materiál pro kování
Obsah
V oblasti zpracování kovů, kde se suroviny transformují na předměty užitku a krásy, materiály pro kování vládnou. Představte si sochaře pečlivě tvarujícího hlínu, ale v průmyslovém měřítku, s obrovským teplem a tlakem tvarujícím tyto materiály do složitých, vysoce pevných součástí. To je podstata kování – a základ pro tento proces spočívá v samotných materiálech, do kterých se chystáme ponořit.
Přehled: Kování cesty k pevnosti
Materiály pro kování jsou speciálně formulované kovy navržené tak, aby odolaly intenzivnímu teplu, tlakovým silám a deformacím spojeným s procesem kování. Na rozdíl od odlévání, kde roztavený kov vyplňuje formu, kování manipuluje s pevným materiálem, zušlechťuje jeho strukturu zrn a zlepšuje jeho mechanické vlastnosti. To se promítá do silnějších, spolehlivějších součástí, které zvládnou náročné aplikace.
Tyto materiály se dodávají v různých variantách, z nichž každá má svou vlastní jedinečnou směs vlastností. Volba materiálu se silně odvíjí od zamýšlené aplikace. Potřebujete součást, která je neuvěřitelně pevná a odolná proti opotřebení? Nebo snad taková, která nabízí vynikající odolnost proti korozi? Svět materiálů pro kování má odpověď na každou potřebu.
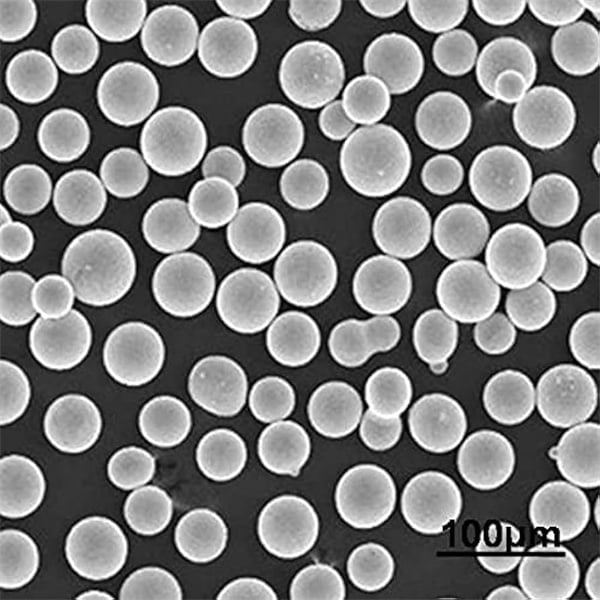
Společné Materiály pro kování
Nyní se ponořme do jádra věci – konkrétních materiálů, které umožňují kování. Zde je bližší pohled na některé z nejrozšířenějších uchazečů:
Tabulka: Běžné materiály pro kování
Materiál | Složení | Klíčové vlastnosti | Aplikace |
---|---|---|---|
Uhlíková ocel | Primárně železo s různým obsahem uhlíku (nízký, střední, vysoký) | Cenově dostupné, dobrá obrobitelnost, pevnost se zvyšuje s obsahem uhlíku | Klikové hřídele, ozubená kola, ojnice, klíče |
Legovaná ocel | Železo s uhlíkem a dalšími prvky, jako je chrom, nikl nebo molybden | Vysoká pevnost, houževnatost, odolnost proti opotřebení, lze tepelně zpracovat pro specifické vlastnosti | Hřídele, ozubená kola, letecké součásti, nástroje |
Nerezová ocel | Železo s chromem pro odolnost proti korozi, často obsahuje nikl a molybden | Vynikající odolnost proti korozi, dobrá pevnost a tvárnost | Ventily, čerpadla, spojovací prvky, lékařské nástroje |
Slitiny niklu | Vysoký obsah niklu, často s chromem a železem | Výjimečná odolnost proti korozi při vysokých teplotách, vynikající pevnost | Lopatky turbíny, výměníky tepla, tlakové nádoby |
Hliníkové slitiny | Primárně hliník s prvky jako měď, hořčík nebo křemík | Lehký, dobrá odolnost proti korozi, střední pevnost | Letecké součásti, automobilové díly, elektrické vodiče |
Titanové slitiny | Primárně titan s prvky jako hliník, vanad nebo molybden | Vysoký poměr pevnosti a hmotnosti, vynikající odolnost proti korozi | Letecké komponenty, lékařské implantáty, sportovní zboží |
Slitiny mědi | Primárně měď s prvky jako zinek, cín nebo olovo | Vynikající elektrická vodivost, dobrá tvárnost, střední pevnost | Elektrické dráty, trubky, výměníky tepla |
Slitiny hořčíku | Primárně hořčík s prvky jako hliník, mangan nebo zinek | Velmi lehký, dobrý poměr pevnosti k hmotnosti | Letecké součásti, elektronické kryty, sportovní zboží |
Superslitiny | Složité kombinace prvků jako nikl, kobalt, chrom a další | Výjimečná pevnost při vysokých teplotách, odolnost proti oxidaci | Součásti proudových motorů, raketové motory, plynové turbíny |
Nástrojové oceli | Vysoký obsah uhlíku s prvky jako chrom, wolfram nebo vanad | Výjimečná tvrdost, odolnost proti opotřebení | Řezné nástroje, razníky, matrice |
Specifické kovové prášky
Zatímco výše uvedená tabulka poskytuje solidní základ, svět materiálů pro kování přesahuje tradiční tvářené formy. Kovové prášky se stávají stále populárnějšími pro kovářské aplikace a nabízejí jedinečné výhody, jako je výroba téměř čistého tvaru a snížený odpad. Zde jsou některé pozoruhodné kovové prášky používané při kování:
- Plynem atomizované ocelové prášky: Vyrábí se rychlým ochlazováním kapek roztavené oceli, což má za následek vysoce sférické prášky s vynikající tekutostí a hustotou balení. Tyto prášky jsou ideální pro složité geometrie a nabízejí
- Vodou atomizované ocelové prášky: Nákladově efektivní alternativa k práškům atomizovaným plynem, vyráběná vysokotlakými vodními paprsky rozbíjejícími proudy roztavené oceli. Tyto prášky jsou obvykle méně sférické, ale stále vhodné pro různé aplikace kování, zejména pro jednodušší geometrie.
- Slitiny na bázi niklu: Podobné výrobními metodami jako ocelové prášky, nabízejí výjimečnou pevnost za vysokých teplot a odolnost proti korozi, což je činí ideálními pro náročné letecké a energetické aplikace.
- Prášky z hliníkové slitiny: Lehká povaha hliníku vyniká v práškové formě, což umožňuje vytváření složitých, vysoce pevných součástí pro automobilový a letecký průmysl.
- Prášky ze slitin titanu: Navzdory problémům se zpracováním v důsledku reaktivity titanu, pokroky v technikách výroby prášků činí prášky z titanových slitin životaschopnějšími pro aplikace kování.
- Prášky z měděných slitin: Tyto prášky nabízejí vynikající elektrickou vodivost a lze je kovat do složitých tvarů pro aplikace v elektronice a výměnících tepla.
- Prášky ze slitin hořčíku: Extrémní lehkost hořčíku se dobře promítá do kování prášků, což umožňuje vytváření vysoce pevných, lehkých součástí pro aplikace, kde je zásadní snížení hmotnosti, například v letectví a přenosné elektronice.
- Prášky z nástrojové oceli: Vlastní tvrdost a odolnost proti opotřebení nástrojových ocelí jsou zachovány v práškové formě, což je činí vhodnými pro kování složitých řezných nástrojů a razníků.
aplikace z materiál pro kování
S tak rozmanitou škálou uchazečů se výběr správného materiálu pro kování scvrkává na pečlivé zhodnocení požadavků aplikace. Zde jsou některé klíčové faktory, které je třeba zvážit:
- Síla: Součást musí odolat silám, se kterými se setká během provozu. Vysoce pevné slitiny, jako jsou niklové slitiny a nástrojové oceli, jsou ideální pro náročné aplikace.
- Houževnatost: Schopnost absorbovat náraz bez prasknutí je zásadní pro součásti, které zažívají rázové zatížení. Střední a vysoce uhlíkové oceli, stejně jako některé hliníkové slitiny, nabízejí dobrou houževnatost.
- Odolnost proti korozi: Vystavení drsným prostředím vyžaduje materiály, které odolávají korozi a degradaci. Nerezové oceli a niklové slitiny v této oblasti vynikají.
- Hmotnost: Pro aplikace, kde je prvořadé snížení hmotnosti, přicházejí ke slovu lehké materiály, jako jsou hliník, hořčík a slitiny titanu.
- Obrobitelnost: Snadnost obrábění materiálu po kování může být rozhodujícím faktorem. Uhlíkové oceli a některé hliníkové slitiny nabízejí dobrou obrobitelnost.
- Náklady: Náklady na materiál jsou vždy třeba zvážit. Uhlíkové oceli jsou obvykle nejlevnější variantou, zatímco exotické slitiny, jako jsou superslitiny, nesou prémiovou cenovku.
Nad rámec základů: Pohled na vlastnosti materiálu
Proces výběru nekončí u základního typu materiálu. Hlubší ponoření do specifických vlastností materiálu poskytuje nuancovanější pochopení jeho vhodnosti. Zde jsou některé zásadní vlastnosti, které je třeba zvážit:
- Pevnost v tahu: Maximální napětí, které materiál vydrží, než dojde k plastické deformaci. Vyšší mez kluzu se promítá do pevnější součásti.
- Mez pevnosti v tahu: Maximální napětí, které materiál vydrží, než se zlomí. To je důležité pro součásti vystavené vysokým tahovým silám.
- Prodloužení: Míra, do jaké se materiál může natáhnout, než se zlomí. Vysoké prodloužení naznačuje dobrou tažnost, což umožňuje určité tvarování po kování.
- Tvrdost: Odolnost proti vtlačení nebo poškrábání. Nástrojové oceli a některé vysoce uhlíkové oceli mají výjimečnou tvrdost.
- Únavová pevnost: Schopnost odolávat opakovanému namáhání bez selhání. To je zásadní pro součásti vystavené cyklickému zatížení.
Pochopení těchto vlastností ve spojení s požadavky aplikace vám umožňuje učinit informované rozhodnutí při výběru optimálního materiálu pro kování.
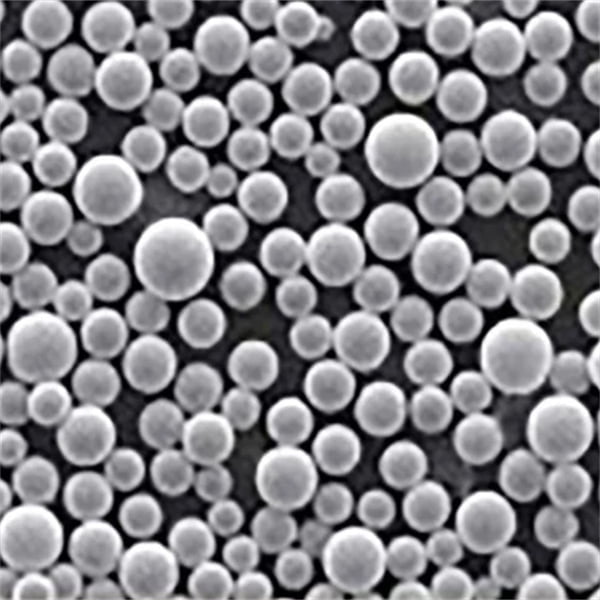
Výhody a omezení
Výhody materiálů pro kování:
- Vynikající pevnost a odolnost: Proces kování zušlechťuje strukturu zrna, což vede k výjimečné pevnosti a houževnatosti ve srovnání s litými nebo obráběnými součástmi.
- Zvýšená únavová pevnost: Řízené proudění zrna dosažené kováním zlepšuje schopnost materiálu odolávat opakovanému namáhání bez selhání.
- Flexibilita designu: Kování umožňuje vytváření složitých tvarů se složitými prvky, na rozdíl od některých procesů lití.
- Zlepšená obrobitelnost: Proces kování může zlepšit obrobitelnost určitých materiálů, což usnadňuje jejich dokončování po kování.
- Rozměrová přesnost: Kování může produkovat součásti s užšími tolerancemi ve srovnání s některými metodami lití.
Omezení materiálů pro kování:
- Vysoká cena: Proces kování je často náročnější na práci a vyžaduje specializované vybavení, což vede k vyšším nákladům na materiál ve srovnání s některými jinými výrobními metodami.
- Omezení velikosti: Velikost výkovků je omezena kapacitou kovacích zařízení. Velmi velké nebo složité součásti nemusí být možné kovat.
- Tvorba odpadu: Kování může generovat značný odpadní materiál, zejména pro složité tvary.
- Povrchová úprava: Kovací součásti mohou vyžadovat další obrábění pro dosažení hladkého povrchu.
Navzdory těmto omezením je výjimečná pevnost, houževnatost a flexibilita designu nabízená materiály pro kování činí cennou volbou pro širokou škálu náročných aplikací.
Aplikace z Materiály pro kování
Materiály pro kování hrají zásadní roli v nesčetných průmyslových odvětvích a formují samotné nástroje a součásti, které pohánějí náš svět. Zde jsou některé významné aplikace:
Průmysl | Příklady součástí | Úvahy o materiálu |
---|---|---|
Automobilový průmysl | Klikové hřídele, ojnice, ozubená kola, součásti zavěšení | Vysoká pevnost, odolnost proti únavě, dobrá obrobitelnost |
Aerospace | Součásti podvozku, nosníky křídel, disky motorů | Vysoký poměr pevnosti k hmotnosti, vynikající odolnost proti korozi, dobrá únavová pevnost (hliníkové slitiny, slitiny titanu, niklové slitiny) |
Ropa a plyn | Vrtací trubky, tlakové nádoby, ventily | Vysoká pevnost, dobrá odolnost proti korozi při vysokých teplotách (legované oceli, nerezové oceli) |
Konstrukce | Jeřáby, háky, spojovací prvky | Vysoká pevnost, dobrá houževnatost (uhlíkové oceli, legované oceli) |
Lékařský | Chirurgické nástroje, implantáty | Vysoká pevnost, biokompatibilita, odolnost proti korozi (nerezové oceli, slitiny titanu) |
Výroba elektřiny | Oběžné lopatky turbín, hřídele, tlakové nádoby | Výjimečná pevnost za vysokých teplot, odolnost proti tečení, odolnost proti oxidaci (superslitiny, niklové slitiny) |
Spotřební zboží | Nože, klíče, golfové hole | Vysoká pevnost, tvrdost, odolnost proti opotřebení (nástrojové oceli) |
Kromě těchto zavedených aplikací se materiály pro kování neustále zkoumají pro nová a inovativní použití. Pokroky ve vědě o materiálech a technikách kování posouvají hranice toho, co je možné. Zde jsou některé vzrušující možnosti na obzoru:
- Odlehčování vozidel: Použití pokročilých hliníkových a titanových slitin v kovaných součástech může výrazně snížit hmotnost vozidla, zlepšit spotřebu paliva a výkon.
- Integrace aditivní výroby: Kombinace kování s aditivními výrobními technikami, jako je 3D tisk, umožňuje vytváření ještě složitějších a lehčích součástí.
- Zkoumání nových materiálů: Probíhá výzkum nových materiálů s výjimečnými vlastnostmi, který otevírá dveře ještě pevnějším a odolnějším kovaným součástem.
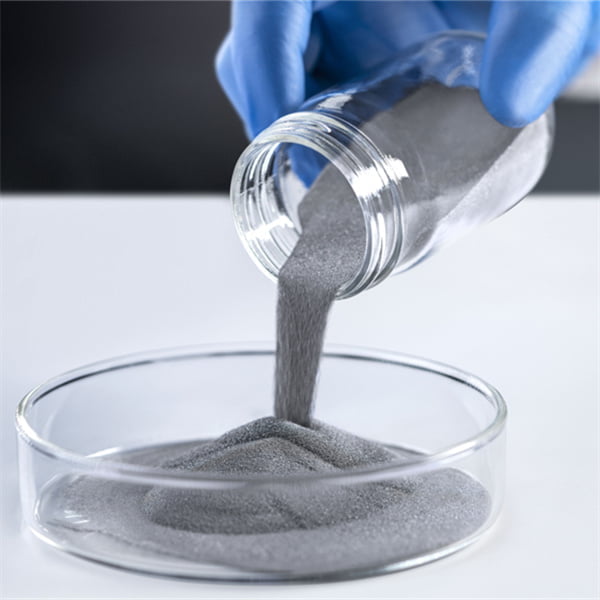
Nejčastější dotazy
Tabulka: Často kladené otázky o materiálech pro kování
Otázka | Odpovědět |
---|---|
Jaký je rozdíl mezi materiálem pro kování a běžnou ocelí? | Materiál pro kování je speciálně formulován tak, aby odolával vysokým teplotám a tlakům spojeným s procesem kování. Obvykle má rafinovanější strukturu zrna a vynikající mechanické vlastnosti ve srovnání s běžnou ocelí. |
Můžete kovat jakýkoli typ kovu? | Většinu kovů lze kovat, ale některé jsou vhodnější než jiné. Faktory jako bod tání, obrobitelnost a odolnost proti oxidaci hrají roli při výběru kovu pro kování. |
Jaké jsou výhody použití kovových prášků při kování? | Kovové prášky nabízejí několik výhod, včetně schopnosti vytvářet součásti téměř čistého tvaru, sníženého odpadu a potenciálu pro složitější geometrie. |
Jaké jsou některé z problémů spojených s kováním? | Vysoké náklady na zařízení a práci, omezení velikosti a tvorba odpadu jsou některé z problémů spojených s kováním. |
Jak volba materiálu pro kování ovlivňuje hotový výrobek? | Volba materiálu má významný dopad na pevnost, houževnatost, odolnost proti korozi, hmotnost a další vlastnosti hotové kované součásti. |
Sdílet na
MET3DP Technology Co., LTD je předním poskytovatelem řešení aditivní výroby se sídlem v Qingdao v Číně. Naše společnost se specializuje na zařízení pro 3D tisk a vysoce výkonné kovové prášky pro průmyslové aplikace.
Dotaz k získání nejlepší ceny a přizpůsobeného řešení pro vaše podnikání!
Související články
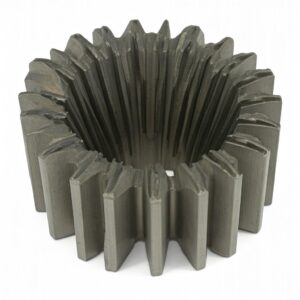
Vysoce výkonné segmenty lopatek trysek: Revoluce v účinnosti turbín díky 3D tisku z kovu
Přečtěte si více "O Met3DP
Nedávná aktualizace
Náš produkt
KONTAKTUJTE NÁS
Nějaké otázky? Pošlete nám zprávu hned teď! Po obdržení vaší zprávy obsloužíme vaši žádost s celým týmem.
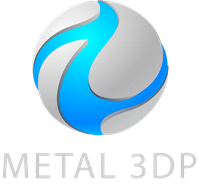
Kovové prášky pro 3D tisk a aditivní výrobu