3D-gedruckte Ansaugkrümmer für leistungsstarke Fahrzeuge
Inhaltsübersicht
Einführung: Revolutionierung der Leistung mit 3D-gedruckten Ansaugrohren
Das unerbittliche Streben nach Leistung in der Automobilindustrie erfordert ständige Innovation. Ingenieure und Konstrukteure sind ständig auf der Suche nach Möglichkeiten, mehr Leistung zu erzielen, die Effizienz zu verbessern, das Gewicht zu reduzieren und jede Komponente für maximale Wirkung zu optimieren. In diesem komplizierten Zusammenspiel der Motorkomponenten spielt der Ansaugkrümmer eine entscheidende, oft unterschätzte Rolle. Es ist die entscheidende Leitung, die für die Verteilung des lebenswichtigen Luft-Kraftstoff-Gemischs (oder nur der Luft bei Motoren mit Direkteinspritzung) an die einzelnen Zylinder verantwortlich ist. Der Wirkungsgrad, die Strömungsdynamik und die Wärmemanagementeigenschaften dieser Komponente wirken sich direkt auf die Motorleistung, die Gasannahme und die Gesamtleistung des Fahrzeugs aus. Jahrzehntelang waren traditionelle Fertigungsmethoden wie Gießen und CNC-Bearbeitung der Standard für die Herstellung von Ansaugrohren. Diese Methoden sind zwar zuverlässig, aber oft mit erheblichen Einschränkungen hinsichtlich der Komplexität des Designs, der Materialauswahl und der Produktionsvorlaufzeiten verbunden, insbesondere bei Kleinserien, Hochleistungsanwendungen oder schnellen Prototyping-Zyklen. Hier kommt die bahnbrechende Kraft von Additive Fertigung von Metall (AM)die allgemein als 3D-Druck von Metall bekannt ist. Diese transformative Technologie verändert die Landschaft des Designs und der Produktion von Automobilkomponenten rapide und bietet beispiellose Freiheiten und Möglichkeiten. Speziell für AnsaugkrümmerMetall-AM eröffnet die Möglichkeit, hoch optimierte, leichte und komplexe Geometrien zu schaffen, deren Herstellung bisher unmöglich oder unerschwinglich war. Stellen Sie sich Ansaugkanäle vor, die präzise auf bestimmte Drehzahlbereiche abgestimmt sind, integrierte Befestigungspunkte, die die Komplexität der Montage reduzieren, oder interne Strukturen, die für ein hervorragendes Wärmemanagement ausgelegt sind - all das wird direkt aus robusten Hochleistungsmetallpulvern hergestellt. Das ist keine Science-Fiction, sondern die Realität, die durch Technologien wie Selektives Laserschmelzen (SLM), Direktes Metall-Laser-Sintern (DMLS) und Elektronenstrahlschmelzen (EBM) ermöglicht wird. Unternehmen, die an der Spitze dieser Revolution stehen, wie Met3dpstellen die fortschrittliche Ausrüstung und die hochwertigen Materialien zur Verfügung, die erforderlich sind, um diese komplexen digitalen Entwürfe in funktionale, leistungsstarke Hardware zu verwandeln. In diesem einführenden Abschnitt wird erläutert, dass der 3D-Druck von Metall nicht nur eine Alternative, sondern oft eine überlegene Lösung für die Herstellung von Ansaugrohren der nächsten Generation ist, die die Grenzen des Erreichbaren in Bezug auf Motorleistung und Design für den anspruchsvollen Hochleistungsfahrzeugsektor verschiebt. Wir werden uns mit den spezifischen Vorteilen, Materialüberlegungen, Konstruktionsprinzipien und Beschaffungsstrategien befassen, die für Ingenieure, Designer und Beschaffungsmanager die diese Spitzentechnologie nutzen wollen, um sich einen Wettbewerbsvorteil auf dem Markt zu verschaffen Additive Fertigung für die Automobilindustrie Raum. Die Möglichkeit, Designs schnell zu iterieren, Krümmer für bestimmte Motorenkonstruktionen oder Rennserien anzupassen und eine erhebliche Gewichtsreduzierung zu erreichen, ohne die Festigkeit zu beeinträchtigen, macht Metall-AM zu einem unverzichtbaren Werkzeug für Hersteller, die die Spitze der Automobiltechnik und -leistung anstreben. Die Integration von fortschrittlichen Simulationswerkzeugen wie Computational Fluid Dynamics (CFD) mit der geometrischen Freiheit von AM ermöglicht die Entwicklung von Krümmern, die nicht nur anders hergestellt werden, sondern auch grundlegend anders sind. besser in Bezug auf die Effizienz und Verteilung des Luftstroms, was zu spürbaren Leistungs- und Drehmomentsteigerungen über den gewünschten Betriebsbereich führt. Darüber hinaus vereinfacht die Möglichkeit der Teilekonsolidierung - die Integration von Merkmalen wie Kraftstoffverteilerhalterungen, Sensoranschlüssen oder Unterdruckanschlüssen direkt in die Krümmerstruktur - die Montage, reduziert potenzielle Leckstellen und trägt weiter zur Optimierung des Gesamtsystems bei. Wenn wir in diesem Beitrag die Feinheiten dieser Technologie untersuchen, wird deutlich, warum Metall 3D-Druck Einführung in den Arbeitsablauf für leistungsstarke Fahrzeugkomponenten wie Ansaugrohre ist nicht länger ein Nischenexperiment, sondern eine strategische Notwendigkeit für Innovation und schnelle Markteinführung. Die Nachfrage nach maßgeschneiderten Lösungen im Motorsport, bei Hypercars und in spezialisierten Tuning-Märkten passt perfekt zu den Möglichkeiten von AM, da sie maßgeschneiderte Leistungsmerkmale ermöglicht, die mit Massenproduktionstechniken nur schwer oder gar nicht zu realisieren sind.
Leistung freisetzen: Die Rolle von Ansaugrohren in Hochleistungsmotoren
Um die Auswirkungen des 3D-Drucks in vollem Umfang zu verstehen, muss man zunächst die entscheidende Funktion des Ansaugkrümmers in einem Hochleistungs-Verbrennungsmotor begreifen. Es ist weit mehr als nur ein einfaches Rohr; es ist ein hochentwickeltes Bauteil, das entwickelt wurde, um den Luftstrom (oder das Luft-Kraftstoff-Gemisch) von der Drosselklappe zu den einzelnen Einlassöffnungen der Zylinder zu steuern und zu optimieren. Die Effektivität dieses Zuführungsprozesses hat einen großen Einfluss auf mehrere wichtige Leistungskennzahlen:
- Volumetrischer Wirkungsgrad (VE): Damit wird gemessen, wie effektiv die Motorzylinder mit dem Luft-Kraftstoff-Gemisch im Vergleich zu ihrem theoretischen Maximalvolumen gefüllt werden. Ein gut konzipierter Ansaugkrümmer maximiert die VE, insbesondere im Ziel-Drehzahlbereich des Motors, indem er Strömungsbeschränkungen minimiert und die Druckwellendynamik (akustische Abstimmung) nutzt. Ein höherer VE-Wert führt direkt zu mehr potenzieller Leistung. Bei Hochleistungsmotoren ist die Maximierung der VE über einen breiten Drehzahlbereich oder die spezielle Abstimmung für Spitzenleistung bei hohen Drehzahlen von größter Bedeutung. Die komplizierten Kanallängen, Durchmesser, das Plenumvolumen und die Übergänge zwischen den Kanälen, die mit Metall AM ermöglichen eine noch nie dagewesene Kontrolle über diese Automobil-Luftströmungsdynamik.
- Luft/Kraftstoff-Verteilung: Für einen reibungslosen Betrieb, eine gleichmäßige Leistungsentfaltung und die Langlebigkeit des Motors ist es wichtig, dass jeder Zylinder die gleiche Menge und Qualität des Kraftstoff-Luft-Gemischs erhält. Eine ungleichmäßige Verteilung kann dazu führen, dass die Zylinder zu mager (Gefahr von Detonationen) oder zu fett (Kraftstoffverschwendung, Leistungsminderung) laufen, was zu Unwuchten, Vibrationen und möglichen Motorschäden führt. Die komplexen Innengeometrien, die mit dem 3D-Druck möglich sind, ermöglichen Konstruktionen, die eine symmetrische und homogene Gemischverteilung fördern und die Einschränkungen überwinden, die häufig bei gegossenen oder gefertigten Krümmern auftreten, bei denen Kernverschiebungen oder Schweißunregelmäßigkeiten die Strömungswege beeinträchtigen können.
- Gaspedal-Reaktion: Das Volumen des Ansaugkrümmers (insbesondere des Plenums) und die Länge/Durchmesser der Kanäle beeinflussen, wie schnell der Motor auf Drosseleingaben reagiert. Größere Ansaugkrümmer können manchmal die Gasannahme dämpfen, während optimierte Kanaldesigns die Ansauggeschwindigkeit bei niedrigeren Drehzahlen und damit die Unmittelbarkeit verbessern können. Bei Hochleistungsmotoren ist ein sofortiges Ansprechen erforderlich, und AM ermöglicht es den Konstrukteuren, diese Volumina und Formen mit unglaublicher Präzision fein abzustimmen und die Anforderungen an die Spitzenleistung mit einem scharfen Einschwingverhalten in Einklang zu bringen.
- Formung der Drehmomentkurve: Die Länge und der Durchmesser der Einlasskanäle spielen eine wichtige Rolle bei der Bestimmung der Drehmomentcharakteristik des Motors. Längere, engere Kanäle begünstigen im Allgemeinen die Drehmomenterzeugung im unteren bis mittleren Drehzahlbereich, da sie die Ansaugimpulsabstimmung (Helmholtz-Resonanz) bei niedrigeren Motordrehzahlen effektiv nutzen. Umgekehrt begünstigen kürzere, breitere Kanäle in der Regel die Leistung bei hohen Drehzahlen, indem sie die Strömungsbegrenzung verringern, wenn der Motor schnell große Luftmengen anfordert. Die längenvariablen Ansaugkanäle (VLIM) sind eine komplexe mechanische Lösung für diesen Kompromiss. Allerdings, 3D-Druck von Metall ermöglicht die Erstellung von Krümmern mit fester Geometrie, die durch CFD-Simulationen sorgfältig optimiert werden, um eine bestimmte gewünschte Drehmomentkurve zu erreichen - vielleicht eine breite, flache Drehmomentkurve für Fahrbarkeit oder eine stark ansteigende Kurve für Spitzenleistung bei Rennanwendungen - ohne die mechanische Komplexität von VLIM-Systemen.
- Wärmemanagement: Die Ansauglufttemperatur wirkt sich erheblich auf die Motorleistung und die Detonationsfestigkeit aus. Mit kühlerer, dichterer Luft kann mehr Kraftstoff verbrannt werden, was die Leistung erhöht. Ansaugkrümmer, insbesondere bei Anwendungen mit Turbo- oder Kompressoraufladung, können erhebliche Wärme vom Motorblock und den Zylinderköpfen absorbieren. Die Wahl des Materials (z. B. Legierungen mit geringerer Wärmeleitfähigkeit) und die Möglichkeit, integrierte Hitzeschilde oder optimierte Luftströmungswege zu konstruieren um Der Krümmer kann mit Hilfe von AM dazu beitragen, die Ansauglufttemperaturen (IAT) zu steuern. Bei einigen Entwürfen könnten sogar Kanäle für die Flüssigkeitskühlung in die Krümmerstruktur selbst integriert werden - ein Kunststück, das mit herkömmlichen Methoden nur schwer zu erreichen ist.
Traditionelle Fertigungsbeschränkungen:
- Gießen: Das Gießen (Sandguss, Feinguss) ist zwar bei hohen Stückzahlen kosteneffizient, doch ist die Komplexität der inneren Gänge aufgrund der Kernanforderungen begrenzt. Das Erreichen gleichbleibend dünner Wände kann eine Herausforderung sein, die Oberflächenbeschaffenheit ist oft rau und erfordert eine Nachbearbeitung, und Porosität kann ein Problem darstellen. Die Länge der Kanäle und die Form des Plenums sind oft Kompromisse, die durch das Gießverfahren selbst vorgegeben sind.
- CNC-Bearbeitung: Die Bearbeitung von Knüppeln bietet hervorragende Präzision und Materialeigenschaften, ist aber unglaublich verschwenderisch (hohes Einkaufs-zu-Flug-Verhältnis) und zeitaufwändig, was sie sehr teuer macht, insbesondere bei komplexen Formen, die eine mehrachsige Bearbeitung erfordern. Interne Merkmale sind besonders schwierig und kostspielig zu bearbeiten. Die Erstellung wirklich optimierter, gekrümmter Laufbahnen ist oft nicht praktikabel.
- Fabrikation (Schweißen): Die Herstellung von Verteilern durch Schweißen von Rohren und Flanschen ermöglicht zwar eine gewisse Anpassung an die Kundenwünsche, birgt aber auch die Gefahr von Fehlern an den Schweißnähten, kann zu internen Turbulenzen führen und erschwert das Erreichen perfekt gleichmäßiger Kanallängen und glatter Übergänge. Es ist oft arbeitsintensiv.
Im Kontext der Tuning von Hochleistungsfahrzeugen und Teile von Verbrennungsmotoren Optimierung ist der Ansaugkrümmer ein Hauptkandidat für Innovationen. Egal, ob es sich um Saugmotoren handelt, die einen maximalen VE-Wert erreichen sollen, oder um Zwangsansaugsysteme, die eine robuste Konstruktion und einen optimierten Durchfluss unter Druck benötigen, die Designfreiheit, die der 3D-Druck bietet, ist ein leistungsstarkes Werkzeug. Ingenieure können folgende Vorteile nutzen Optimierung der Motorleistung Techniken wie CFD-Simulationen, um zahlreiche virtuelle Entwürfe zu iterieren und verschiedene Laufradlängen, Verjüngungen, Plenumvolumina und Geschwindigkeitsstapel zu testen, bevor man sich für einen physischen Druck entscheidet. Diese schnelle Iterationsfähigkeit in Verbindung mit der Fähigkeit, komplexe, organische Formen zu produzieren, die perfekt auf die Anforderungen der Luftströmung zugeschnitten sind, ist der Grund, warum Metall-Additiv-Fertigung entwickelt sich zur bevorzugten Lösung für Teams und Hersteller, die den ultimativen Vorteil in der Motorleistung. Das Streben nach höheren spezifischen Leistungen, breiteren Leistungsbändern und schärferem Ansprechverhalten in allen Bereichen, von Rennwagen über Hypercars bis hin zu spezialisierten Nachrüstungen, treibt die Einführung von Technologien voran, die die inhärenten Grenzen älterer Fertigungsparadigmen überwinden.
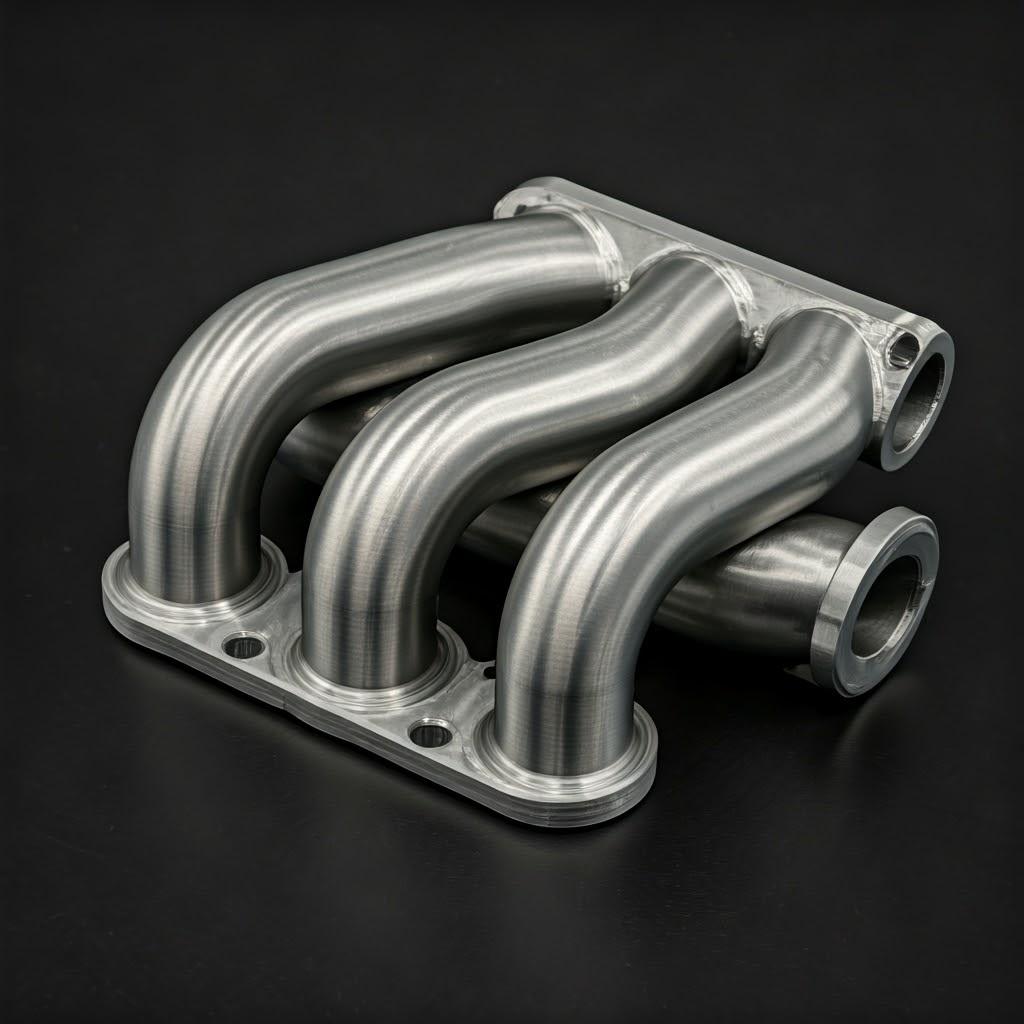
Warum Metall-Additive Fertigung für Ansaugkrümmer? Vorteile gegenüber traditionellen Methoden
Der Übergang zu Additive Fertigung von Metall (AM) für die Herstellung von Ansaugrohren, insbesondere im Hochleistungs-Automobilsektor, wird durch eine Reihe von überzeugenden Vorteilen vorangetrieben, die die Grenzen traditioneller Methoden wie Gießen, CNC-Bearbeitung und Fertigung direkt ansprechen. Diese Vorteile gehen über die bloße Neuheit hinaus und bieten spürbare Verbesserungen bei Leistung, Designflexibilität, Gewicht und Entwicklungsgeschwindigkeit. Für Automobilbeschaffung Fachleuten und Ingenieuren, die Fertigungsoptionen bewerten und diese verstehen Vorteile von Metal AM für die Automobilindustrie Anwendungen ist entscheidend.
Die wichtigsten Vorteile von Metal AM für Ansaugkrümmer:
- Unerreichte Gestaltungsfreiheit und Komplexität: Dies ist wohl der bedeutendste Vorteil. AM baut Teile Schicht für Schicht direkt aus einem 3D-CAD-Modell auf und befreit die Konstrukteure von den Zwängen, die durch Formen, Kerne oder den Zugang zu Schneidwerkzeugen entstehen.
- Optimierter Luftstrom: Die Konstrukteure können unglaublich komplexe interne Geometrien erstellen, einschließlich sanft gekrümmter Kanäle, genau berechneter Verjüngungen, optimierter Plenumformen und integrierter Geschwindigkeitsstapel, die alle durch CFD-Analysen auf maximale volumetrische Effizienz und ausgewogene Zylinderverteilung zugeschnitten sind. Dieses Niveau der Herstellung komplexer Geometrien ist mit konventionellen Methoden einfach unerreichbar oder unerschwinglich.
- Topologie-Optimierung: Mit Hilfe von Software kann Material aus unkritischen Bereichen entfernt werden, während die strukturelle Integrität erhalten bleibt. Das Ergebnis sind organisch aussehende, hocheffiziente Strukturen, die das Gewicht minimieren und gleichzeitig alle funktionalen Anforderungen erfüllen.
- Teil Konsolidierung: Merkmale wie Sensorbuchsen, Unterdruckanschlüsse, Kraftstoffleitungshalterungen und Halterungen können direkt in die Verteilerkonstruktion integriert werden, was die Anzahl der Teile, die Montagezeit, potenzielle Leckstellen und das Gesamtgewicht des Systems reduziert.
- Gewichtsreduzierung: Hochleistungsfahrzeuge streben ständig nach einer Gewichtsreduzierung. Metal AM zeichnet sich hier aus:
- Materialeffizienz: Im Gegensatz zur subtraktiven Fertigung (CNC-Bearbeitung) wird bei AM nur dort Material eingesetzt, wo es benötigt wird, was den Abfall erheblich reduziert.
- Optimierte Strukturen: Wie bereits erwähnt, ermöglicht die Topologieoptimierung erhebliche Gewichtseinsparungen im Vergleich zu sperrigen gegossenen oder maschinell bearbeiteten Teilen, ohne die Festigkeit zu beeinträchtigen. Durch die Verwendung von inhärent leichteren Legierungen wie Aluminium-Silizium-Magnesium (AlSi10Mg) wird dieser Vorteil noch verstärkt. Selbst bei der Verwendung dichterer Werkstoffe wie IN625 für Hochtemperaturanwendungen bleibt das Gewicht dank der Möglichkeit, dünnwandige, optimierte Strukturen zu schaffen, geringer als bei vergleichbaren, traditionell hergestellten Teilen. Leichtbau von Automobilkomponenten ist ein wichtiger Faktor für die Einführung von AM.
- Rapid Prototyping und Iteration: Der Weg vom digitalen Entwurf zum physischen Teil wird drastisch verkürzt.
- Schnellere Entwicklungszyklen: Ingenieure können Krümmerentwürfe innerhalb von Tagen oder Wochen entwerfen, drucken, testen und überarbeiten, anstatt Monate für das Gießen von Werkzeugen oder komplexe CNC-Programmierung zu benötigen. Dies beschleunigt die Entwicklung und ermöglicht eine bessere Leistungsoptimierung vor der endgültigen Produktion.
- Individuelle Anpassung und geringe Stückzahlen: AM eignet sich ideal für die Herstellung maßgeschneiderter Krümmer für spezielle Motorenkonstruktionen, Rennserien mit besonderen Vorschriften oder Hochleistungsfahrzeuge in Kleinserie. Die Kosten pro Teil sind im Vergleich zu werkzeugintensiven Verfahren wie dem Gießen weniger volumenabhängig.
- Materialvielfalt und Leistung: Metal AM bietet Zugang zu einer wachsenden Palette von Hochleistungslegierungen, die für anspruchsvolle Ansaugkrümmeranwendungen geeignet sind.
- Fortschrittliche Legierungen: Werkstoffe wie AlSi10Mg (leicht, gute Wärmeleitfähigkeit) und IN625 (hervorragende Hochtemperaturfestigkeit und Korrosionsbeständigkeit, ideal für Bauteile mit extremem Ladedruck oder für abgasnahe Bauteile) können problemlos verarbeitet werden. Unternehmen wie Met3dp haben sich auf die Herstellung hochwertiger Pulver, einschließlich innovativer Legierungen, spezialisiert, die für AM-Verfahren optimiert sind.
- Konsistente Eigenschaften: Bei korrekter Verarbeitung mit qualitätsgeprüften Geräten und Pulvern (wie denen von vertrauenswürdigen Lieferanten von Metallpulver) können AM-Teile mechanische Eigenschaften erreichen, die mit denen von Gussteilen vergleichbar oder ihnen sogar überlegen sind, und das bei hervorragender Dichte und Integrität.
- Verbessertes Leistungspotenzial: Der Höhepunkt der Designfreiheit, der Leichtbauweise und der Materialoptionen führt direkt zu einer potenziellen Leistungssteigerung.
- Verbesserte VE und Leistung: Optimierte Luftströmungswege führen zu einer besseren Zylinderfüllung und potenziell zu mehr Leistung und Drehmoment.
- Verbesserte Drosselklappenreaktion: Fein abgestimmte Plenumvolumina und Kanaldesigns tragen zu einem schnelleren Ansprechverhalten des Motors bei.
- Thermische Stabilität: Materialauswahl und Konstruktionsmerkmale können dazu beitragen, die Ansauglufttemperaturen effektiver zu steuern, was vor allem bei Zwangsansaugsystemen von entscheidender Bedeutung ist.
Vergleichstabelle: Metall-AM vs. traditionelle Methoden für Ansaugkrümmer
Merkmal | Additive Fertigung von Metall (AM) | Casting | CNC-Bearbeitung (Billet) | Fabrikation (Schweißen) |
---|---|---|---|---|
Entwurfskomplexität | Sehr hoch (Komplexe interne/externe Geometrien) | Mäßig (begrenzt durch Kerne/Formen) | Mäßig (begrenzt durch den Zugang zu Werkzeugen) | Gering-Mäßig (Geometrische Einschränkungen) |
Gewichtsreduzierung | Ausgezeichnet (Topologieoptimierung, dünne Wände) | Ordentlich (kann sperrig sein, Wandstärke begrenzt) | Gut (aber hoher Materialabfall) | Angemessen (abhängig von Design/Material) |
Prototyping-Geschwindigkeit | Sehr schnell | Langsam (Werkzeuge erforderlich) | Langsam-Mäßig (Programmierung/Einrichtungszeit) | Mäßig |
Niedrige Volumenkosten | Mäßig-hoch (keine Abschreibung der Werkzeugkosten) | Sehr hoch (Werkzeugkosten dominieren) | Sehr hoch (Materialabfall, Maschinenzeit) | Hoch (arbeitsintensiv) |
Hohe Volumenkosten | Hoch (langsamere Produktionsraten pro Teil) | Niedrig (Werkzeugkosten amortisiert) | Sehr hoch | Hoch |
Materialabfälle | Sehr niedrig | Niedrig-Mäßig (Tore, Steigleitungen) | Sehr hoch (Buy-to-fly-Ratio) | Niedrig |
Teil Konsolidierung | Ausgezeichnet | Begrenzt | Begrenzt | Schlecht |
Interne Oberflächenbehandlung | Mittelmäßig-gut (Nachbearbeitung erforderlich) | Schlecht-Fair (Erfordert Nachbearbeitung) | Ausgezeichnet (sofern zugänglich) | Fair (Schweißperlen beeinflussen den Fluss) |
Typische Materialien | Al-Legierungen, Ti-Legierungen, Ni-Superlegierungen, Stähle | Al-Legierungen, Gusseisen, Magnesium-Legierungen | Al-Legierungen, Ti-Legierungen, Stähle | Al-Legierungen, Stähle, Ti-Legierungen |
In Blätter exportieren
Während Gusseinschränkungen Ansaugkrümmer Design und die Kosten/Verschwendung von CNC-Bearbeitung vs. 3D-Druck sind erhebliche Nachteile, und AM ist nicht ohne Überlegungen. Die anfänglichen Investitionen in die Ausrüstung können hoch sein (obwohl Servicebüros dies abmildern), die Herstellungsgeschwindigkeiten für Einzelteile können langsamer sein als bei der Massenproduktion von Gussteilen, und oft ist eine Nachbearbeitung erforderlich, um die endgültigen Toleranzen und Oberflächengüten zu erreichen. Für die angestrebte Anwendung - Hochleistungsfahrzeuge, bei denen Leistungsoptimierung, kundenspezifische Anpassung und schnelle Markteinführung im Vordergrund stehen - überwiegen die Vorteile der Metall-AM jedoch oft diese Faktoren. Die Zusammenarbeit mit einem erfahrenen Dienstleistungsanbieter wie Met3dpDas Unternehmen verfügt nicht nur über eine fortschrittliche Drucktechnologie, sondern auch über umfassendes Fachwissen in der Werkstoffkunde und stellt damit sicher, dass diese Vorteile voll zum Tragen kommen. Die Fähigkeit, CFD-optimierte Designs schnell in funktionale Hardware umzusetzen, macht Metall-AM zu einer transformativen Kraft in der Entwicklung und Produktion von kritischen leistungsstarke Fahrzeugkomponenten.
Materialauswahl für Spitzenleistungen: AlSi10Mg und IN625 Ansaugkrümmer
Die Wahl des richtigen Materials ist von grundlegender Bedeutung für den Erfolg eines jeden technischen Projekts, und 3D-gedruckte Ansaugrohre bilden da keine Ausnahme. Die Betriebsumgebung eines Ansaugkrümmers - die Dynamik des Luftstroms, die Verbindung mit einem vibrierenden Motor, die Exposition gegenüber Kraftstoffdämpfen (bei der Saugrohreinspritzung) und erhebliche Temperaturschwankungen (insbesondere bei Anwendungen mit Ladedruck oder in der Nähe heißer Motorkomponenten) - diktiert spezifische Anforderungen an die Materialeigenschaften. Die additive Fertigung von Metallen bietet eine vielseitige Palette von Werkstoffen, aber für Hochleistungs-Saugrohre in Kraftfahrzeugen stechen zwei Legierungen häufig hervor: AlSi10Mg und IN625 (Inconel 625). Das Verständnis ihrer jeweiligen Eigenschaften und Anwendungseignung ist für Ingenieure und Beschaffungsmanager die Beschaffung dieser Komponenten.
AlSi10Mg: Der Leichtgewichts-Champion
AlSi10Mg ist eine silizium- und magnesiumhaltige Aluminiumlegierung, die sowohl in der traditionellen Gießerei als auch in der additiven Fertigung weit verbreitet ist. Sie wird oft als das Arbeitspferd unter den Aluminiumlegierungen für Pulverbettschmelzverfahren wie SLM und DMLS angesehen.
- Wichtige Eigenschaften:
- Geringe Dichte: (~2,67 g/cm³) Dies ist sein Hauptvorteil und trägt erheblich zum Leichtbau von Fahrzeugen bei. Die Verringerung der Masse, insbesondere im oberen Bereich des Motorraums, verbessert die Fahrdynamik.
- Gutes Verhältnis von Stärke zu Gewicht: Bietet eine beachtliche mechanische Festigkeit und Steifigkeit, insbesondere nach einer entsprechenden Wärmebehandlung, und ist damit für die strukturellen Anforderungen eines Ansaugkrümmers geeignet.
- Ausgezeichnete Wärmeleitfähigkeit: Hilft bei der Wärmeableitung, was für niedrigere Ansauglufttemperaturen von Vorteil sein kann, obwohl dies ein zweischneidiges Schwert sein kann, wenn zu viel Wärme vom Motorblock aufgenommen wird. Durch konstruktive Überlegungen kann die unerwünschte Wärmeübertragung gemindert werden.
- Gute Korrosionsbeständigkeit: Im Allgemeinen beständig gegen atmosphärische Korrosion und Kfz-Flüssigkeiten.
- Schweißeignung: Kann bei Bedarf für Reparaturen oder Änderungen geschweißt werden, ist aber bei AM-Teilen weniger üblich.
- Verarbeitbarkeit: Es ist eine der gebräuchlichsten und bekanntesten Legierungen für das Laser-Pulver-Bett-Schmelzen und daher weithin erhältlich bei Lieferanten von 3D-Druckmaterialien und Dienstleistern.
- Anwendungen für Ansaugkrümmer:
- Motoren mit Saugmotoren.
- Anwendungen mit mäßiger Aufladung (Turbolader oder Kompressor), bei denen die Spitzentemperaturen innerhalb des Betriebsbereichs der Legierung bleiben.
- Anwendungen, bei denen die Gewichtsminimierung oberste Priorität hat (z. B. im Motorsport).
- Schnelles Prototyping und Designvalidierung aufgrund seiner Kosteneffizienz im Vergleich zu Superlegierungen.
- Erwägungen:
- Temperaturbegrenzung: AlSi10Mg verliert bei hohen Temperaturen (typischerweise über 150-200°C oder 300-390°F) erheblich an Festigkeit, so dass es für Anwendungen mit extrem hoher Leistung oder an Orten, an denen es ohne sorgfältiges Wärmemanagement zu einer übermäßigen Wärmeeinwirkung durch Abgaskomponenten oder den Motorblock kommt, nicht geeignet ist.
- Duktilität: Kann weniger dehnbar sein als einige andere Aluminiumlegierungen oder Stähle und erfordert eine sorgfältige Konstruktion, um Spannungskonzentrationen zu vermeiden.
IN625 (Inconel 625): Das Hochtemperatur-Schwergewicht
IN625 ist eine Nickel-Chrom-Molybdän-Niob-Superlegierung, die für ihre außergewöhnliche Leistungsfähigkeit unter extremen Bedingungen bekannt ist. Es ist zwar wesentlich dichter und teurer als Aluminiumlegierungen, aber seine Eigenschaften sind unerlässlich, wenn die Bedingungen die Möglichkeiten von AlSi10Mg übersteigen.
- Wichtige Eigenschaften:
- Hervorragende Hochtemperaturfestigkeit: Behält hervorragende mechanische Eigenschaften (Zugfestigkeit, Kriechfestigkeit, Ermüdungsfestigkeit) bei sehr hohen Temperaturen (bis zu 800-900°C oder 1470-1650°F und darüber hinaus für kurze Zeit).
- Ausgezeichnete Korrosions- und Oxidationsbeständigkeit: Hochgradig widerstandsfähig gegen eine Vielzahl von korrosiven Umgebungen, einschließlich Verbrennungsnebenprodukten und Hochtemperaturoxidation.
- Hohe Ermüdungsfestigkeit: Entscheidend für Bauteile, die Motorvibrationen und Druckzyklen ausgesetzt sind.
- Gute Schweißbarkeit (im Vergleich zu anderen Superlegierungen): Kann mit AM-Technologien wie SLM und EBM effektiv bearbeitet werden.
- Anwendungen für Ansaugkrümmer:
- Extreme forcierte Induktion: Hochdruck-Turbolader oder Aufladesysteme, bei denen die Temperaturen der Ansaugluft und der Krümmeroberfläche aufgrund von Wärmestau und Druckluftwärme erheblich ansteigen können.
- Integrierte Komponenten für die Abgasrückführung (EGR): Wenn AGR-Kanäle in das Krümmerdesign integriert sind, kann der IN625 den hohen Temperaturen der Abgase standhalten.
- Nähe zu heißen Komponenten: Situationen, in denen der Krümmer sehr nahe an Auspuffkrümmern oder Turboladern liegt, was zu einer hohen Strahlungs- und Leitungswärmeübertragung führt.
- Anforderungen an die maximale Dauerhaftigkeit: Anwendungen, die ein Höchstmaß an Zuverlässigkeit und Langlebigkeit unter schwierigen Betriebsbedingungen erfordern (z. B. Langstreckenrennen).
- Erwägungen:
- Hohe Dichte: (~8,44 g/cm³) Erheblich schwerer als Aluminium, was sich auf die Ziele der Leichtbauweise auswirkt. Die Designfreiheit von AM kann dazu beitragen, dies durch Optimierung der Geometrie abzumildern, aber es wird von Natur aus schwerer sein als ein entsprechendes AlSi10Mg-Teil.
- Höhere Kosten: Sowohl das Rohpulver als auch der Druckprozess sind wesentlich teurer als bei Aluminiumlegierungen.
- Geringere Wärmeleitfähigkeit: Im Vergleich zu Aluminium leitet IN625 die Wärme weniger gut. Dies kann bei der Isolierung der Ansaugluft von der Motorwärme von Vorteil sein, erfordert aber möglicherweise Überlegungen zur Wärmeableitung, wenn der Krümmer selbst übermäßig heiß wird.
- Herausforderungen bei der Verarbeitung: Erfordert einen höheren Energieaufwand und eine sorgfältige Kontrolle der Parameter während des AM-Prozesses.
Leitfaden zur Materialauswahl: Schlüsselfaktoren
Faktor | Priorität Bevorzugt AlSi10Mg | Vorrangig begünstigt IN625 | Überlegungen |
---|---|---|---|
Betriebstemperatur | Niedriger (< 150-200°C / 300-390°F) | Höher (> 200°C / 390°F) | Präzise Vorhersage von Spitzentemperaturen durch Simulation oder Tests. |
Gewichtsreduzierung | Höchste Priorität | Geringere Priorität (Stärke/Temperatur ist entscheidend) | Die Optimierung des AM-Designs trägt dazu bei, das Gewicht des IN625 zu minimieren. |
Haushalt | Niedrigeres Budget | Höheres Budget verfügbar | Berücksichtigen Sie die Kosten für Pulver, die Druckzeit und die Komplexität der Nachbearbeitung. |
Ladezustand/Druck | Natürlich angesaugt / Moderater Boost | Hoher / extremer Boost | Höhere Drücke korrelieren oft mit höheren Temperaturen und Belastungen. |
Nähe zu Wärmequellen | Größerer Abstand zum Auspuff/Turbo | Ganz in der Nähe | Unabhängig vom Material kann eine thermische Abschirmung oder Beschichtung erforderlich sein. |
Bedenken hinsichtlich Korrosion | Standard-Automobilumgebung | Aggressive Chemikalienexposition / EGR | Beide bieten eine gute Beständigkeit, aber IN625 ist unter extremen Bedingungen überlegen. |
Produktionsvolumen | Prototyping / Geringes Volumen / Kostensensitiv | Leistungskritisch / Geringes Volumen | Der Kostenunterschied wird in größerem Umfang bedeutsamer (auch wenn AM oft ein geringes Volumen hat). |
In Blätter exportieren
Der Met3dp-Vorteil:
Die Wahl des richtigen Materials ist nur ein Teil der Gleichung. Die Qualität des Metallpulvers selbst ist ausschlaggebend, um dichte, fehlerfreie Teile mit vorhersehbaren mechanischen Eigenschaften zu erhalten. Unternehmen wie Met3dp spielen eine entscheidende Rolle als Lieferanten von hochwertigem Metallpulver. Met3dp nutzt fortschrittliche Techniken zur Pulverherstellung, wie z. B. branchenführende Technologien zur Gaszerstäubung und zum Plasma-Rotations-Elektroden-Verfahren (PREP)zur Herstellung von Metallpulvern wie AlSi10Mg und IN625 mit:
- Hohe Sphärizität: Gewährleistet eine gute Fließfähigkeit des Pulvers und eine dichte Packung im Pulverbett, was für die Druckqualität entscheidend ist.
- Kontrollierte Partikelgrößenverteilung (PSD): Eine optimierte PSD führt zu besseren Schmelzeigenschaften und einer feineren Auflösung der Merkmale.
- Niedrige Verunreinigungswerte: Hochreine Materialien führen zu hervorragenden mechanischen Eigenschaften und einer hohen Konsistenz.
- Konsistenz von Charge zu Charge: Wesentlich für zuverlässige und wiederholbare Fertigungsprozesse.
Durch die Beschaffung von Hochleistungspulvern wie AlSi10Mg und IN625 von renommierten Herstellern wie Met3dp können Ingenieure und Beschaffungsmanager mehr Vertrauen in die endgültige Integrität und Leistung ihrer 3D-gedruckten Ansaugrohre haben. Das Know-how von Met3dp geht über die Lieferung von Pulver hinaus; das Verständnis für die Wechselwirkung zwischen Materialien und Metall-AM-Verfahren stellt sicher, dass die Kunden Pulver erhalten, die für bestimmte Drucktechnologien wie SLM, DMLS oder ihre eigenen spezialisierten Selective Electron Beam Melting (SEBM)-Systeme optimiert sind, was die Qualität und Zuverlässigkeit dieser kritischen Prozesse weiter verbessert. Hochleistungskomponenten. Eine frühzeitige Beratung mit Materialexperten und AM-Dienstleistern in der Entwurfsphase ist entscheidend für die optimale Materialauswahl auf der Grundlage der spezifischen Leistungsanforderungen, Betriebsbedingungen und Budgetbeschränkungen des Projekts. Quellen und verwandte Inhalte
Design für additive Fertigung (DfAM): Optimierung von Ansaugrohren für den 3D-Druck
Ein CAD-Modell, das für den Guss oder die spanabhebende Bearbeitung entwickelt wurde, einfach an einen 3D-Metalldrucker zu schicken, führt selten zu optimalen Ergebnissen. Um das Potenzial der additiven Fertigung für Komponenten wie Hochleistungssaugrohre wirklich auszuschöpfen, müssen die Konstrukteure die folgenden Aspekte berücksichtigen Design für additive Fertigung (DfAM) Grundsätze. Bei DfAM geht es nicht nur um die Sicherstellung eines Teils dürfen Es geht darum, die einzigartigen Fähigkeiten des AM-Prozesses zu nutzen und seine Grenzen zu verstehen, um Teile zu schaffen, die leichter, stärker, leistungsfähiger und kostengünstiger zu produzieren sind. Für Ansaugrohre bedeutet dies, dass man sich gleichzeitig auf die Strömungsdynamik, die strukturelle Integrität, das Wärmemanagement und die Druckbarkeit konzentrieren muss. Implementierung von DfAM-Grundsätze Automotive Anwendungen wie diese erfordern ein Umdenken.
Wichtige DfAM-Überlegungen für Ansaugkrümmer:
- Optimieren Sie für Fluss UND Druckbarkeit: Die Hauptfunktion ist der Luftstrom. CFD-Simulationen sind von unschätzbarem Wert, wenn es darum geht, die Länge, den Durchmesser, die Verjüngung, das Plenumvolumen und die Einlässe in der Einströmdüse für die angestrebte VE und Verteilung zu optimieren. Diese idealen Strömungswege müssen jedoch herstellbar sein.
- Selbsttragende Winkel: Entwerfen Sie Innenkanäle und Laufschienenbögen mit Überhangwinkeln, die in der Regel größer als 45 Grad von der horizontalen Ebene (in Bezug auf die Baurichtung) sind, um den Bedarf an internen Stützkonstruktionen zu minimieren, die schwer und kostspielig zu entfernen sind. Wo Stützen sind Sie sollten so gestaltet sein, dass sie sich leicht entfernen lassen, oder sie sollten Verfahren wie die Fließbearbeitung für die Endbearbeitung in Betracht ziehen.
- Reibungslose Übergänge: Vermeiden Sie scharfe Ecken oder abrupte Querschnittsänderungen innerhalb der Fließwege, da diese zu Turbulenzen führen und das genaue Drucken erschweren können. Verwenden Sie großzügige Verrundungen und glatte Keilformen.
- Interne Merkmale: Überlegen Sie, wie interne Merkmale wie Strömungsgleichrichter oder Teiler gebaut und unterstützt werden sollen. Bei komplexen inneren Geometrien kann es manchmal praktischer sein, den Verteiler in Abschnitte aufzuteilen, die separat gedruckt und dann zusammengefügt werden (z. B. durch Schweißen oder Verschrauben), obwohl dies zusätzliche Montageschritte bedeutet.
- Nutzen Sie Topologieoptimierung und generatives Design: Diese Rechentools sind revolutionär für die Verschlankung und Leistungssteigerung.
- Strukturelle Optimierung: Wenden Sie die Topologieoptimierung auf das Plenumgehäuse, die Montageflansche und alle integrierten Halterungen an. Die Software identifiziert Bereiche, in denen das Material unter definierten Lastfällen (Motorvibrationen, Montagekräfte, Ladedruck) nicht wesentlich zur Steifigkeit oder Festigkeit beiträgt, und entfernt es, so dass eine organische, lastpfadoptimierte Struktur übrig bleibt. Dies kann zu erheblichen Gewichtseinsparungen bei der Krümmerstruktur selbst führen.
- Flusspfad-Anleitung: Während die Topologieoptimierung in erster Linie struktureller Natur ist, können generative Entwurfswerkzeuge manchmal dabei helfen, neue, effiziente Strömungswege innerhalb definierter Randbedingungen zu finden, wobei sie synergetisch mit CFD arbeiten.
- Gitterförmige Strukturen: Ziehen Sie in Erwägung, dickere Abschnitte des Plenums oder der Montagebereiche mit internen Gitterstrukturen auszufüllen. Diese können eine hervorragende Steifigkeit und Festigkeit bei einem Bruchteil des Gewichts von Vollmaterial bieten und gleichzeitig zur Schwingungsdämpfung beitragen.
- Stützstrukturen minimieren: Stützstrukturen sind bei der Metall-AM (insbesondere bei PBF-Prozessen) oft notwendig, um das Teil auf der Bauplatte zu verankern, überhängende Merkmale zu stützen und thermische Spannungen zu bewältigen. Sie verursachen jedoch zusätzliche Materialkosten, Bauzeit und einen erheblichen Nachbearbeitungsaufwand für die Entfernung.
- Orientierung aufbauen: Wählen Sie die Bauausrichtung sorgfältig aus, um Überhänge und das Gesamtvolumen der erforderlichen Stützen zu minimieren. Die horizontale Ausrichtung großer ebener Flächen (wie z. B. der Oberseiten von Luftschächten) kann das Risiko des Verziehens erhöhen, weshalb oft ein leichter Winkel bevorzugt wird. Die vertikale Ausrichtung zylindrischer Läufer minimiert oft die internen Stützen, kann aber die Bauhöhe und -zeit erhöhen. Es gibt immer einen Kompromiss.
- Änderungen am Design: Ändern Sie die Winkel geringfügig, fügen Sie Opferrippen oder Abrundungen (Fasen) hinzu, um die Elemente selbsttragend zu machen. Gestalten Sie scharfe Überhänge in konische oder tropfenförmige Formen um, wenn dies funktionell akzeptabel ist.
- Optimierung der Unterstützung: Verwenden Sie spezialisierte Software, um optimierte Stützstrukturen (z. B. Baumstützen, Blockstützen mit Perforation) zu erstellen, die während des Baus stabil genug sind, sich aber anschließend leichter entfernen lassen. Sorgen Sie für einen ausreichenden Zugang für die Werkzeuge zum Entfernen der Stützen, insbesondere im Bereich der Flansche und Öffnungen. Planung Tragwerksplanung Metall AM ist entscheidend.
- Wanddicke und Größe der Merkmale: Bei AM-Prozessen gibt es Einschränkungen hinsichtlich der Mindestwandstärke und der Auflösung der Merkmale.
- Mindestwanddicke: Normalerweise etwa 0,4-1,0 mm, je nach Material, Maschine und Geometrie. Stellen Sie sicher, dass die Wände dick genug sind, um dem Betriebsdruck (vor allem bei erhöhtem Druck) und den Vibrationen standzuhalten, sowie für die Handhabung während der Nachbearbeitung. In der Nähe von Flanschen kann eine dickere Wandstärke zur Abdichtung erforderlich sein. Wenden Sie sich an Ihren AM-Dienstleister, wie Met3dp, für spezifische Wandstärkenrichtlinien 3D-Druck auf der Grundlage ihrer Ausrüstung und des gewählten Materials.
- Größen der Löcher: Kleine Löcher (z. B. für Vakuumleitungen oder Sensoren) müssen möglicherweise nach dem Druck gebohrt oder aufgerieben werden, da kleine Löcher im Druckzustand leicht unregelmäßig oder unterdimensioniert sein können. Entwerfen Sie sie leicht unterdimensioniert für die spätere Bearbeitung oder planen Sie ausreichend Material ein.
- Merkmal Auflösung: Feine Details wie Logos oder Oberflächentexturen können eingearbeitet werden, sind aber durch die Größe des Laser-/Elektronenstrahls und die Größe der Pulverpartikel begrenzt.
- Teil Konsolidierungsstrategie: Identifizieren Sie Möglichkeiten zur Integration benachbarter Komponenten oder Merkmale.
- Klammerung: Integrieren Sie Halterungen für Sensoren, Aktuatoren oder die Kabelführung direkt in den Verteilerkörper.
- Flüssigkeitsanschlüsse: Entwerfen Sie Anschlüsse mit Gewinde oder O-Ring-Abdichtung für Sensoren, Unterdruckleitungen oder Einspritzdüsen direkt in den Druck, so dass möglicherweise keine separaten Fittings erforderlich sind. Stellen Sie sicher, dass um die Anschlüsse herum ausreichend Material für die Abdichtung und Festigkeit vorgesehen ist.
- Flansch-Design: Optimieren Sie die Flanschkonstruktionen für die Abdichtung (erwägen Sie das Anbringen von Nuten für O-Ringe) und den Zugang zu den Schrauben, um einen ausreichenden Freiraum für Werkzeuge während der Montage zu gewährleisten.
- Überlegungen zum Wärmemanagement:
- Wärmeableitung/Isolierung: Je nach Zielsetzung (kühle Luft oder hohe Hitzebeständigkeit) können dünne Wände und Rippen (AlSi10Mg) zur Wärmeableitung verwendet werden, oder es kann eine Topologieoptimierung für eine minimale Kontaktfläche und möglicherweise Materialien mit geringerer Leitfähigkeit wie IN625 genutzt werden, wenn Isolierung der Schlüssel ist.
- Verhinderung von Verformungen: Große, flache Abschnitte (wie Plenum-Oberflächen) können sich aufgrund thermischer Spannungen während der Bauphase verziehen. Erwägen Sie das Hinzufügen von temporären Versteifungsrippen (die später entfernt werden) oder verwenden Sie Fertigungsstrategien, die die Spannungsakkumulation minimieren. Eine sorgfältige Ausrichtung ist entscheidend.
DfAM-Workflow für Ansaugrohre:
- Definieren Sie Anforderungen: Skizzieren Sie klar die Leistungsziele (Durchflussmenge, Druckverarbeitung, Temperaturbereich), Gewichtsziele, Montagepunkte, Schnittstellen und Kostenbeschränkungen.
- Erster Entwurf und Simulation: Erstellen Sie ein erstes CAD-Modell auf der Grundlage traditioneller Konstruktionsprinzipien oder Ihrer Intuition. Durchführung einer CFD-Analyse zur Bewertung der Luftstromeigenschaften (Strömungssimulation CFD).
- Topologie-Optimierung (optional, aber empfohlen): Anwendung der Topologieoptimierung auf Strukturelemente auf der Grundlage simulierter oder erwarteter Belastungen (Druck, Vibration).
- DfAM-Verfeinerung: Ändern Sie die Geometrie auf der Grundlage der DfAM-Prinzipien (selbsttragende Winkel, Minimierung der Stützen, Wandstärke, Integration von Merkmalen). Iterieren Sie mit CFD, um sicherzustellen, dass die Leistung nicht beeinträchtigt wird.
- Simulation aufbauen (empfohlen): Verwenden Sie spezielle Software, um den AM-Herstellungsprozess zu simulieren und potenzielle Spannungskonzentrationen, Verformungen und Stützanforderungen vorherzusagen. Verfeinern Sie Ausrichtung und Stützen auf der Grundlage der Simulationsergebnisse.
- Endgültiger Entwurf und Vorverarbeitung: Fertigstellung des CAD-Modells und Vorbereitung der Konstruktionsdatei (STL oder anderes Format), einschließlich optimierter Ausrichtung und Stützstrukturen.
Durch die proaktive Einbeziehung dieser DfAM-Strategien können Ingenieure über die einfache Nachbildung bestehender Krümmerdesigns hinausgehen und mit der Entwicklung wirklich optimierter Komponenten beginnen, die die transformativen Fähigkeiten der additiven Metallfertigung voll ausschöpfen. Die Zusammenarbeit mit einem erfahrenen AM-Anbieter wie Met3dp, der die Feinheiten der Druckverfahren und Materialien können in der Entwurfsphase unschätzbare Rückmeldungen geben und ein erfolgreiches Ergebnis sicherstellen.
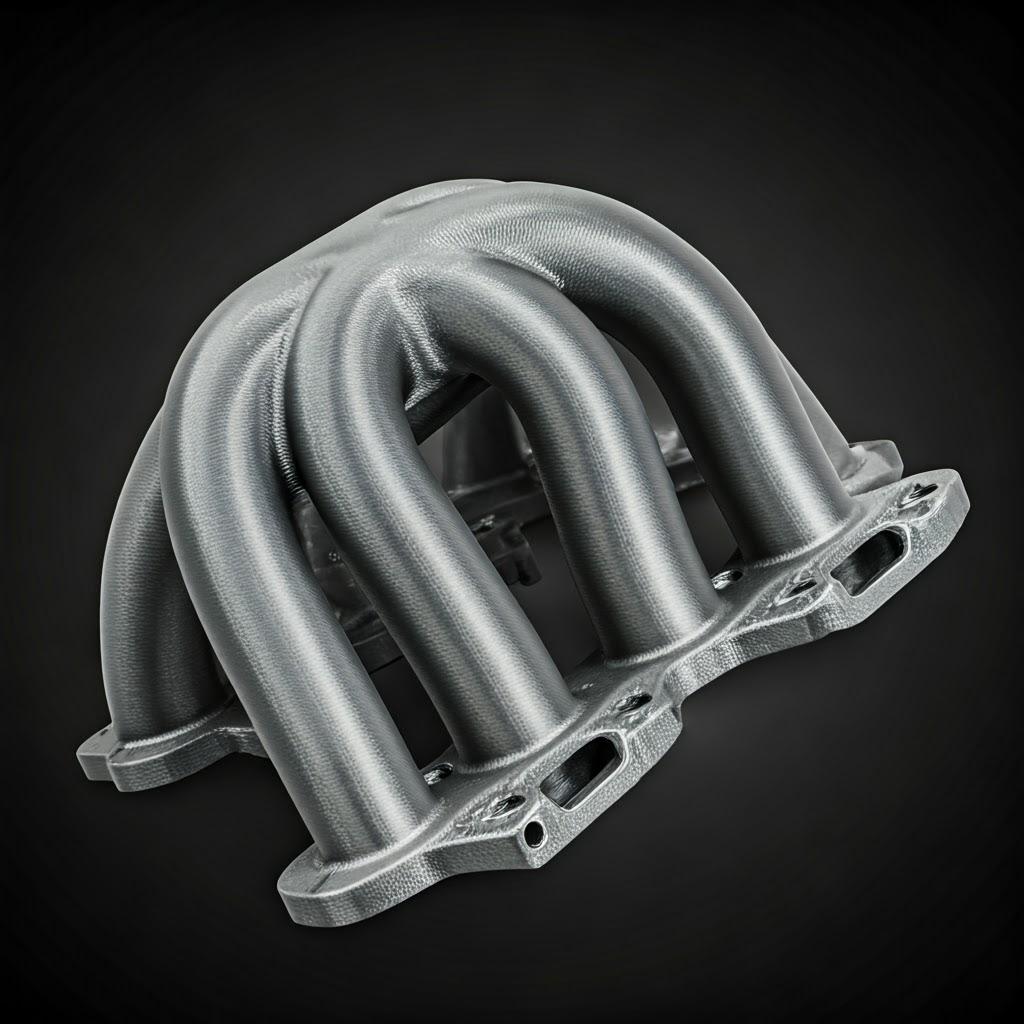
Erreichen von Präzision: Toleranzen, Oberflächengüte und Maßgenauigkeit bei 3D-gedruckten Verteilern
Während die additive Fertigung von Metallen eine unglaubliche Designfreiheit bietet, ist es für Ingenieure und Beschaffungsmanager von entscheidender Bedeutung, den Grad der erreichbaren Präzision in Bezug auf Maßtoleranzen, Oberflächengüte und Gesamtgenauigkeit zu verstehen. Im Gegensatz zur hochgradig kontrollierten Umgebung der mehrachsigen CNC-Bearbeitung sind bei der additiven Fertigung komplexe thermische Prozesse im Spiel, die die endgültige Geometrie und Oberflächenbeschaffenheit des gedruckten Teils beeinflussen können. Mit einer angemessenen Prozesssteuerung, hochwertigen Materialien und einer häufigen Nachbearbeitung können 3D-gedruckte Ansaugrohre jedoch die anspruchsvollen Anforderungen von Hochleistungsanwendungen in der Automobilindustrie erfüllen.
Abmessungstoleranzen:
Die Maßtoleranz bezieht sich auf die zulässige Abweichung in der Größe eines Bauteilmerkmals. Bei der Metall-AM, insbesondere bei Pulverbettschmelzverfahren (Powder Bed Fusion, PBF) wie SLM, DMLS und EBM, liegen die typischen "As-built"-Toleranzen oft im Bereich von:
- Allgemeine Toleranzen: ±0,1 mm bis ±0,3 mm (±0,004″ bis ±0,012″) für kleinere Merkmale (z. B. bis zu 50-100 mm).
- Größere Merkmale: Die Toleranz kann proportional zur Größe zunehmen und bei größeren Teilen aufgrund akkumulierter thermischer Effekte möglicherweise ±0,2% des Nennmaßes betragen.
Faktoren, die die Maßgenauigkeit beeinflussen:
- Thermische Spannung und Verzug: Die wiederholten Erwärmungs- und Abkühlungszyklen, die bei AM auftreten, können innere Spannungen verursachen, die zu Verformungen oder Verzug führen, insbesondere bei großen oder komplexen Geometrien wie Ansaugrohren mit großen flachen Plenumabschnitten oder langen Kanälen. Eine sorgfältige Ausrichtung, robuste Stützstrukturen und ein Spannungsabbau nach der Fertigung sind entscheidend für die Schadensbegrenzung.
- Kalibrierung der Maschine: Die Genauigkeit des Laser- oder Elektronenstrahl-Positionierungssystems, die Kalibrierung des Scanners und die Kontrolle der Schichtdicke wirken sich direkt auf die Genauigkeit der Teile aus. Gut gewartete, hochwertige Maschinen sind unerlässlich.
- Qualität des Pulvers: Eine gleichmäßige Partikelgrößenverteilung und Morphologie des Metallpulvers (wie die hochwertigen AlSi10Mg- und IN625-Pulver, die von Met3dp mit fortschrittlichen Verdüsungstechniken hergestellt werden) tragen zu einem vorhersehbaren Schmelzverhalten und zur Dimensionsstabilität bei.
- Prozessparameter: Laser-/Elektronenstrahlleistung, Scangeschwindigkeit, Schraffurabstand und Schichtdicke müssen sorgfältig für das jeweilige Material und die Geometrie optimiert werden, um ein genaues Schmelzen und Erstarren zu gewährleisten.
- Schrumpfung: Metalle schrumpfen beim Abkühlen und Erstarren. Diese Schrumpfung wird in der Software für die Bauvorbereitung kompensiert, aber dennoch können Abweichungen auftreten.
- Interaktion der Unterstützungsstruktur: Die Art und Weise, wie die Stützen mit dem Teil verbunden sind und wie sie entfernt werden, kann die Abmessungen der Oberflächen, die sie berührt haben, leicht beeinflussen.
Erzielung engerer Toleranzen:
Für kritische Schnittstellen, wie z. B. Motorflansche, Drosselklappenhalterungen, Sensoranschlüsse und Einspritzdüsenbohrungen, reichen die Toleranzen von AM im Ist-Zustand möglicherweise nicht aus. In diesen Fällen:
- Zulagen für die Bearbeitung: Konstruieren Sie das Teil mit zusätzlichem Material (z. B. 0,5 mm bis 1,5 mm) speziell auf diesen kritischen Oberflächen.
- Postprozessor-CNC-Bearbeitung: Nach dem Druck und dem Spannungsabbau werden durch CNC-Bearbeitung die endgültigen Toleranzen erreicht, die oft ±0,025 mm (±0,001″) oder mehr betragen und mit denen vollständig bearbeiteter Teile vergleichbar sind. Dieser hybride Ansatz kombiniert die geometrische Freiheit von AM mit der Präzision der subtraktiven Fertigung für kritische Schnittstellen.
Oberflächengüte (Rauhigkeit):
Ein weiteres wichtiges Merkmal ist die Oberflächengüte, die in der Regel als Ra (durchschnittliche Rauheit) gemessen wird. AM-Teile aus Metall haben im Vergleich zu maschinell gefertigten Teilen in der Regel eine rauere Oberfläche, was auf den schichtweisen Prozess und die teilweise geschmolzenen Pulverpartikel zurückzuführen ist, die an der Oberfläche haften.
- Typische As-Built Ra:
- Obere Oberflächen: Oft glatter, möglicherweise Ra 5-10 µm (200-400 µin).
- Vertikale Mauern: Ra 8-15 µm (315-590 µin) ist üblich und zeigt Schichtlinien.
- Daunenbelag/gestützte Oberflächen: Sie sind in der Regel am rauesten, möglicherweise Ra 15-25 µm (590-980 µin) oder höher, je nach Art des Trägers und der Abtragsmethode. Interne Kanäle, die auf Stützen angewiesen sind, sind besonders rau.
- EBM vs. Laser PBF: Das Elektronenstrahlschmelzen (EBM) erzeugt aufgrund des höheren Energieeintrags und der unterschiedlichen Pulvereigenschaften in der Regel rauere Oberflächen als laserbasierte Systeme (SLM/DMLS), kann aber mitunter innere Spannungen besser bewältigen.
Auswirkungen auf Ansaugrohre:
- Interne Oberflächen: Raue Innenflächen in den Kanälen und im Plenum können die Reibungsverluste erhöhen und den Luftstrom im Vergleich zu einem vollkommen glatten Durchgang leicht stören. Auch wenn die Auswirkungen in manchen Fällen gering sind, ist eine Optimierung der Glätte für eine optimale Leistung wünschenswert.
- Versiegeln von Oberflächen: Für kritische Dichtungsflansche sind die Oberflächen im Bauzustand in der Regel ungeeignet. Eine maschinelle Bearbeitung oder spezielle Nachbearbeitung ist erforderlich.
Verbesserung der Oberflächengüte:
Verschiedene Nachbearbeitungstechniken können die Oberflächengüte von 3D-gedruckten Verteilern erheblich verbessern:
- CNC-Bearbeitung: Bietet das beste Finish auf zugänglichen Oberflächen.
- Abrasives Strahlen (Perlenstrahlen, Sandstrahlen): Erzeugt ein gleichmäßiges, mattes Finish, entfernt loses Pulver und glättet die Oberflächen leicht (Ra 5-10 µm erreichbar).
- Taumeln/Gleitschleifen: Verwendet Schleifmittel in einer Trommel oder einem Rütteltopf, um Außenflächen zu glätten und scharfe Kanten zu brechen. Effektiv für Chargen von kleineren Teilen oder robusten Designs.
- Abrasive Fließbearbeitung (AFM): Drückt eine abrasive Spachtelmasse unter Druck durch innere Kanäle. Hervorragend geeignet zum Glätten von inneren Kanälen und Passagen, die mit anderen Mitteln nicht zugänglich sind.
- Elektropolieren: Ein elektrochemisches Verfahren, bei dem eine dünne Materialschicht abgetragen wird, was zu einer sehr glatten, glänzenden Oberfläche führt. Häufiger bei bestimmten Legierungen wie rostfreien Stählen oder bestimmten Superlegierungen.
- Manuelles Polieren: Arbeitsintensiv, kann aber Hochglanzoberflächen erzielen, wenn dies für die Ästhetik oder für bestimmte Fließanforderungen erforderlich ist.
Qualitätskontrolle und Inspektion:
Um sicherzustellen, dass der endgültige Ansaugkrümmer den Spezifikationen entspricht, sind robuste Qualitätskontrolle additive Fertigung Protokolle:
- Prüfung der Abmessungen: Koordinatenmessmaschinen (KMG) für hochpräzise Punktmessungen an kritischen Merkmalen. 3D-Laserscanning bietet einen umfassenden Vergleich der gesamten Teilegeometrie mit dem ursprünglichen CAD-Modell und erstellt Abweichungskarten.
- Messung der Oberflächengüte: Profilometer werden zur Quantifizierung der Oberflächenrauheit (Ra) eingesetzt.
- Zerstörungsfreie Prüfung (NDT): Verfahren wie die Computertomographie (CT) können die innere Geometrie untersuchen, Hohlräume oder Porosität erkennen und die Integrität der inneren Kanäle überprüfen, ohne das Teil zu beschädigen. Mit der Farbeindringprüfung oder der Magnetpulverprüfung kann die Oberfläche auf Risse untersucht werden.
- Druckprüfung: Unverzichtbar für Ansaugkrümmer, insbesondere bei verstärkten Anwendungen, zur Überprüfung der Integrität und zur Kontrolle auf Lecks bei Betriebsdruck.
Rolle des Lieferanten:
Das Erreichen einer gleichbleibenden Präzision hängt in hohem Maße von den Fähigkeiten und Qualitätssystemen der Metall-AM-Servicebüro. Anbieter wie Met3dp, deren Schwerpunkt auf branchenführendes Druckvolumen, Genauigkeit und ZuverlässigkeitSie investieren in High-End-Ausrüstung, strenge Kalibrierungspläne, optimierte Prozessparameter, die durch umfangreiche Forschung und Entwicklung entwickelt wurden, und robuste Qualitätsmanagementsysteme (oft zertifiziert nach Normen wie ISO 9001 oder AS9100 für die Luft- und Raumfahrt). Erkundigen Sie sich bei der Bewertung potenzieller Lieferanten nach deren Maßhaltigkeitsstandards Automobil Teile, typische erreichbare Toleranzen, Möglichkeiten der Oberflächenbearbeitung und verfügbare Prüfmethoden sind für die Beschaffungsteams von entscheidender Bedeutung. Eine klare Kommunikation kritischer Abmessungen und erforderlicher Toleranzen auf technischen Zeichnungen ist entscheidend, um sicherzustellen, dass das endgültige Teil den Erwartungen entspricht.
Mehr als nur der Druck: Wichtige Nachbearbeitung für 3D-gedruckte Ansaugrohre
Die Reise eines 3D-gedruckten Ansaugkrümmers aus Metall endet nicht, wenn der Drucker anhält. Das "grüne" Teil, das frisch von der Bauplatte kommt, benötigt mehrere entscheidende Nachbearbeitung von Metall AM Schritte, um es in ein funktionelles, zuverlässiges und leistungsstarkes Bauteil zu verwandeln. Diese Schritte sind keine optionalen Extras; sie sind ein wesentlicher Bestandteil, um die gewünschten mechanischen Eigenschaften, die Maßgenauigkeit, die Oberflächengüte und die Gesamtqualität zu erreichen. Das Verständnis dieser Anforderungen ist entscheidend für die Planung der Produktionszeiten und -kosten im Zusammenhang mit Beschaffung im Bereich der additiven Fertigung.
Gemeinsame Nachbearbeitungsschritte für AM-Ansaugrohre aus Metall:
- Entfernung des Pulvers (De-Powdering):
- Prozess: Unmittelbar nach Beendigung des Bauprozesses und Abkühlung der Kammer wird der Bauauftrag (das auf der Bauplatte befestigte Teil, umgeben von ungeschmolzenem Pulver) entfernt. Überschüssiges Pulver wird sorgfältig zurückgewonnen, oft durch manuelles Bürsten, Absaugen oder automatische Siebstationen für das Recycling. Die internen Kanäle innerhalb des Verteilers erfordern besondere Aufmerksamkeit, um sicherzustellen, dass das gesamte lose Pulver entfernt wird, was manchmal mit Vibration oder Druckluft geschieht.
- Wichtigkeit: Pulverrückstände, vor allem in den internen Kanälen, können den Luftstrom einschränken, Motoreinbauten verunreinigen oder nachfolgende Prozesse beeinträchtigen. Gründliches Entpulvern ist entscheidend.
- Stressabbau Wärmebehandlung:
- Prozess: Dies ist in der Regel die erste Schritt nach dem Entpudern, der häufig durchgeführt wird, während das Teil noch an der Bauplatte befestigt ist. Die Baugruppe Teil/Platte wird in einem Ofen auf eine bestimmte Temperatur unterhalb des kritischen Umwandlungspunkts des Materials erhitzt, eine Zeit lang gehalten und dann langsam abgekühlt. Die Parameter (Temperatur, Zeit, Atmosphäre) sind materialspezifisch (z. B., Wärmebehandlung AlSi10Mg unterscheidet sich erheblich von IN625).
- Wichtigkeit: Die schnellen Erwärmungs-/Abkühlungszyklen während des Drucks führen zu erheblichen inneren Spannungen. Die Spannungsentlastung reduziert diese Spannungen, verhindert Verformungen oder Risse beim Entfernen der Halterung oder bei der Bearbeitung und verbessert die Dimensionsstabilität und die mechanischen Eigenschaften (insbesondere die Ermüdungsfestigkeit). Sie ist absolut notwendig für zuverlässige Teile.
- Entfernen des Teils von der Bauplatte:
- Prozess: Nach dem Spannungsabbau wird der Ansaugkrümmer von der Bauplatte getrennt. Dies geschieht in der Regel durch Drahterodieren (Electrical Discharge Machining) oder mit einer Bandsäge. Dabei muss darauf geachtet werden, dass das Teil nicht beschädigt wird.
- Wichtigkeit: Befreit das Teil für die weitere Handhabung und Bearbeitung. Die Grundfläche, an der es befestigt war, muss nachbearbeitet werden.
- Entfernung der Stützstruktur:
- Prozess: Die Stützstrukturen, die zur Verankerung des Teils und zur Abstützung von Überhängen während des Drucks dienen, müssen nun entfernt werden. Dies kann manuell mit Zangen, Cuttern, Schleifmaschinen oder CNC-Bearbeitung erfolgen. Der Zugang kann sich als schwierig erweisen, insbesondere bei internen Stützen innerhalb von Kufen oder komplexen Plenum-Geometrien. Unterstützung von Entfernungstechniken erfordern Geschick und Sorgfalt, um eine Beschädigung der Werkstückoberfläche zu vermeiden.
- Wichtigkeit: Stützen sind nicht funktionsfähig und behindern den Luftstrom oder die Montage. Ihre vollständige Entfernung ist erforderlich. Die von den Stützen hinterlassenen Markierungen oder "Zeugenlinien" erfordern oft eine weitere Nachbearbeitung.
- CNC-Bearbeitung (für kritische Merkmale):
- Prozess: Wie bereits erwähnt, werden kritische Schnittstellen wie Zylinderkopfflansche, Drosselklappenhalterungen, Sensoranschlüsse und Einspritzdüsenbohrungen häufig CNC-gefräst, um enge Toleranzen und spezifische Oberflächengüten zu erreichen, die für die Abdichtung und präzise Ausrichtung erforderlich sind. Dazu muss das AM-Teil auf einer Fräsmaschine oder Drehbank eingerichtet werden.
- Wichtigkeit: Garantiert Maßhaltigkeit und ordnungsgemäße Abdichtung/Paarung mit anderen Motorkomponenten. CNC-Bearbeitung von 3D-Drucken ist eine gängige Praxis für hochpräzise Anwendungen.
- Oberflächenveredelung / Glättung:
- Prozess: Je nach Anforderungen werden verschiedene Methoden zur Verbesserung der Oberflächenbeschaffenheit im Ist-Zustand eingesetzt:
- Perlstrahlen: Erzeugt ein gleichmäßiges, mattes Finish, reinigt Oberflächen.
- Taumeln/Gleitschleifen: Glättet Außenflächen und Kanten.
- Abrasive Fließbearbeitung (AFM): Ideal zum Glätten von Innenkanälen zur Verbesserung der Luftstromeigenschaften.
- Manuelles Schleifen/Polieren: Für besondere ästhetische Anforderungen oder gezielte Glättung.
- Elektropolieren: Erzielt bei kompatiblen Legierungen sehr glatte, saubere Oberflächen.
- Wichtigkeit: Verbessert die Ästhetik, kann die Luftströmung verbessern (glattere innere Durchgänge), beseitigt Oberflächenmängel und bereitet die Oberflächen bei Bedarf auf Beschichtungen vor. Oberflächenpolieren von Metallteilen kann für die Leistung entscheidend sein.
- Prozess: Je nach Anforderungen werden verschiedene Methoden zur Verbesserung der Oberflächenbeschaffenheit im Ist-Zustand eingesetzt:
- Weitere Wärmebehandlungen (optional):
- Prozess: Je nach Werkstoff (insbesondere AlSi10Mg) und gewünschten Eigenschaften können zusätzliche Wärmebehandlungen wie Lösungsglühen und Auslagern (z. B. T6-Zustand bei Aluminium) durchgeführt werden. nach Spannungsabbau und möglicherweise Bearbeitung. Diese Behandlungen erhöhen die Festigkeit und Härte erheblich, können aber manchmal leichte Maßänderungen verursachen, die berücksichtigt werden müssen. IN625 erfordert in der Regel spezielle Lösungsglüh- oder Alterungsbehandlungen, um seine Eigenschaften für den Hochtemperatureinsatz zu optimieren.
- Wichtigkeit: Stellt die endgültigen mechanischen Eigenschaften (Festigkeit, Härte, Duktilität) auf die spezifischen Anforderungen der Anwendung ein.
- Reinigung und Inspektion:
- Prozess: Gründliche Reinigung zur Entfernung von Bearbeitungsflüssigkeiten, Schleifmitteln oder Ablagerungen. Die Endkontrolle umfasst Maßprüfungen (CMM, Scannen), Überprüfung der Oberflächenbeschaffenheit, Sichtprüfung und ggf. zerstörungsfreie Prüfung (CT-Scannen, Druckprüfung) gemäß dem Qualitätsplan.
- Wichtigkeit: Stellt sicher, dass das fertige Teil sauber ist, alle Spezifikationen erfüllt und keine kritischen Mängel aufweist, bevor es ausgeliefert oder montiert wird.
- Beschichtungen oder Oberflächenbehandlungen (optional):
- Prozess: Anwendung von Spezialbeschichtungen:
- Wärmedämmschichten (TBCs): Keramische Beschichtungen, die (häufig durch Plasmaspritzen) auf Außen- oder Innenflächen aufgebracht werden, um die Wärmeübertragung zu verringern - nützlich, um die Ansaugluft kühl zu halten oder das Material des Verteilers vor extremer Hitze zu schützen.
- Eloxieren (für Aluminium): Verbessert die Korrosionsbeständigkeit und Oberflächenhärte, ermöglicht die Einfärbung.
- Pulverbeschichtung/Lackierung: Für die Ästhetik und den grundlegenden Schutz der Umwelt.
- Trockenfilm-Schmierstoffe: Wird innerlich angewendet, um den Luftstrom zu verbessern.
- Wichtigkeit: Verbessert die Leistung (Wärmemanagement), die Haltbarkeit (Korrosions-/Verschleißfestigkeit) oder die Ästhetik. Beschichtungsoptionen für Automobilkomponenten sollte je nach Betriebsumgebung in Betracht gezogen werden.
- Prozess: Anwendung von Spezialbeschichtungen:
Planung für die Nachbearbeitung:
Es ist von entscheidender Bedeutung, die Nachbearbeitung in die anfänglichen Design-, Budget- und Vorlaufzeitberechnungen einzubeziehen. Komplexe interne Stützen, die nicht entfernt werden können, oder Designs, die eine umfangreiche manuelle Politur erfordern, erhöhen die Kosten und Verzögerungen erheblich. Die Zusammenarbeit mit einem erfahrenen AM-Dienstleister wie Met3dp, der eine Anleitung zu DfAM zur Minimierung des Nachbearbeitungsaufwands bieten kann und über eigene oder etablierte Partnerschaften zur effizienten Durchführung dieser notwendigen Schritte verfügt, ist von großem Vorteil. Ihre umfassenden Lösungen, die von fortschrittlichen Pulvern und SEBM-Drucker bis hin zu Anwendungsentwicklungsdiensten, umfassen ein Verständnis des gesamten Arbeitsablaufs, einschließlich dieser kritischen Nachbearbeitungsphasen. Wird die Nachbearbeitung nicht ordnungsgemäß geplant und durchgeführt, können die Vorteile, die sich aus dem Einsatz von AM ergeben, zunichte gemacht werden, was zu einem Bauteil führt, das die Leistungs- oder Zuverlässigkeitsstandards nicht erfüllt.
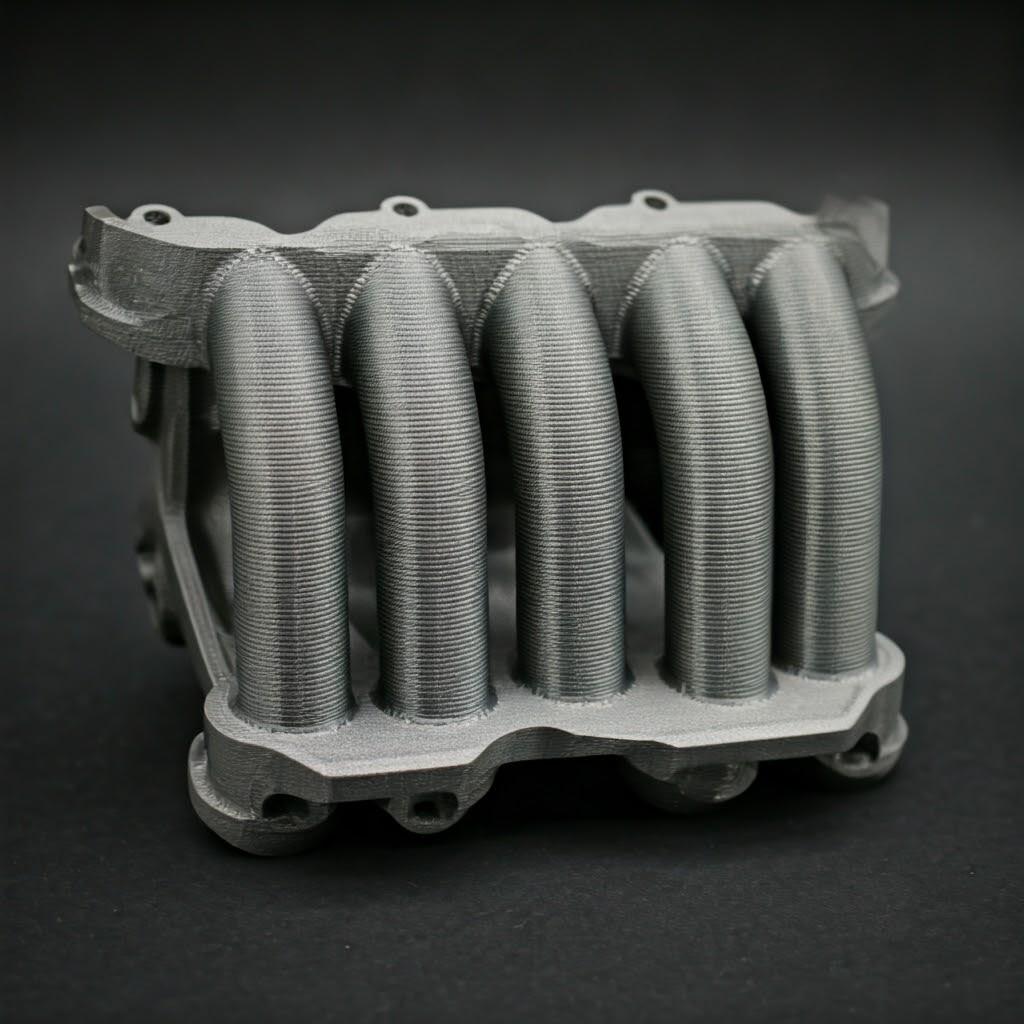
Herausforderungen bei der Metall-AM für Ansaugrohre meistern: Lösungen und bewährte Praktiken
Obwohl die additive Fertigung von Metallen enorme Vorteile für die Herstellung von Hochleistungssaugrohren bietet, ist diese Technologie nicht ohne Herausforderungen. Das Potenzial verstehen Fehler beim 3D-Druck von MetallProzessschwierigkeiten und Hürden bei der Qualitätskontrolle ist sowohl für Designer als auch für Beschaffung Teams, die sich mit Metall AM Servicebüros. Proaktive Planung, robuste Prozesskontrolle und die Einhaltung bewährter Praktiken sind der Schlüssel, um diese Probleme zu mildern und die Lieferung hochwertiger, zuverlässiger Komponenten zu gewährleisten.
Gemeinsame Herausforderungen und Abhilfestrategien:
- Verformung und Verzerrung:
- Herausforderung: Erhebliche Temperaturgradienten während des PBF-Prozesses führen zu inneren Spannungen, die dazu führen können, dass sich das Teil, insbesondere große flache Abschnitte wie Plenum-Oberflächen oder lange Kufen, während der Herstellung oder nach der Entnahme von der Bauplatte verziehen oder verzerren. Dies ist ein großes Problem für die Beibehaltung der Flanschebenheit und der allgemeinen Maßgenauigkeit.
- Lösungen und bewährte Praktiken:
- Optimierte Gebäudeausrichtung: Vermeiden Sie es, große ebene Flächen parallel zur Bauplatte auszurichten. Eine leichte Neigung kann helfen.
- Robuste Stützstrukturen: Verwenden Sie gut konzipierte Stützen, insbesondere in der Nähe von Kanten und Ecken großer Bauteile, um das Teil fest zu verankern und thermischen Spannungen entgegenzuwirken. Ziehen Sie thermische Stützen in Betracht, die speziell für die Wärmeableitung ausgelegt sind.
- Build Plate Heating: Das Vorheizen der Bauplatte (üblich beim EBM, zunehmend auch beim Laser-PBF) reduziert die thermischen Gradienten zwischen dem Teil und der Platte und verringert so die Spannungen.
- Optimierung der Prozessparameter: Die Feinabstimmung von Laser-/Strahlleistung, Scan-Geschwindigkeit und Scan-Strategie (z. B. Insel-Scanning, Schachbrettmuster) kann die lokale Wärmeentwicklung und Eigenspannung minimieren.
- Stressabbau Wärmebehandlung: Durchführung von Stressabbau vor Das Entfernen des Teils von der Bauplatte ist entscheidend für die Stabilisierung der Geometrie.
- Änderungen am Design: Fügen Sie großen ebenen Flächen leichte Wölbungen hinzu oder fügen Sie temporäre Versteifungsrippen ein (die nach dem Druck entfernt werden), um Verformungen zu vermeiden.
- Porosität:
- Herausforderung: Kleine Hohlräume oder Poren im gedruckten Material können dessen strukturelle Integrität, Ermüdungslebensdauer und Druckhaltefähigkeit beeinträchtigen. Porosität kann durch eingeschlossenes Gas (Gasporosität) oder unvollständiges Schmelzen/Schmelzen zwischen Schichten oder Scannerspuren (fehlende Schmelzporosität) entstehen.
- Lösungen und bewährte Praktiken:
- Hochwertiges Pulver: Verwenden Sie kugelförmige, trockene, hochreine Metallpulver mit optimierter Partikelgrößenverteilung (wie die von Met3dp). Schlechte Qualität oder verunreinigtes Pulver ist eine häufige Ursache für Gasporosität. Eine ordnungsgemäße Handhabung und Lagerung des Pulvers ist unerlässlich.
- Optimierte Prozessparameter: Achten Sie auf eine ausreichende Energiedichte (Verhältnis Leistung/Drehzahl), um das Material vollständig zu schmelzen. Falsche Parameter sind die Hauptursache für mangelndes Schmelzen. Eine ausführliche Parameterentwicklung für jede Material/Maschinen-Kombination ist entscheidend.
- Abschirmgas-Atmosphäre: Halten Sie eine hochreine Inertgasatmosphäre (Argon oder Stickstoff) in der Baukammer aufrecht, um Oxidation zu verhindern und Prozessnebenprodukte zu verdrängen, die Gasporosität verursachen könnten. Überwachen Sie den Sauerstoffgehalt.
- Heiß-Isostatisches Pressen (HIP): Ein Nachbearbeitungsschritt unter Einsatz von Hochtemperatur und Hochdruck-Inertgas. HIP kann innere Poren (sowohl Gas als auch fehlende Schmelze) wirksam schließen und so die Dichte und die mechanischen Eigenschaften erheblich verbessern. Es verursacht zusätzliche Kosten, kann aber für kritische Anwendungen notwendig sein.
- NDT-Inspektion: Verwenden Sie CT-Scans, um den Grad der inneren Porosität zu ermitteln und sicherzustellen, dass er innerhalb der für die Anwendung erforderlichen Grenzen liegt.
- Rissbildung (Verfestigungs-/Verflüssigungsrissbildung):
- Herausforderung: Risse können sich während der Erstarrung oder in der Wärmeeinflusszone aufgrund thermischer Spannungen bilden, insbesondere bei Legierungen mit einem breiten Erstarrungsbereich oder solchen, die zur Entmischung neigen (wie einige Aluminiumlegierungen, wenn sie nicht korrekt verarbeitet werden).
- Lösungen und bewährte Praktiken:
- Auswahl der Materialien: Wählen Sie Legierungen aus, die für ihre gute Druckbarkeit bekannt sind, oder machen Sie sich mit den besonderen Herausforderungen vertraut, die mit den gewählten Legierungen verbunden sind (z. B. sind bestimmte hochfeste Aluminiumlegierungen anfälliger für Rissbildung).
- Optimierung der Prozessparameter: Steuerung der Abkühlungsraten durch Scan-Strategie und Parametereinstellungen.
- Build Plate Heating: Verringert thermische Gradienten, was die Anfälligkeit für Risse verringert.
- Stressabbau: Nach dem Druck ist ein sofortiger Stressabbau unerlässlich.
- Entwurf: Vermeiden Sie scharfe innere Ecken oder Merkmale, die als Spannungskonzentratoren wirken.
- Unterstützung bei der Beseitigung von Schwierigkeiten:
- Herausforderung: Das Entfernen von Stützstrukturen, insbesondere von dichten oder internen Stützen in komplexen Verteilerkanälen oder Plenumsräumen, kann zeitaufwändig und kostspielig sein und die Oberfläche des Teils beschädigen. Unzugängliche interne Stützen lassen sich unter Umständen nicht vollständig entfernen.
- Lösungen und bewährte Praktiken:
- DfAM für die Minimierung der Unterstützung: Konstruieren Sie Teile mit selbsttragenden Winkeln (>45°), wo immer dies möglich ist.
- Optimierte Gebäudeausrichtung: Wählen Sie eine Ausrichtung, die den Bedarf an kritischen internen Stützen minimiert.
- Optimiertes Support-Design: Verwenden Sie Stützstrukturen (z. B. dünnwandig, perforiert, baumartig), die das Entfernen erleichtern. Sorgen Sie für ausreichende Zugänge für Werkzeuge.
- Spezialisierte Entfernungstechniken: Ziehen Sie das Drahterodieren zum präzisen Schneiden von Stützen in der Nähe der Werkstückoberfläche in Betracht oder die Fließschleifbearbeitung für die Endbearbeitung von Innenkanälen, die auch dazu beitragen kann, Reste von Innenstützen zu entfernen.
- Design für den Zugang: Wenn interne Stützen unvermeidbar sind, konstruieren Sie Zugangsöffnungen oder erwägen Sie, das Teil in druckbare Abschnitte zu unterteilen.
- Reststress-Management:
- Herausforderung: Selbst wenn der Verzug kontrolliert wird, können erhebliche Restspannungen im Bauteil verbleiben, die die Ermüdungslebensdauer und die langfristige Dimensionsstabilität beeinträchtigen oder zu unerwarteten Ausfällen im Betrieb führen können.
- Lösungen und bewährte Praktiken:
- Umfassende Stressbewältigung: Implementierung geeigneter Spannungsabbauzyklen auf der Grundlage von Material und Geometrie. Dies ist nicht verhandelbar.
- Prozess-Simulation: Verwendung von Simulationswerkzeugen zur Vorhersage von Eigenspannungsmustern und Optimierung der Fertigungsstrategie (Ausrichtung, Scanmuster) zur Minimierung von Spannungsspitzen.
- Strategie für die Bearbeitung: Berücksichtigen Sie bei der Bearbeitung von Teilen mit Eigenspannungen das Potenzial für Verzug. Manchmal ist eine stufenweise Bearbeitung mit Zwischenschritten zum Spannungsabbau erforderlich.
- Build Plate Heating: Wie bereits erwähnt, wird dadurch die Stressakkumulation während des Baus erheblich reduziert.
- Qualitätssicherung und Konsistenz:
- Herausforderung: Die Gewährleistung einer gleichbleibenden Qualität und gleichbleibender Eigenschaften von Teil zu Teil und von Charge zu Charge erfordert eine strenge Prozesssteuerung und -überwachung. Schwankungen bei den Pulverchargen, der Maschinenkalibrierung oder den atmosphärischen Bedingungen können die Ergebnisse beeinflussen.
- Lösungen und bewährte Praktiken:
- Robustes Qualitätsmanagementsystem (QMS): Arbeiten Sie mit Lieferanten wie Met3dp zusammen, die nach strengen QMS (z. B. ISO 9001, AS9100) arbeiten und Rückverfolgbarkeit, Prozesskontrolle und Dokumentation gewährleisten. Informationen über das Qualitätsengagement von Met3dp finden Sie häufig auf dem Unternehmensprofil (Über Met3dp).
- Pulvermanagement: Strenge Verfahren für die Handhabung, Lagerung, Prüfung (Chemie, PSD) und Rückverfolgbarkeit von Pulver. Das Pulverrecycling erfordert eine sorgfältige Überwachung, um eine Verschlechterung zu verhindern.
- Prozessbegleitende Überwachung: Moderne AM-Systeme enthalten Sensoren zur Überwachung der Eigenschaften des Schmelzbads, der Temperatur, des Sauerstoffgehalts usw. und liefern Qualitätsindikatoren in Echtzeit.
- Post-Build-Qualifizierung: Umsetzung eines klaren Plans für die Inspektion und Prüfung von Teilen (Abmessungen, zerstörungsfreie Prüfung, Prüfung mechanischer Eigenschaften an Prüfmustern), um die Erfüllung der Anforderungen zu überprüfen.
Schlussfolgerung zu den Herausforderungen:
Die erfolgreiche Herstellung von 3D-gedruckten Hochleistungs-Saugrohren erfordert die Anerkennung und proaktive Bewältigung dieser potenziellen Herausforderungen. Dies erfordert eine Kombination aus intelligentem Design (DfAM), sorgfältiger Materialauswahl, präzise gesteuerter Metall-AM-Verfahrengründliche Nachbearbeitung und strenge qualitätssicherung additive fertigung Protokolle. Die Zusammenarbeit zwischen Designern, Ingenieuren, Beschaffungsteams und erfahrenen AM-Dienstleistern ist von größter Bedeutung. Durch den Einsatz von Fachwissen, fortschrittlicher Technologie und bewährten Verfahren können die Herausforderungen effektiv gemeistert werden, so dass die Automobilindustrie die Vorteile der additiven Fertigung von Metallen für kritische Komponenten wie Ansaugrohre in Bezug auf Leistung, Leichtbau und Anpassung voll ausschöpfen kann.
Die Wahl Ihres Partners: Die Auswahl des richtigen 3D-Druckdienstleisters für Metall
Die Auswahl der geeigneten Additive Fertigung von Metall (AM) Dienstleisters ist wohl ebenso entscheidend wie die Optimierung des Designs oder die Wahl des richtigen Materials für Ihren 3D-gedruckten Ansaugkrümmer. Die Qualität, Leistung, Zuverlässigkeit und Kosteneffizienz des endgültigen Bauteils werden direkt von den Fähigkeiten, dem Fachwissen und den Qualitätssystemen des von Ihnen gewählten Partners beeinflusst. Mit dem rasanten Wachstum der AM-Branche bieten zahlreiche Anbieter Metalldruckdienstleistungen an, aber nicht alle sind gleich, insbesondere wenn es um anspruchsvolle Anwendungen wie Hochleistungskomponenten für die Automobilindustrie geht. Ingenieure und Beschaffung Fachleute brauchen einen strukturierten Ansatz, um einen Lieferanten zu bewerten und auszuwählen, der ihren technischen Anforderungen, Qualitätsstandards und Projektzielen gerecht wird. Eine kluge Wahl erfordert, dass man nicht nur auf das Preisangebot schaut, sondern eine Reihe von kritischen Faktoren bewertet.
Schlüsselkriterien für die Bewertung von Anbietern von Metall-AM-Dienstleistungen:
- Technische Fähigkeiten und Ausrüstung:
- Drucktechnik: Bieten sie das spezifische PBF-Verfahren (SLM, DMLS, EBM) an, das für das von Ihnen gewählte Material (AlSi10Mg, IN625) und die Komplexität des Designs am besten geeignet ist? Die verschiedenen Technologien weisen Nuancen bei der Oberflächengüte, der Auflösung der Merkmale und dem Eigenspannungsmanagement auf. Unternehmen wie Met3dp bieten neben laserbasierten Systemen auch spezialisierte Technologien wie das Selektive Elektronenstrahlschmelzen (SEBM) an und stellen damit eine breitere Palette von Optionen zur Verfügung.
- Maschinenflotte und Bauvolumen: Verfügt das Unternehmen über ausreichende Maschinenkapazitäten, um Ihre Anforderungen an die Vorlaufzeit zu erfüllen, insbesondere für eine mögliche Serienproduktion oder mehrere Prototypen? Vergewissern Sie sich, dass der maximale Bauraum für die Größe Ihres Ansaugkrümmerdesigns geeignet ist. Anbieter mit branchenführenden Druckvolumen bieten mehr Flexibilität.
- Material-Portfolio: Verarbeiten sie regelmäßig die von Ihnen benötigte Legierung (AlSi10Mg, IN625)? Verfügt er über Erfahrung und validierte Parameter für diese Werkstoffe? Können sie hochwertige, zertifizierte Pulver beziehen? Suchen Sie nach Anbietern wie Met3dp, die nicht nur verwenden, sondern auch herstellen Hochleistungsmetallpulverund gewährleisten eine umfassende Werkstoffkenntnis. Bieten sie andere relevante Legierungen an, wenn sich die Konstruktionsanforderungen ändern?
- Genauigkeit und Auflösung: Wie lauten die dokumentierten typischen Toleranzen und die erreichbaren Mindestgrößen der Merkmale für die relevanten Materialien und Maschinen? Können sie nachweisen, dass sie die für Ihre kritischen Merkmale erforderliche Präzision erreichen?
- Fachwissen, Erfahrung und technische Unterstützung:
- Erfahrung in der Anwendung: Haben sie ähnliche Bauteile, insbesondere Saugrohre oder andere komplexe Automobilteile, erfolgreich hergestellt? Können sie Fallstudien vorlegen oder einschlägige Erfahrungen in der Hochleistungsautomobilbranche nachweisen?
- DfAM-Fachwissen: Bieten sie Designberatung oder Feedback auf der Grundlage der DfAM-Prinzipien an? Können ihre Ingenieure Ihren Entwurf überprüfen und Änderungen vorschlagen, um die Druckbarkeit zu verbessern, die Kosten zu senken oder die Leistung zu steigern? Dieser kooperative Ansatz ist von unschätzbarem Wert.
- Materialwissenschaftliche Kenntnisse: Verfügt das Team über ein umfassendes Verständnis der Metallurgie, der Wärmebehandlungen und der spezifischen Materialeigenschaften von AM-Teilen? Dies ist entscheidend für die Gewährleistung einer optimalen Materialleistung und die Auswahl geeigneter Nachbearbeitungen. Met3dp, mit seinem jahrzehntelange Erfahrung in der additiven Fertigung von Metallenist ein Beispiel für diese Tiefe.
- Problemlösung: Wie gehen sie mit potenziellen Herausforderungen wie dem Verziehen oder dem Entfernen von Stützen bei komplexen Geometrien um? Erfahrene Anbieter haben robuste Lösungen und Fehlerbehebungsprotokolle entwickelt.
- Qualitätsmanagementsysteme und Zertifizierungen:
- Zertifizierungen: Sind sie nach den einschlägigen Qualitätsnormen wie ISO 9001 (allgemeines Qualitätsmanagement) oder AS9100 (Luft- und Raumfahrt, häufig von Hochleistungs-Automobilsektoren übernommen) zertifiziert? Die Zertifizierung zeigt, dass strenge Prozesskontrolle, Dokumentation und kontinuierliche Verbesserung eingehalten werden.
- Prozesskontrolle: Welche Maßnahmen ergreifen sie, um Prozessstabilität und Wiederholbarkeit zu gewährleisten? Dazu gehören Maschinenkalibrierung, Umgebungskontrollen, Protokolle für die Pulverhandhabung und möglicherweise eine prozessbegleitende Überwachung.
- Rückverfolgbarkeit: Kann der Anbieter eine vollständige Rückverfolgbarkeit der für Ihr spezifisches Teil verwendeten Materialien (Pulverchargen) und Verfahren gewährleisten? Dies ist entscheidend für die Qualitätssicherung und die Ursachenanalyse, wenn Probleme auftreten.
- Inspektionskapazitäten: Über welche ZfP- und Messgeräte verfügt das Unternehmen (CMM, 3D-Scanning, CT-Scanning, Oberflächenprofilometrie, Materialprüfung)? Können sie umfassende, auf Ihre Anforderungen zugeschnittene Prüfberichte erstellen?
- Nachbearbeitungsmöglichkeiten:
- In-House vs. Outsourced: Führen sie kritische Nachbearbeitungsschritte wie Spannungsabbau, Wärmebehandlung, CNC-Bearbeitung und Oberflächenveredelung im eigenen Haus durch oder arbeiten sie mit einem Netz von zuverlässigen Zulieferern zusammen? Eigene Kapazitäten bieten oft eine bessere Kontrolle über Qualität und Vorlaufzeiten.
- Angebot an Dienstleistungen: Kann er die für Ihren Ansaugkrümmer erforderliche spezifische Nachbearbeitung anbieten (z. B. AFM für interne Kanäle, Präzisionsbearbeitung von Flanschen, spezifische Beschichtungen)? Prüfen Sie, ob das Unternehmen über Fachwissen in diesen sekundären Arbeitsschritten verfügt.
- Kundenservice, Kommunikation und Projektmanagement:
- Reaktionsfähigkeit: Wie schnell und gründlich reagieren sie auf Anfragen und Angebotsanfragen?
- Kommunikation: Ist die Kommunikation klar, professionell und proaktiv? Werden Sie einen festen Ansprechpartner für Ihr Projekt haben?
- Kollaboration: Sind sie bereit, bei der Lösung von Design- oder Fertigungsproblemen zusammenzuarbeiten?
- Projektleitung: Verfügen sie über klare Prozesse für die Auftragsverfolgung, Fortschrittsaktualisierungen und die Verwaltung von Fristen?
- Kosten, Wert und Vorlaufzeit:
- Transparente Preisgestaltung: Ist das Angebot detailliert und leicht verständlich und werden die Kosten nach Möglichkeit aufgeschlüsselt? Seien Sie vorsichtig bei Angeboten, die zu niedrig erscheinen, da sie möglicherweise Kompromisse bei der Qualität eingehen oder notwendige Nachbearbeitungen auslassen.
- Wert-Angebot: Berücksichtigen Sie den Gesamtwert, einschließlich Fachwissen, Qualitätssicherung, Support und Zuverlässigkeit, und nicht nur den Anschaffungspreis. Ein geringfügig höherer Preis bei einem seriösen Anbieter kann in der Folgezeit viel Zeit und Geld sparen, da Ausfälle oder Verzögerungen vermieden werden.
- Zitierte Vorlaufzeiten: Sind die angegebenen Durchlaufzeiten angesichts der Komplexität des Teils und der erforderlichen Prozesse realistisch? Wie zuverlässig sind die Schätzungen der Durchlaufzeiten auf der Grundlage früherer Leistungen oder Referenzen?
Warum sollte man Met3dp in Betracht ziehen?
Auf der Grundlage dieser Kriterien kann ein Anbieter wie Met3dp stellt ein überzeugendes Argument für Unternehmen dar, die hochwertige 3D-gedruckte Ansaugrohre suchen:
- Umfassende Lösungen: Wir bieten eine synergetische Kombination aus fortschrittlichen SEBM-Druckern, hochwertiger Metallpulverherstellung (AlSi10Mg, IN625, kundenspezifische Legierungen) und Anwendungsentwicklungsdienstleistungen.
- Technische Führerschaft: Beschäftigung von branchenführendes Druckvolumen, Genauigkeit und Zuverlässigkeit über ihre Systeme hinweg, unterstützt durch fundierte materialwissenschaftliche und verfahrenstechnische Kenntnisse.
- Schwerpunkt Qualität: Wir nutzen die fortschrittliche Pulverproduktion (Gaszerstäubung, PREP) für hervorragende Pulvereigenschaften und arbeiten unter strengen Qualitätskontrollstandards sowohl für Pulver als auch für Druckdienstleistungen.
- Partnerschaftlicher Ansatz: Sie positionieren sich als Partner, der Unternehmen bei der Implementierung von AM und der Beschleunigung der digitalen Transformation in der Fertigung unterstützt, indem sie eine kooperative und unterstützende Kundenbeziehung vorschlagen.
Checkliste zur Lieferantenbewertung (Beispiel):
Kriterien | Gewichtung (1-5) | Anbieter A Bewertung (1-5) | Anbieter B Bewertung (1-5) | Met3dp Punktzahl (1-5) | Anmerkungen |
---|---|---|---|---|---|
Technologievergleich (SLM/EBM) | 5 | 4 | 5 | 5 | Met3dp bietet SEBM, potenziell vorteilhaft |
Werkstoffkompetenz (AlSi10Mg/IN625) | 5 | 3 | 4 | 5 | Met3dp stellt diese Pulver her |
Volumen aufbauen | 4 | 5 | 4 | 5 | Überprüfen Sie die spezifischen Abmessungen |
DfAM-Unterstützung | 4 | 3 | 3 | 4 | Suchen Sie nach proaktivem Design-Feedback |
Erfahrung im Automobilbereich | 4 | 2 | 4 | 4 | Fragen Sie nach relevanten Fallstudien |
Qualitätszertifizierungen (ISO/AS) | 5 | 3 | 5 | 5 | Überprüfen Sie aktuelle Zertifizierungen |
Nachbearbeitung (Inhouse-Bearbeitung) | 4 | 2 | 5 | 4 | Überprüfung spezifischer Fähigkeiten (z. B. AFM) |
Inspektionsmöglichkeiten (CT-Scan) | 4 | 1 | 4 | 4 | Bestätigung der Verfügbarkeit für interne Kontrollen |
Vorlaufzeit Zuverlässigkeit | 4 | 3 | 4 | 4 | Referenzen prüfen, wenn möglich |
Kosten (Angebotspreis) | 3 | 5 | 3 | 3 | Gleichgewicht mit Qualität/Wert |
Kommunikation/Unterstützung | 3 | 4 | 4 | 5 | Bewertung der Reaktionsfähigkeit bei der Angebotserstellung |
Gewichtete Punktzahl Gesamt | — | 126 | 156 | 168 | Illustratives Scoring |
In Blätter exportieren
Letztendlich kann das Auswahlverfahren die Einholung von Angeboten und möglicherweise Musterteilen von Anbietern, die in die engere Wahl kommen, beinhalten. Die Durchführung von Audits oder Standortbesichtigungen (falls möglich) kann ebenfalls wertvolle Erkenntnisse liefern. Investieren Sie Zeit in gründliche Bewertung des Metall-AM-Servicebüros ist von entscheidender Bedeutung für die Risikominderung und die Gewährleistung einer erfolgreichen Partnerschaft für die Produktion kritischer Hersteller von Hochleistungsteilen Kooperationen wie 3D-gedruckte Ansaugkrümmer.
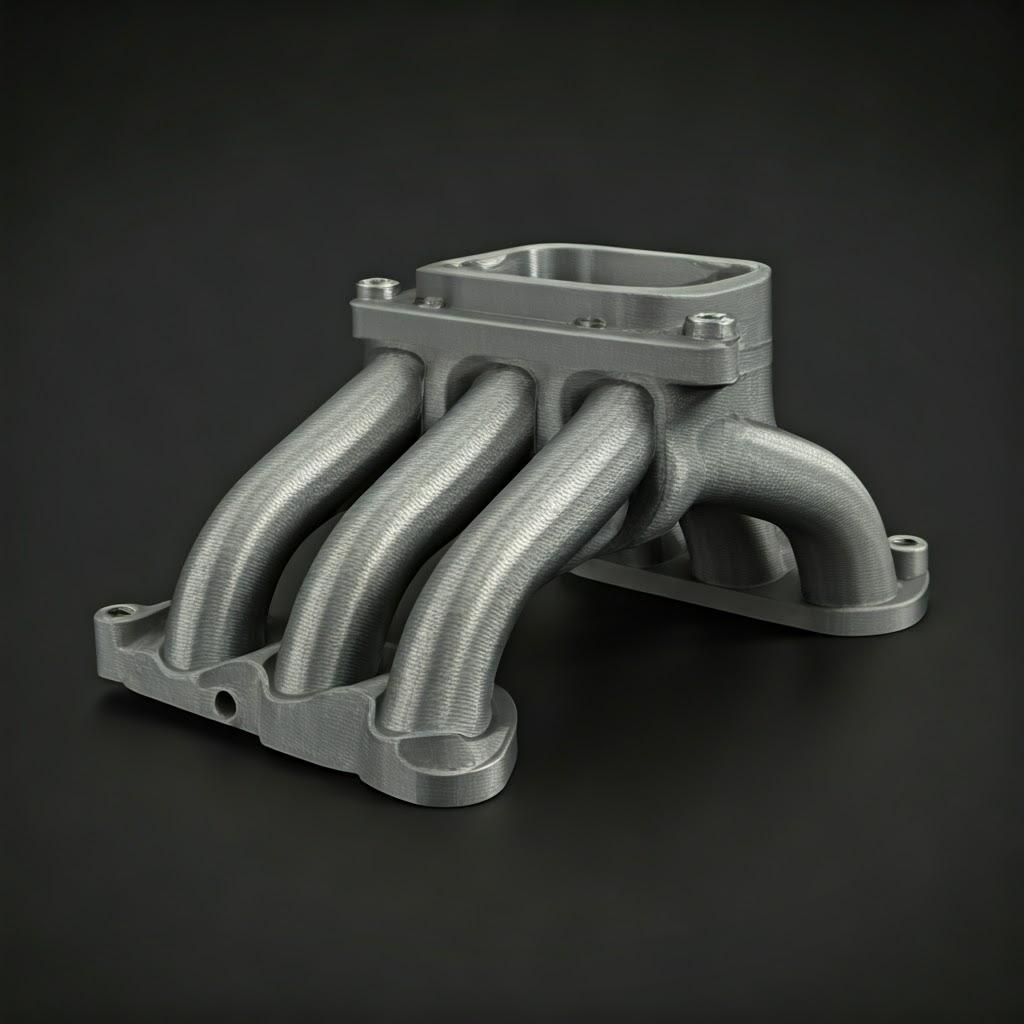
Die Investition verstehen: Kostenfaktoren und Vorlaufzeiten für 3D-gedruckte Ansaugrohre
Eine der häufigsten Fragen von Ingenieuren und Beschaffung Manager, die die additive Fertigung von Metallen in Erwägung ziehen, haben Bedenken hinsichtlich der Kosten und des Zeitaufwands für die Herstellung eines Teils wie eines Ansaugkrümmers. Durch AM entfallen zwar die mit dem Gießen verbundenen Werkzeugkosten, aber die Kostenanalyse für den 3D-Druck von Metall hängt von mehreren verschiedenen Faktoren ab. Auch die Vorlaufzeiten können deutlich kürzer sein als die traditionellen Werkzeugzyklen, werden aber von verschiedenen Faktoren beeinflusst. Das Verständnis dieser Faktoren ist der Schlüssel zu einer effektiven Budgetierung und zur Festlegung realistischer Projektzeitpläne.
Die wichtigsten Kostenfaktoren für AM-Ansaugrohre aus Metall:
- Materialkosten:
- Pulvertyp: Dies ist ein wichtiges Unterscheidungsmerkmal. Hochleistungs-Nickel-Superlegierungen wie IN625 sind pro Kilogramm deutlich teurer als Aluminiumlegierungen wie AlSi10Mg. Für exotische oder kundenspezifische Legierungen werden noch höhere Preise verlangt.
- Pulververbrauch: Das Gesamtvolumen des Teils, einschließlich der erforderlichen Stützstrukturen, wirkt sich direkt auf die Menge des verbrauchten Pulvers aus. Mit DfAM optimierte Designs (Topologieoptimierung, reduzierte Stützstrukturen) können den Materialverbrauch senken.
- Qualität des Pulvers: Hochwertige, kugelförmige Pulver mit kontrollierter PSD von renommierten Anbietern wie Met3dp sind zwar mit höheren Anschaffungskosten verbunden, tragen aber zu einer besseren Druckqualität, weniger Fehlern und gleichmäßigeren Ergebnissen bei, was die Gesamtkosten senken kann.
- Recycling: Ungeschmolzenes Pulver ist zwar weitgehend recycelbar, aber der Recyclingprozess selbst ist mit Kosten und Qualitätskontrollmaßnahmen verbunden.
- Maschinenzeit (Bauzeit):
- Teil Volumen & Höhe: Bei größeren Teilen oder höheren (vertikal ausgerichteten) Bauteilen dauert es länger, Schicht für Schicht zu drucken.
- Komplexität: Hochkomplexe Geometrien können langsamere Scan-Geschwindigkeiten oder kompliziertere Scan-Strategien erfordern, was den Zeitaufwand erhöht.
- Schichtdicke: Dünnere Schichten bieten eine bessere Auflösung und Oberflächengüte, erhöhen aber die Anzahl der Schichten und damit die Bauzeit erheblich.
- Maschinentyp und Wirkungsgrad: Verschiedene Maschinen (z. B. Multilasersysteme) haben unterschiedliche Produktionsraten. Die stündliche Betriebsrate der Maschine (Abschreibung, Energie, Wartung, Verbrauchsmaterial) ist eine wichtige Kostenkomponente.
- Verschachtelung: Wenn mehrere Teile (oder mehrere Kopien desselben Teils) effizient auf einer einzigen Bauplatte verschachtelt werden können, lassen sich die Maschinenzeitkosten pro Teil senken.
- Arbeitskosten:
- Vorverarbeitung: Die Vorbereitung von CAD-Dateien, die Simulation des Aufbaus, die Optimierung der Ausrichtung und die Erstellung von Hilfestellungen erfordern Zeit für qualifizierte Ingenieure.
- Einrichten und Abrüsten der Maschine: Das Vorbereiten der Maschine, das Laden des Pulvers, das Entladen des Aufbaus und die Grundreinigung erfordern Zeit vom Bediener.
- Entpudern: Die manuelle Entfernung von ungeschmolzenem Pulver, insbesondere aus den inneren Kanälen, kann arbeitsintensiv sein.
- Unterstützung bei der Entfernung: Dabei handelt es sich oft um einen erheblichen Anteil an Handarbeit, der sorgfältige Arbeit mit Handwerkzeugen, Schleifmaschinen oder EDM erfordert.
- Nachbearbeitung und Veredelung: Arbeit im Zusammenhang mit der Bearbeitung, dem Trowalisieren, Polieren, Reinigen und Prüfen.
- Nachbearbeitungskosten:
- Wärmebehandlung: Kosten für Ofenzeit, Energieverbrauch und möglicherweise kontrollierte Atmosphäre für Stressabbau oder immobilienverbessernde Behandlungen.
- Bearbeitungen: Kosten im Zusammenhang mit CNC-Maschinenzeit, Werkzeugen und Programmierung für die Endbearbeitung kritischer Merkmale.
- Oberflächenveredelung: Kosten für spezielle Verfahren wie AFM, Elektropolieren oder umfangreiches manuelles Polieren.
- HIP (Heiß-Isostatisches Pressen): Falls dies für eine maximale Dichte und Ermüdungslebensdauer erforderlich ist, bedeutet HIP aufgrund der damit verbundenen Spezialausrüstung einen erheblichen Kostenfaktor.
- Inspektion und Qualitätssicherung: Kosten im Zusammenhang mit CMM-Messungen, 3D-Scans, NDT (CT-Scans sind besonders teuer) und Qualitätsdokumentation.
- Gemeinkosten und Gewinn der Lieferanten: Die Dienstleister berücksichtigen ihre Betriebskosten (Gebäude, Verwaltung, F&E) und ihre Gewinnspanne.
Faktoren, die die Vorlaufzeit beeinflussen:
- Bauzeit: Wie oben beschrieben, ist dies oft die größte Einzelkomponente des Zeitplans, die je nach Größe und Komplexität des Verteilers zwischen Stunden und mehreren Tagen liegen kann.
- Verfügbarkeit der Maschine: Die aktuelle Auslastung des Dienstleisters und die Warteschlange bei der Maschinenplanung wirken sich darauf aus, wann der Druck Ihres Teils beginnen kann. Zeiten hoher Nachfrage können zu längeren Warteschlangen führen.
- Nachbearbeitung Dauer: Jeder Schritt kostet Zeit:
- Stressabbau: In der Regel 8-24 Stunden (einschließlich kontrollierter Abkühlung).
- Bearbeitungen: Stunden bis Tage, je nach Komplexität und Einrichtung.
- Ausbau/Fertigstellung der Stütze: Stunden bis Tage, je nach Konstruktion sehr unterschiedlich.
- HIP/Spezialisierte Beschichtungen: Kann aufgrund von Logistik und Chargenverarbeitung mehrere Tage in Anspruch nehmen.
- Inspektion: Stunden bis Tage.
- Versand: Zeit, die für den Transport vom Dienstleister zu Ihrer Einrichtung benötigt wird.
- Iterationen: Wenn bei Prototypen Designänderungen und Neudrucke erforderlich sind, verlängert sich der Gesamtzeitplan des Projekts erheblich.
Typische Vorlaufzeitspannen (Schätzungen):
- Einfacher Prototyp (minimale Nachbearbeitung): 5-10 Werktage
- Komplexer Verteiler (AlSi10Mg, Standard-Nachbearbeitung): 2-4 Wochen
- Komplexer Verteiler (IN625, umfangreiche Nachbearbeitung + HIP): 4-8 Wochen+
Kosten im Vergleich zu traditionellen Methoden:
- Prototyping: Metall-AM ist oft schneller und kostengünstiger als die Erstellung von Prototypwerkzeugen für den Guss oder die aufwändige CNC-Programmierung für die Bearbeitung komplexer Krümmer aus Knüppeln.
- Kleinserienproduktion (1-100 Einheiten): AM kann sehr wettbewerbsfähig sein, vor allem bei komplexen Konstruktionen, bei denen die Herstellung von Gusswerkzeugen teuer ist und sich nur über wenige Teile amortisieren lässt, oder bei denen die maschinelle Bearbeitung zu verschwenderisch und zeitaufwändig ist.
- Mittlere bis hohe Produktionsmengen (100-1000+): Das traditionelle Gießen ist in der Regel aufgrund der Amortisation der Werkzeuge und der schnelleren Zykluszeiten pro Teil kostengünstiger, es sei denn, die einzigartigen Leistungs- oder Leichtgewichtsvorteile, die nur durch AM möglich sind, rechtfertigen höhere Kosten pro Teil, oder wenn die Komplexität des Designs das Gießen unmöglich macht.
Genaue Angebote einholen:
Um ein genaues Angebot und einen Kostenvoranschlag für Ihr Ansaugkrümmerprojekt zu erhalten, geben Sie potenziellen Lieferanten die folgenden Informationen:
- 3D-CAD-Modell: In einem Standardformat (STEP, STL).
- Spezifikation des Materials: AlSi10Mg, IN625, oder andere.
- Erforderliche Menge: Einschließlich potenzieller künftiger Mengen.
- Kritische Toleranzen: Die wesentlichen Merkmale sind in den Zeichnungen klar definiert.
- Anforderungen an die Oberflächenbeschaffenheit: Geben Sie Ra-Werte für kritische innere/äußere Oberflächen an.
- Post-Processing-Bedarf: Detaillierte Angaben zu den erforderlichen Wärmebehandlungen, Bearbeitungen, Endbearbeitungen, Prüfungen (NDT) oder Beschichtungen.
- Details zur Anwendung: Die Kenntnis der Betriebsbedingungen (Druck, Temperatur) hilft dem Lieferanten bei der Beurteilung der Machbarkeit und der Empfehlung der besten Verfahren.
Großhandel 3D-Druck Dienstleistungen: Für Unternehmen, die regelmäßig oder in größeren Mengen AM-Teile herstellen müssen, bietet sich eine Untersuchung der 3D-Druckdienste für den Großhandel oder der Aufbau kontinuierlicher Partnerschaften mit Anbietern wie Met3dp kann im Vergleich zu einmaligen Aufträgen zu optimierten Preisstrukturen, dedizierten Kapazitäten und rationalisierten Arbeitsabläufen führen. Die Erörterung von Volumenprognosen und langfristigen Bedürfnissen kann potenzielle Effizienzgewinne freisetzen. Die ROI Additive Fertigung Automotive Die Vorteile, die ein Projekt mit sich bringt, liegen oft in der schnelleren Entwicklung, der besseren Leistung und dem geringeren Gewicht, was in bestimmten Fällen die potenziell höheren Kosten pro Teil im Vergleich zu herkömmlichen Methoden aufwiegen kann.
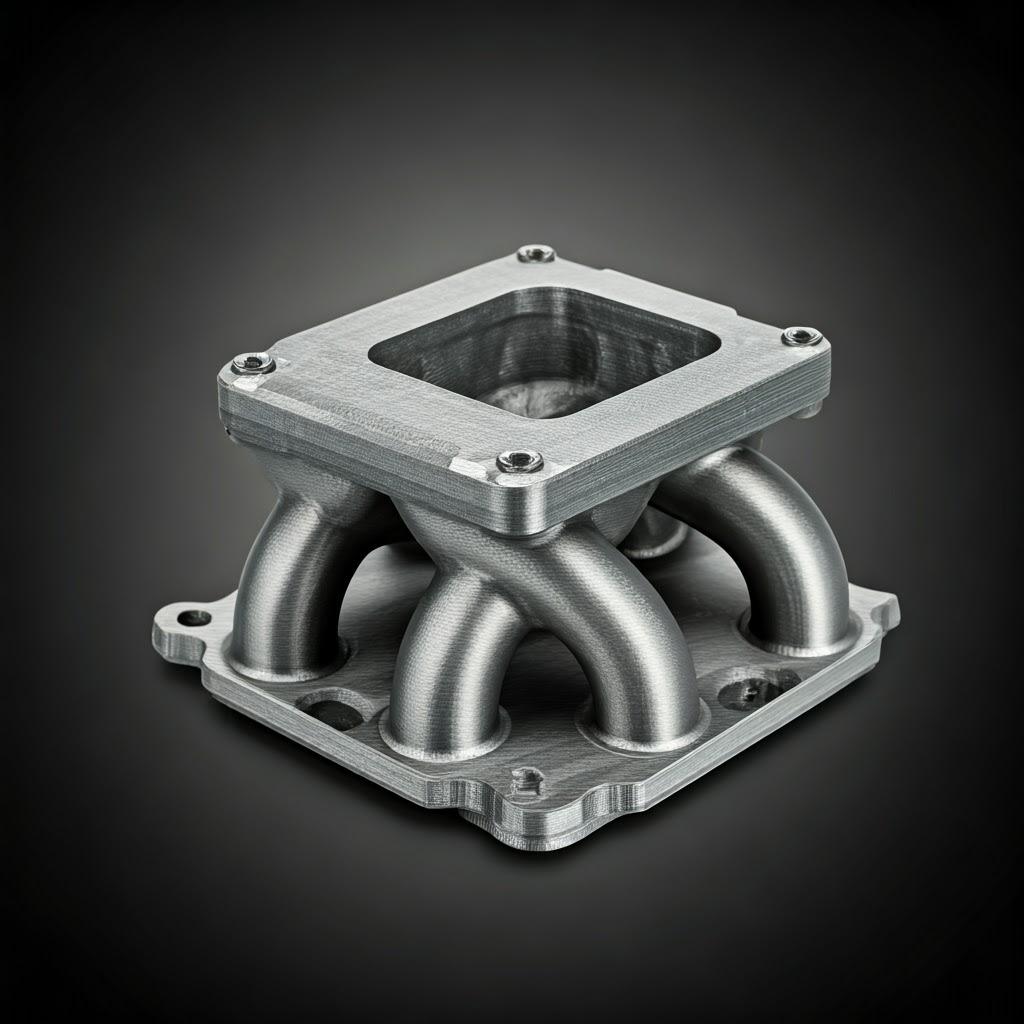
Häufig gestellte Fragen (FAQ) zu 3D-gedruckten Ansaugrohren
Hier finden Sie Antworten auf einige häufig gestellte Fragen zur Verwendung der additiven Fertigung von Metall für Ansaugrohre:
1. Wie haltbar sind 3D-gedruckte Ansaugrohre aus Metall im Vergleich zu gegossenen oder gefrästen?
Bei korrektem Entwurf, der Herstellung unter Verwendung hochwertiger Materialien und Verfahren und einer angemessenen Nachbearbeitung (insbesondere Spannungsentlastung und möglicherweise HIP) können 3D-gedruckte Ansaugkrümmer aus Metall eine vergleichbare oder sogar bessere Haltbarkeit als herkömmliche Gegenstücke aufweisen.
- Materialeigenschaften: AM-Teile aus Legierungen wie AlSi10Mg oder IN625 können Dichten von mehr als 99,5% und mechanische Eigenschaften (Zugfestigkeit, Streckgrenze, Ermüdungsfestigkeit) erreichen, die den Gussnormen für dieselben Legierungen entsprechen oder diese übertreffen, insbesondere nach optimierten Wärmebehandlungen.
- Optimierung des Designs: Die Möglichkeit, das Design mit Hilfe von Topologieoptimierung und DfAM-Prinzipien zu optimieren, ermöglicht die Platzierung von Material genau dort, wo es für die Festigkeit erforderlich ist, so dass im Vergleich zu konstruktiv beeinträchtigten Gussteilen stärkere Strukturen bei ähnlichem oder geringerem Gewicht entstehen können.
- Potenzielle Schwachstellen: Unsachgemäß verarbeitete Teile können Porosität oder Eigenspannungen aufweisen, was die Haltbarkeit beeinträchtigen kann. Die Wahl eines seriösen Anbieters mit einer soliden Qualitätskontrolle wie Met3dp ist entscheidend, um diese Risiken zu minimieren. Interne Oberflächenrauhigkeit könnte, wenn sie nicht durch Nachbearbeitung wie AFM behoben wird, theoretisch die langfristige Ermüdungslebensdauer unter hohen Zyklusbedingungen beeinflussen, obwohl dies oft zweitrangig gegenüber den Materialeigenschaften ist.
- Vergleich: Im Vergleich zu gefertigten/geschweißten Krümmern gibt es bei monolithischen AM-Teilen keine potenziellen Fehlerstellen an Schweißnähten. Im Vergleich zu maschinell gefertigten Teilen hängen die Eigenschaften von AM-Teilen stark von der Prozesssteuerung ab, können aber sehr ähnlich sein, insbesondere nach HIP.
2. Ist der 3D-Druck von Ansaugrohren kosteneffizient?
Das Kosten-Nutzen-Verhältnis hängt stark von der jeweiligen Anwendung, dem Produktionsvolumen, der Komplexität der Konstruktion und dem Wert, der auf Leistungssteigerungen oder eine beschleunigte Entwicklung gelegt wird, ab.
- Prototyping und Kleinserien: Äußerst kosteneffizient. Es vermeidet die hohen Vorlaufkosten und langen Vorlaufzeiten für Gusswerkzeuge und ist oft billiger und schneller als die komplexe mehrachsige CNC-Bearbeitung von Knüppeln für Einzelstücke oder Kleinserien (1-50 Stück).
- Komplexe Entwürfe: Für Verteiler mit komplizierten internen Geometrien, die für den Durchfluss optimiert sind, kann AM die beste Lösung sein. nur praktikable Herstellungsmethode, so dass die Kosten für die Erzielung der gewünschten Leistung eine untergeordnete Rolle spielen.
- Leistungswert: Wenn das AM-fähige Design messbare Verbesserungen in Bezug auf Leistung, Drehmoment, Ansprechverhalten oder entscheidende Gewichtseinsparungen bietet (insbesondere bei Motorsport- oder Hochleistungsfahrzeugen), können die höheren Kosten pro Teil im Vergleich zu Großseriengussteilen leicht durch den gewonnenen Wettbewerbsvorteil gerechtfertigt werden.
- Hohe Lautstärke: Für Standarddesigns in der Massenproduktion (Tausende von Einheiten) bleibt das traditionelle Gießen in der Regel pro Teil kostengünstiger.
- Zusammenfassung: Betrachten Sie die Gesamtbetriebskosten, einschließlich der Einsparungen bei der Entwicklungszeit, der Leistungsvorteile und des Potenzials für die Teilekonsolidierung, und nicht nur die Herstellungskosten pro Stück. Für hochleistungsfähige Ansaugrohre in kleinen bis mittleren Stückzahlen oder hochgradig kundenspezifische Ansaugrohre, 3D-Druck von Metall bietet oft ein ausgezeichnetes Preis-Leistungs-Verhältnis.
3. Welche Informationen sind wichtig, um einem Anbieter von Metall-AM-Dienstleistungen ein genaues Angebot machen zu können?
Um einen zeitnahen und genauen Kostenvoranschlag zu erhalten, sollten Sie so viele Details wie möglich angeben. Zu den wichtigsten Informationen gehören:
- 3D-CAD-Daten: Ein gut definiertes Volumenmodell in einem neutralen Format wie STEP wird bei Fertigungsangeboten gegenüber Netzdateien wie STL bevorzugt, obwohl STL selbst oft für den Druck verwendet wird. Legen Sie 2D-Zeichnungen bei, wenn bestimmte Toleranzen oder Merkmale klar benannt werden müssen.
- Auswahl der Materialien: Geben Sie die gewünschte Legierung (z. B. AlSi10Mg, IN625) und alle erforderlichen Materialzertifizierungen deutlich an.
- Menge: Anzahl der für diesen Auftrag benötigten Teile und voraussichtliche künftige Mengen (hilft bei der Beurteilung des Potenzials für Mengenpreise).
- Kritische Abmessungen und Toleranzen: Heben Sie Merkmale hervor, die enge Toleranzen erfordern (z. B. Flanschebene, Bohrungsdurchmesser), und geben Sie die erforderlichen Werte an. Verwenden Sie gegebenenfalls geometrische Bemaßung und Tolerierung (GD&T).
- Anforderungen an die Oberflächenbeschaffenheit: Geben Sie die gewünschten Ra-Werte für kritische Oberflächen an (z. B. Innenlaufflächen, Dichtflächen).
- Nachbearbeitungsanforderungen: Führen Sie alle erforderlichen Schritte auf: spezifische Wärmebehandlungszyklen (z. B. Spannungsarmglühen, T6-Anlassen), erforderliche Bearbeitungsvorgänge, Endbearbeitung (z. B. Perlstrahlen, AFM, Polieren), Prüfanforderungen (z. B. Druckprüfung, CT-Scan) und etwaige Beschichtungen.
- Anwendungskontext: Beschreiben Sie kurz den Motortyp (NA, Turbo, Kompressor), die erwarteten Betriebsdrücke und -temperaturen sowie die primären Leistungsziele. Dies hilft dem Anbieter, eine entsprechende Beratung anzubieten.
4. Können die internen Passagen eines 3D-gedruckten Ansaugkrümmers für einen optimalen Luftstrom perfekt glatt gemacht werden?
Das Erzielen perfekt glatter interner Passagen erfordert besondere Aufmerksamkeit bei der Gestaltung und Nachbearbeitung.
- As-Built Ausführung: Die Innenflächen von AM-Teilen, insbesondere solche, die Stützstrukturen erfordern oder ungünstig ausgerichtet sind, weisen einen gewissen Grad an Rauheit auf (typischerweise Ra 10-25 µm oder mehr). Die nach unten gerichteten Oberflächen sind in der Regel am rauesten.
- DfAM Auswirkungen: Die Konstruktion von Kufen mit selbsttragenden Winkeln (>45°) minimiert den Bedarf an internen Stützen, was zu vergleichsweise glatteren Oberflächen führt als bei gestützten Abschnitten. Die vertikale Ausrichtung der Kufen kann ebenfalls hilfreich sein.
- Post-Processing-Lösungen:
- Abrasive Fließbearbeitung (AFM): Dies ist oft die wirksamste Methode zum Glätten komplexer interner Passagen, indem ein abrasiver Kitt durch sie hindurchfließt. Sie kann die Rauheit erheblich reduzieren (und möglicherweise Ra < 5 µm erreichen).
- Taumeln/Gleitschleifen: Kann eine gewisse Glättung bewirken, wenn das Medium interne Bereiche effektiv erreichen kann, ist aber weniger zielgerichtet als AFM.
- Elektropolieren: Wirksam für bestimmte Legierungen und Geometrien, die sehr glatte Oberflächen ergeben.
- Abstriche: Die Erzielung ultraglatter Innenoberflächen verursacht aufgrund der zusätzlichen Nachbearbeitungsschritte zusätzliche Kosten und Vorlaufzeiten. Der Leistungsvorteil einer schrittweisen Verbesserung der Glätte muss gegen diese Kosten abgewogen werden. Während glattere Oberflächen im Allgemeinen besser für eine ideale laminare Strömung sind, bieten die komplexen Geometrien, die durch AM möglich sind, oft größere Leistungsgewinne durch optimierte Formen, selbst mit einer etwas raueren Oberfläche als bei einem spiegelpolierten Rohr.
Schlussfolgerung: Die Zukunft der automobilen Leistung mit additiver Fertigung von Metallen
Der Ansaugkrümmer, ein entscheidendes Bauteil für die Atmung und Leistung des Motors, ist ein gutes Beispiel dafür, wie Metall-Additiv-Fertigung ist dabei, die Landschaft des Hochleistungsautomobilbaus neu zu gestalten. Wie wir erforscht haben, werden die Einschränkungen, die mit dem traditionellen Gießen und der maschinellen Bearbeitung einhergehen - Einschränkungen der Designkomplexität, langwierige Werkzeugprozesse, Materialabfall und Schwierigkeiten bei der kundenspezifischen Anpassung von Kleinserien - durch die schichtweise Präzision und Freiheit, die Metall-3D-Drucktechnologien wie SLM, DMLS und SEBM bieten, effektiv überwunden.
Die Vorteile sind überzeugend: unvergleichlich Gestaltungsfreiheit Ermöglichung CFD-optimierter Laufwege und integrierter Funktionen; erhebliche Leichtbau durch Topologieoptimierung und effizienten Materialeinsatz; die Fähigkeit zur Nutzung von Hochleistungsmaterialien wie leichtes AlSi10Mg und Hochtemperatur-IN625, die auf spezifische Betriebsbedingungen zugeschnitten sind; und drastische beschleunigte Prototyping- und Entwicklungszyklen. Diese Vorteile schlagen sich direkt in spürbaren Leistungssteigerungen nieder - verbesserter volumetrischer Wirkungsgrad, verbesserte Gasannahme, optimierte Drehmomentkurven und höhere Gesamtmotorleistung - und verschaffen Herstellern und Rennteams einen entscheidenden Wettbewerbsvorteil.
Um dieses Potenzial auszuschöpfen, ist jedoch ein ganzheitlicher Ansatz erforderlich. Der Erfolg hängt ab von der Einbeziehung Design für additive Fertigung (DfAM) Grundsätze, die sorgfältige Auswahl der geeigneten MaterialienVerständnis und Planung für wesentliche Nachbearbeitung Schritte (vom Spannungsabbau bis zur Präzisionsbearbeitung und Oberflächenveredelung) und die Navigation durch potenzielle Fertigungs Herausforderungen durch robuste Prozesskontrolle und Qualitätssicherung.
Entscheidend für die Reise ist die Auswahl des richtigen Produktionspartners. Ein Anbieter wie Met3dp verkörpert die notwendige Kombination aus Spitzentechnologie, umfassender Materialkenntnis (sowohl als Pulverhersteller als auch als Druckdienstleister), strengen Qualitätssystemen und einem kooperativen Ansatz. Ihr umfassende Lösungendie fortschrittliche Drucker, optimierte Metallpulver und Unterstützung bei der Anwendungsentwicklung umfassen, machen sie zu einem wichtigen Partner für Unternehmen, die die Vorteile der Metall AM für anspruchsvolle Anwendungen wie Ansaugrohre.
Die Zukunft des AutomobilbausInsbesondere in den Bereichen Leistung, Motorsport und Spezialfahrzeuge wird der Einsatz der additiven Fertigung zweifelsohne zunehmen. Für Komponenten wie Ansaugkrümmer, bei denen die Optimierung des Luftstroms, die Gewichtsreduzierung und die Anpassung an Kundenwünsche im Vordergrund stehen, ist der 3D-Metalldruck nicht mehr nur eine praktikable Alternative, sondern wird schnell zum Maßstab für Innovation und Leistung. Durch die Zusammenarbeit mit kompetenten Zulieferern und die strategische Integration von AM in ihre Konstruktions- und Produktionsabläufe können Automobilunternehmen die Grenzen der Motorleistung weiter verschieben und die nächste Generation von Hochleistungsfahrzeugen vorantreiben.
Teilen auf
MET3DP Technology Co., LTD ist ein führender Anbieter von additiven Fertigungslösungen mit Hauptsitz in Qingdao, China. Unser Unternehmen ist spezialisiert auf 3D-Druckgeräte und Hochleistungsmetallpulver für industrielle Anwendungen.
Fragen Sie an, um den besten Preis und eine maßgeschneiderte Lösung für Ihr Unternehmen zu erhalten!
Verwandte Artikel
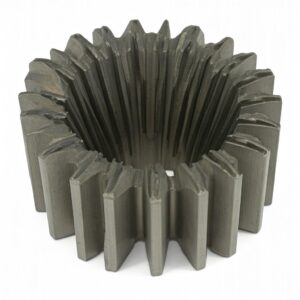
Hochleistungs-Düsenschaufelsegmente: Revolutionierung der Turbineneffizienz mit 3D-Metalldruck
Mehr lesen "Über Met3DP
Aktuelles Update
Unser Produkt
KONTAKT US
Haben Sie Fragen? Senden Sie uns jetzt eine Nachricht! Wir werden Ihre Anfrage mit einem ganzen Team nach Erhalt Ihrer Nachricht bearbeiten.
Holen Sie sich Metal3DP's
Produkt-Broschüre
Erhalten Sie die neuesten Produkte und Preislisten
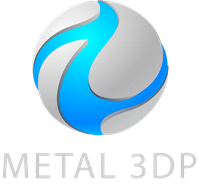
Metallpulver für 3D-Druck und additive Fertigung