High-Strength Clamps via Metal 3D Printing
Obsah
Introduction: The Critical Role of High-Strength Custom Clamps in Industry
In the intricate dance of modern manufacturing, seemingly simple components often play pivotal roles. Among these unsung heroes are industrial clamps – devices designed to hold, secure, position, or fasten objects with precision and reliability. From delicate medical device assembly lines to the high-stress environments of aerospace manufacturing and heavy machinery operation, the need for robust, reliable clamping solutions is universal. However, not all clamps are created equal. Standard, off-the-shelf solutions frequently fall short when faced with unique geometries, extreme operating conditions, or demanding performance requirements. This is where custom industrial clamps become essential, tailored specifically to the task at hand.
Traditionally, producing these custom clamps presented significant hurdles. Engineers designing specialized workholding fixtures, unique assembly jigs, or non-standard mounting brackets often faced a difficult trade-off. Conventional manufacturing methods like CNC machining from billet or casting, while capable of producing strong parts, often involve long lead times, high initial tooling costs (especially for casting), and limitations in geometric complexity. Machining intricate internal features or highly organic shapes can be time-consuming and generate substantial material waste. Casting, while suitable for volume, struggles with rapid prototyping and design iterations, and achieving the fine detail or thin walls sometimes required for optimized clamp designs can be problematic. Furthermore, achieving the absolute highest strength often required selecting bulkier designs or more expensive materials, impacting overall system weight and cost. These challenges often led to compromises: designs might be simplified, lead times extended, or performance margins reduced, impacting overall productivity and innovation. Procurement managers faced the challenge of sourcing these low-volume, high-complexity parts efficiently, often dealing with multiple vendors for machining, finishing, and assembly.
Vstupte výroba aditiv kovů (AM), běžně známý jako kov 3D tisk. This transformative technology offers a fundamentally different approach to creating complex metal components. Instead of subtracting material from a larger block or using molds, AM builds parts layer by layer directly from metal powder, guided by a digital design file. This layer-wise construction unlocks unprecedented design freedom, enabling the creation of highly complex, optimized, and customized metal 3D printing clamps that were previously difficult or impossible to manufacture. Technologies like Selective Laser Melting (SLM) and Electron Beam Melting (EBM), core competencies at leading AM solution providers like Met3dp, fuse fine metal powders precisely where needed, building dense, high-strength metal parts. For engineers and procurement specialists grappling with the limitations of traditional methods for high-strength clamps, metal AM presents a powerful alternative, promising faster turnaround times for custom designs, reduced material waste, the ability to consolidate multiple components into a single printed part, and the potential to create clamping solutions optimized for specific performance criteria like strength-to-weight ratio or conformal contact. This technology is not just a prototyping tool; it’s a viable production method for demanding manufacturing clamps and specialized industrial components.
Applications & Use Cases: Where Metal 3D Printed Clamps Excel
The versatility and design freedom offered by metal additive manufacturing unlock a vast array of applications for custom clamps across numerous high-stakes industries. The ability to tailor a clamp’s geometry, material properties, and functionality precisely to the task allows engineers to overcome challenges and enhance processes in ways previously unachievable. Here’s a deeper look into specific sectors and applications where metal 3D printed clamps are making a significant impact:
1. Aerospace:
- Výzva: Need for lightweight, high-strength components that can withstand extreme temperatures and vibrations, often with complex geometries to fit within tight spaces or conform to aerodynamic surfaces. Holding delicate or complex components during assembly and inspection without causing damage is crucial.
- AM Clamp Solutions:
- Complex Workholding Fixtures: Creating custom jigs and fixtures that perfectly match the contours of complex aerospace parts (e.g., turbine blades, fuselage sections) for machining, inspection, or assembly. Metal AM allows for conformal surfaces and integrated cooling channels if needed.
- Lightweight Mounting Clamps: Designing structurally optimized brackets and clamps using topology optimization to minimize weight while maintaining high strength for securing wiring harnesses, hydraulic lines, or instrumentation. Materials like Titanium alloys (Ti6Al4V), which Met3dp offers expertise in, are often employed.
- Assembly Jigs: Precise clamps for holding components during intricate assembly processes, ensuring alignment and preventing movement.
- Výhody: Significant weight reduction, improved part accessibility during manufacturing, reduced lead times for tooling, ability to create clamps for previously un-holdable parts. Procurement benefits from faster tooling availability for new programs or modifications.
2. Automotive:
- Výzva: High-volume production requires durable, repeatable, and often automated clamping solutions for welding, assembly, machining, and quality control. Rapid iteration for new model tooling and fixtures is essential. Strength and fatigue resistance are critical for long tool life.
- AM Clamp Solutions:
- Robotic End-Effector Grippers/Clamps: Custom-designed grippers for robotic arms that precisely match the part being handled, improving grip security and reducing cycle times in automated assembly lines. Integration of pneumatic channels or sensor mounts directly into the printed clamp is possible.
- Welding Fixtures: High-strength, heat-resistant clamps made from materials like M300 Maraging Steel or specialized Stainless Steels (like 17-4PH) to hold components securely during automated or manual welding processes. Conformal designs can minimize part distortion.
- Machining Fixtures: Robust clamps designed via DfAM to provide maximum rigidity and vibration damping while ensuring clear tool paths during CNC machining operations.
- Inspection Fixtures: Precise clamps to hold parts consistently for CMM or vision system inspection, ensuring measurement repeatability.
- Výhody: Enhanced automation efficiency, longer tool life due to optimized design and material selection, rapid deployment of new tooling, reduced fixture weight improving robot performance. Enables automotive workholding suppliers to offer highly customized solutions quickly.
3. Medical:
- Výzva: Requires clamps and fixtures with high precision, biocompatibility (for certain applications), sterilizability, and often complex, ergonomic designs for surgical instruments or device assembly. Holding delicate or small components securely is paramount.
- AM Clamp Solutions:
- Surgical Instrument Components: Clamping mechanisms within specialized surgical tools, potentially made from biocompatible materials like Titanium alloys or specific Stainless Steels.
- Medical Device Assembly Fixtures: Highly precise, custom jigs and clamps for assembling intricate medical devices (e.g., pacemakers, diagnostic equipment), ensuring components are held securely and accurately without damage.
- Orthopedic Tooling: Custom clamps used in surgical procedures or the manufacture of orthopedic implants.
- Výhody: Ability to create highly ergonomic and complex shapes, use of biocompatible materials, rapid prototyping of new instrument designs, precise holding of miniature components. Streamlines sourcing for specialized medical device fixtures.
4. Heavy Machinery & Industrial Manufacturing:
- Výzva: Dealing with large, heavy components requiring extremely robust clamping solutions. Clamps may need to withstand high forces, impacts, and harsh operating environments (e.g., high temperatures, abrasive materials). Customization is often needed for specific equipment or processes.
- AM Clamp Solutions:
- Heavy-Duty Workholding: Large-scale, high-strength clamps manufactured from materials like M300 or robust tool steels for securing large castings, forgings, or fabrications during machining or assembly.
- Maintenance & Repair Clamps: Custom clamps designed for specific repair tasks or holding components during maintenance operations in the field or factory.
- Pipe Clamps & Brackets: Specialized clamps for securing pipes, conduits, or structural elements in demanding industrial settings, potentially optimized for vibration damping or specific load paths.
- Výhody: Ability to create clamps capable of handling extreme loads, customization for unique tasks, potential for on-demand replacement parts reducing downtime. Provides industrial clamp suppliers with a method to produce specialized, low-volume clamps cost-effectively.
5. Robotics & Automation:
- Výzva: Need for lightweight, strong, and highly customized grippers and clamps for robotic end-effectors to handle a wide variety of parts efficiently and reliably. Integration with sensors and actuators is often required.
- AM Clamp Solutions:
- Custom End-of-Arm Tooling (EOAT): Highly integrated clamping solutions designed specifically for the robot and the task, often combining gripping fingers, mounting structures, and channels for pneumatics or wiring into a single printed part.
- Adaptive Clamping Systems: Designs incorporating lattice structures or compliant mechanisms, printed from flexible metal alloys if needed, to gently grip delicate or irregularly shaped objects.
- Výhody: Optimized robot performance through lighter EOAT, increased gripping versatility, reduced complexity through part consolidation, faster development of custom automation solutions. Essential for robotic clamping solutions providers.
Across these industries, metal AM empowers engineers and B2B clamp manufacturing partners to rethink clamp design, moving beyond the constraints of traditional methods to create solutions that are stronger, lighter, more functional, and faster to produce, directly addressing the specific needs of the application.
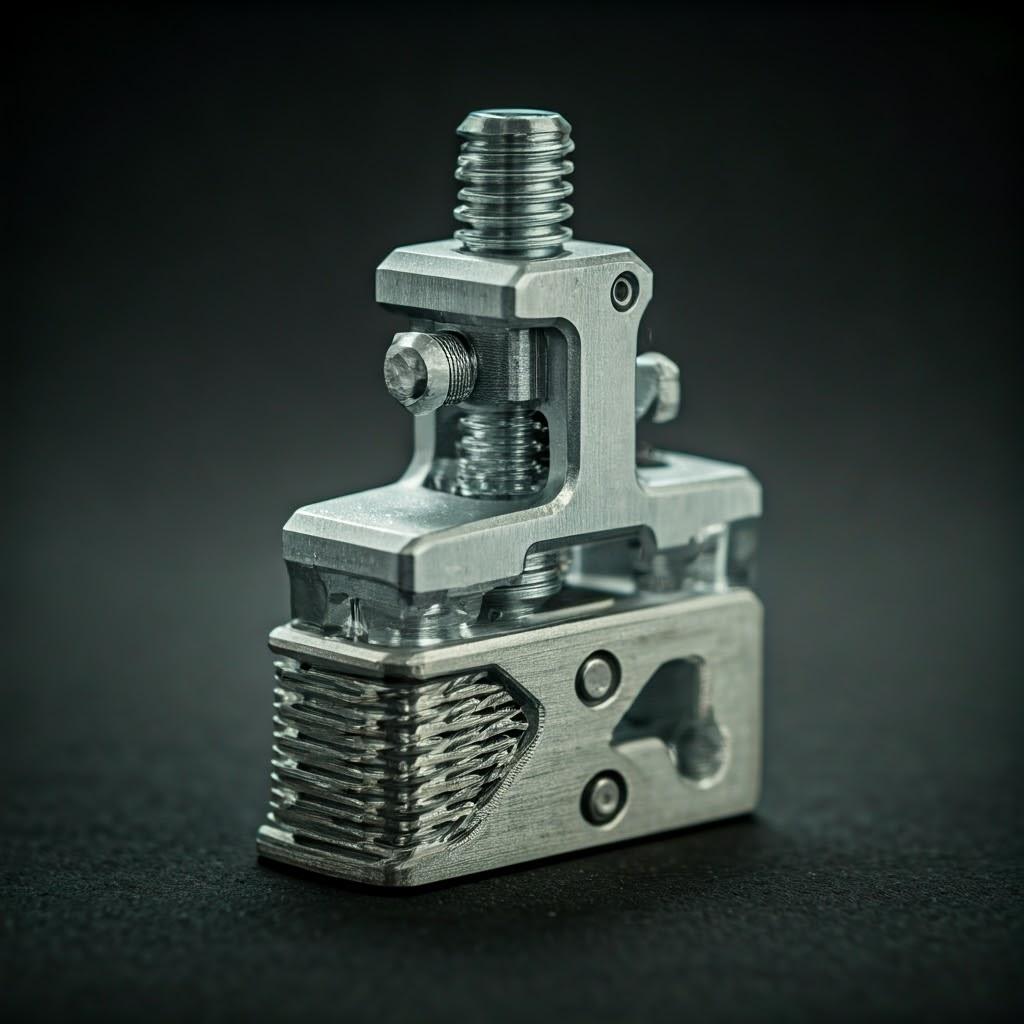
Why Choose Metal 3D Printing for Custom Industrial Clamps?
While traditional manufacturing methods like CNC machining and casting have long served the industry, metal additive manufacturing presents a compelling value proposition, particularly for custom industrial clamps where complexity, speed, and performance are key drivers. Understanding the distinct advantages of AM helps engineers and procurement managers make informed decisions about the best production method for their specific needs.
Comparison: Additive Manufacturing vs. Traditional Methods for Clamps
Vlastnosti | Metal Additive Manufacturing (e.g., SLM/EBM) | CNC obrábění | Casting |
---|---|---|---|
Složitost návrhu | Very High (Internal channels, lattices, organic shapes feasible) | Moderate to High (Limited by tool access) | Moderate (Limited by mold design, draft angles) |
Customization Speed | High (Directly from CAD, no tooling required) | Moderate (Requires programming, setup) | Low (Requires pattern/mold creation) |
Lead Time (Prototype) | Fast (Days) | Moderate (Days to Weeks) | Slow (Weeks to Months) |
Lead Time (Production) | Moderate (Scalable with machine capacity) | Fast (For established processes) | Moderate to Fast (Once tooling exists) |
Materiálový odpad | Low (Powder recycled) | High (Subtractive process) | Moderate (Gates, runners, sprues) |
Náklady na nástroje | Žádný | Low (Standard cutting tools) | High (Pattern/Mold cost) |
Konsolidace částí | High Potential (Combine multiple parts into one print) | Low Potential | Low Potential |
Poměr síly a hmotnosti | Excellent (Topology optimization enables optimized designs) | Good (Limited optimization potential) | Fair (Often requires bulkier designs) |
Výběr materiálu | Growing Range (Specific alloys optimized for AM) | Very Wide (Any machinable stock) | Wide (Castable alloys) |
Ideal Volume | Prototypes, Low-to-Medium Volume, Highly Custom | Prototypes, Medium-to-High Volume | Medium-to-High Volume |
Export do archů
Key Advantages of Metal AM for Clamps:
- Bezkonkurenční volnost designu: This is arguably the most significant advantage. AM allows engineers to design clamps with intricate internal cooling channels (for high-temperature applications), complex conformal surfaces (for gripping unusually shaped parts), negative draft angles, and internal lattice structures to reduce weight while maintaining stiffness. This enables the creation of highly optimized and functional manufacturing clamps that simply cannot be made subtractively or through molding.
- Rapid Prototyping & Iteration: Need to test a new clamp design quickly? Metal AM allows for the production of functional metal prototypes in a matter of days directly from a CAD file. This accelerates the design validation process, allowing engineers to test, refine, and perfect clamp designs much faster than waiting for traditional tooling or complex machining setups. This agility is crucial in fast-paced industries like automotive and aerospace.
- On-Demand Production & Digital Inventory: Metal AM enables manufacturing directly from digital files, facilitating an on-demand production model. Instead of holding physical inventory of numerous custom clamp variations, companies can maintain a digital inventory and print clamps as needed. This reduces warehousing costs, minimizes obsolescence risk, and enhances supply chain resilience, a key concern for procurement departments seeking industrial clamp manufacturers.
- Účinnost materiálu: Subtractive methods like CNC machining can generate significant material waste, sometimes starting with a large block of expensive metal to produce a small, complex clamp. AM, being an additive process, uses material primarily where it’s needed. Unfused powder within the build chamber can typically be recycled and reused, making it a more sustainable option, especially with high-value alloys.
- Konsolidace částí: Complex clamping assemblies often consist of multiple individual components that need to be machined, sourced, and assembled. Metal AM allows designers to consolidate several parts into a single, monolithic printed component. This reduces assembly time, eliminates potential points of failure at joints or fasteners, simplifies the bill of materials, and potentially lowers overall weight and cost.
- High Strength-to-Weight Ratios: By combining advanced materials (like 17-4PH or M300) with design optimization techniques (like topology optimization), metal AM can produce clamps that are exceptionally strong yet significantly lighter than their traditionally manufactured counterparts. This is critical in weight-sensitive applications like aerospace and robotics.
For procurement managers and engineers looking for wholesale 3D printed parts or reliable custom clamp production, partnering with an AM expert like Met3dp provides access to these benefits, leveraging advanced printing technologies and material science to deliver superior clamping solutions. The ability to get custom, high-performance clamps quickly and efficiently changes the equation for tooling and fixture design.
Material Focus: 17-4PH Stainless Steel & M300 Maraging Steel for Demanding Clamps
The performance, durability, and suitability of a custom industrial clamp are fundamentally tied to the material from which it’s made. Metal additive manufacturing offers a growing portfolio of advanced metal powders, but for applications demanding high strength, toughness, and reliability, two materials stand out: 17-4 Precipitation Hardening (PH) Stainless Steel and M300 Maraging Steel. Understanding their distinct properties is crucial for selecting the optimal material for your specific clamping needs. Companies like Met3dp specialize in producing and utilizing such vysoce kvalitní kovové prášky, leveraging advanced atomization techniques to ensure the consistency and spherical morphology required for reliable additive manufacturing.
1. 17-4PH Stainless Steel:
- Přehled: 17-4PH is a versatile, chromium-nickel-copper precipitation-hardening stainless steel known for its excellent combination of high strength, good corrosion resistance, and good toughness. It’s widely used across various industries and is a popular choice for metal AM due to its relatively good printability and well-understood post-processing requirements.
- Key Properties (Post-Heat Treatment):
- High Strength & Hardness: Can achieve high tensile strength (often exceeding 1100 MPa or 160 ksi) and hardness (around 40 HRC) through appropriate heat treatment (aging).
- Dobrá odolnost proti korozi: Offers corrosion resistance comparable to 304 stainless steel in many environments, suitable for general industrial atmospheres and chemical exposure.
- Good Toughness: Maintains reasonable toughness even at high strength levels.
- Weldability/Printability: Generally considered to have good printability in powder bed fusion processes.
- Tepelné zpracování: This is critical for 17-4PH to achieve its desired properties. Parts are typically solution annealed after printing and then subjected to an aging (precipitation hardening) treatment at a specific temperature. A common condition is H900 (aged at 900°F / 482°C), which provides the highest strength and hardness, though other conditions (H1025, H1075, H1150) can be chosen to optimize toughness or ductility at the expense of some strength.
- Typical Clamp Applications: General-purpose industrial workholding, automotive fixtures, aerospace tooling components, medical instrument parts (where high strength is needed but biocompatibility isn’t the primary driver), food processing equipment clamps. It’s often the go-to material for metal 3D printing clamps requiring a balance of strength, corrosion resistance, and cost-effectiveness.
- Why it Matters for Clamps: Its high strength ensures clamps can withstand significant forces without yielding. The hardness provides wear resistance on clamping faces, and the corrosion resistance ensures longevity in typical factory environments. Its availability and well-understood behavior make it a reliable choice for many custom clamp production potřeby.
Table: Typical Properties of 17-4PH (Condition H900)
Vlastnictví | Typical Value (Metric) | Typical Value (Imperial) | Poznámky |
---|---|---|---|
Maximální pevnost v tahu | > 1310 MPa | > 190 ksi | Highly dependent on print quality & HT |
Mez kluzu (0,2%) | > 1170 MPa | > 170 ksi | Highly dependent on print quality & HT |
Prodloužení po přetržení | ~10-14% | ~10-14% | Varies with build direction |
Tvrdost (Rockwell C) | ~40-45 HRC | ~40-45 HRC | Post-heat treatment |
Hustota | ~7,8 g/cm³ | ~0.28 lbs/in³ |
Export do archů
2. M300 Maraging Steel:
- Přehled: M300 is an ultra-high-strength maraging steel. These steels are known for achieving exceptional strength and hardness while maintaining relatively good toughness, superior to many conventional high-carbon tool steels. They contain very little carbon, instead deriving their strength from the precipitation of intermetallic compounds during an aging heat treatment. M300 is often chosen for the most demanding applications.
- Key Properties (Post-Heat Treatment):
- Velmi vysoká pevnost: Capable of achieving yield strengths exceeding 1800 MPa (260 ksi) and ultimate tensile strengths approaching 2000 MPa (290 ksi).
- Výjimečná tvrdost: Can reach hardness levels above 50 HRC, providing excellent wear resistance.
- Good Toughness: Despite its extreme strength and hardness, M300 retains good fracture toughness, making it resistant to brittle failure.
- Good Machinability (in annealed state): Easier to machine before the final aging treatment compared to other steels of similar hardness.
- Dobrá potiskovatelnost: Prints well in powder bed fusion systems, although careful control over parameters and heat treatment is essential.
- Tepelné zpracování: Similar to 17-4PH, M300 requires post-print heat treatment. This typically involves solution annealing followed by aging at around 480-500°C (896-932°F) for several hours. This aging process causes the precipitation of strengthening intermetallic phases within the low-carbon martensitic matrix.
- Typical Clamp Applications: High-performance tooling (injection molds, die casting components), high-load workholding fixtures, clamps used in high-stress or high-impact environments, performance automotive components, aerospace brackets requiring maximum strength-to-weight. Ideal for clamps where failure is not an option and maximum clamping force or rigidity is required.
- Why it Matters for Clamps: Its ultra-high strength allows for smaller, lighter clamp designs capable of exerting or resisting enormous forces. The exceptional hardness ensures long life even under abrasive conditions or high contact stresses on clamp faces. It’s the material of choice when standard steels like 17-4PH might deform or wear prematurely under extreme load. Sourcing high-quality M300 powder, like that produced using Met3dp’s advanced gas atomization systems, is critical for achieving these properties reliably in printed parts.
Table: Typical Properties of M300 Maraging Steel (Aged)
Vlastnictví | Typical Value (Metric) | Typical Value (Imperial) | Poznámky |
---|---|---|---|
Maximální pevnost v tahu | ~1900-2100 MPa | ~275-305 ksi | Highly dependent on print & HT |
Mez kluzu (0,2%) | ~1800-2000 MPa | ~260-290 ksi | Highly dependent on print & HT |
Prodloužení po přetržení | ~5-10% | ~5-10% | Lower ductility than 17-4PH |
Tvrdost (Rockwell C) | ~50-56 HRC | ~50-56 HRC | Post-aging |
Hustota | ~8.0-8.1 g/cm³ | ~0.29 lbs/in³ | Slightly denser than stainless steel |
Export do archů
Choosing Between 17-4PH and M300:
The choice depends on the specific requirements of the clamp:
- Choose 17-4PH if: You need a good balance of strength, corrosion resistance, and toughness for general industrial use. Cost is a significant factor, and the operating environment is not extremely harsh.
- Choose M300 if: Absolute maximum strength, hardness, and wear resistance are critical. The clamp will experience extreme loads or high contact stresses. Weight savings through a stronger, potentially smaller design are highly desirable, and the higher material/processing cost is justified by the performance demands. Corrosion resistance is secondary to mechanical properties (M300 has lower corrosion resistance than 17-4PH).
Partnering with knowledgeable metal powder suppliers and AM service providers like Met3dp, who possess deep expertise in processing these advanced materials via their industry-leading print technology, ensures that the selected material is printed and post-processed correctly to deliver the optimal performance for your high-strength custom industrial clamps. Their experience spans materials like TiNi, TiTa, TiAl, TiNbZr, CoCrMo, various stainless steels, and superalloys, ensuring a comprehensive approach to material selection.
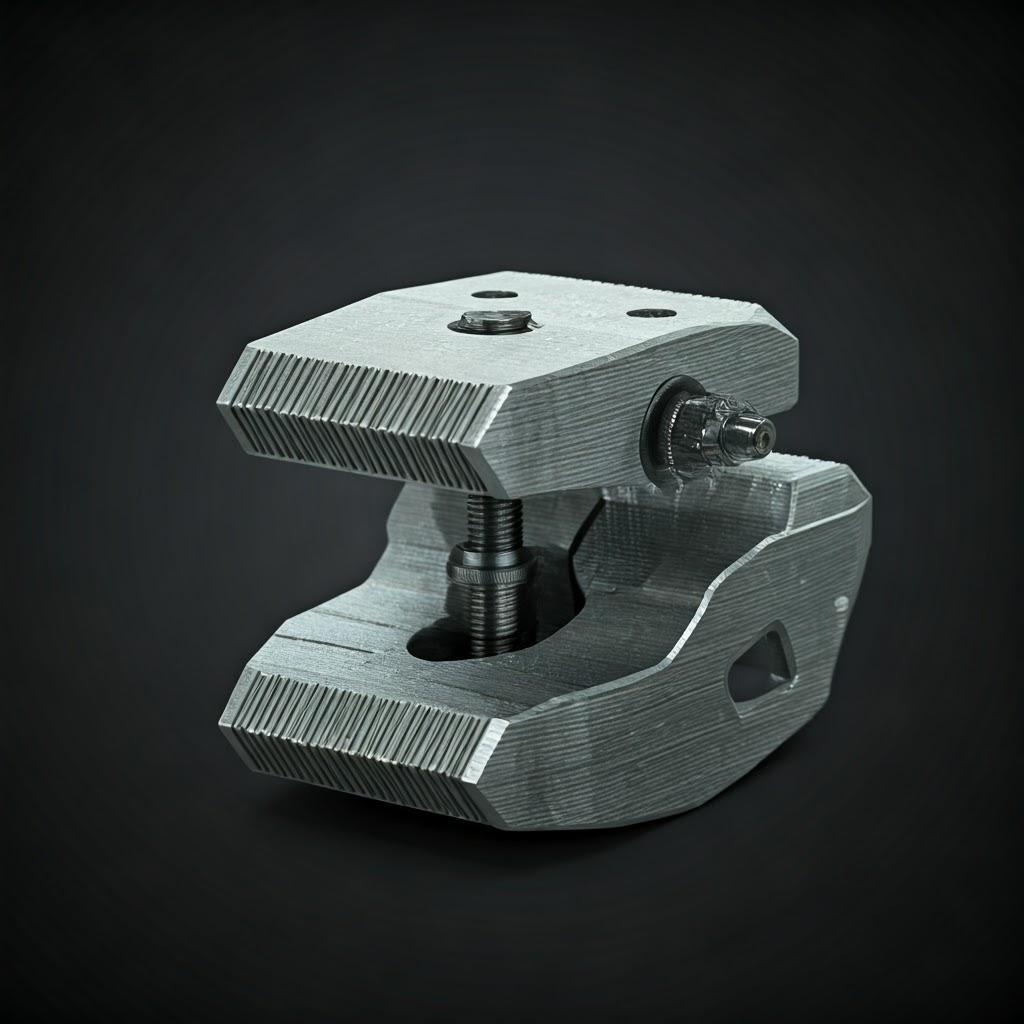
Design for Additive Manufacturing (DfAM): Optimizing Your Custom Clamp Design
Simply replicating a design intended for CNC machining or casting using metal additive manufacturing often fails to capitalize on the technology’s true potential and can even lead to suboptimal results or printing failures. To truly leverage the power of metal AM for high-strength industrial clamps, engineers must embrace Design pro aditivní výrobu (DfAM) principles. DfAM is not just about making a part printable; it’s about designing it intelligently to maximize performance, minimize cost, and reduce lead times by considering the unique capabilities and constraints of the layer-by-layer building process from the outset. Collaborating with experienced additive manufacturing design optimization partners during the design phase is often crucial for success.
Key DfAM Principles for Robust Metal Clamps:
- Optimalizace topologie:
- Concept: This is a computational design technique where software algorithms determine the most efficient material distribution within a defined design space, subject to specific loads, constraints, and performance targets (e.g., minimize weight, maximize stiffness).
- Application for Clamps: For a clamp body, topology optimization can identify areas where material is not contributing significantly to strength or stiffness and remove it, resulting in organic-looking, lightweight structures that maintain or even exceed the performance of their solid counterparts. This is invaluable for reducing inertia in robotic clamps or minimizing weight in aerospace applications.
- Výhody: Significant weight reduction (often 20-50% or more), improved material efficiency, high strength-to-weight ratios. Requires specialized software and expertise to set up and interpret results effectively.
- Lattice Structures & Infill:
- Concept: Replacing solid sections of a part with internal lattice structures (e.g., cubic, gyroid, honeycomb). These structures can be engineered for specific properties.
- Application for Clamps: Can be used to further reduce weight in bulky clamp sections while maintaining structural integrity. Certain lattice types can also improve vibration damping or allow for fluid flow (e.g., for integrated cooling or hydraulic actuation within the clamp body). Variable density lattices can strategically place stiffness where needed.
- Výhody: Drastic weight reduction, potential for multi-functional design (e.g., integrated cooling), improved impact absorption or vibration damping characteristics.
- Designing for Minimal Support Structures:
- Concept: Support structures are temporary features printed alongside the part to anchor overhanging sections and manage thermal stresses during the build. However, they consume extra material, increase print time, and require post-processing for removal, which can be challenging and costly, especially for internal features.
- Application for Clamps: Orienting the clamp design on the build plate to minimize steep overhangs (typically angles < 45 degrees from the horizontal require support). Designing features with self-supporting angles (chamfers instead of sharp horizontal overhangs). Incorporating sacrificial ribs or modifying geometry slightly to avoid the need for supports in hard-to-reach areas.
- Výhody: Reduced material consumption, faster print times, significantly easier and cheaper post-processing, improved surface finish on previously supported surfaces.
- Konsolidace částí:
- Concept: Leveraging AM’s ability to create complex assemblies as single, monolithic parts.
- Application for Clamps: Combining multiple components of a traditional clamp assembly (e.g., base, arm, fastening mechanism elements, brackets) into one printed part. Integrating features like spring-loaded mechanisms, channels for pneumatics, or mounting points directly into the clamp body.
- Výhody: Reduced part count, elimination of assembly labor and potential assembly errors, removal of fasteners or joints which can be failure points, often results in a lighter and stronger overall design. Simplifies the Bill of Materials (BOM) for procurement.
- Feature Design Considerations:
- Tloušťka stěny: Designing walls thick enough to be reliably printed and handle expected loads, but avoiding unnecessarily thick sections which increase print time and thermal stress. Minimum printable wall thickness depends on the material and AM process (often around 0.4-0.8 mm).
- Holes: Small holes (typically < 6-10 mm diameter, depending on orientation) may be printed without supports but might not be perfectly round or accurate. Consider designing holes slightly undersized for post-print drilling or reaming if high precision is required. Horizontal holes often require teardrop shapes or support.
- Threads: Fine threads are challenging to print accurately and achieve required strength. It’s often better to print holes undersized and tap threads post-print, or design for threaded inserts. Larger, coarser threads might be printed directly but may require chasing.
- Clearances: Account for achievable tolerances when designing mating parts or interfaces within the clamp mechanism.
- Material & Process Selection:
- Concept: The choice of material (e.g., 17-4PH vs. M300) and AM process (e.g., Laser Powder Bed Fusion – LPBF/SLM, Electron Beam Melting – EBM) influences design rules (e.g., minimum feature size, support strategies).
- Application for Clamps: Designing features compatible with the resolution of the chosen process. Considering the material’s specific heat treatment requirements during the design phase (e.g., ensuring features can withstand furnace temperatures without distortion).
Effectively implementing DfAM often requires a shift in thinking for designers accustomed to traditional methods. Partnering with AM service providers like Met3dp, who offer 3D print design services or consultation, can bridge this knowledge gap, ensuring that your custom clamp design is fully optimized for additive manufacturing, leading to superior performance and cost-effectiveness.
Achievable Tolerances, Surface Finish, and Dimensional Accuracy in Metal AM Clamps
While metal additive manufacturing offers incredible design freedom, it’s crucial for engineers and procurement managers to have realistic expectations regarding the achievable precision, surface quality, and dimensional accuracy of printed parts, including custom industrial clamps. These factors are influenced by the specific AM process, machine calibration, material properties, build orientation, part geometry, and post-processing steps. Understanding these aspects helps in specifying requirements correctly and determining where secondary finishing operations might be necessary.
Typical Tolerances in Powder Bed Fusion (LPBF/SLM, EBM):
Metal AM processes like Selective Laser Melting (SLM), also known as Laser Powder Bed Fusion (LPBF), and Electron Beam Melting (EBM) – technologies central to providers like Met3dp – offer good dimensional accuracy, but they are not inherently as precise as high-end CNC machining across all features straight off the printer.
- General Tolerances: A common rule of thumb for as-built metal AM parts is tolerances in the range of ±0.1 mm to ±0.2 mm (±0.004″ to ±0.008″) for smaller dimensions (e.g., up to 100 mm), plus an additional ±0.001 mm/mm to ±0.002 mm/mm for larger dimensions.
- Factors Influencing Tolerance:
- Kalibrace stroje: Regular calibration of the printer’s lasers/electron beam, optics, and motion systems is critical.
- Tloušťka vrstvy: Thinner layers generally allow for finer feature resolution but increase build time.
- Beam Spot Size: The diameter of the laser or electron beam affects the minimum feature size and achievable precision.
- Tepelné účinky: Heating and cooling cycles during the layer-by-layer process inevitably cause some thermal expansion, contraction, and residual stress, which can lead to minor warping or deviation from the intended geometry. Complex geometries are more susceptible.
- Orientace na stavbu: The orientation of the part on the build platform significantly impacts accuracy, surface finish on different faces, and the need for support structures, which can affect surface quality upon removal.
- Vlastnosti prášku: The size distribution, morphology, and flowability of the metal powder influence packing density and melt pool stability. Met3dp’s focus on high-quality, spherical powders produced via advanced atomization contributes to process stability and dimensional control.
- Následné zpracování: Stress relief and heat treatment can cause minor dimensional changes. Support removal can affect surface accuracy in localized areas.
Povrchová úprava (drsnost):
The as-built surface finish of metal AM parts is typically rougher than machined surfaces due to the layered nature of the process and the adherence of partially sintered powder particles.
- Drsnost povrchu (Ra) podle stavu: Values commonly range from 6 µm to 25 µm (240 µin to 1000 µin), depending heavily on:
- Orientace: Upward-facing surfaces tend to be smoother than downward-facing surfaces (which require support) or vertical walls (which show layer lines).
- Parametry procesu: Laser/beam power, scan speed, and layer thickness affect melt pool dynamics and surface texture.
- Materiál: Different materials can exhibit different surface characteristics.
- Zlepšení povrchové úpravy: If a smoother finish is required for clamp faces, sealing surfaces, or aesthetic reasons, post-processing is necessary. Common methods include:
- Bead Blasting/Sand Blasting: Creates a uniform matte finish, typically improving Ra slightly (e.g., 5-15 µm).
- Tumbling/Vibratory Finishing: Uses media to smooth surfaces and edges, effective for batches of smaller parts.
- CNC obrábění: Can achieve very smooth and precise finishes (Ra < 1 µm / 40 µin) on specific features.
- Leštění: Manual or automated polishing can achieve mirror-like finishes (Ra < 0.1 µm / 4 µin) but is labor-intensive.
Table: Typical Tolerances & Surface Finish for Metal AM (LPBF/SLM)
Parametr | As-Built Typical Range | Post-Processed Potential | Poznámky |
---|---|---|---|
Rozměrová tolerance | ±0.1 to ±0.2 mm (+0.002 L) | ±0.01 to ±0.05 mm (Machined) | L = Length in mm. Dependent on geometry, size, orientation. |
Drsnost povrchu (Ra) | 6 – 25 µm (240 – 1000 µin) | < 1 µm (Machined/Polished) | Highly dependent on surface orientation & post-processing method. |
Minimální velikost funkce | ~0.4 – 0.8 mm | N/A | Depends on machine resolution & process parameters. |
Minimální tloušťka stěny | ~0.4 – 1.0 mm | N/A | Thicker walls generally recommended for robustness. |
Export do archů
Setting Expectations for Industrial Clamps:
For many industrial clamp applications, the as-built tolerances and surface finish may be perfectly acceptable, especially for non-critical surfaces or robust workholding. However, if the clamp includes precise locating features, datum surfaces, smooth sliding mechanisms, or requires sealing against a workpiece, post-processing machining or finishing of those specific features will likely be required. It’s essential to clearly define critical tolerances and surface finish requirements on drawings and communicate these to the AM service provider. Understanding these achievable levels helps manage expectations and budget appropriately for necessary finishing steps, ensuring the final precision clamps manufacturing meets the application’s demands.
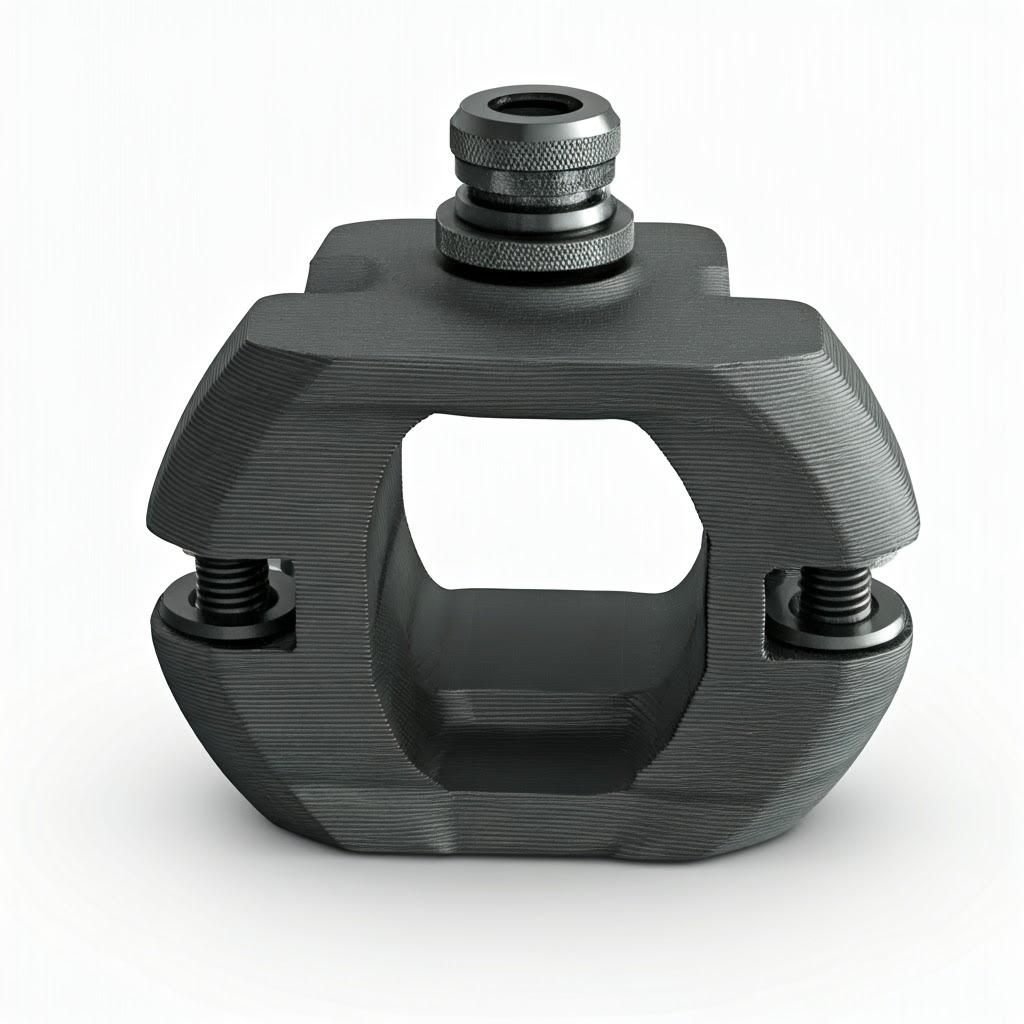
Essential Post-Processing Steps for Metal 3D Printed Clamps
Creating a custom industrial clamp doesn’t end when the 3D printer finishes its job. Metal additive manufacturing is typically the first major step in a multi-stage production process. Post-processing encompasses a series of essential operations performed after printing to transform the raw printed part into a functional, durable, and dimensionally accurate component ready for use. These steps are particularly critical when working with high-strength materials like 17-4PH and M300 Maraging Steel to unlock their full mechanical properties and ensure the clamp meets performance specifications. Engaging with a metal AM post-processing supplier or an AM service provider with integrated capabilities is vital for a seamless workflow.
Common Post-Processing Workflow for AM Clamps:
- Powder Removal / Depowdering:
- Účel: Removing unfused metal powder trapped within the build chamber and potentially within internal channels or complex features of the clamp.
- Metody: Manual brushing, compressed air blow-off, ultrasonic cleaning baths, specialized depowdering stations. Careful execution is needed, especially for complex internal geometries, to recover valuable powder for recycling and ensure no loose powder remains.
- Úleva od stresu:
- Účel: The rapid heating and cooling cycles inherent in powder bed fusion create significant residual stresses within the printed part. These stresses can cause distortion or cracking during printing, upon removal from the build plate, or during subsequent machining. A stress relief heat treatment, typically performed while the part is still attached to the build plate, reduces these internal stresses.
- Method: Heating the part and build plate in a furnace to a specific temperature (below the aging/hardening temperature, e.g., ~650°C for 17-4PH, ~820°C for M300 solution anneal which also relieves stress) for a set duration, followed by controlled cooling. Atmosphere control (vacuum or inert gas) is often required to prevent oxidation.
- Důležitost: Absolutely critical for dimensional stability and preventing premature failure, especially for high-precision clamps or those made from stress-sensitive materials like M300.
- Part Removal from Build Plate:
- Účel: Separating the printed clamp(s) from the metal build plate they were fused to during printing.
- Metody: Typically done using Wire Electrical Discharge Machining (Wire EDM) or a bandsaw. Care must be taken not to damage the parts.
- Odstranění podpůrné konstrukce:
- Účel: Removing the temporary support structures printed to anchor overhangs and aid thermal management.
- Metody: Supports are designed to be weaker than the main part. They can often be removed manually (breaking, pliers) or require machining (milling, grinding), or specialized tools. Access can be difficult for internal supports. This step can be labor-intensive and requires careful handling to avoid damaging the part surface. DfAM plays a key role in minimizing support needs.
- Heat Treatment (Hardening/Aging):
- Účel: To achieve the final desired mechanical properties (strength, hardness, toughness) of the chosen alloy (e.g., 17-4PH, M300). As-printed parts typically do not possess the full strength potential.
- Method: Performed after support removal and potentially rough machining. Involves heating the parts in a precisely controlled furnace environment (atmosphere, temperature profile, duration) specific to the alloy and desired condition (e.g., H900 for 17-4PH, aging at ~480°C for M300). This is a critical heat treatment services AM step requiring metallurgical expertise.
- Důležitost: Essential for developing the high-strength characteristics required for demanding industrial clamps. Incorrect heat treatment can lead to suboptimal properties or part failure.
- Machining (Subtractive Finishing):
- Účel: To achieve tight tolerances on critical dimensions, create precise mating surfaces, drill/tap threads, or improve surface finish on specific features where the as-built AM accuracy is insufficient.
- Method: Using standard CNC milling, turning, grinding, or EDM processes on specific areas of the 3D printed clamp. Requires careful fixture design to hold the potentially complex AM part securely.
- Důležitost: Bridges the gap between AM’s design freedom and the high precision often required for functional interfaces, locating pins, or sealing surfaces on clamps.
- Povrchová úprava:
- Účel: To improve the surface roughness, appearance, wear resistance, or corrosion resistance of the clamp beyond the as-built state.
- Metody:
- Bead Blasting: Creates a uniform matte finish, removes partially sintered particles.
- Tumbling/Vibratory Finishing: Smooths surfaces and edges, good for batch processing.
- Leštění: For smooth, reflective surfaces (e.g., medical clamps).
- Coating/Plating: Applying coatings (e.g., PVD, plating) for enhanced wear resistance, corrosion protection, or lubricity on specific clamp faces or mechanisms.
- Důležitost: Tailors the surface properties to the specific functional or aesthetic requirements of the application. Provides options for surface treatment for 3D prints.
- Inspection and Quality Control:
- Účel: Verifying that the finished clamp meets all dimensional, material, and performance specifications.
- Metody: Dimensional inspection (CMM, 3D scanning), material testing (hardness checks, tensile tests on representative samples), Non-Destructive Testing (NDT) like CT scanning or X-ray to check for internal defects (e.g., porosity), visual inspection.
- Důležitost: Ensures the reliability and safety of the final component, crucial for quality assurance metal printing.
Integrating these post-processing steps effectively requires careful planning and coordination. Leading AM providers often offer a suite of in-house or tightly managed external post-processing capabilities to provide a turnkey solution from design to finished part.
Overcoming Common Challenges in 3D Printing High-Strength Clamps
While metal additive manufacturing enables the creation of exceptional high-strength clamps, the process is complex and not without potential challenges. Awareness of these common issues and the strategies to mitigate them is crucial for successful implementation, particularly when dealing with demanding industrial applications and materials like 17-4PH and M300. Partnering with experienced AM providers who possess robust process controls and troubleshooting expertise is key to navigating these potential pitfalls.
1. Warping and Distortion:
- Issue: Parts curling up, distorting, or detaching from the build plate during printing due to uneven heating/cooling and the buildup of residual thermal stresses. Complex geometries and large, flat sections are more prone to this.
- Causes: High thermal gradients between the molten pool and surrounding powder/solidified material; insufficient anchoring to the build plate or inadequate support structures.
- Strategie zmírnění dopadů:
- Simulation: Using process simulation software to predict thermal behavior and stress accumulation, allowing for design modifications (e.g., adding sacrificial ribs) or optimized build orientation before printing.
- Build Plate Heating: Preheating the build plate (common in EBM, also used in some LPBF systems) reduces thermal gradients.
- Optimalizovaná orientace: Printing the part in an orientation that minimizes large, flat surfaces parallel to the build plate and reduces unsupported overhangs.
- Robust Support Strategies: Designing effective support structures that anchor the part securely and help conduct heat away.
- Optimalizované parametry procesu: Fine-tuning laser/beam power, scan speed, and scan strategy to manage heat input.
- Úleva od stresu: Performing a stress relief cycle immediately after printing, often before removal from the build plate.
2. Difficulty in Support Removal:
- Issue: Support structures proving difficult, time-consuming, or impossible to remove without damaging the part, especially in complex internal channels or delicate features common in optimized clamp designs.
- Causes: Poor DfAM (excessive need for supports); supports placed in inaccessible areas; supports fused too strongly to the part due to incorrect parameters.
- Strategie zmírnění dopadů:
- DfAM Focus: Prioritizing designs that minimize or eliminate the need for supports through smart orientation and self-supporting angles (>45°).
- Optimized Support Design: Using support structures with appropriate density, contact points, and perforation patterns designed for easier removal (often software-generated with user control).
- Process Parameter Control: Ensuring parameters prevent excessive bonding between support and part.
- Specialized Removal Techniques: Utilizing tools like ultrasonic cutters, micro-blasting, or chemical etching in some cases (material dependent). Planning for access during the design phase.
3. Achieving Desired Material Properties Consistently:
- Issue: Final clamp properties (strength, density, ductility, hardness) not meeting specifications due to inconsistencies in the printing or heat treatment process.
- Causes: Porosity (see below); incomplete melting/fusion; incorrect heat treatment parameters (temperature, time, atmosphere); variations in powder quality.
- Strategie zmírnění dopadů:
- Strict Process Control: Utilizing AM systems with closed-loop monitoring and control features. Implementing rigorous machine calibration and maintenance schedules. Met3dp emphasizes the reliability and accuracy of its 3D tisk z kovu systémy.
- Powder Quality Management: Using high-quality, consistent metal powders with controlled sphericity, size distribution, and chemistry (a core strength of Met3dp’s powder production). Proper powder handling and recycling protocols.
- Parameter Optimization: Developing and validating robust process parameters specific to the material and machine.
- Heat Treatment Expertise: Employing precise, calibrated furnaces and adhering strictly to validated heat treatment cycles specific to the alloy and desired condition (e.g., H900, M300 aging).
- Testing & Validation: Performing metallurgical analysis and mechanical testing on witness coupons printed alongside parts to verify properties.
4. Porosity:
- Issue: Small voids or pores within the printed material, which can act as stress concentrators and reduce the clamp’s strength, fatigue life, and density.
- Causes: Trapped gas within the powder or melt pool; insufficient energy density leading to incomplete melting (Lack-of-Fusion porosity); keyholing porosity caused by excessive energy density creating unstable melt pools.
- Strategie zmírnění dopadů:
- Vysoce kvalitní prášek: Using powder with low internal gas content and optimized morphology.
- Optimalizované parametry procesu: Careful tuning of laser/beam power, scan speed, hatch spacing, and layer thickness to ensure stable melting and full consolidation.
- Inert Atmosphere Control: Maintaining a high-purity inert gas atmosphere (Argon or Nitrogen) in the build chamber to minimize oxidation and gas pickup.
- Izostatické lisování za tepla (HIP): A post-processing step involving high temperature and high pressure to close internal pores (adds cost and lead time but can achieve near 100% density). Often used for critical aerospace or medical parts.
5. Managing Residual Stresses:
- Issue: Even if warping doesn’t occur during printing, high residual stresses remain in the as-built part, potentially compromising strength or causing distortion during post-machining.
- Causes: Inherent thermal cycles of the AM process.
- Strategie zmírnění dopadů:
- Stress Relief Heat Treatment: Essential step, as described in post-processing.
- Optimalizované strategie skenování: Using techniques like island scanning or checkerboard patterns to distribute heat more evenly.
- Design Modifications: Avoiding large variations in cross-sectional thickness within the design where possible.
- Careful Machining: Using appropriate cutting parameters and potentially performing machining in stages with intermediate stress relief if significant material removal is required.
Successfully navigating these metal AM troubleshooting scenarios requires a deep understanding of materials science, process physics, and robust quality control measures. This underscores the importance of selecting an AM partner with proven experience and a commitment to quality, from powder production to final inspection, ensuring the reliability of your high-strength industrial clamps.
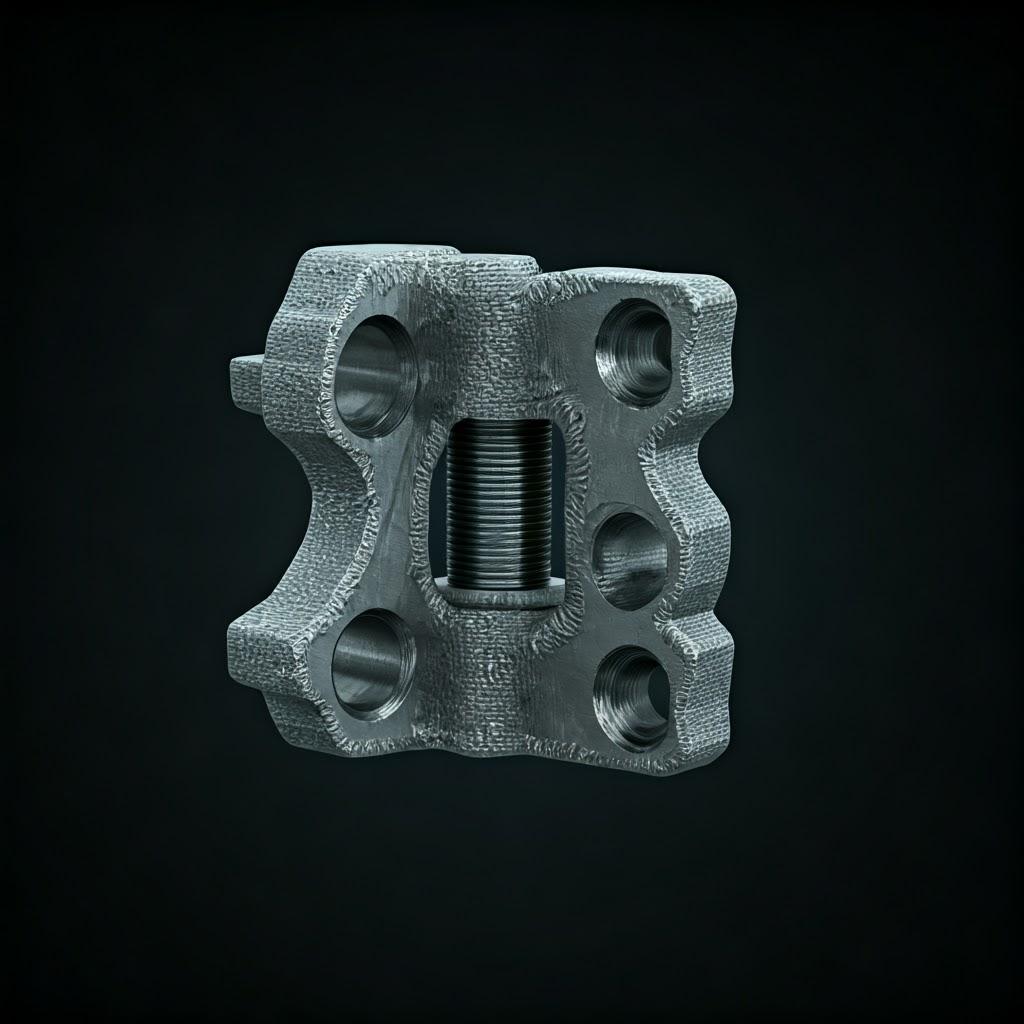
Selecting the Right Metal 3D Printing Service Provider for Industrial Clamps
Choosing the right manufacturing partner is paramount when sourcing high-strength custom industrial clamps via additive manufacturing. The quality, performance, and reliability of your final components depend heavily on the expertise, equipment, processes, and quality systems of your chosen supplier. For engineers and procurement managers evaluating potential metal additive manufacturing partners, especially for B2B relationships involving critical components or wholesale 3D printing volumes, a thorough vetting process is essential. Look beyond just price and consider the following crucial criteria:
Key Criteria for Evaluating Metal AM Suppliers:
- Expertise with High-Strength Materials:
- Requirement: Demonstrated experience and success in printing and post-processing the specific high-strength alloys required for your clamps, such as 17-4PH Stainless Steel and M300 Maraging Steel. This includes understanding their unique print parameters, support strategies, and critical heat treatment cycles.
- Evaluation: Ask about their experience with these specific materials. Request case studies or examples of similar parts they have produced. Do they have metallurgists or materials scientists on staff?
- Relevant Industry Certifications:
- Requirement: Certifications indicate adherence to recognized quality management systems. For general industrial applications, ISO 9001 certified AM providers are essential. For aerospace clamps, AS9100 certification is often mandatory. Medical applications may require ISO 13485.
- Evaluation: Verify current certifications relevant to your industry. Understand the scope of their certification. Companies like Met3dp, focused on industrial applications, often prioritize robust quality systems – you can learn more about their company philosophy and commitment on their O nás strana.
- Machine Capabilities and Technology:
- Requirement: The supplier should possess well-maintained, industrial-grade metal AM systems (e.g., LPBF/SLM, EBM) suitable for the required materials and part size. Consider build volume, achievable accuracy, and machine features (e.g., build plate heating, process monitoring).
- Evaluation: Inquire about their specific printer fleet (manufacturers, models, build envelopes). Does their technology align with your needs for precision and scale? Met3dp prides itself on printers offering industry-leading print volume, accuracy, and reliability.
- Integrated Post-Processing Services:
- Requirement: As discussed, post-processing is critical. Ideally, the provider offers comprehensive in-house capabilities (stress relief, heat treatment, support removal, basic finishing). If certain steps (e.g., complex CNC machining, specialized coatings) are outsourced, they should have a well-managed and qualified supply chain.
- Evaluation: Ask for a detailed list of their in-house post-processing capabilities. How do they manage outsourced processes? A single point of contact for the entire workflow simplifies procurement and project management.
- Robust Quality Control Systems:
- Requirement: A systematic approach to quality throughout the entire process, from incoming powder inspection to final part verification. This includes material traceability, process monitoring, adherence to procedures, and final inspection capabilities (CMM, NDT if required).
- Evaluation: Ask about their Quality Management System (QMS). What checks are performed during and after printing? How do they ensure material traceability? How is powder quality controlled (vital for consistent properties)? Met3dp’s emphasis on producing its own vysoce kvalitní kovové prášky provides an advantage here.
- Technical Support and DfAM Expertise:
- Requirement: The ability to provide guidance on Design for Additive Manufacturing (DfAM) is a significant value-add. A good partner can help optimize your clamp design for printability, performance, and cost-effectiveness.
- Evaluation: Do they offer DfAM consultation? Can their engineers review your design and suggest improvements? What software tools do they use for simulation or optimization?
- Track Record and Case Studies:
- Requirement: Proven success in delivering parts similar to yours, preferably within your industry.
- Evaluation: Request relevant case studies, customer testimonials, or references. How long have they been providing metal AM services?
- Capacity and Scalability:
- Requirement: Ability to meet your volume requirements, whether for single prototypes or larger production/wholesale orders, within acceptable lead times.
- Evaluation: Discuss their current capacity and typical lead times for different order sizes. How do they handle fluctuating demand?
- Communication and Project Management:
- Requirement: Clear, responsive communication and a defined process for project management, quoting, order tracking, and reporting.
- Evaluation: Assess their responsiveness during the initial inquiry and quoting process. Who will be your main point of contact?
Questions Procurement Should Ask Potential Suppliers:
- Can you provide details on your experience printing [Specific Material, e.g., M300]?
- What certifications does your facility hold (ISO 9001, AS9100, etc.)?
- What metal AM systems do you operate, and what are their build volumes?
- What post-processing steps do you perform in-house versus outsource?
- Can you describe your quality control process for incoming powder and finished parts?
- Do you offer DfAM support services?
- What are your standard lead times for prototypes vs. production quantities of parts like this?
- Can you provide references or case studies relevant to industrial clamping applications?
- How do you ensure material traceability throughout the process?
Výběr správného metal AM supplier selection goes beyond a simple transaction; it’s about finding a reliable B2B additive manufacturing partnership that can consistently deliver high-quality, mission-critical components like industrial clamps.
Understanding Cost Factors and Lead Times for AM Clamp Production
Additive manufacturing offers unique advantages, but understanding the cost structure and typical lead times is essential for budgeting, project planning, and managing expectations within procurement and engineering teams. Unlike traditional manufacturing where tooling often dominates initial costs, the cost of metal 3D printing is driven primarily by material consumption and machine time, alongside necessary post-processing.
Breakdown of Cost Drivers for Metal AM Clamps:
- Náklady na materiál:
- Factors: Type of metal powder (e.g., M300 is significantly more expensive than 17-4PH), the total volume of powder consumed (including the part itself and support structures), and powder recycling efficiency. High-performance alloys naturally command higher prices.
- Dopad: Directly proportional to the volume of the final part and its supports. DfAM techniques like topology optimization can significantly reduce material consumption and thus cost.
- Strojový čas:
- Factors: This is often the most significant cost component. It depends on:
- Part Volume/Size: Larger parts take longer to print.
- Část Složitost: Intricate details and complex geometries can increase scan time per layer.
- Výška stavby: Taller parts require more layers, directly impacting print duration.
- Nesting & Build Density: How efficiently multiple parts can be packed onto a single build plate. Printing multiple clamps simultaneously is more cost-effective per part than printing one at a time.
- Required Supports: Dense or extensive support structures add significant print time.
- Dopad: Calculated based on the hours the machine is occupied for the build. Optimizing design for faster printing (e.g., minimizing height, reducing supports) directly impacts cost.
- Factors: This is often the most significant cost component. It depends on:
- Náklady na pracovní sílu:
- Factors: Time spent by technicians for build setup, machine operation monitoring, depowdering, support removal (can be very labor-intensive), basic finishing, and quality inspection.
- Dopad: Skilled labor is required for these tasks. Complex support removal or intricate finishing increases labor hours.
- Náklady na následné zpracování:
- Factors: Costs associated with necessary secondary operations beyond basic finishing. This includes:
- Stress Relief & Heat Treatment: Furnace time, energy consumption, controlled atmospheres.
- CNC obrábění: Machine time, programming, setup for achieving tight tolerances or specific features.
- Povrchová úprava: Costs for bead blasting, polishing, coating, etc.
- Dopad: Can be a significant portion of the total cost, especially if extensive machining or specialized treatments are required. Must be factored in early.
- Factors: Costs associated with necessary secondary operations beyond basic finishing. This includes:
- Engineering & Setup:
- Factors: Initial file preparation, build simulation (if performed), DfAM consultation (if utilized as a separate service), and quality documentation setup.
- Dopad: Usually a smaller component for repeat orders but relevant for initial prototypes or complex projects.
- Quality Assurance & Inspection:
- Factors: The level of inspection required (e.g., standard dimensional checks vs. CMM reports vs. NDT like CT scanning).
- Dopad: More stringent inspection requirements increase time and cost but may be necessary for critical applications.
- Order Volume (Wholesale Factor):
- Factors: Economies of scale apply. Setting up a build is largely a fixed effort, so printing multiple copies of a clamp in one build reduces the per-part cost compared to a single prototype.
- Dopad: Významné wholesale 3D printing quotes discounts are often available for larger batch sizes or production runs.
Typical Lead Times for Metal AM Clamps:
Lead times can vary significantly based on complexity, volume, supplier backlog, and required post-processing.
- Prototypes (1-5 units): Typically range from 5 to 15 business days. This includes printing, basic post-processing (stress relief, support removal, bead blast), and standard inspection. Expedited options may be available at a higher cost.
- Low-Volume Production (10-100 units): Lead times might extend to 3 až 6 týdnů, depending on part size, complexity, nesting efficiency, and the extent of post-processing and QA required.
- Factors Influencing Lead Time:
- Machine Availability/Queue: Current workload at the service provider.
- Print Time: Can range from hours for small parts to several days for large, complex clamps or full build plates.
- Post-Processing Complexity: Heat treatment cycles take time; extensive CNC machining adds days; outsourced processes add logistical time.
- Quality Assurance Steps: Detailed inspections or NDT add to the timeline.
- Doprava: Transit time to your facility.
Obtaining an accurate additive manufacturing pricing estimate and lead time requires submitting a detailed RFQ (Request for Quote) package to potential suppliers, including:
- 3D CAD file (STEP format preferred)
- Material specification (e.g., 17-4PH H900, M300 Aged)
- Quantity required
- 2D drawings indicating critical dimensions, tolerances, and surface finish requirements
- Any specific post-processing or inspection needs
Understanding these 3D printing cost breakdown elements and industrial AM lead times allows for better project planning and cost management when incorporating metal AM clamps into your operations.
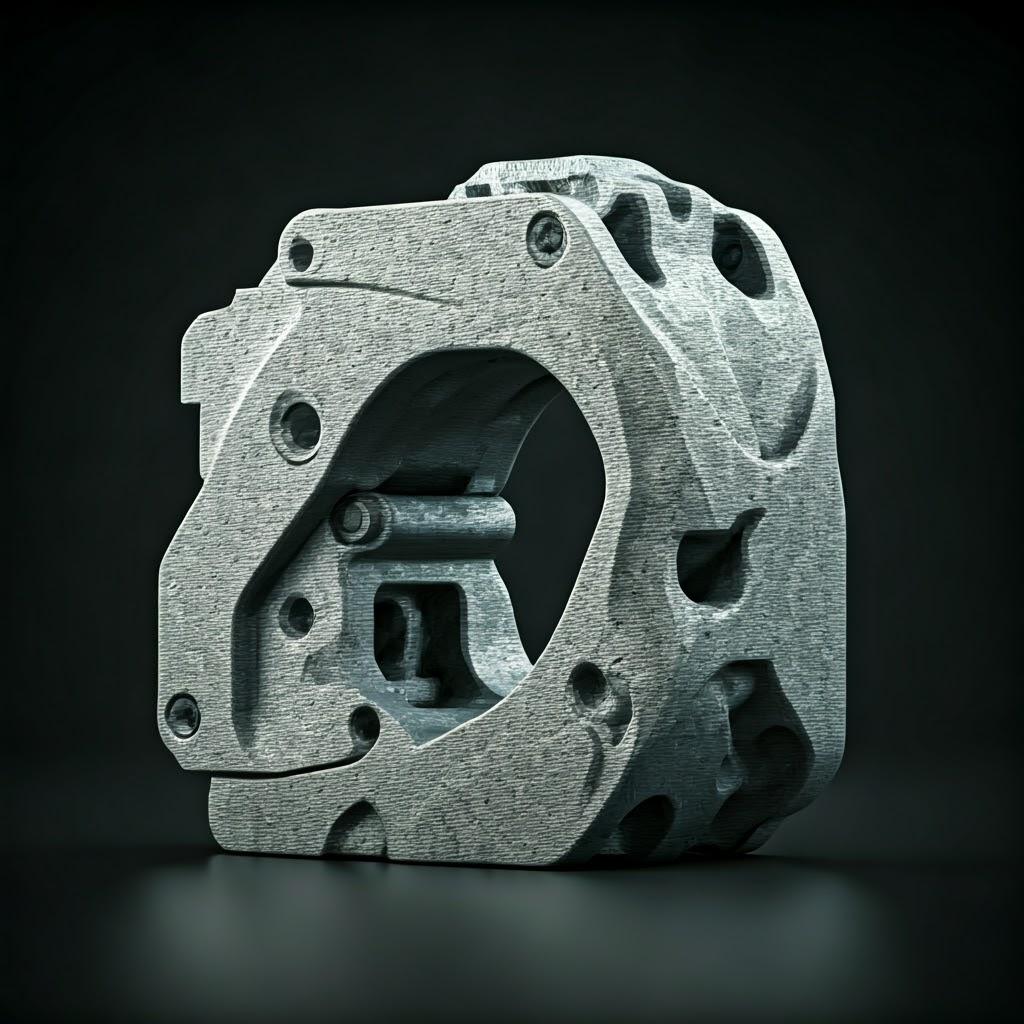
Frequently Asked Questions (FAQ) about Metal 3D Printed Clamps
Here are answers to some common questions engineers and procurement specialists ask when considering metal additive manufacturing for custom industrial clamps:
1. How strong are 3D printed metal clamps compared to machined ones?
- Odpověď: When printed correctly using appropriate materials (like 17-4PH or M300) and undergoing proper post-processing (especially heat treatment), metal AM clamps can achieve mechanical properties (tensile strength, yield strength, hardness) that are comparable, and sometimes superior, to those of parts machined from wrought bar stock or forgings of the same alloy. Furthermore, DfAM allows for topology optimization, potentially creating clamps with higher strength-to-weight ratios than traditionally manufactured counterparts. The key is partnering with an expert provider who ensures process control and proper heat treatment.
2. What is the maximum size clamp that can be 3D printed?
- Odpověď: The maximum size is primarily limited by the build volume of the metal 3D printer used. Industrial LPBF/SLM systems typically range from build volumes around 250x250x300 mm to larger format machines exceeding 500x500x500 mm, with some specialized systems being even larger. For example, Met3dp offers printers with industry-leading print volumes. For very large clamps exceeding single-build capabilities, designs can sometimes be printed in sections and then joined (e.g., by welding) post-print, though this requires careful design and process validation. Discuss your size requirements with potential suppliers to understand their specific large scale metal AM schopnosti.
3. Can existing clamp designs (made for machining) be easily converted for 3D printing?
- Odpověď: While existing CAD files can be used as a starting point, a direct conversion without considering DfAM principles is often suboptimal. Designs created for machining may have features that are difficult or inefficient to print (e.g., sharp overhangs, unnecessarily thick sections). To fully benefit from AM, designs should ideally be reviewed and potentially optimized to reduce supports, minimize mass using topology optimization or lattices, consolidate parts, and ensure features are suitable for the layer-wise process. A simple “print as-is” approach might work but misses significant opportunities for performance improvement and cost reduction.
4. What information is needed to get an accurate quote for custom 3D printed clamps?
- Odpověď: To provide an accurate quote, suppliers typically need:
- 3D model CAD: In a standard format like STEP or STL (STEP preferred for detail).
- Specifikace materiálu: Clearly state the desired metal alloy (e.g., 17-4PH, M300) and the required final condition (e.g., heat treatment state like H900).
- Množství: Number of clamps needed (for prototypes or production runs).
- 2D Drawings (Recommended): To specify critical dimensions, tolerances, surface finish requirements on specific faces, threads, and any other key features or annotations.
- Potřeby následného zpracování: Specify required heat treatments, machining operations, surface finishes, or coatings.
- Inspection Requirements: Detail any specific quality assurance checks, tests, or certifications needed.
5. Are metal 3D printed clamps suitable for high-temperature environments?
- Odpověď: Suitability depends heavily on the material choice and the specific operating temperature.
- Nerezová ocel 17-4PH: Generally suitable for continuous use up to around 315°C (600°F). Strength decreases at higher temperatures.
- M300 Maraging Steel: Retains high strength up to moderately elevated temperatures, potentially around 400-450°C (750-840°F), often outperforming 17-4PH in this range.
- Higher Temperatures: For applications exceeding these limits, other AM materials like Nickel-based superalloys (e.g., Inconel 625, Inconel 718) or certain Cobalt-Chrome alloys would be required. These materials maintain excellent strength and creep resistance at much higher temperatures but come at a higher cost. Discuss your temperature requirements with your AM provider to select the appropriate material.
Tento metal printing FAQ addresses some initial queries, but specific project details should always be discussed directly with your chosen AM partner.
Conclusion: Revolutionizing Clamp Manufacturing with Metal Additive Technology
The landscape of industrial manufacturing is continually evolving, demanding greater efficiency, higher performance, and increased customization. Custom industrial clamps, while seemingly basic components, are critical enablers of productivity and precision across aerospace, automotive, medical, and general manufacturing sectors. As we’ve explored, traditional methods for producing these specialized clamps often hit limitations in terms of design complexity, lead time, and optimization potential.
Metal additive manufacturing emerges as a powerful, transformative solution. By building high-strength clamps layer by layer from advanced metal powders like Nerezová ocel 17-4PH a M300 Maraging Steel, AM overcomes many traditional constraints. It unlocks unparalleled svoboda designu, enabling engineers to create highly optimized, lightweight, and complex clamps perfectly tailored to the task. The ability for rapid prototyping and on-demand production dramatically shortens development cycles and improves supply chain agility, directly benefiting procurement managers. Furthermore, the potential for konsolidace částí and achieving superior poměry pevnosti a hmotnosti delivers tangible performance advantages.
For engineers striving for innovative workholding solutions and procurement managers seeking reliable, efficient sourcing for custom components, metal AM offers a compelling value proposition. However, realizing these benefits requires more than just access to a printer; it demands expertise in DfAM, materials science, process control, and comprehensive post-processing.
This is where partnering with a knowledgeable and capable leader in metal additive manufacturing becomes crucial. Companies like Met3dp, headquartered in Qingdao, China, represent the forefront of this technology. With decades of collective expertise, Met3dp provides comprehensive solutions encompassing pokročilé kovové prášky produced using industry-leading atomization techniques, state-of-the-art Selektivní tavení elektronovým paprskem (SEBM) and other powder bed fusion printers delivering exceptional accuracy and reliability, and vital služby vývoje aplikací. Their integrated approach ensures quality and consistency from the raw material to the finished, high-performance clamp.
Whether you are developing complex aerospace fixtures, robust automotive tooling, precise medical device clamps, or heavy-duty industrial workholding, embracing metal additive manufacturing can provide a significant competitive edge. It enables the creation of clamping solutions that are not just manufactured, but truly engineered pro optimální výkon.
Ready to explore how metal AM can revolutionize your custom clamp production?
Contact Met3dp today to discuss your specific requirements and discover how our cutting-edge systems, high-performance powders, and expert services can power your organization’s additive manufacturing goals. Visit https://met3dp.com/ dozvědět se více.
Sdílet na
MET3DP Technology Co., LTD je předním poskytovatelem řešení aditivní výroby se sídlem v Qingdao v Číně. Naše společnost se specializuje na zařízení pro 3D tisk a vysoce výkonné kovové prášky pro průmyslové aplikace.
Dotaz k získání nejlepší ceny a přizpůsobeného řešení pro vaše podnikání!
Související články
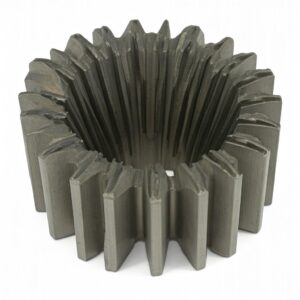
Vysoce výkonné segmenty lopatek trysek: Revoluce v účinnosti turbín díky 3D tisku z kovu
Přečtěte si více "O Met3DP
Nedávná aktualizace
Náš produkt
KONTAKTUJTE NÁS
Nějaké otázky? Pošlete nám zprávu hned teď! Po obdržení vaší zprávy obsloužíme vaši žádost s celým týmem.
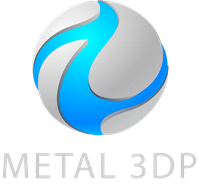
Kovové prášky pro 3D tisk a aditivní výrobu
SPOLEČNOST
PRODUKT
kontaktní informace
- Město Qingdao, Shandong, Čína
- [email protected]
- [email protected]
- +86 19116340731