Lehké tepelné štíty pro letecký průmysl prostřednictvím AM
Obsah
Úvod: Revoluce v tepelné ochraně pomocí tepelných štítů AM Aerospace
Letecký a kosmický průmysl pracuje v extrémních výkonnostních, teplotních a environmentálních podmínkách. Účinná tepelná ochrana není jen požadavkem - je to kritická nutnost, ať už jde o sálavé teplo při vstupu do atmosféry nebo intenzivní tepelné zatížení součástí motorů a hypersonických vozidel. Výroba složitých geometrií a robustních struktur potřebných pro tepelné štíty tradičně zahrnovala složité, vícestupňové procesy, často omezené subtraktivním obráběním a dlouhými dodacími lhůtami. Výsledkem těchto metod byly často těžší součásti, než bylo žádoucí, což mělo přímý dopad na nosnost a palivovou účinnost - klíčové ukazatele v leteckém designu.
Vstupte do aditivní výroby (AM), běžně známé jako 3D tisk z kovu. Tato transformační technologie rychle mění podobu výroby leteckých součástek, zejména systémů tepelné ochrany (TPS), jako jsou tepelné štíty. Díky tomu, že se díly vytvářejí vrstvu po vrstvě přímo z digitálních návrhů za použití vysoce výkonných kovových prášků, nabízí AM nebývalou volnost v komplexnosti konstrukce, umožňuje výrazné snížení hmotnosti díky optimalizaci a zrychluje prototypovací a výrobní cykly. Pro inženýry a manažery nákupu, kteří se potýkají s výzvami extrémního tepelného managementu, 3D tisk z kovu poskytuje výkonnou sadu nástrojů pro vytváření lehkých tepelných štítů nové generace, které posouvají hranice výkonu a účinnosti.
Tepelné štíty jsou v podstatě bariéry určené k odvádění, izolaci nebo ablaci extrémního tepla vznikajícího během letu, které chrání citlivé konstrukce, užitečné zatížení a personál. Jejich konstrukce vyžaduje pečlivou rovnováhu mezi tepelnou odolností, strukturální integritou, nízkou hustotou a odolností při velkém mechanickém a tepelném zatížení. Aditivní výroba je při řešení těchto mnohostranných požadavků vynikající. Umožňuje vytvářet integrované chladicí kanály, složité mřížkové struktury pro úsporu hmotnosti a odvod tepla a používat pokročilé materiály speciálně vybrané pro jejich vysokoteplotní výkon a nízkou tepelnou vodivost.
Společnosti, které stojí v čele tohoto technologického posunu, jako je Met3dp, poskytují základní stavební kameny pro tuto revoluci. Díky hlubokým odborným znalostem v oblasti pokročilé výroby kovových prášků i průmyslových systémů AM pro kovy umožňuje společnost Met3dp výrobcům v leteckém průmyslu plně využít potenciál aditivní výroby. Jejich závazek ke kvalitě, který se odráží v jejich pokročilých technologiích plynové atomizace a plazmového procesu s rotujícími elektrodami (PREP) pro výrobu prášků, zajišťuje vysokou sféricitu, tekutost a čistotu požadovanou pro kritické letecké díly. Když se hlouběji ponoříme do aplikací, výhod a možností výběru materiálů pro tepelné štíty AM, je zřejmé, že tato technologie není jen alternativní výrobní metodou; je to klíčový faktor pro budoucnost tepelného managementu v letectví a kosmonautice, který přináší lehčí, efektivnější a výkonnější řešení. Tento posun je zásadní pro dodavatele, distributory a výrobce, kteří usilují o udržení konkurenceschopnosti na náročném trhu B2B v leteckém průmyslu.
Aplikace: Kde se tepelné štíty AM používají v letectví a kosmonautice?
Schopnost aditivní výroby (AM) vytvářet složité, lehké a vysoce výkonné součásti ji předurčuje k výrobě tepelných štítů pro nejrůznější aplikace v leteckém průmyslu. Poptávka po pokročilých řešeních tepelné ochrany je všudypřítomná, což je dáno zvyšující se rychlostí letu, ambicióznějšími vesmírnými misemi a potřebou opakovaně použitelných systémů. Kov 3D tisk nachází kritické případy použití v následujících oblastech:
- Vozidla pro návrat do atmosféry (kosmické lodě, kapsle):
- Výzva: Ochrana kosmických lodí a kapslí s posádkou před extrémními teplotami (často přesahujícími 1650 °C nebo 3000 °C), které vznikají v důsledku atmosférického tření při návratu do atmosféry.
- Řešení AM: AM umožňuje vytvářet tepelné štíty s optimalizovanými tvary a potenciálně integrovanými transpiračními chladicími kanály nebo složitými vnitřními strukturami, které zlepšují odvod tepla. Materiály, jako jsou slitiny titanu (např. Ti-6Al-4V), nabízejí dobrý poměr pevnosti a hmotnosti a odolnosti vůči vysokým teplotám vhodný pro určité profily při návratu do atmosféry nebo specifické součásti štítu, ačkoli v oblastech s nejvyšším tepelným tokem zůstává dominantní keramika a ablativní materiály. Kovové díly AM mohou sloužit jako konstrukční nosiče nebo upevňovací body pro tyto primární materiály TPS, které těží z odlehčení a geometrické složitosti. Manažeři nákupu B2B, kteří hledají spolehlivé dodavatele konstrukčních součástí pro návratové systémy, se stále častěji obracejí na specialisty na AM.
- Hypersonická vozidla (rakety, letadla):
- Výzva: Při trvalém letu rychlostí Mach 5 a vyšší dochází k intenzivnímu a trvalému aerodynamickému ohřevu náběžných hran, kuželů přídě a povrchů motoru. Materiály musí odolávat vysokým teplotám a zároveň zachovávat strukturální integritu při značném mechanickém namáhání.
- Řešení AM: Metal AM umožňuje vyrábět konformní tepelné štíty a součásti horkých konstrukcí se složitými chladicími kanály (s použitím kapalných nebo plynových chladicích kapalin) integrovanými přímo do dílu. To je při tradiční výrobě velmi obtížné nebo nemožné. Lze použít vysokoteplotní superslitiny a potenciálně žáruvzdorné kovy (zpracované specializovanými technikami AM). Pro hypersoniku je rozhodující odlehčení pomocí optimalizace topologie a AM tuto možnost poskytuje. Distributoři leteckých komponentů potřebují partnery, kteří dokáží spolehlivě dodávat tyto geometricky složité díly odolné vůči vysokým teplotám.
- Raketové motory a pohonné systémy:
- Výzva: Součásti, jako jsou nástavce trysek, spalovací komory a systémy vektorování výfukových plynů, jsou vystaveny extrémním tepelným gradientům a vysokým tepelným tokům ze spalin. Ochrana přilehlých konstrukcí a zajištění dlouhé životnosti komponent je životně důležité.
- Řešení AM: AM může vyrábět lehké nástavce trysek s vnitřními výztužnými prvky nebo integrovanými stínicími prvky. Tepelné štíty pro ochranu citlivých součástí motoru (pohony, elektronika) mohou být navrženy ve složitých tvarech, aby se těsně vešly do omezeného prostoru, a často obsahují montážní prvky přímo ve štítu. Často se používají materiály jako Ti-6Al-4V a superslitiny na bázi niklu. Možnost konsolidace dílů (např. integrace držáku do štítu) zkracuje dobu montáže a snižuje počet potenciálních poruchových míst, což je pro letecké výrobce klíčovou výhodou.
- Tepelný management satelitů:
- Výzva: Na satelitech dochází k extrémním teplotním výkyvům, protože na jedné straně jsou vystaveny přímému slunečnímu záření a na druhé straně chladnému vesmírnému vakuu. K ochraně citlivé elektroniky a přístrojů se používají tepelné štíty nebo tepelné přikrývky, které udržují provozní teplotní rozsahy.
- Řešení AM: Zatímco se často používá vícevrstvá izolace (MLI), konstrukční součásti a štíty vyžadující specifické tvary, tuhost a nízkou hmotnost mohou využívat AM. Slitiny hliníku, jako je AlSi10Mg, nabízejí vynikající tepelnou vodivost (užitečnou pro šíření tepla) a nízkou hustotu, takže jsou vhodné pro určité struktury tepelného managementu nebo komponenty chladičů, které fungují vedle tradičního stínění. AM umožňuje vytvářet konstrukce na míru specifickým geometriím satelitů a tepelným požadavkům, což je cenné pro velkoodběratele, kteří potřebují řešení na míru.
- Nacely a pilony motorů (komerční letadla a vojenská letadla):
- Výzva: Oblasti kolem leteckých motorů jsou vystaveny značnému tepelnému záření a vyžadují důkladnou protipožární ochranu a tepelnou izolaci, která chrání konstrukci křídla a trupu.
- Řešení AM: Pomocí technologie AM lze vytvářet složité držáky, segmenty tepelného štítu a ventilační komponenty s optimalizovaným prouděním vzduchu pro chlazení. Titanové slitiny jsou často upřednostňovány pro svou odolnost proti ohni a pevnost při zvýšených teplotách. Schopnost rychlého prototypování a výroby náhradních dílů prostřednictvím AM je také významnou výhodou pro provozy údržby, oprav a generálních oprav (MRO), což má dopad na dodavatele a distributory v leteckém průmyslu.
Tabulka: Aplikace tepelného štítu AM & Výhody
Oblast použití | Klíčová tepelná výzva | Výhody AM | Potenciální materiály | Cílová skupina B2B |
---|---|---|---|---|
Vozidla pro opětovný vstup | Extrémní přechodový ohřev (1650 °C) | Složité konstrukční nosiče, integrované prvky, potenciál pro chladicí kanály | Ti-6Al-4V (struktury) | Vesmírné agentury, výrobci kapslí, dodavatelé Tier 1 |
Hypersonické systémy | Trvale vysoké teploty, tepelná zátěž | Integrované chlazení, složité geometrie, odlehčování, rychlé prototypování | Superslitiny, Ti-slitiny | Dodavatelé v oblasti obrany, letecký výzkum a vývoj, hypersonické startupy |
Raketový pohon | Vysoký tepelný tok, tepelné gradienty | Konsolidace dílů, konformní provedení, lehké trysky/štítky | Ti-6Al-4V, superslitiny | Poskytovatelé startovacích služeb, výrobci motorů, dodavatelé součástí |
Satelity | Extrémní výkyvy teplot, záření | Lehké konstrukce, vlastní geometrie, tepelná vodivost (AlSi10Mg) | AlSi10Mg, Ti-slitiny | Výrobci družic, integrátoři užitečného zatížení |
Letecké motory | Tepelné vyzařování motoru, požární odolnost | Komplexní držáky, optimalizované proudění vzduchu, náhradní díly pro MRO, požární odolnost | Ti-6Al-4V | Výrobci OEM letadel, výrobci motorů, poskytovatelé MRO |
Export do archů
Všestrannost technologie AM umožňuje konstruktérům přehodnotit konstrukci tepelných štítů a odklonit se od objemných, nadměrně konstruovaných součástí k vysoce optimalizovaným, integrovaným řešením tepelné ochrany přizpůsobeným specifickým požadavkům každé letecké aplikace.
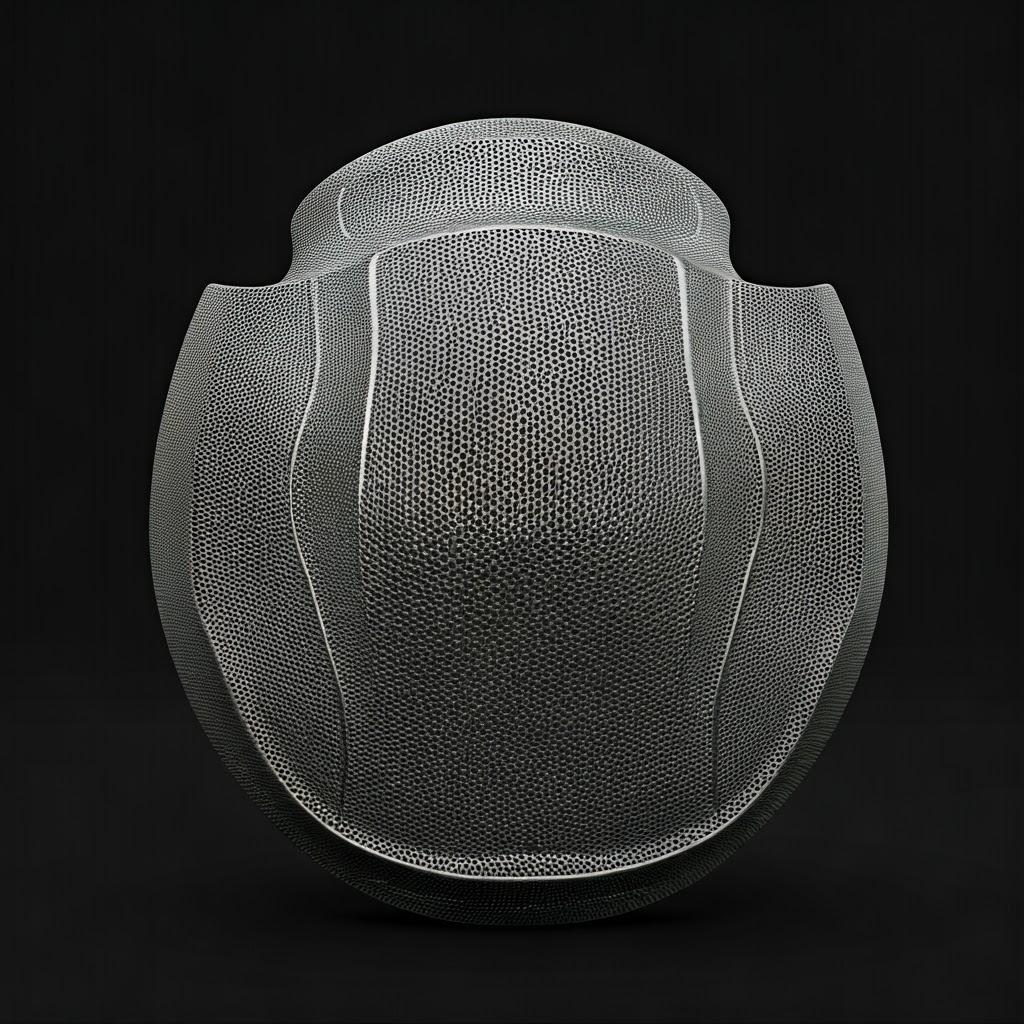
Aditivní výhoda: Proč 3D tisk kovů pro tepelné štíty v letectví?
Tradiční výrobní metody, jako je obrábění, tváření a odlévání, sice již dlouho slouží leteckému průmyslu, ale při výrobě složitých součástí tepelné ochrany, jako jsou tepelné štíty, často představují značná omezení. Aditivní výroba kovů nabízí přesvědčivý soubor výhod, které přímo řeší tyto problémy, a proto se stává stále oblíbenější metodou výroby tepelných štítů nové generace. Pro manažery nákupu a inženýry, kteří posuzují možnosti výroby, je pochopení těchto výhod zásadní pro přijímání informovaných rozhodnutí, která ovlivňují výkon, náklady a dobu realizace.
K hlavním výhodám použití kovového AM pro tepelné štíty v leteckém průmyslu patří:
- Bezkonkurenční volnost designu & Komplexnost:
- Výzva: Tradiční metody se potýkají se složitými vnitřními prvky, podřezáním a nejednotnými tvary, které jsou nutné pro optimální tepelný výkon a integraci.
- Řešení AM: AM vytváří díly vrstvu po vrstvě, což umožňuje vytvářet dříve nemožné geometrie. To zahrnuje:
- Vnitřní chladicí kanály: Konformní kanály, které přesně kopírují obrysy povrchu tepelného štítu, lze integrovat přímo do dílu, což umožňuje vysoce účinné aktivní chladicí systémy.
- Mřížové struktury: V rámci objemu štítu lze navrhnout lehké porézní struktury, které výrazně sníží hmotnost při zachování tuhosti konstrukce a případně zlepší tepelně izolační nebo rozptylové vlastnosti.
- Optimalizace topologie: Algoritmy dokáží určit nejefektivnější rozložení materiálu tak, aby odolával určitému tepelnému a mechanickému zatížení, čímž se odstraní nepotřebný materiál a výrazně se sníží hmotnost.
- B2B Impact: Dodavatelé v leteckém průmyslu mohou nabízet vysoce diferencované tepelné štíty s optimalizovaným výkonem, které nelze vyrábět konvenčně, což jim dává konkurenční výhodu.
- Výrazné snížení hmotnosti (odlehčení):
- Výzva: Každý ušetřený kilogram v leteckém průmyslu se přímo promítá do úspory paliva, zvýšení nosnosti nebo manévrovatelnosti. Tradiční tepelné štíty jsou kvůli výrobním omezením často těžší, než je nutné.
- Řešení AM: Díky optimalizaci topologie, mřížkovým strukturám a schopnosti vytvářet tenkostěnné konstrukce s integrovanými výztužnými žebry může AM snížit hmotnost tepelných štítů o 20-50 % nebo více ve srovnání s konvenčně vyráběnými protějšky, aniž by došlo ke snížení výkonu. Použití přirozeně lehčích materiálů, jako je titan (Ti-6Al-4V) a hliník (AlSi10Mg), tuto výhodu dále zvyšuje.
- B2B Impact: Manažeři veřejných zakázek, kteří hledají lehké komponenty, aby splnili přísné požadavky leteckého průmyslu, považují AM za atraktivní řešení. Úspory hmotnosti se projevují kaskádovitě v celé konstrukci letadla nebo kosmické lodi a nabízejí podstatné výhody na úrovni systému.
- Konsolidace částí:
- Výzva: Složité sestavy zahrnující více součástí (např. štít, držáky, spojovací prvky) zvyšují hmotnost, dobu montáže, náklady a potenciální místa poruchy.
- Řešení AM: AM umožňuje spojit více funkčních prvků do jediného monolitického tištěného dílu. Tepelný štít lze vytisknout s integrovanými montážními šrouby, upevňovacími prvky nebo výztužnými prvky, čímž se eliminuje potřeba samostatných součástí a spojovacích prvků.
- B2B Impact: Snižuje složitost dodavatelského řetězce pro odběratele, snižuje náklady na montáž pro výrobce a zvyšuje celkovou spolehlivost komponent díky minimalizaci spojů a rozhraní.
- Zrychlené prototypování a vývojové cykly:
- Výzva: Vytváření prototypů a opakování návrhů pomocí tradičních nástrojů a obrábění může být časově i finančně náročné.
- Řešení AM: AM umožňuje rychlou výrobu funkčních prototypů přímo z dat CAD, často během několika dnů. Inženýři tak mohou rychle testovat různé konstrukce, materiály a konfigurace, což výrazně zkracuje dobu vývoje nových konceptů tepelných štítů.
- B2B Impact: Rychlejší uvádění nových leteckých systémů na trh a rychlejší kvalifikace součástí. Dodavatelé mohou rychleji reagovat na změny konstrukce u zákazníků.
- Efektivní využití materiálu a snížení množství odpadu:
- Výzva: Subtraktivní výroba (obrábění) začíná s pevným blokem materiálu a odebírá velké množství, čímž vzniká značný odpad (zmetky), zejména u drahých leteckých slitin, jako je titan.
- Řešení AM: Aditivní výroba je ze své podstaty proces, který se blíží čistému tvaru a používá pouze materiál potřebný k výrobě dílu a požadované podpěry. Ačkoli se používá určitý podpůrný materiál a některé následné zpracování může zahrnovat drobné odstranění materiálu, celkový odpad materiálu je ve srovnání se subtraktivními metodami drasticky snížen. Společnosti jako Met3dp, které se specializují na výrobu vysoce kvalitních prášků, se také zaměřují na recyklovatelnost prášků v rámci procesu AM, což dále zvyšuje udržitelnost.
- B2B Impact: Nižší náklady na materiál, zejména u vysoce hodnotných slitin, a lepší ekologické vlastnosti jsou atraktivní pro týmy zadavatelů, které dbají na náklady a udržitelnost.
- Přizpůsobení a výroba na vyžádání:
- Výzva: Výroba malých sérií nebo vysoce přizpůsobených tepelných štítů tradičními metodami často vyžaduje vysoké náklady na přípravu a dlouhé dodací lhůty.
- Řešení AM: AM je vhodný pro nízké až střední výrobní série a vytváření návrhů na míru bez nutnosti nákladného nástrojového vybavení. To usnadňuje výrobu na vyžádání a výrobu náhradních dílů pro starší systémy.
- B2B Impact: Umožňuje distributorům leteckých součástek a poskytovatelům MRO nabízet řešení na míru a efektivněji udržovat zásoby kritických náhradních dílů.
Tabulka: Tradiční vs. AM pro výrobu tepelného štítu
Vlastnosti | Tradiční výroba (obrábění, tváření) | Výroba aditiv kovů (AM) | Výhoda tepelných štítů AM |
---|---|---|---|
Složitost návrhu | Omezeno přístupem k nástroji, úhly tahu | Vysoká geometrická volnost, vnitřní kanály, mřížky | Optimální tepelný výkon, integrované funkce |
Hmotnost | Často těžší kvůli omezením | Významný potenciál pro odlehčení | Vyšší spotřeba paliva, vyšší nosnost |
Počet dílů | Často vyžaduje sestavy | Umožňuje konsolidaci dílů | Zkrácení doby montáže, snížení nákladů a snížení poruchovosti |
Vytváření prototypů | Pomalé, vyžaduje nástroje | Rychlé vytváření prototypů přímo z CAD | Rychlejší iterace návrhu a doba uvedení na trh |
Materiálový odpad | Vysoká (subtraktivní proces) | Nízká (proces blízký tvaru sítě) | Nižší náklady na materiál, udržitelnější |
Nástroje | Potřebné (formy, zápustky, přípravky) | Výroba bez nástrojů | Cenově výhodné pro malé objemy a přizpůsobení |
Doba realizace | Může být zdlouhavé, zejména u složitých dílů | Potenciálně kratší, zejména u prototypů/malých objemů | Rychlejší dodávky komponent, agilní výroba |
Export do archů
Využitím těchto výhod umožňuje AM kovů leteckým inženýrům a výrobcům překonat omezení konvenčních metod a připravit tak půdu pro lehčí, složitější a výkonnější tepelné štíty, které jsou důležité pro současné i budoucí letecké mise. Výběr zkušeného partnera AM, jako je Met3dp, zajišťuje nejen přístup k tiskových metod ale také odborné znalosti v oblasti materiálových věd, které jsou nezbytné pro úspěch.
Výběr materiálu: Optimalizace výkonu s prášky Ti-6Al-4V a AlSi10Mg
Výběr správného materiálu je při navrhování tepelných štítů pro letectví a kosmonautiku velmi důležitý, protože vlastnosti materiálu přímo určují výkonnost součásti při extrémním tepelném a mechanickém zatížení. Aditivní výroba rozšiřuje paletu použitelných materiálů a umožňuje jejich strategické nasazení ve složitých geometriích. Pro mnoho aplikací lehkých tepelných štítů vyráběných pomocí AM vynikají dva kovové prášky: Slitina titanu Ti-6Al-4V a slitina hliníku AlSi10Mg. Volba mezi nimi (nebo případně dalšími pokročilými slitinami) závisí do značné míry na konkrétních provozních podmínkách, konstrukčních požadavcích a cílové hmotnosti.
Vysoce kvalitní kovové prášky jsou základem spolehlivé technologie AM. Společnosti jako Met3dp, které využívají pokročilé výrobní techniky, jako je plynová atomizace a PREP, vyrábějí sférické kovové prášky s vysokou čistotou, kontrolovanou distribucí velikosti částic (PSD) a vynikající tekutostí. Tyto vlastnosti jsou klíčové pro dosažení hustých dílů bez vad s předvídatelnými mechanickými vlastnostmi - což je pro letecké komponenty nepominutelný požadavek.
1. Slitina titanu Ti-6Al-4V (třída 5): Pracovní kůň pro letectví a kosmonautiku
- Popis: Ti-6Al-4V je alfa-beta titanová slitina proslulá vynikající kombinací vysokého poměru pevnosti a hmotnosti, odolnosti proti korozi a dobrých vlastností při mírně zvýšených teplotách (do přibližně 350-400 °C, krátkodobě případně i vyšších). Jedná se o jednu z nejpoužívanějších titanových slitin v leteckém průmyslu pro konstrukční součásti, části motorů a podvozky.
- Výhody tepelných štítů:
- Vysoký poměr pevnosti k hmotnosti: Výrazně lehčí než ocel nebo slitiny niklu při stejné pevnosti, což je rozhodující pro odlehčení štítů.
- Dobrá retence při vysokých teplotách: Zachovává si užitečnou pevnost při teplotách, při kterých by hliníkové slitiny selhaly.
- Vynikající odolnost proti korozi: Odolává oxidaci a působení leteckých kapalin a prostředí.
- Nízká tepelná vodivost: V porovnání s hliníkem může být jeho nižší vodivost výhodná pro izolační účely, protože zpomaluje přenos tepla přes konstrukci štítu (i když při velmi vysokých tepelných tocích je často stále nutné aktivní chlazení nebo izolační vrstvy).
- Biokompatibilita: Ačkoli je jeho biokompatibilita méně důležitá pro tepelné štíty, rozšiřuje jeho použití v jiných aplikacích v letectví a kosmonautice (např. lékařské implantáty pro astronauty).
- Odolnost proti ohni: Titan má ve srovnání se slitinami hliníku nebo hořčíku poměrně dobré ohnivzdorné vlastnosti.
- Úvahy o AM: Ti-6Al-4V je snadno zpracovatelný pomocí technik laserového tavení v práškovém loži (LPBF/SLM) a tavení elektronovým svazkem (EBM). Vyžaduje pečlivou kontrolu inertní atmosféry (argon) během tisku, aby se zabránilo zachycení kyslíku, který může materiál zkřehnout. Následné zpracování často zahrnuje tepelné zpracování pro snížení napětí a případně lisování za tepla (HIP), aby se uzavřela jakákoli zbytková vnitřní pórovitost a maximalizovala únavová životnost.
- Případy použití: Konstrukční prvky TPS návratového vozidla, substruktury hypersonických náběžných hran (často v kombinaci s jinými materiály/chlazením), součásti motorových gondol, tepelné štíty pylonů, součásti výfukového systému.
- B2B Focus: Dodavatelé nabízející certifikovaný prášek Ti-6Al-4V a tiskové služby v souladu s leteckými normami (např. specifikace AMS) jsou velmi žádaní výrobci OEM a výrobci Tier 1.
2. Hliníková slitina AlSi10Mg: Lehká a tepelně vodivá
- Popis: AlSi10Mg je hliníková slitina obsahující křemík a hořčík, která je známá svou dobrou pevností, odlévatelností (což se projevuje dobrou tisknutelností v AM) a vynikající tepelnou vodivostí. Je výrazně lehčí než titan.
- Výhody tepelných štítů:
- Extrémně nízká hustota: Nabízí maximální úsporu hmotnosti v případech, kdy není hlavní podmínkou vysoká pevnost nebo odolnost vůči vysokým teplotám.
- Vysoká tepelná vodivost: Vynikající pro aplikace, kde je cílem rychlé rozložení a rozptýlení tepla po celé konstrukci štítu, často s připojením k většímu chladiči nebo chladicímu systému.
- Dobrá potiskovatelnost: Dobře se zpracovává pomocí LPBF, což umožňuje jemné rysy a složité geometrie.
- Nižší náklady: Obecně jsou levnější než titanové slitiny, a to jak z hlediska nákladů na suroviny, tak z hlediska času a energie potřebných k tisku.
- Úvahy o AM: Tiskne dobře, ale jeho nižší teplota tání vyžaduje pečlivou kontrolu parametrů. Stejně jako u titanu je nutná inertní atmosféra. Následné zpracování obvykle zahrnuje uvolnění napětí a případně tepelné zpracování T6 (rozpuštění a umělé stárnutí) pro dosažení optimálních mechanických vlastností (pevnost a tvrdost).
- Omezení: Jeho hlavním omezením je relativně nízká provozní teplota (obvykle pod 150-200 °C při trvalém použití), což omezuje jeho použití na případy tepelných štítů s nižší teplotou nebo na oblasti vzdálenější od primárního zdroje tepla. Ve srovnání s Ti-6Al-4V má také nižší absolutní pevnost a únavovou odolnost.
- Případy použití: Součásti tepelného managementu družic (chladiče, konstrukční podpěry, kde je potřeba šířit teplo), kryty pro elektroniku vyžadující stínění a odvod tepla, některé součásti v chladnějších částech motorových gondol, prototypy, kde je klíčová funkční geometrie, ale pro počáteční testy není potřeba vysokoteplotní výkon.
- B2B Focus: Distributoři a výrobci, kteří hledají cenově výhodná a lehká řešení pro aplikace při mírných teplotách, často uvádějí AlSi10Mg. Klíčová je dostupnost prášku letecké kvality a certifikovaných tiskových procesů.
Tabulka: Srovnání Ti-6Al-4V a AlSi10Mg pro tepelné štíty AM
Vlastnictví | Ti-6Al-4V (třída 5) | AlSi 10Mg | Hlavní důsledky pro tepelné štíty |
---|---|---|---|
Hustota | ~4,43 g/cm³ | ~2,67 g/cm³ | AlSi10Mg nabízí vynikající potenciál pro odlehčování. |
Maximální provozní teplota. | ~350-400 °C (trvale) | ~150-200 °C (trvale) | Ti-6Al-4V vhodný do prostředí s vyšší teplotou. |
Pevnost (konečná) | Vysoká (~900-1100 MPa, v závislosti na HT) | Mírná (~250-350 MPa, v závislosti na HT) | Ti-6Al-4V poskytuje mnohem vyšší strukturální integritu. |
Poměr síly a hmotnosti | Velmi vysoká | Vysoký | Obě jsou vynikající, ale Ti-6Al-4V se často upřednostňuje kvůli struktuře. |
Tepelná vodivost | Nízká (~7 W/m-K) | Vysoká (~130-150 W/m-K) | AlSi10Mg vyniká šířením tepla; Ti-6Al-4V zajišťuje izolaci. |
Možnost tisku (LPBF) | Dobrý (vyžaduje pečlivou kontrolu) | Vynikající | Obě se dobře hodí pro složitost AM. |
Odolnost proti korozi | Vynikající | Dobrý (může vyžadovat povrchovou úpravu) | Ti-6Al-4V je obecně odolnější v drsném prostředí. |
Relativní náklady | Vyšší | Dolní | AlSi10Mg nabízí ekonomičtější řešení. |
Export do archů
Nad rámec Ti-6Al-4V a AlSi10Mg:
Je důležité si uvědomit, že portfolio kovových AM prášků se neustále rozšiřuje. Pro ještě náročnější vysokoteplotní aplikace mohou letečtí inženýři zvážit např:
- Superslitiny na bázi niklu (např. Inconel 718, Inconel 625): Nabízejí vynikající zachování pevnosti při velmi vysokých teplotách (až 700 °C nebo vyšších) a dobrou odolnost proti korozi. Často se používají v horkých částech motoru a výfukových systémech.
- Žáruvzdorné kovy (např. molybden, slitiny wolframu): Pro aplikace při extrémních teplotách, jako jsou hypersonické náběžné hrany nebo hrdla raketových trysek, však zpracování těchto materiálů pomocí AM představuje značnou výzvu.
- Pokročilé slitiny titanu: Portfolio společnosti Met3dp’ zahrnuje inovativní slitiny, jako jsou TiNi, TiTa, TiAl a TiNbZr, které mohou nabídnout vlastnosti přizpůsobené specifickým tepelným nebo strukturálním výzvám nad rámec standardního Ti-6Al-4V. Prozkoumání celé škály produkty dostupné od specializovaných dodavatelů, je zásadní.
Závěr o materiálech:
Volba mezi Ti-6Al-4V a AlSi10Mg pro tepelný štít AM závisí na důkladné analýze tepelného prostředí, konstrukčního zatížení, cílové hmotnosti a nákladových omezení. Ti-6Al-4V poskytuje pevnost při vysokých teplotách potřebnou pro náročnější aplikace, zatímco AlSi10Mg nabízí maximální úsporu hmotnosti a schopnost šíření tepla v chladnějším prostředí. Spolupráce s poskytovatelem AM, jako je Met3dp, který má hluboké znalosti v oblasti materiálových věd a nabízí vysoce kvalitní prášky pro letecký průmysl, zaručuje, že se vybraný materiál promění ve spolehlivou a vysoce výkonnou součást tepelného štítu.
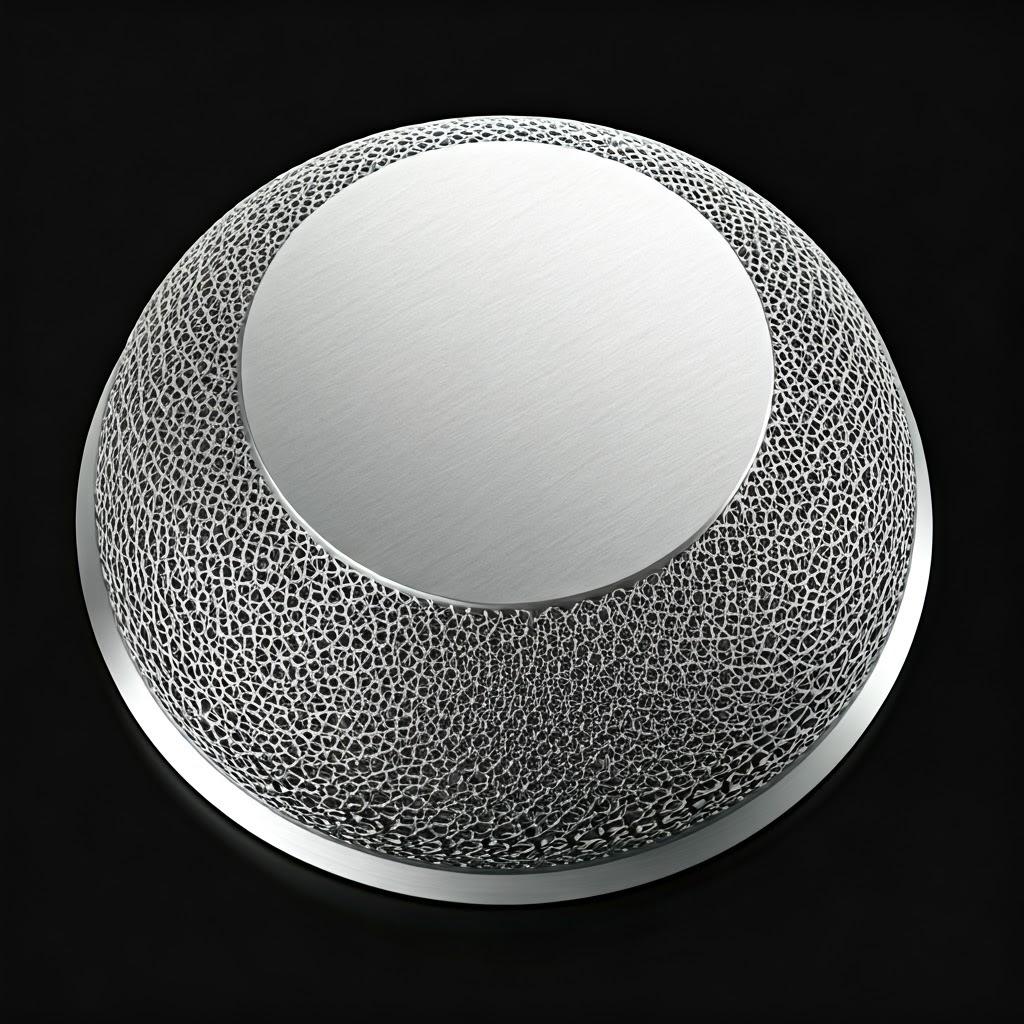
Design pro aditivní výrobu (DfAM): Optimalizace geometrie a výkonu tepelného štítu
Pouhá replikace návrhu určeného pro tradiční výrobu pomocí aditivní výroby jen zřídkakdy uvolní plný potenciál této technologie. Aby inženýři skutečně využili výhody, o kterých jsme hovořili dříve - zejména odlehčení, konsolidaci dílů a lepší tepelný výkon - musí přijmout následující opatření Design pro aditivní výrobu (DfAM) zásady. DfAM je způsob myšlení a metodika zaměřená na navrhování dílů speciálně pro proces sestavování po vrstvách s ohledem na jeho jedinečné možnosti i přirozená omezení. Použití DfAM je rozhodující pro vývoj optimalizovaných tepelných štítů pro letecký průmysl AM, které splňují přísné výkonnostní cíle.
Mezi klíčové aspekty DfAM pro tepelné štíty AM patří:
- Optimalizace topologie:
- Koncept: Pomocí specializovaných softwarových algoritmů se odstraňuje materiál z oblastí, kde není konstrukčně nezbytný, aby odolal definovanému tepelnému a mechanickému zatížení, a výsledkem jsou organicky vypadající, vysoce účinné struktury.
- Aplikace pro tepelné štíty: Výrazně snižuje hmotnost a zároveň zajišťuje zachování tuhosti a pevnosti tam, kde je to potřeba. To je ideální pro vytváření lehkých konstrukčních nosičů pro materiály TPS nebo pro optimalizaci vlastního konstrukčního rámu štítu. Software bere v úvahu případy zatížení (tepelné gradienty, tlakové rozdíly, vibrace) a modeluje díl.
- Výhody: Maximalizuje úsporu hmotnosti, což vede k přímému zlepšení palivové účinnosti a nosnosti.
- Mřížkové a buněčné struktury:
- Koncept: Začlenění vnitřních porézních struktur (jako jsou voštiny, gyroidy nebo stochastické pěny) do pevného objemu součásti. Tyto struktury lze přesně řídit z hlediska velikosti buněk, tloušťky vzpěr a celkové hustoty.
- Aplikace pro tepelné štíty:
- Odlehčení: Nahrazení pevného materiálu porézními mřížkami výrazně snižuje hmotnost.
- Tepelný management: Některé typy mřížek mohou bránit přenosu tepla (izolace) nebo naopak zvětšovat plochu pro výměnu tepla, pokud jsou integrovány s chladicími kanály. Mohou také měnit vlastnosti tlumení vibrací.
- Absorpce energie: Mohou být navrženy tak, aby absorbovaly energii nárazu, což je potenciálně užitečné pro štíty chránící před úlomky.
- Výhody: Poskytuje multifunkční výhody nad rámec prostého snížení hmotnosti a umožňuje přizpůsobit tepelné a mechanické reakce.
- Konsolidace částí:
- Koncept: Přepracování sestavy více komponent, které se mají tisknout jako jediný integrovaný díl.
- Aplikace pro tepelné štíty: Kombinace povrchu štítu s montážními konzolami, vzpěrami, výztužnými žebry nebo dokonce konektory kapalinových kanálů do jednoho monolitického kusu.
- Výhody: Snižuje počet dílů, eliminuje spojovací prvky a spoje (potenciální místa poruch), zjednodušuje montáž, snižuje celkovou hmotnost a potenciálně zlepšuje integritu konstrukce.
- Integrace funkcí:
- Koncept: Navrhování funkčních prvků přímo do dílu AM, které by jinak bylo obtížné nebo nemožné vytvořit.
- Aplikace pro tepelné štíty:
- Konformní chladicí kanály: Vnitřní kanály, které přesně kopírují složité zakřivení povrchu tepelného štítu, zajišťují vysoce účinné a cílené chlazení.
- Texturované povrchy: Vytváření specifických povrchových textur během procesu tisku za účelem zlepšení radiačních vlastností nebo ovlivnění aerodynamických mezních vrstev.
- Integrovaná pouzdra senzorů: Návrh dutin nebo montážních bodů pro vestavěné senzory (teploty, tlaku, tahu) v rámci struktury štítu.
- Výhody: Zvyšuje výkon (chlazení, snímání) a přidává funkce, aniž by zvyšoval počet dílů nebo složitost montáže.
- Budování orientačních a podpůrných struktur:
- Koncept: Zvážení toho, jak bude díl orientován na konstrukční desce a kde budou během tisku potřeba dočasné podpůrné konstrukce (např. při použití LPBF nebo EBM).
- Aplikace pro tepelné štíty:
- Povrchová úprava: Kritické povrchy, které vyžadují vysokou hladkost, by měly být v ideálním případě orientovány vzhůru nebo pod strmým úhlem, aby se minimalizoval “schodišťový efekt”, který je vlastní výrobě na bázi vrstev, a aby se snížil počet kontaktních bodů podpory.
- Převisy a úhly: Mělké úhly (obvykle méně než 45 stupňů od vodorovné roviny) a velké převisy vyžadují podpůrné konstrukce, aby se zabránilo zhroucení při tisku. DfAM se snaží minimalizovat potřebu podpěr nebo navrhnout samonosné úhly, kde je to možné.
- Odstranění podpory: Podpěry musí být po tisku odstranitelné, obvykle ručním lámáním nebo obráběním. DfAM zahrnuje návrh přístupu pro odstranění podpěr a minimalizaci podpěr na kritických nebo těžko přístupných plochách.
- Zbytkové napětí: Orientace sestavy ovlivňuje tepelné gradienty během tisku, což má vliv na zbytkové napětí a potenciální deformace. Strategická orientace může pomoci tyto problémy zmírnit.
- Výhody: Optimalizuje úspěšnost tisku, snižuje čas a náklady na následné zpracování a zlepšuje kvalitu finálního dílu.
- Minimální velikost prvku a tloušťka stěny:
- Koncept: Pochopení limitů konkrétního procesu AM a stroje, pokud jde o nejmenší prvky (otvory, drážky, kolíky) a nejtenčí stěny, které lze spolehlivě vyrobit.
- Aplikace pro tepelné štíty: Zajištění, aby tenké stěny určené pro odlehčení nebo jemné detaily, jako jsou vstupy/výstupy chladicích kanálů, byly v rámci dosažitelných limitů zvoleného systému AM (např. tiskárny Met3dp’ jsou známé svou přesností). Tloušťka stěn má také vliv na přenos tepla a stabilitu konstrukce.
- Výhody: Zajišťuje vyrobitelnost a zabraňuje selhání prvků během tisku nebo v provozu.
Tabulka: Strategie DfAM pro tepelné štíty AM
Strategie DfAM | Cíl | Jak to platí pro tepelné štíty | Klíčový přínos |
---|---|---|---|
Optimalizace topologie | Maximalizace tuhosti/pevnosti při dané hmotnosti | Odstranění nepodstatného materiálu na základě zatěžovacích stavů | Maximální snížení hmotnosti |
Mřížové struktury | Snížení hmotnosti, přizpůsobení vlastností | Nahrazení pevných objemů vnitřními porézními strukturami | Multifunkční: odlehčení, tepelná regulace |
Konsolidace částí | Snížení počtu dílů a montáže | Kombinace štítu, držáků a prvků do jednoho kusu | Vyšší spolehlivost, nižší náklady na montáž & hmotnost |
Integrace funkcí | Přidání funkcí | Vložení chladicích kanálů, držáků senzorů, povrchových textur | Vylepšený výkon, rozšířené možnosti |
Orientace/podpora | Optimalizujte tisk, minimalizujte postproces. | Plánování sestavení, navrhování samonosných úhlů | Kratší doba tisku/náklady, lepší povrchová úprava |
Omezení velikosti funkce | Zajištění vyrobitelnosti | Dodržujte minimální tloušťku stěny a omezení velikosti otvorů | Zaručená vyrobitelnost, prevence selhání prvků |
Export do archů
Implementace DfAM vyžaduje úzkou spolupráci mezi konstruktéry a specialisty na AM. Partneři, jako je Met3dp, s rozsáhlými znalostmi materiálů, procesů a zařízení, mohou poskytnout neocenitelné poradenství při efektivním uplatňování těchto principů a přeměnit standardní konstrukci tepelného štítu na vysoce optimalizovanou aditivně vyráběnou součást. Spolupráce s odborníky na AM v rané fázi návrhu je klíčová pro maximalizaci přínosů a zajištění úspěšného výsledku pro dodavatele B2B v leteckém průmyslu a jejich zákazníky.
Na přesnosti záleží: Dosažení přesných tolerancí a povrchové úpravy u tepelných štítů AM
Letecké komponenty vyžadují mimořádnou přesnost. Výjimkou nejsou ani tepelné štíty, které vyžadují přesné rozměry pro správné uložení a montáž, kontrolované povrchové charakteristiky pro předvídatelný tepelný a aerodynamický výkon a celkovou geometrickou integritu pro zajištění strukturální spolehlivosti. Ačkoli aditivní výroba nabízí neuvěřitelnou geometrickou volnost, dosažení přísných tolerancí a specifických povrchových úprav požadovaných pro letecké aplikace vyžaduje pečlivou kontrolu procesu, porozumění možnostem technologie’ a často i následné kroky zpracování. Manažeři a inženýři pro zadávání zakázek musí mít realistická očekávání a jasné specifikace týkající se dosažitelné přesnosti dílů AM.
1. Rozměrová přesnost a tolerance:
- Definice: Přesnost rozměrů znamená, jak přesně odpovídá konečný vytištěný díl jmenovitým rozměrům uvedeným v modelu CAD. Tolerance definuje přípustný rozsah odchylek pro daný rozměr.
- Schopnosti AM: Dosažitelná přesnost v kovovém AM závisí na několika faktorech:
- Kalibrace stroje: Přesnost navádění laserového nebo elektronového paprsku, konzistence tloušťky vrstvy. Společnosti, jako je Met3dp, investují velké prostředky do tiskáren se špičkovou přesností a spolehlivostí v oboru.
- Vlastnosti materiálu: Rychlost smršťování, charakteristiky tepelné roztažnosti konkrétního kovového prášku (např. Ti-6Al-4V vs. AlSi10Mg).
- Geometrie dílu & Velikost: Větší díly a složité geometrie jsou obecně náchylnější k deformaci a odchylkám.
- Orientace na stavbu: Ovlivňuje tepelnou historii a možné deformace.
- Strategie podpory: Jak dobře podpěry omezují díl během tisku.
- Následné zpracování: Tepelné zpracování s uvolněním napětí může způsobit drobné rozměrové změny.
- Typické tolerance: Tolerance při výrobě se u kovových LPBF/EBM často pohybují v rozmezí ±0,1 mm až ±0,3 mm u menších rozměrů (např. do 100 mm), u větších dílů mohou být odchylky větší (např. ±0,2 % rozměru). Pečlivou optimalizací procesu však lze často dosáhnout těsnějších tolerancí u specifických kritických prvků, které se s rozvojem technologie AM běžně zlepšují.
- Požadavky na letectví a kosmonautiku: Kritické rozměry rozhraní, montážní body a aerodynamické povrchy často vyžadují větší tolerance, než je standardní schopnost AM. Těchto přísnějších tolerancí se obvykle dosahuje následným obráběním.
2. Povrchová úprava (drsnost):
- Definice: Povrchová úprava, často kvantifikovaná pomocí Ra (průměrná drsnost), popisuje strukturu povrchu součásti.
- Charakteristika AM: Povrchy při výrobě kovů AM, zejména při tavení v práškovém loži, jsou ze své podstaty drsnější než povrchy při obrábění. To je způsobeno:
- Linie vrstev: Charakteristický “schodovitý” efekt, zejména na šikmých nebo zakřivených plochách.
- Částečně roztavený prášek: Práškové částice ulpívající na povrchu.
- Kontaktní místa podpůrné struktury: Stopy po odstranění podpěry.
- Typické hodnoty Ra: Hodnoty Ra při sestavování se u kovových LPBF/EBM obvykle pohybují v rozmezí od 6 µm do 25 µm (240 µin až 1000 µin) v závislosti na materiálu, parametrech, orientaci a na tom, zda je povrch během sestavování obrácen nahoru, dolů nebo do strany. Povrchy směřující dolů bývají drsnější v důsledku kontaktu s podpěrou.
- Požadavky na letectví a kosmonautiku: Zatímco některé vnitřní povrchy mohou tolerovat drsnost jako při výrobě, kritické aerodynamické povrchy, těsnicí plochy nebo oblasti vyžadující specifické radiační vlastnosti často vyžadují mnohem hladší povrch (např. Ra < 3,2 µm nebo dokonce < 0,8 µm). Tyto hladší povrchy vyžadují metody následného zpracování.
3. Dosažení požadované přesnosti:
- Řízení procesu: Zásadní význam má použití špičkových systémů AM s přesnou kontrolou parametrů laseru/záření, průtoku plynu a tepelného řízení. Zaměření společnosti Met3dp’ na vysoce přesné tiskárny je zde klíčovým faktorem.
- Design pro přesnost: Navrhování dílů s tolerancemi vhodnými pro AM, pokud je to možné, a jasné určení kritických rozměrů a povrchů, které budou vyžadovat následné zpracování. Optimální orientace dílů pro dosažení nejlepší možné povrchové úpravy kritických povrchů.
- Následné zpracování: To je často nezbytné pro splnění přísných specifikací pro letecký průmysl:
- CNC obrábění: Používá se k dosažení přísných tolerancí u specifických prvků (otvory, styčné plochy, kritické průměry).
- Povrchové úpravy: Techniky jako broušení, leštění, abrazivní obrábění (AFM) nebo chemické leptání mohou výrazně zlepšit kvalitu povrchu.
- Tepelné zpracování (HIP): Izostatické lisování za horka sice primárně ovlivňuje mechanické vlastnosti, ale může také vést k menšímu zlepšení konzistence povrchu uzavřením pórů v blízkosti povrchu.
Tabulka: Úvahy o přesnosti tepelných štítů AM
Parametr | Typický stav AM (LPBF/EBM) | Běžné požadavky na letecký a kosmický průmysl | Metoda k dosažení požadavku (je-li třeba) |
---|---|---|---|
Tolerance | ±0,1 až ±0,3 mm (nebo ±0,2 %) | < ±0,1 mm (často těsněji) | CNC obrábění kritických prvků |
Povrchová úprava (Ra) | 6 µm – 25 µm | < 3,2 µm (nebo hladší) | Broušení, leštění, AFM, obrábění, povlakování |
Pórovitost | < 0,5 % (často <0,1 %) | Téměř 100% hustota (<0,01%) | Optimalizace procesu, lisování za tepla (HIP) |
Geometrická celistvost | Dobrý (podléhá deformaci) | Vysoká (musí odpovídat záměru CAD) | Odlehčení napětí, upínání při HT, obrábění |
Export do archů
Závěr o přesnosti:
Inženýři a manažeři nákupu musí již na začátku procesu jasně definovat rozměrové tolerance a požadavky na povrchovou úpravu pro každý prvek tepelného štítu. Ačkoli AM zpracování kovů poskytuje dobrou základní přesnost, dosažení přísných požadavků běžných v leteckém průmyslu často vyžaduje zahrnutí kroků následného zpracování do výrobního plánu. Spolupráce s dodavatelem AM, který těmto nuancím rozumí, disponuje vysoce kvalitním vybavením a má navázané vztahy se specialisty na následné zpracování, je klíčová pro získání komponent tepelného štítu, které splňují všechny specifikace. Předchozí diskuse o těchto požadavcích zajistí realistická očekávání ohledně nákladů, doby realizace a kvality finálního dílu.
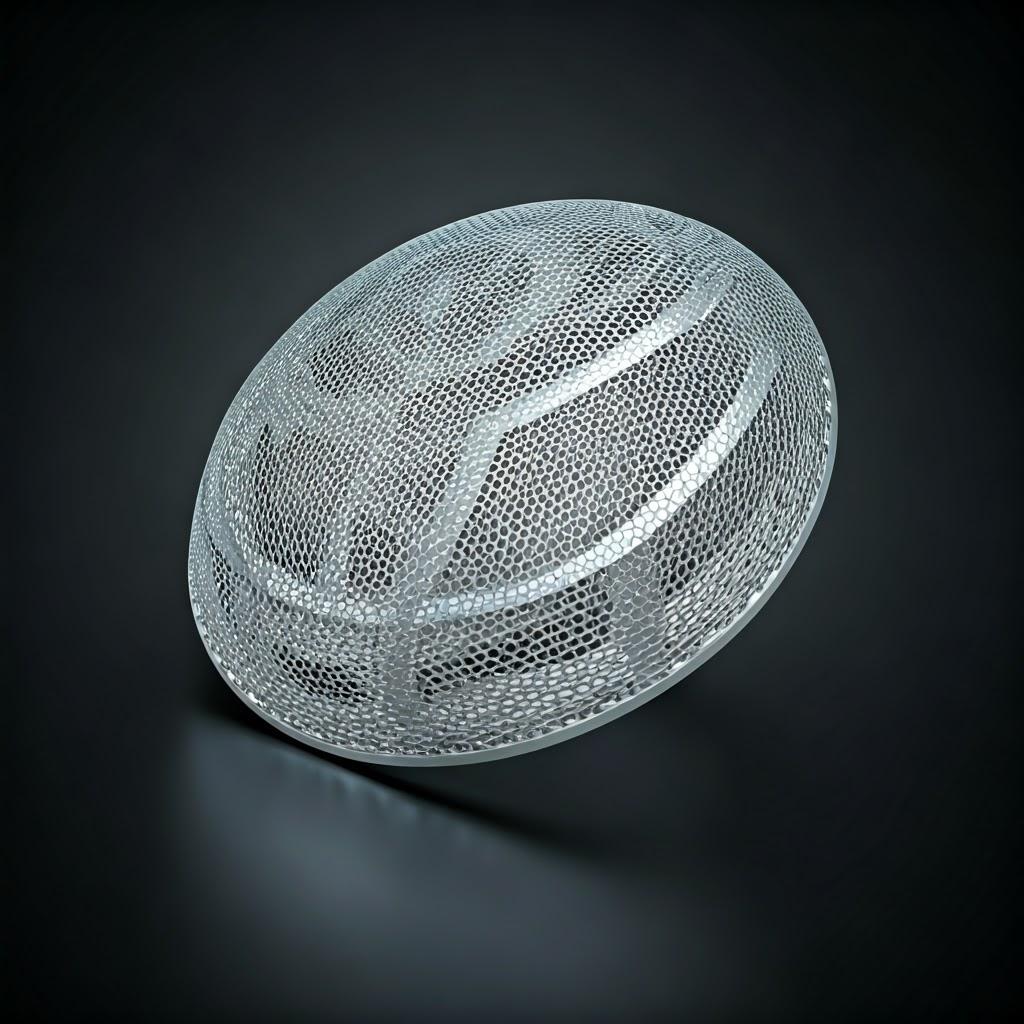
Za hranice stavby: Základní následné zpracování tepelných štítů pro letectví a kosmonautiku
Cesta aditivně vyráběného kovového tepelného štítu nekončí, když se tiskárna zastaví. Součástka, která je čerstvě po vyjmutí z konstrukční desky, obvykle vyžaduje několik zásadních kroků následného zpracování, aby se z ní stala součástka připravená k letu, která splňuje přísné požadavky leteckých aplikací. Tyto kroky jsou nezbytné pro zajištění požadovaných mechanických vlastností, rozměrové přesnosti, povrchové úpravy a celkové integrity dílu. Pochopení těchto běžných požadavků na následné zpracování je zásadní pro přesný odhad nákladů, dodacích lhůt a pro výběr schopného dodavatele AM nebo řízení výrobního procesu.
Mezi běžné kroky následného zpracování tepelných štítů AM pro letecký průmysl patří:
- Odstranění prášku:
- Účel: Odstranění volného nebo částečně spečeného kovového prášku zachyceného ve vnitřních kanálech, mřížkových strukturách nebo ulpělého na povrchu.
- Metody: Ruční kartáčování, vyfukování stlačeným vzduchem, ultrazvukové čisticí lázně, specializované systémy pro regeneraci prášku integrované s tiskárnou. Důkladné odstranění prášku je velmi důležité, zejména z vnitřních chladicích kanálů, aby se zabránilo ucpání a zajistila se funkčnost. U složitých vnitřních geometrií to může být náročné.
- Důležitost: Zajišťuje čistotu dílů, zabraňuje kontaminaci v dalších krocích a umožňuje přesnou kontrolu.
- Tepelné ošetření proti stresu:
- Účel: Rychlé cykly ohřevu a chlazení, které jsou vlastní procesům AM po vrstvách (zejména LPBF), vyvolávají v dílu zbytková napětí. Tato napětí mohou způsobit deformace, trhliny a sníženou únavovou životnost, pokud nejsou odstraněna.
- Metody: Zahřátí dílu v řízené peci (často ve vakuu nebo inertní atmosféře, aby se zabránilo oxidaci) na určitou teplotu nižší, než je bod přeměny slitiny, její udržování po stanovenou dobu a následné pomalé ochlazování. Parametry se výrazně liší v závislosti na slitině (např. Ti-6Al-4V vs. AlSi10Mg) a geometrii dílu. Tento postup se často provádí, když je díl ještě připevněn k sestavovací desce, aby se minimalizovalo jeho deformování.
- Důležitost: Rozměrově stabilizuje díl, snižuje riziko vzniku trhlin a zlepšuje celkové mechanické vlastnosti. Povinné pro většinu leteckých konstrukčních součástí.
- Vyjmutí dílu ze stavební desky:
- Účel: Oddělení vytištěného tepelného štítu od kovové stavební desky, ke které byly během procesu AM přitaveny.
- Metody: Obvykle se provádí pomocí elektroerozivního obrábění (EDM) nebo pásové pily. Při odstraňování je třeba dbát na to, aby nedošlo k poškození dílu.
- Důležitost: Uvolní díl pro další kroky zpracování.
- Odstranění podpůrné konstrukce:
- Účel: Odstranění dočasných podpůrných konstrukcí potřebných během tisku k ukotvení dílu a podpůrných přesahů.
- Metody: Podpěry jsou často navrženy s oslabenými rozhraními pro snadnější demontáž. Mezi metody patří ruční lámání (kleště, dláta), obrábění (frézování) nebo někdy elektroerozivní obrábění. Tento krok může být pracný, zejména u složitých dílů s vnitřními podpěrami.
- Důležitost: Dosáhne konečné geometrie dílu a odhalí podkladový povrch.
- Izostatické lisování za tepla (HIP):
- Účel: Odstranění zbytkové vnitřní pórovitosti (mikroskopických dutin), která by mohla zůstat po tisku, a tím dosažení plné teoretické hustoty. HIPování výrazně zlepšuje únavovou životnost, lomovou houževnatost a celkovou konzistenci mechanických vlastností.
- Metody: Současné vystavení dílu vysoké teplotě (pod bodem tání) a vysokému izostatickému tlaku (za použití inertního plynu, např. argonu) ve specializované nádobě HIP.
- Důležitost: Často povinné pro kritické letecké součásti, zejména ty, které podléhají únavovému zatížení nebo vyžadují maximální integritu materiálu. Zvyšuje spolehlivost a předvídatelnost výkonu dílů AM.
- Obrábění (CNC):
- Účel: Dosažení přísných tolerancí kritických rozměrů, styčných ploch, těsnicích ploch nebo otvorů se závitem, které nelze splnit procesem AM ve výchozím stavu. Používá se také ke zlepšení kvality povrchu specifických prvků.
- Metody: Použití konvenčních CNC frézovacích, soustružnických nebo brusných operací. Upínání dílů AM pro obrábění může být někdy náročné kvůli jejich složitým nebo topologicky optimalizovaným tvarům.
- Důležitost: Zajišťuje přesné uložení a funkci v rámci větší letecké sestavy.
- Povrchová úprava:
- Účel: Dosažení požadované drsnosti povrchu (Ra) pro aerodynamické vlastnosti, těsnění, přilnavost povlaku nebo z estetických důvodů.
- Metody: V závislosti na požadované povrchové úpravě a geometrii lze použít širokou škálu technik:
- Tumbling / hromadné dokončování: Použití abrazivních médií ve vibračním nebo rotačním bubnu pro všeobecné vyhlazování a odstraňování otřepů.
- Abrazivní tryskání (pískování, tryskání kuličkami): Vytváří jednotný matný povrch, čistí povrchy.
- Broušení/leštění: Mechanické postupy pro dosažení velmi hladkých, zrcadlově lesklých povrchů na přístupných plochách.
- Obrábění abrazivním tokem (AFM): Vtlačování brusného tmelu do vnitřních kanálků nebo na složité povrchy za účelem jejich vyhlazení.
- Elektrolytické leštění: Elektrochemický proces, který odstraňuje tenkou povrchovou vrstvu, čímž vzniká velmi hladký a čistý povrch (vhodný pro některé slitiny).
- Důležitost: Jsou důležité pro splnění výkonnostních specifikací týkajících se průtoku kapalin, přenosu tepla, těsnění nebo snížení tření.
- Čištění a kontrola:
- Účel: Závěrečné čištění za účelem odstranění zbytků z předchozích kroků (obráběcí kapaliny, lešticí směsi) a důkladná kontrola za účelem ověření rozměrové přesnosti, povrchové úpravy a celistvosti.
- Metody: Čištění vodou nebo rozpouštědlem, vizuální kontrola, souřadnicový měřicí stroj (CMM) pro kontrolu rozměrů, metody nedestruktivního testování (NDT), jako je rentgenové nebo CT skenování pro ověření vnitřní integrity a odhalení vad (pórovitost, praskliny).
- Důležitost: Poslední krok zajištění kvality před certifikací tepelného štítu pro použití.
Tabulka: Přehled kroků následného zpracování tepelných štítů AM
Krok následného zpracování | Primární účel | Typická metoda (metody) | Klíčový výsledek |
---|---|---|---|
Odstranění prášku | Čistota, čištění kanálů | Kartáčování, čištění proudem vzduchu, čištění ultrazvukem | Část bez sypkého prášku |
Úleva od stresu | Snížení vnitřního napětí, prevence deformace | Řízené vytápění/chlazení pecí | Rozměrová stabilita, lepší vlastnosti |
Odstranění části | Oddělení dílu od stavební desky | Drátové elektroerozivní obrábění, řezání | Část připravená k manipulaci |
Odstranění podpory | Dosažení konečné geometrie | Ruční lámání, obrábění, elektroerozivní obrábění | Díl bez opory, mohou zůstat povrchové stopy |
HIP | Odstranění vnitřní pórovitosti, zlepšení vlastností | Vysokoteplotní & amp; Tlaková pec | Plná hustota, zvýšená únavová životnost |
Obrábění (CNC) | Dosahování těsných tolerancí, hladkých povrchů | Frézování, soustružení, broušení | Přesné rozměry, specifická povrchová úprava |
Povrchová úprava | Dosažení požadovaného Ra, čištění/příprava povrchů | Tryskání, leštění, AFM, elektrolytické leštění | Požadovaná struktura a hladkost povrchu |
Čištění & amp; Inspekce | Finální kontrola kvality, ověření specifikací | Čisticí lázně, CMM, NDT (RTG/CT) | Certifikovaná součást připravená k letu |
Export do archů
Manažeři a inženýři veřejných zakázek musí tyto nezbytné kroky po zpracování zahrnout do plánování projektu. Spolupráce s vertikálně integrovaným poskytovatelem AM nebo s poskytovatelem s dobře řízenou sítí partnerů pro následné zpracování zajišťuje zefektivnění pracovního postupu a zaručuje, že konečný tepelný štít AM splňuje všechny přísné požadavky leteckého průmyslu.
Zvládání výzev: Překonávání překážek při výrobě tepelných štítů AM
Přestože aditivní výroba kovů nabízí významné výhody při výrobě lehkých a složitých tepelných štítů pro letecký průmysl, není tato technologie bez problémů. Úspěšná implementace AM vyžaduje hluboké pochopení potenciálních úskalí a strategií potřebných k jejich zmírnění. Povědomí o těchto problémech umožňuje konstruktérům a nákupním týmům aktivně spolupracovat s dodavateli AM, aby byla zajištěna robustní a spolehlivá výroba. Společnost Met3dp se díky svému zaměření na vysoce kvalitní prášky a spolehlivé tiskové systémy, aktivně pracuje na minimalizaci mnoha těchto běžných problémů.
Mezi hlavní výzvy při výrobě tepelných štítů AM patří:
- Zbytkové napětí, deformace a zkreslení:
- Problém: Rychlé, lokalizované zahřívání a ochlazování, které je vlastní procesům AM, vytváří značné tepelné gradienty, což vede k tvorbě vnitřních zbytkových napětí. Tato napětí mohou způsobit deformaci nebo zkroucení dílů během sestavování nebo po něm, zejména u velkých, tenkých nebo složitých geometrií typických pro tepelné štíty. V závažných případech mohou tato napětí způsobit praskání.
- Strategie zmírnění dopadů:
- Simulace procesu: Použití softwaru k předvídání tepelného chování a akumulace napětí, což umožňuje optimalizovat orientaci sestavy a podpůrné strategie před tiskem.
- Optimalizované strategie skenování: Použití specifických vzorů skenování laserem/paprskem (např. ostrovní skenování, sektorové skenování) pro řízení distribuce tepla.
- Vytápění platformy: Udržování zvýšené teploty konstrukční desky a prostředí komory snižuje tepelné gradienty.
- Robustní podpůrné struktury: Strategicky umístěné podpěry bezpečně ukotví díl ke stavební desce a odolávají deformačním silám.
- Tepelné ošetření proti stresu: Zásadní krok následného zpracování, který se provádí ihned po sestavení (často před vyjmutím dílu) za účelem uvolnění vnitřních pnutí.
- DfAM: Navrhování dílů s vlastnostmi, které ze své podstaty minimalizují koncentraci napětí a možnost deformace.
- Kontrola pórovitosti:
- Problém: V tištěném materiálu mohou vznikat malé dutiny nebo póry v důsledku zachyceného plynu, neúplného spojení mezi vrstvami nebo kontaminace práškem. Pórovitost zhoršuje mechanické vlastnosti, zejména únavovou pevnost, která je pro letecké komponenty kritická.
- Strategie zmírnění dopadů:
- Vysoce kvalitní prášek: Použití vysoce sférického prášku s nízkým obsahem vnitřního plynu a řízenou distribucí velikosti částic, jako jsou částice vyrobené pokročilými technikami atomizace společnosti Met3dp’. Správná manipulace s práškem a jeho skladování jsou zásadní, aby se zabránilo zachycení vlhkosti a kontaminaci.
- Optimalizované parametry procesu: Přesné řízení výkonu laseru/paprsku, rychlosti skenování, tloušťky vrstvy a atmosféry v komoře (čistota inertního plynu) pro zajištění úplného roztavení a tavení.
- Izostatické lisování za tepla (HIP): Účinný krok následného zpracování, který uzavře vnitřní póry a dosáhne téměř plné hustoty.
- Monitorování procesů: Monitorovací systémy in-situ mohou někdy odhalit tvorbu pórovitosti v průběhu stavby a umožnit její úpravu.
- Odstranění podpůrné konstrukce a kvalita povrchu:
- Problém: Podpůrné konstrukce jsou nezbytné, ale jejich odstranění může být obtížné a časově náročné, zejména ze složitých vnitřních kanálů nebo jemných mřížových struktur. Procesy odstraňování mohou na povrchu dílu zanechat stopy po svědcích nebo drsné skvrny, které ovlivňují povrchovou úpravu a případně vyžadují další ošetření.
- Strategie zmírnění dopadů:
- DfAM pro minimalizaci podpory: Navrhování dílů se samonosnými úhly (obvykle > 45°) a optimalizace orientace sestavy pro snížení potřeby podpěr.
- Optimalizovaný design podpory: Použití nosných konstrukcí s minimem kontaktních bodů nebo snadno porušitelných rozhraní. Softwarové nástroje mohou generovat optimalizované geometrie podpěr.
- Pokročilé techniky odstraňování: Využití metod, jako je elektrochemické obrábění nebo specializované nástroje pro těžko přístupné podpěry.
- Plánování dokončovacích prací: Počítejte s tím, že povrchy, na které byly připevněny podpěry, budou pravděpodobně vyžadovat další obrábění nebo dokončovací práce.
- Dosažení těsných tolerancí a povrchové úpravy:
- Problém: Jak již bylo uvedeno, přesnost a povrchová úprava dílů AM nemusí splňovat přísné požadavky na všechny prvky tepelného štítu. Dosažení přesnosti letecké třídy často vyžaduje další kroky.
- Strategie zmírnění dopadů:
- Vysoce přesné systémy AM: Použití strojů známých svou přesností a opakovatelností.
- Kalibrace a řízení procesů: Důkladná kalibrace stroje a optimalizace parametrů.
- Integrace následného zpracování: Plánování a zahrnutí nezbytných kroků obrábění a povrchové úpravy do výrobního postupu a rozpočtu. Klíčová je spolupráce mezi dodavatelem AM a specialisty na obrábění a dokončovací práce.
- Soulad a kvalifikace vlastností materiálu:
- Problém: Zajištění toho, aby mechanické vlastnosti (pevnost, tažnost, únavová životnost) finálního dílu AM byly konzistentní od výroby k výrobě a splňovaly specifikace pro letecký průmysl, vyžaduje přísnou kontrolu a validaci procesu. Kvalifikace nových dílů nebo materiálů AM pro letové aplikace zahrnuje rozsáhlé testování a dokumentaci.
- Strategie zmírnění dopadů:
- Standardizované postupy: Dodržování přísných provozních postupů pro manipulaci s práškem, obsluhu stroje a následné zpracování.
- Certifikace materiálu: Používání certifikovaných prášků pro letecký průmysl od renomovaných dodavatelů.
- Monitorování procesů & Záznam dat: Sledování klíčových parametrů v průběhu sestavování za účelem sledovatelnosti a kontroly kvality.
- Komplexní testování: Provádění tahových zkoušek, únavových zkoušek, metalografické analýzy a nedestruktivního zkoušení na zkušebních kuponech vyrobených společně s díly a/nebo na samotných dílech.
- Spolupráce s certifikačními orgány: Úzká spolupráce s regulačními orgány (FAA, EASA) a hlavními dodavateli při plnění kvalifikačních požadavků.
- Řízení nákladů a doby realizace:
- Problém: Ačkoli AM může urychlit výrobu prototypů, celkové náklady a dobu realizace výrobních dílů mohou ovlivnit faktory, jako je strojní čas, cena prášku, pracnost následného zpracování (zejména odstranění podpěr a dokončovací práce) a kvalifikační požadavky.
- Strategie zmírnění dopadů:
- DfAM pro efektivitu: Optimalizace návrhů nejen z hlediska výkonu, ale také z hlediska tisknutelnosti (např. minimalizace podpěr, snížení konstrukční výšky).
- Vkládání a optimalizace sestavení: Tisk více dílů najednou na jedné konstrukční desce pro maximální využití stroje.
- Realistické plánování: Přesný odhad času a nákladů spojených se všemi kroky, včetně následného zpracování a kontroly.
- Odbornost dodavatele: Spolupráce se zkušenými poskytovateli AM, kteří mohou optimalizovat celý pracovní postup.
Tabulka: Společné výzvy AM & přístupy k jejich zmírnění
Výzva | Primární příčina (příčiny) | Klíčové strategie pro zmírnění dopadů | Význam tepelných štítů |
---|---|---|---|
Deformace/zkreslení | Zbytkové napětí z tepelných gradientů | Simulace, strategie skenování, podpory, odbourávání stresu HT, DfAM | Vysoký (zajišťuje správné uložení/montáž) |
Pórovitost | Zachycený plyn, neúplná fúze | Vysoce kvalitní prášek, optimalizované parametry, HIP | Kritické (ovlivňuje únavovou životnost) |
Odstranění/ukončení podpory | Potřeba podpory, proces stěhování | DfAM (minimalizace podpěr), optimalizovaný návrh podpěr, pokročilé odstraňování, plánování dokončovacích prací | Vysoká (ovlivňuje náklady, kvalitu povrchu) |
Tolerance/přesnost | Omezení procesu, tepelné účinky | Vysoce přesné stroje, kalibrace, následné obrábění | Kritické (zajišťuje vhodnost a funkčnost) |
Konzistence majetku | Variabilita procesu, kvalita prášku | Standardní postupy, certifikovaný prášek, testování, monitorování, kvalifikace | Povinné (zajišťuje spolehlivost) |
Náklady/doba přípravy | Čas stroje, náklady na prášek, následné zpracování | DfAM pro efektivitu, optimalizaci stavby, realistické plánování, zkušený dodavatel | Vysoká (ovlivňuje životaschopnost projektu) |
Export do archů
Úspěšné zvládnutí těchto výzev vyžaduje odborné znalosti, důslednou kontrolu procesů a spolupráci mezi konstruktéry, specialisty na AM a týmy zajišťujícími kvalitu. Uvědomíme-li si tyto potenciální překážky a zavedeme-li vhodné strategie jejich zmírnění, mohou výrobci bez obav využívat technologii AM pro výrobu vysoce výkonných a spolehlivých tepelných štítů pro letecký průmysl.
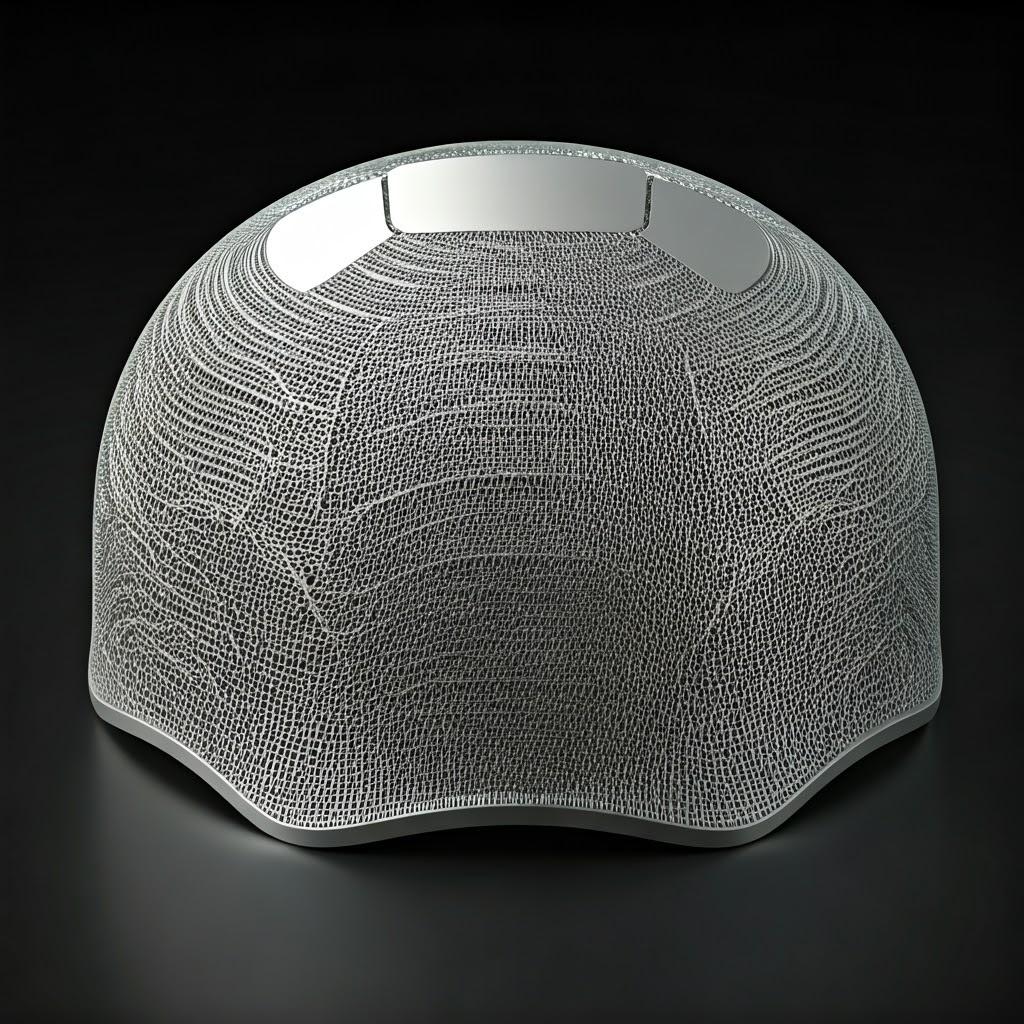
Výběr dodavatele: Výběr správného partnera pro AM zpracování kovů pro letecké komponenty
Výběr správného poskytovatele služeb aditivní výroby je pro výrobu vysoce kvalitních tepelných štítů pro letecký průmysl stejně důležitý jako návrh a výběr materiálu. Jedinečné požadavky leteckého průmyslu - přísné požadavky na kvalitu, složité geometrie, pokročilé materiály a potřeba absolutní spolehlivosti - znamenají, že ne všechny servisní kanceláře AM jsou stejné. Manažeři nákupu a inženýrské týmy musí provést důkladnou prověrku, aby našli partnera s potřebnými odbornými znalostmi, schopnostmi a certifikacemi.
Klíčová kritéria pro hodnocení a výběr dodavatele kovových tepelných štítů pro letecký průmysl zahrnují:
- Odborné znalosti a zkušenosti v oblasti letectví a kosmonautiky:
- Požadavek: Prokazatelná zkušenost s úspěšnou výrobou součástí pro letecký a obranný průmysl. Znalost leteckých materiálů, specifikací (např. AMS, MIL-STD) a očekávání kvality.
- Hodnocení: Případové studie, reference zákazníků v oblasti leteckého průmyslu, znalost aplikací tepelných štítů nebo podobných vysokoteplotních konstrukčních prvků. Rozumí dodavatel kritičnosti a specifickým problémům systémů tepelné ochrany?
- Příslušné technologie a vybavení:
- Požadavek: Vlastnictví systémů AM pro průmyslové zpracování kovů (LPBF, EBM) vhodných pro zvolený materiál (Ti-6Al-4V, AlSi10Mg, superslitiny) a požadovanou velikost/objem dílu. Nejmodernější vybavení často znamená lepší kontrolu procesu, přesnost a spolehlivost.
- Hodnocení: Konkrétní použité modely tiskáren, velikost konstrukční obálky, typ paprsku (laserový/elektronový paprsek), možnosti monitorování procesu. Dodavatelé jako Met3dp, kteří vyrábějí vlastní pokročilé tiskárny, mají často hluboké technické znalosti o možnostech a omezeních svých systémů. Posuďte jejich postupy údržby a kalibrace.
- Schopnosti a kvalita materiálu:
- Požadavek: Schopnost zpracovávat určené letecké slitiny (např. Ti-6Al-4V, AlSi10Mg) s ověřenými parametry. A co je zásadní, musí používat vysoce kvalitní kovové prášky letecké kvality s doloženou sledovatelností a certifikací.
- Hodnocení: Rozsah nabízených materiálů, získávání prášků (vlastní výroba, např. pokročilá atomizace Met3dp, vs. externí dodavatelé), protokoly pro manipulaci s prášky, možnosti testování materiálů, dostupnost certifikací materiálů (např. certifikát shody).
- Systém řízení kvality (QMS) a certifikace:
- Požadavek: Robustní systém řízení kvality je pro letecký průmysl nepostradatelný. Hledejte certifikace, jako je AS9100 (specifická pro letecký průmysl), ISO 9001 a případně i akreditaci NADCAP pro speciální procesy, jako je tepelné zpracování nebo NDT, pokud jsou prováděny ve firmě.
- Hodnocení: Vyžádejte si kopie certifikátů, zprávy o auditu (pokud je to možné) a informujte se o jejich postupech kontroly kvality, systémech sledovatelnosti (od šarže prášku po finální díl) a postupech při řešení neshod.
- Možnosti následného zpracování a síť:
- Požadavek: Jak již bylo řečeno, následné zpracování je nezbytné. Ideální dodavatel má buď vlastní kapacity (odlehčování napětí, obrábění, dokončovací práce, HIP, NDT), nebo dobře řízenou síť kvalifikovaných partnerů pro tyto služby.
- Hodnocení: Seznam vlastních a externě zadaných kroků následného zpracování. Pokud se zadává externě, jak jsou partneři kvalifikováni a řízeni? Mohou poskytnout kompletní, hotový díl? Posuďte jejich zkušenosti se správou celého pracovního postupu.
- Technická odbornost a podpora:
- Požadavek: Přístup ke zkušeným AM inženýrům a metalurgům, kteří mohou poskytovat podporu DfAM, radit s výběrem materiálu, optimalizovat strategie výroby a řešit případné problémy.
- Hodnocení: Kvalifikace a zkušenosti inženýrského týmu, dostupnost pro revize návrhu, schopnost reagovat na technické dotazy, ochota spolupracovat na vývojových projektech.
- Kapacita a doba realizace:
- Požadavek: Dostatečná kapacita strojů pro dodržení časového harmonogramu projektu, od výroby prototypů až po potenciální výrobní objemy. Schopnost poskytovat realistické a spolehlivé odhady doby realizace.
- Hodnocení: Počet příslušných strojů, aktuální pracovní zatížení, historické výsledky v oblasti závazků týkajících se dodacích lhůt. Zeptejte se na jejich procesy plánování a rozvrhování výroby.
- Nákladová konkurenceschopnost:
- Požadavek: Transparentní a konkurenceschopná cenová struktura. I když je cena vždy faktorem, měla by být vyvážena kvalitou, spolehlivostí a odborností, zejména u kritických leteckých komponentů.
- Hodnocení: Vyžádejte si podrobné cenové nabídky s náklady na tisk, materiál, podpěry, následné zpracování, NDT a případné poplatky NRE (Non-Recurring Engineering). Porovnejte nabídky na základě obdobných cen s přihlédnutím k celému rozsahu dodávky.
Tabulka: Kontrolní seznam pro výběr dodavatele tepelných štítů AM
Kritéria | Klíčové otázky, které je třeba položit | Hodnocení důležitosti |
---|---|---|
Zkušenosti z leteckého průmyslu | Můžete poskytnout případové studie/reference z leteckého průmyslu? Rozumíte výzvám TPS? | ★★★★★ |
Technologie a vybavení | Jaké konkrétní tiskárny/systémy používáte? Jaký je objem sestavení? Jak nové je zařízení? | ★★★★☆ |
Schopnost/kvalita materiálu | Můžete zpracovat [Slitina]? Jak zajišťujete kvalitu/sledovatelnost prášku? Máte k dispozici certifikáty? | ★★★★★ |
QMS & Certifikace | Jste certifikováni podle AS9100? Můžeme vidět vaši příručku kvality/certifikáty? Jak je řízena sledovatelnost? | ★★★★★ |
Následné zpracování | Jaké kroky jsou prováděny interně a jaké externě? Jak řídíte partnery? Můžete dodávat hotové díly? | ★★★★★ |
Technická podpora | Jakou podporu DfAM nabízíte? Kdo jsou technické kontakty? | ★★★★☆ |
Kapacita & amp; doba dodání | Jaká je vaše kapacita pro tento projekt? Jaké jsou reálné dodací lhůty? | ★★★★☆ |
Nákladová konkurenceschopnost | Můžete poskytnout podrobný rozpis nákladů? Jaké jsou platební podmínky? | ★★★☆☆ |
Export do archů
Výběr správného partnera AM je investicí do kvality a spolehlivosti. Společnosti jako např Met3dp, které nabízejí komplexní řešení zahrnující pokročilé tiskárny, vysoce kvalitní kovové prášky a služby vývoje aplikací, představují typ integrovaného poskytovatele, který může výrazně snížit riziko zavádění AM pro kritické součásti, jako jsou tepelné štíty pro letecký průmysl. Pokud věnujete čas důkladnému prověření potenciálních dodavatelů podle těchto kritérií, zajistíte si úspěšné partnerství a vysoce kvalitní výsledky pro náročné B2B projekty v leteckém průmyslu.
Pochopení nákladů a dodacích lhůt pro tepelné štíty AM pro letecký průmysl
Pro manažery nákupu a projektové inženýry je přesný odhad nákladů a doby realizace výroby tepelných štítů pro letecký průmysl pomocí aditivní výroby zásadní pro sestavení rozpočtu, plánování a realizovatelnost projektu. Na rozdíl od tradiční velkosériové výroby jsou náklady a termíny AM ovlivněny jiným souborem faktorů. Pochopení těchto faktorů umožňuje realističtější očekávání a lepší komunikaci s poskytovateli AM služeb.
Faktory ovlivňující náklady:
- Objem a hmotnost části:
- Dopad: Větší nebo těžší díly spotřebují více materiálu a jejich tisk trvá déle, což přímo zvyšuje náklady. Techniky DfAM, jako je optimalizace topologie a mřížkové struktury, jsou klíčem k minimalizaci objemu při splnění požadavků.
- Úvaha: Hlavním faktorem je cena materiálu na kilogram (např. Ti-6Al-4V je výrazně dražší než AlSi10Mg). Efektivní vnořování více dílů v rámci jedné sestavy může snížit náklady na jeden díl, ale vyžaduje pečlivé plánování.
- Část Složitost a geometrie:
- Dopad: Velmi složité geometrie se složitými prvky, tenkými stěnami nebo rozsáhlými vnitřními kanály mohou vyžadovat delší dobu nastavení, nižší rychlost tisku pro zajištění přesnosti a výrazně větší úsilí při následném zpracování (zejména odstranění prášku a podpěr).
- Úvaha: AM sice umožňuje komplexnost, ale příliš složité návrhy mohou zbytečně zvyšovat náklady. DfAM by měl vyvažovat nárůst výkonu s vyrobitelností a náročností následného zpracování.
- Typ materiálu:
- Dopad: Náklady na práškové suroviny se u jednotlivých slitin výrazně liší. Slitiny titanu a superslitiny niklu jsou podstatně dražší než slitiny hliníku nebo oceli. Kvalita prášku (sféricita, čistota, PSD) také ovlivňuje náklady - vysoce kvalitní prášky jsou dražší, ale přinášejí lepší výsledky. Cílem investic společnosti Met3dp’ do pokročilé výroby prášků je efektivní zajištění vysoce kvalitních materiálů.
- Úvaha: Ujistěte se, že zvolený materiál je skutečně nezbytný pro danou aplikaci.
- Výška stavby (Z-výška):
- Dopad: Doba tisku je silně závislá na počtu vrstev, který je určen výškou dílu v orientaci sestavení. Tisk vyšších dílů trvá déle, což zvyšuje náklady na strojní čas.
- Úvaha: Optimalizace orientace dílu s cílem minimalizovat výšku sestavení (při zohlednění potřeb podpory a povrchové úpravy) může zkrátit dobu tisku a snížit náklady.
- Požadavky na podpůrnou strukturu:
- Dopad: Díly vyžadující rozsáhlé podpůrné konstrukce spotřebují více materiálu (podpěry jsou často vyrobeny ze stejné drahé slitiny) a výrazně prodlužují dobu práce při následném zpracování při odstraňování a následné povrchové úpravě.
- Úvaha: Pro snížení nákladů je zásadní snaha DfAM o minimalizaci podpor.
- Intenzita následného zpracování:
- Dopad: To je často hlavní příčinou nákladů. Požadavky na HIP, rozsáhlé CNC obrábění s ohledem na přísné tolerance, povrchové úpravy na vysoké úrovni (leštění, AFM) a důkladné NDT zvyšují značné náklady a čas.
- Úvaha: Jasně definujte, které funkce skutečně vyžadují přísné tolerance nebo specializovanou povrchovou úpravu, aby se zabránilo zbytečným nákladům.
- Zajištění kvality a certifikace:
- Dopad: Letecký průmysl vyžaduje přísnou kontrolu kvality, včetně certifikace materiálů, dokumentace procesů, kontroly rozměrů (CMM), NDT (RTG/CT) a případně kvalifikačních zkoušek. Tyto činnosti zvyšují náklady.
- Úvaha: Počítejte s náklady na dodržování předpisů a certifikaci již při plánování projektu.
- Objem objednávky:
- Dopad: Stejně jako ve většině výrobních odvětví se i v AM uplatňují úspory z rozsahu, i když možná méně výrazně než v případě tradičních metod založených na výrobě nástrojů. Náklady na seřizování a čas programování lze amortizovat na větší série, čímž se sníží náklady na jeden díl.
- Úvaha: Diskutujte o možných množstevních slevách pro sériovou výrobu nebo opakované objednávky.
Faktory ovlivňující dobu realizace:
- Doba inženýringu a nastavení: Počáteční příprava souboru, kontrola DfAM, simulace sestavení, generování podpory a nastavení stroje přispívají k počáteční době přípravy.
- Dostupnost stroje a tisková fronta: Doba dodání závisí do značné míry na aktuálním vytížení dodavatele a dostupnosti konkrétního požadovaného stroje.
- Skutečná doba tisku: Určuje se především podle objemu, výšky a složitosti dílu. Může se pohybovat od hodin u malých dílů až po mnoho dní u velkých, složitých součástí nebo celých stavebních desek.
- Doba chlazení: Díly se po tisku musí ve stroji ochladit v inertní atmosféře, což může trvat i několik hodin.
- Sekvence následného zpracování: Každý krok (uvolnění napětí, odstranění dílu, odstranění podpěry, HIP, obrábění, dokončovací práce, kontrola) přidává čas. Celková doba následného zpracování může často přesáhnout dobu tisku, zejména pokud se jedná o více kroků nebo je nutná přeprava mezi různými zařízeními (pokud je zadávána externě).
- Zajištění kvality a kontrola: Důkladná kontrola a dokumentace vyžadují čas.
- Přeprava a logistika: Platí standardní dodací lhůty.
Typické odhady doby realizace:
- Prototypy: Často 1-3 týdny, v závislosti na složitosti a potřebě následného zpracování.
- Malosériová výroba: Obvykle 3-8 týdnů, silně závisí na intenzitě následného zpracování a kvalifikačních požadavcích.
- Poznámka: Jedná se o hrubé odhady; konkrétní časový harmonogram projektu vyžaduje podrobnou cenovou nabídku od dodavatele.
Tabulka: Klíčové náklady & amp; Hnací síly doby realizace pro tepelné štíty AM
Řidič | Dopad na náklady | Dopad na dobu realizace | Zmírnění / zvážení |
---|---|---|---|
Objem/hmotnost dílu | Vysoká (materiál, doba tisku) | Vysoká (doba tisku) | DfAM (odlehčení), efektivní vnořování |
Složitost části | Střední/vysoká (nastavení, postprofesionální úsilí) | Střední/vysoká (nastavení, tisk, postproces) | Vyvážení složitosti a vyrobitelnosti, DfAM |
Typ materiálu | Vysoká (cena prášku) | Minimální | Odůvodnění výběru materiálu, zajištění kvality |
Výška stavby (Z) | Mírná (doba tisku) | Vysoká (doba tisku) | Optimalizace orientace |
Podpůrné struktury | Mírná (materiál, práce při odstraňování) | Mírná (doba odstranění) | DfAM (Minimalizovat podpory) |
Následné zpracování | Velmi vysoká (HIP, obrábění, dokončovací práce, NDT) | Velmi vysoká (více postupných kroků) | Uveďte pouze nezbytné kroky, integrovaný dodavatel |
QA / Certifikace | Střední/vysoká (testování, dokumentace) | Mírná (testování, podávání zpráv) | Plánování požadavků na shodu |
Objem objednávky | Mírná (amortizace nastavení) | Mírná (efektivní plánování) | Diskutujte o výhodách dávkové výroby |
Export do archů
Pochopení těchto faktorů umožňuje produktivnější diskuse s dodavateli AM a pomáhá stanovit realistická očekávání pro zavedení pokročilých, lehkých tepelných štítů AM do leteckých aplikací. Včasná spolupráce se zkušenými dodavateli umožňuje optimalizační strategie, které mohou pozitivně ovlivnit náklady i dobu realizace.
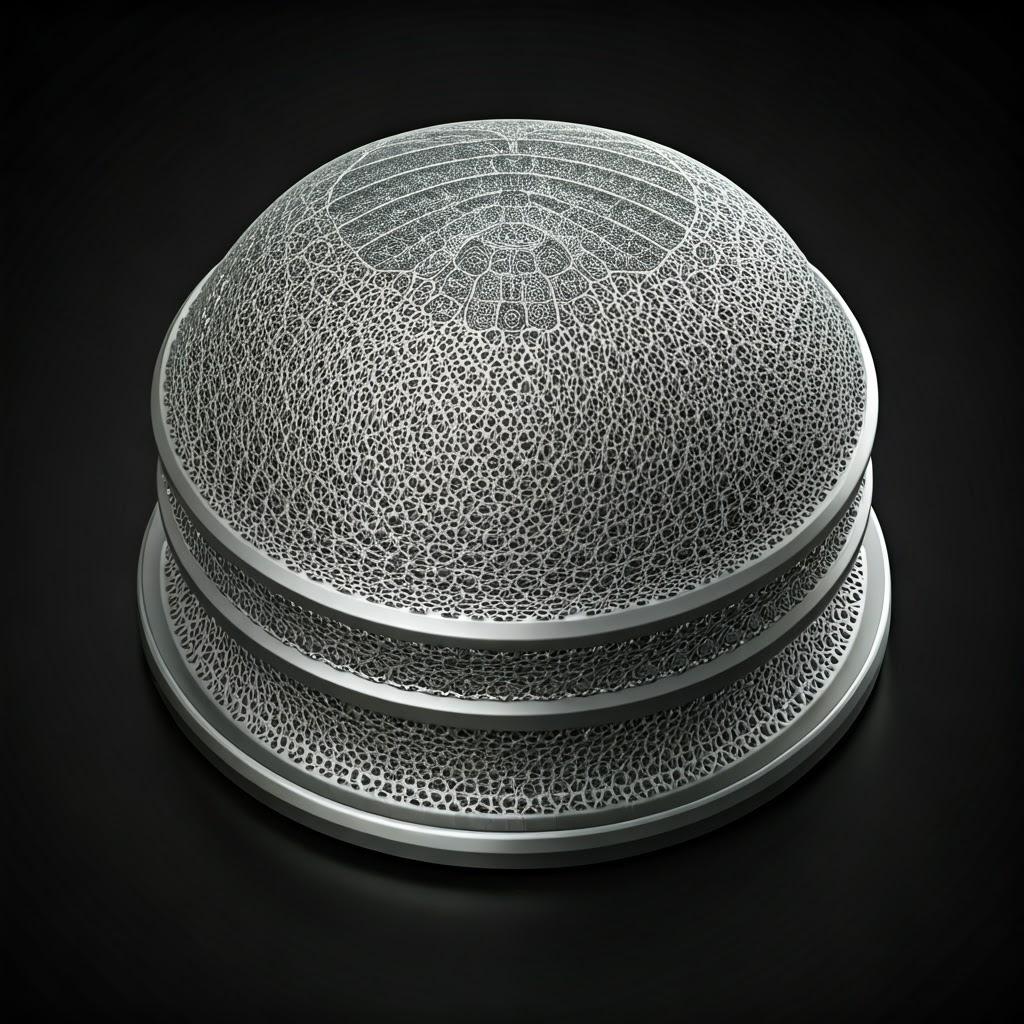
Často kladené otázky (FAQ) o tepelných štítech AM
Zde jsou některé časté otázky, které mají inženýři a manažeři nákupu ohledně použití aditivní výroby kovů pro tepelné štíty v leteckém průmyslu:
- Otázka: Může společnost AM vyrábět tepelné štíty, které se svým výkonem vyrovnají tradičně vyráběným štítům?
- A: Ano, a často ji překračují. AM umožňuje optimalizované konstrukce (optimalizace topologie, vnitřní chladicí kanály, mřížkové struktury) a konsolidaci dílů, která je u tradičních metod nemožná. To vede k lehčím součástem s potenciálně lepšími možnostmi tepelného managementu. Dosažení rovnocenného nebo lepšího výkonu vyžaduje správný DfAM, ověřené parametry procesu, vysoce kvalitní materiály (jako Ti-6Al-4V nebo AlSi10Mg) a nezbytné následné zpracování (jako HIP pro optimální vlastnosti materiálu). Klíčem k úspěchu je využití jedinečných předností AM’, nikoliv pouze replikace starých konstrukcí.
- Otázka: Jaké jsou hlavní problémy při zajišťování kvality a spolehlivosti tepelných štítů AM pro letecký průmysl?
- A: Mezi hlavní výzvy patří řízení zbytkového napětí a deformace během sestavování, minimalizace vnitřní pórovitosti pro zajištění integrity materiálu (zejména únavové životnosti), dosažení přísných rozměrových tolerancí a požadované povrchové úpravy (často prostřednictvím následného zpracování), důsledné odstranění podpůrných struktur bez poškození součásti a zajištění opakovatelných mechanických vlastností sestavení po sestavení. Jejich překonání vyžaduje přísnou kontrolu procesu, vysoce kvalitní výchozí prášek, vhodné následné zpracování (odlehčení od napětí, HIP), komplexní NDT kontrolu (např. CT skenování) a dodržování přísných systémů řízení kvality v leteckém průmyslu (např. AS9100).
- Otázka: Je výroba tepelných štítů metodou AM z kovu ve srovnání s tradičními metodami cenově výhodná?
- A: Záleží na několika faktorech. U velmi složitých konstrukcí, nízkých až středních objemů výroby nebo u součástí, u nichž výrazné odlehčení přináší podstatné výhody na úrovni systému (úspora paliva, zvýšení užitečného zatížení), může být AM velmi efektivní, zejména při zohlednění celkových nákladů životního cyklu. Konsolidace dílů pomocí AM také snižuje náklady na montáž. U jednodušších geometrií vyráběných ve velkých objemech však mohou být tradiční metody, jako je lisování nebo obrábění, stále levnější v přepočtu na jeden díl. Poměr “buy-to-fly” (použitý materiál vs. hmotnost finálního dílu) je u AM mnohem lepší u drahých materiálů, jako je titan, což snižuje množství odpadu ve srovnání s obráběním. Pro každý konkrétní případ je třeba provést podrobnou analýzu nákladů s ohledem na složitost konstrukce, objem, materiál a následné zpracování.
Závěr: Budoucnost tepelné ochrany v letectví a kosmonautice je aditivní
Požadavky na systémy tepelné ochrany v letectví a kosmonautice se stále zvyšují v souvislosti s ambicemi na hypersonické lety, účinnější letecké motory, opakovaně použitelné kosmické lodě a pokročilé satelitní technologie. Tradiční výrobní metody jsou sice spolehlivé, ale často se potýkají se současnými požadavky na extrémní teplotní odolnost, složitou geometrii, strukturální integritu a agresivní odlehčení, které tyto aplikace nové generace vyžadují.
Aditivní výroba kovů se stala výkonnou technologií, která dokáže tato omezení překonat. Jak jsme již prozkoumali, AM nabízí bezkonkurenční svobodu designu a umožňuje inženýrům vytvářet tepelné štíty s integrovanými chladicími kanály, optimalizovanou topologií a lehkými mřížkovými strukturami - dříve nedosažitelné vlastnosti. Schopnost konsolidovat více komponent do jediného tištěného dílu snižuje hmotnost, složitost a potenciální místa poruch. S využitím pokročilých leteckých slitin, jako jsou Ti-6Al-4V a AlSi10Mg, dodává AM vysoce výkonné materiály přesně tam, kde je to potřeba, čímž minimalizuje odpad a maximalizuje efektivitu.
Přestože existují problémy související s řízením procesů, následným zpracováním a kvalifikací, jsou systematicky řešeny prostřednictvím pokroku v oblasti zásad DfAM, technologie strojů, monitorování procesů, vědy o materiálech a standardizačního úsilí v rámci odvětví. Výběr správného partnera - partnera s hlubokými odbornými znalostmi v oblasti leteckých aplikací, robustními systémy kvality (AS9100), pokročilým vybavením, dodávkami vysoce kvalitních materiálů a komplexními možnostmi následného zpracování - je pro úspěšné využití AM pro kritické součásti, jako jsou tepelné štíty, zásadní.
Společnosti jako Met3dp jsou v čele této transformace výroby a poskytují nejenom pokročilé kovové prášky a špičkové tiskárny ale také odborné znalosti v oblasti vývoje aplikací, které jsou potřebné k tomu, aby pomohly leteckým organizacím efektivně implementovat AM. Přijetím aditivní výroby může letecký průmysl uvolnit nové úrovně výkonu, účinnosti a inovací v oblasti tepelného řízení. Lehké, komplexní a vysoce optimalizované tepelné štíty vyráběné pomocí AM nejsou jen komponenty, ale klíčové nástroje pro budoucnost letů a průzkumu vesmíru.
Sdílet na
MET3DP Technology Co., LTD je předním poskytovatelem řešení aditivní výroby se sídlem v Qingdao v Číně. Naše společnost se specializuje na zařízení pro 3D tisk a vysoce výkonné kovové prášky pro průmyslové aplikace.
Dotaz k získání nejlepší ceny a přizpůsobeného řešení pro vaše podnikání!
Související články
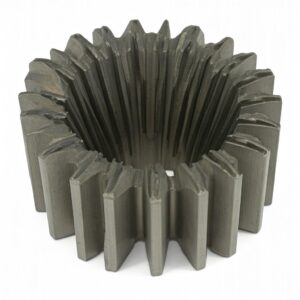
Vysoce výkonné segmenty lopatek trysek: Revoluce v účinnosti turbín díky 3D tisku z kovu
Přečtěte si více "O Met3DP
Nedávná aktualizace
Náš produkt
KONTAKTUJTE NÁS
Nějaké otázky? Pošlete nám zprávu hned teď! Po obdržení vaší zprávy obsloužíme vaši žádost s celým týmem.
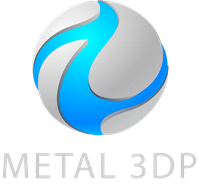
Kovové prášky pro 3D tisk a aditivní výrobu