Atomizace kovů: přehled, dodavatelé, výhody
Obsah
Rozprašování kovů je proces, při kterém se kov přeměňuje ze sypké formy na jemný kovový prášek rozprašováním. Běžně se používá při výrobě kovových prášků pro různé aplikace v různých průmyslových odvětvích. Tento článek poskytuje komplexního průvodce atomizací kovů, který se podrobně zabývá klíčovými aspekty.
Přehled atomizace kovů
Rozprašování kovu spočívá v rozbíjení roztaveného kovu na jemné kapičky pomocí vysokorychlostního proudu plynu nebo kapaliny. Kapky za letu rychle tuhnou a vznikají jemné kulovité kovové prášky.
Klíčové údaje:
- Používá se k výrobě jemných sférických kovových prášků z kovů, jako je hliník, měď, železo, nikl atd.
- Podle způsobu rozprašování se dělí na rozprašování plynem, rozprašování vodou a odstředivé rozprašování.
- Prášky o velikosti od 10 mikronů do 250 mikronů s těsným rozdělením.
- Dosahuje rychlého tuhnutí kapiček a výsledkem jsou jemnozrnné prášky.
- Používá se hlavně v kovové práškové metalurgii a k výrobě kovových práškových součástí.
Metody atomizace
Metoda | Podrobnosti |
---|---|
Rozprašování plynu | Proud roztaveného kovu dezintegrovaný vysokotlakými proudy inertního plynu |
Rozprašování vody | Používá vodní paprsky k rozkladu kovového proudu |
Odstředivá atomizace | Roztavený kov nalitý na rotující kotouč a odlétávající od okrajů |
Aplikace kovových prášků
aplikace | Podrobnosti |
---|---|
Prášková metalurgie | Lisování a spékání prášku pro výrobu dílů PM |
Aditivní výroba kovů | Použití atomizovaných prášků jako vstupní suroviny pro procesy AM, jako je DED, PBF. |
Vstřikování kovů | Smíchejte prášky s pojivem, vstříkněte do forem a odvápněte/spalte. |
Tepelné nástřiky | Rozprašování prášků na povrchy pomocí plazmového/spalovacího spreje |
Pájení | Použití rozprašovaných práškových mezivrstev pro vysokoteplotní pájení |
Svařování | Rozprašované kovové prášky používané jako přídavný materiál při svařování |
Specifikace atomizace kovů
Parametr | Typický rozsah |
---|---|
Velikost prášku | 10 až 250 mikronů |
Rozložení velikosti | Těsná, kulovitá morfologie |
Čistota | Až 99,9% |
Zdánlivá hustota | Přibližně 40-50% skutečné hustoty |
Obsah oxidů | <1%, nižší při atomizaci v inertním plynu |
Rychlost výroby | 10 - 100 kg/hod. |
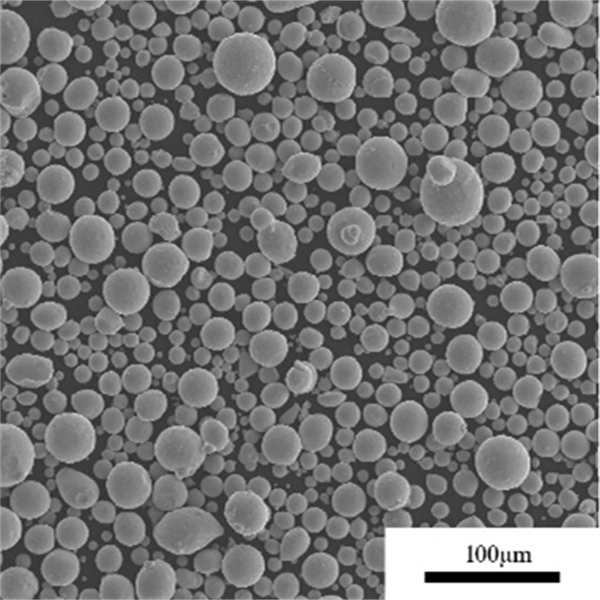
Zařízení pro atomizaci kovů
Klíčová zařízení zapojená do procesu atomizace kovů zahrnují:
Průvodce zařízením pro atomizaci kovů
Zařízení | Účel |
---|---|
Indukční pec | Taví kovový náplňový materiál do kapalného stavu |
Crucible | Podrží roztavený kov před nalitím do rozprašovače |
Tundish | Funguje jako zásobník usnadňující lití kovu. |
Mechanismus atomizace | Rozkládá roztavený kov na kapičky pomocí proudu plynu/kapaliny. |
Systém sběru prášku | Sbírá a odděluje rozprašovaný prášek od dopravního plynu/kapaliny. |
Typy a vlastnosti rozprašovačů
Rozprašovač | Princip | Funkce |
---|---|---|
Rozprašovač plynu | Vysokotlaký proud inertního plynu | Jemnější prášek, nižší oxidace |
Rozprašovač vody | Vysokorychlostní proud vody | Vyšší rychlost výroby, větší částice |
Odstředivý rozprašovač | Nalití roztaveného kovu na rotující kotouč/šálek | Kompaktní, snadno ovladatelný |
Pomocné vybavení
Kategorie | Funkce | Popis | Vliv na kovový prášek |
---|---|---|---|
Příprava surovin | Kondicionování a čištění surovin | Odplyňovací pece: Odstraňte rozpuštěné plyny, jako je vodík a kyslík, abyste zabránili vzniku pórovitosti v konečném prášku. Indukční tavicí pece: Tavení a přesná regulace teploty kovové suroviny. Legovací systémy: Přesně navažte a smíchejte různé kovy, abyste dosáhli požadovaného konečného složení slitiny. | Minimalizuje vady plynu v prášku. Zajišťuje konzistentní vlastnosti prášku. Dosahuje požadovaných vlastností materiálu konečného výrobku. |
Manipulace s kovy a dodávky | Bezpečný přenos roztaveného kovu | Kelímky: Žáruvzdorné nádoby pro uchovávání a přepravu roztaveného kovu. Přečerpávací nádoby (misky, naběračky): Izolované nádoby pro přenos roztaveného kovu z pece do rozprašovací komory. Systémy pro čištění inertním plynem: Zajistěte atmosféru inertního plynu, abyste zabránili oxidaci a kontaminaci během přenosu kovu. | Minimalizuje oxidaci a kontaminaci kovů. Udržuje stálou teplotu kovu pro optimální rozprašování. |
Řízení procesu atomizace | Přesné řízení provozních parametrů | Systémy řízení průtoku: Regulujte průtok rozprašovacího média (plynu nebo vody) pro dosažení konzistentní velikosti kapek a morfologie prášku. Systémy řízení teploty: Sledujte a udržujte optimální teplotu roztaveného kovu pro správnou atomizaci. Systémy řízení tlaku: Regulace tlaku rozprašovacího média (při plynové atomizaci) pro účinnou tvorbu kapek. | Umožňuje konzistentní kvalitu prášku a distribuci velikosti částic. Optimalizuje výtěžnost prášku. |
Sběr a klasifikace prášku | Oddělování a dimenzování částic prášku | Cyklony: Odstředivou silou oddělte větší částice prášku od proudu plynu. Mokré čističe: Zachyťte jemné částice prášku a ochlaďte je pomocí vodního spreje. Systémy prosévání a klasifikace: Rozdělte částice prášku na různé velikostní frakce pomocí sít nebo vzduchových třídičů. | * Zajišťuje požadovanou distribuci velikosti prášku pro konkrétní aplikace. <br> * Minimalizuje ztráty prášku. |
Manipulace s práškem a skladování | Bezpečná správa a skladování kovového prášku | Systémy pro manipulaci s inertními plyny: Při přenosu a skladování prášku udržujte inertní atmosféru, abyste zabránili oxidaci a absorpci vlhkosti. Systémy pro balení prášků: Kovový prášek zabalte do vzduchotěsných nádob pro bezpečnou přepravu a skladování. Sila na prášek: Velké uzavřené skladovací nádoby na sypký kovový prášek s řízenou atmosférou. | Udržuje kvalitu prášku a zabraňuje jeho degradaci. Zajišťuje bezpečnou a efektivní manipulaci s práškem. |
Kontrola životního prostředí | Minimalizace dopadu na životní prostředí | Systémy úpravy vody: Úprava a recyklace procesní vody používané při rozprašování vody, aby se minimalizoval odpad a dodržovaly předpisy na ochranu životního prostředí. Systémy pro odsávání kouře: Zachytávání a filtrování výfukových plynů z procesu rozprašování, aby se minimalizovalo znečištění ovzduší. Systémy pro regulaci hluku: Snížení hluku vznikajícího během procesu rozprašování, aby byly splněny bezpečnostní předpisy. | Dosahuje udržitelné výroby kovového prášku. Zajišťuje dodržování předpisů v oblasti životního prostředí. |
Bezpečnostní systémy | Zajištění bezpečnosti obsluhy | Nouzové uzavírací systémy: V případě nouze rychle zastavte proces rozprašování. Systémy ochrany proti výbuchu: Zabraňte výbuchu v důsledku nahromadění hořlavého plynu nebo kovového prachu. Osobní ochranné prostředky (OOP): Poskytuje obsluze vhodný oděv, respirátory a ochranu očí. | Minimalizuje riziko nehod a zranění. Vytváří bezpečné pracovní prostředí. |
Konstrukční normy a požadavky na instalaci
Komponent | Normy pro navrhování | Požadavky na instalaci |
---|---|---|
Tlakové nádoby | Kodex ASME pro kotle a tlakové nádoby (oddíl VIII, divize 1) EN 13445 (evropská norma) PD 5500 (britská norma) | Dostatečný prostor pro umístění nádoby a přístup k údržbě. Certifikovaná zvedací oka pro bezpečnou přepravu a instalaci. Návrh základů s ohledem na hmotnost, vibrace a potenciální seismickou aktivitu. Sekundární kontejnment k zachycení rozlitých nebo uniklých látek. |
Potrubí | ASME B31.3 Procesní potrubí Příruby a přírubové šroubení ANSI B16.5 | Výběr průměru a materiálu potrubí podle jmenovitého tlaku, teploty a kompatibility s procesními kapalinami. Výběr příruby s ohledem na tlakovou třídu a materiál šroubů. Šikmé potrubí pro správné odvodnění a minimalizaci mrtvých ramen. Přístupné uzavírací ventily pro izolaci a údržbu. Vysoce kvalitní svařovací postupy a kvalifikace personálu. |
Tavicí jednotka | Výběr materiálu z hlediska odolnosti vůči vysokým teplotám a kompatibility s výchozí surovinou | Vyrovnání indukční cívky a chladicí systém pro účinný přenos tepla. Výběr materiálu tyglíku a harmonogram výměny na základě vstupní suroviny a vlastností opotřebení. Napájecí kapacita a řídicí systém pro přesnou regulaci teploty. |
Atomizační komora | Výběr žáruvzdorného obložení na základě provozní teploty a procesních podmínek | Možnost proplachování inertním plynem pro minimalizaci oxidace. Návrh kalicího systému pro rychlé tuhnutí kovových kapek. Sběrný systém pro účinné zachycení kovového prášku. Odvzdušnění při výbuchu ke zmírnění nárůstu tlaku při případném výbuchu prachu. |
Trysky | ASME MFC-7M Měření průtoku tekutin pomocí Venturiho trubic | Pravidelná kontrola a výměna trysek pro udržení stálé distribuce velikosti částic. Seřízení a umístění trysek pro optimální účinnost rozprašování. |
Systém manipulace s práškem | NFPA 654 Standard pro prevenci výbuchů prachu ve výrobních, zpracovatelských a manipulačních zařízeních EN 14460 Ovzduší na pracovišti - Požadavky na manipulaci s hořlavým prachem | Inertizace sběrných a přenosových nádob na prášek inertním plynem, aby se zabránilo výbuchům. Systémy pro odvzdušnění a potlačení výbuchu pro další bezpečnostní opatření. Uzavřené přenosové systémy pro minimalizaci tvorby prachu a fugitivních emisí. Filtrace HEPA pro čištění vzduchu a ochranu zdraví pracovníků. |
Řídicí systémy | Programovací jazyky programovatelných automatů (PAC) podle normy IEC 61131 NFPA 850 Doporučené postupy požární ochrany pro elektrárny a související zařízení | Monitorování a řízení procesních parametrů v reálném čase (teplota, tlak, průtok). Alarmové systémy pro hlášení odchylek od provozních parametrů. Bezpečnostní blokády, které zabraňují poruchám zařízení a potenciálnímu nebezpečí. Redundantní řídicí systémy pro kritické operace k zajištění stability procesu. |
Dodavatelé kovových rozprašovačů
Klíčoví dodavatelé
Dodavatel | Umístění | produkty |
---|---|---|
PSI | Kanada | Plynové, vodní a odstředivé rozprašovače |
Vakuové technologie ALD | Německo | Rozprašovače plynu a vody |
Sino Steel Thermo | Čína | Rozprašovače vody a plynu |
VTI Vacuum Technologies | Spojené království | Špičkové rozprašovače plynu |
Stanovení cen
- Malé laboratorní jednotky začínají na $100,000
- Rozprašovače pro průmyslovou výrobu v rozsahu od $500 000 do $2 000 000.
- Větší systémy na míru mohou stát až $4 000 000.
- Další náklady na pomocné prostředky, instalaci, spotřební materiál
Cena zařízení pro atomizaci kovů:
Faktor | Popis | Dopad na cenu |
---|---|---|
Typ atomizace | Existují dva hlavní typy atomizace kovů: atomizace plynem a atomizace vodou. Plynová atomizace využívá inertní plyn, obvykle argon, k rozbití roztaveného kovu na jemné částice. Vodní atomizace využívá ke stejnému výsledku vysokotlaký vodní paprsek. | Rozprašování plynu je obecně dražší než rozprašování vody. Je to proto, že zařízení pro rozprašování plynu je složitější a vyžaduje vyšší provozní náklady. Plynová atomizace však může vytvářet jemnější a sféričtější částice prášku, které jsou pro některé aplikace žádoucí. |
Rozprašování kovu | Cena zařízení pro atomizaci kovů se může lišit také v závislosti na typu atomizovaného kovu. Reaktivní kovy, jako je titan a zirkon, se atomizují obtížněji než nereaktivní kovy, jako je železo a měď. Reaktivní kovy totiž mohou reagovat s atomizačním plynem nebo vodou, což může vést k problémům s kvalitou prášku a korozí zařízení. | Rozprašování reaktivních kovů obvykle vyžaduje specializovanější zařízení a vyšší provozní náklady. To může výrazně zvýšit cenu zařízení. |
Výrobní kapacita | Zařízení pro atomizaci kovů jsou k dispozici v širokém rozsahu výrobních kapacit, od malých dávkových systémů, které mohou produkovat několik kilogramů prášku za hodinu, až po velké systémy, které mohou produkovat několik tun prášku za hodinu. | Cena zařízení pro rozprašování kovů roste s výrobní kapacitou. Větší systémy jsou složitější a vyžadují dražší komponenty. |
Požadované vlastnosti prášku | Požadované vlastnosti kovového prášku ovlivňují také cenu rozprašovacího zařízení. Pokud je například požadován velmi jemný prášek, bude zapotřebí sofistikovanější rozprašovací systém, který bude dražší. | Pokud musí prášek splňovat přísné specifikace týkající se velikosti částic, morfologie nebo jiných vlastností, bude to pravděpodobně vyžadovat další zařízení nebo procesní kroky, což může zvýšit náklady. |
Úroveň automatizace | Zařízení na rozprašování kovů může být ruční, poloautomatické nebo plně automatizované. Plně automatizované systémy jsou nejdražší, ale mohou také nabídnout nejvyšší úroveň kontroly a konzistence procesu. | Vyšší úroveň automatizace obvykle znamená vyšší cenu. Ta však může být kompenzována zvýšenou produktivitou a snížením nákladů na pracovní sílu. |
Výrobce | Cena zařízení pro rozprašování kovů se může lišit v závislosti na výrobci. Někteří výrobci se specializují na špičková zařízení pro náročné aplikace, zatímco jiní nabízejí základnější zařízení pro méně kritické aplikace. | Známé značky s pověstí kvality a spolehlivosti mohou mít vyšší cenu. |
Výběr dodavatele rozprašovače
- Pověst a úroveň zkušeností
- Přizpůsobení a možnost výběru velikosti
- Výrobní kapacita a dodací lhůty
- Rozpočtová omezení
- Umístění a servisní podpora
- Požadavky na specifikaci prášku
- Nabídka pomocného vybavení
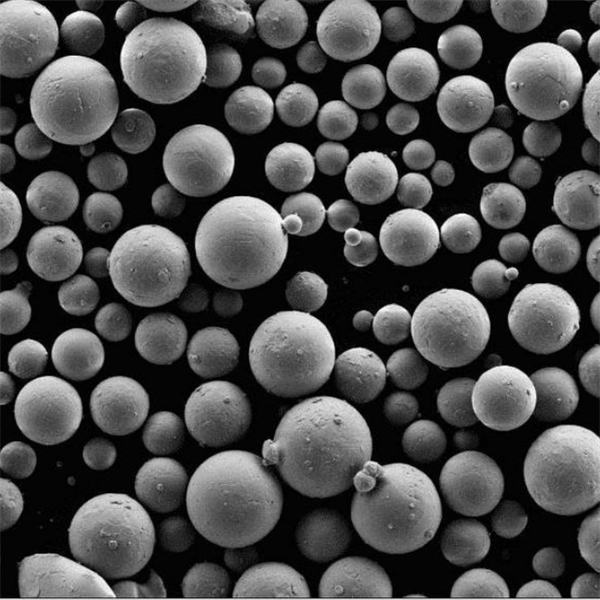
Provoz kovového rozprašovače
Typický proces atomizace
Krok | Aktivita |
---|---|
1 | Plnění indukční pece kovem určeným k rozprašování |
2 | Úplné roztavení kovu a dosažení teploty přehřátí. |
3 | Spuštění průtoku inertního plynu v rozprašovači při požadovaném tlaku |
4 | Otevření indukční pece a nalití roztaveného kovu do pánve / kelímku. |
5 | Nechte kov proudit do rozprašovače, aby se rozpadl na prášek. |
6 | Prášek unášený plynem do cyklonových odlučovačů ke sběru |
7 | Prosévání prášku pro odstranění velkých částic a jemných částic |
8 | Po vychladnutí zabalte hotový prášek do nádob |
Kritické parametry procesu
- Teplota přehřátí kovu
- Průtok roztaveného kovu do rozprašovače
- Průtok a tlak plynu/vody
- Konfigurace lití a množství kovové náplně
- Konstrukce a geometrie trysek
- Sběr a prosévání
Aspekty údržby
- Pravidelně kontrolujte a vyměňujte opotřebované trysky, ventily a vložky.
- Zkontrolujte plynové potrubí, vodní trysky, zda nejsou ucpané a neovlivňují průtok.
- Monitorování pohonu a ložisek odstředivého rozprašovače
- Čisté usazování prášku uvnitř potrubí a nádob
- Údržba indukční pece, teplotních čidel atd.
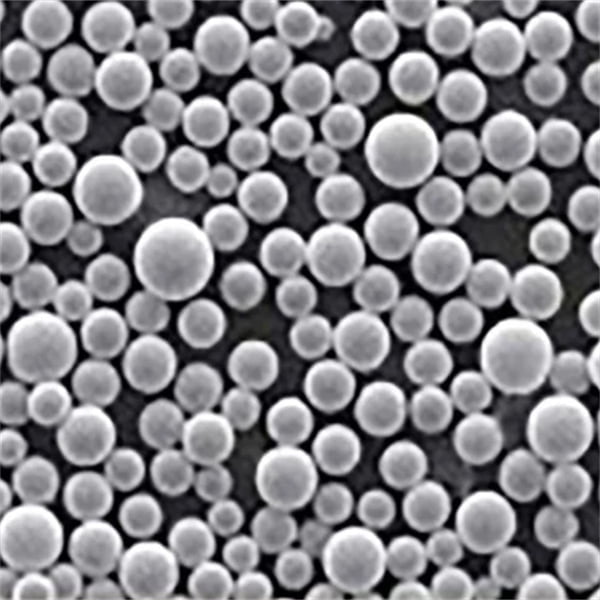
Výhody a omezení
Výhoda | Popis | Omezení | Popis |
---|---|---|---|
Přesné vlastnosti prášku | Zařízení pro atomizaci kovů vyniká při výrobě prášků s přísně kontrolovanou distribucí velikosti částic a morfologií. To umožňuje vytvářet prášky speciálně vhodné pro techniky aditivní výroby (AM), jako je selektivní laserové tavení (SLM) nebo tavení elektronovým svazkem (EBM). Přesná kontrola sférického tvaru a úzké rozmezí velikosti se promítá do optimálních tokových vlastností pro podávání do strojů AM, což vede ke konzistentní tvorbě vrstev a lepší kvalitě finálních výrobků. | Vysoké investiční a provozní náklady | Zřízení a provoz zařízení na rozprašování kovů vyžaduje značné počáteční kapitálové výdaje. Systémy jsou složité, vyžadují specializovanou infrastrukturu, kvalifikovaný personál pro obsluhu a údržbu a průběžné náklady na spotřební materiál, jako jsou inertní plyny a náhradní díly. |
Vysoké výrobní rychlosti a škálovatelnost | Moderní rozprašovací zařízení umožňuje nepřetržitý a automatizovaný provoz, což umožňuje vysokou výtěžnost výroby prášku. To má zásadní význam pro aplikace AM v průmyslovém měřítku, kde je zapotřebí velkých objemů materiálu. Modulární konstrukce mnoha systémů navíc umožňuje škálovatelnost, což znamená, že výrobní kapacitu lze zvýšit přidáním dalších jednotek podle rostoucí poptávky. | Omezená kompatibilita se surovinami | Zatímco atomizace kovů zvládá širokou škálu slitin, některé materiály s vysokým tlakem par nebo reaktivitou mohou představovat problém. Proces atomizace může přinést nečistoty nebo změnit chemické složení prášku, což může mít vliv na výkonnost konečného výrobku. |
Široká použitelnost | Zařízení pro atomizaci kovů je všestranná technologie, která dokáže zpracovávat širokou škálu kovů a slitin. Patří sem materiály běžně používané v AM, jako je titan, hliník, nikl a kobaltové slitiny, i exotičtější možnosti, jako jsou žáruvzdorné kovy a vysoce výkonné slitiny. | Úvahy o životním prostředí | Při procesu rozprašování mohou v závislosti na zvolené metodě vznikat odpadní produkty a emise. Například při atomizaci vodou může vznikat odpadní voda obsahující oxidy kovů. Rozprašování inertním plynem má menší dopad na životní prostředí, ale stále vyžaduje zodpovědné nakládání s výfukovými plyny. |
Vysoká čistota prášku | Oblíbená technika atomizace inertním plynem využívá prostředí inertního plynu, aby se minimalizovala kontaminace během procesu atomizace. Výsledkem je vysoká čistota prášku, která je nezbytná pro aplikace, kde jsou vlastnosti materiálu kritické. | Složitost procesu | Rozprašování kovů zahrnuje množství parametrů, které je třeba přesně řídit, aby bylo dosaženo požadovaných vlastností prášku. Faktory jako teplota taveniny, atomizační tlak a rychlost chlazení významně ovlivňují konečné vlastnosti prášku. Optimalizace těchto parametrů vyžaduje odborné znalosti a průběžné sledování procesu, aby byla zajištěna stálá kvalita. |
Jak vybrat kovový rozprašovač
Faktor | Úvaha | Důležitost | Podrobnosti |
---|---|---|---|
Kompatibilita s kovy | Materiál, který chcete rozprašovat | Kritické | Různé techniky atomizace vynikají u specifických kovů. Plynová atomizace je ideální pro reaktivní kovy, jako je titan a hliník, zatímco vodní atomizace funguje dobře pro méně reaktivní kovy, jako je železo a měď. |
Velikost a distribuce částic | Požadovaná velikost a konzistence kovového prášku | Vysoká důležitost | Velikost částic přímo ovlivňuje vlastnosti konečného produktu. Jemnější prášek vytváří hladší povrchy při 3D tisku, zatímco hrubší prášek může být vhodný pro vstřikování kovů. Rovnoměrné rozložení částic zajišťuje konzistentní vlastnosti materiálu v celém loži prášku. |
Objem výroby | Předpokládané množství potřebného kovového prášku | Mírný význam | Zvažte kapacitu rozprašovače, aby vyhovoval vašim výrobním potřebám. Velkoobjemový plynový atomizátor by mohl být pro malou prototypovou výrobu příliš náročný, zatímco nízkoobjemový vodní atomizátor by měl problém udržet krok s masovou výrobou. |
Provozní náklady | Spotřeba energie, nároky na údržbu | Mírný význam | Plynová atomizace má obecně vyšší počáteční náklady, ale nižší provozní náklady díky energetické účinnosti. Vodní atomizace má často nižší počáteční náklady, ale vyšší provozní náklady kvůli spotřebě vody a možným problémům s korozí. |
Bezpečnost | Rizika spojená s procesem atomizace | Kritické | Plynová i vodní atomizace zahrnuje roztavený kov a prostředí pod tlakem. Plynová atomizace představuje riziko výbuchu kvůli použití inertních plynů. Při atomizaci vodou může vznikat hořlavý plynný vodík. Upřednostněte bezpečnostní prvky a dodržujte správné bezpečnostní protokoly. |
Úroveň automatizace | Požadovaný stupeň automatizace procesu atomizace | Liší se podle uživatele | Vysoce automatizovaný systém minimalizuje lidské zásahy a snižuje počet chyb, ale je spojen s vyššími náklady. Manuální systém nabízí lepší kontrolu, ale vyžaduje více zkušeností obsluhy. |
Budoucí rozšiřitelnost | Potenciální potřeba manipulace s různými kovy nebo objemy | Zvažte, zda je to nutné | Pokud předpokládáte, že budete v budoucnu pracovat s různými kovy nebo zvyšovat výrobu, vyberte si atomizér, který bude flexibilní a bude se těmto změnám přizpůsobovat. |
Pověst výrobce | Záznamy o dodavateli rozprašovače | Důležité | Zjistěte si, jaké má výrobce zkušenosti, zákaznickou podporu a záruční podmínky. Vyberte si renomovanou společnost s prokazatelnými zkušenostmi v oblasti technologie rozprašování kovů. |
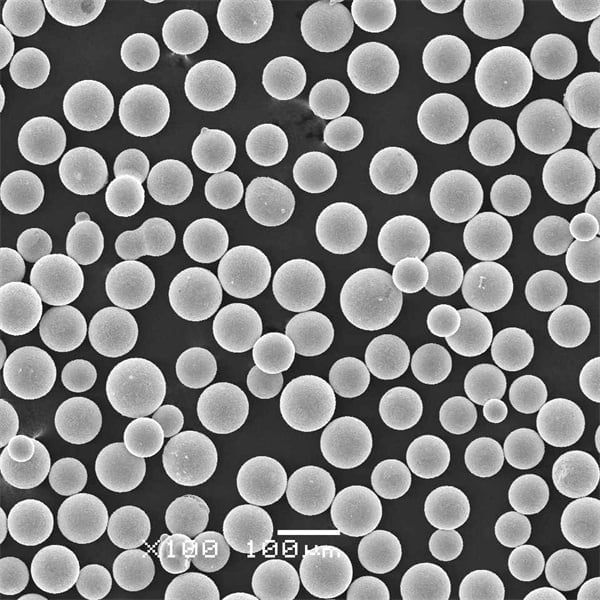
Nejčastější dotazy
Otázka: Jaký je typický rozsah velikostí rozprašovaného kovového prášku?
Odpověď: Rozsah velikosti částic u většiny rozprašovačů je přibližně 10 mikronů až 250 mikronů. Plynové rozprašovače mohou dosáhnout jemnějšího prášku do 10 mikronů, zatímco vodní rozprašovače vytvářejí hrubší prášek nad 100 mikronů.
Otázka: Jaké kovy lze rozprašovat do formy prášku?
Odpověď: Mezi běžné atomizované kovy patří hliník, měď, železo, nikl, kobalt, titan, tantal a nerezová ocel. Atomizovat lze dokonce i slitiny a reaktivní kovy, jako je hořčík.
Otázka: Jak kulovité jsou rozprašované prášky?
Odpověď: Rozprašované prášky mají vysoce kulovitou morfologii, protože kapičky za letu rychle tuhnou. Dosahuje se sféricity 0,9 až 1. Plynová atomizace vytváří sféričtější prášek.
Otázka: Jaké je hlavní použití atomizovaného kovového prášku?
Odpověď: Primární použití je v práškové metalurgii pro lisování a spékání součástí. Jemné prášky jsou také ideální pro aditivní výrobu kovů pomocí tavení v práškovém loži nebo usměrněného energetického nanášení.
Otázka: Jak se řídí distribuce velikosti prášku při rozprašování?
O: Konstrukce trysky, průtok roztaveného kovu, tlak plynu a konfigurace rozprašování určují distribuci velikosti částic. Vícestupňové prosévání po atomizaci pomáhá zúžit distribuci.
Otázka: Vyžaduje atomizace kovů speciální dovednosti?
Odpověď: Přestože se jedná o automatizovaný proces, k optimalizaci a správnému řízení rozprašovače pro kvalitní výrobu kovového prášku jsou zapotřebí znalosti v oblastech, jako je metalurgie, tepelné stříkání a manipulace s práškem.
Otázka: Co určuje rychlost výroby rozprašovače?
Odpověď: Rychlost výroby určuje průtok kovu, tlak plynu a kapacita rozprašovače. Průmyslové rozprašovače mohou vyrábět 100 kg prášku za hodinu, zatímco laboratorní rozprašovače mohou vyrábět pouze několik kg za hodinu.
Otázka: Jak určit správnou velikost a typ rozprašovače?
Odpověď: Klíčovými faktory jsou požadované množství prášku, rozpočet, podpora stávající infrastruktury a požadované vlastnosti prášku. Ty pomáhají při výběru mezi plynovým, vodním nebo odstředivým typem v potřebné kapacitě.
Otázka: Vznikají při atomizaci kovů nějaké vedlejší produkty?
Odpověď: Pevného odpadu není mnoho, ale je třeba čistit odpadní plyn/vodu. Je také nutné odsávání prachu z prostor pro manipulaci s práškem. Je nutná řádná likvidace použitých filtrů a spotřebního materiálu.
Závěr
Rozprašování kovů umožňuje přeměnit sypký kov na jemný sférický prášek pomocí plynu, vody nebo odstředivé energie. Díky přísné kontrole procesních parametrů lze vyrábět vysoce čisté prášky na míru ideální pro AM. Tento průvodce shrnul fungování, typy, aplikace, dodavatele a technické aspekty systémů atomizace kovů. Strukturované informace umožňují snadné porovnání jednotlivých možností pro výběr vhodného rozprašovače.
Sdílet na
MET3DP Technology Co., LTD je předním poskytovatelem řešení aditivní výroby se sídlem v Qingdao v Číně. Naše společnost se specializuje na zařízení pro 3D tisk a vysoce výkonné kovové prášky pro průmyslové aplikace.
Dotaz k získání nejlepší ceny a přizpůsobeného řešení pro vaše podnikání!
Související články
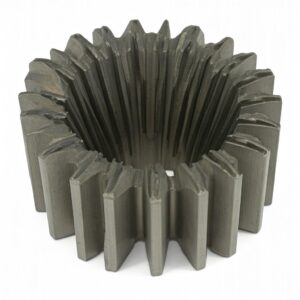
Vysoce výkonné segmenty lopatek trysek: Revoluce v účinnosti turbín díky 3D tisku z kovu
Přečtěte si více "O Met3DP
Nedávná aktualizace
Náš produkt
KONTAKTUJTE NÁS
Nějaké otázky? Pošlete nám zprávu hned teď! Po obdržení vaší zprávy obsloužíme vaši žádost s celým týmem.
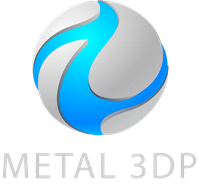
Kovové prášky pro 3D tisk a aditivní výrobu