Konformní chladicí kanály prostřednictvím kovu AM
Obsah
Úvod: Revoluce v tepelném managementu v letectví a kosmonautice díky technologii AM pro kovy
Letecký a kosmický průmysl pracuje v extrémních výkonnostních podmínkách a vyžaduje komponenty, které jsou nejen lehké a pevné, ale také odolné vůči vysokým teplotám a tlakům. Efektivní tepelný management je prvořadý a přímo ovlivňuje účinnost, spolehlivost a životnost kritických systémů, od pohonných jednotek až po citlivou avioniku. Tradiční výrobní metody jsou sice vyspělé, ale často přinášejí značná omezení při navrhování chladicích prvků, zejména vnitřních kanálů. Zde je třeba Aditivní výroba kovů (Metal AM), známý také jako kov 3D tisk, se stává transformační technologií, která umožňuje vytvářet vysoce komplexní systémy Konformní chladicí kanály které bylo dříve nemožné nebo neúnosně drahé vyrobit.
Konformní chladicí kanály jsou složité sítě vnitřních průchodů navržené tak, aby přesně kopírovaly obrysy povrchu dílu. Na rozdíl od běžných chladicích kanálů, které jsou často omezeny na přímé vrtání, mohou konformní kanály obtékat rohy, mít různý průřez a optimální polohu v blízkosti zdrojů tepla. Tento těsný kontakt umožňuje výrazně účinnější a rovnoměrnější odvod tepla, což výrazně zlepšuje výkon tepelného managementu.
Proč je to v letectví a kosmonautice tak důležité?
- Vylepšený výkon: Díky efektivnějšímu řízení tepla mohou součásti, jako jsou lopatky turbín, pracovat při vyšších teplotách, což vede ke zvýšení účinnosti a tahu motoru. Chlazená elektronika udržuje stabilní provozní podmínky a zajišťuje spolehlivost.
- Snížení hmotnosti: Optimalizované chlazení umožňuje kompaktnější konstrukci komponent. Kromě toho AM umožňuje integrovat chladicí prvky přímo do konstrukčních součástí, čímž se eliminuje potřeba samostatných objemných chladicích sestav a přispívá k celkové úspoře hmotnosti letadla - což je rozhodující faktor v ekonomice leteckého průmyslu.
- Zvýšená životnost komponent: Rovnoměrné chlazení minimalizuje koncentraci tepelného napětí a horkých míst, čímž snižuje opotřebení a prodlužuje provozní životnost drahých a kritických dílů.
- Svoboda designu: Technologie AM na bázi kovů zbavuje inženýry omezení tradiční výroby. Umožňuje vytvářet organické, komplexní geometrie optimalizované výhradně pro tepelný výkon, což vede k inovativním řešením dříve neřešitelných tepelných problémů.
Schopnost vyrábět tyto pokročilé chladicí geometrie je do značné míry závislá na procesech, jako je selektivní laserové tavení (SLM), tavení elektronovým svazkem (EBM) a přímé laserové spékání kovů (DMLS). Tyto techniky tavení po vrstvách využívají vysokoenergetické zdroje (lasery nebo elektronové paprsky) k selektivnímu tavení jemných kovových prášků a vytvářejí díly přímo z digitálních modelů. Tato přesná kontrola umožňuje složité vnitřní cesty charakteristické pro konformní chlazení.
Pro manažery nákupu a inženýry v letectví a kosmonautice již není pochopení potenciálu AM kovů pro konformní chlazení volitelné, ale je nezbytné pro udržení konkurenceschopnosti. Představuje změnu paradigmatu v řešení tepelných problémů, kdy se přechází od kompromisních návrhů zaměřených na vyrobitelnost k vysoce optimalizovaným řešením zaměřeným na výkon. Tato technologie umožňuje vývoj letadel a kosmických lodí nové generace s bezprecedentními schopnostmi. Firmy hledající dodavatelé leteckých komponentů specializující se na pokročilé výrobní techniky se stále častěji obracejí na poskytovatelé služeb v oblasti AM kovů schopné dodávat tyto složité díly s požadovanou přesností a vlastnostmi materiálu. Jako přední poskytovatel komplexních 3D tisk z kovu řešení, včetně pokročilého vybavení a vysoce výkonných prášků, stojí Met3dp v čele této revoluce a podporuje inovace v leteckém průmyslu.
Integrace technologie AM pro kovy není jen alternativní výrobní cestou, ale i prostředkem k dosažení vynikajícího designu a funkčnosti. Umožňuje sloučit více dílů do jediné komplexní součásti s integrovaným chlazením, čímž se zkracuje doba montáže, zkracují se potenciální cesty úniku a celková složitost systému. Tento úvod připravuje půdu pro zkoumání konkrétních aplikací, výhod, materiálů a úvah spojených s využitím AM kovů pro výrobu vysoce výkonných konformních chladicích kanálů v náročném leteckém a kosmickém sektoru. Prozkoumáme, jak tato technologie řeší konkrétní bolestivé body, jaké materiály jsou pro tento úkol nejvhodnější a jak úspěšně projít procesem návrhu a výroby. Důraz zůstává kladen na poskytování letecká a kosmická inženýrská řešení které posouvají hranice tepelného výkonu díky pokročilým technologiím aditivní výroba v letectví a kosmonautice techniky.
Kritické aplikace: Kde konformní chlazení v letectví a kosmonautice vyniká
Výhody konformních chladicích kanálů realizovaných prostřednictvím aditivní výroby kovů nejsou teoretické; aktivně se uplatňují v celém spektru kritických leteckých systémů, kde je efektivní tepelný management neoddiskutovatelný. Schopnost umístit chlazení přesně tam, kde je potřeba, podle složitých obrysů součásti, uvolňuje dříve nedosažitelné výkonnostní a konstrukční možnosti. Prozkoumejme některé klíčové oblasti použití:
1. Plynové turbínové motory (proudové motory & turbíny pro výrobu energie):
- Lopatky a lopatky turbíny: Tyto součásti pracují v pravděpodobně nejnáročnějším prostředí v letadle, kde jsou vystaveny extrémně vysokým teplotám (často překračujícím teplotu tání použitých slitin) a mechanickému namáhání. Konformní chladicí kanály, složitě vetknuté do vnitřní struktury lopatek a kopírující složitý tvar křídla, umožňují účinnější chlazení s využitím menšího množství vzduchu odváděného z kompresoru motoru.
- Dopad: Lze dosáhnout vyšších vstupních teplot turbíny (TIT), což přímo zvyšuje tah motoru a účinnost paliva. Rovnoměrné chlazení snižuje tepelné gradienty, minimalizuje tečení a tepelnou únavu, čímž prodlužuje životnost lopatek a zvyšuje spolehlivost motoru. Kovový AM umožňuje složité vnitřní geometrie, jako jsou turbulátory a soustavy pin-fin v kanálech pro lepší přenos tepla. Materiály jako např IN625 (Inconel 625) se často používají díky své výjimečné pevnosti při vysokých teplotách a odolnosti proti korozi.
- Spalovací komory: Vložky a součásti spalovacího prostoru jsou vystaveny intenzivnímu teplu vznikajícímu při spalování paliva. Konformní chlazení integrované do těchto konstrukcí pomáhá udržovat strukturální integritu, zabraňuje prohýbání a zajišťuje úplné spalování, čímž snižuje škodlivé emise.
- Trysky: Výfukové trysky, zejména složité trysky s proměnlivou geometrií, využívají integrované konformní chlazení, které zvládá extrémní teploty výfukových plynů a zároveň optimalizuje aerodynamický výkon.
2. Chlazení letecké elektroniky a elektroniky:
- Integrované chladicí desky & chladiče: Moderní letadla jsou vybavena výkonnou elektronikou pro navigaci, komunikaci, řízení a systémy pro plnění úkolů. Ty v často těsně zaplněných prostorech vytvářejí značné množství tepla. Technologie Metal AM umožňuje vytvářet vysoce přizpůsobené chladicí desky a chladiče s konformními kanály, které přesně odpovídají rozložení komponent generujících teplo (CPU, FPGA, výkonové zesilovače).
- Dopad: Účinnější odvod tepla zajišťuje, že elektronika pracuje v bezpečných teplotních mezích, čímž se předchází poruchám a zajišťuje spolehlivost systému. Volnost designu AM umožňuje lehká a kompaktní řešení chlazení integrovaná přímo do elektronických skříní, což šetří cenný prostor a hmotnost. Materiály jako např AlSi10Mg (slitina hliníku, křemíku a hořčíku) jsou ideální díky své vynikající tepelné vodivosti a nízké hustotě. Velkoobchodní dodavatelé kovového prášku v odvětví letecké a kosmické elektroniky zaznamenávají rostoucí poptávku po těchto lehkých slitinách.
- Moduly výkonové elektroniky: Chlazení vysoce výkonných komponent, jako jsou měniče a konvertory v elektrických nebo hybridních elektrických pohonných systémech, má zásadní význam. Konformní chlazení zajišťuje účinný odvod tepla, což umožňuje vyšší hustotu výkonu.
3. Systémy kontroly prostředí (ECS):
- Výměníky tepla: Systém ECS v letadle řídí teplotu, tlak a kvalitu vzduchu v kabině. To zahrnuje složité výměníky tepla pracující s cykly vzduchu a chladiva. Kovová AM umožňuje navrhovat vysoce kompaktní a účinné výměníky tepla se složitou strukturou žeber a konformními průtokovými cestami optimalizovanými pro maximální přenos tepla při minimálních omezeních objemu a hmotnosti.
- Dopad: Lehčí a menší součásti ECS přispívají k celkové efektivitě letadla. Vylepšený výkon výměníku tepla zvyšuje pohodlí cestujících a odezvu systému. Konsolidace dílů pomocí AM může snížit počet spojů a potenciálních míst netěsnosti ve srovnání s tradičně pájenými nebo svařovanými sestavami.
4. Raketové motory a tepelné řízení kosmických lodí:
- Spalovací komory a trysky: Součásti raketových motorů, které jsou podobné proudovým motorům, ale pracují při ještě extrémnějších teplotách a tlacích, jsou do značné míry závislé na pokročilém chlazení. Běžné je regenerativní chlazení, kdy kryogenní palivo prochází kanály ve stěnách komory a trysky. Kovový AM umožňuje vysoce optimalizovanou geometrii kanálů regenerativního chlazení, čímž se maximalizuje absorpce tepla a výkon motoru (specifický impuls).
- Tepelná kontrola satelitů: Udržování stabilních teplot pro citlivé přístroje a elektroniku ve vesmírném vakuu s extrémními výkyvy teplot mezi slunečním svitem a stínem je životně důležité. Technologie AM umožňuje použití složitých chladičových panelů a tepelných trubek s integrovanými konformními smyčkami kapaliny.
Cílová odvětví a funkce:
Hlavními příjemci jsou jednoznačně letecká a obranná výroba odvětví. Principy a technologie se však vztahují i na související vysoce výkonná odvětví:
- Motorsport: Formule 1 a další závodní série používají AM pro konformní chlazení součástí motoru, brzd a převodovek pro zvýšení výkonu.
- Vysoce výkonná průmyslová zařízení: Těžit z toho mohou plynové turbíny pro výrobu energie, specializované nástroje vyžadující chlazení (např. vstřikovací formy - i když obvykle z jiných materiálů) a výkonné laserové systémy.
Hlavní funkcí, kterou konformní chladicí kanály AM umožňují, je přesné tepelné řízení - účinně a rovnoměrně odvádí teplo z kritických míst složitých, vysoce výkonných součástí. To se přímo promítá do vyšší účinnosti, spolehlivosti, delší životnosti komponent a často i do výrazného snížení hmotnosti, což z ní činí základní technologii pro letecké výrobní služby zaměřené na systémy nové generace. Manažeři veřejných zakázek, kteří hledají průmysloví partneři pro 3D tisk potřebují poskytovatele s prokazatelnými zkušenostmi s těmito náročnými aplikacemi.
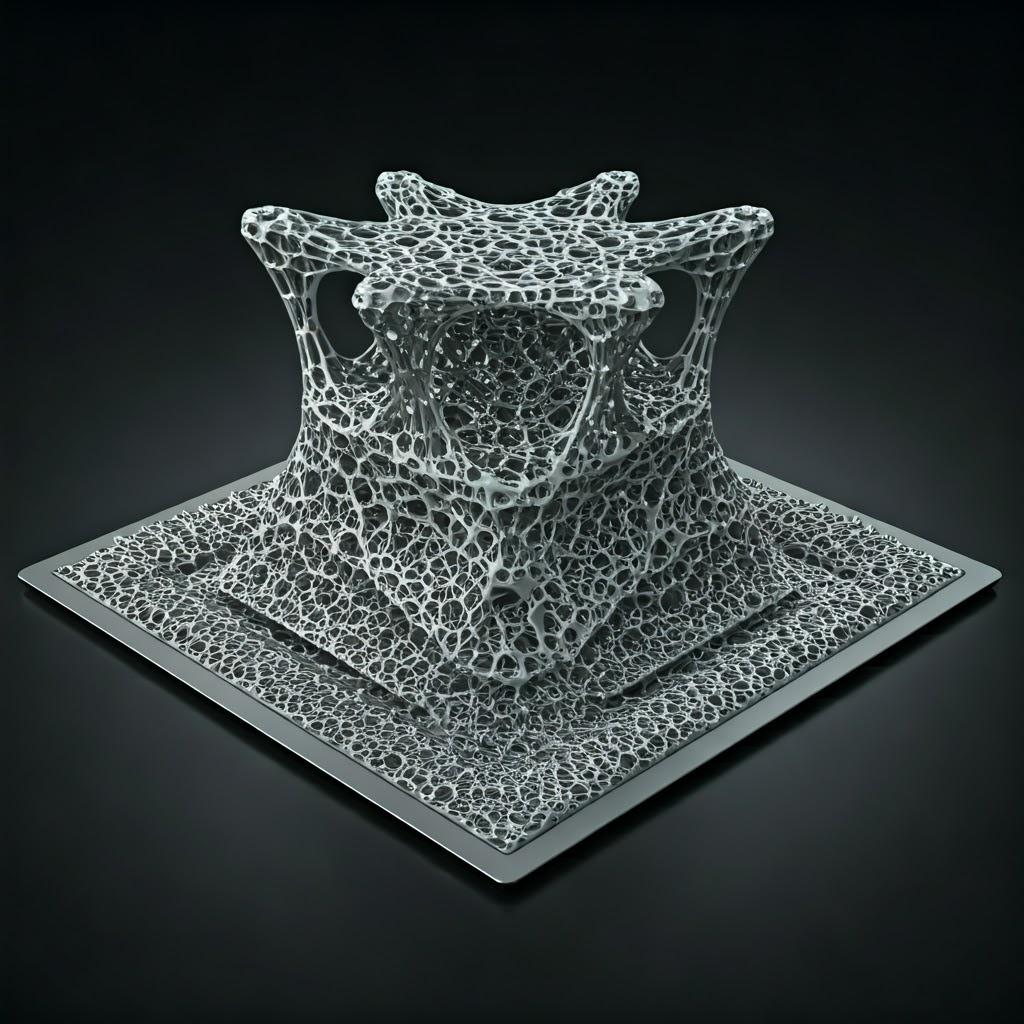
Aditivní výhoda: Proč 3D tisk z kovu pro složité chladicí geometrie?
Tradiční výrobní metody, jako je odlévání, obrábění (vrtání) a pájení, sice slouží leteckému průmyslu již desítky let, ale ze své podstaty omezují složitost a účinnost konstrukce chladicích kanálů. Aditivní výroba kovů tato omezení zásadním způsobem překonává a nabízí řadu výhod, které jsou obzvláště přesvědčivé při vytváření konformních chladicích kanálů. Inženýři a nákup kovů AM odborníci považují tyto výhody za hnací sílu pro zavedení této technologie:
1. Bezkonkurenční volnost designu & Geometrická složitost:
- Tradiční: Omezuje se na lineární dráhy vrtání, jednoduché ohyby (vyžadující vícenásobné nastavení nebo složité nástroje) nebo sestavení více obrobených kusů (zavádějící spoje a potenciální místa poruch). Dosažení skutečné shody se zakřivenými povrchy je velmi obtížné a nákladné.
- Metal AM: Vytváří díly po vrstvách přímo z 3D modelu CAD. To umožňuje:
- Pravé konformní cesty: Kanály mohou přesně kopírovat obrysy složitých povrchů (např. tvary křídel, stěny spalovací komory, rozložení elektronických součástek).
- Proměnlivé průřezy: Průměr a tvar kanálu lze na trase měnit, aby se optimalizovala rychlost proudění a přenos tepla na místě.
- Komplexní vnitřní vybavení: Prvky, jako jsou vypínací lišty, turbulátory, kolíkové lamely a složité rozdělovače, lze integrovat přímo uvnitř kanálů během procesu sestavování, aby se zvýšila turbulence a výměna tepla, aniž by byla nutná dodatečná montáž.
- Organické tvary: Návrhy lze optimalizovat pomocí optimalizace topologie a generativních návrhových algoritmů, což vede k lehkým a vysoce výkonným strukturám, které by jinak nebylo možné vytvořit.
2. Konsolidace dílů & Redukovaná montáž:
- Tradiční: Komplexní chladicí systémy často vyžadují výrobu více jednotlivých součástí (např. desek, trubek, rozdělovačů) a jejich následné spojení svařováním, pájením nebo spojovacími prvky. Každý spoj představuje potenciální cestu úniku, přidanou hmotnost a další výrobní/kontrolní krok.
- Metal AM: Umožňuje tisk jediné monolitické součásti s plně integrovanými vnitřními chladicími kanály.
- Výhody: Eliminuje spoje, čímž výrazně snižuje potenciální netěsnosti a zvyšuje celkovou spolehlivost systému. Snižuje počet dílů, čímž zjednodušuje dodavatelské řetězce a montážní procesy. Často vede ke snížení hmotnosti konečných součástí, protože odpadají spojovací příruby a spojovací prvky. To představuje klíčovou hodnotu pro smluvní výroba v letectví a kosmonautice poskytovatelé využívající AM.
3. Zvýšený tepelný výkon & Účinnost:
- Tradiční: Přímočaré kanály často vedou k neoptimální vzdálenosti od zdroje tepla a nerovnoměrnému chlazení, což vede ke vzniku horkých míst a tepelných gradientů. Omezené vnitřní prvky omezují zlepšení přenosu tepla.
- Metal AM: Konformní kanály minimalizují vzdálenost mezi chladivem a zdrojem tepla v celé kritické ploše.
- Výhody: Účinnější odvod tepla vede k nižším teplotám komponent a/nebo umožňuje provozovat systémy při vyšších výkonech a teplotách. Rovnoměrné chlazení minimalizuje tepelné namáhání a prodlužuje životnost komponent. Integrované prvky pro zvýšení turbulence maximalizují koeficient přenosu tepla mezi chladicí kapalinou a stěnou kanálu.
4. Výrazné snížení hmotnosti:
- Tradiční: Kompromisy v konstrukci kvůli vyrobitelnosti často vedou k silnějším stěnám nebo objemnějším chladicím sestavám, než je nezbytně nutné pro tepelný výkon.
- Metal AM: Volnost konstrukce umožňuje umístit materiál pouze tam, kde je to z konstrukčního nebo tepelného hlediska nutné. Optimalizace topologie může dále odstranit zbytečnou hmotnost. Konsolidace dílů ze své podstaty snižuje hmotnost.
- Výhody: To je důležité pro letectví a kosmonautiku, kde každý ušetřený kilogram znamená úsporu paliva nebo zvýšení nosnosti. To se dokonale shoduje s cíli lehké kovové součásti vývoj.
5. Zrychlené prototypování & Iterace návrhu:
- Tradiční: Vytváření prototypů se složitými vnitřními chladicími prvky často vyžaduje nákladné nástroje (odlévací formy) nebo pracné vícestupňové obrábění a montážní procesy. Iterace návrhu jsou pomalé a nákladné.
- Metal AM: Prototypy lze tisknout přímo z dat CAD relativně rychle, bez nutnosti použití nástrojů.
- Výhody: Umožňuje inženýrům rychle testovat a ověřovat různé návrhy chladicích kanálů, provádět funkční testování a mnohem rychleji a úsporněji provádět iterace směrem k optimálnímu řešení. Zkracuje vývojový cyklus nových leteckých komponent.
6. Rozmanitost materiálů a optimalizace:
- Metal AM: Podporuje rostoucí škálu slitin pro letecký průmysl, včetně vysokoteplotních superslitin (např IN625), lehké hliníkové slitiny (jako např AlSi 10Mg), slitiny titanu a slitiny mědi, což umožňuje vybrat optimální materiál pro konkrétní tepelné a konstrukční požadavky. Dodavatelé kovových prášků jako Met3dp nabízí portfolio optimalizované pro procesy AM.
- Tradiční: Výběr materiálu může být omezen samotným výrobním procesem (např. odlévatelnost, obrobitelnost).
Srovnávací shrnutí:
Vlastnosti | Tradiční výroba (vrtání/pájení) | Výroba aditiv kovů (AM) | Výhoda AM |
---|---|---|---|
Geometrická složitost | Nízká (rovné linie, jednoduché ohyby) | Vysoká (konformní cesty, proměnné úseky, vnitřní prvky) | Optimální tepelný návrh, volnost návrhu |
Shoda | Špatný / obtížný | Vynikající | Rovnoměrný & účinné chlazení |
Konsolidace částí | Nízká (více dílů, nutná montáž) | Vysoký (možnost jedné monolitické části) | Snížení netěsností, hmotnosti a doby montáže |
Tepelný výkon | Středně těžké / kompromitované | Vysoká / optimalizovaná | Vyšší provozní teploty, delší životnost, účinnost |
Hmotnost | Často vyšší | Potenciálně výrazně nižší | Úspora paliva, vyšší užitečné zatížení |
Rychlost prototypování | Pomalé / nákladné | Rychlost / relativně nižší náklady (pro složité díly) | Rychlejší vývojové cykly, rychlá iterace |
Požadavek na nástroje | Vysoký (formy, přípravky, přípravky) | Nízká / žádná | Úspora nákladů, flexibilita |
Interní funkce | Velmi omezené / Post-machined | Vysoká (integrovaná během sestavování) | Zvýšený přenos tepla |
Export do archů
Aditivní výroba kovů v podstatě posouvá paradigma od “navrhování pro vyrobitelnost” k “výrobě optimálního návrhu.” Pro konformní chladicí kanály v letectví a kosmonautice, kde je nejdůležitější výkon a spolehlivost, poskytují výhody aditivní výroby přesvědčivé důvody pro její zavedení, což je hnací silou inovací v oblasti řešení tepelného managementu v letectví a kosmonautice.
Materiální záležitosti: Výběr optimálních prášků pro chlazení v letectví a kosmonautice
Výkonnost, spolehlivost a vyrobitelnost aditivně vyráběných konformních chladicích kanálů jsou zásadně závislé na volbě kovového prášku. Materiál musí nejen odolávat náročným provozním podmínkám leteckého prostředí, ale musí být také vhodný pro konkrétní použitý proces AM s kovy (např. SLM, EBM). Pro aplikace chlazení v letectví a kosmonautice často vynikají dva materiály: AlSi 10Mg a IN625 (Inconel 625). Výběr závisí na kompromisu mezi tepelnými vlastnostmi, teplotní odolností, hmotností a cenou.
Vysoce kvalitní prášky: Základ spolehlivých AM dílů
Než se pustíme do konkrétních materiálů, je třeba zdůraznit důležitost kvality prášku. Konzistentní distribuce velikosti částic (PSD), vysoká sféricita, dobrá tekutost, nízký obsah satelitů a kontrolované chemické složení jsou nezbytné pro dosažení hustých dílů bez vad s předvídatelnými mechanickými a tepelnými vlastnostmi. Horší prášek může vést k problémům, jako je pórovitost, špatná povrchová úprava, nedůsledné spojování vrstev a v konečném důsledku k selhání součásti.
Zde se specializují dodavatelé kovových prášků hrají zásadní roli. Společnosti, jako je Met3dp, využívající pokročilé techniky výroby prášků, jako je vakuová indukční tavná plynová atomizace (VIGA) a plazmový proces s rotujícími elektrodami (PREP), se zaměřují na výrobu vysoce čistých, vysoce sférických kovových prášků speciálně optimalizovaných pro procesy aditivní výroby. Jejich přísná kontrola kvality zajišťuje konzistenci jednotlivých šarží, což je pro certifikovanou výrobu leteckých komponentů zásadní. Závazek společnosti Met3dp’přesahuje rámec standardních slitin; disponují odbornými znalostmi v oblasti vývoje a výroby inovativních materiálů, jako jsou TiNi, TiTa, TiAl, TiNbZr a různé superslitiny, přizpůsobené pro náročné aplikace. Partnerství s poskytovatelem, jako je Met3dp, zajišťuje přístup k vysoce kvalitní kovové prášky které tvoří základ spolehlivých komponent AM.
1. AlSi10Mg: Lehký tepelně výkonný materiál
- Popis: AlSi10Mg je slitina hliníku obsahující křemík a hořčík. Je to dobře zavedená slitina pro odlévání, která je také široce přizpůsobena a optimalizována pro procesy AM, jako je SLM.
- Klíčové vlastnosti a výhody chladicích kanálů:
- Vynikající tepelná vodivost: Hliníkové slitiny mají obecně velmi dobrou tepelnou vodivost (přibližně 120-150 W/m-K pro AM AlSi10Mg, v závislosti na následném zpracování), což umožňuje účinný přenos tepla z komponenty do chladicí kapaliny.
- Nízká hustota: S hustotou přibližně 2,67 g/cm³ je výrazně lehčí než oceli nebo slitiny niklu, což přímo přispívá k úspoře hmotnosti, která je v leteckém průmyslu hlavním faktorem. Díky tomu je ideální pro lehké kovové součásti.
- Dobrý poměr pevnosti a hmotnosti: Ačkoli není tak pevný jako ocel nebo superslitiny, zejména při zvýšených teplotách, nabízí slušný poměr pevnosti a hmotnosti, který je vhodný pro mnoho konstrukčních součástí zahrnujících chlazení.
- Dobrá odolnost proti korozi: Vykazuje dobrou odolnost proti atmosférické korozi.
- Vynikající tisknutelnost: Obecně je považována za jednu z nejsnáze zpracovatelných hliníkových slitin pomocí SLM, která umožňuje jemné rysy a složité geometrie.
- Omezení:
- Omezený výkon při vysokých teplotách: Mechanické vlastnosti (pevnost, odolnost proti tečení) se výrazně zhoršují při teplotách nad ~150-200 °C. To omezuje jeho použití v součástech vystavených velmi vysokým teplotám, jako jsou horké části turbínových motorů.
- Nižší tažnost ve srovnání s tepanými slitinami.
- Typické aplikace chlazení v letectví a kosmonautice: Skříně pro avioniku, chladicí desky pro elektroniku, chladiče, výměníky tepla ECS, konstrukční držáky s integrovaným chlazením, komponenty pro drony. Ideální tam, kde je rozhodující úspora hmotnosti a kde jsou provozní teploty mírné.
2. IN625 (Inconel 625): Vysokoteplotní šampión
- Popis: IN625 je superslitina niklu, chromu, molybdenu a niobu, která je proslulá svou vynikající pevností při vysokých teplotách, odolností proti korozi a únavovou životností.
- Klíčové vlastnosti a výhody chladicích kanálů:
- Vynikající pevnost při vysokých teplotách & Odolnost proti tečení: Zachovává si značnou pevnost a odolnost proti deformaci (creepu) při teplotách až 800-900 °C a krátkodobě si zachovává užitné vlastnosti i při vyšších teplotách. To má zásadní význam pro součásti v horkých částech motorů.
- Vynikající odolnost proti korozi a oxidaci: Odolává širokému spektru korozivních prostředí, včetně vysokoteplotní oxidace, takže je vhodný pro náročná prostředí spalování a výfukových plynů.
- Vysoká únavová pevnost: Kritické pro součásti vystavené cyklickému tepelnému a mechanickému zatížení.
- Dobrá svařitelnost / tisknutelnost: Přestože je tisk IN625 náročnější než tisk AlSi10Mg (vyžaduje pečlivou kontrolu parametrů pro zvládnutí zbytkových napětí), je to jedna z nejlépe zpracovatelných niklových superslitin pomocí AM.
- Omezení:
- Nižší tepelná vodivost: V porovnání s hliníkovými slitinami má IN625 výrazně nižší tepelnou vodivost (přibližně 10-12 W/m-K). To znamená, že pro dosažení stejné úrovně odvodu tepla může být nutné chladicí kanály navrhnout jinak (např. větší povrch, vylepšené turbulenční prvky).
- Vysoká hustota: S hustotou přibližně 8,44 g/cm³ je podstatně těžší než hliníkové slitiny.
- Vyšší cena materiálu: Niklové superslitiny jsou ze své podstaty dražší než hliníkové slitiny.
- Typické aplikace chlazení v letectví a kosmonautice: Lopatky a lopatky turbín (vnitřní chladicí kanály), vložky spalovacích komor, součásti výfukových systémů, klapky trysek, tepelné štíty - aplikace vyžadující výjimečný výkon při extrémních teplotách. Často specifikované dodavatelé leteckých komponentů pro pohonné systémy.
Úvahy o výběru materiálu:
Volba mezi AlSi10Mg a IN625 (nebo jinými potenciálními slitinami, jako jsou slitiny titanu, např. Ti6Al4V) zahrnuje pečlivou analýzu konkrétních požadavků na použití:
Faktor | AlSi 10Mg | IN625 (Inconel 625) | Klíčové úvahy |
---|---|---|---|
Maximální provozní teplota. | Nízká až střední teplota (max. ~150-200 °C) | Velmi vysoká (~800-900 °C+) | Dominantní faktor pro výběr materiálu. |
Tepelná vodivost | Vysoký | Nízký | Vliv konstrukce kanálů na účinnost přenosu tepla. |
Hustota / hmotnost | Nízký | Vysoký | Kritické pro aplikace citlivé na hmotnost. |
Síla | Středně těžká (dobrá pevnost/hmotnost) | Velmi vysoká (zejména při teplotě) | Konstrukční integrita při zatížení a teplotě. |
Odolnost proti korozi | Dobrý | Vynikající | Nutné pro drsné chemické/oxidační prostředí. |
Náklady | Dolní | Vyšší | Rozpočtová omezení versus výkonnostní potřeby. |
Možnost tisku | Obecně jednodušší | Náročnější (zvládání stresu) | Složitost procesu a dosažitelný detail funkce. |
Export do archů
Proč je Met3dp’s prášky důležité zde:
Met3dp se zaměřuje na výrobu vysoce kvalitní kovové prášky pomocí pokročilých atomizačních technik (plynová atomizace, PREP) zajišťuje, že ať už si konstruktér vybere AlSi10Mg pro lehký chladič avioniky nebo IN625 pro náročnou lopatku turbíny, výchozí materiál splňuje přísné požadavky pro letecké aplikace. Jejich schopnosti se rozšiřují na inovativní slitiny, což nabízí potenciál pro budoucí pokrok v oblasti materiálů pro tepelný management. Konzistentní sféricita a tekutost, jak zdůrazňuje Met3dp, se přímo promítají do spolehlivějších tiskových procesů a hustších koncových komponent, což je zásadní pro integritu vnitřních chladicích kanálů, kde mohou defekty ohrozit výkon nebo vést ke katastrofickému selhání. Spolupráce se znalým poskytovatelem, jako je společnost Met3dp, který nabízí jak nejmodernější tiskové zařízení, tak prémiové prášky, poskytuje pevný základ pro využití plného potenciálu technologie tisku kov AM pro chlazení v letectví a kosmonautice.
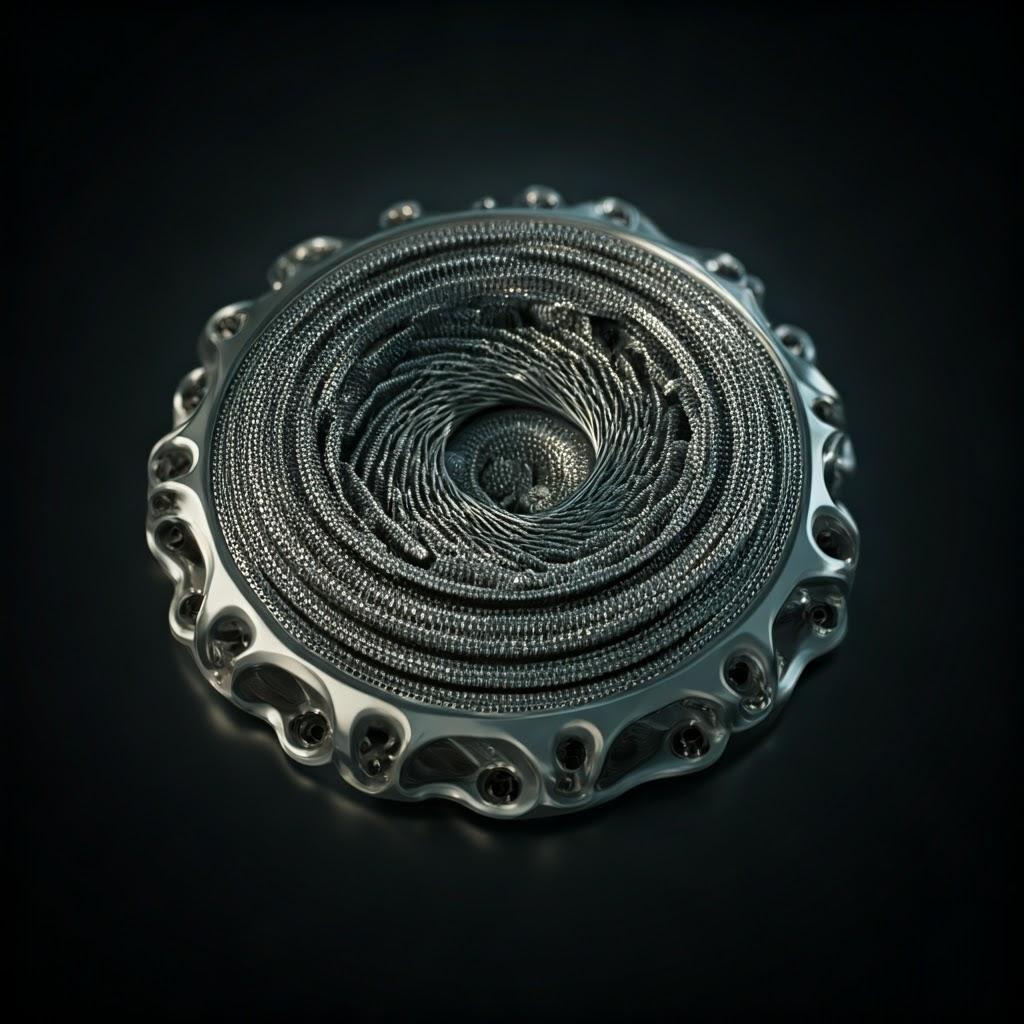
Design pro aditivní výrobu (DfAM): Optimalizace kanálů pro tisk a výkon
Pouhá replikace návrhu určeného pro tradiční výrobu pomocí aditivní výroby kovů (AM) jen zřídkakdy uvolní plný potenciál této technologie, zejména pokud se jedná o složité vnitřní geometrie, jako jsou konformní chladicí kanály. Design pro aditivní výrobu (DfAM) je klíčová metodika, která zahrnuje přizpůsobení konstrukce součásti tak, aby využila silné stránky AM a zároveň zohlednila její specifická omezení a nuance. Uplatňování zásad DfAM od samého počátku je nezbytné pro dosažení funkčních, spolehlivých a nákladově efektivních chladicích komponent pro letecký průmysl. Inženýři pracující s pravidla pro navrhování AM kovů musí vzít v úvahu několik klíčových faktorů:
1. Plánování trasy a geometrie kanálu:
- Optimalizace toku: Hlavním cílem je účinné chlazení. Nedílnou součástí procesu návrhu by měla být analýza počítačové dynamiky tekutin (CFD). CFD simuluje proudění tekutin a přenos tepla v rámci navržené geometrie kanálu, což inženýrům umožňuje:
- Identifikujte potenciální stagnační zóny nebo oblasti se slabým průtokem.
- Optimalizujte průřezy kanálů (kruhové, eliptické, obdélníkové) a rozměry podél cesty, abyste zachovali požadované průtoky a maximalizovali přenos tepla tam, kde je to nejvíce potřeba.
- Ověřte účinnost integrovaných prvků pro zvýšení turbulence.
- Minimální poloměry a plynulé přechody: Ačkoli AM umožňuje vytvářet složité křivky, příliš ostré ohyby mohou zvyšovat tlakové ztráty, vytvářet stagnační zóny a potenciálně ztěžovat spolehlivý tisk nebo odstraňování prášku. Snažte se o hladké, pozvolné přechody a dodržujte minimální poloměry ohybu doporučené pro konkrétní proces AM a materiál.
- Shodnost: Zajistěte, aby trasa kanálu skutečně co nejpřesněji kopírovala obrysy oblasti zdroje tepla a zachovávala stejnou vzdálenost pro rovnoměrný odběr tepla. DfAM toto přesné umístění umožňuje.
2. Samonosné úhelníky a podpěrné konstrukce:
- Převisy a úhly: Procesy AM kovů, jako je SLM, vytvářejí vrstvu po vrstvě. Strmé převisy nebo vodorovné prvky vyžadují během procesu sestavování podpůrné struktury, aby se zabránilo jejich zborcení nebo deformaci. Vnitřní kanály ze své podstaty vytvářejí převisy (“střecha” kanálu).
- Samonosné geometrie: Je velmi žádoucí navrhovat kanály s průřezy, které minimalizují potřebu vnitřních podpěr. Úhly obvykle větší než 45 stupňů od vodorovné roviny mohou být často samonosné (v závislosti na materiálu, stroji a parametrech). Pro vodorovné průřezy kanálů se někdy místo čistě kruhových používají slzovité nebo kosočtvercové tvary, aby se vytvořily samonosné geometrie.
- Strategie podpory (pokud je to nevyhnutelné): Pokud jsou v kanálech nutné vnitřní podpěry, musí být navrženy tak, aby je bylo možné během následného zpracování účinně odstranit. To zvyšuje složitost a náklady. DfAM se zaměřuje na minimalizaci nebo odstranění této potřeby prostřednictvím chytré orientace a geometrických voleb. Vnější podpěry, které drží díl na konstrukční desce, jsou standardní a odstraňují se později.
3. Tloušťka stěny a minimální velikost prvku:
- Minimální tloušťka stěny: Existuje určitý limit, jak tenké stěny lze spolehlivě vytisknout. To závisí na rozlišení stroje AM, velikosti laserového paprsku, vlastnostech prášku a materiálu. U chladicích kanálů musí být stěna oddělující chladicí kapalinu od horkého materiálu součásti dostatečně silná kvůli strukturální integritě a prevenci úniku, ale dostatečně tenká, aby se minimalizoval tepelný odpor. Typická minimální tloušťka stěny pro tisk se může pohybovat od 0,3 mm do 0,8 mm, ale konstrukční pokyny často doporučují o něco silnější stěny kvůli robustnosti, zejména v kritických leteckých aplikacích.
- Minimální průměr kanálu: Stejně tak je stanoven minimální průměr kanálků, které lze spolehlivě vytisknout a, což je rozhodující, po sestavení vyčistit od neroztaveného prášku. To často určuje spodní hranici pro velikost kanálů, obvykle kolem 0,5 mm až 1,0 mm, ačkoli konkrétní možnosti by měly být potvrzeny u výrobce servisní kancelář pro 3D tisk kovů.
- Poměr stran: Velmi vysoké a tenké stěny mohou být náchylné k deformaci nebo nestabilitě během tisku. DfAM zohledňuje poměry stran prvků, aby byla zajištěna vyrobitelnost.
4. Integrace funkcí pro vylepšení toku:
- Turbulátory: AM umožňuje přímou integraci vnitřních prvků, jako jsou žebra, hrbolky, spirály (trip strips) nebo pole pin-fin do chladicích kanálů. Tyto prvky narušují laminární mezní vrstvu proudění, vyvolávají turbulence a významně zvyšují konvekční součinitel přestupu tepla mezi chladivem a stěnou kanálu.
- Složitost návrhu: Návrh těchto prvků vyžaduje pečlivou analýzu CFD, aby bylo zajištěno, že účinně zlepšují přenos tepla, aniž by způsobovaly nadměrné tlakové ztráty. Schopnost spolehlivého tisku těchto složitých prvků je klíčovou výhodou AM.
5. Navrhování pro odstraňování prášku:
- Zachycený prášek: Netavený kovový prášek ve složitých, často spletitých cestách konformních chladicích kanálů představuje velkou výzvu. Konstrukce musí usnadnit odstraňování prášku při následném zpracování.
- Přístupová místa: Vložte strategicky umístěné přístupové otvory nebo otvory (které mohou být později utěsněny), aby bylo možné proplachovat, vyfukovat nebo vibrovat prášek z kanálů.
- Kontinuita kanálu: Vyhněte se konstrukcím, které vytvářejí zcela izolované vnitřní dutiny, z nichž nelze odstranit prášek. Zajistěte, aby všechny úseky kanálů měly vstupní a výstupní cestu.
- Hladké vnitřní povrchy: Ačkoli AM vytváří ze své podstaty drsnější povrchy, může to být ovlivněno volbou konstrukce. Hladší vnitřní povrchy (dosažené orientací, parametry nebo volbou geometrie, například vyhnutím se ostrým vnitřním rohům) mohou usnadnit odstraňování prášku.
6. Využití simulačních nástrojů:
- Optimalizace topologie: Softwarové nástroje mohou optimalizovat rozložení materiálu pro maximální tuhost nebo tepelný výkon při současné minimalizaci hmotnosti, což často vede k organicky vypadajícím strukturám ideálním pro AM. To lze aplikovat na celkovou konstrukci součásti zahrnující chladicí kanály.
- Simulace procesu: Simulace samotného procesu výroby AM může pomoci předvídat potenciální problémy, jako je akumulace zbytkového napětí a deformace, což konstruktérům umožní proaktivně upravit geometrii nebo strategii podpory.
Úloha Met3dp v DfAM:
Úspěšná implementace DfAM vyžaduje nejen teoretické znalosti, ale také praktické zkušenosti s konkrétními procesy a materiály AM. Spolupráce se zkušeným služby aditivní výroby poskytovatele, jako je Met3dp, může být neocenitelný. Jejich služby vývoje aplikací mohou klientům pomoci:
- Optimalizace návrhů pro jejich konkrétní zařízení AM (včetně špičkového objemu a přesnosti tisku).
- Poradenství v oblasti konstrukčních omezení specifických pro daný materiál (např. samonosné úhly pro IN625 vs. AlSi10Mg).
- Efektivní využití simulačních nástrojů.
- Vývoj strategií pro generování podpory a odstraňování prášku na základě rozsáhlých znalostí procesu.
Integrací principů DfAM se mohou inženýři posunout od pouhého tisku stávajících konstrukcí ke skutečnému využití technologie AM pro tvorbu nové generace chladicích řešení pro letectví a kosmonautiku s vynikajícím výkonem a spolehlivostí.
Dosažení přesnosti: Tolerance, povrchová úprava a rozměrová přesnost v chladicích kanálech AM
Ačkoli aditivní výroba kovů nabízí bezkonkurenční geometrickou volnost, dosažení úzkých tolerancí, specifických povrchových úprav a celkové rozměrové přesnosti, které jsou vyžadovány pro mnoho leteckých aplikací, včetně konformních chladicích kanálů, vyžaduje pečlivou kontrolu procesu, porozumění chování materiálu a často i následné zpracování. Manažeři a inženýři pro zadávání zakázek potřebují realistická očekávání ohledně přesnosti dosažitelné přímo v procesu AM a ohledně toho, jaké dokončovací kroky mohou být nezbytné.
1. Tolerance v kovovém AM:
- Obecné dosažitelné tolerance: Obecně lze říci, že procesy AM pro kovy, jako je SLM a EBM, mohou obvykle dosáhnout rozměrových tolerancí v rozmezí ±0,1 mm až ±0,3 mm na středních vzdálenostech (např. 100 mm), přičemž u menších prvků je možné dosáhnout ještě větších tolerancí (např. ±0,05 mm) s optimalizovanými procesními parametry a špičkovými stroji. Jedná se však o obecné údaje, které se mohou výrazně lišit v závislosti na:
- Kalibrace a kvalita strojů: Klíčové jsou vysoce přesné a dobře udržované stroje, které kladou důraz na přesnost a spolehlivost. Společnost Met3dp zdůrazňuje tyto aspekty ve své nabídce zařízení.
- Materiál: Různé materiály vykazují během zpracování různou míru smrštění a deformace (např. vyšší tepelné gradienty IN625’ mohou vyvolat větší napětí/deformaci než AlSi10Mg).
- Geometrie dílu & Velikost: Větší díly a složité geometrie s výraznými teplotními změnami hmotnosti jsou náchylnější k deformaci.
- Orientace na stavbu: Orientace dílu na konstrukční desce má vliv na přesnost vzhledem k vrstevnatosti a požadavkům na podporu.
- Parametry procesu: Výkon laseru/ paprsku, rychlost skenování, tloušťka vrstvy a strategie skenování ovlivňují konečné rozměry.
- Požadavky na letectví a kosmonautiku: Letecké součásti často vyžadují přísnější tolerance, zejména u styčných ploch, rozhraní a kritických průtokových cest. Zatímco AM může dosáhnout tvar blízký tvaru sítě, kritické tolerance často vyžadují dodatečné obrábění.
- standardy: Normy jako řada ISO/ASTM 52900 poskytují rámec pro specifikaci tolerancí AM.
2. Povrchová úprava (drsnost):
- Drsnost povrchu podle stavu: Kovové díly AM mají ve srovnání s obráběnými díly ze své podstaty hrubší povrch. Drsnost závisí do značné míry na:
- Distribuce velikosti částic (PSD): Jemnější a rovnoměrnější prášky obecně vedou k hladším povrchům. To podtrhuje význam vysoce kvalitní kovové prášky jako jsou ty z Met3dp.
- Tloušťka vrstvy: Tenčí vrstvy obvykle vedou k hladším povrchům, ale prodlužují dobu výstavby.
- Orientace povrchu: Povrchy vytvořené rovnoběžně s konstrukční deskou (směrem dolů) nebo pod strmým úhlem bývají drsnější v důsledku “schodovitého” efektu a ulpívání částečně roztavených částic prášku. Svislé stěny jsou obecně hladší. Povrchy směřující vzhůru jsou často nejhladší.
- Parametry procesu: Příkon energie a strategie skenování ovlivňují dynamiku taveniny a strukturu povrchu.
- Typické hodnoty Ra: Drsnost povrchu (Ra) dílů vyrobených metodou SLM/EBM se často pohybuje v rozmezí od 6 µm do 25 µm (nebo více pro určité orientace/materiály).
- Vliv na chladicí kanály: Důležitá je zejména drsnost vnitřního povrchu kanálu:
- Pokles tlaku: Drsnější povrchy zvyšují třecí ztráty, což vede k vyšším tlakovým ztrátám při průtoku chladicí kapaliny.
- Přenos tepla: Drsnost může někdy zvýšit turbulentní přenos tepla, ale nadměrná drsnost může bránit rozvoji proudění nebo vytvářet zárodky varu, pokud není zamýšlena.
- Odstranění prášku: Drsnější vnitřní povrchy mohou ztížit úplné odstranění prášku.
- Únavový život: Drsnost povrchu může být místem vzniku únavových trhlin, což může mít vliv na životnost součásti při cyklickém zatížení.
- Zlepšení povrchové úpravy: K dosažení hladšího povrchu vnitřních kanálů (např. Ra < 5 µm nebo dokonce nižšího), pokud je to nutné z hlediska výkonu nebo čistitelnosti, jsou často zapotřebí techniky následného zpracování, jako je abrazivní průtokové obrábění (AFM), chemické leptání/leštění nebo elektrochemické leštění (ECP).
3. Rozměrová přesnost a metrologie:
- Kontrola zkreslení: Zbytková napětí vznikající během rychlých cyklů ohřevu a chlazení při AM mohou způsobit deformaci dílů, zejména po vyjmutí z konstrukční desky nebo během tepelného zpracování. Strategie pro kontrolu tohoto jevu zahrnují optimalizované podpůrné struktury, specifické strategie skenování (např. ostrovní skenování), ohřev konstrukční desky a tepelné zpracování po odstranění napětí.
- Metrologie a kontrola: Ověřování rozměrové přesnosti a vnitřní geometrie složitých dílů AM s konformními kanály vyžaduje pokročilé metrologické techniky:
- Souřadnicové měřicí stroje (CMM): Vnější rozměry a přístupné prvky.
- Optické / laserové skenování: Zachycení celkového tvaru a porovnání s modelem CAD.
- Počítačová tomografie (CT): Klíčové pro nedestruktivní kontrolu a měření vnitřních kanálů, detekci defektů (pórovitost, trhliny), ověření tloušťky stěn a kvalitativní posouzení drsnosti vnitřního povrchu. CT skenování se stává nepostradatelným nástrojem pro kvalifikaci kritických leteckých dílů AM.
- Dosažení konečné přesnosti: Pro prvky vyžadující velmi vysokou přesnost (např. těsnicí plochy, rozhraní ložisek, přesné průměry vstupních/výstupních kanálů), CNC obrábění se obvykle používá jako krok následného zpracování dílu AM s blízkým tvarem sítě.
Dosažení přesnosti u poskytovatelů služeb:
Práce s servisní kancelář pro 3D tisk kovů zkušenostmi z leteckých aplikací je rozhodující pro dosažení požadované přesnosti. Měli by mít:
- Kalibrované systémy AM s vysokým rozlišením.
- Robustní řízení a monitorování procesu.
- Odborné znalosti parametrů specifických pro materiál a DfAM pro kontrolu tolerance.
- Zavedené možnosti následného zpracování (nebo silné partnerství).
- Pokročilé metrologické vybavení, včetně možnosti CT skenování pro interní validaci prvků.
Pochopení vzájemného vztahu mezi designem (DfAM), zvoleným AM procesem (např. SLM, EBM - viz informace Met3dp’ o tiskových metod), vlastnosti materiálu a následné zpracování je klíčem k úspěšné výrobě leteckých konformních chladicích kanálů, které splňují náročné požadavky na přesnost.
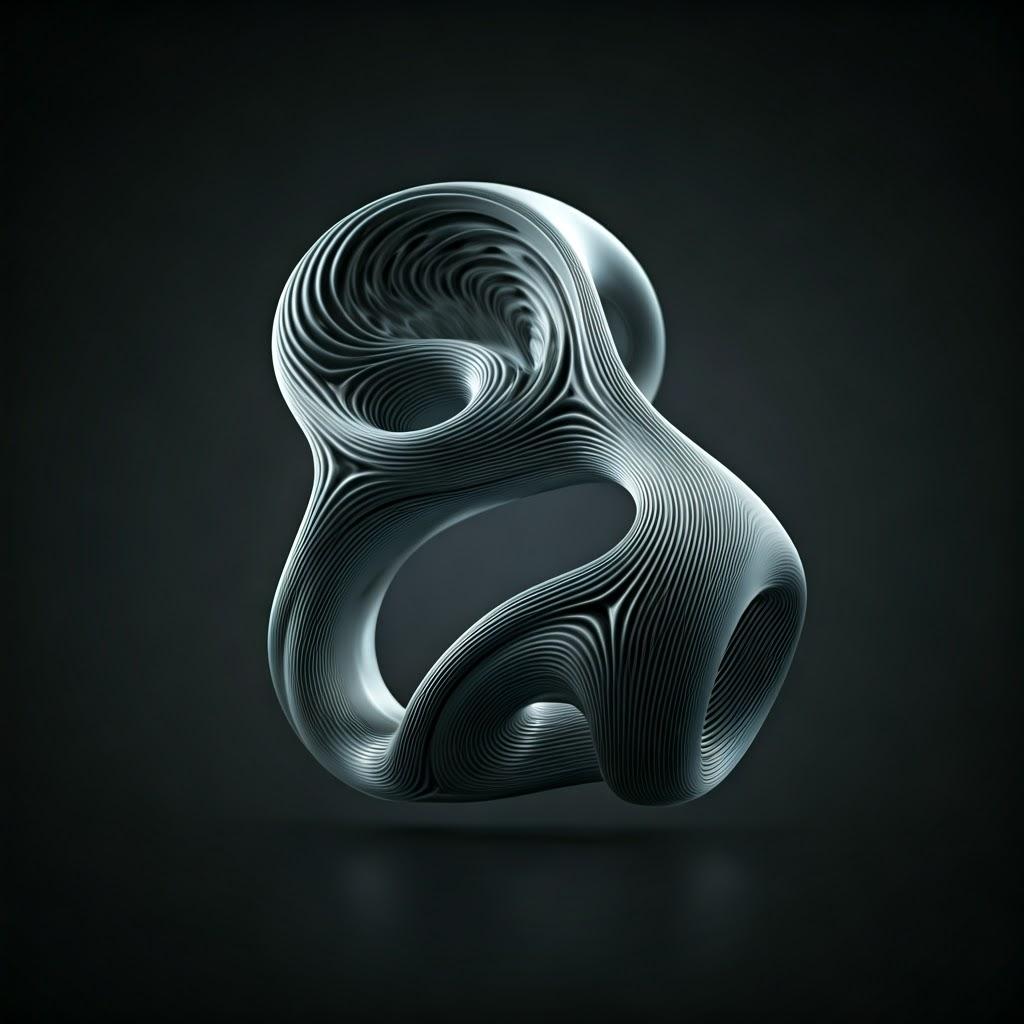
Za hranice tisku: Zásadní následné zpracování chladicích komponentů pro letectví a kosmonautiku
Výroba kovového dílu po vrstvách pomocí aditivní výroby je často pouze prvním krokem ve výrobním procesu, zejména u vysoce výkonných leteckých komponent, jako jsou konformní chladicí kanály. Řada následné zpracování kovů AM obvykle je nutné provést kroky, které z hotového dílu vytvoří funkční certifikovanou součást, která splňuje přísné letecké normy pro mechanické vlastnosti, rozměrovou přesnost, povrchovou úpravu a čistotu. Zanedbání nebo nesprávné provedení těchto kroků může ohrozit integritu a výkonnost konečného výrobku.
Klíčové fáze následného zpracování zahrnují:
1. Tepelné ošetření proti stresu:
- Účel: Rychlé zahřívání a ochlazování, které je vlastní procesům tavení v práškovém loži, vyvolává v tištěném dílu značná zbytková napětí. Tato napětí mohou způsobit deformaci při vyjmutí z konstrukční desky nebo při následném obrábění a mohou mít negativní vliv na únavovou životnost.
- Proces: Díly jsou obvykle tepelně zpracovávány ještě na konstrukční desce v peci s řízenou atmosférou. Konkrétní teplotní cyklus (rychlost ohřevu, teplota namáčení, doba, rychlost chlazení) závisí do značné míry na materiálu (např. různé cykly pro AlSi10Mg vs. IN625) a geometrii dílu.
- Důležitost: Často se jedná o povinný první krok před jakoukoli mechanickou prací (jako je odstranění podpěr nebo obrábění), aby byla zajištěna rozměrová stabilita.
2. Vyjmutí dílu ze stavební desky:
- Proces: Po uvolnění napětí je třeba díl(y) oddělit od konstrukční desky. To se obvykle provádí pomocí:
- Drátové elektroerozivní obrábění (EDM): Nabízí přesné řezání s minimálním indukovaným napětím.
- Pásové řezání: Rychlejší, ale méně přesné a může vyvolat mechanické namáhání.
- Obrábění: Frézování základny dílu od desky.
- Úvaha: Zvolená metoda závisí na geometrii dílu, požadované přesnosti na základně a na nákladových faktorech.
3. Odstranění podpůrné konstrukce:
- Účel: Podpěrné konstrukce, které jsou při stavbě nutné kvůli přesahům a stabilitě, musí být odstraněny.
- Proces: To může být pracný proces, který často zahrnuje:
- Ruční lámání/řezání (u snadno přístupných podpěr).
- CNC obrábění (frézování, broušení) pro integrovanější nebo hůře dostupné podpěry.
- Drátové elektroerozivní obrábění nebo v některých případech elektrochemické obrábění.
- Výzva: Odstranění podpěr bez poškození povrchu dílu vyžaduje opatrnost. Vnitřní podpěry v chladicích kanálech jsou obzvláště náročné a je ideální se jim vyhnout pomocí DfAM. Konstrukce často zahrnuje svědecké značky nebo prvky, které slouží k přesnému odstranění při obrábění.
4. Odstranění prášku (zbavení prachu):
- Účel: Velmi důležité pro komponenty s vnitřními kanály. Ze složitých kanálků je třeba odstranit veškerý nerozpuštěný prášek.
- Proces: Vyžaduje kombinaci metod:
- Vyfukování stlačeného vzduchu.
- Vibrační tabulky.
- Ultrazvukové čisticí lázně.
- Proplachování vhodnými rozpouštědly nebo kapalinami.
- Tepelné cyklování (někdy může pomoci uvolnit slinutý prášek).
- Ověření: Často se ověřuje pomocí vizuální kontroly (boreskopy kanálů), vážení dílu nebo CT skenování, aby se zajistilo, že jsou kanály čisté. Neúplné odstranění prášku může bránit průtoku chladicí kapaliny, snižovat tepelný výkon nebo se z něj mohou stát uvolněné úlomky, které způsobí problémy v následném procesu.
5. Lisování za tepla (HIP):
- Účel: Odstranění vnitřní mikroporozity (dutin), která může zůstat po procesu AM, zlepšení hustoty materiálu a výrazné zlepšení mechanických vlastností, zejména únavové pevnosti, tažnosti a lomové houževnatosti.
- Proces: Díly jsou vystaveny vysoké teplotě (pod bodem tání) a vysokému tlaku inertního plynu (obvykle argonu) současně ve specializované nádobě HIP. Tlak sbalí vnitřní dutiny a materiál se difuzně spojí přes rozhraní dutin.
- Důležitost: Často povinné pro kritické Letecké komponenty HIP, zejména rotujících dílů nebo dílů vystavených vysokému cyklickému zatížení, jako jsou součásti turbín vyrobené z IN625. Zajišťuje, že vlastnosti materiálu se blíží kovaným nebo litým ekvivalentům.
6. Obrábění (CNC):
- Účel: Dosažení konečných rozměrových tolerancí u kritických prvků, styčných ploch, rozhraní (např. přípojných míst pro vedení kapalin), těsnicích ploch a v případě potřeby zlepšení kvality povrchu.
- Proces: Standard CNC obrábění operace (frézování, soustružení, vrtání, broušení) se provádějí na dílu AM ve tvaru blízkém tvaru sítě. Upínání složitých geometrií AM může být náročné.
- Integrace: DfAM by měl zohlednit potřebný zásobník pro obrábění na příslušných plochách.
7. Vnitřní úprava kanálů:
- Účel: Zlepšení kvality povrchu uvnitř konformních chladicích kanálů, pokud je drsnost povrchu ve výchozím stavu nedostatečná pro požadavky na průtok nebo normy čistoty.
- Proces: Specializované techniky mohou zahrnovat:
- Obrábění abrazivním tokem (AFM): Čerpání tmelu s abrazivními částicemi tam a zpět přes kanály, aby se vyhladily povrchy a zaoblily hrany.
- Chemické leštění/leptání: Použití chemických roztoků k selektivnímu odstranění materiálu a vyhlazení povrchu. Vyžaduje pečlivou kontrolu a kompatibilitu materiálu.
- Elektrochemické leštění (ECP): Podobné chemickému leštění, ale k lepšímu odstranění materiálu se používá elektrický proud.
8. Povrchové úpravy a nátěry:
- Účel: Pro zvýšení odolnosti proti opotřebení, ochrany proti korozi, tepelné bariéry nebo jednoduše z kosmetických důvodů.
- Proces: V závislosti na požadavcích mohou ošetření zahrnovat:
- Zpevňování povrchu (zvyšuje únavovou životnost).
- Leštění nebo elektrolytické leštění (vnější povrchy).
- Eloxování (pro hliníkové slitiny jako AlSi10Mg).
- Lakování nebo práškové lakování.
- Specializované povlaky pro letecký průmysl (např. tepelně bariérové povlaky (TBC) pro součásti horké části).
9. Kontrola a testování:
- Účel: Konečné ověření, zda díl splňuje všechny specifikace.
- Proces: Zahrnuje:
- Rozměrová kontrola (CMM, skenování).
- Nedestruktivní zkoušení (NDT): (vnitřní geometrie/defekty), fluorescenční penetrační kontrola (FPI) (povrchové defekty), ultrazvukové testování (UT) (vnitřní defekty).
- Testování těsnosti: Pro zajištění integrity chladicích kanálů je to nezbytné. Může být použita tlaková zkouška nebo zkouška těsnosti pomocí helia.
- Kontroly certifikace materiálu.
Správa pracovních postupů:
Řízení této složité posloupnosti kroků následného zpracování vyžaduje značné odborné znalosti a koordinaci. Poskytovatelé služeb v oblasti AM kovů jako Met3dp často spolupracují se sítí kvalifikovaných partnerů pro specializované procesy, jako je HIP, NDT a povrchová úprava, a nabízejí tak svým zákazníkům efektivnější pracovní postup. Přístup k robustní tiskové technologii, jak je podrobně popsáno na stránkách, jako je Met3dp’s produkt přehled, je výchozím bodem, ale zajištění efektivního řízení celého procesu od začátku do konce je klíčem k dodání leteckých komponentů připravených k letu.
Zvládání výzev: Překonávání překážek při výrobě konformního chlazení AM
Přestože aditivní výroba kovů otevírá neuvěřitelný potenciál pro složité letecké komponenty, jako jsou konformní chladicí kanály, není tato technologie bez problémů. Pochopení těchto potenciálních překážek a zavedení účinných strategií jejich zmírnění je pro úspěšné zavedení a výrobu klíčové. Inženýři a specialisté na zásobování by si měli být vědomi běžných problémů, které se vyskytují při výrobě dílů AM se složitou vnitřní geometrií:
1. Zbytkové napětí a deformace:
- Problém: Rychlé, lokalizované cykly zahřívání a ochlazování, které jsou vlastní fúzi v laserovém nebo elektronovém svazku v práškovém loži, vytvářejí významné tepelné gradienty. Při tuhnutí a smršťování vrstev vznikají v dílu vnitřní pnutí. Tato napětí mohou způsobit:
- Deformace/zkreslení: Díl se může deformovat během sestavování, po vyjmutí ze sestavovací desky nebo během následného tepelného zpracování.
- Praskání: U náchylných materiálů nebo špatně navržených dílů může vysoké zbytkové napětí vést k praskání během výroby nebo později během provozu.
- Dotčené materiály: Ačkoli se vyskytuje ve většině kovů, je obzvláště náročný v materiálech s vysokým koeficientem tepelné roztažnosti nebo v materiálech zpracovávaných při velmi vysokých teplotách, jako jsou niklové superslitiny (IN625) a některé slitiny titanu.
- Strategie zmírnění dopadů:
- Optimalizované podpůrné struktury: Dobře navržené podpěry pevně ukotví díl ke stavební desce a zabrání jeho deformaci během sestavování.
- Vytápění stavebních desek: Předehřívání konstrukční desky (běžné u EBM, stále častěji používané u SLM) snižuje tepelné gradienty mezi tuhnoucím dílem a okolním práškem/deskou.
- Optimalizace strategie skenování: Použití specifických vzorů (např. skenování ostrůvků, střídání směrů šrafování) rovnoměrněji rozděluje tepelný příkon a snižuje lokální špičky napětí.
- Řízení procesních parametrů: Přesné nastavení výkonu, rychlosti a zaměření laseru/paprsku ovlivňuje velikost taveniny a rychlost chlazení.
- DfAM: Navrhování dílů s rovnoměrnějšími průřezy, zamezení vzniku velkých tepelných hmot spojených tenkými průřezy a začlenění prvků snižujících napětí.
- Úleva od stresu po stavbě: Kritický krok tepelného zpracování, který se provádí před vyjmutím dílu z konstrukční desky.
2. Odstranění zachyceného prášku:
- Problém: Zajištění úplného odstranění netaveného kovového prášku z dlouhých, úzkých a klikatých vnitřních chladicích kanálů je značnou výzvou. Zachycený prášek může:
- Blokuje nebo omezuje průtok chladicí kapaliny, což zhoršuje tepelný výkon.
- Stane se slinutým (částečně roztaveným), což ještě více ztěžuje jeho odstranění.
- Se během provozu uvolňují nečistoty, které mohou poškodit navazující součásti.
- Strategie zmírnění dopadů:
- DfAM pro Depowdering: Navrhování kanálů s přiměřeným průměrem (vyhnout se extrémně jemným průchodům), hladkými ohyby a strategicky umístěnými přístupovými otvory pro čištění. Vyvarování se slepých dutin.
- Optimalizovaná orientace sestavení: Orientace dílu pro usnadnění gravitačního odvodu prášku během sestavování a po něm.
- Účinné techniky vyprazdňování: Využívá kombinaci stlačeného vzduchu, vibrací, ultrazvukového čištění a případně specializovaných proplachovacích zařízení.
- Kvalita prášku: Vysoce kulovité prášky s dobrou sypností (na které se zaměřují dodavatelé jako Met3dp) se obecně odstraňují snadněji než nepravidelné prášky.
- Ověření: Pomocí boroskopů, testů proudění vzduchu, vážení nebo CT vyšetření ověřte, zda jsou kanály čisté.
3. Pórovitost:
- Problém: V tištěném materiálu se mohou vytvořit malé dutiny nebo póry v důsledku neúplného spojení mezi vrstvami, zachycení plynu z prášku nebo ochranného plynu nebo keyholingu (rozpadu v důsledku deprese páry) v důsledku nadměrného příkonu energie. Pórovitost může:
- Snížení mechanických vlastností (zejména únavové pevnosti a tažnosti).
- Fungují jako iniciační místa pro crack.
- Pokud se póry propojí, mohou potenciálně vzniknout netěsnosti.
- Strategie zmírnění dopadů:
- Optimalizované parametry procesu: Přesné řízení hustoty energie (výkon, rychlost, rozteč šraf, tloušťka vrstvy) je zásadní pro zajištění úplného roztavení a tavení bez přehřátí. Různé aditivní výrobní metody mohou mít různou citlivost.
- Vysoce kvalitní prášek: Použití prášku s nízkou vnitřní pórovitostí plynu, kontrolovaným chemickým složením a konzistentním PSD minimalizuje problémy se zachycováním plynu. Met3dp’s využitím pokročilé atomizace (Gas Atomization, PREP) se zaměřuje na prášky s nízkou pórovitostí.
- Správný stínicí plyn: Udržování vysoce čisté atmosféry inertního plynu (argonu nebo dusíku) ve stavební komoře zabraňuje oxidaci a kontaminaci.
- Izostatické lisování za tepla (HIP): Vysoce účinné při uzavírání vnitřních pórů, což výrazně zlepšuje integritu materiálu (často povinné u kritických dílů).
- Detekce: Základní metodou pro nedestruktivní detekci a kvantifikaci vnitřní pórovitosti je CT vyšetření.
4. Zajištění integrity úniku:
- Problém: U chladicích kanálů, kterými se přenášejí kapaliny, je nejdůležitější zabránit únikům přes stěny kanálů nebo na rozhraních. Netěsnosti mohou vznikat v důsledku propojené pórovitosti, trhlin nebo defektů na rozhraních.
- Strategie zmírnění dopadů:
- Robustní DfAM: Zajištění dostatečné tloušťky stěn, aby nedocházelo ke koncentraci napětí.
- Řízení procesu & Optimalizace parametrů: Minimalizace pórovitosti a prasklin během stavby.
- HIP: Uzavření vnitřních dutin významně snižuje riziko vzniku propojených pórů, které vedou k netěsnostem.
- Post-Machining: Zajištění hladkých a přesných těsnicích ploch na rozhraních.
- Důkladné testování těsnosti: Zavedení vhodných protokolů o rozpadu tlaku, stopovacím plynu (např. helium) nebo hydrostatických zkouškách jako součásti procesu zajištění kvality.
5. Kontrola povrchové úpravy:
- Problém: Dosažení požadované vnitřní povrchové úpravy pro optimální dynamiku kapalin nebo čistotu může být vzhledem k povaze výroby po vrstvách náročné.
- Strategie zmírnění dopadů:
- Optimalizovaná orientace a parametry: Výběr orientace sestavení a parametrů, o nichž je známo, že vytvářejí hladší povrchy kritických vnitřních prvků.
- DfAM: Použití tvarů kanálů méně náchylných k drsnosti spodní vrstvy.
- Následné zpracování: Použití technik, jako je AFM nebo chemické/elektrochemické leštění, pokud je povrchová úprava podle stavu konstrukce nedostatečná.
Řešení těchto problémů výzvy pro aditivní výrobu v letectví a kosmonautice vyžaduje kombinaci důkladných konstrukčních postupů (DfAM), pečlivé kontroly procesu během výroby AM, vysoce kvalitních materiálů, vhodných technik následného zpracování a důkladných kontrolních a testovacích protokolů. Spolupráce se zkušenými poskytovatelé služeb v oblasti AM kovů kteří těmto výzvám rozumí a mají osvědčené strategie pro jejich zmírnění, je klíčem k úspěšnému zavedení AM pro náročné aplikace, jako jsou konformní chladicí kanály v letectví a kosmonautice.
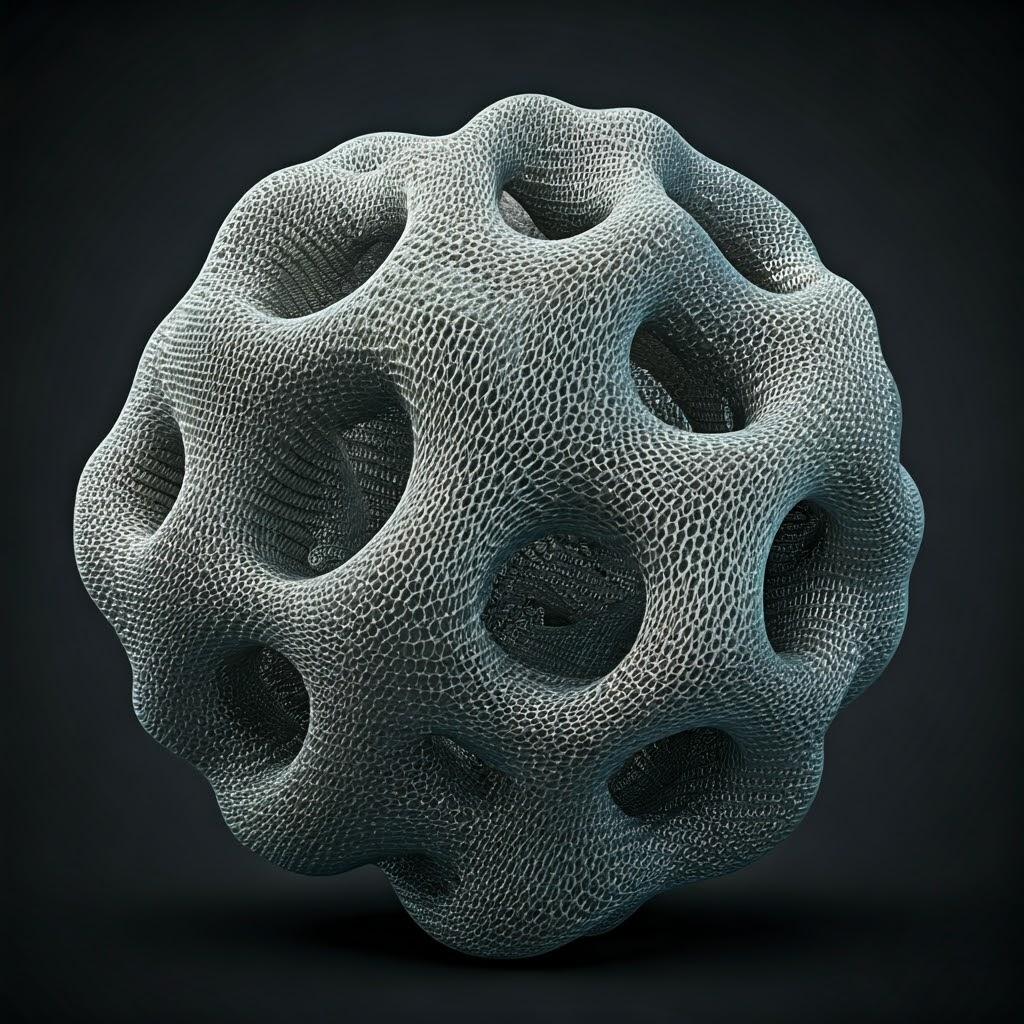
Partnerství pro úspěch: Výběr poskytovatele služeb v oblasti AM pro aplikace v letectví a kosmonautice
Výběr správného výrobního partnera je vždy velmi důležitý, ale v případě složitých leteckých komponentů s vysokými nároky, jako jsou konformní chladicí kanály vyráběné aditivní výrobou kovů, vyžaduje výběr mimořádnou pečlivost. Ne všechny poskytovatelé služeb v oblasti AM kovů disponuje specializovanými odbornými znalostmi, přísnými systémy kvality a certifikovanými procesy, které jsou nezbytné pro splnění náročných standardů leteckého průmyslu. Inženýři a manažeři nákupu musí potenciální partnery hodnotit na základě komplexního souboru kritérií, aby zajistili úspěšné výsledky a zmírnili rizika.
Na co se zaměřit při výběru svého dodavatel AM pro letecký průmysl:
1. Certifikace pro letectví a kosmonautiku a systém řízení kvality (QMS):
- Certifikace AS9100: Jedná se o mezinárodně uznávaný standard QMS pro letecký, kosmický a obranný průmysl. Certifikace podle AS9100 (nebo ekvivalentních norem, jako je EN 9100) prokazuje, že poskytovatel zavedl přísné procesy pro kontrolu kvality, sledovatelnost, řízení rizik a neustálé zlepšování speciálně přizpůsobené požadavkům leteckého průmyslu. Často je to neoddiskutovatelný předpoklad pro 3D tisk certifikovaný pro letecký průmysl.
- Certifikace ISO 9001: Základní norma QMS, která označuje robustní obecné procesy kvality.
- Dokumentovaný systém řízení jakosti: Kromě certifikací si prostudujte jejich příručku kvality. Pochopte jejich postupy pro kontrolu při příjmu materiálu, manipulaci s práškem a sledovatelnost, monitorování procesu sestavování, kontrolu parametrů, řízení neshod, nápravná opatření a závěrečnou kontrolu.
2. Schopnosti a technologie stroje:
- Vhodná technologie AM: Provozují správný typ strojů pro AM obrábění kovů (např. SLM, EBM) vhodných pro vámi zvolený materiál (AlSi10Mg, IN625) a požadavky na aplikaci (rozlišení, kvalita povrchu, produktivita)?
- Strojový park & Stav: Posoudit velikost, stáří a stav údržby strojového parku. Mají dostatečnou kapacitu a redundanci? Jsou stroje pravidelně kalibrovány? Poskytovatelé, jako je Met3dp, nabízející vlastní řadu tiskáren s důrazem na špičkový objem, přesnost a spolehlivost tisku, prokázat hlubokou znalost požadavků na hardware.
- Objem sestavení: Ujistěte se, že jejich stroje mohou pojmout velikost vaší součásti.
- Monitorování procesů: Informujte se o možnostech monitorování in-situ (např. monitorování taveniny, termovizní snímkování), které mohou poskytnout cenné údaje pro zajištění kvality.
3. Odbornost a manipulace s materiálem:
- Prokazatelné zkušenosti s leteckými slitinami: Klíčový je prokazatelný úspěch při tisku konkrétních požadovaných slitin (např. AlSi10Mg, IN625, Ti6Al4V). Požádejte o příklady nebo případové studie.
- Získávání a kontrola kvality prášků: Kde získávají prášky? Mají přísné postupy vstupní kontroly a testování kvality prášku (PSD, morfologie, chemie, tekutost)? Používají vysoce kvalitní prášky od renomovaných dodavatelů nebo výrobců, jako je Met3dp, známý svými pokročilými systémy výroby prášků (plynová atomizace, PREP)?
- Správa prášku a sledovatelnost: Přísné protokoly pro manipulaci s práškem, skladování (prevence kontaminace a absorpce vlhkosti), segregaci mezi různými slitinami a sledovatelnost šarží v celém výrobním procesu jsou nezbytné pro zajištění shody s předpisy pro letecký průmysl. Jak je řízen a dokumentován životní cyklus prášku (použití, recyklace)?
4. Možnosti následného zpracování (vlastní nebo spravovaná síť):
- Komplexní pracovní postup: Jak již bylo řečeno, následné zpracování je velmi důležité. Nabízí poskytovatel potřebné služby, jako je odlehčení napětí, HIP, odstranění podpěr, CNC obrábění, povrchová úprava (AFM, leštění), NDT a zkoušky těsnosti, a to buď přímo u sebe, nebo prostřednictvím sítě kvalifikovaných a auditovaných partnerů?
- Integrované řízení: Existence jediného kontaktního místa, které řídí celý pracovní postup, včetně externích partnerů, zjednodušuje řízení projektu a zajišťuje odpovědnost.
5. Technická podpora a odbornost DfAM:
- Podpora návrhu pro aditivní výrobu (DfAM): Může vám jejich technický tým poradit s optimalizací vašeho návrhu z hlediska tisknutelnosti, výkonu a hospodárnosti? Mohou pomoci s optimalizací topologie nebo strategií podpůrné struktury?
- Simulace procesu: Využívají nástroje pro simulaci procesů sestavování k předvídání a zmírnění potenciálních problémů, jako je zkreslení?
- Znalost aplikace: Rozumí specifickým výzvám a požadavkům aplikací tepelného managementu v letectví a kosmonautice? Společnost Met3dp, která se zaměřuje na průmyslové aplikace a služby vývoje aplikací, se prezentuje jako více než jen tiskárna; je poskytovatelem řešení.
6. Kontrolní a metrologické schopnosti:
- Pokročilé vybavení: Zásadní význam má přístup k vhodným metrologickým nástrojům, včetně souřadnicových měřicích strojů, 3D skenerů a především CT skenování pro nedestruktivní vnitřní kontrolu chladicích kanálů.
- Kvalifikovaný personál: Jsou požadováni certifikovaní inspektoři NDT a metrologové.
- Podávání zpráv: Základními výstupy jsou přehledné a komplexní inspekční zprávy dokumentující soulad se specifikacemi.
7. Dosavadní výsledky a pověst:
- Zkušenosti v letectví a kosmonautice: Úspěšně realizovali podobné projekty pro jiné klienty z oblasti letectví a kosmonautiky? Mohou poskytnout reference nebo případové studie (při zachování důvěrnosti)?
- Spolehlivost a komunikace: Zhodnoťte jejich schopnost reagovat, srozumitelnost komunikace a dodržování termínů.
Hodnocení potenciálních partnerů:
Kritéria | Klíčové otázky, které je třeba položit | Proč je to důležité pro chladicí kanály v letectví a kosmonautice | Jak se Met3dp přizpůsobuje (na základě poskytnutých informací) |
---|---|---|---|
Certifikace & QMS | Jste certifikováni podle AS9100? Můžeme zkontrolovat vaši dokumentaci QMS? Jak zajišťujete sledovatelnost? | Zajišťuje dodržování předpisů, kontrolu procesů a řízení rizik, které jsou důležité pro bezpečnost letů. | Ačkoli AS9100 není výslovně uveden, zaměření na “průmyslové aplikace ” “přesnost ” “spolehlivost” naznačuje závazek k dodržování vysokých standardů. QMS implikuje zaměření na kvalitu prášků/zařízení. |
Schopnosti stroje | Jaké stroje/technologie AM používáte? Jaký je váš objem výroby? Jak jsou stroje kalibrovány a udržovány? | Zajišťuje schopnost pro konkrétní materiály, velikost dílů a požadovanou přesnost. | Nabízí vlastní tiskárny SEBM; klade důraz na špičkový objem, přesnost a spolehlivost. |
Materiálová odbornost | Jaké máte zkušenosti s AlSi10Mg/IN625? Jak prášky kvalifikujete & spravujete? Můžete poskytnout materiálové certifikáty? | Zaručuje správné vlastnosti materiálu, minimalizuje vady způsobené problémy s práškem. | Specializuje se na vysoce výkonné prášky (AlSi10Mg, IN625, Ti slitiny, superslitiny); používá pokročilou atomizaci (plyn/PREP); klade důraz na kvalitu. |
Následné zpracování | Jaké následné zpracování nabízíte? Jak spravujete externí partnery (např. pro HIP, NDT)? | Zajišťuje kompletní, řízený pracovní postup od tisku až po hotový díl. | Poskytuje “komplexní řešení,” což znamená řízení nezbytných kroků. |
Technická podpora (DfAM) | Můžete pomoci s optimalizací designu? Nabízíte simulaci sestavení? Jaké jsou vaše zkušenosti s aplikacemi v leteckém průmyslu? | Plně využívá výhod AM, předchází nákladným chybám a zajišťuje funkční design. | Nabízí “služby vývoje aplikací”; kolektivní odborné znalosti v oblasti metal AM. |
Inspekce & amp; Metrologie | Jaké metody kontroly používáte (zejména interní)? Máte CT vyšetření? Jak ověřujete těsnost? | Klíčové pro ověření vnitřních kanálů, odhalení vad a zajištění integrity dílu. | Zaměření na “přesnost” naznačuje silnou metrologii, i když konkrétní metody je třeba potvrdit. |
Záznamy o činnosti | Můžete se podělit o relevantní případové studie nebo odkazy z oblasti letectví a kosmonautiky? | Buduje důvěru v jejich schopnost dodávat složité, kritické díly. | Prezentuje se jako “lídr v oblasti AM kovů ” což znamená, že má silné výsledky v příslušných oblastech (letectví, lékařství, automobilový průmysl). |
Export do archů
Výběr správného metal AM partner je investice do kvality, spolehlivosti a úspěchu. Důkladné prověření podle těchto kritérií pomůže zajistit, aby vaše aditivně vyráběné konformní chladicí kanály splňovaly přísné požadavky leteckého průmyslu. Zjistěte si více informací o potenciálních partnerech, třeba počínaje jejich firemním profilem, jako je Met3dp’s O nás je dobrým prvním krokem.
Porozumění investicím: Hnací síly nákladů a doba realizace pro konformní chladicí kanály AM
Aditivní výroba kovů sice umožňuje revoluční konstrukce, jako jsou konformní chladicí kanály, ale pro plánování projektu a sestavování rozpočtu je nezbytné pochopit související náklady a časový harmonogram výroby. Jak analýza nákladů na AM kovů a doba realizace aditivní výroby odhad zahrnuje několik vzájemně se ovlivňujících faktorů specifických pro danou technologii a složitost aplikace.
Hnací síly nákladů na konformní chladicí kanály AM:
Konečnou cenu aditivně vyráběné součásti ovlivňuje více než jen hmotnost surovin. Mezi klíčové faktory ovlivňující náklady patří:
- Složitost návrhu & Geometrie dílů:
- Podpůrné struktury: Konstrukce vyžadující rozsáhlé podpůrné struktury (zejména vnitřní) zvyšují spotřebu materiálu, dobu tisku a pracnost následného zpracování při odstraňování. Optimalizace DfAM pro minimalizaci podpěr přímo snižuje náklady.
- Hustota/objem dílu: Ačkoli AM umožňuje odlehčení, skutečný objem tištěného materiálu přímo ovlivňuje náklady (spotřeba materiálu a doba tisku). Topologicky optimalizované struktury vyplněné mřížkou mohou být nákladově efektivnější než pevné bloky.
- Minimální velikosti prvků: Velmi jemné rysy nebo tenké stěny mohou vyžadovat nižší rychlost tisku nebo specializované parametry, což prodlužuje strojní čas.
- Typ materiálu a spotřeba:
- Náklady na prášek: Náklady na suroviny se výrazně liší. Niklové superslitiny pro letectví a kosmonautiku, jako je IN625, jsou na kilogram podstatně dražší než hliníkové slitiny, jako je AlSi10Mg, nebo dokonce titanové slitiny. Vysoce kvalitní, přísně specifikované prášky pro letecký průmysl jsou dražší.
- Množství použitého materiálu: Zahrnuje materiál v konečné části a případné podpůrné konstrukce a případně zkušební kupony vytištěné spolu s ním. Efektivní vnoření více dílů na sestavovací desku může snížit režijní náklady na materiál na díl spojené se základnou sestavovací platformy.
- Čas procesu AM (strojový čas):
- Výška stavby: To je často dominantní faktor doby tisku. U vyšších dílů trvá tisk déle bez ohledu na to, kolik jich je na desce umístěno. Orientace dílů tak, aby se minimalizovala jejich výška, může zkrátit dobu tisku.
- Část Objem & Hustota: Celkový objem taveného materiálu přímo ovlivňuje dobu skenování jednotlivých vrstev.
- Tloušťka vrstvy & amp; Parametry: Tenčí vrstvy zlepšují rozlišení, ale zvyšují počet vrstev a tím i dobu tisku. Optimalizované parametry vyvažují rychlost a kvalitu.
- Hodinová sazba stroje: Náklady na provoz sofistikovaných systémů AM na kovy (včetně odpisů, údržby, energie, inertního plynu a práce) se promítají do hodinové sazby účtované za čas strávený na stroji.
- Požadavky na následné zpracování:
- Intenzita práce: Odstranění podpěr, ruční dokončování a kontrola mohou být pracné.
- Specializované procesy: Kroky jako HIP, CNC obrábění, AFM pro vnitřní kanály, NDT (zejména CT skenování) a specializované povlaky zvyšují náklady na vybavení, odborné znalosti a čas. Rozsah potřebného následného zpracování je hlavní proměnnou nákladů.
- Zajištění kvality a certifikace:
- Úroveň kontroly: Přísné kontrolní protokoly (více metod NDT, podrobné rozměrové zprávy, zkoušky těsnosti) vyžadované pro letecký průmysl zvyšují náklady.
- Dokumentace: Vytváření komplexní dokumentace o sledovatelnosti, certifikace materiálů a certifikátů shody vyžaduje čas a zdroje.
- Objem objednávky:
- Náklady na zřízení: S přípravou každé sestavy jsou spojeny fixní náklady (příprava souboru, nastavení stroje, nakládání prášku). Rozložení těchto nákladů na větší počet stejných dílů snižuje náklady na jeden díl.
- Křivka učení: U opakovaných objednávek lze často dosáhnout vyšší efektivity při tisku a následném zpracování.
Úvahy o době realizace:
Dodací lhůty aditivní výroby pro certifikované letecké díly se často měří v týdnech, nikoli ve dnech. Je důležité mít realistická očekávání:
- Předběžné zpracování: Kontrola návrhu, kontroly DfAM, simulace sestavení, příprava souborů a plánování sestavení mohou trvat několik dní, zejména u složitých dílů nebo při prvním sestavení.
- Doba čekání ve frontě: Díl je třeba naplánovat na dostupný stroj, což závisí na stavu nevyřízených zakázek poskytovatele služeb.
- Doba tisku: Může se pohybovat od mnoha hodin až po několik dní, především v závislosti na výšce a objemu stavby. Tisk vysokého a složitého dílu IN625 může snadno trvat 5-10 dní i déle.
- Následné zpracování: To často představuje nejdelší část doby přípravy.
- Ochlazení a úleva od stresu: 1-2 dny.
- Demontáž dílu/odstranění podpěry: 1-3 dny (velmi variabilní).
- Cyklus HIP (včetně přepravy k poskytovateli HIP nebo od něj, pokud je zadáván externě): 5-10 dní.
- CNC obrábění: 2-7 dní (v závislosti na složitosti a časovém plánu).
- Vnitřní povrchová úprava (AFM atd.): 2-5 dní.
- NDT & amp; kontrola: 2-5 dní.
- Potenciální iterace/přepracování: V případě zjištění problémů může dojít k výraznému zpoždění.
- Doprava: Platí standardní dodací lhůty.
Typická celková doba realizace: U složitého leteckého konformního chladicího kanálu, který vyžaduje více kroků následného zpracování a přísnou kontrolu kvality, se typická doba realizace může pohybovat od 4 až 10 týdnůnebo případně delší dobu u velmi složitých prvních článků.
Náklady vs. tradiční metody:
Zatímco přímý cena 3D tisku v letectví a kosmonautice komponenty se mohou zdát vysoké ve srovnání s jednoduchým obráběným dílem, skutečné srovnání vyžaduje zvážení celkových nákladů na vlastnictví (TCO) a hodnotové nabídky:
- Zvýšení výkonu: Lepší tepelná účinnost může vést k významným provozním úsporám (palivo) nebo umožnit vyšší výkon (tah, hustota výkonu).
- Snížení hmotnosti: Snížení hmotnosti se přímo promítá do úspory nákladů v leteckém provozu.
- Konsolidace částí: Eliminace více dílů, montážních kroků a potenciálních míst poruch snižuje složitost výroby, skladové zásoby a riziko dlouhodobé údržby.
- Rychlost vývoje: Rychlejší prototypování a iterační cykly mohou zkrátit dobu uvedení nových leteckých systémů na trh.
Kovový AM je často nákladově nejefektivnější pro vysoce komplexní díly s malým až středním objemem, kde jeho jedinečné geometrické schopnosti poskytují významné výhody na úrovni výkonu nebo systému, které převažují nad potenciálně vyššími výrobními náklady na jeden díl.
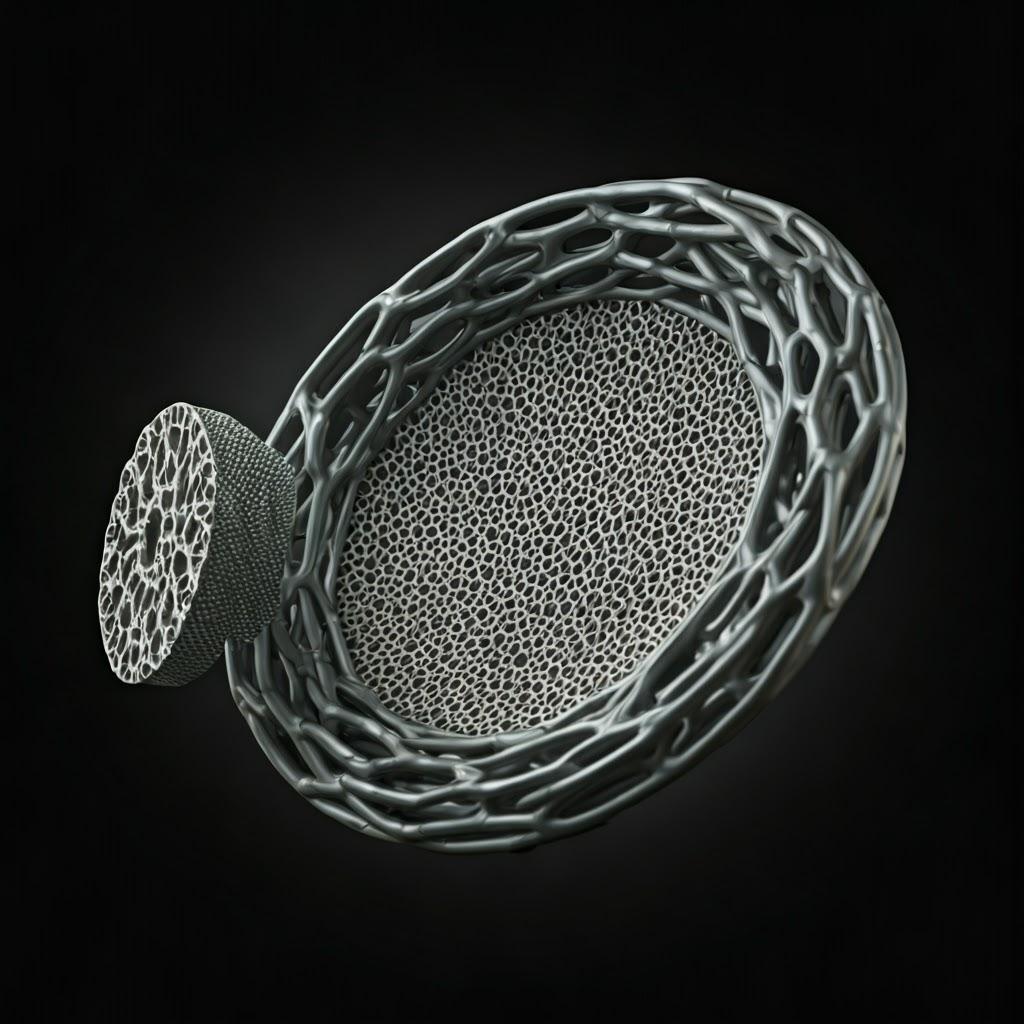
Často kladené otázky (FAQ): AM kovů pro chladicí kanály v leteckém průmyslu
Zde jsou odpovědi na některé časté otázky týkající se použití aditivní výroby kovů pro výrobu konformních chladicích kanálů v letectví a kosmonautice:
Otázka 1: Jak se ověřuje výkon a spolehlivost konformních chladicích kanálů AM, aby se zajistilo, že splňují nebo překonávají tradiční metody?
A: Validace je mnohostranný proces, který je rozhodující pro kvalifikaci jakékoli letecké součásti, zejména té, která je vyráběna novějšími technikami, jako je AM. Obvykle zahrnuje kombinaci simulace, nedestruktivního testování (NDT) a fyzického testování:
- Výpočetní dynamika tekutin (CFD) & Analýza konečných prvků (FEA): Ve fázi návrhu (DfAM) se používají rozsáhlé CFD simulace k předpovědi chování tekutin při proudění (tlaková ztráta, rozložení proudění) a výkonu přenosu tepla v kanálech. Metoda konečných prvků se používá k analýze tepelného namáhání a integrity konstrukce při provozním zatížení a teplotách. Tyto simulace porovnávají předpokládaný výkon konstrukce AM se základními tradičními konstrukcemi nebo požadavky na výkon.
- Nedestruktivní zkoušení (NDT):
- CT vyšetření: Je nezbytný pro ověření vnitřní geometrie chladicích kanálů po tisku, zajištění jejich shody s modelem CAD, kontrolu překážek (zachycený prášek), měření tloušťky stěn a odhalení vnitřních vad, jako jsou pórovitost nebo praskliny.
- Fluorescenční penetrační kontrola (FPI) / Dye Penetrant Inspection (DPI): Používá se k detekci defektů porušujících povrch (trhliny, pórovitost).
- Ultrazvukové zkoušení (UT) / radiografické zkoušení (RT): Ve specifických případech lze použít pro objemovou kontrolu, ačkoli pro složité vnitřní geometrie se často upřednostňuje CT.
- Fyzikální testování:
- Testování průtoku: Měření skutečné tlakové ztráty v závislosti na průtoku v kanálech pomocí vzduchu nebo příslušné chladicí kapaliny. Tím se ověřují předpovědi CFD a kontroluje se, zda nedochází k ucpávání.
- Zkoušky tepelného výkonu: Montáž součásti do zkušebního zařízení simulujícího provozní tepelné zatížení a podmínky proudění chladicí kapaliny. Termočlánky nebo termovizní měření měří povrchové teploty a rychlost odvodu tepla, aby se potvrdilo, že účinnost chlazení odpovídá konstrukčnímu záměru.
- Testování těsnosti: Kriticky důležité. Použití tlaku (hydrostatického nebo pneumatického, někdy s použitím značkovacího plynu, např. helia) k ověření integrity stěn kanálu a všech rozhraní.
- Zkouška zkušebním tlakem / zkouška na roztržení: Vystavení součásti tlakům výrazně vyšším, než je provozní tlak, za účelem ověření strukturální integrity a bezpečnostních rezerv.
- Zkoušky mechanických vlastností: Tisk reprezentativních “svědeckých kupónů” vedle hlavního dílu za použití stejné dávky materiálu a parametrů. Tyto kupony se podrobují zkouškám v tahu, únavovým zkouškám atd., aby se ověřilo, že vlastnosti materiálu po všech krocích zpracování (včetně HIP) splňují specifikace.
- Testování odolnosti/únavy: U součástí vystavených cyklickému zatížení (tepelné cykly, tlakové cykly) podrobení prototypových dílů zrychlenému testování životnosti za účelem ověření odolnosti proti únavě a předpovědi provozní životnosti.
Validace spočívá v porovnání výsledků těchto testů se zavedenými leteckými normami, specifikacemi součástí a případně s údaji z tradičně vyráběných protějšků. Přísné validace leteckých komponentů AM proces zajišťuje, že díly jsou vhodné pro daný účel a bezpečné pro let.
Otázka 2: Jakou úroveň sledovatelnosti materiálů a certifikace procesů lze očekávat při pořizování kritických leteckých dílů pomocí technologie AM?
A: Sledovatelnost a certifikace jsou základními kameny bezpečnosti a kvality letecké výroby a renomovaní poskytovatelé služeb AM v tomto odvětví musí dodržovat přísné požadavky, často stanovené normami jako AS9100. Měli byste očekávat:
- Sledovatelnost prášku: Kompletní sledování kovového prášku od kolébky do hrobu”. To zahrnuje:
- Certifikáty shody dodavatele (CoC) pro každou šarži prášku s podrobnými údaji o chemickém složení, distribuci velikosti částic (PSD), morfologii a tokových vlastnostech.
- Jedinečná identifikace a sledování každé šarže prášku použitého v zařízení poskytovatele AM.
- Záznamy spojující konkrétní šarže prášku (a dokonce i historii použití recyklovaného prášku) s konkrétními konstrukčními úlohami a jednotlivými díly.
- Protokolování parametrů procesu: Podrobný záznam všech kritických parametrů během procesu sestavování AM pro každý díl. Patří sem ID stroje, ID operátora, verze souboru sestavení, tloušťka vrstvy, výkon laseru/paprsku, rychlost skenování, rozteč šraf, teplota sestavovací desky, úroveň kyslíku/průtok plynu atd. Tento datový protokol je součástí rodného listu dílu’“”
- Sledovatelnost sestavení: Každý díl je jednoznačně identifikován (např. sériovým číslem, fyzicky označen nebo označen) a spojen s konkrétní výrobní úlohou, pozicí na výrobní desce a souvisejícími údaji o procesu/prachu.
- Testování svědeckých kupónů: Jak již bylo zmíněno, testovací kupony se často tisknou s každým sestavením. Výsledky testování těchto kupónů (tah, tvrdost, analýza mikrostruktury) jsou zdokumentovány a propojeny s díly vyrobenými v rámci daného sestavení, což umožňuje ověřit vlastnosti materiálu ve stavu po sestavení a po zpracování.
- Záznamy z následného zpracování: Dokumentace potvrzující, že všechny požadované kroky následného zpracování (uvolnění napětí, HIP, obrábění, NDT) byly provedeny podle stanovených postupů, včetně záznamů o použitých parametrech (např. grafy HIP, protokoly o obrábění, výsledky NDT).
- Certifikáty shody (CoC): Konečný dokument dodaný poskytovatelem služeb AM, který potvrzuje, že díl odpovídá požadavkům objednávky, výkresovým specifikacím a příslušným leteckým normám. Tento CoC shrnuje nebo odkazuje na veškerou podpůrnou dokumentaci o sledovatelnosti a testování.
Tento komplexní sledovatelnost materiálu aditivní výroba systém zajišťuje odpovědnost a umožňuje důkladné prošetření, pokud se později v životním cyklu komponenty objeví nějaké problémy.
Otázka 3: Je u složitých konformních chladicích kanálů technologie AM skutečně cenově konkurenceschopná s tradičními výrobními metodami?
A: Na tuto otázku nelze odpovědět jednoduše ano/ne. Velmi záleží na konkrétní součásti, její složitosti, objemu výroby a na tom, jak jsou definovány “náklady” (náklady na jeden díl vs. celková hodnota životního cyklu).
- Přímé náklady na díl: U relativně jednoduchých geometrií, které lze vyrobit konvenčním vrtáním/frézováním/pájením, mohou mít tradiční metody nižší náklady na jeden díl, zejména při velkých objemech, kdy je amortizace nástrojů široce rozložena. Kovový AM často zahrnuje vyšší investiční náklady na zařízení, dražší suroviny (zejména vysoce kvalitní prášky) a potenciálně rozsáhlé následné zpracování, což vede k vyšším přímým výrobním nákladům na díl, zejména u jednodušších konstrukcí nebo velmi vysokých objemů.
- Kde se AM stává konkurencí:
- Extrémní složitost: Pokud je konstrukce konformního chladicího kanálu natolik složitá (vysoce zakřivené dráhy, vnitřní prvky, proměnlivé průřezy), že je fyzicky nemožné nebo neúměrně nákladné a časově náročné ji vyrobit tradičním způsobem (vyžaduje četná složitá nastavení obrábění, složité pájení/svařování s vysokou mírou poruchovosti), stává se AM technologií, která umožňuje, a je tedy ve srovnání s ní nákladově efektivní, neboť může vyrobit díl.
- Konsolidace částí: Pokud AM umožňuje sloučit více tradičně vyráběných dílů (např. blok rozdělovače, více trubek, montážní držáky) do jediné tištěné součásti, může úspora montážní práce, snížení počtu dílů (zásoby, logistika) a eliminace spojů (potenciální místa netěsnosti, spojovací materiál) vyvážit vyšší náklady na tisk.
- Výkonnost & Zvýšení efektivity (hodnota životního cyklu): To je často nejsilnější argument pro AM v letectví a kosmonautice. Pokud vynikající tepelný výkon umožněný konformním chlazením vede k výraznému zlepšení palivové účinnosti motoru, prodloužení životnosti součástek (snížení nákladů na výměnu) nebo umožňuje celkově lehčí konstrukci systému (což zvyšuje úsporu paliva), mohou tyto provozní výhody v průběhu životnosti letadla výrazně převážit nad vyššími počátečními náklady na součástku. To je klíčový aspekt návratnost investic do 3D tisku kovů analýzu.
- Rapid Prototyping & Vývoj: AM výrazně urychluje cyklus návrhu, výroby a testování složitých prototypů, čímž zkracuje dobu vývoje a snižuje náklady ve srovnání s tradičními metodami vyžadujícími výrobu nástrojů.
- Výroba v malém až středním objemu: AM se vyhýbá vysokým počátečním nákladům na nástroje spojeným s odléváním nebo vstřikováním, takže je ekonomičtější pro výrobní série, kde tyto náklady na nástroje nelze efektivně amortizovat.
Závěr o nákladech: Pro konformní chladicí kanály se obvykle nevybírá metoda AM, a to především proto, aby se ušetřily přímé výrobní náklady na samotný kanál ve srovnání s technologií AM jednoduchý tradiční design. Je zvolen proto, že umožňuje složité konstrukce které přinášejí výhody v oblasti výkonu, hmotnosti nebo spolehlivosti, jichž nelze dosáhnout tradičními prostředky. Zdůvodnění nákladů často vychází z hodnota na úrovni systému a přínosy životního cyklu plynoucí z těchto rozšířených schopností, díky čemuž je cenově konkurenceschopný nebo dokonce lepší, pokud se vezme v úvahu celkový obraz.
Závěr: Budoucnost je chladná - Využití technologie AM pro tepelná řešení příští generace v letectví a kosmonautice
Efektivní řízení tepla zůstává kritickým místem při posouvání hranic výkonnosti v letectví a kosmonautice. Tradiční výrobní metody, ačkoli se po desetiletí zdokonalovaly, ze své podstaty omezují geometrickou složitost vnitřních chladicích prvků, což často nutí ke kompromisům mezi tepelnou účinností, vyrobitelností a hmotností. Jak jsme již prozkoumali, Aditivní výroba kovů (Metal AM) představuje zásadní změnu paradigmatu, která ruší tato omezení a zahajuje novou éru řešení tepelného managementu v letectví a kosmonautice.
Schopnost vytvářet Konformní chladicí kanály - složité dráhy, které přesně kopírují obrysy kritických součástí, jako jsou lopatky turbín, kryty motorů a moduly avioniky - je pravděpodobně jedním z nejvýznamnějších přínosů AM’ pro letecký průmysl. Umístěním chlazení přesně tam, kde je ho nejvíce potřeba, umožňuje AM:
- Bezprecedentní tepelný výkon: Dosažení rovnoměrnějšího rozložení teploty, eliminace horkých míst a umožnění spolehlivého provozu součástí při vyšších teplotách nebo hustotách výkonu, což přímo vede ke zvýšení účinnosti motoru, většímu tahu a vyšší spolehlivosti elektroniky.
- Revoluční svoboda designu: Umožňuje konstruktérům překonat omezení vrtání a frézování, využívat organické tvary, variabilní průřezy a integrované prvky zlepšující proudění optimalizované výhradně pro tepelné a konstrukční vlastnosti prostřednictvím DfAM.
- Výrazné snížení hmotnosti: Umožňuje odlehčené konstrukce díky optimalizaci topologie a konsolidaci dílů, což přímo přispívá k úspoře paliva a zvýšení nosnosti - klíčovým ukazatelům v ekonomice letectví a kosmonautiky.
- Zvýšená spolehlivost: Konsolidace více dílů do jediné monolitické součásti eliminuje spoje, pájky a sváry, čímž výrazně snižuje potenciální netěsnosti a zjednodušuje montáž. Důsledná kontrola procesu a následné zpracování, jako je HIP, dále zvyšují integritu materiálu.
Realizace těchto výhod však vyžaduje komplexní přístup. Úspěch závisí na pečlivém Design pro aditivní výrobu (DfAM), pečlivý výběr vhodných vysoce výkonných materiálů, jako je např AlSi 10Mg nebo IN625 pochází jako vysoce kvalitní kovové prášky, pečlivé provádění základních následné zpracování (včetně odlehčování, HIP, obrábění a dokončovacích prací) a důkladné ověřování prostřednictvím pokročilé kontroly a testování.
Orientace ve složitých procesech optimalizace, vědy o materiálech a zajištění kvality vyžaduje odborné znalosti. Spolupráce se správnými Poskytovatel služeb metal AM je proto prvořadá. Výběr dodavatele s prokazatelnými zkušenostmi v leteckém průmyslu, certifikací AS9100, robustním systémem řízení kvality, moderním vybavením, odbornými znalostmi v oblasti materiálů, komplexními možnostmi následného zpracování a silnou technickou podporou je nejen vhodný, ale i nezbytný pro výrobu letuschopných součástí.
Společnost Met3dp stojí v čele této technologické vlny a nabízí synergickou kombinaci těchto technologií špičkové zařízení pro 3D tisk z kovu a pokročilé sférické kovové prášky. Díky desítkám let společných zkušeností a závazku umožnit výrobu nové generace poskytuje společnost Met3dp komplexní řešení - zahrnující tiskárny, prémiové materiály, jako jsou TiNi, TiTa, TiAl, TiNbZr, CoCrMo, nerezové oceli a superslitiny, a služby vývoje aplikací - potřebná k řešení nejnáročnějších problémů v leteckém průmyslu. Naše zaměření na kvalitu prášku prostřednictvím špičkových technologií plynové atomizace a PREP v kombinaci s přesností a spolehlivostí našich tiskových systémů poskytuje základ pro výrobu kritických dílů.
Budoucnost letectví a kosmonautiky je neoddělitelně spjata s rozvojem výrobních technologií. Technologie AM pro kovy, zejména pro aplikace, jako je konformní chlazení, není jen alternativní výrobní metodou; je klíčovým faktorem pro vývoj lehčích, rychlejších, účinnějších a spolehlivějších letadel a kosmických lodí. Přijetí této technologie dnes připravuje půdu pro letecké inovace zítřka.
Jste připraveni prozkoumat, jak může aditivní výroba kovů změnit vaše problémy s tepelným managementem? Návštěva Met3dp se dozvíte více o našem komplexním Met3dp aerospace solutions a zjistěte, jak mohou naše špičkové systémy a vysoce výkonné prášky podpořit cíle vaší organizace v oblasti aditivní výroby. Kontaktujte nás ještě dnes a začněte rozhovor.
Sdílet na
MET3DP Technology Co., LTD je předním poskytovatelem řešení aditivní výroby se sídlem v Qingdao v Číně. Naše společnost se specializuje na zařízení pro 3D tisk a vysoce výkonné kovové prášky pro průmyslové aplikace.
Dotaz k získání nejlepší ceny a přizpůsobeného řešení pro vaše podnikání!
Související články
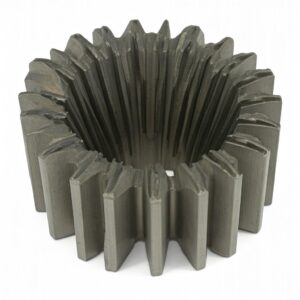
Vysoce výkonné segmenty lopatek trysek: Revoluce v účinnosti turbín díky 3D tisku z kovu
Přečtěte si více "O Met3DP
Nedávná aktualizace
Náš produkt
KONTAKTUJTE NÁS
Nějaké otázky? Pošlete nám zprávu hned teď! Po obdržení vaší zprávy obsloužíme vaši žádost s celým týmem.