3D tisk palivových čerpadel: Revoluce v letecké výrobě
Obsah
Úvod - Vývoj aditivní výroby v palivových systémech pro letectví a kosmonautiku
V náročné oblasti letectví a kosmonautiky, kde je nejdůležitější přesnost, spolehlivost a snížení hmotnosti, integrace pokročilých výrobních technologií neustále posouvá hranice strojírenství. Mezi tyto inovace patří kovové 3D tisk, známá také jako aditivní výroba kovů (AM), se stala transformační silou. Tato technologie rychle rozvíjí konstrukci a výrobu kritických součástí pro letecký průmysl a jednou z oblastí, kde je její dopad obzvláště významný, je výroba palivových čerpadel. Tato složitá zařízení, která jsou životně důležitá pro provoz letadel a kosmických lodí, jsou nyní díky 3D tisku z kovu nově koncipována a vyráběna s lepšími výkonnostními vlastnostmi a nebývalou konstrukční svobodou.
Neustálá snaha o efektivitu a bezpečnost v leteckém průmyslu již dlouho vede k zavádění nejmodernějších materiálů a výrobních postupů. 3D tisk z kovu těmto cílům dokonale odpovídá, protože nabízí možnost vytvářet složité geometrie s optimalizovaným využitím materiálu, zkrácením dodacích lhůt a zlepšením funkčnosti. U palivových čerpadel pro letectví a kosmonautiku to znamená potenciál pro lehčí, odolnější a výkonnější komponenty, které vydrží extrémní podmínky letu a cestování do vesmíru. Vzhledem k tomu, že se průmysl stále více orientuje na transformaci digitální výroby, stojí AM zpracování kovů v popředí, což umožňuje inovace a urychluje vývoj nové generace technologií pro letectví a kosmonautiku.
Společnost Metal3DP Technology Co., LTD, se sídlem v čínském městě Čching-tao, je předním poskytovatelem řešení pro aditivní výrobu, který se specializuje jak na zařízení pro 3D tisk, tak na vysoce výkonné kovové prášky. Technologie společnosti Metal3DP’ jsou díky snaze o dosažení špičkového objemu tisku, přesnosti a spolehlivosti vhodné pro náročné požadavky leteckého, lékařského, automobilového a dalších kritických oborů. Náš pokročilý systém výroby prášků, využívající špičkové technologie plynové atomizace a PREP, zajišťuje výrobu vysoce kvalitních sférických kovových prášků s vynikající tekutostí - což je klíčový faktor pro dosažení hustých a vysoce kvalitních kovových dílů vytištěných 3D tiskem s vynikajícími mechanickými vlastnostmi. Nabídkou komplexní sady řešení, včetně tiskáren SEBM (Selective Electron Beam Melting) a široké škály vysoce kvalitních kovových prášků, jako jsou inovativní slitiny TiNi, TiTa, TiAl, TiNbZr, CoCrMo, nerezové oceli a superslitiny, umožňuje společnost Metal3DP organizacím přijmout kovový 3D tisk a dosáhnout svých cílů v oblasti aditivní výroby. Kontaktujte společnost Met3DP ještě dnes a zjistěte, jak mohou naše schopnosti podpořit cíle vaší organizace v oblasti aditivní výroby.
K čemu slouží palivové čerpadlo? - Pohon letu a vesmírného výzkumu
V letectví a kosmonautice jsou palivová čerpadla kritickými součástmi, které jsou zodpovědné za dodávku paliva pod požadovaným tlakem a průtokem z palivových nádrží do motoru (motorů) letadla nebo kosmické lodi. Jejich funkce je nezbytná pro udržení spalovacího procesu, který vytváří tah, umožňuje let a pohání vesmírné průzkumné mise. Nároky kladené na palivová čerpadla v letectví a kosmonautice jsou obrovské. Musí spolehlivě fungovat v širokém rozsahu teplot, tlaků a vibrací a zároveň musí být lehká, aby se maximalizovala jejich účinnost.
Palivová čerpadla pro letectví a kosmonautiku plní několik klíčových funkcí:
- Dodávka paliva: Zajišťují nepřetržitou a přesně řízenou dodávku paliva do motoru, která odpovídá požadavkům na výkon v různých fázích letu, od vzletu a letu po přistání.
- Regulace tlaku: Udržují potřebný tlak paliva na vstupu do motoru, překonávají tlakové ztráty v palivovém potrubí a zajišťují optimální výkon motoru.
- Oběh paliva: V některých systémech palivová čerpadla rovněž zajišťují cirkulaci paliva pro chlazení součástí motoru nebo jiných systémů před jeho spálením.
- Prevence kavitace: Udržováním dostatečného tlaku pomáhají palivová čerpadla předcházet vzniku bublinek páry v palivovém potrubí (kavitace), které mohou narušit průtok paliva a poškodit čerpadlo.
Tato čerpadla jsou nedílnou součástí různých typů leteckých vozidel, včetně:
- Komerční letadla: Zajištění bezpečného a efektivního provozu proudových motorů pro osobní a nákladní dopravu.
- Vojenská letadla: Zajišťuje spolehlivou dodávku paliva pro výkonné stíhací letouny, bombardéry a dopravní letadla provozovaná v extrémních podmínkách.
- Rakety a kosmické lodě: Dodávání kryogenních pohonných hmot, jako je kapalný vodík a kapalný kyslík, do raketových motorů, což umožňuje manévry na oběžné dráze a cesty do vesmíru.
Spolehlivost a výkon palivových čerpadel přímo ovlivňují bezpečnost a efektivitu leteckého provozu. Jakékoli selhání může mít katastrofální následky, což podtrhuje potřebu robustních konstrukčních a výrobních procesů. 3D tisk z kovu nabízí cestu ke zvýšení výkonu a spolehlivosti těchto kritických součástí prostřednictvím optimalizace konstrukce a použití vysoce výkonných materiálů. Více informací o pokročilých materiálech vhodných pro takto náročné aplikace naleznete na naší produktové stránce.
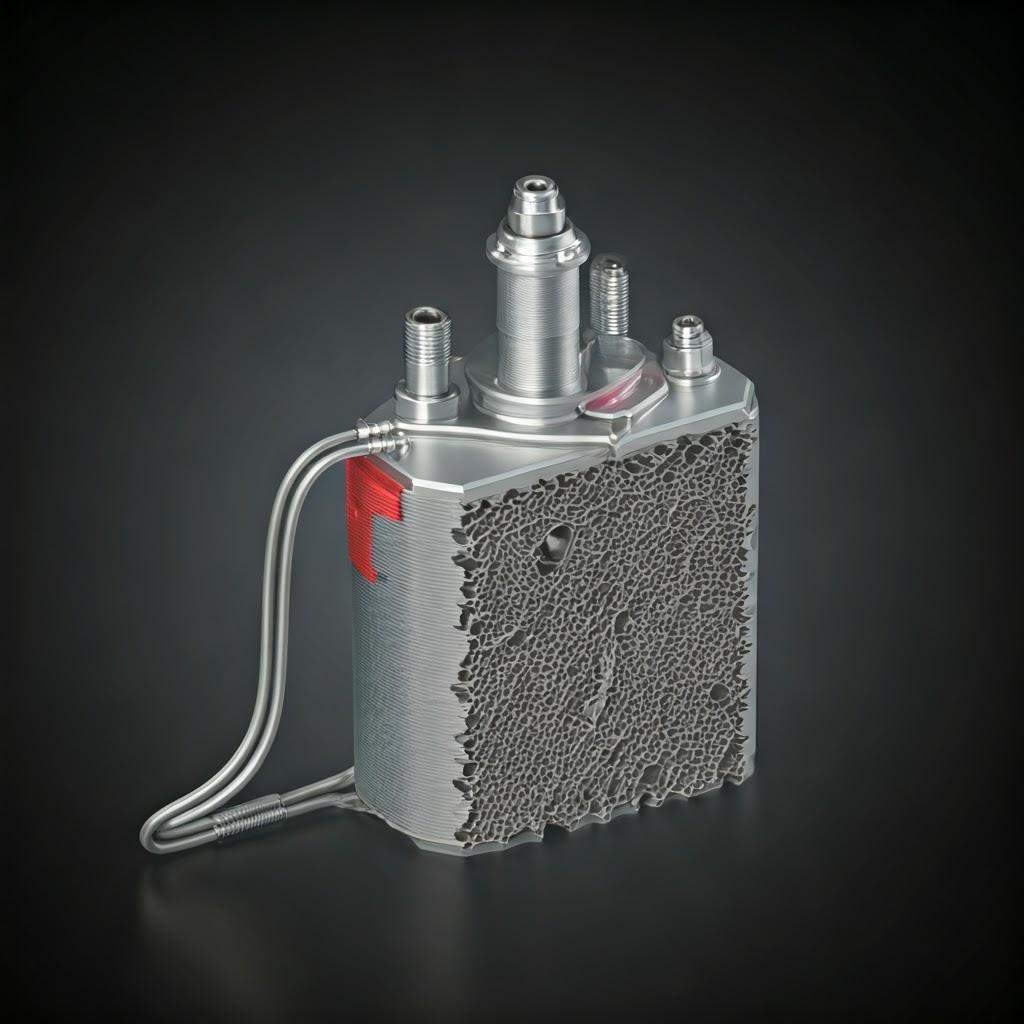
Proč používat 3D tisk z kovu pro palivová čerpadla? - Výhody oproti tradičním metodám
Přechod na kovový 3D tisk palivových čerpadel pro letecký průmysl je dán řadou výhod, které nabízí oproti tradičním výrobním metodám, jako je odlévání, obrábění a svařování. Tyto výhody jsou obzvláště přesvědčivé v leteckém průmyslu, kde jsou rozhodujícími faktory složitost, hmotnost, efektivita materiálu a doba realizace.
Zde je několik klíčových výhod použití kovového 3D tisku pro výrobu palivových čerpadel:
- Svoboda a složitost návrhu: Technologie AM umožňuje vytvářet složité vnitřní geometrie a komplexní tvary, kterých je obtížné nebo nemožné dosáhnout tradičními metodami. To umožňuje inženýrům optimalizovat průtok kapaliny v čerpadle, snížit hmotnost a integrovat více součástí do jediného dílu, čímž se minimalizují požadavky na montáž a potenciální místa poruch.
- Snížení hmotnosti: Optimalizací konstrukce a použitím pokročilých lehkých materiálů lze pomocí kovového 3D tisku výrazně snížit hmotnost součástí palivového čerpadla. To má zásadní význam v leteckém průmyslu, kde každý ušetřený kilogram znamená nižší spotřebu paliva a vyšší nosnost.
- Účinnost materiálu: Aditivní výrobní procesy vytvářejí díly vrstvu po vrstvě a používají pouze materiál potřebný pro danou součást. Tím se výrazně snižuje plýtvání materiálem ve srovnání se subtraktivními metodami, jako je obrábění, kdy se odstraňuje velká část surového materiálu.
- Zkrácené dodací lhůty: 3D tisk z kovu může výrazně zkrátit výrobní cyklus součástí palivových čerpadel. Složité díly lze vyrábět přímo z digitálních návrhů bez nutnosti rozsáhlého nástrojového vybavení a upevnění, což vede k rychlejší výrobě prototypů a výrobě.
- Přizpůsobení a výroba na vyžádání: AM umožňuje výrobu individuálních konstrukcí palivových čerpadel přizpůsobených specifickým požadavkům motoru nebo profilům mise. Umožňuje také výrobu na vyžádání, což snižuje potřebu velkých zásob a umožňuje rychlou výměnu zastaralých dílů.
- Zvýšený výkon a odolnost: Možnost použití vysoce výkonných kovových prášků, jako jsou prášky nabízené společností Metal3DP, a vytvoření optimalizovaných vnitřních struktur může vést k palivovým čerpadlům se zvýšenou účinností, vyššími tlakovými schopnostmi a zvýšenou odolností proti opotřebení, korozi a únavě.
- Integrace funkcí: 3D tisk z kovu umožňuje integrovat prvky, jako jsou chladicí kanály, senzory a montážní rozhraní, přímo do konstrukce palivového čerpadla, což dále snižuje počet dílů a zlepšuje celkovou účinnost systému.
Tyto výhody vedou k rostoucímu rozšíření kovového 3D tisku v leteckém a kosmickém průmyslu pro širokou škálu součástí, včetně kritických palivových čerpadel, která pohánějí naše letadla a kosmické lodě. Chcete-li porozumět různým technologiím kovového 3D tisku, které lze pro takové aplikace využít, můžete si prohlédnout naši stránku o metodách tisku.
Doporučené materiály a jejich význam - Vysoce výkonné prášky pro palivová čerpadla v leteckém průmyslu
Výběr správného kovového prášku má zásadní význam pro dosažení požadovaných výkonnostních charakteristik 3D tištěných palivových čerpadel pro letecký průmysl. Tyto součásti pracují v extrémních podmínkách, včetně vysokých tlaků, různých teplot a vystavení korozivním palivům. Proto musí použité materiály vykazovat výjimečnou pevnost, trvanlivost, odolnost proti korozi a tepelnou stabilitu. Společnost Metal3DP nabízí řadu vysoce kvalitních kovových prášků, které jsou speciálně vhodné pro takto náročné aplikace, včetně IN718, IN625 a Hastelloy X.
IN718 (Inconel 718)
IN718 je nikl-chromová superslitina známá svou vynikající pevností při vysokých teplotách, vlastnostmi při tečení a trhání a odolností proti korozi. Mezi jeho klíčové vlastnosti, díky nimž je vhodný pro palivová čerpadla v leteckém průmyslu, patří:
- Vysoká pevnost při zvýšených teplotách: Zachovává si značnou pevnost až do 700 °C, což je zásadní pro odolnost vůči provozním teplotám uvnitř a v okolí leteckých motorů.
- Vynikající odolnost proti korozi: Odolává oxidaci a korozi v náročných podmínkách, včetně působení různých paliv a atmosférických podmínek.
- Dobrá odolnost proti únavě a tečení: Je nezbytný pro součásti vystavené cyklickému zatížení a dlouhodobému působení vysokých teplot, což zajišťuje dlouhodobou spolehlivost.
- Svařitelnost a vyrobitelnost: Ačkoli je tradičně náročný na obrábění, jeho dobrá svařitelnost je výhodná pro případné opravy nebo integraci s jinými součástmi. Jeho vhodnost pro aditivní výrobu umožňuje vytvářet složité geometrie bez omezení tradičního obrábění.
IN625 (Inconel 625)
IN625 je další nikl-chrom-molybdenová superslitina, která nabízí jedinečnou kombinaci vysoké pevnosti, vynikající odolnosti proti korozi a dobré svařitelnosti. Mezi jeho výhody pro palivová čerpadla v leteckém průmyslu patří:
- Vynikající odolnost proti korozi: Vykazuje výjimečnou odolnost vůči široké škále korozivních prostředí, včetně kyselin, louhů a slané vody, takže je ideální pro součásti, které přicházejí do styku s různými druhy paliv a pracují v různých klimatických podmínkách.
- Vysoká pevnost a odolnost: Poskytuje dobrou pevnost až do středně vysokých teplot (přibližně 650 °C nebo 1200 °F) spolu s vynikající houževnatostí, což zajišťuje strukturální integritu při namáhání.
- Dobrá únavová pevnost: Nabízí odolnost proti únavovému selhání, což je důležité pro součásti vystavené vibracím a kolísání tlaku během letu.
- Vynikající svařitelnost: Snadněji se svařuje ve srovnání s některými jinými superslitinami na bázi niklu, což může být výhodné pro výrobní a opravárenské procesy. Hodí se také pro složité konstrukce dosažitelné pomocí kovového 3D tisku.
Hastelloy X
Hastelloy X je superslitina niklu, chromu, železa a molybdenu, která je známá svou vynikající odolností proti oxidaci a pevností při vysokých teplotách až do 1200 °C. Mezi jeho vlastnosti výhodné pro některé aplikace palivových čerpadel v letectví a kosmonautice patří:
- Výjimečná odolnost proti oxidaci: Dobře se osvědčuje v oxidačním prostředí s extrémně vysokou teplotou, což je důležité pro součásti umístěné v blízkosti horkých částí motoru.
- Dobrá odolnost při vysokých teplotách: Zachovává si značnou pevnost při zvýšených teplotách, vhodný pro náročné provozní podmínky.
- Odolnost vůči nauhličování a nitridaci: Nabízí odolnost proti chemické degradaci při vysokých teplotách, což zvyšuje životnost součástí.
- Dobrá zpracovatelnost a svařitelnost: Lze jej snadno tvarovat a svařovat, takže je vhodný pro složité 3D tištěné konstrukce a integraci s dalšími částmi systému.
Volba mezi těmito materiály závisí na specifických požadavcích palivového čerpadla, včetně rozsahu provozních teplot, typu zpracovávaného paliva, požadavků na tlak a celkové konstrukce systému. Odborné znalosti společnosti Metal3DP v oblasti kovových prášků a aditivních výrobních procesů zajišťují, že si zákazníci mohou vybrat optimální materiál pro svá palivová čerpadla v leteckém průmyslu a dosáhnout tak nejvyšší úrovně výkonu a spolehlivosti. Náš rozsáhlý sortiment vysoce kvalitních kovových prášků si můžete prohlédnout na našich webových stránkách. Zdroje a související obsah
Konstrukční hlediska pro aditivní výrobu - optimalizace geometrie palivového čerpadla
Navrhování pro 3D tisk z kovu vyžaduje odlišné myšlení ve srovnání s tradičními výrobními metodami. Proces sestavování po vrstvách nabízí jedinečné příležitosti pro geometrickou složitost a funkční integraci, ale také zavádí specifické konstrukční aspekty pro zajištění úspěšného tisku a optimálního výkonu dílů. Pro palivová čerpadla v leteckém průmyslu jsou tyto úvahy rozhodující pro dosažení lehkých, odolných a účinných součástí.
Zde jsou uvedeny klíčové aspekty konstrukce aditivně vyráběných palivových čerpadel:
- Optimalizace topologie: 3D tisk z kovu umožňuje vytvářet organické geometrie volných tvarů, které lze optimalizovat z hlediska hmotnosti a konstrukčních vlastností. Software pro optimalizaci topologie lze použít k identifikaci oblastí s nízkým namáháním a odstranění nepotřebného materiálu, což vede k lehčím dílům se srovnatelnou nebo dokonce vyšší pevností. U palivových čerpadel to může vést k optimalizaci průtokových cest a snížení celkové hmotnosti, což je pro letecké aplikace klíčové.
- Mřížové struktury: Začlenění mřížkových struktur do konstrukce palivového čerpadla může výrazně snížit hmotnost při zachování strukturální integrity. Tyto složité, opakující se buněčné struktury lze přizpůsobit specifickým požadavkům na nosnost a nabízejí lehkou alternativu k pevným výplním.
- Konsolidace částí: Aditivní výroba umožňuje integrovat více komponent do jednoho komplexního dílu. U palivových čerpadel to může znamenat spojení krytu čerpadla, vnitřních kanálů a montážních prvků do jediného tištěného kusu, což zkrátí dobu montáže, sníží počet spojovacích prvků a potenciálních míst úniku.
- Vnitřní kanály a konformní chlazení: 3D tisk z kovu usnadňuje vytváření složitých vnitřních kanálů pro proudění tekutin nebo konformní chlazení. U palivových čerpadel mohou optimalizované vnitřní průtokové cesty zvýšit účinnost a snížit tlakové ztráty. Konformní chladicí kanály mohou být integrovány do nástrojů formy používaných pro následné výrobní kroky (pokud je to vhodné) nebo dokonce přímo do tělesa čerpadla v určitých provedeních, aby bylo možné řídit odvod tepla.
- Samonosné geometrie a podpůrné konstrukce: Ačkoli AM nabízí volnost při navrhování, převislé prvky vyžadují podpůrné konstrukce, aby se během tisku nezhroutily. Navrhování dílů se samonosnými úhly (obvykle 45 stupňů nebo více) může minimalizovat potřebu podpěr, což snižuje spotřebu materiálu a dobu následného zpracování. Pokud jsou podpěry nezbytné, je třeba pečlivě zvážit jejich konstrukci a umístění, aby se zajistilo snadné odstranění a minimalizovalo poškození povrchu.
- Orientace a směr stavby: Orientace dílu na konstrukční platformě a směr, ve kterém je tištěn, může významně ovlivnit kvalitu povrchu, mechanické vlastnosti a potřebu podpůrných konstrukcí. Pečlivé zvážení těchto faktorů je zásadní pro dosažení požadovaných tolerancí a výkonnosti finální součásti palivového čerpadla.
- Tloušťka stěny a minimální velikost prvku: Procesy 3D tisku kovů mají omezení minimální tloušťky stěn a velikosti prvků, které lze spolehlivě vyrobit. Konstruktéři musí tyto zásady dodržovat, aby byla zajištěna strukturální integrita a funkčnost palivového čerpadla. Společnost Metal3DP může poskytnout podrobné pokyny pro návrh na základě zvolené technologie tisku a materiálu.
- Úvahy o povrchové úpravě: Povrchová úprava po vytištění v kovovém AM může být drsnější než při tradičním obrábění. Pokud je pro těsnění nebo průtok tekutin vyžadován hladký povrch, mohou být nutné následné kroky zpracování, jako je leštění nebo obrábění. Návrh s ohledem na tuto skutečnost může pomoci minimalizovat rozsah nutného následného zpracování.
Při pečlivém zvážení těchto konstrukčních zásad mohou konstruktéři využít jedinečné možnosti 3D tisku z kovu k vytvoření inovativních a vysoce výkonných palivových čerpadel pro letecký průmysl, která překonávají omezení tradiční výroby. Odborné znalosti společnosti Met3DP’v oblasti aditivní výroby mohou pomoci při optimalizaci návrhů z hlediska vyrobitelnosti a výkonu.
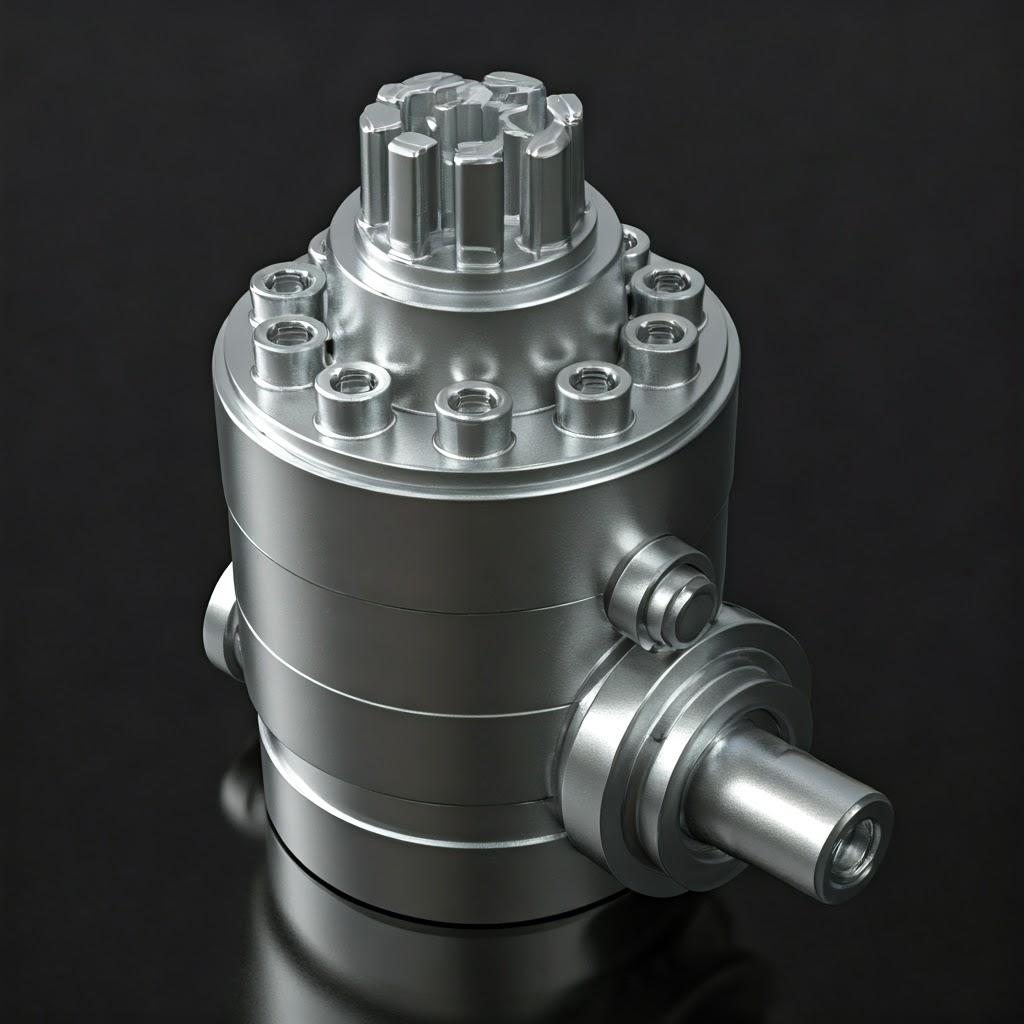
Tolerance, povrchová úprava a rozměrová přesnost - dosažení přesnosti u 3D tištěných palivových čerpadel
V leteckém průmyslu je přesnost nejdůležitější. Součásti, jako jsou palivová čerpadla, musí dodržovat přísné rozměrové tolerance a mít odpovídající povrchovou úpravu, aby bylo zajištěno správné uložení, těsnění a výkon. Technologie 3D tisku kovů výrazně pokročily ve schopnosti dosáhnout vysoké úrovně přesnosti a kvality povrchu, ale pochopení jejich možností a omezení je pro návrh a výrobu funkčních součástí palivových čerpadel zásadní.
Tolerance a rozměrová přesnost
Rozměrová přesnost dosažitelná při 3D tisku z kovu závisí na několika faktorech, včetně technologie tisku (např. DMLS, SLM, EBM), použitého materiálu, velikosti a geometrie dílu a parametrů procesu. Obecně lze říci, že procesy slučování kovového prášku (PBF), jako je přímé laserové spékání kovů (DMLS) a selektivní laserové tavení (SLM), nabízejí poměrně vysokou rozměrovou přesnost, obvykle v rozmezí ±0,1 až ±0,5 mm u menších prvků. Větší díly mohou vykazovat větší odchylky.
Mezi klíčové faktory ovlivňující rozměrovou přesnost patří:
- Kalibrace a přesnost stroje: Zásadní význam má vlastní přesnost a kalibrace 3D tiskárny. Tiskárny Metal3DP’ jsou konstruovány s ohledem na špičkovou přesnost v oboru, aby splňovaly přísné požadavky leteckých aplikací.
- Smršťování a deformace materiálu: Během procesu slinování nebo tavení dochází k tuhnutí a ochlazování kovových prášků, což může vést ke smršťování a případnému zkreslení. Pochopení míry smršťování specifické pro daný materiál a její kompenzace v konstrukci a parametrech procesu je zásadní.
- Orientace na stavbu: Orientace dílu během tisku může ovlivnit rozměrovou přesnost, zejména u prvků sestavených ve směru Z (vrstva po vrstvě). Stupňovité povrchy a rozdíly v přilnavosti vrstev mohou ovlivnit konečné rozměry.
- Podpůrné struktury: Upevnění a odstranění podpěrných konstrukcí může někdy zanechat na povrchu dílu drobné stopy nebo odchylky, které ovlivňují rozměrovou přesnost v těchto oblastech. Je nutné pečlivě navrhnout podpěry a techniky jejich odstraňování.
- Následné zpracování: V případě kritických rozměrů lze po prvotním procesu 3D tisku použít kroky následného zpracování, jako je CNC obrábění nebo broušení, aby se dosáhlo přísnějších tolerancí konkrétních prvků.
Povrchová úprava
Povrchová úprava po vytištění v kovovém AM se obvykle vyznačuje určitým stupněm drsnosti způsobeným procesem vrstveného vytváření a částečně slinutými nebo roztavenými částicemi kovového prášku na povrchu. Hodnoty drsnosti povrchu (Ra) se mohou pohybovat v rozmezí od 5 do 20 µm nebo i více, v závislosti na technologii tisku, tloušťce vrstvy a velikosti částic prášku.
Mezi faktory ovlivňující kvalitu povrchu patří:
- Technologie tisku: Různé procesy AM poskytují různou povrchovou úpravu. Například při EBM je povrch často o něco drsnější než při SLM nebo DMLS, a to kvůli větší velikosti částic prášku a vyšším teplotám při sestavování.
- Tloušťka vrstvy: Tenčí vrstvy obecně vedou k hladšímu povrchu, ale také prodlužují dobu výstavby.
- Velikost a morfologie částic prášku: Jemnější, kulovité částice prášku mají tendenci vytvářet hladší povrchy. Pokročilý systém výroby prášku Metal3DP’ zajišťuje vysokou sféričnost a řízenou distribuci velikosti částic pro optimální povrchovou úpravu.
- Orientace na stavbu: Šikmé nebo zakřivené povrchy mohou vykazovat stupňovitý efekt v důsledku vrstvené povahy tiskového procesu.
- Následné zpracování: Ke zlepšení povrchové úpravy 3D tištěných kovových dílů lze použít různé techniky následného zpracování, včetně:
- Výbuch v médiích: Použití abrazivních médií k odstranění částečně slinutých částic a snížení drsnosti povrchu.
- Leštění: Mechanické nebo chemické leštění pro dosažení hladšího, zrcadlového povrchu.
- Obrábění: Přesné obrábění pro dosažení specifické povrchové úpravy a přísnějších tolerancí na kritických plochách.
- Povlaky: Aplikací nátěrů lze nejen zlepšit povrchovou úpravu, ale také zvýšit odolnost proti korozi nebo jiné vlastnosti.
U palivových čerpadel pro letectví a kosmonautiku závisí požadovaná povrchová úprava na konkrétní aplikaci a na rozhraních s ostatními součástmi. Například těsnicí povrchy budou vyžadovat hladší povrchovou úpravu než nekritické vnější povrchy. Pochopení dosažitelných tolerancí a povrchových úprav při 3D tisku z kovu a plánování nezbytného následného zpracování je pro úspěšnou výrobu vysoce výkonných součástí palivových čerpadel zásadní.
Požadavky na následné zpracování - zdokonalování komponent palivového čerpadla vytištěných na 3D tiskárně
Ačkoli 3D tisk z kovu nabízí možnosti výroby téměř čistého tvaru, pro dosažení konečných požadovaných vlastností, rozměrů a povrchové úpravy součástí palivových čerpadel pro letectví a kosmonautiku jsou často nutné následné kroky zpracování. Tyto kroky jsou nezbytné k zajištění toho, aby díly splňovaly přísné výkonnostní a kvalitativní normy leteckého průmyslu.
Mezi běžné požadavky na následné zpracování kovových 3D tištěných palivových čerpadel patří:
- Odstranění podpory: Během tisku jsou často nutné podpůrné konstrukce, aby se zabránilo zhroucení nebo deformaci převislých prvků. Tyto podpěry musí být po tisku opatrně odstraněny, obvykle metodami, jako je ruční lámání, řezání nebo obrábění. Konstrukce podpěr a jejich upevňovacích bodů by měla minimalizovat riziko poškození povrchu dílu při odstraňování.
- Tepelné zpracování: Tepelné zpracování je důležitým krokem pro mnoho kovových 3D tištěných dílů, včetně dílů vyrobených z materiálů IN718, IN625 a Hastelloy X. Pomáhá zmírnit zbytková napětí vzniklá během rychlého tuhnutí v procesu tisku, zlepšit mikrostrukturu materiálu a dosáhnout požadovaných mechanických vlastností, jako je pevnost, tvrdost a tažnost. Specifické cykly tepelného zpracování jsou přizpůsobeny slitině a zamýšlenému použití.
- Izostatické lisování za tepla (HIP): HIP je proces, který zahrnuje vystavení tištěného dílu vysokému tlaku a teplotě v prostředí inertního plynu. Tento proces pomáhá odstranit vnitřní pórovitost, zvýšit hustotu a dále zlepšit mechanické vlastnosti a únavovou odolnost materiálu, což je důležité zejména u kritických leteckých součástí, jako jsou palivová čerpadla.
- CNC obrábění: Zatímco 3D tiskem z kovu lze vytvářet složité geometrie, některé prvky vyžadující velmi přísné tolerance nebo specifickou povrchovou úpravu může být nutné dodatečně opracovat pomocí CNC (Computer Numerical Control) obrábění. To může zahrnovat závity, přesné otvory, těsnicí plochy a kritická rozhraní s jinými součástmi.
- Povrchová úprava: Jak již bylo uvedeno dříve, povrchová úprava v podobě, v jaké byla vytištěna, nemusí být vhodná pro všechny aplikace. Lze použít různé techniky povrchové úpravy, včetně:
- Výbuch v médiích: K odstranění volných částic prášku a snížení drsnosti povrchu.
- Leštění (mechanické nebo chemické): Pro dosažení hladšího povrchu pro lepší těsnění nebo snížení tření.
- Elektrolytické leštění: K vyhlazení a odjehlení složitých geometrických tvarů a ke zlepšení odolnosti proti korozi.
- Kontrola a řízení kvality: Důsledné kontrolní procesy jsou nezbytné k zajištění toho, aby 3D tištěné komponenty palivového čerpadla splňovaly požadovanou rozměrovou přesnost, povrchovou úpravu a vlastnosti materiálu. To může zahrnovat metody nedestruktivního testování, jako je vizuální kontrola, kontrola penetrací barvivem, ultrazvukové testování a rentgenová počítačová tomografie (CT) k odhalení vnitřních vad.
- Čištění: Odstranění zbytků prášku nebo nečistot z povrchu a vnitřních kanálků tištěného dílu je zásadní před jeho zabudováním do palivového systému.
- Povrchová úprava: V některých případech mohou být použity povlaky pro zvýšení odolnosti proti korozi, opotřebení nebo jiných povrchových vlastností součástí palivového čerpadla.
Konkrétní kroky následného zpracování závisí na materiálu, použité technologii tisku, konstrukci palivového čerpadla a výkonnostních požadavcích aplikace. Komplexní pochopení těchto požadavků a možností různých technik následného zpracování je nezbytné pro úspěšnou výrobu vysoce kvalitních, k letu připravených součástí palivových čerpadel pro letectví a kosmonautiku pomocí kovového 3D tisku. Společnost Metal3DP nabízí poradenství a podporu při výběru vhodných kroků následného zpracování pro vaši konkrétní aplikaci. Naše odborné znalosti celého procesu aditivní výroby zajišťují bezproblémový přechod od návrhu k hotovému dílu.
Běžné problémy a jak se jim vyhnout - zajištění úspěšného 3D tisku palivových čerpadel
3D tisk z kovu sice nabízí řadu výhod pro výrobu palivových čerpadel v letectví a kosmonautice, ale zároveň přináší určité problémy, které je třeba řešit, aby byly výsledky úspěšné. Pochopení těchto potenciálních problémů a zavedení vhodných strategií může zmírnit rizika a vést k výrobě vysoce kvalitních a spolehlivých součástí.
Zde jsou uvedeny některé běžné problémy, se kterými se setkáváme při 3D tisku z kovu, a jak se jim vyhnout:
- Deformace a zkreslení: Tepelné namáhání vyvolané během rychlých cyklů ohřevu a chlazení při tisku může vést k deformaci nebo zkreslení dílu, zejména u velkých nebo složitých geometrií.
- Jak se tomu vyhnout: Optimalizujte konstrukci dílů pomocí zaoblených rohů a rovnoměrných tlouštěk stěn, abyste minimalizovali koncentraci napětí. Použijte předehřev konstrukční desky ke snížení tepelných gradientů. Pečlivě orientujte díl na konstrukční plošině a použijte vhodné podpůrné konstrukce pro ukotvení kritických oblastí. Zvažte použití softwaru pro simulaci procesu k předvídání a kompenzaci možných deformací.
- Odstranění poškození podpůrné konstrukce: Odstranění nosných konstrukcí může někdy zanechat povrchové vady nebo dokonce poškodit jemné prvky palivového čerpadla.
- Jak se tomu vyhnout: Navrhujte samonosné geometrie, kdykoli je to možné. Optimalizujte návrh podpůrné konstrukce pro snadné odstranění s minimální kontaktní plochou. Používejte rozpustné podpůrné materiály, pokud jsou kompatibilní se zvoleným kovovým práškem. Pro odstraňování podpěr použijte kvalifikované techniky a vhodné nástroje.
- Problémy s pórovitostí a hustotou: Neúplné roztavení nebo spékání kovového prášku může mít za následek vnitřní pórovitost, která může ohrozit mechanickou pevnost a únavovou životnost palivového čerpadla.
- Jak se tomu vyhnout: Optimalizujte parametry tisku, jako je výkon laseru, rychlost skenování a tloušťka vrstvy, na základě materiálu a stroje. Zajistěte, aby kovový prášek měl dobrou tekutost a hustotu balení. Zvažte použití izostatického lisování za tepla (HIP) jako kroku následného zpracování, abyste odstranili vnitřní pórovitost a dosáhli téměř plné hustoty. Vysoce kvalitní kovové prášky Metal3DP’jsou navrženy pro optimální hustotu a výkon.
- Drsnost povrchu: Drsnost povrchu po vytištění nemusí splňovat požadavky na kritické těsnicí plochy nebo průtokové kanály palivových čerpadel.
- Jak se tomu vyhnout: Optimalizujte parametry tisku, například snižte tloušťku vrstvy. Použijte jemnější velikosti částic prášku. Naplánujte kroky následného zpracování, jako je tryskání, leštění nebo obrábění, abyste dosáhli požadované povrchové úpravy.
- Zbytková napětí: Rychlé tuhnutí během tisku může vést ke zbytkovým napětím v dílu, která mohou způsobit praskání nebo rozměrovou nestabilitu.
- Jak se tomu vyhnout: Po tisku proveďte vhodné cykly tepelného zpracování, abyste odstranili zbytková napětí. Optimalizujte orientaci sestavy a podpůrné struktury, abyste minimalizovali nárůst napětí.
- Změny vlastností materiálu: Nedůsledné tavení nebo spékání může vést k odchylkám v mikrostruktuře a mechanických vlastnostech celého tištěného dílu.
- Jak se tomu vyhnout: Používejte dobře kalibrované a udržované zařízení pro 3D tisk. Optimalizujte a pečlivě kontrolujte parametry procesu. Zajistěte konzistentní a vysoce kvalitní dodávky kovového prášku, například od společnosti Metal3DP.
- Manipulace s práškem a kontaminace: Kovové prášky mohou být citlivé na vlhkost a kontaminaci, což může negativně ovlivnit kvalitu tisku.
- Jak se tomu vyhnout: Dodržujte přísné postupy manipulace s práškem v kontrolovaném prostředí. Zajistěte správné skladování kovových prášků. Pravidelně udržujte a čistěte 3D tiskárnu a systémy pro manipulaci s práškem.
- Rozšíření a nákladová efektivita: Zatímco 3D tisk je ideální pro komplexní výrobu v malých až středních objemech, rozšíření na velké objemy může představovat problém v oblasti nákladů a výkonnosti ve srovnání s tradiční výrobou.
- Jak řešit: Pečlivě analyzujte požadavky na objem výroby a porovnejte nákladovou efektivitu 3D tisku s tradičními metodami. Optimalizujte návrh dílu pro efektivní tisk. Prozkoumejte hybridní výrobní přístupy, které kombinují 3D tisk s tradičními technikami pro velkoobjemovou výrobu.
Pochopením těchto běžných problémů a zavedením vhodných preventivních a nápravných opatření mohou výrobci efektivně využít 3D tisk kovů k výrobě vysoce výkonných palivových čerpadel pro letecký průmysl, která splňují přísné požadavky tohoto odvětví. Odborné znalosti a komplexní řešení společnosti Metal3DP’mohou pomoci zvládnout tyto výzvy a zajistit úspěšné výsledky aditivní výroby.
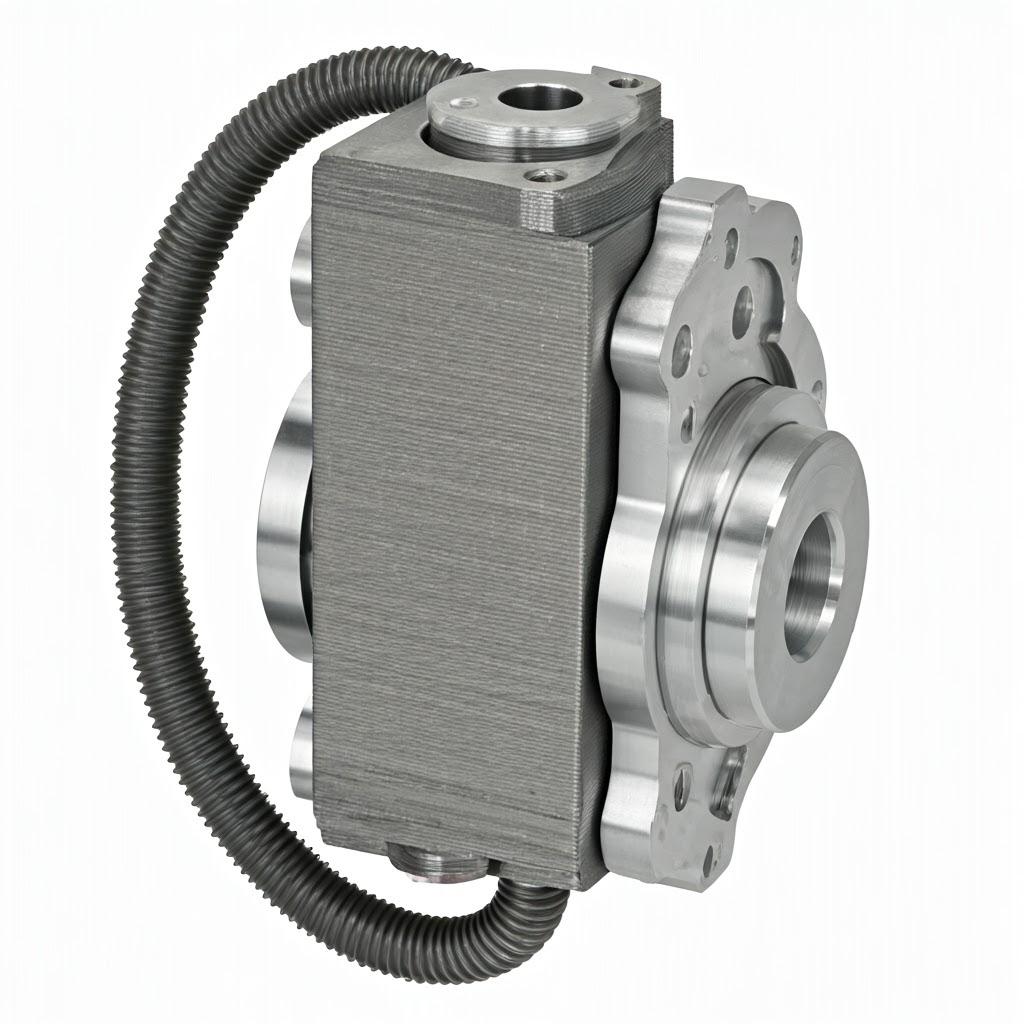
Jak vybrat správného poskytovatele služeb 3D tisku kovů - výběr důvěryhodného partnera
Výběr správného poskytovatele služeb 3D tisku z kovu je zásadním rozhodnutím, které může významně ovlivnit úspěch vašeho projektu výroby palivového čerpadla pro letecký průmysl. Spolehlivý partner bude disponovat odbornými znalostmi, vybavením, materiály a procesy kontroly kvality, které jsou nezbytné k dodání vysoce výkonných komponentů splňujících přísné požadavky leteckého průmyslu.
Zde jsou klíčové faktory, které je třeba zvážit při výběru poskytovatele služeb 3D tisku z kovu:
- Materiálové schopnosti: Ujistěte se, že poskytovatel nabízí řadu vysoce výkonných kovových prášků vhodných pro letecké aplikace, jako jsou IN718, IN625 a Hastelloy X. Ověřte si kvalitu a sledovatelnost jeho materiálů. Společnost Metal3DP vyrábí širokou škálu vysoce kvalitních kovových prášků optimalizovaných pro laserovou fúzi a fúzi v práškovém loži elektronového svazku.
- Tiskové technologie: Různé technologie 3D tisku kovů (např. DMLS, SLM, EBM) mají různé silné stránky a omezení, pokud jde o přesnost, povrchovou úpravu, objem a kompatibilitu materiálů. Vyberte si poskytovatele s vhodnou technologií pro konkrétní konstrukci palivového čerpadla a požadavky na výkon. Společnost Metal3DP se specializuje na tiskárny SEBM (Selective Electron Beam Melting), které jsou známé svou schopností vyrábět husté a vysoce kvalitní kovové díly.
- Vybavení a odborné znalosti: Zhodnoťte flotilu 3D tiskáren poskytovatele, jeho protokoly údržby a odborné znalosti jeho inženýrských a technických týmů. Zkušení odborníci mohou nabídnout cenné poznatky o optimalizaci konstrukce, výběru materiálů a parametrech procesů. Díky desítkám let kolektivních zkušeností v oblasti aditivní výroby kovů poskytuje společnost Metal3DP komplexní řešení zahrnující tiskárny SEBM, pokročilé kovové prášky a služby vývoje aplikací.
- Zajištění kvality a certifikace: V leteckém průmyslu je nezbytná přísná kontrola kvality. Zajímejte se o systém řízení kvality, certifikace (např. AS9100), kontrolní postupy a možnosti testování materiálů.
- Podpora návrhu a inženýrské služby: Dobrý poskytovatel služeb by měl nabízet konzultace k návrhu a optimalizační služby, aby zajistil, že návrh palivového čerpadla je vhodný pro aditivní výrobu a splňuje požadavky na výkon. Metal3DP spolupracuje s organizacemi na implementaci 3D tisku a urychlení transformace digitální výroby.
- Možnosti následného zpracování: Zjistěte, zda poskytovatel nabízí nezbytné služby následného zpracování, jako je odstranění podpěr, tepelné zpracování, HIP, CNC obrábění a povrchová úprava, abyste mohli dodat hotový komponent.
- Dodací lhůty a výrobní kapacita: Posuďte, jak dlouho trvá výroba prototypů a výroba u poskytovatele a jak je schopen zvládnout vaše očekávané objemy.
- Struktura nákladů: Pochopte cenový model poskytovatele a ujistěte se, že odpovídá vašemu rozpočtu. Zvažte celkové náklady na vlastnictví, včetně optimalizace návrhu, tisku, následného zpracování a kontroly kvality.
- Komunikace a zákaznická podpora: Efektivní komunikace a pohotová zákaznická podpora jsou pro úspěšné partnerství klíčové. Vyberte si poskytovatele, který je proaktivní, transparentní a ochotný spolupracovat.
- Důvěrnost a ochrana duševního vlastnictví: Ujistěte se, že poskytovatel má zavedeny spolehlivé zásady a postupy na ochranu vašeho duševního vlastnictví a zachování důvěrnosti vašich návrhů.
Pečlivým vyhodnocením těchto faktorů si můžete vybrat poskytovatele služeb 3D tisku z kovu, který je spolehlivým a schopným partnerem při výrobě vysoce kvalitních komponent palivového čerpadla pro letecký průmysl. Kontaktujte společnost Metal3DP a zjistěte, jak mohou naše schopnosti podpořit cíle vaší organizace v oblasti aditivní výroby. Díky našemu závazku zajistit špičkový objem tisku, přesnost a spolehlivost jsme důvěryhodným partnerem pro kritické díly. Více informací o naší společnosti a naší oddanosti kvalitě se dozvíte na stránce O nás.
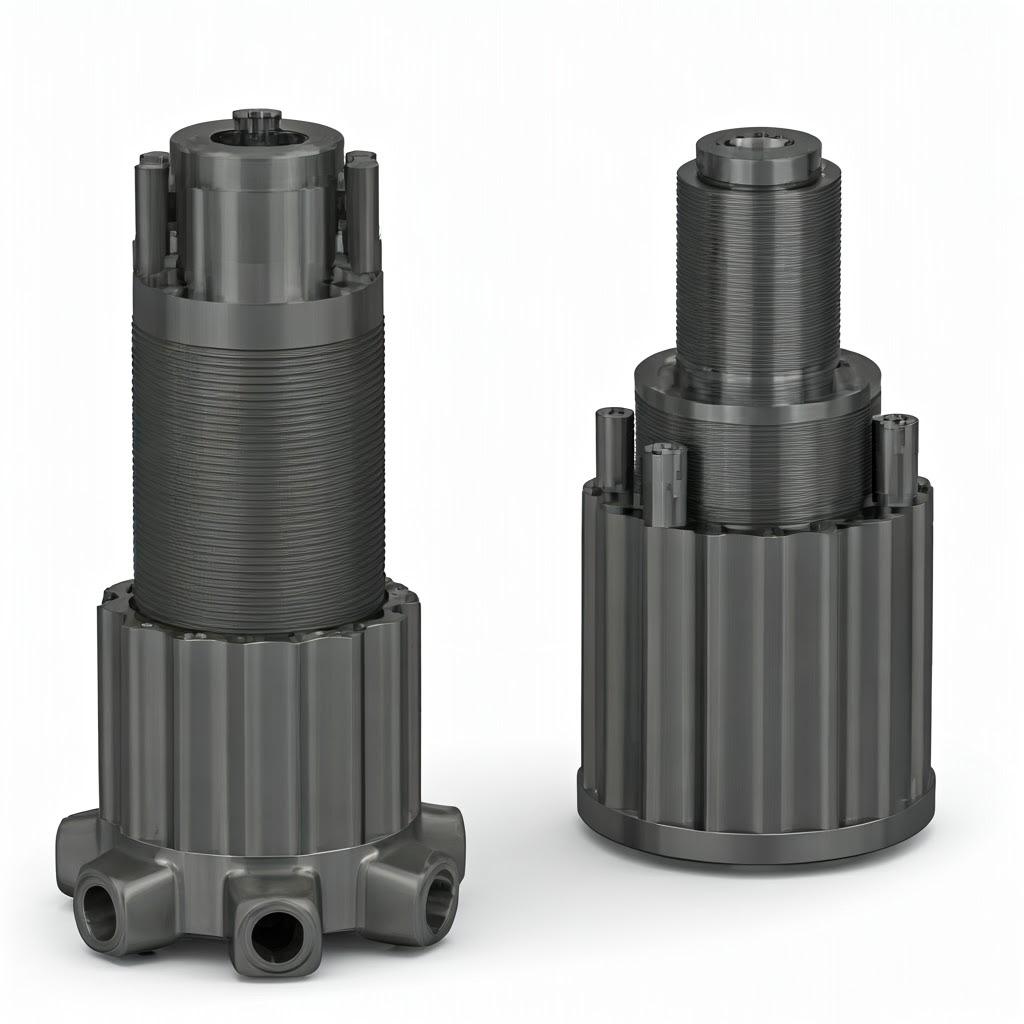
Nákladové faktory a doba realizace - porozumění ekonomice palivových čerpadel tištěných 3D tiskem
Náklady a doba realizace spojené s 3D tiskem kovových palivových čerpadel pro letecký průmysl jsou pro manažery a inženýry odpovědné za zadávání zakázek důležitými faktory. Ačkoli by se mohlo zdát, že AM je vždy dražší a časově náročnější, při bližším pohledu se ukáže diferencovanější obraz, kdy jsou tyto faktory ovlivněny několika proměnnými a v mnoha případech mohou nabídnout významné výhody oproti tradiční výrobě.
Nákladové faktory
Náklady na 3D tisk kovového palivového čerpadla pro letecký průmysl jsou ovlivněny několika klíčovými faktory:
- Náklady na materiál: Významný podíl na tom mají náklady na samotný kovový prášek. Vysoce výkonné slitiny jako IN718, IN625 a Hastelloy X mohou být drahé. Materiálový odpad je u AM obecně nižší ve srovnání se subtraktivními metodami, což může kompenzovat část počátečních nákladů na materiál.
- Doba výstavby: Doba tisku palivového čerpadla závisí na jeho velikosti, složitosti a zvolené technologii tisku. Delší doba sestavení se promítá do vyšších provozních nákladů stroje (spotřeba energie, údržba) a mzdových nákladů.
- Náklady na následné zpracování: Rozsah a složitost požadovaných kroků následného zpracování (odstranění podpory, tepelné zpracování, HIP, obrábění, povrchová úprava) významně ovlivňují celkové náklady.
- Složitost návrhu: Ačkoli AM vyniká při výrobě složitých geometrií, velmi složité konstrukce mohou vyžadovat větší optimalizaci návrhu, delší dobu výroby a rozsáhlejší následné zpracování, což může zvýšit náklady.
- Objem výroby: U nízkých až středních objemů výroby může být 3D tisk z kovu cenově konkurenceschopný nebo dokonce výhodnější než tradiční metody díky absenci nákladů na nástroje a zkrácení doby přípravy. Pro velmi vysoké objemy však mohou tradiční metody nabídnout úspory z rozsahu.
- Odpisy a údržba strojů: Náklady na zařízení pro 3D tisk a jeho údržbu jsou zahrnuty do celkových nákladů na služby.
- Náklady na pracovní sílu: Pro návrh, tisk, následné zpracování, kontrolu kvality a řízení projektu jsou zapotřebí kvalifikovaní pracovníci, což přispívá k celkovým nákladům.
Doba realizace
Doba výroby 3D tištěného kovového palivového čerpadla pro letecký průmysl je rovněž ovlivněna několika faktory:
- Návrh a optimalizace: Doba potřebná pro návrh nebo optimalizaci palivového čerpadla pro aditivní výrobu.
- Doba tisku: Skutečná doba potřebná k vytištění dílu na 3D tiskárně.
- Doba následného zpracování: Doba trvání nezbytných kroků následného zpracování, která se může pohybovat od několika hodin až po několik dní v závislosti na složitosti.
- Kontrola kvality a inspekce: Čas potřebný na důkladnou kontrolu a kontrolu kvality.
- Přeprava a logistika: Doba potřebná k odeslání hotového dílu zákazníkovi.
V porovnání s tradiční výrobou může 3D tisk z kovu nabídnout výrazně kratší dodací lhůty pro složité díly, zejména pro výrobu prototypů a malosériovou výrobu. Eliminace výroby nástrojů a možnost rychlé iterace návrhů může urychlit vývojový cyklus. U velmi velkých výrobních sérií však může doba sestavení jednoho dílu v AM vést k delším celkovým dodacím lhůtám ve srovnání s vysokorychlostními tradičními výrobními procesy.
Pochopení souhry těchto faktorů nákladů a doby realizace je zásadní pro informované rozhodování o tom, zda je 3D tisk z kovu tím správným výrobním řešením pro vaše potřeby palivového čerpadla v leteckém průmyslu. Spolupráce se zkušeným poskytovatelem služeb, jako je Metal3DP, vám může poskytnout podrobnou analýzu nákladů a přínosů a realistické odhady doby realizace na základě vašich konkrétních požadavků.
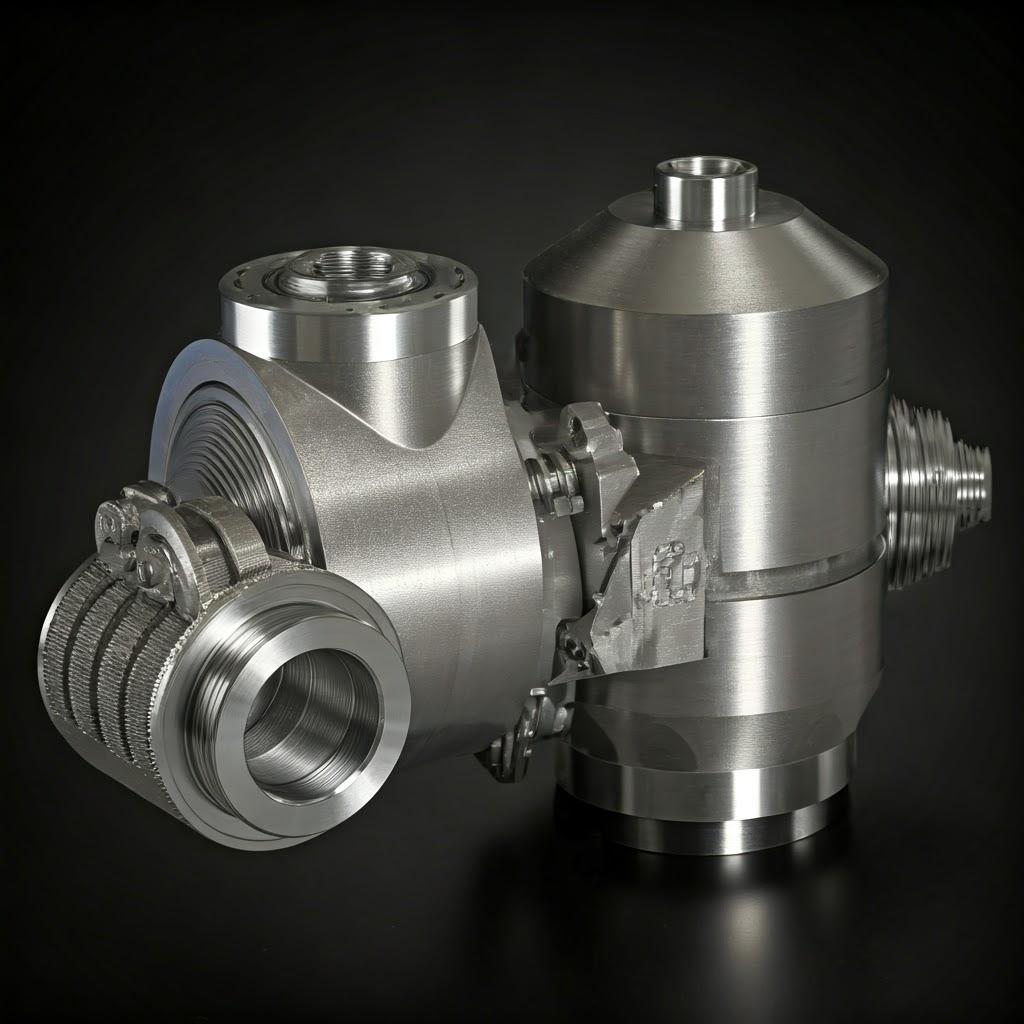
Často kladené otázky (FAQ)
- Jaké jsou typické aplikace kovových 3D tištěných dílů v leteckém průmyslu? Kovový 3D tisk se používá k výrobě široké škály leteckých komponent, včetně dílů palivového systému (jako jsou palivová čerpadla, rozdělovače a vstřikovače), lopatek turbín, konstrukčních konzol, potrubí, výměníků tepla a nástrojů na míru. Díky schopnosti vytvářet složité geometrie a používat lehké a vysoce výkonné materiály je ideální pro optimalizaci výkonu letadel a kosmických lodí.
- Je kovový 3D tisk dostatečně pevný pro použití palivových čerpadel v letectví? Ano, při použití správného kovového prášku a optimalizaci procesu tisku mohou kovové 3D tištěné díly dosahovat mechanických vlastností srovnatelných nebo dokonce lepších než díly vyráběné tradičními výrobními metodami. Techniky následného zpracování, jako je HIP, dále zvyšují hustotu a pevnost materiálu. Vysoce kvalitní kovové prášky společnosti Metal3DP’a odborné znalosti technologie SEBM zajišťují výrobu pevných a odolných součástí vhodných pro náročné letecké aplikace.
- Jaká jsou omezení použití kovového 3D tisku pro palivová čerpadla? Přestože 3D tisk z kovu nabízí mnoho výhod, může mít svá omezení, jako jsou omezení objemu tisku (ačkoli Metal3DP nabízí špičkové objemy tisku), požadavky na povrchovou úpravu, které mohou vyžadovat následné zpracování, a nákladová efektivita pro velmi vysoké výrobní objemy. Pečlivá optimalizace návrhu a výběr vhodné tiskové technologie a materiálů jsou pro zmírnění těchto omezení zásadní.
Závěr - Budoucnost letectví a kosmonautiky díky aditivní výrobě
3D tisk z kovu přináší revoluci v konstrukci a výrobě důležitých součástí pro letecký průmysl a palivová čerpadla stojí v čele této transformace. Možnost vytvářet složitá, lehká a vysoce výkonná palivová čerpadla s použitím materiálů, jako jsou IN718, IN625 a Hastelloy X, nabízí významné výhody oproti tradičním výrobním metodám. Svoboda návrhu, efektivita materiálu, zkrácení dodacích lhůt a lepší funkčnost jsou jen některé z výhod, které vedou k zavádění technologie AM pro zpracování kovů v leteckém průmyslu.
S rostoucí poptávkou po efektivnějších, spolehlivějších a udržitelnějších řešeních pro letecký průmysl bude 3D tisk z kovů hrát stále důležitější roli. Společnosti jako Metal3DP se svými pokročilými tiskovými technologiemi, vysoce kvalitními kovovými prášky a hlubokými odbornými znalostmi v oblasti aditivní výroby umožňují leteckým organizacím posouvat hranice inovací a dosahovat svých cílů v oblasti digitální výroby. Využitím možností kovového 3D tisku může letecký průmysl odemknout nové možnosti konstrukce palivových systémů, což povede k lehčím letadlům, účinnějším motorům a v konečném důsledku k udržitelnější budoucnosti letecké a vesmírné dopravy. Kontaktujte společnost Metal3DP ještě dnes a zjistěte, jak mohou naše špičkové systémy a materiály podpořit cestu vaší organizace k aditivní výrobě.
Sdílet na
MET3DP Technology Co., LTD je předním poskytovatelem řešení aditivní výroby se sídlem v Qingdao v Číně. Naše společnost se specializuje na zařízení pro 3D tisk a vysoce výkonné kovové prášky pro průmyslové aplikace.
Dotaz k získání nejlepší ceny a přizpůsobeného řešení pro vaše podnikání!
Související články
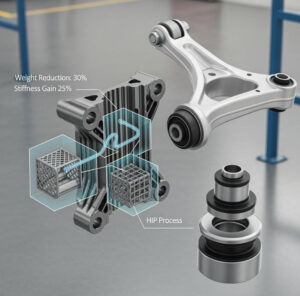
Metal 3D Printed Subframe Connection Mounts and Blocks for EV and Motorsport Chassis
Přečtěte si více "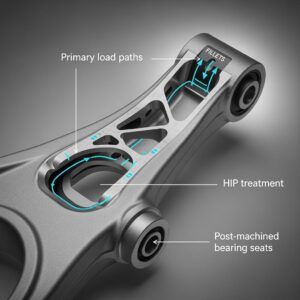
Metal 3D Printing for U.S. Automotive Lightweight Structural Brackets and Suspension Components
Přečtěte si více "O Met3DP
Nedávná aktualizace
Náš produkt
KONTAKTUJTE NÁS
Nějaké otázky? Pošlete nám zprávu hned teď! Po obdržení vaší zprávy obsloužíme vaši žádost s celým týmem.