Aplikace DED v leteckém oboru
Obsah
Představte si svět, kde lze složité letecké součásti stavět vrstvu po vrstvě, na vyžádání, s minimálním odpadem. To není sci-fi; je to realita Depozice řízené energií (DED), špičkové technologie aditivní výroby (AM), která rychle transformuje letecký průmysl.
DED, známá také jako Laser Engineered Net Shaping (LENS), využívá fokusovaný zdroj energie, jako je laser nebo elektronový paprsek, k tavení a nanášení kovového prášku, pečlivě budující trojrozměrný objekt. Představte si to jako high-tech 3D tiskárnu na kov, která nabízí bezkonkurenční svobodu designu a přizpůsobení pro letecké aplikace.
Ale jak přesně DED dobývá letecký průmysl? Připoutejte se, protože se ponoříme do fascinujícího světa aplikací DED, prozkoumáme různé kovové prášky používané a zodpovíme některé palčivé otázky o této revoluční technologii.
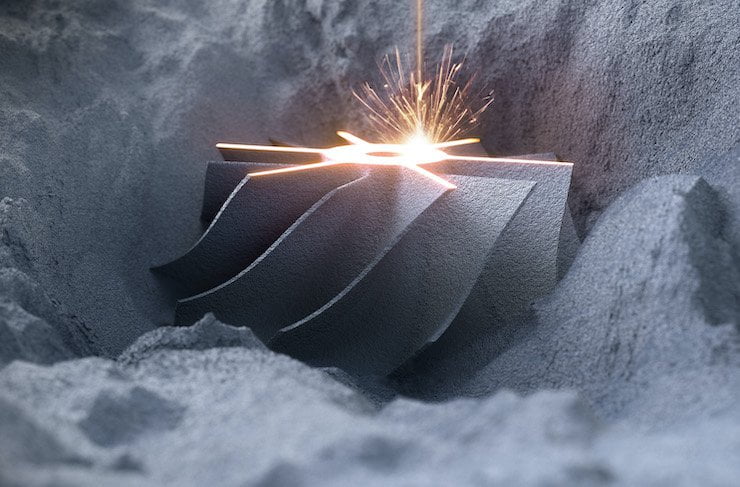
DED: Změna hry pro letecký průmysl
Tradičně se letecké součásti vyráběly konvenčními metodami, jako je odlévání, kování a obrábění. Tyto procesy často vedou k významnému plýtvání materiálem a omezením složitosti návrhu. DED narušuje toto paradigma tím, že nabízí celou řadu výhod:
- Odlehčení: DED umožňuje vytváření složitých dutých struktur, což výrazně snižuje hmotnost – kritický faktor pro palivovou účinnost a nosnost letadel.
- Svoboda designu: DED, neomezený tradičními výrobními omezeními, umožňuje vytváření složitých geometrií s vnitřními kanály a mřížkami, optimalizující výkon a rozložení hmotnosti.
- Rychlé prototypování: DED umožňuje rychlou výrobu prototypů, urychluje cyklus návrhu a vývoje nových leteckých komponent.
- Výroba na vyžádání: DED usnadňuje vytváření náhradních dílů v místě potřeby, čímž se snižuje závislost na předem vyrobených komponentech a minimalizuje prostoje.
- Účinnost materiálu: DED využívá přístup téměř čistého tvaru, minimalizující odpad materiálu ve srovnání s tradičními metodami.
- Opravy a restaurování: DED lze použít k opravě poškozených komponent, prodlužující jejich životnost a snižující potřebu nákladných výměn.
Tyto výhody se promítají do řady vzrušujících aplikací v leteckém oboru:
- Výroba součástí leteckých motorů: DED dělá vlny ve výrobě složitých součástí motorů, jako jsou lopatky turbín, spalovací komory a výměníky tepla. DED umožňuje vytváření součástí s pokročilými vnitřními chladicími kanály, což zvyšuje účinnost a výkon.
- DED pro trup letadla a další konstrukční komponenty: Schopnost DED vytvářet lehké, vysoce pevné struktury je ideální pro výrobu částí trupu letadla, komponentů podvozku a dalších konstrukčních prvků.
- Přizpůsobení a opravy: DED umožňuje přizpůsobení leteckých dílů na vyžádání, což umožňuje úpravy pro splnění specifických požadavků mise. DED lze navíc použít pro opravy poškozených komponent na místě, čímž se snižují prostoje a náklady na údržbu.
Kovové prášky: Stavební kameny úspěchu DED
Úspěch DED závisí na použitých kovových prášcích. Tyto prášky s přesně řízenou velikostí a morfologií (tvarem) hrají zásadní roli v kvalitě a výkonu konečného produktu. Zde je pohled na některé z nejběžnějších kovových prášků používaných v leteckých aplikacích DED:
**Kovový prášek | Popis | Vlastnosti |
---|---|---|
Inconel 625 | Univerzální superslitina na bázi niklu a chromu, známá pro svou výjimečnou pevnost při vysokých teplotách, odolnost proti oxidaci a dobrou svařitelnost. | Nabízí vynikající mechanické vlastnosti při zvýšených teplotách, díky čemuž je ideální pro lopatky turbín, spalovací komory a další komponenty horké sekce. |
Titan 6Al-4V | Vysoce pevná, lehká titanová slitina široce používaná v leteckém průmyslu. | Poskytuje dobrou rovnováhu mezi pevností, tažností a úsporou hmotnosti, díky čemuž je vhodná pro komponenty draku letadla, části podvozku a úchyty motoru. |
Hliníkové slitiny | Rodina lehkých hliníkových slitin s různými vlastnostmi v závislosti na specifickém složení. | Nabízejí vynikající poměr pevnosti k hmotnosti a dobrou odolnost proti korozi, díky čemuž jsou vhodné pro nekritické konstrukční komponenty a lehké kryty. |
Nerezová ocel 316L | Univerzální austenitická nerezová ocel známá svou vynikající odolností proti korozi. | Nabízí dobré mechanické vlastnosti a odolnost proti korozi, díky čemuž je vhodná pro různé aplikace, jako jsou komponenty pro manipulaci s kapalinami a nestrukturální části. |
Inconel 718 | Superslitina na bázi niklu a chromu vytvrzovaná srážením s vysokou pevností a dobrou obrobitelností. | Nabízí kombinaci vysoké pevnosti, dobré odolnosti proti korozi a vynikající obrobitelnosti, díky čemuž je ideální pro různé konstrukční komponenty a aplikace s vysokým tlakem. |
Maraging Steel | Rodina vysoce pevných, nízkolegovaných ocelí s vynikající houževnatostí a rozměrovou stabilitou. | Poskytuje výjimečnou pevnost a houževnatost, díky čemuž jsou vhodné pro komponenty podvozku a vysoce namáhané konstrukční prvky. |
Slitiny niklu | Široká kategorie slitin na bázi niklu s různými vlastnostmi v závislosti na specifickém složení. | Nabízejí širokou škálu vlastností, včetně pevnosti při vysokých teplotách, odolnosti proti korozi a odolnosti proti opotřebení, díky čemuž jsou vhodné pro různé součásti motoru a aplikace s vysokým opotřebením. |
Slitiny kobaltu a chromu | Rodina slitin kobaltu a chromu známá pro svou vysokou odolnost proti opotřebení a biokompatibilitu. | Nabízejí výjimečnou odolnost proti opotřebení a dobrou biokompatibilitu, díky čemuž jsou ideální pro aplikace, jako jsou ložiska proudových motorů a biomedicínské implantáty (ačkoli aplikace DED v biomedicíně spadají mimo rozsah tohoto článku). |
Slitiny mědi | Rodina slitin mědi s různými vlastnostmi v závislosti na specifickém složení. | Nabízejí vysokou elektrickou vodivost a dobrou tepelnou vodivost, díky čemuž jsou vhodné pro výměníky tepla a elektrické komponenty. |
Žáruvzdorné kovy | Skupina kovů s vysokou teplotou tání, jako je wolfram, tantal a molybden. | Vyznačují se výjimečnou pevností při vysokých teplotách a odolností vůči drsným prostředím, díky čemuž jsou vhodné pro aplikace, jako jsou trysky raketových motorů a re-entry vozidla. |
Je důležité poznamenat, že se nejedná o vyčerpávající seznam a probíhající výzkum neustále vyvíjí nové a vylepšené kovové prášky speciálně přizpůsobené pro DED aplikace. Výběr optimálního kovového prášku závisí na různých faktorech, jako jsou požadované konečné vlastnosti komponenty, provozní prostředí a úvahy o nákladech.
Výhody a omezení DED
Zatímco DED nabízí leteckému průmyslu nepřeberné množství výhod, není bez svých omezení. Zde je vyvážený pohled na obě strany mince:
výhody:
- Svoboda designu: Jak již bylo zmíněno, DED otevírá svět konstrukčních možností a umožňuje vytváření složitých geometrií, které si bylo dříve s tradičními technikami nemožné představit.
- Odlehčení: Schopnost vytvářet duté struktury s vnitřními mřížkami se promítá do významné úspory hmotnosti, což je kritický faktor pro výkon letadla.
- Snížení množství odpadu: DED využívá přístup téměř čistého tvaru, minimalizující odpad materiálu ve srovnání s tradičními metodami.
- Rychlé prototypování: DED usnadňuje rychlé vytváření prototypů, urychluje cyklus návrhu a vývoje nových leteckých komponent.
- Výroba na vyžádání: DED umožňuje výrobu náhradních dílů na vyžádání, čímž se snižuje závislost na předem vyrobených komponentech a minimalizují prostoje.
- Opravy a restaurování: DED lze použít k opravě poškozených komponent, prodlužující jejich životnost a snižující potřebu nákladných výměn.
Omezení:
- Doba výstavby: I když je DED rychlejší než tradiční metody, může být ve srovnání s některými subtraktivními technikami stále relativně pomalý proces, zejména u větších komponent.
- Povrchová úprava: Komponenty vyrobené pomocí DED často vyžadují další kroky následného zpracování, aby se dosáhlo požadované povrchové úpravy.
- Dostupnost materiálu: Dostupnost určitých kovových prášků, zejména vysoce výkonných slitin, může být omezená a drahá.
- Řízení procesu: DED je složitý proces, který vyžaduje pečlivou kontrolu parametrů, jako je výkon laseru, rychlost skenování a rychlost podávání prášku, aby byla zajištěna konzistentní kvalita a zabránilo se vadám.
- Kvalifikace a certifikace: Komponenty DED vyžadují přísné testování a certifikaci, aby splňovaly přísné bezpečnostní normy pro letectví.
Budoucnost DED v letectví
Navzdory těmto omezením je budoucnost DED v letectví jasná. S pokrokem technologie se zkrátí doby výroby, zlepší se kvalita povrchu a zvýší se dostupnost vysoce výkonných kovových prášků. Probíhající výzkum se navíc zaměřuje na vývoj nových technik DED, jako je více-materiálový tisk a monitorování procesu in-situ, čímž se dále rozšiřují jeho možnosti.
Potenciální dopad DED na letecký průmysl je obrovský. Může revolučně změnit návrh a výrobu letadel, což povede k lehčím, účinnějším a nákladově efektivnějším vozidlům. Dále může DED umožnit opravy na vyžádání v terénu, což snižuje prostoje údržby a zlepšuje provozní připravenost.
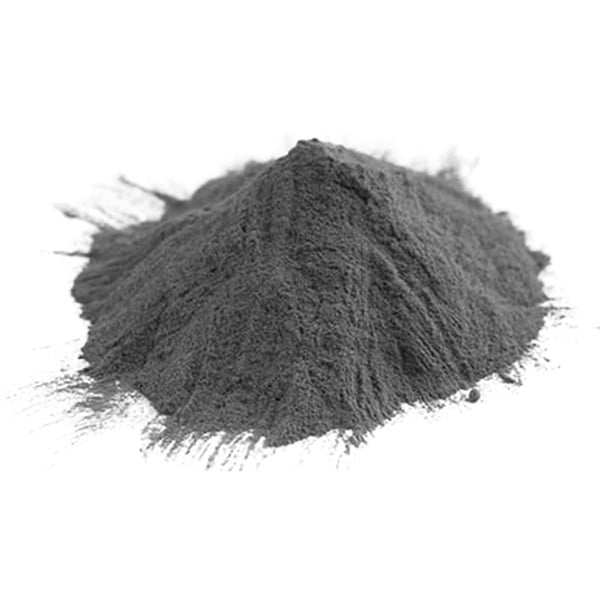
Nejčastější dotazy
Zde je několik často kladených otázek o DED v leteckém průmyslu, prezentovaných v tabulkovém formátu pro snadnou orientaci:
Otázka | Odpovědět |
---|---|
Jaké jsou hlavní výhody použití DED v leteckých aplikacích? | DED nabízí svobodu designu, odlehčení, snížení odpadu, rychlé prototypování, výrobu na vyžádání a možnosti oprav. |
Jaké jsou některé z problémů spojených s DED? | Doba výroby, povrchová úprava, dostupnost materiálu, řízení procesu a kvalifikace pro letecké aplikace jsou některá z klíčových omezení. |
Jaké jsou nejběžnější kovové prášky používané v DED pro letectví? | Inconel 625, Titanium 6Al-4V, hliníkové slitiny, nerezová ocel 316L, Inconel 718, Maraging Steel, slitiny niklu, slitiny kobaltu a chromu, slitiny mědi a žáruvzdorné kovy jsou některé z významných možností. |
Jaký dopad bude mít DED na budoucnost letecké výroby? | DED má potenciál revolučně změnit leteckou výrobu tím, že umožní vytváření lehčích, účinnějších a nákladově efektivnějších letadel. Opravy na vyžádání a snížené prostoje jsou další výhody. |
Je DED vyspělá technologie pro letecké aplikace? | DED je stále ve vývoji, ale rychle se vyvíjí. Probíhající výzkum se zabývá omezeními, jako je doba výroby a povrchová úprava. |
Jaké jsou některé z největších překážek pro širší přijetí DED v letectví? | Kvalifikace a certifikace komponent DED pro použití v letadlech je významnou překážkou. Kromě toho je zapotřebí širší dostupnost vysoce výkonných kovových prášků za konkurenceschopné ceny. |
Lze DED použít pro opravy mimo kontrolované prostředí? | Probíhá výzkum mobilních systémů DED, které by mohly umožnit opravy v terénu. Taková technologie je však stále v rané fázi. |
Lidský faktor: Proč na DED záleží
Kromě technického pokroku představuje DED posun ve způsobu, jakým přemýšlíme o letecké výrobě. Umožňuje agilnější a pohotovější přístup, podporuje inovace a přizpůsobení. Představte si svět, kde lze náhradní díly tisknout na vyžádání ve vzdálených lokalitách nebo kde lze poškozené komponenty opravit v terénu, což minimalizuje prostoje a maximalizuje provozní efektivitu. To se nejen promítá do úspory nákladů, ale také zvyšuje bezpečnost a připravenost mise.
Příběh DED v letectví není jen o technologii; je o lidské vynalézavosti a duchu řešení problémů, který pohání pokrok. Je to o posouvání hranic toho, co je možné, a vytváření budoucnosti, kde je letecká doprava nejen rychlejší a efektivnější, ale také šetrnější k životnímu prostředí. Jak se DED nadále vyvíjí, je jedna věc jistá: obloha je limitem pro jeho potenciální dopad na letecký průmysl.
Sdílet na
MET3DP Technology Co., LTD je předním poskytovatelem řešení aditivní výroby se sídlem v Qingdao v Číně. Naše společnost se specializuje na zařízení pro 3D tisk a vysoce výkonné kovové prášky pro průmyslové aplikace.
Dotaz k získání nejlepší ceny a přizpůsobeného řešení pro vaše podnikání!
Související články
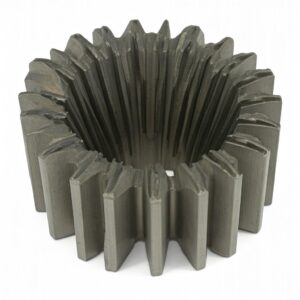
Vysoce výkonné segmenty lopatek trysek: Revoluce v účinnosti turbín díky 3D tisku z kovu
Přečtěte si více "O Met3DP
Nedávná aktualizace
Náš produkt
KONTAKTUJTE NÁS
Nějaké otázky? Pošlete nám zprávu hned teď! Po obdržení vaší zprávy obsloužíme vaši žádost s celým týmem.
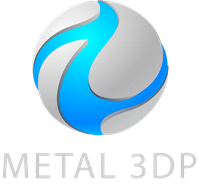
Kovové prášky pro 3D tisk a aditivní výrobu