Prášky z hliníkových slitin
Obsah
Prášky z hliníkové slitiny nabízejí nízkou hmotnost kombinovanou s pevností, trvanlivostí a odolností proti korozi v automobilovém, leteckém a průmyslovém průmyslu. Tato příručka pokrývá běžné složení, vlastnosti, výrobní metody, velikosti, dodavatele, aplikace a výběr.
prášek ze slitiny hliníku Přehled
Sférické hliníkové prášky s řízenou velikostí částic umožňují vysoce výkonné komponenty z lehkých kovů prostřednictvím PM, MIM a AM:
Slitiny | Řada 2xxx, 6xxx, 7xxx hliník |
Vlastnosti | Nízká hustota, pevnost, tvrdost, odolnost proti opotřebení |
Procesy | Prášková metalurgie, Vstřikování kovů, Hliník AM |
Aplikace | Automobilový, letecký, průmyslový |
Výhody | Snížení hmotnosti, výkon, recyklovatelnost |
Pokročilé hliníkové prášky vyvažují ultralehkou hustotu se zlepšenými mechanickými vlastnostmi oproti litým nebo tvářeným slitinám.
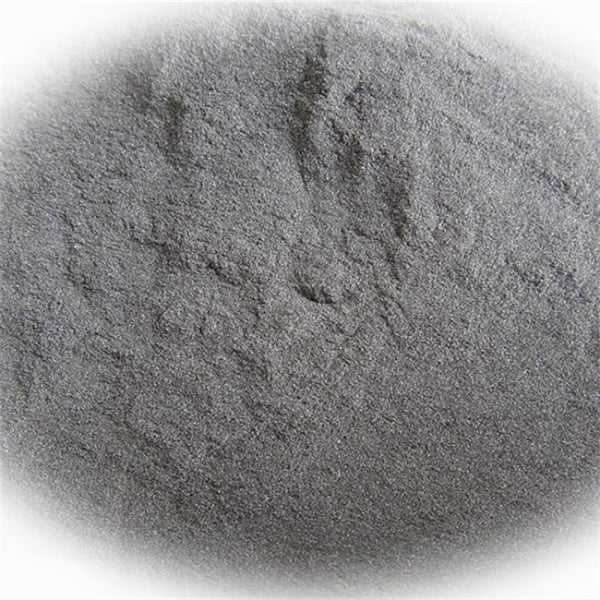
prášek ze slitiny hliníku Typy
Řada hliníkových slitin | Klíčové legující prvky | Vlastnosti | Aplikace |
---|---|---|---|
Řada 1XXX (čistý hliník) | Minimální legující prvky (< 1% celkem) | * Výborná zpracovatelnost a tvarovatelnost * Vysoká elektrická vodivost * Dobrá odolnost proti korozi * Nízká pevnost | * Elektrické vodiče (vodiče, přípojnice) * Výměníky tepla * Balení potravin * Dekorativní aplikace |
Řada 2XXX (Al-Cu) | Především měď (Cu) | * Vysoká pevnost * Dobrá obrobitelnost * Tepelně zpracovatelné pro další zpevnění * Nižší odolnost proti korozi ve srovnání s řadou 1XXX | * Letecké komponenty * Automobilové díly * Sportovní zboží (kola, baseballové pálky) * Stavební a konstrukční materiály |
3XXX Series (Al-Mn) | Mangan (Mn) je hlavním legujícím prvkem * Dobrá zpracovatelnost a tvarovatelnost * Střední pevnost * Vynikající vlastnosti pájení * Nižší odolnost proti korozi ve srovnání s řadou 1XXX | * Kuchyňské náčiní * Vložky tlakového hrnce * Tvarování plechu * Svařovací drát | |
Řada 4XXX (Al-Si) | Křemík (Si) je hlavním legujícím prvkem | * Dobrá slévatelnost * Svařitelnost * Střední pevnost * Nižší odolnost proti korozi ve srovnání s řadou 1XXX | * Bloky motorů * Hlavy válců * Automobilové díly * Stavební a konstrukční odlitky |
Řada 5XXX (Al-Mg) | Hořčík (Mg) je primární legující prvek * Vynikající odolnost proti korozi, zejména v prostředí se slanou vodou * Dobrá svařitelnost * Střední pevnost * Nižší zpracovatelnost ve srovnání s řadami 1XXX a 3XXX | * Námořní aplikace (trupy lodí, paluby) * Skladovací nádrže * Zařízení na chemické zpracování * Svařované konstrukce | |
Řada 6XXX (Al-Mg-Si) | Hořčík (Mg) a křemík (Si) jsou hlavní legující prvky * Vynikající kombinace pevnosti, zpracovatelnosti a odolnosti proti korozi * Tepelně zpracovatelné pro další zpevnění * Široce používané pro extrudované aplikace | * Stavba a konstrukce (rámy oken, dveře) * Doprava (díly letadel, kola nákladních aut) * Nábytek * Obráběné součásti | |
Řada 7XXX (Al-Zn) | Zinek (Zn) je primární legující prvek * Vysoká pevnost * Dobrá obrobitelnost * Výborná odolnost proti opotřebení * Nižší odolnost proti korozi ve srovnání s jinými řadami | * Letecké komponenty (křídla, trup) * Sportovní zboží (golfové hole, lyže) * Vysoce pevné konstrukční aplikace | |
Řada 8XXX (další prvky) | Legováno různými prvky jako lithium (Li) nebo lithium a měď (Li-Cu) * Velmi nízká hustota * Vysoký poměr pevnosti k hmotnosti * Omezená svařitelnost * Drahé | * Letecké aplikace vyžadující minimální hmotnost * Vysoce výkonné závodní komponenty * Speciální vojenské aplikace |
prášek ze slitiny hliníku Vlastnosti
Vlastnictví | Popis | Výhody aditivní výroby |
---|---|---|
Složení | Prášek z hliníkové slitiny není čistý hliník. Je to směs hliníku s různými prvky, jako je měď, hořčík, křemík nebo lithium, v závislosti na požadovaných konečných vlastnostech. Tyto prvky jsou uvedeny ve čtyřmístném kódu (např. AA2024), který definuje sérii slitin a hlavní legující prvky. | Použitím různých legujících prvků mohou výrobci dosáhnout široké škály vlastností konečného tištěného dílu, včetně pevnosti, odolnosti proti korozi a hmotnosti. |
Velikost a distribuce částic | Velikost a distribuce částic prášku z hliníkové slitiny významně ovlivňuje proces tisku a kvalitu finálního dílu. Velikosti částic se typicky pohybují od 15 do 150 mikronů, s těsnou distribucí (podobné velikosti částic) preferovanou pro optimální tok a balení během tisku. | Správná velikost částic zajišťuje hladký tok prášku během procesu tisku, minimalizuje dutiny a defekty v konečné části a ovlivňuje povrchovou úpravu. |
Morfologie prášku | Morfologie prášku se týká tvaru jednotlivých částic. Kulovité tvary jsou ideální pro aditivní výrobu, protože volně tečou, jsou hustě zabaleny a minimalizují tření mezi částicemi během tisku. Nepravidelně tvarované částice mohou bránit toku a vést k nekonzistentnosti tištěného dílu. | Sférický prášek nabízí několik výhod, včetně zlepšené tekutosti, lepší hustoty plnění a snížené poréznosti v konečné části. |
Tekutost | Tekutost označuje snadnost, s jakou se prášek pohybuje gravitací nebo aplikovaným tlakem. Dobrá tekutost je rozhodující pro konzistentní tvorbu vrstvy a přesný tisk. Faktory jako velikost částic, tvar a povrchové charakteristiky ovlivňují tekutost. | Správná tekutost zajišťuje hladké nanášení prášku během tisku, minimalizuje problémy s vrstvením a přispívá k rozměrové přesnosti ve finální části. |
Zdánlivá hustota | Zdánlivá hustota je hmotnost prášku na jednotku objemu s ohledem na prostory mezi částicemi. Je to zásadní faktor pro odhad využití prášku a kalibraci stroje v aditivní výrobě. | Pochopení zdánlivé hustoty umožňuje přesnou přípravu práškového lože a pomáhá optimalizovat využití materiálu během tisku. |
Hustota balení | Hustota balení se týká maximálního množství prášku, které může být zabaleno do určitého objemu. Je vyjádřena jako procento teoretické hustoty (hustota pevného materiálu bez dutin). Vyšší hustota balení vede k pevnějším a hustším tištěným dílům. | Vysoká hustota balení se promítá do vyššího objemu materiálu na jednotku objemu v tištěném dílu, což vede ke zlepšení mechanických vlastností. |
Bod tání | Teplota tání prášku hliníkové slitiny se liší v závislosti na konkrétním složení slitiny. Znalost bodu tání je nezbytná pro výběr vhodných parametrů tisku, jako je výkon laseru nebo hustota energie. | Bod tání určuje množství energie potřebné k roztavení částic prášku během tisku, což zajišťuje správné spojení a spojení mezi vrstvami. |
Tepelná vodivost | Tepelná vodivost označuje schopnost materiálu vést teplo. Hliníkové slitiny mají obecně dobrou tepelnou vodivost, což může být výhodné v aplikacích vyžadujících odvod tepla. | Tepelná vodivost prášku ovlivňuje přenos tepla během tisku a může ovlivnit faktory, jako je deformace nebo zbytkové napětí ve finální části. |
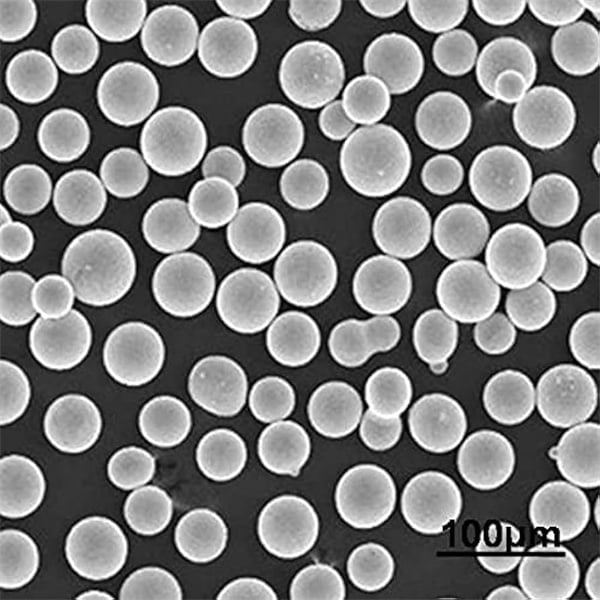
Výrobní metoda
Metoda | Popis | Výhody | Nevýhody | Aplikace |
---|---|---|---|---|
Atomizace plynu | Roztavená hliníková slitina je protlačována malou tryskou pod vysokým tlakem. Inertní plyn, typicky argon nebo dusík, rozbíjí proud kapaliny na jemné kapičky, které rychle tuhnou na sférické nebo téměř sférické částice prášku, když padají do sběrné komory. | * Vyrábí vysoce kvalitní kulovité prášky s dobrou tekutostí pro aditivní výrobní procesy. * Nabízí dobrou kontrolu nad velikostí a distribucí částic. * Vhodné pro širokou škálu hliníkových slitin. | * Vyžaduje vysokou spotřebu energie kvůli potřebě roztaveného kovu a stlačeného plynu. * Může to být složitý a kapitálově náročný proces. * Pokud není pečlivě kontrolováno, může do prášku vnášet kyslík a další nečistoty. | * Aditivní výroba (3D tisk) leteckých součástí, automobilových dílů, lékařských implantátů a lehkých konstrukcí. * Výroba surovin pro vstřikování kovů (MIM). |
Atomizace vody | Podobně jako atomizace plynu, ale vysokotlaký vodní paprsek narušuje proud roztaveného kovu. Tato metoda se obvykle používá pro hrubší prášky. | * Nižší náklady ve srovnání s atomizací plynu díky použití vody místo inertního plynu. * Vhodné pro výrobu větších částic prášku. | * Produkuje méně kulovité a nepravidelnější tvarované částice ve srovnání s atomizací plynu. * Může do prášku vnášet vodík v důsledku interakce s vodou. * Omezená kontrola distribuce velikosti částic. | * Výroba filtračních médií, pyrotechniky a některých kompozitů s kovovou matricí. |
Elektrolýza | Elektrický proud se používá k rozkladu roztavené hliníkové soli na její základní prvky. Hliníkové částice se shromažďují na katodě. | * Vyrábí velmi jemné a čisté hliníkové prášky. * Lze použít k vytvoření specifických morfologií prášku. | * Vysoká spotřeba energie díky procesu elektrolýzy. * Omezená výrobní kapacita ve srovnání s jinými metodami. * Není široce používán pro prášky hliníkových slitin kvůli problémům při legování během elektrolýzy. | * Výroba vysoce čistých hliníkových prášků pro elektronické aplikace a pyrotechniku. |
Plazmová atomizace | Vysokoteplotní a vysokorychlostní plazmový hořák taví a atomizuje surovinu z hliníkové slitiny. Tato metoda nabízí rychlé zahřívání a chlazení, což vede k velmi jemným práškům. | * Vyrábí nejjemnější prášky z hliníkové slitiny s úzkou distribucí velikosti částic. * Nabízí rychlé rychlosti tuhnutí pro potenciálně unikátní mikrostruktury. | * Extrémně vysoká spotřeba energie díky tvorbě plazmy. * Složitý a nákladný proces s omezeným komerčním přijetím. * Vyžaduje pečlivou kontrolu, aby se zabránilo nadměrné oxidaci a nitridaci prášku. | * Potenciální budoucí aplikace ve vysoce výkonné aditivní výrobě a pokročilém výzkumu materiálů. |
Techniky rychlého tuhnutí (RS). | Do této kategorie spadá několik specializovaných technik, včetně zvlákňování taveniny a laserového plátování. Roztavený kov je rychle ochlazen za vzniku pásu nebo jemných kapiček, které jsou následně rozdrceny na prášek. | * Může produkovat prášky s unikátní mikrostrukturou a metastabilními fázemi, které nelze konvenčními metodami dosáhnout. | * Vysoce komplexní a řízené procesy s omezenou výrobní kapacitou. * Prášky mohou mít nepravidelný tvar a velikost. * Vysoké náklady díky speciálnímu vybavení a požadavkům na proces. | * Výzkum a vývoj nových hliníkových slitin s vynikajícími vlastnostmi. |
prášek ze slitiny hliníku Velikosti částic
aplikace | Typický rozsah velikosti částic (mikrometry) | Požadované vlastnosti | Příklady |
---|---|---|---|
Aditivní výroba (3D tisk) | 15-100 | – Dobrá tekutost pro rovnoměrné nanášení prášku – Vysoká hustota balení pro pevné finální díly – Kulovitá morfologie pro minimální povrchové vady | Slitiny hliníku jako AlSi10Mg a 2024 pro letecké komponenty, lékařské implantáty a lehké konstrukce |
Tepelné nástřiky | 45-150 | – Dostatečně velké částice pro účinnou depozici – Odolnost proti nárazu pro aplikace s opotřebením – Regulovatelná poréznost pro tepelnou izolaci | Slitiny hliníku jako Al2O3 a NiAl pro součásti motoru, chladiče a povrchy odolné proti opotřebení |
Pyrotechnika (světlice, ohňostroje) | 1-45 | – Vysoce reaktivní pro rychlé spalování – Široká škála velikostí částic pro barevné efekty – Řízená rychlost hoření pro bezpečnost a vizuální dopad | Slitiny hliníku s pyrotechnickými přísadami, jako je hořčík a dusičnan barnatý |
Vstřikování kovů (MIM) | 10-30 | – Jemné částice pro dobré plnění formy – Rovnoměrná distribuce, aby se zabránilo defektům smršťování – Omezená aglomerace pro hladké povrchy | Hliníkové slitiny jako 316L a 17-4PH pro složité, vysoce přesné součástky v elektronickém a automobilovém průmyslu |
Exotermické svařování | 75-250 | – Rychlé tavení pro silnou tvorbu spojů – Řízená exotermická reakce pro minimální tepelné poškození – Odolnost proti oxidaci pro dlouhodobou integritu spoje | Slitiny hliníku a křemíku pro elektrické uzemnění, opravy a svařování potrubí |
Energetické materiály (výbušniny, pohonné hmoty) | 2-20 | – Vysoce reaktivní pro účinné uvolňování energie – Přizpůsobená distribuce velikosti pro řízenou rychlost hoření – Potažené částice pro lepší bezpečnost a manipulaci | Slitiny hliníku smíchané s oxidačními činidly, jako je chloristan amonný, a palivy, jako jsou uhlovodíkové polymery |
Přední dodavatelé
Název dodavatele | Klíčové produkty a aplikace | Diferenciátory | Region |
---|---|---|---|
NanoAL (prostřednictvím KBM Advanced Materials) | Sférické hliníkové prášky pro aditivní výrobu (AM) | – Vysoká čistota prášku (>99,7%) pro vynikající kvalitu dílů – Úzká distribuce velikosti částic pro konzistentní potiskovatelnost – Zaměření na vysoce výkonné hliníkové slitiny (např. AlSi10Mg, Al7075) pro náročné AM aplikace | Severní Amerika |
Elementum3D | Hliníkové prášky pro aditivní výrobu, vstřikování kovů (MIM) a tepelné nástřiky | – Široké portfolio prášků z hliníkových slitin, včetně standardních a zakázkových složení – Odbornost v přizpůsobení vlastností prášku pro konkrétní aplikace – Globální přítomnost s výrobními závody v Severní Americe a Evropě | Nadnárodní |
Höganäs AB | Hliníkové prášky pro vstřikování kovů (MIM) a aditivní výrobu | – Přední výrobce plynem atomizovaných hliníkových prášků – Zavedené procesy kontroly kvality pro konzistentní výkon prášku – Silná technická podpora pro zákazníky | Evropa |
Společnost APEX Powder Company | Hliníkové prášky pro pyrotechniku, barvy a nátěry a energetické materiály | – Zaměření na vysoce čisté a reaktivní hliníkové prášky – Přísné bezpečnostní protokoly pro manipulaci a skladování pyrotechnických prášků – Hluboké pochopení chování hliníkového prášku v různých aplikacích | Severní Amerika |
Eckert granule (ECKA granule) | Hliníkové prášky pro barvy a nátěry, pájení a svařování a exotermické reakce | – Široký sortiment hliníkových vloček a granulovaných prášků – Aplikační prášky s přizpůsobenými vlastnostmi (např. odolnost proti oxidaci, velikost částic) – Dlouhá historie inovací v technologii hliníkového prášku | Evropa |
AMetal (SLM řešení) | Hliníkové prášky speciálně optimalizované pro selektivní laserové tavení (SLM) | – Prášky vyvinuté a testované pro použití se stroji SLM od společnosti SLM Solutions – Zaměření na dosažení dílů s vysokou hustotou a vynikajícími mechanickými vlastnostmi – Omezená nabídka ve srovnání s širšími dodavateli hliníkového prášku | Evropa |
DLP prášek (kov pro stolní počítače) | Hliníkové prášky pro aditivní výrobu jednoprůchodových tryskových pojiv (SPJB). | – Prášky navržené pro použití s technologií SPJB Desktop Metal – Důraz na vysokou tekutost a hustotu balení pro efektivní tisk – Omezená nabídka specifická pro AM platformu Desktop Metal | Severní Amerika |
Aplikace z prášek ze slitiny hliníku
aplikace | Popis | Specifické příklady slitin | Výhody |
---|---|---|---|
Aditivní výroba (AM) | Také známý jako 3D tisk, AM využívá prášek z hliníkové slitiny k vytvoření složitých součástí téměř čistého tvaru. Vrstvy prášku se selektivně spojují dohromady pomocí technik, jako je tavení laserovým paprskem (SLM) nebo tavení elektronovým paprskem (EBM), aby se vytvořil konečný díl. | AlSi10Mg (pro dobrou svařitelnost), AlSi7Mg0,3 (pro vysokou pevnost), Scalmalloy (pro vysokou pevnost a teplotní odolnost) | * Svoboda designu: Jsou dosažitelné složité geometrie a vnitřní prvky. * Odlehčení: Komponenty mohou být navrženy z méně materiálu, což snižuje hmotnost. * Výroba na vyžádání: Díly lze vyrábět rychle a efektivně pro prototypování nebo malosériovou výrobu. * Účinnost materiálu: Nepoužitý prášek lze recyklovat a znovu použít. |
Vstřikování kovů (MIM) | MIM zahrnuje smíchání prášku z hliníkové slitiny s pojivem za účelem vytvoření suroviny, kterou lze vstřikovat do dutiny formy. Pojivo je poté odstraněno procesem odstraňování pojiva a zanechává za sebou součást téměř síťového tvaru. | 316L (nerezová ocel pro srovnání), 2219 (vysoká pevnost), 7075 (vysoká pevnost a odolnost proti opotřebení) | * Vysoká přesnost a rozměrová přesnost: Lze dosáhnout složitých tvarů s úzkými tolerancemi. * Hromadná výroba: MIM umožňuje efektivní výrobu velkého množství dílů. * Tvar sítě nebo tvar blízký síti: Vyžaduje se minimální následné zpracování. * Univerzálnost materiálu: MIM lze použít s širší škálou materiálů než tradiční techniky odlévání. |
Tepelný nástřik | Roztavený prášek z hliníkové slitiny se nastříká na substrát, aby se vytvořil povlak se specifickými vlastnostmi. | Al5052 (pro odolnost proti korozi), AlSi (pro odolnost proti opotřebení), nikl hliník (NiAl) pro vysokoteplotní aplikace | * Úprava povrchu: Nátěry mohou zlepšit vlastnosti, jako je odolnost proti opotřebení, odolnost proti korozi a tepelná vodivost. * Oprava a restaurování: Opotřebené nebo poškozené součásti lze opravit pomocí žárového nástřiku. * Selektivní nátěr: Specifické oblasti součásti mohou být zaměřeny na nátěr. * Široká škála podkladových materiálů: Tepelný nástřik lze použít na různé materiály, včetně kovů, plastů a keramiky. |
Pyrotechnika | Hliníkový prášek je klíčovou složkou ohňostrojů díky své schopnosti jasně hořet a vytvářet bílou nebo stříbrnou barvu. | Jemnost (<45 mikronů) pro lepší barevné efekty | * Pyrotechnické efekty: Hliníkový prášek přispívá k vizuálním efektům ohňostrojů. * Řízení rychlosti hoření: K řízení rychlosti hoření ohňostrojné kompozice lze použít různé velikosti částic. |
Energetické materiály | Hliníkový prášek se používá v pohonných hmotách a výbušninách díky své vysoké hustotě energie. | Vojenská kvalita se specifickými požadavky na velikost částic a čistotu | * Vysoký energetický výkon: Hliníkový prášek přispívá k výbušné síle materiálu. * Směs paliva a oxidačního činidla: Hliníkový prášek lze smíchat s oxidačními činidly, jako je dusičnan amonný, za účelem vytvoření energetických materiálů. |
Pigmenty a barvy | Hliníkový prášek lze použít jako pigment v barvách a inkoustech k vytvoření stříbrného nebo kovového povrchu. | Ultra jemné prášky (<10 mikronů) pro lepší disperzi | * Dekorativní efekty: Hliníkový prášek poskytuje reflexní a kovový vzhled. * Odraz tepla: Hliníkové pigmenty mohou odrážet teplo, takže jsou vhodné pro tepelně odolné barvy. * Odolnost proti korozi: Hliníkové pigmenty mohou zlepšit odolnost barev proti korozi. |
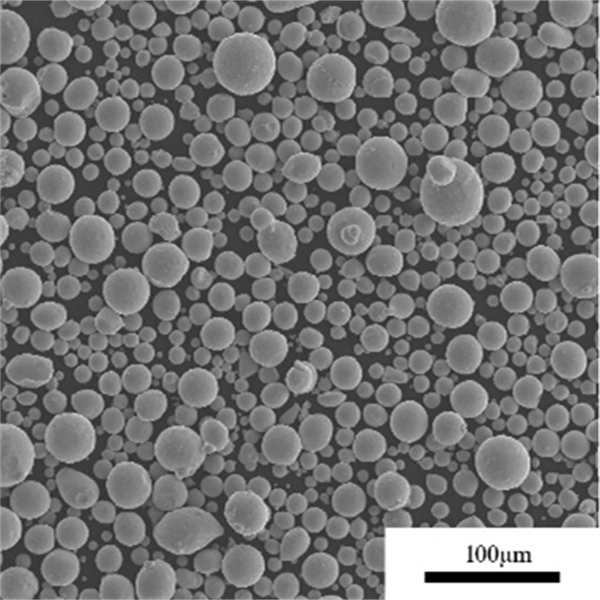
Pokyny pro výběr
Faktor | Popis | Klíčové úvahy |
---|---|---|
Výběr slitiny | První a nejdůležitější krok zahrnuje identifikaci slitiny hliníku, která nejlépe vyhovuje požadavkům vaší aplikace. | * Mechanické vlastnosti: Zvažte požadovanou pevnost v tahu, mez kluzu, únavovou pevnost a tažnost hotové součásti. Různé řady slitin (např. 1xxx, 6xxx, 7xxx) nabízejí spektrum pevnostních a hmotnostních charakteristik. * Odolnost proti korozi: Pokud bude součást vystavena drsnému prostředí, vyberte slitinu s vynikající odolností proti korozi, jako je například řada 5xxx námořní třídy. * Svařitelnost: Posoudit potřebu technik následného zpracování, jako je svařování. Některé slitiny, jako je řada 2xxx, mají nižší svařitelnost. * Tvarovatelnost: Určete úroveň tvarování potřebnou pro konečný díl. Vysoce čistý hliník (řada 1xxx) nabízí vynikající tvarovatelnost, zatímco pevnější slitiny mohou vyžadovat další tvářecí techniky. |
Chemie prášků | Chemické složení prášku přímo ovlivňuje vlastnosti finálního dílu. | * Legující prvky: Konkrétní prvky přidané do hliníkové báze (např. hořčík, křemík, měď) určují konečné vlastnosti. Technické listy od renomovaných dodavatelů uvádějí přesné složení každého prášku. * Úrovně nečistot: Minimalizujte přítomnost nečistot, jako jsou oxidy, železo a křemík, protože mohou negativně ovlivnit mechanické vlastnosti a potiskovatelnost. * Chemická homogenita: Zajistěte konzistentní distribuci prvků v částicích prášku pro jednotné vlastnosti v hotovém dílu. Renomovaní dodavatelé s přísnými postupy kontroly kvality to mohou zaručit. |
Morfologie prášku | Tvar a velikost částic významně ovlivňují tekutost prášku, hustotu balení a potiskovatelnost v procesech aditivní výroby (AM). | * Distribuce velikosti částic: Dobře distribuovaný rozsah velikosti částic s minimálními nadměrnými nebo podměrečnými částicemi optimalizuje tok prášku a hustotu balení. * Tvar částic: V ideálním případě sférické nebo téměř sférické částice nabízejí vynikající tekutost a minimalizují tření mezi částicemi během AM procesů. * Plocha povrchu: Vyšší povrch může zvýšit reaktivitu s atmosférickými prvky, takže některé AM techniky mohou vyžadovat prášky s řízenou povrchovou plochou, aby se minimalizovala oxidace. |
Tekutost prášku | Snadnost, s jakou prášek teče, je rozhodující pro konzistentní tvorbu vrstvy v procesech AM. | * Zdánlivá hustota: To se týká hmotnosti prášku na jednotku objemu, přičemž se bere v úvahu jak pevných částic, tak vzduchových dutin mezi nimi. Vyšší zdánlivá hustota se často promítá do lepší tekutosti. * Úhel klidu: Úhel, pod kterým hromada prášku přirozeně spočívá, je indikátorem tekutosti. Nižší sypný úhel znamená lepší průtok. * Průtok: Měří rychlost, kterou prášek protéká otvorem. To přímo ovlivňuje rychlost a efektivitu AM procesů. |
Vyrobitelnost prášku | Způsob výroby prášku z hliníkové slitiny může ovlivnit jeho vlastnosti. | * Technika atomizace: Plynová atomizace nabízí lepší kontrolu nad velikostí a morfologií částic ve srovnání s technikami, jako je atomizace vody. * Čistota prášku: Atomizační prostředí inertním plynem minimalizuje kontaminaci během procesu atomizace, což vede k vyšší čistotě prášků. |
Prášková aditiva | V některých případech se do prášku začleňují specifická aditiva pro zlepšení potiskovatelnosti nebo vlastností finálního dílu. | * Průtokové látky: Ty zlepšují tekutost prášku pro konzistentnější tiskový proces. * Slinovací pomůcky: Tato aditiva mohou být použita ke snížení slinovací teploty požadované pro zhuštění, což může být výhodné pro některé AM techniky. |
Kvalifikace dodavatele | Výběr spolehlivého dodavatele s osvědčenými výsledky je nezbytný pro kvalitu a konzistenci. | * Postupy kontroly kvality: Zajistěte, aby dodavatel dodržoval přísná opatření kontroly kvality během celého výrobního procesu. * Certifikace: Hledejte dodavatele s certifikacemi relevantními pro AM průmysl, jako jsou normy ASTM nebo NADCAP. * Údaje o charakterizaci prášku: Renomovaní dodavatelé poskytnou podrobné datové listy s chemickým složením, distribucí velikosti částic a dalšími relevantními charakteristikami prášku. |
Výhody vs. nevýhody prášku z hliníkové slitiny
Klady | Nevýhody |
---|---|
Vynikající poměr pevnosti k hmotnosti: Slitiny hliníku v práškové formě se vyznačují mimořádnou pevností v poměru ke své hmotnosti. Díky tomu jsou ideální pro aplikace v leteckém, automobilovém a dopravním průmyslu, kde jsou klíčové lehké a vysoce výkonné komponenty. Ve srovnání s ocelí může prášek z hliníkové slitiny nabídnout až 30% snížení hmotnosti při dosažení srovnatelných nebo dokonce vynikajících pevnostních vlastností. | Výzvy při zpracování: Prášek z hliníkové slitiny může být jemný a vyžaduje pečlivé zacházení v různých fázích výroby. Tekutost prášku musí být přesně řízena, aby byla zajištěna konzistentní hustota v konečné části. Některé hliníkové slitiny mohou navíc vyžadovat specifické atmosféry nebo specializované vybavení během aditivních výrobních procesů, jako je 3D tisk, aby se minimalizovala oxidace a zajistily se optimální výsledky. |
Odemyká komplexní geometrie: Na rozdíl od tradičních subtraktivních výrobních technik, jako je obrábění, umožňuje prášek z hliníkové slitiny vytvářet složité a složité geometrie. Aditivní výrobní procesy využívající tento prášek mohou vyrábět díly s vnitřními kanály, mřížkami a dalšími prvky, kterých by bylo obtížné nebo nemožné dosáhnout konvenčními metodami. Tato svoboda designu otevírá dveře inovacím v oblasti odlehčení, odvodu tepla a funkčnosti dílů. | Omezená velikost dílu: Přestože technologie prášku z hliníkové slitiny nabízí výhody v geometrické složitosti, může mít omezení, pokud jde o konečnou velikost součásti. Současné možnosti 3D tiskových strojů a procesů fúze práškového lože mohou omezit výrobu velmi velkých součástí. Pokrok v technologii však tyto hranice neustále posouvá a očekává se, že maximální dosažitelná velikost dílů v následujících letech poroste. |
Snížení množství materiálového odpadu: Ve srovnání se subtraktivními výrobními procesy, které generují významný odpadový materiál, nabízí prášek z hliníkové slitiny udržitelnější přístup. Při 3D tisku lze nepoužitý prášek často recyklovat a znovu použít, čímž se minimalizuje odpad a výrobní náklady. Toto zaměření na materiálovou efektivitu je v souladu s rostoucími obavami o životní prostředí a podporuje odpovědné výrobní postupy. | Úvahy o ceně: Cena prášku z hliníkové slitiny může být vyšší než u tradičních hliníkových ingotů nebo tyčí. To je částečně způsobeno dodatečným zpracováním spojeným s vytvořením prášku a speciálními požadavky na manipulaci. Výhody nižší hmotnosti, složitých geometrií a sníženého odpadu však mohou ve specifických aplikacích kompenzovat počáteční náklady. Kromě toho, jak technologie dospívá a objem výroby se zvyšuje, očekává se, že cena prášku z hliníkové slitiny bude konkurenceschopnější. |
Vynikající povrchová úprava: Prášek z hliníkové slitiny může vyrábět díly s výjimečnými povrchovými úpravami. Aditivní výrobní procesy mohou dosáhnout vysokého stupně detailů a rozlišení, výsledkem čehož jsou součásti s hladkým a esteticky příjemným vzhledem. To eliminuje potřebu rozsáhlých kroků následného zpracování, jako je broušení nebo leštění, což dále zjednodušuje výrobní proces. | Potenciál anizotropie: Vrstvení, které je vlastní aditivním výrobním procesům využívajícím prášek hliníkové slitiny, může vnést mírnou anizotropii do mechanických vlastností konečné součásti. To znamená, že pevnost a chování materiálu se může lišit v závislosti na směru zatížení. Optimalizací parametrů tiskového procesu a potenciálním použitím technik následného zpracování, jako je tepelné zpracování, však mohou inženýři zmírnit účinky anizotropie a zajistit konzistentní výkon. |
Vlastnosti na míru: Slitiny hliníku mohou být formulovány se specifickými prvky, jako je křemík, hořčík nebo měď, aby se dosáhlo požadovaných mechanických vlastností. To umožňuje vytvoření prášku z hliníkové slitiny přizpůsobeného pro konkrétní aplikace. Například přidání křemíku může zvýšit pevnost, zatímco hořčík zlepšuje tažnost. Výběrem vhodného složení slitiny mohou inženýři optimalizovat prášek pro zamýšlené použití. | Bezpečnostní opatření: Prášek z hliníkové slitiny, stejně jako většina kovových prášků, může být hořlavý a při vdechování může představovat zdravotní riziko. Správné manipulační postupy, ventilační systémy a osobní ochranné prostředky jsou nezbytné pro zajištění bezpečného pracovního prostředí při práci s tímto materiálem. |
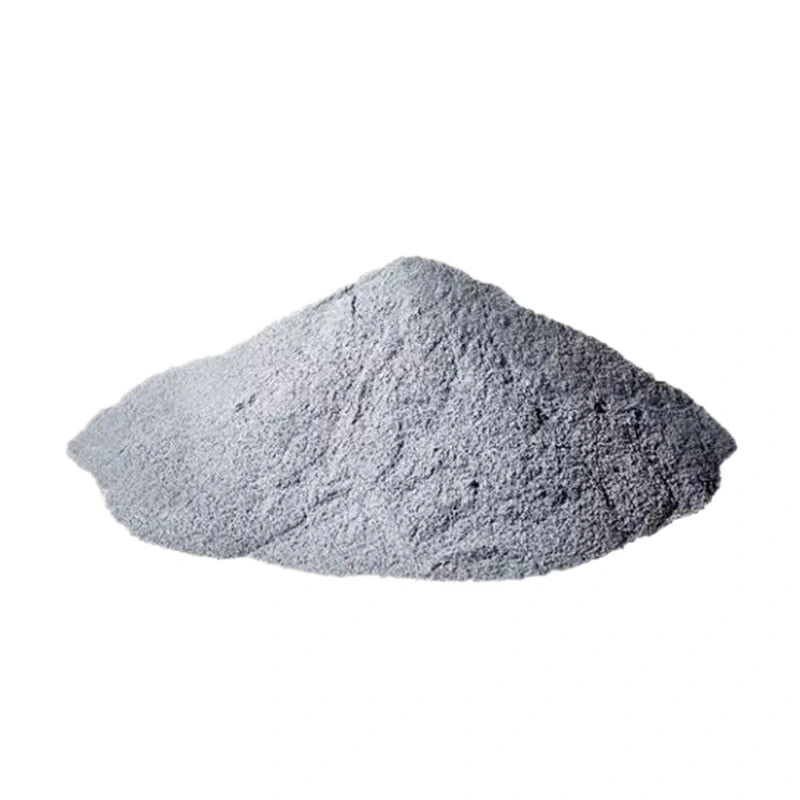
Nejčastější dotazy
Otázka: Jaký je nejrozšířenější prášek z hliníkové slitiny?
A: Hliník 6061 je těžká slitina využívaná v automobilovém a všeobecném strojírenství pro své všestranné mechanické vlastnosti, odolnost proti korozi a nízké náklady.
Otázka: Jaká je cena hliníkového prášku ve srovnání s titanem?
Odpověď: Hliníkové prášky začínají kolem $5/lb oproti $50+/lb pro titan, což prokazuje významné výhody z hlediska nákladů na konverzi pro odlehčení navzdory nižším mechanickým vlastnostem.
Otázka: Oxiduje hliníkový prášek?
Odpověď: Jemné hliníkové prášky představují oxidační rizika během manipulace, skladování a zpracování vyžadující inertní prostředí a přísné kontroly kvality, aby se rizika minimalizovala.
Otázka: Můžete 3D tisknout díly z hliníkové slitiny?
Odpověď: Ano, hliník DED a pojivo jet AM rychle dozrávají pro konstrukční součásti leteckého průmyslu využívající pokročilé prášky a zdokonalení zpracování k dosažení hustoty přes 99% po slinování.
Sdílet na
MET3DP Technology Co., LTD je předním poskytovatelem řešení aditivní výroby se sídlem v Qingdao v Číně. Naše společnost se specializuje na zařízení pro 3D tisk a vysoce výkonné kovové prášky pro průmyslové aplikace.
Dotaz k získání nejlepší ceny a přizpůsobeného řešení pro vaše podnikání!
Související články
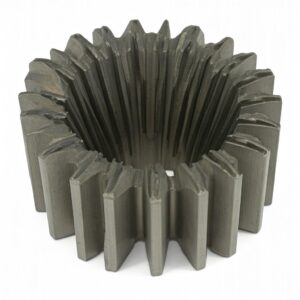
Vysoce výkonné segmenty lopatek trysek: Revoluce v účinnosti turbín díky 3D tisku z kovu
Přečtěte si více "O Met3DP
Nedávná aktualizace
Náš produkt
KONTAKTUJTE NÁS
Nějaké otázky? Pošlete nám zprávu hned teď! Po obdržení vaší zprávy obsloužíme vaši žádost s celým týmem.
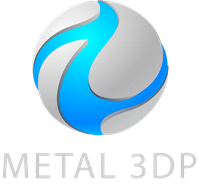
Kovové prášky pro 3D tisk a aditivní výrobu