Redukční pouzdro pro elektrická vozidla
Obsah
Úvod - Zásadní role lehkých redukčních skříní v elektrických vozidlech
Revoluce v oblasti elektromobilů (EV) je hnací silou inovací v celém automobilovém průmyslu, přičemž se neustále zaměřuje na zvyšování účinnosti, prodlužování dojezdu a zlepšování celkového výkonu vozidel. Jádrem této transformace je hnací ústrojí a jeho klíčovou součástí je skříň reduktoru. Tato zdánlivě nenápadná součást hraje zásadní roli při přenosu výkonu z elektromotoru na kola a řídí točivý moment a rychlost tak, aby optimalizovala jízdní vlastnosti. Vzhledem k tomu, že poptávka po vysoce výkonných elektrických vozidlech neustále roste, stává se potřeba lehkých, odolných a geometricky optimalizovaných skříní reduktorů prvořadou. Tradiční výrobní metody často představují omezení při současném plnění těchto požadavků. Právě zde se projevuje transformační potenciál kovových 3D tisk, známá také jako aditivní výroba kovů, která nabízí nebývalou svobodu designu a efektivitu materiálu pro výrobu skříní reduktorů elektromobilů nové generace. Společnosti jako např Metal3DP stojí v čele této revoluce a poskytuje pokročilé zařízení pro 3D tisk a vysoce výkonné kovové prášky, které splňují vyvíjející se potřeby průmyslu elektrických vozidel.
Co je to redukční pouzdro EV a proč je důležité?
Skříň reduktoru v elektromobilu slouží jako ochranný kryt a konstrukční podpěra pro redukční převodovku. Na rozdíl od tradičních vozidel se spalovacími motory s vícestupňovými převodovkami využívají elektrická vozidla obvykle jednorychlostní nebo dvourychlostní redukční převodovku. Tato převodovka je nezbytná z několika klíčových důvodů:
- Násobení točivého momentu: Elektromotory často pracují s vysokými otáčkami, ale při rozběhu mají relativně nižší točivý moment. Redukční převodovka znásobuje točivý moment motoru a poskytuje potřebný výkon pro zrychlení a stoupání do kopce.
- Snížení rychlosti: Převodovka naopak snižuje vysoké otáčky motoru na rozsah vhodný pro kola vozidla.
- Tlumení hluku a vibrací: Skříň pomáhá zadržet mechanické součásti převodovky a minimalizuje hluk a vibrace přenášené do kabiny vozidla, což přispívá k plynulejší a tišší jízdě.
- Ochrana: Skříň reduktoru chrání vnitřní převody a mazací systém před vnějšími nečistotami, nárazy a vlivy prostředí, čímž zajišťuje dlouhou životnost a spolehlivost hnacího ústrojí.
Účinnost a hmotnost skříně reduktoru přímo ovlivňují celkový výkon a dojezd elektromobilu. Lehčí skříň přispívá k nižší celkové hmotnosti vozidla, což vede ke zlepšení energetické účinnosti a prodloužení dojezdu. Optimalizovaná konstrukce navíc může zlepšit tepelné řízení převodovky, které je klíčové pro zachování výkonu a životnosti. Vzhledem k tomu, že průmysl elektromobilů usiluje o vyšší účinnost a delší dojezd, staly se konstrukce a výroba vysoce výkonných skříní reduktorů kritickou oblastí zájmu.
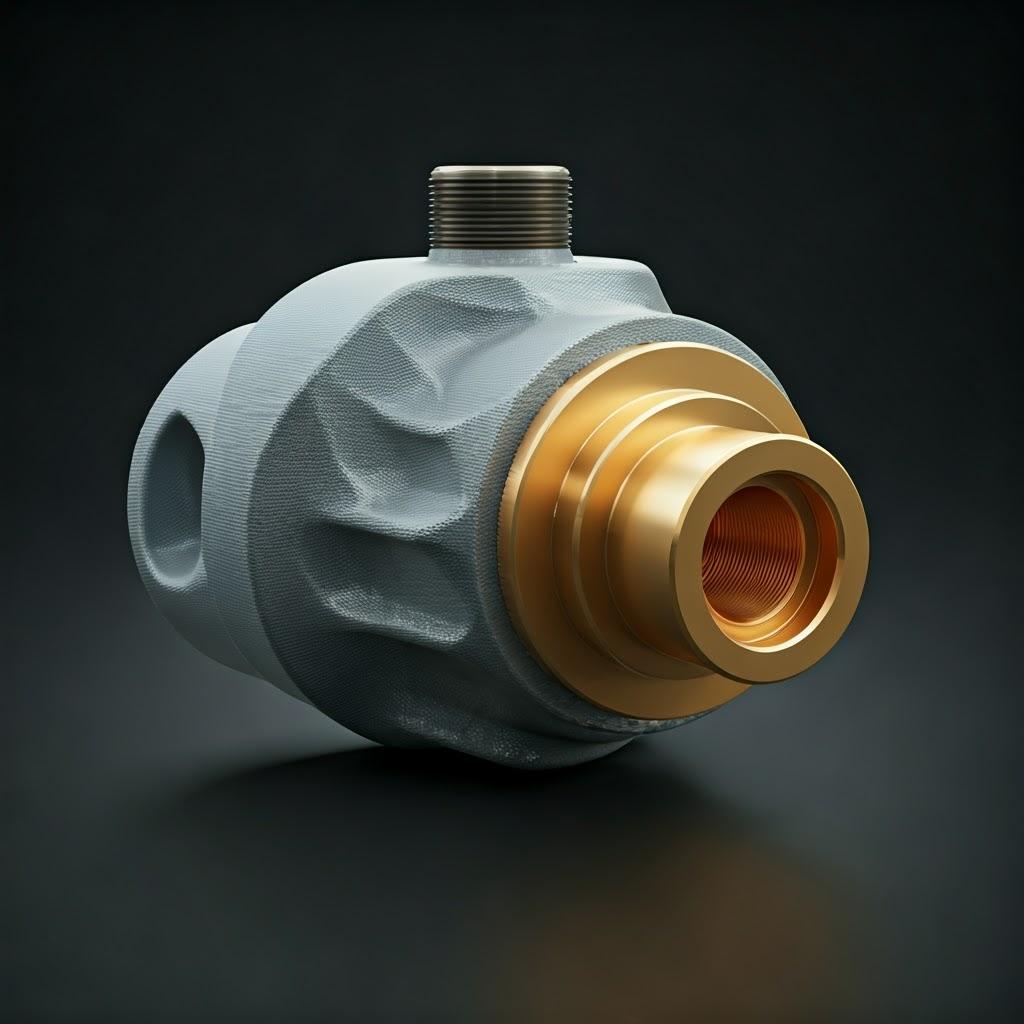
Výhody 3D tisku kovů pro výrobu skříní redukcí pro elektromobily
Kovový 3D tisk nabízí přesvědčivou alternativu k tradičním výrobním metodám, jako je odlévání nebo obrábění, pro výrobu skříní reduktorů pro elektromobily a přináší několik klíčových výhod:
- Odlehčení pomocí optimalizace designu: Aditivní výroba umožňuje vytvářet složité geometrie a vnitřní mřížkové struktury, které je nemožné nebo nákladově neúnosné dosáhnout konvenčními metodami. Inženýři mohou navrhovat pouzdra s optimalizovaným rozložením materiálu, který se umisťuje pouze tam, kde je to z konstrukčního hlediska nezbytné, což vede k výraznému snížení hmotnosti bez snížení pevnosti nebo tuhosti. To má zásadní význam pro zlepšení energetické účinnosti a dojezdu elektromobilů.
- Složité geometrie a funkční integrace: 3D tisk z kovu umožňuje vytvářet složité tvary s integrovanými prvky, jako jsou chladicí kanály, montážní body a pouzdra senzorů přímo v dílu. Tím se snižuje potřeba více komponent a montážních kroků, což zefektivňuje výrobu a zvyšuje spolehlivost.
- Rychlé prototypování a iterace: Rychlost a flexibilita 3D tisku urychlují konstrukční a vývojový cyklus. Inženýři mohou rychle iterovat návrhy, vyrábět prototypy a testovat je, což vede k rychlejší inovaci a rychlejšímu uvedení nových modelů elektromobilů na trh. Metody 3D tisku kovů nabízené společnostmi, jako je Metal3DP, jsou pro tento agilní vývoj ideální.
- Účinnost materiálu: Aditivní výrobní procesy obvykle zahrnují méně materiálového odpadu ve srovnání se subtraktivními metodami, jako je obrábění, kdy se pro vytvoření finálního dílu odebírá značná část surového materiálu. To je důležité zejména při práci s drahými, vysoce výkonnými kovovými prášky.
- Přizpůsobení a malosériová výroba: Kovový 3D tisk je vhodný pro výrobu krytů reduktorů na míru pro konkrétní modely elektromobilů nebo pro nízké výrobní série, kde mohou být náklady na nástroje spojené s tradičními metodami neúměrně vysoké.
- Zvýšený výkon díky výběru materiálu: 3D tisk z kovu umožňuje použití pokročilých materiálů s přizpůsobenými vlastnostmi, jako je vysoký poměr pevnosti a hmotnosti a vynikající tepelná vodivost, což může dále zvýšit výkon a odolnost krytů reduktorů EV. Metal3DP vyrábí širokou škálu vysoce kvalitních kovových prášků optimalizované pro tyto aplikace.
Doporučené kovové prášky pro vysoce výkonná pouzdra redukcí EV
Volba kovového prášku je rozhodující pro dosažení požadovaných výkonnostních charakteristik 3D tištěného pouzdra EV reduktoru. Několik materiálů nabízí přesvědčivou kombinaci vlastností vhodných pro tuto náročnou aplikaci:
- AlSi10Mg: Tato hliníková slitina se hojně používá při kovovém 3D tisku díky vynikajícímu poměru pevnosti a hmotnosti, dobré tepelné vodivosti a odolnosti proti korozi. Díky své nízké hmotnosti je ideální pro snížení celkové hmotnosti elektromobilu, což přispívá k lepší energetické účinnosti. Dobré tepelné vlastnosti také pomáhají odvádět teplo vznikající v převodovce. | Vlastnosti | Hodnota | Význam pro skříně redukcí EV | :——————————- | :————————————— | :——————————————————————– | | Density | ~2.7 g/cm³ | Odlehčení pro lepší energetickou účinnost | | Pevnost v tahu (mez pevnosti) | ~420 MPa | Vysoká pevnost odolávající provoznímu zatížení | Mez kluzu | ~300 MPa | Odolnost proti trvalé deformaci | Tepelná vodivost | ~160 W/m-K | Účinný odvod tepla | Odolnost proti korozi | Dobrá | Zajišťuje dlouhodobou životnost v různých podmínkách prostředí | Vhodnost pro 3D tisk | Vynikající (laserová fúze v práškovém loži) | Vytváří složité geometrie s dobrou přesností a povrchovou úpravou |
- IN625 (Inconel 625): Tato superslitina na bázi niklu nabízí výjimečnou pevnost při vysokých teplotách, vynikající odolnost proti korozi a vysokou únavovou pevnost. Je sice hustší než AlSi10Mg, ale díky svým vynikajícím mechanickým vlastnostem je vhodná pro aplikace, kde je vyžadována extrémní odolnost a výkon, zejména v oblastech skříně reduktoru vystavených vysokému namáhání. | Vlastnosti | Hodnota | Význam pro pouzdra reduktorů EV | :——————————- | :———————————— | :——————————————————————– | | Density | ~8.4 g/cm³ | Vyšší hustota, ale vynikající pevnost | | Pevnost v tahu (mezní) | ~900 MPa (žíhaná) | Velmi vysoká pevnost, vhodná pro náročné aplikace | | Mez kluzu | ~550 MPa (žíhaná) | Vynikající odolnost proti trvalé deformaci při zvýšených teplotách | | Tepelná vodivost | ~10 W/m-K | Nižší tepelná vodivost ve srovnání s hliníkem | Odolnost proti korozi | Vynikající | Vynikající odolnost proti drsnému prostředí | Vhodnost pro 3D tisk | Dobrá (laserová fúze v práškovém loži) | Možnost výroby složitých dílů s vysokou integritou |
Pokročilý systém výroby prášku Metal3DP’s zajišťuje výrobu vysoce kvalitních sférických prášků, jako jsou AlSi10Mg a IN625, s vysokou sféricitou a tekutostí, což je nezbytné pro konzistentní a spolehlivé procesy 3D tisku. Výběr vhodného prášku závisí na konkrétních požadavcích na výkon, cílové hmotnosti a na nákladech na pouzdro EV reduktoru.
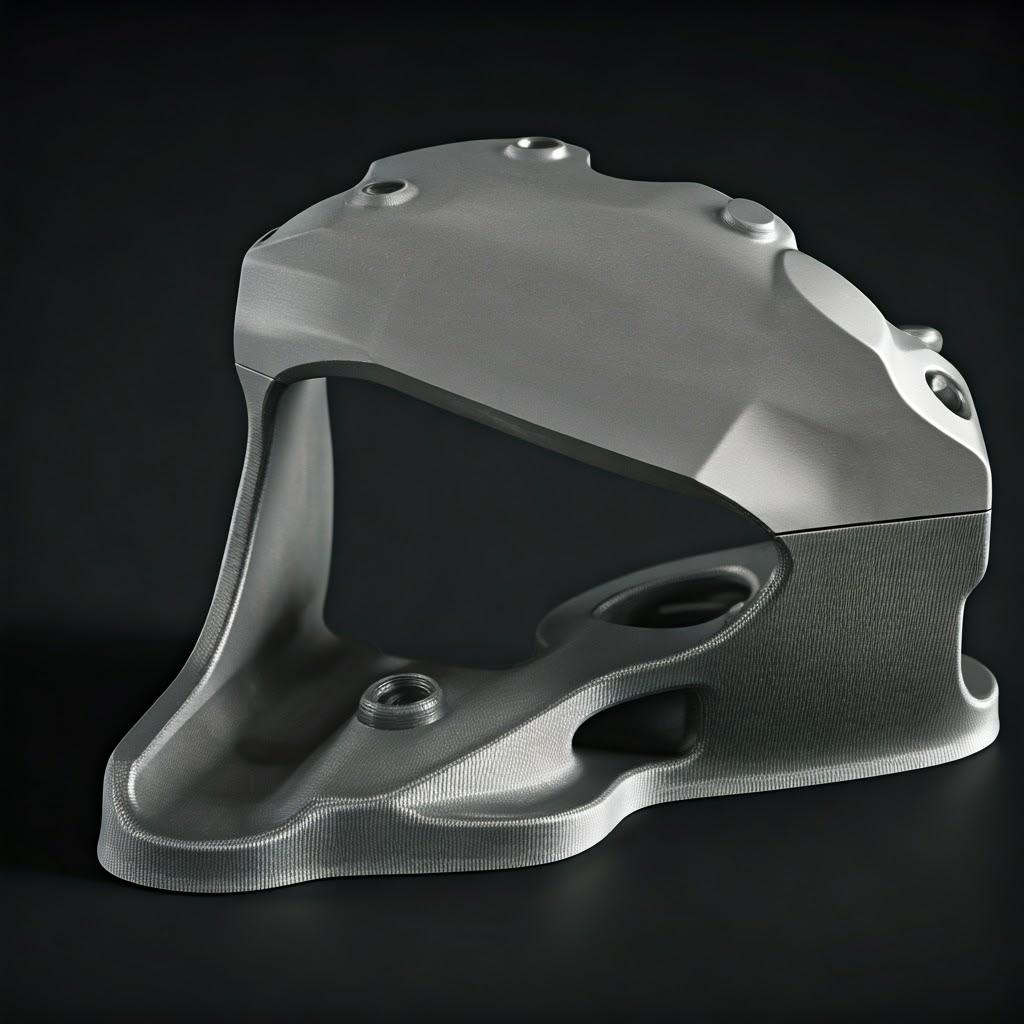
Konstrukční hlediska pro optimalizaci 3D tištěných krytů redukcí pro elektromobily
Navrhování pro aditivní výrobu kovů vyžaduje jiné myšlení než tradiční metody. Pro plné využití možností 3D tisku a dosažení optimálního výkonu skříní reduktorů pro elektromobily je zásadních několik konstrukčních aspektů:
- Optimalizace topologie: Tato výpočetní metoda pomáhá určit nejefektivnější rozložení materiálu pro danou sadu zatížení a omezení. Odstraněním nepotřebného materiálu v málo namáhaných oblastech může optimalizace topologie vést k výraznému snížení hmotnosti při zachování integrity konstrukce. Kovový 3D tisk vyniká při realizaci těchto složitých, organicky vypadajících konstrukcí.
- Mřížové struktury: Začlenění vnitřních mřížových struktur do stěn skříně může zajistit vynikající poměr tuhosti a hmotnosti. Tyto složité sítě vzájemně propojených vzpěr nabízejí výraznou úsporu hmotnosti ve srovnání s plnými stěnami při zachování nebo dokonce zvýšení konstrukčních vlastností. Na základě konkrétních požadavků na zatížení lze zvolit a přizpůsobit různé vzory mřížek.
- Integrace funkcí: Design pro aditivní výrobu umožňuje integrovat více funkcí přímo do pouzdra. To může zahrnovat:
- Chladicí kanály: Vnitřní kanály mohou být navrženy tak, aby usnadňovaly účinný odvod tepla z převodovky, což zvyšuje výkon a životnost.
- Montážní prvky: Integrované montážní body a šrouby mohou snížit potřebu samostatných spojovacích prvků a montážních kroků.
- Integrace senzorů: Přímo do konstrukce lze zabudovat čidla pro sledování teploty, vibrací nebo mazání.
- Kapalinové kanály: Pokud je třeba vést mazací nebo jiné kapaliny skrz pouzdro, lze vytvořit složité vnitřní kanály.
- Samonosné geometrie: Navrhování dílů se samonosnými úhly minimalizuje potřebu podpůrných konstrukcí během procesu tisku. Odstranění podpěr může být časově náročné a může ovlivnit kvalitu povrchu. Pečlivá orientace a konstrukční úpravy mohou snížit nebo eliminovat potřebu podpěr.
- Tloušťka stěny a žebrování: Optimalizace tloušťky stěny a strategicky umístěná žebra mohou zvýšit tuhost a pevnost skříně, aniž by se zvýšila její hmotnost. Minimální dosažitelná tloušťka stěny závisí na zvoleném materiálu a procesu tisku.
- Úvahy o povrchové úpravě: Povrchová úprava kovových 3D tištěných dílů po vytištění se může lišit v závislosti na procesu a materiálu. Konstrukční prvky, které minimalizují strmé převisy a povrchy směřující dolů, mohou zlepšit kvalitu povrchu. U kritických povrchů lze naplánovat kroky následného zpracování, jako je obrábění nebo leštění.
- Integrace sestavy: Pokud se skříň reduktoru skládá z více dílů, může návrh pro 3D tisk umožnit konsolidaci součástí, čímž se sníží počet montážních kroků a potenciálních míst poruch. Lze začlenit zaklapávací prvky nebo integrované spojovací mechanismy.
Dosažení přesnosti: Tolerance, povrchová úprava a rozměrová přesnost u 3D tištěných pouzder
U kritických automobilových součástí, jako jsou skříně reduktorů EV, je nejdůležitější dosáhnout úzkých tolerancí, vhodné povrchové úpravy a vysoké rozměrové přesnosti. Technologie 3D tisku kovů v těchto oblastech významně pokročily:
- Tolerance: Dosažitelná tolerance při 3D tisku z kovu závisí na konkrétní technologii tisku (např. laserová fúze v práškovém loži (LPBF), tavení elektronovým svazkem (EBM)), použitém materiálu a geometrii dílu. Obecně lze u kritických rozměrů dosáhnout tolerance v rozmezí ±0,1 mm až ±0,05 mm. Mezi faktory ovlivňující toleranci patří velikost laserového bodu, distribuce velikosti částic prášku a tepelné řízení během procesu sestavování.
- Povrchová úprava: Povrchová úprava po vytištění se obvykle pohybuje v rozmezí Ra 5-20 μm u LPBF a Ra 10-30 μm u EBM. Drsnost povrchu je ovlivněna velikostí částic prášku a tloušťkou vrstvy. Pro aplikace vyžadující hladší povrch se používají metody následného zpracování, jako je obrábění, leštění nebo abrazivní proudové obrábění.
- Rozměrová přesnost: Rozměrová přesnost se týká schopnosti procesu 3D tisku vyrábět díly, které přesně odpovídají zamýšleným rozměrům modelu CAD. Mezi faktory ovlivňující přesnost patří:
- Smršťování a deformace: Kovy během tisku podléhají tepelné roztažnosti a smršťování, což může vést ke smršťování a deformacím. Pečlivá optimalizace parametrů procesu a návrh nosné konstrukce jsou pro minimalizaci těchto vlivů zásadní.
- Kalibrace a přesnost stroje: Přesnost samotné 3D tiskárny, včetně umístění laserového nebo elektronového paprsku, přímo ovlivňuje rozměrovou přesnost vytištěných dílů. Pravidelná kalibrace je nezbytná.
- Orientace na část: Orientace dílu na konstrukční plošině může ovlivnit přesnost rozměrů, zejména u složitých geometrií. Optimální orientace minimalizuje převisy a maximalizuje samonosné prvky.
Tiskárny Metal3DP’poskytují špičkovou přesnost a spolehlivost v oboru, což zajišťuje, že kritické součásti, jako jsou skříně reduktorů EV, splňují přísné rozměrové požadavky.
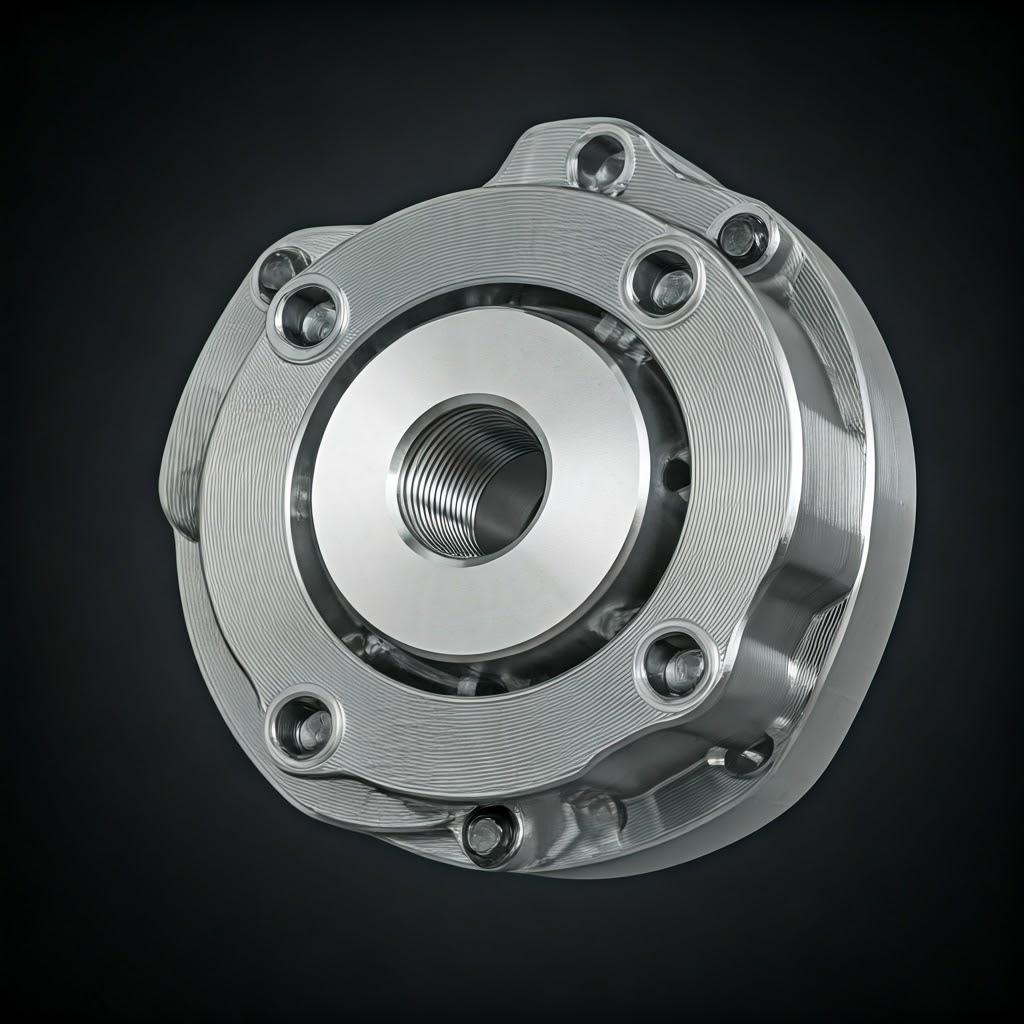
Požadavky na následné zpracování pouzder redukcí EV
Ačkoli 3D tisk z kovu nabízí značné výhody při výrobě složitých geometrií, pro dosažení konečných požadovaných vlastností a povrchové úpravy krytů reduktorů EV jsou často nutné kroky následného zpracování:
- Odstranění podpory: Podpěrné konstrukce, které se používají k zabránění zhroucení nebo deformaci během tisku, je třeba opatrně odstranit. To lze provést ručně pomocí nástrojů nebo automatizovanými procesy, jako je elektroerozivní obrábění (EDM). Cílem návrhu by mělo být minimalizovat potřebu podpěr v kritických oblastech.
- Tepelné ošetření proti stresu: V kovových 3D tištěných dílech mohou v důsledku rychlých cyklů zahřívání a chlazení vznikat zbytková napětí. Ke snížení těchto vnitřních napětí se často provádí tepelné zpracování, které zlepšuje rozměrovou stabilitu a mechanické vlastnosti pouzdra.
- Izostatické lisování za tepla (HIP): HIP zahrnuje vystavení tištěného dílu vysokému tlaku a teplotě v prostředí inertního plynu. Tento proces pomáhá uzavřít všechny vnitřní póry, zvyšuje hustotu a zlepšuje mechanickou pevnost a únavovou životnost materiálu.
- CNC obrábění: V případě kritických styčných ploch nebo prvků vyžadujících velmi přísné tolerance a hladký povrch může být jako sekundární operace nezbytné CNC obrábění. Tím je zajištěna přesná rozměrová přesnost a kvalita povrchu tam, kde je to nutné.
- Povrchová úprava: V závislosti na požadavcích aplikace lze použít různé techniky povrchové úpravy, včetně:
- Leštění: Pro dosažení hladkého, reflexního povrchu.
- Odstřelování: Ke zlepšení drsnosti povrchu pro lepení nebo k vytvoření rovnoměrného matného povrchu.
- Povrchová úprava: Nanášení ochranných nátěrů, jako jsou antikorozní vrstvy nebo nátěry odolné proti opotřebení, pro zvýšení trvanlivosti a výkonu pouzdra.
Překonávání běžných problémů při 3D tisku krytů redukcí pro elektromobily
3D tisk z kovu nabízí řadu výhod, ale existují také běžné problémy, které je třeba řešit, aby byla zajištěna úspěšná výroba krytů redukcí pro elektromobily:
- Deformace a zkreslení: Tepelné gradienty během tisku mohou vést k deformaci a zkreslení, zejména u velkých nebo složitých dílů. Optimalizace parametrů sestavení, použití vhodných podpůrných struktur a tepelné zpracování pro snížení napětí mohou tyto problémy zmírnit.
- Pórovitost: Ve 3D tištěných kovových dílech se mohou vyskytovat vnitřní dutiny nebo pórovitost, které ovlivňují jejich mechanickou pevnost a únavovou životnost. Optimalizace parametrů tisku, výběr materiálu a použití technik následného zpracování, jako je HIP, mohou pórovitost minimalizovat. Metal3DP’s vysoce kvalitními kovovými sférickými prášky jsou navrženy tak, aby při tisku minimalizovaly pórovitost.
- Podpora odstranění poškození: Odstranění podpůrných struktur může někdy zanechat na povrchu vady nebo poškodit díl, zejména u složitých geometrií. Důležitý je pečlivý návrh pro vyrobitelnost a použití vhodných technik odstraňování podpěr.
- Omezení povrchové úpravy: Dosáhnout hladkého povrchu přímo při 3D tisku může být náročné. Pro splnění specifických požadavků na drsnost povrchu jsou často nutné následné kroky zpracování.
- Náklady a škálovatelnost: Přestože se 3D tisk z kovu stává cenově konkurenceschopnějším, náklady na jeden díl mohou být u velmi vysokých objemů výroby stále vyšší než u tradičních metod. Škálovatelnost pro masovou výrobu je stále předmětem vývoje.
- Konzistence vlastností materiálu: Zajištění konzistentních vlastností materiálu v rámci celého velkého 3D tištěného dílu a při více sestaveních vyžaduje pečlivou kontrolu procesu a opatření pro zajištění kvality.
Řešení těchto problémů prostřednictvím optimalizovaného návrhu, řízení procesu, vysoce kvalitních materiálů a vhodných technik následného zpracování je zásadní pro úspěšné zavedení kovového 3D tisku pro skříně reduktorů elektromobilů.
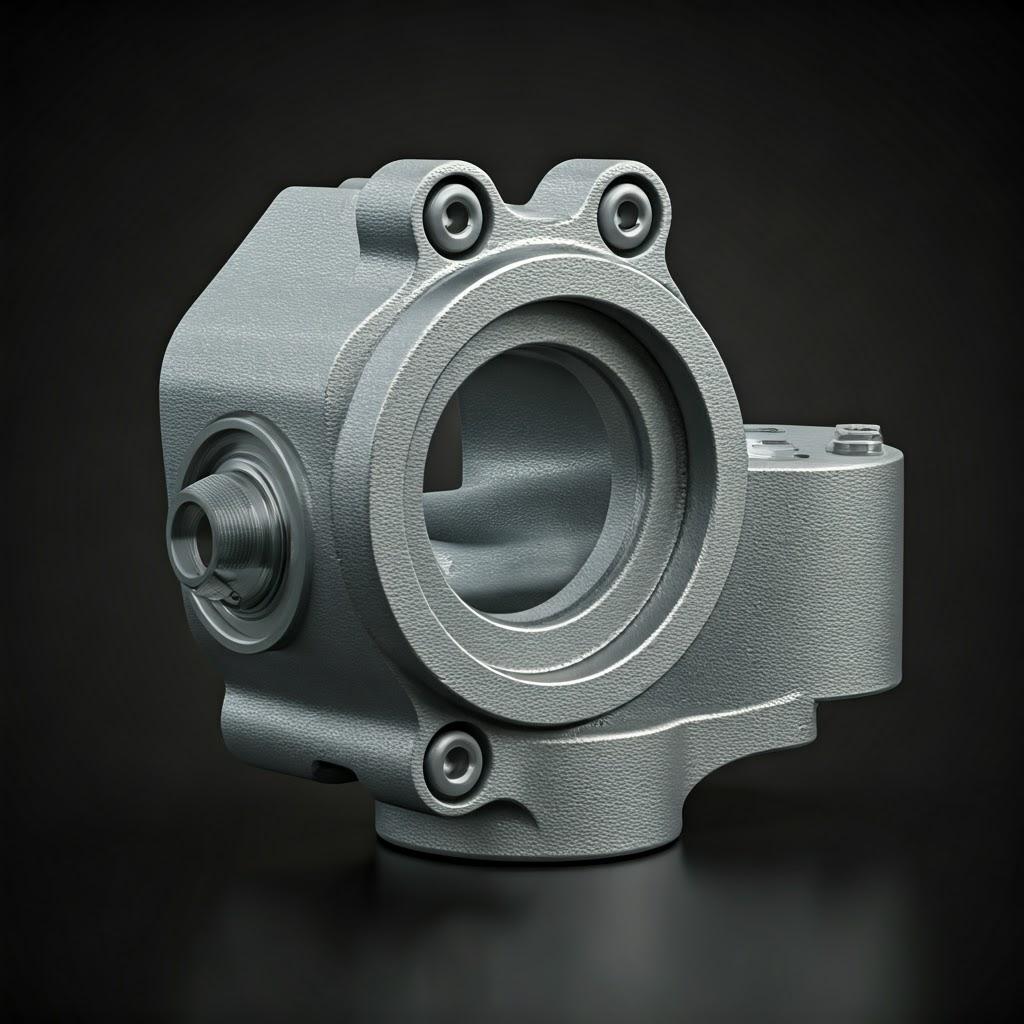
Jak vybrat správného poskytovatele služeb 3D tisku kovů pro komponenty pro elektromobily
Výběr správného poskytovatele služeb 3D tisku z kovu je zásadní pro zajištění úspěšné výroby vysoce kvalitních krytů redukcí pro elektromobily. Zde jsou klíčové faktory, které je třeba zvážit při hodnocení potenciálních dodavatelů:
- Materiálové schopnosti: Ujistěte se, že dodavatel má zkušenosti s prací s doporučenými kovovými prášky, jako jsou AlSi10Mg a IN625, a že má potřebné certifikace a odborné znalosti. Zásadní je jejich znalost vlastností materiálu a parametrů zpracování.
- Tiskové technologie a zařízení: Informujte se o typech technologií 3D tisku kovů, které používají (např. LPBF, DED, Binder Jetting). Volba technologie může ovlivnit dosažitelnou přesnost, kvalitu povrchu a objem výroby. Metal3DP se specializuje na tiskárny SEBM, známé svou přesností a spolehlivostí.
- Zajištění kvality a certifikace: Ověřte si, zda má poskytovatel zavedeny spolehlivé procesy kontroly kvality, včetně testování materiálu, kontroly rozměrů a nedestruktivních metod zkoušení (NDT). Příslušné oborové certifikace (např. ISO 9001, AS9100 pro letecký průmysl) jsou silným ukazatelem jeho závazku ke kvalitě.
- Konstrukční a inženýrská podpora: Dobrý poskytovatel služeb by měl nabízet odborné znalosti v oblasti návrhu pro aditivní výrobu (DfAM), které vám pomohou optimalizovat návrh skříně reduktoru pro 3D tisk a zajistit tak vyrobitelnost, výkon a nákladovou efektivitu.
- Možnosti následného zpracování: Zjistěte, zda poskytovatel nabízí potřebné služby následného zpracování přímo u sebe nebo prostřednictvím důvěryhodných partnerů, včetně odstranění podpory, tepelného zpracování, HIP, CNC obrábění a povrchové úpravy. Komplexní nabídka služeb může zefektivnit výrobní proces.
- Výrobní kapacita a škálovatelnost: Posuďte, zda je poskytovatel schopen zvládnout vaše současné a budoucí objemy výroby. Zjistěte, jaké jsou jeho dodací lhůty a jak je schopen rozšiřovat výrobu podle vývoje vašich potřeb.
- Zkušenosti v oboru: Hledejte poskytovatele s prokazatelnou praxí v automobilovém průmyslu nebo podobných odvětvích s vysokou spolehlivostí. Zkušenosti s komponenty pro elektromobily jsou významnou výhodou.
- Komunikace a transparentnost: Pro úspěšné partnerství je zásadní účinná komunikace a transparentnost v průběhu celého projektu. Poskytovatel by měl reagovat, pravidelně poskytovat aktuální informace a být ochoten spolupracovat při řešení problémů.
- Struktura nákladů: Zjistěte si, jaký je cenový model poskytovatele, včetně nákladů na materiál, tisk, následné zpracování a případných poplatků za nástroje nebo nastavení. Porovnejte nabídky od více poskytovatelů, abyste se ujistili o konkurenceschopných cenách.
Nákladové faktory a doba realizace 3D tištěných krytů redukcí pro elektromobily
Náklady a doba výroby skříní reduktorů pro elektromobily pomocí kovového 3D tisku jsou ovlivněny několika faktory:
Nákladové faktory:
- Náklady na materiál: Cena kovového prášku (např. AlSi10Mg, IN625) významně přispívá k celkovým nákladům. Speciální slitiny, jako je IN625, jsou obecně dražší než hliníkové slitiny.
- Doba výstavby: Délka procesu tisku závisí na velikosti a složitosti dílu a na zvolené technologii tisku. Delší doba sestavení znamená vyšší náklady na používání stroje.
- Náklady na provoz stroje: Patří mezi ně spotřeba energie, údržba a odpisy zařízení pro 3D tisk.
- Náklady na následné zpracování: Rozsah nutného následného zpracování (odstranění podpory, tepelné zpracování, obrábění, dokončovací práce) významně ovlivňuje konečné náklady. Složité pracovní postupy následného zpracování zvyšují náklady.
- Náklady na pracovní sílu: K celkovým nákladům přispívá čas inženýrů na optimalizaci návrhu, přípravu stavby a práci po zpracování.
- Objem výroby: Zatímco 3D tisk může být nákladově efektivní pro malé až střední objemy a složité geometrie, náklady na jeden díl nemusí být konkurenceschopné s tradičními výrobními metodami pro velké objemy u jednoduchých návrhů.
Dodací lhůta:
- Návrh a optimalizace: Čas potřebný k návrhu nebo optimalizaci pouzdra reduktoru pro 3D tisk.
- Příprava stavby: Nastavení tiskové úlohy, včetně optimalizace orientace, generování podpory a řezání.
- Doba tisku: Skutečná doba trvání procesu 3D tisku.
- Doba následného zpracování: Doba potřebná pro odstranění podpory, tepelné zpracování, obrábění a povrchovou úpravu. Tato doba se může výrazně lišit v závislosti na složitosti a požadované povrchové úpravě.
- Kontrola kvality: Čas na kontrolu rozměrů, testování materiálu a další postupy pro zajištění kvality.
- Doprava: Doba dodání hotových dílů.
Kontaktujte společnost Metal3DP a zjistěte, jak mohou naše schopnosti podpořit cíle vaší organizace v oblasti aditivní výroby. Na základě vašich konkrétních požadavků vám můžeme poskytnout podrobné odhady nákladů a doby realizace.
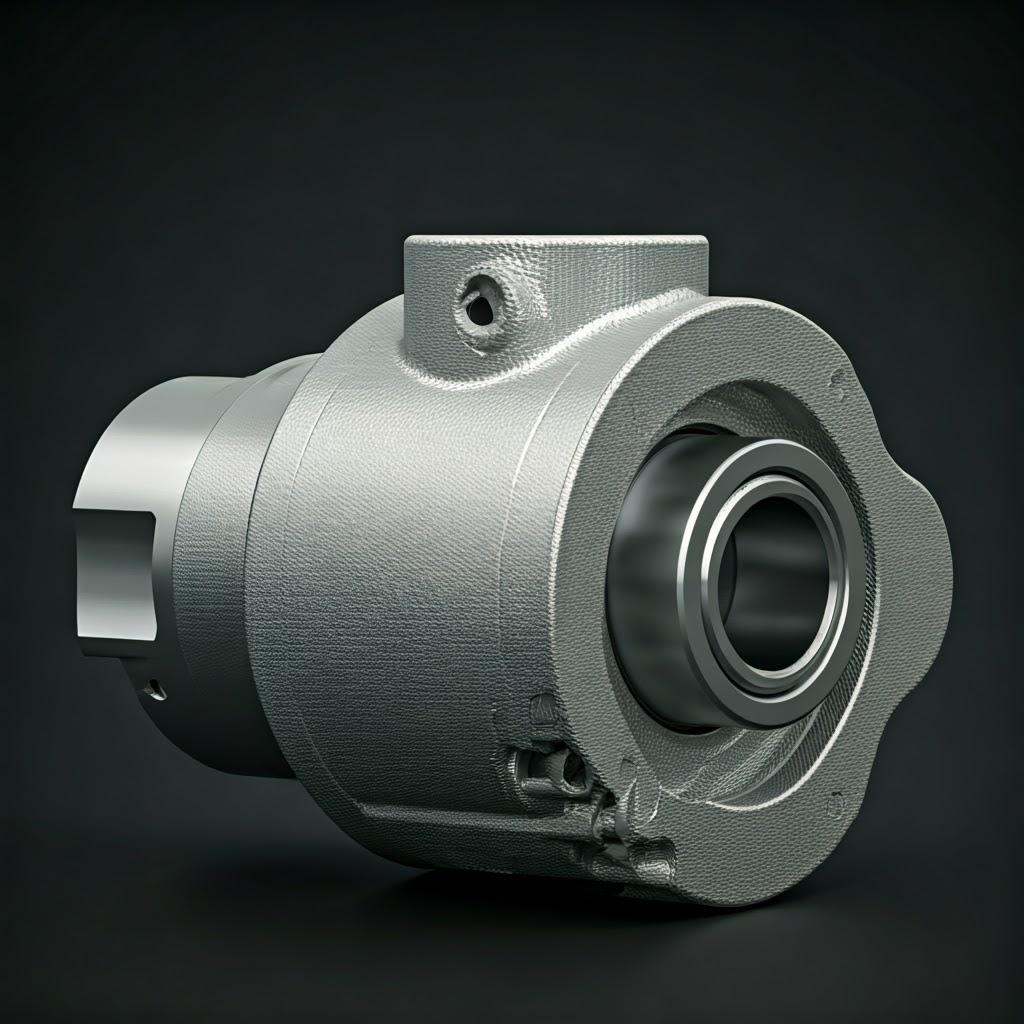
Často kladené otázky (FAQ)
- Otázka: Je kovový 3D tisk dostatečně pevný pro kryty redukcí pro elektromobily?
- A: Ano, kovový 3D tisk s použitím vhodných materiálů, jako jsou AlSi10Mg a IN625, může vyrábět díly s vysokou pevností a odolností vhodné pro náročné zatížení v pohonech elektrických vozidel. Následné zpracování, jako je HIP, může dále zlepšit mechanické vlastnosti.
- Otázka: Jaká je typická tolerance dosažitelná při 3D tisku z kovu pro tuto aplikaci?
- A: V závislosti na technologii tisku a materiálu lze u kritických rozměrů dosáhnout tolerance v rozmezí ±0,1 mm až ±0,05 mm. V případě potřeby lze použít sekundární obrábění pro větší tolerance.
- Otázka: Může 3D tisk z kovu pomoci snížit hmotnost skříní reduktorů EV?
- A: Rozhodně. Díky technikám optimalizace konstrukce, jako je optimalizace topologie a mřížkové struktury, umožňuje kovový 3D tisk výrazné snížení hmotnosti ve srovnání s tradičně vyráběnými pouzdry, aniž by byla narušena strukturální integrita.
Závěr - Využití 3D tisku kovů pro řešení skříní redukcí pro elektromobily nové generace
Průmysl elektromobilů vyžaduje inovace ve všech aspektech konstrukce a výroby vozidel. 3D tisk z kovu představuje transformační technologii pro výrobu redukčních skříní nové generace pro elektromobily. Jeho schopnost umožnit odlehčení díky volnosti designu, integrovat komplexní funkce, urychlit tvorbu prototypů a využívat vysoce výkonné materiály, jako jsou AlSi10Mg a IN625, nabízí významné výhody oproti tradičním výrobním metodám.
Firmy jako Metal3DP Technology Co., LTDdíky svému špičkovému zařízení pro 3D tisk a pokročilým kovovým práškům umožňují výrobcům automobilů posouvat hranice výkonu a účinnosti elektrických vozidel. Pečlivým zvážením konstrukčních zásad, výběru materiálu, požadavků na následné zpracování a výběrem správného poskytovatele služeb lze využít plný potenciál 3D tisku kovů k vytvoření lehčích, účinnějších a výkonnějších skříní redukcí pro elektromobily, což je hnací silou budoucnosti elektromobility.
Sdílet na
MET3DP Technology Co., LTD je předním poskytovatelem řešení aditivní výroby se sídlem v Qingdao v Číně. Naše společnost se specializuje na zařízení pro 3D tisk a vysoce výkonné kovové prášky pro průmyslové aplikace.
Dotaz k získání nejlepší ceny a přizpůsobeného řešení pro vaše podnikání!
Související články
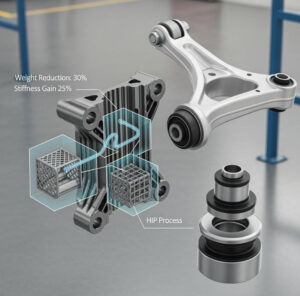
Metal 3D Printed Subframe Connection Mounts and Blocks for EV and Motorsport Chassis
Přečtěte si více "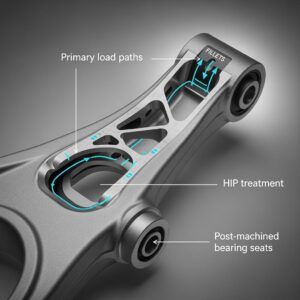
Metal 3D Printing for U.S. Automotive Lightweight Structural Brackets and Suspension Components
Přečtěte si více "O Met3DP
Nedávná aktualizace
Náš produkt
KONTAKTUJTE NÁS
Nějaké otázky? Pošlete nám zprávu hned teď! Po obdržení vaší zprávy obsloužíme vaši žádost s celým týmem.