3D tištěný kovový prášek vhodný pro technologii MIM
Obsah
Představte si, že vyrábíte složité, vysoce přesné kovové součásti se složitými geometriemi – to vše díky revoluční technice 3D tisku. To je kouzlo Metal Injection Molding (MIM) a tajná ingredience? Specializované kovové prášky, které vdechují život těmto miniaturním zázrakům. Připoutejte se, protože se ponoříme hluboko do světa kovových prášků kompatibilních s MIM, prozkoumáme jejich vlastnosti, oblíbené možnosti a faktory, které je činí takovými, jakými jsou.
charakteristika 3D tištěného kovového prášku vhodného pro MIM
- Velikost jemných částic: Představte si pláž přetékající oblázky versus pláž posypanou jemným pískem. Podobně se MIM daří na kovových prášcích s malou velikostí částic, typicky v rozmezí 5 až 20 mikronů. To umožňuje výjimečný tok během vstřikování, což zajišťuje, že složité detaily jsou v konečném dílu bezchybně replikovány.
- Vysoká sféricita: Představte si dokonale kulaté kuličky versus zubaté kameny. Sférické částice v kovových prášcích se mohou pochlubit vynikající hustotou balení, což vede k rovnoměrnější struktuře a vylepšeným mechanickým vlastnostem ve finálním produktu.
- Vynikající tekutost: Představte si nalévání mouky versus hrubé ovesné vločky. Prášky MIM potřebují výjimečnou tekutost, aby se během vstřikování pohybovaly ve složitých kanálech dutiny formy. To se promítá do hladkého procesu lisování a minimalizuje riziko vad.
- Nízký obsah kyslíku: Kyslík může být na večírku v MIM světě vetřelcem. Nadměrné hladiny kyslíku brání slinování, což je zásadní krok, kdy se kovové částice spojují, což ohrožuje pevnost a hustotu konečné součásti.
Zde je praktická tabulka shrnující klíčové vlastnosti kovových prášků připravených pro MIM:
Charakteristický | Důležitost |
---|---|
Jemná velikost částic (5-20 mikronů) | Umožňuje složité detaily a hladký tok |
Vysoká sféricita | Zlepšuje hustotu balení a mechanické vlastnosti |
Vynikající tekutost | Zajišťuje hladké vstřikování a minimalizuje vady |
Nízký obsah kyslíku | Podporuje účinné slinování a optimální pevnost |
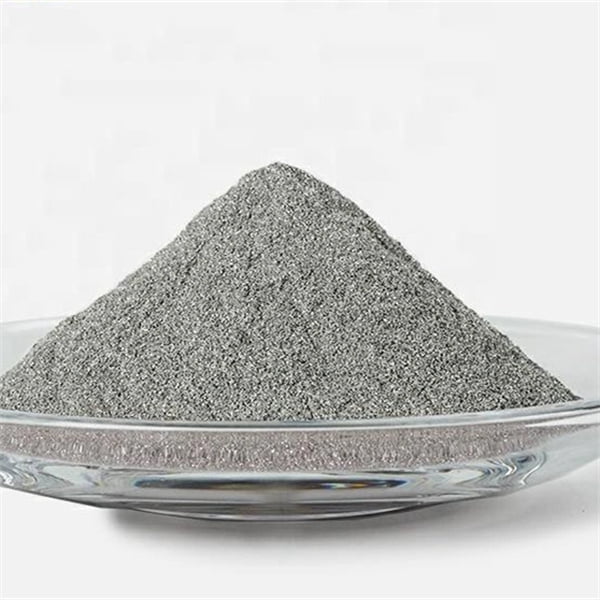
Běžně používané MIM Technologie 3D tisk kovových prášků
Nyní, když rozumíme ideálním vlastnostem, pojďme prozkoumat některé z nejoblíbenějších kovových prášků používaných v technologii MIM:
1. Nerezová ocel 316L:
- Austenitická nerezová ocel, známá svou vynikající odolností proti korozi, díky čemuž je šampionem v aplikacích vystavených drsným prostředím, jako jsou námořní komponenty, lékařské implantáty a zařízení pro chemické zpracování.
- Ve srovnání se svým bratrancem, nerezovou ocelí 17-4PH, nabízí 316L vynikající odolnost proti korozi, ale může být o něco slabší, pokud jde o hrubou pevnost.
2. 17-4PH Nerezová ocel:
- Tato srážkově vytvrzovaná nerezová ocel se může pochlubit výjimečnou pevností a tvrdostí, ideální pro díly vyžadující vysokou odolnost proti opotřebení, jako jsou ozubená kola, vačky a spojovací prvky.
- Ve srovnání s 316L vyniká 17-4PH pevností, ale nemusí být tak vhodná pro vysoce korozivní prostředí. Techniky následného zpracování však mohou do určité míry zvýšit její odolnost proti korozi.
3. Nízkolegovaná ocel:
- Nákladově efektivní možnost pro nekritické aplikace, kde vysoká pevnost není prvořadá.
- Ve srovnání s možnostmi z nerezové oceli může nízkolegovaná ocel vykazovat nižší odolnost proti korozi, takže je méně vhodná pro náročné prostředí. Vyniká však cenovou dostupností, což z ní činí oblíbenou volbu pro velkoobjemovou výrobu jednoduchých komponent.
4. Niklové slitiny:
- Niklové slitiny, které nabízejí výjimečnou pevnost, odolnost vůči vysokým teplotám a vynikající odolnost proti korozi vůči agresivním chemikáliím, jsou tou správnou volbou pro náročné aplikace v leteckém, ropném a plynárenském a chemickém průmyslu.
- Niklové slitiny se sice mohou pochlubit vynikajícím výkonem, ale ve srovnání s jinými možnostmi jsou za prémiovou cenu.
5. Nástrojová ocel:
- Nástrojová ocel, navržená pro výjimečnou odolnost proti opotřebení a rozměrovou stabilitu, se stává hrdinou v aplikacích, jako jsou formy, matrice a řezné nástroje.
- Ve srovnání s jinými možnostmi může nástrojová ocel vyžadovat specifické techniky následného zpracování, aby dosáhla požadovaných vlastností, což zvyšuje složitost výroby.
6. Slitiny mědi:
- Měď, známá svou vynikající tepelnou a elektrickou vodivostí, nachází své uplatnění v aplikacích vyžadujících účinný odvod tepla a elektrické vedení, jako jsou chladiče a elektrické konektory.
- Čistá měď však nemusí mít mechanickou pevnost potřebnou pro určité aplikace. Slitina mědi s prvky, jako je cín nebo chrom, může zvýšit její pevnost při zachování výhod vodivosti.
7. Slitiny titanu:
- Tyto lehké, ale neuvěřitelně pevné slitiny jsou superhvězdami v leteckých a biomedicínských aplikacích, kde je prvořadá redukce hmotnosti a biokompatibilita.
- Slitiny titanu sice nabízejí výjimečný výkon, ale mají vysokou cenovku kvůli složitému výrobnímu procesu a vysokým nákladům na suroviny.
8. Kovar:
- Slitina s řízenou roztažností známá svou schopností odpovídat koeficientu tepelné roztažnosti skla, což z ní činí dokonalého partnera pro utěsnění skla ke kovovým komponentům v elektronice a vědeckých přístrojích.
- Ve srovnání s jinými možnostmi může Kovar vykazovat nižší mechanickou pevnost, takže je nejvhodnější pro aplikace, kde není prvořadá strukturální integrita.
9. Inconel:
- Rodina super slitin známých svou výjimečnou pevností při vysokých teplotách, odolností proti oxidaci a odolností proti tečení. Díky těmto vlastnostem je Inconel ideální pro komponenty horké části v proudových motorech, plynových turbínách a dalších vysokoteplotních aplikacích.
- Podobně jako niklové slitiny má Inconel prémiovou cenu kvůli svému složitému složení a náročnému výrobnímu procesu.
10. Karbid wolframu:
- Tento neuvěřitelně tvrdý a otěruvzdorný materiál nachází své uplatnění v aplikacích vyžadujících výjimečnou odolnost proti otěru, jako jsou řezné nástroje, opěrné desky a trysky.
- Karbid wolframu však může být křehký a náchylný k odštípnutí za určitých podmínek. Pečlivý návrh a výběr jsou zásadní pro úspěšnou implementaci.
Zde je tabulka shrnující tyto běžně používané kovové prášky MIM:
Kovový prášek | Vlastnosti | Typické aplikace |
---|---|---|
Nerezová ocel 316L | Výborná odolnost proti korozi, dobrá tvarovatelnost | Námořní komponenty, lékařské implantáty, zařízení pro chemické zpracování |
Nerezová ocel 17-4PH | Vysoká pevnost, tvrdost a odolnost proti opotřebení | Ozubená kola, vačky, spojovací prvky |
Nízkolegovaná ocel | Nákladově efektivní, dobré pro nekritické aplikace | Jednoduché komponenty, velkoobjemová výroba |
Slitiny niklu | Výjimečná pevnost, odolnost vůči vysokým teplotám, vynikající odolnost proti korozi | Letecký průmysl, ropa a plyn, chemické zpracování |
Nástrojová ocel | Výjimečná odolnost proti opotřebení, rozměrová stabilita | Formy, zápustky, řezné nástroje |
Slitiny mědi | Vynikající tepelná a elektrická vodivost | Chladiče, elektrické konektory |
Titanové slitiny | Lehký, vysoce pevný, biokompatibilní | Letecké, biomedicínské aplikace |
Kovar | Řízený koeficient tepelné roztažnosti | Těsnění skla ke kovovým komponentům |
Inconel | Pevnost při vysoké teplotě, odolnost proti oxidaci a tečení | proudové motory, plynové turbíny |
Karbid wolframu | Výjimečná tvrdost, odolnost proti opotřebení | Řezné nástroje, opěrné desky, trysky |
Další úvahy při výběru MIM Kovové prášky:
Kromě základních vlastností ovlivňuje výběr kovových prášků MIM několik dalších faktorů:
- Dostupnost: Některé exotické kovové prášky mohou mít omezenou dostupnost nebo delší dodací lhůty, což má dopad na plány výroby.
- Náklady: Ceny se mohou výrazně lišit v závislosti na materiálu, složitosti výroby a poptávce na trhu.
- Environmentální předpisy: Na určité prvky v kovových prášcích se mohou vztahovat přísnější předpisy týkající se likvidace nebo manipulace.
Specifikace, velikosti a třídy
Pojďme se hlouběji ponořit a prozkoumat některé technické specifikace kovových prášků MIM:
Charakteristický | Popis | Příklad |
---|---|---|
Distribuce velikosti částic | Rozsah velikostí částic v prášku | Může se pohybovat od 5-20 mikronů, s úzkým rozdělením pro optimální tok |
Zdánlivá hustota | Hmotnost prášku na jednotku objemu v jeho sypkém, nestlačeném stavu | Obvykle vyjádřeno v g/cm³ |
Klepněte na položku Hustota | Hustota prášku po standardizované rutině klepání | Často vyšší než zdánlivá hustota díky vylepšenému balení |
Průtok | Rychlost, jakou prášek teče za specifických podmínek | Měřeno v sekundách/gram |
Obsah vlhkosti | Množství vlhkosti přítomné v prášku | V ideálním případě udržováno nízko, aby se zabránilo problémům se zpracováním |
Obsah kyslíku | Množství kyslíku přítomného v prášku | Nižší obsah kyslíku podporuje lepší slinování |
Tyto specifikace jsou obvykle dokumentovány dodavatelem prášku a mohou se lišit v závislosti na konkrétním materiálu a kvalitě. Kovové prášky MIM jsou navíc často dostupné v různých kvalitách, z nichž každá se stará o specifické požadavky na výkon.
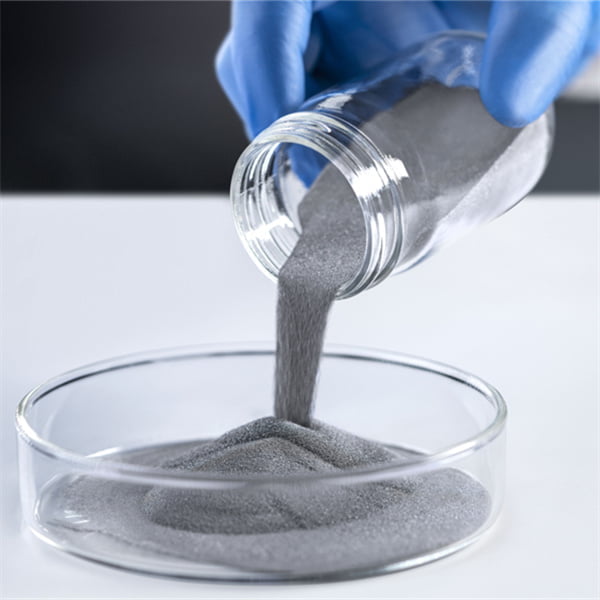
Prozkoumání stránek MIM Dodavatelé kovových prášků
Prostředí dodavatelů kovových prášků MIM je rozmanité a několik zavedených hráčů nabízí řadu materiálů a kvalit. Zde je pohled na některá významná jména:
- Höganäs AB: Přední globální výrobce kovových prášků, který nabízí široký výběr prášků připravených pro MIM napříč různými materiály.
- AMEX Additive Specializuje se na vysoce výkonné kovové prášky pro aditivní výrobu, včetně MIM.
- Carpenter Additive Powder Products: Dceřiná společnost Carpenter Technology Corporation, která poskytuje MIM prášky pro aplikace vyžadující vynikající mechanické vlastnosti.
- Sandvik Additive Manufacturing: Využívá odborné znalosti společnosti Sandvik v oblasti metalurgie k nabídce MIM prášků s výjimečnou kvalitou a konzistencí.
Zvážení cen: Odhalení faktoru nákladů
Cena MIM kovových prášků se může výrazně lišit v závislosti na několika faktorech:
- Materiál: Exotické materiály jako titan nebo Inconel bývají dražší než běžné varianty jako nerezová ocel.
- Vlastnosti prášku: Jemná velikost částic, vysoká sféricita a úzké rozložení velikosti částic si často vyžadují prémii kvůli složitosti výroby takových prášků.
- Objem: Hromadné nákupy obvykle těží z diskontních cen ve srovnání s menšími objednávkami.
- Dodavatel: Různí dodavatelé mohou mít odlišné cenové struktury založené na jejich výrobních nákladech a pozici na trhu.
I když specifické informace o cenách nemusí být snadno dostupné kvůli kolísajícím tržním podmínkám a jednáním s jednotlivými dodavateli, je bezpečné říci, že MIM kovové prášky se mohou pohybovat od několika dolarů za kilogram pro běžné materiály, jako je nízkolegovaná ocel, až po stovky dolarů za kilogram pro vysoce výkonné varianty, jako je Inconel nebo slitiny titanu.
Výhody a omezení MIM kovových prášků
MIM kovové prášky nabízejí jedinečnou kombinaci výhod a omezení. Pojďme se ponořit do obou stran mince:
Výhody MIM kovových prášků:
- Svoboda designu: MIM umožňuje vytváření složitých geometrií se složitými prvky, kterých nelze dosáhnout tradičními obráběcími technikami.
- Vysoká přesnost: MIM vyrábí součásti téměř čistého tvaru s úzkými rozměrovými tolerancemi, což minimalizuje potřebu rozsáhlého následného zpracování.
- Hromadná výroba: MIM usnadňuje nákladově efektivní sériovou výrobu malých, složitých kovových dílů.
- Všestrannost materiálu: K dispozici je široká škála kovových prášků, které uspokojí různé potřeby aplikací.
- Snížení odpadu: MIM využívá proces téměř čistého tvaru, který minimalizuje odpad materiálu ve srovnání s tradičními obráběcími metodami.
Omezení MIM kovových prášků:
- Omezení velikosti dílů: MIM je typicky vhodný pro menší součásti kvůli omezením v plnicích schopnostech formy.
- Vlastnosti materiálu: Díly vyrobené technologií MIM nemusí vždy dosahovat stejných mechanických vlastností jako díly vytvořené tradičními metodami, jako je kování nebo obrábění, zejména u vysoce výkonných materiálů.
- Povrchová úprava: Díly MIM mohou vyžadovat další kroky následného zpracování k dosažení požadované povrchové úpravy.
- Úvahy o návrhu: Návrh pro MIM vyžaduje pečlivou pozornost geometrii dílu a velikosti prvků, aby byla zajištěna úspěšná výroba.
- Náklady: I když je nákladově efektivní pro sériovou výrobu, samotné MIM prášky mohou být drahé, zejména u exotických materiálů.
MIM Kovové prášky: Pohled do budoucnosti
Budoucnost MIM kovových prášků překypuje potenciálem. S pokrokem technologie můžeme očekávat, že uvidíme:
- Vývoj nových kovových prášků: Na obzoru jsou nové materiály se zlepšenými vlastnostmi speciálně navržené pro MIM aplikace.
- Vylepšené charakteristiky prášku: užší rozložení velikosti částic, zlepšená tekutost a nižší obsah kyslíku dále optimalizují proces MIM.
- Snížení nákladů: Pokroky ve výrobních technikách a zvýšené přijetí MIM by mohly vést k nákladově konkurenceschopnějším kovovým práškům.
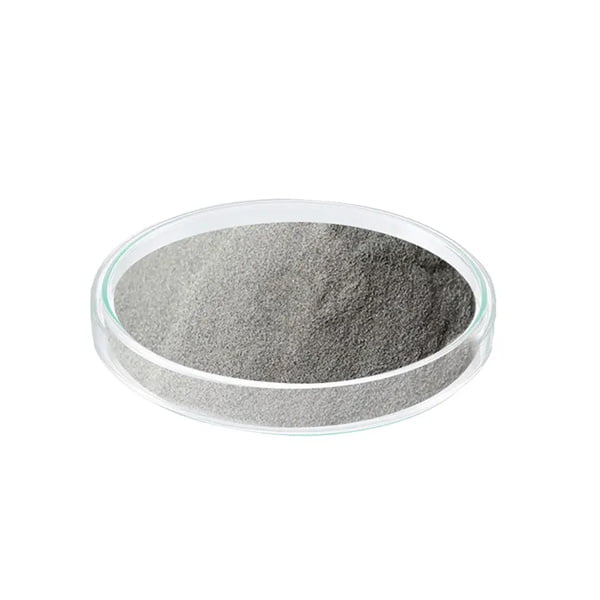
FAQ
Zde je několik často kladených otázek týkajících se MIM kovových prášků:
Otázka | Odpovědět |
---|---|
Jaké jsou výhody použití MIM kovových prášků oproti tradičním obráběcím metodám? | MIM nabízí svobodu designu, vysokou přesnost, schopnost sériové výroby a všestrannost materiálů, často s menším odpadem materiálu. |
Jaká jsou některá omezení MIM kovových prášků? | Omezení velikosti dílů, potenciálně nižší mechanické vlastnosti ve srovnání s některými tradičními metodami, úvahy o povrchové úpravě a omezení designu pro úspěšnou výrobu MIM. |
Jaké faktory ovlivňují výběr MIM kovového prášku? | Vlastnosti, dostupnost, náklady, environmentální předpisy a požadovaná aplikace jsou všechny klíčové faktory. |
Kolik stojí MIM kovové prášky? | Ceny se mohou výrazně lišit v závislosti na materiálu, charakteristikách prášku, objemu a dodavateli. |
Jaký je budoucí výhled pro MIM kovové prášky? | Budoucnost slibuje vývoj nových materiálů, vylepšené charakteristiky prášku a potenciálně nižší náklady. |
Pochopením složitosti MIM kovových prášků můžete využít jejich jedinečné schopnosti k vytváření inovativních a funkčních kovových součástí. S neustálým pokrokem v materiálové vědě a výrobních technikách je technologie MIM připravena hrát stále důležitější roli při utváření budoucnosti výroby kovů.
Sdílet na
MET3DP Technology Co., LTD je předním poskytovatelem řešení aditivní výroby se sídlem v Qingdao v Číně. Naše společnost se specializuje na zařízení pro 3D tisk a vysoce výkonné kovové prášky pro průmyslové aplikace.
Dotaz k získání nejlepší ceny a přizpůsobeného řešení pro vaše podnikání!
Související články
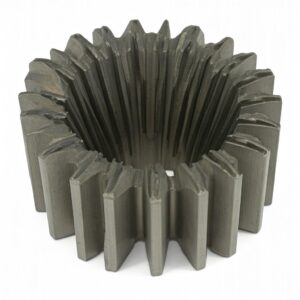
Vysoce výkonné segmenty lopatek trysek: Revoluce v účinnosti turbín díky 3D tisku z kovu
Přečtěte si více "O Met3DP
Nedávná aktualizace
Náš produkt
KONTAKTUJTE NÁS
Nějaké otázky? Pošlete nám zprávu hned teď! Po obdržení vaší zprávy obsloužíme vaši žádost s celým týmem.
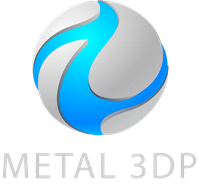
Kovové prášky pro 3D tisk a aditivní výrobu