Prášek z nerezové oceli 17-4PH
Obsah
Přehled
prášková ocel 17-4ph je martenzitická nerezová ocel vytvrzovaná srážením, kterou lze zpracovávat technikami práškové metalurgie pro vysoce výkonné aplikace vyžadující dobré mechanické vlastnosti, odolnost proti korozi a snadnou výrobu.
Tato příručka se zabývá různými typy prášků 17-4PH, jejich charakteristikami, údaji o vlastnostech, metodami zpracování, aplikacemi, specifikacemi, dodavateli, postupy instalace a manipulace, požadavky na údržbu, kritérii výběru pro dodavatele prášků, výhodami a nevýhodami používání prášku 17-4PH a odpověďmi na často kladené otázky.
Typy prášku 17-4PH
prášková ocel 17-4ph je k dispozici v různých formách vhodných pro různé procesy konsolidace prášku:
Typ | Charakteristika |
---|---|
Rozprášený plyn | Kulová morfologie, dobrá tekutost |
Voda atomizovaná | Nepravidelná morfologie, široké rozložení velikosti |
Rozprašování plazmou | Velmi jemný, kulový prášek |
Hydrid-dehydrid | Houbovitá, porézní morfologie |
Karbonylové železo | Vysoce čistý (+99 % Fe) prášek |
Prášek atomizovaný plynem s hladkými kulovými částicemi umožňuje vynikající hustotu balení a slinuté vlastnosti, ale je relativně drahý. Atomizace vodou je ekonomičtější, ale tvar není tak ideální. Pro vstřikování kovů do forem se upřednostňují velmi jemné prášky atomizované plazmou. Prášky HDH a karbonylového železa se používají pro míchání k dosažení vyšší čistoty a zlepšených vlastností.
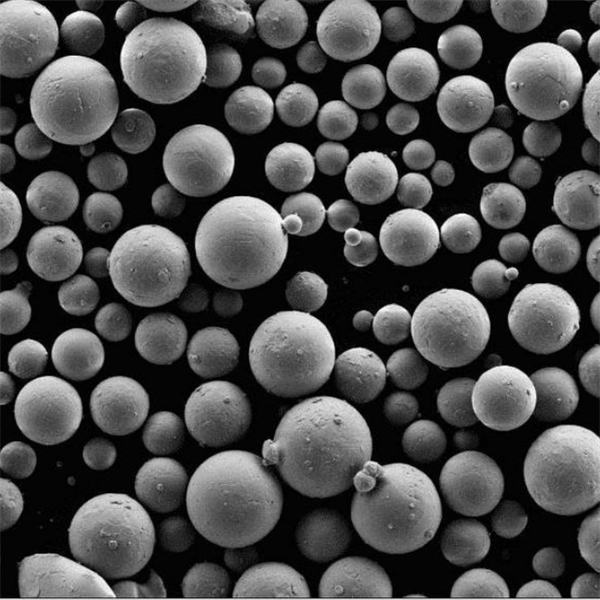
Složení a vlastnosti
Vlastnictví | Popis |
---|---|
Složení | Prášková ocel 17-4 PH se může pochlubit specifickým chemickým složením, které jí propůjčuje žádoucí vlastnosti. Primárním prvkem je železo (Fe), které obvykle tvoří přibližně 73 % hmotnosti prášku. Chrom (Cr), klíčová složka pro odolnost proti korozi, se pohybuje mezi 15,0 a 17,5 %. Obsah niklu (Ni) se pohybuje v rozmezí 3,0 až 5,0 %, což přispívá k pevnosti a houževnatosti. Měď (Cu), další prvek ovlivňující pevnost a obrobitelnost, je přítomna v množství 3,0 až 5,0 %. Mangan (Mn) (přibližně 1,0 %) zlepšuje kalitelnost, zatímco křemík (Si) (také přibližně 1,0 %) zlepšuje pevnost a odolnost proti oxidaci. Pro vytvrzování srážením se přidávají malá množství tantalu (Ta) a niobu (Nb) (společně nepřesahující 0,15 %). |
Charakteristiky částic | Prášek 17-4 PH se obvykle vyrábí pomocí různých technik k dosažení specifických vlastností částic. Běžnou charakteristikou je kulový tvar, který nabízí několik výhod v procesech aditivní výroby, jako je lepší tekutost a hustota balení. Rozložení velikosti částic je dalším zásadním aspektem. Výrobci mohou specifikovat rozložení pomocí notace D-hodnoty. Například D10 označuje průměr, při kterém je 10 % částic menších a 90 % větších. Podobně D50 představuje medián průměru částic a D90 označuje průměr, při kterém je 90 % částic menších a 10 % větších. Velikost částic významně ovlivňuje konečné vlastnosti aditivně vyrobené součásti. Jemnější prášky obecně vedou k hladším povrchovým úpravám, ale mohou být náročnější na zpracování kvůli problémům s tekutostí. Naopak hrubší prášky nabízejí lepší charakteristiky toku, ale mohou vést k hrubší povrchové úpravě. |
Zdánlivá hustota | Zdánlivá hustota se vztahuje k hmotnosti prášku na jednotku objemu, s ohledem na mezery mezi částicemi. Je to zásadní parametr pro manipulaci s práškem a efektivitu skladování. U prášku 17-4 PH se zdánlivá hustota obvykle pohybuje kolem 5,0 g/cm³. Tato hodnota se může lišit v závislosti na rozložení velikosti částic a technikách balení. |
Tekutost | Tekutost popisuje, jak snadno se prášek pohybuje vlastní vahou nebo vnější silou. Je nezbytná pro plynulý provoz v procesech aditivní výroby. Kulové částice obecně vykazují lepší tekutost ve srovnání s nepravidelně tvarovanými částicemi. Kromě toho hraje roli rozložení velikosti částic. Prášky se širším rozložením mohou mít problémy s tekutostí v důsledku segregace, kdy se větší částice mají tendenci oddělovat od jemnějších. Výrobci často používají přísady pro zlepšení tekutosti nebo upravují rozložení velikosti částic, aby optimalizovali tok prášku pro specifické procesy tisku. |
Mechanické vlastnosti | Prášková ocel 17-4 PH nabízí jedinečnou kombinaci mechanických vlastností, když je zpracována do pevné součásti. Ve stavu roztokového žíhání (dosaženého tepelným zpracováním) vykazuje materiál vysokou tažnost a dobrou obrobitelnost. Jeho pevnost je však poměrně nízká. Skutečný potenciál 17-4 PH spočívá ve vytvrzování srážením. Tento sekundární proces tepelného zpracování umožňuje materiálu dosáhnout vysoké pevnosti a tvrdosti při zachování dobré odolnosti proti korozi. Specifické hodnoty pevnosti v tahu, meze kluzu a protažení závisí na zvolených parametrech tepelného zpracování. Typicky mohou díly 17-4 PH dosáhnout pevnosti v tahu přesahující 1000 MPa (145 ksi) a meze kluzu přesahující 830 MPa (120 ksi). |
Odolnost proti korozi | Podobně jako tvářená nerezová ocel 17-4 PH se prášková varianta může pochlubit vynikající odolností proti korozi. Přítomnost chromu poskytuje pasivní vrstvu oxidu, která chrání spodní kov před korozí. Díky tomu je 17-4 PH vhodný pro aplikace vystavené drsným prostředím, včetně slané vody, kyselých nebo alkalických podmínek. Je však důležité poznamenat, že povrchová úprava aditivně vyrobené součásti může ovlivnit její odolnost proti korozi. Hladší povrchová úprava obecně nabízí lepší odolnost proti korozi. |
Svařitelnost | Prášková ocel 17-4 PH vykazuje dobrou svařitelnost pomocí různých technik tavení a odporového svařování. To umožňuje vytváření složitých dílů spojením aditivně vyrobených součástí s dalšími kovovými prvky. Správné postupy svařování a přídavné kovy jsou však zásadní pro zachování integrity a vlastností svarového spoje. |
Tepelné zpracování | Tepelné zpracování hraje zásadní roli při uvolňování plného potenciálu práškové oceli 17-4 PH. Typický proces zahrnuje žíhání roztoku, následované vytvrzováním srážením. Žíhání roztoku zahrnuje zahřátí materiálu na specifickou teplotu a jeho udržování po stanovenou dobu. Tím se rozpustí sraženiny bohaté na měď v mikrostruktuře, čímž se materiál stane měkkým a tvárným. Následné rychlé kalení zmrazí tuto mikrostrukturu v metastabilním stavu. Vytvrzování srážením zahrnuje opětovné zahřátí materiálu žíhaného v roztoku na nižší teplotu a jeho udržování po stanovenou dobu |
Aplikace z prášková ocel 17-4ph
Průmysl | aplikace | Klíčové úvahy |
---|---|---|
Aerospace | Letecké armatury a výztuhy Turbínové lopatky a konstrukční součásti Raketové a raketové díly | Vysoký poměr pevnosti k hmotnosti pro lehké, ale robustní konstrukce Vynikající odolnost proti únavě pro součásti namáhané opakovaným namáháním Zachování mechanických vlastností při zvýšených teplotách (až 600 °F) |
Ropa a plyn | Nástroje a vybavení pro vrtání Ventily a součásti hlavic vrtů Součásti chemického zpracování | Výjimečná odolnost proti korozi v drsných prostředích vrtů obsahujících solanku, kyselý plyn a CO2 – Vysoká odolnost proti opotřebení pro díly, které se opotřebovávají třením a otěrem – Dobrá obrobitelnost pro následné zpracování a přizpůsobení |
Lékařské a zubní služby | Chirurgické nástroje a implantáty Zubní protetika a nástroje | Biokompatibilní vlastnosti pro bezpečnou implantaci do těla Vysoká pevnost a tvrdost pro nástroje vyžadující přesné řezání a manipulaci Dobrá leštitelnost pro hladký, hygienický povrch |
Výroba elektřiny | Komponenty jaderného reaktoru Lopatky parních turbín Dříky ventilů a opotřebovací kroužky | Vynikající odolnost proti obecnému a koroznímu praskání v jaderném prostředí Vysoká odolnost proti tečení pro součásti při dlouhodobém namáhání při vysokých teplotách Dobrá rozměrová stabilita pro přesný provoz a úzké tolerance |
Automotive & Motorsports | Vysoce výkonné součásti zavěšení Ozubená kola a díly převodovky Lehké součásti podvozku | Vysoký poměr pevnosti k hmotnosti pro snížení hmotnosti vozidla a zlepšení spotřeby paliva Výjimečná únavová pevnost pro součásti, které snášejí neustálé vibrace a nárazy Dobrá tvárnost pro složitou výrobu blízkou čistému tvaru |
Spotřební zboží a elektronika | Součásti luxusních hodinek Špičkové příbory a nářadí Sportovní zboží a vybavení | Estetický vzhled díky jasnému, leštěnému povrchu Vysoká pevnost a tvrdost pro odolnost proti opotřebení a trvanlivost Dobrá obrobitelnost pro složité a detailní návrhy |
Specifikace
Typické specifikace pro práškovou ocel 17-4PH zahrnují:
Parametr | Specifikace |
---|---|
Velikost částic | 10 – 45 μm |
Zdánlivá hustota | 2,5 – 4 g/cm³ |
Hustota poklepání | 4 – 6 g/cm³ |
Hallův průtok | < 30 s/50 g |
Složení | Podle ASTM A564 |
Nečistoty | Nízký obsah kyslíku, dusíku |
Tvar | Sférické/nepravidelné |
Plocha povrchu | 0,1 – 1 m²/g |
Jemnější prášky se upřednostňují pro aditivní výrobu, zatímco hrubší velikosti se používají pro lisování a slinování. Vyšší hustota zlepšuje zhutňování prášku, zatímco dobrý tok napomáhá plnění formy. Čistota snižuje inkluze a zlepšuje odolnost proti korozi a mechanické vlastnosti.
Úvahy o návrhu
Funkce designu | Výhoda | Nevýhoda | Strategie zmírnění |
---|---|---|---|
Tloušťka stěny | Podporuje plnou denzifikaci pro optimální pevnost Snižuje vnitřní pórovitost Minimalizuje body koncentrace napětí | Může omezit složitost návrhu pro složité prvky | Udržujte minimální tloušťku stěny 0,3-0,5 mm Využijte principy návrhu pro výrobu (DFM) k dosažení požadovaných prvků s dosažitelnými tloušťkami stěn |
Poměr stran | Zlepšuje strukturální integritu snížením koncentrace napětí Zlepšuje tok prášku během procesů aditivní výroby | Vysoké poměry stran mohou vést k deformaci a praskání | Omezte poměry stran na maximum 8:1 Zvažte přepracování prvků s nadměrně vysokými poměry stran, aby se začlenily zaoblení, žebra nebo alternativní geometrie |
Geometrické prvky | Široká škála svobody návrhu dosažitelná pomocí aditivní výroby Umožňuje vytváření lehkých, složitých součástí | Vnitřní kanály a nepodporované prvky mohou být náročné na výrobu | Použijte principy návrhu pro aditivní výrobu (DFM) k optimalizaci geometrií pro tisknutelnost Strategicky využívejte podpůrné struktury během tisku, abyste zabránili zhroucení nepodporovaných prvků. Zvažte techniky následného zpracování, jako je obrábění, pro prvky vyžadující těsnější tolerance. |
Drsnost povrchu | Díly mohou vykazovat inherentní drsnost povrchu v důsledku povahy materiálu na bázi prášku. | Drsné povrchy mohou ovlivnit tribologické vlastnosti (tření a opotřebení). | Specifikujte požadovanou povrchovou úpravu během fáze návrhu. Zvolte vhodné techniky následného zpracování, jako je leštění nebo otryskávání skleněnými kuličkami, k dosažení požadované povrchové textury. |
Tepelné zpracování | Využijte precipitační kalení k dosažení vysoké pevnosti a tvrdosti. | Nesprávné parametry tepelného zpracování mohou vést k deformaci, zkroucení nebo snížení mechanických vlastností. | Simulujte proces tepelného zpracování virtuálně, abyste optimalizovali parametry. Zaveďte přísné postupy kontroly kvality během cyklů tepelného zpracování. |
Zbytkové napětí | Procesy aditivní výroby mohou zavést zbytkové napětí v rámci součásti. | Vysoké zbytkové napětí může vést k praskání nebo předčasnému selhání. | Optimalizujte parametry tisku, abyste minimalizovali zbytkové napětí. V případě potřeby použijte tepelné zpracování pro uvolnění napětí. |
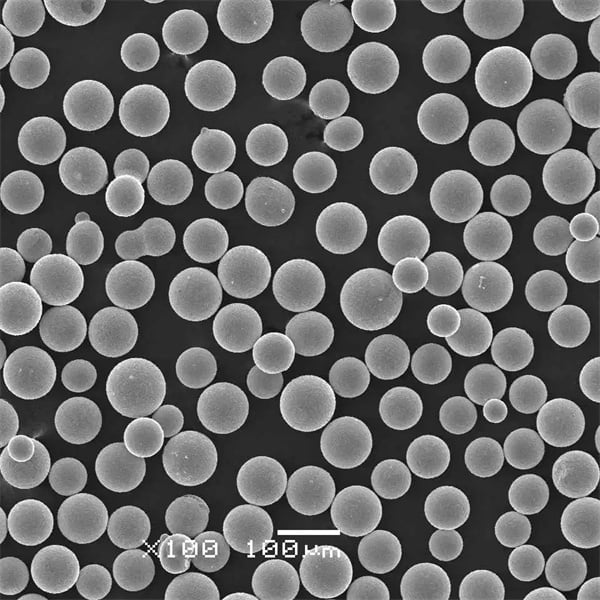
Metody zpracování
Prášek z nerezové oceli 17-4ph lze konsolidovat do plně hustých dílů pomocí:
Metoda | Podrobnosti |
---|---|
Vstřikování kovů (MIM) | Vazba prášku do vsázky pro vstřikování do složitých forem |
Aditivní výroba | Použití laseru/elektronového paprsku k selektivnímu tavení vrstev prášku do 3D tvarů |
Práškové kování | Zhutňuje a za tepla deformuje předlisky prášku do dílů s vysokou hustotou |
Izostatické lisování za tepla | Aplikuje teplo a izostatický tlak k konsolidaci prášku |
Lisování a spékání | Lisuje prášek do formy, poté sintruje pro plnou hustotu |
MIM poskytuje nejvyšší přesnost a je ideální pro složité, malé součásti. AM nabízí maximální svobodu návrhu. Kování produkuje vynikající mechanické vlastnosti. HIP se vyhýbá pórovitosti při slinování. Lisování a slinování kombinuje dobrou přesnost a vlastnosti za nižší cenu.
Správná kontrola teploty, tlaku, atmosféry a dalších parametrů během zpracování je zásadní pro dosažení požadované mikrostruktury a vlastností.
Dodavatelé a ceny
Někteří přední dodavatelé prášku z nerezové oceli 17-4ph zahrnují:
Dodavatel | Cenové rozpětí |
---|---|
Přísada pro tesaře | $50 - $120 za kg |
Sandvik Osprey | $45 - $100 za kg |
Praxair | 40 $ – 90 $ za kg |
Höganäs | $60 - $140 za kg |
Prášek CNPC | $30 - $70 na kg |
Ceny se liší v závislosti na čistotě, vlastnostech prášku, výrobní metodě a objemu nákupu. Malé množství pro výzkum a vývoj je dražší, zatímco hromadné objednávky pro sériovou výrobu mají nižší cenu za kg.
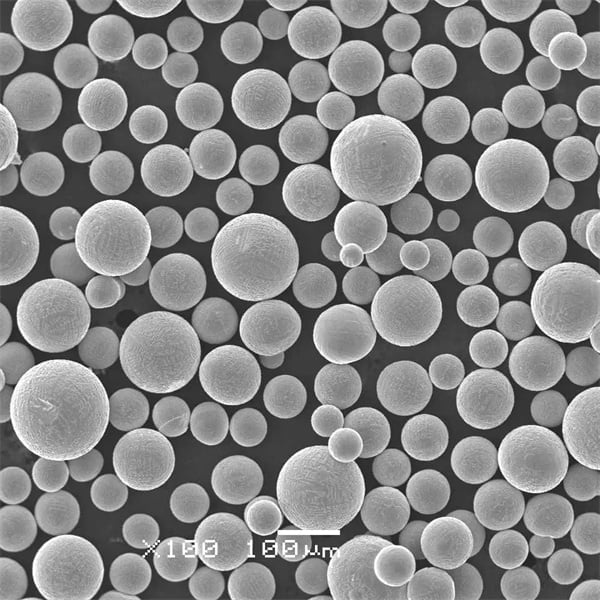
Instalace a manipulace
Aspekt | Popis | Bezpečnostní opatření |
---|---|---|
Úložiště | Skladujte na chladném a suchém místě (ideálně pod 25 °C nebo 77 °F) mimo přímé sluneční světlo a zdroje tepla. Udržujte nádoby těsně uzavřené, aby se zabránilo absorpci vlhkosti, která může ovlivnit tekutost prášku a vést ke shlukování. Zvažte použití vysoušedel uvnitř skladovací nádoby pro dodatečnou kontrolu vlhkosti. | Nikdy neskladujte prášek z nerezové oceli 17-4PH v blízkosti neslučitelných materiálů, jako jsou silné kyseliny, zásady nebo oxidační činidla. Správně označte všechny nádoby typem materiálu, datem přijetí a číslem šarže pro snadnou identifikaci a kontrolu inventáře. |
Kompatibilita zařízení | Ujistěte se, že veškeré zpracovatelské zařízení (násypky, podavače, míchačky) je vyrobeno ze slučitelných materiálů, které neznečistí prášek. Nerezová ocel (304 nebo 316L) je běžnou volbou díky své odolnosti proti korozi. Pravidelně kontrolujte zařízení, zda nevykazuje známky opotřebení nebo poškození, které by mohlo ohrozit integritu prášku. Proveďte zkušební běhy s malým množstvím prášku, abyste ověřili funkčnost zařízení a charakteristiky toku prášku před plnohodnotnou výrobou. | Zaveďte postupy uzemnění a spojování, abyste minimalizovali riziko elektrostatického výboje (ESD) během manipulace s práškem, který může zapálit prachové mraky. Udržujte čisté pracovní prostředí, abyste zabránili kontaminaci prášku cizími předměty nebo úlomky. |
Osobní ochranné prostředky (OOP) | Při manipulaci s práškem z nerezové oceli 17-4PH používejte rukavice z nereaktivního materiálu, jako je nitril nebo butylová guma, abyste zabránili podráždění pokožky nebo alergickým reakcím. Používejte ochranné brýle nebo celoobličejový štít, abyste chránili oči před prachovými částicemi. Při práci v prostředích s významnou koncentrací prachu používejte správně nasazený respirátor s filtrem P100 pro optimální ochranu proti částicím ve vzduchu. | Noste ochranný oděv, jako jsou kombinézy, abyste minimalizovali vystavení pokožky prášku. Po manipulaci s práškem si důkladně umyjte ruce mýdlem a vodou, i když máte nasazené rukavice. Zvažte použití jednorázových návleků na obuv, abyste zabránili zanášení prášku po pracovní ploše. |
Rozlití a čištění | Menší rozlití lze vyčistit vysavačem s filtrem HEPA určeným pro kovové prášky. U větších rozlití izolujte oblast a vyhněte se vytváření prachu ve vzduchu. Použijte metody čištění za mokra s vlhkým hadříkem nebo mopem, abyste minimalizovali tvorbu prachu. Zlikvidujte shromážděný práškový odpad v souladu s místními předpisy. Nikdy nevylévejte prášek do odtoků nebo do životního prostředí. | Vždy ihned vyčistěte rozlití, abyste zabránili šíření kontaminace a potenciálním bezpečnostním rizikům. Pokud dojde k významnému rozlití, evakuujte oblast a informujte příslušný personál o pomoc. |
Školení | Zaveďte komplexní školicí program pro personál zapojený do manipulace s práškem z nerezové oceli 17-4PH. Školení by mělo zahrnovat správné techniky manipulace, bezpečnostní postupy, protokoly pro mimořádné události a důležitost udržování čistého pracovního prostředí. | Pravidelně aktualizujte školicí programy, aby odrážely jakékoli změny v předpisech, postupech manipulace s materiálem nebo bezpečnostních protokolech. Udržujte záznamy o školení, abyste prokázali kompetenci zaměstnanců při manipulaci s tímto materiálem. |
Provoz a údržba
Úkol | Popis | Úvahy o skladování | Bezpečnostní opatření |
---|---|---|---|
Úložiště | |||
– Přijetí | Po příjezdu zkontrolujte nádobu, zda nevykazuje známky poškození nebo úniku. | – Skladujte na chladném a suchém místě (ideálně mezi 10 °C a 25 °C) mimo přímé sluneční světlo a zdroje tepla. | – Při manipulaci s nádobami používejte rukavice, ochranné brýle a prachovou masku. |
– Balení | – Udržujte nádobu těsně uzavřenou, aby se zabránilo absorpci vlhkosti. | – Prášky mohou být za určitých podmínek hořlavé nebo výbušné. Zaveďte postupy uzemnění při manipulaci s nádobami, abyste zabránili statickému výboji. | |
– Separace | Oddělte nádoby s práškem 17-4PH od neslučitelných materiálů, jako jsou silné kyseliny, zásady a oxidační činidla. | – | – |
Úkol | Popis | Úvahy o procesech | Kontrola kvality |
---|---|---|---|
Zpracování | |||
– Přenos | Použijte vhodné zařízení pro přenos prášku, jako jsou uzavřené přenosové systémy nebo uzemněné naběračky, abyste minimalizovali tvorbu prachu. | – Vyhněte se nadměrné manipulaci, protože může zhoršit tekutost prášku. | – Pravidelně sledujte vlastnosti toku prášku, abyste zajistili konzistentní výkon tisku. |
– Míchání/prosévání | V případě potřeby použijte uzavřený míchací systém, abyste minimalizovali vystavení prášku. Prosévání by se mělo provádět v kontrolovaném prostředí, aby se zabránilo kontaminaci. | – Udržujte podrobné záznamy o postupech míchání a parametrech prosévání. | – Pravidelně provádějte analýzu velikosti částic, abyste se ujistili, že prášek splňuje požadované specifikace. |
– Předběžné zahřívání | U některých procesů aditivní výroby může předehřev lože prášku zlepšit tekutost a snížit obsah vlhkosti. | – Dodržujte doporučení výrobce pro teplotu a dobu předehřevu. | – Sledujte a zaznamenávejte parametry předehřevu pro každou stavbu. |
Úkol | Popis | Úvahy o procesech | Kontrola kvality |
---|---|---|---|
Aditivní výroba | |||
– Proces stavby | – Dodržujte stanovené parametry tisku specifické pro prášek 17-4PH a zvolenou technologii AM. | – In-situ monitorovací techniky (např. tepelné zobrazování, monitorování taveniny) lze použít k zajištění konzistentní kvality stavby. | |
– Následné zpracování | Tepelné zpracování je zásadní pro dosažení požadovaných mechanických vlastností v dílech z nerezové oceli 17-4PH. | – Dodržujte stanovené protokoly tepelného zpracování pro 17-4PH, abyste optimalizovali pevnost a tažnost. | – Proveďte mechanické testování (např. zkouška tahem, zkouška tvrdosti) na hotových dílech, abyste ověřili, že splňují konstrukční specifikace. |
Úkol | Popis | Inspekce | Záznamy |
---|---|---|---|
Zajištění kvality | |||
– Vizuální kontrola | Proveďte důkladnou vizuální kontrolu hotového dílu, abyste zjistili případné povrchové vady, jako jsou praskliny, pórovitost nebo delaminace. | – Použijte vhodné kontrolní techniky na základě složitosti dílu a požadavků na aplikaci (např. rentgen, CT sken). | – Dokumentujte všechna zjištění kontroly, včetně typu vady, umístění a přijatých nápravných opatření (je-li to nutné). |
– Rozměrová kontrola | Ověřte, zda rozměry dílu odpovídají konstrukčním specifikacím. | – Použijte kalibrované měřicí přístroje pro přesné rozměrové kontroly. | – Udržujte záznamy všech rozměrových měření pro účely sledovatelnosti. |
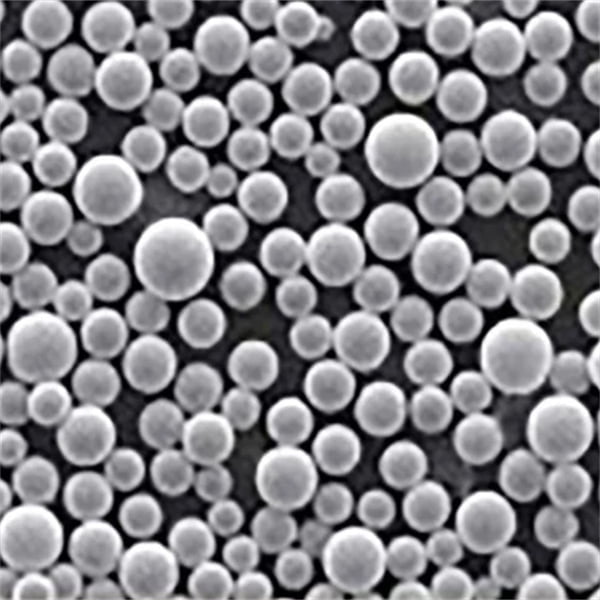
Výběr stránek prášková ocel 17-4ph Dodavatelé
Faktor | Popis | Klíčové úvahy |
---|---|---|
Reputace dodavatele | Zavedená historie dodavatele v průmyslu aditivní výroby kovů (AM) | Hledejte společnosti se zkušenostmi s dodávkou prášku 17-4PH pro AM. Prozkoumejte jejich zákaznické reference a průmyslová ocenění. Ověřte certifikace jako ISO 9001 (řízení kvality) a AS9100 (kvalita pro letectví). |
Kvalita prášku | Chemické složení, distribuce velikosti částic (PSD) a tekutost prášku | Ujistěte se, že prášek splňuje příslušné materiálové normy, jako je ASTM International (ASTM) nebo Aerospace Material Specifications (AMS). Přizpůsobte PSD své specifické technologii AM (např. laserové tavení preferuje jemnější prášky). Upřednostňujte dobrou tekutost pro konzistentní výsledky tisku. |
Postupy kontroly kvality | Opatření dodavatele k zajištění konzistence a čistoty prášku | Zeptejte se na možnosti interní analýzy prášku dodavatele (např. emisní spektrometrie, laserová difrakce). Hledejte certifikace jako ISO 17025 (kompetence laboratoře). Zeptejte se na systém sledovatelnosti šarží dodavatele, abyste udrželi kontrolu kvality. |
Odborné znalosti v oblasti aditivní výroby | Znalost dodavatele o procesech AM a jejich vlivu na výkon prášku | Hledejte dodavatele s vyhrazenými AM týmy, kteří vám mohou poradit s výběrem prášku pro vaši konkrétní aplikaci. Zvažte dodavatele, kteří nabízejí služby následného zpracování, jako je optimalizace tepelného zpracování pro 17-4PH. Spolupracujte s dodavateli, kteří mohou poskytnout technickou podporu a řešení problémů pro výzvy AM. |
Ceny a minimální množství objednávky (MOQ) | Cena za kilogram prášku a minimální množství, které musíte zakoupit | Porovnejte ceny u různých dodavatelů s ohledem na množstevní slevy. Zahrňte náklady na dopravu a případná dovozní cla. Sjednejte MOQ, které odpovídají potřebám vašeho projektu. |
Dodací lhůta | Doba, za kterou dodavatel dodá prášek po vaší objednávce | Zvažte časový harmonogram projektu a potenciální zpoždění výroby. Zeptejte se na dostupnost zásob dodavatele a jeho schopnost plnit naléhavé objednávky. Prozkoumejte možnosti zrychlené dopravy, pokud je to nutné. |
Zákaznický servis | Reakce dodavatele a ochota řešit vaše dotazy | Zhodnoťte snadnost komunikace s prodejními a technickými týmy dodavatele. Hledejte dodavatele, kteří nabízejí specializované account managery pro průběžnou podporu. Ujistěte se, že dodavatel poskytuje jasnou dokumentaci, včetně bezpečnostních listů (SDS) a certifikátů analýzy (COA). |
Výhody a omezení prášku 17-4PH
Výhody | Omezení |
---|---|
Vynikající pevnost a odolnost proti korozi: Prášek 17-4PH nabízí vítěznou kombinaci vysoké pevnosti a vynikající odolnosti proti korozi. Díky tomu je ideální pro aplikace vyžadující jak odolnost, tak schopnost odolávat náročným prostředím. Ve srovnání s jinými prášky z nerezové oceli používanými v aditivní výrobě (AM) je 17-4PH upřednostňován pro své vyvážené vlastnosti, což z něj činí všestrannou volbu napříč různými průmyslovými odvětvími. | Požadavky na následné zpracování: Na rozdíl od některých materiálů používaných v AM vyžadují díly 17-4PH kroky následného zpracování, jako je horké izostatické lisování (HIP) a tepelné zpracování, aby se dosáhlo jejich optimálních mechanických vlastností. To přidává další vrstvu složitosti a nákladů do výrobního procesu. |
Nákladově efektivní: I když to není nejlevnější varianta mezi kovovými prášky, nabízí 17-4PH významnou cenovou výhodu ve srovnání s exotičtějšími slitinami používanými v AM. Díky tomu je to cenově výhodnější varianta pro aplikace, kde je vyžadován výjimečný výkon, ale extrémní vlastnosti nejsou zásadní. | Výzvy při manipulaci a skladování: Vzhledem k jemné velikosti částic a reaktivní povaze vyžaduje prášek 17-4PH pečlivou manipulaci a skladování v řízené atmosféře, aby se zabránilo absorpci vlhkosti a degradaci prášku. To vyžaduje specializované vybavení a postupy manipulace, což zvyšuje celkové náklady. |
Svoboda a flexibilita designu: Významnou výhodou prášku 17-4PH je jeho kompatibilita s technologiemi AM. To umožňuje vytvářet složité, lehké díly se složitými geometriemi, kterých by bylo obtížné nebo nemožné dosáhnout tradičními výrobními metodami. Tato svoboda designu otevírá dveře inovacím a funkční optimalizaci v různých aplikacích. | Svařitelnost a obrobitelnost: I když 17-4PH nabízí vynikající vlastnosti, může být náročné svařovat a obrábět kvůli jeho inherentní pevnosti a charakteristikám zpevňování za studena. To může představovat omezení v situacích, kdy jsou kroky následného zpracování zahrnující svařování nebo obrábění nezbytné pro montáž dílů nebo konečnou úpravu. |
Zavedená historie: 17-4PH má dobře zavedenou historii úspěšného použití v různých průmyslových odvětvích. Tato osvědčená historie poskytuje inženýrům a konstruktérům důvěru ve výkon a spolehlivost materiálu. Stávající data a zavedené technologie zpracování prášku 17-4PH v AM přispívají k plynulejšímu vývoji a výrobnímu procesu. | Omezeno pro extrémní prostředí: I když se 17-4PH může pochlubit působivou pevností a odolností proti korozi, nemusí být optimální volbou pro aplikace ve výjimečně drsných prostředích. Pro situace vyžadující extrémní vysoké nebo nízké teploty nebo vystavení vysoce agresivním chemikáliím by se mohly lépe hodit jiné specializovanější materiály. |
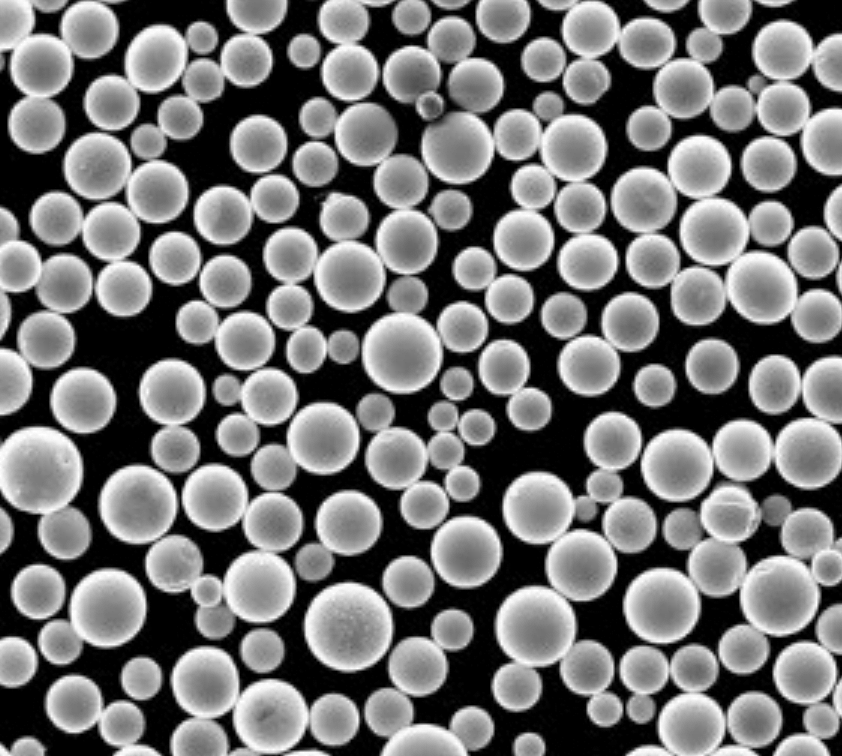
Nejčastější dotazy
Jaké jsou typické aplikace pro prášek z nerezové oceli 17-4PH?
17-4PH se běžně používá v leteckém průmyslu, ropném a plynárenském průmyslu, automobilovém průmyslu, lékařství, zpracování potravin a dalších náročných aplikacích vyžadujících vysokou pevnost, tvrdost a odolnost proti korozi.
Jaké charakteristiky prášku se doporučují pro vstřikování kovů s 17-4PH?
Pro MIM se upřednostňují sférické prášky s d50 8 – 15 mikronů a dobrými vlastnostmi toku (Hallova rychlost toku kolem 20 s/50 g), aby se umožnilo vysoké zatížení práškem v surovině a dobré plnění formy.
Jak se maximalizuje odolnost proti korozi při použití prášku 17-4PH?
Odolnost proti korozi se zlepšuje dostatečným obsahem chromu (>15 %), nízkými úrovněmi nečistot a homogenní mikrostrukturou bez sraženin. Žíhání v roztoku následované rychlým ochlazením pomáhá rozpouštět karbidy a poskytuje nejlepší odolnost proti korozi.
Jaký je typický postup tepelného zpracování 17-4PH a účel každého kroku?
17-4PH se žíhá v roztoku při 1900 °F, kalí se vodou, aby se rozpustily sraženiny, kondicionuje se při 350 °F a poté se stárne při 850 °F, aby se vytvořily jemně rozptýlené sraženiny pro optimální kombinaci tvrdosti, pevnosti a houževnatosti.
Jaká opatření jsou nezbytná při skladování a manipulaci s práškem 17-4PH?
Jako hořlavý kovový prášek vyžaduje 17-4PH skladování v chladné, suché, inertní atmosféře mimo dosah kyslíku a zdrojů zapálení. Při manipulaci s práškem by se mělo používat správné uzemnění, ventilace a OOP, aby se zabránilo požáru, jiskrám a vdechování.
Závěr
Díky své vynikající rovnováze vlastností umožňuje prášek z nerezové oceli 17-4PH výrobu kritických součástí napříč náročnými průmyslovými aplikacemi pomocí účinných metod zpracování práškové metalurgie. Správný výběr a zpracování prášku 17-4PH v kombinaci s tepelným zpracováním přizpůsobeným požadavkům konečného použití vede k optimalizovanému výkonu. Jak se know-how a dostupnost zpracování nadále zlepšuje, bude 17-4PH zaznamenávat rozšířené použití, které nahradí tradičně kované a lité materiály.
Sdílet na
MET3DP Technology Co., LTD je předním poskytovatelem řešení aditivní výroby se sídlem v Qingdao v Číně. Naše společnost se specializuje na zařízení pro 3D tisk a vysoce výkonné kovové prášky pro průmyslové aplikace.
Dotaz k získání nejlepší ceny a přizpůsobeného řešení pro vaše podnikání!
Související články
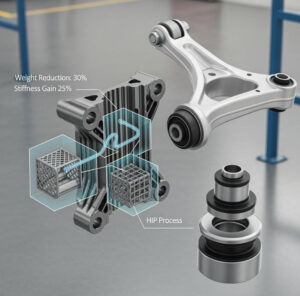
Metal 3D Printed Subframe Connection Mounts and Blocks for EV and Motorsport Chassis
Přečtěte si více "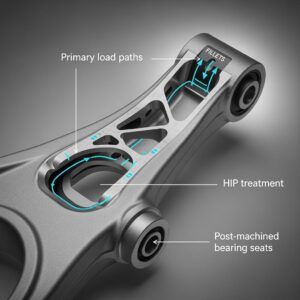
Metal 3D Printing for U.S. Automotive Lightweight Structural Brackets and Suspension Components
Přečtěte si více "O Met3DP
Nedávná aktualizace
Náš produkt
KONTAKTUJTE NÁS
Nějaké otázky? Pošlete nám zprávu hned teď! Po obdržení vaší zprávy obsloužíme vaši žádost s celým týmem.