Vysoce přesné upevnění přístrojů pomocí 3D tisku z kovu
Obsah
Ve složitém světě vyspělých technologií, kde měření posouvají hranice fyziky a zařízení pracují v náročných podmínkách, hraje skromný držák překvapivě důležitou roli. Přesné přístroje - ať už se jedná o seřizování laserů, stabilizaci senzorů v satelitech, držení jemných vzorků v lékařských skenerech nebo zajištění přesnosti v metrologických laboratořích - jsou zcela závislé na svých montážních systémech, pokud jde o stabilitu, seřízení a provozní integritu. Sebemenší vibrace, tepelná roztažnost nebo chybné nastavení mohou ohrozit data, vést k selhání systému nebo znehodnotit výsledky. Výroba těchto vysoce přesných držáků přístrojů tradičně zahrnovala složité víceosé CNC obrábění, často z masivních polotovarů ze specializovaných materiálů. Tento přístup je sice efektivní, ale naráží na omezení v podobě geometrické složitosti, plýtvání materiálem, dodacích lhůt a schopnosti integrovat pokročilé prvky, jako jsou vnitřní chladicí kanály nebo optimalizované lehké struktury. Vstupte do aditivní výroby kovů (AM), běžně známé jako kovová 3D tisk. Tato transformační technologie nabízí výkonnou alternativu, která umožňuje vytvářet držáky přístrojů s nebývalou konstrukční volností, optimalizovanými výkonnostními charakteristikami a potenciálem výrazného snížení nákladů a doby realizace, zejména u složitých nebo nízkoobjemových výrobních sérií. Tento příspěvek se zabývá světem vysoce přesných držáků přístrojů a zkoumá, proč se technologie AM rychle stává řešením pro inženýry a manažery nákupu v leteckém, automobilovém, lékařském a průmyslovém odvětví, se zvláštním zaměřením na materiály, jako je nerezová ocel 316L a pozoruhodná slitina Invar s nízkou roztažností.
Úvod: Kritická úloha přesných držáků přístrojů v technologicky vyspělých odvětvích
Přesné držáky přístrojů jsou mnohem víc než pouhé držáky nebo upevňovací prvky; jsou to konstruované součásti, které jsou nedílnou součástí funkce a spolehlivosti sofistikovaných systémů. Jejich hlavním účelem je bezpečně držet, polohovat a udržovat nastavení citlivých přístrojů vzhledem k referenčnímu rámu nebo jiným součástem, často v náročných podmínkách prostředí. Vzpomeňte si na laserový systém v nástroji pro výrobu polovodičů, optické komponenty v satelitním teleskopu, senzory v systému LiDAR autonomního vozidla nebo sondy v souřadnicovém měřicím stroji (CMM). V každém případě musí držák poskytovat stabilní, předvídatelnou a často izolovanou platformu.
Proč je důležitá stabilita a přesnost:
- Udržování souladu: Optické systémy vyžadují, aby byly komponenty seřízeny s přesností na mikrony nebo dokonce nanometry. Jakékoli posunutí nebo nesouosost držáků v důsledku vibrací, nárazů nebo tepelných změn může systém znehodnotit. Dráhy laserů, orientace senzorů a pozice vzorků musí zůstat přesné.
- Tlumení vibrací: Mnoho přístrojů je citlivých na vnější vibrace (od strojů, akustiky nebo dopravy). Držáky musí často obsahovat tlumicí prvky nebo být vyrobeny z materiálů, které ze své podstaty snižují přenos vibrací na přístroj. Netlumené vibrace mohou do měření vnášet šum nebo způsobovat únavové poruchy.
- Tepelná stabilita: Kolísání teploty může způsobit rozpínání nebo smršťování materiálů. V přesných aplikacích může i nepatrná tepelná roztažnost vést k výraznému nesouososti nebo napětí. Držáky, zejména ty, které se používají v optice, metrologii nebo vesmírných aplikacích, musí často vykazovat minimální změny rozměrů v širokém rozsahu provozních teplot. To vyžaduje použití specializovaných materiálů s nízkým koeficientem tepelné roztažnosti (CTE).
- Strukturální integrita: Držáky musí být dostatečně pevné a tuhé, aby unesly hmotnost přístroje a odolaly jakémukoli provoznímu zatížení (např. zrychlení v leteckém nebo automobilovém průmyslu), aniž by se deformovaly. Deformace při zatížení může způsobit chybné nastavení.
- Odolnost vůči životnímu prostředí: V závislosti na aplikaci může být nutné, aby držáky odolávaly korozi (např. v lékařském nebo námořním prostředí), odplyňování (ve vakuu nebo ve vesmíru) nebo extrémním teplotám.
Omezení tradiční výroby:
Již po desetiletí je CNC obrábění standardem pro výrobu vysoce kvalitních držáků. Představuje však určité výzvy, zejména s tím, jak se konstrukce přístrojů stávají složitějšími a nároky na výkon se zvyšují:
- Geometrická omezení: Obrábění složitých vnitřních prvků, organických tvarů optimalizovaných na poměr tuhosti a hmotnosti (optimalizace topologie) nebo integrovaných funkcí, jako jsou konformní chladicí kanály, může být velmi obtížné, časově náročné nebo nemožné. To často vede ke konstrukcím, které jsou spíše kompromisem než optimálním řešením.
- Materiálový odpad: Subtraktivní výroba začíná s větším blokem materiálu a odstraňuje to, co není potřeba. U drahých nebo specializovaných materiálů, jako je Invar, to může vést ke značnému a nákladnému plýtvání.
- Složitost sestavy: Dosažení složitých geometrií často vyžaduje obrábění více jednotlivých dílů a jejich následné sestavení. Každé rozhraní v sestavě přináší potenciální nárůst tolerancí, chyby v seřízení a místa poruch. Konsolidace dílů, kdy je více funkcí integrováno do jediné součásti, je velmi žádoucí, ale při obrábění často obtížná.
- Doba dodání: Nastavení nástrojů, programování, doba obrábění a montáž mohou vést k dlouhým dodacím lhůtám, zejména u složitých konstrukcí nebo malých výrobních objemů. Iterace prototypů mohou být pomalé a nákladné.
Poptávka po vyšším výkonu, větší konstrukční složitosti, nižší hmotnosti a rychlejších vývojových cyklech v odvětvích využívajících citlivé přístroje vytvořila významnou příležitost pro alternativní výrobní procesy. Aditivní výroba kovů přímo řeší mnohá omezení spojená s tradičními metodami a nabízí přesvědčivou cestu k vytvoření nové generace stabilních montážních řešení pro kritické, high-tech aplikace. Společnosti, které chtějí získat konkurenční výhodu při výrobě nebo používání vysoce přesných zařízení, se stále častěji obracejí na poskytovatele služeb v oblasti AM zpracování kovů, kteří mají odborné znalosti a pokročilé schopnosti, jako je tomu u společnosti Met3dp, aby mohli tyto pokročilé návrhy realizovat.
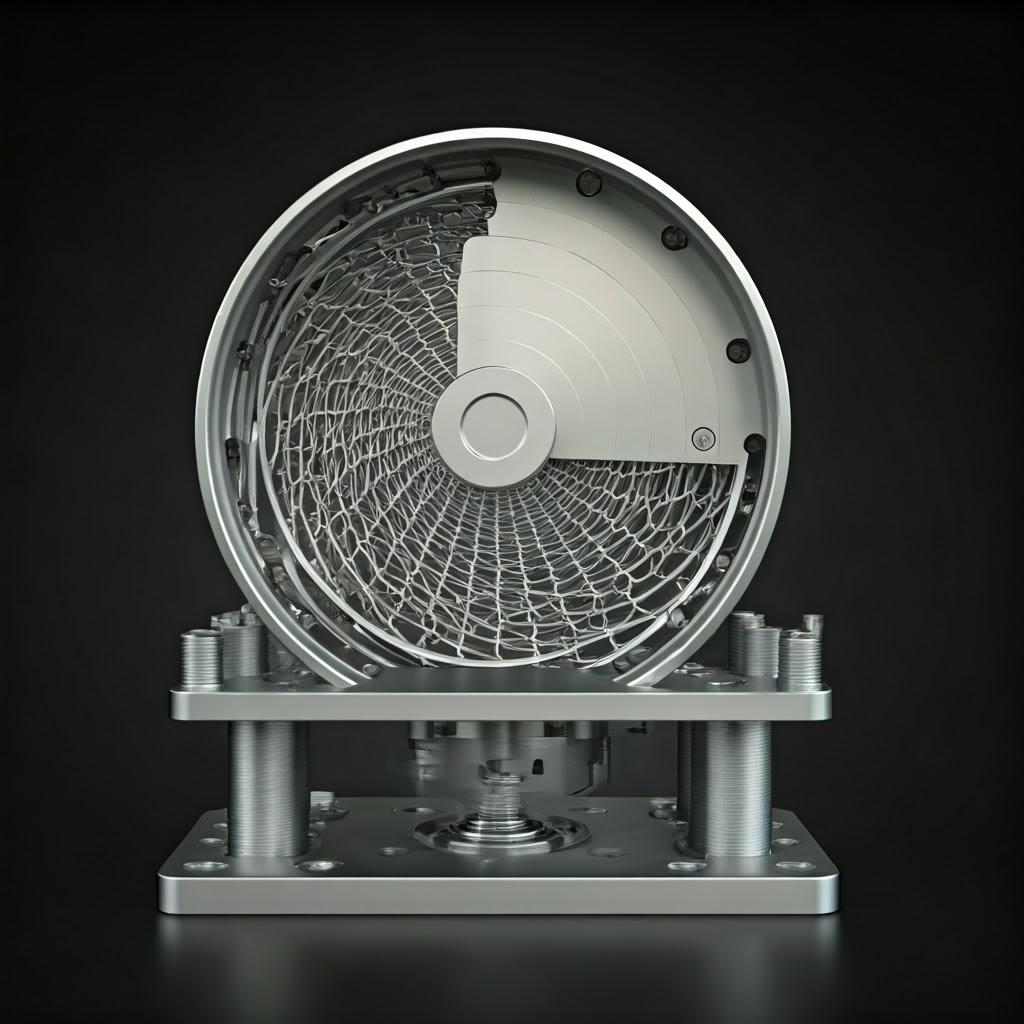
Aplikace & Případy použití: Kde přesná montáž vyniká
Potřeba vysoce přesných a stabilních montážních řešení se týká prakticky všech odvětví vyspělých technologií. Schopnost udržet komponenty stabilní, vyrovnané a izolované od rušivých vlivů prostředí je základem. Aditivní výroba kovů významně proniká do těchto aplikací tím, že umožňuje dříve nedosažitelné konstrukce a kombinace materiálů. Zde se podívejte na klíčová odvětví a konkrétní případy použití, kde 3D tištěné přesné držáky přístrojů přinášejí hodnotu:
1. Letectví a obrana:
- Satelitní přístrojové vybavení: Držáky pro optické užitečné zatížení (teleskopy, kamery), senzory, antény a elektroniku musí odolávat vibracím při startu, tepelným cyklům ve vesmíru (-150 °C až +150 °C nebo více) a udržovat extrémní přesnost zaměření po mnoho let. Materiály s nízkou CTE, jako je Invar, často v kombinaci s optimalizací topologie pro minimální hmotnost (což je kritické pro náklady na vypuštění), jsou ideálními kandidáty pro AM.
- Letecké senzory a avionika: Držáky gyroskopů, akcelerometrů, navigačních systémů a zaměřovacích modulů vyžadují vysokou tuhost, tlumení vibrací a spolehlivost při vysokých přetíženích a proměnlivých teplotách. Technologie AM umožňuje výrobu složitých, lehkých držáků integrovaných přímo do konstrukce letadla.
- Optické lavice a zaměřovací systémy: Pozemní nebo letecké optické systémy potřebují výjimečně stabilní držáky pro lasery, zrcadla a detektory. AM umožňuje vytvářet monolitické optické lavice s integrovanými držáky, což snižuje složitost montáže a zvyšuje stabilitu.
2. Zdravotnické prostředky:
- Diagnostické zobrazovací zařízení (MRI, CT, PET): Citlivé detektory a systémy pro polohování pacientů vyžadují nemagnetické držáky (často vyžadující specifické slitiny), odolné proti vibracím a rozměrově stabilní. Společnost AM dokáže vytvořit držáky na míru specifickým geometriím strojů a rozhraním pro pacienty. Běžně se používají materiály jako nerezová ocel 316L nebo slitiny titanu.
- Chirurgická robotika a nástroje: Držáky pro robotická ramena, kamery a chirurgické nástroje vyžadují vysokou přesnost, tuhost a možnost sterilizace. Technologie AM umožňuje vytvářet složité, ergonomické konstrukce, které často obsahují vnitřní kanály pro chlazení nebo přívod tekutin, a to za použití biokompatibilních materiálů, jako je 316L nebo Ti6Al4V.
- Laboratorní automatizace a analýza: Vysoce výkonné screeningové systémy, mikroskopy a zařízení pro zpracování vzorků jsou závislé na přesném a opakovatelném polohování. Zakázkové 3D tištěné držáky mohou optimalizovat pracovní postupy, zmenšit plochu a zlepšit integraci různých komponent.
3. Metrologie a vědecké přístroje:
- Souřadnicové měřicí stroje (CMM): Hlavy sond, držáky senzorů a konstrukční součásti vyžadují extrémní rozměrovou stabilitu a tuhost, aby byla zajištěna přesnost měření až na submikronovou úroveň. Materiály s nízkým obsahem CTE, jako je Invar, jsou nezbytné a AM umožňuje optimalizovat konstrukci rámů a uchycení sond.
- Mikroskopie (elektronová, atomové síly): Aby bylo možné dosáhnout rozlišení v atomárním měřítku, musí držáky poskytovat výjimečnou izolaci proti vibracím a tepelnou stabilitu. AM umožňuje vytvářet složité, tlumené montážní struktury přizpůsobené konkrétním stupňům mikroskopu a komorám s prostředím.
- Synchrotrony a urychlovače částic: Přístroje beamline, držáky detektorů a manipulátory vzorků pracují v náročných prostředích (vakuum, radiace) a vyžadují přesné nastavení. AM umožňuje vytvářet složité držáky ze specializovaných materiálů odolných vůči těmto podmínkám.
- Optické testování a interferometrie: Držáky pro lasery, zrcadla, děliče paprsků a detektory používané v optických testovacích sestavách vyžadují vysokou stabilitu a možnost jemného nastavení. Společnost AM může vyrábět držáky s integrovanými ohýbacími nebo nastavovacími mechanismy, často s použitím materiálu Invar s nízkou hodnotou CTE.
4. Průmyslová automatizace a výroba:
- Robotické koncové efektory: Držáky pro uchopovače, senzory a nástroje průmyslových robotů musí být lehké (aby se maximalizovalo užitečné zatížení a rychlost) a zároveň pevné. AM umožňuje topologicky optimalizované konstrukce přizpůsobené konkrétním úlohám.
- Systémy strojového vidění: Pro spolehlivou kontrolu a navádění vyžadují držáky kamery a osvětlení stabilní polohu. Zakázkové držáky AM se vejdou do stísněných prostor na výrobních linkách a integrují chladicí nebo ochranné prvky.
- Zařízení pro výrobu polovodičů: Systémy pro manipulaci s destičkami, litografické nástroje a kontrolní stanice vyžadují mimořádně vysokou přesnost a stabilitu, často v čistých prostorách nebo ve vakuu. Materiály s nízkým obsahem plynů a slitiny s nízkým obsahem CTE, jako je Invar, mají zásadní význam a AM poskytuje flexibilitu při navrhování složitých geometrií zařízení. Velkoobchodní dodavatelé přesných součástí se stále častěji poohlížejí po AM, aby uspokojili individuální potřeby tohoto odvětví.
5. Automobilový průmysl:
- Montáž senzorů (LiDAR, radar, kamery): Autonomní řízení a systémy ADAS jsou závislé na přesném nastavení senzorů. Držáky musí odolávat vibracím, teplotním výkyvům a nárazům a zároveň zachovávat kalibraci snímačů. AM umožňuje integrovaná a odolná montážní řešení specifická pro platformy vozidel.
- Zkušební komory motoru: Montáž snímačů pro měření teploty, tlaku a vibrací v dynamometrech motorů vyžaduje robustnost a tepelnou stabilitu. Zakázkové držáky AM mohou optimálně umístit snímače v náročných testovacích prostředích.
- Výrobní přípravky a přípravky: Ačkoli se nejedná přímo o držáky přístrojů, přípravky používané k držení dílů při výrobě nebo kontrole vyžadují vysokou přesnost a stabilitu. AM se hojně využívá k rychlému vytváření vlastních, lehkých a ergonomických upínacích přípravků.
V těchto různých oblastech se často snoubí základní požadavky: přesnost, stabilita (mechanická a tepelná), spolehlivost a často také přizpůsobení nebo složitá geometrie. Aditivní výroba kovů, zejména s využitím pokročilých technik tavení v práškovém loži, jako je selektivní tavení elektronovým svazkem (SEBM) nebo selektivní laserové tavení (SLM), poskytuje nástroje pro splnění těchto náročných požadavků. Poskytovatelé služeb specializující se na 3D tisk z kovu jsou klíčovými partnery pro společnosti, které potřebují tyto vysoce výkonné komponenty, a nabízejí odborné znalosti v oblasti výběru materiálů, optimalizace konstrukce a řízení procesů, aby zajistily, že konečné upevnění splňuje nebo překračuje specifikace. Schopnost získat výrobce držáků přístrojů na zakázku, kteří využívají technologii AM, se stává klíčovou konkurenční výhodou.
Proč aditivní výroba kovů pro držáky přístrojů? Uvolnění výkonu a svobody designu
Rozhodnutí použít aditivní výrobu kovů (AM) pro výrobu vysoce přesných držáků přístrojů vychází z jejích přirozených výhod oproti tradičním subtraktivním metodám, jako je CNC obrábění, zejména pokud jde o složité konstrukce, specializované materiály nebo potřebu optimalizovaného výkonu. Zatímco obrábění je stále vhodné pro jednodušší geometrie nebo velkosériovou výrobu standardizovaných dílů, AM otevírá možnosti, které byly dříve považovány za neproveditelné nebo nákladově neúnosné. Inženýři a manažeři veřejných zakázek si tyto výhody stále více uvědomují:
1. Bezkonkurenční volnost designu & Komplexnost:
- Složité geometrie: AM vytváří díly vrstvu po vrstvě, což umožňuje vytvářet složité vnitřní kanály (pro chlazení, proudění kapalin nebo vedení kabelů), komplexní vnější tvary, záporné úhly ponoru a duté struktury bez omezení daných řeznými nástroji nebo požadavky na formy. Tato svoboda umožňuje konstrukce, které jsou skutečně optimalizované pro funkci, nikoli pouze pro výrobu tradičními prostředky.
- Optimalizace topologie: Inženýři mohou pomocí softwarových nástrojů definovat průběh zatížení, omezení a výkonnostní cíle (např. maximalizovat tuhost, minimalizovat hmotnost) a software vygeneruje organickou, často mřížkovou strukturu, která tyto požadavky splňuje s použitím minimálního množství materiálu. Obrábění takto složitých tvarů je často nemožné nebo ekonomicky neúnosné. U držáků přístrojů to znamená vytvářet struktury, které jsou výjimečně tuhé a stabilní přesně tam, kde je to potřeba, a zároveň výrazně snižují celkovou hmotnost - což má zásadní význam pro letectví, robotiku a přenosná zařízení.
- Konsolidace částí: Více komponent, které by se tradičně vyráběly odděleně a poté sestavovaly (např. držák, chladič, tlumič vibrací), lze často přepracovat a vytisknout jako jediný monolitický díl. Tím se eliminuje čas a náklady na montáž, odstraní se potenciální místa poruchy nebo nesouososti na rozhraních, zlepší se celková strukturální integrita a sníží se problémy s tolerančními sklady.
2. Odlehčení:
- Snížená hmotnost: Díky optimalizaci topologie a schopnosti vytvářet vnitřní mřížkové struktury nebo duté profily může AM výrazně snížit hmotnost držáků přístrojů ve srovnání s pevnými obráběnými součástmi při zachování nebo dokonce zvýšení tuhosti a pevnosti.
- Výhody: Odlehčení je důležité v aplikacích, jako jsou:
- Letectví: Nižší náklady na vypuštění, lepší palivová účinnost, vyšší kapacita užitečného zatížení.
- Automobilový průmysl: Lepší dynamika vozidla, úspora paliva.
- Robotika: Rychlejší pohyby, nižší setrvačnost, vyšší nosnost robotického ramene.
- Lékařské přístroje: Lepší přenosnost, snadnější manipulace s přenosnými nebo nositelnými zařízeními.
3. Vylepšené výkonnostní charakteristiky:
- Integrovaná funkčnost: Volnost designu umožňuje přímou integraci prvků zvyšujících výkon. Příklady zahrnují:
- Konformní chladicí kanály: Vnitřní kanály, které přesně kopírují obrysy součástí generujících teplo nebo kritických oblastí držáku, poskytují mnohem účinnější tepelný management než vrtané kanály nebo připojené chladiče.
- Konstrukce pro tlumení vibrací: Začlenění specifické geometrie mřížky nebo konstrukce ohybů přímo do držáku může pomoci izolovat přístroj od vnějších vibrací.
- Optimalizované cesty toku: Pro držáky, které slouží také jako rozdělovače nebo rozvody kapalin nebo plynů.
- Vlastnosti materiálu: Procesy AM často vedou k jemnozrnné mikrostruktuře, která může vést k vynikajícím mechanickým vlastnostem (pevnost, odolnost proti únavě), které dosahují nebo převyšují vlastnosti litých nebo tepaných materiálů, zejména po vhodném následném zpracování, jako je lisování za tepla (HIP).
4. Materiálové možnosti:
- Specializované slitiny: AM vyniká při zpracování materiálů, které se obtížně nebo draze obrábějí, jako jsou vysokoteplotní superslitiny, některé titanové slitiny a slitiny s nízkou roztažností, jako je Invar (FeNi36). Například obrábění slitiny Invar je kvůli její gumovité povaze a pracovnímu zpevnění velmi náročné. AM poskytuje efektivnější cestu k výrobě složitých dílů Invar, které jsou nezbytné pro tepelně stabilní držáky.
- Nové materiály: Povaha AM po vrstvách otevírá dveře funkčně odstupňovaným materiálům (měnící se složení v rámci celého dílu) nebo kompozitům s kovovou matricí, i když tyto oblasti se teprve rozvíjejí.
- Snížení množství materiálového odpadu: Jako aditivní proces využívá AM pouze materiál potřebný k výrobě dílu a jeho podpěr, což vede k podstatně menšímu množství odpadu ve srovnání se subtraktivním obráběním, zejména u složitých dílů nebo drahých materiálů, jako je Invar nebo titan pro letecký průmysl. Tento poměr “buy-to-fly” je mnohem příznivější.
5. Rychlé prototypování a iterace:
- Rychlost: AM umožňuje rychlou výrobu prototypů přímo z dat CAD, často během několika dnů, bez nutnosti použití nástrojů. To urychluje konstrukční cykly a umožňuje inženýrům rychle otestovat několik iterací a dospět k optimálnímu návrhu mnohem rychleji než při použití tradičních metod.
- Nákladově efektivní iterace: Náklady na výrobu jednoho prototypu nebo malé série pomocí AM jsou často podstatně nižší než náklady na obrábění, což zpřístupňuje zkoumání designu.
6. Přizpůsobení a malosériová výroba:
- Výroba na vyžádání: AM je ideální pro výrobu zakázkových, jednorázových dílů nebo malých sérií bez vysokých nákladů na přípravu spojených s tradiční výrobou. To je ideální pro specializované vědecké přístroje, zakázkové přípravky pro lékařské přístroje nebo náhradní díly pro starší systémy.
- Řešení na míru: Držáky přístrojů lze dokonale přizpůsobit specifickým požadavkům na geometrii, hmotnost a výkon přístroje a jeho provozní prostředí.
Proč upřednostnit AM před CNC obráběním pro držáky? Srovnávací pohled:
Vlastnosti | Výroba aditiv kovů (AM) | CNC obrábění | Výhoda přesných držáků |
---|---|---|---|
Složitost návrhu | Vysoká (vnitřní kanály, mřížky, organické tvary) | Střední až vysoká (omezeno přístupem k nástrojům, nastavením) | AM umožňuje optimalizovat, odlehčit a konsolidovat konstrukce, což je při obrábění nemožné. |
Konsolidace částí | Vynikající | Omezený | AM snižuje chybovost montáže, hmotnost a potenciální poruchovost. |
Odlehčení | Vynikající (optimalizace topologie, vnitřní dutiny) | Omezené (omezení při odstraňování materiálu) | AM výrazně snižuje hmotnost při zachování tuhosti, což je pro dynamické/mobilní aplikace zásadní. |
Materiálový odpad | Nízká (aditivní proces) | Vysoká (subtraktivní proces, zejména složité díly) | AM je nákladově efektivnější a udržitelnější pro drahé materiály, jako je Invar. |
Doba realizace (Proto) | Půst (dny) | Středně pomalý až pomalý (týdny, v závislosti na složitosti) | AM urychluje iteraci a validaci návrhu. |
Dodací lhůta (Prod.) | Středně náročné (doba zpracování + následné zpracování) | Potenciálně rychlejší pro velké objemy (pokud je to jednoduché) | AM může být rychlejší u složitých, nízkoobjemových dílů. |
Výběr materiálu | Široký rozsah, vynikající pro těžko obrobitelné slitiny | Široký sortiment, snadno dostupné standardní materiály | AM efektivně zpracovává kritické materiály, jako je Invar, které jsou potřebné pro tepelnou stabilitu. |
Náklady na nastavení | Nízká (bez nástrojů) | Vysoká (nástroje, programování, přípravky) | AM je nákladově efektivní pro zakázkové díly a malé objemy. |
Povrchová úprava | Středně těžký (vyžaduje následné zpracování pro hladký povrch) | Vynikající (přímo dosažitelné) | Obrábění se upřednostňuje u kritických povrchů, které vyžadují vysokou kvalitu povrchu bez následného zpracování. |
Tolerance | Dobrý (vyžaduje dodatečné obrábění pro dosažení nejvyšší přesnosti) | Vynikající (přímo dosažitelné) | Obrábění preferované pro prvky vyžadující přesnost pod 100 mikronů bez následného zpracování. |
Export do archů
Shrneme-li to, aditivní výroba kovů nabízí pro výrobu vysoce přesných držáků přístrojů řadu přesvědčivých výhod, zejména pokud jsou klíčovými faktory složitost, hmotnost, optimalizace výkonu nebo použití specializovaných materiálů, jako je Invar. Umožňuje inženýrům vymanit se z tradičních výrobních omezení a navrhovat skutečně inovativní montážní řešení. Spolupráce se zkušeným poskytovatelem AM, jako je Met3dp, který kombinuje odborné znalosti v oblasti pokročilé tiskových metod s vysoce kvalitním materiálem, zajišťuje plné využití potenciálu AM pro vaše kritické aplikace.
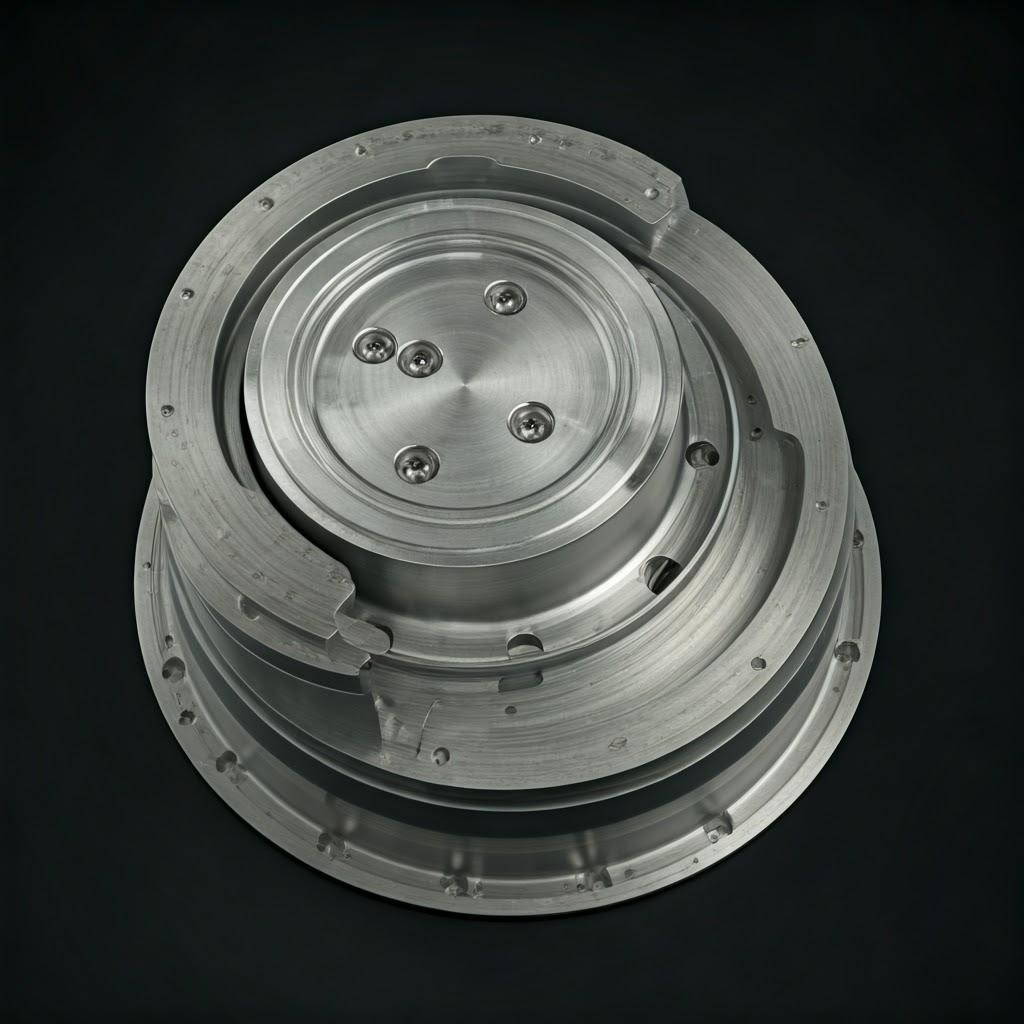
Zaměření materiálu: nerezová ocel 316L & Invar pro optimální výkon
Výkonnost přesného držáku přístroje je zásadně spojena s materiálem, z něhož je vyroben. Ačkoli aditivní výroba kovů dokáže zpracovávat širokou škálu slitin, dva materiály vynikají častým používáním ve vysoce přesných montážních aplikacích díky svým specifickým a často se doplňujícím vlastnostem: Nerezová ocel 316L a Invar (FeNi36). Znalost jejich vlastností je zásadní pro výběr správného materiálu pro vaše konkrétní potřeby.
1. nerezová ocel 316L (austenitická nerezová ocel)
316L je jednou z nejpoužívanějších slitin nerezové oceli v aditivní výrobě, známá pro svou vynikající kombinaci odolnosti proti korozi, mechanických vlastností, biokompatibility a zpracovatelnosti.
- Klíčové vlastnosti & amp; Výhody pro držáky:
- Vynikající odolnost proti korozi: Vysoký obsah chromu a molybdenu dodává oceli 316L výjimečnou odolnost proti korozi v širokém spektru prostředí, včetně chloridů, kyselin a tělních tekutin. Díky tomu je ideální pro úchyty používané ve zdravotnických zařízeních, námořních aplikacích, chemickém zpracování a potravinářském průmyslu.
- Dobrá mechanická pevnost a tažnost: materiál 316L nabízí dobrou rovnováhu mezi pevností v tahu, mezí kluzu a prodloužením, což zajišťuje, že jsou montáže robustní a odolné proti lomu. Jeho vlastnosti jsou obecně srovnatelné s tepaným materiálem 316L.
- Biokompatibilita: materiál 316L je široce akceptován pro lékařské implantáty a přístroje (ISO 10993), takže je vhodný pro upevnění chirurgických nástrojů nebo vnitřních přístrojů.
- Svařitelnost a leštitelnost: Díly vyrobené z materiálu 316L lze snadno svařovat (v případě potřeby montáže, ačkoli cílem AM je konsolidace) a leštit na vysokou kvalitu povrchu, což je důležité pro aplikace v čistých prostorách nebo optické aplikace.
- Nákladová efektivita a dostupnost: Ve srovnání s exotičtějšími slitinami, jako je invar nebo titan, je prášek 316L relativně cenově výhodný a snadno dostupný u kvalitních dodavatelů.
- Dobrá zpracovatelnost AM: materiál 316L je dobře charakterizován a spolehlivě zpracováván pomocí laserové fúze v práškovém loži (LPBF/SLM) a dalších technik AM, což vede k hustým a vysoce kvalitním dílům.
- Omezení:
- Mírná tepelná roztažnost: 316L má koeficient tepelné roztažnosti (CTE) typický pro austenitické nerezové oceli (přibližně 16-17×10-6/K). Ačkoli je tato úroveň roztažnosti pro mnoho aplikací přijatelná, může způsobit významné rozměrové změny a nesouosost v systémech velmi citlivých na kolísání teploty, jako je přesná optika nebo metrologické zařízení.
- Hustota: Je hustší než slitiny hliníku nebo titanu, což může být nevýhodou v aplikacích s kritickou hmotností (ačkoli odlehčovací schopnosti AM’ to mohou zmírnit).
- Typické aplikace pro držáky 316L:
- Součásti zdravotnických přístrojů (chirurgické roboty, diagnostická zařízení)
- Námořní hardware a držáky senzorů
- Přípravky pro chemické zpracování
- Potravinářské strojní součásti
- Obecné montáže průmyslových senzorů a zařízení, kde není primárním zájmem extrémní tepelná stabilita.
2. Invar (FeNi36 / slitina 36)
Invar je slitina železa a niklu, která byla speciálně vyvinuta pro svůj pozoruhodně nízký koeficient tepelné roztažnosti (CTE) při pokojové teplotě a mírně zvýšených teplotách. Jeho název pochází ze slova “neměnný ” což odkazuje na jeho nedostatečnou tepelnou roztažnost.
- Klíčové vlastnosti & amp; Výhody pro držáky:
- Extrémně nízká CTE: To je charakteristický rys společnosti Invar. Jeho CTE se obvykle pohybuje kolem 1,2 × 10-6/K při pokojové teplotě, což je zhruba 10-15krát méně než u nerezové oceli nebo hliníku a výrazně méně než u titanu. Tato výjimečná rozměrová stabilita z něj činí materiál, který je vhodný pro aplikace, kde nelze tolerovat ani nepatrnou tepelnou roztažnost nebo smrštění.
- Dobrá síla a odolnost: Invar poskytuje dostatečnou pevnost a houževnatost pro montážní aplikace, zejména pokud je prvořadým požadavkem rozměrová stabilita.
- Zpracovatelnost AM: I když je tradiční obrábění prášku Invar náročné, lze jej úspěšně zpracovávat pomocí LPBF/SLM, což umožňuje vytvářet složité geometrie, které využívají jeho nízkou CTE. Rozhodující je pečlivá kontrola parametrů a následné tepelné zpracování.
- Omezení:
- Vyšší náklady: Prášek Invar je kvůli vysokému obsahu niklu a specializovanému výrobnímu procesu výrazně dražší než nerezová ocel 316L.
- Nižší odolnost proti korozi: Invar nemá přirozenou odolnost proti korozi jako nerezové oceli. Ve vlhkém prostředí může být náchylný ke korozi, pokud není chráněn povlaky (např. niklováním).
- Obtížnost obrábění: Ačkoli AM obchází většinu obtíží, následné obrábění kritických prvků může být ve srovnání s ocelí stále náročné.
- Citlivost na tepelné zpracování: Dosažení optimálního stavu nízké CTE u Invaru vyžaduje specifické protokoly tepelného zpracování po tisku, aby se uvolnilo napětí a stabilizovala mikrostruktura. Nesprávné tepelné zpracování může ohrozit jeho nízkoexpanzní vlastnosti.
- Hustota: Podobně jako ocel je poměrně hustá.
- Typické aplikace pro držáky Invar:
- Optické držáky (zrcadla, čočky, lasery) v teleskopech, interferometrech a přesných seřizovacích systémech.
- Rámy a přípravky metrologického vybavení (souřadnicové měřicí stroje, měřidla).
- Letecké a kosmické konstrukce vyžadující rozměrovou stabilitu (optické lavice pro družice, kompozitní nástrojové formy).
- Součásti zařízení pro výrobu polovodičů (litografické stupně, manipulace s destičkami).
- Vědecké přístroje vyžadující vysokou stabilitu (fyzikální experimenty, měřicí zařízení).
Srovnání vlastností materiálů:
Vlastnictví | Nerezová ocel 316L | Invar (FeNi36 / slitina 36) | Význam pro montáže |
---|---|---|---|
Primární výhoda | Odolnost proti korozi, cena, dostupnost | Extrémně nízká tepelná roztažnost (CTE) | Volte podle vystavení vlivům prostředí a potřeby maximální rozměrové stability. |
CTE (approx. @ 20°C) | ~16-17×10-6/K | ~1.2×10-6/K | Invar je výrazně lepší pro aplikace citlivé na teplotu. |
Hustota (přibližně) | ~8,0g/cm3 | ~8,1 g/cm3 | Podobná hustota; klíčem k oběma je odlehčení pomocí konstrukce AM. |
Mez kluzu (typická AM) | ~450-550 MPa | ~250-350 MPa (žíhané) | 316L je obecně silnější, ale Invar je vhodný pro většinu statických montážních zatížení. |
Odolnost proti korozi | Vynikající | Špatný (vyžaduje ochranný nátěr) | 316L je vhodný do drsného prostředí; Invar vyžaduje kontrolované prostředí nebo pokovení. |
Relativní náklady | Dolní | Výrazně vyšší | Rozpočtová omezení často dávají přednost materiálu 316L, pokud není nízká CTE Invaru neoddiskutovatelná. |
Zpracovatelnost AM | Dobře zavedené, spolehlivé | Vyžaduje pečlivou kontrolu & tepelné zpracování | Obojí je proveditelné, ale Invar vyžaduje více odborných znalostí. |
Obrobitelnost | Dobrý | Obtížné | AM snižuje závislost na obrábění, což je přínosem pro tvorbu dílů Invar. |
Export do archů
Výběr správného materiálu a dodavatele:
Výběr mezi 316L a Invarem (nebo případně jinými slitinami, jako je titan pro vysoký poměr pevnosti a hmotnosti) závisí v rozhodující míře na konkrétních požadavcích na výkon, provozním prostředí a rozpočtových omezeních aplikace.
- Pokud odolnost proti korozi nebo náklady jsou primárními faktory a mírná tepelná roztažnost je přijatelná: 316L je často tou nejlepší volbou.
- Pokud maximální rozměrová stabilita při změnách teploty (např. optika, metrologie, vesmír): Invar je obvykle vyžadována, a to i přes vyšší náklady a nutnost ochrany životního prostředí.
Kvalita výsledného dílu závisí nejen na výběru materiálu, ale také na kvalitě kovového prášku a odborných znalostech poskytovatele aditivní výroby. Společnosti jako např Met3dp se specializuje na výrobu vysoce kvalitních sférických kovových prášků optimalizovaných pro procesy AM, jako je SEBM a LPBF. Použití pokročilých technologií plynové atomizace a PREP zajišťuje prášky s vysokou sféricitou a dobrou tekutostí, což vede k hustším a spolehlivějším tištěným dílům. Společnost Met3dp vyrábí širokou škálu prášků, včetně nerezových ocelí a potenciálně specializovaných slitin potřebných pro náročné aplikace, a poskytuje tak zákazníkům jak materiály, tak také odborné znalosti potřebné k úspěšné implementaci technologie AM pro vysoce přesné držáky přístrojů. Při hledání dodavatele 3D tisku z materiálu Invar nebo 3D tisku z nerezové oceli 316L je nezbytné ověřit jeho postupy kontroly kvality prášku a zkušenosti s těmito specifickými materiály.
Design pro aditivní výrobu (DfAM): Optimalizace držáků pro tisk & funkčnost
Návrh pro aditivní výrobu (DfAM) představuje zásadní změnu v myšlení ve srovnání s tradičními principy návrhu pro výrobu (DFM) přizpůsobenými subtraktivním procesům, jako je CNC obrábění. Namísto primárního zohlednění přístupu k nástroji, úhlů ponoru a strategií úběru materiálu se DfAM zaměřuje na využití jedinečných možností a přizpůsobení se specifickým omezením výroby po vrstvách. Použití principů DfAM se nedoporučuje pouze pro přesné držáky nástrojů; je nezbytné pro využití plného potenciálu AM z hlediska výkonu, nákladové efektivity a spolehlivosti. Nedostatečný návrh s ohledem na proces AM může vést k poruchám tisku, neoptimálnímu výkonu, nadměrným požadavkům na následné zpracování a zvýšeným nákladům.
Základní zásady DfAM pro přesné přístrojové držáky:
- Využití geometrické volnosti pro funkční zisk:
- Optimalizace topologie: Jedná se pravděpodobně o nejúčinnější techniku DfAM pro montáže. Definováním zatěžovacích stavů (hmotnost přístroje, vibrační vstupy, provozní síly), okrajových podmínek (upevňovací body) a cílů (minimalizace hmotnosti, maximalizace tuhosti, specifická vlastní frekvence) mohou softwarové algoritmy generovat vysoce účinné, často organicky vypadající struktury. Výsledkem je držák, který je tuhý a stabilní přesně tam, kde je to potřeba, s použitím minima materiálu, což vede k výrazné úspoře hmotnosti bez snížení výkonu. To je neocenitelné pro letectví, robotiku a přenosné systémy.
- Mřížové struktury: Začlenění vnitřních příhradových konstrukcí (např. gyroidů, oktetových příhrad) umožňuje další odlehčení při zachování strukturální integrity. Mřížky lze také navrhnout tak, aby poskytovaly specifické vlastnosti tlumení vibrací nebo usnadňovaly odvod tepla - což je velmi důležité pro upevnění přístrojů.
- Konsolidace částí: Aktivně vyhledávejte příležitosti ke spojení více součástí montážní sestavy do jediného tištěného dílu. Lze integrovat držák, chladič a tlumič vibrací? Mohou být prvky pro vyrovnání zabudovány přímo do držáku? Tím se zjednoduší montáž, sníží se tolerance, zvýší se tuhost a sníží se celkové náklady na systém.
- Konformní kanály: Navrhněte vnitřní kanály, které přesně kopírují obrysy zdrojů tepla nebo oblastí vyžadujících tepelný management. U přístrojů, které generují teplo nebo pracují při různých teplotách, nabízejí konformní chladicí/vyhřívací kanály integrované do držáku ve srovnání s tradičními metodami lepší tepelnou regulaci. Lze také integrovat kanály pro vedení kabelů, aby se sestavy staly úhlednějšími.
- Optimalizace orientace sestavení:
- Dopad: Orientace, ve které je držák vytištěn na konstrukční desku, významně ovlivňuje požadavky na podpůrnou konstrukci, povrchovou úpravu na různých plochách, rozložení zbytkového napětí, dobu sestavení a případně i mechanické vlastnosti (anizotropie).
- Úvahy:
- Minimalizujte podporu: Orientujte díl tak, abyste snížili objem a složitost potřebných podpůrných konstrukcí, zejména na kritických funkčních plochách nebo těžko přístupných vnitřních oblastech. Tam, kde je to možné, by se měly používat samonosné úhly (obvykle >45 stupňů od vodorovné roviny).
- Povrchová úprava: Povrchy směřující dolů nebo vyžadující rozsáhlou podporu mají obecně hrubší povrch. Orientujte díl tak, aby kritické povrchy (např. styčné plochy, optické srovnávací body) směřovaly nahoru nebo byly pokud možno svislé, nebo aby byly snadno přístupné pro následné obrábění.
- Mechanické vlastnosti: Vlastnosti se mohou mírně lišit v závislosti na směru sestavení vzhledem ke směru zatížení v konečné aplikaci. Pokud je to kritické, orientujte díl tak, aby nejsilnější osa sestavení byla v jedné přímce s primární dráhou zatížení.
- Tepelný management: Orientace má vliv na odvod tepla během sestavování a ovlivňuje zbytkové napětí.
- Spolupráce: Volba optimální orientace často zahrnuje kompromisy. Spolupráce se zkušeným poskytovatelem AM služeb, jako je Met3dp, je ve fázi návrhu klíčová, protože může simulovat různé orientace a poradit nejlepší strategii na základě jejich specifických vlastností produkt schopnosti a znalosti procesů.
- Navrhování účinných podpůrných struktur:
- Nezbytnost: Podpěry jsou nutné k ukotvení dílu k sestavovací desce, k zabránění jeho deformace v důsledku tepelného namáhání a k podepření převislých prvků a dolů směřujících povrchů během procesu sestavování po vrstvách.
- Optimalizace: Podpěry jsou sice nezbytné, ale spotřebovávají materiál, prodlužují dobu výroby, vyžadují úsilí při odstraňování a mohou poškodit povrch dílu. Cílem DfAM je minimalizovat závislost na podpěrách prostřednictvím chytrých konstrukčních rozhodnutí (např. použití zkosení místo ostrých převisů, orientace prvků tak, aby byly samonosné) a navrhování podpěr, které jsou účinné, ale snadno se odstraňují.
- Typy: V závislosti na umístění a funkci lze použít různé typy podpěr (např. pevné, mřížové, kuželové). Zvažte snadný přístup pro nástroje pro demontáž (kleště, dráty EDM, CNC nástroje).
- Integrace: Někdy mohou být funkční prvky samotného dílu navrženy tak, aby během sestavování fungovaly také jako podpěry, což může snížit potřebu speciálních obětovaných konstrukcí.
- Zohlednění procesních omezení:
- Minimální tloušťka stěny/velikost prvku: Procesy AM mají omezení minimální tloušťky stěn a nejmenších prvků (čepy, otvory), které mohou spolehlivě vyrobit. Ty závisí na konkrétním stroji, velikosti laserového/elektronového paprsku a vlastnostech prášku. Stěny a prvky navrhujte nad tato minima (např. obvykle >0,4-0,5 mm pro jemné prvky v LPBF).
- Orientace a tvar otvorů: Malé otvory se často tisknou přesněji, pokud jsou orientovány vertikálně. Vodorovně orientované malé otvory mohou být vytištěny mírně eliptické a mohou vyžadovat podporu; jejich konstrukce ve tvaru slzy je může učinit samonosnými.
- Odstranění prášku: U dutých profilů nebo vnitřních kanálů zajistěte dostatečné únikové otvory (o průměru nejméně 2-3 mm, nejlépe větší, a strategicky umístěné), aby bylo možné po sestavení odstranit nerozpuštěný prášek. Zachycený prášek zvyšuje hmotnost a může představovat riziko kontaminace.
- Filety a poloměry: V ostrých vnitřních rozích použijte klempířské prvky, abyste snížili koncentraci napětí, která může být slabým místem nebo místem vzniku trhlin, zejména při vibracích nebo zatížení. Hladké přechody obecně zlepšují tisknutelnost a pevnost dílů.
- Návrh pro následné zpracování:
- Přídavky na obrábění: Pokud některé povrchy vyžadují přísné tolerance nebo velmi hladký povrch, kterého nelze dosáhnout přímo pomocí AM, přidejte do těchto specifických oblastí v modelu CAD další materiál (obráběcí materiál, např. 0,5-1,0 mm), aby bylo možné následné obrábění.
- Přístupnost: Zajistěte, aby oblasti vyžadující odstranění podpěr, obrábění, leštění nebo kontrolu byly přístupné i po vytištění dílu. Problematické mohou být hluboké a úzké vnitřní kanály vyžadující povrchovou úpravu.
- Upevnění: Zvažte, jakým způsobem bude díl uchováván pro různé kroky následného zpracování, jako je obrábění nebo měření. Začlenění jednoduchých prvků upevnění do návrhu může později ušetřit značný čas při nastavování.
Iterativní povaha DfAM:
DfAM není vždy lineární proces. Často zahrnuje spolupráci mezi konstruktérem dílu a poskytovatelem služeb AM. Nástroje, jako je software pro simulaci sestavení, mohou předvídat potenciální problémy, jako je deformace nebo přehřátí, což konstruktérům umožňuje proaktivně upravit geometrii nebo nastavení sestavení. Prototypování a testování zůstávají zásadními kroky k ověření konstrukčních rozhodnutí a zajištění toho, aby finální držák přístroje splňoval všechny funkční požadavky. Přijetí principů DfAM od samého počátku je klíčem k maximalizaci výhod kovové AM pro vytváření lehčích, pevnějších, funkčnějších a často nákladově efektivnějších přesných držáků přístrojů ve srovnání s těmi, které jsou omezeny tradičními výrobními paradigmaty.
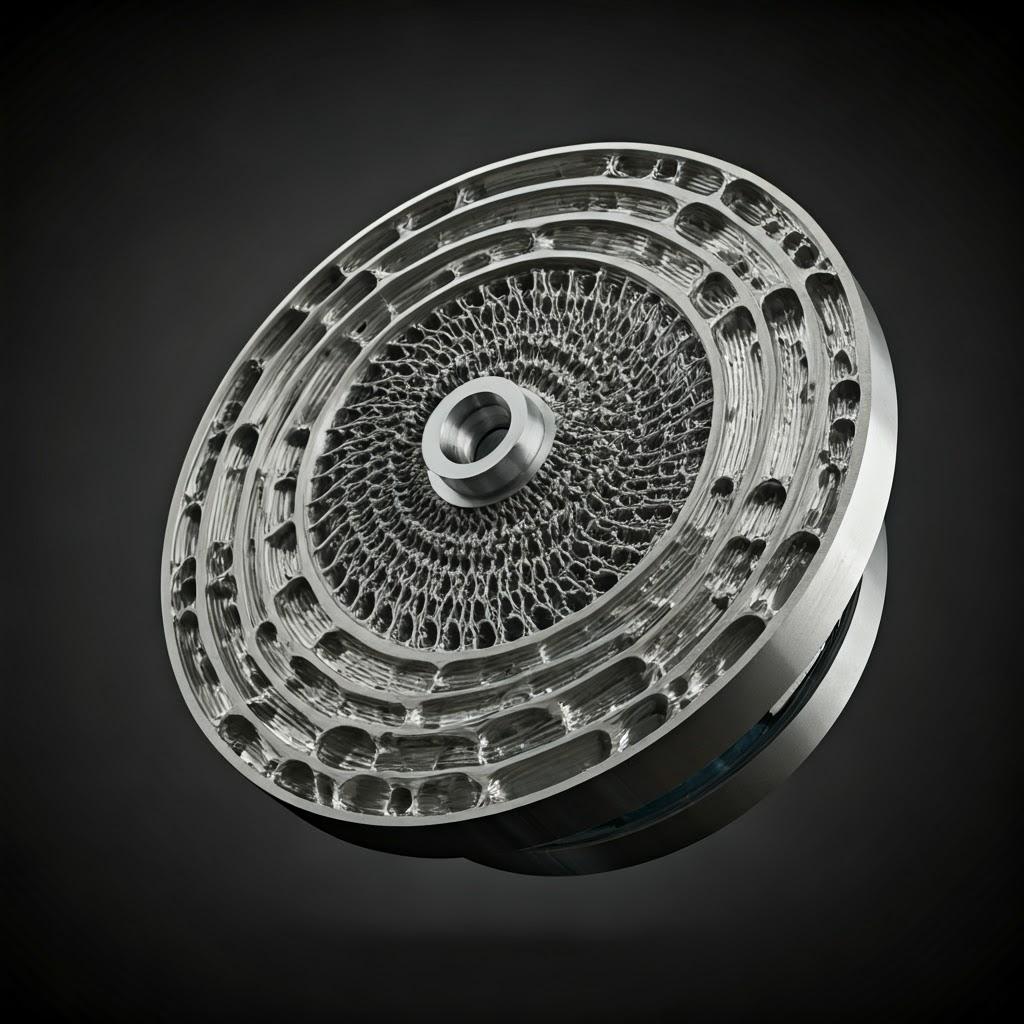
Dosažení přesnosti: Tolerance, povrchová úprava a rozměrová přesnost u 3D tištěných držáků
U součástí určených k uložení citlivých přístrojů je přesnost prvořadá. Pochopení úrovně tolerance, povrchové úpravy a rozměrové přesnosti dosažitelné pomocí aditivní výroby kovů je pro inženýry navrhující držáky a pro manažery nákupu stanovující specifikace a hodnotící dodavatele zásadní. Ačkoli AM výroba kovů nabízí neuvěřitelnou volnost při navrhování, má své vlastní vlastnosti týkající se přesnosti, které se liší od konvenčního obrábění. Pro splnění nejpřísnějších požadavků je často nutná kombinace AM a následného zpracování.
Schopnosti v podobě, v jaké byly vytištěny:
Procesy AM, jako je laserová fúze v práškovém loži (LPBF/SLM) a selektivní tavení elektronovým svazkem (SEBM), vytvářejí díly po vrstvách, obvykle o tloušťce 20-100 mikrometrů. Tento proces ze své podstaty ovlivňuje dosažitelnou přesnost:
- Rozměrová přesnost:
- Obecné tolerance: Obecně lze říci, že u dobře řízených procesů a řádně kalibrovaných strojů se typické rozměrové tolerance kovových dílů tištěných metodou AM často pohybují v rozmezí pm0,1 mm až pm0,2 mm u menších prvků (do ~50-100 mm) nebo pm0,1 až pm0,2 celkového rozměru u větších dílů. Například 200 mm dlouhý prvek může mít toleranci pm0,2 mm až pm0,4 mm.
- Ovlivňující faktory: Skutečná dosažitelná přesnost závisí do značné míry na geometrii dílu (složitost, velikost, objem), materiálu (tepelné vlastnosti), orientaci sestavení, strategii podpory, kalibraci stroje, kvalitě prášku (distribuce velikosti částic, tekutost) a tepelném řízení během sestavení. Zbytková napětí vzniklá během tisku mohou způsobit deformaci nebo zkreslení, což ovlivní konečné rozměry, zejména po vyjmutí z konstrukční desky.
- Přístup společnosti Met3dp’: Dosažení konzistentní přesnosti vyžaduje důkladnou kontrolu procesu. Společnosti jako Met3dp kladou důraz na spolehlivost a přesnost svých tiskových systémů a kvalitu svých kovových prášků, které jsou vyráběny pomocí pokročilých atomizačních technik, aby byla zajištěna konzistentní sférická morfologie a tekutost - faktory, které jsou klíčové pro předvídatelné tavení a tuhnutí, a tím i lepší kontrolu rozměrů.
- Povrchová úprava (drsnost):
- Jak bylo vytištěno Ra: Povrchová úprava kovových dílů vytištěných metodou as-printing je ze své podstaty drsnější než obráběné povrchy, což je dáno tím, že na povrchu ulpívají částečně roztavené částice prášku, a tím, že povrch je tvořen po vrstvách. Typické hodnoty drsnosti povrchu (Ra – Arithmetic Average Roughness) závisí na orientaci a procesu:
- Svislé stěny: Často dosáhnete nejlepšího výsledku, případně Ra 8-15mum.
- Povrchy směřující vzhůru: Mírně drsnější, Ra 10-20mum.
- Plochy směřující dolů (podporované): Výrazně drsnější v místech uchycení podpěr, potenciálně Ra 20-50 mm nebo více, což vyžaduje výraznou úpravu.
- Stupňovité povrchy: K drsnosti přispívají také kroky vrstev na šikmých plochách.
- SEBM vs. LPBF: SEBM obvykle pracuje při vyšších teplotách a používá větší částice prášku, což často vede k drsnější povrchové úpravě (např. Ra 25-45 mm) ve srovnání s LPBF, ale potenciálně nižšímu zbytkovému napětí.
- Důsledky pro montáže: U obecných konstrukčních dílů může stačit povrchová úprava bez tisku. U přesných držáků přístrojů, styčných ploch, těsnicích ploch, rozhraní optických součástí nebo kinematických lokalizačních prvků je však tato drsnost obvykle nepřijatelná a vyžaduje zlepšení pomocí následného zpracování.
- Jak bylo vytištěno Ra: Povrchová úprava kovových dílů vytištěných metodou as-printing je ze své podstaty drsnější než obráběné povrchy, což je dáno tím, že na povrchu ulpívají částečně roztavené částice prášku, a tím, že povrch je tvořen po vrstvách. Typické hodnoty drsnosti povrchu (Ra – Arithmetic Average Roughness) závisí na orientaci a procesu:
Dosažení vyšší přesnosti pomocí následného zpracování:
U většiny vysoce přesných držáků přístrojů budou kritické prvky vyžadovat následné zpracování, především obrábění CNC, broušení nebo lapování, aby se dosáhlo potřebných tolerancí a povrchových úprav.
- Tolerance: Operacemi následného obrábění lze snadno dosáhnout tolerancí v rozsahu pm0,01 mm až pm0,05 mm (10-50mum), a dokonce ještě těsnějších tolerancí až na úroveň jednoho mikronu (mum) pomocí specializovaných procesů broušení nebo lapování na kritických bodech nebo rozhraních. To umožňuje konstruktérům využít geometrickou volnost AM pro celkový tvar a zároveň zajistit přesnost pouze tam, kde je to funkčně nutné.
- Povrchová úprava: Obráběním lze výrazně zlepšit kvalitu povrchu, obvykle se dosahuje Ra 0,8-3,2 mm. Broušením a lapováním lze dosáhnout optické kvality povrchu s Ra hluboko pod 0,1 mm. Techniky leštění mohou také výrazně vyhladit povrchy z estetických nebo funkčních důvodů (např. čistitelnost).
Srovnání: Přesnost v porovnání se stavem po tisku:
Vlastnosti | Kovový AM (typický LPBF) v podobě, v jaké byl vytištěn | Následné zpracování (obrábění/broušení) | Význam pro přesné montáže |
---|---|---|---|
Tolerance | pm0,1-0,2 mm nebo pm0,1-0,2 | pm0,01-0,05 mm (obrábění)<br> pm0,001-0,01 mm (broušení) | AM vhodný pro obecnou formu; následné zpracování je nezbytné pro kritická rozhraní & zarovnání. |
Povrchová úprava (Ra) | 8-25mum (liší se podle zaměření) | 0.8-3.2mum (obrábění)<br> $\< 0.1 \\mu m$ (lapování/leštění) | Pro hladké styčné plochy, těsnění nebo optická rozhraní je nutná následná úprava. |
Schopnost | Složitá celková geometrie | Vysoká přesnost specifických prvků | Kombinací složitosti AM’a přesnosti obrábění dosáhnete optimálních výsledků. |
Export do archů
Kontrola a ověřování kvality:
Zajištění toho, aby konečné upevnění splňovalo stanovené požadavky na přesnost, zahrnuje přísnou kontrolu kvality:
- Monitorování během procesu: Pokročilé systémy AM obsahují senzory, které monitorují bazén taveniny, teplotní gradienty a konzistenci vrstev během procesu, což pomáhá zajistit stabilitu procesu.
- Metrologie po výstavbě: Souřadnicové měřicí stroje (CMM), 3D laserové skenery a optické profilometry se používají k ověření přesnosti rozměrů a kvality povrchu po tisku a po všech krocích následného obrábění.
- Nedestruktivní zkoušení (NDT): Techniky, jako je CT skenování, lze použít ke kontrole vnitřních prvků, kontrole pórovitosti a ověření složitých geometrií, které jsou jinak nepřístupné.
Klíčový závěr:
Aditivní výroba kovů poskytuje dobrou základní rozměrovou přesnost a charakteristickou povrchovou úpravu přímo ze stroje. Pro náročné požadavky vysoce přesných držáků přístrojů však musí konstruktéři počítat s nutností cíleného následného zpracování, především obrábění nebo broušení kritických prvků a povrchů. Strategickým spojením konstrukční svobody AM s přesností subtraktivních dokončovacích technik a partnerstvím s dodavatelem zaměřeným na kvalitu AM mohou konstruktéři vytvářet montážní řešení, která nabízejí jak geometrickou složitost, tak náročnou přesnost. Manažeři nákupu by měli na výkresech jasně definovat požadavky na tolerance a povrchovou úpravu a specifikovat, které prvky vyžadují následné zpracování, aby byla zajištěna přesná cenová nabídka a úspěšná realizace dílu.
Základní kroky následného zpracování funkčních přístrojových držáků
Kovový 3D vytištěný díl je po vyjmutí z tiskárny jen zřídka připraven k finálnímu použití, zejména v souvislosti s vysoce přesnými držáky přístrojů. K přeměně surové vytištěné součásti na funkční, spolehlivý a hotový výrobek je obvykle zapotřebí řada kroků následného zpracování. Tyto kroky jsou klíčové pro uvolnění vnitřních pnutí, odstranění dočasných struktur, dosažení požadovaných vlastností materiálu, zajištění rozměrové přesnosti, dosažení požadované povrchové úpravy a někdy i přidání ochranných vrstev. Pochopení tohoto pracovního postupu je zásadní pro plánování časového harmonogramu výroby a nákladů.
Typický pracovní postup následného zpracování pro kovové držáky AM:
- Tepelné ošetření proti stresu:
- Účel: Rychlé cykly zahřívání a ochlazování, které jsou vlastní procesům tavení v práškovém loži, vytvářejí v tištěném dílu značné vnitřní pnutí. Tato napětí mohou způsobit deformace nebo praskliny, zejména po vyjmutí dílu z konstrukční desky. U většiny kovových AM dílů, zejména u větších dílů nebo dílů vyrobených z materiálů náchylných k tvorbě napětí, jako jsou slitiny titanu nebo Invar, je odstranění napětí prvním kritickým krokem.
- Proces: Díl, často ještě připevněný na konstrukční desce, se zahřeje v peci na určitou teplotu (nižší než teplota přeměny materiálu), po určitou dobu se udržuje a poté se pomalu ochlazuje. To umožňuje uvolnění mikrostruktury, čímž se výrazně sníží zbytková napětí. Konkrétní cykly do značné míry závisí na materiálu (např. Invar vyžaduje pečlivě řízené cykly, aby se zachovaly jeho nízké CTE vlastnosti) a geometrii dílu.
- Důležitost pro držáky: Zajišťuje rozměrovou stabilitu v průběhu času a zabraňuje neočekávanému pokřivení, které by mohlo ohrozit seřízení přístroje.
- Odstranění ze stavební desky:
- Proces: Po uvolnění napětí (pokud se provádí na desce) je třeba díl oddělit od konstrukční desky, na které byl vytištěn. To se obvykle provádí pomocí elektroerozivního obrábění (EDM), řezání nebo někdy CNC obrábění.
- Úvahy: Při demontáži je třeba dbát na to, aby nedošlo k poškození dílu. Rozhraní mezi dílem/podpěrami a deskou je často navrženo tak, aby usnadňovalo demontáž.
- Odstranění prášku (zbavení prachu):
- Účel: Netavený kovový prášek zůstává ve vnitřních kanálech, dutých částech a po tisku ulpívá na povrchu dílu. Tento uvolněný prášek je třeba důkladně odstranit.
- Proces: Obvykle zahrnuje ruční kartáčování, poklepávání a použití stlačeného vzduchu nebo proudů inertního plynu v kontrolovaném prostředí (stanice pro odstraňování prachu) k získání nepoužitého prášku (který lze často prosévat a znovu použít). Mohou se také použít ultrazvukové čisticí lázně nebo specializované vibrační systémy.
- Výzvy: Odstraňování prášku ze složitých vnitřních geometrií nebo mřížkových struktur může být obtížné. Zásady DfAM (např. dostatečné únikové otvory) jsou zde klíčové. Zachycený prášek je nepřijatelný, protože zvyšuje hmotnost a může být zdrojem kontaminace nebo narušovat funkci.
- Odstranění podpůrné konstrukce:
- Účel: Obětní podpůrné konstrukce, které se používají při stavbě k ukotvení dílu a k podpírání převisů, musí být odstraněny.
- Proces: Může se jednat o různé metody, od jednoduchého ručního lámání (u lehce slinutých podpěr) až po náročnější metody, jako je řezání ručními nástroji, elektroerozivní obrábění (zejména u složitých vnitřních podpěr) nebo obrábění na CNC. Metoda závisí na konstrukci podpěry, materiálu a přístupnosti.
- Úvahy: Odstranění podpory může na povrchu dílu zanechat stopy nebo drsné plochy (“jizvy”), které mohou vyžadovat další dokončovací práce. Je třeba dbát na to, aby při odstraňování nedošlo k poškození vlastního dílu. Klíčovým aspektem DfAM je navrhování podpěr pro snadné odstranění.
- Lisování za tepla (HIP) – volitelné, ale často doporučované:
- Účel: HIP je proces, který kombinuje vysokou teplotu a vysoký tlak inertního plynu (obvykle argonu), aby se odstranila vnitřní mikroporozita, která může někdy zůstat po procesu AM. Tím se materiál zhutní, což výrazně zvyšuje únavovou životnost, lomovou houževnatost a celkovou mechanickou integritu.
- Proces: Díly se zahřívají ve specializované nádobě HIP pod vysokým izostatickým tlakem po stanovenou dobu.
- Při použití: Často se vyžaduje pro kritické součásti v letectví a kosmonautice, lékařské implantáty a vysoce zatížené průmyslové díly, kde je integrita materiálu nejdůležitější. V případě přesných držáků vystavených vibracím nebo únavovému zatížení může HIP poskytnout dodatečnou bezpečnostní rezervu a zajistit dlouhodobou spolehlivost. Může také zlepšit konzistenci vlastností materiálu.
- Obrábění / dokončování kritických prvků:
- Účel: Jak již bylo uvedeno, pro dosažení těsných tolerancí (pm0,01-0,05 mm nebo lepších) a hladké povrchové úpravy (Ra $\< 3,2 \\mu m$) na specifických funkčních plochách (styčné plochy, seřizovací body, otvory ložisek, optická rozhraní).
- Proces: Používá standardní CNC frézování, soustružení, broušení nebo lapování. Vyžaduje pečlivou konstrukci upínacích přípravků, aby bylo možné přesně držet často složitý AM díl. Ve fázi DfAM musí být zahrnuty přídavky na obrábění.
- Nezbytnost: Téměř vždy se vyžaduje u vysoce přesných držáků přístrojů, aby bylo zaručeno přesné polohování a montáž.
- Povrchová úprava a zušlechťování:
- Účel: Zlepšení celkové povrchové úpravy, vyčištění dílu, zlepšení estetiky nebo příprava na lakování.
- Procesy:
- Otryskávání kuliček / kuličkování: Vytváří rovnoměrný matný povrch, odstraňuje uvolněné částice a může vyvolat tlakové zbytkové napětí (kuličkování), které zvyšuje únavovou životnost.
- Třískové/vibrační dokončování: Vyhlazuje povrchy a hrany pomocí brusných médií v bubnovém válci nebo vibrační míse. Vhodné pro dávkové zpracování menších dílů.
- Elektrolytické leštění: Elektrochemický proces, při kterém se odstraní tenká vrstva materiálu a výsledkem je velmi hladký, čistý a lesklý povrch. Často se používá pro lékařské (316L) nebo vakuové aplikace.
- Ruční leštění/leštění: Pro dosažení specifických vysoce lesklých povrchů nebo vyhlazení lokalizovaných oblastí.
- Povlakování nebo pokovování:
- Účel: K zajištění ochrany proti korozi (což je pro materiály jako Invar ve vlhkém prostředí nezbytné), zvýšení odolnosti proti opotřebení, změně elektrických nebo tepelných vlastností povrchu nebo zlepšení estetiky.
- Procesy: Niklování (běžné pro Invar), práškové lakování, lakování, eloxování (pro titan), povlaky z fyzikálního napařování (PVD) atd.
- Úvahy: Tloušťku nátěru je třeba zohlednit, pokud je aplikován na rozměrově kritické povrchy. Příprava povrchu je klíčová pro dobrou přilnavost.
- Čištění a kontrola:
- Účel: Závěrečné čištění k odstranění zbytků obráběcích kapalin, lešticích směsí nebo nečistot. Konečná kontrola ověřuje rozměry, povrchovou úpravu a kontroluje případné vady před expedicí.
- Procesy: Ultrazvukové čištění, vizuální kontrola, měření souřadnicovým měřicím přístrojem, profilometrie povrchu, v případě potřeby NDT.
Konkrétní pořadí a nutnost těchto kroků závisí do značné míry na materiálu (např. u Invaru je nutné specifické tepelné zpracování a povrchová úprava), složitosti dílu a přísných požadavcích na konečnou aplikaci. Plánování následného zpracování není dodatečnou záležitostí, ale nedílnou součástí výrobního procesu kovových dílů AM, která ovlivňuje dobu výroby a celkové náklady. Spolupráce s poskytovatelem komplexních služeb, který nabízí komplexní možnosti následného zpracování nebo má pro tyto služby navázaná partnerství, je pro získání funkčních, aplikačně připravených přesných přístrojových držáků klíčová.
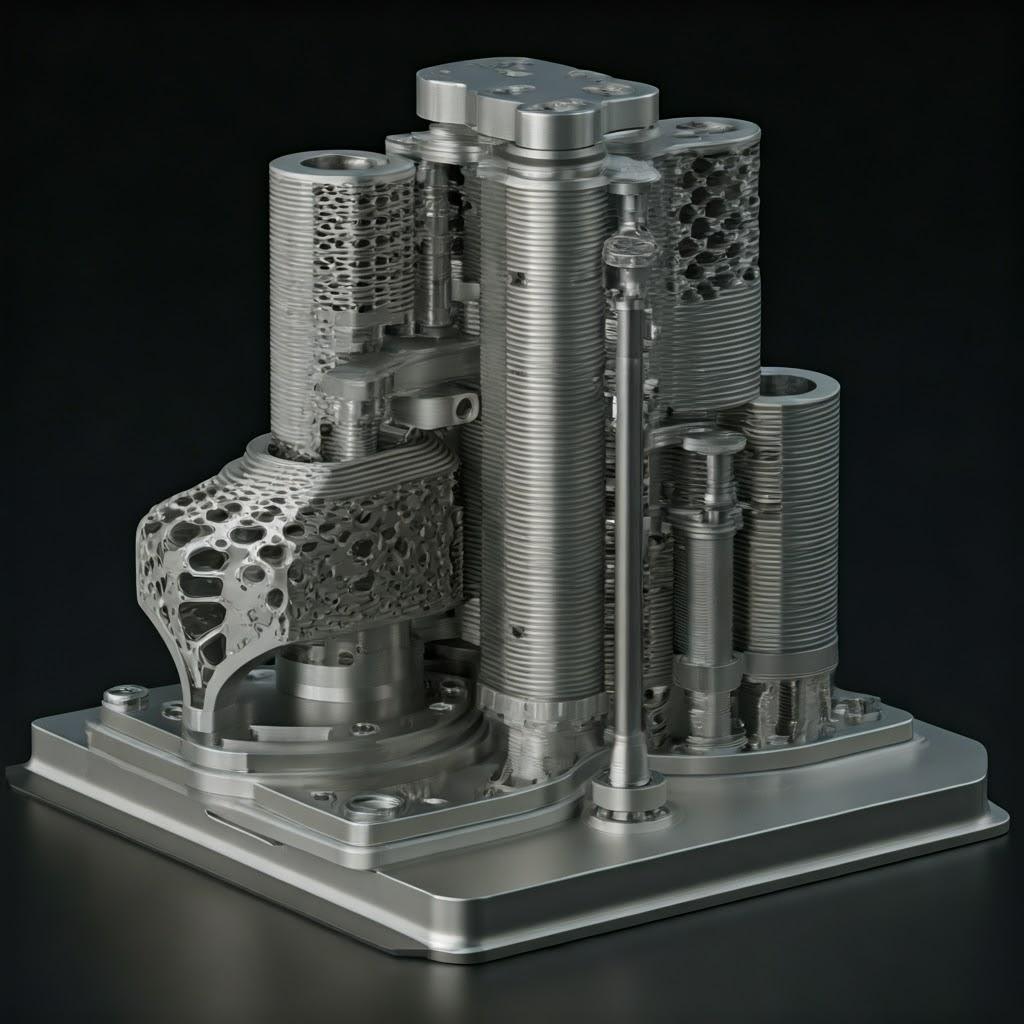
Překonávání problémů při 3D tisku kovových přesných držáků
Přestože aditivní výroba kovů nabízí významné výhody pro výrobu složitých a vysoce výkonných držáků přístrojů, není tato technologie bez problémů. Dosažení požadované přesnosti, integrity materiálu a spolehlivosti vyžaduje pečlivou kontrolu procesu, porozumění materiálovým vědám a často i opakované zdokonalování. Povědomí o těchto potenciálních překážkách umožňuje inženýrům a výrobcům aktivně zavádět strategie pro jejich zmírnění.
Společné výzvy a strategie pro jejich zmírnění:
- Zbytkové napětí, deformace a zkreslení:
- Výzva: Intenzivní, lokalizovaný ohřev laserovým nebo elektronovým paprskem a následné rychlé ochlazení vytváří prudké tepelné gradienty, které vedou k vnitřnímu pnutí v dílu, který je vytvářen vrstvu po vrstvě. Tato napětí mohou způsobit deformaci, zkreslení nebo dokonce prasknutí dílu, zejména po vyjmutí z konstrukční desky nebo během následného zpracování. To je hlavní problém pro zachování rozměrové přesnosti požadované pro přesné montáže.
- Zmírnění:
- Simulace procesu: Softwarové nástroje mohou simulovat proces sestavování a předvídat oblasti s vysokým namáháním a možným zkreslením, což umožňuje upravit orientaci nebo podpůrné strategie před tiskem.
- Optimalizované parametry sestavení: Přesné nastavení výkonu laseru/paprsku, rychlosti skenování, tloušťky vrstvy a strategie skenování pomáhá řídit přívod tepla a snižovat tepelné gradienty.
- Vytápění stavebních desek: Předehřívání konstrukční desky (běžné u LPBF, vlastní SEBM pracující ve vakuu) snižuje teplotní rozdíl mezi tuhnoucím materiálem a okolním práškovým ložem, čímž se snižuje nárůst napětí.
- Chytré strategie podpory: Robustní podpůrné struktury pevně ukotvují díl během sestavování a odolávají deformacím. Podpěry slouží také jako chladiče.
- Tepelné ošetření proti stresu: Jak již bylo uvedeno, jedná se o kritický krok po zpracování, který uvolňuje vnitřní napětí před odstraněním podpěr nebo rozsáhlým obráběním. Specifické protokoly jsou nezbytné, zejména pro citlivé materiály, jako je Invar.
- Odstranění podpůrné konstrukce:
- Výzva: Podpěry jsou nezbytné, ale musí být odstraněny čistě, aniž by došlo k poškození dílu. Přístup k podpěrám ve složitých vnitřních geometriích nebo jemných mřížkových strukturách může být velmi obtížný. Neúplné odstranění zanechává nežádoucí materiál, zatímco agresivní odstranění může poškodit funkční povrchy.
- Zmírnění:
- DfAM pro minimalizaci podpory: Orientace dílu a použití samonosných úhlů (>45°) výrazně snižuje potřebu podpěr. Pomáhá i navrhování prvků, jako jsou zkosení místo ostrých převisů.
- Optimalizovaný design podpory: Použití snadno odstranitelných typů podpěr (např. tenká rozhraní, perforované struktury), zajištění dostatečných vzdáleností pro nástroje a zvážení způsobu odstranění (ruční, elektroerozivní, obrábění) ve fázi návrhu.
- Pokročilé techniky odstraňování: Použití drátového elektroerozivního obrábění pro složité nebo těžko přístupné podpěry umožňuje přesné odstranění s minimálním zatížením dílu.
- Výběr materiálu: Z některých materiálů se podpěry odstraňují snadněji než z jiných.
- Pórovitost (plyn a nedostatek fúze):
- Výzva: V tištěném materiálu se někdy mohou vytvořit malé dutiny nebo póry. Plynové póry vznikají v důsledku plynu zachyceného v prášku nebo rozpuštěného v bazénu taveniny. K pórovitosti při nedostatečném roztavení dochází, když energie laseru/ paprsku není dostatečná k úplnému roztavení a spojení sousedních stop taveniny nebo vrstev. Pórovitost zhoršuje mechanické vlastnosti (zejména únavovou pevnost) a může být škodlivá pro integritu přesného držáku.
- Zmírnění:
- Vysoce kvalitní prášek: Základem je použití vysoce kvalitních, plynem atomizovaných sférických prášků s nízkou vnitřní pórovitostí a kontrolovanou distribucí velikosti částic. Zaměření společnosti Met3dp’na pokročilou výrobu prášků pomocí technologií plynové atomizace a PREP na to přímo reaguje a usiluje o prášky s vysokou sféricitou, dobrou tekutostí a nízkým obsahem satelitů, což podporuje husté balení a konzistentní tavení.
- Optimalizované parametry procesu: Vývoj a přísná kontrola parametrů (výkon, rychlost, rozteč šraf, tloušťka vrstvy) specifických pro materiál a stroj zajišťuje úplné roztavení a tavení.
- Řízená atmosféra: Udržování vysoce čisté atmosféry inertního plynu (argonu nebo dusíku) v konstrukční komoře minimalizuje oxidaci a zachycování plynů během tisku.
- Izostatické lisování za tepla (HIP): Nejúčinnější způsob, jak odstranit zbývající vnitřní pórovitost a zhutnit díl na téměř 100 % teoretické hustoty. Často povinné pro kritické aplikace.
- Omezení povrchové úpravy:
- Výzva: Jak již bylo uvedeno, povrch po vytištění je ze své podstaty drsnější než povrch po obrábění. I když je pro některé aplikace přijatelná, často je nedostatečná pro styčné plochy, těsnicí rozhraní nebo uchycení optických součástí, které vyžadují hladkost pro vyrovnání nebo nízké tření.
- Zmírnění:
- Orientační strategie: Optimální umístění kritických povrchů při plánování stavby (směrem nahoru, vertikálně).
- Optimalizace parametrů: Jemnější prášky a tenčí vrstvy mohou někdy přinést o něco lepší povrchovou úpravu, často na úkor rychlosti vytváření. Strategie skenování obrysů mohou také zlepšit povrchovou úpravu bočnic.
- Cílené následné zpracování: Přijmout povrchovou úpravu v podobě, v jaké byla vytištěna, pokud je to možné, a plánovat specifické dokončovací operace (obrábění, leštění, otryskávání kuličkami, elektrolytické leštění) pouze na plochách, kde je z funkčního hlediska požadována lepší povrchová úprava.
- Anizotropie (vlastnosti závislé na směru):
- Výzva: Vzhledem k procesu vytváření vrstev a sloupcovitému růstu zrn, který je často pozorován podél směru vytváření (osa Z), se mechanické vlastnosti (např. pevnost, tažnost) dílů AM mohou někdy lišit v závislosti na tom, zda jsou měřeny rovnoběžně nebo kolmo na směr vytváření. Tuto anizotropii je třeba brát v úvahu, zejména u montáží vystavených specifickým směrům zatížení.
- Zmírnění:
- Zohlednění orientace na stavbu: Sladění kritické dráhy zatížení v aplikaci s nejvýhodnější orientací sestavení (často rovina XY nebo 45 stupňů), pokud je pro zvolený materiál/proces významná anizotropie.
- Tepelné zpracování: Určité tepelné zpracování může pomoci homogenizovat mikrostrukturu a snížit stupeň anizotropie.
- Výběr procesu: Některé procesy (jako například SEBM s vysokou teplotou sestavení) mohou mít za následek méně výraznou anizotropii ve srovnání s jinými.
- Charakteristika materiálu: Spoléhání se na údaje dodavatele nebo provádění testů, které umožňují pochopit anizotropní chování konkrétního materiálu zpracovávaného zvolenou metodou AM.
- Správa prášku a manipulace s ním:
- Výzva: Kovové prášky mohou být reaktivní, nebezpečné (riziko vdechnutí) a vyžadují pečlivou manipulaci, skladování a sledovatelnost, zejména v regulovaných odvětvích, jako je letecký průmysl a zdravotnictví. Zajištění kvality prášku a zabránění křížové kontaminaci mezi různými materiály je velmi důležité.
- Zmírnění:
- Přísné protokoly: Zavedení přísných postupů pro manipulaci s práškem, prosévání, míchání, skladování (např. v řízené atmosféře) a sledovatelnost (sledování šarží).
- Vyhrazené vybavení: Používání samostatných zařízení (např. sít, stavebních modulů) pro různé typy materiálů, aby se zabránilo křížové kontaminaci.
- Kontrola kvality dodavatele: Spolupráce s renomovanými dodavateli prášků, jako je Met3dp, kteří poskytují certifikované materiály s dokumentovanou kontrolou kvality, zajišťuje spolehlivý výchozí bod.
Úspěšné zvládnutí těchto výzev vyžaduje kombinaci důkladných postupů DfAM, hluboké znalosti vědy o materiálech, pečlivou kontrolu procesů během tisku, vhodné techniky následného zpracování a důsledné zajištění kvality. Spolupráce se zkušeným poskytovatelem služeb v oblasti kovové AM, který má prokazatelné zkušenosti s výrobou vysoce přesných komponent, disponuje moderním vybavením a udržuje přísné systémy řízení kvality, je často nejefektivnějším způsobem, jak zmírnit rizika a zajistit úspěšnou výrobu spolehlivých a vysoce výkonných držáků přístrojů.
Výběr partnera pro Metal AM: Výběr správného dodavatele přesných přístrojových montáží
Úspěch vašeho projektu přesné montáže přístrojů do značné míry závisí na schopnostech, odborných znalostech a standardech kvality vybraného poskytovatele služeb aditivní výroby kovů. Ne všechny kanceláře AM jsou si rovny, zejména pokud se zabývají přísnými požadavky na vysoce přesné součásti a specializované materiály, jako je Invar. Učinit informované rozhodnutí vyžaduje vyhodnotit potenciální partnery podle několika klíčových kritérií. Manažeři nákupu a technické týmy by měli během tohoto procesu výběru dodavatele B2B úzce spolupracovat.
Klíčová kritéria pro hodnocení poskytovatelů služeb AM v oblasti kovů:
- Technická odbornost a poradenství:
- Porozumění aplikaci: Rozumí poskytovatel specifickým výzvám a požadavkům na přesné přístrojové držáky (např. stabilita, vyrovnání, tepelné řízení, vibrace)?
- Podpora DfAM: Nabízejí konzultační služby v oblasti návrhu, které vám pomohou optimalizovat návrh držáku pro aditivní výrobu? Mohou poskytnout odborné poradenství ohledně optimalizace topologie, podpůrných strategií, rozlišení prvků a odstraňování prášku pro složité geometrie?
- Znalosti z oblasti materiálových věd: Mají hluboké znalosti požadovaných materiálů, zejména specializovaných slitin, jako je Invar (FeNi36)? Rozumí nuancím zpracování těchto materiálů a potřebným tepelným úpravám pro dosažení požadovaných vlastností (např. nízké CTE)?
- Řešení problémů: Mají zkušenosti s řešením složitých výrobních problémů souvisejících s přesnými díly AM?
- Technologie, vybavení a schopnosti:
- Příslušné procesy AM: Používají vhodnou technologii AM pro vaše potřeby? Laserová fúze v práškovém loži (LPBF/SLM) je běžná pro vysoké rozlišení, zatímco selektivní tavení elektronovým svazkem (SEBM) nabízí výhody, jako je nižší zbytkové napětí a vhodnost pro některé reaktivní materiály, často upřednostňované pro lékařské a letecké aplikace. Například společnost Met3dp se specializuje na tiskárny SEBM spolu s pokročilou výrobou prášků.
- Machine Park: Jaká je velikost, stáří a stav údržby jejich strojového parku? Mají dostatečnou kapacitu? Jsou jejich stroje řádně kalibrovány a udržovány, aby dosahovaly konzistentních výsledků?
- Kontrola kvality prášku: Jak řídí a kvalifikují své kovové prášky? Používají vysoce kvalitní prášky z renomovaných zdrojů nebo si vyrábějí vlastní s přísnou kontrolou kvality? Ptejte se na získávání prášků, testování (např. chemie, distribuce velikosti částic, morfologie, tekutost), manipulaci, skladování a sledovatelnost. Významnou výhodou je zde důraz společnosti Met3dp’na vlastní výrobu prášků pomocí pokročilých technologií plynové atomizace a PREP, které zajišťují kontrolu nad tímto kritickým vstupním materiálem.
- Vlastní následné zpracování: Jaké mají vlastní kapacity pro následné zpracování (např. pece pro tepelné zpracování, CNC obráběcí centra, zařízení pro povrchovou úpravu, metrologické laboratoře)? Spoléhání se na subdodavatele třetích stran v kritických krocích může někdy přinést zpoždění nebo problémy s kontrolou kvality. Poskytovatel s integrovanými kapacitami často nabízí lepší kontrolu a potenciálně rychlejší realizaci.
- Portfolio materiálů a odbornost:
- Potřebné materiály: Zpracovávají běžně specifické materiály potřebné pro vaši montáž (např. nerezová ocel 316L, Invar)?
- Zkušenosti: Kolik úspěšných projektů s použitím těchto konkrétních materiálů dokončili? Mohou poskytnout katalogové listy materiálů založené na jejich skutečných procesních parametrech a testování?
- Vývoj nových materiálů: Jsou schopni v případě potřeby pracovat s méně běžnými nebo nestandardními slitinami nebo vyvinout jejich parametry?
- Systém řízení kvality (QMS) a certifikace:
- ISO 9001: Jedná se o základní certifikaci systému řízení kvality, která označuje zdokumentované procesy a závazek ke kvalitě.
- Certifikace specifické pro dané odvětví: V závislosti na vašem použití hledejte příslušné certifikáty:
- AS9100: Norma řízení kvality v letectví a kosmonautice.
- ISO 13485: Norma pro řízení kvality zdravotnických prostředků.
- Řízení a monitorování procesů: Jaká opatření přijímají k monitorování a řízení procesu tisku v reálném čase? Jak zajišťují konzistenci mezi jednotlivými sestavami a stroji?
- Kontrola a testování: Jaké metrologické vybavení (souřadnicové měřicí stroje, skenery) a metody nedestruktivního zkoušení (např. CT skenování, penetrační barvení) používají? Odpovídají jejich kontrolní schopnosti požadavkům na přesnost vašeho upevnění?
- Sledovatelnost: Dokáží zajistit úplnou sledovatelnost materiálů, procesních parametrů a kontrol kvality v celém výrobním procesu?
- Dosavadní výsledky, případové studie a reference:
- Osvědčené zkušenosti: Požádejte o příklady minulých projektů s podobnou přesností, složitostí nebo materiály. Cenným ukazatelem jsou případové studie, které prokazují úspěšné výsledky.
- Reference zákazníků: Rozhovor se stávajícími zákazníky, zejména těmi z podobných odvětví nebo se srovnatelnými aplikacemi, může poskytnout upřímné informace o výkonu, spolehlivosti a komunikaci poskytovatele.
- Kapacita, doba realizace a škálovatelnost:
- Objem projektu: Zvládnou požadovaný objem výroby, ať už se jedná o prototypy, malé série nebo případně větší sériovou výrobu?
- Citovaná doba vedení: Jsou jimi uváděné dodací lhůty realistické a konkurenceschopné? Jak zvládají plánování výroby a případná úzká místa (zejména při následném zpracování)?
- Škálovatelnost: Pokud vaše potřeby porostou, dokáží podle toho rozšířit výrobu?
- Komunikace, spolupráce a podpora:
- Reakce: Jak rychle a efektivně reagují na dotazy a žádosti o cenovou nabídku?
- Transparentnost: Mluví otevřeně o svých procesech, schopnostech a možných problémech?
- Spolupráce: Podporují přístup založený na spolupráci a spolupracují s vaším týmem inženýrů na dosažení nejlepšího možného výsledku?
- Zákaznická podpora: Jakou úroveň technické podpory nabízejí před projektem, v jeho průběhu a po něm?
Shrnutí kontrolního seznamu pro výběr dodavatele:
Kritéria | Klíčové otázky |
---|---|
Technické znalosti | Rozumějí přesným montážím? Nabízejí podporu DfAM? Znáte nuance Invar/316L? |
Technologie a vybavení | Vhodný proces AM (LPBF/SEBM)? Kvalita/kapacita stroje? Robustní kontrola kvality prášku (jako Met3dp)? Vlastní následné zpracování? |
Materiálové schopnosti | Nabídka požadovaných slitin? Máte s nimi prokazatelné zkušenosti? Poskytujete spolehlivé údaje o materiálu? |
Systém kvality & Certifikáty | Certifikát ISO 9001? AS9100/ISO 13485, pokud je to nutné? Silné řízení procesů? Pokročilé možnosti kontroly/NDT? Plná sledovatelnost? |
Záznamy o činnosti & Reference | Jsou k dispozici relevantní případové studie? Pozitivní reference zákazníků? |
Kapacita, doba realizace, měřítko | Zvládne požadovaný objem? Reálné dodací lhůty? Schopnost škálování? |
Komunikace & amp; Podpora | Reaguje? Transparentní? Spolupracující? Dobrá technická podpora? |
Export do archů
Výběr správného partnera v oblasti AM kovů je strategickým rozhodnutím. Důkladné prověření potenciálních dodavatelů podle těchto kritérií výrazně zvýší pravděpodobnost, že obdržíte vysoce kvalitní a spolehlivé přesné držáky přístrojů, které splní vaše specifikace, budou dodány včas a v rámci rozpočtu. Hledejte partnery, jako jsou např Met3dp kteří se vyznačují komplexním přístupem, kombinujícím pokročilou tiskovou technologii, vynikající kvalitu materiálu a hluboké zkušenosti s aplikacemi.
Úvahy o nákladech a dodací lhůty pro 3D tištěné držáky přístrojů
Pochopení faktorů, které určují náklady a dobu realizace aditivní výroby kovů, je zásadní pro plánování projektů, sestavování rozpočtů a porovnávání AM s tradičními výrobními metodami. Ačkoli AM nabízí jedinečné výhody, její struktura nákladů a výrobní lhůty se výrazně liší od CNC obrábění nebo odlévání.
Faktory ovlivňující náklady na AM kovů:
Konečná cena 3D tištěného držáku přesných přístrojů je ovlivněna složitou souhrou faktorů:
- Typ materiálu a náklady:
- Hlavním faktorem jsou náklady na práškové suroviny. Specializované slitiny, jako je Invar, jsou na kilogram výrazně dražší než běžné materiály, jako je nerezová ocel 316L. Také titanové slitiny a superslitiny mají vyšší ceny.
- Kvalita prášku (kulovitost, čistota, distribuce velikosti částic) má také vliv na náklady, ale vyšší kvalita často vede k lepším výsledkům tisku a potenciálně k menšímu množství odpadu nebo k menšímu počtu poruch.
- Objem a hmotnost části:
- Přímo určuje množství spotřebovaného drahého kovového prášku. Větší a hustší díly jsou přirozeně dražší.
- Techniky DfAM, jako je optimalizace topologie a mřížkové struktury, jsou klíčem k minimalizaci objemu při současném splnění požadavků na výkon, čímž se přímo snižují náklady na materiál.
- Část Složitost a geometrie:
- Zatímco AM si se složitostí poradí dobře, velmi složité návrhy mohou vyžadovat složitější podpůrné struktury nebo delší dobu tisku kvůli složitým skenovacím drahám.
- Snadné odstraňování prášku z vnitřních kanálků hraje také roli; konstrukce vyžadující rozsáhlé ruční odstraňování prášku zvyšují náklady na pracovní sílu.
- Velikost a orientace ohraničujícího rámečku části:
- Celkové rozměry (délka x šířka x výška) určují, kolik místa zabere díl v konstrukční komoře. Větší díly využívají větší kapacitu stroje a potenciálně vyžadují delší dobu sestavování, což zvyšuje náklady na jeden díl.
- Výška sestavy (rozměr Z) je často nejvýznamnějším faktorem ovlivňujícím dobu tisku, protože stroj musí zpracovávat jednotlivé vrstvy postupně. Optimalizace orientace za účelem minimalizace výšky může někdy snížit náklady.
- Objem a složitost struktury podpory:
- Podpěry spotřebovávají materiál (zvyšují náklady) a vyžadují čas a práci na odstranění (zvyšují náklady na následné zpracování). Konstrukce minimalizující potřebu podpěr jsou nákladově efektivnější.
- Čas stroje (čas sestavení):
- Vypočítá se na základě počtu vrstev, skenované plochy na vrstvu, zvolené strategie skenování a provozních parametrů stroje. Delší doba sestavení znamená vyšší náklady na využití stroje.
- Vliv na to mají faktory jako tloušťka vrstvy (tenčí vrstvy = lepší rozlišení, ale delší čas), výkon laseru/paprsku a rychlost skenování.
- Požadavky na následné zpracování:
- To může být velmi významné část celkových nákladů, které někdy převyšují samotné náklady na tisk. Každý krok zvyšuje náklady na pracovní sílu, strojní čas a případně i náklady na specializované nástroje:
- Odstraňování napětí / tepelné zpracování (čas, energie, specializované cykly pro Invar).
- Odstranění podpory (práce, nástroje, případně čas strávený elektroerozivním obráběním).
- HIP (drahé specializované vybavení a dlouhé časy cyklů).
- CNC obrábění (programování, seřizování, strojní čas, nástroje - zejména pro tvrdé materiály nebo přísné tolerance).
- Povrchová úprava (tryskání, bubnování, leštění, práce/média/zařízení).
- Povlakování/pokovování (materiály, doba zpracování).
- To může být velmi významné část celkových nákladů, které někdy převyšují samotné náklady na tisk. Každý krok zvyšuje náklady na pracovní sílu, strojní čas a případně i náklady na specializované nástroje:
- Množství (velikost dávky):
- AM má relativně nízké náklady na zřízení ve srovnání s nástroji pro odlévání nebo vstřikování. Stále však existují seřizovací úkony (příprava sestavy, nastavení stroje). Náklady na jeden díl se obecně snižují s většími velikostmi dávek, protože náklady na nastavení se amortizují a konstrukční komory mohou být potenciálně vnořeny s více díly. Úspory z rozsahu jsou však obvykle méně dramatické než u metod hromadné výroby.
- Zajištění kvality a kontrola:
- Základní rozměrové kontroly jsou standardní. Požadavky na rozsáhlé protokoly ze souřadnicových měřicích strojů, nedestruktivní zkoušení (např. CT), certifikační zkoušky materiálu nebo podrobnou dokumentaci však zvyšují náklady na práci a vybavení.
Úvahy o době realizace:
Dodací lhůta je celková doba od zadání objednávky do dodání dílu. V případě AM se skládá z několika fází:
- Předzpracování (1-3 dny):
- Kontrola objednávky, příprava souboru CAD, simulace sestavení (volitelně), generování souboru sestavení, plánování výroby.
- Tisk (doba výroby) (1-7+ dní):
- Velmi variabilní v závislosti na velikosti dílu (zejména na výšce), složitosti, množství (vnoření) a zvolených parametrech. Malý držák se může vytisknout přes noc, velký a složitý držák nebo celá stavební deska mohou trvat několik dní až týden.
- Následné zpracování (3 dny – 2+ týdny):
- To často představuje nejdelší a nejproměnlivější část doby přípravy. Každý krok přidává čas:
- Chlazení a odprášení: ~0,5-1 den.
- Úleva od stresu: ~1-2 dny (včetně doby pece a řízeného chlazení).
- Stavební deska/odstranění podpory: ~0,5-2 dny (v závislosti na složitosti a metodě).
- HIP: ~2-4 dny (včetně přepravy do/z zařízení HIP, pokud se nejedná o vlastní zařízení).
- Obrábění: ~2-10+ dní (v závislosti na složitosti, počtu prvků, vytížení dílny).
- Povrchová úprava/povlak: ~1-5 dní.
- Kontrola: ~0,5-1 den.
- To často představuje nejdelší a nejproměnlivější část doby přípravy. Každý krok přidává čas:
- Doprava (1-5 dní):
- Záleží na lokalitě a způsobu dopravy.
Celková odhadovaná doba realizace:
- Prototypy (jednoduché, minimální následné zpracování): ~5-10 pracovních dnů.
- Prototypy/malý objem (složité, vyžadující obrábění/tepelnou úpravu): ~2-4 týdny.
- Výrobní šarže: ~3-6+ týdnů (v závislosti na množství a složitosti následného zpracování).
Srovnání doby přípravy AM vs. obrábění:
- Komplexní, nízký objem: AM je často podstatně rychlejší než obrábění z polotovarů, protože se vyhýbá složitému programování, vícenásobnému nastavování a potenciálně i výrobě vlastních nástrojů.
- Jednoduchý, velký objem: CNC obrábění může být po nastavení rychlejší, zejména pokud lze na výkonných strojích současně obrábět více dílů.
- Klíčový faktor: Rozsah následného obrábění, které je nutné pro díl AM, významně ovlivňuje srovnání celkové doby přípravy. Pokud díl AM vyžaduje rozsáhlé obrábění, může se výhoda doby přípravy snížit.
Klíčový závěr pro zadávání veřejných zakázek a inženýrskou činnost:
Získání přesné nabídky vyžaduje poskytnutí podrobných modelů CAD, jasných specifikací (materiál, tolerance, povrchová úprava, požadované certifikace) a požadovaného množství. Včas se spojte s potenciálními dodavateli a prodiskutujte s nimi možnosti DfAM, které mohou snížit náklady i dobu realizace. Uvědomte si, že následné zpracování je často hlavním faktorem ovlivňujícím náklady i dodací lhůty u vysoce přesných kovových komponent AM.
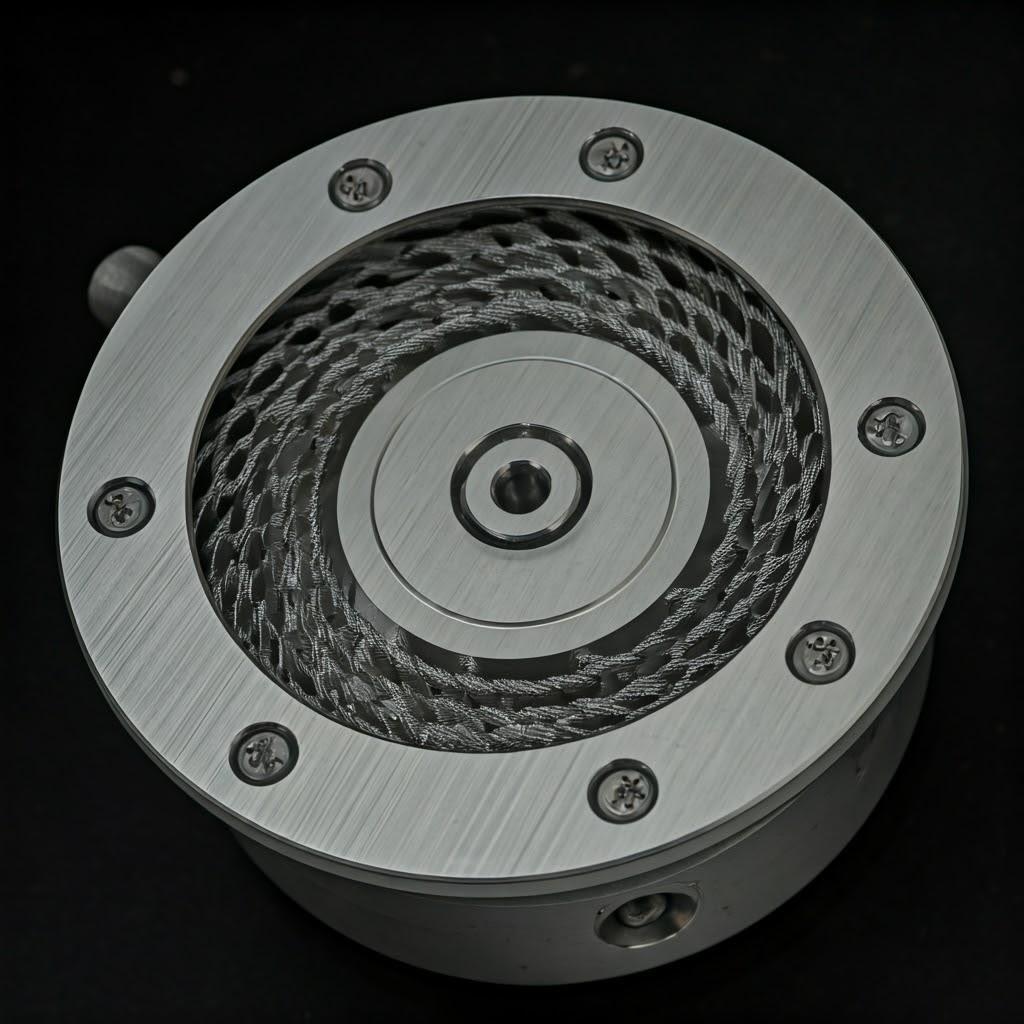
Často kladené otázky (FAQ) o 3D tištěných držácích na přístroje
Zde jsou odpovědi na některé časté otázky, které mají konstruktéři a manažeři nákupu, když zvažují aditivní výrobu kovů pro přesné držáky přístrojů:
Otázka 1: Jaká je cena kovového 3D tištěného držáku na přístroje ve srovnání s držákem obráběným na CNC stroji?
A: Neexistuje jediná odpověď, protože záleží na několika faktorech:
- Složitost: U velmi složitých geometrií (vnitřní kanály, optimalizace topologie, mřížkové struktury), které je obtížné nebo nemožné obrábět, je AM často nákladově efektivnější, a to i při malých objemech. Obrábění takových dílů může vyžadovat několik složitých nastavení nebo výrobu a montáž více kusů, což zvyšuje náklady.
- Objem: U jednoduchých geometrií vyráběných ve velkých objemech je CNC obrábění obvykle nákladově efektivnější díky zavedené automatizaci a rychlejším časům cyklů po nastavení. AM má nižší náklady na nastavení, takže je konkurenceschopná pro prototypy a nízkoobjemové výrobní série (typicky 1-100 dílů).
- Materiál: U drahých materiálů, jako je Invar, které se obtížně obrábějí (což vede k vysokému opotřebení nástrojů a pomalým rychlostem) a při subtraktivních procesech vytvářejí značný odpad, může být AM konkurenceschopnější díky lepšímu využití materiálu (nižšímu poměru nákupu a letu), a to i v případě, že náklady na surový prášek jsou vysoké.
- Konsolidace částí: Pokud AM umožňuje sloučit více obráběných dílů do jediné tištěné součásti, může být díl vyrobený AM levnější, pokud vezmeme v úvahu celkové náklady (cena dílu + montážní práce + snížené riziko chyby při montáži).
- Následné zpracování: Pokud díl AM vyžaduje rozsáhlé dodatečné obrábění, aby byly dodrženy tolerance, výrazně to zvyšuje náklady, takže CNC obrábění od začátku je potenciálně výhodnější, pokud to geometrie umožňuje.
- Doporučení: Pro informované rozhodnutí si nechte vypracovat cenové nabídky pro obě metody na základě konkrétní konstrukce, materiálu, množství a požadavků na tolerance. Zvažte celkové náklady na životní cyklus, včetně flexibility konstrukce a potenciálního zvýšení výkonu díky AM.
Otázka 2: Jakou úroveň přesnosti a tepelné stability mohu reálně očekávat od 3D tištěného držáku Invar?
A:
- Přesnost: Rozměrové tolerance po vytištění se u Invaru obvykle pohybují v rozmezí ±0,1 mm až ±0,2 mm nebo ±0,1-0,2 %. Kvalita povrchu (Ra) se může pohybovat kolem 10-25 μm (LPBF). Pro dosažení tolerancí na mikronové úrovni ($ \pm 0,01 – 0,05$ mm nebo lepších) a hladké povrchové úpravy (Ra <1,6μm), které jsou obvykle vyžadovány pro kritické zarovnávací prvky na přesných optických nebo metrologických držácích, je nezbytné následné opracování těchto specifických prvků.
- Tepelná stabilita: To je klíčová výhoda společnosti Invar. Při správném zpracování (včetně vhodného odlehčení napětí a stabilizačních tepelných úprav po tisku) si 3D tisk Invaru zachovává extrémně nízký koeficient tepelné roztažnosti (CTE), který se při pokojové teplotě pohybuje obvykle kolem 1,2×10-6/K. To zajišťuje minimální změny rozměrů při kolísání teploty, což je rozhodující pro zachování souososti v citlivých systémech. Pro zajištění této vlastnosti je zásadní spolupracovat s dodavatelem, který má zkušenosti se zpracováním a tepelným zpracováním materiálu Invar.
Otázka 3: Jsou 3D tištěné kovové díly stejně pevné a spolehlivé jako komponenty vyrobené z tradičních kovaných nebo litých materiálů?
A: Ano, potenciálně. Při dokonalé kontrole procesu a vhodném následném zpracování mohou kovové díly AM vykazovat vynikající mechanické vlastnosti:
- Hustota: Techniky jako LPBF a SEBM mohou při optimalizaci dosáhnout hustoty dílů >99,5 %, někdy až >99,9 % relativní hustoty, srovnatelné s litými nebo tepanými materiály.
- Pevnost & tažnost: Vlastnosti vytištěných dílů se někdy vyrovnají nebo dokonce předčí vlastnosti odlitých ekvivalentů. Díky následnému zpracování, jako je lisování za tepla (HIP), které eliminuje vnitřní pórovitost, a vhodnému tepelnému zpracování mohou mechanické vlastnosti (mez kluzu, mez pevnosti v tahu, prodloužení, únavová pevnost) dílů AM často odpovídat standardním specifikacím pro tepané materiály, nebo je dokonce překračovat, zejména u některých slitin, jako je titan.
- Spolehlivost: Klíčem je důslednost. Spolupráce s renomovaným dodavatelem AM, který používá vysoce kvalitní prášek, udržuje přísnou kontrolu procesu, provádí nezbytné NDT a může poskytnout certifikace materiálů a údaje o zkouškách, je klíčová pro zajištění spolehlivosti potřebné pro kritické aplikace, jako jsou držáky přístrojů. U náročných aplikací by měly být vlastnosti vždy ověřeny testováním, které odráží provozní podmínky.
Otázka 4: Jak zajistit kvalitu a konzistenci 3D tištěných držáků, zejména pro kritické aplikace vyžadující certifikaci?
A: Zajištění kvality vyžaduje mnohostranný přístup v celém dodavatelském řetězci:
- Výběr dodavatele: Vyberte si poskytovatele s robustním systémem řízení kvality (QMS), ideálně certifikovaným podle normy ISO 9001 a případně AS9100 (letecký průmysl) nebo ISO 13485 (zdravotnictví). Ověřte si jeho zkušenosti s vaším konkrétním materiálem a typem aplikace.
- Kontrola materiálu: Trvejte na použití prášku z renomovaných zdrojů s možností sledování šarží a certifikací materiálu podle příslušných norem (ASTM, ISO, AMS). Seznamte se s postupy dodavatele při manipulaci s práškem a jeho recyklaci.
- Řízení procesu: Ujistěte se, že poskytovatel používá stroje s možností monitorování procesu a udržuje přísnou kontrolu kritických procesních parametrů, dokumentovanou pro každou sestavu.
- Čiré specifikace: Poskytněte podrobné výkresy s jednoznačnými tolerancemi, požadavky na povrchovou úpravu (s uvedením, které povrchy je třeba dokončit), požadované následné zpracování (tepelné úpravy, HIP) a případné požadavky na NDT.
- Ověřování po zpracování: Zajistěte správné provedení všech požadovaných kroků následného zpracování (např. ověření cyklů tepelného zpracování).
- Kontrola a testování: Definujte požadovanou úroveň kontroly (např. protokoly z CMM pro kritické rozměry, měření drsnosti povrchu) a NDT (např. CT skenování pro vnitřní integritu, penetrační barvivo pro povrchové vady). Vyžádejte si závěrečné kontrolní zprávy.
- Dokumentace: Vyžadujte komplexní dokumentaci, včetně certifikace materiálu, protokolů o sestavení (pokud jsou k dispozici/schváleny), záznamů o tepelném zpracování, kontrolních zpráv a certifikátů o shodě.
Závěr: Vylepšete své přístroje pomocí pokročilé aditivní výroby kovů
V náročných oblastech letectví, lékařské techniky, metrologie a pokročilé průmyslové automatizace je snaha o vyšší přesnost, vyšší výkon a větší flexibilitu konstrukce neúprosná. Přesné držáky přístrojů, ačkoli jsou často přehlíženy, jsou základním faktorem pokroku v těchto oblastech. Jak jsme již prozkoumali, aditivní výroba kovů nabízí změnu paradigmatu v navrhování a výrobě těchto kritických součástí.
Překročením omezení tradičního obrábění umožňuje AM technologie inženýrům vytvářet držáky přístrojů, které jsou:
- Geometricky optimalizované: Využití optimalizace topologie a generativního návrhu pro bezkonkurenční poměr tuhosti a hmotnosti.
- Funkčně integrované: Zahrnuje prvky, jako je konformní chlazení, struktury tlumící vibrace a konsolidované sestavy přímo do držáku.
- Lehké: Drastické snížení hmotnosti pro aplikace, kde je hmotnost kritická, aniž by byla obětována stabilita.
- Materiálně pokročilé: Umožňuje efektivní použití specializovaných slitin, jako je Invar s nízkou roztažností pro maximální tepelnou stabilitu nebo korozivzdorný 316L pro drsné prostředí.
- Rychle vytvořený prototyp a přizpůsobený: Urychlení vývojových cyklů a umožnění řešení na míru pro specifické potřeby přístrojů.
Úspěšné využití těchto výhod vyžaduje komplexní přístup, který zahrnuje přísné zásady návrhu pro aditivní výrobu (DfAM), jasné pochopení dosažitelné přesnosti a nezbytných kroků následného zpracování a pečlivou pozornost věnovanou potenciálním problémům, jako je zbytkové napětí a pórovitost. Kriticky důležité je, že vyžaduje partnerství se znalým a schopným poskytovatelem služeb v oblasti AM obrábění kovů.
Výběr dodavatele, jako je Met3dp, která kombinuje desítky let společných zkušeností s nejmodernějšími technologiemi - od pokročilých tiskových systémů SEBM známých svou přesností a spolehlivostí až po vlastní výrobu vysoce kvalitních sférických kovových prášků - zajišťuje základ kvality a schopností. Společnost Met3dp poskytuje komplexní 3d tisk kovů řešení, zahrnující zařízení, materiály a služby vývoje aplikací, a spolupracuje s organizacemi na urychlení zavádění aditivní výroby.
Využitím technologie AM pro zpracování kovů mohou společnosti nejen zlepšit výkon a spolehlivost svých současných přístrojů, ale také odemknout zcela nové možnosti v oblasti konstrukce a možností zařízení. Ať už potřebujete výjimečnou tepelnou stabilitu materiálu Invar pro optické systémy, biokompatibilitu a odolnost proti korozi materiálu 316L pro lékařské přístroje nebo topologicky optimalizované lehké konstrukce pro letecké senzory, aditivní výroba kovů poskytuje nástroje, které vaše přístroje povýší na vyšší úroveň.
Jste připraveni prozkoumat, jak může aditivní výroba kovů přinést revoluci v řešeních pro přesnou montáž přístrojů? Kontaktujte společnost Met3dp ještě dnes, abyste s naším týmem odborníků prodiskutovali požadavky na vaši aplikaci a zjistili, jak mohou naše pokročilé možnosti podpořit inovace ve vaší organizaci.
Sdílet na
MET3DP Technology Co., LTD je předním poskytovatelem řešení aditivní výroby se sídlem v Qingdao v Číně. Naše společnost se specializuje na zařízení pro 3D tisk a vysoce výkonné kovové prášky pro průmyslové aplikace.
Dotaz k získání nejlepší ceny a přizpůsobeného řešení pro vaše podnikání!
Související články
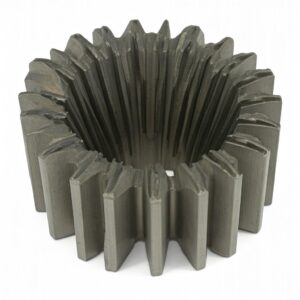
Vysoce výkonné segmenty lopatek trysek: Revoluce v účinnosti turbín díky 3D tisku z kovu
Přečtěte si více "O Met3DP
Nedávná aktualizace
Náš produkt
KONTAKTUJTE NÁS
Nějaké otázky? Pošlete nám zprávu hned teď! Po obdržení vaší zprávy obsloužíme vaši žádost s celým týmem.
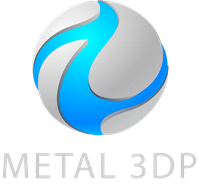
Kovové prášky pro 3D tisk a aditivní výrobu