Lehké držáky pro gimbaly fotoaparátů
Obsah
Úvod - Zásadní role lehkých držáků kamer s kardanem v moderních dronech
V rychle se vyvíjejícím prostředí technologie dronů je požadavek na vysoce výkonné a lehké komponenty prvořadý. Mezi těmito kritickými prvky je kardanový držák kamery základním prvkem, který přímo ovlivňuje stabilitu a kvalitu leteckého snímkování a videografie. Ať už se jedná o profesionální kinematografii, sledování, průmyslovou inspekci nebo rekreační účely, robustní a zároveň lehký držák kardanu je nezbytný pro pořizování plynulých a přesných záběrů. Schopnost dronu provádět složité manévry a udržovat stabilní orientaci kamery závisí na konstrukci a materiálových vlastnostech této klíčové součásti. S tím, jak se aplikace dronů stávají stále sofistikovanějšími, se stále více projevují omezení tradičně vyráběných držáků kardanu - často těžších a méně optimalizovaných pro specifické užitečné zatížení. To vyžaduje inovativní výrobní přístupy, které mohou zajistit složitou geometrii, nižší hmotnost a vyšší odolnost. Kov 3D tisk, známá také jako aditivní výroba kovů, se stala transformační technologií, která nabízí nebývalou svobodu designu a možnost vytvářet lehké držáky kardanových kloubů kamer s vynikajícími výkonnostními vlastnostmi. Tento příspěvek na blogu se zabývá výhodami využití kovového 3D tisku pro tyto kritické součásti dronů, zkoumá vhodné materiály, diskutuje o konstrukčních aspektech a poskytuje poznatky pro inženýry a manažery nákupu, kteří chtějí využít tuto špičkovou výrobní techniku. V čele této inovace stojí Metal3DP Technology Co., LTD, předního poskytovatele řešení pro aditivní výrobu, který se zavázal poskytovat špičkový objem, přesnost a spolehlivost tisku. Jejich odborné znalosti v oblasti zařízení pro 3D tisk i vysoce výkonných kovových prášků je staví do pozice důvěryhodného partnera pro vývoj pokročilých součástí dronů, jako jsou lehké držáky kardanových křídel kamer.
K čemu se používají lehké držáky pro fotoaparáty? Zkoumání klíčových aplikací a odvětví
Lehké kardanové držáky kamer jsou nepostradatelnými součástmi v široké škále aplikací dronů v různých odvětvích. Jejich hlavní funkcí je stabilizace kamer a senzorů, která umožňuje plynulý a kontrolovaný pohyb nezávisle na pohybu dronu. To zajišťuje pořizování vysoce kvalitních, nerozmazaných snímků a dat, což je pro úspěch mnoha operací zásadní.
Zde je přehled klíčových aplikací a odvětví, která se spoléhají na lehké kardanové držáky kamer:
- Letectví a obrana:
- Sledování a průzkum: Lehké kardany umožňují dronům nést sofistikované kamery pro sledování kritické infrastruktury, hranic a taktického prostředí, aniž by to bylo na úkor doby letu nebo manévrovatelnosti.
- Kontrola: Drony vybavené stabilizovanými kamerami se používají ke kontrole letadel, větrných turbín a elektrického vedení a poskytují podrobné vizuální údaje pro údržbu a posouzení bezpečnosti.
- Mapování a geodézie: Snímky s vysokým rozlišením pořízené z dronů namontovaných na kardanových závěsech jsou nezbytné pro vytváření přesných 3D map a provádění průzkumu území.
- Automobilový průmysl:
- Inspekce infrastruktury: Podobně jako v letectví se drony s kamerami namontovanými na kardanu používají ke kontrole konstrukční integrity mostů, silnic a tunelů.
- Logistika a doručování: S rozšiřováním doručovacích služeb pomocí dronů lze pro sledování a ověřování zásilek používat lehké a stabilní kamerové systémy.
- Lékařský:
- Reakce na mimořádné události: Drony se stabilizovanými kamerami mohou poskytovat přehled o situaci v reálném čase během pomoci při katastrofách a pomáhat při pátracích a záchranných operacích.
- Dodávka zdravotnických potřeb: V odlehlých oblastech mohou drony přepravovat důležité zdravotnické potřeby a stabilní kamera může zajistit bezpečné doručení a potvrzení.
- Průmyslová výroba:
- Kontrola majetku: Monitorování velkých průmyslových zařízení, jako jsou ropovody, plynovody nebo chemické závody, je díky vizuálním kontrolám prováděným pomocí dronů efektivnější a bezpečnější.
- Kontrola kvality: Kamery s vysokým rozlišením na stabilizovaných kardanových závěsech lze použít k identifikaci vad vyráběného zboží nebo stavebních projektů.
- Média a zábava:
- Kamera a videografie: Profesionální filmaři a tvůrci obsahu spoléhají na lehké kardanové držáky, které jim umožňují pořizovat filmové letecké záběry s plynulým a hladkým pohybem.
- Přímé přenosy z událostí: Drony poskytují jedinečnou perspektivu pro vysílání živých přenosů a jejich stabilní kamery zajišťují profesionální zážitek ze sledování.
- Zemědělství:
- Monitorování plodin: Multispektrální kamery namontované na kardanových závěsech mohou vyhodnocovat zdravotní stav plodin, identifikovat oblasti vyžadující zavlažování nebo hnojení a odhadovat výnosy.
- Řízení chovu hospodářských zvířat: Drony lze používat k monitorování hospodářských zvířat na velkých plochách a stabilní kamera umožňuje přesné pozorování.
Poptávka po stále sofistikovanějších schopnostech dronů vyžaduje kardanové držáky, které jsou nejen lehké, ale také mají vysokou tuhost a stabilitu. 3D tisk z kovu poskytuje cestu k dosažení těchto náročných specifikací a nabízí svobodu designu a přizpůsobení materiálu, které se tradičním výrobním metodám často nevyrovnají. Metal3DP chápe tyto kritické potřeby průmyslu a nabízí pokročilá řešení 3D tisku z kovu pro vytváření vysoce výkonných kardanových držáků na míru konkrétním aplikacím. Jejich služby kovového 3D tisku můžete dále prozkoumat na adrese https://met3dp.com/metal-3d-printing/.
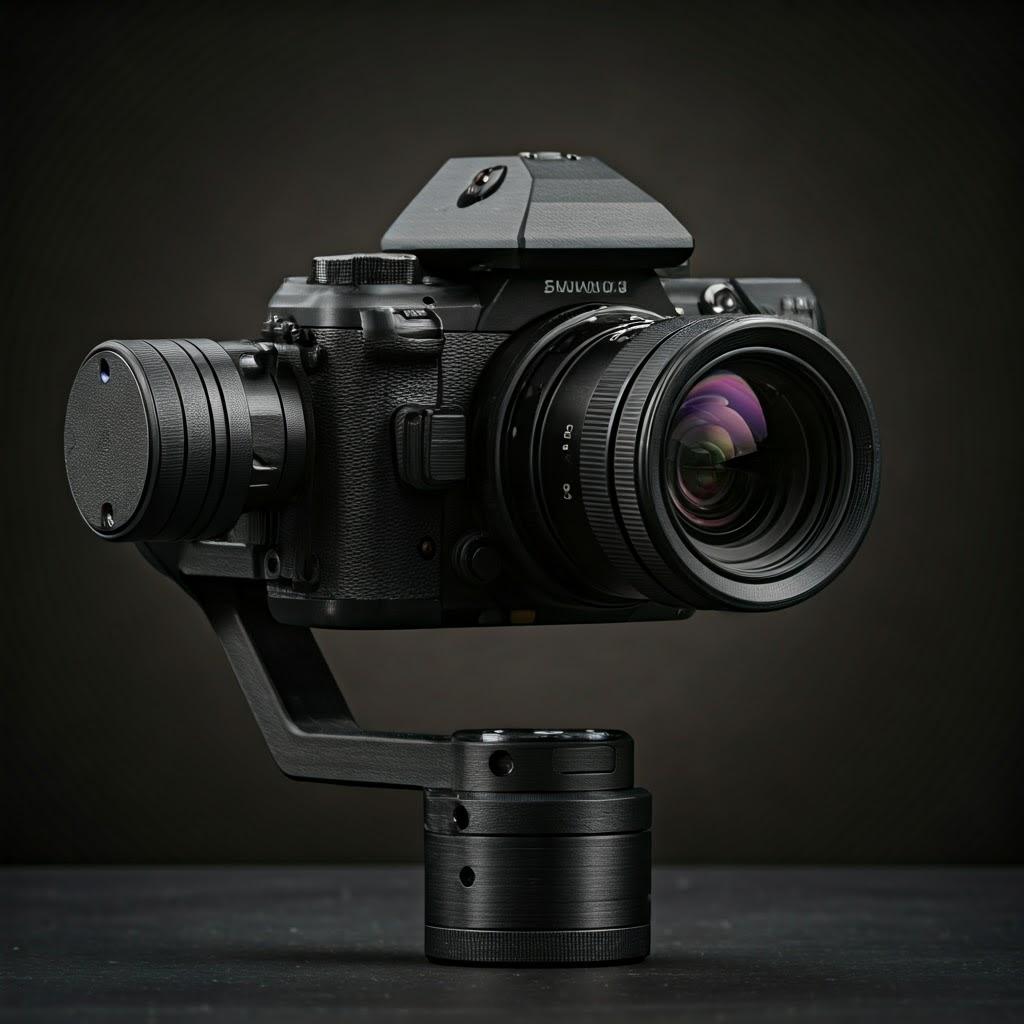
Proč zvolit 3D tisk z kovu pro lehké držáky gimbalů kamer? Výhody oproti tradiční výrobě
Volba kovového 3D tisku pro výrobu lehkých držáků kardanu kamery nabízí oproti tradičním výrobním metodám, jako je CNC obrábění nebo tlakové lití, řadu přesvědčivých výhod. Tyto výhody přímo reagují na kritické požadavky aplikací dronů, včetně snížení hmotnosti, zvýšení výkonu a flexibility konstrukce.
Zde jsou hlavní výhody použití kovového 3D tisku pro držáky kardanu:
- Optimalizace hmotnosti díky volnosti designu: Aditivní výroba umožňuje vytvářet složité geometrie, které jsou při použití tradičních metod nemožné nebo nákladově neúnosné. Patří sem složité vnitřní mřížkové struktury a optimalizace topologie, které strategicky odstraňují materiál v nekritických oblastech, čímž vznikají výrazně lehčí díly bez ztráty pevnosti nebo tuhosti. To má zásadní význam pro drony, kde každý ušetřený gram znamená delší dobu letu a vyšší nosnost.
- Vyšší výkon a stabilita: 3D tisk z kovu umožňuje sloučit více součástí do jediného optimalizovaného dílu. Snížením počtu spojů a spojovacích prvků se zlepšuje celková strukturální integrita a tuhost držáku kardanu, což vede ke zvýšení stability kamery a snížení vibrací. To se přímo promítá do vyšší kvality leteckých záběrů.
- Přizpůsobení a opakování návrhu: Aditivní výroba nabízí bezkonkurenční flexibilitu při navrhování. Inženýři mohou rychle vytvářet prototypy a iterovat různé konstrukce držáků kardanu, aby optimalizovali výkon pro konkrétní modely dronů a kamerové systémy. Tato agilita v procesu návrhu urychluje vývojové cykly a umožňuje vytvářet řešení na míru, která splňují přesné požadavky aplikací.
- Účinnost materiálu: Na rozdíl od subtraktivních metod, jako je obrábění, které odebírají materiál z pevného bloku, 3D tisk z kovu vytváří díly vrstvu po vrstvě a používá pouze nezbytný materiál. To snižuje plýtvání materiálem a může vést k úspoře nákladů, zejména u složitých geometrií a nízkých až středních objemů výroby.
- Výroba na vyžádání a zkrácení dodacích lhůt: 3D tisk z kovu eliminuje potřebu nástrojů, jako jsou formy nebo zápustky, jejichž výroba může být nákladná a časově náročná. To umožňuje zrychlení doby od návrhu po hotový díl, což usnadňuje rychlou tvorbu prototypů a výrobu na vyžádání. Pro podniky, které hledají rychlá a efektivní řešení, je vhodné prozkoumat metody tisku nabízené společností Metal3DP na adrese https://met3dp.com/printing-methods/ může být velmi prospěšné.
- Integrace funkcí: 3D tisk z kovu umožňuje integrovat funkční prvky přímo do konstrukce držáku kardanu, jako jsou chladicí kanály, integrované montážní body nebo dokonce kryty senzorů. Tím se dále snižuje počet součástí a zjednodušuje montáž.
- Vysoce výkonné materiály: Kovový 3D tisk je kompatibilní s celou řadou vysoce výkonných kovových slitin, včetně slitin hliníku, jako jsou AlSi10Mg a A7075, které nabízejí vynikající poměr pevnosti a hmotnosti - ideální pro lehké, ale odolné držáky kardanu. Metal3DP se specializuje na poskytování vysoce kvalitních kovových prášků optimalizovaných pro aditivní výrobu, které zajišťují vynikající mechanické vlastnosti finálních tištěných dílů. Jejich pokročilý systém výroby prášků zaručuje kvalitu a výkon požadovaný pro náročné aplikace.
Využitím možností kovového 3D tisku mohou výrobci a provozovatelé dronů dosáhnout významného zlepšení výkonu, efektivity a všestrannosti svých leteckých platforem. Schopnost vytvářet vysoce optimalizované, lehké držáky kardanových křídel kamer je klíčovým faktorem umožňujícím posouvat hranice technologie dronů.
Doporučené kovové prášky pro vysoce výkonné držáky kardanu: AlSi10Mg a A7075
Výběr vhodného kovového prášku má zásadní význam pro dosažení požadovaných vlastností u lehkých 3D tištěných držáků kardanu kamery. Dvě hliníkové slitiny vynikají vynikající kombinací lehkých vlastností, vysoké pevnosti a vhodnosti pro aditivní výrobu: AlSi10Mg a A7075. Metal3DP nabízí oba tyto vysoce kvalitní kovové prášky, které zajišťují optimální výkon pro náročné aplikace s drony.
1. AlSi10Mg:
- Složení: Slitina hliníku s přibližně 10 % křemíku a 0,3 % hořčíku.
- Klíčové vlastnosti a výhody:
- Vynikající poměr pevnosti k hmotnosti: AlSi10Mg nabízí dobrou rovnováhu mezi pevností a nízkou hustotou, takže je ideální pro lehké aplikace, kde je důležitá strukturální integrita.
- Vysoká tvrdost a odolnost proti opotřebení: Obsah křemíku zvyšuje tvrdost a odolnost slitiny proti opotřebení, což přispívá k trvanlivosti držáku kardanu.
- Dobrá tepelná vodivost: Tato vlastnost pomáhá odvádět teplo generované kamerou nebo motory a zajišťuje stabilní provoz.
- Vynikající tisknutelnost: AlSi10Mg se dobře hodí pro procesy laserové fúze v práškovém loži (LPBF) a poskytuje husté, vysoce kvalitní díly s dobrou povrchovou úpravou.
- Odolnost proti korozi: Slitina vykazuje dobrou odolnost proti korozi, což je důležité pro venkovní aplikace dronů.
- Typické aplikace v držácích gimbalů: Komponenty vyžadující rovnováhu mezi pevností a hmotností, jako jsou konstrukční rámy, konzoly a montážní rozhraní.
2. A7075:
- Složení: Slitina hliníku se zinkem jako hlavním legujícím prvkem spolu s hořčíkem a mědí.
- Klíčové vlastnosti a výhody:
- Velmi vysoká pevnost: A7075 je známá svou výjimečnou pevností, často srovnatelnou s některými ocelemi, takže je vhodná pro vysoce namáhané součásti.
- Lehké: Navzdory své vysoké pevnosti zůstává A7075 lehkou hliníkovou slitinou, což je zásadní pro maximalizaci doby letu dronu a nosnosti.
- Dobrá odolnost proti únavě: Tato vlastnost je důležitá pro součásti vystavené vibracím a cyklickému zatížení při provozu dronů.
- Obrobitelnost: A7075 je sice potisknutelný, ale může vyžadovat následné obrábění, aby se dosáhlo velmi přísných tolerancí a povrchové úpravy.
- Odolnost proti korozi: Obvykle vyžaduje povrchovou úpravu, například eloxování, aby se zvýšila odolnost proti korozi.
- Typické aplikace v držácích gimbalů: Díly vyžadující maximální pevnost a tuhost při minimální hmotnosti, jako jsou kritické konstrukční podpěry a nosné prvky.
Volba mezi AlSi10Mg a A7075 závisí na konkrétních požadavcích aplikace kardanového držáku. AlSi10Mg nabízí dobrý všestranný výkon s vynikající potisknutelností, zatímco A7075 poskytuje vynikající pevnost pro vysoce náročné scénáře.
Metal3DP využívá pokročilé technologie plynové atomizace a PREP k výrobě vysoce kvalitních kovových prášků pro 3D tisk a zajišťuje, že materiály jako AlSi10Mg a A7075 vykazují vysokou sféricitu a dobrou tekutost, což je nezbytné pro konzistentní a spolehlivé tiskové procesy. Jejich závazek ke kvalitě zajišťuje, že zákazníci mohou 3D tisknout husté, vysoce kvalitní kovové díly s vynikajícími mechanickými vlastnostmi. Další informace o jejich vysoce kvalitních kovových prášcích naleznete na adrese https://met3dp.com/product/.
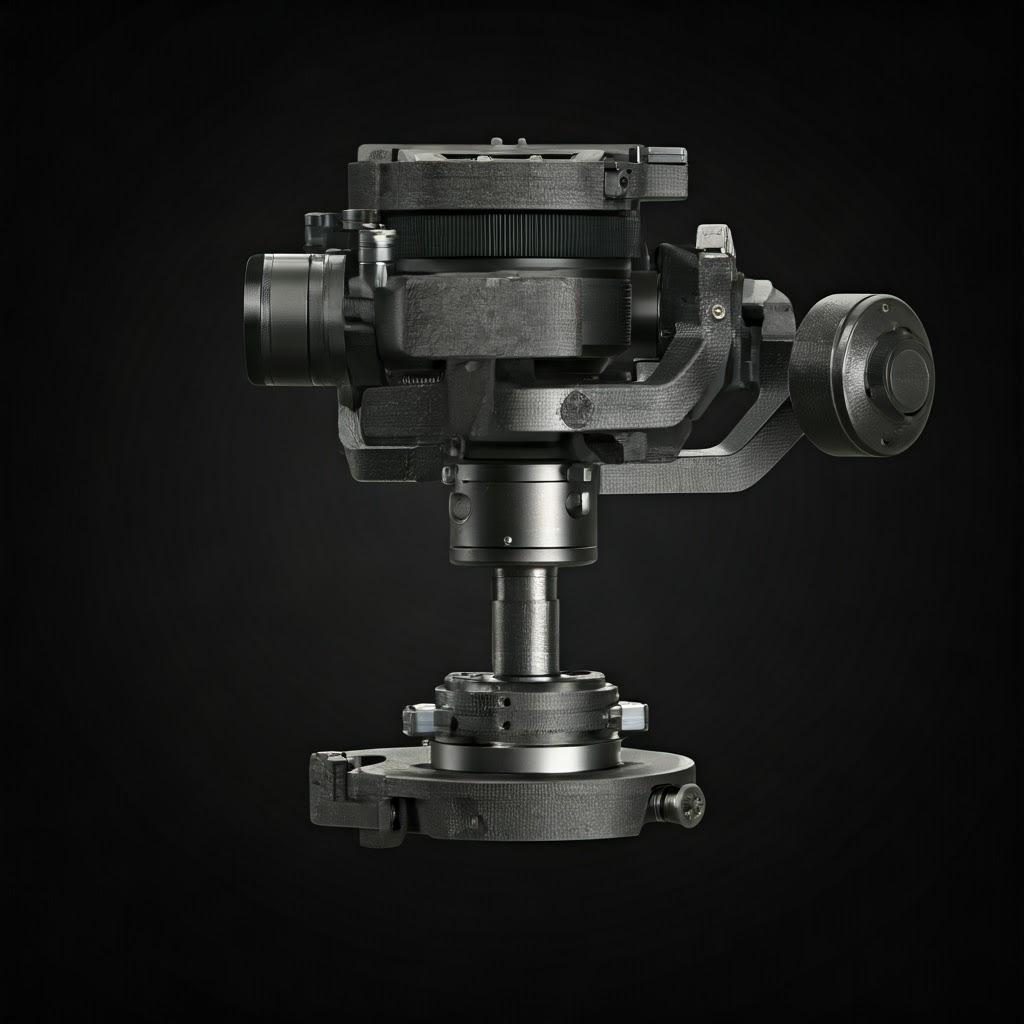
Optimalizace návrhu pro aditivní výrobu lehkých držáků kardanu
Navrhování pro 3D tisk z kovu, známé také jako návrh pro aditivní výrobu (DfAM), se zásadně liší od navrhování pro tradiční výrobní procesy. Aby bylo možné plně využít možností aditivní výroby kovů a vytvořit optimální lehké držáky kardanových křídel kamer, musí konstruktéři zohlednit několik klíčových konstrukčních zásad:
- Optimalizace topologie: Tento výpočetní přístup k návrhu identifikuje a odstraňuje materiál v nekritických oblastech namáhání při zachování integrity konstrukce. Definováním požadavků na nosnost a omezení mohou softwarové algoritmy generovat složité, organicky vypadající geometrie, které výrazně snižují hmotnost, aniž by byla ohrožena pevnost. U lehkých kardanových držáků lze optimalizaci topologie aplikovat na hlavní konstrukční prvky, což vede k vysoce efektivním návrhům.
- Mřížové struktury: Zavedení vnitřních mřížkových struktur v rámci hmoty kardanového držáku může výrazně snížit hmotnost a zároveň zajistit vynikající tuhost a absorpci energie. Různé mřížkové struktury (např. gyroidní, kubické, diamantové) nabízejí různé mechanické vlastnosti. Pečlivý výběr a optimalizace hustoty mřížky a velikosti buněk jsou rozhodující pro vyvážení snížení hmotnosti a konstrukčních vlastností.
- Konsolidace částí: 3D tisk z kovu umožňuje integrovat více dílů do jedné komplexní součásti. Konsolidací například ramene kardanu, montážní desky kamery a krytu motoru lze snížit celkovou hmotnost, dobu montáže a potenciální poruchové body spojené se spojovacími prvky. Tím se také zvýší tuhost a stabilita celého systému.
- Minimalizace materiálu: Konstrukční prvky, jako jsou tenké stěny, žebra a strategicky umístěné podpůrné konstrukce, mohou minimalizovat množství použitého materiálu. Je však nutné zajistit, aby tyto prvky byly navrženy s ohledem na konkrétní kovový prášek a proces tisku, aby se předešlo problémům, jako je deformace nebo nedostatečná strukturální podpora během tisku.
- Orientace a podpůrné struktury: Orientace dílu během tisku významně ovlivňuje kvalitu povrchu, požadavky na podporu a celkovou dobu sestavení. Optimalizace orientace může minimalizovat potřebu rozsáhlých podpůrných struktur, což nejen šetří materiál, ale také snižuje nároky na následné zpracování. Při návrhu zvažte samonosné úhly a minimalizujte převisy.
- Tepelný management: U držáků kardanu, v nichž jsou umístěny motory nebo citlivá elektronika, lze pomocí 3D tisku z kovu integrovat chladicí kanály nebo chladiče přímo do konstrukce. To umožňuje účinný odvod tepla a zajišťuje spolehlivý výkon integrovaných součástí.
- Ergonomie a funkčnost: Zvažte snadnost použití a integrace se systémem dronů. Konstrukční prvky, jako jsou rychloupínací mechanismy, nastavitelné montážní body a kanály pro vedení kabelů, lze začlenit přímo do 3D tištěného držáku kardanu.
Využitím těchto principů DfAM mohou konstruktéři plně využít potenciál kovového 3D tisku a vytvořit lehké držáky kardanových kloubů pro kamery s vynikajícím výkonem, sníženou hmotností a vylepšenou funkčností. Metal3DP‘jejich odborné znalosti v oblasti aditivní výroby a porozumění chování materiálů jim umožňují pomáhat zákazníkům optimalizovat jejich návrhy pro úspěšné výsledky 3D tisku. Jejich služby vývoje aplikací vás mohou provést složitostmi DfAM, abyste dosáhli svých specifických výkonnostních cílů.
Dosažení přesnosti: Tolerance, povrchová úprava a rozměrová přesnost u 3D tištěných držáků kardanu
V aplikacích, kde je nejdůležitější stabilita kamery a přesné zarovnání, je rozhodující tolerance, povrchová úprava a rozměrová přesnost držáku kardanu. Technologie 3D tisku z kovu dosáhly významného pokroku v dosahování přísných specifikací, ale pochopení možností a omezení tohoto procesu je pro navrhování a výrobu vysoce přesných součástí zásadní.
- Rozměrová přesnost: Rozměrová přesnost dosažitelná při 3D tisku z kovu závisí na několika faktorech, včetně technologie tisku (např. Laser Powder Bed Fusion – LPBF, Direct Metal Laser Sintering – DMLS), použitého materiálu, geometrie dílu a parametrů procesu. U menších prvků lze obvykle dosáhnout tolerancí v rozmezí ±0,1 až ±0,2 mm, u větších rozměrů se mohou vyskytnout větší odchylky. Pečlivá kalibrace tiskárny a optimalizované parametry procesu jsou pro dosažení maximální přesnosti zásadní.
- Tolerance: Zásadní význam má stanovení vhodných tolerancí v návrhu. Je důležité zvážit, které prvky vyžadují přísné tolerance pro funkčnost a montáž, a uvolnit tolerance v méně kritických oblastech, aby se snížily výrobní náklady a případné problémy. Kovovým 3D tiskem lze dosáhnout přísných tolerancí na kritických rozhraních, což zajistí přesné uchycení a sladění s kamerou a rámem dronu.
- Povrchová úprava: Povrchová úprava při 3D tisku z kovu je ve srovnání s obráběnými povrchy obvykle drsnější, často se pohybuje v rozmezí Ra 5-20 µm v závislosti na velikosti prášku a tloušťce vrstvy. U kardanových držáků se požadavky na povrchovou úpravu mohou lišit v závislosti na funkčních a estetických aspektech. Povrchy, které se stýkají s jinými součástmi, mohou vyžadovat hladší povrchovou úpravu, aby se zajistilo správné uchycení a zabránilo opotřebení.
- Následné zpracování pro zvýšení přesnosti: Pro dosažení přesnějších tolerancí a hladšího povrchu se často používají kroky následného zpracování. Mezi běžné techniky patří:
- CNC obrábění: U kritických rozměrů a rozhraní vyžadujících velmi přísné tolerance lze použít obrábění CNC jako sekundární proces k dosažení požadované přesnosti a kvality povrchu.
- Broušení a leštění: Tyto metody mohou zlepšit povrchovou úpravu držáku kardanu, což může být nezbytné z estetických důvodů nebo pro snížení tření pohyblivých částí.
- Povrchové úpravy: K dosažení rovnoměrnější povrchové úpravy celého dílu lze použít techniky, jako je tryskání nebo chemické leptání.
- Úvahy o přesnosti návrhu:
- Minimalizace velkých rovných ploch: Ty jsou během tisku náchylné k deformacím, které mohou ovlivnit přesnost rozměrů. Vložení žeber nebo křivek může tento problém zmírnit.
- Zvažte orientaci na stavbu: Orientace dílu tak, aby se minimalizoval schodovitý efekt, může v určitých směrech zlepšit kvalitu vytištěného povrchu a rozměrovou přesnost.
- Návrh minimálních podpůrných konstrukcí: Podpěry jsou sice často nezbytné, ale jejich odstranění může někdy zanechat stopy na povrchu. Optimalizace konstrukce s cílem minimalizovat kontaktní plochy podpěr může zlepšit konečnou kvalitu povrchu.
Metal3DP‘pokročilé zařízení pro 3D tisk z kovu je navrženo pro vysokou přesnost a opakovatelnost. Jejich odborné znalosti v oblasti optimalizace procesů a vědy o materiálech zajišťují, že zákazníci mohou dosáhnout požadovaných tolerancí a povrchových úprav pro své lehké držáky kardanových křídel kamer. Díky pochopení souhry mezi konstrukcí, materiálem a zpracováním mohou konstruktéři využívat kovový 3D tisk k vytváření vysoce přesných a funkčních součástí.
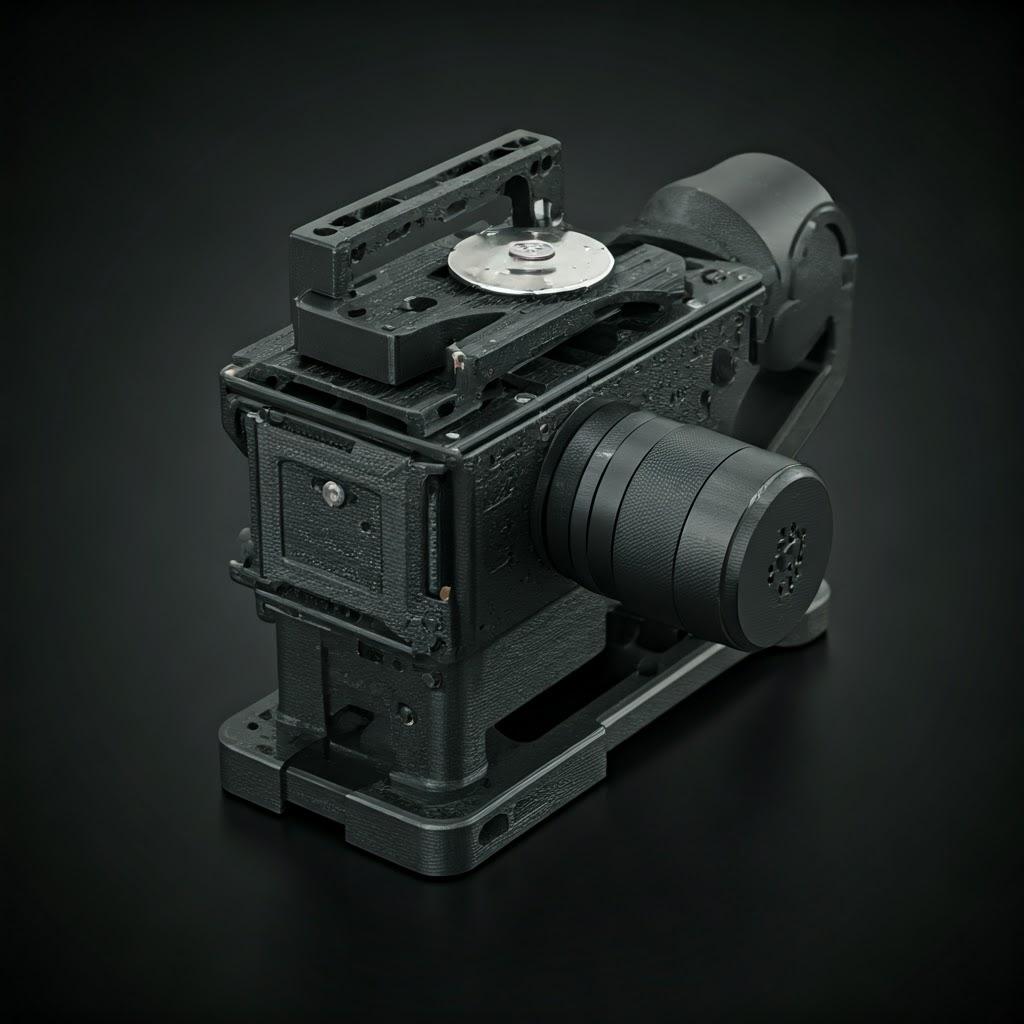
Základní postprocesing pro odolné a vysoce kvalitní držáky gimbalů pro fotoaparáty
Přestože 3D tisk z kovu nabízí značné výhody při vytváření složitých geometrií, jsou často nutné kroky následného zpracování, aby bylo dosaženo konečných požadovaných vlastností, povrchové úpravy a rozměrové přesnosti lehkých držáků kardanových hřídelí pro kamery. Konkrétní požadavky na následné zpracování závisí na aplikaci, materiálu a schopnostech použitého procesu 3D tisku.
Zde jsou uvedeny některé běžné a zásadní kroky následného zpracování kovových 3D tištěných držáků kardanu:
- Odstranění prášku: Po procesu tisku zůstává na povrchu a ve vnitřních kanálech nebo mřížkových strukturách volný kovový prášek. Efektivní odstranění prášku má zásadní význam pro funkčnost a hmotnost dílu. Mezi tyto techniky patří:
- Kartáčování a tryskání vzduchem: Pro vnější povrchy a snadno přístupné vnitřní prvky.
- Vibrační čištění: K uvolňování prášku ze složitých geometrických tvarů.
- Ultrazvukové čištění: Pro jemnější odstraňování prášku, zejména ze složitých vnitřních struktur.
- Odstranění podpůrné konstrukce: Často jsou vyžadovány podpůrné konstrukce, aby se zabránilo zhroucení nebo deformaci během tisku, zejména u převislých prvků. Opatrné odstranění těchto podpěr je nezbytné, aby nedošlo k poškození povrchu dílu. Mezi tyto metody patří:
- Ruční odstranění: Použití ručního nářadí, jako jsou kleště nebo štípací kleště, pro snadno dostupné podpěry.
- Obrábění: Pro výraznější podpěry nebo v případě, že je vyžadován čistý zlom.
- Odstranění na bázi rozpouštědel: Pro specifické materiály a typy podpěr.
- Tepelné ošetření proti stresu: Kovové 3D tištěné díly mohou obsahovat zbytková napětí v důsledku rychlých cyklů zahřívání a ochlazování během procesu tisku. Žíhání na uvolnění napětí při vhodných teplotách pomáhá tato vnitřní pnutí snížit a zlepšuje rozměrovou stabilitu a mechanické vlastnosti dílu. To má zásadní význam pro zachování přesnosti a dlouhodobé spolehlivosti držáku kardanu.
- Povrchová úprava: Jak již bylo zmíněno, povrchová úprava v podobě, v jaké byla vytištěna, nemusí být vhodná pro všechny aplikace. Lze použít různé techniky povrchové úpravy:
- Výbuch v médiích: Pro dosažení rovnoměrného matného povrchu a odstranění drobných nedokonalostí povrchu.
- Leštění a broušení: Pro dosažení hladšího povrchu z estetických nebo funkčních důvodů, jako je snížení tření nebo opotřebení.
- Chemické leptání: K odstranění tenké vrstvy materiálu a dosažení hladšího povrchu.
- Přesné obrábění: Pro kritická rozhraní nebo rozměry vyžadující velmi přísné tolerance lze jako sekundární operaci použít CNC obrábění. Tím je zajištěno přesné uložení a sladění s ostatními součástmi systému dronu.
- Povrchové úpravy pro zlepšení vlastností: V závislosti na materiálu a prostředí použití lze použít povrchové úpravy pro zvýšení odolnosti proti korozi, odolnosti proti opotřebení nebo tvrdosti:
- Eloxování (pro hliníkové slitiny): Zvýšení odolnosti proti korozi a vytvoření tvrdého povrchu odolného proti opotřebení.
- Povlaky (např. keramické, polymerní): K zajištění dodatečné ochrany před vlivy prostředí nebo k úpravě vlastností povrchu.
Volba vhodných kroků následného zpracování je rozhodující pro dosažení požadovaného výkonu a dlouhé životnosti lehkých kardanových držáků kamer. Metal3DP nabízí komplexní služby následného zpracování, které zajišťují, že 3D vytištěné díly splňují nejvyšší standardy kvality a výkonu. Jejich odborné znalosti v oblasti materiálové vědy a aditivní výroby jim umožňují doporučit a provést nezbytné kroky následného zpracování, aby optimalizovali vaše kardanové držáky pro jejich konkrétní použití.
Řešení problémů při 3D tisku lehkých konstrukcí: Deformace, podpora a pórovitost
Ačkoli 3D tisk z kovu nabízí řadu výhod, výroba vysoce kvalitních a lehkých konstrukcí, jako jsou držáky kardanu kamery, může představovat určitou výzvu, kterou je třeba pečlivě řešit optimalizací návrhu a řízením procesu.
- Deformace a zkreslení: Tenkostěnné konstrukce a velké rovné plochy jsou náchylné k deformacím a deformaci v důsledku tepelných napětí, která vznikají při rychlých cyklech zahřívání a ochlazování v procesu tisku.
- Strategie zmírnění dopadů:
- Optimalizovaná orientace sestavení: Orientace dílu tak, aby se minimalizovaly tepelné gradienty a kumulace napětí.
- Strategické využití podpůrných struktur: Ukotvení tenkých profilů do stavební desky a zajištění podpory, aby se zabránilo deformaci.
- Optimalizace parametrů procesu: Nastavení výkonu laseru, rychlosti skenování a tloušťky vrstvy pro minimalizaci tepelného příkonu a zbytkových napětí.
- Tepelné ošetření proti stresu: Žíhání dílů po tisku za účelem snížení vnitřních pnutí.
- Strategie zmírnění dopadů:
- Návrh a odstranění podpůrné konstrukce: Lehké konstrukce se často vyznačují složitou geometrií a převisy, které vyžadují podpůrné konstrukce. Klíčové je navrhnout účinné podpůrné struktury, které zajistí dostatečnou stabilitu během tisku a zároveň je lze snadno odstranit bez poškození povrchu dílu.
- Strategie zmírnění dopadů:
- Optimalizované umístění a hustota podpory: Strategické umístění podpěr v kritických oblastech při minimalizaci celkového objemu podpěr.
- Použití odlamovacích podpěr: Navrhování podpěr se slabšími spoji k dílu pro snadnější demontáž.
- Softwarové nástroje pro generování podpory: Využití pokročilého softwaru k automatickému generování optimalizovaných podpůrných struktur.
- Opatrné techniky odstraňování: Použití vhodných nástrojů a technik k odstranění podpěr bez poškození povrchu.
- Strategie zmírnění dopadů:
- Pórovitost a hustota: Dosažení vysoké hustoty a minimální pórovitosti je zásadní pro mechanické vlastnosti lehkých kardanových držáků, zejména těch, které jsou vyrobeny z vysoce pevných slitin, jako je A7075. Pórovitost může oslabit strukturu a vést k selhání při namáhání.
- Strategie zmírnění dopadů:
- Optimalizované parametry procesu: Přesné nastavení výkonu laseru, rychlosti skenování a vzdálenosti mezi šrafami pro zajištění úplného roztavení a roztavení kovového prášku.
- Vysoce kvalitní kovové prášky: Použití prášků s konzistentní distribucí velikosti částic a vysokou sféricitou, jako jsou prášky poskytované společností Metal3DP, aby byla zajištěna dobrá tekutost a hustota balení.
- Inertní stavební atmosféra: Tisk v kontrolované atmosféře s nízkým obsahem kyslíku, aby se zabránilo oxidaci a tvorbě pórů.
- Izostatické lisování za tepla (HIP): Technika následného zpracování, při níž se za použití vysokého tlaku a teploty materiál dále zhutní a odstraní se vnitřní dutiny.
- Strategie zmírnění dopadů:
- Problémy s povrchovou úpravou: Dosažení hladké povrchové úpravy u složitých, lehkých geometrií může být náročné vzhledem k povaze procesu tisku po vrstvách a možnosti ulpívání prášku.
- Strategie zmírnění dopadů:
- Optimalizovaná orientace sestavení: Minimalizace krokového efektu na kritických plochách.
- Menší velikost částic prášku a tloušťka vrstvy: Použití jemnějších prášků a tenčích vrstev může vést k hladšímu povrchu po tisku.
- Techniky povrchové úpravy: Použití tryskání, leštění nebo chemického leptání ke zlepšení drsnosti povrchu.
- Strategie zmírnění dopadů:
Pochopením těchto potenciálních problémů a zavedením vhodných strategií návrhu a řízení procesů je možné úspěšně tisknout 3D tiskem vysoce kvalitní a lehké držáky kardanových kloubů kamer, které splňují náročné požadavky aplikací pro drony. Metal3DP‘rozsáhlé zkušenosti s aditivní výrobou kovů jim umožňují pomáhat zákazníkům překonávat tyto výzvy a dosahovat optimálních výsledků.
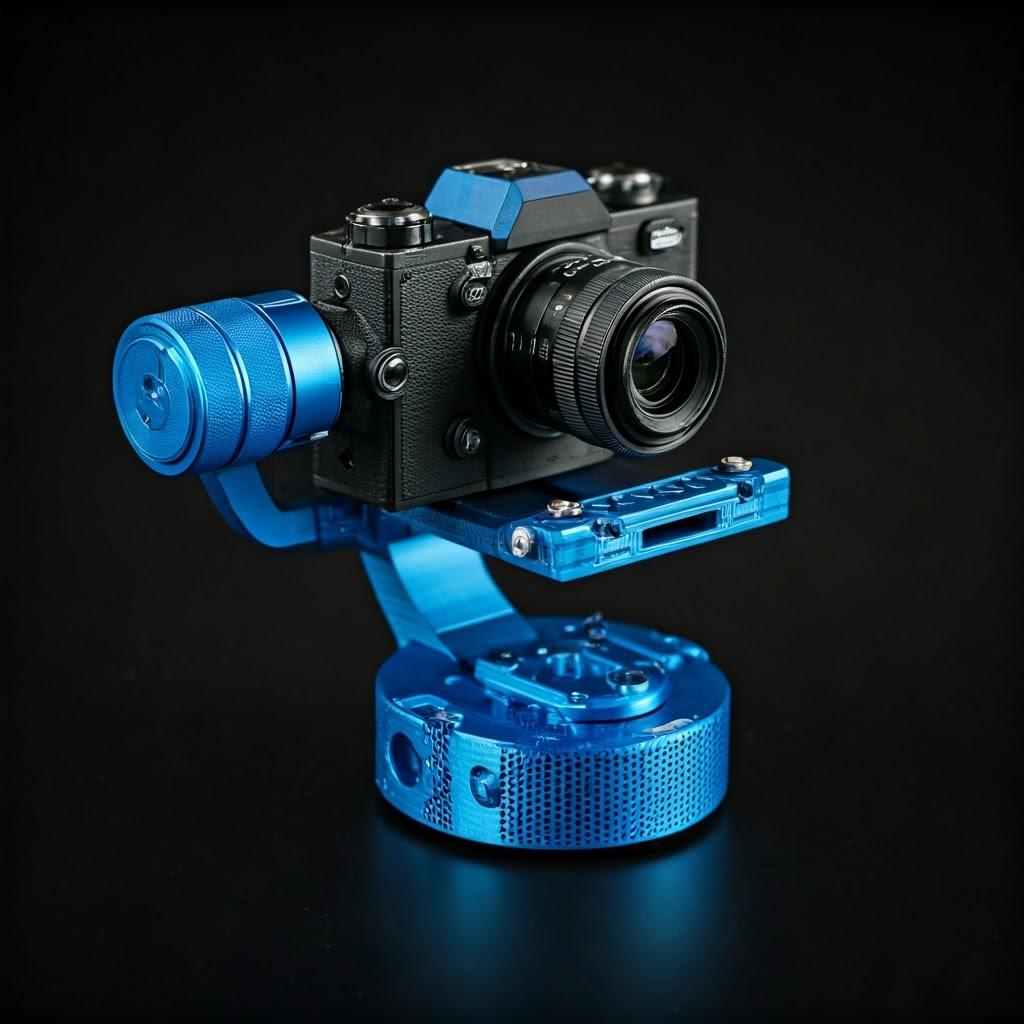
Výběr spolehlivého poskytovatele služeb 3D tisku kovů pro potřeby držáku kardanu
Výběr správného poskytovatele služeb 3D tisku z kovu je zásadním rozhodnutím, které může významně ovlivnit kvalitu, náklady a dobu realizace vašich lehkých držáků kardanu pro kamery. Zde jsou klíčové faktory, které je třeba při hodnocení potenciálních dodavatelů zvážit:
- Materiálové schopnosti: Ujistěte se, že dodavatel má zkušenosti s prací s doporučenými kovovými prášky AlSi10Mg a A7075 a může prokázat odborné znalosti při dosahování požadovaných mechanických vlastností. Informujte se o jeho procesech získávání materiálu a kontroly kvality. Metal3DP se pyšní svým pokročilým systémem výroby prášku a vysokou kvalitou svých kovových prášků, které zajišťují vynikající výkon vašich 3D tištěných komponent.
- Tiskové technologie a zařízení: Porozumět typům technologií 3D tisku kovů, které poskytovatel používá (např. LPBF, DMLS, EBM). Volba technologie může ovlivnit dosažitelnou přesnost, povrchovou úpravu a objem sestavení. Metal3DP nabízí špičkový objem, přesnost a spolehlivost tisku díky svému pokročilému zařízení pro 3D tisk.
- Odborné znalosti v oblasti návrhu pro aditivní výrobu (DfAM): Znalý poskytovatel služeb by vám měl být schopen poskytnout poradenství ohledně optimalizace konstrukce držáku kardanu pro aditivní výrobu. To zahrnuje rady ohledně optimalizace topologie, mřížkových struktur, konsolidace dílů a minimalizace požadavků na podporu. Metal3DP poskytuje komplexní řešení včetně služeb vývoje aplikací, které vám pomohou využít plný potenciál kovového 3D tisku.
- Služby následného zpracování: Zjistěte, zda poskytovatel nabízí nezbytné služby následného zpracování, které splňují vaše požadavky, jako je odstranění prášku, odstranění podpěr, tepelné zpracování pro snížení napětí, povrchová úprava (např. tryskání, leštění, eloxování) a přesné obrábění. Poskytovatel komplexních služeb může zefektivnit výrobní proces a zajistit stálou kvalitu.
- Zajištění kvality a certifikace: Informujte se o systému řízení kvality poskytovatele a o případných příslušných certifikátech (např. ISO 9001, AS9100 pro letecký průmysl). To prokazuje jeho závazek ke kvalitě a řízení procesů.
- Zkušenosti a portfolio: Zjistěte, jaké má dodavatel zkušenosti s výrobou podobných komponentů nebo s průmyslovými odvětvími souvisejícími s technologií dronů (např. letecký a automobilový průmysl). Prozkoumejte jejich portfolio minulých projektů, abyste posoudili kvalitu a složitost jejich práce.
- Komunikace a zákaznická podpora: Pro hladký a úspěšný průběh projektu je nezbytná efektivní komunikace a pohotová zákaznická podpora. Posuďte, jak poskytovatel reaguje na dotazy, zda je schopen poskytnout technickou podporu a zda je ochoten spolupracovat na konstrukčních a výrobních problémech.
- Dodací lhůty a výrobní kapacita: Proberte s nimi typické doby realizace podobných projektů a zhodnoťte jejich výrobní kapacitu, abyste se ujistili, že jsou schopni splnit vaše objemové požadavky a časové plány.
- Struktura nákladů a transparentnost: Získejte jasnou a podrobnou cenovou nabídku, ve které budou uvedeny všechny náklady včetně tisku, materiálů, následného zpracování a případných dalších služeb. Pochopte jejich cenový model a ujistěte se, že neobsahuje žádné skryté poplatky.
Pečlivým vyhodnocením těchto faktorů si můžete vybrat spolehlivého poskytovatele služeb 3D tisku z kovu, který vám dodá vysoce kvalitní a lehké držáky kardanu pro kameru, které splní vaše specifické požadavky na výkon a použití. Zvažte oslovení Metal3DP a zjistěte, jak mohou jejich komplexní schopnosti podpořit cíle vaší organizace v oblasti aditivní výroby. Více informací o jejich společnosti se dozvíte na adrese https://met3dp.com/about-us/.
Analýza nákladů a dodacích lhůt pro kovové 3D tištěné držáky gimbalů pro kamery
Pochopení nákladových faktorů a dodacích lhůt spojených s kovovými 3D tištěnými držáky kardanu kamery je zásadní pro plánování rozpočtu a rozvrhování projektů. Tyto aspekty se mohou výrazně lišit v závislosti na několika faktorech:
- Náklady na materiál: Významným faktorem je cena kovového prášku (např. AlSi10Mg, A7075). Speciální slitiny nebo objednávky menších sérií mohou vést k vyšším materiálovým nákladům. Metal3DP vyrábí širokou škálu vysoce kvalitních kovových prášků a nabízí cenově výhodná řešení v závislosti na požadavcích na materiál a objemu.
- Objem sestavy a velikost dílu: Větší díly, které zabírají větší objem 3D tiskárny, mají obecně vyšší náklady na tisk kvůli vyšší spotřebě materiálu a delší době sestavení. Velikost a složitost konstrukce držáku kardanu přímo ovlivňují spotřebu materiálu a délku procesu tisku.
- Doba výstavby: Doba potřebná k vytištění dílu závisí na jeho velikosti, složitosti, výšce vrstvy a počtu dílů, které lze vložit do jednoho sestavení. Delší doba sestavení znamená vyšší provozní náklady stroje.
- Podpůrné struktury: Objem a složitost podpůrných konstrukcí potřebných pro konstrukci kardanového držáku ovlivní spotřebu materiálu a dobu následného zpracování při demontáži, což ovlivní celkové náklady. Optimalizované konstrukce, které minimalizují potřebu podpěr, mohou vést k úspoře nákladů.
- Požadavky na následné zpracování: Rozsah potřebného následného zpracování (např. odstranění prášku, odstranění pnutí, povrchová úprava, obrábění) zvyšuje celkové náklady a dobu realizace. Díly vyžadující rozsáhlé následné zpracování budou mít vyšší výrobní náklady a delší dobu realizace.
- Množství a objem výroby: Náklady na jeden díl obecně klesají s rostoucím objemem výroby díky úsporám z rozsahu. Kovový 3D tisk je však nákladově efektivní zejména u malých až středních objemů a složitých geometrií, kde by náklady na tradiční nástroje byly neúnosné.
- Náklady poskytovatele služeb: Různí poskytovatelé služeb mají různé cenové struktury založené na jejich vybavení, odborných znalostech, procesech kontroly kvality a režijních nákladech. Pro porovnání nákladů je nezbytné získat nabídky od více renomovaných poskytovatelů.
- Doba dodání: Dodací lhůty pro kovové 3D tištěné držáky kardanu závisí na faktorech, jako je složitost dílu, dostupnost materiálu, aktuální vytížení poskytovatele služeb a požadované kroky následného zpracování. Jednoduché konstrukce se standardními materiály mohou mít kratší dodací lhůty, zatímco složité díly vyžadující specializované materiály nebo rozsáhlé následné zpracování mohou trvat déle. Rychlého prototypování lze často dosáhnout relativně rychle pomocí 3D tisku z kovu.
Je důležité vést podrobné rozhovory s potenciálními poskytovateli služeb, jako je např Metal3DP a získat přesné odhady nákladů a dodacích lhůt na základě vašich specifických požadavků na design a objem výroby. Poskytnutí podrobných modelů CAD a specifikací jim umožní nabídnout přesné cenové nabídky a termíny.
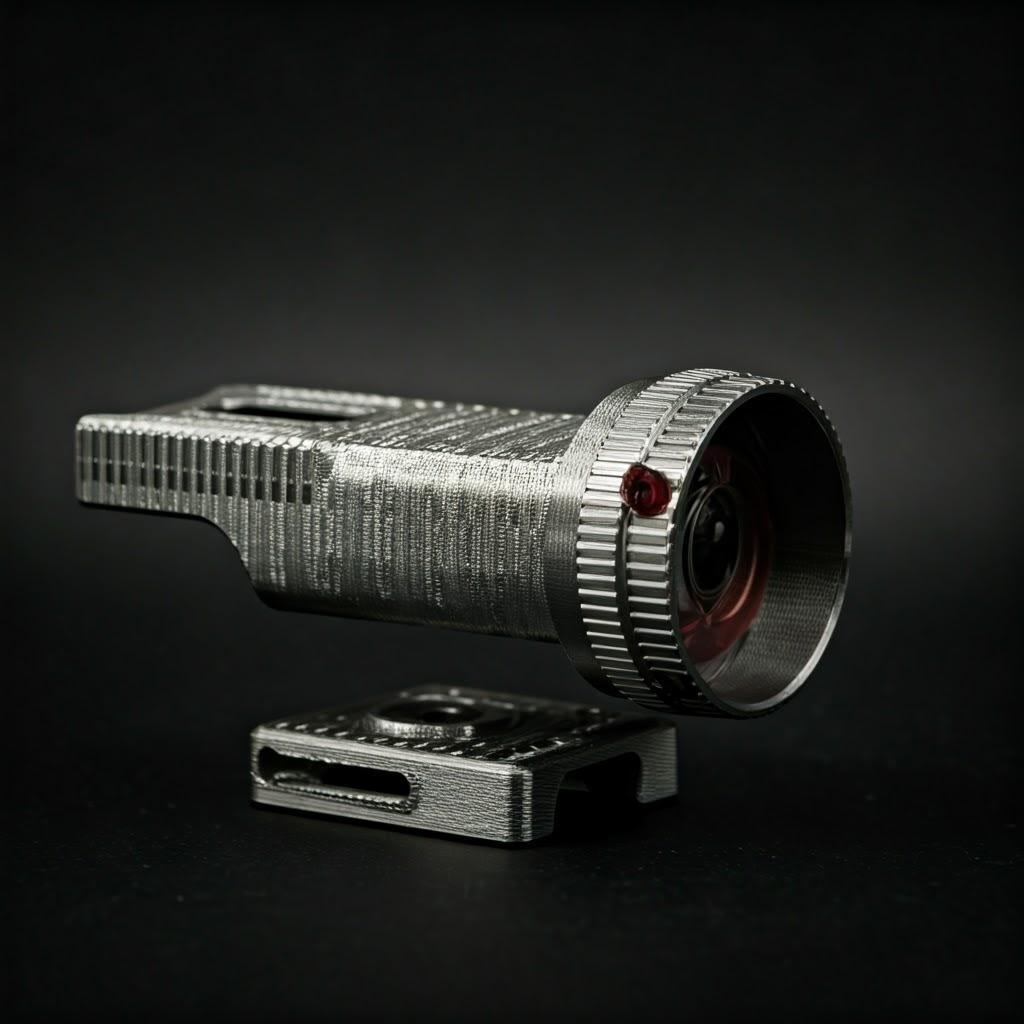
Často kladené otázky (FAQ)
Zde je několik nejčastějších otázek týkajících se použití kovového 3D tisku pro lehké držáky kardanu fotoaparátu:
- Otázka: Mohou být kovové 3D tištěné držáky kardanu stejně pevné jako ty vyrobené tradičními metodami?
- A: Ano, pokud je konstrukce optimalizována pro aditivní výrobu a jsou použity správné parametry kovového prášku a tisku, mohou kovové 3D tištěné díly dosahovat srovnatelného nebo dokonce lepšího poměru pevnosti a hmotnosti než tradičně vyráběné součásti. Slitiny jako A7075 nabízejí výjimečnou pevnost. Metal3DP‘vysoce kvalitní kovové prášky zajišťují vynikající mechanické vlastnosti finálních tištěných dílů.
- Otázka: Jaké je typické snížení hmotnosti dosažitelné při 3D tisku z kovu pro držáky kardanu?
- A: Snížení hmotnosti se může výrazně lišit v závislosti na původní konstrukci a rozsahu optimalizace pro aditivní výrobu. Pomocí technik, jako je optimalizace topologie a mřížkové struktury, lze často dosáhnout snížení hmotnosti o 20-50 % nebo více při zachování nebo zlepšení konstrukčních vlastností.
- Otázka: Jsou kovové 3D tištěné díly vhodné pro drsné podmínky prostředí, s nimiž se setkávají drony?
- A: Ano, při výběru vhodných materiálů a povrchových úprav lze kovové 3D tištěné držáky kardanu vyrobit tak, aby byly odolné vůči korozi, opotřebení a teplotním změnám. Například eloxování hliníkových slitin zvyšuje jejich odolnost proti korozi.
- Otázka: Jaké úrovně detailů a složitosti lze dosáhnout u 3D tištěných návrhů držáků kardanu?
- A: 3D tisk z kovu nabízí značnou volnost při navrhování, umožňuje složité geometrie, vnitřní prvky a konsolidaci dílů, které jsou obtížně dosažitelné nebo nemožné při použití tradičních výrobních metod. To umožňuje vysoce optimalizované a funkční návrhy držáků kardanu.
- Otázka: Jaké jsou typické tolerance dosažitelné při 3D tisku z kovu?
- A: V závislosti na technologii tisku a procesních parametrech lze u menších prvků obecně dosáhnout tolerancí v rozmezí ±0,1 až ±0,2 mm. V případě potřeby lze pro větší tolerance použít techniky následného zpracování, jako je CNC obrábění.
- Otázka: Jaké jsou náklady na kovové 3D tištěné držáky kardanu ve srovnání s tradiční výrobou?
- A: U malých až středních objemů výroby a složitých geometrií může být kovový 3D tisk cenově konkurenceschopný nebo dokonce výhodnější než tradiční metody, které vyžadují nástroje. Absence nákladů na nástroje a možnost vytvářet vysoce optimalizované návrhy může vést k celkové úspoře nákladů.
V případě jakýchkoli dalších otázek nebo konkrétních dotazů týkajících se vašeho projektu se můžete obrátit na odborníky na adrese Metal3DP prostřednictvím svých webových stránek.
Závěr - Uvolnění potenciálu 3D tisku kovů pro pokročilé technologie dronů
3D tisk z kovu představuje transformační technologii pro konstrukci a výrobu lehkých držáků kardanových hřídelí pro kamery, která nabízí řadu přesvědčivých výhod oproti tradičním výrobním metodám. Schopnost vytvářet složité, optimalizované geometrie s vysoce výkonnými materiály, jako jsou AlSi10Mg a A7075, umožňuje vyvíjet lehčí, pevnější a funkčnější součásti, které mají zásadní význam pro rozvoj technologie dronů.
Využitím principů návrhu pro aditivní výrobu mohou konstruktéři dosáhnout výrazného snížení hmotnosti díky optimalizaci topologie a mřížkových struktur, zvýšit výkon díky konsolidaci dílů a přizpůsobit návrhy konkrétním požadavkům aplikace. I když je třeba pečlivě zvážit problémy, jako je deformace, řízení podpůrné struktury a pórovitost, pokrok v technologii tisku a technikách následného zpracování neustále zlepšuje kvalitu a přesnost kovových 3D tištěných dílů.
Výběr spolehlivého poskytovatele služeb 3D tisku kovů, jako je např Metal3DP, se svými odbornými znalostmi v oblasti vysoce kvalitních kovových prášků, pokročilých tiskových zařízení a rozsáhlých možností následného zpracování, je zásadní pro plné využití potenciálu této technologie. Pochopení nákladových faktorů a dodacích lhůt spojených s kovovým 3D tiskem umožňuje informované rozhodování a efektivní řízení projektů.
Závěrem lze říci, že 3D tisk z kovu není jen výrobní proces, ale i nástroj pro inovace v odvětví dronů. Využitím jeho schopností mohou inženýři a manažeři veřejných zakázek odemknout nové možnosti pro vytváření pokročilých, vysoce výkonných součástí dronů, které posunou hranice dosažitelného v oblasti leteckého snímkování i mimo ni. My v Metal3DP se zavázaly poskytovat špičkové systémy a prášky, které vaší organizaci usnadní cestu k aditivní výrobě a urychlí transformaci digitální výroby. Kontaktujte nás ještě dnes a zjistěte, jak mohou naše možnosti podpořit cíle vaší organizace v oblasti aditivní výroby.
Sdílet na
MET3DP Technology Co., LTD je předním poskytovatelem řešení aditivní výroby se sídlem v Qingdao v Číně. Naše společnost se specializuje na zařízení pro 3D tisk a vysoce výkonné kovové prášky pro průmyslové aplikace.
Dotaz k získání nejlepší ceny a přizpůsobeného řešení pro vaše podnikání!
Související články
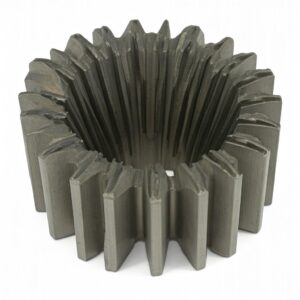
Vysoce výkonné segmenty lopatek trysek: Revoluce v účinnosti turbín díky 3D tisku z kovu
Přečtěte si více "O Met3DP
Nedávná aktualizace
Náš produkt
KONTAKTUJTE NÁS
Nějaké otázky? Pošlete nám zprávu hned teď! Po obdržení vaší zprávy obsloužíme vaši žádost s celým týmem.