Sférické prášky
Obsah
Sférické prášky se vztahují k jemným částicovým materiálům se zaoblenou morfologií používaným v oblastech, jako je aditivní výroba kovového prášku, vstřikování keramiky a karbidů, farmaceutika a výroba pokročilé elektroniky. Jejich vylepšené vlastnosti toku a balení odemykají výhody výkonu ve srovnání s prášky nepravidelného tvaru.
Přehled kulovitého prášku
Konstruované kulovité prášky poskytují vynikající hustotu, tekutost, roztíratelnost, účinnost balení a reologické chování, které jsou zásadní pro výrobní procesy vyžadující homogenní a stabilní vstupní materiály.
Přísná kontrola distribuce velikosti částic, uniformity tvaru, chemické čistoty, mikrostruktury a chemie povrchu umožňuje přizpůsobení výkonu náročným aplikacím v oblastech, jako jsou:
- Aditivní výroba
- Vstřikování kovů
- Tepelně stříkané povlaky
- Zpracování pokročilé keramiky
- Materiály baterií
- Katalyzátory
- Kosmetické a dentální formulace
- Chemické mechanické leštění
Submikronové i větší kulovité prášky hrají kritickou roli v nově vznikajících nanotechnologických výrobních technikách až po operace lisování ve velkém objemu.
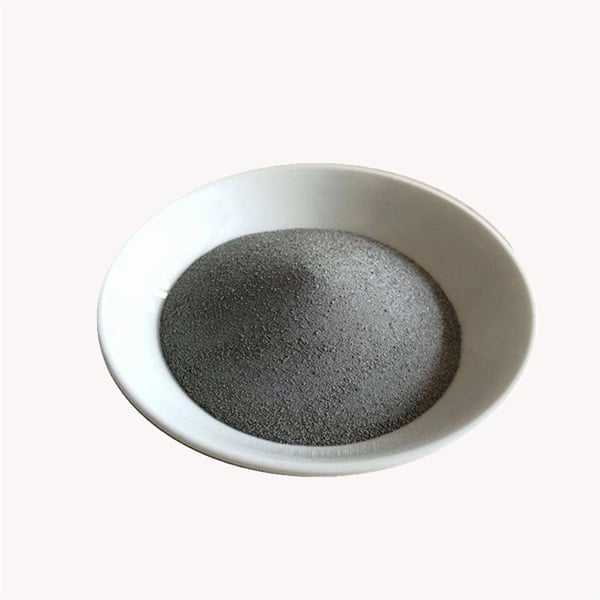
sférický prášek Vlastnosti
Kulovitá morfologie a hladký povrch konstruovaných práškových částic minimalizuje tření mezi částicemi a maximalizuje hustotu ve srovnání s nekulovitými protějšky. To dává vzniknout žádoucím vlastnostem.
Vylepšená tekutost a hustota balení
Zaoblené částice se snadněji přeskupují a klouzají po sobě pod vlivem gravitace, pneumatické dopravy nebo míchání, což vede ke zlepšení průtoku, menšímu shlukování a snadnější manipulaci. Dosahuje se také objemové hustoty blížící se skutečné hustotě materiálu, což minimalizuje prázdné prostory.
To umožňuje rychlejší plnění forem, matric a loží, což je nezbytné pro ekonomiku procesů na bázi prášku. Očekává se průtok přesahující 15 s/50 g pomocí standardního testu Hallova přístroje.
Úzké distribuce velikosti částic
Řízené výrobní techniky umožňují šarže kulovitého prášku s úzkými distribucemi velikosti v rozmezí 10-99 % procházejícími v odchylkách 5 μm. Tato konzistence zajišťuje předvídatelné chování v krocích dávkování, míchání, ohřevu a konsolidace.
Vysoká slinutá hustota
Kulovité morfologie umožňují větší zhutnění během procesů slinování nebo tavení s menšími póry mezi částicemi. To maximalizuje dosažitelné mechanické vlastnosti ve finálních dílech. Hustoty nad 90 % teoretických úrovní jsou typické.
Zlepšená disperze
Nižší poměr povrchu k objemu kulovitých prášků snižuje agregaci ve srovnání s nepravidelnými tvary při disperzi v kapalných nosičích pro nanášení pomocí termického nástřiku, inkoustového tisku, lití do formy nebo jiných mokrých cest. To napomáhá rovnoměrnosti a stabilitě povlaku.
Další atributy
- Lepší retence tekutosti po vystavení zvýšené teplotě
- Snížené otěry a opotřebení zařízení v průběhu času
- Řízenější elektrické rezistivity a defekty
- Rovnoměrné smršťování a rozměrová přesnost
sférický prášek Výrobní metody
Aplikace dostatečné kinetické energie na proudy roztaveného materiálu umožňuje rozpad povrchovým napětím na jemně rozptýlené kapičky, které ztuhnou na práškové částice. Řízení procesních podmínek určuje konečné charakteristiky kulovitého prášku.
Rozprašování plynu
Vysokorychlostní trysky inertního plynu dopadají na kovové taveniny a rozpadají je na jemné kapičky, které se rychle ochlazují na zaoblené pevné prášky při letu z atomizační komory. Použitelné pro reaktivní slitiny, jako je titan, nikl a materiály na bázi železa.
Rozprašování vody
Podobný koncept, ale s vodou jako médiem pro rozbití taveniny. Nižší rychlosti chlazení než plynové přístupy, ale vyšší výtěžky a levnější provozní náklady lépe vyhovují slitinám s vyšší teplotou tání, jako jsou oceli a superslitiny, když je přijatelná nižší kvalita prášku.
Plazmový proces s rotujícími elektrodami (PREP)
Elektrický oblouk taví špičky rotujících drátů s vysokou čistotou, které se rozpadají na koule ochlazené v proudu inertního plynu nasávaného do plazmového paprsku. Vysoce řízené podmínky umožňují těsné distribuce. Používá se pro reaktivní kovy, jako je hliník a hořčík.
Indukční atomizace tavicího plynu na elektrodách (EIGA)
Kombinuje indukční cívkové tavení drátěných elektrod s těsně spojenými plynovými tryskami, což usnadňuje velmi rychlé kalení rodících se kapiček. Nejlepší pro výrobu vysoce uniformních nano a submikronových kulovitých kovových prášků s přizpůsobenými chemickými složeními slitin.
Zpracování sol-gel
Chemické cesty umožňují srážení ultrajemných částic z kapalných prekurzorů, které se poté kalcinují a melou na prášky optimalizované podle tvaru. Používá se pro keramiku, oxidy a karbidy vyžadující čistotu a nanorozměry.
Další metody
Sušení rozprašováním, kondenzační reakce, emulgace, technologie založené na kavitaci, chemické depozice z plynné fáze, elektrodepozice a reakce v pevném stavu nabízejí speciální přístupy k kulovitým kovovým, keramickým a polymerním částicím.
sférický prášek Materiály a velikosti
Nejběžnější materiály kulovitého prášku zahrnují kovy, keramiku, polymery a speciální slitiny – od nanometrové stupnice po velikosti částic přes 100 mikronů.
Třída materiálu | Materiály | Rozsah velikostí |
---|---|---|
Kovy | Nerezové oceli, nástrojové oceli, superslitiny, titan, wolfram, chrom kobalt, měď, hliník | 0,5 μm – 150 μm |
Keramika | Oxid hlinitý, oxid zirkoničitý, karbidy jako WC nebo SiC | 0,01 μm – 45 μm |
Polymery | Nylon, PEEK, PEKK, Ultem | 5 μm – 100 μm |
Ostatní | Sklo, magnetické slitiny, slitiny s tvarovou pamětí, slitiny s vysokou entropií | 0,1 μm – 50 μm |
Dražší slitiny, keramika a speciální prášky směřují k menším rozměrům částic pro vysoce výkonnou aditivní výrobu, zatímco procesy s vyšší propustností fungují lépe s většími distribucemi téměř jedné velikosti.
Klasifikace velikosti
Skupina | Rozsah průměru částic |
---|---|
Ultrafine | < 20 μm |
Pokuta | 20-45 μm |
Střední | 45-105 μm |
Hrubý | 105-150 μm |
Průměrná velikost, kulovitost, chemická čistota, morfologie, mikrostruktura, průtok a vlastnosti hustoty při poklepávání jsou potvrzeny podle požadavků aplikace a potřeb zpracování.
kulovitý prášek z Klíčové aplikace
Aditivní výroba
Selektivní laserové tavení, tavení elektronovým paprskem a tryskové spojování využívají ultrajemné kulovité prášky s řízenými distribucemi velikosti a složeními, které umožňují výrobu složitých kovových dílů přímo z dat CAD.
Vstřikování kovů (MIM)
Kulovité prášky smíchané se spojivy se vstřikují do formy a poté se slinují, aby se vyrobily malé složité díly ve velkém objemu, které kombinují schopnosti blízkého tvaru a dokončování plastového lisování s vysoce výkonnými vlastnostmi materiálů, jako jsou nerezové oceli, nástrojové oceli a superslitiny.
Tepelně stříkané povlaky
Vstupní kovové, karbidové, oxidové a polymerní kulovité prášky se přivádějí přes vyhřívané plazmové nebo spalovací trysky, čímž se vytvářejí povlaky odolné proti korozi, opotřebení a teplu s přizpůsobenými mechanickými nebo dielektrickými atributy.
Pokročilá keramika
Kulovité keramické prášky s úzkou distribucí velikosti slouží jako prekurzory pro výrobu vysoce výkonných elektrických, konstrukčních a žáruvzdorných součástí pomocí lisování za studena, lití do formy, pásových formulací a pokročilých technik slinování vyžadujících optimalizovaná prášková lože.
Další specializované aplikace
Kosmetické podklady, dentální polymery, pájecí pasty, částice nosiče katalyzátoru, kalové leštící suspenze, vodiče práškového kování, prekurzory amorfního kovu atd. se spoléhají na speciální kulovité prášky splňující náročné standardy.
Dodavatelé globálního sférického prášku
Přední výrobci materiálů a zpracovatelé prášků v Americe, Evropě a Asii dodávají sférické prášky pro výzkum a vývoj i pro komerční kupce. Ceny se liší v závislosti na čistotě, uniformitě, velikosti, složení a objemu nákupu.
Možnosti kovů a slitin
Společnost | Umístění |
---|---|
Sandvik | Německo |
Kovové prášky Rio Tinto | Kanada |
Höganäs | Švédsko |
Materiály Mitsubishi | Japonsko |
BÖHLER Edelstahl | Rakousko |
AMETEK | NÁS |
Tekna | Kanada |
Keramické, karbidové a oxidové prášky
Společnost | Umístění |
---|---|
HC Starck | Německo |
Reade Advanced Materials | NÁS |
Pokročilé materiály Inframat | NÁS |
Stanford Advanced Materials | NÁS |
Nanoshel | NÁS |
Ostatní dodavatelé sférických prášků uspokojují potřeby farmaceutických, polymerních, magnetických materiálů, materiálů pro baterie, katalyzátorů a aplikací elektronických prekurzorů.
sférický prášek Analýza nákladů
Sférické prášky z kovů a slitin se pohybují od 5 USD/kg za obecný hliník a železo až po 500 USD/kg za specializované druhy.
Cena silně závisí na:
- Základní složení (např. nerezová ocel stojí 2-4x více než uhlíková ocel)
- Způsob výroby (atomizace plynem vs. vodou, plazma vs. spalování)
- Konzistence distribuce velikosti
- Morfologie a struktura částic
- Množství nákupu a požadované dodací lhůty
- Úrovně čistoty a konzistence
Ceny keramických/karbidových sférických prášků se pohybují od 50 USD/kg do 5000 USD/kg na základě:
- Materiál (oxid křemičitý vs. aluminát lithný, WC vs. HfC)
- Čistota – od 98 do 99,999 %
- Rozměry částic – nanorozměry stojí 100x více
- Objem objednávky
- Plocha povrchu
- Rozsah kalcinace/mletí
- Tendence k aglomeraci
- Citlivost na vlhkost
Úspory z rozsahu platí pro hromadné objednávky, zatímco zakázkové šarže jsou spojeny s prémiemi. Nižší konzistence prášku také snižuje náklady.
Normy a specifikace
Konstruované sférické prášky musí splňovat potřeby aplikace a standardizované zkušební metody, které kontrolují vlastnosti jako:
Parametr | Běžné metody |
---|---|
Distribuce velikosti částic | Laserová difrakce, sedimentace, prosévání |
Tvar částic | Skenovací elektronová mikroskopie, optické hodnocení |
Tekutost prášku | Nálevka Hallova průtokoměru |
Hustota poklepání | Standardní přístroj pro stanovení hustoty kapek |
Ověření složení | ICP-OES/MS, FTIR, XRF, GDMS |
Morfologie | SEM, TEM |
Specifický povrch | BET adsorpce dusíku |
Hustota práškového lože | Geometrická měření |
Tepelná analýza | TGA, DSC |
Mezinárodní (ISO), národní (ASTM) a průmyslové směrnice se vztahují na přijatelné techniky měření použitelné pro kovové, keramické, elektronické a další materiály. sférické prášky.
Používání konzistentních metod oproti standardizovaným požadavkům zajišťuje spolehlivý výkon při použití ve složitých výrobních procesech a aplikacích kritických pro život.
Výhody vs. omezení
Výhody | Nevýhody |
---|---|
– Předvídatelné chování při balení a toku | – Vyšší náklady oproti drcenému/nepravidelnému prášku |
– Zlepšená kvalita produktu a výtěžnost procesu | – Omezená schopnost pro extrémně vysoké teploty pro kovy |
– Lepší kontrola nad mikrostrukturou a výkonem | – Tendence k aglomeraci v určitých případech |
– Přizpůsobitelné distribuce velikosti | – Rizika kontaminace a konzistence |
– Flexibilita složení se slitinami | – Zapouzdření částic během depozice |
– Vyšší dosažitelná slinutá hustota | – Zvláštní bezpečnostní opatření při manipulaci |
– Snížená pórovitost | – Často je nutné prosévání nebo klasifikace |
– Použitelné pro vícesložkové komponenty | – Problémy se zachováním tvaru při nejmenších velikostech |
– Vhodné pro výrobu malých rozměrů a tenkých filmů |
Vyvážení výhod a omezení na základě trasy zpracování a zamýšlené aplikace prášku.
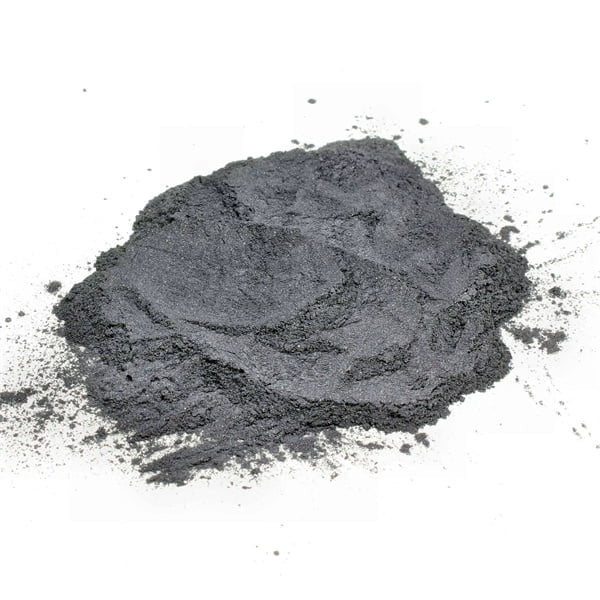
FAQ
Otázka: Jaká je hlavní výhoda sférických prášků oproti práškům nepravidelného tvaru?
Odpověď: Sférické prášky tečou mnohem snadněji díky nižšímu tření mezi částicemi, což umožňuje rychlejší plnění forem, tisk, stříkání a zhutňování, což je zásadní pro přesnou výrobu - zvyšuje rychlost výroby, kvalitu a spolehlivost. Jejich zaoblený tvar také umožňuje vyšší slinutou hustotu.
Otázka: Jak malé lze vyrábět sférické kovové prášky?
Odpověď: Techniky atomizace inertním plynem umožňují prášky z nerezové oceli až do 10 mikronů, zatímco slitiny mědi atomizované plynem mohou dosáhnout průměru 5 mikronů. Speciální směsi vícesložkových slitin byly vyrobeny pod 20 nm pomocí chemie mini-emulze.
Otázka: Co určuje distribuce velikosti sférického prášku?
Odpověď: Konstrukce trysky, dynamika proudění plynu, nástup nestability proudu taveniny a rychlá kinetika chlazení řídí tvorbu kapiček a fyziku tuhnutí v procesech atomizace plynem – vyžadující modelování plus pečlivé parametrické testování pro optimalizaci distribucí.
Otázka: Co je levnější – sférické prášky atomizované plynem nebo vodou?
Odpověď: Atomizace vodou má 5-10x nižší provozní náklady než atomizace plynem, ale produkuje nepravidelnější prášky vyžadující následné zpracování pro zlepšení sférickosti a distribuce. Nákladová výhoda tedy závisí na přijatelné úrovni kvality pro danou aplikaci.
Otázka: Můžete vyrobit sférické částice prášku jedné velikosti?
Odpověď: Mokré chemické výrobní trasy umožňují velmi těsné distribuce až do relativních směrodatných odchylek pod 5 % průměrné velikosti částic, ale zbytkové frakce satelitů vedou k určitému rozptylu. Specializovaná klasifikace nebo prosévání pomáhá izolovat primární modální frakce, pokud je to nutné.
Sdílet na
MET3DP Technology Co., LTD je předním poskytovatelem řešení aditivní výroby se sídlem v Qingdao v Číně. Naše společnost se specializuje na zařízení pro 3D tisk a vysoce výkonné kovové prášky pro průmyslové aplikace.
Dotaz k získání nejlepší ceny a přizpůsobeného řešení pro vaše podnikání!
Související články
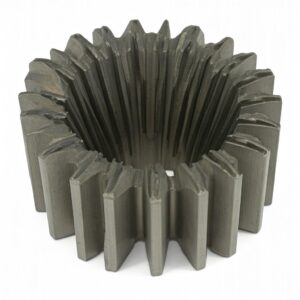
Vysoce výkonné segmenty lopatek trysek: Revoluce v účinnosti turbín díky 3D tisku z kovu
Přečtěte si více "O Met3DP
Nedávná aktualizace
Náš produkt
KONTAKTUJTE NÁS
Nějaké otázky? Pošlete nám zprávu hned teď! Po obdržení vaší zprávy obsloužíme vaši žádost s celým týmem.
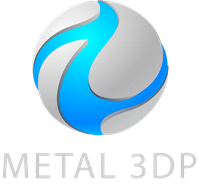
Kovové prášky pro 3D tisk a aditivní výrobu