Plynem atomizovaný prášek: Komplexní průvodce
Obsah
Plynem atomizovaný prášek je druh kovového prášku vyráběného plynovou atomizací, což je proces, při kterém se roztavený kov rozbíjí na kapičky a rychle se ochlazuje vysokotlakým proudem plynu. Touto metodou vzniká velmi jemný, sférický prášek ideální pro aplikace, jako je vstřikování kovů, aditivní výroba a procesy povrchové úpravy.
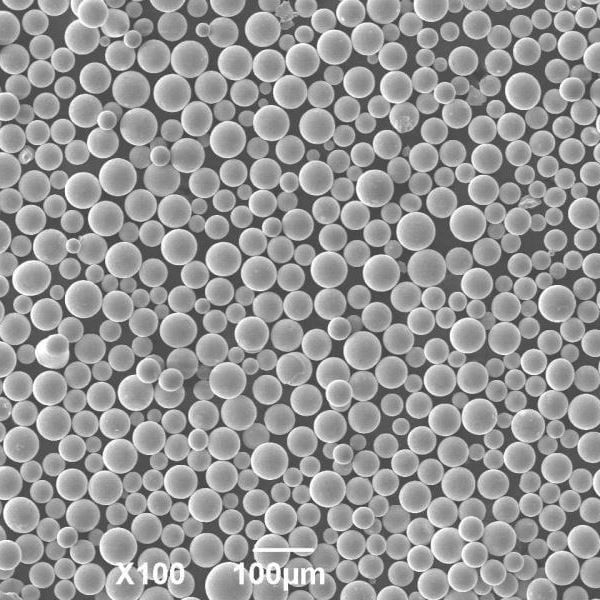
Jak se vyrábí plynný atomizovaný prášek
Plyn rozprašování proces začíná tavením požadovaného kovu v indukční peci. Jakmile kov dosáhne optimální teploty, nalije se v tenkém proudu do rozprašovací komory. Vysokotlaký inertní plyn (obvykle dusík nebo argon) je vháněn přes specializované trysky a vytváří silné proudy plynu, které rozbíjejí proud roztaveného kovu na velmi jemné kapičky.
Jak kapky padají komorou, rychle tuhnou na částice prášku díky vysokému poměru povrchu k objemu. Plyn také zabraňuje aglomeraci částic. Prášek propadá komorou na sběrné síto, kde se prosévá, aby se dosáhlo požadované distribuce velikosti částic.
Klíčové kroky při výrobě prášku v plynovém rozprašovači
Krok | Popis |
---|---|
Tání | Kov se taví v indukční peci |
Nalévání | Roztavený kov se nalije do rozprašovací komory |
Atomizace | Vysokotlaký plyn rozbíjí proud kovu na jemné kapičky |
Tuhnutí | Kapky se rychle ochladí na pevné částice prášku |
Sbírka | Prášek se shromažďuje na dně komory |
Screening | Prášek se prosévá, aby se dosáhlo cílové distribuce velikosti částic |
Výhody prášku rozprašovaného plynem
Mezi hlavní výhody prášku rozprašovaného plynem patří:
- Sférická morfologie – Kapky tuhnou do velmi kulovitých částic ideálních pro spékání a tavení.
- Velikost jemných částic – Lze dosáhnout velikosti částic od 10 – 150 mikronů. Mnohem jemnější než jiné metody.
- Úzká distribuce – Distribuce velikosti částic je velmi úzká, což zlepšuje spékavost.
- Vysoká čistota – Inertní plyn zabraňuje oxidaci a minimalizuje kontaminaci.
- Dobrá tekutost – Sférický tvar zlepšuje vlastnosti toku prášku.
- Široká použitelnost – Většinu kovů a slitin lze rozprašovat na prášek.
Díky těmto vlastnostem jsou prášky rozprašované plynem vhodné pro vstřikování kovů, aditivní výrobu a pokročilé spékání. Vysoká čistota a sférická morfologie mají za následek vynikající hutnící chování.
Kovy a slitiny používané pro atomizaci plynu
Materiál | Příklady |
---|---|
Nerezové oceli | Austenitické, feritické, duplexní a martenzitické nerezové oceli jako 316L, 17-4PH, 420 |
Nástrojové oceli | H13, M2 |
Kobaltové slitiny | CoCrMo |
Slitiny niklu | Inconel, Rene |
Slitiny titanu | Ti-6Al-4V |
Žáruvzdorné kovy | Wolfram, molybden, tantal |
Slitiny mědi | Mosaz, bronz, měď |
Slitiny hliníku | Hliník 6061 |
Drahé kovy | Stříbro, zlato, skupina platiny |
- Nerezové oceli – Austenitické, feritické, duplexní a martenzitické nerezové oceli se běžně atomizují plynem. Oblíbené jsou třídy jako 316L, 17-4PH a 420.
- Nástrojové oceli – Nástrojové oceli jako H13 a M2 lze atomizovat. Používá se pro lisování nástrojových součástí.
- Kobaltové slitiny – Biokompatibilní kobaltové slitiny pro zubní a lékařské použití jako CoCrMo.
- Slitiny niklu – Superslitiny, jako je Inconel a slitiny Rene, jsou pro součásti turbín atomizovány plynem.
- Slitiny titanu – Prášek ze slitiny Ti-6Al-4V pro letecké komponenty a implantáty.
- Žáruvzdorné kovy – Wolfram, molybden, tantal běžně atomizované.
- Slitiny mědi – Rozprašovaná mosaz, bronz a měď pro elektronické/elektrické použití.
- Slitiny hliníku – Hliník 6061 běžně atomizovaný pro automobilový a letecký průmysl.
- Drahé kovy – Stříbro, zlato, kovy platinové skupiny atomizované pro šperkařské účely.
Téměř každou slitinu, která se taví, aniž by se rozkládala, lze atomizovat plynem, pokud jsou optimalizovány parametry, jako je přehřátí taveniny a tlak plynu.
Související produkty:
Typická distribuce velikosti částic
Prášky rozprašované plynem se vyznačují distribucí velikosti částic. Ta udává průměrnou velikost a rozsah velikostí produkovaného prášku. Typická distribuce velikosti částic může vypadat takto:
Velikost částic (mikrony) | Procento |
---|---|
10-25 | 10% |
25-45 | 40% |
45-75 | 30% |
75-105 | 15% |
105-150 | 5% |
- Většina částic je v rozmezí 25-75 mikronů
- Minimální velikost částic kolem 10 mikronů
- Maximálně kolem 150 mikronů
- Úzké rozložení se směrodatnou odchylkou kolem 30 mikronů
Rozsah a distribuce velikosti částic ovlivňuje vlastnosti prášku a vhodnost použití. Jemnější distribuce se používají pro mikroformování, zatímco hrubší velikosti pro kinetické stříkání.
Jak vybrat vhodný prášek rozprašovaný plynem
Zde je několik doporučení pro výběr správného práškového plynu pro vaši aplikaci:
- Složení slitiny přizpůsobte požadavkům na konečné použití, jako je odolnost proti korozi nebo pevnost při vysokých teplotách.
- Zvažte velikost částic podle zamýšleného použití. Jemnější prášky (~15 μm) pro mikro MIM, hrubší (~60 μm) pro stříkání za studena.
- Sférická morfologie nad 90 % zajišťuje maximální hustotu při spékání nebo tavení.
- Úzká distribuce velikosti částic zlepšuje průtok a zvyšuje hustotu zeleně.
- Prášek s vyšší čistotou a nižším obsahem kyslíku pro lepší mechanické vlastnosti.
- Oceli se obvykle atomizují v argonu, reaktivní slitiny jako titan v dusíkové atmosféře.
- Vyberte si renomované dodavatele prášků, kteří vám poskytnou kompletní analytické zprávy.
- Zvažte parametry procesu atomizace používané dodavatelem, abyste zajistili vhodné vlastnosti prášku.
- Před nákupem velkého množství si vyžádejte vzorky pro vyhodnocení a testy.
Jak se používá plynný atomizovaný prášek
aplikace | Používá |
---|---|
Vstřikování kovů | Jemné prášky pro mikro MIM, vysoké zatížení práškem, sférická morfologie pro pevnost |
Aditivní výroba | Sférická morfologie pro SLS/DMLS, jemné prášky pro tryskání pojiva |
Tepelný nástřik | Plynová rozprašovaná surovina pro studený nástřik, jemná distribuce pro nástřik roztoku prekurzoru |
Povrchové inženýrství | Sférický prášek pro kinetickou metalizaci, práškové lakování |
Vstřikování kovů (MIM)
- Jemnější prášky rozprašované plynem pro mikro MIM malých a složitých dílů.
- Vynikající tekutost umožňuje vysoké zatížení práškem a hustotu zelené barvy.
- Sférická morfologie zajišťuje vynikající pevnost a hustotu spékání.
Aditivní výroba
- Ideální sférická morfologie pro procesy tavení v práškovém loži, jako je selektivní laserové spékání (SLS) a přímé laserové spékání kovů (DMLS).
- Rozprašování inertním plynem zlepšuje opětovné použití prášku díky nízkému obsahu kyslíku.
- Jemný prášek používaný při tryskání pojivem a inkoustovém tisku na kov.
Tepelný nástřik
- Plynová rozprašovaná surovina se upřednostňuje pro procesy stříkání vysokou rychlostí, jako je stříkání za studena.
- Husté povlaky z deformace tvárných sférických částic prášku při nárazu.
- Jemnější distribuce prášku pro nástřik suspenzí a roztoků prekurzorů.
Povrchové inženýrství
- Sférické prášky umožňují hladkou povrchovou úpravu při kinetických metalizačních procesech.
- Vynikající tekutost se hodí k procesům nanášení práškových nátěrových hmot pro ochranu proti korozi a opotřebení.
- Jemné kontrolované velikosti pro aplikace strukturování povrchu a třídění.
Problémy spojené s práškovým rozprašováním plynu
Plynem rozprašovaný prášek má sice mnoho výhod, ale přináší také některé problémy:
- Vysoká počáteční investice do zařízení pro rozprašování plynu.
- Vyžaduje technické znalosti pro obsluhu a optimalizaci procesu atomizace.
- Při nesprávné manipulaci a skladování může být náchylný k oxidaci.
- Sférická morfologie prášku ztěžuje dosažení vysoké hustoty zelené barvy při lisování.
- Jemné prášky náchylné k problémům s prášením při manipulaci a zpracování.
- Nákladnější ve srovnání s prášky rozprašovanými vodou a předem legovanými prášky.
- Rizika kontaminace způsobená nevhodnou atmosférou pro rozprašování plynu.
- Různá kvalita různých dodavatelů prášků a tříd.
Abyste mohli plně využít všech výhod prášku rozprašovaného plynem, je třeba přijmout vhodná opatření k minimalizaci těchto problémů.
Nejnovější pokroky v technologii prášků rozprašovaných plynem
Mezi novější vývoj v oblasti výroby prášku rozprašovaného plynem patří:
- Rozprašování více tryskami pro vyšší výtěžnost prášku a rychlejší výrobu.
- Úzce spřažená atomizace pro minimalizaci oxidace taveniny.
- Hladká výroba prášku z ultrazvukové plynové atomizace.
- Nové rozprašovací plyny, jako je helium, pro jemnější rozprašování.
- Systémy úpravy plynu pro recyklaci a čištění rozprašovacího plynu.
- Pokročilé techniky třídění pro užší rozdělení velikosti částic.
- Specializované konstrukce plynových rozprašovačů pro reaktivní slitiny, jako je hořčík a hliník.
- Automatizované systémy manipulace s práškem pro minimalizaci kontaminace.
- Vysokotlaká mikrotrysková atomizace pro submikronové velikosti prášku.
- Integrované systémy výroby, manipulace a kontroly kvality prášku.
Často kladené otázky
Zde je několik nejčastějších dotazů týkajících se prášků rozprašovaných plynem:
Otázka: Jaká je hlavní výhoda prášku rozprašovaného plynem?
Odpověď: Největší výhodou je velmi kulovitá morfologie částic, která vzniká při plynové atomizaci. To vede k vynikajícím tokovým a zhutňovacím vlastnostem.
Otázka: V jakých průmyslových odvětvích se nejčastěji používá práškový plyn?
Odpověď: Automobilový a letecký průmysl jsou hlavními spotřebiteli prášku rozprašovaného v plynu pro vstřikování kovů a aditivní výrobu.
Otázka: Jaký je typický plyn používaný pro atomizaci ocelí?
Odpověď: Většina ocelí se díky svým inertním vlastnostem rozprašuje plynem, a to buď dusíkem, nebo argonem.
Otázka: Jak malé mohou být částice prášku rozprašovaného plynem?
Odpověď: Pomocí specializovaných rozprašovačů s mikrotryskami je možné rozprašovat prášky s velikostí částic pod 1 mikron. Obvyklý rozsah je 10-150 mikronů.
Otázka: Lze prášky rozprašované plynem legovat?
Odpověď: Ano, předlegované prášky rozprašované plynem se vyrábějí tak, že se slitiny před rozprašováním nejprve roztaví a smíchají.
Otázka: Co je příčinou satelitů v plynném rozprašovaném prášku?
Odpověď: Satelity vznikají neúplným rozpadem roztaveného kovu na jemné kapičky. Vyšší tlak plynu snižuje množství satelitů.
Otázka: Má prášek rozprašovaný plynem dobré spékací vlastnosti?
Odpověď: Sférická morfologie a vysoká čistota prášku rozprašovaného plynem vedou k vynikajícímu chování při spékání. Lze dosáhnout více než 98% hustoty.
Otázka: Jak se rozprašují reaktivní kovy, jako je titan a hořčík?
Odpověď: Reaktivní kovy jsou atomizovány pomocí systému s inertním plynem, který zabraňuje působení kyslíku a dusíku.
Zahrnuje klíčové aspekty výroby prášku v plynovém rozprašovači, vlastnosti, aplikace a technologie. Dejte mi vědět, pokud potřebujete nějaké vysvětlení nebo máte další otázky!
Sdílet na
MET3DP Technology Co., LTD je předním poskytovatelem řešení aditivní výroby se sídlem v Qingdao v Číně. Naše společnost se specializuje na zařízení pro 3D tisk a vysoce výkonné kovové prášky pro průmyslové aplikace.
Dotaz k získání nejlepší ceny a přizpůsobeného řešení pro vaše podnikání!
Související články
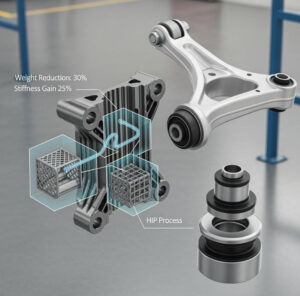
Metal 3D Printed Subframe Connection Mounts and Blocks for EV and Motorsport Chassis
Přečtěte si více "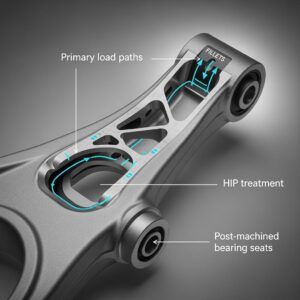
Metal 3D Printing for U.S. Automotive Lightweight Structural Brackets and Suspension Components
Přečtěte si více "O Met3DP
Nedávná aktualizace
Náš produkt
KONTAKTUJTE NÁS
Nějaké otázky? Pošlete nám zprávu hned teď! Po obdržení vaší zprávy obsloužíme vaši žádost s celým týmem.