3D tištěné žebrové konstrukce pro snížení hmotnosti v letectví a kosmonautice
Obsah
Úvod: Kritická role žebrových konstrukcí a hledání lehčích leteckých komponentů
Ve složitém fyzikálním a technickém tanci, který umožňuje masivním letadlům vzdorovat gravitaci, hrají konstrukční prvky zásadní roli. Mezi nejzásadnější z nich patří žebrové konstrukce. Žebra, která se nacházejí v křídlech, trupech a řídicích plochách, jsou neopěvovanými hrdiny, kteří udržují aerodynamický tvar, rozkládají provozní zatížení a zajišťují celkovou integritu draku letadla. Fungují jako kostra, přenášejí napětí z potahu a nosníků, zabraňují vybočení a poskytují upevňovací body pro další kritické systémy. Konstrukce a výroba těchto součástí byla vždy ústředním bodem vývoje letadel, který vyvažoval nepominutelné požadavky na bezpečnost a pevnost se stále přítomnou snahou o efektivitu.
Snaha o efektivitu v leteckém průmyslu je neúprosná a často se zaměřuje především na. snížení hmotnosti. Každý kilogram ušetřené hmotnosti konstrukce letadla se přímo promítá do hmatatelných přínosů po celou dobu jeho životnosti. Lehčí letadla spotřebují méně paliva, což vede k významným úsporám nákladů pro provozovatele a ke snížení ekologické stopy - což je v dnešním světě, který dbá na ochranu životního prostředí, velmi důležité. Kromě toho může snížená hmotnost znamenat zvýšení nosnosti (více cestujících nebo nákladu), prodloužení doletu nebo zlepšení manévrovatelnosti a výkonnosti, což je důležité zejména v obranných a kosmických aplikacích. Tato neúnavná snaha o odlehčení, často označovaná jako "lightweighting", proniká do všech aspektů leteckého designu, od výběru materiálů až po geometrii součástí. Manažeři a inženýři zabývající se zadáváním veřejných zakázek u výrobců OEM v leteckém průmyslu a jejich dodavatelé leteckých komponentů neustále hledají inovativní materiály a výrobní postupy, které by ušetřily drahocenné gramy, aniž by byla ohrožena bezpečnost nebo výkon.
Letecká žebra se tradičně vyrábějí subtraktivními metodami, především CNC obráběním z pevných bloků nebo desek z vysokopevnostního hliníku nebo titanových slitin. Tento přístup je sice efektivní a dobře pochopitelný, ale často zahrnuje vyřezávání obrovského množství drahého surového materiálu, což má za následek špatný poměr "buy-to-fly" (poměr hmotnosti zakoupené suroviny a hmotnosti finálního dílu). Složité geometrie žeber mohou vyžadovat složité operace víceosého obrábění, rozsáhlé programování, specializované nástroje a dlouhé doby obrábění, což významně přispívá k dodacím lhůtám a nákladům, zejména v případě nízkoobjemové výroby nebo výroby prototypů.
Vstupte Výroba aditiv kovů (AM), běžně známý jako kov 3D tisk. Tato transformační technologie rychle překračuje rámec prototypování a přechází do oblasti sériové výroby pro náročná průmyslová odvětví, jako je letectví a kosmonautika. Při AM se místo odebírání materiálu vytvářejí díly vrstvu po vrstvě přímo z digitálního modelu, obvykle pomocí vysokoenergetických zdrojů, jako jsou lasery nebo elektronové paprsky, které spojují jemné kovové prášky. Tento zásadní rozdíl odemyká změnu paradigmatu v tom, jak lze navrhovat a vyrábět součásti pro letectví a kosmonautiku, včetně žebrových konstrukcí.
Technologie AM nabízí leteckým inženýrům nebývalou volnost při navrhování. Složité organické tvary optimalizované pro specifické dráhy zatížení, které dříve nebylo možné vyrobit nebo jejichž výroba byla neúnosně drahá, jsou nyní realizovatelné. Vnitřní mřížkové struktury mohou být začleněny tak, aby zajistily tuhost a zároveň výrazně snížily hmotnost. Více součástí sestavy žeber lze potenciálně konsolidovat do jediného tištěného dílu, čímž se sníží počet spojovacích prvků, doba montáže a potenciální místa poruchy. Kromě toho jsou procesy AM ze své podstaty materiálově efektivnější než tradiční subtraktivní metody, což výrazně zlepšuje poměr mezi nákupem a letem a snižuje plýtvání vysoce hodnotnými leteckými slitinami.
Pro manažeři nákupu v leteckém průmyslu a B2B kupující při hledání špičkových výrobních řešení představuje AM kovů mocný nástroj k dosažení strategických cílů: snížení hmotnosti součástek, zkrácení dodacích lhůt pro složité díly, umožnění inovace designu a potenciální zjednodušení dodavatelských řetězců prostřednictvím konsolidace dílů. Společnosti jako Met3dp se sídlem v čínském Čching-tao stojí v čele této revoluce a poskytují nejen pokročilá zařízení pro 3D tisk z kovu, jako jsou jejich systémy SEBM (Selective Electron Beam Melting) známé špičkovou přesností a spolehlivostí, ale specializují se také na výzkum a výrobu vysoce výkonných, kovové prášky pro letectví a kosmonautiku nezbytné pro výrobu kritických dílů. Tento příspěvek na blogu se zabývá specifiky použití kovové AM pro letecké žebrové konstrukce, zkoumá aplikace, přesvědčivé výhody oproti tradičním metodám, doporučené materiály, jako jsou Scalmalloy® a AlSi10Mg, zásadní konstrukční úvahy a to, co hledat u poskytovatele AM služeb.
Aplikace a funkce: Kde se v letectví a kosmonautice používají 3D tištěné žebrové konstrukce?
Žebrové konstrukce v letectví, bez ohledu na způsob výroby, jsou nedílnou součástí zachování tvaru a funkce různých částí draku letadla. Jejich hlavní úlohou je udržovat aerodynamický profil (zejména u křídel a řídicích ploch), přenášet zatížení mezi potahem, nosníky a podélníky, zabraňovat vybočení při působení tlakových a smykových sil a poskytovat pevné upevňovací body pro jiné systémy. Nástup aditivní výroby kovů tyto základní funkce nezměnil, ale je to má adresu rozšířil možnosti jak těchto funkcí a kde mohou optimalizovaná odlehčená žebra přinést nejvýznamnější výhody. Schopnost vytvářet složité, topologicky optimalizované konstrukce činí AM obzvláště atraktivní pro aplikace, kde je konstrukční účinnost prvořadá.
Podívejme se na klíčové oblasti, kde se 3D tištěné žebrové konstrukce stále více uplatňují:
- Křídlová žebra: To je asi nejklasičtější aplikace. Žebra křídla určují tvar křídla, který je rozhodující pro generování vztlaku. Přenášejí aerodynamické zatížení z potahu křídla na hlavní nosníky a rozdělují zatížení od palivových nádrží, motorů a podvozku umístěných v křídle nebo k němu připevněných. Použití technologie AM umožňuje vysoce optimalizované konstrukce žeber křídla, které sledují přesné dráhy napětí a odstraňují materiál tam, kde není potřeba. To může vést k výrazné úspoře hmotnosti celého křídla, což má přímý dopad na palivovou účinnost. Kromě toho lze během procesu tisku přímo do struktury žeber integrovat vnitřní kanály pro kabeláž, palivové vedení nebo dokonce systémy tepelného řízení, což konsoliduje díly a zjednodušuje montáž. Technologie AM umožňuje vytvářet v žebrech mřížkové struktury s proměnlivou hustotou, které poskytují přizpůsobenou tuhost a pevnost přesně tam, kde je to potřeba.
- Rámy trupu/pruty: Podobně jako žebra křídel udržují rámy nebo žebra trupu tvar průřezu těla letadla, podpírají potah proti vybočení a rozdělují tlakové zatížení (u dopravních letadel) a aerodynamické síly. Slouží také jako montážní body pro interiér kabiny, nákladní systémy a různé vybavení. AM umožňuje navrhovat lehké rámy, které integrují upevňovací držáky a systémová rozhraní, čímž se snižuje počet dílů a složitost montáže. U beztlakových úseků nebo v kosmických aplikacích může optimalizace topologie přinést vysoce efektivní skeletové rámové konstrukce.
- Nosné konstrukce (ocasní části): Žebra v horizontálním stabilizátoru, vertikálním stabilizátoru (ploutvi), výškovkách a směrovce plní podobné funkce jako žebra křídla - udržují aerodynamický profil a přenášejí zatížení na nosníky. Vzhledem k umístění v zadní části letounu může mít úspora hmotnosti v empennage také pozitivní dopad na celkové vyvážení a stabilitu letounu, což může snížit potřebnou velikost a hmotnost protiváhy. AM umožňuje výrobu vysoce integrovaných žeber pro řídicí plochy, potenciálně kombinujících body závěsů nebo upevnění pohonů do jediné tištěné součásti.
- Podpěry součástí motoru a konstrukce Nacelle: Žebra a konzoly v motorových gondolách poskytují strukturální podporu, udržují aerodynamický tvar a zajišťují vedení základních služeb. Často pracují v prostředí s vysokou teplotou nebo vysokými vibracemi. AM s využitím materiálů, jako jsou vysokoteplotní slitiny nebo optimalizované konstrukce hliníku/titanu, může vytvořit lehké a tuhé nosné konstrukce schopné odolat těmto náročným podmínkám. Klíčovým faktorem je zde opět konsolidace dílů, která snižuje počet vyráběných plechových dílů a spojovacích prvků typických pro sestavy gondol.
- Sestavy podvozku: Žebra a podpůrné konstrukce v podvozkových prostorech i samotný podvozek musí při přistání odolávat obrovskému nárazovému zatížení. Zatímco některé součásti z oceli s velmi vysokou pevností mohou zůstat tradičně vyráběné, AM nabízí možnosti odlehčení souvisejících podpůrných konstrukcí, konzol a žeber kapotáže pomocí vysokopevnostního hliníku (jako je Scalmalloy®) nebo titanových slitin.
- Žebra ovládací plochy: Křidélka, klapky, výškovky a kormidla se opírají o vnitřní žebra, která zajišťují jejich tvar a tuhost. Technologie AM umožňuje vytvářet složité tenkostěnné konstrukce žeber optimalizované pro aerodynamickou účinnost a minimální hmotnost, což zlepšuje odezvu řízení.
- Konstrukce družic a nosných raket: V kosmických aplikacích je každý gram rozhodující. AM se hojně využívá k vytváření ultralehkých žeber a izomřížových konstrukcí pro satelitní autobusy, solární panely, anténní podpěry a propojovací struktury pohonných nádrží v nosných raketách. Schopnost rychle iterovat návrhy a vyrábět velmi složité geometrie činí AM ideálním řešením pro často jedinečné a nízkoobjemové požadavky kosmického průmyslu.
Funkční integrace: Kromě konstrukční podpory umožňuje AM integrovat další funkce přímo do konstrukce žeber:
- Tepelný management: Do žeber umístěných v blízkosti zdrojů tepla (např. motorů nebo elektroniky) lze navrhnout vnitřní kanály, které umožňují chlazení vzduchem nebo kapalinou a vytvářejí multifunkční komponenty.
- Směrování systému: Lze do nich zabudovat kanály pro svazky elektrické kabeláže nebo hydraulická vedení, které je chrání a zjednodušují montáž letadla.
- Integrované držáky/držáky: Upevňovací body pro další součásti mohou být součástí žebra, takže není třeba používat samostatné držáky a spojovací prvky.
Pro manažeři nákupu v leteckém průmyslu a specialisté na dodavatelský řetězec, zajišťování těchto pokročilých, často složitých struktur žeber AM vyžaduje partnerství se schopnými poskytovatelé služeb v oblasti AM kovů. Tito dodavatelé musí nejen disponovat správnou tiskovou technologií, ale také prokázat odborné znalosti v oblasti leteckých materiálů, řízení procesů, zajištění kvality a následného zpracování, které jsou nezbytné pro splnění přísných požadavků tohoto odvětví. Schopnost AM konsolidovat sestavy také představuje příležitost k zefektivnění dodavatelského řetězce, protože snižuje počet jednotlivých čísel dílů, které je třeba sledovat, vyhledávat a spravovat.
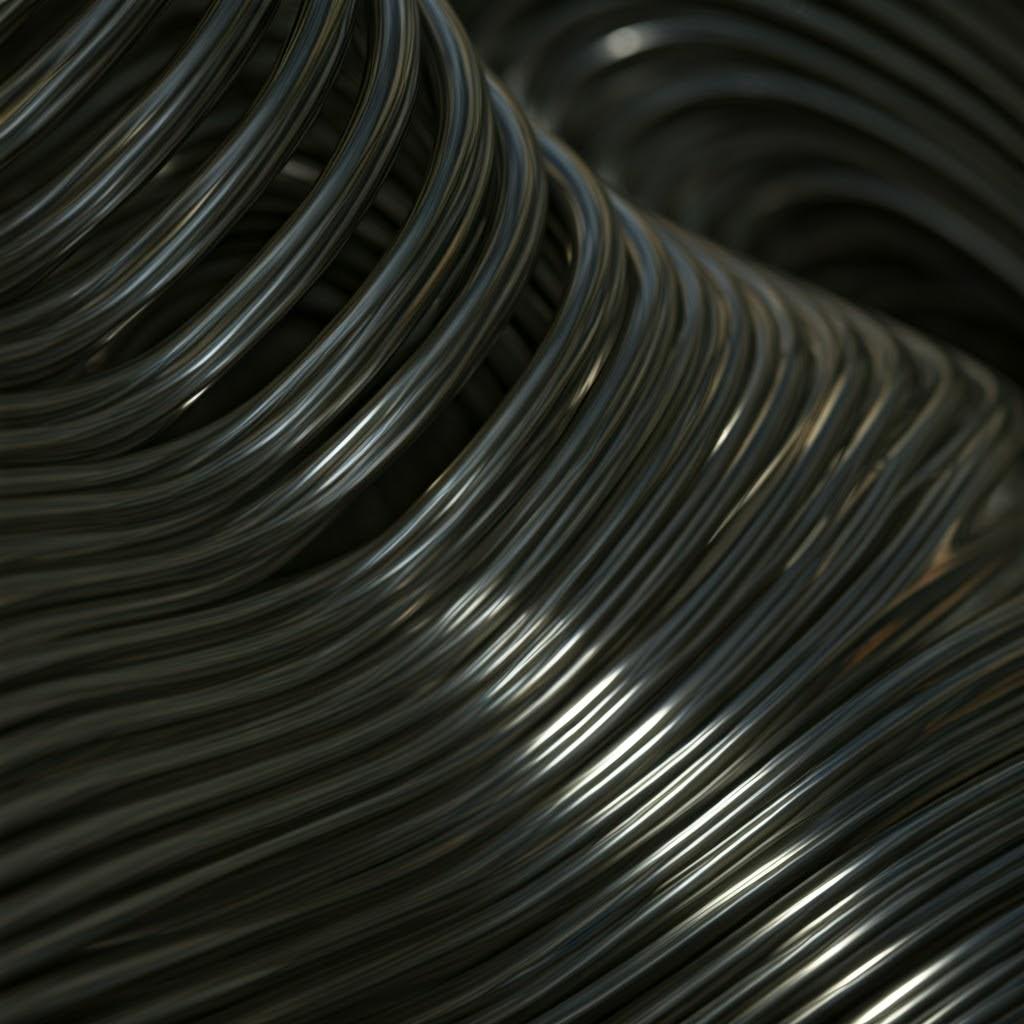
Proč 3D tisk z kovu pro žebra v letectví a kosmonautice? Odemknutí výkonu a zvýšení efektivity
Letecký a kosmický průmysl se již po desetiletí spoléhá na subtraktivní výrobu, zejména na CNC obrábění, při výrobě vysoce přesných konstrukčních součástí, jako jsou žebra. Tato metoda spočívá v tom, že se začíná s pevným blokem, deskou nebo výkovkem z materiálu (často z hliníku nebo titanu) a pečlivě se odřezává přebytečný materiál, dokud se nedosáhne konečného tvaru. Tento tradiční přístup je sice schopen vyrábět vysoce kvalitní díly, ale naráží na přirozená omezení, zejména při použití na složité letecké konstrukce optimalizované pro minimální hmotnost. Aditivní výroba kovů nabízí přesvědčivá řešení, která tato omezení překonávají a umožňují dosáhnout významného zvýšení výkonu a efektivity.
Pojďme si rozebrat klíčové výhody použití technologie AM pro výrobu kovů (konkrétně techniky fúze v práškovém loži, jako je laserová fúze v práškovém loži - LPBF, známá také jako selektivní laserové tavení - SLM a selektivní tavení elektronovým svazkem - SEBM) pro výrobu žeber pro letecký průmysl:
- Revoluční odlehčení pomocí optimalizace topologie: To je pravděpodobně nejvýznamnější výhoda. Tradiční výrobní omezení často nutí konstruktéry k prizmatickým tvarům nebo konstrukcím snadno dosažitelným pomocí řezných nástrojů. AM mnoho těchto omezení odstraňuje. Použití optimalizace topologie softwaru mohou inženýři definovat zatěžovací stavy, okrajové podmínky a návrhový prostor pro žebro a softwarový algoritmus iterativně odstraní materiál z oblastí s nízkým namáháním, přičemž zůstane organická struktura, často podobná kosti, která představuje nejefektivnější cestu zatížení.
- Výhody: Výsledkem jsou součásti, které jsou výrazně lehčí (běžné je snížení hmotnosti o 30-60% nebo i více ve srovnání s tradičně navrženými protějšky) a zároveň splňují nebo překračují požadovaná kritéria pevnosti a tuhosti. To se přímo promítá do úspory paliva a zvýšení výkonnosti, o nichž jsme hovořili dříve.
- Kontrast: Dosažení takto složitých, optimalizovaných tvarů pomocí CNC obrábění by bylo neuvěřitelně obtížné, časově náročné a potenciálně nemožné kvůli omezením přístupu k nástrojům.
- Výrazné zlepšení poměru nákupů a letů: Letecké slitiny jsou drahé. CNC obrábění žeber z plných předvalků často vede k tomu, že poměry nákupů a letů přesahující 10:1, což znamená, že více než 90% nákladné suroviny je zpracováno na třísky (šrot). To představuje značné plýtvání náklady a zdroji.
- Výhody: AM vytváří díly vrstvu po vrstvě, přičemž používá pouze materiál potřebný pro daný díl a jeho podpůrné struktury. Ačkoli se používá určitý podpůrný materiál a netavený prášek je třeba recyklovat, celkové využití materiálu je výrazně lepší. Je možné dosáhnout poměru nákup/výlisek blížícího se 1,5:1 nebo 2:1, což výrazně snižuje náklady na suroviny a odpad.
- Dopad: Díky tomu je ekonomika výroby příznivější, zejména u vysoce hodnotných materiálů, jako je titan, nebo specializovaných slitin, jako je Scalmalloy®.
- Konsolidace dílů pro snížení složitosti a hmotnosti: Žebrové konstrukce v sestavách často zahrnují více obráběných součástí, držáků, spojovacích prvků (nýtů, šroubů) a těsnicích prvků. Každý spoj a spojovací prvek zvyšuje hmotnost, zavádí potenciální místa poruch a prodlužuje dobu a složitost montáže.
- Výhody: AM umožňuje inženýrům přepracovat konstrukci sestav a sloučit více komponent do jediného monolitického tištěného dílu. Složitá sestava žeber s mnoha připojenými konzolami by se tak mohla stát jednou integrovanou konstrukcí.
- Dopad: Tím se snižuje počet dílů, eliminuje se spojovací materiál, snižuje se celková hmotnost, zjednodušují se montážní procesy, snižuje se správa zásob pro oddělení veřejných zakázeka potenciálně zlepšuje strukturální integritu odstraněním spojů.
- Výroba složitých geometrií: AM vyniká při vytváření složitých vnitřních prvků a komplexních vnějších tvarů, kterých je obtížné nebo nemožné dosáhnout tradičními metodami.
- Výhody: Patří sem vnitřní chladicí kanály, optimalizované mřížkové struktury pro přizpůsobení poměru tuhosti a hmotnosti, skryté dutiny pro další snížení hmotnosti a složité konformní tvary, které dokonale odpovídají aerodynamickým profilům nebo spojovacím součástem.
- Použití: U žeber, která potřebují integrovaný tepelný management nebo vyžadují vysoce optimalizované vnitřní struktury, je AM často jedinou schůdnou výrobní metodou.
- Zrychlená tvorba prototypů a iterace návrhu: Nastavení tradiční výroby složitého žebra často zahrnuje vytvoření specializovaných přípravků a složité programování CNC. Změny konstrukce mohou vyžadovat značné přepracování těchto prvků.
- Výhody: AM je řízena digitálně. Návrhy lze upravovat v CAD a odesílat přímo do tiskárny, což umožňuje mnohem rychlejší iterační cykly během vývojové fáze. V rámci jednoho sestavení lze potenciálně vytisknout více variant konstrukce současně pro srovnávací testování.
- Dopad: To urychluje životní cyklus vývoje produktu a umožňuje inženýrům rychleji a efektivněji testovat a ověřovat optimalizované návrhy před zahájením sériové výroby.
- Potenciál zkrácení dodacích lhůt (zejména u složitých/malosériových dílů): Zatímco samotný proces tisku může trvat hodiny nebo dny. celkově doba přípravy od finálního návrhu k hotovému dílu může být u vysoce složitých nebo nízkoobjemových komponent často kratší než u tradičních metod.
- Odůvodnění: AM eliminuje potřebu návrhu a výroby nástrojů, snižuje složité programování a seřizovací časy spojené s víceosým obráběním a zjednodušuje dodavatelský řetězec díky konsolidaci dílů.
- Úvaha: To je velmi závislé na složitosti dílu, materiálu, požadovaném následném zpracování a Poskytovatel služeb AM kapacity a nevyřízených zakázek. Pro naléhavé potřeby nebo díly s dlouhými tradičními dodacími lhůtami však AM nabízí cennou alternativu.
Ačkoli AM nabízí tyto podstatné výhody, je nezbytné spolupracovat se zkušenými poskytovateli, jako je Met3dp. Jejich zaměření na špičkový objem tisku, přesnost a spolehlivost, podpořené hlubokými odbornými znalostmi v oblasti strojní technologie (SEBM) i práškové metalurgie (plynová atomizace, PREP), zajišťuje, že se teoretické výhody AM promítnou do hmatatelných, vysoce kvalitních leteckých komponent. Výběr správného metal AM aerospace partner je klíčem k úspěšnému využití těchto výhod pro náročné aplikace, jako jsou žebrové konstrukce.
Doporučené materiály pro 3D tisk žeber: Scalmalloy® a AlSi10Mg Deep Dive
Výběr vhodného materiálu je základem úspěchu každé technické aplikace, což platí zejména pro letecké komponenty, u nichž je rozhodující výkon, bezpečnost a hmotnost. Ačkoli aditivní výroba kovů dokáže zpracovávat širokou škálu slitin (včetně titanu, niklových superslitin a ocelí), pro žebrové konstrukce se často volí hliníkové slitiny díky jejich přirozené nízké hustotě a dobrým mechanickým vlastnostem. V rodině hliníkových slitin pro AM vynikají dva materiály pro aplikace žeber v leteckém průmyslu, i když s různou pevností a ideálními případy použití: Scalmalloy® a AlSi 10Mg.
Pochopení vlastností těchto materiálů je zásadní jak pro konstruktéry, kteří díl specifikují, tak pro manažeři veřejných zakázek zajištění výrobních služeb a dodavatelé kovových prášků pro letecký a kosmický průmysl potřeby.
Scalmalloy® (slitina Al-Mg-Sc): Vysoce výkonný šampión
Scalmalloy® je patentovaná vysoce výkonná slitina hliníku, hořčíku a skandia vyvinutá speciálně pro náročné požadavky aditivní výroby. Její jedinečné složení vede po tisku a vhodném tepelném zpracování k jemnozrnné mikrostruktuře, která poskytuje mechanické vlastnosti výrazně převyšující vlastnosti tradičních litých nebo tepaných hliníkových slitin běžně používaných v AM.
- Klíčové vlastnosti a výhody:
- Výjimečná specifická síla: To je charakteristická vlastnost slitiny Scalmalloy®. Může se pochlubit velmi vysokou mezí kluzu a pevností v tahu v poměru k nízké hustotě, což z ní činí jednu z nejpevnějších hliníkových slitin zpracovatelných AM. Tento vysoký poměr pevnosti a hmotnosti umožňuje výrazné odlehčení nad rámec toho, čeho lze dosáhnout u standardních slitin, a to i po optimalizaci topologie.
- Vynikající tažnost a únavová životnost: Na rozdíl od některých vysokopevnostních materiálů, které mohou být křehké, si slitina Scalmalloy® zachovává dobré prodloužení (tažnost), což jí umožňuje značnou deformaci před zlomením. Pro letecké součásti vystavené cyklickému zatížení (např. žebra křídel) je rozhodující, že ve srovnání s jinými hliníkovými slitinami AM, jako je AlSi10Mg, vykazuje vyšší únavovou pevnost.
- Dobrá svařitelnost a zpracovatelnost: Obecně se dobře zpracovává v systémech laserové fúze v práškovém loži (LPBF) a v případě potřeby jej lze svařovat pro větší sestavy nebo opravy (i když konsolidace dílů tuto potřebu často vylučuje).
- Odolnost proti korozi: Vyznačuje se dobrou odolností proti korozi, je vhodný do typických provozních prostředí v letectví a kosmonautice.
- Mikrostrukturní stabilita: Přídavek skandia pomáhá stabilizovat mikrostrukturu a přispívá ke stálému vysokému výkonu.
- Ideální aplikace:
- Vysoce zatížené konstrukční prvky, u nichž je hlavním požadavkem maximální úspora hmotnosti.
- díly kritické z hlediska únavy (žebra křídla, rámy trupu, součásti podvozku).
- Aplikace zaměřené na výkon v motoristickém sportu, obraně a vesmíru.
- Přímá náhrada/upgrade komponentů tradičně vyráběných z vysoce pevných hliníkových slitin řady 7xxx.
- Úvahy:
- Náklady: Prášek Scalmalloy® je výrazně dražší než standardní hliníkové slitiny kvůli obsahu skandia a licencování. Tyto vyšší náklady na materiál musí být odůvodněny dosaženým zvýšením výkonu a snížením hmotnosti.
- Tepelné zpracování: Vyžaduje specifické, optimalizované cykly tepelného zpracování, aby dosáhl svých špičkových vlastností. Je nezbytné spolupracovat s poskytovatelem AM služeb, který má zkušenosti s následným zpracováním slitiny Scalmalloy®.
AlSi10Mg: Zavedený pracovní kůň
AlSi10Mg je jednou z nejpoužívanějších a nejlépe charakterizovaných hliníkových slitin při aditivní výrobě kovů. Je to v podstatě slitina hliníkových odlitků upravená pro procesy AM, známá svou vynikající tisknutelností a vyváženými vlastnostmi.
- Klíčové vlastnosti a výhody:
- Vynikající tisknutelnost: Obsah křemíku zajišťuje dobrou tekutost v tavenině, což umožňuje relativně snadné zpracování na různých LPBF strojích s dobrou hustotou a povrchovou úpravou. To vede ke spolehlivé a opakovatelné výrobě.
- Dobrá pevnost a tvrdost: Nabízí dobré mechanické vlastnosti vhodné pro mnoho konstrukčních aplikací, zejména po vhodném tepelném zpracování (např. stav T6). Nedosahuje sice úrovně slitiny Scalmalloy®, ale její pevnost je dostatečná pro středně zatížené součásti.
- Dobré tepelné vlastnosti: Má dobrou tepelnou vodivost, takže je vhodný pro aplikace, kde je důležitý odvod tepla (např. žebra integrovaná s výměníky tepla nebo v blízkosti elektroniky).
- Cenově výhodné a široce dostupné: Prášek AlSi10Mg je podstatně levnější než slitina Scalmalloy® a nabízí jej řada dodavatelů prášků a poskytovatelů služeb AM.
- Dobře pochopeno: Pro AlSi10Mg jsou k dispozici rozsáhlé výzkumné a aplikační údaje, které poskytují vysoký stupeň důvěry v jeho výkonnostní charakteristiky.
- Ideální aplikace:
- Konstrukční součásti pro všeobecné použití, u nichž je vedle snížení hmotnosti hlavním faktorem cena.
- Prototypy a komponenty vyžadující rychlé opakování.
- Konstrukce s integrovanými prvky tepelného managementu.
- Komponenty, u nichž není absolutně maximální poměr pevnosti a hmotnosti primárním požadavkem, ale je třeba dobrých celkových vlastností.
- Nahrazuje tradiční hliníkové odlitky.
- Úvahy:
- Nižší pevnost a životnost při únavě: Jeho mez pevnosti v tahu, mez kluzu a zejména únavová pevnost jsou nižší než u slitiny Scalmalloy®. To omezuje jeho použití ve vysoce namáhaných nebo únavově kritických aplikacích ve srovnání s jeho vysoce výkonným protějškem.
- Tažnost: Může vykazovat nižší tažnost ve srovnání se slitinou Scalmalloy®, zejména ve stavu po dokončení stavby.
Srovnání materiálů:
Vlastnictví | Scalmalloy® (tepelně zpracovaná) | AlSi10Mg (tepelně zpracovaný - typicky T6) | Jednotky | Poznámky |
---|---|---|---|---|
Hustota | ~2.67 | ~2.67 | g/cm³ | Obě jsou si velmi podobné a nabízejí přirozené výhody nízké hmotnosti. |
Pevnost v tahu (UTS) | > 520 | ~300 – 350 | MPa | Scalmalloy® výrazně silnější. |
Mez kluzu (YS) | > 480 | ~230 – 280 | MPa | Scalmalloy® výrazně silnější. |
Prodloužení po přetržení | > 12 | ~6 – 10 | % | Slitina Scalmalloy® má obecně lepší tažnost. |
Únavová pevnost | Výrazně vyšší | Mírný | (Relativní) | Zásadní výhoda slitiny Scalmalloy® v aplikacích s cyklickým zatížením. |
Možnost tisku | Dobrý | Vynikající | (Relativní) | AlSi10Mg je obecně považován za materiál, který lze spolehlivě vytisknout. |
Relativní náklady | Vysoký | Nízká - mírná | (Relativní) | Prášek Scalmalloy® je výrazně dražší. |
Klíčová výhoda | Nejvyšší poměr pevnosti k hmotnosti, únavová životnost | Nákladová efektivita, tisknutelnost, termální tisk | Vyberte si podle primárních požadavků na aplikaci. |
Export do archů
Důležitost kvality prášku:
Bez ohledu na zvolenou slitinu je pro dosažení požadovaných mechanických vlastností a integrity dílů, zejména v leteckém průmyslu, nejdůležitější kvalita kovového prášku použitého v procesu AM. Vlastnosti prášku, jako např:
- Sféricita: Ovlivňuje sypnost prášku a hustotu balení ve stavební komoře.
- Distribuce velikosti částic (PSD): Ovlivňuje dynamiku taveniny a konečné rozlišení dílu/povrchovou úpravu.
- Čistota a nízký obsah kyslíku: Kontaminanty a nadměrné množství kyslíku mohou vést k pórovitosti a křehnutí, což zhoršuje mechanické vlastnosti.
- Tekutost: Zajišťuje rovnoměrné nanášení prášku na celou konstrukční desku.
Zde je partnerství se společností, jako je Met3dp, výraznou výhodou. Společnost Met3dp využívá špičkové technologie výroby prášků, včetně. pokročilý proces atomizace plynu a plazmové rotační elektrody (PREP) systémy. Tyto metody jsou speciálně navrženy pro výrobu vysoce sférických kovových prášků s kontrolovanou velikostí částic, vynikající tekutostí a vysokou čistotou, což jsou základní vlastnosti pro tisk hustých, vysoce kvalitních kovových dílů s vynikajícími a opakovatelnými mechanickými vlastnostmi, které jsou požadovány v leteckém a kosmickém průmyslu. Jejich odborné znalosti přesahují rámec běžných slitin a zahrnují inovativní materiály, jako je TiNi, TiTa a superslitiny, což je důkazem hlubokého porozumění práškové metalurgii. Při získávání služeb AM je zásadní informovat se o postupech poskytovatele v oblasti získávání prášků, kontroly kvality a manipulace s nimi. Závazek společnosti Met3dp poskytovat vysoce kvalitní kovové prášky zajišťuje pevný základ pro výrobu spolehlivých, vysoce výkonných leteckých komponentů, jako jsou žebrové konstrukce.
Volba mezi slitinou Scalmalloy® a AlSi10Mg závisí do značné míry na konkrétních požadavcích na konstrukci žeber - na vyvážení potřeby maximální výkonnosti a úspory hmotnosti s rozpočtovými omezeními a výrobními hledisky.
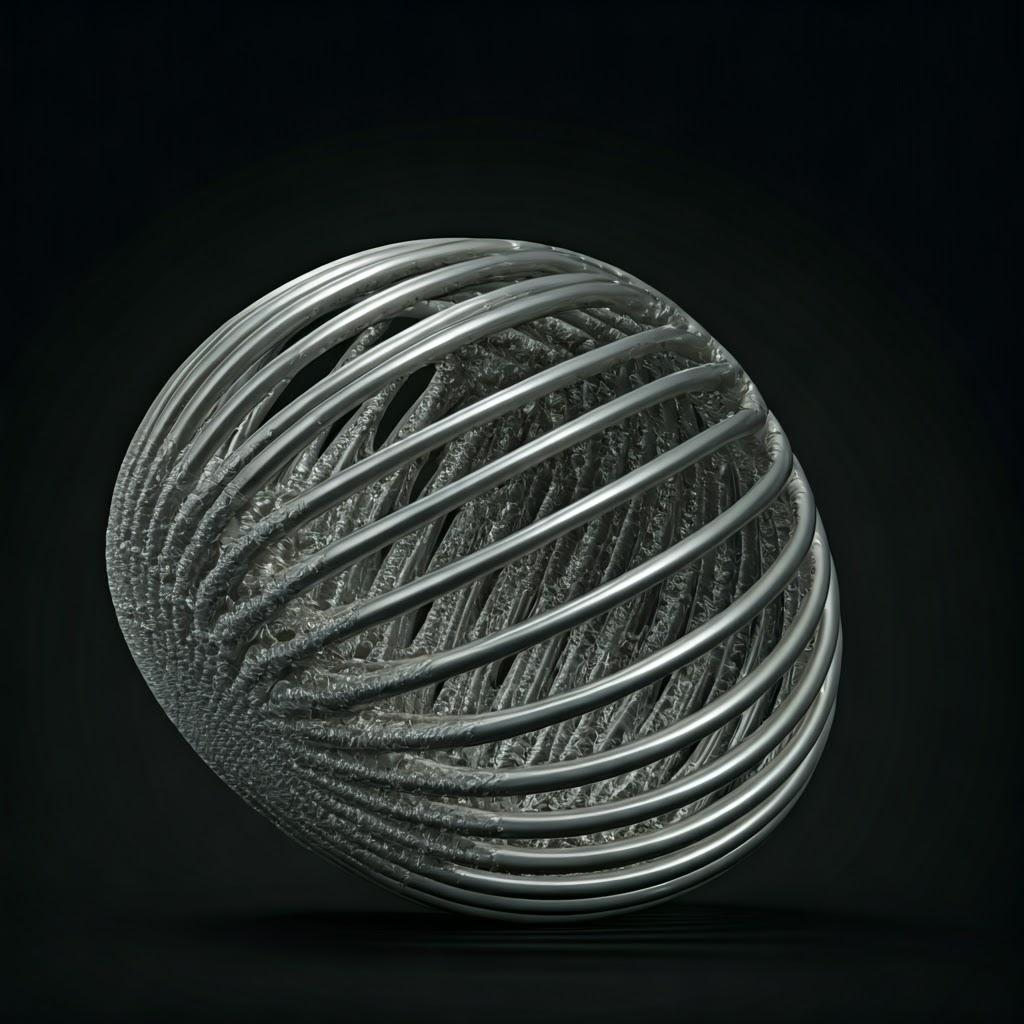
Design pro aditivní výrobu (DfAM): Optimalizace struktury žeber pro úspěšný tisk
Pouhým převzetím žebrové konstrukce určené pro CNC obrábění a jejím odesláním na kovovou 3D tiskárnu se málokdy dosáhne optimálního výsledku, ať už z hlediska výkonu nebo nákladové efektivity. Aby inženýři skutečně využili potenciál aditivní výroby pro letecké komponenty, musejí se chopit Design pro aditivní výrobu (DfAM). Jde o víc než jen o soubor pravidel, ale o zásadní změnu myšlení, která se odklání od omezení subtraktivních metod a využívá jedinečných možností výroby po vrstvách. U leteckých žeber se DfAM zaměřuje na maximalizaci strukturální účinnosti (poměr pevnosti a hmotnosti), integraci funkcí a zajištění vyrobitelnosti a snadného následného zpracování.
Zde jsou uvedeny klíčové zásady DfAM, které jsou zásadní pro navrhování efektivních 3D tištěných žeber pro letecký průmysl:
- Využití optimalizace topologie a generativního návrhu: Jak již bylo uvedeno dříve, tyto výpočetní nástroje jsou základem pro odlehčování pomocí AM.
- Optimalizace topologie: Vychází z definovaného návrhového prostoru a zatěžovacích podmínek a poté algoritmicky odstraňuje materiál z oblastí s nízkým namáháním, čímž odhalí nejefektivnější cestu zatížení. Výsledkem jsou často organické, volně tvarované tvary optimalizované výhradně pro mechanické vlastnosti. Inženýři musí pečlivě definovat zatěžovací stavy, omezení (zóny s ochranou proti zatížení, výrobní omezení, jako je minimální tloušťka) a optimalizační cíle (např. maximalizovat tuhost, minimalizovat hmotnost).
- Generativní design: Často zkoumá širší škálu řešení generováním více alternativních návrhů na základě funkčních požadavků, výběru materiálů a výrobních omezení (včetně AM). To může konstruktérům poskytnout nové koncepty návrhu, které by je jinak nenapadly.
- Výsledek: Tyto nástroje umožňují vytvářet žebrové konstrukce, které jsou výrazně lehčí než jejich tradičně navržené protějšky při zachování nebo dokonce překročení požadavků na výkon.
- Začlenění mřížových struktur: AM umožňuje navrhovat díly se složitou vnitřní strukturou, například mřížky.
- Typy: Ty mohou sahat od rovnoměrných mříží založených na vzpěrách (např. oktetový příhradový nosník) až po složitější, matematicky definované struktury, jako jsou trojnásobně periodické minimální plochy (TPMS) (např. Gyroid).
- Výhody: Mřížky nabízejí mimořádně vysokou tuhost a pevnost v poměru ke své hustotě, což umožňuje další snížení hmotnosti nad rámec toho, čeho lze dosáhnout optimalizací topologie pevných látek. Mohou být také navrženy pro specifické vlastnosti absorpce energie nebo pro usnadnění přenosu tepla, pokud jsou integrovány s funkcemi tepelného managementu. Mřížky s proměnlivou hustotou umožňují konstruktérům přizpůsobit tuhost lokálně v rámci žebra.
- Úvahy: Návrh efektivních mřížek vyžaduje specializované softwarové moduly. Zajištění odstranění prášku ze složitých vnitřních mřížek je kritické a musí být plánováno (vyžaduje únikové otvory). Požadavky na podporu v rámci mřížové struktury je také třeba zvážit.
- Dodržování minimálních rozměrů a tloušťky prvků: Procesy AM mají omezení týkající se nejmenších prvků, které mohou spolehlivě vyrábět.
- Tloušťka stěny: Existuje minimální tloušťka potisknutelné stěny (obvykle 0,3 mm - 1,0 mm v závislosti na stroji, materiálu a orientaci), pod kterou se prvky nemusí správně vytvarovat nebo se mohou nadměrně deformovat. Konstrukce žeber musí tyto limity respektovat.
- Otvory a kanály: Malé otvory (zejména vodorovné) mohou vyžadovat specifické úpravy konstrukce nebo podporu. Minimální průměr často souvisí s možnostmi tloušťky stěny. Únikové otvory (obvykle o průměru > 3-5 mm) jsou nezbytné pro odstranění nesetřeného prášku z vnitřních dutin a mřížkových struktur.
- Nepodporované funkce: Převislé prvky vyžadují podpůrné konstrukce nad určitým úhlem (obvykle se za samonosné považuje úhel > 45 stupňů od svislice, ale tento úhel se liší). Navrhování žeber se zkosenými hranami nebo filety namísto ostrých vodorovných převisů může výrazně snížit potřebu podpěr. Je také třeba zvážit maximální nepodepřené délky mostů.
- Plánování strategické podpůrné struktury: Podpěrné konstrukce jsou v kovovém AM často nezbytné, zejména u složitých geometrií, jako jsou optimalizovaná žebra s převisy. Slouží k několika účelům: ukotvení dílu ke stavební desce, zabránění deformaci v důsledku tepelného namáhání, podepření převislých prvků a odvádění tepla z oblasti taveniny.
- Cíl DfAM: Minimalizujte potřebujete pro podpěry a konstrukci pro snadná demontáž.
- Techniky:
- Orientace: Prvním krokem je výběr optimální orientace stavby. To zahrnuje vyvážení požadavků na povrchovou úpravu, minimalizaci úhlů převisu, řízení zbytkového napětí a zohlednění anizotropie mechanických vlastností. Simulační nástroje mohou pomoci předpovědět napětí a deformace pro různé orientace.
- Navrhování pro vlastní podporu: Použití zkosení (např. úhel 45 stupňů) nebo tvaru slzy u vodorovných otvorů může eliminovat potřebu vnitřních podpěr.
- Přístupnost: Zajištění fyzického přístupu k podpůrným konstrukcím, zejména vnitřním, pro nástroje na odstraňování (ruční nebo automatizované).
- Typ podpory: Využití pokročilého softwaru pro generování podpěr umožňuje vytvářet různé typy podpěr (plný blok, tenké pásy/lamely, stromové/kostkové podpěry), které lze snáze odstranit a minimalizovat kontaktní body ("svědecké stopy") na povrchu finálního dílu. Perforované nebo fragmentované podpěry mohou rovněž usnadnit odstraňování.
- Zohlednění anizotropie: Vzhledem k procesu vytváření po vrstvách a směrovému toku tepla mohou kovové díly AM vykazovat anizotropní mechanické vlastnosti, což znamená, že jejich pevnost a tažnost se může lišit v závislosti na směru zatížení vzhledem ke směru vytváření (X, Y vs. Z).
- Úvaha: Konstruktéři si musí být vědomi této potenciální anizotropie (zejména z hlediska únavové životnosti) a musí ji zohlednit ve fázi návrhu a výběru orientace. Kritické dráhy zatížení by měly být v ideálním případě vyrovnány se směrem optimálních vlastností materiálu (často rovnoběžně se stavební deskou v rovině X-Y). V materiálových listech renomovaných dodavatelů jsou často uvedeny vlastnosti v různých orientacích.
- Navrhování pro následné zpracování: V případě leteckých aplikací je hotový díl AM zřídkakdy konečným produktem. DfAM musí zohlednit navazující procesy.
- Přídavky na obrábění: Pokud povrchy vyžadují přísné tolerance, specifickou povrchovou úpravu nebo kritickou geometrii rozhraní (např. montážní otvory, styčné plochy), je třeba k těmto prvkům v modelu CAD přidat další materiál ("obráběcí materiál" nebo "odsazení") (obvykle 0,5 mm - 2,0 mm).
- Upevnění: Zvažte, jakým způsobem bude složitý díl AM uložen (upevněn) pro následné obrábění nebo kontrolu. Výhodné může být přidání dočasných lokalizačních prvků nebo datových prvků, které se později odstraní.
- Tepelné zpracování: Ujistěte se, že konstrukce vydrží tepelné cykly odlehčování a tepelného zpracování bez nadměrné deformace.
Efektivní DfAM vyžaduje spolupráci mezi konstruktéry a specialisty na AM. Spolupráce s poskytovatelem služeb, jako je Met3dp, který má hluboké odborné znalosti v oblasti AM procesů (včetně SEBM a LPBF) a materiálů, zajišťuje, že návrhy jsou nejen inovativní, ale také vyrobitelné, nákladově efektivní a splňují přísné požadavky leteckých aplikací.
Dosažitelná tolerance, povrchová úprava a rozměrová přesnost u kovových žeber AM
Inženýři a manažeři nákupu, kteří jsou zvyklí na vysokou přesnost CNC obrábění, musí pochopit typické možnosti a omezení aditivní výroby kovů, pokud jde o rozměrovou přesnost, tolerance a povrchovou úpravu. Ačkoli lze pomocí AM obrábění kovů vyrábět velmi složité díly, dosažení extrémně přísných tolerancí, které se často vyskytují na výkresech pro letecký průmysl, obvykle vyžaduje kroky následného zpracování. Pro efektivní plánování projektu a odhad nákladů je zásadní stanovit realistická očekávání pro stav po dokončení.
Rozměrová přesnost a tolerance:
- Typické tolerance podle konstrukce: Pro většinu průmyslových systémů laserového tavení v práškovém loži (LPBF) a selektivního tavení elektronovým svazkem (SEBM) jsou typické dosažitelné tolerance pro dobře navržené a správně zpracované díly v rozmezí:
- +/- 0,1 mm až +/- 0,2 mm pro menší rozměry (např. do 50-100 mm).
- +/- 0,1% až +/- 0,2% jmenovitého rozměru pro větší prvky.
- Tyto hodnoty mohou často odpovídat obecným tolerančním normám, jako je ISO 2768-m (střední) nebo někdy ISO 2768-f (jemná) pro určité prvky, ale bez specifické validace to není zaručeno pro celou geometrii dílu.
- Faktory ovlivňující přesnost: Dosažení konzistentní rozměrové přesnosti závisí na mnoha faktorech:
- Tepelné účinky: Opakované cykly zahřívání a ochlazování, které jsou pro AM typické, způsobují roztahování a smršťování, což vede k vnitřním pnutím, možnému smršťování a deformacím, zejména u velkých nebo složitých geometrií, jako jsou žebra. Pokročilá simulace procesu může pomoci předvídat a kompenzovat některé deformace.
- Kalibrace stroje: Pravidelná a přesná kalibrace skenerů tiskárny, zdroje energie a systému nanášení prášku je velmi důležitá.
- Parametry procesu: Výkon laserového/elektronového paprsku, rychlost skenování, tloušťka vrstvy a strategie šrafování významně ovlivňují stabilitu taveniny a výslednou přesnost dílů. Optimalizované parametry vyvinuté zkušenými poskytovateli jsou nezbytné.
- Kvalita prášku: Konzistentní vlastnosti prášku (PSD, morfologie, tekutost) zajišťují rovnoměrné tání a tuhnutí.
- Geometrie a orientace dílů: Složité tvary s velkými převisy nebo různými průřezy jsou náchylnější k deformaci. Orientace konstrukce ovlivňuje tepelný průběh a akumulaci napětí.
- Podpůrné struktury: Vhodně navržené podpěry pomáhají ukotvit díl a řídit tepelné namáhání, čímž se zlepšuje rozměrová stabilita během sestavování.
- Dosažení přísnějších tolerancí: Pro prvky vyžadující tolerance přísnější, než je obecná schopnost procesu AM (např. kritická montážní rozhraní, otvory ložisek, přesné zarovnávací prvky na žebru), následné CNC obrábění je obvykle vyžadováno. To zahrnuje obrábění specifických povrchů sestaveného dílu AM, aby se dosáhlo potřebné přesnosti. Zásady DfAM vyžadují přidání obráběcího materiálu k těmto prvkům v původním návrhu.
Povrchová úprava (drsnost):
- Drsnost povrchu (Ra) podle stavu: Povrchová úprava kovových dílů vyrobených metodou AM je ze své podstaty drsnější než povrch obrobený. Typické hodnoty Ra se mohou výrazně lišit:
- Vrchní plochy: Obecně hladší (Ra 5 - 15 µm).
- Svislé stěny (osa Z): Mírná drsnost, ovlivněná tloušťkou vrstvy a přilnavostí částic (Ra 8 - 20 µm).
- Úhlové plochy směřující nahoru/dolů: Vykazují charakteristické "schodovité uspořádání" v důsledku vrstevnatého procesu výstavby. Povrchy směřující dolů a podepřené konstrukcemi jsou typicky drsnější kvůli kontaktním místům podpěr (Ra 15 - 30 µm nebo vyšší).
- Faktory ovlivňující povrchovou úpravu:
- Tloušťka vrstvy: Tenčí vrstvy obecně vytvářejí hladší povrchy, ale prodlužují dobu výstavby.
- Velikost částic prášku: Jemnější prášky mohou vést k lepší povrchové úpravě, ale mohou představovat problém z hlediska tekutosti nebo vyžadovat jiné procesní parametry.
- Energetický vstup a strategie skenování: ovlivňují dynamiku taveniny a povrchové tuhnutí.
- Orientace: U strmě skloněných povrchů se projeví výraznější schodovitost než u povrchů postavených rovnoběžně nebo kolmo k základní desce.
- Zlepšení povrchové úpravy: Pokud je drsnost ve výchozím stavu nepřijatelná z funkčních (např. průtok kapalin, únava) nebo estetických důvodů, lze použít různé metody následného zpracování:
- Tryskání kuličkami / pískování: Vytváří rovnoměrný, matný povrch, odstraňuje částečně roztavené částice a může mírně zlepšit Ra (např. na Ra 5-10 µm).
- Obrábění / vibrační úprava: Používá brusná média k vyhlazení povrchů a hran, zvláště účinná pro dávky menších dílů.
- CNC obrábění: Zajišťuje nejlepší možnou povrchovou úpravu specifických prvků.
- Leštění (ruční nebo automatické): V případě potřeby lze dosáhnout velmi hladkého, zrcadlového povrchu, ale je to často pracné.
- Elektrolytické leštění / chemické leštění: Dokáže vyhladit složité povrchy, ale nemusí být vhodný pro všechny geometrie nebo slitiny.
Metrologie a ověřování:
Vzhledem ke geometrické složitosti, kterou AM často umožňuje, a kritické povaze leteckých komponent je robustní metrologie nezbytná.
- Techniky: Souřadnicové měřicí stroje (CMM) se používají k přesnému měření rozměrů kritických prvků. Bezkontaktní metody, jako je 3D laserové skenování nebo skenování strukturovaným světlem, jsou neocenitelné pro porovnání geometrie celého vytištěného dílu s původním modelem CAD, identifikaci odchylek a ověření složitých povrchů.
- Důležitost: Ověřování zajišťuje, že konečná konstrukce žebra splňuje všechny specifikace návrhu z hlediska uložení, tvaru a funkce. Tyto údaje mají zásadní význam pro dokumentaci zajištění kvality vyžadovanou leteckými normami.
Společnosti jako Met3dp chápou význam přesnosti v letectví a kosmonautice. Zaměřují se na špičkovou přesnost a spolehlivost ve svém oboru. tiskových metod v kombinaci s přísnou kontrolou kvality zajišťuje, že díly splňují náročné specifikace, ať už ve stavu po sestavení, nebo po nezbytném následném zpracování. Jasná komunikace mezi konstrukčním týmem a poskytovatelem služeb AM ohledně kritických rozměrů, tolerancí a požadavků na povrchovou úpravu je od počátku prvořadá.
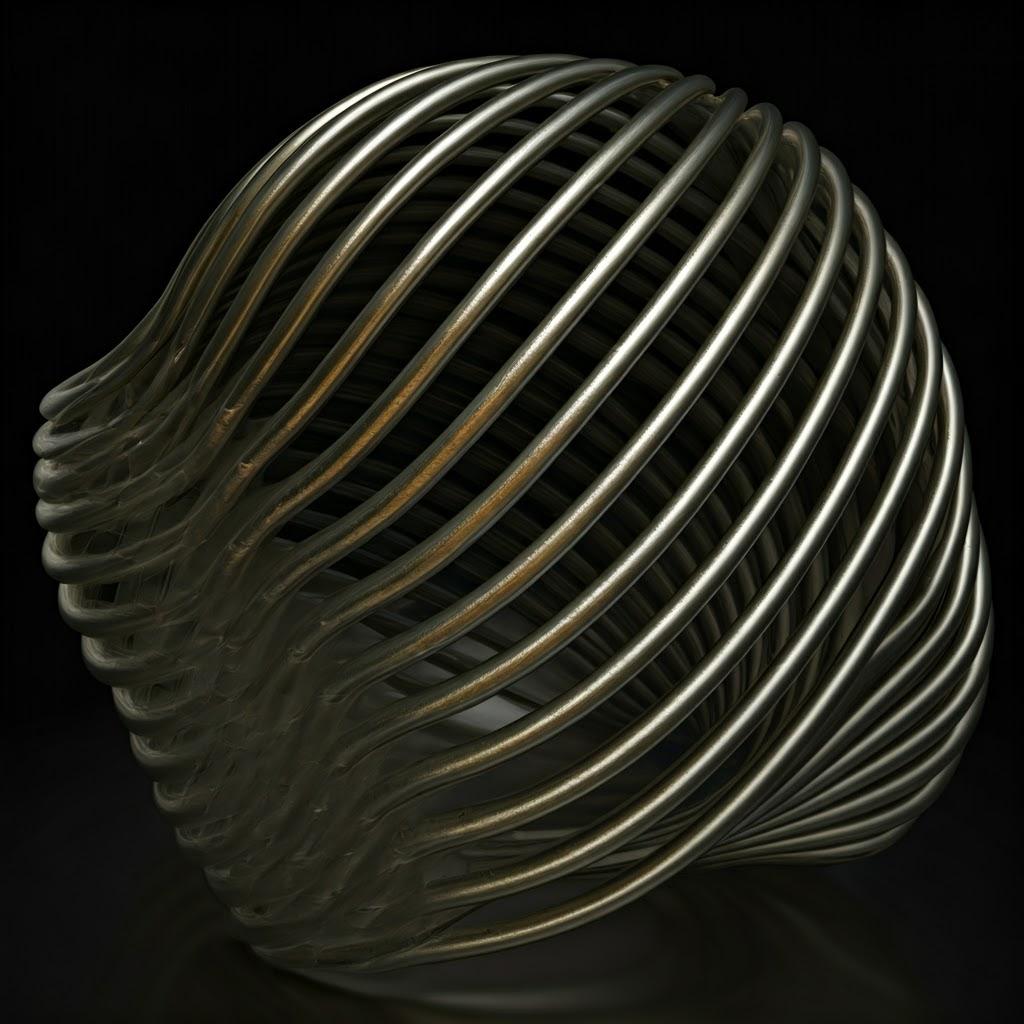
Základní kroky následného zpracování žebrových konstrukcí pro letectví a kosmonautiku
Získání hotové letecké žebrové konstrukce připravené k letu zahrnuje mnohem více než jen samotný proces aditivní výroby. Kroky následného zpracování jsou rozhodující pro uvolnění vnitřních pnutí, dosažení požadovaných vlastností materiálu, odstranění podpůrných struktur, dosažení požadovaných tolerancí a povrchových úprav a ověření integrity součásti. Tyto kroky jsou často povinné pro splnění přísných požadavků na certifikaci v leteckém průmyslu a zajištění bezpečnosti a spolehlivosti finálního dílu.
Zde je přehled základních postupů následného zpracování, které se obvykle používají u kovových žeber AM pro letecký průmysl:
- Úleva od stresu:
- Účel: Rychlé cykly zahřívání a ochlazování během procesu PBF vyvolávají v tištěném dílu značná zbytková napětí. Tato napětí mohou způsobit deformaci (zejména po vyjmutí z konstrukční desky) a negativně ovlivnit mechanické vlastnosti, zejména únavovou životnost. Odlehčení napětí je tepelný cyklus určený ke snížení těchto vnitřních napětí, aniž by se výrazně změnila mikrostruktura.
- Proces: Obvykle se provádí, dokud je díl ještě připevněn na konstrukční desce (někdy se však provádí i po vyjmutí), a zahrnuje zahřátí dílu na určitou teplotu nižší, než je teplota stárnutí nebo rozpouštění, jeho udržení po určitou dobu a následné pomalé ochlazení. To se obvykle provádí ve vakuu nebo v peci s inertní atmosférou (např. argonovou), aby se zabránilo oxidaci.
- Důležitost: Považuje se za povinný první krok pro většinu kritických kovových dílů AM, aby byla zajištěna rozměrová stabilita a předvídatelný výkon.
- Odstranění ze stavební desky:
- Proces: Po dokončení uvolnění napětí a ochlazení dílu je třeba jej oddělit od konstrukční desky. To se běžně provádí pomocí elektroerozivního obrábění, pásového řezání nebo někdy CNC obrábění.
- Úvahy: Při demontáži je třeba dbát na to, aby nedošlo k poškození dílu. Zvolená metoda závisí na geometrii dílu, materiálu a požadované přesnosti základního povrchu.
- Tepelné zpracování (žíhání v roztoku, stárnutí atd.):
- Účel: Dosažení konečné požadované mikrostruktury a mechanických vlastností (pevnost, tvrdost, tažnost) pro zvolenou slitinu. U hliníkových slitin, jako jsou Scalmalloy® a AlSi10Mg, to často zahrnuje úpravu roztokem s následným umělým stárnutím (precipitační kalení), běžně označovanou jako T6 nebo podobný temperační stav.
- Proces: Zahříváním dílu na vyšší teplotu (teplota rozpuštění) se prvky slitiny rozpustí do pevného roztoku, ochlazením (rychlým ochlazením) se tato struktura uzamkne a následným stárnutím (opětovným zahřátím na nižší teplotu po určitou dobu) se ve struktuře zrna vysráží jemné kalitelné částice. Tyto cykly jsou přesně definovány pro každou slitinu a požadovaný temperační stupeň. I v tomto případě jsou rozhodující pece s řízenou atmosférou.
- Důležitost: Je naprosto zásadní pro rozvinutí plného pevnostního potenciálu tepelně zpracovatelných slitin, jako jsou Scalmalloy® a AlSi10Mg, a zajišťuje, že žebro splňuje své konstrukční výkonnostní cíle.
- Izostatické lisování za tepla (HIP):
- Účel: K odstranění vnitřní mikroporozity, která může být přítomna i v dobře zpracovaných dílech AM. Pórovitost působí jako koncentrátor napětí a může výrazně snížit únavovou životnost a lomovou houževnatost.
- Proces: Zahrnuje vystavení součásti vysoké teplotě (pod bodem tání) a vysokému izostatickému tlaku (obvykle 100-200 MPa) za použití inertního plynu (např. argonu) ve specializované nádobě HIP. Kombinace tepla a tlaku způsobí kolaps vnitřních dutin a uzavření difuzní vazby.
- Důležitost: Často je předepsána leteckými normami (např. pro komponenty třídy A / kritické pro let), protože výrazně zvyšuje únavovou pevnost, tažnost a celkovou integritu materiálu, což vede ke spolehlivějším a předvídatelnějším dílům. Zvyšuje náklady, ale u náročných aplikací je často neoddiskutovatelným krokem.
- Odstranění podpůrné konstrukce:
- Účel: Odstranění dočasných podpůrných konstrukcí použitých při stavbě.
- Proces: Může jít o jeden z nejpracnějších kroků, zejména u složitých geometrií žeber s vnitřními podpěrami. Mezi tyto metody patří:
- Ruční odstranění: Lámání nebo odřezávání snadno přístupných podpěr.
- CNC obrábění: Frézování nebo broušení podpěrných konstrukcí, často používané u blokových podpěr nebo k dosažení čisté povrchové úpravy na rozhraní podpěr.
- Drátové elektroerozivní obrábění / ponorné elektroerozivní obrábění: Používá se pro přesné odstranění nebo na těžko přístupných místech.
- Úvahy: Vyžaduje pečlivé provedení, aby nedošlo k poškození povrchu dílu. Velkou roli zde hraje DfAM - klíčový je návrh přístupnosti podpory. Svědecké stopy (malé vady v místech, kde byly připevněny podpěry) mohou vyžadovat další úpravu.
- Povrchová úprava a obrábění:
- Účel: Dosažení požadované konečné drsnosti povrchu, rozměrových tolerancí kritických prvků a kosmetického vzhledu.
- Procesy (podle potřeby):
- CNC obrábění: Je nezbytný pro vytvoření přesných styčných ploch, otvorů pro ložiska, montážních otvorů a dosažení těsných tolerancí uvedených na výkresu, které přesahují možnosti AM.
- Tryskání kuličkami / kuličkování: Poskytuje rovnoměrný matný povrch, čistí povrchy a kuličkování vyvolává příznivé tlakové namáhání, které zvyšuje únavovou životnost.
- Tumbling / leštění: Pro všeobecné vyhlazení povrchu nebo specifické aerodynamické/estetické požadavky.
- Odstraňování otřepů: Odstranění všech ostrých hran nebo otřepů vzniklých při obrábění nebo odstraňování podpěr.
- Nedestruktivní zkoušení (NDT) a inspekce:
- Účel: Ověřit vnitřní a vnější celistvost hotové konstrukce žebra, aniž by došlo k jejímu poškození, a zajistit, aby neobsahovala kritické vady a splňovala všechny rozměrové specifikace.
- Běžné metody NDT pro letecké díly AM:
- Počítačová tomografie (CT): Metoda založená na rentgenovém záření, která umožňuje detailní 3D vizualizaci vnitřních struktur, je vysoce účinná pro detekci pórovitosti, inkluzí, trhlin a provádění vnitřní rozměrové analýzy. Stále častěji se používá u kritických dílů AM.
- Ultrazvukové testování (UT): Využívá zvukové vlny k detekci vnitřních vad.
- Dye Penetrant Inspection (DPI) / Liquid Penetrant Inspection (LPI): Detekuje trhliny porušující povrch.
- Radiografické testování (RT): Tradiční rentgenové zobrazování.
- Rozměrová kontrola: Použití souřadnicových měřicích strojů a 3D skenerů k ověření všech kritických rozměrů a celkové geometrie podle specifikací návrhu.
- Důležitost: Konečná kontrola kvality před certifikací součásti pro použití. Povinné pro zajištění bezpečnosti letu.
Úspěšné zvládnutí tohoto složitého řetězce následného zpracování vyžaduje značné odborné znalosti a specializované vybavení. Výrobci letecké techniky a specialisté na veřejné zakázky by měly usilovat o poskytovatelé služeb v oblasti AM kovů kteří nabízejí komplexní, integrovaná řešení, ať už vlastní, nebo prostřednictvím kvalifikovaných partnerů, pokrývající celý pracovní postup od tisku až po konečnou kontrolu a zajišťující sledovatelnost a kontrolu kvality v každé fázi.
Běžné problémy při 3D tisku žeber v letectví a strategie jejich řešení
Přestože aditivní výroba kovů nabízí transformační potenciál pro letecké žebrové konstrukce, realizace těchto výhod vyžaduje překonání několika neodmyslitelných problémů. Pochopení těchto potenciálních překážek a zavedení účinných strategií pro jejich zmírnění je pro úspěšné zavedení zásadní, zejména pro inženýry, kteří navrhují díly, a manažery nákupu, kteří vybírají. AM kontrola kvality letectví a kosmonautiky partnery.
Zde jsou uvedeny některé běžné problémy, se kterými se setkáváme při 3D tisku složitých leteckých žeber:
- Zbytkové napětí a deformace:
- Výzva: Intenzivní, lokalizovaný ohřev a rychlé ochlazení během procesu PBF vytváří uvnitř dílu značné teplotní gradienty. To vede k rozdílné roztažnosti a smršťování, což má za následek vznik zbytkových napětí. Pokud tato napětí překročí mez kluzu materiálu, mohou způsobit deformaci (pokřivení) během sestavování, po vyjmutí ze sestavovací desky nebo dokonce během následného zpracování. Zvláště náchylné mohou být složité geometrie žeber s různou tloušťkou a velké ploché úseky.
- Strategie zmírnění dopadů:
- Simulace procesu: Použití softwaru pro tepelnou simulaci ve fázi návrhu k předpovědi oblastí koncentrace napětí a možného narušení na základě geometrie a navrhované orientace.
- Optimalizovaná orientace: Výběr takové orientace sestavení, která minimalizuje velké průřezy rovnoběžné se sestavovací deskou a snižuje tepelné gradienty.
- Robustní podpůrné struktury: Navrhování účinných podpěr, které díl nejen ukotví, ale také fungují jako chladiče a rovnoměrněji odvádějí teplo.
- Optimalizované strategie skenování: Použití specifických vzorů skenování laserem/paprskem (např. skenování ostrůvků, šrafování sektorů), které jsou navrženy tak, aby rovnoměrněji rozváděly teplo a snižovaly vznik napětí.
- Okamžitá úleva od stresu: Rozhodující je provedení cyklu tepelného zpracování bezprostředně po sestavení, ideálně před vyjmutím dílu ze sestavovací desky.
- Odstranění podpůrné konstrukce Obtížnost:
- Výzva: Topologicky optimalizovaná žebra se často vyznačují složitými převisy a vnitřními dutinami, které vyžadují rozsáhlé podpůrné konstrukce. Odstranění těchto podpěr, zejména z vnitřních nebo obtížně přístupných oblastí, může být velmi náročné, časově náročné a nákladné. Nesprávné odstranění může také poškodit povrch dílu.
- Strategie zmírnění dopadů:
- DfAM Focus: Nejdůležitější je navrhnout konstrukci s ohledem na minimalizaci podpěr (použití samonosných úhlů, pokud možno zamezení vnitřních převisů) a snadný přístup. Navrhněte prvky, které umožní nástrojům nebo rukám dosáhnout na vnitřní podpěry.
- Pokročilý podpůrný software: Využití softwaru, který generuje snadno odstranitelné typy podpěr (např. tenké pásy, kuželové/stromové podpěry s malými kontaktními body, perforované konstrukce).
- Vhodné techniky odstraňování: Výběr správné metody (ruční obrábění, CNC obrábění, elektroerozivní obrábění drátem nebo dřezem) podle typu podpěry, umístění a materiálu.
- Orientace na stavbu: Orientace dílu tak, aby se minimalizoval objem a složitost potřebných podpěr.
- Kontrola pórovitosti:
- Výzva: Dosažení plné hustoty (>99,5% nebo často >99,9% pro letecký průmysl) je kritické. Vnitřní póry (pórovitost plynů ze zachycených argonových/prachových nečistot nebo pórovitost klíčových otvorů z nestabilních bazénů taveniny) působí jako defekty a výrazně zhoršují mechanické vlastnosti, zejména únavovou pevnost.
- Strategie zmírnění dopadů:
- Vysoce kvalitní prášek: Použití prášku s kontrolovanou sféricitou, PSD, nízkým obsahem vnitřního plynu a přísnými manipulačními postupy, aby se zabránilo absorpci vlhkosti a kontaminaci. To zdůrazňuje význam poskytovatelů, jako je Met3dp, s pokročilými možnostmi výroby prášků (Další informace o Met3dp).
- Optimalizované parametry procesu: Důkladný vývoj a validace parametrů tisku (výkon laseru/ paprsku, rychlost, zaostření, tloušťka vrstvy, řízení atmosféry) specifických pro materiál a stroj, aby bylo zajištěno stabilní tavení.
- Monitorování procesů: Využití nástrojů pro monitorování in-situ (např. monitorování taveniny) k odhalení potenciálních nestabilit během stavby.
- Izostatické lisování za tepla (HIP): Jak již bylo uvedeno, HIP je vysoce účinný při uzavírání zbytkové mikroporozity a je často povinný pro kritické letecké díly, aby byla zaručena hustota a zvýšena únavová odolnost.
- Dosažení konzistentních mechanických vlastností:
- Výzva: Zajištění konzistentního dosažení stanovených mechanických vlastností (pevnost, tažnost, únavová životnost) v celé složité žebrové konstrukci a jejich opakovatelnost při jednotlivých konstrukcích. Odchylky mohou vznikat v důsledku drobných nesrovnalostí v prášku, kalibraci stroje nebo parametrech procesu. Svou roli hraje také anizotropie.
- Strategie zmírnění dopadů:
- Přísná správa prášku: Důsledná kontrola kvality vstupujícího prášku, definované strategie recyklace prášku (omezení cyklů opakovaného použití, pravidelné testování) a správné skladování/manipulace.
- Robustní kalibrace a údržba stroje: Pravidelná preventivní údržba a kalibrace systémů AM.
- Standardizované procesy: Zavedení a dodržování kvalifikovaných, standardizovaných postupů tisku a následného zpracování (včetně tepelného zpracování a HIP).
- Monitorování procesů a zajištění kvality: Využití údajů z monitorování procesu a zavedení přísných protokolů pro zajištění kvality, včetně zkušebních vzorků (zkušebních vzorků vyrobených společně s dílem) pro destruktivní zkoušky k ověření vlastností šarže.
- Porozumění anizotropii: Charakterizace vlastností materiálu v různých orientacích stavby a zohlednění této skutečnosti při návrhu a kvalifikaci.
- Omezení povrchové úpravy:
- Výzva: Povrchová úprava dílů AM nemusí ve stavu po výrobě splňovat požadavky na některé aerodynamické povrchy nebo oblasti kritické z hlediska únavy. Dosažení velmi hladkých povrchů vyžaduje dodatečné úsilí a náklady na následné zpracování. Důležité je řídit očekávání týkající se hotových povrchů v porovnání s povrchy po sestavení.
- Strategie zmírnění dopadů:
- Optimalizace orientace: Orientace kritických povrchů vertikálně nebo horizontálně, pokud je to možné, aby se dosáhlo co nejlepší původní povrchové úpravy.
- Optimalizované parametry: Jemné doladění parametrů obrysu může někdy zlepšit povrchovou úpravu bočnic.
- Cílené následné zpracování: Použití vhodných dokončovacích metod (tryskání, obrábění, leštění) speciálně na povrchy, kde je požadována lepší povrchová úprava, nikoli na celý díl.
- Čirá specifikace: Jasné definování požadavků na povrchovou úpravu na výkresech pro konkrétní prvky.
- Řízení nákladů:
- Výzva: Ačkoli AM umožňuje neuvěřitelné návrhy, extrémní složitost může prodloužit dobu sestavení (více vrstev, složité dráhy skenování), objem podpůrného materiálu a dobu následného zpracování (zejména odstranění podpěr a dokončovací práce), což zvyšuje náklady. Faktorem je také vysoká cena materiálů, jako je Scalmalloy®.
- Strategie zmírnění dopadů:
- Holistická DfAM: Vyvážení optimalizace výkonu a vyrobitelnosti. Někdy jsou o něco méně optimalizované návrhy výrazně jednodušší a levnější na tisk a zpracování.
- Efektivní hnízdění: Maximalizace počtu dílů, které se na konstrukční desce vyrábějí současně, zkracuje dobu přípravy/chlazení jednoho dílu.
- Výběr materiálu: Výběr nákladově nejefektivnějšího materiálu, který splňuje požadavky na výkon (např. AlSi10Mg místo Scalmalloy®, pokud je to možné).
- Zkušení partneři: Spolupráce s poskytovateli služeb AM, kteří mohou nabídnout poradenství ohledně nákladově efektivních strategií návrhu a zpracování.
Úspěšné překonání těchto výzev vyžaduje kombinaci sofistikovaných konstrukčních nástrojů, pokročilého řízení procesů, důsledného řízení kvality a hlubokých odborných znalostí v oblasti materiálových věd a aditivních výrobních procesů. Partnerství s vertikálně integrovaným nebo vysoce zkušeným poskytovatel služeb 3D tisku kovů je často nejúčinnější strategií pro zmírnění dopadů pro letecké společnosti, které se pouštějí do AM pro kritické struktury, jako jsou žebra.
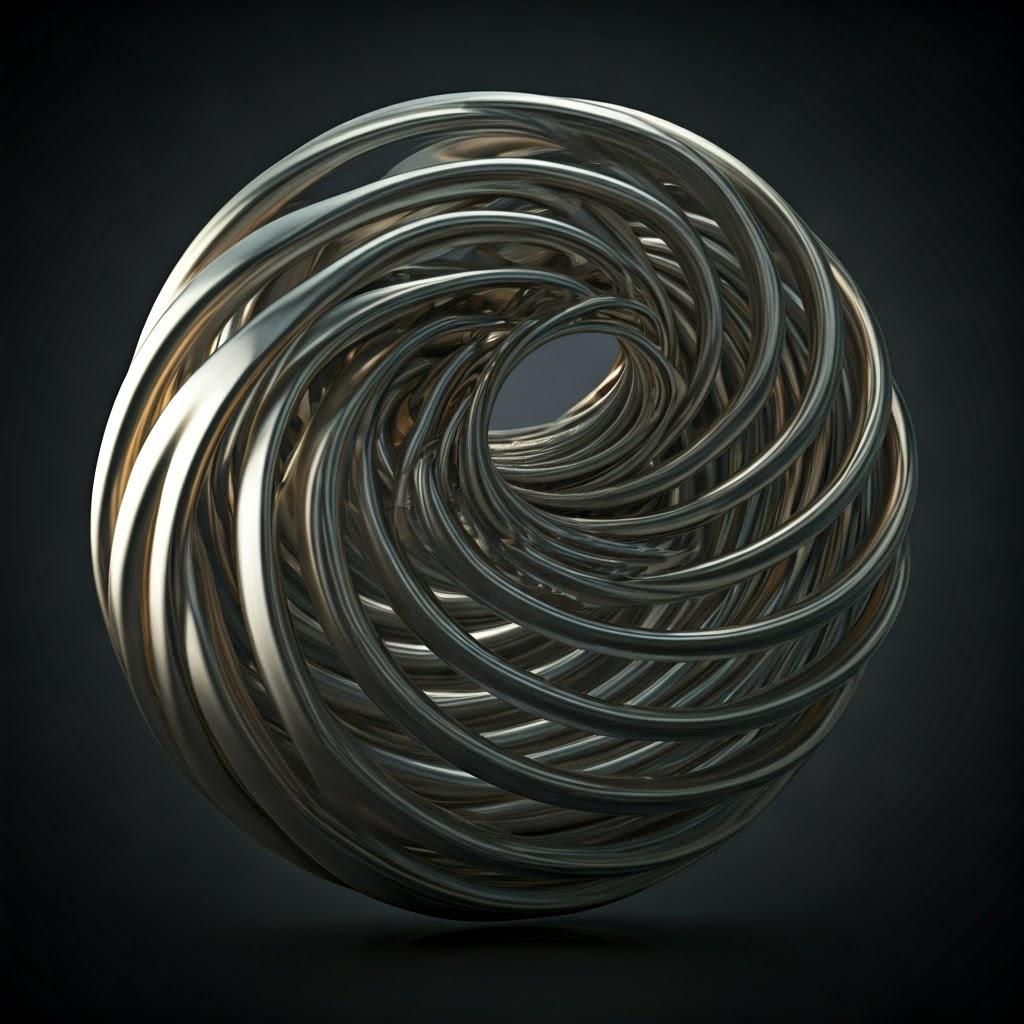
Výběr správného poskytovatele služeb 3D tisku kovů pro letecké komponenty
Výběr výrobního partnera pro kritické letecké komponenty, jako jsou 3D tištěná žebra, je rozhodnutí, které má značnou váhu. Kvalita, spolehlivost a letová způsobilost finálního dílu do značné míry závisí na schopnostech, procesech a odborných znalostech vybraného výrobce. Poskytovatel služeb metal AM. Pro inženýry a manažeři nákupu v leteckém průmyslu, vyhodnocení potenciálu dodavatelé aditivní výroby pro letecký průmysl vyžaduje důkladný proces hloubkové kontroly zaměřený na specifická kritéria, která jsou pro letecký průmysl klíčová. Pouhý výběr na základě nejnižší cenové nabídky může přinést nepřijatelná rizika.
Zde je komplexní průvodce hodnocením a výběrem vhodného partnera pro vaši firmu. 3D tisk kovů pro letectví a kosmonautiku potřeby:
- Zkušenosti a certifikace v leteckém průmyslu (AS9100):
- Certifikace AS9100: Jedná se o mezinárodně uznávaný standard systému řízení kvality (QMS) pro letecký, kosmický a obranný průmysl. Pro výrobu letově kritických součástí je neoddiskutovatelný. Ověřte si, zda je dodavatel držitelem platné certifikace AS9100, a co je důležité, zda je dodavatel rozsah jejich certifikace se vztahuje na konkrétní procesy (např. tisk LPBF/SEBM, tepelné zpracování, NDT) a materiály relevantní pro váš projekt.
- Osvědčené výsledky: Hledejte důkazy o úspěšných projektech s jinými leteckými výrobci OEM nebo renomovanými dodavateli. Cennými ukazateli jsou případové studie, reference (jsou-li k dispozici) a prokázané zkušenosti s podobnými součástmi (např. konstrukčními díly, odlehčenými konstrukcemi).
- Dodržování předpisů ITAR: Pokud pracujete na projektech souvisejících s obranou, které podléhají americkým předpisům o mezinárodním obchodu se zbraněmi, ujistěte se, že poskytovatel splňuje požadavky na registraci a dodržování předpisů ITAR.
- Znalost materiálů a sledovatelnost:
- Specifické schopnosti slitin: Ověřte si, že poskytovatel má ověřené a kvalifikované postupy pro konkrétní letecké slitiny, které požadujete (např. Scalmalloy®, AlSi10Mg, Ti-6Al-4V, IN718). Zeptejte se na úroveň jejich zkušeností s těmito materiály.
- Kontrola kvality prášku: Informujte se o jejich postupech při získávání, testování (např. chemie, distribuce velikosti částic (PSD), morfologie, tekutost), manipulaci, skladování a recyklaci kovových prášků. Poskytovatelé jako Met3dp, kteří vyrábějí vlastní vysoce kvalitní prášky pomocí pokročilých atomizačních technik, mohou nabídnout větší kontrolu nad tímto kritickým vstupním materiálem.
- Úplná sledovatelnost materiálu: Je třeba zavést spolehlivé systémy pro sledování šarží prášku od získání přes zpracování, tisk (propojení konkrétních šarží s konkrétními sestavami/dílci) až po finální uvolnění komponent. To je nezbytné pro zajištění kvality a certifikaci.
- Technologické schopnosti a kapacita:
- Vhodná technologie AM: Nabízejí nejvhodnější technologii (např. LPBF pro jemné rysy, SEBM pro určité materiály nebo výhody produktivity) pro vaši konkrétní konstrukci žebra a materiál? Například společnost Met3dp se specializuje na systémy SEBM, které jsou známé svou přesností a spolehlivostí.
- Strojový park a objem výroby: Zhodnoťte jejich konkrétní modely tiskáren, velikosti obálek pro sestavení (mohou se přizpůsobit rozměrům vašich žeber?) a počet dostupných strojů. Je zapotřebí dostatečná kapacita, aby bylo možné dodržet dobu realizace projektu a případně ji rozšířit na výrobní objemy.
- Monitorování procesů: Jaké možnosti monitorování procesu in-situ mají jejich stroje (např. monitorování bazénu taveniny, termovizní snímání)? Tato data mohou být cenná pro zajištění kvality a konzistence procesu.
- Integrované možnosti následného zpracování:
- Komplexní služby: Posuďte, zda nabízejí požadované kroky následného zpracování (uvolnění napětí, tepelné zpracování, HIP, odstranění podpěr, CNC obrábění, povrchové úpravy, NDT) přímo ve firmě nebo prostřednictvím přísně kontrolované sítě kvalifikovaných partnerů.
- Odborné znalosti: Ujistěte se, že mají (nebo jejich partneři) specifické odborné znalosti v oblasti následného zpracování dílů AM, které se mohou chovat jinak než kované nebo lité materiály. Cykly tepelného zpracování, strategie obrábění a interpretace NDT mohou vyžadovat přizpůsobení pro komponenty AM.
- Řízení kvality: Pokud využíváte externí partnery, jak primární dodavatel řídí kvalitu a sledovatelnost v celém dodavatelském řetězci? Integrovaný přístup často zjednodušuje logistiku a dohled nad kvalitou.
- Robustní systém řízení kvality (QMS):
- Nad rámec certifikace: I když je AS9100 zásadní, prozkoumejte hlouběji jejich každodenní postupy v oblasti kvality. Ptejte se na postupy validace procesů, programy školení obsluhy, harmonogramy kalibrace zařízení, postupy hlášení neshod a nápravných opatření a kontrolu dokumentace.
- Kontrolní schopnosti: Mají potřebné metrologické vybavení (souřadnicové měřicí stroje, 3D skenery) a možnosti NDT (nebo certifikované partnery) pro důkladnou kontrolu dílů podle náročných specifikací pro letecký průmysl?
- Technická podpora a podpora DfAM:
- Partnerství pro spolupráci: Působí poskytovatel pouze jako tisková kancelář, nebo nabízí technickou podporu s přidanou hodnotou? Hledejte odborné znalosti DfAM, které vám pomohou optimalizovat návrh žebra z hlediska tisknutelnosti, výkonu a nákladové efektivity.
- Simulační schopnosti: Mohou provádět simulaci procesu, aby předpověděly tepelné namáhání a deformace a pomohly tak předem optimalizovat orientační a podpůrné strategie?
- Řešení problémů: Zhodnoťte jejich ochotu a schopnost spolupracovat při řešení technických problémů, které mohou vzniknout během vývoje nebo výroby.
- Řízení projektů a komunikace:
- Jasné citování: Je jejich proces tvorby cenové nabídky transparentní a podrobný a jsou v něm jasně popsány všechny zahrnuté kroky a související náklady?
- Komunikace: Budete mít vyhrazené kontaktní místo? Jak často bude poskytovat aktuální informace o projektu? Jasná a proaktivní komunikace je pro řízení složitých projektů v leteckém průmyslu zásadní.
- Podávání zpráv: Jaká úroveň dokumentace (materiálové certifikáty, protokoly o výrobě, kontrolní zprávy, certifikáty shody) bude dodána s hotovými díly?
- Zařízení, bezpečnost a stabilita:
- Čistota a kontroly: Čisté, dobře organizované zařízení s vhodnou kontrolou prostředí svědčí o profesionálním provozu.
- Zabezpečení dat: Ujistěte se, že mají odpovídající opatření na ochranu vašich citlivých údajů o návrhu (IP).
- Finanční stabilita: Zhodnoťte stabilitu poskytovatele, zejména pokud o něm uvažujete pro dlouhodobou spolupráci při výrobě.
Výběr správného dodavatele spočívá v nalezení skutečného partnera, který rozumí vysokým nárokům letecké výroby. Společnosti jako Met3dp, které nabízejí komplexní řešení zahrnující pokročilé SEBM tiskárny, specializované vysoce kvalitní kovové prášky vyvinutý pomocí špičkových technik v oboru, a služby vývoje aplikací jsou příkladem integrovaných odborných znalostí, které jsou přínosem pro náročné projekty. Návštěvy zařízení, provádění auditů a podrobné technické diskuse jsou doporučenými kroky v rámci projektu. hodnocení partnerů pro 3D tisk kovů proces. Můžete se dozvědět více O společnosti Met3dp a jejich odhodlání rozvíjet aditivní výrobu.
Odhad nákladových faktorů a doby realizace pro 3D tisk žeber pro letecký průmysl
Pro zadávání zakázek na letecké komponenty AM aby byly strategie účinné, je nezbytné jasně pochopit faktory, které ovlivňují náklady a dobu realizace 3D tištěných žeber. Na rozdíl od tradiční výroby, kde může být hlavním počátečním nákladem výroba nástrojů, jsou náklady na AM těsněji spjaty se spotřebou materiálu, časem stroje a složitostí následného zpracování. Dodací lhůty jsou ovlivněny různými fázemi, od revize návrhu až po konečnou kontrolu.
Klíčové faktory ovlivňující náklady na kovové žebrové konstrukce AM:
- Spotřeba materiálu:
- Typ prášku: To je často hlavní hnací silou. Vysoce výkonné slitiny, jako např. Náklady na tisk Scalmalloy® výrazně více na kilogram než standardní slitiny, jako je např. Náklady na tisk AlSi10Mg.
- Část Objem: Skutečný geometrický objem finální struktury žebra přímo ovlivňuje množství nataveného prášku.
- Objem podpůrné struktury: Podpěrné konstrukce rovněž spotřebovávají prášek a složité konstrukce vyžadující rozsáhlé podpěry si vyžádají vyšší náklady na materiál. Efektivní DfAM se snaží tyto problémy minimalizovat.
- Efektivita hnízdění: Efektivita uspořádání více dílů na konstrukční desce má vliv na poměr objemu dílů a potenciálně zbytečně použitého prášku v okolním loži (ačkoli netavený prášek se obvykle recykluje).
- Strojový čas:
- Výška stavby: Hlavní faktor určující počet potřebných vrstev. Vyšší díly potřebují více času.
- Část Plocha průřezu a složitost: Ovlivňuje dobu skenování potřebnou pro každou vrstvu. Velmi složité vnitřní struktury nebo rozsáhlé šrafování prodlužují čas.
- Počet dílů na sestavení: Vkládání více žeber efektivněji využívá čas stroje než tisk jednotlivých dílů.
- Hodinová sazba stroje: Liší se v závislosti na konkrétním systému AM (LPBF vs. SEBM), jeho schopnostech a cenové struktuře poskytovatele služeb.
- Práce:
- Nastavení a demontáž: Čas potřebný na přípravu stroje, vložení prášku, vyjmutí hotové sestavy a vyčištění systému.
- Práce po zpracování: Zejména u složitých dílů se na tom může významně podílet ruční odstraňování podpěr, dokončování, kontrola a manipulace.
- Náklady na následné zpracování:
- Úleva od stresu / tepelné ošetření: Doba pece, spotřeba energie, náklady na řízenou atmosféru.
- Izostatické lisování za tepla (HIP): Kvůli specializovanému vybavení a dlouhým časům cyklů se často výrazně zvyšují náklady. Cena se obvykle stanovuje za cyklus nebo podle objemu/hmotnosti.
- Odstranění podpory: Mohou být náročné na ruční práci nebo vyžadovat strojní obrábění (CNC, EDM).
- CNC obrábění: Náklady spojené s programováním, seřizováním, konstrukcí přípravků (pokud je potřeba), časem stroje a nástroji pro dokončování kritických prvků.
- Povrchová úprava: Náklady na tryskání, bubnování, leštění atd.
- NDT a inspekce: Náklady na specializované vybavení (CT skenery, CMM) a čas kvalifikovaných techniků.
- Inženýrství a zajištění kvality:
- Konzultace DfAM: Pokud vyžaduje významnou podporu návrhu ze strany poskytovatele.
- Kvalifikace procesu: Náklady spojené s kontrolou prvního výrobku (FAI), vývojem kvalifikovaných procesních parametrů a případným destruktivním testováním prvních šarží.
- Dokumentace: Čas strávený přípravou komplexních balíčků dokumentace kvality.
- Množství:
- Úspory z rozsahu: Ačkoli je AM často nákladově efektivní pro malé objemy, existují určité úspory z rozsahu. Náklady na nastavení, kvalifikaci a programování lze amortizovat v rámci větších sérií. Náklady na prášek se mohou při hromadných nákupech mírně snížit. Nicméně primární nákladové faktory (materiál, strojní čas) se škálují poměrně lineárně.
Typická doba dodání komponentů:
Odhadování doba realizace aditivní výroby vyžaduje zvážení všech dotčených fází:
- Citace & Design Review: 1-5 pracovních dnů (v závislosti na složitosti a rychlosti reakce poskytovatele).
- Tisková fronta a plánování: Velmi variabilní, od několika dnů po několik týdnů, v závislosti na počtu nevyřízených objednávek poskytovatele a dostupnosti strojů.
- Tisk: Hodiny až několik dní (např. 12 hodin až 72 hodin a více), především v závislosti na výšce a objemu stavby.
- Ochlazení: Několik hodin.
- Úleva od stresu / tepelné ošetření: 1-3 dny (včetně doby pece a řízeného chlazení).
- HIP: 2-5 dní (cykly HIP jsou dlouhé a díly se často dávkují; může se jednat o přepravu ke specializovanému poskytovateli HIP).
- Odstranění podpory / obrábění / dokončovací práce: Velmi variabilní, od 1 dne pro jednoduchou demontáž až po 1-2 a více týdnů pro složité obrábění a dokončovací práce.
- NDT a inspekce: 1-3 dny (v závislosti na požadovaných metodách a hlášení).
- Doprava: 1-5 dní (vnitrostátní/mezinárodní).
Celková předpokládaná doba dodání:
- Jednoduché prototypy (AlSi10Mg, minimální následné zpracování): 1-3 týdny.
- Komplexní žebra (Scalmalloy®, kompletní tepelné zpracování, HIP, obrábění, NDT): 6-12 týdnů, případně déle, v závislosti na všech faktorech.
Strategie optimalizace nákladů:
- Optimalizujte návrh pomocí DfAM, abyste minimalizovali objem a podpůrné struktury.
- Vyberte cenově nejefektivnější materiál, který splňuje všechny požadavky na výkon.
- Jasně definujte pouze nezbytné tolerance a povrchové úpravy, abyste se vyhnuli nadměrnému obrábění.
- Konsolidace dílů do jednotlivých sestav, pokud je to možné.
- Ve fázi návrhu úzce spolupracujte s poskytovatelem AM, abyste pochopili kompromisy v nákladech.
Pochopení této dynamiky nákladů a dodacích lhůt je zásadní pro sestavování rozpočtu, plánování projektů a integraci. 3D tisk z kovu účinně zapojit do dodavatelského řetězce v leteckém průmyslu.
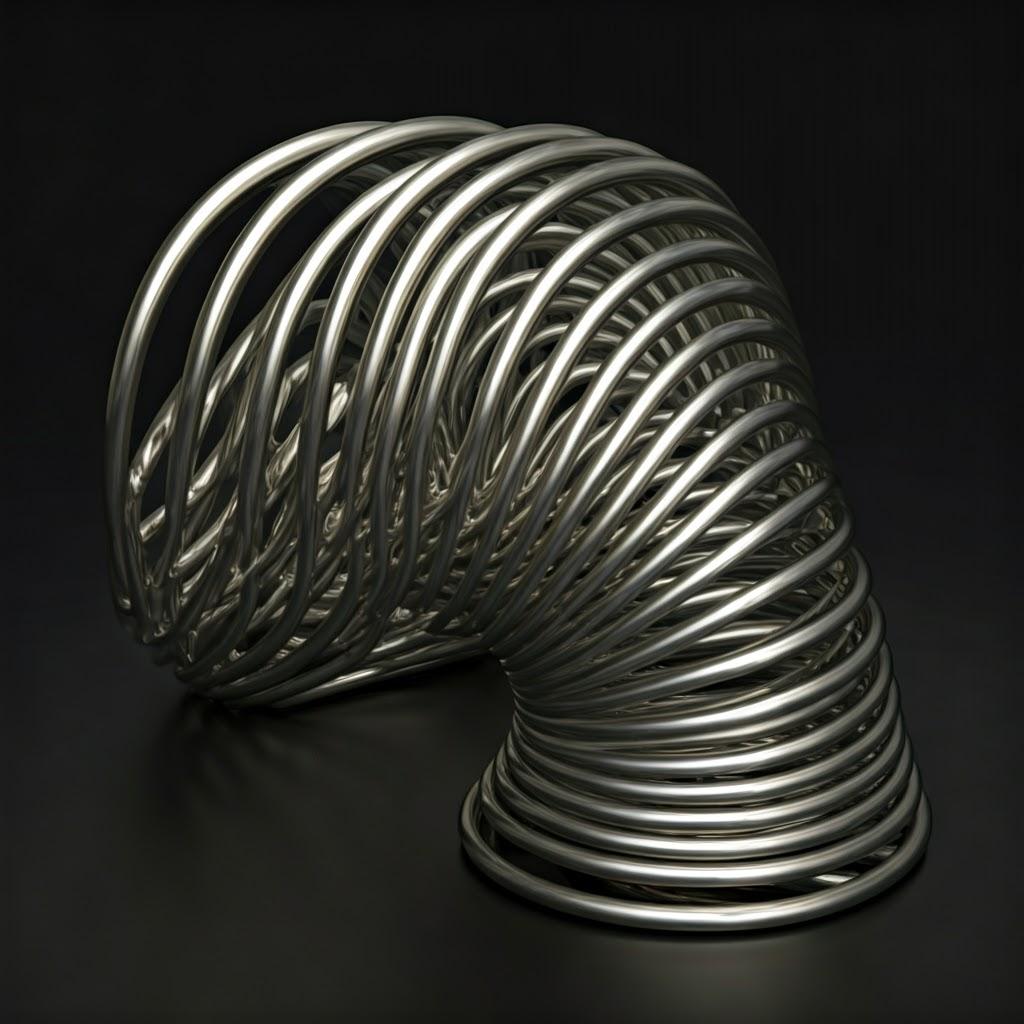
Často kladené otázky (FAQ) o 3D tištěných žebrech pro letectví a kosmonautiku
Zde jsou odpovědi na některé časté otázky inženýrů a specialistů na veřejné zakázky týkající se použití aditivní výroby kovů pro letecké žebrové konstrukce:
- Jaká je pevnost 3D tištěných slitin Scalmalloy® nebo AlSi10Mg ve srovnání s tradičními tepanými hliníkovými slitinami, jako je 7075-T6?
- Scalmalloy® (tepelně zpracovaná): Jeho pevnostní vlastnosti (UTS > 520 MPa, YS > 480 MPa) jsou vysoce konkurenceschopné a často překonávají vlastnosti mnoha tradičních vysokopevnostních hliníkových slitin, jako je 7075-T6 (typické UTS ~570 MPa, YS ~500 MPa). při posuzování měrné pevnosti (pevnost k hmotnosti). Je důležité, že slitina Scalmalloy® často vykazuje lepší únavové vlastnosti ve srovnání s mnoha tepanými slitinami, zejména v přítomnosti vrubů nebo typických povrchových rysů AM.
- AlSi10Mg (tepelně zpracovaný - T6): Je výrazně méně pevný než 7075-T6. Její vlastnosti (UTS ~300-350 MPa, YS ~230-280 MPa) jsou srovnatelné spíše se středně pevnými kovanými slitinami, jako je 6061-T6.
- Klíčový závěr: Slitina Scalmalloy® umožňuje přímou konkurenci vysokopevnostním kovaným slitinám na bázi výkonu, zejména pokud je klíčová nízká hmotnost a únava. AlSi10Mg je vhodný pro méně náročné konstrukční aplikace. Pro obě AM slitiny je zásadní správné tepelné zpracování.
- Mohou 3D tištěná žebra splnit přísné certifikační požadavky pro letově důležité komponenty?
- Ano, rozhodně. Kovové komponenty AM jsou stále častěji certifikovány pro kritické letové aplikace (třída A). Získání certifikace však vyžaduje velmi přísný a kontrolovaný přístup, který zahrnuje:
- Zralý a stabilní proces AM: Používání kvalifikovaných strojů s uzamčenými a ověřenými procesními parametry.
- Kvalifikovaný materiál: Přísná kontrola a testování vstupních práškových surovin a postupů recyklace. Vlastnosti materiálu musí splňovat stanovené přípustné hodnoty (často vytvořené prostřednictvím rozsáhlých testovacích programů podobných MMPDS pro tradiční materiály nebo prostřednictvím specifické kvalifikace dílů).
- Robustní systém řízení kvality: Předpokladem je certifikace AS9100, podrobné řízení procesů, sledovatelnost a dokumentace.
- Komplexní následné zpracování: Standardizované a kvalifikované postupy pro odlehčení napětí, tepelné zpracování, HIP (často vyžadováno), obrábění a dokončovací práce.
- Důsledná nedestruktivní kontrola a inspekce: Využití ověřených technik NDT (jako je CT skenování) a rozměrové kontroly k ověření integrity a shody dílů.
- Spolupráce: Úzká spolupráce mezi projektantem, poskytovatelem služeb AM a certifikačními orgány.
- Ano, rozhodně. Kovové komponenty AM jsou stále častěji certifikovány pro kritické letové aplikace (třída A). Získání certifikace však vyžaduje velmi přísný a kontrolovaný přístup, který zahrnuje:
- Jaká je typická úspora hmotnosti dosažená přepracováním konstrukce žeber pro AM?
- Úspora hmotnosti se obvykle pohybuje v rozmezí 20% až 60% nebo dokonce vyšší ve srovnání s tradičně vyráběnými (např. obráběnými polotovary) protějšky určenými pro stejné zatěžovací stavy. Skutečná úspora do značné míry závisí na:
- Složitost a účinnost původního návrhu.
- Volnost, která je k dispozici pro optimalizaci topologie (návrhový prostor, zatěžovací stavy).
- Zvolený materiál AM (např. použití slitiny Scalmalloy® s vysokou měrnou pevností umožňuje větší úspory).
- Zda je dosaženo konsolidace částí.
- Úspora hmotnosti se obvykle pohybuje v rozmezí 20% až 60% nebo dokonce vyšší ve srovnání s tradičně vyráběnými (např. obráběnými polotovary) protějšky určenými pro stejné zatěžovací stavy. Skutečná úspora do značné míry závisí na:
- Je lisování za tepla (HIP) u 3D tištěných hliníkových dílů pro letecký průmysl vždy nutné?
- Ne vždy, ale je to velmi doporučené a často povinné pro únavově kritické nebo lomově kritické letecké součásti. HIP výrazně zlepšuje integritu materiálu uzavřením vnitřní mikroporozity, což zvyšuje tažnost, lomovou houževnatost a především únavovou životnost. U primárních konstrukčních prvků, jako jsou žebra, kde je únavová odolnost rozhodující, regulační orgány a hlavní dodavatelé obvykle vyžadují ošetření HIP jako součást kvalifikačního procesu, aby byla zajištěna maximální spolehlivost a bezpečnost. U méně kritických (např. sekundárních konstrukcí) nebo nenosných částí může být vynechána, pokud je to odůvodněno analýzou a zkouškami.
- Jaké informace jsou potřeba k získání přesné nabídky od poskytovatele služeb Metal AM, jako je Met3dp?
- K poskytnutí přesné nabídky a posouzení vyrobitelnosti poskytovatelé obvykle potřebují:
- 3D model CAD: Nativní formát CAD nebo nejlépe STEP (.stp/.step).
- Specifikace materiálu: Jasně definovaná slitina (např. Scalmalloy®, AlSi10Mg) a požadovaný stav popouštění/tepelného zpracování (např. T6).
- 2D výkresy (pokud jsou k dispozici): Zadání kritických rozměrů, tolerancí (pomocí GD&T), požadované povrchové úpravy pro konkrétní prvky a dalších klíčových požadavků.
- Množství: Počet požadovaných dílů (pro prototyp vs. výrobní sérii).
- Požadovaná osvědčení: Uveďte, zda je třeba zajistit shodu s AS9100, materiálové certifikáty, certifikáty shody (CoC) nebo zprávy o kontrole prvního výrobku (FAI).
- Požadavky na NDT: Podrobně popište všechny požadované nedestruktivní zkoušky (např. kritéria přijatelnosti CT vyšetření, LPI).
- Potřeby následného zpracování: Zadejte požadované obrábění, povrchové úpravy, nátěry atd.
- Požadovaná doba dodání: Uveďte cílové datum dodání.
- K poskytnutí přesné nabídky a posouzení vyrobitelnosti poskytovatelé obvykle potřebují:
Závěr: Vylepšení leteckých konstrukcí pomocí aditivní výroby kovů
Cesta za složitostí 3D tištěných leteckých žebrových konstrukcí odhaluje přesvědčivý příběh, v němž se inovace setkávají s nutností. Aditivní výroba kovů již není futuristickým pojmem, ale hmatatelným, výkonným nástrojem, který umožňuje leteckým inženýrům a výrobcům posouvat hranice výkonnosti a efektivity. Pro součásti, jako jsou žebra, kde musí strukturální integrita koexistovat s neúnavnou snahou o snížení hmotnosti, nabízí AM transformační cestu.
Pákovým efektem optimalizace topologie a volnosti konstrukce, která je vlastní technologii AM, mohou konstruktéři vytvářet žebrové konstrukce, které jsou radikálně lehčí, ale zároveň splňují náročné požadavky na pevnost a tuhost. Schopnost sloučit více součástí do jediného tištěného dílu zjednodušuje montáž, snižuje počet možných poruchových míst a dále přispívá k úspoře hmotnosti. Vysoce výkonné materiály přizpůsobené pro AM, jako je například výjimečný poměr pevnosti a hmotnosti materiálu Scalmalloy® nebo spolehlivou zpracovatelnost AlSi 10Mg, poskytují řešení na míru pro různé aplikace v letectví a kosmonautice.
Realizace těchto výhod však vyžaduje komplexní přístup. Efektivní Design pro aditivní výrobu (DfAM) zásady musí být vodítkem pro počáteční koncepci a musí zohledňovat nejen optimalizaci, ale také vyrobitelnost, podpůrné strategie a následné zpracování. Dosažení potřebné rozměrové přesnosti a povrchové úpravy často závisí na pečlivém zpracování. následné zpracování, včetně kritických kroků, jako je uvolňování napětí, tepelné zpracování, izostatické lisování za tepla (HIP), přesné obrábění a důkladné nedestruktivní testování (NDT). Zvládnutí běžných problémů spojených se zbytkovým napětím, odstraňováním podpěr a kontrolou pórovitosti vyžaduje hluboké odborné znalosti procesů a důkladné řízení kvality.
Úspěšná implementace technologie AM pro kritické komponenty v letectví a kosmonautice významně závisí na výběru správného výrobního partnera. Nejdůležitější jsou odborné znalosti požadavků leteckého průmyslu, certifikace AS9100, osvědčené materiálové možnosti, pokročilá technologická infrastruktura, integrovaný postprocesing a neochvějný závazek ke kvalitě.
Společnost Met3dp je v tomto prostředí pokročilé výroby kompetentním partnerem. Díky komplexním řešením zahrnujícím špičkovou technologii tisku SEBM, která je proslulá svou přesností a spolehlivostí, vlastní schopnosti vyrábět vysoce čisté sférické kovové prášky optimalizované pro AM pomocí pokročilé atomizace a specializované podpoře vývoje aplikací umožňuje společnost Met3dp organizacím plně využít potenciál aditivní výroby kovů.
Budoucnost leteckých konstrukcí je nesporně spojena s možnostmi aditivní výroby. U svého příštího projektu zahrnujícího složité a lehké konstrukční prvky, jako jsou žebra, zvažte transformační možnosti. Prozkoumejte, jak vám AM zpracování kovů může pomoci dosáhnout bezprecedentních úspor hmotnosti, zvýšit výkon a urychlit inovační cykly.
Jste připraveni prozkoumat, jak může aditivní výroba kovů zlepšit vaše letecké komponenty? Kontaktujte společnost Met3dp ještě dnes, abyste prodiskutovali požadavky vašeho projektu a zjistili, jak naše odborné znalosti mohou podpořit cíle vaší organizace v oblasti aditivní výroby.
Návštěva Met3dp dozvědět se více.
Sdílet na
MET3DP Technology Co., LTD je předním poskytovatelem řešení aditivní výroby se sídlem v Qingdao v Číně. Naše společnost se specializuje na zařízení pro 3D tisk a vysoce výkonné kovové prášky pro průmyslové aplikace.
Dotaz k získání nejlepší ceny a přizpůsobeného řešení pro vaše podnikání!
Související články
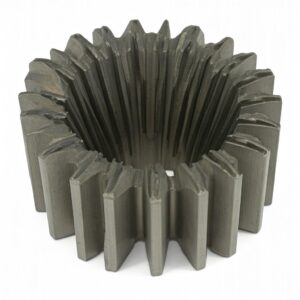
Vysoce výkonné segmenty lopatek trysek: Revoluce v účinnosti turbín díky 3D tisku z kovu
Přečtěte si více "O Met3DP
Nedávná aktualizace
Náš produkt
KONTAKTUJTE NÁS
Nějaké otázky? Pošlete nám zprávu hned teď! Po obdržení vaší zprávy obsloužíme vaši žádost s celým týmem.
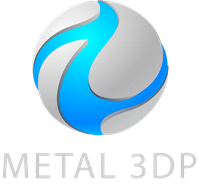
Kovové prášky pro 3D tisk a aditivní výrobu