C22 výroba práškové kyseliny fosforečné
Obsah
Kyselina fosforečná, základní kámen moderního průmyslu, se nachází ve všem od hnojiv po potravinářské přísady a detergenty. Její výrobní proces však může být energeticky náročný a spoléhat na agresivní chemikálie. Vstupte do prášku C22, revoluční technologie, která má za cíl transformovat výrobu kyseliny fosforečné se zaměřením na účinnost a udržitelnost.
Tento komplexní průvodce proniká hluboko do světa C22 výroba práškové kyseliny fosforečné. Prozkoumáme složitosti procesu, odhalíme prášek různých modelů kovových prášků a osvětlíme aplikace, výhody a omezení tohoto inovativního přístupu. Připravte se, nadšenci do chemie i profesionálové z oboru, protože se vydáváme na cestu do budoucnosti výroby kyseliny fosforečné!
Přehled Výroba kyseliny fosforečné z prášku C22
Technologie prášku C22 narušuje tradiční mokrý proces výroby kyseliny fosforečné. Zde je podstata:
- Mokrý proces: Tato konvenční metoda zahrnuje reakci fosfátové horniny se sírovou kyselinou, která generuje velké množství tepla a uvolňuje škodlivé vedlejší produkty, jako jsou fluoridy.
- Prášek C22: Tento inovativní přístup využívá proces tepelného rozkladu. Fosfátová hornina se zahřívá v reaktoru za řízených podmínek, čímž se rozkládá na páru kyseliny fosforečné a další plynné produkty. Kovové prášky, speciálně vybrané pro své katalytické vlastnosti, hrají zásadní roli při zvyšování účinnosti reakce.
Metoda prášku C22 se může pochlubit několika výhodami:
- Snížená spotřeba energie: Ve srovnání s mokrým procesem vyžaduje prášek C22 výrazně méně energie, což se promítá do menší ekologické stopy.
- Čistší výroba: Eliminací potřeby kyseliny sírové minimalizuje prášek C22 tvorbu škodlivých vedlejších produktů.
- Zlepšená účinnost: Kovové prášky působí jako katalyzátory, urychlují reakci a zvyšují výtěžek kyseliny fosforečné.
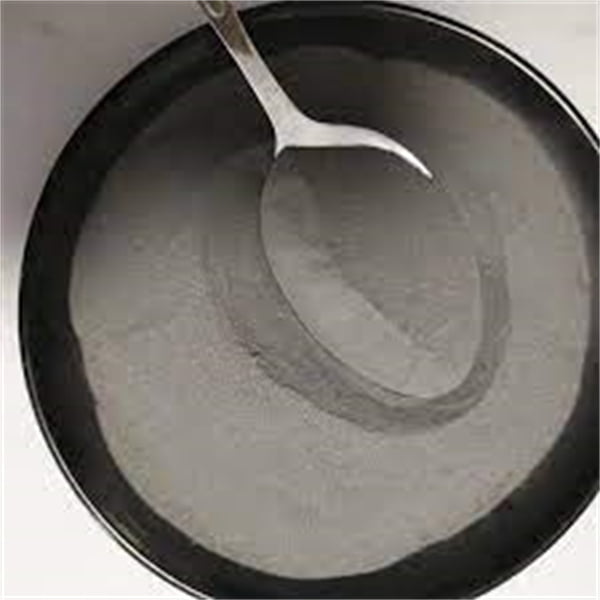
10+ kovových prášků pro prášek C22
Volba kovového prášku v technologii prášku C22 významně ovlivňuje účinnost reakce. Pojďme se ponořit do výběru těchto kovových divů:
1. Železo (Fe): Snadno dostupná a nákladově efektivní možnost, železný prášek vykazuje slušnou katalytickou aktivitu pro rozklad kyseliny fosforečné. Jeho účinnost se však může časem snižovat v důsledku oxidace a slinování (tvorba větších částic).
2. Nikl (Ni): Nikl, známý pro své vynikající katalytické vlastnosti, podporuje účinnou výrobu kyseliny fosforečné. Ve srovnání se železem nabízí nikl lepší odolnost proti oxidaci, ale za vyšší cenu.
3. Kobalt (Co): Podobně jako nikl vykazuje kobaltový prášek výjimečnou katalytickou aktivitu. Navíc vykazuje zlepšenou stabilitu při vysokých teplotách. Relativní nedostatek kobaltu a vyšší cena však mohou být nevýhodou.
4. Měď (Cu): Měděný prášek, všestranný kov, vykazuje určitou katalytickou aktivitu pro rozklad kyseliny fosforečné. Často se kombinuje s jinými kovy (jako je železo nebo nikl) za účelem vytvoření bimetalických katalyzátorů, které potenciálně nabízejí synergické účinky pro zvýšený výkon.
5. Molybden (Mo): Tato méně běžná možnost vykazuje slibnou katalytickou aktivitu při výrobě kyseliny fosforečné. Katalyzátory na bázi molybdenu často vyžadují specifické aktivační postupy pro optimální výkon.
6. Wolfram (W): Wolframový prášek, známý pro svůj vysoký bod tání a stabilitu, nachází uplatnění v procesech prášku C22 při vysokých teplotách. Jeho vysoká cena však může být omezujícím faktorem.
7. Cer (Ce): Tento kov vzácných zemin ve formě prášku vykazuje vynikající katalytickou aktivitu a odolnost proti slinování. Jeho nedostatek a vysoká cena z něj však činí méně komerčně životaschopnou variantu pro velkovýrobu.
8. Lanthan (La): Lanthanový prášek, další kov vzácných zemin, má zajímavé katalytické vlastnosti pro rozklad kyseliny fosforečné. Podobně jako cer jeho vysoká cena a omezená dostupnost brání širokému přijetí.
9. Bimetalické a multimetalické prášky: Kombinací různých kovů vyvinuli výzkumníci inovativní bimetalické a multimetalické katalyzátory. Tyto katalyzátory často využívají přednosti jednotlivých kovů, což potenciálně vede k vynikajícímu výkonu a zlepšené stabilitě katalyzátoru. Mezi příklady patří kombinace železo-nikl, měď-kobalt a cer-molybden.
10. Kovové slitiny: Inženýrství kovových slitin speciálně přizpůsobených pro aplikace prášku C22 je probíhající oblastí výzkumu. Cílem těchto slitin je optimalizovat katalytickou aktivitu, stabilitu při vysokých teplotách a nákladovou efektivitu.
Výběr ideálního kovového prášku (nebo kombinace) závisí na různých faktorech, včetně:
- Katalytická aktivita: Schopnost kovu urychlit reakci rozkladu kyseliny fosforečné.
- Stálost při vysokých teplotách: Schopnost prášku zachovat si svou strukturu a katalytické vlastnosti při vysokých teplotách, se kterými se setkáváme v procesu prášku C22.
- Nákladová efektivita: Cenová dostupnost kovového prášku hraje zásadní roli ve velkovýrobě.
Náklady, stabilita a výkon
Prozkoumali jsme rozmanitou škálu kovových prášků pro aplikace prášku C22. Nyní se ponořme hlouběji a porovnejme jejich silné a slabé stránky, abychom pochopili, který by mohl být šampionem:
Železo (Fe):
- Klady: Hojný, levný
- Nevýhody: Nižší katalytická aktivita, náchylný k oxidaci a slinování
Představte si železný prášek jako pracovního koně skupiny. Je snadno dostupný a cenově výhodný, což z něj činí atraktivní možnost pro výrobce, kteří si uvědomují náklady. Jeho katalytická aktivita však není nejimpozantnější a jeho účinnost se může časem snižovat, protože oxiduje a tvoří větší částice. Představte si to jako spolehlivého, ale potenciálně unaveného pracovníka, který potřebuje častou výměnu.
Nikl (Ni):
- Klady: Vynikající katalytická aktivita, dobrá odolnost proti oxidaci
- Nevýhody: Vyšší náklady ve srovnání se železem
Nikl se staví jako vysoce výkonný spoluhráč. Může se pochlubit vynikající katalytickou aktivitou ve srovnání se železem, což vede k produktivnějšímu výtěžku kyseliny fosforečné. Navíc vykazuje lepší odolnost proti oxidaci, což zajišťuje, že zůstane ve hře déle. Tento zvýšený výkon se však dodává s vyšší cenovkou, kterou musí výrobci zvážit.
Kobalt (Co):
- Klady: Výjimečná katalytická aktivita, stabilita při vysokých teplotách
- Nevýhody: Relativně vzácný, drahý
Kobalt vstupuje do ringu jako prémiový hráč. Může se pochlubit fenomenální katalytickou aktivitou, která posouvá hranice účinnosti výroby kyseliny fosforečné. Jeho stabilita při vysokých teplotách je navíc ideální pro náročné procesy prášku C22. Ale stejně jako hvězdný sportovec se kobalt dodává s vysokou cenovkou a omezenou dostupností, což z něj činí méně dostupnou možnost pro některé výrobce.
Bitva mezi niklem a kobaltem je zajímavá. Nikl nabízí dobrou rovnováhu mezi výkonem a náklady, zatímco kobalt vyniká aktivitou a stabilitou. Volba nakonec závisí na prioritách výrobce a rozpočtových omezeních.
Měď (Cu):
- Klady: Všestranný, lze jej kombinovat s jinými kovy pro zvýšení výkonu
- Nevýhody: Mírná katalytická aktivita sama o sobě
Měď působí jako adaptabilní spoluhráč. Zatímco jeho sólová katalytická aktivita pro rozklad kyseliny fosforečné je mírná, jeho skutečná síla spočívá v jeho schopnosti vytvářet silná partnerství. V kombinaci s jinými kovy, jako je železo nebo nikl, vytváří měď bimetalické katalyzátory, které mohou odemknout synergické efekty, což může vést k výraznému zvýšení výkonu. Představte si měď jako týmového stratéga, který vytváří aliance, aby maximalizoval výsledky.
Molybden (Mo) a wolfram (W):
- Molybden: Slibná katalytická aktivita, vyžaduje specifickou aktivaci
- Wolfram: Vynikající stabilita při vysokých teplotách, vysoké náklady
Molybden a wolfram představují specializované specialisty. Molybden vykazuje slibné katalytické schopnosti, ale často vyžaduje specifické aktivační postupy, než dosáhne svého plného potenciálu. Představte si to jako talentovaného nováčka, který potřebuje nějaký trénink, aby uvolnil své skutečné dovednosti. Wolfram na druhou stranu září v prostředí s vysokou teplotou díky své výjimečné stabilitě. Jeho vysoká cena z něj však činí méně praktickou volbu pro velkovýrobu, což ho staví jako veterána, který vyžaduje prémiový plat.
Kovy vzácných zemin: Cer (Ce) a lanthan (La):
- Klady: Vynikající katalytická aktivita a odolnost proti slinování
- Nevýhody: Vzácné, drahé (omezující komerční životaschopnost)
Cer a lanthan, kovy vzácných zemin, jsou superhvězdy s vysokými nároky na údržbu. Mají výjimečnou katalytickou aktivitu a odolávají slinování, což zajišťuje konzistentní výkon. Představte si je jako celebrity kovového světa, které poskytují špičkové výsledky. Ale stejně jako celebrity je jejich nedostatek a vysoká cena činí méně vhodnými pro velkovýrobu nákladově efektivní.
Bimetalické a multimetalické prášky:
- Klady: Potenciál pro vynikající výkon a stabilitu kombinací předností jednotlivých kovů
Bimetalické a multimetalické prášky jsou snovými týmy světa prášků C22. Výzkumníci neustále zkoumají kombinace jako železo-nikl, měď-kobalt a cer-molybden. Cílem těchto partnerství je využít přednosti každého kovu, což může vést k vynikající katalytické aktivitě, zlepšené stabilitě a celkově robustnějšímu katalyzátoru. Představte si je jako dobře koordinovaný tým, kde každý hráč přispívá svými jedinečnými dovednostmi k vítěznému výsledku.
Slitiny kovů:
- Klady: Vlastnosti na míru pro optimální výkon a nákladovou efektivitu
Kovové slitiny jsou řešení na míru v oblasti prášků C22. Výzkumníci aktivně vyvíjejí slitiny speciálně navržené pro tuto aplikaci. Cílem těchto slitin je dosáhnout dokonalé rovnováhy mezi vysokou katalytickou aktivitou, stabilitou při vysokých teplotách a cenovou dostupností. Představte si je jako sportovce, kteří prošli náročným tréninkem, aby vynikli ve specifických požadavcích prášku C22.
Závod o objevení ideálního kovového prášku (nebo kombinace) pro prášek C22 pokračuje. Výrobci
-
Ti45Nb prášek pro aditivní výrobu
-
Prášek ze slitiny TiNb
-
Prášek ze slitiny TiNbZrSn
-
Ti6Al4V prášek Kovový prášek na bázi titanu pro aditivní výrobu
-
CPTi prášek
-
TC18 Powder : Odemknutí síly karbidu titanu
-
TC11 Powder: Komplexní průvodce
-
TC4 ELI prášek
-
Nejlepší prášek Ti-6Al-4V (TC4 Powder) pro aditivní výrobu
Použití prášku kyseliny fosforečné C22
Kyselina fosforečná vyrobená procesem s práškem C22 se může pochlubit stejnou kvalitou a chemickými vlastnostmi jako konvenčně vyráběná kyselina fosforečná. To otevírá dveře k nepřebernému množství aplikací v různých průmyslových odvětvích:
- Hnojiva: Kyselina fosforečná je klíčovou složkou hnojiv, která poskytuje nezbytný fosfor pro růst rostlin. Technologie prášku C22 může přispět k udržitelnějšímu řetězci výroby hnojiv.
- Potraviny a nápoje: Kyselina fosforečná se používá v konkrétních aplikacích v potravinách a nápojích, například jako kypřící činidlo v pekařských výrobcích a jako regulátor kyselosti v některých nealkoholických nápojích. Kyselina fosforečná vyrobená z prášku C22 může uspokojit tuto poptávku a zároveň potenciálně snížit dopad na životní prostředí.
- Doplňky krmiv pro zvířata: Kyselina fosforečná hraje roli v doplňcích krmiv pro zvířata a zajišťuje správný vývoj kostí a minerální rovnováhu u hospodářských zvířat. Technologie prášku C22 může přispět k udržitelnější výrobě těchto základních aditiv.
- Zpomalovače hoření: Určité typy kyseliny fosforečné se používají ve zpomalovačích hoření pro textilie a plasty. Prášek C22 může potenciálně hrát roli v udržitelné výrobě těchto materiálů pro požární bezpečnost.
- Čištění kovů a povrchová úprava: Kyselina fosforečná se používá v roztocích pro čištění kovů a procesech povrchové úpravy. Kyselina fosforečná vyrobená z prášku C22 může uspokojit tuto průmyslovou poptávku s potenciálně sníženým dopadem na životní prostředí.
- Léčiva: Kyselina fosforečná má určité aplikace ve farmaceutickém průmyslu, například v určitých lécích a procesech výroby léčiv. Technologie prášku C22 může přispět k udržitelnějšímu dodavatelskému řetězci pro tyto aplikace.
- Výzkum a vývoj: Kyselina fosforečná je cenný materiál v různých výzkumných a vývojových aktivitách. Prášek C22 může zajistit spolehlivý a potenciálně udržitelnější zdroj pro tyto snahy.
Aplikace kyseliny fosforečné vyrobené z prášku C22 jsou rozsáhlé a přesahují výše uvedené příklady. Jak technologie dozrává a výrobní náklady se stávají konkurenceschopnějšími, můžeme očekávat ještě širší přijetí v různých průmyslových odvětvích.
Výhody výroby kyseliny fosforečné z prášku C22
Technologie prášku C22 nabízí několik přesvědčivých výhod oproti tradičnímu mokrému procesu výroby kyseliny fosforečné:
- Snížená spotřeba energie: Proces s práškem C22 výrazně snižuje spotřebu energie ve srovnání s metodou mokré kyseliny. To se promítá do menší uhlíkové stopy a nižších výrobních nákladů.
- Čistší výroba: Vyloučením potřeby kyseliny sírové minimalizuje prášek C22 tvorbu škodlivých vedlejších produktů, jako jsou fluoridy. To vede k čistšímu a ekologičtějšímu výrobnímu procesu.
- Krása prášků odolných proti opotřebení spočívá v jejich přizpůsobivosti. Od těžebních zařízení a automobilových dílů až po řezné nástroje a ventily nacházejí tyto prášky uplatnění v široké škále průmyslových odvětví. Katalyzátory kovového prášku urychlují reakci rozkladu kyseliny fosforečné, což vede k vyššímu výtěžku a potenciálně zkracuje dobu zpracování.
- Potenciál pro výrobu na místě: Modulární povaha technologie prášku C22 umožňuje možnost výroby kyseliny fosforečné na místě v závodech na výrobu hnojiv nebo na jiných místech, kde se přímo používá. To může zefektivnit logistiku a potenciálně snížit náklady na dopravu.
- Snížené využití vody: Proces s práškem C22 vyžaduje výrazně méně vody ve srovnání s metodou mokré kyseliny, což z něj činí přístup šetrnější k vodě, což je zvláště cenné v regionech, které čelí nedostatku vody.
Prášek C22: Potenciální změna hry
Vznik technologie prášku C22 je nesmírně slibný pro průmysl kyseliny fosforečné. Tím, že nabízí čistší, účinnější a potenciálně udržitelnější výrobní metodu, může prášek C22 přispět k ekologičtější budoucnosti pro průmysl hnojiv a řadu dalších aplikací, které se spoléhají na kyselinu fosforečnou.
Omezení a výzvy Výroba kyseliny fosforečné z prášku C22
I když se prášek C22 může pochlubit významnými výhodami, je nezbytné uznat omezení a výzvy spojené s touto vyvíjející se technologií:
- Zralost technologie: Prášek C22 je ve srovnání s dobře zavedeným procesem mokré kyseliny relativně nová technologie. K optimalizaci procesu a zajištění jeho dlouhodobé stability a spolehlivosti je zapotřebí další výzkum a vývoj.
- Nákladová konkurenceschopnost: V současné době mohou být náklady na technologii prášku C22 vyšší než tradiční metody mokré kyseliny. Jak technologie dozrává a výroba se zvyšuje, můžeme očekávat, že se náklady stanou konkurenceschopnějšími.
- Výběr kovového prášku: Identifikace optimálního kovového prášku (nebo kombinace) pro nákladově efektivní a vysoce výkonný provoz prášku C22 zůstává trvalou výzvou. Výzkumné úsilí je zásadní pro vývoj nových a vylepšených katalyzátorů.
- Počáteční investice: Implementace technologie prášku C22 vyžaduje počáteční investice do nového zařízení a infrastruktury. To může být překážkou pro některé výrobce, zejména pro malé a střední podniky.
- Předpisy a normy: Vzhledem k tomu, že technologie prášku C22 je relativně nová, regulační rámce a průmyslové standardy pro tento proces se stále vyvíjejí. Stanovení jasných pokynů bude zásadní pro širší přijetí.
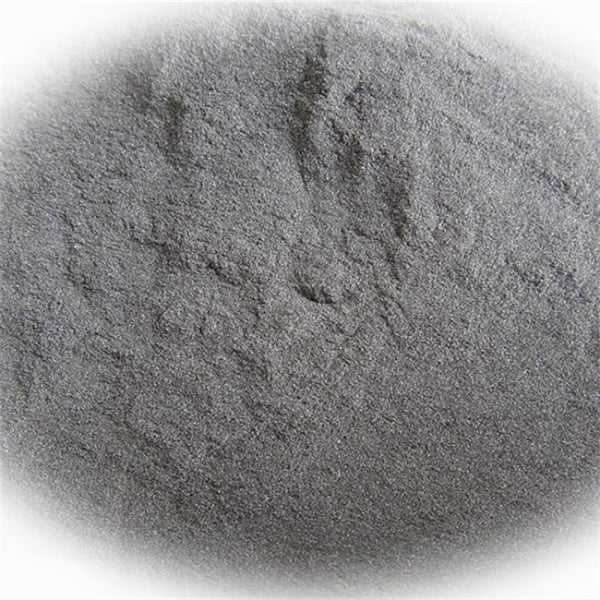
FAQ
Zde jsou některé často kladené otázky týkající se výroby kyseliny fosforečné z prášku C22:
Otázka: Jaké jsou environmentální výhody prášku C22 ve srovnání s procesem mokré kyseliny?
Odpověď: Prášek C22 nabízí několik environmentálních výhod:
- Snížená spotřeba energie: Nižší spotřeba energie se promítá do menší uhlíkové stopy a menších emisí skleníkových plynů.
- Čistší výroba: Eliminace kyseliny sírové minimalizuje tvorbu škodlivých vedlejších produktů, jako jsou fluoridy, což vede k čistšímu výrobnímu procesu.
- Snížená spotřeba vody: Prášek C22 vyžaduje výrazně méně vody ve srovnání s metodou mokré kyseliny, což z něj činí přístup šetrnější k vodě.
Otázka: Je kyselina fosforečná vyrobená z prášku C22 stejná jako konvenčně vyráběná kyselina fosforečná?
Odpověď: Ano, kyselina fosforečná vyrobená z prášku C22 má stejné chemické vlastnosti a kvalitu jako konvenčně vyráběná kyselina fosforečná. To zajišťuje její kompatibilitu se stávajícími aplikacemi v různých průmyslových odvětvích.
Otázka: Jaké jsou úvahy o nákladech na technologii prášku C22?
Odpověď: V současné době mohou být počáteční investice do technologie prášku C22, včetně zařízení a infrastruktury, vyšší než tradiční metody mokré kyseliny. Výhody snížené spotřeby energie, potenciálně nižší spotřeby vody a čistšího procesu však mohou vést k dlouhodobým úsporám nákladů. Kromě toho, jak technologie dozrává a výroba se zvyšuje, můžeme očekávat, že se náklady stanou konkurenceschopnějšími.
Otázka: Jaké jsou některé z výzev, které brání širšímu přijetí prášku C22?
Odpověď: Zde jsou některé klíčové výzvy:
- Zralost technologie: Prášek C22 je relativně nová technologie, která vyžaduje další výzkum a vývoj pro dlouhodobou stabilitu a optimalizaci.
- Nákladová konkurenceschopnost: V současné době mohou být náklady na technologii prášku C22 vyšší než u stávajících metod.
- Výběr kovového prášku: Nalezení optimálního a nákladově efektivního katalyzátoru kovového prášku zůstává trvalou výzvou.
- Počáteční investice: Implementace prášku C22 vyžaduje počáteční investice do nového zařízení, což může být pro některé výrobce překážkou.
Otázka: Jaký je budoucí výhled pro technologii prášku C22?
Odpověď: Budoucnost prášku C22 vypadá slibně. Probíhající výzkum, strategie snižování nákladů a spolupráce mezi průmyslem a akademickou sférou mohou řešit výzvy a připravit cestu pro širší přijetí. Prášek C22 má potenciál revolučně změnit výrobu kyseliny fosforečné, což z ní činí čistší, účinnější a udržitelnější proces pro budoucnost.
Závěrem
Technologie prášku C22 představuje přesvědčivou alternativu pro výrobu kyseliny fosforečné. Tím, že nabízí čistší, účinnější a potenciálně udržitelnější přístup, má prášek C22 potenciál transformovat toto odvětví. I když výzvy přetrvávají, probíhající výzkum a vývoj jsou klíčem k odemknutí plného potenciálu této inovativní technologie. Jak prášek C22 dozrává a stává se nákladově konkurenceschopnějším, můžeme očekávat, že bude hrát významnou roli při utváření budoucnosti udržitelné výroby kyseliny fosforečné pro zelenější zítřek.
Sdílet na
MET3DP Technology Co., LTD je předním poskytovatelem řešení aditivní výroby se sídlem v Qingdao v Číně. Naše společnost se specializuje na zařízení pro 3D tisk a vysoce výkonné kovové prášky pro průmyslové aplikace.
Dotaz k získání nejlepší ceny a přizpůsobeného řešení pro vaše podnikání!
Související články
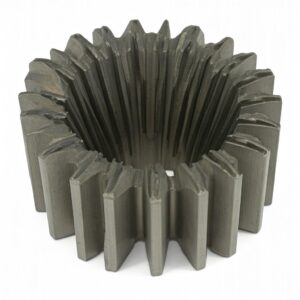
Vysoce výkonné segmenty lopatek trysek: Revoluce v účinnosti turbín díky 3D tisku z kovu
Přečtěte si více "O Met3DP
Nedávná aktualizace
Náš produkt
KONTAKTUJTE NÁS
Nějaké otázky? Pošlete nám zprávu hned teď! Po obdržení vaší zprávy obsloužíme vaši žádost s celým týmem.
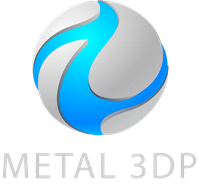
Kovové prášky pro 3D tisk a aditivní výrobu