Přepážky raketových motorů z aditivně vyráběných superslitin
Obsah
Úvod: Kritická úloha přepážek v moderním raketovém pohonu
Neustálá snaha o vyšší výkon, účinnost a spolehlivost raketových pohonných systémů je hnací silou neustálých inovací v celém leteckém průmyslu. Požadavky kladené na raketové motory jsou obrovské, od meziplanetárních misí po komerční vypouštění družic a obranné aplikace. Tyto složité stroje pracují v podmínkách extrémních teplot, tlaků a vibrací, což vyžaduje komponenty navržené a vyrobené tak, aby odolávaly nejnáročnějšímu prostředí, jaké si lze představit. Jedním z kritických prvků sestavy náporové komory raketového motoru jsou přepážky - zdánlivě jednoduché součásti, které hrají velmi důležitou roli při zajišťování stabilního a účinného spalování.
Přepážky raketových motorů jsou strategicky umístěné konstrukce, často v čelní desce vstřikovače nebo ve spalovací komoře, určené především k potlačení nestability spalování. Tyto nestability, projevující se jako vysokofrekvenční tlakové oscilace, mohou vážně snížit výkon motoru, poškodit kritický hardware a dokonce vést ke katastrofickému selhání. Přerušením cest šíření akustických vln a změnou dynamiky proudění fungují přepážky jako zásadní tlumiče, které zajišťují plynulé a kontrolované uvolňování energie, jež pohání kosmické lodě. Kromě toho mohou přepážky přispívat k tepelnému řízení, chránit citlivé součásti, jako je čelní stěna vstřikovače, před intenzivním teplem spalování a ovlivňovat způsoby míchání paliva s oxidačním prostředkem. Vzhledem k tomu, že výrobci nosných raket a agentury pro výzkum vesmíru posouvají hranice výkonnosti, stává se návrh a výroba sofistikovaných, vysoce odolných přepážek prvořadým úkolem. Výroba těchto součástí tradičně zahrnovala složité procesy obrábění, spojování a montáže, což často omezovalo možnosti konstrukce a přinášelo značné dodací lhůty a náklady. S příchodem 3D tisk z kovu, neboli aditivní výroba (AM), zejména s využitím vysoce výkonných superslitin, přináší revoluční změny v koncepci, návrhu a výrobě přepážek raketových motorů. Tato technologie uvolňuje nebývalou konstrukční svobodu a umožňuje vytvářet složité vnitřní chladicí kanály, komplexní geometrie optimalizované pro akustický útlum a konsolidované konstrukce dílů, jejichž výroba byla dříve nemožná nebo nepraktická. Společnosti, které hledají spolehlivé dodavatele a výrobce leteckých komponent, se stále častěji obracejí na specialisty na AM, kteří jsou schopni zpracovávat náročné superslitiny a splňovat přísné požadavky na kvalitu. Tento posun znamená velký skok vpřed v technologii pohonu, který slibuje lehčí, účinnější a spolehlivější raketové motory pro budoucí průzkum a využití vesmíru. Tento článek se zabývá specifiky využití aditivní výroby, zejména s pokročilými superslitinami, jako jsou IN718 a Haynes 282, k výrobě vysoce výkonných přepážek raketových motorů a zkoumá aplikace, výhody, materiálové aspekty a výrobní nuance.
Problém nestability spalování trápí vývoj raketových motorů od jejich počátku. První raketové motory na kapalná paliva, zejména ty větší, se často potýkaly s destruktivními oscilacemi, které konstruktéry mátly. Pochopení a zmírnění těchto nestabilit se stalo hlavním předmětem výzkumu a vývoje. Přepážky se staly jedním z nejúčinnějších pasivních regulačních zařízení. Jejich účinnost spočívá ve schopnosti zasahovat do smyčky zpětné vazby, která udržuje nestabilitu spalování. Tato smyčka obvykle zahrnuje vazbu mezi spalovacím procesem (kolísání uvolňovaného tepla) a akustikou komory (tlakové vlny). Tlakové vlny vznikající při spalování se mohou šířit komorou, odrážet se od povrchů a vracet se zpět do spalovací zóny a ovlivňovat další uvolňování tepla způsobem, který posiluje oscilace. Přepážky zavádějí akustické impedanční nesoulady a tlumení, čímž účinně přerušují tuto rezonanční vazbu. Toho dosahují několika mechanismy:
- Akustické tlumení: Přepážky fungují jako fyzické bariéry, které pohlcují, rozptylují a rozptylují akustickou energii. Jejich geometrie, umístění a vnitřní struktura (pokud existuje) jsou pečlivě navrženy tak, aby se zaměřily na specifické režimy nestability (frekvence a tvary) předpovězené výpočtovou dynamikou tekutin (CFD) a akustickým modelováním.
- Narušení toku: Přepážky, které vyčnívají do spalovací komory nebo rozdělují čelo vstřikovače, mění způsob proudění hnacích a spalovacích plynů. To může narušit uspořádané struktury vírů nebo recirkulačních zón, které by jinak mohly přispívat k nestabilnímu spojení.
- Kompartmentalizace: V některých konstrukcích, zejména na čele vstřikovače, vytvářejí přepážky oddělení, která izolují různé oblasti spalování. To zabraňuje snadnému šíření nestabilit vznikajících v jedné zóně a jejich zesilování v celé komoře.
Kromě kontroly stability plní přepážky často i druhotné, ale důležité funkce:
- Tepelná ochrana: Čelní desky vstřikovačů jsou vystaveny intenzivnímu tepelnému toku. Přepážky mohou stínit části čelní desky nebo obsahovat vnitřní chladicí kanály (umožněné technologií AM), aby bylo možné regulovat teploty a zabránit přehřátí nebo erozi.
- Vylepšení/kontrola míchání: Umístění a tvar přepážek může ovlivnit míchání proudů paliva a okysličovadla v blízkosti vstřikovače, což může mít vliv na účinnost a výkonnost spalování, i když jejich hlavní funkcí zůstává stabilita.
Tradiční způsoby výroby přepážek, jako je obrábění z předlitku nebo odlévání s následným obráběním a svařováním/pájením, narážejí na značná omezení, zejména s tím, jak se konstrukce přepážek stávají složitějšími pro motory s vyššími výkony:
- Geometrická omezení: Obrábění složitých vnitřních prvků, jako jsou zakřivené chladicí kanály nebo jemné struktury akustického tlumení, je velmi obtížné, nákladné a někdy nemožné. Složité podříznutí a vnitřní dutiny často nelze vyrobit.
- Materiálový odpad: Při subtraktivních procesech, jako je obrábění, může vznikat značný materiálový odpad, zejména pokud se začíná s velkými polotovary drahých superslitin.
- Procesy spojování: Montáž přepážek z více obrobených nebo odlitých kusů přináší potenciální slabá místa ve spojích (sváry nebo pájky), které musí odolávat extrémnímu namáhání a teplotním gradientům. Tyto spoje vyžadují důkladnou kontrolu a mohou komplikovat tepelný management.
- Doba dodání: Vícestupňová povaha tradiční výroby, zahrnující výrobu nástrojů, odlévání, obrábění, spojování a kontrolu, vede k dlouhým dodacím lhůtám, což brání rychlému opakování návrhu a vývojovým cyklům, které jsou v leteckém průmyslu klíčové.
Aditivní výroba tato omezení přímo řeší. Díky výrobě přepážek vrstvu po vrstvě z kovového prášku nabízí AM:
- Bezkonkurenční svoboda designu: Umožňují komplexní vnitřní kanály, optimalizované topologie, mřížkové struktury pro odlehčení a lepší tlumení a konformní chladicí cesty, které těsně kopírují povrch přepážky.
- Konsolidace částí: Umožňuje vytisknout více součástí sestavy přepážky jako jediný monolitický díl, čímž se eliminují spoje, snižuje hmotnost a zjednodušuje montáž.
- Snížení množství materiálového odpadu: Použití materiálu pouze tam, kde je to nutné, což z AM činí udržitelnější variantu, zejména u drahých superslitin.
- Zrychlený vývoj: Usnadňuje rychlou tvorbu prototypů a iterací konstrukce, čímž výrazně zkracuje vývojový cyklus nových součástí motoru.
Integrace aditivní výroby do výroby kritických součástí, jako jsou přepážky raketových motorů, představuje změnu paradigmatu a umožňuje leteckým inženýrům navrhovat a vyrábět pohonné systémy, které jsou robustnější, účinnější a výkonnější než kdykoli předtím. Vzhledem k tomu, že specializovaní poskytovatelé AM, jako je Met3dp, zdokonalují procesy pro superslitiny a prokazují konzistentní kvalitu a spolehlivost, bude zavádění AM pro takto náročné aplikace jen růst a posouvat hranice kosmických technologií. Společnost Met3dp se sídlem v čínském městě Čching-tao využívá své odborné znalosti v oblasti pokročilé práškové výroby a zpracování kovů 3D tisk systémy pro podporu právě těchto náročných aplikací v letectví a kosmonautice, které nabízejí vysoce kvalitní superslitinové prášky a tiskové služby.
K čemu se používají přepážky raketových motorů? Definice funkce a významu
Přepážky raketového motoru jsou nedílnou součástí spalovací komory nebo vstřikovací sestavy a jejich hlavním úkolem je zajistit stabilitu a účinnost spalovacího procesu. Jejich funkce je kritická, protože nekontrolované spalování může vést k selhání mise. Pochopení jejich specifické úlohy vyžaduje proniknutí do fyziky raketového pohonu a problémů spojených se spalováním obrovského množství pohonné hmoty v extrémních podmínkách.
Primární funkce: Potlačení nestabilit spalování
Hlavním účelem téměř všech přepážek raketových motorů je zabránit nestabilitě spalování nebo ji potlačit. Jedná se o samovolné kolísání tlaku v komoře, často spojené s kolísáním rychlosti uvolňování tepla z hořících pohonných hmot. Mohou se pohybovat od relativně nízkofrekvenčního “chrčení” až po škodlivé vysokofrekvenční “ječení” nebo “křik”
- Mechanismus nestability: Zjednodušeně si představte malé, náhodné zvýšení tlaku v komoře. Tato tlaková vlna se šíří, odráží a případně vrací do spalovací zóny. Pokud dorazí v okamžiku, kdy podporuje více hoření pohonné hmoty (např. zvýšením rychlosti míchání nebo reakce), vznikne ještě silnější tlakový puls. Při správném načasování (fázi) se tato zpětnovazební smyčka zesiluje, což vede k rozsáhlým, potenciálně destruktivním oscilacím. Geometrie komory, typy pohonných hmot, způsob vstřikování a provozní podmínky ovlivňují, které frekvence jsou nejvíce náchylné k nestabilitě.
- Jak zasahují baffle: Přepážky fungují jako akustické tlumiče a rušiče proudění a přerušují tento zpětnovazební cyklus.
- Akustické tlumení: Zavádějí fyzické bariéry, které zvyšují akustické ztráty v komoře. Zvukové vlny odrážející se od přepážek nebo procházející jimi ztrácejí energii v důsledku viskózních efektů, tepelné vodivosti na povrchu a geometrického rozptylu. Složité vnitřní struktury v přepážkách, které lze vyrobit pomocí AM, lze speciálně vyladit tak, aby tlumily problematické frekvence. Představte si je jako akustické dlaždice v nahrávacím studiu, ale navržené pro pekelně energické prostředí.
- Modifikace průtokového pole: Přepážky fyzicky rozdělují vstřikovací plochu nebo vystupují do komory a mění tak dráhy proudů hnacího plynu a spalin. To může zabránit vzniku velkých souvislých struktur (jako jsou víry), které by se jinak mohly silně spojit s akustickými módy. Účinně rozdělují spalovací proces, takže je obtížnější, aby lokální poruchy přerostly v nestabilitu celé komory.
Typy přepážek a jejich umístění:
Konkrétní konstrukce a umístění přepážek do značné míry závisí na typu motoru (např. kapalinový dvouproudový motor, raketový motor na tuhé palivo), na konkrétních předpokládaných režimech nestability a na celkové architektuře motoru. Mezi běžné typy patří:
- Čelní stěny vstřikovačů: Jedná se pravděpodobně o nejběžnější typ v kapalinových dvouproudových motorech. Často se skládají z radiálních “paprsků” nebo “náboje a paprsků” namontovaných přímo na čelní desku vstřikovače. Toto uspořádání rozděluje oblast vstřikování na menší segmenty (ve tvaru koláče nebo prstence), čímž omezuje komunikaci akustických vln napříč komorou a ruší příčné režimy nestability. Mohou být integrovány přímo do konstrukce injektoru nebo připojeny jako samostatné součásti. AM umožňuje zabudovat do těchto přepážek složité chladicí kanály, které chrání tyto přepážky a pod nimi ležící čelní plochu injektoru.
- Akustické dutiny/rezonátory: Někdy konstruktéři místo pevných přepážek zabudovávají do stěn komory nebo do čela vstřikovače dutiny nebo Helmholtzovy rezonátory. Ty fungují jako vyladěné absorbéry, které tlumí specifické rezonanční frekvence. AM umožňuje přesnou výrobu těchto složitých rezonančních geometrií.
- Komorové přepážky: V kapalinových motorech jsou méně obvyklé, ale někdy se používají, a mohou to být prstence nebo jiné konstrukce umístěné hlouběji ve spalovací komoře, které ruší podélné nebo objemové nestabilní režimy.
- Přepážky pro raketové motory na tuhé pohonné hmoty (SRM): U SRM může rovněž docházet k nestabilitě, která je často způsobena interakcí mezi prouděním plynu a povrchem hořícího paliva (zrna paliva). Do konstrukce zrna nebo izolace komory mohou být začleněny ploutve nebo jiné struktury podobné přepážkám, aby se narušily akustické režimy, ačkoli mechanismy se poněkud liší od kapalinových motorů.
Sekundární funkce:
Stabilita je sice nejdůležitější, ale přepážky přispívají i k dalším aspektům provozu motoru:
- Tepelný management: Čelní plochy vstřikovačů, zejména v blízkosti středu, jsou extrémně tepelně zatíženy. Přepážky mohou fyzicky stínit části vstřikovače nebo, v případě AM efektivněji, obsahovat sofistikované vnitřní chladicí kanály využívající proudění pohonné hmoty (regenerativní chlazení) nebo samostatný chladicí okruh. To zabraňuje degradaci materiálu a zajišťuje strukturální integritu a funkční životnost injektoru. Návrh konformních chladicích kanálů, které přesně kopírují obrysy přepážky, umožněný technologií AM, maximalizuje účinnost chlazení.
- Kontrola míchání: Přítomnost přepážek nevyhnutelně ovlivňuje místní proudové pole v blízkosti vstřikovačů. Ačkoli tato interakce obvykle není jejich primárním cílem, může jemně ovlivnit účinnost míchání pohonných látek. Konstruktéři s tím musí počítat, aby zajistili splnění výkonnostních cílů a požadavků na stabilitu. Špatně navržené přepážky mohou potenciálně bránit účinnému míchání, což může vést ke ztrátám výkonu.
- Strukturální podpora: V některých integrovaných konstrukcích mohou přepážky zajišťovat konstrukční vyztužení samotné čelní desky vstřikovače.
Význam v kontextu letectví a kosmonautiky:
Vzhledem k požadavkům na spolehlivost raketových motorů, zejména pro lety s lidmi do vesmíru a vysoce cenná užitečná zatížení, je účinná konstrukce přepážek nepominutelná.
- Úspěšná mise: Nestability spalování mohou vést ke snížení tahu, neefektivní spotřebě pohonných látek, silným vibracím poškozujícím motor nebo kosmickou loď a v nejhorším případě k rychlému zničení motoru. Přepážky jsou hlavní obrannou linií proti těmto způsobům poruch.
- Podpora výkonu: S tím, jak konstruktéři usilují o vyšší tlaky v komoře a energetičtější pohonné hmoty, aby zvýšili výkon motoru (tah a specifický impuls), se často zvyšuje tendence k nestabilitě. Pokročilé konstrukce přepážek, které umožňuje AM, mají zásadní význam pro spolehlivé dosažení těchto vyšších výkonů.
- Náklady a harmonogram: Selhání motoru během testování nebo letu je neuvěřitelně nákladné. Robustní rezervy stability, zajištěné účinnými přepážkami, snižují riziko nákladných nezdarů během vývoje a provozu. Výroba přepážek sama o sobě sice něco stojí, ale v porovnání s náklady na selhání motoru je to bledší. Využití AM může potenciálně zkrátit vývojové cykly díky rychlejšímu opakování návrhů přepážek ve srovnání s tradičními metodami.
Manažeři nákupu a inženýři, kteří zajišťují komponenty pro letecké projekty, si musí uvědomit kritickou důležitost přepážek. Nejsou to jen pasivní kusy kovu, ale pečlivě navržená zařízení nezbytná pro bezpečný a efektivní provoz celého pohonného systému. Klíčové je spolupracovat s dodavateli, kteří mají hluboké odborné znalosti jak v oblasti materiálových věd (zejména superslitin), tak v oblasti pokročilých výrobních technik, jako je AM. Společnost Met3dp se svým zaměřením na vysoce výkonné kovové prášky a průmyslová řešení 3D tisku dokonale odpovídá potřebám leteckých výrobců, kteří hledají špičkové možnosti výroby přepážek. Jejich znalosti vlastností materiálů a řízení procesů jsou zásadní pro výrobu přepážek, které splňují přísné požadavky raketového pohonu.
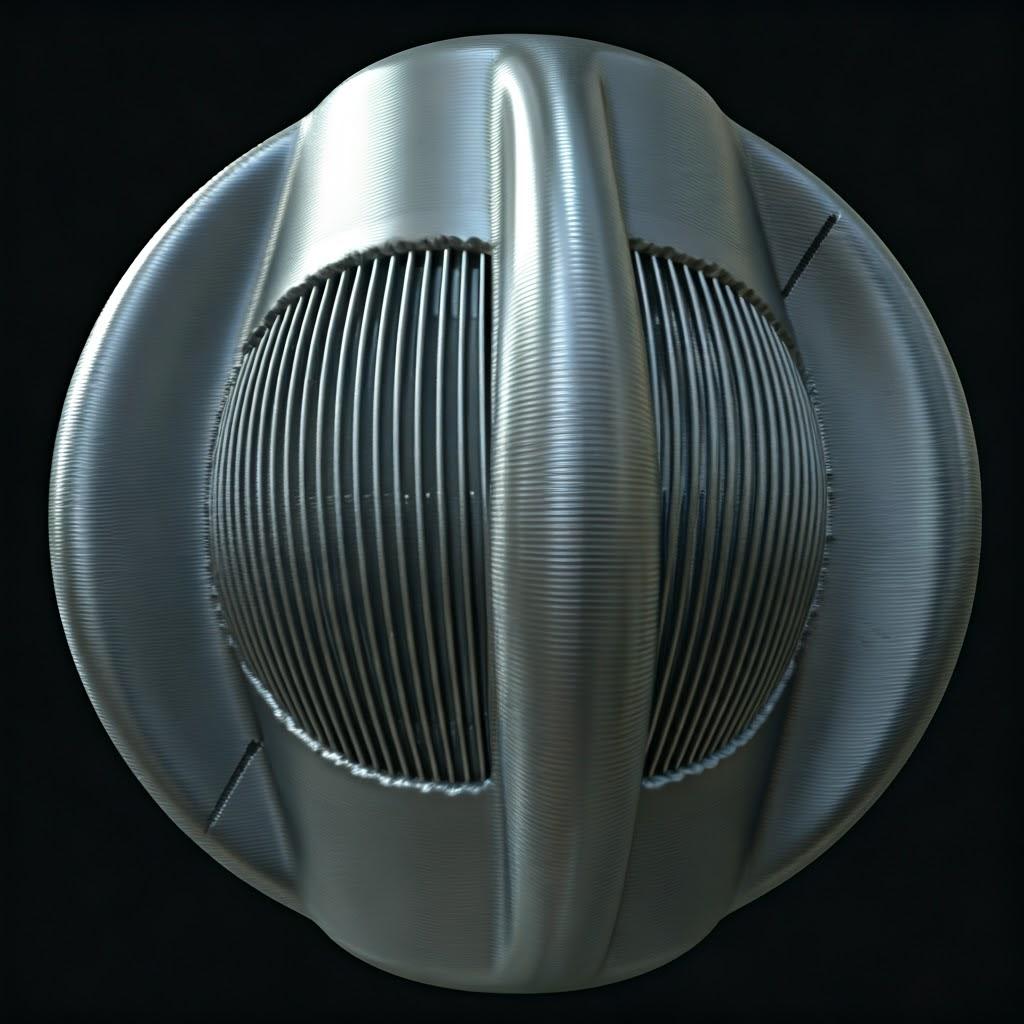
Proč 3D tisk z kovu pro přepážky raketových motorů? Výhody oproti běžným metodám
Rozhodnutí o zavedení aditivní výroby kovů (AM) pro kritické komponenty, jako jsou přepážky raketových motorů, není jen o přijetí novinky, ale o hmatatelných technických a ekonomických výhodách, které přímo odstraňují nedostatky tradičních výrobních technik (odlévání, kování, obrábění, pájení/svařování). Pro letecké inženýry a manažery nákupu, kteří hodnotí výrobní metody, je pochopení těchto výhod klíčem k využití plného potenciálu AM, zejména při práci se složitými geometriemi a vysoce výkonnými superslitinami, jako jsou IN718 a Haynes 282.
1. Bezprecedentní volnost designu a geometrická složitost:
- Tradiční omezení: Obrábění se potýká s vnitřními rysy, podříznutími a složitými křivkami. Představte si, že se snažíte obrobit složité, hladce zakřivené chladicí kanály hluboko uvnitř masivního bloku kovu. Odléváním lze dosáhnout určité složitosti, ale často chybí přesnost a vyžaduje sekundární obrábění. Spojování více jednoduchých dílů přináší slabá místa a zvyšuje složitost montáže.
- Výhoda AM: AM vytváří díly vrstvu po vrstvě přímo z 3D modelu CAD. Tento zásadní rozdíl osvobozuje konstruktéry od mnoha tradičních výrobních omezení.
- Interní kanály: Společnost AM vyniká vytvářením složitých vnitřních chladicích kanálů, které se přesně přizpůsobují tvaru přepážky (konformní chlazení). To umožňuje vysoce efektivní tepelné řízení, které má zásadní význam pro ochranu přepážek a čel vstřikovačů před extrémními teplotami. Kanály mohou mít zakřivené dráhy, různý průřez a mohou zasahovat do oblastí nepřístupných vrtáním nebo frézováním.
- Optimalizované topologie: Konstruktéři mohou pomocí softwaru pro optimalizaci topologie odstranit materiál z oblastí s nízkým namáháním a vytvořit tak lehké, ale pevné konstrukce přepážek. Často tak vznikají organické, mřížkovité geometrie, které nelze obrábět konvenčním způsobem, ale pro AM je to snadné. Odlehčení je v leteckém průmyslu klíčové pro maximalizaci nosnosti.
- Akustické ladění: Geometrie přepážek významně ovlivňuje jejich akustické tlumicí vlastnosti. AM umožňuje vytvářet složité vnitřní prvky, rezonanční komory nebo specifické povrchové struktury, které jsou navrženy tak, aby pohlcovaly nebo rozptylovaly akustickou energii na cílových frekvencích nestability účinněji než jednoduché pevné tvary.
- Integrované funkce: Prvky, jako jsou montážní body, otvory pro senzory nebo vedení průtoku, mohou být integrovány přímo do přepážky během procesu tisku, což snižuje počet dílů a montážních kroků.
2. Konsolidace částí:
- Tradiční přístup: Složité sestavy přepážek se mohou skládat z více strojně opracovaných nebo odlitých dílů, které je třeba přesně připevnit a spojit (např. svařit nebo připájet). Každý spoj představuje potenciální místo poruchy, vyžaduje kontrolu a zvyšuje hmotnost a čas montáže.
- Výhoda AM: AM umožňuje tisk celé složité sestavy přepážek jako jediné monolitické součásti.
- Eliminace kloubů: To odstraňuje rizika spojená se svary nebo pájkami v prostředí s vysokým namáháním a vysokou teplotou. Monolitické díly jsou často konstrukčně lepší.
- Snížený počet dílů: Zjednodušuje správu zásob, logistiku dodavatelského řetězce a konečnou montáž motoru.
- Snížení hmotnosti: Eliminace spojovacích prvků, přírub a překrývajícího se materiálu potřebného ke spojení přispívá k celkové úspoře hmotnosti.
3. Zrychlený vývoj a rychlé prototypování:
- Tradiční časové osy: Vytváření nástrojů pro odlévání nebo složité obráběcí sestavy vyžaduje značný čas a investice. Iterace návrhu tradičně zahrnuje opakování těchto zdlouhavých procesů.
- Výhoda AM: AM je proces bez použití nástrojů. Přechod od upraveného modelu CAD k fyzickému prototypu lze často provést během několika dnů nebo týdnů, nikoli měsíců.
- Rychlejší iterace: Inženýři mohou rychle testovat různé geometrie přepážek (např. různý počet paprsků, provedení kanálů, tlumicí prvky) a najít optimální konfiguraci pro stabilitu a tepelný výkon. Tato rychlá zpětná vazba výrazně zkracuje vývojový cyklus motoru.
- Snížení nákladů na vývoj: I když se jednotlivé díly AM mohou zpočátku zdát drahé, možnost rychlé iterace a vyhnutí se nákladům na nástroje může výrazně snížit celkové náklady na vývojový program.
4. Efektivní využití materiálu a snížení množství odpadu:
- Tradiční odpad: Při subtraktivní výrobě, zejména při obrábění z předvalků, může vznikat značné množství odpadního materiálu (třísek a hoblin). U drahých superslitin, jako je IN718 nebo Haynes 282, představuje tento odpad značné náklady.
- Výhoda AM: AM je aditivní proces, při kterém se používá pouze materiál potřebný k výrobě dílu a některé podpůrné struktury. Přestože je nutné provádět určitý management prášku a odstraňovat podpůrné prvky, celkové využití materiálu je obvykle mnohem vyšší než u subtraktivních metod.
- Úspora nákladů: Snížení spotřeby surovin se přímo promítá do nižších nákladů na součástky, zejména v případě poměru "buy-to-fly", který je běžný v leteckém průmyslu.
- Udržitelnost: Menší produkce odpadu přispívá k ekologičtějším výrobním postupům.
5. Vhodnost pro vysoce výkonné materiály:
- Výzvy při obrábění: Superslitiny jako IN718 a Haynes 282 jsou notoricky známé jako obtížně obrobitelné díky své vysoké pevnosti, houževnatosti a tvrdosti. To vede k pomalému obrábění, rychlému opotřebení nástrojů a zvýšeným výrobním nákladům.
- Výhoda AM: Zatímco tisk superslitin představuje vlastní řadu výzev (vyžaduje pečlivou kontrolu procesu), procesy AM, jako je laserová fúze v práškovém loži (L-PBF) a tavení elektronovým svazkem (EBM), jsou vhodné pro tavení a tavení těchto vysokoteplotních materiálů vrstvu po vrstvě.
- Přizpůsobivost procesů: Parametry AM (výkon laseru, rychlost skenování, zaostření paprsku, tloušťka vrstvy, teplota v komoře) lze přesně řídit a optimalizovat pro konkrétní superslitiny, aby bylo dosaženo hustých a vysoce kvalitních dílů s žádoucí mikrostrukturou a mechanickými vlastnostmi. Společnosti jako Met3dp se specializují na optimalizaci těchto parametrů pomocí svých pokročilých tiskových systémů a vysoce kvalitních kovových prášků.
Srovnávací souhrnná tabulka:
Vlastnosti | Tradiční výroba (obrábění/odlévání/spojování) | Výroba aditiv kovů (AM) | Výhody AM pro přepážky |
---|---|---|---|
Geometrická složitost | Omezené, zejména vnitřní funkce | Vysoká, umožňuje složité vnitřní kanály, mřížky | Optimalizované chlazení, akustický útlum, možnost odlehčení |
Konsolidace částí | Vyžaduje spojování více částí | Umožňuje monolitickou jednodílnou konstrukci | Eliminuje spoje (slabá místa), snižuje počet dílů, zjednodušuje montáž |
Rychlost vývoje | Pomalé (nástroje, vícestupňový proces) | Rychlé (bez použití nástrojů, přímo z CAD) | Rychlá tvorba prototypů a iterace návrhu, kratší vývojové cykly |
Materiálový odpad | Vysoká (subtraktivní procesy) | Nízká (aditivní proces) | Úspora nákladů na drahé superslitiny, udržitelnější provoz |
Doba realizace | Dlouhé (nástroje, více operací) | Potenciálně kratší (zejména u složitých dílů) | Rychlejší dodání prototypů a potenciálně malosériové výroby |
Manipulace se superslitinou | Obtížné a nákladné obrábění | Vhodné (L-PBF, EBM), i když vyžaduje odborné znalosti | Umožňuje použití ideálních vysokoteplotních materiálů bez extrémních nákladů na obrábění |
Počáteční náklady (jednorázové) | Může být nižší pro velmi jednoduché tvary/velký objem | U jednoduchých dílů může být vyšší, u složitých konkurenční | Nákladově efektivní pro složité geometrie, výhody konsolidace dílů |
Náklady na nástroje | Vysoká (formy, zápustky, přípravky) | Žádný | Eliminuje velké počáteční investice, flexibilní výroba |
Export do archů
Závěr pro zadávání veřejných zakázek a inženýrskou činnost:
U přepážek raketových motorů, kde je stále více zapotřebí složitých geometrií pro tepelné řízení a akustický útlum a kde jsou nezbytné vysokoteplotní superslitiny, jsou výhody technologie AM pro kovy přesvědčivé. Umožňuje vytvářet komponenty, které jsou potenciálně lehčí, účinnější, spolehlivější (díky konsolidaci dílů) a rychleji se vyvíjejí než ty, které se vyrábějí konvenčním způsobem. I když jsou odborné znalosti v oblasti řízení procesů, vědy o materiálech a následného zpracování klíčové, partnerství se znalým poskytovatelem AM, jako je Met3dp, který nabízí jak pokročilé tiskové zařízení, tak optimalizované vysoce kvalitní kovové prášky, umožňuje leteckým společnostem plně využít těchto výhod. Přechod na AM u těchto kritických dílů není jen trendem, ale’strategickým krokem ke zvýšení schopností pohonných systémů a konkurenceschopnosti v náročném leteckém odvětví.
Zaměření na materiál: superslitiny IN718 a Haynes 282 pro extrémní prostředí
Výběr materiálů pro součásti raketových motorů je dán mimořádně náročným provozním prostředím: extrémní teploty (často přesahující 1000 °C, ve spalovacím jádře mohou dosáhnout až 3000 °C), vysoké tlaky, náročné tepelné cykly, intenzivní vibrace a vystavení korozivním produktům spalování. Přepážky raketových motorů, které se nacházejí přímo v této nehostinné zóně nebo v její blízkosti, vyžadují materiály, které si v těchto podmínkách zachovávají výjimečné mechanické vlastnosti a odolnost vůči okolnímu prostředí. Superslitiny na bázi niklu jsou pro takové aplikace jako stvořené a mezi nimi vynikají Inconel 718 (IN718) a Haynes 282, které jsou obzvláště vhodné pro aditivní výrobu. Pochopení jejich vlastností je zásadní pro inženýry navrhující přepážky a manažery nákupu, kteří zajišťují materiály a výrobní služby.
Co jsou superslitiny?
Superslitiny jsou kovové slitiny, obvykle na bázi niklu, kobaltu nebo železa, které se vyznačují mimořádnou mechanickou pevností, odolností proti tečení (deformace při dlouhodobém namáhání za vysoké teploty), dobrou stabilitou povrchu a výjimečnou odolností proti korozi a oxidaci při zvýšených teplotách (obvykle nad 540 °C nebo 1000 °F). Jejich výkonnost závisí na složité mikrostruktuře, která se často vyznačuje austenitovou matricí s centrovanou krychlí (FCC), zesílenou precipitáty (jako je gama prvočíslo γ’ a gama dvojčíslo γ”) a prvky zpevňujícími pevný roztok.
Inconel 718 (IN718 / slitina 718): Zavedený pracovní kůň
IN718 je pravděpodobně nejpoužívanější superslitinou na bázi niklu díky své vynikající kombinaci vlastností, dobré zpracovatelnosti (včetně svařitelnosti a tisknutelnosti) a relativně nižší ceně ve srovnání s některými jinými vysoce výkonnými superslitinami.
- Složení: Především nikl (Ni), chrom (Cr), železo (Fe), niob+tantal (Nb+Ta), molybden (Mo), titan (Ti), hliník (Al). Klíčové zpevnění pochází z precipitace γ” (Ni3Nb) a γ’ (Ni3(Al,Ti)) fází v matrici FCC.
- Klíčové vlastnosti:
- Vysoká pevnost: Vynikající pevnost v tahu, v kluzu, při tečení a při roztržení až do teploty přibližně 700 °C (1300 °F). Jeho pevnost je z velké části odvozena od precipitace fáze γ”, která vyžaduje specifický cyklus tepelného zpracování.
- Dobrá odolnost proti korozi: Vysoký obsah chromu zajišťuje dobrou odolnost proti oxidaci a korozi v různých prostředích, včetně spalovacích atmosfér.
- Vynikající svařitelnost/tiskovatelnost: V porovnání s mnoha jinými precipitačně zpevněnými superslitinami vykazuje IN718 vynikající odolnost proti deformačnímu praskání při svařování nebo při tepelných cyklech AM po vrstvách. Díky tomu je relativně snadnější zpracovávat ji pomocí L-PBF a EBM, čímž se dosahuje hustých dílů bez trhlin.
- Dobrá životnost při únavě: Důležité pro součásti vystavené vibračnímu zatížení.
- Široká dostupnost a databáze: O jeho vlastnostech a zpracování existují rozsáhlé údaje, které poskytují jistotu konstruktérům a výrobcům.
- Úvahy o aditivní výrobě:
- IN718 je jedním z nejvyspělejších materiálů pro kovové AM. Optimalizované parametry pro L-PBF a EBM jsou dobře známé.
- Vyžaduje následné tepelné zpracování (žíhání v roztoku a stárnutí) pro vytvoření požadované mikrostruktury a dosažení optimálních mechanických vlastností. Často se používá izostatické lisování za tepla (HIP) k uzavření zbytkové vnitřní pórovitosti a dalšímu zlepšení únavových vlastností.
- Společnost Met3dp vyrábí vysoce kvalitní, plynem atomizovaný prášek IN718 speciálně optimalizovaný pro procesy AM, který zajišťuje vysokou sféricitu, dobrou tekutost a kontrolovanou distribuci velikosti částic, což je rozhodující pro dosažení konzistentních výtisků s vysokou hustotou.
- Omezení: I když je vynikající, její pevnost začíná výrazněji klesat nad 700 °C ve srovnání s některými pokročilejšími superslitinami. Pro součásti, u kterých dochází k ještě vyšším trvalým teplotám, může být nutné použít jiné materiály.
Haynes 282: Pokročilý uchazeč o vyšší teploty
Haynes 282 je novější generace superslitiny vyztužené gama-křemenem (γ’), která byla vyvinuta speciálně pro lepší pevnost při tečení, tepelnou stabilitu, vyrobitelnost a svařitelnost ve srovnání s jinými vysokopevnostními slitinami, jako je Waspaloy nebo R-41, a je určena pro aplikace v rozsahu teplot 650-930 °C (1200-1700 °F).
- Složení: Především nikl (Ni), chrom (Cr), kobalt (Co), molybden (Mo), titan (Ti), hliník (Al) s příměsemi, jako je bór (B) pro zvýšení odolnosti proti tečení. Její zpevnění je do značné míry založeno na precipitaci fáze γ’.
- Klíčové vlastnosti:
- Vynikající pevnost v tahu: Nabízí výrazně lepší odolnost proti tečení než IN718 a Waspaloy, zejména v rozsahu teplot 750 °C – 900 °C. To má zásadní význam pro součásti dlouhodobě zatěžované při velmi vysokých teplotách.
- Vynikající tepelná stabilita: Odolává mikrostrukturní degradaci při dlouhodobém vystavení vysokým teplotám.
- Dobrá odolnost proti oxidaci: Srovnatelné nebo lepší než jiné vysoce výkonné superslitiny.
- Dobrá vyrobitelnost: Je navržen pro lepší svařitelnost a odolnost proti deformačnímu praskání ve srovnání s podobně pevnými slitinami, jako je Waspaloy, takže je vhodný pro AM.
- Dobrá životnost při únavě: Dobře si zachovává pevnost při cyklickém zatížení za vysokých teplot.
- Úvahy o aditivní výrobě:
- Vývoj procesu pro Haynes 282 je sice v oblasti AM novější než IN718, ale rychle dozrává. Dosažení optimálních vlastností vyžaduje pečlivou kontrolu parametrů AM a následného tepelného zpracování (žíhání v roztoku + vícestupňové stárnutí).
- Jeho dobrá svařitelnost se promítá do relativně dobré tisknutelnosti, i když potenciálně vyžaduje přísnější kontrolu procesu než IN718, aby se zvládla zbytková napětí a zabránilo se defektům.
- Klíčová je dostupnost vysoce kvalitního prášku Haynes 282 vhodného pro AM. Dodavatelé zaměřující se na pokročilou výrobu prášků, jako je Met3dp využívající technologie plynové atomizace a PREP, jsou nezbytní pro zajištění prášků s potřebnou čistotou, sféricitou a distribucí velikosti částic pro náročné aplikace.
- Aplikace Niche: Ideální pro přepážky nebo jiné součásti motoru, které trvale pracují při teplotách, při nichž se pevnost při tečení IN718’ stává okrajovou, což posouvá výkonnostní hranice dále.
Zdůvodnění výběru materiálu pro přepážky:
Volba mezi IN718 a Haynes 282 pro konkrétní přepážku raketového motoru závisí na podrobné analýze provozních podmínek:
- Špičkové a trvalé teploty: Pokud provozní teploty trvale přesahují ~700-750 °C, zejména při značném mechanickém zatížení (tlakové rozdíly, vibrace), stává se vynikající pevnost v tečení Haynes 282’ velmi výhodnou.
- Složitost a tisknutelnost: IN718 má v současné době zavedenější a potenciálně šetrnější zpracovatelské okno pro AM, které by mohlo být upřednostněno pro extrémně složité geometrie, kde je nejdůležitější minimalizovat vady tisku, za předpokladu, že jeho vlastnosti jsou dostatečné.
- Náklady: IN718 je obecně levnější než Haynes 282, a to jak z hlediska nákladů na suroviny, tak i z hlediska případné zralosti zpracování. Pokud IN718 splňuje požadavky na výkon, může být ekonomicky výhodnější volbou.
- Schopnost dodavatele: Rozhodující je schopnost vybraného poskytovatele služeb AM spolehlivě zpracovat vybranou slitinu. To zahrnuje ověřené procesní parametry, vhodné možnosti následného zpracování (vakuové pece pro tepelné zpracování, HIP) a přísnou kontrolu kvality.
Úloha Met3dp’v materiálním zajištění:
Společnost jako Met3dp hraje zásadní roli v umožnění používání těchto pokročilých materiálů. Jejich schopnosti jsou klíčové v základu procesu AM:
- Pokročilá výroba prášků: S využitím špičkových technik v oboru, jako je vakuová indukční tavná plynová atomizace (VIGA) a plazmový proces s rotujícími elektrodami (PREP), může společnost Met3dp vyrábět prášky superslitin (včetně IN718 a případně Haynes 282 nebo vlastních variant) s:
- Vysoká čistota: Minimalizace kontaminantů, které by mohly zhoršit vlastnosti materiálu.
- Vysoká sféricita: Zajištění dobré tekutosti prášku ve strojích AM, což vede k rovnoměrnému rozprostření vrstvy a konzistentnímu chování taveniny.
- Řízená distribuce velikosti částic (PSD): Optimalizace PSD pro vysokou hustotu balení a předvídatelné vlastnosti tání.
- Nízký obsah satelitu: Snížení problémů souvisejících s rozptylem prášku a možnými vadami.
- Materiálové znalosti: Díky desítkám let společných zkušeností v oblasti AM s kovy společnost Met3dp rozumí nuancím tisku náročných materiálů, jako jsou superslitiny, a může nabídnout poradenství při výběru materiálu a optimalizaci procesu.
- Integrovaná řešení: Díky nabídce vysoce kvalitních prášků a pokročilých tiskových systémů (jako jsou tiskárny SEBM, které jsou známé tím, že zvládají vysokoteplotní slitiny a snižují zbytkové napětí) poskytuje společnost Met3dp komplexní řešení pro výrobce v leteckém průmyslu, kteří chtějí implementovat AM pro kritické komponenty, jako jsou přepážky.
Závěrem lze říci, že IN718 a Haynes 282 představují vynikající materiál pro aditivně vyráběné přepážky raketových motorů, protože nabízejí potřebnou pevnost při vysokých teplotách a odolnost vůči vlivům prostředí. IN718 poskytuje osvědčené, spolehlivé a nákladově efektivní řešení pro mnoho aplikací, zatímco Haynes 282 posouvá teplotní odolnost dále pro náročnější scénáře. Úspěch výroby přepážek z těchto materiálů prostřednictvím AM do značné míry závisí na kvalitě vstupního prášku a odborných znalostech výrobního partnera, což podtrhuje význam specializovaných dodavatelů v dodavatelském řetězci pro letecký průmysl. Zdroje a související obsah
Design pro aditivní výrobu (DfAM): Optimalizace přepážek pro 3D tisk
Přechod z tradičních výrobních paradigmat na aditivní výrobu (AM) vyžaduje více než jen konverzi stávajícího souboru CAD. Aby inženýři skutečně využili výhod 3D tisku z kovu pro složité součásti, jako jsou přepážky raketových motorů, musí přijmout návrh pro aditivní výrobu (DfAM). DfAM je metodika, která zahrnuje navrhování dílů speciálně s cílem využít jedinečné schopnosti a zohlednit omezení procesů AM, jako je laserová fúze v práškovém loži (L-PBF) a tavení elektronovým svazkem (EBM). Uplatnění principů DfAM na přepážky raketových motorů může vést k výraznému zlepšení výkonu (tepelné řízení, akustický útlum), snížení hmotnosti a efektivity výroby. Spolupráce se zkušeným poskytovatelem služeb AM, který rozumí nuancím různých tiskových metod, je často pro úspěšné zavedení DfAM rozhodující.
Klíčové principy DfAM pro přepážky raketových motorů:
- Využití geometrické volnosti pro funkční vylepšení:
- Konformní chladicí kanály: Jedná se o jednu z nejvýkonnějších aplikací AM pro tepelně zatížené komponenty. Namísto rovných vyvrtaných otvorů umožňuje AM chladicí kanály přesně kopírovat složité obrysy povrchů přepážek a udržovat stálou vzdálenost od horkých spalin.
- Úvahy o návrhu: Rozhodující je průměr kanálku (obvykle >0,5-1 mm pro čistitelnost), poměr stran, minimální poloměry ohybu, hladké přechody a konstrukce pro tisk bez podpěr, pokud je to možné. Analýza CFD se používá k optimalizaci tras kanálů pro maximální odvod tepla tam, kde je to nejvíce potřeba.
- Výhody: Výrazné zlepšení účinnosti chlazení, což vede ke snížení povrchových teplot přepážek, zvýšení životnosti součástí a potenciálně umožňuje vyšší provozní teploty motoru nebo použití materiálů s mírně nižšími teplotními limity.
- Optimalizované funkce akustického tlumení: Jednoduché pevné přepážky poskytují určité tlumení, ale AM umožňuje mnohem sofistikovanější konstrukce.
- Mřížové struktury: Začlenění vnitřních mřížkových nebo gyroidních struktur může výrazně zvětšit plochu uvnitř přepážky, čímž se zvýší rozptyl akustické energie prostřednictvím viskózních efektů. Hustota a typ buněk mřížky mohou být odstupňovány v celém dílu, aby se zaměřily na konkrétní frekvence nebo poskytly strukturální podporu v případě potřeby.
- Rezonanční komory: Konstrukce vnitřních Helmholtzových rezonátorů nebo složitých dutinových sítí naladěných na konkrétní problematické frekvence nestability může zajistit vysoce cílené akustické tlumení.
- Výhody: Účinnější potlačení nestabilit spalování v širším rozsahu provozních podmínek, což vede ke stabilnějšímu a spolehlivějšímu chodu motoru.
- Optimalizace průtokové cesty: Tvar přepážky ovlivňuje místní míchání pohonné hmoty a proudění plynu. Technologie AM umožňuje aerodynamicky optimalizované tvary, které mohou v případě potřeby obsahovat prvky, jako jsou usměrňovače proudění nebo generátory řízené turbulence, integrované přímo do struktury přepážky.
- Konformní chladicí kanály: Jedná se o jednu z nejvýkonnějších aplikací AM pro tepelně zatížené komponenty. Namísto rovných vyvrtaných otvorů umožňuje AM chladicí kanály přesně kopírovat složité obrysy povrchů přepážek a udržovat stálou vzdálenost od horkých spalin.
- Konsolidace částí:
- Strategie: Identifikujte sestavy přepážek, které byly dříve vyrobeny z více pájených nebo svařovaných součástí. Přepracujte je jako jediný monolitický díl AM.
- Úvahy: Zajistěte, aby konsolidovaný návrh bylo možné vyrobit pomocí AM (např. přístup pro odstranění prášku z vnitřních dutin). Analyzujte koncentrace napětí, abyste zajistili odolnost monolitického návrhu.
- Výhody: Eliminuje poruchy spojů, snižuje hmotnost, zjednodušuje montáž, zkracuje dodavatelský řetězec, zlepšuje integritu konstrukce.
- Odlehčení pomocí optimalizace topologie:
- Strategie: Použijte analýzu konečných prvků (MKP), abyste pochopili rozložení napětí v přepážce při provozním zatížení (tlak, vibrace, tepelné namáhání). Použijte software pro optimalizaci topologie k systematickému odstraňování materiálu z oblastí s nízkým namáháním při zachování strukturální integrity a funkčních ploch.
- Výsledek: Často vytváří organické konstrukce optimalizované pro zatížení, které jsou výrazně lehčí než tradiční konstrukce. Tyto složité tvary jsou pro AM ideální.
- Výhody: Snížení hmotnosti součástek je v letectví a kosmonautice zásadní pro zvýšení nosnosti a snížení nákladů na vypuštění.
- Navrhování pro vyrobitelnost (AM Constraints):
- Minimalizace podpůrné struktury: U L-PBF a EBM jsou často nutné podpůrné konstrukce, které slouží k ukotvení dílu na konstrukční desce, podpírají převislé prvky a odvádějí teplo. Podpěry však spotřebovávají další materiál, prodlužují dobu tisku, vyžadují odstranění (což může být obtížné, zejména u vnitřních kanálů) a mohou ovlivnit kvalitu povrchu.
- Techniky: Díl strategicky orientujte na konstrukční desce tak, abyste minimalizovali přesahy. Používejte samonosné úhly (u mnoha procesů/materiálů obvykle >40-45° od vodorovné roviny, i když se to liší). Navrhněte vnitřní kanály s kosočtvercovým nebo slzovitým průřezem namísto kruhového, aby byly samonosné. Používejte obětované prvky nebo konstrukce navržené pro snadnější odlomení.
- Minimální velikost prvku a tloušťka stěny: Procesy AM mají omezení týkající se nejmenších prvků, které mohou spolehlivě vyrábět. Příliš tenké stěny se mohou deformovat nebo se správně nerozlišují. Typické minimální tloušťky stěn se často pohybují v rozmezí 0,3-0,5 mm, ale do značné míry závisí na konkrétním stroji, materiálu a geometrii prvku.
- Odstranění prášku: U konstrukcí s vnitřními dutinami nebo složitými kanály zajistěte, aby byly k dispozici odpovídající otvory určené k odstranění nerozpuštěného prášku po sestavení. Zachycený prášek zvyšuje hmotnost a může být škodlivý. Zvažte vibrace nebo cesty proudění vzduchu pro odvádění prášku.
- Tepelný management během sestavování: Velmi velké nebo husté díly mohou být značně tepelně namáhány. DfAM může zahrnovat návrh odlehčovacích prvků nebo optimalizaci uspořádání sestavy, aby se zmírnily deformace a zkreslení. EBM se svým vysokoteplotním konstrukčním prostředím ze své podstaty snižuje tepelné gradienty a zbytkové napětí ve srovnání s L-PBF.
- Minimalizace podpůrné struktury: U L-PBF a EBM jsou často nutné podpůrné konstrukce, které slouží k ukotvení dílu na konstrukční desce, podpírají převislé prvky a odvádějí teplo. Podpěry však spotřebovávají další materiál, prodlužují dobu tisku, vyžadují odstranění (což může být obtížné, zejména u vnitřních kanálů) a mohou ovlivnit kvalitu povrchu.
Úvahy o pracovním postupu DfAM:
- Úzká spolupráce: Efektivní DfAM vyžaduje úzkou spolupráci mezi konstruktéry (kteří rozumí funkčním požadavkům) a specialisty na AM (kteří rozumí možnostem a omezením procesu). Poskytovatelé, jako je Met3dp, s hlubokými odbornými znalostmi materiálů a tiskových procesů, mohou nabídnout neocenitelné vstupy během fáze návrhu.
- Návrh řízený simulací: Důrazně se doporučuje využití CFD pro tepelnou analýzu a analýzu proudění, FEA pro strukturální analýzu a analýzu napětí a simulaci procesu AM k předvídání potenciálních problémů, jako je deformace nebo přehřátí během sestavování.
- Iterativní přístup: DfAM je často opakující se proces. Počáteční návrhy se vyhodnocují z hlediska vyrobitelnosti a výkonu a poté se zdokonalují na základě výsledků simulací nebo zpětné vazby od poskytovatele AM. Schopnost rychlého prototypování AM usnadňuje tuto opakující se smyčku.
Promyšleným uplatněním principů DfAM mohou konstruktéři překročit pouhou replikaci tradičně navržených přepážek pomocí AM a místo toho vytvořit komponenty nové generace, které nabízejí vynikající výkon, nižší hmotnost a vyšší spolehlivost, a plně tak využít transformační potenciál aditivní výroby v oblasti leteckých pohonů.
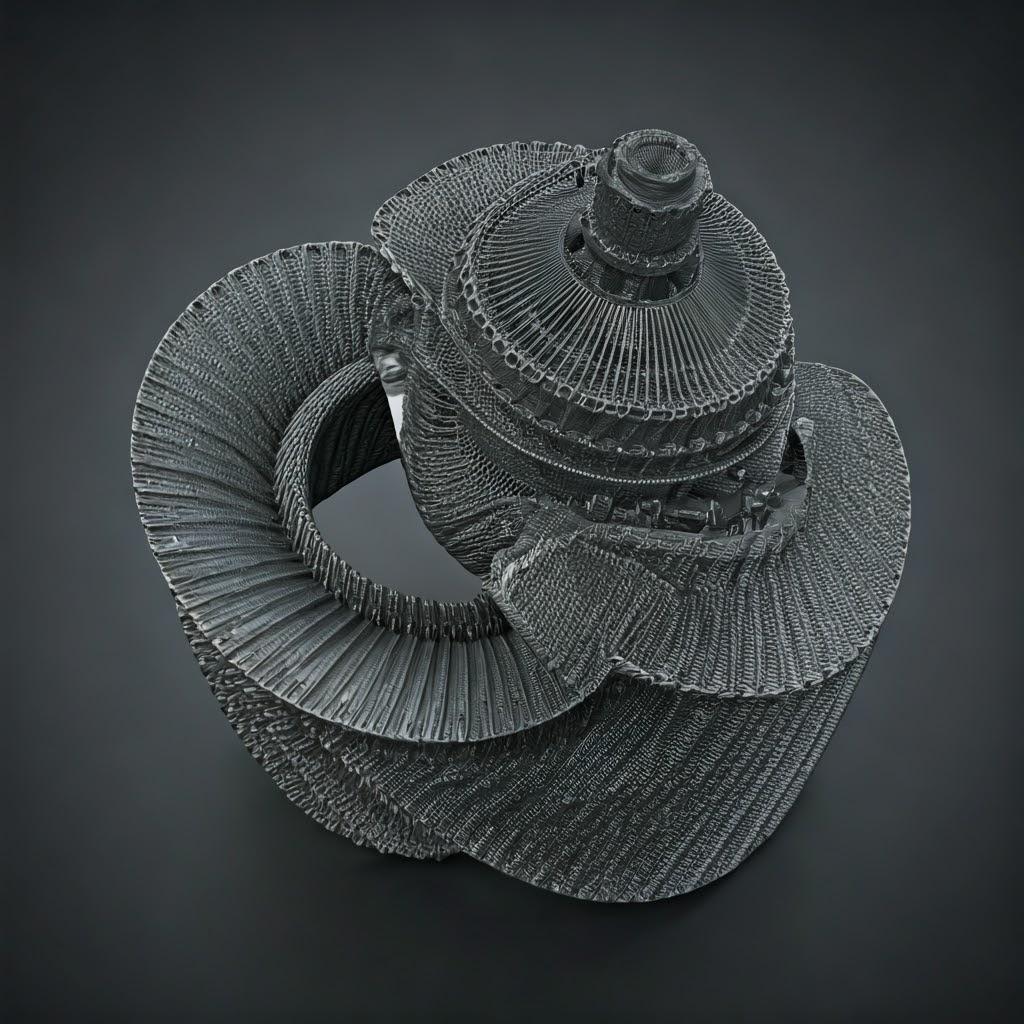
Dosažitelné tolerance, povrchová úprava a rozměrová přesnost u AM přepážek
Ačkoli aditivní výroba nabízí bezkonkurenční volnost při navrhování, je pro inženýry a manažery nákupu zásadní mít realistická očekávání ohledně dosažitelných tolerancí, povrchové úpravy a celkové rozměrové přesnosti komponent vyráběných technologií AM, zejména u kritických aplikací, jako jsou přepážky raketových motorů ze superslitin. Tyto faktory mají přímý vliv na lícování součástí, těsnění, dynamiku kapalin, tepelný výkon a potřebu následných dokončovacích operací. Konkrétní výsledky do značné míry závisí na zvoleném procesu AM (L-PBF vs. EBM), materiálu (IN718, Haynes 282), kalibraci stroje, geometrii součásti a krocích následného zpracování.
Rozměrová přesnost a tolerance:
Rozměrová přesnost znamená, jak přesně se konečné rozměry dílu shodují se jmenovitými rozměry uvedenými v modelu CAD. Tolerance definuje přípustný rozsah odchylek pro daný rozměr.
- Typické tolerance podle konstrukce:
- L-PBF (Laser Powder Bed Fusion): Obecně se má za to, že je schopen vyšší přesnosti a jemnějších rysů než EBM. Typické dosažitelné tolerance u dobře řízených procesů se často pohybují v rozmezí ±0,1 mm až ±0,2 mm (±0,004″ až ±0,008″) u menších rozměrů, případně se mírně zvyšují u větších dílů (např. ±0,1 % až ±0,2 % celkového rozměru). Specifické stroje a optimalizované procesy mohou lokálně dosáhnout ještě větších tolerancí.
- EBM (tavení elektronovým svazkem): EBM pracuje při vyšších teplotách, což snižuje zbytkové napětí, ale někdy může vést k mírně nižší rozměrové přesnosti ve srovnání s L-PBF kvůli faktorům, jako je tepelná roztažnost/kontrakce a potenciální vliv spékání prášku. Typické tolerance se mohou pohybovat v rozmezí ±0,2 mm až ±0,4 mm (±0,008 až ±0,016), i když se neustále pracuje na zlepšeních.
- Faktory ovlivňující přesnost:
- Kalibrace stroje: Pravidelná a přesná kalibrace systému skeneru, zaostření paprsku a konstrukční platformy je nezbytná.
- Tepelné účinky: Nerovnoměrné zahřívání a chlazení během sestavování může způsobit deformace a zkreslení, které ovlivní konečné rozměry. Svou roli hrají procesní parametry, strategie skenování a řízení teploty v konstrukční komoře (zejména zvýšená teplota EBM).
- Geometrie a velikost dílu: Velké, objemné díly nebo díly s výraznými změnami průřezu jsou náchylnější k tepelnému zkreslení. Vnitřní napětí kumulující se v mnoha vrstvách může ovlivnit přesnost.
- Vlastnosti materiálu: Proces ovlivňuje tepelná vodivost, koeficient roztažnosti a chování taveniny konkrétní superslitiny.
- Podpůrné struktury: Způsob podepření dílu může ovlivnit kumulaci napětí a případné deformace při demontáži.
- Následné zpracování: Odlehčovací cykly a cykly HIP mohou způsobit drobné, obecně předvídatelné rozměrové změny, které je třeba zohlednit.
- Dosažení přísnějších tolerancí: U kritických prvků, jako jsou styčné plochy, průměry těsnění nebo rozhraní vyžadující vysokou přesnost, nemusí být tolerance AM od výroby dostatečné. V těchto případech, po obrábění je zaměstnán. Oblasti vyžadující přísné tolerance se často navrhují s přídavným materiálem (přídavek na obrábění nebo “zásoba”), který se po sestavení AM a tepelném zpracování přesně odstraní pomocí CNC obrábění. Tolerance dosažitelné dodatečným obráběním jsou srovnatelné s konvenčními standardy obrábění (např. ±0,01 mm až ±0,05 mm nebo lepší).
Povrchová úprava (drsnost):
Povrchová úprava, obvykle kvantifikovaná pomocí průměrné drsnosti (Ra), popisuje strukturu povrchu součásti. Díly AM mají přirozeně drsnější povrch než obráběné povrchy, což je dáno konstrukcí po vrstvách a částečně roztavenými částicemi prášku ulpívajícími na povrchu.
- Typická drsnost povrchu (Ra):
- L-PBF: Obecně poskytuje lepší povrchovou úpravu než EBM. Hodnoty Ra se často pohybují od 6 µm do 15 µm (přibližně 240 µin až 600 µin) na svislých nebo téměř svislých stěnách, ale mohou být výrazně drsnější (např. >20 µm) na površích směřujících nahoru a zejména dolů (podepřené povrchy).
- EBM: V porovnání s L-PBF jsou povrchy obvykle drsnější, často s hodnotami Ra od 20 µm do 40 µm (přibližně 800 µin až 1600 µin) nebo vyššími. To je částečně způsobeno větší velikostí paprskového bodu a vyšším příkonem energie, což vede k většímu spékání prášku.
- Faktory ovlivňující povrchovou úpravu:
- Tloušťka vrstvy: Tenčí vrstvy obecně vedou k hladším povrchům, zejména u šikmých prvků, ale prodlužují dobu vytváření.
- Distribuce velikosti částic (PSD): Jemnější prášky mohou přispět k lepší povrchové úpravě, ale mohou představovat problém z hlediska tekutosti a manipulace.
- Parametry procesu: Výkon laserového/elektronového paprsku, rychlost skenování a vzdálenost mezi šrafami ovlivňují dynamiku taveniny a kvalitu povrchové taveniny.
- Orientace na část: Svislé stěny bývají hladší než šikmé nebo vodorovné plochy. Povrchy směřující dolů, které jsou podepřeny konstrukcemi, jsou po odstranění podpěr obvykle nejhrubší.
- Průtok plynu (L-PBF): U L-PBF může kvalitu povrchu ovlivnit proudění inertního plynu, který odstraňuje vedlejší produkty zpracování.
- Důsledky drsnosti povrchu:
- Dynamika tekutin: Drsné vnitřní povrchy kanálů mohou zvyšovat tlakovou ztrátu a ovlivňovat charakteristiky proudění.
- Termotransfer: Drsnost povrchu může ovlivnit součinitele přestupu tepla.
- Únavový život: Drsné povrchy mohou sloužit jako iniciační místa pro vznik únavových trhlin, což může snížit životnost součásti při cyklickém zatížení. Zpracování HIP má zásadní význam pro zmírnění účinků povrchové a podpovrchové pórovitosti spojené s drsností.
- Těsnění: Povrchy ve stavu, v jakém jsou, jsou obecně nevhodné pro dynamická nebo vysokotlaká těsnění.
- Zlepšení povrchové úpravy: Když je potřeba hladší povrch:
- Post-Machining: Nejúčinnější pro vnější povrchy nebo přístupné vnitřní prvky vyžadující vysokou hladkost a těsné tolerance.
- Obrábění abrazivním tokem (AFM): Používá se k leštění vnitřních kanálů a složitých průchodů prouděním brusného média.
- Hromadné dokončování: Techniky jako bubnové nebo vibrační dokončování mohou zlepšit celkovou hladkost povrchu, ale nemusí být vhodné pro jemné prvky nebo zachování ostrých hran.
- Elektrolytické leštění: Může poskytnout velmi hladký povrch, ale vyžaduje specifické elektrolyty a kontrolu procesu.
Závazek společnosti Met3dp’:
Dosažení konzistentní rozměrové přesnosti a řízení kvality povrchu vyžaduje hluboké znalosti procesu a důkladnou kontrolu kvality. Společnosti jako Met3dp, které se zaměřují na průmyslové aplikace v odvětvích, jako je letectví a kosmonautika, upřednostňují:
- Vysoce kvalitní prášky: Použití prášků s kontrolovanou sféricitou a PSD přispívá ke stabilnějším taveninám a lepší kvalitě povrchu.
- Pokročilé tiskové systémy: Využití tiskáren s přesnou kalibrací, stabilním tepelným managementem (včetně funkcí SEBM výhodných pro superslitiny) a optimalizovanými procesními parametry.
- Řízení a monitorování procesů: Zavedení důsledných kontrol kvality a případného monitorování na místě, aby se zajistila konzistence mezi jednotlivými stavbami.
- Odborné znalosti v oblasti následného zpracování: Pochopení vlivu tepelného zpracování a HIP na rozměry a nabídka integrovaných řešení po obrábění.
Souhrnná tabulka: Tolerance AM přepážek & povrchová úprava
Parametr | Typický rozsah L-PBF | Typický rozsah EBM | Klíčové ovlivňující faktory | Metody zlepšování |
---|---|---|---|---|
Tolerance (ve stavu po dokončení) | ±0,1 až ±0,2 mm (nebo ±0,1-0,2 %) | ±0,2 až ±0,4 mm (nebo ±0,2-0,4 %) | Kalibrace stroje, tepelné účinky, geometrie, materiál | Optimalizace procesu, následné obrábění (pro kritické) |
Povrchová úprava Ra (podle stavu) | 6-15 µm (svislé stěny) >20 µm (směrem dolů) | 20-40+ µm | Tloušťka vrstvy, PSD, parametry, orientace, typ procesu | Post-Machining, AFM, hromadné dokončování, leštění |
Export do archů
Inženýři, kteří navrhují raketové přepážky AM, musí specifikovat požadované tolerance a povrchové úpravy na základě funkčních požadavků, přičemž si uvědomují, že přísnější specifikace často vyžadují kroky následného zpracování, což zvyšuje náklady a dobu realizace. Pro úspěšnou výrobu komponent je nezbytná jasná komunikace s dodavatelem AM, pokud jde o kritické vlastnosti a kritéria přijatelnosti.
Základní kroky následného zpracování aditivně vyráběných přepážek
Samotným vyjmutím kovové přepážky 3D tištěného raketového motoru ze stavební desky výrobní proces zdaleka nekončí. U kritických leteckých součástí vyrobených ze superslitin, jako je IN718 nebo Haynes 282, je třeba provést řadu zásadních kroků následného zpracování, aby se uvolnila vnitřní napětí, odstranily podpůrné struktury, dosáhlo požadované mikrostruktury materiálu a mechanických vlastností, zajistila rozměrová přesnost, dosáhlo se požadované povrchové úpravy a ověřila se integrita součásti. Tyto kroky jsou nepominutelné pro zajištění bezpečnosti, spolehlivosti a výkonu finální součásti v náročném prostředí raketového motoru. Zanedbání nebo nesprávné provedení kterékoli z těchto fází může ohrozit celou součást.
Typický pracovní postup následného zpracování pro AM přepážky ze superslitiny:
- Úleva od stresu:
- Účel: Rychlé cykly ohřevu a chlazení, které jsou vlastní L-PBF a v menší míře EBM, vytvářejí v tištěném dílu značná zbytková napětí. Tato napětí mohou způsobit deformace (zejména po vyjmutí z konstrukční desky), praskání a snížení mechanických vlastností. Odlehčení napětí je tepelný cyklus určený k uvolnění těchto vnitřních napětí předtím, než je díl odstraněn z konstrukční desky nebo je podroben výrazné manipulaci/obrábění.
- Proces: Obvykle se jedná o zahřátí dílu (často ještě připevněného na konstrukční desce) v peci s řízenou atmosférou (inertní plyn jako argon nebo vakuum, aby se zabránilo oxidaci) na teplotu nižší než teplota stárnutí nebo žíhání roztokem, jeho udržování po určitou dobu a následné pomalé ochlazování. Přesné parametry závisí na slitině a geometrii dílu. Díly EBM, vyráběné při vyšších teplotách, mají obecně nižší zbytkové napětí, ale přesto mohou mít prospěch z cyklu uvolňování napětí.
- Důležitost: První krok, který je důležitý, aby se zabránilo praskání nebo deformaci při následné manipulaci a odstraňování podpěr.
- Vyjmutí dílu ze stavební desky:
- Proces: Obvykle se používá elektroerozivní obrábění (EDM), řezání nebo někdy frézování/broušení, v závislosti na geometrii dílu a materiálu.
- Úvahy: Je třeba postupovat opatrně, aby nedošlo k poškození dílu. Vrstva rozhraní mezi dílem a deskou je často navržena tak, aby se dala snadněji oddělit.
- Odstranění podpůrné konstrukce:
- Účel: Odstraňte dočasné struktury použité během procesu sestavování.
- Proces: Může se jednat o jednoduché ruční lámání/řezání pro přístupné podpěry až po složitější obrábění (frézování, broušení) nebo elektroerozivní obrábění pro podpěry ve složitých nebo vnitřních místech. To může být jeden z nejpracnějších a nejnáročnějších kroků následného zpracování, zejména u přepážek se složitými vnitřními kanály nebo mřížovými strukturami.
- Výzvy: Riziko poškození povrchu dílu, obtížný přístup k vnitřním podpěrám, zajištění úplného odstranění. DfAM hraje zásadní roli při navrhování snadno odstranitelných podpěr.
- Tepelné zpracování (vývoj mikrostruktury a vlastností):
- Účel: Superslitiny AM ve stavu, v jakém jsou vyrobeny, obvykle nemají optimální mikrostrukturu ani mechanické vlastnosti (pevnost, tažnost, odolnost proti tečení) požadované pro náročné aplikace. Tepelné zpracování homogenizuje mikrostrukturu, rozpouští nežádoucí fáze vzniklé během tisku a řízeně precipituje zpevňující fáze (γ’ a/nebo γ”).
- Proces (příklad pro IN718):
- Žíhání roztoků: Zahřátí na vysokou teplotu (např. ~980 °C – 1065 °C v závislosti na požadovaných vlastnostech), aby se rozpustily existující sraženiny a homogenizovala matrice, a následné rychlé ochlazení.
- Léčba stárnutí: Dvoustupňový proces stárnutí (např. ~ 720 °C a následně ~ 620 °C) pro vysrážení zpevňujících fází γ’ a γ” v optimální velikosti a rozložení.
- Proces (příklad pro Haynes 282): Obvykle zahrnuje vyšší teplotu žíhání roztoku (např. ~1135 °C – 1177 °C) a následný vícestupňový proces stárnutí (např. ~1010 °C a následně ~790 °C).
- Prostředí: Musí se provádět ve vakuu nebo v peci s řízenou inertní atmosférou, aby se zabránilo oxidaci, zejména při vysokých teplotách. Přesné řízení teploty a rychlosti ochlazování jsou rozhodující.
- Důležitost: Naprosto nezbytné pro dosažení požadovaných mechanických vlastností (pevnost v tahu, mez kluzu, odolnost proti tečení, únavová životnost) stanovených pro danou aplikaci. Vlastnosti ve stavu, v jakém se vyrábí, jsou obecně horší.
- Izostatické lisování za tepla (HIP):
- Účel: Uzavření vnitřních pórů (mikrodutin), které mohou zůstat po procesu AM v důsledku faktorů, jako je zachycený plyn nebo neúplná fúze. Pórovitost působí jako koncentrátor napětí a výrazně zhoršuje mechanické vlastnosti, zejména únavovou životnost a lomovou houževnatost. HIP materiál zhutňuje, čímž zlepšuje jeho integritu.
- Proces: Díl je vystaven vysoké teplotě (obvykle těsně pod teplotou žíhání roztoku) a vysokému tlaku (např. 100-200 MPa nebo 15 000-30 000 psi) za použití inertního plynu (obvykle argonu) ve specializované nádobě HIP. Kombinace tepla a tlaku způsobí, že se vnitřní dutiny zhroutí a metalurgicky se uzavřou.
- Důležitost: Všeobecně se považuje za povinnou pro kritické letecké součásti, zejména ty, které jsou vystaveny únavovému zatížení. Výrazně zlepšuje mechanické vlastnosti, snižuje rozptyl dat a zlepšuje možnost kontroly. Často se provádí před krokem žíhání roztokem při tepelném zpracování nebo se s ním integruje.
- Povrchová úprava:
- Účel: Dosažení požadované drsnosti povrchu z funkčních důvodů (např. průtok kapalin, těsnění) nebo odstranění nedokonalostí povrchu, které by mohly působit jako iniciační místa únavy.
- Procesy (podle potřeby):
- CNC obrábění: Pro kritické rozměry, tolerance a hladké povrchy specifických prvků (např. styčných ploch, těsnicích drážek). Vyžaduje pečlivý návrh upínacích přípravků pro potenciálně složité tvary AM.
- Obrábění abrazivním tokem (AFM), extrudní broušení: K vyhlazení vnitřních kanálů a průchodů.
- Hromadné dokončování (bubnové, vibrační): Pro všeobecné odjehlování a vyhlazování, pokud je to vhodné pro geometrii dílu.
- Ruční broušení/leštění: Pro lokální dokončovací práce nebo složité tvary.
- Kontrola a nedestruktivní zkoušení (NDT):
- Účel: Ověření celistvosti finálního dílu a zajištění, aby před uvedením do provozu splňoval všechny specifikace a normy kvality.
- Běžné techniky pro letecké díly AM:
- Rozměrová kontrola: Použití souřadnicových měřicích strojů (CMM), laserového skenování nebo skenování strukturovaným světlem k ověření rozměrů a tolerancí podle modelu CAD.
- Počítačová tomografie (CT): Metoda založená na rentgenovém záření, která umožňuje 3D zobrazení vnitřní struktury dílu a umožňuje odhalit vnitřní dutiny, inkluze, trhliny a ověřit geometrii vnitřních kanálů. Stále důležitější pro složité díly AM.
- Dye Penetrant Inspection (DPI) nebo Fluorescent Penetrant Inspection (FPI): K odhalení trhlin porušujících povrch nebo pórovitosti.
- Ultrazvukové testování (UT): Dokáže odhalit podpovrchové vady, i když složité geometrie mohou být náročné.
- Vizuální kontrola: Důkladné vyšetření pod zvětšením.
- Důležitost: Konečná kontrola kvality, která zajistí, že přepážka nemá kritické vady a splňuje všechny technické požadavky. Důsledná nedestruktivní kontrola je standardní praxí pro letově kritický letecký hardware.
Schopnost dodavatele:
Provedení této složité sekvence kroků následného zpracování vyžaduje značné odborné znalosti, specializované vybavení (vakuové pece, jednotky HIP, systémy NDT) a robustní systémy řízení kvality (např. certifikace AS9100). Při výběru poskytovatele AM služeb pro přepážky raketových motorů je zásadní ověřit jeho vlastní schopnosti nebo zavedené vztahy s certifikovanými partnery pro všechny nezbytné fáze následného zpracování. Poskytovatel jako Met3dp, který se zaměřuje na poskytování komplexních řešení pro průmyslové aplikace, chápe kritičnost těchto kroků a integruje je do svých protokolů o zajištění kvality. Jejich znalosti přesahují rámec tisku a zahrnují celý výrobní řetězec potřebný pro komponenty letecké a kosmické kvality.
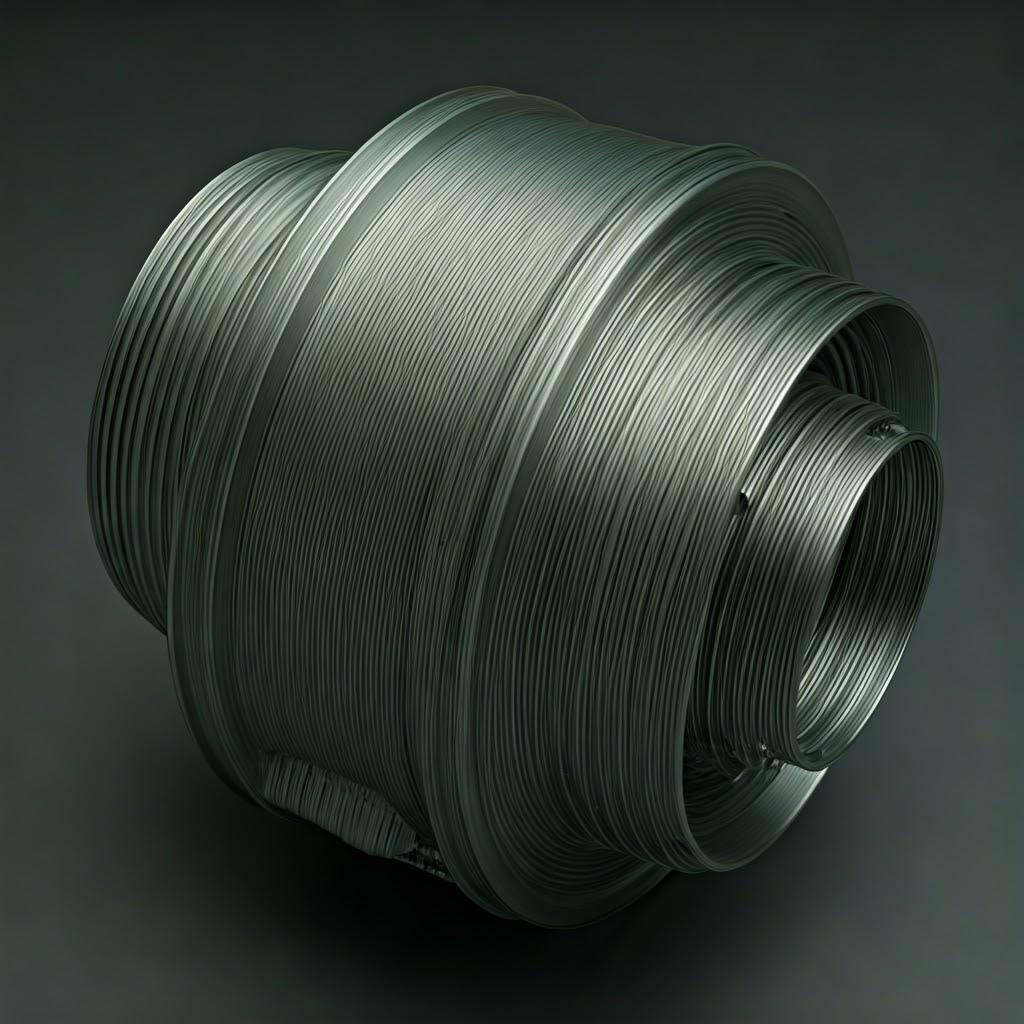
Překonávání běžných problémů při 3D tisku raketových motorů
Ačkoli aditivní výroba kovů otevírá významný potenciál pro výrobu pokročilých přepážek raketových motorů, není tento proces bez problémů, zejména pokud jde o složité geometrie a náročné superslitiny, jako jsou IN718 a Haynes 282. Úspěšná výroba letuschopných součástí vyžaduje předvídání, pochopení a zmírnění těchto potenciálních problémů prostřednictvím pečlivého návrhu, důsledné kontroly procesu a pokročilých znalostí v oblasti materiálových věd. Výrobci a dodavatelé v leteckém průmyslu musí být zběhlí v překonávání těchto překážek.
1. Zbytkové napětí a deformace:
- Výzva: Rychlé, lokalizované zahřívání a ochlazování, které je vlastní L-PBF a EBM, vytváří prudké tepelné gradienty, které vedou ke vzniku vnitřních zbytkových napětí při tuhnutí a smršťování vrstev. Nadměrné napětí může způsobit:
- Zkreslení/pokřivení: Díl se během sestavování nebo po vyjmutí ze sestavovací desky deformuje, což vede k rozměrovým nepřesnostem.
- Praskání: Napětí překračující pevnost materiálu při zvýšených teplotách může způsobit tuhnutí nebo kapalné trhliny během stavby.
- Snížený výkon: Vysoká zbytková napětí mohou negativně ovlivnit únavovou životnost a lomovou houževnatost.
- Strategie zmírnění dopadů:
- Optimalizované strategie skenování: Použití technik, jako je skenování ostrůvků, sektorování nebo úprava délky a orientace vektorů skenování, pomáhá rovnoměrněji rozvádět teplo a snižovat lokální špičky napětí.
- Ohřev stavební desky (L-PBF): Předehřátí konstrukční desky snižuje tepelný gradient mezi ztuhlým materiálem a novou vrstvou, čímž se snižuje akumulace napětí.
- Vysokoteplotní prostředí (EBM): EBM ze své podstaty pracuje se stavební komorou při zvýšených teplotách (několik set °C), což výrazně snižuje tepelné gradienty a zbytková napětí ve srovnání s většinou systémů L-PBF. To je klíčová výhoda při zpracování slitin citlivých na trhliny nebo velkých a složitých dílů.
- Návrh podpůrné konstrukce: Podpěry fungují jako chladiče a mechanické kotvy a ovlivňují namáhání. Je třeba pečlivě navrhnout rovnováhu mezi účinností podpěr a snadnou demontáží.
- Tepelné následné zpracování: Povinné cykly uvolňování napětí (často prováděné na konstrukční desce) jsou klíčové pro uvolnění nahromaděných napětí před vyjmutím dílu. HIP také pomáhá snižovat zbytková napětí.
- Simulace procesů AM: Softwarové nástroje mohou předvídat akumulaci napětí a deformace na základě geometrie dílu a parametrů procesu, což umožňuje úpravu konstrukce nebo procesu před tiskem.
2. Návrh a odstranění podpůrné konstrukce:
- Výzva: Přepážky mají často složité vnitřní průchody, převisy a mřížové konstrukce, které vyžadují podporu při stavbě. Je obtížné navrhnout podpěry, které jsou účinné (zabraňují zhroucení, vedou teplo) a zároveň jsou snadno a zcela odstranitelné bez poškození dílu. Zvláště náročné nebo nemožné může být mechanické odstranění vnitřních podpěr.
- Strategie zmírnění dopadů:
- DfAM pro snížení podpory: Nejúčinnějším přístupem je navrhnout prvky tak, aby byly samonosné (s použitím vhodných úhlů, slzných/ diamantových kanálů). Klíčová je optimální orientace dílu na konstrukční desce.
- Optimalizovaný design podpory: Použití typů podpěr (např. kvádr, kužel, strom) a parametrů (např. hustota, fragmentace), které vyvažují pevnost a lámavost. Specializovaný software pomáhá při generování účinných podpor.
- Výběr materiálu: Některé podpůrné materiály jsou určeny k chemickému rozpouštění, což je však u vysokoteplotních superslitin méně obvyklé.
- Přístup pro odstranění: Navrhování přístupových otvorů nebo cest pro odstranění vnitřních podpěr nebo zachyceného prášku.
- Metody následného zpracování: Využití CNC obrábění, elektroerozivního obrábění nebo AFM pro přesné odstranění podpory v obtížných oblastech. Pro ověření úplného odstranění je nutná důkladná kontrola (např. boreskop, CT).
3. Řízení kvality prášku a manipulace s ním:
- Výzva: Kvalita a konzistence kovového prášku (IN718, Haynes 282) jsou nejdůležitější. Mezi tyto problémy patří:
- Kontaminace: Vnášení cizích částic nebo křížová kontaminace s jinými slitinami mohou způsobit vady a zhoršit vlastnosti materiálu.
- Degradace prášku: Opakované použití prášku může změnit jeho chemický složení (např. zachycení kyslíku) nebo morfologii (tvar/rozložení velikosti částic), což ovlivňuje zpracovatelnost a kvalitu dílů.
- Problémy s plynulostí: Špatný tok prášku může vést k nerovnoměrnému rozprostření vrstvy a způsobit vady.
- Bezpečnost: Manipulace s jemnými kovovými prášky vyžaduje vhodná bezpečnostní opatření (inertní prostředí, uzemnění, osobní ochranné prostředky), aby se zmírnilo riziko výbuchu nebo vdechnutí.
- Strategie zmírnění dopadů:
- Vysoce kvalitní panenský prášek: Získávání prášku od renomovaných dodavatelů, jako je Met3dp, kteří používají pokročilé techniky atomizace (VIGA, PREP) a přísnou kontrolu kvality, aby zajistili vysokou čistotu, sféricitu, kontrolovanou PSD a nízký obsah satelitů. Informace o nás a náš závazek ke kvalitě prášku najdete na našich webových stránkách.
- Přísné protokoly pro manipulaci s práškem: Speciální vybavení, kontrolované prostředí (např. boxy s rukavicemi), postupy prosévání a pečlivé sledování šarží prášku a cyklů opakovaného použití.
- Charakterizace prášku: Pravidelné testování primárního a opakovaně použitého prášku (chemický složení, PSD, tekutost, morfologie), aby se zajistilo, že zůstane v souladu se specifikací.
- Řízení atmosféry: Udržování inertní plynné atmosféry vysoké čistoty (argon, dusík) v tiskárně a manipulačních systémech, aby se minimalizovalo zachycování kyslíku a vlhkosti.
4. Pórovitost:
- Výzva: Přítomnost malých vnitřních dutin (pórů) v tištěném materiálu. Pórovitost výrazně zhoršuje mechanické vlastnosti, zejména únavovou životnost. Mezi příčiny patří:
- Pórovitost plynu: Zachycený plyn v částicích prášku nebo rozpuštěný plyn v tavenině, který se během tuhnutí dostává z roztoku.
- Nedostatečná pórovitost fúze: Nedostatečný příkon energie nebo nesprávné překrytí taveniny vedoucí k neúplnému roztavení mezi vrstvami nebo sousedními skenovacími stopami.
- Pórovitost klíčové dírky: Nadměrná hustota energie způsobuje odpařování kovu, což vede k nestabilitě a zachycení plynu při zhroucení dutiny páry.
- Strategie zmírnění dopadů:
- Optimalizované parametry procesu: Pečlivé řízení výkonu laseru/ paprsku, rychlosti skenování, tloušťky vrstvy, vzdálenosti mezi šrafami a zaostření zajišťuje stabilní tavení a úplné tavení. Vývoj parametrů je specifický pro jednotlivé slitiny.
- Vysoce kvalitní prášek: Použití prášku s nízkým obsahem vnitřního plynu. Vakuové indukční tavení (VIM) během atomizace pomáhá minimalizovat množství rozpuštěných plynů.
- Řízení atmosféry: Zajištění čistého prostředí s vysokou čistotou inertního plynu ve stavební komoře.
- Izostatické lisování za tepla (HIP): Nejúčinnější metoda uzavírání zbytkové pórovitosti (nedostatek pórů Fusion a Gas) po tisku. Je považována za nezbytnou pro kritické součásti.
5. Cracking:
- Výzva: Tvorba trhlin během tuhnutí (solidifikační trhliny) nebo v tepelně ovlivněné zóně během následných tepelných cyklů (liquační trhliny). Superslitiny, zejména vysoce legované, mohou být náchylné vzhledem ke svému širokému rozsahu tuhnutí a precipitačnímu chování.
- Strategie zmírnění dopadů:
- Výběr slitiny: IN718 a Haynes 282 jsou obecně považovány za slitiny s relativně dobrou odolností proti praskání během AM ve srovnání s některými jinými superslitinami, a proto jsou upřednostňovány.
- Optimalizace parametrů: Řízení příkonu energie a rychlosti chlazení pomocí strategie a parametrů skenování může minimalizovat náchylnost k praskání.
- Tepelný management: Ohřev stavebních desek (L-PBF) nebo provoz při vysoké teplotě (EBM) snižuje tepelné gradienty a riziko vzniku trhlin.
- Vhodné tepelné zpracování: Tepelné zpracování po stavbě musí být pečlivě zvoleno, aby se zabránilo škodlivému fázovému srážení nebo relaxačním mechanismům, které by mohly vést k praskání.
Úspěšné zvládnutí těchto výzev vyžaduje kombinaci robustní strojní technologie, vysoce kvalitních materiálů, optimalizovaných procesních parametrů vyvinutých na základě důkladných experimentů, pečlivé kontroly procesu, komplexního následného zpracování a hlubokých metalurgických znalostí. Spolupráce se zkušeným poskytovatelem AM služeb vybaveným správnými nástroji a znalostmi je klíčová pro výrobu spolehlivých, vysoce výkonných přepážek raketových motorů, které splňují přísné požadavky leteckého průmyslu.
Výběr partnera: Výběr správného poskytovatele služeb v oblasti AM pro komponenty pro letectví a kosmonautiku
Úspěšné zavedení aditivní výroby pro kritické letové komponenty, jako jsou přepážky raketových motorů, závisí nejen na pokročilém designu a materiálech, ale také na schopnostech a spolehlivosti vybraného výrobního partnera. Výběr správného poskytovatele služeb v oblasti AM výroby kovů je pro letecké inženýry a manažery nákupu zásadním rozhodnutím. Sázky jsou neuvěřitelně vysoké a vyžadují dodavatele, který prokáže nejen technickou zdatnost, ale také neochvějný závazek ke kvalitě, sledovatelnosti a kontrole procesů, odpovídající standardům leteckého průmyslu. Vyhodnocení potenciálních partnerů vyžaduje mnohostranný přístup, který přesahuje pouhé tiskové schopnosti.
Klíčová kritéria pro hodnocení dodavatelů AM pro letecký průmysl:
- Certifikace a systém řízení kvality (QMS):
- Certifikace AS9100: Jedná se o mezinárodně uznávaný standard QMS pro letecký, kosmický a obranný průmysl. AS9100 zahrnuje požadavky normy ISO 9001, ale přidává přísnější kritéria specifická pro letectví a kosmonautiku, která zahrnují aspekty, jako je řízení konfigurace, řízení rizik, sledovatelnost a ověřování nakupovaných výrobků. U hardwaru kritického pro let je spolupráce s dodavatelem s certifikací AS9100 často povinná nebo velmi preferovaná. Prokazuje to závazek k přísným procesům kontroly kvality.
- Certifikace ISO 9001: Základní standard řízení kvality, který označuje robustní procesy pro zajištění konzistence a spokojenosti zákazníků.
- Dokumentovaný systém řízení jakosti: I nad rámec certifikací by měl mít dodavatel dobře zdokumentovaný a důsledně zavedený systém řízení jakosti, který by měl pokrývat všechny fáze od manipulace s práškem až po konečnou kontrolu a expedici.
- Technické znalosti a zkušenosti:
- Věda o materiálech: Hluboké znalosti metalurgie, zejména u superslitin na bázi niklu, jako jsou IN718 a Haynes 282. To zahrnuje znalost jejich chování během AM zpracování, požadovaných tepelných úprav a dosažitelných vlastností.
- Znalost procesů (L-PBF/EBM): Prokázaná schopnost provozovat a optimalizovat konkrétní technologii AM (např. L-PBF, EBM), která je pro přepážku vyžadována. Zkušenosti s vybranou superslitinou jsou prvořadé. Požadujte případové studie nebo doklady o úspěšných projektech s podobnými materiály a složitostí.
- Podpora DfAM: Ideální partner může spolupracovat na návrhu pro aditivní výrobu, poskytovat zpětnou vazbu ohledně proveditelnosti návrhu, navrhovat optimalizace pro tisk, snížení podpory nebo zvýšení výkonu.
- Zkušenosti s aplikacemi v letectví a kosmonautice: Prokazatelné zkušenosti s výrobou součástí pro letecký průmysl nebo podobně náročná odvětví. Významnou výhodou je porozumění specifickým požadavkům a výzvám pohonných systémů.
- Vybavení, technologie a zařízení:
- Vhodné systémy AM: Vlastnit dobře udržované stroje L-PBF nebo EBM průmyslové třídy vhodné pro zpracování reaktivních superslitin. Mezi tyto faktory patří objem sestavy, výkon laseru/paprsku, řízení atmosféry, možnosti tepelného řízení (např. vysoký ohřev sestavovací desky u L-PBF, vysoká teplota v komoře u EBM, jako jsou systémy Met3dp’s SEBM) a možnosti monitorování.
- Manipulace s práškem: Vyhrazené, kontrolované prostředí a postupy pro manipulaci, skladování, prosévání a správu prášků superslitin, aby se zabránilo kontaminaci a zajistila konzistence.
- Zařízení pro následné zpracování: Vlastní nebo přísně kontrolovaný přístup prostřednictvím certifikovaných partnerů ke všem nezbytným krokům následného zpracování: pece pro uvolňování napětí, vakuové pece pro tepelné zpracování, jednotky pro izostatické lisování za tepla (HIP), CNC obráběcí centra, nástroje pro povrchovou úpravu a komplexní vybavení pro NDT.
- Kalibrace a údržba: Pravidelné, zdokumentované plány kalibrace a preventivní údržby všech kritických zařízení (AM stroje, pece, kontrolní nástroje).
- Komplexní možnosti následného zpracování:
- Jak již bylo popsáno dříve, rozhodující je následné zpracování. Ověřte si, zda je dodavatel schopen řídit celý pracovní postup, včetně:
- Úleva od stresu
- Odborné znalosti v oblasti odstraňování podpory (zejména u složitých interních funkcí)
- Přesné tepelné zpracování (vakuum/inertní atmosféra, přesná regulace teploty)
- Zpracování HIP (přístup k certifikovaným zařízením)
- CNC obrábění (pro přísné tolerance a kritické prvky)
- Povrchová úprava (včetně vnitřních kanálů, pokud jsou vyžadovány, např. AFM)
- Jak již bylo popsáno dříve, rozhodující je následné zpracování. Ověřte si, zda je dodavatel schopen řídit celý pracovní postup, včetně:
- Důkladná kontrola a možnosti nedestruktivního zkoušení:
- Vlastní nebo partnerský přístup k základním metodám NDT, jako je CT skenování, FPI/DPI, UT a nástroje pro kontrolu rozměrů (CMM, skenery).
- Kvalifikovaný personál NDT certifikovaný podle příslušných norem (např. NAS 410 / EN 4179).
- Robustní kontrolní protokoly integrované do celého výrobního procesu.
- Sledovatelnost materiálu:
- Schopnost zajistit úplnou sledovatelnost materiálů od kolébky až po hrob”, propojení finálního dílu s konkrétními šaržemi prášku, parametry zpracování, cykly tepelného zpracování a výsledky kontrol. Jedná se o základní požadavek normy AS9100.
- Kapacita, doba realizace a komunikace:
- Dostatečná kapacita strojů a pracovní síla pro spolehlivé dodržování termínů projektů.
- Transparentní komunikace ohledně doby realizace, možných rizik a stavu projektu.
- Schopnost reagovat a ochota úzce spolupracovat s technickým týmem zákazníka.
Proč spolupracovat s Met3dp?
Přestože konkrétní certifikace by měly být vždy ověřeny na základě aktuálních požadavků projektu, společnost Met3dp ztělesňuje mnoho vlastností, které jsou u vysoce kvalitního partnera v oblasti AM pro letecký průmysl žádány:
- Nadace v oblasti materiálů: Společnost Met3dp, která vyvíjí a vyrábí vysoce kvalitní kovové prášky pomocí pokročilých technologií VIGA a PREP, má základní znalosti o vlastnostech materiálů a jejich interakci s procesem AM. Tyto odborné znalosti se vztahují i na náročné superslitiny, jako je IN718.
- Pokročilé systémy AM: Nabídka průmyslových tiskáren, včetně technologie SEBM (Selective Electron Beam Melting), která je známá svými výhodami při zpracování vysokoteplotních slitin náchylných k praskání díky vysokoteplotnímu prostředí, které snižuje zbytkové napětí.
- Integrovaná řešení: Společnost Met3dp se prezentuje jako poskytovatel komplexních řešení zahrnujících tiskárny, prášky a služby vývoje aplikací, což naznačuje schopnost podporovat zákazníky od návrhu až po výrobu.
- Zaměření na průmyslové aplikace: Jejich cílovými odvětvími jsou letecký, lékařský a automobilový průmysl, což svědčí o zkušenostech s požadavky na vysokou specifikaci a kvalitu.
- Závazek ke kvalitě: Jejich důraz na špičkovou přesnost a spolehlivost ukazuje na kulturu zaměřenou na splnění přísných požadavků odvětví, jako je letecký průmysl.
Výběr správného dodavatele je otázkou řízení rizik. Důkladné hodnocení založené na těchto kritériích pomůže zajistit, aby vaše aditivně vyráběné přepážky pro raketové motory byly vyráběny podle nejvyšších standardů kvality, spolehlivosti a výkonu a plně využívaly možností této transformační technologie.

Porozumění nákladovým faktorům a dodacím lhůtám pro raketové přepážky AM
Ačkoli aditivní výroba nabízí významné technické výhody pro výrobu složitých přepážek raketových motorů, je pro manažery a inženýry odpovědné za zadávání zakázek důležité pochopit faktory, které ovlivňují náklady a dobu realizace. Jasná představa o těchto prvcích umožňuje lépe sestavit rozpočet, plánovat a porovnávat s tradičními výrobními metodami nebo alternativními dodavateli AM. Struktura nákladů na AM se liší od tradičních metod, často zahrnuje vyšší počáteční náklady na jeden díl u jednoduchých položek, ale stává se konkurenceschopnou nebo dokonce výhodnou u velmi složitých nebo konsolidovaných konstrukcí, zejména při zvážení celkových nákladů na životní cyklus a vývoj.
Hlavní hnací síly nákladů na raketové přepážky AM:
- Náklady na materiál:
- Cena prášku: Superslitiny na bázi niklu, jako jsou IN718 a Haynes 282, jsou ve srovnání se standardními ocelemi nebo hliníkovými slitinami ze své podstaty drahé suroviny. Haynes 282 je obecně dražší než IN718. Cenu ovlivňuje také kvalita prášku (čistota, sféricita, PSD).
- Použitý objem: Skutečný objem přepážky a objem potřebných podpůrných konstrukcí určuje množství prášku spotřebovaného přímo v dílu.
- Ztráta prášku/účinnost recyklace: Při manipulaci, tisku a obnově se nevyhnutelně ztratí část prášku. Účinnost procesů prosévání a recyklace prášku ovlivňuje celkové náklady na materiál na jeden díl. U znovu použitého prášku je nutná přísná kontrola kvality, což zvyšuje určité režijní náklady.
- Poměr nákupů a letů: AM má obecně mnohem lepší poměr nákupu k hmotnosti (hmotnost nakoupených surovin vs. hmotnost finálního dílu) ve srovnání se subtraktivním obráběním, což je významná výhoda u drahých materiálů.
- AM Machine Time:
- Doba výstavby: To je často nejvýznamnějším faktorem ovlivňujícím náklady. Je určován:
- Část Objem & Výška: Tisk větších a vyšších dílů trvá déle.
- Složitost: Složité prvky, tenké stěny a mřížkové struktury mohou vyžadovat nižší rychlost skenování nebo specifické strategie, což prodlužuje čas.
- Počet dílů na sestavení: Současný tisk více dílů (nesting) může výrazně snížit efektivní časové náklady stroje na jeden díl díky optimalizaci využití plochy konstrukční platformy a doby seřizování.
- Tloušťka vrstvy: Tenčí vrstvy zlepšují rozlišení a kvalitu povrchu na svazích, ale zvyšují počet vrstev, a tím i dobu vytváření.
- Hodinová sazba stroje: Tato sazba zahrnuje odpisy stroje, spotřebu energie, údržbu, režijní náklady zařízení a spotřebu inertního plynu. Průmyslové systémy AM na kovy představují významnou kapitálovou investici.
- Doba výstavby: To je často nejvýznamnějším faktorem ovlivňujícím náklady. Je určován:
- Náklady na pracovní sílu:
- Nastavení a demontáž: Příprava stroje, nakládání prášku, nastavení souboru sestavení a následné odstranění hotového sestavení, vyčištění stroje a sklízení dílů vyžaduje kvalifikovanou práci.
- Práce po zpracování: To může být podstatné zejména pro:
- Odstranění podpory: Ruční nebo poloautomatické odstraňování podpěr, zejména složitých vnitřních, může být časově náročné.
- Základní povrchová úprava: Prvotní čištění nebo vyhlazení povrchu.
- Kontrola & QA: Práce spojené s rozměrovými kontrolami, přípravou NDT a dokumentací.
- Náklady na následné zpracování (externí nebo interní):
- Tepelné ošetření: Odlehčování napětí, žíhání roztokem, stárnutí a cykly HIP vyžadují specializované pece a jednotky HIP. Tyto procesy zvyšují náklady na provoz zařízení (energie, inertní plyn) a dobu cyklu. Zvláště nákladný, ale často povinný je proces HIP.
- Obrábění: Pokud jsou u některých prvků vyžadovány přísné tolerance nebo specifické povrchové úpravy, zvyšuje CNC obrábění náklady na základě složitosti, doby seřízení a doby obrábění. Obrábění superslitin je ze své podstaty pomalejší a vyžaduje robustnější nástroje.
- Povrchová úprava: Náklady spojené s AFM, leštěním nebo jinými metodami dokončování závisí na požadované úrovni a složitosti přístupu k povrchům (zejména vnitřním).
- NDT: Náklady spojené s prováděním CT vyšetření, FPI, UT atd., včetně času stráveného na zařízení a práce certifikované obsluhy.
- Náklady na konstrukci a inženýrské práce:
- DfAM: Pokud je nutné provést významnou změnu designu nebo optimalizaci pro AM, čas strávený inženýringem zvyšuje počáteční náklady na projekt, i když se často vyplatí ve formě nižších výrobních nákladů nebo lepšího výkonu.
- Simulace: Náklady spojené s prováděním simulací procesu AM nebo CFD/FEA pro ověření návrhu.
- Zajištění kvality a certifikace:
- Udržování certifikace AS9100 a dodržování přísných požadavků na dokumentaci, sledovatelnost a kontrolu procesů zvyšuje režijní náklady, které se promítají do konečné ceny dílu. Tato investice je však klíčová pro zajištění kvality a spolehlivosti na úrovni letecké techniky.
Typické dodací lhůty pro raketové nástavce AM:
Dodací lhůta je celková doba od zadání objednávky do dodání dílu. U složitých komponent ze superslitin AM se může pohybovat od několika týdnů až po několik měsíců v závislosti na různých faktorech:
- Dokončení návrhu & Příprava: Čas potřebný pro závěrečné kontroly DfAM, generování podpory, přípravu souboru sestavení a simulaci (pokud se provádí). (ve dnech)
- Fronta strojů & Plánování: Dostupnost vhodného stroje AM. Vysoká poptávka nebo údržba může způsobit vznik nedodělků. (Dny až týdny)
- Doba tisku: Skutečný čas, který díl stráví při výrobě ve stroji. Může se pohybovat od ~ 24 hodin až po více než týden nebo více u velkých/komplexních konstrukcí. (Dny až týdny)
- Následné zpracování: To často představuje významnou část doby přípravy:
- Chlazení & amp; úleva od stresu: (1-2 dny)
- Demontáž dílů & Čištění: (1 den)
- Tepelné zpracování & amp; HIP: Často zahrnuje dávkování dílů a dlouhé cykly pece/HIP, plus dobu přepravy, pokud se zadává externě. (1-3 týdny)
- Odstranění podpěr a obrábění: Závisí na složitosti. (Dny až týdny)
- Dokončovací práce & amp; NDT: (Dny do týdne)
- Doprava: (Dny)
Faktory ovlivňující dobu realizace:
- Část Složitost: Složitější díly vyžadují delší dobu tisku a intenzivnější následné zpracování.
- Kapacita dodavatele & nevyřízené objednávky: Aktuální pracovní vytížení poskytovatele služeb AM.
- Řetězec následného zpracování: Efektivita a plánování vlastních a externích kroků následného zpracování (cykly HIP, dávky tepelného zpracování).
- Množství: Prototypování jednotlivých dílů může být zpočátku rychlejší, ale optimalizace sestav s více díly může snížit na díl ve výrobních scénářích, i když celková doba výroby může být delší.
- Požadavky na kvalitu: Přísnější požadavky na kontrolu a dokumentaci prodlužují čas.
Shrnutí:
Klíčem k přesnému odhadu nákladů a doby realizace aditivně vyráběných přepážek raketových motorů je pochopení vzájemného vztahu materiálových nákladů, strojního času, práce, rozsáhlého následného zpracování a zajištění kvality. Zatímco AM může urychlit vývoj fáze rychlého prototypování, doba výroby dílů ve výrobní kvalitě zahrnuje řadu dalších kroků než jen tisk. Pro úspěšnou realizaci projektu je nezbytná jasná komunikace s dodavateli, jako je Met3dp, ohledně očekávání, specifikací a harmonogramů.
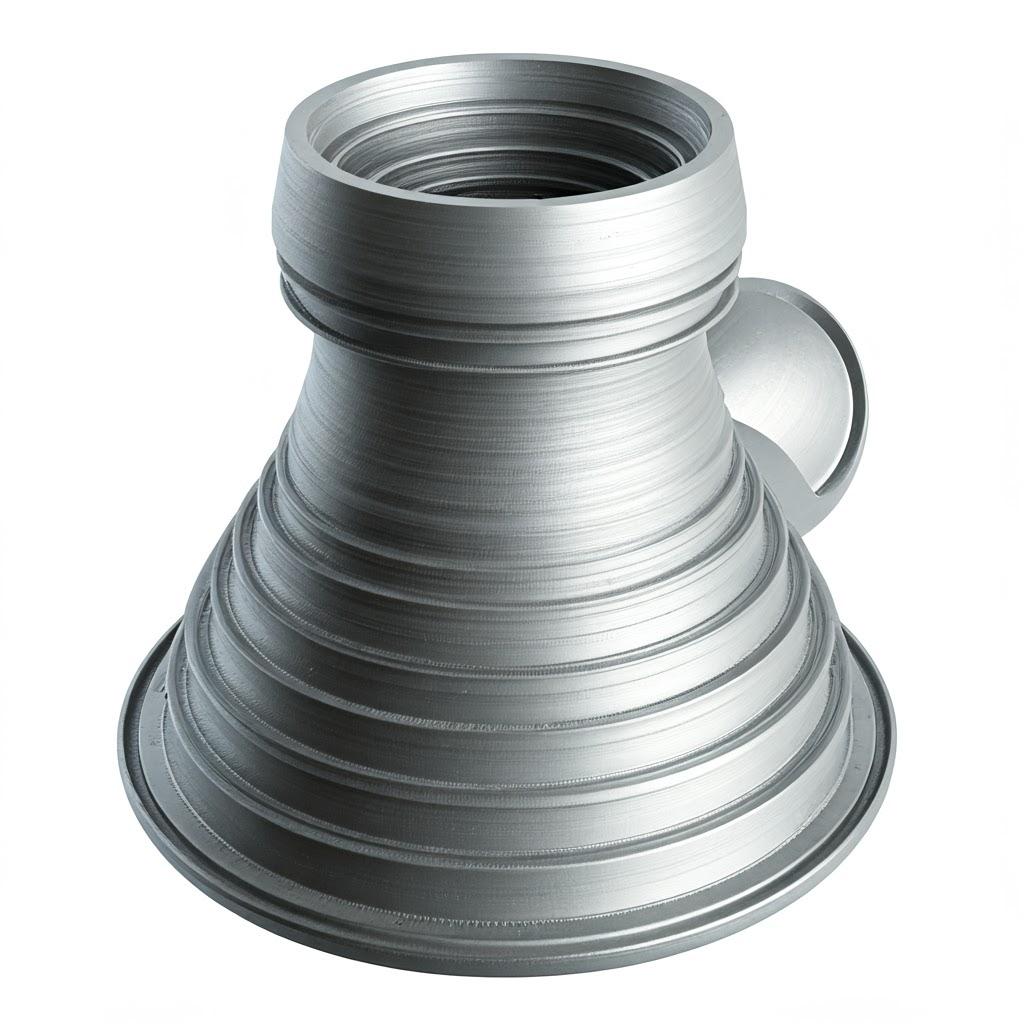
Často kladené dotazy (FAQ) o přepážkách raketových motorů AM
Při zvažování aditivní výroby kritických součástí, jako jsou přepážky raketových motorů, s použitím superslitin, mají inženýři a manažeři nákupu často specifické otázky týkající se výkonu, kvality a specifik procesu. Zde jsou odpovědi na některé časté dotazy:
1. Jaká je spolehlivost a únavová životnost přepážek AM (IN718, Haynes 282) ve srovnání s tradičně vyráběnými přepážkami?
- Odpověď: Při výrobě pomocí dobře řízených a optimalizovaných procesů AM a následném vhodném následném zpracování, včetně Izostatické lisování za tepla (HIP) a důkladným tepelným zpracováním lze mechanické vlastnosti (včetně pevnosti v tahu, odolnosti proti tečení a únavové životnosti) přepážek ze superslitin AM splňují nebo dokonce překračují komponenty vyrobené tradičními metodami, jako je odlévání nebo kování.
- Klíčové faktory: Dosažení vlastností, které jsou stejné nebo lepší než u tepané oceli, závisí především na dosažení plné hustoty materiálu (HIP je rozhodující pro uzavření vnitřní pórovitosti), získání správné mikrostruktury tepelným zpracováním a minimalizaci vad.
- Výhody AM: Konsolidace dílů eliminuje spoje (svary/spoje), které jsou v tradičních sestavách často slabými místy nebo místy iniciace únavy. DfAM může umožnit optimalizované konstrukce s lepším rozložením napětí.
- Požadavek: Důkladná validace procesů, testování materiálů (pomocí zkušebních kuponů vytištěných spolu s díly) a nedestruktivní testování (NDT) jsou nezbytné pro zajištění spolehlivosti hardwaru kritického pro let.
2. Jaká úroveň sledovatelnosti materiálu je zajištěna pro letecké díly AM a proč je důležitá?
- Odpověď: Pro letecké komponenty vyráběné kvalifikovanými dodavateli (zejména těmi, kteří jsou certifikováni podle AS9100), úplná sledovatelnost materiálu je standardní a povinný. To znamená:
- Sledování šarží prášku: Každá šarže kovového prášku (panenského nebo opakovaně použitého) je sledována pomocí jedinečných identifikátorů, včetně jejího zdroje, chemické certifikace a historie zpracování.
- Vytvořit propojení: Každý vytištěný díl je spojen s konkrétním použitým strojem AM, souborem sestavení obsahujícím všechny parametry procesu, konkrétními vloženými dávkami prášku a datem/časem sestavení.
- Záznamy z následného zpracování: Všechny následné kroky (odlehčení, tepelné zpracování, HIP, obrábění, NDT) jsou zdokumentovány a propojeny s dílem nebo výrobní dávkou, včetně diagramů pece, protokolů HIP, záznamů o obrábění a zpráv o NDT.
- Důležitost: Sledovatelnost je klíčová pro kontrolu kvality, protože umožňuje výrobcům prozkoumat případné problémy až k jejich zdroji (např. konkrétní šarži prášku nebo odchylku procesu). Konečnému uživateli (výrobci raketového motoru) poskytuje jistotu, že díl byl vyroben v souladu se specifikací za použití kvalifikovaných materiálů a procesů.
3. Lze stávající konstrukce přepážek, původně vytvořené pro tradiční výrobu, přímo vytisknout pomocí AM?
- Odpověď: Technicky je často možné vytisknout existující design přímo pomocí AM. Je to však možné zřídka využívá klíčové výhody aditivní výroby a mohou být dokonce neoptimální nebo neefektivní.
- Promarněné příležitosti: Přímý tisk nevyužívá schopnost AM vytvářet složité vnitřní chladicí kanály, optimalizované mřížkové struktury nebo konsolidované sestavy. Konstrukce pravděpodobně zahrnuje kompromisy vytvořené speciálně pro tradiční výrobní omezení (např. rovné vrtatelné chladicí otvory, více dílů vyžadujících montáž).
- Potenciální problémy: Konstrukce určené pro odlévání nebo obrábění mohou mít vlastnosti (např. velké převisy, tenké nepodporované stěny), které je obtížné nebo neefektivní tisknout pomocí AM, což vyžaduje rozsáhlé podpůrné konstrukce.
- Doporučení: Zatímco přímý tisk lze použít pro počáteční posouzení nebo nekritické prototypy, doporučuje se přepracovat konstrukci přepážky podle zásad DfAM plně využít možností AM’, pokud jde o zvýšení výkonu (lepší chlazení, tlumení), snížení hmotnosti a potenciální snížení složitosti výroby (konsolidace dílů).
4. Jaké jsou nejkritičtější metody kontroly kvality používané při kvalifikaci přepážek raketových motorů AM pro let?
- Odpověď: Kvalifikace AM přepážek zahrnuje komplexní soubor kontrolních a nedestruktivních metod, které zajišťují geometrickou shodu i vnitřní integritu. Mezi klíčové metody patří:
- Rozměrová kontrola: Použití vysoce přesných souřadnicových měřicích strojů nebo 3D skenování k ověření všech kritických rozměrů a tolerancí podle technického výkresu a modelu CAD.
- Počítačová tomografie (CT): Považuje se za zásadní pro složité díly AM. Poskytuje detailní 3D rentgenový pohled, který umožňuje nedestruktivní kontrolu vnitřních prvků (např. chladicích kanálků), odhalení vnitřních vad (pórovitost, inkluze, praskliny) a ověření celkové geometrické integrity.
- Fluorescenční penetrační kontrola (FPI): Používá se k detekci trhlin, pórů nebo jiných nespojitostí na povrchu. Standardní metoda NDT pro kritické kovové součásti.
- Testování materiálů: Destruktivní testování reprezentativních vzorků nebo “svědeckých kupónů” vytištěných spolu se skutečnými díly (často na stejné konstrukční desce) k ověření tahových vlastností, mikrostruktury (metalografie) a případně únavových nebo creepových vlastností, které po následném zpracování splňují specifikace.
- Zkušební testování/funkční testování: V závislosti na kritičnosti součásti lze provést tlakovou zkoušku nebo zkoušku průtoku, aby se ověřila funkčnost za simulovaných provozních podmínek.
Závěr: Podpora inovací v letectví a kosmonautice pomocí aditivně vyráběných přepážek
Cesta do nitra raketového motoru odhaluje součásti vystavené nejextrémnějším podmínkám, kterým jsou technické systémy vystaveny. Přepážka je mezi nimi klíčovým prvkem, který zajišťuje stabilní a účinné spalování. Konstrukce přepážek, tradičně omezovaná subtraktivní výrobou a montáží, nyní vstupuje do nové éry poháněné aditivní výrobou kovů.
Jak je popsáno v tomto článku, využití pokročilých procesů AM, jako je laserová fúze v práškovém loži (L-PBF) a tavení elektronovým svazkem (EBM), v kombinaci s vysoce výkonnými superslitinami, jako jsou IN718 a Haynes 282, nabízí transformační výhody pro přepážky raketových motorů:
- Bezkonkurenční volnost designu: Umožňuje složité vnitřní chladicí kanály, akusticky optimalizované geometrie a lehké mřížkové struktury, které dříve nebyly dosažitelné.
- Vylepšený výkon: To vede k lepšímu tepelnému managementu, účinnějšímu potlačení nestability spalování a potenciálně vyšším stropům výkonu motoru.
- Konsolidace částí: Snížení složitosti, hmotnosti a potenciálních míst poruchy integrací více komponent do jediného monolitického dílu.
- Zrychlený vývoj: Usnadnění rychlých iterací návrhu a cyklů prototypů, které jsou pro rychlý letecký průmysl klíčové.
Využití těchto výhod však vyžaduje víc než jen přístup k 3D tiskárně. Vyžaduje to komplexní přístup zahrnující:
- Design pro aditivní výrobu (DfAM): Přehodnocení návrhových strategií pro plné využití možností AM.
- Vysoce kvalitní materiály: Využití prvotřídních prášků z vysoce kvalitních slitin s kontrolovanými vlastnostmi.
- Důsledná kontrola procesu: Optimalizace a pečlivá správa parametrů AM.
- Komplexní následné zpracování: Provádění zásadních kroků, jako je odlehčení napětí, tepelné zpracování, HIP a přesné dokončování.
- Přísné zajištění kvality: Používání důkladných protokolů o nedestruktivním zkoušení a kontrolách.
Orientace v tomto složitém prostředí vyžaduje silná partnerství. Spolupráce se zkušeným a schopným poskytovatelem služeb v oblasti AM obrábění kovů, který má hluboké odborné znalosti v oblasti materiálů, procesů, následného zpracování a přísných požadavků na kvalitu v leteckém a kosmickém odvětví, je prvořadá. Společnosti jako Met3dp, které mají základy v pokročilé práškové výrobě, špičkové tiskové technologie (včetně SEBM) a zaměřují se na komplexní průmyslová řešení, představují typ partnera potřebného k úspěšnému zavedení AM pro kritické aplikace, jako jsou přepážky raketových motorů.
Aditivní výroba není jen alternativní výrobní metodou, ale i katalyzátorem inovací v oblasti pohonných technologií. Díky tomu, že umožňuje vytvářet sofistikovanější, spolehlivější a účinnější komponenty, pomáhá kovová AM utvářet budoucnost průzkumu a využití vesmíru. S tím, jak se tato technologie stále zdokonaluje a její přijetí roste, můžeme očekávat, že aditivně vyráběné díly budou hrát stále důležitější roli při pohonu příští generace nosných raket a kosmických lodí.
Chcete-li zjistit, jak mohou pokročilé možnosti aditivní výroby kovů společnosti Met3dp podpořit projekty vaší organizace v leteckém průmyslu, navštivte naše webové stránky nebo kontaktujte náš tým ještě dnes. https://met3dp.com/
Sdílet na
MET3DP Technology Co., LTD je předním poskytovatelem řešení aditivní výroby se sídlem v Qingdao v Číně. Naše společnost se specializuje na zařízení pro 3D tisk a vysoce výkonné kovové prášky pro průmyslové aplikace.
Dotaz k získání nejlepší ceny a přizpůsobeného řešení pro vaše podnikání!
Související články
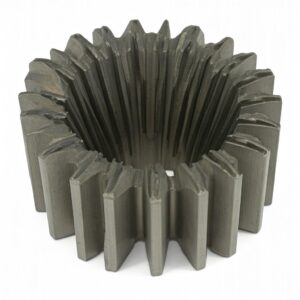
Vysoce výkonné segmenty lopatek trysek: Revoluce v účinnosti turbín díky 3D tisku z kovu
Přečtěte si více "O Met3DP
Nedávná aktualizace
Náš produkt
KONTAKTUJTE NÁS
Nějaké otázky? Pošlete nám zprávu hned teď! Po obdržení vaší zprávy obsloužíme vaši žádost s celým týmem.
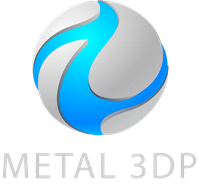
Kovové prášky pro 3D tisk a aditivní výrobu