3D tištěné skříně turbodmychadel pro vysoce výkonná vozidla
Obsah
Revoluční výkon díky 3D tištěným tělesům turbodmychadel
Při neúnavné snaze o zvyšování výkonu automobilů inženýři neustále posouvají hranice technologie motorů. Turbodmychadlo, které je ústředním prvkem systémů nuceného sání, je kritickou součástí a jeho skříň hraje mnohem významnější roli než jen to, že obsahuje kompresor a turbínu. skříň turbodmychadla-skládající se ze skříně kompresoru na chladné straně a skříně turbíny na horké straně, musí odolávat extrémním teplotám, vysokým tlakům, značným vibracím a korozivním výfukovým plynům a zároveň přesně řídit proudění vzduchu, aby se maximalizovala účinnost a výkon motoru. Výroba těchto složitých součástí tradičně zahrnovala odlévání nebo rozsáhlé obrábění, což jsou metody, které často znamenají kompromisy v konstrukci, vlastnostech materiálu nebo době realizace, zejména u specializovaných aplikací.
Vstupte do éry aditivní výroba (AM), běžně známý jako 3D tisk. Konkrétně, 3D tisk z kovu se rychle stává transformující se silou ve výrobě vysoce výkonných automobilových komponentů, včetně skříní turbodmychadel. Tato technologie umožňuje konstrukci složitých kovových dílů po vrstvách přímo z digitálních návrhů, čímž uvolňuje nebývalou úroveň konstrukční svobody, umožňuje použití pokročilých materiálů a výrazně zrychluje vývojové cykly. Pro inženýry, kteří usilují o optimální aerodynamickou účinnost, odlehčení a tepelný management, a pro manažery nákupu, kteří hledají flexibilní výrobní řešení s vysokou hodnotou pro zakázkové komponenty turbodmychadla, nabízí technologie AM pro zpracování kovů přesvědčivou alternativu ke konvenčním metodám.
Tento posun je zvláště důležitý v náročných odvětvích, jako je motoristický sport, vysoce výkonný poprodejní tuning a výroba specifických vozidel, kde hotové komponenty často nedostačují. Schopnost vytvářet na míru vysoce výkonná turbodmychadla s optimalizovanou geometrií přizpůsobenou specifickým požadavkům motoru poskytuje hmatatelnou konkurenční výhodu. Společnosti jako Met3dp stojí v čele této revoluce a poskytují nejen špičkové tiskárny pro AM tisk kovů, které jsou známé svou přesností a spolehlivostí, ale také vysoce výkonné kovové prášky navržené pro náročné podmínky v oblasti AM kovový 3D tisk hnacího ústrojí aplikace. Jakmile se dostaneme hlouběji, prozkoumáme, jak přesně tato technologie mění konstrukci a výrobu turbodmychadel a nabízí významné výhody pro podniky působící v oblasti vysoce výkonných automobilů.
Základní aplikace: Kde mají 3D tištěná pouzdra turbodmychadel vliv?
Jedinečné možnosti aditivní výroby kovů jsou hnací silou zavádění 3D tištěných krytů turbodmychadel v několika klíčových segmentech automobilového průmyslu. Ačkoli AM zatím není hlavním proudem pro hromadně vyráběná vozidla pro dojíždění (kde stále převládá tradiční efektivita odlévání ve velkých objemech), září jasně tam, kde je nejdůležitější přizpůsobení, špičkový výkon a rychlý vývoj. Specialisté na nákupy a inženýři, kteří zajišťují zdroje výroba komponentů pro motorsport řešení nebo hledání dodavatelů pro vylepšení výkonných vozidel se stále častěji obracejí na AM.
Zde je rozpis základních aplikací:
- Motorsport a závodění:
- Konkurenční výhoda: Ve formuli 1, vytrvalostních závodech (jako je WEC), rallye šampionátech a dalších špičkových sériích se počítá každý gram hmotnosti a každý zlomek aerodynamické účinnosti. Technologie AM umožňuje týmům vytvářet vysoce optimalizované, lehké skříně se složitými vnitřními spirálami a kanály, které jsou přesně přizpůsobeny provozním vlastnostem motoru a omezením spojeným s balením.
- Rychlá iterace: Změny v konstrukci lze provést a otestovat během několika dnů nebo týdnů, místo měsíců potřebných pro nové odlévací nástroje. Tato rychlost je klíčová pro udržení konkurenceschopnosti během celé závodní sezóny.
- Materiálová nadřazenost: Závodní prostředí posouvá materiály až na samé hranice jejich možností. AM umožňuje použití vysokoteplotních superslitin, jako je Inconel 625 nebo 718, a zajišťuje tak odolnost při extrémním tepelném zatížení, které by mohlo být pro běžné materiály nebo výrobní metody složitých tvarů náročné.
- Nízký objem, vysoká hodnota: Závodní týmy obvykle vyžadují pouze malý počet vysoce specializovaných komponent, takže beznástrojová povaha AM je ekonomicky životaschopná a strategicky výhodná.
- Vysoce výkonný trh s náhradními díly:
- Vylepšený výkon: Dodavatelé turbodmychadel pro trh s náhradními díly a tuningové firmy se zaměřují na nadšence, kteří chtějí výrazně zvýšit výkon. 3D tisk jim umožňuje navrhovat a nabízet skříně s vynikajícími charakteristikami proudění vzduchu, vylepšenou konstrukcí wastegate a případně integrovanými prvky, které se v dílech OEM nenacházejí.
- Unikátní geometrie: AM umožňuje vytvářet skříně se složitými tvary, jako jsou skříně turbín twin-scroll s vysoce optimalizovanými oddělenými průchody nebo kryty kompresorů s pokročilými ochrannými prvky proti přepětí, které lze obtížně nebo vůbec nelze efektivně dosáhnout odléváním.
- Přizpůsobení: Pro specifické výměny motorů nebo jedinečné konstrukce umožňuje systém AM vytvářet skříně na míru, které se dokonale přizpůsobí dostupnému prostoru a správně se propojí s ostatními součástmi motoru.
- Diferenciace značky: Nabídka vyspělých, 3D tištěných komponent může sloužit jako významný diferenciátor v konkurenčním prostředí trhu s náhradními díly.
- Prototypy OEM a specifická vozidla:
- Zrychlený vývoj: Během Vývoj turbodmychadla OEM fázi nových motorů, AM umožňuje konstruktérům rychle vytvořit prototyp a funkčně otestovat více návrhů skříní. To výrazně zkracuje lhůty výzkumu a vývoje a náklady spojené s tradičními metodami prototypování. Chyby v konstrukci lze rychle odhalit a opravit ještě předtím, než se přistoupí k nákladné sériové výrobě nástrojů.
- Výroba specifických vozidel: U hyperaut, superaut a dalších speciálních vozidel vyráběných v omezeném množství (malosériová výroba automobilů), jsou vysoké náklady na odlévací nástroje často neúnosné. Metal AM poskytuje nákladově efektivní výrobní řešení pro výrobu finálních funkčních skříní turbodmychadel pro tato exkluzivní vozidla, aniž by bylo nutné investovat do speciálních forem.
- Konsolidace částí: AM umožňuje konstruktérům integrovat prvky, jako jsou držáky, šachty senzorů nebo tepelné štíty, přímo do konstrukce pouzdra, čímž se potenciálně snižuje počet dílů, doba montáže a počet míst poruchy.
Funkční přínosy realizované prostřednictvím AM:
V těchto aplikacích se funkční výhody přímo promítají do měřitelného zvýšení výkonu:
- Optimalizovaná aerodynamika: Přesně řízená vnitřní geometrie (spirály, difuzory) vede k vyšší účinnosti kompresoru a turbíny, což má za následek vyšší výkon a rychlejší reakci na plyn (snížení prodlevy turba).
- Vylepšený tepelný management: Integrace důmyslných vnitřních chladicích kanálů, zejména v tělese turbíny, pomáhá zvládat extrémní teploty, zvyšuje odolnost materiálu a udržuje stálý výkon při zatížení.
- Snížení hmotnosti: Algoritmy pro optimalizaci topologie, které umožňuje AM, odstraňují materiál z nekritických oblastí, což vede k lehčím součástem. To je v motoristickém sportu zásadní a přispívá to k celkové efektivitě vozidla.
- Vylepšené balení: Volnost konstrukce umožňuje tvarovat skříně tak, aby se vešly do těsných motorových prostorů, což je u moderních vozidel plných technologií zásadní.
Pro odběratele B2B znamená pořízení 3D tištěných skříní turbodmychadel přístup ke špičkové technologii, která přináší hmatatelné výkonnostní výhody, rychlejší vývojové cykly pro zakázkové projekty a flexibilní výrobní řešení pro specializované komponenty s vysokou hodnotou.
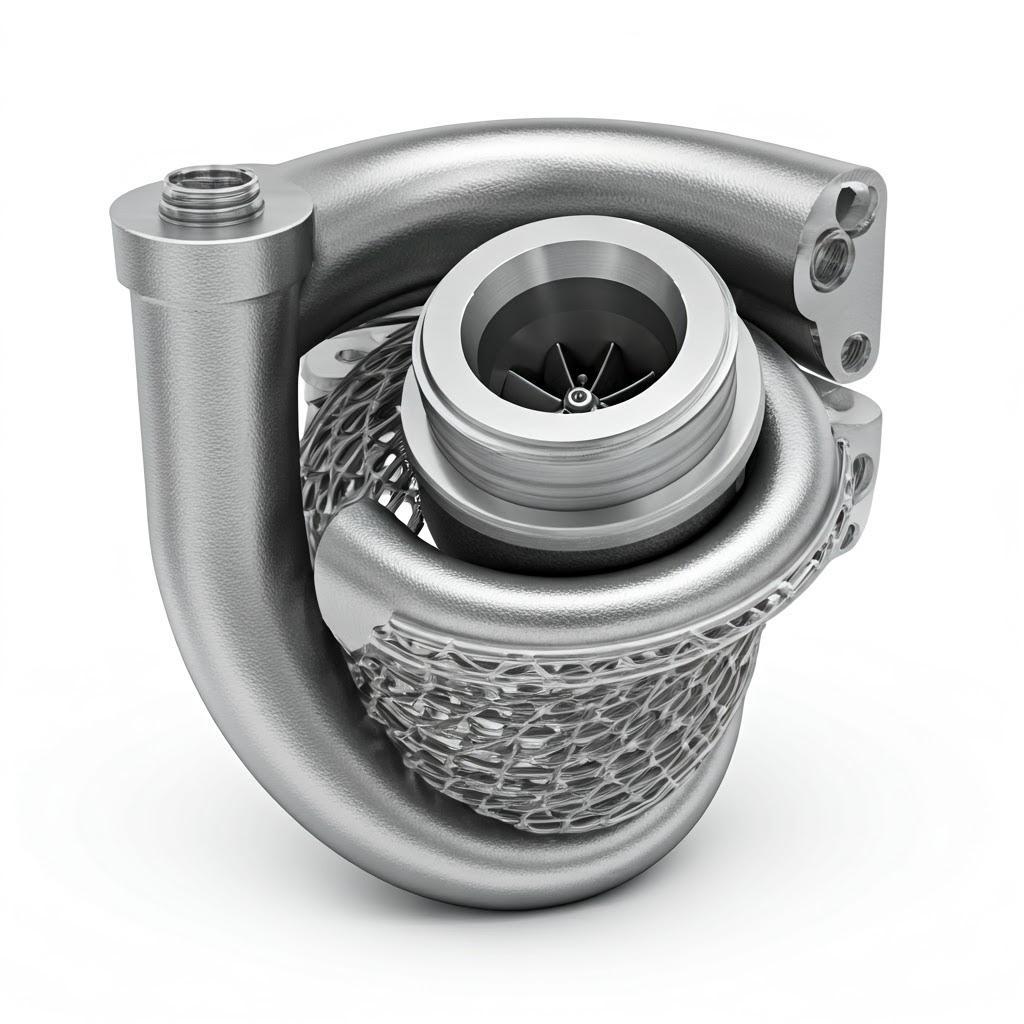
Aditivní výhoda: Proč zvolit 3D tisk z kovu pro skříně turbodmychadel?
Zatímco tradiční výrobní metody, jako je odlévání a obrábění, sloužily automobilovému průmyslu dobře po celá desetiletí, aditivní výroba kovů představuje změnu paradigmatu a nabízí výrazné výhody, zejména pro složité, výkonově kritické komponenty, jako jsou skříně turbodmychadel. Pochopení těchto výhod je klíčové pro inženýry a manažery nákupu, kteří hodnotí výrobní metody pro komponenty hnacích ústrojí nové generace. Srovnejme AM s konvenčními technikami a zdůrazněme výhody kovu AM pro automobilový průmysl aplikace přinášejí.
AM vs. tradiční metody:
- Investiční lití:
- Klady: Vynikající kvalita povrchu, dobrá rozměrová přesnost, vhodné pro složité tvary, cenově výhodné při velkých objemech.
- Nevýhody: Vyžaduje nákladné a časově náročné nástroje (voskové vzory, keramické pláště), značná konstrukční omezení (např. úhly tahu, rovnoměrná tloušťka stěn), omezená vnitřní složitost (jádra mohou být křehká), dlouhé dodací lhůty pro první díly. Obtížné rychlé iterace návrhů.
- Odlévání do písku:
- Klady: Nižší náklady na nástroje než u investičního lití, vhodné pro větší díly.
- Nevýhody: Horší kvalita povrchu a rozměrová přesnost, vyžaduje dodatečné obrábění, značná konstrukční omezení, méně vhodné pro velmi tenké stěny nebo velmi složité detaily.
- Obrábění ze sochorů:
- Klady: Vysoká přesnost, vynikající vlastnosti materiálu (kovaný materiál), žádné náklady na nástroje.
- Nevýhody: Extrémně vysoký odpad materiálu (poměr nákup/let), velmi obtížné nebo nemožné vytváření složitých vnitřních prvků (jako jsou spirály), dlouhá doba obrábění složitých vnějších tvarů, potenciálně vysoké náklady na díl kvůli odpadu a strojnímu času.
- Aditivní výroba kovů (LPBF/SEBM):
- Klady: Výroba bez nástrojů, umožňující rychlé prototypování turbo dílů a nízkoobjemovou výrobu s nízkými náklady. Bezkonkurenční výroba automobilů s komplexní geometrií schopnost, včetně složitých vnitřních kanálků a organických tvarů. Usnadňuje lehká konstrukce turbodmychadla prostřednictvím optimalizace topologie. Umožňuje konsolidaci dílů. Široká škála materiálů, včetně vysoce výkonných superslitin. Významné zkrácení dodací lhůty v automobilovém průmyslu vývojové cykly.
- Nevýhody: Vyšší náklady na díl ve srovnání s odléváním při velmi vysokých objemech. Obvykle vyžaduje následné zpracování (tepelné zpracování, odstranění podpory, povrchová úprava, konečné obrábění). Omezení velikosti sestavy v závislosti na stroji. Vyžaduje odborné znalosti v oblasti návrhu pro aditivní výrobu (DfAM).
Hlavní výhody AM pro skříně turbodmychadel:
- Bezprecedentní svoboda designu: To je pravděpodobně nejvýznamnější výhoda. AM osvobozuje konstruktéry od omezení tradičních metod.
- Příklad: Inženýři mohou navrhovat spirály kompresorů a turbín s plynule se měnícím průřezem optimalizovaným výhradně pro dynamiku tekutin, čímž se maximalizuje účinnost v celém provozním rozsahu. Vnitřní chladicí kanály mohou sledovat složité dráhy přímo v sousedství nejteplejších oblastí skříně turbíny, což je u odlitků prakticky nemožné. Průchody odpadního potrubí lze plynule integrovat do optimálních průtokových cest.
- Odlehčení pomocí optimalizace topologie: AM pracuje synergicky s výpočetními návrhovými nástroji. Software dokáže analyzovat rozložení napětí a odstranit materiál z míst, kde není konstrukčně nutný, a vytvořit tak pevné a zároveň lehké organické tvary.
- Příklad: Skříň turbíny vytištěná na 3D tiskárně může mít zvenčí složitou mřížkovou strukturu, která zachovává tuhost a zároveň výrazně snižuje hmotnost ve srovnání s pevným odlitkem. Tím se sníží celková hmotnost vozidla a může se potenciálně zlepšit přechodová odezva.
- Vylepšený tepelný management: Možnost zabudovat komplexní vnitřní chladicí kanály přímo do stěn skříně je převratná, zejména na straně turbíny, která je vystavena extrémním teplotám výfukových plynů.
- Příklad: Kanály pro chlazení kapalinou nebo vzduchem lze vytisknout jen milimetry od nejžhavějších plynových kanálů, což výrazně snižuje teplotu materiálu, zlepšuje životnost, zabraňuje zahřívání a umožňuje agresivnější ladění motoru.
- Rychlé prototypování a iterace: Beznástrojová povaha AM znamená, že změny konstrukce lze realizovat a fyzicky testovat během několika dní.
- Příklad: Inženýrský tým může během týdne na dynamometru otestovat tři různé konstrukce spirál a shromáždit empirická data pro výběr optimální konfigurace. Při odlévání by tento proces mohl trvat mnoho měsíců a pro každou iteraci by vznikly značné náklady na nástroje.
- Pokročilé využití materiálů: Procesy AM, jako je SEBM (Selective Electron Beam Melting) a LPBF (Laser Powder Bed Fusion), vynikají při zpracování vysoce výkonných materiálů nezbytných pro turbodmychadla.
- Příklad: Superslitiny na bázi niklu, jako jsou IN718 a IN625, známé svou pevností při vysokých teplotách a odolností proti korozi, lze snadno zpracovat pomocí AM do hustých dílů ve tvaru blízkém tvaru sítě. Tyto materiály jsou často náročné nebo drahé na zpracování tradičními metodami, zejména v případě složitých geometrií.
- Konsolidace částí: Komponenty, které byly dříve oddělené a vyžadovaly montáž (např. kryt, montážní držáky, tepelné štíty), lze potenciálně integrovat do jediného tištěného dílu.
- Příklad: Skříň turbodmychadla by mohla být vytištěna s integrovanými montážními body a konstrukčními výztuhami, což by snížilo počet dílů, pracnost montáže, hmotnost a potenciální netěsnosti nebo místa poruch.
Pro zákazníky B2B se tyto výhody promítají do hmatatelné hodnoty: rychlejší uvádění inovativních výrobků na trh, vynikající výkonnost komponentů vedoucí ke konkurenční výhodě, zjednodušená logistika pro malosériové díly a schopnost vytvářet řešení, která byla dříve považována za nemožná. Spolupráce se zkušeným poskytovatelem AM zajišťuje, že tyto výhody budou plně realizovány prostřednictvím optimalizovaného návrhu, výběru materiálu a řízení procesu.
Zaměření materiálu: IN718 & amp; IN625 pro náročná prostředí turbodmychadel
Výběr správného materiálu je pro skříně turbodmychadel velmi důležitý vzhledem k neuvěřitelně náročným provozním podmínkám, kterým čelí: teploty na straně turbíny mohou přesahovat 1000 °C, vysoké tlaky, cyklické tepelné zatížení, vibrace a působení korozivních vedlejších produktů výfukových plynů. Zatímco v sériově vyráběných turbodmychadlech se používají různé materiály (například litina nebo nerezová ocel), vysoce výkonné a náročné aplikace vyžadují použití superslitin na bázi niklu. Mezi nimi vynikají Inconel 718 (IN718) a Inconel 625 (IN625) jako hlavní kandidáti pro aditivní výrobu kovů, které nabízejí výjimečnou kombinaci vlastností snadno zpracovatelných pomocí AM. Pochopení jejich vlastností pomáhá při výběru optimálního materiálu pro konkrétní požadavky na pouzdro.
Proč superslitiny?
Superslitiny na bázi niklu jsou konstruovány tak, aby si zachovaly vynikající mechanickou pevnost, stabilitu povrchu a odolnost proti korozi/oxidaci při extrémně vysokých teplotách, při kterých by běžné oceli selhaly. Díky tomu jsou ideální pro náročné prostředí turbodmychadla, zejména pro skříň turbíny, která je přímo vystavena působení horkých výfukových plynů.
Inconel 718 (IN718 / slitina 718)
- Složení: Slitina niklu a chromu obsahující značné množství železa, niobu a molybdenu s příměsí hliníku a titanu.
- Klíčové vlastnosti:
- Vysoká pevnost & amp; Odolnost proti tečení: Zachovává si vynikající pevnost v tahu, únavu a trhlinu při tečení až do teploty přibližně 700 °C.
- Stářím odolné: Její pevnost je odvozena především z precipitačního kalení (tepelné zpracování stárnutím) za účasti fází Ni3(Nb, Ti, Al). To umožňuje dosáhnout velmi vysoké pevnosti.
- Dobrá odolnost proti korozi: Nabízí dobrou odolnost proti oxidaci a korozi v typickém prostředí motoru.
- Vynikající potisknutelnost/svařitelnost: V porovnání s jinými precipitačně vytvrzenými superslitinami vykazuje IN718 velmi dobrou zpracovatelnost při svařování i aditivní výrobě, což z něj činí oblíbenou volbu pro komplexní komponenty AM.
- Význam turbodmychadla: Často se používá pro skříně kompresorů (kde jsou teploty nižší) a případně pro skříně turbín v aplikacích, kde jsou špičkové teploty výfukových plynů středně vysoké. Jeho vynikající poměr pevnosti a hmotnosti po tepelném zpracování je velmi výhodný. Je obecně o něco levnější než IN625.
Inconel 625 (IN625 / slitina 625)
- Složení: Slitina niklu, chromu, molybdenu a niobu.
- Klíčové vlastnosti:
- Vynikající odolnost při vysokých teplotách: Spoléhá na zpevnění pevným roztokem molybdenu a niobu, které zajišťuje vynikající pevnost a houževnatost při teplotách až do 815 °C a při krátkodobých výkyvech i vyšších. Zachovává si pevnost lépe než IN718 při nejvyšších teplotách, které se vyskytují v agresivních turbo aplikacích.
- Vynikající odolnost proti korozi: Vysoký obsah chromu a molybdenu zajišťuje vynikající odolnost vůči široké škále korozivních prostředí, včetně důlkové koroze, štěrbinové koroze a kyselých kondenzátů, které se vyskytují ve výfukových plynech. V odolnosti proti korozi obecně překonává IN718.
- Vynikající zpracovatelnost a potisknutelnost: Je známá pro svou snadnou výrobu a vynikající svařitelnost/ tisknutelnost, takže je velmi vhodná pro složité geometrie AM.
- Houževnatost: Vykazuje vysokou houževnatost a únavovou pevnost v širokém rozsahu teplot.
- Význam turbodmychadla: Přednostní volba pro vysoce výkonné turbínové skříně, zejména ty, které jsou vystaveny nejextrémnějším teplotám a potenciálně korozivním palivovým směsím (např. s vysokým obsahem etanolu). Jeho vynikající odolnost vůči teplu a korozi poskytuje větší rezervu bezpečnosti a trvanlivosti v náročných aplikacích v motorsportu nebo vysoce vyladěných aplikacích na trhu s náhradními díly.
IN718 vs. IN625 pro 3D tištěná pouzdra turba:
Vlastnosti | Inconel 718 (IN718) | Inconel 625 (IN625) | Význam pro turbo skříně |
---|---|---|---|
Maximální provozní teplota | ~700°C (1300°F) | ~815°C+ (1500°F+) | IN625 je vhodnější pro extrémní teploty výfukových plynů (na straně turbíny) |
Mechanismus pevnosti | Srážkové vytvrzování (požadavek na stárnutí) | Zpevnění pevným roztokem | IN718 potenciálně vyšší pevnost <700°C, vyžaduje tepelné zpracování |
Pevnost při >700 °C | Rychleji klesá | Lépe si udržuje sílu | IN625 lepší pro nejteplejší části skříně turbíny |
Odolnost proti korozi | Dobrý | Vynikající | IN625 nabízí větší odolnost proti agresivním výfukovým plynům |
Tisknutelnost/svařitelnost | Velmi dobře | Vynikající | Oba jsou dobře zavedené materiály pro AM kovů |
Náklady | Obecně nižší | Obecně vyšší | Náklady je třeba porovnat s požadavky na výkonnost/trvanlivost |
Typická aplikace | Skříň kompresoru, mírná strana turbíny | Pouzdro turbíny, vysoce náročné aplikace | Přizpůsobení výběru materiálu konkrétnímu provoznímu prostředí |
Export do archů
Úloha Met3dp’ v oblasti materiálové excelence:
Úspěšný 3D tisk skříní turbodmychadel z náročných materiálů, jako jsou IN718 a IN625, vyžaduje nejen pokročilé tiskové vybavení, ale také mimořádně kvalitní kovový prášek. A právě zde Met3dp vyniká. S využitím špičkových technik výroby prášků, jako je vakuová plynová atomizace (VIGA) a plazmový proces s rotujícími elektrodami (PREP), vyrábí společnost Met3dp kovové prášky s vlastnostmi, které jsou pro úspěšnou aditivní výrobu rozhodující:
- Vysoká sféricita: Zajišťuje vynikající tekutost prášku a vysokou hustotu balení v loži prášku, což vede k hustším a pevnějším finálním dílům.
- Nízký obsah satelitu: Minimalizuje množství jemných částic navázaných na větší koule, čímž dále zlepšuje tekutost a snižuje možné vady.
- Řízená distribuce velikosti částic (PSD): Optimalizovaný PSD pro specifické procesy AM (jako LPBF nebo SEBM) zajišťuje konzistentní tavení a tvorbu vrstev.
- Vysoká čistota: Minimalizuje kontaminanty, které by mohly ohrozit vlastnosti materiálu.
Společnost Met3dp vyrábí širokou škálu vysoce kvalitních kovových prášků, včetně inovativní slitiny a standardní superslitiny jako IN718 a IN625, optimalizované pro laserové a elektronové procesy fúze v práškovém loži. Jejich hluboké odborné znalosti v oblasti práškové výroby i systémů AM tisku zajišťují, že zákazníci dostanou materiály dokonale vhodné pro výrobu kritických komponent, jako jsou vysoce výkonné skříně turbodmychadel. Výběr dodavatele, jako je Met3dp, který má kontrolu nad vědou o materiálu i nad procesem tisku, poskytuje jistotu dosažení požadovaných vlastností materiálu a spolehlivosti součástky.
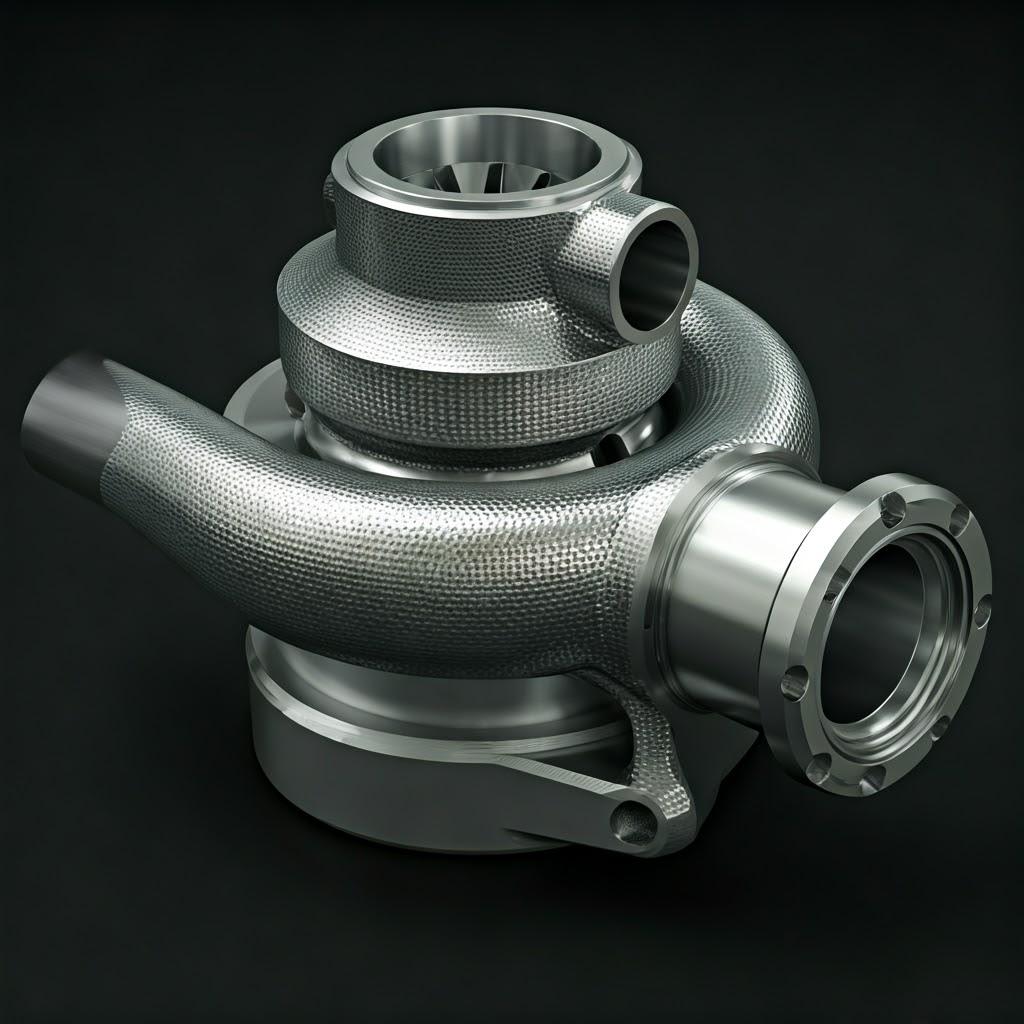
Design pro aditivní výrobu (DfAM): Optimalizace skříní turbodmychadel pro 3D tisk
Častým omylem při zavádění aditivní výroby kovů je, že stávající konstrukce, původně určené pro odlévání nebo obrábění, lze jednoduše poslat do tiskárny. Tento přístup je sice technicky možný, ale nevyužívá jedinečných předností AM a často vede k neoptimálním výsledkům, zvýšeným nákladům nebo dokonce k selhání tisku. Chcete-li skutečně využít potenciál 3D tištěných skříní turbodmychadel, Design pro aditivní výrobu (DfAM) je nejen doporučená, ale i nezbytná. DfAM zahrnuje přehodnocení procesu navrhování od základu, přičemž se zohledňují jak svobody, tak omezení procesu vytváření jednotlivých vrstev. Inženýři a konstruktéři zapojení do Automobilové díly DfAM vývoj se zaměřuje na maximalizaci výkonu při zajištění vyrobitelnosti.
Klíčové zásady DfAM pro skříně turbodmychadel:
- Optimalizace průtokové cesty: V této oblasti je AM pro turbodmychadla opravdu skvělý. Zapomeňte na omezení spojená s odléváním jader. Navrhněte hladké, plynule se měnící spirály a kanály, které přesně odpovídají aerodynamickým požadavkům kompresoru a turbínových kol. Ve fázi návrhu hojně využívejte výpočetní dynamiku tekutin (CFD) k iteraci a zdokonalování cest proudění vzduchu, minimalizaci tlakových ztrát a optimalizaci průtoku přes wastegate pro lepší regulaci zvýšení tlaku. Zvažte integraci prvků, jako jsou vstupy do zvonu nebo optimalizované difuzory přímo do skříně.
- Integrované komplexní funkce: Využijte schopnost AM’ vytvářet složité vnitřní struktury.
- Vnitřní chladicí kanály: Navrhněte konformní chladicí kanály, které kopírují obrysy nejteplejších částí skříně turbíny (např. v blízkosti jazyka spirály nebo vstupu do turbíny). Tyto kanály, které nelze vytvořit tradičními metodami, umožňují cílené chlazení (kapalinou nebo vzduchem), což výrazně zlepšuje tepelné řízení, životnost materiálu a stálost výkonu při zatížení. Zajistěte, aby byly kanály navrženy tak, aby se daly tisknout (pokud možno samonosné úhly) a aby byl zcela odstraněn prášek.
- Integrace senzorů: Do konstrukce lze bez problémů integrovat šroubení a porty pro snímače tlaku, teploty nebo otáček, případně na optimalizovaná místa, která dříve nebyla přístupná.
- Minimalizace a optimalizace struktury podpory: V kovovém AM (zejména LPBF) jsou často nutné podpůrné struktury, které slouží k ukotvení dílu, zvládnutí tepelného namáhání a podpoře převislých prvků. Spotřebovávají však další materiál, prodlužují dobu tisku a vyžadují odstranění při následném zpracování.
- Strategická orientace: Způsob orientace dílu na konstrukční desce má zásadní vliv na potřebu podpory, kvalitu povrchu a potenciální deformace. Analyzujte různé orientace a najděte nejlepší rovnováhu.
- Samonosné úhly: Přesahy navrhněte pokud možno samonosné. Úhly větší než přibližně 45 stupňů od vodorovné roviny se často úspěšně tisknou bez podpěr (to však závisí na konkrétním procesu a materiálu). Místo ostrých vodorovných převisů používejte zkosení nebo filety.
- DfAM pro odstranění podpory: Zajistěte, aby byly podpěry, zejména vnitřní, přístupné pro demontáž. V případě potřeby navrhněte přístupové otvory nebo zvažte procesy, jako je SEBM, které mohou vyžadovat méně podpěr kvůli vyšším teplotám ve stavební komoře.
- Tloušťka stěny a odlehčení:
- Optimalizace topologie: Pomocí specializovaného softwaru identifikujte a odstraňte materiál z oblastí s nízkým namáháním a vytvořte organické struktury optimalizované pro zatížení. To je klíčové pro optimalizace topologie turbodmychadla konstrukce zaměřené na motoristický sport nebo maximální výkon, snížení setrvačnosti otáčení (pokud je použita na rotující součásti) a celkové hmotnosti vozidla.
- Minimální tloušťka stěny: AM umožňuje poměrně tenké stěny (např. 0,4 mm – 1,0 mm v závislosti na procesu a nepodpořeném rozpětí), ale zajišťuje dostatečnou tloušťku stěn pro strukturální integritu, manipulaci a tisk. Vyhněte se velkým nepodporovaným tenkým vodorovným řezům.
- Vyhněte se tlustým řezům: Velmi tlusté masivní profily mohou akumulovat nadměrné tepelné napětí, což zvyšuje riziko praskání nebo deformace. Zvažte návrh vnitřních mřížových struktur nebo dutých profilů namísto plných objemů, kde je to vhodné.
- Tepelný management při tisku: Intenzivní přívod energie při AM kovů vytváří značné tepelné gradienty. Konstrukční prvky, které je zmírňují: přidání obětních žeber nebo chladičů v kritických oblastech, které odvádějí teplo; zajištění plynulých přechodů mezi tlustými a tenkými částmi; orientace dílu tak, aby se minimalizovaly velké rovné plochy rovnoběžné s konstrukční deskou. Software pro simulaci sestavení je zde neocenitelný.
- Konsolidace částí: Prozkoumejte sestavu turbodmychadla a zjistěte možnosti integrace přilehlých součástí (držáků, úchytů, tepelných štítů) přímo do konstrukce skříně. Tím se sníží počet dílů, doba montáže, hmotnost a potenciální místa poruch (např. šroubové spoje nebo svary).
- Design otvorů: Svislé otvory se obecně tisknou s lepší kulatostí. Horizontální nebo šikmé otvory se často tisknou mírně nekulaté (eliptické nebo slzovité) kvůli vrstvené konstrukci. Pokud je nutná přísná tolerance, navrhněte otvory podměrečné pro pozdější obrábění nebo do nich zakomponujte specifické tvary (např. slzy), abyste zlepšili přesnost při sestavování.
Spolupráce se zkušeným aditivní výroba poskytovatele, jako je Met3dp, na počátku procesu návrhu, může být velmi přínosný. Jejich inženýři mají hluboké znalosti principů DfAM a mohou poskytnout cennou zpětnou vazbu pro optimalizaci návrhu skříně turbodmychadla pro úspěšný tisk, optimální výkon a nákladovou efektivitu s využitím pokročilých technologií CAD pro AM automotive pracovní postupy.
Dosažení přesnosti: Tolerance, povrchová úprava a rozměrová přesnost v pouzdrech AM
Přestože aditivní výroba kovů nabízí bezkonkurenční volnost při navrhování, je pro konstruktéry a manažery nákupu zásadní mít realistická očekávání ohledně dosažitelné přesnosti přímo z tiskárny. Součásti vyrobené metodou AM obvykle nemají stejně přísné tolerance a jemnou povrchovou úpravu všech prvků jako součásti plně obráběné ze sochorů pomocí víceosých CNC center. Nicméně díky pečlivé kontrole procesu, vhodnému následnému zpracování a pokročilému zajištění kvality, přesný 3D tisk kovů pro automobilový průmysl komponenty, jako jsou skříně turbodmychadel, mohou splňovat náročné specifikace.
Tolerance:
- Tolerance podle stavu konstrukce: Typická rozměrová přesnost dosažitelná přímo při procesu laserového tavení v práškovém loži (LPBF) nebo selektivního tavení elektronovým svazkem (SEBM) se často pohybuje v rozmezí od ±0,1 mm až ±0,3 mm nebo ±0,1 % až 0,2 % jmenovitého rozměru, podle toho, která hodnota je větší. Tyto hodnoty jsou obecným vodítkem a mohou se výrazně lišit v závislosti na konkrétním stroji, materiálu, geometrii dílu, velikosti, orientaci a použitých procesních parametrech. U velkých a složitých dílů je ze své podstaty náročnější dodržet přísné tolerance v důsledku tepelných vlivů.
- Dosažení přísnějších tolerancí: U kritických rozhraní, jako jsou příruby skříně turbíny a kompresoru, styčné plochy pro středovou rotační sestavu skříně (CHRA), spoje V-pásu nebo montážní body, jsou tolerance při výrobě často nedostatečné. Tyto prvky obvykle vyžadují cNC obrábění po tisku k dosažení potřebné přesnosti (např. ±0,025 mm až ±0,05 mm) pro správné utěsnění, vyrovnání a montáž. DfAM zde hraje roli tím, že zahrnuje dostatečný počet obráběných dílů pouze na těchto kritických prvcích.
Drsnost povrchu (průměrná drsnost – Ra):
- Povrchová úprava podle stavu: Strukturu povrchu dílu AM ovlivňuje několik faktorů:
- Velikost částic prášku: Jemnější prášky mají obecně hladší povrch.
- Tloušťka vrstvy: Tenčí vrstvy obvykle vedou k hladším povrchům, zejména na šikmých plochách.
- Orientace: Svislé stěny bývají hladší než povrchy směřující nahoru nebo dolů. Povrchy směřující dolů, které se opírají o podpěry nebo samotné lože prášku, jsou obvykle nejhrubší v důsledku přilnutí částečně roztaveného prášku.
- Proces: LPBF obecně vytváří hladší povrchy (např. Ra 6-20 µm) ve srovnání se SEBM (kde může být Ra 20-35 µm nebo vyšší) v důsledku rozdílů v energii paprsku a velikosti prášku.
- Následně zpracovaná povrchová úprava: Povrchová úprava v základním stavu je často příliš drsná pro utěsnění povrchů nebo optimální proudění vzduchu v kritických oblastech. K vylepšení povrchové úpravy se používá následné zpracování:
- Výbuch v médiích: (např. kuličkový, pískový, zrnitý) zajistí rovnoměrný matný povrch a odstraní sypký prášek (Ra se může mírně zlepšit nebo změnit strukturu).
- Třískové/vibrační dokončování: Dokáže vyhladit vnější povrchy, ale je méně účinný pro vnitřní kanály.
- Obrábění: Poskytuje nejlepší kvalitu povrchu na specifických prvcích (Ra < 1,6 µm nebo lepší).
- Leštění: Lze dosáhnout velmi hladkého, zrcadlového povrchu, pokud je to vyžadováno ze specifických aerodynamických nebo estetických důvodů, ale je to pracné.
Rozměrová přesnost & Kontrola kvality:
- Faktory ovlivňující přesnost: Dosažení konzistentního přesnost rozměrů turbodmychadla vyžaduje kontrolu celého pracovního postupu: kalibraci stroje, optimalizované a ověřené parametry procesu, strategie tepelného řízení (orientace, podpěry), minimalizaci zbytkového napětí a zohlednění drobných deformací při tepelném zpracování po tisku.
- Význam kontroly kvality (QC): Rigorózní kontrola kvality aditivní výroby kovů je zásadní. To zahrnuje:
- Monitorování během procesu: Některé pokročilé systémy AM nabízejí sledování taveniny a konzistence vrstvy v reálném čase.
- Kontrola po dokončení stavby: Vysoké rozlišení 3D skenování se běžně používá k porovnávání geometrie finálního dílu s původním modelem CAD a k vytváření podrobných map odchylek.
- Kontrola na souřadnicovém měřicím stroji (CMM): Používá se k přesnému měření kritických rozměrů, tolerancí a geometrických rozměrů a tolerancí (GD&T), zejména po konečném obrábění.
- Ověřování vlastností materiálu: Zkoušení tahových tyčí vytištěných vedle hlavního dílu, aby se potvrdilo, že vlastnosti materiálu po tepelném zpracování splňují specifikace.
Met3dp’s Contribution to Precision: Společnost Met3dp si uvědomuje, jak důležitá je přesnost pro náročné aplikace v automobilovém průmyslu. Jejich tiskárny jsou konstruovány pro špičkový objem, přesnost a spolehlivost tisku. Díky kombinaci robustní konstrukce stroje, pokročilého softwaru pro řízení procesu, vysoce kvalitních sférických kovových prášků a přísných systémů řízení kvality umožňuje společnost Met3dp zákazníkům spolehlivě vyrábět husté a přesné skříně turbodmychadel, které splňují náročné normy požadované pro kritické díly vysoce výkonných vozidel.
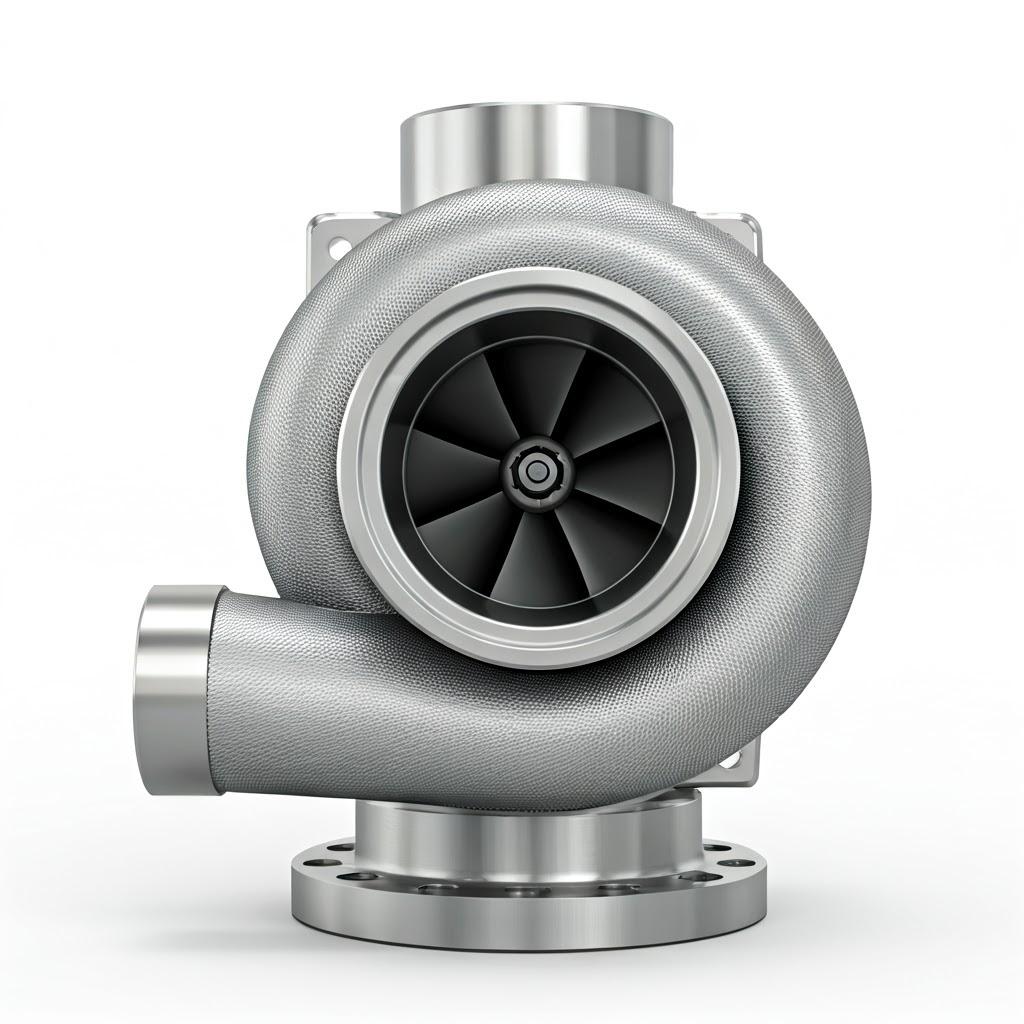
Za hranice tisku: Základní následné zpracování krytů turbodmychadel
Častým nedopatřením při plánování aditivní výroby kovů je podcenění významu a rozsahu následného zpracování. Přijetí krytu turbodmychadla z 3D tiskárny je významným milníkem, ale zdaleka ne posledním krokem. K přeměně surového vytištěného dílu na funkční a spolehlivou součástku připravenou k použití je zapotřebí řada zásadních operací následného zpracování, které se týkají sestava skříně turbodmychadla. Tyto kroky jsou rozhodující pro dosažení požadovaných vlastností materiálu, rozměrové přesnosti, kvality povrchu a celkové integrity.
Typický pracovní postup následného zpracování pro pouzdra AM Turbo (IN718/IN625):
- Tepelné ošetření proti stresu:
- Proč: Rychlé cykly zahřívání a ochlazování, které jsou pro AM typické, vytvářejí v tištěném dílu značná zbytková napětí. Tato napětí mohou způsobit deformace nebo praskliny při následných krocích, jako je odstraňování podpěr nebo obrábění, nebo dokonce později při provozu. Odstraňování napětí je obvykle prvním krokem po dokončení sestavení a ochlazení dílu.
- Jak: Díl (často ještě připevněný na konstrukční desce) se zahřeje v peci s řízenou atmosférou (vakuum nebo inertní plyn, např. argon) na určitou teplotu nižší než teplota stárnutí nebo žíhání, po určitou dobu se udržuje a poté se pomalu ochlazuje. To umožňuje uvolnění vnitřních pnutí, aniž by se výrazně změnila mikrostruktura.
- Vyjmutí dílu ze stavební desky:
- Proč: Během tisku je díl nataven na silnou kovovou konstrukční desku.
- Jak: Obvykle se provádí pomocí elektroerozivního obrábění (EDM) nebo pásové pily. Pečlivé naplánování připojení dílu k desce (např. použití minimálního počtu kontaktních bodů nebo podpěr) může tento krok zjednodušit.
- Odstranění podpůrné konstrukce:
- Proč: Podpěry jsou potřebné během stavby, ale poté musí být odstraněny.
- Jak: Může se jednat o různé způsoby, od jednoduchého ručního odlomení/vypnutí přístupných podpěr až po náročnější odstranění podpěrného kovu AM techniky jako broušení, frézování nebo elektroerozivní obrábění pro houževnaté nebo vnitřní podpěry. Obtížnost do značné míry závisí na materiálu (podpěry z Inconelu jsou silné) a na účinnosti DfAM při minimalizaci a optimalizaci umístění podpěr. Vnitřní průchody vyžadují pečlivou kontrolu, aby se zajistilo odstranění veškerého podpůrného materiálu a volného prášku.
- Konečné tepelné zpracování (žíhání roztokem / stárnutí):
- Proč: Tímto krokem se získají konečné požadované mechanické vlastnosti superslitiny. Požadovaná úprava závisí na konkrétní slitině:
- Tepelné zpracování dílů IN718: IN718 je typicky srážkově kalený. To zahrnuje žíhání v roztoku (zahřátí na vysokou teplotu za účelem rozpuštění precipitátů), po kterém následuje řízené ochlazení a poté jeden nebo dva kroky stárnutí při nižších teplotách za účelem vysrážení zpevňujících fází (gama prime a gama double prime). Pro dosažení cílové tvrdosti a pevnosti se dodržují specifické cykly (např. podle AMS 5662/5663).
- IN625: Obvykle se používá ve stavu žíhaném roztokem pro dosažení nejlepší rovnováhy vlastností ve vysokoteplotním korozivním prostředí. To zahrnuje zahřátí na vysokou teplotu (např. ~1150 °C) a rychlé ochlazení, aby se zpevňující prvky (Mo, Nb) udržely v pevném roztoku. Ačkoli se nejedná o ‘stárnutí’ jako u IN718, je tento krok žíhání (často spojený s uvolněním napětí) klíčový.
- Jak: Provádí se v kalibrovaných pecích s řízenou atmosférou podle přesných časově-teplotních profilů definovaných specifikacemi materiálu nebo leteckými/automobilovými normami.
- Proč: Tímto krokem se získají konečné požadované mechanické vlastnosti superslitiny. Požadovaná úprava závisí na konkrétní slitině:
- CNC obrábění:
- Proč: Pro dosažení přísných tolerancí, specifických povrchových úprav a přesných geometrických vlastností, které jsou vyžadovány pro těsnění a montážní rozhraní.
- Jak: Použití více os CNC obrábění 3D tištěných komponent vyžaduje pečlivý návrh a programování přípravků. Mezi hlavní obráběné oblasti obvykle patří:
- Vstupní a výstupní příruby turbíny (rovinnost, povrchová úprava Ra u těsnění/pásů).
- Vstupní a výstupní připojení kompresoru.
- Párovací plocha pro středové rotační pouzdro (CHRA).
- Sedlo ventilu Wastegate nebo rozhraní pohonu.
- Montážní body a závitové otvory.
- Všechny kritické vnitřní průměry otvorů.
- Ve fázi DfAM měl být přidán obráběcí materiál speciálně pro tyto funkce.
- Povrchová úprava:
- Proč: K dosažení rovnoměrného vzhledu, odstranění nečistot, potenciálnímu zvýšení únavové životnosti (kuličkování) nebo dosažení specifických cílů drsnosti na neobráběných površích.
- Jak: Mezi běžné metody patří:
- Výbuch v médiích: Tryskání kuličkami nebo pískem pro čistý, matný povrch (povrchová úprava AM automotive standardní praxe).
- Třískové/vibrační dokončování: Dokáže vyhladit vnější hrany a povrchy.
- Ruční broušení/leštění: Pro specifické požadavky na lokalizované oblasti.
- Čištění a kontrola:
- Proč: Před montáží se ujistěte, že díl neobsahuje nečistoty, řezné kapaliny a splňuje všechny specifikace.
- Jak: Důkladné čištění. Konečná rozměrová kontrola (CMM/skenování), vizuální kontrola a případně nedestruktivní testování (NDT), jako je kontrola fluorescenčním penetrantem (FPI) pro kontrolu povrchových trhlin nebo počítačová tomografie (CT) pro ověření vnitřní integrity a kontrolu zachyceného prášku, zejména u kritických aplikací.
Každý z těchto kroků následného zpracování je časově i finančně náročný, ale je nezbytný pro zajištění spolehlivé funkce 3D tištěného krytu turbodmychadla a splnění přísných požadavků vysoce výkonného automobilového průmyslu. Často je výhodné spolupracovat s poskytovatelem služeb, který nabízí integrované možnosti následného zpracování.
Zvládání výzev: Obvyklé problémy při 3D tisku turbínových pouzder a jejich řešení
Aditivní výroba kovů sice otevírá neuvěřitelné možnosti pro skříně turbodmychadel, ale jedná se o pokročilý proces, který s sebou přináší řadu potenciálních problémů. Povědomí o těchto běžných problémech spolu s důkladnými strategiemi jejich zmírnění je klíčem k úspěšné výrobě vysoce kvalitních a spolehlivých součástí. Zkušenosti a odborné znalosti procesu, které nabízí například společnost Met3dp, jsou pro zvládnutí těchto složitostí neocenitelné.
Společné výzvy a strategie pro jejich zmírnění:
- Deformace a zkreslení:
- Problém: Výrazné tepelné gradienty při tisku vytvářejí vnitřní pnutí (řízení zbytkového stresu AM). Při ochlazování a smršťování vrstev mohou tato napětí způsobit deformaci dílu, jeho zvednutí z konstrukční desky nebo zkreslení jeho zamýšlené geometrie. To se vyskytuje zejména u deformace kovových dílů AM s velkými plochami nebo výraznou asymetrií.
- Řešení:
- Simulace sestavení: Použití softwaru pro simulaci procesů k předpovědi akumulace napětí a vzorců deformace před tisk. Na základě výsledků upravte orientaci nebo podpůrné konstrukce.
- Optimalizovaná orientace: Orientujte díl tak, abyste minimalizovali velké průřezy rovnoběžné se stavební deskou a vyrovnali rozložení tepelné hmoty.
- Robustní strategie podpory: Použijte strategicky umístěné podpěry (tepelné a mechanické), abyste díl pevně ukotvili a účinně odváděli teplo.
- Řízení procesních parametrů: Optimalizujte strategie skenování (např. ostrovní skenování, střídání směrů poklopů) pro rovnoměrnější rozložení tepla.
- Okamžitá úleva od stresu: Tepelné zpracování na uvolnění napětí proveďte ihned po sestavení, často ještě před vyjmutím dílu ze sestavovací desky.
- Zbytkové napětí a praskání:
- Problém: Vysoká zbytková napětí, pokud nejsou správně řízena, mohou překročit pevnost materiálu, což může vést k praskání během tisku, při chlazení, odstraňování podpěr nebo i později během životnosti. Superslitiny na bázi niklu, zejména ty srážkově kalitelné, jako je IN718 (praskání při tisku Inconelu), mohou být náchylné, pokud nejsou pečlivě kontrolovány procesní parametry a tepelné zpracování. Tlusté profily a ostré vnitřní rohy toto riziko ještě zvyšují.
- Řešení:
- Tepelný management: Výše uvedené strategie pro deformace pomáhají také zvládat zbytkové napětí.
- Optimalizované tepelné zpracování: Implementujte vědecky ověřené cykly uvolňování napětí a konečného tepelného zpracování specifické pro slitinu a proces AM.
- DfAM: Konstrukce s velkorysými poloměry řezu namísto ostrých rohů. Vyhněte se náhlým změnám tloušťky průřezu.
- Optimalizace parametrů procesu: Zajistit stabilní dynamiku tání a zamezit nadměrnému přívodu energie do lokálních oblastí.
- Obtíže při odstraňování podpory:
- Problém: Podpěry z vysokopevnostních superslitin lze velmi obtížně a časově náročně odstranit, zejména ze složitých vnitřních kanálů nebo složitých vnějších prvků. Agresivní odstraňování může poškodit povrch dílu. Nepřístupné vnitřní podpěry může být nemožné zcela odstranit (potíže s odstraněním podpory).
- Řešení:
- DfAM: Nejúčinnější řešení! Konstrukce pro samonosné úhly (>45°). Orientujte díl tak, abyste minimalizovali potřebu podpěr v kritických nebo nepřístupných oblastech. Navrhněte podpěry pro snadnější demontáž (např. se specifickými kontaktními body nebo konstrukcemi).
- Specializované podpůrné struktury: Využijte softwarové funkce pro snadno odnímatelné typy podpěr (např. stromové podpěry, blokové podpěry s perforací).
- Volba procesu: SEBM často vyžaduje méně podpěr než LPBF kvůli vyšší teplotě procesu, která udržuje díly déle nad teplotami relaxace napětí.
- Plánování následného zpracování: Zohledněte metody odstraňování podpory (ruční, obrábění, elektroerozivní obrábění) v celkovém plánu výroby.
- Kontrola pórovitosti:
- Problém: Malé dutiny nebo póry (kontrola pórovitosti 3D tisku) se může v tištěném materiálu vytvořit v důsledku zachyceného plynu (např. argonu používaného v komorách LPBF), neúplného splynutí mezi vrstvami nebo keyholingu (kolapsu v důsledku deprese páry) způsobeného nadměrnou hustotou energie. Pórovitost může snížit mechanické vlastnosti, zejména únavovou pevnost.
- Řešení:
- Kvalita prášku: Použijte vysoce kvalitní, suchý, sférický prášek s optimalizovaným PSD (jako jsou prášky Met3dp’), abyste zajistili dobrou tekutost a hustotu balení.
- Optimalizace parametrů: Vyvinout a ověřit robustní procesní parametry (výkon laseru/paprsku, rychlost, rozteč šraf, tloušťka vrstvy) pro zajištění úplného roztavení a tavení.
- Řízení atmosféry: Udržujte atmosféru inertního plynu vysoké čistoty (LPBF) nebo vysokého vakua (SEBM), aby se minimalizovalo zachycení plynu.
- Izostatické lisování za tepla (HIP): Volitelný krok následného zpracování, kdy jsou díly vystaveny vysoké teplotě a izostatickému tlaku. Tím lze účinně uzavřít vnitřní póry, což výrazně zlepší hustotu a únavové vlastnosti, ale zvyšuje náklady a čas.
- Drsnost povrchu:
- Problém: Povrchy ve stavu, v jakém jsou postaveny, zejména svahy směřující dolů a povrchy přímo podepřené práškem, mohou být drsnější, než je žádoucí pro těsnění nebo optimální dynamiku proudění.
- Řešení:
- Orientace: Pokud je to možné, upřednostněte kritické plochy orientované vzhůru nebo vertikálně.
- Ladění parametrů: Jemnější prášky a tenčí vrstvy mohou zlepšit povrchovou úpravu, ale mohou prodloužit dobu tisku.
- Následné zpracování: Naplánujte příslušné kroky povrchové úpravy (tryskání, obrábění, leštění), jak je popsáno v předchozí části.
Úspěšné zvládnutí těchto výzev vyžaduje kombinaci robustních postupů DfAM, optimalizovaných a validovaných procesních parametrů, vysoce kvalitních materiálů, pečlivého následného zpracování a přísné kontroly kvality. Spolupráce se zkušeným poskytovatelem AM služeb s hlubokými odbornými znalostmi v oblasti zpracování superslitin pro náročné aplikace je rozhodující pro dosažení spolehlivých a vysoce výkonných 3D tištěných skříní turbodmychadel.
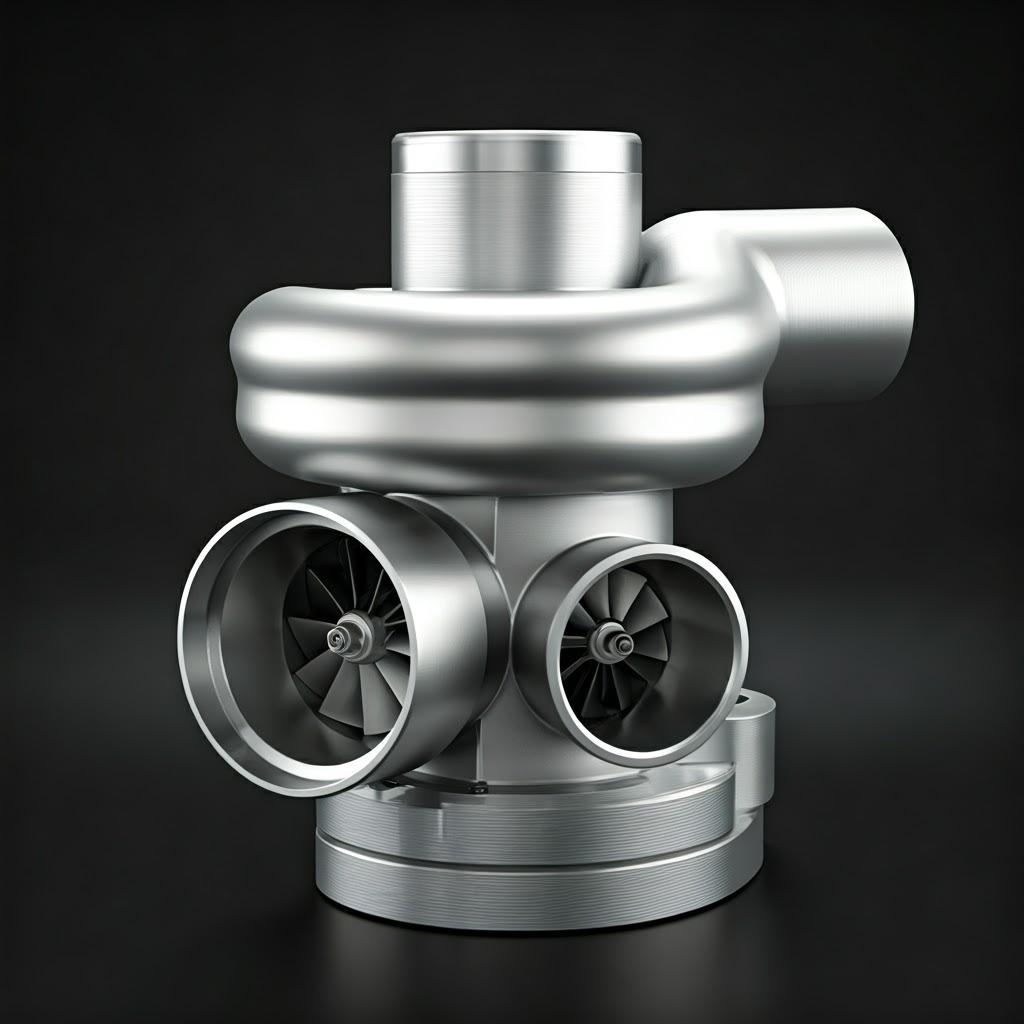
Výběr dodavatele: Výběr správného partnera pro automobilové komponenty v oblasti AM zpracování kovů
Výběr výrobního partnera je vždy zásadním rozhodnutím, ale v případě pokročilých procesů, jako je aditivní výroba kovů pro vysoce výkonné automobilové komponenty, vyžaduje výběr mimořádnou pečlivost. Kvalita, spolehlivost a výkon vašeho 3D tištěného krytu turbodmychadla přímo souvisí se schopnostmi a odbornými znalostmi zvoleného dodavatele. Pro inženýry a manažery veřejných zakázek, kteří shánějí zdroje poskytovatel služeb AM pro automobilový průmysl řešení, je hodnocení potenciálních partnerů na základě komplexního souboru kritérií zásadní pro zmírnění rizik a zajištění úspěchu projektu.
Klíčová kritéria pro hodnocení dodavatelů AM kovů:
- Zkušenosti v oboru & Zkušenosti s aplikacemi: Má dodavatel prokazatelné zkušenosti v automobilovém průmyslu, konkrétně s komponenty hnacího ústrojí nebo díly vystavenými podobně náročným podmínkám (vysoká teplota, vysoké namáhání)? Požádejte o případové studie, příklady minulých projektů nebo reference týkající se vysoce výkonná turbodmychadla nebo podobné náročné aplikace. Obecné zkušenosti s AM nemusí být dostačující.
- Odborné znalosti materiálů (IN718/IN625): Hluboké znalosti zpracování superslitin na bázi niklu pomocí AM jsou nepominutelné. Zajímejte se o jejich zkušenosti s IN718 a IN625, o jejich procesní parametry, o způsob ověřování vlastností materiálu (např. tahové zkoušky svědeckých kupónů) a o jejich postupy při manipulaci s práškem. Dodavatelé s odborné znalosti materiálů aditivní výroba jsou klíčové. Klíčové je také porozumět jejich zdrojům prášku - vyrábějí si prášek sami a zajišťují kontrolu kvality, nebo se spoléhají výhradně na externí dodavatele?
- Technologické schopnosti & amp; Kapacita: Zhodnoťte jejich portfolio vybavení. Provozují dobře udržované stroje průmyslové třídy LPBF nebo SEBM vhodné pro slitiny Inconelu? Jaké jsou rozměry konstrukčního pole? Mohou dosáhnout požadované přesnosti a opakovatelnosti? Investují do udržování své technologie v aktuálním stavu? Neméně důležitá je jejich kapacita - dokáží splnit vaše požadavky? doba dodání kovových dílů AM pro prototypy a potenciální malosériovou výrobu?
- Systém řízení kvality & Certifikace: To je v automobilovém průmyslu nejdůležitější. Hledejte robustní systémy řízení kvality (QMS).
- ISO 9001: Základní požadavek na prokázání procesů kvality.
- AS9100: Ačkoli se jedná o leteckou normu, její důsledné zaměření na řízení procesů, sledovatelnost a řízení rizik je velmi důležité a často přebírané dodavateli pro vysoce výkonný automobilový průmysl/motorový sport.
- IATF 16949: Globální automobilový standard. Ačkoli se plná certifikace může mezi specializovanými poskytovateli AM teprve objevovat, prokázání dodržování jejích zásad (např. řízení procesu, APQP, případně prvky PPAP) je významnou výhodou. Zeptejte se potenciálních dodavatelů na jejich certifikace kvality AM.
- Integrované možnosti následného zpracování: Skříň turbodmychadla vyžaduje rozsáhlé následné zpracování. Může dodavatel zvládnout celý tento pracovní postup (odlehčení napětí, tepelné zpracování podle specifikace, přesné CNC obrábění, povrchovou úpravu, NDT) buď ve vlastní režii, nebo prostřednictvím přísně kontrolované sítě kvalifikovaných partnerů? Jedno kontaktní místo, které řídí celý procesní řetězec, zjednodušuje logistiku a odpovědnost.
- Engineering & DfAM Support: Nejlepší výsledky přináší spolupráce. Nabízí dodavatel odborné konzultace DfAM? Může vám pomoci optimalizovat návrh z hlediska tisknutelnosti, výkonu a hospodárnosti? Tento partnerský přístup je často cennější než čistě transakční vztah.
- Transparentnost a komunikace: Zhodnoťte jejich postup tvorby nabídek - je jasný a podrobný? Jak řeší komunikaci a aktualizace projektu? Reagují na technické dotazy? S transparentním a komunikativním partnerem se lépe spolupracuje.
Proč uvažovat o Met3dp?
Když hodnocení dodavatelů 3D tisku, Met3dp se stává přesvědčivým partnerem pro náročné aplikace v automobilovém průmyslu. Společnost Met3dp se sídlem v čínském městě Qingdao nabízí jedinečnou kombinaci silných stránek:
- Poskytovatel integrovaných řešení: Met3dp není jen servisní kancelář, ale navrhuje a vyrábí i své vlastní špičkové tiskárny známé svou přesností, spolehlivostí a vhodností pro kritické díly. Zásadní je, že disponují také pokročilými vlastními kapacitami pro výrobu vysoce kvalitních sférických kovových prášků (včetně IN718, IN625 a inovativních slitin) pomocí technologií Gas Atomization a PREP. Tato vertikální integrace poskytuje výjimečnou kontrolu nad základními prvky ovlivňujícími kvalitu finálních dílů.
- Hluboké odborné znalosti: Společnost Met3dp má desítky let společných zkušeností v oblasti aditivní výroby kovů a rozumí nuancím zpracování náročných materiálů a složitých geometrií.
- Komplexní partnerství: Kromě tiskových služeb poskytuje společnost Met3dp komplexní řešení, která zahrnují služby vývoje aplikací, která pomáhá organizacím efektivně implementovat AM a urychlit jejich transformaci výroby. Spolupracují s klienty na dosažení konkrétních technických cílů.
- Osvědčené výsledky: Společnost Met3dp se zaměřuje na dodávání špičkových systémů a prášků pro náročné obory, jako je letectví, lékařství a automobilový průmysl, a prokazuje tak své schopnosti při manipulaci s kritickými součástmi.
Výběr osvědčeného dodavatele Možnosti Met3dp znamená partnerství se společností, která investuje do celého ekosystému AM, od vědy o materiálech až po realizaci finálních dílů.
Porozumění investicím: Nákladové faktory a dodací lhůty pro skříně turbodmychadel AM
Pro manažery nákupu a inženýry, kteří plánují projekty zahrnující 3D tištěné skříně turbodmychadel, je pochopení faktorů, které určují náklady a dobu realizace, zásadní pro efektivní sestavení rozpočtu, plánování a porovnání nabídek. Ačkoli AM nabízí významné výhody, zahrnuje odlišnou strukturu nákladů ve srovnání s tradiční výrobou. Poskytování jasných informací pro Citace B2B AM je zásadní.
Klíčové faktory ovlivňující náklady na skříně turbodmychadel AM:
- Spotřeba materiálu:
- Část Objem: Čistý objem konečného návrhu bydlení.
- Objem podpůrné struktury: Podpory spotřebovávají materiál a je třeba s nimi počítat. Efektivní DfAM to minimalizuje.
- Náklady na prášek: Vysoce výkonné superslitiny, jako jsou IN718 a IN625, jsou ve srovnání s běžnými ocelemi nebo slitinami hliníku ze své podstaty drahé suroviny. Náklady ovlivňuje také kvalita prášku a způsob výroby.
- Obnovení/recyklace prášku: Nepoužitý prášek lze sice často recyklovat, ale vícenásobné použití může mírně změnit jeho vlastnosti, což vyžaduje specifické strategie obnovy, které ovlivňují celkové náklady na materiál.
- Strojový čas: To je často nejvýznamnější nákladový faktor.
- Výška stavby: Doba tisku závisí především na počtu vrstev (výška Z), nikoli pouze na objemu dílu nebo složitosti jednotlivých vrstev. Vyšší díly potřebují více času.
- Doba skenování: Doba, za kterou laserový nebo elektronový paprsek naskenuje každou vrstvu. U velmi složitých geometrií se tato doba na vrstvu může mírně prodloužit.
- Rychlost stroje: Hodinové provozní náklady průmyslového systému AM na kov (zahrnují energii, spotřebu inertního plynu, údržbu, odpisy).
- Využití stavební desky (hustota): Tisk více dílů současně na jedné konstrukční desce amortizuje pevně stanovené časy nastavení, ohřevu, chlazení a odebírání dílů na více jednotek, čímž se snižují náklady na jeden díl. To je klíčové pro optimalizaci nízkoobjemové výroby.
- Složitost struktury podpory: Složité nebo husté podpěry nejenže spotřebují více materiálu, ale také vyžadují podstatně více času a úsilí při odstraňování během následného zpracování, což zvyšuje náklady na pracovní sílu.
- Intenzita následného zpracování: To je hlavní faktor, který přispívá ke konečnému náklady na 3D tisk kovů v automobilovém průmyslu komponenty. Každý krok zvyšuje náklady:
- Odlehčení od napětí a konečné tepelné zpracování (doba pece, kontrola atmosféry).
- Pracnost/obráběcí čas při odstraňování podpory.
- CNC obrábění (doba seřizování, programování, strojní čas, nástroje - potenciálně komplexní pětiosé obrábění).
- Povrchová úprava (tryskání, bubnování, ruční leštění).
- NDT a podrobné kontroly.
- Požadavky na zajištění kvality: Úroveň specifikované kontroly (např. standardní rozměrová kontrola vs. úplná zpráva CMM, FPI povrchu, interní CT skenování) přímo ovlivňuje náklady.
- Objem objednávky: Ačkoli se AM vyhýbá nákladům na nástroje, stále existuje efektivita nastavení a programování u větších sérií. Cena za díl obecně klesá při přechodu od jednotlivých prototypů k desítkám nebo stovkám kusů, i když křivka je mnohem plošší než u odlévání.
- Technická podpora/DfAM: Pokud je od dodavatele vyžadována významná optimalizace konstrukce nebo konzultace, může být tento čas inženýrské činnosti zahrnut do počátečních nákladů projektu.
Úvahy o době realizace:
The doba dodání aditivní výroby dílů zahrnuje více než jen dobu tisku:
- Předběžné zpracování: Příprava souboru CAD, simulace sestavení, krájení, nastavení úlohy sestavení (může trvat hodiny až dny).
- Tisk: Velmi variabilní v závislosti na výšce a hustotě dílů (u složitých skříní se může pohybovat od 12 hodin až po několik dní).
- Chlazení: Před vyjmutím musí díly ve stroji dostatečně vychladnout (několik hodin).
- Fronta strojů: Dostupnost příslušného systému AM u dodavatele.
- Následné zpracování: Často se jedná o nejdelší část přípravné doby. Tepelné zpracování trvá hodiny/dny na cyklus; obrábění může trvat dny v závislosti na složitosti a plánování dílny; dokončovací práce a kontrola přidávají další čas (dohromady mohou trvat 1-4+ týdny).
- Doprava: Doba přepravy do vašeho zařízení.
Typické rozmezí dodací lhůty:
- Prototypy: Často 1-4 týdny, v závislosti na složitosti a potřebě následného zpracování.
- Malosériová výroba (např. 10-50 kusů): Obvykle 4-8 týdnů a více, což je silně ovlivněno požadavky na následné zpracování a efektivitou dávkování.
Optimalizace nákladů & amp; Doba realizace:
- Agresivní využití DfAM ke snížení spotřeby materiálu a minimalizaci podpůrných struktur.
- Jasně definujte potřebné tolerance a povrchové úpravy pouze v kritických případech, abyste se vyhnuli zbytečnému obrábění nebo leštění.
- Konsolidace objednávek, pokud je to možné, za účelem zvýšení hustoty stavebních desek.
- Poskytněte předem jasné a úplné technické specifikace, abyste předešli zpoždění.
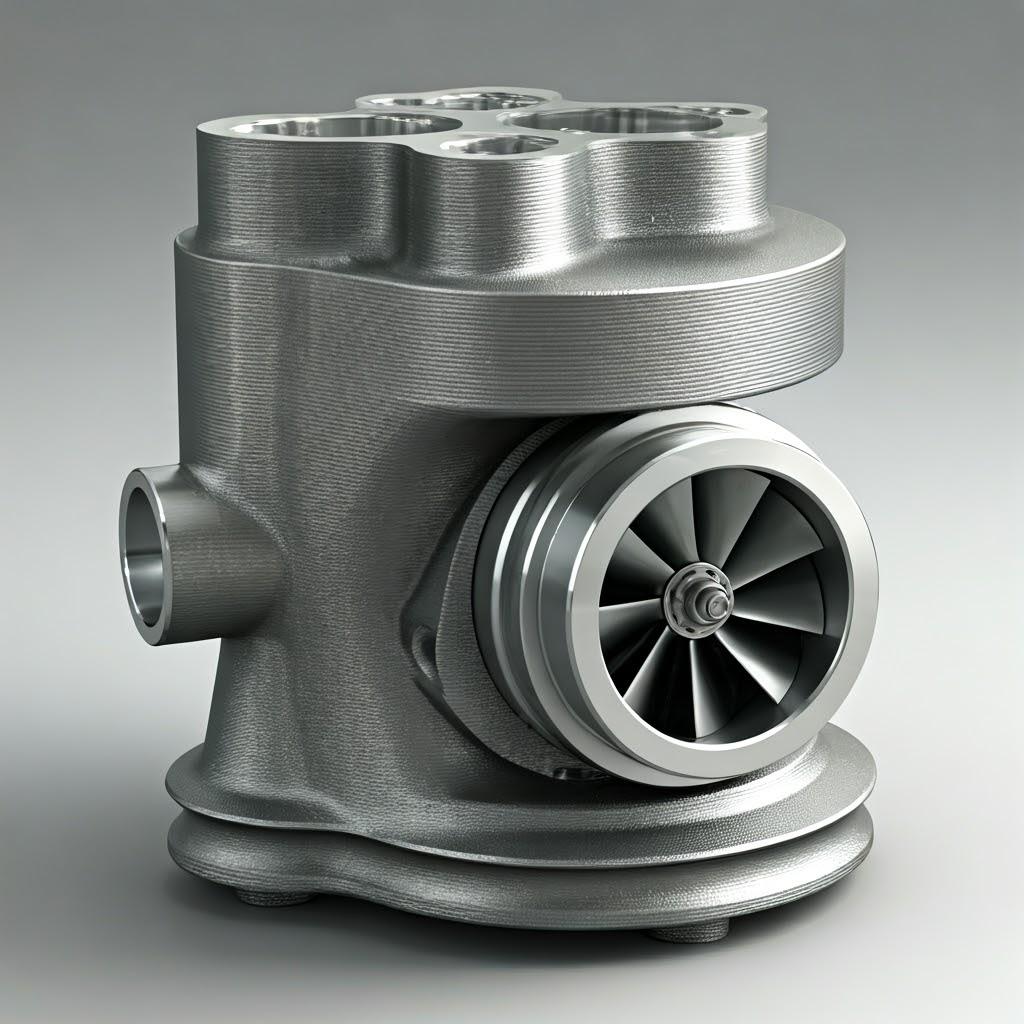
Často kladené otázky (FAQ) o 3D tištěných pouzdrech turbodmychadel
Vzhledem k tomu, že aditivní výroba kovů získává v automobilovém průmyslu na popularitě, inženýři a manažeři nákupu se často ptají na její použití pro komponenty, jako jsou skříně turbodmychadel. Zde jsou odpovědi na některé časté dotazy:
Otázka 1: Jsou skříně turbodmychadel vytištěné 3D tiskem stejně spolehlivé jako tradičně vyráběné?
A: Ano, rozhodně, pokud jsou správně navrženy a vyrobeny. Pokud jsou navržena s využitím robustních principů DfAM speciálně pro aditivní výrobu, vytištěna pomocí ověřených procesů na strojích průmyslové třídy s vysoce kvalitními superslitinami, jako je IN718 nebo IN625, a podrobena vhodnému následnému zpracování (zejména tepelnému zpracování a obrábění kritických prvků) a přísné kontrole kvality, vykazují 3D tištěná pouzdra vynikající výsledky spolehlivost turbodmychadla vytištěného na 3D tiskárně. V mnoha případech mohou díly AM díky optimalizované geometrii (např. integrovanému chlazení, vynikajícím průtokovým cestám) a použití pokročilých materiálů nabídnout vyšší výkon a trvanlivost ve srovnání s jejich konvenčními protějšky, zejména v extrémních provozních podmínkách. Spolehlivost je podmíněna odbornými znalostmi v celém řetězci návrhu, výroby a validace.
Otázka 2: Jaké jsou náklady na 3D tištěné pouzdro ve srovnání s odléváním při malých objemech?
A: Jedná se o zásadní porovnání nákladů na automobilové díly AM otázka. Pro prototypy, jednorázové zakázkové díly a malosériovou výrobu (obvykle v rozsahu od jednoho kusu až po 50-100 kusů, i když přesný bod přechodu závisí do značné míry na složitosti dílu a způsobu odlévání) je obecně kovový AM ekonomičtější než tradiční investiční odlévání. Je to především proto, že AM eliminuje značné počáteční investice a dlouhé dodací lhůty spojené s vytvářením odlévacích vzorů a forem (nástrojů). S rostoucím objemem výroby v řádech stovek nebo tisíců kusů náklady na odlitek výrazně klesají v důsledku amortizace nástrojů, takže je nakonec levnější než AM. Je však nezbytné zvážit celkovou hodnotu nabídky: AM často umožňuje dosáhnout úrovně výkonu, odlehčení nebo konstrukčních prvků nedosažitelných při odlévání, což může ospravedlnit vyšší náklady na jeden díl v aplikacích zaměřených na výkon. Kromě toho rychlost AM’dodávání počátečních dílů urychluje vývojové cykly.
Otázka 3: Jaké zlepšení výkonu lze očekávat od optimalizované skříně turba AM?
A: Optimalizovaná pouzdra AM mohou přinést hmatatelné zvýšení výkonu:
- Zlepšená aerodynamická účinnost: Přesně vytvořené spirály a průtočné cesty, navržené pomocí CFD a neomezené omezeními odlitků, mohou zvýšit účinnost kompresoru i turbíny. To se projeví v potenciálně rychlejším náběhu (zkrácení prodlevy), vyšší schopnosti zvyšování tlaku a zvýšení výkonu/ točivého momentu motoru v celém provozním rozsahu.
- Vylepšený tepelný management: Integrované chladicí kanály ve stěnách skříně turbíny mohou výrazně snížit teplotu materiálu, což zlepšuje životnost, zabraňuje zahřívání, snižuje potřebu nadměrného tepelného stínění výfuku a umožňuje konzistentnější výkon při dlouhodobém provozu s vysokým zatížením (např. při použití na závodní dráze).
- Odlehčení: Optimalizace topologie může výrazně snížit hmotnost skříně ve srovnání s objemnými litými konstrukcemi, což přispívá k celkovému snížení hmotnosti vozidla - což je v motoristickém sportu a u výkonných vozidel rozhodující faktor.
- Optimalizované balení: Volnost konstrukce umožňuje tvarovat skříně tak, aby se vešly do těsných motorových prostorů, což umožňuje kompaktnější nebo efektivnější uspořádání motoru.
Otázka 4: Lze stávající konstrukce skříní turbodmychadel přímo vytisknout na 3D tiskárně?
A: Zatímco vy může technicky poslat soubor CAD s návrhem odlévaného pouzdra do 3D tiskárny, se důrazně nedoporučuje a zpravidla přináší špatné výsledky. Návrhy optimalizované pro odlévání se často vyznačují rovnoměrnou tloušťkou stěn, úhly ponoru a velkými poloměry vhodnými pro plnění formy a vyhazování dílů - prvky, které jsou v AM zbytečné nebo dokonce škodlivé. Přímý tisk takové konstrukce má obvykle za následek:
- Příliš těžké a objemné díly (chybějící možnosti odlehčení).
- Požadavek na rozsáhlé interní a externí podpůrné struktury, což zvyšuje dobu tisku, náklady na materiál a náročnost následného zpracování.
- Možnost vyššího zbytkového napětí a deformace v důsledku neoptimalizované geometrie.
- Nevyužití klíčových výhod AM (např. interní kanály, komplexní cesty toku). Pro dosažení diskutovaných výhod je nezbytné přepracovat návrh skříně s využitím principů DfAM. Srovnání AM vs litá skříň turba vyžaduje navrhování s ohledem na silné stránky každého procesu.
Závěr: Inovace v automobilovém průmyslu pomocí aditivní výroby
Prostředí vysoce výkonného automobilového inženýrství se neustále vyvíjí a aditivní výroba kovů je silným katalyzátorem inovací, zejména v oblasti nuceného sání. Jak jsme již prozkoumali, 3D tištěné skříně turbodmychadel vyrobené z pokročilých superslitin, jako jsou IN718 a IN625, nabízejí přesvědčivý balíček výhod, které přímo reagují na extrémní požadavky motorsportu, poprodejního tuningu a speciálních aplikací pro vozidla.
Bezpříkladné svoboda designu umožňují vytvářet pouzdra s optimalizovanou aerodynamikou a integrovanými prvky tepelného managementu, kterých dříve nebylo možné dosáhnout. To se projevuje v hmatatelném zvýšení výkonu - rychlejší odezva, vyšší účinnost a zvýšená odolnost při zatížení. Schopnost využít optimalizace topologie výsledkem jsou výrazně lehčí součásti, což má zásadní význam pro konkurenční výhodu. Kromě toho AM usnadňuje rychlé prototypování a bez nástrojů malosériová výroba, což urychluje vývojové cykly a poskytuje flexibilní výrobní cestu pro zakázkové nebo specifické komponenty.
Využití tohoto potenciálu však vyžaduje víc než jen přístup k 3D tiskárně. Úspěch závisí na holistickém přístupu zahrnujícím odborníky Design pro aditivní výrobu (DfAM), pečlivý řízení procesu, komplexní následné zpracování, přísný zajištění kvality, a co je zásadní, partnerství se správným poskytovatel řešení AM pro kovy. Zvládnutí problémů se zbytkovým napětím, podpůrnými konstrukcemi a dosažením přesných tolerancí vyžaduje hluboké odborné znalosti a zkušenosti.
The budoucnost výroby turbodmychadel pro výkonné aplikace bude nepochybně docházet k rostoucímu zavádění aditivní výroby. Pro inženýry, kteří se snaží posouvat hranice výkonnosti, a manažery veřejných zakázek, kteří hledají špičková a flexibilní výrobní řešení pro pokročilé automobilové komponenty, představuje AM kovů strategický imperativ.
Pokud je vaše organizace připravena prozkoumat transformační potenciál kovového 3D tisku pro skříně turbodmychadel nebo jiné náročné automobilové komponenty, zvažte spolupráci s lídrem v této oblasti. Zveme vás, abyste Kontaktovat Met3dp a prodiskutovat s vámi vaše konkrétní požadavky. Využijte jejich komplexní řešení - špičkové tiskárny SEBM, pokročilé plynové atomizované a PREP kovové prášky a odborné služby vývoje aplikací - k dosažení cílů vaší organizace v oblasti aditivní výroby a urychlení vaší cesty k inovacím nové generace v automobilovém průmyslu.
Sdílet na
MET3DP Technology Co., LTD je předním poskytovatelem řešení aditivní výroby se sídlem v Qingdao v Číně. Naše společnost se specializuje na zařízení pro 3D tisk a vysoce výkonné kovové prášky pro průmyslové aplikace.
Dotaz k získání nejlepší ceny a přizpůsobeného řešení pro vaše podnikání!
Související články
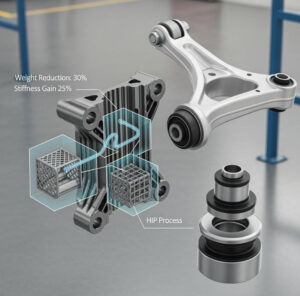
Metal 3D Printed Subframe Connection Mounts and Blocks for EV and Motorsport Chassis
Přečtěte si více "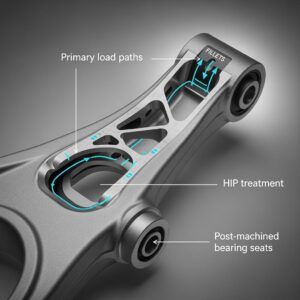
Metal 3D Printing for U.S. Automotive Lightweight Structural Brackets and Suspension Components
Přečtěte si více "O Met3DP
Nedávná aktualizace
Náš produkt
KONTAKTUJTE NÁS
Nějaké otázky? Pošlete nám zprávu hned teď! Po obdržení vaší zprávy obsloužíme vaši žádost s celým týmem.