Vysoce výkonné držáky pro letadla pomocí 3D tisku z kovu
Obsah
Úvod: Kritická role montážních konzol v letectví a aditivní výhody
V náročném světě leteckého inženýrství záleží na každé součásti. Od největších konstrukčních prvků až po nejmenší spojovací prvky - každá součást hraje klíčovou roli při zajišťování bezpečnosti letu, provozní efektivity a celkové výkonnosti letadla. Mezi tyto zásadní součásti patří montážní konzoly - zdánlivě jednoduché díly, které plní kritickou funkci upevnění, podpory a umístění životně důležitých systémů a konstrukcí letadla. Letecké montážní konzoly, které se tradičně vyráběly metodami jako CNC obrábění nebo odlévání, nyní vstupují do nové éry inovací díky transformačním schopnostem technologie kov 3D tisk, známé také jako aditivní výroba (AM).
Letecké montážní konzoly slouží k mnoha účelům, od podepření hydraulických vedení a elektrických svazků až po montáž avionického vybavení a upevnění vnitřního vybavení. Musí odolávat značnému statickému a dynamickému zatížení, vibracím, kolísání teplot a potenciálně korozivnímu prostředí, a to vše při minimálním podílu na celkové hmotnosti letadla. Poměr “buy-to-fly” - poměr hmotnosti nakoupené suroviny a hmotnosti finálního dílu - je v letecké výrobě kritickým ukazatelem. Tradiční subtraktivní metody, při nichž se materiál odebírá z většího bloku, často vedou k vysokým poměrům nákupu a úletu, což se projevuje plýtváním materiálem a zvýšenými náklady.
Toto je místo aditivní výroba kovů nabízí přesvědčivou alternativu. Namísto odebírání materiálu vytváří AM díly vrstvu po vrstvě přímo z kovového prášku podle digitálního konstrukčního souboru. Tento přístup otevírá nebývalou svobodu návrhu a umožňuje vytvářet vysoce komplexní, topologicky optimalizované a lehké konzoly, které je nemožné nebo neúměrně drahé vyrobit běžnými technikami. Společnosti specializující se na 3D tisk z kovu přinášejí revoluci v tom, jak tyto kritické letecké a kosmické komponenty jsou navrženy a vyrobeny.
Výhody přesahují flexibilitu designu. Metal AM umožňuje:
- Výrazné snížení hmotnosti: Optimalizace geometrie držáků snižuje spotřebu materiálu, aniž by byla narušena integrita konstrukce, což přímo přispívá k úspornosti paliva a zvýšení nosnosti.
- Konsolidace částí: Složité sestavy, které dříve vyžadovaly více držáků a spojovacích prvků, lze často přepracovat a vytisknout jako jedinou integrovanou součást, čímž se sníží počet dílů, doba montáže a potenciální místa poruchy.
- Zkrácené dodací lhůty: AM umožňuje rychlou výrobu prototypů a konzolí na vyžádání, což zrychluje vývojové cykly a zlepšuje dobu realizace údržby, oprav a generálních oprav (MRO).
- Zlepšený poměr nákupu k letu: Výroba dílů aditivním způsobem výrazně snižuje materiálový odpad ve srovnání se subtraktivním obráběním, což z něj činí udržitelnější a nákladově efektivnější přístup, zejména u drahých leteckých slitin, jako je titan.
- Vylepšený výkon: Technologie AM umožňuje vytvářet vnitřní chladicí kanály nebo prvky určené speciálně k tlumení vibrací, což vede ke konzolám s vynikajícími výkonnostními vlastnostmi.
Vzhledem k tomu, že letecký a kosmický průmysl stále posouvá hranice výkonnosti a efektivity, stává se 3D tisk z kovu nejen životaschopnou výrobní metodou, ale i strategickým imperativem pro výrobu nové generace vysoce výkonných letadel montážní konzoly pro letectví. Tato technologie umožňuje inženýrům a manažerům nákupu přehodnotit konstrukci součástí, optimalizovat dodavatelské řetězce a nakonec vyrábět lepší letadla.
Odhalení aplikací: Kde se používají 3D tištěné letecké držáky?
Všestrannost aditivní výroby kovů umožňuje vyrábět širokou škálu montážních držáků přizpůsobených specifickým potřebám celého letadla. Zatímco tradičně vyráběné držáky zůstávají převládající, zavádění 3D tištěných alternativ rychle roste v různých oblastech letecké a kosmické aplikace, které se řídí výhodami snížení hmotnosti, složitosti konstrukce a zvýšení výkonu. Tyto konzoly nacházejí uplatnění v konstrukčních i nekonstrukčních úlohách, což dokazuje schopnost této technologie splnit přísné požadavky v leteckém průmyslu.
Zde je přehled běžných oblastí, ve kterých se uplatňují 3D tištěné letecké držáky:
1. Směrování a podpora systému:
- Popis: Upevnění hydraulických a palivových vedení, elektrických kabelových svazků a pneumatických kanálů v celém draku letadla. Tyto držáky zabraňují oděru, zajišťují správné vedení a udržují integritu systému při vibracích a G-silách.
- Výhoda AM: AM umožňuje vytvářet vysoce přizpůsobené tvary, které přesně odpovídají složitým trasám v omezeném prostoru. Pro snížení hmotnosti při zachování potřebné tuhosti lze použít lehké mřížové struktury. Konsolidace dílů může spojit několik jednoduchých svorek a držáků do jediné, efektivnější součásti.
- Materiály: Často AlSi10Mg pro svou lehkost a dobrou zpracovatelnost.
2. Montáž letecké elektroniky a zařízení:
- Popis: Montáž černých skříněk, senzorů, komunikačních zařízení, výpočetních jednotek a dalších citlivých součástí avioniky do trupu nebo kokpitu. Tyto držáky musí zajistit bezpečnou montáž a často i tlumení vibrací.
- Výhoda AM: Lze vytvářet složité geometrie pro dokonalé přizpůsobení specifickým tvarům zařízení. Přímo do držáku lze navrhnout prvky pro odvod tepla (např. integrované chladiče) nebo izolaci vibrací. Rychlé prototypování umožňuje rychlé iterace během vývoje letadla.
- Materiály: AlSi10Mg pro lehčí součásti, Ti-6Al-4V tam, kde je požadována vyšší pevnost, tuhost nebo teplotní odolnost.
3. Konstrukční podpora (sekundární konstrukce):
- Popis: Konzoly spojující sekundární konstrukční prvky, jako jsou podpěry kapotáže, rámy přístupových panelů nebo podpěry podlahových panelů. I když se nejedná o primární nosné konstrukce, přesto vyžadují značnou pevnost a spolehlivost.
- Výhoda AM: Pomocí softwaru pro optimalizaci topologie lze vytvářet vysoce efektivní konstrukce, které umisťují materiál pouze tam, kde je to z konstrukčního hlediska nutné, čímž se dosahuje výrazných úspor hmotnosti ve srovnání s obráběnými ekvivalenty. Složité dráhy zatížení lze přizpůsobit efektivněji.
- Materiály: Ti-6Al-4V je často upřednostňován pro svůj vynikající poměr pevnosti a hmotnosti a odolnost proti únavě. Používají se také vysokopevnostní slitiny hliníku.
4. Součásti motoru a nosné rakety:
- Popis: Držáky v oblasti motorové gondoly nebo pylonu, které mohou být vystaveny vyšším teplotám a náročným podmínkám zatížení. Příkladem jsou montážní body pro senzory, pohony nebo podpěry potrubí.
- Výhoda AM: Možnost použití vysokoteplotních slitin (ačkoli AlSi10Mg a Ti-6Al-4V pokrývají mnoho potřeb držáků, v případě potřeby lze vytisknout i jiné superslitiny). Někdy lze integrovat složité chladicí kanály nebo tepelné štíty.
- Materiály: Převážně Ti-6Al-4V díky své vysoké pevnosti, teplotní odolnosti a únavovým vlastnostem.
5. Vnitřní vybavení kabiny:
- Popis: Držáky pro upevnění sedadel, horních přihrádek, památníků v kuchyňce, dělicích stěn a dalších prvků interiéru kabiny. Klíčovým faktorem je často estetika a hmotnost.
- Výhoda AM: Volnost designu umožňuje vytvořit držáky, které se hladce začlení do estetiky kabiny. Odlehčení má zásadní význam pro snížení celkové hmotnosti letadla. Přizpůsobení pro nízkoobjemové konfigurace kabiny je snadno dosažitelné.
- Materiály: Především AlSi10Mg kvůli nižší hustotě a cenové výhodnosti pro méně konstrukčně kritické aplikace.
Tabulka: Běžné aplikace leteckých držáků & vhodnost AM
Oblast použití | Typická funkce | Hlavní výhody AM | Doporučené materiály (příklady) |
---|---|---|---|
Směrování systému | Zajistěte šňůry/poutka, zabraňte odření | Tvarování na zakázku, odlehčování, konsolidace dílů | AlSi 10Mg |
Montáž letecké elektroniky | Zabezpečení citlivých zařízení, tlumení vibrací | Komplexní geometrie, integrované funkce, rychlý výzkum a vývoj | AlSi10Mg, Ti-6Al-4V |
Sekundární struktury | Připojení panelů, rámů, podpěr | Optimalizace topologie, úspora hmotnosti, návrh zátěžové trasy | Ti-6Al-4V, vysokopevnostní Al |
Motor/maketa | Podpora komponentů v prostředí s vysokou teplotou a zátěží | Možnost vysokých teplot, komplexní integrace chlazení | Ti-6Al-4V, superslitiny |
Interiéry kabin | Zabezpečení sedadel, odpadkových košů, pomníků | Odlehčení, přizpůsobení, estetická integrace | AlSi 10Mg |
Export do archů
Míra přijetí se liší v závislosti na kritičnosti aplikace, certifikačních požadavcích a konkrétním programu letadla. Trend je však jasný: 3D tisk z kovu je stále více uznáván výrobci letecké techniky a distributoři komponentů jako výkonný nástroj pro výrobu optimalizovaných, vysoce výkonných montážních konzol pro letectví v rostoucím rozsahu aplikací.
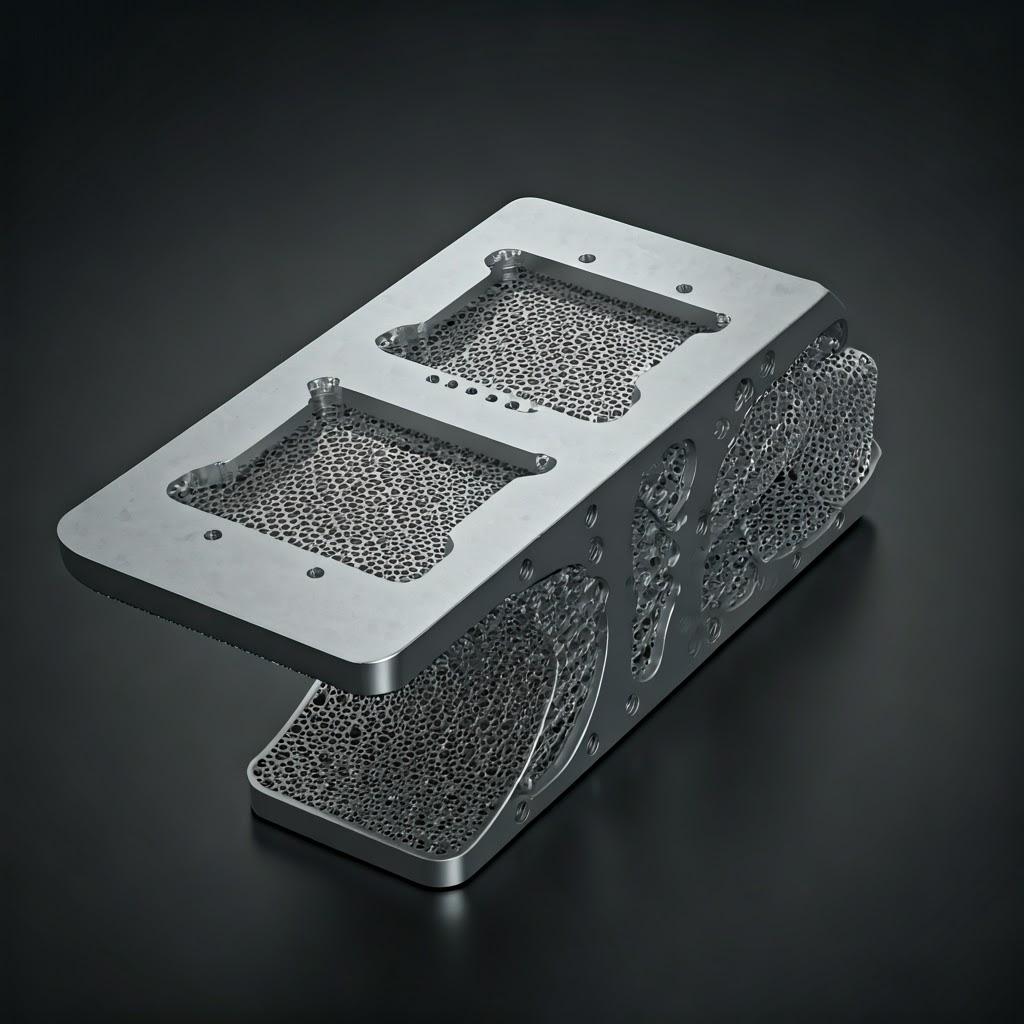
Proč zvolit aditivní výrobu kovů pro letecké konzoly?
Rozhodnutí o zavedení nové výrobní technologie v leteckém průmyslu se nikdy nepřijímá lehce. Bezpečnost, spolehlivost a výkon jsou prvořadé. Přesto aditivní výroba kovů (AM) představuje tak přesvědčivé výhody oproti tradičním metodám výroby leteckých konzol, že se její zavádění urychluje. Inženýrům zaměřeným na optimalizaci konstrukce a manažerům nákupu, kteří hodnotí celkové náklady životního cyklu a efektivitu dodavatelského řetězce, nabízí kovová AM hmatatelné výhody, které je těžké ignorovat.
Pojďme se hlouběji podívat, proč se kovový AM stává pro mnohé preferovanou volbou letadlová část výrobci a dodavatelé leteckého průmyslu:
1. Bezkonkurenční volnost designu & Komplexnost:
- Tradiční omezení: CNC obrábění je omezeno přístupem k nástroji, což vyžaduje více nastavení pro složité díly a často omezuje vnitřní prvky. Odlévání má omezení související s tvorbou forem a dosažitelnými detaily.
- Výhoda AM: Technologie AM vytváří díly po vrstvách, což umožňuje vytvářet složité vnitřní kanály, komplexní křivky, tenké stěny a organické tvary odvozené z optimalizace topologie. To umožňuje konstruktérům navrhovat držáky, které dokonale odpovídají funkčním požadavkům, což je při použití tradičních metod často nemožné. Představte si duté struktury, integrované prvky nebo mřížky s proměnlivou hustotou - to vše je dosažitelné pomocí AM.
2. Významný potenciál odlehčení:
- Letecký a kosmický imperativ: Snížení hmotnosti je hlavním cílem při konstrukci letadel, protože se přímo promítá do snížení spotřeby paliva, zvýšení nosnosti nebo prodloužení doletu.
- Výhoda AM: Algoritmy optimalizace topologie používané ve spojení s technologií AM analyzují dráhy zatížení a odstraňují materiál z nekritických oblastí, čímž vytvářejí vysoce efektivní a lehké konstrukce. Výrazně se zlepšují poměry mezi nákupem a letem, protože materiál se přidává pouze tam, kde je to potřeba, na rozdíl od subtraktivních procesů, které začínají s velkým blokem a u složitých leteckých dílů odebírají potenciálně 80-90 % materiálu. Díky tomu je AM zvláště atraktivní pro drahé materiály, jako je titan.
3. Konsolidace částí:
- Tradiční přístup: Složité systémy často vyžadují více konzol, spojovacích prvků a konektorů, které se montují dohromady. Každá součást zvyšuje hmotnost, prodlužuje dobu montáže a zvyšuje počet možných poruch (např. uvolnění spojovacích prvků).
- Výhoda AM: AM umožňuje konstruktérům sloučit více komponent do jediného monolitického tištěného dílu. Sestava držáku, která se dříve skládala z pěti obráběných dílů a deseti spojovacích prvků, může být přepracována na jednu 3D tištěnou součást, čímž se výrazně sníží počet dílů, zjednoduší montáž, zlepší konstrukční integrita a sníží režijní náklady na správu zásob.
4. Zkrácení dodacích lhůt & Výroba na vyžádání:
- Tradiční dodací lhůty: Vytváření nástrojů (pro odlévání) nebo složité víceosé programování a seřizování (pro obrábění) může vést k dlouhým dodacím lhůtám, zejména u prototypů nebo malosériové výroby.
- Výhoda AM: AM nevyžaduje žádné specifické nástroje pro jednotlivé díly. Jakmile je soubor návrhu připraven, tisk může být často zahájen během několika hodin nebo dnů. To usnadňuje rychlou tvorbu prototypů a umožňuje rychlejší iterace a ověřování návrhu. Umožňuje také výrobu na vyžádání pro náhradní díly nebo MRO, což snižuje potřebu velkých zásob a minimalizuje prostoje letadel. Tato agilita je významným přínosem pro B2B dodavatelé pro letecký průmysl řízení složitých dodavatelských řetězců.
5. Efektivita materiálů & Udržitelnost:
- Poměr nákupů a letů: Jak již bylo zmíněno, tradiční subtraktivní výroba, zejména u složitých leteckých dílů, vytváří značný materiálový odpad (třísky a třísky).
- Výhoda AM: Procesy tavení v práškovém loži, jako je selektivní laserové tavení (SLM) nebo tavení elektronovým svazkem (EBM), využívají materiál efektivněji. Netavený prášek v konstrukční komoře lze obvykle recyklovat a znovu použít při následných výtiscích, což vede k výrazně nižšímu poměru nákupu a výroby a nižší spotřebě surovin. To je nákladově efektivní a přínosné pro životní prostředí.
6. Zvýšený funkční výkon:
- Nad rámec struktury: AM umožňuje integrovat funkční prvky přímo do konstrukce držáku. Může jít například o optimalizované vlastnosti tlumení vibrací díky specifickým mřížkovým strukturám, integrované kanály pro proudění chladicího vzduchu nebo upevňovací body určené pro konkrétní typy senzorů.
Tabulka: AM vs. tradiční obrábění pro letecké držáky
Vlastnosti | Výroba aditiv kovů (AM) | Tradiční CNC obrábění | Zvýraznění výhody |
---|---|---|---|
Složitost návrhu | Vysoká (složité vnitřní prvky, organické tvary) | Středně vysoká (omezená přístupem k nástrojům) | AM umožňuje vysoce optimalizovaný & integrovaný design |
Odlehčení | Vynikající (optimalizace topologie, mřížky) | Dobrý (kapsy, odstraňování materiálu) | AM dosahuje maximálního snížení hmotnosti |
Konsolidace částí | Vynikající (více částí v jedné) | Omezené (montáž diskrétních dílů) | AM snižuje počet dílů, dobu montáže a počet poruchových míst |
Poměr nákupů a letů | Nízká (materiál přidávaný vrstvu po vrstvě, opětovné použití prášku) | Vysoká (materiál odečtený z bloku) | AM výrazně snižuje množství materiálového odpadu & náklady |
Doba realizace (Proto) | Rychle (bez nutnosti použití nástrojů) | Středně pomalý (programování, nastavení) | AM zrychluje vývojové cykly |
Doba realizace (Prod) | Škálovatelné; potenciálně rychlejší pro složité nízkoobjemové systémy | Zavedené; rychlejší pro jednoduché vysokoobjemové | AM nabízí flexibilitu na vyžádání pro náhradní díly/MRO |
Náklady na nástroje | Žádné (přímá digitální výroba) | Potřebné (přípravky, případně specifické nástroje) | AM eliminuje investice do nástrojů |
Export do archů
Tradiční výrobní metody si jistě zachovávají své místo, zejména pro velkosériovou výrobu jednodušších geometrií, ale díky specifickým výhodám, které nabízí AM z kovu, jsou stále přesvědčivější volbou pro výrobu vysoce výkonných, hmotnostně optimalizovaných a složitých výrobků montážní konzoly pro letectví, což je hnací silou inovací v rámci letecká a kosmická výroba odvětví. Společnosti jako Met3dp, které mají zkušenosti s pokročilými kovovými prášky i tiskovými technologiemi, jsou klíčovými hybateli tohoto přechodu.
Zaměření materiálu: AlSi10Mg a Ti-6Al-4V pro vysoce výkonné konzoly
Výkon, spolehlivost a hmotnost leteckého montážního držáku zásadně závisí na materiálu, ze kterého je vyroben. Aditivní výroba kovů nabízí možnost tisku z celé řady slitin pro letecký průmysl, ale dva materiály vynikají jako primární volba pro držáky díky svým dobře známým vlastnostem, zpracovatelnosti a vynikající rovnováze vlastností: AlSi10Mg (hliníková slitina) a Ti-6Al-4V (slitina titanu).
Výběr vhodného materiálu je velmi důležitý a závisí na konkrétních požadavcích aplikace, včetně podmínek zatížení, provozní teploty, cílové hmotnosti a cenových omezení. Jako přední dodavatel pokročilé kovové prášky, společnost Met3dp rozumí nuancím těchto materiálů a využívá nejmodernější výrobní techniky, jako je plynová atomizace, aby zajistila vysokou kulovitost, vynikající tekutost a optimální hustotu finálního tištěného dílu.
Podívejme se na vlastnosti a typické aplikace těchto klíčových leteckých slitin v kontextu 3D tištěných konzol:
1. AlSi10Mg (slitina hliníku, křemíku a hořčíku):
- Popis: AlSi10Mg je litá hliníková slitina, která je široce přizpůsobena pro procesy tavení v práškovém loži (SLM/DMLS). Je známá pro svůj dobrý poměr pevnosti a hmotnosti, vynikající tepelné vlastnosti, odolnost proti korozi a relativně snadné zpracování v systémech AM.
- Klíčové vlastnosti:
- Nízká hustota: Přibližně 2,67 g/cm³ (výrazně lehčí než ocel nebo titan).
- Dobrá síla: Nabízí střední pevnost, po vhodném tepelném zpracování (např. T6) je vhodný pro mnoho aplikací s konzolami.
- Vynikající tepelná vodivost: Je výhodné, pokud držák plní také funkci odvodu tepla.
- Dobrá odolnost proti korozi: Vhodné pro typické prostředí v letectví a kosmonautice.
- Vynikající zpracovatelnost: Tiskne se poměrně snadno s dobrou povrchovou úpravou a detaily prvků.
- Nákladově efektivní: Obecně jsou levnější než slitiny titanu.
- Typické aplikace držáků:
- Držáky pro vedení systému (kabeláž, hydraulika).
- Skříně a montážní vaničky pro avioniku.
- Vybavení interiéru kabiny.
- Sekundární konstrukční podpěry, kde je zatížení mírné.
- Prototypy pro kontrolu lícování a tvaru.
- Úvahy: Nižší pevnost a teplotní odolnost ve srovnání s titanem. Není vhodný pro vysoce zatížené konstrukční díly nebo pro prostředí s vysokou teplotou v blízkosti motorů.
2. Ti-6Al-4V (titanová slitina třídy 5):
- Popis: Ti-6Al-4V (často nazývaný Ti64) je pracovní kůň leteckého průmyslu. Tato alfa-beta titanová slitina je proslulá výjimečným poměrem pevnosti a hmotnosti, vynikající odolností proti korozi, biokompatibilitou a schopností odolávat středně vysokým teplotám.
- Klíčové vlastnosti:
- Vysoký poměr pevnosti k hmotnosti: Nabízí pevnost srovnatelnou s mnoha ocelemi při zhruba o 40 % nižší hustotě (cca 4,43 g/cm³).
- Vynikající odolnost proti korozi: Vysoce odolné proti atmosférické a slané vodě.
- Dobrá únavová pevnost: Kritické pro součásti vystavené cyklickému zatížení.
- Mírná teplotní odolnost: Vhodný pro aplikace do teploty přibližně 350-400 °C (660-750 °F).
- Biokompatibilní: Hojně se používá také u lékařských implantátů (i když u rovnátek je to méně důležité).
- Typické aplikace držáků:
- Vysoce zatížené konstrukční nebo polokonstrukční konzoly.
- Součásti uchycení motoru a držáky gondoly.
- Součásti podvozku (v případě potřeby).
- Konzoly vyžadující vysokou tuhost a únavovou odolnost.
- Aplikace, kde je navzdory vyšším materiálovým nákladům nejdůležitější úspora hmotnosti.
- Úvahy: Vyšší náklady na materiál ve srovnání s hliníkem. Náročnější na následné zpracování (obrábění). Vyžaduje pečlivou kontrolu procesu AM (často v inertní atmosféře), aby se zabránilo zachycení kyslíku. Vyžaduje tepelné zpracování pro snížení napětí.
Tabulka: Srovnání materiálů pro letecké držáky AM
Vlastnictví | AlSi 10Mg | Ti-6Al-4V (třída 5) | Pokyny pro výběr |
---|---|---|---|
Hustota | ~2,67 g/cm³ (nízká) | ~4,43 g/cm³ (mírný) | Pro maximální úsporu hmotnosti v aplikacích s nízkým/středním namáháním zvolte AlSi10Mg. |
Pevnost v tahu (typická) | Mírná (300-450 MPa, po ošetření) | Vysoká (900-1100 MPa, po ošetření) | Zvolte Ti-6Al-4V pro vysokou nosnost a strukturální integritu. |
Tuhost (modul) | Mírná (~70 GPa) | Vysoká (~114 GPa) | Tam, kde je vyžadována vysoká tuhost, aby se zabránilo průhybu, zvolte Ti-6Al-4V. |
Maximální provozní teplota | ~150-200 °C | ~350-400 °C | Pro aplikace vystavené vyšším provozním teplotám zvolte Ti-6Al-4V. |
Odolnost proti korozi | Dobrý | Vynikající | Oba materiály jsou vhodné pro většinu prostředí v letectví a kosmonautice; Ti-6Al-4V je lepší. |
Zpracovatelnost (AM) | Obecně jednodušší | Citlivější (kontrola atmosféry je kritická) | AlSi10Mg často umožňuje rychlejší tisk a potenciálně jemnější rysy. |
Post-Machining | Snadnější | Obtížnější | V případě potřeby přísných tolerancí počítejte se složitostí a náklady na následné obrábění. |
Relativní náklady | Dolní | Vyšší | Vyvážit požadavky na výkonnost a rozpočtová omezení. |
Export do archů
Role společnosti Met3dp jako dodavatele materiálu:
Výběr správného dodavatel kovového prášku je stejně důležitý jako výběr samotného materiálu. Kvalita prášku - jeho sféricita, distribuce velikosti částic (PSD), tekutost a čistota - přímo ovlivňuje hustotu, mechanické vlastnosti a povrchovou úpravu finální 3D tištěné konzoly. Met3dp využívá špičkové technologie rozprašování plynu a technologie PREP (Plasma Rotating Electrode Process) k výrobě vysoce kvalitních prášků AlSi10Mg a Ti-6Al-4V optimalizovaných pro různé druhy tavení v práškovém loži tiskových metod. Naše přísná kontrola kvality zajišťuje konzistenci a spolehlivost a dává výrobcům v leteckém průmyslu důvěru v suroviny používané pro jejich kritické komponenty. Spolupracujeme s organizacemi, kterým dodáváme nejen prášky, ale také odborné znalosti v oblasti výběru materiálů a vývoje aplikací, čímž zajišťujeme, že pro každý jedinečný požadavek na leteckou konzolu je vybrán a správně zpracován optimální materiál.
Volba mezi AlSi10Mg a Ti-6Al-4V nakonec závisí na pečlivé analýze specifických funkčních požadavků, provozního prostředí a výkonnostních cílů konzoly, které jsou vyváženy náklady a výrobními hledisky.
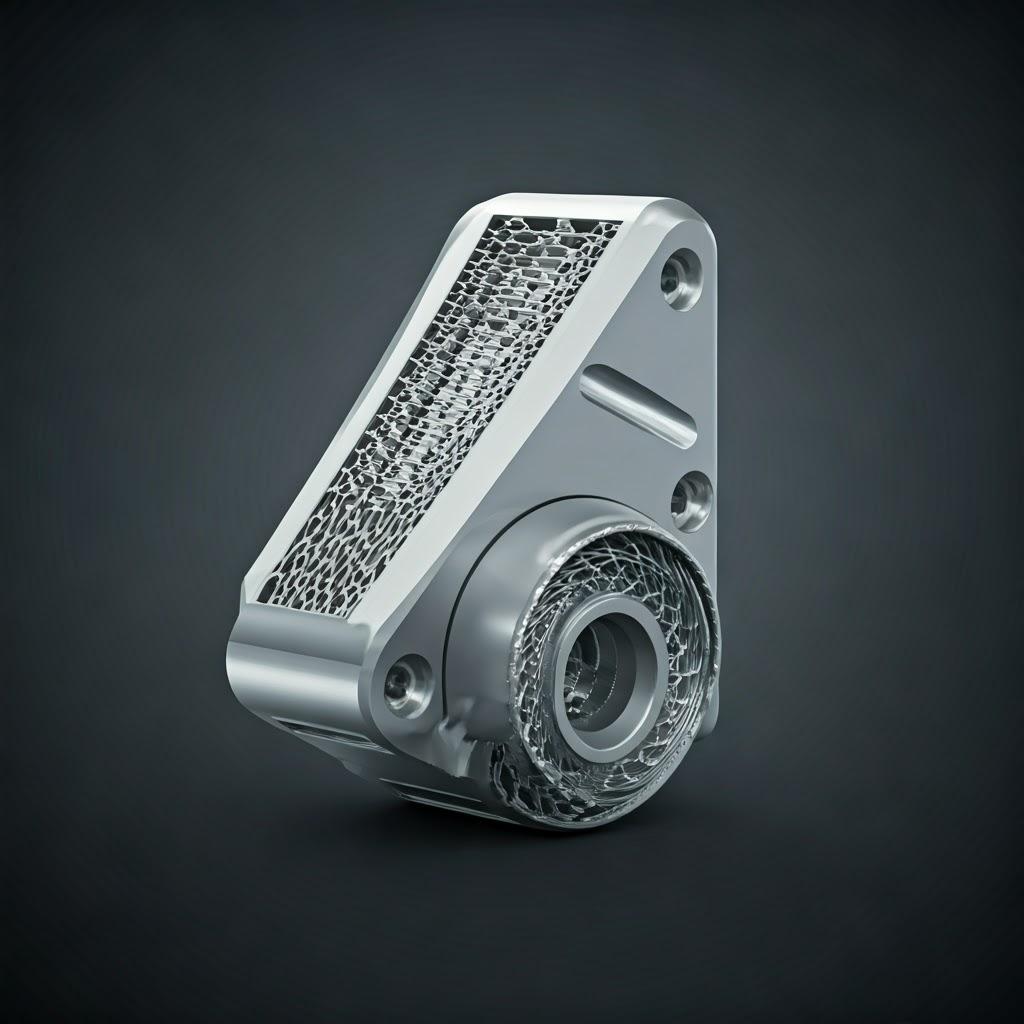
Design pro aditivní výrobu (DfAM): Optimalizace výkonu držáku
Pouhá replikace tradičně navrženého držáku pomocí 3D tisku z kovu často opomíjí nejvýznamnější výhody této technologie. Aby inženýři skutečně využili potenciál pro odlehčení, zvýšení výkonu a nákladovou efektivitu, musí přijmout následující opatření Design pro aditivní výrobu (DfAM) zásady. DfAM není jen o zajištění části může tisknout; jde o aktivní využívání jedinečných schopností aditivních procesů k vytváření vynikajících komponent. V případě leteckých montážních konzolí je použití DfAM klíčové pro splnění přísných požadavků letecká a kosmická výroba odvětví.
Efektivní DfAM pro kovové AM držáky zahrnuje několik klíčových strategií:
1. Optimalizace topologie:
- Koncept: Tento výpočetní přístup využívá algoritmy k optimálnímu rozložení materiálu v definovaném návrhovém prostoru na základě aplikovaných zatížení, omezení a výkonnostních cílů (např. minimalizace hmotnosti při zachování tuhosti).
- Výhoda pro závorky: Vytváří organické, často složitě vypadající tvary, které umisťují materiál pouze tam, kde je to strukturálně nezbytné. To vede k maximálnímu snížení hmotnosti ve srovnání s konvenčními konstrukcemi, což má přímý dopad na spotřebu paliva. Výsledné geometrie je často nemožné nebo nepraktické dosáhnout subtraktivním obráběním.
- Provádění: Vyžaduje specializované softwarové nástroje (např. Altair OptiStruct, Ansys Discovery, nTopology) a jasnou definici zatěžovacích stavů a okrajových podmínek.
2. Generativní design:
- Koncept: Podobně jako optimalizace topologie, ale často v širším rozsahu, generativní návrhové nástroje autonomně generují více návrhových řešení, která splňují předem definovaná omezení a cíle. Inženýr pak vybere nejvhodnější možnost.
- Výhoda pro závorky: Urychluje fázi zkoumání návrhu a potenciálně odhaluje neintuitivní, ale vysoce účinné návrhy konzol. Umožňuje konstruktérům prozkoumat širší škálu možností optimalizovaných pro AM.
- Provádění: Využívá cloud computing a algoritmy AI v rámci CAD nebo specializovaných platforem.
3. Příhradové konstrukce & výplně:
- Koncept: Začlenění vnitřních mřížkových struktur (např. voštin, gyroidů, stochastických pěn) nebo různé hustoty výplně v pevném objemu konzoly.
- Výhoda pro závorky: Výrazně snižuje hmotnost a spotřebu materiálu při zachování strukturální integrity pro určité případy zatížení. Mřížky lze také navrhnout tak, aby v případě potřeby poskytovaly specifické vlastnosti tlumení vibrací nebo usnadňovaly přenos tepla.
- Provádění: Vyžaduje software CAD schopný generovat složité geometrie mřížek a zajistit, aby byly vhodné pro zvolený proces AM (např. samonosné úhly).
4. Minimalizace podpůrných struktur:
- Koncept: Při tavení v práškovém loži jsou často nutné podpůrné konstrukce pro ukotvení převisů a odvádění tepla během tisku. Spotřebovávají však další materiál, prodlužují dobu tisku a vyžadují následné zpracování pro odstranění, což zvyšuje náklady a může mít vliv na kvalitu povrchu.
- Výhoda pro závorky: Konstrukce držáků se samonosnými úhly (obvykle > 45 stupňů od vodorovné roviny), začlenění obětovaných prvků nebo pečlivá orientace dílu na konstrukční desce mohou minimalizovat nebo vyloučit potřebu podpěr v kritických oblastech.
- Provádění: Vyžaduje pochopení specifických omezení procesu AM. Prvky, jako jsou zkosení nebo filety, mohou nahradit ostré převisy. Klíčové je pečlivé zvážení orientace sestavení.
5. Orientace prvků a anizotropie:
- Koncept: Orientace, ve které je držák vytištěn na konstrukční desku, může ovlivnit jeho mechanické vlastnosti (vzhledem k tomu, že AM probíhá po vrstvách, je běžný určitý stupeň anizotropie), povrchovou úpravu na různých plochách a množství potřebné podpory.
- Výhoda pro závorky: Optimální orientace dílu může sladit nejsilnější vlastnosti materiálu s primárním směrem zatížení, minimalizovat podpěry na kritických plochách a zlepšit celkovou úspěšnost tisku.
- Provádění: Analyzujte cesty zatížení a kritické funkce. Použijte simulační nástroje nebo se spolehněte na odborné znalosti poskytovatele služeb AM, abyste určili nejlepší orientaci.
6. Minimální tloušťka stěny a velikost prvku:
- Koncept: Každý proces AM a kombinace materiálů má omezení minimální tloušťky stěny, průměru otvoru a velikosti prvku, které lze spolehlivě vyrobit.
- Výhoda pro závorky: Návrh v těchto mezích zajišťuje vyrobitelnost a zabraňuje poškození nebo deformaci prvků během tisku nebo manipulace.
- Provádění: Projděte si specifikace vybraného AM stroje a materiálu nebo spolupracujte s odborníkem na dodavatel AM pro letecký průmysl abyste zajistili tisknutelnost konstrukčních prvků. Typické minimální tloušťky stěn pro SLM/DMLS se často pohybují v rozmezí 0,4-0,8 mm, ale do značné míry závisí na geometrii a orientaci.
Tabulka: Klíčové strategie DfAM pro letecké závorky
Strategie DfAM | Primární cíl (cíle) | Klíčové výhody pro závorky | Úvahy o provádění |
---|---|---|---|
Optimalizace topologie | Minimalizace hmotnosti, maximalizace tuhosti | Výrazné snížení hmotnosti, optimalizované dráhy zatížení | Vyžaduje specializovaný software, jasnou definici zatěžovacího stavu |
Generativní design | Prozkoumejte optimální konstrukční řešení | Zrychlený průzkum návrhu, neintuitivní řešení | Vyžaduje generativní návrhové nástroje, jasná omezení/cíle |
Mřížové struktury | Snížení hmotnosti, přizpůsobení vlastností | Odlehčení, tlumení vibrací, úspora materiálu | Možnost CAD, zajištění tisknutelnosti (samonosnost) |
Minimalizace podpory | Zkrácení doby tisku, materiálu, následného zpracování | Nižší náklady, lepší povrchová úprava, rychlejší realizace | Konstrukce samonosných úhlů, pečlivá orientace |
Orientace funkcí | Optimalizace vlastností, minimalizace podpor | Sladění pevnosti se zatížením, lepší povrchová úprava | Pochopení anizotropie, umístění kritických prvků |
Tloušťka/velikost stěny | Zajištění vyrobitelnosti | Předcházení chybám tisku, dosažení požadovaných vlastností | Dodržujte procesní/materiálová omezení, konzultujte s poskytovatelem |
Export do archů
Integrací těchto Zásady DfAM od samého počátku mohou konstruktéři přejít od pouhého nahrazení obráběného držáku držákem tištěným. Mohou vytvořit skutečně optimalizované letecké a kosmické komponenty které využívají plný potenciál aditivní výroby kovů, což vede k lehčím, pevnějším a funkčnějším leteckým montážním držákům. Pro úspěch je zásadní spolupráce se zkušenými poskytovateli AM, kteří rozumí DfAM.
Dosažení přesnosti: Tolerance, povrchová úprava a rozměrová přesnost v AM konzolách: tolerance, povrchová úprava a rozměrová přesnost v AM konzolách
Přestože aditivní výroba kovů nabízí neuvěřitelnou volnost při navrhování, častá otázka inženýrů a manažerů nákupu v oborech zaměřených na přesnost, jako je letectví a kosmonautika, se týká dosažitelné úrovně tolerance, kvality povrchu a celkové rozměrové přesnosti. Pochopení možností a omezení procesů AM, jako je selektivní laserové tavení (SLM) a přímé laserové spékání kovů (DMLS) - běžné techniky pro tisk konzol AlSi10Mg a Ti-6Al-4V - je zásadní pro stanovení realistických očekávání a plánování nezbytných kroků po zpracování.
Rozměrová přesnost & Tolerance:
- Obecné schopnosti: Procesy tavení kovového prášku (PBF) obvykle dosahují rozměrové přesnosti v rozmezí ±0,1 mm až ±0,2 mm u menších prvků (např. do 50-100 mm), přičemž toleranční rozsahy se mohou mírně zvýšit u větších rozměrů (např. ±0,1 % až ±0,2 % celkového rozměru). Jedná se o obecné pokyny, které mohou být ovlivněny mnoha faktory.
- Ovlivňující faktory:
- Kalibrace stroje: Pravidelná kalibrace a údržba systému AM jsou velmi důležité.
- Vlastnosti materiálu: Různé slitiny vykazují během tisku různou míru smrštění a napětí.
- Geometrie dílu & Velikost: Větší díly a složité geometrie jsou náchylnější k tepelnému zkreslení.
- Orientace na stavbu: Orientace ovlivňuje tepelné gradienty a potenciální deformace.
- Strategie podpory: Podpěry pomáhají ukotvit díl, ale mohou ovlivnit místní přesnost.
- Tepelný management: Parametry procesu, jako je výkon laseru, rychlost skenování a tloušťka vrstvy, ovlivňují stabilitu taveniny a výslednou přesnost.
- Dosažení přísnějších tolerancí: Pro kritické prvky, jako jsou styčné plochy, ložisková rozhraní nebo přesná umístění otvorů, které vyžadují větší tolerance, než je možné při standardním procesu AM, následné CNC obrábění se obvykle používá. Často je ekonomičtější vytisknout držák ve tvaru blízkém síťovému s přídavky na obrábění kritických ploch než se pokoušet o extrémně přísné tolerance přímo z tiskárny.
Povrchová úprava (drsnost):
- Povrch ve stavu, v jakém se nachází: Povrchová úprava kovových dílů vyrobených metodou AM je ze své podstaty drsnější než povrch obrobený. To je způsobeno procesem tavení po vrstvách a částečně roztavenými částicemi prášku ulpívajícími na povrchu. Typické hodnoty drsnosti povrchu (Ra) u dílů vyrobených metodou SLM/DMLS se pohybují v rozmezí od 6 µm až 20 µm (mikrometrů), v závislosti na:
- Orientace: Povrchy směřující nahoru bývají hladší než povrchy směřující dolů (které vyžadují podpěry) nebo svislé stěny (na kterých se objevují linie vrstev).
- Materiál: Různé kovové prášky mohou mít mírně odlišnou strukturu povrchu.
- Parametry procesu: Parametry laseru a tloušťka vrstvy ovlivňují taveninu a kvalitu povrchu.
- Velikost částic: Rozložení velikosti použitého kovového prášku ovlivňuje dosažitelnou drsnost. Zaměření společnosti Met3dp’ na vysoce kvalitní prášky s řízenou distribucí velikosti částic, vyráběné pomocí pokročilé atomizace, přispívá k lepší kvalitě povrchu.
- Zlepšení povrchové úpravy: Pokud je z funkčních (např. únavová životnost, těsnicí plochy) nebo estetických důvodů požadován hladší povrch, jsou k dispozici různé techniky následného zpracování:
- Tryskání abrazivem (kuličkové/ pískové): Poskytuje rovnoměrný matný povrch a obvykle mírně snižuje hodnoty Ra.
- Třískové/vibrační dokončování: Vyhlazuje povrchy a hrany, účinné pro dávky menších dílů.
- Leštění: Mechanickým nebo elektrochemickým leštěním lze dosáhnout velmi hladkého, zrcadlového povrchu (Ra < 1 µm), ale je to spojeno se značnými náklady a časem.
- Obrábění: Poskytuje nejhladší a nejpřesnější povrchy na specifických prvcích.
Kontrola kvality & Ověřování:
Zajištění toho, aby 3D tištěné držáky splňovaly požadované specifikace, zahrnuje přísnou kontrolu kvality v průběhu celého procesu:
- Řízení kvality prášku: Ověřování kvality vstupního prášku (chemie, PSD, tekutost).
- Monitorování procesů: Monitorování taveniny a usazování vrstvy na místě (pokud je k dispozici).
- Rozměrová kontrola: Použití souřadnicových měřicích strojů (CMM), 3D skenování nebo tradičních metrologických nástrojů k ověření rozměrů a tolerancí po tisku a obrábění.
- Měření drsnosti povrchu: Použití profilometrů ke kvantifikaci kvality povrchu.
- Nedestruktivní zkoušení (NDT): Techniky jako CT nebo radiografie ke kontrole vnitřních defektů, jako je pórovitost (popsáno dále v části Post-Processing).
Tabulka: Typická přesnost pro kovové držáky PBF (AlSi10Mg, Ti-6Al-4V)
Parametr | Schopnost ve stavu po dokončení (typická) | Potenciál následného zpracování | Klíčové úvahy |
---|---|---|---|
Rozměrová tolerance | ±0,1 až ±0,2 mm (nebo ±0,1-0,2 %) | Těsnější obrábění na CNC (±0,025 mm) | Složitost geometrie, velikost, materiál, orientace |
Drsnost povrchu (Ra) | 6 – 20 µm | < 1 µm (leštění), 1-5 µm (obrábění) | Orientace povrchu, požadovaná funkce, náklady |
Minimální velikost funkce | ~0,4 – 0,8 mm (stěny) | Omezeno procesem AM | Schopnost stroje, velikost prášku, konstrukční pravidla |
Minimální průměr otvoru | ~0,5 – 1,0 mm | Omezeno procesem AM; zlepšeno vrtáním | Poměr stran, orientace |
Export do archů
Pochopení těchto úrovní přesnosti umožňuje konstruktérům vhodně navrhovat konzoly a zadávat kroky následného zpracování, jako je například obrábění, pouze v případě potřeby. Spolupráce se zkušeným Poskytovatel služeb metal AM jako je Met3dp, který rozumí nuancím různých tiskových metod a materiálů zajišťuje, že konečné letecké držáky splňují náročné rozměrové a povrchové požadavky leteckého průmyslu.
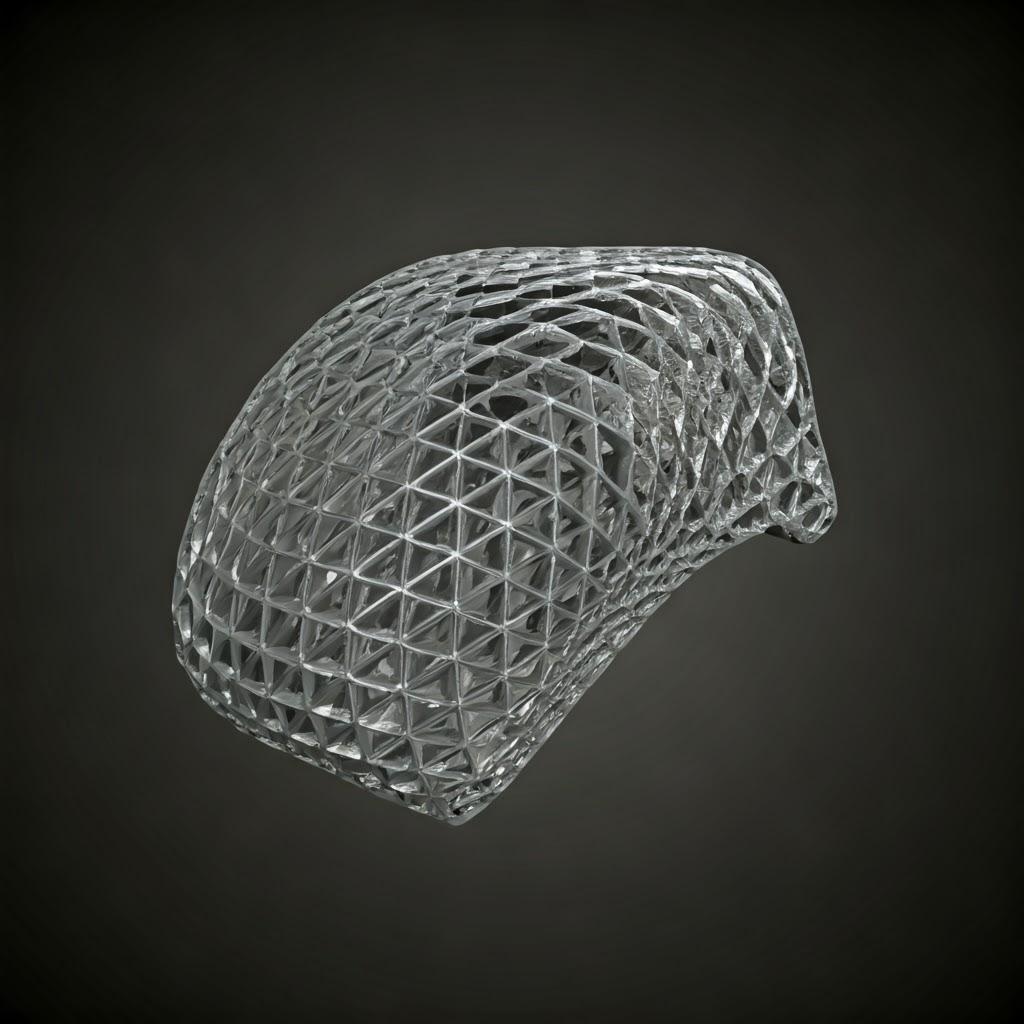
Za hranice tisku: Základní postprocesing pro letecké závorky
Tvorba kovového leteckého držáku nekončí, když se 3D tiskárna zastaví. Součástka “v podobě, v jaké je postavena”, vyžaduje několik zásadních věcí následné zpracování kroky k přeměně ze surového tisku na funkční součástku připravenou k letu, která splňuje letecké normy. Tyto kroky jsou nezbytné pro dosažení požadovaných mechanických vlastností, rozměrové přesnosti, povrchové úpravy a celkové integrity. Manažeři veřejných zakázek by měli tyto nezbytné fáze zohlednit v časovém plánu projektu a kalkulacích nákladů.
Zde je typický pracovní postup pro následné zpracování 3D tištěných kovových leteckých držáků (AlSi10Mg nebo Ti-6Al-4V):
1. Úleva od stresu:
- Účel: Rychlé cykly zahřívání a ochlazování, které jsou vlastní tavení v práškovém loži, vytvářejí v tištěném dílu vnitřní zbytková napětí. Tato napětí mohou způsobit deformace nebo praskliny během nebo po vyjmutí z konstrukční desky nebo negativně ovlivnit únavovou životnost. Odstraňování napětí je tepelné zpracování prováděné před vyjmutí dílu z konstrukční desky.
- Proces: Celá konstrukční deska s připevněnými držáky se zahřeje v peci (často v inertní atmosféře nebo ve vakuu) na určitou teplotu nižší, než je teplota stárnutí nebo žíhání slitiny, po určitou dobu se udržuje a poté se pomalu ochlazuje. To umožňuje uvolnění vnitřních pnutí, aniž by se výrazně změnila mikrostruktura jádra.
- Důležitost: Naprosto zásadní pro rozměrovou stabilitu a prevenci selhání dílu, zejména u složitých geometrií a materiálů, jako je Ti-6Al-4V.
2. Odstranění části:
- Účel: Oddělení tištěných držáků od stavební desky.
- Proces: Obvykle se provádí pomocí elektroerozivního obrábění (EDM) nebo pásové pily. Je třeba dbát na to, aby nedošlo k poškození dílů. Konstrukční desku lze často znovu obrobit a znovu použít.
3. Odstranění podpůrné konstrukce:
- Účel: Odstranění dočasných podpůrných konstrukcí vytvořených během tisku za účelem ukotvení převisů a usnadnění přenosu tepla.
- Proces: Tento krok může být pracný a často se provádí ručně pomocí ručního nářadí, kleští nebo brusky. U složitých vnitřních podpěr může být zapotřebí specializované nářadí nebo někdy elektrochemické obrábění. Zásady DfAM zaměřené na minimalizaci podpěr (viz předchozí oddíl) zde výrazně snižují potřebnou námahu.
- Výzvy: V místech, kde byly připevněny podpěry, mohou zůstat stopy po svědcích nebo drsný povrch, což může vyžadovat další úpravy. Přístup k vnitřním podpěrám může být obtížný.
4. Tepelné ošetření (HIP & amp; roztok/stárnutí):
- Účel: Zlepšení mechanických vlastností (pevnost, tažnost, únavová životnost) a odstranění vnitřní pórovitosti.
- Izostatické lisování za tepla (HIP): Kombinace vysoké teploty a vysokého tlaku inertního plynu (např. argonu) účinně uzavírá vnitřní dutiny a pórovitost a dosahuje téměř plné teoretické hustoty (>99,9 %). To má zásadní význam pro únavově kritické letecké součásti.
- Žíhání v roztoku & stárnutí (pro příslušné slitiny): Další tepelné zpracování přizpůsobené konkrétní slitině (například T6 pro AlSi10Mg nebo specifické zpracování pro Ti-6Al-4V) pro optimalizaci mikrostruktury a dosažení požadovaných konečných mechanických vlastností (tvrdost, pevnost, tažnost).
- Proces: Provádí se ve specializovaných jednotkách HIP a pecích s řízenou atmosférou podle přesných specifikací pro letecký průmysl (např. norem AMS).
- Důležitost: HIP je často považován za povinný pro kritické letecké díly, aby byla zajištěna integrita materiálu a optimální mechanické vlastnosti.
5. Povrchová úprava:
- Účel: Pro dosažení požadované drsnosti povrchu odstraňte podpůrné značky nebo připravte povrchy pro lakování či kontrolu.
- Proces: Jak již bylo uvedeno, mezi možnosti patří:
- Tryskání abrazivem (kuličkami, pískem atd.): Vytváří jednotný matný povrch.
- Třískové/vibrační dokončování: Vyhlazuje povrchy a hrany, vhodné pro dávky.
- Ruční broušení/odstraňování otřepů: Řeší specifické oblasti, jako jsou kontaktní místa podpory.
- Leštění (mechanické/elektrochemické): Pro velmi hladké povrchy na kritických plochách.
- Výběr: Záleží na funkci držáku, materiálu a specifických požadavcích na povrch.
6. CNC obrábění:
- Účel: Dosažení přísných tolerancí kritických rozměrů, styčných ploch, průměrů/umístění otvorů nebo specifických hladkých povrchů, které nelze splnit procesem AM podle stavu konstrukce nebo jinými metodami dokončování.
- Proces: Využívá standardní CNC frézovací nebo soustružnická centra. Upínání často složité geometrie dílů AM může vyžadovat pečlivé plánování. Ve fázi DfAM by měly být zahrnuty přídavky na obrábění.
- Důležitost: Je nezbytný pro zajištění přesných rozhraní a zaměnitelnosti v leteckých sestavách.
7. Čištění & amp; Kontrola:
- Účel: Odstranění všech zbytků prášku, obráběcích kapalin nebo nečistot a ověření, zda konečný díl splňuje všechny specifikace.
- Proces: Zahrnuje postupy závěrečného čištění a důkladnou kontrolu:
- Rozměrová kontrola: CMM, 3D skenování.
- Měření povrchové úpravy: Profilometrie.
- Nedestruktivní zkoušení (NDT): Klíčové pro letectví a kosmonautiku. Mezi běžné metody patří:
- Vizuální kontrola (VT): Základní kontrola povrchových vad.
- Kontrola kapalinovým penetrantem (LPI): Detekuje trhliny porušující povrch.
- Radiografické (rentgenové) nebo počítačové tomografické (CT) vyšetření: Zjišťuje vnitřní dutiny, pórovitost, inkluze a ověřuje vnitřní vlastnosti. CT skenování je obzvláště výkonné u složitých dílů AM.
- Ultrazvukové testování (UT): Dokáže odhalit podpovrchové vady.
- Dokumentace: Podrobné záznamy o všech krocích následného zpracování a výsledcích kontroly jsou uchovávány za účelem zpětné sledovatelnosti, což je požadavek v leteckém průmyslu.
Tabulka: Přehled kroků následného zpracování pro AM letecké konzoly
Krok | Účel | Typická metoda (metody) | Klíčové výsledky |
---|---|---|---|
Úleva od stresu | Snížení vnitřního napětí, prevence deformace | Tepelné zpracování v peci (na stavební desce) | Rozměrová stabilita |
Odstranění části | Oddělení dílu od stavební desky | Drátové elektroerozivní obrábění, pásová pila | Část uvolněná pro další kroky |
Odstranění podpory | Odstranění dočasných tiskových podpěr | Ruční (nástroje), Obrábění, ECM | Díl ve tvaru sítě (může vyžadovat retušování povrchu) |
Tepelné zpracování (HIP) | Odstranění vnitřní pórovitosti, zlepšení vlastností | Vysokoteplotní a tlaková pec (jednotka HIP) | Plná hustota (99,9 %), zvýšená únavová životnost |
Tepelné zpracování (ostatní) | Optimalizace mikrostruktury & mechanické vlastnosti | Žíhání roztokem, stárnutí (specifické pro slitinu) | Požadovaná pevnost, tvrdost, tažnost |
Povrchová úprava | Dosažení požadovaných Ra, čistých povrchů | Tryskání, obrušování, leštění | Specifická struktura povrchu, estetické zlepšení |
CNC obrábění | Dosahování přísných tolerancí, kritických povrchů | Frézování, soustružení | Přesné rozměry, hladké styčné plochy |
Čištění & amp; Inspekce | Odstranění kontaminantů, ověření specifikací | Čistící postupy, CMM, NDT (CT, LPI atd.) | Díl připravený k letu, zajištění kvality, sledovatelnost |
Export do archů
Úspěšné zvládnutí těchto požadavky na následné zpracování je zásadní pro každou organizaci, která zavádí technologii AM pro aplikace v letectví a kosmonautice. Vyžaduje specifické vybavení, odborné znalosti a dodržování přísných norem kvality. Spolupráce se zkušenými poskytovateli služeb zajistí, že tyto kroky budou provedeny správně, a dodá letecké konzoly připravené pro náročné letové podmínky.
Zvládání výzev: Překonávání překážek při 3D tisku leteckých držáků
Přestože výhody aditivní výroby kovů pro letecké držáky jsou značné, není tato technologie bez problémů. Úspěšná implementace AM výroby kovů vyžaduje hluboké porozumění procesu, potenciálním úskalím a strategiím pro jejich zmírnění. Povědomí o těchto problémech je pro konstruktéry i manažery nákupu při hodnocení projektů AM a výběru dodavatelů klíčové.
Zde jsou uvedeny některé běžné překážky, se kterými se setkáváme při 3D tisku kovových leteckých držáků, a jak je řeší zkušení poskytovatelé:
1. Zbytkové napětí, deformace a zkreslení:
- Výzva: Intenzivní, lokalizovaný ohřev a rychlé ochlazení během laserového tavení vytváří značné tepelné gradienty, které vedou k nárůstu zbytkového napětí v dílu a konstrukční desce. Pokud se toto napětí nezvládne, může způsobit deformaci dílů během tisku, prasknutí nebo deformaci po vyjmutí z konstrukční desky.
- Strategie zmírnění dopadů:
- Optimalizované podpůrné struktury: Dobře navržené podpěry bezpečně ukotvují díl a pomáhají odvádět teplo.
- Optimalizace parametrů procesu: Jemné nastavení výkonu laseru, rychlosti skenování, strategie skenování (např. skenování ostrůvků) a tloušťky vrstvy pomáhá řídit tepelný vstup.
- Vytápění platformy: Předehřátí konstrukční desky snižuje tepelné gradienty.
- Tepelné ošetření proti stresu: Provedení tohoto klíčového kroku před je nezbytné odstranit díl (jak bylo popsáno výše).
- Simulace: Software pro tepelnou simulaci může předpovídat nárůst napětí a informovat o rozhodnutích o konstrukci/orientaci.
2. Pórovitost:
- Výzva: Dosažení plné hustoty (>99,9 %) je kritické pro mechanickou integritu (zejména únavovou životnost) leteckých součástí. Pórovitost (malé vnitřní dutiny) může vzniknout v důsledku zachycení plynu během tavení, neúplného tavení mezi vrstvami nebo keyholingu (propadů páry) způsobeného nadměrným přívodem energie.
- Strategie zmírnění dopadů:
- Vysoce kvalitní prášek: Použití sférických, plynem atomizovaných prášků s nízkou vnitřní pórovitostí a řízenou distribucí velikosti částic, jako jsou prášky vyráběné společností Met3dp, je zásadní. Správná manipulace s práškem a jeho skladování jsou rovněž nezbytné, aby se zabránilo absorpci vlhkosti.
- Optimalizované parametry procesu: Vývoj robustních sad parametrů specifických pro kombinaci stroj/materiál zajišťuje stabilní chování taveniny a úplné tavení.
- Kontrola inertní atmosféry: Udržování prostředí inertního plynu vysoké čistoty (argonu nebo dusíku) v konstrukční komoře zabraňuje oxidaci a snižuje pórovitost plynu.
- Izostatické lisování za tepla (HIP): Tento krok následného zpracování účinně uzavírá zbytkový plyn a nedostatek pórovitosti.
3. Odstranění podpůrné konstrukce:
- Výzva: Podpory jsou sice nezbytné, ale zvyšují náklady a složitost. Jejich odstraňování, zejména ze složitých vnitřních kanálů nebo jemných prvků na složitých konstrukcích držáků, může být obtížné, časově náročné a hrozí riziko poškození dílu. Zbytky podpěrného materiálu nebo svědecké stopy mohou také negativně ovlivnit výkon nebo vyžadovat další dokončovací práce.
- Strategie zmírnění dopadů:
- DfAM pro snížení podpory: Konstrukce dílů se samonosnými úhly a prvky minimalizuje potřebu podpěr.
- Optimalizovaný design podpory: Použití podpůrných konstrukcí (např. tenkostěnných nebo příhradových podpěr), které jsou dostatečně pevné během stavby, ale po jejím skončení je lze snáze odstranit.
- Strategická orientace: Orientace dílu tak, aby se minimalizovaly podpěry na kritických plochách nebo v těžko přístupných místech.
- Vhodné techniky odstraňování: Použití správných nástrojů a metod (ruční, obrábění, ECM) v závislosti na typu a umístění podpory.
4. Variace povrchové úpravy:
- Výzva: Povrchová úprava při stavbě se liší v závislosti na orientaci vzhledem ke směru stavby (nahoře, dole, svislé stěny). Dosažení konzistentní nebo velmi hladké povrchové úpravy v celé konzole často vyžaduje značné dodatečné zpracování.
- Strategie zmírnění dopadů:
- Optimalizovaná orientace: Upřednostnění kritických povrchů pro orientaci, která přináší lepší vnitřní povrchovou úpravu.
- Vhodné následné zpracování: Výběr správné dokončovací techniky (tryskání, bubnování, leštění, obrábění) na základě požadované hodnoty Ra a geometrie.
- Ladění parametrů procesu: Některé parametry mohou mírně ovlivnit kvalitu povrchu.
5. Opakovatelnost procesu a zajištění kvality:
- Výzva: Zajištění toho, aby každá vyrobená konzola splňovala přesně stejné specifikace, vyžaduje přísnou kontrolu procesů a protokoly pro zajištění kvality, které jsou v leteckém průmyslu neoddiskutovatelné. Odchylky v dávkách prášku, kalibraci stroje nebo podmínkách prostředí mohou potenciálně ovlivnit kvalitu dílů.
- Strategie zmírnění dopadů:
- Robustní systém řízení kvality (QMS): Zavedení systému řízení kvality v souladu s normami pro letecký průmysl (např. AS9100).
- Řízení životního cyklu prášku: Důsledné testování a sledovatelnost kovových prášků od výroby až po recyklaci.
- Kalibrace a monitorování strojů: Pravidelná kalibrace, preventivní údržba a případně monitorování procesu in-situ.
- Standardizované postupy: Zdokumentované postupy pro tisk, následné zpracování a kontrolu.
- Komplexní NDT: Využití vhodných metod nedestruktivního zkoušení (zejména CT skenování vnitřní integrity) k ověření kvality dílů.
6. Řízení nákladů a dodací lhůty:
- Výzva: Ačkoli AM nabízí výhody, náklady na jeden díl mohou být ve srovnání s tradičními metodami u jednoduchých geometrií nebo velmi velkých objemů stále vysoké. Efektivní řízení dodacích lhůt vyžaduje pečlivé plánování celého pracovního postupu, včetně následného zpracování.
- Strategie zmírnění dopadů:
- DfAM pro snížení nákladů: Optimalizace návrhů nejen z hlediska výkonu, ale také z hlediska vyrobitelnosti (např. minimalizace objemu, redukce podpěr, rozmístění dílů na konstrukční desce).
- Realistické modelování nákladů: Přesné účtování strojního času, materiálu, práce, následného zpracování a zajištění kvality.
- Spolupráce s dodavateli: Úzká spolupráce se zkušenými poskytovateli AM, kteří mohou optimalizovat proces a poskytnout přesné nabídky a odhady doby realizace.
Úspěšné zvládnutí těchto výzev vyžaduje značné odborné znalosti, investice do vybavení a systémů kvality a závazek neustálého zlepšování. To je důvod, proč je partnerství se zavedenými specialisté na aditivní výrobu kovů kteří mají prokazatelné zkušenosti v náročných průmyslových odvětvích, jako je letecký průmysl, je často nejefektivnějším přístupem pro společnosti, které chtějí využít AM pro kritické komponenty, jako jsou montážní konzoly pro letectví. Disponují znalostmi a infrastrukturou, které jim umožní překonat tyto překážky a spolehlivě dodávat díly vhodné pro let.
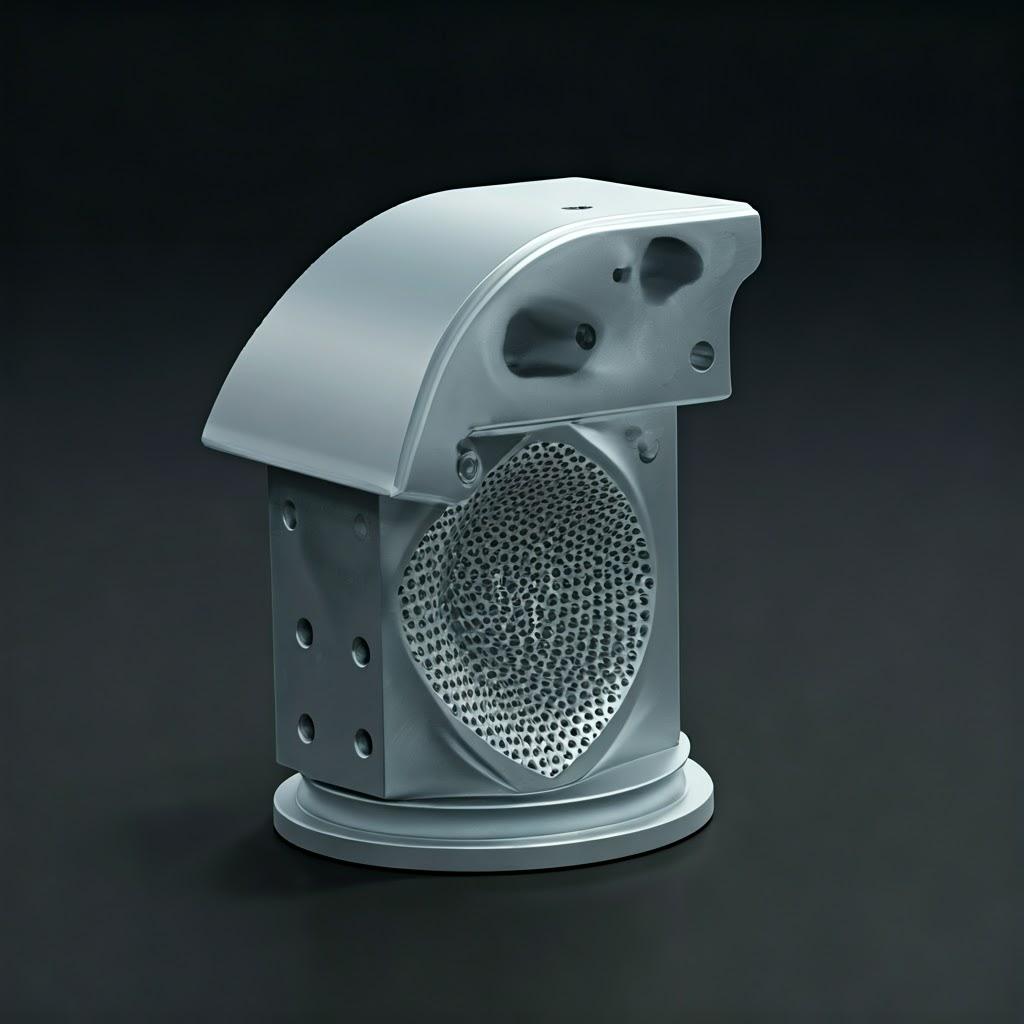
Výběr partnera: Jak si vybrat správného poskytovatele služeb 3D tisku kovů pro letecké komponenty?
Výběr správného výrobního partnera je vždy velmi důležitý, ale v případě leteckých komponentů vyráběných pomocí aditivní výroby kovů je sázka mimořádně vysoká. Složitost technologie, přísné požadavky na kvalitu a kritičnost finálních dílů vyžadují dodavatele s osvědčenými odbornými znalostmi, robustními procesy a správnými certifikacemi. Výběr nevhodného dodavatele může vést ke zpoždění projektu, překročení rozpočtu, nekvalitním dílům a potenciálnímu ohrožení bezpečnosti.
Při hodnocení potenciálních poskytovatelé služeb kovového 3D tisku nebo dodavatelé AM pro letecký průmysl pro vaše potřeby v oblasti letectví zvažte následující klíčová kritéria:
1. Certifikace a dodržování předpisů v leteckém průmyslu:
- Certifikace AS9100: Jedná se o standardní požadavek na systém řízení kvality (QMS) pro letecký, kosmický a obranný průmysl. Certifikace podle AS9100 prokazuje závazek poskytovatele ke kvalitě, sledovatelnosti a neustálému zlepšování, speciálně přizpůsobenému pro letecký průmysl. Neoddiskutovatelné pro letově kritické komponenty.
- Soulad s ITAR (pokud je to relevantní): Pokud váš projekt zahrnuje komponenty související s obranou nebo technická data podléhající předpisům o mezinárodním obchodu se zbraněmi, ujistěte se, že je poskytovatel registrován a splňuje požadavky ITAR.
- Akreditace Nadcap (potenciálně): Zatímco AS9100 se vztahuje na systém řízení jakosti, Nadcap poskytuje akreditaci pro specifické speciální procesy, jako je tepelné zpracování, nedestruktivní kontrola a případně samotná aditivní výroba. Zkontrolujte, zda je držitelem akreditace pro příslušné procesy.
2. Znalost materiálů a sledovatelnost:
- Materiálové schopnosti: Ověřte si, že poskytovatel má zdokumentované zkušenosti s tiskem konkrétní slitiny, kterou požadujete (např. AlSi10Mg, Ti-6Al-4V), a že má pro ni validované procesní parametry.
- Kvalita prášku & amp; Sourcing: Ptejte se na jejich kovový prášek postupy získávání a kontroly kvality. Používají prášky od renomovaných dodavatelů? Provádí vstupní kontrolu materiálu? Poskytovatelé jako Met3dp, kteří vyrábějí vlastní vysoce kvalitní prášky pomocí pokročilých metod, jako je plynová atomizace a PREP, nabízejí výhodu při kontrole tohoto klíčového vstupu.
- Sledovatelnost materiálu: Úplná sledovatelnost šarží kovových prášků, od počáteční šarže přes tisk, zpracování a konečnou kontrolu, je pro odpovědnost v leteckém průmyslu nezbytná. Ujistěte se, že poskytovatel má zavedeny systémy pro udržování tohoto řetězce kontroly.
3. Vybavení a technologie:
- Vhodná technologie AM: Ověřte si, že provozují dobře udržované systémy AM pro průmyslové zpracování kovů vhodné pro zvolený materiál a požadavky na díl (např. SLM, DMLS nebo případně SEBM pro určité aplikace). Společnost Met3dp využívá vedle dalších potenciálních systémů PBF také vlastní špičkové průmyslové tiskárny SEBM, které jsou známé svou spolehlivostí a přesností.
- Objem sestavení: Ujistěte se, že jejich stroje mohou pojmout velikost vašich držáků.
- Monitorování procesů: Zeptejte se na možnosti monitorování in-situ (např. monitorování taveniny), které může poskytnout cenné údaje pro zajištění kvality.
4. Technická podpora a podpora DfAM:
- Odborné znalosti: Má poskytovatel zkušené aplikační inženýry, kteří rozumí principům DfAM a mohou spolupracovat s vaším týmem na optimalizaci konstrukce držáku pro aditivní výrobu? Tato podpora může být neocenitelná pro maximalizaci úspory hmotnosti, minimalizaci podpěr a zajištění tisknutelnosti.
- Simulační schopnosti: Poskytovatelé nabízející tepelnou nebo strukturální simulaci mohou pomoci předpovědět výkon a zmírnit rizika, jako je například deformace.
5. Komplexní možnosti následného zpracování:
- In-House vs. Outsourcing: Určete, které kroky následného zpracování (uvolnění napětí, HIP, obrábění, NDT, dokončovací práce) se provádějí ve firmě a které se zadávají externě. Vlastní kapacity obecně umožňují lepší kontrolu kvality, doby realizace a nákladů.
- Letecké a kosmické normy: Zajistěte, aby veškeré následné zpracování, zejména tepelné zpracování a NDT, bylo prováděno v souladu s příslušnými leteckými specifikacemi (např. normami AMS).
6. Systém řízení kvality (QMS) a kontrola:
- Robustní QMS: Kromě AS9100 zhodnoťte vyspělost a implementaci jejich celkového systému řízení kvality.
- Kontrolní schopnosti: Ověřte si, že disponují potřebným metrologickým vybavením (souřadnicové měřicí stroje, 3D skenery) a možnostmi nedestruktivního zkoušení (u dílů AM se doporučuje CT skenování) pro důkladnou kontrolu a validaci vašich držáků.
- Dokumentace: Zajistěte, aby poskytovali komplexní dokumentaci, včetně certifikací materiálu, certifikátů shody, kontrolních zpráv a záznamů o sledovatelnosti.
7. Zkušenosti a výsledky:
- Zkušenosti v letectví a kosmonautice: Upřednostněte dodavatele s prokazatelnými zkušenostmi s výrobou součástí pro letecký průmysl. Požádejte o případové studie nebo reference (v rámci zachování důvěrnosti).
- Řízení projektů: Zhodnoťte jejich komunikaci, vstřícnost a přístup k řízení projektu během cenové nabídky a zaváděcího procesu.
Tabulka: Kontrolní seznam pro hodnocení dodavatelů AM pro letecký průmysl
Kritéria | Klíčové otázky, které je třeba položit | Úroveň důležitosti |
---|---|---|
Certifikace | Certifikát AS9100? Splňujete požadavky ITAR (pokud je to nutné)? Nadcap pro speciální procesy? | Povinné |
Materiálová odbornost | Zkušenosti s požadovanými slitinami? Ověřené parametry? QC prášku & sledovatelnost? | Vysoký |
Zařízení | Vhodná technika AM? Dostatečný objem stavby? Údržba a kalibrace stroje? Monitorování na místě? | Vysoký |
Technická podpora | Jsou k dispozici odborné znalosti DfAM? Nabídka spolupráce? Možnosti simulace? | Vysoký |
Následné zpracování | Vlastní kapacity (HIP, obrábění, NDT)? Dodržování specifikací AMS? | Vysoký |
Kvalita & amp; Inspekce | Robustní QMS? Vhodná metrologie & NDT (CT)? Komplexní dokumentace? | Povinné |
Zkušenosti & Komunikace | Prokazatelné výsledky v leteckém průmyslu? Případové studie/reference? Jasná komunikace & řízení projektu? | Vysoký |
Náklady a dodací lhůta | Transparentní ceny? Reálné odhady doby realizace? | Středně vysoká a vysoká |
Export do archů
Výběr správného partnera vyžaduje důkladnou prověrku. Nezakládejte své rozhodnutí pouze na ceně; upřednostněte kvalitu, odborné znalosti a shodu s předpisy, zejména v případě letového hardwaru. Schopný partner, jako je Met3dp, nabízející komplexní řešení od pokročilých prášků a tiskáren až po služby vývoje aplikací, může výrazně snížit riziko vašeho projektu a zajistit úspěšnou výrobu vysoce výkonného montážní konzoly pro letectví.
Pochopení investice: Nákladové faktory a dodací lhůty pro 3D tištěné konzoly
Přestože aditivní výroba kovů přináší významné výkonnostní a konstrukční výhody pro letecké držáky, je pro plánování projektu a sestavování rozpočtu zásadní pochopit související náklady a typické doby realizace. Manažeři veřejných zakázek potřebují transparentnost ohledně toho, co určuje konečnou cenu za díl a jak dlouho trvá výrobní proces od zadání objednávky po dodání.
Nákladové faktory pro 3D tištěné kovové držáky:
Náklady na výrobu držáku AM jsou ovlivněny kombinací několika faktorů:
- Typ materiálu a spotřeba:
- Náklady na materiál: Kovové prášky pro letectví a kosmonautiku, zejména slitiny titanu jako Ti-6Al-4V, jsou ze své podstaty dražší než standardní technické slitiny. AlSi10Mg je obecně cenově výhodnější.
- Část Objem & amp; Hmotnost: Čím větší a těžší je držák, tím více materiálu se spotřebuje, což přímo ovlivňuje náklady. Techniky DfAM, jako je optimalizace topologie a mřížkové struktury, jsou klíčem k minimalizaci spotřeby materiálu.
- Objem podpůrné struktury: Materiál použitý na podpůrné konstrukce rovněž zvyšuje náklady, což posiluje potřebu minimalizace podpěr při návrhu.
- Strojový čas:
- Doba výstavby: To je často nejvýznamnějším faktorem ovlivňujícím náklady. Závisí na celkovém objemu, který se má vytisknout (díl + podpěry), tloušťce vrstvy, parametrech laseru (rychlost skenování) a režijních nákladech stroje (nastavení, čištění). Vyšší díly obecně trvají déle.
- Hnízdění & amp; Hustota zástavby: Tisk více držáků současně v jednom sestavení (nesting) může optimalizovat využití stroje a snížit náklady na jeden díl, zejména u menších komponent.
- Práce a inženýrství:
- Příprava souborů & Nastavení: Čas strávený inženýry/techniky přípravou souboru pro sestavení, nastavením stroje a programováním parametrů.
- Práce po zpracování: Ruční práce při odstraňování dílů, odstraňování podpěr, povrchové úpravě a kontrole. Zejména odstranění podpěr může být u složitých dílů pracné.
- Technická podpora (DfAM): Pokud je vyžadována významná pomoc při projektování, může být zahrnuta do celkových nákladů na projekt nebo uvedena samostatně.
- Požadavky na následné zpracování:
- Tepelné zpracování: Náklady spojené s časem pece na uvolnění stresu a/nebo cykly HIP. HIP je relativně nákladný proces vzhledem k potřebě specializovaného vybavení.
- Obrábění: Náklady závisí na složitosti požadovaného obrábění, počtu prvků, které je třeba obrobit, a požadovaných tolerancích.
- Povrchová úprava: Náklady se liší podle zvolené metody (tryskání je levnější než vícestupňové leštění).
- Zajištění kvality a kontrola:
- Náklady na NDT: Nedestruktivní testování, zejména CT skenování, zvyšuje náklady na díl, ale u kritických leteckých komponent je často povinné.
- Rozměrová kontrola: Čas a prostředky na CMM nebo 3D skenování.
- Dokumentace: Úsilí potřebné k sestavení nezbytného balíčku dokumentace kvality.
- Objem objednávky:
- Úspory z rozsahu: Ačkoli je AM vhodný pro malé objemy, lze při větších sériích dosáhnout určitých úspor z rozsahu díky optimalizovanému vnořování a potenciálně vyhrazeným strojům, což snižuje podíl nákladů na seřízení na jeden díl. Velkoobchodní odběratelé nebo ti, kteří chtějí vyrábět pravidelné série, mohou vyjednávat o cenách na základě objemu.
Typické dodací lhůty:
Doba výroby 3D tištěného leteckého držáku zahrnuje několik fází:
- Kontrola objednávek & příprava spisu (1-3 dny): Počáteční kontrola návrhu, kontroly DfAM (pokud je to nutné), finalizace nabídky, příprava souboru pro sestavení a plánování.
- Tisk (1-5+ dní): Skutečný strojní čas závisí do značné míry na velikosti dílu, složitosti a počtu dílů vložených do sestavy. Jedna velká konzola nebo celá sestavovací deska menších konzol může trvat několik dní.
- Následné zpracování (3-10+ dní): To je často nejdelší část přípravné doby. Zahrnuje:
- Doba chlazení po tisku.
- Cyklus tepelného ošetření pro zmírnění stresu (může trvat den nebo déle, včetně náběhu/poklesu).
- Odstranění dílu a podpěry.
- Cyklus HIP (pokud je vyžadován, často se zadává externě, což prodlužuje čas - potenciálně 1-2 týdny včetně logistiky).
- CNC obrábění (závisí na složitosti).
- Povrchová úprava.
- Inspekce a razítko; dokumentace (1-3 dny): Konečná kontrola rozměrů, nedestruktivní zkoušení a příprava dokumentace.
- Doprava (proměnná): Záleží na lokalitě a způsobu dopravy.
Celková odhadovaná doba realizace se může pohybovat od 1-2 týdnů u jednoduchých prototypů bez HIPu až po 4-8 týdnů nebo více u složitých, letově certifikovaných držáků vyžadujících HIP a rozsáhlé následné zpracování.
Tabulka: Náklady & amp; Úvahy o době realizace
Faktor | Primární řidič (řidiči) | Dopad na náklady | Dopad na dobu realizace | Zmírnění / optimalizace |
---|---|---|---|---|
Materiál | Typ slitiny, Objem dílu, Objem nosiče | Vysoký | Nízký | DfAM (odlehčení), Výběr materiálu |
Strojový čas | Výška/objem dílu, Účinnost hnízdění, Parametry | Vysoký | Vysoký | DfAM (složitost), Nesting, Optimalizace procesu |
Práce | Příprava souborů, Odstranění podpory, Dokončovací práce | Mírný | Mírný | DfAM (snížení podpory), Automatizace (kde je to možné) |
Následné zpracování | HIP, složitost obrábění, úroveň dokončování | Středně vysoká a vysoká | Vysoký | Návrh pro minimální zpracování, vlastní kapacity |
Zajištění kvality | Požadavky na NDT (CT), úroveň kontroly | Mírný | Mírný | Jasně definovat požadavky, Efektivní pracovní postupy |
Svazek | Počet stejných dílů | Mírný | Nízký | Dávková výroba, Optimalizované vnoření |
Export do archů
Pochopení těchto faktorů ovlivňujících náklady a dobu realizace umožňuje přesnější sestavování rozpočtu a plánování. Spolupráce s potenciálním distributor leteckých komponentů nebo poskytovatelem služeb AM na počátku procesu návrhu může pomoci optimalizovat konzolu pro nákladově efektivní výrobu a poskytnout realistické termíny dodání.
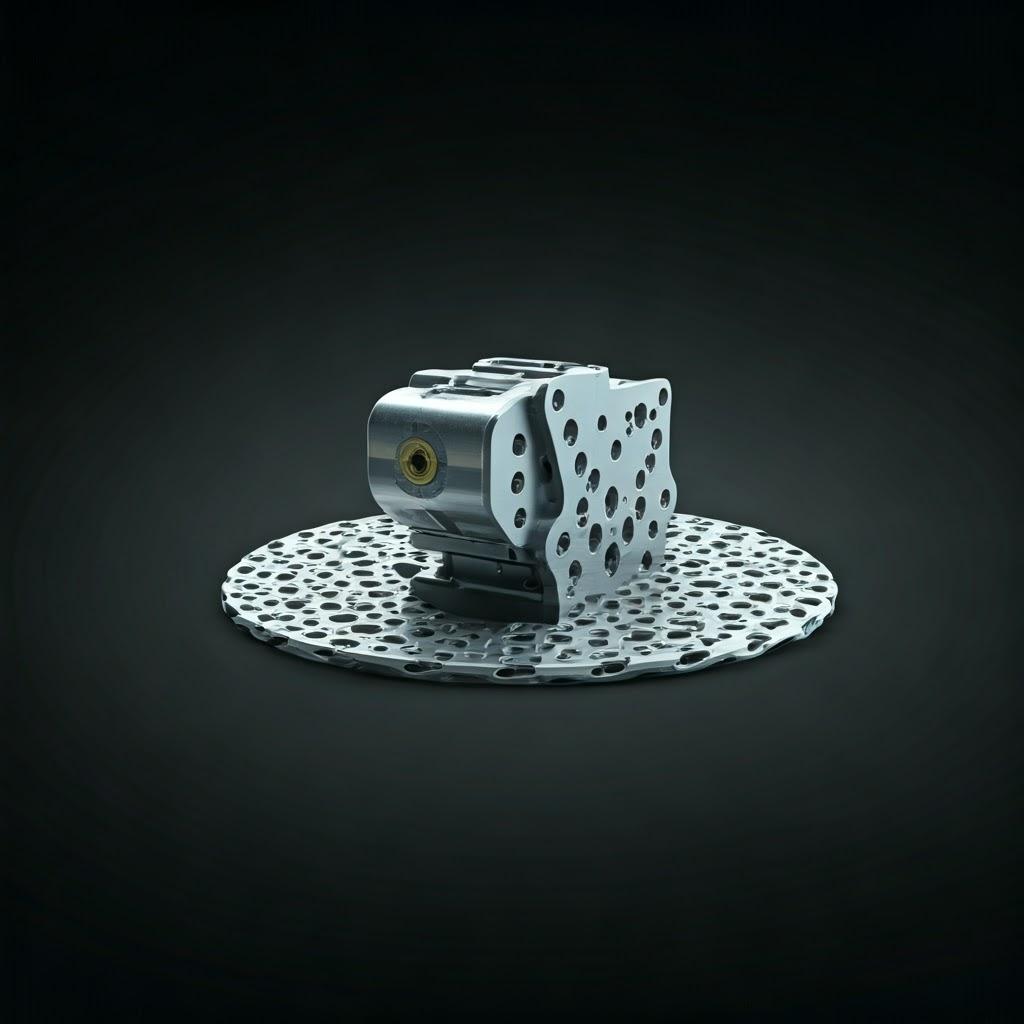
Často kladené otázky (FAQ) o 3D tištěných leteckých držácích
Vzhledem k tomu, že se aditivní výroba kovů stává v letectví a kosmonautice stále rozšířenější, inženýři a manažeři nákupu mají často konkrétní dotazy ohledně jejího použití pro komponenty, jako jsou montážní konzoly. Zde jsou odpovědi na některé časté dotazy:
1. Jaká je pevnost 3D tištěných kovových držáků ve srovnání s tradičně obráběnými držáky?
- Odpověď: Při výrobě pomocí ověřených postupů, vhodných materiálů (jako je Ti-6Al-4V nebo AlSi10Mg) a zásadních kroků následného zpracování, jako je HIP a tepelné zpracování, mohou 3D tištěné kovové konzoly dosáhnout mechanických vlastností (pevnost v tahu, mez kluzu, únavová životnost), které jsou srovnatelné nebo dokonce lepší s kovanými nebo litými protějšky. HIP je zvláště důležitý pro odstranění vnitřní pórovitosti, která je rozhodující pro dosažení únavových vlastností kovaných materiálů. Klíčem je přísná kontrola procesu, kvalitní materiály a dodržování leteckých norem. Optimalizace konstrukce prostřednictvím DfAM může dále využít AM k vytvoření dílů s lepším poměrem tuhosti k hmotnosti nebo pevnosti k hmotnosti než konvenčně navržené obráběné díly.
2. Jsou 3D tištěné letecké držáky certifikované pro let? Jak probíhá certifikační proces?
- Odpověď: Ano, 3D tištěné kovové díly, včetně držáků, dnes létají na mnoha komerčních a vojenských letadlech. Získání letové certifikace je přísný proces, který zahrnuje:
- Kvalifikace procesu: Kvalifikace konkrétního stroje AM, dávky materiálu a sady procesních parametrů podle průmyslových norem (např. specifikace SAE AMS pro AM) a specifických požadavků zákazníka.
- Přípustné množství materiálu: Stanovení statisticky spolehlivých údajů o vlastnostech materiálu (přípustných hodnotách) pro konkrétní kombinaci procesu AM/materiálu prostřednictvím rozsáhlého testování.
- Specifická kvalifikace pro danou část: Prokázání prostřednictvím analýzy a zkoušek (včetně nedestruktivního zkoušení a případného destruktivního zkoušení vzorových dílů), že konkrétní konstrukce držáku splňuje všechny výkonnostní a bezpečnostní požadavky při výrobě kvalifikovaným procesem AM.
- Řízení kvality: Výroba musí probíhat v rámci certifikovaného systému řízení jakosti (AS9100). Tento kvalifikační proces vyžaduje značné investice a odborné znalosti, často ve spolupráci mezi poskytovatelem AM a výrobcem OEM pro letecký průmysl nebo dodavatelem Tier 1.
3. Jaké materiály kromě AlSi10Mg a Ti-6Al-4V se běžně používají nebo zkoumají pro 3D tištěné letecké držáky?
- Odpověď: V současné době se pro konzoly nejčastěji volí AlSi10Mg a Ti-6Al-4V, ale v závislosti na konkrétních požadavcích se používají nebo zkoumají i jiné materiály:
- Ostatní slitiny hliníku: Slitiny hliníku s vyšší pevností vyvinuté speciálně pro AM (např. Scalmalloy® nebo varianty řady 7000) nabízejí vyšší pevnost než AlSi10Mg, ale jejich tisk může být náročnější.
- Superslitiny na bázi niklu: Pro držáky používané v prostředí s velmi vysokými teplotami (např. uvnitř horkých částí motoru) se často tisknou slitiny jako Inconel 718 (IN718) nebo Inconel 625 (IN625).
- Nerezové oceli: Slitiny jako 17-4PH nebo 316L lze použít pro specifické aplikace, které vyžadují dobrou odolnost proti korozi a střední pevnost, často tam, kde je hlavním faktorem cena a hmotnost není tak důležitá.
- Pokročilé slitiny titanu: Pokračuje výzkum slitin, jako je TiAl (aluminid titanu) pro aplikace při velmi vysokých teplotách a nízké hmotnosti, nebo specializovaných slitin, jako jsou TiNi, TiTa, TiAl a TiNbZr, které nabízí společnost Met3dp pro jedinečné funkční vlastnosti, i když ty jsou pro standardní držáky méně obvyklé. Výběr materiálu vždy zahrnuje vyvážení požadavků na výkon (pevnost, teplota, hmotnost) s náklady a vyrobitelností.
Závěr: Zvyšování výkonnosti letadel pomocí aditivně vyráběných konzolí
Neustálá snaha o lehčí, rychlejší a efektivnější letadla vyžaduje neustálé inovace v konstrukci a výrobě. Aditivní výroba kovů se rozhodujícím způsobem posunula za hranice prototypování a stala se rozhodujícím nástrojem pro výrobu vysoce výkonných součástí připravených k letu. Jak jsme již prozkoumali, montážní konzoly pro letectví představují hlavní aplikaci, kde AM zpracování kovů přináší hmatatelnou hodnotu.
Využitím možností technologie AM mohou letečtí inženýři:
- Navrhování a výroba vysoce komplexních, topologicky optimalizovaných konzolí které výrazně snižují hmotnost ve srovnání s tradičními konstrukcemi, což přímo přispívá k úspoře paliva a zvýšení výkonu.
- Konsolidace více obráběných součástí do jednotlivých integrovaných tištěných dílů, což zkracuje dobu montáže, snižuje počet dílů a snižuje počet možných poruch.
- Využití vysoce výkonných leteckých slitin jako je Ti-6Al-4V a AlSi10Mg, minimalizuje plýtvání materiálem díky výrobě téměř čistého tvaru a výrazně zlepšuje poměr mezi nákupem a letem.
- Urychlení vývojových cyklů prostřednictvím rychlého prototypování a umožňují výroba na zakázku pro náhradní díly a MRO, což zvyšuje agilitu dodavatelského řetězce.
Úspěšná implementace technologie AM pro tyto kritické součásti vyžaduje překonání problémů souvisejících s optimalizací konstrukce, řízením procesu, následným zpracováním a zajištěním kvality. To podtrhuje důležitost spolupráce se znalými a zkušenými odborníky.
Met3dp stojí v čele této výrobní revoluce. Jako poskytovatel komplexních řešení se sídlem v čínském Čching-tao nabízíme:
- Špičkové kovové 3D tiskárny (včetně pokročilých systémů SEBM), které zajišťují přesnost a spolehlivost kritických dílů.
- Vysoce kvalitní sférické kovové prášky, včetně AlSi10Mg, Ti-6Al-4V a inovativních slitin, vyráběných pomocí pokročilých technologií plynové atomizace a PREP.
- Desítky let společných zkušeností v oblasti aditivní výroby kovů, poskytuje služby v oblasti vývoje aplikací a spolupracuje s organizacemi s cílem urychlit zavádění AM.
Ať už jste inženýr, který se snaží optimalizovat konstrukci držáku, nebo manažer nákupu, který hledá spolehlivého dodavatele B2B dodavatel pro letecký průmysl pro aditivně vyráběné součásti, společnost Met3dp disponuje technologiemi, materiály a odbornými znalostmi, které podpoří vaše cíle.
Prozkoumejte budoucnost letecké výroby. Kontaktujte společnost Met3dp a poraďte se s ní, jak mohou naše pokročilá řešení aditivní výroby kovů zvýšit výkon a efektivitu vašich leteckých komponentů.
Sdílet na
MET3DP Technology Co., LTD je předním poskytovatelem řešení aditivní výroby se sídlem v Qingdao v Číně. Naše společnost se specializuje na zařízení pro 3D tisk a vysoce výkonné kovové prášky pro průmyslové aplikace.
Dotaz k získání nejlepší ceny a přizpůsobeného řešení pro vaše podnikání!
Související články
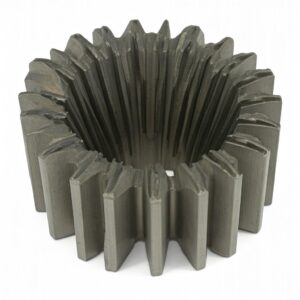
Vysoce výkonné segmenty lopatek trysek: Revoluce v účinnosti turbín díky 3D tisku z kovu
Přečtěte si více "O Met3DP
Nedávná aktualizace
Náš produkt
KONTAKTUJTE NÁS
Nějaké otázky? Pošlete nám zprávu hned teď! Po obdržení vaší zprávy obsloužíme vaši žádost s celým týmem.
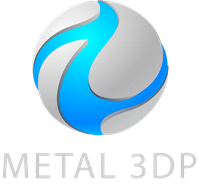
Kovové prášky pro 3D tisk a aditivní výrobu