Odolné součásti ventilů prostřednictvím společnosti Metal AM
Obsah
Úvod
Součásti ventilů jsou neopěvovanými hrdiny nesčetných průmyslových procesů. Jejich spolehlivost a životnost jsou nejdůležitější - od řízení průtoku kritických kapalin v leteckém průmyslu a chemických závodech přes regulaci hydraulických systémů v automobilovém průmyslu až po zajištění přesné dodávky kapalin a plynů v lékařských přístrojích. Tradiční výrobní metody jsou sice dobře zavedené, ale často představují omezení z hlediska složitosti konstrukce, účinnosti materiálu a schopnosti rychlé iterace a přizpůsobení dílů pro konkrétní aplikace.
Vstupte do aditivní výroby kovů (AM), transformační technologie, která přináší revoluci ve způsobu navrhování a výroby odolných součástí ventilů. Známá také jako kovová 3D tisk, tento pokročilý výrobní proces vytváří díly vrstvu po vrstvě z kovových prášků, což nabízí nebývalou volnost při navrhování, snížení plýtvání materiálem a možnost zlepšení výkonnostních charakteristik. Pro průmyslová odvětví, která vyžadují vysoce výkonné a spolehlivé součásti ventilů, představuje technologie AM z kovu přesvědčivou alternativu, která umožňuje vytvářet složité geometrie a optimalizované konstrukce, jež byly dříve nedosažitelné nebo nákladově neúnosné při použití konvenčních technik.
V čele této inovace stojí společnost Metal3DP Technology Co., LTD, přední poskytovatel řešení aditivní výroby se sídlem v čínském městě Čching-tao. Společnost Metal3DP, která se specializuje na špičková zařízení pro 3D tisk i vysoce výkonné kovové prášky, umožňuje průmyslovým odvětvím plně rozvinout potenciál kovové AM. Naše špičkové tiskárny poskytují výjimečný objem tisku, přesnost a spolehlivost, které jsou klíčové pro výrobu kritických ventilových součástí v náročných odvětvích, jako je letecký průmysl, zdravotnictví, automobilový průmysl a průmyslová výroba. Náš závazek vyrábět vysoce kvalitní kovové sférické prášky navíc zajišťuje, že naši zákazníci mohou 3D tisknout husté, vysoce kvalitní kovové díly s vynikajícími mechanickými vlastnostmi, které jsou nezbytné pro odolnost a dlouhou životnost ventilových součástí. Chcete-li se dozvědět více o našich rozsáhlých možnostech, navštivte naši stránku Stránka O nás.
K čemu se používají odolné součásti ventilů?
Odolné součásti ventilů hrají klíčovou roli v celé řadě průmyslových odvětví, z nichž každé má své vlastní jedinečné požadavky a provozní prostředí. Pochopení těchto rozmanitých aplikací zdůrazňuje význam spolehlivosti komponent, integrity materiálu a přesné funkčnosti.
- Ropa a plyn: V tomto odvětví jsou komponenty ventilů nezbytné pro řízení průtoku ropy, zemního plynu a různých chemikálií pod vysokým tlakem a často v korozivním prostředí. Aplikace sahají od regulačních ventilů pro potrubí a zařízení na ústí vrtů až po komponenty v rafinérských procesech. Rozhodující je trvanlivost a odolnost vůči drsným chemikáliím a extrémním teplotám.
- Chemické zpracování: Chemické provozy se při řízení průtoku širokého spektra agresivních a nebezpečných chemických látek ve velké míře spoléhají na ventily. Součásti ventilů zde musí vykazovat výjimečnou odolnost proti korozi a zachovávat svou integritu při různých teplotách a tlacích, aby byl zajištěn bezpečný a efektivní provoz.
- Výroba energie: Ventily mají zásadní význam pro řízení průtoku páry, vody a dalších pracovních kapalin, a to od běžných elektráren až po jaderná zařízení. Klíčovými požadavky na součásti ventilů v tomto odvětví jsou odolnost vůči vysokým teplotám, omezení tlaku a dlouhodobá spolehlivost.
- Úprava vody: Součásti ventilů jsou nedílnou součástí systémů pro čištění a distribuci vody a regulují průtok vody a různých chemikálií pro její úpravu. Odolnost proti korozi a trvanlivost v nepřetržitém provozu jsou nezbytné pro zajištění dodávky čisté vody.
- Letectví: V letadlech a kosmických lodích řídí ventily průtok paliva, hydraulických kapalin a vzduchu v kritických systémech. Snížení hmotnosti, vysoký poměr pevnosti a hmotnosti a spolehlivost v extrémních podmínkách jsou prvořadé.
- Automobilový průmysl: Ventily se používají v různých automobilových systémech, včetně řízení motoru, brzdových systémů a klimatizace. Součásti musí být odolné, spolehlivě fungovat v širokém rozsahu teplot a často se musí vyrábět ve velkých objemech.
- Lékařský: Ventily ve zdravotnických přístrojích řídí průtok kapalin a plynů v aplikacích, jako jsou chirurgické nástroje, systémy pro podávání léků a dýchací přístroje. Rozhodujícími faktory jsou biokompatibilita, přesnost a spolehlivost.
- Průmyslová výroba: V širokém spektru výrobních procesů se ventily používají k řízení průtoku různých materiálů, včetně kapalin, plynů a kalů. Trvanlivost a odolnost proti opotřebení jsou nezbytné pro zachování efektivní výroby.
Konkrétní funkce těchto součástí ventilů se mohou značně lišit, včetně:
- Ovládání zapnutí/vypnutí: Jednoduché ventily, které se otevírají nebo zavírají a umožňují nebo zastavují průtok.
- Regulace průtoku: Ventily určené k regulaci průtoku.
- Odlehčení tlaku: Ventily, které automaticky uvolňují tlak, když překročí nastavenou mez.
- Zpětné ventily: Ventily, které umožňují průtok pouze jedním směrem.
- Míchání a přesměrování: Ventily, které spojují nebo přesměrovávají proudy kapalin.
Vzhledem ke kritické povaze těchto aplikací a funkcí je poptávka po odolných a vysoce výkonných komponentech ventilů neustálá. 3D tisk z kovu nabízí výkonný nástroj, jak těmto požadavkům vyhovět díky rozšířeným možnostem konstrukce a optimalizaci materiálu.
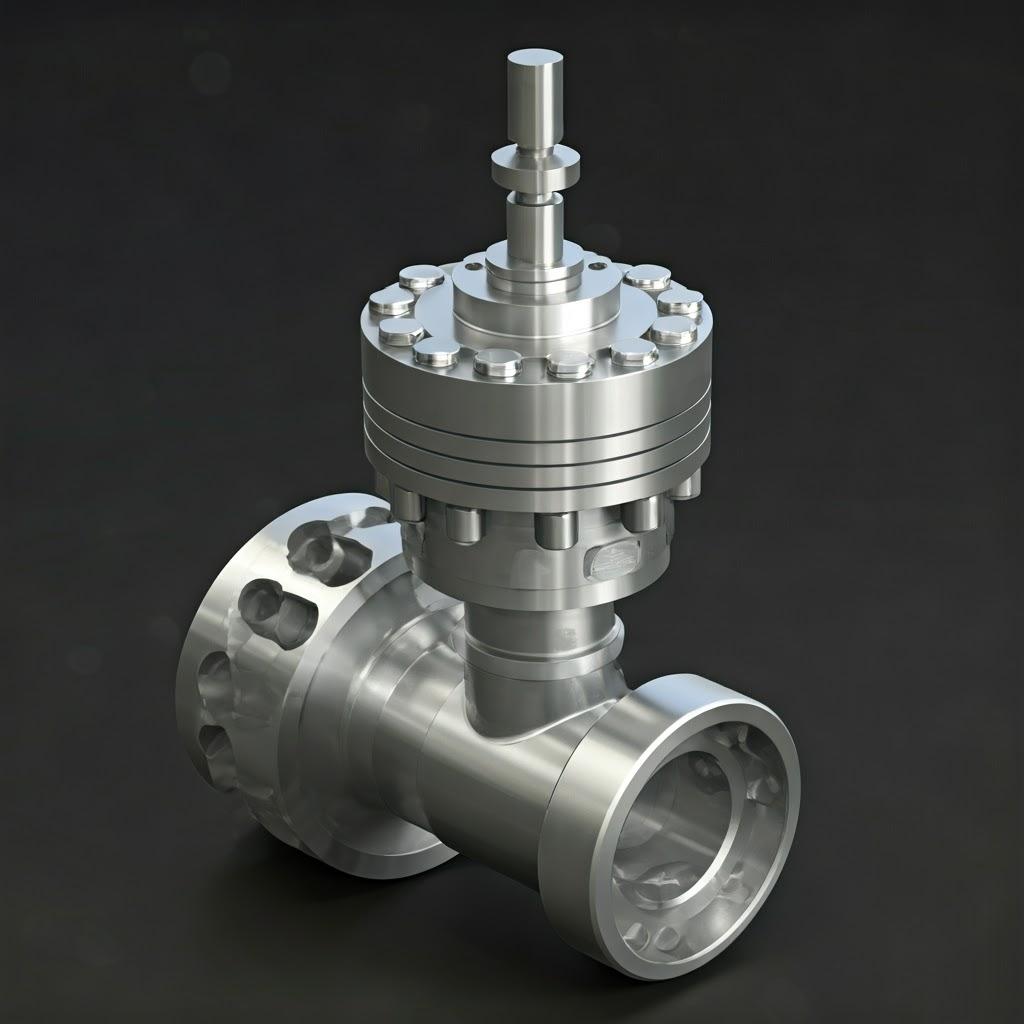
Proč používat 3D tisk z kovu pro odolné součásti ventilů?
Zatímco tradiční výrobní metody, jako je odlévání, kování a obrábění, jsou již dlouho standardem pro výrobu součástí ventilů, 3D tisk kovů nabízí řadu přesvědčivých výhod, které jsou obzvláště výhodné pro vytváření odolných a vysoce výkonných dílů:
- Flexibilita a složitost návrhu: Technologie AM umožňuje vytvářet složité vnitřní geometrie, komplexní průtokové kanály a přizpůsobené prvky, kterých je obtížné nebo nemožné dosáhnout tradičními metodami. Tato konstrukční svoboda umožňuje optimalizovat součásti ventilů pro zvýšení účinnosti průtoku, snížení hmotnosti a zlepšení funkčnosti. Lze například začlenit vnitřní mřížkové struktury pro snížení hmotnosti bez snížení pevnosti, což je významná výhoda v leteckých aplikacích.
- Rychlé prototypování a iterace: Možnost rychlé výroby prototypů pomocí kovového 3D tisku urychluje konstrukční a vývojový cyklus. Inženýři mohou rychle testovat různé iterace součásti ventilu, včas identifikovat potenciální problémy a efektivněji zdokonalovat návrhy, což vede k rychlejšímu uvedení na trh a snížení nákladů na vývoj.
- Účinnost materiálu: Na rozdíl od subtraktivních výrobních procesů, které odebírají materiál z pevného bloku, kovový 3D tisk vytváří díly vrstvu po vrstvě a používá pouze nezbytný materiál. Tím se výrazně snižuje plýtvání materiálem, zejména při práci s drahými speciálními slitinami.
- Přizpůsobení a výroba na vyžádání: Metal AM je ideální pro výrobu komponent ventilů na míru podle specifických aplikačních požadavků nebo pro malosériovou výrobu. Odpadá tak potřeba drahých nástrojů a nákladů na seřizování spojených s tradičními metodami, což je ekonomicky výhodné pro specializované nebo náhradní díly.
- Vylepšené výkonnostní schopnosti: Využitím pokročilých kovových prášků a optimalizovaných konstrukcí lze pomocí 3D tisku kovů vyrábět součásti ventilů s vynikajícími mechanickými vlastnostmi, jako je zvýšená pevnost, zvýšená odolnost proti korozi a zvýšená teplotní tolerance. Jemná kontrola nad mikrostrukturou materiálu, které lze dosáhnout některými procesy AM, může vést ke zlepšení výkonnosti, které je obtížné dosáhnout běžnými technikami.
- Integrace více složek: 3D tisk z kovu umožňuje sloučit více dílů do jediné součásti, čímž se snižuje počet spojů a montážních kroků. To může vést ke zvýšení spolehlivosti, snížení hmotnosti a zjednodušení dodavatelských řetězců. Představte si, že vytisknete tělo ventilu s integrovanými montážními prvky, čímž odpadá potřeba samostatných spojovacích prvků.
- Odlehčení: V průmyslových odvětvích, jako je letecký a automobilový průmysl, je snížení hmotnosti součástí zásadní pro zlepšení palivové účinnosti a výkonu. Technologie AM umožňuje vytvářet lehké konstrukce se složitými vnitřními strukturami, které zachovávají strukturální integritu.
- Rapid Tooling: Ačkoli to není přímý přínos pro finální součást ventilu, lze kovový 3D tisk použít k vytvoření nástrojů (např. forem, zápustek) pro tradiční výrobní procesy rychleji a levněji než konvenční metody výroby nástrojů.
Závazek společnosti Metal3DP’poskytovat špičkový objem a přesnost tisku tyto výhody dále zvyšuje. Větší objemy sestavení umožňují výrobu větších součástí ventilů nebo více menších dílů v jednom sestavení, což zvyšuje efektivitu. Vysoká přesnost zajišťuje, že tištěné součásti splňují přísné rozměrové požadavky kritických ventilových aplikací. Výběrem technologie Metal3DP mohou podniky využít plnou sílu 3D tisku z kovu a vytvářet odolné, vysoce výkonné součásti ventilů s bezkonkurenční konstrukční svobodou a efektivitou. Můžete si prohlédnout různé Služby 3D tisku kovů nabízíme, abyste pochopili, jak lze tyto výhody využít pro vaše konkrétní potřeby.
Doporučené materiály a jejich význam
Výběr vhodného kovového prášku má zásadní význam pro dosažení požadované odolnosti, výkonu a životnosti 3D tištěných součástí ventilů. Společnost Metal3DP nabízí řadu vysoce kvalitních kovových prášků a pro odolné ventilové aplikace se díky svým specifickým vlastnostem jako vynikající volba jeví nerezová ocel 316L a slitina mědi a niklu CuNi30Mn1Fe:
Nerezová ocel 316L:
- Odolnost proti korozi: 316L je austenitická nerezová ocel známá svou vynikající odolností proti korozi, zejména důlkové a štěrbinové korozi, v širokém spektru prostředí, včetně prostředí s obsahem chloridů. To má zásadní význam pro součásti armatur, které přicházejí do styku s různými kapalinami, včetně korozivních chemikálií a slané vody.
- Vysoká pevnost a tažnost: Tato slitina nabízí dobrou kombinaci pevnosti a tažnosti, takže součásti ventilů odolávají vysokým tlakům a mechanickému namáhání bez porušení.
- Svařitelnost: materiál 316L vykazuje dobrou svařitelnost, což může být důležité pro spojování 3D tištěných součástí s jinými částmi systému nebo pro opravy po zpracování.
- Výkon při vysokých a nízkých teplotách: materiál 316L si zachovává své mechanické vlastnosti v širokém rozsahu teplot, takže je vhodný pro aplikace při vysokých i nízkých teplotách.
- Biokompatibilita: V lékařských aplikacích se často používá materiál 316L díky své biokompatibilitě.
CuNi30Mn1Fe (slitina mědi a niklu):
- Vynikající odolnost proti korozi: Slitiny mědi a niklu, včetně CuNi30Mn1Fe, jsou známé svou vynikající odolností vůči korozi mořské vody a biologickému znečištění. Díky tomu jsou ideální pro námořní a pobřežní aplikace, kde jsou součásti ventilů vystaveny drsnému prostředí slané vody.
- Dobrá síla a odolnost: Tato slitina nabízí dobrou rovnováhu mezi pevností a houževnatostí a zajišťuje odolnost v náročných aplikacích.
- Tepelná vodivost: Slitiny mědi a niklu mají dobrou tepelnou vodivost, což může být výhodné v aplikacích, kde je důležitý odvod tepla.
- Antimikrobiální vlastnosti: Měď a její slitiny vykazují přirozené antimikrobiální vlastnosti, které mohou být výhodné v určitých aplikacích, jako je úprava vody nebo lékařské přístroje.
- Svařitelnost a vyrobitelnost: CuNi30Mn1Fe obecně vykazuje dobrou svařitelnost a zpracovatelnost.
Pokročilý systém výroby prášků Metal3DP’s využitím špičkových technologií plynové atomizace a PREP (Plasma Rotating Electrode Process) zajišťuje výrobu vysoce kvalitních kovových prášků pro 3D tisk s vysokou sféricitou a dobrou tekutostí. Tyto vlastnosti jsou zásadní pro dosažení hustých, stejnorodých dílů s vynikajícími mechanickými vlastnostmi během procesu 3D tisku. Náš závazek ke kvalitě se vztahuje na širokou škálu vysoce výkonných kovových prášků, včetně inovativních slitin přizpůsobených pro konkrétní aplikace. Výběrem prášků 316L nebo CuNi30Mn1Fe od společnosti Metal3DP si výrobci mohou být jisti trvanlivostí a výkonem svých 3D tištěných součástí ventilů. Komplexní přehled našich dostupných materiálů naleznete na stránkách Stránka produktu.
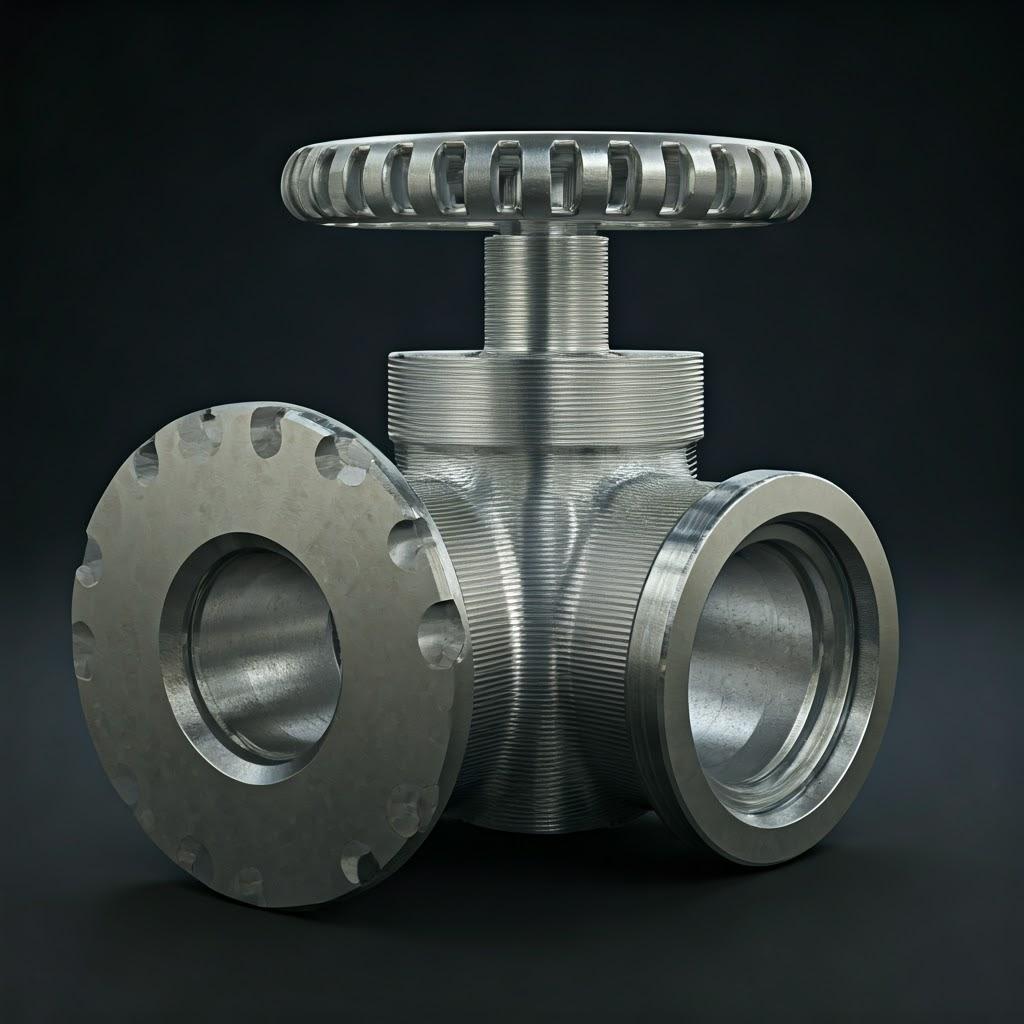
Konstrukční hlediska pro aditivní výrobu součástí ventilů
Optimalizace konstrukce součástí ventilů pro aditivní výrobu kovů je zásadní pro plné využití možností této technologie a dosažení požadovaného výkonu, odolnosti a nákladové efektivity. Na rozdíl od tradičních subtraktivních metod ukládá AM vlastní soubor konstrukčních pravidel a úvah. Zde je několik klíčových aspektů, které je třeba vzít v úvahu při navrhování komponent ventilů pro kovový 3D tisk:
- Minimalizace podpůrných struktur: Podpůrné struktury jsou v kovovém AM často nezbytné, aby se zabránilo deformaci dílů během procesu sestavování a aby se ukotvily převislé prvky. Podpěry však vyžadují odstranění po zpracování, což může prodlužovat čas a náklady a potenciálně ovlivňovat kvalitu povrchu. Navrhování dílů se samonosnou geometrií, jako jsou například slzovité tvary nebo minimalizace strmých převisů, může snížit potřebu rozsáhlých podpůrných struktur. Pečlivá orientace dílu v konstrukční komoře může rovněž významně ovlivnit požadavky na podpěry.
- Navrhování pro odstraňování prášku: 3D tisk z kovu spočívá ve výrobě dílů v loži z prášku. Složité vnitřní kanály nebo dutiny v součástech ventilů mohou zachytit nespečený prášek, který je třeba po tisku účinně odstranit. Zásadní je navrhnout přístupové otvory nebo kanály, které usnadní odvádění prášku. Zvažte velikost a umístění těchto prvků, abyste zajistili důkladné odstranění bez narušení integrity součásti.
- Začlenění vnitřních kanálů a funkcí: Jednou z významných výhod technologie AM pro kovy je možnost vytvářet složité vnitřní geometrie. U ventilových součástí se tak otevírají možnosti optimalizace průtokových cest, integrace chladicích kanálů nebo zabudování senzorů přímo do dílu. Při navrhování vnitřních prvků zvažte minimální velikost prvku a omezení procesu tisku, aby byla zajištěna vyrobitelnost.
- Tloušťka stěny a strukturální integrita: Určení vhodné tloušťky stěny je rozhodující pro zajištění strukturální integrity a tlakové únosnosti součástí ventilů. Technologie AM umožňuje vytvářet tenkostěnné konstrukce, což může snížit hmotnost a spotřebu materiálu. Minimální dosažitelná tloušťka stěny však závisí na materiálu a procesu tisku. Cenným nástrojem pro optimalizaci tloušťky stěny a zajištění toho, že součást vydrží zamýšlené provozní tlaky a zatížení, může být analýza konečných prvků (FEA).
- Úvahy o povrchové úpravě: Povrchová úprava po tisku v kovovém AM se může lišit v závislosti na materiálu, velikosti částic prášku a parametrech tisku. U těsnicích povrchů ventilů je často vyžadován hladký povrch, aby byla zajištěna těsnost. K dosažení požadované drsnosti povrchu může být nutné navrhnout kritické povrchy s ohledem na následné obrábění nebo leštění.
- Tolerance a uložení: Pochopení dosažitelných tolerancí při 3D tisku z kovu je zásadní pro návrh součástí, které budou správně zapadat do sestavy. Tolerance mohou být ovlivněny faktory, jako je velikost dílu, geometrie a materiál. Pro správnou funkčnost je nezbytné navrhovat rozhraní s vhodnými vůlemi nebo interferenčními uloženími s ohledem na možnosti zvoleného tiskového procesu.
- Strategie spojování: Zvažte, jak bude 3D tištěná součást ventilu integrována do většího systému. Technologie AM pro kovy umožňuje vytvářet integrované prvky pro spojování, jako jsou závity, příruby nebo blokovací mechanismy. Alternativně lze použít standardní metody spojování, jako je svařování nebo pájení. Konstrukční úvahy by měly zohlednit zvolenou strategii spojování.
- Výběr materiálu a kompatibilita procesů: Zvolený kovový prášek musí být kompatibilní se zvoleným procesem 3D tisku kovů (např. selektivní laserové tavení (SLM), přímé laserové spékání kovů (DMLS)). Každý proces má svůj vlastní soubor parametrů a omezení, které mohou ovlivnit konstrukční možnosti a dosažitelné vlastnosti. Konzultace s odborníky společnosti Metal3DP’může pomoci zajistit, aby byl návrh optimalizován pro zvolený materiál a metodu tisku. Více informací o různých tiskových metod využíváme.
Při pečlivém zvážení těchto konstrukčních aspektů mohou konstruktéři využít plný potenciál aditivní výroby kovů a vytvořit odolné a vysoce výkonné součásti ventilů s optimalizovanou geometrií, sníženou hmotností a lepší funkčností.
Tolerance, povrchová úprava a rozměrová přesnost 3D tištěných ventilů
Dosažení požadované tolerance, povrchové úpravy a rozměrové přesnosti má zásadní význam pro funkční výkon a spolehlivost 3D tištěných součástí ventilů, zejména těch, které pracují pod tlakem nebo vyžadují těsné těsnění. Technologie 3D tisku z kovů výrazně pokročily a nabízejí stále přesnější a konzistentnější výsledky. Je však’nezbytné pochopit faktory, které tyto aspekty ovlivňují, a jakou úroveň přesnosti lze reálně očekávat.
Tolerance:
- Tolerance označuje přípustnou odchylku určeného rozměru. Dosažitelná tolerance při 3D tisku z kovu závisí na několika faktorech, včetně technologie tisku (SLM, DMLS atd.), použitého materiálu, velikosti a geometrie dílu a orientace při tisku.
- Obecně lze u procesů slučování kovového prášku (PBF), jako je SLM a DMLS, dosáhnout tolerancí v rozmezí ±0,05 mm až ±0,1 mm (±0,002 palce až ±0,004 palce) pro menší prvky. Větší rozměry mohou vykazovat o něco větší tolerance.
- Kritická funkční rozhraní, jako jsou těsnicí plochy nebo závity, mohou vyžadovat následné zpracování, například přesné obrábění, aby se dosáhlo větších tolerancí, než jakých lze dosáhnout přímo tiskem.
- Úzká spolupráce s inženýry Metal3DP’během fáze návrhu může pomoci optimalizovat geometrii dílu a parametry tisku, aby se maximalizovala rozměrová přesnost a minimalizovala potřeba rozsáhlého následného zpracování.
Povrchová úprava:
- Povrchová úprava kovových dílů vytištěných metodou as-printing je obvykle drsnější ve srovnání s obráběnými povrchy. Je ovlivněn velikostí částic prášku, tloušťkou vrstvy a efektem "schodovitého" postupu, který vzniká při vytváření jednotlivých vrstev, zejména na šikmých površích.
- Typické hodnoty drsnosti povrchu (Ra) u kovových dílů po tisku se mohou pohybovat od 5 do 20 µm (200 až 800 µin) v závislosti na parametrech tisku a materiálu.
- U součástí ventilů, které vyžadují hladký těsnicí povrch nebo zvýšenou odolnost proti korozi, se k dosažení požadované povrchové úpravy běžně používají techniky následného zpracování, jako je tryskání, leštění nebo obrábění.
- Zohlednění požadované povrchové úpravy ve fázi návrhu může ovlivnit orientaci dílu během tisku, aby se minimalizovala potřeba rozsáhlého následného zpracování kritických povrchů.
Rozměrová přesnost:
- Rozměrová přesnost se vztahuje k míře, do jaké vytištěný díl odpovídá zamýšleným rozměrům modelu CAD. Je ovlivněna faktory, jako je smršťování materiálu během tuhnutí, tepelné namáhání a kalibrace 3D tiskárny.
- Nejmodernější tiskové zařízení Metal3DP’a optimalizované parametry procesu jsou navrženy tak, aby poskytovaly vysokou rozměrovou přesnost. Náš závazek přesnosti a spolehlivosti zaručuje, že vaše 3D tištěné součásti ventilů splňují přísné specifikace.
- U kritických rozměrů se často doporučuje zahrnout do návrhu přídavky na obrábění, které umožní přesné dokončování po procesu tisku.
- Pravidelná kalibrace a postupy kontroly kvality jsou nezbytné pro zachování rozměrové přesnosti procesu 3D tisku. Společnost Metal3DP dodržuje přísné standardy kvality, aby zajistila konzistentní a přesné výsledky.
Dosažení přesnosti u komponentů ventilů:
- Návrh pro výrobu (DFM): Začlenění principů DFM přizpůsobených pro AM kovů může výrazně zlepšit dosažitelnou toleranci a kvalitu povrchu.
- Výběr materiálu: Volba kovového prášku může ovlivnit konečnou rozměrovou přesnost a povrchovou úpravu. Jemnější prášky mají obecně za následek hladší povrchy.
- Optimalizace procesů: Jemné doladění parametrů tisku, jako je tloušťka vrstvy, výkon laseru a rychlost skenování, může ovlivnit přesnost a kvalitu povrchu.
- Následné zpracování: Plánování nezbytných kroků následného zpracování, jako je CNC obrábění, broušení nebo leštění kritických povrchů, je často nezbytné pro splnění náročných specifikací.
Pochopením možností a omezení kovového 3D tisku z hlediska tolerance, povrchové úpravy a rozměrové přesnosti a navázáním spolupráce se zkušeným poskytovatelem, jako je Metal3DP, mohou inženýři bez obav vyrábět vysoce přesné součásti ventilů pro náročné aplikace.
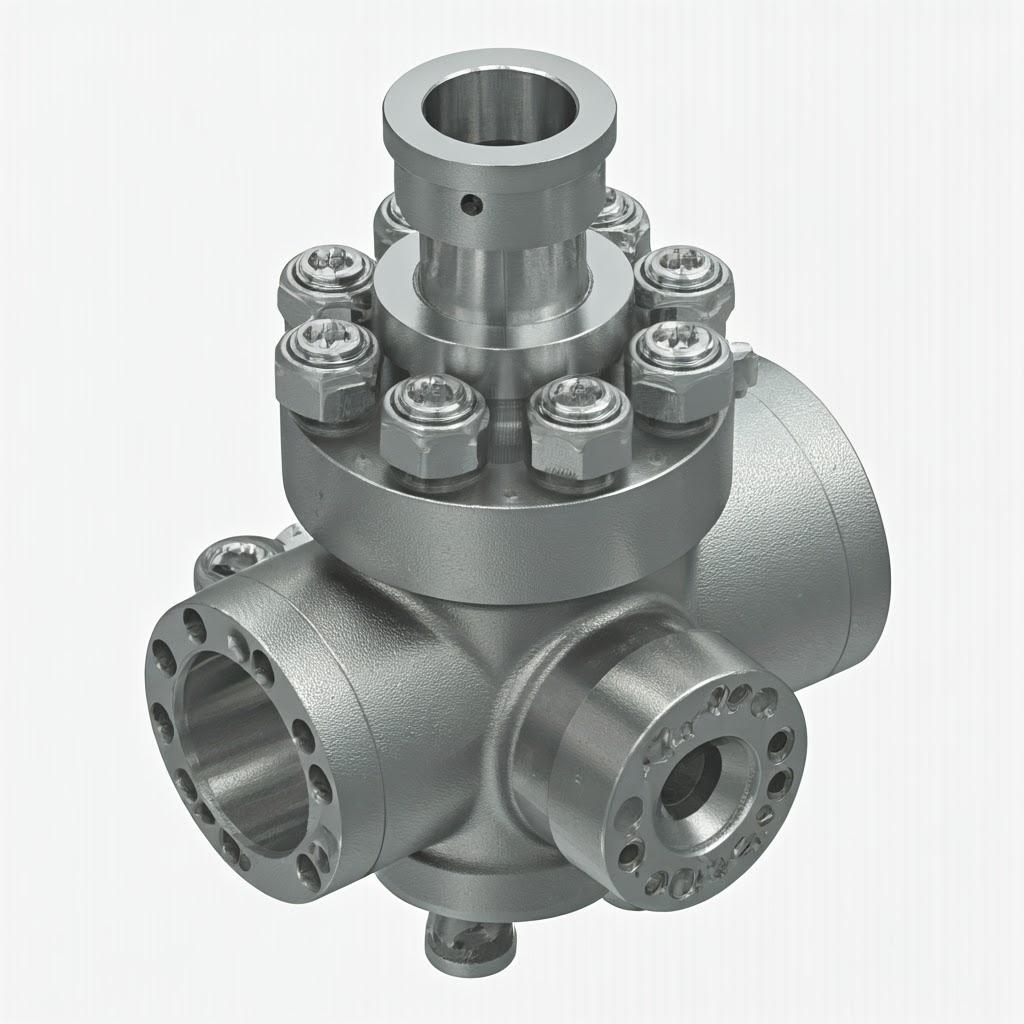
Požadavky na následné zpracování kovových komponent ventilů AM
Ačkoli 3D tisk z kovu nabízí značné výhody při vytváření složitých geometrií, následné zpracování je často nezbytným krokem k dosažení konečných požadovaných vlastností, povrchové úpravy a rozměrové přesnosti funkčních součástí ventilů. Konkrétní požadavky na následné zpracování závisí na aplikaci, použitém materiálu a požadovaných funkčních vlastnostech. Zde jsou uvedeny některé běžné kroky následného zpracování kovových komponent ventilů AM:
- Odstranění podpůrné konstrukce: Jak již bylo zmíněno, během tisku se často používají podpůrné konstrukce, které zajišťují stabilitu a podpírají převislé prvky. Tyto podpěry je třeba po tisku pečlivě odstranit. Způsob odstranění se může lišit v závislosti na materiálu a geometrii podpěr, od ručního odstranění pomocí ručních nástrojů až po automatizované metody, jako je obrábění nebo rozpustné podpěry. Správný návrh může minimalizovat potřebu rozsáhlého odstraňování podpěr.
- Odstranění prášku: U součástí s vnitřními kanálky nebo složitou geometrií je třeba odstranit zachycený nespečený prášek. To může zahrnovat techniky, jako je vyfukování stlačeným vzduchem, čištění ultrazvukem nebo vysávání. Zajištění dostatečného přístupu pro odstranění prášku ve fázi návrhu je zásadní.
- Tepelné ošetření proti stresu: Při 3D tisku kovů dochází k rychlému zahřívání a ochlazování, což může v dílu vyvolat zbytková napětí. Často se provádí tepelné zpracování za účelem snížení těchto vnitřních pnutí, což zlepšuje mechanické vlastnosti a rozměrovou stabilitu součásti. Konkrétní cyklus tepelného zpracování závisí na materiálu.
- Izostatické lisování za tepla (HIP): HIP je proces, při kterém se na tištěný díl působí vysokým tlakem a teplotou, čímž se snižuje vnitřní pórovitost a materiál se dále zhušťuje. Tím se mohou výrazně zlepšit mechanické vlastnosti, zejména únavová pevnost a tažnost, které jsou pro náročné ventilové aplikace kritické.
- Povrchová úprava: Kovové povrchy s potiskem mohou být drsné. V závislosti na aplikaci lze použít různé techniky povrchové úpravy:
- Výbuch v médiích: Používá se k odstranění částečně spečeného prášku a ke zlepšení celkové povrchové úpravy.
- Broušení a leštění: Používá se k dosažení hladších povrchů, zejména pro těsnění rozhraní.
- CNC obrábění: Přesné obrábění může být vyžadováno pro kritické rozměry a dosažení úzkých tolerancí na funkčních plochách, jako jsou závity nebo sedla ventilů.
- Testování těsnosti: U součástí ventilů určených k uchovávání kapalin nebo plynů pod tlakem je zkouška těsnosti klíčovým krokem po zpracování, aby byla zajištěna integrita těsnění a celé součásti. To může zahrnovat tlakové zkoušky vzduchem, vodou nebo jinými vhodnými kapalinami.
- Nátěry a povrchové úpravy: V závislosti na provozním prostředí mohou součásti ventilů vyžadovat povlaky pro zvýšení odolnosti proti korozi, opotřebení nebo jiných specifických vlastností. Příklady zahrnují galvanické pokovování, chemické napařování (CVD) nebo tepelné stříkání.
- Nedestruktivní zkoušení (NDT): K identifikaci vnitřních vad nebo pórovitosti, které by mohly ohrozit integritu součásti, lze použít techniky, jako je rentgenová kontrola nebo ultrazvukové testování.
- Montáž: Pokud se ventil skládá z více 3D tištěných dílů nebo musí být integrován s konvenčně vyráběnými součástmi, bude nutné použít montážní postupy, jako je svařování, pájení nebo mechanické upevnění.
Společnost Metal3DP disponuje odbornými znalostmi a schopnostmi k provedení mnoha z těchto kroků následného zpracování, které zajistí, že konečné součásti ventilů budou splňovat požadované specifikace pro vaši aplikaci. Na základě materiálu, konstrukce a zamýšleného použití vašich 3D tištěných součástí ventilů vám můžeme poradit nejvhodnější postupy následného zpracování. Cílem našich komplexních řešení je poskytnout vám funkční a vysoce kvalitní díly připravené k integraci do vašich systémů.
Běžné problémy a jak se jim vyhnout při 3D tisku ventilů
3D tisk z kovu nabízí řadu výhod, ale existují také potenciální problémy, které mohou vzniknout během procesu výroby komponentů ventilů. Pochopení těchto problémů a zavedení vhodných strategií, jak jim předejít, je zásadní pro dosažení úspěšných a spolehlivých výsledků. Zde jsou uvedeny některé běžné problémy a způsoby, jak je zmírnit:
- Deformace a zkreslení: Tepelné namáhání při rychlých cyklech ohřevu a chlazení v kovovém AM může vést k deformaci nebo pokřivení tištěného dílu, zejména u velkých nebo složitých geometrií.
- Zmírnění: Optimalizujte konstrukci dílu tak, abyste minimalizovali koncentrace napětí a velké ploché plochy. Použijte správné strategie přilnavosti konstrukční desky. Pečlivě kontrolujte parametry tisku a zvažte tepelné zpracování po tisku. Orientace dílu v konstrukční komoře může také významně ovlivnit deformace.
- Obtíže při odstraňování podpůrné konstrukce: Odstranění agresivně připevněných nebo obtížně přístupných podpěrných konstrukcí může být náročné a zdlouhavé, což může vést k poškození povrchové úpravy dílu.
- Zmírnění: Pokud je to možné, navrhujte díly se samonosnou geometrií. Optimalizujte umístění a typ podpěr pro snadnější demontáž. V případě potřeby zvažte použití rozpustných podpůrných materiálů.
- Pórovitost a nedostatečná hustota: Nedostatečné tavení a tavení kovového prášku může mít za následek vnitřní pórovitost, která může součást oslabit a ovlivnit její schopnost nést tlak.
- Zmírnění: Optimalizujte parametry tisku, jako je výkon laseru, rychlost skenování a tloušťka vrstvy prášku. Zajistěte použití vysoce kvalitních kovových prášků s dobrou tekutostí, jako jsou prášky vyráběné pokročilým systémem výroby prášků Metal3DP. Zvažte možnost lisování za tepla (HIP) po tisku, abyste snížili pórovitost a zvýšili hustotu.
- Drsnost povrchu: Kovové povrchy s potiskem mohou být pro některé aplikace ventilů příliš drsné, zejména pro těsnicí povrchy.
- Zmírnění: Optimalizujte parametry tisku tak, abyste minimalizovali drsnost povrchu. Naplánujte kroky následného zpracování, jako je tryskání, leštění nebo obrábění, abyste dosáhli požadované kvality povrchu.
- Dosažení těsných tolerancí: Splnění přísných požadavků na rozměrovou přesnost může být náročné, zejména u složitých geometrií nebo velkých dílů.
- Zmírnění: Navrhujte díly s ohledem na jejich vyrobitelnost a tolerance dosažitelné při zvoleném tiskovém procesu. Zahrňte přídavky na obrábění kritických funkčních povrchů. Využívejte vysoce přesná zařízení pro 3D tisk a optimalizované parametry procesu, které nabízí společnost Metal3DP.
- Konzistence vlastností materiálu: Zajištění konzistentních mechanických vlastností celého tištěného dílu může být problém, pokud nejsou parametry tisku řádně kontrolovány.
- Zmírnění: Spolupracujte se zkušenými poskytovateli 3D tisku z kovu, jako je Metal3DP, kteří mají zavedené a ověřené tiskové procesy. Proveďte přísná opatření pro kontrolu kvality a zvažte následné zpracování, jako je HIP, abyste homogenizovali vlastnosti materiálu.
- Netěsnosti v součástech nesoucích tlak: Dosažení těsnosti u 3D tištěných součástí ventilů může být náročné kvůli možné vnitřní pórovitosti nebo nedokonalosti povrchu.
- Zmírnění: Optimalizujte parametry tisku tak, abyste minimalizovali pórovitost. Použijte techniky následného zpracování ke zlepšení kvality povrchu těsnicích ploch. Po tisku a následném zpracování proveďte důkladné zkoušky těsnosti.
- Úvahy o ceně: 3D tisk kovů může být pro velkosériovou výrobu dražší než tradiční metody.
- Zmírnění: Zaměřte se na aplikace, u nichž jedinečné výhody technologie AM z kovu, jako je složitost konstrukce, přizpůsobení nebo rychlá výroba prototypů, ospravedlňují náklady. Optimalizujte konstrukce pro efektivní využití materiálu a minimalizujte potřebu nákladného následného zpracování. Pro určité objemy může prozkoumání výrobních možností Metal3DP’nabídnout nákladově efektivní řešení.
Pochopením těchto potenciálních problémů a zavedením vhodných konstrukčních strategií, procesních kontrol a technik následného zpracování mohou výrobci efektivně využít 3D tisk kovů k výrobě odolných a spolehlivých součástí ventilů. Klíčem k překonání těchto problémů a dosažení úspěšných výsledků je spolupráce se znalým a zkušeným poskytovatelem AM tisku kovů, jako je Metal3DP.
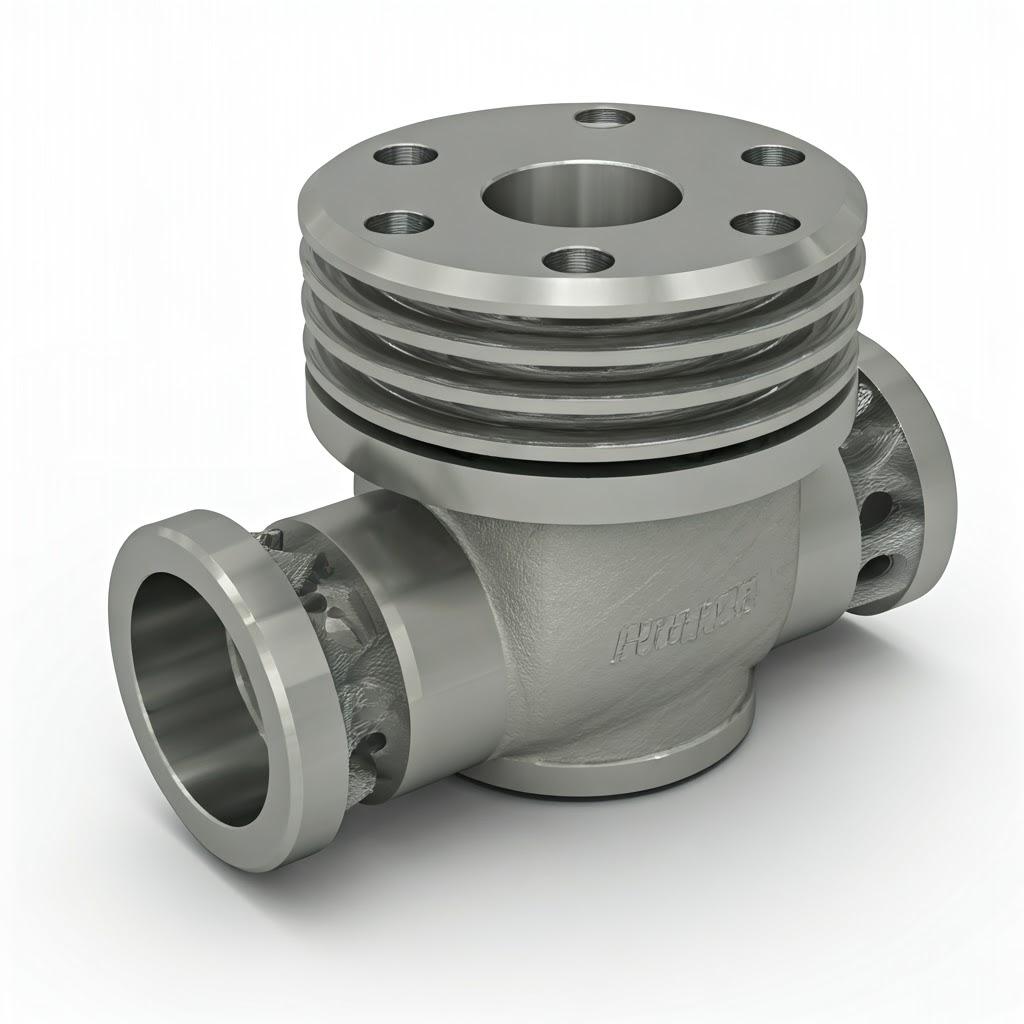
Jak vybrat správného poskytovatele služeb 3D tisku kovů pro ventily
Výběr správného poskytovatele služeb 3D tisku kovů je zásadní rozhodnutí, které může významně ovlivnit kvalitu, náklady a dobu realizace vašich 3D tištěných komponentů ventilů. Zde je několik klíčových faktorů, které je třeba vzít v úvahu při hodnocení potenciálních dodavatelů:
- Odborné znalosti a schopnosti v oblasti materiálů: Ujistěte se, že dodavatel má zkušenosti s prací s konkrétními slitinami kovů, které jsou pro vaše součásti ventilů vyžadovány, jako je nerezová ocel 316L nebo CuNi30Mn1Fe. Informujte se o jeho schopnostech charakterizace a testování materiálů, abyste zajistili, že tištěné díly splňují potřebné materiálové specifikace. Například společnost Metal3DP nabízí širokou škálu vysoce kvalitních kovových prášků a disponuje hlubokými odbornými znalostmi v oblasti jejich použití.
- Tiskové technologie a zařízení: Porozumět typům technologií 3D tisku kovů, které poskytovatel používá (např. SLM, DMLS, EBM). Různé technologie nabízejí různé úrovně přesnosti, povrchové úpravy a objemu sestavení. Ujistěte se, že jejich zařízení je dobře udržované a schopné splnit požadavky na rozměrovou přesnost a složitost vašich ventilových součástí. Špičkové tiskárny Metal3DP’jsou známé svou přesností a spolehlivostí.
- Kontrola kvality a certifikace: Informujte se o systému řízení kvality poskytovatele a o případných příslušných certifikátech (např. ISO 9001, AS9100 pro letecký průmysl). Pro zajištění spolehlivosti a výkonnosti kritických součástí ventilů jsou nezbytné důkladné postupy kontroly kvality, včetně sledování v průběhu procesu a kontroly po vytištění.
- Zkušenosti s průmyslovými aplikacemi: Hledejte poskytovatele s prokazatelnou zkušeností s výrobou kovových 3D tištěných dílů pro náročné průmyslové aplikace, nejlépe v leteckém, automobilovém, lékařském nebo podobném odvětví, kde je výkonnost ventilů kritická. Zkušenosti s podobnými aplikacemi mohou naznačovat, že rozumí specifickým požadavkům a výzvám. Společnost Metal3DP má rozsáhlé zkušenosti v těchto klíčových odvětvích.
- Konstrukční a inženýrská podpora: Dobrý poskytovatel služeb by měl nabízet konzultace k návrhu a technickou podporu pro optimalizaci návrhů komponent ventilů pro technologii AM. To zahrnuje pokyny týkající se návrhu pro vyrobitelnost (DFM), výběru materiálu a následného zpracování. Společnost Metal3DP poskytuje komplexní řešení zahrnující služby vývoje aplikací.
- Možnosti následného zpracování: Zjistěte, zda poskytovatel nabízí nezbytné služby následného zpracování požadované pro vaše součásti ventilů, jako je odstranění podpěr, tepelné zpracování, povrchová úprava a obrábění. Vlastní nebo dobře spravovaná síť kapacit následného zpracování může zefektivnit výrobní proces.
- Dodací lhůty a výrobní kapacita: Diskutujte o dodacích lhůtách pro výrobu prototypů a sériovou výrobu. Ujistěte se, že poskytovatel je schopen splnit vaše požadavky na objem a harmonogramy dodávek. Cílem efektivních procesů společnosti Metal3DP’ je efektivně plnit časové plány zákazníků.
- Struktura nákladů a transparentnost: Pochopte cenový model poskytovatele a zajistěte transparentnost rozdělení nákladů. Porovnejte nabídky od více poskytovatelů a zvažte nejen náklady na tisk, ale také náklady na materiál, poplatky za návrh a následné zpracování.
- Komunikace a zákaznická podpora: Efektivní komunikace a pohotová zákaznická podpora jsou pro hladký a úspěšný průběh projektu klíčové. Posuďte, jak poskytovatel reaguje a zda je ochoten spolupracovat.
- Důvěrnost a ochrana duševního vlastnictví: Ujistěte se, že má poskytovatel spolehlivé zásady a dohody na ochranu vašeho duševního vlastnictví a zachování důvěrnosti vašich návrhů.
Pečlivým vyhodnocením potenciálních poskytovatelů služeb 3D tisku kovů na základě těchto faktorů si můžete vybrat partnera, který bude odpovídat vašim specifickým potřebám a zajistí výrobu vysoce kvalitních a odolných součástí ventilů. Kontaktujte společnost Metal3DP a zjistěte, jak mohou naše schopnosti podpořit cíle vaší organizace v oblasti aditivní výroby.
Nákladové faktory a dodací lhůty pro 3D tištěné komponenty ventilů
Pochopení nákladových faktorů a doby realizace spojené s kovovým 3D tiskem součástí ventilů je nezbytné pro sestavení rozpočtu a plánování projektu. Tyto aspekty se mohou výrazně lišit v závislosti na několika parametrech:
Nákladové faktory:
- Náklady na materiál: Významným faktorem je cena kovového prášku. Speciální slitiny, jako je titan nebo superslitiny na bázi niklu, jsou obecně dražší než nerezové oceli. Náklady přímo ovlivňuje také objem materiálu použitého při tisku. Optimalizované návrhy, které snižují spotřebu materiálu, mohou vést k úspoře nákladů. Řada vysoce kvalitních kovových prášků Metal3DP’nabízí různé cenové kategorie v závislosti na slitině.
- Doba výstavby: Doba potřebná k vytištění součásti ventilu závisí na jeho velikosti, složitosti a zvolené technologii tisku. Delší doba sestavení znamená vyšší provozní náklady stroje. Celkovou dobu sestavení ovlivňují faktory, jako je tloušťka vrstvy a počet dílů, které se tisknou současně na jedné sestavovací platformě.
- Náklady na provoz stroje: Patří mezi ně náklady na spotřebu energie, údržbu 3D tiskárny a odpisy zařízení.
- Náklady na předběžné zpracování: To může zahrnovat optimalizaci návrhu pro AM, přípravu konstrukce a generování podpůrných struktur.
- Náklady na následné zpracování: Jak již bylo uvedeno dříve, kroky následného zpracování, jako je odstranění podpory, tepelné zpracování, povrchová úprava a obrábění, zvyšují celkové náklady. Tyto náklady ovlivňuje složitost a rozsah požadovaného následného zpracování.
- Náklady na pracovní sílu: K celkovým nákladům přispívají odborné znalosti potřebné k obsluze 3D tiskárny, následnému zpracování a kontrole kvality.
- Množství a objem: Ačkoli je technologie AM na bázi kovů často výhodná pro nízké až střední objemy výroby a přizpůsobení, náklady na jeden díl se mohou snížit při větších výrobních sériích díky úsporám z rozsahu při pořizování materiálu a využití konstrukční platformy.
Dodací lhůta:
- Návrh a předběžné zpracování: Počáteční fáze zahrnuje optimalizaci konstrukce pro AM kovů a přípravu konstrukce, která může v závislosti na složitosti trvat několik dní až několik týdnů.
- Doba tisku: Skutečná doba tisku závisí na velikosti a složitosti součásti ventilu a na počtu současně tištěných dílů. Ta se může pohybovat od několika hodin až po několik dní.
- Doba následného zpracování: Doba potřebná pro kroky následného zpracování se liší v závislosti na konkrétních potřebných ošetřeních. Odstranění podpěr může trvat hodiny, zatímco tepelné zpracování nebo rozsáhlé obrábění může dobu přípravy prodloužit o několik dní nebo týdnů.
- Kontrola kvality a inspekce: Před odesláním dílů je nutné provést důkladné kontroly a inspekce kvality, což prodlužuje celkovou dobu realizace.
- Doba přepravy: Doba dodání hotových dílů zákazníkovi závisí na místě a způsobu přepravy.
Strategie řízení nákladů a doby realizace:
- Optimalizace designu: Navrhování pro vyrobitelnost v AM může snížit spotřebu materiálu, dobu výroby a potřebu rozsáhlých podpěr a následného zpracování.
- Výběr materiálu: Výběr nejvhodnějšího materiálu, který splňuje požadavky na výkon a není příliš drahý, může pomoci kontrolovat náklady.
- Plánování stavby: Optimalizace orientace a umístění dílů na sestavovací platformě může maximalizovat počet dílů vytištěných na jedno sestavení a zkrátit celkovou dobu tisku jednoho dílu.
- Efektivní následné zpracování: Zjednodušení pracovních postupů následného zpracování a výběr nákladově nejefektivnějších metod pro dosažení požadované povrchové úpravy a tolerancí může snížit náklady i dobu realizace.
- Spolupráce se zkušeným poskytovatelem: Spolupráce se znalým poskytovatelem služeb, jako je Metal3DP, který má optimalizované procesy a efektivní pracovní postupy, může pomoci minimalizovat náklady i dobu realizace.
Pochopení těchto faktorů nákladů a doby realizace vám umožní činit informovaná rozhodnutí o využití 3D tisku kovů pro vaše ventilové komponenty a efektivně plánovat vaše projekty.
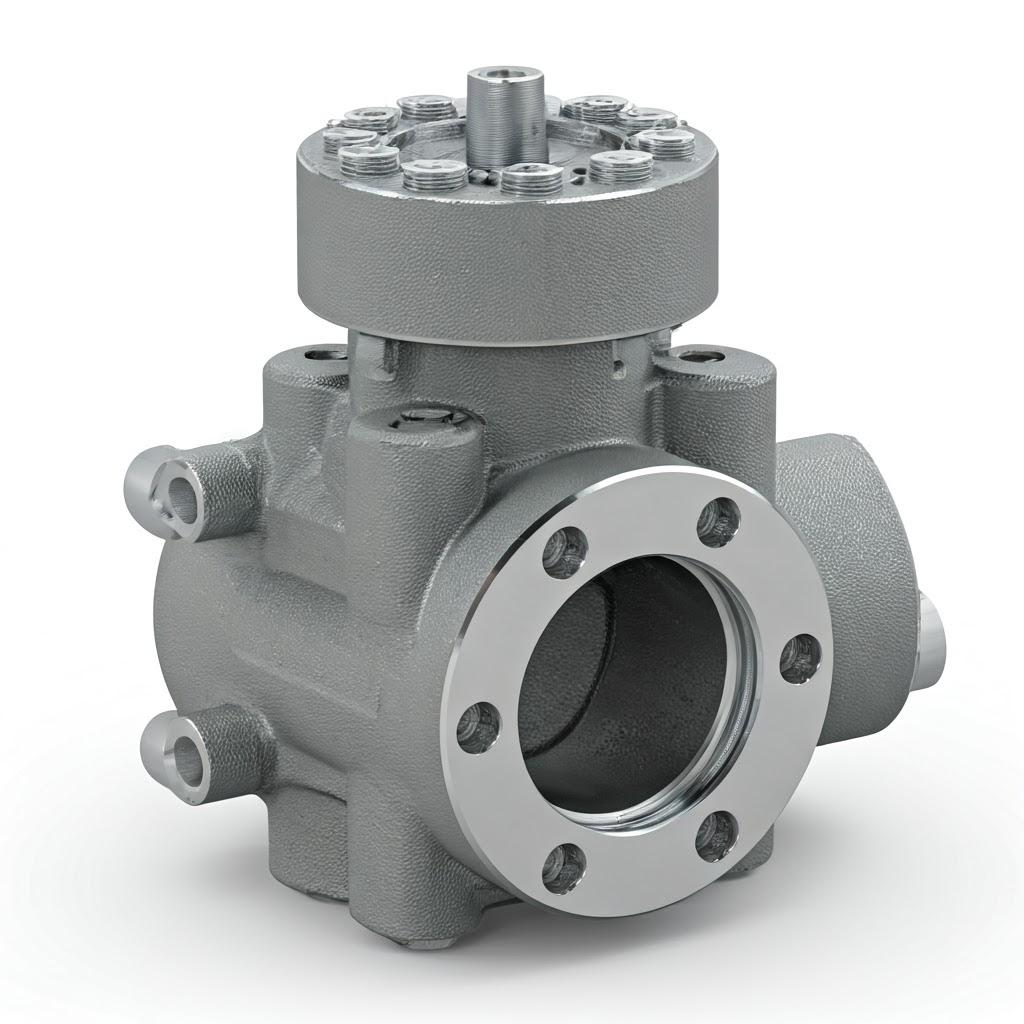
Často kladené otázky (FAQ)
- Jaké typy kovových slitin lze použít pro 3D tisk součástí ventilů? Kovový 3D tisk je kompatibilní s celou řadou slitin, včetně nerezových ocelí (např. 316L), slitin mědi a niklu (např. CuNi30Mn1Fe), titanových slitin, superslitin na bázi niklu, slitin hliníku a dalších. Výběr materiálu závisí na konkrétních požadavcích aplikace, jako je odolnost proti korozi, pevnost, teplotní tolerance a biokompatibilita. Společnost Metal3DP nabízí rozmanité portfolio vysoce kvalitních kovových prášků.
- Jsou 3D tištěné kovové součásti ventilů stejně pevné a odolné jako tradičně vyráběné? Ano, při použití vysoce kvalitních kovových prášků a optimalizovaných parametrů tisku mohou 3D tištěné kovové součásti ventilů dosahovat srovnatelné nebo dokonce vyšší pevnosti a odolnosti než ty, které se vyrábějí tradičními metodami, jako je odlévání nebo kování. Následné zpracování, jako je lisování za tepla (HIP), může dále zlepšit mechanické vlastnosti snížením vnitřní pórovitosti.
- Jaká je obvyklá doba dodání prototypů kovových ventilů vytištěných na 3D tiskárně? Doba realizace prototypů se může lišit v závislosti na složitosti návrhu, zvoleném materiálu a vytíženosti poskytovatele služeb. Kovový 3D tisk však obecně nabízí rychlejší realizaci prototypů ve srovnání s tradičními metodami založenými na nástrojích, často v rozmezí několika dnů až několika týdnů. Společnost Metal3DP se snaží o efektivní prototypování, které urychlí váš proces návrhu a vývoje.
- Lze kovový 3D tisk použít pro hromadnou výrobu součástí ventilů? Zatímco kovový 3D tisk je často ideální pro nízké až střední objemy výroby a vysoce přizpůsobené díly, díky pokroku v technologii a velikosti stavebních platforem se stává stále životaschopnějším pro větší výrobní série. U velkoobjemových aplikací je třeba pečlivě vyhodnotit faktory, jako jsou náklady na jeden díl a rychlost výroby.
- Jak zajistím, aby 3D tištěná součást ventilu splňovala požadované tlakové parametry? Splnění požadavků na tlakovou odolnost zahrnuje pečlivý výběr materiálu, optimalizovaný návrh pro udržení tlaku, hustý a bezchybný tisk a přísné testování. Nedestruktivní metody zkoušení (NDT) a tlakové zkoušky mají zásadní význam pro ověření integrity tištěných součástí. Spolupráce se zkušeným dodavatelem, jako je Metal3DP, který těmto požadavkům rozumí, je zásadní.
Závěr
3D tisk z kovu se stal výkonnou a všestrannou výrobní technologií pro výrobu odolných součástí ventilů v mnoha průmyslových odvětvích. Jeho schopnost usnadnit komplexní konstrukce, optimalizovat použití materiálu, urychlit výrobu prototypů a dokonce zlepšit výkonnostní charakteristiky nabízí významné výhody oproti tradičním výrobním metodám. Využitím správných materiálů, jako je nerezová ocel 316L a CuNi30Mn1Fe, a spoluprací se znalým a zkušeným poskytovatelem, jako je Metal3DP, mohou inženýři a manažeři nákupu odhalit nové možnosti pro vytváření vysoce výkonných a spolehlivých komponent ventilů přizpůsobených specifickým potřebám jejich aplikací. Od složitých vnitřních průtokových kanálů až po lehké a přitom robustní konstrukce - technologie Metal AM umožňuje inovace a efektivitu při výrobě ventilů. Doporučujeme vám prozkoumat potenciál kovového 3D tisku se společností Metal3DP a zjistit, jak naše špičkové systémy, pokročilé kovové prášky a služby vývoje aplikací mohou podpořit cíle vaší organizace’v oblasti aditivní výroby.
Sdílet na
MET3DP Technology Co., LTD je předním poskytovatelem řešení aditivní výroby se sídlem v Qingdao v Číně. Naše společnost se specializuje na zařízení pro 3D tisk a vysoce výkonné kovové prášky pro průmyslové aplikace.
Dotaz k získání nejlepší ceny a přizpůsobeného řešení pro vaše podnikání!
Související články
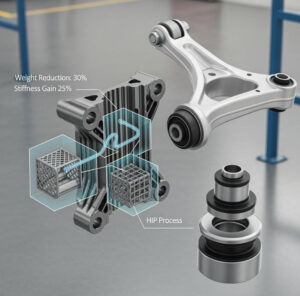
Metal 3D Printed Subframe Connection Mounts and Blocks for EV and Motorsport Chassis
Přečtěte si více "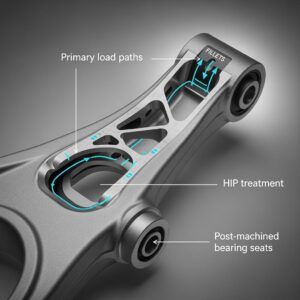
Metal 3D Printing for U.S. Automotive Lightweight Structural Brackets and Suspension Components
Přečtěte si více "O Met3DP
Nedávná aktualizace
Náš produkt
KONTAKTUJTE NÁS
Nějaké otázky? Pošlete nám zprávu hned teď! Po obdržení vaší zprávy obsloužíme vaši žádost s celým týmem.