Pouzdra konektorů na zakázku pro letecké a kosmické systémy
Obsah
Úvod: Definice pouzder leteckých konektorů a jejich funkce
Ve složitém a náročném světě leteckého inženýrství hraje každá součástka, bez ohledu na to, jak je malá, zásadní roli při zajišťování bezpečnosti, spolehlivosti a výkonu. Mezi tyto zásadní prvky patří pouzdra konektorů pro letectví a kosmonautiku. Tyto součásti nemusí být vždy středem pozornosti jako motory nebo křídla, ale jsou základem složité sítě elektrických a datových systémů, které umožňují bezchybné fungování moderních letadel, kosmických lodí a obranných platforem.
V jádru slouží pouzdro leteckého konektoru jako ochranný kryt pro elektrické nebo optické konektory. Mezi jeho hlavní funkce patří:
- Fyzická ochrana: Stínění citlivých rozhraní konektorů (kolíky, zásuvky, koncovky optických vláken) před fyzickým poškozením způsobeným nárazy, vibracemi, otřesy a oděrem. To má zásadní význam v prostředích, kde je mechanické namáhání trvalé a intenzivní.
- Ekologické těsnění: Zabránění vniknutí nečistot, jako je prach, vlhkost, odmrazovací kapaliny, letecké palivo, hydraulické kapaliny a další potenciálně korozivní látky, které mohou narušit elektrické spoje a vést k poruchám systému. Účinné utěsnění má zásadní význam pro zachování integrity signálu a prevenci zkratů.
- Elektrické stínění (EMI/RFI): V mnoha aplikacích v letectví a kosmonautice, zejména v těch, které se týkají citlivé avioniky nebo komunikačních systémů, poskytují pouzdra konektorů stínění proti elektromagnetickému rušení (EMI) a radiofrekvenčnímu rušení (RFI). To zabraňuje rušení přenosu signálu vnějšími elektromagnetickými poli a chrání ostatní blízké systémy před šumem generovaným samotným konektorem.
- Úleva od napětí: Poskytuje mechanickou oporu kabelům vstupujícím do konektoru, čímž zabraňuje přenášení napětí přímo do koncových bodů. Tím se zvyšuje odolnost a životnost celé kabelové sestavy.
- Vyrovnání a párování: Zajišťuje správnou orientaci a bezpečné zajištění párových konektorů, čímž zaručuje vytvoření a udržení spolehlivého spojení i v náročných provozních podmínkách.
Tato pouzdra jsou víc než jen pouhé krabice; jsou to přesně navržené komponenty určené k zachování integrity životně důležitých datových a energetických spojů v letadle nebo kosmické lodi. Selhání jediného konektoru, často způsobené nedostatečnou ochranou pouzdra, může mít kaskádovité účinky, které mohou vést k selhání kritických systémů. Proto jsou konstrukce, výběr materiálu a způsob výroby těchto pouzder předmětem intenzivního zkoumání v leteckém a kosmickém průmyslu. Jak se systémy stávají složitějšími a integrovanějšími, nároky kladené na tyto zdánlivě jednoduché součásti se stále zvyšují, což vyvolává potřebu inovativních řešení.
Nelítostné prostředí v letectví a kosmonautice: Proč jsou robustní pouzdra nepostradatelná?
Provozní prostředí pro letecké a kosmické komponenty je pravděpodobně jedním z nejnáročnějších v jakémkoli inženýrském oboru. Pouzdra konektorů musí odolávat neustálému náporu extrémních podmínek, což z nich činí nepominutelné požadavky na robustnost a spolehlivost. Vezměte si spektrum výzev:
- Extrémní teploty: Komponenty zažívají obrovské teplotní výkyvy, od teplot pod bodem mrazu ve velkých výškách nebo ve vesmíru (-55 °C nebo méně) až po vysoké teploty v blízkosti motorů nebo v prostorech pro vybavení (+125 °C, +175 °C nebo ve specifických zónách ještě vyšší). Materiály si musí v těchto rozmezích zachovat strukturální integritu, těsnicí vlastnosti a rozměrovou stabilitu, aniž by došlo k jejich popraskání, deformaci nebo degradaci.
- Vibrace a nárazy: Letadla a nosné rakety vytvářejí během vzletu, letu a přistání značné vibrace. Pouzdra konektorů musí vydržet toto trvalé vibrační zatížení i náhlé otřesy s vysokým G, aniž by se uvolnila, unavila nebo způsobila přerušované problémy s elektrickými kontakty (fretting). Nezbytné jsou bezpečné zajišťovací mechanismy a robustní konstrukce.
- Tlakové rozdíly: Součásti musí spolehlivě fungovat od tlaků na úrovni moře až po nízké tlaky ve velkých výškách nebo ve vesmírném vakuu. Integrita těsnění je rozhodující pro zabránění ztrátě tlaku v přetlakových kabinách nebo modulech a pro ochranu vnitřních součástí před vnějším prostředím.
- Koroze a kontaminace: Vystavení vlhkosti, slané mlze (v mořském prostředí nebo na pobřežních letištích), hydraulickým kapalinám, palivům, čisticím rozpouštědlům a odmrazovacím prostředkům vyžaduje materiály s vynikající odolností proti korozi. Nebezpečí pro rozhraní konektorů představuje také kontaminace prachem, pískem a jinými částicemi.
- Radiace: Vesmírné aplikace představují výzvu v podobě ionizujícího záření, které může v průběhu času degradovat některé materiály a potenciálně ohrozit dlouhodobou spolehlivost krytů konektorů v družicích a sondách v hlubokém vesmíru.
- Odplyňování (vesmír): Ve vesmírném vakuu mohou materiály uvolňovat zachycené plyny (outgassing), které mohou kontaminovat citlivé optické povrchy nebo elektroniku. Pro vesmírné komponenty jsou často vyžadovány materiály s nízkým obsahem plynů.
- Omezení hmotnosti: V leteckém průmyslu se počítá každý gram. Pouzdra musí poskytovat maximální ochranu a výkon při minimálním podílu na celkové hmotnosti systému. Tato neustálá snaha o odlehčování pohání hledání pokročilých materiálů a výrobních postupů.
Nesplnění těchto přísných požadavků na životní prostředí může vést ke katastrofickým selháním systému. Proto letečtí inženýři a manažeři nákupu upřednostňují pouzdra konektorů vyrobená z vysoce výkonných materiálů za použití procesů, které zaručují konzistenci, spolehlivost a dodržování přísných průmyslových norem (např. AS9100).
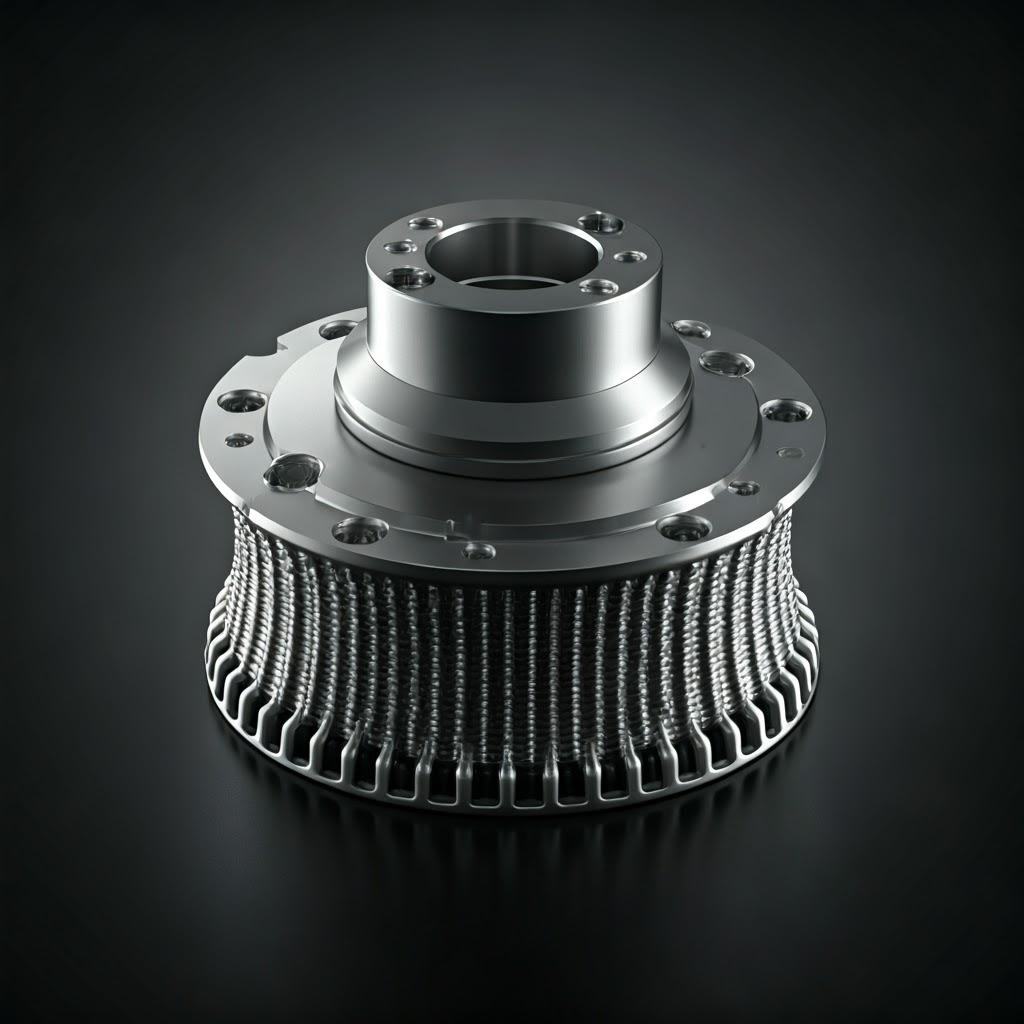
Nutnost přizpůsobení v moderním leteckém designu
Ačkoli existují standardní hotové konektory a pouzdra, rostoucí složitost, miniaturizace a specifické funkční požadavky moderních leteckých systémů často vyžadují pouzdra konektorů na zakázku. Tuto potřebu vyvolává několik faktorů:
- Prostorová omezení: Vzhledem k tomu, že letadla a vesmírné lodě umísťují stále více elektroniky do těsnějších prostor (např. do prostorů pro avioniku, kořenů křídel, užitečného zatížení bezpilotních letounů), potřebují pouzdra konektorů často jedinečné tvary, profily nebo montážní prvky, aby se přesně vešly do přidělených prostor. Standardní obdélníková nebo kruhová pouzdra nemusí být proveditelná.
- Specifické požadavky na páření: Pro propojení s jedinečným nebo nestandardním zařízením, přizpůsobení specifickým úhlům výstupu kabelů nebo integraci více typů konektorů do jediného konsolidovaného pouzdra může být zapotřebí vlastní provedení.
- Integrovaná funkčnost: Roste trend integrovat prvky přímo do krytu, jako jsou integrované stínicí přepážky, chladicí kanály, montážní držáky nebo držáky senzorů. Tím se snižuje počet dílů, doba montáže a potenciální místa poruchy.
- Optimalizace hmotnosti: Přizpůsobení umožňuje konstruktérům přizpůsobit geometrii pouzdra konkrétně požadavkům na zatížení, odstranit zbytečný materiál díky optimalizaci topologie a dosáhnout maximální úspory hmotnosti nad rámec standardních komponent.
- Jedinečné environmentální potřeby: Specifické aplikace mohou vyžadovat specializované konfigurace těsnění, jedinečná řešení stínění EMI/RFI nebo kompatibilitu s nestandardními kapalinami či teplotami, což vede k potřebě vlastních konstrukcí a výběru materiálů.
- Integrace starších systémů: Dodatečná montáž nových systémů do starších letadel často vyžaduje vlastní řešení konektorů pro propojení moderní elektroniky se stávajícími kabelovými svazky a montážními body.
Tradiční výrobní metody, jako je CNC obrábění z polotovarů nebo vstřikování/odlévání (pro velké objemy), mohou mít potíže s efektivním nebo nákladově efektivním splněním těchto požadavků na přizpůsobení, zejména pro nízké až střední objemy, které jsou často vyžadovány v leteckých projektech. Obrábění složitých, organicky tvarovaných nebo vnitřně kanalizovaných zakázkových pouzder může být neuvěřitelně časově náročné a vytvářet značný materiálový odpad. Vytváření forem nebo nástrojů pro odlévání nebo vstřikování je pro malé výrobní série nebo prototypy často neúměrně nákladné. Zde se jedinečné možnosti aditivní výroby kovů stávají transformujícími.
Aditivní výroba kovů: Změna paradigmatu pro výrobu konektorových pouzder
Aditivní výroba kovů (AM), běžně známá jako kovová 3D tisk, nabízí výkonnou alternativu pro výrobu vysoce výkonných, zakázkových krytů konektorů pro letecký průmysl. Technologie jako PBF (Powder Bed Fusion) - která zahrnuje selektivní laserové tavení (SLM), přímé laserové spékání kovů (DMLS) a tavení elektronovým svazkem (EBM) - vytvářejí díly vrstvu po vrstvě přímo z digitálního modelu pomocí jemných kovových prášků. Tento přístup zásadně mění výrobní prostředí pro komponenty, jako jsou pouzdra konektorů:
- Bezprecedentní svoboda designu: AM odstraňuje mnoho tradičních výrobních omezení. Inženýři mohou navrhovat velmi složité geometrie, vnitřní mřížkové struktury pro snížení hmotnosti, konformní chladicí kanály a organicky tvarovaná pouzdra optimalizovaná pro specifický prostor - prvky, které často není možné nebo praktické opracovat nebo odlít.
- Rychlé prototypování a iterace: Vlastní návrhy pouzder lze vytisknout, otestovat a zdokonalit během několika dnů, což výrazně urychluje vývojový cyklus ve srovnání s týdny nebo měsíci, které jsou nutné pro tradiční nástroje a obrábění. Tato pružnost je v rychle se rozvíjejících leteckých programech klíčová.
- Nákladově efektivní přizpůsobení: Vzhledem k tomu, že AM je proces bez použití nástrojů, je rozdíl v nákladech na tisk jednoho vlastního návrhu nebo deseti mírně odlišných variant minimální ve srovnání s vysokými náklady na nástroje spojenými s tradičními metodami. Díky tomu je AM ideální pro nízké až střední výrobní série specializovaných pouzder.
- Konsolidace částí: Do jediného komplexního 3D tištěného dílu lze potenciálně integrovat více součástí sestavy konektoru (např. pouzdro, držák, odlehčení tahu). Tím se zkrátí doba montáže, eliminují se potenciální cesty úniku nebo místa poruch v místech spojů a může se dále snížit hmotnost.
- Účinnost materiálu: Procesy AM obvykle využívají pouze materiál potřebný k výrobě dílu a jeho podpěr, což vede k podstatně menšímu plýtvání materiálem ve srovnání se subtraktivními metodami, jako je CNC obrábění, které může u složitých dílů odstranit až 80-90 % původního bloku materiálu. To je výhodné zejména při použití drahých slitin pro letecký průmysl, jako je titan.
- Výroba na vyžádání: Digitální návrhy lze ukládat a tisknout podle potřeby, což umožňuje distribuované výrobní modely a snižuje potřebu velkých fyzických zásob. Náhradní díly nebo aktualizované návrhy lze vyrábět rychle, aniž by bylo nutné používat stávající nástroje.
Pro letecké inženýry a manažeři veřejných zakázek hledá dodavatelé leteckých komponentů schopné efektivně dodávat vysoce přizpůsobená a výkonná pouzdra konektorů, představuje technologie AM pro kov přesvědčivou nabídku hodnoty. Umožňuje inovace, zrychluje časové lhůty a nabízí nákladově efektivní cestu pro složité, nízkoobjemové díly, které jsou v průmyslu stále častější.
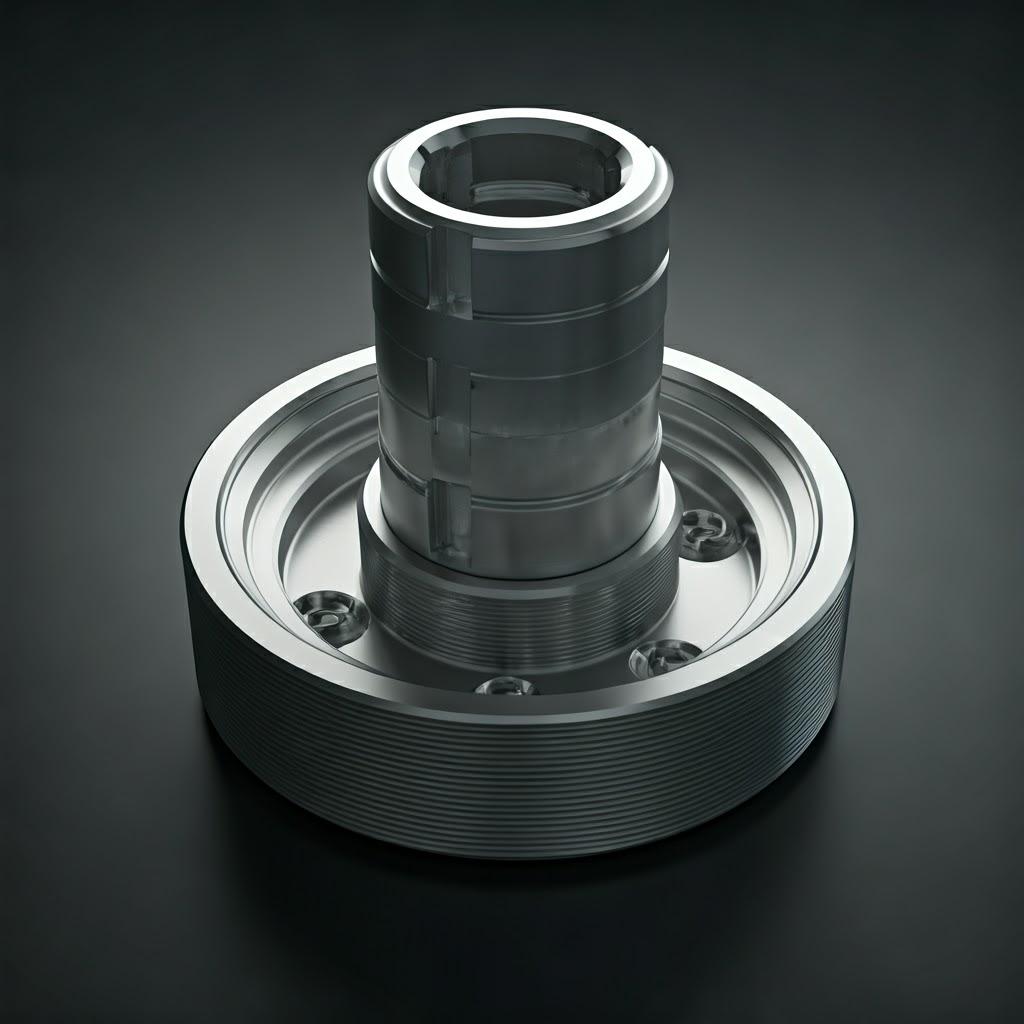
Spolupráce s odbornými dodavateli pro AM zpracování kovů, jako je Met3dp
Úspěšné využití technologie AM pro kritické komponenty, jako jsou pouzdra konektorů pro letectví a kosmonautiku, vyžaduje spolupráci se znalými a schopnými odborníky poskytovatel služeb 3D tisku kovů. Složitost optimalizace procesních parametrů, nauka o materiálech, kontrola kvality a následné zpracování vyžadují specializované odborné znalosti.
Met3dp, se sídlem v čínském městě Čching-tao, je předním poskytovatelem komplexních řešení aditivní výroby šitých na míru náročným průmyslovým aplikacím, včetně leteckého průmyslu. Naše odborné znalosti pokrývají celý ekosystém AM:
- Pokročilé kovové prášky: Společnost Met3dp vyrábí širokou škálu vysoce kvalitních sférických kovových prášků optimalizovaných speciálně pro procesy PBF. S využitím nejmodernějších technologií plynové atomizace a plazmového rotačního elektrodového procesu (PREP) zajišťujeme, že naše prášky, včetně leteckých tříd, jako je Ti-6Al-4V, a nerezových ocelí, jako je 316L, vykazují vysokou sféričnost, vynikající tekutost, kontrolovanou distribuci velikosti částic a vysokou čistotu - což jsou kritické faktory pro dosažení hustých, spolehlivých a vysoce výkonných tištěných dílů.
- Moderní tiskové vybavení: Naše portfolio zahrnuje tiskárny pro selektivní tavení elektronovým svazkem (SEBM), které jsou známé svou schopností efektivně zpracovávat materiály náchylné k praskání při vysokých teplotách a vyrábět díly s nízkým zbytkovým napětím, což často snižuje potřebu rozsáhlého tepelného zpracování. Naše systémy poskytují špičkový objem výroby, přesnost a spolehlivost vhodnou pro kritické letecké komponenty.
- Desítky let kolektivní odbornosti: Náš tým má hluboké znalosti v oblasti AM kovů, materiálové vědy a aplikačního inženýrství. Úzce spolupracujeme s klienty a nabízíme jim podporu při návrhu pro aditivní výrobu (DfAM), optimalizaci procesů a komplexní řešení, která pomáhají organizacím úspěšně implementovat 3D tisk a urychlit jejich transformaci digitální výroby.
Výběr dodavatele, jako je společnost Met3dp, zajišťuje nejen přístup k pokročilé technologii, ale také k zásadním odborným znalostem potřebným pro zvládnutí složitosti výroby leteckých komponentů vhodných k letu. Rozumíme přísným požadavkům na kvalitu a výkon v tomto odvětví a jsme připraveni dodávat pouzdra konektorů na zakázku, která splňují nejvyšší standardy.
Mapování oblohy: Kde se převážně používají zakázková pouzdra leteckých konektorů?
Potřeba robustních, spolehlivých a často přizpůsobených krytů konektorů se týká prakticky všech segmentů leteckého průmyslu. Tyto komponenty jsou všudypřítomné a tvoří neviditelnou páteř elektrických a datových sítí v širokém spektru aplikací. Pochopení toho, kde jsou nejkritičtěji využívány, poukazuje na rozmanité výzvy, které musí překonávat. Manažeři veřejných zakázek, kteří nakupují od velkoobchodní distributoři leteckých komponentů nebo přímo z výrobci konektorů na zakázku potřebují ocenit tato různorodá aplikační prostředí.
Komerční letectví: Zvyšování bezpečnosti a efektivity letových systémů
V dopravních letadlech jsou miliony cestujících a nespočet tun nákladu každý den závislé na bezchybném fungování složitých elektronických systémů. Zakázková pouzdra konektorů jsou nezbytná v mnoha oblastech:
- Prostory pro avioniku: V těchto hustě zaplněných prostorách se nachází mozek letadla - počítače pro řízení letu, navigační systémy (GPS, INS), komunikační rádia (VHF, HF, SATCOM), meteorologické radary a displeje v kokpitu. Pouzdra konektorů musí poskytovat výjimečné stínění EMI/RFI, aby se zabránilo rušení mezi systémy, odolávat vibracím a vejít se do extrémně omezeného prostoru. Běžně se používají vlastní tvary a integrované montážní prvky.
- Nacely a pylony motoru: Prostředí v blízkosti motorů je obzvláště drsné a vyznačuje se vysokými teplotami (což vyžaduje materiály jako Ti-6Al-4V nebo vysokoteplotní slitiny niklu), intenzivními vibracemi a možným působením paliva a hydraulických kapalin. Konektory pro snímače motoru (teploty, tlaku, vibrací), systémy FADEC (Full Authority Digital Engine Control) a akční členy vyžadují mimořádně robustní a tepelně odolná pouzdra.
- Systémy FBW (Fly-by-Wire): Moderní letadla se ve velké míře spoléhají na systémy FBW, kdy jsou vstupy pilota elektronicky přenášeny na řídicí plochy. Integrita těchto datových spojů má zásadní význam. Pouzdra konektorů v síti FBW musí zajišťovat absolutní spolehlivost spojení za všech letových podmínek a vyžadovat vysokou odolnost proti vibracím, nárazům a vlivům prostředí.
- Zábava za letu (IFE) a palubní systémy: Rozsáhlá síť konektorů pro obrazovky IFE, osvětlení kabiny, obslužné jednotky pro cestující a vybavení kuchyně vyžaduje spolehlivé kryty, které často musí splňovat specifické předpisy o hořlavosti a toxicitě kouře (např. FAR 25.853). Pro estetickou integraci nebo jedinečné montážní scénáře může být zapotřebí přizpůsobení.
- Podvozkové systémy: Konektory spojené se snímači polohy podvozku, brzdovými systémy (brake-by-wire) a ovládacími prvky řízení jsou vystaveny silným nárazům, vibracím a působení úlomků z dráhy, vody a odmrazovacích kapalin. Pouzdra zde vyžadují mimořádnou těsnost (krytí IP) a mechanickou odolnost.
Obrana a vojenský letecký průmysl: Zajištění spolehlivosti v kritických aplikacích
Vojenská letadla, vrtulníky a raketové systémy pracují v ještě extrémnějších podmínkách a vyžadují nejvyšší úroveň spolehlivosti a odolnosti. Zakázková pouzdra konektorů jsou důležitá pro:
- Systémy elektronického boje (EW): Pody a vnitřní systémy pro rušení radarů, zpravodajství o signálech (SIGINT) a protiopatření obsahují citlivou vysokofrekvenční elektroniku. Pouzdra konektorů musí poskytovat vynikající účinnost stínění EMI/RFI (>80 dB nebo vyšší) a často vyžadují speciální povrchové úpravy nebo materiály.
- Zabezpečená komunikace: Šifrované datové spoje a zabezpečené systémy hlasové komunikace se spoléhají na konektory chráněné pouzdry odolnými proti neoprávněné manipulaci nebo speciálně opatřenými klíči, aby byla zachována bezpečnost signálu.
- Integrace zbraňových systémů: Konektory spojující pylony letadel s raketami, bombami nebo zaměřovacími moduly vyžadují robustní, rychle odpojitelná pouzdra schopná odolat extrémním přetížení při manévrech a uvolňování zbraní. Spolehlivost je naprosto zásadní.
- Radarové a senzorové systémy: Pokročilé radary AESA (Active Electronically Scanned Array) a různé optické/infračervené senzory používají řadu konektorů. Pouzdra musí odolávat vibracím, zvládat odvod tepla (někdy vyžadující integrované chladicí prvky) a udržovat výkon v širokém rozsahu teplot. Pro konformní instalace jsou často vyžadovány vlastní tvarové faktory.
- Odolná výpočetní technika a Vetronics: Vojenská pozemní vozidla a letadla používají odolné počítače a displeje navržené tak, aby odolaly drsným podmínkám na bojišti. Vnější konektory představují klíčová zranitelná místa, která vyžadují extrémně robustní, ekologicky utěsněná a často na míru navržená pouzdra.
B2B dodavatelé leteckých dílů sloužící obrannému sektoru musí dodržovat přísné vojenské specifikace (MIL-STD, DEF STAN) týkající se materiálů, výkonu a testování všech komponent, včetně krytů konektorů.
Výzkum vesmíru: Extrémní nároky mimo zemskou atmosféru
Vesmírné lodě, satelity a nosné rakety představují vrchol ekologických výzev a posouvají hranice materiálové vědy a inženýrství. Pouzdra konektorů pro vesmírné aplikace se potýkají s jedinečnými překážkami:
- Vakuové prostředí: Materiály musí vykazovat nízké odplyňovací vlastnosti, aby nedošlo ke kontaminaci citlivé optiky nebo elektroniky. Těsnění musí zabránit úniku ve vakuu.
- Extrémní teplotní cykly: Družice na oběžné dráze kolem Země zažívají rychlé a extrémní výkyvy teplot, když přecházejí mezi přímým slunečním světlem a stínem. Pouzdra musí odolávat tepelným cyklům, aniž by došlo k jejich degradaci nebo k namáhání konektorů.
- Zpevnění zářením: Vystavení kosmickému záření a nabitým částicím ve vesmíru vyžaduje materiály a konstrukce, které jsou odolné proti poškození zářením po dlouhou dobu trvání mise (roky nebo desetiletí). Některé materiály mohou při ozáření zkřehnout nebo změnit elektrické vlastnosti.
- Spouštěcí napětí: Pouzdra musí odolávat intenzivním vibracím, akustickému hluku a vysokým přetlakovým silám, které vznikají při startu rakety.
- Minimalizace hmotnosti: Náklady na start jsou přímo úměrné hmotnosti. Každý ušetřený gram je rozhodující. Lehké materiály, jako je Ti-6Al-4V, jsou v kombinaci s optimalizací topologie, kterou umožňuje AM, velmi výhodné pro pouzdra kosmických konektorů. Mezi aplikace patří elektronika družicových sběrnic, přístroje pro užitečné zatížení, komunikační antény a senzory pohonných systémů.
Získávání zdrojů materiály pro letectví a kosmonautiku a komponenty pro vesmír vyžadují dodavatele se specifickými odbornými znalostmi a dodržování standardů kosmických agentur (např. NASA, ESA).
Bezpilotní letadla (UAV): Umožnění kompaktních a lehkých konstrukcí
Rychle se rozvíjející oblast bezpilotních letounů (dronů), od malých průzkumných letounů až po velké platformy pro dlouhou výšku a vytrvalost (HALE), klade důraz na velikost, hmotnost a výkon (SWaP). Klíčovým faktorem jsou vlastní pouzdra konektorů:
- Miniaturizace: UAV mají velmi omezený prostor pro elektroniku. Zakázková pouzdra umožňují integrovat konektory do velmi stísněných prostor, často s nestandardními tvary a montáží.
- Snížení hmotnosti: Použití lehkých materiálů, jako je Ti-6Al-4V, a topologicky optimalizovaných konstrukcí dosažených pomocí AM má zásadní význam pro maximalizaci letové výdrže a nosnosti.
- Integrace užitečného zatížení: Pouzdra pro konektory spojující vyměnitelné užitečné zatížení (kamery, senzory, komunikační relé) musí být robustní, spolehlivá a často vybavená mechanismy pro rychlé nasazení a demontáž.
- Expozice prostředí: V závislosti na profilu mise mohou bezpilotní letouny čelit značným vibracím, různým teplotám a vystavení dešti nebo prachu, což vyžaduje vhodně utěsněné a odolné kryty.
Vyhledávání velkoobchodních distributorů a výrobců leteckých komponentů
Inženýři a odborníci na veřejné zakázky, kteří hledají dodavatele těchto kritických komponent, často hledají “velkoobchodní dodavatelé leteckých konektorů,” “výrobci leteckých krytů na zakázku,” nebo “B2B distributoři leteckých dílů.” Při hledání správného partnera je třeba posoudit nejen jeho nabídku výrobků, ale také jeho výrobní schopnosti, certifikace kvality (AS9100), odborné znalosti materiálů a porozumění specifickému aplikačnímu prostředí. Specialisté na aditivní výrobu, jako je společnost Met3dp, kteří ovládají jak výrobu vysoce kvalitního prášku, tak pokročilé tiskové procesy, nabízejí vertikálně integrované řešení, které je stále atraktivnější pro výrobu zakázkových, vysoce výkonných krytů leteckých konektorů přizpůsobených těmto různorodým a náročným aplikacím.
Aditivní výhoda: Proč 3D tisk kovů přináší revoluci ve výrobě krytů konektorů pro letectví a kosmonautiku?
Po desetiletí se výroba krytů leteckých konektorů opírala především o tradiční výrobní postupy, jako je CNC obrábění ze sochorů (pro kovy) nebo vstřikování (pro velkoobjemové polymery). Tyto metody jsou sice efektivní, ale mají svá omezení, zejména pokud jde o rostoucí požadavky na přizpůsobení, složitost a rychlé vývojové cykly v moderním leteckém průmyslu. Aditivní výroba kovů (AM) nabízí řadu přesvědčivých výhod, které zásadně mění způsob navrhování a výroby těchto kritických součástí. Letečtí inženýři a manažeři veřejných zakázek se stále více obracejí poskytovatelé služeb v oblasti AM kovů využít těchto výhod.
Uvolněná svoboda designu: Složité geometrie a integrované funkce
Pravděpodobně nejvýznamnější výhodou technologie AM pro zpracování kovů, zejména procesů PBF (Powder Bed Fusion), jako jsou SLM a SEBM, je osvobození od tradičních omezení týkajících se designu pro vyrobitelnost (DfM).
- Složité vnější tvary: AM umožňuje vytvářet vysoce organické a složité vnější geometrie skříní, které jsou přizpůsobeny tak, aby se dokonale vešly do omezeného prostoru nebo zlepšily aerodynamické profily, a to bez složitého nastavení nebo omezení dráhy nástroje při CNC obrábění.
- Složité vnitřní prvky: Vnitřní kanály pro konformní chlazení (pro odvádění tepla z výkonných konektorů), integrované stínicí přepážky proti EMI/RFI nebo složité cesty pro optická vlákna mohou být navrženy přímo v konstrukci pouzdra. Obrábění takových vnitřních prvků je často nemožné nebo vyžaduje montáž více kusů.
- Mřížové struktury: Vnitřní mřížkové nebo gyroidní struktury mohou být začleněny tak, aby se výrazně snížila hmotnost při zachování strukturální integrity, což je schopnost jedinečná pro AM.
- Integrace funkcí: Montážní příruby, zarovnávací klíče, prvky pro vedení kabelů a dokonce i pružinové prvky mohou být potenciálně integrovány přímo do jediného tištěného dílu, což snižuje potřebu následné montáže.
Tato konstrukční svoboda umožňuje konstruktérům vytvářet pouzdra konektorů, která jsou skutečně optimalizovaná pro funkci a prostředí aplikace, a neomezují je omezení, která vyplývají z možnosti jejich obrábění nebo lisování.
Strategie odlehčování: Optimalizace topologie a efektivita materiálu
Hmotnost je v leteckém designu věčným problémem. Technologie Metal AM poskytuje výkonné nástroje pro vytváření lehkých, ale pevných pouzder konektorů:
- Optimalizace topologie: Softwarové nástroje mohou analyzovat rozložení napětí v pouzdře při očekávaném zatížení a automaticky odstraňovat materiál z nekritických oblastí, což vede k vysoce optimalizovaným, často organicky vypadajícím tvarům, které využívají minimální množství potřebného materiálu. AM je jedinečně schopna tyto složité, optimalizované geometrie vyrábět přímo.
- Výběr materiálu: AM umožňuje efektivnější využití materiálů s vysokým poměrem pevnosti k hmotnosti, jako je Ti-6Al-4V. Zatímco titan může obrábět, je to obtížné a vzniká při tom značný a drahý odpad. Při AM se používá pouze nezbytný prášek, takže titan je ekonomicky výhodnější volbou pro složitá pouzdra s kritickou hmotností.
- Duté struktury a mříže: Jak již bylo zmíněno, možnost vytvářet duté profily nebo zabudovat vnitřní mřížkové struktury výrazně snižuje hmotnost dílů ve srovnání s pevnými obráběnými součástmi při zachování požadované tuhosti a pevnosti.
Tyto strategie mohou vést ke snížení hmotnosti krytů konektorů o 30-50 % nebo i více v porovnání s tradičně vyráběnými ekvivalenty, což se přímo projeví ve zlepšení palivové účinnosti, zvýšení nosnosti nebo výkonu.
Konsolidace částí: Snížení složitosti sestavy a potenciálních míst poruch
Tradiční konektorové sestavy často zahrnují více komponent: hlavní těleso, zadní kryty, odlehčovače tahu, montážní držáky, těsnění proti elektromagnetickému rušení atd. Každý díl vyžaduje samostatnou výrobu, správu zásob a montáž. Každé rozhraní mezi díly představuje potenciální místo poruchy (např. uvolnění při vibracích, porušené utěsnění vlivem prostředí).
Metal AM umožňuje konsolidace částí, kde je více funkcí integrováno do jediné monolitické tištěné součásti. Například:
- Pouzdro a jeho montážní držák lze vytisknout jako jeden kus.
- Odlehčovací prvky mohou být navrženy přímo v zadní části krytu.
- Vnitřní stínicí stěny mohou v některých provedeních eliminovat potřebu samostatných těsnění nebo vložek proti elektromagnetickému rušení.
Konsolidace dílů přináší významné výhody:
- Zkrácení doby montáže a snížení nákladů na práci: Menší počet dílů znamená jednodušší a rychlejší montáž.
- Zvýšená spolehlivost: Eliminace spojů a rozhraní snižuje počet potenciálních míst poruchy.
- Snížení počtu dílů a zásob: Zjednodušuje logistiku a řízení dodavatelského řetězce.
- Zvýšená strukturální integrita: Monolitické díly mohou být ze své podstaty pevnější a tužší.
Zrychlené časové plány: Rychlá výroba prototypů a zkrácení dodacích lhůt pro výrobu
Letecký průmysl vyžaduje agilitu. Technologie AM pro kovy výrazně zkracuje dobu od návrhu po funkční díl:
- Rychlé prototypování: Iterace návrhu vlastních krytů lze vytisknout a fyzicky otestovat během několika dnů, zatímco u tradičních prototypů vyžadujících nástroje nebo složité obráběcí nastavení to jsou týdny nebo měsíce. To umožňuje rychlejší ověřování a optimalizaci návrhu.
- Výroba bez nástrojů: AM eliminuje nutnost nákladné a časově náročné výroby forem nebo zápustek (pro odlévání/lisování) nebo složité konstrukce přípravků (pro CNC). Výroba může začít téměř okamžitě po schválení konečného návrhu.
- Zkrácené dodací lhůty: U nízkých až středních objemů výroby, které jsou typické pro mnoho zakázkových leteckých komponent, je celková doba přípravy AM (včetně tisku a následného zpracování) často výrazně kratší než u tradičních metod, zejména u složitých geometrií. To má zásadní význam pro dodržení napjatých programových harmonogramů.
- Výroba na vyžádání: Digitální soubory dílů umožňují výrobu blíže k místu potřeby nebo rychlou výrobu náhradních dílů bez závislosti na starším nástrojovém vybavení.
Všestrannost materiálů a zvýšení výkonu pomocí technologie AM pro kovy
Procesy AM mohou pracovat se širokou škálou slitin vhodných pro letecký průmysl, včetně nerezových ocelí (např. 316L), titanových slitin (např. Ti-6Al-4V), hliníkových slitin, niklových superslitin (např. Inconel 625 nebo 718) a slitin mědi. To umožňuje konstruktérům vybrat optimální materiál pro specifické požadavky na výkon pouzdra konektoru (např. teplotní odolnost, odolnost proti korozi, poměr pevnosti a hmotnosti).
Kromě toho může proces vrstvení někdy vést k jemnozrnným mikrostrukturám s vynikajícími mechanickými vlastnostmi. Společnosti, jako je Met3dp, se výrazně zaměřují na optimalizaci propojení mezi vysoce kvalitním kovové prášky a jejich tiskových procesů (jako je SEBM), aby výsledné díly splňovaly nebo překonávaly vlastnosti tepaných nebo litých materiálů a poskytovaly konzistentní, vysoce výkonné komponenty vhodné pro náročné letecké aplikace.
Srovnání AM (PBF) a tradiční výroby (CNC, odlévání)
Abychom plně docenili výhodu aditivních metod, je užitečné porovnat PBF metal AM s tradičními metodami výroby krytů konektorů na zakázku:
Vlastnosti | Kovový AM (PBF: SLM/SEBM) | CNC obrábění | Investiční odlévání |
---|---|---|---|
Složitost návrhu | Velmi vysoká (vnitřní kanály, mřížky) | Střední až vysoká (omezená přístupem k nástrojům) | Mírná (omezená složitostí formy) |
Náklady na přizpůsobení | Nízká (bez nářadí) | Vysoká (programování, nastavení, příslušenství) | Velmi vysoká (náklady na nástroje/lisy) |
Doba realizace (Proto) | Půst (dny) | Středně těžká (dny až týdny) | Pomalý (týdny až měsíce) |
Dodací lhůta (nízký objem) | Mírný | Mírná až vysoká | Pomalé (vyžaduje nástroje) |
Materiálový odpad | Nízká (recyklace prášku) | Vysoká (subtraktivní proces) | Středně těžké (Gates, běžci) |
Snížení hmotnosti | Výborně (Topology opt., lattices) | Omezené (především výběr materiálu) | Mírný (tvar blízký síti) |
Konsolidace částí | Vynikající | Omezený | Omezený |
Povrchová úprava (ve stavu po dokončení) | Středně těžké až těžké | Dobrý až výborný | Dobrý |
Dosažitelná tolerance | Dobrý (často je nutné dodatečné obrábění) | Vynikající | Dobrý |
Ideální objem | Prototypy, nízká až střední úroveň | Prototypy, nízké až vysoké | Střední až vysoká |
Export do archů
Tato tabulka zdůrazňuje, že zatímco CNC nabízí vynikající toleranci a povrchovou úpravu přímo a odlévání je ekonomické při velkých objemech, kovové AM vyniká svobodou designu, přizpůsobením, rychlostí pro složité prototypy a potenciálem snížení hmotnosti, díky čemuž se jedinečně hodí pro náročné úkoly moderní zakázkové výroby krytů konektorů pro letecký průmysl.
Úloha pokročilých technologií 3D tisku kovů
Efektivita technologie AM pro kovy do značné míry závisí na vyspělosti technologie tisku a kvalitě použitých materiálů. Met3dp využívá pokročilé procesy, jako např Selektivní tavení elektronovým paprskem (SEBM). SEBM používá místo laseru elektronový paprsek, který obvykle pracuje ve vakuu a při vyšších teplotách v konstrukční komoře. To přináší specifické výhody pro některé aplikace v letectví a kosmonautice:
- Snížené zbytkové napětí: Vyšší teploty zpracování přirozeně snižují napětí v dílech během výroby, což často snižuje nebo eliminuje potřebu rozsáhlých tepelných úprav po výrobě, a šetří tak čas a náklady.
- Zpracování materiálů náchylných k tvorbě trhlin: SEBM je obzvláště zdatný při zpracování materiálů, jako je Ti-6Al-4V a další vysokoteplotní slitiny, které mohou být náchylné k praskání v laserových systémech.
- Vysoká produktivita: Elektronové paprsky mohou často skenovat rychleji než lasery, což může vést k vyšší rychlosti vytváření určitých geometrií.
Spojení pokročilých tiskových systémů, jako je SEBM, s pečlivě vyrobenými, vysoce sférickými kovovými prášky získanými procesy, jako je plynová atomizace nebo PREP, jak to dělá společnost Met3dp, zajišťuje nejvyšší kvalitu a konzistenci pro náročné letecké komponenty, jako jsou pouzdra konektorů.
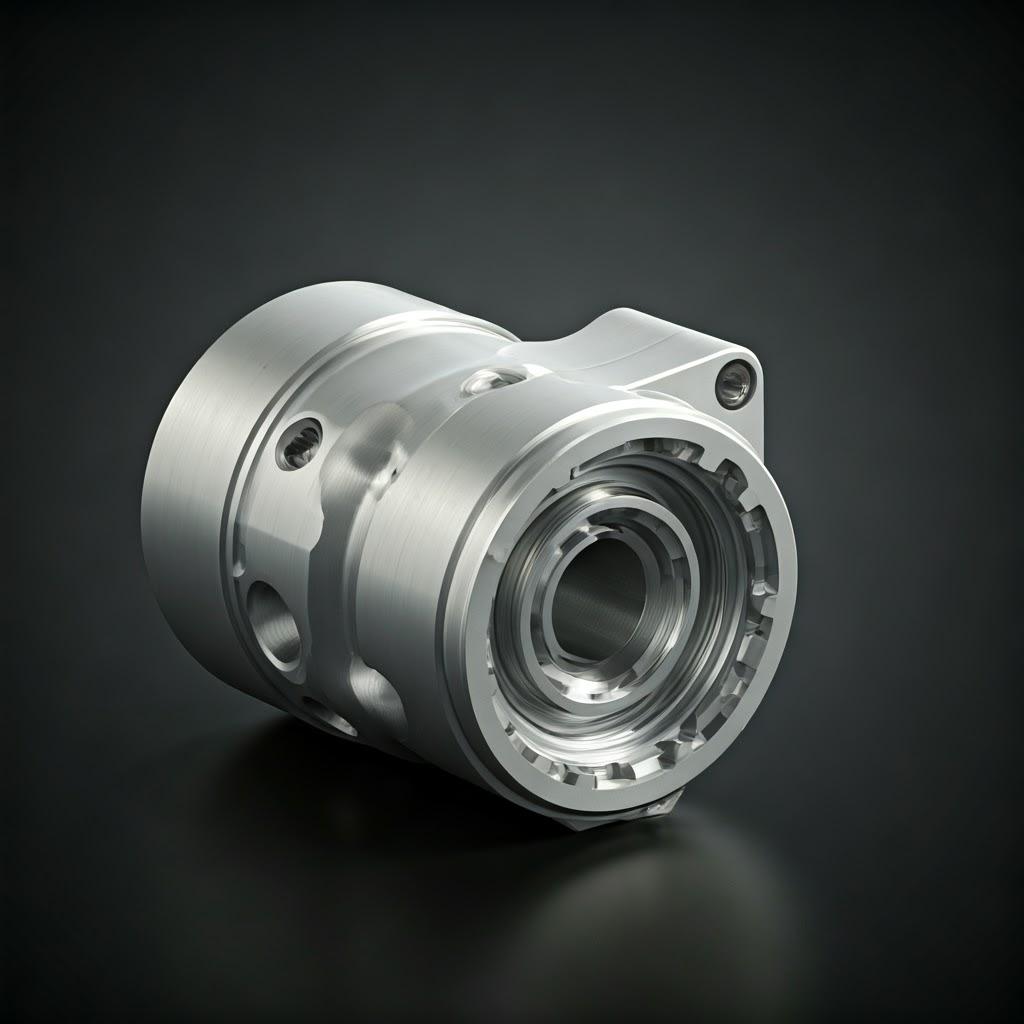
Materiální záležitosti: Výběr optimálního kovového prášku (316L & Ti-6Al-4V) pro letecké konektory
Výběr správného materiálu je základem pro výkon a spolehlivost každé letecké součásti a pouzdra konektorů nejsou výjimkou. Materiál určuje schopnost pouzdra odolávat náročným podmínkám, chránit citlivá rozhraní konektorů, splňovat hmotnostní cíle a požadavky na elektromagnetickou kompatibilitu (EMC). Ačkoli AM s kovem otevírá dveře k použití různých slitin, dva materiály vynikají jako obzvláště vhodné a běžně používané pro 3D tištěná pouzdra konektorů pro letectví a kosmonautiku: Nerezová ocel 316L a Slitina titanu Ti-6Al-4V. Porozumění jejich vlastnostem a významu kvality prášku ze spolehlivého dodavatelé kovových prášků je zásadní pro úspěch.
Porozumění požadavkům: Klíčové vlastnosti materiálů pro pouzdra konektorů
Než se budeme věnovat konkrétním materiálům, nastíníme si klíčové vlastnosti, které inženýři hodnotí při výběru materiálu pro pouzdro leteckého konektoru:
- Odolnost proti korozi: Je nezbytný pro odolnost proti degradaci vlivem vlhkosti, solné mlhy, paliv, hydraulických kapalin a čisticích prostředků, které jsou v leteckém a kosmickém provozu běžné.
- Pevnost a odolnost: Schopnost odolávat mechanickému zatížení, nárazům, vibracím a otřesům bez deformace nebo lomu. Kritickými parametry jsou mez kluzu, mez pevnosti v tahu a únavová pevnost.
- Teplotní stabilita: Zachování mechanických vlastností a rozměrové stability v širokém rozsahu provozních teplot (-55 °C až +175 °C nebo vyšším).
- Hmotnost (hustota): Vysoký poměr pevnosti a hmotnosti je velmi žádoucí pro minimalizaci celkové hmotnosti letadla nebo kosmické lodi.
- Účinnost stínění EMI/RFI: Vrozená schopnost materiálu (často zvýšená geometrií a povlaky) blokovat elektromagnetické rušení. Dobrá elektrická vodivost obecně koreluje s lepším stíněním.
- Vyrobitelnost (tisknutelnost): Jak snadno a spolehlivě lze materiál zpracovávat pomocí zvolené technologie AM kovů (např. SLM, SEBM), aby bylo dosaženo hustých dílů bez vad.
- Náklady: Náklady na suroviny a náklady spojené s tiskem a následným zpracováním.
- Kompatibilita s prostředím: V závislosti na konkrétním použití mohou být důležité faktory jako odplyňování (pro prostor), hořlavost a toxicita.
nerezová ocel 316L: Robustní a spolehlivý pracovní kůň
316L je austenitická slitina nerezové oceli obsahující chrom, nikl a molybden. Pro svou vynikající kombinaci vlastností a zpracovatelnosti pomocí AM se široce používá v mnoha průmyslových odvětvích, včetně leteckého průmyslu.
- Klíčové vlastnosti oceli 316L:
- Vynikající odolnost proti korozi: Přídavek molybdenu zajišťuje vyšší odolnost proti celkové korozi, důlkové korozi a korozi ve štěrbinách, zejména v prostředí s obsahem chloridů (např. v pobřežních oblastech nebo při působení odmrazovacích solí). Odolává také působení mnoha průmyslových chemikálií a leteckých kapalin.
- Dobrá pevnost a tažnost: materiál 316L nabízí dobrou rovnováhu mezi pevností v tahu (obvykle >500 MPa po tisku a odlehčení) a tažností (prodloužení >40 %), díky čemuž je houževnatý a odolný proti lomu.
- Dobrý výkon při vysokých teplotách: Ačkoli 316L nepatří mezi vysokoteplotní superslitiny, zachovává si užitečnou pevnost až do středních teplot, které se vyskytují v mnoha aplikacích v letectví a kosmonautice (výrazně nad 200 °C).
- Nemagnetické: V žíhaném stavu je ocel 316L obvykle nemagnetická, což může být důležité pro aplikace citlivé na magnetická pole.
- Svařitelnost/spojitelnost: V případě potřeby montáže nebo úpravy je lze snadno svařit (ačkoli konsolidace dílů pomocí AM se snaží toto minimalizovat).
- Vynikající tisknutelnost: 316L je jednou z nejsnadněji zpracovatelných a zavedených kovových slitin, které lze spolehlivě zpracovávat technikou laserové fúze v práškovém loži (L-PBF/SLM) a dosáhnout tak vysoké hustoty (>99,5 %).
- Efektivita nákladů: V porovnání s titanovými slitinami nebo niklovými superslitinami je prášek 316L výrazně levnější, což z něj činí atraktivní volbu, pokud není vyžadován absolutně nejvyšší poměr pevnosti a hmotnosti nebo extrémní teplotní odolnost.
- Letecké aplikace pro pouzdra 316L:
- Obecné konektory pro avioniku a kabinové systémy, kde je zapotřebí robustní ochrana proti vlivům prostředí a dobrá pevnost, ale hmotnost není absolutně primárním faktorem.
- Konektory pozemního podpůrného zařízení (GSE).
- Aplikace vyžadující vynikající odolnost proti korozi v náročných atmosférických podmínkách.
- Prototypy, u nichž je v počátečních fázích návrhu důležitá nákladová efektivita.
- Konektory v méně teplotně kritických zónách letadla.
Manažeři veřejných zakázek hledá velkoobchodní dodavatelé nerezové oceli pro prášky AM by měl ověřit, zda kvalita prášku splňuje požadavky na čistotu a konzistenci v leteckém průmyslu.
Slitina titanu Ti-6Al-4V (třída 5): Vysoce výkonný lehký šampion
Ti-6Al-4V (často označovaná zkratkou Ti64) je nejpoužívanější titanová slitina, která představuje více než 50 % veškeré celosvětové tonáže titanu. Je to alfa-beta slitina proslulá výjimečnou kombinací vysoké pevnosti, nízké hustoty a vynikající odolnosti proti korozi, což z ní činí materiál vhodný pro náročné aplikace v letectví a kosmonautice.
- Klíčové vlastnosti Ti-6Al-4V:
- Velmi vysoký poměr pevnosti k hmotnosti: To je charakteristická vlastnost Ti64’. Nabízí pevnost srovnatelnou s mnoha ocelemi, ale má zhruba o 40-45 % nižší hustotu. Díky tomu je ideální pro komponenty pro letectví a kosmonautiku s kritickou hmotností. Typická pevnost v tahu po tisku a tepelném zpracování může přesáhnout 1000 MPa.
- Vynikající odolnost proti korozi: Ti64 vytváří stabilní ochrannou vrstvu oxidu, která zajišťuje vynikající odolnost proti korozi ve většině přírodních prostředí, včetně mořské vody a mnoha průmyslových chemikálií a leteckých kapalin.
- Schopnost pracovat při vysokých teplotách: Zachovává si dobrou pevnost při zvýšených teplotách a je vhodný pro použití až do teploty 350-400 °C, takže je použitelný i v horkých zónách v blízkosti motorů nebo ve vysokorychlostních letadlech.
- Nízká tepelná roztažnost: V porovnání s ocelí a hliníkovými slitinami má titan nižší koeficient tepelné roztažnosti, což snižuje tepelné namáhání v sestavách, u nichž dochází ke kolísání teploty.
- Biokompatibilita: Zatímco pro pouzdra konektorů je méně vhodný, díky své vynikající biokompatibilitě je vhodný pro lékařské implantáty (což dokazuje jeho inertnost).
- Dobrá tisknutelnost (zejména v systému SEBM): I když lze Ti64 zpracovávat pomocí L-PBF, je poněkud reaktivní a těží z vakuového prostředí a vyšších teplot sestavování technologie SEBM (jako je ta, kterou používá společnost Met3dp), která pomáhá zvládat zbytková napětí a zajišťuje optimální vlastnosti materiálu. Je možné dosáhnout vysoké hustoty (>99,7 %).
- Letecké aplikace pro pouzdra Ti-6Al-4V:
- Aplikace s kritickou hmotností: všude tam, kde je nejdůležitější minimalizovat hmotnost (satelity, bezpilotní letouny, výkonná letadla).
- Aplikace vyžadující vysokou pevnost a odolnost v náročných mechanických prostředích (např. podvozky, systémy řízení letu).
- Skříně umístěné v oblastech s vysokými teplotami (motorové gondoly, pylony, systémy kontroly prostředí).
- Pro vesmírné aplikace, kde je rozhodující nízká plynatost a poměr pevnosti a hmotnosti.
- Komponenty vyžadující výjimečnou odolnost proti korozi v kombinaci s vysokou pevností.
Vyhledání spolehlivých distributory titanových slitin specializace na vysoce kvalitní prášky certifikované pro procesy AM v leteckém průmyslu je při specifikaci Ti-6Al-4V zásadní.
Srovnání 316L vs. Ti-6Al-4V pro pouzdra konektorů (formát tabulky)
Vlastnictví | Nerezová ocel 316L | Slitina titanu Ti-6Al-4V (třída 5) | Úvahy o pouzdrech konektorů |
---|---|---|---|
Hustota | ~7,9-8,0 g/cm³ | ~4,43 g/cm³ | Výrazná úspora hmotnosti s Ti-6Al-4V (přibližně o 45 % lehčí). |
Typická pevnost v tahu (AM) | ~500-600 MPa | ~950-1100 MPa (tepelně zpracované) | Ti-6Al-4V nabízí mnohem vyšší pevnost. |
Poměr pevnosti k hmotnosti | Mírný | Vynikající | Klíčová výhoda pro Ti-6Al-4V v leteckém průmyslu. |
Odolnost proti korozi | Výborný (všeobecně, důlkové vrypy) | Vynikající (zejména v oxidačním prostředí) | Obě jsou vynikající; Ti-6Al-4V může mít výhodu v některých specifických médiích. |
Maximální provozní teplota | Mírné (~300 °C limit pro nepřetržité použití) | Vyšší (~350-400 °C) | Ti-6Al-4V se upřednostňuje pro aplikace při vyšších teplotách. |
Tepelná vodivost | Nižší (~16 W/m-K) | Velmi nízká (~7 W/m-K) | Může mít vliv na odvod tepla z konektorů; může vyžadovat konstrukční prvky. |
Elektrická vodivost | Nižší (ve srovnání s Al, Cu) | Velmi nízká | Ovlivňuje účinnost stínění EMI (geometrie/povlaky často kompenzují). |
Možnost tisku (AM) | Vynikající (zejména L-PBF) | Dobrá (zejména SEBM); reaktivnější | Oba jsou dobře zavedené materiály AM. |
Náklady na prášek | Dolní | Výrazně vyšší | Hlavní faktor v celkových nákladech na díl. |
Následné zpracování | Standardní (uvolnění stresu, dokončovací práce) | Často vyžaduje specifické tepelné zpracování | Zpracování Ti-6Al-4V vyžaduje větší péči. |
Export do archů
Závěr: Vyberte si 316L kdy je hlavním faktorem cena, hmotnost není tak kritická a provozní teploty jsou mírné, ale stále je vyžadována dobrá odolnost proti korozi a trvanlivost. Vyberte si Ti-6Al-4V pokud jsou hlavními požadavky maximální úspora hmotnosti, vysoká pevnost a/nebo vyšší teplotní odolnost a vyšší cena je odůvodněna zvýšením výkonu.
Význam vysoce kvalitních kovových prášků od důvěryhodných dodavatelů
Výsledné vlastnosti 3D tištěného kovového pouzdra konektoru jsou neoddělitelně spjaty s kvalitou použitého kovového prášku. Pouhé zadání “316L” nebo “Ti-6Al-4V” nestačí. U náročných aplikací v leteckém průmyslu je nutné spolupracovat se společností dodavatel kovového prášku AM který zaručuje konzistentní a vysoce kvalitní materiál. Mezi klíčové vlastnosti prášku ovlivňující kvalitu dílů patří:
- Sféricita: Vysoce kulovité částice prášku rovnoměrně proudí a hustě se nabalují v práškovém loži, což vede k rovnoměrnějšímu tavení a vyšší hustotě finálního dílu (méně dutin).
- Distribuce velikosti částic (PSD): Řízený PSD zajišťuje dobrou tekutost a rozlišení, což má vliv na kvalitu povrchu a definici prvků. Letecké normy často specifikují přijatelné rozsahy PSD.
- Tekutost: Dobrá tekutost, měřená podle Hallova průtoku, zajišťuje rovnoměrné nanášení prášku po celé konstrukční desce vrstvu po vrstvě a zabraňuje vzniku defektů.
- Chemická čistota: Znečišťující látky (např. kyslík, dusík, uhlík v titanu; vměstky v oceli) mohou výrazně zhoršit mechanické vlastnosti (zejména únavovou životnost a tažnost). Pro minimalizaci nečistot je nutná přísná kontrola procesu výroby prášku.
- Absence satelitů: Malé, nepravidelné částice připojené k větším kulovitým částicím (tzv. satelity”) mohou zhoršovat tekutost a hustotu balení.
- Konzistence mezi jednotlivými šaržemi: Spolehliví dodavatelé provádějí přísnou kontrolu kvality, aby zajistili, že vlastnosti prášku zůstanou konzistentní v jednotlivých šaržích, což zaručuje opakovatelný výkon dílů.
Horší kvalita prášku může vést k pórovitosti, špatným mechanickým vlastnostem, rozměrovým nepřesnostem a nekonzistentním výsledkům - to vše je pro letově kritické součásti nepřijatelné.
Závazek společnosti Met3dp’k výrobě prémiových prášků (plynová atomizace, PREP)
Společnost Met3dp si uvědomuje zásadní souvislost mezi kvalitou prášku a výkonem dílů, a proto investovala značné prostředky do nejmodernějších technologií výroby prášků. Náš závazek zaručuje, že námi dodávané prášky 316L, Ti-6Al-4V a další pokročilé slitiny splňují přísné požadavky leteckého průmyslu.
- Pokročilé technologie atomizace: Používáme špičkové Atomizace plynu (GA) a Proces plazmové rotující elektrody (PREP) techniky.
- Atomizace plynu: Používá vysokotlaké proudy inertního plynu k rozbití proudu roztaveného kovu na jemné kapičky, které ztuhnou v kulovitý prášek. Naše patentované konstrukce trysek a proudění plynu optimalizují tento proces pro dosažení vysoké sféricity a kontrolované velikosti částic.
- PŘÍPRAVA: Vysokou rychlostí otáčí spotřební tyč elektrody a zároveň taví její špičku plazmovým hořákem. Odstředivá síla vyvrhuje roztavené kapičky, které tuhnou v inertní atmosféře, čímž vznikají výjimečně čisté a sférické prášky s minimem satelitů, ideální pro nejnáročnější aplikace, jako je letectví a lékařství.
- Přísná kontrola kvality: Každá šarže prášku Met3dp prochází rozsáhlým testováním chemického složení, distribuce velikosti částic, morfologie (sféricity), tekutosti a hustoty, které zajišťuje, že splňuje nebo překračuje průmyslové normy.
- Optimalizováno pro procesy AM: Naše prášky jsou speciálně vyvinuty a charakterizovány pro optimální výkon v systémech Powder Bed Fusion, včetně našich vlastních tiskáren SEBM, což zajišťuje kompatibilitu a předvídatelné výsledky.
Řízením procesu výroby prášku pomocí pokročilých technik a přísné kontroly kvality poskytuje společnost Met3dp výrobcům v leteckém a kosmickém průmyslu B2B kupující s jistotou, že základní materiál pro jejich 3D tištěná pouzdra konektorů je nejvyšší možné kvality, což umožňuje výrobu hustých, spolehlivých a vysoce výkonných komponent. Prozkoumejte více informací o našem komplexním 3D tisk z kovu řešení.
Design pro aditivní výrobu (DfAM): Optimalizace geometrie pouzdra konektoru pro úspěšný 3D tisk z kovu
Úspěšné využití možností aditivní výroby kovů pro komponenty, jako jsou pouzdra leteckých konektorů, vyžaduje více než jen odeslání existujícího souboru CAD do tiskárny. Vyžaduje to zásadní posun v konstrukčním myšlení, odklon od omezení tradičních subtraktivních nebo formativních procesů směrem k přijetí možností a respektování nuancí výroby po vrstvách. Tento přístup je známý jako Design pro aditivní výrobu (DfAM). Zavedení zásad DfAM od samého počátku je zásadní pro maximalizaci přínosů AM - dosažení odlehčení, konsolidace dílů, optimálního výkonu a nákladové efektivity. Spolupráce se zkušenými Poskytovatelé služeb DfAM nebo dodavatelé AM kovů jako je Met3dp, která má hluboké odborné znalosti v oblasti DfAM, může tento proces výrazně zefektivnit a plně využít potenciál této technologie.
Aditivní myšlení: Klíčové principy DfAM pro bydlení
DfAM není jen soubor pravidel, ale metodika, která integruje možnosti výrobního procesu do fáze návrhu. Pro kovová pouzdra leteckých konektorů vyráběná technologií PBF (Powder Bed Fusion) patří mezi klíčové zásady DfAM:
- Přijímání složitosti (tam, kde je to prospěšné): Na rozdíl od obrábění, kde složitost zvyšuje náklady a čas, zvládá AM složité geometrie relativně snadno. DfAM podporuje inženýry, aby toho využili při navrhování prvků, jako jsou vnitřní kanály, konformní tvary a integrované funkce, které byly dříve nepraktické.
- Navrhování orientace: Způsob orientace dílu na konstrukční desce významně ovlivňuje dobu tisku, požadavky na podpůrnou konstrukci, povrchovou úpravu na různých plochách a dokonce i mechanické vlastnosti (kvůli anizotropnímu chování některých procesů/materiálů AM). DfAM zahrnuje zvážení optimální orientace již v počáteční fázi procesu návrhu.
- Minimalizace podpůrných struktur: U PBF jsou často nutné podpůrné konstrukce pro ukotvení dílu ke stavební desce a podepření převislých prvků. Spotřebovávají však další materiál, prodlužují dobu tisku a vyžadují odstranění při následném zpracování, což zvyšuje náklady na práci a může ovlivnit kvalitu povrchu. Hlavním cílem DfAM je navrhovat díly, které minimalizují potřebu podpěr, často s využitím samonosných úhelníků.
- Zvažte odstranění prášku: U pouzder s vnitřními dutinami nebo kanálky vyžaduje DfAM návrh únikových otvorů nebo cest, které umožňují odstranění nerozpuštěného prášku po tisku. Zachycený prášek zvyšuje hmotnost a může představovat riziko, pokud se později uvolní.
- Optimalizace pro následné zpracování: DfAM předpokládá navazující procesy. Navrhování prvků tak, aby byly snadno přístupné pro odstranění podpěr, obrábění kritických rozhraní nebo povrchovou úpravu, může výrazně snížit čas a náklady na následné zpracování.
- Využití konsolidace částí: DfAM aktivně hledá možnosti, jak spojit více součástí sestavy (např. pouzdro, držák, zadní kryt) do jediného integrovaného dílu AM, čímž se snižuje složitost sestavy a zvyšuje spolehlivost.
- Porozumění materiálu & amp; Omezení procesu: DfAM zohledňuje specifické možnosti a omezení zvoleného procesu AM (např. SLM, SEBM) a materiálu (např. 316L, Ti-6Al-4V), jako je minimální velikost prvku, dosažitelné tolerance a tepelné chování.
Přijetí myšlenky DfAM zajišťuje, že finální návrh je nejen funkční, ale také efektivně vyrobitelný pomocí 3D tisku z kovu, čímž se maximalizují výhody této technologie pro konstrukce leteckých součástí.
Úvahy o tloušťce stěny a minimální velikosti prvků
Procesy AM pro kovy mají omezení týkající se minimální velikosti prvků a stěn, které mohou spolehlivě vyrobit. Navrhování pod těmito hranicemi může vést k neúplnému vytvoření, špatnému rozlišení nebo strukturálním slabinám.
- Minimální tloušťka stěny: To závisí na konkrétním stroji AM (velikost paprsku, tloušťka vrstvy), tištěném materiálu a orientaci stěny.
- U procesů PBF, jako je SLM a SEBM, se obecné vodítko pro robustní stěny často pohybuje v rozmezí 0.4 mm až 1,0 mm. Tenčí stěny by mohly být možné, ale vyžadují pečlivou validaci a mohou být náchylnější k deformaci nebo poškození při manipulaci a následném zpracování.
- Svislé stěny se obecně tisknou spolehlivěji při minimální tloušťce než stěny vodorovné nebo stěny s malým úhlem (které se v podstatě stávají převisy).
- Minimální velikost prvku: Jedná se o drobné detaily, jako jsou kolíčky, šéfy nebo vyražený text.
- Pozitivní prvky (výstupky) se obecně tisknou snáze než negativní prvky (otvory, drážky).
- Minimální spolehlivě potisknutelné rozměry prvků jsou často o něco větší než minimální tloušťka stěny, obvykle začínají kolem 0.5 mm až 1,0 mm. Velmi jemné detaily mohou ztratit ostrost v důsledku dynamiky taveniny a velikosti částic prášku.
- Poměr stran: Vysoké a tenké stěny mohou být náchylné k deformaci nebo nestabilitě během stavby. DfAM zvažuje omezení nadměrných poměrů stran, pokud je to možné, nebo přidání zpevňujících prvků (žeber).
Konstruktéři navrhující pouzdra konektorů musí zajistit, aby všechny kritické konstrukční prvky, těsnicí povrchy a funkční prvky splňovaly tato minima. Pokusy o replikaci návrhů určených pro mikroobrábění bez zohlednění omezení AM pravděpodobně povedou k selhání tisku nebo nefunkčním dílům.
Strategie podpůrné struktury: Minimalizace odpadu a následného zpracování
Podpěrné konstrukce jsou při tisku kovů PBF kritickou, ale často nežádoucí nutností. Plní několik funkcí:
- Ukotvení: Zajistěte díl na konstrukční desce, aby se během sestavování nedeformoval nebo neposouval.
- Podpěrné převisy: Zajistěte podklad pro prvky skloněné pod určitým úhlem vzhledem k základní desce (obvykle 45 stupňů). Bez podpěr by se tyto převisy deformovaly nebo zřítily do práškového lože.
- Vedení tepla: Pomáhají odvádět teplo z roztavené zóny, čímž snižují tepelné namáhání a zabraňují přehřátí choulostivých prvků.
Podpory však představují výzvu:
- Materiálový odpad: Podpěry jsou obětované a představují zbytečně vynaložený drahý kovový prášek.
- Prodloužení doby sestavení: Tiskové podpory prodlužují celkový čas stroje.
- Obtížné odstranění: Odstranění kovových podpěr může být pracné (ruční lámání, řezání, obrábění) a může vést k poškození povrchu dílu.
- Povrchová úprava Impact: Oblasti, kde se podpěry připevňují k dílu, mají obvykle hrubší povrch, který je třeba zušlechtit.
Účinné strategie DfAM pro podpůrné struktury zahrnují:
- Navrhování samonosných úhlů: Pokud je to možné, navrhněte převisy a prvky tak, aby byly nad kritickým úhlem samonosnosti (často ~45 stupňů, ale záleží na stroji/materiálu). Běžnou technikou je použití zkosení místo ostrých vodorovných převisů.
- Optimalizace orientace dílů: Zvolte takovou orientaci konstrukce, která minimalizuje celkovou plochu vyžadující podporu. Často se jedná o kompromis s dalšími faktory, jako jsou požadavky na povrchovou úpravu nebo doba sestavení.
- Použití optimalizovaných typů podpory: Moderní software AM umožňuje různé struktury podpěr (např. kvádrové, liniové, kuželové, stromové, mřížové podpěry). Klíčový je výběr typu, který poskytuje dostatečnou podporu s minimální spotřebou materiálu a snadnějším odstraněním. Například mřížové podpěry mohou být pevné, ale zároveň spotřebovávají méně materiálu a snadněji se odstraňují než pevné bloky.
- Navrhování pro přístupnost: Ujistěte se, že jsou podpěrné konstrukce umístěny tak, aby byly snadno přístupné pro nástroje na odstraňování. Neumisťujte podpěry do hlubokých vnitřních dutin, pokud to není nezbytně nutné a přístupné.
- Minimalizace kontaktních míst: Podpěry navrhněte tak, aby se k dílu připojovaly pokud možno v minimálních kontaktních bodech nebo na nekritických plochách, čímž se sníží dopady při odstraňování.
Vnitřní kanály pro chlazení nebo stínění
Jednou ze silných schopností AM je schopnost vytvářet složité vnitřní kanály uvnitř dílu - což je při použití tradičních metod velmi obtížné nebo nemožné. V případě krytů konektorů pro letectví a kosmonautiku lze tuto možnost využít pro:
- Konformní chlazení: Vysoce výkonné konektory generují teplo. Vnitřní kanály těsně přiléhající ke zdroji tepla mohou být navrženy tak, aby umožňovaly proudění vzduchu nebo dokonce cirkulaci kapalné chladicí kapaliny, což zlepšuje tepelný management a zabraňuje přehřívání.
- Integrované stínění: Vnitřní stěny nebo přihrádky mohou být v pouzdře navrženy tak, aby zajišťovaly stínění EMI/RFI mezi různými sekcemi konektorů nebo svazky kabelů ve stejném pouzdře, což zlepšuje integritu signálu.
- Směrování vodičů: Složité vnitřní cesty mohou potenciálně vést vodiče nebo optická vlákna v samotné konstrukci pouzdra.
Navrhování účinných interních kanálů však vyžaduje pečlivé DfAM:
- Odstranění prášku: To je největší výzva. Kanály musí mít dostatečný průměr (obvykle >1-2 mm, v závislosti na délce a složitosti) a přístupné otvory (únikové otvory), aby bylo možné po sestavení zcela odstranit nerozpuštěný prášek. Zachycený prášek je nepřijatelný. U složitých sítí může být zapotřebí více přístupových bodů.
- Samonosný design: Vnitřní kanály mají často “střechy”, které slouží jako vodorovné převisy. Navrhování průřezů kanálů se samonosnými tvary (např. kosočtverec, slza) může eliminovat potřebu vnitřních podpěr, jejichž odstranění je velmi obtížné nebo nemožné.
- Povrchová úprava: Vnitřní povrchová úprava kanálů AM bude poměrně drsná (stav po dokončení stavby). Pokud je požadován hladký vnitřní povrch (např. pro průtok tekutin), může to vyžadovat sekundární kroky zpracování, jako je abrazivní průtokové obrábění nebo chemické leštění, což zvyšuje složitost a náklady.
Návrh orientace a umístění stavební desky
Jak již bylo zmíněno, orientace pouzdra konektoru na konstrukční desce je kritickým rozhodnutím DfAM s mnoha důsledky:
- Podpůrné struktury: Orientace dílu tak, aby se minimalizovaly strmé převisy, snižuje potřebu podpěr.
- Povrchová úprava: Povrchy směřující vzhůru nebo svisle mají obecně lepší povrchovou úpravu než povrchy směřující dolů (které jsou ovlivněny kontaktními body podpěr) nebo povrchy s malým úhlem (které vykazují schodovitý efekt). Kritické povrchy by měly být v ideálním případě orientovány pro optimální povrchovou úpravu nebo umístěny tak, aby bylo možné je snadno dodatečně opracovat.
- Doba výstavby: Vyšší postavy obvykle potřebují více času. Orientace dílu tak, aby se minimalizovala jeho výška (rozměr Z), může někdy zkrátit dobu tisku, i když je to často v rozporu s minimalizací podpěr.
- Mechanické vlastnosti: Díky konstrukci po vrstvách mohou díly AM vykazovat anizotropní mechanické vlastnosti (pevnost se může lišit v závislosti na směru zatížení vzhledem k vrstvám konstrukce). Při volbě orientace je třeba brát v úvahu kritické směry namáhání, ačkoli u optimalizovaných parametrů a materiálů, jako je Ti-6Al-4V zpracovávaný metodou SEBM, je tento efekt často méně výrazný.
- Tepelný management: Orientace může ovlivnit nahromadění a rozptýlení tepla během sestavování, což může mít vliv na zbytkové napětí a deformace.
- Balení stavební desky: Při tisku více pouzder ovlivňuje jejich orientace a umístění to, kolik dílů se vejde na jednu konstrukční desku, což má vliv na celkovou propustnost a náklady na jeden díl.
DfAM zahrnuje použití simulačních nástrojů a odborných znalostí procesů k nalezení optimální orientace, která vyvažuje tyto konkurenční faktory pro konkrétní požadavky na konstrukci a použití pouzdra.
Využití simulačních nástrojů pro validaci návrhu
Moderní inženýrské pracovní postupy stále častěji zahrnují simulační nástroje již v rané fázi procesu návrhu, což je pro DfAM obzvláště cenné:
- Optimalizace topologie: Jak již bylo uvedeno, tyto nástroje automaticky generují lehké geometrie optimalizované pro zatížení, které jsou ideální pro výrobu AM.
- Simulace procesu: Specializovaný software pro simulaci AM dokáže předvídat potenciální problémy před tisk, například:
- Tepelné zkreslení a deformace: Simulace nárůstu tepla a ochlazování během procesu po vrstvách pomáhá identifikovat místa náchylná k deformaci. To umožňuje konstruktérům upravit orientaci, přidat nebo posílit podpěry nebo upravit konstrukci tak, aby se tato rizika zmírnila.
- Zbytkové napětí: Předvídání vzniku vnitřních pnutí pomáhá optimalizovat strategie tepelného zpracování.
- Efektivita podpůrné struktury: Simulace, zda plánované podpěry budou dostatečné k tomu, aby zabránily selhání konstrukce.
- Simulace výkonu: K ověření strukturální integrity, tepelného výkonu (např. účinnosti chladicích kanálů) a vibrační odezvy konstrukce pouzdra AM při provozním zatížení lze použít standardní nástroje pro analýzu konečných prvků (FEA).
Proaktivní využití simulace umožňuje konstruktérům digitálně opakovat a zdokonalovat návrh skříně, což výrazně snižuje riziko nákladných chyb při výrobě a zajišťuje, že konečný díl splňuje požadavky na výkon. Společnosti, jako je Met3dp, často využívají takové nástroje jako součást svých inženýrské podpůrné služby pomáhat klientům optimalizovat návrhy pro úspěšnou aditivní výrobu.
Přesnost zdokonalena: Dosažení těsných tolerancí, vynikající povrchové úpravy a rozměrové přesnosti u 3D tištěných pouzder
Ačkoli technologie AM pro kovy vyniká při vytváření složitých geometrií, dosažení vysoké úrovně přesnosti, která je často vyžadována u leteckých součástí, zejména u styčných ploch a těsnicích ploch na pouzdrech konektorů, vyžaduje pečlivou kontrolu procesu a často zahrnuje sekundární dokončovací operace. Pochopení dosažitelných limitů tolerance 3D tisku kovů, povaha povrchová úprava v kovu AMa faktory, které ovlivňují celkový rozměrová přesnost je pro inženýry a manažery veřejných zakázek, kteří vyhodnocují dodavatelé přesné výroby.
Pochopení dosažitelných tolerancí při fúzi v kovovém práškovém loži
Tolerance označuje přípustný rozsah odchylek rozměru součásti. V případě kovového AM jsou dosažitelné tolerance ovlivněny mnoha faktory, včetně stroje, materiálu, velikosti a geometrie dílu a následného zpracování.
- Obecné tolerance (ve stavu po dokončení): Pro typické procesy PBF (SLM, SEBM) se často uvádějí obecné dosažitelné tolerance pro dobře řízené procesy v rozsahu:
- ± 0,1 mm až ± 0,2 mm pro menší rozměry (např. do 50-100 mm).
- ± 0,1 % až ± 0,2 % jmenovitého rozměru u větších prvků.
- Specifičnost stroje: Vyšší stroje s lepší kalibrací, tepelnou kontrolou a jemnějšími paprsky mohou často dosáhnout větších tolerancí v tomto rozsahu. K dosažení vysoké přesnosti přispívá zaměření společnosti Met3dp’ na špičkové vybavení.
- Závislost na geometrii: Složité geometrie, tenké stěny a velké rovné plochy mohou být náchylnější k drobným odchylkám nebo deformaci ve srovnání s jednoduššími, robustnějšími díly.
- Potřeba následného obrábění: U prvků vyžadujících velmi přísné tolerance, jako jsou styčné plochy konektorů, drážky pro O-kroužky, otvory se závitem nebo přesné montážní plochy, je důležité, aby se tolerance AM podle stavu konstrukce jsou často nedostatečné. Tyto kritické prvky se obvykle navrhují s použitím dodatečného materiálu (přídavek na obrábění”) a dokončují se pomocí CNC obrábění po fázi tisku a uvolnění stresu. Tento hybridní přístup využívá geometrickou volnost AM a přesnost CNC tam, kde je to potřeba. Tolerance dosažitelné při následném obrábění jsou obvykle ± 0,01 mm až ± 0,05 mm nebo ještě těsnější, splňující standardní požadavky pro letecký průmysl.
Je nezbytné jasně definovat kritické rozměry a tolerance na technických výkresech a uvést, které povrchy je třeba dodatečně opracovat, aby bylo dosaženo konečných specifikací.
Faktory ovlivňující přesnost rozměrů
Dosažení konzistentní rozměrové přesnosti při AM obrábění kovů závisí na pečlivé kontrole mnoha faktorů:
- Kalibrace tiskárny: Pravidelná kalibrace systému skeneru, zaostření paprsku a vyrovnání stavební plošiny je nezbytná.
- Parametry procesu: Výkon laserového/elektronového paprsku, rychlost skenování, tloušťka vrstvy, vzdálenost mezi šrafami a strategie skenování ovlivňují velikost a stabilitu taveniny, což má vliv na rozměrovou přesnost. Klíčové jsou optimalizované sady parametrů vyvinuté zkušenými poskytovateli, jako je Met3dp.
- Vlastnosti materiálu: Rozdíly v charakteristikách prášku (PSD, tekutost, morfologie) mohou ovlivnit hustotu balení a chování při tavení. Použití konzistentního, vysoce kvalitního prášku je zásadní. Svou roli hraje také koeficient tepelné roztažnosti materiálu.
- Tepelné účinky: Nerovnoměrné zahřívání a ochlazování během procesu sestavování vede k tepelnému namáhání, které může způsobit deformace a zkreslení a ovlivnit konečné rozměry. Vliv na to mají faktory, jako je orientace dílu, strategie podpory a tepelné řízení stroje (např. vyhřívaná konstrukční deska/komora, jako je tomu u SEBM).
- Velikost a geometrie dílu: U větších dílů dochází k většímu kumulativnímu tepelnému namáhání. Složité geometrie mohou vytvářet lokální tepelné pasti nebo koncentrace napětí.
- Orientace na stavbu: Jak bylo uvedeno v části DfAM, orientace ovlivňuje tepelné chování a potřeby podpory, což má vliv na přesnost.
- Následné zpracování: Tepelné opracování s uvolněním napětí je důležité pro rozměrovou stabilitu, ale může způsobit mírné, předvídatelné rozměrové změny, se kterými je třeba počítat. Nesprávné odstranění podpěr může rovněž deformovat díly.
Dosažení vysoké přesnosti vyžaduje komplexní přístup, který kombinuje robustní strojní technologii, kvalitní materiály, optimalizované procesní parametry, správné zásady DfAM a kontrolované následné zpracování.
Charakteristika povrchové úpravy: Postavený vs. dodatečně zpracovaný
Povrchová úprava, obvykle kvantifikovaná průměrnou drsností (Ra), je další kritickou vlastností krytů konektorů, která ovlivňuje těsnění, estetiku a někdy i elektrický kontakt nebo tření.
- Povrchová úprava podle stavu: Povrchová úprava dílů přímo po tisku PBF je ze své podstaty drsnější než u obráběných povrchů. Typické hodnoty Ra se pohybují od 5 µm až 20 µm, v závislosti na:
- Orientace: Povrchy směřující k horní straně jsou obecně nejhladší. Na svislých stěnách jsou patrné vrstevnice. Povrchy směřující dolů, které jsou podepřeny konstrukcemi, jsou obvykle nejhrubší kvůli kontaktním místům podpěr. U šikmých povrchů se projevuje “schodovitost” vlastní procesu vrstvení, přičemž nižší úhly vedou k drsnějším povrchům.
- Parametry procesu: Tloušťka vrstvy (tenčí vrstvy = hladší), příkon paprsku a strategie skenování ovlivňují stabilitu taveniny a výslednou strukturu povrchu.
- Velikost částic prášku: Jemnější prášky mohou přispět k hladšímu povrchu, ale mohou mít kompromisy v tekutosti.
- Typ stroje: Různé optické a řídicí systémy stroje mohou přinést mírně odlišné vlastnosti povrchu.
- Následně zpracovaná povrchová úprava: U mnoha aplikací krytů konektorů je povrchová úprava v podobě, v jaké byla vyrobena, přijatelná pro nekritické vnější povrchy. Těsnicí povrchy, styčné plochy nebo esteticky důležité oblasti však často vyžadují vylepšení následnou úpravou. Mezi běžné metody patří:
- Tryskání kuličkami / pískování: Poskytuje rovnoměrný matný povrch, odstraňuje některé volné částice a mírně snižuje Ra (např. na 5-10 µm Ra).
- Obrábění / vibrační úprava: K vyhlazení povrchů a zaoblení hran se používají brusná média v bubnovém válci nebo vibrační míse. Lze dosáhnout hladších povrchů (např. 1-5 µm Ra), ale obecně se omezuje na vnější povrchy a méně přesnou kontrolu prvků.
- CNC obrábění: Používá se pro kritické povrchy vyžadující hladký povrch (Ra < 1 µm často dosažitelné) a přísné tolerance.
- Leštění: Ručním nebo automatickým leštěním lze dosáhnout velmi hladkého, zrcadlového povrchu (Ra << 1 µm) pro specifické požadavky.
- Elektrolytické leštění: Elektrochemický proces, který odstraňuje mikroskopickou vrstvu materiálu, vyhlazuje povrch a zlepšuje odolnost proti korozi, zvláště účinný u nerezových ocelí, jako je 316L.
Techniky pro zlepšení drsnosti povrchu (Ra)
Kromě sekundárního zpracování mohou některé strategie během tisku pomoci optimalizovat výsledný vzhled:
- Orientace: Pokud je to možné, orientujte kritické plochy přednostně svisle nebo vzhůru.
- Optimalizace parametrů: Jemným doladěním parametrů, jako je skenování obrysů (průjezdy laseru kolem okraje každé vrstvy), lze zlepšit povrchovou úpravu bočnic.
- Tenčí vrstvy: Použití menších tlouštěk vrstev vede k jemnějšímu odstupňování na šikmých plochách, což zlepšuje vnímanou hladkost, ale prodlužuje dobu vytváření.
- Kompenzace posunu paprsku: Software může mírně upravit dráhu paprsku, aby kompenzoval vlastnosti taveniny a zlepšil rozměrovou přesnost, což nepřímo souvisí s efektivní hladkostí povrchu prvků.
Dosažení povrchové úpravy srovnatelné s obráběním však obvykle vyžaduje speciální kroky následného zpracování. Prozkoumejte Met3dp’s tiskových metod a schopnosti pro dosažení požadovaných vlastností dílů.
Metrologie a kontrola kvality leteckých komponentů
Ověření, zda finální 3D vytištěné a následně zpracované pouzdro konektoru splňuje stanovené rozměrové požadavky a požadavky na povrchovou úpravu, je kriticky důležité, zejména pro letecký průmysl. Mezi běžné metrologické techniky patří:
- Souřadnicové měřicí stroje (CMM): Vysoce přesné dotykové sondy měří diskrétní body pro ověření kritických rozměrů a geometrických tolerancí (GD&T). Nezbytné pro konečnou přejímku obrobených prvků.
- 3D laserové skenování / skenování strukturovaným světlem: Bezkontaktní metody, které zachycují miliony bodů a vytvářejí 3D model tištěného dílu. Ten lze porovnat s původním modelem CAD a zobrazit odchylky na celém povrchu, což je užitečné pro složité geometrie a ověření celkového tvaru.
- Testery drsnosti povrchu (profilometry): Přístroje na bázi stylusu měří profil povrchu a kvantifikují Ra a další parametry drsnosti.
- Vizuální kontrola: Zvětšená vizuální kontrola povrchových vad, neúplných prvků nebo zbytků podpůrného materiálu.
- Počítačová tomografie (CT): Průmyslová rentgenová technika používaná pro nedestruktivní kontrolu vnitřních prvků, kontrolu zachyceného prášku, vnitřních dutin nebo defektů v objemu dílu. Stále důležitější pro kvalifikaci kritických AM dílů pro letecký a kosmický průmysl.
Důkladný systém řízení kvality (QMS), ideálně certifikovaný podle leteckých norem, jako je AS9100, zajišťuje, že tyto kontroly jsou prováděny důsledně a jsou důkladně zdokumentovány. Výrobci letecké techniky požadovat tuto úroveň zajištění kvality od svých dodavatelé komponentů.
Úloha tiskových systémů s vysokým rozlišením
Základem pro dosažení přesných dílů jsou přesné schopnosti samotného systému AM pro obrábění kovů. Systémy s vysokým rozlišením, které se vyznačují:
- Jemný paprsek Velikost skvrny: Umožňuje vytvářet menší rysy a ostřejší detaily.
- Přesné ovládání skeneru: Přesné a rychlé polohování laserového nebo elektronového paprsku zajišťuje geometrickou věrnost.
- Pokročilé softwarové algoritmy: Sofistikované řízení parametrů a strategií skenování optimalizuje tavení a minimalizuje odchylky.
- Stabilní tepelný management: Stálé teploty ve stavební komoře snižují deformace a zlepšují předvídatelnost.
Investice společnosti Met3dp’do špičkového tiskového zařízení poskytuje pevný základ pro výrobu pouzder konektorů s vysokou přesností a jemným rozlišením prvků, což minimalizuje množství nutných kompenzačních dodatečných úprav.
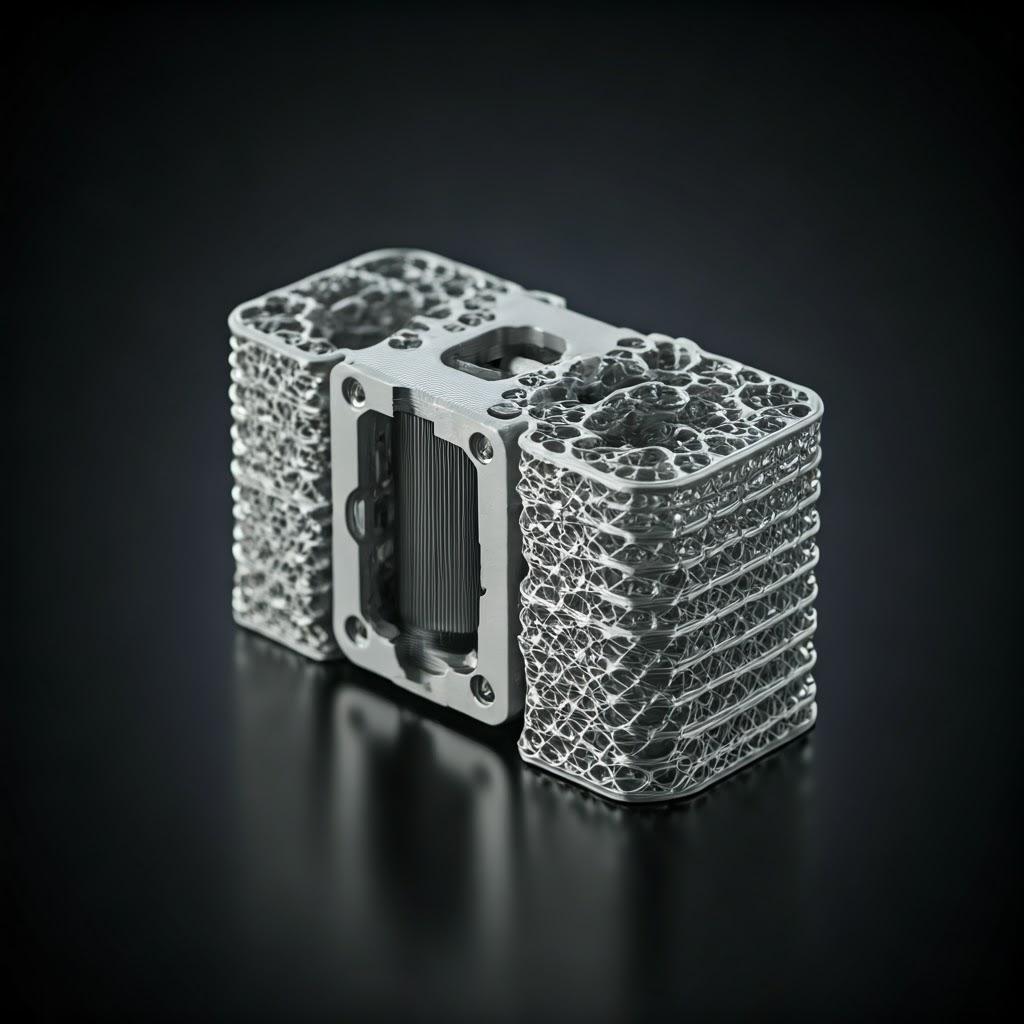
Za hranice stavby: Základní kroky následného zpracování pro pouzdra konektorů pro letectví a kosmonautiku
Běžnou mylnou představou o 3D tisku z kovu je, že díly vyjíždějí ze stroje připravené k použití. Ve skutečnosti, zejména u náročných aplikací, jako jsou pouzdra konektorů pro letecký průmysl, je proces tisku pouze prvním krokem. Řada klíčových následné zpracování 3D tisku kovů téměř vždy je nutné provést kroky k přeměně hotového dílu na funkční a spolehlivou součást, která splňuje přísné specifikace pro letecký průmysl. Tyto kroky se týkají zbytkového napětí, odstraňování prášku, podpůrných struktur, povrchové úpravy, rozměrových tolerancí a vlastností materiálu. Pochopení těchto požadavků je zásadní při hodnocení poskytovatelé služeb v oblasti AM kovů a výpočet celkových nákladů na díl a doby realizace.
Úleva od stresu a tepelné ošetření: Zajištění stability a výkonnosti materiálu
Rychlé cykly zahřívání a ochlazování, které jsou vlastní procesům PBF, vytvářejí v hotovém dílu značná vnitřní napětí. Tato napětí mohou vést k deformaci (zejména po vyjmutí z konstrukční desky), snížení mechanických vlastností a případnému praskání v průběhu času.
- Úleva od stresu: To je obvykle první krok po dokončení stavby a odstranění přebytečného prášku. Díl, často ještě připevněný na konstrukční desce, se zahřeje v peci na určitou teplotu pod bodem přeměny, po určitou dobu se udržuje a poté se pomalu ochlazuje. Tím se krystalová mřížka materiálu uvolní, čímž se výrazně sníží vnitřní pnutí.
- Nezbytnost: Naprosto zásadní pro díly vyrobené pomocí L-PBF (SLM/DMLS) kvůli vyšším tepelným gradientům. U SEBM, která pracuje při zvýšených teplotách, lze někdy snížit nebo vyloučit potřebu rozsáhlého odlehčení napětí, což je výhoda technologie Met3dp’s SEBM.
- Typické cykly: U oceli 316L může uvolnění napětí zahrnovat zahřátí na 600-800 °C. U Ti-6Al-4V se často provádí při teplotách kolem 650-800 °C ve vakuu nebo v peci s inertní atmosférou, aby se zabránilo oxidaci.
- Další tepelné zpracování (žíhání v roztoku, stárnutí): Kromě uvolnění napětí může být k dosažení požadované konečné mikrostruktury a mechanických vlastností (např. optimalizace pevnosti, tažnosti, tvrdosti, únavové životnosti) nutné další tepelné zpracování.
- Ti-6Al-4V: Často se podrobuje úpravě roztokem s následným stárnutím (STA) nebo cyklům žíhání, aby se dosáhlo specifických kombinací pevnosti a tažnosti požadovaných leteckými normami (např. specifikace AMS pro Ti-6Al-4V). Tyto procesy obvykle zahrnují vyšší teploty (např. 900-950 °C při úpravě roztokem) ve vakuové peci.
- 316L: V případě potřeby lze žíhat (např. ~1050 °C), aby se maximalizovala tažnost a odolnost proti korozi.
Správné tepelné zpracování leteckých slitin je kriticky důležitá a musí být prováděna pomocí kalibrovaných pecí a přesně kontrolovaných cyklů, po nichž následují příslušné zkoušky (např. tvrdost, tahové zkoušky) pro ověření výsledků.
Odstranění podpůrné konstrukce: Techniky a úvahy
Po uvolnění napětí je třeba díl oddělit od nosných konstrukcí. To může být jeden z nejpracnějších a potenciálně nejškodlivějších kroků následného zpracování, pokud není během DfAM pečlivě naplánován.
- Vyjmutí dílu ze stavební desky: Obvykle se používá elektroerozivní obrábění, řezání na pásové pile nebo někdy ruční lámání menších dílů/podpěr. Drátové elektroerozivní obrábění zajišťuje čistý řez s minimálním působením síly na díl.
- Techniky odstranění podpory:
- Ruční lámání/řezání: Podpěry jsou často konstruovány s oslabenými rozhraními nebo perforačními body, které umožňují jejich ruční odlomení pomocí kleští nebo ručního nářadí. Tento postup je rychlý, ale zanechává hrubé stopy.
- Obrábění (frézování/broušení): K odstranění nosných konstrukcí, zejména objemných nebo na kritických plochách, lze použít CNC obrábění nebo ruční broušení. To nabízí větší kontrolu nad konečným povrchem, ale zvyšuje časovou náročnost a náklady.
- Drátové elektroerozivní obrábění / ponorné elektroerozivní obrábění: Lze ji použít k přesnému odřezání podpěr v těžko přístupných místech, ale je pomalejší.
- Úvahy:
- Přístupnost: Podpěry ukryté v hlubokých kapsách nebo vnitřních kanálech se odstraňují velmi obtížně. DfAM je klíčem k tomu, abyste se tomu vyhnuli.
- Materiál: Titanové slitiny, jako je Ti-6Al-4V, se hůře řežou nebo obrábějí než nerezová ocel, takže odstranění podpory je pracnější.
- Riziko poškození: Použití nadměrné síly při ručním odstraňování může narušit nebo zlomit jemné prvky.
Účinné a pečlivé odstranění podpěr je zásadní pro dosažení konečné geometrie dílu bez narušení jeho integrity.
Operace povrchové úpravy: Obrábění, leštění, tryskání
Jak již bylo zmíněno, povrchová úprava dílů AM po sestavení často vyžaduje zdokonalení. Pouzdra konektorů mohou vyžadovat různé dokončovací operace v závislosti na funkčních a estetických požadavcích:
- Tryskání abrazivem (kuličkové/ pískové): Běžně se používá k dosažení rovnoměrného matného povrchu, čištění povrchů a odstraňování polosintrovaných částic. Různá média (skleněné kuličky, oxid hlinitý) vytvářejí různé povrchové úpravy.
- Třískové/vibrační dokončování: Efektivní pro vyhlazování vnějších povrchů a odstraňování otřepů na hranách dílů v sériích, čímž se výrazně snižují hodnoty Ra.
- CNC obrábění: Je nezbytný pro dosažení těsných tolerancí a hladkých povrchů na kritických rozhraních (styčné plochy, těsnicí drážky, montážní otvory).
- Broušení/leštění: Pro dosažení velmi hladkých povrchů (s nízkým Ra) v případě potřeby, často ručně nebo s robotickou asistencí u složitých tvarů.
- Elektrolytické leštění: Zvláště účinný pro 316L, který elektrochemickým odstraňováním materiálu zajišťuje velmi hladký, čistý a korozivzdorný povrch.
Konkrétní kombinace dokončovacích kroků závisí výhradně na požadavcích definovaných ve specifikaci a výkresu dílu.
Povlaky a nátěry pro zvýšení výkonu
Základní materiály, jako je 316L a Ti-6Al-4V, mají dobré vnitřní vlastnosti, ale někdy se na 3D tištěná pouzdra konektorů nanášejí povlaky nebo pokovení, které dále zlepšují specifické vlastnosti:
- Stínění EMI/RFI: Zatímco samotné kovové pouzdro poskytuje stínění, pokovení vysoce vodivými kovy, jako je např měď, nikl nebo stříbro může výrazně zlepšit účinnost stínění, zejména při vyšších frekvencích. Běžnou volbou je elektrolytické niklování.
- Ochrana proti korozi: Ačkoli jsou oceli 316L a Ti64 vysoce odolné proti korozi, mohou být použity specializované povlaky (např. povlaky chemické přeměny, jako jsou chromátové nebo fosfátové, barvy, PVD povlaky) pro extrémní prostředí nebo pro specifickou kompatibilitu s kapalinami.
- Odolnost proti opotřebení: Tvrdé povlaky (např. TiN, CrN nanášené pomocí PVD) lze použít, pokud dojde k výraznému abrazivnímu opotřebení pouzdra, což je však u standardních konektorů méně obvyklé.
- Elektrická vodivost: Pokovování může zvýšit vodivost povrchu pro účely uzemnění nebo kontaktu.
- Kosmetické úpravy: Eloxování (pro titan), lakování nebo práškové lakování může poskytnout specifické barvy nebo estetické povrchové úpravy.
Aplikace nátěrů vyžaduje správnou přípravu povrchu dílu AM, aby byla zajištěna dobrá přilnavost. Spolupráce s kvalifikovanými povrchová úprava leteckých součástí doporučujeme dodavatele se zkušenostmi s díly AM.
Protokoly o čištění a závěrečné kontrole
V celém řetězci následného zpracování je nutné provádět čisticí kroky, aby se odstranily zbytky chladicích kapalin z obrábění, tryskacích prostředků, lešticích směsí nebo pokovovacích chemikálií.
- Závěrečné čištění: Před konečnou kontrolou a zabalením se provede závěrečné důkladné čištění (často ultrazvukové čištění ve specifických rozpouštědlech nebo čisticích prostředcích), aby se zajistilo, že pouzdro konektoru neobsahuje žádné nečistoty.
- Závěrečná kontrola: Zahrnuje ověření rozměrů (CMM, skenování), kontrolu povrchové úpravy, vizuální kontrolu vad a případně NDT (např. CT skenování kritických dílů), aby se zajistilo, že hotové pouzdro splňuje všechny specifikace uvedené ve výkresu a plánu kvality. Certifikace materiálů a sledovatelnost procesní dokumentace jsou klíčovými výstupy pro letecké komponenty.
Spolupráce s kvalifikovanými partnery pro postprocessing
Rozsah požadovaných kroků následného zpracování často vyžaduje specializované vybavení a odborné znalosti, které nemusí mít jediná servisní kancelář AM. Mnoho poskytovatelé služeb kovového 3D tisku jsme navázali vztahy s kvalifikovanými partnery pro služby, jako je tepelné zpracování, přesné obrábění, pokovování a nedestruktivní kontrola. Při výběru dodavatele je důležité znát jeho vlastní schopnosti ve srovnání se sítí subdodavatelů a zajistit, aby celý dodavatelský řetězec splňoval normy kvality pro letecký průmysl (např. certifikace AS9100, akreditace Nadcap pro speciální procesy). Společnost Met3dp, která se zaměřuje na komplexní řešení, pomáhá klientům orientovat se v těchto požadavcích na následné zpracování, aby zajistila kvalitu od začátku do konce.
Zvládání výzev: Překonávání potenciálních překážek při 3D tisku kovových konektorů pro letectví a kosmonautiku
Přestože aditivní výroba kovů nabízí transformační potenciál pro výrobu zakázkových krytů leteckých konektorů, není bez technických problémů. Dosažení požadované kvality, spolehlivosti a konzistence vyžaduje hluboké znalosti fyziky procesu, nauky o materiálech a možných způsobů poruch. S vědomím těchto problémy s 3D tiskem kovů a implementace robustních strategií pro zmírnění dopadů je klíčem k úspěšnému nasazení AM pro kritické letecké komponenty. Spolupráce se zkušenou a technologicky vyspělou spolehlivý dodavatel AM jako je Met3dp, který tyto problémy aktivně řeší, je pro zmírnění rizik klíčový.
Zmírnění deformací a zbytkového napětí
Pravděpodobně nejrozšířenějším problémem v oblasti kovových PBF je zvládání tepelného namáhání vznikajícího při rychlých cyklech ohřevu a chlazení. Tato napětí mohou způsobit:
- Deformace: Deformace dílu během sestavování, která může způsobit, že se díl zvedne z podpěr nebo narazí na nůž práškového navíječe, což může vést k selhání sestavování.
- Zbytkové napětí: Vnitřní pnutí, která zůstávají v dílu po ochlazení, mohou narušit rozměrovou stabilitu, snížit únavovou životnost a potenciálně vést k praskání.
Strategie zmírnění dopadů:
- Optimalizované podpůrné struktury: Robustní podpěry jsou nezbytné k pevnému ukotvení dílu na stavební desce a odolávají deformačním silám. DfAM zde hraje klíčovou roli.
- Orientace na stavbu: Pomoci může orientace dílu tak, aby se minimalizovaly velké rovné plochy rovnoběžné s konstrukční deskou a snížil se celkový gradient tepelné hmoty.
- Optimalizace strategie skenování: Použití specifických vzorů (např. skenování ostrůvků, šachovnicové vzory) rozbíjí dlouhé souvislé stopy taveniny, rovnoměrněji rozvádí teplo a snižuje nárůst napětí. Rozhodující jsou také parametry, jako je výkon a rychlost paprsku.
- Simulace procesu: Předvídání kumulace napětí ve fázi návrhu umožňuje proaktivní úpravy geometrie nebo podpor.
- Tepelné ošetření proti stresu: Nezbytný krok následného zpracování pro uvolnění vnitřních napětí (jak bylo popsáno dříve).
- Zpracování při zvýšené teplotě (SEBM): Technologie, jako je tavení elektronovým svazkem (SEBM), které využívá společnost Met3dp, pracují s výrazně vyššími teplotami v konstrukční komoře. Díky tomu zůstává díl po celou dobu sestavování horký, což funguje jako proces uvolňování napětí in-situ a výsledkem jsou díly s mnohem nižším zbytkovým napětím ve srovnání s typickým L-PBF, což výrazně snižuje riziko deformace.
Zajištění hustoty dílů a zamezení vzniku pórovitosti
Dosažení téměř plné hustoty (obvykle 99,5 % nebo více pro letecký průmysl) je kritické pro mechanickou integritu. Pórovitost (vnitřní dutiny) může působit jako koncentrátor napětí, což výrazně snižuje únavovou životnost a celkovou pevnost.
Příčiny pórovitosti:
- Nedostatek fúze: Při nedostatečném příkonu energie (nízký výkon, vysoká rychlost) nedojde k úplnému roztavení částic prášku, takže mezi vrstvami zůstávají mezery nebo stopy po skenování.
- Keyholing: Nadměrný přísun energie vytváří hluboké, nestabilní taveniny, které se mohou zhroutit, zachytit plyn a vytvořit póry.
- Pórovitost plynu: Plyny rozpuštěné v roztaveném kovu nebo zachycené v dutých částicích prášku mohou při tuhnutí vytvářet póry.
- Špatná kvalita prášku: Prášek nepravidelného tvaru nebo prášek s vnitřními dutinami se balí méně efektivně a může zadržovat plyn.
Strategie zmírnění dopadů:
- Optimalizované parametry procesu: K nalezení optimálního okna pro výkon laseru/paprsku, rychlost skenování, tloušťku vrstvy a vzdálenost mezi šrafami pro každý materiál je zapotřebí rozsáhlý vývoj procesu, aby bylo dosaženo konzistentního, úplného tavení bez vzniku klíčových děr. Společnost Met3dp intenzivně investuje do vývoje robustních parametrů svých materiálů a systémů SEBM.
- Vysoce kvalitní prášek: Zásadní význam má použití vysoce sférického prášku s nízkým obsahem vnitřního plynu a řízeným PSD, jako je prášek vyrobený společností Met3dp pomocí GA a PREP. Dobrá tekutost prášku zajišťuje rovnoměrné nanášení vrstev.
- Kontrola inertní atmosféry: Udržování vysoce čisté atmosféry inertního plynu (argonu nebo dusíku pro L-PBF) nebo vakua (SEBM) minimalizuje kontaminaci a reakce, které by mohly způsobit pórovitost.
- Izostatické lisování za tepla (HIP): Následné zpracování při vysoké teplotě a vysokém tlaku v inertní atmosféře. HIP může účinně uzavřít vnitřní póry (kromě těch, které jsou otevřené k povrchu) a dosáhnout téměř 100% hustoty. Přináší však značné dodatečné náklady a čas a může ovlivnit rozměry, takže je obvykle vyhrazena pro nejkritičtější aplikace, kde se tolerance vnitřních pórů blíží nule. Dobře řízené procesy AM mohou často dosáhnout dostatečné hustoty bez HIP.
Problémy při odstraňování vnitřních podpěr ze složitých geometrií
Jak bylo zdůrazněno v oddílech DfAM a následného zpracování, odstranění podpůrných konstrukcí ze složitých vnitřních kanálů nebo dutin v pouzdru konektoru je velkou výzvou.
Strategie zmírnění dopadů:
- DfAM má zásadní význam: Nejlepším řešením je design pokud možno odstranit potřebu vnitřních podpěr a použít samonosnou geometrii kanálů (např. tvar slzy, kosočtverce).
- Zajištění přístupu: Pokud se nelze vyhnout vnitřním podpěrám, navrhněte vhodné přístupové otvory pro nástroje nebo proplachování.
- Specializované podpůrné struktury: Pomoci může použití snadno rozdrobitelných nebo rozpustných podpůrných materiálů (v přímém tisku kovů méně obvyklé, ale zkoumané) nebo optimalizovaných mřížkových podpěr.
- Pokročilé techniky odstraňování: Ve specifických případech lze uvažovat o abrazivním proudovém obrábění nebo chemickém leptání, které jsou však složité, nákladné a vyžadují pečlivé ověření, aby nedošlo k poškození dílu nebo změně kritických rozměrů. Konstrukce vyžadující rozsáhlé a nepřístupné vnitřní podpěry jsou často považovány za nevhodné pro současnou technologii AM.
Protokoly o kontaminaci materiálu a manipulaci s práškem
Kovové prášky, zejména reaktivní, jako je Ti-6Al-4V, jsou citlivé na kontaminaci kyslíkem, dusíkem, vlhkostí a křížovou kontaminaci z jiných kovových prášků. Kontaminace vážně zhoršuje mechanické vlastnosti.
Strategie zmírnění dopadů:
- Přísná manipulace s práškem: Používání kontrolovaného prostředí (rukavicové boxy, uzavřené kontejnery), proplachování inertním plynem a speciální zařízení (síta, násypky, stavební moduly) pro každý typ materiálu zabraňuje křížové kontaminaci a vystavení atmosféře.
- Řízení životního cyklu prášku: Sledování spotřeby prášku, recyklace (prosévání za účelem odstranění nadměrných částic nebo rozstřiků) a pravidelné testování chemického složení recyklovaného prášku jsou nezbytné pro zachování integrity materiálu. Společnost Met3dp dodržuje přísné protokoly pro manipulaci s práškem a kontrolu kvality.
- Kvalita inertního plynu: Zajištění čistoty argonu nebo dusíku používaného ve stavební komoře (pro L-PBF) je velmi důležité.
Zajištění konzistence napříč výrobními dávkami
Pro letecký průmysl je zásadní dosáhnout stejně vysoké kvality u každého dílu, ať už se jedná o tisk jednoho nebo sta pouzder konektorů. Výzvy v letecké výrobě se často točí kolem opakovatelnosti.
Strategie zmírnění dopadů:
- Robustní systém řízení kvality (QMS): Zavedení certifikovaného systému řízení jakosti (jako je AS9100) poskytuje rámec pro řízení procesů, dokumentaci, sledovatelnost a neustálé zlepšování.
- Kalibrace a údržba strojů: Pravidelná preventivní údržba a kalibrace zajišťují stálý výkon systému AM.
- Monitorování procesů: Nástroje pro monitorování in-situ (např. monitorování taveniny, termální snímkování) mohou poskytovat údaje o stabilitě konstrukce v reálném čase a potenciálně odhalit vady v okamžiku jejich vzniku (ačkoli tato technologie se pro definitivní posouzení kvality stále vyvíjí).
- Konzistentní suroviny: Zásadní je použití prášku od důvěryhodného dodavatele, jako je Met3dp, s certifikovanou konzistencí jednotlivých šarží.
- Standardizované postupy: Zdokumentované a přísně dodržované postupy pro nastavení sestavy, provoz, manipulaci s práškem a následné zpracování minimalizují lidské chyby a variabilitu.
- Statistická kontrola procesu (SPC): Analýza procesních dat a měření dílů v průběhu času pomáhá identifikovat trendy a udržovat stabilitu procesu.
Pochopením těchto potenciálních problémů a navázáním spolupráce se znalým dodavatelem, jako je společnost Met3dp, který využívá pokročilé technologie (SEBM), vysoce kvalitní materiály, přísnou kontrolu procesů a komplexní podporu DfAM, mohou letečtí inženýři a manažeři nákupu s jistotou využít technologii AM pro výrobu spolehlivých a vysoce výkonných krytů konektorů na zakázku.
Výběr dodavatele: Jak vybrat správného poskytovatele služeb 3D tisku kovů pro letecké komponenty?
Rozhodnutí zavést aditivní výrobu kovů pro kritické součásti, jako jsou pouzdra leteckých konektorů, je významné. Využití plného potenciálu této technologie - dosažení letuschopných dílů, které splňují přísné normy výkonu, kvality a spolehlivosti - však závisí především na výběru správného výrobního partnera. Ne všechny poskytovatelé služeb kovového 3D tisku jsou si rovny, zejména pokud se jedná o náročný letecký průmysl. Inženýři a manažeři veřejných zakázek musí provádět důkladnou hloubkovou kontrolu a hodnotit potenciální dodavatele podle přísného souboru kritérií, aby se ujistil, že mají potřebné odborné znalosti, technologie a kontroly kvality. Spolupráce se schopným a certifikovaným dodavatelem má zásadní význam pro zmírnění rizik a zajištění úspěchu projektu.
Posuzování technických schopností: Vybavení, materiály, odborné znalosti
Základem každého schopného dodavatele AM je jeho technická zdatnost. Mezi klíčové oblasti, které je třeba hodnotit, patří:
- Portfolio zařízení:
- Shoda technologií: Používají vhodnou technologii PBF (SLM, DMLS, SEBM), která je nejvhodnější pro materiál vašeho pouzdra (316L, Ti-6Al-4V) a složitost? Například technologie SEBM, kterou nabízí společnost Met3dp, vyniká u Ti-6Al-4V díky nižšímu zbytkovému napětí a schopnosti zpracovávat reaktivní materiály ve vakuu.
- Kvalita stroje & Funkce: Jsou jejich stroje průmyslové kvality, dobře udržované a vybavené potřebnými funkcemi pro monitorování nebo řízení procesu?
- Objem sestavení: Dokáží jejich stroje přizpůsobit velikost vaší konstrukce pouzdra konektoru?
- Rozlišení & Přesnost: Jaká je udávaná přesnost a minimální velikost prvků jejich systémů?
- Odborné znalosti materiálů:
- Kvalifikované materiály: Mají prokazatelné zkušenosti a ověřené procesní parametry speciálně pro leteckou jakost 316L a Ti-6Al-4V? Mohou poskytnout materiálové listy založené na tištěných vlastnostech?
- Širší portfolio: Nabízejí další vhodné slitiny pro letecký průmysl (např. hliníkové slitiny, Inconel), pokud by se vaše potřeby vyvíjely?
- Získávání prášku a kvalita: Kde získávají prášky? Provádějí přísné vstupní kontroly kvality? Dodavatel jako Met3dp, který vyrábí vlastní vysoce kvalitní prášky pomocí pokročilých metod GA a PREP, nabízí významnou výhodu při kontrole této kritické vstupní proměnné.
- Odborné znalosti procesů:
- Vývoj parametrů: Mají odborné znalosti pro optimalizaci parametrů tisku pro specifické geometrie a požadavky na výkon, nebo se spoléhají pouze na standardní nastavení výrobce stroje?
- Metalurgické porozumění: Zahrnuje jejich tým materiálové vědce nebo metalurgy, kteří rozumí nuancím chování slitin během AM a následného tepelného zpracování?
Systémy řízení kvality a certifikace (např. AS9100)
V leteckém průmyslu je kvalita nejen žádoucí, ale i povinná. Závazek dodavatele ke kvalitě se nejlépe projevuje prostřednictvím jeho systému řízení jakosti a příslušných certifikací:
- Certifikace AS9100: Jedná se o mezinárodně uznávaný standard QMS speciálně pro letecký, kosmický a obranný průmysl. Zahrnuje požadavky normy ISO 9001, ale přidává přísné kontroly bezpečnosti, spolehlivosti, letové způsobilosti, sledovatelnosti, řízení konfigurace a řízení rizik. Aditivní výroba s certifikací AS9100 poskytovatelé prokazují závazek dodržovat nejvyšší oborové standardy. To by mělo být považováno za hlavní požadavek při výběru dodavatele letových součástí.
- Certifikace ISO 9001: Základní norma QMS, která označuje dokumentované procesy pro řízení kvality, konzistenci a neustálé zlepšování. Je to dobrý základ, ale pro hlavní dodavatele v leteckém průmyslu často sám o sobě nestačí.
- Akreditace Nadcap: Zatímco AS9100 se vztahuje na celý systém, Nadcap poskytuje specifickou akreditaci pro “speciální procesy”, jako je tepelné zpracování, nedestruktivní testování (NDT), svařování a povlaky. Pokud váš dodavatel provádí tyto kritické kroky ve vlastní režii nebo je zadává externě, ověření jeho nebo jeho partnera’akreditace Nadcap přidává další vrstvu jistoty.
Vyžadujte doklady o těchto certifikacích a pochopte rozsah jejich implementace QMS.
Standardy sledovatelnosti materiálu a řízení procesů
Letecké komponenty vyžadují pečlivou sledovatelnost - schopnost sledovat historii dílu od šarže suroviny přes každý výrobní a kontrolní krok.
- Sledovatelnost šarží prášku: Dodavatel musí prokázat jasné sledování, která konkrétní šarže prášku (s příslušnými chemickými a PSD certifikáty) byla použita pro každou stavební úlohu. To je nezbytné pro vyšetřování, pokud by se později objevily nějaké problémy. Dodavatelé jako Met3dp, kteří kontrolují výrobu prášků, ze své podstaty nabízejí spolehlivou sledovatelnost.
- Protokolování parametrů procesu: Průmyslové systémy AM zaznamenávají kritické procesní parametry během sestavování (např. výkon paprsku, hladinu kyslíku v komoře, teplotu). Dodavatel by měl tyto záznamy uchovávat jako součást dokumentace sestavení.
- Správa konfigurace: Musí být zavedeny přísné kontroly, aby se zajistilo, že se pro výrobu použije správná revize návrhu (soubor CAD, výkres).
- Dokumentace: Komplexní dokumentační balíčky, včetně materiálových certifikátů, protokolů o sestavení, záznamů o následném zpracování (grafy tepelného zpracování), kontrolních zpráv (CMM, NDT) a certifikátů o shodě, jsou standardními dodávkami pro letecké díly.
Ověřte si postupy dodavatele pro udržování této úrovně sledovatelnosti a kontroly.
Hodnocení technické podpory a odbornosti DfAM
Jak již bylo podrobně popsáno dříve, DfAM má zásadní význam pro optimalizaci pouzder konektorů pro aditivní výrobu. Cenný dodavatel funguje jako partner, který nabízí technickou podporu:
- Konzultace DfAM: Mohou jejich inženýři posoudit váš návrh a poskytnout konstruktivní zpětnou vazbu ohledně optimalizace geometrie, minimalizace podpěr, zajištění odstranění prášku a výběru nejlepší orientace?
- Simulační schopnosti: Nabízejí simulaci procesu pro předvídání deformací nebo napětí nebo služby optimalizace topologie, které pomáhají dosáhnout cílů odlehčení?
- Řešení problémů: Mají odborné znalosti pro řešení potenciálních problémů při sestavování, které souvisejí se složitými geometriemi nebo specifickými požadavky na výkon?
Tento přístup založený na spolupráci zajišťuje, že návrh lze vyrábět efektivně a účinně.
Kapacita, dodací lhůty a škálovatelnost pro výrobní svazky
Zvažte své okamžité potřeby pro výrobu prototypů i potenciální budoucí požadavky na výrobu:
- Kapacita stroje: Mají dostatečnou dostupnost strojů, aby splnili vaše požadované dodací lhůty pro prototypy a případné další objednávky? Jaký je jejich typický objem nevyřízených zakázek?
- Škálovatelnost: Pokud váš projekt přejde z prototypu do malosériové nebo středně velkosériové výroby, má dodavatel kapacitu (více strojů, efektivní pracovní postup, robustní následné zpracování), aby mohl výrobu odpovídajícím způsobem rozšířit?
- Transparentnost doby realizace: Poskytují realistické a spolehlivé odhady dodací lhůty na základě aktuální kapacity a složitosti vašeho dílu a požadavků na jeho následné zpracování?
Porozumění hodnotové nabídce: Proč spolupracovat s Met3dp?
Výběr dodavatele není jen o zaškrtávání políček, ale o nalezení partnera, který se zasadí o váš úspěch. Společnost Met3dp nabízí přesvědčivou nabídku hodnoty pro zákazníky z oblasti leteckého průmyslu, kteří hledají pouzdra konektorů na zakázku:
- Integrované řešení: Jako výrobce vysoce kvalitních kovových prášků pro letecký průmysl (316L, Ti-6Al-4V, slitiny na zakázku) využívající pokročilé technologie GA a PREP a poskytovatel pokročilých služeb tisku SEBM nabízí společnost Met3dp bezkonkurenční kontrolu nad celým procesním řetězcem AM, čímž zajišťuje kvalitu materiálu a synergii procesů.
- Technologická výhoda: Naše odborné znalosti v oblasti SEBM poskytují výrazné výhody pro materiály, jako je Ti-6Al-4V, a poskytují díly s nízkým zbytkovým napětím a vynikajícími vlastnostmi materiálu, což často snižuje potřebu následného zpracování.
- Odborné znalosti: Náš tým se skládá z odborníků s desítkami let zkušeností v oblasti AM kovů, materiálových věd a leteckých aplikací, kteří poskytují odbornou podporu při vývoji DfAM a aplikací.
- Zaměření na kvalitu: Pracujeme podle přísných protokolů kontroly kvality, které zajišťují sledovatelnost materiálu a konzistentní kvalitu dílů vhodných pro náročná průmyslová odvětví. (Další informace O nás).
- Spolupráce se zákazníky: Úzce spolupracujeme s klienty, abychom porozuměli jejich jedinečným výzvám a poskytli jim řešení na míru, která plně využívají potenciál aditivní výroby.
Vyhledání spolehlivých dodavatelů a výrobců kovů B2B AM
Kromě přímého vyhledávání zvažte také oborové adresáře, veletrhy (jako Formnext) a doporučení z důvěryhodných zdrojů. Při zapojování potenciálních B2B partneři pro tisk na kov, připravit podrobnou žádost o cenovou nabídku (RFQ) včetně modelů CAD, výkresů s uvedením kritických rozměrů a tolerancí, specifikací materiálů, požadovaných certifikací, množství a požadovaných dodacích lhůt. To umožňuje přesné cenové nabídky a smysluplné porovnání potenciálních dodavatelů.
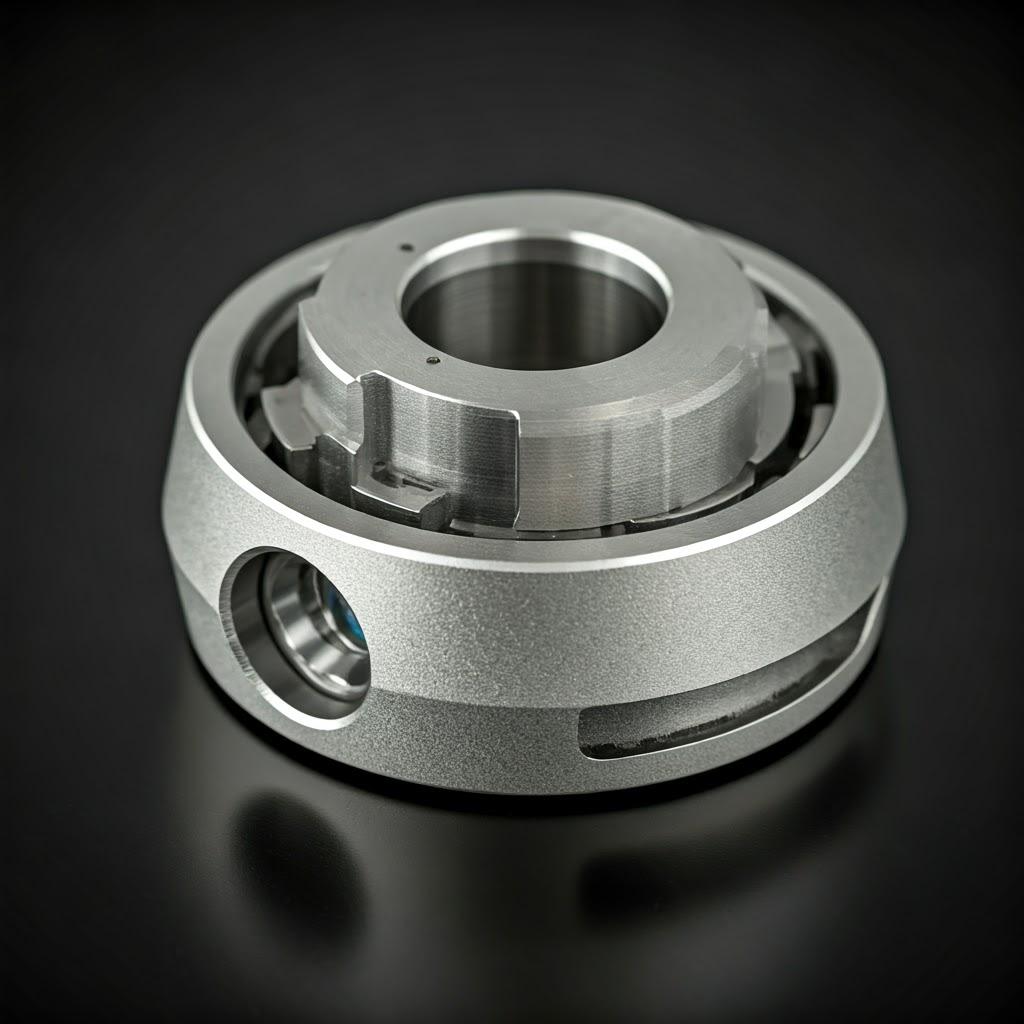
Pochopení investice: Klíčové nákladové faktory a očekávaná doba realizace pro 3D tištěná pouzdra konektorů
Jedním z hlavních faktorů při zavádění jakékoli výrobní technologie je její nákladová efektivita a doba potřebná k získání dílů. Ačkoli AM zpracování kovů nabízí přesvědčivé výhody pro zakázková pouzdra konektorů pro letecký průmysl, je nezbytné pochopit faktory, které ovlivňují náklady na 3D tisk kovů a vliv dodací lhůty pro letecké komponenty. Tyto znalosti pomáhají inženýrům zdůvodnit výběr technologie a manažerům nákupu umožňují efektivně sestavit rozpočet a plánovat. Získání podrobných nabídek od potenciálních distributoři 3D tisku kovů nebo servisních kanceláří je zásadní, ale pochopení základní struktury nákladů poskytuje cenný kontext.
Materiálové náklady: Cena a spotřeba prášku
Materiál je významnou složkou nákladů, zejména u drahých leteckých slitin:
- Cena prášku: Mezi běžnými slitinami je značný rozdíl v ceně za kilogram.
- Nerezová ocel 316L: Relativně úsporné.
- Slitina titanu Ti-6Al-4V: Výrazně dražší (často 5 až 10krát dražší než 316L nebo dražší) kvůli nákladům na suroviny a složitým procesům výroby prášku.
- Ostatní slitiny: Niklové superslitiny (Inconel) mají rovněž prémiovou cenu. Slitiny hliníku jsou obecně levnější než nerezová ocel.
- Spotřebovaný materiál: Náklady nejsou jen na prášek v konečné části, ale zahrnují:
- Část Objem: Skutečný objem pouzdra konektoru.
- Podpůrné struktury: Objem prášku použitého pro obětní podpěry. Efektivní DfAM to minimalizuje.
- Procesní ztráty: Část prášku se nevyhnutelně ztratí při manipulaci, prosévání a tisku (efektivní dodavatelé však minimalizují odpad recyklací).
- Hustota zástavby: Hustě zabalené sestavy (tisk více dílů současně) využívají prášek efektivněji než tisk jednotlivých dílů ve velkém objemu sestavy.
Závěr: Volba materiálu (zejména Ti-6Al-4V vs. 316L) je hlavním faktorem ovlivňujícím náklady. Konstrukce optimalizované pro minimální objem a podpůrné konstrukce (DfAM) přímo snižují náklady na materiál.
Doba sestavení: strojové hodiny a složitost
Dalším významným nákladovým faktorem je doba, kterou stroj AM stráví tiskem dílu, obvykle účtovaná v hodinové sazbě, která pokrývá odpisy stroje, údržbu, energii, inertní plyn/vakuum a režijní náklady zařízení.
- Část Objem & Výška: Tisk dílů s větším objemem trvá přirozeně déle. Doba sestavení často silně souvisí s výškou dílu (rozměr Z), protože nanesení a spojení každé vrstvy trvá určitou dobu.
- Počet dílů na sestavení: Tisk více dílů současně (nesting) rozkládá čas potřebný k nastavení a vychladnutí stroje na více položek, čímž se snižují náklady na jeden díl.
- Složitost & Strategie skenování: Velmi složité geometrie nebo požadavky na specifické strategie skenování (např. pro jemné prvky nebo snížení napětí) mohou ovlivnit celkový čas na vrstvu.
- Technologie stroje: Různé technologie AM a konkrétní modely strojů mají různou rychlost výroby. SEBM může někdy nabídnout rychlejší objemovou rychlost než L-PBF pro určité materiály/geometrie díky rychlejšímu skenování paprsku.
Závěr: Optimalizujte konstrukce pro minimální výšku, pokud je to možné (vyvážení s potřebami podpory), a využijte vnoření konstrukčních desek pro více dílů, abyste snížili náklady na strojní čas na jeden díl.
Náklady na pracovní sílu: Optimalizace návrhu, nastavení, následné zpracování
Lidské úsilí je zapojeno do celého pracovního postupu AM:
- Technická podpora/DfAM: Čas strávený inženýry optimalizací návrhu, simulací procesu a přípravou souboru pro sestavení.
- Nastavení a provoz stroje: Práce při nakládání prášku, nastavení úlohy sestavení, monitorování tisku a vykládání hotové sestavy.
- Manipulace s práškem a recyklace: Čas strávený proséváním, manipulací a bezpečnou a efektivní správou zásob prášku.
- Část & Odstranění podpory: Pečlivé vyjmutí dílů ze stavební desky a pečlivé odstranění podpůrných konstrukcí, zejména složitých nebo vnitřních, může být spojeno se značnou pracností. To často představuje hlavní překážku a nákladový faktor při následném zpracování.
- Povrchová úprava & amp; Kontrola: Ruční práce při povrchové úpravě (leštění, odjehlování), čištění, vizuální kontrole a metrologii.
Závěr: Konstrukce, které minimalizují podpůrné konstrukce a požadavky na ruční dokončování, přímo snižují náklady na pracovní sílu. Automatizace následného zpracování (tam, kde je to možné) může pomoci, ale mnoho kroků zůstává náročných na pracovní sílu.
Požadavky a složitost následného zpracování
Jak již bylo podrobně popsáno dříve, kroky následného zpracování zvyšují náklady a čas:
- Tepelné zpracování: Doba pece, spotřeba energie, náklady na inertní plyn/vakuum. Složité cykly (jako STA pro Ti-6Al-4V) trvají déle a stojí více než jednoduché odlehčení.
- Obrábění: Čas strávený na CNC strojích (frézování, soustružení, elektroerozivní obrábění), náklady na nástroje, čas strávený programováním. Počet a složitost obráběných prvků přímo ovlivňuje náklady.
- Povrchová úprava: Náklady spojené s tryskacími médii, provozem bubnového zařízení, spotřebním materiálem a prací při leštění nebo specializovanými procesy, jako je elektrolytické leštění.
- Nátěry/povlaky: Náklady účtované specializovanými pokovovacími dílnami v závislosti na materiálu povlaku, tloušťce a požadavcích na maskování.
Závěr: Jasně zadejte pouze nezbytné následné zpracování. Nadměrné tolerování nebo požadavek na zbytečně jemnou povrchovou úpravu výrazně zvyšuje náklady. DfAM by se měl snažit minimalizovat závislost na rozsáhlém následném zpracování, pokud je to možné.
Náklady na kontrolu kvality a inspekce
Úroveň požadované kontroly významně ovlivňuje náklady:
- Standardní kontrola: Vizuální kontroly, základní měření rozměrů.
- Pokročilá metrologie: Doba programování a měření na souřadnicové měřicí soupravě, doba 3D skenování a analýzy.
- Nedestruktivní zkoušení (NDT): Náklady na CT vyšetření, radiografické zkoušky nebo penetrační zkoušky, pokud jsou vyžadovány pro detekci vnitřních defektů nebo kontrolu trhlin - zejména CT vyšetření může být nákladné.
- Dokumentace: Čas strávený sestavováním komplexních balíčků kvalitní dokumentace.
Závěr: Definujte vhodnou úroveň kontroly na základě kritičnosti. Vyžadování rozsáhlé nedestruktivní kontroly u nekritických součástí zbytečně zvyšuje náklady.
Faktory ovlivňující dodací lhůty
Doba realizace - celková doba od zadání objednávky do obdržení hotových dílů - je ovlivněna mnoha stejnými faktory jako náklady:
- Design & Příprava: Čas na přezkoumání DfAM, simulaci (je-li třeba) a přípravu souboru sestavení (obvykle 1-3 dny).
- Doba tisku: Velmi variabilní v závislosti na velikosti, složitosti a množství dílů (může se pohybovat od hodin u malých dílů až po mnoho dní u velkých, složitých sestav nebo velkých sérií).
- Fronta strojů: Aktuální vytížení dodavatele a dostupnost strojů významně ovlivňují dobu, kdy může být sestavení zahájeno. Doporučuje se rezervovat kapacitu pro výrobní série s předstihem.
- Doba následného zpracování: To často představuje velkou část celkové doby realizace.
- Tepelné zpracování: Obvykle 1-3 dny (včetně cyklů v peci a chlazení).
- Podpora/odstranění dílu: V závislosti na složitosti se může pohybovat od hodin až po dny.
- Obrábění: U složitých dílů může trvat dny až týdny.
- Povrchová úprava/povlak: V závislosti na procesu a dodacích lhůtách dodavatele se prodlužuje o dny nebo týdny.
- Kontrola a přeprava: Závěrečné kontroly kvality a doba přepravy.
Realistická očekávání:
- Prototypy: Pro relativně jednoduchá pouzdra konektorů, která vyžadují standardní následné zpracování, jsou dodací lhůty následující 1 až 3 týdny jsou často dosažitelné.
- Výrobní série: V případě většího množství nebo dílů, které vyžadují rozsáhlé následné zpracování a přísnou kontrolu kvality, se doba dodání může prodloužit na několik týdnů až měsíců.
Závěr: Spolupracujte s dodavateli včas, poskytněte jim kompletní informace z RFQ a předem projednejte očekávanou dobu realizace. Dobře naplánovaný DfAM a jasně definované požadavky mohou pomoci zefektivnit proces. Kontakt Met3dp prodiskutovat konkrétní časový plán projektu a získat podrobnou cenovou nabídku.
Zvyšování úrovně leteckých a kosmických systémů: Trvalá hodnota 3D tištěných pouzder konektorů z kovu na zakázku
V tomto průzkumu jsme se zabývali kritickou úlohou pouzder konektorů v letectví a kosmonautice, jedinečnými výzvami, kterým čelí, a tím, jak aditivní výroba kovů, zejména s použitím robustních materiálů, jako je nerezová ocel 316L a vysoce výkonná titanová slitina Ti-6Al-4V, nabízí transformativní přístup k jejich výrobě. Výhody, které nabízí technologie AM pro kovy, nejsou jen postupným zlepšováním; představují zásadní posun směrem k větší volnosti návrhu, optimalizaci výkonu a větší výrobní agilitě, což v konečném důsledku přispívá k bezpečnějším, efektivnějším a schopnějším leteckým systémům.
Rekapitulace: Klíčové výhody pro aplikace v letectví a kosmonautice
3D tisk z kovu přináší silnou kombinaci výhod, které jsou přímo použitelné pro požadavky na pouzdra konektorů v letectví a kosmonautice:
- Bezkonkurenční volnost designu: Umožňuje složité geometrie, vnitřní prvky (chlazení, stínění) a optimalizaci topologie pro odlehčení, které jsou tradičními metodami nemožné nebo nepraktické.
- Rychlé přizpůsobení & amp; Prototypování: Zrychlení vývojových cyklů díky možnosti rychlého opakování a výroby zakázkových návrhů krytů přizpůsobených specifickým prostorovým, hmotnostním nebo funkčním omezením.
- Snížení hmotnosti: Výrazné snížení hmotnosti součástí díky optimalizaci topologie a efektivnímu využití materiálů s vysokým poměrem pevnosti a hmotnosti, jako je Ti-6Al-4V, což přispívá k úspoře paliva a zvýšení nosnosti.
- Konsolidace částí: Snížení složitosti montáže, potenciálních míst poruch a logistické režie díky integraci více funkcí do jediného tištěného dílu.
- Zvýšení výkonu: Umožňuje použití optimálních materiálů, jako je Ti-6Al-4V, pro vysokopevnostní, vysokoteplotní nebo korozivní prostředí a umožňuje konstrukce s integrovaným tepelným managementem nebo zvýšeným stíněním EMI.
- Efektivní malosériová výroba: Poskytuje nákladově efektivní metodu výroby přizpůsobených, nízko až středně velkých sérií, které jsou často vyžadovány v projektech v leteckém a kosmickém průmyslu, a vyhýbá se tak vysokým nákladům na nástroje.
Budoucí trendy: Pokroky v materiálech a procesech
Oblast aditivní výroby kovů se neustále vyvíjí a do budoucna slibuje ještě větší možnosti pro letecké komponenty:
- Nové materiály: Vývoj nových slitin speciálně navržených pro AM, které nabízejí lepší vlastnosti (vyšší teplotní odolnost, vyšší pevnost, lepší tisknutelnost). Výzkum tisku keramiky nebo kompozitů s kovovou matricí pro specializované aplikace v pouzdrech.
- Rychlejší tiskové procesy: Inovace zaměřené na zvýšení rychlosti výroby bez snížení kvality, což dále zlepšuje ekonomickou životaschopnost pro větší objemy výroby.
- Vylepšené monitorování in situ & Kontrola: Sofistikovanější monitorování taveniny a procesu výroby v reálném čase spolu se smyčkami zpětné vazby řízenými umělou inteligencí, které automaticky upravují parametry, což vede k lepšímu zajištění kvality a snížení potřeby kontrol po výrobě.
- Zvýšená automatizace: Větší automatizace kroků následného zpracování, jako je odstraňování prášku a podpěr, pro snížení nákladů na pracovní sílu a doby přípravy.
- Hybridní výroba: Užší integrace aditivních a subtraktivních procesů v rámci jedné strojní platformy pro zvýšení efektivity.
Úloha AM kovů v udržitelné letecké výrobě
Aditivní výroba je také v souladu s rostoucím důrazem na udržitelnost v leteckém průmyslu:
- Snížení množství materiálového odpadu: V porovnání se subtraktivním obráběním vzniká při AM výrazně méně odpadu, což je výhodné zejména při použití drahých slitin, jako je titan. Recyklace prášku dále zlepšuje využití materiálu.
- Odlehčení: Nižší hmotnost součástí se přímo promítá do nižší spotřeby paliva během provozu letadla, což snižuje emise.
- Výroba na vyžádání & Distribuovaná výroba: Tisk dílů v okamžiku, kdy jsou potřeba, a na místě, kde jsou potřeba, snižuje množství skladových zásob a emisí z dopravy, které jsou spojeny se složitými globálními dodavatelskými řetězci.
Závěrečné myšlenky: Využití aditivní výroby pro získání konkurenční výhody
Zakázková kovová 3D tištěná pouzdra konektorů jsou víc než jen součástky; jsou to nástroje pro inovace. Tím, že osvobozuje konstruktéry od tradičních omezení a umožňuje optimalizovaná, integrovaná a lehká řešení, umožňuje kovová AM společnostem v leteckém průmyslu stavět letadla, kosmické lodě a obranné systémy nové generace. I když existují problémy, spolupráce se znalými a technologicky vyspělými dodavateli, jako je Met3dp, kteří nabízejí komplexní řešení od výroby vysoce kvalitního prášku až po pokročilý tisk a inženýrskou podporu, umožňuje organizacím s jistotou využít sílu aditivní výroby. Využití této technologie se stále více stává nejen možností, ale i nutností pro udržení konkurenční výhody v dynamickém leteckém průmyslu. Prozkoumejte, jak Met3dp’s komplexní službou řešení kovového 3D tisku může pozvednout váš příští projekt.
Často kladené otázky (FAQ): Odpovědi na vaše nejčastější dotazy týkající se 3D tištěných pouzder leteckých konektorů
Otázka 1: Jaké jsou typické tolerance dosažitelné u 3D tištěných kovových krytů konektorů?
A1: Tolerance při výrobě pomocí technologie SLM (Powder Bed Fusion, SEBM) se obvykle pohybují v rozmezí ±0,1 mm až ±0,2 mm u menších prvků nebo ±0,1 % až ±0,2 % u větších rozměrů. Kritická rozhraní, styčné plochy nebo těsnicí drážky vyžadující přísnější tolerance (např. ±0,01 mm až ±0,05 mm) však obvykle vyžadují následné CNC obrábění. DfAM zahrnuje návrh těchto prvků s přídavkem na obrábění.
Otázka 2: Jaké jsou náklady na 3D tisk v porovnání s CNC obráběním u zakázkových krytů konektorů?
A2: Srovnání nákladů do značné míry závisí na složitosti a objemu dílů.
- Pro velmi složité geometrie nebo malé objemy (prototypy, 1-100 dílů): 3D tisk z kovu je často nákladově efektivnější, protože se vyhne vysokým nákladům na nástroje/přípravky a rozsáhlým časům programování/nastavení spojeným s obráběním složitých tvarů z předvalků.
- Pro jednodušší geometrie nebo větší objemy: CNC obrábění může být ekonomičtější, protože náklady na nastavení se amortizují na více dílů a doba obráběcího cyklu pro jednoduché tvary může být kratší než doba sestavení AM. Velkou roli hraje také volba materiálu; AM snižuje množství odpadu u drahých materiálů, jako je Ti-6Al-4V, čímž se může stát konkurenceschopnější, i když se obrábění jeví jako rychlejší. Vždy se doporučuje podrobné porovnání cenových nabídek.
Otázka 3: Jaké certifikáty bych měl hledat u dodavatele kovových AM dílů pro letecký průmysl?
A3: Nejdůležitější certifikací je AS9100, norma systému řízení jakosti specifická pro letecký, kosmický a obranný průmysl. To prokazuje závazek dodavatele dodržovat přísné procesy kvality, sledovatelnosti a řízení rizik, které jsou vyžadovány pro letové komponenty. Norma ISO 9001 je dobrým základem, ale sama o sobě je obecně nedostatečná. V závislosti na požadovaném následném zpracování je velmi cenná také akreditace Nadcap pro speciální procesy, jako je tepelné zpracování nebo NDT.
Otázka 4: Lze efektivně vytisknout vnitřní prvky, jako je stínění nebo chladicí kanály?
A4: Ano, jednou z klíčových výhod technologie AM pro kovy je možnost vytvářet složité vnitřní prvky. Úspěšná implementace však vyžaduje pečlivý návrh pro aditivní výrobu (DfAM). Mezi klíčové aspekty patří:
- Odstranění prášku: Kanály musí mít dostatečný průměr a přístupné únikové otvory pro úplné odstranění nerozpuštěného prášku.
- Samonosné geometrie: Vnitřní kanálové střechy by měly být v ideálním případě navrženy se samonosnými úhelníky (např. ve tvaru slzy nebo kosočtverce), aby nebylo nutné používat vnitřní podpěry, které se velmi obtížně odstraňují.
- Povrchová úprava: Vnitřní povrchy budou mít drsnost jako při výrobě, pokud se nepoužijí specifické sekundární procesy (např. abrazivní proudové obrábění).
Otázka 5: Jaká je obvyklá doba dodání prototypů nebo výrobních pouzder leteckých konektorů?
A5: Dodací lhůty jsou velmi proměnlivé. Mezi faktory patří složitost dílu, velikost, množství, materiál, dostupnost stroje a rozsah požadovaného následného zpracování (tepelné zpracování, obrábění, dokončovací práce, kontrola).
- Prototypy: Často se pohybují od 1 až 3 týdny.
- Výrobní série: Může se pohybovat od několik týdnů až měsícův závislosti na objemu a složitosti. Včasné zapojení dodavatelů a poskytnutí jasných požadavků umožňuje přesnější odhady doby realizace.
Sdílet na
MET3DP Technology Co., LTD je předním poskytovatelem řešení aditivní výroby se sídlem v Qingdao v Číně. Naše společnost se specializuje na zařízení pro 3D tisk a vysoce výkonné kovové prášky pro průmyslové aplikace.
Dotaz k získání nejlepší ceny a přizpůsobeného řešení pro vaše podnikání!
Související články
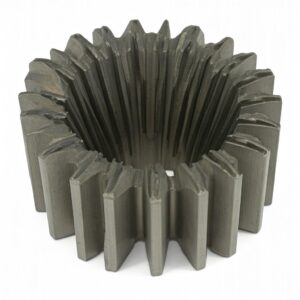
Vysoce výkonné segmenty lopatek trysek: Revoluce v účinnosti turbín díky 3D tisku z kovu
Přečtěte si více "O Met3DP
Nedávná aktualizace
Náš produkt
KONTAKTUJTE NÁS
Nějaké otázky? Pošlete nám zprávu hned teď! Po obdržení vaší zprávy obsloužíme vaši žádost s celým týmem.
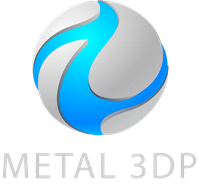
Kovové prášky pro 3D tisk a aditivní výrobu