3D tisk tlakových ventilů ze slitin odolných proti korozi
Obsah
Úvod: Kritická role tlakových ventilů v leteckém průmyslu a nástup aditivní výroby
Letecký a kosmický průmysl se pohybuje na vrcholu inženýrství a vyžaduje komponenty, které bezchybně fungují v extrémních podmínkách. Mezi nejdůležitější, ale často opomíjené patří tlakové ventily. Tato složitá zařízení jsou strážci kapalinových systémů, kteří pečlivě řídí průtok, tlak, směr a teplotu životně důležitých kapalin, jako je palivo, hydraulické oleje, chladicí kapaliny a pneumatické plyny. Tlakové ventily v letectví a kosmonautice jsou nepostradatelné pro bezpečnost letu, řízení a úspěch mise - od řízení tahu mohutných raketových motorů až po ovládání podvozku a zajištění tlaku v kabině. Selhání prostě nepřipadá v úvahu, když se pohybujete kilometry nad Zemí nebo se vydáváte do vesmírného vakua. Proto musí být tyto součásti vyrobeny podle nejvyšších standardů přesnosti, spolehlivosti a materiálové integrity a musí být schopny odolávat obrovským tlakovým rozdílům, extrémním teplotám, intenzivním vibracím a působení potenciálně korozivních médií.
Výroba těchto složitých součástí tradičně zahrnovala vícestupňové procesy, jako je odlévání, kování a rozsáhlé subtraktivní obrábění. Tyto metody se sice osvědčily, ale často s sebou nesou značná omezení. Konstrukční možnosti jsou omezeny požadavky na nástroje a dostupností obrábění, zejména u složitých vnitřních geometrií potřebných pro optimální dynamiku tekutin. Materiálový odpad může být značný, zejména při obrábění z velkých polotovarů drahých, vysoce výkonných slitin. Kromě toho mohou dlouhé dodací lhůty spojené s tvorbou nástrojů, procesy odlévání nebo kování a složitým víceosým obráběním bránit rychlé tvorbě prototypů, opakování konstrukce a celkové pružnosti výroby - což jsou kritické faktory v rychle se rozvíjejícím leteckém odvětví. Manažeři a inženýři zabývající se zadáváním zakázek neustále hledají způsoby, jak zlepšit výkon, snížit hmotnost, zkrátit dodací lhůty a optimalizovat dodavatelské řetězce, čímž posouvají hranice konvenční výroby.
Vstupte do aditivní výroby kovů (AM), známé spíše jako kovová aditivní výroba 3D tisk. Tato transformační technologie rychle mění podobu výroby leteckých součástek. Na rozdíl od subtraktivních metod, které odstraňují materiál, AM vytváří díly vrstvu po vrstvě přímo z digitálního modelu pomocí vysokoenergetických zdrojů, jako jsou lasery nebo elektronové paprsky, které spojují jemné kovové prášky. Tento přístup založený na vrstvení uvolňuje nebývalou konstrukční svobodu a umožňuje vytvářet vysoce komplexní geometrie, složité vnitřní kanály a optimalizované struktury, jejichž výroba byla dříve nemožná nebo neúměrně nákladná. U tlakových ventilů pro letectví a kosmonautiku to znamená možnost významného zvýšení výkonu díky optimalizovaným průtokovým cestám, snížení hmotnosti díky optimalizaci topologie a konsolidaci dílů a výrazné zrychlení vývojových cyklů.
Konkrétně se jako přední procesy AM pro výrobu hustých, vysoce pevných kovových dílů vhodných pro náročné aplikace v letectví a kosmonautice prosadily techniky tavení v práškovém loži (PBF), jako je selektivní laserové tavení (SLM) a přímé laserové spékání kovů (DMLS). Tyto procesy umožňují použití moderních, vysoce výkonných slitin, které jsou důležité pro integritu ventilů. Mezi nejdůležitější materiály pro tlakové ventily pro letecký průmysl, které vyžadují mimořádnou odolnost, patří korozivzdorné superslitiny, jako je Inconel 625 (IN625), a robustní nerezové oceli, jako je 316L. IN625 nabízí pozoruhodnou kombinaci vysoké pevnosti, únavové odolnosti, tepelné stability a mimořádné odolnosti proti korozi a oxidaci v širokém rozsahu teplot. nerezová ocel 316L poskytuje vynikající odolnost proti korozi, zejména proti specifickým chemikáliím, spolu s dobrou pevností a vyrobitelností, což často představuje cenově výhodnější řešení pro méně náročné teplotní aplikace. Možnost přesného zpracování těchto pokročilých materiálů pomocí AM otevírá nové možnosti pro tvorbu tlakových ventilů nové generace, které jsou lehčí, účinnější a vyrábějí se s větší hbitostí. Společnost Met3dp se jako přední poskytovatel řešení pro aditivní výrobu specializuje jak na pokročilé 3D tisk z kovu a vysoce výkonných kovových prášků, jako jsou IN625 a 316L, které jsou nezbytné pro plné využití potenciálu této technologie pro kritické letecké komponenty.
K čemu se používají letecké tlakové ventily? Klíčové aplikace a funkce
Tlakové ventily pro letectví a kosmonautiku nejsou monolitické; zahrnují různorodou skupinu součástí, z nichž každá je přizpůsobena specifickým funkcím ve složité síti systémů letadel a kosmických lodí. Jejich hlavním úkolem je přesné řízení tekutin - kapalin a plynů - zajišťující bezpečný a efektivní provoz systémů v náročných a často rychle se měnících podmínkách. Pochopení jejich specifických aplikací poukazuje na kritickou potřebu spolehlivosti, přesnosti a vhodnosti materiálu, kterou mohou řešit pokročilé výrobní techniky, jako je 3D tisk kovů.
Základní funkce leteckých tlakových ventilů:
- Regulace tlaku: Udržování tlaku v systému v předem definovaném rozmezí, prevence přetlakování nebo podtlakování (např. regulátory tlaku v palivovém nebo hydraulickém potrubí).
- Odlehčení tlaku: Automaticky se otevírají, aby vypustily nadměrný tlak a ochránily součásti systému před poškozením, pokud tlak překročí bezpečnou mez (např. pojistné ventily v hydraulických akumulátorech nebo palivových nádržích).
- Řízení toku: Modulování nebo uzavírání průtoku kapalin (např. škrticí ventily, uzavírací ventily v palivovém potrubí, regulační ventily hydraulických pohonů).
- Směrové řízení: Směrování průtoku kapaliny do různých částí systému (např. přepínací ventily v hydraulických systémech pro podvozek nebo řízení letu).
- Zpětné ventily: Umožňuje průtok kapaliny pouze jedním směrem a zabraňuje zpětnému toku (např. se používá v palivových, hydraulických a pneumatických systémech).
- Míchání/rozdělování: Kombinování nebo oddělování proudů kapalin (např. ventily pro regulaci teploty v systémech pro regulaci prostředí).
Klíčové oblasti použití:
- Pohonné systémy:
- Palivové systémy: Ventily řídí tok paliva z nádrží do motorů, řídí tlak v nádržích, regulují tlak paliva a zajišťují nouzové vypnutí. Musí zvládat těkavá paliva, jako je kerosin (Jet A-1) nebo kryogenní pohonné hmoty (kapalný vodík/kyslík v raketách), a pracovat v širokém rozsahu teplot. Zpětné ventily zabraňují zpětnému toku, zatímco regulační ventily zajišťují stálý tlak paliva. Materiály jako IN625 jsou často upřednostňovány kvůli vysokým teplotám a potenciálně korozivním přísadám do paliva nebo vedlejším produktům spalování.
- Systémy odvzdušnění motoru: Ventily řídí průtok horkého vysokotlakého vzduchu vypouštěného z kompresorových stupňů motoru. Tento vzduch se používá pro různé funkce, jako je startování motoru, ochrana proti námraze a tlak v kabině (ECS). Tyto ventily musí odolávat extrémně vysokým teplotám (často přesahujícím 600 °C) a tlakům.
- Ventily raketových motorů: Ty se potýkají s nejextrémnějšími podmínkami, ovládají kryogenní pohonné hmoty, vysokotlaké spalovací plyny a vyžadují rychlou aktivaci a absolutní spolehlivost. Složitost a potřeba exotických materiálů z nich činí hlavní kandidáty pro AM.
- Hydraulické systémy:
- Ovládání letu: Ventily přivádějí vysokotlakou hydraulickou kapalinu (obvykle Skydrol nebo podobné fosfátové estery) k pohonům, které pohybují řídicími plochami (křidélka, výškovky, směrovka). Přesnost, spolehlivost a rychlá odezva jsou prvořadé.
- Přistávací zařízení: Ventily ovládají vysouvání, zasouvání, řízení a brzdění podvozku, který pracuje pod vysokým zatížením a tlakem. Musí být robustní a odolné proti znečištění.
- Komunální systémy: Hydraulika pohání také nákladové dveře, obraceče tahu a další užitečné funkce, které vyžadují speciální ovládací ventily. Odolnost proti korozi hydraulických kapalin a těsnost jsou kritické. materiál 316L může být vhodný pro mnoho hydraulických aplikací, zatímco materiál IN625 může být zvolen pro scénáře s vyšší teplotou nebo tlakem.
- Pneumatické systémy:
- Podobně jako hydraulika, ale s použitím stlačeného vzduchu nebo dusíku. Často se používá pro startování motoru, nasazení obracečů tahu, nouzové systémy a někdy jako doplněk hydraulických funkcí. Ventily musí zvládnout vysoké tlaky a zajistit těsnost.
- Systémy kontroly prostředí (ECS):
- Ventily řídí průtok vypouštěného vzduchu, recirkulovaného vzduchu v kabině a chladiva a regulují teplotu, tlak a ventilaci v kabině. Musí spolehlivě fungovat při různých teplotách a tlacích a zajišťovat pohodlí a bezpečnost cestujících. Běžně se zde používají zpětné ventily, ventily pro regulaci průtoku a ventily pro směšování teplot.
- Hospodaření s tekutinami (ostatní):
- Pitná voda & amp; Odpadní systémy: Ačkoli jsou ventily v těchto systémech méně důležité pro řízení letu, vyžadují materiály odolné proti korozi vodou a čisticími prostředky, často se upřednostňují nerezové oceli jako 316L.
- Chladicí systémy: Ventily řídí průtok chladicích kapalin (jako jsou glykolové směsi nebo specializované dielektrické kapaliny) pro elektroniku (avioniku), generátory nebo pomocné energetické jednotky (APU).
Nároky na provozní prostředí:
Letecké ventily pracují v prostředí, které je na hony vzdálené typickému průmyslovému prostředí. Mezi hlavní výzvy patří:
- Extrémní teploty: Od kryogenních teplot ve vesmíru nebo při letech ve velkých výškách (-55 °C nebo méně) až po spalující žár v blízkosti motorů nebo v systémech vypouštění vzduchu (až 650 °C nebo více).
- Vysoké tlaky: Hydraulické systémy běžně pracují s tlakem 3000-5000 psi (20-35 MPa), v budoucnu bude tlak vyšší. Palivové a pneumatické systémy také používají značné tlaky.
- Vibrace a nárazy: Neustálé vibrace během letu a značné rázové zatížení při vzletu, přistání a manévrech vyžadují vysokou únavovou pevnost a integritu konstrukce.
- Žíravá média: Vystavení tryskovému palivu, hydraulickým kapalinám (Skydrol), odmrazovacím kapalinám, čisticím prostředkům, solné mlze (v námořním prostředí) a vedlejším produktům spalování vyžaduje vynikající odolnost proti korozi.
- Citlivost na hmotnost: Každý kilogram ušetřený na letadle znamená úsporu paliva nebo zvýšení nosnosti, a proto je odlehčení hlavním faktorem při konstrukci.
- Spolehlivost a bezpečnost: Ventily jsou často kritickými součástmi pro let; jejich selhání může mít katastrofální následky. Přísné testování, certifikace a kontrola kvality jsou povinné.
Složitost vnitřních geometrií potřebných pro účinný průtok v kombinaci s náročnými provozními podmínkami a potřebou vysoce výkonných materiálů činí výrobu tlakových ventilů pro letecký průmysl mimořádně náročnou při použití tradičních metod. Tato složitost však dokonale ladí se silnými stránkami aditivní výroby kovů a umožňuje inženýrům navrhovat a vyrábět ventily optimalizované pro funkci a prostředí dříve nedosažitelným způsobem. Manažeři veřejných zakázek, kteří tyto kritické komponenty pro velkoobchodní nebo OEM aplikace zajišťují, musí zajistit, aby jejich dodavatelé dokázali splnit tyto náročné funkční a environmentální požadavky, což činí pokročilé materiály a výrobní procesy stále nezbytnějšími.
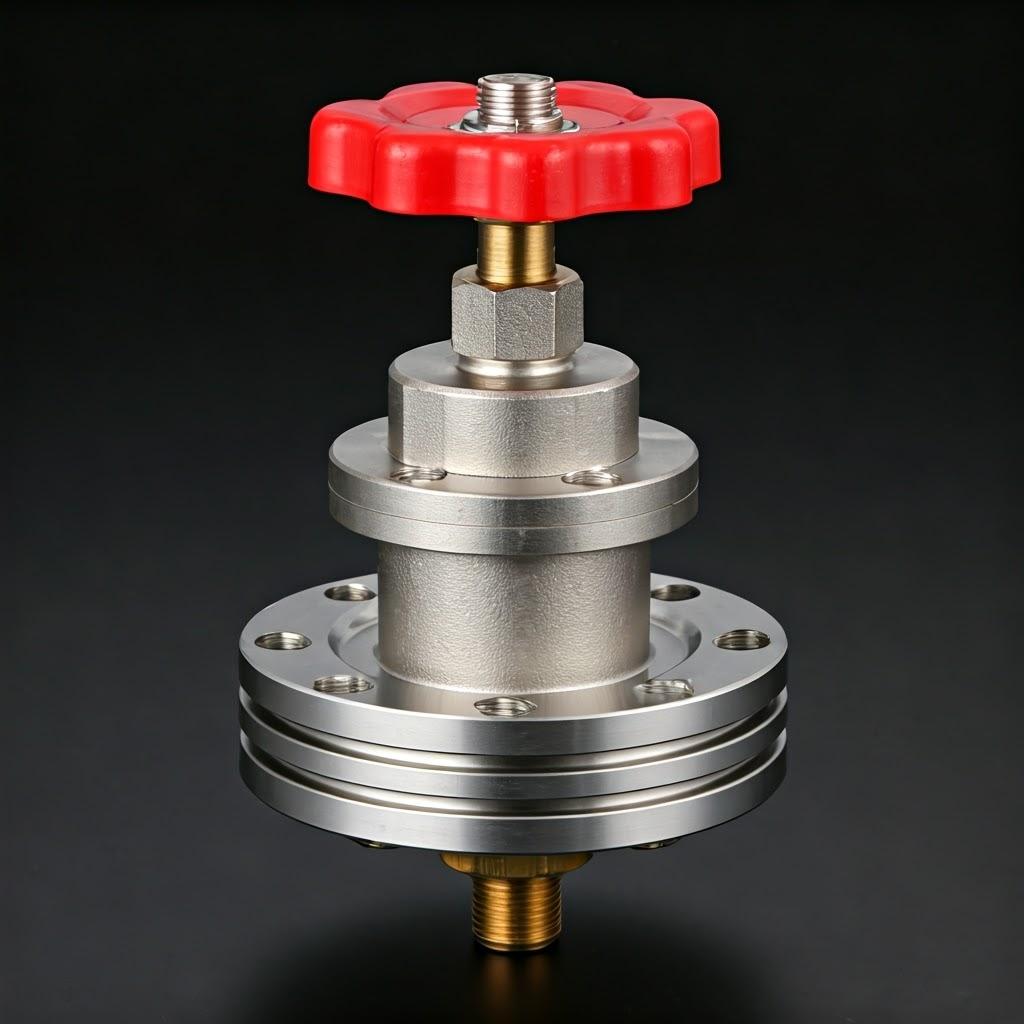
Proč používat 3D tisk kovů pro letecké tlakové ventily? Výhody oproti tradiční výrobě
Rozhodnutí o zavedení aditivní výroby kovů pro výrobu tlakových ventilů v letectví a kosmonautice není jen o přijetí nové technologie, ale o hmatatelných technických a obchodních výhodách, které přímo řeší omezení tradičních metod, jako je odlévání, kování a subtraktivní obrábění. Pro inženýry, kteří navrhují systémy pro řízení tekutin, a manažery nákupu, kteří zajišťují spolehlivé a vysoce výkonné komponenty, je pochopení těchto výhod klíčem k využití plného potenciálu AM’. 3D tisk kovů, zejména technologie Powder Bed Fusion (PBF) využívající materiály jako IN625 a 316L, nabízí pro ventily v leteckém průmyslu přesvědčivou hodnotu.
1. Bezprecedentní volnost a komplexnost návrhu:
- Tradiční limity: Odlévání vyžaduje formy, což omezuje vnitřní složitost a často vyžaduje vícedílné sestavy. Obrábění se potýká s přístupem a vytvářením složitých vnitřních kanálů nebo prvků, zejména zakřivených nebo nelineárních drah.
- Výhoda AM: AM vytváří díly vrstvu po vrstvě přímo z modelu CAD, čímž zbavuje konstruktéry mnoha tradičních výrobních omezení (DfM). To umožňuje:
- Optimalizované vnitřní geometrie: Vytvoření hladkých, zakřivených vnitřních kanálů, které minimalizují turbulence a tlakové ztráty, což vede k efektivnějšímu proudění kapaliny ve srovnání s často hranatými průchody, které jsou dány vrtáním nebo litím.
- Komplexní funkce: Integrace vnitřních přepážek, statických směšovačů nebo jedinečně tvarovaných sedel ventilů přímo do konstrukce dílu.
- Biomimikry & Advanced Flow Paths: Navrhování průtokových cest inspirovaných přírodou nebo komplexními simulacemi (CFD) za účelem maximalizace výkonu.
2. Odlehčování pomocí optimalizace topologie a efektivity materiálu:
- Letecký a kosmický imperativ: Snížení hmotnosti je v letectví a kosmonautice velmi důležité pro zlepšení palivové účinnosti, zvýšení nosnosti nebo zlepšení manévrovatelnosti.
- Tradiční přístup: Snižování hmotnosti často zahrnuje rozsáhlé obrábění přebytečného materiálu z pevných předvalků nebo odlitků, což vede ke značnému plýtvání materiálem (poměr nákup/let může být špatný).
- Výhoda AM:
- Optimalizace topologie: Softwarové algoritmy mohou optimalizovat rozmístění materiálu na základě průběhu zatížení a požadavků na výkon, čímž se odstraní zbytečná hmotnost při zachování integrity konstrukce. Výsledkem jsou organicky vypadající, vysoce účinné konstrukce, které často nelze opracovat.
- Mřížové struktury: Vnitřní mřížkové nebo buněčné struktury mohou být použity k výraznému snížení hmotnosti při zajištění požadované tuhosti a pevnosti, což je ideální pro tělesa ventilů nebo nekritické části.
- Tvar blízký síti: AM vyrábí díly mnohem blíže jejich konečným rozměrům, čímž výrazně snižuje množství potřebného materiálu a následného odpadu při obrábění, což je výhodné zejména při použití drahých slitin, jako je IN625.
3. Konsolidace částí:
- Tradiční shromáždění: Složité ventilové systémy často vyžadují výrobu několika jednotlivých součástí (tělesa, přírub, konektorů, vnitřních prvků), které se vyrábějí odděleně a poté se sestavují pomocí svařování, pájení nebo spojovacích prvků. Každý spoj představuje potenciální cestu úniku, vyžaduje další čas a práci při montáži a zvyšuje hmotnost.
- Výhoda AM: AM umožňuje konstruktérům sloučit více funkčních součástí do jediného monolitického tištěného dílu. To přináší významné výhody:
- Snížený počet dílů: Zjednodušuje řízení zásob, logistiky a dodavatelského řetězce.
- Eliminace kloubů: Omezuje potenciální cesty úniku, čímž zvyšuje spolehlivost a bezpečnost.
- Zkrácení doby montáže & Náklady: Snižuje náklady na pracovní sílu a zefektivňuje výrobní proces.
- Vylepšený výkon: Odstranění spojů může někdy zlepšit strukturální integritu nebo průtokové vlastnosti.
4. Rychlé prototypování a zrychlené vývojové cykly:
- Tradiční časové osy: Vytvoření nástrojů pro odlévání nebo kování, nastavení složitých obráběcích operací a sestavení prototypů může trvat týdny nebo měsíce. Iterace návrhu jsou pomalé a nákladné.
- Výhoda AM:
- Eliminace nástrojů: AM nevyžaduje žádné specifické nástroje, což umožňuje vyrábět prototypy přímo z digitálních souborů během několika dnů, nikoli týdnů či měsíců.
- Rychlá iterace: Inženýři mohou rychle otestovat více variant návrhu, optimalizovat výkon na základě empirických dat a mnohem rychleji dospět ke konečnému návrhu. Tato pružnost je na konkurenčním trhu v leteckém průmyslu klíčová.
- Zkrácení doby uvedení na trh: Rychlejší vývojové cykly se přímo promítají do rychlejšího zprovoznění nových letadel nebo systémů.
5. Optimalizace dodavatelského řetězce a výroba na vyžádání:
- Tradiční dodavatelské řetězce: Spoléhání se na slévárny, kovárny a specializované strojírny může vést ke složitým, geograficky rozptýleným dodavatelským řetězcům s dlouhými dodacími lhůtami a potenciálními zranitelnostmi. Často je nutné udržovat velké zásoby náhradních dílů.
- Výhoda AM:
- Digitální inventář: Díly existují jako digitální soubory, dokud nejsou potřeba, což snižuje požadavky na fyzické zásoby.
- Výroba na vyžádání: Ventily lze tisknout podle potřeby, blíže k místu použití, čímž se zkracují dodací lhůty pro náhradní díly nebo malosériovou výrobu.
- Odolnost dodavatelského řetězce: Snižuje závislost na tradičních dodavatelích z jednoho zdroje a nabízí větší flexibilitu při získávání zdrojů. Společnosti jako Met3dp mohou působit jako spolehlivé poskytovatelé služeb v oblasti AM kovů pro dodavatele leteckých komponentů a výrobce OEM.
6. Zvýšený výkonnostní potenciál:
- Za hranice replikace: Ačkoli AM může replikovat stávající konstrukce ventilů, jeho skutečná síla spočívá ve vytváření nových konstrukcí, které jsou jinými metodami nemožné. Optimalizované průtokové cesty mohou snížit energetické ztráty, zlepšit regulační vlastnosti a zvýšit celkovou účinnost systému. Integrované chladicí kanály nebo pouzdra senzorů mohou zvýšit funkčnost.
Srovnávací tabulka: AM vs. tradiční výroba pro letecké ventily
Vlastnosti | Aditivní výroba kovů (PBF) | Tradiční výroba (odlévání / kování / obrábění) | Výhoda AM |
---|---|---|---|
Složitost návrhu | Velmi vysoká (složité vnitřní kanály, mřížky) | Střední až nízká (omezená nástroji/přístupem) | Umožňuje optimalizovaný tok, integrované funkce, nové návrhy |
Odlehčení | Vysoký potenciál (optimalizace topologie, mřížky) | Mírná (především obráběním) | Výrazná úspora hmotnosti, lepší poměr ceny a výkonu |
Konsolidace částí | Vysoký potenciál (integrace více částí) | Nízká (vyžaduje montáž samostatných dílů) | Menší počet dílů, méně netěsných míst, nižší náklady na montáž |
Rychlost prototypování | Půst (dny) | Pomalé (týdny/měsíce kvůli výrobě nástrojů) | Rychlá iterace návrhu, rychlejší vývojové cykly |
Nástroje | Není vyžadováno | Potřebné (formy, zápustky, přípravky) | Nižší počáteční náklady pro malé objemy, rychlejší nastavení |
Materiálový odpad | Nízká (tvar blízký síti, recyklace prášku) | Vysoká (zejména při rozsáhlém obrábění) | Lepší využití materiálu, nižší náklady na drahé slitiny |
Dodací lhůta (nízký objem) | Krátké | Dlouhé (podle nástrojů a nastavení) | Rychlejší dodávky prototypů, náhradních dílů a malých sérií |
Dodavatelský řetězec | Flexibilní (digitální zásoby, na vyžádání) | Pevné (v závislosti na konkrétních dodavatelích/procesech) | Zvýšená agilita a odolnost |
Náklady (nízký objem) | Potenciálně nižší (bez nástrojů) | Vysoká (amortizace nástrojů) | Ekonomičtější pro prototypy a malé série |
Náklady (velký objem) | Potenciálně vyšší (pomalejší rychlost výstavby) | Potenciálně nižší (úspory z rozsahu) | Nákladová efektivita závisí na složitosti, objemu a aplikaci (existuje přechodový bod) |
Export do archů
Zatímco tradiční výrobní metody budou i nadále hrát svou roli, zejména pro velmi velkosériovou výrobu jednodušších konstrukcí, aditivní výroba kovů nabízí přesvědčivé výhody pro složité, vysoce výkonné tlakové ventily pro letecký průmysl, zejména při použití pokročilých materiálů, jako jsou IN625 a 316L. Umožňuje inženýrům posouvat hranice designu a manažerům nákupu dodávat komponenty s vyšším výkonem, nižší hmotností a větší flexibilitou dodavatelského řetězce.
Doporučené materiály: IN625 a 316L pro odolnost proti korozi a vysoký výkon
Výběr správného materiálu má zásadní význam pro výkon a životnost tlakových ventilů pro letectví a kosmonautiku, které musí spolehlivě fungovat v náročných podmínkách zahrnujících agresivní kapaliny, extrémní teploty a vysoké tlaky. Procesy aditivní výroby kovů, jako je selektivní laserové tavení (SLM), vynikají při zpracování vysoce výkonných slitin, které splňují tyto přísné požadavky. Mezi nejpoužívanější a nejdůvěryhodnější materiály pro 3D tisk leteckých ventilů vyžadujících vynikající odolnost proti korozi patří superslitina na bázi niklu Inconel 625 (IN625) a austenitická nerezová ocel 316L. Pochopení jejich odlišných vlastností je zásadní pro výběr optimálního materiálu pro konkrétní aplikaci ventilu.
Inconel 625 (IN625 / UNS N06625): Vysoce výkonný pracovní kůň
IN625 je slitina niklu, chromu, molybdenu a niobu proslulá výjimečnou kombinací vysoké pevnosti, houževnatosti, tepelné stability a mimořádné odolnosti proti korozi a oxidaci v neuvěřitelně širokém teplotním rozsahu, od kryogenních úrovní až po přibližně 980 °C.
Klíčové vlastnosti a výhody IN625 pro letecké ventily:
- Vynikající odolnost proti korozi: IN625 vykazuje výjimečnou odolnost vůči široké škále korozivních prostředí, včetně:
- Důlková a štěrbinová koroze v prostředí s obsahem chloridů (např. působení mořské vody, odmrazovací kapaliny).
- Prostředí kyselých plynů (obsahujících H₂S).
- Oxidační a redukční kyseliny.
- Alkalické roztoky.
- Vysokoteplotní oxidace a nauhličování. Díky tomu je ideální pro ventily, které pracují s agresivními palivy, hydraulickými kapalinami, vedlejšími produkty spalování nebo pracují v náročných atmosférických podmínkách.
- Vysoká pevnost a únavová životnost: Slitina si zachovává vynikající pevnost v tahu, pevnost při tečení a pevnost v tahu i při zvýšených teplotách. Vysoký obsah niobu přispívá ke zpevnění pevným roztokem. To má zásadní význam pro ventily vystavené vysokým tlakům a cyklickému zatížení.
- Vynikající zpracovatelnost a svařitelnost (tisknutelnost): IN625 je známá svou dobrou tisknutelností v procesech PBF, což umožňuje vytvářet husté díly bez trhlin při vhodné optimalizaci parametrů.
- Tepelná stabilita: Odolává degradaci a zachovává si své mechanické vlastnosti při dlouhodobém vystavení vysokým teplotám, což je nezbytné pro ventily v systémech odvzdušňování nebo v blízkosti motorů.
- Kryogenní houževnatost: Na rozdíl od mnoha materiálů, které při nízkých teplotách křehnou, si IN625 zachovává dobrou houževnatost až do kryogenních hodnot, takže je vhodný pro vesmírné aplikace nebo operace ve velkých výškách.
Aplikace leteckých ventilů pro IN625: Součásti motorů, systémy vypouštění vzduchu, manipulace s palivem pro agresivní nebo vysokoteplotní paliva, součásti raketových motorů, výfukové systémy, některé vysokotlaké/vysokoteplotní hydraulické aplikace.
nerezová ocel 316L (316L / UNS S31603): Všestranný bojovník proti korozi
316L je austenitická chromniklová nerezová ocel obsahující molybden. Označení “L” znamená nízký obsah uhlíku (obvykle <0,03 %), který minimalizuje srážení karbidů při svařování nebo tepelném zpracování, a tím zvyšuje odolnost proti korozi, zejména ve svařovaných profilech. Je to jedna z nejběžnějších a nejuniverzálnějších nerezových ocelí používaných v mnoha průmyslových odvětvích, včetně leteckého průmyslu.
Klíčové vlastnosti a výhody materiálu 316L pro letecké ventily:
- Dobrá obecná odolnost proti korozi: materiál 316L vyniká vynikající odolností proti atmosférické korozi, mnoha organickým i anorganickým chemikáliím a díky obsahu molybdenu je obzvláště účinný proti důlkové korozi způsobené chloridy (i když je obecně méně odolný než materiál IN625 v prostředí s vysokou koncentrací chloridů nebo při vysokých teplotách).
- Dobrá pevnost a tažnost: Poskytuje dobrou rovnováhu mezi pevností v tahu, houževnatostí a tažností při pokojových a mírně zvýšených teplotách (obvykle do přibližně 500-600 °C, nad touto teplotou pevnost výrazně klesá).
- Vynikající tvařitelnost a svařitelnost (tisknutelnost): materiál 316L je jedním z nejjednodušších a nejběžnějších materiálů, které lze zpracovávat technikou PBF, nabízí široký prostor pro zpracování a umožňuje vyrábět díly s vysokou hustotou.
- Biokompatibilita (relevantní pro některé specializované aplikace): materiál 316L se často používá v lékařských implantátech díky své biokompatibilitě.
- Efektivita nákladů: V porovnání se superslitinami na bázi niklu, jako je IN625, je prášek 316L výrazně levnější, což z něj činí ekonomičtější volbu pro aplikace, kde jsou jeho výkonnostní charakteristiky dostatečné.
Aplikace ventilů 316L v leteckém průmyslu: Hydraulické systémy (tam, kde jsou teploty mírné), manipulace s palivem pro méně agresivní paliva, systémy pitné vody a odpadní systémy, systémy kontroly prostředí (ECS), pozemní podpůrná zařízení, konstrukční součásti v rámci ventilových sestav.
Úvahy o výběru materiálu:
Volba mezi IN625 a 316L závisí do značné míry na konkrétních provozních požadavcích tlakového ventilu:
Parametr | Příznivci IN625 | Upřednostňuje 316L | Úvahy |
---|---|---|---|
Provozní teplota | Vysoká (600 °C) nebo kryogenní teplota | Mírná (< 500-600 °C) | IN625 si mnohem lépe udržuje pevnost při vysokých teplotách. |
Korozní prostředí | Těžké (silné kyseliny, vysoký obsah chloridů, vysoká teplota) | Mírná (obecné chemikálie, atmosférické látky, mírné chloridy) | IN625 nabízí širší a robustnější odolnost proti korozi. |
Mechanická pevnost | Potřebná vysoká pevnost, únava, odolnost proti tečení | Mírná síla dostatečná | IN625 má obecně lepší mechanické vlastnosti, zejména při teplotě. |
Hodnocení tlaku | Velmi vysoký tlak | Střední až vysoký tlak | Vyšší pevnost IN625 umožňuje potenciálně tenčí stěny/lehčí konstrukce. |
Citlivost na náklady | Výkon ospravedlňuje vyšší náklady | Náklady jsou hlavním hnacím faktorem | prášek 316L je výrazně levnější. |
Specifická kapalina | Agresivní paliva, specifické chemikálie, horké plyny | Standardní hydraulické kapaliny (Skydrol), voda, vzduch | Vždy se doporučuje testování kompatibility materiálů. |
Export do archů
Met3dp Vysoce kvalitní kovové prášky:
Úspěšný 3D tisk součástí pro letecký průmysl vyžaduje nejen pokročilé tiskové vybavení, ale také mimořádně kvalitní kovové prášky. Vlastnosti prášku - včetně distribuce velikosti částic (PSD), morfologie (sféricity), tekutosti, čistoty a obsahu kyslíku - přímo ovlivňují hustotu, mikrostrukturu a mechanické vlastnosti finálního tištěného dílu.
Met3dp využívá špičkové technologie výroby prášků, mezi které patří atomizace plynu a proces s rotujícími plazmovými elektrodami (PREP), k výrobě vynikajících sférických kovových prášků optimalizovaných pro aditivní výrobu.
- Atomizace plynu: Naše pokročilé plynové atomizační systémy využívají jedinečné konstrukce trysek a proudění plynu k výrobě kovových prášků s vysokou sféricitou, vynikající tekutostí a řízenou PSD, která je rozhodující pro konzistentní hustotu práškového lože v procesech PBF.
- PŘÍPRAVA: Tato technologie poskytuje prášky s výjimečnou kulovitostí a velmi nízkým obsahem satelitů, které jsou ideální pro dosažení maximální hustoty balení a výrobu dílů s vynikající povrchovou úpravou a vnitřní integritou.
Met3dp dodává obě IN625 a 316L prášky, pečlivě vyráběné a kontrolované z hlediska kvality tak, aby splňovaly přísné požadavky leteckého průmyslu. Naše prášky umožňují zákazníkům spolehlivý 3D tisk hustých, vysoce výkonných tlakových ventilů s vynikajícími mechanickými vlastnostmi a odolností proti korozi, kterou vyžadují jejich kritické aplikace. Nabízíme také širší portfolio zahrnující inovativní slitiny, jako jsou TiNi, TiTa, TiAl, TiNbZr, CoCrMo, další nerezové oceli a superslitiny, a poskytujeme tak komplexní materiálová řešení. Výběr poskytovatele, jako je Met3dp, s odbornými znalostmi v obou oblastech pokročilé kovové prášky a tiskové systémy, zajišťuje spolehlivý základ pro výrobu kritických leteckých součástí.
Pečlivým vyhodnocením požadavků na aplikaci a výběrem vhodné vysoce výkonné slitiny mohou inženýři využít výhod 3D tisku kovů k vytvoření tlakových ventilů nové generace pro letecký průmysl se zvýšeným výkonem, spolehlivostí a vyrobitelností.
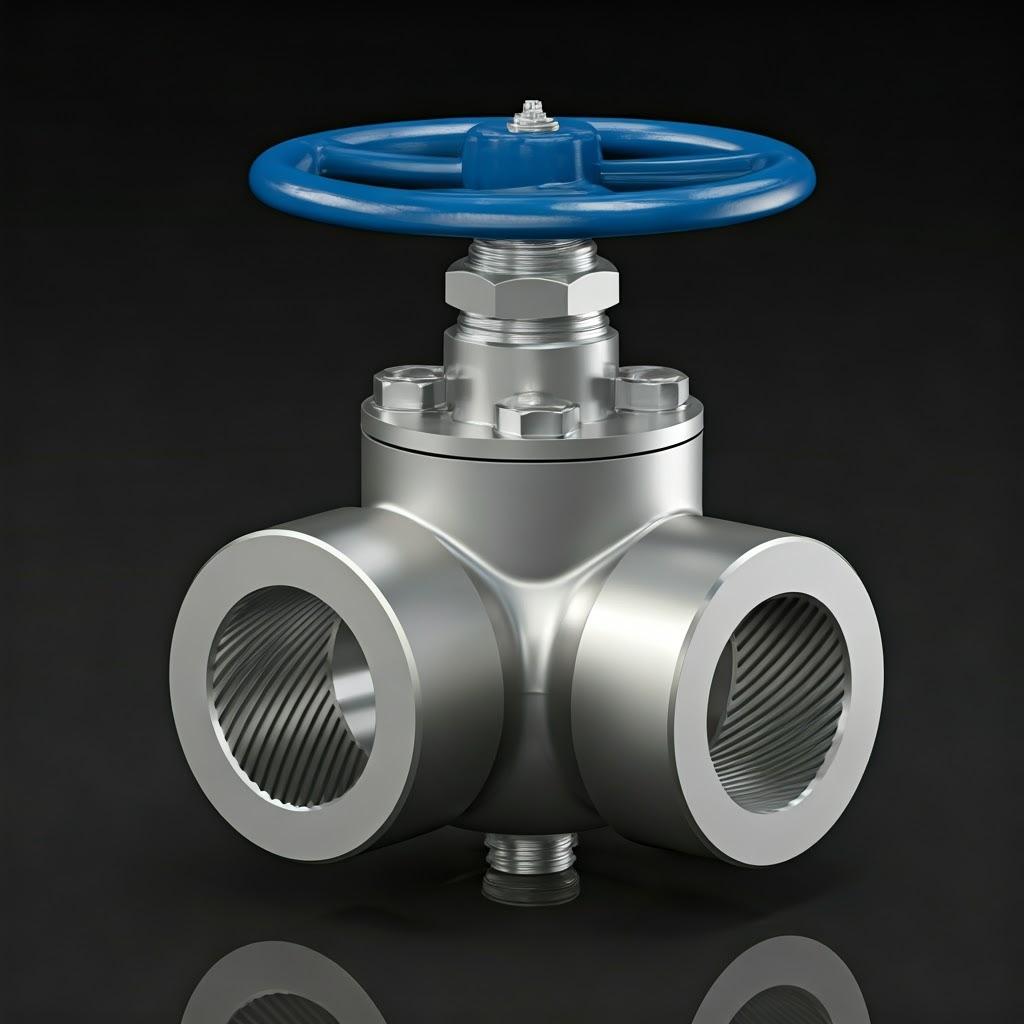
Konstrukční hlediska pro aditivně vyráběné tlakové ventily
Přechod výroby leteckých tlakových ventilů z tradičních metod na aditivní výrobu kovů (AM) není jen otázkou převzetí stávajícího souboru CAD a jeho odeslání do tiskárny. Aby bylo možné skutečně využít sílu AM a dosáhnout optimálního výkonu, úspory hmotnosti a efektivity nákladů, musí konstruktéři a inženýři přijmout následující opatření Design pro aditivní výrobu (DfAM) zásady. DfAM zahrnuje přehodnocení konstrukce součástí tak, aby se využily jedinečné schopnosti AM a zároveň se zmírnila její přirozená omezení. U složitých součástí, jako jsou tlakové ventily, jsou pro úspěch rozhodující specifické strategie DfAM, které ovlivňují vše od dynamiky tekutin po strukturální integritu a vyrobitelnost. Těchto zásad by si měli být vědomi i manažeři nákupu při hodnocení návrhů nebo spolupráci s dodavateli AM služeb.
1. Využití geometrické volnosti pro lepší dynamiku tekutin:
- Hladké vnitřní kanály: Tradiční obrábění často vede k ostrým rohům a stupňovitým přechodům v kanálech kapalin kvůli omezení přístupu nástroje. AM umožňuje vytvářet hladké, organicky zakřivené vnitřní kanály.
- Výhody: Snižuje turbulence, minimalizuje tlakovou ztrátu na ventilu, zlepšuje účinnost průtoku (Cv) a může snížit hlučnost.
- DfAM Tip: Využijte simulaci CFD (Computational Fluid Dynamics) již v rané fázi návrhu k modelování proudění přes složité geometrie AM a optimalizaci tvaru, průměru a zakřivení kanálů pro specifické vlastnosti kapaliny a rychlosti proudění. Vyhněte se náhlým změnám průměru nebo směru proudění.
- Integrované funkce Flow: Složité funkce, jako jsou statické směšovače, usměrňovače průtoku nebo Venturiho trysky, mohou být integrovány přímo do konstrukce tělesa ventilu, aniž by bylo nutné používat samostatné díly nebo složitou montáž.
- Výhody: Zlepšuje funkčnost (např. lepší míchání, přesnější měření průtoku) v menším, případně lehčím balení.
- DfAM Tip: Tyto integrované prvky pečlivě modelujte a zvažte omezení týkající se tisknutelnosti, jako je minimální velikost prvku a potřeba samonosných úhlů nebo snadno odnímatelných vnitřních podpěr.
2. Optimalizace pro odlehčení:
- Optimalizace topologie: Tato výpočetní technika optimalizuje rozložení materiálu v definovaném návrhovém prostoru na základě aplikovaných zatížení, omezení a výkonnostních cílů (např. maximalizace tuhosti při minimalizaci hmotnosti).
- Výhody: Vytváří vysoce účinné, často organicky vypadající struktury, které používají materiál pouze tam, kde je to z konstrukčního hlediska nezbytné, což vede k výraznému snížení hmotnosti, jež je pro letecký průmysl zásadní. Ideální pro tělesa ventilů a konstrukční prvky.
- DfAM Tip: Přesně definujte zatěžovací stavy (tlak, vibrace, montážní síly). Zajistěte, aby optimalizovaný návrh byl vyrobitelný pomocí AM (např. vyhněte se prvkům příliš tenkým pro spolehlivý tisk, zajistěte samonosné úhly, kde je to možné). Při nastavení optimalizace je třeba zohlednit požadavky na následné zpracování (např. přístup pro opracování těsnicích ploch).
- Mřížové struktury: Nahrazení pevných částí vnitřními mřížovými nebo buněčnými strukturami (např. gyroidy, stochastické pěny) může výrazně snížit hmotnost a spotřebu materiálu při zachování požadovaných mechanických vlastností, jako je tuhost nebo absorpce energie.
- Výhody: Výrazná úspora hmotnosti, možnost tlumení vibrací, lepší tepelný management (pokud je navržen tak, aby mřížkou proudila kapalina).
- DfAM Tip: Zvolte typy mřížek a velikosti buněk odpovídající požadované konstrukční výkonnosti a možnostem procesu AM (minimální tloušťka nosníku). Zajistěte, aby bylo možné odstranit prášek z vnitřních mřížek; v případě potřeby návrh zahrnuje přístupové otvory. Analyzujte výkonnost mřížky za příslušných zatěžovacích podmínek pomocí metody konečných prvků.
3. Strategie konsolidace části:
- Identifikace příležitostí: Analyzujte stávající vícedílné sestavy ventilů. Lze příruby, konektory, držáky nebo dokonce některé vnitřní součásti integrovat do jediného tištěného dílu?
- Výhody: Snižuje počet dílů, dobu montáže, potenciální netěsnosti a zjednodušuje skladové zásoby pro dodavatele a distributory, kteří vyřizují velkoobchodní objednávky ventilů.
- DfAM Tip: Pečlivě vyhodnoťte funkční požadavky každého originálního dílu. Ujistěte se, že konsolidovaná konstrukce zachovává přístup pro kontrolu, nezbytné následné zpracování (např. obrábění kritických rozhraní) a neohrožuje montáž nebo údržbu vyměnitelných vnitřních prvků (např. těsnění nebo vyskakovací klapky, pokud zůstávají oddělené). Ověřte strukturální integritu konsolidovaného návrhu pomocí analýzy konečných prvků (MKP).
4. Řešení specifických omezení AM:
- Převisy a podpůrné konstrukce: Procesy PBF se vytvářejí vrstvu po vrstvě. Prvky s malým úhlem vůči konstrukční desce (obvykle pod 45 stupňů, i když to závisí na materiálu a parametrech) vyžadují podpůrné struktury, aby se zabránilo deformaci nebo zhroucení během tisku.
- Výzva: Podpěry spotřebovávají další materiál, prodlužují dobu výroby, vyžadují ruční odstraňování (což zvyšuje náklady a možnost poškození povrchu) a jejich odstranění ze složitých vnitřních kanálů může být obtížné nebo nemožné.
- Tipy DfAM:
- Design pro vlastní podporu: Díl na konstrukční desce strategicky orientujte. Upravte geometrii tak, aby používala samonosné úhly (např. >45 stupňů). Pro vodorovné otvory používejte místo jednoduchých kružnic zkosení nebo kosočtverce/teardropy.
- Minimalizace vnitřních podpěr: Pokud jsou vnitřní podpěry nevyhnutelné (např. složité vnitřní rozvody), navrhněte je tak, aby se daly snadno odstranit. Zahrňte přístupové otvory pro nástroje nebo proplachování. Zvažte rozpustné nebo snadno rozbitné podpůrné materiály/designy, pokud je poskytovatel služeb nabízí. Prozkoumejte alternativní orientace, které by mohly umístit kritické vnitřní prvky do samonosných poloh.
- Obětní funkce: Konstrukční prvky určené k pozdějšímu opracování, které mohou sloužit jako podpěry při tisku.
- Tloušťka stěny a velikost prvků: Procesy AM mají omezení týkající se minimální tloušťky potisknutelné stěny a rozlišení prvků. Velmi tenké stěny se mohou deformovat nebo postrádat strukturální integritu, zatímco velmi jemné rysy nemusí být přesně rozlišeny.
- DfAM Tip: Dodržujte pokyny pro minimální tloušťku stěny poskytnuté poskytovatelem služeb AM (např. Met3dp) pro konkrétní materiál (IN625, 316L) a stroj. Zajistěte, aby kritické prvky, jako jsou sedla ventilů nebo těsnicí drážky, byly dostatečně robustní pro tisk a následné následné zpracování. Vyhněte se velkým, nepodporovaným horizontálním rozpětím (mostům).
- Zbytkové napětí a deformace: Rychlé cykly ohřevu a chlazení, které jsou pro PBF typické, mohou v dílu vyvolat zbytková napětí, která mohou způsobit deformaci nebo zkroucení, zejména u velkých nebo složitých geometrií.
- DfAM Tip: Vyhněte se velkým plochým úsekům rovnoběžným se stavební deskou. Tam, kde je to vhodné, použijte prvky snižující napětí, jako jsou mírné oblouky nebo koutové hrany. Spolupracujte s dodavatelem AM na orientaci sestavy a podpůrných strategiích, které mají zabránit deformaci. Ve fázi návrhu zvažte tepelnou simulaci.
- Odstranění prášku: Z hotového dílu je třeba odstranit netavený prášek, zejména z vnitřních kanálků a dutin, které jsou běžné u ventilů.
- DfAM Tip: Navrhněte vnitřní kanály s dostatečným průměrem a hladkými přechody, které usnadňují odvádění prášku. U složitých vnitřních sítí nebo uzavřených mřížkových struktur zahrňte strategicky umístěné odtokové/přístupové otvory (které lze případně později ucpat nebo opracovat). Vyvarujte se vytváření “pastí na prášek.”
5. Navrhování pro následné zpracování:
- Přídavky na obrábění: Kritická rozhraní, těsnicí plochy, závitové prvky a otvory s přísnou tolerancí často vyžadují dodatečné obrábění pro dosažení konečné přesnosti a povrchové úpravy.
- DfAM Tip: Přidejte k těmto specifickým povrchům v modelu CAD další materiál (obráběcí materiál) (např. 0,5-2 mm, v závislosti na velikosti a variabilitě procesu). Zajistěte, aby konstrukce umožňovala volný přístup k nástroji pro obráběcí operace bez rušení jinými prvky.
- Přístup k inspekci: Zajistěte, aby kritické vnitřní prvky nebo místa potenciálních poruch byly přístupné pro nedestruktivní metody zkoušení (NDT), jako je CT skenování nebo boroskopická kontrola.
Úvahy o pracovním postupu DfAM:
- Spolupráce: Úzká spolupráce mezi konstruktérem, procesním inženýrem AM (u poskytovatele služeb, jako je Met3dp) a případně koncovým uživatelem je klíčová.
- Softwarové nástroje: Využívejte pokročilý software CAD, simulační software (CFD, FEA, optimalizace topologie) a software pro přípravu konstrukce speciálně zaměřený na AM.
- Iterativní proces: DfAM je často iterativní. Původní návrhy může být třeba zdokonalit na základě analýzy tisknutelnosti, výsledků simulace nebo zpětné vazby z prototypování.
Aktivním začleněním těchto principů DfAM mohou konstruktéři navrhovat tlakové ventily pro letectví a kosmonautiku, které lze nejen vyrábět pomocí 3D tisku, ale které jsou skutečně optimalizované z hlediska výkonu, hmotnosti, spolehlivosti a nákladů, což přináší lepší řešení ve srovnání s tradičně vyráběnými protějšky. Tento přístup zaměřený na konstrukci je nezbytný pro realizaci všech výhod, které slibuje aditivní výroba v náročném leteckém a kosmickém odvětví.
Dosažení přesnosti: Tolerance, povrchová úprava a rozměrová přesnost u ventilů tištěných na 3D tiskárně
Ačkoli aditivní výroba kovů umožňuje neuvěřitelnou geometrickou volnost, klíčovým problémem pro inženýry a manažery nákupu, kteří hodnotí 3D tištěné tlakové ventily pro letecký průmysl, je dosažitelná úroveň přesnosti. Parametry, jako je rozměrová přesnost, geometrické tolerance (GD&T) a povrchová úprava, jsou pro funkci ventilů kritické, zejména u těsnicích ploch, styčných ploch a dynamických součástí. Pochopení typických schopností procesů fúze v práškovém loži (PBF), jako je SLM/DMLS, faktorů ovlivňujících přesnost a role následného zpracování je nezbytné pro stanovení realistických očekávání a zajištění toho, aby díly splňovaly přísné požadavky leteckého průmyslu.
Schopnosti v podobě, v jaké byly vytištěny:
Procesy PBF pro kovy vytvářejí díly vrstvu po vrstvě tavením jemného prášku. To vede k určitým vlastnostem, pokud jde o přesnost:
- Rozměrová přesnost: To se týká toho, jak přesně se vytištěný díl shoduje se jmenovitými rozměry uvedenými v modelu CAD.
- Typické hodnoty: U dobře kalibrovaných průmyslových systémů (jako jsou systémy používané společností Met3dp), které tisknou na materiály jako IN625 nebo 316L, se typická přesnost rozměrů po tisku často pohybuje v rozmezí od ±0,1 mm až ±0,2 mm (±0,004″ až ±0,008″) pro menší funkce nebo ±0,1 % až ±0,2 % jmenovitého rozměru u větších prvků. To se však může výrazně lišit v závislosti na geometrii, velikosti, orientaci, materiálu a procesních parametrech dílu.
- Faktory ovlivňující přesnost: Roli hraje velikost bodu laserového paprsku, tloušťka vrstvy, vlastnosti prášku, tepelné napětí způsobující drobné smrštění nebo deformace a účinnost podpůrné konstrukce. U velkých a složitých dílů je obecně obtížnější dodržet přísné tolerance přímo z tiskárny ve srovnání s menšími a jednoduššími geometriemi.
- Povrchová úprava (drsnost): Výsledkem vrstevnatého charakteru PBF je charakteristická struktura povrchu. Drsnost povrchu se obvykle měří jako Ra (průměrná drsnost).
- Typické hodnoty: Drsnost povrchu po tisku závisí do značné míry na orientaci povrchu vzhledem ke směru sestavení a na použitých procesních parametrech.
- Vrchní plochy (rovnoběžné se stavební deskou, poslední vrstvy): Často hladší, Ra 5-10 µm (200-400 µin).
- Svislé stěny (kolmé na stavební desku): Mírná drsnost, Ra 8-15 µm (315-600 µin), s čarami vrstev.
- Zakřivené/úhlové plochy směřující vzhůru: Podobně jako svislé stěny nebo mírně hladší.
- Plochy směřující dolů (převisy): Obecně nejhrubší, Ra 15-25 µm+ (600-1000 µin+), v důsledku rozhraní s podpůrnými konstrukcemi nebo charakteru tiskových převisů s malým úhlem. Odstranění podpěr může mít také lokální vliv na povrchovou úpravu.
- Interní kanály: Drsnost uvnitř kanálů může být náročné přesně předpovědět a změřit, často je podobná povrchům směřujícím dolů, pokud jsou složité a nepodložené, ale potenciálně hladší, pokud jsou svislé a dostatečně široké.
- Proč je to důležité: Povrchová úprava ovlivňuje proudění kapalin (tření), účinnost těsnění, únavovou životnost (drsné povrchy mohou být místem vzniku trhlin) a estetiku. Povrchová úprava v podobě, v jaké byla vytištěna, je často nedostatečná pro dynamická těsnění nebo vysoce přesné styčné plochy.
- Typické hodnoty: Drsnost povrchu po tisku závisí do značné míry na orientaci povrchu vzhledem ke směru sestavení a na použitých procesních parametrech.
- Geometrické tolerance (GD&T): Dosažení přísných geometrických tolerancí (např. rovinnost, kolmost, soustřednost, poloha) přímo z tiskárny může být náročné kvůli možnosti tepelného zkreslení. Zatímco obecná přesnost může být v rozmezí ±0,1-0,2 mm, dosažení těsnějších výzev GD&T často vyžaduje dodatečné obrábění.
Faktory ovlivňující přesnost PBF:
Dosažení co nejvyšší přesnosti samotného procesu AM vyžaduje pečlivou kontrolu mnoha proměnných:
- Kalibrace stroje: Pravidelná kalibrace laserů, skenerů a konstrukční platformy tiskárny je zásadní.
- Parametry procesu: Zásadní jsou optimalizované parametry (výkon laseru, rychlost skenování, rozteč šraf, tloušťka vrstvy) specifické pro daný materiál (IN625, 316L). Společnost Met3dp investuje velké prostředky do vývoje procesů, aby zajistila optimální výsledky.
- Kvalita prášku: Konzistentní distribuce velikosti částic prášku, morfologie a tekutost, jak je zajištěna pokročilou výrobou prášků Met3dp’, významně přispívá ke kvalitě a přesnosti dílů. Chemické složení prášku a obsah kyslíku musí být přísně kontrolovány.
- Tepelný management: Kontrola teploty v konstrukční komoře a řízení teplotních gradientů pomáhá minimalizovat zbytkové napětí a deformace. Software pro simulaci sestavení může předvídat potenciální deformace.
- Orientace na stavbu: Způsob orientace dílu na konstrukční desce významně ovlivňuje přesnost, kvalitu povrchu na různých plochách a požadavky na podporu. Často dochází ke kompromisu mezi optimalizací kvality povrchu, přesností, dobou sestavení a minimalizací podpory.
- Strategie podpory: Správně navržené a umístěné podpěrné konstrukce jsou rozhodující pro ukotvení dílu, zabránění deformacím a zajištění geometrické přesnosti, zejména u převisů.
Úloha následného zpracování pro přesnost:
U mnoha kritických prvků na tlakovém ventilu pro letectví a kosmonautiku je přesnost vytištěná v podobě, v jaké je vytištěna, nedostatečná. Pro splnění konečných technických specifikací jsou obvykle nutné kroky následného zpracování:
- CNC obrábění: Jedná se o nejběžnější metodu pro dosažení úzkých tolerancí a jemné povrchové úpravy specifických prvků.
- Aplikace: Obrábění sedel ventilů pro dokonalé utěsnění, úprava těsnicích ploch pro O-kroužky nebo těsnění, závitování otvorů, vyvrtávání kritických průměrů pro cívky nebo písty, dosažení těsné rovinnosti nebo kolmosti na montážních přírubách.
- Schopnosti: Při obrábění na CNC lze snadno dosáhnout tolerancí ±0,01 mm až ±0,025 mm (±0,0004 až ±0,001) nebo lepších a jemnosti povrchu (Ra) hluboko pod 1 µm (40 µin), často až 0,4-0,8 µm (16-32 µin) nebo hladší při broušení/lapování.
- Úvaha: Vyžaduje konstrukci dílů s obráběcím materiálem a zajištění přístupu k nástrojům (hledisko DfAM).
- Tepelné zpracování (HIP): Tepelné zpracování s uvolněním pnutí sice primárně ovlivňuje mechanické vlastnosti, ale může pomoci minimalizovat deformace, které by mohly vzniknout po odstranění podpory nebo během obrábění. Izostatické lisování za tepla (HIP) může uzavřít vnitřní pórovitost, což může jemně ovlivnit rozměrovou stabilitu, ale jeho hlavní úlohou je zlepšení integrity materiálu a únavové životnosti.
- Techniky povrchové úpravy: Kromě obrábění lze kvalitu povrchu zlepšit i dalšími metodami:
- Obrábění abrazivním tokem (AFM) / Extrude Hone: Protlačováním polymerního tmelu s abrazivem vnitřními kanálky lze účinně vyhladit a vyleštit vnitřní povrchy, což zlepšuje průtok a čistitelnost.
- Elektrolytické leštění: Elektrochemický proces, který odstraňuje tenkou vrstvu materiálu, vyhlazuje povrch (zvláště výhodné pro 316L) a zlepšuje odolnost proti korozi. Může být účinný u složitých vnějších a někdy i vnitřních geometrií.
- Tumbling / hromadné dokončování: Použitím brusných médií v bubnu lze vyhladit vnější povrchy a odjehlit hrany, i když je to méně přesné než obrábění.
- Mikroobrábění / laserové leštění: Pokročilé techniky pro dosažení velmi jemných povrchových úprav na specifických plochách.
Kontrola kvality a metrologie:
Zajištění toho, aby finální 3D vytištěný a následně zpracovaný ventil splňoval požadovanou přesnost, vyžaduje důkladnou kontrolu kvality (QC) a metrologii:
- Souřadnicové měřicí stroje (CMM): Slouží k přesnému měření rozměrové přesnosti a vlastností GD&T.
- Optické skenery / laserové skenery: Poskytuje úplné 3D porovnání geometrie s původním modelem CAD, což je užitečné pro složité tvary a ověření celkového tvaru.
- Povrchové profilometry: Přesné měření drsnosti povrchu (Ra).
- Boreskopy / videoskopy: Umožněte vizuální kontrolu vnitřních kanálů na vady nebo nerovnosti.
- CT vyšetření (počítačová tomografie): Může nedestruktivně kontrolovat vnitřní geometrii, měřit vnitřní prvky a odhalovat vnitřní vady nebo zachycený prášek, i když s omezením přesnosti ve srovnání s CMM pro přístupné prvky.
Nastavení očekávání:
- Hybridní přístup: Očekávejte, že kritické letecké ventily vyráběné pomocí AM budou pravděpodobně hybridním produktem - s využitím AM pro komplexní geometrii a tvorbu téměř čistého tvaru s následným cíleným následným obráběním a dokončováním pro kritické tolerance a povrchy.
- Spolupráce je klíčová: Úzce spolupracujte se svým poskytovatelem AM služeb, jako je Met3dp, abyste porozuměli jejich schopnostem, pokud jde o přesnost tisku pro IN625 a 316L, jejich standardním možnostem následného zpracování a jejich postupům kontroly kvality. Jasně definovat kritické rozměry, tolerance a požadavky na povrchovou úpravu na technických výkresech pomocí standardních výkresů GD&T.
- Nákladové důsledky: Uvědomte si, že dosažení vyšších úrovní přesnosti (přísnější tolerance, jemnější povrchová úprava) obvykle vyžaduje rozsáhlejší následné zpracování, které zvyšuje náklady na konečný díl a dobu realizace.
Pochopením přirozených schopností a omezení kovových PBF, využitím vhodných technik následného zpracování a zavedením přísné kontroly kvality mohou výrobci s jistotou vyrábět vysoce přesné letecké tlakové ventily pomocí aditivní výroby, které splňují nebo překonávají výkonnost svých tradičně vyráběných protějšků.
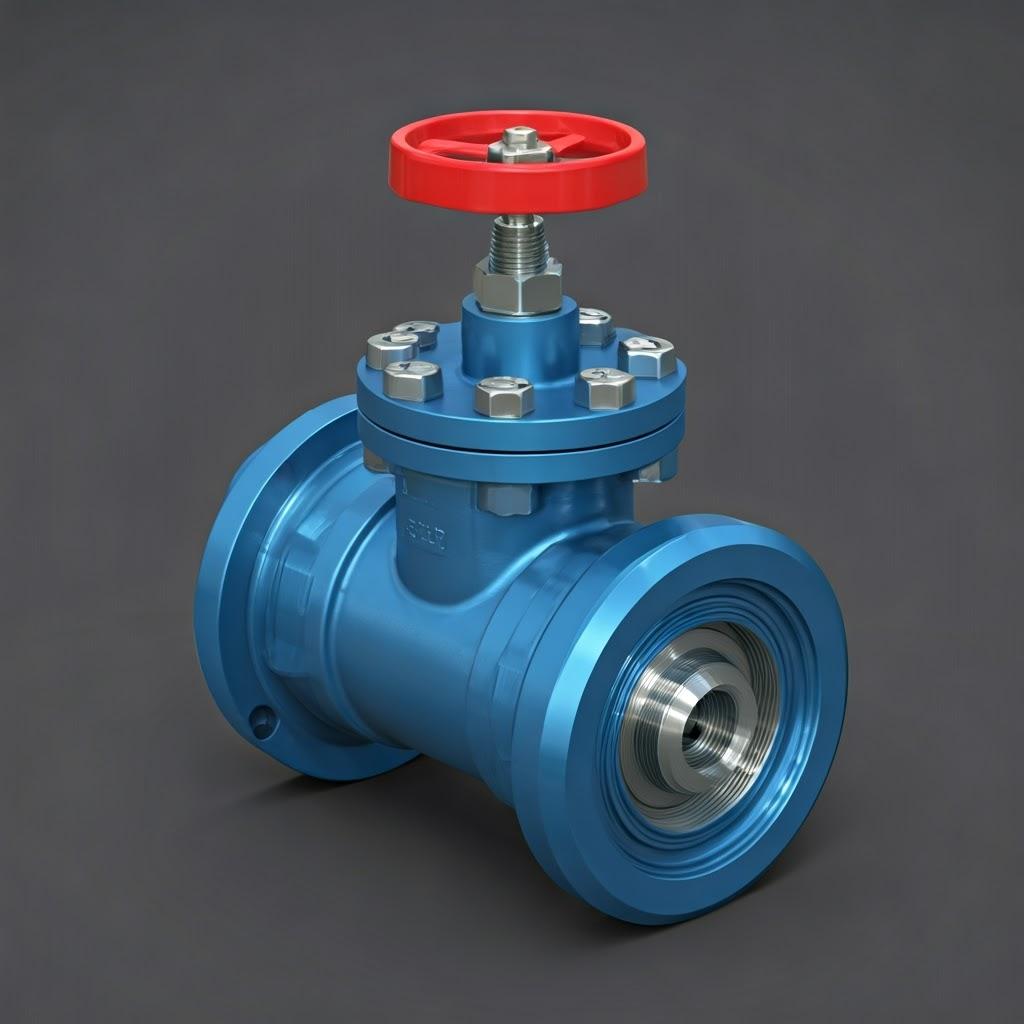
Požadavky na následné zpracování funkčních leteckých ventilů
Vytvoření rozměrově přesného tvaru pomocí aditivní výroby kovů je pouze prvním krokem při výrobě funkčního tlakového ventilu pro letecký průmysl. Díl “po vytištění”, čerstvě vytažený ze stroje PBF po odstranění prášku, vyžaduje řadu pečlivě kontrolovaných kroků následného zpracování, aby bylo dosaženo potřebných mechanických vlastností, povrchových charakteristik, čistoty a celkové integrity, které požaduje letecký průmysl. Tyto kroky přemění téměř čistý tvar součásti na hotový výrobek splňující přísné technické specifikace a požadavky na letovou způsobilost. Jak inženýři, kteří zadávají specifikace dílů, tak manažeři nákupu, kteří zajišťují služby AM, musí tyto zásadní procesy zohlednit ve svém plánování, časovém harmonogramu a analýze nákladů.
Typický pracovní postup následného zpracování pro letecké ventily AM (IN625 / 316L):
- Tepelné ošetření proti stresu:
- Účel: Rychlé cykly ohřevu/chlazení při tisku PBF vyvolávají v dílu značná zbytková napětí. Tato napětí mohou způsobit deformaci při vyjmutí z konstrukční desky nebo při následném obrábění a mohou mít negativní vliv na únavovou životnost. Cyklus uvolnění napětí zahřeje díl na určitou teplotu (nižší než teplota žíhání nebo rozpouštění, např. ~870-900 °C pro IN625, nižší pro 316L), udrží jej po stanovenou dobu a poté jej pomalu ochladí.
- Důležitost: Je naprosto nezbytné pro rozměrovou stabilitu a prevenci praskání nebo kroucení. Obvykle se provádí, když je díl ještě připevněn na konstrukční desce nebo ihned po opatrném vyjmutí.
- Úvahy: Vyžaduje kalibrované pece s řízenou atmosférou (např. vakuum nebo inertní plyn, jako je argon), aby se zabránilo oxidaci, což je obzvláště důležité pro reaktivní slitiny nebo dosažení lesklé povrchové úpravy. Konkrétní parametry cyklu závisí na slitině (IN625 vs. 316L) a geometrii/hmotnosti dílu.
- Odstranění ze stavební desky & Odstranění nosné konstrukce:
- Proces: Díly se obvykle vyřezávají z konstrukční desky pomocí elektroerozivního obrábění (EDM) nebo pásového řezání. Poté se musí odstranit podpůrné konstrukce, které jsou navrženy tak, aby ukotvily díl a zabránily zborcení převisu. Často se jedná o ruční proces s použitím ručního nářadí, kleští, brusek nebo někdy specializovaných nástrojů.
- Důležitost: Nezbytné pro uvolnění částí a přístup ke všem povrchům. Odstranění podpěr je často pracné a vyžaduje zručnost, aby nedošlo k poškození povrchu dílu.
- Výzvy: Vnitřní podpěry ve složitých ventilových kanálech lze ručně odstranit jen velmi obtížně nebo vůbec. To vyžaduje strategie DfAM, které minimalizují nebo odstraňují vnitřní podpěry nebo je navrhují pro snadnější přístup/odstranění. V místech, kde byly podpěry připevněny, mohou zůstat stopy (drobné vady), které mohou vyžadovat místní úpravy.
- Izostatické lisování za tepla (HIP) – volitelné, ale často doporučované pro kritické díly:
- Proces: HIP zahrnuje současné vystavení dílu vysoké teplotě (pod bodem tání, ale obvykle blízko teplotám žíhání roztoku) a vysokému tlaku inertního plynu (např. argonu o tlaku 100-200 MPa / 15 000-30 000 psi) ve specializované nádobě.
- Účel: Hlavním cílem je odstranit vnitřní mikroporozitu, která může zůstat i v dobře vytištěných dílech AM. Póry jsou potenciálními místy iniciace trhlin při únavovém zatížení. HIP tyto vnitřní dutiny účinně uzavírá kombinací plastické deformace a difuzní vazby na atomární úrovni.
- Výhody: Výrazně zlepšuje únavovou životnost, tažnost, lomovou houževnatost a rázovou houževnatost, čímž se vlastnosti materiálu přibližují (nebo někdy i překračují) vlastnosti materiálů vyrobených z kovu. Zvyšuje konzistenci a spolehlivost, což je pro letově kritické součásti zásadní.
- Úvahy: Zvyšuje náklady a dobu realizace. Vyžaduje specializované vybavení. Může způsobit drobné rozměrové změny (smrštění), s nimiž je třeba počítat, pokud se provádí před konečným obráběním. Často se specifikuje pro vysoce namáhané nebo únavově kritické součásti ventilů. Někteří zadavatelé v leteckém průmyslu vyžadují pro určité díly AM HIP.
- Žíhání roztokem / tepelné zpracování stárnutím (pokud to specifikace materiálu vyžaduje):
- Účel: Kromě uvolnění napětí vyžadují některé slitiny specifické cykly tepelného zpracování, aby bylo dosaženo požadované konečné mikrostruktury a mechanických vlastností (pevnost, tvrdost, odolnost proti korozi) uvedených v materiálových specifikacích (např. normy AMS pro IN625). To může zahrnovat žíhání v roztoku (rozpouštění precipitátů), následované kalením a případně stárnutím (řízené precipitační kalení).
- Důležitost: Zajistí, aby materiál splňoval požadované výkonnostní normy pro danou aplikaci.
- Úvahy: Parametry cyklu (teploty, časy, rychlosti chlazení) jsou kritické a specifické pro jednotlivé slitiny. Vyžaduje kalibrované pece s řízenou atmosférou. Může být kombinován s HIP nebo následovat po něm.
- Obrábění pro kritické tolerance a vlastnosti:
- Proces: Použití CNC frézování, soustružení, broušení nebo elektroerozivního obrábění k dosažení přesných rozměrů, úzkých tolerancí (GD&T) a jemných povrchových úprav specifických prvků, kterých nelze spolehlivě dosáhnout “při tisku.”
- Aplikace ve ventilech: Vytváření přesných těsnicích ploch (kov-kov nebo pro elastomerová těsnění), závitování připojovacích otvorů, vyvrtávání vnitřních průměrů cívek/popet, obrábění montážních přírub na plocho a kolmo, zajištění přesného umístění prvků.
- Důležitost: Je nezbytný pro funkčnost, neporušenost těsnění a správnou montáž/spojení s ostatními součástmi.
- Úvahy: Vyžaduje díly navržené s přídavky na obrábění (DfAM). Mohou být zapotřebí vhodné upínací přípravky, někdy složité pro organické tvary AM.
- Povrchová úprava a čištění:
- Účel: Zlepšení kvality povrchu nad rámec stavu po vytištění nebo obrobení z různých důvodů: snížení tření kapalin, zvýšení únavové životnosti, zlepšení čistitelnosti, zajištění správného těsnění nebo z estetických důvodů. Důkladné čištění je nezbytné k odstranění obráběcích kapalin, nečistot a zbytků prášku, zejména z vnitřních kanálků.
- Procesy:
- Odstraňování otřepů: Odstranění ostrých hran po obrábění nebo odstranění podpěr.
- Tumbling / hromadné dokončování: Vyhlazení vnějších povrchů, zaoblení hran.
- Otryskávání abrazivem (zrnitost/šrot): Vytváří jednotný matný povrch, dokáže odstranit drobné nedokonalosti. Je třeba dbát na to, aby nedošlo k poškození kritických povrchů.
- Leštění/leštění: Dosažení velmi hladkých, reflexních povrchů (např. pro specifické typy těsnění nebo požadavky na průtok).
- Elektrolytické leštění: Elektrochemické vyhlazování a zjasňování povrchů (zejména 316L).
- Obrábění abrazivním tokem (AFM): Vyhlazování vnitřních kanálů.
- Ultrazvukové čištění / proplachování: Odstraňování nečistot a volného prášku z vnitřních kanálů pomocí specializovaných čisticích roztoků a postupů. Kritické pro spolehlivost ventilů.
- Důležitost: Kvalita povrchu ovlivňuje výkon a spolehlivost. Čistota je pro kapalinové systémy v letectví a kosmonautice neoddiskutovatelná.
- Nedestruktivní zkoušení (NDT) a inspekce:
- Účel: Ověření neporušenosti dílu bez jeho poškození. Zásadní pro zajištění kvality v letectví a kosmonautice.
- Běžné metody pro ventily AM:
- Vizuální kontrola (VT): Včetně boroskopické kontroly vnitřních kanálů.
- Rozměrová kontrola: Použití souřadnicových měřicích strojů, skenerů, měřidel.
- Počítačová tomografie (CT): Zjišťování vnitřních vad (pórovitost, vměstky, trhliny), ověřování vnitřní geometrie, kontrola zachyceného prášku. Stále častější u kritických dílů AM.
- Zkoušky penetrací barvivem (PT): Zjišťování trhlin nebo defektů narušujících povrch.
- Ultrazvukové testování (UT): Detekce vnitřních defektů (méně časté u složitých tvarů AM než u CT).
- Radiografické testování (RT): Rentgenová kontrola vnitřních závad.
- Důležitost: Poskytuje jistotu, že díl nemá kritické vady a splňuje všechny rozměrové a kvalitativní specifikace před instalací. Požadavky jsou často dány normami pro letecký průmysl (např. AS9100) a specifikacemi zákazníka.
- Povrchové úpravy (specifické pro danou aplikaci):
- Účel: Aplikace specifických povlaků pro zvýšení odolnosti proti opotřebení, snížení tření (mazivosti), další zlepšení odolnosti proti korozi nebo zajištění tepelně bariérových vlastností.
- Příklady: Nitridace, PVD/CVD povlaky (např. TiN, CrN), specializované letecké barvy nebo maziva se suchým filmem.
- Úvahy: Záleží výhradně na konkrétní funkci ventilu a provozním prostředí.
Schopnost dodavatele:
Při pořizování 3D tištěných leteckých ventilů se musí manažeři nákupu ujistit, že vybraný poskytovatel služeb, jako je Met3dp, disponuje nejen schopností tisku, ale také potřebnými certifikovanými možnostmi následného zpracování, ať už vlastními nebo prostřednictvím kvalifikovaných partnerů. To zahrnuje kalibrované vybavení (pece, CNC stroje), robustní systémy řízení kvality (např. certifikace AS9100), odborné znalosti v oblasti manipulace s leteckými materiály a přísné protokoly NDT a kontroly. Vertikálně integrovaný přístup, kdy je tisk a více kroků následného zpracování řízeno pod jednou střechou, může často zefektivnit pracovní postup, zlepšit kontrolu kvality a zkrátit dodací lhůty.
Řetězec následného zpracování je kritickou a neoddiskutovatelnou součástí výroby spolehlivých, vysoce výkonných tlakových ventilů pro letecký průmysl pomocí aditivní výroby. Vyžaduje odborné znalosti, specializované vybavení a pečlivou kontrolu kvality, aby bylo možné přeměnit díl vyrobený metodou AM na letuschopnou součástku.
Běžné problémy při 3D tisku tlakových ventilů a jejich řešení
Ačkoli aditivní výroba kovů nabízí obrovský potenciál pro výrobu pokročilých tlakových ventilů pro letecký průmysl, není tento proces bez problémů. Kombinace složité geometrie, která je ventilům vlastní, náročných výkonnostních požadavků leteckého průmyslu a fyziky slučování práškového lože po vrstvách může vést k potenciálním problémům během tisku nebo následného zpracování. Klíčem k úspěšné a opakovatelné výrobě je rozpoznání těchto běžných problémů a zavedení účinných strategií jejich zmírnění - často vycházejících z robustního DfAM, pečlivé kontroly procesu a porozumění materiálovým vědám. Poskytovatelé služeb, jako je Met3dp, využívají své odborné znalosti k aktivnímu řešení těchto potenciálních úskalí.
1. Deformace a deformace zbytkovým napětím:
- Výzva: Intenzivní, lokalizovaný přívod tepla z laserového/elektronového paprsku a následné rychlé ochlazení vytváří v průběhu výroby významné tepelné gradienty a odpovídající zbytková napětí v dílu. Tato napětí mohou překročit mez kluzu materiálu a způsobit deformaci dílu, zkroucení od konstrukční desky nebo rozměrovou deformaci, zejména u velkých plochých dílů nebo asymetrických konstrukcí.
- Strategie zmírnění dopadů:
- Optimalizovaná orientace sestavení: Orientace dílu tak, aby se minimalizovaly velké rovné plochy rovnoběžné s konstrukční deskou a snížily se tepelné gradienty napříč vrstvami.
- Robustní podpůrné struktury: Návrh a umístění silných, dobře navržených podpěr, které pevně ukotví díl k základní desce a působí proti smršťovacím silám. Klíčové jsou kotevní body.
- Optimalizace parametrů procesu: Jemné doladění výkonu laseru, rychlosti skenování a strategie skenování (např. ostrovní skenování, střídání směrů šrafování), aby se minimalizovalo lokální zahřívání a rovnoměrněji rozložilo napětí.
- Tepelná simulace: Použití softwaru pro simulaci sestavení k předvídání akumulace napětí a možného zkreslení, což umožňuje úpravy konstrukce nebo optimalizovanou podporu/orientaci před tiskem.
- Tepelné ošetření proti stresu: Pro uvolnění vnitřních pnutí a rozměrovou stabilizaci dílu je rozhodující provedení cyklu uvolnění napětí bezprostředně po sestavení (často před odstraněním podpěry).
- DfAM: Vyhnout se konstrukčním prvkům, o nichž je známo, že zvyšují namáhání, jako jsou ostré vnitřní rohy nebo náhlé změny tloušťky. Začlenění koutů a postupných přechodů.
2. Obtíže při odstraňování podpůrné konstrukce (zejména vnitřní):
- Výzva: Tlakové ventily jsou často vybaveny složitými vnitřními kanály, rozdělovači a dutinami potřebnými pro průtok kapaliny. Pokud tyto vnitřní prvky vyžadují podpůrné konstrukce kvůli nízkým úhlům přesahu, může být odstranění těchto podpěr po tisku velmi obtížné, časově náročné, nákladné a může dojít k poškození vnitřních povrchů. Úplné odstranění je často nemožné provést ručně.
- Strategie zmírnění dopadů:
- DfAM pro vlastní podporu: Upřednostnění úprav konstrukce tak, aby vnitřní prvky byly samonosné (např. použití úhlů >45°, slzovitých/diamantových tvarů otvorů, optimalizace orientace). Jedná se o nejefektivnější řešení.
- Navrhování pro přístup: Pokud se vnitřním podpěrám nelze vyhnout, navrhněte volné přístupové otvory nebo cesty pro nástroje nebo proplachování, abyste se k nim mohli dostat a odstranit je. Tyto otvory mohou být později ucpány nebo opracovány.
- Specializované podpůrné struktury: Použití podpůrných konstrukcí navržených pro snadnější demontáž (např. tenčí spojovací body, specifická geometrie). Některé výzkumy zkoumají částečně rozpustné kovové nosiče, ale to zatím není komerčně rozšířeno.
- Metody následného zpracování: Použití technik, jako je abrazivní průtokové obrábění (AFM) nebo chemické leptání (při pečlivém zvážení kompatibility materiálu), může někdy pomoci vyhladit vnitřní povrchy po odstranění nosiče, ale nemusí účinně odstranit objemný materiál nosiče.
- CT vyšetření: Slouží k ověření, zda byly úspěšně odstraněny všechny vnitřní podpěry (a volný prášek).
3. Čištění vnitřních kanálů a odstraňování prášku:
- Výzva: Po tisku je velmi důležité zajistit, aby byl ze složitých, úzkých nebo klikatých vnitřních kanálů ventilů odstraněn veškerý neroztavený kovový prášek. Zachycený prášek může bránit průtoku kapaliny, kontaminovat systémy, uvolnit se během provozu a způsobit poškození nebo zabránit účinnému ošetření HIP.
- Strategie zmírnění dopadů:
- DfAM: Navrhování kanálů s dostatečným průměrem, hladkými ohyby (vyhnout se těsným rohům, kde se může prášek usazovat) a strategicky umístěnými odtokovými/přístupovými otvory. Vyhnout se konstrukcím, které vytvářejí nevyhnutelné pasti na prášek.
- Optimalizovaná orientace & Podporuje: Orientace dílu pro usnadnění odvodu prášku během sestavování a následného vylamování. Podpěry by neměly bránit cestám pro odstraňování prášku.
- Důkladné čištění po stavbě: Zavedení přísných protokolů pro odstraňování prášku zahrnujících vibrace, proudy stlačeného vzduchu a případně ultrazvukové čisticí lázně s vhodnými roztoky.
- Ověření: Použití boroskopů pro vizuální kontrolu a CT skenování k nedestruktivnímu potvrzení úplného odstranění prášku z vnitřních dutin.
4. Kontrola pórovitosti a integrity materiálu:
- Výzva: Dosažení plné teoretické hustoty (100 %) je u PBF obtížné. Může zůstat malé množství pórovitosti (plynové póry ze zachyceného plynu nebo póry s chybějící fúzí mezi vrstvami/skenovacími stopami). Pórovitost zhoršuje mechanické vlastnosti, zejména únavovou pevnost, a může být škodlivá v aplikacích vysokotlakých ventilů.
- Strategie zmírnění dopadů:
- Optimalizované parametry procesu: Vývoj a použití ověřených sad parametrů (výkon laseru, rychlost, šrafování, tloušťka vrstvy) specifických pro materiál (IN625, 316L) a stroj k dosažení maximální hustoty (>99,5 % je běžné, >99,9 % dosažitelné). Met3dp se výrazně zaměřuje na optimalizaci procesních parametrů.
- Vysoce kvalitní prášek: Použití sférického prášku s dobrou tekutostí a řízenou distribucí velikosti částic, jako jsou prášky Met3dp’ rozprašované plynem nebo PREP, zajišťuje rovnoměrnou hustotu práškového lože, čímž se snižuje počet defektů způsobených nedostatečnou fúzí. Výhodný je také nízký obsah plynu v prášku.
- Řízená atmosféra stavby: Udržování vysoce čisté atmosféry inertního plynu (argonu nebo dusíku) v konstrukční komoře minimalizuje oxidaci a kontaminaci, které mohou vést k defektům.
- Izostatické lisování za tepla (HIP): Jak již bylo zmíněno, HIP je vysoce účinný při uzavírání vnitřních pórů, čímž výrazně zlepšuje integritu materiálu a jeho únavové vlastnosti. Často se doporučuje nebo vyžaduje u kritických leteckých dílů.
- NDT (CT skenování): Používá se ke zjištění a kvantifikaci úrovně vnitřní pórovitosti.
5. Omezení povrchové úpravy:
- Výzva: Výsledkem procesu, který je vlastní vrstvení, a velikosti částic prášku jsou povrchy po vytištění, které jsou drsnější, než se obvykle vyžaduje pro těsnicí plochy nebo dynamické součásti ventilů s nízkým třením. Nejdrsnější jsou často povrchy směřující dolů a vnitřní kanály.
- Strategie zmírnění dopadů:
- Optimalizovaná orientace & Parametry: Tisk kritických povrchů pod optimálním úhlem vzhledem ke směru sestavení (svislé nebo horní povrchy jsou často hladší). Jemné doladění parametrů může mít malý vliv na povrchovou úpravu.
- Cílené následné zpracování: Spoléhání se na CNC obrábění, broušení, leštění, AFM nebo elektrolytické leštění k dosažení požadovaných specifikací povrchové úpravy na kritických funkčních plochách.
- DfAM: Navrhování funkcí speciálně pro usnadnění efektivních dokončovacích operací po zpracování.
6. Diagnostika a prevence selhání konstrukce:
- Výzva: Sestavy mohou někdy selhat uprostřed procesu kvůli problémům, jako jsou pády lopatek opakovače (v důsledku deformace dílu nebo úlomků), delaminace nebo jiné nestability procesu. Pro spolehlivou výrobu je zásadní diagnostikovat hlavní příčinu a zabránit jejímu opakování.
- Strategie zmírnění dopadů:
- Monitorování během procesu: Využití senzorů a kamer ve stroji AM ke sledování konstrukce vrstvu po vrstvě, které včas odhalí potenciální problémy (např. přehřátí, deformace, problémy s nátěrem).
- Robustní řízení procesů: Udržování přísné kontroly nad kalibrací stroje, kvalitou prášku, atmosférou při stavbě a ověřenými parametry procesu.
- Zkušení operátoři a inženýři: Kvalifikovaný personál, který dokáže interpretovat monitorovací data, diagnostikovat poruchy a odpovídajícím způsobem upravit parametry nebo nastavení. Tým Met3dp’má desítky let společných zkušeností.
- Simulace sestavení: Předvídání potenciálních míst selhání (např. vysoké namáhání vedoucí k praskání, zásahy do nátěru) předtím, než se odhodláte k fyzickému sestavení.
Řešení těchto výzev vyžaduje komplexní přístup, který kombinuje inteligentní design (DfAM), vysoce kvalitní materiály, přesně řízený aditivní výrobní procesy, vhodným následným zpracováním a důsledným zajištěním kvality. Pro úspěšné zavedení 3D tisku pro náročné aplikace, jako jsou tlakové ventily v letectví a kosmonautice, je zásadní spolupráce se zkušeným poskytovatelem AM technologií pro kovy, jako je Met3dp, který těmto potenciálním problémům rozumí a má zavedené strategie pro jejich zmírnění a systémy kvality (např. dodržování AS9100).
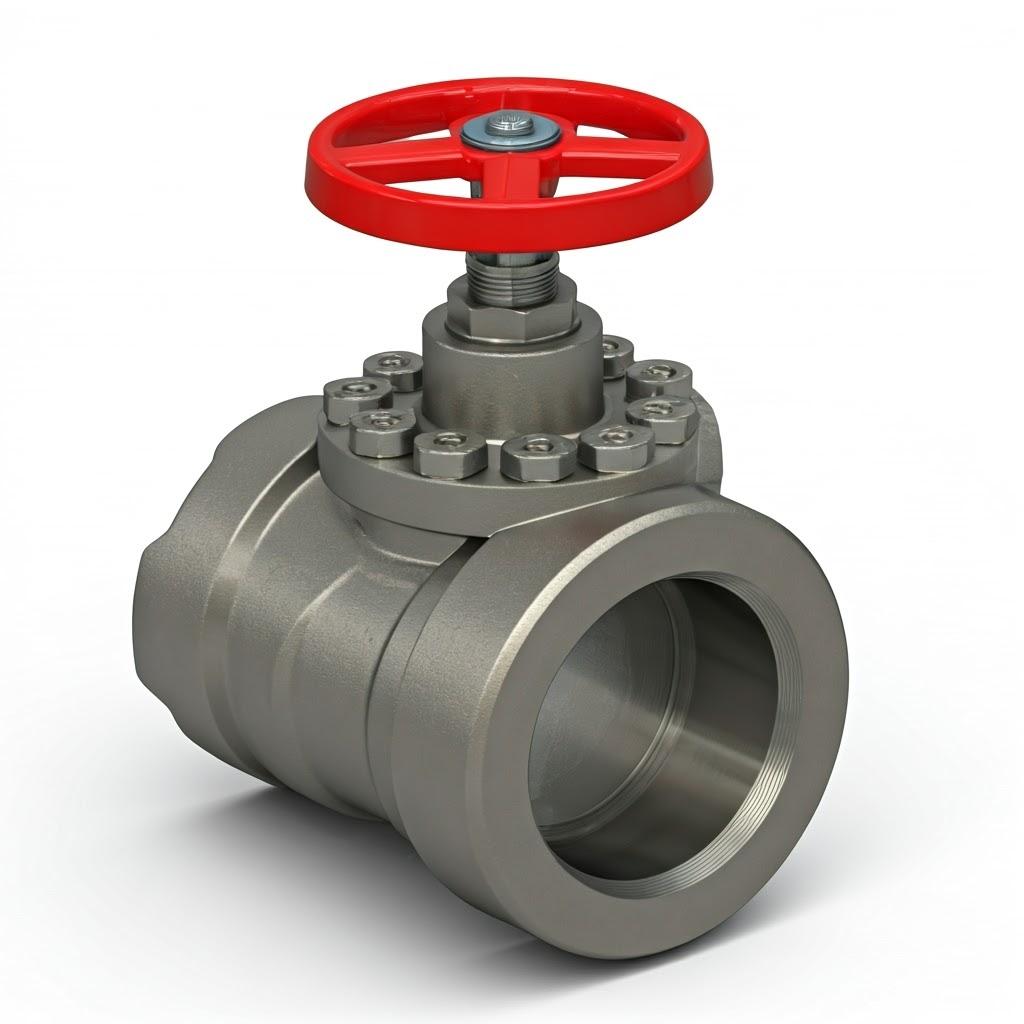
Jak vybrat správného poskytovatele služeb 3D tisku kovů pro letecké komponenty
Výběr správného výrobního partnera je vždy velmi důležitý, ale v případě letově kritických leteckých komponent, jako jsou tlakové ventily vyráběné pomocí pokročilých technologií, jako je aditivní výroba kovů, je sázka podstatně vyšší. Výběr poskytovatele služeb v oblasti AM výroby kovů může přímo ovlivnit kvalitu dílů, spolehlivost, shodu s předpisy, náklady a dodací lhůty. Manažeři nákupu, inženýři a odborníci na dodavatelský řetězec potřebují strukturovaný přístup k hodnocení potenciálních dodavatelů, aby se ujistili, že mají potřebné technické znalosti, robustní systémy kvality, specifické průmyslové certifikace a vhodné vybavení pro náročné letecké aplikace s použitím materiálů, jako jsou IN625 a 316L. Partnerství se zkušeným a schopným dodavatelem, jako je Met3dp, je pro úspěch naprosto zásadní.
Klíčová kritéria pro hodnocení poskytovatelů služeb v oblasti AM pro letectví a kosmonautiku:
- Specifické certifikace pro letecký průmysl a systém řízení kvality (QMS):
- Certifikace AS9100: Jedná se o mezinárodně uznávaný standard QMS pro letecký, kosmický a obranný průmysl. Certifikace podle normy AS9100 (nebo ekvivalentních norem, jako je EN 9100) prokazuje, že dodavatel zavedl přísné procesy pro kontrolu kvality, řízení rizik, řízení konfigurace, sledovatelnost a neustálé zlepšování přizpůsobené požadavkům leteckého průmyslu. To je často neoddiskutovatelný požadavek pro dodavatele Tier 1 a Tier 2 v leteckém průmyslu.
- Certifikace ISO 9001: Certifikace ISO 9001 je sice obecnější, ale ukazuje na zásadní závazek dodržovat zásady řízení kvality.
- Robustní dokumentace QMS: Dodavatel by měl být schopen předložit dokumentaci s podrobnými údaji o své příručce jakosti, postupech řízení procesů, programech školení obsluhy, záznamech o kalibraci zařízení a postupech nápravných/preventivních opatření.
- Závazek Met3dp: Společnost Met3dp pracuje s přísnými protokoly kontroly kvality, které jsou v souladu s nejlepšími průmyslovými postupy, a chápe kritickou povahu výroby leteckých komponentů.
- Prokazatelné zkušenosti a odbornost:
- Dosavadní výsledky v leteckém a kosmickém průmyslu: Má poskytovatel prokazatelné zkušenosti s výrobou dílů pro zákazníky z leteckého průmyslu? Může se podělit o (nedůvěrné) případové studie nebo příklady relevantní pro vaši aplikaci (např. složité fluidní součásti, díly pro vysoké teploty)?
- Odborné znalosti materiálů: Hluboké znalosti zpracování specifických požadovaných slitin (IN625, 316L, případně dalších, jako jsou slitiny titanu). To zahrnuje znalost optimálních procesních parametrů, manipulaci s práškem, protokoly tepelného zpracování a charakterizaci vlastností materiálu. Společnost Met3dp, která se specializuje jak na pokročilé kovové prášky a systémy AM, disponuje těmito základními odbornými znalostmi v oblasti vědy o materiálech.
- Podpora DfAM: Může poskytovatel nabídnout podporu pro aditivní výrobu? Má aplikační inženýry, kteří mohou spolupracovat s vaším konstrukčním týmem na optimalizaci návrhů ventilů z hlediska tisknutelnosti, výkonu a nákladové efektivity?
- Hloubka inženýrství: Dostupnost zkušených metalurgických, strojních a výrobních inženýrů, kteří dohlížejí na projekty a řeší problémy.
- Schopnosti a technologie zařízení:
- Vhodná technologie AM: Pro husté, vysoce výkonné kovové díly, jako jsou tlakové ventily, se obvykle vyžaduje laserová fúze v práškovém loži (L-PBF, včetně SLM/DMLS) nebo tavení elektronovým svazkem (EBM - vhodné zejména pro určité materiály, jako je Ti-6Al-4V). Ujistěte se, že poskytovatel používá stroje průmyslové třídy od renomovaných výrobců.
- Strojový park a kapacita: Má poskytovatel dostatečnou kapacitu strojů, aby zvládl výrobu prototypů a případné požadavky na objem výroby bez výrazných zpoždění? Redundance (více strojů) je také výhodná pro zmírnění rizik výpadků. Met3dp využívá špičkové tiskárny známé svým objemem, přesností a spolehlivostí.
- Manipulace s práškem a jeho správa: Přísné protokoly pro skladování, manipulaci, prosévání a recyklaci kovových prášků jsou nezbytné k zabránění kontaminace (velkým rizikem je křížová kontaminace mezi slitinami) a zajištění stálé kvality prášku. Hledejte kontrolované prostředí a zdokumentované postupy. Základy společnosti Met3dp’v oblasti výroby prášků zajišťují dodržování osvědčených postupů.
- Možnosti následného zpracování: Zhodnoťte jejich vlastní nebo přísně řízené externí kapacity pro nezbytné kroky následného zpracování: odlehčení napětí, HIP (je-li třeba), přesné CNC obrábění, povrchová úprava (včetně vnitřních kanálů), tepelné zpracování, NDT a čištění. Vertikálně integrovaný dodavatel může často nabídnout lepší kontrolu a kratší dodací lhůty.
- Sledovatelnost a kontrola materiálu:
- Získávání a certifikace prášků: Odkud dodavatel získává prášky IN625 a 316L? Může poskytnout certifikaci materiálu (např. protokoly o zkouškách prokazující chemické složení, distribuci velikosti částic) pro každou šarži použitého prášku? V leteckém průmyslu je zásadní úplná sledovatelnost od suroviny až po finální díl. Společnost Met3dp, která vyrábí vlastní vysoce kvalitní prášky, nabízí neodmyslitelné výhody sledovatelnosti.
- Dávkové řízení: Jak řídí dávky prášku v průběhu celého procesu, aby byla zajištěna konzistence a nedocházelo k míchání? Lze zpětně dohledat konkrétní šarži prášku a sestavu stroje, ze kterého pochází?
- Nedestruktivní zkoušení (NDT) a inspekce:
- Vlastní kapacity NDT: Disponuje poskytovatel vlastními kapacitami pro běžné metody nedestruktivního zkoušení požadované pro letecké díly (např. vizuální/boroskopická kontrola, rozměrová kontrola pomocí souřadnicových měřicích přístrojů/skenerů)? Přístup k pokročilým metodám NDT, jako je CT skenování, je pro díly AM stále důležitější.
- Certifikovaní inspektoři: Jsou jejich pracovníci NDT certifikováni podle příslušných norem (např. NAS 410 / EN 4179)?
- Podávání zpráv: Mohou jako součást dokumentace poskytnout komplexní inspekční zprávy dokumentující rozměrovou shodu, výsledky NDT a certifikace materiálů?
- Důvěrnost a zabezpečení dat:
- Ochrana duševního vlastnictví (IP): Letecké konstrukce jsou často citlivé. Ujistěte se, že poskytovatel má spolehlivé postupy (např. dohody o mlčenlivosti – NDA, protokoly o bezpečném nakládání s daty) na ochranu vašeho duševního vlastnictví.
- Komunikace a řízení projektů:
- Jasné komunikační kanály: Vyhrazená kontaktní osoba (projektový manažer nebo account manažer), která rozumí vašim požadavkům a pravidelně vás informuje.
- Reakce: Jak rychle reagují na dotazy, žádosti o cenovou nabídku a technické otázky?
- Transparentnost: Ochota otevřeně diskutovat o svých postupech, schopnostech a omezeních.
- Náklady a doba realizace:
- Transparentní citování: Poskytněte podrobné nabídky s rozpisem nákladů (materiál, doba tisku, následné zpracování, NDT atd.). Pochopte jejich cenovou strukturu (za díl, za sestavení atd.).
- Reálná doba dodání: Nabízejte realistické a spolehlivé odhady dodacích lhůt pro výrobu prototypů a sériovou výrobu. Dávejte si pozor na poskytovatele, kteří slibují nerealisticky rychlé provedení složitých leteckých dílů vyžadujících rozsáhlé následné zpracování a validaci.
- Úvahy o velkoobchodu/objemu: Pokud odebíráte větší množství nebo jako distributor, poraďte se o cenových strukturách a plánování kapacit.
Proces hodnocení:
- Žádost o cenovou nabídku (RFQ): Předložte podrobný balíček RFQ obsahující modely CAD, podrobné výkresy s GD&T, specifikace materiálu (např. normy AMS pro IN625/316L), požadované následné zpracování, požadavky na NDT, množství a požadovaný termín dodání.
- Audit dodavatele: V případě kritických partnerství zvažte provedení auditu na místě nebo virtuálního auditu, abyste si ověřili jejich zařízení, vybavení, procesy, systémy kvality a certifikace z první ruky.
- Hodnocení schopností: Diskutujte o konkrétních technických problémech souvisejících s konstrukcí vašeho ventilu (např. vnitřní podpěry, tenké stěny, přísné tolerance) a zhodnoťte jejich navrhovaná řešení a úroveň důvěry.
- Pilotní projekt/zkušební díly: Zvažte možnost začít s menším pilotním projektem nebo testovacími kupony, abyste mohli posoudit kvalitu a služby poskytovatele, než se rozhodnete pro větší sérii.
Výběr správného poskytovatele služeb AM kovů je strategickým rozhodnutím. Zaměřením se na certifikace specifické pro letecký průmysl, osvědčené odborné znalosti, robustní systémy kvality, vhodné technologie a silnou komunikaci mohou společnosti vybudovat spolehlivé partnerství s dodavateli, jako je Met3dp, a úspěšně tak využít aditivní výrobu pro kritické komponenty, jako jsou tlakové ventily.
Nákladové faktory a dodací lhůty pro 3D tištěné ventily pro letectví a kosmonautiku
Aditivní výroba kovů umožňuje vytvářet vysoce komplexní a optimalizované tlakové ventily pro letecký průmysl, avšak pochopení souvisejících nákladů a typických dodacích lhůt je zásadní pro plánování projektu, sestavování rozpočtu a porovnání AM s tradičními výrobními postupy. Na rozdíl od hromadně vyráběných položek jsou náklady na 3D tisk specializovaných komponent, jako jsou letecké tlakové ventily, ovlivněny mnoha faktory. Manažeři nákupu a inženýři potřebují mít přehled o těchto faktorech ovlivňujících náklady, aby mohli přijímat informovaná rozhodnutí o dodávkách a řídit očekávání týkající se časových harmonogramů projektů.
Klíčové faktory ovlivňující náklady na 3D tištěné ventily:
- Typ materiálu a spotřeba:
- Náklady na prášek: Vysoce výkonné letecké slitiny, jako je IN625, jsou na kilogram výrazně dražší než materiály jako nerezová ocel 316L nebo hliníkové slitiny. Slitiny titanu mají také vyšší cenu. Důležitým faktorem je vlastní cena kovového prášku. Společnost Met3dp se díky vlastní výrobě prášků snaží zajistit konkurenceschopné náklady na materiál a zároveň vysokou kvalitu.
- Část Objem & amp; Hmotnost: Čím větší a těžší je ventil, tím více prášku se spotřebuje, což přímo zvyšuje náklady na materiál.
- Objem podpůrné struktury: Náklady zvyšuje také materiál použitý na podpůrné konstrukce. Optimalizované konstrukce (DfAM), které minimalizují podpěry, snižují spotřebu materiálu.
- Účinnost recyklace prášku: Netavený prášek lze sice recyklovat, ale s nakládáním s práškem jsou spojeny ztráty efektivity a náklady na kontrolu kvality, které se započítávají do režijních nákladů.
- Čas stroje (čas sestavení):
- Velikost dílu & Složitost: Větší díly nebo díly se složitou geometrií se tisknou vrstvu po vrstvě déle.
- Výška stavby: Čím vyšší je díl(y) v orientaci sestavení, tím více vrstev je třeba zpracovat, což přímo ovlivňuje dobu tisku.
- Počet dílů na sestavení (Nesting): Poskytovatelé služeb se snaží maximalizovat počet dílů tištěných současně v rámci jedné úlohy sestavení (nesting), aby byl stroj efektivně využit. Tisk jednoho ventilu může být relativně drahý na jeden díl ve srovnání s tiskem dávky. To významně ovlivňuje velkoobchodní náklady na 3D tisk.
- Tloušťka vrstvy & amp; Parametry: Použití tenčích vrstev pro vyšší rozlišení prodlužuje dobu sestavení. Potřebný čas ovlivňují také specifické parametry procesu (rychlost skenování, šrafování).
- Hodinová sazba stroje AM: Poskytovatelé služeb mají hodinové sazby za své stroje pro průmyslové AM, které zohledňují odpisy stroje, údržbu, spotřebu energie, spotřebu inertního plynu a režijní náklady zařízení.
- Náklady na pracovní sílu:
- Příprava stavby: Kvalifikovaní technici jsou potřební k přípravě souboru pro sestavení (orientace, podpěry), načtení stroje a dohledu nad procesem tisku.
- Práce po zpracování: To může představovat významnou složku nákladů. Ruční odstraňování podpěr, nastavení a obsluha obrábění, povrchová úprava, kontrola a dokumentace vyžadují hodiny kvalifikované práce. U složitých dílů vyžadujících rozsáhlé ruční dokončování nebo odstraňování vnitřních podpěr budou náklady na pracovní sílu vyšší.
- Požadavky na následné zpracování:
- Tepelné zpracování: Náklady spojené s časem pece, energií, řízenou atmosférou (vakuum/inertní plyn) a pracovní silou při uvolňování napětí, HIP nebo žíhání/staření v roztoku. HIP je obzvláště nákladný krok kvůli specializovanému vybavení.
- Obrábění: Čas strávený na CNC stroji, náklady na nástroje, návrh/výrobu přípravků (pokud je potřeba) a práci obráběče. Počet a složitost obráběných prvků přímo ovlivňuje náklady.
- Povrchová úprava: Náklady závisí na použité metodě (např. bubnové leštění je levnější než AFM nebo špičkové leštění) a na ploše/komplexnosti povrchu.
- Čištění: Specializované procesy čištění vnitřních kanálů zvyšují časovou náročnost a náklady.
- Nedestruktivní zkoušení (NDT) a zajištění kvality:
- Úroveň inspekce: Rozsah a typ požadovaných nedestruktivních zkoušek (vizuální, rozměrové, CT, PT atd.) významně ovlivňují náklady. CT vyšetření je sice výkonné, ale relativně drahé.
- Dokumentace: Vytváření komplexních balíčků dokumentace kvality vyžadovaných pro sledovatelnost v letectví a kosmonautice zvyšuje administrativní náklady.
- Náklady na certifikaci: Udržování certifikací, jako je AS9100, zahrnuje průběžné náklady, které jsou započítány do sazeb poskytovatele.
- Design Complexity & DfAM:
- Špatně optimalizované návrhy: Návrhy, které ignorují zásady DfAM (např. vyžadují nadměrné vnitřní podpory, obtížně obrobitelné prvky, velké neoptimalizované pevné části), budou vždy dražší z důvodu delší doby tisku, vyšší spotřeby materiálu a rozsáhlé práce při následném zpracování.
- Topologická optimalizace / mřížky: Tyto techniky sice šetří hmotnost materiálu (snižují náklady na materiál), ale složité geometrie mohou někdy mírně prodloužit dobu tisku nebo vyžadovat složitější nastavení/simulaci sestavení, ačkoli úspory materiálu často převažují.
- Objem objednávky (množství):
- Prototypování vs. výroba: Jednorázové prototypy jsou obvykle drahé v přepočtu na jeden díl, protože náklady na zřízení se amortizují v průběhu jednoho kusu.
- Velikost dávky: Náklady na jeden díl se výrazně snižují při tisku dílů v dávkách díky lepšímu využití stroje (nesting) a amortizaci nákladů na seřízení/programování na více jednotek. To je klíčové pro velkoobchodní odběratele a distributory, kteří usilují o velkoobchodní ceny.
Typická doba dodání komponentů:
Dodací lhůta se vztahuje k celkové době od zadání objednávky po dodání konečného dílu. U složitých leteckých ventilů vyráběných pomocí AM zahrnuje tato doba více fází:
- Revize objednávky & Plánování (1-5 dní): Potvrzení požadavků, revize DfAM (pokud je to relevantní), příprava souboru sestavení (orientace, podpory), plánování.
- Tisk (1-10+ dní): Skutečný strojní čas závisí do značné míry na velikosti dílu, složitosti a efektivitě vnoření. Jeden velký ventil nebo celá stavební deska menších ventilů může trvat několik dní nepřetržitého tisku. Roli hraje také dostupnost stroje/objednávka.
- Následné zpracování (5-20+ dní): To často představuje nejdelší část doby přípravy.
- Léčba stresu/tepla: (včetně cyklů pece, chlazení).
- Stavební deska/odstranění podpory: 1-2 dny.
- HIP (pokud je vyžadován): 3-7 dní (včetně dopravy k poskytovateli HIP, pokud není na místě, a doby cyklu).
- Obrábění: 2-10+ dní (v závislosti na složitosti, počtu prvků a vytížení dílny).
- Povrchová úprava/čištění: 1-5 dní.
- NDT & amp; Inspekce: 1-5 dní.
- Doprava (1-5 dní): V závislosti na místě a způsobu přepravy.
Celková předpokládaná doba realizace:
- Prototypy: Typicky 2-6 týdnův závislosti na složitosti a potřebách následného zpracování.
- Malé výrobní dávky: Typicky 4-10 týdnů, případně déle, pokud se jedná o rozsáhlou kvalifikaci, NDT nebo externí zpracování, jako je HIP.
Faktory doby realizace:
- Část Složitost: Složitější díly vyžadují více času na tisk a následné zpracování.
- Intenzita následného zpracování: Díly, které vyžadují HIP, rozsáhlé obrábění a více dokončovacích kroků, mají delší dodací lhůty.
- Kapacita dodavatele a pracovní zatížení: Aktuální fronta/zásobník u poskytovatele služeb.
- Dostupnost externích služeb: Dodací lhůty pro outsourcované procesy, jako je HIP nebo specializované nátěry.
- Kvalifikační požadavky: Kontrola prvního článku (FAI) nebo jiné kvalifikační kroky mohou prodloužit dobu.
Náklady vs. tradiční metody:
- Vytváření prototypů & nízký objem: AM je často rychlejší a nákladově efektivnější než tradiční metody díky eliminaci nákladů na nástroje (formy, zápustky).
- Vysoká složitost: U velmi složitých ventilů nebo ventilů, které významně využívají konsolidaci dílů a odlehčení, může AM zůstat konkurenceschopná i při vyšších objemech, pokud výkonnostní výhody ospravedlňují náklady.
- Velký objem, jednoduchý design: U relativně jednoduchých konstrukcí ventilů vyžadovaných ve velmi vysokých objemech je tradiční odlévání/obrábění často cenově výhodnější díky úsporám z rozsahu.
Porozumění těmto nákladovým faktorům a složkám doby realizace umožňuje lepší plánování a komunikaci mezi inženýringem, nákupem a poskytovatelem služeb AM. Získání podrobných cenových nabídek od zkušených dodavatelů, jako je Met3dp, kteří rozumí nuancím požadavků leteckého průmyslu a celému výrobnímu procesu, je nezbytné pro přesné posouzení projektu.
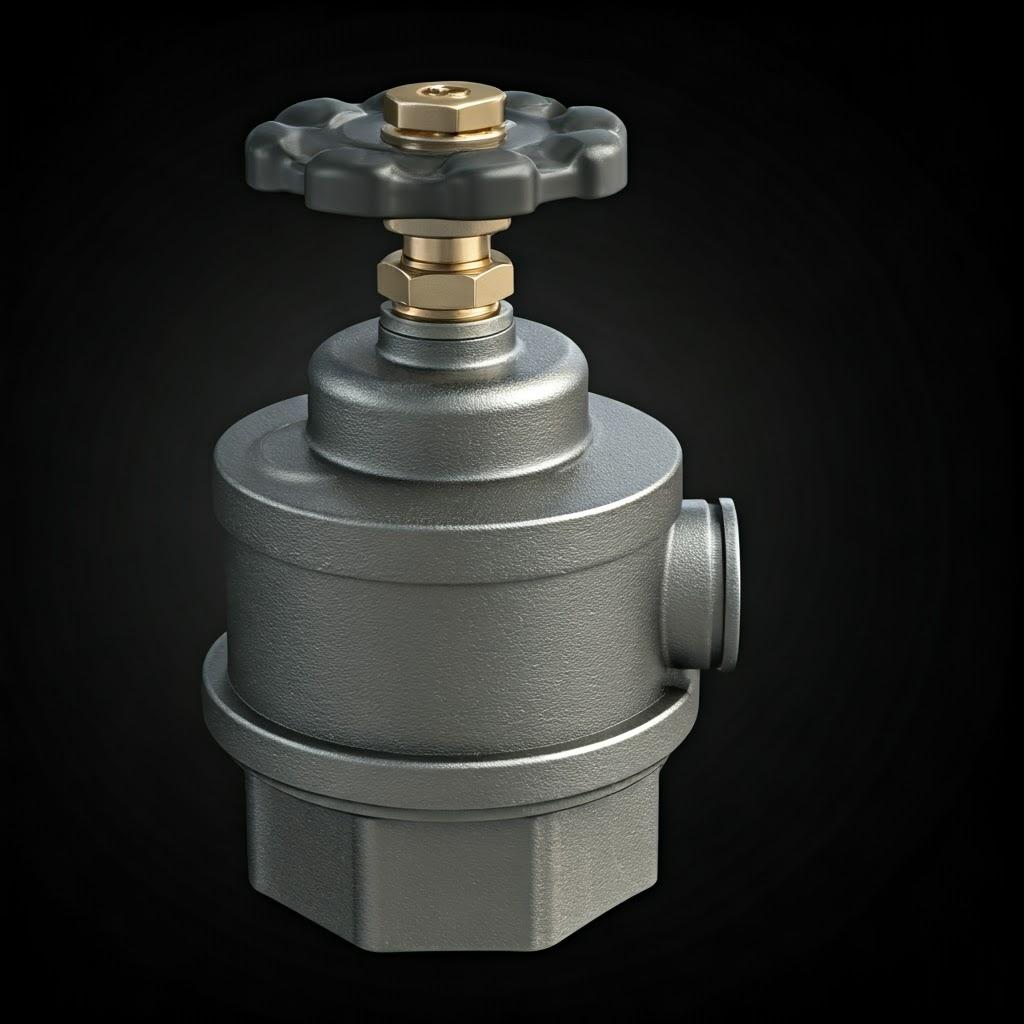
Často kladené otázky (FAQ) o 3D tisku leteckých tlakových ventilů
Zde jsou odpovědi na některé časté otázky, které mají inženýři, konstruktéři a manažeři nákupu, když zvažují aditivní výrobu kovů pro tlakové ventily v letectví a kosmonautice z materiálů jako IN625 a 316L:
1. Mohou 3D tištěné kovové ventily splňovat přísné certifikační požadavky leteckého průmyslu (např. FAA/EASA)?
- Odpověď: Ano, rozhodně, ale vyžaduje to přísný a dobře zdokumentovaný proces. Splnění požadavků na certifikaci v leteckém průmyslu (např. od Federálního úřadu pro letectví nebo Agentury Evropské unie pro bezpečnost letectví) zahrnuje prokázání, že proces AM, materiál a finální díl trvale splňují stanovené výkonnostní, bezpečnostní a spolehlivostní normy. To obvykle zahrnuje:
- Kvalifikace procesu: Kvalifikace konkrétního AM stroje, materiálu (např. prášek IN625 nebo 316L z certifikovaného zdroje, jako je Met3dp) a validované sady procesních parametrů použitých k výrobě dílu.
- Přípustné množství materiálu: Stanovení statisticky ověřených údajů o vlastnostech materiálu (pevnost v tahu, únavová životnost atd.) pro konkrétní materiál a proces AM, často na základě rozsáhlého testování materiálových kupónů vytištěných společně s díly.
- Specifická kvalifikace pro danou část: Provedení výkonnostních zkoušek (tlakové zkoušky, zkoušky těsnosti, průtokové zkoušky, vibrační zkoušky atd.) na konečné konstrukci ventilu vyrobené kvalifikovaným procesem AM.
- Robustní řízení kvality: Dodržování přísných systémů kvality, jako je AS9100, zajištění plné sledovatelnosti, řízení procesů, NDT a dokumentace.
- Spolupráce: Úzká spolupráce s regulačními orgány a zákazníky při vytváření a dodržování schválených kvalifikačních plánů.
- Mnoho kovových dílů vytištěných 3D tiskem, včetně součástí ventilů, již létá v komerčních a vojenských letadlech, což dokazuje, že certifikace je dosažitelná při správném přístupu a partnerství.
2. Jaká je výkonnost (např. jmenovitý tlak, průtokové charakteristiky, únavová životnost) aditivně vyráběných ventilů ve srovnání s tradičně vyráběnými ventily (litými, kovanými, obráběnými)?
- Odpověď: Při správném návrhu, tisku a následném zpracování mohou být kovové ventily AM výkonné se rovnají nebo dokonce převyšují jako u tradičně vyráběných protějšků.
- Mechanické vlastnosti: Díky optimalizovaným parametrům a následnému zpracování, jako je HIP, mohou statické a únavové vlastnosti AM IN625 nebo 316L splňovat nebo překračovat specifikace pro tváření nebo odlévání. HIP výrazně zvyšuje únavovou životnost uzavřením vnitřní pórovitosti.
- Tlaková odolnost: Součástky AM lze navrhovat pomocí optimalizace topologie a metodou konečných prvků, aby efektivně zvládaly vysoké tlaky a potenciálně dosáhly požadovaných hodnot tlaku při nižší hmotnosti ve srovnání s tradičními konstrukcemi.
- Charakteristika toku: Schopnost společnosti AM vytvářet složité, hladké vnitřní geometrie často umožňuje dosáhnout lepších průtokových charakteristik (vyšší Cv, nižší tlaková ztráta) ve srovnání s ventily s úhlovými, obrobenými průchody. CFD lze použít k optimalizaci průtokových cest speciálně pro AM.
- Odolnost proti korozi: Přirozená korozní odolnost slitin, jako jsou IN625 a 316L, je při procesu AM zachována za předpokladu použití vysoce kvalitního prášku a správného zpracování. Určitou roli může hrát povrchová úprava, která někdy vyžaduje povrchovou úpravu pro optimální výkon ve vysoce korozivním prostředí.
- Klíčem je využití zásad DfAM a zajištění vhodného následného zpracování a kontroly kvality zkušenými poskytovateli, jako jsou např Met3dp. Přímá náhrada konstrukce optimalizované pro odlévání pomocí AM bez DfAM nemusí přinést optimální výsledky.
3. Jaká je typická kvalita povrchu (drsnost) dosažitelná uvnitř vnitřních kanálků 3D tištěného ventilu a jak ji lze v případě potřeby zlepšit?
- Odpověď: Jednou z výzev kovových PBF je povrchová úprava vnitřních kanálů po vytištění. Bývá drsnější než vnější povrchy, zejména na svazích směřujících dolů nebo na složitých nepodporovaných prvcích.
- Typický stav po vytištění Ra: Drsnost (Ra) uvnitř kanálů se může pohybovat v širokém rozmezí, často od 15 µm až 30 µm (600 – 1200 µin) nebo případně vyšší v obtížně tisknutelných oblastech. To do značné míry závisí na průměru kanálu, jeho orientaci a na tom, zda byly zapotřebí podpěry. Svislé kanály o větším průměru bývají hladší než vodorovné nebo složité, úzké.
- Metody zlepšování: Pokud je požadován hladší vnitřní povrch (např. pro snížení třecích ztrát, zlepšení čistitelnosti nebo pro specifické těsnicí aplikace), lze použít několik technik následného zpracování:
- Obrábění abrazivním tokem (AFM) / Extrude Hone: To je často nejúčinnější metoda pro vyhlazení vnitřních chodeb. Do kanálků se vtlačí abrazivní tmel, který odře vrcholy a vyhladí povrch. Je možné dosáhnout výrazného snížení Ra.
- Elektrolytické leštění: Dokáže vyhladit vnitřní povrchy přístupné elektrolytu, což je zvláště účinné u nerezových ocelí, jako je 316L.
- Chemické leptání/leštění: Může zajistit určité vyhlazení, ale vyžaduje pečlivou kontrolu a ověření kompatibility materiálu.
- Úvahy o návrhu: Navrhování co nejrovnějších a nejširších kanálů a jejich příznivá orientace při stavbě pomáhá dosáhnout lepšího počátečního povrchu a usnadňuje následné leštění. Zásadní je včasné projednání požadavků na vnitřní povrchovou úpravu s dodavatelem AM.
4. Je kovový 3D tisk nákladově efektivním řešením pro sériovou výrobu leteckých ventilů, nebo je určen především pro výrobu prototypů?
- Odpověď: Nákladová efektivita AM kovů pro sériovou výrobu leteckých ventilů závisí na několika faktorech, především na složitost, objem a nabídka hodnoty plynoucí z výhod AM.
- Vytváření prototypů: AM je téměř vždy rychlejší a nákladově efektivnější pro výrobu počátečních prototypů a velmi malých sérií díky absenci nákladů na nástroje.
- Série s malým až středním objemem výroby: U složitých ventilů, kde AM umožňuje významnou konsolidaci dílů, odlehčení nebo zlepšení výkonu, kterého nelze jinak dosáhnout, může být nákladově efektivní i při sériové výrobě (desítky až stovky či potenciálně tisíce kusů), zejména při zohlednění celkové hodnoty životního cyklu (např. úspora paliva díky lehčím dílům).
- Velkoobjemová výroba: U jednodušších konstrukcí ventilů, které jsou vyžadovány ve velmi vysokých objemech (mnoho tisíc kusů), jsou tradiční metody, jako je odlévání a následné obrábění, často ekonomičtější díky zavedeným úsporám z rozsahu.
- Bod přechodu: V objemu existuje bod přechodu, kdy se tradiční metody stávají levnějšími v přepočtu na jeden díl. Tento bod se však posouvá s tím, jak dozrává technologie AM, zvyšuje se rychlost tisku a potenciálně klesají náklady na materiál. Pro letecký průmysl jsou faktory, které přesahují čistou cenu kusu (jako je zkrácení doby dodání náhradních dílů, zvýšení výkonnosti, zjednodušení dodavatelského řetězce), často atraktivní pro AM, i když jsou náklady na jeden díl o něco vyšší. Klíčová je analýza celkových nákladů na vlastnictví a konkrétní hodnoty, kterou AM přináší pro danou aplikaci. Konzultace se zkušenými poskytovateli, kteří rozumí jak AM, tak tradičním metodám, může pomoci určit nejlepší přístup pro váš konkrétní ventil a objemové požadavky.
Závěr: Zvýšení úrovně řízení tekutin v leteckém průmyslu pomocí aditivní výroby a pokročilých slitin
Náročné prostředí leteckého průmyslu vyžaduje komponenty, které nabízejí nekompromisní spolehlivost, výkon a účinnost. Tlakové ventily, jakožto kritické regulátory kapalinových systémů, jsou pro tento požadavek klíčové. Tradiční výrobní metody jsou sice zavedené, ale často představují omezení z hlediska složitosti konstrukce, využití materiálu a rychlosti výroby, zejména u složitých geometrií a vysoce výkonných materiálů, které jsou potřebné v moderních letadlech a kosmických lodích.
Aditivní výroba kovů, konkrétně technika Powder Bed Fusion využívající pokročilé slitiny odolné proti korozi, jako je např IN625 a Nerezová ocel 316L, představuje významný pokrok ve výrobě těchto kritických komponent. Jak jsme již zjistili, výhody jsou přesvědčivé:
- Bezkonkurenční volnost designu: Umožňuje optimalizovat vnitřní průtokové cesty pro vyšší efektivitu a integraci složitých funkcí.
- Významné odlehčení: Využití optimalizace topologie a mřížkových struktur ke snížení hmotnosti součástí, což je rozhodující faktor pro úsporu paliva a nosnost v letectví.
- Konsolidace částí: Snížení složitosti montáže, potenciálních míst úniku a zjednodušení dodavatelských řetězců.
- Zrychlený vývoj: Usnadňuje rychlé vytváření prototypů a iterace designu, čímž se inovace rychleji dostávají na trh.
- Vylepšené vlastnosti materiálu: Dosažení vynikajících mechanických vlastností a využití vynikající odolnosti proti korozi a vysokoteplotní pevnosti slitin, jako je IN625, a univerzálnosti slitiny 316L.
Realizace těchto výhod však vyžaduje hluboké pochopení principů DfAM, pečlivou kontrolu procesu, vhodné následné zpracování (včetně tepelného zpracování, přesného obrábění a povrchové úpravy) a přísné protokoly zajištění kvality v souladu s přísnými normami pro letecký průmysl, jako je AS9100. Řešení problémů, jako je zbytkové napětí, odstranění podpěr a dosažení kritických tolerancí, vyžaduje odborné znalosti a pokročilé schopnosti.
Výběr správného výrobního partnera je proto klíčový. Poskytovatel jako např Met3dp, se sídlem v čínském městě Čching-tao, vyniká tím, že nabízí komplexní, vertikálně integrované řešení. Odborné znalosti společnosti Met3dp’ zahrnují celý ekosystém AM:
- Pokročilá výroba prášků: Využití špičkových technologií atomizace plynu a PREP k výrobě vysoce sférických, vysoce průtočných materiálů IN625, 316L a dalších specializované kovové prášky na míru pro AM.
- Moderní tiskové systémy: Tiskárny, které jsou proslulé špičkovým objemem tisku, přesností a spolehlivostí, jsou vhodné pro kritické díly.
- Desítky let kolektivní odbornosti: Využíváme hluboké znalosti v oblasti aditivní výroby kovů, vědy o materiálech a vývoje aplikací v leteckém, lékařském, automobilovém a dalších náročných odvětvích.
- Komplexní řešení: Spolupracujeme s organizacemi při zavádění 3D tisku a poskytujeme podporu od optimalizace návrhu až po následné zpracování a kvalifikaci.
Využitím aditivní výroby kovů z vysoce výkonných slitin a partnerstvím se zkušenými poskytovateli zaměřenými na kvalitu, jako je Met3dp, mohou letecké společnosti zvýšit výkon, spolehlivost a účinnost svých systémů pro řízení tekutin. AM není jen nástrojem pro tvorbu prototypů; je to výkonné výrobní řešení, které umožní vytvořit novou generaci lehčích, rychlejších a schopnějších leteckých vozidel.
Jste připraveni prozkoumat, jak může aditivní výroba kovů revolučně změnit vaše konstrukce tlakových ventilů pro letectví a kosmonautiku? Kontaktujte Met3dp ještě dnes a prodiskutujte s našimi odborníky požadavky na vaše aplikace a zjistěte, jak mohou naše špičkové systémy a pokročilé kovové prášky podpořit cíle vaší organizace v oblasti aditivní výroby a urychlit transformaci digitální výroby.
Sdílet na
MET3DP Technology Co., LTD je předním poskytovatelem řešení aditivní výroby se sídlem v Qingdao v Číně. Naše společnost se specializuje na zařízení pro 3D tisk a vysoce výkonné kovové prášky pro průmyslové aplikace.
Dotaz k získání nejlepší ceny a přizpůsobeného řešení pro vaše podnikání!
Související články
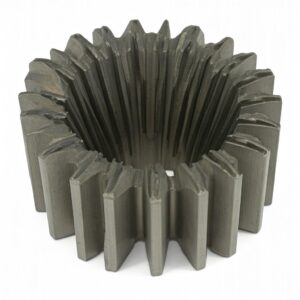
Vysoce výkonné segmenty lopatek trysek: Revoluce v účinnosti turbín díky 3D tisku z kovu
Přečtěte si více "O Met3DP
Nedávná aktualizace
Náš produkt
KONTAKTUJTE NÁS
Nějaké otázky? Pošlete nám zprávu hned teď! Po obdržení vaší zprávy obsloužíme vaši žádost s celým týmem.
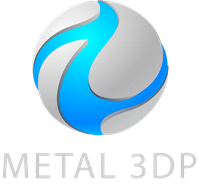
Kovové prášky pro 3D tisk a aditivní výrobu