3D tisk držáků senzorů pro elektromobily a autonomní vozidla
Obsah
Automobilový průmysl prochází seismickou změnou, kterou způsobuje dvojí revoluce v podobě elektrifikace (EV) a autonomního řízení. Tyto pokroky vyžadují vozidla vybavená sofistikovanými senzory - LiDAR, RADAR, kamery, ultrazvuk - neustále vnímajícími okolí. Zajištění optimální funkce těchto senzorů vyžaduje robustní, přesná a často složitá montážní řešení: držáky senzorů. Tyto držáky, tradičně vyráběné metodami jako CNC obrábění, odlévání nebo lisování, čelí stále větším výzvám souvisejícím s komplexností konstrukce, optimalizací hmotnosti a rychlými vývojovými cykly, které vyžaduje moderní automobilový průmysl. Zde se uplatní aditivní výroba kovů (AM), běžně známá jako kovová aditivní výroba (AM) 3D tisk, se stává transformativní technologií.
3D tisk z kovu nabízí bezkonkurenční svobodu při navrhování a umožňuje vytvářet složité, topologicky optimalizované a lehké držáky senzorů, které jsou běžnými metodami jednoduše nerealizovatelné. Pro elektrická vozidla (EV) je pro prodloužení dojezdu nejdůležitější odlehčení a společnost AM dodává komponenty s výjimečným poměrem pevnosti a hmotnosti. V oblasti autonomních vozidel (AV) vytváří obrovské množství a rozmanitost senzorů, z nichž každý vyžaduje přesné umístění a stabilitu, složité problémy s balením, které může AM elegantně vyřešit prostřednictvím konsolidace dílů a přizpůsobené geometrie. Tato technologie umožňuje automobilovým inženýrům a manažerům nákupu přejít od konceptu k funkčnímu prototypu a sériové výrobě rychleji než kdykoli předtím, urychlit inovační cykly a získat konkurenční výhodu.
Tento komplexní průvodce se zabývá specifiky použití kovového 3D tisku pro držáky automobilových senzorů se zaměřením na aplikace v rychle se rozvíjejícím odvětví elektromobilů a autonomních vozidel. Prozkoumáme funkční požadavky, výrazné výhody, které AM nabízí oproti tradiční výrobě, vhodné vysoce výkonné materiály, jako jsou slitiny hliníku (konkrétně AlSi10Mg a A7075), kritické aspekty návrhu (DfAM), dosažitelné úrovně přesnosti, nezbytné kroky následného zpracování, potenciální problémy a pokyny pro výběr správného výrobního partnera. Ať už jste inženýr, který navrhuje systémy ADAS nové generace, manažer nákupu, který hledá spolehlivé dodavatele automobilových komponent, nebo výrobní specialista zkoumající pokročilé výrobní techniky, pochopení možností kovové AM pro držáky senzorů je pro orientaci v budoucnosti automobilového inženýrství klíčové. Společnosti jako např Met3dp, která se specializuje na pokročilé kovové prášky a tiskové systémy, stojí v čele a umožňuje tento přechod k efektivnějším, přizpůsobeným a vysoce výkonným automobilovým součástem.
Kritické funkce: K čemu se používají držáky automobilových senzorů?
Držáky automobilových senzorů se mohou zdát jako jednoduché komponenty, ale hrají klíčovou roli ve funkčnosti a bezpečnosti moderních vozidel, zejména elektromobilů a vozidel vybavených pokročilými asistenčními systémy řidiče (ADAS) a funkcemi plné autonomie. Jejich hlavním úkolem je bezpečně upevnit, přesně umístit, chránit a někdy i tepelně řídit rozmanitou škálu senzorů integrovaných v celém vozidle. Spolehlivost a přesnost údajů zachycených těmito snímači přímo závisí na stabilitě a správné orientaci, kterou zajišťují jejich držáky.
Klíčové funkce a aplikace:
- Bezpečné upevnění: Nejzásadnějším úkolem je pevné připevnění snímačů k podvozku, karoserii, nárazníku, mřížce chladiče, střešní linii nebo vnitřním konstrukcím vozidla. Držák musí odolávat neustálým vibracím, nárazům a namáhání okolním prostředím, ke kterému dochází během provozu vozidla, aniž by se uvolnil nebo selhal. Selhání by mohlo vést k chybnému nastavení snímače, jeho nesprávné funkci nebo úplnému odpojení.
- Přesné polohování a zarovnání: Systémy ADAS a autonomní řízení se spoléhají na senzory s přesným a pevným zorným polem. Skenery LiDAR potřebují stabilní platformy pro přesné generování mračna bodů, jednotky RADAR vyžadují specifické úhly pro detekci a sledování cílů a kamery potřebují přesné nastavení pro zpracování obrazu, udržování jízdních pruhů a rozpoznávání objektů. Držáky snímačů jsou navrženy tak, aby udržovaly tyto kritické orientace po celou dobu životnosti vozidla, a často obsahují funkce pro přesné nastavení zarovnání během montáže nebo servisu. Dokonce i drobné nesouososti mohou výrazně zhoršit výkonnost a bezpečnost systému.
- Ochrana životního prostředí: Senzory, zejména ty, které jsou namontovány externě, jsou vystaveny nepříznivým podmínkám: vlhkosti, nečistotám, úlomkům, kamenným úlomkům, extrémním teplotám a čisticím chemikáliím. Držáky často tvoří součást krytu snímače nebo fungují ve spojení s dalšími ochrannými prvky, aby chránily citlivou elektroniku a optiku před poškozením nebo znečištěním. K této ochranné funkci významně přispívá výběr materiálu (např. korozivzdorné hliníkové slitiny) a konstrukce.
- Tlumení vibrací: Při provozu vozidla vznikají vibrace, které mohou negativně ovlivnit výkon a životnost snímače. Držáky snímačů mohou být navrženy tak, aby někdy obsahovaly specifickou geometrii nebo materiály, které tlumí nebo izolují snímač od škodlivých frekvencí a zajišťují čistší signály a nižší mechanické namáhání.
- Tepelný management: Některé senzory během provozu vytvářejí teplo nebo jsou namontovány v blízkosti zdrojů tepla, jako jsou pohonné jednotky nebo elektronika. Držáky vyrobené z tepelně vodivých materiálů, jako jsou hliníkové slitiny, mohou pomoci odvádět teplo pryč od snímače, čímž se zabrání jeho přehřátí a zajistí stabilní provoz ve stanoveném teplotním rozsahu. To je důležité zejména v hustě osazených elektronických architekturách elektromobilů.
- Integrace a balení: V moderních vozidlech je místa málo. Držáky snímačů usnadňují integraci snímačů do složitých sestav, často se pohybují ve stísněných prostorech a pojmou kabelové svazky a konektory. Technologie AM pro kovy umožňuje vytvářet vysoce přizpůsobené tvary, které se dokonale vejdou do dostupné konstrukční obálky, a případně sloučit více montážních bodů nebo prvků do jediného tištěného dílu.
Specifické typy snímačů a požadavky na držáky:
- LiDAR (Light Detection and Ranging): Často vyžaduje velké a stabilní držáky, které jsou schopné unést hmotnost snímače a udržet přesnou úhlovou orientaci pro snímání v rozsahu 360 stupňů. Pro přesnost mračna bodů je rozhodující tlumení vibrací. Držáky lze namontovat na střechu, mřížku nebo blatníky.
- RADAR (radiová detekce a měření vzdálenosti): Potřebuje držáky, které zajišťují správné zaměření (azimut a elevaci) a jsou často integrovány za mřížkami nebo nárazníky. Materiál držáku nesmí rušit přenos rádiových vln (i když u kovových držáků namontovaných na držáku je to menší problém) za nekovové fasády). Stabilita je klíčová pro adaptivní tempomat a prevenci kolize.
- Kamery (viditelné, infračervené): Vyžadují extrémně stabilní montáž, aby se zabránilo chvění obrazu, které ovlivňuje varování před opuštěním jízdního pruhu, rozpoznávání dopravních značek a autonomní navigaci. Držáky jsou často umístěny za čelním sklem, v bočních zrcátkách, mřížkách nebo náraznících a vyžadují přesné zarovnání.
- Ultrazvukové senzory: Tyto snímače, které se obvykle používají pro asistenci při parkování a detekci objektů na krátkou vzdálenost, se často montují do nárazníků. Držáky je musí pevně držet v jedné rovině s povrchem nárazníku, chránit je před menšími nárazy a zároveň umožnit účinné šíření akustických vln.
- Inerciální měřicí jednotky (IMU): Tyto snímače (gyroskopy, akcelerometry) mají zásadní význam pro dynamiku vozidla a autonomní navigaci. Jejich držáky musí zajistit pevné a od vibrací izolované spojení s podvozkem vozidla pro přesné snímání pohybu.
Rostoucí složitost a počet senzorů v elektromobilech a AV vyvolává potřebu sofistikovanějších, lehčích a na míru navržených držáků. Manažeři veřejných zakázek, kteří hledají spolehlivá řešení pro montáž senzorů, a velkoobchodní dodavatelé automobilových dílů si musí uvědomit rostoucí poptávku po držácích, které splňují tyto pokročilé požadavky, jež často nejlépe řeší technologie, jako je 3D tisk z kovu.
Proč zvolit 3D tisk z kovu pro výrobu držáků senzorů?
Zatímco tradiční výrobní metody, jako je CNC obrábění, výroba plechů (lisování a ohýbání) a odlévání, se již dlouho používají pro výrobu automobilových držáků, aditivní výroba kovů představuje přesvědčivý soubor výhod, zejména pro složité, přizpůsobené a výkonné držáky senzorů, které jsou vyžadovány u elektromobilů a autonomních vozidel. Volba kovové AM může vést k významnému zlepšení designu, výkonu, rychlosti výroby a efektivity dodavatelského řetězce.
Klíčové výhody AM kovu pro držáky senzorů:
- Bezkonkurenční volnost designu & Komplexnost:
- Optimalizace topologie: Algoritmy mohou na základě průběhu zatížení přepracovat konstrukci konzol a odstranit nepotřebný materiál při zachování konstrukční integrity. Výsledkem jsou vysoce organické, lehké tvary, které nelze ekonomicky opracovat ani odlít. U držáků snímačů to znamená minimální zvýšení hmotnosti vozidla (což je pro dojezd elektromobilu zásadní) bez snížení tuhosti.
- Konsolidace částí: Více součástí sestavy držáku (např. držák, rameno, upevňovací prvky) lze potenciálně přepracovat a vytisknout jako jediný komplexní díl. Tím se sníží počet dílů, doba montáže, potenciální místa poruchy a celková hmotnost.
- Vnitřní kanály a složité geometrie: Pomocí AM lze vytvářet držáky s vnitřními chladicími kanály (pro senzory generující teplo), integrované kabelové trasy nebo složité mřížkové struktury pro optimální poměr tuhosti a hmotnosti. Tyto vlastnosti jsou obtížné nebo nemožné při použití subtraktivních (obrábění) nebo formovacích (odlévání, lisování) metod.
- Rychlé prototypování a iterace:
- Rychlost: Funkční kovové prototypy držáků snímačů lze vyrobit během několika dnů namísto týdnů nebo měsíců, které jsou často nutné pro nastavení nástrojů při odlévání nebo složité programování CNC.
- Flexibilita: Na základě zpětné vazby z testování lze návrhy rychle upravit a znovu vytisknout, aniž by vznikly značné náklady na nové zpracování. To urychluje vývojový cyklus pro nové integrace senzorů do elektromobilů a AV a umožňuje inženýrům rychle iterovat návrhy pro optimální umístění a výkon senzorů.
- Odlehčení:
- Jak již bylo zmíněno, optimalizace topologie a použití přirozeně pevných, ale lehkých materiálů, jako jsou hliníkové slitiny (AlSi10Mg, A7075), umožňují výrazně snížit hmotnost ve srovnání s tradičně navrženými a vyrobenými držáky. Každý ušetřený gram přispívá k lepší účinnosti a ovladatelnosti vozidla a v případě elektromobilů k prodloužení dojezdu.
- Přizpůsobení a malosériová výroba:
- Výroba na vyžádání: AM je ideální pro výrobu držáků přizpůsobených konkrétním modelům vozidel, typům snímačů nebo montážním místům bez nutnosti použití speciálních nástrojů. To je výhodné pro specifické platformy vozidel, řešení pro trh s náhradními díly nebo přizpůsobení se variacím hardwaru snímačů.
- Úsporné malé šarže: Výroba malých až středních objemů (desítky až tisíce kusů) konzol pomocí AM může být nákladově efektivnější než tradiční metody, které často spoléhají na úspory z rozsahu spojené s vysokými náklady na nástroje. To dobře odpovídá často nižším počátečním objemům pro specializované modely elektromobilů nebo autonomní testovací flotily.
- Výkonnost materiálu:
- Metal AM využívá vysoce výkonné technické materiály, včetně doporučených slitin hliníku AlSi10Mg a A7075, které nabízejí vynikající pevnost, trvanlivost, odolnost proti korozi a tepelné vlastnosti vhodné pro náročné prostředí automobilového průmyslu. Společnosti specializující se na 3D tisk z kovu, jako je Met3dp, poskytují přístup k široké škále certifikovaných prášků optimalizovaných pro tyto aplikace.
- Výhody dodavatelského řetězce pro B2B:
- Zkrácené dodací lhůty: V porovnání s pořizováním složitých obráběných dílů nebo čekáním na odlévací nástroje může AM výrazně zkrátit dodací lhůty pro prototypy i výrobní díly, čímž se zlepší rychlost reakce automobilových výrobců OEM a dodavatelů Tier 1.
- Decentralizovaná výroba: Digitální návrhové soubory lze elektronicky zasílat certifikovaným poskytovatelům služeb AM po celém světě, což umožňuje lokalizovat výrobu blíže k montážním linkám, snížit náklady na dopravu a logistické komplikace.
- Snížení závislosti na nástrojích: Eliminace potřeby drahého a časově náročného nástrojového vybavení snižuje rizika dodavatelského řetězce spojená s poškozením nástroje, údržbou nebo zablokováním dodavatele. Tisk na vyžádání poskytuje větší flexibilitu.
Srovnávací tabulka: AM vs. tradiční metody pro držáky snímačů
Vlastnosti | Kovové AM (např. PBF) | CNC obrábění | Odlévání (např. tlakové lití) | Lisování/ohýbání plechů |
---|---|---|---|---|
Složitost návrhu | Velmi vysoká (vnitřní kanály, mřížky) | Vysoká (omezená přístupem k nástrojům) | Středně těžký (vyžadován návrh úhlů) | Nízká až střední |
Odlehčení | Vynikající (optimalizace topologie) | Dobrý (odstranění materiálu) | Fair (minimální tloušťka stěny) | Fair (výběr materiálu) |
Konsolidace částí | Vysoký potenciál | Nízký | Mírný | Nízký |
Rychlost prototypování | Velmi rychle (dny) | Mírná (dny/týdny) | Pomalé (týdny/měsíce – výroba nástrojů) | Středně těžká (závisí na nástroji) |
Náklady na nástroje | Žádný | Nízká (může být zapotřebí příslušenství) | Vysoká (Dies) | Vysoká (Dies) |
Ekonomika nízkých objemů | Dobrý | Mírný | Špatný | Špatný |
Materiálový odpad | Nízká (opětovné použití prášku) | Vysoká (subtraktivní) | Středně těžká (brány/běžci) | Mírná (odřezky) |
Možnosti materiálu | Rostoucí rozsah (Al, Ti, ocel atd.) | Široký rozsah | Dobrý rozsah (Al, Zn, Mg) | Široký rozsah (listová forma) |
Dodací lhůta (výroba) | Rychlý až středně rychlý | Mírný | Mírný až pomalý | Mírný |
Export do archů
Zatímco tradiční metody jsou i nadále vhodné pro velmi velkosériovou výrobu jednoduchých konstrukcí držáků, kde jsou náklady na díl naprosto zásadní, metoda AM nabízí přesvědčivou hodnotu pro stále složitější, výkonově kritické a rychle se vyvíjející držáky senzorů, které jsou nedílnou součástí moderní automobilové technologie, zejména pro velkoodběratele, dodavatele Tier 1 a výrobce OEM zaměřené na inovace v oblasti elektromobilů a autonomních vozidel.
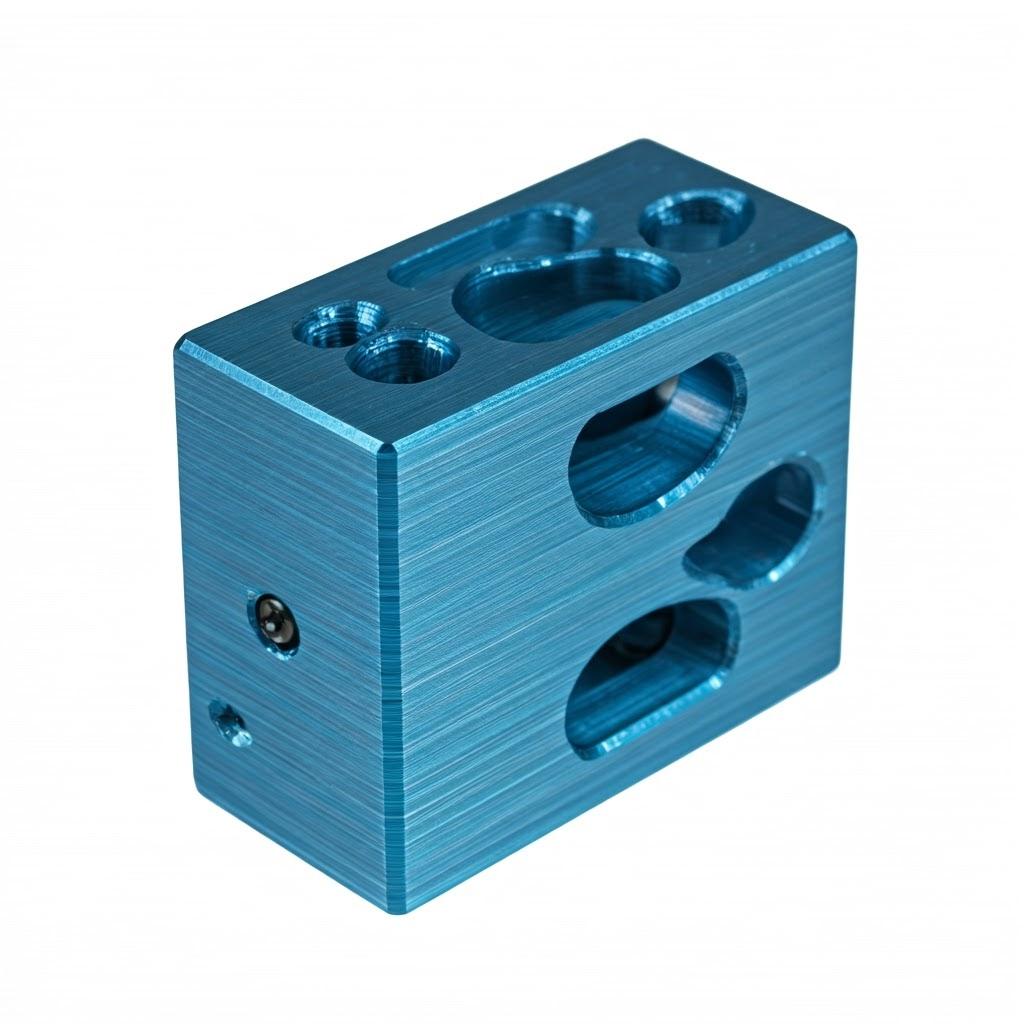
Výběr materiálu: AlSi10Mg a slitiny hliníku A7075
Výběr správného materiálu je zásadní pro výkon, trvanlivost a nákladovou efektivitu jakékoli vyráběné součásti a 3D tištěné držáky automobilových senzorů nejsou výjimkou. Pro aplikace v elektromobilech a autonomních vozidlech musí materiály často vyvažovat pevnost, nízkou hmotnost, odolnost proti korozi, tepelnou vodivost a zpracovatelnost prostřednictvím aditivní výroby. Pro tyto aplikace jsou často upřednostňovány hliníkové slitiny, přičemž AlSi10Mg a A7075 se jeví jako obzvláště relevantní volba pro kovovou AM. Pochopení jejich odlišných vlastností je klíčové pro inženýry a specialisty na nákupy, kteří se rozhodují o materiálu.
AlSi10Mg: Všestranný pracovní kůň
AlSi10Mg je jednou z nejběžnějších a nejlépe charakterizovaných hliníkových slitin používaných v procesech tavení kovového prášku (PBF), jako je selektivní laserové tavení (SLM) a přímé laserové spékání kovů (DMLS). Je to v podstatě slitina hliníkových odlitků upravená pro aditivní výrobu.
- Složení: Převážně hliník (Al) s významným množstvím křemíku (Si, cca 9-11 %) a hořčíku (Mg, cca 0,2-0,45 %). Křemík zlepšuje tekutost a odlévatelnost (výhodné pro tavení/tuhnutí v AM), zatímco hořčík umožňuje precipitační kalení tepelným zpracováním.
- Klíčové vlastnosti:
- Dobrý poměr pevnosti a hmotnosti: Nabízí slušnou mechanickou pevnost, zejména po vhodném tepelném zpracování, v kombinaci s nízkou hustotou, která je hliníku vlastní. Ideální pro odlehčování elektrických vozidel.
- Vynikající odolnost proti korozi: Vytváří pasivní oxidovou vrstvu, která poskytuje dobrou ochranu proti atmosférické korozi, což je zásadní pro držáky vystavené povětrnostním vlivům.
- Dobrá tepelná vodivost: Pomáhá odvádět teplo od senzorů nebo okolní elektroniky a přispívá tak ke strategiím tepelného managementu.
- Vynikající zpracovatelnost v AM: Široce dostupný jako prášek s dobře zavedenými parametry tisku, které vedou k relativně vysoké spolehlivosti a opakovatelnosti v systémech PBF. Obecně vykazuje dobrou svařitelnost během procesu tavení po vrstvách.
- Možnosti následného zpracování: Dobře reaguje na standardní kroky následného zpracování, jako je uvolnění napětí, tepelné zpracování T6 (rozpuštění a umělé stárnutí) pro výrazné zlepšení mechanických vlastností (mez kluzu, pevnost v tahu, tvrdost), obrábění a povrchová úprava.
- Typické aplikace pro držáky senzorů: Vhodné pro širokou škálu držáků, u nichž je vyžadována dobrá rovnováha mezi pevností, hmotností, cenou a odolností vůči životnímu prostředí. Často se používá pro držáky podpírající kamery, ultrazvukové senzory a některé jednotky RADAR, kde není primární extrémní pevnost.
A7075 (hliníková slitina 7075): Vysoce odolný soupeř
A7075 je vysoce výkonná hliníková slitina známá svou výjimečnou pevností, srovnatelnou s mnoha ocelemi, ale s výrazně nižší hustotou. Tradičně se používá v leteckém průmyslu a ve vysoce namáhaných konstrukčních aplikacích, jeho adaptace pro aditivní výrobu je novější a náročnější než u AlSi10Mg, ale nabízí významné výkonnostní výhody. Primárním legujícím prvkem je zinek (Zn), dále hořčík (Mg) a měď (Cu).
- Klíčové vlastnosti:
- Velmi vysoký poměr pevnosti k hmotnosti: Výrazně vyšší mez kluzu a pevnost v tahu než AlSi10Mg, zejména po tepelném zpracování (např. stav T6). To umožňuje ještě lehčí konstrukce držáků při stejné nosnosti nebo vytváření držáků pro vysoce namáhané aplikace.
- Vynikající únavová pevnost: Odolává poruchám při cyklickém zatížení, což je důležité pro součásti vystavené stálým vibracím vozidla.
- Dobrá obrobitelnost: Přestože je pevný, lze jej v tepelně zpracovaném stavu dobře obrábět pro kritické toleranční prvky.
- Výzvy v oblasti zpracovatelnosti AM: A7075 je notoricky známý tím, že je obtížné jej spolehlivě zpracovávat pomocí laserové PBF kvůli širokému rozsahu tuhnutí a náchylnosti k praskání při tuhnutí (praskání za tepla) a pórovitosti. Vyžaduje pečlivě kontrolované procesní parametry, specializované možnosti strojů a často modifikované složení slitiny nebo strategie zpracování (např. použití specifických parametrů laseru nebo vyhřívaných stavebních plošin). Výhodou může být tavení elektronovým svazkem (EBM) nebo novější laserové techniky.
- Odolnost proti korozi: Obecně nižší obecná odolnost proti korozi ve srovnání s AlSi10Mg, zvláště náchylné k praskání pod napětím (SCC) v určitých prostředích, pokud nejsou řádně tepelně zpracovány a chráněny (např. eloxováním nebo lakováním). Důležitá je pečlivá konstrukce a následné zpracování.
- Typické aplikace pro držáky senzorů: Nejlépe se hodí pro vysoce zatížené nebo bezpečnostně kritické držáky senzorů, kde je nejdůležitější maximální pevnost a tuhost a kde je rozhodující úspora hmotnosti. Příkladem jsou držáky pro těžké jednotky LiDAR, konstrukční montážní body pro klastry senzorů nebo komponenty vystavené značnému dynamickému zatížení, pokud lze spolehlivě překonat problémy při zpracování AM.
Srovnávací tabulka materiálů:
Vlastnictví | AlSi 10Mg | A7075 (zpracováno AM) | Význam pro držáky senzorů |
---|---|---|---|
Primární legující prvky | Si, Mg | Zn, Mg, Cu | Vlivy na základní vlastnosti a reakce na tepelné zpracování. |
Hustota | ~2,67 g/cm³ | ~2,81 g/cm³ | Oba jsou lehké; A7075 o něco hustší, ale mnohem pevnější. |
Typická mez kluzu (T6) | ~230-280 MPa | ~450-500+ MPa | A7075 nabízí výrazně vyšší pevnost pro náročná zatížení. |
Typická pevnost v tahu (T6) | ~300-350 MPa | ~520-570+ MPa | Vyšší pevnost v tahu znamená lepší odolnost proti porušení v tahu. |
Elastický modul | ~70 GPa | ~71 GPa | Podobná tuhost; konstrukce zde určuje tuhost více než materiál. |
Odolnost proti korozi | Dobrý až výborný | Slušný (náchylný k SCC, pokud není ošetřen) | AlSi10Mg je vhodnější pro běžnou expozici; A7075 vyžaduje ochranu. |
Tepelná vodivost | Dobrý (~130-150 W/m-K) | Dobrý (~130 W/m-K) | Obě jsou vhodné pro mírné potřeby odvodu tepla. |
Zpracovatelnost AM (L-PBF) | Vynikající / dobře zavedený | Náročné (vyžaduje odborné znalosti/kontrolu) | AlSi10Mg se v současnosti tiskne snadněji a spolehlivěji. |
Relativní náklady | Dolní | Vyšší (Prášek & amp; Zpracování) | A7075 je vzhledem k obtížnosti a výkonu dražší. |
Export do archů
Využití vysoce kvalitních prášků:
Konečná kvalita a výkonnost 3D tištěného držáku senzoru do značné míry závisí na kvalitě použitého kovového prášku. Získávání prášků s kontrolovanou distribucí velikosti částic (PSD), vysokou sféricitou, dobrou tekutostí a nízkým obsahem kyslíku/nečistot je klíčové pro dosažení hustých dílů bez vad s konzistentními mechanickými vlastnostmi.
Firmy jako Met3dp se specializuje na výrobu vysoce výkonných kovových prášků pro aditivní výrobu s využitím pokročilých technik, jako je vakuová indukční tavná plynová atomizace (VIGA) a plazmový proces s rotační elektrodou (PREP). Jejich odborné znalosti zajišťují, že prášky jako AlSi10Mg a případně specializované varianty vhodné pro vysokopevnostní aplikace splňují přísné požadavky automobilového průmyslu. Při výběru poskytovatele AM služeb nebo při přímém nákupu prášků je pro spolehlivou výrobu kritických součástí, jako jsou držáky senzorů, nezbytné ověřit kvalitu prášku, certifikaci a sledovatelnost. Spolupráce s dodavateli, kteří prokazují přísnou kontrolu kvality svého pokročilé systémy pro výrobu prášku zajišťuje základ pro úspěšnou složku AM.
Souhrnně lze říci, že AlSi10Mg i A7075 nabízejí přesvědčivé vlastnosti pro 3D tištěné držáky automobilových senzorů. AlSi10Mg poskytuje robustní, nákladově efektivní a snadno zpracovatelné řešení pro mnoho aplikací. A7075 poskytuje vynikající pevnost pro nejnáročnější scénáře, i když s větší složitostí zpracování a vyššími náklady. Optimální volba závisí na konkrétních požadavcích na výkon, podmínkách zatížení, provozním prostředí a proveditelnosti výroby pro cílovou aplikaci držáku snímače v kontextu elektromobilů a autonomních vozidel. Zdroje a související obsah
Design pro aditivní výrobu (DfAM): Optimalizace držáků senzorů pro 3D tisk
Pouhým převzetím návrhu držáku snímače určeného pro obrábění CNC nebo odlévání a jeho odesláním na kovovou 3D tiskárnu se málokdy dosáhne optimálního výsledku. Aby inženýři skutečně využili výhod aditivní výroby - odlehčení, konsolidace dílů, zvýšení výkonu a nákladové efektivity - musí přijmout návrh pro aditivní výrobu (DfAM). DfAM je filozofie a soubor metodik zaměřených na navrhování součástí speciálně pro jedinečné možnosti a omezení AM procesů, jako je například Powder Bed Fusion (PBF). Pro automobilové držáky senzorů je použití zásad DfAM rozhodující pro úspěch, zejména pokud se zaměřují na náročné aplikace v elektrických a autonomních vozidlech.
Myšlení DfAM: Aditivní myšlení
Namísto subtraktivního (odebírání materiálu) nebo formativního (tvarování materiálu ve formě) podporuje DfAM inženýry v přemýšlení po vrstvách. To zahrnuje zvažování faktorů, jako je orientace konstrukce, požadavky na podpůrnou konstrukci, tepelné řízení během konstrukce a možnost vytváření složitých vnitřních a vnějších prvků, které dříve nebyly možné. Cílem není pouze replikovat existující konzolu, ale nově ji vytvořit pro lepší výkon a vyrobitelnost pomocí AM.
Klíčové principy DfAM pro kovové držáky senzorů AM:
- Strategie orientace na budování:
- Dopad: Orientace dílu na konstrukční platformě významně ovlivňuje kvalitu povrchu (povrchy směřující nahoru a dolů), množství a umístění potřebných podpůrných struktur, potenciální anizotropii (směrové změny mechanických vlastností), akumulaci zbytkových napětí a celkovou dobu a náklady na konstrukci.
- Úvahy o závorkách: Orientace kritických montážních ploch nebo prvků, které vyžadují vysokou přesnost, směrem nahoru může minimalizovat schodovitý efekt a snížit potřebu dodatečného obrábění. To však může zvýšit potřebu podpěr na jiných místech. Minimalizace výšky dílu (osa Z) obecně zkracuje dobu tisku. Orientace za účelem snížení velkých ploch průřezu na jednu vrstvu může zmírnit tepelné namáhání. Často je zapotřebí kompromisu, který vyvažuje kvalitu povrchu, potřeby podpor a mechanické vlastnosti.
- Minimalizace a návrh podpůrné struktury:
- Nezbytnost: Kovové PBF vyžadují podpěrné konstrukce pro převisy a mosty, které přesahují určitý samonosný úhel (obvykle kolem 45 stupňů u hliníkových slitin, i když závisí na procesu). Podpěry ukotvují díl ke stavební desce, zabraňují jeho deformaci a odvádějí teplo z převisů.
- Přístup DfAM: Hlavním cílem je minimalizovat potřebujete pro podpěry navrhováním prvků se samonosnými úhly, kdekoli je to možné. Tam, kde se podpěrám nelze vyhnout, by měly být navrženy:
- Snadná demontáž: Začlenění bodů pro vylomení, použití podpěrných konstrukcí s nižší hustotou, zajištění přístupu k nástroji pro demontáž.
- Minimální zjizvení povrchu: Optimalizace styčných bodů mezi podpěrou a dílem.
- Efektivní přenos tepla: Zajištění podpěr, které dostatečně zabraňují přehřátí a deformaci převisů.
- Příklad závorky: Namísto ostrého 90stupňového přesahu montážní příruby ji navrhněte se 45stupňovým zkosením nebo koutem. Kulaté nebo slzovité tvary vodorovných otvorů mohou často zajistit jejich samonosnost.
- Optimalizace topologie a generativní návrh:
- Koncept: Jedná se o výkonné výpočetní nástroje, které optimalizují rozložení materiálu v definovaném návrhovém prostoru s ohledem na zatěžovací podmínky a omezení. Optimalizace topologie odstraňuje materiál z oblastí s nízkým namáháním a zanechává často organicky vypadající nosnou konstrukci. Generativní návrh zkoumá více konstrukčních řešení na základě výkonnostních kritérií.
- Aplikace na závorky: Ideální pro odlehčení držáků senzorů při zachování nebo dokonce zvýšení tuhosti. Inženýři definují montážní body, ochranné zóny (kde se senzor nachází nebo kudy procházejí vodiče) a působící zatížení (vibrace, statická hmotnost, rázy). Software poté vygeneruje optimalizovanou geometrii držáku, čímž se často dosáhne snížení hmotnosti o 30-70 % ve srovnání s tradičními návrhy. To je nesmírně výhodné pro dojezd elektromobilu a celkovou dynamiku vozidla.
- Mřížové struktury:
- Definice: Inženýrské porézní struktury složené z opakujících se jednotkových buněk. Lze je integrovat do konstrukcí pevných dílů.
- Výhody pro závorky:
- Extrémní odlehčení: Vyplnění méně kritických objemů držáku mřížkovou strukturou výrazně snižuje hmotnost a spotřebu materiálu.
- Tlumení vibrací: Určité geometrie mřížek mohou být navrženy tak, aby absorbovaly nebo tlumily vibrace, což může zlepšit kvalitu a životnost signálu ze snímače.
- Tuhost na míru: Umožňuje nastavení tuhosti držáku v různých směrech.
- Výzvy: Může být obtížné odstranit prášek ze složitých vnitřních mřížek; vyžaduje pečlivou simulaci pro zajištění strukturální integrity.
- Tloušťka stěny a velikost prvků:
- Minimální požadavky: Procesy AM mají omezení minimální tloušťky stěny a velikosti prvku, které mohou spolehlivě vyrobit (často kolem 0,4-0,8 mm, v závislosti na stroji a parametrech). Konstrukce pod těmito limity může vést k neúplným prvkům nebo k selhání.
- Optimalizace: Tenké stěny sice šetří hmotnost, ale mohou být náchylné k deformaci nebo poškození. DfAM zahrnuje nalezení správné rovnováhy - použití silnějších profilů tam, kde je vysoké namáhání, a tenčích profilů jinde, často na základě výsledků optimalizace topologie. Doporučují se plynulé přechody mezi silnými a tenkými úseky, aby se snížila koncentrace napětí.
- Design otvorů:
- Malé otvory: Velmi malé vertikální otvory se někdy mohou samy uzavřít v důsledku dynamiky taveniny. Minimální doporučené průměry se často pohybují kolem 0,5-1,0 mm.
- Vodorovné otvory: Náchylné k poklesu nebo vyžadující vnitřní podpěry. Konstrukce ve tvaru slzy nebo kosočtverce umožňuje, aby horní část byla samonosná.
- Závitové otvory: Vlákna lze sice někdy tisknout přímo, ale často jim chybí potřebná přesnost a pevnost. Standardním postupem DfAM je tisk pilotních otvorů a jejich následné závitování při následném zpracování (obrábění).
- Konsolidace částí:
- Cíl: Snížení počtu komponent v sestavě jejich přepracováním do jediného integrovaného dílu AM.
- Příklad držáku senzoru: Namísto držáku vyrobeného z několika lisovaných, obráběných nebo odlévaných dílů sešroubovaných dohromady by DfAM mohl umožnit výrobu jediného tištěného dílu, který by obsahoval držák snímače, body pro upevnění k šasi a možná i prvky pro vedení kabelů nebo odvod tepla. Tím se sníží pracnost montáže, skladové zásoby, hmotnost a potenciální místa poruch.
- Úvahy o tepelném managementu při návrhu:
- Výzva: Velké rovné plochy tištěné rovnoběžně s konstrukční deskou nebo náhlé změny průřezu mohou vést k nadměrnému zahřívání a zbytkovému napětí, které může způsobit deformace nebo praskání.
- DfAM Solutions: Pokud je to možné, vyhněte se velkým plochým základnám, použijte žebra nebo vlnovky k vyztužení tenkých profilů, zajistěte plynulé přechody v geometrii a strategicky orientujte díl (jak je uvedeno v bodě 1). Simulační nástroje mohou předvídat tepelné chování a řídit úpravy konstrukce.
Spolupráce a nástroje:
Efektivní DfAM často vyžaduje specializované softwarové nástroje (např. nTopology, Altair Inspire, Autodesk Fusion 360 generative design) a především spolupráci mezi konstruktérem a specialisty na výrobu AM nebo poskytovatelem služeb. Zkušený partner v oblasti AM, jako je Met3dp, může poskytnout neocenitelnou zpětnou vazbu ohledně vyrobitelnosti návrhu, navrhnout optimalizace na základě jejich specifického tiskových metod a schopnosti strojů a pomáhají vyhnout se možným úskalím. U složitých komponent, jako jsou držáky senzorů, se doporučuje spolupracovat s dodavatelem AM již na počátku procesu návrhu. Manažeři veřejných zakázek by měli hledat dodavatele, kteří v rámci svých služeb nabízejí podporu DfAM.
Uplatněním těchto principů DfAM mohou automobilové společnosti využívat technologii AM pro výrobu lehčích, pevnějších, funkčnějších a rychleji vyvinutých držáků senzorů, čímž získají významnou výhodu na konkurenčním trhu elektromobilů a autonomních vozidel.
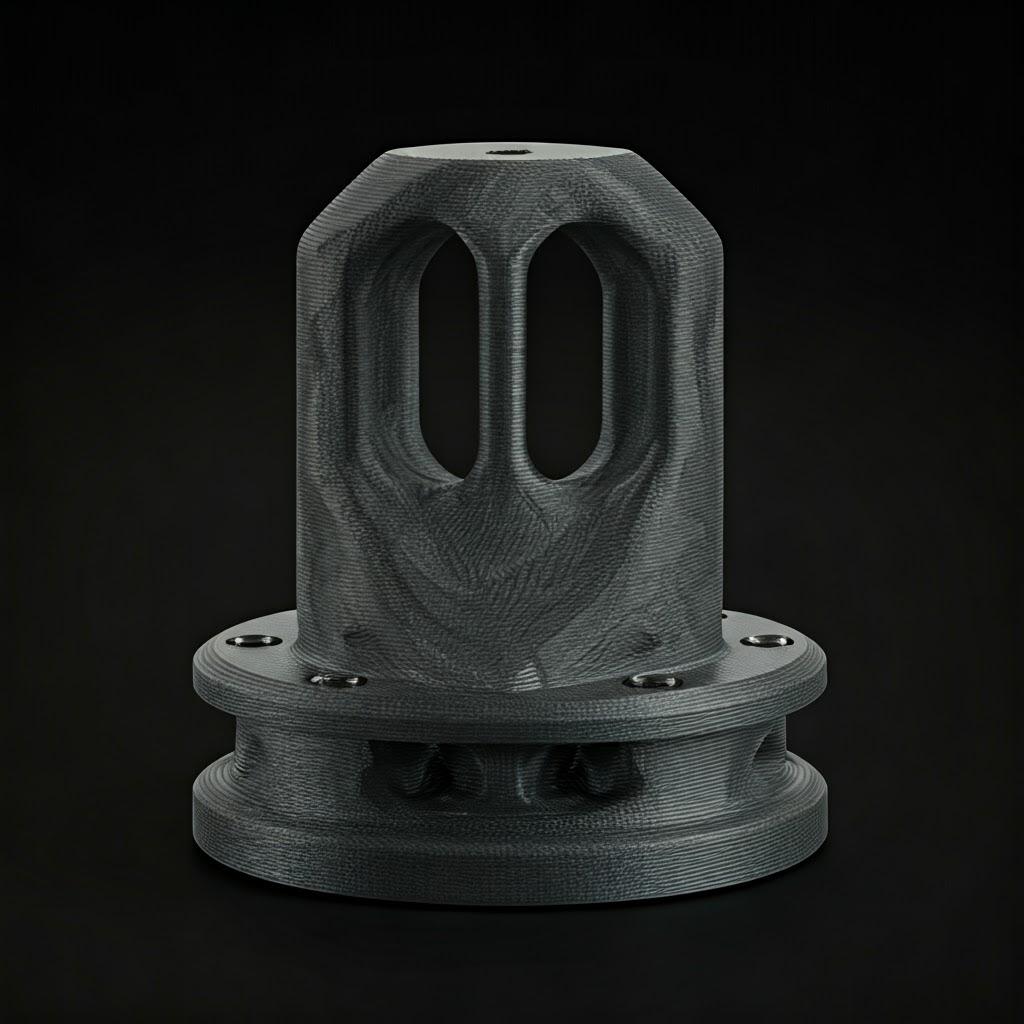
Dosažení přesnosti: Tolerance, povrchová úprava a rozměrová přesnost v AM konzolách: tolerance, povrchová úprava a rozměrová přesnost v AM konzolách
Přestože aditivní výroba kovů nabízí neuvěřitelnou volnost při navrhování, častá otázka inženýrů a manažerů nákupu se týká dosažitelné úrovně přesnosti. Mohou kovové držáky senzorů vytištěné 3D tiskem splňovat přísné tolerance a požadavky na povrchovou úpravu, které jsou u automobilových komponent často nutné, zejména pro přesné nastavení senzorů a propojení s jinými díly? Pochopení pojmů tolerance, povrchová úprava a rozměrová přesnost spolu s faktory, které je v případě kovové AM ovlivňují, je klíčové.
Definice pojmů:
- Rozměrová přesnost: Jak přesně se rozměry vytištěného dílu shodují se jmenovitými rozměry uvedenými v modelu CAD. Často se vyjadřuje jako procentuální odchylka (např. ±0,1 %) nebo absolutní odchylka (např. ±0,1 mm).
- Tolerance: Přípustný rozsah odchylek pro určitý rozměr. Technické výkresy definují tolerance pro kritické vlastnosti (např. průměry montážních otvorů, rovinnost povrchu rozhraní), aby se zajistilo správné uložení a funkce.
- Drsnost povrchu: Měří strukturu a jemné nerovnosti povrchu dílu. Běžně se kvantifikuje pomocí parametrů jako Ra (aritmetický průměr drsnosti) nebo Rz (průměrná maximální výška profilu). Nižší hodnoty Ra/Rz označují hladší povrchy.
Typické přesné schopnosti kovových PBF (L-PBF):
Pro hliníkové slitiny, jako jsou AlSi10Mg a A7075, zpracovávané metodou laserové fúze v práškovém loži (L-PBF), se typické dosažitelné hodnoty obecně pohybují v následujících rozmezích:
- Rozměrová přesnost:
- Obecná přesnost: Často se uvádí ±0,1 % až ±0,2 % jmenovitého rozměru.
- Minimální přesnost: U malých prvků je často možné dosáhnout absolutní minimální odchylky přibližně ±0,05 mm až ±0,2 mm, což do značné míry závisí na prvku, orientaci a kalibraci stroje.
- Tolerance:
- V původním stavu: Tolerance dosažitelné přímo z tiskárny se obvykle pohybují v rozmezí ISO 2768-m (střední) nebo někdy -f (jemné) pro určité prvky. V závislosti na velikosti a geometrii očekávejte tolerance kolem ±0,1 mm až ±0,5 mm.
- Post-Machined: U kritických prvků, které vyžadují přísnější tolerance (např. uložení ložisek, přesné montážní plochy), se standardně používá následné CNC obrábění. Obráběním lze snadno dosáhnout tolerancí běžných v automobilových aplikacích (např. ±0,01 mm až ±0,05 mm).
- Povrchová úprava (Ra):
- V původním stavu:
- Stěny směřující vzhůru / svislé stěny: Obvykle se pohybují v rozmezí 6 µm až 15 µm Ra.
- Plochy směřující dolů / převislé plochy (podporované): Obecně drsnější v důsledku kontaktních bodů podpory a částečného spékání, často v rozmezí 15 až 25 µm Ra nebo více.
- Boční stěny (vzhledem k nátěrové hmotě): Může zobrazovat linie vrstev.
- Po následném zpracování:
- Tryskání kuličkami: Dokáže zajistit rovnoměrný matný povrch, obvykle 5-10 µm Ra, ale mikroskopicky povrch výrazně nevyhladí.
- Tumbling / hromadné dokončování: Může zlepšit Ra, zejména na vnějších površích a hranách, a to až pod 5 µm Ra.
- Obrábění/leštění: V případě potřeby lze dosáhnout velmi hladkých povrchů s Ra hluboko pod 1 µm.
- V původním stavu:
Faktory ovlivňující přesnost:
Dosažení konzistentní přesnosti a kvality povrchu při AM obrábění kovů je složitou souhrou různých faktorů:
- Systém AM:
- Kalibrace stroje: Pravidelná kalibrace laserů, skenerů (galvanometrů) a pohybových systémů je zásadní.
- Stav stroje: Na konzistenci má vliv opotřebení, čistota optiky a prostředí stavební komory (průtok plynu, hladina kyslíku).
- Typ technologie: Různé procesy AM (L-PBF, EBM, Binder Jetting) mají ze své podstaty různé charakteristiky přesnosti.
- Parametry procesu:
- Tloušťka vrstvy: Tenčí vrstvy obecně umožňují vytvářet jemnější prvky a lepší povrchovou úpravu na šikmých plochách, ale prodlužují dobu vytváření.
- Výkon laseru, rychlost skenování, vzdálenost mezi šrafami: Tyto parametry jádra ovlivňují velikost a stabilitu taveniny, mají vliv na hustotu, strukturu povrchu a zbytkové napětí (které ovlivňuje deformaci). Klíčové jsou optimalizované sady parametrů.
- Strategie skenování: Způsob, jakým laser skenuje jednotlivé vrstvy, ovlivňuje rozložení tepla a napětí.
- Vlastnosti materiálu:
- Kvalita prášku: Konzistentní distribuce velikosti částic, sféricita a tekutost vedou k rovnoměrným vrstvám prášku a předvídatelnému tavení. Nekvalitní prášek může způsobit vady ovlivňující rozměry a povrchovou úpravu.
- Tepelné vlastnosti: Koeficient tepelné roztažnosti a vodivosti ovlivňuje smršťování a deformace během cyklů ohřevu/chlazení.
- Návrh části (DfAM):
- Geometrie: Složité tvary, tenké stěny, velké rovné plochy a ostré přechody mohou být náchylnější k deformaci.
- Orientace: Jak již bylo uvedeno, orientace výrazně ovlivňuje kvalitu povrchu na různých plochách a možnost deformace.
- Podpůrné struktury:
- Strategie: Hustota, kontaktní body a umístění ovlivňují stabilitu dílu během sestavování a kvalitu povrchu po odstranění. Nedostatečná podpora vede k deformaci; příliš husté podpory se obtížně odstraňují a zanechávají výraznější stopy po svědcích.
- Následné zpracování:
- Úleva od stresu: Je to důležité pro minimalizaci deformace po vyjmutí z konstrukční desky. Nedůsledné tepelné zpracování může samo o sobě způsobit deformaci.
- Odstranění podpory: Při neopatrném odstraňování může dojít k poškození povrchu dílů.
- Obrábění: Zavádí vlastní soubor tolerancí, ale umožňuje dosáhnout vysoké přesnosti u specifických prvků.
Specifikace a ověřování:
- Přehledné výkresy: Pro konstruktéry je důležité jasně specifikovat kritické rozměry a tolerance na technických výkresech pomocí geometrického dimenzování a tolerování (GD&T). Uveďte, které tolerance jsou požadovány “při stavbě” a kterých bude dosaženo dodatečným obráběním.
- Dohody o kvalitě: Pro dodavatelské řetězce B2B jsou zásadní jasné dohody o kvalitě mezi zákazníkem a poskytovatelem služeb AM. Ty by měly definovat přijatelné rozsahy tolerancí, požadavky na povrchovou úpravu, kontrolní metody a standardy pro podávání zpráv.
- Metrologie: Ověřování rozměrů a tolerancí obvykle vyžaduje pokročilé metrologické vybavení:
- Souřadnicové měřicí stroje (CMM): Vysoce přesné bodové měření kritických prvků.
- 3D skenery (laserové nebo se strukturovaným světlem): Zachycení celkové geometrie složitých tvarů pro porovnání s modelem CAD.
- Povrchové profilometry: Měření parametrů drsnosti povrchu, jako jsou Ra a Rz.
Závěrem lze říci, že ačkoli se technologie AM v oblasti kovů nemůže rovnat přesnosti špičkového CNC obrábění ve všech prvcích, lze s ní přímo z tiskárny dosáhnout přesnosti vhodné pro mnoho aplikací v automobilovém průmyslu, včetně držáků senzorů. Kombinací správných postupů DfAM, pečlivé kontroly procesu a cíleného následného zpracování (zejména obrábění kritických rozhraní) mohou výrobci spolehlivě splnit přísné požadavky na tolerance a povrchovou úpravu v automobilovém průmyslu. Manažeři nákupu by měli navázat kontakt s potenciálními dodavateli AM, aby porozuměli jejich specifickým schopnostem, procesům kontroly kvality a typické dosažitelné přesnosti pro materiály jako AlSi10Mg a A7075.
Za hranice tiskového lůžka: Základní následné zpracování kovových držáků senzorů
Běžnou mylnou představou o 3D tisku z kovu je, že díly vyjíždějí ze stroje připravené k použití. Ve skutečnosti je u funkčních technických součástí, jako jsou držáky automobilových senzorů z AlSi10Mg nebo A7075, proces tisku pouze prvním krokem. K přeměně surového vytištěného dílu na hotovou součást, která splňuje výkonnostní, odolnostní a bezpečnostní normy, je zapotřebí řada nezbytných operací následného zpracování. Pochopení těchto kroků je zásadní pro inženýry, kteří specifikují požadavky, a pro manažery nákupu, kteří zohledňují celkové náklady a dobu realizace.
Proč je nutné následné zpracování?
- Zbytkové napětí: Rychlé cykly zahřívání a ochlazování, které jsou pro PBF typické, vytvářejí v dílu vnitřní pnutí. Tato napětí je třeba zmírnit, aby se zabránilo pozdějšímu zkroucení nebo prasknutí.
- Podpůrné struktury: Převisy a složité prvky vyžadují při stavbě podpůrné konstrukce, které je třeba odstranit.
- Povrchová úprava: Povrchy ve stavu, v jakém jsou postaveny, jsou obvykle drsnější, než je nutné pro těsnění, propojení nebo estetické účely.
- Mechanické vlastnosti: Díly ve stavu, v jakém jsou vyrobeny, zejména u slitin jako AlSi10Mg a A7075, často nemají plnou potenciální pevnost nebo tvrdost. Pro optimalizaci těchto vlastností je nutné tepelné zpracování.
- Tolerance: Ačkoli AM dosahuje přiměřené přesnosti, kritické rozměry často vyžadují obrábění, aby byly splněny přísné technické tolerance.
- Odstranění prášku: Z vnitřních kanálků a povrchových štěrbin je třeba odstranit volný nebo částečně spečený prášek.
Běžné kroky následného zpracování hliníkových držáků senzorů AM:
- Tepelné ošetření proti stresu:
- Účel: To je často úplně první krok po dokončení sestavování, někdy se provádí, když je díl ještě připevněn k sestavovací desce. Zahřívání zahrnuje zahřívání dílu v peci na určitou teplotu (nižší než teplota stárnutí slitiny, obvykle 200-300 °C pro AlSi10Mg) po stanovenou dobu a následné pomalé ochlazování. To umožňuje uvolnění vnitřních pnutí, čímž se výrazně snižuje riziko deformace nebo prasklin při odstraňování podpěr nebo následném obrábění.
- Důležitost: Naprosto zásadní pro rozměrovou stabilitu, zejména u složitých geometrií nebo vysokopevnostních slitin, jako je A7075, které jsou náchylnější k namáhání. Vynechání nebo nesprávné provedení odlehčení může vést k selhání dílu.
- Vyjmutí dílu ze stavební desky:
- Metoda: Díly se obvykle tisknou na silnou kovovou konstrukční desku. Je třeba je oddělit, obvykle pomocí:
- Drátové elektroerozivní obrábění (EDM): Přesné, s minimální silou, vhodné pro jemné díly, ale pomalejší.
- Pásová pila: Je rychlejší, častější pro robustní díly, ale vyžaduje opatrné zacházení a zanechává drsnější povrch na linii řezu.
- Úvaha: Způsob odstranění může ovlivnit následné požadavky na povrchovou úpravu podkladu.
- Metoda: Díly se obvykle tisknou na silnou kovovou konstrukční desku. Je třeba je oddělit, obvykle pomocí:
- Odstranění podpůrné konstrukce:
- Metody: V závislosti na konstrukci podpěry (např. plná, mřížová, kuželové body) může odstranění zahrnovat:
- Ruční rozbití: Podpěry navržené s lámacími body lze někdy odlomit ručně nebo pomocí jednoduchého nářadí.
- Řezné nástroje: Mohou být zapotřebí kleště, brusky nebo specializované nástroje.
- Obrábění (frézování/broušení): Někdy se vyžaduje pro podpěry v obtížně přístupných oblastech nebo tam, kde je na rozhraní podpěr nutná čistá povrchová úprava.
- Výzvy: Může být pracné, zejména v případě složitých vnitřních podpěr. Nebezpečí poškození povrchu dílu, pokud se neprovádí pečlivě. To zdůrazňuje význam DfAM při minimalizaci potřeby podpěr.
- Metody: V závislosti na konstrukci podpěry (např. plná, mřížová, kuželové body) může odstranění zahrnovat:
- Odstranění prášku / čištění:
- Účel: Odstraňte veškerý sypký nebo polosyntetický prášek zachycený ve vnitřních kanálech, mřížkových strukturách nebo povrchových pórech.
- Metody: Stlačený vzduch, tryskání kuličkami, ultrazvukové čisticí lázně.
- Důležitost: Zachycený prášek může zvýšit hmotnost, potenciálně kontaminovat systémy nebo se během provozu uvolnit. Důkladné čištění je nezbytné, zejména u dílů s vnitřními prvky.
- Tepelné zpracování roztokem a stárnutí (např. T6 Temper):
- Účel: Pro dosažení požadovaných konečných mechanických vlastností (tvrdost, mez kluzu, pevnost v tahu) u srážením kalitelných slitin, jako jsou AlSi10Mg a A7075.
- Proces (typický T6 pro hliník):
- Řešení Ošetření: Zahřejte díl na vysokou teplotu (např. ~500-540 °C), aby se legující prvky rozpustily v hliníkové matrici.
- Kalení: Rychle ochlaďte součást (např. ve vodě nebo polymeru), aby se prvky zachytily v přesyceném pevném roztoku.
- Umělé stárnutí: Díl znovu zahřejte na nižší teplotu (např. ~150-190 °C) po určitou dobu, což umožní řízené vysrážení zpevňujících fází.
- Výsledek: Výrazně zvyšuje pevnost a tvrdost v porovnání se stavem po zabudování nebo po uvolnění napětí. Konkrétní parametry závisí na slitině a požadovaných vlastnostech.
- Povrchová úprava:
- Cíl: Zlepšete hladkost povrchu, zajistěte jednotný vzhled, odstraňte otřepy na hranách nebo připravte povrch na lakování.
- Běžné metody pro závorky:
- Tryskání abrazivem (kuličkami, pískem, zrnem): Používá vysokotlaké médium k čištění povrchu, odstraňuje oxidy, vytváří rovnoměrnou matnou strukturu a může poskytnout určitý kuličkovací efekt zlepšující únavovou životnost. Typ média (skleněné kuličky, oxid hlinitý atd.) ovlivňuje konečnou povrchovou úpravu.
- Tumbling (vibrační dokončování / hromadné dokončování): Díly se umístí do vany s abrazivním médiem a vibrují nebo tromlují. Hodí se k odstraňování otřepů na hranách, zlepšování Ra a dosažení konzistentní povrchové úpravy na sériích dílů, zejména těch se složitými vnějšími tvary.
- Ruční odstraňování otřepů/odstraňování otřepů: Ruční dokončování pomocí pilníků nebo brusek k odstranění podpěrných svědků nebo ostrých hran.
- CNC obrábění:
- Účel: Dosažení přísných tolerancí u kritických prvků, které nelze splnit procesem AM as-built nebo jinými metodami dokončování.
- Aplikace pro závorky: Obrábění montážních otvorů s přesnými průměry a polohovými tolerancemi, vytváření rovných styčných ploch pro montáž senzorů, obrábění rozhraní pro konektory nebo jiné součásti.
- Úvaha: Vyžaduje vhodné upevnění; obrobitelnost se může mírně lišit v závislosti na procesu AM a podmínkách tepelného zpracování.
- Povlaky a povrchové úpravy:
- Účel: Zvýšit odolnost proti korozi, zlepšit odolnost proti opotřebení, zajistit elektrickou izolaci nebo dosáhnout požadovaného estetického vzhledu/barvy.
- Možnosti hliníkových držáků:
- Eloxování (tvrdý povlak typu II nebo III): Vytváří kontrolovanou, odolnou vrstvu oxidu. Zlepšuje odolnost proti korozi a opotřebení. Nezbytné pro A7075 v potenciálně korozivním prostředí. Lze barvit různými barvami (typ II).
- Chemické konverzní povlaky (např. alodové, chromátové/nechromátové): Poskytuje ochranu proti korozi a vynikající základ pro přilnavost barvy.
- Lakování / práškové lakování: Poskytuje ochranu proti korozi a širokou škálu barevných/finišových variant.
Integrace následného zpracování do pracovního postupu:
Pořadí a výběr kroků následného zpracování závisí do značné míry na konkrétních požadavcích držáku senzoru.
Příklad pracovního postupu (vysoce přesný držák): Build -> Stress Relief -> Wire EDM Removal -> Support Removal -> Bead Blast (Cleaning) -> Solution & amp; Aging (T6) -> CNC Machining (Critical Features) -> Deburr -> Anodize -> Final Inspection.
Konstruktéři musí na výkresech dílů a ve specifikacích jasně definovat všechny nezbytné požadavky na následné zpracování. Manažeři nákupu se musí ujistit, že potenciální poskytovatelé AM služeb mají schopnosti (vlastní nebo prostřednictvím důvěryhodných partnerů) provést všechny požadované kroky, a při rozhodování o výběru dodavatelů musí zohlednit související náklady a dodací lhůty. Poskytovatel komplexních služeb, který nabízí komplexní řešení od tisku až po finální úpravu a kontrolu, může často zefektivnit proces pro B2B zákazníky.
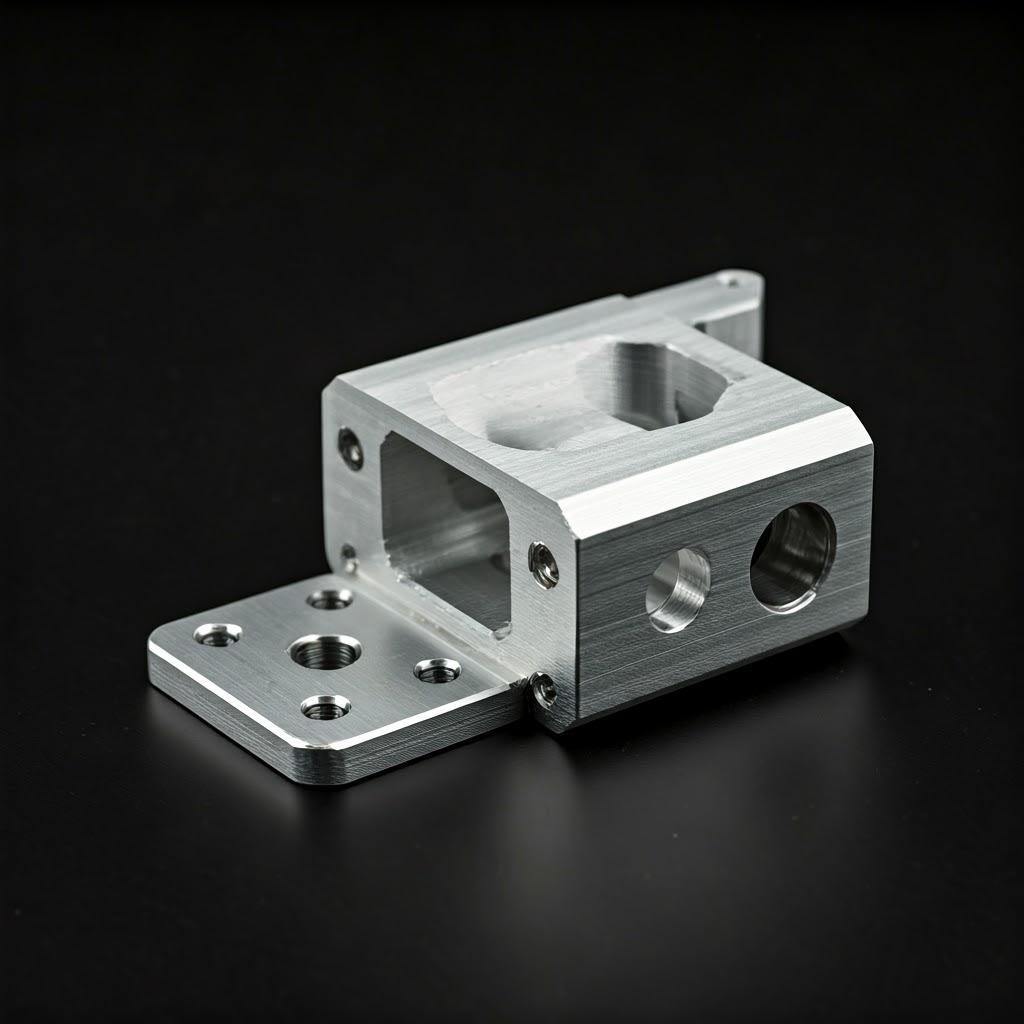
Překonávání potenciálních překážek: Obvyklé problémy při 3D tisku držáků senzorů a jejich řešení
Aditivní výroba kovů sice nabízí významné výhody pro výrobu držáků automobilových senzorů, ale není bez problémů. Pochopení potenciálních překážek ve fázi tisku a následného zpracování umožňuje konstruktérům a výrobcům aktivně zavádět strategie pro jejich zmírnění, a zajistit tak konzistentní kvalitu a spolehlivou výrobu. Klíčem k překonání těchto složitostí je spolupráce se zkušeným poskytovatelem AM služeb.
Společné výzvy a strategie pro jejich zmírnění:
- Deformace a zkreslení:
- Příčina: Nerovnoměrné zahřívání a ochlazování během procesu tavení po vrstvách vytváří v dílu zbytková napětí. Jak tato napětí narůstají, mohou překonat kotevní účinek podpěr nebo vlastní tuhost dílu a způsobit jeho deformaci nebo zkroucení, zejména po vyjmutí z konstrukční desky. Tenké stěny, velké ploché profily a asymetrické geometrie jsou náchylnější.
- Zmírnění:
- DfAM: Navrhněte konstrukci s ohledem na minimální tepelné gradienty (vyhněte se náhlým změnám tloušťky), přidejte ztužující prvky (žebra).
- Orientace: Orientujte díl tak, abyste minimalizovali velké průřezy na vrstvu a omezili nepodporované přesahy.
- Strategie podpory: Použijte robustní podpůrné konstrukce strategicky umístěné tak, aby působily proti smršťovacím silám a účinně ukotvily díl.
- Parametry procesu: Optimalizujte parametry (např. strategii skenování, výkon laseru), abyste minimalizovali lokální přehřátí.
- Tepelná simulace: Pomocí simulačního softwaru můžete předvídat oblasti s vysokým namáháním a potenciální deformace, a tím se řídit při úpravách konstrukce nebo podpory.
- Úleva od stresu: Tepelné zpracování na uvolnění napětí proveďte ihned po tisku, před vyjmutím dílu.
- Zbytkové napětí:
- Příčina: Příznačné pro PBF v důsledku rychlého tuhnutí a velkých tepelných gradientů. I když je deformace kontrolována, mohou přetrvávat vysoká vnitřní napětí.
- Dopad: Může vést k předčasnému selhání při zatížení (zejména únavě), praskání při následném zpracování (obrábění) nebo dlouhodobé rozměrové nestabilitě.
- Zmírnění:
- Optimalizace procesů: Parametry jemného doladění mohou ovlivnit úroveň napětí.
- Tepelné ošetření proti stresu: Základní metoda pro snížení zbytkového napětí na přijatelnou úroveň. Rozhodující je správné provedení.
- Design: Hladké geometrické přechody snižují koncentraci napětí.
- Povědomí o následném zpracování: Uvědomte si, že při obrábění může dojít k uvolnění napětí, což může způsobit drobné rozměrové změny. Někdy se obrábění provádí částečně před konečným uvolněním napětí.
- Pórovitost (plyn a nedostatek fúze):
- Příčina:
- Pórovitost plynu: Zachycené plyny (např. argon ze stavební komory, vodík rozpuštěný v prášku/tavenině) vytvářejí během tuhnutí malé, obvykle kulovité póry. Často jsou způsobeny kontaminovaným práškem nebo nedostatečnou kontrolou atmosféry v komoře.
- Pórovitost v důsledku chybějící fúze: Nedostatečný příkon energie (příliš nízký výkon laseru, příliš vysoká rychlost skenování) nebo špatná rovnoměrnost vrstvy prášku brání úplnému roztavení a splynutí mezi vrstvami nebo sousedními skenovacími stopami, což zanechává nepravidelně tvarované dutiny.
- Dopad: Snižuje hustotu dílu, zhoršuje mechanické vlastnosti (zejména únavovou pevnost a tažnost), vytváří potenciální cesty k úniku a působí jako místo iniciace trhlin.
- Zmírnění:
- Vysoce kvalitní prášek: Použijte prášek s kontrolovaným nízkým obsahem plynu, dobrou kulovitostí a tekutostí. Pořizujte si zboží od renomovaných dodavatelů, jako je např Met3dp, známé svými pokročilými procesy atomizace (VIGA, PREP), které zajišťují čistotu a kvalitu prášku, je zásadní.
- Optimalizace parametrů: Vyvíjet a důsledně kontrolovat ověřené procesní parametry pro konkrétní materiál a stroj.
- Údržba stroje: Zajistěte správný průtok inertního plynu, nízkou hladinu kyslíku ve stavební komoře a čistou optiku.
- Manipulace s práškem: Proveďte správné skladovací a manipulační postupy, abyste zabránili absorpci vlhkosti nebo plynu.
- Izostatické lisování za tepla (HIP): Krok následného zpracování zahrnující vysokou teplotu a tlak, který může uzavřít vnitřní póry (plynné i LoF), čímž se výrazně zlepší hustota a mechanické vlastnosti. Často se používá pro kritické aplikace, ale zvyšuje náklady a dobu realizace.
- Nedestruktivní zkoušení (NDT): Ke zjištění vnitřní pórovitosti kritických dílů použijte metody, jako je CT skenování.
- Příčina:
- Krakování (tuhnutí/kvašení):
- Příčina: Zvláště náročné je to u slitin s širokým rozsahem mrznutí, jako je A7075. Napětí vyvolaná během tuhnutí mohou způsobit vznik trhlin podél hranic zrn nebo v oblastech, kde se vyskytují fáze s nižším bodem tání (liquační trhliny). Rychlé ochlazování tento problém ještě zhoršuje.
- Zmírnění:
- Úprava slitiny: Někdy se pro AM používají mírně upravené kompozice, aby se zlepšila svařitelnost.
- Řízení procesu: Přesné řízení parametrů laseru, případně pomocí pulzních laserů nebo specifických strategií skenování (např. řízení teploty taveniny).
- Tepelný management: Použití vyhřívaných stavebních plošin nebo optimalizovaných cyklů ohřevu/chlazení.
- Úleva od stresu: Včasné uvolnění napětí může zabránit vzniku trhlin způsobených namáháním po sestavení.
- HIP: Někdy může pomoci zacelit mikrotrhliny, ale na velké trhliny po tuhnutí je méně účinný. Vyžaduje pečlivý vývoj parametrů poskytovatelem AM.
- Obtíže při odstraňování podpory & Kvalita povrchu:
- Příčina: Špatně navržené podpěrné konstrukce (příliš husté, špatný typ, špatné umístění) nebo příliš složité geometrie dílů vyžadující rozsáhlé vnitřní podpěry.
- Dopad: Zvýšené náklady na práci při odstraňování, potenciální poškození povrchu dílu (škrábance, rýhy), zbytky podpůrného materiálu (dříky) ovlivňující lícování nebo estetiku, špatná povrchová úprava v místech rozhraní podpěr.
- Zmírnění:
- DfAM Focus: Upřednostněte navrhování dílů tak, aby byly samonosné nebo aby se minimalizovala potřeba podpory. Místo ostrých převisů používejte koutové profily.
- Optimalizované generování podpory: Používejte pokročilé funkce softwaru pro vytváření podpěr (např. blokové podpěry, stromové podpěry, kuželové podpěry), které jsou navrženy pro snadnější demontáž a minimální kontakt s dílem.
- Kvalifikovaní technici: Zkušení technici umí lépe opatrně odstranit podpěry bez poškození dílu.
- Následné zpracování: Naplánujte nezbytné dokončovací kroky (obrábění, tryskání, otryskávání) k vyčištění stop po podpěrách.
- Rozměrová nepřesnost:
- Příčina: Kumulativní účinek drobných změn smrštění, mírné deformace, posunu parametrů při dlouhých stavbách nebo nepřesností při kompenzaci tepelné roztažnosti/smrštění.
- Dopad: Díly nemusí splňovat kritické tolerance požadované pro montáž nebo funkci.
- Zmírnění:
- Kalibrace a monitorování strojů: Zajistěte přesnou kalibraci a stabilitu systému AM. Zavedení monitorování v průběhu procesu, pokud je k dispozici.
- Kompenzace smrštění: V softwaru pro přípravu konstrukce použijte vhodné faktory měřítka na základě empirických údajů pro konkrétní materiál a stroj.
- Řízení procesu: Udržujte přísnou kontrolu nad všemi kritickými parametry procesu.
- Post-Machining: Smiřte se s tím, že dosažení co nejtěsnějších tolerancí často vyžaduje obrábění kritických prvků po tisku a tepelném zpracování. Navrhujte díly s přídavky na obrábění, kde je to nutné.
Partnerství pro úspěch:
Úspěšné zvládnutí těchto výzev vyžaduje kombinaci důkladných konstrukčních postupů, pečlivé kontroly procesu, důkladného následného zpracování a přísného zajištění kvality. Pro výrobce OEM a dodavatele Tier 1 v automobilovém průmyslu je nejdůležitější spolupracovat se znalým a zkušeným poskytovatelem služeb v oblasti AM zpracování kovů. Hledejte poskytovatele, kteří:
- Prokázat odborné znalosti s konkrétními slitinami (AlSi10Mg, A7075).
- Mějte dobře udržované a kalibrované vybavení.
- Používat přísné systémy řízení procesů a kvality (např. ISO 9001, ideálně IATF 16949 pro automobilový průmysl).
- Používejte vysoce kvalitní, sledovatelné prášky.
- Nabízet pokyny a zpětnou vazbu DfAM.
- Mít komplexní schopnosti následného zpracování (nebo silné partnerství).
- Zajistit důkladnou kontrolu a podávání zpráv (metrologie, NDT, pokud je to nutné).
Pochopením těchto potenciálních překážek a spoluprací se schopnými partnery mohou společnosti bez obav využít technologii AM pro výrobu vysoce výkonných a spolehlivých držáků senzorů pro náročné požadavky elektromobilů a autonomních vozidel.
Partnerství pro úspěch: Jak vybrat správného poskytovatele služeb 3D tisku kovů pro automobilové komponenty?
Využití aditivní výroby kovů pro kritické komponenty, jako jsou držáky automobilových senzorů, vyžaduje více než jen přístup k tiskárně; vyžaduje strategické partnerství se schopným a spolehlivým poskytovatelem služeb. Kvalita, výkon a konzistence vašich finálních dílů jsou přímo závislé na odborných znalostech, procesech a kontrolách kvality vybraného dodavatele. Pro inženýry a manažery nákupu v náročném automobilovém odvětví, zejména pro ty, kteří se podílejí na vývoji elektromobilů a autonomních vozidel, je výběr správného partnera v oblasti kovové AM zásadním rozhodnutím, které ovlivňuje časový harmonogram projektu, spolehlivost součástek a celkový úspěch. Informovaný výběr vyžaduje pečlivé vyhodnocení na základě řady technických a provozních kritérií.
Klíčová hodnotící kritéria pro výběr poskytovatele služeb v oblasti AM:
- Technické znalosti a zkušenosti s aplikacemi:
- Specializace na materiál: Má poskytovatel prokazatelné zkušenosti s tiskem a následným zpracováním konkrétních hliníkových slitin, které potřebujete (AlSi10Mg, A7075)? Požádejte o případové studie nebo příklady podobných dílů, které vyrobil.
- Zaměření na automobilový průmysl: Rozumí specifickým požadavkům a výzvám automobilového průmyslu (např. odolnost, environmentální testování, procesy PPAP)? Zkušenosti s držáky senzorů nebo podobnými konstrukčními prvky jsou výhodou.
- Podpora DfAM: Mohou vám poskytnout odbornou zpětnou vazbu k vašim návrhům a optimalizovat je pro aditivní výrobu, čímž se potenciálně zlepší výkon a sníží náklady? Mají inženýry, kteří mohou aktivně spolupracovat na optimalizaci návrhů?
- Řešení problémů: Technologie AM pro kovy může představovat nečekané výzvy. Má poskytovatel tým s hlubokými technickými znalostmi, který dokáže vyřešit problémy související s tiskem, materiály nebo následným zpracováním? Hledejte poskytovatele se silným zázemím v oblasti výzkumu a vývoje nebo s kolektivními odbornými znalostmi, jako je tým společnosti Met3dp, který se zabývá materiálovou vědou a vývojem aplikací.
- Schopnosti a technologie stroje:
- Vhodnost procesu: Především L-PBF pro hliník, ale mají dobře udržované stroje průmyslové třídy vhodné pro požadovanou přesnost a materiál?
- Objem sestavení: Mohou jejich stroje vyhovět velikosti vašich držáků snímačů?
- Pokročilé funkce: Využívají stroje s funkcí monitorování procesu (např. monitorování taveniny, termovizní snímání), které mohou pomoci zajistit kvalitu a konzistenci výroby?
- Údržba & Kalibrace: Jaké jsou jejich postupy pro údržbu strojů a pravidelnou kalibraci, aby byla zajištěna konzistentní produkce?
- Kvalita, kontrola a sledovatelnost materiálu:
- Získávání prášku: Získávají vysoce kvalitní kovové prášky od renomovaných výrobců (nebo vyrábějí vlastní, jako Met3dp)? Jaké jsou jejich postupy vstupní kontroly a testování prášků?
- Certifikace: Mohou poskytnout materiálové certifikáty (certifikáty analýzy/výhody) pro konkrétní šarži prášku použitou pro vaše díly?
- Sledovatelnost: Existuje spolehlivý systém pro sledování šarží prášku v průběhu celého procesu, který spojuje konečný díl s konkrétním použitým materiálem? To je zásadní pro odpovědnost v automobilovém průmyslu.
- Manipulace & amp; Skladování: Jsou zavedeny správné postupy pro skladování a manipulaci s prášky, aby se zabránilo kontaminaci (zejména vlhkostí u hliníku) a zachovala se tekutost? Jak se prášek znovu používá/obnovuje?
- Systém řízení kvality (QMS):
- Certifikace ISO 9001: Jedná se o základní požadavek, který označuje zdokumentovaný systém kontroly kvality a neustálého zlepšování.
- Certifikace/soulad s IATF 16949: Ačkoli plná certifikace může být u čistě AM servisních kanceláří ve srovnání s dodavateli Tier 1 méně obvyklá, prokázaná shoda nebo soulad se zásadami IATF 16949 je pro projekty v automobilovém průmyslu významnou výhodou. Prokazuje závazek k přísné kontrole procesů, řízení rizik (FMEA), sledovatelnosti a dokumentačním postupům (jako je APQP – pokročilé plánování kvality výrobků a PPAP – proces schvalování výrobních dílů). Ptejte se na jejich znalost a schopnost podporovat tyto požadavky automobilového průmyslu.
- Možnosti následného zpracování:
- Komplexní řešení: Nabízí poskytovatel komplexní sadu vlastních služeb následného zpracování (uvolnění napětí, tepelné zpracování specifické pro Al slitiny, odstranění podpěr, základní povrchová úprava)?
- Řízená partnerská síť: Pokud jsou služby, jako je přesné CNC obrábění, pokročilá povrchová úprava (např. bubnové leštění, leštění) nebo specializované povlaky (eloxování, lakování), zadávány externě, má poskytovatel síť kvalifikovaných a auditovaných partnerů? Jak řídí kontrolu kvality těchto externích procesů?
- Odborné znalosti: Existují specifické odborné znalosti v oblasti tepelného zpracování hliníkových dílů AM (které se mohou jemně lišit od kovaných/odlévaných materiálů) a obrábění komponent AM?
- Metrologie a kontrola:
- Zařízení: Disponují potřebným metrologickým vybavením (souřadnicové měřicí stroje, 3D skenery, profilometry) pro ověření rozměrové přesnosti a požadavků na kvalitu povrchu?
- Schopnosti NDT: Pokud je to vyžadováno u kritických dílů, mohou provádět nebo řídit nedestruktivní testování, jako je CT skenování (pro vnitřní vady) nebo penetrační testování barvivem (pro povrchové trhliny)?
- Podávání zpráv: Jakou úroveň kontrolního hlášení mohou poskytnout? Dokáží se přizpůsobit specifickým požadavkům GD&T a formátům hlášení?
- Kapacita, škálovatelnost a dodací lhůty:
- Současná kapacita: Dokáží splnit vaše požadované objemy (prototyp a potenciální výroba) v přijatelných dodacích lhůtách? Jaké je jejich typické vytížení strojů?
- Plán škálovatelnosti: Jak by se v případě nárůstu objemů rozšířila výroba? Mají více strojů nebo plánují rozšíření?
- Včasné dodání: Jaká je jejich historie v dodržování uvedených dodacích lhůt? Pokud je to možné, vyžádejte si reference nebo údaje o výkonnosti.
- Komunikace a podpora:
- Reakce: Reagují rychle na dotazy a poskytují nabídky?
- Transparentnost: Je komunikace ohledně technické proveditelnosti, možných problémů, nákladů a časového harmonogramu jasná?
- Řízení projektů: Je pro vaše projekty vyhrazeno kontaktní místo?
- Efektivita nákladů:
- Transparentní ceny: Je cenová nabídka jasná a podrobná a pokud možno rozděluje náklady?
- Nabídka hodnoty: Zvažte celkovou hodnotu, včetně technické podpory, zajištění kvality, spolehlivosti a následného zpracování, nejen cenu za díl. Nejlevnější varianta nemusí nabízet potřebnou kvalitu nebo podporu pro aplikace v automobilovém průmyslu.
Due Diligence:
Nespoléhejte se pouze na webové stránky nebo brožury. Zapojte se do technických diskusí, pokládejte podrobné otázky, vyžádejte si vzorky dílů (třeba tiskem vzorového návrhu), a pokud je to možné, proveďte audit zařízení (buď osobní, nebo virtuální), abyste si ověřili možnosti a procesy. Klíčem k úspěšné integraci 3D tištěných držáků snímačů do vašich projektů v automobilovém průmyslu je vybudování pevného a kooperativního vztahu s poskytovatelem AM služeb.
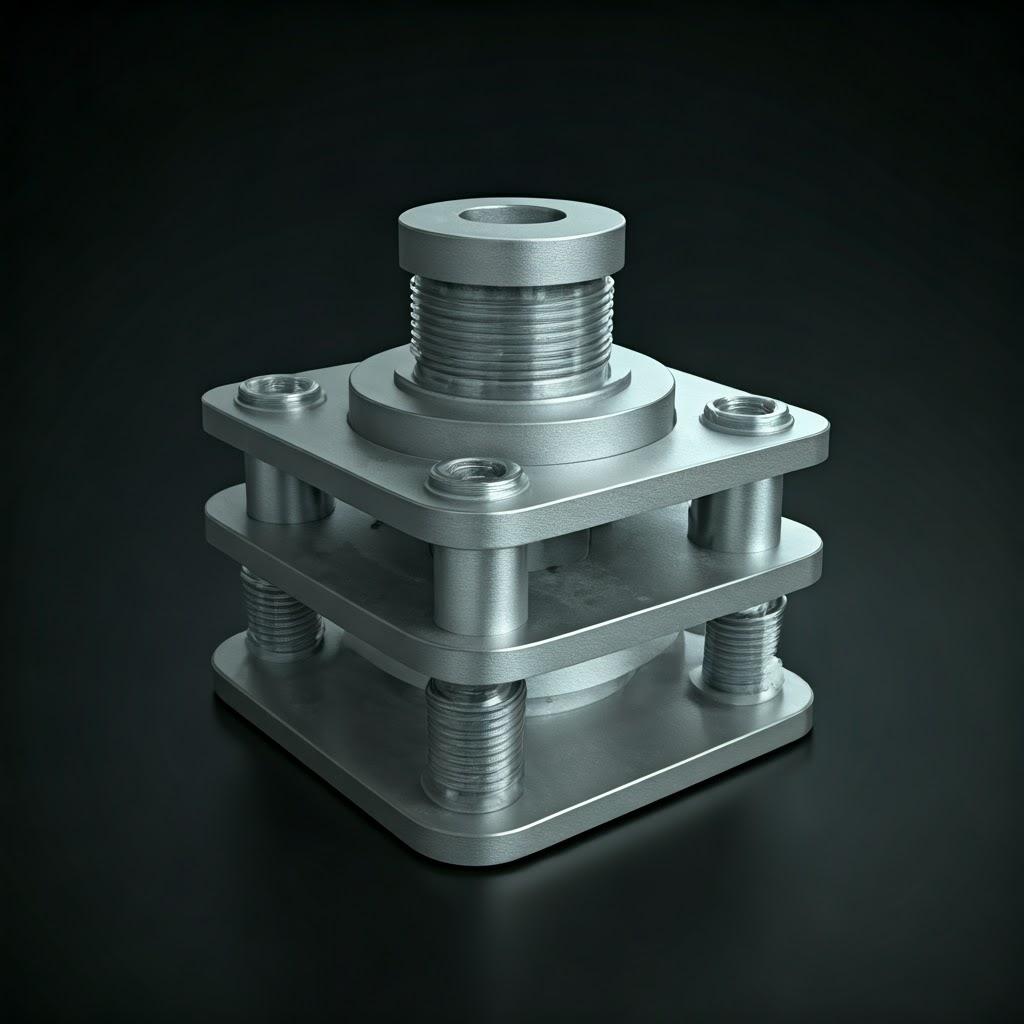
Porozumění investicím: Nákladové faktory a dodací lhůty pro 3D tištěné držáky senzorů
Jednou z nejnaléhavějších otázek pro inženýry a manažery nákupu, kteří uvažují o aditivní výrobě kovů, je: “Kolik to bude stát a jak dlouho to bude trvat?” Ačkoli AM eliminuje značné počáteční investice do nástrojů spojené s odléváním nebo lisováním, struktura nákladů a výpočet doby realizace se liší od tradičních metod. Pochopení klíčových faktorů pomáhá při sestavování rozpočtu, porovnávání nabídek a informovaném rozhodování o zavedení AM pro výrobu držáků senzorů.
Klíčové faktory ovlivňující náklady na kovové držáky senzorů AM:
Konečná cena uvedená poskytovatelem služeb AM je obvykle souhrnem několika faktorů:
- Náklady na materiál:
- Cena prášku: Náklady na kilogram kovového prášku. Vysoce výkonné slitiny, jako je A7075, jsou obecně dražší než standardní AlSi10Mg kvůli nákladům na suroviny a náročnosti zpracování. Cenu ovlivňuje také kvalita prášku (sféricita, čistota, PSD).
- Spotřeba materiálu: To zahrnuje objem závěrečné části plus objem potřebných podpůrných konstrukcí. Konstrukce optimalizované pro minimální podporu (DfAM) přímo snižují náklady na materiál.
- Obnovení/recyklace prášku: Nepoužitý prášek lze sice často prosévat a znovu použít, ale existují určité limity. Obvykle je třeba přimíchat určité procento původního prášku (míra obnovení) a část prášku se časem nevyhnutelně ztratí nebo znehodnotí. Tyto faktory jsou započítány do nákladů na materiál poskytovatele.
- Čas stroje (čas sestavení):
- Primární řidič: To je často nejvýznamnější složka nákladů. Je určena především celkovou výškou sestavy (Z-výška), protože tisk probíhá po jednotlivých vrstvách. Vyšší díly se tisknou déle.
- Další faktory: Celkový objem taveného materiálu na jednu vrstvu (související s průřezem a hustotou dílu), počet dílů umístěných na konstrukční desce a specifické parametry procesu (tloušťka vrstvy, rychlost skenování) ovlivňují celkový počet hodin stroje.
- Výpočet: Poskytovatelé služeb mají obvykle hodinovou sazbu za své stroje, která zahrnuje odpisy, spotřebu energie, spotřebu inertního plynu, údržbu a režijní náklady na obsluhu. Software pro simulaci sestavení odhaduje celkovou dobu tisku.
- Náklady na pracovní sílu:
- Předběžné zpracování: Příprava souborů, optimalizace rozložení sestavy (vnoření), generování struktury podpory.
- Nastavení a provoz stroje: Vkládání prášku, nastavení sestavení, monitorování procesu, vyložení sestavovací desky.
- Práce po zpracování: Může jít o značný objem práce, včetně vyjmutí dílu z desky, odstranění/čištění prášku, ručního odstranění podpěr (často složitého a časově náročného), základní povrchové úpravy a kontroly. Čím složitější jsou podpěry nebo vnitřní prvky, tím vyšší jsou náklady na práci.
- Náklady na následné zpracování (nad rámec základní práce):
- Tepelné zpracování: Čas a energie pece pro uvolnění napětí a/nebo rozpuštění & cykly stárnutí (T6). Ty vyžadují specializované, kalibrované zařízení.
- Obrábění: Náklady do značné míry závisí na počtu obráběných prvků, požadovaných tolerancích, složitosti upínacích přípravků a době obrábění. Účtuje se obvykle hodinová sazba za čas strávený na CNC stroji plus programování/nastavení.
- Povrchová úprava: Náklady na tryskání, bubnování, eloxování, lakování atd. závisí na procesu, velikosti dílu, velikosti dávky a požadovaných specifikacích. Často je provádějí specializované třetí strany, což zvyšuje marži a logistické náklady.
- Kontrola: Čas potřebný na měření na souřadnicovém měřicím stroji, 3D skenování, nedestruktivní zkoušení a tvorbu protokolů zvyšuje náklady, zejména u dílů vyžadujících rozsáhlou validaci (např. na úrovni PPAP).
- Část Složitost a design:
- Podporuje: Složitější díly často vyžadují rozsáhlejší podpůrné struktury, což zvyšuje spotřebu materiálu, (mírně) prodlužuje dobu tisku a výrazně zvyšuje pracnost a riziko následného zpracování.
- Vnitřní funkce: AM sice umožňuje vytvářet složité vnitřní kanály nebo mřížky, ale jejich odstranění a kontrola prášku mohou být náročnější a nákladnější.
- Optimalizace topologie: Může snížit objem materiálu (což snižuje náklady na materiál a potenciálně i dobu tisku), ale může vést ke složitým tvarům, které vyžadují pečlivé podpůrné strategie a potenciálně více práce při dokončování.
- Hustota zástavby (hnízdění):
- Efektivita: Schopnost efektivně umístit více držáků snímačů na jednu konstrukční desku má zásadní význam pro snížení nákladů na jeden díl. Poskytovatelé služeb používají k optimalizaci vnoření software. Malé díly často výrazně profitují ze sériové výroby.
- Požadavky na kvalitu:
- Přísnost: Vyšší požadavky na kvalitu (přísnější tolerance, rozšířená kontrola, NDT, rozsáhlá dokumentace, např. úplný PPAP) přirozeně zvyšují náklady na práci, vybavení a případný zmetek, což vede k vyšší ceně za díl.
Typické dodací lhůty:
Dodací lhůty pro kovové držáky senzorů AM se mohou výrazně lišit v závislosti na podobných faktorech, jako jsou náklady:
- Výroba prototypů (1-10 kusů):
- Typické: 5 až 15 pracovních dnů.
- Rozdělení: 1-2 dny na přípravu souboru/vypracování fronty, 1-4 dny na tisk (v závislosti na výšce/komplexnosti), 3-10+ dní na následné zpracování (uvolnění napětí, odstranění podpěr, základní povrchová úprava, případně tepelné zpracování a zrychlené obrábění).
- Nízký až střední objem výroby (10 až 1000 kusů):
- Typické: 3 až 8+ týdnů.
- Rozdělení: Zahrnuje čas na optimalizaci rozvržení sestavy pro sériovou výrobu, potenciálně delší tiskové série, plánování času v peci pro tepelné zpracování sérií, koordinaci sériového obrábění nebo dokončování a provádění kontrol sérií. Přispívá k tomu i logistika a potenciální řazení do front v různých krocích procesu.
- Faktory ovlivňující dobu realizace:
- Dostupnost stroje/zácpa: Aktuální pracovní vytížení u poskytovatele služeb.
- Doba výstavby: Přímo souvisí s výškou dílu a počtem dílů na sestavení.
- Složitost následného zpracování: Obrábění, specializované povlaky a rozsáhlá kontrola jsou často nejdelšími tyčemi ve stanu. Externě zajišťované kroky zvyšují logistické zpoždění.
- Velikost dávky: Větší šarže mohou trvat celkově déle, ale v některých krocích mohou být efektivnější.
- Požadavky na kvalitu/kontrolu: Důsledná kontrola prodlužuje čas.
- Doprava: Doba přepravy do místa zákazníka.
Úvahy B2B:
V případě trvalých vztahů B2B zahrnujících velkoobchodní nebo hromadné objednávky mohou poskytovatelé služeb AM nabízet odstupňované ceny na základě objemových závazků nebo uzavírat dlouhodobé dohody s pevnou cenovou strukturou. Pro získání realistických cenových nabídek a spolehlivé plánování dodavatelského řetězce je zásadní předem projednat očekávané roční objemy a požadavky na kvalitu. Nabídky vždy porovnávejte na základě podrobného porozumění tomu, co je zahrnuto v ceně a době realizace (např. které kroky následného zpracování, úroveň kontroly, přepravní podmínky).
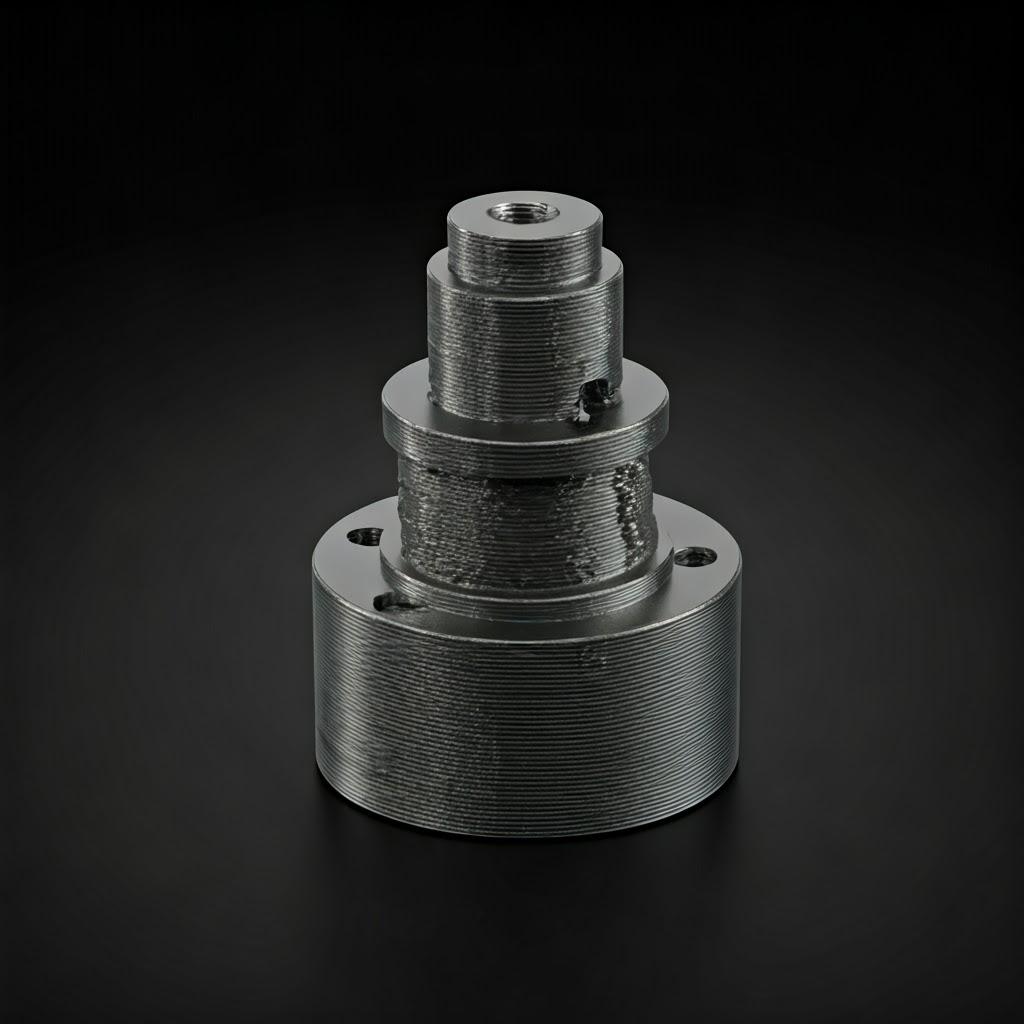
Často kladené otázky (FAQ) o 3D tisku držáků automobilových senzorů
Zde jsou odpovědi na některé časté otázky, které mají konstruktéři a manažeři nákupu, když zvažují aditivní výrobu kovů pro držáky automobilových senzorů:
Otázka 1: Je kovový 3D tisk cenově konkurenceschopný s CNC obráběním nebo odléváním pro držáky senzorů?
A: To do značné míry závisí na několika faktorech:
- Složitost: U velmi složitých, topologicky optimalizovaných nebo konsolidovaných konstrukcí konzol, které je obtížné nebo nemožné obrábět nebo odlévat, může být AM nákladově efektivní i při nižších objemech, protože se vyhne složitému nastavování nebo výrobě nástrojů.
- Objem:
- Nízký objem (prototypy, 1-100 kusů): AM je často více nákladově efektivnější než odlévání (kvůli vysokým nákladům na nástroje) a konkurenceschopné se složitým CNC obráběním (kvůli programování a době seřizování).
- Střední objem (100-10 000): Jedná se o šedou zónu. Optimalizovaná výroba AM (kvalitní nesting, zjednodušené následné zpracování) může konkurovat obrábění, zejména pokud DfAM umožňuje výrazné odlehčení nebo zvýšení výkonu. Odlévání se stává konkurenceschopnější s rostoucími objemy, aby se amortizovaly nástroje, ale pouze pokud je konstrukce odlévatelná.
- Velký objem (100 000 a více): Tradiční metody, jako je tlakové lití nebo lisování (pro jednodušší konstrukce), jsou obecně nákladově efektivnější na jeden díl, pokud je konstrukce vhodná.
- Dodací lhůta: Pokud je rychlost kritická (např. rychlá výroba prototypů, naléhavé náhradní díly), nabízí AM’schopnost vyrábět díly ve dnech/týdnech bez použití nástrojů významnou hodnotu, která může převážit vyšší náklady na jeden díl.
- Celkové náklady na vlastnictví: Zvažte i jiné faktory než jen cenu za díl, například investice do nástrojů/údržby (které se díky AM vyhnete), potenciální úsporu hmotnosti (zlepšení efektivity vozidla), zjednodušení montáže (konsolidace dílů) a zkrácení doby uvedení na trh.
Otázka 2: Jaká je pevnost 3D tištěných hliníkových držáků (AlSi10Mg, A7075) ve srovnání s tradičním tepaným nebo litým hliníkem?
A: Při správném zpracování a tepelném zpracování mohou kovové hliníkové díly AM vykazovat vynikající mechanické vlastnosti:
- AlSi10Mg: Obvykle dosahuje vlastností srovnatelných nebo mírně lepších než hliníkové odlitky A356/A360, zejména po tepelném zpracování T6. Rychlé tuhnutí při AM často vede k jemnější mikrostruktuře, která může zvýšit pevnost.
- A7075: Zde může společnost AM skutečně zazářit, při odborném zpracování. Správně vytištěný a tepelně zpracovaný A7075 T6 může dosáhnout pevnosti v tahu a meze kluzu srovnatelné s tepaným 7075-T6, který je výrazně pevnější než většina litých hliníkových slitin a AlSi10Mg. Nabízí poměr pevnosti k hmotnosti blížící se pevnosti některých ocelí.
- Klíčové faktory: Dosažení těchto vlastností závisí především na použití vysoce kvalitního prášku, optimalizovaných parametrech tisku (pro zajištění vysoké hustoty >99,5 %) a správném tepelném zpracování po výrobě (odlehčení od napětí a cyklus T6). Vlastnosti mohou také vykazovat určitou anizotropii (změny se směrem sestavování), což je třeba zohlednit při návrhu a testování. Vždy si vyžádejte údaje o vlastnostech materiálu od svého dodavatele AM na základě jeho specifického procesu.
Otázka 3: Může se kovový AM rozšířit na sériovou výrobu držáků senzorů pro automobilový průmysl?
A: Ano, AM z kovu se stále častěji používá pro sériovou výrobu v automobilovém průmyslu, i když obvykle spíše pro výklenkové nebo středně velkoobjemové aplikace (tisíce až desetitisíce dílů ročně) než pro masová vozidla (miliony ročně).
- Faktory životaschopnosti: Škálovatelnost závisí na velikosti konzoly (menší díly se snáze vyrábějí ve velkém), složitosti, počtu dostupných tiskáren a efektivitě celého pracovního postupu (včetně automatizace následného zpracování).
- Trendy: Náklady na jeden díl se snižují s tím, jak se zrychlují stroje, zlepšují materiály a zvyšuje automatizace. AM je obzvláště atraktivní pro aplikace, kde přizpůsobení, vysoký výkon (odlehčení) nebo složitá geometrie přinášejí významnou hodnotu, například ve výkonných vozidlech, elektrických vozidlech, autonomních systémech a na trhu s náhradními díly.
- Hybridní přístupy: Někdy se AM používá pro počáteční výrobní série nebo složité varianty, zatímco jednodušší, velkoobjemové verze mohou později přejít na tradiční metody.
Otázka 4: Jakou dokumentaci kvality mohu očekávat od renomovaného dodavatele kovových AM dílů pro automobilový průmysl?
A: Pro aplikace v automobilovém průmyslu je zásadní sledovatelnost a dokumentace. Renomovaný dodavatel, který se zavázal dodržovat normy kvality pro automobilový průmysl, by měl být schopen zajistit:
- Certifikace materiálu: Certifikát o analýze (CoA) nebo certifikát o shodě (CoC) pro konkrétní použitou šarži prášku, který potvrzuje jeho chemické složení a klíčové vlastnosti.
- Zpráva o stavbě: Protokol s podrobnými údaji o použitých parametrech sestavení, ID stroje, datu sestavení, umístění dílu na sestavovací desce a všech významných událostech během sestavení.
- Záznamy z následného zpracování: Potvrzení a parametry používané pro cykly odlehčování a tepelného zpracování (např. diagramy pece). Sledovatelnost všech externě zadávaných procesů (obrábění, povrchová úprava).
- Zpráva o rozměrové kontrole: Výsledky měření kritických rozměrů uvedených ve výkresu (např. protokol ze souřadnicového měřicího stroje, protokol o porovnání 3D skenů). Úroveň podrobnosti by měla odpovídat dohodnutému plánu kvality.
- Zpráva o nedestruktivním zkoušení (NDT): Pokud je to vyžadováno (např. zpráva z CT vyšetření pro zjištění pórovitosti, zpráva o penetraci barvivem pro zjištění povrchových trhlin).
- Dokumentace PPAP: V případě sériové výroby by dodavatelé, kteří jsou obeznámeni s IATF 16949, měli být schopni poskytnout prvky dokumentace procesu schvalování výrobních dílů podle požadavků zákazníka (např. schéma průběhu procesu, PFMEA, plán kontroly, analýza systému měření, výsledky měření rozměrů, certifikace materiálů). Vyjasněte si požadavky PPAP již na počátku zakázky.
Závěr: Urychlení inovací v automobilovém průmyslu pomocí aditivní výroby kovů pro držáky senzorů
Neustálý vývoj automobilového průmyslu směrem k elektrifikaci a autonomii závisí na bezproblémové integraci a bezchybném fungování stále většího množství sofistikovaných senzorů. Zajištění stabilní, přesné a spolehlivé montáže těchto kritických komponent je prvořadé a držáky automobilových snímačů se vyvinuly z jednoduchých přípravků na složité, výkonné díly. Klíčovou technologií se stala aditivní výroba kovů, která nabízí transformační přístup k navrhování a výrobě těchto životně důležitých součástí.
Využitím možností technologie AM pro zpracování kovů, zejména vysoce výkonných hliníkových slitin, jako je univerzální AlSi10Mg a vysoce pevná slitina A7075, mohou automobiloví inženýři překonat omezení tradiční výroby. Bezkonkurenční svoboda konstrukce, kterou AM poskytuje, otevírá možnosti pro:
- Významné odlehčení: Optimalizace topologie a mřížové struktury, snížení hmotnosti vozidla pro lepší dojezd a ovladatelnost elektromobilu.
- Složité geometrie: Vytváření složitých tvarů, které dokonale zabalí senzory do stísněných prostor a integrují více funkcí.
- Konsolidace částí: Snížení složitosti montáže, hmotnosti a potenciálních míst poruchy spojením více komponent do jediného tištěného dílu.
- Rychlé prototypování a iterace: Urychlení vývojových cyklů pro nové integrace senzorů a platformy vozidel.
- Přizpůsobení: Umožňuje konstrukci držáků na míru pro konkrétní modely snímačů, varianty vozidel nebo aplikace na trhu s náhradními díly bez omezení v oblasti nástrojů.
Realizace těchto výhod však vyžaduje komplexní přístup. Úspěch závisí na přijetí zásad návrhu pro aditivní výrobu (DfAM), pochopení zásadní úlohy pečlivého následného zpracování (včetně odlehčení napětí a tepelného zpracování) pro dosažení požadovaných vlastností a rozměrové přesnosti a zvládnutí potenciálních problémů procesu prostřednictvím pečlivé kontroly a odborných znalostí.
Zásadní význam má spolupráce se správným poskytovatelem služeb AM pro kovy. Výběr dodavatele s prokazatelnými odbornými znalostmi v oblasti automobilových aplikací, robustními systémy řízení kvality, pokročilými možnostmi v oblasti materiálů a zpracování a komplexními řešeními následného zpracování zaručuje, že konečné držáky snímačů splňují přísné požadavky tohoto odvětví. Společnosti jako např Met3dp, která nabízí synergii pokročilé výroby kovových prášků, nejmodernějších tiskových systémů a hlubokých aplikačních znalostí, představuje typ integrovaného partnera schopného podpořit automobilové společnosti na jejich cestě k AM.
Kovový 3D tisk již není jen nástrojem pro tvorbu prototypů, ale životaschopným a stále přesvědčivějším výrobním řešením pro složité a vysoce hodnotné automobilové komponenty. Pro držáky senzorů v elektromobilech a autonomních vozidlech nabízí AM cestu ke zvýšení výkonu, urychlení inovací a získání konkurenční výhody při utváření budoucnosti mobility.
Jste připraveni prozkoumat, jak může aditivní výroba kovů změnit vaše návrhy držáků automobilových senzorů? Kontaktujte společnost Met3dp ještě dnes, abyste prodiskutovali své konkrétní požadavky a zjistili, jak mohou naše komplexní řešení AM posunout vaše projekty kupředu.
Sdílet na
MET3DP Technology Co., LTD je předním poskytovatelem řešení aditivní výroby se sídlem v Qingdao v Číně. Naše společnost se specializuje na zařízení pro 3D tisk a vysoce výkonné kovové prášky pro průmyslové aplikace.
Dotaz k získání nejlepší ceny a přizpůsobeného řešení pro vaše podnikání!
Související články
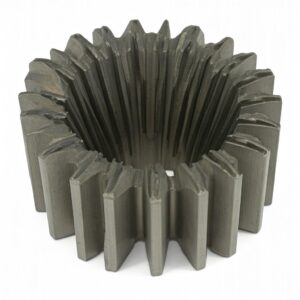
Vysoce výkonné segmenty lopatek trysek: Revoluce v účinnosti turbín díky 3D tisku z kovu
Přečtěte si více "O Met3DP
Nedávná aktualizace
Náš produkt
KONTAKTUJTE NÁS
Nějaké otázky? Pošlete nám zprávu hned teď! Po obdržení vaší zprávy obsloužíme vaši žádost s celým týmem.
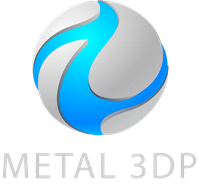
Kovové prášky pro 3D tisk a aditivní výrobu