3D tištěná pouzdra termočlánků pro proudové motory
Obsah
Letecký a kosmický průmysl se pohybuje na špičkové technické úrovni a vyžaduje komponenty, které splňují extrémní výkonnostní, spolehlivostní a bezpečnostní standardy. Proudové motory, které jsou srdcem moderních letadel, jsou zázraky složitých strojů pracujících za intenzivního tepla, tlaku a vibrací. V tomto náročném prostředí hrají i zdánlivě malé součásti kritickou roli. Jednou z takových klíčových součástí je pouzdro termočlánku, které je zodpovědné za ochranu citlivých teplotních čidel důležitých pro sledování stavu motoru a optimalizaci jeho výkonu. Výroba těchto pouzder, která se tradičně vyrábí odléváním nebo složitým obráběním, s sebou nese značné problémy, včetně konstrukčních omezení, dlouhých dodacích lhůt a plýtvání materiálem.
Transformační technologie však mění způsob navrhování a výroby těchto kritických součástí: Výroba aditiv kovů (AM), běžně známý jako kov 3D tisk. Tento inovativní přístup nabízí bezprecedentní volnost při navrhování, rychlejší vývojové cykly a možnost používat pokročilé materiály, které jsou dokonale vhodné pro drsné podmínky uvnitř proudového motoru. Pro inženýry, kteří usilují o zlepšení výkonu, a manažery nákupu, kteří se zaměřují na efektivní a spolehlivé zásobování, představuje technologie AM kovů přesvědčivou nabídku.
Tento blogový příspěvek se zabývá specifiky použití kovového 3D tisku pro pouzdra termočlánků proudových motorů. Prozkoumáme jejich kritickou funkci, významné výhody, které AM nabízí oproti konvenčním metodám, ideální vysoce výkonné materiály, jako jsou IN718 a 316L, a klíčové aspekty návrhu, výroby a výběru dodavatele. Pochopení těchto aspektů je klíčové pro letecké výrobce, poskytovatele MRO (údržba, opravy a generální opravy) a dodavatele součástí, kteří chtějí využít sílu aditivní výroby pro letecký hardware nové generace. Jako lídr v oblasti průmyslových řešení AM pro kovy, Met3dp poskytuje pokročilé tiskové systémy a vysoce kvalitní kovové prášky, které umožňují společnostem využívat výhody této technologie. Přinášíme desítky let společných zkušeností, abychom pomohli organizacím implementovat 3D tisk a urychlit jejich transformaci digitální výroby.
Kritická role termočlánkových pouzder v proudových motorech: Funkce a význam pro bezpečnost a výkonnost v letectví a kosmonautice
Abychom pochopili význam využití pokročilé výroby pro pouzdra termočlánků, musíme nejprve pochopit jejich zásadní roli v komplexním ekosystému proudového motoru. Samotný termočlánek je čidlo používané k měření teploty. Obvykle se skládá ze dvou různorodých elektrických vodičů, které tvoří elektrický spoj. Změna teploty na přechodu vyvolá napětí, které lze interpretovat pro přesné odečtení teploty. V proudovém motoru je přesné sledování teploty nejen přínosné, ale z několika důvodů naprosto nezbytné:
- Optimalizace výkonu: Řídicí systémy motorů se spoléhají na přesné údaje o teplotě z různých stupňů (kompresor, spalovací komora, turbína), aby optimalizovaly spalování paliva, tah a celkovou účinnost. Udržování teplot v optimálním rozmezí zajišťuje, že motor funguje tak, jak byl navržen.
- Monitorování bezpečnosti a stavu motoru: Odchylky od normálních provozních teplot mohou naznačovat potenciální problémy, například nestabilitu spalování, poruchy chladicího systému nebo degradaci součástí. Včasná detekce pomocí přesných údajů z termočlánků umožňuje včasné zásahy údržby a předchází tak katastrofickým poruchám. Zvláště důležité je sledování teploty výfukových plynů (EGT).
- Správa životnosti komponent: Mnoho součástí motoru má teplotní limity. Důsledný provoz pod těmito limity, ověřený pomocí termočlánků, prodlužuje životnost drahých dílů, jako jsou lopatky turbín. Nadměrné teploty mohou životnost součástek drasticky zkrátit.
- Dodržování předpisů: Letecké úřady nařizují přísné sledování a kontrolu parametrů motoru, včetně teploty, aby byla zajištěna bezpečnost letu.
Vzhledem k významu senzoru je pouzdro termočlánku slouží jako jeho základní ochránce a rozhraní. Mezi jeho hlavní funkce patří:
- Ochrana životního prostředí: Stínění citlivého spoje termočlánku a kabeláže před extrémním prostředím uvnitř motoru - teplotami přesahujícími 1000∘C (1832∘F) v horkých částech, vysokými tlaky, korozivními plyny a intenzivními vibracemi.
- Bezpečné upevnění: Poskytuje stabilní a spolehlivý montážní bod pro přesné umístění termočlánkového snímače v plynové cestě nebo na konkrétní skříni motoru. Montáž musí odolávat vibracím motoru a tepelné roztažnosti/kontrakci.
- Těsnění: Zabraňuje úniku plynu v místech, kde kryt proniká do skříně motoru, a zajišťuje tak zachování tlaku a účinnosti motoru.
- Tepelný management: V některých provedeních může pouzdro hrát roli při řízení tepelného toku do samotného senzoru nebo z něj, což zajišťuje přesnost měření.
- Elektrická izolace/vodivost: V závislosti na konstrukci zajištění správného elektrického uzemnění nebo izolace.
Kryt tedy není pouhý držák, ale konstrukční součást, která si musí zachovat svou strukturální integritu, těsnost a stabilitu montáže v těch nejnáročnějších podmínkách, které se v moderním strojírenství vyskytují. Porucha krytu může vést k poškození snímače, nepřesným údajům, úniku plynu nebo dokonce k tomu, že se kryt sám stane součástí motoru - to vše s potenciálně vážnými následky. To podtrhuje potřebu robustní konstrukce, vysoce kvalitních materiálů a pokročilých výrobních procesů, které jsou schopny splnit tyto přísné požadavky, což z nich dělá hlavní kandidáty pro možnosti nabízené společností 3D tisk z kovu.
Proč se 3D tisk z kovu prosazuje u pouzder termočlánků: Výhody oproti tradiční výrobě pro dodavatele v leteckém průmyslu
Po desetiletí se pouzdra termočlánků vyráběla především pomocí investičního odlévání nebo rozsáhlého CNC obrábění z kovaných polotovarů. Tyto tradiční metody se sice osvědčily, ale mají svá omezení, zejména pokud jde o snahu leteckého průmyslu o lehčí, složitější a rychle vyvíjené komponenty. Aditivní výroba kovů nabízí změnu paradigmatu a přináší významné výhody, které jsou pro letecké inženýry, výrobce a dodavatele přesvědčivé:
Omezení tradičních metod:
- Omezení návrhu: Odlévání vyžaduje formy a vzory, které omezují geometrickou složitost (např. vnitřní kanály, tenké stěny, složité prvky). Obrábění je sice přesné, ale může se potýkat se složitými vnitřními prvky a vytváří značný materiálový odpad (poměr "buy-to-fly").
- Náklady na nástroje & Dodací lhůty: Investiční lití vyžaduje nákladnou a časově náročnou tvorbu nástrojů. Obrábění složitých dílů může vyžadovat několik nastavení a specializovaných přípravků. To zpomaluje a prodražuje malosériovou výrobu nebo iterace konstrukce.
- Problémy s konsolidací částí: Pouzdra často zahrnují více pájených nebo svařovaných dílčích komponent (příruby, šrouby, tělesa), což zvyšuje počet výrobních kroků, hmotnost a potenciální místa poruch.
- Materiálový odpad: Subtraktivní výroba (obrábění) může vést k plýtvání značným množstvím drahého leteckého materiálu.
Výhody aditivní výroby kovů (AM):
Procesy AM, jako je selektivní laserové tavení (SLM) nebo tavení elektronovým svazkem (EBM), vytvářejí díly vrstvu po vrstvě přímo z kovového prášku a nabízejí řešení těchto problémů:
- Bezprecedentní svoboda designu:
- Složité geometrie: AM vyniká při vytváření složitých tvarů, podříznutí a vnitřních prvků, které je obtížné nebo nemožné odlévat nebo obrábět. To umožňuje optimalizovat průtokové cesty kolem snímače, integrované montážní prvky nebo v případě potřeby konformní chladicí kanály.
- Optimalizace topologie a odlehčení: Inženýři mohou pomocí softwarových nástrojů odstranit materiál z nekritických oblastí a vytvořit tak lehčí skříně bez snížení pevnosti, což přispívá k celkové úspornosti letadla.
- Konsolidace částí: Více komponent tradiční sestavy pouzdra lze přepracovat a vytisknout jako jediný monolitický díl. Tím se sníží počet dílů, odpadnou kroky pájení/svařování, zjednoduší se montáž, sníží se hmotnost a potenciálně se zvýší spolehlivost odstraněním spojů.
- Zkrácení dodacích lhůt & Rychlejší iterace:
- Eliminace nástrojů: AM vytváří přímo z digitálního souboru CAD, čímž odpadá potřeba fyzických nástrojů. To výrazně zkracuje dodací lhůty, zejména u prototypů, zakázkových návrhů nebo malosériové výroby.
- Rychlé prototypování: Úpravy návrhu lze rychle provést jednoduchou změnou souboru CAD a vytištěním nové iterace, což urychluje proces vývoje a kvalifikace.
- Účinnost materiálu: AM je aditivní proces, při kterém se používá pouze materiál potřebný k výrobě dílu a jeho podpěr. To výrazně snižuje plýtvání materiálem ve srovnání se subtraktivním obráběním, což je výhodné zejména při použití drahých superslitin, jako je IN718.
- Zvýšený výkonnostní potenciál: Komplexní vnitřní geometrie umožněná technologií AM může potenciálně zlepšit funkci pouzdra, například optimalizací proudění vzduchu kolem senzoru pro zrychlení odezvy nebo začleněním prvků, které zlepšují tlumení vibrací.
- Flexibilita dodavatelského řetězce:
- Výroba na vyžádání: Díly lze tisknout podle potřeby, čímž se snižují požadavky na zásoby náhradních dílů.
- Distribuovaná výroba: Soubory digitálních dílů lze elektronicky odesílat do certifikovaných zařízení AM po celém světě pro lokalizovanou výrobu.
Tabulka: AM vs. tradiční výroba pro pouzdra termočlánků
Vlastnosti | Výroba aditiv kovů (AM) | Tradiční (odlévání/obrábění) | Výhoda dodavatele B2B (AM) |
---|---|---|---|
Svoboda designu | Vysoká (složité geometrie, vnitřní kanály, konsolidace) | Střední až nízká (omezení v oblasti nástrojů/obrábění) | Nabídka vysoce optimalizovaných, konsolidovaných a lehkých řešení |
Nástroje | Žádný (digitální soubor) | Potřebné (formy, vzory, složité přípravky) | Rychlejší zavádění nových produktů (NPI), nižší počáteční náklady na zřízení |
Doba realizace | Krátké (zejména pro prototypy, nízký objem) | Dlouhé (tvorba nástrojů, vícestupňové procesy) | Rychlá reakce na potřeby zákazníků, rychlejší uvedení na trh |
Materiálový odpad | Nízká (aditivní proces) | Vysoký (obrábění) nebo střední (podavače/brány odlitků) | Úspora nákladů na drahé suroviny, ekologičtější proces |
Konsolidace částí | Vynikající schopnost | Obtížná montáž (pájení, svařování) | Jednodušší výrobní postup, snížené riziko montáže, potenciální zvýšení spolehlivosti |
Ideální objem | Nízké až střední, složité díly | Velký objem (odlévání), střední objem (obrábění) | Konkurenceschopnost pro specializované, vysoce hodnotné letecké komponenty |
Rychlost iterace | Rychle (úprava CAD, dotisk) | Pomalé (úprava nástrojů nebo přeprogramování) | Agilní vývoj, rychlé přizpůsobení změnám designu |
Export do archů
Pro velkoobchodní nákupčí a manažery nákupu v leteckém a kosmickém sektoru znamená spolupráce s dodavatelem AM, jako je Met3dp, přístup ke špičkovým výrobním kapacitám, které mohou dodávat špičkové komponenty rychleji a potenciálně nákladově efektivněji (zejména při zohlednění celkových nákladů na životní cyklus a výkonnostních přínosů).
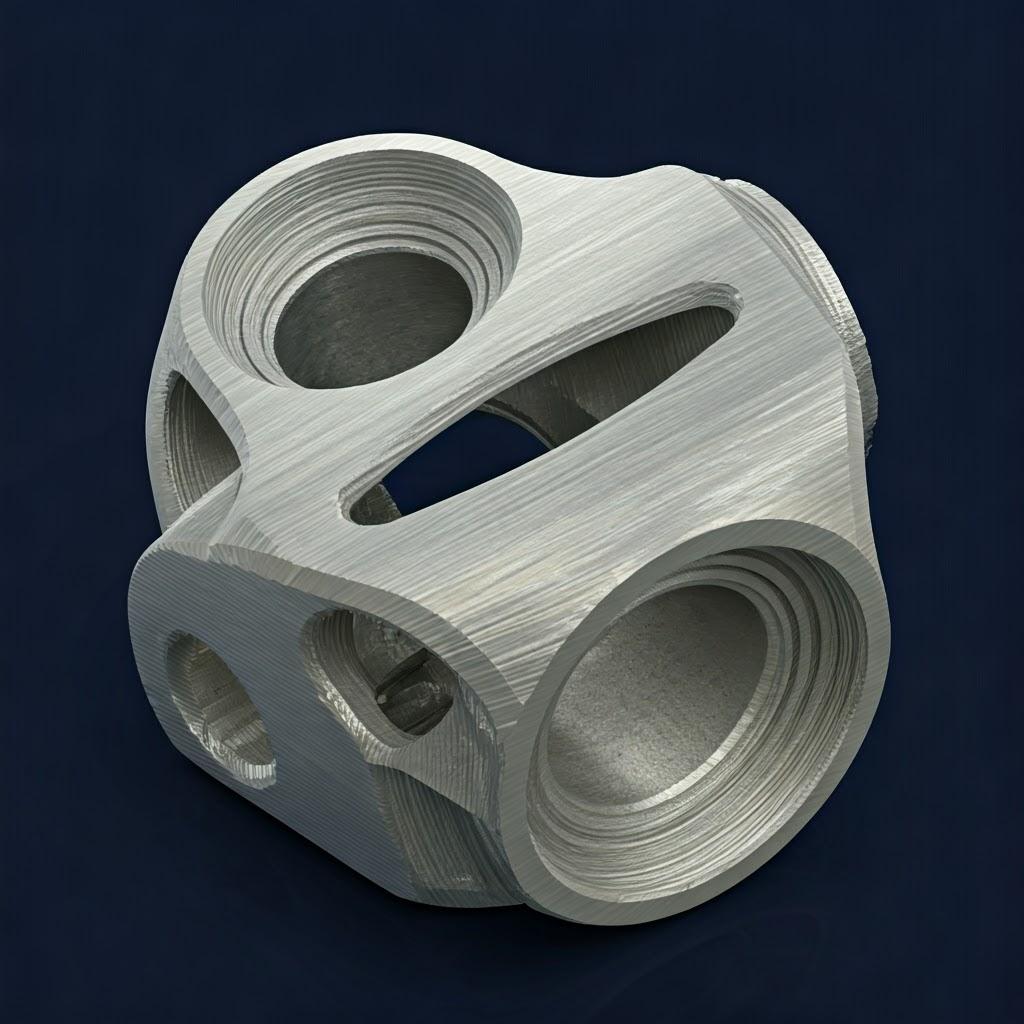
Výběr materiálu Deep Dive: IN718 a 316L pro optimální výkon (získávání vysoce kvalitních prášků)
Výběr správného materiálu je pro komponenty pracující v extrémním prostředí proudového motoru velmi důležitý. Materiál musí odolávat vysokým teplotám, odolávat oxidaci a korozi, zachovat si pevnost při namáhání a vibracích a být kompatibilní s okolními součástmi motoru. Pro 3D tištěná pouzdra termočlánků vynikají dva materiály díky svým vlastnostem a zavedenému použití v leteckém průmyslu a náročných průmyslových aplikacích: IN718 (Inconel 718) a Nerezová ocel 316L. Vhodnost každého z nich závisí na konkrétních provozních podmínkách a výkonnostních požadavcích umístění skříně v motoru.
IN718 (Inconel 718): Vysoce výkonný pracovní kůň
IN718 je precipitačně kalitelná superslitina na bázi niklu a chromu, která je známá svou výjimečnou kombinací vlastností, díky nimž je oblíbeným materiálem pro náročné aplikace v leteckém průmyslu, včetně dílů v horkých částech proudových motorů.
- Klíčové vlastnosti:
- Pevnost při vysokých teplotách: Zachovává si vynikající pevnost v tahu, únavu, tečení a trhlinu při teplotách do přibližně 700∘C (1300∘F).
- Vynikající odolnost proti korozi: Odolává oxidaci a korozi v agresivním prostředí, včetně vedlejších produktů spalování.
- Dobrá svařitelnost: V porovnání s jinými niklovými superslitinami vykazuje IN718 relativně dobrou svařitelnost (což je důležité pro tradiční výrobu, méně pro monolitické díly AM, ale svědčí to o dobrých zpracovatelských vlastnostech).
- Zpracovatelnost v AM: Dobře charakterizované a široce používané v procesech AM s kovy, jako je SLM a EBM, umožňující výrobu hustých dílů s vysokou pevností.
- Proč je to důležité pro pouzdra termočlánků: Díky své schopnosti odolávat vysokým teplotám a namáhání v turbíně a výfukové části proudového motoru je ideální pro skříně umístěné v těchto kritických horkých zónách. Jeho pevnost zajišťuje strukturální integritu při aerodynamickém zatížení a vibracích, zatímco jeho odolnost proti korozi jej chrání před drsným chemickým prostředím.
nerezová ocel 316L: Všestranná a spolehlivá volba
316L je austenitická chromniklová nerezová ocel obsahující molybden, který zvyšuje její odolnost proti korozi, zejména proti chloridům a dalším průmyslovým rozpouštědlům. Je široce používán v různých průmyslových odvětvích, včetně leteckého průmyslu, pro komponenty vyžadující dobrou pevnost a vynikající odolnost proti korozi při mírných teplotách.
- Klíčové vlastnosti:
- Vynikající odolnost proti korozi: Vyšší odolnost proti celkové korozi, důlkové korozi a štěrbinové korozi ve srovnání s nerezovou ocelí 304.
- Dobrá pevnost a tažnost: Nabízí dobrou rovnováhu mechanických vlastností při pokojových a mírně zvýšených teplotách (obvykle do cca 550∘C / 1022∘F, i když pevnost výrazně klesá nad 425∘C / 800∘F).
- Dobrá tvářitelnost a svařitelnost: Snadno se zpracovává různými technikami.
- Efektivita nákladů: Obecně jsou levnější než superslitiny na bázi niklu, jako je IN718.
- Dobře zavedené v AM: Běžně používané a dobře pochopené v procesech 3D tisku z kovu.
- Proč je to důležité pro pouzdra termočlánků: Pro pouzdra umístěná v chladnějších částech motoru (např. ve stupních kompresoru, obtokových kanálech nebo vnějších skříních), kde teploty nejsou tak extrémní, ale odolnost proti korozi a spolehlivost jsou stále klíčové, nabízí materiál 316L robustnější a ekonomičtější řešení než materiál IN718.
Tabulka: Srovnání materiálů pro pouzdra termočlánků
Vlastnosti | IN718 (niklová superslitina) | Nerezová ocel 316L | Úvahy o získávání zdrojů |
---|---|---|---|
Maximální provozní teplota. | ~ 700∘C (1300∘F) | ~ 425-550∘C (800-1022∘F) | Přizpůsobení materiálu specifickým požadavkům motorové zóny |
Pevnost při vysokých teplotách | Vynikající | Mírný | Kritické pro součásti horkého řezu |
Odolnost proti korozi | Vynikající | Vynikající (zejména chloridy) | Obě nabízejí dobrou odolnost; konkrétní potřeby se mohou lišit |
Relativní náklady | Vysoký | Mírný | Důsledky pro rozpočet v případě hromadného zadávání veřejných zakázek |
Hustota | ~ 8,19 g/cm3 | ~ 8,0 g/cm3 | Drobný rozdíl, ale důležitý pro odlehčení |
Zpracovatelnost AM | Dobře zavedené | Dobře zavedené | Ujistěte se, že dodavatel má ověřené parametry pro vybraný materiál |
Typické umístění motoru | Část turbíny, plášť spalovacího motoru, výfuk | Kompresorová část, skříň ventilátoru, obtokové potrubí | Výběr na základě tepelného a mechanického zatížení |
Export do archů
Zásadní význam kvality prášku
Bez ohledu na zvolenou slitinu je kvalita kovového prášku použitého v procesu AM zásadní pro dosažení požadovaných mechanických vlastností a integrity konečného dílu. U leteckých aplikací je to neoddiskutovatelné. Mezi klíčové vlastnosti prášku patří:
- Sféricita: Vysoce kulovité částice prášku zajišťují dobrou tekutost a vysokou hustotu balení v práškovém loži, což vede k hustším a pevnějším finálním dílům s menším počtem dutin a defektů.
- Distribuce velikosti částic (PSD): Pro konzistentní tavení a nanášení vrstev je rozhodující kontrolovaná PSD. Různé stroje AM jsou optimalizovány pro specifické rozsahy PSD.
- Čistota: Zásadní je nízký obsah nečistot (jako je kyslík, dusík, uhlík) a nepřítomnost kontaminantů. Nečistoty mohou zhoršit mechanické vlastnosti a odolnost proti korozi.
- Tekutost: Prášek musí rovnoměrně a hladce proudit v systému pro nanášení nátěru tiskárny, aby se vytvořily rovnoměrné vrstvy.
Met3dp: Váš zdroj vysoce kvalitních prášků pro letecký průmysl
Ve společnosti Met3dp chápeme, že výjimečné díly začínají výjimečnými materiály. Naše společnost využívá špičkové technologie výroby prášků, včetně Atomizace plynu (GA) a Proces plazmové rotující elektrody (PREP), k výrobě vysoce kvalitních sférických kovových prášků speciálně optimalizovaných pro aditivní výrobu.
- Naše pokročilé zařízení pro rozprašování plynu využívá jedinečné konstrukce trysek a proudění plynu k výrobě kovových kuliček s vysokou sféricitou a vynikající tekutostí, což je zásadní pro dosažení vynikající hustoty a mechanických vlastností dílů v náročných aplikacích, jako jsou součásti proudových motorů.
- Nabízíme komplexní portfolio vysoce výkonných kovových prášků, včetně IN718 a 316L, přísně testované a kontrolované z hlediska kvality, aby splňovaly přísné požadavky leteckého průmyslu.
- Kromě těchto slitin vyrábí společnost Met3dp také inovativní slitiny, jako jsou TiNi, TiTa, TiAl, TiNbZr, CoCrMo, další nerezové oceli a superslitiny, což ukazuje naše široké odborné znalosti v oblasti materiálů.
Výběr dodavatele, jako je Met3dp, zaručuje, že základní prvek vašeho 3D tištěného pouzdra termočlánku - kovový prášek - splňuje nejvyšší standardy, což umožňuje výrobu spolehlivých, vysoce výkonných komponent vhodných pro kritické použití v letectví a kosmonautice. Manažeři nákupu a inženýři se mohou spolehnout na společnost Met3dp, která zajišťuje konzistentní kvalitu a dodávky těchto pokročilých materiálů, za nimiž stojí hluboké odborné znalosti v oblasti procesy a aplikace aditivní výroby.
Design pro aditivní výrobu (DfAM): Optimalizace geometrie pouzdra termočlánku pro výkon a tisknutelnost
Jedním z nejpřesvědčivějších důvodů, proč se výrobci v leteckém průmyslu obracejí na aditivní výrobu kovů, je možnost radikálně přehodnotit konstrukci součástí. Pouhá replikace konstrukce původně určené pro odlévání nebo obrábění často nedokáže plně využít možností AM. Design pro aditivní výrobu (DfAM) je klíčová metodika, která zahrnuje navrhování dílů speciálně pro proces stavění po vrstvách, což přináší výhody v oblasti výkonu, hmotnosti a vyrobitelnosti. U krytů termočlánků proudových motorů může použití principů DfAM vést k podstatně lepším součástem.
Klíčové zásady DfAM pro pouzdra termočlánků:
- Využití geometrické složitosti:
- Integrované funkce: AM umožňuje bezproblémovou integraci prvků, které by obvykle tvořily samostatné díly nebo vyžadovaly složité obrábění. V případě pouzdra termočlánku to může znamenat vytištění montážních přírub, šachet pro senzory, kanálů pro vedení vodičů nebo dokonce prvků proti otáčení přímo do hlavního těla.
- Optimalizované vnitřní struktury: V případě potřeby lze navrhnout a vytisknout složité vnitřní kanály pro proudění chladicího vzduchu kolem snímače nebo specifické průtokové cesty pro kalibrační plyny, což jsou funkce, které jsou při použití tradičních metod často nemožné.
- Tenké stěny & Složité zakřivení: AM může vyrábět díly s tenčími stěnami (pokud je to konstrukčně vhodné) a složitými, organickými tvary, které sledují linie napětí, což může snížit hmotnost a zlepšit aerodynamickou interakci v dráze plynů motoru.
- Konsolidace částí:
- Snížení složitosti sestavy: Tradiční pouzdra termočlánků se mohou skládat z tělesa, příruby, závitové hlavice a případně krycích desek, často spojených pájením nebo svařováním. Každý spoj představuje potenciální místo poruchy a zvyšuje počet výrobních kroků a tolerancí.
- Výhoda AM: DfAM podporuje přepracování této sestavy jako jediné monolitické součásti. Tisk pouzdra jako jednoho kusu eliminuje procesy spojování, snižuje počet dílů v kusovníku, zjednodušuje skladové zásoby a montáž, snižuje celkovou hmotnost a díky odstranění spojů ze své podstaty zvyšuje strukturální integritu. To je významná výhoda pro zadavatele veřejných zakázek, kteří usilují o zefektivnění logistiky, a pro inženýry, kteří se snaží o vyšší spolehlivost.
- Optimalizace topologie a odlehčení:
- Inteligentní umístění materiálu: Pomocí specializovaného softwaru mohou konstruktéři definovat zatěžovací stavy a okrajové podmínky skříně. Software pak iterativně odstraňuje materiál z oblastí s nízkým namáháním a ponechává materiál pouze tam, kde je to z konstrukčního hlediska nezbytné.
- Výsledek: Výsledkem jsou často organicky vypadající, vysoce optimalizované konstrukce, které splňují nebo překračují pevnostní požadavky původního návrhu, ale mají výrazně nižší hmotnost. I malé úspory hmotnosti jednotlivých součástí se výrazně sčítají v rámci celého motoru, což přispívá ke zvýšení palivové účinnosti a výkonu, což jsou klíčové faktory v leteckém průmyslu.
- Navrhování pro tisk:
- Orientace na stavbu: Způsob orientace dílu na konstrukční desce významně ovlivňuje potřeby podpory, kvalitu povrchu, dobu tisku a akumulaci zbytkového napětí. DfAM zahrnuje zvážení optimální orientace již v počáteční fázi návrhu.
- Minimalizace podpory: Podpěrné konstrukce jsou často nutné pro prvky vyčnívající nad stavební desku pod úhlem obvykle menším než 45 stupňů od vodorovné roviny. Podpěry spotřebovávají další materiál, prodlužují dobu tisku, vyžadují odstranění (následné zpracování) a mohou na povrchu zanechat stopy po svědcích. Správná praxe DfAM zahrnuje:
- Navrhování prvků se samonosnými úhly (>= 45 stupňů), pokud je to možné.
- Použití zkosení místo ostrých převisů.
- Orientace dílu tak, aby kritické plochy směřovaly co nejméně dolů.
- Navrhování vnitřních kanálů, které jsou samonosné nebo umožňují snadné odstraňování prášku.
- Plánování následného zpracování: Zajištění přístupu k podpůrným nástrojům pro demontáž a v případě potřeby k přípravkům pro CNC obrábění. Navrhování obětních prvků, které pomáhají při tisku nebo následném zpracování, ale později se odstraní.
- Zvládání tepelného stresu:
- Design funkcí: Ostré rohy mohou při rychlých cyklech zahřívání a ochlazování při AM koncentrovat napětí. Začlenění koutů a zaoblených hran může pomoci rovnoměrněji rozložit napětí a snížit riziko deformace nebo prasklin.
- Distribuce materiálu: Velké, objemné úseky spojené s tenkými úseky mohou zhoršovat tepelné namáhání. DfAM podporuje plynulejší přechody tloušťky materiálu.
Použití DfAM vyžaduje jiné myšlení než navrhování pro tradiční výrobu. Vyžaduje úzkou spolupráci mezi konstruktéry a odborníky na AM procesy. Spolupráce se znalým poskytovatelem služeb AM, který rozumí principům DfAM, je zásadní pro plné využití výhod tisku krytů termočlánků a dalších kritických součástí.
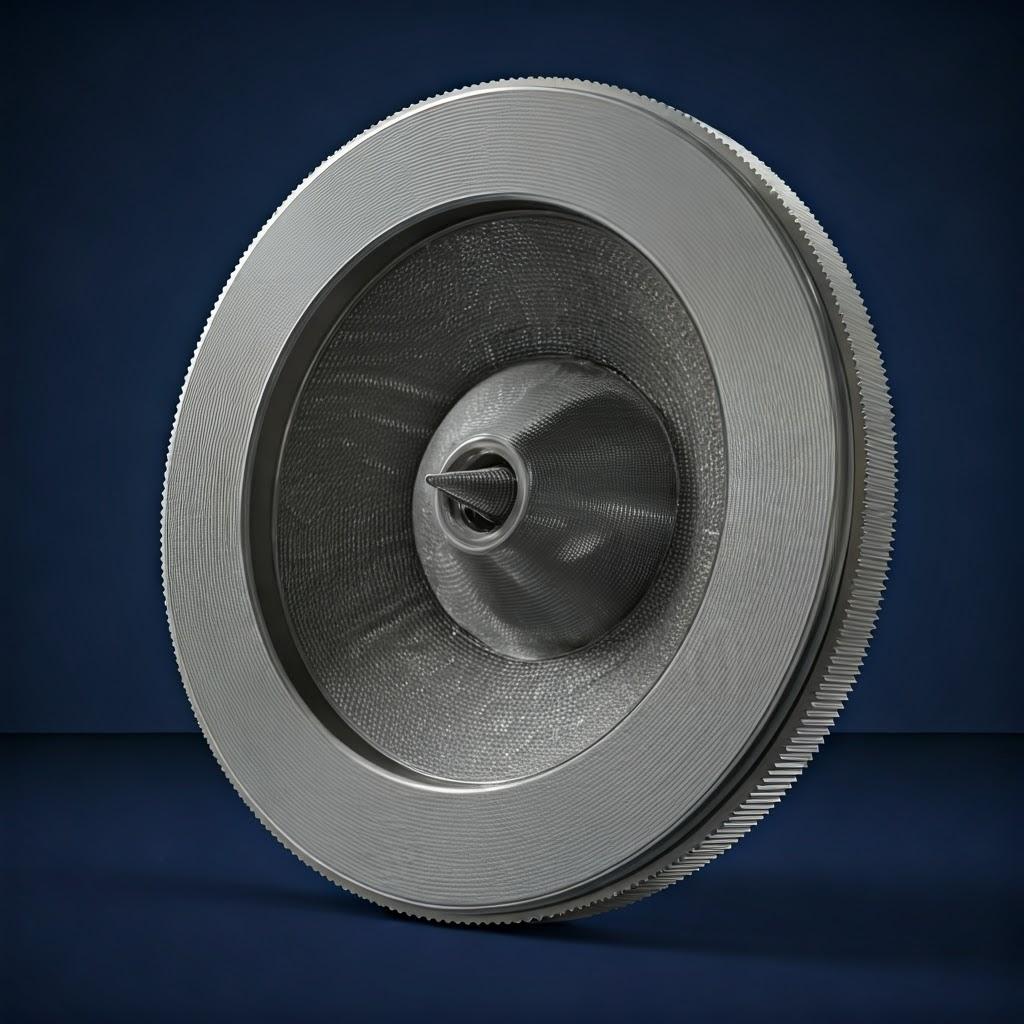
Dosažení přesnosti: Tolerance, povrchová úprava a rozměrová přesnost v kovovém AM: normy pro přesnost v kovovém AM
Ačkoli AM nabízí volnost při navrhování, součásti určené pro proudové motory musí splňovat přísné požadavky na lícování, tvar a funkci. To znamená dosažení specifické úrovně přesnosti, pokud jde o tolerance, povrchovou úpravu a celkovou rozměrovou přesnost. Pochopení možností a omezení technologie AM pro kovy v těchto oblastech je pro konstruktéry a manažery nákupu zásadní.
Tolerance:
- Obecná dosažitelnost: Typické tolerance “as-built” pro procesy AM s kovem, jako je SLM a EBM, se často pohybují v rozmezí ±0,1 mm až ±0,2 mm (±0,004″ až ±0,008″) pro menší prvky, přičemž u větších rozměrů se mohou mírně zvýšit v důsledku tepelných vlivů. To se však může výrazně lišit v závislosti na:
- Systém AM: Konkrétní stroj, jeho kalibrace a kvalita zaostření paprsku.
- Materiál: Různé slitiny vykazují různé chování při smršťování a deformaci.
- Geometrie dílu & Velikost: Větší díly nebo složité geometrie jsou náchylnější k tepelnému zkreslení.
- Parametry sestavení: Výkon laserového/elektronového paprsku, rychlost skenování, tloušťka vrstvy atd.
- Následné zpracování: Odlehčení od napětí a HIP mohou způsobit drobné rozměrové změny.
- Kritické rozměry: U prvků vyžadujících přísnější tolerance - jako jsou montážní rozhraní, těsnicí povrchy nebo přesné vnitřní průměry pro uložení snímače následné CNC obrábění je téměř vždy nutné. AM se používá k efektivnímu vytvoření téměř síťového tvaru a obrábění zajišťuje konečnou přesnost.
- Úvaha DfAM: Tolerance by měly být zváženy ve fázi návrhu. Identifikujte kritické prvky vyžadující přísné tolerance a zajistěte, aby konstrukce umožňovala přístup pro následné obráběcí operace.
Povrchová úprava (drsnost):
- Povrchová úprava podle stavu: Povrchová úprava kovových dílů vyrobených metodou AM je ze své podstaty drsnější než povrch obrobený. Typické hodnoty Ra (průměrná drsnost) se mohou pohybovat od 6 µm do 20 µm (240 µin až 800 µin) nebo více, v závislosti na:
- Orientace na stavbu: Povrchy směřující nahoru (up-skins) bývají hladší, zatímco na bočních stěnách se objevují linie vrstev a povrchy směřující dolů (down-skins) podepřené konstrukcemi jsou po odstranění podpěr obvykle nejhrubší.
- Velikost prášku: Jemnější prášky obecně vedou k hladšímu povrchu, ale mohou se zpracovávat odlišně.
- Parametry procesu: Tloušťka vrstvy, příkon energie a strategie skenování ovlivňují chování taveniny a výsledný povrch.
- Význam pro pouzdra: Drsné povrchy mohou být problematické pro těsnicí aplikace (např. plochy přírub) a mohou působit jako koncentrátory napětí, což může mít vliv na únavovou životnost. Vnitřní povrchy mohou vyžadovat hladkost kvůli průtoku nebo aby se zabránilo zachycování částic.
- Zlepšení povrchové úpravy: K dosažení požadované povrchové úpravy na kritických místech se používají kroky následného zpracování, jako je tryskání kuličkami, bubnování, leštění nebo CNC obrábění.
Rozměrová přesnost:
- Definice: Jak přesně odpovídá konečný vytištěný díl jmenovitým rozměrům zadaným v modelu CAD.
- Ovlivňující faktory: Podobně jako tolerance je přesnost ovlivněna kalibrací stroje, vlastnostmi materiálu, tepelným řízením během sestavování, strategií podpory a kroky následného zpracování (zejména odlehčení a HIP, které mohou způsobit předvídatelné smrštění).
- Dosažení přesnosti: Vyžaduje pečlivou kontrolu procesu, dobře popsané parametry materiálu a často i kompenzační faktory zabudované do tiskového souboru, aby se zohlednily očekávané tepelné účinky. Zkušení poskytovatelé AM využívají simulační nástroje a empirická data k maximalizaci rozměrové přesnosti.
Met3dp’s Commitment to Precision:
Ve společnosti Met3dp si uvědomujeme, že přesnost je pro letecké komponenty kritická. Naše průmyslové 3D tiskové systémy jsou navrženy tak, aby poskytovaly špičkovou přesnost a spolehlivost. Používáme přísné procesní kontroly, kalibrační protokoly strojů a optimalizované parametry vyvinuté na základě rozsáhlého testování pro materiály jako IN718 a 316L. Zatímco dosahujeme vynikající přesnosti při výrobě, úzce spolupracujeme se zákazníky na integraci nezbytných kroků následného zpracování, čímž zajišťujeme, že kritické tolerance a povrchová úprava součástí, jako jsou pouzdra termočlánků, splňují náročné specifikace leteckého průmyslu.
Za hranice tisku: Zásadní kroky následného zpracování pro kryty proudových motorů pro mise
Častou mylnou představou o 3D tisku z kovu je, že díly jsou připraveny k použití ihned po dokončení procesu sestavení. U nekritických aplikací tomu tak někdy může být, ale u vysoce výkonných a kritických součástí, jako jsou pouzdra termočlánků proudových motorů, je díl “as-built” pouze mezistupněm. Je zapotřebí řada zásadních kroků následného zpracování, aby bylo zajištěno, že díl splňuje rozměrové specifikace, dosahuje požadovaných vlastností materiálu a je bez vad.
Společný pracovní postup následného zpracování pro pouzdra termočlánků AM:
- Odstranění prášku:
- Proces: Pečlivé odstranění neroztaveného prášku z povrchu dílu a všech vnitřních kanálků nebo dutin, obvykle pomocí stlačeného vzduchu, kartáčování nebo specializovaných stanic pro manipulaci s práškem.
- Důležitost: Zajišťuje, že nezůstane žádný volný prášek, který by mohl kontaminovat systémy motoru nebo narušit následné procesy. DfAM zde hraje roli při navrhování snadno čistitelných kanálů.
- Tepelné ošetření proti stresu:
- Proces: Zahřátí dílu (často ještě připevněného na konstrukční desce) v peci s řízenou atmosférou na určitou teplotu nižší, než je teplota stárnutí nebo žíhání, jeho udržování a následné pomalé ochlazování.
- Důležitost: Při rychlém zahřívání a ochlazování během AM vznikají značná vnitřní pnutí. Odlehčení napětí tato napětí snižuje, čímž zabraňuje deformaci při odstraňování podpěr nebo obrábění a zlepšuje rozměrovou stabilitu a celkovou integritu dílu. Jedná se o kritické první krok.
- Vyjmutí dílu ze stavební desky:
- Proces: Oddělení vytištěného dílu (dílů) od kovové konstrukční desky, obvykle pomocí elektroerozivního obrábění (EDM) nebo pásové pily.
- Důležitost: Uvolní díl pro následnou manipulaci a zpracování. Vyžaduje opatrnost, aby nedošlo k poškození dílu.
- Odstranění podpůrné konstrukce:
- Proces: Odstranění podpůrných struktur vzniklých během tisku pomocí ručních metod (lámání, řezání, broušení), CNC obrábění nebo někdy elektrochemického leštění.
- Důležitost: Podpěry jsou nezbytné pro tisk, ale nejsou součástí finální součásti. Odstranění je třeba provádět opatrně, aby nedošlo k poškození povrchu součásti, zejména v blízkosti kritických prvků. Povrch, na který byly podpěry připevněny, je obvykle drsný a může vyžadovat další úpravu.
- Žíhání roztokem / tepelné zpracování stárnutím (specifické pro materiál, např. pro IN718):
- Proces: Podrobení dílu specifickým, přísně kontrolovaným tepelným cyklům (zahřátí na vysoké teploty, ochlazení a následné stárnutí při středních teplotách).
- Důležitost: Tím se vytvoří požadovaná mikrostruktura a precipitáty (v případě precipitačně kalitelných slitin, jako je IN718) potřebné k dosažení konečných specifikovaných mechanických vlastností (tvrdost, pevnost v tahu, odolnost proti tečení). Parametry jsou specifické pro jednotlivé slitiny a jsou rozhodující pro jejich výkon.
- Izostatické lisování za tepla (HIP):
- Proces: Umístění dílů do specializované nádoby a jejich současné vystavení vysokému tlaku inertního plynu (např. 100-200 MPa) a zvýšené teplotě (pod bodem tání) po stanovenou dobu.
- Důležitost: Tento proces účinně uzavírá vnitřní mikroporozitu, která může být přítomna i v dobře vytištěných dílech AM. Odstranění pórovitosti výrazně zvyšuje únavovou pevnost, tažnost a celkovou integritu materiálu. HIP je často předepsán leteckými normami (např. AS9100) pro kritické letové součásti.
- CNC obrábění:
- Proces: Použití tradičního subtraktivního obrábění (frézování, soustružení, vrtání, řezání závitů) k dosažení úzkých tolerancí kritických rozměrů, vytvoření přesných těsnicích ploch, obrábění závitů a zlepšení kvality povrchu specifických prvků.
- Důležitost: Překlenuje mezeru mezi schopností téměř čistého tvaru AM’ a požadavky na konečné rozměry a povrchovou úpravu, které samotná AM u kritických rozhraní obvykle nedokáže splnit.
- Povrchová úprava:
- Proces: Použití technik, jako je tryskání kuličkami, kuličkování (může zvýšit únavovou životnost), abrazivní obrábění (AFM) pro vnitřní kanály, leštění nebo elektrolytické leštění.
- Důležitost: Zlepšuje celkovou kvalitu povrchu, odstraňuje nečistoty, dosahuje specifických hodnot drsnosti (Ra) a v případě potřeby může připravit povrch pro následné nátěry.
- Čištění a kontrola:
- Proces: Důkladně očistěte díly, abyste odstranili zbytky prášku, obráběcích kapalin nebo nečistot. Následuje důkladná kontrola různými metodami.
- Důležitost: Konečné ověření před certifikací dílu pro použití. Metody kontroly jsou popsány v části “Výzvy.”
Rozsah a pořadí těchto kroků závisí na materiálu, složitosti konstrukce a specifických požadavcích na pouzdro termočlánku. Spolupráce s poskytovatelem komplexních služeb, který má zkušenosti s těmito technikami následného zpracování, je pro získání komponent AM připravených k letu klíčová.
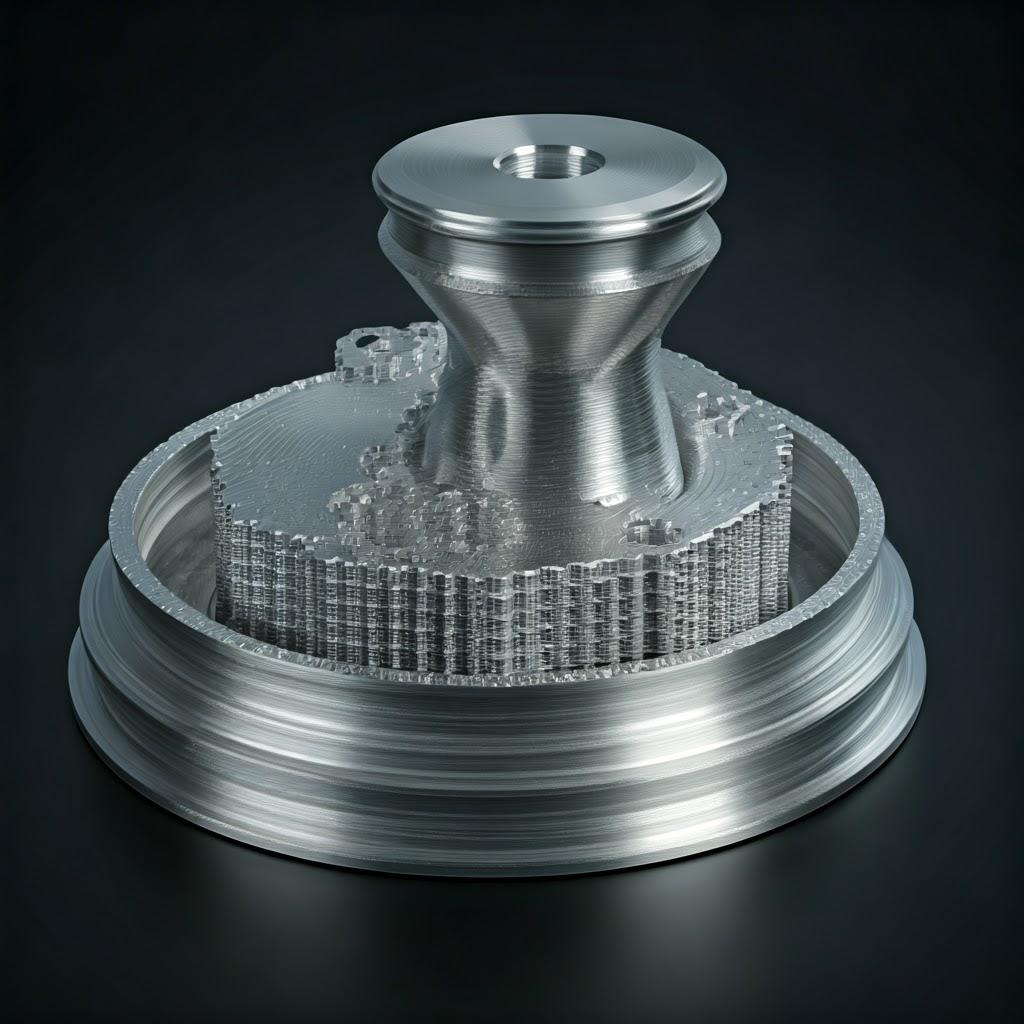
Zvládání výzev: Překonávání potenciálních problémů při 3D tisku termočlánkových pouzder (Kontrola kvality pro průmyslové dodávky)
Ačkoli technologie AM nabízí řadu výhod, jedná se také o složitý proces s potenciálními problémy, které je třeba pochopit a zmírnit, zejména při výrobě dílů pro kritické bezpečnostní aplikace v letectví a kosmonautice. Zajištění konzistentní kvality a spolehlivosti pro průmyslové dodávky vyžaduje důkladnou kontrolu procesu a efektivní řešení běžných problémů.
Společné výzvy a strategie pro jejich zmírnění:
- Zbytkové napětí, deformace a zkreslení:
- Příčina: Nerovnoměrné zahřívání a chlazení, které je vlastní procesu vrstvení, vytváří vnitřní napětí, které může způsobit deformaci dílů nebo odchylky od zamýšlené geometrie, zejména po vyjmutí z konstrukční desky.
- Zmírnění:
- Simulace procesu: Použití softwaru k předvídání akumulace napětí a deformace před tiskem.
- Optimalizované parametry: Jemné doladění výkonu laseru/paprsku, strategie skenování a případně předehřívání konstrukční komory (běžné u EBM).
- Strategie inteligentní podpory: Navrhování robustních podpěr pro ukotvení dílu a účinný odvod tepla.
- DfAM: Navrhování dílů s prvky, které minimalizují koncentraci napětí (např. koutová pole, postupné změny tloušťky).
- Povinná úleva od stresu: Provádění tepelného ošetření pro uvolnění napětí před vyjmutí dílu z konstrukční desky.
- Pórovitost:
- Příčina: Malé vnitřní dutiny v tištěném materiálu, které mohou sloužit jako místa iniciace trhlin a zhoršovat mechanické vlastnosti (zejména únavovou životnost). Příčinou je zachycený plyn, neúplné spojení mezi vrstvami nebo nesoulad prášku.
- Zmírnění:
- Vysoce kvalitní prášek: Použití prášku s vysokou sféricitou, kontrolovaným PSD, nízkým obsahem plynu a dobrou tekutostí (jako jsou prášky Met3dp’s GA/PREP). Správná manipulace s práškem, aby se zabránilo absorpci vlhkosti.
- Optimalizované parametry procesu: Zajištění dostatečné hustoty energie a vhodných strategií skenování pro úplné roztavení a fúzi.
- Řízená atmosféra: Udržování prostředí s vysoce čistým inertním plynem (argon nebo dusík) ve stavební komoře, aby se minimalizovala oxidace a zachytávání plynů.
- Izostatické lisování za tepla (HIP): Jak již bylo zmíněno, HIP je velmi účinný při uzavírání vnitřní pórovitosti plynu a zlepšování hustoty. Často se vyžaduje u kritických dílů.
- Problémy s odstraněním podpory:
- Příčina: Podpěry potřebné pro tisk převisů nebo složitých prvků lze obtížně odstranit, zejména z vnitřních kanálků nebo choulostivých oblastí, což může vést k poškození dílu nebo zanechání nežádoucích povrchových artefaktů.
- Zmírnění:
- DfAM: Navrhování dílů tak, aby byly pokud možno samonosné a minimalizovaly potřebu podpěr. Strategická orientace dílu. Navrhování podpěr pro snadnější demontáž (např. se specifickými body rozhraní).
- Pokročilé strategie podpory: Použití specializovaných typů podpěr (např. stromové podpěry, kuželové podpěry), které zajišťují stabilitu a snadnější demontáž.
- Kvalifikovaní technici: Zaměstnání zkušených techniků s vhodnými nástroji (ruční nástroje, mikroobrábění, elektroerozivní obrábění) pro pečlivé odstranění podpěr.
- Drsnost povrchu:
- Příčina: Vlastní povaha tavení po vrstvách, schodovitý efekt na zakřivených površích, částečně roztavené částice prášku ulpívající na povrchu, podpůrné kontaktní body.
- Zmírnění:
- Optimalizace procesů: Použití jemnějších tlouštěk vrstev (na úkor času sestavení), optimalizace parametrů obrysového skenování.
- Orientace na stavbu: Optimální umístění kritických ploch (např. nahoru nebo vertikálně) pro lepší povrchovou úpravu.
- Následné zpracování: Použití obrábění, leštění, tryskání nebo AFM podle potřeby ke splnění požadavků na povrchovou úpravu.
- Konzistence a opakovatelnost:
- Výzva: Zajištění, aby díly vytištěné v různých sestavách, na různých strojích nebo v různých časech splňovaly konzistentně stejné specifikace - což je zásadní pro průmyslové dodávky a kvalifikaci v leteckém průmyslu.
- Zmírnění:
- Robustní systém řízení kvality (QMS): Zavádění a dodržování přísných norem kvality (např. AS9100 pro letecký průmysl).
- Monitorování a řízení procesů: Monitorování klíčových procesních parametrů v reálném čase (výkon laseru, vlastnosti taveniny, hladina kyslíku, teplota).
- Kalibrace stroje: Pravidelná a důkladná kalibrace systémů AM.
- Správa prášku: Přísná kontrola získávání, testování, skladování, manipulace a sledovatelnosti prášku. Protokoly o testování šarží a recyklaci.
- Standardizované postupy: Zdokumentované postupy pro nastavení sestavy, tisk, následné zpracování a kontrolu.
- Kontrola a řízení kvality (QC):
- Výzva: Ověřování vnitřní integrity a rozměrové přesnosti složitých dílů AM.
- Metody:
- Rozměry: Souřadnicové měřicí stroje (CMM), 3D skenování.
- Vlastnosti materiálu: Zkoušky tahu, zkoušky tvrdosti (často na svědeckých kuponech vytištěných vedle dílů).
- Vnitřní vady (pórovitost, trhliny): Rentgenová počítačová tomografie (CT) je neocenitelná pro nedestruktivní kontrolu vnitřní struktury složitých dílů AM. Dye penetrant testing (PT) a Magnetic Particle testing (MT) lze použít pro defekty porušující povrch.
- Mikrostruktura: Metalografická analýza řezaných vzorků nebo svědeckých kupónů.
Překonání těchto výzev vyžaduje hluboké znalosti procesů, moderní vybavení, přísnou kontrolu kvality a závazek neustálého zlepšování. Manažeři nákupu v leteckém průmyslu by měli upřednostňovat dodavatele, jako je Met3dp, kteří prokazují odborné znalosti v oblasti řízení těchto složitostí a mají potřebné certifikace (např. AS9100 nebo připravenost na ni), aby zajistili dodávku spolehlivých a vysoce kvalitních pouzder termočlánků vhodných pro let.
Výběr partnera: Jak vybrat správného poskytovatele služeb 3D tisku kovů (Hodnocení dodavatelů leteckých komponentů)
Úspěch implementace 3D tištěných pouzder termočlánků nebo jakékoli jiné kritické součásti pro letectví a kosmonautiku významně závisí na výběru správného výrobního partnera. V leteckém průmyslu je v sázce mnoho, proto výběr poskytovatele služeb aditivní výroby kovů vyžaduje důkladné vyhodnocení, které přesahuje pouhé porovnání cenových nabídek. Manažeři nákupu a inženýři musí posoudit potenciální dodavatele na základě jejich technických schopností, systémů kvality, odborných znalostí materiálů a porozumění požadavkům leteckého průmyslu.
Klíčová kritéria pro hodnocení dodavatelů kovového AM pro letectví:
- Odborné znalosti v oblasti letectví a kosmonautiky &; Certifikace:
- Znalosti v oboru: Rozumí dodavatel specifickým požadavkům, předpisům (FAA, EASA) a očekáváním kvality v leteckém průmyslu?
- Certifikace AS9100: Jedná se o mezinárodně uznávaný standard systému řízení kvality pro letecký, kosmický a obranný průmysl. Certifikace (nebo prokazatelná shoda a cesta k certifikaci) je často nezbytnou podmínkou pro výrobu letového hardwaru. Zajišťuje robustní procesy pro sledovatelnost, řízení konfigurace, řízení rizik a další.
- Technické schopnosti & Řízení procesů:
- Vhodná technologie: Používají příslušné technologie AM (např. SLM, EBM) vhodné pro IN718 nebo 316L?
- Kvalita zařízení & Údržba: Jsou jejich stroje dobře udržovány a pravidelně kalibrovány, aby byl zajištěn stálý výkon?
- Monitorování procesů: Využívají ke sledování konzistence stavby monitorování in-situ nebo jiné techniky?
- Vývoj parametrů: Mají zavedené a ověřené parametry pro výrobu konkrétních požadovaných slitin?
- Odborné znalosti materiálů a kvalita:
- Prokazatelné zkušenosti s materiálem: Úspěšný tisk s leteckými slitinami, jako jsou IN718 a 316L.
- Kontrola kvality prášku: Přísné postupy pro vstupní kontrolu prášku, skladování, manipulaci a sledovatelnost. Jak řídí opětovné použití/recyklaci prášku, aby byla zachována kvalita? (Dodavatel jako Met3dp, který vyrábí vlastní vysoce kvalitní prášky pomocí pokročilých metod GA a PREP, zde nabízí významné výhody).
- Certifikace materiálu: Schopnost poskytnout úplnou certifikaci materiálu s vysledováním původní šarže prášku.
- Komplexní možnosti následného zpracování:
- Vlastní vs. spravované služby: Nabízejí nezbytné kroky následného zpracování (uvolnění napětí, tepelné zpracování specifické pro slitinu, HIP, přesné obrábění, NDT) přímo ve firmě, nebo je zajišťují prostřednictvím sítě kvalifikovaných a nejlépe letecky certifikovaných dodavatelů?
- Integrovaný pracovní postup: Jak hladce jsou tyto kroky integrovány do jejich výrobního procesu a systému kvality?
- Robustní systém řízení kvality (QMS):
- Nad rámec certifikace: Hledejte důkazy o vyspělém systému řízení kvality v praxi - dokumentované postupy, přísné kontrolní protokoly (včetně vhodných metod NDT, jako je CT skenování pro interní kontrolu), validace procesů, případně statistická kontrola procesů (SPC) a účinné řešení neshod.
- Engineering & DfAM Support:
- Spolupráce: Dokáže jejich tým inženýrů efektivně spolupracovat na návrhu pro aditivní výrobu (DfAM), aby optimalizoval návrh pouzdra z hlediska výkonu a tisknutelnosti?
- Simulační schopnosti: Nabízejí simulační služby pro předvídání tepelného namáhání nebo výsledků tisku?
- Kvalifikační podpora: Mohou pomoci s vypracováním zkušebních plánů a poskytnutím údajů potřebných pro kvalifikaci součástí?
- Kapacita, škálovatelnost & Záznamy o činnosti:
- Objem výroby: Dokáží splnit vaše požadavky na objem výroby, od prototypů po potenciální sériovou výrobu nebo hromadné objednávky náhradních dílů pro MRO?
- Spolehlivost: Mají prokazatelné zkušenosti s dodáváním vysoce kvalitních dílů včas? Vyžádejte si případové studie nebo reference, zejména z leteckého nebo podobně náročného odvětví.
Hledání profilu ideálního partnera:
Ideálním partnerem není pouze tisková kancelář, ale poskytovatel řešení. Disponuje certifikacemi, technickými znalostmi, spolehlivými systémy kvality a přístupem založeným na spolupráci, který je nezbytný pro zvládnutí složitostí letecké výroby. Chápou kritickou povahu součástí, jako jsou pouzdra termočlánků, a mají infrastrukturu, která jim umožní dodávat spolehlivé díly vhodné pro let. Společnosti jako např Met3dp ztělesňuje tento profil, protože kombinuje pokročilou tiskovou technologii s vlastní výrobou vysoce výkonných kovových prášků a desítky let společných zkušeností v oblasti aditivní výroby kovů a je připravena spolupracovat s organizacemi na dosažení jejich cílů v oblasti AM.
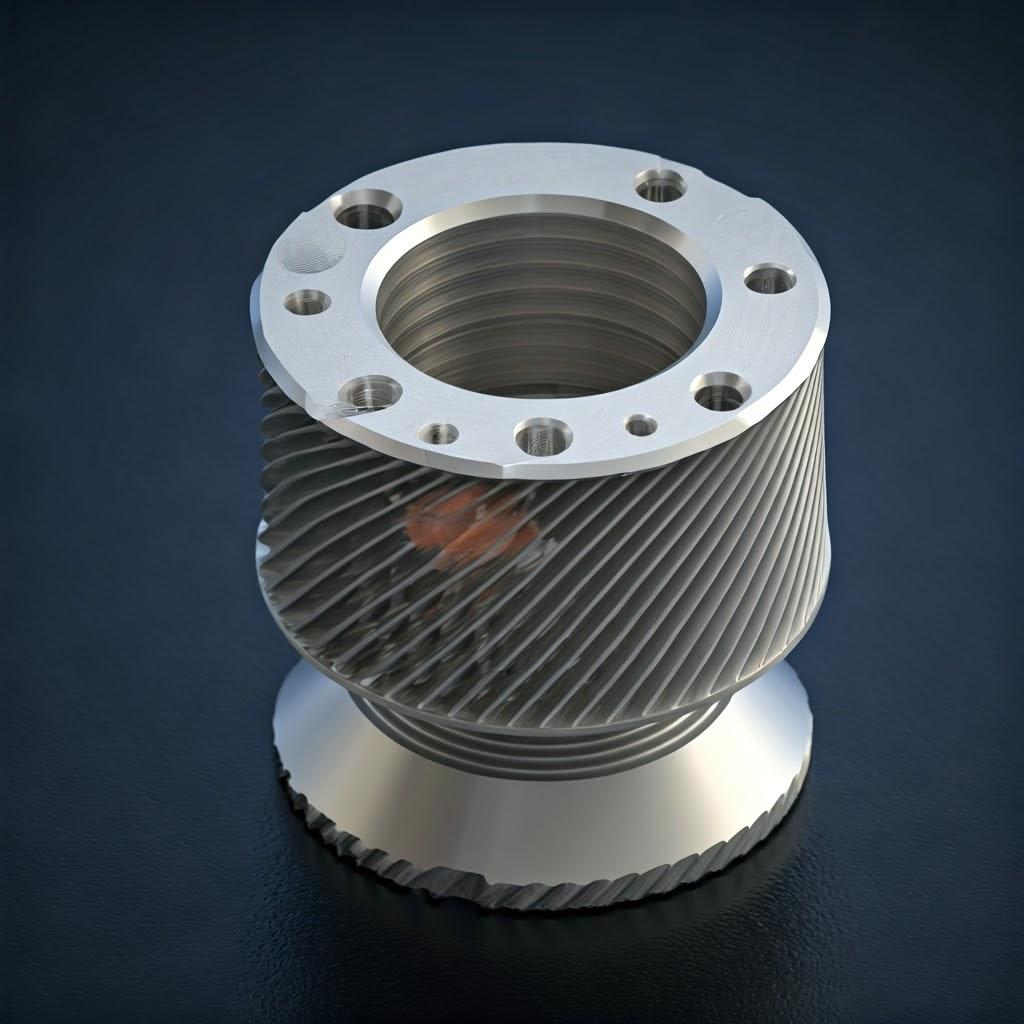
Pochopení investice: Faktory nákladů a dodací lhůty pro průmyslové zakázky a hromadné nákupy
Ačkoli technologie AM pro kovy nabízí přesvědčivé technické výhody, pro plánování projektů a rozhodování o zadávání zakázek je zásadní pochopit strukturu nákladů a očekávané doby realizace. Ekonomika AM se výrazně liší od tradiční výroby.
Klíčové faktory ovlivňující náklady na 3D tištěná pouzdra termočlánků:
- Náklady na materiál:
- Typ slitiny: Prášky pro letectví a kosmonautiku jsou drahé. IN718 je podstatně dražší než 316L.
- Spotřeba: Obsahuje materiál v závěrečné části plus materiál použitý na nosné konstrukce. Konstrukce dílů (hustota, velikost) má na to přímý vliv.
- Stav prášku: Panenský prášek vs. správně recyklovaný prášek (který může přinést úspory nákladů, pokud je spravován pod přísnou kontrolou kvality).
- AM Machine Time:
- Doba trvání stavby: Primární nákladový faktor, který je určen objemem dílu, výškou, tloušťkou vrstvy, rychlostí skenování a počtem dílů umístěných na jedné konstrukční desce. Větší nebo složitější díly vyžadují delší dobu.
- Hodinová sazba stroje: Odráží kapitálové investice, údržbu, provozní náklady (energie, plyn) a čas obsluhy.
- Náklady na pracovní sílu:
- Nastavení a demontáž: Příprava souboru pro sestavení, nastavení stroje a odebrání sestavovací desky/dílů.
- Následné zpracování: Práce spojené s odstraňováním prášku, odstraňováním podpěr, tepelným zpracováním, nastavením obrábění, dokončovacími pracemi a kontrolou. Odstraňování podpěr a obrábění může být náročné na pracovní sílu.
- Náklady na následné zpracování:
- Externí služby: Náklady spojené se specializovanými procesy, jako je HIP, specifické tepelné zpracování, NDT (zejména CT skenování) nebo pokročilé obrábění, pokud jsou zadávány externě.
- Spotřební materiál: Materiály používané při dokončování, čištění atd.
- Zajištění kvality & Inspekce:
- NDT: Nedestruktivní metody zkoušení zvyšují náklady, ale jsou nezbytné pro ověření integrity. CT skenování je sice důkladné, ale dražší než metody, jako je penetrační testování barvivem.
- Rozměrová kontrola: Čas potřebný pro CMM nebo 3D skenování.
- Dokumentace: Generování zpráv o dodržování předpisů a certifikací.
- Design & Engineering:
- Počáteční DfAM: Čas potřebný k optimalizaci konstrukce pro AM, zejména v případě konverze z tradiční konstrukce nebo konsolidace dílů.
- Objem objednávky:
- Amortizace: Náklady na seřízení (příprava souboru, seřízení stroje) se amortizují na počet dílů v sestavě. U větších sérií jsou náklady na tyto fixní prvky na jeden díl obecně nižší.
- Hnízdění: Tisk více dílů současně v jedné sestavovací úloze optimalizuje strojní čas a snižuje náklady na jeden díl ve srovnání s tiskem jednotlivých jednotek. Hromadný nákup umožňuje lepší plánování sestavení.
Typická doba realizace:
Dodací lhůty pro plně zpracované a zkontrolované díly AM pro letectví a kosmonautiku se obvykle pohybují v řádech týdnů, nikoliv dnů. Celková doba zahrnuje:
- Předběžné zpracování: Kontrola objednávky, konzultace DfAM (v případě potřeby), příprava souboru konstrukce, plánování zakázky (1-5 dní).
- Tisk: V závislosti na velikosti, složitosti a množství dílů na sestavení (1-7 dní).
- Následné zpracování: Tato fáze je často časově nejnáročnější.
- Úleva od stresu & amp; ochlazení: (1-2 dny)
- Odstranění podpory/základní úprava: (1-3 dny)
- Tepelné zpracování / stárnutí (např. IN718): Vyžaduje specifické cykly v peci (2-5 dní včetně náběhu/namáčení/chlazení).
- HIP: Vyžaduje plánování ve specializovaném zařízení, samotný cyklus může trvat ~ 1 den plus přeprava (celkem 3-10 dní).
- CNC obrábění: Záleží na složitosti a dostupnosti dílny (2-10 dní).
- Kontrola (NDT, rozměrová): (1-5 dní).
- Doprava: (1-5 dní v závislosti na lokalitě/metodě).
Celková předpokládaná doba realizace: Obvykle 3 až 8 týdnů, velmi variabilní v závislosti na konkrétním dílu a požadovaných krocích zpracování. Za vyšší cenu mohou být k dispozici zrychlené možnosti, ale kritické procesy, jako je tepelné zpracování a HIP, mají minimální dobu cyklu. Jasná komunikace s dodavatelem je zásadní pro řízení očekávání.
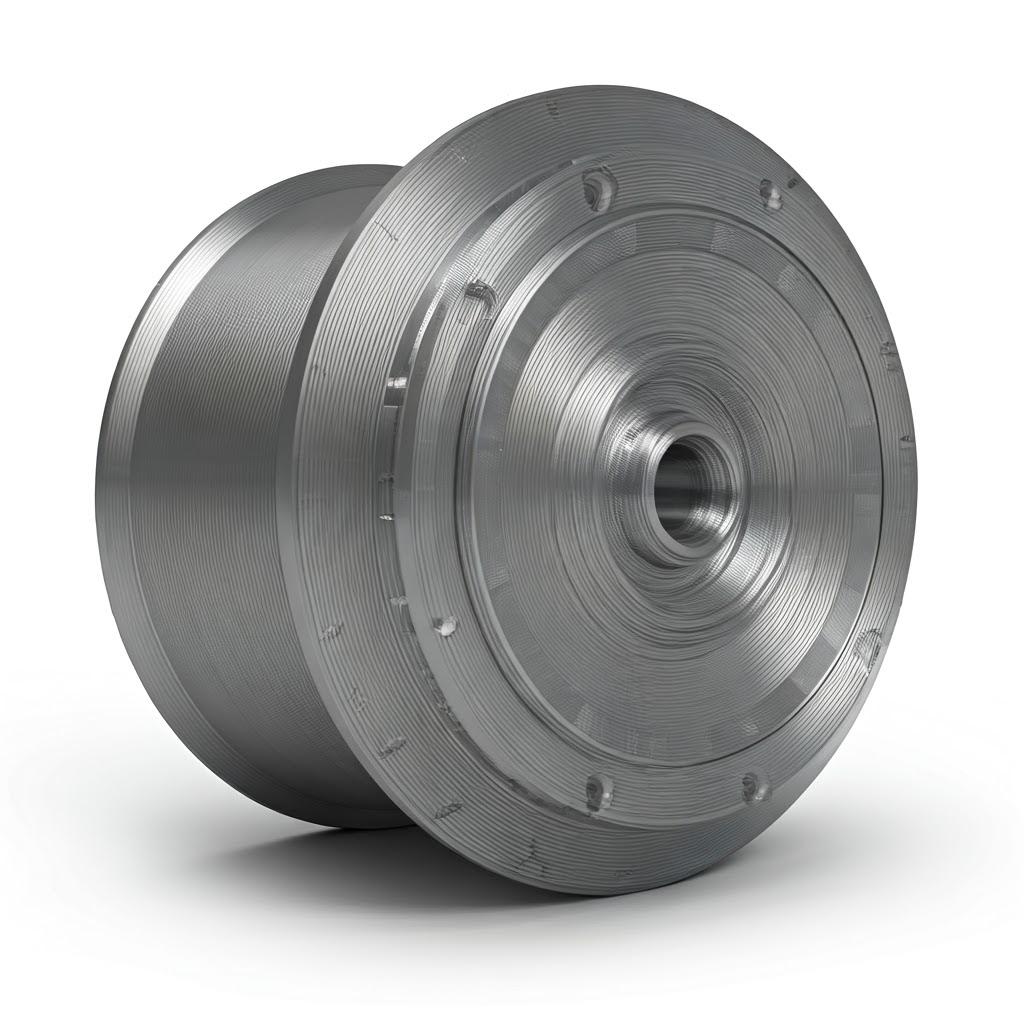
Závěr: Budoucnost leteckých komponentů je aditivní - partnerství s Met3dp pro úspěch
Aditivní výroba kovů představuje významný pokrok ve výrobě složitých, vysoce výkonných součástí pro náročná prostředí, jako jsou například proudové motory. V případě krytů termočlánků nabízí AM oproti tradičním metodám přesvědčivé výhody, včetně bezprecedentní konstrukční svobody umožňující konsolidaci a odlehčení dílů, možnosti využití pokročilých vysokoteplotních superslitin, jako je IN718, a potenciálu zkrácení vývojových cyklů.
Využití těchto výhod však vyžaduje víc než jen přístup k 3D tiskárně. Vyžaduje to komplexní přístup zahrnující přísné zásady návrhu pro aditivní výrobu (DfAM), pečlivý výběr materiálu podpořený výjimečnou kvalitou prášku, pečlivou kontrolu procesu během tisku a komplexní kroky následného zpracování včetně tepelného zpracování, HIP a přesného obrábění, aby byly splněny konečné specifikace. Kromě toho jsou pro zajištění spolehlivosti a bezpečnosti vyžadované leteckým průmyslem nepostradatelné důkladné protokoly pro zajištění kvality a kontroly.
Výběr správného výrobního partnera - partnera s hlubokými odbornými znalostmi v oblasti leteckého průmyslu, osvědčenými technickými schopnostmi, vyspělým systémem řízení kvality a zkušenostmi v celém pracovním procesu AM od prášku až po hotový díl - má zásadní význam.
Met3dp je připraven být tímto partnerem. Jako lídr v oboru kovové AM poskytujeme komplexní řešení, která zahrnují naše vlastní pokročilé tiskárny SEBM (Selective Electron Beam Melting), pečlivě vyráběné vysoce kvalitní kovové prášky optimalizované pro aditivní výrobu (včetně IN718, 316L, Ti-slitin, CoCrMo a dalších) a odborné služby vývoje aplikací. Náš závazek ke kvalitě, který se opírá o špičkové technologie atomizace prášku a desítky let společných zkušeností, zaručuje, že můžeme dodávat komponenty splňující přísné požadavky leteckého průmyslu a dalších kritických odvětví.
Budoucnost letecké výroby je stále více aditivní. Využitím možností 3D tisku z kovu mohou společnosti vytvářet lehčí, pevnější a efektivnější komponenty rychleji než kdykoli předtím. Spolupracujte se společností Met3dp a prozkoumejte, jak mohou naše špičkové systémy, pokročilé materiály a znalosti aplikací urychlit transformaci digitální výroby a podpořit cíle vaší organizace v oblasti aditivní výroby krytů termočlánků a dalších materiálů. Kontaktujte nás ještě dnes a začněte rozhovor.
Často kladené otázky (FAQ): Odpovědi na vaše otázky týkající se 3D tištěných pouzder termočlánků
Otázka 1: Je 3D tisk IN718 stejně pevný jako kovaný nebo litý IN718?
A: Vhodnou optimalizací procesu a následným zpracováním, zejména izostatickým lisováním za tepla (HIP) pro odstranění vnitřní pórovitosti a specifickým tepelným zpracováním pro dosažení požadované mikrostruktury, mohou být mechanické vlastnosti (pevnost v tahu, mez kluzu, prodloužení) AM IN718 vysoce srovnatelné s litým IN718. Dosažení vlastností rovnocenných s tvářeným IN718, zejména pokud jde o únavovou pevnost, je náročné, ale v určitých orientacích a při důsledné kontrole procesu a následném zpracování je možné. U kritických aplikací se vlastnosti ověřují rozsáhlým testováním podle leteckých norem.
Otázka 2: Jaké úrovně detailů a minimální velikosti prvků lze dosáhnout na 3D tištěném pouzdru termočlánku?
A: Dosažitelná úroveň detailů závisí na konkrétním procesu AM kovů (SLM obecně nabízí jemnější rozlišení než EBM), schopnostech stroje a velikosti částic prášku. Minimální velikost tisknutelných prvků se obvykle pohybuje kolem 0,4-0,5 mm (0,016″-0,020″). U prvků vyžadujících vysokou přesnost nebo velmi ostré hrany (jako jsou závity nebo kritické těsnicí plochy) se však obvykle používá následné CNC obrábění, aby se dosáhlo konečných tolerancí a definice.
Otázka 3: Jaká je cena 3D tištěného pouzdra termočlánku ve srovnání s tradičně vyráběným pouzdrem?
A: Srovnání nákladů je složité a do značné míry závisí na faktorech, jako je geometrie dílu, objem zakázky, materiál a konkrétní tradiční metoda (odlévání vs. obrábění).
- AM může být nákladově efektivnější pro: Velmi složité geometrie, konsolidované díly (omezení montáže), nízké až střední objemy výroby (bez nákladů na nástroje) a rychlý vývoj prototypů. U drahých slitin může být významná i úspora materiálu díky snížení množství odpadu (oproti obrábění).
- Tradiční metody mohou být levnější pro: Velmi jednoduché geometrie vyráběné ve velmi vysokých objemech, kde se náklady na nástroje výrazně amortizují. Analýza celkových nákladů na vlastnictví, která bere v úvahu faktory, jako je úspora hmotnosti, zkrácení doby montáže a potenciálně lepší výkon, často upřednostňuje AM pro vhodné letecké komponenty.
Otázka č. 4: Jaké informace potřebuje společnost Met3dp k poskytnutí cenové nabídky na 3D tištěné pouzdro termočlánku?
A: Abychom vám mohli poskytnout přesnou nabídku, potřebujeme obvykle následující informace:
- 3D CAD model dílu (upřednostňuje se formát STEP).
- Specifikovaný materiál (např. IN718, 316L).
- Požadované množství (případně včetně předpokládaných budoucích objemů).
- Technické výkresy s uvedením kritických rozměrů, tolerancí a požadovaných povrchových úprav.
- Podrobnosti o nezbytném následném zpracování (tepelné zpracování, HIP, požadavky na obrábění, povrchové úpravy).
- Jakékoli specifické požadavky na testování, kontrolu (např. CT skenování) nebo certifikaci (např. materiálové certifikáty, osvědčení o shodě).
Otázka 5: Jsou 3D tištěná pouzdra termočlánků automaticky certifikována pro let?
A: Ne, díly nejsou automaticky certifikovány jen proto, že jsou vytištěny na 3D tiskárně. Jakákoli součást určená pro letový hardware, bez ohledu na způsob výroby, musí projít přísným kvalifikačním a certifikačním procesem definovaným výrobcem motoru nebo letadla a leteckými úřady (jako je FAA nebo EASA). To zahrnuje rozsáhlé testování materiálů, validaci procesů (prokazující konzistenci a opakovatelnost) a testování na úrovni dílů (funkční, environmentální, únavové atd.). Spolupráce s dodavatelem, jako je Met3dp, který pracuje pod přísnou kontrolou kvality (v souladu se zásadami AS9100) a poskytuje úplnou sledovatelnost a dokumentaci procesů, je rozhodujícím faktorem pro dosažení případné certifikace dílu zákazníkem.
Sdílet na
MET3DP Technology Co., LTD je předním poskytovatelem řešení aditivní výroby se sídlem v Qingdao v Číně. Naše společnost se specializuje na zařízení pro 3D tisk a vysoce výkonné kovové prášky pro průmyslové aplikace.
Dotaz k získání nejlepší ceny a přizpůsobeného řešení pro vaše podnikání!
Související články
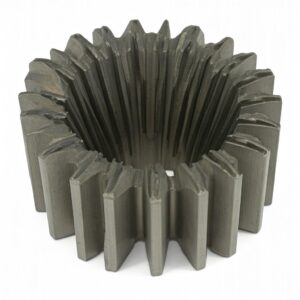
Vysoce výkonné segmenty lopatek trysek: Revoluce v účinnosti turbín díky 3D tisku z kovu
Přečtěte si více "O Met3DP
Nedávná aktualizace
Náš produkt
KONTAKTUJTE NÁS
Nějaké otázky? Pošlete nám zprávu hned teď! Po obdržení vaší zprávy obsloužíme vaši žádost s celým týmem.
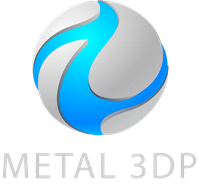
Kovové prášky pro 3D tisk a aditivní výrobu