Palivové rozdělovače navržené pro optimalizaci průtoku aditiv
Obsah
Úvod: Revoluce v dodávkách paliva pomocí 3D tištěných rozdělovačů z vlastního kovu
Složitý tanec techniky, který pohání náš moderní svět, často závisí na přesném řízení a distribuci kapalin. Od řevu proudového motoru pronikajícího stratosférou přes vytříbené hučení vysoce výkonného automobilového motoru obepínajícího zatáčky na trati až po neúnavný provoz průmyslových turbín na výrobu energie - účinná dodávka paliva je nejdůležitější. V srdci těchto složitých systémů se nachází kritická, ale často podceňovaná součást: rozdělovač paliva. Ve své podstatě slouží rozdělovač paliva jako důmyslná spojovací skříňka pro kapaliny, která přijímá palivo ze zdroje a pečlivě ho rozvádí do několika míst za ním, jako jsou vstřikovače, trysky nebo spalovací komory. Jeho funkce je zásadní - zajišťuje, aby se správné množství paliva dostalo na správné místo ve správný čas, pod správným tlakem a s minimálními ztrátami nebo kolísáním. Porucha nebo neefektivita rozdělovače může vést k neoptimálnímu výkonu, zvýšeným emisím, snížené spotřebě paliva a v kritických aplikacích, jako je letecký průmysl, i k potenciálně katastrofickým následkům. Požadavky kladené na tyto součásti jsou značné, často zahrnují složité vnitřní cesty, odolnost vůči vysokým tlakům a teplotám, kompatibilitu s agresivními palivy a přísné požadavky na hmotnost a prostor, zejména v leteckém a automobilovém průmyslu.
Historicky se při výrobě palivových rozvodů používaly především tradiční techniky, především odlévání, subtraktivní obrábění (frézování a vrtání) a montážní postupy, jako je pájení nebo svařování. Tyto metody sice slouží průmyslu již desítky let, ale ze své podstaty s sebou nesou značná omezení, zejména pokud konstruktéři usilují o maximální výkon a účinnost.
- Obsazení: Odlévání je sice vhodné pro výrobu složitých vnějších tvarů, ale při vytváření složitých a optimalizovaných vnitřních kanálů je obtížné. Vnitřní jádra mohou být složitá a křehká, což omezuje volnost konstrukce. Spolehlivé dosažení tenkých stěn může být obtížné a problémem může být pórovitost, která může vést k netěsnostem nebo slabým místům. Povrchová úprava vnitřních litých kanálů je často drsná, což brání plynulému proudění kapaliny a zvyšuje tlakovou ztrátu. Kromě toho je výroba a úprava nástrojů pro odlévání drahá a časově náročná, takže opakování návrhu je pomalé a nákladné.
- Obrábění: Subtraktivní obrábění, které obvykle vychází z masivního bloku kovu, vyniká vysokou přesností a vynikající povrchovou úpravou na externí povrchy a přístupné vnitřní vlastnosti. Vytvoření složitých, hladce zakřivených vnitřních průchodů nebo vnitřních prvků s ostrými podříznutími je však často nemožné nebo vyžaduje obrábění rozdělovače z více kusů. Operace hlubokého vrtání pro dlouhé, rovné kanály jsou možné, ale vytváření optimalizovaných, nelineárních průtokových cest je značně omezené. Toto omezení si vynucuje návrhy, které jsou kompromisem mezi vyrobitelností a ideální dynamikou tekutin. Subtraktivním procesům je také vlastní značný odpad materiálu.
- Montáž (pájení/svařování): Aby se překonala omezení monolitického odlévání nebo obrábění, jsou složité rozdělovače často konstruovány z více jednodušších dílů spojených pájením nebo svařováním. To sice umožňuje vytvořit složitější vnitřní sítě, ale každý spoj vytváří potenciální cesty úniku, zvyšuje hmotnost, prodlužuje dobu montáže a její složitost a vytváří místa možného selhání při namáhání nebo tepelném cyklování. Zajištění integrity mnoha spojů vyžaduje důkladnou kontrolu a řízení kvality, což zvyšuje celkové náklady a dobu výroby.
Tato tradiční výrobní omezení často nutí konstruktéry ke kompromisům v ideálních návrzích. Průtokové cesty mohou být neoptimální, což vede ke zbytečným tlakovým ztrátám a nerovnoměrnému rozložení paliva. Počet dílů se zvyšuje, aby se dosáhlo požadované složitosti, což zvyšuje hmotnost a potenciální místa poruch. Dodací lhůty pro nové návrhy nebo úpravy se mohou protáhnout na měsíce kvůli potřebě nových nástrojů nebo složitých obráběcích nastavení. V průmyslových odvětvích, kde jsou výkon, hmotnost a rychlost uvedení na trh rozhodujícími faktory, představují tato omezení významné překážky.
Vstupte do říše výroba aditiv kovů (AM), častěji známý jako 3D tisk z kovu. Tato transformační technologie zásadně mění způsob navrhování a výroby složitých součástí, jako jsou palivové rozvody. Namísto odebírání materiálu z pevného bloku nebo odlévání roztaveného kovu do formy se při AM vyrábějí díly vrstvu po vrstvě přímo z digitálního modelu (CAD), přičemž se jemné částice kovového prášku spojují pomocí cíleného zdroje energie, jako je laser nebo elektronový paprsek. Tento přístup založený na vrstvách účinně osvobozuje návrháře od mnoha omezení, která ukládají tradiční metody.
Důsledky pro konstrukci a výrobu palivových rozvodů jsou zásadní:
- Bezprecedentní svoboda designu: AM umožňuje vytvářet velmi složité vnitřní geometrie, které dříve nebylo možné vyrobit. Hladce zakřivené kanály, které přesně kopírují optimalizované průtokové dráhy, vnitřní zásobníky, integrované filtry a variabilní průřezy lze navrhnout a zabudovat přímo do monolitického dílu. Tato schopnost umožňuje konstruktérům navrhovat především pro funkci a optimalizovat dynamiku tekutin, nikoliv dělat kompromisy s ohledem na vyrobitelnost.
- Optimalizace toku: Díky možnosti vytvářet složité vnitřní kanály mohou konstruktéři minimalizovat ostré ohyby, snížit turbulence a zajistit rovnoměrnější rozložení průtoku do každého výstupního bodu. To vede ke snížení tlakových ztrát v rozdělovači, zlepšení účinnosti spalování a potenciálně vyššímu výkonu motoru nebo systému. K návrhu vysoce optimalizovaných vnitřních cest lze použít simulace počítačové dynamiky tekutin (CFD) a společnost AM může tyto složité digitální návrhy převést přímo na fyzický hardware.
- Výrazné snížení hmotnosti: AM umožňuje použití algoritmů optimalizace topologie. Tyto softwarové nástroje analyzují rozložení napětí v dílu při provozním zatížení a inteligentně odstraňují materiál z nekritických oblastí, čímž vytvářejí lehké, ale pevné a organicky vypadající struktury. U palivových rozvodů to může vést k výrazným úsporám hmotnosti - což je rozhodující faktor v leteckém průmyslu, kde každý ušetřený gram znamená úsporu paliva nebo zvýšení nosnosti, a ve výkonném automobilovém průmyslu, kde snížení hmotnosti zlepšuje ovladatelnost a zrychlení.
- Konsolidace částí: Složité sestavy, které se dříve vyráběly z několika obráběných a pájených součástí, lze často přepracovat a vytisknout jako jediný monolitický díl. To výrazně snižuje počet dílů, eliminuje potenciální netěsnosti spojené se spoji, zjednodušuje montážní procesy, snižuje správu zásob a ze své podstaty zvyšuje spolehlivost součásti.
Kov 3D tisk není jen nástrojem pro tvorbu prototypů, je to technologie připravená k výrobě, která je schopna vyrábět díly pro konečné použití v nejnáročnějších aplikacích. Společnosti jako Met3dp jsou v čele a poskytují pokročilá řešení AM, včetně sofistikovaných tiskáren a vysoce výkonných kovových prášků, speciálně přizpůsobených pro průmyslová odvětví, jako je letecký, automobilový a lékařský průmysl. Jejich odborné znalosti v oblasti materiálové vědy a řízení procesů zajišťují výrobu hustých, vysoce kvalitních kovových dílů s vynikajícími mechanickými vlastnostmi, díky čemuž je aditivní výroba kritických komponent, jako jsou například palivové rozvody na zakázku, spolehlivou a výhodnou realitou. Tento technologický posun otevírá dveře k navrhování a konstrukci palivových rozvodů, které jsou lehčí, účinnější, spolehlivější a jejichž vývoj je rychlejší než kdykoli předtím - což představuje skutečnou revoluci v dodávkách paliva v mnoha odvětvích špičkových technologií. Manažeři veřejných zakázek a inženýři, kteří hledají konkurenční výhody díky optimalizovanému výkonu palivových systémů, se stále častěji obracejí na specializované dodavatele kovových AM komponentů, kteří jsou schopni tyto komponenty nové generace dodávat.
Základní aplikace: Kde se používají rozdělovače paliva AM na zakázku?
Jedinečné výhody, které nabízí aditivní výroba kovů - zejména volnost návrhu pro optimalizaci průtoku, snížení hmotnosti a konsolidaci dílů - z ní činí mimořádně vhodnou technologii pro výrobu rozvodů paliva na zakázku v celé řadě náročných průmyslových odvětví. Zatímco základní funkce zůstává stejná (distribuce paliva), specifické požadavky a výhody realizované prostřednictvím AM se výrazně liší v závislosti na kontextu aplikace. Pokrokově smýšlející inženýrské týmy a výrobní stratégové aktivně nasazují rozdělovače paliva AM v odvětvích, kde jsou výkon, účinnost a spolehlivost neoddiskutovatelné. Pojďme’prozkoumat klíčová odvětví a konkrétní funkce, kde tyto pokročilé komponenty mají významný dopad:
1. Letectví a obrana: Toto odvětví je pravděpodobně nejvýznamnějším prvopočátkem a příjemcem výhod palivových rozdělovačů AM. Extrémní provozní podmínky (vysoké teploty, tlaky, vibrace) v kombinaci s neúnavnou snahou o snižování hmotnosti činí z AM ideální řešení.
- Plynové turbínové motory (proudové motory): Palivové rozvody a související součásti, jako jsou palivové trysky, mají zásadní význam pro výkon a účinnost motoru. AM umožňuje:
- Optimalizované vnitřní geometrie: Vytvoření složitých vnitřních kanálů, které zajišťují rovnoměrný přísun paliva do spalovacího prostoru, zlepšují stabilitu a účinnost spalování a zároveň snižují emise. Vířivé prvky nebo směšovací prvky mohou být integrovány přímo.
- Snížení hmotnosti: Optimalizace topologie může výrazně snížit hmotnost rozdělovače ve srovnání s tradičně obráběnými nebo litými verzemi. To přímo přispívá ke zlepšení spotřeby paliva letadla nebo zvýšení doletu/nákladu. Například nahrazení vícedílné pájené sestavy jediným tištěným rozdělovačem s optimalizovanou topologií může přinést úsporu hmotnosti 30-50 % nebo více pro danou součást.
- Konsolidace částí: Spojení těla rozdělovače, montážních konzol a případně i částí palivových trysek do jediné tištěné součásti snižuje složitost montáže, eliminuje netěsnosti spojů (což je hlavní problém spolehlivosti) a zjednodušuje dodavatelský řetězec. Přední výrobci leteckých motorů již do svých nejnovějších konstrukcí motorů začleňují 3D tištěné palivové trysky a součásti rozdělovače.
- Výběr materiálu: Použití vysokoteplotních superslitin, jako je Inconel 625 (IN625), nebo specializovaných titanových slitin, které lze snadno zpracovat pomocí AM, zajišťuje výkon a odolnost v náročném prostředí motoru. Odborné znalosti společnosti Met3dp’ve zpracování těchto pokročilých slitin pomocí technik, jako je selektivní tavení elektronovým svazkem (SEBM) a laserová fúze v práškovém loži (L-PBF), spolu s vysoce kvalitními prášky rozprašovanými plynem z ní činí cenného partnera pro dodavatele leteckých rozvodů.
- Raketové pohonné systémy: Zde jsou požadavky ještě extrémnější, zahrnují kryogenní paliva, vysoké tlaky a krátkou provozní životnost, kdy je klíčový maximální výkon.
- Komplexní chladicí kanály: AM umožňuje integrovat složité chladicí kanály přímo do stěn sběrného potrubí, což je nezbytné pro řízení intenzivního tepla vznikajícího při spalování, zejména v blízkosti vstřikovačů.
- Čelní desky vstřikovačů/panely: Kombinace rozdělovačů paliva a okysličovadla do složitých vstřikovacích sestav s přesně řízenými průtokovými cestami zvyšuje účinnost míchání a spalování, což je rozhodující pro maximalizaci tahu.
- Rychlá iterace: Rychlost AM umožňuje dodavatelům nosných raket rychle opakovat návrhy rozdělovačů a vstřikovačů během vývoje a optimalizovat výkon rychleji, než by to umožnily tradiční metody.
- Satelity a kosmické lodě: Hmotnost je zde pravděpodobně nejkritičtějším faktorem vzhledem k nákladům na start.
- Miniaturní a lehké systémy: AM usnadňuje vytváření vysoce kompaktních a lehkých palivových rozdělovačů pro trysky pro řízení polohy a pohonné systémy s použitím materiálů, jako je titan nebo slitiny hliníku (např. AlSi10Mg pro aplikace při nižších teplotách).
- Integrované funkce: Porty snímačů, montážní body a konektory pro připojení kapalin lze bez problémů integrovat do konstrukce rozdělovače, což snižuje celkovou složitost systému.
2. Vysoce výkonný automobilový průmysl: I když je citlivost na náklady vyšší než v leteckém průmyslu, výkonnostní výhody palivových rozvodů AM jsou stále atraktivnější, zejména v závodních, luxusních/výkonných vozidlech a při výrobě pokročilých prototypů.
- Motorsport (F1, vytrvalostní závody atd.): Týmy pracují na špičkové technologické úrovni a hledají každou výkonnostní výhodu.
- Optimalizovaný průtok pro maximální výkon: Na míru navržené rozdělovače s vnitřními kanály optimalizovanými pomocí CFD zajišťují vyvážený přísun paliva do každého válce, čímž maximalizují účinnost spalování a výkon. Možnost rychlého vytvoření prototypu a testování různých konstrukcí rozdělovačů umožňuje týmům vyladit výkon motoru pro konkrétní tratě nebo podmínky.
- Snížení hmotnosti: I malá úspora hmotnosti má zásadní význam pro zlepšení ovladatelnosti, zrychlení a brzdění. Topologicky optimalizované rozvody AM přispívají k celkovému snížení hmotnosti vozidla.
- Kompaktní balení: Motorové prostory závodních vozů jsou těsně u sebe. AM umožňuje navrhovat rozvody tak, aby přesně zapadaly do dostupných prostor a zahrnovaly složité křivky a tvary.
- Výkonné silniční vozy & Luxusní vozidla: Funkce původně vyvinuté pro závodní účely se často přenášejí i na ostatní.
- Zvýšená účinnost motoru & amp; Odezva: Optimalizovaný rozvod paliva může přispět ke zlepšení spotřeby paliva a odezvy na sešlápnutí plynu.
- Diferenciace designu: Unikátní součásti motoru mohou být na trhu s luxusními vozy prodejním argumentem.
- Vývoj prototypů a motorů: AM výrazně urychluje vývojový cyklus motoru. Inženýři mohou navrhnout, vytisknout a otestovat nové koncepty rozdělovačů během několika dnů nebo týdnů ve srovnání s měsíci u tradičních nástrojů a výroby, což umožňuje rychlejší inovace a optimalizace.
3. Průmyslové aplikace: Výhody rozdělovačů AM se vztahují na různá průmyslová prostředí, zejména ta, která zahrnují turbíny, těžké stroje a specializovanou manipulaci s kapalinami.
- Energetické turbíny (plynové a parní): Velké průmyslové turbíny vyžadují podobně jako proudové motory přesnou dodávku paliva pro zajištění účinnosti a regulace emisí.
- Odolnost & Výkon při vysokých teplotách: AM umožňuje použití robustních superslitin (jako je IN625), které jsou schopny odolávat náročným provozním podmínkám po delší dobu.
- Zvýšená účinnost & Emise: Optimalizované míchání paliva a vzduchu díky pokročilé konstrukci trysek a rozdělovačů přispívá k vyšší tepelné účinnosti a nižším emisím NOx.
- Oprava & amp; Výměna: AM lze použít k výrobě náhradních rozdělovačů pro starší turbíny, u nichž již nemusí být k dispozici původní díly nebo nástroje, a případně i ke konstrukčním vylepšením. Manažeři průmyslových zakázek, kteří hledají spolehlivé průmyslové kapalinové systémy komponenty mohou využívat AM jak pro nové konstrukce, tak pro MRO (údržba, opravy, generální opravy).
- Těžké stroje a terénní vozidla: Motory ve stavebních, důlních a zemědělských zařízeních využívají robustní a účinné palivové systémy. I když jsou hlavním faktorem náklady, stále větší pozornost si získává potenciál pro zvýšení úspory paliva a spolehlivosti díky optimalizovaným rozdělovačům AM.
- Specializované testovací soupravy a výzkumná zařízení: V prostředí výzkumu a vývoje je neocenitelná schopnost rychle vytvářet vlastní rozdělovače pro specifické experimenty s kapalinami nebo testovací sestavy. AM poskytuje flexibilitu při vytváření jednorázových nebo malosériových komponentů přizpůsobených jedinečným experimentálním potřebám.
Ve všech těchto odvětvích je společným znakem snaha o zvýšení výkonu, zlepšení účinnosti, zvýšení spolehlivosti a často i snížení hmotnosti nebo velikosti. Rozvody paliva na zakázku vyráběné metodou AM s využitím kovu představují účinný nástroj k dosažení těchto cílů a posouvají hranice možností při navrhování kapalinových systémů. S tím, jak technologie dozrává a náklady se dále vyvíjejí, se očekává, že se nasazení rozdělovačů paliva AM bude dále rozšiřovat a stane se standardním řešením pro náročné aplikace vyžadující optimalizovaný průtok a složité geometrie. Podniky, které hledají velkoobchodní výroba palivových rozvodů nebo specializované výrobci palivových rozvodů pro automobilový průmysl stále častěji navazují partnerství s odbornými poskytovateli AM, jako je Met3dp, aby tyto pokročilé možnosti využili.
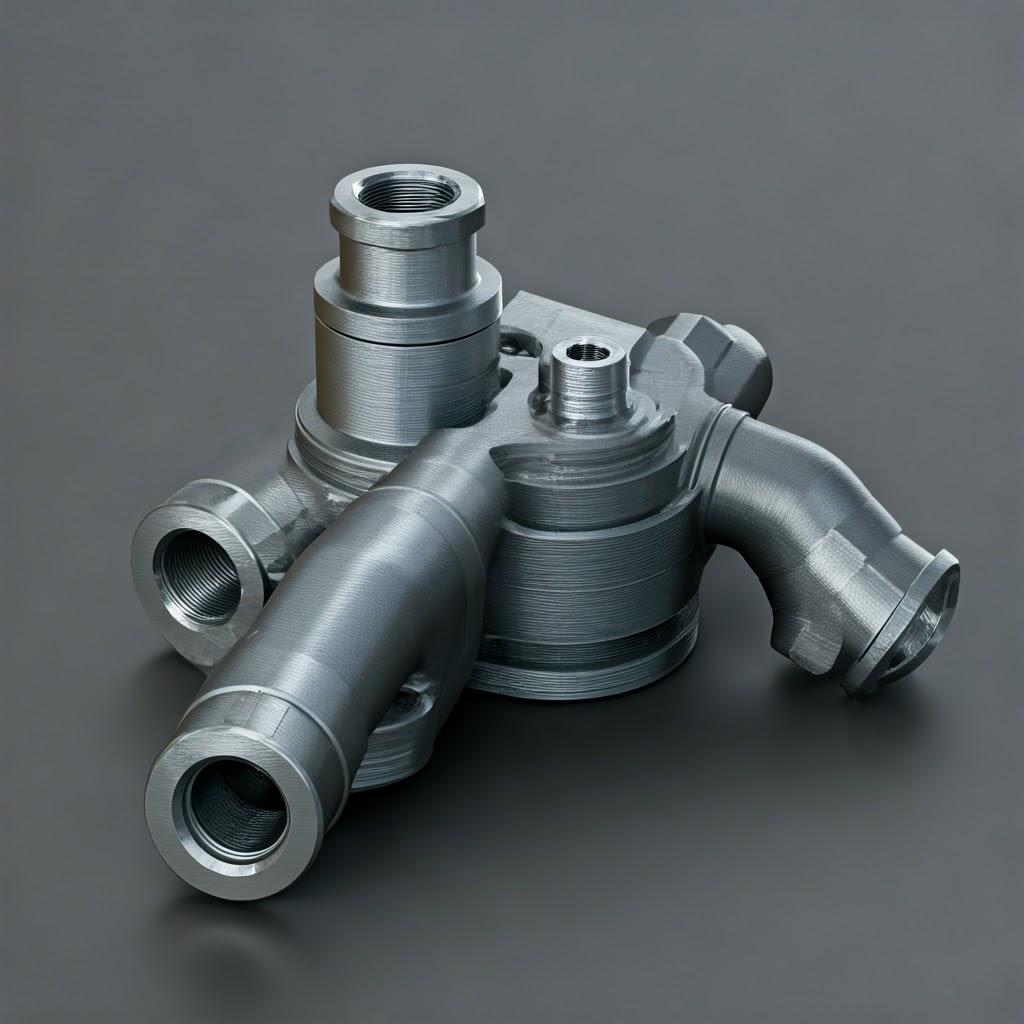
Aditivní výhoda: Proč zvolit 3D tisk z kovu pro palivové rozvody?
Rozhodnutí přejít od tradičních výrobních metod starých desítky let k relativně novější technologii, jako je aditivní výroba kovů, u kritické součásti, jako je palivové potrubí, se nepřijímá lehce. Je vedeno řadou přesvědčivých výhod, které přímo řeší přirozená omezení odlévání, obrábění a pájení, což v konečném důsledku umožňuje vytvářet vynikající komponenty. Pro inženýry a manažery nákupu, kteří hodnotí výrobní metody, je pochopení těchto specifických výhod klíčové pro přijímání informovaných rozhodnutí a uvolnění významných výkonnostních a logistických přínosů. Výhoda “aditivních materiálů” pro palivové rozvody vyplývá ze synergie konstrukční svobody, zvýšení výkonu, zlepšení fyzikálních vlastností a efektivity výroby. Pojďme se’hlouběji seznámit s tím, proč se AM zpracování kovů rychle stává preferovanou volbou pro špičkové palivové rozvody:
1. Bezkonkurenční volnost designu: To je pravděpodobně nejvýznamnější přínos AM. Konstrukce po vrstvách osvobozuje konstruktéry od “konstrukce pro vyrobitelnost” omezení tradičních metod. * Složité vnitřní geometrie: AM vyniká při vytváření složitých vnitřních kanálků, které je prostě nemožné vytvořit vrtáním nebo odléváním. Návrháři mohou implementovat: * Hladké, zakřivené dráhy toku: Eliminace ostrých 90stupňových ohybů, které jsou běžné u vrtaných rozvodů, snižuje rozdělení proudění a turbulence, což vede k nižším tlakovým ztrátám a efektivnějšímu transportu kapaliny. * Proměnlivé průřezy: Kanály mohou plynule měnit tvar a velikost po celé své délce, aby bylo možné přesně regulovat rychlost proudění a tlak. * Vnitřní přepážky a směšovací prvky: Konstrukce pro zlepšení míchání paliva nebo řízení distribuce průtoku mohou být integrovány přímo do tělesa rozdělovače bez nutnosti montáže. * Optimalizované křižovatky: Tam, kde se více kanálů spojuje nebo rozděluje, lze geometrii pečlivě navrhnout pomocí analýzy CFD, aby byly zajištěny plynulé přechody a vyvážené proudění. * Optimalizace topologie: Tato výpočetní konstrukční technika, která se dokonale hodí pro AM, umožňuje inženýrům definovat podmínky zatížení a požadavky na výkon (např. tuhost) a umožňuje softwaru navrhnout optimální rozložení materiálu. Často tak vznikají organické, mřížkovité struktury, které si zachovávají pevnost a tuhost a zároveň výrazně snižují spotřebu materiálu a hmotnost, což je mnohem více, než je možné dosáhnout běžným obráběním. V případě palivového rozdělovače to znamená snížit jeho hmotnost a zároveň zajistit, aby odolával provozním tlakům a vibracím. * Integrované funkce: Montážní body, šachty pro senzory, chladiče nebo konektory pro připojení kapalin, které by obvykle byly samostatnými díly vyžadujícími montáž, lze navrhnout a vytisknout jako integrální prvky tělesa rozdělovače, což zjednodušuje celý systém.
2. Přímé zvýšení výkonu: Volnost konstrukce, kterou umožňuje AM, se přímo promítá do měřitelného zlepšení výkonu palivových rozvodů. * Optimalizovaná dynamika tekutin: Jak již bylo zmíněno, hladké, zakřivené vnitřní kanály navržené pomocí simulace CFD minimalizují tlakové ztráty. To znamená, že palivové čerpadlo pracuje méně intenzivně, čímž se šetří energie, a tlak dodávaný do vstřikovačů je konzistentnější a předvídatelnější, což vede k lepšímu rozprašování a spalování. * Rovnoměrné rozložení průtoku: Složité vnitřní geometrie lze pečlivě vyladit tak, aby každý výstupní otvor obdržel stejné množství průtoku a tlaku paliva, což je rozhodující pro vyvážený výkon motoru, zejména u víceválcových motorů nebo spalovacích motorů s více tryskami. Tradiční rozdělovače mají často potíže s dosažením dokonalého rozdělení kvůli výrobním omezením. * Vylepšený tepelný management: U vysokoteplotních aplikací (např. u leteckých motorů) umožňuje technologie AM integrovat sofistikované vnitřní chladicí kanály přímo do stěn rozdělovače, a to pomocí samotného paliva nebo samostatného chladicího okruhu. To pomáhá zachovat strukturální integritu materiálu rozdělovače a zabraňuje přehřátí paliva nebo vzniku koksování.
3. Výrazné snížení hmotnosti: Hmotnostní optimalizace je hlavním motorem pro zavádění AM, zejména v dopravním průmyslu. * Optimalizace topologie: Jak již bylo řečeno, jedná se o významný příspěvek, který odstraňuje nepotřebný materiál. * Výběr materiálu: AM umožňuje efektivní využití lehkých a vysoce pevných materiálů, jako jsou slitiny hliníku (AlSi10Mg) a titanu (Ti6Al4V), které by bylo obtížné nebo nákladné tradičně obrábět do složitých tvarů. * Konsolidace částí: Snížení počtu jednotlivých součástí neodmyslitelně snižuje celkovou hmotnost přírub, spojovacích prvků a těsnění. * Dopad: Běžně se uvádí, že u leteckých a automobilových součástí přepracovaných pro AM dochází k úspoře hmotnosti o 20 % až 60 % nebo dokonce více ve srovnání s jejich konvenčními protějšky. To se přímo promítá do úspory paliva, zvýšení užitečného zatížení nebo zlepšení dynamiky vozidla.
4. Konsolidace částí a zjednodušení systému: To přináší řadu logistických výhod a výhod v oblasti spolehlivosti. * Zkrácení doby montáže & Náklady: Tisk jediného integrovaného rozdělovače eliminuje čas a práci potřebnou k montáži více součástí, nanášení těsnicích materiálů a utahování spojovacích prvků. * Eliminace únikových cest: Pájené nebo svařované spoje a mechanické armatury jsou potenciálními zdroji netěsností, zejména při vysokém tlaku, vibracích nebo tepelných cyklech. Monolitický díl AM má výrazně méně potenciálních míst úniku, což výrazně zvyšuje spolehlivost a bezpečnost systému, což je pro palivové systémy kritický faktor. * Zjednodušený dodavatelský řetězec & Zásoby: Správa jednoho čísla dílu namísto více komponent zjednodušuje nákup, logistiku, správu zásob a údržbu. To přímo oslovuje manažery veřejných zakázek, kteří usilují o zefektivnění provozu a snížení režijních nákladů. * Zvýšená spolehlivost: Méně dílů a spojů znamená méně možných poruch, což vede k robustnějšímu a spolehlivějšímu konečnému výrobku.
5. Rychlé prototypování, iterace a přizpůsobení: AM urychluje životní cyklus vývoje produktu a umožňuje řešení na míru. * Rychlost: Funkční kovové prototypy lze vyrobit během několika dnů nebo týdnů přímo z dat CAD, aniž by bylo nutné používat drahé a časově náročné nástroje (např. formy nebo zápustky). To umožňuje inženýrským týmům rychle testovat a ověřovat návrhy, identifikovat chyby a provádět iterace mnohem rychleji, než to umožňují tradiční metody. * Nákladově efektivní iterace: Změny návrhu zahrnují úpravu souboru CAD a tisk nové verze. To je podstatně levnější a rychlejší než úprava nebo znovuvytvoření tradičního nástroje. * Přizpůsobení & Malosériová výroba: AM je ekonomicky výhodná pro výrobu vysoce přizpůsobených rozdělovačů nebo malých sérií, protože není třeba amortizovat náklady na nástroje. To je ideální pro specializované aplikace, motoristický sport nebo náhradní díly pro starší systémy. Společnosti, které potřebují rychlé prototypování palivových systémů považují AM za neocenitelnou.
6. Efektivita materiálů a udržitelnost: * Snížení množství odpadu: Při aditivní výrobě se obvykle používá pouze materiál potřebný k výrobě dílu a jeho podpěr, což vede k podstatně menšímu plýtvání materiálem ve srovnání se subtraktivním obráběním, které začíná s větším blokem a odebírá materiál. Přestože opětovné použití prášku a recyklace jsou důležitými aspekty, poměr "buy-to-fly" (poměr nakoupených surovin k hmotnosti finálního dílu) je u AM často mnohem lepší. * Umožnění lehkých konstrukcí: Snížená hmotnost součástí přispívá k lepší palivové účinnosti v konečné aplikaci (letadlo, vozidlo), což vede ke snížení emisí po celou dobu životnosti výrobku.
Volba kovového 3D tisku pro palivové rozvody je proto strategickým rozhodnutím, které je vedeno potenciálem vyššího výkonu, nižší hmotnosti, vyšší spolehlivosti a rychlejších vývojových cyklů. Ačkoli počáteční náklady na díl mohou být někdy vyšší než u jednoduchého obráběného dílu, analýza celkových nákladů na vlastnictví často odhalí významné úspory při zohlednění redukce montáže, lepšího výkonu, výhod úspory hmotnosti a zjednodušení logistiky. Spolupráce se zkušeným dodavatel AM kovů jako je Met3dp, která má hluboké znalosti materiálů, procesů jako L-PBF a SEBM a principů DfAM, je klíčem k plnému využití těchto výhod aditiv pro vaše kritické aplikace distribuce paliva. Zkoumání různých tiskových metod a možností materiálů je pro optimalizaci výsledku zásadní.
Výběr materiálu: AlSi10Mg a IN625 pro optimální výkonnost
Výběr vhodného materiálu je pravděpodobně jedním z nejdůležitějších rozhodnutí při návrhu a výrobě jakékoli součásti, ale u rozvodů paliva nabývá na významu vzhledem k náročným provozním požadavkům, kterým často čelí. Materiál musí zajistit nejen strukturální integritu při tlaku a vibracích, ale také odolávat možným teplotním extrémům, odolávat korozi způsobené různými typy paliva a v ideálním případě přispívat k dosažení cílů optimalizace hmotnosti. Aditivní výroba rozšiřuje paletu dostupných materiálů a kombinací jejich zpracování, ale je třeba pečlivě zvážit, zda výsledný díl splňuje všechny požadavky na výkon, bezpečnost a životnost.
U 3D tištěných palivových rozvodů na zakázku jsou často na prvním místě dva materiály, a to díky jejich vynikající rovnováze vlastností a zpracovatelnosti pomocí běžných technik AM, jako je laserová fúze v práškovém loži (L-PBF): Slitina hliníku, křemíku a hořčíku (AlSi10Mg) a Nikl-chromová superslitina Inconel 625 (IN625). Pochopení odlišných vlastností a ideálních aplikací pro každou z nich je pro inženýry a specialisty na zadávání zakázek, kteří chtějí efektivně využívat AM, zásadní.
1. Hliník křemík hořčík (AlSi10Mg): Lehký pracovní kůň
AlSi10Mg je široce používaná hliníková slitina v aditivní výrobě, která přesně kopíruje vlastnosti tradičních litých hliníkových slitin, jako je A360. Jeho oblíbenost vyplývá z kombinace žádoucích vlastností, díky nimž je vhodný pro širokou škálu aplikací, včetně mnoha palivových systémů.
- Klíčové vlastnosti:
- Nízká hustota / nízká hmotnost: S hustotou přibližně 2,67 g/cm3 je výrazně lehčí než oceli nebo slitiny niklu, takže je ideální pro aplikace, kde je snížení hmotnosti hlavním faktorem (letectví, automobilový průmysl, drony).
- Dobrý poměr pevnosti a hmotnosti: I když není tak pevný jako ocel nebo titan, nabízí slušnou mechanickou pevnost, zejména po vhodném tepelném zpracování, takže je vhodný pro mírné tlakové a konstrukční požadavky. Typická mez pevnosti v tahu (UTS) tepelně zpracovaného materiálu L-PBF AlSi10Mg může přesáhnout 300 MPa.
- Vynikající tepelná vodivost: Hliníkové slitiny velmi dobře vedou teplo, což může být výhodné při odvádění tepla od paliva nebo při použití samotného rozdělovače jako chladiče v některých konstrukcích.
- Dobrá odolnost proti korozi: Vykazuje dobrou odolnost vůči atmosférické korozi a různým kapalinám, avšak vždy je třeba ověřit kompatibilitu s konkrétním palivem.
- Zpracovatelnost: Je relativně snadno zpracovatelný pomocí systémů L-PBF, což umožňuje jemné rysy a dobrou povrchovou úpravu (v porovnání s AM).
- Ideální aplikace palivového rozdělovače:
- Automobilový průmysl: Široce se používá pro prototypové a sériové rozvody ve výkonných vozidlech, standardních osobních automobilech (kde je to možné) a v motorsportu díky své nízké hmotnosti a odpovídajícímu výkonu pro typické automobilové tlaky a teploty paliva.
- Bezpilotní letadla (UAV / drony): Hmotnost je rozhodující a provozní podmínky jsou obecně méně extrémní než u leteckých motorů s posádkou.
- Letectví a kosmonautika (méně náročné role): Vhodné pro sekundární palivové potrubí, hydraulické rozdělovače nebo součásti v systémech řízení prostředí, kde jsou teploty a tlaky mírné.
- Průmyslová zařízení: Aplikace, kde jsou provozní teploty relativně nízké a agresivní chemická koroze nepředstavuje hlavní problém.
- Úvahy o zpracování (L-PBF):
- Vyžaduje pečlivou kontrolu parametrů (výkon laseru, rychlost skenování, tloušťka vrstvy), aby se minimalizovala pórovitost a dosáhlo se hustých dílů.
- Obvykle vyžaduje po tisku tepelné zpracování za účelem snížení vnitřních pnutí vzniklých během rychlých cyklů zahřívání a ochlazování. Pro maximalizaci pevnosti a tvrdosti se často používá tepelné zpracování T6 (rozpuštění a umělé stárnutí).
- Podpěrné konstrukce jsou obvykle nutné pro převisy a obvykle se odstraňují ručně nebo pomocí CNC obrábění.
- Schopnosti Met3dp’: Společnosti jako Met3dp využívají pokročilé techniky výroby prášků, jako např rozprašování plynu, k výrobě vysoce kvalitního prášku AlSi10Mg. Tím je zajištěna vysoká sféricita, dobrá sypnost, kontrolovaná distribuce velikosti částic a nízký obsah kyslíku - všechny tyto faktory jsou rozhodující pro dosažení konzistentních, vysoce hustých a spolehlivých dílů během procesu L-PBF. Získávání prášku od renomovaného dodavatele s důkladnou kontrolou kvality, jako je společnost Met3dp, je nezbytné pro zajištění materiálové integrity konečného rozdělovače. Jejich sortiment produkty obsahuje různé vysoce výkonné prášky optimalizované pro AM.
2. Inconel 625 (IN625): Šampion odolný vůči korozi a vysokým teplotám
IN625 je superslitina niklu, chromu, molybdenu a niobu, která je proslulá svými výjimečnými vlastnostmi v náročných podmínkách. Pokud palivové rozvody čelí extrémním teplotám, vysokým tlakům a korozivním médiím, je IN625 často vhodným materiálem.
- Klíčové vlastnosti:
- Vynikající odolnost při vysokých teplotách: Zachovává si značnou pevnost a odolává tečení při zvýšených teplotách (až 800-900∘C nebo vyšších, v závislosti na podmínkách), takže je ideální pro komponenty v blízkosti spalovacích komor nebo výfukových systémů.
- Vynikající odolnost proti korozi: Vykazuje výjimečnou odolnost vůči široké škále korozních prostředí, včetně oxidačních a redukčních kyselin, důlkové koroze, štěrbinové koroze a chloridového korozního praskání. To má zásadní význam při práci s agresivními nebo alternativními druhy paliv.
- Vysoká únavová pevnost: Účinně odolává cyklickému zatížení a vibracím, což má zásadní význam v prostředí motorů.
- Vynikající svařitelnost/obrobitelnost (v AM): Přestože je slitina IN625 složitá, lze ji snadno zpracovávat pomocí L-PBF i tavení elektronovým svazkem (EBM), což umožňuje vytvářet husté díly bez trhlin s vhodnou kontrolou parametrů.
- Kryogenní houževnatost: Zachovává si dobrou houževnatost i při velmi nízkých teplotách, což je důležité pro některé aplikace paliv v letectví a kosmonautice.
- Ideální aplikace palivového rozdělovače:
- Letecké plynové turbínové motory: Palivové sběrné potrubí, palivové trysky a součásti spalovacího motoru pracující v horkých částech motoru.
- Raketové pohonné systémy: Součásti vstřikovačů, rozvody paliva a okysličovadla, které zvládají extrémní teploty a tlaky.
- Vysokoteplotní průmyslové systémy: Dodávka paliva v průmyslových pecích, reaktorech pro chemické zpracování nebo v energetických turbínách pracujících v náročných podmínkách.
- Mořské aplikace: Díky odolnosti vůči korozi ve slané vodě je vhodný pro palivové systémy lodních dieselových motorů.
- Aplikace s korozivními palivy: Systémy využívající biopaliva, syntetická paliva nebo jiné alternativy, které mohou být korozivnější než tradiční ropné produkty.
- Úvahy o zpracování (L-PBF/EBM):
- Vyžaduje vyšší příkon energie ve srovnání s hliníkovými slitinami.
- Náchylnost na vznik zbytkového napětí v důsledku velkých tepelných gradientů; je nutná pečlivá kontrola ohřevu, strategie skenování a často i ohřevu stavební desky (běžné u EBM).
- Téměř vždy je nutné po tisku provést žíhání na uvolnění napětí, aby se snížila zbytková napětí a zabránilo se deformaci nebo praskání. Pro optimalizaci mechanických vlastností může být nutné další tepelné zpracování (žíhání v roztoku, stárnutí).
- Podpůrné struktury jsou obvykle hustší a jejich odstranění může být náročnější než u hliníkových slitin, což často vyžaduje obrábění nebo elektroerozivní obrábění.
- Met3dp’s Expertise: Společnost Met3dp má značné zkušenosti s výrobou a zpracováním superslitin, jako je IN625. Jejich pokročilé systémy výroby prášků zajišťují výrobu prášků se specifickými vlastnostmi potřebnými pro úspěšné AM zpracování těchto náročných materiálů. Jejich zkušenosti s různými systémy AM, včetně potenciálně selektivního tavení elektronovým svazkem (SEBM), které může být výhodné pro řízení napětí v niklových slitinách, jim navíc umožňují poradit klientům s optimální kombinací materiálů a procesů pro náročné materiály Letecký rozdělovač IN625 aplikace. Jejich portfolio přesahuje tyto dva materiály a zahrnuje inovativní slitiny, jako jsou TiNi, TiTa, TiAl, TiNbZr, CoCrMo, nerezové oceli a další, a poskytuje tak komplexní materiálová řešení.
Volba mezi AlSi10Mg a IN625:
Výběr závisí především na provozním prostředí:
Vlastnosti | AlSi 10Mg | IN625 |
---|---|---|
Primární výhoda | Lehký, dobrá tepelná vodivost | Pevnost při vysokých teplotách, odolnost proti korozi |
Hustota | Nízká (~2,67 g/cm3) | Vysoká (~8,44 g/cm3) |
Maximální teplota použití | Mírná (~150-200∘C) | Velmi vysoká (~800-1000∘C) |
Odolnost proti korozi | Dobrý (všeobecný) | Vynikající (agresivní prostředí) |
Náklady | Dolní | Vyšší |
Hmotnost | Lehčí | Těžší |
Typické aplikace | Automobilový průmysl, Drony, Nízkoteplotní letecký průmysl | Letecké motory, rakety, vysokoteplotní průmyslová zařízení |
Zpracování AM | L-PBF (běžné) | L-PBF, EBM (běžné) |
Export do archů
Další potenciální materiály:
Ačkoli AlSi10Mg a IN625 pokrývají mnoho aplikací, lze uvažovat i o dalších materiálech:
- Slitiny titanu (např. Ti6Al4V): Nabízejí vynikající poměr pevnosti k hmotnosti, lepší než AlSi10Mg, a dobrou odolnost proti korozi se středně vysokou teplotní odolností (až ~400∘C). Často se používají v leteckém průmyslu, kde je hmotnost kritická, ale teploty nevyžadují IN625.
- Nerezové oceli (např. 316L, 17-4PH): Poskytují dobrou odolnost proti korozi a střední pevnost při nižších nákladech než IN625, vhodné pro různé průmyslové a automobilové aplikace, kde nehraje roli vysoká teplota a hmotnost není hlavním problémem.
Proces výběru materiálu nakonec vyžaduje důkladnou analýzu provozních podmínek rozdělovače, požadavků na výkon, cílové hmotnosti a rozpočtových omezení. Konzultace s odborníky na materiály a zkušenými dodavateli AM, jako je Met3dp, kteří rozumí nuancím různých kovové prášky a jejich zpracování, je zásadní pro zajištění optimální volby spolehlivého a vysoce výkonného palivového rozvodu vytištěného 3D tiskem. Jejich zázemí jako dodavatelé kovových prášků s využitím špičkových technologií v oboru jim dává jedinečný přehled o možnostech materiálů.
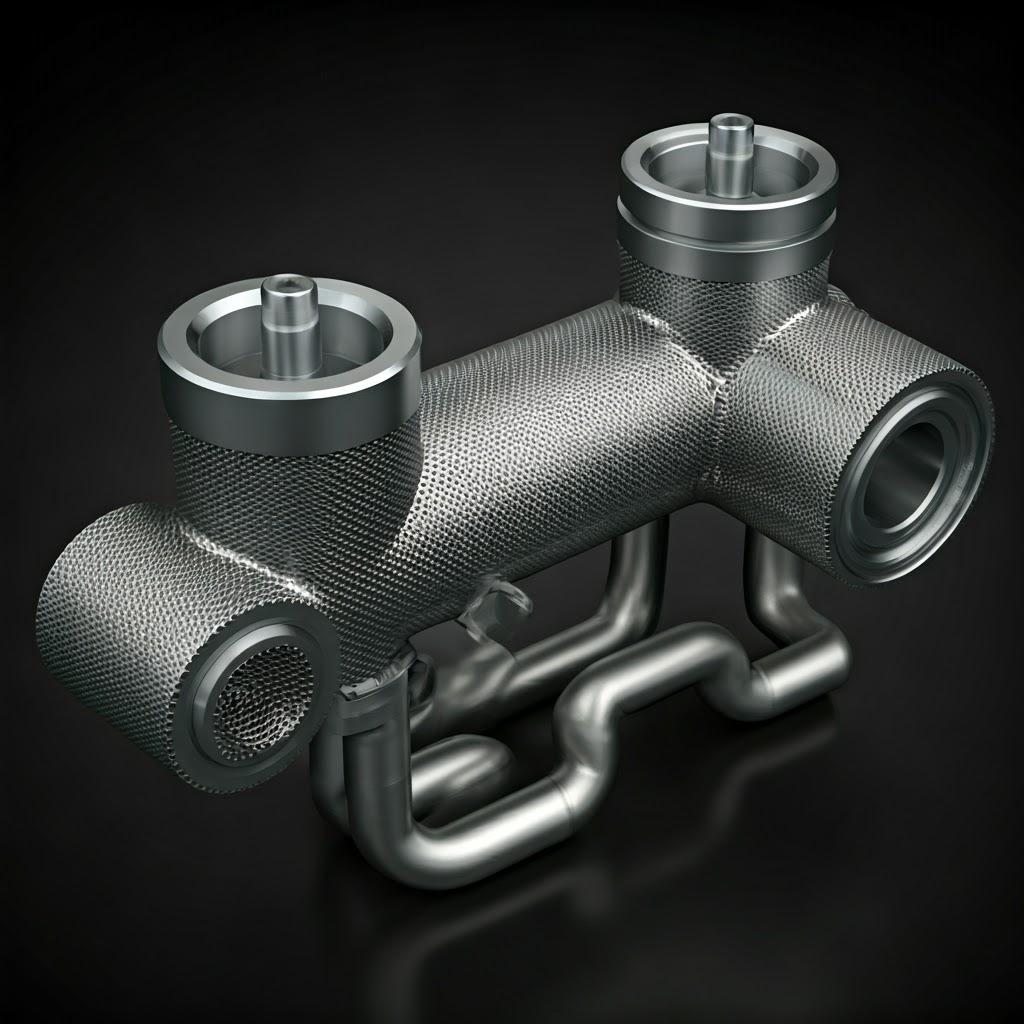
Design pro aditivní výrobu (DfAM): Optimalizace palivových rozvodů pro tisk
Pouhým převzetím návrhu palivového rozvodu určeného pro tradiční výrobu a jeho odesláním do kovové 3D tiskárny se málokdy dosáhne optimálních výsledků. Ve skutečnosti to může často vést k selhání tisku, špatné kvalitě dílů, nadměrným požadavkům na následné zpracování a zbytečně vysokým nákladům. Aby inženýři skutečně využili transformační potenciál aditivní výroby - optimalizaci průtoku, snížení hmotnosti a konsolidaci dílů, o nichž jsme hovořili dříve - musí přijmout Design pro aditivní výrobu (DfAM). DfAM není jen návrh, ale zásadní posun v myšlení o designu, který zohledňuje jedinečné možnosti a omezení stavebního procesu po jednotlivých vrstvách již od koncepční fáze. U složitých fluidních součástí, jako jsou palivové rozvody, je použití zásad DfAM rozhodující pro úspěch.
DfAM zahrnuje holistický přístup, který zahrnuje úvahy o vlastnostech materiálu, možnostech tiskárny, požadavcích na podpůrnou konstrukci, krocích následného zpracování a požadované funkčnosti dílu. Často vyžaduje úzkou spolupráci mezi konstruktéry a poskytovatelem AM služeb s využitím praktických zkušeností a znalostí procesů poskytovatele. Rozebereme si klíčové principy DfAM, které se konkrétně týkají navrhování optimalizovaných palivových rozvodů pro kovovou AM:
1. Design vnitřního kanálu: Právě zde nabízí AM oproti tradičním metodám pro rozdělovače nejvýznamnější výhody. * Samonosné úhly: Většina procesů tavení v práškovém loži (např. L-PBF a EBM) může tisknout převislé prvky bez podpůrných struktur až do určitého úhlu, obvykle kolem 45 stupňů od vodorovné roviny (vzhledem ke konstrukční desce). Navrhování vnitřních kanálů s mírným sklonem a vyhýbání se plochým vodorovným stropům minimalizuje potřebu vnitřních podpěr, jejichž odstranění z uzavřených průchodů může být velmi obtížné nebo nemožné. Tam, kde se vodorovným úsekům nelze vyhnout, je možné je navrhnout s “slzovitým” nebo kosočtvercovým průřezem, aby byly samonosné. * Hladké křivky a filety: Ostré vnitřní rohy koncentrují napětí a mohou narušit proudění kapaliny, což způsobuje turbulence a pokles tlaku. DfAM podporuje používání hladkých, velkorysých poloměrů a filetů v místech křížení kanálů a ohybů. Procesy AM mohou snadno vytvářet tyto složité křivky, což vede ke zlepšení dynamiky tekutin a lepší strukturální integritě. * Vyhýbání se tenkým a hlubokým slotům: Velmi úzké nebo hluboké vnitřní prvky mohou být obtížné pro přesný tisk a náročné na čištění zbytků prášku. Při návrhu je třeba dbát na to, aby kanály byly dostatečně velké pro účinné odstraňování prášku a v případě potřeby i pro následné zpracování, jako je abrazivní proudové obrábění. * Optimalizace průtokové cesty (návrh řízený CFD): DfAM umožňuje konstruktérům používat nástroje pro simulaci počítačové dynamiky tekutin (CFD) k modelování proudění tekutin v navrhovaných rozdělovačích. Výsledky mohou být vodítkem pro optimalizaci tvarů, velikostí a uspořádání kanálů za účelem dosažení specifických cílů, jako je minimalizace tlakové ztráty, zajištění rovnoměrného rozdělení průtoku do všech výstupů nebo podpora specifických charakteristik míchání. Společnost AM pak může tyto vysoce optimalizované, často neintuitivní geometrie přímo vyrábět.
2. Úvahy o tloušťce stěny: * Minimální tloušťka potisku: Procesy AM mají omezení minimální tloušťky stěny, kterou mohou spolehlivě vyrobit, obvykle v rozmezí od 0,3 mm do 1,0 mm v závislosti na materiálu, stroji a geometrii prvku. Konstrukce musí tyto limity respektovat, aby se zajistilo úplné vytvarování prvků. * Strukturální integrita a omezení tlaku: Stěny musí být dostatečně silné, aby odolaly provozním tlakům palivového systému, aniž by se propadly nebo praskly. K simulaci rozložení napětí pod tlakem a zajištění dostatečné tloušťky stěn, zejména v oblastech s vysokým tlakem nebo v oblastech, které byly optimalizací topologie označeny jako vysoce namáhané, by měla být použita analýza konečných prvků (FEA). DfAM zahrnuje vyvážení snahy o odlehčení s potřebou robustnosti konstrukce. * Jednotnost (pokud je to možné): Proměnlivá tloušťka stěny je sice možná a často i žádoucí (např. prostřednictvím optimalizace topologie), ale velké a náhlé změny tloušťky mohou někdy vést k rozdílné rychlosti chlazení během tisku, což může vést ke zvýšení zbytkového napětí nebo deformace. Upřednostňují se postupné přechody.
3. Strategie podpůrné struktury: Podpěrné konstrukce jsou v kovovém AM často nutné k ukotvení dílu k sestavovací desce, k podepření převislých prvků (strmějších než samonosný úhel) a k odvádění tepla od dílu během tisku, čímž se snižuje jeho deformace. * Minimalizace vnitřních podpor: Jak již bylo uvedeno, vnitřní podpěry v uzavřených kanálech jsou velmi nežádoucí. DfAM se zaměřuje na orientaci dílu na konstrukční desce a návrh geometrie kanálů (s použitím samonosných úhlů a tvarů), aby se jejich potřeba eliminovala nebo výrazně snížila. * Konstrukce pro snadnou demontáž: Pokud jsou nutné vnější podpěry (např. pod přírubami nebo vnějšími prvky), měly by být navrženy tak, aby byly přístupné a snadno odstranitelné pomocí ručního nářadí nebo obrábění, aniž by došlo k poškození povrchu dílu. To může zahrnovat použití specifických typů podpěr (např. mřížové nebo kuželové podpěry) s minimálním počtem styčných bodů nebo navržení svědeckých linií, kde lze podpěry čistě odříznout obráběním. * Funkce podpory: Podpěry hrají zásadní roli také v tepelném managementu. V místech náchylných k přehřívání nebo deformaci mohou být zapotřebí husté podpěry. Simulační nástroje mohou pomoci předvídat tepelné chování a řídit optimální umístění a typ podpěr.
4. Integrace funkcí: AM umožňuje kombinovat více funkcí do jediného dílu. * Konsolidace součástí: Hledejte možnosti integrace držáků, montážních otvorů, otvorů pro senzory, krytů nebo dokonce prvků výměníku tepla přímo do těla rozdělovače. Tím se sníží počet dílů, náročnost montáže a potenciální netěsnosti. * Navrhování integrovaných funkcí pro AM: Zajistěte, aby integrované prvky dodržovaly zásady DfAM (např. samonosné úhly pro montážní otvory, dostatečná tloušťka stěny kolem portů). Zvažte, jak budou na integrovaných prvcích prováděny kroky následného zpracování, jako je řezání závitů nebo obrábění těsnicích ploch.
5. Optimalizace topologie a odlehčení: * Použití zatížení a omezení: Definujte provozní zatížení (tlak, vibrace, montážní síly) a omezení (ochranné zóny, místa připojení) pro rozdělovač. * Spouštění optimalizačních algoritmů: Pomocí softwaru pro optimalizaci topologie založeného na metodě konečných prvků lze iterativně odstraňovat materiál z nekritických oblastí a zároveň zajistit, aby konstrukce stále splňovala požadavky na výkon (tuhost, pevnost, vlastní frekvence). * Interpretace a zpřesnění výsledků: Surový výstup topologické optimalizace často vyžaduje vyhlazení a interpretaci, aby bylo možné vytvořit vyrobitelný návrh. To může zahrnovat převod složitých mřížkových struktur na lépe zvládnutelné geometrie nebo zajištění dodržení minimálních velikostí prvků. Mřížkové struktury sice nabízejí maximální úsporu hmotnosti, ale mohou být náročné na vnitřní čištění a kontrolu, takže u palivových rozdělovačů je třeba najít rovnováhu. Generativní návrhové nástroje nabízejí podobné možnosti a často zkoumají více možností návrhu na základě definovaných omezení.
Spolupráce je klíčová: Úspěšná implementace DfAM, zejména u kritických komponent, jako jsou palivové rozvody, často velmi těží z včasné spolupráce se zkušeným poskytovatelem služeb AM, jako je Met3dp. Jejich inženýři mají hluboké praktické znalosti o specifických schopnostech strojů, chování materiálů, podpůrných strategiích a důsledcích následného zpracování. Mohou poskytnout zásadní zpětnou vazbu ohledně proveditelnosti návrhu, navrhnout úpravy pro zlepšení tisknutelnosti nebo snížení nákladů a pomoci zajistit, aby byl konečný návrh skutečně optimalizován pro aditivní proces. Využití řešení aditivní výroby nabízené kompetentními partnery zefektivňují cestu od konceptu k funkčnímu a vysoce výkonnému dílu. Tento přístup založený na spolupráci zajišťuje, že návrhy jsou nejen teoreticky optimální, ale také prakticky vyrobitelné, spolehlivé a nákladově efektivní. Ignorování zásad DfAM je častým úskalím, které vede k nákladným selháním a promarněným příležitostem při zavádění technologie AM pro kovy.
Dosažení přesnosti: Tolerance, povrchová úprava a rozměrová přesnost v rozdělovačích AM
Přestože aditivní výroba kovů nabízí nebývalou svobodu při navrhování, je pro inženýry a manažery nákupu zásadní mít realistická očekávání ohledně dosažitelné přesnosti, povrchové úpravy a rozměrové přesnosti 3D tištěných dílů, zejména u funkčních součástí, jako jsou palivové rozvody, kde mohou být rozhodující úzké tolerance a specifické vlastnosti povrchu. Na rozdíl od vysoce přesného CNC obrábění, při kterém lze dosáhnout přesnosti na úrovni mikronů, procesy AM ze své podstaty zahrnují tepelné výkyvy, konstrukci po vrstvách a vlastnosti částic prášku, které ovlivňují konečný rozměrový výsledek a strukturu povrchu. Pochopení těchto aspektů je klíčem k efektivnímu návrhu a určení nezbytných kroků následného zpracování.
1. Rozměrové tolerance: * Typické dosažitelné tolerance: Obecně lze říci, že procesy tavení kovového prášku (L-PBF a EBM) obvykle dosahují rozměrových tolerancí v rozmezí ±0,1 mm až ±0,2 mm u menších dílů (např. do 100 mm) a procenta celkového rozměru (např. ±0,1 % až ±0,2 %) u větších dílů. To se však může výrazně lišit v závislosti na několika faktorech: * Kalibrace strojů & Stav: Dobře udržované a přesně kalibrované stroje poskytují vyšší přesnost. * Materiál: Různé materiály vykazují během zpracování různou míru smrštění a tepelné roztažnosti (např. slitiny hliníku se smršťují více než slitiny niklu). * Geometrie dílu & Velikost: Složité geometrie, velké rovné plochy a vysoké, tenké prvky jsou náchylnější ke zkreslení a odchylkám. Tepelné namáhání se kumuluje různě v závislosti na tvaru dílu. * Orientace na stavbu: Orientace dílu na konstrukční desce ovlivňuje rozložení tepla, požadavky na podporu a možnost deformace, což má vliv na konečné rozměry. * Tepelné namáhání: Zbytková napětí vzniklá během tisku mohou způsobit deformaci nebo zkroucení po vyjmutí dílu z konstrukční desky nebo během tepelného zpracování po tisku. * Navrhování pro toleranci: Kritické rozměry, které vyžadují větší tolerance než standardní proces AM (např. těsnicí plochy, rozhraní ložisek, průměry otvorů), musí být obvykle řešeny následným zpracováním, obvykle CNC obráběním. DfAM zahrnuje identifikaci těchto kritických prvků a návrh dílu s dostatečným množstvím dodatečného materiálu (přídavek na obrábění nebo zásoba) v těchto oblastech, aby bylo možné provést přesné dokončovací práce. * Důslednost: Dosažení tolerancí pod 0,1 mm přímo z tiskárny je sice náročné, ale řízení procesu a konzistence se zlepšují. Zkušení poskytovatelé se zaměřují na udržování stabilních procesů, aby zajistili opakovatelné rozměrové výsledky od dílu k dílu a od dávky k dávce.
2. Drsnost povrchu: * Drsnost povrchu (Ra) podle stavu: Povrchová úprava dílů přímo ze stroje AM je ze své podstaty drsnější než u obráběných povrchů. To je způsobeno částečně roztavenými částicemi prášku, které ulpívají na povrchu, a vrstevnatým “schodovitým” efektem na zakřivených nebo šikmých plochách. Typické hodnoty drsnosti povrchu (Ra) po sestavení se u L-PBF často pohybují v rozmezí od 6 μm do 25 μm (240 μin až 1000 μin) v závislosti na materiálu, parametrech, orientaci a na tom, zda povrch během sestavování směřoval nahoru nebo dolů. Díly EBM mají obvykle drsnější povrch. * Vnitřní vs. vnější povrchy: Vnitřní kanály a povrchy směřující dolů (podepřené povrchy) mají obecně drsnější povrchovou úpravu než vnější stěny směřující nahoru nebo svislé stěny, což je způsobeno faktory, jako jsou kontaktní body podpěr a adhezní vlastnosti prášku. To je kritický faktor u palivových rozdělovačů, kde hladkost vnitřních kanálů ovlivňuje průtok kapaliny. * Vliv drsnosti: Drsné vnitřní povrchy mohou zvyšovat tření, což vede k vyšším tlakovým ztrátám a může přispívat k turbulencím. Mohou také zachycovat nečistoty nebo vytvářet iniciační místa pro únavové trhliny v aplikacích s vysokým namáháním. * Zlepšení povrchové úpravy: Ke zlepšení kvality povrchu se používají různé techniky následného zpracování (podrobněji popsané v následující části), včetně tryskání kuličkami, bubnového obrábění, CNC obrábění, leštění, elektrolytického leštění a obrábění abrazivním tokem (AFM). Volba závisí na požadované úrovni povrchové úpravy, přístupnosti (vnitřní vs. vnější), materiálu a na finančních aspektech.
3. Ověřování rozměrové přesnosti: Zajištění, aby finální rozdělovač splňoval specifikace, vyžaduje důkladnou kontrolu kvality a kontrolní metody. * Souřadnicové měřicí stroje (CMM): Poskytují vysoce přesná bodová měření pro ověřování kritických rozměrů, umístění otvorů a prvků geometrického dimenzování a tolerování (GD&T). Vyžaduje fyzické sondování. * 3D skenování (strukturované světlo / laser): Rychle zachytí celou 3D geometrii dílu a umožní porovnání s původním modelem CAD, čímž vytvoří barevné mapy zobrazující odchylky na celém povrchu. Vynikající pro celkové ověření tvaru, ale může být méně přesný než CMM pro konkrétní kritické rozměry. * CT vyšetření (počítačová tomografie): Využívá rentgenové snímky k vytvoření 3D modelu dílu včetně vnitřních prvků. To je neocenitelné pro kontrolu rozměrů a celistvosti složitých vnitřních kanálů v rozdělovačích, ověřování tloušťky stěn a odhalování vnitřních vad, jako je pórovitost, aniž by došlo k destrukci dílu. * Tradiční metrologie: Ke specifickým měřením se používají také kalipery, mikrometry, výškoměry a funkční kontroly (např. lícování dílů).
Met3dp’s Commitment to Precision: Dosažení požadované přesnosti u náročných aplikací, jako je letecký průmysl nebo lékařské komponenty, vyžaduje více než jen moderní stroje. Vyžaduje to přísnou kontrolu procesu, pečlivou kalibraci stroje, vysoce kvalitní vstupní materiály (prášky) a hluboké porozumění tepelným a fyzikálním jevům, které se při výrobě vyskytují. Společnosti, jako je Met3dp, zdůrazňují svou schopnost dodávat špičkový objem tisku, přesnost a spolehlivost pro kritické díly. Tento závazek zahrnuje robustní systémy řízení kvality (QMS), investice do přesného metrologického vybavení (jako je souřadnicová měřicí soustava a případně 3D skenování) a odborné znalosti v oblasti řízení celého pracovního postupu - od konzultace DfAM přes tisk a následné zpracování až po konečnou kontrolu - s cílem splnit náročné požadavky na tolerance a povrchovou úpravu kritických součástí, jako jsou palivové rozvody. Při hodnocení partnerů pro vysoce přesné projekty AM by se inženýři a manažeři nákupu měli zajímat o konkrétní metrologické schopnosti a postupy zajištění kvality potenciálního dodavatele.
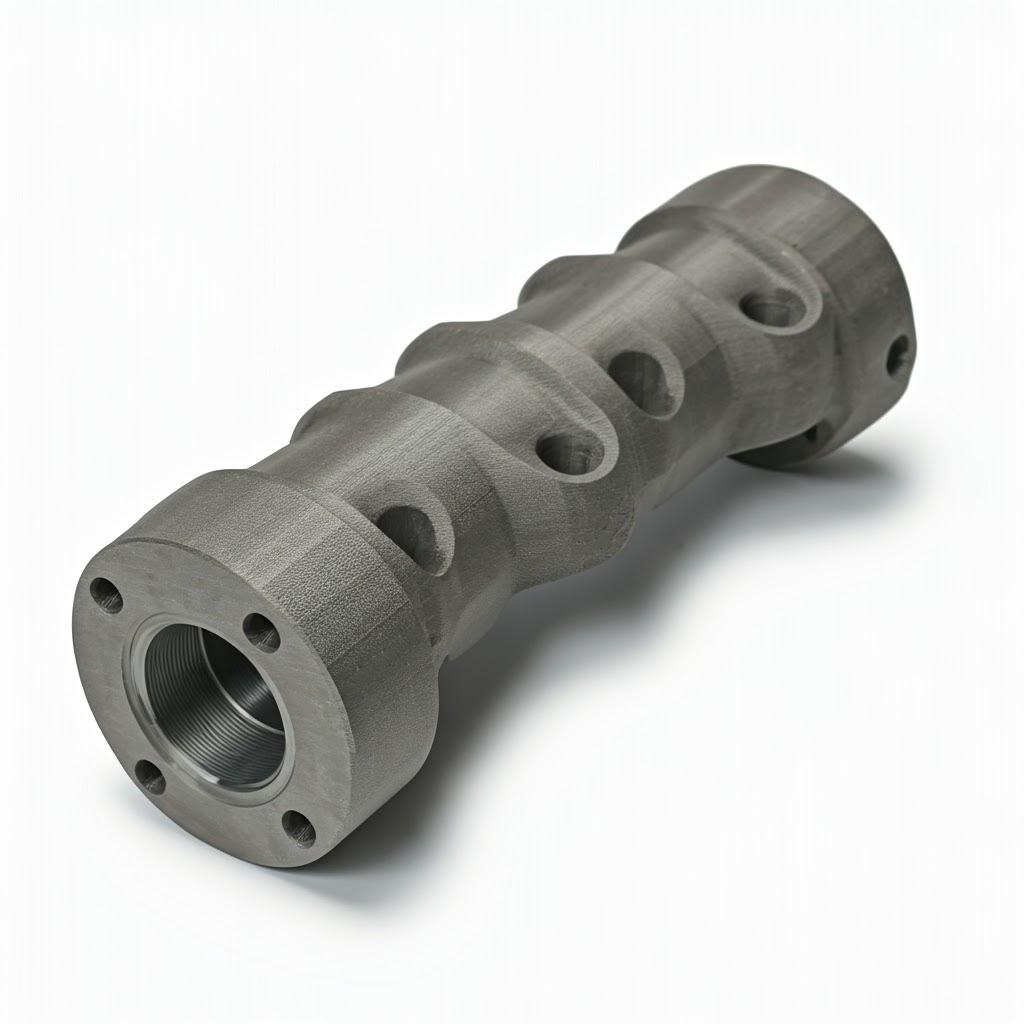
Kromě tisku: Základní kroky následného zpracování palivových rozvodů
Běžnou mylnou představou o 3D tisku z kovu je, že díly vyjíždějí ze stroje připravené k okamžitému použití. Ačkoli AM výrazně zjednodušuje tvorbu složitých geometrií, realita, zejména u náročných aplikací, jako jsou palivové rozvody, je taková, že fáze “tisku” je často jen jedním krokem ve vícestupňovém výrobním procesu. Téměř vždy je nutné následné zpracování, aby se z hotového dílu stala funkční a spolehlivá součást, která splňuje všechny technické specifikace týkající se vlastností materiálu, rozměrové přesnosti, povrchové úpravy a čistoty. Pochopení těchto nezbytných kroků je klíčové pro přesný odhad celkové doby výroby a nákladů.
Zde je přehled základních operací následného zpracování, které se běžně používají u kovových palivových rozvodů AM:
1. Úleva od stresu / tepelné ošetření: * Účel: Rychlé cykly zahřívání a ochlazování, které jsou vlastní procesům tavení v práškovém loži, vytvářejí v hotovém dílu značná vnitřní pnutí. Tato napětí mohou způsobit deformaci nebo pokřivení po vyjmutí dílu z konstrukční desky, snížit únavovou životnost materiálu a potenciálně vést k jeho předčasnému selhání. Tepelné zpracování pro uvolnění napětí se provádí před vyjmutí dílu z konstrukční desky (kdykoli je to možné), aby se tato vnitřní napětí uvolnila. * Proces: Díl, který je stále připevněn ke stavební desce, se zahřeje v peci s řízenou atmosférou na určitou teplotu (pod kritické body přeměny materiálu), po určitou dobu se udržuje a poté se pomalu ochlazuje. Přesný cyklus (teplota, čas, atmosféra) závisí do značné míry na materiálu (např. cykly AlSi10Mg se výrazně liší od cyklů IN625) a geometrii dílu. * Další tepelné úpravy: Kromě uvolnění napětí může být pro dosažení požadovaných konečných mechanických vlastností (tvrdost, pevnost, tažnost) specifikovaných pro danou aplikaci nezbytné další tepelné zpracování, jako je žíhání v roztoku a stárnutí (např. zpracování T6 pro AlSi10Mg nebo specifické cykly stárnutí pro IN625). Tyto úpravy mění mikrostrukturu materiálu.
2. Vyjmutí dílu ze stavební desky: * Metoda: Po dokončení odlehčování (pokud se provádí na desce) je třeba díl oddělit od kovové konstrukční desky, na které byl vytištěn. To se obvykle provádí pomocí elektroerozivního obrábění (EDM) nebo pásové pily. Při tomto procesu je třeba dbát na to, aby nedošlo k poškození dílu.
3. Odstranění podpůrné konstrukce: * Účel: Odstranění dočasných podpůrných konstrukcí použitých při stavbě. * Metody: Může se jednat o různé způsoby, od jednoduchého ručního vylamování u snadno přístupných, lehce natavených podpěr až po náročnější metody, jako je broušení, frézování nebo elektroerozivní obrábění drátem u hustších nebo hůře přístupných podpěr. Přístup může být obzvláště náročný u podpěr uvnitř vnitřních kanálů rozdělovače, pokud nebyly důsledně uplatněny zásady DfAM, aby se jim zabránilo. Mohou být zapotřebí specializované nástroje nebo techniky. Tento krok může být pracný a vyžaduje kvalifikované techniky, aby nedošlo k poškození kritických povrchů.
4. CNC obrábění: * Účel: K dosažení přesnějších tolerancí, specifických povrchových úprav a prvků, které nelze přesně vyrobit samotným procesem AM. * Aplikace na množinách: * Kritická rozhraní: Obrábění těsnicích ploch (např. drážky pro O-kroužky, ploché plochy pro těsnění) pro zajištění těsnosti spojů. * Obrábění v přístavu: Přesné dimenzování a úprava připojovacích otvorů. * Závitování/frézování: Vytváření závitových otvorů pro upevňovací prvky nebo senzory. * Těsná tolerance Funkce: Dosažení rozměrové přesnosti nad rámec standardních možností AM u specifických prvků určených v návrhu. * Zlepšení povrchové úpravy: Frézování nebo soustružení specifických vnějších povrchů pro dosažení velmi hladkého povrchu (Ra<1μm). * Úvahy: Vyžaduje pečlivé nastavení a upevnění dílu AM. Ve fázi DfAM musí být zahrnuto dostatečné množství obráběného materiálu.
5. Povrchová úprava & Povrchová úprava: * Účel: Zlepšení drsnosti povrchu, zlepšení estetiky, zvýšení únavové životnosti, zvýšení odolnosti proti opotřebení nebo zvýšení odolnosti proti korozi. * Společné techniky pro rozdělovače: * Tryskání kuličkami / pískování: Zajišťuje rovnoměrný matný povrch, odstraňuje částečně spečené částice a může přenášet tlaková napětí zlepšující únavovou životnost. Různá média (skleněné kuličky, oxid hlinitý) vytvářejí různé povrchové úpravy. * Obrábění / vibrační úprava: Používá abrazivní média v rotujícím nebo vibrujícím bubnu k odjehlování hran a vyhlazování povrchů, zejména u dávek menších dílů. * Leštění: Ruční nebo automatizované leštění za použití postupně jemnějších brusných materiálů k dosažení hladkého, zrcadlového povrchu vnějších povrchů. * Elektrolytické leštění: Elektrochemický proces, který odstraňuje tenkou vrstvu materiálu, vyhlazuje povrch a zvyšuje odolnost proti korozi, zvláště účinný pro nerezové oceli a některé slitiny niklu. V závislosti na geometrii může někdy zasáhnout i vnitřní oblasti. * Obrábění abrazivním tokem (AFM) / Extrude Hone: Používá se speciálně k vyhlazování a leštění vnitřních kanálů. Polymerový tmel s abrazivem je pod vysokým tlakem protlačován vnitřními kanály rozdělovače tam a zpět, čímž postupně eroduje vrcholy a vyhlazuje povrchy. Je nezbytný pro optimalizaci průtoku v kritických vnitřních kanálech, kam se jiné metody nedostanou. * Povrchová úprava: Nanášení specializovaných povlaků (např. tepelně bariérových povlaků, povlaků odolných proti opotřebení, vrstev zabraňujících korozi) v závislosti na požadavcích aplikace.
6. Čištění a kontrola: * Účel: Odstranění všech zbytků prášku, obráběcích kapalin, úlomků podpěr a dalších nečistot a ověření, zda díl před konečným použitím splňuje všechny specifikace. * Metody: * Odstranění prášku: Používá se vyfukování stlačeným vzduchem, ultrazvukové čisticí lázně, specializované proplachovací soupravy, které jsou obzvláště důležité pro složité vnitřní kanály rozdělovačů. Zajištění úplného odstranění prášku je nezbytné, aby se zabránilo následné kontaminaci nebo ucpání. * Ověřování čistoty: Boroskopická kontrola vnitřních kanálů, odběr vzorků závěrečných oplachových kapalin. * Testování těsnosti: Nezbytné pro palivové rozvody. Mezi metody patří zkouška rozpadu tlaku (natlakování rozdělovače a sledování poklesu tlaku) nebo zkouška těsnosti pomocí helia (použití helia jako stopovacího plynu detekovaného hmotnostním spektrometrem) pro vyšší citlivost. Zkoušky penetrací barvivem mohou někdy odhalit trhliny porušující povrch. * Rozměrová kontrola a kontrola NDT: Závěrečné kontroly souřadnicovým měřicím přístrojem, vizuální kontrola a případně metody nedestruktivního zkoušení, jako je CT skenování, aby se zajistila vnitřní integrita a průchodnost kanálů.
Integrace těchto Následné zpracování AM kroků do celkového výrobního plánu je zásadní. Významně ovlivňují konečnou cenu dílu a celkovou dobu výroby. Znalý partner v oblasti AM, jako je Met3dp, rozumí tomuto kompletnímu pracovnímu postupu a může poskytnout pokyny ohledně nejúčinnějších a nejefektivnějších strategií následného zpracování na základě specifických požadavků na palivový rozdělovač, čímž zajistí, že dodaná finální součást bude skutečně vhodná pro daný účel. Nezohlednění těchto kroků může vést k nečekaným zpožděním a překročení rozpočtu.
Zvládání výzev: Potenciální problémy při výrobě AM rozvodů a jejich řešení
Přestože aditivní výroba kovů nabízí pozoruhodné možnosti pro výrobu složitých palivových rozvodů, není tato technologie bez problémů. Dosažení konzistentních a vysoce kvalitních výsledků vyžaduje hluboké pochopení fyziky procesu, pečlivou kontrolu parametrů, vysoce kvalitní materiály a často i sofistikované strategie pro zmírnění dopadů. Inženýři a manažeři nákupu by si měli být vědomi potenciálních problémů, aby mohli lépe spolupracovat s poskytovateli AM a zajistit robustní výrobní procesy. Zde jsou uvedeny některé běžné problémy, se kterými se setkáváme při výrobě rozdělovačů AM, a jak zkušení poskytovatelé, jako je Met3dp, pracují na jejich překonání:
1. Deformace a zkreslení: * Problém: Nerovnoměrné zahřívání a ochlazování během procesu tavení po vrstvách vyvolává tepelné napětí. Tato napětí se hromadí a mohou způsobit deformaci nebo zkroucení dílu a odchýlit se od zamýšlené geometrie, zejména u velkých plochých profilů nebo tenkých prvků. * Zmírnění: * Optimalizovaná orientace sestavení: Umístění dílu na konstrukční desku, aby se minimalizovaly velké ploché plochy rovnoběžné s deskou a snížil se tepelný gradient. * Robustní podpůrné struktury: Strategicky umístěné podpěry pevně ukotví díl k sestavovací desce a fungují jako chladiče, které rovnoměrněji odvádějí teplo. Konstrukce podpěr má zásadní význam. * Tepelná simulace: Použití softwaru k předvídání rozložení teplot a kumulace napětí během stavby, což umožňuje proaktivní úpravy orientace nebo podpěr. * Optimalizace parametrů procesu: Nastavení výkonu laseru/ paprsku, rychlosti skenování a strategie skenování (např. ostrovní skenování) pro řízení tepelného příkonu a snížení nárůstu napětí. * Vytápění stavebních desek: Předehřívání základní desky (běžné u EBM, používá se také u některých systémů L-PBF, zejména u slitin náchylných k praskání) snižuje teplotní rozdíl a minimalizuje napětí. * Tepelné ošetření proti stresu: Provedení tohoto kroku před vyjmutím dílu z konstrukční desky je zásadní pro uvolnění nahromaděných napětí.
2. Řízení zbytkového stresu: * Problém: I když se podaří zabránit výraznému zkroucení, může v hotovém dílu zůstat zablokováno vysoké zbytkové napětí. To může negativně ovlivnit únavovou životnost, lomovou houževnatost a rozměrovou stabilitu v průběhu času nebo způsobit deformace při následném obrábění. * Zmírnění: * Strategie uvedené v části Deformace/zkreslení (orientace, podpěry, simulace, parametry, ohřev desek) jsou primárními metodami zmírnění. * Efektivní cykly pro odbourání stresu: Zajištění cyklu tepelného zpracování po výrobě vhodného pro daný materiál a geometrii, aby se maximálně snížilo napětí bez negativního vlivu na mikrostrukturu. * Monitorování procesů: In-situ monitorovací techniky (experimentální) se zaměřují na sledování nárůstu napětí během tisku. * Měření & Validace: Techniky, jako je rentgenová difrakce (XRD), mohou měřit úroveň zbytkového napětí v hotových dílech, aby se ověřila účinnost strategií zmírnění.
3. Praskání: * Problém: Některé slitiny, zejména některé vysokopevnostní hliníkové slitiny, niklové superslitiny (jako IN625 za neoptimálních podmínek) a titanové slitiny, mohou být náchylné k praskání během tisku (praskání při tuhnutí) nebo během ochlazování nebo tepelného zpracování po výrobě (praskání vlivem deformačního stáří). * Zmírnění: * Výběr materiálu & Kvalita: Zásadní je použití vysoce kvalitního prášku s řízeným chemickým složením určeným speciálně pro zpracování AM. Zaměření společnosti Met3dp’na pokročilou výrobu prášku (plynová atomizace, PREP) zajišťuje optimální vlastnosti prášku a snižuje jeho náchylnost. * Optimalizace parametrů: Přesné vyladění příkonu energie, strategie skenování a případně použití specializovaných parametrů (např. pulzní lasery) může minimalizovat tendenci k praskání. * Řízení ohřevu stavební desky / prostředí komory: Udržování zvýšené teploty snižuje tepelné gradienty. * Optimalizované tepelné zpracování: Rozhodující jsou pečlivě navržené cykly uvolňování napětí a žíhání. * Izostatické lisování za tepla (HIP): Viz níže - může uzavřít vnitřní dutiny a případně zacelit mikrotrhliny.
4. Obtíže při odstraňování podpůrné konstrukce: * Problém: Podpěry, zejména husté nebo umístěné ve složitých vnitřních kanálech rozdělovače, je velmi obtížné a časově náročné zcela odstranit bez poškození dílu. Neúplné odstranění může bránit průtoku nebo působit jako kontaminace. * Zmírnění: * DfAM Focus: Nejlepší strategií je upřednostnit volbu konstrukce (samonosné úhly, optimální orientace), která minimalizuje nebo eliminuje potřebu vnitřních podpěr. * Optimalizovaný design podpory: Použití typů podpěr (např. kuželových, mřížových), které se snáze odstraňují a mají pokud možno minimální kontaktní body. * Specializované techniky odstraňování: Využití elektroerozivního obrábění, specializovaných nástrojů nebo případně chemického leptání (v závislosti na materiálu) pro náročné podpěry. Obrábění abrazivním tokem může někdy pomoci odstranit zbytky vnitřních podpěr a zároveň vyhladit kanál. * Plánování přístupnosti: Navrhování přístupových portů (které lze později zapojit), pokud je odstranění vnitřní podpěry nevyhnutelné.
5. Dosažení požadavků na vnitřní povrchovou úpravu: * Problém: Vnitřní povrchy ve stavu, v jakém jsou postaveny, jsou ze své podstaty drsné. U palivových rozvodů může tato drsnost bránit průtoku, zvyšovat tlakovou ztrátu a potenciálně zachycovat nečistoty nebo zbytky prášku. Dosažení hladkého vnitřního povrchu, zejména ve složitých kanálech bez přímé viditelnosti, je náročné. * Zmírnění: * Orientace & Účinky parametrů: Orientace konstrukce ovlivňuje drsnost vnitřního povrchu (‘up-skin’ vs ‘down-skin’). Optimalizované parametry mohou mírně zlepšit povrchovou úpravu. * Obrábění abrazivním tokem (AFM) / Extrude Hone: Nejúčinnější metoda pro zlepšení povrchové úpravy vnitřních kanálů ve složitých rozdělovačích. Vyžaduje pečlivou kontrolu procesu, aby bylo dosaženo požadované hladkosti bez nadměrného úběru materiálu. * Elektrolytické leštění: Může být účinný, pokud elektrolyt může dostatečně protékat všemi vnitřními kanály. * Úvahy o návrhu: Důležité je navrhnout dostatečně velké kanály, které umožní účinnou AFM nebo proplachování.
6. Kontrola pórovitosti: * Problém: V tištěném materiálu mohou vznikat malé dutiny nebo póry v důsledku zachyceného plynu (plynová pórovitost) nebo neúplného roztavení/splynutí mezi vrstvami nebo skenovacími stopami (nedostatečná pórovitost). Pórovitost snižuje hustotu materiálu, zhoršuje mechanické vlastnosti (zejména únavovou pevnost) a může vytvářet potenciální cesty úniku. * Zmírnění: * Vysoce kvalitní prášek: Použití prášku s nízkým obsahem zachyceného plynu, kontrolovanou distribucí velikosti částic a dobrou morfologií (jako je prášek Met3dp’) minimalizuje pórovitost plynu. Zásadní je správné zacházení s práškem (skladování, sušení). * Optimalizované parametry procesu: Zajištění dostatečné hustoty energie (výkon laseru/paprsku, rychlost) a správného překrytí mezi skenovacími stopami podporuje úplné roztavení a tavení, čímž se snižuje počet defektů způsobených nedostatečnou fúzí. * Stabilní procesní prostředí: Udržování kontrolované atmosféry inertního plynu (např. argonu, dusíku) zabraňuje oxidaci a snižuje kontaminaci. * Izostatické lisování za tepla (HIP): Tento krok následného zpracování zahrnuje vystavení dílu vysoké teplotě a vysokému izostatickému tlaku (obvykle za použití argonu). Tím se účinně uzavřou vnitřní dutiny a póry, výrazně se zvýší hustota a zlepší mechanické vlastnosti. Často se specifikuje pro kritické letecké nebo lékařské součásti. * NDT inspekce: Ke zjištění a kvantifikaci vnitřní pórovitosti se běžně používá CT vyšetření.
7. Odstraňování prášku ze složitých průchodů: * Problém: Zajištění odstranění veškerého volného nebo částečně slinutého prášku ze složité vnitřní sítě rozdělovače je velmi důležité, ale náročné. Zachycený prášek může způsobit kontaminaci v dalším proudu nebo bránit průtoku. * Zmírnění: * Design pro čištění: Vyhýbejte se slepým otvorům nebo prvkům, které zachycují prach. Navrhování kanálků pro účinné proplachování. * Důkladné čisticí postupy: Použití stlačeného vzduchu, vibrací, ultrazvukových čisticích lázní a případně specializovaných proplachovacích zařízení s vhodnými rozpouštědly nebo kapalinami. * Kontrola: Použití boroskopu nebo CT k ověření úplného odstranění prášku z vnitřních kanálů.
Navigace v těchto výzvy v oblasti AM kovů vyžaduje kombinaci důkladných postupů DfAM, vysoce kvalitních materiálů, optimalizovaných a přísně kontrolovaných tiskových procesů, vhodných technik následného zpracování a přísného zajištění kvality. Spolupráce se zkušeným poskytovatelem AM, jako je Met3dp, který disponuje potřebnými odbornými znalostmi, pokročilým vybavením (včetně potenciálně výhodných tiskáren SEBM pro určité slitiny) a systémy kvality, výrazně zvyšuje pravděpodobnost úspěšné výroby spolehlivých a vysoce výkonných produktů 3D tisk z kovu palivových rozdělovačů a zároveň zmírnit tato potenciální úskalí. Jejich komplexní přístup, od výroby prášku až po finální validaci dílu, pomáhá zajistit efektivní zvládnutí složitostí AM.
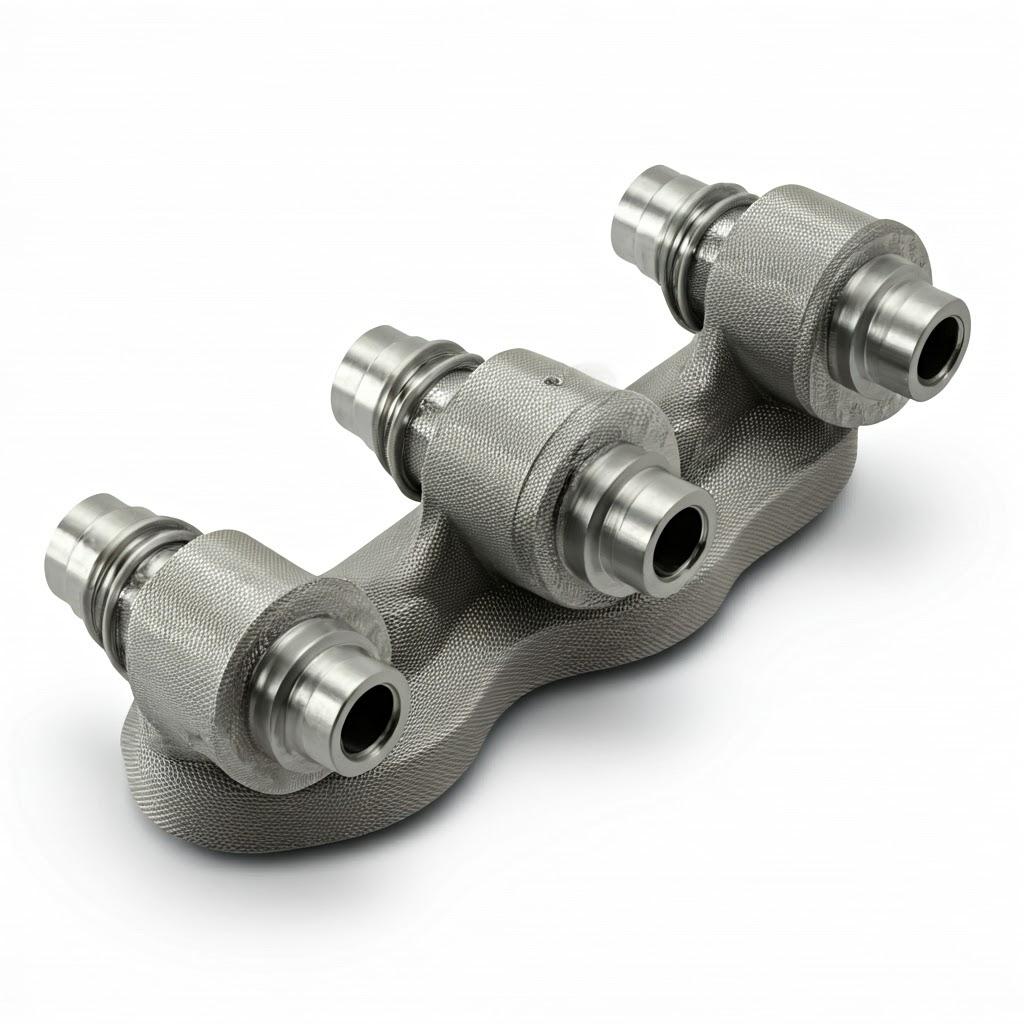
Výběr dodavatele: Výběr správného partnera pro 3D tisk kovů pro palivové rozvody
Úspěch výroby složité, vysoce výkonné součásti, jako je palivové potrubí na zakázku, pomocí aditivní výroby nezávisí jen na dobrém návrhu a výběru správného materiálu, ale také na výběru správného výrobního partnera. V oblasti AM výroby kovů existuje široká škála poskytovatelů služeb, od malých dílen až po velké specializované průmyslové hráče. Pro kritické komponenty pracující v náročných prostředích, jako je letecký a kosmický průmysl nebo vysoce výkonný automobilový průmysl, je nejdůležitější spolupracovat s poskytovatelem, který disponuje správnou kombinací technických znalostí, robustních procesů, pokročilých technologií a přísné kontroly kvality. Špatná volba může vést ke zpoždění projektu, překročení nákladů, nevyhovující kvalitě dílů, nebo dokonce ke katastrofálním poruchám v provozu.
Jaká kritéria by tedy měli inženýři a manažeři veřejných zakázek upřednostňovat při hodnocení potenciálních projektů? Poskytovatel služeb metal AM partnery pro výrobu palivových rozvodů? Zde je podrobný kontrolní seznam:
1. Technické znalosti & amp; Prokazatelné zkušenosti: * Záznamy o činnosti: Má poskytovatel prokazatelné zkušenosti s tiskem dílů podobné složitosti a materiálu, z jakého je vyroben váš palivový rozvod? Požádejte o případové studie nebo příklady týkající se zejména manipulace s kapalinami, vysokoteplotních aplikací nebo příslušných průmyslových odvětví (letecký a automobilový průmysl). * Specializace na materiál: Specializují se na konkrétní materiály, které požadujete (např. IN625, AlSi10Mg, Ti6Al4V)? Hluboké znalosti metalurgie materiálů a jejich interakce s procesem AM jsou klíčové, zejména u náročných slitin. Poskytovatelé, kteří vyrábějí vlastní prášky, jako je Met3dp, často disponují hlubšími znalostmi v oblasti materiálových věd. * Inženýrský důvtip: Zhodnoťte kvalifikaci a zkušenosti jejich inženýrského týmu. Dokáží se zapojit do smysluplných diskusí o DfAM a poskytnout cennou zpětnou vazbu k optimalizaci návrhu? Rozumějí fyzice proudění tekutin a strukturální mechanice relevantní pro rozdělovače? * Průmyslové certifikace: Pro aplikace v letectví a kosmonautice je certifikace AS9100 často neoddiskutovatelná. Pro automobilový průmysl je výhodná znalost norem IATF 16949. Tyto certifikace svědčí o závazku dodržovat přísné procesy kvality, které jsou v těchto odvětvích vyžadovány. Společnost Met3dp zdůrazňuje své zaměření na “kritické díly v leteckém, zdravotnickém, automobilovém a dalších oborech,” což naznačuje zkušenosti s plněním přísných požadavků tohoto odvětví.
2. Vybavení, technologie a schopnosti: * Flotila tiskáren: Jaké typy strojů pro AM na kovy provozují (L-PBF, EBM)? Jaké jsou značky, modely a objemy výroby? Různorodý a moderní vozový park naznačuje investice a schopnosti. Například společnost Met3dp uvádí, že poskytuje komplexní řešení zahrnující např tiskárny SEBM, což může u některých materiálů, jako jsou slitiny niklu, přinést výhody díky vlastnímu snížení napětí v důsledku zahřátého prostředí při stavbě. * Řízení a monitorování procesů: Jaká opatření jsou zavedena pro monitorování a kontrolu procesu výstavby (např. hladina kyslíku, monitorování taveniny, termovizní snímky)? Důsledná kontrola procesu je klíčem k opakovatelné kvalitě. * Vlastní následné zpracování: Nabízí poskytovatel kritické kroky následného zpracování přímo ve firmě (pece na uvolňování napětí/tepelné zpracování, CNC obráběcí centra, možnost odstranění podpěr, základní dokončovací práce)? Vlastní kapacity obecně vedou k lepší integraci, kontrole kvality a potenciálně kratším dodacím lhůtám ve srovnání s outsourcingem více kroků. * Metrologická laboratoř: Jaké mají kontrolní zařízení (souřadnicové měřicí stroje, 3D skenery, profilometry, případně CT)? Schopnost přesně měřit a ověřovat geometrii a vnitřní vlastnosti dílů je klíčová.
3. Kvalita materiálu, portfolio & manipulace: * Získávání materiálu & Kvalifikace: Kde získávají kovové prášky? Vyrábějí si vlastní, jako Met3dp se svými pokročilými technologiemi? technologie atomizace plynu a PREP, nebo od kvalifikovaných externích dodavatelů? Jak kvalifikují nové materiály nebo šarže? * Portfolio materiálů: Nabízejí širokou škálu relevantních materiálů, které přesahují vaši okamžitou potřebu, což svědčí o širších odborných znalostech? Například společnost Met3dp uvádí mezi svými produkty inovativní slitiny, jako jsou TiNi, TiTa, TiAl, TiNbZr, CoCrMo, nerezové oceli a superslitiny vysoce kvalitní kovové prášky. * Kontrola kvality prášku: Jaké jsou jejich postupy pro testování vstupního prášku (chemismus, distribuce velikosti částic, tekutost, morfologie, hustota)? Jak se prášek skladuje, jak se s ním manipuluje, jak se sleduje (sledovatelnost šarží) a jak se recykluje, aby se zabránilo kontaminaci a zajistila konzistence? Konzistentní, vysoce kvalitní prášek je základem dobrého AM dílu. * Certifikace materiálu: Mohou poskytnout materiálové certifikáty potvrzující, že prášek splňuje konkrétní průmyslové normy (např. ASTM, AMS)?
4. Systém řízení kvality (QMS): * certifikace: Jsou certifikovány podle příslušných norem kvality, jako je ISO 9001? Jak již bylo zmíněno, AS9100 je pro letectví a kosmonautiku zásadní. Tyto certifikace vyžadují dokumentované postupy, řízení procesů, sledovatelnost, řízení rizik a neustálé zlepšování. * Dokumentace a sledovatelnost: Dokáží zajistit úplnou sledovatelnost od dávky surového prášku až po hotový díl, včetně protokolů o sestavení, záznamů o následném zpracování a kontrolních zpráv? To je u kritických součástí zásadní. * Inspekční protokoly: Jaké jsou jejich standardní kontrolní postupy? Jak se identifikují a ověřují kritické prvky? Jaké metody statistické kontroly procesu (SPC) se používají, pokud existují? * Zpracování neshod: Jaký je jejich postup pro identifikaci, dokumentaci a řešení neshodných dílů nebo odchylek v procesu?
5. Inženýrství & Podpora vývoje aplikací: * Konzultace DfAM: Nabízejí služby, které vám pomohou optimalizovat váš návrh pro aditivní výrobu, identifikovat potenciální problémy a navrhnout zlepšení pro tisk, výkon a nákladovou efektivitu? * Simulační schopnosti: Mohou poskytnout nebo využít výsledky simulací (FEA pro analýzu napětí/tepelnou analýzu, CFD pro analýzu proudění) na podporu validace návrhu? * Vývoj aplikací: Jsou ochotni spolupracovat na vývoji nových aplikací nebo na řešení obzvláště náročných projektů? Společnosti jako Met3dp se prezentují jako poskytovatelé komplexní řešení zahrnující tiskárny SEBM, pokročilé kovové prášky a služby vývoje aplikací, což naznačuje partnerský přístup. Zkoumání způsobu Met3dp poskytuje komplexní řešení může odhalit jejich hloubku jako potenciálního partnera.
6. Kapacita, dodací lhůta & Komunikace: * Produkční kapacita: Zvládnou váš požadovaný objem, ať už jde o prototypy, malé série nebo případně větší výrobní série? Mají dostatečnou kapacitu strojů a kvalifikovanou pracovní sílu? * Transparentnost doby realizace: Poskytují realistické a spolehlivé odhady doby realizace? Jak informují o stavu projektu a případných zpožděních? * Reakce: Jak rychle reagují na dotazy a žádosti o cenovou nabídku? Dobrá komunikace je zásadní v průběhu celého životního cyklu projektu. Hledejte partnery, kteří se chovají jako spolehlivá výroba AM zdroje.
7. Struktura nákladů & Value Proposition: * Citace Transparentnost: Je jejich cenová nabídka jasná a podrobná, s rozpisem nákladů spojených s materiálem, tiskem, podporou, následným zpracováním a kontrolou? Dejte si pozor na příliš nízké cenové nabídky, protože mohou vynechat nezbytné kroky nebo slevit z kvality. * Celkové náklady na vlastnictví: Vyhodnoťte hodnotu nad rámec ceny za díl. Nabízí spolupráce s tímto dodavatelem výhody, jako je rychlejší uvedení na trh, lepší výkonnost dílů, nižší náklady na následnou montáž nebo vyšší spolehlivost, které ospravedlňují investici?
Výběr správného dodavatel kovového 3D tisku je strategické rozhodnutí. Vyžaduje důkladnou prověrku, kladení podrobných otázek a případnou návštěvu zařízení nebo provedení pilotních projektů. V případě náročných aplikací palivových rozvodů spolupráce se zavedeným, technicky zdatným a na kvalitu zaměřeným poskytovatelem, jako je Met3dp, který kontroluje klíčové aspekty od výroby prášku až po pokročilé tiskové systémy a nabízí komplexní technickou podporu, výrazně odlehčuje proces a maximalizuje potenciální přínosy zavedení aditivní výroby.
Porozumění investicím: Nákladové faktory a dodací lhůty pro palivové rozvody AM
Přechod na aditivní výrobu palivových rozvodů zahrnuje pochopení souvisejících nákladů a typických časových lhůt. Ačkoli AM nabízí významné výkonnostní a konstrukční výhody, je nezbytné mít jasnou představu o potřebných ekonomických a časových investicích. Náklady i doba realizace jsou ovlivněny složitou souhrou faktorů souvisejících s konstrukcí dílu, výběrem materiálu, specifiky procesu a požadovanou úrovní kvality. Manažeři a inženýři zabývající se zadáváním zakázek musí tyto faktory pochopit, aby mohli efektivně sestavovat rozpočet, řídit harmonogramy projektů a provádět přesná srovnání s tradičními výrobními metodami.
Klíčové faktory ovlivňující náklady na kovové palivové rozvody AM:
- Konstrukce dílů & Geometrie:
- Složitost: Velmi složité konstrukce s mnoha vnitřními prvky, tenkými stěnami nebo prvky vyžadujícími rozsáhlé podpůrné struktury vyžadují obecně delší dobu tisku a následného zpracování, což zvyšuje náklady. Konstrukce optimalizované pomocí principů DfAM pro minimalizaci podpěr a usnadnění následného zpracování mohou být nákladově efektivnější.
- Část Objem & Ohraničující rámeček: Celková velikost rozdělovače má přímý vliv na množství spotřebovaného materiálu a čas potřebný na stroji AM. Větší díly zabírají na konstrukční desce více místa a jejich tisk po vrstvách trvá déle. Výška dílu v orientaci sestavení je často hlavním faktorem ovlivňujícím dobu tisku.
- Objem podpůrné struktury: Podpěry spotřebovávají materiál a jejich odstranění vyžaduje značný čas práce/stroje. U konstrukcí, které vyžadují rozsáhlé nebo obtížně odstranitelné podpěry, budou náklady vyšší.
- Výběr materiálu:
- Náklady na prášek: Náklady na suroviny se výrazně liší. Vysoce výkonné superslitiny, jako je IN625, jsou na kilogram výrazně dražší než hliníkové slitiny jako AlSi10Mg nebo nerezové oceli. Slitiny titanu se nacházejí někde uprostřed.
- Hustota materiálu: Hustší materiály (jako IN625) vedou k tomu, že při stejném objemu jsou díly těžší, což přímo zvyšuje složku materiálových nákladů na základě hmotnosti.
- Možnost tisku: Některé materiály jsou náročnější na spolehlivý tisk, což může vyžadovat nižší rychlost tisku nebo složitější sady parametrů, což nepřímo ovlivňuje náklady na strojní čas.
- Proces aditivní výroby:
- Strojový čas: To je často hlavní příčinou nákladů. Ovlivňují ho:
- Doba výstavby: Určuje se výškou dílu, tloušťkou použité vrstvy (tenčí vrstvy = lepší rozlišení, ale delší sestavení), rychlostí skenování a počtem dílů vložených na jednu sestavovací desku.
- Hodinová sazba stroje: Liší se v závislosti na typu, velikosti a sofistikovanosti stroje AM. U špičkových strojů s pokročilým monitorováním jsou sazby vyšší.
- Efektivita hnízdění: Tisk více dílů současně na jedné konstrukční desce (nesting) pomáhá amortizovat čas přípravy a maximalizovat využití stroje, čímž se snižují náklady na jeden díl, zejména u menších dílů.
- Příprava stavby & Nastavení: Čas potřebný na přípravu souboru pro sestavení (orientace, podpěry), vložení prášku a nastavení stroje.
- Strojový čas: To je často hlavní příčinou nákladů. Ovlivňují ho:
- Požadavky na následné zpracování: To může představovat podstatnou část (často 30-70 % a více) celkových nákladů.
- Tepelné zpracování: Čas, spotřeba energie a práce v peci na uvolnění napětí a další potřebné cykly. Pece s řízenou atmosférou zvyšují náklady.
- Odstranění podpory: Pracovní náročnost závisí do značné míry na složitosti a dostupnosti podpory. Ruční odstraňování, obrábění nebo specializované techniky, jako je elektroerozivní obrábění, jsou spojeny s náklady.
- CNC obrábění: Strojní čas a kvalifikovaná práce při vytváření kritických prvků, těsnicích ploch, závitů atd. Počet a složitost obráběných prvků přímo ovlivňuje náklady.
- Povrchová úprava: Náklady se značně liší v závislosti na metodě (jednoduché tryskání vs. vícestupňové leštění nebo komplexní AFM pro vnitřní kanály) a požadované úrovni drsnosti povrchu (Ra).
- Čištění: Čas a prostředky na odstranění prášku (zejména vnitřního) a závěrečné čištění.
- Zajištění kvality & Inspekce:
- Úroveň inspekce: Základní vizuální a rozměrové kontroly jsou standardní. Důkladnější kontrola (souřadnicový měřicí přístroj, 3D skenování, zkoušky těsnosti, NDT, např. CT) zvyšuje náklady, ale může být vyžadována u kritických aplikací.
- Dokumentace: Vytváření podrobných kontrolních zpráv a dokumentace o sledovatelnosti vyžaduje čas a zdroje.
- Objednávkové množství:
- Prototypy vs. výroba: U jednorázových prototypů se hradí plné náklady na zřízení. Malá až střední sériová výroba umožňuje lepší využití stroje (nesting) a amortizaci nákladů na seřízení a programování, což vede k nižším cenám za díl. S rostoucím množstvím jsou typické výrazné cenové zlomy. Vyhodnocení velkoobjemová výroba AM náklady vyžadují konkrétní nabídky na základě objemu.
Faktory ovlivňující dobu dodání:
Doba realizace je celková doba od zadání objednávky (nebo dokončení návrhu) do dodání finálního dílu. Ovlivňuje ji několik postupných a souběžných činností:
- Dokončení návrhu & Engineering Review: Čas na kontrolu DfAM, optimalizaci a přípravu sestavení.
- Čas fronty stroje: Čeká se, až bude k dispozici vhodný stroj. To se může výrazně lišit v závislosti na počtu nevyřízených objednávek poskytovatele služeb.
- Doba tisku: Určeno výškou dílu, složitostí a vnořením. Může se pohybovat od hodin u malých dílů až po mnoho dní u velkých a složitých konstrukcí.
- Doba vychladnutí: Před vyjmutím nechte stavební komoru a díl dostatečně vychladnout.
- Následné zpracování: Jedná se často o nejproměnlivější a potenciálně nejdelší část doby přípravy, která zahrnuje postupné kroky, jako je tepelné zpracování, odstranění podpěr, obrábění, dokončovací práce a čištění. Úzká místa mohou nastat, pokud má konkrétní zařízení (např. velké pece, specializované dokončovací stroje) omezenou kapacitu.
- Kontrola kvality: Čas potřebný k měření a validaci.
- Doprava: Doba logistiky závisí na lokalitě a způsobu přepravy.
Typické rozmezí dodací lhůty:
- Prototypy: Často se pohybuje v rozmezí 1 až 4 týdnů, což závisí na složitosti, materiálu, dostupnosti stroje a rozsahu následného zpracování.
- Výroba malých sérií: V závislosti na množství a výše uvedených faktorech se může pohybovat od 3 do 8 týdnů nebo déle.
Získání přesných cenových nabídek a časových harmonogramů: Chcete-li získat spolehlivé odhady nákladů a doby realizace pro váš konkrétní projekt palivového rozvodu, musíte potenciálním dodavatelům poskytnout podrobné informace, včetně:
- Finální 3D model CAD (preferovaný formát STEP).
- Specifikace materiálu (např. AlSi10Mg, IN625) a všechny požadované normy.
- Podrobné výkresy s uvedením kritických rozměrů, tolerancí (GD&T), požadovaných povrchových úprav (vnitřních a vnějších) a všech specifických prvků, jako jsou závity.
- Požadované množství (prototyp, odhad malosériové výroby).
- Specifické požadavky na testování nebo kontrolu (např. parametry zkoušek těsnosti, potřeby NDT).
- Požadované datum dodání (pokud je to relevantní).
Úzká spolupráce s transparentním a zkušeným poskytovatelem AM, jako je Met3dp, může pomoci optimalizovat návrhy z hlediska efektivity nákladů a poskytnout realistické odhady jak pro náklady na 3D tisk kovů a Dodací lhůta AM, čímž se zajistí soulad mezi očekáváními a skutečností projektu.
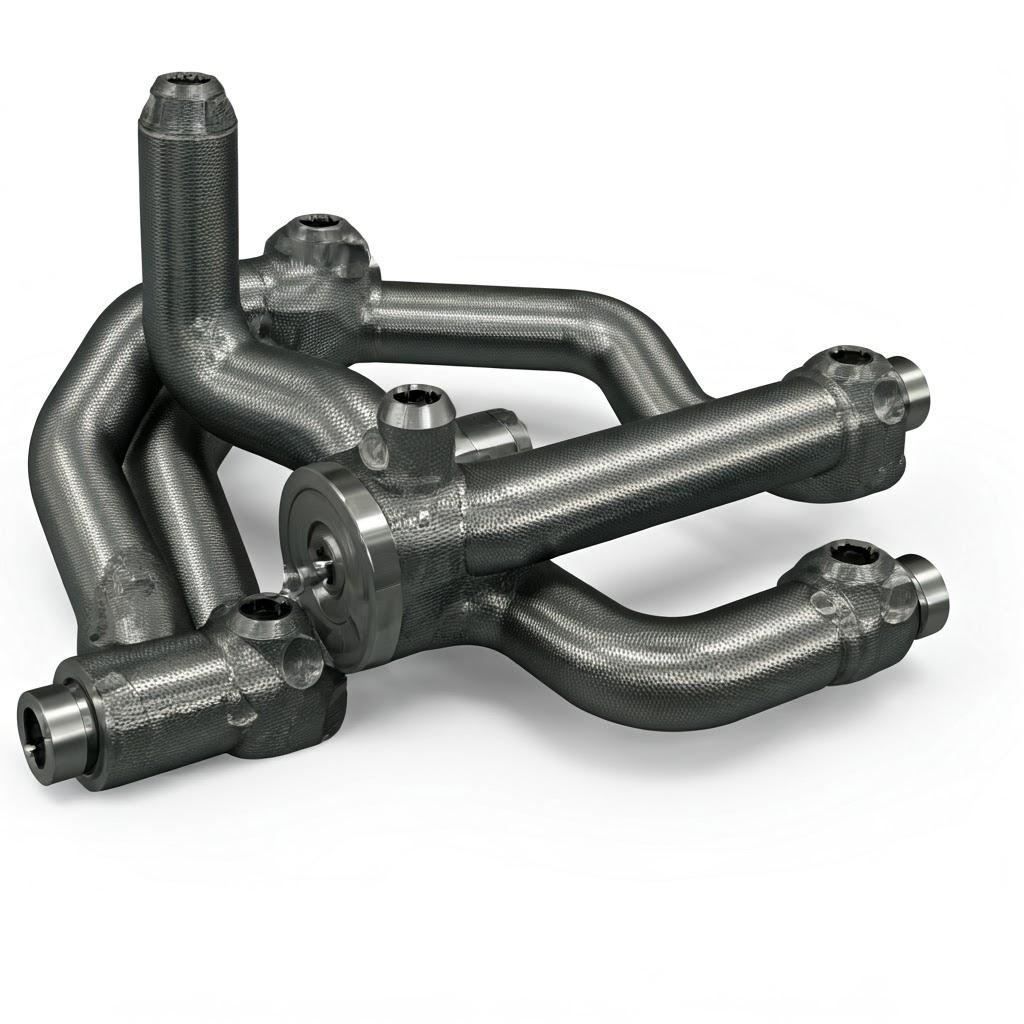
Často kladené otázky (FAQ) o 3D tištěných palivových rozvodech
Zde jsou odpovědi na některé časté otázky, které inženýři a manažeři nákupu řeší, když zvažují aditivní výrobu kovů pro rozvody paliva:
Otázka 1: Jaké jsou hlavní výhody 3D tištěného palivového rozvodu oproti tradičně vyráběnému?
- A1: Mezi hlavní výhody patří:
- Svoboda designu: Možnost vytvářet velmi složité vnitřní kanály optimalizované pro průtok kapaliny (snížení tlakové ztráty, zlepšení rovnoměrnosti distribuce) a integrovat prvky, což je často nemožné při odlévání nebo obrábění.
- Snížení hmotnosti: Významné úspory hmotnosti díky optimalizaci topologie a konsolidaci dílů, což je klíčové pro letecký a výkonný automobilový průmysl.
- Zvýšení výkonu: Optimalizované průtokové cesty vedou ke zlepšení účinnosti motoru/systému, potenciálně vyššímu výkonu a lepším emisím.
- Konsolidace částí: Spojení více komponent do jednoho tištěného dílu zkracuje dobu montáže, eliminuje potenciální netěsnosti spojů, zjednodušuje inventarizaci a zvyšuje spolehlivost.
- Rapid Prototyping & Iterace: Rychlejší vývojové cykly ve srovnání s tradičními metodami založenými na nástrojích umožňují rychlejší validaci a optimalizaci návrhu.
Otázka č. 2: Mohou 3D tištěné rozvody zvládnout tlaky a teploty v leteckých motorech?
- A2: Rozhodně. Výběrem vhodných vysoce výkonných materiálů, jako je niklová superslitina Inconel 625 (IN625), mohou 3D tištěné rozvody spolehlivě odolávat extrémním teplotám (až 800-1000∘C) a vysokým tlakům, které se vyskytují v motorech plynových turbín a raketových pohonných systémech. Správné ověření návrhu (FEA), dodržování zásad DfAM, optimalizované parametry tisku, nezbytné tepelné úpravy (snížení napětí, stárnutí) a přísná kontrola kvality (včetně NDT, jako je CT skenování a zkoušky těsnosti) jsou nezbytné pro zajištění strukturální integrity a výkonnosti v těchto náročných prostředích.
Otázka 3: Jak hladké mohou být vnitřní kanály palivového potrubí vytištěného na 3D tiskárně?
- A3: Drsnost vnitřního povrchu (Ra) kovových dílů AM se obvykle pohybuje od 6 μm do 25 μm nebo více, což je drsnější než u obráběných povrchů. I když je to pro některé aplikace přijatelné, pro optimální průtok tekutin je často požadován hladší povrch. Techniky následného zpracování, jako např Obrábění abrazivním tokem (AFM) nebo Extrude Hone jsou speciálně navrženy tak, aby výrazně zlepšily kvalitu povrchu vnitřních kanálů, a to i složitých, a potenciálně dosáhly hodnot Ra pod 1-5 μm v závislosti na počáteční drsnosti, materiálu a době zpracování. U některých materiálů a geometrií může být účinné také elektrolytické leštění. Dosažitelná hladkost závisí na zvolené metodě následného zpracování a na konstrukci dílu (velikost kanálků/přístupnost).
Otázka 4: Jaké informace musím poskytnout, abych získal nabídku na 3D tištěný palivový rozvod na zakázku?
- A4: Chcete-li získat přesnou cenovou nabídku a odhad doby realizace, měli byste svému potenciálnímu dodavateli AM poskytnout:
- 3D CAD model konstrukce rozdělovače (preferuje se formát STEP).
- Specifikovaný materiál (např. AlSi10Mg, IN625, Ti6Al4V) a všechny příslušné materiálové normy (ASTM, AMS).
- 2D výkresy s jasným uvedením kritických rozměrů, geometrického dimenzování a tolerování (GD&T), požadované povrchové úpravy (uveďte vnitřní a vnější povrchy) a umístění všech prvků, jako jsou závity nebo těsnicí plochy.
- Množství požadovaných dílů (rozlišujte mezi prototypovými a výrobními objemy).
- Jakékoli specifické požadavky na následné zpracování (např. konkrétní cyklus tepelného zpracování, specifická povrchová úprava).
- Požadavky na povinné zkoušky a inspekce (např. tlak a doba trvání zkoušky těsnosti, potřeby NDT, požadovaná dokumentace/certifikační balíček).
- Zamýšlené použití (pomáhá poskytovateli pochopit kontext a kritičnost).
Otázka 5: Nabízí Met3dp pomoc při návrhu optimalizace mého rozdělovače pro aditivní výrobu?
- A5: Ano, společnost Met3dp klade důraz na poskytování komplexních řešení, která přesahují pouhý tisk. Jejich služby zahrnují služby vývoje aplikací a využití jejich desítky let společných zkušeností v aditivní výrobě kovů. To znamená, že nabízíme konzultace v oblasti designu pro aditivní výrobu (DfAM), abychom klientům pomohli optimalizovat jejich stávající konstrukce nebo vyvinout nové koncepty rozdělovačů, které plně využívají výhod AM. Tento přístup založený na spolupráci pomáhá zajistit, aby byly díly navrženy pro úspěšný tisk, optimální výkon, spolehlivost a nákladovou efektivitu. Důrazně doporučujeme zapojit jejich konstrukční tým již v rané fázi procesu návrhu.
Závěr: Budoucnost proudění tekutin je aditivní – partnerství pro optimalizované rozdělovače
Cesta složitostí návrhu, výroby a kvalifikace rozvodů paliva na zakázku pomocí aditivní výroby kovů ukazuje jasný obraz: AM není pouhou alternativou, ale transformační silou, která mění budoucnost systémů proudění tekutin. Schopnost vymanit se z okovů tradičních výrobních omezení uvolňuje nebývalé příležitosti pro inovace a umožňuje vytvářet rozdělovače, které jsou lehčí, lépe fungují, integrují více funkcí a dostávají se na trh rychleji než kdykoli předtím.
Z náročných prostředí letectví a kosmonautiky motorů a raketového pohonu do konkurenčního světa vysoce výkonný automobilový průmysl a robustní potřeby průmyslové turbíny, 3D tisk z kovu přináší hmatatelné výhody. Optimalizované vnitřní kanály vzniklé na základě analýzy CFD a realizované pomocí AM minimalizují tlakové ztráty a zajišťují rovnoměrnou dodávku paliva, čímž zvyšují účinnost a výkon. Optimalizace topologie snižuje kritickou hmotnost, čímž se zvyšuje úspora paliva a nosnost. Konsolidace dílů výrazně snižuje složitost, odstraňuje místa úniku a zefektivňuje dodavatelské řetězce. Materiály, jako je lehký AlSi 10Mg a robustní, vysokoteplotní IN625 poskytují řešení na míru pro různé provozní podmínky.
Realizace těchto výhod však vyžaduje zvládnutí nuancí designu pro aditivní výrobu (DfAM), pochopení dosažitelné přesnosti, implementaci nezbytného následného zpracování a zmírnění potenciálních výrobních problémů. Úspěch závisí na pečlivém plánování, důsledné kontrole procesů a především na výběru správného výrobního partnera.
Partner, jako je Met3dp, vyniká integrovaným přístupem. Díky špičkovým schopnostem v oboru pokročilá výroba prášků (plynová atomizace, PREP), které zajišťují kvalitu materiálu, a sofistikovaný Zařízení pro 3D tisk (včetně technologie SEBM), kontrolují kritické prvky hodnotového řetězce. Jejich komplexní řešení zahrnují konzultace DfAM, vývoj aplikací, rozmanité možnosti materiálů a závazek k přesnosti a spolehlivosti požadované pro kritické komponenty. Díky spolupráci s odborným poskytovatelem mohou společnosti bez obav využít technologii AM kovů a získat konkurenční výhodu prostřednictvím špičkové technologie palivových rozvodů.
Budoucnost efektivní a vysoce výkonné distribuce kapalin je bezesporu aditivní. Pokud navrhujete palivové systémy nové generace nebo se snažíte vylepšit ty stávající, zkoumání potenciálu kovového 3D tisku již není volitelné - je nezbytné.
Jste připraveni na revoluci v palivových rozvodech? Využijte sílu aditivní výroby. Kontaktovat Met3dp ještě dnes, abyste mohli prodiskutovat své projektové požadavky a zjistit, jak vám naše odborné znalosti v oblasti zařízení pro AM zpracování kovů, pokročilých materiálů a vývoje aplikací mohou pomoci navrhnout a vyrobit palivové rozvody optimalizované z hlediska průtoku, hmotnosti a výkonu, a urychlit tak vaši cestu k digitální transformaci výroby.
Sdílet na
MET3DP Technology Co., LTD je předním poskytovatelem řešení aditivní výroby se sídlem v Qingdao v Číně. Naše společnost se specializuje na zařízení pro 3D tisk a vysoce výkonné kovové prášky pro průmyslové aplikace.
Dotaz k získání nejlepší ceny a přizpůsobeného řešení pro vaše podnikání!
Související články
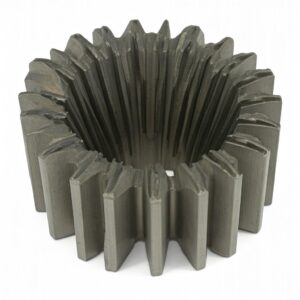
Vysoce výkonné segmenty lopatek trysek: Revoluce v účinnosti turbín díky 3D tisku z kovu
Přečtěte si více "O Met3DP
Nedávná aktualizace
Náš produkt
KONTAKTUJTE NÁS
Nějaké otázky? Pošlete nám zprávu hned teď! Po obdržení vaší zprávy obsloužíme vaši žádost s celým týmem.
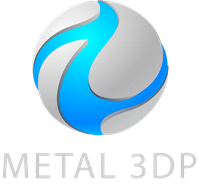
Kovové prášky pro 3D tisk a aditivní výrobu