3D tištěné chirurgické nástroje z nerezové oceli a titanu
Obsah
Revoluční chirurgie: Vzestup 3D tištěných chirurgických nástrojů z nerezové oceli a titanu
Operační sál je precizní pracoviště, kde je nejdůležitější zručnost chirurga, ale stejně důležitá je i kvalita a konstrukce jeho nástrojů. Po staletí se chirurgické nástroje vyráběly tradičními metodami, jako je kování, odlévání a obrábění. Tyto techniky jsou sice účinné, ale často narážejí na omezení při výrobě velmi složitých geometrií, návrhů specifických pro pacienta nebo umožňují rychlé opakování během vývoje. Přichází aditivní výroba kovů (AM), známější jako 3D tisk kovů - transformační technologie, která je připravena nově definovat design chirurgických nástrojů, jejich výrobu a v konečném důsledku i výsledky pro pacienty.
Kov 3D tisk vytváří díly vrstvu po vrstvě přímo z digitálního modelu pomocí vysoce výkonných kovových prášků. Tento přístup uvolňuje nebývalou konstrukční svobodu a umožňuje vytvářet chirurgické nástroje se složitými prvky, vnitřními kanály, mřížkovými strukturami pro snížení hmotnosti a ergonomickými tvary, které dříve nebylo možné vyrobit nebo jejichž výroba byla neúnosně drahá. Představte si kleště dokonale přizpůsobené ruce chirurga, vodítka přesně přizpůsobená jedinečné anatomii pacienta odvozené z CT snímků nebo komplexní retraktory kombinující více funkcí do jediného optimalizovaného nástroje. To není science fiction, to je realita, kterou umožňuje technologie metal AM.
Tato technologie je obzvláště důležitá v náročných oborech, jako je ortopedie, neurochirurgie, kardiovaskulární chirurgie a minimálně invazivní zákroky, kde standardní nástroje nemusí vždy stačit. Možnost rychlého prototypování a výroby zakázkových, nízkoobjemových nebo velmi složitých nástrojů nabízí významné výhody oproti konvenční výrobě, která často vyžaduje nákladné nástroje a dlouhé dodací lhůty, zejména u specializovaných konstrukcí.
Kromě toho se při AM s kovy využívají materiály, které jsou známé svou vhodností pro lékařské aplikace. Dvěma význačnými druhy jsou nerezová ocel 316L a titanová slitina Ti-6Al-4V (třída 5). Obě nabízejí vynikající biokompatibilitu, odolnost proti korozi a mechanickou pevnost potřebnou k tomu, aby odolaly náročným chirurgickým zákrokům a opakovaným sterilizačním cyklům. Využitím pokročilých technik atomizace prášku zajišťují poskytovatelé, jako je Met3dp, že tyto materiály mají v práškové formě vysokou sféricitu a tekutost nezbytnou pro výrobu hustých, vysoce kvalitních tištěných dílů s vynikajícími mechanickými vlastnostmi, které jsou pro kritické chirurgické aplikace klíčové. Integrace 3D tisk z kovu do dodavatelského řetězce chirurgických nástrojů není jen alternativou, ale i vylepšením, které slibuje vyšší výkon, personalizaci a potenciálně rychlejší inovační cykly pro život zachraňující zařízení.
Aplikace aditivně vyráběných chirurgických nástrojů: Přesnost napříč lékařskými specializacemi
Univerzálnost kovového 3D tisku umožňuje jeho použití v širokém spektru chirurgických oborů. Jeho schopnost vytvářet složité, přizpůsobené a lehké nástroje z něj činí neocenitelný nástroj tam, kde je klíčová přesnost a specifická funkčnost. Manažeři veřejných zakázek a dodavatelé chirurgických nástrojů si stále více uvědomují potenciál AM’tisku k řešení neuspokojených potřeb a zlepšení efektivity zákroků.
- Ortopedie: Tento obor byl v počátcích využívání AM pro chirurgická vodítka pro pacienty (PSI) pro náhrady kolenních a kyčelních kloubů, která zajišťují přesné umístění implantátu. Běžně se používají také komplexní vrtací vodítka, osteotomy a nástroje na míru pro spinální fúzi nebo úrazovou chirurgii. Možnost integrace porézních nebo mřížkových struktur může pomoci při manipulaci s nástroji a vizualizaci.
- Neurochirurgie: Jemná povaha neurochirurgie vyžaduje mimořádně přesné a často miniaturní nástroje. AM umožňuje vytvářet vlastní vodítka pro umístění elektrod při hluboké mozkové stimulaci, specializované mikroforceptory, disektory a retraktory přizpůsobené pro navigaci složitých nervových a cévních struktur.
- Kardiovaskulární chirurgie: Nástroje, jako jsou vlastní rozdělovače chlopní, složité svorky nebo specializované součásti podávacích systémů pro minimálně invazivní zákroky, těží z volnosti designu AM’. Možnost vytvářet nástroje s integrovanými funkcemi může snížit počet potřebných nástrojů a potenciálně zkrátit dobu zákroku.
- Minimálně invazivní chirurgie (MIS): Laparoskopické a endoskopické zákroky se opírají o dlouhé, tenké nástroje se složitými koncovými efektory. AM umožňuje vytvářet ergonomické rukojeti, kloubové koncovky nástrojů a nástroje s vnitřními kanály pro irigaci, odsávání nebo optická vlákna, což zlepšuje kontrolu chirurga a možnosti postupu.
- Kraniomaxillofaciální chirurgie (CMF): Pro rekonstrukční operace se používají vodítka pro řezání specifická pro pacienta, vodítka pro repozici a vlastní nástroje založené na datech z CT/MRI, které zajišťují přesnost řezů a repozice kostí.
- Zubní a ústní chirurgie: Pomocí technologie AM lze přesně vyrobit vlastní vodítka vrtáků pro zavádění implantátů, specializované extrakční nástroje a ortodontické nástroje.
- Všeobecná chirurgie: Zatímco mnoho standardních nástrojů je dostačujících, AM nachází uplatnění při vytváření specializovaných retraktorů, svorek nebo kleští pro náročné případy nebo nové chirurgické přístupy.
- Rychlý vývoj prototypů a nástrojů: Kromě nástrojů pro koncové použití je AM neocenitelná pro rychlé opakování návrhů během vývojové fáze. Chirurgové mohou rychle a s nízkými náklady testovat různé ergonomické tvary nebo funkční prvky, než se rozhodnou pro finální výrobu.
Tabulka: Příklady 3D tištěných chirurgických nástrojů podle specializace
Lékařská specializace | Příklady aplikací AM | Klíčové přínosy |
---|---|---|
Ortopedie | Specifické nástroje pro pacienty (PSI), vlastní vrtací vodítka, páteřní instrumentárium | Přesnost, zkrácený čas operačního sálu, složitá geometrie |
Neurochirurgie | Mikropřístroje, vlastní vodítka elektrod, specializované retraktory | Miniaturizace, přesnost, přizpůsobení konkrétnímu pacientovi |
Kardiovaskulární | Rozdělovače ventilů, komplexní svorky, součásti systému MIS Delivery System | Přizpůsobení, integrované funkce, složité geometrie |
Minimálně invazivní | Kloubové koncové efektory, ergonomické rukojeti, nástroje s vnitřními kanály | Funkčnost, ergonomie, miniaturizace |
Kraniomaxillofaciální | Vodítka pro řezání a polohování specifická pro pacienta, vlastní fixační nástroje | Přesnost, předvídatelnost, zkrácení doby operace |
Zubní/ústní chirurgie | Vodítka pro vrtání implantátů, specializované extrakční nástroje | Přesnost, přizpůsobení na míru, efektivita |
Všeobecná chirurgie | Specializované retraktory, svorky na míru pro jedinečné případy | Specifické aplikace, které řeší specifické anatomické potřeby |
Vývoj nástrojů | Funkční prototypy, ergonomické modely | Rychlost, nákladová efektivita, opakování návrhu |
Export do archů
Schopnost přizpůsobit nástroje nejen zákroku, ale potenciálně i anatomii konkrétního pacienta nebo preferencím chirurga znamená významný posun směrem k personalizované chirurgické péči, který je dán pokrokem v aditivní výrobní technologii.
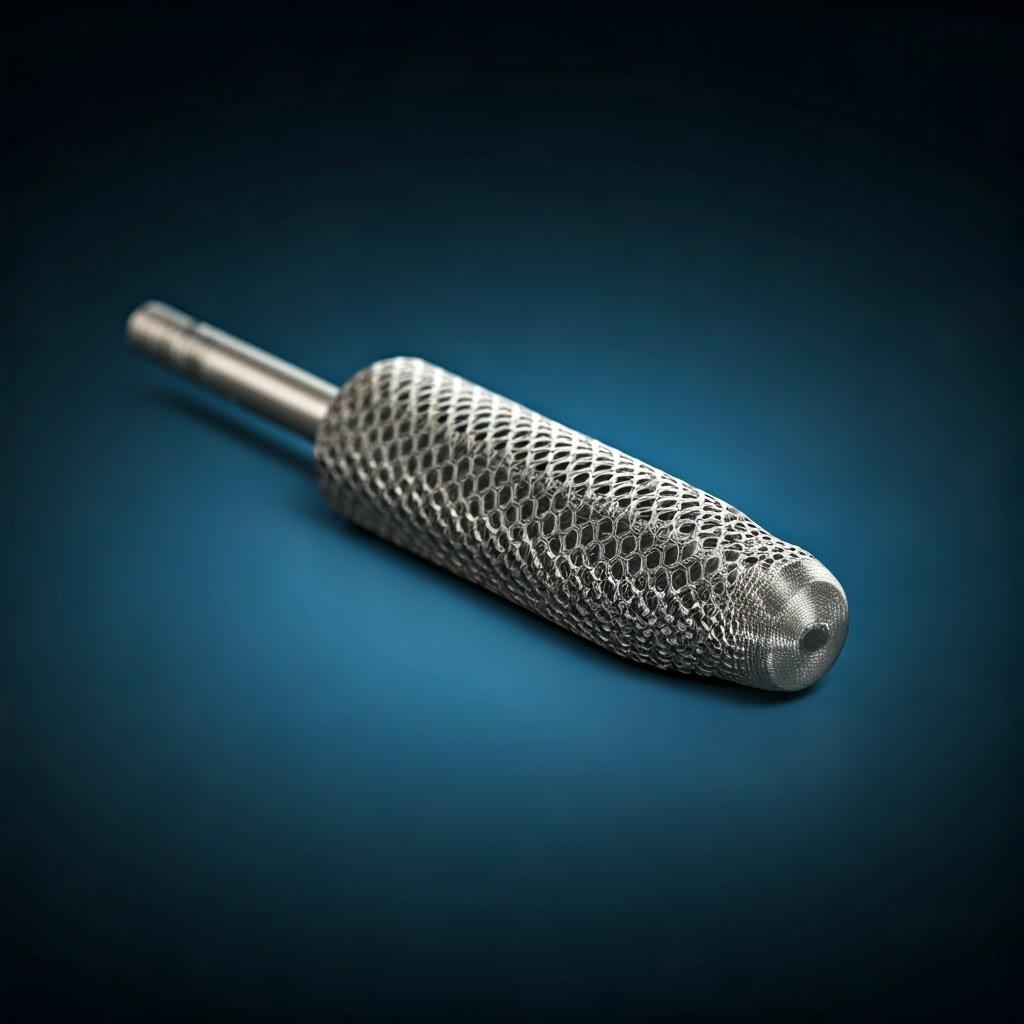
Proč 3D tisk kovů mění výrobu chirurgických nástrojů
Tradiční výroba chirurgických nástrojů je založena na subtraktivních metodách (obrábění materiálu) nebo na formovacích metodách (odlévání, kování). Tyto postupy jsou sice vyspělé a spolehlivé pro standardní nástroje, ale představují překážky, které aditivní výroba kovů účinně překonává, zejména u specializovaných, zakázkových nebo složitých nástrojů. Pro velkoodběratele a společnosti vyrábějící zdravotnické prostředky, které hledají inovativní řešení a spolehlivé dodavatele zakázkových chirurgických nástrojů, je pochopení těchto výhod klíčové.
Klíčové výhody technologie AM pro chirurgické nástroje:
- Bezkonkurenční volnost designu: AM vytváří díly vrstvu po vrstvě, což umožňuje vytvářet geometrie, které jsou tradičními metodami nemožné. To zahrnuje:
- Interní kanály: Pro zavlažování, odsávání nebo umístění optických vláken.
- Mřížové struktury: Snížení hmotnosti bez ztráty pevnosti, zlepšení ergonomie a snížení únavy chirurgů.
- Složité křivky a obrysy: Pro přizpůsobení konkrétnímu pacientovi nebo lepší manipulaci.
- Konsolidace částí: Spojení více komponent tradiční sestavy do jediného tištěného dílu, což snižuje složitost, potenciální místa poruch a dobu montáže.
- Hromadné přizpůsobení a nástroje pro konkrétní pacienty (PSI): AM vyniká při výrobě unikátních dílů přímo z digitálních modelů (např. CT/MRI skenů). To umožňuje:
- Průvodci pro pacienty: Zlepšení přesnosti operací v ortopedii, CMF a neurochirurgii.
- Ergonomie specifická pro chirurga: Nástroje navržené pro optimální pohodlí a ovládání pro jednotlivé chirurgy.
- Výroba na vyžádání: Výroba specializovaných nástrojů podle potřeby, čímž se sníží požadavky na zásoby zřídka používaných položek.
- Rychlé prototypování a zrychlené inovace: Nové návrhy chirurgických nástrojů lze prototypovat, testovat a iterovat mnohem rychleji a nákladově efektivněji než tradičními metodami, které vyžadují speciální nástroje. To urychluje vývojový cyklus nových chirurgických přístupů a zařízení.
- Účinnost materiálu: Při AM se obvykle používá pouze materiál potřebný k výrobě dílu a jeho podpěr, což vede k menšímu plýtvání materiálem ve srovnání se subtraktivní výrobou, zejména u složitých konstrukcí (poměr "buy-to-fly").
- Optimalizace dodavatelského řetězce: Digitální výroba umožňuje decentralizovanou výrobu. Návrhy nástrojů lze digitálně odesílat do certifikovaných tiskařských zařízení blíže místu použití, což může zkrátit dodací lhůty a logistickou náročnost, ačkoli v oblasti zdravotnictví je i nadále nejdůležitější přísná kontrola kvality.
- Potenciál rozšířené funkčnosti: Volnost konstrukce umožňuje integrovat prvky, které zlepšují výkon, jako jsou texturované povrchy pro lepší uchopení, optimalizované břity nebo integrované snímací funkce (ve vývoji).
Srovnání: Kovové AM vs. tradiční výroba pro chirurgické nástroje
Vlastnosti | Výroba aditiv kovů (AM) | Tradiční výroba (kování, obrábění, odlévání) |
---|---|---|
Složitost | Vysoká složitost dosažitelná s minimálním zvýšením nákladů | Složitost výrazně zvyšuje náklady & obtížnost |
Přizpůsobení | Ideální pro specifické pacienty & amp; zakázkové díly v malých objemech | Drahé a pomalé pro unikátní/obvyklé díly |
Doba realizace (Proto) | Půst (dny) | Mírně až pomalu (týdny/měsíce na výrobu nástrojů) |
Doba realizace (Prod) | Mírná (závisí na objemu, následném zpracování) | Rychle pro velkoobjemové standardní díly |
Náklady na nástroje | Žádné (beznástrojová výroba) | Vysoké počáteční náklady na nástroje |
Materiálový odpad | Obecně nižší (lepší poměr nákupu k letu) | Mohou být významné, zejména při obrábění |
Svoboda designu | Velmi vysoká (vnitřní kanály, mřížky, organické tvary) | Omezeno omezeními při obrábění/lisování |
Konsolidace částí | Vynikající schopnost | Omezené, často vyžaduje montáž |
Ideální objem | Nízký až střední objem, prototypy, zakázka | Velkoobjemové, standardní provedení |
Export do archů
Ačkoli AM nenahradí tradiční výrobu pro všechny chirurgické nástroje (zejména pro velkoobjemové, jednoduché nástroje, kde jsou náklady na jeden díl při použití konvenčních metod nejnižší), představuje výkonnou, doplňkovou cestu pro inovace, přizpůsobení a řešení složitých chirurgických problémů. Společnosti jako Met3dp, které mají hluboké odborné znalosti jak v oblasti pokročilé práškové výroby, tak v oblasti přesných tiskových procesů, jsou v této transformaci klíčovými hybateli.
Biokompatibilní materiály: nerezová ocel 316L vs. titan Ti-6Al-4V pro chirurgické nástroje
Výběr materiálu je při konstrukci chirurgických nástrojů zásadní. Nástroje musí být pevné, trvanlivé, odolné vůči korozi způsobené tělesnými tekutinami a drsnými sterilizačními procesy a především biokompatibilní - to znamená, že při styku s biologickou tkání nevyvolávají škodlivé reakce. Pro kovový 3D tisk chirurgických nástrojů dominují dva materiály: 316L nerezová ocel a slitina titanu Ti-6Al-4V (třída 5). Pochopení jejich vlastností je pro inženýry a manažery nákupu, kteří specifikují materiály pro aditivní výrobu zdravotnických prostředků, zásadní.
Nerezová ocel 316L:
- Složení: Austenitická slitina nerezové oceli obsahující chrom, nikl a molybden. Písmeno ‘L’ označuje nízký obsah uhlíku (<0,03 %), který zlepšuje odolnost proti korozi, zejména po svařování nebo odlehčování - což je důležité po tepelných cyklech 3D tisku.
- Klíčové vlastnosti:
- Vynikající odolnost proti korozi: Vysoce odolné proti celkové korozi, důlkové korozi a štěrbinové korozi, což je rozhodující pro vystavení tělním tekutinám a sterilizačním prostředkům (např. autoklávování).
- Dobrá biokompatibilita: Široce akceptované pro dočasné a některé trvalé kontaktní aplikace v lidském těle (podle norem jako ISO 10993).
- Vysoká tažnost a tvárnost: Ačkoli je u AM méně relevantní než u tradičních metod, svědčí o dobré houževnatosti.
- Dobrá pevnost a tvrdost: Dostatečné pro mnoho chirurgických aplikací, jako jsou retraktory, rukojeti a obecné nástroje.
- Nemagnetické: Obecně se považují za nemagnetické v žíhaném stavu, což může být důležité pro kompatibilitu s magnetickou rezonancí, ačkoli určitý zbytkový magnetismus může být vyvolán obráběním za studena nebo případně během AM zpracování.
- Nákladově efektivní: Obecně jsou levnější než slitiny titanu.
- Dobře zavedené: Dlouhá historie použití ve zdravotnických prostředcích, která poskytuje rozsáhlé údaje a znalosti.
Slitina titanu Ti-6Al-4V (třída 5):
- Složení: Slitina titanu alfa-beta obsahující 6 % hliníku a 4 % vanadu. Často se specifikuje jako Ti-6Al-4V ELI (Extra Low Interstitials, Grade 23) pro kritické chirurgické implantáty kvůli lepší tažnosti a lomové houževnatosti, ačkoli pro nástroje je běžná třída 5.
- Klíčové vlastnosti:
- Výjimečná biokompatibilita: Považuje se za jeden z nejlépe biokompatibilních kovů, široce používaný pro dlouhodobé implantáty (klouby, zubní) a nástroje. Vytváří stabilní, pasivní oxidovou vrstvu.
- Vynikající odolnost proti korozi: Vynikající odolnost vůči tělesným tekutinám a různým chemickým prostředím.
- Vysoký poměr pevnosti k hmotnosti: Výrazně lehčí než ocel (přibližně o 40-45 % nižší hustota), ale se srovnatelnou nebo vyšší pevností. To má zásadní význam pro snížení únavy chirurga u ručních nástrojů a u nástrojů používaných v aplikacích citlivých na hmotnost.
- Dobrá únavová pevnost: Důležité pro přístroje vystavené opakovaným zátěžovým cyklům.
- Kompatibilní s nemagnetickou magnetickou rezonancí: Je nemagnetický, takže je ideální pro nástroje používané při zákrocích MRI.
- Potenciál osteointegrace: Povrch je sice důležitější pro implantáty, ale v případě potřeby lze povrch ošetřit tak, aby se podpořil růst kosti u některých specializovaných zařízení.
- Vyšší náklady: Dražší surovina a potenciálně náročnější na zpracování ve srovnání s materiálem 316L.
Tabulka: Srovnání materiálů 316L a Ti-6Al-4V pro 3D tištěné chirurgické nástroje
Vlastnictví | Nerezová ocel 316L | Slitina titanu Ti-6Al-4V | Význam pro chirurgické nástroje |
---|---|---|---|
Biokompatibilita | Dobrý (ISO 10993) | Vynikající (ISO 10993) | Důležité pro bezpečnost pacientů, Ti-6Al-4V se často upřednostňuje pro implantáty |
Odolnost proti korozi | Vynikající | Vynikající / nadstandardní | Kritické pro dlouhou životnost, odolnost proti sterilizaci |
Hustota | ~8,0 g/cm³ | ~4,4 g/cm³ | Ti-6Al-4V nabízí výraznou úsporu hmotnosti (ergonomie) |
Pevnost v tahu (typická) | Středně vysoká (~550-700 MPa, tištěná) | Velmi vysoká (~900-1100 MPa, tištěná) | Vyšší pevnost umožňuje jemnější/robustnější konstrukce s Ti |
Tuhost (Youngův modul) | Vysoká (~193 GPa) | Mírná (~114 GPa) | 316L je tužší; Ti-6Al-4V je pružnější |
Tvrdost | Dobrý | Dobrý | Důležité pro odolnost proti opotřebení, zachování ostrých hran |
Kompatibilita s MRI | Obecně nemagnetické (závisí na procesu) | Plně nemagnetické | Klíčové pro použití v prostředí MRI |
Náklady | Dolní | Vyšší | Významný faktor při výběru materiálu |
Typické aplikace AM | Obecné nástroje, rukojeti, retraktory | Implantáty, vysokopevnostní nástroje, lehké nástroje, nástroje pro MRI | Přizpůsobuje vlastnosti materiálu potřebám aplikace |
Export do archů
Na kvalitě materiálu záleží: Bez ohledu na zvolenou slitinu je rozhodující kvalita kovového prášku použitého v procesu AM. Faktory, jako je distribuce velikosti částic, sféricita, tekutost a čistota, přímo ovlivňují hustotu, mechanické vlastnosti a povrchovou úpravu konečného vytištěného dílu. Společnost Met3dp využívá špičkové technologie plynové atomizace a plazmového rotačního elektrodového procesu (PREP) k výrobě vysoce kvalitních sférických kovových prášků, včetně lékařské třídy 316L a Ti-6Al-4V, které zajišťují optimální výkon a konzistenci pro náročné aplikace chirurgických nástrojů. Výběr dodavatele s robustní výrobou prášků a schopností kontroly kvality je pro spolehlivou výrobu lékařských přístrojů nejdůležitější.
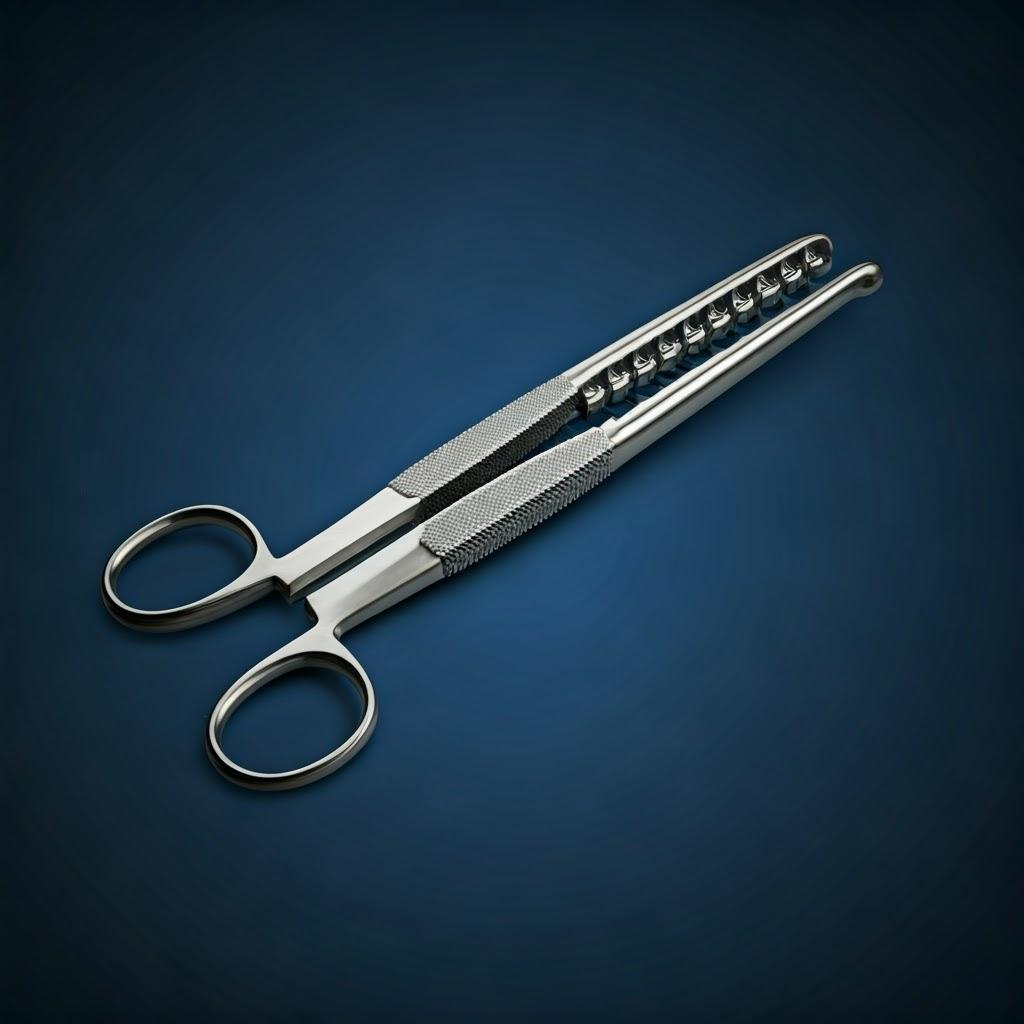
Principy návrhu pro aditivní výrobu (DfAM) pro vysoce výkonné chirurgické nástroje
Pouhá replikace tradičně navrženého chirurgického nástroje pomocí 3D tisku jen zřídkakdy odhalí plný potenciál aditivní výroby. Aby inženýři skutečně využili výhod komplexnosti, přizpůsobení a zvýšení výkonu, musí přijmout návrh pro aditivní výrobu (DfAM). DfAM zahrnuje navrhování dílů s ohledem na specifické možnosti a omezení procesu AM. U chirurgických nástrojů to znamená optimalizaci z hlediska funkčnosti, ergonomie, sterilizovatelnosti a efektivity výroby.
Použití principů DfAM má zásadní význam pro vytvoření nástrojů, které lze nejen tisknout, ale které mají také vynikající výkon a manipulaci. Spolupráce se zkušeným poskytovatelem AM, jako je Met3dp, který rozumí nuancím různých typů výroby tiskových metod a materiálů, může významně pomoci při optimalizaci návrhů.
Klíčové aspekty DfAM pro chirurgické nástroje:
- Optimalizace podpůrné struktury: Procesy AM často vyžadují podpůrné konstrukce pro ukotvení dílu na konstrukční desce a podporu přečnívajících prvků během tisku.
- Minimalizujte převisy: Orientujte díl na konstrukční desce tak, abyste omezili strmé úhly nebo vodorovné převisy (>45° často vyžaduje podpěru).
- Konstrukce samonosných úhlů: Pokud je to možné, používejte zkosení nebo mírnější úhly.
- Přístupnost pro stěhování: Zajistěte, aby bylo možné fyzicky dosáhnout na podpěry a odstranit je bez poškození choulostivých prvků. V případě potřeby zvažte návrh přístupových otvorů.
- Vliv na povrchovou úpravu: Podporované povrchy mají obvykle drsnější povrch a mohou vyžadovat intenzivnější následné zpracování. Kritické povrchy navrhujte pokud možno samonosné.
- Tloušťka stěny a velikost prvků: Procesy AM mají minimální tloušťky stěn a velikosti prvků, které lze tisknout.
- Minimální tloušťka stěny: Obvykle se pohybuje od 0,3 mm do 0,8 mm v závislosti na technologii (např. LPBF vs. SEBM) a materiálu. Zajistěte, aby stěny byly dostatečně silné pro strukturální integritu a manipulaci.
- Rozlišení malých funkcí: Při navrhování velmi jemných prvků, jako jsou vroubky nebo kolíky, zvažte velikost laserového bodu nebo průměr elektronového paprsku.
- Průměry otvorů: Přesný tisk malých otvorů (1 mm) může být náročný a může vyžadovat dodatečné vrtání. Navrhněte odpovídajícím způsobem nebo počítejte s obráběním.
- Vnitřní kanály a dutiny: Společnost AM vyniká při vytváření složitých vnitřních geometrií pro funkce, jako je přívod kapalin, sání nebo vedení kabelů.
- Samonosné tvary: Vnitřní kanály navrhněte ve tvaru slzy nebo kosočtverce, abyste se vyhnuli potřebě vnitřních podpěr, jejichž odstranění je velmi obtížné nebo nemožné.
- Odstranění prášku: Obsahují odtokové otvory nebo přístupové body, aby bylo zajištěno odstranění veškerého nerozpuštěného prášku z vnitřních dutin po tisku - což je důležité pro biokompatibilitu.
- Plynulé přechody: Vyhněte se ostrým vnitřním rohům, které by mohly zachycovat nečistoty nebo bránit průtoku.
- Mřížové konstrukce a odlehčování: Začlenění vnitřních mřížek nebo topologicky optimalizovaných struktur může výrazně snížit hmotnost nástroje, zlepšit ergonomii a snížit únavu chirurga při zachování potřebné tuhosti a pevnosti. To je výhodné zejména u titanových nástrojů.
- Konsolidace částí: Identifikujte možnosti kombinace více komponent tradiční sestavy přístroje do jediného monolitického tištěného dílu. Tím se zkrátí doba montáže, sníží náklady, sníží se počet možných poruch a zjednoduší se dodavatelský řetězec.
- Textura povrchu: Navrhněte funkční textury přímo do dílu, například úchyty na rukojetích nebo specifickou drsnost na pracovních koncích, čímž můžete snížit počet kroků následného zpracování.
- Sterilizace a čištění: Navrhněte nástroje s hladkým povrchem, zaoblenými hranami a minimem štěrbin, ve kterých by se mohly zachytit biologické nečistoty. Vyhněte se prvkům, které ztěžují důkladné čištění a sterilizaci. Zajistěte, aby odstranění prášku z vnitřních kanálků bylo proveditelné a ověřitelné.
- Integrace výběru materiálu: Výběr konstrukce může být ovlivněn vlastnostmi materiálu. Například nižší tuhost titanu může vyžadovat jiné konstrukční úvahy než u nerezové oceli pro stejnou aplikaci.
Tabulka: Souhrn pokynů DfAM pro chirurgické nástroje
Zásada DfAM | Pokyn | Odůvodnění chirurgických nástrojů |
---|---|---|
Orientace | Optimalizace pro minimální podpěry, nejlepší povrchová úprava na kritických místech | Omezuje následné zpracování, zajišťuje kritickou kvalitu povrchu |
Podporuje | Minimalizujte převisy (45°), zajistěte přístup k odstranění | Náklady, doba realizace, povrchová úprava, zamezení poškození |
Tloušťka stěny | Dodržujte procesní minima (např. 0,4 mm), zajistěte strukturální integritu | Tisknutelnost, pevnost, manipulace |
Vnitřní kanály | Použití samonosných tvarů, konstrukce pro odstraňování prášku | Funkčnost, zabraňuje zachycení prášku (riziko biokompatibility) |
Odlehčení | Využití mřížek/optimalizace topologie, kde je to vhodné | Zlepšená ergonomie, snížení únavy chirurgů |
Konsolidace částí | Spojení více komponent do jednoho tištěného dílu | Omezená montáž, méně poruchových bodů, jednodušší dodavatelský řetězec |
Čistitelnost | Navrhněte hladké povrchy, vyhněte se hlubokým trhlinám, zajistěte dráhu pro odstranění prášku | Účinná sterilizace, zabraňuje hromadění biologické zátěže |
Export do archů
Díky aditivnímu myšlení od samého počátku mohou výrobci vytvářet chirurgické nástroje nové generace, které nabízejí vynikající výkon, ergonomii a přizpůsobení a překonávají omezení tradičních výrobních paradigmat.
Dosažení kritických tolerancí, povrchové úpravy a přesnosti u 3D tištěných chirurgických nástrojů
Zatímco volnost designu je hlavním lákadlem, chirurgické nástroje vyžadují přesnost. Kritické rozměry, styčné prvky a vhodné vlastnosti povrchu jsou pro funkčnost a bezpečnost nepominutelné. Pochopení dosažitelných úrovní tolerance, kvality povrchu a rozměrové přesnosti při použití technologie metal AM je pro inženýry a manažery nákupu, kteří tuto technologii hodnotí pro výrobu zdravotnických prostředků, zásadní.
Tolerance:
- Obecné tolerance: Kovové díly vytištěné metodou AM as-printing obvykle dosahují tolerancí v rozsahu ISO 2768 medium (m) nebo někdy fine (f). To znamená zhruba ±0,1 mm až ±0,3 mm u menších rozměrů, přičemž u větších dílů se toleranční rozsahy zvyšují v důsledku tepelných vlivů při sestavování.
- Kritické tolerance: U prvků vyžadujících přísnější tolerance (např. styčné plochy, zajišťovací mechanismy, přesné průměry) je často nutné následné obrábění (CNC frézování, soustružení, broušení). Těmito sekundárními operacemi lze u specifických prvků dosáhnout tolerancí srovnatelných s konvenčním obráběním (např. ±0,01 mm až ±0,05 mm).
- Závislost na procesu: Tolerance se mohou mírně lišit mezi různými procesy AM (např. Laser Powder Bed Fusion – LPBF vs. Selective Electron Beam Melting – SEBM) a stroji. Špičkové průmyslové systémy, jako jsou ty, které využívá společnost Met3dp, nabízejí lepší kontrolu procesu a konzistenci, což vede k lepší přesnosti při tisku.
Povrchová úprava (drsnost):
- Jak bylo vytištěno: Povrchová úprava dílů AM je ze své podstaty drsnější než u obráběných povrchů, a to kvůli procesu vrstvení a částečně roztaveným částicím prášku ulpívajícím na povrchu.
- Typické hodnoty Ra (průměrná drsnost) se pohybují od 5 µm do 20 µm v závislosti na materiálu, procesních parametrech, rozložení velikosti částic a orientaci povrchu (povrchy směřující vzhůru jsou obecně hladší než povrchy směřující dolů nebo povrchy na podložce).
- Následné zpracování pro zlepšení: Pro většinu chirurgických aplikací je povrch v podobě, v jaké byl vytištěn, příliš drsný. Používají se různé techniky následného zpracování:
- Tryskání abrazivem (kuličkové/ pískové): Poskytuje rovnoměrný matný povrch a odstraňuje volné částice (Ra obvykle 3-6 µm).
- Třískové/vibrační dokončování: Používá média k vyhlazení povrchů a hran, účinná pro dávky dílů (Ra může dosahovat 1-3 µm).
- Elektrolytické leštění: Elektrochemický proces, který odstraňuje tenkou vrstvu materiálu, čímž vzniká velmi hladký, lesklý, čistý a vysoce korozivzdorný povrch. Často se upřednostňuje pro chirurgické nástroje z nerezové oceli (Ra < 0,8 µm, někdy < 0,4 µm).
- Ruční leštění: Pro dosažení zrcadlového povrchu na určitých plochách, i když je to pracné.
- Obrábění: Vytváří hladké a přesné povrchy kritických prvků.
- Význam pro chirurgické nástroje: Hladké povrchy mají zásadní význam pro čistitelnost, snižují tření, minimalizují trauma tkáně a zabraňují adhezi biologické zátěže. V závislosti na funkci nástroje a typu kontaktu jsou často vyžadovány specifické cíle Ra.
Rozměrová přesnost a validace:
- Řízení procesu: Dosažení konzistentní rozměrové přesnosti vyžaduje přísnou kontrolu nad celým procesem AM, včetně kalibrace stroje, konzistentní kvality prášku (jako jsou prášky s vysokou sféricitou od společnosti Met3dp), optimalizovaných procesních parametrů a řízeného tepelného managementu.
- Ověřování: Přesnost rozměrů musí být ověřena pomocí vhodného metrologického zařízení.
- Třmeny/mikrometry: Pro základní rozměrové kontroly.
- Souřadnicové měřicí stroje (CMM): Pro vysoce přesné měření složitých geometrií a ověřování GD&T (Geometrické rozměry a tolerance).
- 3D skenování: Pro porovnání výsledné geometrie dílu s původním modelem CAD.
- Systém řízení kvality (QMS): Robustní systém řízení jakosti (ideálně certifikovaný podle normy ISO 13485 pro zdravotnické prostředky) zajišťuje, že procesy jsou dokumentovány, kontrolovány a validovány, aby se důsledně vyráběly díly splňující rozměrové specifikace.
Tabulka: Typické úrovně přesnosti v kovovém AM pro chirurgické nástroje
Parametr | Rozsah podle tisku | Potenciál po zpracování | Důležitost |
---|---|---|---|
Tolerance | ±0,1 až ±0,3 mm (ISO 2768-m/f) | ±0,01 až ±0,05 mm (obráběním) | Uložení, funkce, párové díly |
Povrchová úprava (Ra) | 5 µm – 20 µm | < 0,8 µm (elektrolytické leštění/leštění) | Čistitelnost, biokompatibilita, tření, opotřebení |
Rozlišení prvků | ~0,3 – min. 0,8 mm stěna/výbava | Definováno procesem AM | Schopnost vytvářet jemné detaily |
Metoda ověřování | Souřadnicové měřicí stroje, 3D skenování, měřidla | CMM, profilometrie povrchu | Zajištění shody dílů s konstrukčními specifikacemi & standardy |
Export do archů
Ačkoli AM nabízí neuvěřitelnou flexibilitu designu, dosažení potřebné přesnosti chirurgických nástrojů často vyžaduje kombinaci řízeného tisku a cíleného následného zpracování, které se řídí přísnými postupy kontroly kvality.
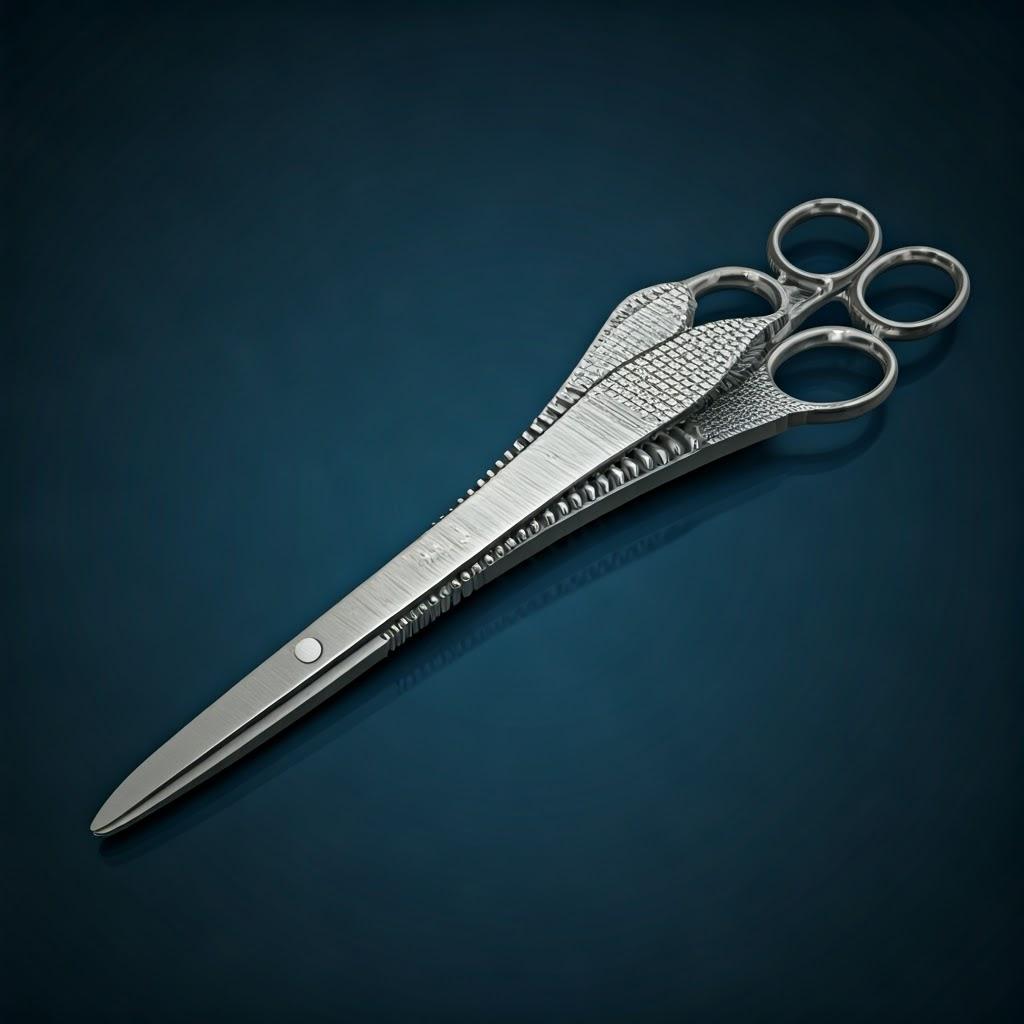
Základní kroky následného zpracování pro funkční a bezpečné 3D tištěné chirurgické nástroje
Kovový 3D tištěný díl je zřídkakdy připraven k použití ihned po vyjetí ze stroje, zejména ne pro kritické aplikace, jako jsou chirurgické nástroje. K přeměně surového vytištěného dílu na funkční, bezpečný a sterilní zdravotnický prostředek je zapotřebí řada nezbytných kroků následného zpracování. Tyto kroky řeší zbytková napětí, odstraňují dočasné struktury, dosahují požadované povrchové úpravy a tolerancí a zajišťují čistotu. Konkrétní pracovní postup se může lišit v závislosti na materiálu, složitosti konstrukce a požadavcích aplikace.
Typický pracovní postup následného zpracování:
- Úleva od stresu / tepelné ošetření:
- Proč: Rychlé cykly zahřívání a ochlazování při AM vyvolávají v dílu vnitřní pnutí. Tepelné zpracování (žíhání, uvolňování napětí) při specifických teplotách homogenizuje mikrostrukturu, uvolňuje tato napětí (zabraňuje potenciální deformaci nebo praskání) a může optimalizovat mechanické vlastnosti, jako je tažnost a pevnost podle materiálových norem (např. normy ASTM pro 316L nebo Ti-6Al-4V).
- Jak: Provádí se v peci s řízenou atmosférou (vakuum nebo inertní plyn) podle validovaných protokolů specifických pro danou slitinu.
- Vyjmutí dílu ze stavební desky:
- Jak: Díly se obvykle vyřezávají z konstrukční desky pomocí elektroerozivního obrábění (EDM) nebo pásové pily.
- Odstranění podpůrné konstrukce:
- Proč: Podpěry jsou nutné během stavby, ale poté musí být odstraněny.
- Jak: To lze provést ručně (lámáním nebo řezáním), pomocí CNC obrábění nebo někdy pomocí elektroerozivního obrábění. Je třeba dbát na to, aby nedošlo k poškození samotného dílu. U složitých vnitřních podpěr může být přístup náročný.
- Čištění & amp; Odstraňování prášku:
- Proč: Veškeré zbytky kovového prášku, zejména z vnitřních kanálků nebo složitých prvků, musí být pečlivě odstraněny. Zachycený prášek představuje významné riziko pro biokompatibilitu.
- Jak: Mezi metody patří ofukování stlačeným vzduchem, ultrazvukové čisticí lázně a případně mikrotryskání. Konstrukční prvky (odtokové otvory) tento proces usnadňují.
- Povrchová úprava:
- Proč: Pro dosažení požadované hladkosti pro čistitelnost, snížení tření a biokompatibilitu.
- Jak: Jak již bylo řečeno, zahrnuje to kroky jako:
- Otryskání abrazivem (např. tryskáním kuličkami) pro dosažení rovnoměrného matného povrchu.
- Obrábění / vibrační dokončování pro vyhlazení hran a povrchů.
- Elektrolytické leštění (zejména pro 316L) pro velmi hladký, čistý a pasivní povrch.
- Ruční leštění pro specifické požadavky na vysoký lesk.
- Obrábění (pokud je vyžadováno):
- Proč: K dosažení kritických tolerancí, přesných průměrů otvorů, rovných styčných ploch nebo ostrých řezných hran, které nelze spolehlivě vyrobit pouhou technologií AM.
- Jak: CNC frézování, soustružení, broušení nebo vrtání specifických prvků.
- Konečné čištění a pasivace:
- Proč: K odstranění zbytků po obrábění nebo manipulaci a, zejména u nerezové oceli a titanu, k zajištění tvorby stabilní pasivní oxidové vrstvy, která zvyšuje odolnost proti korozi a biokompatibilitu.
- Jak: Zahrnuje ověřené vícestupňové čisticí procesy s použitím čisticích prostředků, rozpouštědel a čištěné vody, po nichž případně následuje specifická pasivační úprava (např. lázeň s kyselinou dusičnou nebo kyselinou citronovou u nerezových ocelí).
- Kontrola a řízení kvality:
- Proč: Ověřit, zda rozměrová přesnost, povrchová úprava, vlastnosti materiálu a čistota odpovídají všem specifikacím.
- Jak: CMM, vizuální kontrola, profilometrie povrchu, případně testování materiálu na vzorcích vytištěných vedle dílů.
- Validace sterilizace (provádí výrobce zdravotnických prostředků):
- Proč: Ačkoli to poskytovatel služeb AM obvykle neprovádí, přístroj musí být kompatibilní se standardními metodami sterilizace (např. autoklávování, gama záření, EtO). Výrobní proces, včetně čištění, musí zajistit, aby bylo možné přístroj účinně sterilizovat. Validační protokoly potvrzují, že zvolená metoda sterilizace trvale dosahuje požadované úrovně zajištění sterility (SAL).
Příklad zjednodušeného vývojového diagramu následného zpracování:
Úryvek kódu
graf TD
A[3D Print Complete] --> B{Stress Relief / Heat Treatment};
B --> C{Vyjmutí dílu z desky};
C --> D{Vyjmutí podpěry};
D --> E{Počáteční čištění / odstranění prášku};
E --> F{Povrchová úprava (otryskání/otlučení atd.)};
F --> G{Obrábění (je-li třeba)};
G --> H{Závěrečné čištění a pasivace};
H --> I[Kontrola (rozměry, povrch)];
I --> J(Připraveno k balení/sterilizaci);
%% Volitelné cesty
F --> H; %% Vynechat obrábění
E --> G; %% Obrábění před celkovou povrchovou úpravou
Každý krok vyžaduje pečlivou kontrolu a validaci, zejména v rámci systému řízení kvality zdravotnických prostředků, jako je ISO 13485, aby bylo zajištěno, že výsledný chirurgický nástroj je bezpečný a účinný.
Překonávání výzev při aditivní výrobě kovů pro chirurgické aplikace
Ačkoli AM zpracování kovů nabízí významné výhody pro výrobu chirurgických nástrojů, není bez problémů. Úspěšná výroba vysoce kvalitních a spolehlivých zdravotnických prostředků vyžaduje předvídání a zmírnění potenciálních problémů v průběhu fází návrhu, tisku a následného zpracování. Pochopení těchto problémů pomáhá při výběru schopných výrobních partnerů a stanovení realistických očekávání.
Společné výzvy a strategie pro jejich zmírnění:
- Zbytkové napětí a deformace:
- Výzva: Rychlé cykly zahřívání/chlazení vytvářejí vnitřní napětí, které může způsobit deformaci nebo zkroucení dílů během tisku nebo po něm, nebo dokonce jejich prasknutí.
- Zmírnění:
- Simulace: Použití softwaru pro tepelnou simulaci k předvídání nárůstu napětí a optimalizaci orientace dílů a podpůrných strategií.
- Parametry procesu: Optimalizace výkonu laseru/paprsku, rychlosti skenování a tloušťky vrstvy.
- Vytápění platformy: Předehřívání stavební platformy (běžné u SEBM, možné u některých LPBF) snižuje tepelné gradienty.
- Strategie podpory: Robustní podpůrné konstrukce pomáhají ukotvit díl a odvádět teplo.
- Úleva od stresu: Tepelné zpracování po tisku je zásadní pro odstranění zbytkových napětí.
- Odstranění podpůrné konstrukce:
- Výzva: Odstraňování podpěr, zejména ze složitých vnitřních geometrií nebo choulostivých prvků, může být obtížné, časově náročné a hrozí při něm riziko poškození dílu. Podepřené povrchy jsou obvykle drsné.
- Zmírnění:
- DfAM: Návrh pro minimální použití podpory a snadný přístup (viz oddíl DfAM).
- Optimalizované podpory: Použití podpůrných konstrukcí, které jsou během stavby dostatečně pevné, ale jsou navrženy tak, aby se snadněji rozlomily.
- Pokročilé techniky odstraňování: Využití drátového elektroerozivního obrábění nebo přesného obrábění pro obtížné podpěry.
- Výběr procesu: Některé procesy mohou pro určité geometrie vyžadovat méně podpěr.
- Dosažení požadované povrchové úpravy a čistoty:
- Výzva: Povrchy vytištěné ve formě tisku jsou drsné a nevhodné pro většinu chirurgických aplikací. Dosažení konzistentní hladkosti (často je požadováno Ra 0,8 µm) a zajištění odstranění veškerého prášku/odpadků, zejména z vnitřních kanálků, je velmi důležité, ale náročné.
- Zmírnění:
- Optimalizované parametry: Jemné doladění parametrů tisku může mírně zlepšit výslednou kvalitu tisku.
- Efektivní následné zpracování: Použití vhodných technik, jako je elektrolytické leštění, bubnové leštění nebo tryskání, přizpůsobených materiálu a geometrii.
- DfAM pro čistitelnost: Konstrukce dílů bez prvků, které zachycují prach nebo nečistoty.
- Ověřené protokoly čištění: Zavedení přísných, vícestupňových čisticích procesů s ověřovacími kroky.
- Kontrola pórovitosti:
- Výzva: V tištěném materiálu mohou někdy vznikat malé dutiny nebo póry v důsledku neúplného roztavení, zachycení plynu nebo efektu "keyholing". Pórovitost může zhoršovat mechanické vlastnosti (zejména únavovou pevnost) a potenciálně se v ní mohou vyskytovat bakterie.
- Zmírnění:
- Vysoce kvalitní prášek: Použití prášku s konzistentní sféricitou, distribucí velikosti a nízkým obsahem plynu, jako je prášek vyrobený pomocí pokročilé atomizace Met3dp’. Příklady naleznete na našich stránkách stránka produktu.
- Optimalizované parametry procesu: Vývoj a ověřování sad parametrů, které zajišťují úplné roztavení a hustotu (>99,5 % je běžné, často lze dosáhnout >99,9 %).
- Monitorování procesů: Využití monitorovacích systémů in-situ (např. monitorování taveniny) k odhalení potenciálních problémů během výstavby.
- Izostatické lisování za tepla (HIP): Krok následného zpracování zahrnující vysokou teplotu a tlak k uzavření vnitřních pórů (často se používá u kritických dílů zatížených únavou, zvyšuje náklady).
- Konzistence a opakovatelnost procesu:
- Výzva: Zajištění toho, aby každý vyrobený díl splňoval stejné specifikace, vyžaduje přísnou kontrolu mnoha proměnných (stroj, materiál, parametry, prostředí).
- Zmírnění:
- Robustní QMS: Zavedení normy ISO 13485 nebo srovnatelného systému kvality.
- Kalibrace a údržba strojů: Pravidelná, zdokumentovaná kalibrace a preventivní údržba.
- Správa prášku: Přísná kontrola získávání prášku, manipulace s ním, skladování a protokolů o recyklaci/omlazování.
- Validace procesu (IQ/OQ/PQ): Důkladná instalační kvalifikace (IQ), provozní kvalifikace (OQ) a výkonnostní kvalifikace (PQ) pro stroje a procesy.
- Statistická kontrola procesu (SPC): Sledování klíčových procesních ukazatelů pro zajištění stability.
- Dodržování předpisů a validace:
- Výzva: Zdravotnické prostředky jsou přísně regulovány. Prokázání, že procesy AM a výsledné díly splňují přísné požadavky (biokompatibilita, mechanické vlastnosti, sterilita), vyžaduje rozsáhlé testování a dokumentaci.
- Zmírnění:
- Spolupráce se zkušenými dodavateli: Výběr dodavatelů, jako je Met3dp, kteří mají zkušenosti s výrobou zdravotnických prostředků a příslušné certifikace (např. ISO 13485).
- Certifikace materiálu: Použití certifikovaných materiálů lékařské kvality s plnou sledovatelností.
- Důkladné ověření: Provádění komplexních zkoušek (mechanických, chemických, biokompatibility) podle příslušných norem (ISO, ASTM).
- Dokumentace: Vedení podrobných záznamů o všech krocích výroby a kontroly kvality.
Překonání těchto výzev vyžaduje kombinaci pokročilých technologií, odborných znalostí v oblasti materiálových věd, důsledné kontroly procesů a hlubokého porozumění požadavkům na zdravotnické prostředky. Výběr výrobního partnera s prokazatelnými schopnostmi v těchto oblastech je pro úspěšné uvedení 3D tištěných chirurgických nástrojů na trh zásadní.
Výběr správného partnera pro 3D tisk kovů pro výrobu zdravotnických prostředků
Výběr správného výrobního partnera je při vývoji 3D tištěných chirurgických nástrojů pravděpodobně stejně důležitý jako návrh a výběr materiálu. Jedinečné požadavky průmyslu zdravotnických prostředků - přísné předpisy, požadavky na vysokou přesnost, biokompatibilitu a absolutní spolehlivost - vyžadují spolupráci s poskytovatelem aditivní výroby kovů, který má specifické odborné znalosti a robustní systémy kvality. Manažeři nákupu a technické týmy by měli potenciální dodavatele hodnotit na základě komplexního souboru kritérií.
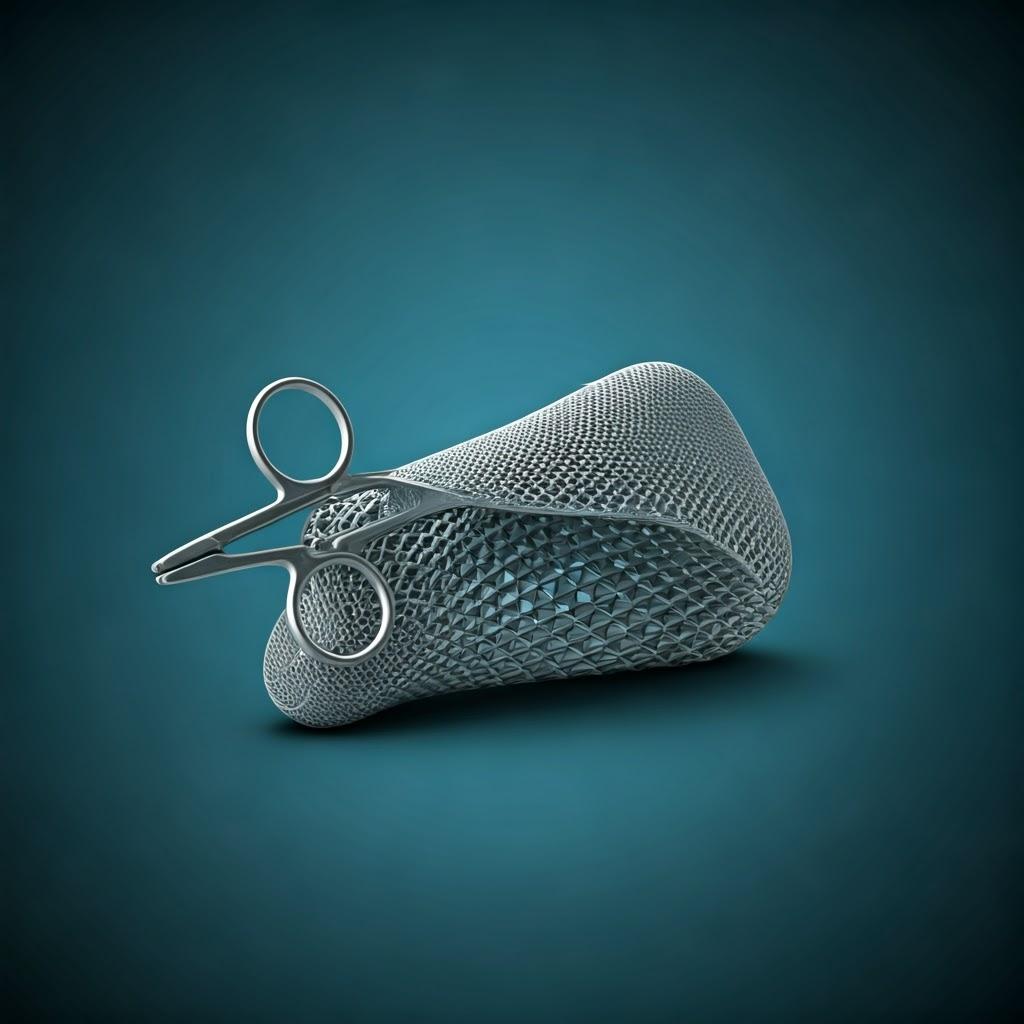
Klíčová kritéria pro hodnocení dodavatelů kovů pro chirurgické nástroje:
- Systém řízení kvality (QMS) a certifikace:
- Certifikace ISO 13485: Jedná se o mezinárodní normu pro systémy řízení kvality zdravotnických prostředků. Certifikace prokazuje, že dodavatel zavedl procesy pro kontrolu návrhu, řízení rizik, sledovatelnost, validaci procesů a nápravná/preventivní opatření přizpůsobená zdravotnickému průmyslu. Mělo by se jednat o primární požadavek.
- Certifikace ISO 9001: Obecná norma QMS, která se často používá společně s normou ISO 13485 a která označuje širší řízení procesů kvality.
- Zkušenosti s lékařskými přístroji:
- Osvědčené výsledky: Má dodavatel prokazatelné zkušenosti s výrobou lékařských komponent, zejména chirurgických nástrojů nebo implantátů? Požádejte o případové studie, příklady (v případě potřeby pod NDA) a reference.
- Porozumění předpisům: Klíčová je znalost předpisů FDA (např. 21 CFR Part 820), EU MDR a dalších relevantních předpisů.
- Odbornost a manipulace s materiálem:
- Certifikované materiály: Získávají a používají certifikované kovové prášky lékařské kvality (např. 316L, Ti-6Al-4V ELI) s plnou sledovatelností?
- Kontrola kvality prášku: Jaké jsou jejich postupy pro vstupní kontrolu prášku, skladování, manipulaci a recyklaci/obnovu, aby se zabránilo kontaminaci a zajistila konzistence? Společnosti jako Met3dp, které vyrábějí vlastní vysoce kvalitní prášky pomocí pokročilých technik atomizace, nabízejí významné výhody v oblasti kontroly materiálu a sledovatelnosti. Více informací o našem závazku ke kvalitě se můžete dozvědět na našich stránkách Stránka O nás.
- Rozsah materiálů: Nezbytná je schopnost pracovat se specifickými slitinami (316L, Ti-6Al-4V).
- Technologie a vybavení:
- Vhodná technologie AM: Provozují dobře udržované, průmyslové systémy AM pro kovy (např. LPBF, SEBM) vhodné pro požadovanou přesnost a materiál?
- Vytváření objemu a kapacity: Dokáží pojmout požadovanou velikost a množství dílů?
- Monitorování procesů: Jsou jejich stroje vybaveny funkcí monitorování in-situ pro lepší kontrolu kvality?
- Možnosti následného zpracování:
- In-House vs. Outsourcing: Nabízejí potřebné kroky následného zpracování (tepelné zpracování, odstranění podpěr, obrábění, leštění, čištění, pasivace) přímo ve firmě nebo prostřednictvím kvalifikovaných partnerů? Vlastní kapacity často poskytují lepší kontrolu a potenciálně kratší dodací lhůty.
- Ověřené procesy: Jsou jejich kroky následného zpracování, zejména čištění a pasivace, validovány pro lékařské aplikace?
- Technická odbornost a podpora:
- Podpora DfAM: Mohou poskytnout odborné poradenství při optimalizaci návrhů pro aditivní výrobu?
- Inženýrská spolupráce: Jsou jejich inženýři přístupní a spolupracují s vámi během celého životního cyklu projektu?
- Řešení problémů: Mají odborné znalosti pro řešení potenciálních výrobních problémů?
- Kontrola a metrologie:
- Zařízení: Disponují kalibrovanými souřadnicovými měřidly, profilometry, skenery a dalším potřebným metrologickým vybavením?
- Podávání zpráv: Mohou poskytnout komplexní kontrolní zprávy dokumentující přesnost rozměrů, povrchovou úpravu a shodu se specifikacemi?
- Důvěrnost a ochrana duševního vlastnictví:
- NDA: Jsou ochotni a zvyklí pracovat na základě dohod o mlčenlivosti, aby ochránili citlivé duševní vlastnictví?
Tabulka: Kontrolní seznam pro hodnocení dodavatelů
Kritéria | Klíčové otázky, které je třeba položit | Proč je to důležité pro chirurgické nástroje |
---|---|---|
Certifikace ISO 13485 | Je dodavatel certifikován? Může poskytnout certifikát? | Prokazuje shodu se systémem řízení jakosti zdravotnických prostředků |
Lékařské zkušenosti | Jaké konkrétní lékařské díly jste vyráběli? Můžete se podělit o případové studie/příklady? | Zajišťuje porozumění zdravotním požadavkům |
Kontrola materiálu | Jak získáváte, testujete, zpracováváte a sledujete prášky pro lékařské účely (316L, Ti-6Al-4V)? | Zaručuje biokompatibilitu materiálu & vlastnosti |
Technologie & Kapacita | Jaké stroje AM používáte? Jaký je objem/přesnost sestavení? Máte kapacitu pro můj projekt? | Zajišťuje technickou způsobilost & včasné dodávky |
Následné zpracování | Jaké kroky se provádějí ve firmě? Jsou procesy čištění/pasivace validovány? | Kritické pro vlastnosti finálního dílu, bezpečnost, povrchovou úpravu |
Technická podpora | Nabízíte recenzi DfAM? Jak řešíte technické problémy? | Optimalizuje design, zajišťuje plynulou výrobu |
Inspekce & amp; QC | Jaké máte metrologické vybavení? Jaká úroveň kontrolního hlášení je standardní/ dostupná? | Ověřuje, zda díly splňují kritické specifikace |
Důvěrnost | Jaké postupy jsou zavedeny na ochranu duševního vlastnictví? | Chrání citlivé informace o návrhu |
Export do archů
Výběr partnera, jako je společnost Met3dp, s desetiletími společných zkušeností zahrnujících pokročilou výrobu kovových prášků, přesnou technologii tisku SEBM a komplexní služby vývoje aplikací, poskytuje silný základ pro vývoj a výrobu vysoce kvalitních a spolehlivých 3D tištěných chirurgických nástrojů.
Porozumění struktuře nákladů a dodací lhůtě pro 3D tištěné chirurgické nástroje
Ačkoli technologie AM umožňuje inovace, pro plánování projektů, sestavování rozpočtů a zadávání zakázek je nezbytné znát související náklady a časový harmonogram výroby. Na rozdíl od tradiční hromadné výroby, kde dominuje amortizace nástrojů, jsou náklady na AM řízeny jinými faktory.
Klíčové faktory ovlivňující náklady na 3D tištěné chirurgické nástroje:
- Typ materiálu a spotřeba:
- Výběr materiálu: Titanové slitiny (Ti-6Al-4V) jsou výrazně dražší než nerezové oceli (316L), a to jak z hlediska ceny surového prášku, tak často i z hlediska požadavků na zpracování.
- Část Objem: Skutečný objem materiálu použitého v samotném dílu. Větší/hustší díly stojí více.
- Podpůrné struktury: Materiál použitý na podpěry zvyšuje spotřebu a vyžaduje čas/náklady na odstranění. Optimalizovaná orientace a DfAM mohou tento problém minimalizovat.
- Práškový odpad/recyklace: Neefektivní manipulace s práškem nebo nadměrný odpad zvyšují náklady.
- Čas stroje (čas sestavení):
- Výška dílu (Z-výška): Doba sestavení je dána především počtem vrstev, což znamená, že vyšší díly trvají déle bez ohledu na to, kolik se jich vejde na desku. Efektivní rozmístění více dílů na konstrukční desce je klíčové pro snížení nákladů na strojní čas na jeden díl.
- Část Složitost: Velmi složité prvky mohou vyžadovat pomalejší parametry tisku.
- Hodinová sazba stroje: Liší se v závislosti na technologii stroje, jeho velikosti a nákladech na obsluhu.
- Složitost návrhu:
- Optimalizace DfAM: Dobře optimalizované návrhy minimalizují potřebu podpory a případně i dobu tisku. Špatně navržené díly mohou vyžadovat nadměrné množství podpěr nebo složitou orientaci, což zvyšuje náklady.
- Vnitřní funkce: Složité vnitřní kanály, které vyžadují obtížné odstraňování prášku, mohou prodloužit dobu následného zpracování a zvýšit náklady.
- Požadavky na následné zpracování:
- Intenzita: Počet a složitost kroků významně ovlivňují náklady. Základní odstranění podpory a tryskání jsou levnější než víceosé CNC obrábění, elektrolytické leštění a rozsáhlé ruční dokončovací práce.
- Tolerance/povrchová úprava: Přísnější tolerance a jemnější povrchové úpravy vyžadují intenzivnější (a nákladnější) následné zpracování.
- Zajištění kvality a kontrola:
- Úroveň inspekce: Základní rozměrové kontroly jsou méně nákladné než kompletní protokoly ze souřadnicových měřicích strojů, testování materiálu (pokud je pro danou šarži vyžadováno) a podrobná analýza povrchu.
- Dokumentace: Rozsáhlá dokumentace vyžadovaná pro dodržování předpisů zvyšuje režijní náklady.
- Objednávkové množství:
- Náklady na zřízení: Ačkoli se nejedná o žádné nástroje, vznikají náklady na přípravu souboru pro sestavení, nastavení stroje a pracovní postupy po zpracování. Tyto náklady se amortizují ve větším množství, čímž se snižuje cena za díl.
- Efektivita sestavení talíře: Větší množství umožňuje efektivnější ukládání dílů na konstrukční desku, čímž se zkracuje čas stroje na jeden díl.
Tabulka: Souhrn nákladových faktorů
Hnací síla nákladů | Primární vliv | Jak optimalizovat |
---|---|---|
Materiál | Typ slitiny (Ti vs. ocel), objem dílu, objem nosiče | Výběr vhodného materiálu, DfAM pro odlehčení |
Strojový čas | Výška dílu (Z), Účinnost vnoření stavební desky | Optimalizace orientace, maximální využití stavební desky |
Složitost návrhu | Potřeby podpory, Interní funkce | Uplatňovat zásady DfAM, zjednodušovat, kde je to možné |
Následné zpracování | Počet/typ kroků, požadavky na toleranci/dokončení | Zadejte pouze nezbytné kroky, Navrhněte snadnější dokončování |
Zajištění kvality | Úroveň inspekce, potřeby dokumentace | Definujte jasné a vhodné požadavky na kontrolu kvality |
Množství | Amortizace zřizovacích nákladů, efektivita hnízdění | Pokud je to možné, objednávejte v dávkách |
Export do archů
Doba dodání:
- Vytváření prototypů: U jednotlivých kusů nebo velmi malých šarží se standardním následným zpracováním mohou být dodací lhůty relativně krátké, často v rozmezí od 5 až 15 pracovních dnů, v závislosti na složitosti a nevyřízených objednávkách dodavatele.
- Výroba (malý až střední objem): U validovaných výrobních dílů, které vyžadují kompletní následné zpracování a zajištění kvality, jsou dodací lhůty obvykle delší a pohybují se v rozmezí od 3 až 8 týdnů. To zohledňuje plánování, dobu výroby (která může být u celé desky i několik dní), cykly tepelného zpracování, vícestupňové následné zpracování a důkladnou kontrolu.
- Faktory ovlivňující dobu realizace: Složitost, množství, náročnost následného zpracování, dostupnost materiálu, kapacita dodavatele a požadovaná validace/dokumentace - to vše má vliv na konečný harmonogram dodávek.
Jasná komunikace s poskytovatelem AM ohledně požadavků a očekávání je klíčem k získání přesných odhadů nákladů a realistických odhadů doby realizace.
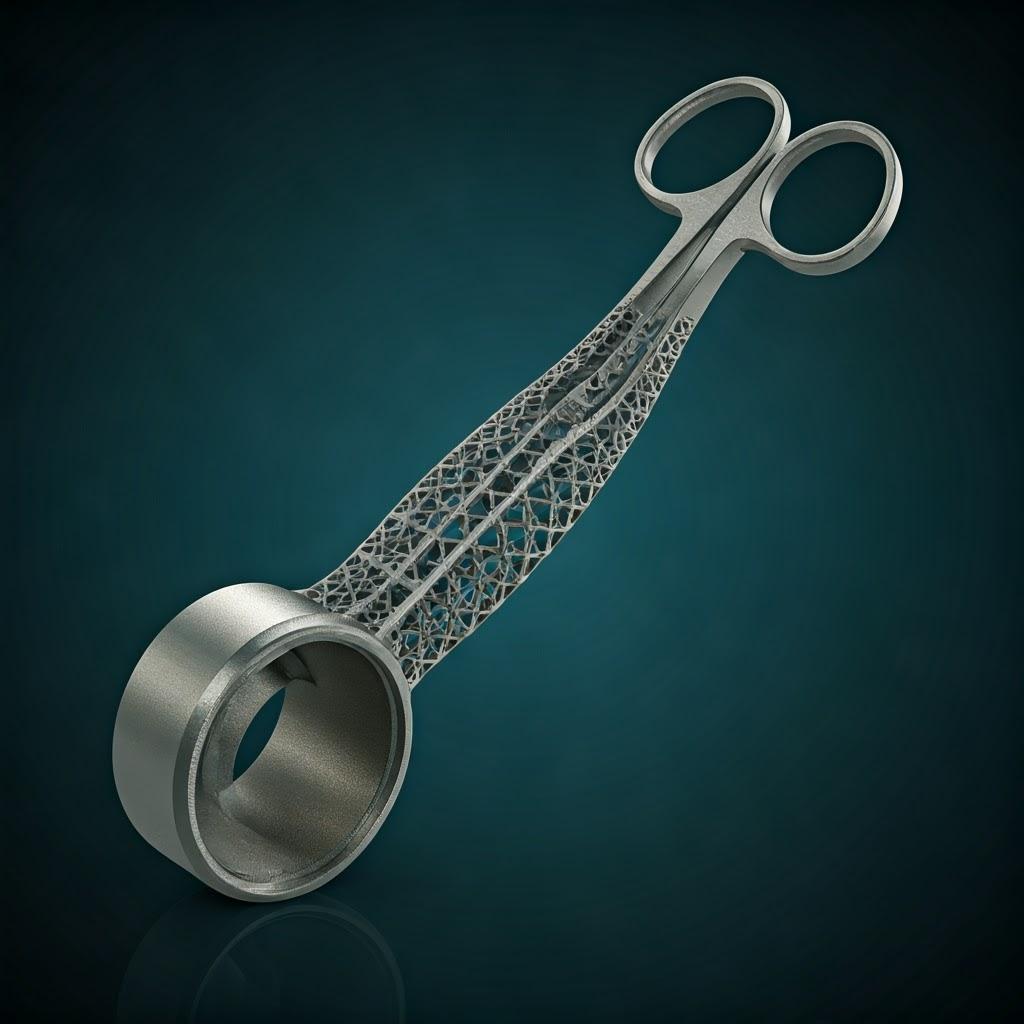
Často kladené otázky (FAQ) o 3D tištěných chirurgických nástrojích
Zde jsou odpovědi na některé časté otázky týkající se použití nerezové oceli 316L a titanu Ti-6Al-4V pro 3D tištěné chirurgické nástroje:
- Jsou 3D tištěné chirurgické nástroje z materiálů 316L a Ti-6Al-4V skutečně biokompatibilní? Ano, pokud jsou správně vyrobeny. Jak nerezová ocel 316L, tak Ti-6Al-4V (zejména třída ELI) jsou široce uznávané a používané biokompatibilní materiály splňující normy jako ISO 10993. Biokompatibilita však nezávisí pouze na surovině, ale v rozhodující míře na celém procesu: použití certifikovaného prášku lékařské kvality, dosažení vysoké hustoty (>99,5 %), zajištění úplného odstranění prášku, použití vhodného následného zpracování (např. pasivace) a zavedení validovaných protokolů čištění. Spolupráce s poskytovatelem certifikovaným podle normy ISO 13485, který má zkušenosti s výrobou ve zdravotnictví, je zásadní pro zajištění splnění požadavků na biokompatibilitu.
- Jaká je pevnost a odolnost 3D tištěných chirurgických nástrojů ve srovnání s tradičně vyráběnými nástroji? Mechanické vlastnosti (pevnost, tvrdost, odolnost proti únavě) kovových AM dílů vyrobených z 316L a Ti-6Al-4V mohou být srovnatelné, a někdy dokonce lepší než u dílů vyrobených tradičními metodami, jako je kování nebo odlévání, zejména pokud vezmeme v úvahu kované nebo žíhané stavy. Správné tepelné zpracování po tisku je zásadní pro dosažení optimálních vlastností stanovených normami ASTM nebo ISO. Kromě toho konstrukční svoboda AM umožňuje optimalizovat geometrii (např. pomocí optimalizace topologie), aby se v případě potřeby zvýšila tuhost nebo pevnost, což může vést k vytvoření pevnějších nebo lehčích nástrojů než u tradičních protějšků.
- Lze chirurgické nástroje z nerezové oceli a titanu vytištěné na 3D tiskárně sterilizovat standardními nemocničními metodami? Rozhodně. Materiály 316L i Ti-6Al-4V vykazují vynikající odolnost vůči běžným sterilizačním metodám používaným ve zdravotnických zařízeních, včetně:
- Autoklávování (parní sterilizace): Nejběžnější metoda; tyto materiály odolávají vysokým teplotám a tlakům.
- Sterilizace etylenoxidem (EtO): Kompatibilní.
- Záření gama: Kompatibilní.
- Nízkoteplotní plynné plazma s peroxidem vodíku: Kompatibilní. Klíčové je, aby konstrukce nástroje umožňovala průnik sterilizačního prostředku a jeho kontakt se všemi povrchy (DfAM pro čistitelnost) a aby byly součásti před sterilizací důkladně vyčištěny a odstraněna veškerá biologická zátěž nebo výrobní zbytky.
- Jaké informace musím poskytnout, abych získal nabídku na 3D tištěný chirurgický nástroj? Abyste získali přesnou nabídku, musíte obvykle poskytnout:
- 3D model CAD: Vysoce kvalitní model ve standardním formátu (např. STEP, IGES).
- Specifikace materiálu: Jasně uveďte požadovaný materiál (např. nerezová ocel 316L nebo Ti-6Al-4V).
- Množství: Počet požadovaných stejných dílů.
- Kritické tolerance: Uveďte všechny specifické rozměry, které vyžadují přísnější tolerance, než jsou standardní možnosti AM.
- Požadavky na povrchovou úpravu: Zadejte požadovanou drsnost povrchu (Ra) nebo typ povrchové úpravy (např. matné tryskání, elektrolytické leštění).
- Potřeby následného zpracování: Uveďte podrobnosti o požadovaném tepelném zpracování, obrábění nebo specifických dokončovacích krocích.
- Kontext aplikace: Stručně popište zamýšlené použití (pomůže poskytovateli pochopit funkční požadavky).
- Požadovaná osvědčení/dokumentace: Uveďte všechny potřebné certifikáty materiálu nebo inspekční zprávy.
Závěr: Budoucnost chirurgie je personalizovaná a přesná díky technologii Metal AM
Aditivní výroba kovů se rychle vyvíjí z prototypové technologie v životaschopnou a často lepší výrobní metodu pro složité a vysoce hodnotné komponenty, zejména v náročné oblasti chirurgie. Možnost používat osvědčené biokompatibilní materiály, jako je nerezová ocel 316L a titan Ti-6Al-4V, v kombinaci s bezkonkurenční volností designu, kterou AM nabízí, umožňuje konstruktérům zdravotnických přístrojů a chirurgům vytvářet nástroje, které byly dříve považovány za nemožné.
Kovový 3D tisk přináší hmatatelné výhody - od chirurgických vodítek pro pacienty, která zvyšují přesnost zákroků, přes lehké ergonomické nástroje snižující únavu chirurgů až po konsolidované nástroje zjednodušující složité zákroky. Umožňuje zrychlení inovačních cyklů, usnadňuje masové přizpůsobení a otevírá nové cesty ke zlepšení chirurgických technik a výsledků u pacientů.
Realizace těchto výhod však vyžaduje pečlivé dodržování zásad návrhu pro aditivní výrobu, přísnou kontrolu procesu, ověřené techniky následného zpracování a důsledné zajištění kvality. Výběr vysoce kvalitních kovových prášků a znalý, zkušený výrobní partner s příslušnými lékařskými certifikacemi (jako je ISO 13485) je pro úspěch nejdůležitější.
Vzhledem k tomu, že tato technologie se stále zdokonaluje a její náklady se potenciálně snižují, bude se zavádění 3D tištěných chirurgických nástrojů zrychlovat, což povede k další personalizaci chirurgie a pokroku ve všech lékařských oborech.
Jste připraveni prozkoumat, jak může aditivní výroba kovů změnit konstrukci vašich chirurgických nástrojů? Využijte odborné znalosti a špičkové schopnosti společnosti Met3dp. Jako lídr v oblasti pokročilé výroby kovových prášků i přesného řešení kovového 3D tisku, poskytujeme komplexní podporu od optimalizace návrhu až po finální výrobu dílů. Kontaktujte společnost Met3dp ještě dnes, abyste prodiskutovali své projektové požadavky a zjistili, jak mohou naše schopnosti podpořit cíle vaší organizace v oblasti aditivní výroby.
Sdílet na
MET3DP Technology Co., LTD je předním poskytovatelem řešení aditivní výroby se sídlem v Qingdao v Číně. Naše společnost se specializuje na zařízení pro 3D tisk a vysoce výkonné kovové prášky pro průmyslové aplikace.
Dotaz k získání nejlepší ceny a přizpůsobeného řešení pro vaše podnikání!
Související články
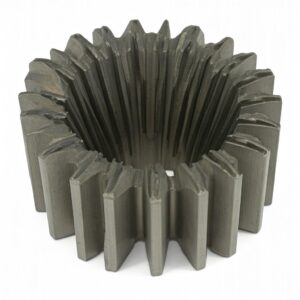
Vysoce výkonné segmenty lopatek trysek: Revoluce v účinnosti turbín díky 3D tisku z kovu
Přečtěte si více "O Met3DP
Nedávná aktualizace
Náš produkt
KONTAKTUJTE NÁS
Nějaké otázky? Pošlete nám zprávu hned teď! Po obdržení vaší zprávy obsloužíme vaši žádost s celým týmem.
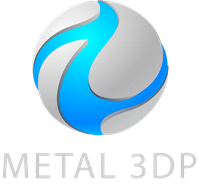
Kovové prášky pro 3D tisk a aditivní výrobu