Bracing Arms for Structural Integrity in Flight Systems
Obsah
Introduction: The Critical Role of Aerospace Bracing Arms
The aerospace industry operates at the cutting edge of engineering, demanding components that meet extraordinary standards for performance, reliability, and safety. Every gram of weight carries a significant cost penalty over the operational lifetime of an aircraft or spacecraft, while structural integrity is non-negotiable. Within the complex ecosystem of a flight system, structural components form the essential skeleton, bearing immense loads and withstanding harsh operating conditions, from extreme temperatures to constant vibrations. Among these critical elements are Aerospace Bracing Arms.
At their core, bracing arms are structural members designed primarily to provide stiffness, support, and stability between different parts of an assembly. They counteract bending moments, transfer loads efficiently, maintain critical alignments, and contribute significantly to the overall rigidity and robustness of structures like airframes, landing gear assemblies, and engine pylons. Traditionally, these components were manufactured through subtractive methods like CNC machining from solid billets or via forging and casting processes. While reliable, these methods often impose limitations on design complexity, lead to significant material waste, and can involve long lead times due to tooling requirements.
Vstupte Výroba aditiv kovů (AM), more commonly known as metal 3D tisk. This transformative technology is revolutionizing how aerospace components, including bracing arms, are designed and produced. By building parts layer by layer directly from digital models using high-performance metal powders, AM unlocks unprecedented design freedom. Engineers can now create highly optimized, lightweight structures with complex internal features, consolidating multiple parts into a single, more efficient component. This paradigm shift addresses the core aerospace challenges of weight reduction, performance enhancement, and supply chain optimization.
For procurement managers, engineers, and designers in aerospace manufacturing, understanding the capabilities of metal AM for producing parts like bracing arms is crucial. It represents an opportunity to enhance product performance, reduce operational costs, and shorten development cycles. Companies seeking reliable dodavatelé leteckých komponentů and manufacturing partners need providers with deep expertise not just in printing, but also in materials science, design for AM (DfAM), and rigorous quality control processes essential for flight-critical applications.
Toto je místo Met3dp emerges as a leader. Specializing in advanced metal additive manufacturing solutions, including industry-leading Selective Electron Beam Melting (SEBM) printers and high-performance metal powders produced via state-of-the-art Gas Atomization and Plasma Rotating Electrode Process (PREP) technologies, Met3dp provides comprehensive capabilities tailored for demanding industries like aerospace. Our expertise spans the entire AM workflow, enabling the production of dense, high-quality metal parts with superior mechanical properties, perfectly suited for applications like next-generation aerospace bracing arms.
This article will delve into the specifics of using metal 3D printing for aerospace bracing arms, exploring applications, the compelling advantages over traditional methods, recommended materials like Ti-6Al-4V and Scalmalloy®, crucial design considerations, and how to partner with the right AM service provider.
Applications and Use Cases: Where Aerospace Bracing Arms Take Flight
Aerospace bracing arms are ubiquitous, performing vital structural roles across virtually all types of flight vehicles. Their specific design and material depend heavily on the application’s unique load case, environmental conditions, and weight targets. Understanding these diverse applications highlights the versatility required from both the component and its manufacturing process. Key use cases include:
- Konstrukce draku letadla:
- Function: Connecting ribs, spars, and stringers within wings and fuselage sections; reinforcing bulkheads; providing attachment points for other systems.
- Důležitost: Maintaining the aerodynamic shape under load, distributing stress evenly across the airframe, preventing buckling and structural failure. Airframe bracing requires high stiffness and fatigue resistance. AM allows for topology-optimized designs that follow complex load paths precisely.
- Průmyslová odvětví: Commercial Aviation OEMs, Defense Aircraft Manufacturers, Business Jet Producers.
- Sestavy podvozku:
- Function: Connecting shock struts, retraction mechanisms, and wheel assemblies; transferring landing impact loads into the airframe structure; providing structural stability during ground operations (taxiing, takeoff, landing).
- Důležitost: Must withstand extreme impact loads, cyclic fatigue, and potential corrosion. Weight reduction here directly impacts overall aircraft efficiency. Part consolidation via AM can reduce assembly complexity and potential failure points in these critical systems.
- Průmyslová odvětví: Landing Gear System Suppliers, Aircraft OEMs, MRO Providers (for spare parts).
- Engine Mounts and Pylons:
- Function: Supporting the engine, isolating vibrations from the airframe, transferring engine thrust loads, holding engine components and nacelles securely.
- Důležitost: Requires exceptional strength, fatigue resistance, and often high-temperature tolerance, especially for bracing near the engine core or exhaust sections. Complex geometries are often needed to fit within confined nacelle spaces.
- Průmyslová odvětví: Engine Manufacturers, Nacelle Suppliers, Aircraft OEMs.
- Control Surface Linkages:
- Function: Connecting actuators to control surfaces (ailerons, elevators, rudders); transmitting control inputs accurately.
- Důležitost: Requires high stiffness for precise control response, low weight to minimize inertia, and high reliability. AM enables integrated designs with optimized kinematics.
- Průmyslová odvětví: Flight Control System Suppliers, Aircraft Manufacturers.
- Satellite Structures:
- Function: Supporting deployable appendages (solar arrays, antennas), reinforcing primary bus structures, mounting sensitive equipment.
- Důležitost: Extreme weight sensitivity (launch costs are paramount), need for high stiffness-to-weight ratio, often complex geometries to integrate with multiple systems within tight volume constraints. Thermal stability can also be crucial. AM is ideal for creating bespoke, highly optimized satellite components.
- Průmyslová odvětví: Satellite Manufacturers, Space Exploration Agencies, Aerospace Component Distributors specializing in space hardware.
- Unmanned Aerial Vehicles (UAVs) / Drones:
- Function: Forming part of the airframe structure, supporting payloads (cameras, sensors), connecting wing/rotor assemblies to the fuselage.
- Důležitost: Weight is critical for endurance and payload capacity. Rapid prototyping and design iteration enabled by AM are highly beneficial in this fast-developing sector. Ability to produce complex, integrated structures is key for compact designs.
- Průmyslová odvětví: UAV/Drone Manufacturers, Defense Contractors, Aerial Surveying Companies.
- Interior Structures:
- Function: Supporting overhead bins, cargo bay structures, monuments (galleys, lavatories).
- Důležitost: While perhaps less critical than primary structures, weight savings here still contribute to fuel efficiency. AM allows for optimized designs and potentially part consolidation for faster cabin integration.
- Průmyslová odvětví: Cabin Interior Suppliers, Aircraft OEMs.
- Maintenance, Repair, and Overhaul (MRO):
- Function: Producing replacement bracing arms for aging aircraft or components damaged in service.
- Důležitost: AM enables on-demand manufacturing of obsolete or hard-to-source spare parts, reducing aircraft downtime and inventory costs. Digital inventories replace physical ones.
- Průmyslová odvětví: MRO Service Providers, Airlines, Military Logistics Commands.
The breadth of these applications underscores the need for manufacturing processes that offer flexibility, material diversity, and the ability to create highly optimized parts. Aerospace component manufacturers a structural parts suppliers are increasingly turning to metal AM to meet these demanding requirements, providing superior solutions compared to traditional approaches.
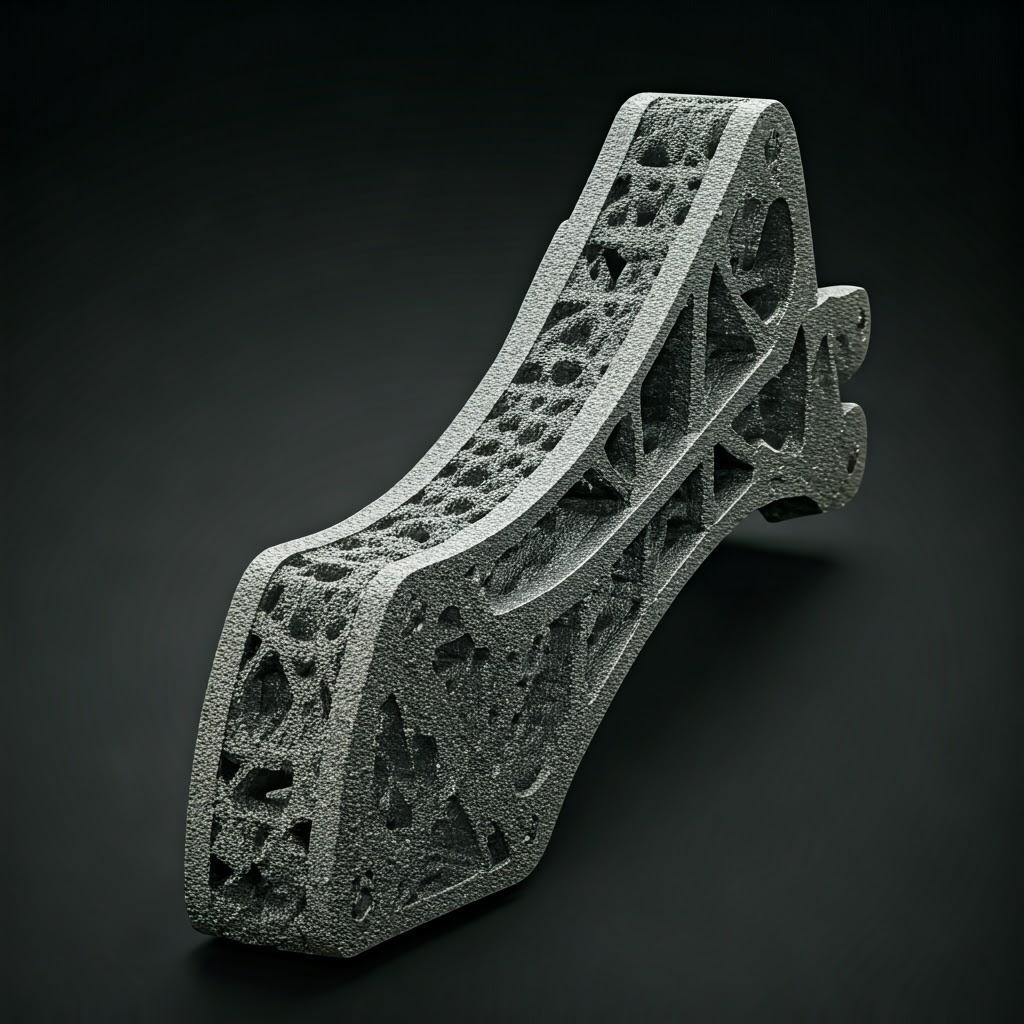
Why Metal 3D Printing for Aerospace Bracing Arms? Unlocking Performance Gains
While traditional manufacturing methods like CNC machining, forging, and casting have served the aerospace industry for decades, they present inherent limitations, particularly when pushing the boundaries of performance and efficiency. Metal additive manufacturing offers compelling advantages specifically suited to overcoming these limitations for components like bracing arms:
Limitations of Traditional Manufacturing for Bracing Arms:
- CNC obrábění: Although precise, it’s a subtractive process, often starting with a large billet of material and removing excess. This leads to:
- Significant material waste (buy-to-fly ratio can be high, especially with expensive materials like titanium).
- Geometric limitations – undercuts, complex internal channels, and highly organic shapes optimized for load paths can be difficult or impossible to machine.
- Longer machining times for complex parts.
- Forging/Casting: These methods can produce near-net shapes but:
- Require expensive tooling (dies, molds) with long lead times, making them unsuitable for low-volume production or prototypes.
- Design changes necessitate costly tooling modifications.
- Often have limitations in achieving fine details or highly complex internal structures.
- May require significant post-machining to achieve final tolerances.
Key Advantages of Metal Additive Manufacturing:
Metal AM fundamentally changes the design and production paradigm, offering tangible benefits for aerospace bracing arms:
- Massive Weight Reduction: This is arguably the most significant driver for AM in aerospace.
- Optimalizace topologie: Software algorithms can sculpt the bracing arm’s geometry, placing material only where structurally necessary based on load paths, resulting in highly organic, efficient shapes impossible to machine conventionally. Weight savings of 30-50% or even more are achievable compared to traditionally designed parts.
- Mřížové struktury: AM allows the integration of internal lattice structures – complex networks of struts and nodes – providing high stiffness and strength at a fraction of the weight of solid material.
- Bezprecedentní svoboda designu: AM builds parts layer by layer, freeing designers from many constraints of traditional methods.
- Složité geometrie: Internal cooling channels, conformal pathways, complex curvatures, and intricate features can be built directly into the part.
- Biomimicry: Designs inspired by natural structures (like bone) that are inherently lightweight and strong can be realized.
- Konsolidace částí: Multiple individual components that would traditionally be assembled (e.g., a brace, mounting brackets, fasteners) can often be redesigned and printed as a single, monolithic part.
- Výhody: Reduces part count, eliminates fasteners (potential failure points), simplifies assembly, reduces weight, and improves structural integrity.
- Rapid Prototyping and Accelerated Development:
- Producing functional metal prototypes directly from CAD data without tooling allows for faster design iteration and validation.
- Reduces the overall time-to-market for new aircraft programs or component upgrades.
- Snížení množství materiálového odpadu: AM is an additive process, using primarily only the material needed for the part and its supports.
- Significantly improves the buy-to-fly ratio compared to subtractive machining, especially critical for expensive aerospace alloys like titanium. This offers substantial cost savings on raw materials.
- Supply Chain Optimization & On-Demand Manufacturing:
- Digital Inventory: Parts can be stored as digital files and printed when needed, reducing physical inventory requirements and warehousing costs.
- MRO & Spare Parts: Enables rapid production of obsolete or low-demand spare parts, minimizing aircraft-on-ground (AOG) time.
- Distributed Manufacturing: Potential for parts to be printed closer to the point of need.
- Vylepšený výkon: Optimized designs can lead to improved stiffness, better load distribution, and potentially enhanced fatigue life compared to conventionally designed counterparts.
The table below summarizes the key advantages of Metal AM for aerospace bracing arms compared to traditional methods:
Vlastnosti | Výroba aditiv kovů (AM) | Traditional Manufacturing (CNC, Forging, Casting) | Advantage for Bracing Arms |
---|---|---|---|
Hmotnost | Significant reduction via topology optimization & lattices | Often heavier due to design/process constraints | Lower fuel consumption, increased payload capacity |
Složitost návrhu | High freedom for complex internal/external features | Limited by tooling, machining access, or draft angles | Optimized performance, functional integration |
Konsolidace částí | Enables integration of multiple parts into one | Requires assembly of multiple components | Reduced weight, fewer failure points, simplified assembly |
Materiálový odpad | Low (Near-net shape) | High (Machining) or Moderate (Casting/Forging + Machining) | Lower material costs, improved sustainability |
Lead Time (Proto) | Fast (Days/Weeks – no tooling) | Slow (Weeks/Months – tooling required for C/F) | Faster design iteration and validation |
Náklady na nástroje | Žádný | High (Dies/Molds for C/F) | Economical for low-volume, prototypes, and complex designs |
Dodavatelský řetězec | Flexible, on-demand, digital inventory | Reliant on traditional inventory & logistics | Reduced inventory costs, faster MRO response times |
Export do archů
By leveraging these advantages, aerospace manufacturers a B2B dodavatelé can produce bracing arms that are lighter, stronger, and more tailored to their specific function, contributing directly to the next generation of more efficient and capable flight systems. Engaging with knowledgeable 3D tisk z kovu providers is key to unlocking this potential.
Recommended Materials: Ti-6Al-4V and Scalmalloy® for Peak Performance
The choice of material is paramount in aerospace design, directly influencing a component’s weight, strength, durability, and resistance to environmental factors. For metal 3D printed aerospace bracing arms, two materials stand out due to their exceptional properties and proven track record in additive manufacturing: Ti-6Al-4V (titanová třída 5) a Scalmalloy® (a high-performance Aluminum alloy).
The quality of the final printed part is intrinsically linked to the quality of the metal powder feedstock. Characteristics such as:
- Sféricita: How close the powder particles are to perfect spheres impacts powder bed density and flowability.
- Tekutost: The ability of the powder to spread evenly across the build platform is crucial for consistent layers.
- Čistota: Contaminants can lead to defects and compromised mechanical properties in the final part.
- Distribuce velikosti částic (PSD): A controlled PSD ensures optimal packing density and melting behavior.
Met3dp utilizes industry-leading Atomizace plynu a Proces plazmové rotující elektrody (PREP) technologies to produce metal powders with high sphericity, excellent flowability, low oxygen content, and controlled PSD. Our rigorous quality control ensures that powders meet the stringent requirements for critical aerospace applications, leading to denser, stronger, and more reliable 3D printed components. Explore our diverse range of high-quality kovové prášky.
Let’s delve into the specifics of Ti-6Al-4V and Scalmalloy®:
1. Ti-6Al-4V (Titanium Grade 5): The Aerospace Workhorse
Ti-6Al-4V is the most widely used titanium alloy in aerospace and is exceptionally well-suited for AM processes like Laser Powder Bed Fusion (LPBF) and Electron Beam Melting (EBM). Its popularity stems from a highly desirable combination of properties:
- Vysoký poměr pevnosti k hmotnosti: Titanium alloys offer strength comparable to many steels but at roughly 40-45% lower density. This is a primary driver for its use in aerospace where weight reduction is critical. Bracing arms made from Ti-6Al-4V can be significantly lighter than steel equivalents for the same strength requirement.
- Vynikající odolnost proti korozi: Titanium forms a stable, passive oxide layer, providing outstanding resistance to corrosion from jet fuel, hydraulic fluids, saltwater, and atmospheric conditions. This enhances durability and reduces maintenance needs.
- Good High-Temperature Performance: Ti-6Al-4V retains useful strength up to around 315°C (600°F), making it suitable for applications in engine pylons or near warmer sections of the airframe.
- Fatigue Strength & Fracture Toughness: It exhibits good resistance to fatigue crack growth, crucial for components subjected to cyclic loading, like landing gear or airframe structures.
- Biokompatibilita: While less relevant for bracing arms, its biocompatibility makes it suitable for medical implants, showcasing its non-reactive nature.
AM Considerations for Ti-6Al-4V:
- Requires careful control of the build atmosphere (inert gas like Argon) due to its reactivity, especially at elevated temperatures.
- Often requires post-print stress relief heat treatment and potentially Hot Isostatic Pressing (HIP) to achieve optimal mechanical properties and reduce internal porosity. Met3dp’s SEBM process operates under vacuum and at higher temperatures, which can reduce residual stress compared to LPBF.
2. Scalmalloy®: High-Performance Aluminum Alloy
Scalmalloy® is a patented high-strength aluminum-magnesium-scandium alloy specifically developed for additive manufacturing. It offers performance characteristics that bridge the gap between traditional high-strength aluminum alloys and titanium, making it an attractive alternative for certain applications.
- Výjimečná síla: Scalmalloy® boasts mechanical properties (yield and tensile strength) significantly higher than conventional AM aluminum alloys (like AlSi10Mg) and approaching those of Ti-6Al-4V, especially considering its lower density.
- Nízká hustota: Being an aluminum alloy, it is significantly lighter than Ti-6Al-4V (approx. 2.67 g/cm³ vs. 4.43 g/cm³). This allows for even greater weight savings in stiffness-driven designs where its specific strength (strength divided by density) is advantageous.
- Excellent Ductility & Weldability: Compared to some other high-strength aluminum alloys, Scalmalloy® exhibits good ductility, making it more resistant to fracture. It’s also weldable, which can be beneficial for post-processing or integration.
- Good Dynamic Load Performance: It performs well under cyclic loading conditions.
- Odolnost proti korozi: Offers good corrosion resistance suitable for many aerospace environments.
AM Considerations for Scalmalloy®:
- Primarily processed using LPBF technology.
- Requires specific heat treatment cycles after printing to achieve its optimal high-strength properties.
- The addition of Scandium contributes significantly to its strength through grain refinement and precipitation hardening mechanisms.
Material Selection – Ti-6Al-4V vs. Scalmalloy®:
The choice between these two leading materials often depends on the specific requirements of the bracing arm application:
Vlastnictví | Ti-6Al-4V (Typical AM Values) | Scalmalloy® (Typical AM Values, Heat Treated) | Considerations for Bracing Arms |
---|---|---|---|
Hustota | ~4,43 g/cm³ | ~2.67 g/cm³ | Scalmalloy® offers significant density advantage (~40% lighter). |
Yield Strength (Rp0.2) | 830 – 1100 MPa | 480 – 520 MPa | Ti-6Al-4V generally offers higher absolute strength. |
Tensile Strength (Rm) | 900 – 1170 MPa | 520 – 540 MPa | Ti-6Al-4V generally offers higher absolute strength. |
Specific Strength (Rm/ρ) | Vysoký | Velmi vysoká | Scalmalloy® excels in stiffness/strength-critical, weight-sensitive designs. |
Prodloužení po přetržení | 5 – 15% | 10 – 16% | Both offer reasonable ductility for structural parts. |
Maximální provozní teplota | ~315°C (600°F) | ~125°C (257°F) | Ti-6Al-4V is superior for higher temperature applications. |
Odolnost proti korozi | Vynikající | Dobrý | Ti-6Al-4V generally superior, especially in harsh environments. |
Relative Cost (Powder) | Vyšší | Dolní | Titanium powder is typically more expensive than aluminum alloys. |
Export do archů
Conclusion on Materials:
- Vyberte si Ti-6Al-4V when: Maximum absolute strength, higher operating temperatures, or superior corrosion resistance are primary requirements. It remains the benchmark for many demanding aerospace structural parts.
- Vyberte si Scalmalloy® when: The absolute highest weight savings are paramount (stiffness-driven designs), operating temperatures are moderate, and its strength profile meets the design requirements. It provides a compelling high-strength, low-weight alternative.
Partnering with a provider like Met3dp, who possesses deep material science expertise and utilizes premium, quality-controlled powders, ensures that the selected material performs to its maximum potential in the final 3D printed aerospace bracing arm.
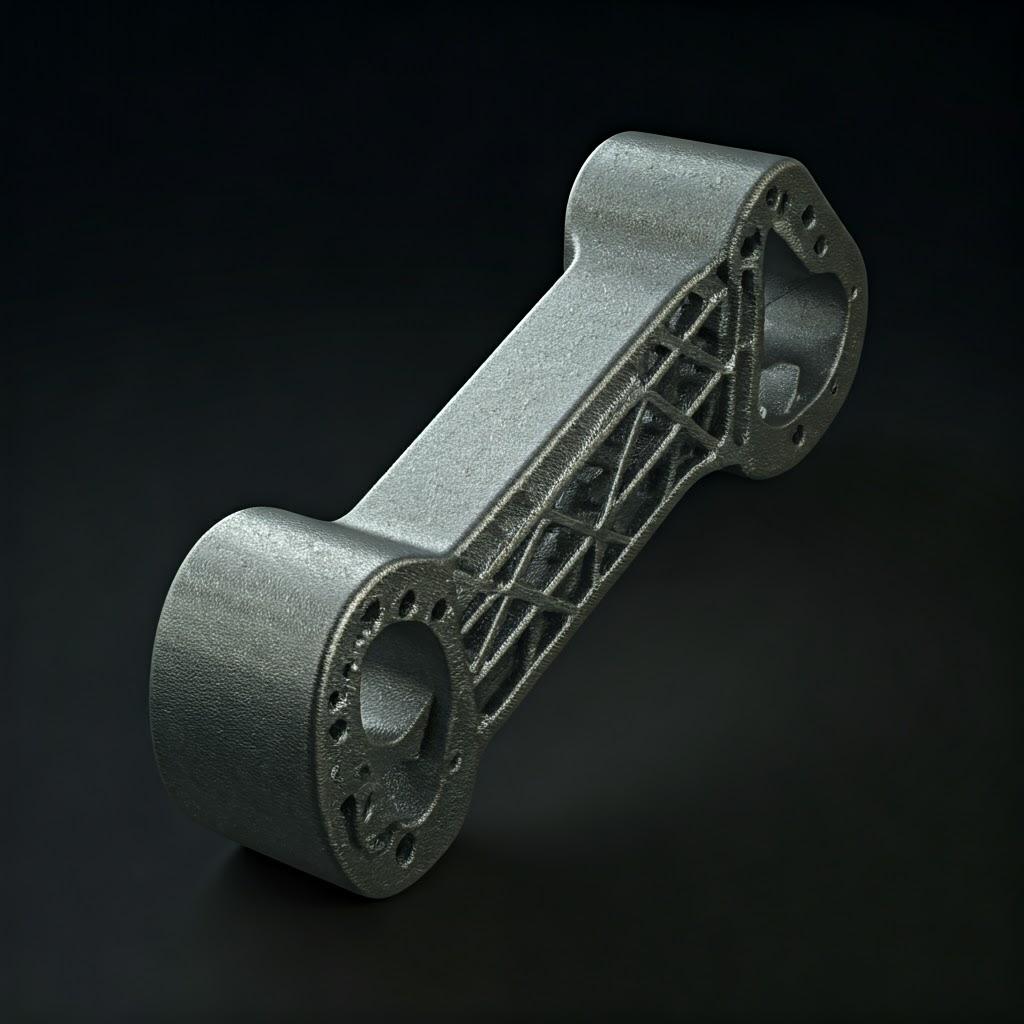
Design for Additive Manufacturing (DfAM): Optimizing Bracing Arms for 3D Printing
Simply recreating a traditionally designed bracing arm using metal 3D printing often fails to leverage the technology’s true potential and can even lead to suboptimal results. To unlock the significant weight savings, performance gains, and part consolidation benefits discussed earlier, engineers must embrace Design pro aditivní výrobu (DfAM). DfAM is a mindset and a set of principles that considers the unique capabilities and constraints of the AM process right from the conceptual design stage. For aerospace bracing arms, applying DfAM principles is not just beneficial; it’s essential for creating truly optimized, flight-ready components.
Key DfAM considerations for aerospace bracing arms include:
- Optimalizace topologie: This is arguably the most powerful DfAM tool for structural components.
- Concept: Using specialized software (e.g., Altair Inspire, nTopology, Ansys Discovery), engineers define the design space, load cases (tension, compression, torsion, vibration), constraints (mounting points, keep-out zones), and performance goals (maximize stiffness, minimize weight).
- Proces: The software iteratively removes material from areas experiencing low stress, leaving behind an organic, load-path-optimized structure.
- Výhody: Results in highly efficient, lightweight designs that place material precisely where it’s needed, often achieving weight reductions of 30-50% or more compared to conventional designs, while meeting or exceeding stiffness requirements. These complex, often bone-like structures are typically only manufacturable via AM.
- Lattice Structure Integration: AM allows the seamless integration of internal lattice structures within the bracing arm’s volume.
- Typy: Various lattice types exist (e.g., cubic, octet-truss, gyroid) offering different balances of stiffness, strength, energy absorption, and surface area.
- Použití: Can be used to fill voids in topology-optimized parts, further reducing weight while maintaining structural integrity or providing specific vibration damping characteristics. Can also create multi-functional structures (e.g., incorporating heat exchange capabilities if needed).
- Výhody: Maximizes stiffness-to-weight ratio, allows for tailored mechanical properties, and can enhance performance beyond solid optimized designs.
- Overhangs and Support Structures: Metal AM processes build layer by layer, meaning downward-facing surfaces (overhangs) beyond a certain angle relative to the build plate typically require support structures.
- Self-Supporting Angles: Designs should aim to utilize self-supporting angles (often > 45 degrees, depending on the material and process) wherever possible to minimize the need for supports.
- Support Strategy: When supports are unavoidable, they must be designed strategically:
- Minimize contact points with the final part surface to reduce witness marks.
- Ensure they are strong enough to prevent distortion during printing but easy enough to remove during post-processing.
- Avoid placing supports on critical surfaces or within complex internal channels where removal is difficult or impossible.
- Výhody: Reducing supports saves material, reduces print time, simplifies post-processing, lowers cost, and improves surface finish on downward-facing areas.
- Minimum Feature Size and Wall Thickness: AM processes have limitations on the smallest features they can accurately produce.
- Úvahy: Designers must adhere to minimum wall thicknesses (depends on material, machine, parameters – often 0.4-1.0 mm), hole diameters, and slot widths recommended by the AM service provider (like Met3dp) to ensure features are fully formed and robust.
- Výhody: Prevents feature failure during printing or handling and ensures the part meets functional requirements.
- Build Orientation Planning: The orientation of the bracing arm on the build plate significantly impacts several factors:
- Podpůrné struktury: Orientation determines which surfaces become overhangs requiring support.
- Povrchová úprava: Upward and downward-facing surfaces typically have different roughness characteristics. Vertical walls often have the best finish.
- Mechanické vlastnosti: Anisotropy (directionally dependent properties) can occur in AM parts. Orientation should align critical load paths with the direction of optimal material properties (often the X-Y plane).
- Build Time & Cost: Taller builds generally take longer. Packing multiple parts efficiently on the build plate is crucial for production cost.
- Výhody: Strategic orientation optimizes for the most critical factors – minimizing supports, achieving required surface finish on key features, maximizing mechanical performance, and reducing manufacturing time/cost.
- Functional Integration & Part Consolidation: DfAM encourages designers to think beyond single-function parts.
- Opportunity: Can mounting brackets, vibration damping features, fluid channels, or sensor housings be integrated directly into the bracing arm design?
- Výhody: Reduces overall part count, eliminates fasteners and assembly steps, lowers weight, minimizes potential failure points, and can create more elegant and efficient system-level solutions.
- Filleting and Smoothing: Sharp corners can act as stress concentrators.
- Practice: Applying generous fillets and smoothing transitions, particularly in topology-optimized designs, helps distribute stress more evenly and improves fatigue life. AM easily accommodates these complex curvatures.
- Výhody: Enhanced structural integrity and durability under cyclic loading.
Successfully implementing DfAM requires close collaboration between design engineers and AM specialists. Experienced aerospace 3D printing service providers like Met3dp offer crucial expertise in guiding customers through the DfAM process, ensuring that bracing arm designs are fully optimized for additive manufacturing and meet all functional and quality requirements.
Achievable Tolerances, Surface Finish, and Dimensional Accuracy in AM Bracing Arms
While metal AM offers incredible design freedom, it’s crucial for engineers and procurement managers to understand the achievable levels of precision, surface finish, and dimensional accuracy. These factors directly impact component fit, function, and the need for subsequent post-processing steps. Expectations should be realistic and aligned with the capabilities of the chosen AM process and material.
Rozměrová přesnost a tolerance:
- As-Printed Accuracy: The accuracy achievable directly from the printer depends on the specific technology (LPBF, EBM), machine calibration, material properties, part geometry, size, and build orientation.
- Typical Ranges: For well-calibrated industrial systems printing Ti-6Al-4V or Scalmalloy®, general tolerances often fall within ±0.1 mm to ±0.3 mm or ±0.1% to ±0.2% of the dimension, whichever is larger. Specific features might achieve tighter tolerances.
- ISO Standards: Often referenced against general tolerance standards like ISO 2768 (e.g., class ‘m’ for medium or ‘f’ for fine might be achievable for certain dimensions as-printed, but this needs verification per part).
- Faktory ovlivňující přesnost: Thermal stresses during printing can cause minor warping or shrinkage, part orientation affects geometric stability, and support structures can influence adjacent surfaces.
- Post-Processing for High Precision: For critical interfaces, mating surfaces, bearing bores, or features requiring tolerances tighter than the as-printed capability, post-machining (CNC milling, turning, grinding) is typically required. This allows achieving tolerances comparable to traditional machining (e.g., down to ±0.01 mm or tighter).
Povrchová úprava (drsnost):
- As-Printed Surface Roughness (Ra): The surface texture of AM parts is inherently rougher than machined surfaces due to the layer-by-layer process and partially melted powder particles adhering to surfaces.
- Typical Ra Values:
- LPBF (Laser Powder Bed Fusion): Generally offers finer finishes than EBM. Ra values often range from 6 µm to 20 µm (240 µin to 800 µin) depending on orientation (vertical walls smoother, up/down-facing surfaces rougher) and material.
- EBM (Electron Beam Melting): Typically produces rougher surfaces, often Ra 20 µm to 35 µm (800 µin to 1400 µin), due to larger layer thicknesses and powder particle sizes. However, the higher build temperatures in EBM can reduce residual stress.
- Support Structure Influence: Surfaces where supports were attached will typically be rougher and require more extensive finishing.
- Typical Ra Values:
- Zlepšení povrchové úpravy: Various post-processing techniques can significantly improve surface finish:
- Tryskání kuličkami / pískování: Provides a uniform matte finish, removing loose powder (Ra typically 5-15 µm).
- Obrábění / vibrační úprava: Smoothens surfaces and edges, suitable for batches of smaller parts (Ra can reach 1-5 µm).
- Leštění: Manual or automated polishing can achieve very smooth, mirror-like finishes (Ra < 0.8 µm or even < 0.1 µm) for specific requirements like fatigue life improvement or aesthetics.
- Obrábění: Provides the smoothest and most controlled surface finish on specific features.
Metrology and Quality Control:
Verifying the dimensional accuracy and integrity of flight-critical components like bracing arms is non-negotiable.
- Inspection Methods:
- Coordinate Measuring Machines (CMM): Provide high-accuracy point measurements for verifying critical dimensions and tolerances.
- 3D Laser Scanning / Structured Light Scanning: Capture the full geometry of the part, allowing comparison to the original CAD model and analysis of overall form and dimensional deviations. Ideal for complex, organic shapes from topology optimization.
- Traditional Gauges: Calipers, micrometers, height gauges for specific feature checks.
- Quality Management System (QMS): Partnering with an AS9100 certified 3D printing supplier is crucial for aerospace applications. AS9100 mandates rigorous process control, traceability, documentation, and inspection protocols, ensuring consistent quality and reliability. Met3dp operates under stringent quality standards, ensuring our processes and parts meet demanding aerospace requirements. Our expertise across various tiskových metod, including SEBM and LPBF, allows us to select the optimal approach for specific accuracy and surface needs.
Summary Table: Tolerances & Surface Finish
Parametr | As-Printed (Typical Range) | Achievable with Post-Processing | Method for Improvement |
---|---|---|---|
General Tolerance | ±0.1 to ±0.3 mm / ±0.1% to ±0.2% | Down to ±0.01 mm or tighter | CNC Machining, Grinding |
Surface Roughness (Ra) – LPBF | 6 µm – 20 µm | < 0.8 µm (Polished) | Blasting, Tumbling, Polishing, Machining |
Surface Roughness (Ra) – EBM | 20 µm – 35 µm | < 1 µm (Polished) | Blasting, Tumbling, Polishing, Machining |
Export do archů
Understanding these capabilities allows engineers to design bracing arms effectively, specifying post-processing only where necessary, thereby optimizing both performance and cost.
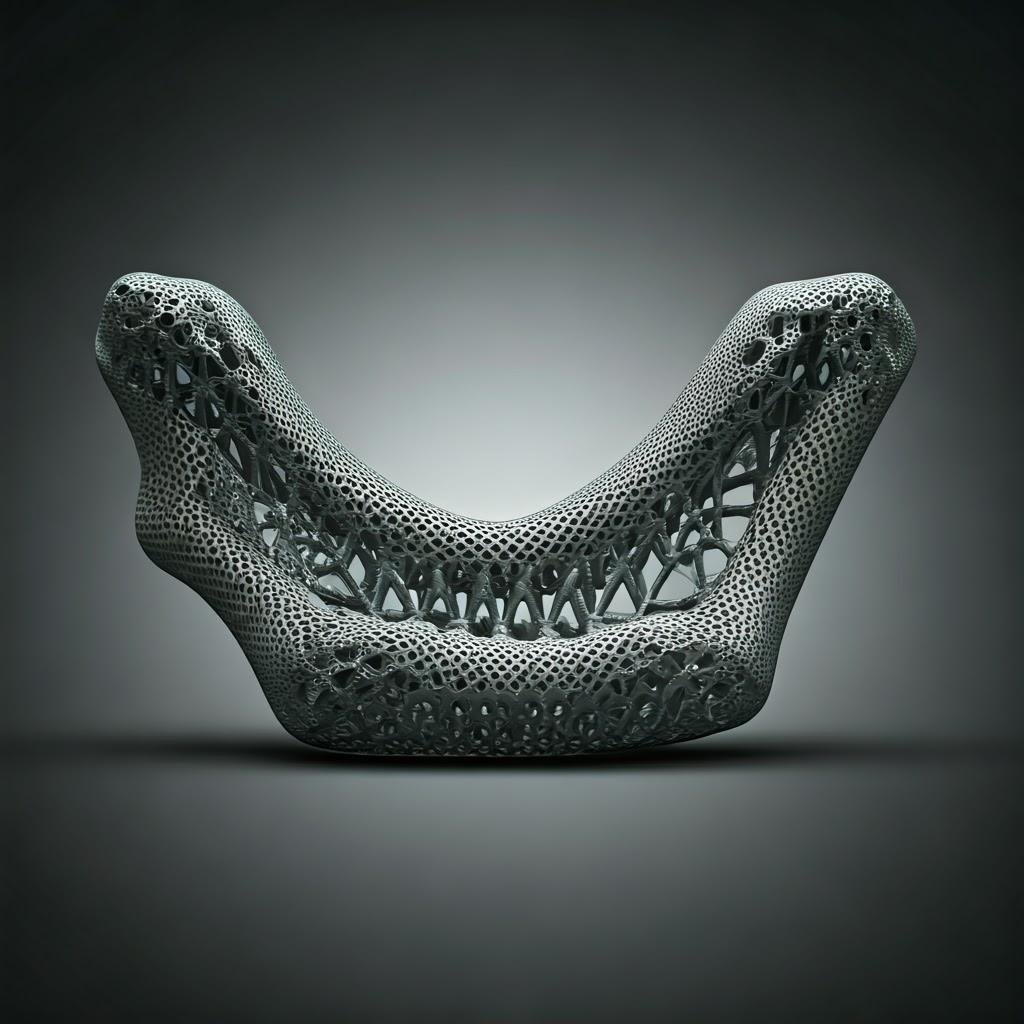
Essential Post-Processing Steps for Flight-Ready Bracing Arms
A metal 3D printed part, as it comes off the build plate, is rarely ready for its final application, especially in the demanding aerospace sector. A series of crucial post-processing steps are required to transform the near-net-shape part into a finished, flight-certified component. This workflow ensures the bracing arm meets dimensional specifications, achieves the required mechanical properties, possesses the necessary surface characteristics, and is free from internal defects.
The typical post-processing workflow for AM aerospace bracing arms includes:
- De-Powdering: Carefully removing loose metal powder from the part, especially from internal channels or complex features. This often involves manual brushing, vacuuming, or using compressed air within controlled environments to safely handle potentially reactive powders like titanium.
- Úleva od stresu: Heat treatment performed shortly after printing (often while still on the build plate) to alleviate internal stresses built up during the rapid heating and cooling cycles of the AM process. This minimizes the risk of distortion or cracking during subsequent steps like removal from the build plate.
- Part Removal: Separating the printed bracing arm(s) from the build plate, typically using wire EDM (Electrical Discharge Machining), sawing, or grinding.
- Odstranění podpůrné konstrukce: A often labor-intensive step involving manually breaking, cutting, or machining away the support structures designed during the DfAM phase. Care must be taken to avoid damaging the part surface. Accessing supports within internal cavities can be particularly challenging.
- Izostatické lisování za tepla (HIP): This is a critical step for most flight-critical AM metal parts, especially those made from titanium alloys.
- Proces: Parts are subjected to high temperature (below the melting point) and high isostatic pressure (typically using Argon gas) simultaneously in a specialized furnace.
- Výhody:
- Closes Internal Porosity: Eliminates small internal voids (like gas porosity or lack-of-fusion defects) that can act as crack initiation sites.
- Improves Density: Increases the part’s density closer to theoretical maximum (typically > 99.9%).
- Enhances Mechanical Properties: Significantly improves ductility, fatigue life, fracture toughness, and overall property consistency, making the part more reliable under demanding aerospace load conditions.
- Requirement: Often mandated by aerospace standards for Class A / flight-critical AM components.
- Solution Annealing / Aging / Heat Treatment (Post-HIP): Depending on the alloy (e.g., Scalmalloy®, certain titanium treatments), additional specific heat treatment cycles may be required after HIP to achieve the final desired microstructure and mechanical properties (e.g., target strength, hardness, ductility).
- Final Machining (CNC): As discussed previously, machining critical interfaces, mounting holes, bearing surfaces, and any features requiring tight tolerances or specific surface finishes that cannot be achieved by AM alone.
- Povrchová úprava: Applying processes to achieve the final desired surface texture.
- Blasting (Bead, Sand): Creates a uniform matte finish, improves aesthetics, and can provide minor peening effect beneficial for fatigue life.
- Obrábění / vibrační úprava: Smoothens surfaces and deburrs edges.
- Leštění: For very low Ra values or specific aerodynamic/fatigue requirements.
- Cleaning: Thoroughly cleaning the part to remove any machining fluids, blasting media, or contaminants before final inspection or coating.
- Coatings and Surface Treatments: Applying specific surface treatments based on application requirements:
- Anodizing (Type II or III for Ti): Improves wear resistance and provides an optional surface for primer/paint adhesion.
- Chemical Conversion Coating: Enhances corrosion resistance and provides a good base for paint.
- Painting / Priming: For corrosion protection and final livery.
- Dry Film Lubricants / PVD Coatings: For wear resistance on specific surfaces.
- Non-Destructive Testing (NDT) / Inspection: Final verification of the part’s integrity and dimensions.
- Rozměrová kontrola: CMM, 3D scanning.
- Internal Integrity Inspection:
- Computed Tomography (CT) Scanning: Provides detailed 3D X-ray imaging to detect internal porosity, inclusions, or cracks. Increasingly standard for critical AM parts.
- Radiographic Testing (X-ray): 2D imaging for defect detection.
- Surface Defect Inspection:
- Fluorescent Penetrant Inspection (FPI): Detekuje trhliny porušující povrch.
- Visual Inspection: Under magnification.
This comprehensive post-processing sequence is integral to the value chain of aerospace additive manufacturing. Partnering with a provider like Met3dp, who offers or manages these critical downstream processes alongside core printing capabilities, ensures a streamlined path to obtaining fully qualified, flight-ready bracing arms.
Common Challenges in 3D Printing Aerospace Bracing Arms and Mitigation Strategies
While metal additive manufacturing offers significant advantages, producing high-quality, flight-critical aerospace components like bracing arms is complex and presents unique challenges. Awareness of these potential issues and implementing effective mitigation strategies are crucial for successful adoption and reliable production. Experienced AM providers develop robust processes to overcome these hurdles.
Common challenges include:
- Warping and Distortion:
- Cause: Uneven heating and cooling during the layer-wise fusion process induce thermal gradients and internal stresses, which can cause the part to warp or distort, deviating from the intended geometry. This is particularly prevalent in large or geometrically complex parts.
- Mitigation:
- Build Simulation: Using process simulation software to predict thermal behavior and distortion, allowing for pre-compensation in the build file or optimization of build parameters/orientation.
- Optimized Support Structures: Strategically placed supports anchor the part to the build plate and counteract warping forces.
- Process Parameter Control: Fine-tuning laser/electron beam power, scan speed, and layer thickness.
- Stress Relief Heat Treatment: Performing this step promptly after printing is critical.
- Build Plate Heating (LPBF) / Higher Build Temps (EBM): Reduces thermal gradients.
- Zbytkové napětí:
- Cause: Similar to distortion, thermal gradients lead to locked-in stresses within the material even after cooling. High residual stress can reduce fatigue life, cause cracking, and lead to distortion upon removal from the build plate or during machining.
- Mitigation:
- Optimalizované strategie skenování: Using specific laser/beam scanning patterns (e.g., island scanning) to manage heat distribution.
- Post-Print Heat Treatment: Stress relief and HIP cycles are essential for reducing residual stress to acceptable levels.
- Design Optimization (DfAM): Avoiding overly thick sections or sharp transitions that concentrate stress.
- Process Selection: EBM generally results in lower residual stress than LPBF due to higher, more uniform build temperatures.
- Pórovitost:
- Cause: Small voids within the printed material. Can be caused by gas trapped during melting (gas porosity) or incomplete fusion between layers/scan tracks (lack-of-fusion porosity). Porosity acts as stress concentrators, degrading mechanical properties, especially fatigue life.
- Mitigation:
- Vysoce kvalitní prášek: Using powder with low trapped gas content and controlled morphology (like Met3dp’s powders).
- Optimalizované parametry procesu: Ensuring sufficient energy density for complete melting and fusion (laser/beam power, speed, hatch spacing).
- Controlled Build Atmosphere: Maintaining a pure inert gas environment (LPBF) or high vacuum (EBM) to prevent gas pickup.
- Izostatické lisování za tepla (HIP): Highly effective at closing internal pores and achieving full density.
- Cracking:
- Cause: Can occur during printing (solidification cracking) or subsequent heat treatment (liquation cracking), often related to high thermal stresses, alloy composition (certain alloys are more prone), or unfavorable grain structures.
- Mitigation:
- Výběr materiálu: Choosing alloys well-suited for AM.
- Parameter Optimization: Adjusting parameters to control cooling rates and thermal gradients.
- Appropriate Heat Treatment Protocols: Carefully designed cycles to avoid inducing cracking.
- DfAM: Designing to minimize stress concentrations.
- Support Removal Difficulties:
- Cause: Supports placed in hard-to-reach internal channels or complex geometries can be extremely difficult or impossible to remove completely, potentially leaving stress risers or unwanted material.
- Mitigation:
- DfAM Focus: Designing for minimal support structures (self-supporting angles, optimized orientation).
- Specialized Support Structures: Using support designs (e.g., easily breakable or soluble) where applicable, though less common in robust metal AM.
- Accessibility Planning: Ensuring tool access for manual removal during the design phase.
- Post-Processing Expertise: Utilizing skilled technicians and appropriate tools (machining, EDM).
- Powder Handling and Safety:
- Cause: Many metal powders (especially Titanium and Aluminum alloys) are reactive and pose fire or explosion risks if not handled correctly. They also present inhalation hazards.
- Mitigation:
- Controlled Environments: Using inert atmospheres (glove boxes), proper grounding, and specialized handling equipment.
- Osobní ochranné prostředky (OOP): Respirators, conductive clothing, safety glasses are mandatory.
- Powder Management Systems: Automated sieving, blending, and loading systems minimize exposure and ensure powder quality/traceability.
- Strict Safety Protocols: Following established industry best practices (e.g., NFPA standards).
- Process Repeatability and Consistency:
- Cause: Ensuring every part produced in a batch, or across multiple builds, meets the exact same specifications is critical for aerospace certification and serial production. Variations in powder batches, machine calibration, or environmental factors can affect outcomes.
- Mitigation:
- Robust Quality Management System (AS9100): Implementing strict process controls, machine calibration schedules, and material traceability.
- Monitorování během procesu: Utilizing sensors (melt pool monitoring, thermal imaging) to track build consistency in real-time.
- Powder Lifecycle Management: Tracking powder reuse and refreshing batches to maintain consistent properties.
- Standardized Operating Procedures: Ensuring all steps are performed consistently.
Overcoming these challenges requires a deep understanding of materials science, AM processes, thermal dynamics, and rigorous process control. Working with an established additive manufacturing partner like Met3dp, who possesses this expertise and has invested in the necessary technology and quality systems, significantly de-risks the adoption of AM for critical components like aerospace bracing arms. Our team leverages decades of collective experience to anticipate and mitigate these challenges, ensuring the delivery of reliable, high-performance parts. Learn more about our company and commitment to quality on our O nás strana.
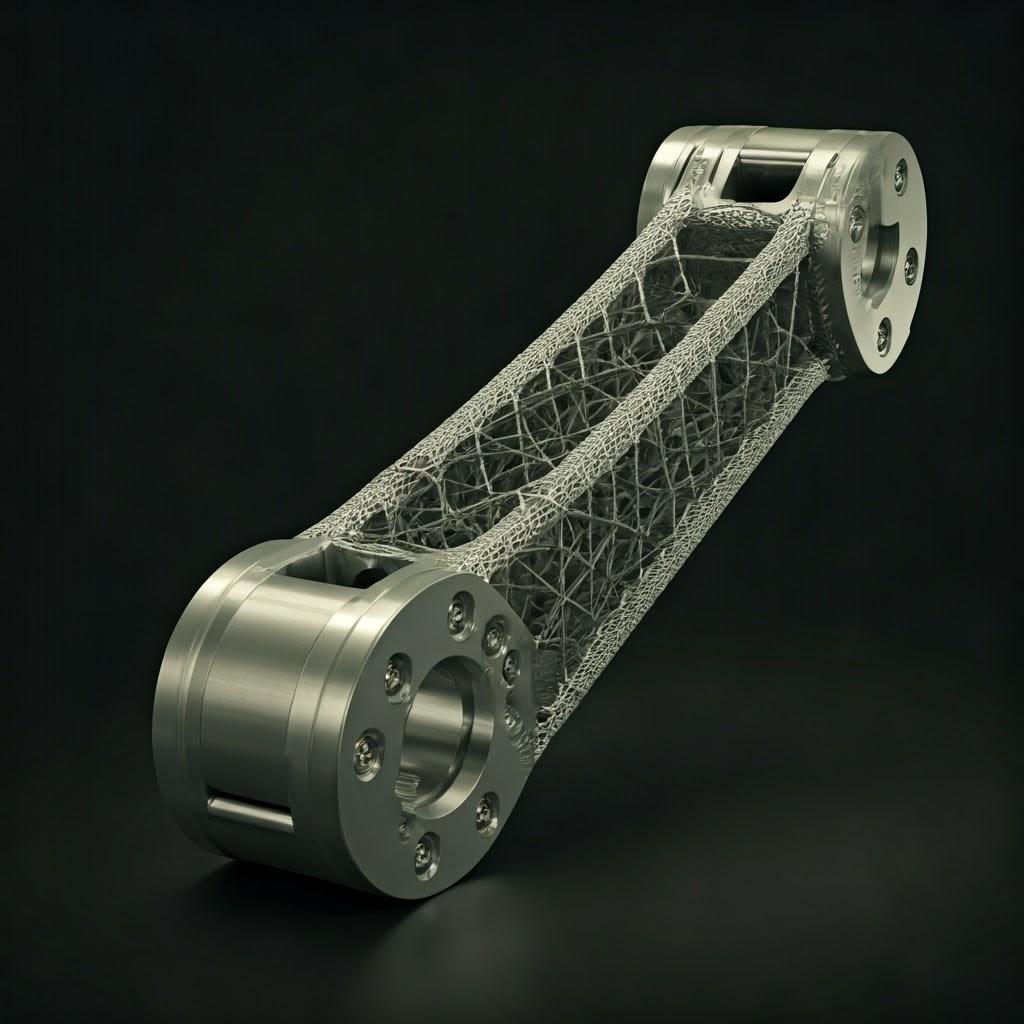
Choosing Your Aerospace Metal 3D Printing Partner: Key Evaluation Criteria
Selecting the right additive manufacturing partner is arguably as critical as the technology itself, especially when dealing with flight-critical components like aerospace bracing arms. The aerospace industry demands the highest levels of quality, reliability, and traceability. A subpar supplier can lead to project delays, cost overruns, and potentially catastrophic component failures. Therefore, procurement managers and engineering teams must conduct thorough due diligence when evaluating potential aerospace metal 3D printing service providers.
Here are key criteria to assess when choosing your AM partner:
- Aerospace Certifications (AS9100): This is non-negotiable. AS9100 is the internationally recognized Quality Management System (QMS) standard for the aviation, space, and defense industries. Certification demonstrates that the provider has implemented rigorous processes for traceability, configuration management, risk management, process control, and continuous improvement, specifically tailored to aerospace requirements. Ask for proof of current certification.
- Proven Aerospace Experience & Track Record: Look beyond certifications to demonstrated experience.
- Has the provider successfully produced similar components (structural parts, flight hardware) for other aerospace clients?
- Can they provide relevant case studies or references (while respecting confidentiality)?
- Do they understand the specific challenges and requirements of the aerospace sector, such as stringent qualification processes and documentation needs?
- Materiálové znalosti: Deep knowledge of the specific materials required (e.g., Ti-6Al-4V, Scalmalloy®) is crucial.
- Do they have qualified processes for these materials on their machines?
- Do they understand the material’s behavior during printing and post-processing (heat treatment response, etc.)?
- Do they source high-quality, aerospace-grade powders with verifiable traceability? Met3dp’s foundation in producing high-performance metal powders provides us with inherent material expertise.
- Equipment Capabilities & Technology: Assess their manufacturing infrastructure.
- Do they operate industrial-grade AM systems (LPBF, EBM) suitable for the required material and part size? Consider specific 3D tisk z kovu technologies and their suitability.
- What is the build volume capacity? Can they accommodate the size of your bracing arm?
- Are the machines well-maintained and calibrated?
- Do they have sufficient machine capacity for your prototyping and potential production volume needs?
- Robustní systém řízení kvality (QMS): Beyond AS9100 certification, probe deeper into their quality practices.
- How do they ensure powder quality and traceability throughout its lifecycle (receiving, testing, use, recycling)?
- What are their process monitoring and control procedures during the build?
- What NDT and metrology equipment do they have in-house or through certified partners?
- How is data (build logs, sensor data, inspection reports) managed and archived?
- Engineering & DfAM Support: True partners offer more than just printing services.
- Can they provide expert guidance on Design for Additive Manufacturing (DfAM) to optimize your bracing arm design for weight, performance, and manufacturability?
- Do they offer simulation capabilities (build process simulation, topology optimization support)?
- Can they assist with developing test plans and qualification strategies?
- Comprehensive Post-Processing Capabilities: As highlighted earlier, post-processing is critical.
- Does the provider offer essential services like heat treatment (stress relief, HIP), CNC machining, surface finishing, and NDT either in-house or through tightly controlled, qualified partners?
- An integrated workflow simplifies project management and ensures accountability.
- Production Capacity & Scalability: Consider both current needs and future potential.
- Can they handle your required volumes, whether for prototypes, low-rate initial production (LRIP), or eventual serial production?
- Do they have plans for capacity expansion if needed?
- Communication & Project Management: Clear, transparent communication is vital.
- Are they responsive and easy to work with?
- Do they provide clear project timelines, status updates, and documentation?
- Is there a dedicated point of contact for your project?
Met3dp is committed to meeting and exceeding these criteria. As a company deeply rooted in both advanced metal powder production and additive manufacturing system technology (including SEBM printers), we offer an integrated approach. Our focus on aerospace, medical, and other demanding industries drives our commitment to quality (including preparations for AS9100), material science excellence, and providing comprehensive solutions from powder to finished part. We partner with organizations to leverage AM strategically, ensuring the production of reliable, high-performance components like aerospace bracing arms.
Understanding Cost Factors and Lead Times for AM Bracing Arms
While metal additive manufacturing enables significant performance improvements and potential long-term cost savings (e.g., through fuel efficiency from weight reduction), the direct manufacturing cost and lead time are key considerations for project planning and B2B procurement. Understanding the primary drivers helps in optimizing designs for cost-effectiveness and setting realistic timelines.
Key Cost Factors:
- Náklady na materiál:
- Typ prášku: High-performance aerospace alloys like Ti-6Al-4V are significantly more expensive than standard steels or even Scalmalloy®.
- Powder Volume: The amount of powder consumed, determined by the part volume and the necessary support structures. Efficient design (topology optimization, minimizing supports) directly reduces material cost.
- Powder Refresh/Recycling: Costs associated with managing powder lifecycle and refreshing batches impact overall material overhead.
- Strojový čas:
- Doba výstavby: Directly related to the part’s height (number of layers) and the volume of material being fused per layer. Taller parts take longer. Denser packing of multiple parts on a build plate can improve machine utilization and reduce per-part time cost.
- Machine Depreciation & Operating Costs: High-value industrial AM systems have significant capital and operational costs (power, inert gas, maintenance) factored into hourly rates.
- Práce:
- Pre-Processing: CAD preparation, build setup simulation, support structure generation.
- Machine Operation: Skilled technicians required for setup, operation, monitoring.
- Následné zpracování: De-powdering, support removal, heat treatment, machining, finishing, inspection – can be very labor-intensive depending on complexity.
- Zajištění kvality: Engineering review, documentation, certification efforts.
- Post-Processing Complexity:
- Tepelné zpracování: Standard stress relief is common; Izostatické lisování za tepla (HIP) adds significant cost due to specialized equipment and long cycle times but is often mandatory for fatigue-critical parts.
- Obrábění: The extent of required CNC machining for tight tolerances or specific finishes heavily impacts cost.
- Surface Finishing/Coating: Costs vary widely depending on the chosen method (blasting, polishing, anodizing, painting).
- NDT: Non-destructive testing, especially CT scanning, adds cost but is crucial for quality verification.
- Part Complexity and Size: While AM handles complexity well, highly intricate designs might require more complex support structures or more intensive post-processing, impacting labor costs. Larger parts consume more material and machine time.
- Quality Assurance & Certification: The level of documentation, inspection, and testing required (especially for flight certification) adds overhead.
- Objem objednávky:
- Prototypy: Typically have a higher per-part cost due to setup and lack of economies of scale.
- Serial Production: Allows for process optimization, efficient build plate packing, and potential wholesale 3D printing volume discounts or negotiated contract pricing for B2B dodavatelé.
Typical Lead Times:
Lead times for AM bracing arms can vary significantly based on several factors:
- Vytváření prototypů: Often ranges from 1 to 4 weeks, depending on complexity, material availability, and current machine queue. The ability to skip tooling offers a major speed advantage over traditional methods.
- Production Parts (Low-Rate): May range from 4 to 10 weeks, accounting for potential HIP cycles, extensive post-processing, machining, and rigorous QA/testing.
- Serial Production: Once processes are fully qualified and optimized, lead times can be more predictable and potentially shorter per batch, but initial qualification can take months.
- Influencing Factors:
- Machine availability and scheduling queue at the AM service provider.
- Complexity of the part and build setup.
- Required post-processing steps (HIP and extensive machining add significant time).
- Testing and qualification requirements.
- Raw material (powder) availability.
It’s crucial to work closely with your AM provider to get accurate cost estimates and realistic lead time projections based on your specific bracing arm design and requirements. Early collaboration during the design phase can help optimize for both cost and speed.
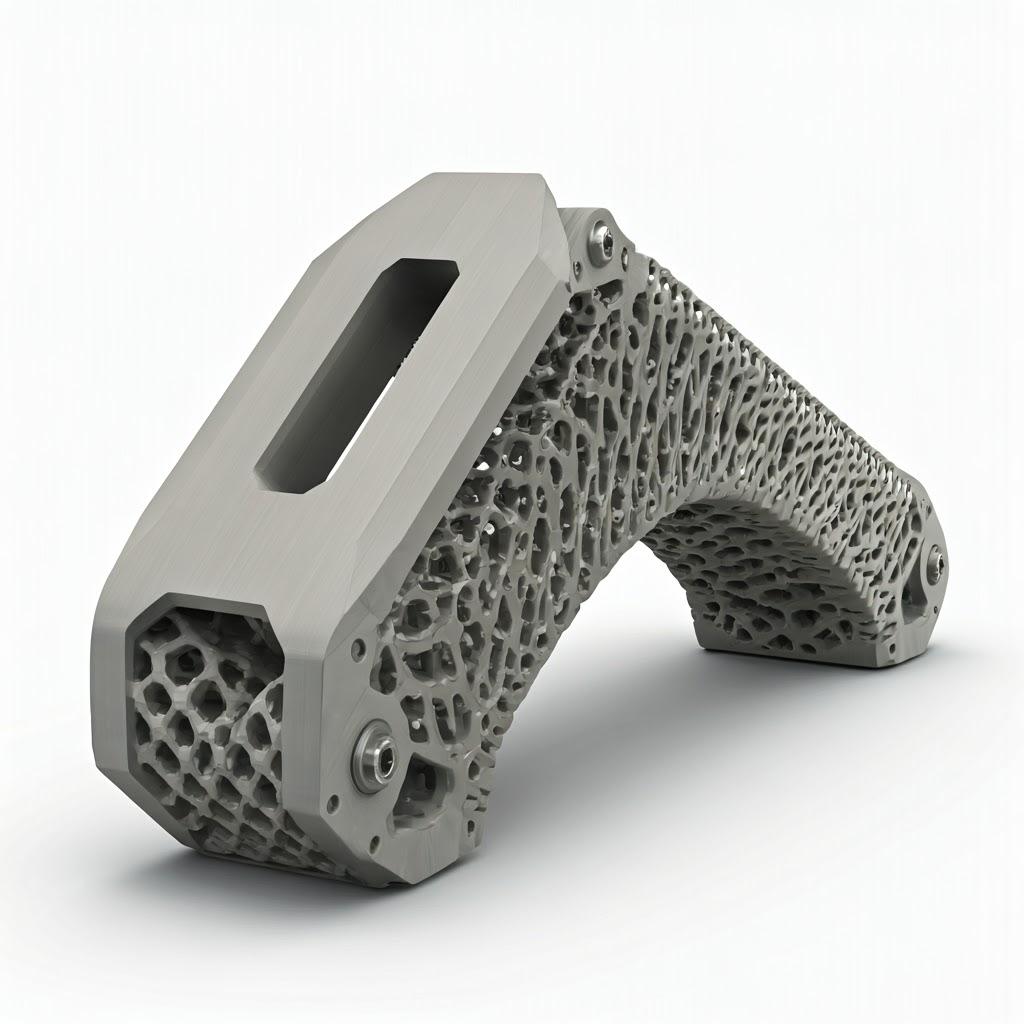
Frequently Asked Questions (FAQ) about 3D Printed Aerospace Bracing Arms
Here are answers to some common questions regarding the use of metal additive manufacturing for aerospace bracing arms:
- What typical weight savings can be achieved compared to traditional methods?
- Weight savings are highly dependent on the original design, the load cases, and the extent to which DfAM principles (especially topology optimization and lattice structures) are applied. However, it is common to see weight reductions ranging from 20% to over 50% for aerospace structural components like bracing arms when redesigned for AM compared to traditionally manufactured (e.g., machined billet) counterparts, while maintaining or even increasing stiffness.
- Are 3D printed metal bracing arms certifiable for flight applications?
- Ano, rozhodně. However, it requires a rigorous qualification process defined by aerospace regulatory bodies (like FAA, EASA) and OEMs. This involves establishing a stable, repeatable manufacturing process (including printing and all post-processing steps like HIP), comprehensive material characterization (developing material allowables based on extensive testing), component-level testing (static, fatigue, fracture mechanics), and robust quality assurance (AS9100). Many 3D printed metal parts, including structural components, are already flying on commercial and military aircraft and spacecraft. Partnering with an experienced provider familiar with aerospace qualification is key.
- How does the fatigue performance of AM bracing arms compare to forged or machined parts?
- With proper process control, DfAM, and essential post-processing (especially HIP to close internal porosity), the fatigue performance of AM components made from materials like Ti-6Al-4V can be comparable or even superior to cast parts and approach the performance of wrought/forged materials. HIP is critical for minimizing defects that can initiate fatigue cracks. Surface finish also plays a significant role; critical areas may require machining or polishing to achieve optimal fatigue life. Extensive testing is always part of the qualification process to verify fatigue performance for specific applications.
- What are the primary benefits of Scalmalloy® over Ti-6Al-4V for certain bracing arm applications?
- The main advantage of Scalmalloy® is its significantly lower density (~2.67 g/cm³ vs. ~4.43 g/cm³) while offering very high strength for an aluminum alloy. This results in a superior specific strength (strength-to-weight ratio), making it ideal for stiffness-driven designs where minimizing mass is the absolute top priority, provided its absolute strength and lower maximum service temperature (~125°C) are sufficient for the application. It can enable lighter bracing arms than Ti-6Al-4V in such scenarios.
- Can Met3dp handle the production of large or complex bracing arm structures?
- Met3dp utilizes industry-leading printing equipment, including systems with substantial build volumes suitable for many aerospace components. Our expertise in both SEBM and LPBF technologies, combined with advanced DfAM support, allows us to tackle complex geometries effectively. We recommend contacting us directly with your specific part dimensions and requirements to discuss feasibility and capabilities for large-scale or intricate bracing arm production.
- What quality documentation is provided for flight-critical AM parts?
- For flight-critical components produced under an AS9100 certified system, comprehensive documentation is standard. This typically includes:
- Certificate of Conformance (CoC).
- Full material traceability (powder batch records, chemistry certification).
- Build log data (machine parameters used).
- Post-processing records (heat treatment charts, machining reports).
- Dimensional inspection reports (CMM, scan data).
- NDT reports (e.g., CT scan analysis, FPI results).
- Final inspection reports confirming compliance with all drawing specifications.
- For flight-critical components produced under an AS9100 certified system, comprehensive documentation is standard. This typically includes:
Závěr: Vylepšení leteckých konstrukcí pomocí aditivní výroby kovů
Aerospace bracing arms, though seemingly simple components, play a vital role in ensuring the structural integrity and performance of flight systems. The relentless drive for lighter, stronger, and more efficient aircraft and spacecraft has paved the way for aditivní výroba kovů to revolutionize how these critical parts are designed and produced.
By leveraging the power of AM, aerospace engineers can break free from the constraints of traditional manufacturing. Techniques like topology optimization and lattice structure integration, combined with advanced materials such as Ti-6Al-4V a Scalmalloy®, enable the creation of bracing arms that are significantly lighter, highly optimized for specific load paths, and potentially integrate multiple functions into a single component. This translates directly into tangible benefits: reduced fuel consumption, increased payload capacity, simplified assembly, and enhanced overall system performance.
However, unlocking this potential requires more than just access to a 3D printer. It demands a holistic approach encompassing rigorous Design pro aditivní výrobu (DfAM) principles, meticulous process control during printing, essential post-processing steps like HIP and precision machining, and unwavering adherence to stringent aerospace quality standards (AS9100). Addressing challenges related to distortion, porosity, and residual stress requires deep expertise and robust mitigation strategies.
Choosing the right manufacturing partner is therefore paramount. An experienced, certified provider with deep material science knowledge, advanced technological capabilities, comprehensive engineering support, and a proven track record in aerospace is essential for success.
Met3dp stands ready to be that partner. With our roots in high-performance metal powder production and expertise in leading AM technologies like SEBM, we provide end-to-end solutions tailored for the unique demands of the aerospace industry. We collaborate with our clients to push the boundaries of what’s possible, delivering reliable, flight-ready components that elevate structural performance.
Ready to explore how metal additive manufacturing can optimize your aerospace bracing arms and other critical components? Visit our website at https://met3dp.com/ or contact our expert team today to discuss your specific project requirements.
Sdílet na
MET3DP Technology Co., LTD je předním poskytovatelem řešení aditivní výroby se sídlem v Qingdao v Číně. Naše společnost se specializuje na zařízení pro 3D tisk a vysoce výkonné kovové prášky pro průmyslové aplikace.
Dotaz k získání nejlepší ceny a přizpůsobeného řešení pro vaše podnikání!
Související články
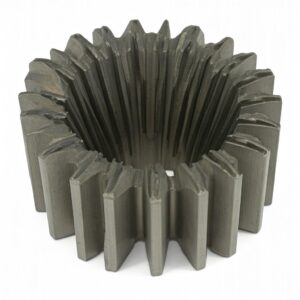
Vysoce výkonné segmenty lopatek trysek: Revoluce v účinnosti turbín díky 3D tisku z kovu
Přečtěte si více "O Met3DP
Nedávná aktualizace
Náš produkt
KONTAKTUJTE NÁS
Nějaké otázky? Pošlete nám zprávu hned teď! Po obdržení vaší zprávy obsloužíme vaši žádost s celým týmem.
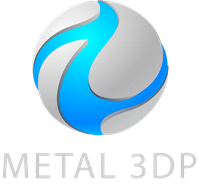
Kovové prášky pro 3D tisk a aditivní výrobu
SPOLEČNOST
PRODUKT
kontaktní informace
- Město Qingdao, Shandong, Čína
- [email protected]
- [email protected]
- +86 19116340731