Pouzdra ventilů pro kryogenní raketové systémy prostřednictvím AM
Obsah
Úvod: Kritická úloha krytů ventilů v kryogenním raketovém pohonu
Neustálá snaha o průzkum vesmíru a rozmísťování družic závisí na spolehlivosti a výkonnosti nosných raket. Srdcem těchto důmyslných strojů jsou složité pohonné systémy, které jsou zodpovědné za generování obrovského tahu potřebného k překonání zemské gravitace. V těchto systémech je nejdůležitější řídit tok těkavých kryogenních pohonných látek - především kapalného kyslíku (LOX) a kapalného vodíku (LH2), které jsou skladovány při teplotách stovky stupňů pod bodem mrazu. Tento kritický úkol připadá na řadu komponent, mezi nimiž vyniká pouzdro ventilu jako základní prvek provozní integrity.
Pouzdra raketových ventilů jsou mnohem víc než jen pouhé kryty. Jsou to sofistikované, tlakově odolné konstrukce určené k zadržování a usměrňování toku kryogenních kapalin při extrémních tlakových rozdílech a tepelných gradientech. Tvoří tělesa různých typů ventilů - zpětných ventilů, regulačních ventilů, uzavíracích ventilů, pojistných ventilů - z nichž každý je nezbytný pro přesné řízení pohonných hmot během různých fází letu, od startu motoru a řízení vektoru tahu až po oddělení stupně a ukončení mise. Selhání i jediného pouzdra ventilu může mít katastrofální následky, které mohou vést k selhání mise nebo ještě k horšímu.
Tradičně se při výrobě těchto kritických součástí používaly především subtraktivní metody, jako je CNC obrábění z předlitků nebo investiční odlévání, často následované rozsáhlými spojovacími procesy, jako je svařování. Tyto metody se sice osvědčily, ale při aplikaci na náročné požadavky moderní raketové techniky se potýkají se značnými problémy:
- Geometrická složitost: Optimální dynamika tekutin často vyžaduje složité vnitřní průchody a vnější montážní prvky, což posouvá hranice možností obrábění a zvyšuje náklady. Složité geometrie mohou vyžadovat výrobu více jednotlivých kusů, které jsou později svařeny nebo sešroubovány dohromady, čímž vznikají potenciální cesty úniku a místa poruch.
- Materiálový odpad: Subtraktivní výroba ze své podstaty zahrnuje vyřezávání konečného tvaru z většího bloku materiálu, což vede ke značnému plýtvání, zejména pokud se jedná o drahé superslitiny pro letecký průmysl.
- Dlouhé dodací lhůty: Vícestupňový proces zahrnující tvorbu nástrojů (pro odlévání), složité nastavení obrábění a montáž může vést k tomu, že se doba realizace protáhne na několik měsíců, což brání rychlým vývojovým cyklům, které jsou v konkurenčním vesmírném průmyslu klíčové.
- Omezení hmotnosti: Každý kilogram vynesený na oběžnou dráhu s sebou nese značné náklady. Tradiční metody často vedou k nadměrně konstruovaným a těžším součástem, než je nutné, protože optimalizace pro snížení hmotnosti pomocí obrábění složitých vnitřních struktur je obtížná a nákladná.
- Úzká místa dodavatelského řetězce: Závislost na specializovaných slévárnách nebo strojírenských dílnách může vytvářet úzká místa, zejména u výklenkových slitin nebo složitých dílů v malých objemech.
Vstupte Aditivní výroba (AM), častěji známý jako 3D tisk. Konkrétně se jako převratná síla objevují techniky AM pro kovy, jako je laserová fúze v práškovém loži (LPBF), které nabízejí transformační přístup k výrobě vysoce výkonných leteckých komponent, jako jsou pouzdra raketových ventilů. Technologie AM vytváří díly vrstvu po vrstvě přímo z digitálního modelu pomocí jemného kovového prášku, což umožňuje vytvářet geometrie dříve nedosažitelné běžnými prostředky. Tato technologie umožňuje inženýrům přehodnotit konstrukci součástek a zaměřit se na funkci a výkon, nikoli na omezení vyrobitelnosti. V případě kryogenních ventilových skříní nabízí AM přesvědčivou cestu ke zvýšení výkonu, snížení hmotnosti, zrychlení vývojových cyklů a zvýšení odolnosti dodavatelského řetězce, což jsou v náročném světě leteckého inženýrství zásadní výhody. Vzhledem k tomu, že letečtí výrobci a specialisté na zásobování hledají efektivnější a vysoce výkonná řešení, pochopení potenciálu AM pro výrobu těchto životně důležitých komponent již není volitelné, ale nezbytné.
Aplikace a požadavky: Kde se používají pouzdra raketových ventilů AM?
Zavedení aditivní výroby pro pouzdra raketových ventilů není futuristickým konceptem, ale rychle se rozvíjející realitou, která je poháněna hmatatelnými výkonnostními a výrobními přínosy. Tyto součásti nacházejí své místo v nejnáročnějších částech moderních nosných raket a kosmických lodí, kde přesnost, spolehlivost a hmotnost jsou neoddiskutovatelné. Pochopení jejich specifických aplikací poukazuje na náročné provozní prostředí, kterému odolávají, a na to, proč je AM jedinečně vhodná pro řešení těchto výzev.
Klíčové oblasti použití:
- Pohonné systémy hlavního motoru: Jedná se pravděpodobně o nejkritičtější aplikaci. Ventilové skříně zde řídí obrovské průtoky LOX a LH2 (nebo jiných pohonných hmot, jako je RP-1 a metan) do hlavní spalovací komory.
- Funkce: Hlavní uzavírací ventily pohonných hmot (zajišťují bezpečný start a vypnutí motoru), škrticí ventily (regulují tah), předventily (regulují průtok do turbočerpadel) a zpětné ventily (zabraňují zpětnému toku).
- Požadavky: Musí odolávat extrémním tlakům (často stovky barů), kryogenním teplotám (-183 °C pro LOX, -253 °C pro LH2), vysokým vibracím při zážehu motoru a vyžadují absolutní těsnost. AM umožňuje komplexní vnitřní průtokové cesty navržené pro optimální dynamiku kapaliny a minimální tlakové ztráty, spolu s integrovanými porty pro senzory nebo montážními prvky, což snižuje počet dílů a potenciálních míst úniku.
- Motory horního stupně: Tyto motory pracují ve vesmírném vakuu a často je nutné je opakovaně restartovat. Jejich ventilové systémy zvládají menší množství pohonných látek, ale vyžadují vysokou přesnost pro manévrování na oběžné dráze a vynesení užitečného zatížení.
- Funkce: Izolační ventily pohonných hmot, ventily pro regulaci poměru směsi, ventily pro regulaci plnicího tlaku.
- Požadavky: Vysoká spolehlivost po potenciálně dlouhou dobu trvání mise, přesné řízení průtoku, minimální hmotnost, schopnost odolávat tepelným cyklům (zahřívání během střelby, chlazení během pobřežních fází). Potenciál odlehčení AM je zde obzvláště cenný, protože hmotnost ušetřená v horním stupni se přímo promítá do zvýšení kapacity užitečného zatížení.
- Systémy řízení reakce (RCS) / systémy řízení polohy (ACS): Tyto systémy používají malé trysky k řízení orientace (polohy) nosné rakety nebo kosmické lodi. Jejich ventily zvládají menší průtoky hypergolických pohonných hmot nebo studeného plynu.
- Funkce: Oddělovací ventily náporového motoru, regulátory tlaku.
- Požadavky: Rychlá doba odezvy, vysoká životnost (vyžadující vynikající odolnost proti únavě), kompatibilita s potenciálně korozivními pohonnými hmotami, extrémní miniaturizační potenciál. AM umožňuje vysoce integrované rozdělovače a bloky ventilů, které kombinují více funkcí ventilů do jediné, kompaktní a lehké tištěné součásti.
- Satelitní pohonné systémy: Podobně jako horní stupně a RCS vyžaduje pohon družic miniaturizaci, spolehlivost a dlouhodobou výkonnost pro udržení stanice a úpravu oběžné dráhy.
- Funkce: Západkové ventily, regulátory, ovládací ventily trysek.
- Požadavky: Velmi nízká těsnost, dlouhá provozní životnost (často více než 15 let), odolnost proti záření, minimální hmotnost. AM usnadňuje vytváření konstrukcí ventilů na míru optimalizovaných pro konkrétní satelitní platformy a profily misí.
Splnění přísných požadavků průmyslu:
Letecký a kosmický průmysl, zahrnující komerční poskytovatele kosmických startů (jako SpaceX, Blue Origin, Rocket Lab), dodavatele obranných zařízení a vládní agentury (jako NASA, ESA), klade neuvěřitelně vysoké nároky. Pouzdra ventilů AM musí splňovat nebo překonávat výkonnost svých tradičně vyráběných protějšků.
- Spolehlivost a bezpečnost: Neoddiskutovatelné. Rozsáhlé testování, kvalifikace a kontrola procesů jsou nutné k zajištění bezchybné funkčnosti dílů v extrémních podmínkách. Vlastnosti materiálu musí být konzistentní a předvídatelné.
- Výkonnost: Klíčové je dosažení přesných průtoků, minimalizace tlakových ztrát, zajištění těsnosti a splnění specifických požadavků na ovládání. AM umožňuje konstruktérům optimalizovat vnitřní geometrii pro dynamiku tekutin způsobem, který byl dříve nemožný.
- Snížení hmotnosti: Hlavní hnací síla pro zavedení AM. Snížení hmotnosti součástek, zejména u horních stupňů a družic, přináší významné úspory nákladů a zvýšení výkonu (např. vyšší nosnost, schopnost delta-v). AM umožňuje optimalizaci topologie a použití vnitřních mřížkových struktur pro snížení hmotnosti bez narušení strukturální integrity.
- Efektivita nákladů: Zatímco strojní čas AM a specializované prášky mohou být drahé, celkové náklady na vlastnictví mohou být nižší díky snížení plýtvání materiálem, eliminaci nákladů na nástroje (zejména u malosériové výroby), konsolidovaným dílům (snížení pracnosti a času montáže) a výrazně kratším dodacím lhůtám, které umožňují rychlejší iteraci a rychlejší uvedení na trh. Společnosti, které hledají Dodavatel leteckých ventilů nebo Partner AM Production se kvůli těmto výhodám stále častěji obracejí k aditivním metodám.
Náročnost těchto aplikací podtrhuje, proč se pokročilé techniky AM kovů ve spojení s vysoce výkonnými materiály, jako jsou IN625 a IN718, stávají nepostradatelnými nástroji pro letecké inženýry a manažery nákupu odpovědné za zásobování Součásti raketových motorů a kritické Aplikace kryogenních ventilů.
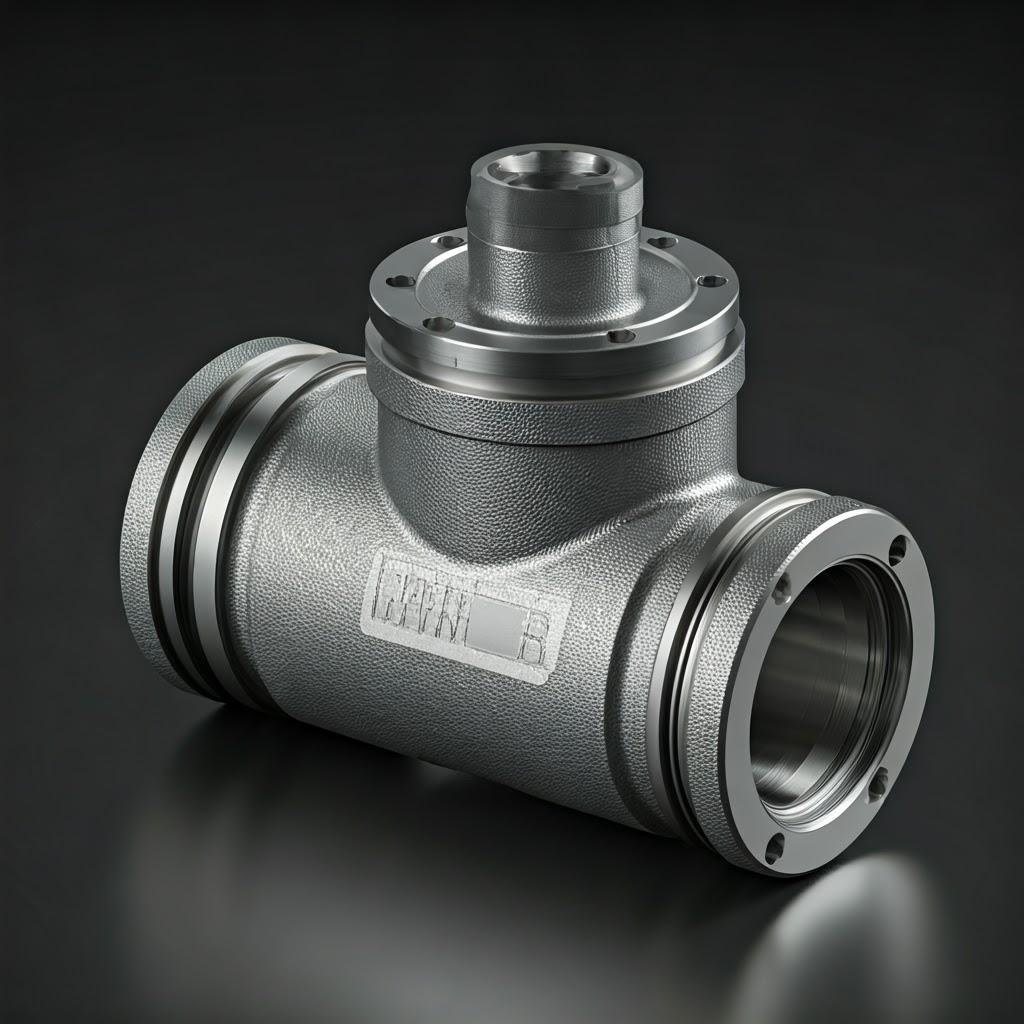
Proč aditivní výroba kovů pro pouzdra raketových ventilů? Odemykání výkonnostních výhod
Rozhodnutí přejít od zavedených výrobních postupů, jako je odlévání nebo obrábění, k aditivní výrobě kovů pro kritické součásti, jako jsou pouzdra raketových ventilů, je vedeno řadou přesvědčivých výhod. Zatímco tradiční metody průmyslu dobře sloužily, AM nabízí jedinečné možnosti, které přímo řeší hlavní výzvy leteckého designu a výroby: složitost, hmotnost, rychlost a nákladovou efektivitu, zejména pro náročné kryogenní aplikace. Porovnejme AM, konkrétně laserovou fúzi v práškovém loži (LPBF), s tradičními metodami a prozkoumejme konkrétní výhody, které přináší.
AM vs. tradiční výroba těles ventilů:
Vlastnosti | CNC obrábění (subtraktivní) | Investiční odlévání | Kování | Kov AM (LPBF) (aditivum) |
---|---|---|---|---|
Složitost | Omezeno přístupem k nástrojům, těžko dostupné vnitřní funkce | Vhodné pro složité tvary, vyžaduje nástroje | Jednodušší tvary, vysoká pevnost | Vysoká geometrická volnost, možnost použití složitých vnitřních kanálů |
Konsolidace částí | Obtížné, často vyžaduje montáž | Možné, ale složitost nástrojů se zvyšuje | Omezený | Vynikající, více dílů lze integrovat do jednoho tisku |
Odlehčení | Omezeno subtraktivní povahou | Určitý potenciál, vyžaduje úpravy nástrojů | Omezený | Vysoký potenciál prostřednictvím optimalizace topologie, mříže |
Materiálový odpad | Vysoká (odstraněný materiál) | Středně těžké (brány, běžci) | Nízký | Nízká (recyklovaný prášek), nosiče vytvářejí určitý odpad |
Doba realizace | Středně náročné (programování, nastavení) až Dlouhé (složité) | Dlouhé (návrh nástrojů & výroba) | Dlouhé (návrh matrice & výroba) | Krátké (prototypy) až středně dlouhé (výroba), žádné tvrdé nástroje |
Náklady na nástroje | Nízká (přípravky) až střední (vlastní nástroje) | Vysoká (voskové vzory, keramické skořápky) | Velmi vysoká (umírá) | Žádné (digitální výroba) |
Možnosti materiálu | Široká škála obrobitelných slitin | Odlévané slitiny | Kujné slitiny | Rostoucí sortiment svařitelných slitin (vhodné IN625, IN718) |
Ideální objem | Nízká až vysoká | Střední až vysoká | Vysoký | Nízká (prototypy, zakázka) až střední (sériová výroba) |
Export do archů
Klíčové výhody AM kovů pro pouzdra raketových ventilů:
- Bezprecedentní geometrická volnost & Konsolidace dílů:
- Výzva: Tradiční metody se potýkají se složitými vnitřními cestami proudění, které jsou nutné pro optimální dynamiku tekutin nebo kompaktní konstrukci. Často je nutné svařit nebo připájet více obrobených nebo odlitých dílů, což přináší potenciální netěsnosti, koncentrace napětí a další kontrolní body.
- Řešení AM: Technologie LPBF vytváří díl po vrstvách, což umožňuje vytvářet velmi složité vnitřní kanály, konformní chladicí kanály a organicky tvarované struktury optimalizované pro proudění a rozložení napětí. Zásadní je, že do jediného tištěného dílu lze často sloučit více součástí (např. těleso skříně, příruby, držáky, vnitřní přepážky).
- Výhody: Snížení počtu dílů zjednodušuje montáž, snižuje hmotnost, eliminuje potenciální netěsnosti spojené se spoji, zlepšuje integritu konstrukce a snižuje celkový kusovník a související logistické náklady. Tato schopnost mění pravidla hry při navrhování vysoce výkonných a spolehlivých konstrukcí Složité letecké díly.
- Významný potenciál odlehčení:
- Výzva: Minimalizace hmotnosti je v letectví a kosmonautice zásadní. Tradiční metody ztěžují selektivní odstraňování materiálu z oblastí s nízkým namáháním, aniž by došlo ke snížení pevnosti nebo výraznému prodloužení doby obrábění.
- Řešení AM: AM umožňuje pokročilé strategie odlehčování:
- Optimalizace topologie: Softwarové algoritmy analyzují rozložení napětí a odstraňují materiál z nekritických oblastí, čímž vytvářejí vysoce efektivní, organicky vypadající struktury, které udržují pevnost pouze tam, kde je to nutné.
- Mřížové struktury: Vnitřní dutiny lze vyplnit konstrukčními mřížovými strukturami, které poskytují oporu a tuhost při zlomku hmotnosti pevného materiálu.
- Výhody: Drastické snížení hmotnosti (často o 20-50 % a více) ve srovnání s tradičně vyráběnými protějšky, což přímo zvyšuje kapacitu užitečného zatížení a výkonnost mise. Díky tomu je AM ideální pro výrobu Lehké raketové komponenty.
- Zrychlená tvorba prototypů, iterace a výroba:
- Výzva: Návrh, výroba a testování prototypu tradičními metodami může trvat týdny nebo měsíce. Iterace návrhu jsou pomalé a nákladné kvůli úpravám nástrojů nebo novým obráběcím programům.
- Řešení AM: AM pracuje přímo z digitálního souboru CAD, čímž odpadá potřeba fyzických nástrojů. Prototypy lze často vytisknout během několika dnů. Úpravy návrhu spočívají v jednoduché změně modelu CAD a zahájení nového tisku.
- Výhody: Povolí Rychlé prototypování v letectví a kosmonautice, což inženýrům umožňuje rychle a levně testovat více variant návrhu. To výrazně zkracuje vývojový cyklus, podporuje inovace a umožňuje dříve odhalit chyby v návrhu. U výrobních dílů může AM navíc výrazně zkrátit dodací lhůty ve srovnání s odléváním nebo kováním, což nabízí větší pružnost dodavatelského řetězce - klíčový faktor pro podniky, které usilují o rychlou reakci na změny Partner AM Production. Prozkoumejte různé tiskových metod k dispozici, abyste pochopili možnosti.
- Snížení plýtvání materiálem a poměru nákupů a letů:
- Výzva: Při obrábění vysoce hodnotných superslitin, jako je Inconel, vzniká značné množství odpadního materiálu (třísek a hoblin), což vede ke špatnému poměru “buy-to-fly” (poměr hmotnosti nakoupené suroviny k hmotnosti finálního dílu).
- Řešení AM: LPBF je aditivní proces, při kterém se používá pouze materiál potřebný pro díl a jeho podpůrné struktury. Nerozpuštěný prášek v konstrukční komoře lze obvykle prosévat a recyklovat pro další konstrukce.
- Výhody: Výrazně snižuje množství materiálového odpadu, čímž se proces stává udržitelnějším a nákladově efektivnějším, zejména v případě drahých leteckých materiálů. Výrazně zlepšuje poměr nákupu a letu.
- Výroba na vyžádání a flexibilita dodavatelského řetězce:
- Výzva: Tradiční výroba se často spoléhá na velké výrobní série, aby se amortizovaly vysoké náklady na nástroje. Udržování velkých skladových zásob vázne na kapitálu a obstarávání specializovaných komponent může znamenat dlouhé čekání a zranitelnost dodavatelských řetězců.
- Řešení AM: AM umožňuje ekonomicky výhodnou výrobu malých sérií nebo dokonce jednotlivých zakázkových dílů bez nákladů na nástroje. Díly lze vyrábět “na vyžádání” blíže k místu potřeby.
- Výhody: Snižuje požadavky na skladové zásoby, umožňuje vytvářet vysoce přizpůsobená pouzdra ventilů pro specifické profily misí a poskytuje cestu pro digitální skladové zásoby a distribuovanou výrobu, čímž zvyšuje odolnost dodavatelského řetězce proti narušení.
Využitím těchto výhod poskytuje aditivní výroba kovů leteckým inženýrům a manažerům nákupu výkonný nástroj k překonání omezení tradičních postupů, který umožňuje vývoj a výrobu kryogenních raketových ventilů nové generace, které jsou lehčí, složitější, potenciálně dlouhodobě levnější a dostupné rychleji než kdykoli předtím.
Zaměření materiálu: IN625 a IN718 pro extrémní kryogenní podmínky
Extrémní provozní prostředí kryogenních raketových ventilů - zahrnující teploty od okolního prostředí až po -253 °C, vysoké tlaky, tepelné cykly a potřebu absolutní spolehlivosti - vyžaduje použití vysoce specializovaných materiálů. Mezi přední materiály pro tyto náročné aplikace, zejména při použití aditivní výroby, patří superslitiny na bázi niklu Inconel 625 (IN625) a Inconel 718 (IN718). Tyto materiály mají výjimečnou kombinaci vlastností, díky nimž se ideálně hodí pro náročné úkoly kosmického pohonu, a co je důležité, jsou dobře charakterizované a snadno zpracovatelné pomocí technik laserové práškové fúze (LPBF).
Porozumění superslitinám na bázi niklu:
Superslitiny na bázi niklu jsou třídou kovových materiálů určených pro provoz v náročných podmínkách vysokých teplot, vysokého namáhání a korozivního nebo oxidačního prostředí. Jejich výjimečné vlastnosti vyplývají z jejich austenitové matrice s centrovaným kubickým jádrem (FCC), zesílené různými legujícími prvky, které vytvářejí stabilní precipitáty (jako gama primární a gama double-primární fáze v IN718) nebo zajišťují zesílení v pevném roztoku (jako molybden a niob v IN625). Ačkoli jsou často spojovány s vysokoteplotními aplikacemi (turbíny proudových motorů, spalovací komory), mnoho niklových superslitin vykazuje také vynikající houževnatost a zachovává si pevnost při kryogenních teplotách, což je činí univerzálními pro extrémní podmínky v leteckém průmyslu.
Inconel 625 (IN625 / UNS N06625 / slitina 625): Korozivzdorný pracovní kůň
IN625 je nemagnetická slitina niklu, chromu, molybdenu a niobu, která je známá svou vynikající zpracovatelností a mimořádnou odolností proti korozi v široké škále agresivních prostředí.
- Klíčové vlastnosti a výhody kryogenních ventilů:
- Vynikající kryogenní houževnatost: Na rozdíl od mnoha ocelí, které při nízkých teplotách křehnou, si IN625 zachovává vynikající tažnost a houževnatost až do kryogenních teplot (-196 °C a méně), což zabraňuje křehkému lomu při namáhání.
- Vysoká pevnost: Přestože IN625 není při pokojové teplotě nebo při zvýšených teplotách tak pevná jako slitiny kalené precipitací, jako je IN718, nabízí dobrou pevnost v tahu a únavovou pevnost v širokém rozsahu teplot, včetně kryogenních podmínek. Její pevnost pochází především ze zpevňujících účinků molybdenu a niobu v pevném roztoku v nikl-chromové matrici.
- Vynikající odolnost proti korozi: Vysoce odolný proti důlkové korozi, štěrbinové korozi a celkové korozi v různých prostředích, včetně oxidačních a redukčních kyselin a chloridového korozního praskání. To je výhodné, pokud se mohou vyskytovat stopové kontaminanty nebo různé typy kapalin.
- Vynikající svařitelnost & Fabricability: IN625 je známý tím, že se poměrně snadno svařuje a zpracovává pomocí technik AM, jako je LPBF. Ve srovnání s některými jinými superslitinami má nižší náchylnost k praskání po svařování. To se promítá do dobré tisknutelnosti s nižším rizikem vzniku trhlin během procesu tavení po vrstvách v AM.
- Tepelná odolnost proti únavě: Dobře zvládá tepelné cykly mezi okolní a kryogenní teplotou.
- Úvahy o AM: IN625 obecně tiskne dobře s LPBF a dosahuje vysoké hustoty (>99,5 %). Po tisku je obvykle nutné provést standardní tepelné zpracování pro snížení napětí, aby se minimalizovala zbytková napětí vzniklá během rychlých cyklů zahřívání a ochlazování. Žíhání roztokem může dále zlepšit vlastnosti.
Inconel 718 (IN718 / UNS N07718 / Alloy 718): Vysokopevnostní standard
IN718 je pravděpodobně nejpoužívanější superslitinou na bázi niklu, zejména v leteckém průmyslu. Jedná se o precipitačně kalitelnou slitinu, což znamená, že její výjimečná pevnost je výsledkem tepelného zpracování, které způsobuje vznik jemně rozptýlených zpevňujících fází (gama prime a gama double prime) v matrici materiálu.
- Klíčové vlastnosti a výhody kryogenních ventilů:
- Výjimečná síla: V porovnání s IN625 nabízí výrazně vyšší pevnost v tahu, mez kluzu, creep a pevnost v tahu, zejména při teplotách do přibližně 700 °C. Tato vysoká pevnost se do značné míry udržuje až do kryogenních teplot. To umožňuje tenčí stěny a lehčí konstrukce při zachování požadavků na tlak.
- Dobrý kryogenní výkon: Přestože je IN718 při nejnižších kryogenních teplotách možná o něco méně tvárný než IN625, stále vykazuje dobrou houževnatost a je široce používán v kryogenních aplikacích vyžadujících vysoký poměr pevnosti k hmotnosti.
- Vynikající odolnost proti únavě: Kritické pro součásti vystavené vibračnímu zatížení a tlakovým cyklům, které jsou běžné v raketových motorech.
- Dobrá svařitelnost (u slitiny kalitelné srážením): Díky pomalejší kinetice srážení je svařitelnější (a tedy i lépe zpracovatelná pomocí AM) než mnoho jiných srážením zpevněných superslitin, což snižuje náchylnost k praskání během výroby nebo po tepelném zpracování.
- Dobrá odolnost proti korozi: Přestože IN718 není obecně považován za tak odolný proti korozi jako IN625 ve vysoce agresivním prostředí, nabízí dostatečnou odolnost pro typické aplikace v leteckém a kosmickém průmyslu.
- Úvahy o AM: IN718 je jednou z nejběžnějších a nejznámějších superslitin zpracovávaných společností LPBF. Dosažení optimálních vlastností vyžaduje pečlivou kontrolu parametrů tisku a především specifické následné tepelné zpracování. Ty obvykle zahrnují uvolnění napětí, následované žíháním v roztoku a dvoustupňovým procesem stárnutí (precipitační kalení), aby se vyvinuly zpevňující fáze a dosáhlo se požadované vysoké pevnosti a tvrdosti. U kritických součástí IN718 se často doporučuje izostatické lisování za tepla (HIP), aby se uzavřela případná zbytková vnitřní pórovitost a dále se zlepšily únavové vlastnosti.
Proč jsou tyto materiály důležité pro pouzdra ventilů AM:
Volba mezi IN625 a IN718 často závisí na specifických požadavcích na těleso ventilu:
- Pokud maximální pevnost a únavová životnost jsou hlavními pohony, které umožňují co nejlehčí konstrukci, IN718 se často upřednostňuje za předpokladu, že jsou správně provedeny nezbytné vícestupňové tepelné úpravy.
- Pokud maximální odolnost proti korozi nebo o něco lepší tažnost/houževnatost při nejnižších kryogenních teplotách nebo pokud je požadováno jednodušší následné zpracování, IN625 může být lepší volbou.
- Oba materiály nabízejí vysoký poměr pevnosti a hmotnosti nezbytné pro letecký průmysl.
- Obě tyto společnosti prokázaly, že dobrá zpracovatelnost prostřednictvím LPBF, což umožňuje vytvářet složité geometrie a konsolidované konstrukce, díky nimž je AM pro tyto součásti tak atraktivní.
Úloha vysoce kvalitních kovových prášků:
Úspěch výroby pouzder ventilů IN625 a IN718 pomocí AM je zásadně závislý na kvalitě vstupního materiálu - kovového prášku. Nekvalitní prášek může vést k defektům finálního dílu a narušit jeho integritu. Mezi klíčové vlastnosti prášku patří:
- Sféricita: Vysoce kulovité částice prášku zajišťují dobrou tekutost v systému AM stroje, což vede k rovnoměrnému vrstvení prášku a konzistentnímu tavení.
- Distribuce velikosti částic (PSD): Řízená PSD má zásadní význam pro dosažení vysoké hustoty balení v práškovém loži, což přispívá k výrobě plně hustých finálních dílů s minimální pórovitostí.
- Chemické složení: Musí striktně dodržovat specifikace pro letecký průmysl pro příslušnou slitinu (např. normy AMS). Nečistoty mohou zhoršit mechanické vlastnosti.
- Nízký obsah kyslíku/dusíku: Nadměrný obsah intersticiálního plynu může vést k pórovitosti a křehkosti.
- Absence satelitů: Malé, nepravidelné částice připojené k větším kulovitým částicím (satelitům) mohou bránit tekutosti a hustotě balení.
Zde hrají zásadní roli specializovaní výrobci prášků. Společnosti jako např Met3dps využitím pokročilých výrobních technik, jako je např Vakuová indukční tavicí plynová atomizace (VIGA) a Proces plazmové rotující elektrody (PREP), zaměřit se na výrobu Vysoce výkonné kovové prášky s optimalizovanou sféricitou, kontrolovaným PSD, vysokou čistotou a vynikající tekutostí, speciálně přizpůsobenou pro náročné aplikace AM. Odborné znalosti společnosti Met3dp’v oblasti práškové metalurgie zajišťují, že použité prášky IN625 a IN718 mají ideální vlastnosti potřebné pro spolehlivý tisk hustých, vysoce kvalitních kryogenních ventilových skříní splňujících přísné požadavky leteckého průmyslu. Jejich angažovanost přesahuje prášky a nabízí pohled na celou oblast 3D tisk z kovu ekosystém. Pro letecké výrobce a specialisty na nákup těchto kritických komponent je zásadní spolupracovat s dodavatelem, který rozumí materiálovým vědám i nuancím procesu AM. Zdroje a související obsah
Design pro aditivní výrobu (DfAM): Optimalizace těles ventilů pro tisk
Pouhé převzetí návrhu určeného pro tradiční výrobu a jeho odeslání na kovovou 3D tiskárnu málokdy přinese optimální výsledky, zejména u náročných komponent, jako jsou kryty ventilů kryogenních raket. Aby bylo možné plně využít výhod aditivní výroby - odlehčení, konsolidace dílů, zvýšení výkonu - musí konstruktéři přijmout Design pro aditivní výrobu (DfAM) zásady. DfAM není jen o zajištění části může je třeba aktivně navrhnout díl tak, aby se využily jedinečné schopnosti AM a zároveň se zmírnila jeho omezení. U pouzder ventilů to znamená, že je třeba od počátku zvažovat faktory, jako je orientace sestavy, podpůrné struktury, konstrukce vnitřních kanálů a rozlišení prvků.
Klíčové zásady DfAM pro pouzdra ventilů AM:
- Strategie orientace na budování:
- Co to je: Rozhodnutí o tom, jak bude těleso ventilu orientováno na konstrukční desce ve stroji AM.
- Proč je to důležité: Orientace významně ovlivňuje:
- Podpůrné struktury: Plochy, které přesahují určitý úhel (obvykle 45 stupňů od vodorovné roviny, avšak v závislosti na materiálu a parametrech), vyžadují podpůrné konstrukce, aby se zabránilo jejich zřícení během stavby. Orientace určuje, kde jsou podpěry potřeba, jak jsou rozsáhlé a jak snadno je lze později odstranit. Klíčová je minimalizace podpěr, zejména na kritických vnitřních nebo vnějších plochách.
- Povrchová úprava: Povrchy směřující dolů (spodní strana) a povrchy přímo připevněné k podpěrám mají obvykle horší povrchovou úpravu než povrchy směřující nahoru nebo svislé stěny. Kritické těsnicí povrchy nebo vnitřní průtokové cesty by měly být v ideálním případě orientovány tak, aby se minimalizoval kontakt s podpěrami nebo aby byly samonosné.
- Mechanické vlastnosti: Vzhledem k tomu, že díly AM jsou vyráběny po vrstvách, mohou vykazovat mírnou anizotropii (směrové rozdíly ve vlastnostech). Orientace může ovlivnit pevnost a únavovou životnost vzhledem ke směru primárního zatížení.
- Doba výstavby & Náklady: Vyšší postavy obvykle potřebují více času. Orientace dílu tak, aby se minimalizovala jeho výška (osa Z) v konstrukční komoře, může zkrátit dobu tisku.
- Optimalizace: Konstruktéři musí strategicky orientovat těleso ventilu tak, aby tyto faktory vyvážili, a často používají simulační software k předvídání potřeb podpory a možného zkreslení.
- Optimalizace podpůrné struktury:
- Co to je: Navrhování dočasných konstrukcí, které během tisku ukotvují díl na konstrukční desku a podpírají přečnívající prvky.
- Proč je to důležité: Špatně navržené podpěry lze obtížně a časově náročně odstranit (což zvyšuje náklady na následné zpracování), při odstraňování mohou poškodit povrch dílu a spotřebovat cenný materiál a čas potřebný k tisku. Naopak nedostatečné podpory mohou vést k selhání sestavy nebo deformaci dílu.
- Optimalizace:
- Minimalizace potřeby: Navrhujte prvky tak, aby byly “samonosné” všude tam, kde je to možné, používejte úhly menší, než je mezní hodnota kritického přesahu (např. zkosení ostrých přesahů namísto použití úhlů 90 stupňů). Tvar slzy pro vodorovné otvory může často eliminovat potřebu vnitřních podpor.
- Přístupnost: Zajistěte, aby podpěrné konstrukce byly umístěny na místech přístupných pro nástroje pro demontáž (ruční nebo případně drátové elektroerozivní obrábění). Vyvarujte se navrhování podpěr hluboko ve složitých vnitřních dutinách, kde nejsou dosažitelné.
- Minimalizace kontaktních bodů: Používejte takové typy podpěr (např. kuželové nebo tenkostěnné podpěry), které minimalizují kontaktní plochu s vlastním povrchem dílu, což usnadňuje odstraňování a omezuje vznik povrchových vad (“svědeckých stop”).
- Odvod tepla: Podpěry také pomáhají odvádět teplo od převisů. Jejich konstrukce musí zohledňovat tepelný management při stavbě.
- Tloušťka stěny & amp; Rozlišení funkce:
- Co to je: Vezměte v úvahu minimální a maximální tloušťku potisknutelné stěny a nejmenší pozitivní nebo negativní prvky (jako jsou otvory nebo kolíky), které může konkrétní proces AM a materiál spolehlivě vyrobit.
- Proč je to důležité: Příliš tenké stěny nemusí spolehlivě tisknout, mohou se deformovat nebo nemají dostatečnou strukturální integritu. Velmi tlusté části mohou akumulovat nadměrné teplo, což může vést k deformaci nebo nežádoucí mikrostruktuře. Malé prvky mohou ztratit definici kvůli velikosti laserového bodu a dynamice taveniny.
- Optimalizace: Dodržujte pokyny specifické pro daný stroj/materiál (např. minimální tloušťka stěny se často pohybuje kolem 0,4-0,8 mm u LPBF). Zajistěte, aby kritické prvky, jako jsou těsnicí drážky, porty snímačů nebo malé otvory, byly navrženy v rámci dosažitelných limitů rozlišení. Pečlivě používejte nástroje pro optimalizaci topologie, abyste se vyhnuli vytváření příliš tenkých prvků pro spolehlivý tisk. Tam, kde je to možné, udržujte relativně stejnou tloušťku stěn, abyste podpořili rovnoměrné zahřívání a chlazení.
- Vnitřní kanály & průchody:
- Co to je: Navrhování složitých vnitřních cest, které jsou rozhodující pro proudění kapaliny v tělese ventilu.
- Proč je to důležité: AM vyniká při vytváření složitých vnitřních geometrií, ale zachycený prášek a odstraňování podpěry představují hlavní problémy. Vnitřní kanály musí být navrženy tak, aby byly samonosné (vyhnout se plochým vodorovným stropům) nebo umožňovaly odstranění prášku po tisku.
- Optimalizace:
- Samonosné tvary: Pokud je to možné, navrhněte vnitřní kanály se slzovitým, kosočtvercovým nebo kruhovým průřezem a zajistěte, aby úhly převisu byly pod kritickou mezí. Vyhněte se velkým plochým vnitřním stropům, které by vyžadovaly rozsáhlé vnitřní podpěry.
- Přístup k odstraňování prášku: Ujistěte se, že jsou k dispozici dostatečné vstupní/výstupní otvory nebo strategicky umístěné přístupové otvory (které mohou být později ucpány), aby bylo možné po sestavení zcela odstranit nerozpuštěný prášek z vnitřních dutin pomocí vibrací, stlačeného vzduchu nebo proplachování. Zachycený prášek je kritickou závadou.
- Drsnost povrchu: Uvědomte si, že povrchová úprava vnitřních kanálů bude ve výchozím stavu drsnější než opracované povrchy, což může mít vliv na charakteristiky proudění. Pokud je požadována hladší povrchová úprava vnitřních kanálů, navrhněte je s ohledem na tuto drsnost nebo zařaďte kroky následného zpracování, jako je abrazivní průtokové obrábění nebo elektrolytické leštění.
- Možnosti konsolidace částí:
- Co to je: Aktivně hledá možnosti, jak spojit více komponent z tradiční sestavy do jediného monolitického tištěného dílu.
- Proč je to důležité: To je jedna z nejvýznamnějších výhod systému AM’. Konsolidace dílů, jako je hlavní těleso ventilu, montážní příruby, držáky nebo dokonce vnitřní prvky pro usměrňování průtoku, zkracuje dobu montáže a snižuje pracnost, eliminuje potenciální netěsnosti ze spojů/svařenců/pájky, snižuje celkovou hmotnost a zjednodušuje dodavatelský řetězec.
- Optimalizace: Zkontrolujte celou sestavu ventilu. Mohou být držáky integrovány přímo do skříně? Lze kombinovat více průtokových cest v rámci jednoho tištěného rozdělovače? Lze do něj zabudovat držáky senzorů? DfAM podporuje holistický pohled na funkci součásti’v rámci většího systému.
Využití softwaru a odborných znalostí:
Úspěšná implementace DfAM pro složité díly, jako jsou kryogenní ventilové skříně, často vyžaduje sofistikované softwarové nástroje pro:
- Optimalizace topologie: Automatické generování lehkých nosných konstrukcí.
- Generování mřížky: Vytváření vnitřních mřížových struktur, které šetří hmotnost.
- Simulace sestavení: Předvídání tepelného namáhání, deformace a optimálních podpůrných strategií před tiskem.
- CAD pro AM: Návrhové nástroje specificky zohledňující omezení a možnosti AM.
Úzká spolupráce se zkušeným Poskytovatel služeb v oblasti AM kovů je neocenitelný. Poskytovatelé jako Met3dp mají hluboké zkušenosti nejen s obsluhou strojů LPBF, ale také s nuancemi DfAM pro materiály jako IN625 a IN718. Jejich inženýři mohou poskytnout zásadní zpětnou vazbu ohledně vyrobitelnosti konstrukce, navrhnout optimalizace z hlediska nákladů a výkonu a pomoci se zorientovat ve složitostech strategie a orientace podpory. Pochopení schopností poskytovatele a využití jeho zkušeností již v rané fázi návrhu je klíčem k maximalizaci přínosů AM pro Optimalizace konstrukce ventilů.
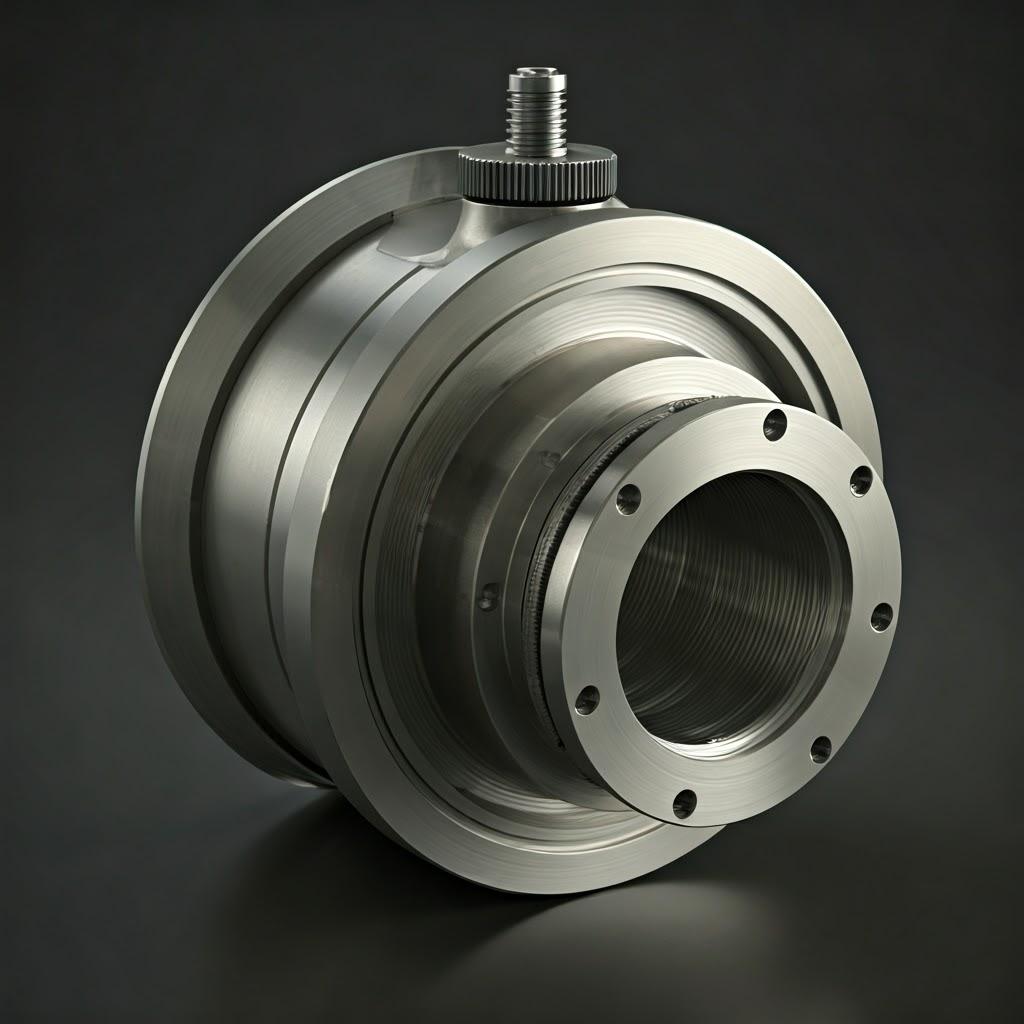
Dosažitelná přesnost: Tolerance, povrchová úprava a rozměrová přesnost v pouzdrech ventilů AM
Ačkoli aditivní výroba nabízí bezkonkurenční geometrickou volnost, je pro inženýry a manažery nákupu zásadní pochopit, jaké úrovně přesnosti lze dosáhnout přímo v procesu tisku a jaké kroky následného zpracování mohou být nezbytné pro splnění přísných požadavků na kryogenní pouzdra raketových ventilů. Faktory jako rozměrová tolerance, povrchová úprava (drsnost) a celková přesnost jsou rozhodující pro zajištění správného těsnění, montážního uložení a funkčního výkonu.
Typické tolerance při laserové fúzi v práškovém loži (LPBF):
LPBF je jedním z nejpřesnějších procesů AM, ale ze své podstaty není tak přesný jako špičkové CNC obrábění ve všech rozměrech přímo z konstrukční desky. Typické dosažitelné tolerance pro dobře řízené procesy LPBF s použitím materiálů jako IN625 a IN718 se často pohybují v rozmezí:
- Obecná rozměrová tolerance: ±0,1 mm až ±0,2 mm pro menší prvky (např. do 50-100 mm).
- Větší rozměry: Tolerance se mohou měnit s velikostí, často se uvádí ±0,1 % až ±0,2 % jmenovitého rozměru u větších dílů.
- Tolerance specifické pro danou funkci: Průměry otvorů, tloušťky stěn a přesnost umístění prvků se mohou lišit v závislosti na orientaci, umístění v rámci sestavy a tepelných účincích.
Faktory ovlivňující toleranci:
- Kalibrace stroje: Přesnost laserového skenovacího systému, kontrola tloušťky vrstvy a tepelné řízení stroje.
- Vlastnosti materiálu: Teplotní roztažnost a smršťovací charakteristiky IN625/IN718.
- Geometrie a orientace dílů: Složité tvary a orientace mohou vést k různým tepelným gradientům a potenciálnímu zkreslení.
- Tepelné namáhání: Zbytková napětí vzniklá během tisku mohou způsobit deformace, pokud nejsou správně zvládnuty pomocí podpůrných strategií a tepelného zpracování pro snížení napětí.
- Následné zpracování: Odlehčení od napětí a HIP mohou způsobit drobné, předvídatelné rozměrové změny.
Povrchová úprava (drsnost):
Povrchová úprava dílů přímo vytištěných pomocí LPBF je ze své podstaty drsnější než u obráběných povrchů. Drsnost do značné míry závisí na orientaci povrchu vzhledem ke směru sestavení a na vlastnostech prášku.
- Povrchy směřující vzhůru & Svislé stěny: Obvykle vykazují nejlepší povrchovou úpravu, často v rozsahu Ra 6 µm až 15 µm (Průměrná drsnost).
- Plochy směřující dolů (převisy): Bývají drsnější v důsledku interakce s podpůrnými konstrukcemi nebo částečně roztaveným práškem pod nimi, často Ra 15 µm až 25 µm nebo vyšší.
- Plochy směřující do stran: U šikmých povrchů vzniká vlivem vrstev drsnost, která má vliv na drsnost.
Faktory ovlivňující povrchovou úpravu:
- Tloušťka vrstvy: Tenčí vrstvy obecně vedou k hladším povrchům, ale prodlužují dobu výstavby.
- Distribuce velikosti částic prášku: Jemnější prášky mohou vést k hladšímu povrchu.
- Parametry laseru: Parametry tavení (výkon, rychlost, rozteč poklopů) ovlivňují vlastnosti taveniny a výslednou strukturu povrchu.
- Orientace: Jak již bylo zmíněno, hlavním faktorem je úhel povrchu vzhledem ke směru stavby.
- Průtok plynu: Proudění stínicího plynu v konstrukční komoře může ovlivnit stabilitu taveniny a rozstřiku, což má vliv na kvalitu povrchu.
Dosažení přesnějších tolerancí a hladších povrchů:
U kritických prvků kryogenního ventilového tělesa, jako jsou těsnicí plochy, montážní rozhraní, umístění závitů nebo přesné vnitřní průměry, jsou tolerance a povrchová úprava LPBF často nedostatečné. Po obrábění je obvykle vyžadováno.
- CNC obrábění: Kritické rozměry, těsnicí drážky (např. pro O-kroužky nebo kovová těsnění), plochy přírub a otvory se závity se po tisku a tepelném zpracování běžně dokončují. To umožňuje dosáhnout tolerancí typických pro konvenční obrábění (např. ±0,01 mm až ±0,05 mm nebo těsnějších) a specifických požadavků na kvalitu povrchu (např. Ra < 1,6 µm nebo ještě nižší pro těsnicí povrchy).
- Další dokončovací procesy: V závislosti na požadavcích lze k dosažení velmi hladkých povrchů (Ra < 0,8 µm nebo lepší) použít postupy jako broušení, leštění, elektroleštění nebo abrazivní proudové obrábění (pro vnitřní kanály).
Kontrola rozměrů a zajištění těsnosti:
Důkladná kontrola je pro letecké komponenty povinná.
- Souřadnicové měřicí stroje (CMM): Slouží k ověření kritických rozměrů podle modelu CAD a technických výkresů po tisku a následném obrábění.
- 3D skenování: Bezkontaktní optické nebo laserové skenery mohou zachytit celou geometrii dílu pro porovnání se jmenovitým návrhem, což je užitečné pro složité tvary a ověření celkového tvaru.
- Testování těsnosti: Naprosto nezbytné pro skříně ventilů. To zahrnuje stlačení součásti (často za použití helia ve vakuové komoře pro vysokou citlivost), aby se zajistilo, že nedochází k únikům přes stěny pouzdra nebo kritická těsnicí rozhraní, což splňuje přísné letecké normy. Netěsné součásti jsou základním požadavkem.
Důsledky pro navrhování a zadávání veřejných zakázek:
- Design pro následné obrábění: Konstruktéři musí navrhnout AM díl s dostatečným množstvím dodatečného materiálu (přídavek na obrábění nebo “zásoba”) na površích, které budou vyžadovat dokončovací obrábění.
- Jasně specifikujte požadavky: Technické výkresy musí jasně definovat konečné rozměrové tolerance, požadavky na povrchovou úpravu (s použitím vhodných symbolů, např. Ra) a kontrolní kritéria pro prvky AM ve stavu po sestavení i po obrobení.
- Schopnost dodavatele: Manažeři veřejných zakázek musí zajistit, aby jimi zvolené Poskytovatel služeb v oblasti AM kovů má schopnost nejen přesně vytisknout díl, ale také řídit nebo provádět nezbytné procesy následného obrábění a kontroly, aby splňovaly konečné specifikace, nebo má k tomu certifikované partnery.
Pochopení vzájemného vztahu mezi Tolerance 3D tisku kovů, Povrchová úprava AM, a následné zpracování je klíčové pro úspěšnou výrobu funkčních a spolehlivých kryogenních raketových ventilů, které splňují náročné požadavky Rozměrová přesnost Letectví a kosmonautika normy.
Kromě tisku: Základní kroky následného zpracování pro pouzdra raketových ventilů
Výroba rozměrově přesného kovového tvaru vrstvu po vrstvě je pouze prvním krokem při výrobě funkčního kryogenního raketového ventilu připraveného k letu pomocí aditivní výroby. Součástka, která je čerstvě po vyjetí z tiskárny, vyžaduje řadu zásadních kroků Následné zpracování AM kroky k uvolnění vnitřních pnutí, odstranění dočasných struktur, dosažení požadovaných vlastností materiálu, zajištění vnitřní pevnosti a splnění požadavků na konečné rozměry a povrchovou úpravu. Zanedbání nebo nesprávné provedení těchto kroků může ohrozit integritu a výkonnost součásti.
U vysoce výkonných niklových superslitin, jako jsou IN625 a IN718, které se používají v kritických aplikacích v letectví a kosmonautice, není následné zpracování volitelné, ale je nedílnou součástí výrobního procesu.
Běžné a základní kroky následného zpracování:
- Tepelné ošetření proti stresu:
- Proč: Rychlé cykly zahřívání a ochlazování, které jsou pro LPBF typické, vytvářejí v tištěném dílu značná zbytková napětí. Tato napětí mohou způsobit deformace (zejména po vyjmutí z konstrukční desky), deformace při následném obrábění a mohou mít negativní vliv na mechanické vlastnosti, zejména na únavovou životnost.
- Proces: Obvykle se provádí, když je díl ještě připevněn k desce, často ve vakuu nebo v peci s inertní atmosférou. Díl se zahřeje na určitou teplotu nižší, než je teplota žíhání nebo stárnutí (např. ~870-980 °C pro IN718, ~870-900 °C pro IN625, ale konkrétní cykly závisí na přesných požadavcích a geometrii), po určitou dobu se udržuje a poté se pomalu ochlazuje. To umožňuje uvolnění mikrostruktury materiálu, čímž se výrazně sníží vnitřní napětí.
- Důležitost: U dílů IN625 a IN718 AM je to naprosto nezbytné, aby byla zajištěna rozměrová stabilita a zabránilo se vzniku trhlin.
- Vyjmutí dílu ze stavební desky:
- Proč: Během tisku je díl nataven na silnou kovovou konstrukční desku.
- Proces: Obvykle se provádí pomocí drátového elektroerozivního obrábění (EDM) nebo pásové pily. Drátové elektroerozivní obrábění nabízí vyšší přesnost a hladší povrch řezu.
- Odstranění podpůrné konstrukce:
- Proč: Dočasné podpěry použité při tisku musí být odstraněny.
- Proces: To může být náročné, zejména v případě složitých geometrií nebo podpěr ve vnitřních prostorách. Mezi tyto metody patří:
- Ruční odstranění: Použití kleští, štípacích kleští, brusek nebo specializovaných nástrojů. Může být pracné a vyžaduje kvalifikované techniky, aby nedošlo k poškození povrchu dílu.
- Obrábění: Frézováním nebo soustružením lze odstranit přístupné podpěry.
- Drátové elektroerozivní obrábění: Někdy lze použít k přesnému odstranění, zejména v blízkosti choulostivých prvků.
- Důležitost: Důkladné odstranění je nezbytné. Zbylý podpůrný materiál může působit jako koncentrátor napětí nebo narušovat funkci. Snadnost Podpora Odstranění AM je třeba zvážit ve fázi DfAM.
- Žíhání roztokem a tepelné zpracování stárnutím (zejména pro IN718):
- Proč: Vytvoření požadované mikrostruktury a dosažení cílových mechanických vlastností (vysoká pevnost, tvrdost, tažnost). Mikrostruktura ve stavu, v jakém je vyrobena, často není optimální.
- Žíhání roztoků: Rozpouští precipitáty vzniklé během tisku a homogenizuje mikrostrukturu. Zahřívá se na vysokou teplotu (např. ~950-1050 °C pro IN718) a následně se rychle ochladí.
- Stárnutí (srážkové vytvrzování): Následné dvoustupňové tepelné zpracování při nižší teplotě (např. ~ 720 °C a následně ~ 620 °C u IN718) způsobí řízenou precipitaci zpevňujících fází (gama prime/double prime). Tento krok je rozhodující pro dosažení charakteristické vysoké pevnosti IN718.
- Proces: Provádí se v přesně řízených vakuových pecích nebo pecích s inertní atmosférou podle specifických specifikací leteckých materiálů (např. normy AMS pro letecké a kosmické materiály) Tepelné zpracování IN718).
- Důležitost: Jsou nezbytné pro dosažení vysoce výkonných mechanických vlastností požadovaných pro letecké komponenty. IN625 obvykle vyžaduje žíhání v roztoku pouze v případě, že je požadována maximální tažnost nebo odolnost proti korozi, protože je primárně zpevněn pevným roztokem.
- Proč: Vytvoření požadované mikrostruktury a dosažení cílových mechanických vlastností (vysoká pevnost, tvrdost, tažnost). Mikrostruktura ve stavu, v jakém je vyrobena, často není optimální.
- Izostatické lisování za tepla (HIP):
- Proč: Navzdory optimalizaci procesu mohou díly z LPBF někdy obsahovat mikroskopické vnitřní póry (v důsledku zachyceného plynu nebo neúplné fúze). Tyto póry mohou působit jako místa iniciace trhlin a výrazně snižovat únavovou životnost, což je u kritických součástí nepřijatelné.
- Proces: Díl je vystaven vysoké teplotě (pod bodem tání, často blízko teploty žíhání roztoku) a vysokému izostatickému tlaku (obvykle 100-200 MPa) za použití inertního plynu (např. argonu) ve specializované nádobě HIP. Kombinace tepla a tlaku způsobí, že se vnitřní dutiny zhroutí a difúzně spojí, čímž se účinně odstraní pórovitost.
- Důležitost: Stále častěji se stává standardní praxí pro kritické letecké komponenty AM, zejména ty vyrobené z IN718, aby se dosáhlo maximální hustoty (>99,9 %), zlepšila se únavová pevnost, tažnost a zajistila se homogenita materiálu. HIP Treatment Aerospace je klíčovým krokem k zajištění kvality.
- CNC obrábění:
- Proč: Jak již bylo řečeno, pro dosažení přísných tolerancí na kritických rozhraních, těsnicích plochách, závitech a přesných průměrech otvorů.
- Proces: Použití frézek, soustruhů nebo víceosých obráběcích center k selektivnímu odebírání materiálu z určitých oblastí tepelně zpracovaného a HIPovaného dílu. Vyžaduje pečlivou konstrukci upínacích přípravků, které udrží často složitou geometrii AM.
- Důležitost: Překlenuje mezeru mezi geometrickou volností AM’ a požadavky na přesnost funkčního leteckého hardwaru. CNC obrábění 3D tištěných dílů vyžaduje odborné znalosti v oblasti manipulace se složkami blízkými síťovému tvaru.
- Povrchová úprava:
- Proč: Zlepšení hladkosti povrchu nad rámec stavu při výrobě nebo obrábění, což může zvýšit průtok kapalin, čistitelnost nebo únavovou životnost.
- Proces: Možnosti zahrnují:
- Ruční leštění/broušení: Pro specifické přístupné oblasti.
- Hromadné dokončování: Obrábění nebo vibrační úprava s médii (může být agresivní).
- Obrábění abrazivním tokem (AFM): Čerpání abrazivních médií vnitřními kanály za účelem jejich vyhlazení.
- Elektrolytické leštění: Elektrochemický proces vyhlazování povrchů, často používaný pro zlepšení odolnosti proti korozi a čistitelnosti.
- Povlaky: Aplikace specializovaných povlaků pro tepelnou bariéru, odolnost proti opotřebení nebo jiné funkce (méně časté pro samotné těleso skříně, pokud nejsou potřeba specifické povrchové vlastnosti).
- Důležitost: Používá se na základě specifických funkčních požadavků na určité povrchy tělesa ventilu.
- Nedestruktivní zkoušení (NDT):
- Proč: Ověření vnitřní a vnější integrity hotového dílu bez jeho poškození.
- Proces: Mezi běžné metody NDT pro letecké díly AM patří:
- Počítačová tomografie (CT): Průmyslová rentgenová technika k detekci vnitřních vad, jako je pórovitost, inkluze nebo trhliny, a k ověření geometrie vnitřních kanálů.
- Fluorescenční penetrační kontrola (FPI): K odhalení trhlin nebo defektů narušujících povrch.
- Ultrazvukové testování (UT): Dokáže odhalit podpovrchové vady.
- Radiografické vyšetření (rentgen): Tradiční rentgen pro detekci vnitřních defektů.
- Důležitost: Povinný krok zajištění kvality, který potvrzuje, že díl splňuje přísné normy kvality pro letecký průmysl. NDT pro komponenty AM je pro letovou certifikaci rozhodující.
Složitost a kritičnost těchto kroků po zpracování podtrhuje potřebu vertikálně integrovaného nebo dobře řízeného dodavatelského řetězce. Ideální Letecké a kosmické dokončovací služby partner nebo poskytovatel AM se silnými vlastními schopnostmi je nezbytný pro spolehlivou transformaci tištěného tvaru do kryogenního ventilového pouzdra připraveného k použití v misi.
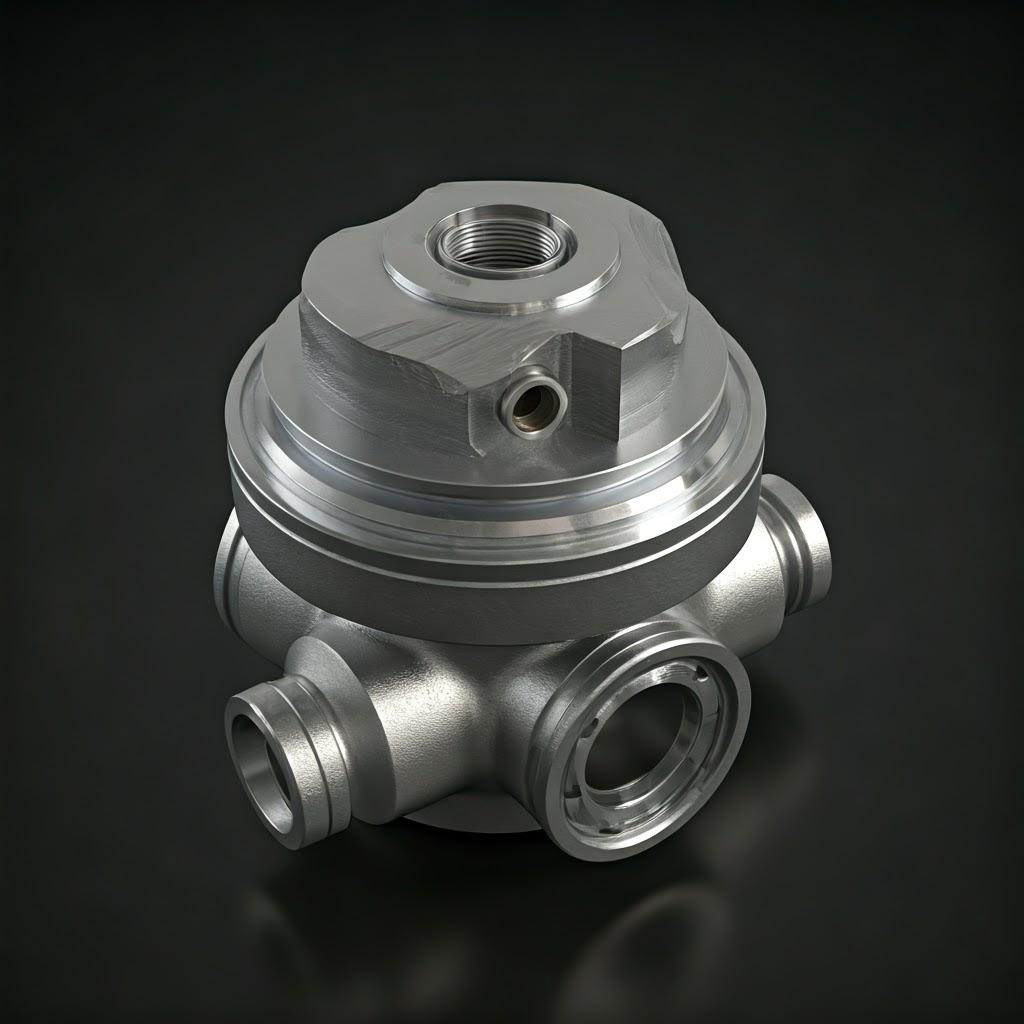
Zvládání výzev: Běžné problémy při výrobě pouzder ventilů AM a jejich řešení
Ačkoli aditivní výroba kovů nabízí významné výhody pro výrobu složitých součástí, jako jsou kryty ventilů kryogenních raket, není tento proces bez problémů. Pochopení potenciálních problémů a zavedení účinných strategií pro jejich zmírnění je zásadní pro konzistentní a vysoce kvalitní výrobu. Inženýři a manažeři nákupu v leteckém průmyslu by si měli být vědomi těchto běžných překážek při zavádění AM.
Běžné problémy při LPBF těles ventilů IN625/IN718:
- Deformace a zkreslení (zbytkové napětí):
- Problém: Intenzivní, lokalizovaný ohřev a rychlé ochlazování během LPBF vytváří značné tepelné gradienty, které vedou k tvorbě vnitřních zbytkových napětí. Po vyjmutí z konstrukční desky nebo během následného zpracování mohou tato napětí způsobit deformaci, zkreslení nebo dokonce prasknutí dílu, což ohrožuje rozměrovou přesnost.
- Řešení:
- Simulace sestavení: Využití softwaru pro simulaci procesu před tiskem pomáhá předvídat tepelné chování a deformace a umožňuje optimalizovat orientaci a podpůrné struktury, aby se zabránilo deformačním tendencím.
- Optimalizovaná strategie podpory: Robustní, dobře navržené podpěry pevně ukotví díl k sestavovací desce a pomáhají zvládat tepelné namáhání během sestavování. Konstrukce podpěr má zásadní význam.
- Optimalizovaná strategie skenování: Vzor a parametry používané laserem k tavení vrstev prášku ovlivňují přívod tepla a akumulaci napětí. Strategie, jako je ostrovní skenování nebo skenování podle sektorů, mohou pomoci zmírnit napětí.
- Povinná úleva od stresu: Provedení správného tepelného ošetření pro uvolnění napětí před vyjmutí součásti z konstrukční desky je nezbytné pro uvolnění vnitřních pnutí a stabilizaci součásti.
- Krakování (tuhnutí nebo následné tepelné zpracování):
- Problém: Niklové superslitiny, zejména srážecí, jako je IN718, mohou být náchylné k praskání buď během tuhnutí v procesu AM (praskání při tuhnutí), nebo během tepelného zpracování po svařování (praskání po deformačním stárnutí nebo po tepelném zpracování).
- Řešení:
- Kontrola kvality prášku: Použití vysoce čistého prášku s kontrolovaným chemickým složením minimalizuje prvky, které podporují praskání.
- Optimalizace parametrů: Přesné nastavení výkonu laseru, rychlosti a vzdálenosti mezi šrafami pro kontrolu velikosti bazénu taveniny, rychlosti chlazení a tepelných gradientů.
- Optimalizované cykly tepelného zpracování: Pečlivé řízení rychlosti ohřevu/chlazení a doby zdržení během uvolňování napětí, žíhání v roztoku a stárnutí podle zavedených osvědčených postupů pro AM verze těchto slitin je zásadní pro zamezení vzniku trhlin, zejména u slitiny IN718. Může být zapotřebí pomalé rychlosti ohřevu v určitých teplotních rozmezích.
- DfAM: Vyhněte se příliš silným profilům nebo ostrým vnitřním rohům, kde se může koncentrovat napětí.
- Obtíže při odstraňování podpory:
- Problém: Podpěry, zejména ty, které se nacházejí ve složitých vnitřních dutinách nebo jsou vyrobeny z houževnatých materiálů, jako je Inconel, lze velmi obtížně, časově i finančně náročně odstranit bez poškození dílu. Neúplné odstranění ohrožuje funkci a čistotu.
- Řešení:
- DfAM Focus: Pokud je to možné, upřednostněte samonosné konstrukce. Používejte optimalizované typy podpěr (např. tenké stěny, malé kontaktní body, odlamovací konstrukce). Ve fázi návrhu zajistěte přístupnost pro nástroje pro demontáž.
- Pokročilé techniky odstraňování: Použití drátového elektroerozivního obrábění nebo specializovaných elektrochemických či abrazivních metod v případech, kdy je ruční odstraňování nepraktické.
- Výběr materiálu: V některých nekritických aplikacích (i když u skříní ventilů je to vzácné) by se mohlo zkoušet použití jiných, snadněji odnímatelných podpůrných materiálů, pokud to systém AM umožňuje.
- Vnitřní pórovitost:
- Problém: V tištěném materiálu mohou vznikat mikroskopické dutiny v důsledku zachyceného plynu (např. argonového stínícího plynu), keyholingu (nestabilita v důsledku deprese par v bazénu taveniny) nebo nedostatečného spojení mezi vrstvami/stopami. Pórovitost snižuje hustotu a výrazně zhoršuje mechanické vlastnosti, zejména únavovou pevnost.
- Řešení:
- Optimalizované parametry procesu: Vývoj robustních sad parametrů (výkon laseru, rychlost, tloušťka vrstvy, vzdálenost mezi šrafami, průtok plynu) ověřených pro výrobu plně hustého (>99,5 % nebo více) materiálu.
- Kvalita prášku & manipulace: Použití vysoce kvalitního, suchého, sférického prášku s nízkým obsahem plynu a správné postupy manipulace, aby se zabránilo zachycení vlhkosti.
- Izostatické lisování za tepla (HIP): Nejúčinnější způsob, jak odstranit zbytkovou vnitřní pórovitost, dosáhnout téměř 100% hustoty a výrazně zlepšit únavové vlastnosti. Často se považuje za povinný pro kritické aplikace vyžadující vysoké nároky na kvalitu Kontrola pórovitosti.
- Odstraňování prášku z vnitřních kanálů:
- Problém: Úplné odstranění veškerého nerozpuštěného prášku ze složitých vnitřních chodeb po sestavení může být velmi obtížné. Zachycený prášek je kontaminant a může vést k poruše nebo selhání součásti.
- Řešení:
- DfAM pro odstraňování prášku: Navrhování kanálů s hladkými přechody, dostatečnými průměry a strategicky umístěnými přístupovými otvory pro vypouštění a proplachování. Vyhnout se “slepým uličkám”, kde se může prášek trvale zachytit.
- Postprocesy následného zpracování: Zavedení přísných čisticích postupů zahrnujících vibrační stoly, vyfukování stlačeným vzduchem (v kontrolovaném prostředí), čištění ultrazvukem a případně proplachování vhodnými kapalinami.
- Kontrola: Použití technik, jako je CT skenování nebo boroskop, k ověření úplného odstranění prášku z kritických vnitřních oblastí.
- Omezení povrchové úpravy:
- Problém: Drsnost povrchu ve stavu, v jakém je postaven, zejména na převisech nebo vnitřních kanálech, nemusí splňovat požadavky na těsnění, účinnost proudění nebo odolnost proti únavě.
- Řešení:
- Orientační strategie: Optimální orientace kritických povrchů při sestavování.
- Optimalizace parametrů: Jemné doladění parametrů může mírně zlepšit povrchovou úpravu, ale omezení zůstávají.
- Následné zpracování: Zařazení nezbytných kroků, jako je obrábění, leštění, AFM nebo elektrolytické leštění kritických povrchů, u nichž je povrchová úprava v základním stavu nedostatečná. Klíčové je uvědomit si potřebu těchto kroků již ve fázi plánování.
Zmírňování problémů pomocí odbornosti a partnerství:
Úspěšné zvládnutí těchto Výzvy v oblasti AM kovů vyžaduje více než jen přístup k tiskárně. Vyžaduje hluboké znalosti procesů, odborné znalosti v oblasti materiálových věd, přísnou kontrolu kvality a často i značné investice do následného zpracování a kontrolních kapacit. Proto je třeba spolupracovat se zkušenou a renomovanou firmou Poskytovatel služeb v oblasti AM kovů je často nejefektivnějším přístupem pro společnosti, které vstupují do oblasti AM v letectví a kosmonautice.
Organizace jako např Met3dp přinášejí desítky let společných zkušeností v oblasti aditivní výroby kovů, které zahrnují vše od pokročilé výroby prášku až po sofistikované tiskové techniky a vývoj aplikací. Jejich znalosti materiálů, jako jsou IN625 a IN718, spolu s robustními systémy řízení kvality pomáhají zajistit, aby byly potenciální problémy předvídány a řešeny proaktivně prostřednictvím optimalizovaného DfAM, pečlivé kontroly procesu a důkladného následného zpracování. Více informací o nás a náš závazek ke kvalitě může poskytnout jistotu při řešení složitých projektů AM. Využitím takových partnerství mohou letecké společnosti výrazně snížit riziko zavádění AM pro kritické komponenty, jako jsou kryogenní ventilové skříně, a urychlit svou cestu k výrobě nové generace.
Výběr partnera: Výběr správného poskytovatele služeb v oblasti AM pro komponenty pro letectví a kosmonautiku
Úspěšné zavedení aditivní výroby pro kritické komponenty, jako jsou kryogenní raketové ventily, závisí nejen na robustním návrhu a výběru materiálu, ale také na schopnostech a odborných znalostech vašeho výrobního partnera. Výběr správného Poskytovatel služeb v oblasti AM kovů je strategické rozhodnutí, které významně ovlivňuje kvalitu, spolehlivost, náklady a dobu uvedení na trh. Vzhledem k přísným požadavkům leteckého průmyslu, zejména u komponentů pro kryogenní pohonné hmoty, vyžaduje proces výběru pečlivé vyhodnocení, které přesahuje pouhé uvedení nejnižší ceny. Inženýři a manažeři nákupu musí hledat partnery, kteří prokazují hluboké znalosti leteckých norem, materiálových věd, řízení procesů a celého pracovního postupu AM, od optimalizace návrhu až po konečnou kontrolu.
Klíčová kritéria pro hodnocení poskytovatelů služeb v oblasti AM pro letectví a kosmonautiku:
- Certifikace pro letectví a kosmonautiku & Systém řízení kvality (QMS):
- Požadavek: Hledejte poskytovatele, kteří jsou držiteli příslušných certifikací pro letectví a kosmonautiku, především AS9100. Tato certifikace prokazuje robustní systém řízení kvality, který je speciálně přizpůsoben přísným požadavkům leteckého, kosmického a obranného průmyslu. Zahrnuje aspekty jako sledovatelnost, řízení procesů, řízení rizik a neustálé zlepšování.
- Ověření: Vyžádejte si kopie certifikátů a informujte se o vyspělosti a implementaci jejich QMS. Seznamte se s jejich postupy pro sledovatelnost materiálu, dokumentaci procesů, školení obsluhy a řízení neshod.
- Prokazatelné zkušenosti s cílovými materiály & Aplikace:
- Požadavek: Klíčové jsou specifické zkušenosti s tiskem a následným zpracováním požadovaných niklových superslitin (IN625, IN718) pro náročné aplikace. Zkušenosti z leteckého průmyslu jsou vysoce upřednostňovány před obecným průmyslovým tiskem.
- Ověření: Požádejte o případové studie, příklady vyrobených podobných součástí a údaje prokazující dosažitelné vlastnosti materiálu (pevnost v tahu, mez kluzu, prodloužení, údaje o únavě) pro IN625/IN718 vyrobené na jejich strojích. Pokud je to možné, prodiskutujte jejich zkušenosti s kryogenními aplikacemi.
- Schopnosti, kapacita a údržba stroje:
- Požadavek: Ujistěte se, že poskytovatel má vhodné stroje LPBF (např. dostatečný objem pro velikost tělesa ventilu, dostatečný výkon laseru pro efektivní zpracování niklových slitin) a dostatečnou kapacitu pro splnění vašich potřeb v oblasti prototypování a potenciální sériové výroby. Stroje by měly být dobře udržované a kalibrované.
- Ověření: Informujte se o jejich konkrétních modelech strojů, rozměrech konstrukční obálky, konfiguracích laserů a plánech údržby. Pochopte jejich plánování výroby a kapacitní plánování, abyste zajistili, že budou schopni dodržet požadované dodací lhůty.
- Kontrola kvality prášku & sledovatelnost:
- Požadavek: Poskytovatel musí mít přísné postupy pro získávání, testování, manipulaci, skladování a recyklaci kovových prášků, aby zabránil kontaminaci a zajistil konzistenci jednotlivých šarží. Nezbytná je úplná sledovatelnost od šarže prášku až po finální díl.
- Ověření: Zeptejte se na jejich dodavatele prášků (zda spolupracují s renomovanými firmami) Vysoce výkonné kovové prášky ), procesy vstupní kontroly prášku (chemie, PSD, morfologie, kontroly tekutosti), protokoly pro manipulaci s práškem (inertní prostředí, třídění) a řízení životního cyklu prášku (sledování spotřeby, postupy recyklace, omezení opětovného použití). Společnosti jako např Met3dp, které vyrábějí vlastní vysoce kvalitní prášky pomocí pokročilých technik atomizace, nabízejí přirozené výhody při řízení této kritické vstupní veličiny.
- Vlastní nebo spravované možnosti následného zpracování:
- Požadavek: Jak již bylo uvedeno, následné zpracování (uvolnění napětí, tepelné zpracování, HIP, odstranění podpěr, obrábění, NDT) je rozsáhlé a kritické. Ideální partner má silné vlastní schopnosti nebo tyto procesy bezproblémově zvládá prostřednictvím certifikovaných a důvěryhodných externích partnerů.
- Ověření: Zjistěte, které kroky následného zpracování se provádějí ve firmě a které se zadávají externě. Pokud jsou zadávány externě, ověřte si, jaké standardy kontroly kvality a certifikace se uplatňují u jejich subdodavatelů. Ujistěte se, že mají ověřené postupy pro správné tepelné zpracování IN718 (roztok + stárnutí) a přístup k akreditovaným nebo rovnocenným službám NADCAP v oblasti HIP a NDT.
- Inženýrská podpora & DfAM Expertise:
- Požadavek: Poskytovatel by měl nabízet víc než jen služby “print-to-print”. Hledejte partnery s inženýrskými týmy se zkušenostmi v oblasti DfAM, kteří mohou spolupracovat na optimalizaci návrhu, vývoji podpůrné strategie, simulaci sestavení a řešení problémů.
- Ověření: Diskutujte o jejich schopnostech DfAM. Mohou poskytnout zpětnou vazbu k vašemu návrhu z hlediska vyrobitelnosti? Využívají simulační nástroje? Jsou jejich inženýři přístupní pro technické diskuse? Skutečný Partner pro aditivní výrobu spolupracuje na zlepšení konečného produktu.
- Nedestruktivní zkoušení (NDT) a inspekce:
- Požadavek: Robustní možnosti nedestruktivního zkoušení a kontroly rozměrů jsou neoddiskutovatelné pro Certifikát AS9100 AM díly. To zahrnuje CT skenování, FPI, CMM a případně další metody relevantní pro tělesa ventilů.
- Ověření: Zkontrolujte jejich postupy NDT, seznam zařízení a osvědčení obsluhy. Pochopte jejich možnosti kontroly rozměrů a formáty hlášení. Potvrďte, že jsou schopni splnit specifické požadavky na kontrolu uvedené ve vaší technické dokumentaci.
- Časové závazky & Komunikace:
- Požadavek: Poskytovatel by měl nabídnout realistické odhady doby realizace celého procesu (tisk a veškeré následné zpracování) a udržovat jasnou a proaktivní komunikaci po celou dobu trvání projektu.
- Ověření: Diskutujte o jejich typických dodacích lhůtách pro podobné díly. Zhodnoťte jejich přístup k řízení projektů a komunikační protokoly. Reakce a transparentnost jsou klíčovými ukazateli spolehlivého dodavatele.
Hledání vhodného partnera: Kromě kontrolního seznamu
I když tato kritéria představují pevný rámec, zvažte také kulturní soulad a ochotu spolupracovat. Výroba složitých leteckých komponentů pomocí AM často zahrnuje učební křivku a vyžaduje silné partnerství mezi zákazníkem a dodavatelem. Hledejte dodavatele, kteří jsou transparentní, pokud jde o problémy, ochotní investovat do vývoje procesů, je-li to nutné, a zavázaní k dlouhodobému úspěchu.
Firmy jako Met3dp jako poskytovatelé komplexních řešení, kteří využívají své hluboké odborné znalosti v oblasti pokročilých technologií 3D tisk z kovu zařízení, výroba vysoce kvalitních prášků a služby vývoje aplikací. Jejich zaměření na kritická průmyslová odvětví, jako je letectví a kosmonautika, v kombinaci s desítkami let společných zkušeností z nich činí silného kandidáta pro organizace, které hledají spolehlivého partnera pro výrobu komponentů, jako jsou kryogenní pouzdra raketových ventilů. Spolupráce s potenciálními dodavateli, provádění auditů (virtuálních nebo osobních) a zahájení menších pilotních projektů může pomoci vybudovat důvěru předtím, než se zavážete k rozsáhlé výrobě. Výběr správného Výrobce kovových dílů na zakázku specializace v oblasti AM je pro úspěch v leteckém průmyslu klíčová.
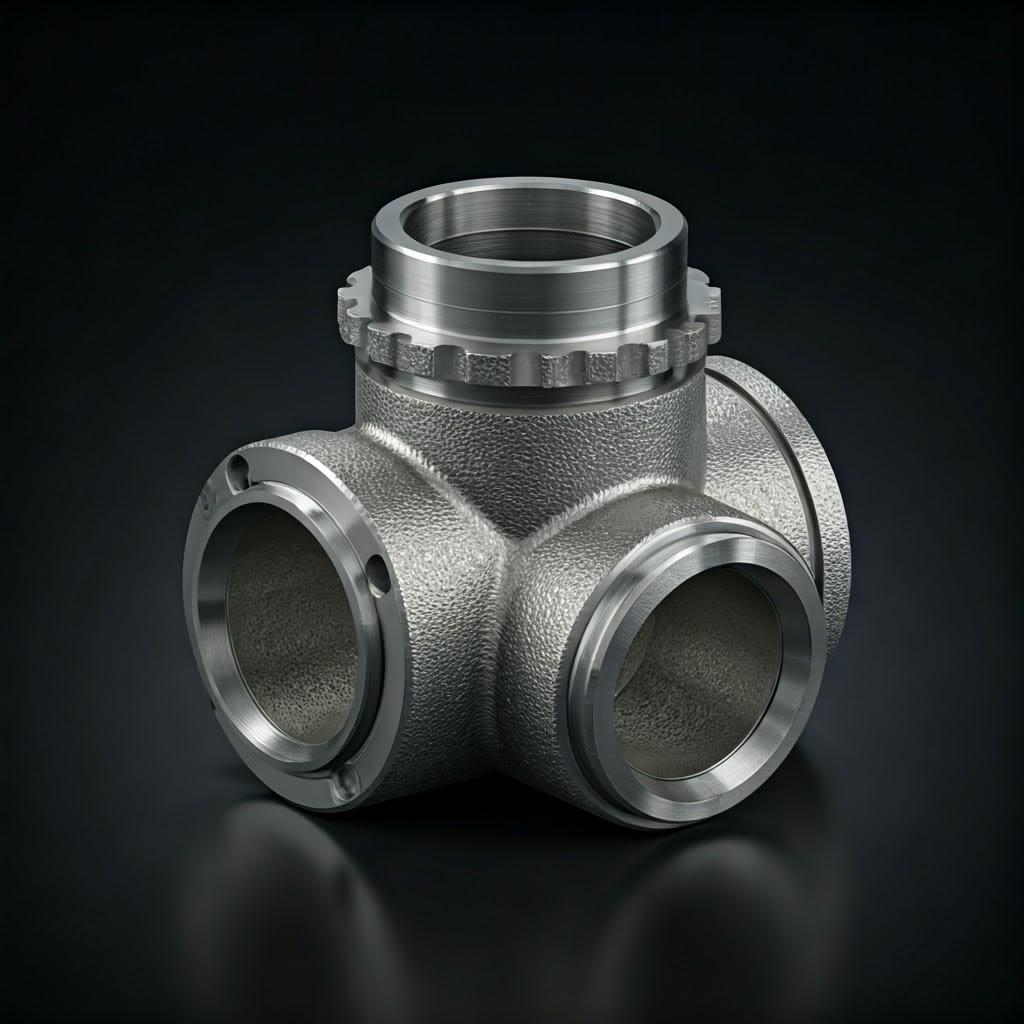
Pochopení investice: Nákladové faktory a dodací lhůty pro pouzdra ventilů AM
Aditivní výroba přináší ve srovnání s tradičními metodami, jako je odlévání nebo obrábění, odlišnou strukturu nákladů a dynamiku dodacích lhůt. Pochopení těchto faktorů je nezbytné pro přesné sestavení rozpočtu projektů, informované rozhodování o zavedení AM a stanovení realistických očekávání pro výrobu kryogenních raketových ventilů. Zatímco AM může nabídnout dlouhodobé úspory díky odlehčení a konsolidaci dílů, počáteční náklady na jeden díl, zejména u složitých superslitinových komponent, vyžadují pečlivou analýzu.
Klíčové faktory ovlivňující náklady na pouzdra ventilů AM:
- Část Svazek & Složitost:
- Objem: Větší díly spotřebují více materiálu a vyžadují delší dobu výroby, což přímo zvyšuje náklady. Ohraničující rámeček (nejmenší krychle, do které se díl vejde) ovlivňuje, kolik dílů se vejde do jednoho sestavení.
- Složitost: Ačkoli AM dobře zvládá složitost, velmi složité konstrukce mohou vyžadovat rozsáhlejší podpůrné struktury, potenciálně delší dobu výroby (kvůli zvýšenému laserovému skenování) a intenzivnější následné zpracování (odstranění podpěr, kontrola), což má dopad na náklady. Složitost dosažená konsolidací dílů však může snížit celkové náklady na systém díky eliminaci montážních kroků.
- Typ materiálu & Spotřeba:
- Výběr materiálu: Vysoce výkonné superslitiny niklu, jako jsou IN625 a IN718, jsou ze své podstaty drahé materiály. Náklady na kilogram prášku optimalizovaného pro letectví a kosmonautiku jsou značné.
- Spotřeba: To zahrnuje materiál použitý na samotný díl a materiál použitý na podpůrné konstrukce. Minimalizace objemu podpěr pomocí DfAM přímo snižuje náklady na materiál. Efektivní vnořování více dílů v rámci jednoho sestavení pomáhá amortizovat náklady na prášek.
- Doba sestavení (využití stroje):
- Náklady na stroj: Průmyslové systémy AM pro obrábění kovů představují velkou kapitálovou investici. Hlavním nákladovým faktorem je strojní čas (náklady na hodinu).
- Faktory: Doba sestavení je ovlivněna výškou dílu (počtem vrstev), objemem dílu (skenovaná plocha na jednu vrstvu), tloušťkou použité vrstvy a konkrétní použitou strategií laserového skenování. Optimalizace orientace a vnoření za účelem maximalizace počtu dílů na sestavení a minimalizace výšky sestavení snižuje náklady na strojní čas na jeden díl.
- Požadavky na podpůrnou strukturu:
- Objem: Jak již bylo zmíněno, podpěry spotřebovávají materiál a čas na stavbu.
- Odstranění: Pracovní síla a specializované postupy (např. elektroerozivní obrábění) potřebné pro odstranění podpěr zvyšují náklady, zejména u složitých vnitřních podpěr. DfAM zaměřený na minimalizaci podpěr je pro kontrolu nákladů klíčový.
- Intenzita následného zpracování:
- Tepelné zpracování: Odstraňování napětí, žíhání roztokem a stárnutí vyžadují specializované vakuové pece a zvyšují časovou náročnost a náklady.
- HIP: Izostatické lisování za tepla je nákladný sériový proces vyžadující specializované vybavení; je třeba počítat s jeho náklady, zejména pokud je vyžadováno pro díly kritické z hlediska únavy.
- Obrábění: Dokončovací obrábění kritických prvků zvyšuje náklady na strojní čas, nástroje, programování a pracovní sílu. Rozsah požadovaného obrábění přímo ovlivňuje konečnou cenu.
- Povrchová úprava: Leštění, AFM atd. zvyšují náklady v závislosti na ploše a požadované hladkosti.
- NDT a inspekce: CT skenování, FPI, CMM atd. vyžadují specializované vybavení a certifikovaný personál, což významně přispívá ke konečným nákladům, zejména u dílů vyžadujících 100% kontrolu.
- Zajištění kvality & Dokumentace:
- Úroveň dokumentace, sledovatelnosti, validace procesů a podávání zpráv o kvalitě, které jsou vyžadovány pro letecké komponenty, zvyšuje režijní náklady ve srovnání se standardními průmyslovými díly.
- Objednávkové množství:
- Náklady na zřízení: Ačkoli se AM vyhýbá výrobě pevných nástrojů, stále vznikají náklady na nastavení spojené s přípravou souboru pro sestavení, nastavením stroje a vývojem pracovního postupu po zpracování. Tyto náklady se amortizují při větších sériích.
- Množstevní slevy: Velkoobchodní ceny 3D tisku lze sjednat pro větší výrobní série nebo opakované objednávky, což odráží efektivitu využití strojů, nákupu prášků a optimalizace procesů.
Typické dodací lhůty pro pouzdra ventilů AM:
Doba realizace se může výrazně lišit v závislosti na složitosti, požadavcích na následné zpracování a počtu nevyřízených zakázek poskytovatele. AM však obecně nabízí výhody, zejména ve fázi prototypů.
- Vytváření prototypů: Od finálního modelu CAD k hotovému prototypu (odlehčenému od napětí a s odstraněnou podpěrou) může trvat 1-3 týdny. Tento rychlý obrat je velkou výhodou pro iteraci návrhu.
- Výroba (včetně kompletního následného zpracování): U plně kvalifikovaného, tepelně zpracovaného, HIPovaného, obráběného, kontrolovaného a dokumentovaného tělesa ventilu jsou dodací lhůty delší, ale často podstatně kratší než u tradičních způsobů odlévání nebo kování, a to v rozmezí od 4 až 12 týdnů, což do značné míry závisí na výše uvedených faktorech a množství.
- Srovnání: Tradiční odlévání může vyžadovat dodací lhůty v délce 3-6 měsíců nebo delší, což je z velké části způsobeno výrobou nástrojů. Komplexní obrábění z předlitků může být někde mezi, v závislosti na složitosti a dostupnosti strojů.
Shrnutí porovnání nákladů a doby realizace:
Metoda | Náklady na nástroje | Materiálový odpad | Složitost části | Odlehčení | Doba realizace (Proto) | Doba realizace (Prod) | Náklady na díl (nízký objem) | Náklady na díl (vysoký objem) |
---|---|---|---|---|---|---|---|---|
CNC obrábění | Nízká/střední | Vysoký | Střední | Nízký | Med | Med | Vysoký | Med |
Casting | Vysoký | Med | Vysoký | Med | Dlouho | Dlouho | Med | Nízký |
Kování | Velmi vysoká | Nízký | Nízký | Nízký | Velmi dlouhý | Dlouho | Neuplatňuje se (pouze pro vysoký objem) | Nejnižší |
Kov AM (LPBF) | Žádný | Nízký | Velmi vysoká | Vysoký | Krátké | Střední/krátký | Velmi vysoká | Střední/vysoká |
Export do archů
Závěr o investicích: Zatímco Náklady na 3D tisk kovů na jeden díl u složitého pouzdra ventilu ze superslitiny se může zpočátku zdát vyšší než u tradičních metod (zejména ve srovnání s velkoobjemovým odléváním/kovením), je nutné provést analýzu celkových nákladů na vlastnictví. Při zohlednění eliminovaných nákladů na nástroje, snížení plýtvání materiálem, výrazné úspory hmotnosti (snížení nákladů na uvedení na trh), konsolidovaných dílů (zkrácení montáže) a drasticky kratšího Doba realizace AM (urychlení vývoje a zlepšení reakce dodavatelského řetězce), představuje AM často přesvědčivou nabídku hodnoty pro výrobu kritických leteckých komponentů v malých až středních objemech. Vyhodnocení Ceny aditivní výroby vyžaduje, aby se hledělo nejen na samotný díl, ale i na jeho dopad na celý systém a životní cyklus.
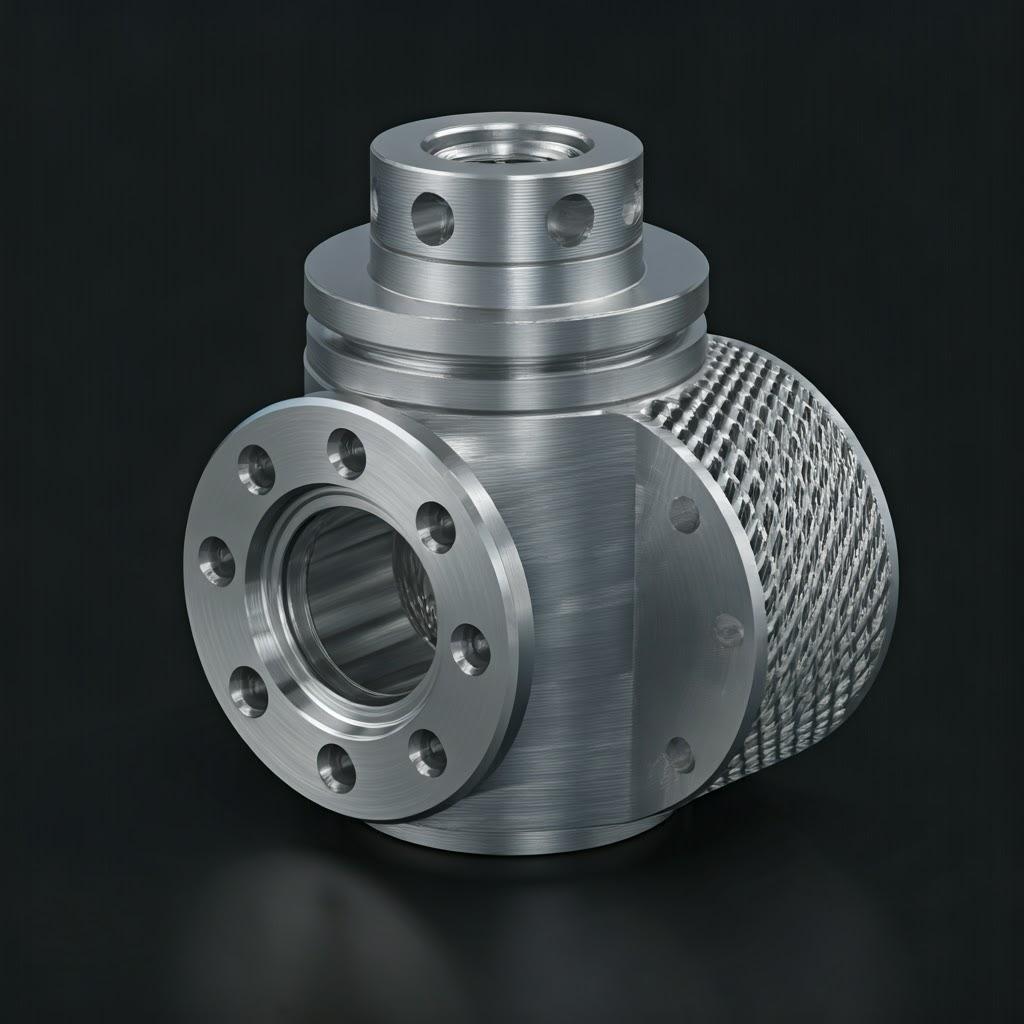
Závěr: Pohon budoucích raketových systémů s aditivně vyráběnými pouzdry ventilů
Cesta do vesmíru je dlážděna technologickými inovacemi a vyžaduje komponenty, které posouvají hranice výkonu, spolehlivosti a účinnosti. Příkladem této výzvy jsou kryogenní pouzdra raketových ventilů, která pracují v náročném prostředí extrémních teplot a vysokých tlaků. Jak jsme již prozkoumali, aditivní výroba kovů, zejména laserová prášková fúze využívající pokročilé niklové superslitiny, jako jsou IN625 a IN718, představuje změnu paradigmatu ve způsobu navrhování a výroby těchto kritických součástí.
AM osvobozuje inženýry od omezení tradiční výroby a umožňuje vytvářet pouzdra ventilů s bezkonkurenční geometrickou složitostí. To přináší hmatatelné výhody: vysoce optimalizované vnitřní průtokové cesty pro lepší dynamické vlastnosti kapalin, integrované prvky, které konsolidují více dílů do jedné monolitické konstrukce (snižují hmotnost, čas montáže a potenciální netěsnosti), a schopnost implementovat sofistikované strategie odlehčování, jako je optimalizace topologie a mřížkové struktury, které jsou klíčové pro snížení nákladů na vypuštění a maximalizaci kapacity užitečného zatížení.
Výhody přesahují čistý výkon. Možnosti rychlého prototypování, které jsou vlastní AM, výrazně zkracují vývojové cykly a umožňují rychlejší opakování a ověřování nových konstrukcí ventilů. Kromě toho schopnost vyrábět díly na vyžádání bez speciálních nástrojů zvyšuje odolnost dodavatelského řetězce a nabízí nebývalou flexibilitu - což jsou v rychlém leteckém průmyslu zásadní vlastnosti. Přestože existují problémy spojené s řízením procesu, složitostí následného zpracování a přísným zajištěním kvality, jsou systematicky řešeny prostřednictvím pokroku v principech DfAM, simulačního softwaru, monitorování procesu a odborných znalostí specializovaných poskytovatelů řešení AM.
Úspěšná implementace AM pro kryogenní ventilové skříně závisí na komplexním přístupu:
- Inteligentní design (DfAM): Přizpůsobení součásti speciálně pro aditivní proces.
- Pokročilé materiály: Použití vysoce kvalitních prášků optimalizovaných pro AM, jako jsou IN625 a IN718, které jsou známé svým kryogenním výkonem.
- Robustní zpracování: Přesné řízení procesu LPBF a pečlivé provádění základních kroků následného zpracování, jako je tepelné zpracování, HIP a obrábění.
- Strategické partnerství: Spolupráce se zkušenými Poskytovatelé služeb v oblasti AM kovů kteří mají potřebná osvědčení, vybavení a odborné znalosti.
Firmy jako Met3dp stojí v čele této výrobní revoluce a nabízí integrovaná řešení, která zahrnují jak nejmodernější technologii tisku, tak výrobu vysoce čistých kovových prášků optimalizovaných pro nejnáročnější aplikace. Jejich závazek ke kvalitě a inovacím umožňuje leteckým společnostem využít plný potenciál Raketový pohon AM technologie. Prozkoumejte, jak může Met3dp podpořit vaše cíle v oblasti aditivní výroby, a navštivte naše stránky domovskou stránku.
Závěrem lze říci, že aditivní výroba není pouze alternativní metodou výroby kryogenních raketových ventilů, ale je to technologie, která umožní budoucnost výzkumu vesmíru. Díky uvolnění nových úrovní konstrukční svobody, optimalizace výkonu a pružnosti výroby bude AM hrát stále důležitější roli při vytváření lehčích, rychlejších, výkonnějších a nákladově efektivnějších nosných raket a kosmických lodí potřebných k dosažení hvězd.
Často kladené otázky (FAQ)
Otázka 1: Jakým typickým kryogenním teplotám musí odolávat pouzdra ventilů AM?
A1: Pouzdra raketových ventilů obvykle pracují s pohonnými látkami, jako je kapalný kyslík (LOX), který vře při -183 °C, a kapalný vodík (LH2), který vře při -253 °C. Proto musí pouzdra ventilů zachovat strukturální integritu, zabránit křehkému lomu a zajistit správnou těsnost při těchto extrémně nízkých provozních teplotách. Materiály jako IN625 a IN718 jsou vybírány speciálně pro jejich vynikající houževnatost a zachování pevnosti při těchto kryogenních úrovních.
Otázka 2: Jaká je únavová životnost materiálů AM IN625/IN718 ve srovnání s kovanými (tradičně vyráběnými) materiály?
A2: Při správném zpracování (optimalizované parametry tisku, vhodné tepelné zpracování a povinné izostatické lisování za tepla – HIP) může být únavová životnost IN625 a IN718 vyrobených z LPBF srovnatelná s životností tepaných protějšků, a v některých případech ji dokonce překračuje, zejména ve specifických orientacích. HIP má zásadní význam pro minimalizaci vnitřních defektů (pórů), které obvykle omezují únavové vlastnosti dílů vyrobených metodou AM. Roli však hrají i faktory, jako je kvalita povrchu a zbytkové napětí, a vždy je nutné provést důkladné testování a kvalifikaci specifickou pro danou aplikaci, aby bylo možné dosáhnout Vlastnosti 3D tisku kovů validace v kritických součástech.
Otázka 3: Lze pomocí AM přímo vytisknout stávající konstrukce tělesa ventilů (vyrobené pro odlévání/obrábění)?
A3: I když je technicky možné vytisknout starší design, je to zřídka optimální a nevyužívá to klíčových výhod AM. Přímý tisk konstrukce určené pro odlévání nebo obrábění často vede k nadměrným podpůrným strukturám, neoptimální orientaci, potenciálním problémům s tisknutelností a zbytečné hmotnosti. Aby bylo možné plně využít výhod AM, je třeba Redesign DfAM se doporučuje. To zahrnuje přehodnocení návrhu na základě zásad DfAM s cílem optimalizovat topologii, konsolidovat díly, minimalizovat podpěry, zajistit odstranění prášku a případně zvýšit výkon nad rámec původního návrhu.
Otázka 4: Jaká specifická opatření pro kontrolu kvality jsou nezbytná pro letecké díly AM, jako jsou pouzdra ventilů?
A4: Kontrola kvality v letectví a kosmonautice pro kritické díly AM je mnohostranná a přísná. Mezi klíčová opatření patří:
Dokumentace: Komplexní záznamy o sledovatelnosti, které spojují šarži prášku, parametry stroje, údaje o sestavení, záznamy o následném zpracování a výsledky kontroly s každým jedinečným pa
Kontrola prášku: Přísné přejímací zkoušky (chemie, PSD, tekutost), manipulační protokoly a sledovatelnost.
Monitorování procesů: Monitorování taveniny, parametrů laseru a prostředí stavby (hladina kyslíku, teplota) na místě.
Ověřování po zpracování: Přesná kontrola a ověření všech cyklů tepelného zpracování (pomocí termočlánků na dílech), parametrů HIP a přesnosti obrábění.
Nedestruktivní zkoušení (NDT): Povinné CT vyšetření vnitřních defektů/geometrie, FPI pro povrchové defekty a případně UT/X-ray.
Rozměrová kontrola: CMM a/nebo 3D skenování k ověření shody se specifikacemi výkresu.
Mechanické zkoušky: Dávkové testování vlastností materiálu pomocí tištěných zkušebních kuponů (tah, únava).
Dokumentace: Komplexní záznamy o sledovatelnosti, které spojují dávku prášku, parametry stroje, údaje o sestavení, záznamy o následném zpracování a výsledky kontroly s každým jedinečným dílem.
Sdílet na
MET3DP Technology Co., LTD je předním poskytovatelem řešení aditivní výroby se sídlem v Qingdao v Číně. Naše společnost se specializuje na zařízení pro 3D tisk a vysoce výkonné kovové prášky pro průmyslové aplikace.
Dotaz k získání nejlepší ceny a přizpůsobeného řešení pro vaše podnikání!
Související články
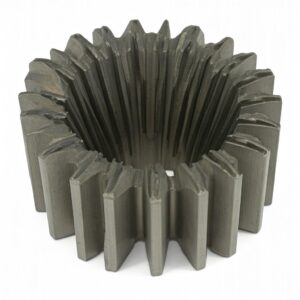
Vysoce výkonné segmenty lopatek trysek: Revoluce v účinnosti turbín díky 3D tisku z kovu
Přečtěte si více "O Met3DP
Nedávná aktualizace
Náš produkt
KONTAKTUJTE NÁS
Nějaké otázky? Pošlete nám zprávu hned teď! Po obdržení vaší zprávy obsloužíme vaši žádost s celým týmem.
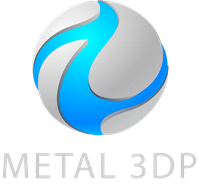
Kovové prášky pro 3D tisk a aditivní výrobu