Prášky z kovových slitin
Obsah
Prášky z kovových slitin odkazuje na částicové směsi dvou nebo více kovových prvků používané v celé výrobě, aditivních technikách a výzkumných aplikacích. Tato příručka slouží jako hloubková reference na kovové slitinové prášky – zkoumá typy, výrobní metody, klíčové vlastnosti, specifikace, dodavatele, ceny, aplikace, srovnání a další.
Přehled prášků ze slitin kovů
Charakteristický | Popis |
---|---|
Složení | Kovové slitinové prášky jsou jemně rozdělené kovové částice vytvořené rozkladem kombinace dvou nebo více kovů do práškové formy. Tyto slitiny jsou navrženy tak, aby dosahovaly specifických vlastností, jako je zvýšená pevnost, odolnost proti korozi nebo vodivost, které jednotlivé kovy nemusí mít samy o sobě. |
Výrobní proces | Kovové slitinové prášky se vyrábějí různými technikami, přičemž atomizace je nejběžnější. Při atomizaci se roztavená slitina rozbije na jemnou mlhu kapiček, které rychle ztuhnou na sférické nebo téměř sférické práškové částice. Mezi další metody patří elektrolýza, redukce v pevném stavu a mechanické mletí, z nichž každá nabízí výhody pro specifické materiály nebo aplikace. |
Vlastnosti částic | Velikost, tvar a distribuce částic kovového slitinového prášku významně ovlivňují konečné vlastnosti dílů, které se používají k jejich vytvoření. Sférické částice obecně lépe tečou a hustěji se balí, což vede ke zlepšení výkonu v procesech aditivní výroby, jako je 3D tisk. Velikost částic může také ovlivnit mechanické vlastnosti, povrchovou úpravu a celkovou kvalitu konečného produktu. |
Aplikace | Prášky z kovových slitin způsobily revoluci ve výrobě napříč různými průmyslovými odvětvími. Rozsáhle se používají v aditivní výrobě (3D tisk) k vytváření složitých, lehkých součástí pro letecký, automobilový a lékařský průmysl. Kromě toho se prášky z kovových slitin používají v procesech, jako je vstřikování kovů (MIM), k výrobě složitých dílů blízkých konečnému tvaru pro různé aplikace. |
Výhody | Ve srovnání s tradičními výrobními metodami, jako je obrábění nebo odlévání, nabízejí prášky z kovových slitin několik výhod. Umožňují výrobu blízkou konečnému tvaru, čímž se minimalizuje odpad materiálu. Schopnost přizpůsobit složení a charakteristiky částic prášku navíc umožňuje vytvářet díly se specifickými vlastnostmi. Prášky z kovových slitin také usnadňují výrobu složitých geometrií a lehkých konstrukcí, díky čemuž jsou ideální pro různé špičkové aplikace. |
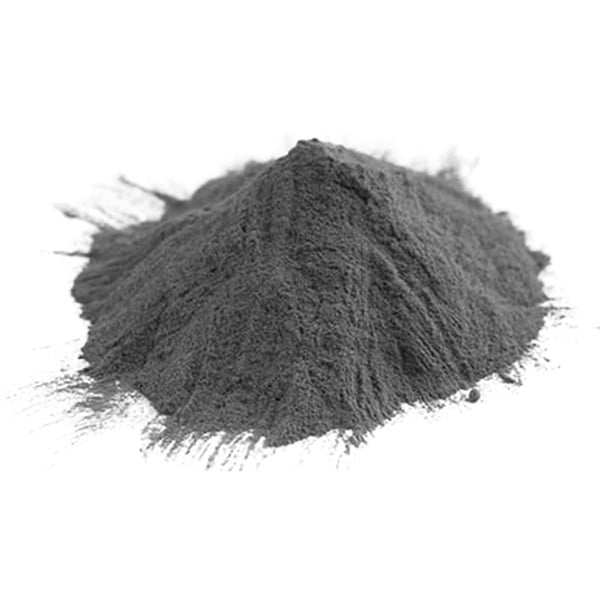
Typy prášků z kovových slitin
Hlavní kategorie:
- Ocelové slitiny – nerezové, nástrojové, legované oceli…
- Slitiny titanu – Ti6Al4V, TiAl, titanové aluminidy
- Slitiny hliníku – hliník 2024, 7075, AlSiMg
- Kobaltové slitiny – kobaltový chrom, MP35N
- Slitiny niklu – Inconel 625, Inconel 718, Hastelloy
A jedinečnost založená na:
Legující prvky
Typ | Běžné prvky | Příkladné materiály |
---|---|---|
Nízko legované | <5 % Ni, Cr, Mo | 4140, 4340 |
Středně legované | 5-15 % Ni, Cr, Mo atd. | H13, 420 nerez |
Vysoce legované | 15-30 % Al, Co, Ti atd. | 316 nerez, MP35N |
Způsob výroby
Metoda | Slitinové systémy | Charakteristika |
---|---|---|
Rozprašovaný plyn | Většina slitin | Sférické, řízené rozložení velikosti |
Atomizovaná voda | Ocel | Nepravidelný tvar, široká distribuce |
Plazmová atomizace | Reaktivní materiály jako slitiny Ti a Al | Řízená atmosféra, sférická |
Elektrolytické | Měď, Ni | Dendritické vločky, houba |
Míchání prvků, jako je hliník, kobalt, chrom, wolfram atd., se základními kovy vytváří vylepšené schopnosti slitinových prášků. Výrobní technika také ovlivňuje morfologii a vlastnosti prášku.
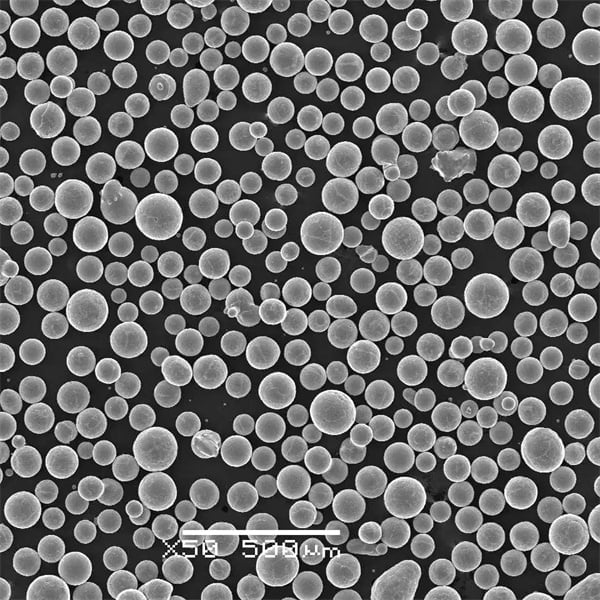
Výrobní procesy prášků z kovových slitin
Proces | Popis | Výhody | Nevýhody | Aplikace |
---|---|---|---|---|
Atomizace | Nejběžnější metoda, atomizace, zahrnuje tavení kovové slitiny a následné rozdělení na jemnou mlhu kapiček pomocí vysokotlakého plynu (plynová atomizace) nebo rychle rotujícího disku (odstředivá atomizace). Kapičky rychle tuhnou, když padají v řízené atmosféře, čímž se vytvářejí sférické nebo téměř sférické částice prášku. | Vysoká rychlost výroby Přizpůsobitelná velikost a distribuce částic Vhodné pro širokou škálu slitin | Vysoká spotřeba energie Možnost oxidace během atomizace Může vyžadovat další zpracování pro specifické tvary | Ozubená kola Ložiska Řezné nástroje Letecké komponenty Lékařské implantáty |
Elektrolýza | Tento proces využívá elektrický proud k extrakci kovových iontů z roztoku kovové soli a jejich usazování na katodě (záporně nabité elektrodě) jako jemný prášek. Specifické vlastnosti prášku lze řídit úpravou složení elektrolytu a parametrů depozice. | Prášky vysoké čistoty Vynikající kontrola nad velikostí a morfologií částic Vhodné pro reaktivní kovy | Relativně pomalý proces Omezená rychlost výroby Vysoká spotřeba energie | Elektrické kontakty Součásti baterií Filtry Specializované slitiny |
Redukce pevných látek | V této metodě se oxid kovu přímo převede na kovový prášek prostřednictvím redukční reakce s redukčním činidlem, jako je vodík nebo oxid uhelnatý, při zvýšených teplotách. Redukce v pevném stavu se často používá pro kovy s vysokou afinitou ke kyslíku, jako je titan a zirkonium. | Vhodné pro reaktivní kovy Může být kontinuální proces Potenciálně nižší spotřeba energie ve srovnání s atomizací | Omezená kontrola nad velikostí a morfologií částic Může vyžadovat další kroky následného zpracování Možnost kontaminace z redukčního činidla | Pyrotechnika Vstupní suroviny pro vstřikování kovů Třecí materiály |
Chemická redukce | Tento proces zahrnuje použití chemické reakce k přeměně sloučeniny kovu na kovový prášek. Lze použít různé chemické reakce v závislosti na konkrétním kovu a požadovaných vlastnostech prášku. | Lze použít pro různé kovy Relativně jednoduchý proces Možnost levné výroby | Omezená kontrola nad vlastnostmi prášku Může vyžadovat rozsáhlé kroky čištění Environmentální problémy spojené s některými chemickými reaktanty | Nosné katalyzátory Pigmenty Pájení slitin |
Mechanické frézování | Tato metoda zahrnuje broušení objemového materiálu (ingotů, třísek) na jemný prášek pomocí vysokovýkonných mlýnů. Mechanické mletí lze použít k výrobě prášků z široké škály materiálů, včetně kovů, slitin a keramiky. | Všestrannost – použitelná pro různé materiály Lze použít pro malosériovou výrobu | Široké rozložení velikosti částic Možnost kontaminace z mlecího média. Vznik tepla během zpracování může ovlivnit vlastnosti prášku | Amorfní kovové prášky Kompozitní materiály Speciální slitiny |
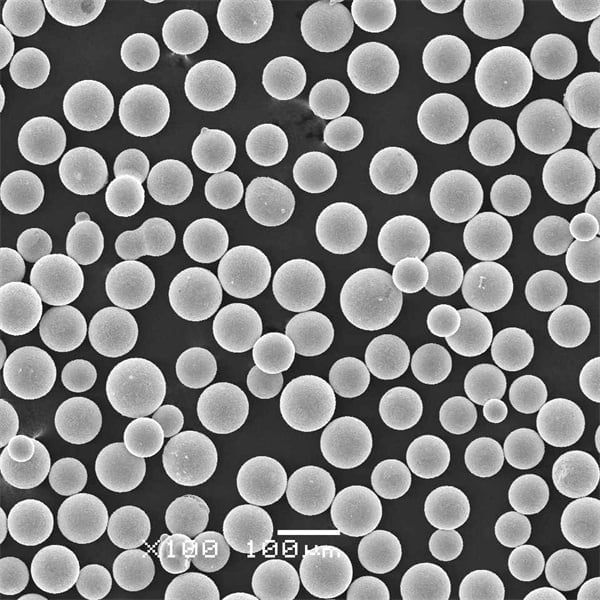
Vlastnosti Prášky z kovových slitin
Fyzikální vlastnosti
Atribut | Charakteristika |
---|---|
Stát | Prášek z pevných částic |
Barva | Šedostříbrný/černý prášek |
Magnetismus | Feritické/martenzitické materiály jsou feromagnetické |
Zápach | Obvykle bez zápachu |
Chuť | Bez chuti |
Rozpustnost | Nerozpustný ve vodě a běžných rozpouštědlech |
Mechanické vlastnosti
Metrický | Popis |
---|---|
Tvrdost | Rozsah od měkkých drahých slitin < 100 HV po kalené nástrojové oceli > 700 HV |
Síla | Rozpětí od < 100 MPa pro uhlíkové oceli až po více než 2 000 MPa pro některé niklové superslitiny |
Tažnost | Míra tvárnosti – vysoká pro ocel C, střední pro pracovní oceli, nízká pro materiály s vysokým obsahem Cr/Co |
Tepelné vlastnosti
Opatření | Podrobnosti |
---|---|
Bod tání | Závislé na slitinovém systému – 500 až 1500 °C+ |
Tepelná vodivost | 15 – 90 W/mK mezi typy slitin |
CTE | Liší se od ~5 x10-6 K-1 (Invar) do ~18 x10-6 K-1 (hliníkové slitiny) |
Tabulka 2: Přehled běžných fyzikálních, mechanických a tepelných vlastností prášků z kovových slitin
Volba specifické slitiny vyvažuje tvrdost, mez kluzu, tažnost, hustotu, odolnost vůči teplu/korozi a další atributy podle aplikace.
Specifikace
Komerční prášky z kovových slitin jsou testovány a certifikovány podle specifikací:
Distribuce velikosti částic
Standard | Mikrony | Způsob výroby |
---|---|---|
Pokuta | 1-25 | Rozprašování plynu |
Střední | 25-75 | Rozprašování plynu |
Hrubý | 75-150 | Rozprašování vody |
Stupně čistoty
Hodnocení | Kontrola chemického složení | Nečistoty |
---|---|---|
Standard | Široké rozsahy slitin | Až 1 % ostatních |
Vlastní | Fixní cíl slitiny | <1000 ppm nečistot |
Vysoká čistota | Úzké pásmo slitiny | <100 ppm kontaminantů |
Tabulka 3: Typické rozsahy velikostí, chemie a stupně čistoty pro komerční prášky z kovových slitin
Splnění nebo překročení certifikovaných specifikací zajišťuje opakovatelný výkon mezi šaržemi prášku a následnými výrobními sériemi.
Výrobci prášků z kovových slitin
Kategorie výrobce | Popis | Klíčové produkty | Použité aplikace | Geografický dosah |
---|---|---|---|---|
Globální lídři | Tyto nadnárodní korporace mají rozsáhlé výrobní kapacity, rozmanitou nabídku kovových slitin a pokročilé programy výzkumu a vývoje. Uspokojují širokou škálu průmyslových odvětví a často provozují výrobní závody na několika kontinentech. | Superslitiny na bázi niklu, železa a kobaltu Titanové a hliníkové slitiny Speciální slitiny pro aditivní výrobu | Letectví a obrana (lopatky turbín, součásti motorů) Ropa a plyn (vrtací zařízení, nástroje pro vrtání) Automobilový průmysl (ozubená kola, ložiska) Lékařství (implantáty, protézy) Elektronika (chladiče, elektrické kontakty) | Severní Amerika Evropa Asia Jižní Amerika |
Regionální hráči | Tito výrobci se zaměřují na specifické geografické trhy a uspokojují regionální průmyslové potřeby. Mohou se specializovat na konkrétní slitiny nebo uspokojovat specializované aplikace. | Prášky z nerezové oceli Nástrojové oceli Prášky z mosazi a bronzu Surovina pro vstřikování kovů (MIM). | Spotřební zboží (příbory, hardware) Součásti průmyslových strojů Elektrické komponenty Automobilové díly (ozubená kola, filtry) Lékařské přístroje (chirurgické nástroje) | Severní Amerika Evropa Asia (Může mít omezenou přítomnost v jiných regionech) |
Nově vznikající výrobci | Tyto společnosti jsou často menší a zaměřují se na inovativní technologie nebo uspokojují nové požadavky trhu. Mohou se specializovat na prášky pro aditivní výrobu (AM) nebo zkoumat nové výrobní metody. | Vysoce výkonné kovové prášky pro AM Nanoprášky pro specializované aplikace Prášky z kovových slitin z recyklovaných materiálů Biokompatibilní slitiny pro lékařské implantáty | Průmysl aditivní výroby Nové technologie (např. 3D tisk pro letectví) Výzkumné a vývojové instituce Iniciativy v oblasti udržitelnosti životního prostředí | Primárně zaměřeno na rozvinuté regiony (Severní Amerika, Evropa, Asie), ale může se globálně rozšířit s růstem trhu |
Smluvní výrobci | Tito výrobci vyrábějí prášky z kovových slitin na základě specifikací zákazníka. Nabízejí flexibilitu z hlediska složení slitiny, velikosti částic a objemu výroby, což uspokojuje specifické aplikace a výzkumné potřeby. | Vlastní prášky z kovových slitin Malosériová výroba Prášky pro prototypování a pilotní projekty | Výzkum a vývoj v různých průmyslových odvětvích Projekty aditivní výroby vyžadující unikátní materiály Specializované aplikace v leteckém, lékařském a elektronickém průmyslu | Globální dosah (může být umístěn kdekoli, ale často přítomen v hlavních výrobních centrech) |
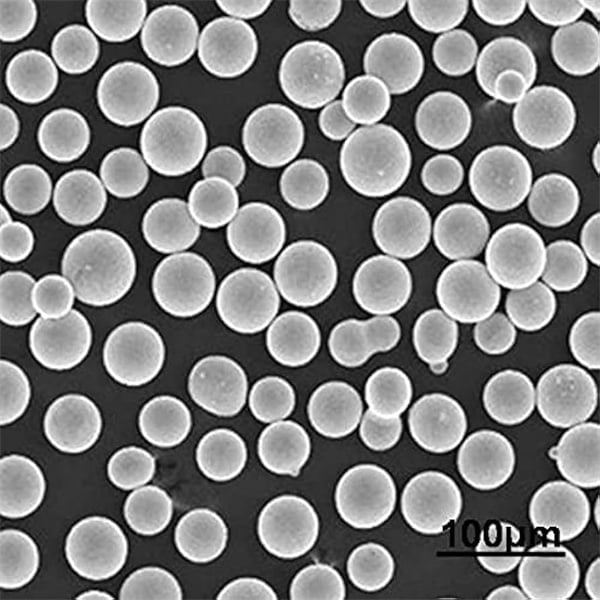
Aplikace z Prášky z kovových slitin
Průmysl | Aplikace | Výhody |
---|---|---|
Aerospace | Lopatky turbín, součásti draku | Vysoká pevnost, tepelná odolnost |
Automobilový průmysl | Ozubená kola, součásti hnacího ústrojí | Ochrana proti opotřebení |
Výrobní | Nástroje pro vlastní produkty | Kratší vývojové cykly |
Ropa a plyn | Těsnění, součásti ventilů, nástroje pro vrty | Zlepšení trvanlivosti |
Tabulka 5: Prášek z kovových slitin umožňuje vysoce výkonné aplikace napříč sektory
Využití vlastností, jako je tepelná tolerance, tvrdost a odolnost proti korozi, usnadňuje spolehlivost v náročných prostředích zařízení oproti stávajícím alternativám, jako jsou plasty nebo tradiční slitiny.
Pro a proti prášků z kovových slitin
Klady | Nevýhody |
---|---|
Flexibilita designu: Prášky z kovových slitin umožňují vytváření složitých geometrií se složitými prvky, kterých je obtížné nebo nemožné dosáhnout tradičními výrobními metodami, jako je obrábění nebo odlévání. To otevírá dveře lehkým a vysoce výkonným součástem v různých průmyslových odvětvích. | Omezená velikost dílu: Současné technologie 3D tisku práškového lože mají omezení maximální velikosti tisknutelného dílu. Větší díly navíc mohou vyžadovat kroky následného zpracování, jako je horké izostatické lisování (HIP), pro zlepšení mechanických vlastností, což zvyšuje složitost a náklady. |
Účinnost materiálu: Prášky z kovových slitin podporují výrobu téměř čistého tvaru, minimalizují odpad materiálu ve srovnání s úběrovými technikami, jako je obrábění. To je zvláště výhodné pro drahé nebo vysoce výkonné slitiny. | Vyšší náklady: Prášky z kovových slitin samotné mohou být dražší než objemové kovy kvůli dodatečnému zpracování, které je součástí jejich výroby. Za vyšší celkové výrobní náklady se navíc mohou podílet zařízení pro 3D tisk a kroky následného zpracování, zejména u malosériové výroby. |
Vlastnosti na míru: Vlastnosti prášků z kovových slitin lze přesně řídit úpravami ve výrobním procesu a složení slitiny. To umožňuje vytvářet materiály se specifickou pevností, hmotností, odolností proti korozi nebo jinými požadovanými vlastnostmi. | Povrchová úprava: Povrchová úprava dílů vyrobených z prášků z kovových slitin může být drsnější ve srovnání s obráběnými nebo litými součástmi. Pro dosažení požadované kvality povrchu mohou být nezbytné techniky následného zpracování, jako je leštění nebo obrábění. |
Lehký design: Prášky z kovových slitin usnadňují vytváření lehkých konstrukcí s vysokým poměrem pevnosti k hmotnosti. To je zásadní pro aplikace v leteckém, automobilovém a jiném průmyslu citlivém na hmotnost. | Anizotropie: Díly vytištěné prášky z kovových slitin mohou vykazovat anizotropní vlastnosti, což znamená, že jejich mechanická pevnost se může lišit v závislosti na směru tisku. To je třeba zohlednit ve fázi návrhu, aby byl zajištěn optimální výkon. |
Rychlé prototypování: Prášky z kovových slitin jsou ideální pro rychlé prototypování složitých dílů. To umožňuje rychlejší iterace návrhu a rychlejší uvedení nových produktů na trh. | Obavy o bezpečnost: Manipulace s prášky z kovových slitin může představovat bezpečnostní rizika v důsledku potenciální hořlavosti, rizik vdechování a podráždění kůže. Zásadní jsou správné manipulační postupy a osobní ochranné prostředky. |
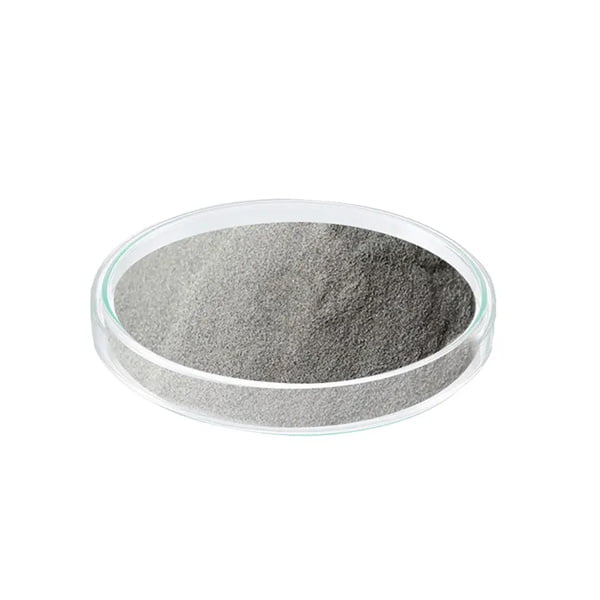
Nejčastější dotazy
Otázka: Jaký je hlavní rozdíl mezi ingotami z kovových slitin a prášky?
Odpověď: Prášky dodávají rafinované mikrostruktury bez segregace a poskytují vsázku pro nové výrobní techniky. Ingoty slouží konvenčním tvářecím procesům.
Otázka: U kterého prášku z kovové slitiny se v nadcházejících letech očekává největší růst?
Odpověď: Prášky ze slitin titanu a hliníku pro letecké aplikace vzhledem k výjimečným schopnostem poměru pevnosti k hmotnosti a zpracovatelnosti.
Otázka: Jaký rozsah velikosti částic funguje nejlépe pro běžné zpracování AM kovových slitin?
Odpověď: 15–45 mikronů poskytuje dobrou hustotu balení práškového lože a soudržnost vrstev a zároveň se vyhýbá problémům, které se vyskytují u ultrajemných prášků.
Otázka: Jak se prášky z kovových slitin liší od prášků z oxidů kovů nebo keramiky?
Odpověď: Prášky z kovových slitin obsahují 2+ kovové prvky tvořící substituční směsi, zatímco oxidy/keramika zahrnují iontové chemické změny s hluboce odlišnými vlastnostmi.
Závěr
Optimalizované kompozice prášků z kovových slitin, mikrostruktury a morfologie rozšiřují možnosti výroby dílů, prototypování a výkonu v leteckém, kosmickém, automobilovém a energetickém sektoru – jak je zde dokumentováno prostřednictvím poznatků o vlastnostech, pokynů pro výrobu, parametrů specifikace a příkladů použití. V případě jakýchkoli dalších otázek týkajících se výběru, nákupu nebo zpracování speciálních slitin se obraťte na nás.
Sdílet na
MET3DP Technology Co., LTD je předním poskytovatelem řešení aditivní výroby se sídlem v Qingdao v Číně. Naše společnost se specializuje na zařízení pro 3D tisk a vysoce výkonné kovové prášky pro průmyslové aplikace.
Dotaz k získání nejlepší ceny a přizpůsobeného řešení pro vaše podnikání!
Související články
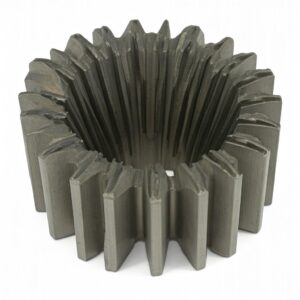
Vysoce výkonné segmenty lopatek trysek: Revoluce v účinnosti turbín díky 3D tisku z kovu
Přečtěte si více "O Met3DP
Nedávná aktualizace
Náš produkt
KONTAKTUJTE NÁS
Nějaké otázky? Pošlete nám zprávu hned teď! Po obdržení vaší zprávy obsloužíme vaši žádost s celým týmem.
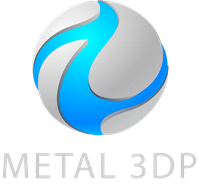
Kovové prášky pro 3D tisk a aditivní výrobu