Úvod do technologie atomizace
Obsah
Technologie atomizace se týká procesů, které mění objemné kapaliny na malé kapičky nebo jemný sprej. Je široce používán v aplikacích, jako je spalování, nátěry, čištění, zvlhčování a další. Tento článek poskytne podrobného průvodce atomizačním zařízením, pracovními principy, aplikacemi, konstrukčními úvahami, výběrem dodavatele, instalací, provozem, údržbou a často kladenými otázkami.
Úvod do technologie atomizace
Atomizace je proces rozbíjení objemných kapalin na jemné kapičky předáním energie. Převádí kapaliny z kontinuálních proudů nebo tlakového toku na rozptýlené mlhy.
Atomizace umožňuje zlepšený kontakt mezi kapalinou a plynem, substrátem nebo jinou nemísitelnou kapalinou. Umožňuje rychlý přenos tepla a hmoty, chemické reakce a změny skupenství.
Některé klíčové výhody atomizační technologie zahrnují:
- Vyšší povrchový kontakt má za následek rychlejší reakce a přenosové procesy
- Lepší míchání a interakce mezi různými fázemi
- Jednotnější úprava a nátěry
- Zlepšené spalování, odpařování, zvlhčování nebo čištění
- Přesná kontrola distribuce velikosti kapiček
Atomizace je široce používána v aplikacích, jako jsou:
- Vstřikování paliva do motorů
- Sušení rozprašováním potravin, chemikálií a léčiv
- Zvlhčování a zamlžování
- Malování a nátěry
- Zemědělské chemické postřiky
- Lékařské nebulizéry
- Dávkovače parfémů
- Hašení požáru
- Čištění odpadních vod
- Čištění spalin
Základní technologie zahrnuje protlačování stlačené kapaliny otvorem trysky vysokou rychlostí. To dodává energii k destabilizaci proudu kapaliny a jeho rozbití na kapičky.
Různé atomizační techniky předávají energii různými způsoby. Klíčové metody jsou:
Typy atomizačních technik
Metoda | Princip |
---|---|
Tlaková atomizace | Protlačování kapaliny tryskou pod vysokým tlakem |
Rotační atomizace | Odstřeďování kapaliny z vysokorychlostního rotačního pohárku nebo disku |
Pneumatická atomizace | Vystavení proudu kapaliny vysokorychlostnímu proudu plynu |
Ultrazvuková atomizace | Použití vysokofrekvenčních zvukových vln k narušení proudu kapaliny |
Elektrostatická atomizace | Aplikace elektrostatického náboje k destabilizaci povrchu kapaliny |
Technika atomizace určuje distribuci velikosti kapiček, vzor spreje, rychlost kapiček a další parametry. Výběr závisí na potřebách aplikace.
Nyní se podívejme na některé hlavní typy atomizačních zařízení a jejich pracovní principy podrobněji.
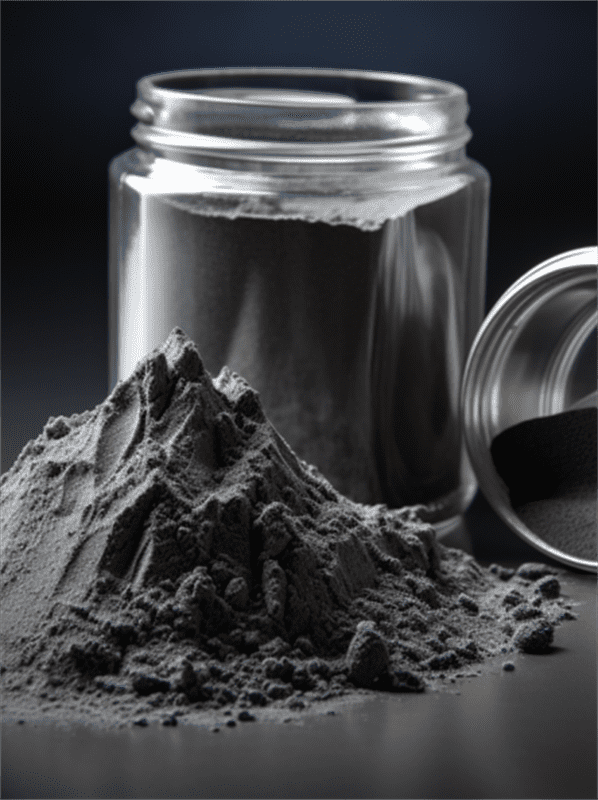
Typy atomizérů
Atomizéry jsou zařízení navržená tak, aby rozmělňovala kapaliny na spreje nebo mlhu. Zde jsou některé běžné typy a jejich klíčové vlastnosti:
Tlakové atomizéry
Typ | Princip | Velikost kapek | Průtok | Tlak | Vzor |
---|---|---|---|---|---|
Tryska s jednoduchým otvorem | Kapalina protlačená malým otvorem | 50-500 um | Nízký | 2-10 bar | Dutý kužel |
Jednokapalinová tryska | Krouživý pohyb před výstupním otvorem | 15-250 μm | Střední | 5-30 bar | Plný kužel |
Dvoukapalinová tryska | Rozprašovací plyn urychluje kapalinu | 5-150 μm | Středně vysoká | 1-10 bar | Plný kužel |
Deflektorová tryska | Dopad kapaliny na deflekční desku | 10-150 μm | Střední | 5-20 bar | Široký plochý sprej |
Vzduchová tryska | Vysokorychlostní vzduch rozbíjí vrstvu kapaliny | 50-400 um | Středně vysoká | 1-5 bar | Plochý ventilátor |
Tlakové rozprašovače, jako jsou rozprašovací trysky a jednokapalinové vířivé trysky, jsou široce používány díky své jednoduché konstrukci a schopnosti pokrýt široké rozsahy proudění. Mohou být navrženy tak, aby produkovaly spreje s různými velikostmi kapek, vzorů a rychlostí.
Rotační atomizéry
Typ | Princip | Velikost kapek | Průtok | Rychlost | Vzor |
---|---|---|---|---|---|
Disk | Kapalina přiváděná do středu, rotuje mimo okraj | 10-75 μm | Nízko-střední | 8 000-35 000 ot./min | Oběžník |
Pohár | Kapalina přiváděná do pohárku, rotuje z okraje | 40-150 um | Středně vysoká | 3 000-15 000 ot./min | Ve tvaru koblihy |
Rotační atomizéry se skládají z rotujících součástí, jako jsou disky nebo kelímky, které odstřeďují kapalinu pomocí odstředivé síly. Dosahují jemných velikostí kapiček vhodných pro aplikace, jako je nanášení sprejem a sušení. Nevýhodou jsou složité požadavky na pohonné systémy.
Pneumatické atomizéry
Typ | Princip | Velikost kapek | Průtok | Rychlost plynu | Vzor |
---|---|---|---|---|---|
Vnitřní mix | Plyn se vnitřně mísí s kapalinou | 10-100 μm | Nízko-střední | 100-250 m/s | Dutý kužel |
Externí mix | Plyn fouká kolmo na kapalinu | 50-400 um | Středně vysoká | 75-100 m/s | Plochý ventilátor |
Tryska na píšťalku | Vysokorychlostní plyn vytváří nízký tlak | 25-75 μm | Nízký | 100-350 m/s | Dutý kužel |
Pneumatické atomizéry využívají hybnost plynu k rozdrcení kapaliny na kapičky. Nabízejí výhody, jako je potřebný nízký tlak kapaliny a zvládají viskozity. Vyžadují však velké objemy stlačeného vzduchu nebo plynu.
Ultrazvukové atomizéry
Typ | Princip | Velikost kapek | Průtok | Frekvence | Vzor |
---|---|---|---|---|---|
Vibrační povrch | Kapalina umístěná na vibrační desce | 5-100 μm | Velmi nízká | 20-200 kHz | Široký rozptyl |
Vibrační tryska | Kapalina prošla vibrační tryskou | 15-150 μm | Velmi nízká | 20-120 kHz | Rozprašovací kužel |
Ultrazvukové atomizéry pracují pomocí vysokofrekvenčních vibrací k destabilizaci toku kapaliny. Mohou dosáhnout velmi jemných velikostí kapiček vhodných pro mlžení a zvlhčování. Ale mají omezenou průtokovou kapacitu.
Pokročilé atomizéry
Některé další pokročilé metody atomizace, jako je elektrostatická atomizace, atomizace ultrazvukovým plynem a efervescentní atomizace, se také používají pro specializované aplikace.
Nyní, když jsme viděli různé typy atomizérů, podívejme se na kritické konstrukční a provozní parametry.
Konstrukční parametry atomizéru
Níže jsou uvedeny některé klíčové parametry, které je třeba vzít v úvahu při výběru a navrhování atomizérů:
Velikost kapek
Klíčový výsledek atomizace. Pro aplikace, jako je povlakování, jsou zapotřebí jemné kapičky pod 100 μm. Větší kapky fungují pro kropení nebo zvlhčování. Dosažitelné velikosti závisí na technologii.
Průtok
Kapacita atomizéru se pohybuje od méně než 1 LPH do více než 50 000 LPH. Přizpůsobte velikost atomizéru potřebám aplikace.
Vzor ve spreji
Dutý kužel, plný kužel, plochý vějíř nebo kruhové vzory. Vyberte tvar vzoru na základě potřeb pokrytí.
Rychlost kapky
Typický rozsah 5 – 100 m/s v závislosti na tlaku a typu atomizéru. Vyšší rychlosti zlepšují přenos hybnosti.
Vlastnosti kapaliny
Viskozita, povrchové napětí a teplota ovlivňují atomizaci. Při výběru atomizéru zohledněte vlastnosti kapaliny.
Provozní tlak
Tlakové atomizéry potřebují vysoký tlak kapaliny 2-30 barů. Nižší tlak potřebný pro pneumatické typy.
Rychlost průtoku plynu
Pneumatické atomizéry vyžadují vysoké průtoky plynu. Rozhodující pro získání požadovaných velikostí kapek.
Rychlost otáčení
Rychlost odstřeďování od 3 000 do 100 000 ot./min pro rotační atomizéry. Vyšší rychlost dává menší kapky.
Spotřeba energie
Důležitý faktor. Tlakové a rotační typy spotřebovávají značnou energii.
Kompatibilita materiálů
Materiály atomizéru musí být kompatibilní s kapalnými chemickými vlastnostmi.
Náklady
Široký sortiment podle typu, velikosti, materiálů. Vyvážit potřeby výkonu a rozpočtu.
Zvažte všechny parametry a vyberte atomizér tak, aby vyhovoval požadavkům aplikace optimálním způsobem.
Aplikace atomizační technologie
Atomizéry se používají v široké řadě průmyslových, komerčních a spotřebitelských aplikací. Zde je několik hlavních příkladů:
Sušení rozprašováním
Přeměňuje kapalná krmiva na sušený prášek atomizací krmiva na horký vzduch. Používá se pro potraviny, chemikálie, léčiva.
aplikace | Použitý atomizér | Velikost kapky | Vzor |
---|---|---|---|
Sušené mléko | Rotary | 40-150 um | Oběžník |
Káva | Tlak | 50-150 um | Plný kužel |
Čisticí prostředek | Rotary | 20-100 μm | Oběžník |
Keramické | Ultrazvukový | 5-20 um | Široký rozptyl |
Spalovací systémy
Atomizéry rozprašují palivo do motorů a kotlů pro lepší míchání a spalování.
aplikace | Použitý atomizér | Velikost kapky | Vzor |
---|---|---|---|
IC motory | Víceotvorová tryska | 15-90 μm | Dutý kužel |
Průmyslové hořáky | Parní tryska | 80-150 μm | Pevný kužel |
Olejové pece | Otočný pohár | 50-200 μm | Kobliha |
Natírání a lakování
Rozprašovače rovnoměrně nanášejí barvy, maziva, lepidla na povrchy.
aplikace | Použitý atomizér | Velikost kapky | Vzor |
---|---|---|---|
Lakování automobilů | Otočný zvonek | 40-90 um | Oběžník |
Povrchová úprava nábytku | Vzduchová stříkací pistole | 80-250 um | Plochý ventilátor |
Lepidla | Ultrazvukový | 10-30 μm | Široký rozptyl |
Mazání stroje | Vnitřní míchací tryska | 50-150 um | Dutý kužel |
Zvlhčování a chlazení
Ultrazvukové a tlakové atomizéry vytvářejí jemnou mlhu pro kontrolu vlhkosti a chlazení.
aplikace | Použitý atomizér | Velikost kapky | Vzor |
---|---|---|---|
Skleníky | Otáčející se disk | 50-100 μm | Oběžník |
datová centra | Ultrazvuková deska | 5-20 um | Široký rozptyl |
Obrábění | Prstencová tryska | 75-150 μm | Pevný kužel |
Zemědělské postřiky
Hydraulické trysky rozprašují pesticidy, hnojiva a další agrochemikálie pro péči o plodiny.
aplikace | Použitý atomizér | Velikost kapky | Vzor |
---|---|---|---|
Vysílací nástřik | Deflektorová tryska | 80-250 um | Plochý ventilátor |
Postřik řádkových plodin | Dvojitá kapalinová tryska | 150-400 um | Dutý kužel |
Sadový postřik | Vířivá komora | 100-250 um | Dutý kužel |
Provzdušňování odpadních vod
Jemné bublinkové difuzory rozprašují vzduch do odpadní vody pro přenos kyslíku během čištění.
aplikace | Použitý atomizér | Velikost bubliny | Vzor |
---|---|---|---|
Nádrž na aktivovaný kal | Ponořená turbína | 1-5 mm | Rozptýlené |
Oxidační příkop | Porézní membrána | 0,5-2 mm | Široký rozptyl |
Provzdušňovaná laguna | Mechanický povrchový provzdušňovač | 3-8 mm | Náhodný |
To ukazuje pozoruhodnou škálu průmyslových odvětví a procesů, které využívají technologii atomizace díky jejím výhodám.
Nyní se podívejme na technické úvahy pro výběr a design atomizéru.
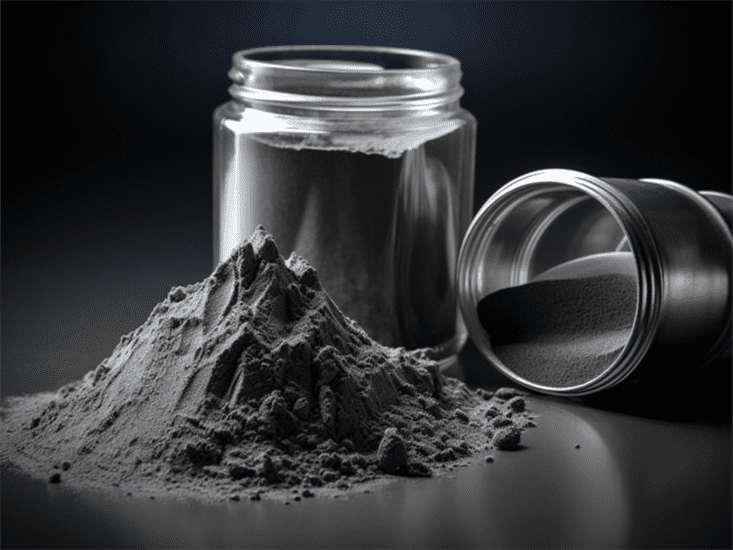
Směrnice inženýrského návrhu
Správný design je klíčem k dosažení optimálního výkonu atomizéru pro danou aplikaci. Zde je několik pokynů:
Distribuce velikosti kapiček
Klíčové kritérium. Vyberte technologii atomizéru na základě požadované cílové velikosti kapky. Použijte měření jako DV10, DV50, DV90.
Vlastnosti kapaliny
Zvažte viskozitu, povrchové napětí, korozivnost a teplotu. Slaďte materiály a provozní podmínky.
Kapacita průtoku
Velikost atomizéru pro zajištění potřebného rozsahu průtoku. Přidejte bezpečnostní rezervu 20-30%.
Krytí sprejem
Zvolte úhel stříkání, vzor a výšku pro dosažení požadovaného pokrytí. Zohledněte překrývání.
Hodnocení tlaku
Rozprašovač a potrubí musí odolat potřebnému tlaku kapaliny a plynu. Přidejte bezpečnostní faktor.
Montážní konfigurace
Uspořádání pro zajištění správného cílení postřiku, odvodnění a dostupnosti pro údržbu.
Provozní kontrola
Nainstalujte přístrojové vybavení pro řízení průtoku, tlaku, rychlosti otáčení a průtoku plynu v provozním rozsahu.
Filtrace kapalin
Nainstalujte filtry k odstranění částic, které by mohly ucpat malé otvory. Zadejte jmenovitou hodnotu 10-25 mikronů.
Přístup ke službě
Umožněte bezpečný přístup k vnitřním součástem vyžadujícím kontrolu nebo výměnu.
Stavební materiály
Vyberte materiály odolné vůči vlastnostem kapaliny a podmínkám prostředí. Zabraňte korozi.
Dodržování těchto pokynů bude mít za následek systém atomizéru optimalizovaný pro špičkový výkon a spolehlivost.
Výběr dodavatele a náklady
Mnoho výrobců nabízí atomizéry přizpůsobené různým aplikacím. Zde jsou pokyny pro výběr a rozpočet:
Přední výrobci atomizérů
Společnost | Umístění | produkty |
---|---|---|
Spraying Systems Co. | USA | Kompletní sortiment trysek |
EXAIR | USA | Trysky na stlačený vzduch |
Lechler | Německo | Tlakové trysky |
Schlick | Německo | Rotační atomizéry |
Düsen-Schlick | Německo | Pneumatické trysky |
Sono-Tek | USA | Ultrazvukové rozprašovače |
Odhadované náklady na atomizér
Typ | Kapacita | Materiály | Cenové rozpětí |
---|---|---|---|
Tlaková tryska | 1–20 GPH | Průmyslová povinnost | $50 – $500 |
Pneumatická tryska | 5 – 100 GPH | Průmyslová povinnost | $100 – $1,000 |
Rotační disk | 5 – 30 GPH | Standard | $2,000 – $5,000 |
Ultrazvukový | 0,1 – 2 GPH | Standard | $1,000 – $3,000 |
- Ceny se liší v závislosti na materiálech, velikostech a specifikacích
- Rozpočet 2-4X pro vysoce propracované návrhy specifické pro konkrétní aplikace
- Přední dodavatelé OEM nabízejí spolehlivý výkon a podporu
Tipy pro výběr dodavatele atomizéru
- Ověřte odborné znalosti a záznamy ve vaší oblasti použití
- Zkontrolujte řadu dostupných konstrukcí trysek a průtokové kapacity
- Zajistěte dostupnost místního prodeje a technické podpory
- Vyžádejte si vzorky pro testování výkonu atomizéru
- Zkontrolujte záruky a záruky životnosti
- Porovnejte ceny mezi 3-5 dodavateli pro rozpočtování
- Upřednostněte kvalitu před nejnižšími náklady, abyste se vyhnuli problémům s údržbou
To poskytuje výchozí bod pro zdroj a rozpočet pro kvalitní atomizéry vhodné pro potřeby vaší aplikace.
Instalace, provoz a údržba
Správná instalace, používání a údržba jsou životně důležité pro optimalizaci výkonu atomizéru, životnosti a bezpečnosti.
Pokyny pro instalaci
- Namontujte bezpečně pomocí hardwaru doporučeného výrobcem
- Věnujte pozornost výšce, orientaci a míření spreje
- Ponechte dostatečný prostor pro proudění vzduchu a rozprašování
- Připojte potrubí kapaliny a plynu bezpečně podle norem
- Nainstalujte filtraci, ventily a přístrojové vybavení podle návrhu
- Před uvedením do provozu zkontrolujte netěsnosti, vibrace, ucpání
Bezpečný provoz
- Pracujte v doporučeném rozsahu tlaku, teploty a zatížení
- V těsné blízkosti používejte ochranné prostředky, jako jsou obličejové štíty
- Ucpané otvory čistěte pouze stlačeným vzduchem nebo měkkým kartáčkem
- Monitorujte průtok, pokles tlaku, vzor stříkání pro případné problémy
- V případě abnormálního hluku nebo silných vibrací okamžitě vypněte
Plán údržby
Aktivita | Frekvence |
---|---|
Zkontrolujte vnější stav | Týdenní |
Zkontrolujte upevnění, připojení | Měsíční |
Vyčistěte vnější povrchy | Čtvrtletně nebo podle potřeby |
Monitorujte filtry, těsnění, těsnění | Čtvrtletně nebo podle OEM |
Zkontrolujte vnitřní průchody | Každoročně |
Vyměňte opotřebované součásti | Při zhoršení výkonu nebo podle OEM |
Skladování a manipulace
- Otvory uzávěru, když se tryska nepoužívá
- Skladujte v čistém a suchém prostředí mimo vibrace
- Zabraňte fyzickému poškození citlivých součástí
Správná instalace v kombinaci se správnými provozními a údržbovými postupy zajistí dlouhý a bezproblémový provoz atomizéru.
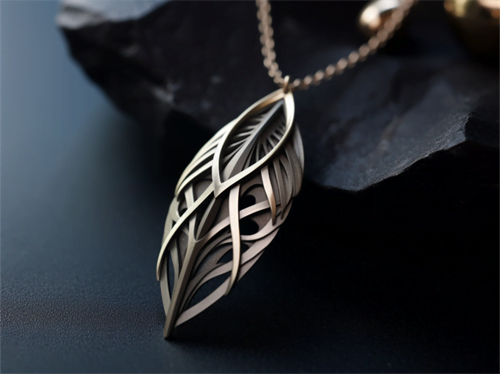
Nejčastější dotazy
Zde jsou odpovědi na některé často kladené otázky týkající se výběru atomizéru a řešení problémů:
Jaké jsou typické důvody špatné atomizace?
- Ucpané nebo opotřebované otvory trysek v důsledku nedostatečné filtrace
- Viskozita kapaliny je pro konstrukci atomizéru příliš vysoká
- Provozní tlak je příliš nízký
- Rychlost rotačního atomizéru je příliš nízká
- Průtok plynu nedostatečný pro pneumatické typy
Jak opravit nerovnoměrné vzory stříkání?
- Vyčistěte nebo vyměňte otvory trysek, pokud jsou ucpané
- Upravte tlak kapaliny a vzduchu v doporučeném rozsahu
- Vyměňte opotřebované součásti trysky
- Ověřte vyrovnání a nastavení podle výrobce
Co způsobuje problémy s ucpáním trysek?
- Nedostatečná filtrace kapalin – instalujte jemnější filtry
- Provoz pod minimálním tlakem – zvyšte tlak
- Nechání atomizované kapaliny zaschnout a uložit se na otvory
Jak snížit provozní hluk atomizéru?
- Zajistěte, aby provozní podmínky odpovídaly specifikacím
- Zkontrolujte, zda nejsou poškozené nebo opotřebované součásti
- Izolujte atomizér pomocí tlumičů a pružných spojů
- Upravte akustické prostředí tak, aby absorbovalo hluk
Jaká údržba pomáhá maximalizovat životnost atomizéru?
- Pravidelně dodržujte doporučené postupy čištění
- Vyměňte filtrační prvky, když se tlakový pokles zvýší
- K čištění používejte měkké kartáče a stlačený vzduch – vyhněte se tvrdým předmětům
- Namažte ložiska a těsnění podle postupů OEM
- Pravidelně kontrolujte opotřebení kritických dílů, jako jsou disky a misky
Kdy je nutné atomizér přestavět nebo vyměnit?
- Pokud jsou otvory silně opotřebované a zvětšují se
- Pokud dojde k poškození povrchů dopadajících na kapalinu, což má vliv na sprej
- Pokud má povrch disku/hrnku viditelné nepravidelnosti nebo vady
- Pokud těsnění netěsní a ložiska jsou opotřebovaná
- Pokud kritické náhradní díly již nejsou k dispozici
Kde najdu výrobce a dodavatele atomizérů?
- Přední společnosti jako Spraying Systems, Schlick, Lechler, EXAIR, Sono-Tek
- Distributoři průmyslových dodávek jako Grainger, McMaster-Carr, WW Grainger
- Online prodejci na platformách jako Alibaba, Made-in-China, globalsources.com
- Místní prodejci ve vašem regionu specializující se na technologii sprejů
Závěr
Atomizace je životně důležitý proces používaný v různých aplikacích napříč průmyslovými odvětvími k přeměně kapalin na spreje a mlhu. Výběr správné technologie atomizéru a designu pro vaše potřeby je zásadní. Tlakové, rotační, pneumatické a ultrazvukové atomizéry mají klady i zápory. Rozsah použití je od sušení rozprašováním přes natírání až po zemědělské postřiky.
Sdílet na
MET3DP Technology Co., LTD je předním poskytovatelem řešení aditivní výroby se sídlem v Qingdao v Číně. Naše společnost se specializuje na zařízení pro 3D tisk a vysoce výkonné kovové prášky pro průmyslové aplikace.
Dotaz k získání nejlepší ceny a přizpůsobeného řešení pro vaše podnikání!
Související články
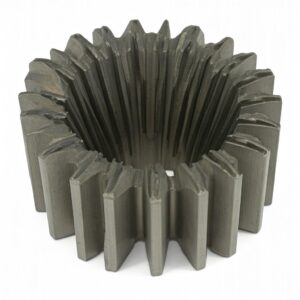
Vysoce výkonné segmenty lopatek trysek: Revoluce v účinnosti turbín díky 3D tisku z kovu
Přečtěte si více "O Met3DP
Nedávná aktualizace
Náš produkt
KONTAKTUJTE NÁS
Nějaké otázky? Pošlete nám zprávu hned teď! Po obdržení vaší zprávy obsloužíme vaši žádost s celým týmem.