Komponenty rámu baterie pro chlazení elektromobilů pomocí 3D tisku z kovu
Obsah
Úvod: Revoluce v tepelném managementu elektromobilů s kovovými 3D tištěnými rámy pro chlazení baterií
Revoluce v oblasti elektromobilů (EV) se zrychluje díky pokroku v technologii baterií, účinnosti pohonných jednotek a celosvětovému úsilí o udržitelnou dopravu. Srdcem každého výkonného elektromobilu je akumulátor - sofistikovaný systém pro ukládání energie, který vyžaduje přesnou kontrolu nad svým provozním prostředím. Efektivní tepelné řízení má zásadní význam a přímo ovlivňuje životnost, výkon, bezpečnost a rychlost nabíjení baterie. Tradiční výrobní metody mají často problémy s výrobou složitých, lehkých a vysoce účinných chladicích komponent, které jsou nutné pro splnění stále rostoucích požadavků moderních elektromobilů. V tomto případě je výroba aditiv kovů (AM), běžně známý jako kov 3D tisk, se stává transformativní technologií.
Konkrétně se jedná o chladicí rám baterie, kritické součásti zodpovědné za odvádění tepla vznikajícího během nabíjecích a vybíjecích cyklů, může AM výrazně prospět. Díky využití pokročilých kovových prášků, jako jsou slitiny hliníku, křemíku a hořčíku (AlSi10Mg) a mědi, chromu a zirkonu (CuCrZr), mohou nyní výrobci vytvářet chladicí rámy se složitým designem vnitřních kanálů, optimalizovanými cestami proudění tekutin a výrazně nižší hmotností ve srovnání s konvenčně vyráběnými díly. Kovový 3D tisk umožňuje integraci složitých prvků, konsolidaci více dílů do jediné součásti a rychlou iteraci návrhu, což urychluje vývojové cykly a odemyká nové úrovně výkonu. Pro inženýry a manažery nákupu v konkurenčním automobilovém odvětví již není pochopení potenciálu AM kovů pro komponenty, jako jsou chladicí rámy baterií, volitelné; je to nezbytné pro udržení náskoku. Tato technologie nabízí cestu ke zdokonalení Chlazení baterií elektromobilů, lepší dojezd vozidla a vyšší celková spolehlivost systému, což představuje významný pokrok v oblasti bezpečnosti inovace v automobilovém průmyslu. Společnosti, které hledají spolehlivé aditivní výroba kovů řešení se stále častěji obracejí na zkušené partnery, kteří jsou schopni trvale dodávat vysoce kvalitní komponenty.
Společnost Met3dp, která je lídrem v oblasti AM technologií pro zpracování kovů, poskytuje komplexní řešení a využívá desítky let zkušeností v oblasti pokročilých tiskových technologií i vysoce výkonných materiálů. Náš závazek ke kvalitě, od výroby prášku až po finální ověření dílu, zajišťuje, že zákazníci z automobilového průmyslu dostanou komponenty, které splňují přísné požadavky průmyslu elektrických vozidel. Prozkoumejte, jak naše schopnosti mohou podpořit vaši novou generaci systémů tepelného řízení.
Kritická role chladicích rámů baterií v elektrických vozidlech
Akumulátor je pravděpodobně nejdůležitější a nejdražší součástí elektromobilu. Její stav a účinnost přímo určují dojezd, zrychlení, dobu nabíjení a celkovou životnost vozidla. Lithium-iontové baterie, které jsou v současnosti standardem pro elektromobily, jsou citlivé na výkyvy teplot. Provoz mimo jejich optimální teplotní okno (obvykle 15 °C až 35 °C) může vést ke zrychlené degradaci, snížení kapacity, riziku tepelného vyčerpání a ohrožení Výkon baterie elektromobilu. Efektivní systém tepelného managementu (BTMS) je proto nejen přínosný, ale i zásadní pro bezpečnost elektrických vozidel a spolehlivost.
The chladicí rám baterie často plní v rámci systému BTMS a celkové struktury akumulátoru více funkcí. Jeho hlavní funkcí je odvod tepla. Obvykle obsahuje kanálky nebo desky, kterými cirkuluje chladicí kapalina (kapalina nebo někdy vzduch), která pohlcuje přebytečné teplo z článků baterie a odvádí je do chladiče nebo výměníku tepla. Konstrukce těchto chladicích kanálů má zásadní význam pro zajištění rovnoměrného rozložení teploty ve všech buňkách, což zabraňuje vzniku lokálních horkých míst, která mohou způsobit degradaci nebo poruchu.
Kromě tepelné regulace může chladicí rám přispívat také ke strukturální integritě akumulátoru. Může tvořit součást krytu, chránit články před vnějšími nárazy a vibracemi a poskytovat montážní body pro další součásti. Tento aspekt strukturální integrace umožňuje odlehčení klíčovým faktorem návrhu. Snížení hmotnosti rámu přímo přispívá ke zlepšení celkové energetické účinnosti a dojezdu vozidla, což jsou klíčové parametry na konkurenčním trhu s elektromobily.
Funkce chladicího rámu baterie lze shrnout takto:
- Odvod tepla: Účinně odvádí teplo vznikající při provozu a nabíjení bateriových článků.
- Rovnoměrnost teploty: Zajištění konzistentních teplot v celém modulu baterie pro maximalizaci životnosti a výkonu.
- Strukturální podpora: Zajišťuje mechanickou podporu a ochranu článků baterie.
- Integrace komponent: Slouží jako montážní bod pro senzory, kabelové svazky a další součásti systému řízení baterie.
- Těsnění a uzavírání: Zabraňuje úniku chladicí kapaliny a chrání buňky před vlivy prostředí.
Vzhledem k těmto kritickým úlohám vyžaduje konstrukce a výroba chladicích rámů baterií vysokou přesnost, specifické vlastnosti materiálů (jako je vysoká tepelná vodivost a dobrý poměr pevnosti a hmotnosti) a složitou geometrii. Tradiční metody, jako je odlévání, vytlačování nebo obrábění, často narážejí na omezení při výrobě složitých vnitřních kanálků a tenkých stěn, které jsou nutné pro optimální tepelný výkon a nízkou hmotnost. Zde se uplatní jedinečné schopnosti výroba automobilových součástek prostřednictvím 3D tisku z kovu poskytují výraznou výhodu, umožňují konstrukce, které byly dříve považovány za nemožné, a zlepšují celkovou účinnost hnacího ústrojí. Manažeři veřejných zakázek, kteří hledají spolehlivé dodavatele těchto kritických komponent, musí zvážit výrobce s prokazatelnými zkušenostmi v oblasti pokročilých materiálů a procesů.
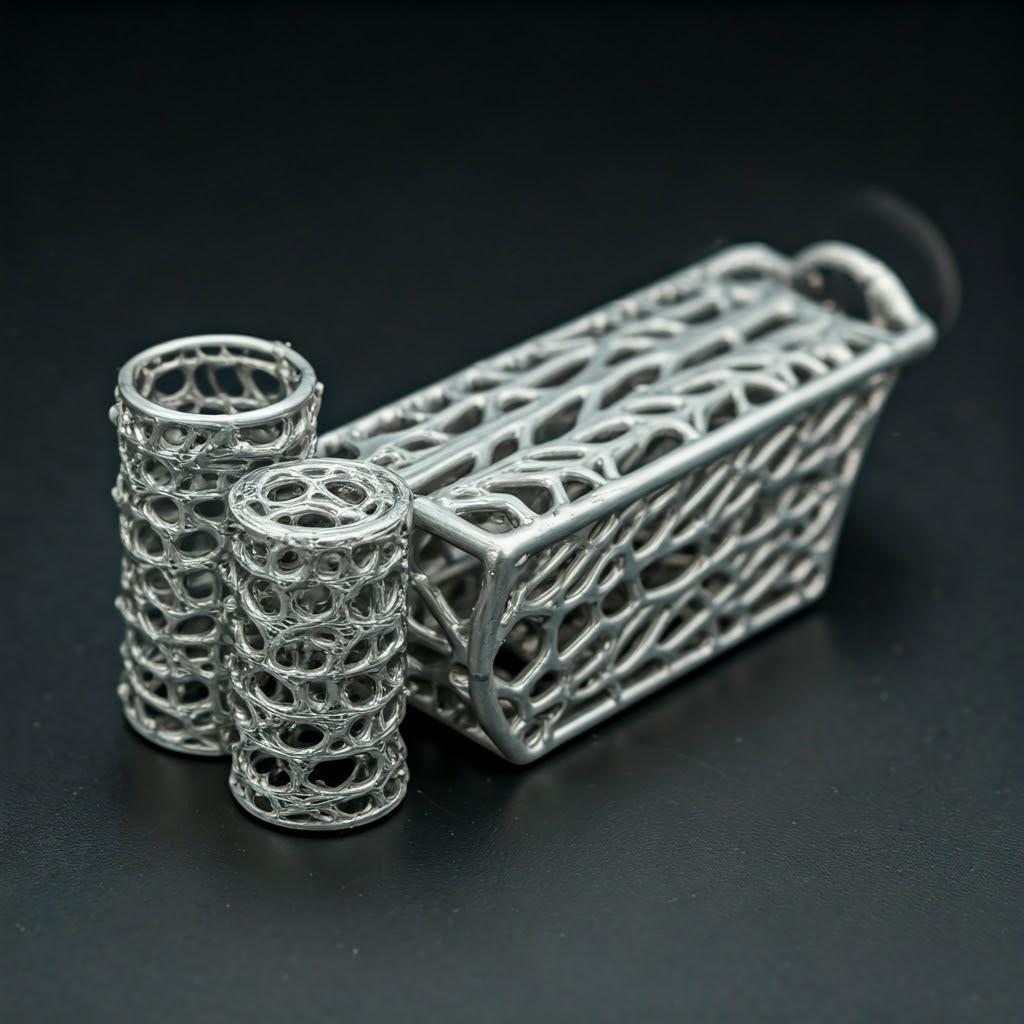
Proč je aditivní výroba kovů ideální pro komponenty chlazení baterií pro elektromobily
Přechod na elektrifikaci představuje pro výrobce automobilů významné technické výzvy, zejména v oblasti tepelného managementu a odlehčování. Aditivní výroba kovů nabízí přesvědčivá řešení těchto problémů a stává se tak stále atraktivnější možností pro výrobu komponent, jako jsou chladicí rámy baterií pro elektromobily. Výhody oproti tradičním výrobním metodám (odlévání, CNC obrábění, lisování, pájení) jsou četné a působivé:
- Bezkonkurenční volnost designu & Komplexnost:
- Složité chladicí kanály: Technologie AM umožňuje vytvářet velmi složité geometrie vnitřních chladicích kanálů, včetně konformních kanálů, které přesně kopírují obrysy bateriových článků, čímž se maximalizuje kontaktní plocha a účinnost přenosu tepla. Návrhy mohou obsahovat prvky, jako jsou turbulátory nebo optimalizované průtokové cesty, které je nemožné nebo neúměrně nákladné dosáhnout tradičními metodami. Přemýšlejte o mikrokanálech, proměnlivých průřezech a strukturách inspirovaných biotechnologiemi pro dosažení maximálního tepelného výkonu.
- Optimalizace topologie: Inženýři mohou pomocí výpočetních nástrojů optimalizovat konstrukci rámu a odstranit materiál z málo namáhaných oblastí a zároveň zesílit kritická místa. Výsledkem jsou výrazně lehčí díly (**lehké konstrukce**), aniž by byla narušena integrita konstrukce, což je pro prodloužení dojezdu elektromobilů klíčové.
- Konsolidace částí: Více komponent (např. rozdělovače průtoku, montážní konzoly, části rámu), které by se tradičně vyráběly odděleně a následně montovaly (často s nutností pájení nebo svařování, což může být příčinou poruch), lze integrovat a vytisknout jako jediný monolitický díl. Tím se snižuje doba montáže, náklady, hmotnost a potenciální netěsnosti, což vede k větší robustnosti konsolidované části.
- Zrychlený vývoj & Prototypování:
- Rychlá iterace: Metal AM umožňuje rychlé prototypování v automobilovém průmyslu komponenty přímo z dat CAD. Úpravy konstrukce chladicích kanálů nebo konstrukčních prvků lze realizovat a otestovat během několika dnů namísto týdnů nebo měsíců, které jsou nutné pro úpravy nástrojů při odlévání nebo vytlačování. To výrazně urychluje vývojový cyklus nových konstrukcí akumulátorů.
- Výroba bez nástrojů: AM eliminuje potřebu drahého a časově náročného nástrojového vybavení (formy, zápustky). To je výhodné zejména pro nízké až střední výrobní série, zakázkovou výrobu nebo výrobu starších dílů, u nichž již neexistuje původní nástrojové vybavení.
- Výhody materiálu a optimalizace:
- Pokročilé slitiny: Procesy AM mohou efektivně využívat vysoce výkonné slitiny vybrané speciálně pro jejich tepelnou vodivost (např. slitiny mědi) nebo poměr pevnosti a hmotnosti (např. slitiny hliníku), přesně přizpůsobené potřebám aplikace. Společnost Met3dp se specializuje na zpracování materiálů, jako je AlSi10Mg, a nabízí odborné znalosti při vývoji parametrů pro slitiny, jako je CuCrZr.
- Optimalizované použití materiálu: AM je aditivní proces, což znamená, že materiál se vkládá pouze tam, kde je to potřeba. To často vede k menšímu plýtvání materiálem ve srovnání se subtraktivními metodami, jako je CNC obrábění, což přispívá k úspoře nákladů a udržitelnosti.
- Flexibilita dodavatelského řetězce a výroba na vyžádání:
- Decentralizovaná výroba: Díly lze potenciálně vytisknout blíže k místu montáže, čímž se sníží přepravní náklady a doba realizace.
- Digitální inventář: Návrhy jsou uloženy v digitální podobě, což umožňuje tisknout díly na vyžádání a snižuje potřebu velkých fyzických zásob.
Zatímco tradiční metody jsou i nadále vhodné pro velmi velkosériovou výrobu jednodušších vzorů, unikátní výhody kovu AM - komplexnost, konsolidace, rychlost a optimalizace - je mimořádně vhodný pro náročné požadavky na chladicí rámy baterií nové generace pro elektromobily. Vzhledem k tomu, že průmysl usiluje o vyšší hustotu energie a rychlejší nabíjení, bude schopnost vytvářet vysoce optimalizované komponenty tepelného managementu pomocí AM stále důležitější. Výběr kompetentního 3D tisk z kovu klíčem k efektivnímu využití těchto výhod je partner, jako je Met3dp, s odbornými znalostmi v oblasti příslušných materiálů a procesů.
Hloubkový ponor do materiálů: AlSi10Mg a CuCrZr pro optimální tepelný výkon
Volba materiálu je pro výkonnost chladicího rámu baterie elektromobilu zásadní. Materiál musí mít kombinaci vlastností: vysokou tepelnou vodivost, aby účinně odváděl teplo od článků, dobrou mechanickou pevnost, aby zvládl konstrukční zatížení a vibrace, nízkou hustotu pro odlehčení, odolnost proti korozi chladicími kapalinami a vynikající zpracovatelnost prostřednictvím aditivní výroby. Dva výrazní kandidáti, kteří jsou pro tuto aplikaci často zvažováni, jsou AlSi10Mg (slitina hliníku) a CuCrZr (slitina mědi). Pochopení jejich příslušných silných a slabých stránek je zásadní pro výběr materiálů pro automobilový průmysl.
1. AlSi10Mg (slitina hliníku, křemíku a hořčíku): Lehký pracovní kůň
AlSi10Mg je jednou z nejpoužívanějších hliníkových slitin při aditivní výrobě kovů, zejména při laserové práškové fúzi (LPBF). Jeho obliba pramení z vynikající rovnováhy vlastností a dobré zpracovatelnosti.
- Vlastnosti:
- Dobrá tepelná vodivost: Přestože AlSi10Mg nemá tak vysokou tepelnou vodivost jako čistý hliník nebo slitiny mědi, nabízí slušnou tepelnou vodivost (obvykle 120-140 W/m-K po tepelném zpracování), která je dostatečná pro mnoho aplikací kapalinového chlazení.
- Vynikající poměr pevnosti k hmotnosti: To je velká výhoda. Hliníkové slitiny jsou výrazně lehčí než ocel nebo měď, což přímo přispívá k odlehčení vozidla a zvýšení dojezdu. AlSi10Mg nabízí dobrou mechanickou pevnost a tvrdost, zejména po vhodném tepelném zpracování.
- Dobrá odolnost proti korozi: Hliník přirozeně vytváří ochrannou vrstvu oxidů, která zajišťuje slušnou odolnost vůči běžným automobilovým chladicím kapalinám.
- Vynikající tisknutelnost: AlSi10Mg je dobře známý a relativně snadno zpracovatelný systém LPBF, který vykazuje dobrou stabilitu v bazénu taveniny a výsledkem jsou husté díly.
- Efektivita nákladů: V porovnání se slitinami mědi jsou hliníkové prášky obecně cenově výhodnější.
- Vhodnost pro chladicí rámy: AlSi10Mg je vynikající volbou, pokud je hlavním požadavkem odlehčení a tepelné zatížení je zvládnutelné. Jeho zpracovatelnost umožňuje vytvářet složité geometrie potřebné pro účinné chladicí kanály. Často je výchozí volbou pro konstrukční součásti s integrovanými chladicími funkcemi. Pro dosažení optimálních mechanických vlastností je obvykle nutné následné zpracování, včetně tepelného zpracování (např. stárnutí T6).
- Nabídka Met3dp’s: Společnost Met3dp má rozsáhlé zkušenosti se zpracováním prášku AlSi10Mg a využívá pokročilé techniky plynové atomizace k výrobě vysoce sférických prášků s vynikající tekutostí, která je klíčová pro dosažení konzistentní hustoty a mechanických vlastností tištěných dílů. Naše přísná kontrola kvality zajišťuje, že šarže prášku splňují přísné specifikace pro automobilový průmysl.
Tabulka: AlSi10Mg (typické hodnoty pro AM)
Vlastnictví | Typická hodnota (po tepelném zpracování) | Jednotka | Význam pro chladicí rámy |
---|---|---|---|
Hustota | ~2.67 | g/cm³ | Vynikající pro odlehčování |
Tepelná vodivost | 120 – 140 | W/(m-K) | Dobrá schopnost odvodu tepla |
Mez kluzu | 230 – 280 | MPa | Dobrá strukturální integrita |
Maximální pevnost v tahu | 330 – 400 | MPa | Odolnost proti mechanickému zatížení |
Prodloužení po přetržení | 6 – 10 | % | Tažnost, odolnost proti lomu |
Možnost tisku | Vynikající | N/A | Umožňuje komplexní návrhy, spolehlivou výrobu |
Relativní náklady | Mírný | N/A | Nákladově efektivní řešení |
Export do archů
2. CuCrZr (slitina mědi, chromu a zirkonia): Šampion tepelné vodivosti
Pokud je absolutní prioritou maximální odvod tepla, přicházejí na řadu slitiny mědi jako CuCrZr. Měď se může pochlubit výrazně vyšší tepelnou vodivostí než hliník.
- Vlastnosti:
- Výjimečná tepelná vodivost: To je hlavní výhoda CuCrZr. Jeho tepelná vodivost (obvykle >300 W/m-K) je více než dvojnásobná oproti AlSi10Mg, což umožňuje mimořádně účinný přenos tepla, který je zásadní pro vysoce výkonné akumulátory nebo scénáře rychlého nabíjení.
- Dobrá odolnost při vysokých teplotách: CuCrZr si ve srovnání s čistou mědí zachovává přiměřenou pevnost při zvýšených teplotách.
- Dobrá elektrická vodivost: Ačkoli je pro chladicí rámy méně důležitý, jeho vysoká elektrická vodivost je pozoruhodná.
- Vyšší hustota: Slitiny mědi jsou výrazně hustší (~8,9 g/cm³) než slitiny hliníku, což představuje výzvu pro cíle odlehčení. Hmotnostní postih musí být odůvodněn lepšími tepelnými vlastnostmi.
- Výzvy při zpracování: Měděné slitiny jsou notoricky známé jako náročnější pro zpracování pomocí laserového AM kvůli své vysoké odrazivosti a tepelné vodivosti, což může vést k nestabilitě procesu a vadám, jako je pórovitost, pokud se s nimi nepracuje s odbornými znalostmi a optimalizovaným vybavením. Tavení elektronovým svazkem (EBM/SEBM), jako jsou systémy potenciálně nabízené nebo využívané partnery Met3dp, může někdy nabídnout výhody pro zpracování mědi díky lepší absorpci energie.
- Vyšší náklady: Prášky ze slitin mědi jsou obecně dražší než prášky ze slitin hliníku.
- Vhodnost pro chladicí rámy: CuCrZr je preferovaným materiálem, pokud je tepelný výkon nejdůležitější a převažuje nad obavami z vyšší hmotnosti a nákladů. Je ideální pro lokalizované oblasti s vysokým tepelným tokem nebo náročné aplikace vyžadující rychlý odvod velkého množství tepla. Konstrukce musí využívat tepelné vlastnosti materiálu, aby bylo jeho použití opodstatněné, což často vyžaduje vysoce optimalizované tenkostěnné struktury dosažitelné pomocí AM.
- Přístup společnosti Met3dp’: Zatímco slitiny mědi představují výzvu, společnost Met3dp se díky svému zaměření na pokročilou výrobu prášků a řízení procesů prostřednictvím svých Tiskárny a odborné znalosti SEBM umožňuje zpracovávat náročné materiály. Úzce spolupracujeme s klienty na stanovení proveditelnosti a optimalizaci parametrů materiálů, jako je CuCrZr, a zajišťujeme, aby díly splňovaly přísné tepelné a mechanické požadavky. Klíčový je přístup k vysoce kvalitnímu, plynem atomizovanému prášku CuCrZr s kontrolovanými vlastnostmi, což je oblast, kde Met3dp’s pokročilý systém výroby prášku vyniká.
Tabulka: CuCrZr Vlastnosti (typické hodnoty pro AM)
Vlastnictví | Typická hodnota (po tepelném zpracování) | Jednotka | Význam pro chladicí rámy |
---|---|---|---|
Hustota | ~8.9 | g/cm³ | Výrazná hmotnostní nevýhoda oproti hliníku |
Tepelná vodivost | >300 | W/(m-K) | Výjimečná schopnost odvádět teplo |
Mez kluzu | 350 – 450 | MPa | Dobrá mechanická pevnost |
Maximální pevnost v tahu | 450 – 550 | MPa | Vysoká odolnost |
Prodloužení po přetržení | 10 – 20 | % | Dobrá tažnost |
Možnost tisku | Náročné (vyžaduje odbornost) | N/A | Řízení procesu je pro kvalitu dílů zásadní |
Relativní náklady | Vysoký | N/A | Náklady odůvodněné potřebami výkonu |
Export do archů
Závěr o materiálech:
Volba mezi AlSi10Mg a CuCrZr závisí do značné míry na konkrétních požadavcích aplikace chladicího rámu baterie pro elektromobily.
- Vyberte si AlSi 10Mg pokud: Pokud je kriticky důležité odlehčení, tepelné zatížení je mírné, cena je hlavním faktorem a je požadováno snadné zpracování.
- Vyberte si CuCrZr pokud: Pokud je hlavním cílem maximální odvod tepla, vyšší hmotnost je přijatelná a rozpočet umožňuje použití kvalitnějšího materiálu a případně složitější zpracování.
Často lze uvažovat o hybridních přístupech nebo lokalizovaném použití měděných vložek v hliníkovém rámu, ačkoli AM umožňuje monolitické konstrukce z obou materiálů. Práce s dodavatel vysoce výkonných slitin a odborník na AM, jako je Met3dp, zajistí, že výběr materiálu bude optimalizován z hlediska výkonu, nákladů a vyrobitelnosti, a využije tak plný potenciál kovového 3D tisku pro pokročilý tepelný management elektromobilů.
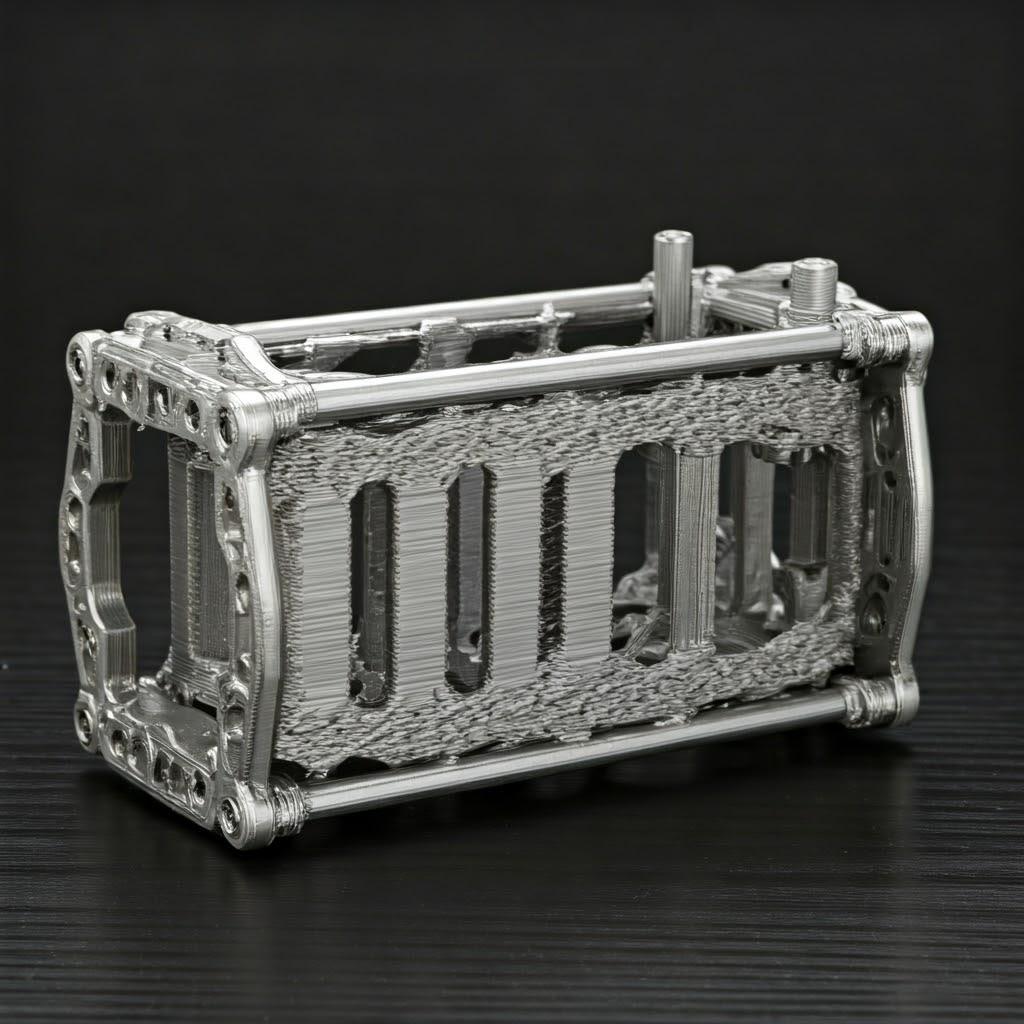
Principy návrhu pro aditivní výrobu (DfAM) pro chladicí rámy baterií
Pouhá replikace návrhu určeného pro tradiční výrobu pomocí 3D tisku z kovu jen zřídkakdy uvolní plný potenciál aditivní technologie. Aby inženýři skutečně využili výhod AM pro komponenty, jako jsou chladicí rámy baterií pro elektromobily, musí přijmout následující opatření Design pro aditivní výrobu (DfAM) zásady. DfAM zahrnuje přehodnocení procesu návrhu tak, aby se maximalizovaly výhody, které nabízí výroba po vrstvách, jako je geometrická složitost, konsolidace dílů a odlehčení, a zároveň se zohlednila omezení konkrétního procesu AM (např. laserové tavení v práškovém loži – LPBF nebo selektivní tavení elektronovým svazkem – SEBM). Použití Automobilový průmysl DfAM strategie je zásadní pro vývoj vysoce výkonných a nákladově efektivních řešení chlazení.
Mezi klíčové zásady DfAM, které se týkají chladicích rámů baterií pro elektromobily, patří:
- Optimalizace vnitřních chladicích kanálů:
- Složité geometrie: Překročte rámec jednoduchých rovných nebo kruhových kanálů. AM umožňuje hladce zakřivené dráhy, variabilní průřezy a konformní kanály, které přesně kopírují tvar bateriových článků nebo modulů. Tím se maximalizuje kontaktní plocha pro přenos tepla a může se snížit tlaková ztráta.
- Funkce optimalizace toku: Integrujte prvky, jako jsou vnitřní žebra, turbulátory nebo optimalizované rozdělovače, přímo do konstrukce, abyste zvýšili míchání chladicí kapaliny a účinnost přenosu tepla. Výpočetní simulace dynamiky tekutin (CFD) se stávají mocným nástrojem v kombinaci s geometrickou volností AM pro optimalizace chladicích kanálů.
- Samonosné kanály: Navrhněte vnitřní kanály s průřezy (např. slza, kosočtverec) a orientací, které minimalizují nebo eliminují potřebu vnitřních podpůrných konstrukcí, jejichž odstranění po tisku může být velmi obtížné nebo nemožné. Úhly větší než 45 stupňů od vodorovné roviny jsou obecně samonosné.
- Strategie odlehčování:
- Optimalizace topologie: Využijte softwarové nástroje k analýze konstrukčního zatížení rámu a automatickému odstranění materiálu z nekritických oblastí, což vede k organicky vypadajícím a vysoce efektivním konstrukcím. To je základním kamenem lehká konstrukce součástí pro elektromobily.
- Mřížové struktury: V silnějších částech rámu zabudujte vnitřní mřížové nebo buněčné struktury. Tyto struktury výrazně snižují hmotnost a spotřebu materiálu při zachování požadované tuhosti a pevnosti. Mohou také potenciálně zvýšit výkonnost při nárazu díky absorpci energie.
- Tenké stěny: AM umožňuje vytvářet velmi tenké, ale přesto konstrukčně pevné stěny (až do tloušťky cca 0,3-0,5 mm v závislosti na materiálu a stroji), což dále snižuje hmotnost ve srovnání s minimálními tloušťkami stěn dosažitelnými při odlévání.
- Konsolidace částí:
- Integrované funkce: Navrhněte montážní konzoly, kryty snímačů, průtokové konektory a konstrukční prvky jako nedílné součásti chladicího rámu. Tím se eliminují montážní kroky, snižuje se počet dílů, minimalizují se potenciální místa úniku (jako jsou těsnění nebo pájené spoje) a často se snižuje celková hmotnost a náklady.
- Minimalizace podpůrných struktur:
- Orientace: Pečlivě zvažte orientaci dílu na konstrukční desce. Orientace prvků tak, aby byly samonosné (zpravidla s přesahem >45°), snižuje objem potřebných podpůrných konstrukcí.
- Optimalizace podpory: Tam, kde se podpěrám nelze vyhnout (např. velké ploché spodní strany), navrhněte je tak, aby se daly snadno odstranit a měly minimální dopad na kritické povrchy. Využijte specializované typy podpěr (např. stromové podpěry, blokové podpěry), které nabízí software pro přípravu AM.
- Snížení stresu: Zvažte, jak geometrie a orientace dílu ovlivňují vznik zbytkového napětí během tisku. Velké rovné plochy nebo náhlé přechody mohou zvyšovat napětí a možnost deformace.
- Úvahy specifické pro daný proces:
- Minimální velikost prvku: Pochopení limitů rozlišení zvoleného procesu AM (LPBF obvykle nabízí jemnější rysy než SEBM). Ujistěte se, že kritické prvky, jako jsou tenké stěny nebo malé detaily kanálů, jsou v rámci možností stroje.
- Odstranění prášku: Zajistěte, aby konstrukce obsahovala cesty nebo otvory, které umožní snadné odstranění nerozpuštěného prášku z vnitřních kanálků a dutin po tisku. Zachycený prášek může zvýšit hmotnost a potenciálně narušit provoz.
Uplatněním těchto zásad DfAM mohou konstruktéři překročit rámec postupných zlepšení a dosáhnout zásadních změn v oblasti chladicího výkonu, snížení hmotnosti a integrace součástí. Spolupráce s odborníkem na AM, jako je Met3dp, ve fázi návrhu může poskytnout neocenitelné poznatky o možnostech a omezeních procesu a zajistit optimalizaci návrhu z hlediska vyrobitelnosti a výkonu. Tým společnosti Met3dp může pomoci s DfAM, přičemž využije různých tiskových metod aby co nejlépe vyhovoval specifickým požadavkům chladicího rámu baterie vašeho elektromobilu.
Dosažení přesnosti: Přesnost: tolerance, povrchová úprava a přesnost při AM zpracování kovů
Přestože aditivní výroba kovů nabízí nebývalou volnost při navrhování, je pro konstruktéry a manažery nákupu zásadní, aby si uvědomili, jaké úrovně přesnosti lze dosáhnout, pokud jde o rozměrovou přesnost, tolerance a povrchovou úpravu. Tyto faktory přímo ovlivňují funkčnost, montáž a výkonnost chladicích rámů baterií pro elektromobily, zejména pokud jde o těsnicí povrchy, rozhraní s moduly baterií a charakteristiky proudění chladicí kapaliny. Dosažení požadovaných tolerance 3D tisku kovů a normy pro povrchovou úpravu v automobilovém průmyslu aplikací vyžaduje pečlivou kontrolu nad celým pracovním postupem AM.
Rozměrová přesnost a tolerance:
Přesnost kovového dílu AM znamená, jak přesně se jeho konečné rozměry shodují s původním modelem CAD. Tolerance definují přípustné odchylky pro konkrétní rozměry. Typická dosažitelná přesnost a tolerance závisí na několika faktorech:
- AM proces: LPBF obecně nabízí vyšší přesnost a jemnější detaily ve srovnání se SEBM, i když SEBM může být pro určité geometrie a materiály rychlejší.
- Kalibrace stroje: Přesnost a kalibrace 3D tiskárny jsou velmi důležité. Zásadní jsou dobře udržované, vysoce kvalitní stroje, jaké používá společnost Met3dp.
- Materiál: Různé materiály se během tavení a tuhnutí chovají různě, což ovlivňuje jejich smršťování a případné deformace. AlSi10Mg a CuCrZr mají různé tepelné vlastnosti, které ovlivňují konečnou přesnost.
- Velikost a geometrie dílu: Větší díly nebo složité geometrie jsou náchylnější k tepelnému namáhání a možným odchylkám.
- Orientace na stavbu: Orientace dílu na konstrukční desce ovlivňuje přesnost kvůli anizotropní povaze procesu po vrstvách.
- Následné zpracování: Kroky, jako je tepelné zpracování, mohou způsobit drobné rozměrové změny, zatímco obrábění CNC se často používá k dosažení velmi přísných tolerancí u kritických prvků.
Typické hodnoty:
- Obecné tolerance (podle tisku): U dobře řízených procesů LPBF se obecné rozměrové tolerance často pohybují v rozmezí ±0,1 mm až ±0,2 mm u menších prvků (např. do 50-100 mm), případně se mírně zvyšují u větších rozměrů (např. ±0,2 % jmenovitého rozměru).
- Přísnější tolerance (s obráběním): U kritických rozhraní, montážních bodů nebo těsnicích ploch vyžadujících přísnější kontrolu se obvykle používá následné CNC obrábění. Obráběním lze snadno dosáhnout tolerancí ±0,025 mm až ±0,05 mm nebo ještě těsnějších, což odpovídá běžným výrobním standardům.
Povrchová úprava (drsnost):
Dalším zásadním aspektem, zejména u vnitřních chladicích kanálů a těsnicích povrchů, je kvalita povrchu, která se často udává pomocí aritmetického průměru drsnosti (Ra).
- Drsnost povrchu po vytištění: Povrchová úprava dílů AM je ze své podstaty drsnější než u obráběných povrchů, a to v důsledku vrstvení a ulpívání částečně roztavených částic prášku na povrchu.
- Vrchní plochy: Obecně hladší (Ra 5-10 µm).
- Svislé stěny: Střední drsnost (Ra 8-15 µm).
- Povrchy směřující nahoru/dolů: Drsnost závisí do značné míry na úhlu vzhledem ke stavební desce. Povrchy směřující dolů (<45°) vyžadují podpůrné struktury a jejich odstranění zanechává stopy po svědcích, což výrazně zvyšuje drsnost (Ra > 15-20 µm).
- Interní kanály: Drsnost uvnitř úzkých nebo složitých vnitřních kanálů je obzvláště náročná na kontrolu a zlepšení. Drsnost může ovlivnit dynamiku kapaliny a potenciálně zvýšit tlakové ztráty nebo ovlivnit koeficienty přenosu tepla. Roli zde hrají úvahy DfAM (např. tvar kanálu, orientace).
- Zlepšení povrchové úpravy: Pro dosažení hladších povrchů jsou zásadní metody následného zpracování:
- Obrábění abrazivním tokem (AFM): Lze použít k vyhlazení vnitřních kanálků.
- Otryskávání kuličkami/pískování: Poskytuje jednotný matný povrch a odstraňuje sypký pudr, ale jen mírně redukuje Ra.
- Třískové/vibrační dokončování: Efektivní pro vyhlazení vnějších povrchů menších dílů.
- Leštění: Ruční nebo automatizované leštění pro dosažení velmi hladkého, zrcadlového povrchu (Ra < 0,8 µm) na specifických plochách.
- Obrábění: Poskytuje nejlepší kontrolu povrchové úpravy na přístupných prvcích.
Kontrola kvality:
Zajištění konzistentního rozměrová přesnost kovu AM dílů vyžaduje přísnou kontrolu kvality v průběhu celého procesu. To zahrnuje:
- Ověřování kvality prášku.
- Pravidelná kalibrace a údržba stroje.
- Monitorování během procesu (např. monitorování taveniny).
- Kontrola rozměrů po sestavení pomocí souřadnicových měřicích strojů (CMM) nebo 3D skenování.
- Měření drsnosti povrchu.
Společnost Met3dp klade velký důraz na kontrolu kvality a využívá pokročilé metrologické vybavení a přísné monitorování procesů, aby zajistila, že chladicí rámy baterií pro elektromobily splňují přesné specifikace požadované zákazníky z automobilového průmyslu. Pochopení dosažitelné přesnosti a plánování nezbytných kroků následného zpracování je klíčovou součástí procesu zadávání zakázek pro 3D tisk z kovu komponenty.

Základní kroky následného zpracování 3D tištěných chladicích rámů
Kovové 3D tištěné díly, včetně chladicích rámů baterií pro elektromobily z AlSi10Mg nebo CuCrZr, se z tiskárny málokdy sundávají připravené ke konečnému použití. Následné zpracování je kritickou fází výrobního procesu, která je nezbytná k dosažení požadovaných vlastností materiálu, rozměrových tolerancí, povrchové úpravy a celkové funkčnosti. Pochopení těchto kroků je pro manažery nákupu a inženýry zásadní při plánování výrobních harmonogramů a odhadování nákladů.
Mezi běžné kroky následného zpracování kovových chladicích rámů baterií AM patří:
- Úleva od stresu / tepelné ošetření:
- Účel: Rychlé cykly ohřevu a chlazení, které jsou vlastní procesům AM (zejména LPBF), vyvolávají v tištěném dílu vnitřní pnutí. Tato zbytková napětí mohou způsobit deformace nebo praskliny během tisku, odstraňování podpěr nebo později v průběhu životního cyklu dílu. Tepelné zpracování tato napětí zmírňuje a, což je důležité, upravuje mikrostrukturu materiálu, aby se dosáhlo požadovaných mechanických vlastností (pevnost, tvrdost, tažnost).
- Postup:
- Úleva od stresu: Obvykle se provádí, když je díl ještě připevněn k desce, a zahrnuje zahřátí dílu na určitou teplotu (pod teplotu stárnutí pro AlSi10Mg) a jeho udržování po stanovenou dobu, po níž následuje pomalé ochlazení.
- Žíhání v roztoku a stárnutí (např. T6 pro AlSi10Mg): U slitin, jako je AlSi10Mg, je pro výrazné zvýšení pevnosti a tvrdosti často nutné vícestupňové tepelné zpracování (rozpuštění při vysoké teplotě, kalení a následné umělé stárnutí při nižší teplotě). Specifické tepelné zpracování AlSi10Mg cyklů závisí na požadovaných konečných vlastnostech. Pro optimalizaci pevnosti a vodivosti CuCrZr se rovněž využívá specifické tepelné zpracování.
- Úvahy: Tepelné zpracování musí být pečlivě řízeno (atmosféra, teplotní náběhy, doby udržování), aby bylo dosaženo konzistentních výsledků. Může způsobit mírné rozměrové změny, které je třeba zohlednit.
- Vyjmutí dílu ze stavební desky:
- Účel: Oddělení vytištěné součásti (součástí) od kovové konstrukční desky, na kterou byly během tisku nataveny.
- Postup: Obvykle se provádí pomocí elektroerozivního obrábění (EDM) nebo pásové pily. Je třeba dbát na to, aby nedošlo k poškození dílu.
- Odstranění podpůrné konstrukce:
- Účel: Odstranění dočasných konstrukcí vytištěných pro podporu převisů a složitých prvků během procesu výstavby.
- Postup: To může být náročný a pracný krok, zejména u složitých vnitřních geometrií. Mezi tyto metody patří:
- Ruční odstranění pomocí kleští, štípacích kleští nebo brusky.
- CNC obrábění.
- Někdy elektrochemické obrábění nebo jiné metody pro těžko přístupná místa.
- Úvahy: Odstranění podpory může na povrchu zanechat stopy nebo otřepy, což často vyžaduje další dokončovací kroky. DfAM hraje zásadní roli při minimalizaci potřeby podpěr a jejich konstrukci pro snadnější odstraňování.
- CNC obrábění:
- Účel: K dosažení přísných tolerancí u kritických rozměrů, vytvoření přesných styčných ploch, zajištění rovinnosti pro těsnění nebo zlepšení kvality povrchu u specifických prvků.
- Postup: Použití standardních CNC frézovacích nebo soustružnických operací pro obrábění specifických oblastí AM dílu.
- Aplikace: Obrábění otvorů pro šrouby na přesné průměry a polohy, vytváření drážek pro O-kroužky, zplošťování těsnicích ploch, dosažení specifických hodnot Ra na styčných prvcích. CNC obrábění kovových dílů AM je pro funkční komponenty velmi běžný.
- Povrchová úprava & Čištění:
- Účel: K odstranění volného prášku, zlepšení hladkosti povrchu, dosažení požadovaného estetického vzhledu nebo přípravě povrchu pro lakování.
- Postupy:
- Odstranění prášku: Odprašování pomocí stlačeného vzduchu, vibrací nebo specializovaného zařízení, které je zvláště důležité pro vnitřní kanály.
- Odstřelování: Tryskáním kuličkami nebo pískováním se vytvoří jednotný matný povrch.
- Třískové/vibrační dokončování: Vyhlazuje vnější povrchy a hrany.
- Leštění: Pro velmi nízké hodnoty Ra na specifických plochách.
- Obrábění abrazivním tokem (AFM) / Extrude Hone: Používá se k vyhlazování vnitřních kanálků prouděním abrazivního média.
- Testování těsnosti:
- Účel: Naprosto zásadní pro všechny součásti určené k přenášení chladicí kapaliny. Zajišťuje integritu chladicích kanálů a zabraňuje únikům.
- Postup: Zahrnuje zvýšení tlaku v chladicích kanálech (obvykle vzduchem nebo heliem pod vodou nebo pomocí snímačů poklesu tlaku), aby se zjistily případné netěsnosti nebo pórovitost, která narušuje stěny kanálu. Testování těsnosti chladicích systémů je neoddiskutovatelným krokem k zajištění kvality.
- Kontrola a řízení kvality:
- Účel: Ověření, zda díl splňuje všechny rozměrové, materiálové a funkční specifikace.
- Postup: Rozměrová kontrola (CMM, 3D skenování), měření drsnosti povrchu, testování vlastností materiálu (v případě potřeby), závěrečná vizuální kontrola.
Konkrétní služby následného zpracování závisí na složitosti konstrukce chladicího rámu, použitém materiálu a specifických požadavcích aplikace. Spolupráce s poskytovatelem komplexních služeb, jako je společnost Met3dp, která rozumí složitostem tisku i následného zpracování, zajišťuje zefektivnění pracovního postupu a vysoce kvalitní finální komponenty připravené k integraci do baterií pro elektromobily.
Překonávání problémů při 3D tisku kovů pro automobilové aplikace
Ačkoli aditivní výroba kovů nabízí významné výhody pro výrobu složitých součástí, jako jsou chladicí rámy baterií pro elektromobily, není bez problémů. Úspěšná implementace AM pro náročné aplikace v automobilovém průmyslu vyžaduje odborné znalosti, pečlivou kontrolu procesu a pochopení možných úskalí. Proaktivní řešení těchto problémů je klíčem k zajištění kvality, spolehlivosti a nákladové efektivity dílů.
Mezi běžné problémy a strategie jejich zmírnění patří:
- Zbytkové napětí a deformace:
- Výzva: Rychlé, lokalizované zahřívání a ochlazování, které je vlastní procesům tavení v práškovém loži, vytváří tepelné gradienty, které vedou k vnitřním pnutím uvnitř dílu. Nadměrné zbytkové napětí kovu AM dílů může způsobit deformaci během sestavování, deformaci po vyjmutí ze sestavovací desky nebo dokonce prasknutí. Velké ploché úseky nebo ostré geometrické přechody tento problém ještě zhoršují.
- Zmírnění:
- DfAM: Navrhování dílů s prvky snižujícími napětí (např. vyhýbání se velkým plným blokům, používání mřížových struktur, přidávání obětovaných žeber).
- Strategie budování: Optimalizace orientace dílu, použití vhodných podpůrných struktur (které rovněž pomáhají ukotvit díl a odvádět teplo) a optimalizace strategií skenování laserem/elektronovým paprskem.
- Parametry procesu: Jemné doladění parametrů, jako je tloušťka vrstvy, příkon energie a ohřev platformy (důležité zejména u SEBM).
- Následné zpracování: Provádění účinných tepelných úprav pro uvolnění napětí ihned po tisku, často před vyjmutím dílu z konstrukční desky.
- Pórovitost:
- Výzva: V tištěném materiálu mohou vznikat malé dutiny nebo póry v důsledku zachyceného plynu, neúplného splynutí mezi vrstvami nebo jevu keyholing (propadání parních prohlubní). Pórovitost může zhoršit mechanické vlastnosti (zejména únavovou životnost) a, což je kritické pro chladicí rámy, může vytvořit netěsné cesty, pokud se póry propojí nebo naruší povrch.
- Zmírnění:
- Kvalita prášku: Použití vysoce kvalitních sférických kovových prášků s nízkou vnitřní pórovitostí a řízenou distribucí velikosti částic, jako jsou prášky vyráběné pomocí pokročilé plynové atomizace Met3dp’. Zajištění správné manipulace s práškem a jeho skladování, aby se zabránilo absorpci vlhkosti.
- Optimalizace parametrů: Vývoj a ověřování robustních procesních parametrů (výkon laseru, rychlost skenování, vzdálenost mezi šrafami, tloušťka vrstvy) specifických pro materiál a stroj, aby bylo zajištěno úplné roztavení a tavení. Společnost Met3dp investuje do vývoje procesních parametrů velké prostředky.
- Monitorování procesů: Využití monitorovacích systémů in-situ (např. monitorování taveniny) k odhalení případných anomálií během výstavby.
- Následné zpracování: K uzavření vnitřních pórů lze v některých případech použít izostatické lisování za tepla (HIP), které však zvyšuje náklady a složitost. Pro zjištění kritické pórovitosti je nezbytné provést řádné zkoušky těsnosti.
- Odstranění podpůrné konstrukce:
- Výzva: Podpůrné konstrukce jsou sice nezbytné, ale zvyšují časovou náročnost a náklady jak ve fázi tisku, tak ve fázi následného zpracování. Jejich odstraňování, zejména ze složitých vnitřních kanálů nebo jemných prvků, může být obtížné, pracné a hrozí při něm poškození povrchu dílu.
- Zmírnění:
- DfAM: Navrhování samonosných úhlů (>45°) všude, kde je to možné, optimalizace tvarů vnitřních kanálů a strategická orientace dílu.
- Podpora designu: Použití specializovaných softwarových funkcí pro generování podpěr, které jsou účinné a zároveň se snadněji odstraňují (např. tenčí kontaktní body, perforované struktury).
- Techniky následného zpracování: Použití vhodných metod odstraňování (ruční, CNC, případně elektrochemické) na základě umístění podpěry a geometrie dílu.
- Povrchová úprava:
- Výzva: Přirozená vrstevnatost a přilnavost prášku vedou k drsnějšímu povrchu ve srovnání s tradičním obráběním. To může být problematické u těsnicích povrchů nebo uvnitř chladicích kanálů, kde to ovlivňuje proudění kapaliny.
- Zmírnění:
- Optimalizace parametrů: Jemným doladěním parametrů lze mírně zlepšit kvalitu povrchu.
- Orientace: Optimální orientace kritických ploch na konstrukční desce.
- Následné zpracování: Provedení nezbytných dokončovacích kroků, jako je obrábění, leštění, tryskání nebo AFM, jak bylo uvedeno výše.
- Konzistence a škálovatelnost:
- Výzva: Zajištění konzistentní kvality dílů ve více sestavách a na různých strojích a efektivní rozšiřování výroby pro splnění požadavků na objem výroby v automobilovém průmyslu vyžaduje robustní systémy řízení procesů a kvality.
- Zmírnění:
- Standardizace: Zavedení standardizovaných pracovních postupů, důsledné kalibrace strojů a konzistentních protokolů pro správu prášků.
- Systémy řízení kvality: Dodržování příslušných certifikací (např. ISO 9001, případně IATF 16949 pro dodavatele v automobilovém průmyslu).
- Monitorování procesů & Analýza dat: Průběžné sledování údajů o sestavení s cílem zajistit konzistenci a identifikovat případné odchylky.
- Partnerství: Spolupráce se zkušenými poskytovateli AM, jako je Met3dp, kteří mají zavedené systémy kvality a zkušenosti s rozšiřováním výroby.
- Náklady:
- Výzva: V porovnání s tradičními metodami může mít AM obrábění kovů vyšší počáteční náklady na jeden díl, zejména u jednoduchých konstrukcí ve velkých objemech, a to kvůli investicím do strojů, nákladům na materiál a časové náročnosti procesu.
- Zmírnění:
- DfAM: Využití konsolidace dílů a odlehčení ke kompenzaci nákladů díky zkrácení doby montáže a snížení spotřeby materiálu.
- Optimalizace procesů: Minimalizace doby výstavby a podpůrných struktur.
- Objem: S rostoucím objemem výroby výrazně klesají náklady na jeden díl.
- Celkové náklady na vlastnictví: Vezměte v úvahu úspory plynoucí z rychlejšího vývoje, vyššího výkonu a flexibility dodavatelského řetězce, nejen náklady na jednotlivé díly.
Překonání těchto výzev vyžaduje hluboké znalosti materiálových věd, fyziky procesů AM, principů DfAM a důslednou kontrolu kvality. Spolupráce se zkušeným 3D tisk z kovu poskytovatel služeb, jako je Met3dp, který disponuje potřebnou technologií, odbornými znalostmi a odhodláním zajištění kvality v automobilovém průmyslu AM je zásadní pro úspěšné zavedení technologie AM pro kritické součásti, jako jsou chladicí rámy baterií pro elektromobily. Náš tým spolupracuje s klienty, aby se s těmito složitostmi vypořádal a poskytl optimalizovaná a spolehlivá řešení.
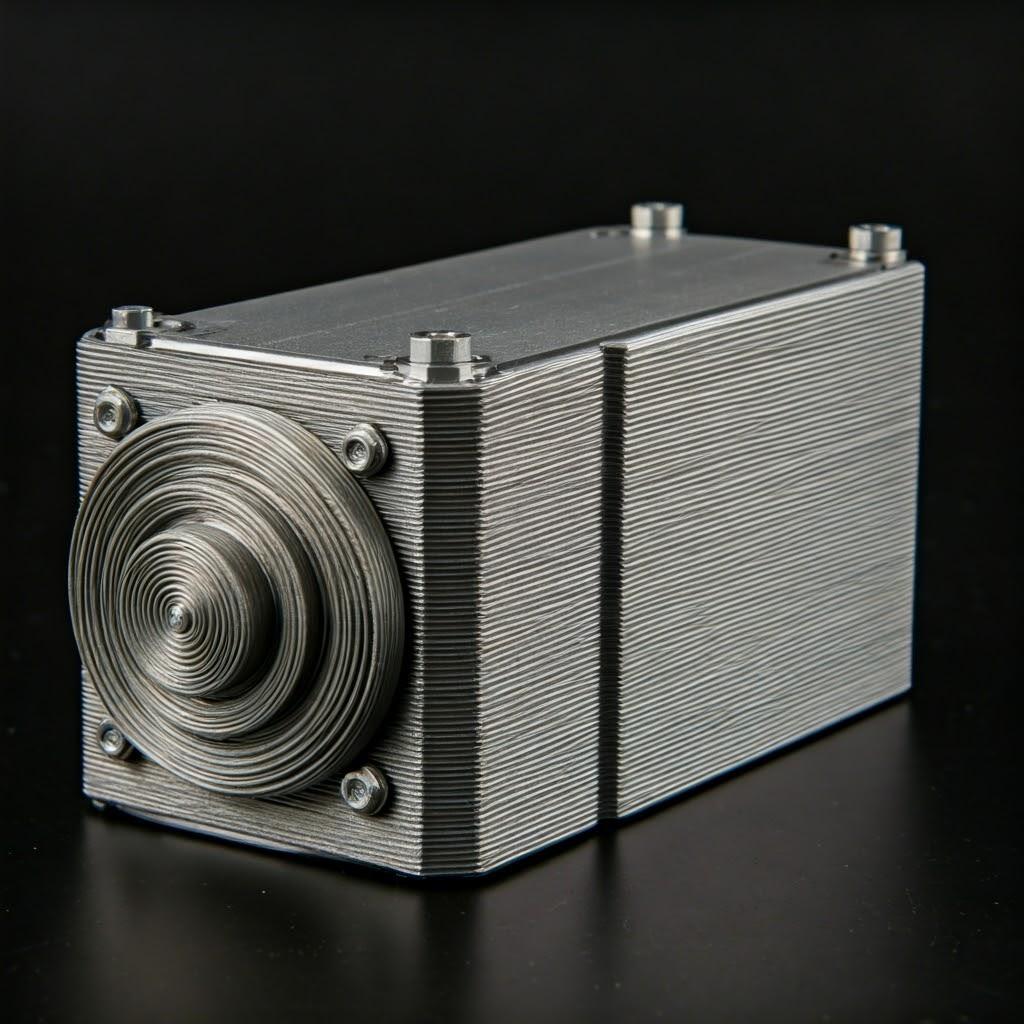
Výběr partnera pro aditivní výrobu kovů: Klíčové úvahy pro dodavatele elektrických vozidel
Výběr správného výrobního partnera je stejně důležitý jako samotná technologie, zejména pokud se jedná o náročné automobilové komponenty, jako jsou chladicí rámy baterií pro elektromobily. Úspěch vašeho projektu závisí na odborných znalostech, spolehlivosti a schopnosti dodavatele splnit přísné normy kvality. Pro inženýry a manažery nákupu, kteří se pohybují v poskytovatel služeb 3D tisku kovů by se mělo řídit několika klíčovými faktory hodnocení dodavatelů AM pro automobilový průmysl proces:
- Technické znalosti a zkušenosti:
- Specializace na materiál: Má dodavatel prokazatelné zkušenosti s konkrétními slitinami, které požadujete (např. AlSi10Mg, CuCrZr)? Požádejte o případové studie nebo příklady podobných projektů. Deep odborné znalosti materiálu AM je zásadní a zahrnuje manipulaci s práškem, vývoj parametrů a pochopení chování materiálu během tisku a následného zpracování.
- Znalost procesů: Ovládají nejvhodnější proces AM (LPBF, SEBM) pro vaši aplikaci? Rozumí nuancím dosažení optimální hustoty, přesnosti a vlastností materiálu?
- Zkušenosti v oboru: Pracovali v automobilovém průmyslu nebo v jiných náročných odvětvích (letecký průmysl, zdravotnictví) s podobnými nároky na kvalitu? Porozumění výroba automobilových součástek požadavky jsou klíčové.
- Technologie a vybavení:
- Kvalita stroje & Schopnosti: Jaké typy tiskáren provozují? Jsou dobře udržované a kalibrované? Mají stroje schopné zvládnout požadovaný objem sestavení a dosáhnout potřebné přesnosti? Společnost Met3dp využívá špičkové tiskárny známé svou přesností a spolehlivostí.
- Kontrola kvality prášku: Jak získávají a spravují své kovové prášky? Mají důkladnou kontrolu kvality vstupních materiálů? Výhodou společnosti Met3dp’ je vlastní výroba vysoce kvalitních sférických kovových prášků pomocí pokročilých atomizačních technik.
- Software & Simulace: Využívají pokročilý software pro přípravu konstrukce a případně simulační nástroje pro optimalizaci orientace, podpěr a předvídání potenciálních problémů, jako je deformace?
- Systémy řízení kvality:
- certifikace: Je poskytovatel držitelem příslušných certifikátů kvality, např ISO 9001? IATF 16949 (norma pro automobilový průmysl) je pro mnoho poskytovatelů AM stále ještě ve vývoji, ale prokázání dodržování přísných protokolů kvality je nezbytné.
- Řízení procesu: Jaká opatření jsou zavedena pro sledování procesu a kontroly kvality v průběhu celého výrobního procesu (manipulace s práškem, tisk, následné zpracování, kontrola)?
- Sledovatelnost: Mohou zajistit úplnou sledovatelnost materiálů a procesních parametrů pro každý vyrobený díl?
- Kapacita a škálovatelnost:
- Objem výroby: Zvládne poskytovatel požadované objemy výroby, od prototypů až po potenciální malosériovou nebo středněsériovou výrobu? Má dostatečnou kapacitu strojů a kvalifikovaný personál?
- Doba dodání: Dokáží dodržet časový plán vašeho projektu? Mají zkušenosti se spolehlivými dodávkami?
- Technické a podpůrné služby:
- Podpora DfAM: Mohou nabídnout odborné poradenství v oblasti návrhu pro aditivní výrobu, které vám pomůže optimalizovat návrh chladicího rámu z hlediska výkonu, nákladů a vyrobitelnosti?
- Možnosti následného zpracování: Nabízí komplexní škálu vlastních nebo úzce řízených služeb následného zpracování (tepelné zpracování, obrábění, dokončovací práce, testování)?
- Komunikace & amp; Spolupráce: Jsou vstřícní, transparentní a ochotní spolupracovat na řešení problémů? Výběr partnera AM jde o budování vztahu, ne jen o transakci.
- Celková nabídka hodnoty:
- Efektivita nákladů: I když jsou náklady důležitým faktorem, zhodnoťte celkem hodnotu, a to s ohledem na kvalitu, spolehlivost, odborné znalosti, rychlost a podporu, nikoli pouze na cenu za díl.
- Umístění & Logistika: Zvažte polohu poskytovatele ve vztahu k vašim montážním zařízením a jeho logistické možnosti.
Společnost Met3dp tyto vlastnosti ztělesňuje a staví se do pozice nejen dodavatele, ale i strategického partnera. S hlubokými kořeny v obou řešení pro aditivní výrobu a pokročilou výrobu kovových prášků, nabízíme jedinečnou kombinaci odborných znalostí v oblasti materiálových věd a mistrovství v tiskových procesech. Díky našemu závazku ke kvalitě, investicím do špičkových technologií v oboru a společnému přístupu jsme ideálním partnerem pro automobilové společnosti, které chtějí využívat technologii AM pro výrobu kovů pro kritické součásti elektromobilů, jako jsou chladicí rámy baterií.
Porozumění nákladovým faktorům a dodacím lhůtám pro 3D tištěné bateriové rámy
Ačkoli AM zpracování kovů umožňuje výrazné zvýšení výkonu a konstrukčních možností chladicích rámů baterií pro elektromobily, pro plánování projektů a zadávání zakázek je zásadní pochopit související náklady a časový harmonogram výroby. Jak analýza nákladů na 3D tisk kovů a odhad dodací lhůty automobilových dílů závisí na řadě vzájemně propojených faktorů.
Klíčové hnací síly nákladů:
- Typ materiálu a spotřeba:
- Náklady na prášek: Náklady na suroviny se u jednotlivých slitin výrazně liší. Slitiny mědi jako CuCrZr jsou podstatně dražší než slitiny hliníku jako AlSi10Mg.
- Část Objem & amp; Hmotnost: Větší a hustší díly přirozeně spotřebují více prášku, což přímo ovlivňuje náklady na materiál. Techniky DfAM, jako je optimalizace topologie a mřížkové struktury, mohou výrazně snížit spotřebu materiálu.
- Podpůrné struktury: Materiál použitý na podpůrné konstrukce zvyšuje celkovou spotřebu a je třeba jej zohlednit. Minimalizace podpěr pomocí DfAM tyto náklady snižuje.
- Strojový čas:
- Doba výstavby: To je často nejvýznamnějším faktorem ovlivňujícím náklady. Závisí na objemu dílu (konkrétně na jeho výšce v konstrukční komoře), složitosti, tloušťce použité vrstvy a účinnosti strategie skenování laserovým/elektronovým paprskem. Vyšší díly nebo díly vyžadující velmi jemné vrstvy se tisknou déle.
- Rychlost stroje: Hodinové provozní náklady na průmyslovou kovovou 3D tiskárnu se zohledněním odpisů, energie, spotřebního materiálu (filtry, plyny) a údržby.
- Složitost návrhu & Nastavení sestavení:
- Podporuje: Složité geometrie vyžadující rozsáhlé podpůrné struktury prodlužují dobu tisku (více materiálu k nanesení) i práci po zpracování (odstranění podpěr).
- Hnízdění & amp; Hustota zástavby: To, jak efektivně lze více dílů vnořit do jednoho konstrukčního svazku, ovlivňuje náklady na strojní čas na jeden díl. Zkušení poskytovatelé optimalizují rozložení sestav.
- Doba přípravy: Čas, který inženýři potřebují k přípravě souboru sestavení (orientace, generování podpory, krájení).
- Následné zpracování:
- Práce & Vybavení: Každý krok následného zpracování (uvolnění napětí, tepelné zpracování, odstranění podpěr, obrábění, dokončovací práce, kontrola) zvyšuje náklady na pracovní sílu a čas zařízení.
- Složitost: Složité vnitřní kanály vyžadující specializované dokončovací práce (jako je AFM) nebo přísné tolerance vyžadující rozsáhlé CNC obrábění výrazně zvýší náklady.
- Požadavky na kvalitu: Vyšší úrovně kontroly (např. rozsáhlá kontrola CMM, CT) zvyšují náklady.
- Objem objednávky:
- Úspory z rozsahu: Stejně jako u většiny výrobních procesů vedou vyšší objemy obecně k nižším nákladům na jeden díl díky amortizaci nákladů na nastavení, optimalizovanému sestavování a efektivnějším pracovním postupům. Objemová výroba AM se stává stále životaschopnější, i když se struktura nákladů liší od tradičních velkoobjemových metod.
Faktory ovlivňující dobu dodání:
- Dokončení návrhu & Příprava: Čas potřebný na konzultaci DfAM (pokud je potřeba) a přípravu stavebního souboru.
- Tisková fronta: Dostupnost vhodných strojů u poskytovatele služeb. Vysoká poptávka může vést ke vzniku front.
- Doba tisku: Skutečná doba, kterou díl stráví tiskem ve stroji (v závislosti na velikosti a složitosti se může pohybovat od několika hodin až po několik dní).
- Následné zpracování: Souhrnná doba potřebná pro všechny nezbytné kroky po tisku (cykly tepelného zpracování, obrábění, dokončovací práce, kontrola). To může často trvat stejně dlouho nebo déle než samotný tisk.
- Přeprava & Logistika: Čas potřebný k přepravě do cílového místa určení.
Typické časové rozvrhy:
Jednoduché prototypy mohou být vyrobeny za 1-2 týdny, ačkoli jejich výroba velmi závisí na projektu. Složitější komponenty vyžadující značné následné zpracování nebo díly vyrobené z náročných materiálů by mohly mít dodací lhůty v rozmezí 3 až 8 týdnů nebo více, zejména u počátečních výrobních sérií. Navázání spolupráce s poskytovatelem, jako je Met3dp, umožňuje lepší plánování a potenciální zrychlení časového harmonogramu po validaci procesů. Přesné nabídky nákladů i dodacích lhůt vyžadují podrobnou kontrolu dat CAD finálního dílu, specifikací materiálů a požadavků na kvalitu. Efektivní zadávání veřejných zakázek 3D tisk z kovu zahrnuje poskytnutí jasných specifikací potenciálním dodavatelům.
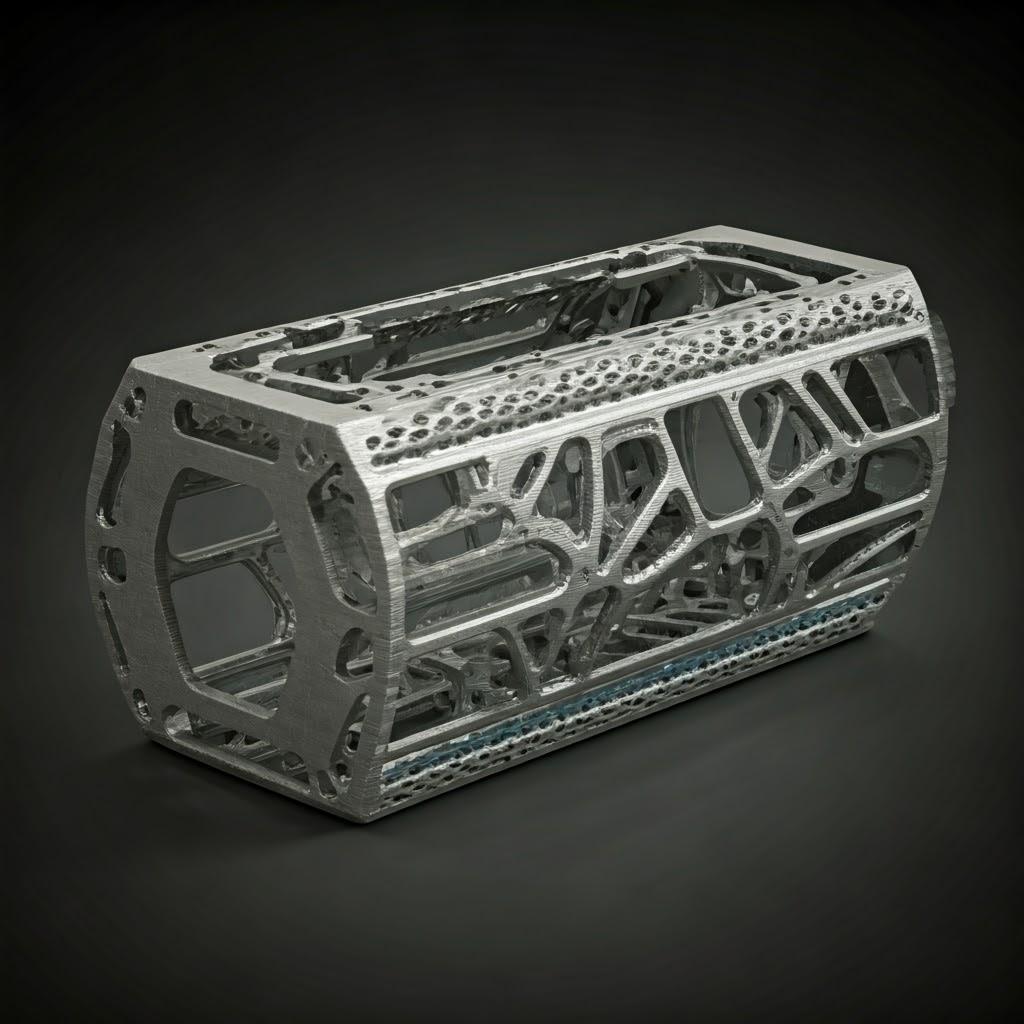
Často kladené otázky (FAQ) o kovových 3D tištěných chladicích rámech pro elektromobily
Zde jsou odpovědi na některé časté otázky inženýrů a manažerů veřejných zakázek týkající se použití kovového AM pro komponenty chlazení baterií pro elektromobily:
1. Jaké jsou hlavní výhody použití kovového AM pro chladicí rámy ve srovnání s tradičními metodami, jako je odlévání nebo pájené sestavy?
Technologie AM pro kovy nabízí několik klíčových výhod:
- Geometrická složitost: Schopnost vytvářet velmi složité vnitřní chladicí kanály (např. konformní, optimalizované průtokové cesty), které jsou nemožné nebo nepraktické při odlévání nebo obrábění, což vede k vynikajícímu tepelnému výkonu.
- Odlehčení: Umožňuje optimalizaci topologie a mřížkové struktury, což výrazně snižuje hmotnost součástek ve srovnání s pevnými odlitky a zvyšuje dojezd elektromobilů.
- Konsolidace částí: Umožňuje integraci více funkcí (chlazení, konstrukce, montáž) do jediného tištěného dílu, což snižuje složitost montáže, potenciální netěsnosti a často i hmotnost/náklady.
- Rychlost pro prototypy/malé objemy: Rychlejší iterace během vývoje a rychlejší výroba pro nízké až střední objemy, protože není potřeba žádné nářadí.
- Možnosti materiálu: Usnadňuje použití vysoce výkonných slitin, jako je AlSi10Mg pro odlehčení nebo CuCrZr pro maximální tepelnou vodivost.
2. Jak jsou chladicí kanály v 3D tištěných rámech odolné proti úniku?
Dosažení těsnosti je nejdůležitější a velmi dobře dosažitelné při správném řízení procesu. Mezi klíčové faktory patří:
- Optimalizace parametrů: Použití ověřených parametrů tisku k zajištění plné hustoty (>99,5 %, často vyšší) a minimalizace pórovitosti materiálu.
- Kvalita prášku: Zásadní je začít s vysoce kvalitním kovovým práškem s nízkou pórovitostí.
- Design: Vyhnout se konstrukčním prvkům, které jsou náchylné k defektům (např. velmi tenké stěny bez řádné podpory).
- Následné zpracování: HIP sice může uzavřít vnitřní póry, ale často není nutný, pokud jsou parametry tisku dobře kontrolovány.
- Důkladné testování: Zavedení povinného testování těsnosti (např. rozpad tlaku, testování těsnosti helia) jako standardního kroku kontroly kvality pro každou vyrobenou chladicí součást. Při správné výrobě zkušeným dodavatelem, jako je Met3dp, splňují kovové chladicí rámy AM přísné požadavky na těsnost.
3. Lze při AM zpracování kovů dosáhnout požadované povrchové úpravy uvnitř chladicích kanálů pro efektivní průtok kapaliny?
Povrchová úprava po vytištění uvnitř kanálů AM je ze své podstaty drsnější (typicky Ra 10-20 µm nebo vyšší) než u konvenčně opracovaných kanálů. To sice může mírně zvýšit tlakovou ztrátu ve srovnání s dokonale hladkou trubicí, ale výkonnostní přínosy optimalizované geometrie kanálů často převáží vliv drsnosti povrchu. Pro aplikace vyžadující hladší vnitřní povrchy:
- Design: Orientace kanálků a použití specifických tvarů (např. slza) může zlepšit povrchovou úpravu některých vnitřních povrchů.
- Následné zpracování: K výraznému zlepšení vnitřní povrchové úpravy lze použít techniky, jako je abrazivní průtokové obrábění (AFM) nebo chemické leštění, i když s dodatečnými náklady. Požadovaná vnitřní povrchová úprava by měla být specifikována a projednána s dodavatelem AM.
4. Jaké informace obvykle potřebuje společnost Met3dp k poskytnutí cenové nabídky na 3D tištěný chladicí rám baterie?
Abychom mohli poskytnout přesnou nabídku, obvykle požadujeme:
- 3D model CAD: STEP nebo STL soubor finálního návrhu dílu.
- Specifikace materiálu: Požadovaná slitina (např. AlSi10Mg, CuCrZr) a případné specifické požadavky na vlastnosti materiálu.
- Technický výkres: Uvedení kritických rozměrů, tolerancí, požadované povrchové úpravy (zejména u těsnicích/spojovacích ploch) a všech specifických prvků, které mají být obráběny.
- Množství: Počet požadovaných dílů (pro prototypovou, malosériovou nebo sériovou výrobu).
- Požadavky na následné zpracování: Podrobnosti o tepelném zpracování, specifických povrchových úpravách, potřebách testování (např. parametry zkoušek těsnosti).
- Časový plán dodání: Požadované datum dodání.
5. Je metoda AM vhodná pro velkosériovou výrobu těchto rámů v automobilovém průmyslu?
Technologie AM se rychle vyvíjí, a přestože vyniká při výrobě prototypů, přizpůsobování a nízko až středně velkoobjemové výrobě, její vhodnost pro tradiční velkoobjemové automobilové váhy (stovky tisíc nebo miliony kusů ročně) se ve srovnání s odléváním nebo lisováním pro automobilový průmysl stále vyvíjí jednoduchý návrhy. U složitých, vysoce výkonných chladicích rámů, kde AM přináší významné výkonnostní nebo konsolidační výhody, jichž nelze jinak dosáhnout, se však stává schůdnou variantou i pro sériovou výrobu v tisících nebo desetitisících kusů. Nákladová efektivita do značné míry závisí na složitosti konstrukce a hodnotě plynoucí z jedinečných schopností AM’. Společnost Met3dp spolupracuje se zákazníky na vyhodnocení obchodních důvodů pro sériová výroba pomocí AM.
Závěr: Budoucnost výkonu elektromobilů díky řešením aditivní výroby Met3dp’
Neustálá snaha o vyšší výkon, delší dojezd a rychlejší nabíjení na trhu elektromobilů vytváří obrovský tlak na systémy tepelného řízení baterií. Aditivní výroba kovů se jednoznačně stala klíčovou technologií, která nabízí bezprecedentní možnosti navrhovat a vyrábět chladicí rámy baterií pro elektromobily, které jsou lehčí, složitější a tepelně lepší než rámy vyrobené konvenčními metodami. Využitím konstrukční svobody AM s pokročilými materiály, jako je lehký AlSi10Mg nebo vysoce vodivý CuCrZr, mohou výrobci automobilů dosáhnout významného zlepšení účinnosti, životnosti a bezpečnosti bateriových bloků - což jsou kritické faktory úspěchu v konkurenčním prostředí elektromobilů.
Od optimalizace složitých vnitřních chladicích kanálů pomocí DfAM až po zajištění přesnosti díky pečlivé kontrole procesu a následnému zpracování poskytuje AM kovů výkonný soubor nástrojů pro pokročilá výroba v automobilovém průmyslu aplikace. Složitost výběru materiálu, optimalizace konstrukce, procesních parametrů a zajištění kvality však vyžaduje hluboké odborné znalosti.
Výběr správného partnera je nejdůležitější. Met3dp stojí v čele této technologické vlny a kombinuje špičková technologie tisku SEBM/LPBF s bezkonkurenčními odbornými znalostmi v oblasti výroba vysoce výkonných kovových prášků. Náš integrovaný přístup, od rozprašovaného prášku až po hotovou a otestovanou součástku, zajišťuje kvalitu, spolehlivost a výkonnost, které vyžaduje automobilový průmysl. Jsme více než jen poskytovatel služeb; jsme partner pro spolupráci, který vám pomůže plně využít potenciál aditivní výroby pro vaše nejdůležitější komponenty pro elektromobily.
Jste připraveni na revoluci v tepelném managementu elektromobilů? Kontaktujte Met3dp ještě dnes a prodiskutovat s vámi váš projekt chladicího rámu baterie a zjistit, jak naše špičkové systémy, pokročilé materiály a služby vývoje aplikací mohou urychlit vaši cestu k elektromobilům nové generace. Pojďme řídit budoucí technologie pro elektromobily společně.
Sdílet na
MET3DP Technology Co., LTD je předním poskytovatelem řešení aditivní výroby se sídlem v Qingdao v Číně. Naše společnost se specializuje na zařízení pro 3D tisk a vysoce výkonné kovové prášky pro průmyslové aplikace.
Dotaz k získání nejlepší ceny a přizpůsobeného řešení pro vaše podnikání!
Související články
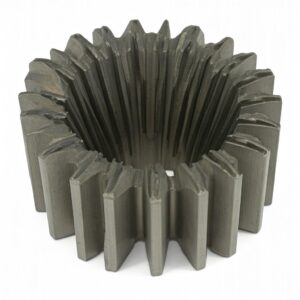
Vysoce výkonné segmenty lopatek trysek: Revoluce v účinnosti turbín díky 3D tisku z kovu
Přečtěte si více "O Met3DP
Nedávná aktualizace
Náš produkt
KONTAKTUJTE NÁS
Nějaké otázky? Pošlete nám zprávu hned teď! Po obdržení vaší zprávy obsloužíme vaši žádost s celým týmem.
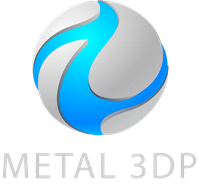
Kovové prášky pro 3D tisk a aditivní výrobu