Prášek hliníku niklu: Vlastnosti, výroba a aplikace
Obsah
Prášek oxidu hlinitého niklu je intermetalická sloučenina složená z niklu a hliníku. Nabízí vysokou pevnost, odolnost proti oxidaci a korozi a tepelnou stabilitu, díky čemuž je vhodný pro použití v průmyslových odvětvích, jako je letecký průmysl, automobilový průmysl, energetika a chemie.
Přehled prášku z niklového aluminidu
Niklový aluminid se vztahuje na řadu slitin složených primárně z niklu a hliníku, přičemž nikl tvoří více než 50 % hmotnosti slitiny. Nejběžnějším typem používaným komerčně je Ni3Al, který poskytuje optimální kombinaci vlastností.
Mezi klíčové vlastnosti a charakteristiky prášku z niklového aluminidu patří:
Složení:
- Primárně nikl (více než 50 % hmotnosti) a hliník
- Malé množství legujících prvků jako chrom, zirkonium, bor
- Přesné složení se liší podle třídy
Výrobní metody:
- Rozprašování plynu
- Plazmový proces s rotujícími elektrodami (PREP)
Tvar částic: Sférické, vysoce tekoucí
Velikost částic: 15 - 150 mikronů
Bod tání: 1638 °F (890 °C)
Hustota: 7,6 g/cm3
Síla: Lepší než superslitiny na bázi niklu
Odolnost proti oxidaci: Vynikající do ~1000 °C
Odolnost proti korozi: Vysoká v redukční a neutrální atmosféře
Náklady: Vyšší než prášky niklu nebo hliníku
Vyváženost vlastností niklového aluminidu jej činí vhodným pro konstrukční použití při vysokých teplotách v korozivním nebo oxidačním prostředí napříč průmyslovými odvětvími.
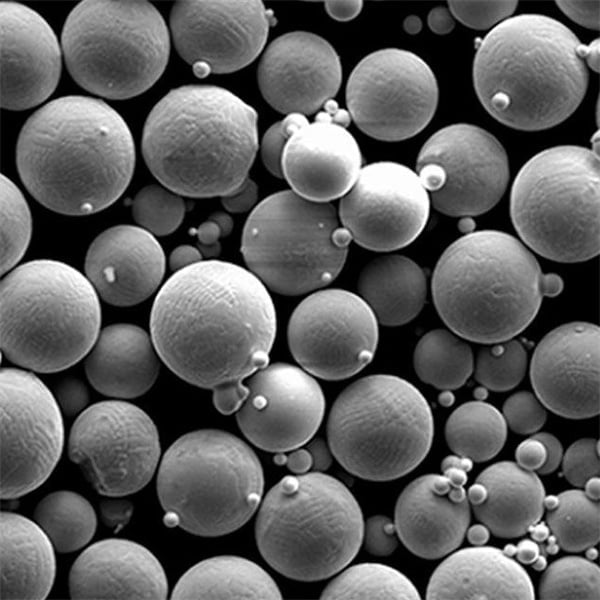
Typy Prášky z niklového aluminidu
Prášky z niklového aluminidu lze kategorizovat podle složení, tvaru prášku, rozsahu velikosti částic, výrobní metody a dalších parametrů.
Podle složení
Poměr niklu a hliníku určuje typ vytvořeného niklového aluminidu. Mezi běžné typy patří:
Typ | Popis |
---|---|
Ni3Al | Nejpoužívanější komerčně. Nabízí optimální rovnováhu vlastností. Bod tání 1638 °F (890 °C). |
NiAl | Vyšší obsah hliníku. Tažnější, ale méně pevný nad 1000 °F (540 °C). Bod tání 2552 °F (1400 °C). |
NiAl3 | Vyšší obsah niklu. Používá se tam, kde je pevnost kritická. Křehký intermetalický. Bod tání 1740 °F (950 °C). |
Legující přísady jako 1-3 % chromu a 0,1 % boru nebo zirkonia se také přidávají pro přizpůsobení specifických mechanických, environmentálních nebo výrobních vlastností.
Podle tvaru a velikosti prášku
Prášek z niklového aluminidu může mít kulovitý nebo nepravidelný tvar. Kulovité prášky mají vyšší tekutost a hustotu balení. Běžné rozsahy velikostí zahrnují:
Velikost ok | Velikost mikronů | Typické použití |
---|---|---|
140 – 325 | 44 – 105 | Aditivní výroba |
325 – 500 | 15 – 44 | Tepelné stříkání |
-140 | <105 | Slisování a slinování |
Jemnější prášky jsou vhodné pro aditivní výrobní techniky, jako je selektivní laserové slinování (SLS) a laserové nanášení kovu (LMD) pro složité, rozměrově přesné díly. Hrubší částice fungují lépe pro jiné techniky konsolidace.
Podle způsobu výroby
Technika výroby niklového aluminidu ovlivňuje složení, tvar, rozložení velikosti, tekutost, mikrostrukturu a náklady. Hlavní metody jsou:
Metoda | Popis | Charakteristika |
---|---|---|
Atomizace plynu | Roztavený proud rozložený vysokotlakými plynovými tryskami | Jemný kulovitý prášek, 15 – 106 μm. Řízené složení a distribuce velikosti. Nákladné. |
Proces plazmové rotující elektrody (PREP) | Elektroda roztavená plazmovým obloukem. Materiál odhozen odstředivou silou | Nepravidelný úhlový prášek, 106 – 250 μm. Nižší náklady, vyšší obsah kyslíku. |
Prášek atomizovaný plynem má kulovitou morfologii ideální pro aditivní výrobu, zatímco prášek PREP je levnější, ale s vyšším obsahem kyslíku.
Aplikace a použití prášku z niklového aluminidu
Jedinečná kombinace vlastností niklového aluminidu vedla k jeho přijetí v průmyslových odvětvích, jako je letecký průmysl, automobilový průmysl, energetika, chemické zpracování a další, kde se cení odolnost vůči teplu, korozi, opotřebení nebo oxidaci.
Podle průmyslu nebo aplikace
Mezi hlavní aplikace patří:
Letectví: Lopaty turbín, rotory turbodmychadel, trysky raket, spalovací komory
Automobilový průmysl: Rotory turbodmychadel, části výfukového systému
Energie: Výměníky tepla pro solární tepelné, jaderné a chemické zpracování
Chemické: Ventily, potrubí a procesní zařízení pro korozivní služby
Aditivní výroba: Komplexní strukturální prototypy a koncové díly
Povlaky: Tepelně stříkané povlaky pro ochranu proti opotřebení a korozi
Podle formy produktu
Prášek z niklového aluminidu lze použít k výrobě hotových dílů pomocí metod, jako jsou:
- Aditivní výroba (SLS, DMLS)
- Vstřikování kovů
- Izostatické lisování za tepla
- Tepelně stříkané povlaky
- Svařování
Slouží buď jako konečný materiál dílu, nebo jako povlak aplikovaný na niklové superslitiny, nerezové oceli nebo jiné substráty.
Podle funkce a výhod
Mezi klíčové vlastnosti, které podporují přijetí napříč aplikacemi, patří:
Odolnost proti oxidaci: Chrání proti oxidaci pro delší životnost součástí při teplotách nad 1000 °C
Tepelná odolnost: Zachovává pevnost v tenkých částech při teplotách nad 1000 °F po delší dobu
Odolnost proti korozi: Odolává napadení sloučeninami síry a solemi
Odolnost proti opotřebení: Poskytuje tvrdý, hladký povrch pro ochranu proti opotřebení
Odlehčování: Umožňuje lehčí komponenty než niklové superslitiny
Tepelná odolnost proti únavě: Odolává praskání z tepelných cyklů
Odolnost vůči tečení: Zachovává tvar při trvalém zatížení při vysokých teplotách
Specifikace niklového aluminidu
Produkty prášku z niklového aluminidu musí splňovat limity složení, rozložení velikosti částic, morfologii, průtok, chemické testy, mikrostrukturu a omezení nečistot v závislosti na aplikaci a potřebách zákazníků.
Specifikace | Podrobnosti |
---|---|
Složení | Primárně nikl + hliník. Různé množství Cr, Zr, B, C, Y, Hf atd. |
Distribuce velikosti částic | Specifické pro aplikaci. <15 μm pro AM, až 150 μm pro lisování. |
Tvar a morfologie prášku | Preferuje se kulovitý. Satelitní částice omezeny. |
Chemická analýza | Odpovídá specifikaci třídy pro Ni, Al a další legující prvky |
Průtoková rychlost | >50 s/50 g pro zajištění dobré tekutosti |
Nečistoty | Limity pro O, N, S. Žádné inkluze ani satelity. |
Zdánlivá hustota | Typicky 4 – 5 g/cm3 |
Mikrostruktura | Homogenní, málo pórů nebo dutin |
Kromě toho se mechanické vlastnosti jako pevnost, modul, tvrdost, tažnost atd. ověřují testováním vzorků vyrobených z prášku.
Prášek hliníku niklu Dodavatelé
Prášek z niklového aluminidu vhodný pro aditivní výrobu, termické stříkání, lisování a další aplikace je k dispozici od řady výrobců po celém světě.
Společnost | Značky | Výrobní metody |
---|---|---|
Sandvik | Osprey® | Rozprašování plynu |
Tesařská technologie | Kulovitý niklový aluminid | Rozprašování plynu |
Hoganas | Hoganas NiAl | Rozprašování plynu |
PyroGenesis | PyroNiAl | Plazmová atomizace |
Atlantik vybavení inženýrů | AEE NiAl | Rozprašování plynu |
Ceny se liší v závislosti na složení, rozsahu velikostí, tvaru a objemu nákupu – od 50 USD/kg za prášek atomizovaný plazmou až po 120+ USD/kg za speciální kulovitý niklový aluminid atomizovaný plynem optimalizovaný pro aditivní výrobu.
Prášek z niklového aluminidu ve srovnání s alternativami
Mezi klíčové alternativy k prášku z niklového aluminidu patří niklové superslitiny, nerezové oceli, kobaltové slitiny a slitiny MCrAlY.
Ve srovnání s niklovými superslitinami:
- Méně hustý (7,6 g/cm3 vs 8 – 9 g/cm3), tedy lehčí
- Nižší pevnost při extrémních teplotách (>1100 °C)
- Lepší odolnost proti oxidaci do 1000 °C
- Nižší náklady
Ve srovnání s nerezovými oceli:
- Vyšší pevnost při zvýšených teplotách
- Vynikající odolnost proti oxidaci a korozi
- Obtížnější obrábění a výroba
- Dražší
Ve srovnání s kobaltovými slitinami:
- Bez rizik dodavatelského řetězce kobaltu
- Nižší náklady na suroviny
- Vyšší odolnost proti oxidaci
- Nižší pevnost v tahu v některých teplotních rozsazích
Ve srovnání se slitinami MCrAlY:
- Vyšší pevnost
- Lepší fázová stabilita při typických provozních teplotách
- Méně tvárný a houževnatější
Zatímco niklový aluminid zaostává za superslitinami ve vlastnostech při extrémních teplotách, jeho dobře zaoblené schopnosti a nižší náklady jej staví jako alternativní materiál volby pro tepelně náročné aplikace napříč průmyslovými odvětvími.
Výhody a omezení niklového aluminidu
Niklový aluminid nabízí vynikající odolnost proti oxidaci a korozi spolu s dobrou pevností při zvýšených teplotách. Existují však i určité nevýhody ve srovnání s alternativami.
Výhody
Pevnost při vysokých teplotách – Zachovává si slušnou pevnost a odolnost proti tečení až do 1100 °C. Tenké profily zůstávají pevné i při vyšších teplotách.
Odolnost proti oxidaci – Tvoří ochrannou vrstvu oxidu hlinitého, která umožňuje použití až do ~1000 °C. 4krát delší životnost ve srovnání se superslitiny.
Hustota – Součásti z niklového aluminidu o hustotě 7,6 g/cm3 jsou lehčí než alternativy, jako je ocel nebo niklové superslitiny. Umožňuje odlehčení.
Odolnost proti korozi – Vysoce odolné vůči sulfidaci a korozi vyvolané chloridy až do 900 °C.
Tepelná vodivost – Dvojnásobek oproti superslitinám, pro lepší odvod tepla ze součástí. Zajišťuje odolnost proti tepelné únavě.
Tepelná roztažnost – Téměř shodné s niklovými superslitinami. Snižuje tepelnou únavu a praskání.
Svařitelnost – Lze svařovat tavným svařováním pro opravu součástí.
Obrobitelnost – O něco lepší obrobitelnost než srovnatelné niklové superslitiny.
Náklady – Levnější než superslitiny na základě ekvivalentního výkonu.
Nevýhody a omezení
Pevnost při extrémních teplotách – Pevnost v tahu klesá nad 1000 °C rychleji ve srovnání se superslitinami. Užitečný limit ~1100 °C.
Tažnost a houževnatost při lomu – Křehká intermetalická sloučenina. Selhává dříve, než vykazuje velkou plastickou deformaci.
Zpracovatelnost – Stejně jako u jiných vysoce výkonných slitin může být tváření a výroba obtížná. Možné je omezené tváření za studena.
Náklady na suroviny – Dražší než ocel nebo hliníkové slitiny. Cena je volatilní s cenami niklu.
Povlakovatelnost – Obtížné nanášení silných, hustých povlaků pomocí termického nástřiku nebo jiných metod.
Dostupnost – Jako novější slitina je dostupnost forem výrobků a znalostí zpracování ve srovnání s tradičními slitinami omezená.
Velikost součásti – Velké, složité díly se obtížně vyrábějí, zejména pomocí nových metod, jako je aditivní výroba.
Niklový aluminid tedy není vhodný pro nejnáročnější tepelné aplikace, kde tažnost, zpracovatelnost a pevnost při extrémních teplotách převyšují všechny ostatní faktory. Jeho dobře vyvážený výkon z něj však činí kandidáta na nahrazení superslitin, nerezových ocelí nebo povlaků v aplikacích s o něco méně agresivními požadavky za potenciálně nižší cenu.
Způsoby zpracování niklového aluminidu
Vzhledem k jeho vysoké pevnosti a křehkosti vyžaduje niklový aluminid pro výrobu dílů a součástí nekonvenční metody zpracování.
Aditivní výroba
Také známý jako 3D tisk, umožňuje vytvářet složité, optimalizované geometrie vrstvu po vrstvě přímo z prášku slitiny. Selektivní laserové tavení (SLM), přímé laserové slinování kovů (DMLS) a laserové nanášení kovu (LMD) jsou oblíbené techniky AM pro niklový aluminid.
Výhody: Maximální svoboda návrhu, přizpůsobené součásti, snížený odpad, kratší dodací lhůty
Omezení: Pomalé rychlosti stavění, vysoké náklady na zařízení, omezené velikosti, často je vyžadováno dodatečné zpracování
Vstřikování kovů
Prášek se smíchá se pojivem, vytvaruje do specializovaného tvaru, pojivo se odstraní a součást se slinuje. Kombinuje všestrannost vstřikování plastů s výkonem kovových dílů.
Výhody: Těsné tolerance, vynikající povrchové úpravy, rychlé, automatizované zpracování
Omezení: Omezení velikosti dílů, vyžaduje se specializovaný materiál, kroky po slinování
Prášková metalurgie
Prášek niklového aluminidu se slisuje do forem a zhutní. HIP lze použít pro plnou hustotu. Konvenční techniky lisování a slinování umožňují vysoké objemy za nižší náklady.
Výhody: Mírně složité geometrie, schopnost vytvářet konečný tvar, husté vlastnosti
Omezení: Méně přesné než aditivní techniky, jednodušší tvary
Tepelné nástřiky
Práškový materiál niklového aluminidu se zahřívá a žene na substráty, aby se pomocí různých technik nanášely silné kovové povlaky – plazmový nástřik, HVOF atd.
Výhody: Ochranné povlaky pro velké součásti, jako jsou potrubí nebo nádrže
Omezení: Vysoká pórovitost, omezení tloušťky povlaku, rozsáhlá příprava substrátu
Investiční odlévání
Roztavený niklový aluminid se nalije do specializovaných forem vytvořených z voskových vzorů pro složité, přesné odlévané díly.
Výhody: Vynikající povrchová úprava, přesnost rozměrů, složité tvary v hotovém stavu
Omezení: Omezení velikosti dílů, nákladné nástroje
Zatímco konvenční výroba na bázi fréz a soustruhů je pro niklový aluminid velmi omezena, tyto nové metody nabízejí rozšířené výrobní možnosti v souladu s vysokým výkonovým potenciálem slitiny.
Výzkum a vývoj
Zatímco niklový aluminid má atraktivní vlastnosti, probíhající výzkum a vývoj se zaměřuje na rozšiřování porozumění mechanismům zpevňování slitiny, zlepšování tažnosti a houževnatosti při lomu při pokojové teplotě, zdokonalování složení a mikrostruktur řízených výpočetním modelováním a kvalifikaci pro aplikace při extrémních teplotách v leteckých motorech, pozemních turbínách a raketových motorech a jaderných reaktorech.
Optimalizace slitiny
Přidávání tantalu, chromu, boru a dalších prvků do slitiny může upravit houževnatost niklového aluminidu při pokojové teplotě a mechanické vlastnosti při vysokých teplotách. Termodynamické simulace spojené s umělou inteligencí pomáhají při identifikaci složení odolných vůči oxidaci, tečení a segregaci.
Manipulace se strukturou zrn
Velikost a morfologie zrn niklového aluminidu ovlivňuje jeho tažnost v tahu a tečení. Použití směrového tuhnutí k vytvoření orientovaných, sloupcovitých zrn zlepšuje houževnatost při lomu při pokojové teplotě a odolnost proti šíření únavových trhlin. Extra velké sloupcovité zrno také zvyšuje životnost při tečení a lomu.
Inženýrství inkluzí
Zavedení nanočástic oxidu zirkoničitého nebo jiné keramiky brání klouzání hranic zrn, což radikálně zlepšuje odolnost proti tečení při vysokých teplotách. Tyto částice také zachycují škodlivé stopové prvky.
Hybridní výroba
Kombinace aditivní výroby s vrstveným nanášením a obrábění umožňuje využít pevnost niklového aluminidu výhradně tam, kde je to potřeba, zatímco tažnější slitiny jsou integrovány do oblastí vyžadujících odolnost proti poškození.
Vývoj povlaků
Aplikace ochranných povlaků s vynikající odolností vůči prostředí na součásti z niklového aluminidu vytváří kompozitní systém, který spojuje teplotní schopnosti niklových aluminidů s extrémní odolností proti korozi.
Spojování a opravy
Niklové aluminidy se ukázaly jako náročné na tavné svařování bez praskání. Vývoj pájení při nižších teplotách, spojování v přechodné kapalné fázi a techniky spojování práškovou metalurgií umožňuje použití niklového aluminidu ve složitějších sestavách a obnovu poškozených součástí.
Zatímco niklový aluminid již dnes prokazuje své zásluhy pro tepelně náročné aplikace, probíhající vědecké a technologické úsilí si klade za cíl plně odemknout jeho potenciální výkonnostní limity v nejagresivnějších prostředích použití napříč průmyslovými odvětvími.
Zásady návrhu niklového aluminidu
Součásti a díly navržené pro niklový aluminid musí zohledňovat jeho jedinečnou kombinaci vysoké pevnosti a nízké tažnosti a odolnosti proti lomu při pokojové teplotě.
Koncentrace napětí
Vyvarujte se zářezů, malých otvorů, ostrých rohů a dalších nerovnoměrných geometrií vytvářejících lokalizované zvýšení napětí, které mohou iniciovat praskliny i při mírném zatížení. Nebo lokálně vyztužte oblast silnějšími průřezy.
Zbytková napětí
Minimalizujte metody zpracování zavádějící zbytková tahová napětí, jako je nadměrné tváření za studena, které se mohou kombinovat s provozními napětími a překročit místní limity lomu.
Tepelná stabilita
Pro provoz nad 1000 °C zajistěte, aby expozice nepřekračovaly dobu, která by vedla k vývoji mikrostruktury negativně ovlivňující mechanické vlastnosti v důsledku elementární distribuce nebo srážení křehkých fází.
Životnost při únavě
Navrhněte pro konečnou životnost při cyklickém namáhání stanovením bezpečných limitů amplitudy střídavého napětí korelovaných s celkovými provozními cykly, s přihlédnutím k průměrným napětím a prostředí.
Odolnost vůči poškození
Navrhněte dostatečnou houževnatost při lomu prostřednictvím výběru složení, řízení struktury zrn a hybridních přístupů ke slitinám, abyste odolali iniciaci a růstu trhlin nebo umožnili detekci pomocí nedestruktivní kontroly.
Tolerance koroze
V podstatě by se niklový aluminid měl v návrhu používat konzervativně, podobně jako keramika – se zaměřením na mírné, rovnoměrné napětí a deformace, přičemž se vyhýbá koncentrátorům napětí a maximalizuje se tloušťka průřezu, jak je povoleno. Tím se zajistí, že se případné lokální vady během používání nešíří, což by vedlo k předčasnému selhání. Díky pečlivému inženýrství informovanému o jedinečných schopnostch niklového aluminidu oproti omezením slouží spolehlivě napříč mnoha tepelně náročnými aplikacemi, které umožňuje.
Kontrola kvality a inspekce niklového aluminidu
Zajištění prášek oxidu hlinitého niklu a vyrobené součásti splňují specifikace, vyžaduje kombinaci pozitivní identifikace materiálu, odběru vzorků a chemické analýzy, charakterizace mikrostruktury, nedestruktivního hodnocení a validace mechanických vlastností.
Prášková analýza potvrzuje chemii pomocí emisní spektroskopie nebo rentgenové fluorescenční spektroskopie v souladu se specifikacemi třídy. Prosévání určuje shodu distribuce velikosti částic. Zdánlivá hustota a rychlost toku podle Halla měří vlastnosti prášku pro vhodnost následného zpracování.
Pozitivní identifikace materiálu (PMI) pomocí laserem indukované spektroskopie rozpadu nebo rentgenové fluorescenční spektroskopie určuje skutečné versus očekávané složení slitiny přítomné pro zajištění kvality.
Optická mikroskopie hodnotí mikrostrukturu – homogenitu, velikost zrn, nežádoucí fáze, vady – při zvětšení až 1000x na připravených vzorcích. Analýza obrazu kvantifikuje charakteristiky zrn.
Skenovací elektronová mikroskopie odhaluje jemnější mikrostrukturní detaily, jako jsou hranice zrn, drobné trhliny, intermetalické sraženiny a inkluze. Elementární mapy potvrzují rovnoměrnost distribuce.
Transmisní elektronová mikroskopie poskytuje nejvyšší zvětšení pohledů na vnitřní struktury, rozlišuje nano-sraženiny, atomové dislokace, fázové hranice a zpevňující částice v kovové matrici.
Chemické testování pomocí emisní spektroskopie nebo hmotnostní spektrometrie detekuje stopové prvky na úrovni částic na milion, čímž se určí, zda nečistoty, jako je síra, kyslík a uhlík, splňují limity.
Rentgenová difrakce identifikuje přítomné fáze podle jejich jedinečných difrakčních vzorců atomové mřížky. Potvrzuje, že složení fáze odpovídá očekáváním.
Mechanické testování určuje, zda pevnost, tažnost, houževnatost při lomu, vysokocyklová únava, odolnost proti tečení, parametry růstu trhlin a další vlastnosti dosahují minimálních hodnot návrhu prostřednictvím standardizovaných zkoušek vzorků v tahu, tlaku, ohybu, lomu a cyklického zatížení v rozsahu teplot.
Nedestruktivní hodnocení pomocí penetrační kapaliny, magnetických částic, ultrazvukové a radiografické kontroly odhaluje povrchové a vnitřní vady. Ověřte integritu kritických oblastí.
Zkouška koroze vystavením prostředí simulujícím provozní podmínky – solná mlha, plyny obsahující síru, produkty spalování, kyseliny – hodnotí výkonnost oproti cílům. Analýza po zkoušce odhaluje režimy napadení.
Hodnocení životnosti Testování při dlouhodobě zvýšené teplotě předpovídá přežití při tečení, pevnosti v tahu a termomechanické únavě odpovídající potřebám aplikace – tisíce hodin pro letecké motory nebo roky pro výrobu energie. Potvrzuje konstrukční rezervy.
U niklového aluminidu je dosažení očekávaného výsledku silně závislé na ověření, že chemické složení, mikrostruktura a vlastnosti odpovídají specifikacím, normám a zamýšleným provozním podmínkám. Validace kvality v kombinaci s řízením procesů zajišťuje spolehlivý výkon v náročných aplikacích.
Kódy a normy pro nikl-aluminid
Použití nikl-aluminidu v různých průmyslových odvětvích vyžaduje shodu na technických specifikacích týkajících se chemického složení, minimálních vlastností, kontrol kvality, výrobních procesů, kontrolních postupů a metodiky návrhu. Standardy specifické pro danou aplikaci mají za cíl zajistit životnost, bezpečnost a funkčnost.
Aerospace
AMS 4001 – Odlitky z nikl-aluminidu
AMS 2774 – Tepelné zpracování práškových slitin niklu a hliníku
Tyto normy pokrývají chemické složení, mechanické vlastnosti při pokojové a zvýšené teplotě, metalografické standardy, zkušební postupy, kroky zajištění kvality a řízení procesů přizpůsobené pro součásti leteckých motorů.
Aditivní výroba
ASTM F3055 – Standardní specifikace pro aditivní výrobu konstrukčních součástí z nikl-aluminidu (Ni3Al) pomocí tavení práškové vrstvy
Poskytuje požadavky na práškový vsázkový materiál, konstrukční principy, základy procesu, následné zpracování, zkušební metody, kontrolu a kritéria přijetí při výrobě dílů z nikl-aluminidu pomocí technologií laserového tavení práškové vrstvy.
Automobilový průmysl
Ačkoli standardy specifické pro automobilový průmysl jsou stále ve vývoji, kontroly a pokyny pro použití vysoce výkonných slitin z leteckého nebo energetického sektoru se často adaptují nebo přijímají.
Průmyslové vytápění
Stupně ASM 2700 definují různé slitiny nikl-aluminidu používané pro sálavé trubice, mufle a další součásti pecí, specifikující chemické složení, mechanické vlastnosti, formy výrobků a kontroly kvality přizpůsobené pro prostředí tepelného zpracování.
Celkově platí, že použití těchto široce akceptovaných kódů a specifikací při výrobě nebo nákupu nikl-aluminidu stanoví soulad mezi výrobci, výrobci dílů a koncovými uživateli v metrikách souvisejících s kvalitou, spolehlivostí a bezpečností pro zamýšlené teplotní zatížení.
Výzkumné publikace o nikl-aluminidu
Mezi klíčová témata nikl-aluminidu, která se celosvětově zkoumají, patří:
- Základní mechanismy deformace, zpevňování a poškození
- Vývoj slitin
- Výroba prášku a začlenění keramických částic
- Aditivní výroba
- Hybridní struktury s jinými slitinami
- Ochranné nátěry
- Zlepšení svařitelnosti
Zvýraznění
- Oxfordská univerzita modelovala mezimolekulární vazby přísad do slitin, aby se snížilo zkřehnutí
- University of Wisconsin prokázala 30-40% zlepšení životnosti při tečení pomocí nano-inkluzí oxidu zirkoničitého
- JAMRI Japonsko vyvinulo lopatky z nikl-aluminidu pro testování turbín při 700 °C
- GE Aviation vyrábí díly turbín pomocí technologie laserového tavení práškové vrstvy
- ANSTO Austrálie vytvořila inovativní metody spojování při nižších teplotách
Přední výzkumné skupiny a hlavní hráči v průmyslu po celém světě nadále rozšiřují možnosti nikl-aluminidu, znalosti zpracování a implementaci v kritických technologiích čisté energie, pohonu a vysokých teplot.
Neustálé publikování zjištění v respektovaných recenzovaných časopisech umožňuje sdílení získaných poznatků s cílem posunout zralost této vysoce výkonné intermetalické sloučeniny. Rostoucí množství výzkumných prací o nikl-aluminidu podtrhuje významný zájem a pokrok ve vědecké komunitě při povyšování jeho současné specializované role na mnohem širší materiálové řešení.
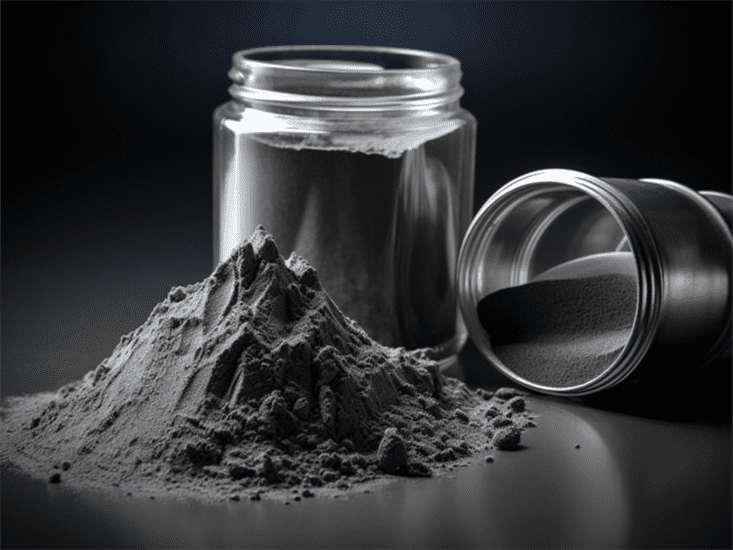
FAQ
Jaké je hlavní použití prášku z nikl-aluminidu?
Hlavním použitím je výroba součástí pro aplikace při vysokých teplotách, zejména v leteckém, energetickém a automobilovém sektoru, kde musí být zachována dobrá mechanická pevnost v intenzivně horkých, oxidačních nebo korozivních atmosférách přesahujících 1000 °F (540 °C).
Proč je nikl-aluminid lepší než nerezová ocel při vysokých teplotách?
Hliník a další legující prvky umožňují nikl-aluminidu odolávat oxidaci, korozi a deformaci mnohem lépe než nerezové oceli nad teplotou přibližně 1000 °F. Obětuje určitou houževnatost při pokojové teplotě pro tepelnou stabilitu.
Který kov má nejvyšší bod tání?
Wolfram má nejvyšší bod tání při 6192 °F (3422 °C). Nikl-aluminid si však zachovává užitečnou pevnost až do teploty přes 2000 °F, což je mnohem více než užitečný horní teplotní limit wolframu.
Je nikl-aluminid lepší než Inconel?
Superslitiny niklu Inconel nabízejí lepší pevnost v tahu při nejvyšších teplotách (>1100 °C), ale jsou těžší, dražší a mají nižší odolnost proti oxidaci než nikl-aluminidy v některých teplotních rozsazích.
V jakých průmyslových odvětvích se používá oxid hlinitý niklu?
Letecký průmysl je předním prvním uživatelem lopatek turbín, turbodmychadel a trysek raket. Použití se rozšiřuje v energetických odvětvích, jako je koncentrovaná solární energie, chemické zpracování a energetické turbíny pro odolnost nikl-aluminidu vůči teplu a korozi.
Rezaví nikl-aluminid?
Ne – Jeho vysoký obsah hliníku tvoří tvrdou vrstvu oxidu hlinitého, která chrání základní kov před útokem kyslíku při vysokých teplotách. Tato samoléčivá vrstva oxidu poskytuje vynikající odolnost proti oxidaci.
Lze nikl-aluminid svařovat?
Nikl-aluminid se obtížně svařuje tavením bez tvorby trhlin, ale probíhá pokrok, který umožňuje svařování pomocí technik pájení. Aditivní výroba laserovým tavením práškové vrstvy poskytuje alternativní přístup „svařování“ v pevném stavu.
Proč se nikl-aluminid obtížně obrábí?
Jeho vysoká pevnost odolává řezání, zatímco nízká tažnost při pokojové teplotě způsobuje praskání a trhání při obráběcím namáhání namísto plynulé deformace jako ocel. Jsou vyžadovány časté výměny nástrojů a speciální třídy s tvrdými povlaky oxidu.
Je nikl-aluminid toxický?
Elementární nikl a hliník mají nízkou toxicitu a jsou běžnými konstrukčními kovy. Jemný prášek z nikl-aluminidu však představuje zdravotní rizika pro dýchací cesty podobná jiným jemným práškům, což vyžaduje protiopatření při manipulaci a zpracování.
To jsou tedy běžné otázky týkající se vlastností, výroby a použití prášku z nikl-aluminidu. Obraťte se na nás s jakýmikoli dalšími dotazy!
Sdílet na
MET3DP Technology Co., LTD je předním poskytovatelem řešení aditivní výroby se sídlem v Qingdao v Číně. Naše společnost se specializuje na zařízení pro 3D tisk a vysoce výkonné kovové prášky pro průmyslové aplikace.
Dotaz k získání nejlepší ceny a přizpůsobeného řešení pro vaše podnikání!
Související články
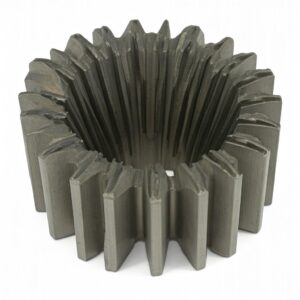
Vysoce výkonné segmenty lopatek trysek: Revoluce v účinnosti turbín díky 3D tisku z kovu
Přečtěte si více "O Met3DP
Nedávná aktualizace
Náš produkt
KONTAKTUJTE NÁS
Nějaké otázky? Pošlete nám zprávu hned teď! Po obdržení vaší zprávy obsloužíme vaši žádost s celým týmem.
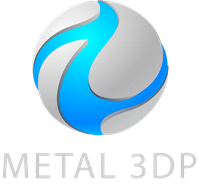
Kovové prášky pro 3D tisk a aditivní výrobu