Skříně pro elektroniku dronů
Obsah
Úvod - Zásadní role kovových 3D tištěných krytů v technologii dronů
Rychlý vývoj technologie dronů zahájil éru nebývalých možností v různých odvětvích, od leteckého fotografování a sledování až po logistiku a průmyslové inspekce. Srdcem každého sofistikovaného dronu je jeho složitý elektronický systém, jemná sestava senzorů, procesorů, komunikačních modulů a rozvodných jednotek. Ochrana těchto životně důležitých součástí před nepříznivými podmínkami prostředí, mechanickým namáháním a elektromagnetickým rušením má zásadní význam pro zajištění spolehlivého a stálého provozu dronů. Zde hrají zásadní roli vysoce kvalitní kryty elektroniky.
Skříně pro elektroniku dronů se tradičně vyrábějí konvenčními metodami, jako je CNC obrábění nebo vstřikování. Tyto techniky sice mají své přednosti, ale často jsou spojeny s omezeními, pokud jde o flexibilitu konstrukce, optimalizaci hmotnosti a přizpůsobení, zejména u složitých geometrií a nízkých až středních objemů výroby. Kov 3D tisk, známá také jako aditivní výroba kovů, se stala transformačním řešením, které nabízí inženýrům a manažerům nákupu jedinečné možnosti vytváření robustních, lehkých a vysoce přizpůsobených krytů pro elektroniku dronů.
3D tisk z kovu umožňuje výrobu složitých konstrukcí krytů, které by bylo obtížné nebo nemožné realizovat při tradiční výrobě. To otevírá možnosti integrace složitých funkcí, optimalizace vnitřního uspořádání pro lepší tepelné řízení a umístění komponent a snížení celkové hmotnosti - což je rozhodující faktor pro efektivitu a výdrž letu dronů. Aditivní výroba navíc umožňuje rychlou tvorbu prototypů a výrobu na vyžádání, což urychluje vývojový cyklus a umožňuje nákladově efektivní přizpůsobení pro konkrétní aplikace dronů.
Jako přední poskytovatel řešení aditivní výroby, Metal3DP Technology Co., LTD stojí v čele této technologické revoluce. Díky špičkovému objemu tisku, přesnosti a spolehlivosti jsou naše tiskárny ideální pro výrobu kritických součástí dronů. Naše odborné znalosti se rozšiřují na komplexní řadu vysoce výkonných kovových prášků, což zajišťuje, že si můžete vybrat optimální materiál pro své specifické požadavky na kryt.
K čemu se používají kovové 3D tištěné kryty elektroniky pro drony?
Kovové 3D tištěné kryty elektroniky pro drony slouží k mnoha důležitým funkcím v různých aplikacích dronů. Jejich hlavním úkolem je chránit citlivé elektronické součásti dronu před různými škodlivými vlivy, a zajistit tak provozní integritu a dlouhou životnost. Zde je přehled jejich klíčových použití:
- Ochrana životního prostředí: Drony často pracují v náročném prostředí, kde jsou vystaveny prachu, vlhkosti, dešti, extrémním teplotám a korozivním látkám. Kovové kryty poskytují robustní bariéru proti těmto prvkům a zabraňují poškození vnitřní elektroniky.
- Mechanická ochrana: Během letu a přistání mohou drony zažívat vibrace, otřesy a nárazy. Robustní kovové kryty poskytují významnou mechanickou ochranu a chrání citlivé desky s obvody a komponenty před fyzickým poškozením.
- Stínění elektromagnetického rušení (EMI) a vysokofrekvenčního rušení (RFI): Elektronické součástky mohou být náchylné k rušení vnějšími elektromagnetickými poli nebo mohou samy vyzařovat záření, které ovlivňuje jiné systémy. Kovové kryty fungují jako účinný štít, který zajišťuje správnou funkci elektroniky dronu a zabraňuje rušení jiných zařízení.
- Tepelný management: Elektronické součástky při provozu vytvářejí teplo. Kov díky své vynikající tepelné vodivosti pomáhá odvádět teplo od kritických součástí, čímž zabraňuje jejich přehřívání a zajišťuje optimální výkon. Složité vnitřní geometrie dosažitelné pomocí 3D tisku mohou dále zlepšit odvod tepla prostřednictvím integrovaných chladicích kanálků nebo žeber.
- Optimalizace hmotnosti: 3D tisk z kovu poskytuje robustní ochranu a zároveň umožňuje vytvářet lehká pouzdra díky optimalizaci designu a použití pokročilých materiálů. Snížení hmotnosti je zásadní pro maximalizaci doby letu dronu, kapacity užitečného zatížení a celkové efektivity.
- Přizpůsobení a integrace: Aditivní výroba umožňuje vytvářet vysoce přizpůsobené kryty na míru specifickým požadavkům na tvar a velikost elektroniky dronu. Funkce, jako jsou montážní body, konektory a kanály pro vedení kabelů, lze integrovat přímo do konstrukce, čímž se zkrátí doba montáže a její složitost.
- Rychlé prototypování a iterace: 3D tisk z kovu usnadňuje rychlou tvorbu prototypů, což inženýrům umožňuje testovat různé návrhy skříní a rychle je vylepšovat na základě zpětné vazby o jejich výkonu. To urychluje vývojový cyklus a zkracuje dobu uvedení na trh.
Tyto všestranné skříně nacházejí uplatnění v různých typech dronů a průmyslových odvětvích, včetně:
- Letectví a obrana: Ochrana systémů řízení letu, komunikačních zařízení a senzorů ve vojenských a komerčních bezpilotních letounech.
- Automobilový průmysl: Pouzdro elektroniky pro systémy autonomního řízení, pole senzorů a komunikační moduly ve vzdušných vozidlech.
- Lékařský: Obalení kritické elektroniky v bezpilotních letounech používaných pro lékařské dodávky, dohled a reakci na mimořádné události.
- Průmyslová inspekce: Ochrana senzorů, kamer a systémů sběru dat v bezpilotních letounech používaných pro inspekci infrastruktury, zemědělství a geodézii.
- Logistika a doručování: Zajištění bezpečnosti a funkčnosti elektroniky v doručovacích dronech provozovaných v různých prostředích.
Využitím možností kovového 3D tisku mohou průmyslová odvětví dosáhnout vynikajícího výkonu, spolehlivosti a přizpůsobení krytů elektroniky pro drony. Prozkoumejte naše služby 3D tisku z kovu a zjistěte, jak můžeme podpořit vaše specifické potřeby.
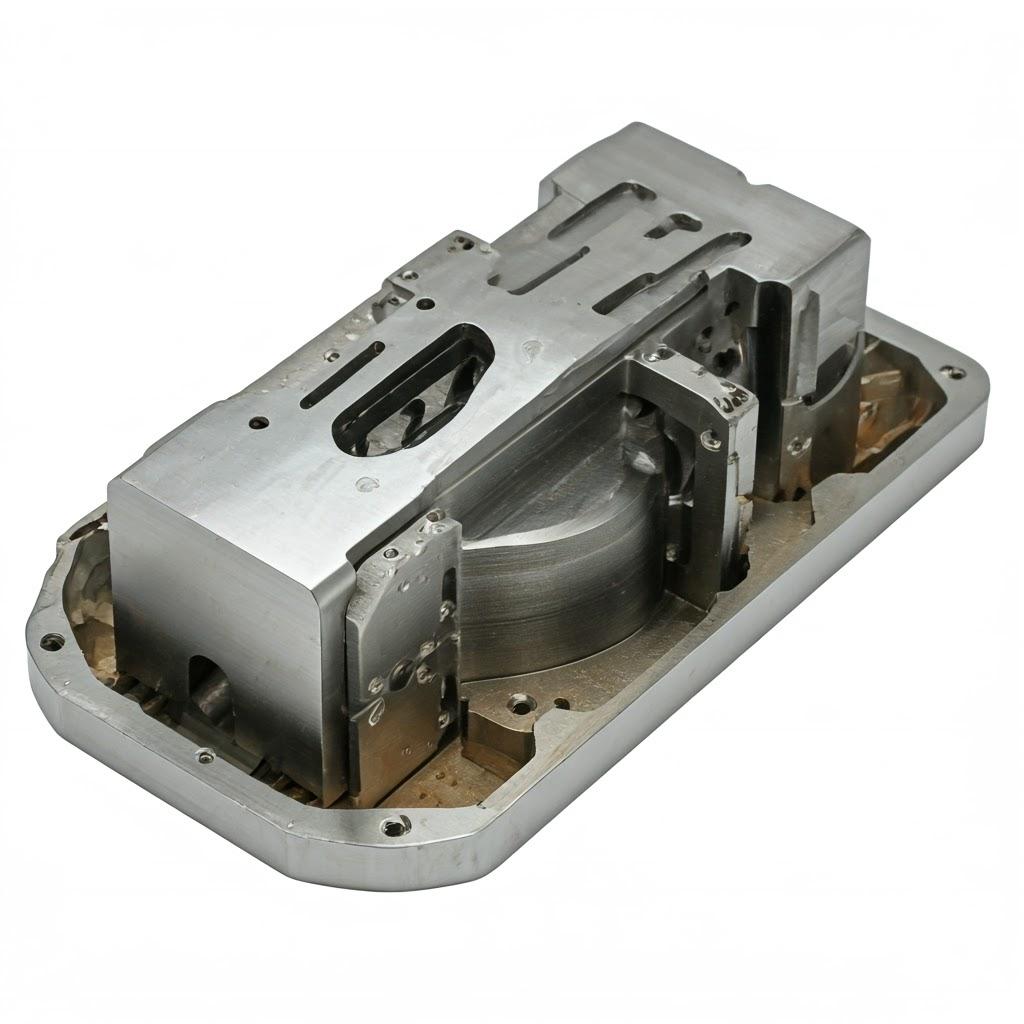
Proč zvolit 3D tisk z kovu pro kryty elektroniky pro drony?
Volba kovového 3D tisku namísto tradičních výrobních metod pro kryty elektroniky pro bezpilotní letouny nabízí řadu přesvědčivých výhod, díky nimž se stává stále atraktivnějším řešením pro inženýry a manažery veřejných zakázek. Zde jsou některé hlavní výhody:
- Svoboda a složitost návrhu: 3D tisk kovů osvobozuje konstruktéry od omezení tradičních výrobních postupů. Snadno lze vytvářet složité geometrie, složité vnitřní prvky, jako jsou chladicí kanály a výztužná žebra, a organické tvary. To umožňuje vysoce optimalizované návrhy skříní, které maximalizují využití prostoru, zlepšují funkčnost a snižují hmotnost.
- Optimalizace hmotnosti: Při konstrukci dronů se počítá každý gram. 3D tisk z kovu v kombinaci s pokročilými konstrukčními technikami, jako jsou mřížkové struktury a optimalizace topologie, umožňuje vytvářet lehké a přitom pevné kryty. To se přímo promítá do prodloužení doby letu, zvýšení nosnosti a energetické účinnosti.
- Účinnost materiálu: Aditivní výrobní procesy obvykle zahrnují méně materiálového odpadu ve srovnání se subtraktivními metodami, jako je CNC obrábění, kdy se při výrobě finálního dílu odebírá velké množství materiálu. To může vést k úspoře nákladů, zejména při použití drahých speciálních kovů.
- Rychlá výroba prototypů a zkrácení dodacích lhůt: 3D tisk z kovu výrazně urychluje proces výroby prototypů. Iterace návrhu lze rychle realizovat a testovat, což zkracuje dobu vývoje a uvádění na trh. Navíc u nízkých až středních objemů výroby může 3D tisk nabídnout kratší dodací lhůty ve srovnání s tradičními metodami náročnými na výrobu nástrojů.
- Přizpůsobení a výroba na vyžádání: Aditivní výroba umožňuje snadné přizpůsobení konstrukce skříní specifickým požadavkům bez nutnosti použití nových nástrojů. To je výhodné zejména u specializovaných aplikací pro drony nebo při řešení různých rozložení elektronických komponent. Výroba na vyžádání také eliminuje potřebu velkých skladových zásob.
- Integrace funkcí: 3D tisk z kovu umožňuje integrovat více funkcí přímo do konstrukce skříně. To může zahrnovat montážní prvky, konektory, kanály pro vedení kabelů a dokonce i struktury tepelného managementu, což snižuje počet samostatných komponent a zjednodušuje montáž.
- Vylepšený výkon: Možnost výběru ze široké škály vysoce výkonných kovových prášků umožňuje vytvářet kryty se specifickými vlastnostmi, jako je vysoký poměr pevnosti a hmotnosti, vynikající tepelná vodivost a účinné stínění EMI/RFI.
- Nákladová efektivita pro malé až střední objemy: Počáteční investice do zařízení pro 3D tisk z kovu může být sice značná, ale může být vysoce nákladově efektivní pro výrobu složitých dílů v malých až středních objemech, kde by náklady na nástroje spojené s tradičními metodami byly neúnosné.
Pokročilé kovové prášky Metal3DP’s jsou speciálně navrženy tak, aby maximalizovaly výhody aditivní výroby a umožnily výrobu vysoce výkonných krytů pro elektroniku dronů s vynikajícími mechanickými vlastnostmi a funkční integrací. Naše odborné znalosti v oblasti technologie SEBM (Selective Electron Beam Melting) dále zvyšují přesnost a spolehlivost tištěných dílů.
Doporučené kovové prášky pro kryty dronů: AlSi10Mg a Scalmalloy®
Výběr správného kovového prášku má zásadní význam pro dosažení požadovaných výkonnostních charakteristik 3D tištěných krytů elektroniky pro drony. Ve společnosti Metal3DP nabízíme řadu vysoce kvalitních kovových prášků optimalizovaných pro aditivní výrobu. Pro aplikace krytů pro drony, kde je nejdůležitější nízká hmotnost, vysoká pevnost a dobrá tepelná vodivost, doporučujeme zejména AlSi10Mg a Scalmalloy®.
AlSi10Mg:
AlSi10Mg je díky své vynikající kombinaci vlastností široce používanou hliníkovou slitinou pro 3D tisk z kovu:
- Vysoký poměr pevnosti k hmotnosti: Tato slitina nabízí značnou pevnost při zachování nízké hmotnosti, což je rozhodující pro maximalizaci efektivity letu dronů a nosnosti.
- Dobrá tepelná vodivost: Slitiny hliníku obecně vykazují dobrou tepelnou vodivost, což umožňuje účinný odvod tepla z přiložené elektroniky.
- Vynikající zpracovatelnost: AlSi10Mg se dobře hodí pro procesy laserové fúze v práškovém loži (LPBF) a poskytuje husté a vysoce kvalitní díly s dobrou povrchovou úpravou.
- Odolnost proti korozi: Hliník má přirozenou odolnost proti korozi a poskytuje ochranu vnitřní elektroniky v různých provozních prostředích.
- Nákladově efektivní: V porovnání s některými jinými vysoce výkonnými slitinami nabízí AlSi10Mg cenově výhodné řešení pro mnoho aplikací krytů pro drony.
Scalmalloy®:
Scalmalloy® je vysoce výkonná slitina hliníku, hořčíku a skandia speciálně vyvinutá pro aplikace aditivní výroby vyžadující výjimečnou pevnost a nízkou hmotnost:
- Velmi vysoká pevnost: Slitina Scalmalloy® vykazuje výrazně vyšší pevnost než běžné hliníkové slitiny, což umožňuje vytvářet tenčí a lehčí stěny skříní bez narušení strukturální integrity.
- Vynikající poměr pevnosti k hmotnosti: Jeho výjimečná pevnost v kombinaci s nízkou hustotou vede k vynikajícímu poměru pevnosti a hmotnosti, takže je ideální pro komponenty dronů s kritickou hmotností.
- Dobrá tažnost: Navzdory své vysoké pevnosti nabízí slitina Scalmalloy® také dobrou tažnost, která zajišťuje odolnost proti lomu při namáhání.
- Zvýšený výkon při únavě: Tato slitina vykazuje vynikající únavovou odolnost, která je pro součásti dronů vystavené vibracím a cyklickému zatížení během letu klíčová.
- Dobrá svařitelnost a odolnost proti korozi: Scalmalloy® nabízí dobrou svařitelnost pro případné následné zpracování nebo montáž a vykazuje dobrou odolnost proti korozi.
Volba mezi slitinou AlSi10Mg a slitinou Scalmalloy® závisí na konkrétních požadavcích aplikace dronu. Pokud je naprosto prvořadým požadavkem hmotnost a je potřeba maximální pevnost, nabízí slitina Scalmalloy® lepší řešení. Pro aplikace, kde je vyžadována dobrá rovnováha mezi pevností, tepelnou vodivostí a cenovou výhodností, je AlSi10Mg vynikající volbou.
Na Metal3DP, máme rozsáhlé zkušenosti s prací s AlSi10Mg i Scalmalloy® a optimalizujeme parametry tisku tak, abychom dosáhli nejvyšší kvality a výkonu pro vaše kryty pro elektroniku dronů. Náš pokročilý systém výroby prášku zajišťuje výrobu sférických prášků s vysokou sféricitou a dobrou tekutostí, což je nezbytné pro konzistentní a spolehlivý 3D tisk.
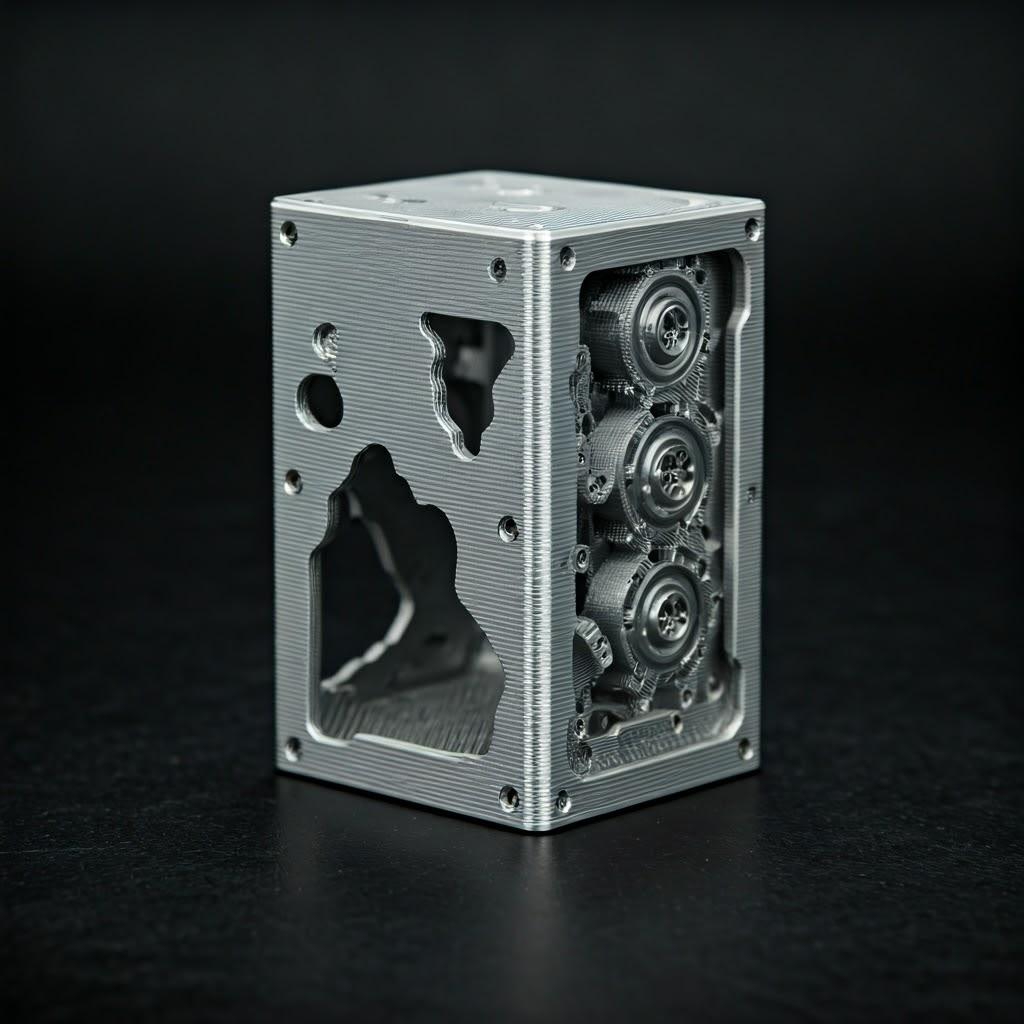
Úvahy o návrhu optimálních kovových krytů pro 3D tisk dronů
Navrhování pro 3D tisk z kovu vyžaduje jiné myšlení než tradiční výroba. Aby bylo možné plně využít možností aditivní výroby a dosáhnout optimálního výkonu krytů elektroniky pro drony, je třeba vzít v úvahu několik klíčových aspektů návrhu:
- Optimalizace topologie: Tento výpočetní přístup k návrhu identifikuje nejefektivnější rozložení materiálu pro danou sadu zatížení a omezení. Odstraněním nepotřebného materiálu může optimalizace topologie vést k výraznému snížení hmotnosti při zachování strukturální integrity - což je pro aplikace v bezpilotních letounech zásadní výhoda.
- Mřížové struktury: Začlenění mřížových nebo buněčných struktur do stěn skříně nebo vnitřních podpěr může dále snížit hmotnost, aniž by se snížila tuhost nebo pevnost. Lze použít různé vzory mřížek, z nichž každá nabízí jiné mechanické vlastnosti.
- Konsolidace částí: 3D tisk z kovu umožňuje integraci více komponent do jednoho vytištěného dílu. Tím se snižuje počet montážních kroků, spojovacích prvků a potenciálních míst poruchy, což vede k robustnějšímu a spolehlivějšímu krytu. Zvažte integraci montážních prvků, kabelových kanálů a dokonce chladičů přímo do konstrukce.
- Tloušťka stěny a žebrování: Optimalizace tloušťky stěny je nezbytná pro vyvážení hmotnosti a pevnosti konstrukce. Začlenění vnitřních nebo vnějších žeber může výrazně zvýšit tuhost, aniž by se zvýšila nadměrná hmotnost. Pro určení optimálního umístění a geometrie žeber je zásadní pečlivá analýza rozložení napětí.
- Podpůrné struktury: Kovový 3D tisk často vyžaduje podpůrné struktury, které zabraňují deformaci dílů během procesu sestavování, zejména u převislých prvků a složitých geometrií. Konstrukce se samonosnými úhelníky a minimalizace potřeby rozsáhlých podpěr může snížit spotřebu materiálu a dobu následného zpracování. Ve fázi návrhu zvažte snadné odstranění podpěr.
- Orientace a směr stavby: Orientace dílu na konstrukční platformě a směr, ve kterém je tištěn, může významně ovlivnit kvalitu povrchu, mechanické vlastnosti a potřebu podpůrných konstrukcí. Pečlivé zvážení těchto faktorů ve fázi návrhu může optimalizovat proces tisku a kvalitu výsledného dílu.
- Funkce tepelné správy: Pro skříně s elektronikou je tepelný management klíčový. Konstrukční prvky, jako jsou integrovaná chladicí žebra, větrací otvory nebo vnitřní kanály pro odvod tepla, lze začlenit přímo do 3D tištěného návrhu. Zvažte požadavky na proudění vzduchu a přenos tepla uzavřené elektroniky.
- Minimalizace koncentrace stresu: Ostré rohy a náhlé změny geometrie mohou vést ke koncentraci napětí a potenciálně oslabit díl při zatížení nebo vibracích. Začlenění koutů a hladkých přechodů do konstrukce může tyto problémy zmírnit a zlepšit celkovou odolnost skříně.
- Tolerance a uložení: Zohledněte tolerance dosažitelné při zvoleném procesu 3D tisku z kovu. Navrhněte rozhraní s ostatními součástmi s odpovídajícími vůlemi a uložením, abyste zajistili správnou montáž a funkčnost. Zvažte vliv tepelné roztažnosti a smršťování na rozměrovou přesnost.
- Požadavky na povrchovou úpravu: Povrchová úprava kovových 3D tištěných dílů po vytištění se může lišit v závislosti na materiálu a procesu tisku. Pokud je požadována hladší povrchová úprava, počítejte ve fázi návrhu s kroky následného zpracování, jako je obrábění nebo leštění.
Promyšleným řešením těchto konstrukčních otázek mohou konstruktéři plně využít potenciál kovového 3D tisku k vytvoření vysoce výkonných, lehkých a vysoce funkčních krytů elektroniky pro drony. Naše služby vývoje aplikací ve společnosti Metal3DP vám může poskytnout odborné poradenství při optimalizaci vašich návrhů pro aditivní výrobu kovů.
Dosažení přesnosti: Tolerance, povrchová úprava a rozměrová přesnost u 3D tištěných skříní
U krytů elektroniky pro drony je nejdůležitější přesnost, aby bylo zajištěno správné uchycení, funkčnost a ochrana vnitřních součástí. V případě kovového 3D tisku jsou tolerance, povrchová úprava a rozměrová přesnost klíčovými aspekty, kterým musí inženýři a manažeři nákupu rozumět:
- Tolerance: Tolerance označuje přípustnou odchylku určeného rozměru. Dosažitelné tolerance v kovovém 3D tisku závisí na několika faktorech, včetně technologie tisku (např. LPBF, SEBM), použitého materiálu, geometrie dílu a parametrů sestavení. Obecně lze při kovovém 3D tisku dosáhnout tolerancí v rozmezí ±0,1 mm až ±0,05 mm, ve specifických případech a při následném zpracování i těsnějších. Je’velmi důležité jasně sdělit požadované tolerance poskytovateli služeb 3D tisku z kovu, aby bylo zajištěno jejich splnění.
- Povrchová úprava: Povrchová úprava kovových 3D tištěných dílů po vytištění je obvykle hrubší ve srovnání s díly vyrobenými obráběním nebo vstřikováním. Drsnost povrchu (Ra) se může pohybovat od 5 do 20 µm nebo i více, v závislosti na procesu tisku a materiálu. Pro aplikace vyžadující hladší povrch lze použít techniky následného zpracování, jako je leštění, tryskání nebo obrábění. Zadání požadované povrchové úpravy na počátku procesu návrhu je důležité pro plánování nezbytného následného zpracování.
- Rozměrová přesnost: Rozměrová přesnost se vztahuje k míře, do jaké se vytištěný díl shoduje se zamýšleným modelem CAD. Přestože 3D tisk z kovu nabízí dobrou celkovou rozměrovou přesnost, mohou se vyskytnout odchylky způsobené faktory, jako je smršťování materiálu během tuhnutí, tepelné namáhání a orientace sestavení. Pro dosažení vysoké rozměrové přesnosti je nezbytná pečlivá optimalizace procesu, přesná kalibrace stroje a zkušená obsluha.
Zde’je tabulka shrnující typické dosažitelné rozsahy:
Vlastnosti | Typický dosažitelný rozsah při 3D tisku kovů | Faktory ovlivňující |
---|---|---|
Tolerance | ±0,1 mm až ±0,05 mm (nebo těsněji při optimalizaci) | Technologie tisku, materiál, geometrie, parametry sestavení |
Drsnost povrchu (Ra) | 5 až 20 µm (nebo hladší při následném zpracování) | Technologie tisku, materiál, tloušťka vrstvy, parametry sestavení |
Rozměrová přesnost | Obecně dobré, ale mohou se vyskytnout odchylky | Smršťování materiálu, tepelné namáhání, orientace konstrukce, kalibrace stroje |
Export do archů
Pro zajištění požadované přesnosti krytů elektroniky pro drony se doporučuje:
- Navrhujte s ohledem na omezení zvoleného tiskového procesu. Vyhněte se příliš přísným tolerancím nebo velmi hladkému povrchu, pokud to není nezbytně nutné, protože to může zvýšit náklady a dobu výroby.
- Na výkresech jasně uveďte kritické rozměry a tolerance.
- Projednejte požadavky na povrchovou úpravu s poskytovatelem služeb 3D tisku z kovu.
- Zvažte možnosti následného zpracování pro dosažení přísnějších tolerancí nebo hladších povrchů.
- Vyberte si renomovaného a zkušeného poskytovatele služeb 3D tisku z kovu, jako je např Metal3DP s důkladnými procesy kontroly kvality. Naše špičková přesnost v oboru zajišťuje, že vaše tištěné skříně splňují nejnáročnější specifikace.
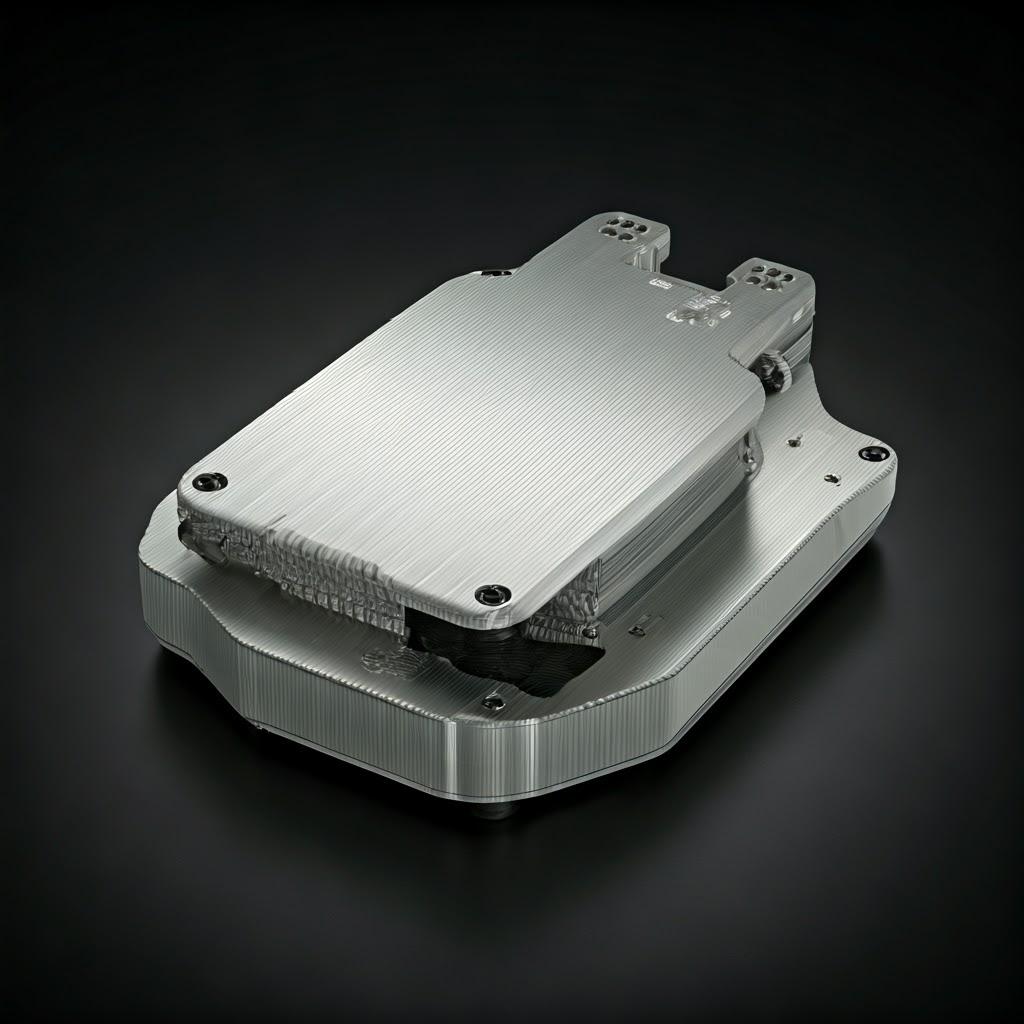
Techniky následného zpracování kovových 3D tištěných krytů elektroniky pro drony
3D tisk z kovu sice nabízí značné výhody při vytváření složitých geometrií, ale k dosažení konečných požadovaných vlastností, povrchové úpravy a rozměrové přesnosti krytů elektroniky pro bezpilotní letouny jsou často nutné kroky následného zpracování. Mezi běžné techniky následného zpracování patří:
- Odstranění podpory: Během tisku jsou často nutné podpůrné konstrukce, aby se zabránilo deformaci. Tyto podpěry je třeba po tisku opatrně odstranit, obvykle ručním lámáním, řezáním nebo obráběním. Konstrukce dílu a strategie podpěr může výrazně ovlivnit snadnost a efektivitu odstraňování podpěr.
- Tepelné zpracování: Tepelné zpracování se často používá ke snížení vnitřních pnutí, zlepšení mechanických vlastností (např. pevnosti a tvrdosti) a dosažení požadované mikrostruktury tištěných kovových dílů. Konkrétní cyklus tepelného zpracování závisí na materiálu a zamýšleném použití.
- Povrchová úprava: Jak již bylo zmíněno, povrchová úprava v podobě, v jaké byla vytištěna, nemusí být vhodná pro všechny aplikace. K dosažení hladšího povrchu, zlepšení estetiky nebo zvýšení odolnosti proti korozi lze použít různé techniky povrchové úpravy. Patří mezi ně:
- Výbuch v médiích: Použití abrazivních médií k odstranění volného prášku a vytvoření rovnoměrnější struktury povrchu.
- Leštění: Mechanické nebo chemické vyhlazení povrchu za účelem snížení drsnosti.
- Obrábění (CNC): Přesné obrábění lze použít k dosažení úzkých tolerancí u kritických prvků a ke zlepšení kvality povrchu.
- Povlakování a pokovování: Povlaky lze nanášet za účelem zlepšení povrchových vlastností, jako je odolnost proti korozi, odolnost proti opotřebení nebo elektrická vodivost. Mezi běžné možnosti patří eloxování hliníku, pokovování pro stínění EMI nebo lakování pro estetické účely.
- Spojování a montáž: U větších nebo složitějších skříní může být nutné spojit více 3D tištěných dílů pomocí metod, jako je svařování, pájení nebo lepení. Pečlivý návrh a zvážení způsobů spojování jsou klíčové.
- Kontrola a řízení kvality: Důkladná kontrola je nezbytná k zajištění toho, aby tištěné kryty splňovaly požadovanou rozměrovou přesnost, povrchovou úpravu a vlastnosti materiálu. Lze použít techniky, jako jsou souřadnicové měřicí stroje (CMM), nedestruktivní zkoušení (NDT) a analýza materiálu.
Konkrétní požadavky na následné zpracování krytu elektroniky pro drony závisí na materiálu, zamýšleném použití a požadovaných výkonnostních vlastnostech. Tyto požadavky je nezbytné prodiskutovat s poskytovatelem služeb 3D tisku z kovu již na počátku projektu, aby byl zajištěn racionální a efektivní výrobní proces. Metal3DP nabízí komplexní služby následného zpracování splnit širokou škálu požadavků a zajistit, aby vaše 3D tištěné skříně splňovaly nejvyšší standardy.
Řešení problémů při 3D tisku kovových krytů pro drony
3D tisk z kovu nabízí řadu výhod, ale zároveň přináší určité problémy, které by měli inženýři a manažeři veřejných zakázek znát:
- Deformace a zkreslení: Tepelné namáhání během tisku může vést k deformaci nebo zkreslení dílu, zejména u velkých nebo složitých geometrií. Pečlivý návrh, optimalizované parametry sestavení a vhodné podpůrné struktury mohou pomoci tyto problémy zmírnit.
- Zbytková napětí: Kovové 3D tištěné díly mohou obsahovat zbytková napětí, která mohou ovlivnit jejich mechanické vlastnosti a rozměrovou stabilitu. K odstranění těchto napětí je často nutné následné tepelné zpracování.
- Pórovitost: Neúplné splynutí kovového prášku během tisku může mít za následek pórovitost dílu, což může snížit jeho pevnost a únavovou odolnost. Optimalizace parametrů tisku, výběr materiálu a kvalita prášku mají zásadní význam pro minimalizaci pórovitosti. Vysoce kvalitní kovové prášky Metal3DP’s jsou navrženy tak, aby minimalizovaly pórovitost a zajistily husté a vysoce výkonné díly.
- Povrchová úprava: Jak již bylo řečeno, povrch po tisku může být drsný, což vyžaduje následné zpracování pro dosažení hladšího povrchu nebo přísnějších tolerancí.
- Odstranění podpůrné konstrukce: Odstranění podpůrných konstrukcí může být u složitých geometrií náročné a může zanechat stopy na povrchu. Důležitá je pečlivá konstrukce a strategie podpory.
- Náklady: Náklady na 3D tisk z kovu mohou být vyšší než u tradičních výrobních metod, zejména u velkých výrobních objemů. Pro malé až střední objemy a složité díly však může být nákladově efektivní. Pochopení faktorů ovlivňujících náklady a optimalizace návrhu pro aditivní výrobu může pomoci řídit výdaje.
- Škálovatelnost: Zvyšování výroby pomocí 3D tisku kovů může představovat výzvu ve srovnání s tradičními velkosériovými výrobními procesy. Pokroky v rychlosti tisku a objemu výroby však neustále zlepšují škálovatelnost.
- Výběr materiálu: Přestože nabídka kovových prášků pro 3D tisk roste, je stále omezenější ve srovnání s materiály dostupnými pro tradiční výrobu. Pečlivý výběr materiálu na základě požadavků aplikace je nezbytný.
Pro efektivní zvládnutí těchto výzev je zásadní:
- Spolupracujte se zkušeným poskytovatelem služeb 3D tisku kovů, jako je např Metal3DP který má odborné znalosti pro optimalizaci tiskového procesu a zmírnění případných problémů.
- Navrhujte díly speciálně pro aditivní výrobu s ohledem na faktory, jako jsou požadavky na podporu, orientace konstrukce a koncentrace napětí.
- Důkladně se seznamte s vlastnostmi materiálu a omezeními vybraného kovového prášku.
- Plánujte nezbytné kroky následného zpracování a náklady s nimi spojené.
- Zvažte požadavky na objem výroby a škálovatelnost již na počátku projektu.
Pokud si inženýři a manažeři nákupu uvědomí tyto problémy a budou je aktivně řešit, mohou úspěšně využít výhod kovového 3D tisku pro své potřeby v oblasti krytů elektroniky pro drony.
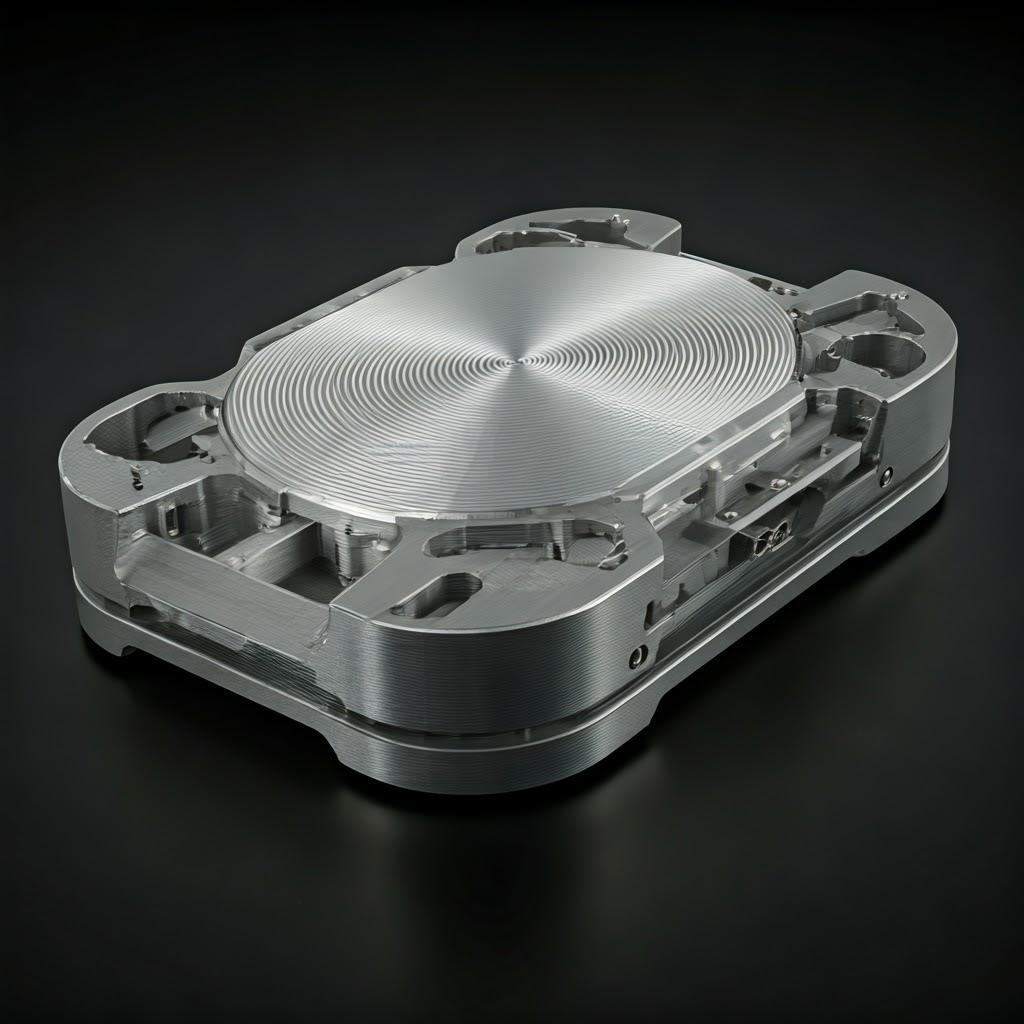
Jak vybrat správného poskytovatele služeb 3D tisku kovů pro komponenty dronů
Výběr správného poskytovatele služeb 3D tisku z kovu je zásadní rozhodnutí, které může významně ovlivnit kvalitu, náklady a dobu realizace krytů elektroniky pro drony. Zde jsou klíčové faktory, které je třeba při hodnocení potenciálních dodavatelů zvážit:
- Materiálové schopnosti: Ujistěte se, že poskytovatel nabízí specifické kovové prášky potřebné pro vaši aplikaci, například AlSi10Mg nebo Scalmalloy®. Zjistěte, zda má se zpracováním těchto materiálů zkušenosti a zda může poskytnout materiálové listy a protokoly o zkouškách. Metal3DP vyrábí širokou škálu vysoce kvalitních kovových práškůvčetně těch, které jsou doporučeny pro kryty dronů.
- Technologie tisku: Různé technologie 3D tisku kovů (např. LPBF, DED, Binder Jetting, SEBM) mají různé silné a slabé stránky, pokud jde o přesnost, povrchovou úpravu, objem a náklady. Pochopte, jakou technologii používají a zda odpovídá vašim požadavkům. Společnost Metal3DP se specializuje na selektivní tavení elektronovým svazkem (SEBM), který nabízí vysokou přesnost a spolehlivost pro náročné aplikace.
- Vybavení a kapacita: Zhodnoťte možnosti zařízení poskytovatele, včetně objemu výroby, přesnosti stroje a počtu tiskáren, které provozuje. To vám napoví, jak jsou schopni zvládnout objem vašeho projektu a velikost dílů, které mohou vyrábět. Naše tiskárny Metal3DP poskytují špičkový objem tisku, přesnost a spolehlivost.
- Kontrola kvality a certifikace: Informujte se o procesech kontroly kvality poskytovatele, včetně kontrolních metod, kontroly přesnosti rozměrů a testování materiálu. Příslušné certifikace (např. ISO 9001, AS9100 pro letecký průmysl) mohou poskytnout záruku, že se poskytovatel zavázal ke kvalitě.
- Konstrukční a inženýrská podpora: Nabízí poskytovatel služby optimalizace návrhu pro aditivní výrobu? Může poskytnout poradenství při výběru materiálu, návrhu nosné konstrukce a úvahách o následném zpracování? Poskytovatel se silnou inženýrskou podporou vám pomůže maximalizovat výhody kovového 3D tisku. Metal3DP poskytuje komplexní řešení zahrnující tiskárny SEBM, pokročilé kovové prášky a služby vývoje aplikací.
- Služby následného zpracování: Zjistěte, zda poskytovatel nabízí nezbytné služby následného zpracování, jako je odstranění podpěr, tepelné zpracování, povrchová úprava a lakování. Komplexní servis může zefektivnit výrobní proces.
- Zkušenosti a odbornost: Hledejte poskytovatele s prokazatelnými zkušenostmi v oblasti 3D tisku z kovu, ideálně se zkušenostmi z leteckého, automobilového, lékařského nebo průmyslového výrobního odvětví, které je relevantní pro aplikace dronů. Projděte si případové studie a reference, pokud jsou k dispozici.
- Komunikace a zákaznický servis: Efektivní komunikace a pohotový zákaznický servis jsou nezbytné pro hladký průběh projektu. Posuďte jejich schopnost reagovat, srozumitelnost komunikace a ochotu spolupracovat.
- Náklady a doba realizace: Získejte jasnou a podrobnou nabídku, ve které budou uvedeny všechny náklady včetně tisku, materiálů a následného zpracování. Zjistěte předpokládanou dobu realizace projektu a ujistěte se, že splňuje vaše požadavky.
- Důvěrnost a ochrana duševního vlastnictví: Pokud je konstrukce krytu vašeho dronu chráněná, ujistěte se, že poskytovatel služeb má uzavřené důkladné dohody o důvěrnosti a zavedená opatření na ochranu vašeho duševního vlastnictví.
Pečlivým vyhodnocením těchto faktorů si můžete vybrat poskytovatele služeb 3D tisku z kovu, který je vhodný pro vaše potřeby výroby komponentů pro drony.
Pochopení nákladových faktorů a dodacích lhůt pro 3D tištěné kryty pro drony
Náklady a doba realizace kovových 3D tištěných krytů elektroniky pro drony jsou ovlivněny několika faktory. Jejich pochopení vám pomůže efektivně naplánovat projekt a učinit informovaná rozhodnutí:
Nákladové faktory:
- Náklady na materiál: Typ a množství použitého kovového prášku jsou významnými faktory ovlivňujícími náklady. Pokročilé slitiny jako Scalmalloy® jsou obvykle dražší než standardní slitiny jako AlSi10Mg. Objem skříně a hustota konstrukce ovlivní spotřebu materiálu.
- Doba výstavby: Doba tisku krytu závisí na jeho velikosti, složitosti, výšce vrstvy a použité technologii tisku. Delší doba sestavení znamená vyšší provozní náklady stroje.
- Náklady na předběžné zpracování: To může zahrnovat optimalizaci návrhu pro aditivní výrobu, generování sestavovacích souborů a přípravu tiskárny.
- Náklady na následné zpracování: Jak již bylo uvedeno dříve, kroky následného zpracování, jako je odstranění podpěr, tepelné zpracování, povrchová úprava a povlakování, zvyšují celkové náklady. Složitost a rozsah těchto procesů ovlivní konečnou cenu.
- Náklady na pracovní sílu: K celkovým nákladům přispívají odborné znalosti potřebné pro obsluhu tiskáren, následné zpracování a kontrolu kvality.
- Odpisy a údržba strojů: Náklady na vlastnictví a údržbu kovového 3D tiskového zařízení jsou zahrnuty v ceně.
- Množství a objem: Zatímco 3D tisk z kovu může být nákladově efektivní pro malé až střední objemy, jednotkové náklady se mohou snížit při větších výrobních sériích díky úsporám z rozsahu při nákupu materiálu a optimalizaci procesu.
Doba dodání:
- Návrh a příprava: Počáteční fáze návrhu a čas potřebný k přípravě 3D modelu pro tisk.
- Doba tisku: Skutečná doba trvání procesu tisku, která závisí na výše uvedených faktorech.
- Doba následného zpracování: Doba potřebná k odstranění podpěr, tepelnému zpracování, povrchové úpravě a dalším krokům následného zpracování. Tato doba se může výrazně lišit v závislosti na složitosti dílu a požadované povrchové úpravě.
- Kontrola kvality a inspekce: Doba potřebná k důkladné kontrole a kontrole kvality.
- Doprava a dodání: Čas potřebný k přepravě hotových skříní na místo.
Optimalizace nákladů a doby realizace pro vaše kovové 3D tištěné kryty pro drony:
- Principy návrhu pro aditivní výrobu minimalizovat spotřebu materiálu, dobu výstavby a potřebu rozsáhlých podpěr.
- Výběr nejvhodnějšího kovového prášku který splňuje požadavky na výkon bez zbytečných nákladů.
- Jasně definujte požadovanou povrchovou úpravu a tolerance abyste se vyhnuli nadměrné specifikaci následného zpracování.
- Konsolidace více částí do jednoho tisku kde je to možné, aby se zkrátila doba montáže a snížily náklady.
- Spolupracujte se zkušeným poskytovatelem služeb 3D tisku kovů, jako je např Metal3DP který dokáže optimalizovat proces tisku a poskytnout přesné odhady nákladů a doby realizace.
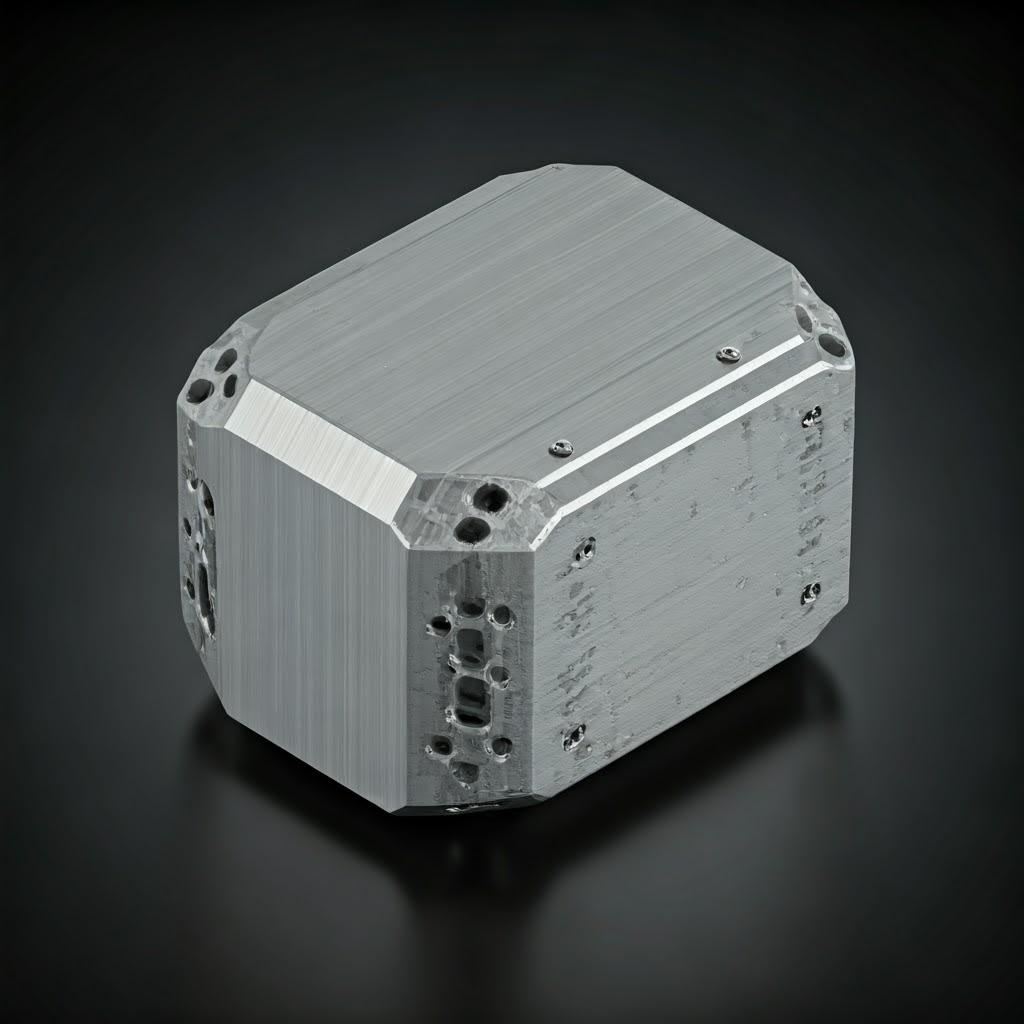
Často kladené otázky (FAQ)
- Jaké je typické snížení hmotnosti dosažitelné u kovových 3D tištěných krytů dronů ve srovnání s tradičními metodami? Snížení hmotnosti se může výrazně lišit v závislosti na konstrukci a materiálu, ale optimalizací topologie a mřížkovými strukturami lze často dosáhnout snížení o 20-50 % nebo více.
- Mohou kovové 3D tištěné kryty poskytnout dostatečné stínění EMI/RFI pro citlivou elektroniku dronů? Ano, kovové materiály ze své podstaty dobře stíní EMI/RFI. Účinnost lze dále zvýšit konstrukčními opatřeními, jako jsou souvislé vodivé cesty a vhodný výběr materiálu.
- Jaká je typická doba realizace malé série zakázkových kovových 3D tištěných krytů elektroniky pro drony? Doba realizace se může lišit v závislosti na složitosti návrhu, dostupnosti materiálu a vytíženosti poskytovatele služeb. U malých sérií se však obvykle pohybuje v rozmezí několika dnů až několika týdnů, což je často rychlejší než tradiční metody založené na výrobě nástrojů.
Závěr - Inovace dronů pomocí 3D tisku kovů
3D tisk z kovu přináší revoluci ve způsobu navrhování a výroby krytů elektroniky pro drony. Jeho schopnost vytvářet složité geometrie, optimalizovat hmotnost, zvyšovat výkon a umožnit rychlé přizpůsobení nabízí významné výhody oproti tradičním výrobním metodám. Využitím pokročilých materiálů, jako jsou AlSi10Mg a Scalmalloy®, a partnerstvím se zkušenými poskytovateli, jako je např Metal3DP Technology Co., LTD, inženýři a manažeři veřejných zakázek v leteckém, automobilovém, lékařském a průmyslovém odvětví mohou odhalit nové možnosti inovací dronů. Od lehkých a zároveň robustních krytů až po integrovaná řešení tepelného managementu - kovový 3D tisk umožňuje vytvářet technologie dronů nové generace. Kontakt Metal3DP a zjistit, jak naše špičkové systémy a vysoce kvalitní kovové prášky mohou podpořit cíle vaší organizace v oblasti aditivní výroby pro aplikace s drony.
Sdílet na
MET3DP Technology Co., LTD je předním poskytovatelem řešení aditivní výroby se sídlem v Qingdao v Číně. Naše společnost se specializuje na zařízení pro 3D tisk a vysoce výkonné kovové prášky pro průmyslové aplikace.
Dotaz k získání nejlepší ceny a přizpůsobeného řešení pro vaše podnikání!
Související články
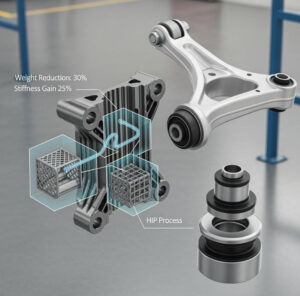
Metal 3D Printed Subframe Connection Mounts and Blocks for EV and Motorsport Chassis
Přečtěte si více "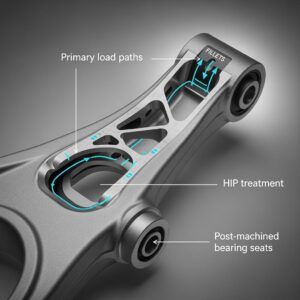
Metal 3D Printing for U.S. Automotive Lightweight Structural Brackets and Suspension Components
Přečtěte si více "O Met3DP
Nedávná aktualizace
Náš produkt
KONTAKTUJTE NÁS
Nějaké otázky? Pošlete nám zprávu hned teď! Po obdržení vaší zprávy obsloužíme vaši žádost s celým týmem.