Vlastní 3D tištěné výfukové štíty
Obsah
Úvod - Kritická role výfukových štítů automobilů a výhody 3D tisku z kovu
V náročném prostředí automobilového průmyslu hraje každá součástka klíčovou roli při zajišťování výkonu, bezpečnosti a životnosti vozidla. Mezi nimi je výfukový štít důležitým prvkem, který chrání okolní díly a cestující před extrémním teplem generovaným výfukovým systémem. Výfukové štíty, které se tradičně vyráběly pomocí procesů, jako je lisování a hluboké tažení, nyní využívají transformačních schopností kovu 3D tisk. Tato pokročilá výrobní technika nabízí bezkonkurenční volnost designu, efektivitu materiálu a potenciál pro zlepšení výkonnostních charakteristik. Vzhledem k tomu, že automobilový průmysl stále posouvá hranice inovací, stávají se zakázkové 3D tištěné výfukové štíty vynikající alternativou, která poskytuje řešení na míru pro stále složitější konstrukce vozidel a přísné požadavky na výkon. Společnosti jako např Metal3DP stojí v čele této revoluce a nabízí špičkové služby aditivní výroby kovů a vysoce výkonné kovové prášky, které splňují vyvíjející se potřeby automobilového průmyslu.
K čemu se v automobilovém průmyslu používají 3D tištěné výfukové štíty na zakázku?
3D tištěné výfukové štíty na zakázku plní v automobilových systémech několik důležitých funkcí. Jejich hlavním účelem je tepelná izolace, která zabraňuje tomu, aby vysoké teploty výfukového potrubí a dalších součástí výfuku poškodily okolní citlivé součásti, jako jsou kabelové svazky, plastové součásti, palivové potrubí, a dokonce i konstrukci karoserie vozidla. Tato ochrana je zásadní pro prevenci předčasného opotřebení, selhání součástí a možného ohrožení bezpečnosti. Kromě tepelného managementu mohou tyto štíty také přispívat ke snížení hluku tím, že tlumí vibrace a minimalizují přenos hluku výfukového systému do kabiny vozidla. V moderním designu vozidel, kde je optimalizace prostoru prvořadá, navíc 3D tisk umožňuje vytvářet výfukové štíty se složitou geometrií, které mohou těsně přiléhat k výfukovým součástem, čímž se maximalizuje ochrana bez zbytečného zvětšování objemu. Možnost přizpůsobení konstrukce také umožňuje integraci prvků, jako jsou kanály pro proudění vzduchu pro lepší odvod tepla nebo montážní body přizpůsobené specifické konstrukci podvozku. Automobiloví inženýři a manažeři nákupu si stále více uvědomují hodnotu těchto zakázkových řešení pro zvýšení spolehlivosti, bezpečnosti a celkového výkonu vozidla. Chcete-li prozkoumat všestrannost kovového 3D tisku v automobilových aplikacích, navštivte stránku Metal3DP’s kovové 3D tiskové služby stránky.
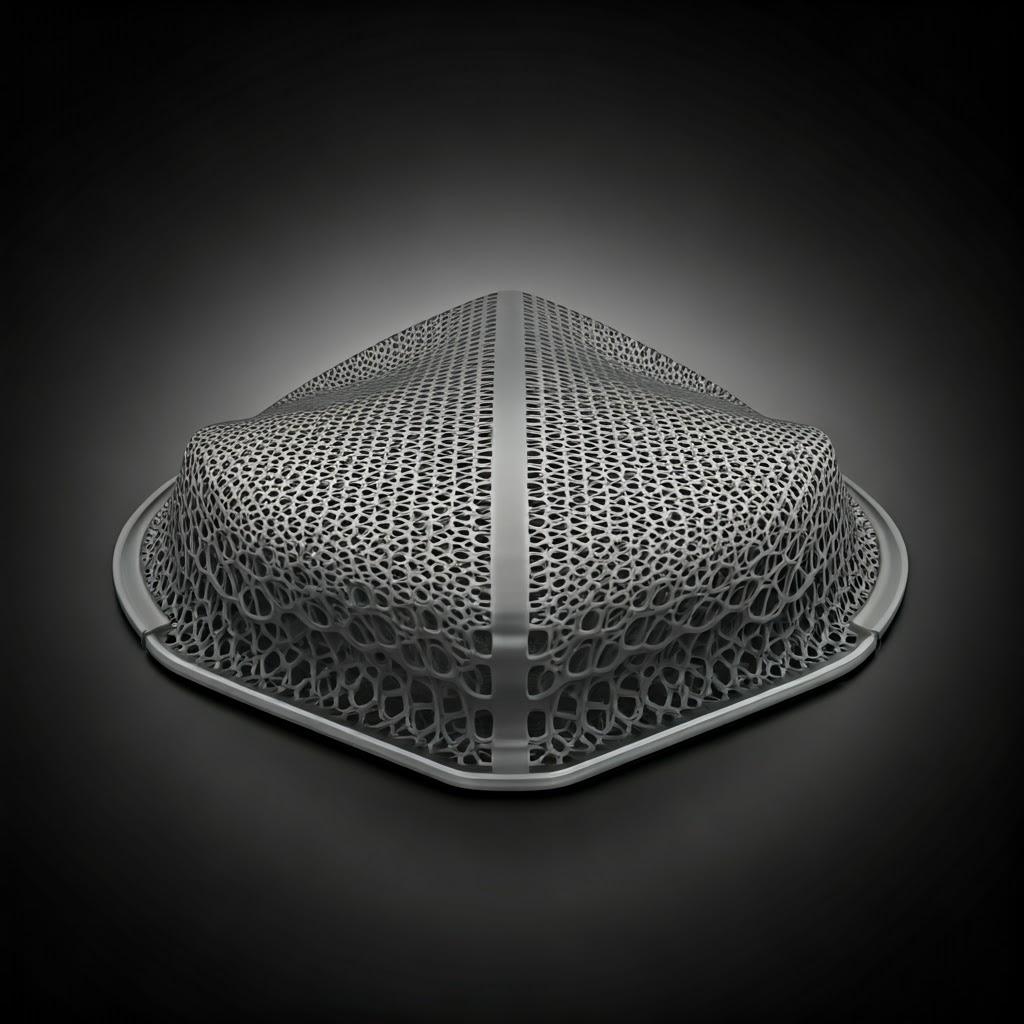
Proč zvolit 3D tisk kovů pro výrobu výfukových štítů automobilů?
Volba kovového 3D tisku namísto tradičních výrobních metod pro automobilové výfukové štíty představuje řadu přesvědčivých výhod.
- Flexibilita a složitost návrhu: Aditivní výroba umožňuje vytvářet složité geometrie, které jsou často nemožné nebo nákladově neúnosné při lisování nebo hlubokém tažení. To umožňuje optimalizovat tvar štítu pro maximální tepelnou ochranu a efektivní využití prostoru v těsných motorových prostorech. Inženýři mohou navrhovat štíty s vnitřními chladicími kanály nebo složitými zakřiveními pro lepší řízení odvodu tepla.
- Účinnost materiálu: Na rozdíl od subtraktivních výrobních procesů, při nichž se materiál odebírá, se při 3D tisku díly vytvářejí vrstvu po vrstvě, čímž se výrazně snižuje plýtvání materiálem. To je výhodné zejména při použití vysoce výkonných slitin, jako jsou AlSi10Mg a IN625, což vede k úspoře nákladů a udržitelnějšímu výrobnímu procesu.
- Potenciál odlehčení: 3D tisk z kovu usnadňuje vytváření lehkých, ale konstrukčně pevných součástí. Optimalizací konstrukce a použitím materiálů s vysokým poměrem pevnosti a hmotnosti mohou výrobci vyrábět výfukové štíty, které snižují celkovou hmotnost vozidla, což přispívá ke zvýšení spotřeby paliva a snížení emisí.
- Rychlé prototypování a iterace: Rychlost a flexibilita 3D tisku umožňují rychlou tvorbu prototypů a iteraci designu. Automobiloví inženýři mohou rychle vyrábět prototypy výfukových štítů, testovat jejich výkon a provádět úpravy designu ve zlomku času ve srovnání s tradičními postupy výroby nástrojů. Tento zrychlený vývojový cyklus je v rychle se rozvíjejícím automobilovém průmyslu klíčový.
- Přizpůsobení a malosériová výroba: Kovový 3D tisk je ideální pro výrobu výfukových štítů na míru pro konkrétní modely vozidel nebo pro nízkoobjemovou výrobu, kde by náklady na tradiční nástroje byly neúnosné. To je výhodné zejména pro speciální vozidla, výkonné vozy nebo aplikace na trhu s náhradními díly.
- Integrace funkcí: Aditivní výroba umožňuje integrovat více funkcí do jednoho dílu. Například montážní prvky, výztužná žebra nebo dokonce senzory lze začlenit přímo do konstrukce výfukového štítu, čímž se sníží potřeba dalších komponent a montážních kroků.
Přední poskytovatelé jako např Metal3DP využívají pokročilé tiskárny SEBM (Selective Electron Beam Melting) k výrobě složitých kovových dílů s vysokou přesností a spolehlivostí, a jsou tak důvěryhodným partnerem pro výrobce automobilů, kteří hledají inovativní řešení.
Doporučené kovové prášky pro 3D tisk výfukových štítů: AlSi10Mg a IN625
Volba kovového prášku je rozhodující pro konečné vlastnosti a výkon 3D tištěného automobilového výfukového štítu. Metal3DP doporučuje AlSi10Mg a IN625 jako vynikající materiál pro tuto aplikaci vzhledem k jejich specifickým vlastnostem:
AlSi10Mg:
- Složení: Slitina hliníku obsahující křemík (Si) a hořčík (Mg).
- Klíčové vlastnosti:
- Vysoká tepelná vodivost: Výborně odvádí teplo z výfukového systému.
- Lehké: Snižuje celkovou hmotnost vozidla, čímž zlepšuje spotřebu paliva.
- Dobrý poměr pevnosti a hmotnosti: Zajišťuje strukturální integritu bez nadměrné hmotnosti.
- Vynikající zpracovatelnost: Dobře se hodí pro procesy laserového tavení v práškovém loži (LPBF) a nabízí dobrou kvalitu povrchu a rozlišení detailů.
- Odolnost proti korozi: Nabízí dostatečnou odolnost vůči korozivnímu prostředí pod vozidlem.
- Aplikace ve výfukových štítech: Ideální pro aplikace, kde jde především o snížení hmotnosti a účinný odvod tepla.
IN625 (slitina niklu a chromu):
- Složení: Slitina niklu, chromu a molybdenu s niobem.
- Klíčové vlastnosti:
- Výjimečná odolnost při vysokých teplotách: Zachovává si své mechanické vlastnosti při zvýšených teplotách, které se vyskytují ve výfukových systémech.
- Vynikající odolnost proti korozi a oxidaci: Odolává náročnému chemickému a tepelnému prostředí výfukových plynů.
- Vysoká odolnost proti tečení: Odolává deformaci při trvalých vysokých teplotách a zatížení.
- Dobrá svařitelnost: V případě potřeby usnadňuje následné zpracování a integraci s dalšími komponentami.
- Aplikace ve výfukových štítech: Přednostně se používá u vysoce výkonných vozidel nebo v oblastech výfukového systému, kde dochází k extrémním teplotám a korozivním podmínkám.
Pokročilý systém výroby prášku Metal3DP’s zajišťuje výrobu vysoce kvalitních kovových prášků s vysokou sféricitou a tekutostí, což je klíčové pro dosažení hustých a bezchybných 3D tištěných dílů s vynikajícími mechanickými vlastnostmi. Výběr mezi AlSi10Mg a IN625 bude záviset na konkrétních požadavcích na výkon, provozních teplotách a nákladových aspektech pro aplikaci automobilového výfukového štítu.
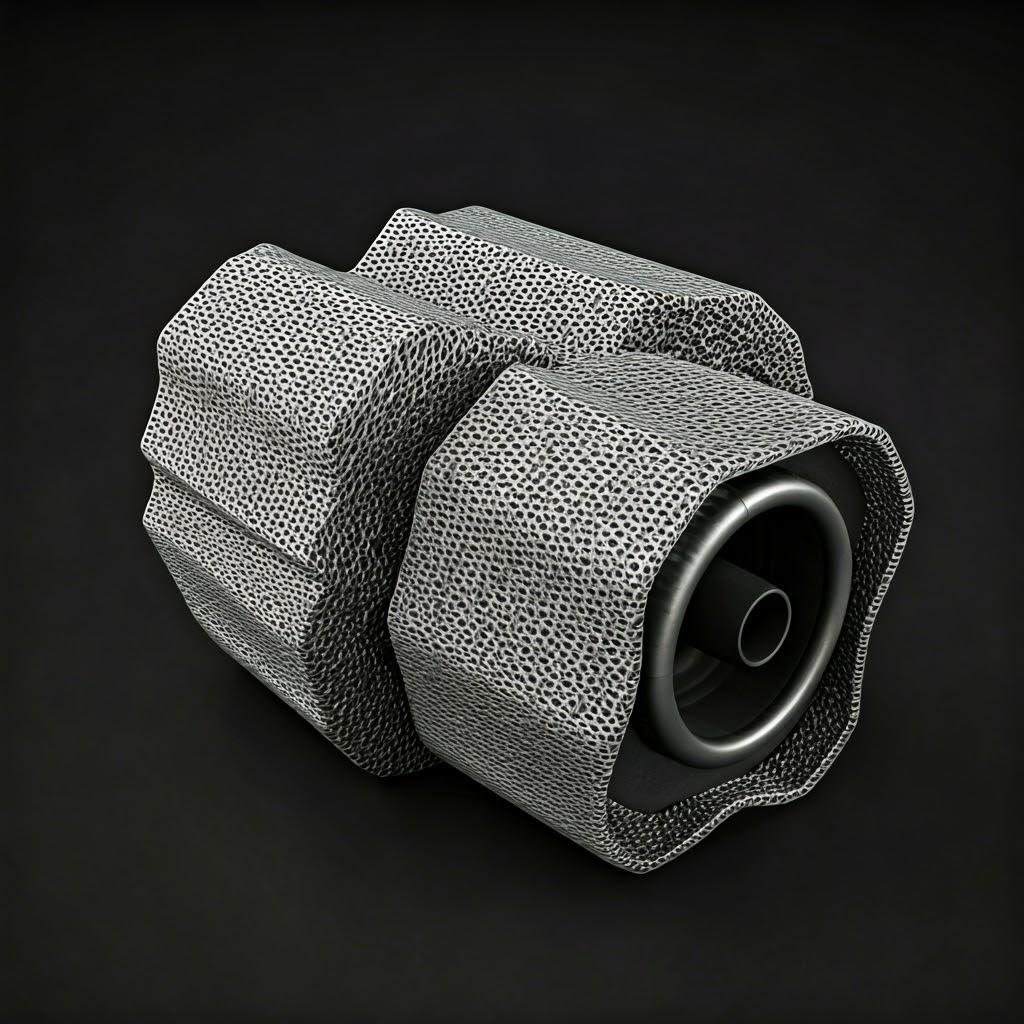
Klíčové aspekty návrhu aditivně vyráběných výfukových štítů automobilů
Navrhování automobilových výfukových štítů pro kovový 3D tisk vyžaduje odlišný přístup ve srovnání s tradičními výrobními metodami. Aby bylo možné plně využít možností aditivní výroby a zajistit optimální výkon, je třeba vzít v úvahu několik klíčových aspektů návrhu:
- Optimalizace topologie: Pomocí specializovaného softwaru mohou inženýři provést optimalizaci topologie a určit nejefektivnější rozložení materiálu pro výfukový štít. Tento proces může vést k výraznému snížení hmotnosti při zachování požadované strukturální integrity a tepelné ochrany. Odstraněním nepotřebného materiálu v málo namáhaných oblastech lze konstrukci přizpůsobit pro dosažení maximálního výkonu při minimální hmotnosti.
- Mřížové struktury: Začlenění mřížkových struktur do konstrukce výfukového štítu může zajistit vynikající tuhost a odolnost proti nárazu a zároveň dále snížit hmotnost. Tyto složité vnitřní geometrie jsou dosažitelné pouze aditivní výrobou a nabízejí vynikající poměr pevnosti a hmotnosti ve srovnání s pevnými konstrukcemi.
- Funkce tepelné správy: 3D tisk umožňuje integrovat složité chladicí kanály nebo žebra přímo do konstrukce výfukového štítu. Tyto prvky mohou zlepšit odvod tepla, dále chránit okolní součásti a zlepšit celkovou účinnost výfukového systému. Umístění a geometrii těchto prvků lze přesně řídit a zaměřit se tak na konkrétní oblasti s vysokou tepelnou zátěží.
- Tloušťka stěny a žebrování: Pečlivé zvážení tloušťky stěny je zásadní pro vyvážení hmotnosti a strukturální integrity. Strategicky umístěná žebra nebo klíny mohou zajistit dodatečnou tuhost a zabránit deformaci při tepelném namáhání, aniž by se výrazně zvýšila celková hmotnost.
- Podpůrné struktury: Při navrhování procesů tavení v práškovém loži, jako je SEBM nebo LPBF, je třeba vzít v úvahu potřebu podpůrných konstrukcí, které zabrání deformacím a zajistí správnou tvorbu dílů. Cílem návrhu by měla být minimalizace objemu a složitosti těchto podpěr, aby se snížila spotřeba materiálu a nároky na následné zpracování. K tomu mohou pomoci funkce, jako jsou samonosné úhelníky a optimalizovaná orientace dílu na konstrukční platformě.
- Spojování a montáž: Pokud se výfukový štít skládá z více částí, měla by konstrukce obsahovat prvky usnadňující snadnou a robustní montáž. Může jít o vzájemně propojené prvky, drážky s klíčem nebo vyhrazené oblasti pro svařování nebo jiné způsoby spojování. Pro efektivní výrobu je nezbytné myslet na celý proces montáže již ve fázi návrhu.
Při zohlednění těchto konstrukčních zásad mohou automobiloví inženýři plně využít potenciál 3D tisku kovů k vytvoření vysoce výkonných, lehkých a vysoce funkčních výfukových štítů. Služby Met3DP’s pro vývoj aplikací může poskytnout cenné odborné znalosti při optimalizaci návrhů pro aditivní výrobu.
Dosažení přesnosti: Tolerance, povrchová úprava a rozměrová přesnost u 3D tištěných výfukových štítů
V automobilovém průmyslu je přesnost nejdůležitější a výfukové štíty nejsou výjimkou. Technologie 3D tisku kovů, které nabízejí společnosti jako např Metal3DP lze dosáhnout působivé úrovně tolerance, kvality povrchu a rozměrové přesnosti, což splňuje přísné požadavky automobilových aplikací.
- Tolerance: Procesy SEBM (Selective Electron Beam Melting) a LPBF (Laser Powder Bed Fusion) umožňují dosáhnout tolerancí v rozmezí ±0,1 až ±0,2 mm pro kritické rozměry. Dosažitelná tolerance závisí na faktorech, jako je velikost dílu, geometrie a materiál. Pro zachování vysoké přesnosti je nezbytná pečlivá kontrola procesu a optimalizované parametry sestavení.
- Povrchová úprava: Povrchová úprava kovových 3D tištěných dílů se obvykle pohybuje v rozmezí 10 až 30 µm Ra (průměrná drsnost). I když to může být pro některé aplikace vhodné, lze použít techniky následného zpracování, jako je leštění, obrábění nebo abrazivní tryskání, k dosažení hladší povrchové úpravy až na několik mikrometrů Ra, pokud je to nutné z aerodynamických nebo estetických důvodů.
- Rozměrová přesnost: Rozměrová přesnost se týká schopnosti procesu 3D tisku vyrábět díly, které přesně odpovídají zamýšlenému modelu CAD. Při správné kalibraci a optimalizaci procesu lze při 3D tisku kovů dosáhnout rozměrové přesnosti ±0,2 % jmenovitého rozměru. Faktory, jako je tepelná roztažnost a smršťování během procesu sestavování, jsou pečlivě kontrolovány, aby se minimalizovaly odchylky.
Přesnost a kvalita povrchu dosažitelná při 3D tisku z kovu se neustále zlepšuje díky pokroku v technologii strojů a procesních parametrech. U kritických automobilových komponent, jako jsou výfukové štíty, zajišťuje přesnost, kterou tyto technologie nabízejí, správné uložení, funkci a dlouhodobou spolehlivost. Automobiloví konstruktéři by měli zvážit požadovanou toleranci a povrchovou úpravu již na počátku procesu návrhu, aby mohli vybrat nejvhodnější technologii 3D tisku a naplánovat všechny nezbytné kroky následného zpracování.

Techniky následného zpracování pro výfukové štíty automobilů vyrobené pomocí 3D tisku z kovu
Přestože 3D tisk z kovu nabízí značné výhody, je často nutné následné zpracování, aby se dosáhlo konečných požadovaných vlastností a povrchové úpravy výfukových štítů pro automobilový průmysl. Mezi běžné techniky následného zpracování patří:
- Odstranění podpory: U dílů vytištěných pomocí technologií tavení v práškovém loži jsou nezbytné podpůrné struktury, které zabraňují zborcení a deformaci během procesu sestavování. Tyto podpěry musí být po tisku pečlivě odstraněny, často pomocí specializovaných nástrojů nebo obráběním. Cílem návrhu dílu by měla být minimalizace potřeby rozsáhlých podpůrných struktur.
- Tepelné zpracování: Pro odstranění zbytkových napětí vzniklých během procesu 3D tisku a dosažení požadovaných mechanických vlastností materiálu (např. tvrdosti, pevnosti v tahu) se často provádí tepelné zpracování. To může zahrnovat procesy, jako je uvolňování napětí, žíhání nebo kalení a popouštění, v závislosti na použité slitině.
- Povrchová úprava: Jak již bylo zmíněno, povrchová úprava ve stavu, v jakém je vyrobena, nemusí být vhodná pro všechny aplikace. Ke zlepšení hladkosti povrchu, odstranění povrchových oxidů nebo dosažení specifických estetických požadavků lze použít techniky, jako je kuličkování, abrazivní tryskání, leštění nebo CNC obrábění.
- CNC obrábění: U kritických prvků vyžadujících velmi přísné tolerance nebo specifické geometrie, které jsou obtížně dosažitelné přímo pomocí 3D tisku, lze jako sekundární proces použít CNC obrábění. To umožňuje vysoce přesné dokončování klíčových rozhraní nebo montážních bodů.
- Povrchová úprava: V závislosti na provozním prostředí a konkrétním použitém materiálu mohou být použity povlaky pro zvýšení odolnosti proti korozi, zlepšení vlastností proti opotřebení nebo zajištění tepelné bariéry. Příkladem jsou keramické povlaky nebo specializované nátěry pro vysoké teploty.
- Kontrola a řízení kvality: Po následném zpracování je nezbytná důkladná kontrola pomocí technik, jako jsou souřadnicové měřicí stroje (CMM), nedestruktivní testování (NDT) a měření drsnosti povrchu, aby bylo zajištěno, že konečný díl splňuje požadované specifikace a normy kvality pro automobilové aplikace.
Při výběru kovového 3D tisku pro automobilové výfukové štíty je důležité pochopit nezbytné kroky následného zpracování a jejich dopad na náklady a dobu realizace. Komplexní řešení Metal3DP’s zahrnuje nejen pokročilý tisk, ale také pokyny k vhodným pracovním postupům následného zpracování.
Překonávání běžných problémů při 3D tisku výfukových štítů automobilů
3D tisk z kovu sice nabízí řadu výhod, ale existují také potenciální problémy, které je třeba řešit, aby byla zajištěna úspěšná výroba automobilových výfukových štítů:
- Deformace a zkreslení: Tepelné namáhání během procesu sestavování může vést k deformaci nebo zkreslení dílu, zejména u složitých geometrií nebo velkých dílů. Optimalizace orientace dílu, použití účinných podpůrných struktur a pečlivá kontrola parametrů sestavování mohou tyto problémy zmírnit.
- Zbytková napětí: Rychlé cykly zahřívání a ochlazování při 3D tisku kovů mohou v dílu vyvolat zbytková napětí, která mohou ovlivnit jeho mechanické vlastnosti a rozměrovou stabilitu. Tepelné úpravy po zpracování mají zásadní význam pro odstranění těchto napětí.
- Pórovitost: Vznik pórů nebo dutin uvnitř tištěného dílu může ohrozit jeho pevnost a únavovou odolnost. Použití vysoce kvalitních kovových prášků, optimalizace procesních parametrů (např. výkonu laseru, rychlosti skenování) a zajištění správného průtoku stínicího plynu jsou zásadní pro minimalizaci pórovitosti. Vysoce kvalitní kovové prášky Metal3DP’s jsou navrženy tak, aby toto riziko minimalizovaly.
- Výzvy při odstraňování podpory: Odstraňování podpůrných konstrukcí ze složitých geometrií může být časově náročné a může zanechat stopy na povrchu. Navrhování dílů se samonosnými prvky a optimalizace umístění podpěr může tento proces zjednodušit.
- Omezení povrchové úpravy: Dosáhnout hladkého povrchu přímo při 3D tisku může být náročné. Pokud je požadována specifická povrchová úprava, je nutné naplánovat vhodné techniky následného zpracování, jako je leštění nebo obrábění.
- Úvahy o ceně: 3D tisk z kovu může být nákladově efektivní pro malé až střední objemy a složité díly, ale počáteční investice do zařízení a náklady na kovové prášky mohou být značné. Důkladná analýza nákladů porovnávající 3D tisk s tradičními metodami je nezbytná.
Pochopením těchto potenciálních problémů a zavedením vhodných konstrukčních strategií, procesních kontrol a technik následného zpracování mohou výrobci automobilů efektivně využít 3D tisk kovů k výrobě vysoce kvalitních výfukových štítů. Spolupráce se zkušenými poskytovateli služeb, jako je např Metal3DP může poskytnout cenné poznatky a řešení k překonání těchto problémů.
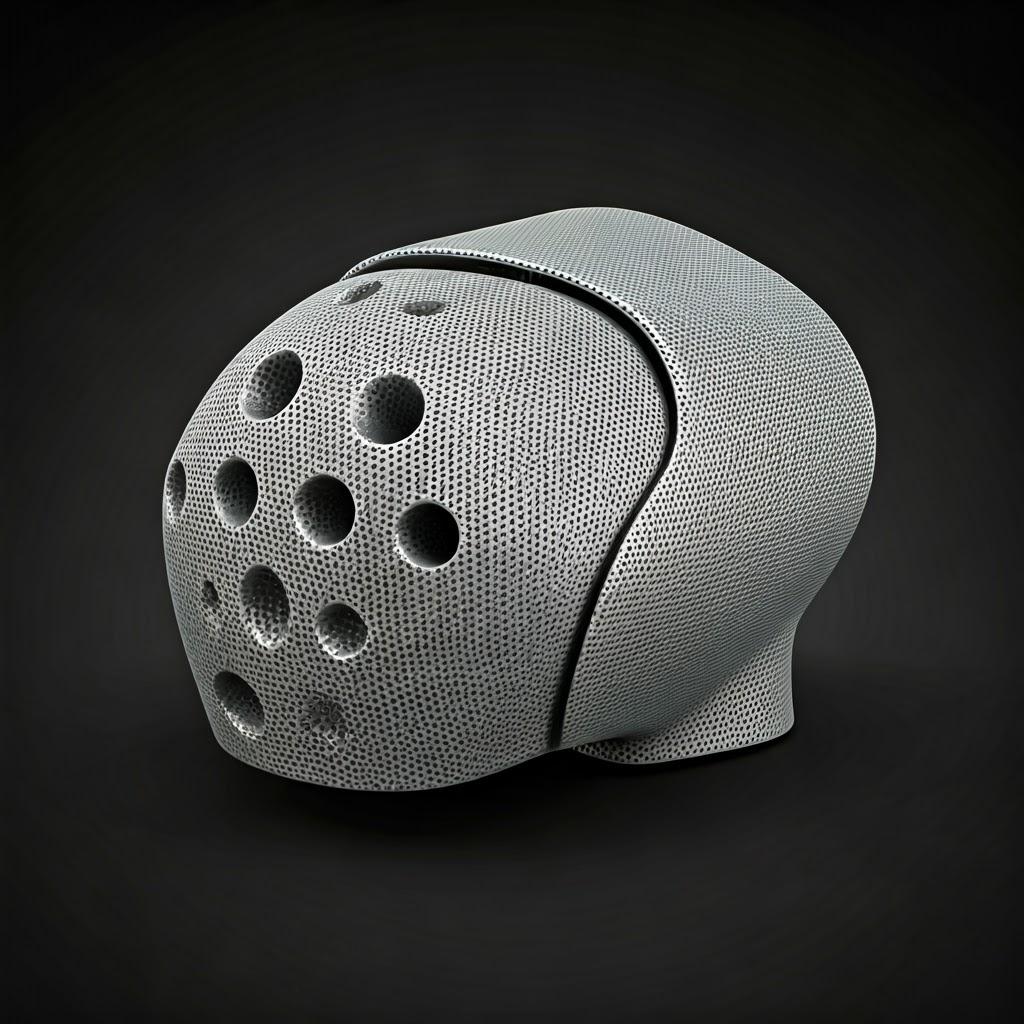
Jak vybrat správného poskytovatele služeb 3D tisku kovů pro automobilové komponenty
Výběr správného poskytovatele služeb 3D tisku z kovu je pro výrobce automobilů, kteří chtějí využít tuto pokročilou technologii pro komponenty, jako jsou výfukové štíty, zásadním rozhodnutím. Zde jsou klíčové faktory, které je třeba zvážit při hodnocení potenciálních dodavatelů:
- Materiálové schopnosti: Ujistěte se, že dodavatel nabízí specifické kovové prášky potřebné pro vaši aplikaci, například AlSi10Mg a IN625. Ověřte si jeho odborné znalosti a zkušenosti se zpracováním těchto materiálů a jeho schopnost zajistit certifikaci a sledovatelnost materiálu. Metal3DP se může pochlubit širokou škálou vysoce kvalitních kovových prášků optimalizovaných pro různé aplikace.
- Technologie a vybavení: Porozumět typům technologií 3D tisku kovů, které poskytovatel používá (např. SEBM, LPBF). Každá technologie má své silné stránky a omezení, pokud jde o objem sestavení, přesnost a povrchovou úpravu. Informujte se o konkrétních tiskárnách, které používají, a o jejich plánech údržby, protože to může mít vliv na kvalitu dílů a dodací lhůty. Metal3DP používá špičkové tiskárny SEBM, které jsou známé svou přesností a spolehlivostí.
- Zajištění kvality a certifikace: Ověřte si, zda má poskytovatel zavedené spolehlivé systémy řízení kvality a zda je držitelem příslušných certifikátů (např. ISO 9001, AS9100 pro letecký průmysl). Tím je zajištěno, že jeho procesy jsou kontrolovány a že vyráběné díly splňují přísné normy kvality vyžadované v automobilovém průmyslu.
- Konstrukční a inženýrská podpora: Zkušený poskytovatel služeb by měl nabídnout konzultace k návrhu a technickou podporu pro optimalizaci návrhu výfukového štítu pro aditivní výrobu. To zahrnuje pokyny pro výběr materiálu, optimalizaci topologie a návrh pro vyrobitelnost. Metal3DP poskytuje komplexní řešení včetně služeb vývoje aplikací.
- Možnosti následného zpracování: Zjistěte, zda poskytovatel nabízí potřebné služby následného zpracování, jako je odstranění podpěr, tepelné zpracování, povrchová úprava a obrábění. Vlastní nebo dobře spravovaná síť služeb následného zpracování může zefektivnit výrobní proces a zajistit konzistentní kvalitu.
- Dodací lhůty a výrobní kapacita: Diskutujte o dodacích lhůtách pro výrobu prototypů a výrobu, jakož i o schopnosti poskytovatele zvládnout vaše očekávané objemy. Ujistěte se, že jeho harmonogramy jsou v souladu s harmonogramem vašeho projektu.
- Struktura nákladů a transparentnost: Získejte jasný rozpis nákladů, včetně nákladů na tisk, materiály, následné zpracování a případné poplatky za návrh nebo inženýrské práce. Transparentní struktura cen vám pomůže přesně stanovit rozpočet projektu.
- Komunikace a zákaznická podpora: Posuďte, jak poskytovatel reaguje, jak komunikuje a jaká je jeho celková zákaznická podpora. Spolehlivý partner bude aktivně řešit vaše dotazy a poskytovat aktuální informace v průběhu celého výrobního procesu.
Pečlivým zvážením těchto faktorů si mohou výrobci automobilů vybrat poskytovatele služeb 3D tisku z kovu, který jim dodá vysoce kvalitní výfukové štíty na zakázku splňující jejich specifické požadavky na výkon a výrobu.
Analýza nákladů a dodacích lhůt pro 3D tištěné výfukové štíty automobilů
Pochopení nákladových faktorů a dodacích lhůt spojených s 3D tiskem kovů je pro manažery nákupu v automobilovém průmyslu zásadní. Zde je rozpis toho, co tyto aspekty ovlivňuje u 3D tištěných výfukových štítů:
Nákladové faktory:
- Náklady na materiál: Významným faktorem je cena kovového prášku (např. AlSi10Mg, IN625). Specializované slitiny jako IN625 jsou obvykle dražší než standardní slitiny jako AlSi10Mg. Množství materiálu použitého na jeden díl má také přímý vliv na náklady. Optimalizace konstrukce s cílem snížit spotřebu materiálu je klíčem k nákladové efektivitě.
- Doba výstavby: Doba tisku dílu závisí na jeho velikosti, složitosti a zvolené technologii 3D tisku. Delší doba sestavení znamená vyšší provozní náklady stroje. Optimalizace orientace dílu a parametrů sestavení může pomoci minimalizovat dobu sestavení.
- Náklady na následné zpracování: Rozsah nutného následného zpracování (např. odstranění podpory, tepelné zpracování, povrchová úprava, obrábění) významně ovlivňuje celkové náklady. Složité kroky následného zpracování zvyšují konečnou cenu. Návrh minimálních podpůrných struktur a včasné zvážení požadované povrchové úpravy může pomoci tyto náklady kontrolovat.
- Náklady na stroje a práci: Poskytovatelé služeb zohledňují náklady na provoz a údržbu svých zařízení pro 3D tisk, jakož i náklady na pracovní sílu související s návrhem, tiskem, následným zpracováním a kontrolou kvality.
- Objem a škálovatelnost: Zatímco 3D tisk z kovu může být nákladově efektivní pro malé až střední objemy a složité geometrie, náklady na jeden díl se mohou snížit při větších výrobních sériích díky úsporám z rozsahu. Doporučujeme projednat s poskytovatelem služeb případné množstevní slevy.
Doba dodání:
- Vytváření prototypů: 3D tisk z kovu nabízí výrazně kratší dodací lhůty pro výrobu prototypů ve srovnání s tradičními metodami výroby nástrojů. Prototypy lze často vyrobit během několika dnů nebo týdnů, což umožňuje rychlé opakování návrhu a testování.
- Výroba: Dodací lhůty pro výrobu závisí na faktorech, jako je složitost dílu, objemové požadavky, dostupnost materiálu a aktuální vytížení poskytovatele služeb. Jednoduché konstrukce a snadno dostupné materiály obvykle vedou ke zkrácení dodacích lhůt. Složitější díly nebo velké výrobní série mohou vyžadovat delší dodací lhůty.
- Následné zpracování: Celkovou dobu zpracování může ovlivnit také doba potřebná pro následné zpracování. Složité tepelné úpravy nebo rozsáhlé povrchové úpravy prodlouží výrobní lhůty.
- Doprava: Do celkové dodací lhůty je třeba započítat také dobu potřebnou k přepravě hotových dílů do vaší lokality.
Je důležité, abyste s vybraným poskytovatelem služeb 3D tisku z kovu hned na začátku projektu prodiskutovali očekávané náklady a dobu realizace. Získání podrobné cenové nabídky a pochopení faktorů, které ovlivňují náklady i dobu realizace, vám pomůže činit informovaná rozhodnutí a efektivně plánovat výrobní harmonogram.
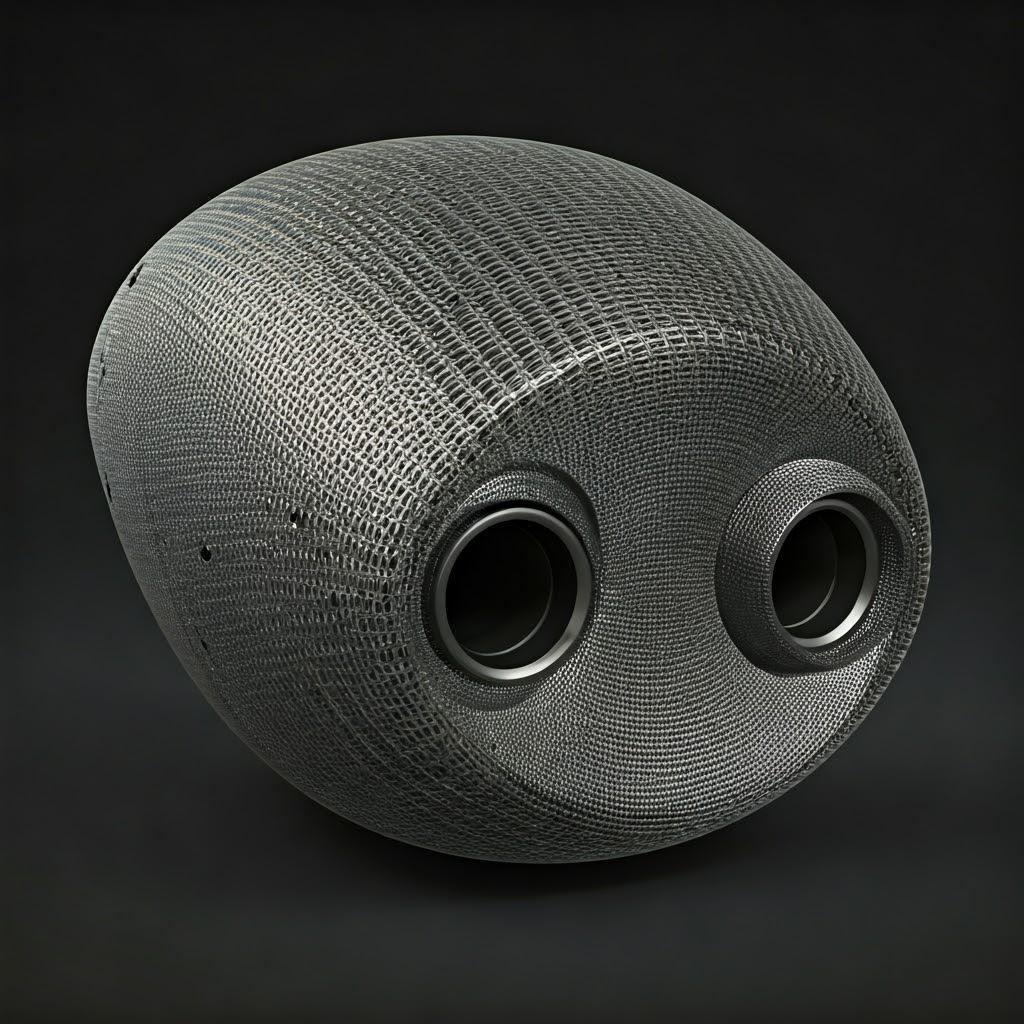
Často kladené otázky (FAQ) o 3D tisku kovů pro výfukové štíty
- Je 3D tisk z kovu dostatečně pevný pro automobilové výfukové štíty? Ano, pokud je zvolen vhodný kovový prášek (například AlSi10Mg nebo IN625) a proces tisku je optimalizován, mohou 3D tištěné kovové díly dosáhnout mechanických vlastností srovnatelných nebo dokonce lepších než díly vyrobené tradičními metodami. Následné úpravy, jako je tepelné zpracování, dále zvyšují jejich pevnost a odolnost.
- Odolají kovové 3D tištěné výfukové štíty vysokým teplotám? Rozhodně. Materiály jako IN625 jsou speciálně vybírány pro svou vynikající pevnost při vysokých teplotách a odolnost proti korozi, takže jsou vhodné pro extrémní podmínky ve výfukovém systému. AlSi10Mg také nabízí dobrou tepelnou vodivost pro odvod tepla.
- Jaká je typická životnost kovového výfukového štítu vytištěného na 3D tiskárně? Životnost 3D tištěného kovového výfukového štítu závisí na faktorech, jako je použitý materiál, provozní podmínky a kvalita výrobního procesu. Při správném výběru materiálu a výrobě mohou tyto štíty dosáhnout životnosti srovnatelné s tradičně vyráběnými součástmi.
- Jaké jsou náklady na 3D tištěné výfukové štíty ve srovnání s tradičními metodami? U malých až středních objemů a složitých geometrií může být kovový 3D tisk nákladově efektivnější než tradiční metody náročné na nástroje. Absence nákladů na nástroje a možnost vytvářet složité konstrukce bez dalších výrobních kroků může vést k výrazným úsporám. U velmi vysokých objemů jednoduchých dílů mohou být tradiční metody stále ekonomičtější.
- Jakou volnost při navrhování nabízí 3D tisk z kovu pro výfukové štíty? 3D tisk z kovu nabízí bezkonkurenční svobodu při navrhování, umožňuje vytvářet složité geometrie, vnitřní prvky, jako jsou chladicí kanály nebo mřížkové struktury, a přizpůsobené tvary, které jsou obtížně dosažitelné nebo nemožné při tradičních výrobních postupech. To umožňuje optimalizovat výfukové štíty pro specifické požadavky na výkon a prostorová omezení.
Závěr - Inovace v automobilovém průmyslu díky kovovým 3D tištěným výfukovým štítům
3D tisk z kovu přináší revoluci ve způsobu navrhování a výroby automobilových komponent, jako jsou výfukové štíty. Schopnost vytvářet složité, lehké a vysoce výkonné díly s přizpůsobenými vlastnostmi materiálu nabízí významné výhody oproti tradičním výrobním metodám. Společnosti jako např Metal3DPdíky pokročilé technologii SEBM a vysoce kvalitním kovovým práškům umožňují automobilovým inženýrům a manažerům nákupu posouvat hranice inovací. Využitím aditivní výroby kovů může automobilový průmysl dosáhnout vyššího výkonu vozidel, lepší palivové účinnosti a rychlejších vývojových cyklů výrobků. Budoucnost automobilové výroby je stále více digitální a kovový 3D tisk je klíčovou technologií, která tuto transformaci pohání. Kontakt Metal3DP a zjistit, jak mohou jejich schopnosti podpořit cíle vaší organizace v oblasti aditivní výroby.
Sdílet na
MET3DP Technology Co., LTD je předním poskytovatelem řešení aditivní výroby se sídlem v Qingdao v Číně. Naše společnost se specializuje na zařízení pro 3D tisk a vysoce výkonné kovové prášky pro průmyslové aplikace.
Dotaz k získání nejlepší ceny a přizpůsobeného řešení pro vaše podnikání!
Související články
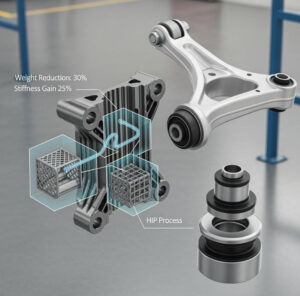
Metal 3D Printed Subframe Connection Mounts and Blocks for EV and Motorsport Chassis
Přečtěte si více "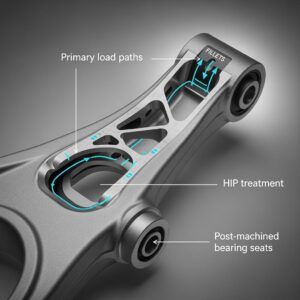
Metal 3D Printing for U.S. Automotive Lightweight Structural Brackets and Suspension Components
Přečtěte si více "O Met3DP
Nedávná aktualizace
Náš produkt
KONTAKTUJTE NÁS
Nějaké otázky? Pošlete nám zprávu hned teď! Po obdržení vaší zprávy obsloužíme vaši žádost s celým týmem.