3D tištěné lodní vrtule ze slitin bronzu a niklu
Obsah
Úvod: Příští vlna v námořním pohonu - aditivní výroba kovů
Neustálý tlak na efektivitu, výkonnost a udržitelnost v námořním průmyslu vyžaduje neustálé inovace. Srdcem pohybu plavidel je lodní šroub - kritická součást, která převádí výkon motoru na tah. Po desetiletí se konstrukce a výroba lodních šroubů do značné míry spoléhala na tradiční metody, jako je odlévání a obrábění. Tyto metody jsou sice efektivní, ale často se potýkají s omezeními, pokud jde o složitost konstrukce, dodací lhůty, náklady na nástroje a plýtvání materiálem. Dnes se nová vlna technologií chystá nově definovat lodní pohon: Výroba aditiv kovů (AM), běžně známý jako kov 3D tisk.
Kovový AM představuje změnu paradigmatu, kdy se přechází od subtraktivních procesů (odebírání materiálu) k aditivním (vytváření vrstvy po vrstvě z kovového prášku). Tento zásadní rozdíl otevírá nebývalé možnosti pro vytváření vysoce optimalizovaných, komplexních a přizpůsobených součástí. Představte si vrtule se složitou geometrií lopatek dokonale přizpůsobenou konkrétnímu tvaru trupu a provoznímu profilu plavidla, vyráběné rychleji a potenciálně nákladově efektivněji, zejména v případě jedinečných nebo nízkoobjemových požadavků. To už není sci-fi, ale rychle se rozvíjející realita, kterou umožňují pokročilé technologie techniky 3D tisku kovů.
Tento článek se zabývá zajímavým využitím technologie AM pro výrobu lodních šroubů, konkrétně se zaměřením na použití vysoce výkonných slitin bronzu a niklu, jako jsou např Nikl-hliníkový bronz (NAB – CuAl10Fe5Ni5) a Měď a nikl (CuNi – CuNi30Mn1Fe). Tyto materiály jsou proslulé svými výjimečnými vlastnostmi v drsném mořském prostředí a nabízejí vynikající odolnost proti korozi, trvanlivost a v případě slitin CuNi i vynikající vlastnosti proti zanášení.
Proč je to důležité pro inženýry a manažery veřejných zakázek v leteckém, automobilovém, lékařském a průmyslovém výrobním odvětví, kromě bezprostředního námořního zaměření? Pokroky a principy, o nichž se zde hovoří - svoboda konstrukce, optimalizace materiálů, narušení dodavatelského řetězce, zvýšení výkonnosti - jsou důležité pro všechna odvětví, která hledají vysoce výkonné kovové součásti. Pochopení toho, jak AM mění náročné aplikace, jako jsou lodní vrtule, poskytuje cenné informace o jejím potenciálu pro vaše vlastní kritické součásti.
Pro inženýři, otevírá technologie AM široký prostor pro navrhování. Umožňuje vytvářet biomimetické struktury, složité vnitřní kanály pro chlazení nebo snižování hluku a variabilní rozložení stoupání/sklonů podél rozpětí lopatek, které jednoduše nejsou proveditelné nebo ekonomické při použití tradičních forem pro odlévání nebo víceosého CNC obrábění. To se přímo promítá do potenciálního zvýšení hydrodynamické účinnosti, úspory paliva, snížení kavitace a nižšího hluku vyzařovaného pod vodou.
Pro manažeři veřejných zakázek a těm, kteří řídí dodavatelské řetězce, nabízí technologie AM na bázi kovů přesvědčivé výhody. Usnadňuje výrobu na vyžádání, čímž výrazně snižuje potřebu velkých zásob náhradních dílů, zejména u starších nebo méně obvyklých plavidel. Dodací lhůty pro zakázkové nebo náhradní vrtule se mohou výrazně zkrátit ve srovnání s týdny nebo měsíci, které jsou často potřebné pro výrobu vzorů, odlévání a obrábění. Kromě toho může AM umožnit lokalizovanou výrobu, což posiluje odolnost dodavatelského řetězce a potenciálně snižuje logistické náklady a složitost. Nalezení spolehlivého poskytovatel řešení pro aditivní výrobu se stává klíčem k využití těchto výhod.
Na Met3dp, stojíme v čele této technologické revoluce. Společnost Met3dp se sídlem v čínském městě Čching-tao se specializuje na průmyslové systémy aditivní výroby kovů a výrobu vysoce výkonných kovových prášků nezbytných pro tyto pokročilé aplikace. Naše špičkové tiskárny SEBM (Selective Electron Beam Melting) poskytují výjimečnou přesnost, spolehlivost a objem výroby vhodný pro náročné komponenty, jako jsou lodní vrtule. Ve spojení s našimi odbornými znalostmi v oblasti práškové metalurgie, využívajícími pokročilé technologie plynové atomizace a plazmového procesu s rotujícími elektrodami (PREP), poskytujeme komplexní ekosystém pro využití plného potenciálu technologie AM kovů. Spolupracujeme s organizacemi napříč náročnými odvětvími, abychom integrovali 3D tisk a urychlili jejich transformaci digitální výroby.
Tento článek se zabývá konkrétními případy použití, ve kterých 3D tištěné vrtule vynikají, podrobně popisuje výhody oproti tradičním metodám, zabývá se vlastnostmi slitin CuAl10Fe5Ni5 a CuNi30Mn1Fe v kontextu AM a provede vás kritickými aspekty návrhu, výroby a partnerství pro úspěšné zavedení této technologie. Připojte se k nám při plavbě v proudech změn v technologii lodních pohonů.
Aplikace & Případy použití: Kde 3D tištěné vrtule vynikají?
Zatímco tradiční výrobní metody jsou i nadále vhodné pro sériově vyráběné, standardizované vrtule, aditivní výroba kovů přináší významné výhody ve specifických mezerách a aplikacích, kde její jedinečné schopnosti nabízejí jedinečnou hodnotu. Zavádění 3D tištěných vrtulí nabírá na síle v různých segmentech námořního průmyslu, což je dáno potřebou přizpůsobení, rychlosti, vyššího výkonu a řešení zastarávání. Zde je uvedeno, kde vrtule AM vytvářejí vlny:
1. Zakázkové a vysoce výkonné jachty:
- Potřebujete: Majitelé superjachet a vysoce výkonných závodních jachet vyžadují maximální účinnost a minimální vibrace/hluk. Pro optimální výkon musí být vrtule dokonale přizpůsobeny konstrukci trupu a charakteristikám motoru.
- Výhoda AM: Technologie AM pro kovy umožňuje vytvářet vysoce přizpůsobené geometrie vrtulí. Hydrodynamická optimalizace pomocí výpočetní dynamiky tekutin (CFD) může vést k návrhům se složitými křivkami a profily lopatek, které je obtížné nebo nemožné přesně odlít. AM umožňuje rychlou iteraci - tisk a rychlé testování více variant návrhu, aby bylo dosaženo požadovaných výkonnostních cílů. Schopnost vyrábět jednorázové návrhy bez speciálních nástrojů činí AM pro tento trh ekonomicky životaschopným.
2. Bezpilotní povrchová vozidla (USV) a autonomní podvodní vozidla (AUV):
- Potřebujete: Tyto platformy často vyžadují kompaktní, vysoce účinné a někdy i akusticky skryté pohonné systémy. Konstrukce se často opakují podle toho, jak se vyvíjí užitečné zatížení senzorů a požadavky na mise. Typické jsou nízké výrobní objemy.
- Výhoda AM: AM vyniká při výrobě složitých a lehkých konstrukcí. Systémy vrtulových potrubí nebo integrované trysky se složitými vnitřními prvky lze tisknout jako jednotlivé jednotky, což snižuje složitost montáže a potenciální netěsnosti. Schopnost rychlého prototypování umožňuje inženýrům rychle přizpůsobit pohonné systémy novým konfiguracím vozidla nebo profilům mise. Pro vojenské nebo výzkumné aplikace umožňuje AM vytvářet vrtule se specifickou akustickou signaturou.
3. Specializované pracovní a servisní lodě:
- Potřebujete: Plavidla určená pro specifické úkoly (např. pilotní čluny, plavidla pro přesun posádky, výzkumná plavidla, pomocná plavidla na moři) mají často jedinečné provozní profily, které vyžadují optimalizovaný pohon z hlediska účinnosti, ovladatelnosti nebo nízké hlučnosti. Výrobní objemy mohou být spíše malosériové než sériové.
- Výhoda AM: AM umožňuje přizpůsobit vrtule konkrétnímu pracovnímu cyklu plavidla - optimalizovat pro vysoký tah při nízkých rychlostech, maximalizovat účinnost paliva během přepravy nebo minimalizovat hluk při výzkumných činnostech. Pro výzkumná plavidla, která potřebují velmi nízkou hlučnost, může AM vyrábět složité tvary lopatek navržené tak, aby se snížil hluk vznikající při kavitaci a hluk způsobený vírem na špičce. Možnost rychlého tisku náhradních lopatek nebo celých vrtulí minimalizuje prostoje těchto kritických prostředků.
4. Rychlé prototypování a hydrodynamický výzkum:
- Potřebujete: Námořní architekti a námořní inženýři se neustále snaží zdokonalovat konstrukce lodních šroubů. Testování nových konceptů vyžaduje přesné fyzické modely.
- Výhoda AM: Metal AM je ideálním nástrojem pro vytváření funkčních prototypů pro testování v nádržích nebo dokonce pro omezené námořní zkoušky. Návrhy lze převzít přímo z modelů CAD a vytisknout je z cílového materiálu (nebo vhodného náhradního materiálu) mnohem rychleji než tradiční způsoby výroby prototypů zahrnující výrobu modelů a odlévání. To urychluje cyklus návrh-konstrukce-zkoušky a podporuje inovace v oblasti hydrodynamické účinnosti, snižování kavitace a potlačování hluku.
5. Náhradní díly pro starší systémy a zastaralé konstrukce:
- Potřebujete: Údržba starších plavidel může být náročná, pokud se původní konstrukce lodních šroubů již nevyrábí nebo pokud se původní nástroje/vzory ztratily či degradovaly. Shánění náhradních dílů může být spojeno s dlouhými dodacími lhůtami a vysokými náklady.
- Výhoda AM: Pokud existuje 3D model CAD nebo jej lze vytvořit pomocí reverzního inženýrství (např. 3D skenování), umožňuje technologie AM z kovu výrobu náhradních vrtulí nebo listů na vyžádání, aniž by bylo nutné použít původní nástroje. To je neocenitelné pro provozovatele flotil, námořní síly a projekty obnovy. Zajišťuje provozní připravenost a prodlužuje životnost cenného majetku. Tato schopnost je zajímavá zejména pro distributoři lodních dílů hledá řešení pro obtížně dostupné komponenty.
6. Niche aplikace a extrémní prostředí:
- Potřebujete: Některé aplikace mohou vyžadovat vrtule vyrobené z exotických slitin, které nejsou běžně dostupné ve standardních slévárnách, nebo vrtule určené pro extrémní provozní podmínky (např. vysokorychlostní plavidla, polární operace).
- Výhoda AM: Poskytovatelé služeb AM často pracují s širší škálou slitin, včetně specializovaných složení. Společnosti jako Met3dp, které mají zkušenosti s vývojem prášků, mohou v případě potřeby zkoumat i vlastní složení slitin. Kromě toho lze pomocí AM vytvářet robustní konstrukce optimalizované tak, aby odolávaly specifickým výzvám prostředí, jako je náraz ledu nebo silná kavitace.
Příležitosti pro dodavatelský řetězec:
Rozvoj vrtule AM vytváří nové příležitosti pro podniky v celém námořním dodavatelském řetězci:
- Distributoři námořních dílů: Mohou rozšířit své portfolio o vrtule AM na zakázku nebo na vyžádání a nabídnout tak rychlejší řešení naléhavých potřeb a přístup k návrhům, které nejsou k dispozici prostřednictvím tradičních kanálů.
- Dodavatelé pro stavbu lodí: Mohou využít AM pro rychlou tvorbu prototypů ve fázi návrhu plavidla nebo nabízet vysoce optimalizované vrtule jako součást s přidanou hodnotou pro nové stavby, čímž se odliší od ostatních.
- Opravárenské dvory a poskytovatelé údržby: Může spolupracovat s poskytovateli služeb AM a nabízet rychlá řešení výměny poškozených vrtulí, čímž se výrazně zkrátí prostoje plavidel. Tím se mění prostředí MRO (údržba, opravy a generální opravy).
Souhrnně řečeno, 3D tisk z kovu nemusí nutně nahradit veškerou tradiční výrobu vrtulí ze dne na den. Místo toho nabízí výkonná řešení tam, kde je nejdůležitější přizpůsobení, rychlost, složitá geometrie, malosériová výroba a rychlé inovace. S tím, jak tato technologie dozrává, snižují se náklady a roste povědomí o ní, bude se nepochybně i nadále rozšiřovat spektrum aplikací, v nichž 3D tištěné vrtule vynikají, což z ní činí klíčovou technologii pro progresivně uvažující námořní inženýry a specialisty na zásobování.
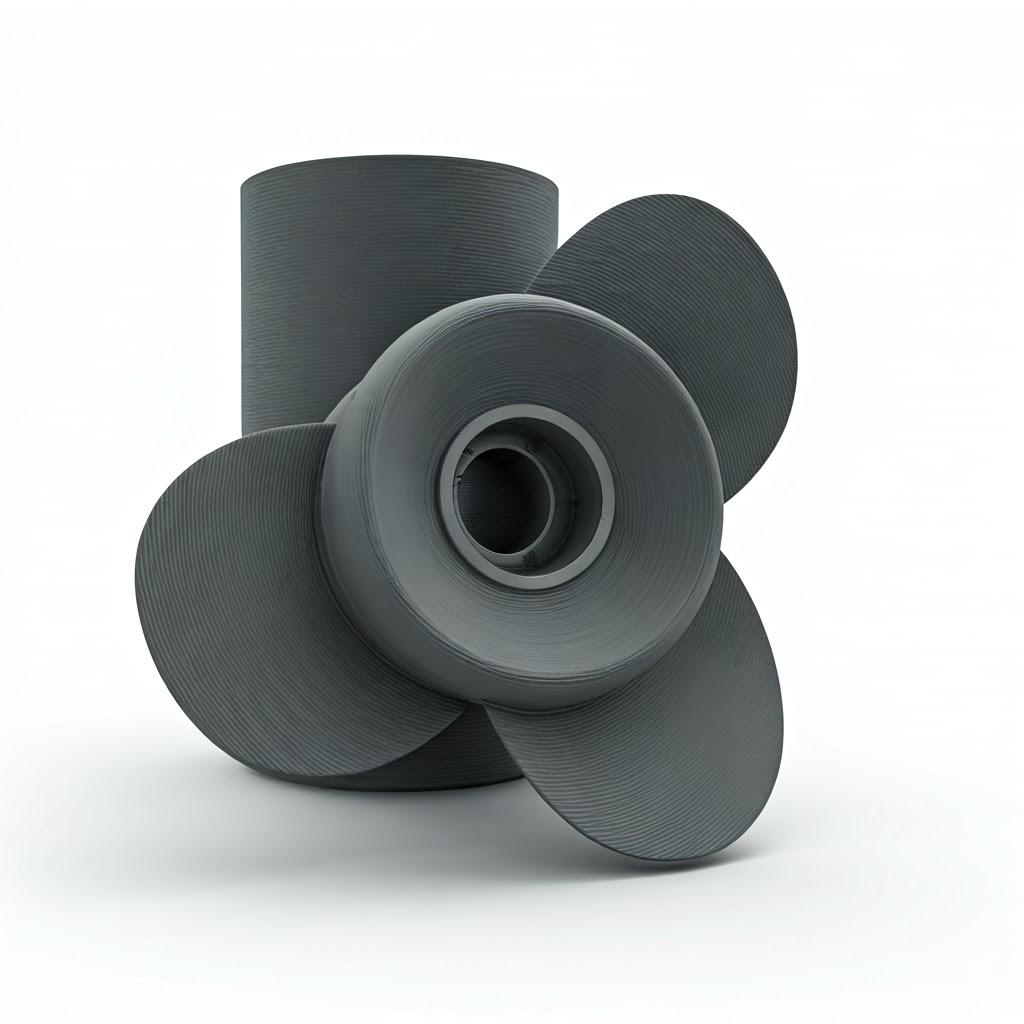
Proč 3D tisk z kovu? Výhody oproti tradiční výrobě vrtulí
Po celé generace se lodní vrtule vyráběly převážně odléváním (obvykle odléváním do písku nebo investičním odléváním), po kterém následovalo rozsáhlé CNC obrábění a dokončovací práce. Tyto metody jsou sice vyspělé a umožňují vyrábět spolehlivé vrtule, ale jejich podstata s sebou nese omezení, která lze účinně překonat aditivní výrobou kovů. Pochopení těchto rozdílů je klíčové pro inženýry, kteří usilují o optimální výkon, i pro manažery nákupu, kteří se snaží o efektivní a flexibilní zásobování.
Srovnejme AM (konkrétně techniky Powder Bed Fusion, jako jsou LPBF a SEBM, kde má společnost Met3dp díky svým pokročilým tiskárnám SEBM značné zkušenosti) s tradičním odléváním a CNC obráběním pro výrobu vrtulí:
Srovnání: Výroba vrtule z kovu vs. tradiční výroba vrtule
Vlastnosti | Aditivní výroba kovů (LPBF/SEBM) | Tradiční odlévání (+CNC) | Tradiční CNC obrábění (ze sochorů) |
---|---|---|---|
Svoboda designu | Velmi vysoká: Umožňuje velmi složité geometrie, vnitřní prvky, tenké stěny, optimalizované tvary lopatek, mřížové struktury. | Mírné: Omezeno možnostmi výroby forem, úhly tahu a rychlostí chlazení. Složité vnitřní prvky obtížné/nemožné. | Vysoká (externí): Vynikající pro vnější povrchy, ale omezené pro vnitřní prvky. Hluboké kapsy/komplikované vnitřní práce jsou obtížné. |
Dodací lhůta (prototyp/malý objem) | Krátký: Dny až týdny. Není třeba žádné nářadí. Přímo z CAD. | Dlouhé: Týdny až měsíce. Vyžaduje vytvoření vzoru/formy. | Středně dlouhá až dlouhá: Záleží na složitosti a programování. Shánění polotovarů může být časově náročnější. |
Náklady na nástroje | Žádné: Výroba bez použití nástrojů. | Vysoká: Značné náklady na vzory a formy, zejména ty složité. | Nízká (Fixturing): Vyžaduje upínací přípravky, ale žádné formy pro konkrétní díl. |
Materiálový odpad | Nízká: Proces téměř síťového tvaru. Netavený prášek je z velké části recyklovatelný. | Mírné: Vyžaduje stoupačky, brány, běhouny (recyklované, ale energeticky náročné). Potřebný značný přídavek na obrábění. | Velmi vysoká: Subtraktivní proces, často se z 50 % surového polotovaru stávají třísky (recyklovatelné, ale neefektivní). |
Zpracování složitosti | Vynikající: Složitost často nepřináší žádné dodatečné náklady ani čas. Umožňuje konsolidaci dílů. | Náročné: Zvýšená složitost výrazně zvyšuje náklady na nástroje a možnost vzniku vad odlitků. | Náročné/nákladné: Velmi složité geometrie vyžadují víceosé stroje, složité programování a dlouhé časy cyklů. |
Minimální množství objednávky (MOQ) | První: Ideální pro jednotlivé kusy, prototypy a malé objemy. | Mírná až vysoká: Náklady na nástroje vyžadují pro ekonomickou rentabilitu sériovou výrobu. | Jedna (teoreticky): Ale doba nastavení prodražuje jednotlivé kusy, pokud nejsou jednoduché. |
Potenciál přizpůsobení | Velmi vysoká: Každý tisk může být jedinečný, aniž by to bylo spojeno s výraznými náklady. Možnost hromadného přizpůsobení. | Nízká: Přizpůsobení vyžaduje nové nebo upravené nástroje, což je nákladné a pomalé. | Mírné: Lze přizpůsobit funkce, ale je to omezeno tvarem polotovaru a omezeními při obrábění. |
Vlastnosti materiálu | Vynikající: Díky rychlému tuhnutí často splňuje nebo překračuje vlastnosti odlitku/tepané oceli. Jemnozrnná struktura. Potenciál pro mikrostruktury na míru. | Dobré: Dobře pochopitelné vlastnosti, ale náchylné k pórovitosti, segregaci a hrubší struktuře zrn. | Vynikající: Vlastnosti kovaných materiálů jsou obvykle měřítkem. Homogenní struktura. |
Export do archů
Vypracování klíčových výhod technologie AM na bázi kovů:
- Bezkonkurenční volnost designu: To je pravděpodobně nejvýznamnější výhoda AM. Inženýři již nejsou omezováni omezeními konstrukce forem nebo dostupností řezných nástrojů.
- Hydrodynamická optimalizace: Vytvářejte lopatky s plynule se měnícím sklonem, sklonem, náklonem a odklonem, přesně optimalizované pomocí CFD pro maximální účinnost a minimální kavitaci v celém provozním profilu plavidla.
- Redukce hluku: Navrhování složitých geometrií špiček (např. winglety, jiné než rovinné tvary) nebo vnitřních tlumicích struktur pro minimalizaci hluku vyzařovaného pod vodou - kritické pro výzkumná plavidla, námořní aplikace a pohodlí cestujících.
- Snížení hmotnosti: Zavedení vnitřních mřížových struktur nebo optimalizace topologie pro snížení hmotnosti vrtule při zachování strukturální integrity. Lehčí vrtule snižují namáhání hřídele a mohou zlepšit dynamickou odezvu.
- Konsolidace částí: Integrujte prvky, jako jsou ochranné kryty lan nebo specializované nástavce nábojů, přímo do tisku vrtule, čímž snížíte počet dílů, dobu montáže a potenciální místa poruch.
- Zkrácení dodacích lhůt pro prototypy a malé objemy: Možnost přímého přechodu od digitálního souboru CAD k fyzickému kovovému dílu během několika dnů nebo týdnů je transformující.
- Zrychlené inovace: Rychle otestujte více iterací návrhu, což umožňuje rychlejší konvergenci k optimálnímu řešení.
- Náhradní díly na vyžádání: Tiskněte náhradní vrtule nebo lopatky pouze v případě potřeby, čímž výrazně snížíte náklady na skladování zásob a minimalizujete prostoje plavidel. To mění pravidla hry pro distributoři lodních dílů a provozovatelé vozových parků, kteří se zabývají různorodými nebo stárnoucími vozovými parky.
- Naléhavé požadavky: Rychle řešte nepředvídaná poškození nebo provozní potřeby bez čekání na tradiční fronty na odlitky a obrábění.
- Výroba bez použití nástrojů: Odstranění potřeby drahých a časově náročných vzorů a forem uvolňuje ekonomickou životaschopnost pro:
- Přizpůsobení: Výroba jednorázových vrtulí pro jachty nebo specializovaná plavidla se stává cenově dostupnou.
- Nízkosériová výroba: Výroba malých sérií vrtulí pro specifické aplikace nebo nové konstrukce plavidel je nákladově efektivní.
- Součásti Legacy: Obnovení zastaralých vrtulí bez nutnosti investovat do obnovy ztraceného nářadí.
- Efektivita materiálů a udržitelnost:
- Tvar blízký síti: Procesy AM obvykle využívají pouze materiál potřebný pro díl a jeho podpůrné struktury, což výrazně snižuje množství odpadu v porovnání se subtraktivním obráběním z velkých polotovarů.
- Recyklovatelnost prášku: Netavený kovový prášek v konstrukční komoře lze obvykle prosévat a znovu použít při dalších výtiscích, což dále zlepšuje využití materiálu. Recyklace odlévaných kanálků/brán a obráběcích třísek je sice možná, ale proces AM je ve své podstatě méně nehospodárný v primární fázi výroby.
- Potenciál pro vynikající vlastnosti materiálu: Proces tavení po vrstvách zahrnuje rychlé zahřívání a ochlazování, což vede ke vzniku jemnozrnných mikrostruktur.
- Zvýšená pevnost & amp; Životnost při únavě: Jemná zrna obecně korelují s vyšší pevností a lepší odolností proti únavě ve srovnání s hrubozrnnými litými materiály.
- Hustota: Vysoce kvalitní procesy AM, jako jsou ty, které používá společnost Met3dp s použitím optimalizovaných parametrů a vysoce kvalitních prášků, mohou dosáhnout hustoty dílů vyšší než 99,5 %, což minimalizuje pórovitost, která může ohrozit odlévané díly.
Zatímco tradiční metody mají své místo, zejména pro velkosériovou výrobu jednoduchých, standardizovaných konstrukcí, aditivní výroba kovů nabízí přesvědčivé technické a ekonomické výhody pro rostoucí rozsah aplikací lodních šroubů. Umožňuje inženýrům navrhovat výkonnější komponenty a manažerům nákupu poskytuje nebývalou flexibilitu a rychlost při zajišťování kritického námořního hardwaru, čímž se AM stává důležitým nástrojem pro služba průmyslového 3D tisku uživatelů v námořním sektoru.
Zaměření materiálu: CuAl10Fe5Ni5 & CuNi30Mn1Fe Mořské slitiny
Výběr materiálu je naprosto zásadní pro lodní vrtule, které pracují v jedinečně náročném prostředí, jež se vyznačuje korozivní mořskou vodou, vysokým mechanickým zatížením, možností kavitační eroze a trvalou hrozbou biologického znečištění. Tradiční materiály vrtulí, jako je manganový bronz a nerezová ocel, mají svá omezení. Aditivní výroba kovů otevírá dveře k využití pokročilých slitin vybraných speciálně pro jejich vynikající vlastnosti v těchto podmínkách. Dvěma výraznými kandidáty, které lze snadno zpracovat pomocí AM, jsou nikl-hliníkový bronz (NAB, konkrétně CuAl10Fe5Ni5) a měď-nikl (CuNi, konkrétně CuNi30Mn1Fe). Pochopení jejich vlastností je zásadní pro výběr správného materiálu pro 3D tištěnou vrtuli.
1. Nikl-hliníkový bronz (NAB) – CuAl10Fe5Ni5:
Materiál NAB, který je často považován za základní materiál pro vysoce výkonné lodní vrtule, nabízí vynikající rovnováhu mezi pevností, houževnatostí a odolností proti korozi. Slitina CuAl10Fe5Ni5 (odpovídá normám, jako je ASTM B148 C95800 pro odlévání, ačkoli vlastnosti AM se mohou mírně lišit) obvykle obsahuje přibližně 9-11 % hliníku, 3-5 % železa a 4-5,5 % niklu, zbytek tvoří měď.
- Klíčové vlastnosti a výhody lodních šroubů:
- Vysoká pevnost & Houževnatost: V porovnání s manganovými bronzy vykazuje NAB výrazně vyšší pevnost v tahu a mez kluzu, což umožňuje tenčí a účinnější konstrukce lopatek nebo vyšší odolnost pro náročné aplikace. Jeho dobrá tažnost a rázová houževnatost zajišťují odolnost proti poškození úlomky nebo drobnými nárazy.
- Vynikající odolnost proti korozi mořskou vodou: NAB vytváří při působení mořské vody houževnatý, komplexní ochranný oxidový film (bohatý na oxid hlinitý). Tento film poskytuje vynikající odolnost proti celkové korozi, důlkové korozi a štěrbinové korozi, a to i ve znečištěných nebo stojatých vodách.
- Vynikající odolnost proti kavitační erozi: Kavitace (vznik a rozpad bublinek páry v důsledku tlakových změn na povrchu lopatek) může rychle zničit materiály vrtule. NAB je proslulá svou vynikající odolností proti kavitačnímu poškození, která je výrazně lepší než u nerezových ocelí nebo manganových bronzů. To má zásadní význam pro zachování geometrie a účinnosti lopatek v průběhu času.
- Dobrá odolnost proti opotřebení a oděru: Mikrostruktura slitiny zajišťuje dobrou odolnost proti abrazivnímu opotřebení, což je výhodné v kalných vodách nebo při manévrování.
- Svařitelnost: Zatímco AM je zaměřen na monolitické díly, NAB obecně nabízí slušnou svařitelnost pro případné opravy v případě potřeby (i když je třeba dodržovat specifické postupy pro díly AM).
- Zpracovatelnost AM: Slitiny NAB, jako je CuAl10Fe5Ni5, prokázaly dobrou zpracovatelnost pomocí technik fúze v práškovém loži (LPBF a SEBM), což při použití kvalitního prášku a optimalizovaných parametrů umožňuje vytvářet husté díly s vysokou integritou.
- Úvahy:
- Biofouling: NAB je sice odolný vůči korozi, ale ve srovnání se slitinami CuNi je pouze mírně odolný vůči mořskému růstu (biofouling). V závislosti na provozním profilu může být stále nutné pravidelné čištění nebo nátěry proti zanášení.
- Náklady: Cena: Obecně dražší než manganové bronzy, ale často je odůvodněna jejich vynikajícím výkonem a dlouhou životností.
2. Měď a nikl (CuNi) – CuNi30Mn1Fe:
Slitiny mědi a niklu, zejména varianty 70/30 (CuNi 70/30) a 90/10 (CuNi 90/10), jsou široce používány v námořních aplikacích především pro svou vynikající odolnost proti biologickému znečištění a vynikající obecnou odolnost proti korozi. Slitina CuNi30Mn1Fe (podobně jako C71500) obvykle obsahuje přibližně 30 % niklu, 0,5-1,5 % manganu a 0,4-1,0 % železa.
- Klíčové vlastnosti a výhody lodních šroubů:
- Výjimečná odolnost proti biologickému znečištění: To je hlavní výhoda slitin CuNi. Povrch přirozeně odolává usazování a růstu mořských organismů, jako jsou mlži, řasy a škeble. Je to způsobeno tvorbou filmu bohatého na měďnaté látky, který je poloadherentní a brání biologickému uchycení, případně v kombinaci s minimálním uvolňováním měďnatých iontů. Tato vlastnost je velmi cenná pro udržení účinnosti vrtule po dlouhou dobu, snížení spotřeby paliva a nutnosti častého čištění.
- Velmi dobrá odolnost proti korozi mořskou vodou: Slitiny CuNi vytvářejí stabilní, přilnavý ochranný film, který poskytuje vynikající odolnost proti korozi v proudící mořské vodě. Jsou obzvláště odolné vůči nárazovému napadení způsobenému turbulentním prouděním nebo suspendovanými pevnými látkami.
- Dobrá tvárnost a tvařitelnost: Tyto slitiny jsou obecně tvárné, což může být výhodné z hlediska odolnosti proti poškození.
- Zpracovatelnost AM: Slitiny CuNi lze také zpracovávat pomocí technologií AM, které umožňují vytvářet složité tvary při zachování jejich klíčových materiálových výhod.
- Úvahy:
- Nižší síla: V porovnání s NAB má CuNi30Mn1Fe výrazně nižší pevnost v tahu a mez kluzu. To znamená, že lopatky vrtule mohou být silnější nebo jejich konstrukce upravena tak, aby zvládly vyšší namáhání, což může mít vliv na špičkovou hydrodynamickou účinnost ve srovnání s tenčí konstrukcí NAB.
- Odolnost proti kavitaci: Přestože má dobrou obecnou odolnost proti korozi, jeho odolnost proti kavitační erozi je obecně považována za nižší než u NAB. Konstrukční hlediska pro minimalizaci kavitace jsou ještě důležitější.
- Náklady: Vysoký obsah niklu činí tyto slitiny relativně drahými.
Srovnání materiálů pro 3D tištěné vrtule:
Vlastnictví | CuAl10Fe5Ni5 (nikl-hliníkový bronz) | CuNi30Mn1Fe (měď-nikl 70/30) | Význam pro vrtule |
---|---|---|---|
Pevnost v tahu | Vysoká (~585+ MPa / 85+ ksi typický odlitek) | Mírná (~380+ MPa / 55+ ksi typicky žíhané) | Vysoká (zatížení čepele) |
Mez kluzu | Vysoká (~240+ MPa / 35+ ksi typický odlitek) | Nízká (~150+ MPa / 22+ ksi typicky žíhané) | Vysoká (odolnost proti deformaci) |
Odolnost proti korozi | Vynikající | Velmi dobře | Kritické |
Odolnost proti kavitaci | Vynikající | Slušný až dobrý | Velmi vysoká |
Odolnost proti biologickému znečištění | Mírný | Výjimečné | Vysoký (efektivita) |
Hustota | ~7,6 g/cm³ | ~8,9 g/cm³ | Mírná (setrvačnost) |
Možnost tisku (LPBF/SEBM) | Dobrý | Dobrý | Základní |
Relativní náklady | Vysoký | Velmi vysoká | Střední (náklady na životní cyklus) |
Export do archů
Poznámka: Specifické vlastnosti dílů vyrobených metodou AM závisí do značné míry na parametrech procesu, kvalitě prášku a následném zpracování (např. tepelném zpracování) a mohou se lišit od typických hodnot odlitků nebo tvářených dílů.
Klíčová role kvality kovových prášků – Příspěvek společnosti Met3dp’s:
Dosažení požadovaných mechanických vlastností a korozní odolnosti u 3D tištěné vrtule není jen o volbě správného označení slitiny, ale zásadním způsobem závisí na kvalita kovového prášku používané v procesu AM. Zde hrají důležitou roli specializovaní výrobci prášků, jako je Met3dp, kteří jsou důvěryhodnými partnery dodavatel kovového prášku.
Společnost Met3dp využívá špičkové technologie výroby prášků:
- Atomizace plynu (GA): Tento proces využívá vysokotlaké proudy inertního plynu k rozbití proudu roztaveného kovu na jemné kapičky, které ztuhnou v kulovitý prášek. Met3dp využívá jedinečné konstrukce trysek a proudění plynu k optimalizaci tohoto procesu, čímž vzniká prášek s:
- Vysoká sféricita: Sférické částice snadno proudí a hustě se v práškovém loži nabalují, což je zásadní pro dosažení vysoké hustoty (>99,5 %) tištěných dílů s minimální pórovitostí.
- Nízký obsah satelitu: Minimalizuje množství jemných, nepravidelných částic navázaných na větší koule, což dále zlepšuje tekutost a hustotu balení.
- Řízená distribuce velikosti částic (PSD): Přizpůsobení PSD pro konkrétní stroje AM (jako je SEBM nebo LPBF) zajišťuje konzistentní tavení a tvorbu vrstev.
- Proces plazmové rotující elektrody (PREP): Metoda PREP je vhodná zejména pro výrobu vysoce sférických prášků z reaktivních nebo žáruvzdorných kovů (jako jsou slitiny titanu, které jsou důležité i v některých námořních odvětvích) a spočívá v otáčení tyče spotřební elektrody při tavení jejího hrotu plazmovým hořákem. Odstředivá síla rozptyluje roztavený kov do kapiček, které za letu tuhnou. Tato metoda obvykle produkuje prášky s výjimečnou kulovitostí a velmi vysokou čistotou, bez plynné pórovitosti uvnitř částic.
Proč je pro vrtule důležitá kvalita prášku Met3dp’s:
- Předvídatelný výkon: Sférické prášky s vysokou čistotou a konzistentní PSD vedou ke spolehlivému tavení a tuhnutí, což vede k vytištěným vrtulím s předvídatelnými mechanickými vlastnostmi (pevnost, tažnost, únavová životnost) a konzistentní odolností proti korozi, které splňují přísné námořní požadavky.
- Snížení počtu závad: Špatná kvalita prášku (nepravidelné tvary, vnitřní pórovitost, nečistoty, nekontrolovaná PSD) může vést k defektům konečného dílu, jako je pórovitost, nedostatečné tavení nebo praskání, což může ohrozit strukturální integritu a výkon kritické součásti, jako je vrtule.
- Optimalizovaný tisk: Vysoce kvalitní prášky umožňují plynulejší zpracování, což potenciálně umožňuje vyšší rychlost sestavování a snižuje pravděpodobnost selhání tisku.
Využitím pokročilých technik výroby prášků a přísné kontroly kvality společnost Met3dp zajišťuje, že dodávané prášky CuAl10Fe5Ni5 a CuNi30Mn1Fe splňují náročné specifikace požadované pro 3D tisk vysoce integrovaných lodních vrtulí. Naše rozsáhlé portfolio kovových prášků, podrobně popsané na našich webových stránkách (viz nabídka materiálů Met3dp’s), poskytuje inženýrům a manažerům veřejných zakázek základy potřebné pro bezpečné zavedení aditivní výroby pro náročné námořní aplikace. Výběr správné slitiny je prvním krokem; pro úspěch je nejdůležitější zajistit, aby byla vyrobena z prvotřídního prášku optimalizovaného pro AM.
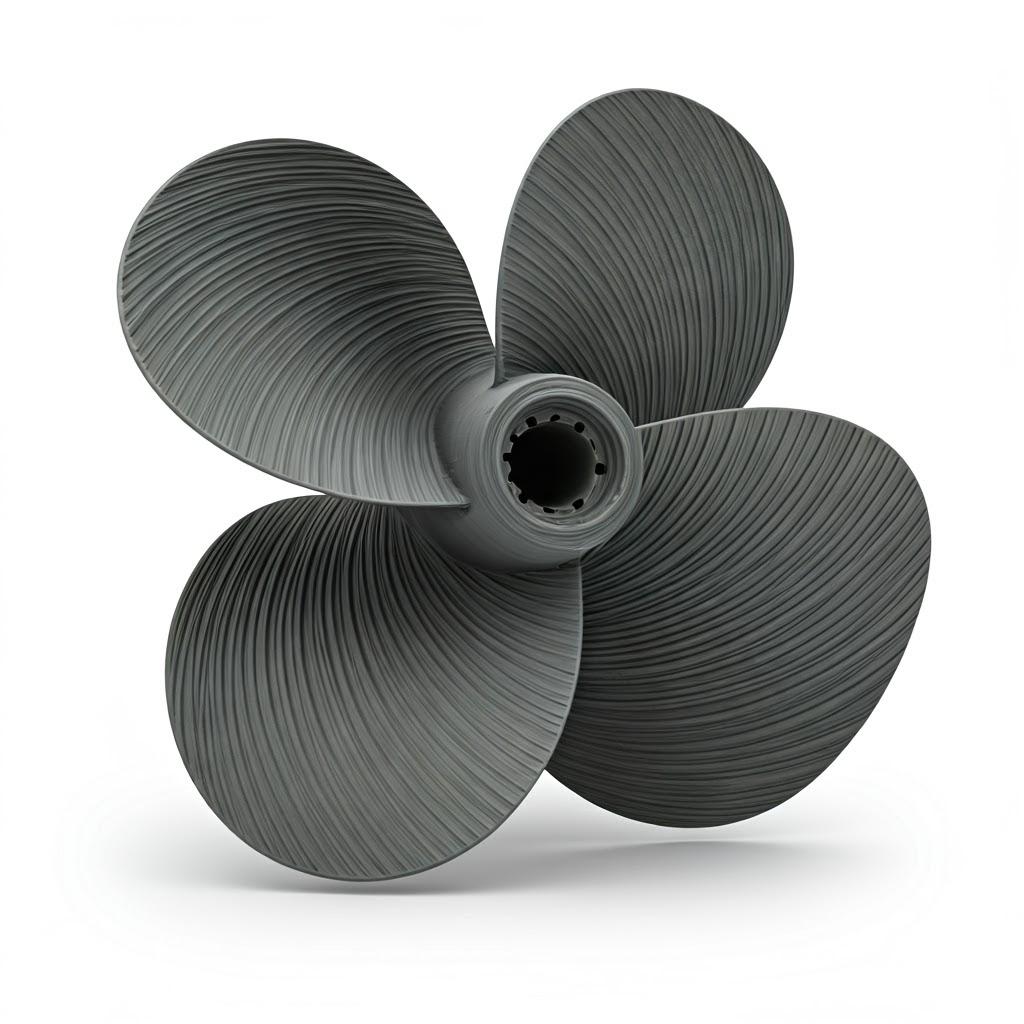
Design pro aditivní výrobu (DfAM): Optimalizace vrtulí pro 3D tisk
Jedním z nejzásadnějších posunů, které přináší aditivní výroba kovů, je nutnost přehodnotit samotný design. Pouhé převzetí návrhu vrtule optimalizovaného pro odlévání nebo CNC obrábění a jeho odeslání do 3D tiskárny jen zřídkakdy uvolní plný potenciál AM a může dokonce vést k neoptimálním výsledkům nebo selhání tisku. Design pro aditivní výrobu (DfAM) je metodika, která integruje znalosti o procesu AM, materiálech a následných krocích zpracování přímo do fáze návrhu. U lodních vrtulí je použití principů DfAM klíčové pro maximalizaci výkonu, minimalizaci nákladů a zajištění vyrobitelnosti.
Proč je DfAM důležitý pro vrtule:
- Využití geometrické volnosti: AM odstraňuje mnohá tradiční výrobní omezení a umožňuje vytvářet složité tvary, které mohou zlepšit hydrodynamické vlastnosti.
- Minimalizace podpory: Podpůrné konstrukce jsou často nezbytné, ale zvyšují náklady na materiál, čas tisku a značnou náročnost následného zpracování. Cílem DfAM je minimalizovat jejich použití.
- Zvládání tepelného namáhání: Proces tavení po vrstvách vytváří tepelné gradienty a zbytková napětí. DfAM je může pomoci zmírnit.
- Zajištění tisknutelnosti: Návrh s ohledem na omezení AM (např. minimální velikost prvku, úhly přesahu) předchází problémům při sestavování.
- Optimalizace pro následné zpracování: Zvážení způsobu tepelného zpracování, dokončování a kontroly dílu ve fázi návrhu může tyto navazující kroky zjednodušit.
Klíčové zásady DfAM pro 3D tištěné vrtule:
- Využití geometrické složitosti pro zvýšení výkonu:
- Pokročilé profily čepelí: Překročte jednoduché poměry P/D a standardní průřezy. Implementujte plynule se měnící rozložení sklonu, sklonu, náklonu a zakřivení optimalizované pomocí analýzy CFD pro konkrétní podmínky proudění. Navrhujte lopatky s neplanárními tvary nebo winglety, abyste snížili kavitaci ve špičkovém víru a indukovaný odpor.
- Optimalizace náběžné/následné hrany: AM umožňuje dosáhnout ostřejších a přesnějších hran, než je běžné u odlitků (extrémní ostrost však může vyžadovat dodatečné opracování nebo může představovat problém s trvanlivostí/ tisknutelností). Pečlivě navrhněte profily hran, abyste vyvážili zvýšení efektivity se strukturální integritou a výrobními omezeními. Zvažte biomimetické návrhy hran inspirované přírodou (např. tubery jako na ploutvích keporkaků), pokud analýza naznačuje výhody.
- Integrace rozbočovače: Navrhněte integrované prvky, jako jsou řezačky lana, specializované kryty nebo držáky senzorů, přímo do konstrukce náboje, čímž se zkonsolidují díly a zlepší průtok.
- Minimalizace strategické podpůrné struktury:
- Samonosné úhly: Konstrukční prvky musí dodržovat limity samonosného úhlu zvoleného procesu AM (obvykle 45° nebo více od vodorovné roviny pro LPBF/SEBM, i když záleží na materiálu). Klíčová je strategická orientace vrtule ve stavební komoře.
- Vyhněte se vodorovným plochám: Velké rovné plochy směřující dolů vyžadují rozsáhlou podporu. Upravte konstrukce tak, abyste použili zkosení nebo oblouky, kde je to možné.
- Přístupné podpory: Tam, kde se podpěrám nelze vyhnout (např. pod nábojem, strmé převisy lopatek), navrhněte je tak, aby byly snadno přístupné a odstranitelné. Používejte perforace nebo specifické konstrukce, které se čistě odlamují nebo jsou snadno dosažitelné nástroji. Zvažte použití různých typů podpěr (např. kvádr vs. mříž) v závislosti na umístění a funkci.
- Podpory specifické pro daný proces: Pochopení podpůrných strategií společných pro konkrétní proces AM (např. SEBM často vyžaduje méně robustnějších podpěr než LPBF kvůli vyšší teplotě procesu, která snižuje tepelné gradienty). V tomto případě je neocenitelná spolupráce s poskytovatelem AM služeb, jako je Met3dp, který má hluboké znalosti o svých systémech SEBM.
- Optimalizace tloušťky stěny a velikosti prvků:
- Minimální tloušťka stěny: Dodržujte minimální tloušťku stěny pro tisk pro zvolený materiál (CuAl10Fe5Ni5 nebo CuNi30Mn1Fe) a proces (obvykle kolem 0,4-1,0 mm, ale silnější je často bezpečnější pro strukturální integritu a tisknutelnost). Vyhněte se příliš tenkým vlečným hranám, které se mohou deformovat nebo je obtížné je přesně vytisknout.
- Rozlišení malých funkcí: Rozumějte limitům pro rozlišení velmi malých otvorů, čepů nebo složitých detailů. Pokud je u malých prvků nutná vysoká přesnost, plánujte dodatečné obrábění.
- Interní kanály: Pokud navrhujete vnitřní kanály (např. pro tlumení nebo budoucí integraci senzorů), zajistěte jejich samonosnost nebo navrhněte přístupová místa pro odstraňování prášku. Odstraňování prášku ze složitých vnitřních kanálů může být velmi náročné.
- Design pro zvládání stresu:
- Orientační dopad: Orientace vrtule ve stavební komoře významně ovlivňuje potřeby podpory, kvalitu povrchu, rozměrovou přesnost a průběh zbytkových napětí. Optimální orientaci určete simulací nebo ve spolupráci s odborníky. Stavba lopatek ve svislé poloze může minimalizovat počet podpěr, ale může prodloužit výšku a dobu stavby. Stavba ve vodorovné poloze může vyžadovat více podpěr, ale může snížit výšku.
- Tepelné aspekty: Vyhněte se náhlým změnám průřezu, které mohou koncentrovat napětí. V místech křížení (např. od kořene lopatky k náboji) používejte velkorysé křídla a poloměry, aby se napětí rozložilo rovnoměrněji.
- Návrh řízený simulací: Využití tepelné a strukturální analýzy konečných prvků (FEA) kalibrované pro procesy AM k předpovědi koncentrací napětí a potenciálních ohnisek deformace před tisk. Upravte návrh na základě výsledků simulace.
- Zvažte odlehčení (s opatrností):
- Optimalizace topologie: Použijte softwarové nástroje k odstranění materiálu z oblastí s nízkým namáháním (především náboje, případně silnějších částí lopatek) při zachování cílových parametrů.
- Mřížové struktury: Vnitřní mřížové struktury umožňují výrazné snížení hmotnosti. U vrtulí však zvažte důsledky pro únavovou životnost při cyklickém zatížení, možnost vnitřní koroze, pokud nejsou zcela utěsněny, a obtížnost čištění/kontroly vnitřních povrchů vystavených mořskému prostředí. Často se kvůli robustnosti a spolehlivosti dává přednost pevným lopatkám.
Význam spolupráce:
Efektivní DfAM se málokdy provádí izolovaně. Vyžaduje úzkou spolupráci mezi konstruktérem součásti (který rozumí funkčním požadavkům) a odborníkem na AM procesy (který rozumí možnostem a omezením výroby). Spolupráce se znalým poskytovatel řešení pro aditivní výrobu jako je Met3dp na počátku návrhového cyklu, je velmi doporučeno. Tým společnosti Met3dp přináší desítky let společných zkušeností v oblasti kovové AM, materiálové vědy a optimalizace procesů s využitím svých pokročilých tiskáren SEBM a vysoce kvalitních prášků. Tato spolupráce zajišťuje, že návrh vrtule je nejen inovativní, ale také vyrobitelný, spolehlivý a nákladově efektivní. Díky využití technologie DfAM mohou inženýři skutečně využít transformační sílu 3D tisku k vytvoření lodních vrtulí nové generace.
Dosažitelná přesnost: Tolerance, povrchová úprava a rozměrová přesnost
Přestože aditivní výroba kovů nabízí neuvěřitelnou volnost při navrhování, je pro inženýry a manažery nákupu nezbytné mít realistická očekávání ohledně dosažitelné přesnosti, povrchové úpravy a celkové rozměrové přesnosti 3D tištěných lodních vrtulí “v hotovém stavu ” Pochopení těchto aspektů je zásadní pro stanovení nezbytných kroků následného zpracování a zajištění toho, aby finální součástka splňovala funkční požadavky. Dosažitelná přesnost závisí na konkrétním procesu AM (např. LPBF vs. SEBM), kalibraci stroje, použitém materiálu, velikosti a složitosti dílu, orientaci sestavení a tepelném řízení během tisku.
1. Rozměrové tolerance:
- Obecné tolerance: Obecně platí, že procesy fúze kovového prášku (PBF), jako je laserová PBF (LPBF/SLM) a selektivní tavení elektronovým svazkem (SEBM), mohou obvykle dosáhnout obecných rozměrových tolerancí v rozsahu ISO 2768-m (střední) nebo někdy -f (jemné) pro díly po vytištění. To znamená zhruba ±0,1 mm až ±0,5 mm nebo více, v závislosti na velikosti rozměru.
- LPBF: Díky menší velikosti laserového bodu ve srovnání s elektronovým paprskem je často možné dosáhnout mírně přísnějších tolerancí a jemnějšího rozlišení prvků.
- SEBM: Pracuje při vyšších teplotách, což pomáhá snižovat zbytková napětí, ale někdy může vést k mírně nižší rozměrové přesnosti ve srovnání s LPBF, ačkoli s dobře kalibrovanými stroji, jaké používá společnost Met3dp, lze dosáhnout vynikajících výsledků. Zaměření společnosti Met3dp’na špičkovou přesnost a spolehlivost v oboru zajišťuje optimální výkonnost jejich systémů SEBM.
- Faktory ovlivňující toleranci:
- Velikost dílu: Větší díly obecně vykazují větší absolutní odchylku v důsledku kumulovaných tepelných vlivů a možného zkreslení.
- Geometrie: U složitých geometrií s tenkými stěnami nebo velkými převisy je dodržování přísných tolerancí náročnější.
- Materiál: Různé slitiny vykazují různý stupeň smrštění a deformačního potenciálu.
- Orientace: Směr budování významně ovlivňuje přesnost u různých prvků.
- Tepelný management: Rozhodující roli hrají procesní parametry a stabilita stroje.
- Kritické tolerance: Rozměry vyžadující vysokou přesnost - jako je průměr otvoru vrtule, geometrie drážky, kuželové rozhraní hřídele a montážní plochy - téměř vždy vyžadují dodatečné opracování (např. CNC soustružení, frézování, broušení), aby bylo dosaženo nezbytných malých tolerancí (často v rozmezí ±0,01 mm až ±0,05 mm) pro správné uložení a funkci. DfAM by měl počítat s přidáním dostatečné zásoby obrábění (např. 0,5 mm až 2 mm) na těchto kritických plochách.
2. Povrchová úprava (drsnost):
- Drsnost při tisku (Ra): Povrchová úprava kovových dílů vytištěných metodou AM je podstatně drsnější než obráběné nebo dokonce lité povrchy.
- LPBF: Obvykle dosahuje hodnot Ra mezi 5 µm a 20 µm (mikrometry).
- SEBM: Výsledkem je obecně drsnější povrch, často mezi 20 a 40 µm Ra, někdy i více. To je částečně způsobeno větší velikostí paprsku a vyšším příkonem energie, což vede k většímu spékání částic na povrchu.
- Textura povrchu:
- Linie vrstev: Přirozený charakter vrstvení vytváří viditelné linie, zejména na svislých stěnách.
- Schodiště: Zakřivené nebo šikmé povrchy vykazují “schodovitý” efekt, kdy se hrany vrstvy přibližují hladké křivce. Závažnost závisí na tloušťce vrstvy a úhlu povrchu vzhledem ke konstrukční desce. Menší úhly mají za následek výraznější schodovitost.
- Up-skin vs. Down-skin: Povrchy směřující při stavbě nahoru (up-skins) mají obecně lepší povrchovou úpravu než povrchy směřující dolů (down-skins), které jsou ovlivněny podpůrnými konstrukcemi nebo interakcí prášku pod nimi.
- Důsledky pro vrtule: Drsnost povrchu vrtule AM po vytištění je obvykle příliš vysoká pro optimální hydrodynamické vlastnosti, protože zvyšuje třecí odpor a může podporovat brzký vznik kavitace. Proto, obvykle je nutná výrazná povrchová úprava, zejména na tlakové a sací straně lopatek, jak je podrobně popsáno v následující části. Manažeři veřejných zakázek by měli zajistit, aby nabídky od služba průmyslového 3D tisku poskytovatelé jasně specifikují cílovou povrchovou úpravu a metody použité k jejímu dosažení.
3. Rozměrová přesnost a deformace:
- Celková přesnost: Kromě tolerancí konkrétních prvků je zásadní celková geometrická věrnost dílu ve srovnání s původním modelem CAD. Tepelné cykly během tisku mohou způsobit deformace a zkreslení, zejména u velkých, tenkých nebo asymetricky navržených dílů, jako jsou lopatky vrtule.
- Strategie zmírnění dopadů:
- Simulace: Prediktivní modelování pomáhá předvídat zkreslení.
- Orientace & Podporuje: Strategické umístění minimalizuje namáhání a ukotvuje díl.
- Parametry procesu: Optimalizovaný přívod energie a strategie skenování snižují tepelné gradienty.
- Stabilita stroje & Kalibrace: Kvalitní a dobře udržované stroje, jako jsou tiskárny Met3dp’s SEBM, poskytují stabilní prostředí pro zpracování, které je nezbytné pro přesnost. Jejich závazek ke spolehlivosti se promítá do předvídatelnějších rozměrových výsledků.
- Úleva od stresu: Tepelné zpracování po tisku je nezbytné pro uvolnění vnitřních pnutí, která by jinak mohla způsobit deformaci při vyjmutí z konstrukční desky nebo při obrábění.
- Požadavek na vyvážení: I při vynikající rozměrové přesnosti dosažené pomocí AM a následného obrábění je nutné provést konečné statické a dynamické vyvážení drobných hmotnostních nerovnováh, které jsou vlastní každému výrobnímu procesu (AM nebo tradičnímu). To zajistí, že se vrtule otáčí hladce, aniž by vyvolávala vibrace v hřídelovém vedení a trupu, což je rozhodující pro výkon, pohodlí a dlouhou životnost součástí pohonného ústrojí.
Závěrem lze říci, že ačkoli technologie AM nabízí možnost vytvářet složité geometrie vrtulí, není to ze své podstaty ‘dokonale přesný’ proces přímo ze stroje. Inženýři musí navrhovat s ohledem na dosažitelné tolerance a povrchové úpravy a manažeři nákupu musí počítat s nezbytnými kroky následného zpracování, zejména s obráběním a povrchovou úpravou, aby byly splněny konečné funkční požadavky. Klíčem k dosažení požadované přesnosti pro náročné námořní aplikace je spolupráce se zkušeným poskytovatelem AM, který těmto nuancím rozumí a disponuje správným vybavením a řízením procesu, jako je Met3dp.
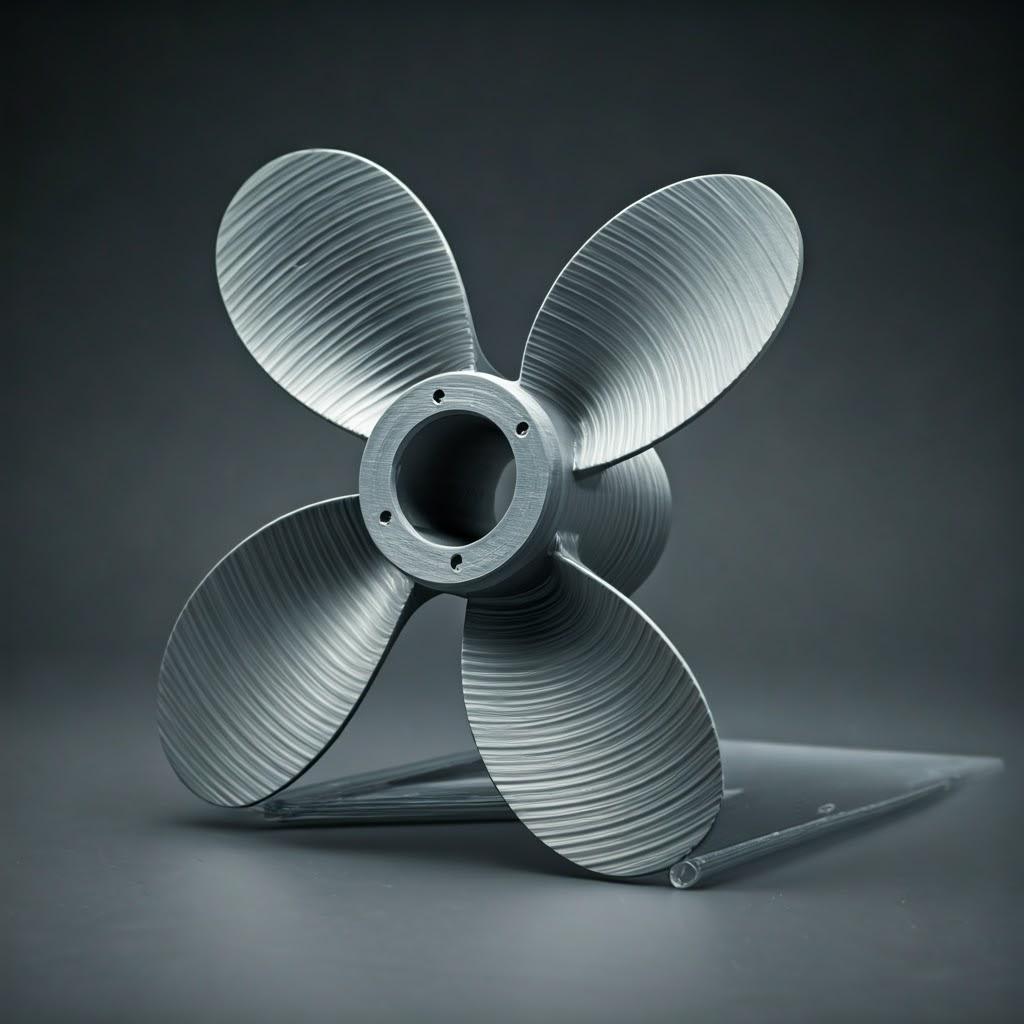
Cesta následného zpracování: Od vytištěného dílu k hotové vrtuli
Cesta 3D tištěné kovové vrtule nekončí, když se tiskárna zastaví. Ve skutečnosti je “tisk” často jen prvním významným krokem v komplexním výrobním procesu. Následné zpracování není pouhou dodatečnou myšlenkou; je to’zásadní sled kroků nutných k přeměně surové, vytištěné součásti na funkční, spolehlivou a hotovou lodní vrtuli připravenou k instalaci a provozu. Konkrétní kroky a jejich pořadí se mohou lišit v závislosti na použitém procesu AM (LPBF vs. SEBM), materiálu (NAB vs. CuNi), složitosti konstrukce vrtule a konečných požadavcích na výkon.
Zde’je typický postup následného zpracování 3D tištěné lodní vrtule s použitím CuAl10Fe5Ni5 nebo CuNi30Mn1Fe:
1. Tepelné ošetření proti stresu:
- Proč: To je pravděpodobně nejkritičtější úvodní krok následného zpracování. Rychlé cykly zahřívání a ochlazování, které jsou vlastní procesům PBF, vytvářejí v tištěném dílu značná zbytková napětí. Tato napětí mohou způsobit deformace nebo praskliny během následných kroků (jako je vyjmutí z konstrukční desky nebo obrábění) nebo ohrozit výkonnost a únavovou životnost dílu v provozu.
- Jak: Díl, často ještě připevněný na konstrukční desce, se zahřeje v peci s řízenou atmosférou (např. inertním plynem, jako je argon, nebo ve vakuu) na určitou teplotu pod kritickým bodem přeměny slitiny, udržuje se po stanovenou dobu a poté se pomalu ochlazuje.
- Typické pro NAB (CuAl10Fe5Ni5): Teploty se mohou pohybovat od 300 °C do 650 °C v závislosti na požadované rovnováze mezi uvolněním napětí a zachováním pevnosti. Doba se liší v závislosti na tloušťce dílu.
- Typické pro CuNi (CuNi30Mn1Fe): Teploty žíhání/odlehčování mohou být v rozmezí 550 °C až 750 °C.
- Výsledek: Výrazně snižuje vnitřní napětí, stabilizuje mikrostrukturu a zlepšuje tažnost. Je třeba pečlivě plánovat, protože díly se během tohoto procesu mohou stále mírně deformovat, pokud nejsou správně podepřeny.
2. Vyjmutí dílu ze stavební desky:
- Proč: Vrtule je během tisku přitavena k silné kovové konstrukční desce. Pro další zpracování je třeba ji oddělit.
- Jak: Mezi běžné metody patří:
- Drátové elektroerozivní obrábění (EDM): Přesná metoda, vhodná pro složitá rozhraní, minimální síla působící na díl.
- Pásové řezání: Rychlejší a levnější pro jednodušší rozhraní, ale působí větší mechanickou silou.
- Obrábění: Frézování nebo broušení rozhraní základny a podpěry.
- Úvaha: Zvolená metoda závisí na geometrii dílu, požadované přesnosti na základně a na nákladových faktorech.
3. Odstraňování a čištění sypkého prášku:
- Proč: Na povrchu dílu a v případných vnitřních dutinách nebo podpůrných strukturách zůstává netavený kovový prášek. Ten je třeba důkladně odstranit.
- Jak:
- Ruční kartáčování/vysávání: Pro přístupné povrchy.
- Foukání stlačeného vzduchu: Účinné, ale vyžaduje omezení šíření prášku vzduchem.
- Tryskání kuličkami (jemné): Může pomoci uvolnit zachycený prášek, ale je třeba postupovat opatrně, aby nedošlo k poškození jemných rysů.
- Ultrazvukové čištění: Někdy se používá s vhodnými rozpouštědly pro složité díly.
- Výzva: Úplné odstranění prášku ze složitých vnitřních kanálků nebo hustých mřížkových struktur (pokud jsou použity) může být velmi obtížné a vyžaduje pečlivé zvážení konstrukce (DfAM). Neúplné odstranění prášku představuje riziko kontaminace a zvyšuje mrtvou hmotnost.
4. Odstranění podpůrné konstrukce:
- Proč: Podpěry jsou dočasné konstrukce, které jsou nezbytné pro proces stavby, ale nejsou součástí konečné konstrukce vrtule.
- Jak: Tento krok je často náročný na práci:
- Ruční lámání/řezání: Pro snadno přístupné, lomené podpěry. Lze použít kleště, dláta, brusky.
- Obrábění (CNC nebo ruční): Frézování nebo broušení nosných konstrukcí, zejména v místech rozhraní (“svědecké stopy”).
- Drátové elektroerozivní obrábění: Pro přesné odstraňování v úzkých oblastech.
- Výzva: Po odstranění podpory mohou na povrchu dílu zůstat stopy nebo drobné nedokonalosti, které vyžadují smíchání. Přístup k podpěrám ve složitých geometriích nožů může být obtížný. DfAM hraje velkou roli při navrhování podpěr pro snadnější odstraňování. Tento krok významně ovlivňuje konečné náklady a dobu realizace, zejména u složitých dílů vyžadujících rozsáhlé podpory. Manažeři nákupu vyhodnocují nabídky od velkoobchodní 3D tištěná vrtule dodavatelé by se měli informovat o čase a metodách určených pro odstranění podpory.
5. Žíhání roztokem / zpevňující tepelné zpracování (volitelné, ale běžné):
- Proč: Kromě uvolnění napětí může být k optimalizaci konečných mechanických vlastností (např. zvýšení pevnosti, další zlepšení odolnosti proti korozi, homogenizace mikrostruktury) zapotřebí další tepelné zpracování. Konkrétní ošetření do značné míry závisí na slitině a požadovaných vlastnostech.
- NAB: Může zahrnovat zpracování při vyšších teplotách (např. > 800 °C), po kterém následuje řízené chlazení nebo kalení a případně popouštění pro dosažení specifických fází a úrovní tvrdosti.
- CuNi: Obvykle se používá v žíhaném stavu po odlehčení napětí pro optimální odolnost proti korozi a biologickému znečištění.
- Jak: Provádí se v pecích s řízenou atmosférou podle přesných teplotních a časových profilů definovaných specifikacemi materiálu nebo požadavky aplikace.
6. Lisování za tepla (HIP) (volitelné):
- Proč: Odstranění zbývající vnitřní mikroporozity, která zůstala po procesu AM. Pórovitost může působit jako iniciační místo únavových trhlin, což snižuje životnost součásti při cyklickém zatěžování (velmi důležité pro vrtule).
- Jak: Díl je vystaven vysoké teplotě (pod bodem tání) a vysokému izostatickému tlaku (za použití inertního plynu, např. argonu) současně ve specializované nádobě HIP. Tlak sbalí vnitřní dutiny a materiál se difuzně spojí přes rozhraní dutin.
- Kdy: Doporučuje se pro kritické aplikace vyžadující maximální únavovou životnost a strukturální integritu. Zvyšuje náklady a dobu realizace, ale poskytuje nejvyšší kvalitu materiálu. Společnost Met3dp může poradit, zda je HIP výhodný na základě aplikace a svých procesních možností.
7. Obrábění kritických rozměrů a vlastností:
- Proč: Jak bylo uvedeno v části ‘Přesnost’, tolerance AM jsou často nedostatečné pro kritická rozhraní.
- Jak: Použití CNC soustruhů, frézek nebo brusek k dosažení konečných tolerancí na:
- Vrtulový otvor (průměr, kužel, drážka)
- Montážní plochy
- Hroty nebo břity vyžadující specifické profily/ostrost.
- Veškeré povrchy vyžadující velmi specifický, hladký povrch pro hydrodynamické těsnění nebo uložení.
8. Povrchová úprava:
- Proč: Zlepšení hydrodynamické účinnosti (snížení odporu), minimalizace vzniku kavitace, zvýšení únavové životnosti (hladké povrchy mají méně nárůstů napětí) a zlepšení estetiky.
- Jak: Lze použít různé metody, často v kombinaci:
- Broušení/pískování: Ruční nebo robotické procesy s použitím brusných pásů nebo kotoučů k vyhlazení povrchu ostří a smíchání podpůrných stop. Používají se postupně jemnější zrna.
- Leštění: Použití lešticích směsí a lešticích kotoučů k dosažení velmi nízkých hodnot Ra (v případě potřeby zrcadlového povrchu), obvykle zaměřené na přítlačné a sací plochy lopatek.
- Hromadné dokončování (bubnové/vibrační): Lze použít pro menší součásti nebo k dosažení rovnoměrného saténového povrchu, případně s použitím abrazivních nebo neabrazivních médií. Méně obvyklé pro velké vrtule.
- Elektrolytické leštění: Elektrochemický proces, který odstraňuje tenkou vrstvu materiálu, přednostně z vrcholů, čímž vzniká velmi hladký a čistý povrch. Může být účinný pro složité tvary, ale vyžaduje specifické elektrolyty pro slitiny mědi.
9. Nedestruktivní zkoušení (NDT) a zajištění kvality:
- Proč: Ověřit celistvost hotové vrtule a zajistit, aby před dodáním splňovala všechny specifikace. Je to nezbytné pro kontrolu kvality a certifikaci.
- Jak: Kombinace metod:
- Vizuální kontrola: Důkladná kontrola povrchových vad, prasklin, neúplného odstranění podpěr.
- Rozměrová kontrola: Použití souřadnicových měřicích strojů (CMM), 3D skenerů nebo tradičních metrologických nástrojů k ověření kritických rozměrů a celkové geometrie podle modelu CAD a výkresů.
- Zkouška penetrací barvivem (DPT): K odhalení trhlin porušujících povrch nebo pórovitosti.
- Radiografické vyšetření (rentgen) nebo počítačová tomografie (CT): K odhalení vnitřních vad, jako je pórovitost nebo vměstky. CT skenování poskytuje úplný 3D pohled na vnitřní struktury.
- Certifikace materiálu: Ověřování sledovatelnosti šarží prášku a shody se specifikacemi materiálu.
10. Vyvažování:
- Proč: Zajistit plynulý provoz bez vibrací.
- Jak: Umístění hotové vrtule na vyvažovací stroj pro zjištění hmotnostní nerovnováhy. Poté se z určitých míst na náboji nebo lopatkách opatrně odstraní materiál (obvykle broušením), dokud vrtule nesplní požadovaný stupeň vyvážení (např. ISO 1940 G6.3 nebo lepší). Obvykle se provádí statické i dynamické vyvažování.
Tento komplexní postup následného zpracování zdůrazňuje, že 3D tisk je součástí integrovaného výrobního řetězce. Každý krok vyžaduje odborné znalosti, specializované vybavení a pečlivou kontrolu kvality. Společnosti, jako je Met3dp, nabízející komplexní řešení aditivní výroby, rozumí tomuto složitému procesu a zajišťuje, aby finální vrtule vytištěná 3D tiskem a dodaná zákazníkovi splňovala náročné požadavky námořního prostředí.
Zvládání výzev: Běžné překážky při 3D tisku vrtulí & řešení
Přestože potenciál 3D tištěných lodních vrtulí je obrovský, jeho využití vyžaduje překonání několika problémů spojených s aditivní výrobou kovů, zejména při práci se složitými geometriemi a náročnými materiály, jako jsou NAB a CuNi. Povědomí o těchto potenciálních překážkách umožňuje inženýrům, výrobcům a specialistům na zadávání zakázek aktivně zavádět strategie pro jejich zmírnění, často ve spolupráci se zkušenými poskytovateli AM služeb.
1. Deformace a zkreslení:
- Výzva: Intenzivní, lokalizované zahřívání a rychlé ochlazování během procesů PBF vytváří prudké tepelné gradienty. Při tuhnutí a ochlazování se vrstvy smršťují, což vyvolává vnitřní napětí. Nerovnoměrné rozložení napětí, zejména u velkých dílů nebo dílů s různými průřezy, jako jsou například vrtulové lopatky, může způsobit deformaci nebo zkreslení dílu oproti jeho zamýšlenému tvaru, a to jak během sestavování, tak po vyjmutí ze sestavovací desky.
- Řešení:
- Tepelná simulace: Pomocí softwaru FEA předpovídejte rozložení teploty a výsledná napětí/deformace na základě geometrie dílu, vlastností materiálu a strategie skenování. Umožňuje preventivně upravit konstrukci nebo proces.
- Optimalizovaná orientace dílu: Výběr orientace stavby, která minimalizuje velké převisy, vyrovnává tepelné hmoty a případně snižuje výšku stavby, může výrazně ovlivnit zkreslení.
- Robustní podpůrné struktury: Podpěry slouží nejen k ukotvení převisů, ale také jako chladiče a mechanické zábrany proti deformacím. Rozhodující je inteligentní návrh podpěr.
- Optimalizované strategie skenování: Techniky, jako je skenování ostrůvků, sektorování nebo úprava parametrů laseru/paprsku, mohou pomoci zvládnout akumulaci tepla a snížit napětí.
- Procesní teplota (SEBM Advantage): SEBM pracuje s práškovým ložem při zvýšených teplotách (několik set °C). Tím se snižuje tepelný gradient mezi roztavenou lázní a okolním materiálem, což přirozeně snižuje zbytková napětí v porovnání s procesy LPBF při pokojové teplotě, a je tak potenciálně výhodné pro velké nebo složité díly náchylné k deformacím. Tuto výhodu využívá společnost Met3dp’s odbornými znalostmi v oblasti SEBM.
- Povinná úleva od stresu: Tepelné zpracování na uvolnění napětí bezprostředně po tisku a před odstraněním podpěry je bezpodmínečně nutné.
2. Řízení zbytkového stresu:
- Výzva: I když je makroskopická deformace kontrolována, mohou v dílu zůstat zablokována vysoká zbytková napětí. Tato napětí mohou:
- Způsobují neočekávané deformace při dodatečném obrábění při odstraňování vrstev materiálu.
- Vést k předčasnému praskání nebo selhání v provozu, zejména při únavovém zatížení.
- Ztěžují demontáž podpěry nebo způsobují, že díl při demontáži podpěry pruží zpět.
- Řešení:
- DfAM: Navrhování s ohledem na zmírnění namáhání (klempířské prvky, vyhýbání se ostrým rohům, postupné změny tloušťky).
- Optimalizace procesů: Jak bylo uvedeno výše (orientace, strategie skenování, SEBM).
- Účinné tepelné zpracování: Správné cykly uvolňování stresu jsou nejdůležitější. Žíhání v roztoku nebo HIP může dále homogenizovat mikrostrukturu a snížit kolísání napětí.
3. Pórovitost:
- Výzva: V tištěném materiálu mohou z několika důvodů vznikat malé dutiny nebo póry:
- Pórovitost plynu: Zachycený stínicí plyn (argon v LPBF) nebo rozpuštěné plyny v prášku uvolněné během tavení.
- Nedostatečná pórovitost fúze: Nedostatečný příkon energie nebo nesprávné překrytí paprsku/laseru vedoucí k neúplnému roztavení mezi vrstvami nebo skenovacími stopami.
- Problémy s kvalitou prášku: Duté částice prášku nebo nečistoty.
- Dopad: Pórovitost snižuje efektivní plochu průřezu, zhoršuje mechanické vlastnosti (zejména únavovou pevnost a tažnost) a může sloužit jako iniciační místo koroze.
- Řešení:
- Optimalizované parametry procesu: Zajištění správné hustoty energie, rychlosti skenování, tloušťky vrstvy a průtoku plynu (pro LPBF).
- Vysoce kvalitní prášek: Rozhodující je použití prášku s vysokou sféricitou, kontrolovaným PSD, nízkým obsahem vnitřního plynu a vysokou čistotou. To podtrhuje význam nákupu od renomovaných dodavatelů, jako je společnost Met3dp, kteří využívají pokročilé techniky atomizace (plynová atomizace, PREP) a přísnou kontrolu kvality. Další informace o závazku společnosti Met3dp’ke kvalitě.
- Izostatické lisování za tepla (HIP): Nejúčinnější způsob odstranění vnitřní pórovitosti po tisku.
4. Dosažení požadované povrchové úpravy:
- Výzva: As-printed povrchy jsou ze své podstaty drsné (viz předchozí část). Dosažení hladkého povrchu, který je nezbytný pro hydrodynamickou účinnost (typicky Ra < 3-6 µm, nebo dokonce nižší u vysoce výkonných aplikací), vyžaduje značné úsilí při následném zpracování, zejména u složitých, dvakrát zakřivených povrchů vrtulových listů.
- Řešení:
- Orientační strategie: Optimální orientace kritických povrchů (např. čelních ploch lopatek) vzhledem ke směru stavby může minimalizovat schodovitost, ačkoli existují kompromisy (např. zvýšená potřeba podpory).
- Pokročilé následné zpracování: Využití víceosého CNC obrábění, robotického broušení/leštění nebo případně elektrolytického leštění.
- Rozpočtování času & amp; Náklady: Uvědomujeme si, že dosažení vysoce kvalitní povrchové úpravy je významnou součástí celkové doby výroby a nákladů.
5. Obtíže při odstraňování podpory:
- Výzva: Odstranění potenciálně rozsáhlých a složitých podpěrných konstrukcí bez poškození dílu může být časově náročné, nákladné a vyžaduje kvalifikovanou práci. Přístup k vnitřním podpěrám nebo k podpěrám na choulostivých prvcích je obzvláště náročný. Svědecké stopy po podpěrách vždy vyžadují kosmetické úpravy.
- Řešení:
- DfAM pro minimální podporu: Základní strategií je navrhnout díl a zvolit orientaci tak, aby se v první řadě minimalizovala potřeba podpěr.
- Chytrá konstrukce podpory: Použití konstrukcí, které jsou dostatečně pevné při stavbě, ale jsou navrženy tak, aby se daly snadno rozbít nebo aby se k nim dalo přistupovat při řezání/obrábění.
- Vhodné techniky odstraňování: Použití správných nástrojů (ruční, CNC, elektroerozivní obrábění) pro konkrétní typ podpěry a umístění.
- Zkušení technici: Spoléhání se na kvalifikované pracovníky při ručním odstraňování a dokončování podpory.
6. Soulad materiálu a kvalifikace:
- Výzva: Zajištění toho, aby každá tištěná vrtule vykazovala konzistentní vlastnosti materiálu (pevnost, tažnost, odolnost proti korozi), které odpovídají specifikacím, vyžaduje přísnou kontrolu celého procesního řetězce od surového prášku až po hotový díl. Odchylky v jednotlivých šaržích prášku nebo odchylky v parametrech tisku mohou ovlivnit výsledky. Kvalifikace procesu pro námořní aplikace, která může vyžadovat certifikaci klasifikačními společnostmi (např. DNV, ABS, LR), přidává další vrstvu složitosti.
- Řešení:
- Důsledná kontrola kvality prášku: Získávání prášku od dodavatelů s robustními systémy řízení kvality (jako je Met3dp, dodržující normy jako ISO 9001), kteří poskytují podrobné certifikace šarží (chemie, PSD, morfologie, tekutost).
- Validace procesu & Monitorování: Stanovení kvalifikovaných, uzamčených parametrů tisku pro konkrétní kombinace materiálů a strojů. Zavedení monitorování in-situ, pokud je to možné, pro sledování konzistence sestavení.
- Standardizované následné zpracování: Používání konzistentních, zdokumentovaných postupů pro tepelné zpracování, obrábění a dokončovací práce.
- Komplexní NDT: Důkladné testování pro ověření integrity a vlastností každého hotového dílu.
- Spolupráce pro certifikaci: Úzká spolupráce s klasifikačními společnostmi od samého počátku, pokud je vyžadována formální certifikace, zahrnující testování materiálů, kvalifikaci procesů a kontrolu dílů podle jejich pravidel. To má zásadní význam pro velkoobchod s lodními komponenty dodavatelé usilující o široké přijetí na trhu.
7. Nákladová efektivita:
- Výzva: V porovnání s vyspělou technologií odlévání standardních velkoobjemových vrtulí může mít technologie AM vyšší počáteční náklady na jeden díl, které jsou způsobeny drahými stroji, specializovanými materiály a rozsáhlým následným zpracováním.
- Řešení:
- Zaměřte se na hodnotu, nejen na náklady: Zdůrazněte aplikace, kde AM poskytuje jedinečnou hodnotu (přizpůsobení, rychlost, zvýšení výkonu, řešení zastarávání), která převáží potenciálně vyšší cenu kusu.
- Optimalizace pro AM: Pomocí DfAM lze snížit spotřebu materiálu, minimalizovat podpěry a případně konsolidovat díly, čímž se sníží celkové výrobní náklady.
- Celkové náklady na vlastnictví (TCO): Analyzujte náklady na celý životní cyklus, včetně potenciálních úspor paliva díky vyšší účinnosti, snížení údržby díky lepším materiálům (např. odolnost proti biologickému znečištění CuNi) a minimalizaci prostojů díky náhradním dílům na vyžádání.
- Technologický pokrok: Náklady se neustále snižují s tím, jak se technologie AM vyvíjí, stroje jsou rychlejší a materiály dostupnější.
Pochopením těchto výzev a spoluprací se znalými partnery vybavenými správnou technologií a odbornými znalostmi, jako je Met3dp, může námořní průmysl úspěšně využít sílu aditivní výroby kovů k výrobě inovativních, vysoce výkonných lodních vrtulí.
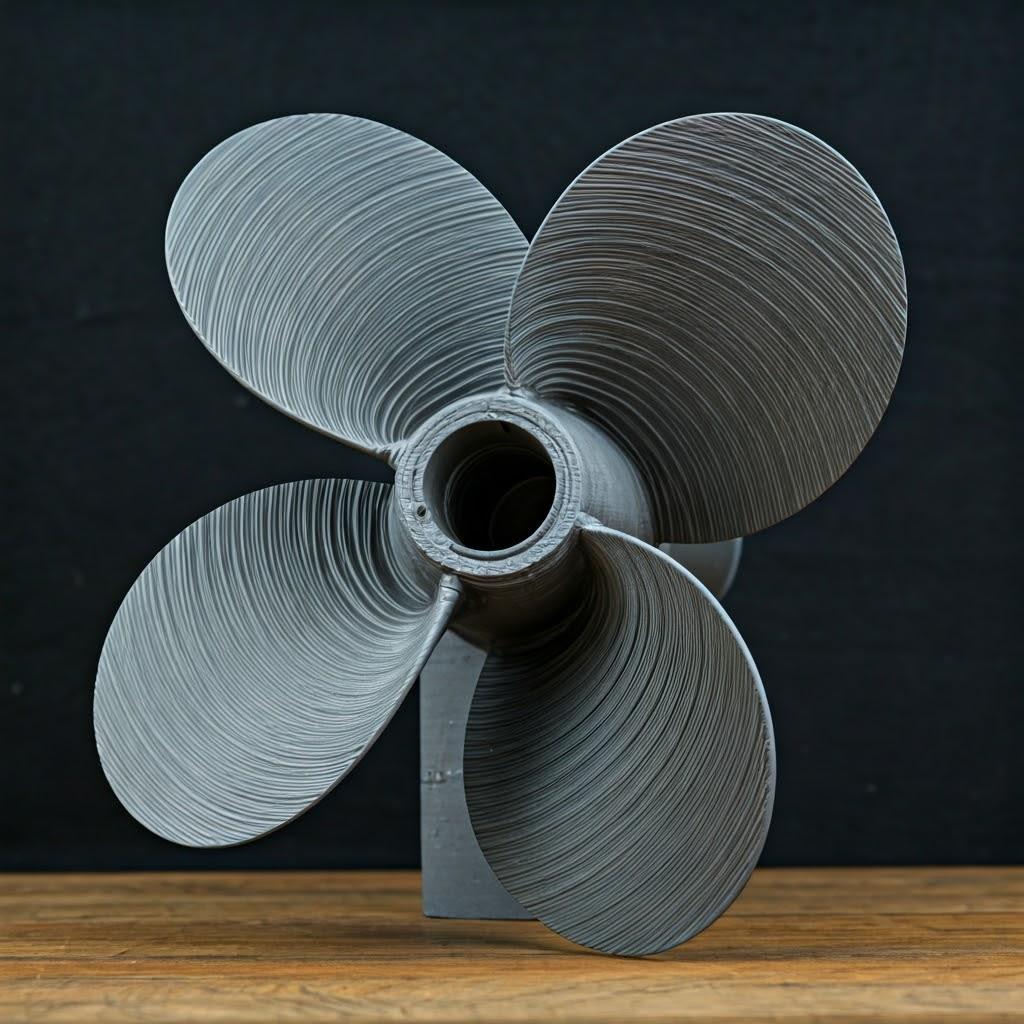
Výběr partnera: Výběr správného poskytovatele služeb Metal AM
Úspěšná implementace 3D tištěných lodních vrtulí vyžaduje více než jen pokročilou technologii, ale také silné partnerství se schopným a zkušeným poskytovatelem služeb v oblasti aditivní výroby kovů. Správný partner působí jako rozšíření vašeho týmu inženýrů a dodavatelů a nabízí odborné znalosti, spolehlivost a zajištění kvality v průběhu celého procesu, od optimalizace návrhu až po finální kvalifikaci dílu. Nesprávná volba může vést ke zpoždění projektu, překročení nákladů, nevyhovující kvalitě součástek a v konečném důsledku k nevyužití výhod AM.
Pro inženýry a manažery veřejných zakázek, kteří hodnotí potenciální služba průmyslového 3D tisku pro projekty lodních šroubů, které používají specializované materiály, jako je CuAl10Fe5Ni5 (NAB) nebo CuNi30Mn1Fe, je třeba zvážit tato kritická kritéria:
1. Prokázané odborné znalosti a relevantní zkušenosti:
- Zaměření na námořní aplikace: Má poskytovatel doložené zkušenosti s námořními součástmi? Rozumí náročnému provoznímu prostředí, problémům s korozí a požadavkům na výkon specifickým pro námořní průmysl? Požádejte o případové studie nebo příklady podobných projektů (při respektování NDA).
- Specializace na materiál: Podařilo se jim úspěšně vytisknout díly s použitím NAB, CuNi nebo jiných příslušných vysoce výkonných slitin mědi? Tisk z těchto materiálů může být náročnější než z běžných ocelí nebo titanu. Ověřte si jejich zkušenosti s konkrétní slitinou, kterou hodláte použít.
- Velikost a složitost: Zahrnuje jejich předchozí práce díly srovnatelné velikosti a geometrické složitosti s vaším návrhem vrtule? Tisk velkých a složitých tvarů vyžaduje specifické schopnosti strojů a odborné znalosti v oblasti řízení procesů.
2. Vhodná technologie a vybavení:
- Vhodnost procesu AM: Nabízejí správnou technologii? Pro robustní, středně velké až velké vrtule z NAB nebo CuNi nabízí selektivní tavení elektronovým svazkem (SEBM) často výhody při řízení zbytkového napětí díky vysokým teplotám zpracování. Pro menší díly nebo díly vyžadující jemnější rysy by mohla být vhodná technologie LPBF (Laser Powder Bed Fusion). Pochopte důvody, které poskytovatele vedou k doporučení konkrétního procesu. Specializace společnosti Met3dp’na špičkové tiskárny SEBM jsou vhodným kandidátem pro náročné aplikace s vrtulemi.
- Schopnosti stroje: Má jejich flotila zařízení potřebný stavební objem (rozměry X, Y, Z), aby se přizpůsobila velikosti vaší vrtule? Jsou jejich stroje dobře udržované a kalibrované z hlediska přesnosti a opakovatelnosti?
- Manipulace s práškem: Mají spolehlivé postupy pro skladování, manipulaci, prosévání a recyklaci kovových prášků, aby se zabránilo kontaminaci a zajistila konzistence? Používají v případě potřeby speciální stroje pro reaktivní nebo citlivé slitiny?
3. Zajištění kvality materiálu:
- Získávání prášku: Odkud pocházejí prášky NAB a CuNi? Spolupracují s renomovanými dodavatelé kovových prášků? Provádějí vstupní kontroly kvality (např. chemie, PSD, morfologie)?
- Vlastní výroba prášku: Poskytovatelé jako např Met3dp, kteří vyrábějí vlastní vysoce kvalitní sférické kovové prášky pomocí pokročilých technologií technologie atomizace plynu a PREP, nabízí významnou výhodu. Tím je zajištěna plná sledovatelnost, optimalizované vlastnosti prášku pro jejich stroje a větší kontrola nad kvalitou materiálu - což je pro náročné aplikace rozhodující faktor.
4. Komplexní možnosti následného zpracování:
- Integrované služby: Nabízí poskytovatel kompletní sadu nezbytných kroků následného zpracování přímo u sebe nebo prostřednictvím úzce řízených kvalifikovaných partnerů? To zahrnuje:
- Tepelné zpracování v řízené atmosféře (uvolňování napětí, žíhání atd.)
- Přesné odstraňování dílů (možnost drátového elektroerozivního obrábění?)
- Důkladné odstranění a čištění prášku
- Kvalifikované odstranění podpůrné konstrukce
- Obrábění na CNC (víceosé obrábění pro složité povrchy a prvky lopatek)
- Povrchová úprava (broušení, leštění pro splnění hydrodynamických požadavků)
- Dostupnost lisování za tepla (HIP) v případě potřeby
- Zařízení pro nedestruktivní zkoušení (NDT) (vizuální, rozměrové/CMM, DPT, RTG/CT)
- Možnosti dynamického vyvažování
- Zjednodušený dodavatelský řetězec: Integrovaná nabídka služeb zjednodušuje řízení projektu, snižuje logistickou náročnost a zajišťuje odpovědnost v celém výrobním procesu.
5. Robustní systém řízení kvality (QMS) a certifikace:
- Certifikace ISO 9001: To by mělo být považováno za minimální požadavek, který prokazuje závazek ke standardizovaným procesům a kontrole kvality.
- Sledovatelnost: Dokáží zajistit úplnou sledovatelnost od šarže surového prášku až po konečný dodávaný díl?
- Zkušenosti s klasifikací námořních plavidel: Pokud vaše vrtule vyžaduje certifikaci od orgánů jako DNV, ABS, Lloyd’s Register atd., má poskytovatel zkušenosti s požadovanými kvalifikačními postupy, dokumentací a zkušebními protokoly? Zkušenosti společnosti Met3dp’v oblasti leteckého, lékařského a automobilového průmyslu dokazují její schopnost zvládat přísné požadavky na kvalitu a připravenost zapojit se do kvalifikačních procesů pro námořní aplikace. O závazku společnosti Met3dp’ke kvalitě se dozvíte na stránce ‘O nás’.
- Audity a transparentnost: Jsou otevřeni zákaznickým auditům nebo návštěvám zařízení v případě významných projektů?
6. Technická podpora a spolupráce:
- Odborné znalosti DfAM: Nabízejí podporu pro návrh aditivní výroby, která vám pomůže optimalizovat návrh vrtule z hlediska tisknutelnosti, výkonu a nákladové efektivity?
- Inženýrský přístup: Jsou jejich inženýři a techničtí pracovníci přístupní pro diskusi o konstrukčních problémech, výběru materiálu, procesních parametrech a strategiích následného zpracování?
- Komunikace: Mají jasné komunikační protokoly a poskytují pravidelné aktualizace projektu?
7. Kapacita, dodací lhůty a logistika:
- Realistické časové plány: Dokáží poskytnout a dodržet realistické odhady dodací lhůty s ohledem na celý pracovní postup od objednávky až po dodání?
- Plánování kapacity: Mají dostatečnou strojní a personální kapacitu, aby zvládli váš projekt bez výrazného zpoždění, zejména pokud zvažujete velkoobchod s lodními komponenty objednávky?
- Odborné znalosti v oblasti přepravy: Mají zkušenosti s balením a mezinárodní přepravou velkých, relativně choulostivých komponentů? (výhodou pro globální logistiku je umístění společnosti Met3dp ve významném přístavním městě Čching-tao).
Shrnutí kontrolního seznamu hodnocení:
Kritérium | Klíčové úvahy |
---|---|
Zažít | Význam pro námořní průmysl, zkušenosti se specifickými slitinami (NAB/CuNi), podobná velikost/složitost dílů |
Technologie | Vhodný proces AM (SEBM/LPBF), odpovídající objem sestavy, stav stroje |
Kvalita materiálu | Renomovaný zdroj prášku (vlastní jako Met3dp je výhodou), postupy kontroly kvality, manipulační protokoly |
Následné zpracování | Komplexní vlastní/spravované kapacity (tepelné zpracování, obrábění, dokončovací práce, NDT, vyvažování) |
Systém kvality | ISO 9001, sledovatelnost, zkušenosti s námořní certifikací (v případě potřeby), připravenost k auditu |
Technická podpora | Služby DfAM, inženýrská spolupráce, přehlednost komunikace |
Kapacita & amp; doba dodání | Reálné termíny, dostatečná kapacita, prokazatelná výkonnost dodávek |
Logistika & Náklady | Zkušenosti s přepravou, jasná struktura cenové nabídky, konkurenceschopná celková hodnota |
Export do archů
Výběr správného partnera AM je strategické rozhodnutí. Důkladné prověření podle těchto kritérií vám pomůže zajistit, že si vyberete poskytovatele, jako je Met3dp, který má technickou zdatnost, závazek kvality a ducha spolupráce nezbytného pro úspěšné dodání vysoce výkonných lodních vrtulí vytištěných na 3D tiskárně.
Ekonomické aspekty: Nákladové faktory a analýza doby realizace
Technické výhody 3D tištěných lodních šroubů jsou přesvědčivé, ale pochopení ekonomických důsledků - konkrétně faktorů ovlivňujících náklady a očekávané doby realizace - je zásadní pro přijímání informovaných rozhodnutí, zejména pro manažery veřejných zakázek a vedoucí projektů. Aditivní výroba kovů představuje odlišnou strukturu nákladů ve srovnání s tradičním odléváním nebo obráběním, což v některých scénářích přináší výhody, zatímco v jiných může být dražší.
Klíčové nákladové faktory pro 3D tištěné vrtule:
Konečnou cenu vrtule vytištěné na 3D tiskárně ovlivňuje složitá souhra faktorů. Jasné pochopení těchto složek je zásadní při vyhodnocování nabídek od poskytovatelé služeb aditivní výroby.
- Náklady na materiál:
- Cena prášku: Náklady na kilogram vybraného kovového prášku (např. CuAl10Fe5Ni5, CuNi30Mn1Fe). Slitiny mědi, zejména s vysokým obsahem niklu, jako je CuNi30Mn1Fe, bývají dražší než standardní oceli nebo slitiny hliníku.
- Část Objem: Množství materiálu, které přímo tvoří geometrii vrtule.
- Objem podpory: Množství materiálu použitého na podpůrné konstrukce, které může být v závislosti na konstrukci a orientaci značné. Cílem DfAM je toto minimalizovat.
- Recyklace prášku: Netavený prášek je sice z velké části recyklovatelný, ale jsou s ním spojeny náklady na prosévání, testování a obnovu zásob prášku. Renomovaní poskytovatelé tuto efektivitu zohledňují ve svých cenách.
- AM Machine Time:
- Doba výstavby: Především podle výšky sestavy a objemu taveného materiálu na jednu vrstvu. Mezi faktory patří tloušťka vrstvy, rychlost skenování a počet dílů vložených do jednoho sestavení.
- Hodinová sazba stroje: Zahrnuje amortizaci stroje, spotřebu energie, inertní plyn (u LPBF), vakuové systémy (u SEBM), údržbu a čas obsluhy. Průmyslové stroje vyšší třídy mají vyšší hodinové sazby.
- Náklady na pracovní sílu:
- Předběžné zpracování: Příprava souborů CAD, simulace sestavení, návrh podpory, nastavení stroje.
- Obsluha stroje: Sledování procesu sestavování.
- Práce s následným zpracováním (často značná):
- Vyjmutí dílu ze stavební desky.
- Odstraňování a čištění sypkého prášku.
- Odstranění nosné konstrukce: To může být velmi pracné, zejména u složitých geometrií.
- Ruční broušení, broušení a leštění pro povrchovou úpravu.
- Kontrola a kontrola kvality práce.
- Náklady na následné zpracování (nepracovní):
- Tepelné zpracování: Doba pece, energie, plyny s řízenou atmosférou/vakuum.
- Izostatické lisování za tepla (HIP): Náklady na specializované vybavení a proces; v případě potřeby mohou být významným přídavkem.
- CNC obrábění: Obráběcí čas pro dosažení kritických tolerancí a specifických vlastností povrchu. Víceosé obrábění zvyšuje náklady.
- Spotřební materiál: Brusiva pro dokončovací práce, chladicí kapaliny pro obrábění, NDT materiály (barviva, fólie).
- Vyvažování: Čas na vybavení a kvalifikovanou práci.
- Zajištění kvality a testování:
- Služby NDT: Náklady spojené s prováděním DPT, rentgenových/ CT vyšetření atd.
- Rozměrová kontrola: Čas stroje CMM, práce metrologů.
- Dokumentace: Generování zpráv o shodě, certifikací materiálů, záznamů o kontrolách.
- Režijní náklady a zisk:
- Provozní režie poskytovatele služeb (zařízení, správa atd.) a ziskové rozpětí.
- Objednávkové množství:
- Nízké objemy (1-10): AM zde často zazáří díky absenci nákladů na nástroje. Náklady na seřízení se amortizují na menší počet dílů.
- Střední objemy: Náklady na jeden díl se snižují, protože se rozkládají náklady na nastavení, a efektivitu lze nalézt v dávkovém následném zpracování.
- Vysoké objemy: Tradiční odlévání je obvykle nákladově efektivnější na jeden díl, ačkoli náklady na AM se neustále zlepšují.
- Velkoobchodní ceny: U opakovaných objednávek nebo větších šarží mohou dodavatelé nabízet množstevní slevy nebo vyjednávat velkoobchodní ceny struktury.
Analýza doby realizace:
Jednou z nejvýznamnějších výhod AM je často zkrácení dodací lhůty ve srovnání s tradičními metodami, zejména u zakázkových nebo nízkoobjemových dílů.
- Srovnání:
- Tradiční odlévání: Vyžaduje výrobu vzorů/forem (týdny/měsíce), odlévání (dny/týdny), obrábění/dokončování (týdny). Celkem: Často 8-16 týdnů nebo více.
- Metal AM: Příprava návrhu/simulace (dny), tisk (dny až 1-2 týdny v závislosti na velikosti), kompletní následné zpracování (1-4 týdny v závislosti na složitosti). Celkem: Často 3-8 týdnů.
- Typický pracovní postup AM & Odhad času (příklad – Středně velká vrtule):
- Zpracování objednávky & amp; Příprava tisku: 1-3 dny
- Tisk (SEBM/LPBF): 3-10 dní (velmi závisí na velikosti/komplexnosti)
- Cooldown & Depowdering: 1 den
- Tepelné ošetření proti stresu: 1-2 dny (včetně doby v peci)
- Odstranění dílu/podpory: 1-3 dny
- HIP (v případě potřeby): 3-5 dní (včetně logistiky k poskytovateli HIP, pokud je zadáván externě)
- CNC obrábění: 2-5 dní
- Povrchová úprava: 2-7 dní (velmi závisí na požadovaném Ra)
- NDT & amp; Inspekce: 1-3 dny
- Vyvažování: 1 den
- Odhadovaná celková částka: ~3 až 8 týdnů
- Faktory ovlivňující dobu realizace AM:
- Velikost dílu & Složitost: Tisk a následné zpracování větších a složitějších dílů trvá déle.
- Dostupnost stroje: Plánování na příslušných strojích.
- Intenzita následného zpracování: Rozsáhlé obrábění nebo leštění výrazně prodlužuje čas. HIP výrazně prodlužuje čas.
- Požadavky na zajištění kvality: Důsledná nedestruktivní kontrola a dokumentace prodlužují čas.
- Efektivita pracovních postupů poskytovatele: Jak zefektivněné jsou jejich operace?
Celkové náklady na vlastnictví (TCO):
Je důležité se dívat dál než jen na počáteční kupní cenu. Hledisko TCO zohledňuje celoživotní náklady a přínosy:
- Potenciální úspory s vrtulemi AM:
- Úspora paliva: Optimalizované konstrukce mohou vést k výrazným úsporám paliva po celou dobu životnosti plavidla.
- Snížená údržba: Špičkové materiály, jako je CuNi, snižují potřebu častého čištění díky odolnosti proti biologickému znečištění. Lepší odolnost proti kavitaci (NAB) prodlužuje životnost lopatek.
- Nižší náklady na zásoby: Tisk náhradních dílů na vyžádání eliminuje nutnost držet nákladné fyzické zásoby.
- Minimalizace prostojů: Rychlejší výměna poškozených lodních šroubů umožňuje rychlejší obnovení provozu plavidel.
- Výpočet TCO: Odhad těchto přínosů po dobu životnosti je sice složitý, ale je nezbytný pro ospravedlnění investic do potenciálně dražších komponent AM, zejména pro komerční nebo námořní provozovatele a náročné majitele jachet.
Závěrem lze říci, že ekonomická výhodnost 3D tištěných vrtulí je příznivá pro prototypy, zakázkové návrhy, malosériovou výrobu a situace, kdy rychlost nebo jedinečné výkonnostní charakteristiky umožněné technologií AM poskytují významnou hodnotu. Ačkoli náklady na materiál a následné zpracování jsou klíčovými faktory, výrazně zkrácené doby realizace a potenciální výhody TCO často činí z AM přesvědčivou ekonomickou volbu pro specifické námořní aplikace. Získání podrobných nabídek od zkušených poskytovatelů, jako je Met3dp, s uvedením všech složek nákladů a reálných dob realizace je prvním krokem k informovanému ekonomickému vyhodnocení.
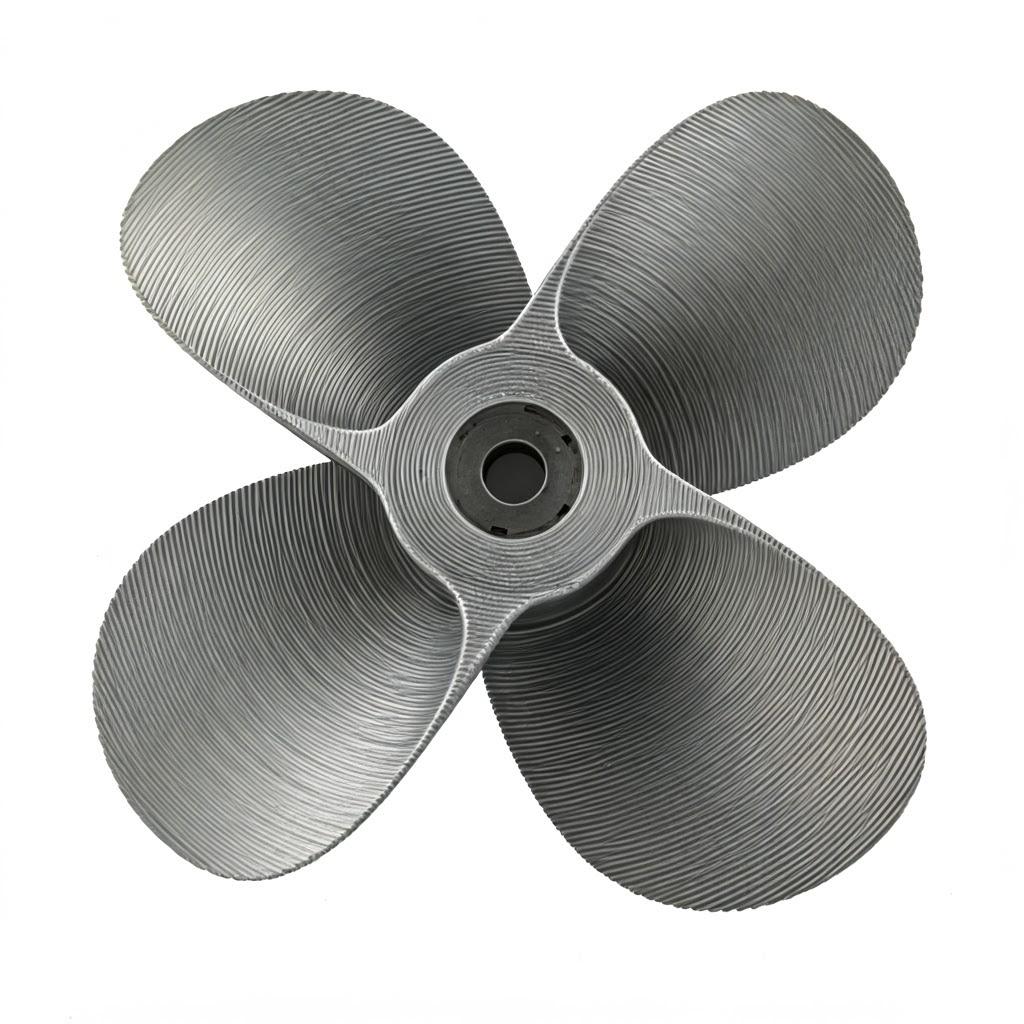
Často kladené otázky (FAQ) o 3D tištěných lodních šroubech
Vzhledem k tomu, že aditivní výroba kovů získává v námořním průmyslu na popularitě, inženýři, konstruktéři, manažeři veřejných zakázek a provozovatelé plavidel se často ptají na možnosti, omezení a praktické aspekty 3D tištěných vrtulí. Zde jsou odpovědi na některé často kladené otázky:
Otázka 1: Jsou vrtule vytištěné 3D tiskem stejně pevné a odolné jako tradičně odlévané vrtule?
A: Ano, a potenciálně ještě pevnější a odolnější, pokud jsou správně navrženy, vyrobeny a následně zpracovány. Zde je důvod:
- Vlastnosti materiálu: Procesy AM kovů, jako je SEBM a LPBF, vedou při správné kontrole a použití vysoce kvalitních prášků (jako jsou prášky vyráběné společností Met3dp) k jemnozrnným mikrostrukturám. Jemná zrna obecně vedou k vyšší pevnosti v tahu, meze kluzu a únavové pevnosti ve srovnání s hrubšími zrny typickými pro pískové odlitky.
- Hustota: Procesy AM s vysokou integritou mohou dosáhnout hustoty dílů přesahující 99,5 %, často až téměř 100% hustoty, zejména pokud se použije izostatické lisování za tepla (HIP). Tím se minimalizuje pórovitost, která může být slabým místem litých součástí.
- Výkon slitiny: Použití vysoce výkonných slitin, jako je NAB (CuAl10Fe5Ni5) nebo CuNi (CuNi30Mn1Fe), poskytuje vynikající pevnost, houževnatost a odolnost proti korozi a kavitaci.
- Optimalizace návrhu (DfAM): AM umožňuje optimalizovat konstrukce z hlediska rozložení napětí, čímž se potenciálně snižují špičková napětí v porovnání s konstrukcemi omezenými omezeními odlévání.
- Kritický faktor: Klíčem k úspěchu je důsledná kontrola procesu, ověřené vlastnosti materiálu, vhodné následné zpracování (zejména tepelné zpracování a případně HIP) a důkladné nedestruktivní testování (NDT), které zajistí absenci kritických vad. Pokud jsou tyto kroky dodrženy zkušenými dodavateli, mohou vrtule AM splňovat nebo překonávat výkonnost svých litých protějšků a odpovídat příslušným námořním normám.
Otázka 2: Jaká je maximální velikost vrtule, kterou lze vytisknout na 3D tiskárně?
A: Ta se s rozvojem technologie AM neustále vyvíjí.
- Aktuální limity PBF: Většina současných průmyslových kovových strojů PBF (LPBF a SEBM) má stavební obálku obvykle v rozmezí zhruba 500 x 500 x 500 mm, přičemž některé větší stroje s rámem dosahují v jednom rozměru 800 nebo dokonce 1000 mm. To umožňuje výrobu vrtulí vhodných pro mnoho malých až středně velkých plavidel, USV, AUV a jachet. Met3dp nabízí špičkové objemy tisku v rámci kategorie SEBM a posouvá tyto hranice.
- Velmi velké vrtule: Vrtule pro velké komerční lodě (často o průměru několika metrů) jsou obecně stále mimo praktické rozměrové limity jednodílného tisku PBF.
- Alternativní metody:
- Directed Energy Deposition (DED) / Wire Arc Additive Manufacturing (WAAM): Tyto procesy AM nejsou omezeny práškovým ložem a teoreticky mohou vyrábět mnohem větší díly, i když obvykle s nižším rozlišením a potenciálně vyžadující více finálního obrábění. Aktivně se zkoumají pro velké námořní součásti.
- Sekční tisk: Dalším možným přístupem je vytištění velké vrtule z více částí a jejich následné spojení (např. svařováním), což však přináší složitosti spojené s integritou a kvalifikací spojů.
- Výhled: Trend směřuje k větším objemům strojů AM, takže maximální tisknutelná velikost se bude pravděpodobně i nadále zvyšovat.
Otázka 3: Lze stávající návrhy vrtulí, které byly původně vyrobeny pro odlévání, snadno upravit pro 3D tisk?
A: Ačkoli je technicky možné vytisknout vrtuli přímo z existujícího modelu CAD (nebo z modelu vytvořeného reverzním inženýrstvím/3D skenováním existujícího dílu), je často’ není optimální.
- Promarněné příležitosti: Pouhá replikace odlitku nevyužívá klíčových výhod AM, jako je geometrická volnost pro hydrodynamickou optimalizaci, potenciál odlehčení nebo integrované prvky.
- Potenciální problémy: Návrhy optimalizované pro odlévání mohou obsahovat prvky (jako jsou velké ploché úseky nebo specifické úhly tahu), které je obtížné nebo neefektivní tisknout pomocí AM nebo mohou vyžadovat nadměrné podpůrné struktury.
- Doporučení: (DfAM): Nejlepším postupem je použít stávající konstrukci jako výchozí, ale poté ji přehodnotit a optimalizovat pomocí zásad návrhu pro aditivní výrobu (DfAM). To zahrnuje spolupráci s odborníky na AM s cílem přizpůsobit geometrii pro lepší výkon, snížení hmotnosti, minimalizaci podpěr a zlepšení tisknutelnosti. Tím se odemkne skutečná hodnota zavedení AM.
Otázka 4: Jaké jsou náklady na 3D tisk ve srovnání s tradičním odléváním vrtulí?
A: Neexistuje jediná odpověď, záleží na několika faktorech:
- Prototypy, jednorázové výrobky, návrhy na zakázku: Pro jednotlivé kusy nebo velmi malá množství (5 až 10 kusů) je AM téměř vždy rychlejší a cenově výhodnější protože eliminuje vysoké počáteční náklady a dlouhou dobu přípravy spojenou s vytvářením vzorů a forem pro odlévání.
- Složité geometrie: Pokud je konstrukce vrtule velmi složitá (např. složité tvary lopatek, vnitřní prvky), může být AM ekonomičtější než odlévání a rozsáhlé víceosé obrábění, protože složitost zvyšuje náklady na samotný proces AM relativně málo (i když může zvýšit potřebu následného zpracování).
- Nízký až střední objem (např. 10-100 jednotek): Jedná se o šedou zónu, kde porovnání nákladů do značné míry závisí na velikosti dílu, složitosti, materiálu a konkrétní srovnávané metodě odlévání. Je třeba provést podrobnou analýzu nákladů a přínosů.
- Velký objem (>100s nebo 1000s) & Jednoduché návrhy: U velkého množství relativně jednoduchých, standardizovaných konstrukcí vrtulí zůstávají tradiční metody odlévání obecně zachovány nákladově efektivnější na díl díky zavedeným úsporám z rozsahu.
- Na TCO záleží: Nezapomeňte zvážit celkové náklady na vlastnictví (TCO). Vyšší počáteční náklady na AM mohou být kompenzovány výhodami po celou dobu životnosti, jako je úspora paliva nebo snížení údržby.
Otázka 5: Mohou 3D tištěné vrtule získat schválení klasifikační společnosti (např. DNV, ABS, Lloyd’s Register)?
A: Ano, získání třídního schválení pro 3D tištěné lodní komponenty, včetně lodních šroubů, je stále více možné, i když to vyžaduje přísný proces.
- Existují pokyny: Hlavní klasifikační společnosti zveřejnily pokyny a rámce pro kvalifikaci AM dílů, materiálů a výrobců (např. DNVGL-CG-0197, ABS Guide for Additive Manufacturing).
- Přísná kvalifikace: Tento proces obvykle zahrnuje:
- Kvalifikace výrobce: Audit zařízení, systému řízení jakosti, procesů a způsobilosti personálu poskytovatele služeb AM.
- Specifikace materiálu: Definování a testování vlastností konkrétní použité šarže prášku.
- Kvalifikace procesu: Kvalifikace konkrétního stroje AM a uzamčených parametrů používaných pro výrobu.
- Kvalifikace dílů: Rozsáhlé zkoušky NDT a mechanické zkoušky (tahové, únavové, rázové, korozní) na zkušebních kuponech vytištěných vedle dílu a případně i na dílu samotném.
- Dokumentace: Komplexní záznamy sledující celý proces od prášku až po hotový díl.
- Spolupráce je klíčová: Dosažení schválení třídy vyžaduje úzkou spolupráci mezi projektantem, dodavatelem AM (jako je Met3dp, který má zkušenosti s přísnými požadavky na kvalitu) a klasifikační společností již od počátečních fází projektu. Přidává to čas a náklady, ale je to nezbytné pro zajištění nejvyšší úrovně bezpečnosti a spolehlivosti kritických aplikací.
Otázka 6: Jaká je odolnost 3D tištěné vrtule z mědi a niklu (CuNi) proti biologickému znečištění v porovnání s tradiční litou nebo tepanou částí z CuNi?
A: Odolnost slitin CuNi proti biologickému znečištění vyplývá z jejich chemického složení a způsobu, jakým interagují s mořskou vodou a vytvářejí specifickou ochrannou povrchovou vrstvu oxidu mědi. Proto by 3D tištěná vrtule z CuNi měla vykazovat srovnatelná vynikající odolnost proti biologickému znečištění k tradičně vyráběným protějškům, za předpokladu, že:
- Správné složení slitiny: Prášek AM (např. CuNi30Mn1Fe) splňuje požadované chemické specifikace.
- Hustá mikrostruktura: Procesem AM se dosáhne plně hustého dílu bez výrazné pórovitosti, která by mohla změnit chemický složení povrchu nebo vytvořit místa pro uchycení.
- Vhodný stav povrchu: Konečná povrchová úprava po následném zpracování je vhodná. Extrémně drsné povrchy mohou zpočátku nabízet více textury pro usazení, ale základní vlastnost materiálu by měla být dominantní.
- Potenciál pro vylepšení? AM by v budoucnu mohla dokonce nabídnout možnosti vytváření specifických mikrotextur na povrchu během tisku, což by mohlo dále zvýšit odolnost proti biologickému znečištění, ačkoli tato oblast je předmětem probíhajícího výzkumu.
Zodpovězení těchto otázek by mělo organizacím, které zvažují zavedení 3D tištěných lodních vrtulí využívajících pokročilé slitiny, jako jsou NAB a CuNi, poskytnout větší jasnost a jistotu.
Závěr: Mapování budoucnosti námořního pohonu pomocí Met3dp
Zavedení aditivní výroby kovů představuje významný zlomový bod ve vývoji technologie lodních pohonů. Jak jsme již v této diskusi zkoumali, 3D tisk, zejména s využitím vysoce výkonných slitin, jako je nikl-hliníkový bronz (CuAl10Fe5Ni5) a měď-nikl (CuNi30Mn1Fe), nabízí silný soubor výhod, které přímo reagují na trvalé požadavky na vyšší účinnost, větší přizpůsobivost, menší dopad na životní prostředí a odolnější dodavatelské řetězce v námořním průmyslu.
Pro inženýři a námořní architekti, kovové AM odemyká bezprecedentní úroveň svobody designu. Osvobozuje konstrukci lodních šroubů od omezení tradičních odlévacích forem a přístupu k obrábění a umožňuje vytvářet vysoce optimalizované, komplexní geometrie přizpůsobené hydrodynamice konkrétních plavidel. To se projevuje v hmatatelných výhodách: vyšší palivová účinnost díky pokročilým profilům lopatek, snížení kavitace a hlučnosti díky propracovaným konstrukcím hran a špiček a možnostem lehčích, integrovaných pohonných komponent. Schopnost rychle vytvářet prototypy a testovat funkční návrhy urychluje inovační cykly a posouvá hranice možností v oblasti výkonu lodních pohonů.
Pro manažeři veřejných zakázek, loděnice a provozovatelé flotil, představuje technologie AM pro kovy přesvědčivé strategické výhody. Beznástrojová povaha této technologie dramaticky zkracuje dodací lhůty pro zakázkové nebo malosériové vrtule, čímž mění ekonomiku výklenkových aplikací a konstrukce plavidel na míru. Výrobní možnosti na vyžádání umožňují výrobu náhradních dílů přesně podle potřeby, čímž se minimalizují nákladné zásoby a výrazně se zkracují prostoje plavidel - což je rozhodující faktor pro provozní připravenost a ziskovost. Tato technologie umožňuje agilnější a pohotovější dodavatelský řetězec, který je schopen řešit problémy se zastaráváním starších systémů a umožňuje lokalizovanou výrobu. Vyhodnocení celkových nákladů na vlastnictví (TCO), včetně zvýšení výkonnosti a snížení nákladů na údržbu, často odhalí silnou nabídku hodnoty AM nad rámec počátečních nákladů na díl, zejména při jednání s dodavateli zaměřenými na velkoobchod s lodními komponenty.
Úspěšné využití tohoto transformačního potenciálu však vyžaduje zvládnutí složitostí DfAM, materiálové vědy, řízení procesů a rozsáhlého následného zpracování. To podtrhuje zásadní význam výběru správného výrobního partnera.
Met3dp je připravena stát se tímto strategickým partnerem. Nabízíme víc než jen tiskové služby řešení aditivní výroby postavené na základech hlubokých odborných znalostí a špičkových technologií. Naše silné stránky dokonale odpovídají požadavkům na výrobu vysoce kvalitních lodních šroubů:
- Pokročilá technologie SEBM: Naše špičkové tiskárny pro selektivní tavení elektronovým svazkem jsou ideální pro výrobu robustních dílů s nízkým namáháním z náročných materiálů, jako jsou NAB a CuNi, a poskytují výjimečnou přesnost a spolehlivost.
- Vysoce výkonné kovové prášky: Jako výrobce vlastních prášků s využitím nejmodernějších technologií plynové atomizace a PREP zajišťujeme nejvyšší kvalitu, konzistenci a sledovatelnost materiálů, které jsou důležité pro výkonnost lodí.
- Materiál & amp; Odborné znalosti v oblasti aplikací: Náš tým má desítky let společných zkušeností a spolupracuje s klienty v oblasti DfAM, výběru materiálů, optimalizace procesů a kvalifikačních postupů.
- Integrovaný přístup: Rozumíme celému výrobnímu procesu, od prášku až po hotovou, vyváženou a zkontrolovanou vrtuli, a zajišťujeme kvalitu a odpovědnost v každé fázi.
Budoucnost lodního pohonu je bezpochyby spjata s rozvojem digitálních výrobních technologií, jako je například technologie AM. Přijetím těchto inovací mohou zúčastněné strany v námořním odvětví dosáhnout nové úrovně výkonnosti, efektivity a provozní flexibility.
Jste připraveni prozkoumat, jak mohou 3D tištěné vrtule změnit vaše námořní aplikace? Ať už navrhujete jachtu na zakázku, vyvíjíte pokročilá USV, hledáte vylepšení výkonu pro pracovní lodě nebo potřebujete řešení pro zastaralé díly, společnost Met3dp má odborné znalosti a technologie, které vám pomohou uspět.
Kontaktujte Met3dp ještě dnes prodiskutovat požadavky vašeho projektu s našimi specialisty na aditivní výrobu a zjistit, jak mohou naše schopnosti podpořit cestu vaší organizace k nové generaci lodního pohonu. Vítáme dotazy od inženýrů, manažerů nákupu, loděnic, dodavatelé lodních šroubů, a distributoři lodních dílů chtějí využít možnosti 3D tisku z kovu.
Sdílet na
MET3DP Technology Co., LTD je předním poskytovatelem řešení aditivní výroby se sídlem v Qingdao v Číně. Naše společnost se specializuje na zařízení pro 3D tisk a vysoce výkonné kovové prášky pro průmyslové aplikace.
Dotaz k získání nejlepší ceny a přizpůsobeného řešení pro vaše podnikání!
Související články
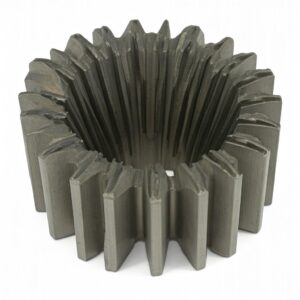
Vysoce výkonné segmenty lopatek trysek: Revoluce v účinnosti turbín díky 3D tisku z kovu
Přečtěte si více "O Met3DP
Nedávná aktualizace
Náš produkt
KONTAKTUJTE NÁS
Nějaké otázky? Pošlete nám zprávu hned teď! Po obdržení vaší zprávy obsloužíme vaši žádost s celým týmem.
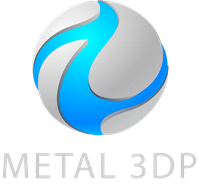
Kovové prášky pro 3D tisk a aditivní výrobu