Einführung in die mechanische Legierung für den 3D-Druck von Metallpulvern
Inhaltsübersicht
Die Welt der 3D-Druck Metallpulver entwickelt sich in erstaunlichem Tempo weiter und verschiebt die Grenzen des Möglichen in Bezug auf Design, Komplexität und Materialauswahl. Insbesondere die additive Fertigung von Metallen hat die Türen zur Herstellung komplizierter und funktionaler Objekte direkt aus digitalen Modellen geöffnet. Aber haben Sie sich jemals gefragt, wie das in diesen Druckern verwendete Metallpulver überhaupt hergestellt wird? Hier kommt das mechanische Legieren ins Spiel, eine faszinierende Technologie, die eine entscheidende Rolle bei der Herstellung von Hochleistungsmetallen spielt. 3D-Druck Metallpulver.
die Grundprinzipien des mechanischen Legierens
Stellen Sie sich vor, Sie haben einen Cocktailshaker, der mit verschiedenfarbigen Bonbons gefüllt ist. Durch kräftiges Schütteln werden die Bonbons vermischt, so dass eine scheinbar gleichmäßige Mischung entsteht. Dies ist im Wesentlichen das Grundprinzip des mechanischen Legierens. Dabei handelt es sich um ein Verfahren zur Verarbeitung von Feststoffpulvern, bei dem durch Hochenergie-Kugelmahlen mehrere Metallpulver auf atomarer Ebene miteinander vermischt und vermengt werden.
Hier finden Sie eine genauere Aufschlüsselung des Prozesses:
- Auswahl des Pulvers: Der erste Schritt besteht in der sorgfältigen Auswahl der gewünschten Metallpulver auf der Grundlage der endgültigen Materialeigenschaften und Anwendungsanforderungen. Dabei kann es sich um einzelne Elemente, vorlegierte Pulver oder sogar um Kombinationen aus beiden handeln.
- Fräsverfahren: Die ausgewählten Pulver werden dann in eine Hochenergie-Kugelmühle gefüllt, die im Wesentlichen wie ein riesiger Rüttler funktioniert. In der Mühle prallen zahlreiche Kugeln aus einem härteren Material (häufig Stahl oder Keramik) mit hoher Geschwindigkeit auf die Pulverpartikel. Durch diese intensive mechanische Kraft werden die Pulverpartikel gebrochen, verformt und verschweißt, wodurch eine innige Vermischung und ein neues Produkt entstehen, homogenisiertes Pulvermaterial mit einzigartigen Eigenschaften.
- Pulversammlung und -verarbeitung: Nach einer vorgegebenen Mahldauer wird das entstandene Pulver gesammelt und weiteren Verarbeitungsschritten wie Sieben und Klassieren unterzogen, um die gewünschte Partikelgrößenverteilung und Morphologie zu erreichen.
Stellen Sie sich das folgendermaßen vor: Stellen Sie sich vor, Sie versuchen, Schokoladenstückchen und Mehl mit der Hand zu mischen. Das Ergebnis ist vielleicht eine einigermaßen vermengte Mischung, aber es gibt immer noch unterschiedliche Anteile von jeder Zutat. Beim mechanischen Legieren hingegen werden diese Zutaten in einen leistungsstarken Mixer gegeben, der eine viel gleichmäßigere und konsistentere Mischung auf der Ebene der einzelnen Partikel erzielt.
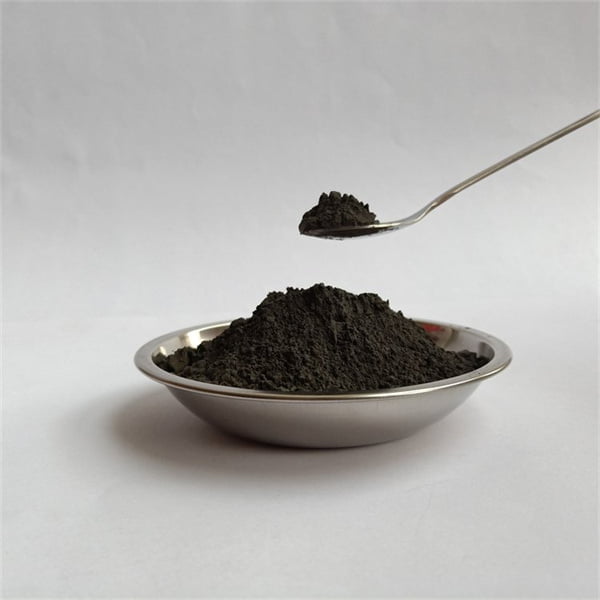
Mechanische Legierung bei der Herstellung von 3D-gedruckten Metallpulvern
Mechanisches Legieren ist ein vielseitiger Ansatz zur Herstellung von Metallpulvern, die speziell für 3D-Druckanwendungen geeignet sind. Hier erfahren Sie, wie es eine Schlüsselrolle spielt:
- Neue Legierungen schaffen: Durch das Mischen verschiedener elementarer Pulver ermöglicht das mechanische Legieren die Herstellung neuartiger Legierungen mit spezifischen Eigenschaften, die in herkömmlicher Form nicht ohne weiteres verfügbar sind. Dies eröffnet die Möglichkeit, Materialeigenschaften wie Festigkeit, Korrosionsbeständigkeit und thermisches Verhalten für bestimmte 3D-Druckanwendungen individuell zu gestalten.
- Verbesserung der Pulvereigenschaften: Mechanisches Legieren kann auch die Fließfähigkeit, die Packungsdichte und die allgemeine Druckfähigkeit bestehender Metallpulver verbessern. Durch die Verfeinerung der Partikelgröße und -morphologie wird das Pulver für verschiedene 3D-Druckverfahren wie Laser Powder Bed Fusion (LPBF) und Electron Beam Melting (EBM) besser geeignet.
- Ermöglichung von Verbundwerkstoff-Pulvern: Diese Technik ebnet auch den Weg für die Entwicklung von Metallmatrix-Verbundwerkstoffen (MMC) für den 3D-Druck. Indem keramische oder andere Verstärkungspartikel durch mechanisches Legieren in die Metallmatrix eingearbeitet werden, bietet das resultierende Pulver verbesserte mechanische Eigenschaften wie Verschleißfestigkeit und Hochtemperaturleistung.
Das mechanische Legieren ist ein leistungsfähiges Werkzeug, um das Potenzial des 3D-Drucks von Metallen zu erschließen. Es ermöglicht die Herstellung neuartiger Werkstoffe mit genau zugeschnittenen Eigenschaften, die den Anforderungen verschiedener Anwendungen gerecht werden.
Die Vorteile des mechanischen Legierens bei 3D-Druck von Metallpulvern
Im Vergleich zu herkömmlichen Pulverherstellungsmethoden wie der Zerstäubung bietet das mechanische Legieren mehrere entscheidende Vorteile für den 3D-Druck:
- Größere kompositorische Kontrolle: Sie ermöglicht die Herstellung präziser und gleichmäßiger Legierungen mit spezifischen Zusammensetzungen, die nicht auf leicht erhältliche vorlegierte Pulver beschränkt sind.
- Verbesserte Pulvereigenschaften: Das Verfahren verfeinert die Pulverpartikel und verbessert ihre Fließfähigkeit, Packungsdichte und Druckfähigkeit, was zu einer besseren Leistung in 3D-Druckverfahren führt.
- Entwicklung von neuartigen Materialien: Sie ermöglicht die Herstellung einzigartiger Legierungen und Metallmatrix-Verbundwerkstoffe mit Eigenschaften, die mit herkömmlichen Methoden nicht erreicht werden können, und erweitert die Möglichkeiten für 3D-Druckanwendungen.
- Skalierbarkeit: Das mechanische Legieren kann für die Herstellung kleiner oder großer Pulverchargen angepasst werden und eignet sich daher sowohl für die Forschung als auch für die industrielle Produktion.
Es ist jedoch wichtig zu wissen, dass das mechanische Legieren auch gewisse Einschränkungen mit sich bringt:
- Bearbeitungszeit: Der Fräsprozess kann zeit- und energieaufwendig sein, insbesondere bei härteren oder komplexeren Materialkombinationen.
- Kontaminationspotenzial: Die sorgfältige Auswahl der Mahlmedien und die Prozesskontrolle sind entscheidend für Verunreinigung minimieren von den Mahlkugeln oder der Umgebung.
- Kostenüberlegungen: Einrichtung und Pflege von High
Spezifische Metallpulvermodelle für den 3D-Druck durch mechanisches Legieren
Während die Kernfunktionalitäten gleich bleiben, werden spezifische Metallpulvermodelle, die durch mechanisches Legieren hergestellt werden, für verschiedene 3D-Druckanwendungen und Leistungsanforderungen eingesetzt. Hier sind 10 bemerkenswerte Beispiele:
1. Inconel 625: Dieses Superlegierungspulver auf Nickel-Chrom-Basis zeichnet sich durch außergewöhnliche Hochtemperaturfestigkeit, Oxidationsbeständigkeit und Kriechfestigkeit aus. Es eignet sich besonders für anspruchsvolle Anwendungen wie Komponenten für die Luft- und Raumfahrt, Gasturbinenteile und Wärmetauscher im Bereich des 3D-Drucks.
2. Ti-6Al-4V: Dieses Pulver aus einer Titanlegierung bietet ein hervorragendes Gleichgewicht aus Festigkeit, Gewicht und Biokompatibilität. Aufgrund seiner günstigen Eigenschaften bei der Herstellung durch mechanisches Legieren wird es häufig in der Medizin- und Luftfahrtindustrie für Anwendungen wie orthopädische Implantate, Flugzeugkomponenten und individuelle Prothesen verwendet.
3. AlSi10Mg: Dieses Pulver aus einer Aluminium-Silizium-Magnesium-Legierung ist für seine gute Gießbarkeit, Schweißbarkeit und Korrosionsbeständigkeit bekannt. Aufgrund seiner Kombination aus Druckbarkeit und mechanischen Eigenschaften, die durch mechanisches Legieren erreicht werden können, findet es in verschiedenen Sektoren Anwendung, unter anderem in der Automobilindustrie, der Luft- und Raumfahrt und der Konsumgüterindustrie.
4. Cu-Sn10: Dieses Kupfer-Zinn-Legierungspulver bietet eine hervorragende elektrische Leitfähigkeit und Verschleißfestigkeit. Es wird häufig bei der Herstellung von elektrischen Bauteilen wie Kühlkörpern, Stromschienen und Steckverbindern verwendet, wo seine durch mechanisches Legieren verbesserten Eigenschaften entscheidend für die Leistung sind.
5. CoCrMo: Dieses Kobalt-Chrom-Molybdän-Legierungspulver ist für seine hohe Biokompatibilität, Verschleißfestigkeit und Korrosionsbeständigkeit bekannt. Es ist eine beliebte Wahl für den 3D-Druck von medizinischen Implantaten wie Hüft- und Knieprothesen, bei denen die Biokompatibilität und die mechanischen Eigenschaften, die durch die mechanische Legierung erreicht werden, von größter Bedeutung sind.
7. Inconel 718: Dieses Superlegierungspulver auf Nickel-Chrom-Basis ist bekannt für seine außergewöhnliche Festigkeit bei hohen Temperaturen, seine gute Oxidationsbeständigkeit und seine hervorragende Kriechfestigkeit. Es wird häufig in anspruchsvollen Anwendungen wie Turbinenschaufeln, Raketentriebwerkskomponenten und anderen Hochleistungsteilen verwendet, bei denen die durch mechanisches Legieren erzielbaren Eigenschaften von entscheidender Bedeutung sind.
8. Martensitaushärtender Stahl 300: Dieses hochfeste Stahlpulver mit niedrigem Kohlenstoffgehalt bietet nach der Wärmebehandlung eine hervorragende Festigkeit und Zähigkeit. Es wird in verschiedenen Anwendungen eingesetzt, die ein hohes Verhältnis von Festigkeit zu Gewicht erfordern, wie z. B. bei Komponenten für die Luft- und Raumfahrt, bei Werkzeugen und bei Verteidigungsausrüstung, wo die durch mechanisches Legieren erzielten Eigenschaften entscheidend sind.
9. Nickel-Aluminium-Bronze (NAB): Dieses Pulver aus einer Kupfer-Aluminium-Nickel-Legierung bietet eine hervorragende Korrosionsbeständigkeit, Verschleißfestigkeit und gute mechanische Eigenschaften. Es findet Anwendung in Schiffskomponenten, Lagern und Verschleißteilen, wo seine Druckbarkeit und seine durch mechanisches Legieren verbesserten Eigenschaften von Vorteil sind.
10. Hastelloy C-276: Dieses Pulver aus einer Nickel-Chrom-Molybdän-Legierung ist für seine außergewöhnliche Korrosionsbeständigkeit in einer Vielzahl von aggressiven Umgebungen bekannt. Es wird in chemischen Verarbeitungsanlagen, Systemen zur Kontrolle der Umweltverschmutzung und anderen Anwendungen eingesetzt, die eine hervorragende Beständigkeit gegen aggressive Chemikalien erfordern und bei denen die durch mechanisches Legieren erzielten Eigenschaften entscheidend sind.
Es ist wichtig, daran zu denken, dass dies nur einige wenige Beispiele sind und die Möglichkeiten mit mechanisch legierten Pulvern ständig erweitert werden. Im Zuge des technologischen Fortschritts können wir mit noch mehr innovativen und spezialisierten Metallpulvern rechnen, die auf die spezifischen Anforderungen der verschiedenen 3D-Druckanwendungen zugeschnitten sind.
Vergleich von Metallpulvermodellen für den 3D-Druck
Bei der Auswahl eines Metallpulvermodells für Ihr 3D-Druckprojekt müssen mehrere Faktoren berücksichtigt werden:
- Gewünschte Eigenschaften: Bestimmen Sie die entscheidenden Eigenschaften, die Ihr fertiges Teil haben muss, wie Festigkeit, Gewicht, Korrosionsbeständigkeit, Biokompatibilität oder elektrische Leitfähigkeit.
- Bewerbungsvoraussetzungen: Berücksichtigen Sie die spezifische Anwendung und die Umgebungsbedingungen, denen das Teil ausgesetzt sein wird.
- 3D-Druckverfahren: Stimmen Sie die Pulvereigenschaften wie Partikelgröße und Fließfähigkeit auf das spezifische 3D-Druckverfahren ab, das Sie verwenden werden (z. B. LPBF, EBM).
Im Folgenden finden Sie einen kurzen Vergleich einiger Schlüsseleigenschaften der genannten Metallpulvermodelle:
Metallpulver-Modell | Festigkeit (MPa) | Dichte (g/cm³) | Schmelzpunkt (°C) | Anwendungen |
---|---|---|---|---|
Inconel 625 | Mit seiner außergewöhnlichen Hochtemperaturfestigkeit eignet es sich ideal für anspruchsvolle Anwendungen wie Komponenten für die Luft- und Raumfahrt und Wärmetauscher. | Besitzt eine hohe Dichte von 8,44 g/cm³, was zu seiner Robustheit beiträgt. | Mit einem Schmelzpunkt von 1455°C hält es auch extremen Temperaturen stand. | Weit verbreitet in der Luft- und Raumfahrt, in Gasturbinen und Wärmetauschern aufgrund seiner Kombination aus Festigkeit, Hochtemperaturbeständigkeit und guter Bedruckbarkeit. |
Ti-6Al-4V | Es bietet ein ausgezeichnetes Gleichgewicht zwischen Festigkeit, Gewicht und Biokompatibilität und ist daher für Anwendungen wie orthopädische Implantate und Prothesen geeignet. | Weist eine moderate Dichte von 4,43 g/cm³ auf und bietet ein gutes Gleichgewicht zwischen Gewicht und Festigkeit. | Es schmilzt bei einer Temperatur von ca. 1600 °C und beweist damit seine Fähigkeit, hohen Temperaturen standzuhalten. | Aufgrund seiner Biokompatibilität, seines günstigen Verhältnisses von Festigkeit zu Gewicht und seiner guten Bedruckbarkeit ist es eine beliebte Wahl in der Medizin- und Luftfahrtindustrie. |
AlSi10Mg | Es ist bekannt für seine gute Gießbarkeit, Schweißbarkeit und Korrosionsbeständigkeit, was es vielseitig einsetzbar macht. | Es besitzt eine geringere Dichte von etwa 2,7 g/cm³, was zu seinen leichten Eigenschaften beiträgt. | Schmelzt im Vergleich zu anderen Materialien bei einer relativ niedrigen Temperatur von etwa 577 °C, was in manchen Fällen eine leichtere Verarbeitung ermöglicht. | Aufgrund seiner Bedruckbarkeit, seiner günstigen mechanischen Eigenschaften und seiner guten Gießbarkeit wird es häufig in der Automobil-, Luft- und Raumfahrt- und Konsumgüterindustrie verwendet. |
Cu-Sn10 | Hervorragende elektrische Leitfähigkeit und Verschleißfestigkeit, was es für Anwendungen wie elektrische Komponenten und Kühlkörper wertvoll macht. | Weist eine moderate Dichte von ca. 8,9 g/cm³ auf, wodurch die elektrische Leitfähigkeit mit dem Gewicht in Einklang gebracht wird. | Schmilzt bei einer Temperatur von ca. 830°C und bietet eine gute Verarbeitbarkeit und Bedruckbarkeit. | Aufgrund seiner außergewöhnlichen elektrischen Leitfähigkeit und Verschleißfestigkeit wird es häufig bei der Herstellung von elektrischen Komponenten wie Kühlkörpern und Stromschienen verwendet. |
CoCrMo | Es ist bekannt für seine hohe Biokompatibilität, Verschleißfestigkeit und Korrosionsbeständigkeit, was es zur ersten Wahl für medizinische Implantate macht. | Es besitzt eine hohe Dichte von etwa 8,3 g/cm³, was zu seiner Haltbarkeit und Verschleißfestigkeit beiträgt. | Es schmilzt bei einer Temperatur von ca. 1350 °C und beweist damit seine Fähigkeit, hohen Temperaturen während verschiedener Prozesse standzuhalten. | Aufgrund seiner ausgezeichneten Biokompatibilität, guten Bedruckbarkeit und Verschleißfestigkeit wird es in der Medizin für Anwendungen wie Hüft- und Kniegelenksprothesen verwendet. |
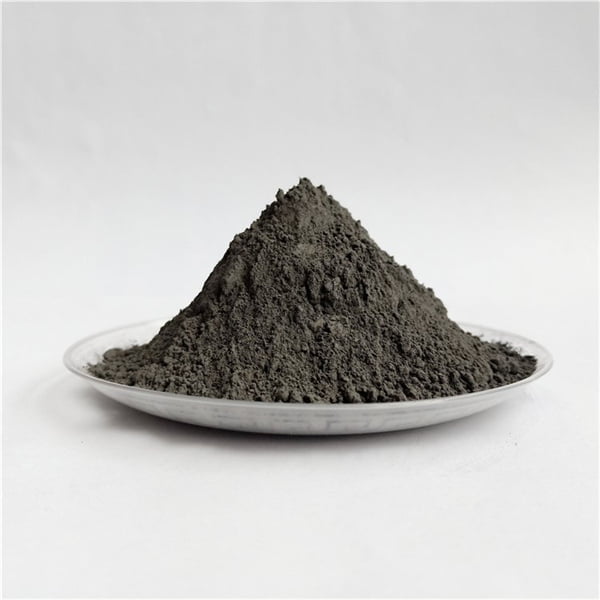
Zusätzliche Überlegungen und Zukunftsaussichten für mechanische Legierungen im 3D-Druck
Das mechanische Legieren bietet zahlreiche Vorteile für 3D-Druck von Metallpulvernist es wichtig, einige zusätzliche Faktoren zu berücksichtigen:
- Kosten: Der Prozess kann sein teurer im Vergleich zu herkömmlichen Pulverherstellungsmethoden wie der Zerstäubung, insbesondere bei größeren Mengen.
- Prozesskontrolle: Strenge Kontrolle Die Kontrolle der Mahlparameter und der Ausrüstung ist von entscheidender Bedeutung, um eine gleichbleibende Pulverqualität zu gewährleisten und das Kontaminationsrisiko zu minimieren.
- Auswirkungen auf die Umwelt: Der mit dem Mahlprozess verbundene Energieverbrauch macht es erforderlich, die Nachhaltigkeit und die potenziellen Umweltauswirkungen zu berücksichtigen.
Trotz dieser Überlegungen scheint die Zukunft des mechanischen Legierens im 3D-Druck vielversprechend zu sein. Hier sind einige spannende Möglichkeiten, auf die man sich freuen kann:
- Entwicklung von neuen Legierungen: Die Technologie wird auch weiterhin den Weg für die Herstellung neuartiger Legierungen mit einzigartigen Eigenschaften ebnen und die Grenzen dessen, was im 3D-Druck möglich ist, verschieben.
- Verbesserte Prozesseffizienz: Fortschritte in der Frästechnologie und Prozessoptimierung können zu höherer Effizienz und geringeren Kosten führen, was sie für verschiedene Anwendungen zugänglicher macht.
- Nanokomposit-Pulver: In der Zukunft könnten Nanokomposit-Pulver mit außergewöhnlichen Eigenschaften entwickelt werden, die das Potenzial des 3D-Drucks für fortschrittliche Anwendungen weiter ausbauen.
Zusammenfassend lässt sich sagen, dass das mechanische Legieren ein leistungsfähiges Werkzeug ist, um das Potenzial des 3D-Drucks von Metallen zu erschließen. Durch die Schaffung neuartiger Werkstoffe mit maßgeschneiderten Eigenschaften und die Förderung von Fortschritten in diesem Bereich ebnet diese Technologie den Weg für die Herstellung von innovative, leistungsstarke und funktionelle Objekte in den verschiedensten Branchen. Mit fortschreitender Forschung und Entwicklung können wir erwarten, dass sich noch mehr aufregende Möglichkeiten ergeben, die die Zukunft des 3D-Drucks von Metallen prägen werden.
FAQ
F: Was sind die Vorteile der Verwendung von mechanisch legierten Pulvern im 3D-Druck?
A: Es gibt mehrere Vorteile, unter anderem:
- Größere Kontrolle über die Zusammensetzung: Ermöglicht die Herstellung präziser und gleichmäßiger Legierungen mit spezifischen Zusammensetzungen.
- Verbesserte Pulvereigenschaften: Verbessert die Fließfähigkeit, die Packungsdichte und die Bedruckbarkeit für eine bessere Leistung in 3D-Druckverfahren.
- Entwicklung von neuartigen Materialien: Ermöglicht die Herstellung einzigartiger Legierungen und Metallmatrix-Verbundwerkstoffe mit Eigenschaften, die mit herkömmlichen Methoden nicht erreicht werden können.
- Skalierbarkeit: Anpassungsfähig an die Herstellung kleiner oder großer Pulverchargen sowohl für die Forschung als auch für die industrielle Produktion.
F: Was sind einige Einschränkungen bei der Verwendung von mechanisch legierten Pulvern?
A: Mögliche Einschränkungen sind:
- Bearbeitungszeit: Der Mahlprozess kann zeitaufwändig und energieintensiv sein, insbesondere bei komplexen Materialkombinationen.
- Kontaminationspotenzial: Eine sorgfältige Auswahl der Mahlmedien und die Prozesskontrolle sind entscheidend, um Verunreinigungen zu minimieren.
- Kostenüberlegungen: Die Einrichtung und Wartung von Hochenergie-Mahlanlagen kann teuer sein.
F: Welche Faktoren sind bei der Auswahl eines Metallpulvermodells für den 3D-Druck zu berücksichtigen?
A: Zu den Schlüsselfaktoren gehören:
- Gewünschte Eigenschaften: Identifizieren Sie die entscheidenden Eigenschaften, die Ihr fertiges Teil benötigt (Festigkeit, Gewicht, Korrosionsbeständigkeit usw.).
- Bewerbungsvoraussetzungen: Berücksichtigen Sie die spezifische Anwendung und die Umgebungsbedingungen, denen das Teil ausgesetzt sein wird.
- 3D-Druckverfahren: Passen Sie die Pulvereigenschaften (Partikelgröße, Fließfähigkeit) an den spezifischen 3D-Druckprozess an, den Sie verwenden werden.
F: Wie sieht die Zukunft der mechanischen Legierung im 3D-Druck aus?
A: Die Zukunft sieht vielversprechend aus, mit Potenzial für:
- Entwicklung von neuen Legierungen: Die Herstellung neuartiger Legierungen mit einzigartigen Eigenschaften, die die Möglichkeiten des 3D-Drucks erweitern.
- Verbesserte Prozesseffizienz: Fortschritte in der Mahltechnologie und Prozessoptimierung können zu höherer Effizienz und reduzierten Kosten führen.
- Nanokomposit-Pulver: Die Entwicklung von Nanokompositpulvern mit außergewöhnlichen Eigenschaften, die das Potenzial des 3D-Drucks für fortschrittliche Anwendungen weiter ausbauen.
Durch das Verständnis des Potenzials und der Einschränkungen der mechanischen Legierung können wir diese Technologie nutzen, um innovative und funktionale 3D-gedruckte Objekte zu erstellen und so die Zukunft verschiedener Branchen zu gestalten.
Teilen auf
MET3DP Technology Co., LTD ist ein führender Anbieter von additiven Fertigungslösungen mit Hauptsitz in Qingdao, China. Unser Unternehmen ist spezialisiert auf 3D-Druckgeräte und Hochleistungsmetallpulver für industrielle Anwendungen.
Fragen Sie an, um den besten Preis und eine maßgeschneiderte Lösung für Ihr Unternehmen zu erhalten!
Verwandte Artikel
Über Met3DP
Aktuelles Update
Unser Produkt
KONTAKT US
Haben Sie Fragen? Senden Sie uns jetzt eine Nachricht! Wir werden Ihre Anfrage mit einem ganzen Team nach Erhalt Ihrer Nachricht bearbeiten.
Holen Sie sich Metal3DP's
Produkt-Broschüre
Erhalten Sie die neuesten Produkte und Preislisten
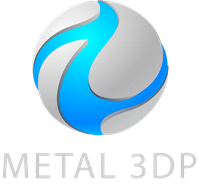
Metallpulver für 3D-Druck und additive Fertigung