Inconel 625 prášek
Obsah
Prášek Inconel 625 označuje práškovou slitinu niklu, chromu a molybdenu, která je známá svou vynikající pevností, odolností proti korozi a vysokou teplotou až do 1000 °C. Díky této kombinaci vlastností je inconel 625 všestrannou superslitinou pro náročné aplikace od leteckých součástí až po zařízení pro chemické zpracování.
Tento průvodce se zabývá různými typy práškového inkonelu 625, včetně variant rozprašovaných plynem, podrobnostmi o složení, klíčovými vlastnostmi a charakteristikami, výrobními metodami, aplikacemi, cenami, dodavateli, jakož i výhodami, nevýhodami a nejčastějšími dotazy při práci s touto vysoce výkonnou kovovou slitinou v práškové formě.
Typy prášku Inconel 625
Mezi běžné varianty prášku inconel 625 patří:
Typ | Složení | Charakteristika |
---|---|---|
Rozprášený plyn | 63% Ni, 21,5% Cr, 9% Mo bal. Fe | Sférické homogenní částice ideální pro AM |
Rozprašování plazmou | Stejně jako rozprašovaný plyn | O něco menší, kulovité částice |
Frézované/legované | Stejné složení | Nepravidelný tvar, vyrobený z práškového směsi |
Třída pojiva pro tryskání | Totéž + pojiva a průtokové látky | Složení pro 3D tisk pomocí pojivového paprsku |
Plynové a plazmové verze vykazují přesnou kontrolu velikosti a tvaru částic, které jsou preferovány pro aditivní výrobu, jako je například laserová fúze v práškovém loži, aby se dosáhlo vysoké konečné hustoty po spékání.
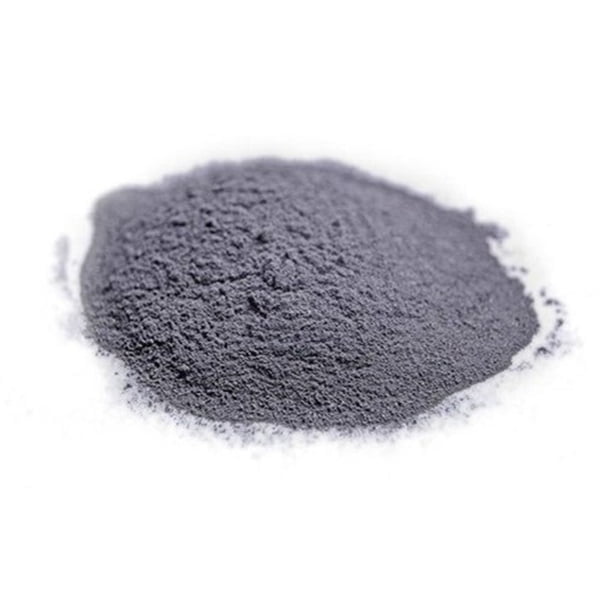
Výrobní metody
Metoda | Popis | Typický výstup |
---|---|---|
Atomizace plynu | Vysokotlaký inertní plyn rozkládá rotující proud taveniny inkonelu na jemné kapičky, které při rychlém tuhnutí vytvářejí prášek slitiny. | Vynikající sférická morfologie ideální pro aplikace AM |
Plazmová atomizace | Podobně jako u plynové atomizace, ale s využitím energie plazmatu k dosažení vyšších teplot a jemnějšího rozpadu taveniny. | Možnost vzniku velmi sférických částic o velikosti pod 45 mikronů; nižší produktivita |
Vakuové indukční tavení | Ingoty s přesným složením se drtí a melou na prášek. | Částice nepravidelného tvaru s vyšší pórovitostí po konsolidaci |
Plynová atomizace zajišťuje rovnováhu mezi laditelnou distribucí velikosti částic a přiměřeným objemem pro konzistentní chemii slitin. Plazmové metody umožňují menší výstupní dávky s přísnějšími tolerancemi částic.
Vlastnosti Inconel 625 prášek
Mezi výhody vyplývající ze složení a výroby patří:
Vlastnictví | Charakteristika | Význam |
---|---|---|
Vysoká pevnost | Pevnost v tahu 110 000 PSI (758 MPa) | Odolává velkému zatížení bez deformace |
Odolnost proti korozi | Vysoký obsah chrómu a molybdenu vytváří ochrannou povrchovou vrstvu oxidů | Spolehlivě funguje ve vlhkém kyselém prostředí, které je běžné v průmyslových závodech. |
Odolnost proti oxidaci | Minimální nikl 65% si zachovává vlastnosti až do 1000 °C | Zvládá výfukové plyny z motoru, chemické reakce a extrémní provozní teplo bez poruchy |
Svařitelnost | Složení pro vynikající spojování a opravy | Snadná integrace do velkých sestav |
Biokompatibilita | Nemagnetické s vynikající únavovou pevností | Vhodné pro implantáty, jako jsou ortopedické kolenní a kyčelní klouby. |
Vyvážená konstrukční kombinace trvanlivosti, vyrobitelnosti a extrémní chemické odolnosti výrazně rozšiřuje možnosti použití ve srovnání s běžnějšími kovy, jako jsou oceli, v horkých a žíravých provozních podmínkách.
Aplikace prášku Inconel 625
Průmysl využívá pákové vlastnosti:
Segment | Běžné použití | Funkce |
---|---|---|
Aerospace | Lopatky turbíny, součásti motoru | Odolává dlouhodobým cyklům extrémního tepla a tlaku. |
Chemické zpracování | Trubky výměníku tepla, ventily, čerpadla | Odolnost proti korozi v širokém spektru chemických prostředí |
Ropa a plyn | Vybavení hlavic vrtů, námořní komponenty na moři | Výkon a snadnější opravy na místě díky svařování |
Lékařské implantáty | Ortopedické klouby, zubní kořeny | Biokompatibilní pevnost přizpůsobená anatomickému zatížení |
Námořní hardware | Matice, šrouby, spojovací materiál, hnací hřídele | Odolnost proti korozi ve slané / mořské vodě |
Aditivní výroba | Složité geometrie ve výše uvedených odvětvích | Svoboda designu AM rozšířená o univerzálnost slitin |
Vytváření jednorázových kování kritických pro letectví a kosmonautiku i komerčních námořních komponentů v sériovém měřítku ukazuje přizpůsobivost materiálu inconel 625 ke konsolidaci složitých a robustních hotových výrobků v těchto klíčových odvětvích.
-
Ti45Nb prášek pro aditivní výrobu
-
Prášek ze slitiny TiNb
-
Prášek ze slitiny TiNbZrSn
-
Ti6Al4V prášek Kovový prášek na bázi titanu pro aditivní výrobu
-
CPTi prášek
-
TC18 Powder : Odemknutí síly karbidu titanu
-
TC11 Powder: Komplexní průvodce
-
TC4 ELI prášek
-
Nejlepší prášek Ti-6Al-4V (TC4 Powder) pro aditivní výrobu
Specifikace z prášek inconel 625
Standard | Definice tříd | Požadavky na chemii |
---|---|---|
ASTM B446 | Třídy prášku Inconel 625: standardní, jemný a ultrajemný | Definuje procenta Ni, Cr, Mo, Ti, Al, C, Si |
AMS 5666 | Žíhané / za tepla izostaticky lisované varianty | Uveďte mezní hodnoty C, Al, Ti v "žíhaném" stavu |
ASME SB-443 | Chemické složení slitiny trubek / trubek | Podobně jako ASTM B446, ale kontroluje také limity Nb a Co |
U náročnějších aplikací, jako jsou jaderné reaktory a systémy kapalného kyslíku se specializovaným hodnocením rizika kontaminace, je třeba zavést přísnější kontroly stopových prvků, jako je uhlík, síra a křemík.
Dodavatelé a ceny
Dodavatel | Klíčové stupně | Odhad ceny |
---|---|---|
Sandvik Osprey | Rozprašování plynem podle normy ASTM B446 | $40 - $100 za kg |
Tesařské práškové výrobky | Více variant velikostí | $60 - $250 za kg |
Technologie povrchů Praxair | Izostatické lisování za tepla, plazmové verze | $150 - $500+ za kg |
Společnost Powder Alloy Corporation | Plynové rozprašování, směsné mletí | $35 - $150 za kg |
Náklady se pohybují v širokém rozmezí od $35/kg pro běžný prášek rozprašovaný plynem vhodný pro obecné použití v aditivní výrobě až po $500/kg pro specializované varianty lisované za tepla, které se používají v aplikacích s vysokou mírou odpovědnosti, jako jsou letecké motory nebo zařízení pro dálkové monitorování ropy a zemního plynu na moři, kde jsou povinné certifikované mechanické vlastnosti.
Nezapomeňte, že při porovnávání možností a cen je třeba kupovat specifikaci, nikoli pouze typ slitiny.
Výhody a nevýhody
Klady | Nevýhody |
---|---|
Odolnost v extrémně náročných prostředích | Stojí více než 5x více než běžné varianty z nerezové oceli |
Zachovává si vlastnosti v teplotním rozsahu stovek °C | Pro méně extrémní procesní podmínky existují možnosti materiálů s nižší teplotou. |
K dispozici jako optimalizovaný tisknutelný prášek | Nedostatek komplexních certifikovaných předpisů a norem pro AM |
Odolává široké škále korozivních chemikálií | Vyžaduje přísná opatření při manipulaci kvůli riziku reaktivity. |
Kombinuje vyrobitelnost, svařitelnost a zpracovatelnost | Stále náchylné ke vzniku chloridových korozních trhlin, takže nejsou odolné. |
Společnosti musejí vyvažovat vynikající výkonnostní okno v náročných provozních podmínkách, jako jsou ropné plošiny na moři a lopatky turbín proudových motorů, s riziky dodavatelského řetězce při řízení speciálních slitin.
Omezení a úvahy
Provozní omezení při práci s práškem Inconel 625:
- Řízení titanových nečistot pod 0,4% potřebných pro požadovanou fázovou rovnoměrnost
- Následné zpracování po aditivní výrobě je obvykle nutné k dosažení plných vlastností
- Cyklické tepelné zpracování může umožnit hrubnutí zrn a nižší tažnost.
- Rizika srážení karbidu při dlouhodobé expozici při teplotách 500-700 °C
- Izostatické lisování za tepla poskytuje největší hustotu, ale obětuje část tažnosti v tahu.
- ověřování přísnosti dodavatelských systémů kvality zamezuje rizikům kontroly kontaminace.
Inženýři využívají modelování metodou konečných prvků ke kontrole konstrukcí z hlediska zatížení. A kontroly prevence od snímačů nečistot vzduchu až po směrovost broušení dále optimalizují výkon.
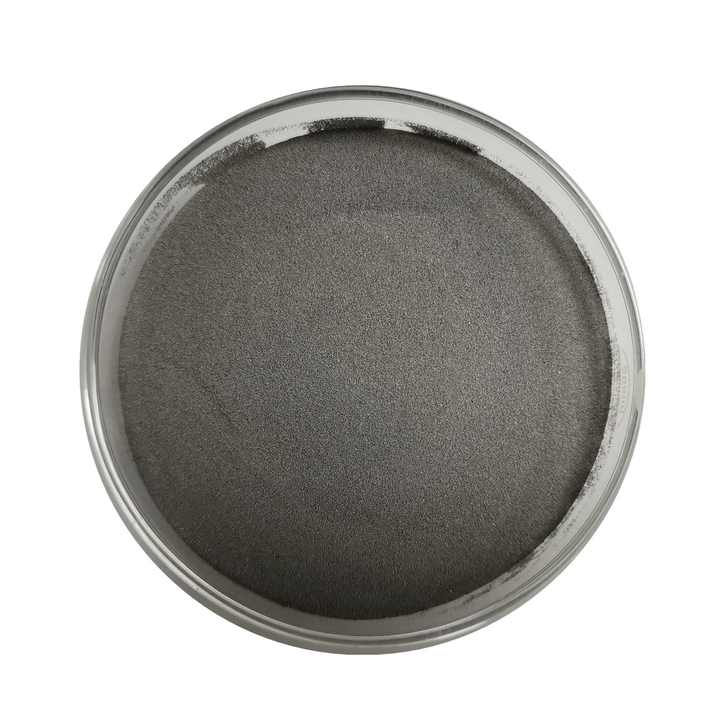
FAQ
Otázka | Odpovědět |
---|---|
Jaký rozsah velikosti částic se používá? | 15-45 mikronů typické pro techniky laserové fúze v práškovém loži |
Jaká je typická objemová hmotnost? | Přibližně 4 g/cc +/- 0,5 g/cc |
Jaký je bod tání? | Rozsah 1290 až 1350 °C |
Jaká metoda následného zpracování poskytuje nejlepší vlastnosti materiálu? | Preferuje se lisování za tepla, ale záleží na aplikaci. |
Jaké jsou typické meze pevnosti v tahu a meze kluzu? | 125 000 psi (862 MPa) v tahu; 110 000 psi (758 MPa) mez kluzu |
Jaká bezpečnostní opatření jsou nutná při manipulaci? | Vzhledem k reaktivitě jemného prášku se upřednostňuje prostředí s inertním plynem. |
Jaká rizika kontaminace je třeba sledovat? | Příměsové prvky síra, křemík, hliník a titan především |
Má prášek neomezenou trvanlivost? | Obecně se doporučuje provést opakovaný test po 1 roce, kdy je zařízení uzavřeno před kyslíkem/vlhkostí. |
Široké využití v leteckém a energetickém průmyslu prokazuje schopnosti, ale řízení speciálních slitin vyžaduje odpovídající kontrolu kvality a škálování hodnocení nebezpečí.
Závěr
Vzhledem k tomu, že aditivní výroba přináší větší svobodu přizpůsobení slitin, poskytuje inconel 625 bezkonkurenční kompatibilitu výrobních procesů od 3D tisku složitých součástí turbín až po svařování 60 stop dlouhých komínů chemických reaktorů. Udržení přístupu ke specializovaným niklovým slitinám však představuje výzvu pro řízení rizik dodavatelského řetězce, protože rozvíjející se trhy vyčerpávají omezené výrobní zdroje. Společnosti proto musí kodifikovat osvědčené postupy manipulace a režimy testování kvality, aby zajistily spolehlivou výkonnost na kritických ropných plošinách a v implantovaných spojích pro pacienty, které mají kromě obsahu niklu společný jen malý podíl, ale jsou vystaveny radikálně odlišným nárokům životního cyklu. Kontrola veřejných zakázek a distribuované výrobní metody pravděpodobně rozšíří dostupnost práškového inkonelu, pokud potřebné odborné znalosti proniknou do kompetencí pracovníků v průmyslovém měřítku. Avšak pouze zohlednění jedinečného kontextu každé aplikace - od extrémních provozních teplot až po stopy nečistot katalyzátorů - může inženýrům umožnit maximalizovat potenciál této skupiny materiálů a zároveň se vypořádat s konkurenční dostupností speciálních kovů, protože složitost výrobků se v různých odvětvích zvyšuje. Příštích 60 let Inconelu 625 bude záviset na spolupráci konstruktérů, metalurgů, tiskařů a kontrolorů, kteří budou převádět složení na komponenty udržující nepřetržitou provozuschopnost navzdory rostoucím ekologickým a bezpečnostním rizikům.
Sdílet na
MET3DP Technology Co., LTD je předním poskytovatelem řešení aditivní výroby se sídlem v Qingdao v Číně. Naše společnost se specializuje na zařízení pro 3D tisk a vysoce výkonné kovové prášky pro průmyslové aplikace.
Dotaz k získání nejlepší ceny a přizpůsobeného řešení pro vaše podnikání!
Související články
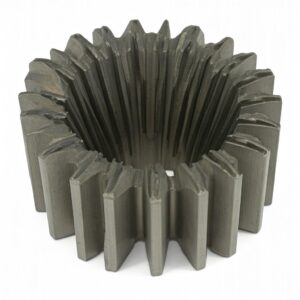
Vysoce výkonné segmenty lopatek trysek: Revoluce v účinnosti turbín díky 3D tisku z kovu
Přečtěte si více "O Met3DP
Nedávná aktualizace
Náš produkt
KONTAKTUJTE NÁS
Nějaké otázky? Pošlete nám zprávu hned teď! Po obdržení vaší zprávy obsloužíme vaši žádost s celým týmem.
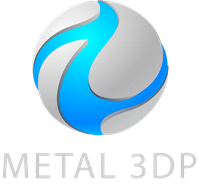
Kovové prášky pro 3D tisk a aditivní výrobu