3D tištěné pohonné trysky pro námořní systémy
Obsah
Úvod: Vývoj lodních pohonných trysek s kovovým AM
Snaha o efektivitu, výkon a spolehlivost byla v námořním průmyslu vždy na prvním místě. Od kolosálních kontejnerových lodí křižujících globální obchodní trasy po agilní námořní plavidla chránící pobřeží a sofistikovaná podvodní vozidla zkoumající hlubiny - pohonný systém je srdcem provozních schopností. Ústředním prvkem mnoha těchto systémů je pohonná tryska - součástka zdánlivě jednoduchá ve své koncepci, ale neuvěřitelně složitá ve své hydrodynamické funkci. Ať už se jedná o Kortovu trysku maximalizující tah vlečného člunu, přesně navržený kanál pro vodní paprsek nebo specializovanou součást trysky pro dynamické polohování, její konstrukce přímo ovlivňuje spotřebu paliva, rychlost, manévrovatelnost a akustickou signaturu.
Tradičně se tyto kritické součásti vyráběly zavedenými metodami, jako je odlévání, kování a rozsáhlé obrábění. Tyto techniky jsou sice spolehlivé, ale často přinášejí omezení, pokud jde o složitost konstrukce, výběr materiálu, dobu realizace a schopnost vytvářet vysoce přizpůsobené nebo optimalizované geometrie. Vstupte do transformační síly výroba aditiv kovů (AM), častěji známý jako kov 3D tisk. Tato technologie rychle mění paradigmata napříč průmyslovými odvětvími a její potenciál v lodním inženýrství, zejména v oblasti pohonných komponent, je obrovský.
Technologie AM umožňuje inženýrům a námořním architektům vymanit se z omezení tradiční výroby. Umožňuje vytvářet pohonné trysky se složitou vnitřní strukturou, optimalizovanými hydrodynamickými profily a konsolidovanými konstrukcemi, jejichž výroba byla dříve nemožná nebo neúměrně nákladná. Díky tomu, že se díly vytvářejí vrstvu po vrstvě přímo z digitálních modelů za použití vysoce výkonných kovových prášků, nabízí AM nebývalou svobodu designu, zrychluje prototypování a výrobní cykly a otevírá dveře k použití pokročilých materiálů přizpůsobených pro drsné námořní prostředí.
Pro inženýry, kteří usilují o vyšší výkonnost plavidel, manažery veřejných zakázek, kteří hledají spolehlivé a inovativní řešení dodavatelé pro stavbu lodía společnosti, které chtějí využít nejmodernější technologie námořní vybavení, porozumění možnostem kov AM pro lodní komponenty již není volitelná - je nezbytná pro udržení konkurenceschopnosti. Tento příspěvek se zabývá specifiky využití kovového 3D tisku pro trysky lodních pohonů, zkoumá aplikace, výhody, klíčové materiály, jako jsou CuNi30Mn1Fe a IN625, konstrukční úvahy a způsoby, jak spolupracovat s odbornými poskytovateli, jako je Met3dp, aby bylo možné tuto výkonnou technologii využít. Společnost Met3dp, která se specializuje jak na pokročilé systémy AM kovů, tak na výrobu vysoce kvalitních sférických kovových prášků prostřednictvím špičkových technologií plynové atomizace a PREP, je připravena podpořit vývoj námořního průmyslu.
Základní aplikace: Kde 3D tištěné pohonné trysky dělají vlny?
Použitelnost kovového 3D tisku se neomezuje jen na výklenkové nebo experimentální použití; nachází praktické a vysoce hodnotné uplatnění při výrobě různých typů pohonných trysek v různých námořních odvětvích. Díky schopnosti vytvářet složité geometrie a využívat specializované materiály je AM zvláště vhodný pro komponenty, u nichž optimalizace výkonu přináší významné provozní výhody.
Zde je několik klíčových oblastí, ve kterých 3D tištěné pohonné trysky prokazují svou hodnotu:
- Kortovy trysky:
- Funkce: Tyto kanálové vrtule jsou určeny k výraznému zvýšení tahu lodních šroubů, zejména při nízkých rychlostech, které se běžně používají na remorkérech, trawlerech a některých velkých plavidlech.
- Výhoda AM: Technologie Metal AM umožňuje vytvářet vysoce optimalizované profily kanálů přizpůsobené konkrétním konstrukcím vrtulí a interakcím s trupem, což maximalizuje zvýšení tahu a potenciálně zlepšuje kavitační výkon. Složité vnitřní výztužné struktury lze integrovat bez svařování, což zlepšuje strukturální integritu a únavovou životnost. Přizpůsobení pro specifickou hydrodynamiku plavidla se stává proveditelnějším.
- Komponenty pro pohon vodním paprskem:
- Funkce: Vodní trysky využívají oběžného kola, které nasává vodu a vypuzuje ji tryskou vysokou rychlostí, čímž zajišťuje pohon a řízení. Mezi klíčové součásti patří sací kanály, statory, oběžná kola (i když u trysek AM je to méně obvyklé) a konečná výtoková tryska.
- Výhoda AM: Složité vnitřní geometrie statorů a trysek vodního paprsku, které jsou klíčové pro efektivní usměrňování proudění, jsou ideálními kandidáty pro AM. Hladké, optimalizované vnitřní průchody minimalizují hydraulické ztráty. Velkou výhodou je konsolidace dílů, která může spojit více tradičně vyráběných dílů do jediné tištěné součásti, čímž se zkrátí doba montáže a zkrátí se potenciální cesty úniku. Vysokopevnostní materiály odolné proti korozi, jako je IN625, se snadno zpracovávají pomocí AM pro náročné podmínky proudění s vysokou rychlostí.
- Trysky trysek (azimut, tunel, dynamické polohování):
- Funkce: Náporové motory zajišťují manévrovací schopnosti a schopnost udržet se na stanici. Jejich trysky usměrňují tah generovaný vrtulí, což často vyžaduje přesné ovládání a odolnost.
- Výhoda AM: AM umožňuje výrobu trysek s optimalizovaným hydrodynamickým tvarem pro maximální účinnost tahu a snížení hlučnosti. U dynamických polohovacích systémů vyžadujících rychlé změny vektoru tahu mohou lehké konstrukce dosažené optimalizací topologie (možné pomocí AM) snížit setrvačnost. Možnost tisku z robustních materiálů, jako je IN625, zajišťuje dlouhou životnost v náročných provozních cyklech. Pro pohonné jednotky s vysokou hustotou výkonu by mohly být potenciálně integrovány vnitřní chladicí kanály.
- Pohon specializovaných podvodních vozidel (AUV, ROV):
- Funkce: Autonomní podmořská vozidla (AUV) a dálkově ovládaná vozidla (ROV) často vyžadují kompaktní, vysoce účinné a někdy i akusticky tiché pohonné systémy.
- Výhoda AM: Technologie AM se dokonale hodí pro výrobu vysoce výkonných trysek na míru, které jsou v malých objemech přizpůsobeny jedinečným požadavkům na mise a omezením velikosti těchto vozidel. Lze realizovat složité, biologicky inspirované návrhy pro zvýšení účinnosti nebo utajení. Odlehčení pomocí AM je rozhodující pro maximalizaci kapacity užitečného zatížení a výdrže u AUV poháněných bateriemi. Materiály s vynikající odolností proti korozi, jako jsou slitiny CuNi nebo specializované třídy titanu, které rovněž nabízí společnost Met3dp, jsou pro dlouhodobý provoz pod vodou nezbytné.
- Kapotážní ploutve vrtule (PBCF) & Zařízení pro zvýšení účinnosti:
- Funkce: Zařízení, jako jsou PBCF, se sice nejedná přímo o trysky, ale připojují se k vrtulím, aby rozbíjely víry v náboji a získávaly zpět rotační energii, čímž se zvyšuje účinnost. Podobné přídavné zařízení zvyšující účinnost může někdy obsahovat prvky podobné tryskám.
- Výhoda AM: Složité, často nesouměrné tvary těchto zařízení mohou být náročné na tradiční výrobu. AM umožňuje přesné vytváření těchto geometrických tvarů, případně jejich přímou integraci s jinými součástmi vrtule nebo rychlé prototypování a testování nových konceptů zvyšujících účinnost.
Odvětví, která z toho mají prospěch:
- Obchodní přeprava: Snaha o zlepšení palivové účinnosti, snížení údržby (materiály proti znečištění) a spolehlivé komponenty.
- Naval & amp; Obrana: Požadavky na vysoký výkon, trvanlivost, potenciální snížení akustické signatury a rychlé nasazení řešení na míru.
- Ropa na moři a plyn / obnovitelné zdroje energie: Využívají systémy DP, ROV pracovní třídy a potřebují robustní komponenty pro drsné prostředí.
- Mořský výzkum & Průzkum: Nasazení AUV a ROV vyžadujících specializovaný, lehký a korozivzdorný pohon.
- Jachting: Hledáte vysoce výkonné komponenty pro vodní paprsek nebo řešení trysek na míru.
Společným znakem těchto aplikací je potřeba vyššího výkonu, přizpůsobení a spolehlivosti v náročných provozních podmínkách - právě zde vyniknou jedinečné schopnosti technologie AM pro zpracování kovů. Manažeři veřejných zakázek, kteří hledají dodavatelé námořního vybavení schopné dodávat tyto pokročilé komponenty, se stále častěji obracejí na specialisty na AM kovů.
Proč 3D tisk z kovu pro pohonné trysky? Výhody oproti tradičním metodám
Tradiční výrobní metody, jako je odlévání a obrábění, sice slouží námořnímu průmyslu již desítky let, ale mají svá omezení, zejména pokud se setkáváme s požadavky na stále složitější a optimalizovanější konstrukce pohonných trysek. Aditivní výroba kovů nabízí přesvědčivý soubor výhod, které tato omezení přímo řeší, a poskytuje tak inženýrům, konstruktérům a provozovatelům plavidel významnou hodnotu.
Srovnejme si kovovou AM (konkrétně procesy Powder Bed Fusion – PBF, jako jsou Selective Laser Melting/Melting (SLM/SLM) a Electron Beam Melting (EBM)) s tradičními přístupy k výrobě trysek:
Srovnání: Kovové AM vs. tradiční výroba pro námořní trysky
Vlastnosti | Aditivní výroba kovů (PBF) | Tradiční výroba (odlévání / kování + obrábění) | Důsledky pro námořní průmysl |
---|---|---|---|
Složitost návrhu | Velmi vysoká: Umožňuje složité vnitřní kanály, komplexní křivky, optimalizaci topologie, mřížkové struktury. Náklady jsou méně závislé na složitosti. | Omezené: Omezeno možnostmi formy/výlisku, přístupem k nástroji pro obrábění. Složité prvky výrazně zvyšují náklady. | AM umožňuje hydrodynamicky lepší konstrukci, integrované funkce a potenciálně tišší provoz. |
Konsolidace částí | Vynikající: Často lze více komponentů přepracovat a vytisknout jako jeden kus. | Špatné: Složité sestavy často vyžadují více dílů, svařování, spojovací materiál. | Kratší doba montáže, méně potenciálních míst poruch (svary, těsnění), lepší konstrukční integrita. |
Využití materiálu | Vysoká: Používá pouze materiál potřebný pro díl a podpěry (recyklovatelný). Minimální množství odpadu. | Nižší: Odlévání může mít přiměřenou výtěžnost, ale obrábění je subtraktivní a vytváří značný odpad (třísky). | Udržitelnější výroba, úspora nákladů na drahé slitiny, jako je IN625. |
Dodací lhůta (prototypy) | Rychle: Dny až týdny od souboru CAD k fyzickému dílu. Umožňuje rychlou iteraci návrhu. | Pomalé: Týdny až měsíce, zejména pokud je zapotřebí nástrojů (forem, zápustek). | Rychlejší vývojové cykly, rychlejší testování a ověřování nových konceptů trysek. |
Dodací lhůta (výroba) | Středně rychlý až rychlý: Závisí na velikosti dílu, množství, následném zpracování. Vhodné pro nízký a střední objem & na vyžádání. | Různě: Může být rychlý pro zavedené velkoobjemové díly, ale doba přípravy nástrojů je předem. Pomalé pro malé objemy. | AM nabízí agilitu, náhradní díly na vyžádání, snížení potřeby zásob určitých dílů. |
Náklady na nástroje | Žádné: Přímá digitální výroba, bez nutnosti výroby specifických nástrojů. | Vysoká: Formy, zápustky nebo složité přípravky mohou představovat značné počáteční investice. | AM je nákladově efektivní pro zakázkové díly, prototypy a malosériovou výrobu. |
Snížení hmotnosti | Významný potenciál: Optimalizace topologie a vnitřní mřížky mohou výrazně snížit hmotnost při zachování pevnosti. | Omezené: Snížení hmotnosti často závisí pouze na výběru materiálu nebo na základním konstrukčním řešení. | Nižší hmotnost plavidla, lepší palivová účinnost, menší setrvačnost pohonných jednotek. |
Možnosti materiálu | Rozsah pěstování: Široká škála svařitelných slitin, které lze tisknout, včetně vysoce výkonných Ni-slitin, Ti-slitin, Cu-slitin, nerezových ocelí. | Dobře zavedené: Velmi široký rozsah, ale konkrétní kombinace nebo geometrie mohou být omezeny procesem. | AM umožňuje použití pokročilých materiálů, jako je IN625 nebo specializované slitiny CuNi, pro dosažení optimálního výkonu. |
Přizpůsobení | Snadné: Každý tisk může být jedinečný, aniž by to bylo spojeno s výraznými náklady. Ideální pro návrhy na míru. | Obtížné/nákladné: Vyžaduje změny nástrojů nebo rozsáhlé přeprogramování variant. | Trysky na míru pro specifickou hydrodynamiku plavidla nebo provozní požadavky jsou možné. |
Export do archů
Vypracované klíčové výhody:
- Bezkonkurenční svoboda designu: To je pravděpodobně nejvýznamnější výhoda. AM umožňuje konstruktérům navrhovat vnitřní průtokové cesty optimalizované čistě pro hydrodynamickou účinnost, bez omezení nutností úhlů ponoru (odlévání) nebo přístupu nástrojů (obrábění). Přímo do struktury trysky lze zabudovat složité chladicí kanály, prvky tlumení hluku nebo integrované kryty senzorů.
- Zrychlené inovace: Možnost přejít od digitálního návrhu k fyzickému kovovému prototypu během několika dní zásadně mění vývojový cyklus. Více iterací návrhu nové koncepce trysky lze vytisknout a otestovat za dobu, která by byla potřebná k získání jediného prototypu tradičním odléváním, což vede k mnohem rychlejšímu získání výkonnějších finálních výrobků. Prozkoumejte možnosti s Met3dp’s kovový 3D tisk řešení.
- Výroba na vyžádání & snížení skladových zásob: Pro některé kritické náhradní díly nebo nízkoobjemové zakázkové trysky umožňuje AM výrobu na vyžádání. Tím se snižuje potřeba rozsáhlých fyzických zásob a uvolňuje se kapitál a skladovací prostor. Stačí pouze digitální soubor.
- Odlehčení: Zvláště důležité pro AUV, vysokorychlostní plavidla nebo součásti vysoko nad těžištěm plavidla je, že AM v kombinaci se softwarem pro optimalizaci topologie může vytvořit trysky, které jsou výrazně lehčí než jejich tradičně vyráběné protějšky a zároveň splňují nebo překračují požadavky na pevnost.
- Vylepšené vlastnosti materiálu: Procesy AM často vedou k jemnozrnným mikrostrukturám, které mohou v některých případech a při správném následném zpracování nabízet lepší mechanické vlastnosti ve srovnání s odlévanými ekvivalenty. Kromě toho AM umožňuje použití materiálů, které by bylo obtížné nebo nemožné odlít nebo vykovat do složitých tvarů trysek.
Zatímco tradiční metody zůstávají životaschopné pro standardní velkoobjemovou výrobu trysek, aditivní výroba kovů představuje výkonnou alternativu pro aplikace vyžadující vyšší výkon, přizpůsobení, rychlejší vývoj nebo složité geometrie. Umožňuje námořním inženýrům a výrobci lodí posunout hranice konstrukce pohonných systémů.
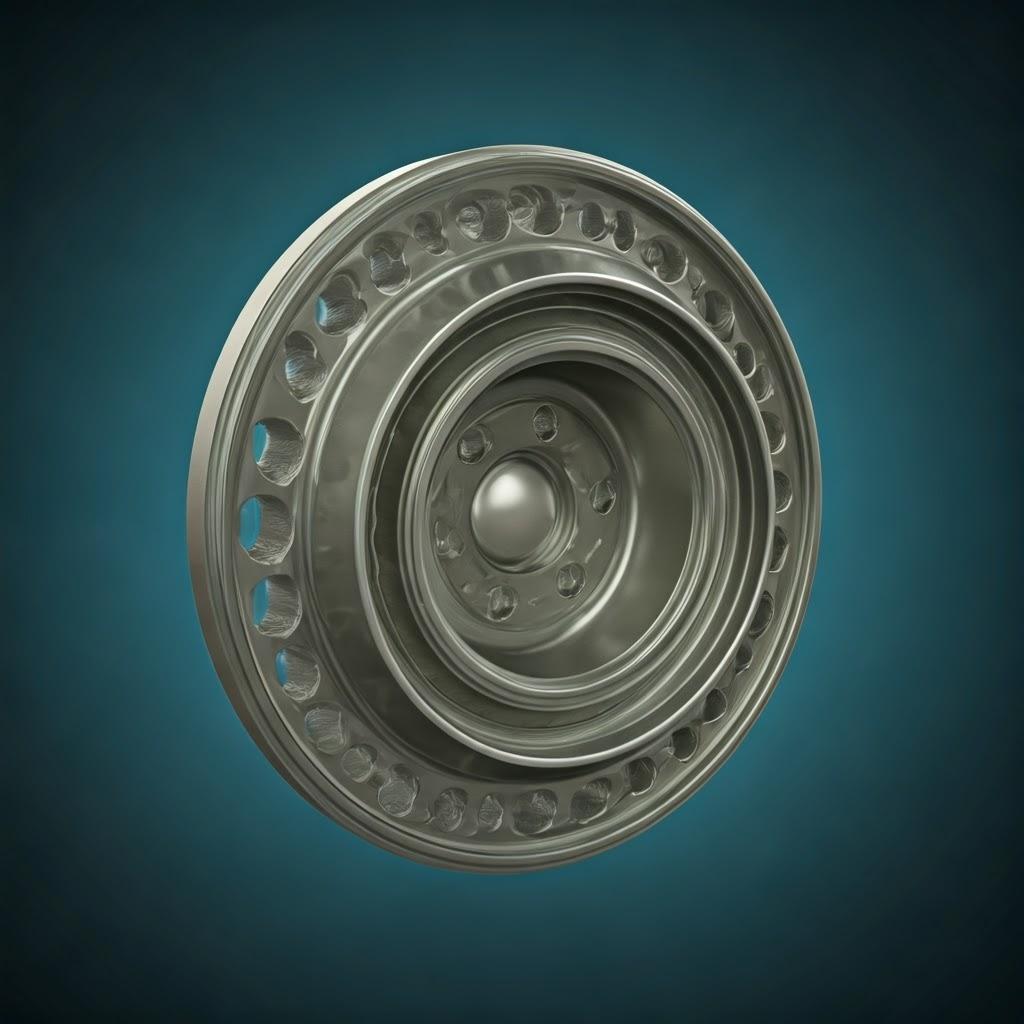
Zaměření materiálu: CuNi30Mn1Fe a IN625 pro vynikající výkon v námořní dopravě
Volba materiálu je rozhodující pro každou lodní součást, zejména pro trysky pohonných jednotek, které jsou neustále vystaveny korozivní mořské vodě, vysokým rychlostem proudění, možné kavitaci a mechanickému namáhání. Aditivní výroba kovů nejenže umožňuje vytvářet složité tvary, ale také používat pokročilé slitiny speciálně vhodné pro tyto náročné podmínky. Dva význačné materiály pro 3D tištěné námořní trysky jsou např CuNi30Mn1Fe (slitina mědi a niklu) a IN625 (superslitina niklu a chromu). Pro úspěšný tisk je nejdůležitější kvalita výchozího kovového prášku a společnost Met3dp využívá své pokročilé technologie technologie atomizace plynu a PREP k výrobě vysoce sférických, sypkých prášků, které jsou nezbytné pro dosažení hustých a vysoce kvalitních dílů.
CuNi30Mn1Fe: Šampion v boji proti korozi a proti znečištění
Slitiny mědi a niklu, často označované jako měďnaté nikly, mají dlouhou a úspěšnou historii v námořních aplikacích díky své výjimečné odolnosti proti korozi mořskou vodou a přirozené odolnosti proti biologickému znečištění. CuNi30Mn1Fe (podobně jako C71500) je specifické složení optimalizované pro rovnováhu mezi pevností, trvanlivostí a výkonem na moři.
Klíčové vlastnosti a výhody námořních trysek:
- Vynikající odolnost proti korozi mořskou vodou: Slitiny mědi a niklu vytvářejí při působení mořské vody stabilní přilnavou ochrannou vrstvu oxidu. Tato vrstva zajišťuje vynikající odolnost proti celkové korozi, důlkové korozi a štěrbinové korozi ve slaném prostředí, a to i ve znečištěných vodách nebo při vyšších průtocích, které se vyskytují v tryskách.
- Vlastní protihnilobné vlastnosti: Ionty mědi přirozeně brání usazování a růstu mořských organismů, jako jsou mlži, škeble a řasy. Pro pohonnou trysku je to významná výhoda. Biofouling zvyšuje drsnost povrchu, což drasticky snižuje hydrodynamickou účinnost, zvyšuje spotřebu paliva a může vést ke zhoršení výkonu nebo nevyváženosti. Použití CuNi30Mn1Fe minimalizuje potřebu častého čištění nebo nátěrů proti zanášení, což snižuje provozní náklady a prostoje.
- Dobrá pevnost a tažnost: CuNi30Mn1Fe sice není tak pevná jako superslitiny, ale nabízí dostatečnou mechanickou pevnost a houževnatost pro mnoho aplikací trysek, zejména tam, kde není primárním problémem extrémní zatížení nebo teplota. Její tažnost umožňuje určitou plastickou deformaci před lomem, což přispívá k celkové trvanlivosti.
- Svařitelnost a zhotovitelnost (tradiční kontext): Ačkoli se zaměřujeme na AM, jeho tradičně dobrá svařitelnost se dobře uplatňuje při procesu tavení po vrstvách v AM, což přispívá k výtiskům bez vad.
- Mírné náklady: V porovnání s niklovými superslitinami nebo titanem je měďnatý nikl obecně cenově výhodnější, což ho činí atraktivním pro aplikace, kde jsou vysoce ceněny jeho specifické výhody.
Proč záleží na kvalitě prášku: V případě AM je dosažení požadované odolnosti proti korozi a mechanických vlastností založeno na tisku hustého, homogenního dílu. To vyžaduje kovový prášek s: * Vysoká sféricita: Zajišťuje dobrou hustotu balení práškového lože a konzistentní tavení. * Dobrá tekutost: Umožňuje rovnoměrné rozprostření prášku během tisku. * Řízená distribuce velikosti částic (PSD): Ovlivňuje balení, tavení a konečnou povrchovou úpravu. * Nízké hladiny nečistot (zejména kyslíku): Kontaminace kyslíkem může zhoršit mechanické vlastnosti a odolnost proti korozi. Pokročilé techniky rozprašování Met3dp’ jsou navrženy tak, aby tyto vlastnosti optimalizovaly pro náročné aplikace.
CuNi30Mn1Fe Shrnutí vlastností (typické hodnoty pro tvářené/odlévané oceli – vlastnosti AM závisí na procesu/postprocesu):
Vlastnictví | Typický rozsah hodnot | Význam pro námořní trysky |
---|---|---|
Hustota | ~ 8,94 g/cm³ | Standardní hustota, zohlednění hmotnosti při návrhu. |
Pevnost v tahu | 380 - 550 MPa | Postačuje pro mnoho aplikací trysek se středním zatížením. |
Mez kluzu | 140 – 415 MPa | Odolnost proti trvalé deformaci při zatížení. |
Prodloužení | 15 – 40% | Označuje dobrou tažnost a houževnatost. |
Odolnost proti korozi | Vynikající v mořské vodě | Primární výhoda, dlouhá životnost, odolnost proti vrypům/vrstvám. |
Odolnost proti biologickému znečištění | Vynikající | Snižuje odpor, udržuje účinnost a snižuje náklady na údržbu. |
Export do archů
Ideální aplikace: Kortové trysky pro pracovní lodě, trysky pro tryskové motory v mírných podmínkách, součásti, kde je hlavním faktorem ochrana proti znečištění, díly vyžadující dlouhou dobu ponoru.
IN625 (Inconel 625): Vysoce pevný a vysoce odolný motor
IN625 je superslitina niklu, chromu, molybdenu a niobu, která je známá svou výjimečnou kombinací vysoké pevnosti, vynikající odolnosti proti korozi (zejména proti důlkové a štěrbinové korozi v agresivním prostředí) a vysokoteplotní stability. Jedná se o materiál, který je vhodný pro některé z nejnáročnějších námořních aplikací.
Klíčové vlastnosti a výhody námořních trysek:
- Vynikající odolnost proti korozi: IN625 vykazuje pozoruhodnou odolnost v širokém spektru korozivních médií, včetně vysoce chloridové mořské vody, kyselých podmínek a stojatých nebo znečištěných vod. Vysoký obsah niklu a chromu zajišťuje obecnou odolnost proti korozi, zatímco molybden významně zvyšuje odolnost proti důlkové a štěrbinové korozi - kritickým způsobům poruch v mořském prostředí.
- Vysoká pevnost & Houževnatost: IN625 si zachovává vysokou pevnost v tahu, pevnost v kluzu a pevnost v tahu při tečení od kryogenních teplot až do ~815 °C. Díky tomu je vhodný pro vysoce výkonné trysky, na které působí značné hydrodynamické síly, kolísání tlaku nebo zvýšené teploty (např. v blízkosti výfuků motorů nebo v systémech s vysokou hustotou výkonu).
- Vynikající únavová pevnost: Vzhledem k cyklickému zatížení, kterému jsou vystaveny součásti pohonu, je klíčová odolnost proti únavě. IN625 se v podmínkách únavy chová výjimečně dobře, což přispívá k dlouhé provozní životnosti.
- Odolnost proti korozi pod napětím (SCC): IN625 je vysoce odolný vůči SCC, což je důležité zejména v mořském prostředí bohatém na chloridy.
- Dobrá vyrobitelnost (kontext AM): IN625 je jednou z nejsnáze potisknutelných niklových superslitin metodami PBF, i když je nezbytná pečlivá kontrola parametrů a následné zpracování (např. odlehčení napětí).
Proč záleží na kvalitě prášku: Stejně jako u CuNi závisí výkonnost dílu AM IN625 na kvalitě prášku. Vzhledem k vyšším výkonnostním nárokům, které jsou na součásti IN625 často kladeny, jsou důležité faktory jako např: * Nízká pórovitost: Zásadní pro únavovou životnost a odolnost proti korozi. Vyžaduje optimalizované vlastnosti prášku (sféricita, tekutost, PSD) a parametry tisku. * Minimální satelitní částice: Drobné částice navázané na větší koule mohou ovlivnit tekutost a hustotu balení. Řízené procesy atomizace je minimalizují. * Přesné chemické složení: Pro dosažení očekávaných mechanických a korozních vlastností je nezbytné zajistit, aby prášek přesně odpovídal specifikaci IN625. Renomovaný dodavatelé kovových prášků jako Met3dp poskytují certifikované prášky s přísně kontrolovanými chemickými látkami.
IN625 Shrnutí vlastností (Typické hodnoty – vlastnosti AM závisí na procesu/následném zpracování):
Vlastnictví | Typický rozsah hodnot (žíhané) | Význam pro námořní trysky |
---|---|---|
Hustota | ~ 8,44 g/cm³ | O něco lehčí než ocel nebo měďnatý nikl. |
Pevnost v tahu | 830 – 1030 MPa | Velmi vysoká pevnost pro náročné zatížení a prostředí s vysokým tlakem. |
Mez kluzu | 415 – 760 MPa | Vysoká odolnost proti trvalé deformaci. |
Prodloužení | 30 – 50% | Vynikající tažnost a houževnatost i při vysokých pevnostech. |
Odolnost proti korozi | Vynikající, zejména Pitting & amp; Crevice | Vhodné do nejagresivnějších mořských podmínek, dlouhá životnost. |
Pevnost při vysokých teplotách | Vynikající až do ~815 °C | Významné, pokud tryska pracuje v blízkosti zdrojů tepla nebo v systémech s vysokou energií. |
Export do archů
Ideální aplikace: Vysoce výkonné trysky a statory pro vodní paprsek, součásti námořních trysek, trysky pro hlubinné ROV/AUV pracující v korozivních nebo vysokotlakých zónách, součásti vyžadující maximální trvanlivost a odolnost proti kavitační erozi.
Volba mezi CuNi30Mn1Fe a IN625 závisí na konkrétních provozních požadavcích, rozpočtu a výkonnostních cílech pohonné trysky. Oba materiály nabízejí při zpracování pomocí vysoce kvalitních prášků a optimalizovaných technik aditivní výroby kovů významné výhody, které umožňují výrobu lodních pohonných komponent nové generace.
Design pro aditivní výrobu (DfAM): Optimalizace trysek pro 3D tisk
Úspěšné využití aditivní výroby kovů pro trysky lodních pohonů přesahuje pouhou konverzi stávajícího modelu CAD určeného pro odlévání nebo obrábění. Aby inženýři skutečně využili výhody AM - komplexnost, konsolidaci, odlehčení a efektivitu - musí přijmout Design pro aditivní výrobu (DfAM) zásady. DfAM zahrnuje navrhování částí konkrétně pro proces výstavby po jednotlivých vrstvách, přičemž od počátku zohledňuje své jedinečné možnosti a omezení. Aplikace DfAM na námořní trysky může výrazně zlepšit tisknutelnost, snížit náklady, minimalizovat následné zpracování a zvýšit výkonnost finálního dílu.
Zde jsou klíčové úvahy o DfAM pro optimalizace geometrie trysky pro AM:
- Optimalizace vnitřních průtokových cest:
- Plynulé přechody: Vyhněte se ostrým rohům a náhlým změnám směru ve vnitřních kanálech. Ty vytvářejí koncentraci napětí, mohou být obtížně přesně tisknutelné a mohou vyžadovat rozsáhlé vnitřní podpůrné konstrukce. Pro zlepšení dynamiky proudění a tisknutelnosti volte pozvolné křivky a koutové plochy.
- Hydrodynamická účinnost: V rané fázi návrhu použijte analýzu CFD (Computational Fluid Dynamics) pro simulaci proudění tryskou. AM umožňuje přímé vytvoření složitých, optimalizovaných vnitřních geometrií identifikovaných pomocí CFD, které by bylo obtížné nebo nemožné dosáhnout pomocí tradičních metod.
- Minimalizace převisů a podpůrných konstrukcí:
- Samonosné úhly: Procesy PBF (Metal Powder Bed Fusion) obvykle umožňují tisknout přesahy vůči konstrukční desce až do určitého úhlu (často kolem 45 stupňů), aniž by pod nimi byly nutné podpůrné konstrukce. Navrhování prvků, jako jsou sbíhající se/rozbíhající se úseky nebo vnitřní kanály s úhly většími, než je tato kritická hranice, výrazně snižuje potřebu podpěr.
- Integrace podpůrné strategie: Tam, kde se podpěrám nelze vyhnout (např. u vodorovných povrchů nebo nízkých úhlů), navrhněte díl s ohledem na odstranění podpěr. Zajistěte dostatečný přístup pro nástroje k odlamování nebo obrábění podpěrných konstrukcí, zejména ve vnitřních dutinách. Zvažte začlenění malých konstrukčních prvků (např. specifických zkosení) v místech, kde se podpěry stýkají s dílem, aby se usnadnilo odstraňování a minimalizovalo zjizvení povrchu.
- Alternativní orientace: Včas vyhodnoťte různá zaměření stavby. Někdy může otočení dílu na sestavovací desce výrazně snížit objem potřebných podpěr, ušetřit materiál, čas tisku a úsilí při následném zpracování.
- Tloušťka stěny a velikost prvků:
- Minimální tloušťka stěny: Zjistěte, jaká je minimální tloušťka potisknutelné stěny pro zvolený materiál a proces AM (často v rozmezí 0,4-1,0 mm pro PBF). Ujistěte se, že všechny konstrukční stěny splňují tento minimální požadavek. Tenké stěny mohou být náchylné k deformaci nebo se nemusí přesně vyřešit.
- Jednotnost: AM sice umožňuje měnit tloušťku stěn, ale náhlé velké změny mohou vést k rozdílné rychlosti chlazení a zvýšenému tepelnému namáhání. Pokud je to možné, snažte se o postupné změny tloušťky.
- Drobné funkce: Dbejte na minimální velikost rozlišitelných prvků (otvory, kolíky, drážky). Velmi jemné prvky by se nemusely vytisknout přesně nebo by se mohly snadno poškodit při následném zpracování.
- Konsolidace částí:
- Přepracování sestav: Aktivně vyhledávejte příležitosti k přepracování vícedílných sestav trysek (např. těleso trysky, vnitřní usměrňovače průtoku, montážní příruby) do jediné integrované součásti. Tím se eliminují kroky svařování/pájení/upevňování, snižuje se hmotnost, zlepšuje se strukturální integrita a zjednodušuje se dodavatelský řetězec.
- Optimalizace topologie a odlehčení:
- Optimalizace cesty zatížení: Využijte software pro optimalizaci topologie k určení míst, kde je materiál z konstrukčního hlediska nezbytný, a odstraňte jej tam, kde není, na základě očekávaného provozního zatížení. To může vést k výrazné úspoře hmotnosti - což je zásadní pro výkonově kritické aplikace, jako jsou AUV nebo vysokorychlostní plavidla - při zachování požadované pevnosti. Technologie AM je jedinečně schopna vyrábět organické, často složité geometrie, které jsou výsledkem optimalizace topologie.
- Mřížové struktury: Začlenění vnitřních mřížových konstrukcí do méně kritických oblastí pro další snížení hmotnosti a spotřeby materiálu při zajištění strukturální podpory.
- Úvahy o tepelném managementu:
- Vyhněte se velkým pevným blokům: Velmi velké a husté úseky mohou během tisku kumulovat značné tepelné napětí. Zvažte možnost dutých profilů (pokud je to konstrukčně možné) nebo zabudování vnitřních prvků, které pomohou řídit distribuci tepla.
- Postupné změny průřezu: Jak již bylo zmíněno u tloušťky stěny, snažte se o plynulé přechody v celkovém průřezu dílu, abyste minimalizovali lokální nahromadění tepla a snížili riziko deformace nebo praskání.
Uplatňování těchto zásad DfAM vyžaduje změnu myšlení, ale přináší značné výhody. Spolupráce se zkušenými poskytovateli služeb AM, jako je například tým, který zdůraznil O společnosti Met3dp, může poskytnout cenné poznatky a pokyny ve fázi návrhu a zajistit, aby byl návrh vaší námořní trysky optimalizován pro úspěšnou aditivní výrobu. Jejich odborné znalosti zahrnují vědu o materiálech, optimalizaci procesů a vývoj aplikací a pomáhají klientům orientovat se ve složitostech DfAM pro náročné komponenty.
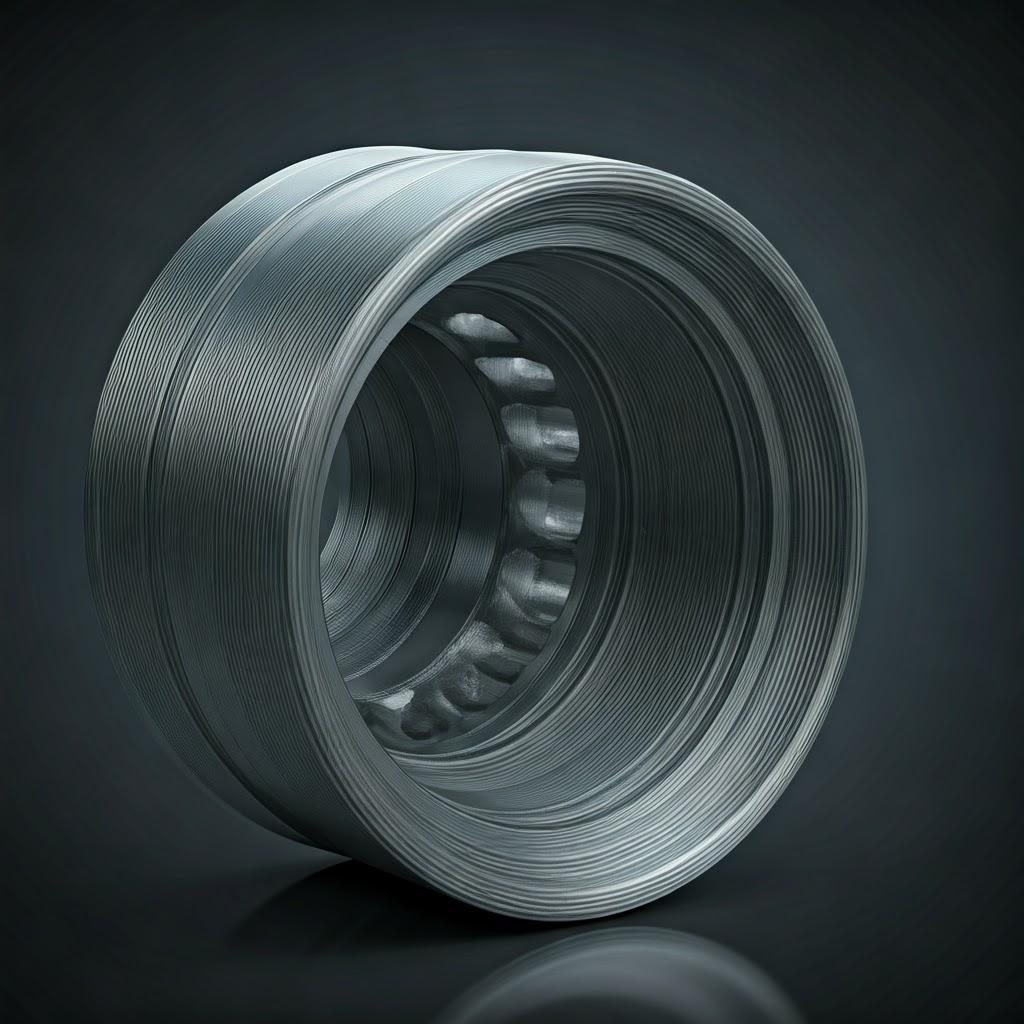
Dosažitelná přesnost: Tolerance, povrchová úprava a rozměrová přesnost u trysek AM
Inženýři a manažeři nákupu, kteří jsou zvyklí na přísné tolerance dosažitelné při přesném obrábění, musí porozumět vlastnostem aditivní výroby kovů, pokud jde o rozměrovou přesnost a povrchovou úpravu. Ačkoli AM nabízí neuvěřitelnou volnost při navrhování, vyrábí díly s odlišnou úrovní přesnosti ve srovnání se subtraktivními metodami. Klíčové je nastavení realistických očekávání a plánování nezbytných kroků následného zpracování.
Rozměrové tolerance:
- Typické tolerance PBF: Procesy fúze v kovovém prášku (jako SLM/DMLS a EBM) obvykle dosahují rozměrových tolerancí v rozmezí ±0,1 mm až ±0,2 mm pro menší prvky (např. do 50-100 mm) nebo ±0,1 % až ±0,2 % pro větší rozměry. Tyto hodnoty se mohou lišit v závislosti na:
- Konkrétní AM stroj a jeho kalibrace.
- Potiskovaný materiál (různé kovy vykazují různé charakteristiky smršťování).
- Geometrie a velikost dílu (u větších a složitějších dílů může dojít k větší odchylce).
- Vytvořit orientační a podpůrnou strategii.
- Tepelná správa během sestavování.
- Srovnání s obráběním: Tyto tolerance jsou obecně volnější než tolerance dosažené standardním CNC obráběním (které často udrží ±0,01 mm až ±0,05 mm nebo těsnější).
- Důsledky: U prvků, které vyžadují velmi vysokou přesnost (např. kritické příruby, ložisková rozhraní, přesné vnitřní průměry určující průtoky), nemusí vyrobený díl AM splňovat specifikace. Tyto prvky obvykle vyžadují sekundární obrábění po tisku. Je nezbytné identifikovat tyto kritické prvky ve fázi návrhu a zahrnout do návrhu AM přídavky na obrábění (dodatečný materiál na skladě).
Povrchová úprava (drsnost):
- Drsnost povrchu (Ra) podle stavu: Povrchová úprava kovových dílů tištěných metodou AM je ze své podstaty drsnější než u obráběných povrchů, což je způsobeno procesem vrstvení a ulpíváním částečně roztavených částic prášku na povrchu. Typické hodnoty Ra pro procesy PBF se pohybují od 5 µm až 25 µm (mikrometrů). Mezi faktory ovlivňující Ra patří:
- Tloušťka vrstvy: Tenčí vrstvy obecně vedou k hladším povrchům, ale prodlužují dobu tisku.
- Velikost částic prášku: Jemnější prášky mohou vést k hladšímu povrchu, ale mohou představovat problém při manipulaci a tekutosti. Roli zde hraje kvalita a kulovitost prášků, jako jsou prášky Met3dp.
- Orientace na stavbu: Povrchy skloněné vzhledem ke směru stavby často vykazují lepší povrchovou úpravu než čistě vodorovné povrchy směřující nahoru nebo dolů. Svislé stěny mají tendenci vykazovat mírnou drsnost.
- Parametry laseru/záření: Příkon energie a strategie skenování ovlivňují dynamiku taveniny a strukturu povrchu.
- Materiál: Různé materiály mohou mít mírně odlišné vlastnosti povrchu.
- Hydrodynamický dopad: U pohonných trysek je rozhodující drsnost povrchu. Drsné vnitřní povrchy zvyšují tření a turbulence, snižují hydrodynamickou účinnost a potenciálně zvyšují hlučnost nebo vznik kavitace. Drsné vnější povrchy zvyšují odpor vzduchu.
- Zlepšení: Zatímco optimalizace procesů může vyladit povrchovou úpravu po výrobě, dosažení hladkého povrchu srovnatelného s leštěnými nebo jemně obrobenými díly (Ra &;lt; 1 µm) obvykle vyžaduje následné kroky zpracování, jako je tryskání kuličkami, bubnové obrábění, abrazivní proudové obrábění (AFM), elektroleštění nebo ruční leštění.
Rozměrová přesnost a kontrola kvality:
- Zdroje nepřesností: Mezi potenciální zdroje patří smršťování materiálu při ochlazování, deformace způsobené zbytkovým tepelným napětím, drobné nepřesnosti při kalibraci stroje a drobné odchylky během procesu roztírání prášku nebo tavení.
- Zmírnění: Pečlivá simulace procesu (předpověď deformace), optimalizované parametry sestavení, robustní podpůrné struktury, kontrolované prostředí sestavení a odlehčení napětí po sestavení přispívají k maximalizaci rozměrové přesnosti. Pochopení specifických tiskových metod a jejich nuance jsou klíčové.
- Zajištění kvality: Renomovaní poskytovatelé služeb AM používají přísná opatření pro kontrolu kvality. Ta často zahrnují:
- Analýza prášku: Zajištění, aby vstupující kovový prášek splňoval specifikace.
- Monitorování během procesu: Některé pokročilé systémy sledují vlastnosti taveniny nebo konzistenci vrstev během sestavování.
- Kontrola po dokončení stavby: Vizuální kontrola, kontrola rozměrů pomocí kalibrovaných nástrojů (třmeny, mikrometry), 3D skenování v porovnání s původním modelem CAD a kontrola kritických rozměrů na souřadnicovém měřicím stroji (CMM).
- Nedestruktivní zkoušení (NDT): U kritických aplikací lze k odhalení povrchových trhlin nebo vnitřní pórovitosti použít metody NDT, jako je penetrační testování barvivem (PT) nebo počítačová tomografie (CT).
Pochopení těchto dosažitelných úrovní přesnosti umožňuje konstruktérům efektivně navrhovat, v případě potřeby zahrnout obráběcí materiál a specifikovat příslušné požadavky na povrchovou úpravu, čímž se zajistí, že finální 3D tištěná tryska splní všechna funkční a výkonnostní kritéria.
Kromě tisku: Základní následné zpracování pro námořní trysky
Častou mylnou představou o 3D tisku z kovu je, že díl je připraven k použití ihned po vyjetí ze stroje. Ve skutečnosti je u náročných aplikací, jako jsou trysky lodních pohonů, fáze tisku pouze jednou částí celkového výrobního procesu. Řada klíčových následné zpracování téměř vždy je nutné provést kroky k přeměně hotového dílu na funkční a spolehlivou součást s požadovanými vlastnostmi materiálu, rozměrovou přesností a povrchovou úpravou.
Klíčové fáze následného zpracování 3D tištěných kovových námořních trysek zahrnují:
- Úleva od stresu / tepelné ošetření:
- Proč je to důležité: Rychlé cykly zahřívání a ochlazování, které jsou vlastní procesům PBF, vytvářejí v tištěném dílu značné vnitřní pnutí. Tato zbytková napětí mohou vést k deformaci (zejména po vyjmutí z konstrukční desky), snížení únavové životnosti a případně k praskání. Tepelné zpracování je nezbytné pro uvolnění těchto napětí a homogenizaci mikrostruktury.
- Proces: Díly se obvykle zahřívají v peci s řízenou atmosférou na určitou teplotu (pod bodem tání, ale dostatečně vysokou, aby umožnila difúzi atomů), po určitou dobu se udržují a poté se pomalu ochlazují. Přesný cyklus (teplota, doba, rychlost chlazení) závisí do značné míry na materiálu (např. cykly pro IN625 se liší od cyklů pro slitiny CuNi nebo nerezové oceli) a na požadovaných konečných vlastnostech materiálu (např. žíhání pro dosažení maximální tažnosti vs. stárnutí pro dosažení maximální pevnosti).
- Optimalizace nemovitostí: Tepelné zpracování se rovněž používá k dosažení cílové mikrostruktury a mechanických vlastností (pevnost, tvrdost, tažnost, odolnost proti korozi) stanovených pro danou aplikaci. U slitin, jako je IN625, se často vyžaduje specifické žíhání v roztoku a/nebo ošetření stárnutím, aby byly splněny specifikace v datasheetu.
- Odstranění ze stavební desky:
- Proces: Díly se obvykle tisknou na silnou kovovou konstrukční desku. Je třeba je oddělit, obvykle pomocí elektroerozivního drátového obrábění (EDM), řezání nebo obrábění. To je třeba provádět opatrně, aby nedošlo k poškození dílu. Často se provádí odlehčení napětí před odstranění z desky, aby se minimalizovalo zkreslení.
- Odstranění podpůrné konstrukce:
- Nezbytnost: Podpěry jsou potřebné při tisku převisů a složitých prvků, ale musí být následně odstraněny.
- Metody: Odstranění může zahrnovat ruční odlomení (u snadno přístupných, lehce připojených podpěr), řezání/broušení nebo obrábění. Přístup k vnitřním podpěrám ve složitých tryskových kanálech a jejich odstranění může být obzvláště náročné a vyžaduje pečlivé plánování ve fázi DfAM. Značky nebo vady zanechané v místech připojení podpěr je často třeba zahladit.
- Obrábění:
- Účel: K dosažení přísných tolerancí u kritických rozměrů, vytvoření specifických těsnicích ploch nebo zlepšení kvality povrchu funkčních oblastí.
- Společné prostory: Čelní plochy přírub, které se spojují s jinými součástmi, vnitřní otvory vyžadující přesné průměry pro ložiska nebo těsnění, otvory se závitem a kritické hydrodynamické plochy často vyžadují obrábění CNC po tisku. Konstruktéři s tím musí počítat a přidat k těmto prvkům v původním modelu AM CAD další materiál (obráběcí materiál).
- Povrchová úprava:
- Cíl: Snížení drsnosti povrchu při stavbě za účelem zlepšení hydrodynamických vlastností, estetiky nebo čistitelnosti.
- Techniky:
- Otryskávání kuliček / kuličkování: Pohání médium (skleněné kuličky, keramické broky) na povrchu. Mírně vyhlazuje, vytváří rovnoměrný matný povrch a může vyvolat příznivé tlakové namáhání (kuličkování).
- Třískové/vibrační dokončování: Umístí díly do vany s brusným médiem, které se bubnováním nebo vibracemi postupně vyhlazuje povrchy a hrany. Vhodné pro hromadné zpracování.
- Obrábění abrazivním tokem (AFM): Vtlačuje abrazivem napuštěný tmel do vnitřních kanálků, což je účinné pro vyhlazování složitých vnitřních chodeb, které jsou běžné v tryskách.
- Elektrolytické leštění: Elektrochemický proces, při kterém se odstraňuje tenká vrstva materiálu a výsledkem je velmi hladký a lesklý povrch. Je účinný zejména u některých slitin, jako jsou nerezové oceli.
- Ruční broušení/leštění: Je to pracné, ale umožňuje cílené vyhlazení a dosažení velmi jemných povrchových úprav na určitých místech.
- Čištění a kontrola:
- Čištění: Důkladné odstranění zbytků prášku (zejména z vnitřních kanálků), obráběcích kapalin nebo lešticích směsí.
- Závěrečná kontrola: Komplexní kontrola zahrnující vizuální kontrolu, finální ověření rozměrů (CMM, skenování), potvrzení vlastností materiálu (pokud byly vedle vytištěny zkušební kupony) a případné požadované NDT (např. zkouška těsnosti, penetrační barvení), aby se zajistilo, že tryska před nasazením splňuje všechny normy kvality.
Rozsah a typ následného zpracování významně ovlivňuje konečné náklady a dobu realizace 3D tištěné trysky. Pečlivé naplánování těchto kroků a jejich začlenění do celkové výrobní strategie je zásadní pro úspěšné zavedení AM pro námořní komponenty.
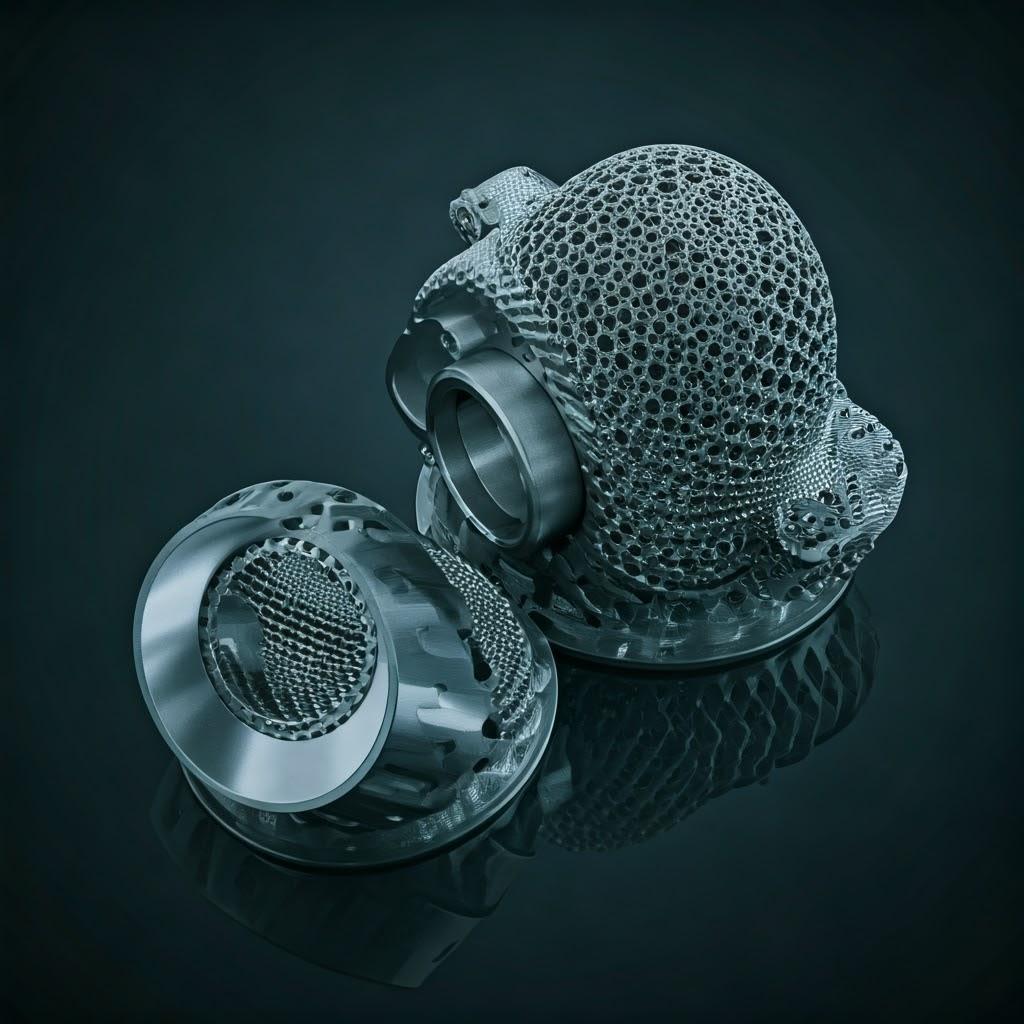
Zvládání výzev: Běžné problémy při 3D tisku námořních trysek a jejich řešení
Aditivní výroba kovů sice nabízí obrovské výhody, ale je to také složitý proces s potenciálními problémy, které je třeba pochopit a zvládnout, zejména při výrobě kritických součástí, jako jsou trysky lodních pohonů. Povědomí o těchto potenciálních problémech umožňuje proaktivní zmírnění pomocí pečlivého návrhu, kontroly procesu a spolupráce se zkušenými poskytovateli AM.
Zde jsou některé běžné problémy a jejich řešení:
Běžné problémy při výrobě kovů AM pro námořní trysky & strategie pro jejich zmírnění
Výzva | Popis / potenciální příčina | Strategie zmírňování dopadů |
---|---|---|
Deformace / zkreslení | Ohýbání dílů nebo odchylky od zamýšlené geometrie v důsledku nerovnoměrného ohřevu/chlazení a vzniku zbytkových napětí. | DfAM: Optimalizujte orientaci dílů, navrhněte je s ohledem na tepelnou stabilitu (vyhněte se náhlým velkým změnám hmotnosti). <br> Podporuje: Použijte robustní podpůrné konstrukce strategicky umístěné k ukotvení dílu. <br> Proces: Optimalizujte strategii skenování, případně použijte ohřev stavební desky. <br> Následné zpracování: Proveďte tepelné zpracování na uvolnění napětí, často před vyjmutím z konstrukční desky. |
Pórovitost (nedostatek fúze / plynu) | Malé vnitřní dutiny uvnitř tištěného materiálu, které snižují hustotu, pevnost, únavovou životnost a odolnost proti korozi. Příčinou jsou nesprávné parametry, plyn zachycený v prášku/bazénu taveniny nebo špatná kvalita prášku. | Kvalita prášku: Použijte vysoce kvalitní suchý sférický prášek s kontrolovaným PSD (např. z pokročilé atomizace Met3dp’). <br> Optimalizace procesů: Přesné nastavení výkonu laseru/paprsku, rychlosti skenování a tloušťky vrstvy pro úplné roztavení. Optimalizujte průtok ochranného plynu. <br> Následné zpracování: Lisování za tepla (HIP) může uzavřít vnitřní póry (zvyšuje náklady a čas). |
Obtížnost odstranění podpory | Podpěry jsou těžko přístupné nebo se čistě odlomí, což může vést k poškození dílu nebo zanechat značné povrchové vady. Obzvláště náročné jsou vnitřní podpěry. | DfAM: Minimalizujte potřebu podpěr díky samonosným úhelníkům. Design pro přístup (např. dočasné přístupové otvory). Používejte optimalizované typy podpěr (např. tenčí připojovací body). <br> Proces: Zvolte vhodné parametry generování podpory v softwaru. <br> Následné zpracování: K odstranění použijte specializované nástroje, případně drátové elektroerozivní obrábění nebo obrábění. |
Zbytkové napětí / praskání | Vysoká vnitřní napětí mohou vést k mikrotrhlinám nebo dokonce k velkým trhlinám během tisku nebo následného zpracování, zejména u slitin citlivých na trhliny nebo u složitých geometrií. | DfAM: Vyhněte se ostrým vnitřním rohům, navrhněte postupné změny tloušťky. <br> Proces: Simulujte tepelnou historii, optimalizujte strategii skenování (např. skenování podle sektorů), abyste zvládli nahromadění tepla. <br> Výběr materiálu: Zvažte náchylnost materiálu. <br> Následné zpracování: Provádějte pečlivě navržené cykly uvolňování napětí ihned po tisku. |
Problémy s drsností povrchu | Povrch ve stavu, v jakém je postaven, je příliš drsný pro hydrodynamické požadavky, což vede k neúčinnosti nebo kavitaci. | DfAM: Optimální orientace kritických povrchů pro finální úpravu. <br> Proces: Optimalizujte parametry (tloušťka vrstvy, příkon energie), pokud je to možné, použijte jemnější prášek. <br> Následné zpracování: Provádět vhodné techniky povrchové úpravy (tryskání, leštění, AFM atd.) podle požadavků aplikace. |
Rozměrová nepřesnost | Konečné rozměry dílu jsou mimo stanovené tolerance. | DfAM: Navrhněte kritické prvky s přídavkem na obrábění. <br> Proces: Zajistěte kalibraci stroje, použijte simulaci procesu k předvídání smrštění/pokřivení a kompenzaci v CAD. <br> Následné zpracování: Správně provádějte úlevu od stresu. Pro kritické tolerance použijte CNC obrábění. <br> QA: Provádění důsledné rozměrové kontroly (skenování, CMM). |
Nekonzistentní vlastnosti materiálu | Mechanické nebo korozní vlastnosti se liší v rámci dílu nebo mezi jednotlivými konstrukcemi. | Kontrola prášku: Zajistěte konzistentní kvalitu prášku, manipulaci s ním a protokoly pro jeho opětovné použití. <br> Řízení procesu: Udržujte přísnou kontrolu nad všemi parametry tisku (výkon, rychlost, průtok plynu, teplota). <br> Následné zpracování: Zajistěte konzistentní, optimalizované cykly tepelného zpracování. <br> Testování: Tisk a testování materiálových kupónů vedle dílů. |
Export do archů
Řešení problémů s kovovým 3D tiskem vyžaduje hluboké porozumění vzájemnému působení konstrukce, materiálů, procesních parametrů a následného zpracování. Klíčem k překonání těchto výzev a spolehlivé výrobě vysoce kvalitních trysek pro kritické lodní pohony je spolupráce se znalým poskytovatelem služeb, který je vybaven spolehlivou kontrolou procesů, systémy řízení kvality a odbornými znalostmi materiálů, jako jsou CuNi30Mn1Fe a IN625.
Výběr partnera: Jak si vybrat správného poskytovatele služeb v oblasti AM pro námořní komponenty?
Výběr správného výrobního partnera je vždy velmi důležitý, ale v případě pokročilých technologií, jako je aditivní výroba kovů pro náročné námořní aplikace, nabývá na významu. Kvalita, spolehlivost a výkonnost vaší 3D tištěné pohonné trysky závisí do značné míry na odborných znalostech, procesech a schopnostech vybraného výrobce servisní kancelář Metal AM. Inženýři a manažeři nákupu, kteří se v tomto prostředí pohybují, se při hodnocení potenciálních dodavatelů musí zaměřit nejen na cenu, ale i na řadu technických a provozních faktorů.
Zde jsou klíčová kritéria, která je třeba zvážit při výběru dodavatel kovového 3D tisku pro lodní komponenty:
- Technická expertíza & Konzultace:
- Věda o materiálech: Mají hluboké znalosti navrhovaných materiálů (např. CuNi30Mn1Fe, IN625)? Mohou poradit s výběrem materiálu na základě vašeho specifického provozního prostředí a požadavků na výkon? Rozumí nuancím zpracování těchto materiálů pomocí AM?
- Podpora DfAM: Mohou poskytnout odborné poradenství při optimalizaci návrhu trysky pro aditivní výrobu? Dobrý partner s vámi spolupracuje, aby zajistil, že návrh bude tisknutelný, nákladově efektivní a bude splňovat funkční potřeby.
- Znalost procesů: Rozumí složitostem konkrétního procesu AM (např. SLM, EBM), včetně optimalizace parametrů pro hustotu, přesnost a kvalitu povrchu?
- Schopnosti stroje & Technologie:
- Vhodná technologie: Pracují se správným typem systému AM pro kovy (typicky laser nebo elektronová fúze v práškovém loži pro trysky) pro váš materiál a aplikaci?
- Objem sestavení: Je konstrukční prostor stroje dostatečně velký, aby se do něj vešla vaše konstrukce trysky?
- Přesnost & Rozlišení: Mohou jejich stroje dosáhnout požadované úrovně detailů a tolerance pro vaši součást (s ohledem na případné dodatečné obrábění)?
- Údržba a kalibrace strojů: Mají přísné protokoly pro údržbu strojů, které zajišťují konzistentní výsledky?
- Kvalita materiálu & manipulace:
- Sourcing prášku & Certifikace: Kde získávají kovové prášky? Poskytují materiálové certifikáty ověřující chemické složení a vlastnosti prášku? Společnosti jako Met3dp, které vyrábějí vlastní vysoce kvalitní prášky pomocí pokročilých metod, jako je plynová atomizace a PREP, nabízejí lepší kontrolu a sledovatelnost. Prozkoumejte jejich nabídku vysoce výkonné kovové prášky a systémy.
- Manipulace s práškem: Mají přísné postupy pro skladování prášků, manipulaci s nimi, jejich prosévání a sledovatelnost, aby se zabránilo kontaminaci a zajistila se konzistence jednotlivých šarží? Například přebírání kyslíku může zhoršit vlastnosti slitin pro námořní použití.
- Systém řízení kvality (QMS) & Certifikace:
- ISO 9001: Jedná se o základní certifikaci, která ukazuje, že je zaveden dokumentovaný systém řízení jakosti.
- Certifikace specifické pro dané odvětví: V závislosti na aplikaci (např. námořní, klasifikované) mohou být vyžadovány nebo žádoucí certifikace jako AS9100 (letecký průmysl, často přijímané pro náročná průmyslová odvětví) nebo specifická schválení námořních klasifikačních společností (např. DNV, ABS, prohlášení Lloyd’s Register nebo schválení pro specifické materiály/procesy). Informujte se o jejich aktuálních certifikacích a plánu.
- Zkušenosti & Případové studie:
- Osvědčené výsledky: Podařilo se jim vyrobit podobné komponenty z hlediska složitosti, velikosti nebo materiálu?
- Zkušenosti v oboru: Mají zkušenosti s obsluhou námořního průmyslu nebo jiných odvětví s podobně náročnými požadavky (např. letecký průmysl, energetika)? Vyžádejte si případové studie nebo reference relevantní pro vaši žádost.
- Možnosti následného zpracování:
- Integrované služby: Dokáží zvládnout nebo provést nezbytné kroky následného zpracování (tepelné zpracování, obrábění, povrchová úprava, NDT) buď vlastními silami, nebo prostřednictvím kvalifikovaných partnerů? Integrovaný pracovní postup zjednodušuje řízení projektu.
- Komunikace & Podpora:
- Reakce: Reagují na dotazy a žádosti o technické informace?
- Transparentnost: Mluví otevřeně o svých procesech, schopnostech a možných problémech?
- Technická konzultace: Je jejich tým přístupný pro technické diskuse během celého životního cyklu projektu?
- Náklady & amp; Doba dodání:
- Jasné citace: Poskytují podrobné nabídky s uvedením všech nákladů (tisk, materiál, podpory, následné zpracování, kontrola kvality)?
- Realistické časové plány: Nabízejí dosažitelné dodací lhůty na základě aktuální kapacity a složitosti vašeho projektu?
Výběr partnera, jako je Met3dp, který kombinuje desítky let společných zkušeností v oblasti AM kovů, špičkové vybavení v oboru, pokročilé možnosti výroby prášků a komplexní služby vývoje aplikací, poskytuje silný základ pro úspěšnou implementaci kov AM pro kritické námořní komponenty. Důkladné prověření potenciálních dodavatelů podle těchto kritérií vám pomůže zajistit, že budete spolupracovat s dodavatelem, který je schopen dodávat vysoce kvalitní a spolehlivé hnací trysky splňující vaše specifikace.
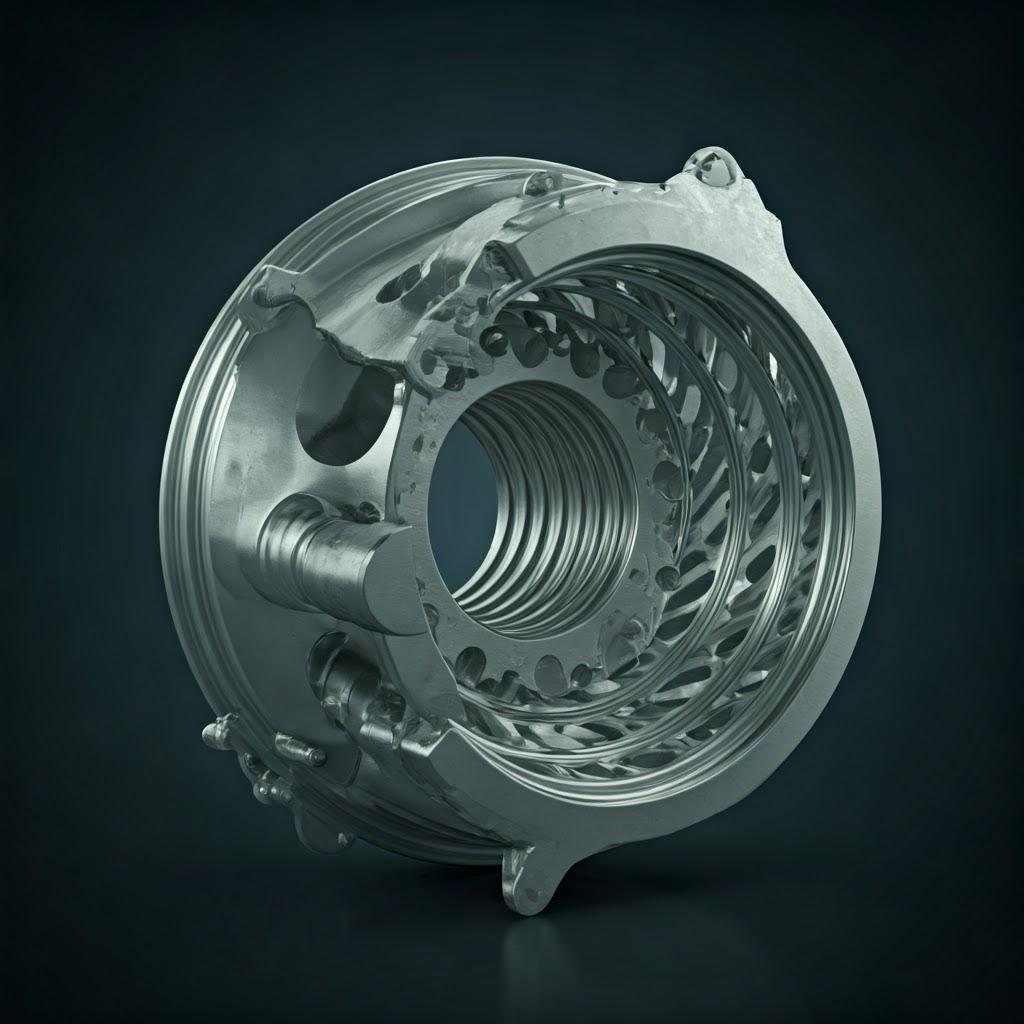
Porozumění investicím: Nákladové faktory a dodací lhůty pro pohonné trysky AM
Jednou z hlavních otázek manažerů nákupu a inženýrů, kteří zvažují AM kovů, jsou náklady a časová náročnost. Ačkoli AM nabízí významné výhody, je třeba pochopit, co stojí za těmito faktory odhad nákladů na 3D tisk kovů a typické dodací lhůty aditivní výroby má zásadní význam pro plánování a sestavování rozpočtu projektu. Náklady na jednotku jsou obecně vyšší než u tradičních metod u jednoduchých, velkoobjemových dílů, ale mohou být vysoce konkurenceschopné u složitých, nízko až středně objemových nebo na míru upravených dílů, jako jsou například hnací trysky.
Klíčové faktory ovlivňující náklady na 3D tištěné námořní trysky:
- Typ materiálu & Spotřeba:
- Náklady na prášek: Náklady na suroviny se výrazně liší. Niklové superslitiny jako IN625 jsou podstatně dražší než slitiny CuNi nebo nerezové oceli.
- Část Objem/hmotnost: Množství materiálu přímo spotřebovaného na díl a jeho nosné konstrukce je hlavním nákladovým faktorem. Větší a hustší díly stojí více. Techniky DfAM, jako je optimalizace topologie, mohou pomoci snížit spotřebu materiálu.
- Doba tisku:
- Výška stavby: Doba tisku v systémech PBF se řídí především počtem vrstev, což znamená, že tisk vyšších dílů trvá déle bez ohledu na to, kolik dílů je na konstrukční desce (až do limitu desky).
- Část Svazek & Složitost: Zatímco výška je primární, celkový objem a složitost skenovacích cest v rámci každé vrstvy také přispívají k času.
- Rychlost stroje: Poskytovatelé služeb počítají s hodinovou sazbou za provoz stroje, která zahrnuje energii, odpisy, údržbu a spotřebu inertního plynu.
- Část Složitost & Design:
- Podpůrné struktury: Složité geometrie s mnoha převisy vyžadují rozsáhlé podpěrné konstrukce. To spotřebovává více materiálu, prodlužuje dobu tisku a výrazně zvyšuje pracnost následného zpracování při odstraňování. Klíčem ke snížení nákladů je zaměření DfAM na samonosné konstrukce.
- Jemné funkce: Velmi složité detaily mohou vyžadovat pomalejší parametry tisku nebo specifické možnosti stroje, což může prodloužit čas a náklady.
- Požadavky na následné zpracování:
- Tepelné zpracování: Doba pece a složitost požadovaného cyklu (zejména u slitin vyžadujících specifické úpravy stárnutím) zvyšují náklady.
- Obrábění: Rozsah požadovaného CNC obrábění (počet prvků, přísnost tolerancí) je významným faktorem ovlivňujícím náklady vzhledem k pracovní síle a strojnímu času.
- Povrchová úprava: Techniky, jako je ruční leštění nebo AFM pro vnitřní kanály, jsou náročné na pracovní sílu a ve srovnání s jednoduššími metodami, jako je tryskání kuliček, zvyšují náklady.
- Zajištění kvality & Inspekce:
- Základní kontrola kvality: Obvykle jsou součástí standardní rozměrové kontroly a vizuální kontrola.
- Pokročilé NDT: Požadavky na penetrační zkoušky barvivem, CT skenování nebo specifické zkoušky vlastností materiálu zvyšují náklady kvůli specializovanému vybavení a odborným znalostem.
- Certifikace: Balíčky dokumentace pro sledovatelnost materiálu a certifikaci procesů vyžadují administrativní úsilí.
- Objem objednávky:
- Náklady na zřízení: S přípravou každého sestavení jsou spojeny fixní náklady (příprava souborů, nastavení stroje). Tyto náklady se amortizují na počet dílů v sestavě.
- Snížení jednotkových nákladů: Tisk více kopií trysky při jednom sestavení obecně snižuje náklady na jednotku v porovnání s tiskem pouze jedné. Diskutujte o velkoobchodní náklady na 3D tisk nebo dávkové ceny u svého poskytovatele pro případné množstevní slevy.
Typické dodací lhůty:
Doba realizace se vztahuje k celkové době od zadání objednávky (a předložení finálního souboru CAD) do obdržení hotového dílu. Je ovlivněna několika faktory:
- Příprava souborů & Čas fronty: Počáteční inženýrská revize, příprava sestavení a aktuální stav nevyřízených zakázek poskytovatele služeb (může se pohybovat v rozmezí dnů až týdnů).
- Doba tisku: Jak již bylo řečeno, řídí se především výškou dílu (může se pohybovat od hodin u malých dílů až po mnoho dní u velkých/vysokých součástí).
- Doba následného zpracování: V závislosti na jednotlivých krocích může být tato část doby přípravy často nejdelší. Cykly tepelného zpracování trvají dlouho, složitá nastavení obrábění přidávají dny a složitá povrchová úprava je náročná na práci (může trvat dny až několik týdnů).
- QA & amp; Doprava: Závěrečná kontrola a doba přepravy.
Celkově: U středně složité kovové námořní trysky se typická doba realizace může pohybovat od 2 až 6 týdnů, ale může se výrazně lišit. Velmi velké nebo složité díly vyžadující rozsáhlé následné zpracování mohou trvat déle. Vždy si vyžádejte konkrétní odhad dodací lhůty na základě konečného návrhu a požadavků.
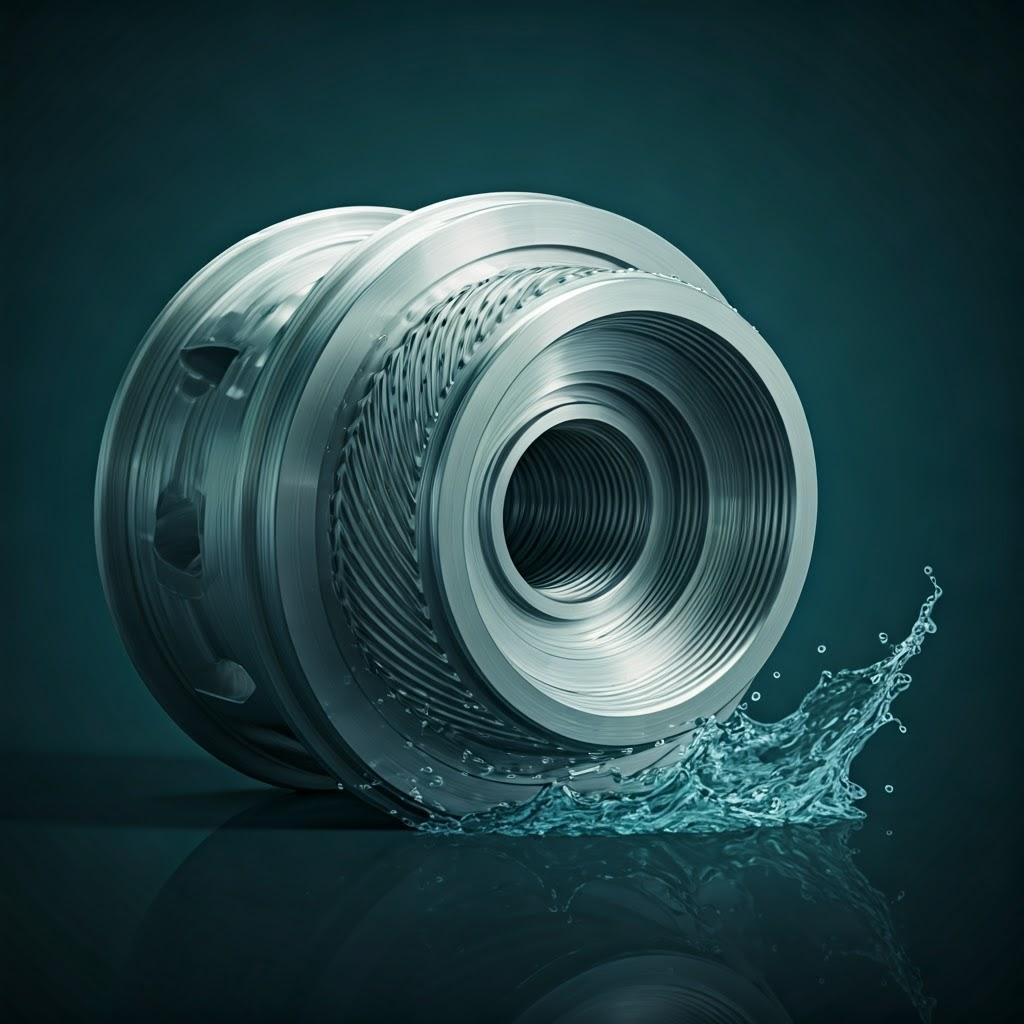
Často kladené otázky (FAQ) o 3D tištěných tryskách pro námořní dopravu
S tím, jak se v námořním průmyslu rozšiřuje aditivní výroba kovů, se inženýři, konstruktéři a specialisté na zadávání zakázek často setkávají s opakujícími se otázkami. Zde jsou odpovědi na některé časté dotazy:
- Jaká je odolnost/životnost 3D tištěné trysky v porovnání s tradičně vyráběnou tryskou (např. odlévanou)?
- Při výrobě za použití optimalizovaných parametrů, vysoce kvalitních prášků a vhodného následného zpracování (zejména tepelného zpracování) mohou kovové díly AM dosahovat mechanických vlastností (pevnost, únavová odolnost, houževnatost), které jsou srovnatelné nebo dokonce převyšují vlastnosti ekvivalentních odlitků. Výhodná může být jemnozrnná mikrostruktura, které se často dosahuje při procesech PBF. Mezi klíčové faktory zajišťující trvanlivost patří:
- Dosažení plné hustoty: Minimalizace pórovitosti prostřednictvím řízení procesu nebo HIP je zásadní pro únavovou životnost a odolnost proti korozi.
- Správné tepelné zpracování: Zásadní pro uvolnění napětí a dosažení požadovaných konečných vlastností materiálu.
- Vhodný výběr materiálu: Použití materiálů, jako je IN625 nebo CuNi30Mn1Fe, které jsou známé svou odolností v moři.
- Kontrola kvality: Důkladná kontrola a kontrola NDT zajistí, že díl před nasazením splňuje normy integrity.
- Souhrnně lze očekávat, že dobře navržená a správně vyrobená tryska AM bude mít vynikající odolnost a životnost a potenciálně překoná tradiční díly, pokud AM umožní lepší konstrukci nebo kombinaci materiálů.
- Při výrobě za použití optimalizovaných parametrů, vysoce kvalitních prášků a vhodného následného zpracování (zejména tepelného zpracování) mohou kovové díly AM dosahovat mechanických vlastností (pevnost, únavová odolnost, houževnatost), které jsou srovnatelné nebo dokonce převyšují vlastnosti ekvivalentních odlitků. Výhodná může být jemnozrnná mikrostruktura, které se často dosahuje při procesech PBF. Mezi klíčové faktory zajišťující trvanlivost patří:
- Jaké certifikace jsou potřebné nebo dostupné pro 3D tištěné námořní komponenty?
- Výchozí hodnota: Certifikace ISO 9001 pro výrobního partnera je důkazem robustního systému řízení kvality.
- Certifikace materiálu: Vždy si vyžádejte materiálové certifikáty potvrzující, že chemický složení prášku splňuje příslušné normy (např. ASTM, specifikace UNS pro slitiny IN625 nebo CuNi).
- Námořní klasifikace: Hlavní námořní klasifikační společnosti (jako DNV, ABS, Lloyd’s Register, Bureau Veritas) aktivně vyvíjejí normy a pokyny pro aditivní výrobu. Zatímco rozšířené certifikace specifické pro jednotlivé díly se stále vyvíjejí, tyto společnosti zveřejnily rámce a pokyny. Někteří poskytovatelé služeb mohou získat specifická schválení pro určité materiály, stroje nebo procesy. U kritických komponent může být nezbytné zapojit se do spolupráce s klasifikačními společnostmi již v počáteční fázi projektu, aby bylo možné pochopit požadavky na kvalifikaci nebo akceptaci.
- Specifické použití: Námořní nebo obranné aplikace mohou mít další specifické vojenské normy (MIL-STD) nebo kvalifikační požadavky.
- Je 3D tisk rentabilní pro sériovou výrobu trysek, nebo pouze pro prototypy?
- Nákladová efektivita závisí do značné míry na několika faktorech, které vytvářejí přechodový bod, kdy se AM stává ekonomičtější než tradiční metody:
- Složitost: Čím složitější je konstrukce trysky (např. složité vnitřní kanály, optimalizace topologie), tím je AM nákladově efektivnější, protože tradiční výrobní náklady se se složitostí rychle zvyšují.
- Objem: AM je vysoce nákladově efektivní pro prototypy a malosériovou výrobu (např. 1-100 kusů), protože se vyhýbá vysokým nákladům na nástroje (odlévací formy, kovací formy). Pro velmi vysoké objemy (tisíce kusů) jsou tradiční metody často levnější pokud konstrukce je dostatečně jednoduchá pro výrobu nástrojů.
- Náklady na nástroje: Pokud tradiční výroba vyžaduje drahé a složité nástroje, bod rentability se posouvá, čímž se AM stává konkurenceschopným při vyšších objemech.
- Hodnota doby realizace: Pokud je rychlost uvedení na trh nebo rychlá dostupnost náhradních dílů kritická, může rychlejší doba realizace AM (zejména zamezení zpoždění při výrobě nástrojů) přinést významnou hodnotu, která ospravedlní potenciálně vyšší jednotkové náklady.
- Zvýšení výkonu: Pokud AM umožňuje konstrukci, která významně zlepšuje palivovou účinnost nebo snižuje údržbu (např. díky materiálům proti znečištění), celkové náklady na vlastnictví po celou dobu životnosti plavidla mohou být ve prospěch komponenty AM, i když počáteční náklady jsou vyšší.
- Proto je AM kovů stále životaschopnější nejen pro prototypy, ale také pro sériová výroba specializovaných, složitých nebo přizpůsobených lodních trysek, zejména tam, kde je klíčovým faktorem výkon a doba realizace.
- Nákladová efektivita závisí do značné míry na několika faktorech, které vytvářejí přechodový bod, kdy se AM stává ekonomičtější než tradiční metody:
Závěr: Budoucnost námořního pohonu s aditivní výrobou
Námořní svět prochází obdobím významného technologického pokroku, který je dán potřebou vyšší efektivity, lepšího výkonu, menšího dopadu na životní prostředí a agilnějších výrobních řešení. V čele této transformace stojí aditivní výroba kovů, která nabízí bezprecedentní možnosti pro kritické komponenty, jako jsou trysky lodních pohonů.
Jak jsme již prozkoumali, využití technologie AM pro zpracování kovů umožňuje konstruktérům a výrobcům:
- Odemkněte svobodu designu: Vytvářejte hydrodynamicky optimalizované trysky se složitou vnitřní geometrií, která byla dříve nedosažitelná.
- Zvýšení výkonu: Zlepšení tahu, účinnosti, odolnosti proti kavitaci a potenciální snížení akustických signatur díky přizpůsobeným konstrukcím.
- Využití pokročilých materiálů: Použití vysoce výkonných slitin, jako jsou korozivzdorné a protihnilobné slitiny CuNi30Mn1Fe nebo vysoce odolné proti vlivům prostředí IN625 přesně tam, kde je to potřeba.
- Urychlení inovací: Rychle vytvářejte prototypy a vylepšujte nové návrhy, a uvádějte tak lepší produkty na trh rychleji.
- Povolení přizpůsobení & Konsolidace: Efektivní výroba trysek na míru a snížení počtu dílů, zjednodušení montáže a zvýšení spolehlivosti.
Úspěšná integrace této technologie vyžaduje překonání problémů souvisejících s optimalizací návrhu (DfAM), řízením procesu, materiálovou vědou a následným zpracováním. Spolupráce se znalým a schopným poskytovatel řešení AM pro kovy je nejdůležitější.
Met3dp má jedinečnou pozici, aby podpořila zavádění aditivní výroby v námořním průmyslu. Díky nejmodernějším tiskárny SEBM poskytuje špičkovou přesnost a spolehlivost v oboru, pokročilou výroba kovového prášku zařízení využívající technologie plynové atomizace a PREP pro vynikající kvalitu prášku a desítky let společných zkušeností nabízí společnost Met3dp komplexní řešení. Od dodávek certifikovaných, vysoce výkonných prášků, jako jsou specializované CuNi, IN625, Ti slitiny a nerezové oceli, až po poskytování služeb vývoje aplikací a špičkových tiskových zařízení, Met3dp pomáhá organizacím urychlit jejich digitální výrobní transformaci.
Cesta k optimalizovanému pohonu lodí je stále více propojena s možnostmi aditivní výroby. Využitím AM mohou výrobci lodí, lodní inženýři a dodavatelé vybavení vytvářet pohonné systémy nové generace, které jsou účinnější, spolehlivější a přizpůsobené náročným podmínkám mořského prostředí.
Jste připraveni prozkoumat, jak může aditivní výroba kovů přinést revoluci do komponentů lodního pohonu? Navštivte Met3dp a dozvíte se více o našich pokročilých kovových prášcích, tiskových systémech a komplexních řešeních AM.
Sdílet na
MET3DP Technology Co., LTD je předním poskytovatelem řešení aditivní výroby se sídlem v Qingdao v Číně. Naše společnost se specializuje na zařízení pro 3D tisk a vysoce výkonné kovové prášky pro průmyslové aplikace.
Dotaz k získání nejlepší ceny a přizpůsobeného řešení pro vaše podnikání!
Související články
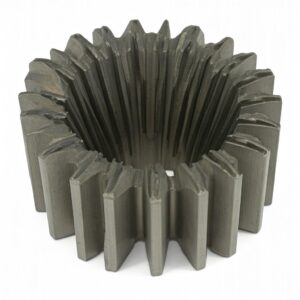
Vysoce výkonné segmenty lopatek trysek: Revoluce v účinnosti turbín díky 3D tisku z kovu
Přečtěte si více "O Met3DP
Nedávná aktualizace
Náš produkt
KONTAKTUJTE NÁS
Nějaké otázky? Pošlete nám zprávu hned teď! Po obdržení vaší zprávy obsloužíme vaši žádost s celým týmem.
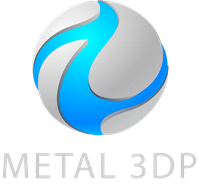
Kovové prášky pro 3D tisk a aditivní výrobu