Titanové držáky pro letecké konstrukce pomocí 3D tisku
Obsah
Titanové držáky pro letecké konstrukce pomocí 3D tisku: Průvodce pro inženýry a zadavatele veřejných zakázek
Letecký a kosmický průmysl se pohybuje na špičce technického vývoje a vyžaduje komponenty, které nabízejí výjimečný výkon, neochvějnou spolehlivost a minimální hmotnost. Mezi nejkritičtější, ale často přehlížené komponenty patří letecké držáky. Tyto důležité součásti hardwaru jsou spojovacím článkem různých systémů a konstrukcí v letadlech, kosmických lodích, satelitech a bezpilotních prostředcích (UAV). Vzhledem k tomu, že konstrukce v letectví a kosmonautice směřují k větší efektivitě a složitosti, tradiční výrobní metody pro tyto klíčové součásti stále častěji narážejí na omezení. Právě zde transformační síla aditivní výroby kovů (AM), běžně známé jako kovový 3D tisk, v kombinaci s vysoce výkonnými materiály, jako jsou titanové slitiny, přináší revoluci v konstrukci a výrobě součástí. Pro inženýry, kteří usilují o inovace v konstrukci, a manažery nákupu, kteří usilují o optimalizaci dodavatelských řetězců a snížení nákladů na životní cyklus, je pochopení potenciálu titanových 3D tištěných leteckých montážních prvků prvořadé.
Úvod: Kritická role leteckých držáků a vzestup aditivní výroby titanu
Co jsou letecké a kosmické držáky? Neopěvovaní hrdinové letu
Letecké závěsy v různých podobách hrají zásadní roli při zajišťování strukturální integrity, stability a funkčnosti kosmických vozidel. Jsou to v podstatě držáky, přípravky nebo rozhraní určená k bezpečnému upevnění, podepření a umístění různých součástí v konstrukci draku letadla nebo kosmické lodi. Jejich funkce jsou mnohostranné a kritické:
- Nosná konstrukce: Upevnění často přenáší značné statické a dynamické zatížení mezi součástmi, jako jsou motory a konstrukce křídel, podvozek a trup nebo těžké vybavení a vnitřní kostra. Musí odolávat obrovským silám při vzletu, přistání, manévrování (vysoké přetížení) a v turbulentních podmínkách.
- Tlumení a izolace vibrací: Letecké prostředí je vystaveno intenzivním vibracím způsobeným motory, aerodynamickými silami a strojním zařízením. Držáky jsou často navrženy tak, aby tyto vibrace pohlcovaly nebo izolovaly, chránily citlivé vybavení (jako je avionika, senzory, kamery) a zabraňovaly únavovému selhání okolních konstrukcí.
- Přesné polohování a zarovnání: Mnohé komponenty, zejména senzory, naváděcí systémy a komunikační pole, vyžadují přesné a stabilní polohování. Držáky zajišťují, aby si tyto součásti zachovaly požadovanou orientaci a vyrovnání při provozním namáhání.
- Tepelný management: V některých aplikacích mohou držáky hrát roli při odvádění tepla nebo zajišťovat tepelné přestávky mezi součástmi pracujícími při různých teplotách.
- Zabezpečení systémů: Udržují důležité systémy na místě, včetně hydraulických vedení, elektrických svazků, součástí palivového systému a systémů řízení prostředí.
Vzhledem k těmto náročným úkolům může mít selhání jediného držáku katastrofální následky. Proto jejich konstrukce, výběr materiálu a výrobní proces podléhají nejvyšším standardům kvality a spolehlivosti.
Tradiční výrobní problémy: Omezení minulosti
Historicky se letecké držáky vyráběly především konvenčními výrobními technikami:
- Subtraktivní obrábění: CNC obrábění dílů z plných bloků (polotovarů) kovů pro letecký průmysl, jako je hliník nebo titan. Tato metoda je sice schopna dosáhnout vysoké přesnosti, ale trpí:
- Vysoký materiálový odpad: Zejména u složitých geometrií je značná část (často 80-95 %) drahého bloku suroviny obrobena, což vede ke špatnému poměru “buy-to-fly”.
- Omezení návrhu: Některé složité tvary, vnitřní prvky nebo vysoce optimalizované struktury lze obtížně nebo vůbec nelze efektivně nebo hospodárně obrábět.
- Náklady na nástroje a nastavení: Mohou být vyžadovány složité přípravky, což zvyšuje náklady a dobu realizace.
- Obsazení: Nalévání roztaveného kovu do forem. Odlévání je sice vhodné pro určité tvary, ale může mít omezení z hlediska dosažitelných tolerancí, vlastností materiálu (možnost vzniku pórovitosti) a nutnosti výrazného dodatečného opracování. Vytvoření počátečních forem je také časově a finančně náročné.
- Výroba/montáž: Svařování nebo spojování více jednodušších kusů. To přináší potenciální místa poruch ve spojích, zvyšuje hmotnost kvůli spojovacím prvkům a prodlužuje dobu a složitost montáže.
Tyto tradiční metody často vedou k delším dodacím lhůtám, zejména u složitých nebo malosériových dílů, brání realizaci vysoce optimalizovaných odlehčených konstrukcí a významně přispívají k plýtvání materiálem, což je hlavní nákladový faktor v letecké výrobě. Manažeři nákupu se často potýkají s problémy při získávání těchto součástí od spolehlivých dodavatelů dodavatelé leteckých komponentů kteří mohou splnit náročné harmonogramy a nákladové cíle pomocí těchto starších technik.
Nástup aditivní výroby kovů v letectví a kosmonautice
Aditivní výroba kovů představuje změnu paradigmatu. Namísto odebírání materiálu vytváří AM díly vrstvu po vrstvě přímo z 3D modelu CAD pomocí vysokoenergetických zdrojů, jako jsou lasery nebo elektronové paprsky, které spojují částice kovového prášku. Tento přístup zásadně překonává mnohá omezení tradičních metod a nabízí leteckým inženýrům a výrobcům nebývalé možnosti. Procesy, jako je laserová fúze v práškovém loži (LPBF, známá také jako selektivní laserové tavení nebo SLM) a tavení elektronovým svazkem (EBM), se stále více uplatňují při výrobě letově kritických součástí. Možnost vytvářet složité, lehké a vysoce výkonné díly přímo z digitálních návrhů je hnací silou významných inovací v celém odvětví. Společnosti, které chtějí tuto technologii využít, často hledají zkušeného kov 3D tisk dodavatel s hlubokou znalostí požadavků leteckého průmyslu.
Titan: Materiál volby pro náročné aplikace
Slitiny titanu, zejména Ti-6Al-4V (třída 5) a jeho varianta s vyšší čistotou Ti-6Al-4V ELI (třída 23), se díky své výjimečné kombinaci vlastností staly referenčními materiály v leteckém průmyslu:
- Vysoký poměr pevnosti k hmotnosti: Titan má pevnost srovnatelnou s mnoha ocelemi, ale výrazně nižší hustotu, takže je ideální pro aplikace v letectví a kosmonautice, kde je kritická hmotnost.
- Vynikající odolnost proti korozi: Titan vytváří stabilní pasivní oxidovou vrstvu, která je mimořádně odolná proti korozi způsobené leteckým palivem, hydraulickými kapalinami, slanou vodou a atmosférickými podmínkami.
- Dobrý výkon při vysokých teplotách: Zachovává si pevnost při mírně zvýšených teplotách, které se vyskytují v motorovém prostoru a v draku letadla.
- Odolnost proti únavě: Klíčové pro součásti vystavené cyklickému zatížení během letového provozu.
Synergie: AM a titan pro letecké držáky
Kombinace konstrukční svobody aditivní výroby s vynikajícími vlastnostmi titanových slitin vytváří silnou synergii pro výrobu leteckých držáků nové generace. Tato kombinace umožňuje:
- Optimalizované návrhy: Vytvoření topologicky optimalizovaných úchytů, které umisťují materiál pouze tam, kde je to nutné pro nesení zatížení, což výrazně snižuje hmotnost.
- Konsolidace částí: Navrhování jednoduchých, složitých držáků, které nahrazují sestavy několika jednodušších dílů, čímž se snižuje počet spojovacích prvků, doba montáže a potenciálních míst poruch.
- Rychlé prototypování a iterace: Rychlá výroba a testování variant návrhu, aby se dospělo k optimálnímu řešení mnohem rychleji než při použití tradičních metod založených na nástrojích.
- Snížení množství materiálového odpadu: Procesy AM, jako je LPBF a EBM, se blíží čistému tvaru a používají pouze materiál potřebný pro díl a podpůrné struktury, což výrazně zlepšuje poměr mezi nákupem a letem ve srovnání s obráběním.
Tento technologický pokrok umožňuje společnostem, jako je Met3dp, s odbornými znalostmi jak v oblasti pokročilých technologií, tak v oblasti 3D tisk z kovu systémy, jako jsou tiskárny SEBM (Selective Electron Beam Melting) a výroba vysoce výkonných kovových prášků, a nabízí tak komplexní řešení pro výrobu složitých a vysoce hodnotných leteckých komponent.
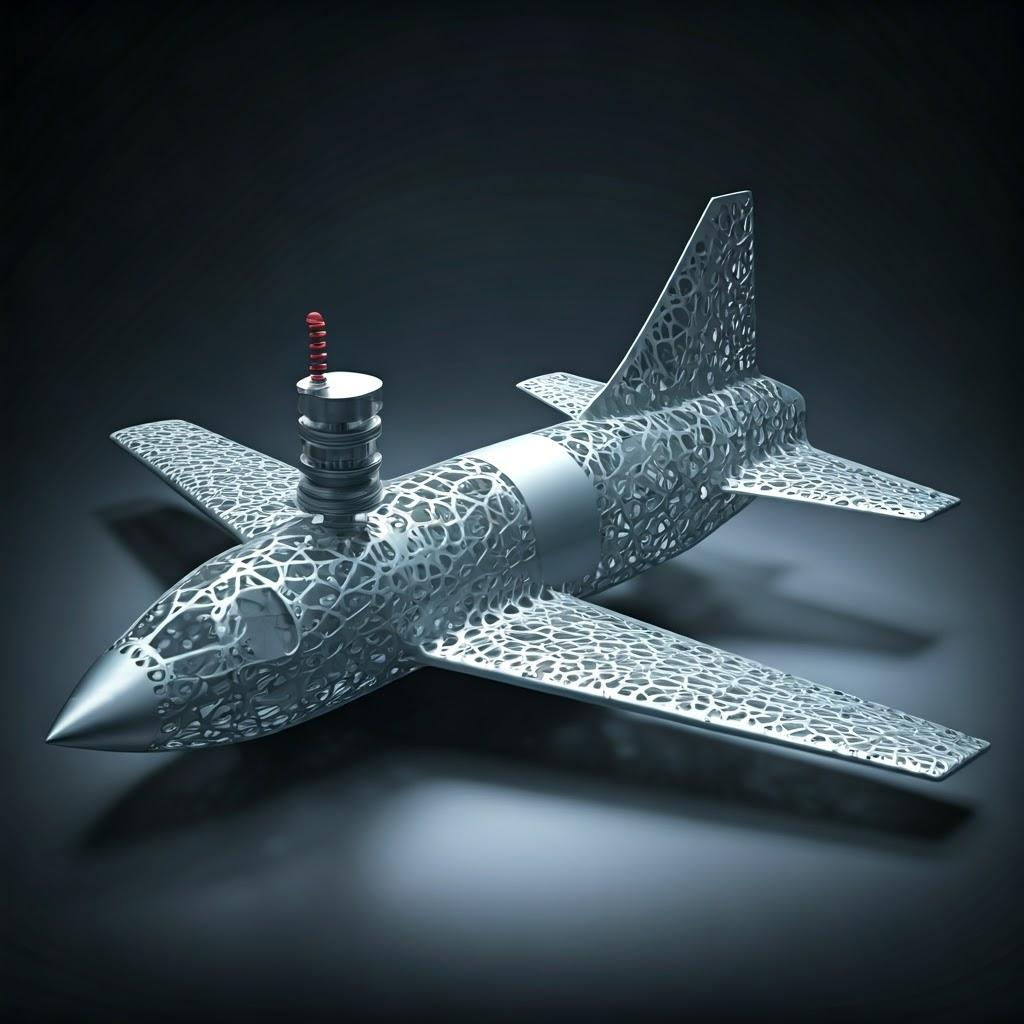
K čemu se používají titanové držáky pro letectví a kosmonautiku vytištěné na 3D tiskárně? Aplikace a funkce
Všestrannost aditivní výroby kovů v kombinaci s robustními vlastnostmi titanových slitin, jako je Ti-6Al-4V, umožňuje výrobu široké škály leteckých držáků přizpůsobených specifickým náročným aplikacím. Tyto součásti již nejsou omezeny omezeními tradičního obrábění nebo odlévání, což umožňuje optimalizovat výkon napříč různými leteckými platformami. Manažeři veřejných zakázek, kteří hledají spolehlivé dodavatel titanových komponentů nebo výroba konzol pro letecký průmysl partner musí pochopit šíři aplikací, ve kterých vynikají titanové držáky vytištěné na 3D tiskárně.
Podrobné rozdělení typů montáže:
Zatímco “montáž” je obecný pojem, 3D tisk umožňuje v rámci této kategorie vytvářet vysoce specializované konstrukce:
- Uchycení motoru a držáky pylonu: Jedná se o velmi důležité konstrukční součásti, které upevňují motory ke křídlu nebo trupu letadla. Musí odolávat extrémnímu zatížení, vysokým teplotám a značným vibracím. Technologie AM umožňuje vytvářet složité konstrukce s optimalizovanou hmotností, které zachovávají strukturální integritu při obrovském namáhání. Často se zde používá optimalizace topologie, aby se vytvořily organicky vypadající tvary, které účinně přenášejí dráhy zatížení.
- Držáky a stojany na vybavení (zásobníky letecké elektroniky): Bezpečné umístění citlivých a často těžkých leteckých zařízení, řídicích jednotek, rozvodů energie a přístrojů. Tyto držáky často vyžadují prvky izolace vibrací, zohlednění tepelného managementu (odvodu tepla) a přesné umístění. Technologie AM umožňuje integrovat složité vnitřní prvky, zásuvné díly nebo kanály pro vedení kabelů přímo do konstrukce držáku.
- Konstrukční konzoly a uzly: Spojení různých částí draku, jako jsou žebra křídla s nosníky, části trupu nebo výztuhy přepážek. Ty mají často složitou geometrii danou okolními konstrukcemi a požadavky na zatížení. AM usnadňuje vytváření lehkých uzlů na míru, které mohou nahradit těžší vícedílné sestavy.
- Držáky senzorů a antén: Zajištění stabilních a přesně nastavených platforem pro kritické senzory (např. senzory leteckých dat, navigační senzory, optické užitečné zatížení) a komunikační antény. Tyto držáky musí být často navrženy s ohledem na specifické aerodynamické profily nebo požadavky na tepelnou stabilitu. Možnost vytvářet pomocí AM vlastní tvary zajišťuje optimální umístění a výkon.
- Upevnění hydraulického, palivového a elektrického vedení (svorky/držáky): Zabezpečení rozsáhlé sítě kabelů a kabelových svazků v letadle nebo kosmické lodi. Ačkoli se zdá, že je to jednoduché, těchto úchytů je mnoho a přispívají k celkové hmotnosti. Technologie AM umožňuje navrhnout vysoce optimalizované, lehké úchyty, které mohou sloučit více držáků vedení do jediné tištěné součásti.
- Uchycení akčních členů: Podpůrné lineární nebo rotační aktuátory používané pro řídicí plochy letu, nasazení podvozku nebo jiné mechanické systémy. Ty musí odolávat značnému provoznímu zatížení a udržovat přesné nastavení.
- Upevnění v interiéru: Držáky pro upevnění prvků kabiny, zádržných systémů nákladu nebo jiného vnitřního vybavení, kde je stále výhodná úspora hmotnosti.
Specifické letecké a kosmické platformy a aplikace:
3D tištěné titanové držáky nacházejí uplatnění napříč celým spektrem leteckého a obranného průmyslu:
- Komerční letadla: Součásti motoru, konstrukční držáky draku, vnitřní vybavení kabiny, součásti mechanismu dveří. Snaha o efektivní využití paliva činí snížení hmotnosti prvořadým.
- Vojenská letadla & amp; Stíhací letouny: Vysoce výkonné konstrukční díly, držáky zbraňových systémů, senzorové moduly, komponenty vyžadující vysokou pevnost a odolnost proti únavě při extrémním přetížení a vibracích. Klíčovou výhodou je také rychlejší realizace náhradních dílů nebo modernizací.
- Satelity a kosmické lodě: Konstrukční uzly, anténní podpěry, držáky pro citlivé optické přístroje, držáky palivových nádrží, držáky vlnovodů. Snížení hmotnosti je naprosto zásadní pro snížení nákladů na vypuštění. Materiály jako Ti-6Al-4V ELI jsou upřednostňovány pro své kryogenní vlastnosti. Vyhledávání dodavatelů pro pořizování satelitních komponentů kteří rozumí AM, je stále důležitější.
- Bezpilotní letadla (UAV / drony): Uchycení motoru/motoru, součásti podvozku, držáky pro integraci senzorů a užitečného zatížení, konstrukční prvky rámu. AM umožňuje rychlé vývojové cykly a vysoce přizpůsobené, lehké konstrukce, které jsou nezbytné pro maximalizaci letové vytrvalosti a nosnosti pro Konstrukční díly UAV.
- Vrtulníky: Upevnění převodovky, součásti rotorového systému, upevnění zařízení citlivých na vibrace. AM může pomoci řešit náročné vibrační prostředí rotorových letadel.
- Kosmické nosné rakety: Držáky a podpěry v sestavách raketových motorů, držáky palivového potrubí, konstrukční spoje schopné odolat extrémním startovním silám a teplotám.
Klíčové funkční požadavky pro přijetí AM:
Náročné provozní prostředí diktuje přísné funkční požadavky na letecké držáky, z nichž mnohé lze lépe splnit pomocí AM:
Funkční požadavek | Jak vynikají titanové držáky vytištěné na 3D tiskárně | Význam pro kupující B2B |
---|---|---|
Vysoká pevnost v poměru k hmotnosti | Vrozená vlastnost titanu, dále vylepšená optimalizací topologie, která je možná pouze při AM, minimalizuje spotřebu materiálu. | Snížení spotřeby paliva, zvýšení kapacity užitečného zatížení, nižší náklady na start. |
Nosnost | Optimalizované konstrukce zajišťují rozložení napětí podél primárních cest zatížení. Následné zpracování HIP zajišťuje integritu materiálu. | Zvýšená konstrukční spolehlivost, splňující výkonnostní normy kritické pro bezpečnost. |
Tlumení vibrací | Složité geometrie, včetně vnitřních mřížkových struktur, mohou být navrženy tak, aby pohlcovaly nebo posouvaly frekvence vibrací. | Zvýšená životnost citlivých zařízení, zvýšený komfort cestujících, snížení únavy. |
Odolnost proti únavě | Vysoce kvalitní prášek Ti-6Al-4V (jako Met3dp’s) a následné zpracování (HIP, povrchová úprava) poskytují vynikající únavové vlastnosti. | Delší životnost součástí, kratší intervaly údržby, vyšší bezpečnost. |
Tepelná stabilita | Titan si zachovává vlastnosti v přiměřeném rozsahu teplot. AM umožňuje v případě potřeby integraci chladicích kanálů. | Spolehlivý výkon v různých tepelných prostředích (např. v blízkosti motorů). |
Odolnost proti korozi | Vnitřní vlastnost titanu zajišťuje dlouhou životnost v náročných podmínkách leteckého průmyslu (vlhkost, kapaliny, solná mlha). | Snížená údržba, delší životnost dílů, vhodnost pro různé provozní podmínky. |
Složité geometrie | AM odstraňuje tradiční výrobní omezení a umožňuje vytvářet velmi složité, integrované a organické tvary přizpůsobené konkrétním potřebám. | Optimální přizpůsobení a funkce, potenciál konsolidace dílů, inovace designu. |
Konsolidace částí | Jeden díl AM může nahradit sestavu více dílů, spojovacích prvků a spojů. | Snížení počtu dílů, úspora hmotnosti, zjednodušení montáže, méně poruchových míst. |
Rychlá dostupnost (MRO) | Možnost tisku náhradních dílů nebo náhradních dílů na vyžádání, což snižuje potřebu skladových zásob a zkracuje dobu AOG (Aircraft on Ground). | Lepší provozní připravenost, nižší náklady na skladování, rychlejší opravy. |
Export do archů
Za hranice letectví a kosmonautiky:
Výhody, které vedou k zavádění titanových držáků vytištěných 3D tiskem v leteckém průmyslu, je činí atraktivními i pro další vysoce výkonná průmyslová odvětví, která vyžadují lehké, pevné a korozivzdorné komponenty, jako jsou např.:
- Vysoce výkonný automobilový průmysl / motoristický sport
- Obranné a vojenské vybavení
- Námořní aplikace
- Lékařské implantáty (s použitím biokompatibilních materiálů)
- Průmyslová robotika a automatizace
Inženýři a specialisté na zadávání veřejných zakázek v těchto oborech se mohou poučit ze zavádění této technologie v leteckém a kosmickém průmyslu. Spolupráce se znalým distributor aditivní výroby kovů nebo poskytovatel služeb, jako je Met3dp, může usnadnit přenos této technologie do nových aplikací.
Proč používat 3D tisk z kovu pro letecké držáky? Hlavní výhody oproti běžným metodám
Rozhodnutí přejít od osvědčených konvenčních výrobních metod k aditivní výrobě kovů u kritických součástí, jako jsou letecké držáky, se nepřijímá lehce. Důvodem je řada přesvědčivých výhod, které řeší klíčové problémy v oblasti konstrukce, výroby a provozu v leteckém průmyslu. Inženýrům, kteří posouvají hranice designu, a týmům pro zadávání zakázek zaměřeným na celkové náklady na vlastnictví a efektivitu dodavatelského řetězce nabízí AM hmatatelné výhody, které je těžké ignorovat. Pojďme se hlouběji ponořit do problematiky proč kovový 3D tisk se stává preferovanou metodou výroby vysoce výkonných titanových držáků pro letecký průmysl.
1. Bezprecedentní volnost designu & Komplexnost:
To je pravděpodobně největší transformační výhoda AM. Tradiční metody jsou ze své podstaty subtraktivní nebo formativní, což omezuje geometrické možnosti. Aditivní metoda AM designéry osvobozuje:
- Optimalizace topologie: Sofistikované softwarové algoritmy mohou analyzovat průběh zatížení a napětí v konstrukčním prostoru součásti a odstraňovat materiál tam, kde není potřeba, a přidávat jej pouze tam, kde je to nutné pro integritu konstrukce. Výsledkem jsou vysoce organické a efektivní tvary, které je často nemožné nebo neúměrně nákladné obrábět. V případě držáků to znamená dosažení požadované pevnosti a tuhosti při minimální hmotnosti.
- Mřížové struktury: AM umožňuje vytvářet vnitřní mřížkové nebo buněčné struktury v pevných dílech. Tyto mřížky mohou výrazně snížit hmotnost při zachování strukturální podpory, pohlcovat energii/vibrace nebo usnadňovat proudění tekutin, pokud jsou navrženy jako kanály. Představte si držák s hustým vnějším pláštěm pro přenos zatížení, ale s lehkým vnitřním mřížkovým jádrem.
- Konsolidace částí: Složité sestavy, které se dříve skládaly z více jednotlivých dílů a vyžadovaly spojovací prvky, svařování nebo lepení, lze často přepracovat a vytisknout jako jedinou monolitickou součást. Upevnění integrované se svými upevňovacími body nebo zahrnující prvky ze sousedních dílů eliminuje pracnost montáže, odstraňuje potenciální místa poruch v místech spojů, snižuje počet dílů (zjednodušuje skladové zásoby a logistiku pro velkoobchod s leteckými díly ) a často vede k dalším úsporám hmotnosti.
- Konformní chladicí/vyhřívací kanály: Pokud držák podporuje zařízení generující teplo nebo vyžaduje tepelnou stabilitu, AM umožňuje integrovat vnitřní kanály, které přesně odpovídají tvaru dílu, přímo během procesu výroby, což umožňuje efektivnější řízení tepla než vrtané kanály.
- Vnitřní prvky & Složité geometrie: Snadno lze vytvářet prvky, jako jsou skryté dutiny, složité vnitřní průchody, výřezy a hladce splývající křivky, což umožňuje vysoce optimalizované funkční návrhy.
2. Výrazné snížení hmotnosti (lepší poměr nákupu a letu):
Hmotnost je v letectví a kosmonautice hlavním faktorem ovlivňujícím náklady. Každý ušetřený kilogram znamená potenciální úsporu paliva po celou dobu životnosti letadla, zvýšení nosnosti nebo prodloužení doletu/doby trvání mise.
- Optimalizované návrhy: Jak bylo uvedeno výše, optimalizace topologie a mřížkové struktury, které AM umožňuje, přímo vedou k lehčím dílům (často o 20-60 % nižší hmotnost ve srovnání s konvenčně vyráběnými ekvivalenty), aniž by došlo ke snížení výkonu.
- Tvar blízký síti: Procesy AM vytvářejí díly blízké jejich konečným rozměrům. I když může být nutné dodatečné opracování kritických rozhraní, počáteční spotřeba materiálu je výrazně nižší než při obrábění z velkého polotovaru. Poměr “buy-to-fly” (hmotnost nakoupené suroviny vs. hmotnost finálního dílu) se výrazně zlepšuje. Snížení plýtvání drahým titanem je hlavním nákladovým přínosem, který je atraktivní pro manažeři nákupu v leteckém průmyslu.
Příklad porovnání poměru nákupů a letů:
Výrobní metoda | Typický poměr nákupů a letů (titan) | Důsledky |
---|---|---|
Tradiční CNC obrábění | 10:1 až 20:1 (nebo vyšší) | 90-95 % materiálového odpadu, vysoké náklady na suroviny. |
Aditivní výroba kovů | 1.5:1 až 3:1 | Minimální odpad materiálu, výrazné úspory nákladů na suroviny. |
Export do archů
3. Efektivita materiálů a udržitelnost:
Se snížením hmotnosti úzce souvisí efektivní využití materiálů.
- Snížení množství odpadu: AM používá pouze materiál potřebný pro díl a jeho podpěry (které lze často minimalizovat díky chytrému návrhu a orientaci). Tím se výrazně snižuje množství vysoce hodnotného titanu, který končí jako třísky při obrábění, což snižuje dopad na životní prostředí a náklady na suroviny.
- Možnost opakovaného použití prášku: Netavený prášek v konstrukční komoře lze obvykle získat zpět, prosévat a smíchat s panenským práškem pro opětovné použití v následujících konstrukcích (při dodržení přísných protokolů kontroly kvality), což dále zlepšuje využití materiálu. Společnosti jako Met3dp, které vyrábějí vlastní prášky, mají optimalizované procesy pro správu životního cyklu prášku.
4. Zkrácení doby realizace a zrychlení iterací:
V rychlém leteckém průmyslu záleží na rychlosti - jak při vývoji, tak při údržbě, opravách a generálních opravách (MRO).
- Rychlé prototypování: AM umožňuje inženýrům vyrábět fyzické prototypy návrhů montáží v řádu dnů namísto týdnů či měsíců spojených s tradičním nastavením nástrojů a obráběním. To umožňuje rychlejší ověřování návrhů, funkční testování a iterační cykly.
- Eliminace nástrojů: AM obvykle nevyžaduje žádné specifické nástroje (formy, zápustky, složité přípravky). Tím se eliminuje značná časová náročnost a náklady spojené s návrhem, výrobou a úpravou nástrojů. Změny lze provést přímo v modelu CAD a rychle vytisknout nový díl.
- Výroba na vyžádání: Pro náhradní díly nebo malosériovou výrobu nabízí AM možnost výroby na vyžádání. To snižuje potřebu velkých zásob fyzických dílů a potenciálně zkracuje dobu AOG (Aircraft on Ground) tím, že se náhradní držáky tisknou podle potřeby. Tato agilita je klíčová pro řešení pro MRO v letectví a kosmonautice.
- Digitální inventář: Návrhy existují jako digitální soubory, což umožňuje distribuovanou výrobu blíže k místu potřeby a potenciálně zjednodušuje globální dodavatelské řetězce.
5. Odolnost a agilita dodavatelského řetězce:
Závislost na složitých, vícestupňových tradičních dodavatelských řetězcích může být zranitelná. AM nabízí alternativy:
- Snížení závislosti na dodavateli: Konsolidace dílů může snížit počet potřebných dodavatelů jednotlivých komponent.
- Distribuovaná výroba: Soubory digitálních dílů lze zasílat elektronicky certifikovaným firmám kovové servisní kanceláře AM nebo interních zařízeních po celém světě pro místní výrobu, čímž se zkracují přepravní lhůty a logistické překážky.
- Rychlejší reakce na změny designu: Technické změny lze provádět mnohem rychleji, aniž by bylo nutné je přebudovávat.
6. Vylepšený výkon a funkčnost:
Kromě pouhého kopírování stávajících konstrukcí může AM skutečně zvýšit výkon součástek:
- Mikrostruktury na míru: V závislosti na použitém procesu AM (např. LPBF vs. EBM) a parametrech lze dosáhnout různých mikrostruktur, které mohou ovlivnit pevnost, únavovou životnost a další vlastnosti. Pro optimalizaci těchto vlastností je zásadní následné zpracování, jako je HIP.
- Integrovaná funkčnost: Jak je uvedeno v části Volnost konstrukce, prvky, jako jsou mřížky tlumící vibrace nebo konformní chladicí kanály, lze zabudovat přímo do držáku, čímž se zlepší celkový výkon systému.
- Biomimikry: AM umožňuje konstruktérům napodobit účinné struktury, které se vyskytují v přírodě (např. struktury kostí), a dosáhnout tak optimálního poměru pevnosti a hmotnosti.
Shrneme-li to, aditivní výroba kovů představuje přesvědčivou nabídku hodnoty pro výrobu titanových leteckých držáků, která nabízí výhody v oblasti flexibility konstrukce, snížení hmotnosti, efektivity materiálu, rychlosti, pružnosti dodavatelského řetězce a potenciálního zvýšení výkonu, kterému se tradiční metody nemohou rovnat. Využití pokročilých platforem, jako jsou tiskárny Met3dp’SEBM, a vysoce kvalitních materiálů je klíčem ke spolehlivému využití těchto výhod.
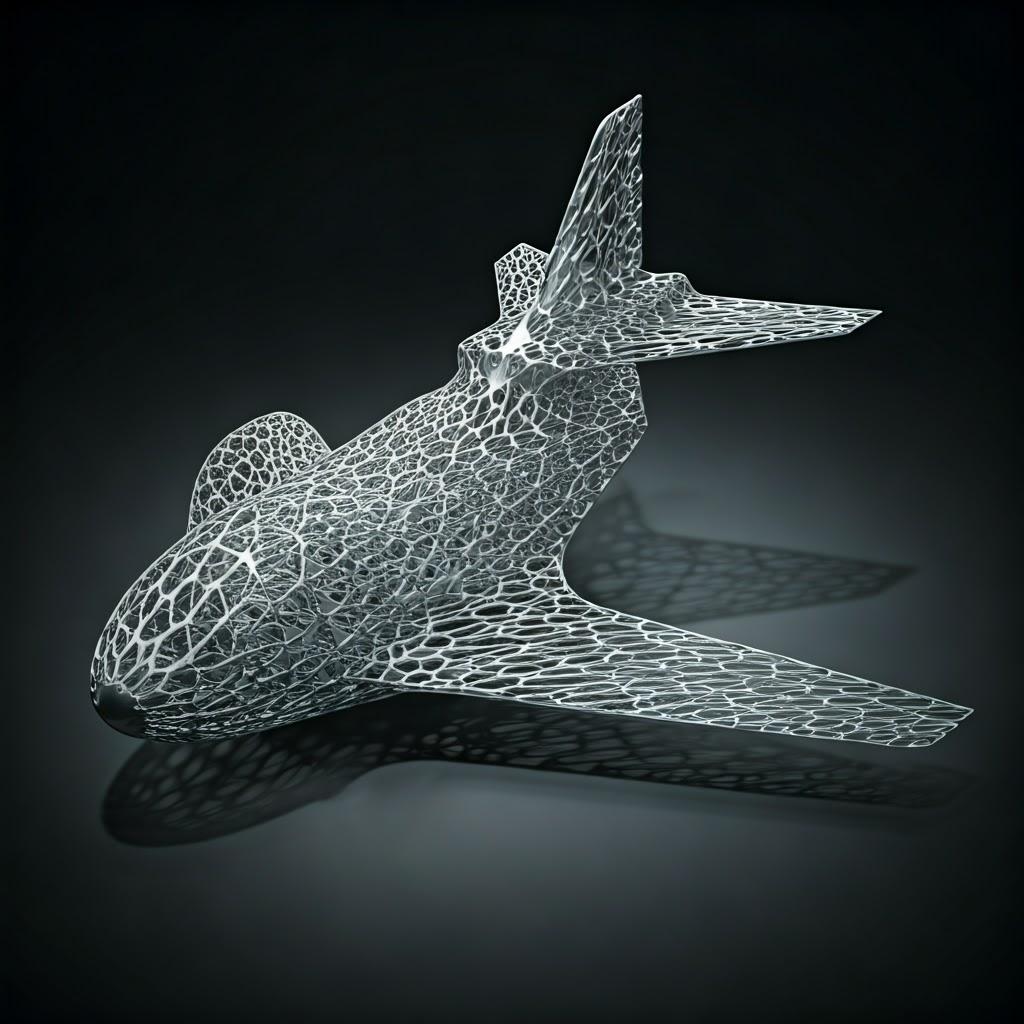
Doporučené materiály pro 3D tištěné letecké držáky: Ti-6Al-4V & Ti-6Al-4V ELI Deep Dive
Výběr správného materiálu je základem úspěchu každé letecké součásti, zejména nosných držáků. I když lze pomocí aditivní výroby kovů zpracovávat různé slitiny, slitiny titanu, konkrétně Ti-6Al-4V (třída 5) a Ti-6Al-4V ELI (třída 23), vynikají jako základní materiály pro 3D tisk leteckých držáků díky své výjimečné vyváženosti vlastností. Pochopení jejich nuancí je zásadní jak pro konstruktéry, kteří materiál specifikují, tak pro manažery nákupu, kteří jej získávají od kvalifikovaných dodavatelů dodavatel titanového prášku nebo poskytovateli služeb AM.
Ti-6Al-4V (třída 5): Standard pro letectví a kosmonautiku
Ti-6Al-4V, často označovaný jednoduše jako “Ti64” nebo titan třídy 5, je nejpoužívanější titanovou slitinou ve všech průmyslových odvětvích, zejména v letectví a kosmonautice. Její obliba pramení z velmi žádoucí kombinace vlastností dosažitelných pomocí AM:
- Vysoký poměr pevnosti k hmotnosti: To je jeho charakteristická vlastnost. Nabízí pevnost srovnatelnou s mnoha ocelovými slitinami při zhruba 56% hustotě. To se přímo promítá do lehčích součástí bez ztráty mechanického výkonu.
- Vynikající odolnost proti korozi: Vytváří vysoce stabilní, houževnatou pasivní vrstvu oxidu (TiO2), která ji chrání před korozí v široké škále agresivních prostředí, včetně leteckého paliva, hydraulických kapalin, odmrazovacích solí a mořské atmosféry.
- Dobrá odolnost vůči zvýšeným teplotám: Může pracovat nepřetržitě při teplotách do přibližně 315 °C a vydrží i přerušované působení vyšších teplot, takže je vhodný pro použití v blízkosti motorů nebo v horkých částech draku letadla.
- Svařitelnost & Zhotovitelnost: Ačkoli se zaměřujeme na AM, jeho základní svařitelnost naznačuje dobré tavné vlastnosti nezbytné pro procesy tavení v práškovém loži.
- Mírné náklady (pro titan): I když je dražší než hliník nebo ocel, jedná se o nejběžnější a obecně cenově nejvýhodnější slitinu titanu.
Ti-6Al-4V ELI (třída 23): Zvýšená houževnatost a čistota
Ti-6Al-4V ELI (Extra Low Interstitials) je verze třídy 5 s vyšší čistotou. Klíčový rozdíl spočívá v přísně kontrolovaných nižších limitech intersticiálních prvků, především kyslíku a železa.
- Zlepšená tažnost a lomová houževnatost: Snížení obsahu intersticiálních prvků významně zvyšuje tažnost (schopnost deformovat se bez porušení) a lomovou houževnatost (odolnost proti šíření trhlin), zejména při kryogenních teplotách.
- Vynikající odolnost proti poškození: Díky tomu je třída 23 preferovanou volbou pro kritické konstrukční součásti, u nichž se používá konstrukční filozofie odolnosti proti selhání nebo poškození nebo u nichž se předpokládá provoz ve velmi chladném prostředí (např. při letech ve vesmíru nebo ve velkých výškách).
- Zvýšená biokompatibilita: Díky vyšší čistotě je třída 23 také běžnou volbou pro lékařské implantáty, ačkoli pro typické letecké montáže je to méně důležité.
- Mírně nižší pevnost: Zvýšená houževnatost je dosažena za cenu mírně nižší pevnosti v tahu a meze kluzu ve srovnání se standardní třídou 5.
Srovnávací vlastnosti (typické hodnoty pro díly AM po odlehčení od napětí/HIP):
Vlastnictví | Ti-6Al-4V (třída 5) AM | Ti-6Al-4V ELI (třída 23) AM | Jednotka | Význam pro letecká a kosmická zařízení |
---|---|---|---|---|
Hustota | ~4.43 | ~4.43 | g/cm³ | Základem je vysoký poměr pevnosti a hmotnosti. |
Pevnost v tahu (UTS) | 950 – 1150 | 860 – 1000 | MPa | Maximální napětí, které materiál vydrží, než se zlomí. |
Mez kluzu (posun 0,2%) | 850 – 1050 | 790 – 930 | MPa | Napětí, při kterém začíná trvalá deformace; rozhodující pro návrhové meze. |
Prodloužení po přetržení | 8 – 15 | 10 – 18 | % | Míra houževnatosti; vyšší hodnota ELI znamená lepší houževnatost. |
Lomová houževnatost (K<sub>IC</sub>) | 55 – 70 | 70 – 95 | MPa√m | Odolnost proti šíření trhlin; výrazně vyšší u ELI, rozhodující pro odolnost proti poškození. |
Únavová pevnost (rotační nosník) | ~500 – 600 | ~500 – 600 | MPa | Odolnost proti selhání při cyklickém zatížení; zásadní pro dlouhou životnost ve vibrujícím prostředí. |
Maximální provozní teplota | ~315 | ~315 | °C | Vhodný pro mnoho draků letadel a některé aplikace spojené s motorem. |
Klíčové mezní hodnoty | O < 0,20 %, N < 0,05 %, Fe < 0,30 % | O < 0,13 %, N < 0,03 %, Fe < 0,25 % | Hmotnost % | Nižší obsah intersticiálů v ELI je hlavním rozlišovacím znakem, který zlepšuje houževnatost. |
Příslušné normy AMS (typické) | AMS 4911, AMS 6931 (LPBF), AMS 7001 (EBM) | AMS 4907, AMS 6930 (LPBF), AMS 7000 (EBM) | – | Certifikace často vyžadují dodržení specifických specifikací leteckých materiálů (AMS/ASTM). |
Export do archů
(Poznámka: Konkrétní vlastnosti do značné míry závisí na parametrech procesu AM, orientaci konstrukce a následném zpracování (zejména tepelném zpracování/HIP). Jedná se o reprezentativní hodnoty.)
Proč jsou tyto slitiny ideální pro letecké a kosmické montáže:
Kombinace vysoké pevnosti, nízké hustoty, vynikající odolnosti proti korozi, dobré únavové životnosti a přiměřené teplotní odolnosti činí Ti-6Al-4V i Ti-6Al-4V ELI výjimečně vhodnými pro náročné požadavky leteckých montáží.
- 5. třída je často dostačující pro širokou škálu montáží, kde je prioritou maximální pevnost a nákladová efektivita.
- Třída 23 se volí pro vysoce kritické montáže, které vyžadují vynikající odolnost proti poškození, pro aplikace s kryogenními teplotami (vesmír, vysoká nadmořská výška) nebo tam, kde je třeba splnit specifické požadavky na lomovou mechaniku.
Zásadní význam vysoce kvalitního kovového prášku:
Úspěch výroby spolehlivých, vysoce výkonných titanových držáků vytištěných 3D tiskem začíná kvalitou suroviny: kovového prášku. Na rozdíl od tradiční metalurgie, kde jsou výchozím bodem vlastnosti objemového materiálu, v AM vlastnosti prášku přímo ovlivňují kvalitu finálního dílu vrstvu po vrstvě. Mezi klíčové vlastnosti prášku patří např:
- Sféricita: Vysoce kulovité částice prášku rovnoměrně proudí a hustě se nabalují v loži prášku. To zajišťuje konzistentní nanášení vrstev a rovnoměrné tavení, čímž se minimalizuje riziko vzniku dutin nebo pórovitosti v konečném dílu. Nepravidelné nebo satelitně vázané částice mohou vést ke špatné tekutosti a hustotě balení.
- Tekutost: Dobrá tekutost, která přímo souvisí se sféricitou a distribucí velikosti částic, zajišťuje, že nanášeč může rozprostřít hladké a rovnoměrné vrstvy prášku po celé konstrukční plošině, což je rozhodující pro rozměrovou přesnost a kvalitu dílů.
- Čistota: Znečišťující látky (např. nadměrné množství kyslíku, dusíku, uhlíku nebo cizích částic) mohou vážně zhoršit mechanické vlastnosti (zejména tažnost a únavovou životnost) titanových slitin. Přísná kontrola procesu výroby prášku je nezbytná pro udržení vysoké úrovně čistoty, zejména nízkého obsahu intersticiálních látek, který je vyžadován u tříd ELI.
- Distribuce velikosti částic (PSD): Rozsah a rozložení velikostí částic ovlivňuje hustotu práškového lože, tekutost a dosažitelné rozlišení a kvalitu povrchu tištěného dílu. Různé stroje AM (LPBF vs. EBM) jsou optimalizovány pro specifické rozsahy PSD. Pro opakovatelnost procesu je zásadní konzistence PSD mezi jednotlivými dávkami.
Met3dp: Zajištění excelence prášků pro kritické aplikace
Protože si uvědomují, že kvalita prášku je nejdůležitější, společnosti jako např Met3dp investovaly velké prostředky do nejmodernějších technologií výroby prášků. Společnost Met3dp využívá špičkové metody v oboru, jako jsou:
- Vakuová indukční tavicí plynová atomizace (VIGA): Při tomto procesu se předlegovaná titanová surovina taví ve vakuu nebo v inertní atmosféře a poté se proud roztaveného kovu dezintegruje pomocí vysokotlakých proudů inertního plynu (argonu nebo dusíku). Tato technika je proslulá výrobou vysoce sférických prášků s dobrou čistotou a kontrolovanou PSD, které jsou ideální pro procesy LPBF. Zařízení Met3dp’ využívá jedinečné konstrukce trysek a proudění plynu pro optimalizaci sféricity a tekutosti.
- Proces plazmové rotující elektrody (PREP): Při PREP se rychle rotující tyč elektrody z cílové slitiny taví na svém hrotu plazmovým hořákem. Odstředivá síla pak vyvrhne roztavené kapičky, které za letu ztuhnou do vysoce kulovitých částic v inertní atmosféře. Metoda PREP je známá tím, že produkuje výjimečně čisté a sférické prášky s minimem satelitů a vnitřní pórovitosti, které jsou velmi žádoucí pro kritické aplikace a často upřednostňované pro procesy EBM.
Díky vlastní kontrole celého procesu výroby prášku, od výběru surovin až po atomizaci a klasifikaci, zajišťuje společnost Met3dp konzistentní dodávky vysoce čistých, vysoce sférických prášků Ti-6Al-4V a Ti-6Al-4V ELI optimalizovaných pro náročné požadavky aditivní výroby v leteckém průmyslu. Jejich portfolio zahrnuje také inovativní slitiny nad rámec standardů, které nabízejí další možnosti. Díky tomuto závazku ke kvalitě materiálů je společnost Met3dp spolehlivým partnerem a dodavatel vysoce výkonných kovových prášků pro společnosti, které chtějí vyrábět 3D tištěné komponenty vhodné pro lety. Nákupní týmy se mohou spolehnout na sledovatelnost a kontrolu kvality, která je vlastní výrobě prášku Met3dp’.
Konstrukční hlediska pro aditivní výrobu leteckých držáků
Přechod od navrhování pro tradiční výrobu (jako je obrábění nebo odlévání) k navrhování pro aditivní výrobu (DfAM) vyžaduje změnu myšlení. Namísto omezení přístupem k nástroji nebo omezením formy mohou konstruktéři využít svobodu AM při vytváření vrstvu po vrstvě a vytvářet vysoce optimalizované, komplexní a lehké letecké držáky. Úspěšná AM však s sebou přináší také vlastní soubor konstrukčních pravidel a úvah týkajících se podpůrných struktur, tepelného managementu a možností procesu. Přijetí principů DfAM je klíčové pro plné využití potenciálních výhod - snížení hmotnosti, konsolidace dílů a zvýšení výkonu - které činí 3D tištěné titanové držáky tak atraktivními pro letecký průmysl. Inženýři spolupracující se zkušeným DfAM aerospace poskytovatele služeb může výrazně zkrátit dobu učení.
Využití principů DfAM (Design for Additive Manufacturing):
DfAM není jen o tom, aby se stávající návrhy daly tisknout, ale o zásadním přehodnocení přístupu k návrhu tak, aby se maximalizovaly výhody procesu AM a zároveň se zmírnila jeho omezení. Klíčové zásady DfAM pro letecké držáky zahrnují:
- Geometrie řízená funkcemi: Zaměřte se na funkční požadavky (dráhy zatížení, tuhost, vibrační režimy, rozhraní) a nechte se jimi řídit při tvorbě geometrie, místo abyste se přizpůsobovali tvarům snadno vytvořeným staršími metodami.
- Složitost je (téměř) zdarma: Na rozdíl od obrábění, kde složitost výrazně zvyšuje náklady, má přidávání složitých prvků, vnitřních kanálků nebo komplexních zakřivení v AM minimální dopad na výrobní náklady, které jsou dány především objemem a výškou. Využijte toho k integraci funkcí.
- Design pro minimální podporu: Podpěry jsou sice často nezbytné, ale zvyšují náklady na materiál, čas tisku a náročnost následného zpracování a mohou poškodit povrch. Pokud je to možné, navrhujte díly se samonosnými úhly a pečlivě zvažte orientaci sestavení.
- Návrh pro následné zpracování: Zajistěte, aby kritické prvky byly přístupné pro odstranění podpěr, kontrolu a případné požadované obrábění nebo povrchovou úpravu. Zvažte přidání obětního materiálu (přídavek na obrábění) na kritické povrchy.
- Úvahy o tepelném managementu: Přemýšlejte o tom, jak se během tisku hromadí a rozptyluje teplo. Vyhněte se velmi tlustým částem sousedícím s velmi tenkými bez plynulých přechodů, protože to může zhoršit tepelné namáhání a deformace.
Optimalizace topologie: Tvarování s napětím:
Optimalizace topologie je základním kamenem DfAM pro konstrukční díly, jako jsou letecké držáky. Je to výpočetní metoda, která optimalizuje rozložení materiálu v definovaném geometrickém návrhovém prostoru na základě daných zatěžovacích podmínek, okrajových omezení a výkonnostních cílů (např. maximalizace tuhosti, minimalizace hmotnosti).
- Proces:
- Definujte prostor návrhu: Zadejte maximální přípustný objem, který může díl zabírat.
- Definice zatížení & Omezení: Aplikujte realistické provozní zatěžovací stavy (tah, tlak, smyk, vibrace) a definujte pevné body nebo zóny, kde se materiál nemůže vyskytovat (např. otvory pro šrouby, styčné plochy).
- Stanovte si cíle: Definujte cíl - obvykle se jedná o minimalizaci hmotnosti při dodržení určitých limitů tuhosti nebo napětí.
- Výrobní omezení: Zadejte omezení procesu AM, jako je minimální velikost prvku nebo samonosné úhly, abyste zajistili, že výsledný návrh bude vyrobitelný.
- Optimalizace běhu: Software iterativně odstraňuje materiál z málo namáhaných oblastí a ponechává optimalizovanou nosnou konstrukci.
- Výsledek: Často organické, “bionické” struktury, které účinně přenášejí zatížení s minimálním použitím materiálu, což vede k výrazné úspoře hmotnosti (často 20-50 % nebo více).
- Softwarové nástroje: Mezi běžné platformy patří Altair Inspire, Ansys Discovery, Dassault Systèmes (SOLIDWORKS Simulation/CATIA Generative Design), nTopology, Autodesk Fusion 360.
- Úvahy: Surový výstup často vyžaduje určité vyhlazení a zjemnění z důvodu vyrobitelnosti a únavy. Pro spolehlivé výsledky je třeba přesně definovat zatěžovací stav.
Podpůrné struktury: Nezbytné lešení:
V procesech tavení v práškovém loži (LPBF, EBM) vyžadují převisy a vodorovné prvky podpůrné struktury, které zabraňují zborcení během sestavování a ukotvují díl k sestavovací desce a působí proti deformačním silám.
- Účel:
- Podepřete povrchy a prvky směřující dolů pod kritickým samonosným úhlem (obvykle 45° od vodorovné roviny).
- Působí jako chladiče, které odvádějí teplo z taveniny, zejména na převisech.
- Zajistěte díl na konstrukční desce proti tepelnému namáhání a silám působícím při přelakování.
- Typy: Může se jednat o celistvé kvádry, jemné mřížky, sítě nebo stromové struktury. Výběr závisí na umístění, požadované pevnosti a snadnosti odstranění.
- Strategie návrhu:
- Minimalizace potřeby: Orientujte díl tak, abyste maximalizovali samonosné plochy. Místo ostrých vodorovných převisů používejte pokud možno zkosení nebo filety.
- Optimalizace pro odstranění: V místech styku s dílem používejte podpůrné konstrukce s malými kontaktními body (perforace, kuželové spoje), které usnadňují odlomení. Pokud je plánováno ruční nebo strojní odstranění, zajistěte fyzický přístup pro nástroje. Vyhněte se podpěrám v nepřístupných vnitřních kanálech, pokud to není nezbytně nutné a pokud nejsou určeny pro odstraňování prášku.
- Tepelné aspekty: V oblastech náchylných k přehřívání nebo deformacím mohou být zapotřebí hustší podpěry.
- Dopad: Podpěry spotřebovávají materiál a strojní čas, vyžadují značné množství práce při následném odstraňování a mohou ovlivnit povrchovou úpravu ploch, kterých se dotýkají. Efektivní strategie podpěr jsou klíčem k nákladově efektivnímu AM.
Orientační strategie: Připravte si půdu pro úspěch:
Způsob orientace dílu na konstrukční desce zásadně ovlivňuje několik aspektů tisku:
- Doba výstavby: Především podle výšky (počtu vrstev) ve směru Z. Plošná orientace dílu obecně zkracuje dobu sestavení, ale zvyšuje plochu průřezu na vrstvu a potenciálně i potřebu podpěr.
- Objem podpory: Různá orientace bude mít za následek různé množství potřebných podpůrných konstrukcí. Minimalizace podpěr je často klíčovým faktorem pro volbu orientace.
- Kvalita povrchu: Povrchy nakloněné vzhledem ke konstrukční desce vykazují “schodovitý” efekt v důsledku vrstevnatého charakteru AM. Svislé stěny mají tendenci mít lepší povrchovou úpravu než mělké úhly. Povrchy směřující dolů, kde se připevňují podpěry, mají po odstranění obvykle horší kvalitu povrchu.
- Mechanické vlastnosti (anizotropie): Vzhledem ke směrové povaze tuhnutí a tepelným gradientům mohou díly AM vykazovat anizotropní vlastnosti (různou pevnost/tažnost v závislosti na směru zkoušení vzhledem ke směru sestavení). Tento efekt je závislý na procesu a materiálu, ale je třeba jej zohlednit, zejména u dílů kritických z hlediska únavy. Dráhy kritického zatížení by měly být v ideálním případě zarovnány se směrem optimálních vlastností (často rovnoběžně s konstrukční deskou).
- Tepelné namáhání & deformace: Orientace ovlivňuje způsob, jakým se akumuluje a rozptyluje teplo, což má vliv na zbytkové napětí a riziko deformace. Orientace velkých plochých povrchů rovnoběžně s konstrukční deskou může zvýšit riziko deformace.
- Rozlišení funkce: Přesnost a definice malých prvků se může mírně lišit v závislosti na jejich orientaci vzhledem k liniím vrstvy.
Výběr optimální orientace často zahrnuje vyvážení těchto konkurenčních faktorů na základě konkrétní geometrie a požadavků na díl.
Tloušťka stěny & Velikost prvků:
Procesy AM mají omezení minimální velikosti prvků, které mohou spolehlivě vyrobit:
- Minimální tloušťka stěny: Obvykle kolem 0,4 – 1,0 mm, v závislosti na procesu (LPBF je obecně jemnější než EBM), stroji, materiálu a poměru výšky stěny a plochy. Velmi tenké a vysoké stěny jsou náchylné k deformaci nebo poruše během tisku.
- Minimální průměr otvoru/kolíku: Malé otvory (obvykle 0,5 – 1,0 mm) se mohou během tisku zalepit nebo je obtížné je vyčistit od prášku. Vodorovné otvory se často tisknou mírně eliptické. Malé kolíky mohou postrádat pevnost nebo definici.
- Samonosné úhly: Prvky skloněné pod úhlem větším než ~45° od vodorovné roviny lze obvykle stavět bez podpěr. Úhly mělčí než tato hodnota vyžadují podpěry.
- Navrhování pro limity: Zajistěte, aby kritické prvky splňovaly požadavky na minimální velikost. Pokud se plánuje dodatečné obrábění (např. vrtání otvorů na konečnou velikost), zvažte návrh mírně větších prvků.
Konsolidace částí: Snížení složitosti:
Jednou z nejvýkonnějších technik DfAM je konsolidace více součástí sestavy do jediného monolitického tištěného dílu.
- Příklad: Složitá sestava leteckého držáku se může skládat z hlavní obrobené konzoly, několika menších plechových výztuh a různých spojovacích prvků (šrouby, matice, nýty). Přístup DfAM by je mohl přepracovat na jediný topologicky optimalizovaný titanový díl vytištěný pomocí AM.
- Výhody:
- Snížený počet dílů: Zjednodušuje kusovník, správu zásob a logistiku dodavatelského řetězce.
- Eliminace spojů/spojovacích prvků: Snižuje hmotnost, odstraňuje potenciální místa poruchy, eliminuje pracnost montáže.
- Zlepšená strukturální účinnost: Umožňuje plynulejší přenos zatížení ve srovnání se šroubovými spoji.
- Potenciál pro integrovanou funkcionalitu: Přímá integrace funkcí, jako jsou kabelové příchytky nebo konstrukce tlumící vibrace.
Začlenění interních prvků:
Přístup AM’layer-by-layer umožňuje snadné vytváření složitých vnitřních geometrií:
- Mřížky: V rámci pevných objemů lze navrhovat periodické (např. krychlové, osmičkové) nebo stochastické (pěnové) mřížky, které výrazně snižují hmotnost a zároveň přizpůsobují tuhost a vlastnosti pohlcování energie. Klíčové hledisko: zajištění možnosti odstranění vnitřního prášku.
- Interní kanály: Konformní kanály pro chladicí kapaliny, hydrauliku nebo kabeláž mohou být integrovány přímo do konstrukce držáku a chráněny před vnějším prostředím. Konstrukce musí umožňovat odvádění prášku.
Při pečlivém zvážení těchto principů DfAM mohou inženýři navrhovat letecké držáky, které jsou nejen vyrobitelné pomocí AM, ale jsou skutečně optimalizované z hlediska výkonu, hmotnosti a nákladové efektivity v kontextu letectví a kosmonautiky.
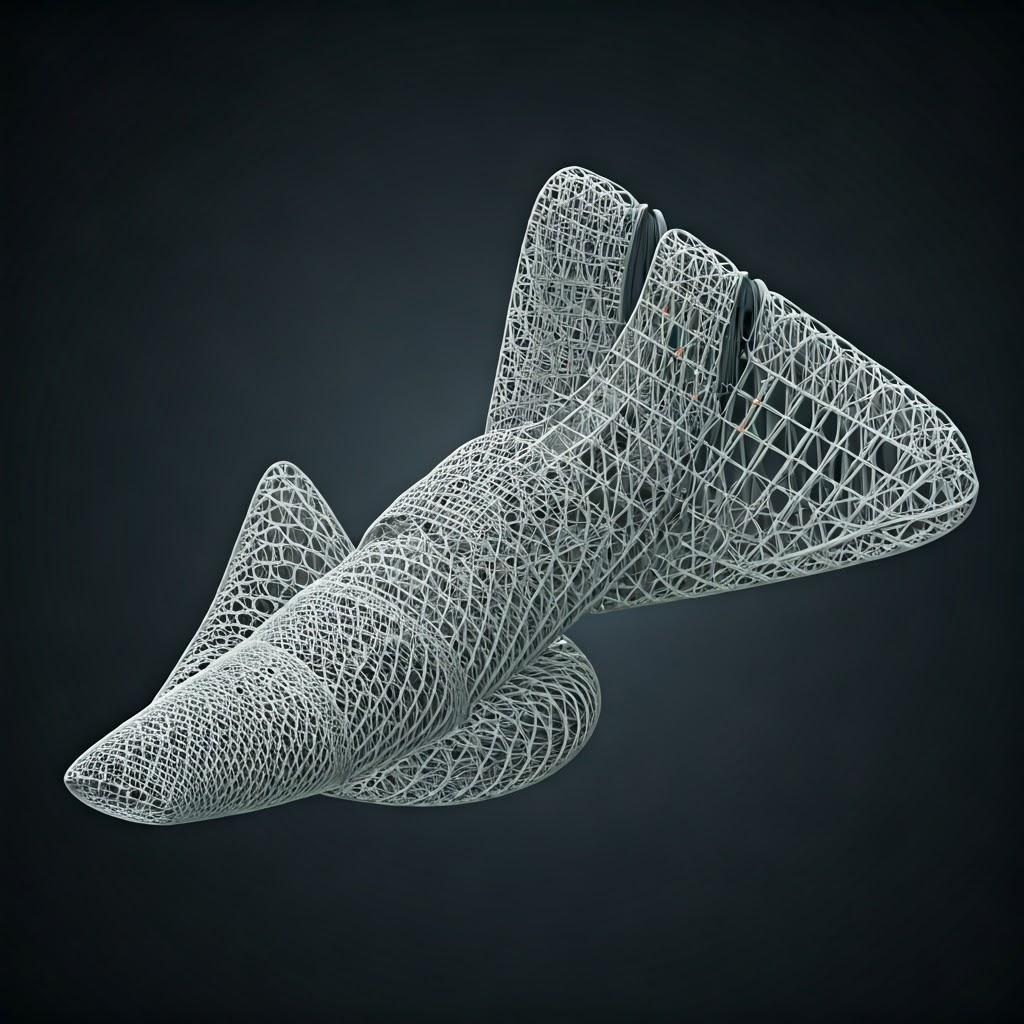
Tolerance, povrchová úprava a rozměrová přesnost 3D tištěných titanových držáků
Ačkoli aditivní výroba nabízí neuvěřitelnou volnost při navrhování, je pro součásti, jako jsou letecké držáky, které mají často přísné požadavky na uložení, montáž a funkci, zásadní pochopit dosažitelnou úroveň přesnosti. Inženýři a manažeři nákupu musí mít realistická očekávání ohledně tolerancí, povrchové úpravy a celkové rozměrové přesnosti 3D tištěných titanových dílů a musí plánovat nezbytné kroky následného zpracování, jako je obrábění, aby splnili nejpřísnější specifikace. Výběr konkrétních kovové metody 3D tisku jako je laserová fúze v práškovém loži (LPBF) nebo tavení elektronovým svazkem (EBM).
Dosažitelné tolerance s technologií Metal AM:
Při procesech AM se kovové díly vyrábějí po vrstvách a faktory, jako je tepelná roztažnost/kontrakce, velikost paprsku/laserového bodu, vlastnosti prášku a kalibrace stroje, ze své podstaty omezují dosažitelné tolerance.
- Obecné rozsahy: Typické dosažitelné tolerance u dobře řízených procesů LPBF nebo EBM, při nichž se vyrábějí titanové díly, se často pohybují v rozmezí ±0,1 mm až ±0,3 mm pro menší rozměry nebo ±0,1 % až ±0,2 % jmenovitého rozměru u větších prvků. To by mohlo zhruba odpovídat ISO 2768-m (střední) nebo někdy -f (jemný) toleranční třídy pro obecné rozměry.
- Faktory ovlivňující tolerance:
- AM proces: LPBF obecně nabízí o něco lepší přesnost a jemnější rozlišení prvků než EBM díky menší tloušťce vrstvy a jemnější velikosti bodu prášku/ paprsku. Vyšší teplota zpracování EBM může snížit zbytkové napětí, ale může ovlivnit jemné rozlišení prvků.
- Kalibrace strojů & Stav: Pravidelná kalibrace a údržba jsou pro přesnost zásadní.
- Velikost dílu & Geometrie: Větší díly nebo díly s výraznými teplotními odchylkami jsou náchylnější k deformaci a tolerančním odchylkám.
- Tepelné namáhání: Nerovnoměrné zahřívání a chlazení způsobuje smršťování a deformace, které je třeba předvídat a kompenzovat (např. simulací, podpůrnými strategiemi nebo úpravami konstrukce).
- Orientace na stavbu: Ovlivňuje kumulaci tepelného namáhání a vliv schodišťových stupňů na šikmé plochy.
- Kvalita prášku: Konzistentní velikost a morfologie částic přispívá k předvídatelnému tání a tuhnutí.
- Následné zpracování: Tepelné zpracování s uvolněním napětí může způsobit drobné rozměrové změny. Odstranění podpěr může ovlivnit přesnost povrchu.
- Dodržování přísných tolerancí: Pro kritické prvky, které vyžadují větší tolerance, než jsou obecné možnosti procesu AM (např. otvory ložisek, přesné styčné plochy, prvky pro zarovnání), následné obrábění (CNC frézování, soustružení, broušení) je téměř vždy nutné. Pro tyto prvky je zásadní zahrnout do fáze DfAM přídavky na obrábění.
Povrchová úprava (drsnost): Dodržení kvality povrchu (hrubost): stavba vs. dodatečné zpracování:
Povrchová úprava dílů AM je ze své podstaty drsnější než u obráběných povrchů, což je způsobeno procesem tavení po vrstvách a částečně roztavenými částicemi prášku ulpívajícími na povrchu.
- Drsnost povrchu (Ra) podle stavu:
- LPBF (SLM): Obvykle se pohybuje od 6 µm až 15 µm Rav závislosti na parametrech, orientaci a materiálu. Svislé stěny jsou obecně hladší než šikmé nebo vodorovné plochy.
- EBM: Obecně drsnější než LPBF, obvykle v rozmezí od 20 µm až 35 µm Ra v důsledku větších částic prášku a vyšších teplot zpracování, které způsobují větší spékání.
- Schodišťový efekt: Povrchy vytvořené pod úhlem vůči konstrukční desce vykazují viditelné linie vrstev, což přispívá k drsnosti. Závažnost závisí na úhlu a tloušťce vrstvy.
- Vliv povrchové úpravy: Drsné povrchy mohou působit jako koncentrátory napětí a negativně ovlivňovat únavovou životnost. Mohou být také nevhodné pro těsnicí povrchy nebo aerodynamické aplikace.
- Zlepšení povrchové úpravy (následné zpracování): Různé metody mohou výrazně zlepšit kvalitu povrchu:
- Tryskání abrazivem (kuličkové/ pískové): Poskytuje jednotný matný povrch, obvykle 3-8 µm Ra. Vhodné pro odstranění sypkého pudru a dosažení kosmetické jednotnosti.
- Obrábění / vibrační úprava: Díly se tromlují médiem, čímž se vyhladí jejich povrch a hrany. Lze dosáhnout 1-5 µm Ra. Nejlepší pro dávky menších, robustních dílů.
- CNC obrábění: Nabízí nejlepší kontrolu kvality povrchu, která umožňuje dosáhnout <1 µm Ra na konkrétní funkce.
- Leštění (ruční nebo automatické): Lze dosáhnout velmi hladkého, zrcadlového povrchu (<0,5 µm Ra), ale je často pracná.
- Elektrochemické leštění: Elektrochemicky vyhlazuje povrchy, účinný na složité tvary, ale vyžaduje specifické elektrolyty.
Rozměrová přesnost a ověřování:
U leteckých součástí je velmi důležité zajistit, aby finální díl splňoval všechny rozměrové specifikace. To vyžaduje důkladnou kontrolu kvality a metrologii.
- Řízení procesu: Udržování přísné kontroly nad parametry procesu AM (výkon laseru/ paprsku, rychlost, tloušťka vrstvy, průtok plynu, teplota), používání vysoce kvalitního a konzistentního prášku a zajištění správné kalibrace stroje jsou základem pro dosažení předvídatelných rozměrových výsledků. Společnosti, jako je Met3dp, kladou důraz na to přesnost a spolehlivost svých tiskáren SEBM, založených na přísné kontrole procesů.
- Metrologie a inspekce:
- Souřadnicové měřicí stroje (CMM): Poskytují vysoce přesná bodová měření pro ověřování kritických rozměrů, prvků GD&T (geometrické dimenzování a tolerování) a celkové tolerance tvaru.
- 3D skenování (laser/strukturální světlo): Snímání hustých dat mračna bodů celého povrchu dílu, které umožňuje porovnání s původním modelem CAD (analýza odchylek barevných map) a ověření složitých geometrií. Užitečné pro identifikaci deformací nebo zkreslení.
- Počítačová tomografie (CT): Využívá rentgenové záření k vytvoření 3D rekonstrukce dílu, což umožňuje nedestruktivní měření vnitřních vlastností, tloušťky stěn a detekci vnitřních defektů (pórovitosti), které jsou jinými metodami nedostupné. Klíčové pro ověření složitých vnitřních kanálů nebo mřížek navržených pomocí DfAM.
- Iterativní zlepšování: Naměřené údaje lze zpětně použít ve fázi návrhu a přípravy konstrukce, aby se použily kompenzační faktory a zlepšila se přesnost následných výtisků.
Splnění přísných požadavků leteckého průmyslu:
Letecké normy vyžadují vysokou úroveň přesnosti a spolehlivosti. Zatímco AM poskytuje počáteční téměř čistý tvar, je nutná kombinace řízení procesu, DfAM (včetně přídavků na obrábění), pečlivě naplánovaného následného zpracování a přísné metrologie, aby bylo zajištěno, že 3D tištěné titanové držáky splňují náročné požadavky na přizpůsobení, tvar a funkci kritických letových aplikací. V průběhu celého procesu je nezbytná spolupráce mezi konstruktéry, specialisty na AM a týmy zajišťujícími kvalitu. Manažeři nákupu by měli zajistit, aby potenciální dodavatelé aditivní výroby pro letecký průmysl mají spolehlivé systémy řízení kvality (QMS) a metrologické schopnosti.
Požadavky na následné zpracování 3D tištěných leteckých držáků
Běžnou mylnou představou o aditivní výrobě kovů je, že díly vyjíždějí z tiskárny připravené k použití. Ve skutečnosti, zejména u náročných aplikací v letectví a kosmonautice, je proces tisku pouze jedním z kroků výrobního procesu. K přeměně hotového dílu na funkční, spolehlivý a letu schopný letecký držák je zapotřebí řada nezbytných kroků následného zpracování. Tyto kroky jsou rozhodující pro uvolnění napětí, odstranění podpěr, dosažení požadovaných tolerancí a povrchové úpravy, zajištění integrity materiálu a ověření kvality. Pochopení těchto požadavků je zásadní pro přesný odhad nákladů, dodacích lhůt a zajištění toho, aby konečná součást splňovala přísné požadavky kvalifikace leteckých dílů normy.
1. Úleva od stresu / tepelné ošetření:
- Proč je to důležité: Rychlé cykly zahřívání a ochlazování, které jsou vlastní procesům tavení v práškovém loži, vytvářejí v tištěném titanovém dílu značná zbytková napětí. Tato napětí mohou způsobit deformace (zejména po vyjmutí z konstrukční desky), mikrotrhliny a vážně ohrozit mechanické vlastnosti dílu, zejména jeho únavovou životnost.
- Proces: Díly jsou obvykle podrobeny řízenému tepelnému cyklu ve vakuu nebo v peci s inertní atmosférou. Mezi běžné úpravy Ti-6Al-4V patří:
- Žíhání na uvolnění stresu: Zahřátí na určitou teplotu pod beta transus (např. 650-800 °C pro Ti-6Al-4V, doba namáčení závisí na tloušťce) a následné řízené ochlazení. Tím se výrazně sníží zbytková napětí při minimálním ovlivnění mikrostruktury a pevnosti.
- Úplné žíhání: Zahřátí na vyšší teplotu, někdy i vyšší než beta transus, po delší dobu, aby se dosáhlo maximální tažnosti a stability, často na úkor určité pevnosti.
- Solution Treating and Aging (STA): Lze je použít k přizpůsobení pevnosti a tažnosti, ale v porovnání s odlehčením napětí nebo HIP jsou pro typické montážní aplikace méně časté.
- standardy: Procesy tepelného zpracování leteckých dílů musí často splňovat normy, jako je AMS-H-81200, nebo specifické požadavky zákazníků.
2. Odstranění podpůrné konstrukce:
- Nezbytnost: Podpěrné konstrukce použité při stavbě musí být odstraněny.
- Metody:
- Ruční odstranění: Podpěry navržené se slabými rozhraními lze někdy odlomit ručně nebo pomocí jednoduchého ručního nářadí. Vyžaduje opatrné zacházení, aby nedošlo k poškození povrchu dílu.
- Obrábění (řezání, frézování, broušení): Často se vyžadují pro robustní podpěry nebo podpěry v těsných místech. CNC obrábění umožňuje přesné řízení.
- Drátové elektroerozivní obrábění (EDM): Lze je použít k přesnému řezání podpěr v blízkosti povrchu dílu, zejména složitých rozhraní nebo vnitřních podpěr, a minimalizovat tak poškození povrchu.
- Úvahy: DfAM zde hraje klíčovou roli - konstrukce podpěr pro snadný přístup a odstranění výrazně snižuje čas a náklady na následné zpracování. Oblasti, kde byly podpěry připevněny, často vyžadují další dokončovací práce.
3. Povrchová úprava:
- Účel: Zlepšení drsnosti povrchu při výrobě, zvýšení únavové životnosti, splnění estetických požadavků, příprava pro nátěry nebo dosažení specifických tolerancí na styčných plochách.
- Společné metody (jak je uvedeno výše):
- Tryskání abrazivem: Jednotný matný povrch, čištění.
- Třískové/vibrační dokončování: Dávkové vyhlazování, lámání hran.
- CNC obrábění: Pro kritické rozměry, GD&T prvky, těsnicí povrchy a dosažení hladkého povrchu (1 µm Ra) na specifických plochách.
- Leštění (ruční/automatické): Pro velmi nízké požadavky na Ra.
- Elektrochemické leštění: Pro složité tvary.
- Vliv na únavu: Drsnost povrchu slouží jako iniciační místo pro vznik únavových trhlin. Vyhlazení povrchů, zejména metodami, které vyvolávají tlakové zbytkové napětí (jako je kuličkování, někdy používané po prvotní povrchové úpravě), může výrazně zvýšit únavovou odolnost - což je kritický faktor pro letecké montáže při cyklickém zatížení.
4. Lisování za tepla (HIP):
- Co to je: Proces, při kterém jsou díly vystaveny současně vysoké teplotě (obvykle těsně pod bodem tání, např. ~900-950 °C pro Ti-6Al-4V) a vysokému tlaku inertního plynu (např. argonu, obvykle 100-200 MPa) ve specializované nádobě.
- Proč se používá (zejména v letectví a kosmonautice):
- Eliminuje vnitřní pórovitost: Vysoký tlak účinně uzavírá vnitřní dutiny (např. pórovitost plynu nebo vady způsobené nedostatečnou fúzí), které mohou být přítomny po tisku, a dosahuje téměř plné teoretické hustoty (~ 100 %).
- Zlepšuje mechanické vlastnosti: Výrazně zvyšuje tažnost, lomovou houževnatost a především únavovou pevnost odstraněním potenciálních míst iniciace trhlin (pórů).
- Snižuje rozptyl majetku: To vede ke konzistentnějším a předvídatelnějším vlastnostem materiálu v celém dílu a mezi různými sestavami.
- Úleva od stresu: Vysoké teploty také účinně snižují zbytková napětí.
- Požadavek: Vzhledem k výraznému zlepšení integrity materiálu a únavového výkonu je HIP často povinný požadavek pro 3D tištěné titanové součásti kritické pro let, včetně mnoha leteckých držáků. Dodavatelé musí mít přístup k certifikovaným kapacitám HIP.
5. Kontrola a testování (zajištění kvality):
- Nezbytnost: Ověření shody dílu se všemi specifikacemi před jeho certifikací pro let.
- Nedestruktivní zkoušení (NDT):
- Vizuální kontrola (VT): Základní kontrola povrchových vad, správný tvar.
- Rozměrová metrologie: CMM, 3D skenování (jak bylo popsáno dříve).
- Dye Penetrant Inspection (FPI/PT): Zjišťuje trhliny nebo pórovitost narušující povrch.
- Radiografické vyšetření (RT – rentgen) / počítačová tomografie (CT): Zjišťuje vnitřní vady (pórovitost, vměstky, trhliny) a ověřuje vnitřní geometrii. CT je stále cennější pro složité díly AM.
- Ultrazvukové testování (UT): Dokáže odhalit podpovrchové vady.
- Destruktivní zkoušky (obvykle na reprezentativních zkušebních vzorcích postavených společně s díly):
- Zkouška tahem: Měří mez kluzu, mez pevnosti v tahu, prodloužení (tažnost).
- Únavové zkoušky: Měří odolnost proti cyklickému zatížení.
- Metalografie: Mikroskopické zkoumání struktury zrn a hustoty materiálu po zpracování.
- Chemická analýza: Ověřuje složení slitiny.
- Dokumentace: V rámci systémů kvality pro letectví a kosmonautiku, jako je AS9100, se vyžaduje přísná dokumentace a sledovatelnost.
6. Volitelné nátěry:
- V závislosti na konkrétní aplikaci mohou být držáky opatřeny dalšími nátěry pro:
- Zvýšená odolnost proti opotřebení: Např. karbid wolframu nebo speciální tvrdé povlaky na kontaktních plochách.
- Tepelně bariérové nátěry (TBC): Pro díly pracující v prostředí s velmi vysokými teplotami.
- Maziva se suchým filmem: Na styčných plochách pro snížení tření.
- Priming/Painting: Pro ochranu životního prostředí nebo identifikaci.
Efektivní řízení celého řetězce následného zpracování vyžaduje značné odborné znalosti, specializované vybavení a důkladnou kontrolu procesu. Při hodnocení potenciálních poskytovatelé služeb kovového 3D tisku, je nezbytné posoudit jejich vlastní schopnosti a síť certifikovaných partnerů pro kroky, jako je tepelné zpracování, HIP, NDT a přesné obrábění.
Běžné problémy při 3D tisku titanových držáků a jejich řešení
Ačkoli aditivní výroba kovů nabízí značné výhody pro výrobu leteckých držáků, není bez problémů. Pochopení těchto potenciálních problémů a strategií k jejich zmírnění je klíčové pro úspěšné zavedení technologie AM pro kritické součásti. Klíčem k překonání těchto překážek je proaktivní plánování, optimalizace procesu, vysoce kvalitní materiály a důkladná kontrola kvality. Inženýři a manažeři nákupu by si měli být vědomi těchto běžných problémů výzvy v oblasti AM kovů při zadávání a získávání 3D tištěných titanových dílů.
1. Deformace a zkreslení:
- Výzva: Výrazné teplotní gradienty mezi roztavenou lázní a okolním materiálem během tisku vyvolávají vnitřní pnutí. Tato napětí se hromadí a mohou způsobit deformaci, zkroucení nebo dokonce odtržení dílu od konstrukční desky, což vede k selhání konstrukce nebo k dílům mimo rozměrové tolerance. Relativně nízká tepelná vodivost titanu může tento problém ještě zhoršit.
- Strategie zmírnění dopadů:
- Optimalizovaná orientace sestavení: Pomoci může orientace dílu tak, aby se minimalizovaly velké rovné plochy rovnoběžné s konstrukční deskou a snížila se výška Z.
- Robustní podpůrné struktury: Dobře navržené podpěry pevně ukotví díl k sestavovací desce a pomáhají odvádět teplo.
- Simulace procesu: Pomocí softwaru pro simulaci procesu sestavování lze předvídat oblasti s vysokým namáháním a možným narušením, což umožňuje předběžnou kompenzaci v souboru sestavení nebo úpravu strategie podpory.
- Optimalizované parametry procesu: Přesným vyladěním výkonu laseru/paprsku, rychlosti skenování a šrafovacích vzorů lze minimalizovat tepelné gradienty.
- Vytápění stavebních desek: Udržování zvýšené teploty v konstrukční komoře (což je důležité zejména u EBM, ale používá se i u některých systémů LPBF) snižuje tepelné gradienty a snižuje zbytkové napětí.
- Tepelné ošetření proti stresu: Nezbytný krok následného zpracování pro uvolnění nahromaděných napětí před odstraněním podpěry.
2. Pórovitost:
- Výzva: Přítomnost malých dutin nebo pórů v tištěném materiálu může výrazně zhoršit mechanické vlastnosti, zejména únavovou pevnost, tažnost a lomovou houževnatost. Pórovitost působí jako koncentrátory napětí, kde mohou vznikat trhliny. Mezi typy patří:
- Pórovitost v důsledku chybějící fúze: Nepravidelně tvarované dutiny způsobené nedostatečným příkonem energie k úplnému roztavení částic prášku nebo nedostatečným překrytím skenovacích stop.
- Pórovitost klíčového otvoru / Pórovitost plynu: Kulovité dutiny jsou často způsobeny nadměrným příkonem energie (odpařováním materiálu, který se zachytí) nebo plynem zachyceným v částicích prášku, který se uvolňuje během tavení.
- Strategie zmírnění dopadů:
- Optimalizované parametry procesu: Pečlivý vývoj a kontrola výkonu laseru/paprsku, rychlosti skenování, zaostření, tloušťky vrstvy a vzdálenosti mezi šrafami jsou rozhodující pro zajištění úplného roztavení a tavení bez přehřátí.
- Vysoce kvalitní kovový prášek: Klíčové je použití prášku s vysokou sféricitou, kontrolovaným PSD, nízkým obsahem vnitřního plynu a vysokou čistotou. Nekvalitní prášek (nepravidelné tvary, satelity, vnitřní pórovitost, kontaminace) je hlavním zdrojem vad. Met3dp’se zaměřuje na výrobu prvotřídního kovové prášky pomocí pokročilých technik atomizace plynu a PREP přímo řeší tuto výzvu.
- Kontrola inertní atmosféry: Udržování vysoce čisté atmosféry inertního plynu (argonu nebo dusíku) v konstrukční komoře zabraňuje oxidaci a kontaminaci během tisku. Správná dynamika proudění plynu je nutná k odstranění vedlejších produktů zpracování (rozstřik, výpary).
- Izostatické lisování za tepla (HIP): Nejúčinnější způsob, jak po tisku odstranit zbývající vnitřní pórovitost, což vede k téměř zcela hustým dílům. Často povinné pro kritické letecké součásti.
3. Zbytkové napětí:
- Výzva: I když je deformace během sestavování kontrolována, zůstávají v sestaveném dílu zablokována značná zbytková napětí. Tato napětí mohou vést k předčasnému selhání při zatížení, snížení únavové životnosti a nepředvídatelným deformacím při následném obrábění.
- Strategie zmírnění dopadů:
- Tepelné následné zpracování: Tepelné zpracování s uvolněním napětí nebo HIP jsou základní metody pro výrazné snížení zbytkového napětí.
- Optimalizace designu: Vyvarování se náhlých změn průřezu a velkých objemů těles může pomoci zvládnout akumulaci napětí.
- Optimalizace parametrů procesu: Stejně jako v případě pórovitosti a deformace mohou vyladěné parametry minimalizovat vznik napětí.
- Strategie budování: Strategie skenování (např. ostrovní skenování, rotace sektorů) mohou rovnoměrněji rozložit teplo.
- Výběr procesu: EBM obecně vede k nižšímu zbytkovému napětí než LPBF díky vysoké a rovnoměrné teplotě udržované v celé konstrukční komoře.
4. Podpora Obtížnost odstranění & Kvalita povrchu:
- Výzva: Odstraňování podpůrných struktur, zejména složitých nebo ve vnitřních dutinách, může být časově i finančně náročné a může vést k poškození povrchu dílu. Povrchy, na které byly podpěry připevněny, mají vždy nižší kvalitu (stopy po svědcích, drsnost).
- Strategie zmírnění dopadů:
- DfAM Focus: Navrhněte díly a zvolte jejich orientaci tak, abyste minimalizovali potřebu podpěr. Navrhujte podpěry se snadno rozbitnými nebo přístupnými rozhraními. Navrhněte dostatečně velké vnitřní kanály pro případné odstranění prášku a podpěr.
- Specializované techniky odstraňování: Použití vhodných nástrojů (ruční nástroje, CNC obrábění, elektroerozivní obrábění) podle typu a umístění podpěry.
- Povrchová úprava: Naplánujte potřebné dokončovací kroky (tryskání, otryskávání, obrábění) k vyčištění stop po opotřebení a dosažení požadované kvality povrchu.
5. Anizotropie (směrové vlastnosti):
- Výzva: Vzhledem ke směrovému tuhnutí taveniny a výsledné struktuře zrn (často podlouhlá sloupcovitá zrna ve směru stavby) se mechanické vlastnosti (např. pevnost, tažnost) dílů AM mohou lišit v závislosti na směru působícího zatížení vzhledem ke směru stavby (X, Y vs. Z). Tuto anizotropii je třeba zohlednit při návrhu a analýze.
- Strategie zmírnění dopadů:
- Charakteristika & Porozumění: Testování vlastností materiálu v různých orientacích vzhledem ke směru stavby, aby se zjistil stupeň anizotropie pro konkrétní proces a materiál.
- Optimalizovaná orientace sestavení: Vyrovnání primárního směru zatížení během provozu s orientací, která vykazuje nejpříznivější vlastnosti (často kolmo na směr stavby/paralelně k vrstvám).
- Následné zpracování (HIP): HIP může pomoci částečně homogenizovat mikrostrukturu a snížit tak stupeň anizotropie, i když ji nemusí zcela odstranit.
- Výběr procesu: Různé procesy AM mohou vést k různým stupňům anizotropie.
6. Manipulace s práškem a bezpečnost:
- Výzva: Jemné kovové prášky, zejména reaktivní materiály jako titan, představují bezpečnostní riziko. Za určitých podmínek mohou být hořlavé nebo výbušné (oblaka prachu) a představují riziko vdechnutí. Kontaminace (např. kyslíkem nebo vlhkostí) může zhoršit kvalitu prášku.
- Strategie zmírnění dopadů:
- Manipulace s inertní atmosférou: Pokud je to možné, manipulujte s titanovým práškem v prostředí inertního plynu (argonu).
- Správné uzemnění: Zabránění hromadění statické elektřiny.
- Osobní ochranné prostředky (OOP): Respirátory, rukavice, ochrana očí.
- Good Housekeeping: Zabránění hromadění prášku.
- Kontrolované prostředí: Udržování skladovacích podmínek s nízkou vlhkostí.
- Školení: Zajištění školení personálu o bezpečném zacházení s práškem.
7. Náklady a škálovatelnost:
- Výzva: V porovnání s některými tradičními metodami hromadné výroby může mít AM výroba kovů vysoké investiční náklady na vybavení a relativně pomalejší rychlost výroby. Náklady na prášek, zejména u vysoce kvalitních leteckých tříd, mohou být také značné. Proto může být AM méně nákladově efektivní pro velmi jednoduché díly nebo extrémně vysoké objemy výroby, kde jsou tradiční metody dobře zavedené.
- Strategie zmírnění dopadů:
- Zaměření na aplikace s vysokou hodnotou: Zaměřte se na komponenty, u nichž výhody AM’ (složitost, snížení hmotnosti, konsolidace, zkrácení dodací lhůty u složitých dílů) přinášejí nejvýznamnější přidanou hodnotu a ospravedlňují náklady. Do této kategorie často spadají montáže pro letectví a kosmonautiku.
- DfAM pro snížení nákladů: Optimalizujte návrhy s cílem minimalizovat spotřebu materiálu a dobu sestavení (např. optimalizace topologie, minimalizace podpěr).
- Hnízdění: Tisk více dílů najednou na konstrukční desku pro maximální využití stroje.
- Efektivita procesu: Využití vysoce produktivních strojů (např. multilaserových systémů) a optimalizace procesních parametrů.
- Spolupráce s dodavateli: Spolupráce se zkušenými poskytovateli služeb AM, kteří mají optimalizované pracovní postupy a úspory z rozsahu.
Uvědomíme-li si tyto problémy a zavedeme-li vhodné strategie pro jejich zmírnění v celé fázi návrhu, výroby a následného zpracování, mohou společnosti úspěšně využívat kovový 3D tisk k výrobě vysoce kvalitních a spolehlivých titanových držáků pro letecký průmysl, které splňují přísné požadavky tohoto odvětví.
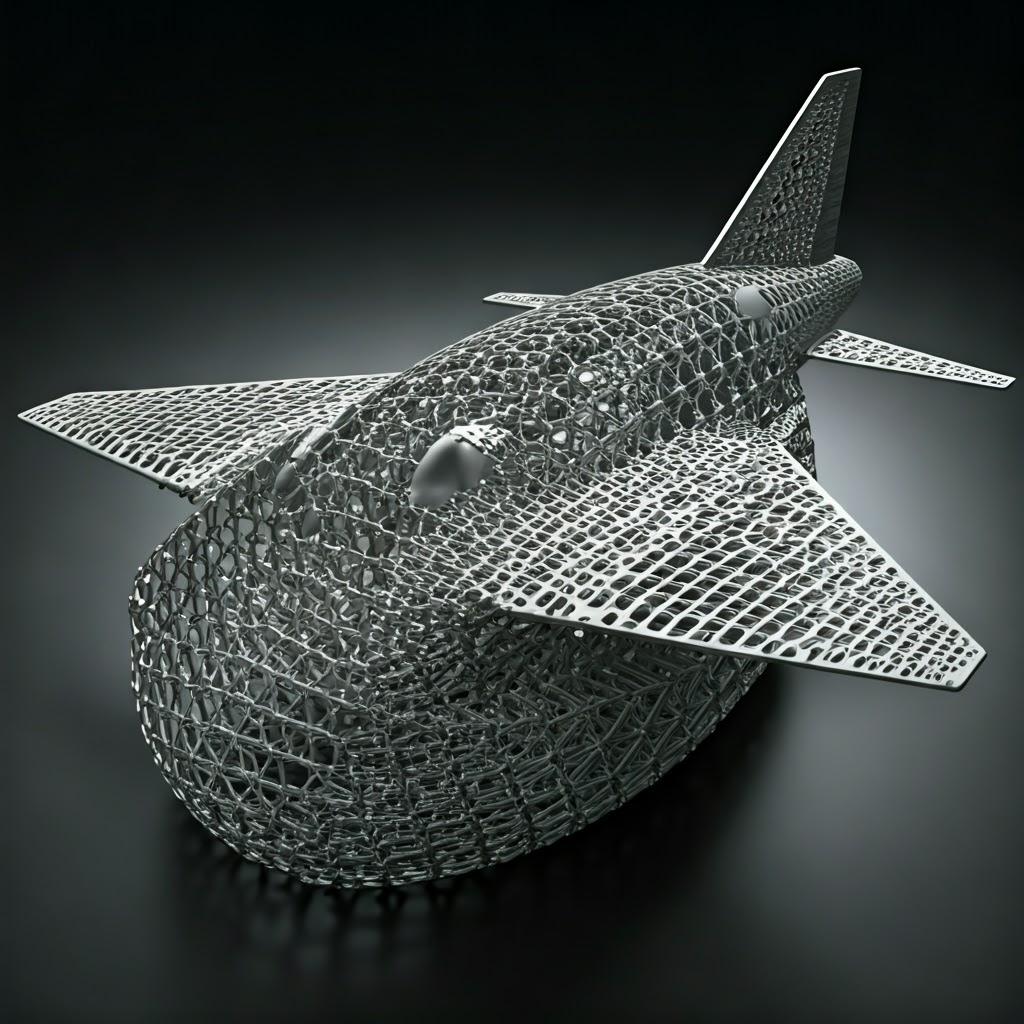
Jak vybrat správného poskytovatele služeb 3D tisku kovů pro letecké a kosmické montáže
Výběr správného výrobního partnera je při výrobě titanových držáků vytištěných na 3D tiskárně pro letecké aplikace pravděpodobně stejně důležitý jako návrh a výběr materiálu. Jedinečné požadavky leteckého průmyslu - přísné požadavky na kvalitu, složité součásti, kritické bezpečnostní funkce a přísné certifikační procesy - znamenají, že ne všichni poskytovatelé služeb aditivní výroby kovů jsou si rovni. Výběr nekvalifikovaného dodavatele může vést k nákladným zpožděním, neshodným dílům a potenciálním rizikům. Manažeři a inženýři nákupu musí provést důkladnou prověrku, aby identifikovali partnera se specifickými odbornými znalostmi, certifikacemi, schopnostmi a přístupem ke kvalitě, které jsou pro letecký průmysl vyžadovány. Zde je průvodce hodnocením potenciálních dodavatelů:
1. Prokázané odborné znalosti a zkušenosti v oblasti letectví a kosmonautiky:
- Záznamy o činnosti: Hledejte dodavatele s prokazatelnými zkušenostmi s výrobou součástí, zejména konstrukčních dílů, jako jsou držáky, pro letecký průmysl. Požádejte o případové studie, reference a příklady podobných dílů, které vyrobili.
- Specializace na materiál: Nezbytné jsou hluboké odborné znalosti v oblasti zpracování Ti-6Al-4V a Ti-6Al-4V ELI. To zahrnuje porozumění jeho metalurgii, vhodným parametrům procesu AM, reakcím na tepelné zpracování a běžným způsobům poruch.
- Porozumění aplikaci: Dodavatel by měl rozumět funkčním požadavkům leteckých držáků (podmínky zatížení, únavová životnost, faktory prostředí) a tomu, jak může AM tyto požadavky nejlépe splnit.
- Povědomí o právních předpisech: Znalost příslušných leteckých norem (AMS, ASTM, AS), doložek kvality (např. od společností Boeing, Airbus, Lockheed Martin, NASA) a případně ITAR (International Traffic in Arms Regulations) nebo jiných požadavků na kontrolu exportu, pokud jsou použitelné.
2. Základní certifikace:
Certifikace jsou neoddiskutovatelným důkazem závazku dodavatele ke kvalitě a řízení procesů, zejména v leteckém průmyslu.
- AS9100: Jedná se o základní normu systému řízení kvality (QMS) pro letecký, kosmický a obranný průmysl. Zahrnuje požadavky normy ISO 9001, ale přidává řadu specifických kontrolních mechanismů pro letectví a kosmonautiku týkajících se bezpečnosti, spolehlivosti, sledovatelnosti, řízení rizik, řízení konfigurace a dalších. Dodavatel 3D tisku s certifikací AS9100 je obvykle považován za minimální požadavek pro letově kritické komponenty.
- ISO 9001: Základní certifikace QMS, která označuje zavedené procesy kontroly kvality, dokumentace a neustálého zlepšování. Často je předpokladem pro AS9100.
- Akreditace Nadcap: Zatímco AS9100 se vztahuje na celkový systém řízení jakosti, Nadcap poskytuje specifickou akreditaci pro speciální procesy. Akreditaci Nadcap (buď vlastní, nebo prostřednictvím certifikovaných partnerů) hledejte pro kritické kroky následného zpracování, jako jsou:
- Tepelné zpracování (HT)
- Nedestruktivní zkoušení (NDT)
- Svařování (WLD) – méně časté pro samotné AM díly, ale může se vztahovat na související procesy.
- Zkušebny materiálů (MTL)
- Chemické zpracování (CP) – Pro určité povrchové úpravy nebo leptání. (Poznámka: Nadcap pro aditivní výrobu se vyvíjí, ale zásadní jsou akreditace pro související speciální procesy).
3. Technologie, vybavení a kapacita:
- Vhodná technologie AM: Ujistěte se, že dodavatel disponuje správným typem technologie AM pro vaše potřeby (např. LPBF pro jemné prvky, EBM pro potenciálně nižší napětí a různé mikrostruktury). Posuďte konkrétní značku/model tiskáren, jejich stav a záznamy o údržbě. Společnosti jako např Met3dp, které nabízejí vlastní pokročilé tiskárny SEBM vedle možností LPBF poskytují technologické možnosti. Můžete se dozvědět více O nás a náš závazek používat špičkové vybavení.
- Kalibrace a údržba strojů: Přísné protokoly pro kalibraci strojů, preventivní údržbu a sledování výkonu jsou nezbytné pro zajištění stálé kvality a přesnosti dílů.
- Kapacita a redundance: Má dodavatel dostatečnou kapacitu strojů, aby splnil časový plán projektu, včetně možného náběhu výroby? Disponuje více stroji, aby zajistil redundanci pro případ výpadku?
- Kontrolované prostředí: Správná kontrola prostředí (teplota, vlhkost, čistota) ve výrobním zařízení je důležitá, zejména při manipulaci s citlivými kovovými prášky.
4. Odborné znalosti materiálů a kontrola kvality:
- Získávání a správa prášků: Jak dodavatel získává, testuje a zpracovává titanový prášek?
- Získávání zdrojů: Nakupují od kvalifikovaných externích dodavatelů, nebo mají vlastní výrobu jako Met3dp, která nabízí lepší kontrolu kvality a sledovatelnosti?
- Příchozí kontrola: Jaké testy se provádějí na vstupních šaržích prášku (chemie, PSD, morfologie, tekutost)?
- Sledovatelnost: Mohou u konkrétního dílu zjistit přesnou šarži použitého prášku?
- Manipulace & amp; Skladování: Jsou dodržovány přísné postupy pro manipulaci s inertní atmosférou, skladování a prevenci křížové kontaminace?
- Strategie recyklace: Jaké jsou jejich ověřené postupy prosévání, testování a míchání opakovaně použitého prášku, aby byla zajištěna trvalá kvalita? Přísná kontrola řízení životního cyklu prášku je pro letecký průmysl zásadní.
5. Komplexní interní schopnosti & amp; partnerská síť:
Výroba hotového leteckého držáku vyžaduje víc než jen tisk. Zhodnoťte schopnost dodavatele zvládnout celý pracovní postup:
- Podpora DfAM: Nabízejí inženýrskou podporu pro optimalizaci návrhů pro aditivní výrobu?
- Tisk: Základní schopnost s robustním řízením procesu.
- Následné zpracování: Zhodnoťte jejich vlastní schopnosti v oblasti odlehčování/tepelného zpracování, odstraňování výztuh, povrchové úpravy a klíčových kroků, jako je HIP. Pokud je zadáváno externím dodavatelům, jsou jejich partneři certifikováni podle Nadcapu a jsou pevně integrováni do jejich systému kvality?
- Obrábění: Mají vlastní kapacity pro přesné CNC obrábění nebo kvalifikované partnery pro dokončování kritických prvků?
- Kontrola & Metrologie: Disponují moderním metrologickým vybavením (souřadnicové měřicí stroje, 3D skenery, CT skenery) a certifikovanými možnostmi nedestruktivního zkoušení (FPI, rentgen)?
Integrovaná nabídka služeb často vede k lepší komunikaci, zkrácení doby realizace a jasnější odpovědnosti.
6. Technická podpora a spolupráce:
- Aplikační inženýři: Neocenitelný je přístup ke kvalifikovaným inženýrům, kteří mohou poskytovat konzultace v oblasti DfAM, radit při výběru materiálů, simulovat procesy sestavování a podporovat kvalifikační úsilí.
- Přístup založený na spolupráci: Hledejte partnera, který je ochoten úzce spolupracovat s vaším týmem, zajišťovat transparentnost a jasnou komunikaci v průběhu celého životního cyklu projektu.
7. Robustní systém řízení kvality (QMS):
- Kromě certifikátu: Hledejte důkazy hluboce zakořeněné kultury kvality. Patří sem důkladná dokumentace procesů, záznamy o školení obsluhy, jasné postupy hlášení neshod a nápravných opatření, důsledné řízení konfigurace a podrobný sběr/uchovávání dat.
8. Dodací lhůty, kapacita a rychlost reakce:
- Realistické citování: Poskytují jasné a realistické odhady doby realizace na základě aktuální kapacity?
- Termíny schůzek: Jaké jsou jejich výsledky v oblasti včasného dodání?
- Škálovatelnost: Dokáží podpořit vaše potřeby od výroby prototypu až po potenciální sériovou výrobu?
Shrnutí kontrolního seznamu hodnocení:
Kritéria | Klíčové úvahy | Důležitost |
---|---|---|
Zkušenosti z leteckého průmyslu | Prokazatelné výsledky, odborné znalosti v oblasti Ti64, znalost aplikací, povědomí o předpisech. | Kritické |
Certifikace | AS9100 (povinné), ISO 9001, Nadcap (pro speciální procesy). | Kritické |
Technologie a vybavení | Vhodná technologie AM (LPBF/EBM), kvalita stroje & údržba, kapacita, redundance. | Vysoký |
Kontrola materiálu | Získávání prášku, testování, sledovatelnost, manipulace, recyklační protokoly. (Vlastní výroba jako Met3dp je výhodou). | Kritické |
Schopnost "od konce ke konci | DfAM, tisk, tepelné zpracování, HIP, obrábění, dokončovací práce, NDT, metrologie (vlastní nebo certifikovaní partneři). | Kritické |
Technická podpora | Konzultace DfAM, simulace procesů, podpora kvalifikace. | Vysoký |
Systém řízení kvality | Dokumentované procesy, sledovatelnost, řízení rizik, kultura neustálého zlepšování nad rámec certifikátu. | Kritické |
Dodací lhůta & amp; Kapacita | Realistické nabídky, včasné dodávky, škálovatelnost. | Vysoký |
Komunikace/Partnerství | Transparentnost, vstřícnost, přístup založený na spolupráci. | Vysoký |
Export do archů
Pečlivým vyhodnocením potenciálních dodavatelů podle těchto kritérií si mohou letecké společnosti s jistotou vybrat schopného a spolehlivého dodavatele partner pro výrobu leteckých komponentů vybavená pro dodávku vysoce kvalitních, letuschopných titanových držáků vytištěných na 3D tiskárně.
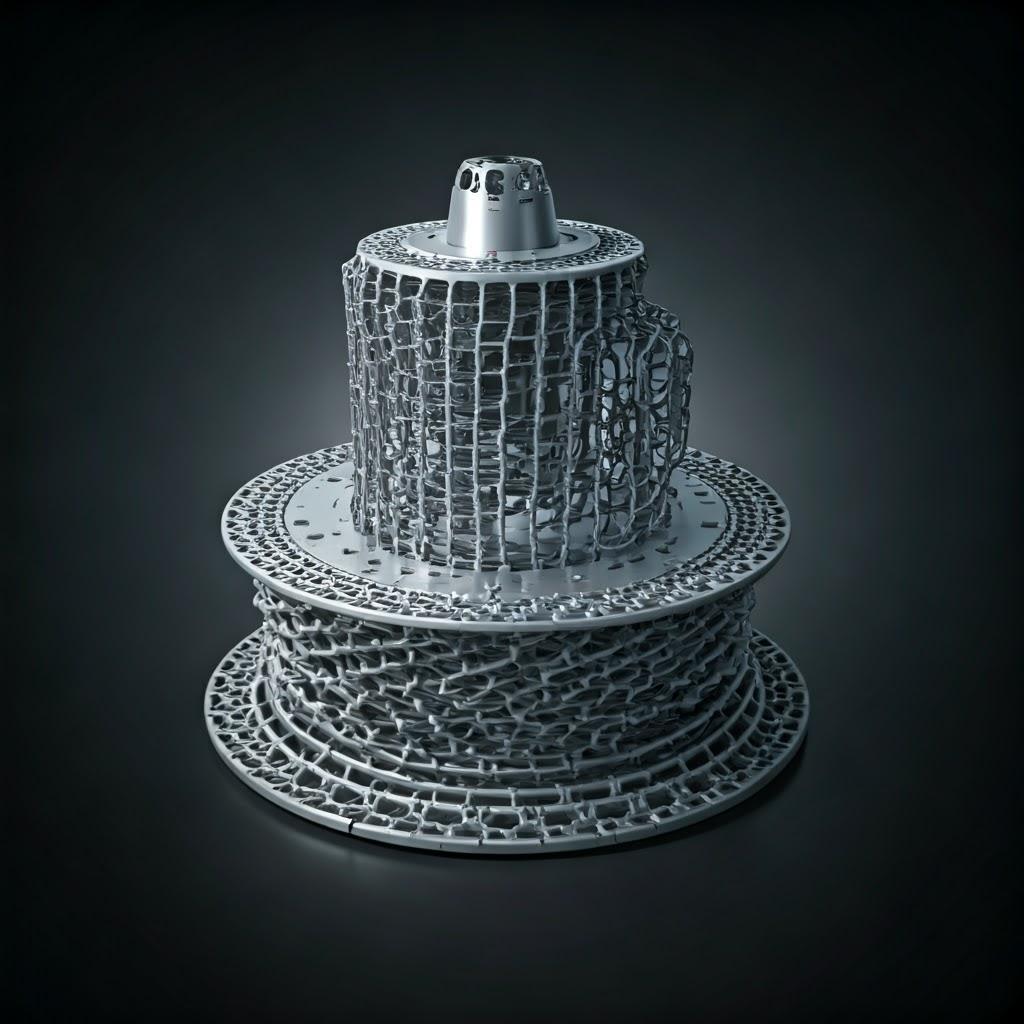
Nákladové faktory a dodací lhůty pro 3D tištěné titanové držáky pro letectví a kosmonautiku
Zatímco výkonnostní a konstrukční výhody 3D tištěných titanových držáků jsou zřejmé, pochopení souvisejících nákladů a typických dodacích lhůt je zásadní pro plánování projektu, sestavování rozpočtu a porovnání AM s tradičními výrobními metodami. Náklady i doba realizace jsou ovlivněny složitou souhrou faktorů souvisejících s materiálem, složitostí konstrukce, strojním časem, prací, následným zpracováním a požadavky na kvalitu, které jsou pro letecký průmysl neodmyslitelné. Manažeři nákupu potřebují mít jasnou představu o těchto faktorech, aby mohli přijímat informovaná rozhodnutí o dodávkách a řídit očekávání.
Klíčové faktory ovlivňující náklady na 3D tištěné titanové držáky:
Konečná cena titanového držáku vytištěného na 3D tiskárně se odvíjí od několika faktorů:
Hnací síla nákladů | Popis & Ovlivňující faktory | Dopad na celkové náklady |
---|---|---|
1. Náklady na materiál | Cena za kilogram vysoce kvalitního leteckého prášku Ti-6Al-4V nebo Ti-6Al-4V ELI. Zahrnuje objem samotného dílu plus objem podpůrných konstrukcí. Roli hraje také míra obnovy prášku a účinnost recyklace. Titanový prášek je ze své podstaty drahý. | Vysoký |
2. Strojový čas | Náklady na hodinu provozu stroje AM na kov vynásobené celkovou dobou výroby. Doba sestavení se řídí především těmito faktory: <br> – Objem dílů: <br> – Výška dílu (osa Z): Více vrstev znamená delší dobu tisku. <br> – Složitost: Složité dráhy skenování mohou prodloužit dobu tisku na jednu vrstvu. <br> – Efektivita hnízdění: Kolik dílů se vejde na jednu konstrukční desku. | Vysoký |
3. Náklady na pracovní sílu | Kvalifikovaná práce je nutná pro: <br> – Příprava stavby: <br> – Obsluha stroje & Monitorování. <br> – Demontáž/odstraňování dílů: <br> – Vyjmutí podpěr: Vyjmutí dílů ze stavební komory, odstranění sypkého prášku: Často ruční nebo poloautomatické, u složitých podpěr může být velmi časově náročné. <br> – Práce po zpracování: Obrábění, dokončovací práce, kontrolní úkony. | Významné |
4. Náklady na následné zpracování | Náklady spojené s nezbytnými kroky po tisku: <br> – Odlehčení od napětí / tepelné zpracování: <br> – Izostatické lisování za tepla (HIP): Často se zadává specializovaným zařízením, což představuje značné navýšení nákladů, ale má zásadní význam pro vlastnosti. <br> – Obrábění: <br> – Povrchová úprava: Tryskání, bubnování, leštění atd. <br> – NDT & Kontrola: Čas zařízení, práce certifikovaného inspektora. | Významné |
5. Složitost návrhu & Podporuje | Zatímco geometrická složitost sama o sobě nijak drasticky nezvyšuje tisk náklady (na rozdíl od obrábění), velmi složité konstrukce mohou vyžadovat rozsáhlé podpůrné konstrukce. To zvyšuje: <br> – Spotřebu materiálu (podpěry). <br> – Čas sestavení (podpěry zvyšují objem/výšku). <br> – Práci po zpracování (odstranění podpěr). | Střední až vysoká |
6. Zajištění kvality & amp; Certifikace | Náklady spojené s důkladnou dokumentací, sledovatelností, zkouškami (destruktivními & NDT), kontrolními zprávami a certifikačními dokumenty, které jsou nutné pro splnění leteckých norem (např. shoda s AS9100, zprávy o kontrole prvního výrobku – FAIR). | Střední |
7. Objem objednávky | Škálování nákladů na AM se liší od tradičních metod. <br> – Náklady na nastavení (příprava souboru, plánování sestavení) se amortizují přes velikost dávky. <br> – Plné sestavovací desky jsou efektivnější z hlediska strojového času. <br> – Možnost množstevních slev od dodavatelů na velkoobchodní 3D tisk <br> – Snížení nákladů na jeden díl je však v závislosti na objemu obecně méně dramatické než u velkoobjemových metod, jako je odlévání nebo lisování. | Střední |
8. Iterace návrhu | Náklady spojené s tvorbou prototypů a změnami designu během vývojové fáze. AM vyniká rychlým opakováním, což může snížit celkové náklady na vývoj ve srovnání s metodami vyžadujícími nástroje. | Proměnná (vývoj) |
Export do archů
Porozumění výpočtu nákladů: Poskytovatelé služeb AM obvykle vypočítávají náklady na základě kombinace spotřeby materiálu (podle hmotnosti nebo objemu), strojního času (na základě simulace sestavení) a odhadované práce/nákladů na následné zpracování. Poskytnutí čistého, optimalizovaného modelu CAD a jasných specifikací pomáhá zajistit přesnou kalkulaci.
Součásti a typické rozsahy dodací lhůty:
Doba realizace - celková doba od zadání objednávky do dodání dílu - je v letectví často stejně důležitá jako náklady, zejména u programů MRO nebo rychlého vývoje. Skládá se z několika fází:
- Citace & Zpracování objednávky (1-5 pracovních dnů): Kontrola modelu CAD a specifikací, vygenerování cenové nabídky, potvrzení objednávky a provedení počáteční přípravy stavby (např. orientace, plánování strategie podpory).
- Doba čekání ve frontě (proměnná: dny až týdny): Čas strávený čekáním na uvolnění vhodného stroje. To do značné míry závisí na aktuálním vytížení a kapacitě dodavatele.
- Doba tisku (hodiny až několik dní): Skutečný čas, který díl(y) stráví tiskem ve stroji AM. Závisí na velikosti, výšce, složitosti a hustotě vnoření dílu. Tisk jednoho velkého držáku nebo celé desky menších držáků může snadno trvat 24-72 hodin i více.
- Ochlazení (několik hodin): Doba potřebná k dostatečnému ochlazení stavební komory a dílů před jejich vyjmutím, často v inertní atmosféře.
- Následné zpracování (proměnná: dny až týdny): To je často nejvýznamnější a nejproměnlivější složka dodací lhůty. Zahrnuje:
- Odstraňování napětí / tepelné zpracování (může trvat 1-3 dny včetně cyklů v peci a manipulace).
- HIP (vyžaduje plánování s poskytovateli HIP, čas na přepravu a samotný cyklus HIP - může přidat 1-2 týdny).
- Odstranění podpory & Základní dokončovací práce (1-3 dny v závislosti na složitosti).
- Přesné obrábění (závisí na složitosti, může trvat několik dní až týdnů).
- NDT inspekce & amp; kontroly kvality (1-5 dní v závislosti na požadavcích).
- Doprava (proměnná): Doba přepravy do místa zákazníka.
Typické rozmezí dodací lhůty (orientační):
- Prototypy (se základním následným zpracováním, jako je odlehčení napětí): 2 – 4 týdny
- Funkční prototypy / kvalifikační díly (včetně HIP, základního obrábění): 4 – 7 týdnů
- Výrobní díly (plně zpracované, zkontrolované, certifikované): 5 – 10+ týdnů
Důležité upozornění (od 16. dubna 2025): Dodací lhůty mohou kolísat v závislosti na celkové poptávce v odvětví, nevyřízených objednávkách konkrétních dodavatelů a dostupnosti specializovaných služeb následného zpracování, jako je HIP. Aktuální dobu dodání si vždy ověřte u vybraného dodavatele ve fázi nabídky.
Strategie pro optimalizaci nákladů a doby realizace:
- Design for AM (DfAM): Optimalizujte návrhy tak, abyste minimalizovali objem, snížili stavební výšku a minimalizovali podpůrné konstrukce. Konsolidujte díly, abyste omezili následnou montáž a kontrolu.
- Hnízdění: Maximalizujte počet dílů vytištěných na jednu sestavovací desku.
- Minimalizace následného zpracování: Navrhujte díly tak, abyste minimalizovali potřebu rozsáhlého obrábění nebo složitého odstraňování podpěr. Jasně definujte, které prvky vyžadují přísné tolerance nebo specifické povrchové úpravy.
- Čiré specifikace: Poskytněte předem úplné a jednoznačné výkresy a specifikace, abyste se vyhnuli zpoždění při cenové nabídce nebo výrobě.
- Spolupráce s dodavateli: Spolupracujte se svým dodavatelem AM již na začátku procesu návrhu a využijte jeho odborných znalostí pro optimalizaci nákladů a doby realizace.
Pochopením těchto faktorů ovlivňujících náklady a dobu realizace mohou letecké společnosti lépe plánovat projekty, řídit rozpočty a efektivně využívat plný potenciál titanových držáků vytištěných 3D tiskem.
Často kladené otázky (FAQ) o 3D tištěných titanových držácích pro letectví a kosmonautiku
Zde jsou odpovědi na některé časté otázky, které mají inženýři a manažeři nákupu, když zvažují aditivní výrobu titanových leteckých držáků:
Otázka 1: Jsou titanové držáky vytištěné 3D tiskem stejně pevné jako tradičně obráběné nebo kované?
A: Ano, při výrobě kvalifikovanými postupy a vhodným následným zpracováním mohou 3D tištěné komponenty Ti-6Al-4V vykazovat mechanické vlastnosti (jako je pevnost v tahu, mez kluzu a únavová pevnost), které jsou srovnatelné s kovanými (obráběnými ze sochoru) nebo kovanými protějšky, a někdy je dokonce překonávají. Dosažení tohoto cíle vyžaduje:
- Optimalizované parametry procesu AM pro zajištění plné hustoty a dobrého spojení vrstev.
- Vysoce kvalitní prášek pro letecký průmysl s kontrolovaným chemickým složením a morfologií.
- Zásadní následné zpracování, zejména Izostatické lisování za tepla (HIP), což eliminuje vnitřní pórovitost a výrazně zlepšuje únavové vlastnosti, takže jsou často rovnocenné nebo lepší než kované materiály, zejména pokud jde o konzistenci únavové životnosti.
- Vhodná tepelná úprava pro snížení napětí nebo žíhání. Výkonnost závisí do značné míry na kontrole kvality prováděné výrobcem dodavatel aditivní výroby pro letecký průmysl.
Otázka 2: Jaké specifické certifikace pro letecký průmysl jsou nezbytně nutné pro dodavatele vyrábějící 3D tištěné držáky?
A: Primární certifikace systému řízení kvality dodavatele je AS9100. To dokazuje, že mají potřebné kontrolní mechanismy pro sledovatelnost, řízení konfigurace, řízení rizik a další procesy důležité pro letecký průmysl. Nad rámec AS9100, Akreditace Nadcap má zásadní význam pro všechny speciální procesy, ať už prováděné ve firmě nebo subdodavateli. To běžně zahrnuje Tepelné zpracování (HT) a Nedestruktivní zkoušení (NDT). Pokud se používá HIP (což se u kritických montáží velmi doporučuje), měl by být poskytovatel HIP rovněž držitelem příslušných certifikátů (často ISO 9001/AS9100 a případně Nadcap HT). Samotná kvalifikace dílu zahrnuje přísné testování a dokumentaci specifickou pro danou součást a požadavky zákazníka, často s odkazem na AMS nebo specifické normy OEM.
Otázka 3: Můžeme jednoduše vzít náš stávající návrh držáku (vyrobený pro obrábění) a vytisknout jej na 3D tiskárně?
A: I když je technicky možné vytisknout konstrukci původně určenou pro obrábění, nevyužívá se tím hlavních výhod aditivní výroby. Přímý “tisk jako takový” přístup často vede k tomu, že díl je těžší a jeho výroba pomocí AM je potenciálně dražší, než je nutné. Aby bylo možné z AM skutečně těžit, měl by být díl přepracován podle zásad designu pro aditivní výrobu (DfAM). To zahrnuje:
- Provedení optimalizace topologie za účelem odstranění nepotřebného materiálu na základě cest zatížení.
- Zvažování možností konsolidace dílů za účelem snížení složitosti montáže.
- Optimalizace konstrukce s cílem minimalizovat podpůrné struktury a usnadnit následné zpracování.
- Využití schopnosti AM’ vytvářet složité vnitřní prvky nebo mřížkové struktury pro snížení hmotnosti nebo zlepšení funkčnosti. Pouhý tisk staré konstrukce je zřídkakdy optimálním přístupem.
Otázka 4: Jaká je typická úspora nákladů při použití AM pro letecké montáže ve srovnání s obráběním?
A: Úspory nákladů jsou velmi variabilní a do značné míry závisí na konkrétní součásti, její složitosti, tradičním výrobním poměru mezi nákupem a letem a objemu výroby.
- Přímé náklady na díl: U jednoduchých držáků vyráběných ve velkých objemech může být tradiční obrábění stále levnější v přímém poměru mezi jednotlivými díly. U velmi složitých držáků však může být AM konkurenceschopná nebo dokonce levnější díky volnosti konstrukce a nižším nákladům na seřízení.
- Snížení množství materiálového odpadu: AM výrazně snižuje plýtvání materiálem v porovnání s obráběním titanových sochorů (špatný poměr mezi nákupem a letem). Úspora drahých titanových surovin může být značná (50-90% snížení odpadu).
- Snížení hmotnosti: AM umožňuje výraznou úsporu hmotnosti (20-60 %) díky optimalizaci topologie. To se projeví v podstatných úsporách provozních nákladů po celou dobu životnosti letadla (spotřeba paliva) nebo ve zvýšení potenciálu příjmů (užitečné zatížení). Tato úspora během životního cyklu často převáží případné zvýšení počátečních nákladů na díl.
- Konsolidace částí: Snížení počtu dílů šetří montážní práci, spojovací materiál, správu zásob a potenciální místa poruch.
- Zkrácení dodací lhůty: Rychlejší tvorba prototypů a možnost náhradních dílů na vyžádání nabízí nepřímé úspory nákladů. Skutečná hodnota často spočívá v kombinaci snížení plýtvání materiálem, provozních úspor v průběhu životního cyklu díky snížení hmotnosti a zlepšení designu/výkonu, nikoli pouze v nižších počátečních výrobních nákladech ve všech případech.
Otázka 5: Jak společnost Met3dp zajišťuje kvalitu svých titanových prášků (jako je Ti-6Al-4V) speciálně pro náročné letecké aplikace?
A: Společnost Met3dp si uvědomuje, že kvalita prášku je základem spolehlivé aditivní výroby v leteckém průmyslu. Dokonalost zajišťujeme prostřednictvím několika strategií:
- Pokročilé výrobní technologie: Využívá špičkové technologie atomizace plynem (VIGA) a plazmového procesu s rotujícími elektrodami (PREP), které jsou navrženy pro výrobu vysoce sférických prášků s minimem satelitů a vysokou čistotou.
- Přísná kontrola surovin: Získávání vysoce kvalitních vstupních materiálů a přesná kontrola chemie v průběhu tavicího procesu.
- Průběžné kontroly: Sledování klíčových parametrů během rozprašování pro zajištění konzistence.
- Důkladné testování kontroly kvality: Každá šarže prášku prochází rozsáhlým testováním na:
- Chemické složení (včetně kritických intersticiálních prvků, jako je kyslík/dusík).
- Distribuce velikosti částic (PSD) pomocí laserové difrakce.
- Morfologie a sféricita (analýza pomocí SEM).
- Průtočnost (např. testování Hallovým průtokoměrem).
- Zdánlivá hustota a hustota kohoutku.
- Sledovatelnost šarží: Zachování úplné sledovatelnosti od surovin až po finální balený prášek.
- Optimalizované balení: prášky jsou baleny v inertních podmínkách, aby se zabránilo kontaminaci a zajistila se dlouhá skladovatelnost. Tento komplexní přístup zajišťuje, že Ti-6Al-4V a další produkty společnosti Met3dp’ kovové prášky důsledně splňují přísné požadavky na hustotu, čistotu, tekutost a morfologii, které jsou vyžadovány v kritických aplikacích pro letecký průmysl, a umožňují našim zákazníkům tisknout vysoce kvalitní a spolehlivé komponenty.
Závěr: Vynášení leteckých konstrukcí pomocí 3D tištěných titanových držáků
Letecká výroba prochází zásadní proměnou, která je způsobena neustálou snahou o lehčí, pevnější a účinnější komponenty. V rámci tohoto vývoje, aditivní výroba kovů v kombinaci s vysoce výkonnými titanovými slitinami, jako jsou Ti-6Al-4V a Ti-6Al-4V ELI, se stala klíčovou technologií, zejména pro kritické součásti, jako jsou letecké držáky. Jak jsme již zjistili, možnost 3D tisku těchto důležitých konstrukčních prvků nabízí přesvědčivé výhody, které přímo řeší hlavní problémy leteckého průmyslu.
Viděli jsme, jak AM osvobozuje designéry od omezení tradiční výroby a umožňuje vytvářet nové výrobky topologicky optimalizované, lehké držáky které byly dříve nemyslitelné. Tato konstrukční svoboda se přímo promítá do významných úspora hmotnosti, zlepšení palivové účinnosti a nosnosti - klíčových ukazatelů pro výkon letadel a kosmických lodí. Schopnost pro konsolidace částínahrazením složitých sestav jednotlivými monolitickými tištěnými součástmi se dále snižuje hmotnost a současně se zjednodušení montáže, snížení počtu dílů a eliminace potenciálních míst poruch spojené se spoji a spojovacími prvky.
Kromě hmotnosti a složitosti přináší technologie AM kovů také účinnost materiálu mnohem lepší než subtraktivní obrábění, což výrazně snižuje plýtvání drahým titanem a zlepšuje klíčový poměr mezi nákupem a letem. Tato technologie také urychluje inovační cykly díky rychlé prototypování a nabízí potenciál pro výroba na vyžádání náhradních dílů, zvýšení odolnosti dodavatelského řetězce a zkrácení dodacích lhůt MRO. V kombinaci s nezbytnými kroky následného zpracování, jako je např Izostatické lisování za tepla (HIP), 3D tištěné titanové držáky demonstrují mechanické vlastnosti srovnatelné nebo lepší s jejich konvenčně vyráběnými protějšky, což zajišťuje strukturální integritu a spolehlivost vyžadovanou pro kritické letové aplikace.
Úspěšné využití této technologie však vyžaduje pečlivé zvážení zásad DfAM, důkladné pochopení možností a omezení procesu, pokud jde o tolerance a povrchovou úpravu, pečlivé řízení požadavků na následné zpracování a aktivní zmírnění potenciálních problémů, jako je zbytkové napětí a pórovitost.
Úspěch implementace 3D tištěných titanových držáků pro letecký průmysl závisí především na výběru správných partnerů. To znamená vybrat dodavatelé materiálu kteří zaručují nejvyšší standardy kvality a konzistence prášku a spolupracují se společností poskytovatelé služeb aditivní výroby kteří mají prokazatelné odborné znalosti v oblasti letectví a kosmonautiky, nezbytné certifikace (jako je AS9100 a příslušné akreditace Nadcap), robustní systémy řízení kvality a komplexní komplexní schopnosti od podpory návrhu přes tisk, následné zpracování až po důkladnou kontrolu.
Společnost Met3dp stojí v čele tohoto technologického pokroku a nabízí jedinečnou kombinaci schopností jako vývojář pokročilých technologií Tiskárny pro selektivní tavení elektronovým svazkem (SEBM) a výrobce vysoce kvalitní sférické kovové prášky vyráběné pomocí nejmodernějších technologií atomizace plynu a PREP. Naše hluboké odborné znalosti v oblasti materiálových věd a aditivních výrobních procesů spolu s naším závazkem ke kvalitě a spolehlivosti z nás činí ideálního partnera pro letecké společnosti, které chtějí zavést 3D tisk a urychlit svou transformaci digitální výroby.
Zavedení 3D tištěných titanových držáků je víc než jen nová výrobní technika; je to strategický faktor pro novou generaci leteckého designu a výkonnosti. Umožňuje konstruktérům vyrábět lehčí letadla, létat dál, nést více a rychleji inovovat.
Jste připraveni prozkoumat, jak může aditivní výroba zvýšit kvalitu vašich leteckých konstrukcí? Kontakt Met3dp ještě dnes, abyste mohli prodiskutovat své specifické potřeby v oblasti komponent a zjistit, jak naše komplexní řešení - od špičkových tiskáren a prémiových prášků až po odborné služby vývoje aplikací - mohou podpořit cíle vaší organizace v oblasti aditivní výroby a pomoci vám dosáhnout nových výšin.
Sdílet na
MET3DP Technology Co., LTD je předním poskytovatelem řešení aditivní výroby se sídlem v Qingdao v Číně. Naše společnost se specializuje na zařízení pro 3D tisk a vysoce výkonné kovové prášky pro průmyslové aplikace.
Dotaz k získání nejlepší ceny a přizpůsobeného řešení pro vaše podnikání!
Související články
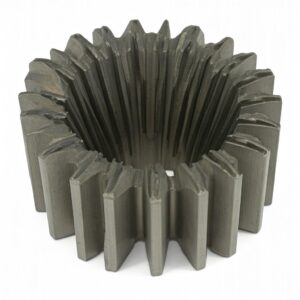
Vysoce výkonné segmenty lopatek trysek: Revoluce v účinnosti turbín díky 3D tisku z kovu
Přečtěte si více "O Met3DP
Nedávná aktualizace
Náš produkt
KONTAKTUJTE NÁS
Nějaké otázky? Pošlete nám zprávu hned teď! Po obdržení vaší zprávy obsloužíme vaši žádost s celým týmem.
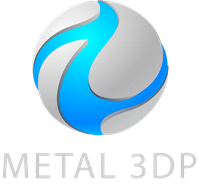
Kovové prášky pro 3D tisk a aditivní výrobu