Montážní držáky pro systémy pohonu elektrických vozidel: Využití 3D tisku kovů pro inovace v automobilovém průmyslu
Obsah
Revoluce v oblasti elektromobilů (EV) mění automobilový průmysl a vyžaduje inovativní přístupy k designu, výrobě a řízení dodavatelského řetězce. Ústředním prvkem této transformace jsou systémy pohonu - srdce každého elektromobilu - zahrnující baterie, elektromotory, výkonovou elektroniku a převodovky. Bezpečná montáž těchto kritických součástí při optimalizaci hmotnosti, výkonu a prostoru pro balení představuje značnou inženýrskou výzvu. Montážní držáky, zdánlivě jednoduché součásti, hrají klíčovou roli v konstrukční integritě, bezpečnosti a celkové účinnosti elektrických vozidel. Vzhledem k tomu, že výrobci automobilů a jejich dodavatelé Tier 1 posouvají hranice výkonu a dojezdu elektromobilů, tradiční výrobní metody pro tyto držáky, jako je odlévání nebo obrábění ze sochoru, jsou stále častěji zpochybňovány schopnostmi výroba aditiv kovů (AM), běžně známý jako kov 3D tisk. Tato technologie nabízí nebývalou konstrukční svobodu a umožňuje vytvářet vysoce optimalizované, lehké a složité držáky, jejichž výroba byla dříve nemožná nebo neúnosně drahá. Pro manažery nákupu, inženýry a konstruktéry v automobilovém průmyslu je pochopení potenciálu technologie AM pro výrobu držáků pohonných jednotek pro elektromobily zásadní pro udržení konkurenceschopnosti a podporu inovací. Tento článek se zabývá specifiky využití kovového 3D tisku pro montážní držáky hnacího ústrojí EV, zkoumá aplikace, výhody, výběr materiálů, konstrukční úvahy a způsoby, jak spolupracovat se správným poskytovatelem výrobních služeb B2B, jako je Met3dp, lídr v oblasti řešení aditivní výroby.
Úvod: Zásadní role hnacích jednotek v elektromobilech a změna výroby
Pohonné jednotky elektrických vozidel jsou sofistikované sestavy vysoce hodnotných komponentů. Na rozdíl od vozidel se spalovacím motorem (ICE) s jediným blokem motoru jsou elektromobily často vybaveny distribuovanými součástmi - bateriovými bloky rozprostírajícími se na podlaze vozidla, jedním nebo více elektromotory pohánějícími nápravy, měniči převádějícími stejnosměrný proud na střídavý a souvisejícími řídicími jednotkami. Každý z těchto prvků vyžaduje robustní montážní řešení nebo držáky:
- Bezpečné umístění součástí: Držáky pevně drží prvky hnacího ústrojí na určených místech v podvozku nebo pomocných rámech vozidla a zabraňují jejich pohybu během provozu, zrychlování, brzdění, zatáčení a případných nárazů.
- Správa zatížení a vibrací: Musí odolávat statickému zatížení (hmotnost součástí) a dynamickému zatížení (vibrace od vozovky a provozu hnacího ústrojí, reakce točivého momentu, setrvačné síly). Účinné tlumení vibrací má zásadní význam pro pohodlí cestujících a dlouhou životnost součástí.
- Zajištění strukturální integrity: Konzoly přispívají k celkové tuhosti a strukturální integritě vozidla tím, že přenášejí zatížení mezi komponenty hnacího ústrojí a karoserií vozidla.
- Usnadnění montáže a údržby: Dobře navržené držáky zjednodušují proces montáže na výrobní lince a umožňují snadnější přístup při servisu nebo výměně součástí.
- Optimalizace balení: V těsném prostředí moderního elektromobilu musí konzoly často odpovídat složitým tvarům a vejít se do minimálního dostupného prostoru.
- Příspěvek k tepelnému managementu: V některých případech mohou být držáky navrženy tak, aby pomáhaly odvádět teplo od součástí, jako jsou motory nebo výkonová elektronika.
Přechod na elektrifikaci přináší jedinečné výzvy pro konstrukci a výrobu držáků. Klíčovou z nich je odlehčení. Snížení hmotnosti vozidla má zásadní význam pro prodloužení dojezdu, zlepšení jízdní dynamiky a kompenzaci značné hmotnosti akumulátorů. Každý ušetřený gram přispívá k celkové efektivitě. Rychlé tempo vývoje elektromobilů navíc vyžaduje kratší konstrukční cykly a rychlejší tvorbu prototypů, což jsou oblasti, kde tradiční výrobní metody, často závislé na drahém nástrojovém vybavení (např. odlévací formy), mohou vytvářet úzká místa.
Dodavatelský řetězec B2B v automobilovém průmyslu se těmto požadavkům přizpůsobuje. Dodavatelé jsou vyhledáváni nejen pro nákladově efektivní výrobu, ale i pro svou schopnost nabídnout inovativní řešení, která řeší snížení hmotnosti, integraci složitostí a rychlost uvedení na trh. Zde vstupuje do hry aditivní výroba kovů. Procesy AM, zejména techniky laserové fúze v práškovém loži (L-PBF), jako je selektivní laserové tavení (SLM) nebo přímé laserové spékání kovů (DMLS), vytvářejí díly vrstvu po vrstvě přímo z 3D CAD dat pomocí vysoce výkonných laserů, které spojují jemné kovové prášky. Tento přístup eliminuje potřebu tradičního obrábění, uvolňuje složité geometrie a umožňuje výrobu vysoce optimalizovaných konstrukčních dílů. Společnosti, jako je Met3dp, se svými odbornými znalostmi v oblasti pokročilých kovových prášků a průmyslových 3D tiskových systémů, jsou klíčové pro to, aby výrobci a dodavatelé automobilů mohli plně využít potenciál AM pro kritické komponenty, jako jsou držáky hnacího ústrojí EV. Jejich zaměření na špičkový objem tisku, přesnost a spolehlivost z nich činí strategického partnera pro podniky, které se pohybují v oblasti přechodu na elektromobilitu a hledají pokročilá výrobní řešení.
K čemu se používají montážní držáky pro hnací ústrojí EV? Klíčové funkce a aplikace
Montážní držáky hnacího ústrojí elektrických vozidel plní různé funkce, které jsou přizpůsobeny konkrétní součásti, kterou podporují, a jejímu umístění v rámci architektury vozidla. Pochopení těchto aplikací poukazuje na všestrannost, kterou vyžaduje konstrukční i výrobní proces. Mezi klíčové aplikace v rámci ekosystému EV patří:
- Uchycení elektromotoru: Tyto držáky upevňují elektromotor(y) k podvozku nebo pomocnému rámu. Musí zvládnout značné reakční síly točivého momentu při zrychlování a rekuperačním brzdění, zvládat vibrace motoru, aby se nepřenášely do kabiny, a odolávat dynamickému zatížení způsobenému nerovnostmi vozovky. Konstrukce musí být často kompaktní a zároveň robustní a musí zahrnovat prvky pro vyrovnání a montáž. Technologie Metal AM umožňuje vytvářet topologicky optimalizované konstrukce, které umisťují materiál přesně tam, kde je to potřeba pro zvládnutí dráhy namáhání, a výrazně tak snižují hmotnost ve srovnání s tradičními odlitky nebo výrobními držáky.
- Držáky a podpěry baterií: Podepření těžkého akumulátoru vyžaduje četné držáky a konstrukční prvky. Tyto součásti mají zásadní význam pro bezpečnost při nárazu a zajišťují, že baterie zůstane během nárazu v bezpečí. Přispívají také k celkové torzní tuhosti podvozku. Konzoly mohou upevňovat přihrádku baterie ke karoserii vozidla, podpírat jednotlivé moduly uvnitř sady nebo montovat související součásti chladicího systému. Technologie AM umožňuje vytvářet složité tvary, které se přizpůsobí tvaru akumulátoru, a integrovat montážní body pro senzory nebo kabelové svazky, případně sloučit více dílů do jednoho.
- Pouzdra a držáky výkonové elektroniky: Měniče, konvertory (DC-DC) a palubní nabíječky (OBC) vyžadují bezpečnou montáž. Tyto držáky musí často vyhovovat složitým tvarům a poskytovat volný prostor pro vysokonapěťovou kabeláž a chladicí vedení. V některých případech může být samotný držák navržen s integrovanými chladicími kanály pomocí AM, což zlepšuje účinnost tepelného managementu - kritický faktor pro výkon a životnost výkonové elektroniky. V tomto případě je obzvláště výhodná konstrukční svoboda AM, která umožňuje optimalizovat proudění vzduchu nebo integrovat kapalinové chlazení přímo do montážní konstrukce.
- Uchycení převodovky a diferenciálu: U elektromobilů s redukčními převodovkami nebo diferenciály plní montážní konzoly podobné funkce jako držáky motoru, které řídí točivý moment, vibrace a zatížení. Zajišťují přesné vyrovnání motoru a součástí hnacího ústrojí. AM dokáže vyrobit tuhé a lehké držáky přizpůsobené specifické konstrukci převodovky a omezením spojeným s balením vozidla.
- Držáky pomocných komponent: Různé další komponenty související s pohonným ústrojím, jako jsou čerpadla pro chladicí systémy, vysokonapěťové propojovací skříňky nebo sestavy nabíjecích portů, rovněž vyžadují speciální držáky. Ačkoli jsou tyto díly potenciálně méně konstrukčně náročné než držáky motoru nebo baterie, může použití AM pro tyto díly stále přinášet výhody v podobě snížení hmotnosti, konsolidace dílů a rychlého opakování konstrukce, zejména ve fázích vývoje vozidla.
Význam pro odvětví:
Primárním průmyslovým odvětvím pro tyto komponenty je v drtivé většině Automobilový průmysl, konkrétně v rámci Elektrická vozidla (EV) segment. Patří sem:
- Osobní automobily (výrobci OEM a začínající výrobci)
- Elektrická užitková vozidla (dodávky, nákladní vozidla, autobusy)
- Výkonná elektrická vozidla a motoristický sport
- Elektrická terénní vozidla (stavebnictví, zemědělství)
- Speciální elektrická vozidla (např. autonomní kyvadlová doprava)
Klíčové funkční požadavky, které řeší AM:
- Konstrukční integrita & Nosnost: AM s vysokopevnostními hliníkovými slitinami, jako je A7075 nebo optimalizovaný AlSi10Mg, poskytuje pevnost srovnatelnou nebo vyšší než tradiční materiály.
- Tlumení vibrací: Složité geometrie a mřížkové struktury umožněné technologií AM mohou být navrženy tak, aby aktivně tlumily vibrace.
- Integrace tepelného managementu: Konformní chladicí kanály lze zabudovat přímo do držáků pro výkonovou elektroniku nebo motory.
- Konsolidace částí: AM umožňuje konstruktérům spojit více tradičně samostatných dílů (např. držák, chladič a montážní desku) do jediné komplexní součásti, čímž se snižuje doba montáže, hmotnost a potenciální místa poruchy. To je významná výhoda pro dodavatele automobilových držáků, kteří chtějí nabízet řešení s přidanou hodnotou.
- Složité geometrie a obaly: Technologie AM vyniká při výrobě organických tvarů, které se vejdou do stísněných prostorů a obepínají ostatní komponenty, což je v moderních elektromobilech zásadní.
Využitím 3D tisku kovů mohou výrobci a dodavatelé vyrábět držáky hnacího ústrojí elektromobilů, které jsou nejen funkční, ale také vysoce optimalizované pro jedinečné požadavky elektromobility.
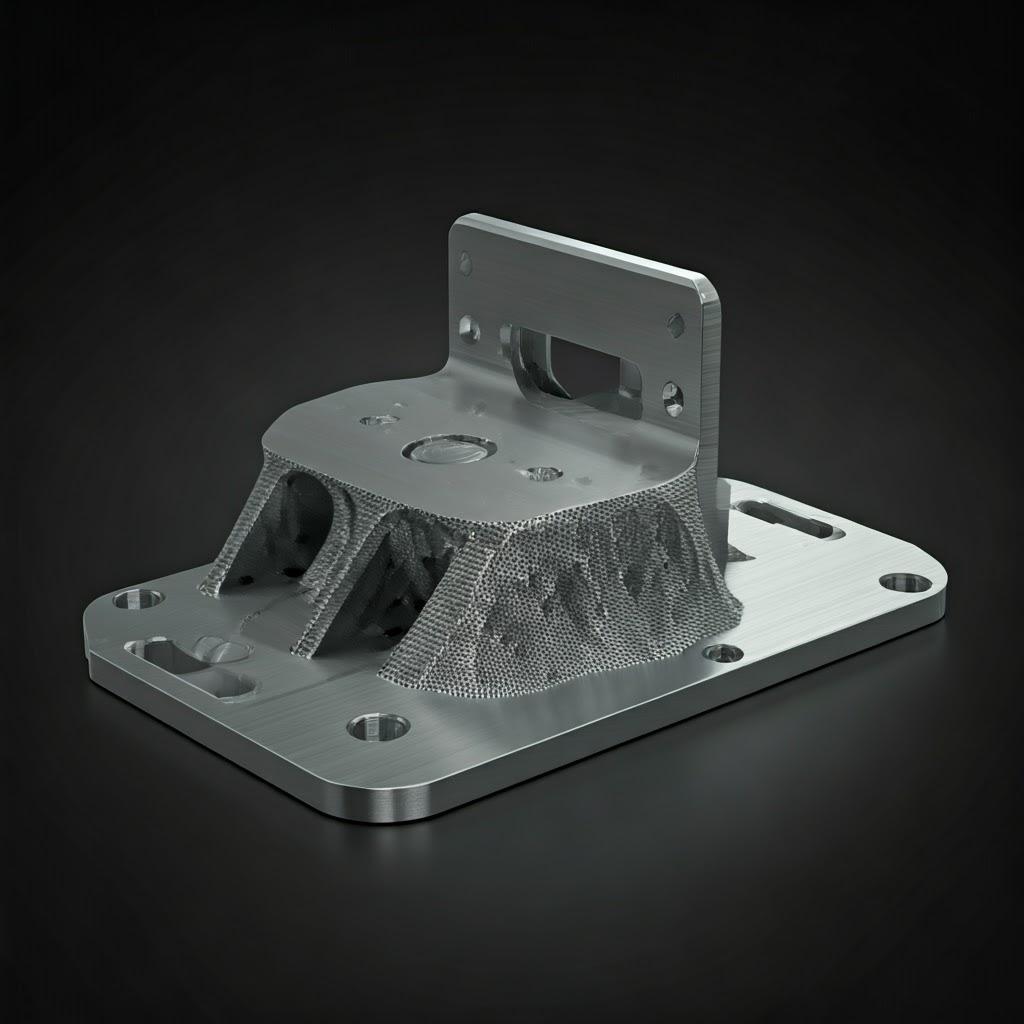
Proč používat 3D tisk z kovu pro držáky hnacího ústrojí elektromobilů? Výhody oproti tradiční výrobě
Zatímco tradiční výrobní metody, jako je odlévání (tlakové lití, odlévání do písku) a CNC obrábění ze sochorů, jsou již dlouho standardem pro výrobu automobilových držáků, aditivní výroba kovů nabízí přesvědčivé výhody, zejména pro výzvy a příležitosti, které představují elektromobily. Pro konstruktéry usilující o optimální výkon a manažery nákupu zaměřené na celkové náklady na vlastnictví a pružnost dodavatelského řetězce je pochopení těchto výhod klíčové.
Zde’je rozpis důvodů 3D tisk z kovu je transformační technologií pro držáky pohonných jednotek elektrických vozidel:
- Bezkonkurenční volnost designu & Komplexnost:
- Tradiční: Odlévání vyžaduje úhly tahu, rovnoměrnou tloušťku stěn a vyhýbá se podřezávání, což omezuje geometrickou složitost. Obrábění je subtraktivní, což ztěžuje nebo znemožňuje vytváření složitých vnitřních prvků a může vést k plýtvání.
- Metal AM: Vytváří díly vrstvu po vrstvě, což umožňuje vytvářet velmi složité organické tvary, vnitřní kanály (např. pro chlazení), tenké stěny a složité mřížkové struktury. To umožňuje optimalizace topologie, kde softwarové algoritmy odstraňují materiál z oblastí s nízkým namáháním, čímž vznikají díly dokonale přizpůsobené jejich dráze zatížení. Tato schopnost je ideální pro vytváření pevných a zároveň velmi lehkých konzol.
- Významný potenciál odlehčení:
- Tradiční: Snížení hmotnosti často zahrnuje použití lehčích materiálů (např. hliníku místo oceli) nebo složité vícestupňové obrábění, které může být nákladné. Konstrukce odlitků jsou často objemnější, než je nutné, kvůli omezením procesu.
- Metal AM: Optimalizace topologie a schopnost vytvářet vnitřní mřížkové struktury umožňují výrazné snížení hmotnosti (často o 20-60 % a více) ve srovnání s tradičně vyráběnými protějšky, aniž by byla snížena pevnost nebo tuhost. To se přímo promítá do zvýšení dojezdu elektromobilů a zlepšení dynamiky vozidla.
- Rychlá tvorba prototypů a zrychlená iterace:
- Tradiční: Vytváření prototypů odléváním vyžaduje nákladné a časově náročné nástroje (formy nebo vzory). Obrábění prototypů může být rychlejší, ale stále vyžaduje čas na programování a nastavení. Změny konstrukce vyžadují nové nástroje nebo přeprogramování.
- Metal AM: Prototypy lze vytisknout přímo z dat CAD během několika dní, bez použití nástrojů. To umožňuje inženýrům rychle otestovat několik iterací návrhu, ověřit výkon a zkrátit celkový cyklus vývoje vozidla, což je na rychle se vyvíjejícím trhu s elektromobily zásadní. Změny lze snadno provést úpravou souboru CAD.
- Konsolidace částí:
- Tradiční: Složité sestavy často vyžadují více jednotlivých držáků, spojovacích prvků a spojovacích postupů.
- Metal AM: Svoboda návrhu umožňuje konstruktérům sloučit více komponent do jediného integrovaného 3D tištěného dílu. Například montážní konzola může obsahovat prvky pro vedení kabelů, montáž senzorů nebo vedení kapalin, což snižuje počet dílů, dobu montáže, hmotnost a potenciální místa poruch. To nabízí významné výhody pro výrobní řešení B2B zaměřená na zefektivnění výroby.
- Efektivní využití materiálu a snížení množství odpadu:
- Tradiční: Obrábění je ze své podstaty neekonomické a často se při něm z masivního bloku odebírá značné množství materiálu. Při odlévání vznikají odpady v podobě vtoků, vtokových lišt a stoupacích lišt.
- Metal AM: Jedná se o aditivní proces, při kterém se používá pouze materiál potřebný k výrobě dílu a jeho podpěr. Přestože se používá určitý podpůrný materiál a vzniká odpadní prášek, je obecně materiálově mnohem úspornější než subtraktivní metody, zejména u složitých dílů. Nepoužitý prášek lze často recyklovat a znovu použít, což dále zlepšuje udržitelnost.
- Výroba na vyžádání a malosériová výroba:
- Tradiční: Odlévání je obvykle nákladově efektivní pouze při velkých objemech kvůli nákladům na nástroje. Obrábění se může vyplatit při nízkých objemech, ale u složitých dílů může být pomalé a nákladné.
- Metal AM: Eliminuje náklady na nástroje, takže je ekonomicky výhodné pro nízké až střední výrobní série, přizpůsobení, náhradní díly nebo aplikace ve výklenkových vozidlech. To podporuje agilní výrobní strategie a distribuované výrobní modely, které upřednostňují moderní dodavatelské řetězce B2B.
- Výroba bez nástrojů:
- Tradiční: Vyžaduje značné investice do forem, zápustek, přípravků a přípravků.
- Metal AM: Vyžaduje pouze 3D tiskárnu a digitální návrhové soubory, což snižuje kapitálové výdaje na nástroje a úložný prostor.
Srovnávací tabulka: Kovové AM vs. tradiční metody pro EV rovnátka
Vlastnosti | Aditivní výroba kovů (L-PBF) | Tradiční casting | Tradiční CNC obrábění |
---|---|---|---|
Složitost návrhu | Velmi vysoká (vnitřní kanály, mřížky) | Mírný (úhly průtahu, rovnoměrné stěny) | Vysoká (omezená přístupem k nástrojům) |
Odlehčení | Vynikající (optimalizace topologie) | Dobrý (výběr materiálu) | Mírná (subtraktivní limity) |
Rychlost prototypování | Velmi rychle (dny) | Pomalé (týdny/měsíce – výroba nástrojů) | Mírná (dny/týdny) |
Náklady na nástroje | Žádný | Vysoký | Nízká (Fixturing) / Žádná |
Konsolidace částí | Vynikající | Omezený | Omezený |
Materiálový odpad | Nízká (přídavné látky, recyklace prášku) | Středně těžké (vtoky, běhouny) | Vysoká (subtraktivní) |
Ideální objem | Prototypy, nízká až střední úroveň | Vysoký objem | Prototypy, nízká až střední úroveň |
Dodací lhůta (výroba) | Mírný | Dlouhé (nástroje) -> Rychlé (na díl) | Mírný |
Náklady (nízký objem) | Konkurenční | Velmi vysoká | Vysoký |
Náklady (velký objem) | Vyšší | Nejnižší | Středně vysoké až vysoké |
Export do archů
Ačkoli může mít metoda AM v případě velmi velkých objemů vyšší náklady na jeden díl ve srovnání se zavedenými metodami odlévání, její výhody v oblasti optimalizace designu, rychlosti uvádění nových návrhů na trh a schopnosti vyrábět složité a lehké konstrukce z ní činí stále strategičtější volbu pro náročné aplikace držáků hnacích ústrojí elektrických vozidel. Spolupráce se znalým poskytovatelem služeb, jako je Met3dp, zajišťuje přístup ke správné technologii a odborným znalostem, které umožňují tyto výhody využít.
Doporučené materiály pro 3D tištěné držáky pro elektromobily: AlSi10Mg & A7075 Deep Dive
Výběr správného materiálu je základem úspěchu každé 3D tištěné součásti, zejména u konstrukčně kritických dílů, jako jsou držáky hnacího ústrojí elektromobilů. Výběr do značné míry závisí na konkrétních požadavcích aplikace, včetně pevnosti, tuhosti, hmotnosti, provozní teploty, odolnosti a nákladů. U hliníkových držáků vyráběných metodou Laser Powder Bed Fusion (L-PBF) vynikají dvě slitiny: AlSi10Mg a vysokopevnostní slitiny řady 7000, jako je A7075 (často označovaná jako AA7075).
Met3dp, s využitím svých odborných znalostí a pokročilý systém výroby prášku využívající technologie plynové atomizace a PREP, zajišťuje dostupnost vysoce kvalitních sférických kovových prášků, které jsou klíčové pro spolehlivou aditivní výrobu. Jejich portfolio zahrnuje řadu slitin vhodných pro náročné průmyslové aplikace. Prozkoumejme’e doporučené hliníkové prášky pro držáky elektromobilů:
1. AlSi10Mg:
- Popis: AlSi10Mg je jednou z nejpoužívanějších hliníkových slitin v aditivní výrobě. Je to v podstatě slitina upravená pro procesy L-PBF. Obsahuje přibližně 9-11 % křemíku (Si) a 0,2-0,45 % hořčíku (Mg).
- Klíčové vlastnosti:
- Dobrý poměr pevnosti a hmotnosti: Nabízí dobré mechanické vlastnosti vhodné pro mnoho konstrukčních aplikací.
- Vynikající tisknutelnost: Relativně snadné zpracování pomocí L-PBF s dobře zavedenými parametry, které vede k hustým a spolehlivým dílům.
- Dobré tepelné vlastnosti: Vhodné pro aplikace vyžadující mírný odvod tepla.
- Dobrá odolnost proti korozi: Dobře funguje v typických automobilových prostředích.
- Svařitelnost: V případě potřeby lze svařovat, ačkoli cílem AM je často eliminovat tyto sekundární procesy prostřednictvím konsolidace dílů.
- Tepelně zpracovatelné: Mechanické vlastnosti lze výrazně zlepšit tepelným zpracováním, například T6 (tepelné zpracování roztokem s následným umělým stárnutím), které zvyšuje mez kluzu a pevnost v tahu.
- Proč je to důležité pro závorky EV:
- Všestrannost: Vhodné pro širokou škálu konzol, od mírně zatížených konstrukčních prvků až po skříně a podpěry, u nichž není extrémní pevnost hlavním faktorem.
- Efektivita nákladů: Tisk je obecně nákladově efektivnější než tisk slitin s vyšší pevností díky zavedeným procesním parametrům a nižším nákladům na suroviny.
- Vytváření prototypů: Vynikající volba pro funkční prototypy díky dobré rovnováze vlastností a tisknutelnosti, která umožňuje rychlé ověření návrhu.
- Zavedený výkon: Dobře pochopené chování a rozsáhlé údaje o jeho výkonu v AM.
2. A7075 (AA7075):
- Popis: A7075 je vysoce výkonný hliník legovaný zinkem, který je známý svou výjimečnou pevností, často srovnatelnou s některými ocelemi, ale s výrazně nižší hustotou. Tradičně se používá v leteckém průmyslu a v konstrukčních aplikacích s vysokým namáháním. Jeho přizpůsobení pro L-PBF bylo náročnější, ale nabízí výrazné zvýšení výkonu.
- Klíčové vlastnosti:
- Velmi vysoká pevnost: Má výrazně vyšší pevnost v tahu a mez kluzu než AlSi10Mg, zejména po vhodném tepelném zpracování (např. T6 nebo T73).
- Vynikající poměr pevnosti k hmotnosti: Ideální pro aplikace, kde je rozhodující minimalizace hmotnosti při maximalizaci pevnosti.
- Dobrá únavová pevnost: Dobře funguje v podmínkách cyklického zatížení.
- Nižší odolnost proti korozi (ve srovnání s AlSi10Mg): Může vyžadovat povrchovou úpravu (např. eloxování nebo lakování) pro ochranu v drsném prostředí.
- Náročná tisknutelnost: V porovnání s AlSi10Mg je náchylnější k problémům, jako je praskání a pórovitost během L-PBF. Vyžaduje přísně kontrolované procesní parametry, specifické možnosti stroje (např. plošný ohřev) a případně specializované složení prášku nebo následné zpracování, jako je lisování za tepla (HIP).
- Proč je to důležité pro závorky EV:
- Aplikace s vysokou zátěží: Primární volba pro vysoce namáhané držáky, jako jsou hlavní držáky motoru nebo kritické styčné body zavěšení, kde může být pevnost AlSi10Mg nedostatečná.
- Maximální odlehčení: Díky svým vynikajícím mechanickým vlastnostem umožňuje navrhovat součásti s minimální spotřebou materiálu.
- Výkonnostní výhoda: Vhodné pro výkonné elektromobily, aplikace v motorsportu nebo situace vyžadující nejvyšší možnou konstrukční účinnost.
- Vyžaduje odbornost: Úspěšný tisk slitiny A7075 vyžaduje poskytovatele služeb s prokazatelnými zkušenostmi a řízením procesů pro tuto specifickou slitinu, což podtrhuje význam spolupráce se specialisty, jako je Met3dp, kteří se zaměřují na vysoce kvalitní kovové prášky a pokročilé procesy AM.
Srovnání vlastností materiálu (typické hodnoty po tepelném zpracování):
Vlastnictví | AlSi10Mg (stav T6) | A7075 (T6 Stav – AM*) | Jednotka | Poznámky |
---|---|---|---|---|
Hustota | ~2.67 | ~2.81 | g/cm³ | A7075 je o něco hustší. |
Mez kluzu (Rp0,2) | 230 – 300 | 450 – 520 | MPa | A7075 výrazně silnější. |
Pevnost v tahu (Rm) | 330 – 430 | 500 – 570 | MPa | A7075 výrazně silnější. |
Prodloužení při přetržení (A) | 6 – 10 | 5 – 10 | % | Podobné rozsahy tažnosti jsou dosažitelné. |
Tvrdost | ~100 – 120 | ~150 – 170 | HV / HB | A7075 je těžší. |
Možnost tisku | Vynikající | Náročný | – | Vyžaduje specializované řízení procesu. |
Odolnost proti korozi | Dobrý | Mírný | – | Může potřebovat ochranu pro A7075. |
Export do archů
*Poznámka: Vlastnosti AM A7075 se mohou výrazně lišit v závislosti na kvalitě prášku, parametrech tisku, orientaci sestavení a specifickém tepelném zpracování. Dosažení optimálních vlastností vyžaduje odborné znalosti.
Volba mezi AlSi10Mg a A7075:
- Pro většinu standardních držáků pro elektromobily, funkční prototypy a aplikace citlivé na náklady: AlSi 10Mg je často upřednostňovanou volbou díky vynikajícímu poměru vlastností, potiskovatelnosti a ceny.
- Pro vysoce zatížené součásti, díly kritické z hlediska bezpečnosti nebo aplikace vyžadující maximální odlehčení: A7075 nabízí vynikající výkon, ale vyžaduje pečlivé zvážení náročnosti zpracování a případné potřeby ochrany povrchu. Vyšší výkon je spojen s vyšší výrobní složitostí a náklady.
Konzultace se zkušeným poskytovatelem služeb v oblasti metal AM, jako je Met3dp, je zásadní. Pomůže vám vyhodnotit specifické požadavky vašeho držáku hnacího ústrojí pro elektromobily, doporučí nejvhodnější materiál a využije své odborné znalosti v oblasti optimalizace parametrů procesu a kontroly kvality prášku, aby zajistil výrobu vysoce výkonných a spolehlivých komponentů přizpůsobených vašim potřebám v oblasti automobilového průmyslu B2B.
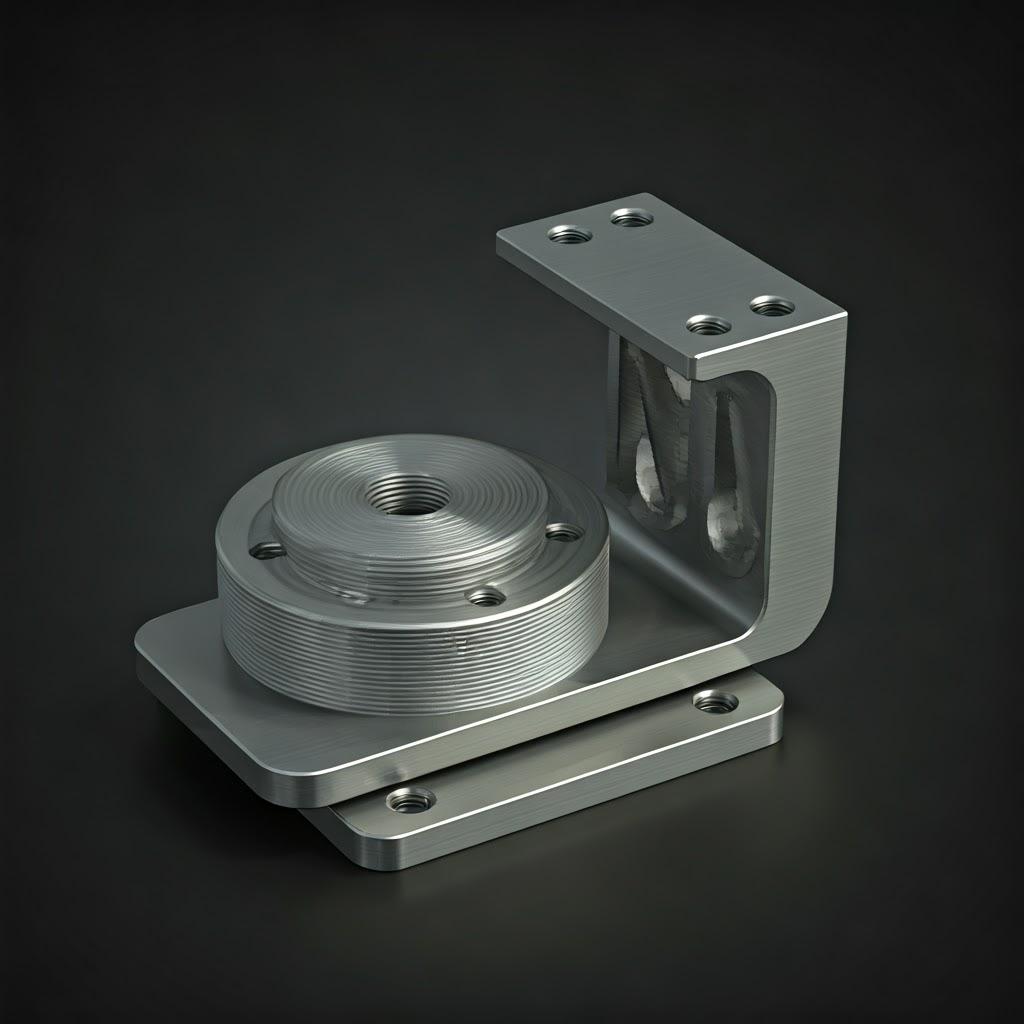
Konstrukční hlediska pro aditivní výrobu (DfAM) držáků pro elektromobily
Pouhá replika konstrukce určené pro odlévání nebo obrábění jen zřídkakdy uvolní plný potenciál aditivní výroby kovů. Aby bylo možné skutečně využít výhod AM pro konzoly pohonných jednotek elektrických vozidel - zejména odlehčení, zvýšení výkonu a konsolidace dílů - musí konstruktéři přijmout Design pro aditivní výrobu (DfAM) zásady. DfAM zahrnuje přehodnocení přístupu k navrhování tak, aby vyhovoval stavebnímu procesu po vrstvách a využíval jeho jedinečných schopností. Pro dodavatele B2B a výrobce OEM v automobilovém průmyslu je zvládnutí DfAM klíčové pro vývoj optimalizovaných komponent pro elektromobily nové generace.
Mezi klíčové aspekty DfAM pro držáky pohonných jednotek EV patří:
- Optimalizace topologie:
- Koncept: Použití specializovaného softwaru (např. Altair Inspire, Ansys Discovery, nTopology) k výpočetnímu určení nejefektivnějšího rozložení materiálu v rámci definovaného návrhového prostoru na základě použitých zatížení, omezení a výkonnostních cílů (např. maximalizace tuhosti, minimalizace hmotnosti).
- Použití: Ideální pro konstrukční držáky, jako jsou držáky motoru nebo držáky baterie. Software vytváří organické, často kostěné struktury, které přesně kopírují průběh napětí a odstraňují zbytečný materiál při zachování nebo dokonce zvýšení pevnosti a tuhosti. To je hlavní hnací silou pro výrazné snížení hmotnosti dílů AM.
- Výhody: Dosahuje maximálního potenciálu odlehčení, což vede ke zlepšení dojezdu a výkonu elektromobilu.
- Příhradové konstrukce a výplně:
- Koncept: Zahrnutí vnitřních mřížkových struktur (opakující se geometrické jednotkové buňky jako krychle, osmiúhelník, gyroid) místo pevného materiálu. Ty mohou být přizpůsobeny pro specifické vlastnosti, jako je vysoký poměr tuhosti a hmotnosti, absorpce energie (pro odolnost proti nárazu) nebo tlumení vibrací. Mřížky s proměnlivou hustotou mohou dále optimalizovat využití materiálu.
- Použití: Lze je použít v tělesech konzol nebo specifických sekcích pro snížení hmotnosti při zachování strukturální podpory nebo přidání funkčních vlastností.
- Výhody: Další snížení hmotnosti nad rámec optimalizace topologie povrchu, potenciál pro lepší tlumení vibrací nebo výkon při nárazu.
- Orientace a podpůrné struktury:
- Koncept: Orientace dílu na konstrukční platformě významně ovlivňuje dobu tisku, kvalitu povrchu, rozměrovou přesnost, potřebné podpůrné struktury a případně i mechanické vlastnosti (v důsledku anizotropie). Kovové procesy L-PBF vyžadují podpůrné struktury pro převislé prvky (obvykle nad 45 stupňů od vodorovné roviny), aby se zabránilo zborcení a ukotvení dílu k sestavovací desce a zvládlo se tepelné namáhání.
- Použití: Návrháři musí včas zvážit orientaci. Snažte se minimalizovat strmé převisy a objem potřebného podpůrného materiálu. Konstrukční prvky, jako jsou zkosení nebo filety na plochách směřujících dolů, mohou změnit strmé převisy na samonosné úhly.
- Výhody: Snižuje se čas tisku, spotřeba materiálu (podpěry jsou odpad) a náročnost následného zpracování (odstranění podpěr). Zlepšuje kvalitu povrchu na kritických plochách směřujících dolů.
- Minimální velikost prvku a tloušťka stěny:
- Koncept: Procesy AM mají omezení, pokud jde o nejmenší prvky (např. kolíky, otvory) a nejtenčí stěny, které mohou spolehlivě vyrobit. To závisí na rozlišení stroje, velikosti laserového bodu a vlastnostech prášku. Typické minimální tloušťky stěn pro L-PBF se často pohybují kolem 0,4-0,8 mm.
- Použití: Zajistěte, aby stěny a prvky byly navrženy nad technologické minimum, aby byl zaručen úspěšný tisk a strukturální integrita.
- Výhody: Zabraňuje selhání tisku, zajišťuje robustnost dílů.
- Design otvorů:
- Koncept: Malé vodorovné otvory často vyžadují vnitřní podpěry, jejichž odstranění může být velmi obtížné nebo nemožné. Svislé otvory se obecně tisknou dobře. Tvar slzy (podlouhlé vertikální otvory) může často zajistit, že vodorovné otvory budou samonosné.
- Použití: Kritické otvory orientujte pokud možno svisle. Pokud jsou nutné vodorovné otvory, zvažte jejich konstrukci jako samonosných tvarů nebo plánujte jejich dodatečné opracování. U závitových otvorů je často nejlepší vytisknout pilotní otvor a závity následně obrobit, aby se dosáhlo přesnosti a pevnosti.
- Výhody: Zamezuje zachycení podpůrného materiálu, zvyšuje přesnost kritických otvorů.
- Strategie konsolidace části:
- Koncept: Aktivně vyhledávejte příležitosti ke kombinaci více sousedních dílů (např. držák + chladič + upevňovací šroub) do jedné komplexní součásti AM.
- Použití: Analyzujte sestavy kolem držáku hnacího ústrojí. Lze integrovat montážní body pro kabelové svazky, snímače nebo chladicí potrubí? Lze do hlavní konstrukce držáku sloučit samostatné výztužné prvky?
- Výhody: Snižuje počet dílů, hmotnost, dobu montáže, správu zásob a potenciální místa poruch (např. šroubové spoje). Nabízí významnou přidanou hodnotu pro dodavatele B2B.
- Koncentrace stresu:
- Koncept: Ostré vnitřní rohy působí jako zvyšující se napětí, což může vést k únavovému selhání při zatížení.
- Použití: U vnitřních rohů a přechodů použijte velkorysé poloměry, podobně jako u tradičních konstrukčních metod, ale při agresivní optimalizaci hmotnosti je to ještě důležitější.
- Výhody: Zvyšuje únavovou životnost a celkovou odolnost držáku.
- Navrhování pro následné zpracování:
- Koncept: Zvažte, jak budou probíhat kroky následného zpracování, jako je odstranění podpěr, obrábění a povrchová úprava.
- Použití: Zajistěte, aby byly podpěrné konstrukce přístupné pro demontážní nástroje. Přidejte další materiál (přídavek na obrábění) na povrchy vyžadující vysokou přesnost nebo specifické povrchové úpravy, které budou dosaženy CNC obráběním. Vyhněte se složitým vnitřním mřížkám, pokud je odstraňování prášku kritické a obtížné.
- Výhody: Zjednodušuje pracovní postup následného zpracování, snižuje náklady a dobu přípravy.
Zavedení DfAM vyžaduje změnu myšlení a často i spolupráci mezi konstruktéry a specialisty na AM. Poskytovatelé služeb, jako je Met3dp, s hlubokými odbornými znalostmi v různých oblastech tiskových metod a materiálů, může nabídnout neocenitelné služby B2B v oblasti designu a konzultace, které klientům pomohou optimalizovat jejich návrhy držáků pro elektromobily pro aditivní výrobu a zajistit, aby plně využili výhod této technologie z hlediska výkonu, hmotnosti a nákladové efektivity.
Tolerance, povrchová úprava a rozměrová přesnost 3D tištěných držáků pro elektromobily
U funkčních automobilových součástí, jako jsou držáky hnacího ústrojí, je dosažení požadované rozměrové přesnosti, tolerancí a povrchové úpravy rozhodující pro správné uložení, montáž a výkon. Manažeři nákupu a inženýři potřebují realistická očekávání ohledně toho, čeho může aditivní výroba kovů, konkrétně L-PBF, dosáhnout “as-built” (přímo po tisku a odlehčení napětí) a co obvykle vyžaduje sekundární následné zpracování. Pochopení těchto aspektů je zásadní pro efektivní získávání B2B a kontrolu kvality.
1. Rozměrová přesnost:
- Definice: Jak moc se výsledný vytištěný díl shoduje s rozměry uvedenými v původním 3D modelu CAD.
- Typické hodnoty L-PBF: Přesnost při výrobě je obecně dobrá, ale ne tak vysoká jako při přesném obrábění. Typické hodnoty se často pohybují v rozmezí ±0,1 mm až ±0,2 mm u menších prvků nebo ±0,1 % až ±0,2 % celkového rozměru u větších dílů.
- Ovlivňující faktory:
- Kalibrace stroje: Klíčová je pravidelná kalibrace skenerů a optiky tiskárny.
- Vlastnosti materiálu: Tepelná roztažnost a smršťování během tisku se liší podle slitiny.
- Geometrie dílu & Velikost: Větší díly a složité geometrie jsou náchylnější k tepelnému zkreslení.
- Orientace na stavbu: Ovlivňuje tepelné gradienty a potenciální smršťování/deformace.
- Strategie podpory: Nevhodné podpěry mohou způsobit deformaci.
- Tepelný management: Pomáhá plošinový ohřev (je-li k dispozici) a stálé procesní teploty.
- Úleva od stresu: Správné tepelné zpracování po tisku je nezbytné k odstranění vnitřních pnutí, která mohou způsobit deformaci při vyjmutí z konstrukční desky.
- Dosažení vysoké přesnosti: Pro kritické rozměry, styčné plochy nebo rozhraní vyžadující přísné tolerance (např. otvory ložisek, přesné montážní plochy) se obvykle používá CNC obrábění po tisku. Renomovaní poskytovatelé služeb, jako je Met3dp, kladou důraz na řízení procesů a spolehlivost strojů, aby se maximalizovala přesnost při výrobě.
2. Tolerance:
- Definice: Přípustná odchylka rozměru. Tolerance jsou uvedeny na technických výkresech (např. pomocí norem ISO).
- Tolerance podle stavu konstrukce: Standardní dosažitelné tolerance přímo z L-PBF se často pohybují kolem ISO 2768-m (střední) nebo někdy -f (jemné) pro určité vlastnosti, ale to je velmi závislé na výše uvedených faktorech. Dosažení přísnějších tolerancí obvykle vyžaduje obrábění.
- Důsledky pro design: Konstruktéři by měli stanovit přísné tolerance pouze v případě, že je to z funkčního hlediska nezbytné. Nadměrné tolerance zvyšují pravděpodobnost nutnosti rozsáhlého dodatečného obrábění, což zvyšuje náklady a dodací lhůty. Jasně rozlišujte kritické prvky vyžadující obrábění od méně kritických povrchů přijatelných ve stavu, v jakém jsou postaveny.
3. Povrchová úprava (drsnost):
- Definice: Míra textury povrchu, obvykle kvantifikovaná aritmetickým průměrem drsnosti (Ra).
- Hodnoty L-PBF podle projektu: Povrchová úprava dílů z L-PBF je přirozeně drsnější než povrch obrobený v důsledku slučování částic prášku po vrstvách. Typické hodnoty Ra se pohybují od 6 µm do 20 µm (mikrometrů), někdy vyšší na površích směřujících dolů nebo silně podepřených.
- Ovlivňující faktory:
- Tloušťka vrstvy: Tenčí vrstvy obecně vedou k hladšímu povrchu, ale prodlužují dobu tisku.
- Velikost částic prášku: Jemnější prášky mohou vést k hladším povrchům.
- Parametry laseru: Podmínky tání ovlivňují strukturu povrchu.
- Orientace na část: Povrchy postavené rovnoběžně se směrem stavby (svislé stěny) bývají hladší než šikmé nebo vodorovné povrchy (“schodišťový efekt”). Povrchy směřující dolů a vyžadující podpěry jsou po odstranění podpěr často nejhrubší.
- Zlepšení povrchové úpravy: Pokud je z funkčních důvodů požadován hladší povrch (např. těsnicí plochy, snížení tření, estetika), používají se různé metody následného zpracování:
- Tryskání abrazivem (kuličkové/ pískové): Běžná metoda pro dosažení rovnoměrného matného povrchu (Ra obvykle 3-10 µm).
- Třískové/vibrační dokončování: Používá média k vyhlazení povrchů a hran, účinná pro dávky menších dílů.
- Leštění: Ruční nebo automatické leštění pro zrcadlovou povrchovou úpravu (Ra < 0,8 µm).
- Obrábění: Poskytuje nejlepší kontrolu nad povrchovou úpravou specifických prvků.
- Eloxování/povlakování: Může poskytnout hladší pocit a zvýšenou ochranu proti korozi, i když nemusí výrazně snížit naměřené Ra v závislosti na výchozím povrchu.
Kontrola kvality v automobilovém průmyslu:
Dosažení konzistentní tolerance, přesnosti a povrchové úpravy vyžaduje důslednou kontrolu kvality v celém pracovním procesu AM. To zahrnuje:
- Řízení kvality prášku: Zajištění konzistentních vlastností prášku.
- Monitorování procesů: Sledování taveniny a ukládání vrstev in-situ.
- Metrologie po tisku: Použití souřadnicových měřicích strojů (CMM), 3D skenerů nebo tradičních měřidel k ověření rozměrů.
- Testování materiálů: Ověření mechanických vlastností, které odpovídají specifikacím.
B2B nákupy automobilových komponentů vyžadují dodavatele s robustními systémy řízení kvality (např. ISO 9001, případně IATF 16949 nebo shoda s normami pro výrobní díly) a metrologickými schopnostmi pro ověření shody. Společnosti jako Met3dp, zaměřené na vysoce přesné, spolehlivé tiskové systémy a komplexní řešení, chápou přísné požadavky automobilového průmyslu.
Souhrnná tabulka: Schopnosti ve stavu po sestavení vs. schopnosti po zpracování
Parametr | Stav L-PBF (typický) | Dosažitelné s následným zpracováním | Poznámky |
---|---|---|---|
Rozměrová přesnost | ±0,1 až ±0,2 mm / ±0,1-0,2 % | S přesností ±0,01 mm (obrábění) | Závisí do značné míry na velikosti prvku a řízení procesu. |
Třída tolerance | ISO 2768-m / -f (přibližně) | ISO 2768-f / -c (obrábění) | Těsné tolerance udávejte pouze v případě potřeby. |
Povrchová úprava (Ra) | 6 – 20 µm+ | < 0,8 µm (leštění/obrábění) | Výrazně se liší podle orientace a podpěr. |
3 – 10 µm (tryskání) | Tryskáním získáte jednotný matný povrch. |
Export do archů
Porozumění těmto možnostem umožňuje inženýrům a manažerům nákupu přijímat informovaná rozhodnutí o specifikacích návrhu, potřebách následného zpracování a výběru dodavatele pro 3D tištěné držáky pohonných jednotek pro elektromobily.
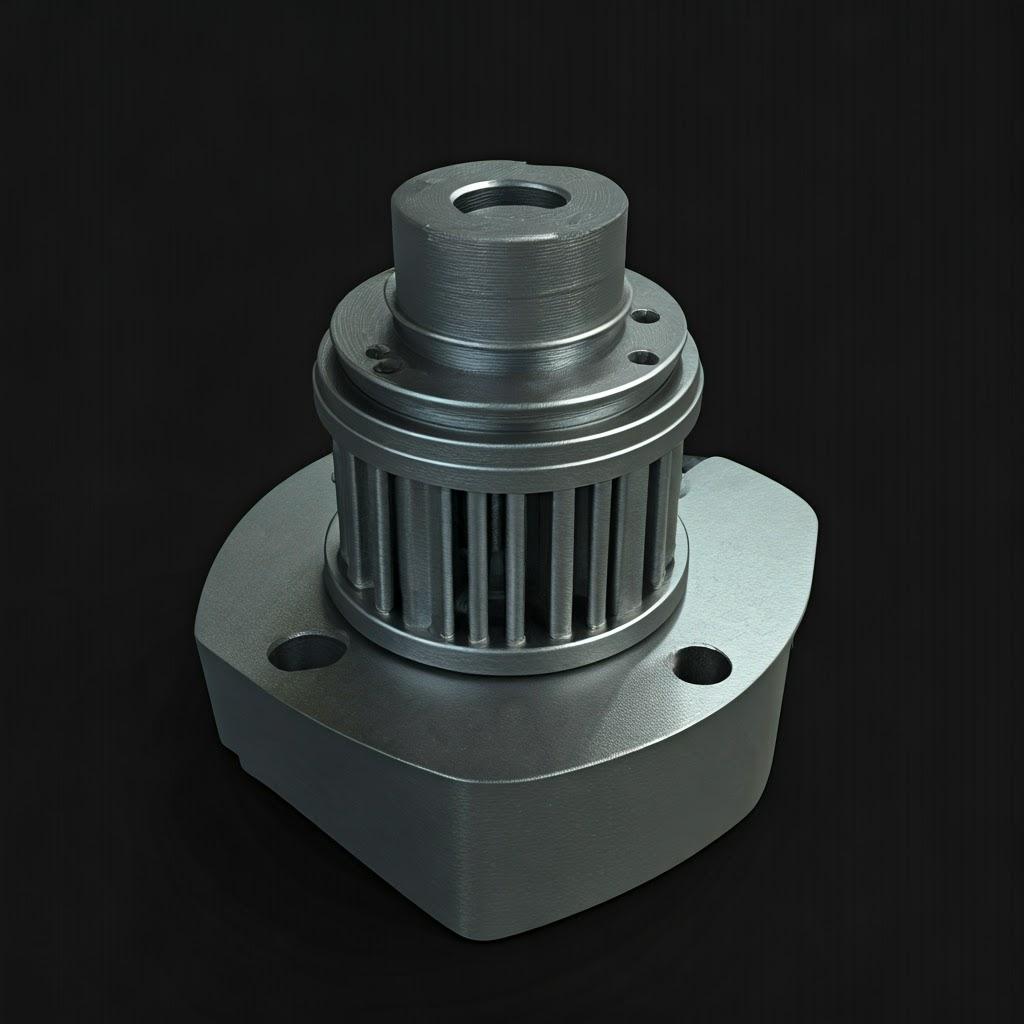
Požadavky na následné zpracování kovových 3D tištěných držáků pro elektromobily: Od tisku po součástku
Běžnou mylnou představou o 3D tisku z kovu je, že díly vyjíždějí ze stroje připravené k použití. Ve skutečnosti téměř všechny kovové díly AM, zejména funkční součásti, jako jsou držáky pohonných jednotek pro elektromobily, vyžadují několik zásadních kroků následného zpracování, aby bylo dosaženo požadovaných konečných vlastností, rozměrů a povrchové úpravy. Tyto kroky prodlužují celkovou dobu výroby a zvyšují náklady, ale jsou nezbytné pro zajištění toho, aby díl splňoval technické specifikace. Služby následného zpracování B2B jsou nedílnou součástí dodavatelského řetězce AM.
Mezi běžné kroky následného zpracování hliníkových držáků EV s potiskem L-PBF (AlSi10Mg, A7075) patří:
- Odstranění prášku:
- Proces: Po dokončení sestavení a vychladnutí se sestavovací komora vybalí a je třeba pečlivě odstranit volný, nerozpuštěný prášek, který obklopuje díly. To se často provádí ručně pomocí kartáčů a vakuových systémů nebo pomocí automatických stanic pro odstraňování prášku. Vnitřní kanály nebo složité mřížkové struktury mohou odstraňování prášku ztěžovat.
- Důležitost: Zajistí, že nezůstane žádný volný prášek, který by mohl narušit další kroky nebo konečnou aplikaci. Umožňuje obnovu a recyklaci prášku.
- Tepelné ošetření proti stresu:
- Proces: Díly se obvykle ponechají připevněné na konstrukční desce a projdou tepelným cyklem v peci. To zahrnuje zahřátí dílů na určitou teplotu (pod bod tání, např. ~300 °C pro AlSi10Mg) po stanovenou dobu, po níž následuje řízené ochlazení.
- Důležitost: Rychlé zahřívání a ochlazování během procesu L-PBF vyvolává v materiálu značné vnitřní pnutí. Odlehčení napětí je klíčové pro snížení těchto zbytkových napětí, aby se zabránilo deformaci nebo praskání při pozdějším vyjmutí dílů z konstrukční desky nebo při obrábění. Rovněž stabilizuje mikrostrukturu.
- Odstranění ze stavební desky:
- Proces: Po uvolnění napětí se díly oddělí od kovové konstrukční desky. Běžně se k tomu používá elektroerozivní obrábění (EDM) nebo pásová pila.
- Důležitost: Uvolní jednotlivé díly pro další zpracování.
- Odstranění podpůrné konstrukce:
- Proces: Podpěrné konstrukce potřebné při tisku musí být odstraněny. To lze provést ručně (pomocí kleští, štípacích kleští, brusek), pomocí CNC obrábění nebo někdy pomocí elektroerozivního obrábění drátem u choulostivých nebo těžko přístupných podpěr. Snadnost odstranění závisí do značné míry na tom, jak dobře byly podpěry navrženy (DfAM).
- Důležitost: Podpěry jsou nefunkční a musí být odstraněny. Tento krok významně ovlivňuje konečnou povrchovou úpravu v podepřených oblastech.
- Tepelné zpracování roztokem a stárnutí (např. T6 pro Al slitiny):
- Proces: U slitin, jako jsou AlSi10Mg a A7075, je k dosažení požadovaných konečných mechanických vlastností (pevnost, tvrdost, tažnost) často nutný celý cyklus tepelného zpracování. To obvykle zahrnuje:
- Řešení Ošetření: Zahřátí na vyšší teplotu (např. ~500-540 °C pro slitiny Al) za účelem rozpuštění legujících prvků do hliníkové matrice.
- Kalení: Rychlé ochlazení (často ve vodě), aby se prvky udržely v roztoku.
- Umělé stárnutí: Opětovným zahříváním na nižší teplotu (např. 150-190 °C) po delší dobu se vysráží jemné částice, které slitinu zpevní.
- Důležitost: Naprosto zásadní pro rozvinutí plného pevnostního potenciálu tepelně zpracovatelných hliníkových slitin. Bez správného tepelného zpracování nesplní konzola konstrukční požadavky na pevnost. Konkrétní cykly (T6, T73 atd.) se volí na základě požadované rovnováhy mezi pevností, houževnatostí a odolností proti korozi pod napětím.
- Proces: U slitin, jako jsou AlSi10Mg a A7075, je k dosažení požadovaných konečných mechanických vlastností (pevnost, tvrdost, tažnost) často nutný celý cyklus tepelného zpracování. To obvykle zahrnuje:
- Povrchová úprava:
- Proces: Jak již bylo řečeno, ke zlepšení povrchové úpravy se na základě požadavků používají různé techniky:
- Tryskání abrazivem (kuličkami, pískem atd.): Standardní krok pro jednotný, čistý a matný povrch. Odstraňuje drobné nedokonalosti.
- Třískové/vibrační dokončování: Pro odstraňování otřepů na hranách a hladší povrchové úpravy dávek.
- Leštění: Pro dosažení velmi hladkých, reflexních povrchů.
- Důležitost: Zlepšuje estetiku, může zvýšit únavové vlastnosti odstraněním povrchových vad, připravuje povrchy pro nátěry nebo splňuje specifické funkční požadavky (např. těsnění).
- Proces: Jak již bylo řečeno, ke zlepšení povrchové úpravy se na základě požadavků používají různé techniky:
- CNC obrábění:
- Proces: Použití frézek, soustruhů nebo brusek k dosažení přísných tolerancí u specifických prvků, vytvoření přesných styčných ploch, vrtání a závitování otvorů nebo zlepšení kvality povrchu na kritických místech.
- Důležitost: Nezbytné v případech, kdy přesnost nebo povrchová úprava AM není dostatečná pro funkční požadavky. Často se vyžaduje pro rozhraní s jinými součástmi hnacího ústrojí.
- Kontrola a zajištění kvality (QA):
- Proces: Konečná rozměrová kontrola (souřadnicová měřicí souprava, skenování), měření drsnosti povrchu, zkoušení materiálu (tahové zkoušky na reprezentativních vzorcích), nedestruktivní zkoušení (NDT), jako je CT skenování (počítačová tomografie) pro kontrolu vnitřní pórovitosti nebo defektů, a konečná vizuální kontrola.
- Důležitost: Před odesláním ověří, zda hotová konzola splňuje všechny specifikace návrhu a normy kvality. Má zásadní význam pro automobilové komponenty, které jsou důležité z hlediska bezpečnosti.
Úvahy o pracovním postupu:
Konkrétní pořadí a nutnost těchto kroků závisí na konstrukci, materiálu a požadavcích na použití držáku. Spolupráce s poskytovatelem komplexních služeb, jako je Met3dp, který nabízí jak pokročilý tisk, tak komplexní možnosti následného zpracování (ať už vlastními silami, nebo prostřednictvím kvalifikovaných partnerů), zjednodušuje dodavatelský řetězec pro B2B zákazníky. Ti mohou řídit celý pracovní postup od souboru CAD až po hotový, zkontrolovaný díl a zajistit kvalitu a konzistenci v celém procesu. Manažeři nákupu by si měli ujasnit, které kroky následného zpracování jsou zahrnuty v nabídkách, a ujistit se, že dodavatel má potřebné odborné znalosti a vybavení.
Obvyklé problémy při 3D tisku držáků pro elektromobily a jejich řešení
Ačkoli aditivní výroba kovů nabízí významné výhody, výroba vysoce kvalitních a spolehlivých držáků hnacího ústrojí elektromobilů pomocí L-PBF není bez problémů. Pochopení těchto potenciálních problémů a způsobu, jakým je zkušení poskytovatelé služeb zmírňují, je klíčové pro úspěšnou implementaci a řízení očekávání v rámci dodavatelského řetězce B2B.
1. Deformace a zkreslení:
- Výzva: Intenzivní, lokalizované teplo laseru a následné rychlé ochlazení vytváří prudké tepelné gradienty, které vyvolávají zbytková napětí. Tato napětí mohou způsobit, že se díly (zejména velké, ploché nebo tenkostěnné) během sestavování deformují nebo se deformují po vyjmutí ze sestavovací desky.
- Zmírnění:
- Optimalizovaná orientace: Výběr orientace sestavení, která minimalizuje velké rovné plochy rovnoběžné se sestavovací deskou a řídí nahromadění tepla.
- Robustní strategie podpory: Použití dobře navržených podpěr k pevnému ukotvení dílu a proti tepelnému namáhání.
- Optimalizace parametrů procesu: Přesné vyladění výkonu laseru, rychlosti a strategie skenování pro minimalizaci indukce napětí (vyžaduje odborné znalosti specifické pro daný materiál).
- Vytápění platformy: Používání tiskáren s vyhřívanými konstrukčními plošinami může snížit teplotní gradienty.
- Účinná úleva od stresu: Provedení správného cyklu tepelného zpracování pro uvolnění napětí před vyjmutí dílu z konstrukční desky je kritické.
2. Pórovitost:
- Výzva: V tištěném materiálu mohou vznikat malé dutiny nebo póry v důsledku zachyceného plynu (z prášku nebo atmosféry) nebo neúplného spojení mezi vrstvami (nedostatečná pórovitost spojení). Pórovitost může výrazně zhoršit mechanické vlastnosti, zejména únavovou pevnost.
- Zmírnění:
- Vysoce kvalitní prášek: Použití sférického prášku s nízkou vnitřní pórovitostí a řízenou distribucí velikosti částic, jako jsou částice vyrobené pomocí pokročilých atomizačních technik společnosti Met3dp’. Zásadní je také správná manipulace s práškem a jeho skladování, aby se zabránilo absorpci vlhkosti.
- Optimalizované parametry tisku: Vývoj a ověřování robustních sad parametrů (výkon laseru, rychlost, tloušťka vrstvy, rozteč šraf) specifických pro slitinu a stroj, aby bylo zajištěno úplné roztavení a tavení.
- Kontrola inertní atmosféry: Udržování prostředí s vysoce čistým inertním plynem (argon nebo dusík) ve stavební komoře, aby se minimalizovala oxidace a zachytávání plynů.
- Izostatické lisování za tepla (HIP): Následný krok zpracování zahrnující vysokou teplotu a vysokotlaký plyn k uzavření vnitřních pórů. Často se používá u kritických aplikací nebo náročných materiálů, jako je A7075, k dosažení téměř plné hustoty a zlepšení únavových vlastností.
3. Obtíže při odstraňování podpory:
- Výzva: Odstranění podpěr může být obtížné, časově i finančně náročné, zejména vnitřních podpěr nebo podpěr na složitých geometriích. Špatné odstranění může poškodit součást nebo zanechat nežádoucí povrchové artefakty.
- Zmírnění:
- DfAM pro minimalizaci podpory: Navrhování dílů se samonosnými úhly a prvky, kde je to možné. Orientace dílů tak, aby se snížila potřeba podpěr na kritických plochách.
- Optimalizovaný design podpory: Použití podpěrných konstrukcí (např. kvádrových, kuželových, stromových podpěr s vhodnou geometrií zubů), které zajišťují dostatečné ukotvení, ale jsou navrženy pro snadnější odpojení (např. použití menších kontaktních bodů, perforace). Softwarové nástroje nabízejí pokročilé strategie generování podpěr.
- Plánování přístupnosti: Zajištění fyzického přístupu k podpěrám pro ruční nebo automatizované nástroje pro odstranění.
- Vhodné techniky odstraňování: Použití správných nástrojů (ruční, CNC, elektroerozivní obrábění) pro konkrétní typ podpěry a umístění.
4. Praskání (zejména u vysokopevnostních slitin):
- Výzva: Vysokopevnostní hliníkové slitiny, jako je A7075, jsou během rychlých cyklů ohřevu/chlazení L-PBF náchylnější k tvorbě trhlin při tuhnutí nebo kapalnění, a to z důvodu jejich širokého rozsahu tuhnutí a tepelného namáhání.
- Zmírnění:
- Modifikace slitin (prášková chemie): Někdy mohou drobné úpravy chemického složení prášku zlepšit tisknutelnost.
- Specializované parametry: Vývoj vysoce specifických parametrů laseru (např. strategie pulzního laseru, specifické vzorce skenování) přizpůsobených ke zmírnění tendencí k praskání.
- Předehřev plošiny: Použití výrazného ohřevu stavební plošiny (někdy i několik set stupňů C) snižuje tepelné gradienty a riziko vzniku trhlin.
- Optimalizované tepelné zpracování: Rozhodující je pečlivě navržené odlehčení a následné cykly tepelného zpracování.
5. Dosažení konzistentních mechanických vlastností:
- Výzva: Mechanické vlastnosti (pevnost, tažnost, únavová životnost) mohou být ovlivněny odchylkami v procesu, umístěním konstrukce, orientací (anizotropie) a účinností následného tepelného zpracování. Zajištění konzistentních vlastností u jednotlivých šarží a dílů je pro aplikace v automobilovém průmyslu zásadní.
- Zmírnění:
- Důsledná kontrola procesu: Provádění přísné kontroly kvality prášku, parametrů stroje a atmosféry.
- Kvalifikace procesu: Důkladné ověření procesu tisku a tepelného zpracování pro každou konkrétní slitinu a aplikaci.
- Homogenizační tepelné zpracování: Specifické tepelné cykly mohou pomoci snížit mikrostrukturní změny.
- Rutinní testování: Pravidelné testování svědeckých kupónů vytištěných vedle dílů za účelem ověření, zda mechanické vlastnosti odpovídají specifikacím.
- Spolupráce s odborníky: Spolupráce s poskytovateli služeb, jako je Met3dp, kteří mají hluboké znalosti v oblasti materiálových věd a odborné znalosti procesů, je klíčem k důslednému dosažení požadovaných vlastností náročných materiálů. Jejich zaměření na špičkovou spolehlivost v oboru pomáhá zajistit spolehlivé výsledky.
Pochopením těchto výzev a navázáním spolupráce se zkušenými poskytovateli AM technologií pro kovy, kteří používají spolehlivé strategie pro jejich zmírnění, mohou automobilové společnosti bez obav přijmout aditivní výrobu pro výrobu vysoce výkonných a spolehlivých držáků hnacího ústrojí pro elektromobily a urychlit tak inovace v rámci svých dodavatelských řetězců B2B.
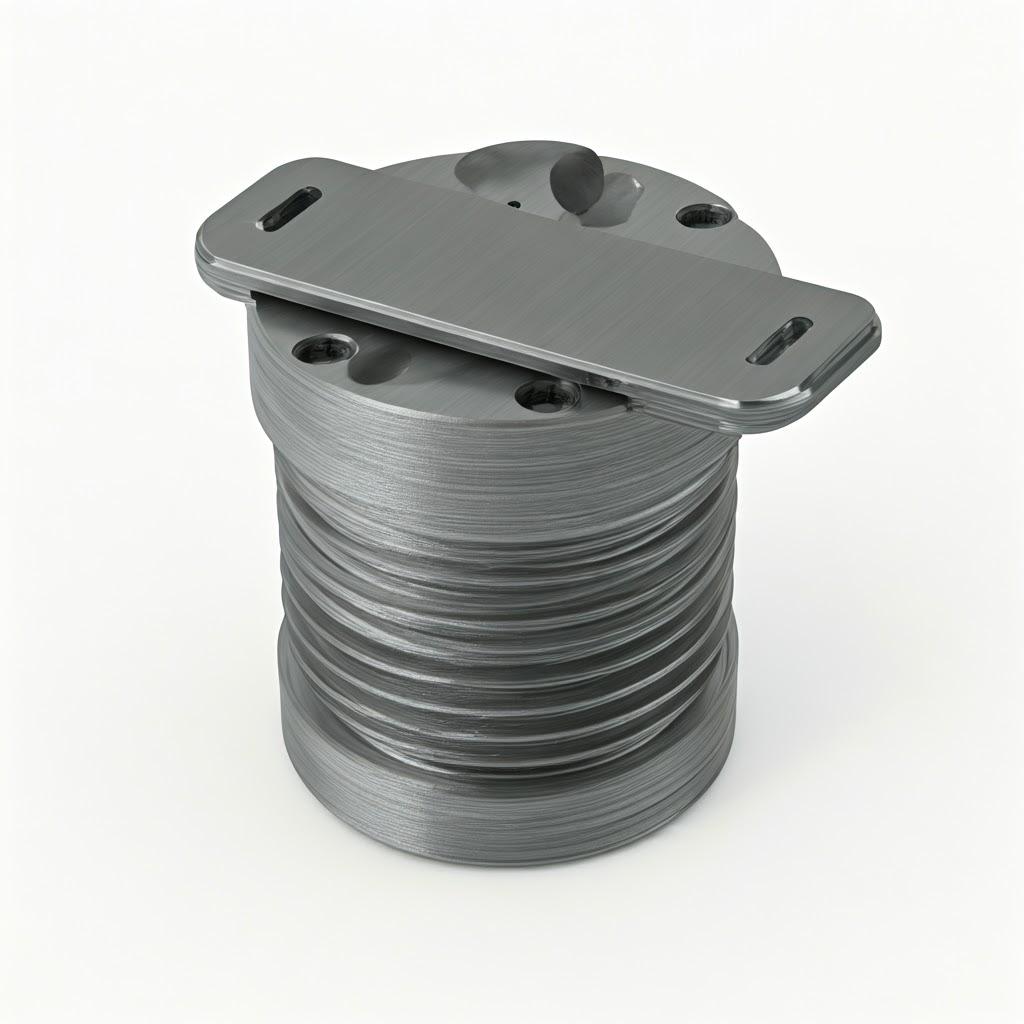
Jak vybrat správného poskytovatele služeb 3D tisku kovů pro komponenty pro elektromobily
Výběr správného partnera pro aditivní výrobu je stejně důležitý jako konstrukce a výběr materiálu pro držáky vašeho elektrického hnacího ústrojí. Kvalita, spolehlivost, nákladová efektivita a včasné dodání vašich komponent do značné míry závisí na schopnostech a odborných znalostech vybraného poskytovatele služeb. Pro manažery nákupu a inženýrské týmy zapojené do B2B sourcingu pro automobilový AM vyžaduje hodnocení potenciálních dodavatelů pečlivé zvážení několika klíčových faktorů.
Zde je návod, na co se zaměřit při výběru poskytovatele služeb 3D tisku z kovu pro náročné aplikace pro elektromobily:
- Prokázané odborné znalosti a zkušenosti:
- Zaměření na automobilový průmysl: Má poskytovatel prokazatelné zkušenosti s prací s klienty z automobilového průmyslu a rozumí přísným požadavkům tohoto odvětví (kvalita, sledovatelnost, výkon)? Vyhledejte případové studie nebo reference týkající se konkrétně automobilového průmyslu nebo komponentů pro elektromobily.
- Specializace na materiál: Mají hluboké zkušenosti s tiskem konkrétních slitin, které potřebujete (např. AlSi10Mg, A7075)? Úspěšný tisk náročných materiálů, jako je vysokopevnostní hliník, vyžaduje specializované znalosti.
- Znalost aplikace: Rozumí funkčním požadavkům na držáky hnacího ústrojí (zatížení, vibrace, tepelný management)?
- Technologie a vybavení:
- Vhodný proces AM: Ujistěte se, že používají vhodné stroje L-PBF (SLM/DMLS), které jsou známé svou kvalitou a spolehlivostí při výrobě kovových dílů.
- Možnosti stroje: Vezměte v úvahu objem sestavy (dokáže se přizpůsobit velikosti vašeho dílu?), výkon laseru, ohřev platformy (důležité zejména pro slitiny jako A7075) a možnosti monitorování procesu. Poskytovatelé, jako je Met3dp, kladou důraz na své špičkový objem, přesnost a spolehlivost tisku, což jsou klíčové ukazatele vyspělého vybavení.
- Údržba a kalibrace strojů: Pravidelná údržba a kalibrace jsou nezbytné pro dosažení konzistentních výsledků.
- Schopnosti a kvalita materiálu:
- Portfolio prášků: Nabízejí specifické certifikované kovové prášky? Umí v případě potřeby zajistit nebo zpracovat slitiny na zakázku?
- Kontrola kvality prášku: Jaké procesy jsou zavedeny pro získávání, testování, manipulaci, skladování a sledovatelnost prášku? Nejdůležitější je konzistentní kvalita prášku. Společnosti jako Met3dp, které vyrábějí vlastní vysoce kvalitní kovové prášky pomocí pokročilé atomizace, mají často lepší kontrolu nad tímto kritickým vstupem.
- Certifikace materiálu: Mohou poskytnout materiálové certifikáty odpovídající příslušným normám (např. ASTM, ISO)?
- Systém řízení kvality (QMS) a certifikace:
- ISO 9001: Základní certifikace indikující robustní QMS.
- AS9100 (letectví a kosmonautika): Tato certifikace je sice specifická pro letecký průmysl, ale často znamená velmi vysokou úroveň kontroly a sledovatelnosti procesů, což je výhodné pro zákazníky z automobilového průmyslu.
- IATF 16949 (automobilový průmysl): Zlatý standard pro dodavatele automobilového průmyslu. Ačkoli ne všichni dodavatelé AM se ho drží (zejména pro výrobu prototypů), povědomí o jeho zásadách nebo jejich dodržování je významnou výhodou pro výrobní díly.
- Sledovatelnost: Zajistěte, aby měly systémy pro sledování dílů a materiálů v průběhu celého výrobního procesu.
- Vlastní možnosti následného zpracování:
- Komplexní služby: Nabízí poskytovatel potřebné kroky následného zpracování přímo ve firmě (uvolnění napětí, tepelné zpracování, odstranění podpěr, základní povrchová úprava)? To může zefektivnit pracovní postup a zlepšit dobu realizace.
- Spravované služby: Pokud jsou některé kroky (např. složité CNC obrábění, specializované nátěry, HIP) zadávány externím dodavatelům, jak dobře tyto externí partnery řídí a zajišťují kvalitu?
- Odborné znalosti: Mají metalurgické znalosti pro tepelné zpracování a vhodné vybavení pro dokončovací a obráběcí práce?
- Technická podpora a podpora DfAM:
- Konzultační přístup: Mohou vám jejich inženýři poradit s návrhem pro aditivní výrobu (DfAM), abyste optimalizovali návrh konzoly z hlediska hmotnosti, výkonu a tisknutelnosti?
- Simulační schopnosti: Nabízejí služby analýzy konečných prvků (FEA) nebo optimalizace topologie?
- Řešení problémů: Jsou proaktivní při identifikaci potenciálních výrobních problémů na základě vašeho návrhu?
- Kapacita a doba realizace:
- Škálovatelnost: Zvládnou vaše požadované objemy, od prototypů až po potenciálně malosériovou výrobu?
- Citovaná doba vedení: Jsou uváděné dodací lhůty realistické a důsledně dodržované? Pochopte jejich proces plánování výroby.
- Reakce: Jak rychle reagují na dotazy a poskytují nabídky?
- Náklady a transparentnost:
- Jasné citace: Je struktura cen jasná a obsahuje podrobné informace o nákladech na tisk, materiál, podpěry a jednotlivé kroky následného zpracování?
- Nabídka hodnoty: Zvažte celkovou hodnotu, včetně kvality, odborných znalostí, spolehlivosti a podpory, nejen cenu za díl.
- Umístění a logistika:
- Doprava: Zvažte náklady na dopravu a logistiku, zejména u mezinárodních B2B dodavatelů. Ujistěte se, že mají zkušenosti s vhodným balením choulostivých AM dílů.
Proč Met3dp vyniká: Met3dp se na základě těchto kritérií řadí mezi silné uchazeče. Jako společnost specializující se na zařízení pro 3D tisk a vysoce výkonné kovové prášky má komplexní odborné znalosti. Jejich zaměření na špičkovou přesnost a spolehlivost v oboru, pokročilé systémy výroby prášků (plynová atomizace, PREP), rozmanité portfolio materiálů (včetně speciálních slitin) a desítky let kolektivních zkušeností v oblasti kovové AM z nich činí cenného partnera pro společnosti, které hledají komplexní řešení pro náročné aplikace, jako jsou držáky pohonných jednotek pro elektromobily. Další zkoumání jejich schopností může odhalit, jak odpovídají vašim specifickým potřebám v oblasti B2B nákupu.
Výběr správného partnera je investicí do kvality a úspěchu vašeho projektu EV. Důkladné prověření potenciálních dodavatelů podle těchto kritérií vám pomůže zajistit výběr dodavatele, který je schopen splnit náročné požadavky automobilového průmyslu.
Analýza nákladových faktorů a doby realizace pro 3D tištěné držáky hnacího ústrojí elektromobilů
Pochopení faktorů, které ovlivňují náklady a dobu dodání kovových 3D tištěných komponent, je nezbytné pro přesné plánování projektu, sestavování rozpočtu a řízení očekávání dodavatelského řetězce B2B. Ačkoli AM nabízí jedinečné výhody, ve srovnání s tradiční výrobou s sebou nese vlastní soubor ekonomických a plánovacích faktorů.
Klíčové nákladové faktory:
- Typ materiálu a spotřeba:
- Volba slitiny: Vysoce výkonné slitiny jako A7075 jsou obvykle dražší na kilogram než standardní slitiny jako AlSi10Mg kvůli nákladům na suroviny a složitosti zpracování. Speciální slitiny (na bázi Ti, superslitiny) jsou výrazně dražší.
- Část Objem & amp; Hmotnost: Skutečné množství materiálu použitého k tisku dílu přímo ovlivňuje náklady. Větší a hustší díly stojí více.
- Objem podpůrné struktury: Materiál použitý na podpůrné konstrukce zvyšuje náklady, protože se jedná v podstatě o odpadní materiál, jehož tisk a odstranění vyžaduje čas. Efektivní DfAM minimalizuje potřebu podpěr.
- Část Složitost a design:
- Geometrická složitost: Velmi složité návrhy mohou vyžadovat složitější podpůrné strategie a potenciálně delší dobu tisku, což mírně ovlivňuje náklady. AM si však se složitostí poradí dobře - hlavním faktorem je poměr objem/čas.
- Tloušťka stěny & Vlastnosti: Velmi tenké stěny nebo jemné rysy mohou vyžadovat nižší rychlost tisku nebo specializované parametry, což může prodloužit strojní čas.
- Čas sestavení (strojový čas):
- Výška dílu (Z-výška): To je často nejvýznamnější faktor ovlivňující dobu tisku, protože stroj vytváří vrstvu po vrstvě. Vyšší díly se tisknou déle, bez ohledu na jejich stopu.
- Část Objem & Hustota: Skenování větších objemů těles trvá laserem déle.
- Počet dílů na sestavení: Efektivní vnoření více dílů na jednu konstrukční desku zkracuje dobu nastavení stroje na jeden díl a může snížit náklady (úspory z rozsahu).
- Tloušťka vrstvy & amp; Parametry: Tenčí vrstvy zlepšují povrchovou úpravu, ale prodlužují dobu vytváření; rychlejší parametry mohou zkrátit dobu, ale vyžadují pečlivou validaci.
- Požadavky na následné zpracování:
- Tepelné zpracování: Odlehčení od napětí a plné cykly tepelného zpracování T6 (nebo podobné) vyžadují čas a energii v peci, což zvyšuje náklady.
- Odstranění podpory: Pracovní náročnost ručního odstraňování nebo čas strávený na stroji (EDM/CNC) zvyšuje náklady. Složité/interní podpěry je výrazně zvyšují.
- CNC obrábění: Obrábění specifických prvků z hlediska tolerance nebo povrchové úpravy je často jedním z nejvýznamnějších nákladů na následné zpracování, které vyžaduje čas strávený na stroji, programování a seřizování.
- Povrchová úprava: Náklady se značně liší v závislosti na metodě (tryskání je relativně nízké, rozsáhlé leštění je vysoké).
- Kontrola: Pokročilá kontrola, jako je CT skenování, zvyšuje náklady, ale může být nezbytná u kritických dílů.
- Množství a objem objednávek:
- Úspory z rozsahu: Ačkoli AM nemá žádné náklady na nástroje, existují určité úspory z rozsahu. Větší série umožňují efektivnější využití konstrukčních desek, potenciálně kratší dobu přípravy jednoho dílu a množstevní slevy na materiály nebo služby. Zadávání zakázek B2B často zahrnuje vyjednávání o cenách pro opakované objednávky nebo větší množství.
- Práce a odbornost:
- Obsluha stroje, konzultace DfAM, následné zpracování a kontrola kvality vyžadují kvalifikovanou pracovní sílu. Potřebné odborné znalosti, zejména u složitých dílů nebo materiálů, se promítají do celkových nákladů.
Faktory doby realizace:
- Kótování a kontrola designu: Počáteční příprava souboru, kontroly DfAM a generování nabídky zaberou určitý čas (obvykle 1-3 dny).
- Plánování strojů: Dostupnost vhodné tiskárny. Vysoká poptávka nebo údržba může vytvořit fronty (proměnlivé, mohou trvat dny až týdny).
- Doba tisku: Určuje se podle výšky, objemu a parametrů dílu (může se pohybovat od hodin u malých dílů až po několik dní u velkých/složitých konstrukcí).
- Chlazení a odprášení: Čas na vychladnutí stavební desky před vybalením a následným odstraněním prášku (hodiny až den).
- Následné zpracování: To často významně přispívá k celkové době realizace:
- Léčba stresu/tepla: Cyklus pece trvá hodiny až dny, včetně náběhu a ochlazení.
- Podpora Odstranění & Základní povrchová úprava: Velmi variabilní v závislosti na složitosti (hodiny až dny).
- CNC obrábění: V závislosti na složitosti a dostupnosti stroje (ve dnech).
- Vnější procesy (HIP, povrchová úprava): V závislosti na plánování dodavatele se může prodloužit o dny nebo týdny.
- Zajištění kvality & Inspekce: Kontrola rozměrů, zkoušky materiálu (pokud jsou vyžadovány), dokumentace (hodiny až dny).
- Doprava: Doba přepravy do místa zákazníka.
Typické rozmezí dodací lhůty:
- Prototypy (jednoduché, minimální následné zpracování): Často 5-10 pracovních dnů.
- Funkční prototypy (s tepelným zpracováním, základní povrchová úprava): Obvykle 10-15 pracovních dnů.
- Malosériová výroba dílů (vyžadující obrábění, plnou kontrolu kvality): Může se pohybovat od 3 do více než 6 týdnů, což velmi závisí na složitosti a velikosti dávky.
Získání přesných odhadů: Nejlepším způsobem, jak zjistit náklady a dodací lhůtu pro konkrétní držák EV, je předložit 3D model CAD a podrobné požadavky (materiál, tolerance, povrchová úprava, množství) renomovaným poskytovatelům služeb, jako je Met3dp, k vypracování oficiální cenové nabídky. Jasná komunikace o kritických vlastnostech a požadovaném následném zpracování je zásadní pro přesné zadání zakázky B2B.
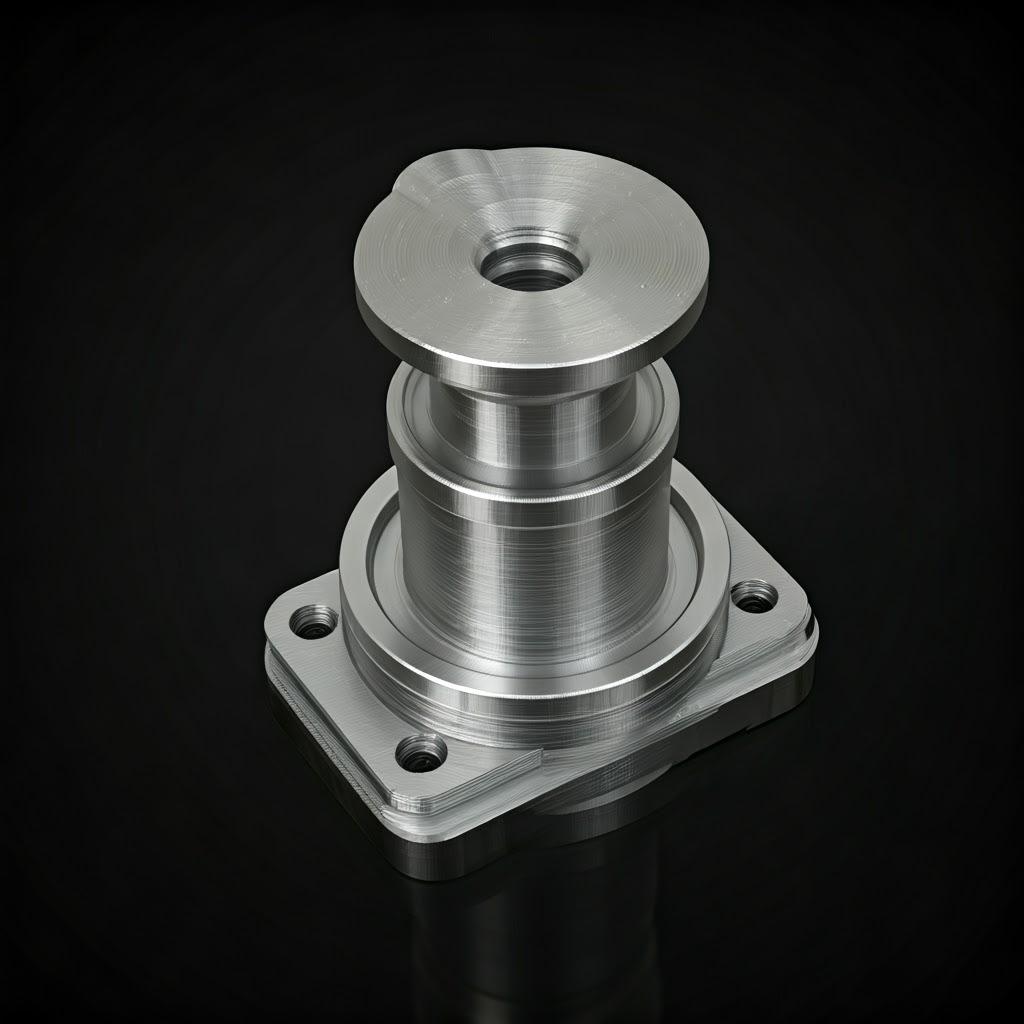
Často kladené otázky (FAQ) o 3D tištěných držácích pro elektromobily
Zde jsou odpovědi na některé časté otázky inženýrů a manažerů nákupu týkající se použití aditivní výroby kovů pro držáky pohonných jednotek elektrických vozidel:
Otázka 1: Je 3D tištěný hliník (jako AlSi10Mg nebo A7075) dostatečně pevný pro náročné aplikace držáků hnacího ústrojí?
A: Rozhodně. Při správném zpracování a vhodném následném tepelném zpracování (např. popouštění T6) mají 3D tištěné hliníkové slitiny vynikající mechanické vlastnosti.
- AlSi10Mg (T6): Poskytuje pevnost srovnatelnou nebo vyšší než typické slitiny hliníkových odlitků, takže je vhodný pro mnoho středně zatížených držáků. Poměr pevnosti k hmotnosti je velmi dobrý.
- A7075 (T6/T73): Nabízí výjimečně vysokou pevnost, která se často blíží pevnosti některých ocelí, ale má zhruba třetinovou hustotu. Díky tomu je ideální pro vysoce namáhané součásti, kde je rozhodující maximální pevnost a minimální hmotnost. Klíčem je správný výběr materiálu na základě požadavků na zatížení, ověřených parametrů procesu a přísné kontroly kvality, včetně nezbytných tepelných úprav. Aditivně vyráběné konzoly, zejména ty, které využívají optimalizaci topologie, mohou často překonat tradičně vyráběné protějšky z hlediska poměru tuhosti a hmotnosti.
Otázka 2: Jaké jsou náklady na 3D tištěné držáky EV ve srovnání s tradičním odléváním nebo CNC obráběním?
A: Srovnání nákladů do značné míry závisí na složitosti dílů, objemu a optimalizaci konstrukce:
- Prototypy a malé objemy (50-100 kusů): Kovový AM je často cenově vysoce konkurenceschopný nebo dokonce levnější než odlévání (kvůli vysokým nákladům na nástroje) a složité CNC obrábění (kvůli plýtvání materiálem a strojnímu času).
- Střední objemy (stovky jednotek): Srovnání se stává bližším. AM může být stále konkurenceschopná, pokud je konstrukční složitost vysoká, umožňuje významnou konsolidaci dílů nebo umožňuje podstatné odlehčení, kterého nelze dosáhnout jinak.
- Velké objemy (více než tisíce kusů): Tradiční tlakové lití se obvykle stává nákladově nejefektivnější metodou na jeden díl za předpokladu, že je konstrukce vhodná pro lití. AM však může být stále používána pro specifické výklenkové aplikace nebo v případech, kdy její jedinečné výhody (složitost, doba přípravy změn návrhu) převáží rozdíl v nákladech na jeden díl.
- Faktor složitosti: U velmi složitých geometrií, které je obtížné nebo nemožné efektivně odlévat nebo obrábět, může AM zůstat konkurenceschopná i při vyšších objemech.
- Celkové náklady na vlastnictví (TCO): Zvažte i jiné faktory než jen cenu za díl, například nižší náklady na montáž (díky konsolidaci dílů), nižší potřebu zásob (výroba na vyžádání) a výkonnostní výhody odlehčení (lepší dojezd/účinnost elektromobilu).
Otázka 3: Jaká je obvyklá doba pro získání prototypu držáků pro elektromobily pomocí 3D tisku z kovu?
A: Doba realizace prototypů je jednou z hlavních výhod AM’. Obvykle můžete očekávat:
- Jednoduché prototypy (minimální následné zpracování): 5-10 pracovních dnů.
- Funkční prototypy (vyžadující tepelné zpracování, základní povrchovou úpravu): 10-15 pracovních dnů. Mezi faktory ovlivňující tuto hodnotu patří kapacita/plánování poskytovatele, velikost/složitost dílu (určující dobu tisku) a rozsah požadovaného následného zpracování. Při žádosti o cenovou nabídku si vždy ověřte dobu realizace. Toto rychlé vyřízení je neocenitelné pro urychlení vývojových cyklů EV.
Otázka 4: Mohou být funkční prvky, jako jsou chladicí kanály nebo závitové otvory, integrovány přímo do 3D tištěných držáků?
A: Ano, to je další významná výhoda kovu AM:
- Chladicí kanály: Technologie AM umožňuje vytvářet složité konformní chladicí kanály přímo v konstrukci držáku. To je velmi výhodné pro odvod tepla z přilehlých součástí, jako je výkonová elektronika nebo motory, a potenciálně tak odpadá potřeba samostatných chladičů a zvyšuje se tepelná účinnost.
- Závitové otvory: Vlákna lze sice někdy tisknout přímo, ale jejich kvalita a pevnost nemusí být optimální, zejména u menších vláken. Obvyklým osvědčeným postupem je navrhnout a vytisknout pilotní otvory a poté při následném zpracování použít tradiční CNC řezání závitů, aby bylo dosaženo přesných, silných a standardizovaných závitů.
- Další funkce: Montážní šrouby, vodicí lišty pro vedení kabelů, zásuvné prvky (při pečlivém návrhu) a složité styčné plochy mohou být integrovány, což podporuje úsilí o konsolidaci dílů.
Závěr: Urychlení inovací elektrických vozidel pomocí pokročilé aditivní výroby kovů
Neustálá snaha o lehčí, účinnější a výkonnější elektromobily vyžaduje změnu paradigmatu v navrhování a výrobě kritických součástí, jako jsou držáky hnacího ústrojí. Aditivní výroba kovů, zejména laserová prášková fúze s využitím pokročilých hliníkových slitin, jako jsou AlSi10Mg a A7075, nabízí výkonné řešení, jak se s těmito výzvami vypořádat.
Jak jsme již prozkoumali, výhody jsou přesvědčivé: bezkonkurenční volnost návrhu umožňující optimalizaci topologie a konsolidaci dílů, významný potenciál odlehčení, který je zásadní pro prodloužení dojezdu elektromobilů, možnost rychlého prototypování, které urychluje vývojové cykly, a schopnost vyrábět složité geometrie nedosažitelné tradičními metodami. Přestože jsou úvahy o tolerancích, povrchové úpravě, následném zpracování a výběru správného výrobního partnera zásadní, strategické výhody, které AM nabízí, mění automobilové inženýrství.
Přijetím zásad DfAM a využitím možností pokročilých kovových prášků a tiskových systémů mohou výrobci automobilů a jejich dodavatelé B2B vytvářet držáky hnacího ústrojí pro elektromobily, které nejsou pouze funkční, ale skutečně optimalizované pro jedinečné požadavky elektromobility. Překonání výzev vyžaduje odborné znalosti a důkladnou kontrolu procesů, což podtrhuje význam spolupráce se znalými poskytovateli služeb.
Společnost Met3dp je se svým komplexním portfoliem zahrnujícím vysoce výkonné kovové prášky, špičková zařízení pro 3D tisk a hluboké zkušenosti s aplikacemi připravena podpořit přechod automobilového průmyslu. Jejich závazek ke kvalitě, spolehlivosti a inovacím poskytuje základ potřebný k využití plného potenciálu technologie AM s kovy.
Chcete-li zjistit, jak může aditivní výroba kovů revolučně změnit výrobu komponentů pro elektromobily a řešit vaše specifické potřeby v oblasti držáků hnacího ústrojí, doporučujeme vám obrátit se na odborníky v této oblasti. Kontaktujte Metal3DP a prodiskutovat s vámi vaše projektové požadavky a zjistit, jak mohou jejich špičkové systémy a pokročilé materiály podpořit cestu vaší organizace k výrobě elektromobilů nové generace. Budoucnost automobilových inovací se buduje vrstvu po vrstvě - zajistěte si správného partnera, který vám ji pomůže vybudovat lépe.
Sdílet na
MET3DP Technology Co., LTD je předním poskytovatelem řešení aditivní výroby se sídlem v Qingdao v Číně. Naše společnost se specializuje na zařízení pro 3D tisk a vysoce výkonné kovové prášky pro průmyslové aplikace.
Dotaz k získání nejlepší ceny a přizpůsobeného řešení pro vaše podnikání!
Související články
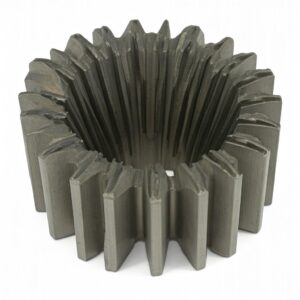
Vysoce výkonné segmenty lopatek trysek: Revoluce v účinnosti turbín díky 3D tisku z kovu
Přečtěte si více "O Met3DP
Nedávná aktualizace
Náš produkt
KONTAKTUJTE NÁS
Nějaké otázky? Pošlete nám zprávu hned teď! Po obdržení vaší zprávy obsloužíme vaši žádost s celým týmem.
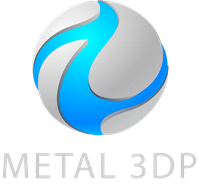
Kovové prášky pro 3D tisk a aditivní výrobu