Vysokoteplotní obložení proudových motorů pomocí 3D tisku
Obsah
Úvod: Revoluce v obložení tryskových motorů pomocí aditivní výroby kovů
Letecký průmysl je neúnavně poháněn snahou o vyšší účinnost, snížení emisí a zvýšení výkonu. Jádrem této snahy je plynový turbínový motor, zázrak techniky pracující v extrémních podmínkách. V těchto motorech čelí součásti, jako je spalovací vložka, nejnáročnějšímu prostředí, jaké si lze představit - spalujícím teplotám, vysokým tlakům a korozivním plynům. Tradičně výroba těchto složitých, vysoce výkonných dílů zahrnovala složité, vícestupňové procesy, jako je odlévání, kování a rozsáhlé obrábění, což často vedlo k dlouhým dodacím lhůtám, značnému plýtvání materiálem a omezením složitosti konstrukce.
Vstupte do aditivní výroby kovů (AM), známé spíše jako 3D tisk z kovu. Tato transformační technologie přepisuje pravidla pro navrhování a výrobu kritických leteckých komponent, včetně vložek proudových motorů. Tím, že AM vytváří díly vrstvu po vrstvě přímo z kovového prášku na základě digitálního modelu, uvolňuje nebývalou svobodu návrhu, umožňuje rychlé prototypování a iterace, snižuje plýtvání materiálem a konsoliduje více dílů do jediné optimalizované součásti. U vysokoteplotních aplikací, jako jsou například vložky spalovacích motorů, nabízí možnost využití pokročilých superslitin a vytvoření složitých vnitřních chladicích kanálů cestu k lehčím, odolnějším a účinnějším motorům. Společnosti, které stojí v čele této revoluce, jako je Met3dp, využívají desetiletí zkušeností s pokročilými kovovými prášky i nejmodernějšími tiskovými systémy, aby mohly dodávat komponenty, které splňují přísné požadavky leteckého průmyslu. Tento posun směrem k aditivní výrobě není jen alternativou, ale zásadním faktorem pro technologii plynových turbín nové generace, který slibuje vyšší výkon a udržitelnější budoucnost letectví. Vzhledem k tomu, že inženýři a manažeři nákupu hledají spolehlivé dodavatele a velkoobchodní řešení pro tyto pokročilé komponenty, stává se pochopení možností a výhod AM výroby kovů klíčovým.
Kritické funkce: Úloha vložek v moderních proudových motorech
Spalovací vložka, často označovaná jednoduše jako “vložka” nebo “vložka spalovacího motoru”, je kritická součást umístěná ve spalovací části motoru s plynovou turbínou. Její hlavní funkcí je omezit vysokoteplotní spalovací proces a chránit okolní součásti motoru (jako je plášť turbíny a konstrukční prvky) před extrémním teplem, které vzniká - často přesahuje 1500∘C (2732∘F). Jeho úloha však zdaleka přesahuje pouhou izolaci.
Klíčové funkce obložení proudového motoru:
- Uzavření a tepelné stínění: Obložení tvoří hranici spalovací zóny a zajišťuje, aby se intenzivní plamen nedostal k tepelně citlivým částem motoru. Musí odolávat přímému dopadu plamene a extrémním tepelným gradientům.
- Definice směšovací zóny: Hraje klíčovou roli při vedení proudu vzduchu ve spalovacím prostoru. Pomáhá správně promíchat přiváděný stlačený vzduch s palivem pro účinné spalování a usměrňuje proudění chladicího vzduchu. Přesně řízené míchání je nezbytné pro dosažení stabilního spalování, minimalizaci tvorby znečišťujících látek (např. NOx) a zajištění rovnoměrného rozložení teploty na vstupu do turbíny.
- Strukturální integrita: Navzdory extrémním teplotám musí obložení zachovat svůj strukturální tvar a integritu při značných tlakových rozdílech a aerodynamickém zatížení v celém provozním rozsahu motoru, od vzletového tahu až po cestovní podmínky. Prohnutí, prasknutí nebo deformace mohou vést ke katastrofickému selhání motoru.
- Odolnost a dlouhá životnost: Obložení jsou během spouštění, provozu a vypínání motoru vystavena silným tepelným cyklům. Tato opakovaná roztažnost a smršťování vyvolává tepelnou únavu. Musí také odolávat oxidaci a korozi způsobené spalinami a případnými nečistotami paliva po tisíce letových hodin. Spolehlivost je prvořadá, takže výběr materiálu a kvalita výroby jsou pro výrobce a dodavatele dílů pro letectví a kosmonautiku kritickým problémem.
- Řízení chlazení: Moderní vložky obsahují sofistikovaná chladicí schémata (např. výtokové chlazení, filmové chlazení) využívající tisíce přesně umístěných malých otvorů nebo složitých vnitřních průchodů. Tato schémata využívají část výstupního vzduchu z kompresoru k vytvoření ochranných vrstev chladnějšího vzduchu podél stěn vložky, čímž se výrazně snižuje teplota kovu a prodlužuje životnost součásti. Účinnost tohoto chlazení přímo ovlivňuje účinnost motoru a životnost vložek.
Výkon spalovací vložky přímo ovlivňuje několik klíčových parametrů motoru:
- Účinnost motoru: Správné míchání a řízené spalování ve vložce přispívá k vyšší tepelné účinnosti. Účinné chlazení umožňuje dosáhnout vyšších teplot na vstupu do turbíny, což je klíčový faktor pro zlepšení celkové termodynamické účinnosti motoru a snížení spotřeby paliva.
- Emise: Konstrukce vložky významně ovlivňuje tvorbu znečišťujících látek, jako jsou oxidy dusíku (NOx), oxid uhelnatý (CO) a nespálené uhlovodíky (UHC). Optimalizovaný způsob míchání paliva se vzduchem může výrazně snížit škodlivé emise.
- Spolehlivost a náklady na údržbu: Odolná, dobře navržená vložka prodlužuje dobu mezi generálními opravami motoru, snižuje náklady na údržbu a zvyšuje dostupnost letadla. Pro letecké společnosti a poskytovatele údržby, oprav a generálních oprav (MRO) je zásadní, aby si opatřili vysoce kvalitní vložky od spolehlivých dodavatelů součástí plynových turbín.
Vzhledem k těmto kritickým funkcím a náročnému provoznímu prostředí vyžaduje výroba obložení proudových motorů pokročilé materiály a přesné výrobní techniky schopné vyrábět složité geometrie s vysokou věrností a integritou materiálu. Zde skutečně vyniknou jedinečné výhody aditivní výroby kovů.
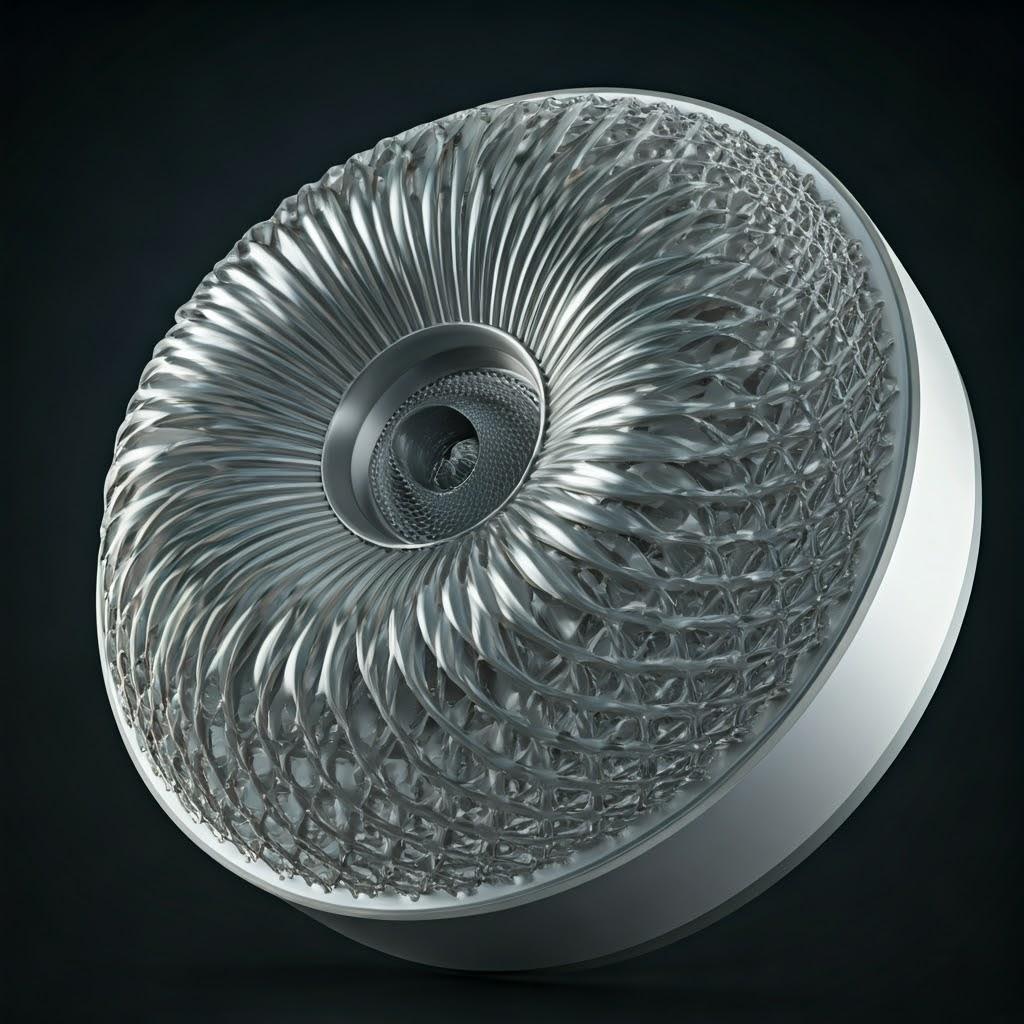
Proč 3D tisk kovů pro vložky proudových motorů? Odblokování zvýšení výkonu
Tradiční výrobní metody pro vložky proudových motorů, zahrnující především výrobu plechů (tváření, svařování, pájení) nebo investiční odlévání, sloužily v tomto odvětví po celá desetiletí. Tyto metody však ze své podstaty mají omezení, která může aditivní výroba kovů překonat, což u těchto vysoce ceněných součástí přináší významné výhody. Komplexní tvary, složité chladicí prvky a náročné požadavky na materiál moderních vložek z nich činí ideální kandidáty pro procesy AM, jako jsou např Selektivní laserové tavení (SLM) nebo tavení elektronovým svazkem (EBM).
Klíčové výhody použití kovových vložek AM:
- Bezprecedentní volnost designu & Komplexnost:
- Složité chladicí geometrie: AM umožňuje vytvářet velmi složité vnitřní chladicí kanály, optimalizované vzory výtokového chlazení (přesně tvarované a orientované otvory) a mřížkové struktury, které je nemožné nebo neúnosně drahé vyrobit tradičními metodami. To umožňuje účinnější chlazení, které umožňuje dosáhnout vyšších teplot spalování, a tím i lepší účinnosti motoru a poměru tahu k hmotnosti.
- Optimalizované tvary: Techniky, jako je optimalizace topologie, mohou být použity k odstranění materiálu z oblastí s nízkým namáháním, což vede k lehčím vložkám bez narušení strukturální integrity. Generativní návrhové algoritmy mohou zkoumat nové tvary optimalizované pro míchání proudění a tepelný management.
- Konsolidace částí:
- Snížená složitost montáže: Obložení tradičně vyráběná z více kusů plechu vyžadují rozsáhlé svařování nebo pájení, což přináší potenciální místa poruch a zvyšuje složitost výroby. AM umožňuje sloučení mnoha dílů do jediné monolitické součásti.
- Vylepšená strukturální integrita: Eliminace spojů a svarů zvyšuje celkovou pevnost a spolehlivost vložky a snižuje riziko vzniku trhlin ve svarech při tepelném cyklování.
- Nižší počet dílů & Logistika: Konsolidace dílů zjednodušuje řízení zásob, montážní procesy a logistiku dodavatelského řetězce pro výrobce v leteckém průmyslu.
- Zrychlený vývoj & Prototypování:
- Rychlá iterace: AM umožňuje konstruktérům rychle vyrobit a otestovat více variant konstrukce obložení. Tato schopnost rychlé výroby prototypů výrazně zkracuje vývojový cyklus nových programů nebo modernizací motorů, což umožňuje rychlejší inovace a zlepšení výkonu.
- Snížení nákladů na nástroje: Na rozdíl od odlévání nebo tváření nevyžaduje AM drahé formy nebo zápustky, takže je nákladově efektivní pro nízkoobjemovou výrobu typickou pro vývojové a testovací fáze, a dokonce i pro výrobu dílů na míru nebo starších dílů.
- Efektivní využití materiálů & Snížení množství odpadu:
- Výroba téměř čistého tvaru: AM vytváří díly vrstvu po vrstvě, přičemž používá pouze materiál nezbytný pro součást a potřebné podpůrné struktury. To je v ostrém kontrastu se subtraktivní výrobou (obrábění z polotovaru), při níž může vznikat značný materiálový odpad, zejména u drahých superslitin.
- Udržitelnost: Snížení spotřeby materiálu je v souladu s průmyslovými cíli pro udržitelnější výrobní postupy.
- Zvýšený výkonnostní potenciál:
- Odlehčení: Díky optimalizaci topologie a použití složitých geometrií, jako jsou vnitřní mřížky, může AM výrazně snížit hmotnost obložení, což přispívá k celkovému snížení hmotnosti motoru - což je rozhodující faktor pro zlepšení palivové účinnosti a výkonu letadla.
- Zvýšená odolnost: Optimalizované chlazení a monolitické konstrukce mohou vést k nižším provozním teplotám kovu a snížení koncentrace napětí, což může prodloužit provozní životnost vložky a zvýšit spolehlivost motoru. Kupující B2B, kteří se zaměřují na celkové náklady na vlastnictví, mají z této zvýšené životnosti prospěch.
- Pokročilé využití materiálů:
- Zpracování superslitin: Techniky AM, jako je SLM a EBM, jsou vhodné pro zpracování vysoce výkonných superslitin na bázi niklu (jako IN738LC a Hastelloy X), které jsou potřebné pro extrémní teploty ve spalovacím zařízení. Společnosti jako Met3dp se specializují na výrobu atomizovaných prášků těchto slitin optimalizovaných pro procesy AM, což zajišťuje vysokou hustotu a vynikající vlastnosti materiálu ve finálním dílu. Přečtěte si více informací o různých tiskových metod vhodné pro tyto materiály.
Srovnávací tabulka: AM vs. tradiční výroba pro vložky
Vlastnosti | Výroba aditiv kovů (AM) | Tradiční výroba (odlévání/výroba) |
---|---|---|
Složitost návrhu | Velmi vysoká (vnitřní kanály, mřížky, optimalizované tvary) | Střední až vysoká (omezeno nástroji, metodami spojování) |
Konsolidace částí | Vynikající (více částí integrovaných do jedné) | Omezené (vyžaduje svařování, pájení, spojovací materiál) |
Doba realizace (Proto) | Krátké (dny/týdny) | Dlouhé (týdny/měsíce – vyžaduje nástroje) |
Náklady na nástroje | Žádné / minimální | Vysoký (formy, zápustky, přípravky, přípravky) |
Materiálový odpad | Nízký (tvar blízký síti) | Střední až vysoká (přídavek na obrábění, systémy brány) |
Účinnost chlazení | Potenciálně vyšší (optimalizovaná, komplexní chladicí schémata) | Dobrý (zavedené metody, ale geometricky omezené) |
Odlehčení | Vynikající (optimalizace topologie, mřížky) | Omezený |
Ideální objem | Nízká až střední, vysoká složitost, rychlá tvorba prototypů, přizpůsobení | Velkoobjemové, jednodušší konstrukce |
Potenciální selhání | Změny v řízení procesu (pórovitost, napětí) | Vady svaru/pájení, pórovitost odlitků/vměstky |
Export do archů
Ačkoli AM přináší přesvědčivé výhody, je pro inženýry a manažery veřejných zakázek zásadní spolupracovat se zkušenými poskytovateli služeb v oblasti AM, kteří mají hluboké odborné znalosti v oblasti řízení procesů, vědy o materiálech a následného zpracování specifického pro náročné aplikace v leteckém průmyslu.
Zaměření na materiály: IN738LC a Hastelloy X pro extrémní prostředí
Výběr materiálů pro obložení spalovacího prostoru proudových motorů má zásadní význam vzhledem k neuvěřitelně náročným provozním podmínkám: extrémním teplotám (teplota plamene často přesahuje 1500∘C, přičemž teplota kovu se udržuje nižší díky chlazení, ale stále dosahuje 800-1100∘C), vysokým tlakům, oxidačním a korozivním prostředím a náročným tepelným cyklům. Superslitiny na bázi niklu jsou pro tyto náročné aplikace vhodným materiálem, který nabízí výjimečnou kombinaci vysokoteplotní pevnosti, odolnosti proti tečení, únavové životnosti a odolnosti proti oxidaci a korozi.
Pro vložky vyráběné aditivní výrobou kovů jsou významní dva kandidáti IN738LC (Inconel 738 Low Carbon) a Hastelloy X. Tyto slitiny mají vlastnosti, díky nimž jsou velmi vhodné pro procesy tavení po vrstvách, které jsou pro AM typické, a jejich výkonnostní charakteristiky dokonale odpovídají požadavkům na spalovací vložku. Získávání vysoce kvalitních prášků těchto superslitin optimalizovaných pro AM je rozhodující pro dosažení požadované hustoty, mikrostruktury a mechanických vlastností dílů.
Met3dp: Váš partner pro vysoce výkonné superslitinové prášky
Ve společnosti Met3dp si uvědomujeme, jak zásadní roli hrají materiály pro úspěch aditivní výroby. Využíváme naše pokročilé možnosti výroby prášků, včetně špičkových technologií v oboru technologie atomizace plynu a plazmového procesu s rotujícími elektrodami (PREP), vyrábíme kovové prášky s vysokou sféricitou a vynikající tekutostí, které jsou speciálně optimalizovány pro procesy AM, jako je SLM a EBM. Naše odborné znalosti zajišťují, že prášky jako IN738LC a Hastelloy X splňují přísné požadavky leteckého průmyslu na čistotu, distribuci velikosti částic a morfologii. Prozkoumejte náš sortiment kovové prášky a výrobky.
IN738LC (Inconel 738 Low Carbon)
IN738LC je precipitačně kalitelná superslitina na bázi niklu, která je známá svou vynikající pevností při vysokých teplotách, odolností proti tečení a korozi za tepla, zejména ve středním teplotním rozsahu (750-950∘C). Označení “LC” znamená nízký obsah uhlíku, který zlepšuje svařitelnost a, což je pro AM důležité, snižuje náchylnost k praskání při tuhnutí během rychlých cyklů zahřívání a ochlazování v procesu tisku.
- Klíčové vlastnosti a výhody pro vložky:
- Vysoká pevnost v tahu: Odolává deformaci při trvalém zatížení za zvýšených teplot, což je zásadní pro zachování tvaru a integrity vložky po dlouhou dobu provozu.
- Vynikající odolnost proti korozi za tepla: Odolává působení síry a dalších znečišťujících látek obsažených v produktech spalování leteckého paliva.
- Dobrá odolnost proti oxidaci: Vytváří ochrannou vrstvu oxidu, která odolává degradaci v prostředí bohatém na kyslík a při vysokých teplotách.
- Dobrá odlévatelnost/ tisknutelnost: Varianta LC vykazuje lepší zpracovatelské vlastnosti vhodné pro investiční lití a, což je velmi důležité, pro aditivní výrobní procesy, jako je SLM.
- Srážkové kalení: Vysoké pevnosti dosahuje tepelným zpracováním, které způsobuje precipitaci gama prvočíselných (γ′) fází v niklové matrici. Pro dosažení požadované mikrostruktury a vlastností je nezbytná pečlivá kontrola procesu AM a následného tepelného zpracování.
Hastelloy X
Hastelloy X je superslitina niklu, chromu, železa a molybdenu zpevněná pevným roztokem. Na rozdíl od srážením vytvrzených slitin, jako je IN738LC, získává svou pevnost především z legujících prvků rozpuštěných v niklové matrici. Je známá pro svou vynikající kombinaci pevnosti při vysokých teplotách, odolnosti proti oxidaci a zpracovatelnosti.
- Klíčové vlastnosti a výhody pro vložky:
- Výjimečná odolnost proti oxidaci: Nabízí vynikající odolnost proti oxidaci až do velmi vysokých teplot (přibližně 1200∘C), takže je vhodný pro nejžhavější části spalovacího prostoru.
- Dobrá odolnost při vysokých teplotách: Přestože při středních teplotách není obecně tak pevná jako srážením vytvrzené slitiny, zachovává si užitečnou pevnost při velmi vysokých teplotách.
- Vynikající tvařitelnost a svařitelnost: Tyto vlastnosti, tradičně známé pro snadnou výrobu v kovaných formách, se dobře promítají do dobré zpracovatelnosti při aditivní výrobě. Ve srovnání s některými jinými superslitinami je méně náchylná k praskání.
- Odolnost proti koroznímu praskání pod napětím: Vykazuje dobrou odolnost proti praskání v prostředí s obsahem chloridů.
- Tepelná stabilita: Zachovává si své vlastnosti i po dlouhodobém vystavení vysokým teplotám.
Srovnávací tabulka: IN738LC vs. Hastelloy X pro vložky AM
Vlastnictví | IN738LC | Hastelloy X | Význam pro liniové společnosti |
---|---|---|---|
Mechanismus posilování | Srážkové kalení (γ′) | Pevné posílení řešení | Ovlivňuje požadavky na tepelné zpracování a mez pevnosti. |
Maximální teplota použití | Vynikající až do ~980∘C | Vynikající až do ~1200∘C (pro oxidaci) | Hastelloy X je upřednostňován pro nejteplejší oblasti díky vyšší odolnosti proti oxidaci. |
Pevnost v tahu | Velmi vysoká (střední teploty) | Dobrý (zejména při velmi vysokých teplotách) | IN738LC se často upřednostňuje tam, kde je kritická dlouhodobá odolnost proti tečení pod 950∘C. |
Odolnost proti oxidaci | Dobrý | Vynikající | Kritické pro dlouhou životnost v prostředí spalovacího zařízení. |
Odolnost proti korozi za tepla | Vynikající | Dobrý | Důležité pro odolnost vůči nečistotám v palivu. |
Zpracovatelnost AM | Dobrý (varianta LC pomáhá) | Vynikající | Ovlivňuje tvorbu defektů (praskání, pórovitost) během tisku. |
Tepelné zpracování | Požadované (roztok + stárnutí) | Obvykle žíhané roztokem | Ovlivňuje kroky následného zpracování a konečné vlastnosti. |
Typické aplikace | Lopatky turbíny, lopatky, součásti spalovacího motoru | Vyzdívky spalovacího prostoru, přechodové kanály, přídavné spalování | Oba materiály se osvědčily v horkých částech plynových turbín. |
Export do archů
Proč jsou prášky Met3dp důležité:
Úspěch tisku vložek proudových motorů s IN738LC nebo Hastelloy X závisí do značné míry na kvalitě výchozího kovového prášku. Met3dp zajišťuje:
- Vysoká sféricita & Tekutost: Je nezbytný pro rovnoměrné vrstvení práškového lože v procesech SLM/EBM, což vede ke konzistentnímu chování taveniny a vysoké hustotě dílů.
- Řízená distribuce velikosti částic (PSD): Optimalizovaná PSD zajišťuje dobrou hustotu balení a předvídatelné vlastnosti tání.
- Vysoká čistota & Nízké satelity: Minimalizuje výskyt nečistot a nerovností, které mohou vést k vadám finální součásti.
- Konzistence dávky: Přísná kontrola kvality zajišťuje spolehlivé a opakovatelné výsledky mezi jednotlivými šaržemi, což má zásadní význam pro kvalifikaci v leteckém průmyslu.
Výběr správného materiálu, správně zpracovaného pomocí vysoce kvalitního prášku od důvěryhodného dodavatele, jako je Met3dp, je základem pro využití plného potenciálu aditivní výroby pro vytváření vynikajících vložek do proudových motorů. Pochopení nuancí mezi slitinami, jako jsou IN738LC a Hastelloy X, umožňuje inženýrům vybrat optimální materiál na základě specifického teplotního profilu a rozložení napětí v rámci konstrukce vložky.
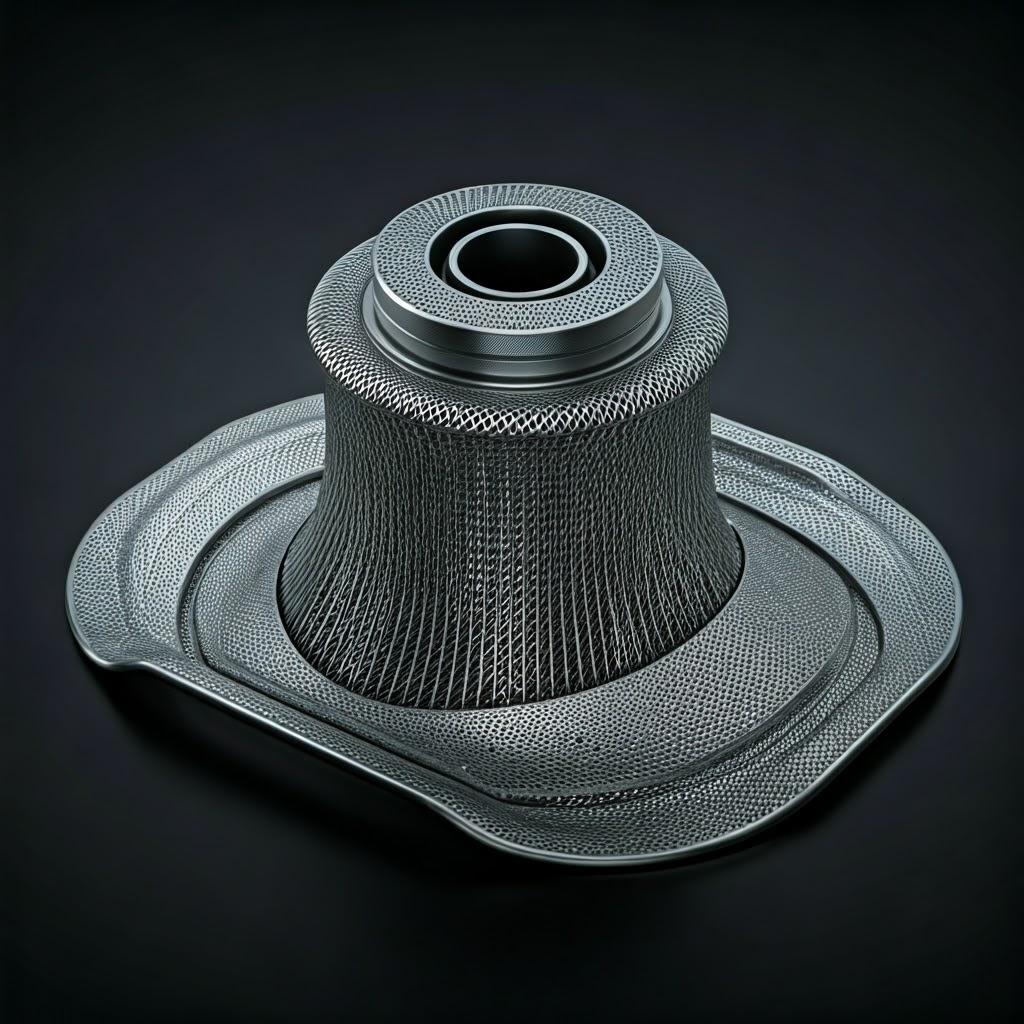
Design pro aditivní výrobu (DfAM): Optimalizace geometrie vložky
Pouhá replika tradičně navrženého obložení proudového motoru pomocí aditivní výroby často nevyužívá plný potenciál této technologie. Aby inženýři skutečně využili výhod AM - odlehčení, lepší chlazení, konsolidace dílů - musí přijmout Design pro aditivní výrobu (DfAM). DfAM je změna paradigmatu, která překračuje omezení konvenční výroby a navrhuje díly speciálně optimalizované pro proces AM po vrstvách. Pro složité a vysoce hodnotné součásti, jako jsou spalovací vložky pracující v extrémních podmínkách, je DfAM nejen přínosem, ale i nezbytným předpokladem pro dosažení významného zvýšení výkonu.
Klíčové principy DfAM pro obložení proudových motorů:
- Využití geometrické volnosti:
- Komplexní chladicí kanály: Společnost AM vyniká vytvářením konformních chladicích kanálů, které kopírují obrysy stěn vložky, vnitřních průchodů s optimalizovanými průřezy (např. tvar slzy pro lepší proudění) a složitých sítí, které maximalizují přenos tepla. To umožňuje účinnější chlazení s využitím menšího množství vypouštěného vzduchu, což přímo zvyšuje účinnost motoru.
- Optimalizované chlazení efuze: Namísto pouhého vrtání kulatých otvorů může společnost AM vytvořit tvarované otvory (jako jsou ventilátory nebo ležaté konstrukce) přesně orientované tak, aby optimalizovaly ochranný film chladicího vzduchu podél povrchu vložky, čímž se zvyšuje účinnost chlazení a životnost.
- Integrované funkce: Konzoly, šrouby, montážní body a další prvky, které by mohly být samostatnými přivařenými díly, mohou být integrovány přímo do konstrukce vložky, čímž se sníží počet dílů a eliminují se potenciální místa poruch v místech spojů.
- Optimalizace topologie a odlehčení:
- Materiál v případě potřeby: Softwarové nástroje analyzují rozložení napětí uvnitř vložky při provozním zatížení. Algoritmy pro optimalizaci topologie pak odstraňují materiál z oblastí s nízkým namáháním a vytvářejí organické struktury optimalizované pro zatížení, které jsou výrazně lehčí než jejich tradiční protějšky, přičemž si zachovávají nebo dokonce zvyšují tuhost a pevnost.
- Mřížové struktury: V oblastech, kde je vyžadována tuhost, ale ne plná hustota, lze použít vnitřní mřížové struktury. Tyto složité sítě výrazně snižují hmotnost a mohou být navrženy tak, aby zlepšily odvod tepla nebo akustický útlum - což jsou funkce důležité v prostředí spalovacího motoru.
- Konsolidace částí:
- Zjednodušení sestav: Jak již bylo zmíněno dříve, AM umožňuje přepracovat a vytisknout více součástí tradiční sestavy vložky (např. různé sekce, chladicí kroužky, montážní příruby) jako jediný monolitický kus. To výrazně zkracuje dobu montáže, eliminuje spoje náchylné k únavě nebo netěsnosti a zjednodušuje řízení dodavatelského řetězce pro letecké výrobce a poskytovatele MRO.
- Zohlednění výrobních omezení (specifických pro AM):
- Podpůrné struktury: Díly AM často vyžadují během procesu sestavování dočasné podpůrné konstrukce pro ukotvení převisů a odvod tepla. DfAM zahrnuje navrhování dílů tak, aby se minimalizovala potřeba podpěr, zejména v těžko přístupných vnitřních oblastech. To zahrnuje strategickou orientaci dílu na konstrukční desce a použití samonosných úhlů (obvykle > 45 stupňů od vodorovné roviny), kde je to možné. Pokud jsou podpěry nezbytné, měl by návrh zajistit jejich přístupnost pro odstranění při následném zpracování.
- Orientace na stavbu: Orientace, ve které je vložka vytištěna, ovlivňuje kvalitu povrchu, umístění a typ potřebných podpěr, akumulaci zbytkových napětí a potenciálně anizotropní vlastnosti materiálu. DfAM zvažuje optimální orientaci již ve fázi návrhu.
- Minimální velikost prvku & Tloušťka stěny: Procesy AM mají omezení, pokud jde o nejmenší prvky (otvory, drážky) a nejtenčí stěny, které mohou spolehlivě vyrobit. Konstruktéři musí dodržovat pokyny specifické pro daný proces, zejména při práci s náročnými superslitinami, jako jsou IN738LC a Hastelloy X. Typické minimální tloušťky stěn se mohou pohybovat od 0,4 mm do 1,0 mm v závislosti na konkrétním stroji a materiálu.
- Odvod tepla: Velké pevné části mohou během tisku akumulovat teplo, což může vést k napětí a deformaci. DfAM může zahrnovat návrh vnitřních dutin nebo kanálů, i když nejsou nezbytně nutné pro funkci, jednoduše proto, aby se zvládly tepelné gradienty během sestavování.
Úvahy o pracovním postupu DfAM:
DfAM Step | Popis | Nástroje/techniky | Relevance B2B/dodavatelů |
---|---|---|---|
Analýza požadavků | Definujte funkční, tepelné a konstrukční požadavky a požadavky na životnost obložení. | Systémové inženýrství, FEA (počáteční) | Jasné specifikace potřebné pro kótování a výrobu poskytovateli služeb AM. |
Koncepční návrh (AM) | Brainstorming návrhů využívajících volnost AM (komplexní chlazení, mřížky, integrace). | CAD, software pro generativní navrhování | Spolupráce mezi konstruktéry OEM a odborníky na AM (jako jsou aplikační inženýři Met3dp). |
Optimalizace topologie | Matematicky odstraňte materiál z nekritických oblastí na základě zatěžovacích stavů. | Optimalizační software na bázi konečných prvků (např. Altair OptiStruct, Ansys Discovery) | Snižuje náklady na materiál & hmotnost, klíčové prodejní body pro velkoobchodní komponenty. |
Podrobný návrh | Zpřesněte geometrii, přidejte funkční prvky, navrhněte prvky minimalizující podporu, definujte vzory chladicích otvorů. | Pokročilé moduly CAD, specifické moduly pro AM | Zásadní jsou kontroly vyrobitelnosti dodavatelem AM. |
Simulace sestavení | Předvídejte tepelné namáhání, deformace a potenciální poruchy sestavy před tiskem. | Software pro simulaci AM (např. Ansys Additive Suite, Simufact Additive) | Snižuje náklady na pokusy a omyly, zajišťuje vyšší úspěšnost prvního sestavení. |
Strategie podpory | Navrhněte potřebné podpůrné konstrukce pro přístupnost a minimální zjizvení dílů. | Software pro přípravu AM (např. Materialise Magics) | Zkušení dodavatelé optimalizují podporu pro kvalitní a efektivní odstranění. |
Plán následného zpracování | Definujte kroky pro tepelné zpracování, odstranění podpory, obrábění a dokončovací práce na základě konstrukčních vlastností. | Procesní inženýrství | Integrované plánování zajišťuje, že finální díl splňuje všechny specifikace. |
Export do archů
Díky integraci principů DfAM od samého počátku mohou inženýři navrhovat obložení proudových motorů, která jsou nejen vyrobitelná pomocí AM, ale jsou také lehčí, tepelně účinnější a potenciálně odolnější než jejich konvenčně vyráběné předchůdkyně. Klíčem k realizaci těchto výhod je spolupráce s dodavatelem AM, který se vyzná v osvědčených postupech DfAM pro superslitiny.
Dosažení přesnosti: Tolerance, povrchová úprava a rozměrová přesnost u AM linerů
Ačkoli aditivní výroba nabízí neuvěřitelnou geometrickou volnost, dosažení úzkých tolerancí, specifické povrchové úpravy a vysoké rozměrové přesnosti, které jsou vyžadovány u kritických leteckých komponent, jako jsou vložky proudových motorů, vyžaduje pečlivou kontrolu procesu a často vyžaduje následné zpracování. Při zadávání požadavků na 3D tištěné vložky musí manažeři a inženýři nákupu rozumět typickým možnostem a omezením procesů AM, jako je selektivní laserové tavení (SLM) a tavení elektronovým svazkem (EBM).
Tolerance:
- Obecné dosažitelné tolerance: Tolerance při výrobě se u procesů AM kovů obvykle pohybují v rozmezí ±0,1 mm až ±0,2 mm (±0,004 až ±0,008) u menších rozměrů a přibližně ±0,1 % až ±0,2 % u větších rozměrů. To se však může výrazně lišit v závislosti na:
- Velikost a geometrie dílu: Větší díly a složité geometrie jsou náchylnější k tepelnému zkreslení, což ovlivňuje celkovou přesnost.
- Materiál: Superslitiny jako IN738LC a Hastelloy X mohou vykazovat značné zbytkové napětí, které ovlivňuje rozměrovou stabilitu.
- Kalibrace stroje: Pravidelná kalibrace a údržba systému AM jsou zásadní.
- Orientace na stavbu: Orientace ovlivňuje tepelné gradienty a umístění podpěr.
- Následné zpracování: Tepelné zpracování s uvolněním napětí může způsobit drobné rozměrové změny, se kterými je třeba počítat.
- Kritické tolerance: Prvky, které vyžadují větší tolerance, než je obecný stav (např. styčné plochy, rozhraní s jinými součástmi motoru, přesné průměry palivových trysek nebo snímačů), obvykle vyžadují po obrábění (CNC frézování, soustružení, broušení). Pro tyto prvky je nezbytné zahrnout do fáze DfAM přídavky na obrábění.
Povrchová úprava (drsnost):
- Povrchová úprava podle stavu: Povrchová úprava kovových dílů vyrobených metodou AM je ze své podstaty drsnější než povrch obrobený. Typické hodnoty Ra (průměrná drsnost) se pohybují od 6 µm do 20 µm (240 µin až 800 µin) a jsou ovlivněny:
- Tloušťka vrstvy: Tenčí vrstvy obecně vedou k hladším povrchům, ale prodlužují dobu výstavby. Typická tloušťka vrstvy je 30-60 µm.
- Velikost částic prášku: Jemnější prášky mohou vést k hladšímu povrchu, ale mohou ovlivnit tekutost. Met3dp optimalizuje vlastnosti prášku pro dosažení rovnováhy mezi tisknutelností a povrchovou úpravou.
- Orientace: Povrchy rovnoběžné s konstrukční deskou (směřující nahoru) bývají hladší než svislé stěny, které jsou hladší než povrchy směřující dolů, které vyžadovaly kontakt s opěrou. Šikmé povrchy vykazují charakteristický “schodovitý” efekt.
- Parametry procesu: Výkon laseru/elektronového paprsku, rychlost skenování a strategie ovlivňují stabilitu taveniny a vlastnosti povrchu.
- Zlepšení povrchové úpravy: Pro aplikace vyžadující hladší povrchy (např. pro aerodynamické vlastnosti uvnitř vložky nebo pro snížení koncentrace napětí) se používají různé techniky následného zpracování:
- Tryskání abrazivem (zrnitostní/perličkové tryskání): Poskytuje rovnoměrný matný povrch, odstraňuje sypký pudr, ale výrazně nesnižuje Ra.
- Třískové/vibrační dokončování: Používá média k vyhlazení povrchů, účinná pro dávky menších dílů nebo přístupných prvků.
- Chemické leštění/leptání: Může vyhlazovat povrchy, ale vyžaduje pečlivou kontrolu.
- Elektrolytické leštění: Elektrochemickým odstraňováním materiálu zajišťuje velmi hladký a lesklý povrch.
- Ruční leštění: Je náročný na pracovní sílu, ale používá se pro specifické kritické oblasti.
- CNC obrábění: Nejpřesnější způsob, jak dosáhnout specifického, hladkého povrchu funkčních ploch.
Rozměrová přesnost & Kontrola kvality:
- Zajištění přesnosti: Dosažení konzistentní rozměrové přesnosti vyžaduje holistický přístup:
- Robustní řízení procesů: Sledování charakteristik taveniny, atmosféry v komoře a tepelných podmínek během sestavování. Výhodou jsou vysoce kvalitní systémy AM s uzavřenou řídicí smyčkou, jako jsou systémy potenciálně používané partnery Met3dp nebo vlastní systémy.
- Simulace: Použití simulačních nástrojů k předvídání a kompenzaci zkreslení.
- Optimalizovaná strategie podpory: Dobře navržené podpěry minimalizují deformace během stavby a zabraňují prohýbání.
- Řízené následné zpracování: Důsledné provádění procesů uvolňování stresu a HIP.
- Kontrola a ověřování: Důsledná kontrola je pro letecké komponenty nepominutelná.
- Souřadnicové měřicí stroje (CMM): Slouží k přesnému měření kritických rozměrů a ověřování geometrických rozměrů a tolerancí (GD&T).
- 3D skenování (laser/strukturální světlo): Zachycuje celkovou geometrii dílu, což umožňuje porovnání s původním modelem CAD a identifikaci odchylek nebo deformací.
- Nedestruktivní zkoušení (NDT): Metody, jako je CT skenování, se používají nejen k detekci defektů (viz další část), ale mohou také poskytnout rozměrovou analýzu vnitřních vlastností.
Souhrnná tabulka: Přesnost u vložek AM
Parametr | Schopnost ve stavu po dokončení (typická) | Faktory ovlivňující | Možnosti následného zpracování pro zlepšení |
---|---|---|---|
Tolerance | ±0,1 až ±0,2 mm / ±0,1 % až ±0,2 % | Velikost, geometrie, materiál, stroj | CNC obrábění |
Povrchová úprava | Ra 6-20 µm (240-800 µin) | Tloušťka vrstvy, prášek, orientace | Obrábění, leštění, tryskání, otryskávání |
Ověřování | CMM, 3D skenování, NDT | Požadavky na inspekci, kritičnost | N/A (Metody kontroly přesnosti) |
Export do archů
Konstruktéři, kteří zadávají AM vložky, musí na výkresech jasně definovat požadavky na tolerance a povrchovou úpravu a uvést, které z nich platí “ve stavu po zabudování” a které vyžadují dodatečné zpracování. Spolupráce se zkušeným dodavatelem AM je klíčová pro zajištění toho, aby tyto požadavky byly splnitelné a nákladově efektivní.
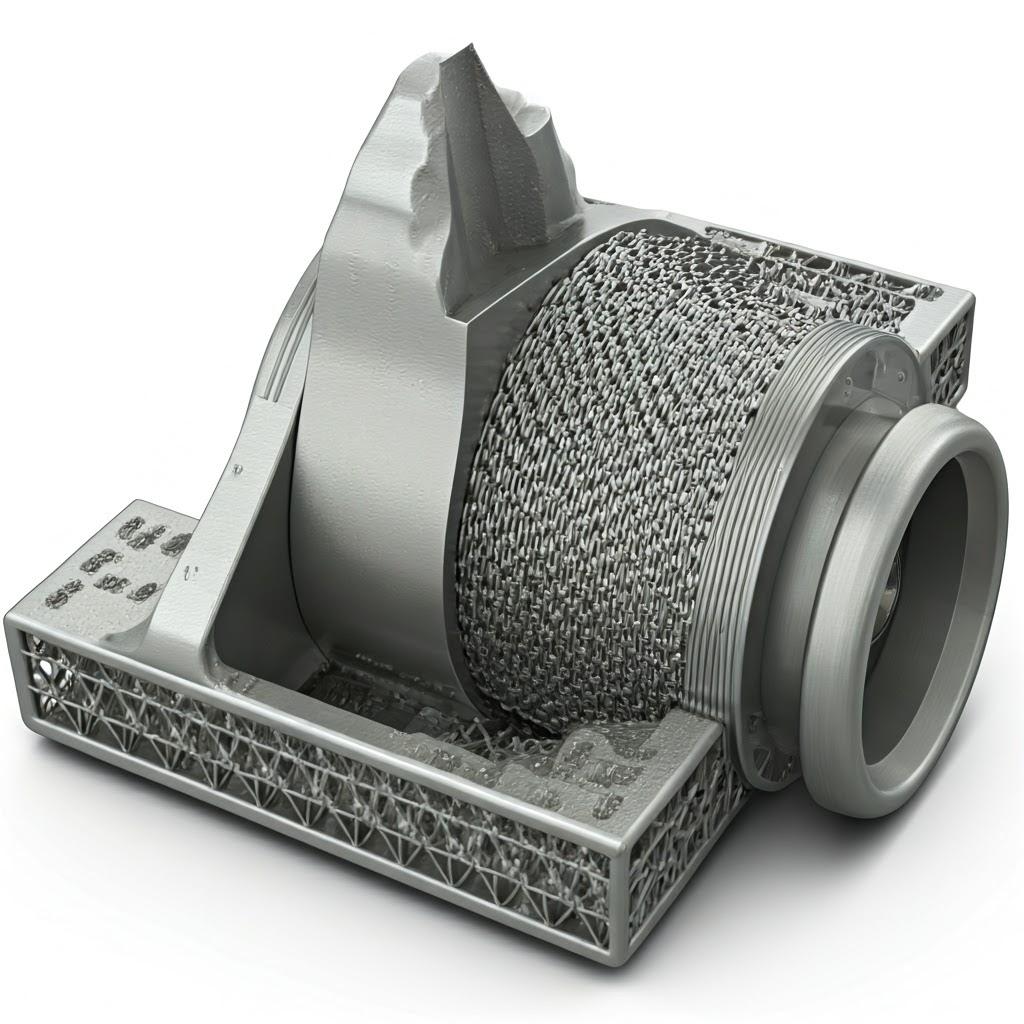
Za hranice stavby: Základní následné zpracování pro 3D tištěné obložení
Tisk obložení proudového motoru je pouze jednou částí pracovního postupu aditivní výroby. U bezpečnostně kritických leteckých součástí vyrobených z vysoce výkonných superslitin jsou kroky následného zpracování naprosto nezbytné pro dosažení požadovaných vlastností materiálu, rozměrové přesnosti, povrchové úpravy a celkové integrity dílu. Vynechání nebo nesprávné provedení těchto kroků může ohrozit výkon a trvanlivost vložky.
Běžné kroky následného zpracování pro AM vložky ze superslitiny:
- Tepelné ošetření proti stresu:
- Účel: Rychlé cykly zahřívání a ochlazování, které jsou vlastní procesům tavení v práškovém loži, vyvolávají v tištěném dílu značná zbytková napětí. Tato napětí mohou způsobit deformaci při vyjmutí z konstrukční desky nebo dokonce vést k praskání. Odlehčení napětí, které se obvykle provádí ještě v době, kdy je díl připevněn ke konstrukční desce v peci s řízenou atmosférou, snižuje tato vnitřní napětí, zlepšuje rozměrovou stabilitu a snižuje náchylnost k prasklinám.
- Proces: Zahřátí dílu na určitou teplotu (nižší než teplota stárnutí u srážením vytvrzených slitin, jako je IN738LC), jeho udržování po určitou dobu a následné pomalé ochlazování. Parametry do značné míry závisí na slitině a geometrii dílu.
- Demontáž ze stavební desky & Demontáž podpěry:
- Účel: Oddělení dílu od stavební desky a odstranění dočasných podpěrných konstrukcí.
- Metody: Často se používá elektroerozivní obrábění (EDM) nebo pásová pila k vyřezání dílu z desky. Odstranění podpory může být náročné, zejména u složitých vnitřních geometrií. Může zahrnovat ruční lámání/řezání u přístupných podpěr nebo CNC obrábění a případně chemické leptání u obtížně přístupných oblastí. Pečlivý návrh (DfAM) minimalizuje složitost podpěr.
- Izostatické lisování za tepla (HIP):
- Účel: HIP je zásadním krokem pro zlepšení metalurgické integrity leteckých dílů AM. Využívá vysokou teplotu (pod bodem tání) a vysoký tlak inertního plynu (obvykle argonu), který se rovnoměrně aplikuje na díl. Tento proces účinně uzavírá vnitřní mikroporéznost (jako je plynová pórovitost nebo malé vady nedostatečného roztavení), která může vzniknout během tisku. Odstranění pórovitosti výrazně zvyšuje únavovou životnost, tažnost a lomovou houževnatost - vlastnosti, které jsou kritické pro životnost vložky při tepelném cyklování.
- Výhody: Výsledkem je téměř plně hustý materiál, který se svými vlastnostmi blíží kovaným nebo litým ekvivalentům. Často se jedná o povinný krok pro kritické rotační nebo tlakové součásti v letectví a kosmonautice.
- Žíhání roztokem & amp; stárnutí Tepelné zpracování (pokud je použitelné):
- Účel: Pro dosažení požadované konečné mikrostruktury a mechanických vlastností, zejména u srážením kalitelných slitin, jako je IN738LC.
- Proces:
- Žíhání roztoků: Zahřátí materiálu na vysokou teplotu za účelem rozpuštění legujících prvků a sraženin do pevného roztoku, po kterém následuje rychlé ochlazení (kalení).
- Stárnutí (srážkové vytvrzování): Zahřívá součást na střední teplotu po delší dobu, což způsobuje řízené srážení zpevňujících fází (jako γ′ v IN738LC).
- Poznámka: U slitin zpevněných pevným roztokem, jako je Hastelloy X, lze po HIP nebo obrábění provést žíhání roztokem pro optimalizaci vlastností, ale srážecí stárnutí se obvykle nevyžaduje. Rozhodující je přesná kontrola teplot, časů a atmosfér.
- CNC obrábění:
- Účel: Pro dosažení malých tolerancí u kritických prvků, vytvoření přesných těsnicích povrchů, vyvrtání nebo vystružení specifických otvorů a dosažení požadovaných povrchových úprav, kterých nelze dosáhnout “jako na stavbě” nebo jinými metodami dokončování.
- Úvahy: Vyžaduje pečlivou konstrukci upínacích přípravků, aby bylo možné udržet potenciálně složitou geometrii dílů AM. Ve fázi DfAM je třeba zahrnout přídavky na obrábění. Důležité je pochopení potenciálně odlišného chování materiálů AM při obrábění ve srovnání s obráběnými materiály.
- Povrchová úprava:
- Účel: Pro dosažení konečné požadované drsnosti povrchu očistěte díl nebo jej připravte pro následné povlakování.
- Metody: Jak bylo popsáno výše (tryskání, leštění, bubnování atd.), volí se na základě specifických požadavků na různé oblasti obložení.
- Tepelně bariérové nátěry (TBC) (volitelné, ale běžné):
- Účel: K další ochraně materiálu vložky před extrémními teplotami hoření. TBC jsou keramické povlaky (často z yttrií stabilizovaného zirkonia – YSZ) nanášené na povrchy horkých plynových cest. Poskytují tepelnou izolaci, čímž výrazně snižují teplotu kovu vložky, což umožňuje dosáhnout vyšších teplot plynu nebo prodloužit životnost vložky.
- Použití: Obvykle se nanáší pomocí plazmového nástřiku nebo fyzikální depozice z par elektronů (EB-PVD) po konečném obrábění a přípravě povrchu.
Integrace pracovních postupů:
Pořadí a konkrétní parametry těchto kroků následného zpracování jsou rozhodující a musí být pečlivě naplánovány a provedeny. Představují významnou část celkového výrobního času a nákladů na AM vložku. Renomovaní poskytovatelé služeb AM v oblasti kovů, kteří se specializují na letecký průmysl, mají pro tyto kritické operace následného zpracování ověřené postupy a certifikované vybavení. Pochopení tohoto kompletního pracovního postupu je zásadní pro přesný odhad nákladů a plánování doby realizace ze strany nákupních týmů B2B.
Zvládání výzev: Zajištění kvality při aditivní výrobě obložení
Ačkoli AM zpracování kovů nabízí transformační potenciál pro vložky proudových motorů, dosažení konzistentních a vysoce kvalitních výsledků, zejména u náročných superslitin, vyžaduje překonání několika neodmyslitelných problémů. Povědomí o těchto potenciálních problémech a spolupráce se zkušenými poskytovateli, kteří používají důkladné strategie pro jejich zmírnění, je pro úspěch v leteckých aplikacích zásadní. Společnost Met3dp díky svému zaměření na vysoce kvalitní prášky a hluboké znalosti procesů AM významně přispívá k překonávání těchto překážek. Více informací o našem odhodlání a odborných znalostech naleznete na našich stránkách O nás strana.
Společné výzvy a strategie pro jejich zmírnění:
- Zbytkové napětí a deformace:
- Výzva: Rychlé, lokalizované zahřívání a ochlazování během tavení po vrstvách vytváří značné teplotní gradienty, které vedou k vnitřním pnutím. Tato napětí mohou způsobit deformaci nebo zkroucení dílů během sestavování, po vyjmutí ze sestavovací desky nebo během následného tepelného zpracování. V závažných případech může napětí vést k praskání.
- Zmírnění:
- Optimalizované strategie skenování: Použití technik, jako je skenování ostrůvků, šachovnicové vzory nebo optimalizované délky vektorů, pomáhá rovnoměrněji rozvádět teplo.
- Vytápění stavebních desek: Předehřátí konstrukční desky snižuje tepelný gradient mezi roztaveným materiálem a podkladovými vrstvami/deskou.
- Simulace procesu: Předvídání akumulace napětí a deformace umožňuje kompenzovat konstrukce nebo optimalizovat orientaci konstrukce a podpůrné strategie.
- Robustní podpůrné struktury: Vhodné podpěry díl pevně ukotví a pomáhají odvádět teplo.
- Okamžitá úleva od stresu: Tepelné zpracování na uvolnění napětí bezprostředně po sestavení, často před odstraněním podpěry, má zásadní význam.
- Pórovitost:
- Výzva: Vnitřní dutiny nebo póry v tištěném materiálu mohou působit jako koncentrátory napětí, což výrazně zhoršuje únavovou životnost a mechanické vlastnosti. Pórovitost může vznikat v důsledku zachyceného plynu v prášku nebo v bazénu taveniny (plynová pórovitost) nebo neúplným natavením mezi vrstvami nebo skenovacími stopami (nedostatečná pórovitost natavení).
- Zmírnění:
- Vysoce kvalitní prášek: Zásadní je použití prášku s nízkým obsahem vnitřního plynu, vysokou sféricitou a kontrolovaným PSD (jako je prášek vyráběný pokročilou atomizací Met3dp). Klíčové je také správné zacházení s práškem a jeho skladování, aby se zabránilo absorpci vlhkosti.
- Optimalizované parametry procesu: Přesné nastavení výkonu laseru/paprsku, rychlosti skenování, tloušťky vrstvy a vzdálenosti mezi šrafami zajišťuje úplné roztavení a tavení.
- Řízená atmosféra: Udržování vysoce čisté atmosféry inertního plynu (argonu nebo dusíku) ve stavební komoře minimalizuje oxidaci a zachycování plynu.
- Izostatické lisování za tepla (HIP): Jak již bylo uvedeno, HIP je vysoce účinný při uzavírání vnitřních pórů, a proto je standardním krokem pro kritické letecké díly.
- Praskání:
- Výzva: Superslitiny, zejména precipitačně kalitelné, jako je IN738LC, mohou být náchylné k tvorbě trhlin při tuhnutí (během ochlazování taveniny) nebo k tvorbě trhlin při kapalnění (opětovné roztavení fází s nižším bodem tání na hranicích zrn) v důsledku tepelného namáhání.
- Zmírnění:
- Výběr/úprava slitiny: Použití variant navržených pro lepší zpracovatelnost při AM (např. IN738LC oproti standardnímu IN738).
- Optimalizace parametrů: Řízení příkonu energie a rychlosti chlazení za účelem minimalizace tepelného namáhání.
- Optimalizace strategie skenování: Snížení zbytkového napětí.
- Vhodné tepelné zpracování: Pečlivě kontrolované zátěžové a homogenizační procedury.
- Odstranění podpůrné konstrukce:
- Výzva: Odstraňování podpěr, zejména hustých nebo vnitřních podpěr v rámci složitých geometrií vložek, může být obtížné, časově náročné a hrozí při něm riziko poškození povrchu dílu.
- Zmírnění:
- DfAM: Navrhování dílů tak, aby byly pokud možno samonosné, s použitím optimalizovaných typů podpěr (např. kuželových, tenkostěnných, perforovaných), které se snáze odstraňují.
- Strategická orientace: Volba orientace konstrukce, která minimalizuje kritické podpěry nebo je umístí na přístupná místa.
- Pokročilé techniky odstraňování: Použití CNC obrábění, elektroerozivního obrábění nebo elektrochemických metod, pokud je ruční odstranění nepraktické nebo hrozí poškození.
- Konzistence materiálových vlastností & Anizotropie:
- Výzva: Mechanické vlastnosti (pevnost, tažnost, únavová životnost) se někdy mohou lišit v závislosti na směru stavby (anizotropie) v důsledku vrstevnaté mikrostruktury a tepelné historie. Zajištění konzistentních vlastností v celém dílu a mezi jednotlivými sestaveními je klíčové.
- Zmírnění:
- Řízení procesních parametrů: Udržování přísné kontroly nad všemi parametry tisku.
- Tepelný management: Pomocí ohřevu stavební desky a řízeného chlazení.
- Následné zpracování (HIP & amp; tepelné zpracování): HIP a vhodné tepelné zpracování pomáhají homogenizovat mikrostrukturu a snížit anizotropii, což vede k rovnoměrnějším vlastnostem.
- Důkladné testování: Rozsáhlé zkoušky materiálu (tahové, únavové, creepové) na zkušebních vzorcích, které jsou postaveny vedle dílů a často se testují v různých orientacích.
- Nedestruktivní zkoušení (NDT):
- Výzva: Spolehlivá detekce kritických vnitřních defektů (póry, trhliny, nedostatečné spojení) ve složitých geometriích AM vyžaduje sofistikované techniky NDT.
- Zmírnění:
- Počítačová tomografie (CT): Poskytuje úplný 3D pohled na vnitřní strukturu, což je velmi efektivní pro detekci objemových defektů a ověření geometrie vnitřních kanálů.
- Další metody: V závislosti na typu dílu a defektu lze použít techniky, jako je fluorescenční penetrační kontrola (FPI) pro povrchové trhliny, ultrazvukové testování (UT) nebo radiografie, ačkoli u složitých leteckých dílů AM se stále více upřednostňuje CT skenování.
Úspěšná výroba vysoce kvalitních vložek proudových motorů pomocí AM vyžaduje hluboké odborné znalosti v oblasti materiálového inženýrství, procesního inženýrství, DfAM, simulace, následného zpracování a kontroly kvality. Partnerství s vertikálně integrovaným poskytovatelem řešení nebo specializovanou servisní kanceláří AM s prokazatelnými výsledky v oblasti leteckých superslitin je pro zmírnění těchto problémů a zajištění shody a spolehlivosti dílů naprosto zásadní.
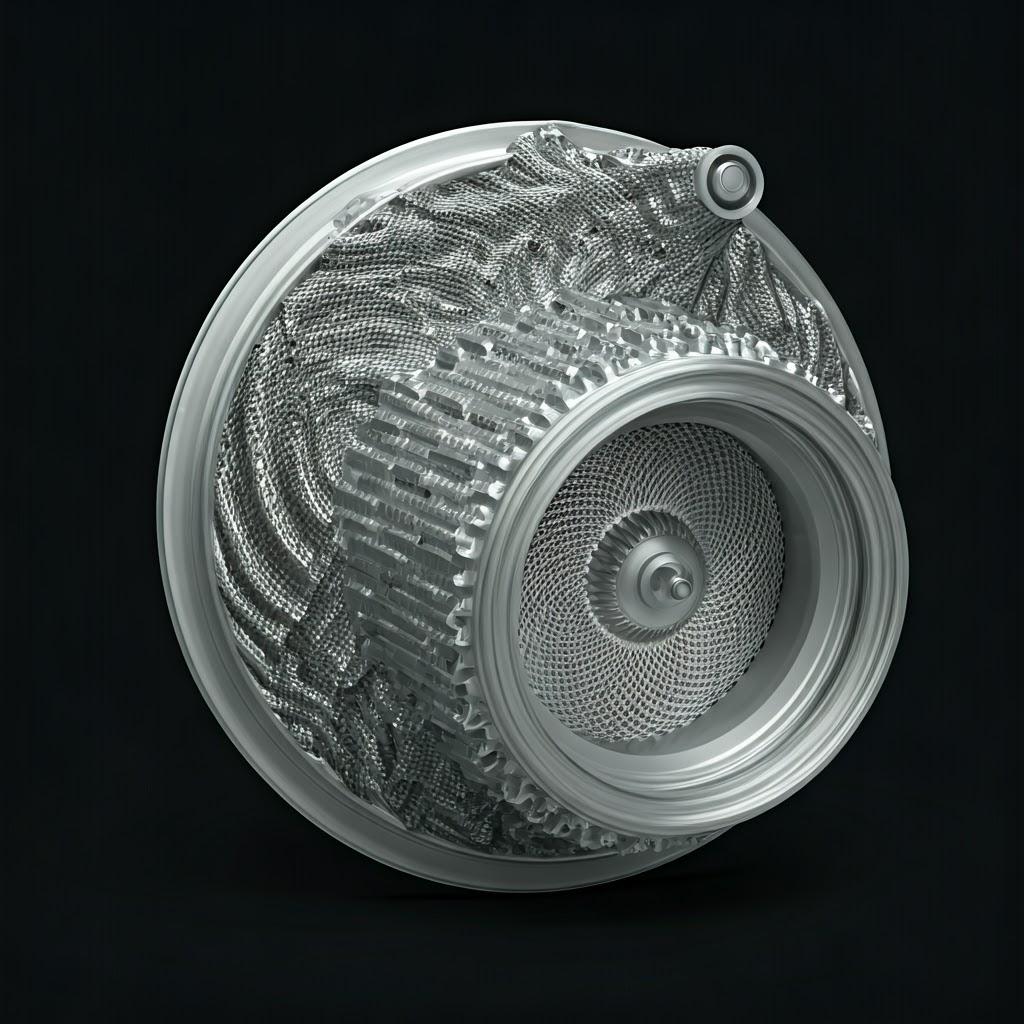
Výběr dodavatele: Výběr správného partnera pro AM zpracování kovů pro letecké komponenty
Výběr správného výrobního partnera je při pořizování aditivně vyráběných vložek do proudových motorů zásadním rozhodnutím. Vzhledem k přísným požadavkům leteckého průmyslu, složitosti součástí a pokročilé povaze použitých materiálů a procesů je prostý výběr dodavatele s nejnižší cenovou nabídkou zřídkakdy tou nejlepší strategií. Manažeři veřejných zakázek a technické týmy musí vyhodnocovat potenciální poskytovatele služeb aditivní výroby kovů na základě komplexního souboru kritérií, aby byla zajištěna kvalita, spolehlivost a shoda s předpisy.
Klíčová kritéria pro hodnocení dodavatelů kovových AM obložení pro letecký průmysl:
- Letecké a kosmické certifikace:
- AS9100: Jedná se o standardní požadavek na systém řízení kvality (QMS) pro letecký, kosmický a obranný průmysl. Ujistěte se, že dodavatel má platnou certifikaci AS9100.
- NADCAP: Národní akreditační program pro letecké a obranné dodavatele. Zatímco AS9100 se vztahuje na systém řízení jakosti, NADCAP poskytuje specifickou akreditaci pro speciální procesy, jako je tepelné zpracování, nedestruktivní zkoušení (NDT), svařování (méně relevantní pro monolitické AM díly, ale svědčí o řízení procesů) a potenciálně specifické AM technologie, jak se budou normy vyvíjet. Hledejte akreditaci NADCAP pro příslušné kroky následného zpracování.
- Schválení OEM: Konkrétní výrobci motorů (např. GE, Rolls-Royce, Pratt & amp; Whitney) mají často vlastní schvalovací procesy pro dodavatele a specifikace materiálů/procesů. V případě potřeby ověřte, zda je dodavatel schválen příslušnými výrobci OEM.
- Prokazatelné zkušenosti se superslitinami:
- Materiálové znalosti: Dodavatel musí prokázat rozsáhlé zkušenosti s tiskem a následným zpracováním konkrétních požadovaných superslitin (např. IN738LC, Hastelloy X). Požádejte o případové studie, příklady vyrobených podobných dílů a údaje o vlastnostech materiálu získané z jejich procesů.
- Vývoj parametrů: Měly by mít dobře vyvinuté a ověřené procesní parametry pro konkrétní kombinaci slitiny a stroje, aby byla zajištěna optimální hustota, mikrostruktura a mechanické vlastnosti.
- Technologie a vybavení:
- Vhodná technologie AM: Ověřte si, zda používají správný typ systému pro tavení v práškovém loži (SLM nebo EBM) vhodný pro danou aplikaci a materiál. Zjistěte, jaké konkrétní modely strojů používají a jaké jsou jejich možnosti (stavební objem, výkon laseru/ paprsku, monitorovací systémy).
- Údržba a kalibrace strojů: Ujistěte se, že mají přísné postupy pro údržbu a kalibraci strojů, které zaručují konzistentní výkon.
- Možnosti následného zpracování: Zhodnoťte jejich vlastní nebo přísně kontrolované externí kapacity pro kritické kroky následného zpracování, jako je odlehčení napětí, HIP, víceosé CNC obrábění, NDT (zejména CT skenování) a případně aplikace TBC. Vlastní kapacity často nabízejí lepší kontrolu a kratší dodací lhůty.
- Sledovatelnost materiálu a manipulace s ním:
- Získávání prášku: Zjistěte, odkud získávají kovové prášky. Spolupracují s renomovanými výrobci prášků, kteří jsou známí kvalitou pro letecký průmysl, jako např Met3dp, nebo vyrobit vlastní? Kvalitní vstupní materiály jsou neoddiskutovatelné.
- Správa prášku: Přísné postupy pro manipulaci s práškem, skladování (kontrola vlhkosti), prosévání, recyklaci (pokud je to vhodné) a sledování šarží jsou zásadní pro prevenci kontaminace a zajištění konzistence. Zásadní je úplná sledovatelnost od šarže surového prášku až po finální díl.
- Systém řízení kvality (QMS) & Dokumentace:
- Robustní QMS: Kromě AS9100 zhodnoťte hloubku a implementaci jejich systému řízení kvality. To zahrnuje dokumentaci řízení procesů, záznamy o školení obsluhy, kontrolní postupy, řešení neshod a procesy nápravných opatření.
- Komplexní dokumentace: Letecký průmysl vyžaduje rozsáhlou dokumentaci, včetně certifikátů o shodě, certifikací materiálů, procesních protokolů, inspekčních zpráv a výsledků nedestruktivního zkoušení. Ujistěte se, že dodavatel může poskytnout požadovaný soubor dokumentace.
- Inženýrská a technická podpora:
- Odborné znalosti DfAM: Mohou poskytnout pokyny k optimalizaci konstrukce vložky pro aditivní výrobu?
- Simulační schopnosti: Používají k předvídání a zmírňování rizik simulační software?
- Aplikační inženýrství: Mají inženýry, kteří rozumí funkčním požadavkům na letecké komponenty a dokáží efektivně spolupracovat? Společnosti jako Met3dp, které nabízejí komplexní řešení, často poskytují silné služby v oblasti vývoje aplikací.
- Řízení projektů a komunikace:
- Jasná komunikace: Hledejte vstřícnou komunikaci, jasná kontaktní místa a proaktivní aktualizace.
- Řízení projektů: Zajistěte, aby měli zavedené systémy pro řízení složitých projektů, sledování jejich průběhu a dodržování dohodnutých termínů.
Shrnutí kontrolního seznamu hodnocení:
Kritéria | Klíčové otázky, které je třeba položit | Význam (letectví a kosmonautika) |
---|---|---|
Certifikace | AS9100? NADCAP (tepelné zpracování, NDT)? Schválení OEM? | Povinné |
Zkušenosti se superslitinami | Které konkrétní slitiny? Podobné vyráběné díly? Jsou k dispozici údaje o materiálu? Ověření parametrů? | Velmi vysoká |
Technologie/vybavení | Správný proces AM (SLM/EBM)? Specifikace stroje? Vlastní následné zpracování (HIP, CNC, NDT)? Kalibrační postupy? | Velmi vysoká |
Sledovatelnost materiálu | Zdroj prášku (kvalitní dodavatel, jako je Met3dp?) Postupy manipulace/skladování/recyklace? Sledování šarží? | Povinné |
QMS & Dokumentace | Hloubka QMS? Řízení procesů? Kontrolní metody? Požadovaná dokumentace (CoC, materiálové certifikáty, zprávy o NDT)? | Povinné |
Technická podpora | Pokyny DfAM? Možnosti simulace? Porozumění aplikacím? | Vysoký |
Řízení projektu/komunikace | Reakce? Kontaktní místo? Sledování pokroku? Záznamy o včasném dodání? | Vysoký |
Export do archů
Výběr dodavatele je o navázání partnerství, zejména u kritických komponent. Důkladné vyhodnocení na základě těchto kritérií vám pomůže zajistit výběr dodavatele kovových AM dílů, který je schopen spolehlivě dodávat vysoce kvalitní a vyhovující obložení proudových motorů.
Pochopení nákladů a časového harmonogramu pro 3D tištěné obložení tryskových motorů
Přestože jsou výkonnostní výhody aditivní výroby vložek do proudových motorů přesvědčivé, pro plánování projektů a sestavování rozpočtů odborníky na zadávání veřejných zakázek a manažery inženýrské činnosti je zásadní pochopit související náklady a typické doby realizace. Struktura nákladů na díly vyrobené metodou AM se výrazně liší od tradiční výroby a konečnou cenu a harmonogram dodávek ovlivňuje několik faktorů.
Klíčové faktory ovlivňující náklady na obložení proudových motorů AM:
- Náklady na materiál:
- Superslitiny: Superslitiny na bázi niklu, jako je IN738LC a Hastelloy X, jsou ze své podstaty drahé materiály. Náklady jsou dány cenou surovin (niklu, chromu, kobaltu, molybdenu atd.) a složitým procesem atomizace, který je nutný k výrobě vysoce kvalitního sférického prášku vhodného pro AM. Množství spotřebovaného prášku (hmotnost dílu + nosiče + potenciální odpad) je hlavním nákladovým faktorem. Zásobování od renomovaných dodavatelů zajišťuje kvalitu, ale je spojeno s vyšší cenou, která je nezbytná pro materiály letecké kvality.
- AM Machine Time:
- Doba výstavby: Často se jedná o největší jednotlivou složku nákladů. Doba výstavby závisí na:
- Část Objem: Větší díly se samozřejmě vyrábějí déle.
- Část Výška: Doba sestavení přímo souvisí s počtem potřebných vrstev (výška dělená tloušťkou vrstvy). Vysoké díly trvají déle než ploché díly stejného objemu.
- Složitost & Podporuje: Složité prvky a rozsáhlé podpůrné konstrukce zvětšují plochu, kterou je třeba skenovat laserovým/elektronovým paprskem, což prodlužuje čas.
- Hnízdění: Současný tisk více dílů na jedné konstrukční desce může amortizovat dobu přípravy, ale může prodloužit celkovou dobu sestavování.
- Odpisy stroje & Provozní náklady: Kapitálové náklady na průmyslové systémy AM na kov jsou vysoké a jsou započítány do hodinových sazeb, stejně jako spotřeba energie, spotřeba inertního plynu, filtry atd.
- Doba výstavby: Často se jedná o největší jednotlivou složku nákladů. Doba výstavby závisí na:
- Náklady na pracovní sílu:
- Nastavení a demontáž: Příprava stroje, vkládání prášku, odstranění nástavby a počáteční čištění vyžadují čas kvalifikovaného technika.
- Následné zpracování: To může být velmi pracné. Ruční odstraňování podpěr, podrobná kontrola, nastavení přípravků pro obrábění, ruční leštění a interpretace NDT - to vše významně přispívá k nákladům na pracovní sílu.
- Engineering & QA: Podpora DfAM, simulace, kontroly kvality a příprava dokumentace rovněž představují mzdové náklady.
- Intenzita následného zpracování:
- Povinné kroky: Odlehčení od napětí a HIP jsou obecně vyžadovány pro vložky a zvyšují fixní náklady na dávku.
- Obrábění: Množství CNC obrábění, které je nutné pro dosažení přísných tolerancí nebo specifických povrchových úprav, významně ovlivňuje náklady. Víceosé obrábění složitých tvarů AM může být nákladné.
- Povrchová úprava: V závislosti na metodě (tryskání vs. leštění) a požadovaném rozsahu.
- Povlaky: Aplikace TBC představuje další, často značné náklady.
- Nedestruktivní zkoušení (NDT):
- CT vyšetření: Přestože CT skenovací zařízení poskytuje neocenitelné údaje, jeho vlastnictví a provoz jsou nákladné, což zvyšuje náklady na jeden díl. Náklady vznikají i u jiných metod nedestruktivního zkoušení.
- Zajištění kvality & Dokumentace:
- Přísná kontrola, testování a dokumentace, které jsou vyžadovány pro letově kritické letecké komponenty, přispívají k celkovým nákladům.
- Objem objednávky:
- Úspory z rozsahu: Ačkoli se AM vyhýbá nákladům na výrobu nástrojů, existují určité úspory z rozsahu. Náklady na seřízení se amortizují ve větších sériích. Optimalizované vnořování na konstrukčních deskách může zlepšit využití stroje. Snížení nákladů na jeden díl s objemem je však obvykle méně dramatické než u tradičních velkoobjemových procesů, jako je odlévání.
Typické dodací lhůty:
Dodací lhůty pro vložky AM se mohou značně lišit, ale obecně nabízejí výhody oproti tradičním metodám, zejména pro prototypy a malosériovou výrobu.
- Prototypování/první článek: Obvykle se pohybuje od 2 až 8 týdnů. To zahrnuje kontrolu DfAM, simulaci sestavení (volitelná, ale doporučená), tisk, všechny kroky následného zpracování (včetně možných prodlev pro externí HIP nebo tepelné zpracování), kontrolu a dokumentaci. Složitost návrhu a požadavky na následné zpracování jsou hlavními faktory.
- Výroba seriálu: Jakmile je proces plně kvalifikován, lze optimalizovat dobu přípravy dalších dávek, která však nadále závisí na době sestavení, pracovním postupu po zpracování a velikosti dávky. Předvídatelné dodací lhůty mohou být stanoveny na základě smluvních ujednání s 3D tisk z kovu dodavatele. Konzistenci mohou ovlivnit faktory dodavatelského řetězce (dostupnost prášku, čekací doba po zpracování).
Náklady vs. tradiční metody:
- Přímé náklady: U jednodušších konstrukcí vložek vyráběných ve velkých objemech může mít tradiční výroba nebo odlévání stále nižší přímé náklady na jeden díl.
- Celkové náklady na vlastnictví: AM se stává konkurenceschopnějším, pokud se zohlední:
- Vysoká složitost: Díly se složitým chlazením nebo geometrií tradičně nemožné/nákladné.
- Konsolidace částí: Snížení pracnosti montáže a zvýšení spolehlivosti.
- Zkrácení doby realizace: Rychlejší vývojové cykly, rychlejší výměna dílů.
- Vylepšený výkon: Odlehčení a lepší chlazení vedoucí k úspoře paliva nebo delší životnosti součástí (hodnotová nabídka).
- Žádné nářadí: Výrazné úspory u malosériových nebo prototypových dílů.
Manažeři veřejných zakázek by si měli vyžádat podrobné nabídky s rozpisem těchto nákladových položek a spolupracovat s dodavateli na optimalizaci návrhů a procesů s ohledem na nákladovou efektivitu, aniž by byla ohrožena kvalita nebo výkon.
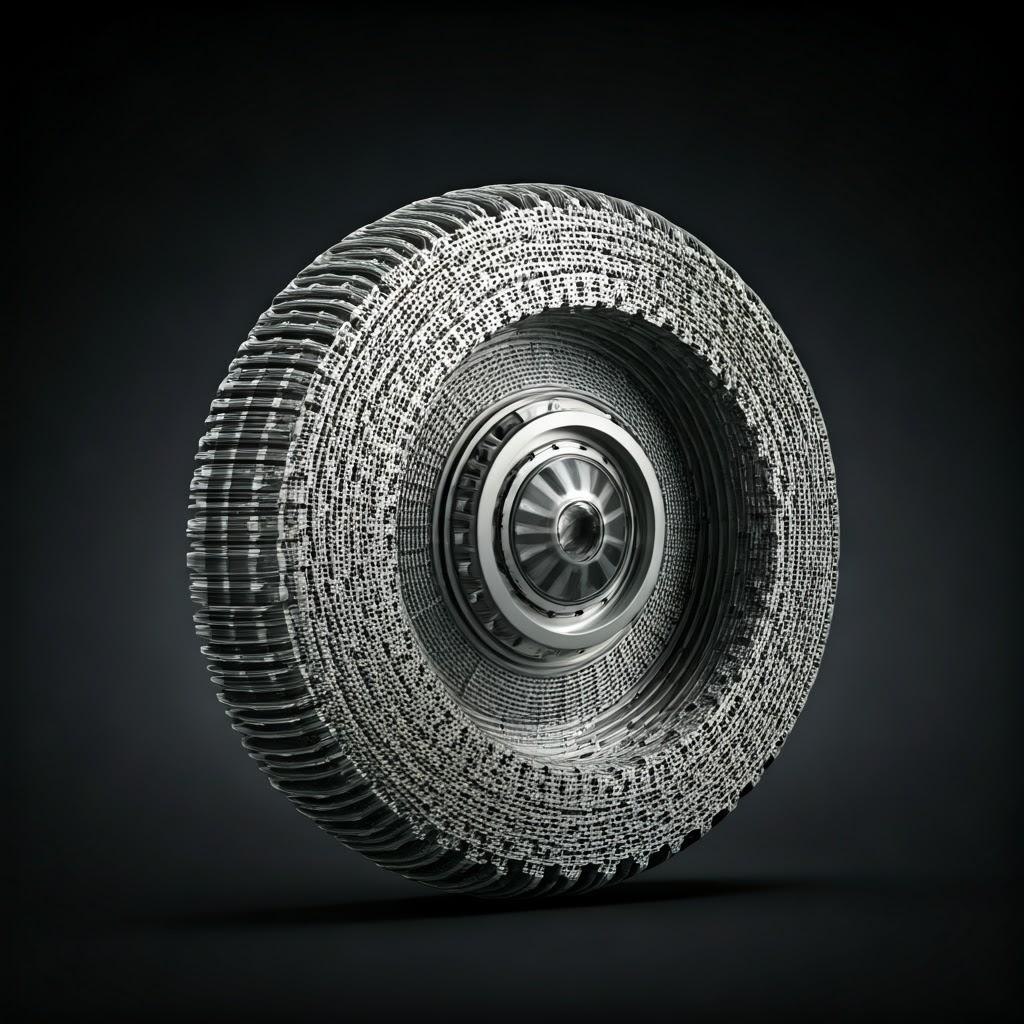
Často kladené otázky (FAQ) o 3D tištěných obloženích proudových motorů
Otázka 1: Jaká je životnost a trvanlivost 3D tištěného obložení proudového motoru ve srovnání s tradičně vyráběným obložením (např. odlévaným nebo vyráběným)?
A1: Cílem použití aditivní výroby pro vložky proudových motorů je často dosáhnout stejné nebo vyšší životnosti a odolnosti než u tradičních dílů. AM umožňuje použití pokročilých superslitin, jako jsou IN738LC a Hastelloy X, zpracovaných na téměř plnou hustotu pomocí technik, jako je SLM/EBM v kombinaci s HIP. Svoboda konstrukce, kterou AM nabízí, navíc umožňuje vytvářet vynikající chladicí schémata (složité kanály, optimalizované výtokové otvory), která mohou výrazně snížit provozní teplotu kovu vložky. Nižší teploty kovu se přímo promítají do snížení tepelné únavy, tečení a oxidace, což může vést k prodloužení životnosti součásti. Dosažení tohoto cíle však vyžaduje přísnou kontrolu procesu, důkladné NDT a rozsáhlé kvalifikační zkoušky (včetně únavových zkoušek, zkoušek tečení a zkoušek odolnosti motoru), aby se ověřila výkonnost a zajistilo se, že splňuje nebo překračuje požadavky stanovené pro tradičně vyráběné vložky. První aplikace ukázaly slibné výsledky, ale kvalifikace je klíčová pro každou konkrétní konstrukci a aplikaci.
Otázka 2: Je 3D tisk vložek proudových motorů cenově konkurenceschopný s tradičními metodami, jako je investiční lití nebo výroba plechů?
A2: Nákladová konkurenceschopnost závisí do značné míry na několika faktorech. U velmi složitých konstrukcí vložek zahrnujících složité chladicí prvky, optimalizaci topologie pro odlehčení nebo konsolidaci dílů (redukce více vyrobených kusů na jeden) může být AM velmi cenově konkurenceschopná nebo dokonce levnější, pokud vezmeme v úvahu celkové náklady na vlastnictví. Je tomu tak proto, že tradiční metody by měly potíže s vytvořením takto složitých prvků nebo by byly neúnosně drahé a náklady na montáž se snižují. U jednodušších konstrukcí nebo velmi vysokých objemů výroby mohou tradiční metody, jako je odlévání (po počáteční investici do nástrojů) nebo výroba plechů, stále nabízet nižší náklady na jeden díl. AM však nabízí významné úspory díky eliminaci nákladů na nástroje (což je výhodné zejména u prototypů a nízkých objemů) a drastickému zkrácení dodacích lhůt pro vývoj a výměnu dílů. Hodnotová nabídka pro obložení AM často spočívá ve zlepšení výkonu (účinnost, hmotnost) a zrychlení inovačních cyklů spíše než pouze v přímém srovnání nákladů na jeden díl u jednoduchých, velkosériových součástí.
Otázka 3: Jaké specifické certifikace a kvalifikace jsou obvykle vyžadovány pro aditivní výrobu dílů kritických pro let, jako jsou například vložky spalovacího prostoru?
A3: Výroba letově kritických leteckých součástí pomocí AM vyžaduje dodržování přísných certifikačních a kvalifikačních protokolů. Mezi klíčové požadavky patří:
- Systém řízení kvality: Výrobce musí pracovat v rámci certifikovaného systému řízení jakosti AS9100.
- Akreditace speciálních procesů: Akreditace NADCAP je obvykle vyžadována pro kritické kroky následného zpracování, jako je tepelné zpracování, nedestruktivní zkoušení a případně svařování (pokud se jedná o spojování, ačkoli cílem AM je toto minimalizovat). S tím, jak AM dozrává, jsou stále běžnější specifické kontrolní seznamy NADCAP pro procesy AM.
- Specifikace materiálu: Konkrétní kovový prášek (např. IN738LC, Hastelloy X) musí splňovat specifikace leteckého materiálu (normy AMS) týkající se složení, vlastností prášku a sledovatelnosti.
- Specifikace procesu: Celý výrobní proces (parametry tisku, orientace sestavení, strategie podpory, kroky následného zpracování včetně HIP, tepelného zpracování, obrábění) musí být důsledně definován, zdokumentován a zakotven ve specifikaci procesu.
- Kvalifikace dílů: U dílů vyrobených definovaným postupem se vyžaduje rozsáhlé testování. To zahrnuje ověření rozměrů, nedestruktivní zkoušky (často 100% CT skenování), destruktivní zkoušky (tahové, únavové, creepové zkoušky na svědeckých kuponech nebo obětních prvcích), mikrostrukturální analýzu a případně zkoušky na plošině nebo na celém motoru, aby se prokázalo, že díl splňuje všechny požadavky na výkon a životnost.
- Požadavky OEM: Velcí výrobci motorů mají často své vlastní dokumenty se specifickými požadavky, které musí dodavatelé dodržovat, případně včetně seznamů schválených dodavatelů materiálů a procesů.
Splnění těchto požadavků vyžaduje značné investice do řízení procesů, systémů kvality, testování a dokumentace.
Závěr: Budoucnost je aditivní - pokrok v technologii tryskových motorů pomocí 3D tisku
Cesta složitostí výroby obložení proudových motorů pomocí aditivní výroby kovů odhaluje technologii, která není pouhou novinkou, ale mocným nástrojem pro budoucnost leteckého pohonu. Schopnost překonat omezení tradičních metod otevírá dveře k nebývalé úrovni složitosti konstrukce, zejména při vytváření vysoce optimalizovaných chladicích systémů, které mají zásadní význam pro zvýšení účinnosti motorů a snížení emisí. Využitím AM mohou konstruktéři konsolidovat díly, výrazně snížit hmotnost díky optimalizaci topologie a mřížkovým strukturám a drasticky zkrátit vývojové cykly, což urychluje tempo inovací.
Úspěšná implementace AM pro kritické součásti, jako jsou vložky, závisí na zvládnutí několika klíčových oblastí: použití zásad návrhu pro aditivní výrobu (DfAM), výběr správných vysoce výkonných superslitin, jako jsou IN738LC a Hastelloy X, použití vysoce kvalitních kovových prášků, přesné řízení procesu tisku a pečlivé provedení základních kroků po zpracování, jako je HIP a tepelné zpracování. Překonání problémů souvisejících se zbytkovým napětím, pórovitostí a dosažením přísných tolerancí vyžaduje hluboké odborné znalosti a důkladnou kontrolu kvality.
Výběr správného výrobního partnera - partnera s ověřenými certifikacemi pro letecký průmysl, hlubokými znalostmi materiálů a procesů, komplexními schopnostmi a závazkem ke kvalitě - je prvořadý. Společnosti jako např Met3dp, která má základy v pokročilé výrobě prášků pomocí technologií plynové atomizace a PREP a jejíž vize směřuje k poskytování komplexních řešení zahrnujících materiály, zařízení a vývoj aplikací, hraje v tomto ekosystému zásadní roli. Umožňujeme výrobcům v leteckém průmyslu využít plný potenciál technologie AM pro zpracování kovů.
Vzhledem k tomu, že letecký průmysl pokračuje ve svém neúnavném úsilí o dosažení udržitelnějších, efektivnějších a výkonnějších letadel, bude aditivní výroba kovů nepochybně hrát stále důležitější roli. Pro součásti, jako jsou obložení proudových motorů, které pracují v srdci výkonu motoru, nabízí AM jasnou cestu k dosažení výkonnostních cílů nové generace. Budoucnost technologie proudových motorů je bezesporu spjata s pokrokem a zaváděním aditivní výroby.
Sdílet na
MET3DP Technology Co., LTD je předním poskytovatelem řešení aditivní výroby se sídlem v Qingdao v Číně. Naše společnost se specializuje na zařízení pro 3D tisk a vysoce výkonné kovové prášky pro průmyslové aplikace.
Dotaz k získání nejlepší ceny a přizpůsobeného řešení pro vaše podnikání!
Související články
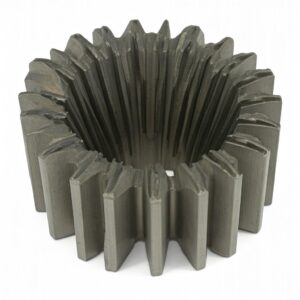
Vysoce výkonné segmenty lopatek trysek: Revoluce v účinnosti turbín díky 3D tisku z kovu
Přečtěte si více "O Met3DP
Nedávná aktualizace
Náš produkt
KONTAKTUJTE NÁS
Nějaké otázky? Pošlete nám zprávu hned teď! Po obdržení vaší zprávy obsloužíme vaši žádost s celým týmem.
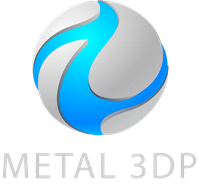
Kovové prášky pro 3D tisk a aditivní výrobu