Pláště elektromotorů pomocí 3D tisku z kovu pro tepelnou účinnost
Obsah
Neustálá snaha o vyšší výkon, delší dojezd a rychlejší nabíjení na trhu elektromobilů (EV) vytváří obrovský tlak na konstrukci komponent, zejména systémů tepelného managementu. Elektromotor, srdce hnacího ústrojí elektromobilu, generuje během provozu značné množství tepla. Efektivní odvádění tohoto tepla má zásadní význam nejen pro výkon a spolehlivost, ale také pro dlouhou životnost motoru a souvisejících součástí. Tradiční řešení chlazení se často potýkají s omezeními v podobě složitosti, hmotnosti a tepelné účinnosti. V tomto případě je nutné použít aditivní výrobu kovů (AM), resp 3D tisk, se ukazuje jako technologie, která mění pravidla hry a umožňuje výrobu vysoce optimalizovaných chladicích plášťů elektromotorů s nebývalou volností konstrukce a tepelným výkonem. Společnosti specializující se na pokročilé kovové prášky a 3D tisk z kovu řešení, jako je Met3dp, stojí v čele této revoluce a umožňují automobilovým inženýrům a manažerům nákupu přehodnotit návrh tepelného managementu.
Úvod: Revoluce v tepelném managementu elektromobilů díky 3D tištěným chladicím plášťům motorů
Chladicí plášť motoru elektromobilu (EV), známý také jako kryt motoru nebo kryt statoru s integrovanými chladicími kanály, je důležitou součástí, která odpovídá za regulaci provozní teploty elektromotoru. Při přeměně elektrické energie na mechanický pohyb vznikají ve vinutí a jádře značné odporové ztráty. Pokud se toto teplo neřídí efektivně, může vést k:
- Snížená účinnost motoru: Vyšší teploty zvyšují elektrický odpor, což vede k větším ztrátám energie.
- Degradace složek: Dlouhodobé vystavení nadměrnému teplu může vést k degradaci izolačních materiálů, ložisek a magnetů a výrazně zkrátit životnost motoru.
- Přiškrcení výkonu: Aby se zabránilo přehřátí, může řídicí systém vozidla omezit výkon motoru, což má negativní dopad na jízdní výkon, zejména při náročných podmínkách, jako je jízda vysokou rychlostí nebo tažení.
- Obavy o bezpečnost: V extrémních případech může přehřátí představovat bezpečnostní riziko.
Základním účelem chladicího pláště je zajistit, aby chladicí kapalina (obvykle směs vody a glykolu) obíhala kolem částí motoru, které vytvářejí teplo, především kolem statoru, absorbovala teplo a odváděla ho do chladiče. Účinnost tohoto přenosu tepla přímo souvisí s konstrukcí chladicích kanálů v plášti - jejich průběhem, tvarem, plochou a blízkostí zdrojů tepla.
Proč je tepelný management u elektromobilů důležitější než kdy jindy:
Požadavky na systémy tepelného řízení elektromobilů se zvyšují v důsledku několika průmyslových trendů:
- Zvýšená hustota výkonu: Motory jsou stále menší a výkonnější, aby splňovaly výkonnostní očekávání a omezení týkající se balení, a soustřeďují produkci tepla do menšího objemu.
- Rychlejší nabíjení: Při vysokorychlostním nabíjení vzniká značné množství tepla nejen v baterii, ale ovlivňuje také tepelné zatížení celého systému hnacího ústrojí během následného provozu.
- Cíle s rozšířeným dosahem: Optimalizace všech aspektů účinnosti vozidla, včetně minimalizace energetických ztrát způsobených teplem, má zásadní význam pro maximalizaci dojezdu.
- Požadavky na výkon: Spotřebitelé očekávají, že elektromobily budou nabízet zrychlení a trvalý výkon srovnatelný nebo vyšší než vozidla se spalovacími motory, což vyžaduje robustní tepelný management.
Tradiční výrobní omezení:
Běžné metody výroby chladicích plášťů motorů, jako je odlévání (odlévání do písku, tlakové lití) a obrábění ze sochoru, mají svá omezení:
- Geometrická omezení: Procesy odlévání se potýkají s problémy při vytváření velmi složitých vnitřních kanálů s tenkými stěnami nebo složitými cestami, které jsou potřebné pro optimální průtok chladicí kapaliny a výměnu tepla. Úhly ponoru, omezení umístění jádra a minimální tloušťky stěn omezují volnost konstrukce.
- Hmotnost: Odlévané součásti často vyžadují silnější stěny, než je z konstrukčního hlediska nutné, a to jednoduše kvůli omezením výrobního procesu, což zbytečně zvyšuje hmotnost - což je u elektromobilů, u nichž je nejdůležitější dojezd, kritický faktor.
- Náklady na nástroje & Dodací lhůty: Vytváření forem a zápustek pro odlévání je nákladné a časově náročné, takže je méně vhodné pro nízké až střední výrobní série nebo rychlé prototypové iterace.
- Složitost sestavy: Složité chladicí okruhy někdy vyžadují sestavení a utěsnění více odlitých nebo opracovaných dílů, což přináší potenciální netěsnosti a další výrobní kroky.
Transformace aditivní výroby:
Kovový 3D tisk tato omezení zásadně překonává. Tím, že se chladicí plášť vytváří vrstvu po vrstvě přímo z kovového prášku (například ze specializovaných slitin, jako je CuCrZr nebo AlSi10Mg), umožňuje AM:
- Bezkonkurenční svoboda designu: Inženýři mohou navrhovat vysoce komplexní, topologicky optimalizované vnitřní chladicí kanály, které přesně kopírují obrysy zdrojů tepla, maximalizují povrch a turbulentní proudění pro vynikající přenos tepla. Funkce, jako jsou tenké stěny, složité mřížkové struktury a konformní kanály, které jsou při použití tradičních metod nemožné nebo neúnosně drahé, jsou nyní realizovatelné.
- Konsolidace částí: Více komponent tradiční chladicí sestavy lze potenciálně integrovat do jediného 3D tištěného dílu, čímž se zkrátí doba montáže, sníží se hmotnost a sníží se počet potenciálních míst poruchy.
- Odlehčení: Materiál lze umístit přesně tam, kde je to nutné pro zajištění strukturální integrity a tepelné funkce, což umožňuje výrazné snížení hmotnosti ve srovnání s odlévanými protějšky.
- Rychlé prototypování a iterace: Návrhy lze rychle upravovat a znovu tisknout bez nutnosti nákladných změn nástrojů, což urychluje vývojové cykly a umožňuje optimalizaci výkonu.
- Přizpůsobení materiálu: AM umožňuje použití pokročilých kovových slitin vybraných speciálně pro jejich tepelnou vodivost, poměr pevnosti a hmotnosti a odolnost proti korozi, které jsou přizpůsobeny náročnému prostředí elektromobilů.
Přední dodavatelé, jako je společnost Met3dp, využívající pokročilé techniky výroby prášků, jako je plynová atomizace a plazmový proces s rotujícími elektrodami (PREP), spolu s nejmodernějšími tiskárnami pro selektivní tavení elektronovým svazkem (SEBM) a laserovou fúzi v práškovém loži (L-PBF), nabízejí vysoce kvalitní materiály a přesnost výroby, které jsou pro tyto kritické komponenty nezbytné. Jejich odborné znalosti pokrývají celý procesní řetězec od výroby prášku až po hotový díl a zajišťují spolehlivost a výkon pro náročné automobilové aplikace. S pokračujícím rychlým rozvojem průmyslu elektrických vozidel se technologie AM z kovu může stát nepostradatelným nástrojem pro návrh a výrobu nové generace vysoce výkonných chladicích plášťů motorů.
Základní aplikace: Kde mají 3D tištěné chladicí pláště motorů elektromobilů dopad?
Přestože potenciál chladicích plášťů tištěných 3D tiskem zahrnuje různé aplikace elektromotorů, jejich využití je v současné době nejvýznamnější a nejvlivnější v odvětvích, kde jsou rozhodujícími rozdíly výkon, hmotnost a optimalizace konstrukce. Výrobci originálního vybavení pro automobilový průmysl (OEM) a jejich dodavatelé Tier 1 jsou hlavními průzkumníky a osvojiteli, kteří jsou vedeni jedinečnými požadavky trhu s elektromobily. Manažeři nákupu a inženýrské týmy v těchto organizacích stále častěji vyhodnocují poskytovatele AM technologií pro kovy, a to jak pro řešení prototypů, tak pro sériovou výrobu.
Klíčové oblasti použití:
- Vysoce výkonná elektrická vozidla (hyperauta a sportovní elektromobily):
- Výzva: Tato vozidla posouvají hranice hustoty výkonu a trvalého výkonu. Motory pracují při extrémním zatížení a vytvářejí obrovské množství tepla, které běžné chladicí systémy jen těžko účinně zvládají v rámci omezených možností balení. Snížení hmotnosti je také nejdůležitější pro ovladatelnost a zrychlení.
- Řešení AM: 3D tisk z kovu umožňuje vytvářet topologicky optimalizované chladicí pláště s velmi složitými vnitřními kanály navrženými pomocí simulací výpočtové dynamiky tekutin (CFD). Tyto pláště maximalizují odvod tepla z kritických oblastí, jako je statorové vinutí a koncové závity, což umožňuje vyšší trvalý výkon bez přehřívání. Materiály jako slitiny mědi (např. CuCrZr), které nabízejí vynikající tepelnou vodivost, jsou často upřednostňovány, a to i přes výrobní problémy, které AM pomáhá překonat. Odlehčení dosažené optimalizovanou konstrukcí dále zlepšuje dynamiku vozidla. Klíčovými velkoodběrateli v této nice jsou specializovaní výrobci a výkonnostní divize.
- Prémiová & Elektrická vozidla hlavního proudu:
- Výzva: Ačkoli to možná není tak extrémní jako u hyperaut, běžné elektromobily stále vyžadují efektivní tepelný management pro zajištění dojezdu, spolehlivosti a možnosti rychlého nabíjení. Výrobci OEM hledají nákladově efektivní řešení, která nabízejí zlepšení oproti tradičnímu odlévání, zejména s tím, jak se v různých segmentech zvyšuje hustota výkonu motorů. Důležitým faktorem je také snížení NVH (hluk, vibrace, drsnost) prostřednictvím optimalizované konstrukce skříně.
- Řešení AM: Aditivní výroba, zejména s využitím nákladově efektivních a dobře pochopených hliníkových slitin, jako je AlSi10Mg, nabízí cestu ke zlepšení tepelného výkonu ve srovnání se základními odlitky. AM umožňuje konformní chladicí kanály, které těsněji objímají stator, čímž se snižuje tepelný odpor. Konsolidace dílů může zjednodušit montážní linky. Zatímco nákladová konkurenceschopnost s velkoobjemovým tlakovým litím zůstává otázkou, AM nabízí významnou hodnotu ve fázi vývoje pro rychlé opakování a ověřování výkonu. S tím, jak technologie AM dozrává a náklady klesají, roste její využití v sériové výrobě pro prémiové segmenty, přičemž distributoři hrají roli při řízení dodavatelského řetězce těchto komponent.
- Elektrický motoristický sport (Formule E, Electric GT atd.):
- Výzva: Motoristický sport představuje vrchol optimalizace výkonu podle přísných předpisů. Týmy vyžadují maximální výkon, minimální hmotnost a extrémní spolehlivost v závodních podmínkách. Vývojové cykly jsou krátké a vyžadují rychlou výrobu prototypů a komponentů na míru.
- Řešení AM: 3D tisk z kovu se v motoristickém sportu hojně využívá pro svou schopnost rychle dodávat vysoce přizpůsobené, lehké komponenty s optimalizovanými výkonnostními vlastnostmi. Chladicí pláště jsou hlavními kandidáty, protože umožňují týmům přesně přizpůsobit tepelný management jejich jedinečným konstrukcím motorů a závodním strategiím. Možnost iterovat návrhy mezi závody na základě údajů o výkonu je neocenitelná. Výběr materiálu (často vysoce pevný hliník nebo specializované slitiny) a složitá vnitřní geometrie jsou klíčovými výhodami, které využívají závodní týmy, které často spolupracují přímo s poskytovateli služeb AM.
- Užitková elektrická vozidla (autobusy, nákladní vozidla):
- Výzva: Těžká elektrická vozidla využívají velké a výkonné motory, které pracují v konstantních zátěžových cyklech. Spolehlivost, životnost a účinnost jsou rozhodující pro minimalizaci provozních nákladů. Tepelný management musí být robustní, aby zvládl trvalé požadavky na vysoký točivý moment a proměnlivé podmínky prostředí.
- Řešení AM: I když je citlivost na náklady vysoká, potenciál vyšší účinnosti a spolehlivosti díky optimalizovanému chlazení může nabídnout dlouhodobou hodnotu. Pomocí AM lze vytvořit chladicí pláště se zlepšeným rozdělením průtoku chladicí kapaliny, což zabraňuje vzniku horkých míst a prodlužuje životnost motoru. Pro specializovaná užitková vozidla nebo při vývoji nových platforem pohonných jednotek poskytuje AM flexibilní výrobní řešení. Nákupní oddělení ve výrobě užitkových vozidel hledají spolehlivé dodavatele průmyslového tisku kovů, kteří jsou schopni splnit normy odolnosti.
- Letecký a kosmický elektrický pohon (městská letecká mobilita, drony):
- Výzva: Elektrický pohon v letectví a kosmonautice se teprve rodí, ale vyžaduje extrémně nízkou hmotnost a mimořádně vysokou spolehlivost. Tepelný management je kriticky důležitý kvůli změnám hustoty vzduchu a závažným důsledkům selhání součástek.
- Řešení AM: 3D tisk z kovu je v letectví a kosmonautice již běžnou záležitostí, protože umožňuje výrobu lehkých a složitých dílů. Pro chlazení elektromotorů v bezpilotních letounech nebo budoucích vozidlech UAM umožňuje AM tisk vysoce integrované a optimalizované systémy tepelného managementu, které často kombinují konstrukční prvky s chladicími kanály v jediné součásti za použití materiálů, jako jsou vysokopevnostní slitiny hliníku nebo titanu. Důležitá je důsledná kontrola kvality a certifikace, kterou nabízejí zkušení poskytovatelé, jako je Met3dp.
Funkce vylepšené 3D tiskem:
Napříč těmito aplikacemi 3D tisk z kovu specificky zlepšuje funkce chladicího pláště:
- Zlepšený přenos tepla: Optimalizovaná geometrie kanálů (složité dráhy, turbulátory, zvětšená plocha) zlepšuje součinitel přestupu tepla mezi součástmi motoru a chladicí kapalinou.
- Cílené chlazení: Průtok chladicí kapaliny lze přesně nasměrovat do identifikovaných horkých míst v motoru.
- Snížení tepelných gradientů: Rovnoměrnější chlazení minimalizuje kolísání teploty v celém motoru, čímž se snižuje namáhání a zlepšuje životnost.
- Zlepšený průtok chladicí kapaliny: Optimalizovaná konstrukce kanálů minimalizuje tlakové ztráty, což potenciálně umožňuje použití menších a účinnějších čerpadel chladicí kapaliny.
- Integrační potenciál: Chladicí kanály lze integrovat přímo do konstrukčních prvků motoru, čímž se snižuje počet dílů a složitost montáže.
Schopnost využít tato funkční vylepšení činí z 3D tištěných chladicích plášťů atraktivní nabídku pro inženýry, kteří hledají zvýšení výkonu, a pro manažery nákupu, kteří hledají inovativní řešení od dodavatelů pokročilých výrobních technologií.
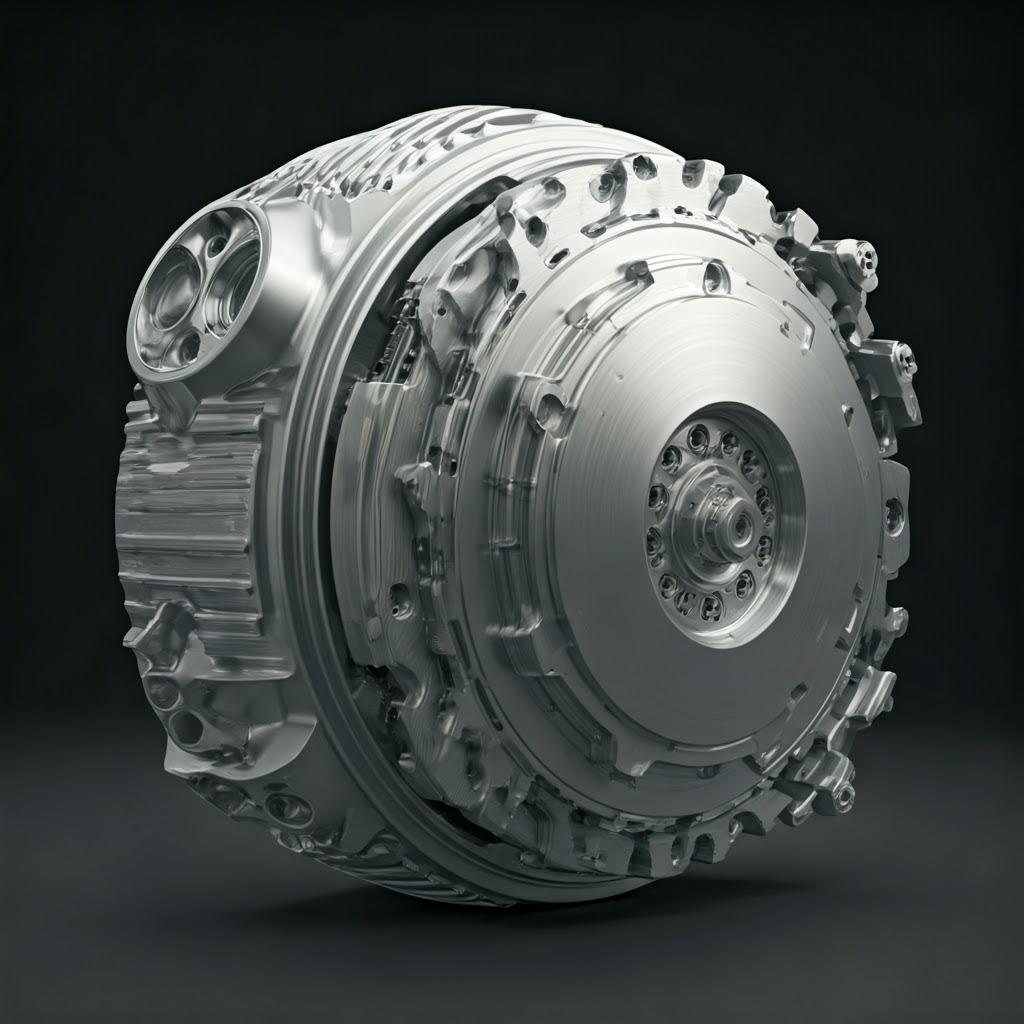
Aditivní výhoda: Proč upřednostnit 3D tisk kovů pro chladicí pláště elektromobilů před tradičními metodami?
Rozhodnutí automobilových výrobců OEM, dodavatelů Tier 1 a výrobců výkonných vozidel využít aditivní výrobu kovů pro chladicí pláště motorů elektromobilů vychází z řady přesvědčivých výhod, které přímo řeší nedostatky konvenčních metod, jako je odlévání a obrábění. Zatímco tradiční postupy jsou pro určité aplikace i nadále vhodné, AM výroba kovů nabízí transformační potenciál, zejména při posouvání hranic výkonu, účinnosti a integrace konstrukce. Vyhodnocení těchto přínosů je pro vedoucí pracovníky v oblasti inženýrství a specialisty na nákupy pokročilých automobilových komponent zásadní.
1. Bezkonkurenční geometrická složitost & volnost designu:
- Tradiční omezení: Procesy odlévání jsou omezeny potřebou forem a jader. Navrhování složitých vnitřních průchodů s podřezáním, ostrými zatáčkami nebo proměnnými průřezy je obtížné, nákladné nebo nemožné. Jsou vyžadovány úhly ponoru a minimální tloušťky stěn často přesahují konstrukční potřeby. Obrábění vnitřních kanálů do masivního bloku je rovněž velmi omezující.
- Výhoda AM: Konstrukce po vrstvách odstraňuje většinu geometrických omezení. Kovová AM umožňuje:
- Kanály s optimalizovanou topologií: Algoritmy určují nejefektivnější cesty zatížení a rozložení materiálu. U chladicích plášťů to znamená, že kanály přesně kopírují zdroje tepla, maximalizují kontaktní plochu a minimalizují spotřebu materiálu a hmotnost.
- Konformní chlazení: Kanály se mohou přesně přizpůsobit tvaru statoru nebo rotoru a zachovávají konzistentní minimální vzdálenost pro vysoce účinný přenos tepla, na rozdíl od často kompromitovaných cest v litých konstrukcích.
- Vnitřní mřížové struktury: Lehké, složité mřížkové struktury mohou být začleněny do stěn kanálů nebo do těla pláště, aby se zvýšila strukturální tuhost a zároveň minimalizovala hmotnost, nebo dokonce do samotných kanálů, aby se podpořilo turbulentní proudění a zvýšila se plocha pro přenos tepla.
- Tenké, rovnoměrné stěny: Stěny lze navrhnout mnohem tenčí (až na submilimetrovou úroveň, pokud to proces dovolí) a rovnoměrnější než při odlévání, což snižuje hmotnost a tepelný odpor.
- Integrované funkce: Funkční prvky, jako jsou montážní body, pouzdra senzorů nebo konektory pro připojení kapalin, lze bez problémů integrovat do jediného tištěného dílu.
2. Vynikající tepelný výkon:
- Tradiční omezení: Geometrická omezení při odlévání často vedou k neoptimálním průtokovým cestám chladicí kapaliny, potenciálním mrtvým zónám, kde chladicí kapalina stagnuje, a větším vzdálenostem mezi chladicí kapalinou a zdrojem tepla, což má za následek vyšší tepelný odpor a méně účinný odvod tepla.
- Výhoda AM: Volnost konstrukce, kterou AM umožňuje, se přímo promítá do vynikajícího tepelného výkonu:
- Maximalizovaná plocha povrchu: Komplexní vnitřní geometrie, včetně žeber nebo mřížkových struktur v kanálech, výrazně zvětšují plochu, která je k dispozici pro výměnu tepla.
- Optimalizované cesty toku: Pomocí simulací CFD lze navrhnout kanály, které zajistí rovnoměrnou rychlost chladicí kapaliny, minimalizují tlakovou ztrátu a v případě potřeby vyvolávají turbulenci, aby se maximalizoval koeficient přenosu tepla.
- Snížení tepelných překážek: Tvarové kanály minimalizují vzdálenost, kterou musí teplo urazit od zdroje (statorového vinutí) k chladicí kapalině, a výrazně tak snižují tepelný odpor.
- Cílené chlazení: Chladicí kapalinu lze přednostně směrovat do známých horkých míst v konstrukci motoru.
3. Významný potenciál odlehčení:
- Tradiční omezení: Odlévání často vyžaduje silnější profily pro vyplnění formy a předpoklady strukturální integrity, což vede k těžším součástem. Obrábění ze sochoru začíná přebytkem materiálu.
- Výhoda AM: Materiál se přidává pouze v případě potřeby. Optimalizace topologie a mřížové struktury umožňují drastické snížení spotřeby materiálu při zachování nebo dokonce zvýšení výkonnosti konstrukce a poměru tuhosti a hmotnosti. Snížení hmotnosti je u elektromobilů zásadní pro zlepšení dojezdu, ovladatelnosti a celkové účinnosti. I několik ušetřených kilogramů významně přispívá.
4. Konsolidace částí:
- Tradiční omezení: Složité chladicí systémy mohou vyžadovat více odlitých nebo opracovaných součástí (např. oddělené poloviny pláště, rozdělovače, konektory), které je třeba sestavit, sešroubovat, svařit nebo připájet, což přináší potenciální netěsnosti, pracnost montáže a problémy s tolerancí.
- Výhoda AM: Kovová AM umožňuje sloučit více funkčních prvků do jediného monolitického tištěného dílu. To zjednodušuje dodavatelský řetězec, zkracuje dobu montáže a snižuje náklady, zvyšuje spolehlivost eliminací spojů a těsnění a často přispívá k dalšímu snížení hmotnosti. To je významným přínosem pro velkoobchodní nákupčí a nákupní týmy spravující složité sestavy.
5. Zrychlený vývoj & Prototypování:
- Tradiční omezení: Vytvoření nástrojů (forem, zápustek) pro odlévání představuje velkou časovou (týdny nebo měsíce) a finanční investici. Iterace návrhu vyžadují nákladné úpravy nástrojů nebo jejich kompletní předělání. Obrábění prototypů může být rychlejší, ale nemusí přesně kopírovat vlastnosti nebo geometrii konečného odlévaného dílu.
- Výhoda AM: AM je proces bez použití nástrojů. Návrhy lze odeslat přímo z CADu do tiskárny. Prototypy lze vyrobit během několika dnů, což inženýrům umožňuje rychle testovat a iterovat návrhy na základě tepelných a strukturálních simulací nebo fyzických testů. To výrazně zkracuje vývojový cyklus, snižuje riziko a umožňuje optimalizovat finální návrhy před zahájením sériové výroby. Společnosti jako Met3dp, které nabízejí pokročilé tiskárny i materiály, mohou tento rychlý iterační proces usnadnit.
6. Pružnost materiálu & Pokročilé slitiny:
- Tradiční omezení: Odlévání je často omezeno na specifické, dobře zavedené slitiny (především slitiny hliníku pro chladicí pláště). Zavádění nových nebo obtížně odlévatelných slitin může být náročné.
- Výhoda AM: Procesy AM s kovy, jako je L-PBF a SEBM, jsou kompatibilní s širší škálou pokročilých kovových prášků, včetně:
- Slitiny mědi s vysokou tepelnou vodivostí (např. CuCrZr): Nabízejí podstatně lepší přenos tepla než hliník, ale jsou známé tím, že je obtížné odlévat složité tvary bez vad. Díky AM je možné odlévat složité pláště ze slitin mědi.
- Vysokopevnostní hliníkové slitiny: Specifické slitiny Al optimalizované pro AM nabízejí vynikající poměr pevnosti a hmotnosti.
- Slitiny titanu: Pro aplikace vyžadující extrémní odlehčení a odolnost proti korozi (i když méně časté pro primární chladicí pláště z důvodu nižší tepelné vodivosti a vyšších nákladů).
- Vlastní slitiny: Poskytovatelé AM, jako je Met3dp, s vlastní výrobou prášku pomocí technik, jako je plynová atomizace, mohou dokonce podporovat vývoj a použití vlastních slitin přizpůsobených specifickým tepelným a mechanickým požadavkům.
Výhody B2B dodavatelského řetězce a výroby:
- Snížení investic do nástrojů: Eliminuje vysoké počáteční náklady spojené s odléváním forem.
- Výroba na vyžádání: Umožňuje výrobu blíže k místu potřeby, což může zjednodušit logistiku.
- Flexibilní velikosti dávek: Ekonomicky výhodné pro nízké až střední výrobní série, ideální pro specifická vozidla, motoristický sport nebo počáteční náběh výroby předtím, než je opodstatněné vyrábět velkoobjemové nástroje.
- Digitální inventář: Návrhy existují jako digitální soubory, což umožňuje tisknout díly podle potřeby a snižuje požadavky na fyzické zásoby.
Srovnávací tabulka: AM vs. tradiční metody pro chladicí pláště pro elektromobily
Vlastnosti | Výroba aditiv kovů (AM) | Tradiční casting | Tradiční obrábění |
---|---|---|---|
Geometrická složitost | Velmi vysoká (vnitřní kanály, mřížky, konformní) | Střední až nízká (úhly ponoru, hranice jádra) | Nízká (omezené interní funkce) |
Tepelný výkon | Potenciálně velmi vysoká (optimalizovaný průtok, max. SA) | Středně těžká (kompromitované průtokové cesty) | Střední až vysoká (pokud to konstrukce umožňuje) |
Odlehčení | Vynikající (optimalizace topologie, mřížky) | Poctivé (minimální tloušťka stěny) | Spravedlivé (limity pro odstranění materiálu) |
Konsolidace částí | Vysoký potenciál | Nízký potenciál | Velmi nízký potenciál |
Rychlost prototypování | Velmi rychle (dny) | Pomalé (týdny/měsíce na výrobu nástrojů) | Mírná (dny/týdny) |
Náklady na nástroje | Žádné / velmi nízké | Vysoký | Nízká (Fixturing) |
Možnosti materiálu | Široký (Al, Cu, Ti, ocel, slitiny na zakázku) | Omezené (hlavně Al, některé slitiny Fe) | Široký (závisí na dostupnosti polotovarů) |
Ideální objem | Nízká až střední, Prototypování | Vysoký | Nízká, Prototypování |
Náklady na díl (nízký objem) | Mírná až vysoká | Velmi vysoká (z důvodu amortizace nástrojů) | Vysoký |
Náklady na díl (vysoký objem) | Vysoká (doba zpracování) | Nízký | Mírná až vysoká |
Dodavatelský řetězec | Potenciálně jednodušší (na vyžádání, digitální) | Komplexní (dodavatelé nástrojů, slévárny) | Jednodušší (dodavatelé materiálu, strojírenské dílny) |
Export do archů
Zatímco náklady na jeden díl ve velmi vysokých objemech mohou být stále výhodnější než tradiční odlévání, přesvědčivé technické výhody, zejména pokud jde o výkon, hmotnost a rychlost vývoje, činí z kovového 3D tisku stále atraktivnější a strategicky důležitější výrobní metodu pro chladicí pláště elektromotorů, zejména pro aplikace zaměřené na výkon a společnosti, které hledají konkurenční výhodu. Výběr zkušeného partnera pro aditivní výrobu je klíčem k realizaci těchto výhod.
Materiální záležitosti: Výběr vysoce výkonných prášků jako CuCrZr a AlSi10Mg
Volba materiálu je zásadní pro výkon a spolehlivost jakékoli konstrukční součásti a chladicí pláště pro elektromotory vytištěné na 3D tiskárně nejsou výjimkou. Zvolený kovový prášek určuje tepelnou vodivost pláště, mechanickou pevnost, hmotnost, odolnost proti korozi a v konečném důsledku i jeho schopnost splnit náročné požadavky pohonných jednotek elektromobilů. Aditivní výroba otevírá dveře k použití materiálů, které by bylo obtížné nebo nemožné tvarovat tradičními metodami, což inženýrům nabízí větší flexibilitu, ale také vyžaduje pečlivé zvážení. U chladicích plášťů pro elektromobily vynikají dvě skupiny materiálů: Slitiny hliníku a slitiny mědi.
Proč je výběr materiálu rozhodující:
- Tepelná vodivost: To je pravděpodobně nejdůležitější vlastnost. Vyšší tepelná vodivost umožňuje snadnější přenos tepla ze zdrojů tepla motoru (statoru) přes materiál pláště do chladicí kapaliny, což minimalizuje tepelný odpor a udržuje motor chladnější.
- Mechanická pevnost a odolnost: Chladicí plášť je často konstrukční součástí sestavy motoru. Musí odolávat vibracím, mechanickému zatížení a vnitřnímu tlaku chladicí kapaliny po celou dobu životnosti vozidla. Tepelné namáhání vyvolávají také teplotní změny.
- Hmotnost: Minimalizace hmotnosti součástek má zásadní význam pro maximalizaci dojezdu a výkonu elektromobilu. K tomuto cíli přímo přispívají lehčí materiály.
- Odolnost proti korozi: Materiál musí být kompatibilní se standardními automobilovými chladicími kapalinami (např. směsmi vody a glykolu) a musí odolávat korozi po mnoho let provozu a vystavení různým podmínkám prostředí.
- Vyrobitelnost (tisknutelnost): Ne všechny slitiny lze stejně snadno zpracovávat pomocí technologií AM na kovy, jako je L-PBF nebo SEBM. Je třeba vzít v úvahu faktory, jako je absorpce laserového/elektronového paprsku, tekutost prášku, svařitelnost a náchylnost k praskání nebo zbytkovému napětí během tisku.
- Náklady: Náklady na materiál jsou významným faktorem v celkové ceně komponent, zejména při výrobě větších objemů. Nákupní týmy musí vyvažovat požadavky na výkonnost s rozpočtovými omezeními.
Doporučené prášky pro chladicí bundy EV:
1. Slitiny hliníku (konkrétně AlSi10Mg):
- Přehled: AlSi10Mg je jednou z nejběžnějších a nejlépe charakterizovaných hliníkových slitin používaných při aditivní výrobě kovů. Je to v podstatě slitina hliníku, křemíku a hořčíku upravená do práškové formy.
- Klíčové vlastnosti:
- Dobrá tepelná vodivost: AlSi10Mg sice nemá tak vysokou tepelnou vodivost jako měď, ale má dobrou tepelnou vodivost (přibližně 150-180 W/m-K po tepelném zpracování), což je výrazně lepší než u ocelí nebo slitin titanu.
- Vynikající poměr pevnosti k hmotnosti: Slitiny hliníku jsou ze své podstaty lehké (hustota ~2,68 g/cm³). Slitiny AlSi10Mg mají dobrou mechanickou pevnost a tuhost, zejména po vhodném tepelném zpracování (T6), takže jsou vhodné pro konstrukční součásti.
- Dobrá potiskovatelnost: Obecně se dobře zpracovává se systémy L-PBF, vykazuje dobrou svařitelnost a relativně nižší zbytkové napětí ve srovnání s některými jinými slitinami. To z něj činí spolehlivou volbu pro složité geometrie.
- Odolnost proti korozi: Vykazuje dobrou odolnost proti korozi, je vhodný pro typické prostředí automobilových chladicích kapalin.
- Efektivita nákladů: Hliníkové prášky jsou obecně cenově dostupnější než slitiny mědi nebo titanu, takže AlSi10Mg je vhodným kandidátem pro aplikace citlivé na náklady a pro rozšiřování sériové výroby.
- Proč je to důležité pro chladicí bundy: AlSi10Mg poskytuje vyváženou kombinaci tepelného výkonu, nízké hmotnosti, přiměřené pevnosti, dobré vyrobitelnosti a rozumné ceny. Často je výchozím bodem pro mnoho aplikací AM v automobilovém průmyslu, včetně komponent tepelného managementu. Jeho široké použití znamená, že parametry zpracování jsou dobře známy zkušeným poskytovatelům AM služeb.
2. Slitiny mědi (konkrétně CuCrZr – měď, chrom, zirkon):
- Přehled: Slitiny mědi jsou díky své výjimečné tepelné vodivosti velmi atraktivní pro tepelný management. CuCrZr je srážením zpevněná slitina mědi navržená tak, aby nabízela dobrou rovnováhu mezi vodivostí a mechanickou pevností při zvýšených teplotách.
- Klíčové vlastnosti:
- Vynikající tepelná vodivost: To je hlavní výhoda. CuCrZr se může pochlubit velmi vysokou tepelnou vodivostí (obvykle >300 W/m-K), která je zhruba dvojnásobná oproti AlSi10Mg. To umožňuje výrazně účinnější odvod tepla z motoru.
- Dobrá mechanická pevnost (při teplotě): Zatímco čistá měď je měkká, příměsi chromu a zirkonia umožňují její zpevnění věkem, což výrazně zvyšuje její pevnost a umožňuje jí zachovat si dobré mechanické vlastnosti i při zvýšených provozních teplotách, které se vyskytují v elektromotorech.
- Dobrá odolnost proti korozi: Obecně kompatibilní s automobilovými chladicími kapalinami.
- Vyšší hustota: Slitiny mědi jsou výrazně hustší (~8,9 g/cm³) než slitiny hliníku, což znamená, že měděný plášť bude těžší než hliníkový plášť s identickou geometrií. Lepší tepelný výkon by však mohl umožnit menší nebo tenčí konstrukce, což by mohlo kompenzovat část hmotnostní ztráty.
- Výzvy:
- Možnost tisku: Tisk měděných slitin pomocí L-PBF je notoricky známý problém, především kvůli vysoké odrazivosti a tepelné vodivosti mědi. Odráží velkou část laserové energie (což vyžaduje lasery s vyšším výkonem, často zelené lasery) a rychle odvádí teplo, což ztěžuje vytvoření stabilní taveniny. To může vést k vadám, jako je pórovitost nebo nedostatečné tavení, pokud se neřídí pečlivě. Zpracování vyžaduje specializované vybavení a přesně vyladěné parametry. SEBM může být výhodná díky lepší absorpci energie.
- Náklady: Prášky ze slitin mědi jsou výrazně dražší než prášky z hliníku.
- Proč je to důležité pro chladicí bundy: U aplikací vyžadujících absolutně nejvyšší úroveň tepelného výkonu (např. vysoce výkonné závodní motory, aplikace s extrémně vysokým výkonem) lze využít vynikající tepelnou vodivost CuCrZr. Umožňuje konstruktérům posunout tepelné limity dále, než je to možné u hliníku, což může vést k vyššímu trvalému výkonu nebo kompaktnějším konstrukcím motorů. Vzhledem k výrobním výzvám je nezbytné spolupracovat s vysoce zkušeným poskytovatelem AM s osvědčenými schopnostmi tisku mědi. Velkoodběratelé na výkonných trzích vyhledávají zejména dodavatele schopné zpracovávat tyto pokročilé materiály.
Úloha Met3dp’ v oblasti materiálové excelence:
Výběr správného prášku je jen částí rovnice kvalita tohoto prášku je stejně důležitý pro dosažení spolehlivých a vysoce výkonných dílů. V této oblasti přináší vertikálně integrovaný partner, jako je Met3dp, významnou hodnotu:
- Pokročilá výroba prášků: Společnost Met3dp využívá špičkové technologie výroby prášků:
- Atomizace plynu (GA): Tento proces využívá vysokotlaké proudy inertního plynu k rozbití proudu roztaveného kovu na jemné kapičky, které ztuhnou na kulovité částice prášku. Zařízení Met3dp’využívá jedinečné konstrukce trysek a proudění plynu k dosažení vysoké sféricity a dobré tekutosti - což je klíčové pro konzistentní vrstvení práškového lože ve strojích AM.
- Proces plazmové rotující elektrody (PREP): Při PREP se rychle rotující elektroda z cílového kovu taví plazmovým hořákem. Odstředivou silou jsou odlévány roztavené kapky, které v inertní atmosféře tuhnou do vysoce kulovitých prášků s velmi malým počtem satelitů (menších připojených částic) a nízkou vnitřní pórovitostí. Výsledkem je často vynikající kvalita prášku, ideální pro náročné aplikace.
- Kontrola kvality: Důležitá je důsledná kontrola distribuce velikosti částic (PSD), morfologie (sféricity), tekutosti, chemického složení a čistoty. Konzistentní kvalita prášku zajišťuje předvídatelné chování při tisku a konečné vlastnosti dílů.
- Široké portfolio materiálů: Zatímco AlSi10Mg a CuCrZr jsou klíčové pro chladicí pláště, společnost Met3dp vyrábí širokou škálu vysoce kvalitních kovových prášků, včetně různých slitin titanu (TiNi, TiTa, TiAl, TiNbZr), kobalt-chromu (CoCrMo), nerezových ocelí a superslitin. Tato šíře odborných znalostí zajišťuje hluboké porozumění vlastnostem kovových prášků a jejich zpracování. Jejich nabídku můžete dále prozkoumat na jejich stránka produktu.
- Materiál & amp; Odborné znalosti procesů: Společnost Met3dp kombinuje své odborné znalosti prášků s hlubokými znalostmi procesů AM tisku (včetně SEBM a L-PBF) a zajišťuje, že vybraný prášek je optimálně zpracován tak, aby bylo dosaženo požadovaných vlastností materiálu v konečném chladicím plášti.
Srovnávací tabulka: Klíčové vlastnosti materiálů
Vlastnictví | AlSi10Mg (typický, tepelně zpracovaný) | CuCrZr (typický, tepelně zpracovaný) | Jednotky | Význam pro chladicí plášť |
---|---|---|---|---|
Tepelná vodivost | ~150 – 180 | >300 | W/m-K | Velmi vysoká |
Hustota | ~2.68 | ~8.9 | g/cm³ | Vysoká (nižší je lepší) |
Mez kluzu | ~250 – 300 | ~400 – 500 | MPa | Vysoký |
Maximální pevnost v tahu | ~400 – 450 | ~500 – 600 | MPa | Vysoký |
Možnost tisku (L-PBF) | Dobrý | Náročný | – | Vysoký |
Relativní náklady | Dolní | Vyšší | – | Vysoký |
Odolnost proti korozi | Dobrý | Dobrý | – | Vysoký |
Export do archů
Závěr o materiálech:
Výběr mezi AlSi10Mg a CuCrZr (nebo jinými možnými slitinami) závisí do značné míry na požadavcích na výkonnost konkrétní aplikace v porovnání s náklady a hmotnostními omezeními. AlSi10Mg nabízí robustní, cenově výhodné řešení s dobrými všestrannými vlastnostmi vhodné pro mnoho aplikací v elektromobilech. CuCrZr poskytuje vynikající tepelný výkon pro nejnáročnější scénáře, i když s vyššími náklady a složitostí výroby. Spolupráce se znalým dodavatelem materiálů a poskytovatelem služeb AM, jako je Met3dp, který kontroluje kvalitu prášku od atomizace až po finální tisk, zajišťuje přístup k vysoce kvalitním materiálům a odborným znalostem potřebným k jejich efektivnímu využití pro optimální výkon chladicího pláště elektromotoru.
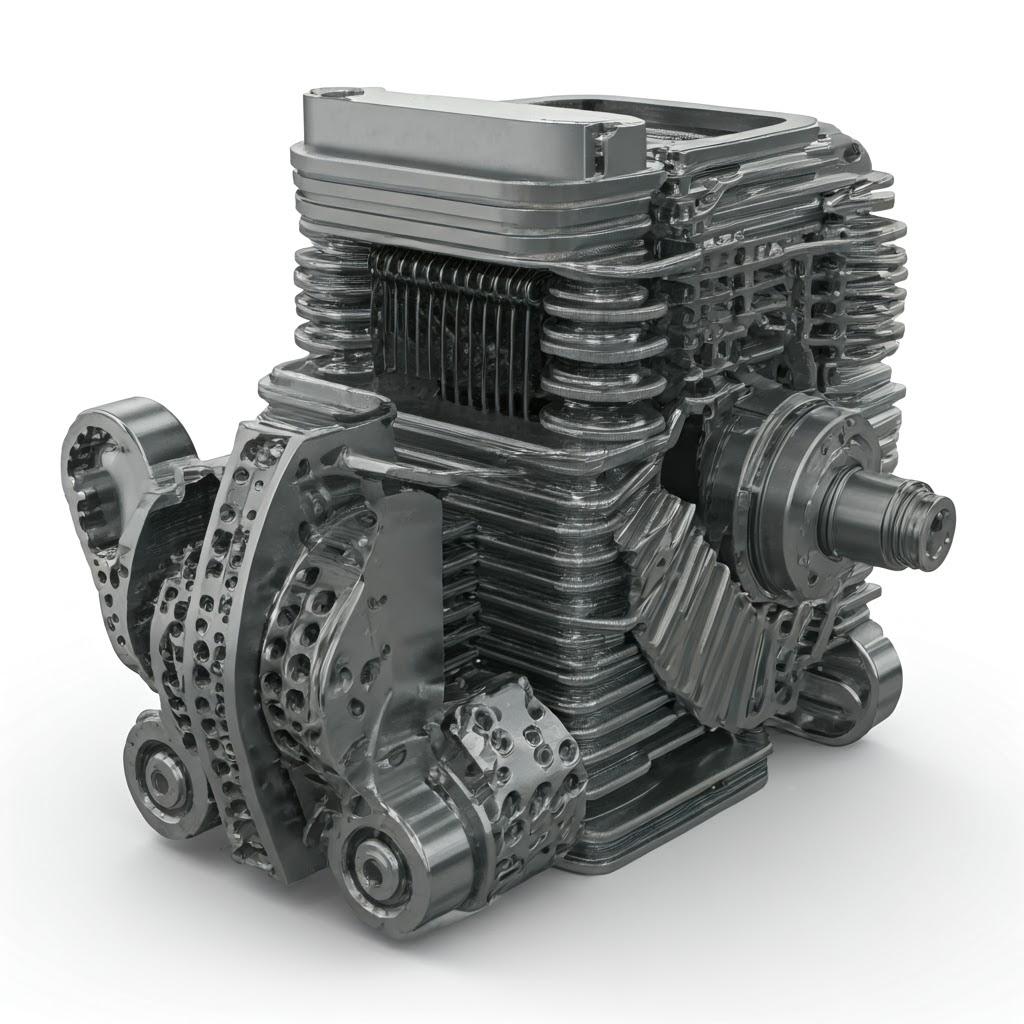
Design pro aditivní výrobu (DfAM): Optimalizace geometrie chladicího pláště pro dosažení špičkového výkonu
Pouhá replikace konstrukce určené k odlévání nebo obrábění pomocí aditivní výroby kovů jen zřídkakdy uvolní plný potenciál této technologie. Aby inženýři skutečně využili výhod 3D tisku pro chladicí pláště elektromotorů - lepší tepelný výkon, nižší hmotnost a konsolidace dílů - musí přijmout návrh pro aditivní výrobu (DfAM). DfAM není jen soubor pravidel, ale změna myšlení, která podporuje konstruktéry, aby přemýšleli v termínech vrstev, optimalizovali pro konkrétní použitý AM proces (jako je Laser Powder Bed Fusion – L-PBF nebo Selective Electron Beam Melting – SEBM) a využívali nabízenou geometrickou volnost. Manažerům veřejných zakázek, kteří spolupracují s dodavateli AM, pomáhá pochopení principů DfAM při vyhodnocování proveditelnosti a úrovně optimalizace navrhovaných konstrukcí.
Základní zásady DfAM pro chladicí pláště EV:
- Přijměte složitost pro funkci:
- Zpochybněte konvenční myšlení: Zapomeňte na omezení v podobě úhlů tahu, tahu jádra a přístupu k obrábění z přímé viditelnosti. AM se daří díky komplexnosti pokud slouží svému účelu.
- Optimalizace interních kanálů: V tomto případě se AM hodí pro chladicí bundy. Namísto jednoduchých kulatých nebo obdélníkových kanálů navrhněte:
- Konformní kanály: Dráhy, které přesně kopírují obrysy statoru nebo jiných zdrojů tepla a zachovávají minimální a stálou vzdálenost pro optimální přenos tepla.
- Proměnlivé průřezy: Kanály, které se zužují nebo rozšiřují za účelem regulace rychlosti chladicí kapaliny, podpory turbulence v určitých oblastech nebo přizpůsobení se omezením při balení.
- Složité cesty: Rozdělujte, spojujte a směrujte kanály složitými způsoby, aby se chladicí kapalina dostala do všech kritických oblastí a horkých míst identifikovaných pomocí tepelné simulace (CFD).
- Vnitřní funkce: Začlenění turbulátorů (žeber, důlků, gyroidních struktur) přímo do stěn kanálu, které vyřazují mezní vrstvu, zvyšují turbulentní proudění a při správném návrhu výrazně zvyšují součinitel přestupu tepla, aniž by docházelo k výraznému snížení tlakové ztráty.
- Integrace funkcí: Kombinujte montážní otvory, porty pro senzory, vstupy/výstupy kapalin a dokonce i konstrukční prvky přímo do jediného tištěného pláště, čímž eliminujete montážní kroky a potenciální místa úniku.
- Optimalizace topologie a odlehčení:
- Nechte softwarového průvodce: Využívejte software pro optimalizaci topologie již na začátku procesu návrhu. Definujte zatěžovací stavy (mechanické, tepelné), zóny s omezeným přístupem a výkonnostní cíle (např. maximalizace tuhosti, minimalizace hmotnosti, optimalizace tepelného toku). Software vygeneruje organické, často neintuitivní tvary, které efektivně rozdělí materiál pouze tam, kde je to potřeba.
- Mřížové struktury: Začlenění vnitřních mřížkových struktur (např. voštin, gyroidů, stochastické pěny) do pevných stěn pláště. Ty mohou výrazně snížit hmotnost při zachování vysoké tuhosti a pevnosti. Různé typy mřížek nabízejí různé vlastnosti (izotropní vs. anizotropní) vhodné pro různé podmínky zatížení. Ujistěte se, že zvolená velikost jednotkové buňky mřížky je tisknutelná se zvoleným procesem AM a rozlišením.
- Tenké žebrované stěny: Nahraďte tlusté masivní profily tenčími stěnami vyztuženými optimalizovanými vzory žeber, čímž dosáhnete podobných konstrukčních vlastností s menším množstvím materiálu a hmotnosti.
- Minimalizace a optimalizace podpůrných struktur:
- Samonosné úhly: Konstrukční prvky s úhly přesahu většími, než je kritický úhel samonosnosti pro zvolený materiál a proces (obvykle kolem 45° pro L-PBF, případně větší pro SEBM). Tím se minimalizuje potřeba obětovaných podpěrných konstrukcí.
- Design vnitřního kanálu: Navrhněte vnitřní vodorovné nebo nízkoúhlové kanály s nekruhovým průřezem (např. slza, kosočtverec), které jsou ze své podstaty samonosné, což snižuje nebo eliminuje potřebu vnitřních podpěr, které je obtížné nebo nemožné odstranit. Vyhněte se dlouhým plochým vnitřním stropům.
- Přístupné podpory: Tam, kde jsou podpěry nevyhnutelné (např. u vstupů/výstupů, složitých vnějších prvků), navrhněte je tak, aby je bylo možné během následného zpracování snadno odstranit bez poškození funkčních povrchů. Zvažte místa pro vylomení nebo konstrukce, které umožňují přístup k nástroji. Podpěry na bázi prášku (běžné při SEBM) se odstraňují snadněji než podpěry na bázi taveniny (L-PBF), ale mohou ovlivnit kvalitu povrchu.
- Na strategii podpory záleží: Projednejte včas strategii podpory se zvoleným poskytovatelem služeb AM, jako je Met3dp. Jejich zkušenosti s konkrétními stroji a materiály mohou být vodítkem při výběru konstrukce, aby se minimalizovaly požadavky na podporu a související náklady/rizika.
- Zvažte tloušťku stěny a rozlišení prvků:
- Minimální tloušťka stěny: Zjistěte, jaká je minimální tloušťka potisknutelné stěny pro daný proces a materiál (často 0,3-0,5 mm pro L-PBF, o něco větší pro SEBM). Navrhněte dostatečně tlusté stěny pro strukturální a tepelné požadavky, ale vyhněte se zbytečnému objemu. Velmi tenké stěny mohou být náchylné k deformaci nebo poškození.
- Rozlišení funkce: Malé prvky, ostré rohy a složité detaily mají limity založené na velikosti paprsku, velikosti částic prášku a tloušťce vrstvy. Zajistěte, aby kritické prvky, jako jsou těsnicí plochy nebo malé detaily kanálů, byly v rámci dosažitelného rozlišení. Vyhněte se nožovým hranám; používejte malé poloměry nebo zkosení.
- Plán následného zpracování:
- Přídavky na obrábění: Identifikujte kritická rozhraní, těsnicí plochy nebo prvky vyžadující přísné tolerance, které bude nutné po tisku opracovat na CNC. Ve fázi návrhu přidejte v těchto oblastech dostatečné množství obětovaného materiálu (např. 0,5-2 mm).
- Odstranění prášku: Navrhněte vnitřní kanály s dostatečným průměrem a hladkými přechody, které usnadní odstraňování netaveného prášku po sestavení. V případě potřeby do složitých vnitřních sítí zabudujte přístupové otvory, které lze později ucpat nebo svařit. Zachycený prášek představuje významné riziko pro kvalitu.
- Úvahy o tepelném zpracování: Pochopte, jak může tepelné zpracování (nutné pro optimální vlastnosti slitin jako AlSi10Mg a CuCrZr) způsobit drobné deformace. Navrhněte robustní prvky nebo naplánujte konečné obrábění po tepelném zpracování.
- Páková simulace (CFD & amp; FEA):
- Iterativní návrhová smyčka: DfAM je nejefektivnější, pokud je úzce propojen se simulací. Použijte výpočetní dynamiku tekutin (CFD) k modelování proudění chladicí kapaliny a přenosu tepla v navrhovaných kanálech. Použijte analýzu konečných prvků (FEA) k posouzení integrity konstrukce při mechanickém a tepelném zatížení.
- Ověřte optimalizaci: Využijte výsledky simulace k upřesnění tras kanálů, optimalizaci tloušťky stěn, ověření výsledků optimalizace topologie a předvídání potenciálních problémových oblastí (např. horkých míst, koncentrace vysokého napětí) před zahájením tisku. Tato opakující se smyčka návrh-simulace-zpřesnění je klíčem k maximalizaci výkonu.
Souhrnná tabulka pokynů DfAM:
Zásada DfAM | Klíčové úvahy o chladicích pláštích pro elektromobily | Benefit |
---|---|---|
Přijměte složitost | Konformní kanály, proměnné průřezy, vnitřní turbulátory, integrace | Vynikající tepelný výkon, snížený tepelný odpor, snížení počtu dílů |
Optimalizace topologie | Včasné podání žádosti, definování zátěže/omezení, efektivní využití softwaru | Maximální odlehčení, optimální využití materiálu, vysoký poměr tuhosti k hmotnosti |
Mřížové struktury | Vnitřní začlenění pro hmotnost/tuhost, kontrola tisknutelnosti | Výrazné snížení hmotnosti, přizpůsobené mechanické vlastnosti |
Minimalizace podpory | Navrhněte samonosné úhly (45°), optimalizujte tvary vnitřních kanálů | Kratší doba/náklady na následné zpracování, nižší riziko poškození povrchu |
Přístupné podpory | Plánujte přístup k odstranění, zvažte místa pro odpojení | Snadnější a čistší odstranění podpěr, zachované funkční povrchy |
Tloušťka stěny | Dodržujte limity min/max, používejte tenké stěny + žebra | Snížení hmotnosti, zkrácení doby tisku, úspora materiálu |
Rozlišení prvků | Dodržování procesních limitů pro malé prvky, otvory, ostré hrany | Zajišťuje vyrobitelnost, zabraňuje selhání nebo nepřesnosti prvků |
Plán následného zpracování | Přidejte obráběcí materiál, navrhněte odstraňování prášku, zvažte účinky tepelného zpracování | Dosahuje konečných tolerancí, zajišťuje čistotu, zabraňuje problémům s deformacemi |
Simulace pákového efektu | Použití CFD pro tepelné/proudové výpočty, FEA pro konstrukční výpočty, iterace návrhu | Předpověď výkonu & optimalizace, zmenšené fyzické prototypy |
Export do archů
Přijetím těchto principů DfAM mohou inženýrské týmy překročit pouhé používání 3D tisku jako náhradní výrobní metody a začít skutečně využívat jeho sílu k vytváření chladicích plášťů motorů elektromobilů nové generace, které výrazně překonávají své tradiční protějšky. Spolupráce se zkušenými dodavateli AM, kteří rozumí nuancím různých tiskových metod a materiály, je pro úspěšnou implementaci DfAM zásadní.
Přesnost uvolněna: Dosažení těsných tolerancí a vynikající povrchové úpravy u 3D tištěných chladicích plášťů
Přestože aditivní výroba kovů vyniká při vytváření složitých geometrií, častá otázka inženýrů a manažerů nákupu, zejména těch, kteří jsou zvyklí na přesné obrábění, se týká dosažitelné rozměrové přesnosti, tolerancí a povrchové úpravy 3D tištěných dílů. U funkčních součástí, jako jsou chladicí pláště elektromotorů, jsou tyto aspekty rozhodující pro správnou montáž, těsnění, dynamiku kapalin a celkový výkon. Pochopení schopností a omezení kovového AM je v tomto ohledu zásadní pro stanovení realistických očekávání a plánování nezbytných kroků následného zpracování.
Pochopení tolerancí při výrobě kovů metodou AM:
- Obecné tolerance: Jako výchozí bod lze uvést, že procesy AM kovů, jako je L-PBF a SEBM, mohou obvykle dosáhnout obecných rozměrových tolerancí srovnatelných s investičním litím. Běžně se používá norma ISO 2768, přičemž díly často spadají do tříd středních (m) nebo hrubých (c) tolerancí stav.
- ISO 2768-m (střední): Často je možné dosáhnout mnoha funkcí přímo z tiskárny. Například u prvku o velikosti 100 mm může být tolerance ±0,3 mm.
- ISO 2768-c (hrubý): Bezpečnější předpoklad pro méně kritické rozměry nebo složitější geometrie. Pro 100 mm to může být ±0,5 mm.
- Přísnější tolerance: Dosažení tolerancí těsnějších než ISO 2768-m obvykle vyžaduje dodatečné opracování specifických prvků. Tolerance typické pro CNC obrábění (např. ±0,05 mm nebo lepší) nejsou obecně dosažitelné přímo v procesu AM pro celou součást.
- Faktory ovlivňující toleranci:
- Kalibrace a kvalita strojů: Špičkové průmyslové tiskárny, jako jsou ty, které používá společnost Met3dp, s přesným řízením pohybu, kalibrací paprsku a systémy tepelného řízení, ze své podstaty produkují přesnější díly. Pravidelná údržba a kalibrace jsou klíčové.
- Vlastnosti materiálu: Různé kovové prášky vykazují během tisku různou míru smršťování, koeficienty tepelné roztažnosti a chování při namáhání, což má vliv na konečné rozměry. Zkušení poskytovatelé vyvíjejí specifické sady parametrů, které kompenzují chování materiálu.
- Geometrie dílu & Velikost: Velké, složité díly nebo díly s výraznými změnami průřezu jsou náchylnější k tepelnému zkreslení a odchylkám od zamýšlené geometrie. Vnitřní pnutí vznikající během procesu po vrstvách mohou způsobit deformace.
- Orientace v budově & Podporuje: Orientace dílu na konstrukční platformě ovlivňuje rozměrovou přesnost v důsledku faktorů, jako je odstupňování vrstev na zakřivených plochách a vliv podpůrných struktur. Podpěry mohou při odstraňování mírně narušit povrchy a lokálně ovlivnit geometrii.
- Tepelný management: Cykly ohřevu a chlazení během procesu výroby významně ovlivňují zbytkové napětí a potenciální deformace. Procesy, jako je SEBM, které pracují při zvýšených teplotách v konstrukční komoře, často vedou k nižšímu zbytkovému napětí ve srovnání s L-PBF, což může u určitých geometrií a materiálů zlepšit rozměrovou stabilitu.
- Následné zpracování: Tepelné zpracování s uvolněním napětí může způsobit drobné rozměrové změny. Odstranění podpěr může ovlivnit místní přesnost. K dosažení konečných přesných tolerancí kritických prvků se používá obrábění.
Povrchová úprava (drsnost):
- Drsnost povrchu (Ra) podle stavu: Povrchová úprava kovových dílů vyrobených metodou AM je ze své podstaty drsnější než povrch obrobený. Je ovlivněna velikostí částic prášku, tloušťkou vrstvy, parametry paprsku a orientací povrchu.
- Typické hodnoty Ra (L-PBF): V závislosti na výše uvedených faktorech se často pohybují v rozmezí od 6 µm do 20 µm (mikrometrů) Ra. Povrchy směřující vzhůru bývají hladší než povrchy směřující dolů (které vyžadují oporu) nebo svislé stěny (na nichž se projevují linie vrstev).
- Typické hodnoty Ra (SEBM): Obecně drsnější než L-PBF v důsledku větších částic prášku a částečného spékání, často v rozmezí 20 až 35 µm Ra nebo vyšším.
- Vliv povrchové úpravy:
- Těsnění: Povrchy ve stavu, v jakém jsou vyrobeny, jsou obvykle příliš drsné pro účinné těsnění O-kroužkem nebo těsněním. Tyto povrchy obvykle vyžadují obrábění nebo leštění.
- Dynamika tekutin: Drsný vnitřní povrch kanálů může zvýšit tlakovou ztrátu a potenciálně změnit charakteristiky přenosu tepla ve srovnání s hladkými kanály. Nadměrná drsnost je sice někdy výhodná pro vyvolání turbulence, ale obvykle je nežádoucí.
- Únavový život: Drsnost povrchu může být iniciačním místem únavových trhlin, i když u chladicích plášťů je to často méně kritické než u vysoce namáhaných konstrukčních součástí.
- Zlepšení povrchové úpravy: Různé techniky následného zpracování mohou výrazně zlepšit kvalitu povrchu:
- CNC obrábění: Poskytuje nejhladší a nejpřesnější povrchovou úpravu, ale obvykle se omezuje na přístupné povrchy.
- Obrábění abrazivním tokem (AFM): Proudí abrazivní média vnitřními kanály a vyhlazuje je.
- Elektrochemické leštění: Elektrochemicky odstraňuje materiál a vytváří lesklý a hladký povrch.
- Hromadné dokončování (bubnové, vibrační): Používá média k vyhlazení vnějších povrchů.
- Mikroobrábění / leštění: Ruční nebo automatické leštění pro specifické oblasti.
Met3dp’s Commitment to Precision:
Dosažení konzistentních tolerancí a požadovaných povrchových úprav vyžaduje nejen pokročilé vybavení, ale i hluboké znalosti procesů. Met3dp klade důraz na:
- Špičkové vybavení v oboru: Základem je použití tiskáren známých svou přesností a spolehlivostí.
- Optimalizované parametry: Rozsáhlé zkušenosti s vývojem a zdokonalováním parametrů sestavování pro specifické slitiny, jako jsou AlSi10Mg a CuCrZr, s cílem minimalizovat odchylky a dosáhnout konzistentních výsledků.
- Přísná kontrola kvality: Provádění metrologických kontrol (např. skenování na souřadnicovém měřicím stroji, 3D skenování) během výroby a po ní za účelem ověření rozměrové přesnosti oproti specifikacím.
- Integrované následné zpracování: Nabídka nebo řízení nezbytných kroků následného zpracování, včetně přesného obrábění a povrchové úpravy, aby byly splněny požadavky na finální výkres.
Tolerance & amp; Očekávání povrchové úpravy Shrnutí:
Parametr | Stav (typický rozsah) | Dosažitelné s následným zpracováním | Význam pro chladicí plášť |
---|---|---|---|
Obecná tolerance | ISO 2768-m / -c (±0.3 to ±0.5mm @100mm) | Tolerance obrábění (±0,05 mm+) | Střední (celková výbava), vysoká (rozhraní) |
Drsnost povrchu (Ra) | 6-35 µm (L-PBF/SEBM) | <1 µm možné (obráběné/leštěné) | Vysoká (těsnicí plochy), střední (vnitřní kanály) |
Opakovatelnost | Dobrý (s řízením procesu) | Vynikající (obrábění) | Vysoká (pro sériovou výrobu) |
Export do archů
Závěr o přesnosti:
Ačkoli kovové díly AM nevycházejí z tiskárny se zrcadlovým povrchem a mikronovou přesností CNC obrábění na všech površích, nabízejí pozoruhodnou komplexnost v kombinaci s úctyhodnou přesností při výrobě. V případě chladicích plášťů pro elektromobily je u kritických rozhraní, která vyžadují přísné tolerance nebo hladké těsnicí povrchy, obvykle nutné dodatečné obrábění. Většinu složité geometrie, včetně vnitřních kanálů, však lze často použít s tolerancemi a povrchovou úpravou, které jsou již zabudovány, nebo v případě potřeby se specializovanými procesy vnitřní povrchové úpravy. Nastavení jasných specifikací na výkresech, pochopení možností procesu a spolupráce se schopným AM partnerem, jako je Met3dp, jsou klíčem k úspěšnému využití kovového 3D tisku pro přesné citlivé aplikace.
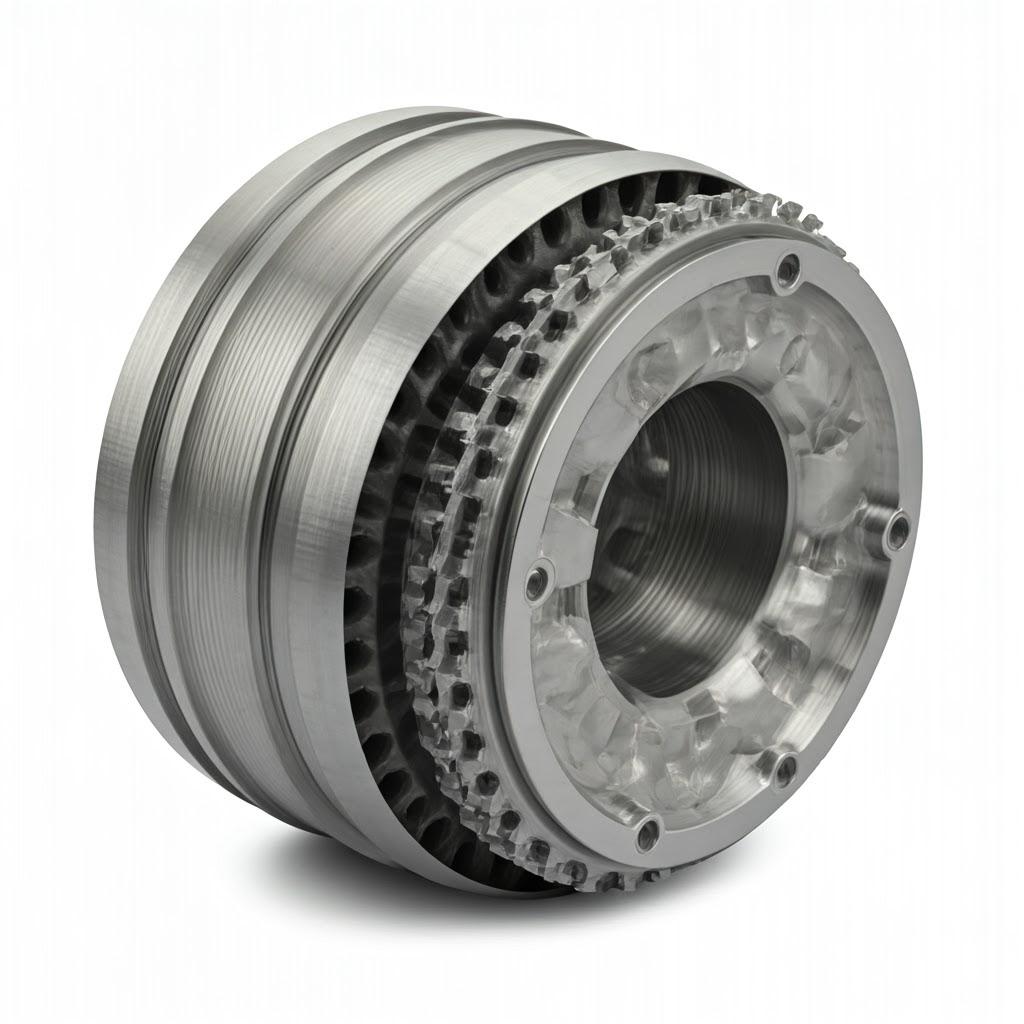
Za hranice stavby: Základní kroky následného zpracování pro funkční chladicí pláště pro elektromobily
Cesta kovové 3D tištěné součásti nekončí, když se tiskárna zastaví. Aby chladicí plášť elektromotoru přešel od surového vytištěného dílu k funkční a spolehlivé součásti připravené k integraci do vozidla, musí projít řadou zásadních kroků následného zpracování. Tyto kroky nejsou volitelným doplňkem; jsou nedílnou součástí dosažení požadovaných mechanických vlastností, rozměrové přesnosti, povrchových vlastností a celkové kvality, kterou požaduje automobilový průmysl. Pochopení tohoto pracovního postupu je zásadní pro inženýry, kteří navrhují díly, a pro nákupní týmy, které vybírají dodavatele AM, protože integrované možnosti následného zpracování významně ovlivňují dobu realizace, náklady a kvalitu finálního dílu.
Společný pracovní postup následného zpracování pro chladicí pláště AM:
- Odprašování / čištění:
- Účel: Odstranění veškerého zbytkového, neroztaveného kovového prášku zachyceného uvnitř součásti, zejména ze složitých vnitřních chladicích kanálků.
- Metody: Obvykle se používá ruční kartáčování, ofukování stlačeným vzduchem, tryskání kuličkami nebo specializované stanice pro manipulaci s práškem, někdy v kombinaci s vibracemi. U složitých vnitřních sítí může být nutné použít specializované proplachovací nebo průtokové systémy. Zde je rozhodující pečlivý návrh (DfAM) zahrnující přístupové otvory a zamezující zachycování prášku.
- Důležitost: Zachycený prášek může bránit průtoku chladicí kapaliny, později se může oddělit a způsobit kontaminaci systému, zvýšit hmotnost a narušit následné kroky, jako je tepelné zpracování nebo svařování. Důkladné čištění je nejdůležitější.
- Úleva od stresu:
- Účel: Rychlé cykly zahřívání a ochlazování, které jsou vlastní L-PBF a v menší míře SEBM, vytvářejí v tištěném dílu značné vnitřní pnutí. Odstraňování napětí je tepelné zpracování prováděné před vyjmutí dílu z konstrukční desky (nebo bezprostředně po něm), aby se snížilo toto vnitřní pnutí.
- Metoda: Zahřátí celé konstrukční desky s přiloženými díly v peci s inertní atmosférou na určitou teplotu (nižší než teplota stárnutí nebo rozpuštění), její udržování a následné pomalé ochlazování. Teploty a časy jsou specifické pro daný materiál (např. ~300-350 °C pro AlSi10Mg).
- Důležitost: Snižuje riziko deformace nebo prasklin při řezání dílu z konstrukční desky a při následném obrábění nebo tepelných cyklech v provozu.
- Vyjmutí dílu ze stavební desky:
- Účel: K oddělení vytištěného chladicího pláště od kovové stavební desky, na kterou byly během tisku nataveny.
- Metody: Obvykle se provádí pomocí elektroerozivního obrábění (EDM) nebo pásové pily. Drátové elektroerozivní obrábění obecně poskytuje čistší řez s menším mechanickým namáháním, ale je pomalejší.
- Důležitost: Je třeba postupovat opatrně, aby nedošlo k poškození dílu.
- Odstranění podpůrné konstrukce:
- Účel: Odstranění obětovaných podpůrných konstrukcí vytvořených během tisku pro ukotvení převisů a složitých prvků.
- Metody: Může zahrnovat ruční lámání a broušení (u přístupných podpěr), obrábění na CNC nebo elektroerozivní obrábění. Odstranění podpěr z vnitřních kanálů je obzvláště náročné a zdůrazňuje význam DfAM pro minimalizaci vnitřních podpěr nebo jejich konstrukci pro odstranění (např. pomocí chemického leptání pro některé materiály/typy podpěr, i když méně časté pro Al/Cu).
- Důležitost: Podpěry jsou nefunkční a zvyšují hmotnost. Jejich odstranění může zanechat stopy po svědcích nebo mírně drsnější povrchy (“jizvy”), které mohou vyžadovat další úpravu v závislosti na místě. Neúplné odstranění je nepřípustné.
- Tepelné zpracování (rozpouštění, stárnutí, žíhání):
- Účel: Dosažení požadovaných konečných mechanických vlastností (pevnost, tvrdost, tažnost) a zajištění mikrostrukturní stability. Většina AM kovů vyžaduje pro optimalizaci vlastností tepelné zpracování, protože mikrostruktura v podobě, v jaké je vyrobena, je často nerovnovážná a anizotropní.
- AlSi10Mg: Obvykle prochází popouštěním T6 (tepelné zpracování roztokem a následné umělé stárnutí), které výrazně zvyšuje pevnost a tvrdost.
- CuCrZr: Vyžaduje ošetření roztokem a následné stárnutí, aby se dosáhlo srážecího vytvrzení, což zvyšuje pevnost při zachování dobré vodivosti.
- Metoda: Řízené cykly zahřívání a ochlazování v kalibrovaných pecích, často ve vakuu nebo inertní atmosféře, aby se zabránilo oxidaci. Specifické teplotní profily a doby trvání jsou kritické a závisí na slitině.
- Důležitost: Nezbytné pro splnění požadavků na mechanické vlastnosti specifikovaných v návrhu. Mírně ovlivňuje konečné rozměry, proto se často provádí před konečným obráběním.
- Účel: Dosažení požadovaných konečných mechanických vlastností (pevnost, tvrdost, tažnost) a zajištění mikrostrukturní stability. Většina AM kovů vyžaduje pro optimalizaci vlastností tepelné zpracování, protože mikrostruktura v podobě, v jaké je vyrobena, je často nerovnovážná a anizotropní.
- CNC obrábění:
- Účel: Dosažení úzkých tolerancí, specifických povrchových úprav a přesných geometrických prvků na kritických rozhraních, kterých nelze dosáhnout přímo procesem AM.
- Společné prostory: Těsnicí plochy (drážky pro O-kroužky, ploché plochy těsnění), montážní otvory, rozhraní konektorů, všechny plochy vyžadující vysokou kolmost, rovinnost nebo rovnoběžnost.
- Metoda: Použití standardních CNC frézek, soustruhů nebo brusek. Vyžaduje pečlivou konstrukci upínacího přípravku, aby složitý AM díl bezpečně držel bez deformace. Vyžaduje krok DfAM spočívající v přidání obráběcího materiálu.
- Důležitost: Zaručuje správnou montáž, neporušenost těsnění a propojení se spárovanými součástmi v sestavě motoru.
- Povrchová úprava:
- Účel: Pro zlepšení hladkosti povrchu (snížení Ra), zlepšení vzhledu nebo přípravu povrchů pro lakování.
- Metody (podle potřeby):
- Vnější povrchy: Tryskání kuličkami (pro rovnoměrný matný povrch), bubnové/vibrační dokončování (pro celkové vyhlazení/odstraňování otřepů), ruční nebo robotické leštění (pro specifické hladké plochy).
- Interní kanály: Obrábění abrazivním tokem (AFM), chemické leštění/leštění (v závislosti na materiálu) nebo případně ponechání v původním stavu, pokud analýza CFD ukáže, že drsnost je přijatelná nebo prospěšná.
- Důležitost: Má zásadní význam pro utěsnění povrchů, může zlepšit dynamiku tekutin v kanálech a ovlivňuje estetický vzhled.
- Čištění a kontrola:
- Účel: Závěrečné čištění za účelem odstranění veškerých obráběcích kapalin, nečistot nebo kontaminantů. Komplexní kontrola pro ověření shody se všemi specifikacemi.
- Metody: Čištění vodou nebo rozpouštědlem, čištění ultrazvukem. Kontrola zahrnuje:
- Rozměry: Souřadnicový měřicí stroj (CMM), 3D skenování.
- Integrita: Zkouška těsnosti (tlakový rozklad nebo ponorná zkouška) je nezbytné pro chladicí plášť, aby se zajistilo, že nedojde k úniku chladicí kapaliny v důsledku pórovitosti nebo prasklin. Nedestruktivní testování (NDT), jako je rentgenové nebo CT skenování, může být použito k odhalení vnitřních vad nebo ověření odstranění prášku ve vysoce kritických aplikacích.
- Materiál: Zkoušky tvrdosti, případně mikrostrukturní analýza na svědeckých kuponech.
- Vizuální: Důkladná vizuální kontrola povrchových vad.
- Důležitost: Finální kontrola kvality zajišťuje, že díl je vhodný pro daný účel a splňuje všechny požadavky výkresu před odesláním k zákazníkovi nebo na montážní linku.
Význam integrovaných služeb:
Správa tohoto vícestupňového řetězce následného zpracování může být složitá. Spolupráce s poskytovatelem AM služeb, jako je Met3dp, který tyto procesy nabízí nebo řídí v integrovaném pracovním postupu, přináší týmům zadavatelů a inženýrů několik výhod:
- Zjednodušená logistika: Jediné kontaktní místo snižuje složitost.
- Řízení procesu: Zajišťuje konzistenci a kontrolu kvality ve všech fázích.
- Optimalizovaný pracovní postup: Zkracuje celkovou dobu dodání v porovnání s přepravou dílů mezi více specializovanými dodavateli.
- Odpovědnost: Jasná odpovědnost za kvalitu finálního dílu.
Souhrnná tabulka následného zpracování:
Krok | Účel | Běžné metody | Klíčové úvahy |
---|---|---|---|
Odprašování | Odstraňte zbytky prášku | Kartáčování, tryskání vzduchem, tryskání, proplachování | Vnitřní kanály, lapače prášku, úplnost |
Úleva od stresu | Snížení vnitřního napětí před odstraněním dílu | Tepelné zpracování v peci (na stavební desce) | Zabraňuje deformaci/praskání, cyklus specifický pro materiál |
Odstranění části | Oddělení dílu od stavební desky | Drátové elektroerozivní obrábění, pásová pila | Zamezení poškození dílů, kvalita řezu |
Odstranění podpory | Odstranění obětních podpěr | Ruční lámání, obrábění, broušení, elektroerozivní obrábění | Přístupnost (vnitřní), povrchové značky, úplnost |
Tepelné zpracování | Dosažení konečných mechanických vlastností (pevnost, tvrdost) | Pecní cykly (rozpouštění, stárnutí), vakuum/nergetický plyn | Specifický materiál (T6 pro Al, stárnutí pro CuCrZr), ovlivňuje rozměry |
CNC obrábění | Dosahování těsných tolerancí & jemná povrchová úprava kritických prvků | Frézování, soustružení, broušení | Obráběcí materiál (DfAM), konstrukce upínacích přípravků, tolerance |
Povrchová úprava | Zlepšení Ra, estetiky, příprava na lakování | Tryskání, leštění, AFM (interní), omílání | Těsnicí plochy, vnitřní kanály, specifické potřeby |
Čištění & amp; Inspekce | Konečná čistota, ověření shody se specifikacemi | Metody čištění, Souřadnicový měřicí stroj, 3D skenování, Zkouška těsnosti, NDT, Vizuální zkouška | ZKOUŠKA ÚNIKŮ JE KRITICKÁ, rozměrové kontroly |
Export do archů
Pro výrobu vysoce kvalitních a funkčních chladicích plášťů elektromotorů pomocí technologie AM je rozhodující úspěšně projít labyrintem následného zpracování. Vyžaduje to pečlivé plánování ve fázi návrhu a úzkou spolupráci se zkušeným výrobním partnerem, který rozumí složitostem každého kroku.
Zvládání výzev: Běžná úskalí při 3D tisku chladicích plášťů a strategie pro jejich zmírnění
Přestože aditivní výroba kovů nabízí významné výhody pro výrobu složitých součástí, jako jsou chladicí pláště elektromotorů, není tato technologie bez problémů. Pochopení potenciálních úskalí a způsobů, jak je zkušení výrobci zmírňují, je pro inženýry navrhující tyto díly a pro manažery nákupu, kteří vybírají spolehlivé dodavatele, zásadní. Aktivní řešení těchto problémů zajistí vyšší kvalitu, lepší konzistenci a snížení rizika při zavádění AM pro kritické aplikace v automobilovém průmyslu.
Společné výzvy & Strategie zmírnění:
- Zbytkové napětí, deformace a zkreslení:
- Výzva: Rychlé, lokalizované zahřívání a ochlazování, které je vlastní procesům tavení po vrstvách (zejména L-PBF), vytváří značné tepelné gradienty, které vedou k vnitřním pnutím. Tato napětí mohou způsobit deformaci dílů během sestavování, deformaci po vyjmutí ze sestavovací desky nebo dokonce prasknutí. Zvláště náchylné jsou velké ploché profily nebo asymetrické konstrukce.
- Strategie zmírnění dopadů:
- Optimalizovaná orientace sestavení: Orientace dílu tak, aby se minimalizovaly velké rovné plochy rovnoběžné s konstrukční deskou a snížil se tepelný gradient napříč vrstvami.
- Tepelná technika: Použití optimalizovaných strategií skenování (např. ostrovní skenování, šachovnicové vzory) pro rovnoměrnější rozložení tepla a snížení lokálních špiček napětí.
- Vhodné podpůrné struktury: Dobře navržené podpěry bezpečně ukotví díl k sestavovací desce a odolávají deformačním silám během sestavování.
- Výběr procesu: Díky vysokoteplotnímu prostředí pro stavbu má SEBM v porovnání s L-PBF obecně nižší zbytkové napětí, což je potenciálně výhodné pro velké nebo složité díly náchylné k deformaci.
- Tepelné ošetření proti stresu: Provedení cyklu na uvolnění stresu před vyjmutí dílu z konstrukční desky má zásadní význam pro uvolnění vnitřních pnutí.
- Simulace: Použití softwaru pro simulaci konstrukce k předvídání akumulace napětí a deformace, což umožňuje úpravy konstrukce nebo optimalizované podpůrné strategie před tiskem.
- DfAM: Navrhování dílů s vlastnostmi, které ze své podstaty snižují koncentraci napětí (např. vyhýbání se ostrým vnitřním rohům, používání koutových profilů).
- Pórovitost:
- Výzva: V tištěném materiálu mohou vznikat malé dutiny nebo póry v důsledku neúplného spojení mezi vrstvami, zachycení plynu z prášku nebo atmosféry nebo defektů typu keyholing (prohlubně po páře) způsobených nadměrným příkonem energie. Pórovitost může zhoršovat mechanické vlastnosti (zejména únavovou životnost) a, což je pro chladicí plášť kritické, vytvářet potenciální netěsnosti.
- Strategie zmírnění dopadů:
- Vysoce kvalitní prášek: Zásadní je použití prášku s vysokou sféricitou, dobrou tekutostí, nízkou vnitřní pórovitostí plynů a kontrolovanou distribucí velikosti částic. Met3dp’ používá technologie GA a PREP zaměřené na tyto vlastnosti.
- Optimalizované parametry procesu: Pečlivé vyladění výkonu laseru/paprsku, rychlosti skenování, tloušťky vrstvy, vzdálenosti mezi šrafami a průtoku plynu (v L-PBF) pro konkrétní materiál, aby se zajistilo úplné roztavení a tavení bez přehřátí. Klíčový je rozsáhlý vývoj parametrů.
- Kontrola inertní atmosféry: Udržování atmosféry vysoce čistého inertního plynu (argonu nebo dusíku pro L-PBF, vakua pro SEBM), aby se minimalizovala oxidace a zachycování plynů během tavení.
- Kontrola kvality (NDT): Zavedení nedestruktivních metod zkoušení, jako je rentgenová radiografie nebo počítačová tomografie (CT), pro zjištění vnitřní pórovitosti, zejména v kritických oblastech nebo jako součást kvalifikace procesu. Měření hustoty (např. Archimédova metoda) může poskytnout celkový údaj o pórovitosti.
- Testování těsnosti: Povinná tlaková zkouška každého chladicího pláště, která potvrdí jeho celistvost a nepřítomnost průchodnosti.
- Obtíže při odstraňování podpory (zejména interní):
- Výzva: Podpěry jsou sice nezbytné, ale jejich čisté odstranění bez poškození dílu může být obtížné, časově náročné a nákladné. Podpěry uvnitř složitých vnitřních chladicích kanálů jsou obzvláště náročné, protože přístup k nim je omezený. Neúplné odstranění může bránit průtoku nebo se později oddělit.
- Strategie zmírnění dopadů:
- DfAM Focus: Základní strategií je navrhnout konstrukci s minimálním použitím podpěr, zejména uvnitř (samonosné úhelníky, optimalizované tvary kanálů).
- Přístupný design podpory: Konstrukce vnějších podpěr pro snadný přístup s nástroji pro demontáž a s prvky pro vylomení.
- Volba procesu: Při SEBM se často používají nosiče na bázi prášku, které se obecně snáze odstraňují tryskáním než plně roztavené nosiče běžné u L-PBF.
- Specializované techniky odstraňování: Využití metod, jako je abrazivní průtokové obrábění (AFM) nebo chemické leptání (pokud to kompatibilita materiálu umožňuje) pro zbytky vnitřních podpěr kanálů nebo vyhlazení povrchu.
- Kontrola: Použití boroskopu nebo CT k ověření úplné podpory a odstranění prášku z vnitřních chodeb.
- Odstraňování prášku & Křížová kontaminace:
- Výzva: Zajištění odstranění veškerého netaveného prášku z vnitřních kanálků může být obtížné. Pokud výrobce zpracovává více typů materiálů, je navíc velmi důležité zabránit křížové kontaminaci mezi prášky (např. smíchání ocelového prášku s hliníkovým), protože i stopové množství může drasticky ovlivnit vlastnosti materiálu.
- Strategie zmírnění dopadů:
- DfAM pro odstraňování prášku: Navrhování kanálů s odpovídajícím průměrem, hladkými ohyby a přístupovými otvory.
- Přísné čisticí protokoly: Provádění vícestupňového čištění (foukání, vibrace, proplachování) a ověřování čistoty.
- Vyhrazené vybavení: V ideálním případě používat speciální tiskárny, sestavovací moduly a zařízení pro manipulaci s práškem pro různé skupiny materiálů (např. reaktivní vs. nereaktivní, ocel vs. hliník vs. měď), aby se zabránilo křížové kontaminaci.
- Přísné postupy při manipulaci s práškem: Zavedení pečlivých postupů pro nakládání, vykládání, prosévání a skladování prášku. Důležitá je sledovatelnost šarží.
- Povrchová úprava & kontrola drsnosti:
- Výzva: Povrchová úprava dílů AM je ve srovnání s obráběním relativně hrubá. Zatímco u některých povrchů je to přijatelné, kritické oblasti, jako jsou těsnicí plochy, vyžadují zlepšení a drsnost vnitřních kanálů může nepředvídatelným způsobem ovlivnit proudění a přenos tepla, pokud není zvládnuta.
- Strategie zmírnění dopadů:
- Optimalizace parametrů: Jemné doladění parametrů (např. obrysové skeny, menší výšky vrstev) může zlepšit povrchovou úpravu některých povrchů, často však za cenu prodloužení doby sestavení.
- Orientace na stavbu: Optimální orientace kritických povrchů vzhledem ke směru sestavování (např. povrchy směřující vzhůru jsou často hladší).
- Následné zpracování: Použití vhodných technik povrchové úpravy (obrábění, leštění, AFM atd.) zaměřených na povrchy, u nichž je požadována hladkost.
- Analýza CFD: Použití CFD k pochopení vlivu očekávané drsnosti vnitřního kanálu na tlakovou ztrátu a přenos tepla, což umožňuje rozhodování o konstrukci nebo požadavcích na povrchovou úpravu.
- Dosažení integrity odolné proti úniku:
- Výzva: U chladicího pláště je nepropustnost neoddiskutovatelná. Pórovitost, mikrotrhliny (způsobené zbytkovým napětím) nebo vady na rozhraních mohou vést k úniku chladicí kapaliny.
- Strategie zmírnění dopadů:
- Robustní řízení procesů: K tomu přispívají všechny strategie zaměřené na snížení pórovitosti a zbytkového napětí.
- Pečlivé následné zpracování: Zajištění, aby při obrábění nebo odstraňování podpěr nedocházelo k defektům.
- 100% testování těsnosti: Zavedení povinných, přísných zkoušek těsnosti (např. zkouška tlakového rozkladu) u každého jednotlivého dílu podle definovaných automobilových norem. Jedná se o kritickou závěrečnou kontrolu kvality.
- Potenciální impregnace: V některých případech (i když méně žádoucích) lze mikroporéznost utěsnit pomocí specializovaných impregnačních pryskyřic, ale obvykle se jedná spíše o obnovovací opatření než o primární strategii.
Řešení výzev vyžaduje odbornost:
Překonání těchto potenciálních úskalí vyžaduje značné odborné znalosti v oblasti materiálových věd, fyziky procesů AM, DfAM a přísné kontroly kvality. Proto je výběr zkušeného výrobního partnera, jako je Met3dp, klíčový. Jejich hluboké znalosti vlastností prášku (z vlastní pokročilé výroby), možností tiskáren, optimalizace parametrů procesu a integrovaného následného zpracování, podpořené robustními systémy řízení kvality, poskytují jistotu, že tyto problémy budou aktivně zvládnuty, aby bylo možné dodat spolehlivé a vysoce výkonné chladicí pláště EV. Spolupráce s dodavateli již v rané fázi návrhu umožňuje inženýrům využít těchto odborných znalostí a zmírnit potenciální problémy ještě před jejich vznikem.
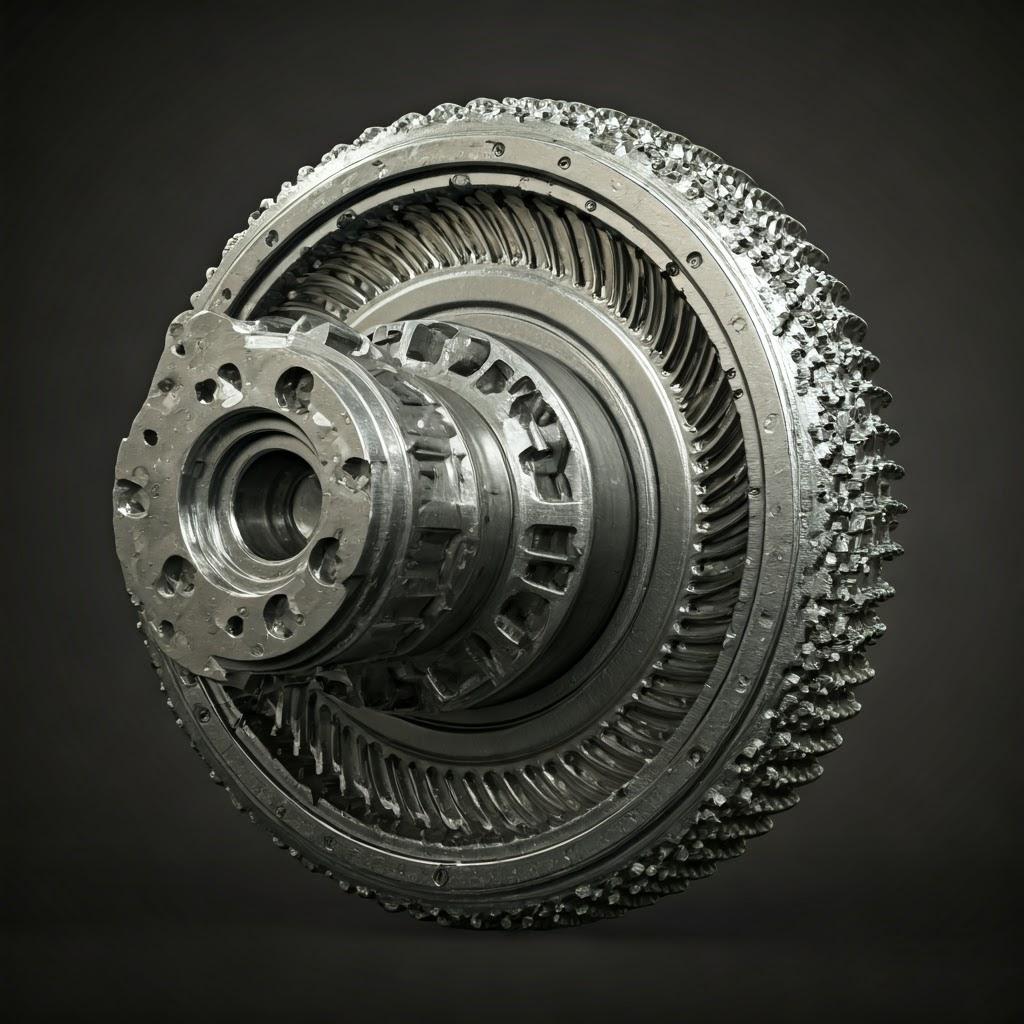
Výběr partnera: Výběr správného poskytovatele služeb 3D tisku kovů pro automobilové komponenty
Úspěch implementace aditivní výroby kovů pro kritické součásti, jako jsou chladicí pláště motorů elektromobilů, závisí nejen na robustním návrhu a výběru materiálu, ale především na schopnostech a spolehlivosti vybraného výrobního partnera. Výběr správného poskytovatele AM služeb je strategickým rozhodnutím pro inženýrské týmy a manažery nákupu, které ovlivňuje kvalitu, náklady, dobu realizace a celkový úspěch projektu. Vzhledem k náročnosti automobilového průmyslu přesahují kritéria hodnocení pouhé tiskové schopnosti.
Klíčová kritéria pro hodnocení dodavatelů technologií AM pro automobilový průmysl:
- Systémy řízení kvality & Certifikace:
- Požadavek: Automobilový průmysl vyžaduje přísnou kontrolu kvality. Hledejte dodavatele s robustním systémem řízení kvality (QMS) certifikovaným podle normy ISO 9001 jako základ. Ačkoli certifikace IATF 16949 (globální norma pro automobilový průmysl) může být v současné době pro poskytovatele čistě AM služeb vzácná, prokázání povědomí o ní, souladu s jejími zásadami (např. řízení procesů, sledovatelnost, řízení rizik) a jasný plán, jak k ní dospět, je významnou výhodou.
- Proč je to důležité: Certifikace jsou důkazem závazku k dokumentovaným procesům, neustálému zlepšování, sledovatelnosti a konzistentní kvalitě, což je nezbytné pro spolehlivé dodávky automobilových součástek.
- Hodnocení: Vyžádejte si aktuální certifikace, zprávy o auditu (pokud je to možné), podrobnosti o jejich systému řízení jakosti, postupy sledovatelnosti (od šarže prášku po finální díl) a záznamy o kalibraci.
- Odborné znalosti materiálů & Kontrola kvality prášku:
- Požadavek: Zásadní je hluboká znalost zpracovávaných materiálů (např. AlSi10Mg, CuCrZr). To zahrnuje znalost jejich metalurgického chování během tisku a tepelného zpracování. Zásadní je, že dodavatel musí mít přísné kontroly kvality vstupního prášku a manipulačních postupů, aby se zabránilo kontaminaci a zajistila konzistence.
- Proč je to důležité: Vlastnosti materiálu přímo určují výkonnost dílu. Nekonzistentní kvalita prášku nebo špatné zacházení s ním vede k nepředvídatelným výsledkům tisku a možným poruchám součástek. Odbornost zajišťuje správné nastavení parametrů a tepelné zpracování.
- Hodnocení: Zajímejte se o jejich strategii získávání prášků (vlastní výroba jako Met3dp vs. externí dodavatelé), postupy testování prášků (PSD, morfologie, chemie, tekutost), sledování šarží, podmínky skladování a manipulační protokoly (zejména pro reaktivní kovy nebo prevenci křížové kontaminace). Prodiskutujte jejich zkušenosti s konkrétními požadovanými slitinami. Poskytovatel jako Met3dp, který vyrábí vlastní vysoce kvalitní prášky pomocí pokročilých metod, jako je PREP a plynová atomizace, nabízí výraznou výhodu v kontrole těchto kritických vstupů. Můžete se dozvědět více o nás a náš integrovaný přístup.
- Technologické schopnosti & amp; Kapacita:
- Požadavek: Dodavatel by měl disponovat nejmodernějším zařízením pro AM (L-PBF, SEBM nebo jiné zařízení vhodné pro danou aplikaci) vhodným pro vybrané materiály a požadovanou přesnost. Neméně důležité jsou komplexní vlastní nebo přísně řízené externí kapacity pro všechny nezbytné kroky následného zpracování (uvolnění napětí, tepelné zpracování, obrábění, dokončovací práce, kontrola). Klíčová je také dostatečná kapacita pro zvládnutí prototypových objemů a rozšíření na malosériovou až středněsériovou výrobu.
- Proč je to důležité: Technologie určuje schopnosti (přesnost, rychlost, kompatibilita materiálů). Integrované následné zpracování zefektivňuje pracovní postup, zkracuje dodací lhůty a zajišťuje odpovědnost. Dostatečná kapacita zabraňuje vzniku úzkých míst a zajišťuje včasné dodání, což je pro časový harmonogram automobilového průmyslu zásadní.
- Hodnocení: Zhodnoťte jejich strojový park (typ, stáří, počet strojů, objem výroby), dostupné postprocesní vybavení, metrologické možnosti (CMM, skenery), softwarové nástroje (příprava výroby, simulace) a uvedenou kapacitu. Zajímejte se o jejich schopnost v případě potřeby rozšířit výrobu. Zaměření společnosti Met3dp’na špičkový objem tisku, přesnost a spolehlivost přímo odpovídá těmto potřebám.
- Technické znalosti a technická podpora:
- Požadavek: Ideální partner funguje více než jen jako tisková kancelář; měl by nabízet poradenství v oblasti DfAM, posouzení proveditelnosti, poznatky o simulaci výstavby a společné řešení problémů. Jeho tým by měl zahrnovat zkušené inženýry a metalurgy, kteří rozumí jak AM, tak požadavkům cílové aplikace.
- Proč je to důležité: Spolupráce zajišťuje optimalizaci návrhů z hlediska vyrobitelnosti, výkonu a nákladové efektivity. Odborná podpora může pomoci překonat konstrukční problémy a urychlit vývoj.
- Hodnocení: Projděte si případové studie nebo příklady podobných projektů. Během úvodních diskusí zhodnoťte technickou úroveň jejich týmu. Ptejte se na jejich proces podpory DfAM a možnosti simulace. Hledejte partnery, kteří jsou ochotni investovat čas do pochopení vašich konkrétních požadavků.
- Záznamy & Zkušenosti v oboru:
- Požadavek: Velmi cenné jsou prokazatelné zkušenosti s výrobou dílů pro náročná průmyslová odvětví, nejlépe automobilový nebo letecký průmysl. Reference nebo případové studie prokazující úspěšné provedení projektu, zejména s podobnými materiály nebo typy součástí, zvyšují důvěru.
- Proč je to důležité: Zkušenosti znamenají znalost očekávání v oboru, běžných problémů a požadavků na kvalitu. Osvědčené zkušenosti snižují riziko spojené s přijetím relativně nové výrobní technologie.
- Hodnocení: Požádejte o relevantní případové studie, reference zákazníků nebo reference (při zachování důvěrnosti). Zajímejte se o jejich zkušenosti s díly vyžadujícími zkoušky těsnosti, přísné tolerance nebo certifikace specifických materiálů.
- Řízení projektů & Komunikace:
- Požadavek: Jasné komunikační kanály, definované časové plány projektu, pravidelné aktualizace a pohotový zákaznický servis jsou zásadní, zejména v průběhu tvorby prototypů a náběhu výroby. Profesionální řízení projektu zajišťuje jeho hladkou realizaci.
- Proč je to důležité: Udržuje projekty na správné cestě, usnadňuje rychlé řešení problémů a buduje pevné pracovní vztahy. Rozhodující pro dodržování napjatých harmonogramů vývoje automobilů.
- Hodnocení: Zhodnoťte vstřícnost ve fázi nabídky a úvodní diskuse. Ptejte se na proces řízení projektu a na určené kontaktní osoby.
- Konkurenceschopnost v oblasti nákladů a doby realizace:
- Požadavek: Zatímco náklady by neměly být pouze musí být cenová struktura dodavatele transparentní a konkurenceschopná vzhledem k nabízené hodnotě a kvalitě. Dodací lhůty musí být v souladu s termíny projektů.
- Proč je to důležité: Dodržování rozpočtu a včasné dodávky jsou základními obchodními požadavky.
- Hodnocení: Získejte podrobné nabídky s rozpisem nákladů (materiál, strojní čas, následné zpracování, NRE). Porovnejte nabídky od více kvalifikovaných dodavatelů. Projednejte realistické odhady doby realizace s ohledem na složitost a potřeby následného zpracování.
Shrnutí kontrolního seznamu hodnocení dodavatele:
Kritéria | Klíčové otázky, které je třeba položit | Proč je to pro automobilový průmysl AM klíčové? |
---|---|---|
Systém kvality/certifikáty | ISO 9001? Povědomí/plány IATF? Proces sledovatelnosti? Výsledky auditů? | Zajišťuje konzistentní kvalitu, spolehlivost a řízení procesů |
Materiálová odbornost | Zkušenosti s požadovanými slitinami? Získávání prášků / kontrola kvality? Manipulační protokoly? | Zaručuje správné vlastnosti materiálu, zabraňuje vadám a kontaminaci |
Technologie & Kapacita | Strojový park (typ/počet/objem)? Možnosti následného zpracování (ve firmě)? Metrologie? Škálovatelnost? | Určuje technickou proveditelnost, efektivitu pracovních postupů, včasnost dodávek |
Technická podpora | Nabízené pokyny DfAM? Možnosti simulace? Odbornost inženýrského týmu? Přístup založený na spolupráci? | Optimalizuje design pro AM, urychluje vývoj, řeší problémy |
Záznamy o činnosti | Zkušenosti v automobilovém průmyslu/odpovídajícím oboru? Případové studie/reference? Podobné vyráběné díly? | Snižuje riziko, prokazuje porozumění požadavkům odvětví |
Řízení projektů | Komunikační proces? Aktualizace projektu? Reakce? Specializované kontakty? | Zajišťuje hladký průběh, dodržuje termíny a buduje důvěru |
Náklady a dodací lhůta | Transparentní ceny? Konkurenční nabídka? Reálné dodací lhůty? Soulad s potřebami projektu? | Splnění rozpočtových a časových omezení |
Export do archů
Výběr správného partnera pro technologii AM na bázi kovů je zásadním krokem pro každou společnost, která chce tuto technologii využít pro náročné aplikace, jako jsou chladicí pláště elektromotorů. Důkladné hodnocení založené na těchto kritériích pomůže identifikovat dodavatele, jako je Met3dp, kteří disponují potřebnou kombinací systémů kvality, kontroly materiálu, technologické zdatnosti, odborných znalostí a zaměření na zákazníka, jež jsou nezbytné pro dodávku spolehlivých a vysoce výkonných komponent pro budoucnost elektromobility.
Pochopení investice: Chladicí pláště vytištěné na 3D tiskárně: nákladové faktory a typické doby realizace
Technické výhody 3D tisku kovů pro chladicí pláště elektromobilů jsou přesvědčivé, ale pochopení souvisejících nákladů a dodacích lhůt je nezbytné pro plánování projektů, sestavování rozpočtů a přijímání informovaných rozhodnutí, zejména pro oddělení veřejných zakázek, která porovnávají AM s tradičními výrobními postupy. Struktura nákladů na AM se výrazně liší od odlévání nebo obrábění, zejména pokud jde o závislost na objemu a nástrojích.
Klíčové faktory ovlivňující náklady na aditivní výrobu kovů:
- Materiálové náklady & amp; Spotřeba:
- Cena prášku: Základní náklady na kilogram kovového prášku jsou hlavním faktorem. Pokročilé slitiny jako CuCrZr jsou výrazně dražší než běžné AlSi10Mg. Vysoce kvalitní prášek se specifickými vlastnostmi (sféricita, PSD) si rovněž žádá příplatek.
- Část Objem & Hustota: Skutečný objem konečného dílu určuje množství taveného prášku. Techniky DfAM, jako je optimalizace topologie a mřížkové struktury, přímo snižují spotřebu materiálu a náklady.
- Podpůrné struktury: K celkové spotřebě přispívá i materiál použitý na nosné konstrukce, i když tento prášek je často recyklovatelný (při pečlivé kontrole kvality). Minimalizace podpěr prostřednictvím DfAM tyto náklady snižuje.
- Odpady/recyklace: Část prášku se při manipulaci a tisku nevyhnutelně ztratí nebo znehodnotí. Účinné procesy recyklace prášku používané dodavatelem mohou pomoci tyto náklady zmírnit, ale vyžadují přísné testování, aby byla zajištěna kvalita recyklovaného prášku.
- Čas stroje (čas sestavení):
- Primární řidič: To je často největší nákladová složka, která představuje dobu, po kterou drahý stroj AM tiskne díl.
- Ovlivňující faktory:
- Výška dílu (osa Z): Doba sestavení je přímo úměrná počtu vrstev, proto je rozhodující výška dílu v orientaci sestavení.
- Objem dílu/plocha na vrstvu: Množství materiálu, který se má v každé vrstvě natavit, ovlivňuje dobu potřebnou pro skenování.
- Složitost: Velmi složité geometrie mohou vyžadovat nižší rychlost skenování nebo složitější strategie skenování.
- Tloušťka vrstvy: Tenčí vrstvy zlepšují rozlišení a kvalitu povrchu, ale výrazně zvyšují počet vrstev, a tím i dobu sestavování.
- Typ stroje & Výkon: Rychlejší stroje s výkonnějšími lasery/paprsky nebo s více paprsky mohou zkrátit dobu sestavení, ale mají vyšší hodinovou provozní sazbu.
- Hustota hnízdění/balení: Tisk více dílů současně v jednom sestavení výrazně zlepšuje využití stroje a snižuje náklady na jeden díl. Zkušení dodavatelé optimalizují rozložení sestav.
- Náklady na pracovní sílu:
- Předběžné zpracování: Příprava sestavy (zpracování souborů CAD, orientace, generování podpory, krájení) vyžaduje kvalifikované techniky/inženýry.
- Obsluha stroje: Sledování procesu sestavování.
- Následné zpracování: To může být velmi pracné a zahrnuje odprášení, odstranění dílu, odstranění podpěry, nastavení tepelného zpracování, nastavení/operaci obrábění, dokončovací práce, čištění a kontrolu. Složitost dílu a požadovaná úroveň dokončovacích prací silně ovlivňují pracnost následného zpracování.
- Náklady na následné zpracování:
- Spotřební materiál & Energie: Tepelné zpracování (čas v peci, inertní plyn/vakuum), obrábění (opotřebení nástroje, chladicí kapalina), dokončovací média (tryskání, leštění).
- Specializované procesy: Náklady spojené se specifickými kroky, jako je elektroerozivní obrábění drátem, AFM, CT skenování nebo specializované aplikace povlakování.
- Kontrola kvality & Inspekce:
- Práce & Vybavení: Čas strávený rozměrovou kontrolou (CMM, skenování), zkouškami těsnosti, NDT, zkouškami materiálu (pokud jsou vyžadovány) a dokumentací. Úroveň požadované kontroly kvality ovlivňuje náklady.
- Non-Recurring Engineering (NRE):
- Počáteční nastavení: Náklady spojené s počáteční konzultací návrhu, optimalizací DfAM, návrhem specifických přípravků (pro obrábění/kontrolu) nebo vývojem procesních parametrů pro jedinečné aplikace. Obvykle se amortizují v průběhu první dávky dílů.
- Množství (velikost dávky):
- Amortizace: Náklady NRE a práce při seřizování se rozloží na počet vyrobených dílů.
- Využití stroje: Větší dávky umožňují lepší vnoření stavebních desek, což výrazně zlepšuje efektivitu strojního času a snižuje náklady na jeden díl.
- Křivka učení: Efektivity při následném zpracování lze často dosáhnout s většími dávkami.
- Přerušení objemu: Dodavatelé často nabízejí odstupňované ceny podle množství.
Upozornění ke srovnání nákladů:
Přímé porovnání nákladů na AM s tradičními metodami vyžaduje pečlivé zvážení objemu.
- Prototypování &; Nízký objem (<100s): AM je často vysoce nákladově konkurenceschopná nebo dokonce levnější díky absenci nákladů na nástroje (formy/lisy pro odlévání).
- Střední objem (100s – nízké 1000s): Srovnání se stává složitým. Optimalizované díly AM (odlehčené, konsolidované) mohou nabízet funkční výhody, které ospravedlňují potenciální zvýšení nákladů, nebo mohou být náklady srovnatelné v závislosti na složitosti a následném zpracování.
- Velký objem (více než 10 000): Tradiční metody, jako je tlakové lití, obvykle nabízejí nižší náklady na díl díky úsporám z rozsahu za předpokladu, že je konstrukce vhodná pro lití. Je však třeba posoudit celkové náklady na vlastnictví (s ohledem na zvýšení výkonu, úsporu hmotnosti, zjednodušení montáže z AM).
Typické dodací lhůty:
Dodací lhůta je doba od zadání objednávky (a potvrzení konečného návrhu) do dodání dílu. Je velmi variabilní, ale má obecný průběh:
- Výroba prototypů (1-10 kusů):
- Typický rozsah: 1 až 4 týdny.
- Ovlivňující faktory: Aktuální dostupnost stroje, doba výroby (často 1-3 dny pro chladicí plášť v závislosti na velikosti/komplexnosti), požadovaná složitost následného zpracování (základní uvolnění napětí a odstranění podpory vs. úplné tepelné zpracování, rozsáhlé obrábění a dokončovací práce). Zrychlené možnosti jsou často k dispozici za příplatek.
- Malosériová výroba (10s – low 100s):
- Typický rozsah: 4 až 8 týdnů.
- Ovlivňující faktory: Potřeba optimalizovaného uspořádání sestav, plánování strojního času pro více sestav, potenciální vývoj specifických přípravků pro obrábění nebo kontrolu, efektivní řízení toku v různých krocích následného zpracování. Roli může hrát i dostupnost materiálu pro větší množství.
- Střední objem výroby (vysoké počty kusů – 1000 kusů):
- Typický rozsah: 8 až 16+ týdnů (často s postupnými dodávkami).
- Ovlivňující faktory: Vyžaduje významné plánování kapacity strojů, případně vyhrazení strojního času, robustní dodavatelský řetězec prášku, případně rozšíření možností následného zpracování a rozsáhlé plánování kontroly kvality. Klíčová je optimalizace procesu a zavedení stabilního výrobního rytmu.
Faktory urychlující/zpomalující dobu dodání:
- Zrychlení: Jasné specifikace návrhu, díly optimalizované pro DfAM (méně podpěr, méně následného zpracování), snadno dostupný prášek, dobré vztahy s dodavatelem/komunikace, výběr dodavatele s integrovanými schopnostmi.
- Zpomalení: Změny návrhu v průběhu procesu, složité geometrie vyžadující rozsáhlé podpěry nebo složité následné zpracování, nestandardní požadavky na materiál, kapacitní omezení dodavatelů, zpoždění při přepravě/logistice.
Dodací lhůta & amp; Souhrnná tabulka nákladů:
Faktor | Dopad na náklady | Dopad na dobu realizace | Zmírnění / optimalizace |
---|---|---|---|
Složitost návrhu | Zvýšení (doba sestavení, podpory, post-proc.) | Zvýšení (Build, post-proc.) | DfAM pro zjednodušení tam, kde je to možné, optimalizuje podporu |
Velikost dílu/objem | Zvýšení (materiál, doba sestavení) | Zvýšení (doba sestavení) | DfAM pro odlehčení, vnoření dílů do sestavy |
Výběr materiálu | Významné (CuCrZr >> AlSi10Mg) | Menší (různé parametry), větší (pokud se zpožďuje dodávka zdrojů) | Výběr na základě skutečné potřeby, ujistěte se, že dodavatel má odborné znalosti o materiálu |
Množství | Snížení na díl (amortizace, efektivita) | Celkové zvýšení, snížení na díl potenciálně (efektivita) | Optimalizace velikosti dávek, plánování výrobního plánu |
Následné zpracování | Významný řidič (práce, čas strávený na zařízení) | Významný řidič | DfAM pro minimalizaci potřeby obrábění/dokončování, integrovaný dodavatel |
Požadavky na kvalitu | Zvýšení (doba kontroly, náklady na nedestruktivní kontrolu) | Zvýšení (doba kontroly) | Jasně definujte požadavky předem |
Export do archů
Pochopení vzájemného působení těchto faktorů umožňuje přesnější sestavení rozpočtu a plánování projektu při zvažování použití AM kovů pro chladicí pláště motorů elektromobilů. Otevřené diskuse s potenciálními dodavateli, jako je Met3dp, o konkrétních požadavcích na konstrukci a očekávaných objemech jsou zásadní pro získání realistických odhadů nákladů a odhadů doby realizace.
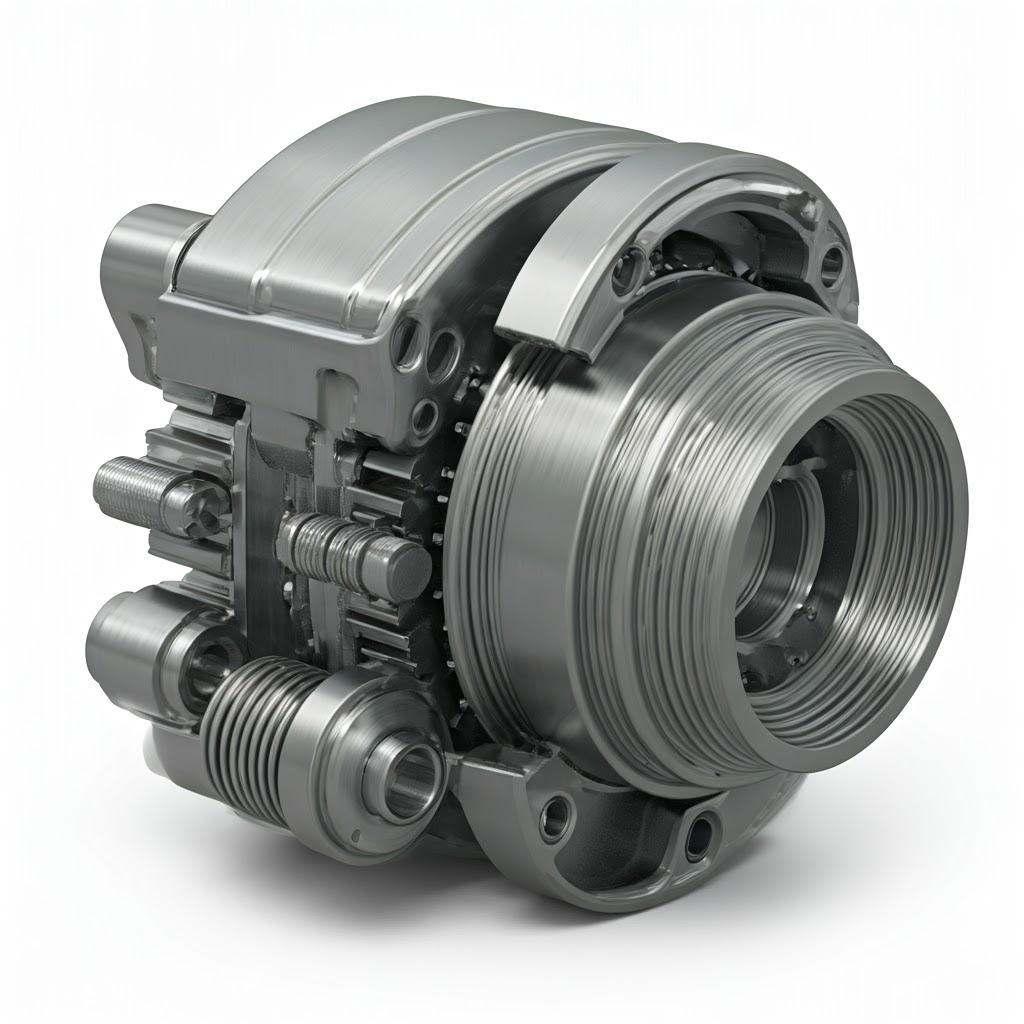
Často kladené otázky (FAQ) pro týmy zadavatelů a inženýrů
Zde jsou odpovědi na některé časté otázky, které mají inženýři a manažeři nákupu, když zvažují kovový 3D tisk pro chladicí pláště motorů elektromobilů:
1. Jaké jsou náklady na 3D tištěný chladicí plášť ve srovnání s tradičním odléváním, zejména s rostoucím objemem výroby?
- Odpověď: Srovnání nákladů do značné míry závisí na objemu a složitosti.
- Prototypy & Low Volume (< ~100 kusů): 3D tisk z kovu je často nákladově efektivnější než odlévání, protože se vyhýbá extrémně vysokým počátečním nákladům a dlouhým dodacím lhůtám spojeným s výrobou odlévacích forem nebo zápustek.
- Střední objem (~100 – 2 000 kusů): Jedná se o přechodovou zónu. Nákladová konkurenceschopnost AM závisí na faktorech, jako je složitost konstrukce (AM zvládá složitost lépe), potenciál pro konsolidaci dílů (snížení nákladů na montáž), výhody odlehčení (hodnota ušetřené hmotnosti) a konkrétní proces/materiál AM oproti metodě odlévání (např. pískové vs. tlakové lití). Optimalizované díly AM by mohly mít vyšší cenu odůvodněnou zvýšením výkonu.
- Velký objem (10 000 a více kusů): U relativně jednoduchých konstrukcí vyrobitelných tlakovým litím se tradičními metodami obvykle dosahuje nižší cena za kus díky zavedeným úsporám z rozsahu. Pokud však AM umožňuje výrazné zlepšení výkonu (lepší chlazení, vyšší účinnost motoru) nebo snížení hmotnosti (lepší dojezd vozidla), analýza celkových nákladů na vlastnictví může být pro určité aplikace stále výhodnější pro AM i při vyšších objemech. Zásadní je vyhodnotit nejen cenu kusu, ale i celkovou nabídku hodnoty.
2. Jaké jsou typické testovací a validační postupy potřebné pro kvalifikaci 3D tištěného kovového chladicího pláště pro použití v automobilovém průmyslu?
- Odpověď: Kvalifikace zahrnuje přísné testování nad rámec standardních rozměrových kontrol, které odráží požadavky na tradičně vyráběné díly, ale navíc se zaměřuje na specifické aspekty AM. Klíčové postupy zahrnují:
- Ověřování vlastností materiálu: Zkoušky v tahu, zkoušky tvrdosti a mikrostrukturní analýza (často s použitím svědeckých kupónů vytištěných vedle dílů), které potvrzují, že materiál po tisku a tepelném zpracování splňuje specifikace. Sleduje se konzistence napříč sestavami.
- Testování těsnosti: Povinná 100% zkouška rozpadu tlaku nebo zkouška těsnosti pomocí helia, která zajišťuje integritu ochranného obalu kapaliny při provozních tlacích. Kritéria přijatelnosti jsou obvykle přísná.
- Ověřování rozměrů: Kompletní kontrola rozvržení pomocí souřadnicového měřicího přístroje nebo 3D skenování pro ověření shody s výkresy, včetně kritických rozměrů rozhraní a výkresů GD&T.
- Nedestruktivní zkoušení (NDT): V závislosti na kritičnosti může být použito CT skenování nebo rentgenová kontrola (zejména během kvalifikace procesu) k odhalení vnitřních vad, jako je pórovitost nebo nedostatečné slícování. Na površích po obrábění lze použít penetrační zkoušku barvivem nebo magnetickými částicemi.
- Tlaková zkouška na roztržení: Zkoušení vzorků do selhání při hydrostatickém tlaku za účelem stanovení bezpečnostní rezervy nad maximálním provozním tlakem.
- Tepelné cyklování & amp; Vibrační testování: Simulace provozních podmínek pro posouzení životnosti a odolnosti proti únavě při kombinovaném tepelném a mechanickém zatížení.
- Testování kompatibility chladicí kapaliny: Zajištění dlouhodobé odolnosti proti korozi a degradaci při působení specifikovaných automobilových chladicích kapalin.
- Validace procesu (prvky PPAP): Sladění s prvky rámce PPAP (Production Part Approval Process), včetně procesních diagramů, FMEA (Failure Modes and Effects Analysis), kontrolních plánů a studií způsobilosti, prokazuje připravenost výroby na sériovou výrobu.
3. Mohou být složité vnitřní chladicí kanály navržené pomocí DfAM spolehlivě a konzistentně vyrobeny a jak se ověřuje jejich vnitřní kvalita?
- Odpověď: Ano, spolehlivá výroba složitých vnitřních kanálů je klíčovou silnou stránkou technologie AM, ale vyžaduje pečlivý návrh a přísnou kontrolu procesu.
- Spolehlivost & konzistence: Dosaženo prostřednictvím:
- DfAM: Navrhování kanálů se samonosnými tvary (např. slza, kosočtverec) a hladkými přechody pro minimalizaci potřeby vnitřních podpěr a usnadnění odstraňování prášku.
- Optimalizované parametry: Použití ověřených parametrů tisku specifických pro materiál a geometrii kanálu k zajištění úplného spojení a minimalizace defektů.
- Kvalita prášku: Použití vysoce kvalitního sypkého prášku.
- Robustní čištění: Zavedení důkladných a ověřených postupů pro odstraňování prachu.
- Ověření: Interní kvalita se ověřuje prostřednictvím:
- Vizuální kontrola (pokud je to možné): Pomocí boroskopů vizuálně zkontrolujte přístupné části kanálů, zda v nich nejsou překážky, zbytky podpěr nebo hrubé vady.
- Testování průtoku: Měření tlakových ztrát v kanálech při definovaných průtocích, aby se zajistilo, že jsou čisté a odpovídají předpovědím CFD. Zablokování nebo výrazné odchylky indikují problémy.
- CT vyšetření: Počítačová tomografie poskytuje podrobný 3D pohled na vnitřní strukturu, což umožňuje ověřit geometrii kanálku, detekovat vnitřní pórovitost nebo zbytky prášku a posoudit tloušťku stěny. Toho se často využívá při vývoji a kvalifikaci procesu a případně při odběru vzorků během výroby vysoce kritických dílů.
- Testování těsnosti: Slouží jako závěrečná kontrola funkčnosti, která potvrzuje celkovou celistvost stěn kanálu.
- Spolehlivost & konzistence: Dosaženo prostřednictvím:
Spolupráce se zkušeným poskytovatelem AM, jako je Met3dp, který má robustní procesy pro DfAM, optimalizaci parametrů, čištění a kontrolu (včetně případné NDT), je nezbytná pro dosažení spolehlivých a ověřitelných komplexních vnitřních geometrií. Prozkoumejte naši nabídku kovové prášky a roztoky vhodné pro tyto náročné aplikace.
Závěr: Budoucnost výkonu elektromobilů díky aditivně vyráběným chladicím plášťům
Přechod na elektrickou mobilitu vyžaduje neustálé inovace všech systémů vozidla a tepelné řízení je klíčovým faktorem pro výkon, dojezd a spolehlivost. Jak jsme již prozkoumali, chladicí pláště motorů elektromobilů představují prvotřídní příležitost, kde lze omezení tradiční výroby překonat transformačními schopnostmi aditivní výroby kovů.
Využitím 3D tisku z kovu získávají konstruktéři nebývalou svobodu při navrhování. Mohou vytvářet chladicí pláště se složitými, konformními vnitřními kanály optimalizovanými pomocí pokročilé simulace, které maximalizují přenos tepla přesně tam, kde je to potřeba. Optimalizace topologie a mřížkové struktury umožňují výrazné odlehčení, což přímo přispívá k účinnosti a dojezdu vozidla. Kromě toho schopnost konsolidovat více součástí do jediného tištěného dílu zjednodušuje montáž, snižuje počet potenciálních poruchových míst a zefektivňuje dodavatelský řetězec.
Tato cesta zahrnuje pečlivý výběr materiálu, volbu mezi vyváženým výkonem slitin, jako je AlSi10Mg, nebo vynikající tepelnou vodivostí CuCrZr, poháněných vysoce kvalitními prášky. Úspěch vyžaduje pečlivé dodržování zásad návrhu pro aditivní výrobu (DfAM), překonávání potenciálních problémů, jako je zbytkové napětí a pórovitost, prostřednictvím odborné kontroly procesu a provádění komplexních kroků po zpracování a validaci, včetně klíčových testů těsnosti.
Výběr správného výrobního partnera - partnera s prověřenými odbornými znalostmi, robustními systémy kvality, pokročilými technologickými schopnostmi a hlubokými znalostmi materiálů - má zásadní význam. Společnosti, jako je Met3dp, s vertikálně integrovanými schopnostmi od pokročilé výroby prášků až po přesný tisk a podporu vývoje aplikací, mají ideální pozici k tomu, aby pomohly výrobcům automobilů využít plný potenciál AM.
Kovový 3D tisk již není jen nástrojem pro tvorbu prototypů, ale životaschopným strategickým výrobním řešením, které nabízí hmatatelné výkonnostní výhody pro náročné komponenty pro elektromobily. S tím, jak se trh s elektromobily stále zrychluje, bude zavádění aditivně vyráběných chladicích plášťů motorů nepochybně hrát stále důležitější roli při posouvání hranic tepelné účinnosti, hustoty výkonu a celkového výkonu vozidel. Spoluprací s předními odborníky a přijetím této pokročilé technologie mohou výrobci OEM a dodavatelé přispět k rozvoji budoucnosti elektromobility.
Navštivte naše webové stránky a zjistěte, jak mohou špičkové systémy a prášky Met3dp’podpořit cíle vaší organizace v oblasti aditivní výroby: https://met3dp.com/.
Sdílet na
MET3DP Technology Co., LTD je předním poskytovatelem řešení aditivní výroby se sídlem v Qingdao v Číně. Naše společnost se specializuje na zařízení pro 3D tisk a vysoce výkonné kovové prášky pro průmyslové aplikace.
Dotaz k získání nejlepší ceny a přizpůsobeného řešení pro vaše podnikání!
Související články
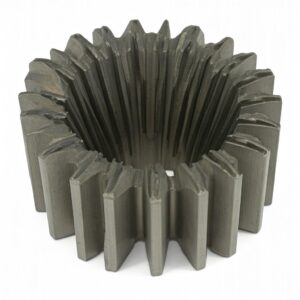
Vysoce výkonné segmenty lopatek trysek: Revoluce v účinnosti turbín díky 3D tisku z kovu
Přečtěte si více "O Met3DP
Nedávná aktualizace
Náš produkt
KONTAKTUJTE NÁS
Nějaké otázky? Pošlete nám zprávu hned teď! Po obdržení vaší zprávy obsloužíme vaši žádost s celým týmem.
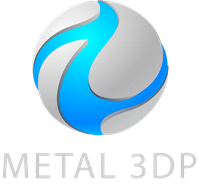
Kovové prášky pro 3D tisk a aditivní výrobu