Tisk nástrojů na zakázku pomocí 3D tisku kovů pro výrobu
Obsah
Úvod: Revoluce ve výrobě pomocí 3D tištěných nástrojů na zakázku
Moderní výrobní odvětví - od leteckého a automobilového průmyslu až po výrobu lékařských přístrojů a spotřebního zboží - se v neustálé snaze o efektivitu, rychlost a inovace neustále snaží hledat transformační technologie. Zakázkové nástroje, zahrnující přípravky, upínací přípravky, formy, zápustky a další výrobní pomůcky, tvoří základ opakovatelných a vysoce kvalitních výrobních procesů. Tradičně byla výroba tohoto nezbytného nástrojového vybavení významným úzkým místem, které se často vyznačovalo dlouhými dodacími lhůtami, vysokými náklady a konstrukčními omezeními, jež jsou vlastní subtraktivním metodám, jako je CNC obrábění nebo odlévání. Nástup a vyspělost výroba aditiv kovů (AM), běžně známý jako kov 3D tisk, zásadně mění prostředí zakázkových nástrojových řešení. Tato technologie nabízí bezprecedentní schopnost vytvářet vysoce komplexní, výkonově optimalizované nástroje s pozoruhodnou rychlostí a rostoucí nákladovou efektivitou, což vede ke změně paradigmatu v přístupu výrobců k nastavení a realizaci výroby.
Kovový 3D tisk překonává omezení tradičních metod tím, že vytváří díly vrstvu po vrstvě přímo z digitálních modelů pomocí specializovaných kovových prášků. Tento aditivní přístup uvolňuje dříve nedosažitelné geometrické svobody a umožňuje integraci složitých vnitřních prvků, topologicky optimalizovaných lehkých struktur a, což je pro mnoho nástrojových aplikací zásadní, konformních chladicích kanálů, které přesně kopírují kontury povrchu nástroje. Důsledky pro efektivitu výroby jsou hluboké. Rychlejší iterační cykly nástrojů, snížení plýtvání materiálem, prodloužení životnosti nástrojů díky optimalizovaným konstrukcím a materiálům a zlepšení kvality finálních dílů díky lepšímu tepelnému managementu jsou jen některé z výhod, které nutí konstruktéry a manažery nákupu zkoumat a zavádět nástroje pro aditivní výrobu.
Představte si, že zkrátíte dobu přípravy složité vložky do vstřikovací formy z měsíců na týdny nebo dokonce dny. Představte si výrobu lehkého, ergonomického montážního přípravku dokonale přizpůsobeného konkrétní součásti, který zvyšuje efektivitu pracovníků a snižuje jejich únavu. Představte si lisovací formy s integrovaným chlazením, které výrazně zkracují dobu cyklu a snižují opotřebení. To nejsou futuristické koncepty, ale hmatatelná realita, kterou umožňuje 3D tisk z kovu. Tato technologie umožňuje výrobcům pružněji reagovat na požadavky trhu, rychleji přizpůsobovat výrobní linky a dosahovat úrovně výkonnosti, která byla dříve považována za nemožnou. Společnost Met3dp si jako přední poskytovatel pokročilých řešení aditivní výroby uvědomuje transformační potenciál této technologie pro zakázkové nástroje. S využitím špičkových tiskáren pro selektivní tavení elektronovým svazkem (SEBM) a vysoce výkonných kovových prášků vyráběných pomocí nejmodernějších technologií plynové atomizace a plazmového procesu s rotujícími elektrodami (PREP) umožňuje společnost Met3dp podnikům plně využít potenciál úvod do 3D tisku kovů pro jejich kritické potřeby v oblasti nástrojů. Nejde jen o to, aby se nástroje vyráběly jinak, ale o zásadní zlepšení celého výrobního hodnotového řetězce.
Přechod na aditivní výrobu nástrojů není pouhým trendem, ale strategickou nutností pro společnosti, které si chtějí udržet konkurenční výhodu. Řeší hlavní výrobní výzvy: zkrácení doby uvedení na trh, snížení výrobních nákladů, zvýšení kvality dílů a umožnění větší inovace designu. Pro manažery veřejných zakázek, kteří hledají spolehlivé zakázková nástrojová řešení dodavatelé, je zásadní porozumět možnostem a nuancím technologie AM na bázi kovů. Pro konstruktéry a výrobní inženýry je přijetí principů návrhu pro aditivní výrobu (DfAM) uvolněním plného potenciálu této technologie. Tento článek slouží jako komplexní průvodce pro technické a nákupní profesionály a zkoumá rozmanité aplikace, přesvědčivé výhody, kritické úvahy o materiálech, osvědčené postupy při navrhování, očekávání kvality, potřeby následného zpracování, potenciální problémy, kritéria výběru dodavatelů, nákladové faktory a často kladené otázky týkající se použití kovového 3D tisku pro zakázkové nástroje. Připojte se k nám a pronikněte do toho, jak tato revoluční technologie vytváří budoucnost efektivní, agilní a vysoce výkonné výroby.
Různorodé aplikace: Kde vynikají kovové 3D tištěné nástroje
Všestrannost aditivní výroby kovů umožňuje řešit široké spektrum požadavků na zakázkové nástroje v mnoha průmyslových odvětvích. Její schopnost rychle vytvářet složité geometrie a využívat vysoce pevné a odolné materiály z ní činí ideální řešení pro aplikace, kde tradiční metody nedostačují z hlediska rychlosti, nákladů nebo optimalizace výkonu. Manažeři nákupu, kteří hledají dodavatele B2B a velkoobchodní možnosti pro případy použití průmyslových nástrojů zjistí, že technologie AM pro kovy nabízí přesvědčivé výhody v několika klíčových kategoriích:
1. Přípravky a přípravky: Tato zařízení jsou nezbytná pro umístění, podepření a vedení obrobků nebo nástrojů během výrobních operací, jako je montáž, obrábění, svařování nebo kontrola.
- Tradiční výzvy: Často vyžadují složité obrábění, což vede k dlouhým dodacím lhůtám a vysokým nákladům, zejména u malosériových nebo vysoce přizpůsobených konstrukcí. Při ručních operacích může být faktorem také hmotnost.
- Výhoda AM:
- Rychlost: Rychlá výroba prototypů a přípravků na zakázku v řádu dnů, nikoli týdnů nebo měsíců.
- Složitost & Shoda: Možnost vytvářet vysoce ergonomické tvary, které dokonale odpovídají složité geometrii dílů, což zvyšuje přesnost a usnadňuje použití. Vnitřní mřížkové struktury mohou výrazně snížit hmotnost bez ztráty tuhosti, což je pro kapesní zařízení klíčové.
- Konsolidace: Často lze více součástí sestavy přípravku sloučit do jediného dílu vytištěného na 3D tiskárně, čímž se zkrátí doba montáže a sníží se počet potenciálních míst poruchy.
- Příklady: Montážní přípravky pro letecké komponenty, přípravky pro kontrolu kvality na souřadnicových měřicích strojích, přípravky pro svařování automobilových rámů, chirurgická vodítka (typ lékařského přípravku). Získávání 3D tištěné přípravky a přípravky umožňuje rychlejší nastavení a výměnu linky.
2. Formy (vstřikování, vyfukování, tepelné tvarování): Nástrojové vložky, jádra a dutiny používané v různých formovacích procesech mají z AM obrovský užitek, zejména díky možnosti konformního chlazení.
- Tradiční výzvy: Obrábění hlubokých a složitých chladicích kanálů je obtížné, nákladné a často nemožné. To vede k neoptimálnímu chlazení, delší době cyklu, deformaci obrobku a nižší životnosti nástroje.
- Výhoda AM:
- Konformní chlazení: Určující přínos. 3D tisk umožňuje navrhnout chladicí kanály přesně podle obrysů povrchu formy, obvykle 1-2 mm pod ní. To zajišťuje rychlé a rovnoměrné chlazení, které výrazně zkracuje dobu cyklu (často o více než 20-50 %), zlepšuje kvalitu dílů (menší deformace, lepší rozměrová stabilita) a prodlužuje životnost formy.
- Složitost: Umožňuje vytvářet složité prvky formy, textury a podříznutí, které je obtížné nebo nemožné obrábět.
- Hybridní přístup: Vložky AM lze integrovat do konvenčně obráběných základů forem, což nabízí nákladově efektivní způsob, jak získat výkonnostní výhody tam, kde je to nejvíce potřeba.
- Příklady: Vložky do vstřikovacích forem pro složité interiérové díly automobilů, nástroje pro vyfukování složitých designů lahví, nástroje pro tepelné tvarování obalů. Aditivní výrobní formy s konformním chlazením představují významnou konkurenční výhodu.
3. Lisovací formy (lisování, tváření, tlakové lití): Nástroje používané k řezání, tvarování nebo formování materiálů, jako jsou plechy nebo roztavené kovové slitiny, jsou vystaveny extrémnímu namáhání a teplotám.
- Tradiční výzvy: Vysoká míra opotřebení, dlouhé dodací lhůty pro tvrdé nástroje, potíže se začleněním účinného chlazení do vysokoteplotních procesů, jako je tlakové lití.
- Výhoda AM:
- Možnosti materiálu: Možnost tisku s vysoce pevnými nástrojovými ocelemi odolnými proti opotřebení (např. H13, M300), které jsou schopny odolávat náročným operacím.
- Konformní chlazení (tlakové lití): Podobně jako u vstřikování mohou integrované chladicí kanály výrazně zlepšit dobu cyklu, snížit tepelné namáhání, minimalizovat pájení dílů a prodloužit životnost formy při tlakovém lití.
- Rapid Prototyping/Bridge Tooling: Rychlá výroba prototypů nebo malosériových lisovacích/ tvářecích forem pro ověření návrhů předtím, než se zavážete k drahému tradičnímu nástroji.
- Složitost: Vytvářejte tvářecí formy se složitými povrchy pro složité plechové díly.
- Příklady: Lisovací formy na plech pro panely automobilových karoserií (zejména pro zkušební nebo malosériové použití), vložky pro tlakové lití složitých hliníkových součástí, tvářecí nástroje pro letecké konzoly. Získávání zdrojů kovové výlisky s potiskem může urychlit vývoj produktů a zvýšit efektivitu vysokoteplotních procesů.
4. Nástroje na konci ramene (EoAT) / uchopovače: Zakázková chapadla pro robotická ramena používaná při automatizované manipulaci, montáži a operacích pick-and-place.
- Tradiční výzvy: Často vyžadují montáž více komponent, mohou být těžké a přizpůsobení konkrétním dílům může být časově náročné.
- Výhoda AM:
- Odlehčení: Optimalizace topologie a mřížkové struktury vytvářejí pevné a zároveň lehké chapadla, která robotům umožňují rychlejší pohyb nebo manipulaci s těžšími náklady.
- Přizpůsobení a složitost: Snadno vytvoříte chapadla dokonale přizpůsobená tvaru manipulovaného předmětu, čímž zvýšíte bezpečnost a spolehlivost uchopení. Lze přímo integrovat vnitřní kanály pro vakuum nebo pneumatiku.
- Konsolidace částí: Snižte složitost a dobu montáže tiskem monolitických konstrukcí chapadel.
- Příklady: Zakázková chapadla pro manipulaci s jemnými elektronickými součástkami, EoAT pro montážní linky v automobilovém průmyslu, specializovaná chapadla pro zpracování potravin.
Specifické průmyslové aplikace:
- Letectví: Vrtací přípravky, montážní přípravky, kontrolní měřidla, nízkoobjemové tvářecí nástroje.
- Automobilový průmysl: Prototypy lisovacích forem, vložky do vstřikovacích forem, montážní přípravky, robotická chapadla.
- Lékařský: Zakázková chirurgická vodítka, přípravky pro montáž lékařských přístrojů, vložky do forem pro výrobu implantátů (v případě potřeby s použitím biokompatibilních materiálů, jako je Ti6Al4V nebo CoCrMo, ačkoli nástroje často používají nástrojové oceli).
- Průmyslová výroba: Součásti obráběcích strojů, upínací zařízení, tvářecí nástroje, specializované nástroje pro opravy.
Rozsah těchto aplikace rychlého obrábění podtrhuje transformační dopad technologie AM na kovy. Díky tomu, že 3D tisk kovů umožňuje rychlejší výrobu, komplexní konstrukce a vyšší výkon díky funkcím, jako je konformní chlazení, umožňuje výrobcům napříč odvětvími překonat tradiční omezení v oblasti nástrojů a uvolnit nové úrovně produktivity a inovací. Společnosti, jako je Met3dp, jsou díky svým odborným znalostem v oblasti pokročilých tiskových technologií i vědy o materiálech klíčovými partnery při realizaci těchto přínosů pro různorodé případy použití průmyslových nástrojů.
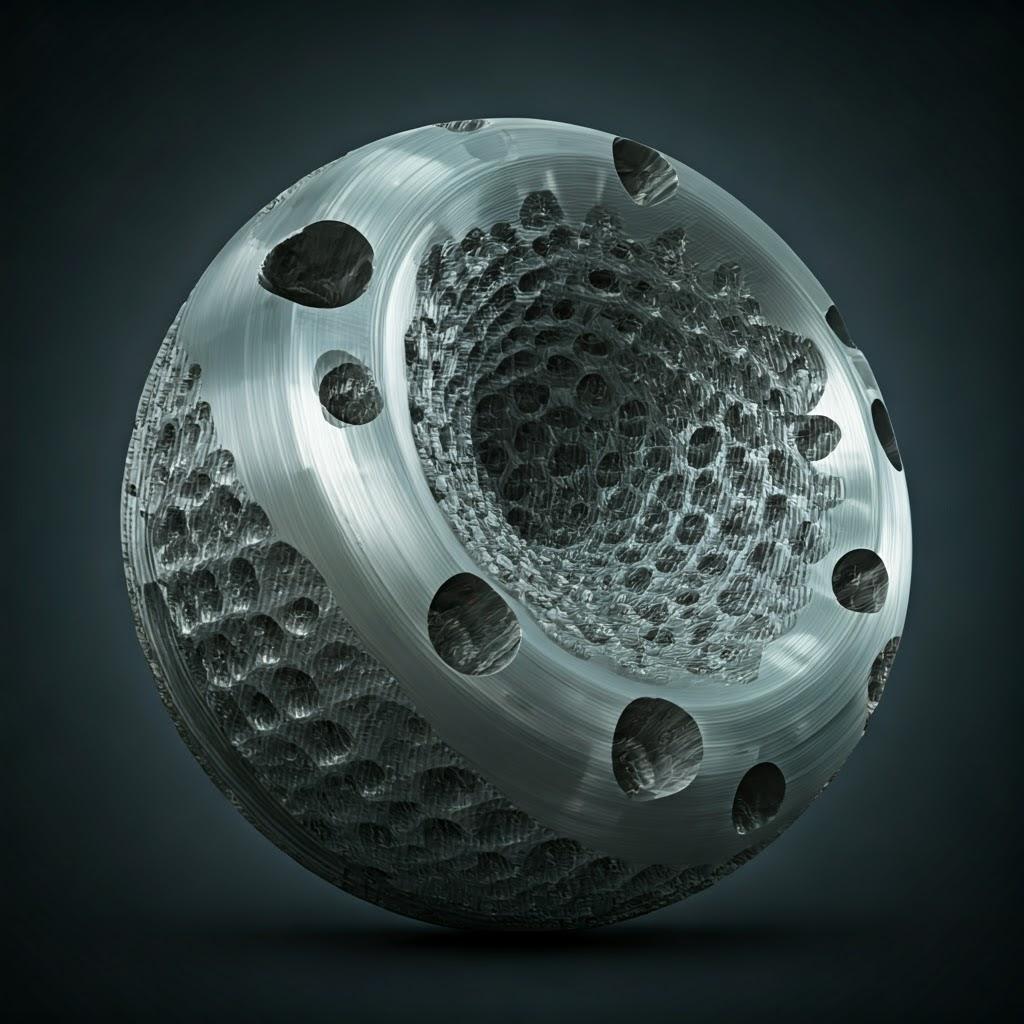
Aditivní výhoda: Proč zvolit 3D tisk kovů pro zakázkové nástroje?
Zatímco tradiční výrobní metody pro výrobu nástrojů, jako je CNC obrábění, elektroerozivní obrábění a odlévání, zůstávají relevantní, aditivní výroba kovů představuje přesvědčivý soubor výhod, které přímo řeší mnoho omezení, jež jsou těmto starším technikám vlastní. Pro konstruktéry usilující o optimální výkon a manažery nákupu zaměřené na celkové náklady na vlastnictví a agilitu dodavatelského řetězce je pochopení těchto výhod klíčové při hodnocení zakázková nástrojová řešení. Rozhodnutí o využití kovového 3D tisku často vychází z jeho schopnosti přinést hodnotu v několika klíčových dimenzích: rychlost, komplexnost, výkon a nákladová efektivita v konkrétních scénářích.
1. Bezprecedentní rychlost a zkrácení dodacích lhůt: To je pravděpodobně nejvýznamnější hnací silou pro zavádění AM v oblasti nástrojů.
- Tradiční: Vytváření složitých nástrojů, zejména forem a zápustek, může trvat týdny nebo dokonce měsíce kvůli složitým procesům obrábění, vícenásobnému nastavení a závislosti na dostupnosti kvalifikované pracovní síly. Iterace návrhu jsou pomalé a nákladné.
- Přísada: Kovové 3D tiskárny mohou často vyrobit složité nástrojové komponenty, jako jsou například vložky do forem nebo vlastní přípravky, během několika dní přímo ze souboru CAD. To usnadňuje:
- Rychlé prototypování: Rychle vytvářejte a testujte funkční prototypy nástrojů, což umožňuje rychlejší ověřování a opakování návrhu.
- Nástroje pro mosty: Rychlá výroba krátkodobých nástrojů pro zahájení výroby v době, kdy se vyrábějí konvenční dlouhodobé nástroje, což zkracuje dobu uvedení na trh.
- Výroba na vyžádání: V případě potřeby rychle vyrobte náhradní nebo specializované nástroje, čímž snížíte nároky na skladové zásoby a prostoje.
- Dopad: Toto zrychlení výrazně zkracuje vývojové cykly výrobků a umožňuje výrobcům mnohem rychleji reagovat na změny na trhu nebo požadavky zákazníků. Rychlé prototypování nástrojů se stává proveditelným a vysoce účinným.
2. Geometrická složitost a svoboda designu: AM vytváří díly vrstvu po vrstvě, což konstruktéry osvobozuje od mnoha omezení, která kladou subtraktivní metody.
- Tradiční: Obráběcí omezení omezují vnitřní prvky, složité tvary a možnost hospodárně vytvářet určité podřezy nebo složité křivky.
- Přísada: Umožňuje vytvářet:
- Konformní chladicí kanály: Jak již bylo uvedeno, tyto složité vnitřní kanály kopírují tvar povrchu nástroje a zajišťují vysoce účinné a rovnoměrné chlazení. Toho je velmi obtížné nebo nemožné dosáhnout konvenčním způsobem, ale u AM je to poměrně snadné. Zvýšení výkonnosti z hlediska doby cyklu a kvality dílů při lisování a tlakovém lití je značné.
- Optimalizace topologie a odlehčení: Algoritmy mohou optimalizovat návrhy nástrojů tak, aby umisťovaly materiál pouze tam, kde je to z konstrukčního hlediska nutné, a vytvářet pevné a zároveň lehké přípravky, upínací přípravky a EoAT pomocí vnitřních mřížkových struktur nebo organických tvarů.
- Konsolidace částí: Složité sestavy lze často přepracovat a vytisknout jako jediný monolitický díl, čímž se zkrátí doba montáže, sníží se potenciální netěsnosti (v chlazených nástrojích) a sníží se počet míst poruchy.
- Dopad: To umožňuje nejen rychlejší výrobu nástrojů, ale i jejich výrazně lepší výkon, ergonomičtější provedení nebo zcela nové výrobní možnosti. Nástroje se složitou geometrií již nepředstavuje velkou nákladovou ani časovou překážku.
3. Zvýšený výkon a životnost nástroje: Kombinace volnosti konstrukce a pokročilých materiálů umožňuje vynikající výkon nástrojů.
- Konformní chlazení: To vede k rychlejším cyklům, nižšímu tepelnému namáhání, menšímu kroucení dílů a často delší životnosti nástrojů díky nižším špičkovým teplotám a rovnoměrnějšímu rozložení teploty.
- Optimalizované materiály: AM umožňuje použití moderních nástrojových ocelí (např. H13, maragingové oceli jako M300/1.2709) a dalších vysoce výkonných slitin vybraných speciálně pro požadavky na opotřebení, tvrdost a teplotu. Společnosti jako Met3dp nabízejí řadu specializovaných prášků optimalizovaných pro náročné nástrojové aplikace.
- Vlastnosti povrchu: Textury, drobné rytiny nebo specifické funkční povrchy lze během tisku integrovat přímo do konstrukce nástroje.
- Dopad: Výkonnější nástroje vedou přímo k vyšší kvalitě finálních dílů, zvýšení produktivity výroby a snížení provozních nákladů.
4. Nákladová efektivita (závisí na kontextu): Počáteční náklady na jeden díl u AM mohou být někdy vyšší než u tradičních metod pro jednoduché geometrie, je celková nabídka hodnoty často nákladově efektivnější, pokud se vezme v úvahu celý životní cyklus a specifické potřeby aplikace.
- Snížení nákladů na dodací lhůty: Rychlejší uvedení na trh znamená rychlejší generování příjmů. Zkrácení prostojů znamená nižší provozní ztráty.
- Snížení pracnosti: Vysoce automatizované procesy AM snižují potřebu neustálého dohledu kvalifikovaného obráběče ve srovnání se složitým vícestupňovým obráběním.
- Účinnost materiálu: AM je aditivní proces, při kterém obvykle vzniká méně materiálového odpadu (zejména ve srovnání s obráběním z velkého polotovaru), ačkoli podpůrné struktury určitý odpad vytvářejí.
- Zvýšení výkonu: Rychlejší časy cyklů a nižší zmetkovitost konformně chlazených nástrojů mají přímý dopad na ziskovost.
- Složitost “zdarma”: Na rozdíl od obrábění, kde složitost dramaticky zvyšuje náklady, v případě AM složitost nepřináší téměř žádné dodatečné náklady kromě potenciálně delší doby tisku nebo většího množství podpůrného materiálu.
- Prodloužení životnosti nástrojů: Nástroje s delší životností snižují četnost výměny a související náklady.
- Dopad: Při hodnocení tradiční vs. aditivní obrábění, analýza celkových nákladů na vlastnictví (TCO) často odhalí významný potenciál úspor pro AM, zejména u složitých, vysoce výkonných nebo časově náročných nástrojových aplikací.
5. Přizpůsobení a agilita: AM je ideální pro výrobu vysoce přizpůsobených nebo jedinečných nástrojových komponent.
- Životaschopnost při nízkém objemu: Ekonomicky výhodná výroba jednorázových nebo velmi malých sérií zakázkových nástrojů bez vysokých nákladů na přípravu tradičních metod.
- Snadné aktualizace designu: Digitálně upravujte návrhy nástrojů a rychle je znovu tiskněte, abyste se přizpůsobili změnám produktu nebo vylepšení procesu.
- Dopad: Poskytuje výrobcům větší flexibilitu při přizpůsobování výrobních linek, testování nových konceptů a uspokojování požadavků specifických trhů.
Souhrnně lze říci, že přesvědčivé výhody 3D tištěných nástrojů - rychlost, svoboda designu umožňující funkce jako konformní chladicí kanály, vyšší výkonnost, potenciální úspora nákladů a agilita - z něj činí výkonnou alternativu a doplněk tradičních metod. Využitím technologie AM pro obrábění kovů mohou výrobci překonat kritická úzká místa, zlepšit provozní efektivitu a odblokovat vyšší úroveň produktivity a inovací ve svých nástrojových strategiích.
Materiální záležitosti: Výběr správných kovových prášků pro vysoce výkonné nástroje
Úspěch jakéhokoli kovového 3D tištěného nástroje na zakázku závisí především na výběru vhodného materiálu. Aplikace nástrojů často zahrnují náročné podmínky: vysoké mechanické namáhání, zvýšené teploty, abrazivní opotřebení a potřebu vynikající rozměrové stability. Aditivní výroba nabízí rostoucí portfolio kovových prášků, které jsou speciálně vhodné pro splnění těchto výzev. Výběr správného prášku vyžaduje pochopení specifických požadavků dané aplikace (např. vstřikování vs. lisovací forma vs. přípravek) a vlastností, které nabízejí různé slitiny. Pro manažery nákupu, kteří obstarávají dodavatelé materiálů pro aditivní výrobu a konstruktérům, kteří specifikují nástroje, je nezbytná znalost běžných vysoce výkonných nástrojových prášků.
Společnost Met3dp s využitím svých pokročilých možností výroby prášků, včetně technologií plynové atomizace a PREP, vyrábí řadu vysoce kvalitních sférických kovových prášků optimalizovaných pro procesy AM, jako je selektivní tavení elektronovým svazkem (SEBM) a laserová fúze v práškovém loži (LPBF). Náš důraz na kvalitu prášků - vysoká sféricita, dobrá tekutost, kontrolovaná distribuce velikosti částic a nízký obsah kyslíku/nečistot - zajišťuje zákazníkům tisk hustých, vysoce integrovaných nástrojových komponent s vynikajícími mechanickými vlastnostmi. Mezi nejvýznamnější materiály pro zakázkové nástroje patří specializované nástrojové oceli a maragingové oceli.
Doporučené nástrojové prášky:
1. Nástrojová ocel H13:
- Popis: Univerzální chrom-molybden-vanadová nástrojová ocel pro obrábění za tepla, široce používaná v tradičním nástrojářství a dobře přizpůsobená pro AM. Je známá pro svou vynikající kombinaci vysoké houževnatosti, odolnosti proti opotřebení, dobré odolnosti proti tepelné únavě a rozměrové stálosti při zvýšených teplotách.
- Klíčové vlastnosti:
- Vysoká tvrdost (po tepelném zpracování obvykle dosahuje 45-52 HRC).
- Vynikající odolnost proti popouštění (zachovává tvrdost při vysokých teplotách).
- Dobrá tepelná vodivost (výhodná pro chladicí aplikace).
- Vysoká houževnatost a tažnost (odolává praskání při nárazu).
- Dobrá obrobitelnost (ve srovnání s jinými nástrojovými ocelemi) po žíhání.
- Úvahy o AM: Vyžaduje pečlivou kontrolu parametrů tisku a povinné tepelné zpracování po tisku (kalení a popouštění), aby bylo dosaženo požadovaných vlastností. Často jsou nutné cykly odlehčení od napětí.
- Typické aplikace: Vstřikovací formy & jádra (zejména s konformním chlazením), zápustky pro tlakové lití, vytlačovací zápustky, kovací nástroje, tvářecí nástroje, konstrukční součásti vyžadující vysokou pevnost a tvrdost. 3D tisk z nástrojové oceli H13 je oblíbenou volbou pro náročné tepelné a mechanické zatížení.
2. Maraging Steels (např. M300 / 1.2709 / MS1):
- Popis: Skupina nízkouhlíkových ocelí s vysokým obsahem niklu, které se zpevňují srážením intermetalických sloučenin během stárnutí, nikoli obsahem uhlíku jako tradiční nástrojové oceli. Nabízejí velmi vysokou pevnost, dobrou houževnatost a vynikající rozměrovou stabilitu při tepelném zpracování. M300 (často označovaná podobně jako 1.2709 nebo MS1 v AM) je běžnou třídou.
- Klíčové vlastnosti:
- Velmi vysoká tvrdost a pevnost (po jednoduchém tepelném zpracování stárnutím lze obvykle dosáhnout tvrdosti až 50-55+ HRC).
- Výjimečná houževnatost ve srovnání s tradičními nástrojovými ocelemi při podobných úrovních tvrdosti.
- Vynikající svařitelnost (vhodné pro opravy nebo hybridní výrobu).
- Minimální a předvídatelné deformace během nízkoteplotního tepelného zpracování při stárnutí (obvykle ~480-500 °C), což zjednodušuje následné zpracování ve srovnání s vysokoteplotním kalením a popouštěním, které je nutné u H13.
- Dobrá obrobitelnost ve stavu po tisku nebo po žíhání v roztoku.
- Úvahy o AM: Relativně snadný tisk s dobrou hustotou. Významnou výhodou je jednoduché tepelné zpracování při stárnutí, které snižuje složitost následného zpracování a riziko deformace.
- Typické aplikace: Vysoce výkonné vstřikovací formy (jádra, vložky, zvedáky), nástroje vyžadující vysokou pevnost a houževnatost, složité komponenty pro tlakové lití, vysoce přesné přípravky, letecké komponenty. Na stránkách M300 maraging steel AM (nebo 1.2709 vlastnosti prášku) je ideální pro vysoce přesné nástroje, u nichž je rozhodující minimální deformace při tepelném zpracování.
Srovnávací tabulka: H13 vs. maragingová ocel (M300/1.2709) pro AM nástroje
Vlastnosti | Nástrojová ocel H13 | Maraging Steel (M300 / 1.2709) | Shrnutí klíčových výhod |
---|---|---|---|
Primární legování | Cr, Mo, V, C | Ni, Co, Mo, Ti | Různé mechanismy posilování |
Typická tvrdost (HRC) | 45-52 | 50-55+ | Maraging ocel obecně dosahuje vyšší tvrdosti/pevnosti |
Houževnatost | Dobrý | Vynikající (při vysoké tvrdosti) | Maraging ocel nabízí lepší houževnatost |
Tvrdost za tepla | Velmi dobře | Dobrý (ale může změknout nad teplotou zrání) | H13 je obecně vhodnější pro velmi vysoké provozní teploty |
Tepelné zpracování | Komplexní (Austenitize, Quench, Temper) | Jednoduché (vytvrzování ve stáří ~480 °C) | Maraging steel mnohem jednodušší, menší riziko deformace |
Rozměrová stabilita (HT) | Mírné (riziko zkreslení) | Vynikající (minimální zkreslení) | Maraging ocel vynikající pro přesné aplikace |
Svařitelnost | Veletrh | Vynikající | Maraging steel se snadněji opravuje/modifikuje |
Náklady | Obecně nižší | Obecně vyšší | H13 často nákladově efektivnější materiál |
Běžné použití AM | Nástroje pro obrábění za tepla, formy, lisovací formy | Vysoce přesné formy, vysoce odolné nástroje | Obojí je široce používáno, výběr závisí na konkrétních potřebách |
Export do archů
Další potenciální materiály: Zatímco H13 a maragingové oceli jsou pracovními koňmi, v závislosti na konkrétní potřebě nástroje lze zvážit i jiné materiály:
- Nerezové oceli (např. 17-4PH, 316L): Používá se pro nástroje vyžadující odolnost proti korozi, například v potravinářství nebo v některých lékařských aplikacích, nebo pro méně náročné přípravky. Často se snadněji tisknou a následně zpracovávají.
- Kobalt-chrom (CoCrMo): Nabízí vynikající odolnost proti opotřebení, vysokou pevnost při zvýšených teplotách a odolnost proti korozi. Používá se pro vysoce náročné opotřebitelné součásti nebo specifické lékařské nástroje.
- Slitiny titanu (např. Ti6Al4V): Lehké, pevné a odolné proti korozi. Používá se pro lehké přípravky, robotická chapadla nebo specifické lékařské/kosmické nástroje (i když méně často pro vysoce opotřebované formy/nástroje). Společnost Met3dp nabízí inovativní slitiny titanu, jako jsou TiNi, TiTa, TiAl, TiNbZr, které by mohly najít využití ve výklencích pro nástroje. Prozkoumejte rozmanité materiály společnosti Met3dp’ nabídka kovových prášků.
- Niklové superslitiny (např. Inconel 718): Používá se pro nástroje pracující v extrémně vysokoteplotním nebo korozivním prostředí.
Výběr správného dodavatele materiálu: Výběr kovový prášek pro nástroje zahrnuje více než jen výběr slitiny. Kvalita prášku přímo ovlivňuje kvalitu výsledného nástroje. Spolupráce s renomovaným dodavatelem, jako je Met3dp, zaručuje:
- Důsledná chemie: Přísná kontrola složení slitiny.
- Optimalizované charakteristiky částic: Vysoká sféricita, řízená distribuce velikosti (PSD) a dobrá tekutost vhodná pro specifické procesy AM (jako je SEBM nebo LPBF).
- Nízký obsah nečistot: Minimalizace obsahu kyslíku a dalších nečistot, které mohou zhoršit mechanické vlastnosti.
- Sledovatelnost šarží: Zajištění konzistence a kontroly kvality.
- Technická podpora: Odborná pomoc při výběru nejlepšího materiálu pro danou aplikaci.
Závěrem lze říci, že výběr materiálu je základním kamenem úspěšného 3D tisku kovových nástrojů. Pečlivým zvážením požadavků na aplikaci a využitím vlastností pokročilých materiálů, jako jsou H13 a M300/1.2709, mohou výrobci vyrábět vysoce výkonné a odolné nástroje, které přinášejí významné provozní výhody. Spolupráce se zkušeným dodavatel materiálů pro aditivní výrobu jako Met3dp poskytuje přístup k vysoce kvalitním práškům a odborným znalostem potřebným k informovanému výběru materiálu.
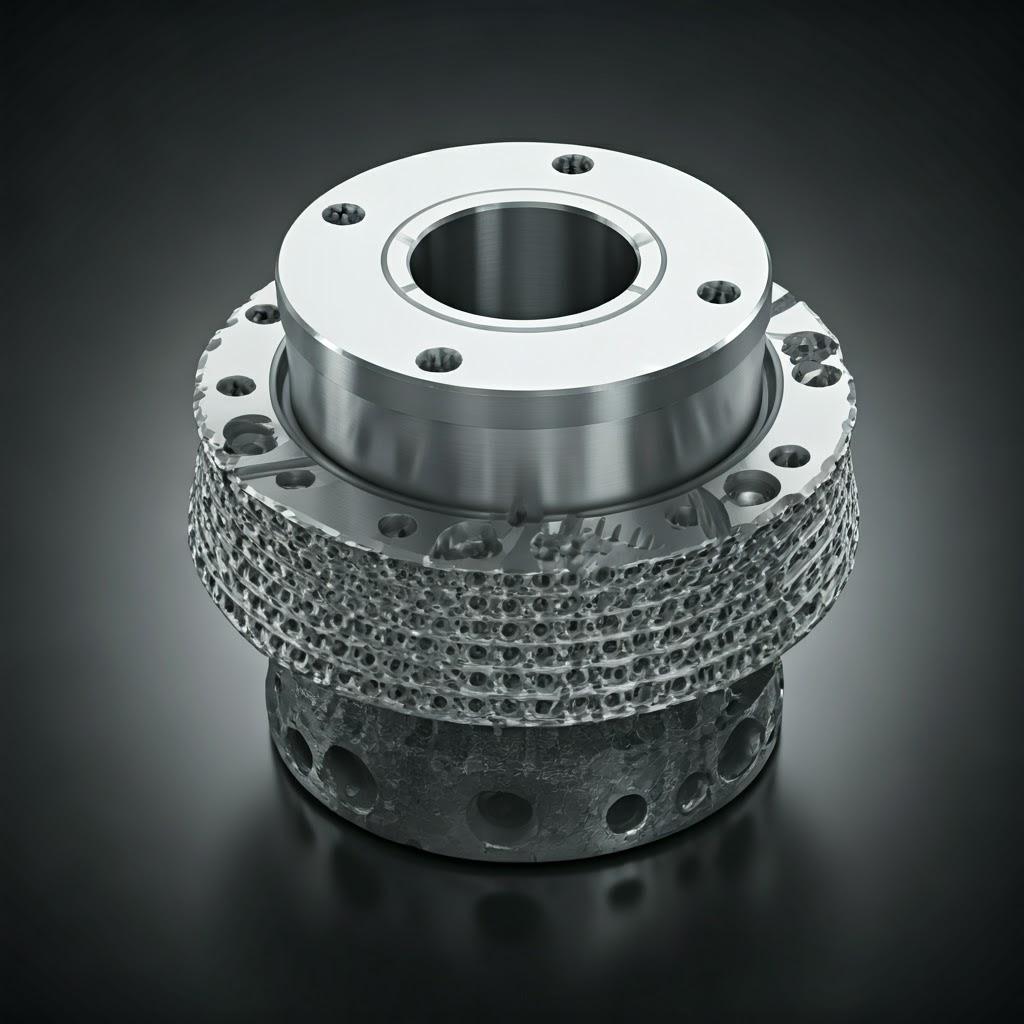
Design pro aditivní výrobu (DfAM): Optimalizace nástrojů pro 3D tisk z kovu
Pouhá replikace tradičně navrženého nástroje pomocí aditivní výroby kovů jen zřídkakdy uvolní plný potenciál této technologie. Aby inženýři skutečně využili rychlost, složitost a výkonnostní výhody, o kterých jsme hovořili dříve, musí přijmout následující opatření Design pro aditivní výrobu (DfAM). DfAM není jen souborem pravidel, ale změnou myšlení, která podporuje konstruktéry v tom, aby od počátku uvažovali aditivně a brali v úvahu proces sestavování po jednotlivých vrstvách, vlastnosti materiálů, požadavky na podpůrné konstrukce a kroky následného zpracování. Uplatňování zásad DfAM konkrétně na zakázkové nástroje - ať už se jedná o formy, zápustky, přípravky nebo přípravky - je rozhodující pro dosažení funkčních, nákladově efektivních a vysoce výkonných výsledků. Manažeři veřejných zakázek by si také měli být vědomi principů DfAM, protože přímo ovlivňují proveditelnost, náklady a kvalitu 3D tištěných nástrojů, které si pořizují. Investice do odborných znalostí v oblasti DfAM, ať už interně, nebo prostřednictvím zkušeného poskytovatele služeb, jako je Met3dp, je klíčem k maximalizaci návratnosti investic do technologie AM pro nástroje z kovů.
Základní zásady DfAM pro zakázkové nástroje:
- Strategie orientace a podpory:
- Orientace na stavbu: Orientace dílu na konstrukční desce významně ovlivňuje dobu tisku, kvalitu povrchu na různých plochách, množství a umístění potřebných podpůrných struktur a potenciální tepelné namáhání. U nástrojů by kritické funkční plochy (např. plochy dutin formy, body pro umístění upínacích přípravků) měly být v ideálním případě orientovány tak, aby se minimalizovaly nebo vyloučily podpěry, často směřují vzhůru nebo jsou samonosné.
- Převisy a úhly: Procesy AM s kovem mají omezení úhlu přesahů, které lze vytvořit bez podpůrných konstrukcí. Úhly typicky větší než 45 stupňů od vodorovné roviny jsou často samonosné, ale to se liší podle materiálu, stroje (mohou platit různé úvahy pro SEBM vs LPBF, pochopení různých tiskových metod je užitečné) a specifickou geometrii. Návrhy by měly maximalizovat samonosné prvky, pokud je to možné.
- Návrh podpůrné konstrukce: Podpěry jsou často nezbytné, ale zvyšují náklady na materiál, čas tisku a náročnost následného zpracování (odstranění). DfAM zahrnuje:
- Minimalizace podpory: Orientace dílu a úprava nekritických prvků (např. použití zkosení místo ostrých převisů), aby se snížila závislost na podpěrách.
- Navrhování pro odstranění: Zajištění přístupu k podpěrám pro nástroje pro demontáž (ruční nebo strojní). Použití optimalizovaných typů podpěr (např. mřížové nebo stromové podpěry) může snížit spotřebu materiálu a kontaktních bodů. Zvažte přidání prvků usnadňujících demontáž, jako jsou přístupová okénka, pokud se nelze vyhnout vnitřním podpěrám.
- Úvahy o podpůrném materiálu: Některé pokročilé systémy nabízejí rozpustné nebo snadno rozbitné podpůrné materiály, což usnadňuje jejich odstraňování.
- Návrh a rozlišení funkcí:
- Minimální tloušťka stěny: Procesy AM mají omezení, jak tenký prvek lze spolehlivě vytisknout. Tento limit se liší podle stroje a materiálu, ale obvykle se pohybuje v rozmezí 0,4-1,0 mm. Návrhy nástrojů musí tyto limity respektovat, aby byla zajištěna strukturální integrita a tisknutelnost.
- Minimální velikost prvku: Malé otvory, čepy nebo složité detaily mají také svá omezení vyplývající z velikosti bodu laserového/elektronového paprsku a velikosti částic prášku. Velmi jemné prvky mohou vyžadovat obrábění po tisku.
- Orientace otvorů: Vodorovné otvory se často tisknou s lepší rozměrovou přesností než svislé otvory díky konstrukci po vrstvách. Velmi malé otvory, zejména horizontální, mohou vyžadovat podpěru nebo je lepší je po tisku vyvrtat.
- Ostré rohy: Ostré vnitřní rohy mohou představovat místa koncentrace napětí. Použití koutů nebo poloměrů může zvýšit únavovou životnost a snížit napětí, což je u vysoce zatížených nástrojů velmi důležité.
- Konstrukce pro konformní chlazení (formy a zápustky):
- Jedná se o ukázkový příklad toho, že DfAM umožňuje dosahovat vynikajícího výkonu. Mezi klíčové aspekty patří:
- Cesta kanálu: Navrhněte kanály tak, aby kopírovaly obrysy povrchů, které vytvářejí teplo (dutina formy, čelo formy), ve stejné vzdálenosti (obvykle 1-3 mm pod povrchem). Vyhněte se ostrým ohybům, které brání proudění.
- Průměr kanálu & Tvar: Průměry se obvykle pohybují od 2 do 10 mm. Běžné jsou kruhové průřezy, ale AM umožňuje optimalizovat tvary (např. slza) pro zlepšení přenosu tepla nebo snížení tlakové ztráty. Dbejte na to, aby byly průměry dostatečně velké, aby se daly tisknout a nedocházelo k jejich ucpávání.
- Optimalizace toku: Navrhněte turbulentní proudění (podporuje přenos tepla) a zajistěte vyvážené proudění v různých chladicích okruzích. K optimalizaci uspořádání kanálů se často používá simulace CFD (Computational Fluid Dynamics).
- Vstupy/výstupy: Navrhněte robustní přípojky pro externí chladicí potrubí, které často obsahují standardní montážní rozhraní, jež mohou vyžadovat dodatečné opracování.
- Depowdering: Zajistěte, aby bylo možné po tisku účinně vyčistit vnitřní kanály od neroztaveného prášku. To může zahrnovat návrh přístupových otvorů nebo zajištění dostatečného průměru kanálů.
- Jedná se o ukázkový příklad toho, že DfAM umožňuje dosahovat vynikajícího výkonu. Mezi klíčové aspekty patří:
- Odlehčení pomocí optimalizace topologie a mřížových struktur:
- Zvláště důležité pro přípravky, přípravky a robotické EoAT, kde snížení hmotnosti zlepšuje ergonomii nebo výkonnost robota.
- Optimalizace topologie: Softwarové nástroje analyzují podmínky zatížení a odstraňují materiál z nekritických oblastí, čímž vznikají organicky vypadající, vysoce účinné konstrukce.
- Mřížové struktury: Nahrazení plných objemů vnitřními opakujícími se jednotkovými buňkami (mřížkami) může výrazně snížit hmotnost a spotřebu materiálu při zachování požadované tuhosti a pevnosti. Různé typy mřížek (např. krychlové, oktetové příhradové) nabízejí různé vlastnosti.
- Použití: Vytvářejte ergonomické, lehké montážní přípravky; snižte setrvačnost robotických chapadel; minimalizujte náklady na materiál u velkých přípravků. Nástroje pro mřížové struktury nabízí významné výhody při manipulaci a automatizaci.
- Konsolidace částí:
- Využijte výhodu komplexnosti AM’ k přepracování vícedílných nástrojových sestav do jediné monolitické tištěné součásti.
- Výhody: Snižuje pracnost a čas montáže, eliminuje potenciální netěsnosti (např. ve spojích v chladicích kanálech), snižuje počet dílů a správu zásob, často zlepšuje celkovou tuhost a pevnost eliminací spojů.
- Příklad: Spojení více kusů složitého přípravku nebo integrace svorek přímo do těla přípravku.
- Navrhování pro následné zpracování:
- Díly AM, zejména nástroje, téměř vždy vyžadují následné zpracování. DfAM zahrnuje plánování těchto kroků:
- Přídavky na obrábění: Přidejte dodatečný materiál (např. 0,5-1,0 mm) na povrchy, které vyžadují vysokou přesnost, specifickou rovinnost nebo hladké povrchy dosažitelné pouze CNC obráběním (např. dělící čáry forem, polohovací body přípravků, těsnicí povrchy).
- Vlastnosti obrobků: Začlenit do konstrukce prvky, které zjednodušují držení dílu při následném obrábění nebo dokončovacích operacích.
- Úvahy o tepelném zpracování: Zjistěte, jak bude zvolený materiál (např. H13 vs. M300) reagovat na tepelné zpracování a zda konstrukce vydrží tepelné namáhání bez nadměrného zkreslení. Jednoduché a robustní geometrie jsou obecně lepší.
- Díly AM, zejména nástroje, téměř vždy vyžadují následné zpracování. DfAM zahrnuje plánování těchto kroků:
Promyšleným použitím těchto DfAM pro nástroje principy, mohou výrobci přejít od pouhého nahrazování tradičních metod ke skutečným inovacím a vytvářet vlastní nástroje, které se vyrábějí rychleji, jsou lehčí, mají delší životnost a fungují lépe než kdykoli předtím. Spolupráce s odborníky na AM, jako je Met3dp, zajišťuje, že návrhy jsou optimalizovány nejen z hlediska funkčnosti, ale také z hlediska vyrobitelnosti s využitím pokročilých technologií pokyny pro navrhování AM kovů.
Přesnost a kvalita: Pochopení tolerance, povrchové úpravy a přesnosti u 3D tištěných nástrojů
Při specifikaci a pořizování zakázkových nástrojů je nejdůležitější dosáhnout požadované úrovně přesnosti, kvality povrchu a celkové rozměrové přesnosti. Nástroje často přímo spolupracují s finálními díly nebo jinými výrobními zařízeními, což vyžaduje přísnou kontrolu kritických rozměrů a vlastností povrchu. Přestože aditivní výroba kovů nabízí pozoruhodnou geometrickou volnost, je nezbytné, aby konstruktéři a manažeři nákupu měli realistická očekávání ohledně vlastních tolerancí a kvality povrchu dosažitelných přímo z tiskárny a aby chápali roli následného zpracování při plnění přísných požadavků. Zajištění kontrola kvality 3D tištěných dílů určené pro nástrojové aplikace zahrnuje pečlivé řízení procesu, vhodnou metrologii a často i sekundární dokončovací operace.
Rozměrová přesnost a tolerance:
- Přesnost podle konstrukce: Přesnost kovového dílu AM bezprostředně po tisku a odlehčení napětí, ale před jakýmkoli obráběním. Typické dosažitelné tolerance závisí do značné míry na:
- Kalibrace stroje: Dobře udržované a kalibrované stroje (jako jsou špičkové systémy používané společností Met3dp) poskytují vyšší přesnost.
- Proces (LPBF vs. SEBM): Různé procesy mohou mít mírně odlišné inherentní schopnosti přesnosti. SEBM často pracuje při vyšších teplotách, což může vést k odlišnému chování napětí/zkreslení než LPBF.
- Materiál: Různé kovové prášky vykazují během tisku a chlazení různé charakteristiky smrštění a napětí.
- Velikost a geometrie dílu: Větší díly a složité geometrie jsou obecně náchylnější k tepelnému zkreslení a odchylkám. Vnitřní pnutí vznikající během tisku mohou způsobit deformace.
- Orientace a podpora: Orientace stavby ovlivňuje akumulaci tepelných gradientů a podpůrné konstrukce ovlivňují stabilitu během stavby.
- Typické tolerance podle konstrukce: Obecné pokyny pro dobře řízené procesy AM s kovy jsou sice specifické pro jednotlivé procesy a materiály, ale mohou se pohybovat v rozmezí:
- ±0,1 mm až ±0,3 mm pro menší prvky (< 50 mm).
- ±0,2 % až ±0,5 % jmenovitého rozměru u větších prvků.
- Poznámka: Jedná se o obecné odhady; konkrétní možnosti je třeba ověřit u poskytovatele AM služeb (jako je Met3dp, známý pro přesnost a spolehlivost). Dosažení větších tolerancí často vyžaduje dodatečné obrábění.
- Tolerance po obrábění: U kritických rozměrů, jako jsou dělící čáry formy, otvory pro vyhazovací čepy, polohovací plochy upínacích přípravků nebo rozhraní ložisek, se obvykle používá CNC obrábění po tisku. Obráběním lze dosáhnout mnohem větších tolerancí, často srovnatelných s tradiční výrobou:
- ±0,01 mm až ±0,05 mm je snadno dosažitelný v závislosti na procesu obrábění a nastavení.
- Význam pro nástroje: Pochopení těchto tolerančních rozsahů je zásadní. Nekritické prvky přípravku mohou být přijatelné s tolerancemi podle konstrukce, zatímco pracovní plochy přesné vložky formy budou téměř jistě vyžadovat obrábění.
Povrchová úprava (drsnost):
- Povrchová úprava podle stavu: Kovové díly AM mají v porovnání s obráběnými povrchy přirozeně drsnější povrch, což je způsobeno procesem vrstvení a částečně roztavenými částicemi prášku ulpívajícími na povrchu. Drsnost povrchu (běžně měřená jako Ra – Arithmetic Average Roughness) závisí na:
- Orientace: Povrchy směřující vzhůru a strmé úhly mají obecně nejlepší povrchovou úpravu. Plochy směřující dolů, které jsou podepřeny konstrukcemi, bývají po odstranění podpěr drsnější. Na bočních stěnách jsou patrné linie vrstev.
- Tloušťka vrstvy: Tenčí vrstvy obecně vedou k hladšímu povrchu, ale prodlužují dobu tisku.
- Velikost částic prášku: Jemnější prášky mohou přispět k hladšímu povrchu.
- Parametry procesu: Výkon laseru/paprsku, rychlost skenování atd. ovlivňují vlastnosti taveniny a výsledný povrch.
- Typické hodnoty Ra ve stavu po dokončení stavby:
- LPBF: Často v rozsahu 6-15 µm Ra (240-600 µin Ra).
- SEBM: Někdy může být mírně drsnější v důsledku vlastností procesu, potenciálně 15-35 µm Ra (600-1400 µin Ra).
- Poznámka: Jedná se o typická rozmezí, která se mohou výrazně lišit.
- Následně zpracovaná povrchová úprava: Pro zlepšení kvality povrchu nástrojů se používají různé dokončovací techniky:
- Otryskávání kuliček / kuličkování: Poskytuje rovnoměrný matný povrch, odstraňuje volný prášek a může vyvolat tlakové napětí (zlepšuje únavovou životnost). Hodnoty Ra se mohou mírně zlepšit nebo zůstat podobné, ale stanou se rovnoměrnějšími.
- Třískové/vibrační dokončování: Dokáže vyhladit povrchy a hrany, zejména u menších dílů. Dosažitelné Ra závisí na médiu a čase.
- Broušení/leštění: Nezbytné pro povrchy forem, které vyžadují hladký povrch pro vyhazování dílů nebo optickou čistotu, a pro povrchy s vysokým opotřebením. Ručním nebo automatizovaným leštěním lze dosáhnout velmi hladkých povrchů, často < 0,1 µm Ra (< 4 µin Ra) pro zrcadlové povrchy forem.
- Obrábění: Poskytuje kontrolovanou, hladkou povrchovou úpravu typickou pro frézování nebo soustružení (např. 0,8-3,2 µm Ra nebo lepší).
- Význam pro nástroje: Povrchová úprava ovlivňuje tření, odolnost proti opotřebení, uvolňování dílů (ve formách), přilnavost barvy (u přípravků) a estetiku. Požadovaná povrchová úprava určuje nezbytné kroky následného zpracování. Porozumění aditivní výroba povrchové úpravy možnosti a omezení jsou klíčové.
Kontrola a ověřování kvality:
- Monitorování procesů: Pokročilé systémy AM zahrnují monitorování in-situ (sledování bazénu taveniny, termální snímkování) pro sledování konzistence konstrukce.
- Kontrola kvality materiálu: Zajištění kvality prášku (chemický složení, velikost částic, tekutost) je klíčové - hlavní zaměření pro integrované poskytovatele, jako je Met3dp.
- Nedestruktivní zkoušení (NDT):
- CT vyšetření (počítačová tomografie): Stále častěji se používá k odhalování vnitřních vad, jako je pórovitost nebo nedostatečné slícování, a k ověřování, zda jsou složité vnitřní prvky, jako jsou konformní chladicí kanály, jasné a odpovídají návrhu.
- Dye Penetrant / Kontrola magnetickými částicemi: Používá se k detekci trhlin porušujících povrch.
- Rozměrová metrologie:
- Souřadnicový měřicí stroj (CMM): Používá se pro vysoce přesné ověřování kritických rozměrů, zejména po obrábění.
- 3D skenování: Optické nebo laserové skenery zachycují celou geometrii vytištěného dílu a umožňují porovnání s původním modelem CAD, aby bylo možné posoudit celkovou odchylku a přesnost. Užitečné pro složité tvary, kde je CMM obtížný.
- Zkouška tvrdosti: Ověření, zda nástroj po tepelném zpracování dosáhl stanovené tvrdosti, je rozhodující pro výkon a odolnost proti opotřebení.
Závěrem lze říci, že ačkoli 3D tisk z kovu nabízí neuvěřitelné konstrukční možnosti pro zakázkové nástroje, dosažení potřebného tolerance 3D tisku kovů, povrchová úprava a celkové rozměrově přesné nástroje často vyžaduje kombinaci pečlivého DfAM, řízených tiskových procesů a vhodných kroků následného zpracování a ověřování kvality. Spolupráce se zkušeným partnerem, který těmto nuancím rozumí a má robustní systémy řízení kvality, je zásadní pro získání spolehlivých, vysoce výkonných nástrojů, které splňují náročné výrobní požadavky.
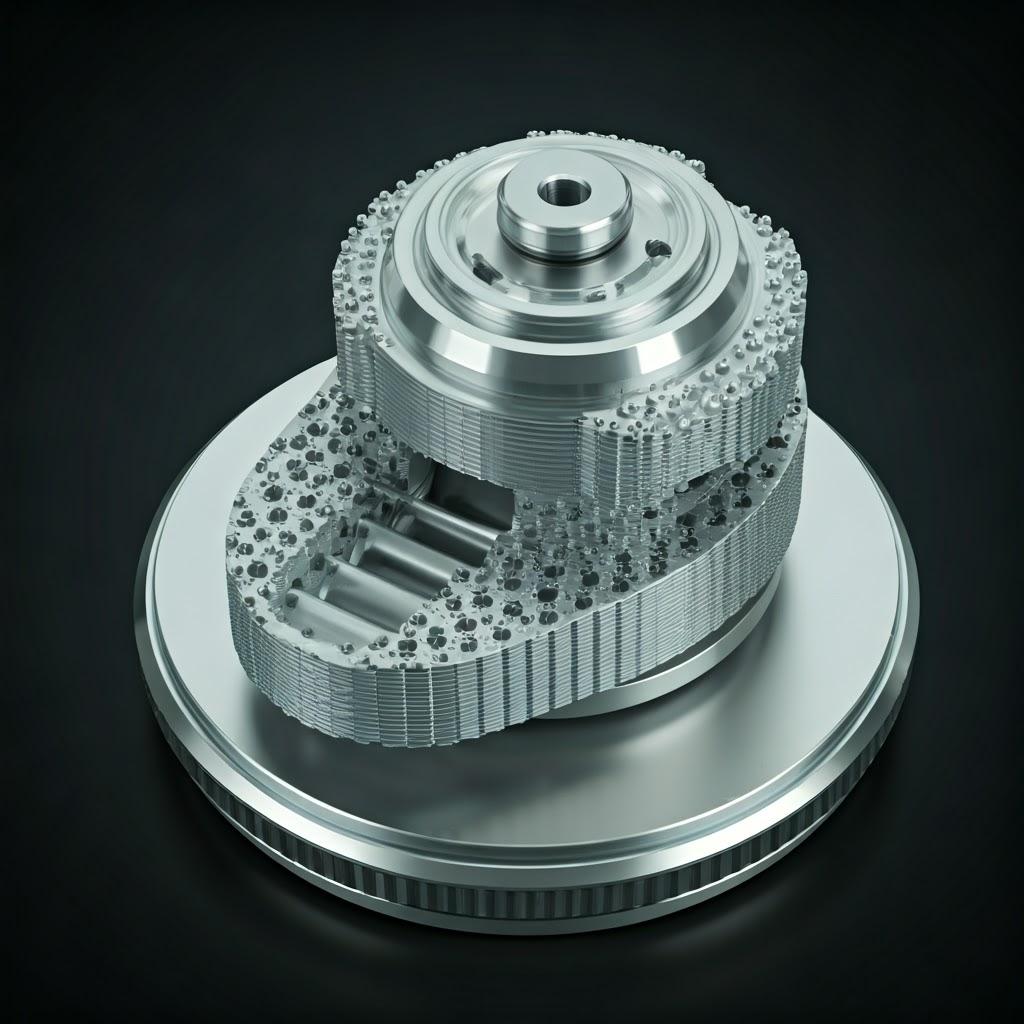
Za hranice tisku: Základní následné zpracování pro 3D tištěné kovové nástroje
Vytvoření vlastního nástroje nekončí, když kovová 3D tiskárna dokončí svou práci. Díl, který je čerstvě vytištěný z konstrukční desky, je jen zřídka připraven k okamžitému použití v náročném výrobním prostředí. Řada kritických postprocesní aditivní výroba je téměř vždy nutné provést kroky, které z hotové součásti vytvoří funkční, odolný a přesný nástroj. Tyto kroky jsou nezbytné k odstranění vnitřních pnutí, odstranění podpůrných struktur, dosažení požadovaných vlastností materiálu (tvrdost, pevnost, houževnatost), dosažení kritických rozměrů a povrchových úprav a zajištění celkové výkonnosti a životnosti nástroje. Pochopení těchto běžných požadavků na následné zpracování je zásadní pro konstruktéry navrhující nástroje a pro manažery nákupu, kteří při rozhodování o dodávkách zohledňují celkové náklady a dobu realizace. Ignorování nebo nesprávné provedení těchto kroků může vést k předčasnému selhání nástroje, špatnému výkonu a zhoršené kvalitě finálního dílu.
Běžné fáze následného zpracování nástrojů pro AM obrábění kovů:
- Úleva od stresu:
- Proč je to potřeba: Rychlé cykly zahřívání a ochlazování, které jsou vlastní procesům AM s kovem po vrstvách, vytvářejí v tištěném dílu značná vnitřní pnutí. Tato napětí mohou způsobit deformace, zkroucení (zejména po vyjmutí z konstrukční desky), a dokonce i praskání, pokud nejsou odstraněna.
- Proces: Obvykle první krok po tisku, který se často provádí, když je díl ještě připevněn ke stavební desce, aby se zachovala jeho stabilita. Zahřívání zahrnuje zahřátí dílu v peci na určitou teplotu (pod transformační teplotu materiálu, např. ~550-650 °C pro H13, nebo žíhací cyklus v závislosti na cíli), jeho udržování po stanovenou dobu a následné pomalé ochlazování. To umožňuje uvolnění mikrostruktury materiálu a snížení vnitřních pnutí.
- Důležitost: Naprosto zásadní pro rozměrovou stabilitu a prevenci následného zkroucení nebo praskání při odstraňování podpěr, obrábění nebo tepelném zpracování.
- Vyjmutí dílu ze stavební desky:
- Proces: Po uvolnění napětí (pokud se provádí na desce) je třeba díl oddělit od kovové konstrukční desky, na které byl vytištěn. Mezi běžné metody patří:
- Drátové elektroerozivní obrábění (EDM): Nabízí přesné řezání s malou silou, ideální pro jemné díly nebo v případě potřeby čistého řezného povrchu.
- Řezání (pásová pila): Rychlejší a běžnější metoda pro robustní díly, která však zanechává drsnější povrch, který obvykle vyžaduje následné obrábění.
- Obrábění: V některých případech lze použít i frézování nebo broušení.
- Proces: Po uvolnění napětí (pokud se provádí na desce) je třeba díl oddělit od kovové konstrukční desky, na které byl vytištěn. Mezi běžné metody patří:
- Odstranění podpůrné konstrukce:
- Proč je to potřeba: Podpěrné konstrukce, které jsou nezbytné pro tisk převisů a složitých geometrií, musí být odstraněny.
- Proces: V závislosti na složitosti a dostupnosti podpěr může jít o jeden z nejnáročnějších kroků. Mezi tyto metody patří:
- Ruční odstranění: Použití kleští, brusek, dlát nebo jiných ručních nástrojů. Vyžaduje zručnost a opatrnost, aby nedošlo k poškození povrchu dílu. Často zanechává stopy, které je třeba dále opracovat.
- CNC obrábění: Frézováním nebo soustružením lze přesně odstranit podpěry, zejména větší nebo integrovanější. Často se používá ve spojení s ručními metodami.
- Drátové elektroerozivní obrábění: Lze je použít pro přístup k podpěrám a jejich řezání v obtížně přístupných místech.
- DfAM Impact: Konstrukce pro odstranění podpěr (přístupnost, minimalizace kontaktních míst) významně ovlivňuje snadnost a náklady na tuto fázi.
- Tepelné zpracování (kalení/stárnutí):
- Proč je to potřeba: Kovové díly vytištěné asynchronně, a to ani po odlehčení od napětí, obvykle nemají optimální tvrdost, pevnost nebo odolnost proti opotřebení, které jsou vyžadovány pro nástrojové aplikace. Tepelným zpracováním se získá konečná požadovaná mikrostruktura a mechanické vlastnosti. Konkrétní zpracování závisí do značné míry na materiálu.
- Proces:
- Nástrojové oceli (např. H13): Vyžaduje vícestupňový proces:
- Austenizace: Zahřátím na vysokou teplotu (např. ~1000-1050 °C) se rozpustí karbidy a vytvoří austenit.
- Kalení: Rychlým ochlazením (na vzduchu, v oleji nebo inertním plynu) se austenit přemění na tvrdý martenzit.
- Temperování: Přehřátí na nižší teplotu (např. ~500-600 °C, často prováděné vícekrát) za účelem snížení křehkosti, zvýšení houževnatosti a dosažení cílové tvrdosti (např. 45-52 HRC). Tepelné zpracování nástrojové oceli jako je H13, je zásadní, ale vyžaduje pečlivou kontrolu, aby se minimalizovalo zkreslení.
- Maraging Steels (např. M300/1.2709): Vyžaduje mnohem jednodušší proces zrání při nižší teplotě:
- Zpevnění věkem: Zahřívání na mírnou teplotu (obvykle ~480-500 °C) po dobu několika hodin. To způsobí vysrážení zpevňujících intermetalických sloučenin. Chlazení není nutné. Hlavní výhodou je minimální deformace během tohoto procesu.
- Nástrojové oceli (např. H13): Vyžaduje vícestupňový proces:
- Řízení atmosféry: Tepelné zpracování se obvykle provádí ve vakuových pecích nebo v řízené inertní atmosféře, aby se zabránilo oxidaci a oduhličení, zejména při vysokých austenitizačních teplotách.
- Obrábění (CNC):
- Proč je to potřeba: Pro dosažení přísných tolerancí kritických rozměrů, vytvoření rovných těsnicích ploch (jako jsou dělící čáry formy), obrábění závitů nebo přesných otvorů a dosažení specifické povrchové úpravy, která je lepší než stav po výrobě.
- Proces: Standard CNC obrábění 3D výtisků používají se techniky jako frézování, soustružení, broušení a elektroerozivní obrábění. V úvahu přicházejí:
- Obrábění: Bezpečné upevnění potenciálně složité části AM.
- Tvrdost materiálu: Obrábění plně kalené nástrojové oceli je náročné a vyžaduje vhodné řezné nástroje a parametry. Obrábění je často snazší před závěrečným krokem kalení (ačkoli maragingové oceli jsou často po obrábění zestárlé kvůli své rozměrové stabilitě).
- Příspěvek na zásoby: DfAM by měl obsahovat dostatečné množství materiálu pro obráběcí operace.
- Povrchová úprava:
- Proč je to potřeba: Dosažení požadované drsnosti povrchu pro funkci (např. hladký povrch formy pro uvolnění dílu, strukturovaný povrch pro přilnavost), estetiku nebo odolnost proti opotřebení.
- Proces: Různé metody v závislosti na cíli:
- Tryskání kuličkami / pískování: Čistí povrch, zajišťuje jednotný matný vzhled, odstraňuje sypký pudr.
- Obrábění / vibrační úprava: Vyhlazuje hrany a povrchy, zejména u dávek menších dílů.
- Broušení: Používá se pro vysoce přesné rovinné a hladké povrchy specifických prvků.
- Leštění: Ruční nebo automatické leštění, nezbytné pro vstřikovací formy vyžadující vysoký lesk nebo optickou čistotu. Lze dosáhnout zrcadlového lesku (Ra 0,1 µm). Leštění kovových dílů je u složitých forem často vysoce kvalifikovaný ruční proces.
- Povlakování (např. PVD, nitridace): Aplikace specializovaných povlaků může dále zvýšit odolnost proti opotřebení, snížit tření nebo zlepšit uvolňovací vlastnosti pro náročné nástrojové aplikace.
Konkrétní pořadí a kombinace těchto nástroje pro povrchovou úpravu a další kroky následného zpracování se liší v závislosti na typu nástroje, materiálu a požadavcích aplikace. Pro výrobce je zásadní spolupracovat s poskytovateli AM služeb, jako je Met3dp, kteří mají nejen pokročilé tiskové schopnosti, ale také rozsáhlé odborné znalosti a vybavení pro následné zpracování, což zajišťuje zefektivnění pracovního postupu od digitálního souboru po hotový funkční nástroj. Zanedbání této “fáze po tisku” podkopává významné investice do aditivní výrobní technologie.
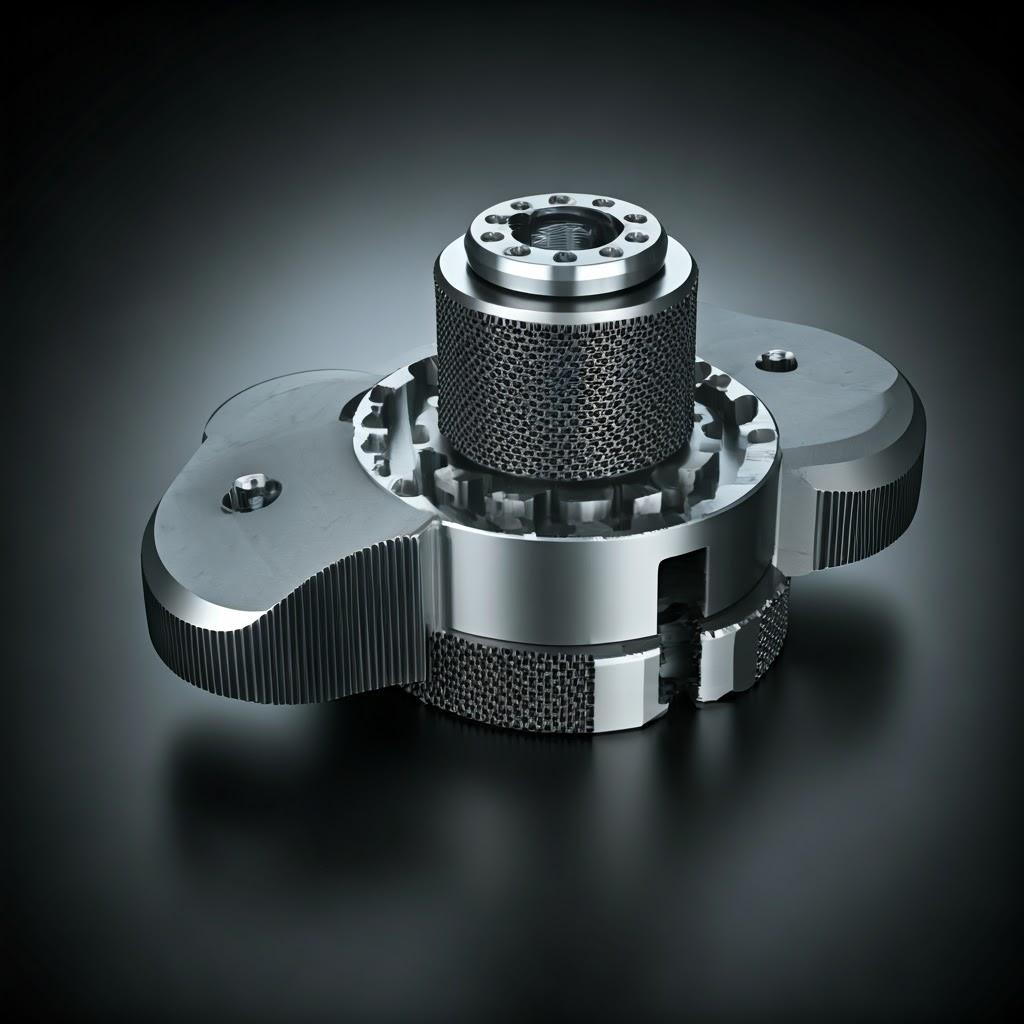
Překonávání překážek: Obvyklé problémy při výrobě nástrojů pro 3D tisk z kovu a jejich řešení
Přestože aditivní výroba kovů nabízí transformační potenciál pro zakázkové nástroje, není bez problémů. Jako každý pokročilý výrobní proces vyžaduje dosažení konzistentních a vysoce kvalitních výsledků pečlivou kontrolu, porozumění procesu a odborné znalosti při řešení problémů. Inženýři a manažeři nákupu by si měli být vědomi potenciálních překážek, aby mohli stanovit realistická očekávání a aktivně spolupracovat se svými partnery v oblasti AM, aby zmírnili rizika. Řešení těchto problémů je klíčem k úspěšné implementaci technologie AM kovů pro náročné nástrojové aplikace. Naštěstí neustálý pokrok v technologiích, materiálech, softwaru a znalostech procesů poskytuje účinná řešení a strategie pro zmírnění dopadů.
Společné výzvy a strategie pro jejich zmírnění:
- Zbytkové napětí, deformace a pokřivení:
- Výzva: Rychlé, lokalizované zahřívání a ochlazování, které je pro AM typické, vytváří vnitřní pnutí. Pokud tato napětí překračují mez kluzu materiálu nebo jsou nerovnoměrně rozložena, mohou způsobit deformaci dílu, deformaci jeho tvaru (zejména po vyjmutí z konstrukční desky) nebo dokonce prasknutí. To se týká zejména velkých dílů nebo složitých geometrií, které jsou běžné u nástrojů. Zmírnění deformace nástrojů je prvořadým zájmem.
- Příčiny: Vysoké tepelné gradienty, rychlé ochlazování, vlastnosti smršťování materiálu, geometrie dílu (např. velké ploché úseky, ostré přechody).
- Řešení & zmírnění:
- Optimalizovaná strategie sestavení: Pečlivý výběr orientace stavby, vhodné podpůrné struktury (fungující jako chladiče a kotvy) a optimalizované strategie skenování (např. ostrovní skenování, rotační vektory skenování) mohou pomoci zvládnout hromadění a distribuci tepla.
- Řízení procesních parametrů: Jemné doladění výkonu laserového/elektronového paprsku, rychlosti skenování a tloušťky vrstvy pro konkrétní materiál a geometrii. Použití předehřevu (běžné u systémů SEBM a některých systémů LPBF) snižuje tepelné gradienty.
- Tepelná simulace: Software dokáže předvídat kumulaci napětí a deformace, což umožňuje úpravu konstrukce nebo kompenzaci geometrie před tiskem.
- Povinná úleva od stresu: Pro uvolnění vnitřních pnutí před dalším zpracováním je zásadní provést správný cyklus tepelného zpracování bezprostředně po tisku, často ještě na konstrukční desce.
- Robustní konstrukce dílů (DfAM): Vyhnout se velkým nepodporovaným plochám, používat postupné přechody mezi tloušťkami a navrhovat konstrukci s ohledem na vlastní tuhost může pomoci zabránit deformacím.
- Odstranění podpůrné konstrukce:
- Výzva: Odstraňování podpůrných struktur, zejména vnitřních nebo složitých, může být časově i finančně náročné a hrozí při něm riziko poškození povrchu dílu. Výzvy spojené s odstraněním podpory jsou významným faktorem celkových nákladů a doby realizace.
- Příčiny: Husté podpěry, špatná přístupnost, silné spojení mezi podpěrou a dílem, choulostivé vlastnosti dílu.
- Řešení & zmírnění:
- DfAM pro minimalizaci podpory: Pokud je to možné, navrhněte díly se samonosnými úhly (>45°). Orientujte díl tak, abyste snížili potřebu podpěr kritických ploch.
- Optimalizovaný design podpory: Používejte takové typy podpěr (např. mřížové, stromové, kuželové), které minimalizují kontaktní body a spotřebu materiálu a zároveň zajišťují potřebnou stabilitu. Využívejte softwarové funkce, které optimalizují umístění a typ podpěr.
- Navrhování pro přístup: Zajistěte, aby nástroje (ruční nebo strojní) dosáhly na podpěry pro demontáž. Pokud se nelze vyhnout vnitřním podpěrám, zvažte přidání dočasných přístupových otvorů nebo oken.
- Výběr materiálu: Z některých materiálů se podpěry odstraňují snáze nebo hůře.
- Techniky následného zpracování: Použití drátového elektroerozivního obrábění nebo specializovaných technik obrábění pro obtížné podpěry.
- Pórovitost:
- Výzva: Přítomnost malých dutin nebo pórů v tištěném kovu. Póry mohou působit jako koncentrátory napětí, snižovat pevnost nástroje, jeho únavovou životnost a potenciálně ovlivňovat tepelnou vodivost nebo povrchovou úpravu po leštění. Detekce a kontrola pórovitost při 3D tisku je pro kritické nástroje zásadní.
- Příčiny: Zachycený plyn při rozprašování nebo tisku, odpařování těkavých prvků, nedostatečná hustota energie (nedostatečné spojení mezi vrstvami/stopami), keyholing (nestabilita způsobená nadměrnou hustotou energie), špatná kvalita prášku nebo manipulace s ním (vlhkost, znečištění).
- Řešení & zmírnění:
- Optimalizované parametry procesu: Přesné řízení výkonu laseru/ paprsku, rychlosti skenování, vzdálenosti mezi šrafami a tloušťky vrstvy je klíčem k dosažení úplného roztavení a tavení. Vývoj parametrů je zásadní pro každou kombinaci materiálu a stroje.
- Vysoce kvalitní prášek: Zásadní je použití prášku s nízkým obsahem plynu, řízenou distribucí velikosti částic a vysokou sféricitou (jako je prášek vyráběný pokročilou atomizací v Met3dp). Správné postupy manipulace s práškem a jeho skladování (např. sušení, prosévání) zabraňují kontaminaci a zachycování vlhkosti.
- Řízená atmosféra stavby: Udržování vysoce čisté atmosféry inertního plynu (argonu nebo dusíku) v konstrukční komoře minimalizuje oxidaci a kontaminaci během tisku.
- Izostatické lisování za tepla (HIP): Krok následného zpracování zahrnující vysoký tlak a teplotu. HIP může účinně uzavřít vnitřní póry, čímž se výrazně zlepší hustota a mechanické vlastnosti. Často se používá pro kritické aplikace, jako jsou letecké komponenty, ale zvyšuje náklady a dobu realizace. Může být zvažována pro vysoce náročné nástroje.
- Kontrola kvality (CT skenování): Použití CT skenů k nedestruktivní kontrole dílů na vnitřní pórovitost.
- Povrchová úprava a vady:
- Výzva: Povrchy v hotovém stavu mohou být drsné a mohou vykazovat vady, jako jsou částečně roztavené částice prášku (tzv. "balling”"), tvorba strusky nebo stopy po podpěrách. Ty ovlivňují tření, opotřebení, uvolňovací vlastnosti (formy) a estetiku.
- Příčiny: Nestability procesu, neoptimální parametry, interakce nosné konstrukce, rozstřik prášku.
- Řešení & zmírnění:
- Optimalizace parametrů: Přesné nastavení parametrů pro zajištění stabilních bazénů taveniny a hladkého nanášení vrstev.
- Optimalizovaná orientace & Podporuje: Optimální umístění kritických povrchů a použití dobře navržených podpěr.
- Následné zpracování: Použití vhodných dokončovacích technik (tryskání, otryskávání, obrábění, leštění) k dosažení požadované kvality povrchu. Viz předchozí oddíl o následném zpracování.
- Praskání:
- Výzva: Trhliny mohou vznikat během tisku nebo následného tepelného zpracování, zejména u slitin s vysokým obsahem uhlíku nebo slitin citlivých na trhliny, nebo v důsledku vysokých zbytkových napětí.
- Příčiny: Vysoké zbytkové napětí, křehké fáze materiálu, rychlé ochlazení, nekompatibilita materiálů (u vícemateriálových výtisků), existující defekty působící jako iniciační místa.
- Řešení & zmírnění:
- Výběr materiálu: Výběr slitin s lepší tisknutelností a nižší náchylností k praskání, pokud je to možné (např. maragingové oceli často vykazují nižší riziko praskání než některé nástrojové oceli během tisku).
- Řízení procesu: Použití předehřevu, optimalizované strategie skenování pro řízení tepelných gradientů a pečlivý výběr parametrů.
- Úleva od stresu: Rychlá a správná úleva od stresu má zásadní význam.
- Kontrola tepelného zpracování: Opatrné zvyšování a rychlost chlazení při tepelném zpracování po tisku, zejména u citlivých materiálů, jako je H13.
Úspěšné zvládnutí těchto výzev vyžaduje hluboké znalosti materiálových věd, fyziky procesů AM, principů DfAM a důkladných postupů kontroly kvality. Spolupráce se zkušeným optimalizace procesu AM kovů odborník jako Met3dp, který kombinuje vysoce kvalitní materiály, pokročilou technologii tisku (včetně SEBM) a komplexní možnosti následného zpracování, tato rizika výrazně zmírňuje. Otevřená komunikace mezi zákazníkem a poskytovatelem AM služeb týkající se požadavků na aplikaci a potenciálních problémů je klíčem k dosažení úspěšných výsledků v oblasti kovových 3D tištěných nástrojů.
Výběr partnera: Výběr ideálního poskytovatele služeb 3D tisku kovů pro výrobu nástrojů
Úspěšné využití aditivní výroby kovů pro zakázkové nástroje není jen o pochopení technologie, ale vyžaduje i spolupráci se správným výrobním partnerem. Kvalita, výkonnost, nákladová efektivita a včasné dodání vašich 3D tištěných nástrojů do značné míry závisí na schopnostech, odborných znalostech a procesech zvoleného poskytovatele služeb. Pro inženýry a manažery veřejných zakázek, kteří mají za úkol obstarávat služby 3D tisku kovů B2B řešení, vyžaduje hodnocení potenciálních dodavatelů důkladné posouzení v několika kritických dimenzích. Informované rozhodnutí zajistí přístup nejen k tiskařské kapacitě, ale také k zásadní technické podpoře a zajištění kvality potřebné pro náročné nástrojové aplikace.
Při hodnocení potenciálních hodnocení dodavatelů nástrojů na zakázku kritéria, zvažte následující faktory:
1. Technické znalosti a zkušenosti s aplikací nástrojů:
- Hluboké znalosti AM: Má poskytovatel základní znalosti metalurgie, fyziky AM procesů (LPBF, SEBM atd.) a materiálových věd relevantních pro nástroje?
- Specializace na nástroje: Vyrobili úspěšně nástroje podobné vaší aplikaci (např. vstřikovací formy s konformním chlazením, vysoce přesné přípravky, lisovací formy)? Mohou poskytnout případové studie nebo příklady? Při předvídání výzev a optimalizaci výsledků pro konkrétní typy nástrojů jsou zkušenosti velmi důležité.
- Podpora DfAM: Nabízejí konzultace k návrhu pro aditivní výrobu? Mohou vašim inženýrům pomoci s optimalizací stávajících návrhů nebo s vývojem nových návrhů speciálně pro AM s cílem maximalizovat výhody, jako je konformní chlazení nebo odlehčení? Tato schopnost spolupráce přináší významnou přidanou hodnotu.
- Dovednosti pro řešení problémů: Jak řeší potenciální problémy, jako jsou poruchy tisku, kontrola zkreslení nebo dosažení specifických vlastností materiálu?
2. Schopnosti a technologie stroje:
- Vhodná technologie: Používají správný typ technologie AM (např. Laser Powder Bed Fusion – LPBF, Selective Electron Beam Melting – SEBM) pro váš materiál a potřeby aplikace? Například technologie SEBM, kterou často používají poskytovatelé jako Met3dp, vyniká u reaktivních materiálů nebo aplikací vyžadujících vysokou produktivitu a snížené zbytkové napětí díky vakuovému prostředí a vyšším teplotám zpracování.
- Objem sestavení: Dokáží jejich stroje pojmout velikost požadovaných nástrojů?
- Kvalita a údržba stroje: Jsou jejich stroje od renomovaných výrobců? Mají přísné plány údržby, které zajišťují stálý výkon a přesnost?
- Monitorování procesů: Jsou jejich stroje vybaveny funkcemi monitorování in-situ, které umožňují sledovat konzistenci sestavení a případně odhalit vady během tisku?
3. Portfolio materiálů a kontrola kvality:
- Příslušné materiály: Nabízejí specifické nástrojové oceli (H13, M300/1.2709) nebo jiné slitiny potřebné pro vaši aplikaci?
- Kvalita prášku: To je nejdůležitější. Informujte se o jejich postupech získávání prášku a kontroly kvality. Řídí důsledně testování prášku, manipulaci, skladování a sledovatelnost? Společnosti jako Met3dp, které vyrábějí vlastní vysoce kvalitní prášky pomocí pokročilých technologií plynové atomizace a PREP, nabízejí výraznou výhodu v oblasti konzistence a optimalizace materiálu. Zajišťují vysokou sféricitu, řízenou distribuci velikosti částic, dobrou tekutost a nízkou úroveň nečistot, které jsou kritické pro husté a vysoce výkonné nástroje.
- Vývoj nových materiálů: Zabývají se výzkumem nebo nabízejí pokročilé nebo specializované slitiny (jako je Met3dp’TiNi, TiTa, TiAl, TiNbZr, CoCrMo), které by mohly nabídnout jedinečné výhody pro budoucí potřeby nástrojů?
4. Komplexní možnosti následného zpracování:
- In-House vs. Outsourcing: Zvládá poskytovatel kritické kroky následného zpracování, jako je uvolňování napětí, tepelné zpracování (s kalibrovanými pecemi a odbornými znalostmi specifických cyklů pro nástrojové oceli), CNC obrábění a povrchovou úpravu, sám, nebo se spoléhá na externí dodavatele? Vlastní kapacity obecně nabízejí lepší kontrolu, potenciálně rychlejší realizaci a zefektivnění odpovědnosti.
- Specifické odborné znalosti: Mají prokazatelné odborné znalosti v oblasti specifického postprocessingu, který je vyžadován pro nástroje? To zahrnuje přesné tepelné zpracování pro dosažení cílové tvrdosti bez nadměrného zkreslení, vysoce přesné obrábění kritických prvků a případně pokročilé leštění forem.
- Zařízení: Disponují potřebným vybavením (pece, CNC stroje, metrologické nástroje), aby mohly efektivně zvládnout požadované kroky následného zpracování?
5. Systém řízení kvality a certifikace:
- QMS: Pracují v rámci spolehlivého systému řízení kvality (QMS)? Certifikace jako ISO 9001 jsou základním ukazatelem zavedených procesů kvality. Pro odvětví, jako je letectví a kosmonautika, může být relevantní certifikace AS9100.
- Sledovatelnost: Mohou zajistit úplnou sledovatelnost od suroviny (dávky prášku) přes tisk a následné zpracování až po finální díl?
- Metrologie a kontrola: Jaké mají možnosti kontroly rozměrů (souřadnicový měřicí stroj, 3D skenování)? Nabízejí možnosti NDT, jako je CT skenování, pokud je vyžadováno pro ověření vnitřní integrity?
6. Doba realizace, kapacita a rychlost reakce:
- Citace rychlosti: Jak rychle dokáží poskytnout podrobné nabídky na základě vašich požadavků?
- Stanovená doba dodání: Jaké jsou jejich typické dodací lhůty pro díly podobné těm vašim? Zjistěte, jaké faktory to mohou ovlivnit (např. aktuální počet nedodělků, složitost následného zpracování).
- Produkční kapacita: Mají dostatečnou kapacitu strojů, aby zvládli váš potenciální objem nebo splnili naléhavé požadavky?
- Komunikace: Jsou vstřícní, transparentní a snadno se s nimi komunikuje? Dobré řízení projektu a komunikace jsou zásadní.
7. Struktura nákladů a transparentnost:
- Jasné ceny: Je jejich cenová struktura transparentní? Rozdělují náklady spojené s tiskem, materiálem, podpěrami a následným zpracováním?
- Nabídka hodnoty: Nehodnoťte náklady pouze izolovaně, ale v kontextu kvality, odborných znalostí, doby realizace a celkové poskytované hodnoty (např. podpora DfAM, integrované následné zpracování). Někdy není nejlevnější varianta tou nejlepší hodnotou, zejména u kritických nástrojů.
8. Umístění a logistika:
- Doprava: Zvažte náklady a dobu přepravy, zejména u mezinárodních dodavatelů. Pochopte celní a případné dovozní/vývozní požadavky. Společnost Met3dp se sídlem v čínském Čching-tao obsluhuje globální trh a využívá efektivní logistiku.
- Návštěvy/audity na místě: Je možné navštívit jejich zařízení nebo provést audit (i virtuálně) a posoudit jejich činnost z první ruky?
Met3dp jako váš partner: Společnost Met3dp je předním poskytovatelem, protože nabízí komplexní integrované řešení. Díky desítkám let společných zkušeností kombinujeme špičkové tiskárny SEBM známé pro přesnost a spolehlivost, pokročilé možnosti výroby kovových prášků zajišťující kvalitu materiálu, široké portfolio zahrnující standardní a inovativní slitiny a robustní služby vývoje aplikací. Náš závazek sahá od počátečních konzultací a podpory DfAM až po pečlivý tisk a následné zpracování, což vám zajistí nástroje optimalizované z hlediska výkonu a spolehlivosti. Chcete-li se dozvědět více o naší společnosti a hodnotách, navštivte naši stránku O nás strana.
Výběr správného partnera je strategické rozhodnutí. Pečlivým vyhodnocením těchto kritérií můžete identifikovat vhodného partnera služby 3D tisku kovů B2B dodavatele, který disponuje technickou zdatností, kvalitou a komplexními schopnostmi potřebnými k úspěšnému dodání vysoce výkonných nástrojů na zakázku pro vaše výrobní potřeby.
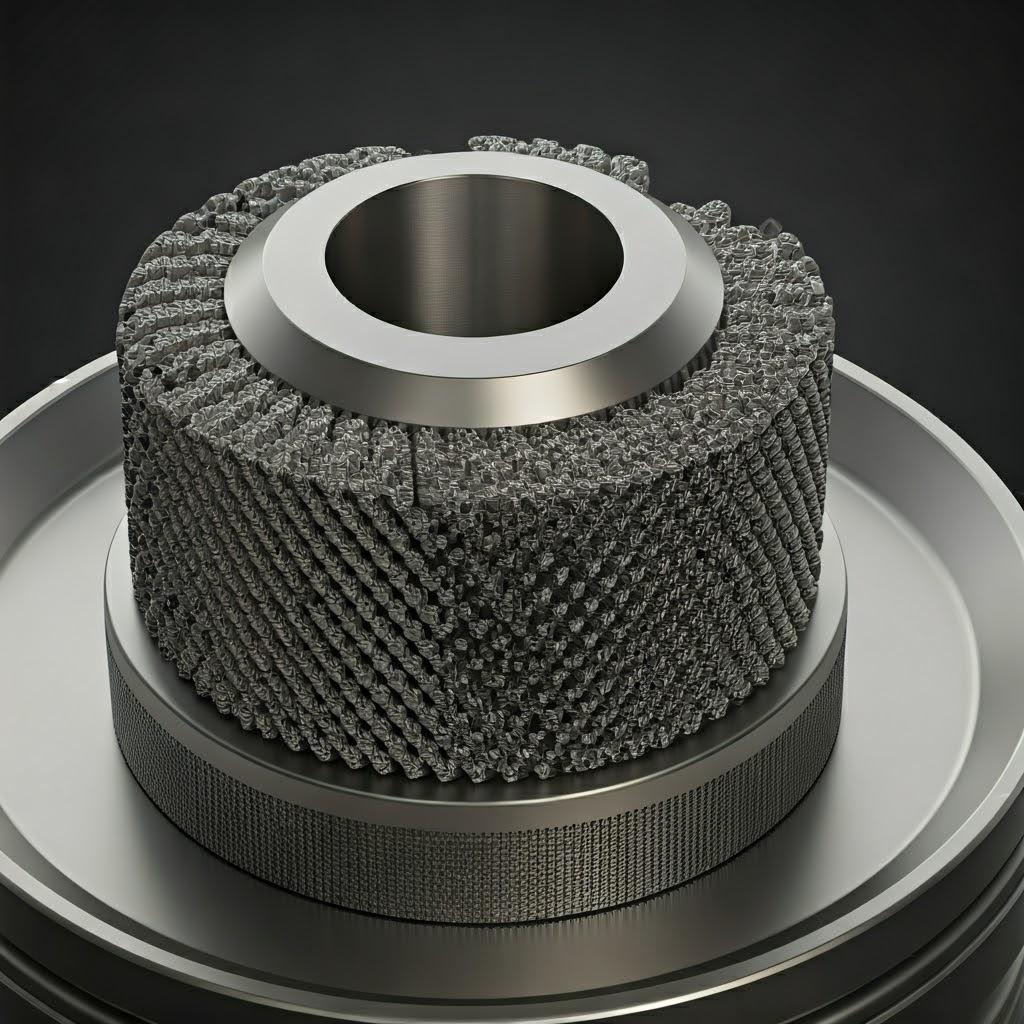
Analýza nákladů a obrat: Faktory ovlivňující cenu a dobu realizace 3D tištěných nástrojů
Jednou z nejpalčivějších otázek pro konstruktéry a manažery nákupu, kteří zvažují použití technologie AM pro výrobu nástrojů na zakázku, jsou náklady a doba realizace. Ačkoli se často propaguje rychlost, pochopení nuancí toho, co určuje rychlost výroby, je velmi důležité odhad nákladů na 3D tisk nástrojů a doba realizace aditivní výroby je zásadní pro přesné plánování projektu, sestavování rozpočtu a porovnávání AM s tradičními metodami nebo jinými dodavateli. Cena není libovolná; ovlivňuje ji kombinace spotřeby materiálu, strojního času, práce a složitosti tisku i následného zpracování. Stejně tak doba realizace je více než jen doba trvání tisku; zahrnuje celý pracovní postup od zadání zakázky až po finální dodání.
Klíčové faktory ovlivňující náklady:
- Typ materiálu a spotřeba:
- Náklady na prášek: Náklady na suroviny se u různých kovových prášků výrazně liší. Maragingové oceli nebo specializované slitiny jsou obvykle dražší než standardní nástrojové oceli jako H13 nebo nerezové oceli.
- Část Objem: Skutečný objem finálního dílu přímo ovlivňuje množství spotřebovaného prášku.
- Podpůrné struktury: Na nákladech se podílí i materiál použitý na nosné konstrukce. Optimalizované konstrukce (DfAM), které minimalizují podpěry, mohou vést k úsporám.
- Odpady: Ačkoli je AM aditivní, při manipulaci, tisku a recyklaci vzniká určitý odpad z prášku.
- Geometrie, velikost a složitost dílů:
- Ohraničující rámeček / výška stavby: Větší nebo vyšší díly zaměstnávají stroj delší dobu a spotřebují více materiálu. Celková velikost v poměru k objemu stroje ovlivňuje, kolik dílů může být vloženo do jednoho sestavení, což má vliv na efektivitu.
- Složitost: Ačkoli AM dobře zvládá složitost, velmi složité konstrukce mohou vyžadovat rozsáhlejší podpůrné struktury, což může prodloužit dobu tisku a práci při následném zpracování a odstranění. Funkce, jako jsou složité vnitřní konformní chladicí kanály, prodlužují dobu návrhu a ověřování.
- Tloušťka/hustota stěny: Tlustší části se tisknou déle. Konstrukce využívající lehké mřížkové struktury mohou snížit spotřebu materiálu a dobu tisku ve srovnání s pevnými tělesy.
- Strojový čas (tisk):
- Hodinová sazba: Stroje AM představují značné kapitálové investice a poskytovatelé obvykle počítají s hodinovou provozní sazbou, která pokrývá odpisy, energii, údržbu, inertní plyn a spotřební materiál.
- Doba trvání tisku: Určuje se podle objemu dílu, výšky, složitosti (počtu skenovaných obrysů), zvolené tloušťky vrstvy a strategie skenování. Delší doba tisku přímo zvyšuje náklady.
- Požadavky na následné zpracování: Často se jedná o hlavní náklady na nástroje.
- Úleva od stresu & amp; Tepelné ošetření: Čas, spotřeba energie a práce v peci. Komplexní cykly pro nástrojové oceli jsou náročnější než jednoduché stárnutí maragingových ocelí.
- Odstranění podpory: Náročné na práci, zejména u složitých dílů nebo obtížně přístupných podpěr. Použití specializovaných metod, jako je elektroerozivní obrábění, zvyšuje náklady.
- CNC obrábění: Požadováno pro kritické tolerance a povrchové úpravy. Náklady závisí na množství obrábění, složitosti nastavení a požadované přesnosti. Obrábění kalené nástrojové oceli je pomalejší a nákladnější.
- Povrchová úprava: Tryskání je relativně levné, ale ruční leštění vysoce kvalitních forem může být časově velmi náročné a vyžaduje kvalifikovanou práci, což výrazně zvyšuje náklady. Další náklady přináší povrchová úprava.
- Zajištění kvality a kontrola:
- Základní kontrola kvality: Obvykle jsou součástí standardní rozměrové kontroly a vizuální kontrola.
- Pokročilé NDT: Požadavky, jako je CT skenování pro zjištění vnitřní pórovitosti nebo podrobné zprávy z CMM pro ověření rozměrů, zvyšují značné náklady vzhledem k potřebnému vybavení a odborným znalostem.
- certifikace: U projektů vyžadujících zvláštní certifikace nebo rozsáhlou dokumentaci mohou vzniknout dodatečné administrativní náklady.
- Práce a odbornost:
- DfAM & amp; Technická podpora: Konzultační služby a služby optimalizace návrhu mohou být účtovány samostatně nebo v balíčku.
- Nastavení a provoz stroje: Kvalifikovaní technici musí připravovat sestavy, obsluhovat stroje a provádět prvotní čištění dílů.
- Práce po zpracování: Jak již bylo zmíněno, odstranění podpěr, obrábění a leštění vyžaduje kvalifikovanou práci.
- Objem objednávek a naléhavost:
- Množství: Zatímco náklady na seřízení jsou ve srovnání s tradičním nástrojem relativně nízké, u větších sérií (např. více stejných vložek do forem) lze dosáhnout úspor z rozsahu díky optimalizovanému vnořování sestav a zjednodušenému následnému zpracování. Informujte se o velkoobchodní 3D tiskové nástroje případné možnosti.
- Zrychlená služba: Za spěšné objednávky, které vyžadují přerušení rozvrhu nebo vyhrazený strojní čas, se obvykle účtují příplatky.
Pochopení složek dodací lhůty:
Dodací lhůta je celková doba od potvrzení objednávky do konečného dodání dílu. Zahrnuje:
- Citování & Zpracování objednávek: Kontrola návrhu, potvrzení požadavků, vytvoření cenové nabídky (hodiny až dny).
- Doba čekání ve frontě: Čekání na dostupnost stroje (může se značně lišit v závislosti na počtu nevyřízených objednávek poskytovatele - potenciálně dny až týdny).
- Příprava stavby: Krájení modelu, plánování podpěr, příprava stroje (hodiny).
- Doba tisku: Skutečná doba provozu stroje (hodiny až několik dní, v závislosti na velikosti/složitosti dílu).
- Doba chlazení: Nechte stavební komoru a díl před vyjmutím dostatečně vychladnout (hodiny).
- Následné zpracování:
- Léčba stresu/tepla: Cykly pece (hodiny až dny, včetně náběhu/máčení/chlazení).
- Odstranění podpory & Základní povrchová úprava: (hodiny až dny).
- Obrábění: (hodiny až dny, v závislosti na složitosti a plánování dílny).
- Leštění/povlakování: (hodiny až dny nebo dokonce týdny u složitých forem).
- Kontrola kvality: (hodiny až dny).
- Doprava: (dnů, v závislosti na lokalitě a způsobu).
Typický obrat: U středně složitých kovových AM nástrojů, které vyžadují standardní následné zpracování (odlehčení napětí, tepelné zpracování, základní obrábění), se dodací lhůty často pohybují od 1 až 4 týdny. Velmi složité nástroje, nástroje vyžadující rozsáhlé leštění (např. vstřikovací formy) nebo zakázky zadané v období špičkové kapacity však mohou tuto dobu přesáhnout. Vždy si u svého dodavatele ověřte dodací lhůty na základě konkrétního projektu. Zkoumání různých aplikací a procesů v rámci 3D tisk z kovu může poskytnout další informace o časových osách.
Pochopením faktorů, které ovlivňují cenové faktory kovů AM a různé fáze, které přispívají k celkovému doba realizace aditivní výroby, mohou výrobci lépe plánovat projekty, řídit rozpočty a nastavit realistická očekávání při začleňování 3D tištěných nástrojů na zakázku do svých výrobních postupů. Klíčem k úspěšnému zvládnutí těchto aspektů je transparentní komunikace s partnerem v oblasti AM.
Často kladené otázky (FAQ) o 3D tisku nástrojů na zakázku z kovu
S tím, jak se aditivní výroba kovů prosazuje v nástrojích, se konstruktéři, designéři a odborníci na zadávání zakázek často ptají na její možnosti, omezení a praktické důsledky. Zde jsou odpovědi na některé často kladené otázky týkající se nejčastější dotazy k 3D tištěným nástrojům:
1. Jaká je odolnost a životnost 3D tištěných nástrojů ve srovnání s tradičně vyráběnými nástroji?
To je zásadní otázka a odpověď na ni do značné míry závisí na několika faktorech: výběru materiálu, kvalitě tisku (hustotě), optimalizaci designu (DfAM) a správném následném zpracování (zejména tepelném zpracování).
- Ekvivalence materiálu: Při použití ekvivalentních materiálů (např. tištěná nástrojová ocel H13 oproti tepané H13) a dosažení vysoké hustoty (>99,5 %) při správném tepelném zpracování mohou být základní mechanické vlastnosti (tvrdost, pevnost) nástroje AM srovnatelné a někdy dokonce o něco lepší díky jemnozrnné mikrostruktuře, které se často dosahuje při AM.
- Vylepšení výkonu: Kovová AM nabízí jedinečné výhody, které mohou rozšířit životnost nástroje přesahující tradiční možnosti. Nejvýznamnější je konformní chlazení ve formách a zápustkách. Díky účinnějšímu a rovnoměrnějšímu odvodu tepla snižuje konformní chlazení tepelné namáhání, minimalizuje opotřebení spojené s vysokými teplotami a může vést k výrazně delší životnosti nástrojů v náročných cyklech.
- Potenciální výzvy: Pokud není proces AM řádně kontrolován, mohou vnitřní vady, jako je pórovitost nebo nedostatečné spojení, působit jako iniciační body pro trhliny, což může snížit únavovou životnost ve srovnání s kovaným materiálem bez vad. Zbytková napětí, pokud nejsou dostatečně odlehčena, mohou rovněž negativně ovlivnit životnost. Povrchová úprava může rovněž ovlivnit vlastnosti opotřebení, pokud není vhodně dodatečně zpracována pro danou aplikaci.
- Závěr: Správně navržené, vytištěné (vysoká hustota) a následně zpracované (správné tepelné zpracování a povrchová úprava) kovové AM nástroje, zejména při využití jedinečných výhod AM, jako je konformní chlazení, mohou v mnoha aplikacích dosáhnout nebo dokonce překročit životnost tradičních nástrojů. Dosažení tohoto cíle však vyžaduje odborné znalosti a důslednou kontrolu procesu ze strany dodavatele AM. Nejde ani tak o samotný proces, jako spíše o dosažení požadované integrity materiálu a konečných vlastností. Poradenství otázky týkající se nástrojů pro AM na kovy se zkušenými poskytovateli, jako je Met3dp.
2. Je 3D tisk z kovu nákladově efektivní pro velkosériovou výrobu nástrojů?
Obecně lze říci, že kovový AM nachází své uplatnění v aplikacích, kde jeho jedinečné výhody převažují nad potenciálně vyššími náklady na díl náklady na tisk ve srovnání s vysoce optimalizovanými tradičními metodami pro velmi jednoduché, velkoobjemové nástroje.
- Silné stránky AM: 3D tisk z kovu je obvykle cenově nejvýhodnější pro:
- Prototypy a nástroje pro mosty: Rychlá výroba funkčních nástrojů pro testování nebo počáteční malosériovou výrobu, zatímco se vyrábí konvenční tvrdé nástroje.
- Složité geometrie: Nástroje se složitými prvky, které se tradičním způsobem obrábějí velmi obtížně nebo nákladně. Složitost AM je spojena s malými nebo žádnými dodatečnými náklady.
- Konformní chlazení: Výkonnostní přínosy (zkrácení doby cyklu, zlepšení kvality) často ospravedlňují investice do AM pro formy a zápustky, a to i při středních objemech, na základě celkových nákladů na vlastnictví (TCO).
- Zakázkové/malosériové nástroje: Přípravky, přípravky nebo specializované nástroje potřebné v malých množstvích, kde jsou tradiční náklady na seřízení neúnosné.
- Opravy/modifikace nástrojů: AM lze někdy použít k opravě opotřebovaných nebo poškozených nástrojů nebo k přidání funkcí.
- Tradiční silné stránky: U jednoduchých geometrií nástrojů požadovaných ve velmi vysokých objemech (např. tisíce stejných jednoduchých destiček) mohou tradiční metody, jako je CNC obrábění ze skladového materiálu, stále nabízet nižší cenu za kus díky zavedené infrastruktuře a úsporám z rozsahu.
- Vyvíjející se krajina: S tím, jak technologie AM dozrává, zvyšuje se rychlost tisku, snižují se náklady na stroje a zlepšuje se automatizace, se nákladová efektivita AM neustále zlepšuje a rozšiřuje se do aplikací s vyššími objemy.
- Závěr: Ačkoli se obvykle nejedná o extrémně velkoobjemové, jednoduché nástroje založené čistě na počáteční ceně kusu, nabízí kovové AM přesvědčivou nákladovou efektivitu pro prototypy, složité konstrukce, nástroje kritické z hlediska výkonu (konformní chlazení) a nízko až středně velkou sériovou výrobu, pokud vezmeme v úvahu TCO, rychlost uvedení na trh a svobodu designu. Vyhodnoťte náklady na 3D tištěné formy nebo svítidla na základě hodnotových faktorů konkrétní aplikace.
3. Jaké informace musím poskytnout, abych získal přesnou nabídku na 3D tištěný nástroj?
Chcete-li od poskytovatele služeb AM pro kovy, jako je Met3dp, obdržet včasnou a přesnou nabídku, je nezbytné poskytnout předem komplexní informace. Chybějící údaje mohou vést ke zpoždění nebo nepřesnému stanovení ceny. Klíčové informace zahrnují:
- Model CAD: 3D model CAD ve standardním neutrálním formátu (např. STEP (.stp/.step), Parasolid (.x_t)) je povinný. Pokud je to možné, vyhněte se při počátečním zadání souborům se sítí (jako je STL), pokud to není výslovně požadováno, protože modely v pevném stavu obsahují přesnější geometrické informace.
- Specifikace materiálu: Jasně uveďte požadovanou slitinu kovu (např. nástrojová ocel H13, maraging ocel M300/1.2709, nerezová ocel 17-4PH). Pokud si nejste jisti, popište požadavky na použití (tvrdost, teplotní odolnost, potřeby opotřebení), aby vám dodavatel mohl doporučit vhodný materiál.
- Kritické rozměry a tolerance: Zřetelně uveďte (např. na 2D výkresu připojeném k 3D modelu) všechny kritické rozměry a jejich požadované tolerance. Uveďte, zda se jedná o tolerance při stavbě, nebo zda vyžadují dodatečné opracování.
- Požadavky na povrchovou úpravu: Zadejte požadovanou drsnost povrchu (např. hodnotu Ra) pro kritické povrchy (např. dutina formy, kontaktní místa přípravku) a nekritické povrchy. Uveďte, zda jsou zapotřebí specifické dokončovací procesy, jako je leštění nebo tryskání.
- Požadavky na následné zpracování: Uveďte podrobnosti o povinném tepelném zpracování (včetně cílového rozsahu tvrdosti, např. HRC 48-52 pro H13), cyklech uvolňování napětí nebo specifických obráběcích operacích, které jsou nutné nad rámec dosažení tolerancí (např. závitování, konečné broušení).
- Popis aplikace: Stručně vysvětlete funkci nástroje (např. vložka do vstřikovací formy pro ABS plast, montážní přípravek pro automobilové součástky, lisovací forma pro hliníkový plech) a provozní podmínky (teplota, zatížení, předpokládaná životnost). Tento kontext pomůže dodavateli lépe pochopit požadavky.
- Množství: Uveďte počet požadovaných stejných nebo podobných dílů.
- Požadavky na dodací lhůtu: Uveďte, zda existují konkrétní dodací lhůty.
- Důvěrnost: Pokud je návrh citlivý, zajistěte, aby byla před sdílením souborů uzavřena dohoda o mlčenlivosti (NDA).
Poskytnutí těchto podrobností umožňuje poskytovateli AM služeb přesně vyhodnotit tisknutelnost, složitost, spotřebu materiálu, požadované následné zpracování a související náklady a dodací lhůty, což vede ke spolehlivé cenové nabídce pro váš produkt trvanlivost nástrojů na zakázku a výrobních potřeb.
Závěr: Budoucnost efektivní výroby se kuje pomocí 3D tištěných nástrojů na zakázku
Prostředí zakázkové výroby nástrojů prochází významnou proměnou, která je způsobena možnostmi aditivní výroby kovů. Jak jsme již prozkoumali, 3D tisk kovů, který překračuje omezení tradičních subtraktivních metod, nabízí výkonnou kombinaci těchto možností rychlost, geometrická složitost a zvýšení výkonu které přímo řeší kritické výrobní problémy. Od rychlé výroby složitých přípravků a přípravků až po vytváření vysoce výkonných vstřikovacích forem s integrovanou technologií konformní chladicí kanály... výhody 3D tištěných nástrojů jsou hmatatelné a mají dopad na různá odvětví, jako je letecký, automobilový, lékařský a všeobecný průmysl.
Schopnost zkrátit dodací lhůty z měsíců na týdny nebo dny urychluje vývojové cykly produktů a umožňuje nebývale pružně reagovat na požadavky trhu. Svoboda konstrukce, která je vlastní AM, umožňuje konstruktérům vytvářet nástroje optimalizované pro funkci - lehké, ergonomické a se složitými vnitřními strukturami, jako je konformní chlazení, které výrazně zvyšují produktivitu a kvalitu finálních dílů. Využití vysoce výkonných materiálů, jako je nástrojová ocel H13 a maragingová ocel M300/1.2709, zajišťuje, že tyto výhody nejsou na úkor odolnosti nebo životnosti, pokud jsou přijaty zásady návrhu pro aditivní výrobu (DfAM) a správně provedeny přísné kroky následného zpracování, zejména tepelné zpracování a dokončovací práce.
Využití plného potenciálu této technologie však vyžaduje zvládnutí jejích nuancí, včetně pochopení tolerancí, povrchových úprav, potenciálních problémů, jako je zbytkové napětí, a zásadního významu následného zpracování. Úspěch závisí nejen na samotné technologii, ale také na výběru správného partnera. Ideální služby 3D tisku kovů B2B poskytovatel nabízí více než jen tiskařskou kapacitu; poskytuje odborné znalosti v oblasti materiálových věd, konzultace DfAM, robustní kontrolu procesů, komplexní interní schopnosti následného zpracování a silný závazek k zajištění kvality.
Met3dp je příkladem takového partnera. Jako lídr v oboru metal AM se sídlem v čínském Čching-tao poskytujeme komplexní řešení zahrnující špičkové tiskárny SEBM, které jsou proslulé tím, že poskytují přesnost a spolehlivost, pokročilé kovové prášky vyráběné přímo ve firmě pomocí nejmodernějších atomizačních technik a hluboké zkušenosti s vývojem aplikací. Spolupracujeme s organizacemi po celém světě při zavádění 3D tisk z kovu efektivně urychlit transformaci digitální výroby a umožnit výrobu nástrojů nové generace.
Budoucnost efektivní, agilní a vysoce výkonné výroby je neoddělitelně spjata s pokrokem v aditivní výrobě. Pro zakázkové nástroje již není 3D tisk z kovu výklenkovou novinkou, ale strategickou schopností, která výrobcům umožňuje rychleji inovovat, snižovat náklady, zlepšovat kvalitu a získávat výraznou konkurenční výhodu. Přijetím této technologie a spoluprací se znalými partnery, jako je Met3dp, mohou společnosti vytvořit nástrojová řešení, která odemknou novou úroveň produktivity a podpoří dokonalost výroby.
Jste připraveni revolučně změnit svou strategii pro zakázkové nástroje? Kontaktujte Met3dp ještě dnes a zjistit, jak naše špičkové systémy, pokročilé kovové prášky a komplexní odborné znalosti mohou podpořit cíle vaší organizace v oblasti aditivní výroby.
Sdílet na
MET3DP Technology Co., LTD je předním poskytovatelem řešení aditivní výroby se sídlem v Qingdao v Číně. Naše společnost se specializuje na zařízení pro 3D tisk a vysoce výkonné kovové prášky pro průmyslové aplikace.
Dotaz k získání nejlepší ceny a přizpůsobeného řešení pro vaše podnikání!
Související články
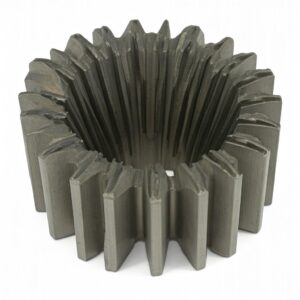
Vysoce výkonné segmenty lopatek trysek: Revoluce v účinnosti turbín díky 3D tisku z kovu
Přečtěte si více "O Met3DP
Nedávná aktualizace
Náš produkt
KONTAKTUJTE NÁS
Nějaké otázky? Pošlete nám zprávu hned teď! Po obdržení vaší zprávy obsloužíme vaši žádost s celým týmem.
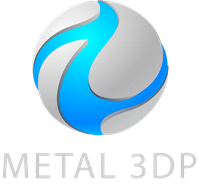
Kovové prášky pro 3D tisk a aditivní výrobu