Výhody technologie DMLS
Obsah
DMLS, neboli Direct Metal Laser Sintering, se stal průlomem ve světě aditivní výroby kovů. Představte si technologii, která dokáže vytvářet složité, vysoce výkonné kovové díly přímo z digitálního souboru, čímž eliminuje potřebu tradičních subtraktivních výrobních metod. To je kouzlo DMLS. Ale co přesně dělá DMLS tak výhodným? Pojďme se ponořit do světa kovových prášků, prozkoumat klíčové výhody této revoluční technologie a zjistit, jak transformuje různá průmyslová odvětví.
Populární kovové prášky pro DMLS
DMLS prosperuje díky rozmanité škále kovových prášků, z nichž každý nabízí jedinečné vlastnosti pro specifické aplikace. Zde je bližší pohled na některé z nejčastěji používaných kovových prášků v DMLS:
Kovový prášek | Složení | Vlastnosti | Aplikace |
---|---|---|---|
Nerezová ocel 316L | 16-18% Chrom, 10-14% Nikl, 2-3% Molybden | Vynikající odolnost proti korozi, vysoká pevnost, biokompatibilní | Letecké komponenty, lékařské implantáty, zařízení pro chemické zpracování |
Titan Ti6Al4V | 90% Titan, 6% Hliník, 4% Vanad | Vysoký poměr pevnosti k hmotnosti, dobrá biokompatibilita, vynikající odolnost proti korozi. | Letecké díly, lékařské implantáty, sportovní zboží |
Inconel 625 | Slitina niklu a chromu s přídavkem molybdenu, niobu a železa | Výjimečná pevnost při vysokých teplotách, odolnost proti oxidaci a korozi | Součásti turbín, výměníky tepla, zařízení pro chemické zpracování |
Hliník AlSi10Mg | Hliníková slitina s 10% křemíku a 0,5% hořčíku | Lehký, dobrá odolnost proti korozi, vysoká pevnost | Automobilové díly, letecké komponenty, chladiče |
Měď | 100% Měď | Vysoká tepelná a elektrická vodivost, dobrá obrobitelnost | Výměníky tepla, elektrické komponenty, elektrody |
Nástrojová ocel (H13) | Legovaná ocel s vysokým obsahem chromu, molybdenu a vanadu | Vysoká odolnost proti opotřebení, dobrá prokalitelnost | Formy, zápustky, řezné nástroje |
Nikl (IN718) | Slitina niklu a chromu s přídavkem železa, niobu a molybdenu | Vysoká pevnost, dobrá odolnost proti tečení při zvýšených teplotách | Lopaty turbín, součásti raketových motorů |
Kobaltový chrom (CoCrMo) | Slitina kobaltu a chromu s molybdenem | Vysoká odolnost proti opotřebení, biokompatibilní | Náhrady kloubů, zubní implantáty |
Zlato | 100% Zlatá | Vysoká elektrická vodivost, vynikající odolnost proti korozi, biokompatibilní | Šperky, elektrické konektory, zdravotnické prostředky |
Platinum | 100% platina | Vysoká teplota tání, vynikající odolnost proti korozi, biokompatibilní | Katalyzátory, zdravotnické prostředky, šperky |
Tento seznam pouze naznačuje rozsáhlou škálu kovových prášků dostupných pro DMLS. Proces výběru závisí na specifických potřebách aplikace. Mezi faktory, které je třeba zvážit, patří:
- Mechanické vlastnosti: Pevnost, tažnost, odolnost proti únavě a odolnost proti opotřebení jsou zásadní pro díly namáhané napětím.
- Tepelné vlastnosti: Teplota tání, tepelná vodivost a koeficient tepelné roztažnosti hrají zásadní roli při vysokoteplotních aplikacích.
- Odolnost proti korozi: Prostředí, kterému bude díl vystaven, určuje potřebu prášků odolných proti korozi.
- Biokompatibilita: U lékařských implantátů je biokompatibilita prvořadá pro zajištění bezpečného kontaktu s tělem.
Kromě této tabulky existuje celý svět speciálních kovových prášků, které se vyvíjejí – od kompozitů s kovovou matricí pro zvýšenou pevnost až po funkčně gradientní materiály s přizpůsobenými vlastnostmi v různých oblastech dílu. Možnosti jsou skutečně nekonečné.
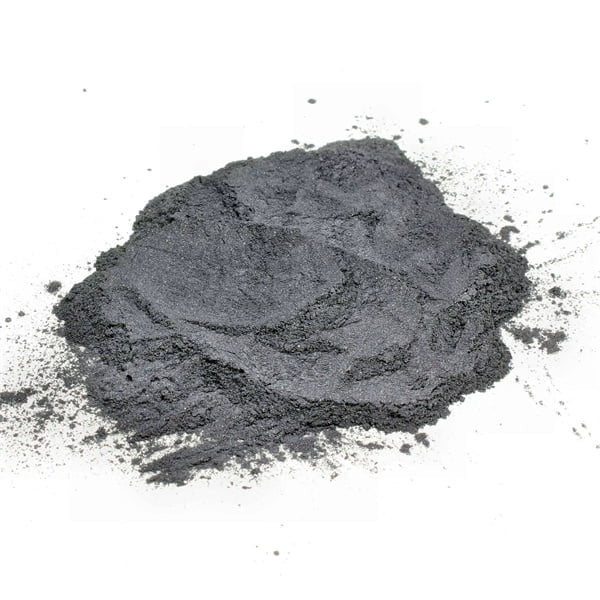
Vysoká přesnost výroby DMLS Technologie
Jednou z nejzajímavějších výhod DMLS je jeho výjimečná přesnost. Na rozdíl od tradičních metod, které zahrnují odebírání materiálu, DMLS staví díly vrstvu po vrstvě pomocí laserového paprsku, který selektivně tavidá kovový prášek. Tento pečlivý proces umožňuje vytváření složitých geometrií s přesností na úrovni mikronů.
Představte si důsledky! DMLS dokáže vyrábět díly s vnitřními kanály, tenkými stěnami a složitými mřížkovými strukturami, které by bylo nemožné nebo neuvěřitelně nákladné dosáhnout tradičními technikami. To otevírá dveře pro lehké, ale robustní konstrukce v leteckém a automobilovém průmyslu. V lékařství může DMLS vyrábět vysoce přizpůsobené implantáty, které dokonale odpovídají anatomii pacienta, což vede ke zlepšení chirurgických výsledků a rychlejší době zotavení.
Představte si to jako stavění z Lega v mikroskopickém měřítku, ale místo plastových kostek používáte kovové částice k vytváření neuvěřitelně detailních a funkčních objektů.
Nízké výrobní náklady technologie DMLS pro složité díly
Zatímco samotné stroje DMLS vyžadují značnou počáteční investici, technologie může být překvapivě nákladově efektivní pro výrobu složitých dílů. Zde je důvod:
- Snížení množství materiálového odpadu: Tradiční subtraktivní výroba často zahrnuje značné plýtvání materiálem během obráběcích procesů. DMLS na druhé straně používá pouze potřebné množství kovového prášku, čímž minimalizuje odpad a snižuje celkové náklady na materiál.
- Konsolidace částí: DMLS umožňuje konstruktérům kombinovat více komponent do jednoho funkčně optimalizovaného dílu. To eliminuje potřebu montážních procesů, což šetří čas a náklady na práci.
- Svoboda designu a snížená potřeba nástrojů: Složité geometrie, které by si v tradičních metodách vyžadovaly složité nástroje, lze vyrábět přímo pomocí DMLS. To eliminuje potřebu drahých nástrojů a zkracuje dodací lhůty.
Je však důležité si uvědomit, že DMLS není univerzálním řešením. Pro jednodušší díly vyráběné ve velkých objemech mohou být tradiční metody stále nákladově efektivnější. Ale pro složité, nízkosériové výrobní série DMLS září.
Představte si scénář, kdy potřebujete vlastní ozubené kolo s unikátní vnitřní strukturou. Tradiční výroba by vyžadovala vytvoření specializovaných nástrojů pro obrábění zubů ozubeného kola a vnitřních prvků. S DMLS můžete navrhnout celé ozubené kolo v jednom souboru CAD a vytisknout jej přímo, čímž se eliminuje potřeba nástrojů a šetří čas i peníze.
Svoboda designu technologie DMLS je vysoká
DMLS uvolňuje pouta tradičních konstrukčních omezení. Zde je návod:
- Bezprecedentní geometrie: DMLS umožňuje vytváření dílů se složitými vnitřními kanály, mřížkami a převislými prvky, které jsou u subtraktivních metod jednoduše nemožné. To otevírá dveře inovativním návrhům se zlepšeným výkonem a nižší hmotností.
- Funkční gradienty: DMLS dokáže vyrábět díly s různými vlastnostmi v celé jejich struktuře. Představte si vrták se silnou špičkou odolnou proti opotřebení, která přechází do pružnější stopky pro lepší tlumení nárazů. DMLS toho může dosáhnout použitím různých kovových prášků nebo změnou úrovní výkonu laseru ve stejném sestavení.
- Přizpůsobení a personalizace: DMLS vyniká ve výrobě přizpůsobených dílů. Potřebujete lékařský implantát, který dokonale odpovídá kostní struktuře pacienta? Nebo lehký, vysoce pevný držák pro vlastní závodní kolo? DMLS to zvládne snadno.
Představte si DMLS jako splněný sen sochaře. Poskytuje svobodu vytvářet složité a funkční formy, které byly dříve omezeny na oblast představivosti.
Další výhody DMLS Technologie
DMLS se může pochlubit řadou dalších výhod, díky nimž je přesvědčivou volbou pro různé aplikace:
- Rychlé prototypování: DMLS umožňuje rychlé a iterativní vytváření funkčních prototypů, což urychluje proces vývoje produktu.
- Snížení zásob: Díky možnosti vyrábět díly na vyžádání pomáhá DMLS snižovat potřebu velkých zásob, minimalizovat náklady na skladování a zefektivňovat logistiku.
- Odlehčení: Díly vyrobené technologií DMLS mohou být výrazně lehčí než tradičně vyráběné protějšky, což nabízí významnou výhodu v aplikacích, jako je letecký a automobilový průmysl, kde je snížení hmotnosti zásadní pro účinnost paliva.
Představte si svět, kde můžete mít plně funkční prototyp svého nového vynálezu v rukou během několika dní, nikoli týdnů. DMLS to umožňuje a podporuje inovace a urychluje cestu od konceptu k vytvoření.
Nevýhody technologie DMLS
I když DMLS nabízí nepřeberné množství výhod, je nezbytné si uvědomit i jeho omezení:
- Omezený výběr materiálů: Ve srovnání s tradičními metodami má DMLS v současnosti poněkud omezený výběr tisknutelných kovových prášků. To se však neustále rozšiřuje s pokračujícím vývojem nových materiálů.
- Drsnost povrchu: Díly vyrobené technologií DMLS mohou vykazovat o něco hrubší povrchovou úpravu ve srovnání s obráběnými součástmi. K dosažení hladší povrchové úpravy lze v případě potřeby použít techniky následného zpracování, jako je leštění nebo otryskávání.
- Náklady na stroje a materiály: Jak již bylo zmíněno, stroje DMLS vyžadují vysokou počáteční investici. Kromě toho mohou být některé kovové prášky dražší než konvenční materiály.
Klíčem je nalezení správného nástroje pro danou práci. DMLS vyniká ve výrobě složitých, malosériových dílů. Ale pro velkoobjemovou výrobu jednodušších komponent mohou být tradiční metody vhodnější.
Aplikace technologie DMLS
DMLS rychle transformuje širokou škálu průmyslových odvětví:
- Letectví: DMLS se používá k vytváření lehkých, vysoce pevných komponent pro letadla, satelity a kosmické lodě.
- Automobilový průmysl: Automobilový průmysl využívá DMLS pro vlastní díly, prototypy a lehké komponenty pro závodní vozy a vysoce výkonná vozidla.
- Lékařský: DMLS hraje zásadní roli při vytváření přizpůsobených lékařských implantátů, protetiky a chirurgických nástrojů.
- Spotřební zboží: Od vlastních šperků a sportovních potřeb až po jedinečné designové prvky si DMLS nachází cestu na trh se spotřebním zbožím. Představte si svět, kde si můžete personalizovat pouzdro na telefon pomocí složitých návrhů nebo mít jedinečný, 3D tištěný rám kola vyrobený přesně podle vašich specifikací. DMLS otevírá dveře pro masové přizpůsobení a výrobu na vyžádání, což by mohlo způsobit revoluci ve způsobu, jakým interagujeme s každodenními předměty.
- Energie: DMLS se používá k vytváření složitých komponent pro výměníky tepla, turbíny a další aplikace související s energií. Schopnost vyrábět složité geometrie s vysokou přesností umožňuje vývoj účinnějších a výkonnějších energetických systémů.
- Nástroje: DMLS se používá k výrobě vlastních přípravků, upevňovacích prvků a dalších prvků nástrojů. Schopnosti rychlého prototypování DMLS umožňují rychlejší iterace návrhu a zefektivněné výrobní procesy v rámci nástrojářského průmyslu.
Aplikace technologie DMLS se neustále rozšiřují, protože její schopnosti jsou stále více známé a dostupné. Můžeme očekávat, že uvidíme DMLS hrát ještě větší roli při utváření budoucnosti výroby napříč různými sektory.
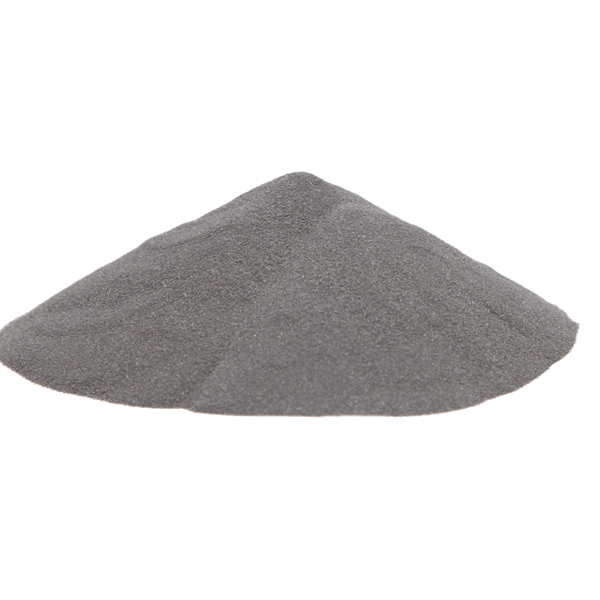
FAQ
Zde jsou některé často kladené otázky o technologii DMLS, zodpovězené jasným a stručným formátem:
Otázka | Odpovědět |
---|---|
Co je DMLS? | DMLS neboli Direct Metal Laser Sintering je technologie aditivní výroby, která používá laserový paprsek k selektivnímu tavení kovového prášku vrstvu po vrstvě a vytváří složité trojrozměrné objekty z digitálního souboru. |
Jaké jsou výhody DMLS? | DMLS nabízí řadu výhod, včetně vysoké přesnosti výroby, potenciální nákladové efektivity pro složité díly, svobody designu, schopností rychlého prototypování a schopnosti vytvářet lehké komponenty. |
Jaká jsou omezení technologie DMLS? | DMLS má v současnosti omezený výběr tisknutelných kovových prášků ve srovnání s tradičními metodami. Kromě toho mohou mít díly vyrobené technologií DMLS o něco hrubší povrchovou úpravu a stroje i některé materiály mohou být drahé. |
Jaké jsou některé aplikace DMLS? | DMLS se používá v různých průmyslových odvětvích, včetně letectví, automobilového průmyslu, lékařství, spotřebního zboží, energetiky a nástrojů. |
Je DMLS vhodný pro mou aplikaci? | Vhodnost DMLS závisí na vašich specifických potřebách. DMLS vyniká ve výrobě složitých, malosériových dílů. Pro jednodušší komponenty vyráběné ve velkých objemech mohou být tradiční metody nákladově efektivnější. |
Technologie DMLS je výkonný nástroj s potenciálem revolučně změnit způsob, jakým navrhujeme a vyrábíme objekty. Pochopením jeho výhod, omezení a různých aplikací se můžete informovaně rozhodnout, zda je DMLS pro váš další projekt tou správnou volbou.
Závěrem lze říci, že technologie DMLS je důkazem lidské vynalézavosti. Jeho schopnost přeměnit kovový prášek na složité a funkční objekty dláždí cestu pro budoucnost plnou inovací, svobody designu a nové éry výrobních možností.
Sdílet na
MET3DP Technology Co., LTD je předním poskytovatelem řešení aditivní výroby se sídlem v Qingdao v Číně. Naše společnost se specializuje na zařízení pro 3D tisk a vysoce výkonné kovové prášky pro průmyslové aplikace.
Dotaz k získání nejlepší ceny a přizpůsobeného řešení pro vaše podnikání!
Související články
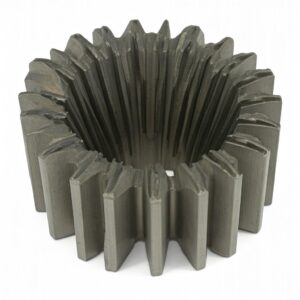
Vysoce výkonné segmenty lopatek trysek: Revoluce v účinnosti turbín díky 3D tisku z kovu
Přečtěte si více "O Met3DP
Nedávná aktualizace
Náš produkt
KONTAKTUJTE NÁS
Nějaké otázky? Pošlete nám zprávu hned teď! Po obdržení vaší zprávy obsloužíme vaši žádost s celým týmem.
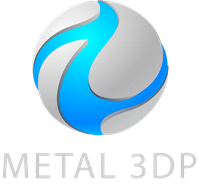
Kovové prášky pro 3D tisk a aditivní výrobu