3D-Druck von Satellitenpaneelen mit leichten Aluminiumlegierungen
Inhaltsübersicht
Einführung: Die Orbitalverschiebung - Wie 3D-gedruckte Satellitenpaneele die Luft- und Raumfahrttechnik revolutionieren
Die Luft- und Raumfahrtindustrie steht an der Schwelle zu einem beispiellosen Wandel, angetrieben durch die unerbittliche Forderung nach leichteren, schnelleren und kostengünstigeren Raumfahrzeugen. Satelliten, die Arbeitspferde der modernen Kommunikation, Navigation, Erdbeobachtung und wissenschaftlichen Forschung, sind von zentraler Bedeutung für diese Entwicklung. Bisher war die Herstellung von Satellitenkomponenten, insbesondere von Strukturteilen, ein komplexer, kostspieliger und zeitaufwändiger Prozess, der eine subtraktive Bearbeitung, eine komplizierte Montage mehrerer Teile und erheblichen Materialabfall erforderte. Doch eine mächtige technologische Welle - Additive Fertigung von Metall (AM), besser bekannt als Metall 3D-Druck - grundlegend umgestaltet, wie Satellitentafeln und andere kritische Raumfahrzeugkomponenten entworfen, entwickelt und produziert werden. Dieser Orbitalwechsel verspricht nicht nur schrittweise Verbesserungen, sondern einen Paradigmenwechsel, der Leistungsniveaus und Einsatzmöglichkeiten ermöglicht, die bisher als unerreichbar galten.
Satellitenpaneele sind weit mehr als einfache Abdeckungen; sie sind multifunktionale Elemente, die für den Erfolg der Mission entscheidend sind. Sie sorgen für strukturelle Integrität, beherbergen empfindliche Elektronik, bewältigen thermische Belastungen und dienen als Montageplattform für wichtige Instrumente und Subsysteme. Der unerbittliche Druck zur Senkung der Startkosten - die oft in Zehntausenden von Dollar pro Kilogramm, das in die Umlaufbahn geschickt wird, berechnet werden - stellt eine enorme Anforderung an Leichtbaukomponenten. Jedes eingesparte Gramm schlägt sich direkt in erheblichen finanziellen Einsparungen oder einer erhöhten Nutzlastkapazität nieder. Dies ist der Punkt, an dem die Synergie zwischen fortschrittlichen Leichtmetalllegierungen und 3D-Druck von Metall glänzt wirklich.
Mit herkömmlichen Fertigungsmethoden ist es oft schwierig, einen optimalen Leichtbau zu erreichen, ohne die strukturelle Integrität zu beeinträchtigen oder zu hohe Kosten zu verursachen. Die maschinelle Bearbeitung großer Metallblöcke zu komplexen Plattengeometrien führt zwangsläufig zu erheblichem Materialabfall (schlechtes Preis-Leistungs-Verhältnis), und der Zusammenbau mehrerer kleinerer Teile führt zu potenziellen Fehlerquellen (Verbindungen, Befestigungselemente) und erhöht gleichzeitig Gewicht und Komplexität. Additive Fertigung von Metallhingegen baut Teile Schicht für Schicht direkt aus digitalen Entwürfen mit Hochleistungsmetallpulvern auf. Dieses Verfahren eröffnet eine beispiellose Designfreiheit, die es den Ingenieuren ermöglicht, hoch optimierte, komplexe Geometrien zu schaffen, einschließlich interner Gitterstrukturen und topologisch optimierter Formen, die natürliche Strukturen wie Knochen nachahmen - stark, wo es nötig ist, minimal anderswo. Diese Fähigkeit ermöglicht die Erstellung von Satellitentafeln die wesentlich leichter sind als ihre traditionell hergestellten Gegenstücke, aber eine gleichwertige oder sogar höhere Festigkeit und Steifigkeit aufweisen.
Die Vorteile gehen über die reine Gewichtsreduzierung hinaus. AM erleichtert das Rapid Prototyping und die Design-Iteration und verkürzt so die Entwicklungszyklen für neue Satellitenplattformen oder -komponenten drastisch. Die Konsolidierung von Teilen, bei der mehrere Komponenten neu entworfen und als ein einziges, monolithisches Teil gedruckt werden, verkürzt die Montagezeit, minimiert potenzielle Fehlerpunkte, vereinfacht die Lieferketten und verringert das Gesamtgewicht weiter. Darüber hinaus ermöglicht AM die Verwendung fortschrittlicher Werkstoffe, die speziell für die raue Umgebung des Weltraums entwickelt wurden und maßgeschneiderte Eigenschaften wie ein hohes Verhältnis von Festigkeit zu Gewicht, eine spezifische Wärmeleitfähigkeit sowie Beständigkeit gegen Strahlung und extreme Temperaturschwankungen bieten.
Um in diesem Bereich führend zu sein, bedarf es nicht nur innovativer Designansätze, sondern auch robuster Fertigungskapazitäten und überlegener Werkstoffkunde. Unternehmen wie Met3dpmit Hauptsitz in Qingdao, China, sind von zentraler Bedeutung B2B-Luftfahrtzulieferer in diesem Bereich. Spezialisiert auf Industriequalität 3D-Druck von Metall Ausrüstungen und die Produktion von Hochleistungs MetallpulverMet3dp bietet die grundlegenden Technologien, die Ingenieure und Beschaffungsmanager in der Luft- und Raumfahrt benötigen, um das volle Potenzial von AM auszuschöpfen. Unsere Drucker zeichnen sich durch ein branchenweit führendes Produktionsvolumen, Präzision und Zuverlässigkeit aus - wesentliche Eigenschaften bei der Produktion von unternehmenskritischen Raumfahrttechnik. Kombiniert mit unserem Fachwissen über fortschrittliche Metallpulvereinschließlich leichte Aluminiumlegierungen wie AlSi10Mg und Scalmalloy® sowie weltraumtaugliche Titanlegierungen wie Ti-6Al-4V, ermöglicht Met3dp Unternehmen die Herstellung von Produkten der nächsten Generation. Satellitentafeln die den strengen Anforderungen der modernen Weltraumforschung und Kommerzialisierung entsprechen. Dieser Technologiesprung verändert nicht nur die wie Satelliten gebaut werden; er expandiert was die sie erreichen können.
Die wichtigsten Erkenntnisse für Fachleute der Luft- und Raumfahrt:
- Das Gewicht ist ausschlaggebend: Metall-AM bietet nie dagewesene Möglichkeiten zur Gewichtsreduzierung von Satellitenpanels, was sich direkt auf die Startkosten und die Nutzlastkapazität auswirkt.
- Komplexität ist ein Vorteil: AM ermöglicht komplizierte Designs (Topologieoptimierung, Gitterstrukturen), die mit herkömmlichen Methoden nicht möglich sind, und verbessert so Leistung und Funktionalität.
- Konsolidierung vereinfacht: Das Drucken mehrerer Teile in einem Stück reduziert den Montageaufwand, mögliche Fehler, das Gewicht und den logistischen Aufwand.
- Geschwindigkeit beschleunigt die Innovation: Schnelles Prototyping und kürzere Produktionsvorlaufzeiten ermöglichen eine schnellere Entwicklung und Einführung von Satellitensystemen.
- Die Wahl des Materials ist wichtig: Hochentwickelte Legierungen, die auf AM- und Weltraumumgebungen zugeschnitten sind, sind der Schlüssel zu einer optimalen Leistung der Platten.
- Die Kompetenz der Lieferanten ist entscheidend: Durch die Zusammenarbeit mit erfahrenen AM-Anbietern wie Met3dp wird der Zugang zu zuverlässigen Anlagen, hochwertigen Materialien und Anwendungsunterstützung sichergestellt.
Diese Einführung bildet die Grundlage für eine eingehendere Untersuchung der spezifischen Anwendungen, Vorteile, Materialien und Überlegungen, die mit dem Einsatz von 3D-Druck von Metall für die Produktion von fortgeschrittenen Satellitentafelndie auf die Bedürfnisse und Interessen von Raumfahrttechnik Teams und B2B-Beschaffung Fachleute, die modernste Fertigungslösungen suchen.
Kernfunktionen: Welche Rolle spielen Satellitenpaneele in der modernen Raumfahrzeugarchitektur?
Um die Auswirkungen der additiven Fertigung von Metallen auf das Satellitendesign in vollem Umfang zu verstehen, ist es unerlässlich, die vielfältigen und kritischen Funktionen zu kennen, die die verschiedenen Teile eines Satelliten erfüllen. Raumfahrzeugarchitektur. Dabei handelt es sich nicht nur um passive Oberflächen, sondern um hochtechnisierte Komponenten, die für das Überleben, den Betrieb und den Gesamterfolg der Mission des Satelliten unerlässlich sind. Die Anforderungen, die an diese Platten gestellt werden - strukturelle Widerstandsfähigkeit während des Starts, Betriebsstabilität in der rauen Weltraumumgebung und spezifische funktionale Leistung - erfordern fortschrittliche Materialien und Fertigungstechniken wie 3D-Druck von Metall.
Satellitenpaneele können grob nach ihrer Hauptfunktion kategorisiert werden, obwohl viele von ihnen oft mehrere Funktionen gleichzeitig erfüllen. Das Verständnis dieser Funktionen verdeutlicht, warum Eigenschaften wie Steifigkeit, Verhältnis von Festigkeit zu Gewicht, Wärmemanagement und Maßgenauigkeit nicht verhandelbare Anforderungen für Raumfahrttechnik und Beschaffungsteams Beschaffung unternehmenskritische Teile.
1. Strukturelle Paneele (Primär- und Sekundärstrukturen): Diese bilden das Rückgrat und das Skelett des Satelliten und stellen das wesentliche Gerüst dar, auf dem alle anderen Komponenten montiert werden.
- Belastbar: Muss während des Starts extremen mechanischen Belastungen standhalten, einschließlich starker Vibrationen, Schalldruck und hoher G-Kräfte, ohne sich zu verformen oder zu versagen.
- Steifigkeit und Stabilität: Bereitstellung einer starren Plattform, um die präzise Ausrichtung empfindlicher Instrumente (wie Teleskope, Antennen, Sensoren) während der gesamten Missionsdauer aufrechtzuerhalten und Mikrovibrationen und thermischen Verzerrungen in der Umlaufbahn zu widerstehen.
- Schnittstellenpunkte: Präzise Montageschnittstellen (Halterungen, Einsätze, Vorsprünge) für die Befestigung von Subsystemen, Nutzlasten und Mechanismen.
- Gebräuchliche Formulare: Sie werden oft als Isogitter- oder Orthogitterstrukturen (traditionell maschinell bearbeitet) oder zunehmend unter Einbeziehung von Topologieoptimierung und Gitterstrukturen (ideal für AM) entworfen, um die Steifigkeit zu maximieren und gleichzeitig die Masse zu minimieren. Wabenförmige Sandwichplatten sind ebenfalls weit verbreitet, wobei AM für die Deckschichten oder komplexe Kerngeometrien verwendet werden kann.
2. Montageplatten für Ausrüstung und Nutzlast: Diese Paneele dienen als spezielle Plattformen für die Anbringung spezifischer Satelliten-Subsysteme und der primären Missionsnutzlast.
- Sichere Anbringung: Sie bieten robuste und zuverlässige Befestigungspunkte für empfindliche und oft schwere Geräte wie Kommunikationstransponder, Antriebstanks, Reaktionsräder, Batterien, Bordcomputer und wissenschaftliche Instrumente.
- Wege der Wärmeleitung: Sie sind oft so konstruiert, dass sie die Wärme von der eingebauten Elektronik weg zu speziellen Kühlerplatten leiten.
- Schwingungsdämpfung: Kann Merkmale oder Materialien enthalten, um empfindliche Geräte von den Vibrationen des Raumfahrzeugbusses zu isolieren.
- Anforderungen an die Präzision: Gefordert sind hohe Maßgenauigkeit und enge Toleranzen für die Schnittstellen, um die korrekte Ausrichtung und Funktion der angebrachten Hardware zu gewährleisten.
3. Wärmemanagement-Paneele (Kühler und Hitzeschutzschilder): Die Kontrolle der Temperatur ist entscheidend für die Langlebigkeit und Leistung der Satelliten. Paneele spielen eine Schlüsselrolle bei der Abstrahlung von Abwärme in den Weltraum und der Abschirmung von Komponenten vor extremen Temperaturen.
- Heizkörperverkleidungen: Sie sind mit speziellen Oberflächenbeschichtungen (Beschichtungen mit hohem Emissionsgrad) und häufig mit internen Strukturen (integrierte Wärmerohre oder Flüssigkeitskreisläufe - möglicherweise verbessert durch AM) ausgestattet, um die von der Elektronik und den Nutzlasten erzeugte Abwärme effizient abzuleiten. Sie benötigen eine gute Wärmeleitfähigkeit über die gesamte Plattendicke.
- Hitzeschutzschilder: Schutz empfindlicher Komponenten vor direkter Sonneneinstrahlung oder der von anderen Teilen des Satelliten (z. B. Antriebssystemen) erzeugten Wärme. Oft wird eine mehrschichtige Isolierung (MLI) verwendet, aber die darunterliegende Strukturplatte muss den Temperaturgradienten standhalten.
- Materialeigenschaften: Erforderlich sind Materialien mit angemessener Wärmeleitfähigkeit, Stabilität über weite Temperaturbereiche (-150°C bis +150°C oder mehr) und geringer Wärmeausdehnung.
4. Elektronik-Gehäuse und -Gehäuse: Diese Paneele bilden Boxen oder Gehäuse, um empfindliche elektronische Komponenten vor den Gefahren der Weltraumumgebung zu schützen.
- Schutz der Umwelt: Schutz der Elektronik vor Strahlung (galaktische kosmische Strahlung, Sonnenpartikel), Mikrometeoroiden, atomarem Sauerstoff (im LEO) und elektrostatischer Entladung.
- EMI/EMC-Abschirmung: Häufig zur Vermeidung elektromagnetischer Störungen zwischen verschiedenen elektronischen Systemen. AM ermöglicht komplexe interne Abschirmungsgeometrien.
- Strukturelle Unterstützung: Bieten mechanische Unterstützung und Befestigungspunkte für Leiterplatten und elektronische Baugruppen.
- Integration des Wärmemanagements: Sie können Merkmale wie Kühlkörper oder Leitungsbahnen enthalten, um die von der eingeschlossenen Elektronik erzeugte Wärme zu bewältigen.
5. Solarmodul-Substrat-Paneele: Diese bilden die strukturelle Grundlage für die Photovoltaikzellen, die den Strom für den Satelliten erzeugen.
- Leichte Struktur: Sie müssen extrem leicht und dennoch steif genug sein, um die empfindlichen Solarzellen während des Einsatzes und des Betriebs zu halten.
- Mechanismen für die Bereitstellung: Oft Teil komplexer, entfaltbarer Flügelstrukturen, die komplizierte Gelenkmechanismen und eine zuverlässige Entfaltungskinematik erfordern. AM kann potenziell einige Mechanismusmerkmale integrieren.
- Thermische Stabilität: Um eine optimale Leistung der Solarzelle zu gewährleisten und Risse in der Zelle zu vermeiden, muss die Ebenheit und Dimensionsstabilität bei unterschiedlichen Temperaturen erhalten bleiben.
6. RF (Radiofrequenz)-Komponenten-Paneele: Einige Panels integrieren oder unterstützen Elemente der Kommunikations- oder Erfassungssysteme des Satelliten.
- Antennenreflektoren/Strukturen: Präzise geformte Platten, die Funkwellen reflektieren oder bündeln. Oberflächengenauigkeit und Stabilität sind von größter Bedeutung.
- Integration von Hohlleitern: AM bietet die Möglichkeit, komplexe Wellenleiterstrukturen direkt in die Strukturplatten zu integrieren, wodurch Verbindungen und potenzielle Signalverluste reduziert werden.
Zusammenfassende Tabelle: Funktionen und Anforderungen des Satellitenpanels
Panel-Typ | Primäre Funktion(en) | Wichtige Anforderungen | Relevanz von Metal AM |
---|---|---|---|
Strukturelle Paneele | Tragfähigkeit, Steifigkeit, Befestigung von Bauteilen | Hohe Festigkeit im Verhältnis zum Gewicht, hohe Steifigkeit, Ermüdungsbeständigkeit, präzise Schnittstellen | Topologie-Optimierung, Gitterstrukturen, Teilekonsolidierung, Leichtbau |
Montage der Ausrüstung | Sichere Befestigung, Wärmeleitfähigkeit, Schwingungsdämpfung | Hohe Festigkeit, Maßgenauigkeit, gute Wärmeleitfähigkeit, Steifigkeit | Komplexe Schnittstellengeometrien, integrierte Klammern, optimierte Leitungswege |
Thermisches Management | Wärmestrahlung (Heizkörper), Wärmeabschirmung | Spezifische Wärmeleitfähigkeit, hohe Emissivität (Oberfläche), thermische Stabilität | Integrierte Kühlkanäle, komplexe Geometrien für Wärmerohre, optimierte Kühlerformen, Leichtbaustrukturen |
Elektronik-Gehäuse | Umweltschutz, EMI-Abschirmung, Struktur | Strahlungsabschirmung, Festigkeit, Wärmemanagement, EMI-Dichtungskompatibilität | Komplexe innere Merkmale, konforme Formen, integrierte Abschirmung, Konsolidierung von Teilen |
Substrate für Solarmodule | Solarzellenträger, Struktur für den Einsatz | Extremer Leichtbau, hohe Steifigkeit, thermische Stabilität, Einsatzfähigkeit | Ultraleichte Gitterkerne, optimierte Versteifungen, Integration von Mechanikschnittstellen |
RF-Komponenten-Panels | Antennenunterstützung/-formung, Integration von Hohlleitern | Hochdimensionale Genauigkeit, Oberflächenglätte, RF-Leistung, Stabilität | Präzise komplexe Formen (Reflektoren), integrierte Wellenleiter, leichtgewichtige Trägerstrukturen |
In Blätter exportieren
Das Verständnis für diese vielfältigen und anspruchsvollen Aufgaben unterstreicht, warum die Luft- und Raumfahrtindustrie ein starkes Interesse an Metall-Additiv-Fertigung. Die Fähigkeit zu schaffen Leichtgewichtkomplex, hoch integriert Satellitentafeln mit weltraumtauglichen Materialien wie AlSi10Mg, Scalmalloy®und Ti-6Al-4V geht direkt auf die zentralen Herausforderungen ein, mit denen die Raumfahrttechnik Teams. Für B2B-Beschaffung Managern bietet die Beschaffung von Platten, die im AM-Verfahren von fähigen Lieferanten wie Met3dp hergestellt werden, einen Weg zu verbesserter Leistung, reduzierten Kosten und rationalisierten Raumfahrzeugkomponente Erwerb.
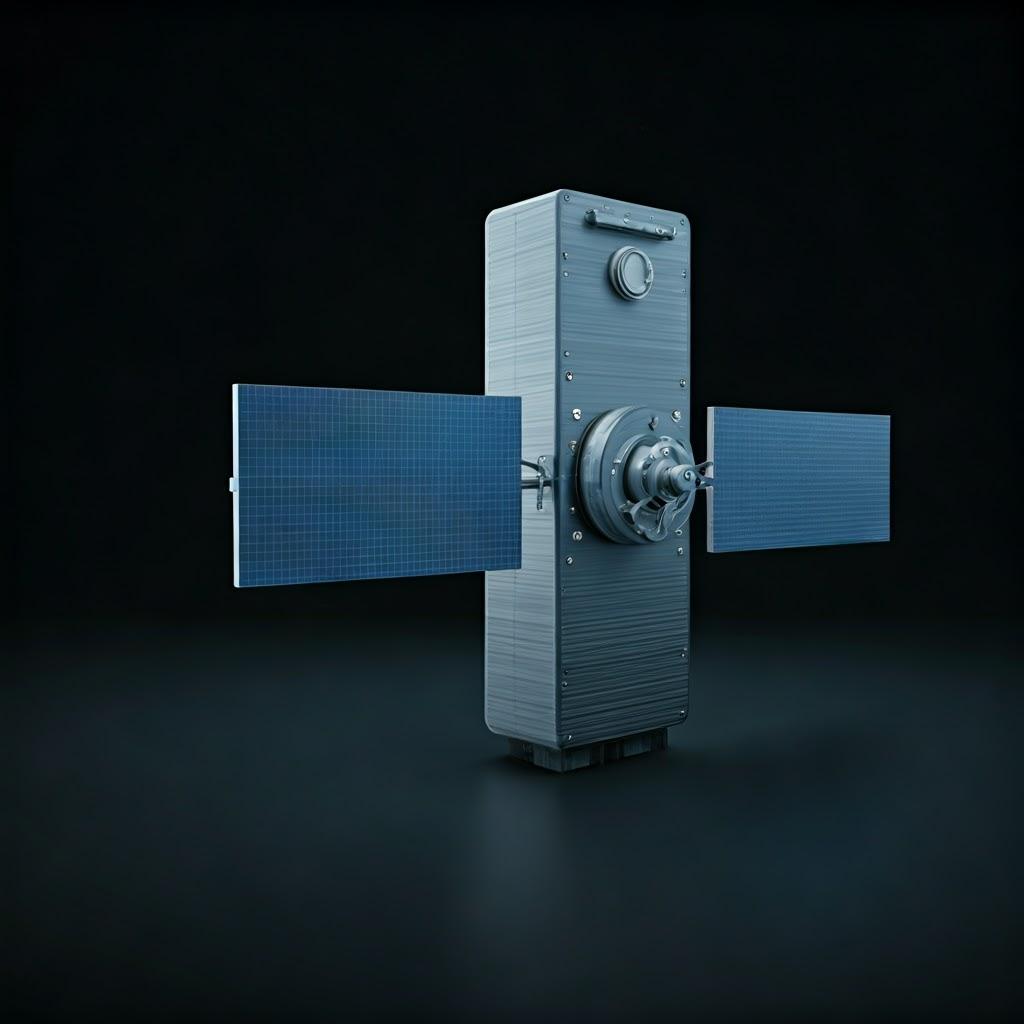
Der Additiv-Vorteil: Warum 3D-Metalldruck für die Produktion von Satellitenpaneelen?
Herkömmliche Fertigungsmethoden wie CNC-Bearbeitung, Blechumformung, Gießen und komplexe Montage haben sich in der Luft- und Raumfahrtindustrie zwar seit Jahrzehnten bewährt, stoßen aber an ihre Grenzen, wenn es darum geht, die steigenden Anforderungen an leichtere, komplexere und schneller entwickelte Satellitenkomponenten zu erfüllen. Additive Fertigung von Metall (AM), oder 3D-Druck von Metallbietet eine Reihe von überzeugenden Vorteilen, die diese Einschränkungen direkt angehen und sie zu einer zunehmend bevorzugten Methode für die Produktion der nächsten Generation machen. Satellitentafeln. Für Raumfahrtingenieure mit Schwerpunkt auf Leistung und Beschaffungsmanager Die Vorteile von AM, die sich auf den Wert und die Effizienz der Lieferkette konzentrieren, sind transformativ.
Sehen wir uns die wichtigsten Vorteile der Verwendung von 3D-Druck von Metall im Vergleich zu traditionelle Fertigung speziell im Zusammenhang mit Satellitentafel Produktion:
1. Unerreichte Leichtbau-Fähigkeiten:
- AM Vorteil: Metall-AM eignet sich hervorragend zur Herstellung komplexer Innengeometrien wie Gitterstrukturen und ermöglicht Topologieoptimierung Algorithmen. Diese Werkzeuge entfernen Material in Bereichen mit geringer Belastung und verstärken gleichzeitig kritische Belastungspfade. Das Ergebnis sind Bauteile, die deutlich leichter sind (oft 20-60% Gewichtsreduzierung) als herkömmlich bearbeitete oder hergestellte Teile, ohne dass die Festigkeit oder Steifigkeit darunter leidet. Dies ist von entscheidender Bedeutung für die Senkung der Kosten von Satellitenstarts.
- Traditionelle Einschränkung: Die maschinelle Bearbeitung komplexer innerer Hohlräume oder Gitter ist oft unmöglich oder unerschwinglich. Bei Blechkonstruktionen sind die Möglichkeiten, wirklich optimierte 3D-Lastpfade zu erreichen, begrenzt. Das Gießen kann dicke Abschnitte für den Fluss erfordern, was zusätzliches Gewicht bedeutet.
- Beispiel: Ein strukturelles Halterungspaneel, das traditionell aus mehreren maschinell bearbeiteten Teilen und Befestigungselementen besteht, kann mithilfe von Topologieoptimierung neu entworfen und als eine einzige, leichtere AM-Komponente gedruckt werden. Scalmalloy® oder Ti-6Al-4V.
2. Radikale Teilkonsolidierung:
- AM Vorteil: Komplexe Baugruppen, die aus zahlreichen Einzelteilen bestehen (Halterungen, Verbindungselemente, Platten, Befestigungen), können oft neu entworfen und als eine einzige, monolithische Komponente gedruckt werden. Dadurch wird die Anzahl der Teile drastisch reduziert, der Arbeits- und Zeitaufwand für die Montage entfällt, potenzielle Fehlerstellen im Zusammenhang mit Verbindungen (Schweißnähte, Befestigungselemente) werden beseitigt, die Lagerverwaltung vereinfacht und das Gesamtgewicht reduziert.
- Traditionelle Einschränkung: Die Komplexität der Fertigung erfordert oft die Zerlegung von Strukturen in einfachere Teilkomponenten, die dann zusammengefügt werden müssen, was zu zusätzlicher Komplexität, Gewicht und Prüfanforderungen führt.
- Beispiel: Ein Elektronikgehäuse, das mehrere interne Befestigungspunkte, Abschirmwände und externe Schnittstellen erfordert, kann als ein integriertes Teil gedruckt werden, wodurch Dutzende von Befestigungselementen und mehrere Montageschritte entfallen.
3. Extreme Gestaltungsfreiheit und Komplexität:
- AM Vorteil: AM baut Teile schichtweise auf und befreit die Konstrukteure von vielen Beschränkungen, die bei herkömmlichen Methoden gelten (z. B. Werkzeugzugang bei der Bearbeitung, Entformungswinkel beim Gießen, Biegeradien bei Blechen). Dies ermöglicht die Herstellung hochkomplexer Merkmale, konformer Formen, die komplexen Kurven folgen, integrierter Kühlkanäle, interner Hohlräume und funktional abgestufter Materialien (wobei letztere noch in der Entwicklung sind).
- Traditionelle Einschränkung: Das Design wird oft durch den Herstellungsprozess diktiert. Komplexe innere Merkmale sind schwierig oder unmöglich. Die Werkzeugkosten können komplexe Formen unwirtschaftlich machen, insbesondere bei der Satellitenproduktion in kleinen Stückzahlen.
- Beispiel: Eine Wärmemanagementplatte kann mit integrierten, konform geformten Innenkanälen für Flüssigkeitskühlkreisläufe gedruckt werden, die genau für die Wärmelastverteilung optimiert sind - ein Design, das nicht maschinell hergestellt werden kann.
4. Beschleunigte Prototyping- und Entwicklungszyklen:
- AM Vorteil: Der Übergang von einer digitalen Konstruktionsdatei (CAD) zu einem physischen Metallteil kann mit AM erheblich schneller erfolgen, insbesondere bei komplexen Geometrien, da oft keine umfangreichen Werkzeuge (Formen, Gesenke, Vorrichtungen) benötigt werden. Dies ermöglicht eine schnelle Iteration - Ingenieure können Komponenten viel schneller entwerfen, drucken, testen und verfeinern, was den gesamten Zeitplan für die Satellitenentwicklung beschleunigt.
- Traditionelle Einschränkung: Die Erstellung von Werkzeugen für den Guss oder von komplexen Vorrichtungen für die Bearbeitung kann Wochen oder Monate dauern, was Konstruktionswiederholungen langsam und kostspielig macht.
- Beispiel: Verschiedene Designvariationen für eine kritische Nutzlast-Montageplatte können mit AM innerhalb von Tagen oder Wochen gedruckt und strukturell getestet werden, im Vergleich zu Monaten bei herkömmlichen Methoden, die die Erstellung von Gussmodellen oder komplexe Mehrachsen-Bearbeitungseinrichtungen beinhalten.
5. Verbesserte Materialeffizienz (Buy-to-Fly-Ratio):
- AM Vorteil: Bei der additiven Fertigung handelt es sich um ein endkonturnahes Verfahren, d. h. es wird in erster Linie nur das Material verwendet, das für das endgültige Teil benötigt wird, zuzüglich der Stützstrukturen (die häufig recycelbar sind). Dadurch wird der Materialabfall im Vergleich zu subtraktiven Verfahren wie der CNC-Bearbeitung, bei der ein großer Prozentsatz eines teuren Rohmaterialblocks abgetragen werden kann, erheblich reduziert. Dies ist besonders wichtig für kostspielige Luftfahrtlegierungen wie Ti-6Al-4V und Scalmalloy®.
- Traditionelle Einschränkung: Bei der subtraktiven Bearbeitung fallen naturgemäß erhebliche Abfälle (Späne) an. Das Verhältnis zwischen dem eingekauften Rohmaterial und dem Endgewicht des Werkstücks (Buy-to-Fly-Ratio) kann sehr hoch sein (z. B. 10:1 oder sogar 20:1 bei komplex bearbeiteten Teilen).
- Beispiel: Das Drucken eines komplexen Ti-6Al-4V-Satellitenpaneels könnte ein Verhältnis von 2:1 oder 3:1 (einschließlich Stützen) ergeben, verglichen mit potenziell viel höheren Verhältnissen bei der Bearbeitung aus einem massiven Block.
6. Reduzierte Durchlaufzeiten für komplexe und kleinvolumige Teile:
- AM Vorteil: Bei hochkomplexen Komponenten oder Teilen, die in geringen Stückzahlen benötigt werden (typisch für viele Satellitenprogramme), kann AM die fertigen Teile oft schneller liefern als herkömmliche Methoden, die mit Vorlaufzeiten für Werkzeuge oder umfangreichen Bearbeitungs-/Montageabläufen verbunden sind. Dies verbessert Luft- und Raumfahrt-Lieferkette Reaktionsfähigkeit.
- Traditionelle Einschränkung: Werkzeugbau, Rüstzeiten und mehrstufige Prozesse können zu langen Vorlaufzeiten führen, insbesondere bei kundenspezifischen oder nicht standardisierten Komponenten.
- Beispiel: Die Herstellung eines Satzes von 5 einzigartigen, hochkomplexen Strukturpaneelen für eine bestimmte Satellitenmission könnte mit AM schneller abgeschlossen werden als die Inbetriebnahme von Gussmodellen oder die Programmierung komplizierter 5-Achsen-Bearbeitungspfade.
7. Verbesserte kundenspezifische Anpassung und On-Demand-Fertigung:
- AM Vorteil: Da AM direkt von digitalen Dateien ausgeht, ist es relativ einfach, ein Design für spezifische Anforderungen zu ändern oder einzigartige Variationen zu schaffen, die nur Änderungen am CAD-Modell und keine physischen Werkzeuge erfordern. Dies unterstützt die Produktion auf Abruf und Ersatzteilstrategien.
- Traditionelle Einschränkung: Die Anpassung an Kundenwünsche erfordert oft erhebliche Umrüstungen oder Neuprogrammierungen, was kostspielig und zeitaufwändig ist.
Vergleichstabelle: Metall-AM vs. traditionelle Fertigung für Satellitenpaneele
Merkmal | Additive Fertigung von Metall (AM) | Traditionelle Fertigung (Bearbeitung, Montage, Gießen) | Vorteil für Satellitentafeln? |
---|---|---|---|
Gewichtsreduzierung | Ausgezeichnet (Topologie Opt., Gitter) | Begrenzt durch Prozesseinschränkungen | Hoch |
Teil Konsolidierung | Hohes Potenzial | Schwierig / Erhöht die Komplexität | Hoch |
Entwurfskomplexität | Hoch (Interne Merkmale, Konforme) | Eingeschränkt durch Werkzeuge, Zugang, Prozessphysik | Hoch |
Prototyping-Geschwindigkeit | Schnell (werkzeuglos für komplexe Teile) | Langsam (abhängig von Werkzeug/Einrichtung) | Hoch |
Materialabfälle | Niedrig (Fast-Netzform) | Hoch (Subtraktiv) / Mäßig (Gießen) | Mittel-Hoch |
Vorlaufzeit (komplex) | Potenziell kürzer | Potenziell länger (Werkzeugbau, mehrstufig) | Mittel-Hoch |
Personalisierung | Einfach (digitale Dateiveränderung) | Kostspielig/zeitaufwendig (Umrüstung) | Mittel |
Oberfläche | Gröber (as-built), erfordert Nachbearbeitung | Glatter (maschinell bearbeitet), aber Einschränkungen bei komplexen Oberflächen | Abhängig von den Anforderungen |
Maßgenauigkeit | Gut, verbessert sich, erfordert Prozesskontrolle und Nachbearbeitung | Sehr hoch (Zerspanung), mäßig (Guss) | Abhängig von den Anforderungen |
Kosten (pro Teil) | Kann bei einfachen Teilen höher sein, bei komplexen/konsolidierten Teilen wettbewerbsfähig | Niedriger für einfache/hohe Stückzahlen, höher für komplexe/geringe Stückzahlen | Abhängig von Komplexität/Volumen |
In Blätter exportieren
Um diese Vorteile nutzen zu können, sind Fachkenntnisse sowohl im Bereich des Designs für die additive Fertigung (DfAM) als auch des Druckverfahrens selbst erforderlich. Die Partnerschaft mit einem sachkundigen Metall-AM-Dienstleister wie Met3dp, das nicht nur den neuesten Stand der Technik bietet Druckverfahren wie das Selektive Elektronenstrahlschmelzen (SEBM), aber auch fundierte materialwissenschaftliche Kenntnisse sind entscheidend. Die Fähigkeiten von Met3dp ermöglichen Luft- und Raumfahrtunternehmen und ihre B2B-Lieferanten die volle Nutzung der Vorteile der additiven Fertigungund die Grenzen der Satellitentafel Design und Leistung bei gleichzeitiger Optimierung der Luft- und Raumfahrt-Lieferkette.
Auf das Material kommt es an: Auswahl optimaler Leichtbau-Legierungen für 3D-gedruckte Satellitenpaneele
Die Wahl des Werkstoffs ist für den Erfolg eines jeden Bauteils in der Luft- und Raumfahrt von grundlegender Bedeutung, und 3D-gedruckte Satellitenpaneele sind keine Ausnahme. Die anspruchsvolle Weltraumumgebung - mit Vakuum, extremen Temperaturzyklen, Strahlung und den gewaltigen Kräften beim Start - stellt hohe Anforderungen an die Materialien. Darüber hinaus ist das übergreifende Ziel von Leichtbau um die Startkosten zu senken, hat großen Einfluss auf die Materialauswahl. Zum Glück, Metall-Additiv-Fertigung ist kompatibel mit einer Reihe von fortschrittlichen Luftfahrtlegierungen perfekt für diese Herausforderungen geeignet. Die drei empfohlenen Puder - AlSi10Mg, Scalmalloy®und Ti-6Al-4V - repräsentieren ein Spektrum von Eigenschaften, die für unterschiedliche Plattenanwendungen und Leistungsanforderungen geeignet sind.
Das Verständnis der Eigenschaften der einzelnen Legierungen ist entscheidend für Raumfahrtingenieure Designentscheidungen zu treffen und für Beschaffungsmanager Beschaffung von Materialien oder 3D-Metalldruckdienste. Zu den wichtigsten zu berücksichtigenden Eigenschaften gehören:
- Dichte (ρ): Wirkt sich direkt auf das Gewicht aus (geringeres Gewicht ist besser für die Gewichtsreduzierung).
- Spezifische Festigkeit (Höchstzugkraft / Dichte): Festigkeit pro Gewichtseinheit - eine wichtige Kennzahl für die Luft- und Raumfahrt.
- Spezifische Steifigkeit (Elastizitätsmodul / Dichte): Steifigkeit pro Gewichtseinheit - wichtig für die strukturelle Stabilität.
- Wärmeleitfähigkeit (k): Fähigkeit, Wärme zu leiten - wichtig für Wärmemanagementplatten.
- Wärmeausdehnungskoeffizient (CTE): Wie stark sich das Material bei Temperaturänderungen ausdehnt/zusammenzieht - ein niedriger WAK ist für die Dimensionsstabilität vorzuziehen.
- Ermüdungsfestigkeit: Widerstandsfähigkeit gegen Versagen bei zyklischer Belastung (z. B. bei Vibrationen).
- Umweltresistenz: Verträglichkeit mit Vakuum (geringe Ausgasung), Strahlung, extremen Temperaturen und potenziell korrosiven Elementen (z. B. Resttreibstoffe).
- Druckbarkeit und Verarbeitbarkeit: Einfaches Drucken hochwertiger, dichter Teile mit AM-Verfahren (wie Laser Powder Bed Fusion - L-PBF oder Electron Beam Melting - EBM) und einfache Nachbearbeitung (Wärmebehandlung, Bearbeitung).
Schauen wir uns die empfohlenen Materialien im Detail an:
1. Aluminium-Silizium-Magnesium-Legierung (AlSi10Mg): Das Arbeitspferd Aluminium
- Zusammensetzung: Hauptsächlich Aluminium, mit ~10% Silizium und <0,5% Magnesium.
- Eigenschaften:
- Vorteile: Relativ geringe Dichte (~2,67 g/cm³), gute Bedruckbarkeit über L-PBF, hervorragende Wärmeleitfähigkeit (~120-150 W/m-K), gute Korrosionsbeständigkeit, leicht verfügbar, relativ kostengünstig im Vergleich zu anderen Legierungen für die Luft- und Raumfahrt. Bietet mäßige Festigkeit nach entsprechender Wärmebehandlung.
- Nachteile: Geringere Festigkeit und Temperaturbeständigkeit im Vergleich zu Scalmalloy® oder Ti-6Al-4V (verliert oberhalb von ~150-200°C erheblich an Festigkeit). Geringere Ermüdungsfestigkeit.
- Typische Anwendungen für Satellitenbildschirme:
- Strukturelle Platten mit mäßigen Belastungsanforderungen.
- Elektronikgehäuse, bei denen eine gute Wärmeableitung erforderlich ist.
- Wärmetauscher und Bauteile von Kühlerverkleidungen (insbesondere innere Strukturen).
- Montagehalterungen für weniger kritische Komponenten.
- Prototypen, bei denen Kosten und Geschwindigkeit die wichtigsten Faktoren sind.
- Warum das wichtig ist: AlSi10Mg ist ein zuverlässiges und gut bekanntes Ausgangsmaterial für viele AM-Anwendungen. Die Ausgewogenheit von geringer Dichte, guten thermischen Eigenschaften und Druckbarkeit macht es für eine Vielzahl von Platten geeignet, bei denen die extreme mechanische Leistung nicht der einzige Faktor ist.
2. Scalmalloy®: Das Hochleistungsaluminium
- Zusammensetzung: Eine Aluminium-Magnesium-Scandium-Legierung (proprietäre Zusammensetzung von APWorks/Airbus). Speziell für die additive Fertigung entwickelt.
- Eigenschaften:
- Vorteile: Sehr hohe spezifische Festigkeit, die an die von Ti-6Al-4V heranreicht, jedoch mit einer geringeren Dichte (~2,66 g/cm³). Ausgezeichnete Duktilität und Zähigkeit im Vergleich zu anderen hochfesten AM-Aluminiumsorten. Gute Ermüdungseigenschaften und Schweißbarkeit (nützlich für mögliche Nachbearbeitungen oder Montage). Behält seine Festigkeit bei leicht erhöhten Temperaturen besser bei als AlSi10Mg. Außergewöhnliche Druckfähigkeit durch L-PBF.
- Nachteile: Höhere Materialkosten im Vergleich zu AlSi10Mg. Scandium ist ein teures Legierungselement. Erfordert eine präzise Prozesssteuerung während des Drucks und der Wärmebehandlung, um optimale Eigenschaften zu erzielen. Geringere Wärmeleitfähigkeit als AlSi10Mg (~100 W/m-K).
- Typische Anwendungen für Satellitenbildschirme:
- Primärstrukturelemente, die bei hohen Belastungen ein Höchstmaß an Leichtigkeit erfordern.
- Hochbelastete Halterungen und Schnittstellenkomponenten.
- Direkter Ersatz für schwerere traditionelle Aluminium- oder sogar einige Titankomponenten.
- Bauteile, die starken Vibrationen oder Ermüdungsbelastungen ausgesetzt sind.
- Leistungskritische Anwendungen, bei denen Gewichtseinsparungen die höheren Materialkosten rechtfertigen.
- Warum das wichtig ist: Scalmalloy® verschiebt die Grenzen dessen, was mit Aluminiumlegierungen in der AM möglich ist. Es ermöglicht Ingenieuren, extrem leichte und dennoch starke und haltbare SatellitentafelnSie konkurrieren in vielen strukturellen Anwendungen direkt mit Titan, bieten aber eine geringere Dichte und sind oft leichter zu verarbeiten.
3. Titanlegierung (Ti-6Al-4V, Grad 5 & Grad 23 ELI): Der weltraumerprobte Standard
- Zusammensetzung: Titan, legiert mit ~6% Aluminium und ~4% Vanadium. Die Sorte 23 (ELI - Extra Low Interstitial) weist einen geringeren Sauerstoff-, Stickstoff- und Kohlenstoffgehalt auf, was die Duktilität und Bruchzähigkeit verbessert.
- Eigenschaften:
- Vorteile: Hervorragende spezifische Festigkeit, insbesondere bei erhöhten Temperaturen (behält die Festigkeit bis zu ~300-400°C bei). Hohe Steifigkeit. Außergewöhnliche Korrosionsbeständigkeit (inert in den meisten Umgebungen). Biokompatibel (allerdings weniger relevant für Platten). Gute Ermüdungsbeständigkeit. Sorte 23 bietet eine erhöhte Schadenstoleranz. Umfangreiche Flugerfahrung in der Luft- und Raumfahrt.
- Nachteile: Höhere Dichte im Vergleich zu Aluminiumlegierungen (~4,43 g/cm³). Erheblich höhere Materialkosten. Schwieriger zu drucken (reaktiv mit Sauerstoff/Stickstoff, erfordert inerte Atmosphäre oder Vakuum - EBM ist gut geeignet) und nachzubearbeiten (schwierig zu bearbeiten, spezielle Wärmebehandlungen wie HIP erforderlich). Geringere Wärmeleitfähigkeit (~6,7 W/m-K).
- Typische Anwendungen für Satellitenbildschirme:
- Kritische Strukturelemente, die hohen Belastungen oder hohen Temperaturen ausgesetzt sind (z. B. in der Nähe von Motoren oder Hochleistungselektronik).
- Halterungen für schwere Bauteile oder solche, die maximale Steifigkeit erfordern.
- Bauteile, die extreme Haltbarkeit, Ermüdungsfestigkeit oder Bruchzähigkeit erfordern (häufig Güteklasse 23 ELI).
- Paneele, die potenziell korrosiven Stoffen ausgesetzt sind (z. B. Schnittstellen zu Treibmitteln).
- Anwendungen, bei denen eine höhere Dichte aufgrund höherer mechanischer oder thermischer Leistungsanforderungen akzeptabel ist.
- Warum das wichtig ist: Ti-6Al-4V ist nach wie vor der Maßstab für Hochleistungsanwendungen in der Luft- und Raumfahrt. Seine nachgewiesene Erfolgsbilanz, seine ausgezeichneten mechanischen Eigenschaften über eine Reihe von Temperaturen und seine hervorragende Korrosionsbeständigkeit machen es zum Material der Wahl für die anspruchsvollsten Satellitentafel trotz des höheren Gewichts und der höheren Kosten im Vergleich zu modernen Aluminiumsorten.
Vergleichstabelle der Materialeigenschaften (typische Werte für AM)
Eigentum | Einheit | AlSi10Mg (wärmebehandelt) | Scalmalloy® (wärmebehandelt) | Ti-6Al-4V (Güteklasse 5, geglüht/HIP) | Ti-6Al-4V (Güte 23, geglüht/HIP) |
---|---|---|---|---|---|
Dichte (ρ) | g/cm³ | ~2.67 | ~2.66 | ~4.43 | ~4.42 |
Höchstzugkraft (UTS) | MPa | ~350 – 450 | ~500 – 540 | ~900 – 1000 | ~830 – 950 |
Streckgrenze (0,2% Offset) | MPa | ~250 – 350 | ~450 – 500 | ~830 – 930 | ~760 – 880 |
Bruchdehnung (%) | % | ~6 – 12 | ~10 – 16 | ~10 – 18 | ~12 – 20 |
Elastizitätsmodul (E) | GPa | ~70 – 75 | ~75 – 80 | ~110 – 115 | ~105 – 110 |
Spezifische Festigkeit (UTS/ρ) | kNm/kg (ca.) | ~131 – 169 | ~188 – 203 | ~203 – 226 | ~188 – 215 |
Spezifische Steifigkeit (E/ρ) | MNm/kg (ca.) | ~26 – 28 | ~28 – 30 | ~25 – 26 | ~24 – 25 |
Wärmeleitfähigkeit (k) | W/m-K | ~120 – 150 | ~100 – 120 | ~6.7 | ~7.0 |
Maximale Betriebstemperatur (ca.) | °C | ~150 | ~200 | ~350 | ~350 |
In Blätter exportieren
Hinweis: Die Eigenschaften können je nach den Parametern des AM-Prozesses, der Bauausrichtung, der Wärmebehandlung und den Prüfbedingungen erheblich variieren. Dies sind repräsentative Werte.
Die Rolle von Met3dp bei der Materialexzellenz: Die Auswahl der richtigen Legierung ist nur ein Teil der Gleichung. Die Qualität und Konsistenz des Metallpulver selbst sind entscheidend für das Erreichen der gewünschten Materialeigenschaften im endgültigen Druckteil. Hier kommt das Know-how von Met3dp als Anbieter von Metallpulver wird von unschätzbarem Wert. Durch den Einsatz von branchenführenden Pulverherstellungstechnologien wie der Vakuum-Induktions-Schmelz-Gaszerstäubung (VIGA) und dem Plasma-Rotations-Elektroden-Verfahren (PREP) produziert Met3dp hochwertige Metallpulver gekennzeichnet durch:
- Hohe Sphärizität: Gewährleistet eine gute Fließfähigkeit des Pulvers und eine hohe Packungsdichte im Pulverbett, was zu dichteren, gleichmäßigeren Teilen führt.
- Niedriger Satellitengehalt: Minimiert feine Partikel, die an größeren Partikeln haften, verbessert den Durchfluss und reduziert mögliche Defekte.
- Kontrollierte Partikelgrößenverteilung (PSD): Maßgeschneiderte PSDs, die für bestimmte AM-Prozesse (L-PBF, EBM) optimiert sind, gewährleisten ein gleichmäßiges Schmelzen und eine gleichmäßige Schichtbildung.
- Hochreine und kontrollierte Chemie: Eine strenge Kontrolle der Legierungszusammensetzung und die Minimierung von Verunreinigungen (wie Sauerstoff und Stickstoff) sind entscheidend für das Erreichen der angestrebten mechanischen und physikalischen Eigenschaften, insbesondere bei reaktiven Legierungen wie Titan.
Met3dp bietet eine umfassende Produktportfolio Dazu gehören nicht nur Standardlegierungen wie AlSi10Mg und Ti-6Al-4V (einschließlich Grade 23 ELI), sondern auch auf speziellere Werkstoffe, die für die Luft- und Raumfahrt von Bedeutung sind, wie Superlegierungen (Inconel 718, 625), andere Titanlegierungen (TiAl, TiNbZr) und rostfreie Stähle, um sicherzustellen, dass B2B-Beschaffung Teams und Ingenieure haben Zugang zu den richtigen Materialien für ihre anspruchsvollen Satellitentafel Anwendungen. Unser Engagement für die Pulverqualität führt direkt zu zuverlässigeren und leistungsfähigeren 3D-gedruckten Komponenten für die Raumfahrtindustrie.
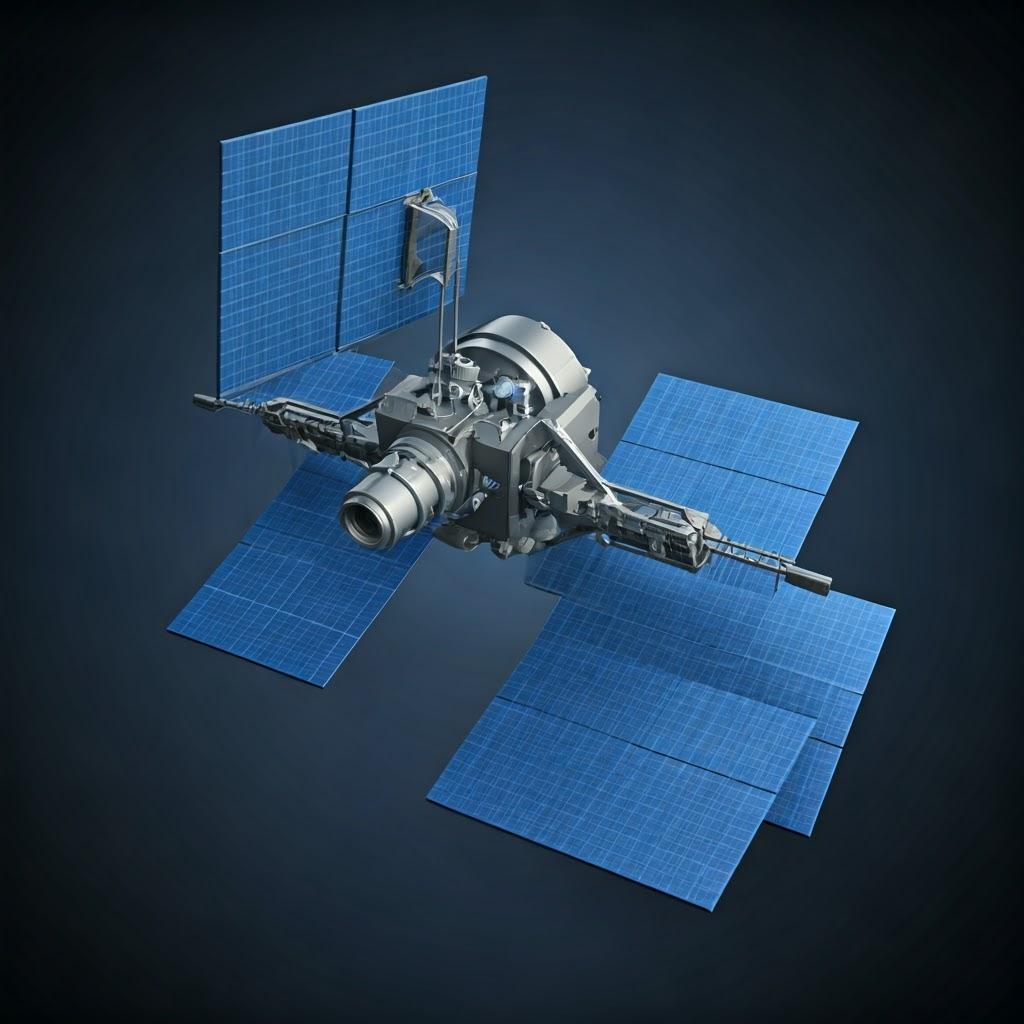
Entwerfen für die Sterne: Wichtige Überlegungen für additiv gefertigte Satellitenpaneele
Erfolgreiche Nutzung der Additive Fertigung von Metall (AM) für Satellitentafeln erfordert mehr als nur die Konvertierung einer bestehenden Designdatei und den Klick auf "Drucken". Es erfordert einen grundlegenden Wandel in der Designphilosophie, der die folgenden Prinzipien einbezieht Design für additive Fertigung (DfAM). Bei DfAM geht es nicht nur um die Anpassung an den Druckprozess, sondern um die aktive Nutzung seiner einzigartigen Fähigkeiten - wie die Erstellung komplexer Geometrien und die Konsolidierung von Teilen -, um eine bessere Leistung, ein geringeres Gewicht und eine schnellere Entwicklung zu erreichen, Ziele, die in der Raumfahrttechnik. Für B2B-Design-Dienstleistungen und internen Entwicklungsteams ist die Beherrschung von DfAM der Schlüssel zur Erschließung des vollen Potenzials von 3D-Druck von Metall für Raumfahrzeugkomponenten.
Hier sind die wichtigsten DfAM-Überlegungen bei der Gestaltung Satellitentafeln für die Metall-AM-Produktion:
1. Umfassen Sie die Topologie-Optimierung:
- Was es ist: Ein rechnergestütztes Konstruktionsverfahren, bei dem Software-Algorithmen anhand eines Konstruktionsraums, von Belastungsbedingungen, Beschränkungen und Materialeigenschaften die effizienteste Materialanordnung ermitteln, um die Leistungsziele (z. B. Steifigkeit, Festigkeit) zu erreichen. Dabei wird im Wesentlichen unnötiges Material weggeschnitten, so dass eine optimierte, oft organisch anmutende Struktur zurückbleibt.
- Warum das für Panels wichtig ist: Dies ist wohl das mächtigste Instrument zur Erreichung drastischer Leichtbau in Struktur- und Montageplatten. Es stellt sicher, dass das Material nur dort platziert wird, wo es strukturell notwendig ist, um die Startlasten und Betriebsbelastungen zu bewältigen, was zu einer erheblichen Gewichtsreduzierung im Vergleich zu herkömmlichen Konstruktionen auf der Grundlage von Standardprofilen oder Aussparungen führt.
- Wie man sich bewirbt:
- Definieren Sie den Planungsraum (maximal zulässiges Volumen).
- Genaue Definition aller Lastfälle (statisch, dynamisch, thermisch).
- Geben Sie Randbedingungen an (Fixpunkte, Sperrzonen für Schnittstellen oder Komponenten).
- Auswahl der für AM geeigneten Herstellungsbedingungen (z. B. Mindestgröße der Bauteile).
- Einsatz robuster Simulationssoftware (FEA integriert mit Topologieoptimierungswerkzeugen wie Altair OptiStruct, Dassault Systèmes TOSCA, Ansys Discovery, usw.).
- Interpretieren und verfeinern Sie die oft komplexen Ergebnisse in ein fertigungsgerechtes AM-Design.
- Erwägungen: Erfordert genaue Lastdefinition und Simulationskenntnisse. Die sich daraus ergebenden Geometrien können komplex sein und erfordern unter Umständen eine sorgfältige Planung der Ausrichtung und Unterstützung für den Druck.
2. Strategische Nutzung von Gitterstrukturen:
- Was sie sind: Technische poröse Strukturen, die sich aus sich wiederholenden Einheitszellen zusammensetzen (z. B. auf Basis von Streben wie kubische oder Oktett-Fachwerke oder auf Basis von Oberflächen wie TPMS (Triply Periodic Minimal Surfaces) wie Gyroide oder Schwarzite). AM ist in einzigartiger Weise in der Lage, diese komplizierten inneren Strukturen zu erzeugen.
- Warum sie für Panels wichtig sind:
- Gewichtsreduzierung: Sie werden als Kernstrukturen in Sandwichpaneelen oder als Füllung für dickere Abschnitte verwendet, wodurch das Gewicht erheblich reduziert wird und gleichzeitig eine gute Steifigkeit und Knickbeständigkeit erhalten bleibt.
- Energie-Absorption: Sie können so konstruiert werden, dass sie vorhersehbar brechen, was die Widerstandsfähigkeit gegenüber Vibrationen oder Stoßbelastungen erhöhen kann.
- Wärmemanagement: Eine große Oberfläche innerhalb von Gittern kann die Wärmeübertragung verbessern, was für integrierte Kühlung oder Kühlerplattenkerne nützlich ist. TPMS-Strukturen bieten glatte, durchgehende Oberflächen, die für den Flüssigkeitsstrom von Vorteil sind.
- Maßgeschneiderte Eigenschaften: Steifigkeit und Festigkeit lassen sich durch Variation von Zelltyp, Größe und Streben-/Wandstärke einstellen.
- Wie man sich bewirbt:
- Wählen Sie den geeigneten Gittertyp auf der Grundlage der Hauptfunktion (Steifigkeit, Wärmeübertragung usw.).
- Integrieren Sie Werkzeuge zur Gittergenerierung in CAD- oder Spezialsoftware.
- Stellen Sie sicher, dass die Streben-/Wanddicke deutlich über der minimalen druckbaren Featuregröße für den gewählten AM-Prozess und das gewählte Material liegt.
- Berücksichtigen Sie die Pulverentfernung aus komplexen inneren Gittern - konstruieren Sie für Zugänglichkeit oder verwenden Sie TPMS-Strukturen, die von Natur aus selbstentleerend sind.
- Erwägungen: Das Entwerfen, Simulieren und Prüfen von komplexen Gittern kann eine Herausforderung sein. Die Gewährleistung einer vollständigen Pulverentfernung ist entscheidend.
3. Aggressive Teilkonsolidierung vorantreiben:
- Was es ist: Überdenken von Baugruppen, die aus mehreren traditionell hergestellten Teilen bestehen (Platten, Halterungen, Befestigungselemente, Rohre), und Neukonzipierung, um sie als eine einzige, monolithische Komponente zu drucken.
- Warum das für Panels wichtig ist: Reduziert den Zeit- und Arbeitsaufwand für die Montage, eliminiert potenzielle Fehlerstellen an Verbindungen/Verbindungselementen, vereinfacht die Lieferkette und das Bestandsmanagement, reduziert häufig das Gesamtgewicht durch den Wegfall von Flanschen und Befestigungselementen und kann die strukturelle Effizienz verbessern.
- Wie man sich bewirbt:
- Analysieren Sie vorhandene Schalttafel-Baugruppen: Identifizieren Sie benachbarte Teile mit einfachen Schnittstellen, zahlreichen Verbindungselementen oder Komponenten mit verwandten Funktionen.
- Neugestaltung von Schnittstellen für eine nahtlose Integration in ein einzelnes AM-Teil.
- Integrieren Sie Befestigungselemente, Flüssigkeitskanäle oder Halterungen direkt in die Struktur der Haupttafel.
- Durchführung einer gründlichen Funktions- und Strukturanalyse (FEA) des konsolidierten Entwurfs, um sicherzustellen, dass er alle ursprünglichen Anforderungen erfüllt.
- Erwägungen: Erhöht die Komplexität des einzelnen AM-Teils. Das Versagen eines konsolidierten Teils kann kritischer sein als das Versagen einer einzelnen Komponente in einer Baugruppe (erfordert eine strenge Validierung). Kann Reparaturen erschweren (Ersatz statt Reparatur einer Unterkomponente).
4. Entwurf zur Minimierung und Beseitigung von Stützen:
- Warum Unterstützung benötigt wird: Metall-AM-Verfahren wie L-PBF erfordern Stützstrukturen für Überhang-Features (typischerweise unter 45° aus der Horizontalen), um sie an der Bauplatte oder den unteren Schichten zu verankern, Verformungen zu verhindern und Wärme abzuleiten. Bei EBM sind oft weniger Stützstrukturen erforderlich, da der Pulverkuchen eine gewisse Unterstützung bietet.
- Warum sie minimieren: Träger verbrauchen zusätzliches Material, verlängern die Druckzeit, erfordern einen erheblichen Nachbearbeitungsaufwand beim Entfernen und können Spuren hinterlassen, die die Oberflächengüte beeinträchtigen.
- Wie man gestaltet:
- Orientierung: Richten Sie die Platte in der Baukammer so aus, dass die kritischen Flächen senkrecht oder nach oben gerichtet sind, und minimieren Sie nach unten gerichtete Überhänge.
- Selbsttragende Winkel: Entwerfen Sie Überhänge so, dass sie nach Möglichkeit über dem kritischen Winkel liegen (z. B. >45°). Verwenden Sie Abschrägungen anstelle von scharfen Überhängen.
- Selbsttragende Merkmale: Verwenden Sie Rauten- oder Tropfenformen für horizontale Löcher anstelle von perfekten Kreisen.
- Zugänglichkeit: Stellen Sie sicher, dass die Stützstrukturen für die Entnahmewerkzeuge (manuell oder automatisch) physisch zugänglich sind. Vermeiden Sie das Einschließen von Trägern in geschlossenen Hohlräumen, es sei denn, es werden auflösbare Träger oder spezielle Strategien verwendet.
- Design unterstützen: Arbeiten Sie mit dem AM-Anbieter zusammen, um die Art der Halterung (z. B. Kegel, Block, Linie) und die Dichte (unter Verwendung von leicht abbrechbaren Kontaktpunkten) zu optimieren, damit sie leichter zu entfernen ist und dennoch die erforderliche Funktion erfüllt.
- Erwägungen: Bei der optimalen Ausrichtung müssen oft Kompromisse zwischen Unterstützungsbedarf, Oberflächengüte, Bauzeit und möglichem Verzug eingegangen werden.
5. Beachten Sie die prozessspezifischen Funktionsbeschränkungen:
- Wanddicke: Gestalten Sie die Wände dicker als die minimale bedruckbare Grenze für das gewählte Verfahren/Material (z. B. typischerweise 0,3-0,5 mm für L-PBF, möglicherweise dicker für EBM). Sehr dünne Wände sind anfällig für Verformungen und Beschädigungen während der Handhabung/Nachbearbeitung. Berücksichtigen Sie das Knickverhalten.
- Merkmal Größe: Kleine Löcher, Stifte, Schlitze und feine Details haben minimale herstellbare Größen. Horizontale Löcher sind oft weniger genau als vertikale.
- Bildseitenverhältnis: Sehr hohe, dünne Elemente können während des Baus anfällig für Vibrationen oder Verzerrungen sein.
- Kanäle: Interne Kanäle benötigen Mindestdurchmesser für eine effektive Pulverentfernung (typischerweise >1-2 mm, je nach Länge und Komplexität).
6. Umgang mit Eigenspannung durch Konstruktion:
- Das Problem: Durch die schnelle Erwärmung und Abkühlung während des AM-Prozesses entstehen erhebliche innere Spannungen, die zu Verformungen, Rissen oder Maßungenauigkeiten führen können.
- Design-Lösungen:
- Vermeiden Sie große, flache, freitragende Bereiche parallel zur Bauplatte.
- Verwenden Sie großzügige Verrundungen und Radien anstelle von scharfen Innenecken, in denen sich die Spannung konzentriert.
- Integrieren Sie gegebenenfalls spannungsmindernde Merkmale oder Topologien.
- Berücksichtigen Sie die Auswirkungen der Gebäudeausrichtung auf die thermischen Gradienten.
- Allmähliche Übergänge in der Dicke sind abrupten Veränderungen vorzuziehen.
7. Design mit Nachbearbeitung im Hinterkopf:
- Zulagen für die Bearbeitung: Wenn enge Toleranzen oder spezielle Oberflächengüten für bestimmte Merkmale erforderlich sind (z. B. Befestigungsschnittstellen, Passflächen), fügen Sie in diesen Bereichen des CAD-Modells zusätzliches Rohmaterial (z. B. 0,5-2 mm) hinzu, das später durch CNC-Bearbeitung entfernt wird.
- Datum Merkmale: Berücksichtigen Sie klare, leicht zugängliche Bezugspunkte in der Konstruktion, um die Einrichtung für die Nachbearbeitung und Prüfung (CMM) zu erleichtern.
- Zugang: Stellen Sie sicher, dass Werkzeuge und Sonden für die Entfernung von Halterungen, die Oberflächenbearbeitung (z. B. Strahlen, Polieren) und die ZfP-Prüfung (z. B. Sichtlinie für bestimmte Verfahren) zugänglich sind.
Partnerschaften für den DfAM-Erfolg: Beherrschung von DfAM, insbesondere für unternehmenskritische Satellitenkomponentenerfordert Erfahrung. Die Zusammenarbeit mit einem sachkundigen AM-Partner ist von unschätzbarem Wert. Met3dpmit seinem umfassenden Fachwissen sowohl in 3D-Druck von Metall Ausrüstung (einschließlich leistungsstarker SEBM-Systeme) und fortschrittliche Metallpulverbietet umfassende Dienstleistungen im Bereich der Anwendungsentwicklung an. Unser Team kann helfen Raumfahrtingenieure und B2B-Lieferanten bei der Optimierung von Bauteildesigns speziell für die additive Fertigung unter Berücksichtigung von Materialeigenschaften, Prozessfähigkeiten, Support-Strategien und Nachbearbeitungsanforderungen, um ein erfolgreiches Ergebnis vom Konzept bis zum flugfertigen Teil zu gewährleisten. Dieser kollaborative Ansatz hilft, Risiken zu minimieren und die Vorteile von AM zu maximieren.
Präzision in der Umlaufbahn: Erzielung enger Toleranzen, Oberflächengüte und Maßgenauigkeit
Während die additive Fertigung von Metallen eine unglaubliche Designfreiheit ermöglicht, müssen Komponenten, die für die Umlaufbahn bestimmt sind, strenge Anforderungen an die Präzision erfüllen. Satellitentafeln enthalten oft kritische Schnittstellen für die Montage empfindlicher Nutzlasten, die Ausrichtung von Strukturelementen oder die Gewährleistung des thermischen Kontakts. Daher ist das Verständnis und die Verwaltung Abmessungsgenauigkeit, Toleranzenund Oberflächengüte ist von entscheidender Bedeutung für Raumfahrtingenieure und qualitätssicherung Teams. Auch wenn AM nicht mit den Ist-Zustand Präzision der High-End-CNC-Bearbeitung über das gesamte Teil, strategisches Design und Nachbearbeitung ermöglichen es, die anspruchsvollen Luftfahrtnormen für unternehmenskritische Teile.
As-Built vs. fertige Präzision: Es ist von entscheidender Bedeutung, zwischen der direkt im AM-Prozess erreichbaren Präzision ("as-built") und der endgültigen Präzision nach Nachbearbeitungsschritten wie der mechanischen Bearbeitung zu unterscheiden.
- As-Built-Genauigkeit: Sie liegt in der Regel zwischen ±0,1 mm und ±0,2 mm bei kleineren Merkmalen bzw. zwischen ±0,5% und ±1% der Gesamtabmessung bei größeren Teilen. Diese Variabilität wird durch zahlreiche Faktoren beeinflusst (siehe unten). Sie ist im Allgemeinen ausreichend für unkritische Merkmale oder Teile, bei denen die Gesamtform wichtiger ist als die genauen Abmessungen.
- Oberflächenbeschaffenheit (Rauheit, Ra) wie gebaut: Stark abhängig vom AM-Verfahren (L-PBF ist im Allgemeinen glatter als EBM), dem Material, den Parametern, der Bauausrichtung und der Position auf dem Teil.
- Vertikale Mauern: Oft die glattesten, möglicherweise 5-15 µm Ra.
- Nach oben gerichtete Flächen: Geringfügig rauer durch teilweise anhaftendes Pulver, vielleicht 10-20 µm Ra.
- Nach unten gerichtete (überhängende) Flächen: Typischerweise die rauesten aufgrund der Kontaktpunkte mit der Trägerstruktur oder der direkten Einwirkung der Energiequelle, möglicherweise >20-25 µm Ra.
- Fertige Genauigkeit und Oberflächengüte: Durch die Einbeziehung von Nachbearbeitungsschritten (CNC-Fräsen, -Drehen, -Schleifen) für kritische Merkmale können bei Bedarf Toleranzen, die mit der traditionellen Fertigung vergleichbar sind (z. B. ±0,01 mm bis ±0,05 mm oder enger), und sehr glatte Oberflächen (Ra < 1 µm) erzielt werden.
Faktoren, die die As-Built-Präzision beeinflussen:
- AM Maschinenkalibrierung & Zustand: Die regelmäßige Kalibrierung von Scannern/Elektronenkanonen, Strahlfokus- und Bewegungssystemen ist unerlässlich.
- Prozessparameter: Laser-/Strahlleistung, Scangeschwindigkeit, Schichtdicke, Schraffurabstand und Scanstrategie wirken sich alle auf die Stabilität des Schmelzbades und die Erstarrung aus und beeinflussen die Genauigkeit und das Finish.
- Qualität des Pulvers: Konsistente Partikelgrößenverteilung (PSD), Morphologie (Sphärizität) und Fließfähigkeit des Metallpulver (eine zentrale Stärke des Met3dp-Angebots) tragen zu gleichmäßigen Schichten und stabilem Schmelzen bei.
- Thermische Effekte: Eigenspannungen, die während der Erhitzungs- und Abkühlungszyklen entstehen, können Verformungen und Verzerrungen verursachen, die sich auf die endgültigen Abmessungen auswirken. Unterstützungsstrategie und Spannungsabbau sind wichtige Kontrollmechanismen.
- Teil Orientierung: Beeinflusst den Unterstützungsbedarf, die Oberflächenrauhigkeit auf den verschiedenen Flächen und die Anfälligkeit für thermische Verformung.
- Strategie unterstützen: Die Dichte und die Lage der Stützen beeinflussen die Wärmeableitung und mögliche Verformungen während der Auf- und Abbauphase.
- Wärmebehandlung: Wärmebehandlungen nach der Herstellung (Spannungsabbau, HIP, Glühen) können geringfügige Maßänderungen verursachen, die berücksichtigt werden müssen.
Verwaltung von Toleranzen und Oberflächenbeschaffenheit für Satellitenpaneele:
- Geometrische Dimensionierung und Tolerierung (GD&T): Wenden Sie GD&T rigoros, aber strategisch an. Definieren Sie enge Toleranzen nur an kritischen Schnittstellen (z. B. Montagebohrungen/-pads, Gegenflächen, Ausrichtungsmerkmale). Verwenden Sie geringere Profiltoleranzen für weniger kritische Oberflächen, bei denen die AM-Genauigkeit im Ist-Zustand ausreichend ist. Dadurch werden unnötige und kostspielige Nachbearbeitungen vermieden.
- Kennzeichnen Sie kritische Oberflächen: Geben Sie auf den Zeichnungen deutlich an, welche Oberflächen nachbearbeitet werden müssen, und geben Sie die Endtoleranz und die Anforderungen an die Oberflächengüte (z. B. Ra-Wert) an.
- Near-Net-Shape-Strategie: Entwerfen Sie das AM-Teil als "Near-Net-Shape"-Rohling und fügen Sie ausreichend Bearbeitungsmaterial (z. B. 0,5-2 mm) speziell für kritische Oberflächen hinzu.
- Datum Merkmale: Integrieren Sie robuste, leicht zugängliche Bezugspunkte in die Konstruktion. Diese sind wichtige Bezugspunkte für die genaue Einrichtung des Teils auf CNC-Maschinen für die Nachbearbeitung und auf KMGs für die Prüfung.
- Verbesserung der Oberflächengüte:
- Allgemeine Glättung: Verfahren wie Perlstrahlen, Sandstrahlen oder Trommeln können die allgemeine Oberflächengüte verbessern und loses Pulver entfernen, was für unkritische Bereiche oft ausreicht.
- Gezieltes Finishing: Für spezielle Anforderungen wie verbesserte Ermüdungsfestigkeit, Dichtheit oder HF-Leistung können nach dem anfänglichen Glätten oder Bearbeiten fortschrittlichere Techniken wie die Fließbearbeitung (AFM), elektrochemisches Polieren (ECP) oder manuelles Polieren eingesetzt werden.
Typischer Vergleich der Oberflächenrauhigkeit (Ra):
Oberflächenbeschaffenheit / Prozess | Typischer Ra-Bereich (µm) | Anmerkungen |
---|---|---|
As-Built Metall AM (L-PBF) | ||
- Vertikale Wand | 5 – 15 | Im Allgemeinen die glatteste Oberfläche im Ist-Zustand |
- Nach oben gerichtete Oberfläche | 10 – 20 | Leichte Unebenheiten durch teilweise gesintertes Pulver |
- Nach unten gerichtet (unterstützt) | 15 – 30+ | Rauher durch Auflagekontaktpunkte / Schmelzdynamik |
As-Built Metal AM (EBM) | 20 – 40+ | Im Allgemeinen rauer als L-PBF aufgrund der größeren Schichtdicke/Partikel |
Nachbearbeitung von Oberflächen | ||
- Perlstrahlen / Sandstrahlen | 2 – 10 | Sorgt für ein gleichmäßiges, mattes Finish, entfernt lose Partikel |
- Taumeln / Vibrationsgleitschleifen | 1 – 5 | Gut für Schüttgutveredelung, Kantenabrundung |
- CNC-Bearbeitung (Fräsen/Drehen) | 0.4 – 6.3 | Standard-Bearbeitungsbereich, steuerbar |
- CNC-Bearbeitung (Schleifen) | 0.1 – 1.6 | Für sehr hohe Präzision und glatte Oberflächen |
- Polieren / Läppen | < 0.1 - 0.8 | Für Hochglanzoberflächen, optische Oberflächen oder Dichtungen |
In Blätter exportieren
Inspektion und Metrologie - Sicherstellung der Konformität: Überprüfung, ob die endgültige Satellitentafel die Einhaltung aller Maß- und Oberflächenspezifikationen ist entscheidend. Häufig wird ein mehrstufiger Prüfansatz verwendet:
- Prozessbegleitende Überwachung: Einige fortschrittliche AM-Maschinen bieten eine Echtzeit-Überwachung der Schmelzepool-Eigenschaften oder der Schichttopografie, was frühzeitige Hinweise auf mögliche Probleme liefert.
- Zerstörungsfreie Prüfung (NDT): Das CT-Scannen ist von unschätzbarem Wert für die Überprüfung der inneren Geometrie, die Erkennung von Hohlräumen/Einschlüssen und die Überprüfung der Pulverentfernung aus den inneren Kanälen. Andere ZfP-Methoden (DPI, UT, RT) prüfen auf Oberflächen- und Untergrundfehler (mehr dazu unter Nachbearbeitung).
- 3D-Scannen: Das Scannen mit Laser oder strukturiertem Licht erfasst die Gesamtgeometrie des gefertigten oder fertigen Teils und ermöglicht den Vergleich mit dem ursprünglichen CAD-Modell sowie die Bewertung der Gesamtform und der Verformung.
- Koordinatenmessmaschine (CMM): Messtaster oder optische KMGs liefern hochpräzise Messungen von spezifischen Merkmalen, Abmessungen und GD&T-Kennzeichnungen, die in der Regel nach der Endbearbeitung kritischer Merkmale durchgeführt werden.
Das Engagement von Met3dp für Präzision: Das Erreichen einer gleichbleibenden Präzision beginnt mit zuverlässigen Geräten und hochwertigen Materialien. Met3dp bietet industrielle Metall-3D-Drucker auf Genauigkeit und Wiederholbarkeit ausgelegt, die für die Herstellung von unternehmenskritische Teile. Unsere strenge Qualitätskontrolle in Metallpulver Die Produktion gewährleistet ein konsistentes Ausgangsmaterial, was für die Erzielung vorhersehbarer Ergebnisse bei jedem Bauvorgang von grundlegender Bedeutung ist. Auch wenn für die engsten Toleranzen oft eine Nachbearbeitung erforderlich ist, wird der Weg zu einem flugfähigen Bauteil durch ein qualitativ hochwertiges, maßhaltiges Bauteil aus einem zuverlässigen System deutlich verkürzt. Satellitentafelund stärkt unsere Rolle als vertrauenswürdiger B2B-Lieferant für anspruchsvolle Raumfahrt-Fertigung Anwendungen.
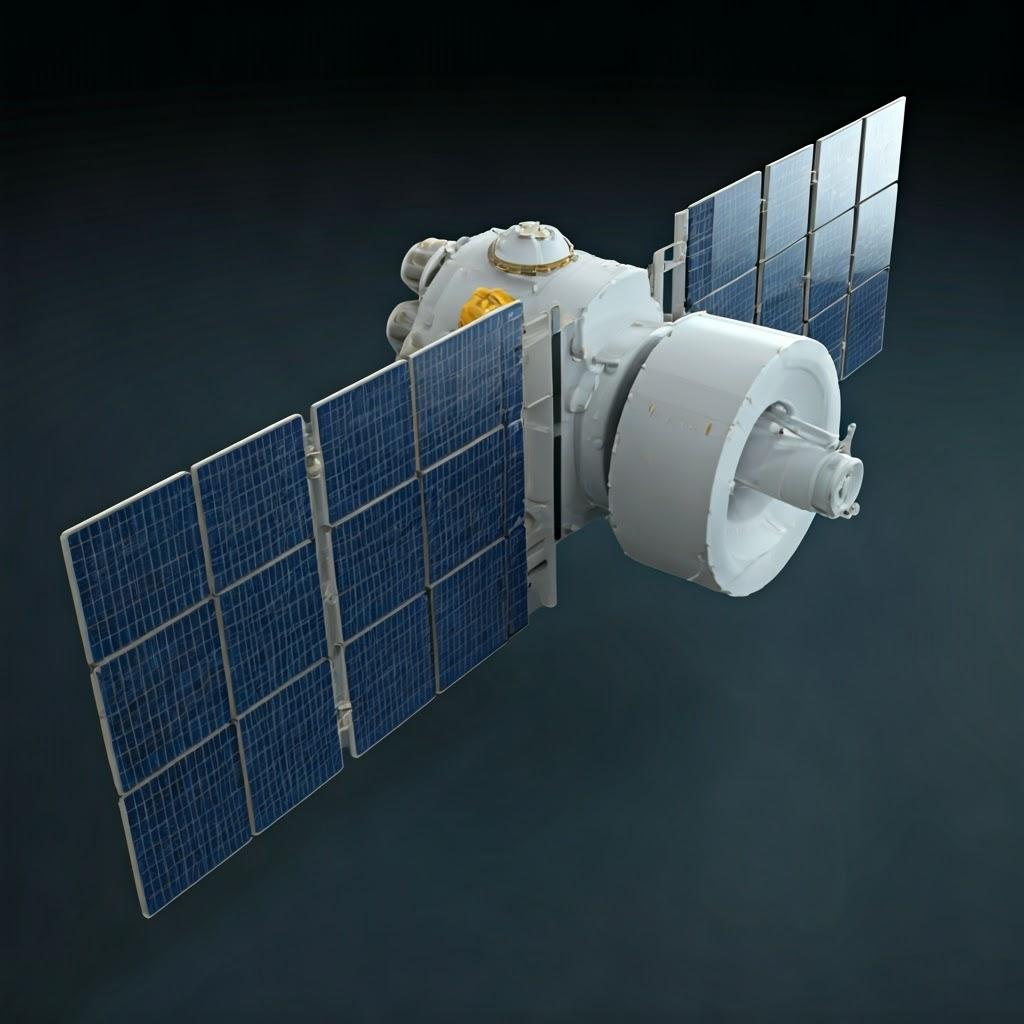
Über den Bau hinaus: Wichtige Nachbearbeitungsschritte für 3D-gedruckte Satellitenpaneele
Ein häufiges Missverständnis über Metall-Additiv-Fertigung ist, dass die Teile aus dem Drucker kommen und sofort einsatzbereit sind. Während AM die endkonturnahe Form erzeugt, wird eine Reihe von entscheidenden Nachbearbeitung Schritte sind fast immer erforderlich, um ein Bauteil im Ist-Zustand in ein flugfähiges Satellitentafel die den strengen Luft- und Raumfahrt Anforderungen an mechanische Eigenschaften, Maßhaltigkeit, Oberflächengüte und Gesamtintegrität. Das Verständnis dieses Arbeitsablaufs ist entscheidend für eine genaue Projektplanung, Kostenkalkulation und Vorlaufzeitabschätzung durch Technik und Beschaffung Teams.
Die einzelnen Schritte und ihre Reihenfolge können je nach Material variieren (z. B., AlSi10Mg, Scalmalloy®, Ti-6Al-4V), das verwendete AM-Verfahren (L-PBF, EBM), die Komplexität des Designs und die spezifischen Anforderungen der Anwendung. Ein typischer Arbeitsablauf umfasst jedoch Folgendes:
1. Thermische Behandlungen (oft erste Schritte):
- Stressabbau: Dies ist in der Regel die allererste Schritt nach Abschluss des Bauprozesses, der häufig durchgeführt wird, während das Teil noch auf der Bauplatte in einem Ofen mit inerter Atmosphäre (z. B. Argon) befestigt ist. Die schnellen Erwärmungs- und Abkühlungszyklen, die dem AM (insbesondere L-PBF) eigen sind, führen zu erheblichen inneren Eigenspannungen. Beim Spannungsabbau wird das Teil auf eine bestimmte Temperatur (unterhalb der Umwandlungspunkte) erhitzt, gehalten und langsam abgekühlt. Dadurch werden die inneren Spannungen reduziert und Verformungen oder Risse bei nachfolgenden Schritten wie der Entnahme oder Bearbeitung des Teils verhindert.
- Wärmebehandlung (für Eigenschaften): Wird nach dem Abtragen der Teile und manchmal nach der Grobbearbeitung durchgeführt. Ziel ist die Optimierung der Mikrostruktur und der mechanischen Eigenschaften des Materials.
- Heiß-Isostatisches Pressen (HIP): Wird als wesentlich für die meisten kritischen Luft- und Raumfahrtkomponenten, insbesondere solche aus Ti-6Al-4V. Die Teile werden mehrere Stunden lang einer hohen Temperatur (knapp unter dem Schmelzpunkt) und einem hohen isostatischen Druck (unter Verwendung eines Inertgases wie Argon, ~100-200 MPa) ausgesetzt. Durch dieses Verfahren werden interne Poren und Hohlräume, die sich während des Drucks gebildet haben könnten, wirksam geschlossen, wodurch sich die Dichte (auf nahezu 100%), die Duktilität, die Ermüdungsfestigkeit und die Bruchzähigkeit erheblich verbessern.
- Lösungsglühen und Alterung (Härten): Spezifische, auf die Legierung zugeschnittene Wärmebehandlungszyklen (z. B. T6-Wärmebehandlung für AlSi10Mg und Scalmalloy®), um Legierungselemente in der Matrix aufzulösen und sie dann kontrolliert auszuscheiden, um die gewünschte Festigkeit, Härte und Duktilität zu erreichen. Die Parameter (Temperatur, Zeit) sind kritisch und legierungsspezifisch.
2. Physische Trennung und Entfernung der Unterstützung:
- Entfernen des Teils von der Bauplatte: Nach dem Spannungsabbau (falls auf der Platte erforderlich) wird die gedruckte Platte vorsichtig von der Bauplatte abgetrennt. Dies geschieht häufig durch Drahterodieren (Electrical Discharge Machining), um einen sauberen Schnitt zu erzielen, oder manchmal auch mit einer Bandsäge.
- Entfernung der Stützstruktur: Dies kann einer der zeitaufwändigsten und arbeitsintensivsten Schritte sein. Stützen werden in der Regel manuell mit Handwerkzeugen (Zangen, Scheren, Schleifmaschinen) oder manchmal durch CNC-Bearbeitung oder spezielle Methoden wie elektrochemische Bearbeitung für schwer zugängliche Bereiche entfernt. Dabei muss darauf geachtet werden, dass die Oberfläche des Teils nicht beschädigt wird. Spuren an den Stellen, an denen Stützen angebracht wurden, sind üblich und erfordern oft eine weitere Nachbearbeitung. DfAM-Strategien, die die Anzahl der Stützen minimieren und die Zugänglichkeit sicherstellen, sind hier von großem Vorteil.
3. Oberflächenveredelung und Endbearbeitung:
- Entfernung und Reinigung von Schüttgut: Gründliches Entfernen von nicht verschmolzenen Resten Metallpulverinsbesondere von internen Kanälen oder komplexen Gitterstrukturen, ist von entscheidender Bedeutung. Dies geschieht in der Regel durch Abblasen mit Druckluft, Perlstrahlen oder Ultraschallreinigung. Eingeschlossenes Pulver kann ein Kontaminationsproblem darstellen oder unerwünschte Masse hinzufügen.
- Allgemeine Oberflächenglättung: AM-Oberflächen sind relativ rau, so wie sie sind. Verschiedene Methoden können für eine gleichmäßigere und glattere Oberfläche sorgen:
- Perlenstrahlen / Sandstrahlen: Treibt feine Medien (Glasperlen, Keramik, Aluminiumoxid) auf die Oberfläche. Erzeugt eine gleichmäßige matte Oberfläche, verbessert das kosmetische Erscheinungsbild und kann Druckspannungen erzeugen, die sich positiv auf die Dauerhaftigkeit auswirken.
- Taumeln / Vibrationsgleitschleifen: Die Teile werden in eine Wanne mit Schleifmittel gelegt, das vibriert oder taumelt. Gut zum Glätten von Oberflächen und Entgraten von Kanten an mehreren Teilen gleichzeitig, jedoch weniger präzise für bestimmte Merkmale.
- Abrasive Fließbearbeitung (AFM): Drückt eine abrasive Spachtelmasse durch innere Kanäle oder über Oberflächen, um sie zu glätten. Wirksam für innere Durchgänge.
- Elektrochemisches Polieren (ECP): Verwendet ein elektrochemisches Verfahren zum Abtragen von Material, was zu einer sehr glatten, glänzenden Oberfläche führt. Besonders effektiv bei bestimmten Legierungen wie rostfreiem Stahl und einigen Titanlegierungen.
- Gezielte Oberflächenveredelung: Spezielle Bereiche, die eine sehr geringe Rauheit (z. B. Ra < 0,8 µm) für die Abdichtung, die optische Montage oder die HF-Leistung erfordern, müssen in der Regel manuell poliert oder präzise bearbeitet/geschliffen werden.
4. Bearbeitungen für Präzision:
- CNC-Bearbeitung: Wie bereits erwähnt, werden kritische Schnittstellen, Montagebohrungen, Gegenflächen und alle Merkmale, die engere Toleranzen als die AM-Fähigkeit erfordern, normalerweise durch CNC-Fräsen, Drehen oder Schleifen bearbeitet. Dies erfordert ein sorgfältiges Vorrichtungsdesign, um das oft komplexe AM-Teil sicher zu halten und die Bezugsmerkmale genau zu referenzieren.
5. Inspektion und Qualitätssicherung (NDT):
- Zerstörungsfreie Prüfung (NDT): Wesentlich für die Überprüfung der Integrität von Flug-Hardware. Die zerstörungsfreie Prüfung wird häufig in mehreren Stufen durchgeführt (z. B. nach dem HIP, nach der Endbearbeitung).
- Computertomographie (CT) Scannen: Bietet eine detaillierte 3D-Visualisierung des Bauteilinneren, um Porosität, Einschlüsse und Risse zu erkennen und die innere Geometrie zu überprüfen, ohne das Bauteil zu beschädigen.
- Farbeindringprüfung (Dye Penetrant Inspection, DPI) oder Fluorescent Penetrant Inspection (FPI): Erkennt Risse, die die Oberfläche durchbrechen.
- Ultraschallprüfung (UT): Spürt mit Hilfe von Schallwellen Fehler im Untergrund auf.
- Durchleuchtungsprüfung (RT): Röntgenbasierte Methode zum Auffinden interner Defekte.
- Endabnahme der Abmessungen: Verwendung von CMM oder 3D-Scanning zur Bestätigung, dass alle Abmessungen und GD&T-Anforderungen erfüllt sind.
6. Endreinigung und Beschichtung:
- Endreinigung: Strenge Reinigungsverfahren zur Entfernung von Rückständen von Bearbeitungsflüssigkeiten, NDT-Chemikalien oder der Handhabung, um sicherzustellen, dass das Teil für die Integration in die Satellitenbaugruppe bereit ist (häufig in einer Reinraumumgebung).
- Beschichtung / Oberflächenbehandlung: Auftragen spezieller Beschichtungen, wenn dies für die Konstruktion erforderlich ist, wie z. B.:
- Thermisch kontrollierte Beschichtungen: Anstriche oder aufgetragene Schichten mit spezifischem Emissions- und Absorptionsvermögen für Heizkörperverkleidungen oder Wärmemanagement.
- Korrosionsschutz: Eloxieren (für Aluminiumlegierungen wie AlSi10Mg, Scalmalloy®) oder Konversionsbeschichtungen.
- Verschleißbeständige Beschichtungen: Für bestimmte Schnittstellenpunkte.
Überlegungen zum Prozessablauf: Die genaue Reihenfolge ist wichtig. So wird z. B. die HIP-Behandlung in der Regel vor der Endbearbeitung durchgeführt, da der Prozess leichte Maßänderungen verursachen kann. Die zerstörungsfreie Prüfung kann nach der Wärmebehandlung und erneut nach der Endbearbeitung erfolgen. Eine effektive Planung und Integration dieser Nachbearbeitung Schritte sind entscheidend für das Management von Kosten und Vorlaufzeiten. B2B-Veredelungsdienstleistungen die auf AM-Teile spezialisiert sind, spielen oft eine Schlüsselrolle in diesem Ökosystem.
Während Met3dp konzentriert sich in erster Linie auf die Bereitstellung branchenführender Metall-3D-Drucker und hochwertige MetallpulverWir wissen, dass dies nur die ersten Schritte zur Herstellung eines flugfähigen Bauteils sind. Unser Team verfügt über das Wissen des gesamten AM-Workflows und kann Kunden wertvolle Einblicke und Anleitungen für die komplexe Nachbearbeitung bieten, um sicherzustellen, dass die mit unseren Systemen und Materialien hergestellten Teile letztendlich die anspruchsvollen Spezifikationen von Endbearbeitung von Luft- und Raumfahrtkomponenten für Satellitentafeln.
Herausforderungen meistern: Häufige Probleme beim 3D-Druck von Satellitenpaneelen und Lösungen von Experten
Während die Vorteile der Metall-Additiv-Fertigung für Satellitentafeln sind überzeugend, aber wie jeder fortschrittliche Fertigungsprozess ist auch dieser nicht ohne potenzielle Herausforderungen. Ein proaktives Verständnis dieser häufigen Probleme und die Implementierung effektiver Strategien zur Schadensbegrenzung sind der Schlüssel zum Erreichen konsistenter, qualitativ hochwertiger Ergebnisse, die geeignet sind für unternehmenskritische Luft- und Raumfahrt Anwendungen. Die Zusammenarbeit mit einem erfahrenen und sachkundigen AM-Lieferant kann wesentlich dazu beitragen, diese Komplexität zu bewältigen.
Hier sind einige häufige Herausforderungen, die bei 3D-Druck von Satellitentafeln und Expertenlösungen:
1. Verformung und Verzerrung:
- Problem: Abweichung von der beabsichtigten Geometrie, die durch den Aufbau und die Freisetzung von inneren Eigenspannungen während des Druckprozesses verursacht wird. Große, flache Platten oder Teile mit abrupten Dickenänderungen sind besonders anfällig.
- Die Ursachen: Hohe thermische Gradienten während schneller Heiz-/Abkühlzyklen, unzureichende Unterstützung, die ein Abheben des Teils von der Bauplatte ermöglicht, unsachgemäße Spannungsentlastung.
- Lösungen:
- Optimierte Ausrichtung: Ausrichtung der Platte, um große flache Bereiche parallel zur Bauplatte zu minimieren und thermische Spannungen zu verringern.
- Wirksame Unterstützungsstrategie: Verwendung robuster Stützen, insbesondere in der Nähe von Kanten und Überhängen, um das Teil fest zu verankern und die Wärme effizient abzuleiten. Simulationswerkzeuge können helfen, die Platzierung der Stützen zu optimieren.
- Optimierung der Prozessparameter: Feinabstimmung der Scan-Strategien (z. B. Insel-Scanning, unterschiedliche Parameter in verschiedenen Abschnitten), um den Wärmeeintrag zu steuern.
- Zeitnahe und korrekte Stressentlastung: Die Durchführung einer Spannungsarmglühung unmittelbar nach der Fertigung, oft vor der Entnahme des Teils aus der Bauplatte, ist von entscheidender Bedeutung.
- Änderungen am Design: Einarbeitung von Rippen oder anderen Versteifungselementen unter Verwendung allmählicher Dickenübergänge.
2. Reststress-Management:
- Problem: Selbst wenn der Verzug kontrolliert wird, können hohe innere Spannungen verbleiben, die bei der Nachbearbeitung (z. B. bei der maschinellen Bearbeitung) zu vorzeitigen Rissen oder zu einer verringerten Ermüdungslebensdauer im Betrieb führen können.
- Die Ursachen: Inhärent für schichtweises Schmelzen und Erstarren. Beeinflusst durch Materialeigenschaften, Teilegeometrie und Prozessparameter.
- Lösungen:
- Effektive thermische Nachbearbeitung: Spannungsabbau und HIP sind die wichtigsten Methoden, um die Restspannung auf ein akzeptables Niveau zu reduzieren.
- Optimierte Prozessparameter: Wie beim Verziehen hilft eine sorgfältige Kontrolle des Energieeintrags und der Scanstrategie, die Stressakkumulation zu kontrollieren.
- Überlegungen zum Design: Vermeidung von scharfen Innenecken (Verwendung von Ausrundungen), Minimierung von großen Querschnittsabweichungen.
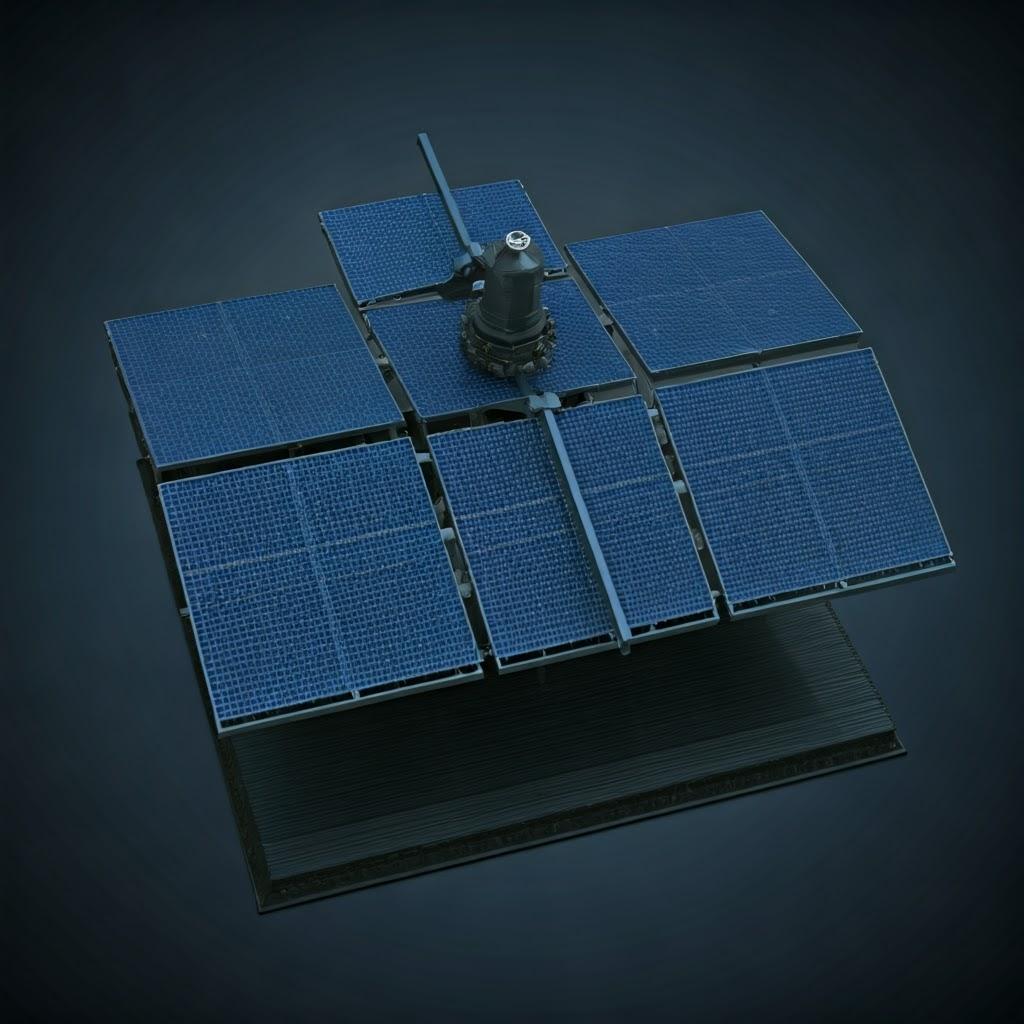
3. Porosität:
- Problem: Kleine innere Hohlräume oder Poren innerhalb des gedruckten Materials. Porosität verschlechtert die mechanischen Eigenschaften, insbesondere die Duktilität, Ermüdungsfestigkeit und Bruchzähigkeit, die für zuverlässige Bauteile in der Luft- und Raumfahrt entscheidend sind.
- Die Ursachen:
- Gas Porosität: Eingeschlossenes Schutzgas (z. B. Argon in L-PBF) im Schmelzbad aufgrund von Instabilität oder Verunreinigung.
- Schlüsselloch-Porosität: Verursacht durch eine übermäßige Energiedichte, die instabile, tiefe Schmelztümpel erzeugt, die zusammenbrechen und Gas einschließen.
- Lack-of-Fusion-Porosität: Unzureichende Energiedichte, die zu unvollständigem Schmelzen zwischen Schichten oder Scannerspuren führt.
- Fragen zur Pulverqualität: Mitgerissene Gase in den Pulverpartikeln, schlechte Pulverpackung aufgrund unregelmäßiger Morphologie oder falscher Partikelgrößenverteilung.
- Lösungen:
- Rigorose Optimierung der Prozessparameter: Entwicklung stabiler Parametersätze (Leistung, Geschwindigkeit, Schichtdicke, Schraffurabstand), die durch umfangreiche Tests validiert werden (z. B. Erstellung und Analyse von Dichtewürfeln).
- Hochwertiges Pulver: Verwenden Metallpulver mit hoher Sphärizität, geringem internen Gasgehalt, kontrollierter PSD und minimalen Satelliten (wie die von Met3dp hergestellten) gewährleistet eine gute Fließfähigkeit, Packungsdichte und gleichmäßiges Schmelzen. Eine ordnungsgemäße Handhabung und Lagerung des Pulvers zur Vermeidung von Feuchtigkeits-/Gasaufnahme ist unerlässlich.
- Effektiver Schutzgasfluss: Sicherstellung einer ordnungsgemäßen laminaren Strömung des Inertgases in L-PBF-Systemen, um Dämpfe zu entfernen, ohne das Schmelzbad zu stören.
- Heiß-Isostatisches Pressen (HIP): Sehr wirksam beim Schließen von Gas- und Schmelzfehlporen, wodurch die Materialintegrität erheblich verbessert wird. Oft obligatorisch für kritische Teile der Klasse A in der Luft- und Raumfahrt.
4. Schwierigkeiten bei der Entfernung von Trägern und Oberflächenmängeln:
- Problem: Halterungen, die sich nur schwer oder gar nicht entfernen lassen, ohne die Oberfläche des Teils zu beschädigen oder deutliche Spuren zu hinterlassen, die eine aufwändige Nachbearbeitung erfordern. Interne Stützen in komplexen Kanälen stellen eine besondere Herausforderung dar.
- Die Ursachen: Zu dichte Stützen, schlechte Zugänglichkeit des Teils, empfindliche Teilemerkmale in der Nähe von Stützen.
- Lösungen:
- DfAM für Unterstützungen: Teile so konstruieren, dass sie möglichst selbsttragend sind, sie so ausrichten, dass möglichst wenig Abstützung erforderlich ist, und den Zugang für Ausbauwerkzeuge sicherstellen.
- Optimiertes Support-Design: Verwendung spezieller Software zur Erstellung von Strukturen, die während der Bauphase stabil genug sind, sich aber leichter entfernen lassen (z. B. kleinere Kontaktpunkte, perforierte Strukturen, materialspezifische Stützstrategien).
- Erweiterte Entfernungstechniken: Erkundung von Drahterosion, elektrochemischer Bearbeitung oder Spezialwerkzeugen für schwierige Träger.
- Planung der Oberflächenbehandlung: Akzeptieren Sie, dass die Kontaktpunkte der Stützen rauer sein werden, und planen Sie die notwendigen Nachbearbeitungsschritte (Schleifen, Verschneiden, Bearbeiten) ein.
5. Pulvermanagement und Sicherheit:
- Problem: Risiko einer Kreuzkontamination zwischen verschiedenen Legierungen, Pulververschlechterung im Laufe der Zeit (Oxidation, Feuchtigkeitsaufnahme) und Sicherheitsrisiken im Zusammenhang mit der Handhabung von feinen, potenziell reaktiven Metallpulvern (insbesondere Aluminium und Titan).
- Die Ursachen: Unzureichende Verfahren, schlechte Lagerbedingungen, fehlende Spezialausrüstung.
- Lösungen:
- Strenge Verfahren: Einführung strenger Protokolle für die Reinigung der Maschinen zwischen den Aufträgen mit verschiedenen Legierungen, spezielle Pulverhandhabungsgeräte (Siebe, Trichter, Lagerbehälter) für jede Materialfamilie.
- Kontrollierte Umgebung: Lagerung von Pulvern in versiegelten Behältern mit Trocknungsmitteln oder unter Inertgas. Kontrolle der Luftfeuchtigkeit in der Produktionsumgebung. Regelmäßige Pulverprüfungen (Chemie, PSD, Fließfähigkeit).
- Sicherheitsmaßnahmen: Ordnungsgemäße Erdung der Geräte zur Verhinderung statischer Entladungen, Verwendung geeigneter PSA (Atemschutzmasken, leitfähige Kleidung), Handhabung von reaktiven Pulvern in inerter Atmosphäre, Staubsauger mit ATEX-Zulassung, Schulung des Bedienpersonals über sichere Handhabungsverfahren und Notfallmaßnahmen (z. B. Feuerlöscher der Klasse D für Metallbrände).
- Zuverlässige Pulverbeschaffung: Durch die Beschaffung von Pulvern mit gleichbleibend hoher Qualität von renommierten Lieferanten wie Met3dp werden Schwankungen und potenzielle Degradationsprobleme minimiert.
6. Erzielung einheitlicher Materialeigenschaften:
- Problem: Sicherstellung, dass die mechanischen Eigenschaften (Festigkeit, Duktilität, Ermüdungslebensdauer) in einem einzigen Bauwerk, zwischen verschiedenen Bauwerken und zwischen verschiedenen Maschinen konsistent sind. Entscheidend für die Zertifizierung und Zuverlässigkeit.
- Die Ursachen: Schwankungen bei den Prozessparametern, Abweichungen bei der Maschinenkalibrierung, uneinheitliches Pulvermaterial, geringfügige Unterschiede in der thermischen Entwicklung innerhalb eines Builds.
- Lösungen:
- Robuste Prozessentwicklung und -validierung: Gründliche Entwicklung und Festlegung von Prozessparametern für jede Material-/Maschinenkombination.
- Kalibrierung und Wartung von Maschinen: Strenge Einhaltung der geplanten Kalibrierungs- und vorbeugenden Wartungsroutinen.
- Gleichbleibende Pulverqualität: Verwendung von Pulver von qualifizierten Lieferanten mit strengen Qualitätskontrollen und effizienter Chargenverwaltung.
- Gutscheine bezeugen: Einbindung von standardisierten Prüfkörpern (Testkupons) in jede Bauplattform für mechanische Tests (Zug, Ermüdung) und Mikrostrukturanalysen zur Überprüfung der Eigenschaften für jeden Produktionslauf.
- Statistische Prozesskontrolle (SPC): Überwachung der wichtigsten Prozessvariablen und Ausgangscharakteristika, um Stabilität zu gewährleisten und Drift im Laufe der Zeit zu erkennen.
Partnerschaften zur Bewältigung von Herausforderungen: Um diese potenziellen Hürden zu überwinden, sind Fachwissen, robuste Ausrüstung, hochwertige Materialien und bewährte Verfahren erforderlich. Hier ist die Zusammenarbeit mit einem Unternehmen wie Met3dp bietet einen erheblichen Wert. Unser Engagement geht über den reinen Verkauf von Druckern und Pulvern hinaus; wir wollen ein zuverlässiger AM-Lieferant und Partner. Unsere branchenführenden Drucker sind auf Stabilität und Konsistenz ausgelegt. Unser fortschrittliches Metallpulver werden unter strengen Qualitätskontrollen hergestellt, um materialbedingte Probleme zu minimieren. Darüber hinaus unterstützt unser technisches Fachwissen unsere Kunden bei der Prozessentwicklung, DfAM und Fehlerbehebung und hilft ihnen bei der erfolgreichen Implementierung 3D-Druck von Metall für anspruchsvolle Raumfahrt-Fertigung Anwendungen wie Satellitentafeln und sicherzustellen, dass sie die erforderliche Qualität und Zuverlässigkeit für ihre B2B-Lösungen für die Fertigung.
Die Wahl Ihres Partners: Die Auswahl des richtigen Metall-AM-Dienstleisters für Luft- und Raumfahrtkomponenten
Die Entscheidung für eine Hebelwirkung Metall-Additiv-Fertigung für kritische Komponenten wie Satellitentafeln ist wichtig. Genauso wichtig ist die Wahl des richtigen Partners, der diese Entwürfe zum Leben erweckt. Ob Sie einen 3D-Druck-Servicebüro für Metall Die Wahl eines Lieferanten ist eine strategische Entscheidung, die weit über den Vergleich von Preisangeboten hinausgeht. Für anspruchsvolle Raumfahrt-FertigungWo Zuverlässigkeit, Präzision und Rückverfolgbarkeit nicht verhandelbar sind, ist die Zusammenarbeit mit einem fähigen, erfahrenen und vertrauenswürdigen Unternehmen von größter Bedeutung. Bewertung von Potenzial AM-Lieferanten erfordert eine gründliche Bewertung ihrer Fähigkeiten, Erfahrungen und Qualitätssysteme.
Hier sind die wichtigsten Kriterien für Beschaffungsmanager und Ingenieurteams die bei der Auswahl eines Metall AM Partner für Luft- und Raumfahrtkomponenten:
1. Erfahrung und Zertifizierungen in der Luft- und Raumfahrt:
- Nachgewiesene Erfolgsbilanz: Hat der Lieferant erfolgreich Komponenten für andere Kunden aus der Luft- und Raumfahrtindustrie hergestellt? Kann er Fallstudien oder Referenzen vorlegen (im Rahmen der NDA-Bestimmungen)? Erfahrungen mit ähnlichen Anwendungen (Strukturteile, thermische Komponenten usw.) sind sehr wertvoll.
- Einschlägige Zertifizierungen: Ist der Lieferant nach den Qualitätsnormen der Luft- und Raumfahrt zertifiziert, insbesondere AS9100? Zwar verfügen noch nicht alle AM-Anbieter über dieses Zertifikat, doch ist es ein Zeichen für ein ausgereiftes Qualitätsmanagementsystem, das den Anforderungen der Luft- und Raumfahrt entspricht. ISO 9001 ist eine Mindestgrundlage. Ein Verständnis der spezifischen Anforderungen von Kunden oder Behörden (z. B. NASA, ESA-Normen) ist ebenfalls von Vorteil.
- Dokumentation und Rückverfolgbarkeit: Sind sie mit dem strengen Dokumentationspaket vertraut, das typischerweise für Flughardware erforderlich ist, einschließlich Materialzertifizierungen, Fertigungsprotokollen, Prozessparametern, NDT-Berichten und Konformitätszertifikaten?
2. Sachkenntnis und Qualifikation:
- Spezifische Legierungserfahrung: Verfügen sie über fundierte Fachkenntnisse bei der Bearbeitung der spezifischen Leichtmetalllegierungen die Sie benötigen (AlSi10Mg, Scalmalloy®, Ti-6Al-4Veinschließlich Klasse 23 ELI)? Können sie konsistente, optimierte Materialeigenschaften für diese auf ihren Maschinen gedruckten Legierungen nachweisen?
- Qualitätskontrolle des Pulvers: Wie beschaffen, testen, handhaben und speichern sie ihre Metallpulver? Welche Maßnahmen werden ergriffen, um Kreuzkontaminationen und Verschlechterungen zu verhindern? Gibt es eine Rückverfolgbarkeit für Pulverchargen? (Dies steht im Einklang mit Met3dp's Kernkompetenz bei der Herstellung von hochwertigen, rückverfolgbaren Pulvern).
- Prozess der Materialqualifizierung: Verfügen sie über etablierte Prozesse zur Qualifizierung von Materialien und Parametern auf ihren Maschinen, um wiederholbare Ergebnisse zu gewährleisten, die den Spezifikationen der Luft- und Raumfahrt entsprechen?
3. Fähigkeiten, Zustand und Kapazität der Ausrüstung:
- Angemessene Technologie: Verfügen sie über die richtige AM-Technologie (z. B. L-PBF, EBM), die für Ihr Material und Ihre Anwendung am besten geeignet ist?
- Spezifikationen der Maschine: Werden die Maschinen gut gewartet und regelmäßig kalibriert? Haben sie ein angemessenes Bauvolumen für die Größe Ihrer Satellitentafeln? Setzen sie Maschinen ein, die für ihre Zuverlässigkeit und Präzision bekannt sind (wie die von Met3dp)?
- Kapazität und Redundanz: Verfügen sie über ausreichende Maschinenkapazitäten, um die von Ihnen geforderten Vorlaufzeiten einzuhalten, auch unter Berücksichtigung möglicher Wartungsarbeiten oder anderer Projekte? Verfügen sie über mehrere Maschinen, die Ihr Teil bearbeiten können, um Redundanz zu gewährleisten?
4. Technische und DfAM-Unterstützung:
- Fachwissen im Bereich Design für additive Fertigung (DfAM): Kann ihr Ingenieurteam wertvolle Beiträge zur Optimierung Ihres Plattenentwurfs für AM leisten? Dazu gehören die Optimierung der Topologie, der Gitterstrukturen, der Stützstrategie, der Ausrichtungsplanung und der Gestaltung der Merkmale für die Herstellung und Nachbearbeitung.
- Anwendungstechnik: Verfügen sie über qualifizierte Anwendungsingenieure, die sowohl das AM-Verfahren als auch die Anforderungen von Luft- und Raumfahrtanwendungen verstehen? Können sie effektiv mit Ihrem Konstruktionsteam zusammenarbeiten? (Met3dp bietet umfassende Dienste zur Anwendungsentwicklung).
- Problemlösung: Haben sie eine Erfolgsbilanz bei der effektiven Fehlersuche und Lösung potenzieller Build-Probleme?
5. Umfassende Nachbearbeitungsmöglichkeiten:
- Integrierter Arbeitsablauf: Bietet der Anbieter kritische Nachbearbeitung (z.B. Spannungsarmglühen, Wärmebehandlung, Grundveredelung), oder verwalten sie ein Netz qualifizierter Partner für Dienstleistungen wie HIP, CNC-Präzisionsbearbeitung, spezielle ZfP und Beschichtung?
- Prozesskontrolle: Wie steuern und kontrollieren sie gegebenenfalls die Qualität dieser externen Nachbearbeitungsschritte? Es ist wichtig, die gesamte Prozesskette zu verstehen.
- Fachwissen: Kennen sie die spezifischen Anforderungen an die Nachbearbeitung von AM-Teilen für die Luft- und Raumfahrt (z. B. spezifische Wärmebehandlungszyklen für Ti-6Al-4V, NDT-Standards)?
6. Ein solides Qualitätsmanagementsystem (QMS):
- Prozesskontrolle: Umfasst ihr QMS strenge Kontrollen in allen Phasen - Entwurfsprüfung, Bauvorbereitung, Maschinenbetrieb, Materialhandhabung, Nachbearbeitung, Inspektion und Dokumentation?
- Rückverfolgbarkeit: Können sie eine durchgängige Rückverfolgbarkeit bieten, die das fertige Teil mit der spezifischen Maschine, den Herstellungsparametern, dem Bediener, der Pulvercharge und allen Nachbearbeitungs- und Prüfprotokollen in Verbindung bringt? Dies ist nicht verhandelbar für Flug-Hardware.
- Inspektionskapazitäten: Verfügen sie über kalibrierte Prüfgeräte (CMM, 3D-Scanner, NDT-Geräte oder Zugang) und geschultes Personal, um zu überprüfen, ob die Teile alle Spezifikationen erfüllen?
7. Vertraulichkeit und Schutz des geistigen Eigentums (IP):
- Sicherheitsmaßnahmen: Über welche Verfahren und Systeme verfügen sie, um Ihre sensiblen Designdaten und Ihr geistiges Eigentum zu schützen? Stellen Sie sicher, dass solide Vertraulichkeitsvereinbarungen (NDAs) abgeschlossen werden.
8. Kommunikation, Reaktionsfähigkeit und Standort:
- Kollaboration: Ist die Kommunikation mit ihnen einfach und gehen sie auf technische Fragen und Projektaktualisierungen ein? Eine kooperative Beziehung ist der Schlüssel.
- Logistik: Berücksichtigen Sie die Auswirkungen ihres Standorts auf die Transportzeiten, die Kosten und die Durchführbarkeit von Besichtigungen oder Audits vor Ort.
Checkliste: Schlüsselfragen für potenzielle AM-Lieferanten
Kategorie | Zu stellende Fragen |
---|---|
Zeugnisse für die Luft- und Raumfahrt | Welche Erfahrungen haben Sie mit Luft- und Raumfahrtprojekten? Sind Sie AS9100-zertifiziert? Wie handhaben Sie die Dokumentation und Rückverfolgbarkeit von Flughardware? |
Werkstoffkompetenz | Welche spezifischen Legierungen (AlSi10Mg, Scalmalloy®, Ti-6Al-4V Gr 5/23) verarbeiten Sie regelmäßig? Wie qualifizieren/kontrollieren Sie die Qualität und die Eigenschaften des Pulvers? |
Ausstattung und Kapazität | Mit welchen Typen/Modellen von AM-Maschinen arbeiten Sie? Wie hoch ist ihr Produktionsvolumen? Wie wird die Wartung/Kalibrierung gehandhabt? Wie hoch ist Ihre Kapazität? |
Technische Unterstützung | Bieten Sie DfAM-Beratung an? Wer leistet technische Unterstützung? Können Sie Beispiele für eine gemeinsame Designoptimierung nennen? |
Nachbearbeitung | Welche Nachbearbeitungsschritte führen Sie selbst durch, welche vergeben Sie extern? Wie qualifizieren/verwalten Sie externe Lieferanten? |
Qualität & Rückverfolgbarkeit | Können Sie Ihr QMS beschreiben? Wie stellen Sie die vollständige Rückverfolgbarkeit von Teilen sicher? Welche Prüf-/NDT-Methoden setzen Sie ein? |
Vertraulichkeit | Welche Maßnahmen gibt es zum Schutz des geistigen Eigentums und der Designdaten der Kunden? |
Kommunikation/Logistik | Wer ist der Hauptansprechpartner? Was sind typische Kommunikationsprotokolle? Was sind die Standardvorlaufzeiten (abhängig von den Projektdetails)? |
In Blätter exportieren
AM mit Met3dp ins Haus holen: Für Organisationen, die den Aufbau oder die Erweiterung ihrer eigenen Metall AM Aus strategischen Gründen (z. B. hohe Stückzahlen, schnelle Iterationen, maximale Kontrolle) ist die Auswahl der richtigen Ausrüstung und des richtigen Materiallieferanten entscheidend. Met3dp zeichnet sich in diesem Szenario als idealer Partner aus. Wir bieten nicht nur branchenführende Metall-3D-Drucker bekannt für ihre Zuverlässigkeit, Genauigkeit und das große Bauvolumen, aber auch für die hochwertige Metallpulver die für die Herstellung konsistenter Komponenten in Luft- und Raumfahrtqualität unerlässlich sind. Entscheidend ist, dass wir unsere Technologie mit umfassenden Schulungen, Unterstützung bei der Anwendungsentwicklung und reaktionsschnellem Service unterstützen, damit unsere Kunden erfolgreich implementieren und skalieren können. Metall-Additiv-Fertigung für anspruchsvolle Anwendungen wie Satellitentafeln. Auswahl von Met3dp ist eine Investition in ein komplettes, zuverlässiges AM-Ökosystem.
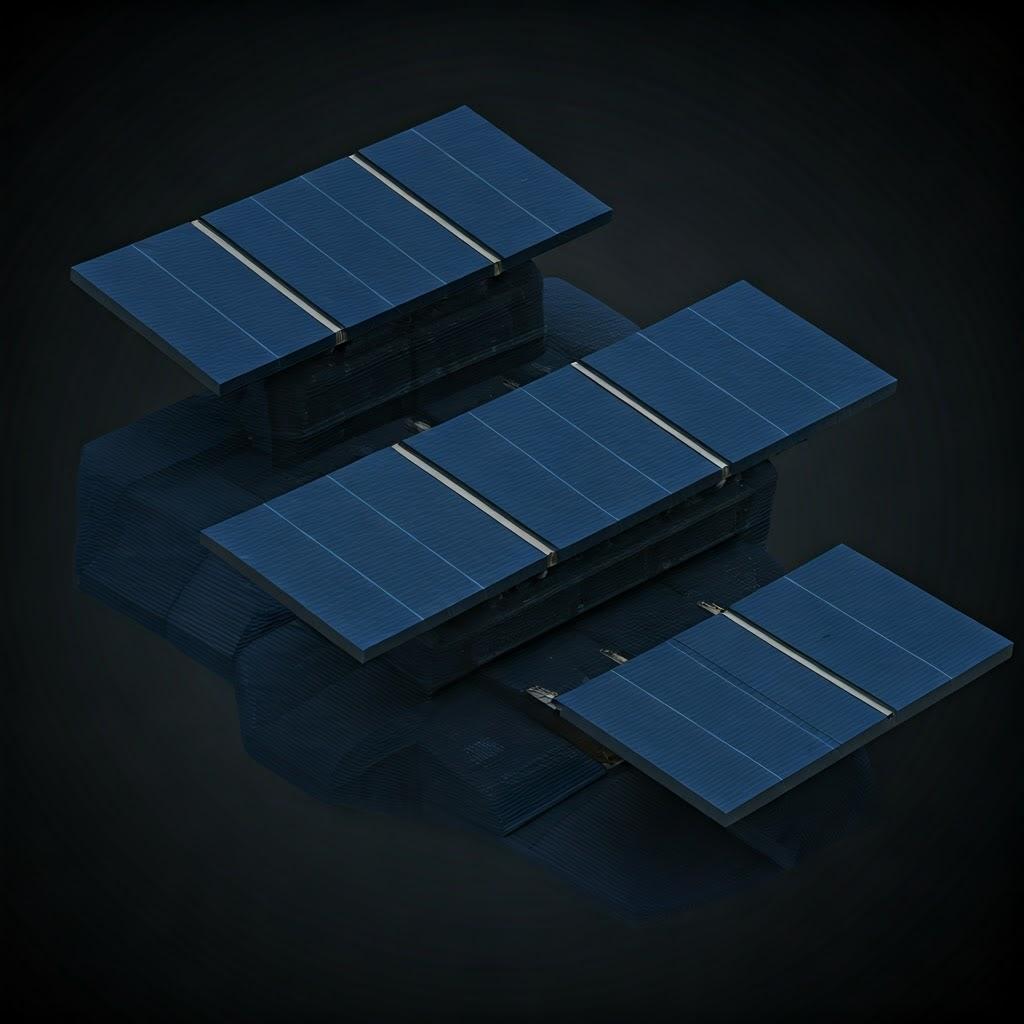
Budgetierung für Innovation: Kostenfaktoren und Vorlaufzeiten für 3D-gedruckte Paneele verstehen
Die additive Fertigung bietet ein transformatives Potenzial, aber die Anwendung für Komponenten wie Satellitentafeln erfordert ein klares Verständnis der damit verbundenen Kosten und Zeitvorgaben. Während AM zu erheblichen Einsparungen in Bereichen wie den Startkosten (aufgrund des geringeren Gewichts) und dem Arbeitsaufwand bei der Montage (aufgrund der Konsolidierung der Teile) führen kann, werden die Produktionskosten des AM-Teils selbst durch ein komplexes Zusammenspiel von Faktoren während des gesamten Arbeitsablaufs bestimmt. B2B-Beschaffung Fachleute und Ingenieure müssen nicht nur den Preis pro Teil im Auge behalten, sondern auch die Gesamtbetriebskosten und das Wertangebot.
Dekonstruktion der Kosten von Metall-AM-Satellitenpaneelen:
Das endgültige Preisschild für eine 3D-gedrucktes Satellitenpanel wird von weit mehr als nur dem verbrauchten Rohmaterial beeinflusst. Zu den wichtigsten Kostentreibern gehören:
- Materialkosten:
- Pulver Preis: Leistungsstarke Luftfahrtlegierungen variieren erheblich im Preis (€/kg), mit Ti-6Al-4V die im Allgemeinen am teuersten sind, gefolgt von Scalmalloy®und dann AlSi10Mg.
- Materialverbrauch: Dazu gehört auch das Volumen des letzten Teils plus das Volumen der während der Bauphase erforderlichen Stützstrukturen. Effiziente DfAM- und Unterstützungsstrategien minimieren dies.
- Pulver-Recycling/Verlust: Ungeschmolzenes Pulver kann zwar oft gesiebt und wiederverwendet werden, doch sind den Auffrischungszyklen Grenzen gesetzt, und ein Teil des Materials geht bei der Handhabung und Verarbeitung unweigerlich verloren. Dieser Effizienzfaktor wirkt sich auf die Gesamtmaterialkosten aus.
- AM-Maschinenbetrieb:
- Abschreibung von Maschinen: Industrielle Metall-AM-Systeme stellen eine beträchtliche Kapitalinvestition dar, deren Kosten über die produzierten Teile amortisiert werden müssen.
- Bauzeit: Ein wichtiger Faktor. Berechnet auf der Grundlage der Anzahl der Schichten (Teilehöhe) multipliziert mit der Zeit pro Schicht (bestimmt durch den Scanbereich und die Parameter). Größere, höhere oder komplexere Teile benötigen mehr Zeit. Effiziente Verschachtelung mehrerer Teile auf einer Bauplatte kann den Durchsatz verbessern, kann aber die Bauhöhe erhöhen.
- Verbrauchsmaterial und Dienstprogramme: Kosten für Inertgas (Argon, Stickstoff), Strom (Maschinen und Hilfsgeräte wie Kältemaschinen), Filter, Wiederaufbereitungsmesser usw.
- Vorbereitungs- und Einrichtungsarbeiten:
- Vorverarbeitung: Entwicklungszeit für DfAM-Überprüfung, Fertigungssimulation (thermisch, Belastung), Ausrichtungsoptimierung, Erzeugung von Stützstrukturen und Zerlegung der CAD-Datei in Maschinenanweisungen.
- Maschine einrichten: Bedienerzeit für das Laden der Build-Datei, die Vorbereitung der Bauplatte, das Laden des Pulvers und das Starten des Bauprozesses.
- Nachbearbeitungskosten (oft >50% der Gesamtkosten):
- Thermische Behandlungen: Kosten für Ofenzeit, Energie und Inertgas für Spannungsarmglühen, HIP und/oder Lösungsglüh-/Alterungszyklen. HIP ist besonders energie- und zeitintensiv.
- Teil/Träger entfernen: Arbeitsaufwand für das Ausschneiden von Teilen aus der Bauplatte und das manuelle oder mechanische Entfernen von Stützstrukturen. Kann bei komplexen Teilen mit umfangreichen Stützstrukturen erheblich sein.
- CNC-Bearbeitung: Kosten im Zusammenhang mit der Konstruktion/Fertigung von Vorrichtungen, der Programmierung von CNC-Werkzeugwegen, der Maschineneinrichtungszeit, der Bearbeitungszeit, dem Werkzeugverschleiß und der Arbeit von Facharbeitern zur Erreichung enger Toleranzen bei kritischen Merkmalen.
- Oberflächenveredelung: Arbeitsaufwand, Gerätezeit und Verbrauchsmaterial für Perlstrahlen, Trommeln, Polieren oder andere Endbearbeitungsmethoden, die zur Erfüllung der Oberflächenspezifikationen erforderlich sind.
- Inspektion und zerstörungsfreie Prüfung: Erheblicher Kostenfaktor, da teure Geräte (CT-Scanner, CMMs) und zertifiziertes Personal für die Durchführung von Tests und die Erstellung detaillierter Berichte (für die Luft- und Raumfahrt erforderlich) benötigt werden.
- Arbeit (Fachkräfte):
- Kosten im Zusammenhang mit geschulten AM-Maschinenbedienern, Anwendungsingenieuren, Nachbearbeitungstechnikern, Qualitätsprüfern und Projektmanagern, die während des gesamten Arbeitsablaufs beteiligt sind.
- Qualitätssicherung und Dokumentation:
- Gemeinkosten im Zusammenhang mit der Aufrechterhaltung eines robusten QMS (z. B. AS9100), der Durchführung von Kalibrierungen, der Verwaltung der Dokumentation und der Gewährleistung einer vollständigen Rückverfolgbarkeit.
Faktoren, die die Vorlaufzeit beeinflussen:
Die Zeit, die von der Fertigstellung des Entwurfs bis zum Erhalt eines flugtauglichen Satellitentafel ist ähnlich komplex:
- Design Iteration & Vorbereitung: Zeitaufwand für DfAM, Simulation und Erstellung von Dateien (kann von Stunden bis zu Tagen reichen).
- Warteschlangenzeit der Maschine: Verfügbarkeit geeigneter AM-Maschinen bei einem Dienstleistungsunternehmen oder im eigenen Haus (kann je nach Bedarf einige Tage bis Wochen dauern).
- AM Aufbauzeit: Reine Druckzeit (kann von Stunden für kleine Teile bis zu vielen Tagen für große, komplexe Paneele oder ganze Bauplatten reichen).
- Post-Processing-Pipeline: Dies ist oft der längste und variabelste Teil der Vorlaufzeit.
- Thermische Behandlungen (Spannungsabbau, HIP, Wärmebehandlung): Jeder Schritt kann 1-3 Tage dauern, einschließlich Erhitzungs-/Abkühlungszyklen.
- Logistik: Die Zeit, die benötigt wird, um die Teile zwischen den verschiedenen Verarbeitungsschritten zu transportieren (z. B. vom Drucker zum Wärmebehandler, von der Maschinenwerkstatt zum NDT-Labor), insbesondere, wenn externe Zulieferer beteiligt sind.
- Entfernen der Halterung und Bearbeitung: Hängt stark von der Komplexität ab (kann von Stunden bis zu Tagen pro Teil reichen).
- Fertigstellung und Inspektion: Kann einige weitere Tage in Anspruch nehmen.
- Qualifizierung und Dokumentation: Zeit für die abschließende Überprüfung, Zusammenstellung der Dokumentation und Abzeichnung.
Typische Vorlaufzeiten: Für ein mäßig komplexes Teil für die Luft- und Raumfahrt, das mehrere Nachbearbeitungsschritte erfordert, beträgt die Gesamtdurchlaufzeit 4 bis 10 Wochen sind üblich, können jedoch stark variieren.
Genaue Kostenvoranschläge einholen: Um zuverlässige Kosten- und Zeitvoranschläge für die Einreichung eines Anfrage für ein Angebot (RFQ)bieten Sie potenziellen Lieferanten an:
- 3D-CAD-Modell (bevorzugt STEP-Format).
- 2D-Zeichnungen mit klaren GD&T, kritischen Abmessungen und Anforderungen an die Oberflächengüte.
- Angegebener Werkstoff (einschließlich Güteklasse, z. B. Ti-6Al-4V Grade 23).
- Erforderliche Wärmebehandlungen (Spannungsarmglühen, HIP, Glühen, usw.).
- ZfP-Anforderungen (z. B. CT-Scan-Klasse/Auflösung, FPI-Standard).
- Gewünschte Menge und Liefertermin.
- Alle anwendbaren Spezifikationen oder Normen (z. B. AS9100-Konformität).
Engagieren Sie sich mit erfahrenen AM-Lieferanten wie Met3dp (für Ausrüstung/Materialien/Unterstützung) oder qualifizierte Servicebüros in einem frühen Stadium des Entwurfsprozesses ermöglicht einen DfAM-Input, der nicht nur Leistung und Gewicht optimieren, sondern auch die Bauzeit und die Komplexität der Nachbearbeitung verringern kann, was zu einer besseren Kontrolle über Preisgestaltung bei der additiven Fertigung und Zeitvorgaben. Unsere zuverlässigen Anlagen und konsistenten Pulver tragen auch zu besser vorhersehbaren Bauzyklen und Qualitätsergebnissen bei, wodurch sich kostspielige Nacharbeiten oder Verzögerungen in den anspruchsvollen Wirtschaft der Luft- und Raumfahrtindustrie Landschaft.
Häufig gestellte Fragen (FAQ) zum 3D-Druck von Satellitenpaneelen
Hier finden Sie Antworten auf einige häufig gestellte Fragen von Ingenieuren und Beschaffungsmanagern zum Einsatz der additiven Fertigung von Metall für Satellitenpaneele:
F1: Wie ist die Festigkeit von 3D-gedruckten Satellitenpaneelen im Vergleich zu traditionell hergestellten? A: Bei korrekter Herstellung, AM-Satellitenpaneele aus Metall können mechanische Eigenschaften aufweisen, die denen herkömmlicher Guss- oder Knetprodukte entsprechen oder diese sogar übertreffen, insbesondere wenn man die spezifische Festigkeit (Verhältnis von Festigkeit zu Gewicht) berücksichtigt. Zu den Schlüsselfaktoren gehören:
- Wahl der Legierung: Die Verwendung von Hochleistungslegierungen wie Scalmalloy® oder Ti-6Al-4V.
- Prozess-Optimierung: Gewährleistung von dichten, fehlerfreien Teilen durch optimierte Druckparameter.
- Nachbearbeiten: Durchführung geeigneter Wärmebehandlungen (wie Spannungsarmglühen, Lösungsglühen/Alterung) und HIP (Heiß-Isostatisches Pressen)Dies ist entscheidend für das Schließen der inneren Porosität und die Maximierung der Ermüdungsfestigkeit und Duktilität, wodurch AM-Teile oft mit Knetwerkstoffen vergleichbar werden.
- Entwurf: Nutzung von Topologieoptimierung und Gitterstrukturen können AM-Teile bei gleicher Steifigkeit und Festigkeit für bestimmte Lastfälle deutlich leichter sein. Es ist wichtig zu beachten, dass AM-Teile eine gewisse Anisotropie aufweisen können (Eigenschaften, die je nach Baurichtung leicht variieren), was während der Design- und Testphasen berücksichtigt werden muss.
F2: Sind 3D-gedruckte Metallteile wie Satellitenpaneele ohne weiteres für die Raumfahrt zugelassen? A: Ja, 3D-gedruckte Metallteile werden in zunehmendem Maße zertifiziert und auf Satelliten und Trägerraketen geflogen, was jedoch einen strengen und gut dokumentierten Qualifikationsprozess erfordert. Die Zertifizierung erfolgt nicht automatisch; sie erfordert:
- Prozessstabilität: Nachweis eines stabilen, wiederholbaren und statistisch kontrollierten Herstellungsprozesses (Druckparameter, Pulverhandhabung, Nachbearbeitung).
- Materialcharakterisierung: Umfassende Prüfung der Materialeigenschaften (Zugfestigkeit, Ermüdung, Bruchzähigkeit usw.) unter Verwendung von Prüfkörpern aus mehreren Produktionen zur Ermittlung zuverlässiger zulässiger Konstruktionswerte.
- Zerstörungsfreie Prüfung (NDT): Gründliche Inspektion (oft einschließlich CT-Scan für die interne Qualität), um die Integrität der Teile und das Fehlen kritischer Fehler zu überprüfen.
- Rückverfolgbarkeit und Dokumentation: Führen akribischer Aufzeichnungen, die das fertige Teil mit allen Prozessschritten, Materialchargen und Prüfergebnissen verknüpfen.
- Einhaltung von Standards: Einhaltung etablierter Luft- und Raumfahrtrichtlinien (z. B. NASA-STD-6016, ECSS-Standards der ESA oder spezifische Kundenanforderungen). Zusammenarbeit mit Lieferanten mit Erfahrung in luftfahrttechnische Qualifizierung Protokollen wird dieser Prozess erheblich vereinfacht.
F3: Was sind die Hauptvorteile der Verwendung von Scalmalloy® gegenüber Ti-6Al-4V für Satellitenpaneele oder umgekehrt? A: Die Wahl zwischen diesen beiden hervorragenden Luftfahrtlegierungen hängt stark von den spezifischen Anforderungen des Satellitentafel:
- Wählen Sie Scalmalloy®, wenn:
- Maximales Lightweighting hat Vorrang: Seine Dichte ist um ~40% geringer als die von Ti-6Al-4V, was erhebliche Gewichtseinsparungen ermöglicht.
- Die Betriebstemperaturen sind moderat: Gut geeignet für Temperaturen bis ~150-200°C.
- Es ist eine hohe spezifische Stärke erforderlich: Sein Verhältnis von Festigkeit zu Gewicht kann in vielen Fällen mit Titanlegierungen mithalten.
- Bearbeitbarkeit/Druckgeschwindigkeit ist ein Faktor: Im Allgemeinen einfacher und schneller zu drucken und zu bearbeiten als Titan.
- Wählen Sie Ti-6Al-4V, wenn:
- Erhöhte Temperaturen werden erwartet: Behält seine ausgezeichnete Festigkeit bis zu ~350°C oder höher bei.
- Außergewöhnliche Korrosionsbeständigkeit ist erforderlich: Titan ist sehr reaktionsträge.
- Maximale absolute Festigkeit, Steifigkeit oder Schadenstoleranz ist kritisch: Insbesondere die Sorte 23 ELI bietet eine hervorragende Bruchzähigkeit.
- Nachgewiesene Flugerfahrung ist erwünscht: Titanlegierungen haben eine längere Geschichte in der Raumfahrt.
- Höhere Dichte ist akzeptabel aufgrund von Leistungsanforderungen, die das Gewicht überwiegen.
- Zusammenfassung: Scalmalloy® eignet sich hervorragend für Leichtbauanwendungen bei moderaten Temperaturen, während Ti-6Al-4V ist die erste Wahl für höhere Temperaturen, maximale Haltbarkeit und extreme Umgebungen.
F4: Können komplexe interne Merkmale wie Kühlkanäle zuverlässig gedruckt und gereinigt werden? A: Ja, die Schaffung komplexer interner Kanäle ist eine der Hauptstärken von Metall-Additiv-Fertigung. Die Zuverlässigkeit hängt jedoch von der richtigen Konstruktion und Prozesskontrolle ab:
- Design for Manufacturability: Die Kanäle müssen einen ausreichenden Durchmesser haben (typischerweise >1-2 mm, je nach Länge/Komplexität), damit das ungeschmolzene Pulver entfernt werden kann. Glatte, geschwungene Biegungen sind besser als scharfe Ecken. Der Einbau von Zugangsöffnungen für Reinigung und Inspektion kann von Vorteil sein. Die Verwendung selbstentleerender Geometrien wie TPMS-Gitter kann ebenfalls hilfreich sein.
- Entfernung von Puder: Gründliche Reinigungsprotokolle mit Vibration, Druckluft und eventuell Lösungsmittelspülung sind nach dem Druck unerlässlich.
- Verifizierung: CT-Abtastung wird häufig als ZfP-Methode eingesetzt, um zu bestätigen, dass die Kanäle vollständig von Pulver befreit sind und die Maßvorgaben erfüllen, bevor die Platte in Betrieb genommen wird. Mit sorgfältiger DfAM und Nachbearbeitung können hocheffiziente und konform gekühlte Satellitentafeln können mit AM zuverlässig hergestellt werden.
Schlussfolgerung: Der Start in die Zukunft - Der bleibende Wert von Metal AM für die Satellitenherstellung
Die Reise durch die Verwicklungen der 3D-Druck von Satellitentafeln offenbart eine Technologie, die weit mehr als nur eine Neuheit ist; Metall-Additiv-Fertigung ist ein grundlegender Wegbereiter für die nächste Generation von Raumfahrtinnovation. Durch das Angebot noch nie dagewesener Möglichkeiten in Leichtbau, Teilkonsolidierungund GestaltungsfreiheitAM setzt direkt bei den wichtigsten Faktoren der modernen Satellitenentwicklung an: Senkung der Startkosten, Erhöhung der Nutzlastkapazität und -funktionalität sowie Beschleunigung der Einsatzzeiten.
Die Fähigkeit zur Nutzung fortgeschrittener Leichtmetalllegierungen wie AlSi10Mgdie leistungsstarke Scalmalloy®und das weltraumerprobte Ti-6Al-4Vin Kombination mit optimierten Entwürfen, die aus DfAM Grundsätze wie Topologieoptimierung und Gitterstrukturenermöglicht Ingenieuren die Erstellung von Satellitentafeln die leichter, stabiler und funktionell besser integriert sind als je zuvor. Der Weg dorthin führt über eine sorgfältige Prüfung der Prozessparameter, strenge Nachbearbeitung einschließlich Wärmebehandlungen wie HIPund gründlich qualitätssicherung und NDTDie Ergebnisse erweisen sich zunehmend als wesentlich für wettbewerbsfähige Satellitenplattformen.
Um sich in dieser fortschrittlichen Fertigungslandschaft erfolgreich zurechtzufinden, bedarf es mehr als nur Technologie, sondern auch Fachwissen und zuverlässiger Partnerschaften. Die Wahl der richtigen AM-Lieferant - eine mit bewährten Luft- und Raumfahrt Erfahrung, tief WerkstoffkompetenzRobuste Ausrüstung, umfassende Unterstützung und eine Verpflichtung zu Qualität und Rückverfolgbarkeit sind entscheidend.
Met3dp steht an der Spitze dieser Technologiewelle und bietet die für den Erfolg erforderlichen Grundelemente. Unser branchenführende Metall-3D-Druckerdie auf Präzision und Zuverlässigkeit ausgelegt sind, kombiniert mit unseren sorgfältig hergestellten hochwertige Metallpulverbilden die Grundlage für eine konsistente und leistungsstarke additive Fertigung. Neben der Technologie ist unser Engagement für Unterstützung bei der Anwendungsentwicklung gewährleistet, dass unsere Partner das Potenzial von AM für ihre anspruchsvollsten Anwendungen voll ausschöpfen können.
Während die Raumfahrtindustrie ihre rasante Expansion fortsetzt, angetrieben durch Konstellationen, Erkundungsmissionen und kommerzielle Unternehmungen, wird die Rolle der Metall-Additiv-Fertigung wird nur wachsen. Sie bietet die Flexibilität, die Leistungsverbesserungen und das Potenzial für Widerstandsfähigkeit der Lieferkette die notwendig sind, um die Zukunft in der Umlaufbahn zu gestalten.
Sind Sie bereit zu erfahren, wie Metal AM Ihre Satellitenfertigung revolutionieren kann? Kontakt Met3dp und erfahren Sie mehr über unsere umfassenden Lösungen - von fortschrittlichen SEBM-Druckern und Hochleistungspulvern bis hin zum fachkundigen Anwendungssupport - und wie wir Sie bei der Verwirklichung der Ziele Ihres Unternehmens im Bereich der additiven Fertigung unterstützen können. Besuchen Sie uns unter https://met3dp.com/ um das Gespräch zu beginnen.
Teilen auf
MET3DP Technology Co., LTD ist ein führender Anbieter von additiven Fertigungslösungen mit Hauptsitz in Qingdao, China. Unser Unternehmen ist spezialisiert auf 3D-Druckgeräte und Hochleistungsmetallpulver für industrielle Anwendungen.
Fragen Sie an, um den besten Preis und eine maßgeschneiderte Lösung für Ihr Unternehmen zu erhalten!
Verwandte Artikel
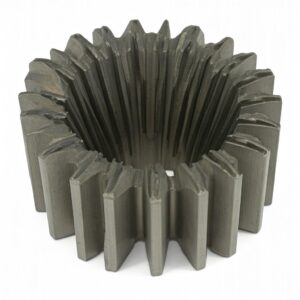
Hochleistungs-Düsenschaufelsegmente: Revolutionierung der Turbineneffizienz mit 3D-Metalldruck
Mehr lesen "Über Met3DP
Aktuelles Update
Unser Produkt
KONTAKT US
Haben Sie Fragen? Senden Sie uns jetzt eine Nachricht! Wir werden Ihre Anfrage mit einem ganzen Team nach Erhalt Ihrer Nachricht bearbeiten.
Holen Sie sich Metal3DP's
Produkt-Broschüre
Erhalten Sie die neuesten Produkte und Preislisten
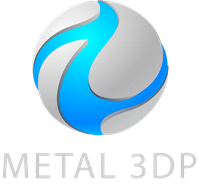
Metallpulver für 3D-Druck und additive Fertigung