UAV-Rahmen 3D-Druck mit leichtem Aluminium
Inhaltsübersicht
Einleitung: Die wachsende Rolle von Metal AM bei der Herstellung moderner UAV-Rahmen
Das unbemannte Luftfahrzeug (UAV), gemeinhin als Drohne bekannt, hat sich über seine Nischenherkunft hinaus zu einer transformativen Technologie für eine Vielzahl von Sektoren entwickelt. Von anspruchsvoller militärischer Aufklärung und Präzisionsüberwachung in der Landwirtschaft bis hin zur schnellen Paketzustellung und Inspektion kritischer Infrastrukturen - UAVs verändern die Einsatzmöglichkeiten weltweit. Das Herzstück jeder Hochleistungsdrohne ist ihr Rahmen - das strukturelle Rückgrat, das die Nutzlastkapazität, die Flugdauer, die Manövrierfähigkeit und die allgemeine Widerstandsfähigkeit bestimmt. Da die Missionsanforderungen immer anspruchsvoller werden, stehen die Hersteller vor der Herausforderung, Rahmen zu entwickeln, die nicht nur außergewöhnlich stark und steif, sondern auch unglaublich leicht sind. Hier kommt die Synergie zwischen fortschrittlichen Materialien wie leichten Aluminiumlegierungen und modernsten Fertigungstechniken wie 3D-Druck von Metall wird zu einem Wendepunkt.
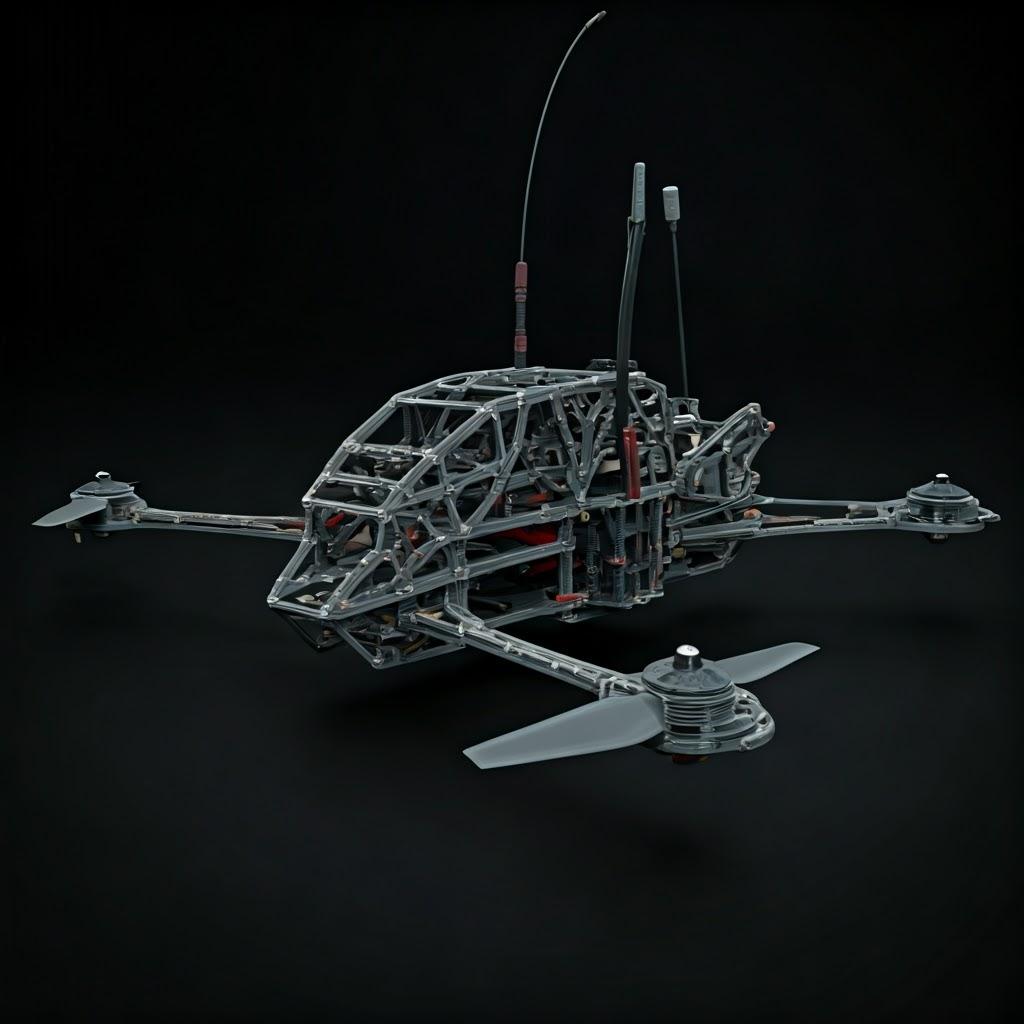
Herkömmliche Fertigungsverfahren, wie die CNC-Bearbeitung von Knüppeln oder die Herstellung von Strukturen aus Blechen und Rohren, setzen der geometrischen Komplexität und der Materialeffizienz oft erhebliche Grenzen. Komplexe innere Strukturen, optimierte Belastungspfade und die nahtlose Integration funktionaler Merkmale sind auf herkömmliche Weise schwer, zeitaufwändig oder schlichtweg unmöglich zu erreichen. Die additive Fertigung von Metallen (AM), insbesondere Pulverbettschmelztechnologien wie Selective Laser Melting (SLM) und Electron Beam Melting (EBM), ändert dieses Paradigma grundlegend. Durch den schichtweisen Aufbau von Teilen direkt aus feinem Metallpulver eröffnet AM eine nie dagewesene Designfreiheit. So können Ingenieure Techniken wie Topologieoptimierung und generatives Design anwenden und organisch geformte, hocheffiziente Strukturen schaffen, die das Gewicht minimieren und gleichzeitig die Festigkeit und Steifigkeit maximieren - Eigenschaften, die sich perfekt für moderne UAV-Rahmen eignen.
Die Luft- und Raumfahrt- sowie die Verteidigungsindustrie, die die AM-Technologie schon früh eingeführt haben, haben den Weg geebnet und die tiefgreifenden Vorteile gedruckter Komponenten für anspruchsvolle Anwendungen demonstriert. Nun durchdringen diese Vorteile rasch den breiteren kommerziellen und industriellen UAV-Markt. Die Möglichkeit, mehrere Komponenten in einem einzigen gedruckten Teil zusammenzufassen, verkürzt die Montagezeit, minimiert potenzielle Fehlerquellen im Zusammenhang mit Verbindungen und Befestigungselementen und vereinfacht die Lieferketten. Darüber hinaus erleichtert AM das Rapid Prototyping und die Design-Iteration und ermöglicht so schnellere Entwicklungszyklen und die Entwicklung hochgradig individueller UAV-Plattformen, die auf spezifische Missionsprofile oder Nutzlastanforderungen zugeschnitten sind. Leichte Aluminiumlegierungen, die für ihr hervorragendes Verhältnis von Festigkeit zu Gewicht, ihre Korrosionsbeständigkeit und ihre relative Kosteneffizienz bekannt sind, sind die besten Kandidaten für diese technologische Revolution. In Kombination mit der Präzision und Designflexibilität der Metall-AM ermöglichen Materialien wie AlSi10Mg, Scalmalloy® und fortschrittliche AM-kompatible A7075-Legierungen die Herstellung von UAV-Rahmen der nächsten Generation, die bisher unerreichbar waren.
Für Beschaffungsmanager und Ingenieure, die Komponenten beschaffen oder Fertigungspartner suchen, ist es wichtig, die Möglichkeiten der Metall-AM für UAV-Rahmen zu verstehen. Es stellt eine Verlagerung hin zu effizienteren, leistungsfähigeren und potenziell kostengünstigeren Lösungen dar, insbesondere für komplexe oder niedrig- bis mittelvolumige Produktionsläufe. Unternehmen wie Met3dp, die sich sowohl auf fortschrittliche Metall-AM-Anlagen als auch auf die Herstellung von Hochleistungsmetallpulvern mit modernsten Zerstäubungstechniken spezialisiert haben, stehen an der Spitze dieses Wandels. Unser Fachwissen erstreckt sich auf das gesamte AM-Ökosystem, von der Entwicklung optimierter Druckparameter bis hin zur Sicherstellung höchster Pulvereigenschaften - Sphärizität, Fließfähigkeit und Reinheit -, die für die Herstellung zuverlässiger, einsatzkritischer UAV-Komponenten unerlässlich sind. Da die UAV-Industrie ihr exponentielles Wachstum fortsetzt, wird Metall-AM zweifellos eine immer wichtigere Rolle bei der Gestaltung der Zukunft des Designs und der Leistung von Flugplattformen spielen.
Wofür werden leichte UAV-Rahmen aus Aluminium verwendet? Wichtige Anwendungen und Branchen

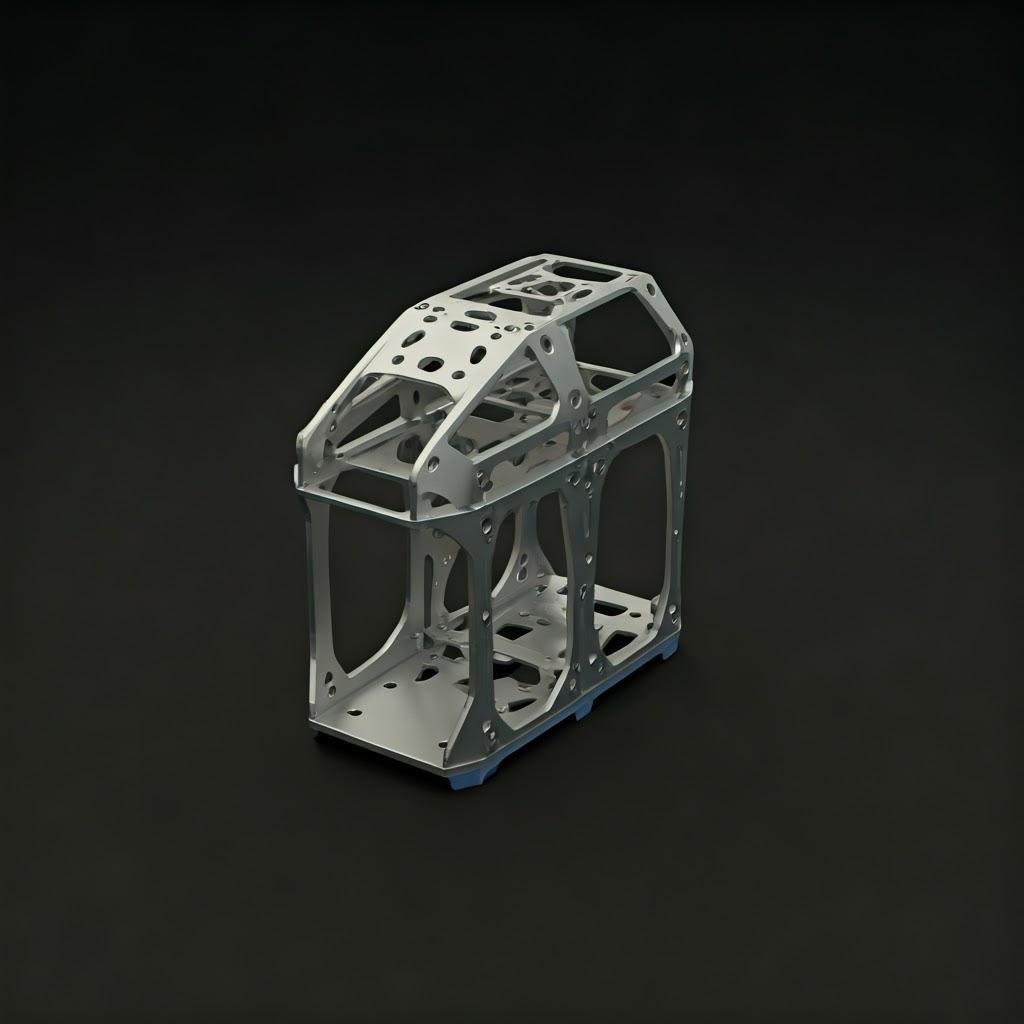
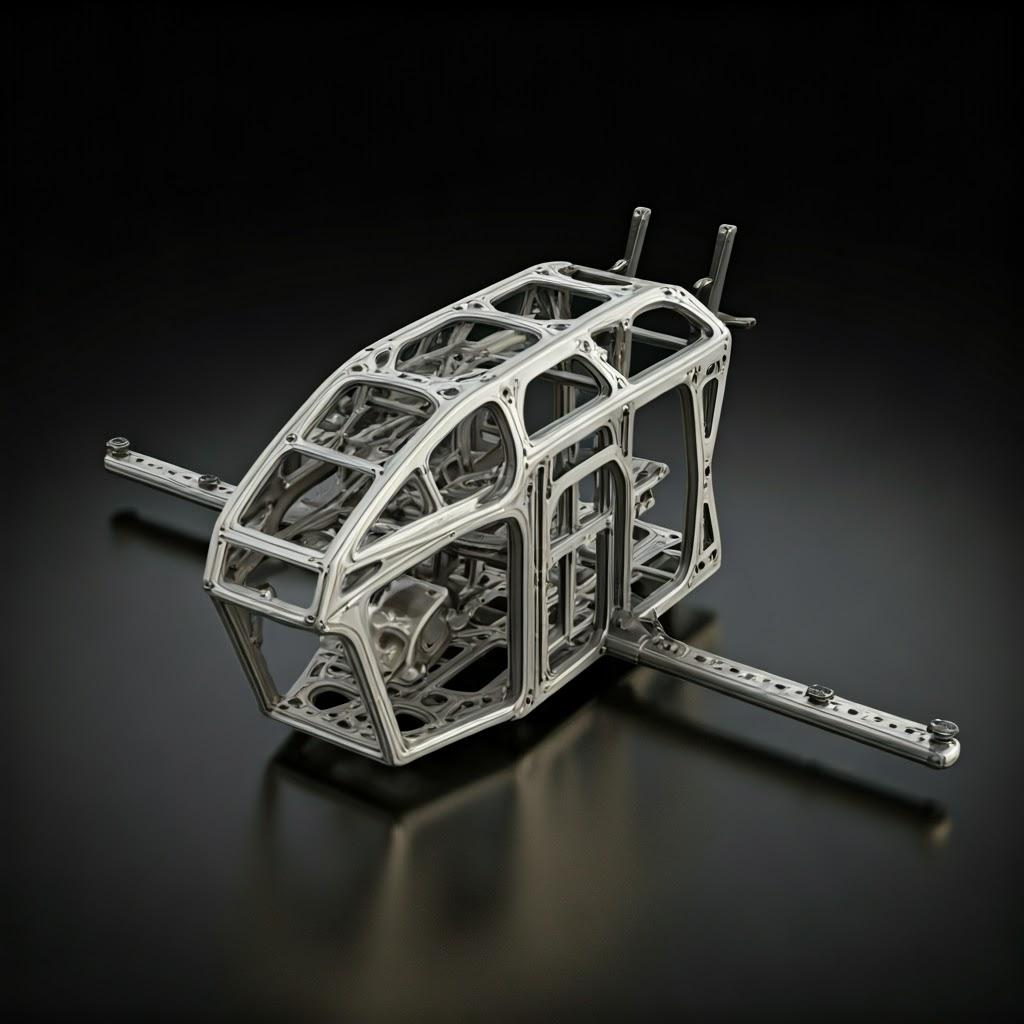
Der UAV-Rahmen ist weit mehr als nur ein Skelett. Er ist ein multifunktionales Chassis, das aerodynamischen Kräften standhält, kritische Subsysteme beherbergt und schützt, Vibrationen bewältigt und unterschiedliche Nutzlasten unter verschiedenen Einsatzbedingungen trägt. Die Nachfrage nach leichten Aluminiumrahmen, insbesondere nach solchen, die durch additive Fertigung verbessert wurden, ergibt sich aus den direkten Auswirkungen der Gewichtsreduzierung auf wichtige Leistungskennzahlen wie Flugdauer, Nutzlastkapazität, Agilität und Energieeffizienz. Folglich finden 3D-gedruckte Aluminiumrahmen in einem breiten Spektrum von Branchen und Anwendungsfällen Anwendung:
- Luft- und Raumfahrt und Verteidigung: In diesem Sektor werden höchste Anforderungen an Leistung, Zuverlässigkeit und oft auch an die Tarnung gestellt.
- Anwendungen: Langstreckenplattformen für Nachrichtengewinnung, Überwachung und Aufklärung (ISR); Zieldrohnen; taktische unbemannte Systeme; Schwarmdrohnenkomponenten.
- Anforderungen an den Rahmen: Extreme Gewichtsreduzierung zur Maximierung der Flugzeit oder Reichweite, hohe strukturelle Integrität für Manövrierfähigkeit und raue Umgebungen, Integration komplexer Sensor- oder Kommunikationsgeräte, potenziell geringe beobachtbare Eigenschaften. AM ermöglicht optimierte, konsolidierte Konstruktionen, bei denen häufig hochfeste Legierungen wie Scalmalloy® oder A7075 verwendet werden.
- Kommerzielle Lieferung und Logistik: Der aufstrebende Markt für Drohnenlieferungen erfordert effiziente, zuverlässige und sichere UAVs, die verschiedene Paketgrößen und -gewichte transportieren können.
- Anwendungen: Zustellung von Paketen auf der letzten Meile, Transport von medizinischem Material, Intralogistik in großen Einrichtungen.
- Anforderungen an den Rahmen: Ausgewogenheit von Stärke, Gewicht und Kosteneffizienz. Langlebigkeit für hochfrequenten Einsatz, standardisierte Befestigungspunkte für Nutzlastbehälter, einfache Wartung. AlSi10Mg ist oft eine geeignete Wahl, da es gute Leistung zu einem vernünftigen Preis bietet.
- Landwirtschaft und Umweltüberwachung: Mit speziellen Sensoren ausgestattete Drohnen helfen in der Präzisionslandwirtschaft, bei der Ernteüberwachung, der Umweltvermessung und der Verfolgung von Wildtieren.
- Anwendungen: Sprühen von Pflanzen, Feldkartierung (NDVI), Bodenanalyse, Überwachung der Küstenerosion, Schutz von Wildtieren.
- Anforderungen an den Rahmen: Fähigkeit zur Beförderung spezifischer Sensornutzlasten (Multispektralkameras, LiDAR), Stabilität für eine präzise Datenerfassung, Widerstandsfähigkeit gegenüber Umwelteinflüssen (Staub, Feuchtigkeit), ausreichende Ausdauer für die Erfassung großer Gebiete. Eine Gewichtsreduzierung führt direkt zu längeren Vermessungszeiten.
- Inspektion und Vermessung der Infrastruktur: UAVs bieten eine sichere und kostengünstige Möglichkeit zur Inspektion von Brücken, Stromleitungen, Windturbinen, Pipelines und Gebäuden sowie zur Landvermessung und Kartierung.
- Anwendungen: Visuelle und thermische Inspektion kritischer Infrastrukturen, LiDAR-Kartierung, Baustellenüberwachung, Katastervermessung.
- Anforderungen an den Rahmen: Hohe Stabilität für den Transport von hochauflösenden Kameras oder LiDAR-Scannern, Vibrationsdämpfung, Einsatz in unmittelbarer Nähe von Strukturen, Langlebigkeit. AM ermöglicht integrierte Dämpfungsfunktionen und kundenspezifische Halterungen.
- Energiesektor: In der Öl- und Gasindustrie, in Solarparks und in der Windenergiebranche werden UAVs für Inspektions- und Wartungsaufgaben eingesetzt, oft an abgelegenen oder gefährlichen Orten.
- Anwendungen: Pipeline-Inspektion, Inspektion von Offshore-Plattformen, thermische Analyse von Solarmodulen, Inspektion von Windturbinenblättern.
- Anforderungen an den Rahmen: Robustheit, Widerstandsfähigkeit gegenüber Umwelteinflüssen, potenziell lange Flugzeiten bei entfernten Einsätzen, Möglichkeit zur Mitnahme spezieller Sensoren (z. B. Methan-Detektoren).
- Kinematographie und Rundfunk: Mit High-End-Kameras ausgestattete Drohnen fangen atemberaubende Luftaufnahmen für Film, Fernsehen und Live-Events ein.
- Anwendungen: Luftaufnahmen, Sportübertragungen, Nachrichtenerfassung.
- Anforderungen an den Rahmen: Außergewöhnliche Stabilität und Vibrationsdämpfung für reibungslose Aufnahmen, Möglichkeit zur Aufnahme professioneller kardanischer Aufhängungen, geringe Geräuschentwicklung (beeinflusst durch das Gesamtdesign einschließlich der Aerodynamik des Rahmens).
- Öffentliche Sicherheit und Notfallmaßnahmen: Polizei, Feuerwehr sowie Such- und Rettungsteams nutzen UAVs zur Situationserkennung, Überwachung und Ortung von Personen.
- Anwendungen: Such- und Rettungseinsätze, Brandüberwachung, Rekonstruktion von Unfallstellen, Verwaltung von Menschenmengen.
- Anforderungen an den Rahmen: Schnelle Einsatzfähigkeit, Robustheit, Möglichkeit zur Mitnahme von Wärmebild- oder optischen Zoomkameras, Zuverlässigkeit bei verschiedenen Wetterbedingungen.
Tabelle: UAV-Anwendungsbeispiele und wichtige Rahmenüberlegungen
Industrie/Anwendung | Anforderungen an den Primärrahmen | Typische Wahl der Aluminiumlegierung (AM) | B2B Fokus |
---|---|---|---|
Luft- und Raumfahrt/Verteidigung (ISR) | Maximale Gewichtsreduzierung, hohe Festigkeit, hohe Steifigkeit, Nutzlastintegration | Scalmalloy®, A7075 | Lieferant von Hochleistungskomponenten, Auftragnehmer im Verteidigungsbereich |
Kommerzielle Lieferung | Langlebigkeit, Kosteneffizienz, standardisierte Halterungen, Gewicht | AlSi10Mg, möglicherweise Scalmalloy® | Logistikintegratoren, Großhandel mit UAV-Teilen |
Präzisionslandwirtschaft | Nutzlastkapazität (Sensoren), Stabilität, Ausdauer | AlSi10Mg | Landwirtschaftliche Technologieanbieter, Dienstleistungsunternehmen |
Inspektion der Infrastruktur | Stabilität, Schwingungsdämpfung, Sensorintegration, Langlebigkeit | AlSi10Mg, Scalmalloy® | Ingenieurbüros, Vermögensverwaltungsgesellschaften |
Energiesektor (Remote) | Robustheit, Ausdauer, Umweltbeständigkeit | AlSi10Mg, Scalmalloy® | Energiekonzerne, Inspektionsdienstleister |
Professionelle Kinematographie | Extreme Stabilität, Schwingungsdämpfung, kardanische Integration | AlSi10Mg, Kundenspezifisch optimierte Ausführungen | Produktionsfirmen, Ausrüstungsverleihfirmen |
In Blätter exportieren
Für UAV-Hersteller und Systemintegratoren ist die Beschaffung von Rahmen, die diese vielfältigen und anspruchsvollen Anforderungen erfüllen, von größter Bedeutung. Leichte Aluminiumlegierungen, insbesondere wenn sie mittels additiver Fertigung hergestellt werden, bieten die erforderlichen Leistungsmerkmale. Die Zusammenarbeit mit einem kompetenten Metall-AM-Anbieter gewährleistet den Zugang zu den richtigen Werkstoffen, Design-Know-how und Produktionskapazitäten, um optimierte Rahmenlösungen zu liefern und Ihre Produkte in diesen wachsenden Märkten wettbewerbsfähig zu positionieren. Suche nach zuverlässigen Anbieter von UAV-Komponenten und Hersteller von kundenspezifischen UAV-Rahmen Die Fähigkeit, AM zu nutzen, wird für den Erfolg immer wichtiger.
Warum 3D-Metalldruck für UAV-Rahmen? Vorteile gegenüber traditioneller Fertigung
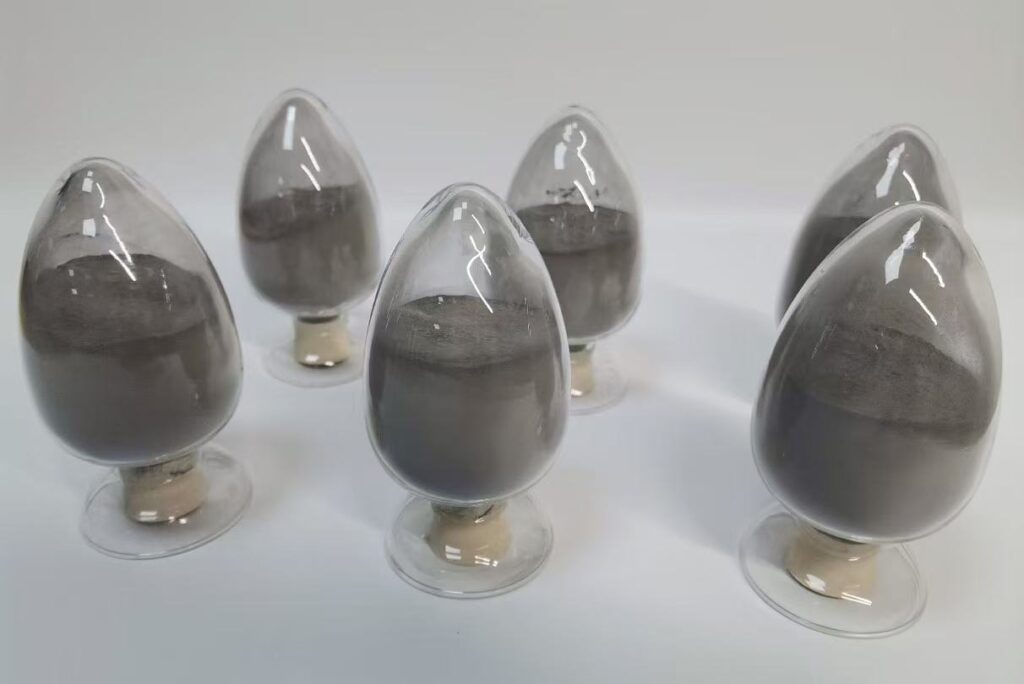
Während die UAV-Industrie seit Jahren auf herkömmliche Fertigungsmethoden zurückgreift, bietet die additive Fertigung von Metallen eine Reihe überzeugender Vorteile, insbesondere bei der Entwicklung und Herstellung von leichten, leistungsstarken Aluminiumrahmen. Diese Vorteile schlagen sich oft direkt in einer besseren UAV-Leistung, schnelleren Entwicklungszyklen und einer effizienteren Produktion nieder, insbesondere bei komplexen Designs oder kundenspezifischen Serien. Lassen Sie uns einen Blick auf die Hauptgründe werfen, warum Konstruktions- und Beschaffungsteams sich zunehmend der Metall-AM zuwenden:
- Unerreichte Gestaltungsfreiheit und Komplexität:
- Herausforderung mit Traditionellem: Die CNC-Bearbeitung ist durch den Zugang zu den Werkzeugen begrenzt, was komplexe innere Merkmale oder hohle Strukturen schwierig und kostspielig macht. Bei der Blechverarbeitung sind die Konstruktionen auf gebogene und verbundene Formen beschränkt.
- AM Vorteil: AM baut Teile Schicht für Schicht auf und ermöglicht so die Herstellung komplizierter Geometrien, die auf andere Weise nicht möglich sind. Dies beinhaltet:
- Topologie-Optimierung: Algorithmen bestimmen die effizienteste Materialverteilung, um bestimmten Belastungen standzuhalten. Das Ergebnis sind organische, knochenähnliche Strukturen, die unglaublich leicht und dennoch stabil sind.
- Interne Gitterstrukturen: Das Ersetzen von massiven Profilen durch interne Gitter reduziert das Gewicht drastisch, während die strukturelle Integrität erhalten bleibt und möglicherweise Funktionen wie Schwingungsdämpfung hinzugefügt werden.
- Integrierte Funktionen: Halterungen für Motoren, Sensoren und Batterien, Kanäle für die Verkabelung und aerodynamische Verkleidungen können nahtlos in das Rahmendesign integriert werden, was die Anzahl der Teile und die Komplexität der Montage reduziert.
- Konformes Design: Die Komponenten können so gestaltet werden, dass sie gekrümmten Oberflächen folgen oder genau in enge Bereiche passen.
- Signifikante Gewichtsreduzierung (Lightweighting):
- Herausforderung mit Traditionellem: Eine signifikante Gewichtsreduzierung erfordert oft eine umfangreiche Bearbeitung (Materialabfall) oder komplexe Zusammenstellungen dünnwandiger Teile.
- AM Vorteil: Topologieoptimierung und Gitterstrukturen, die durch AM ermöglicht werden, sind die Hauptantriebskräfte für die Gewichtsreduzierung. Die Verringerung des Rahmengewichts verbessert direkt die kritischen UAV-Metriken:
- Erhöhte Flugausdauer: Weniger Gewicht erfordert weniger Energie, um in der Luft zu bleiben.
- Höhere Nutzlastkapazität: Das eingesparte Gewicht des Rahmens kann für den Transport von schwereren oder mehr Sensoren, Batterien oder Fracht verwendet werden.
- Verbesserte Beweglichkeit und Manövrierfähigkeit: Leichtere Rahmen ermöglichen eine schnellere Beschleunigung und engere Kurven.
- Teil Konsolidierung:
- Herausforderung mit Traditionellem: Komplexe Baugruppen erfordern oft zahlreiche Einzelteile, Verbindungselemente (Schrauben, Nieten) und Fügeverfahren (Schweißen, Kleben). Jede Schnittstelle ist ein potenzieller Fehlerpunkt und erhöht das Gewicht und die Montagezeit.
- AM Vorteil: Mehrere funktionale Komponenten können als ein einziges, monolithisches Teil entworfen und gedruckt werden. Dies führt zu:
- Reduzierte Montagezeit und -kosten: Weniger zu montierende Teile bedeuten schnellere Produktion und geringere Arbeitskosten.
- Verbesserte strukturelle Integrität: Durch die Beseitigung von Verbindungen und Befestigungselementen werden potenzielle Schwachstellen beseitigt.
- Vereinfachte Lieferkette: Weniger einzelne Teilenummern, die verwaltet und beschafft werden müssen.
- Rapid Prototyping und Design-Iteration:
- Herausforderung mit Traditionellem: Die Erstellung von Prototypen durch maschinelle Bearbeitung oder Herstellung von Werkzeugen kann zeitaufwändig und teuer sein und den Designzyklus verlangsamen.
- AM Vorteil: Digitale Konstruktionsdateien können schnell in physische Metallprototypen umgewandelt werden, oft innerhalb weniger Tage. Dies ermöglicht es Ingenieuren,:
- Schnelleres Testen von Designs: Schnelle Validierung der strukturellen Leistung, Passform und Funktion.
- Iterieren Sie schnell: Nehmen Sie auf der Grundlage von Testergebnissen Designänderungen vor und drucken Sie neue Versionen, ohne dass teure Werkzeugänderungen erforderlich sind.
- Beschleunigen Sie die Markteinführungszeit: Bringen Sie neue oder verbesserte UAV-Modelle schneller auf den Markt.
- Personalisierung und Produktion auf Abruf:
- Herausforderung mit Traditionellem: Die Herstellung von Kleinserien oder kundenspezifischen Versionen von Rahmen mit herkömmlichen Methoden kann aufgrund der Einrichtungs- und Werkzeugkosten unerschwinglich sein.
- AM Vorteil: AM ist ideal für die Produktion kleiner bis mittlerer Stückzahlen und für die kundenspezifische Massenfertigung.
- Maßgeschneiderte Designs: Die Rahmen können leicht an spezifische Missionen, Nutzlasten oder Kundenanforderungen angepasst werden, ohne dass die Kosten für jede Designvariante erheblich steigen.
- Fertigung auf Abruf: Die Teile können nach Bedarf produziert werden, was den Lagerbedarf reduziert und digitale Lagerkonzepte ermöglicht.
- Materialeffizienz:
- Herausforderung mit Traditionellem: Subtraktive Verfahren wie die CNC-Bearbeitung beginnen mit einem großen Materialblock und entfernen überschüssiges Material, wobei möglicherweise erheblicher Abfall entsteht (obwohl die Späne recycelt werden können).
- AM Vorteil: Bei Pulverbettschmelzverfahren wird in der Regel nur das für das Teil und die Stützstrukturen benötigte Material verwendet. Ungeschmolzenes Pulver kann in der Regel recycelt und wiederverwendet werden, was zu höheren Materialausnutzungsraten führt, insbesondere bei komplexen Geometrien. (Hinweis: Bei der Entfernung von Stützstrukturen entsteht ein gewisser Abfall).
Tabelle: Metall-AM vs. traditionelle Fertigung für UAV-Rahmen
Merkmal | Additive Fertigung von Metallen (z. B. SLM/EBM) | Traditionelle Fertigung (z. B. CNC-Bearbeitung, Fertigung) | Hauptvorteil für UAV-Frames |
---|---|---|---|
Geometrische Komplexität | Sehr hoch (interne Kanäle, Gitter, organische Formen) | Mäßig bis gering (begrenzt durch Werkzeugzugang, Biegeradien) | Optimierte Strukturen, integrierte Funktionen |
Gewichtsreduzierung | Hervorragend (Topologieoptimierung, Netze) | Gut (Erfordert umfangreiche Bearbeitung oder komplexe Montage) | Erhöhte Ausdauer, Nutzlast, Agilität |
Teil Konsolidierung | Hervorragend (mehrere Teile als ein Teil druckbar) | Gering (Erfordert die Montage mehrerer Komponenten) | Geringere Montagezeit/-kosten, verbesserte Zuverlässigkeit |
Prototyping-Geschwindigkeit | Fasten (Tage) | Mäßig bis langsam (Wochen, je nach Komplexität/Tooling) | Schnellere Design-Validierung, kürzere Markteinführungszeit |
Kosten der Anpassung | Geringe Schwankungsbreite (keine Werkzeugbestückung) | Hoch (Erfordert neue Werkzeuge oder komplexe Neuprogrammierung) | Einsatzspezifische Entwürfe, Maßgeschneiderte Lösungen |
Materialabfälle | Im Allgemeinen niedriger (Pulverrecycling) | Kann hoch sein (subtraktiver Charakter von CNC) | Nachhaltiger, potenziell niedrigere Rohstoffkosten (komplexe Teile) |
Skalierbarkeit des Volumens | Am besten für geringes bis mittleres Volumen | Am besten für hohe Stückzahlen (sobald die Werkzeuge eingerichtet sind) | Effiziente Produktion für spezialisierte/angepasste UAVs |
In Blätter exportieren
Um diese Vorteile zu nutzen, sind Fachkenntnisse sowohl im Bereich des Designs für die additive Fertigung (DfAM) als auch in den Feinheiten der spezifischen Druckverfahren und Materialien. Die Zusammenarbeit mit einem Dienstleister wie Met3dp, der über fundierte Kenntnisse im Druck von Aluminiumlegierungen verfügt und hochmoderne Anlagen betreibt, stellt sicher, dass diese Vorteile in vollem Umfang genutzt werden können, und verändert die Art und Weise, wie Hochleistungs-Drohnenrahmen konzipiert und produziert werden. Für die Beschaffungsverantwortlichen liegt der Nutzen darin, dass sie leistungsfähigere Komponenten erhalten, die Logistik vereinfachen und ihren Ingenieurteams eine größere Designflexibilität ermöglichen.
Empfohlene Aluminium-Pulver für UAV-Rahmen: AlSi10Mg, Scalmalloy®, A7075
Die Auswahl des richtigen Materials ist von grundlegender Bedeutung, um die gewünschten Leistungsmerkmale eines 3D-gedruckten UAV-Rahmens zu erreichen. Aluminiumlegierungen werden aufgrund ihres geringen Gewichts und ihrer guten Korrosionsbeständigkeit bevorzugt. Im Bereich der additiven Fertigung zeichnen sich mehrere Aluminiumpulver durch ihre Druckfähigkeit und die daraus resultierenden mechanischen Eigenschaften aus. Bei der Auswahl müssen oft Festigkeit, Duktilität, Gewicht, thermische Eigenschaften, Druckbarkeit, Nachbearbeitungsanforderungen und Kosten abgewogen werden. Hier ist ein genauerer Blick auf die Top-Anwärter für leichte UAV-Rahmen:
1. AlSi10Mg:
- Beschreibung: Dies ist eine der gängigsten und bekanntesten Aluminiumlegierungen, die in der Metall-AM verwendet wird, im Wesentlichen eine Aluminium-Silizium-Magnesium-Gusslegierung, die für das Pulverbettschmelzen angepasst wurde.
- Wichtige Eigenschaften:
- Gutes Verhältnis zwischen Stärke und Gewicht.
- Ausgezeichnete Druck- und Verarbeitbarkeit auf verschiedenen SLM/DMLS-Plattformen.
- Gute Wärmeleitfähigkeit.
- Mäßige Duktilität.
- Kann nachbearbeitet werden (wärmebehandelt, maschinell bearbeitet, poliert).
- UAV-Rahmen Eignung: Eine ausgezeichnete Allround-Wahl für eine breite Palette von UAV-Anwendungen, insbesondere dort, wo eine moderate Festigkeit ausreicht und Kosteneffizienz ein wichtiger Faktor ist. Ideal für Prototypen, kommerzielle Allzweckdrohnen und strukturell weniger anspruchsvolle Komponenten. Die breite Verfügbarkeit und die etablierten Druckparameter machen es zu einer zuverlässigen Option für viele Großhandel UAV Teile Lieferanten.
- Erwägungen: Seine Festigkeit ist im Vergleich zu Hochleistungslegierungen wie Scalmalloy® oder optimiertem A7075 geringer. Zur Erzielung optimaler Eigenschaften ist häufig eine Wärmebehandlung (in der Regel Spannungsarmglühen oder T6) erforderlich.
2. Scalmalloy®:
- Beschreibung: Eine patentierte Hochleistungs-Aluminium-Magnesium-Scandium-Legierung, die von APWORKS speziell für die additive Fertigung entwickelt wurde. Durch den geringen Zusatz von Scandium entstehen beim Druck extrem feine Kornstrukturen, die zu außergewöhnlichen mechanischen Eigenschaften führen.
- Wichtige Eigenschaften:
- Sehr hohe spezifische Festigkeit (Verhältnis von Festigkeit zu Gewicht), die oft die von Standard-Aluminiumlegierungen für die Luft- und Raumfahrt wie AlSi10Mg und sogar von einigen Titansorten übertrifft.
- Ausgezeichnete Duktilität und Ermüdungsbeständigkeit im Vergleich zu anderen hochfesten Aluminium-AM-Legierungen.
- Gute Schweißeignung (wichtig, wenn nach der Herstellung Verbindungen erforderlich sind).
- Gute Korrosionsbeständigkeit.
- Behält seine Festigkeit bei mäßig erhöhten Temperaturen besser bei als AlSi10Mg.
- UAV-Rahmen Eignung: Die erste Wahl für anspruchsvolle Anwendungen, die maximale Gewichtseinsparungen ohne Kompromisse bei der Festigkeit und Haltbarkeit erfordern. Ideal für militärische Hochleistungsdrohnen, Schwerlastdrohnen, Kunstflug- oder Renndrohnen und kritische Strukturkomponenten, bei denen ein Versagen nicht in Frage kommt. Seine Eigenschaften ermöglichen hoch optimierte und topologisch komplexe Konstruktionen.
- Erwägungen: Scalmalloy®-Pulver ist aufgrund des Scandiumgehalts und der Lizenzierung wesentlich teurer als AlSi10Mg. Es erfordert sorgfältig kontrollierte Druckparameter und kann spezielle Nachbearbeitungsempfehlungen haben.
3. A7075 (AM-verarbeitbare Varianten):
- Beschreibung: Traditionell eine sehr hochfeste, zinkhaltige Aluminium-Knetlegierung, die in der Luft- und Raumfahrtindustrie weit verbreitet ist (z. B. 7075-T6). In der Vergangenheit galt es als sehr schwierig, diese Legierung mit dem Laser-Pulverbett-Verfahren zu drucken, da Probleme wie Heißrisse auftraten. Fortschritte bei der Modifizierung der Pulverzusammensetzung (z. B. Zugabe von Nukleierungselementen) und ausgefeilte Prozesssteuerungsstrategien haben jedoch AM-Versionen realisierbar gemacht.
- Schlüsseleigenschaften (von AM-Varianten):
- Extrem hohe Festigkeit, die nach geeigneter Wärmebehandlung die Festigkeit von herkömmlichem 7075-T6 erreichen oder übertreffen kann.
- Ausgezeichnetes Verhältnis von Festigkeit zu Gewicht.
- Gute Ermüdungsfestigkeit.
- UAV-Rahmen Eignung: Gezielt für Anwendungen, die höchste Festigkeit erfordern, wie bei traditionell aus 7075 hergestellten Komponenten. Geeignet für hochbelastete Strukturteile in der Luft- und Raumfahrt und in Verteidigungsdrohnen, wo maximale Leistung entscheidend ist und die Komplexität der Verarbeitung bewältigt werden kann.
- Erwägungen: Das Drucken von A7075-Varianten ist nach wie vor eine Herausforderung und erfordert ein hohes Maß an Prozesswissen und streng kontrollierte Parameter, um Defekte wie Rissbildung und Porosität zu vermeiden. Spezifische Wärmebehandlungen sind entscheidend, um die gewünschten hochfesten Eigenschaften zu erreichen. Die Verfügbarkeit und die Kosten des Pulvers könnten höher sein als bei AlSi10Mg, und das Prozesswissen könnte weniger weit verbreitet sein als bei AlSi10Mg oder Scalmalloy®. Erfordert einen hochqualifizierten Metall-AM-Dienstleister.
Tabelle: Vergleich der empfohlenen Aluminium-AM-Pulver für UAV-Rahmen
Eigentum | AlSi10Mg | Scalmalloy® | A7075 (AM-Varianten) |
---|---|---|---|
Primäre Legierungselemente | Silizium (Si), Magnesium (Mg) | Magnesium (Mg), Scandium (Sc), Zirkonium (Zr) | Zink (Zn), Magnesium (Mg), Kupfer (Cu) |
Relative Stärke | Gut | Sehr hoch | Extrem hoch (bei entsprechender Wärmebehandlung) |
Spezifische Stärke | Gut | Ausgezeichnet | Ausgezeichnet |
Duktilität/Dehnung | Mäßig | Gut | Mäßig (kann niedriger sein als Scalmalloy®) |
Druckbarkeit | Ausgezeichnet | Gut (Erfordert bestimmte Parameter) | Anspruchsvoll (erfordert eine fachkundige Prozesskontrolle) |
Korrosionsbeständigkeit | Gut | Gut | Mäßig (kann anfällig für Spannungskorrosion sein) |
Relative Kosten | $$ | $$$$ | $$$ |
Typische UAV-Anwendungsfälle | Allgemeine Zwecke, Prototypen, kommerziell | Hochleistung, Luft- und Raumfahrt/Verteidigung, Heavy-Lift | Komponenten für Luft- und Raumfahrt/Verteidigung mit höchster Festigkeit |
In Blätter exportieren
Warum die Qualität des Pulvers wichtig ist:
Unabhängig von der gewählten Legierung ist die Qualität des Metallpulvers selbst entscheidend für eine erfolgreiche additive Fertigung. Faktoren wie:
- Sphärizität: Glatte, kugelförmige Partikel fließen gleichmäßig und packen dicht, was zu gleichmäßigen Schmelzbädern und lunkerfreien Teilen führt.
- Partikelgrößenverteilung (PSD): Ein kontrollierter PSD gewährleistet eine gute Pulverbettdichte und ein vorhersehbares Schmelzverhalten.
- Fließfähigkeit: Ein gleichmäßiger Pulverfluss ist für eine gleichmäßige Wiederbeschichtung des Pulverbetts während des Drucks unerlässlich.
- Reinheit und niedrige Satellitenzahl: Das Fehlen von Verunreinigungen und unregelmäßigen "Satelliten"-Partikeln verhindert Defekte im fertigen Teil.
Met3dp nutzt fortschrittliche Pulverherstellungstechnologien wie Gaszerstäubung und Plasma-Rotationselektroden-Verfahren (PREP) zu produzieren hochwertige Metallpulvereinschließlich Aluminiumlegierungen, optimiert für AM. Unsere strenge Qualitätskontrolle stellt sicher, dass die Pulver die anspruchsvollen Spezifikationen erfüllen, die für die Luft- und Raumfahrt und andere kritische Anwendungen erforderlich sind. So können unsere Kunden zuverlässig dichte, leistungsstarke UAV-Rahmen mit hervorragenden mechanischen Eigenschaften drucken. Die Wahl des richtigen Pulvers und die Sicherstellung seiner Qualität sind entscheidende erste Schritte bei der Nutzung von Metall-AM für das UAV-Design der nächsten Generation.
Konstruktionsüberlegungen für additiv gefertigte UAV-Rahmen (DfAM)
Die erfolgreiche Nutzung der additiven Fertigung von Metallteilen für UAV-Rahmen erfordert mehr als nur die Konvertierung einer bestehenden CAD-Datei, die für herkömmliche Verfahren entwickelt wurde. Es erfordert eine Verlagerung der Designphilosophie in Richtung Design for Additive Manufacturing (DfAM). Die DfAM-Prinzipien zielen darauf ab, die Vorteile der additiven Fertigung - wie Komplexität, geringes Gewicht und Konsolidierung der Teile - zu maximieren und gleichzeitig ihre Einschränkungen, wie die Notwendigkeit von Stützstrukturen und inhärenten Oberflächenbeschaffenheiten, zu verringern. Die Anwendung von DfAM ist von entscheidender Bedeutung für die Herstellung kostengünstiger, hochleistungsfähiger Aluminium-UAV-Rahmen. Hier sind die wichtigsten Überlegungen für Ingenieure und Designer:
- Topologie-Optimierung und generatives Design einsetzen:
- Diese Software-Tools sind für den Leichtbau von zentraler Bedeutung. Durch die Definition von Lastfällen, Einschränkungen und Designräumen können Algorithmen hoch optimierte, oft organisch anmutende Formen erzeugen, die nur dort Material verwenden, wo es strukturell notwendig ist.
- Anwendung für UAV-Frames: Ideal für Hauptstrukturteile, Motorträger und Fahrwerkskomponenten, die unnötige Masse einsparen und gleichzeitig sicherstellen, dass die Festigkeits- und Steifigkeitsanforderungen erfüllt werden. Dies führt direkt zu längeren Flugzeiten oder einer höheren Nutzlastkapazität.
- Strategisches Design für Orientierung:
- Wie ein Teil auf der Bauplatte ausgerichtet wird, hat einen erheblichen Einfluss auf die Druckzeit, das Volumen der Stützstruktur, die Oberflächenqualität und möglicherweise die mechanischen Eigenschaften (insbesondere in der Z-Achsen-Baurichtung).
- Erwägungen:
- Stützen minimieren: Richten Sie das Teil so aus, dass Überhänge und nach unten gerichtete Flächen, die abgestützt werden müssen, vermieden werden. Selbsttragende Winkel (typischerweise >45 Grad zur Horizontalen) sollten nach Möglichkeit verwendet werden.
- Oberfläche: Kritische Flächen, die eine höhere Qualität erfordern, sollten idealerweise als vertikale Wände oder nach oben gerichtete Flächen ausgerichtet sein. Nach unten weisende Flächen weisen in der Regel rauere Oberflächen auf.
- Druckzeit: Höhere Ausrichtungen bedeuten im Allgemeinen längere Druckzeiten.
- Wärmemanagement: Die Ausrichtung kann die Wärmeverteilung und die Eigenspannungsakkumulation beeinflussen.
- Minimieren und Optimieren von Stützstrukturen:
- Stützstrukturen sind beim Metallpulverbettschweißen oft notwendig, um das Teil auf der Bauplatte zu verankern, überhängende Merkmale zu stützen und die Wärme von der Schmelzzone wegzuleiten. Sie verlängern jedoch die Druckzeit, verbrauchen Material und müssen in der Nachbearbeitung entfernt werden, was arbeitsintensiv sein kann und die Oberfläche des Teils möglicherweise beschädigt.
- DfAM-Strategien:
- Konstruktionsmerkmale müssen selbsttragend sein (mit Winkeln >45 Grad).
- Ersetzen Sie große Überhänge durch Abschrägungen oder Ausrundungen.
- Verwenden Sie im Inneren Gitterstrukturen anstelle von massiven Überhängen, wo dies angebracht ist.
- Gestalten Sie die Halterungen so, dass sie leicht zugänglich und abnehmbar sind (z. B. durch Perforationspunkte, Abreißvorrichtungen).
- Erwägen Sie eine spezielle Software zur Erstellung von Stützen für optimierte, leicht entfernbare Strukturen (z. B. Baumstützen, Blockstützen).
- Halten Sie sich an die Größenbeschränkungen für Features:
- Bei AM-Prozessen gibt es Mindestgrößen für druckbare Merkmale, die von der Größe des Laserstrahlflecks (SLM) oder den Eigenschaften des Elektronenstrahls (EBM), der Größe der Pulverpartikel und der Schichtdicke beeinflusst werden.
- Leitlinien:
- Mindestwanddicke: Stellen Sie sicher, dass die Wände dick genug sind, um zuverlässig zu drucken und der Handhabung/Betriebsbelastung standzuhalten (normalerweise 0,4-1,0 mm, je nach Höhe, Material und Maschine). Dünne, hohe Wände können sich während des Drucks verziehen oder versagen.
- Mindest-Lochgröße: Kleine Löcher (typischerweise <0,5 mm) können während des Drucks versiegeln oder schwer vom Pulver zu befreien sein. Entwerfen Sie Löcher, die groß genug sind, um zuverlässig zu drucken und das Pulver zu entfernen, oder planen Sie ein, sie in der Nachbearbeitung zu bohren/aufzubohren. Horizontale Löcher sind oft schwieriger als vertikale Löcher.
- Geprägt/Graviert Merkmale: Achten Sie auf ausreichende Tiefe/Höhe und Breite für eine klare Auflösung.
- Filets und Radien einbeziehen:
- Scharfe Innenecken können als Spannungskonzentratoren wirken und die Lebensdauer verringern. Sie können auch schwierige Punkte für die Ansammlung von thermischen Spannungen während des Drucks sein.
- Bewährte Praxis: Bringen Sie großzügig Verrundungen an Innenecken und Radien an Außenkanten an, um die Belastung gleichmäßiger zu verteilen und die Druckfähigkeit zu verbessern.
- Design für die Nachbearbeitung:
- Die meisten AM-Teile aus Metall müssen nachbearbeitet werden. Berücksichtigen Sie diese Schritte bereits in der Entwurfsphase:
- Zulagen für die Bearbeitung: Wenn bei bestimmten Merkmalen (z. B. Passflächen, Lagerbohrungen) enge Toleranzen oder spezielle Oberflächengüten erforderlich sind, fügen Sie diesen Bereichen im CAD-Modell zusätzliches Material (Rohmaterial) hinzu, um eine CNC-Bearbeitung nach dem Druck zu ermöglichen.
- Unterstützung bei der Entfernung Zugang: Stellen Sie sicher, dass die Bereiche, an denen die Stützen befestigt sind, für die Entfernungswerkzeuge zugänglich sind, ohne die endgültige Teilegeometrie zu beschädigen.
- Entfernung von Puder: Bei internen Kanälen oder Hohlprofilen sollten Sie strategisch platzierte Abfluss-/Zugangslöcher vorsehen, um das Entfernen von nicht verschmolzenem Pulver nach dem Druck zu erleichtern.
- Wärmebehandlung: Informieren Sie sich, ob das gewählte Material (z. B. A7075 oder AlSi10Mg T6) eine Wärmebehandlung erfordert, und stellen Sie sicher, dass die Konstruktion den thermischen Zyklen ohne übermäßige Verformung standhalten kann.
- Die meisten AM-Teile aus Metall müssen nachbearbeitet werden. Berücksichtigen Sie diese Schritte bereits in der Entwurfsphase:
- Hebelwirkung Teilkonsolidierung:
- Suchen Sie aktiv nach Möglichkeiten, mehrere Komponenten einer herkömmlichen Baugruppe in einem einzigen gedruckten Teil zu kombinieren. Analysieren Sie Schnittstellen, Verbindungselemente und Montageschritte.
- Leistungen Revisited: Geringere Anzahl von Teilen, Wegfall von Verbindungen/Befestigungselementen (potenzielle Fehlerstellen), vereinfachte Montage, oft geringeres Gesamtgewicht und niedrigere Produktionskosten für komplexe Baugruppen.
Die Beherrschung von DfAM erfordert Erfahrung und häufig die Zusammenarbeit zwischen Konstrukteuren und AM-Spezialisten. Die Zusammenarbeit mit einem sachkundigen Metall-AM-Dienstleister der eine DfAM-Beratung anbietet, kann den Prozess erheblich rationalisieren und sicherstellen, dass die Entwürfe von UAV-Rahmen für die additive Fertigung optimiert werden, was zu leichteren, stärkeren und effizienter hergestellten Komponenten führt.
Erreichen von Präzision: Toleranz, Oberflächengüte und Maßgenauigkeit bei gedruckten UAV-Rahmen
Obwohl Metall-AM eine unglaubliche geometrische Freiheit bietet, ist es für Ingenieure und Beschaffungsmanager entscheidend, realistische Erwartungen hinsichtlich der erreichbaren Präzision direkt aus dem Drucker zu haben. AM-Teile aus Metall erreichen in der Regel nicht die extrem hohen Toleranzen und feinen Oberflächengüten, die bei der CNC-Präzisionsbearbeitung ohne Nachbearbeitung möglich sind. Das Verständnis der typischen Fähigkeiten und Einflussfaktoren ermöglicht jedoch eine effektive Konstruktion und Planung, um die spezifischen Anforderungen von UAV-Rahmen zu erfüllen.
Maßgenauigkeit und Toleranzen:
- Typische As-Built-Toleranzen: Bei Verfahren wie SLM/DMLS mit Aluminiumlegierungen liegen die typischen erreichbaren Toleranzen oft im Bereich von:
- ±0,1 mm bis ±0,2 mm für kleine Merkmale (z. B. bis zu 20-50 mm).
- ±0,2% bis ±0,5% des Nennmaßes für größere Merkmale.
- Beeinflussende Faktoren:
- Kalibrierung der Maschine: Die regelmäßige Kalibrierung des Laser-/Elektronenstrahlsystems, des Scanners und der Z-Achsenbewegung ist von entscheidender Bedeutung.
- Materialeigenschaften: Die verschiedenen Legierungen zeigen beim Drucken ein unterschiedliches Schrumpfungs- und Wärmeverhalten.
- Geometrie und Größe des Teils: Große oder komplexe Teile sind anfälliger für thermische Verformung und Abweichung.
- Orientierung: Die Aufbaurichtung beeinflusst die Genauigkeit aufgrund des schichtweisen Aufbaus und der thermischen Gradienten.
- Unterstützende Strukturen: Das Anbringen und Entfernen von Stützen kann die lokale Genauigkeit beeinflussen.
- Thermische Spannungen: Eigenspannungen, die sich während des Drucks aufbauen, können beim Entfernen von der Bauplatte zu Verformungen führen, wenn sie nicht ordnungsgemäß behandelt werden (z. B. durch Spannungsabbau).
- Erzielung engerer Toleranzen: Wenn bestimmte Merkmale des UAV-Rahmens engere Toleranzen erfordern, als sie im Ist-Zustand möglich sind (z. B. Lagergehäuse, Schnittstellen zur Motorbefestigung, Verbindungsflächen), wird das Teil in der Regel mit Bearbeitungszugaben (zusätzliches Material) für diese kritischen Merkmale konstruiert, und die erforderliche Präzision (oft bis zu ±0,01 mm oder besser) wird durch CNC-Nachbearbeitung erreicht.
Oberflächengüte (Rauhigkeit):
- As-Built Oberflächenbeschaffenheit: Die Oberflächenrauhigkeit (in der Regel als Ra gemessen) von AM-Metallteilen ist deutlich höher als bei maschinell bearbeiteten Oberflächen. Sie wird von der Größe der Pulverpartikel, der Schichtdicke und der Oberflächenausrichtung beeinflusst.
- Vertikale Mauern: Sie bieten in der Regel die beste Ausführung im Ist-Zustand.
- Nach oben gerichtete Oberflächen: Aufgrund der Art des Schmelzens der obersten Schicht etwas rauer.
- Nach unten gerichtete Oberflächen (unterstützt): Aufgrund der Wechselwirkung mit den Trägerstrukturen und der Physik des Schmelzens über losem Pulver oder Trägern sind sie in der Regel am rauesten. Ra-Werte können sehr unterschiedlich sein, oft zwischen 6 µm und 25 µm (oder höher bei nach unten gerichteten Oberflächen), je nach spezifischem Prozess, Material und Parametern.
- Verbesserung der Oberflächengüte:
- Orientierung: Bevorzugen Sie kritische Oberflächen wie vertikale Wände, wo dies möglich ist.
- Optimierung der Parameter: Die Feinabstimmung von Parametern wie Schichtdicke oder Laser-/Strahlstrategie kann einen gewissen Einfluss haben.
- Nachbearbeiten: Dies ist die wichtigste Methode zur deutlichen Verbesserung der Oberflächenqualität:
- Perlstrahlen/Shot Peening: Sorgt für eine gleichmäßige matte Oberfläche, entfernt lose Partikel und kann die Ermüdungslebensdauer (durch Druckspannung) verbessern. Ra-Werte verbessern sich typischerweise auf ~3-10 µm.
- Taumeln/Gleitschleifen: Glättet Oberflächen und Kanten, vor allem bei Chargen kleinerer Teile.
- CNC-Bearbeitung: Sorgt für die bestmögliche Oberflächengüte bei bestimmten Merkmalen und erreicht bei Bedarf Ra < 1 µm.
- Polieren: Manuelles oder automatisiertes Polieren für ästhetische Anforderungen oder sehr spezifische funktionale Anforderungen (z. B. aerodynamische Oberflächen).
Tabelle: Typische Präzisionsfähigkeiten für Aluminium-AM-UAV-Rahmen
Parameter | As-Built (Typisch SLM/DMLS) | Nach der CNC-Bearbeitung (Gezielte Merkmale) | Überlegungen zu UAV-Frames |
---|---|---|---|
Toleranz (Kleine Merkmale) | ±0,1 bis ±0,2 mm | ±0,01 bis ±0,05 mm (oder besser) | Entwurf für die Bearbeitung von kritischen Schnittstellen (Motorhalterungen usw.) |
Toleranz (Große Merkmale) | ±0,2% bis ±0,5% | ±0,01 bis ±0,05 mm (oder besser) | Berücksichtigen Sie mögliche Verformungen; nutzen Sie die maschinelle Bearbeitung für präzise Passungen. |
Oberflächengüte (Ra) | 6 µm - 25+ µm | < 1 µm bis 3 µm | Bei unkritischen Oberflächen oft akzeptabel; andere werden gestrahlt/bearbeitet. |
Merkmal Auflösung | ~0,4 mm Mindestwandstärke/Merkmal | Begrenzt nur durch die Bearbeitungsmöglichkeiten | Stellen Sie sicher, dass AM das Basis-Feature für die Bearbeitung herstellen kann. |
In Blätter exportieren
Bei B2B-Transaktionen ist eine klare Kommunikation zwischen dem UAV-Entwickler und dem Metall-AM-Dienstleister in Bezug auf kritische Abmessungen, Toleranzen und Anforderungen an die Oberflächenbeschaffenheit ist von entscheidender Bedeutung. Durch die Festlegung dieser Anforderungen auf Zeichnungen und die Angabe, welche Oberflächen nachbearbeitet werden müssen, wird sichergestellt, dass der endgültige gedruckte und fertige UAV-Rahmen alle Funktions- und Montageanforderungen erfüllt. Qualitätskontroll- und Inspektionsschritte sind unerlässlich, um zu überprüfen, ob die angegebene Präzision erreicht wurde.
Wesentliche Nachbearbeitungsschritte für 3D-gedruckte UAV-Rahmen aus Aluminium
Der Druck des Aluminium-UAV-Rahmens ist oft nur der erste große Schritt im Fertigungsablauf. Um das fertige Teil in ein funktionales, zuverlässiges und einbaufertiges Bauteil zu verwandeln, sind in der Regel eine Reihe von Nachbearbeitungsschritten erforderlich. Die spezifischen Schritte und ihre Reihenfolge hängen von der gewählten Legierung, der Komplexität der Konstruktion und den Anwendungsanforderungen (z. B. Toleranzen, Oberflächengüte, mechanische Eigenschaften) ab. Das Verständnis dieser Schritte ist für die Projektplanung, die Kostenkalkulation und die Abschätzung der Vorlaufzeit von entscheidender Bedeutung. Zu den wichtigsten Nachbearbeitungsschritten gehören:
- Stressabbau Wärmebehandlung (oft zuerst):
- Zweck: Zur Verringerung der inneren Eigenspannungen, die während der schnellen Aufheiz- und Abkühlzyklen des schichtweisen Druckverfahrens entstehen. Hohe Eigenspannungen können zu einer Verformung oder einem Verzug der Teile führen, insbesondere nach der Entnahme von der Bauplatte, und die mechanischen Eigenschaften negativ beeinflussen.
- Prozess: Die gesamte Bauplatte, an der die gedruckten Teile noch befestigt sind, wird in der Regel in einem Ofen auf eine bestimmte Temperatur erhitzt (unter der Alterungstemperatur für wärmebehandelbare Legierungen), eine Zeit lang gehalten und dann langsam abgekühlt. Die Parameter variieren je nach Aluminiumlegierung (z. B. wird AlSi10Mg typischerweise bei 300 °C spannungsfrei gemacht).
- Wichtigkeit: Wird oft als obligatorisch für maßkritische Teile oder komplexe Geometrien angesehen, um die Stabilität während der nachfolgenden Schritte zu gewährleisten.
- Entfernen des Teils von der Bauplatte:
- Zweck: Um den/die gedruckten UAV-Rahmen von der Metallgrundplatte zu trennen, auf der sie gedruckt wurden.
- Methoden: Üblicherweise wird dies verwendet:
- Drahterodieren (Electrical Discharge Machining): Präzise, minimale Krafteinwirkung auf das Teil, gut für empfindliche Strukturen.
- Bandsägen: Schneller und kostengünstiger, aber weniger präzise und erfordert eine sorgfältige Handhabung. Erfordert einen ausreichenden Abstand zwischen dem Teil und der Platte.
- Entfernung der Stützstruktur:
- Zweck: Um die während des Druckvorgangs erforderlichen temporären Stützstrukturen zu entfernen.
- Methoden: Das Spektrum reicht vom manuellen Brechen/Schneiden (für leicht zugängliche, leicht verbundene Stützen) bis hin zur CNC-Bearbeitung oder zum Schleifen für integrale oder schwer zugängliche Stützen.
- Herausforderungen: Kann arbeitsintensiv und zeitaufwendig sein. Es muss darauf geachtet werden, dass die Oberfläche des Teils nicht beschädigt wird, insbesondere an den Kontaktpunkten der Stützen. DfAM spielt eine große Rolle bei der Vereinfachung dieses Schritts.
- Lösungsglühen und Alterungswärmebehandlung (falls zutreffend):
- Zweck: Zur Erzielung der gewünschten endgültigen mechanischen Eigenschaften (Festigkeit, Härte, Duktilität) bei wärmebehandelbaren Aluminiumlegierungen wie AlSi10Mg (für den Zustand T6) oder A7075-Varianten. Für Scalmalloy® ist dies in der Regel nicht erforderlich, um die hohe Festigkeit zu erreichen, obwohl spezielle Alterungsbehandlungen durchgeführt werden können.
- Verfahren (Beispiel: T6 für AlSi10Mg):
- Lösung Behandlung: Erhitzen auf eine hohe Temperatur (z.B. ~530°C), um die Legierungselemente in der Aluminiummatrix aufzulösen.
- Abschrecken: Schnelle Abkühlung (in der Regel in Wasser), um die Elemente in einer übersättigten festen Lösung einzuschließen.
- Künstliche Alterung: Erneutes Erhitzen auf eine niedrigere Temperatur (z. B. ~160 °C) für mehrere Stunden, um Verfestigungsphasen auszufällen.
- Wichtigkeit: Entscheidend für die Maximierung der Leistung von Legierungen wie AlSi10Mg und A7075 in anspruchsvollen Strukturanwendungen. Erfordert eine präzise Steuerung des Ofens.
- Oberflächenveredelung:
- Zweck: Zur Verbesserung der Oberflächenrauhigkeit, zur Beseitigung kleinerer Unebenheiten, zur Erzielung einer gewünschten Ästhetik oder zur Vorbereitung von Oberflächen für Beschichtungen.
- Methoden (wie zuvor beschrieben):
- Perlstrahlen / Shot Peening: Erzeugt ein gleichmäßiges, mattes Finish, reinigt Oberflächen und kann die Ermüdungsfestigkeit verbessern.
- Taumeln / Vibrationsgleitschleifen: Glättet Oberflächen und Kanten, gut für Chargen.
- Polieren: Für glatte, spiegelnde Oberflächen (weniger häufig für strukturelle Rahmen, es sei denn, dies ist aerodynamisch kritisch).
- CNC-Bearbeitung:
- Zweck: Zum Erreichen enger Toleranzen bei bestimmten Merkmalen, zur Herstellung präziser Passflächen, zum Bohren/Gewindeschneiden von Löchern oder zur Verbesserung der Oberflächengüte in kritischen Bereichen.
- Prozess: Verwendet standardmäßige CNC-Fräs- oder Drehzentren. Erfordert eine sorgfältige Vorrichtungskonstruktion, um das potenziell komplexe AM-Teil sicher und ohne Verformung zu halten. Wie in DfAM erwähnt, muss für diese Vorgänge zusätzliches Material in die Konstruktion einbezogen werden.
- Wichtigkeit: Unverzichtbar, wenn die AM-Toleranzen im Ist-Zustand für die funktionalen Anforderungen nicht ausreichen (z. B. Lagersitze, Schnittstellen).
- Reinigung und Inspektion:
- Zweck: Zur Entfernung von Pulverresten, Bearbeitungsflüssigkeiten oder Ablagerungen und zur Überprüfung, ob das Teil alle Spezifikationen erfüllt.
- Methoden: Ultraschallreinigung, Sichtprüfung, Dimensionsprüfung (CMM, 3D-Scannen), möglicherweise zerstörungsfreie Prüfung (NDT) wie CT-Scannen oder Farbeindringprüfung für kritische Komponenten in der Luft- und Raumfahrt zur Prüfung auf innere Defekte oder Oberflächenrisse.
Die Integration und Optimierung dieser Nachbearbeitungsschritte sind Schlüsselkompetenzen von erfahrenen Metall-AM-Lohnhersteller. Die Unternehmen müssen über robuste Qualitätskontrollsysteme und möglicherweise Zertifizierungen (wie AS9100 für die Luft- und Raumfahrt) verfügen, die diese sekundären Vorgänge abdecken, um sicherzustellen, dass das endgültige UAV-Gestell für den jeweiligen Zweck geeignet ist.
Allgemeine Herausforderungen beim 3D-Druck von UAV-Rahmen und Strategien zur Abhilfe
Der 3D-Metalldruck eröffnet zwar ein erhebliches Potenzial für UAV-Rahmen, ist aber nicht ohne Herausforderungen. Das Bewusstsein für potenzielle Probleme und die Umsetzung wirksamer Strategien zur Schadensbegrenzung, die oft auf fundierten Prozesskenntnissen und materialwissenschaftlichem Fachwissen beruhen, sind entscheidend für einen dauerhaften Erfolg. Hier sind einige der häufigsten Herausforderungen, die beim Druck von Aluminium-Drohnenrahmen auftreten:
- Verformung und Verzerrung:
- Die Ursache: Hohe thermische Gradienten während des Druckens führen zum Aufbau von Eigenspannungen. Wenn das Teil von der Bauplatte gelöst wird, können diese Spannungen dazu führen, dass es sich verzieht oder verformt und von der vorgesehenen Geometrie abweicht. Große, flache Teile oder asymmetrische Designs sind besonders anfällig.
- Strategien zur Schadensbegrenzung:
- Optimierte Ausrichtung: Ausrichten des Teils, um große ebene Flächen parallel zur Bauplatte zu minimieren.
- Robuste Unterstützungsstrategie: Verwendung von gut durchdachten Halterungen zur sicheren Verankerung des Teils und zur Steuerung der Wärmeableitung.
- Kontrolle der Prozessparameter: Feinabstimmung von Laser-/Strahlleistung, Scangeschwindigkeit und Strategie zur Minimierung des Spannungsaufbaus.
- Stressabbau Wärmebehandlung: Die Durchführung dieses Schrittes vor dem Ausbau der Teile ist oft unerlässlich.
- Simulation: Einsatz von Simulationssoftware zur Vorhersage von Spannungen und Verformungen, die eine Anpassung des Designs oder der Ausrichtung vor dem Druck ermöglicht.
- Schwierigkeiten bei der Beseitigung von Stützstrukturen:
- Die Ursache: Halterungen sind notwendig, können aber dicht sein, sich in schwer zugänglichen Bereichen befinden oder fest mit dem Teil verbunden sein, was die Entfernung zeitaufwändig und potenziell schädlich macht.
- Strategien zur Schadensbegrenzung:
- DfAM: Der effektivste Ansatz ist eine Konstruktion, die den Bedarf an Stützen minimiert (selbsttragende Winkel, Optimierung der Topologie unter Vermeidung von Überhängen).
- Optimiertes Support-Design: Verwendung von Software zur Erzeugung von Stützen, die während des Drucks stabil genug sind, sich aber leichter entfernen lassen (z. B. reduzierte Kontaktpunkte, Perforation, spezielle Stütztypen wie Baumstützen).
- Nachbearbeitungsplanung: Auswahl geeigneter Entfernungsmethoden (manuell, CNC-Bearbeitung) auf der Grundlage der Lage und Konstruktion des Trägers. Ermöglichung eines angemessenen Zugangs in der Konstruktion.
- Porosität (Gas oder Lack-of-Fusion):
- Die Ursache: Hohlräume innerhalb des gedruckten Materials. Gasporosität entsteht durch gelöste Gase im Pulver oder Schmelzbad. Lack-of-Fusion-Porosität tritt auf, wenn Schichten oder benachbarte Schmelzspuren nicht vollständig verschmelzen, was häufig auf einen unzureichenden Energieeintrag oder eine schlechte Verteilung des Pulvers zurückzuführen ist. Porosität verschlechtert die mechanischen Eigenschaften, insbesondere die Ermüdungsfestigkeit.
- Strategien zur Schadensbegrenzung:
- Hochwertiges Pulver: Verwendung von Pulver mit geringem Gehalt an eingeschlossenen Gasen, kontrolliertem PSD und hoher Sphärizität/Fließfähigkeit. Beschaffung bei renommierten Lieferanten von Metallpulver ist der Schlüssel.
- Optimierte Druckparameter: Gewährleistung einer ausreichenden Energiedichte (Laser-/Strahlleistung, Geschwindigkeit) für vollständiges Schmelzen und Fusion bei gleichzeitiger Vermeidung von Überhitzung, die die Gasporosität erhöhen kann.
- Richtige Maschinenumgebung: Aufrechterhaltung der Reinheit der Inertgasatmosphäre (Argon/Stickstoff) in der Baukammer zur Minimierung von Oxidation und Gasaufnahme.
- Heiß-Isostatisches Pressen (HIP): Ein Nachbearbeitungsschritt (Erhitzen unter hohem Druck), der die inneren Poren schließen kann, jedoch zusätzliche Kosten verursacht und in der Regel hochkritischen Komponenten vorbehalten ist.
- Oberflächenrauhigkeit und Merkmalsauflösung:
- Die Ursache: Naturgemäß schichtweiser Aufbau mit geschmolzenen Pulverpartikeln, insbesondere auf schrägen oder nach unten gerichteten Oberflächen. Die Mindestgröße des Merkmals ist durch die Größe des Strahlflecks und die Pulvereigenschaften begrenzt.
- Strategien zur Schadensbegrenzung:
- Optimierung der Orientierung: Wie bereits erwähnt, müssen kritische Flächen optimal platziert werden.
- Einstellung der Parameter: Die Verwendung feinerer Schichtdicken (erhöht die Druckzeit) oder spezieller Strahlstrategien kann das Ergebnis leicht verbessern.
- Nachbearbeiten: Perlstrahlen, Trommeln, Zerspanen oder Polieren sind die wichtigsten Methoden, um die gewünschte Oberflächenbeschaffenheit zu erreichen.
- DfAM: Entwurf von Merkmalen, die weit über die minimale druckbare Größe hinausgehen, um robust zu sein.
- Rissbildung (insbesondere bei hochfesten Legierungen):
- Die Ursache: Einige hochfeste Legierungen (wie das herkömmliche A7075 vor den AM-spezifischen Modifikationen) sind aufgrund ihrer Zusammensetzung und der schnellen Erstarrung bei AM anfällig für Erstarrungsrisse oder Heißrisse.
- Strategien zur Schadensbegrenzung:
- Auswahl/Änderung der Legierung: Verwendung von Legierungen, die speziell für AM entwickelt oder modifiziert wurden (z. B. Scalmalloy®, AM-optimierte A7075-Varianten mit Kornfeinern).
- Optimierte Parameter: Präzise Kontrolle über thermische Gradienten durch Parameterabstimmung.
- Substrat/Bauplattenheizung: Erhöhte Bauplattentemperaturen können thermische Gradienten reduzieren.
- Prozess-Know-how: Wir stützen uns auf fundierte materialwissenschaftliche und verfahrenstechnische Kenntnisse.
Die Bewältigung dieser Herausforderungen erfordert eine Kombination aus guten Designpraktiken (DfAM), hochwertigen Materialien, gut gewarteten und kalibrierten Anlagen, optimierten Prozessparametern und robusten Nachbearbeitungsmöglichkeiten. An dieser Stelle ist die Zusammenarbeit mit einem erfahrenen und sachkundigen AM-Anbieter wie Met3dp von unschätzbarem Wert. Unsere jahrzehntelange Erfahrung in der additiven Fertigung von Metallen, die fortschrittliche SEBM-Drucker, eine ausgefeilte Pulverproduktion mittels Gaszerstäubung und PREP sowie umfassende Anwendungsentwicklungsdienste umfasst, versetzt uns in die Lage, diese Herausforderungen effektiv zu bewältigen. Wir arbeiten vom Entwurf bis zur Endkontrolle eng mit unseren Kunden zusammen und nutzen unser Know-how, um hochwertige und zuverlässige Aluminium-Drohnenrahmen zu liefern. Mehr über die Grundlagen und das Know-how unseres Unternehmens erfahren Sie auf unserer Über uns Seite. Die Zusammenarbeit mit einem Partner, der sich der Prozesskontrolle und Qualitätssicherung verschrieben hat, erleichtert die Einführung von Metall-AM für anspruchsvolle Anwendungen wie UAV-Komponenten erheblich.
Auswahl des richtigen 3D-Druckpartners für UAV-Komponenten aus Metall
Die Wahl des richtigen Fertigungspartners ist ebenso wichtig wie die Optimierung des Designs und die Auswahl des geeigneten Materials für Ihren UAV-Rahmen. Die Fähigkeiten, das Fachwissen und die Qualitätssysteme des von Ihnen gewählten Dienstleisters für die additive Fertigung von Metallen wirken sich direkt auf die endgültige Qualität, Leistung, Kosten und rechtzeitige Lieferung Ihrer Komponenten aus. Für Ingenieure und Beschaffungsmanager, die sich in der Landschaft der Metall-AM-DienstleisterHier sind die wichtigsten Kriterien zur Bewertung:
- Technische Kompetenz und Erfahrung:
- Werkstoffkunde: Tiefes Verständnis der spezifischen Aluminiumlegierungen (AlSi10Mg, Scalmalloy®, A7075-Varianten), einschließlich ihrer Metallurgie, ihrer Druckeigenschaften und der erforderlichen Nachbearbeitung, um die gewünschten Eigenschaften zu erzielen.
- DfAM-Kenntnisse: Nachgewiesene Fähigkeit, Designberatung zu leisten und Teile für die additive Fertigung zu optimieren, um Vorteile wie Leichtbau zu maximieren und Herausforderungen wie Stützstrukturen zu minimieren.
- Prozess-Optimierung: Nachgewiesene Erfahrung in der Entwicklung und Kontrolle robuster Druckparameter für konsistente, hochwertige Ergebnisse.
- Erfahrung in der Industrie: Achten Sie auf Fallstudien oder Erfahrungen speziell in den Bereichen Luft- und Raumfahrt, Verteidigung oder UAV. Die Vertrautheit mit den Standards und Erwartungen der Branche ist entscheidend.
- Technologie und Ausrüstung:
- Angemessene Technologie: Wird dort die beste AM-Technologie für Ihre Bedürfnisse eingesetzt? (z. B. ist SLM/DMLS für Aluminium üblich).
- Maschinenqualität und Kalibrierung: Verwendung von branchenführenden Geräten, die für ihre Genauigkeit und Zuverlässigkeit bekannt sind. Erkundigen Sie sich nach Wartungsplänen und Kalibrierungsprotokollen.
- Bauvolumen: Vergewissern Sie sich, dass die Maschinen die Größe Ihrer UAV-Rahmenkomponenten aufnehmen können.
- Handhabung des Pulvers: Robuste Verfahren für die Lagerung, Handhabung, Siebung und das Recycling von Pulver, um die Qualität des Pulvers zu erhalten und die Rückverfolgbarkeit zu gewährleisten.
- Materialkapazitäten und Qualitätskontrolle:
- Legierung Verfügbarkeit: Bestätigung, dass sie die von Ihnen benötigte Aluminiumlegierung verarbeiten können.
- Pulverbeschaffung und -prüfung: Strenge Qualitätskontrolle für eingehende Metallpulver (chemische Zusammensetzung, Partikelgrößenverteilung, Morphologie, Fließfähigkeit). Anbieter wie Met3dp, die ihre eigenen Pulver mit fortschrittlichen Methoden wie Gaszerstäubung und PREP herstellen, haben oft einen Vorteil bei der Kontrolle und Überprüfung der Pulverqualität von der Quelle an.
- Rückverfolgbarkeit von Materialien: Fähigkeit zur Rückverfolgung von Pulverchargen während des gesamten Herstellungsprozesses, unerlässlich für die Qualitätssicherung, insbesondere in der Luft- und Raumfahrt.
- Qualitätsmanagementsystem (QMS) und Zertifizierungen:
- ISO 9001: Die Basiszertifizierung für ein seriöses Fertigungsunternehmen.
- AS9100: Äußerst wünschenswert, oft sogar obligatorisch für Zulieferer in der Lieferkette der Luft- und Raumfahrt- sowie der Verteidigungsindustrie. Zeigt ein ausgereiftes QMS an, das auf die strengen Anforderungen der Branche zugeschnitten ist.
- NADCAP: Akkreditierung für spezielle Verfahren wie Wärmebehandlung, zerstörungsfreie Prüfung (ZfP) oder Schweißen, wenn diese kritische Teile des Arbeitsablaufs sind und für Ihre Anwendung erforderlich sind.
- Umfassende Nachbearbeitungsmöglichkeiten:
- Eigenes vs. verwaltetes Netzwerk: Beurteilen Sie die Fähigkeiten des Unternehmens in Bezug auf die erforderlichen Nachbearbeitungsschritte (Spannungsabbau, Wärmebehandlung, Entfernen von Halterungen, CNC-Bearbeitung, Oberflächenbehandlung). Führen sie diese intern oder über qualifizierte Partner durch?
- Fachwissen: Vergewissern Sie sich, dass sie über das Fachwissen verfügen, um diese kritischen Schritte, insbesondere die für AM-Aluminiumlegierungen spezifische Wärmebehandlung, korrekt durchzuführen oder zu verwalten.
- Kapazität, Vorlaufzeit und Kommunikation:
- Produktionskapazität: Können sie Ihre Mengenanforderungen erfüllen, vom Prototyp bis zur potenziellen Serienproduktion?
- Transparente Vorlaufzeiten: Fähigkeit, realistische Schätzungen für den gesamten Prozess (Druck + Nachbearbeitung + Kontrolle) abzugeben und proaktiv über mögliche Verzögerungen zu informieren.
- Reaktionsfähigkeit: Gute Kommunikation und Kundenbetreuung während des gesamten Projektzyklus.
- Zusammenarbeit und Unterstützung:
- Partnerschaftlicher Ansatz: Suchen Sie nach einem Anbieter, der bereit ist, als Partner zu agieren, der technische Beratung anbietet und bei der Lösung von Problemen mitarbeitet.
- DfAM-Unterstützung: Bereitschaft, Entwürfe zu überprüfen und Verbesserungen für die additive Fertigung vorzuschlagen.
Die Auswahl eines Partners ist eine strategische Entscheidung. Unternehmen wie Met3dp zeichnet sich durch das Angebot umfassender Lösungen aus, die branchenführende SEBM-Drucker, fortschrittliche Metallpulverproduktion und Anwendungsentwicklungsdienste umfassen. Unsere jahrzehntelange Erfahrung in der Metall-AM stellt sicher, dass wir die Feinheiten der Produktion von einsatzkritischen Teilen für anspruchsvolle Branchen wie die Luft- und Raumfahrt kennen. Wir legen großen Wert auf Partnerschaften und nutzen unsere vertikal integrierten Fähigkeiten, um hochwertige, zuverlässige Komponenten wie leichte Aluminium-UAV-Rahmen zu liefern. Wenn Sie sich die Zeit nehmen, potenzielle Lieferanten anhand dieser Kriterien gründlich zu prüfen, erhöht sich die Wahrscheinlichkeit eines erfolgreichen Projektergebnisses erheblich.
Verständnis der Kostenfaktoren und Vorlaufzeiten für gedruckte UAV-Rahmen
Metall-AM bietet zwar überzeugende technische Vorteile, aber das Verständnis der damit verbundenen Kosten und Vorlaufzeiten ist für die Projektplanung und Budgetierung von entscheidender Bedeutung, insbesondere für die B2B-Beschaffung. Anders als bei der traditionellen Fertigung, bei der die Werkzeugkosten bei geringen Stückzahlen oft dominieren, werden die AM-Kosten von anderen Faktoren bestimmt.
Die wichtigsten Kostentreiber für AM-UAV-Rahmen aus Metall:
- Materialverbrauch:
- Pulvertyp: Die Kosten pro Kilogramm Metallpulver sind sehr unterschiedlich. Hochleistungslegierungen wie Scalmalloy® sind aufgrund der Legierungselemente (Scandium) und der Lizenzierung erheblich teurer als Standard-AlSi10Mg. Auch die A7075 AM-Varianten sind teurer.
- Teilband: Das tatsächliche Volumen des fertigen Teils hat einen direkten Einfluss auf die Menge des geschmolzenen Pulvers.
- Unterstützende Strukturen: Die Verwendung von Pulver für Stützen erhöht den Materialverbrauch. Ein optimiertes DfAM zur Minimierung der Stützen hilft, diese Kosten zu senken.
- Effizienz des Pulverrecyclings: Ungeschmolzenes Pulver ist zwar größtenteils recycelbar, doch kommt es bei der Handhabung und Verarbeitung zu gewissen Verlusten.
- Maschinennutzungszeit:
- Druckzeit: Dies ist oft ein Hauptkostentreiber. Er wird bestimmt durch das zu scannende Gesamtvolumen (Teil + Träger) und die Höhe des Teils (Anzahl der Schichten). Zu den Faktoren, die ihn beeinflussen, gehören:
- Größe und Komplexität der Teile: Größere und komplexere Teile brauchen länger.
- Schichtdicke: Dünnere Schichten verbessern die Auflösung, verlängern aber die Druckzeit erheblich.
- Suchstrategie und Parameter: Durch optimierte Parameter können Geschwindigkeit und Qualität in Einklang gebracht werden.
- Kosten der Maschine: Die stündlichen Betriebskosten von teuren Metall-AM-Systemen (einschließlich Abschreibung, Wartung, Energie, Inertgas).
- Druckzeit: Dies ist oft ein Hauptkostentreiber. Er wird bestimmt durch das zu scannende Gesamtvolumen (Teil + Träger) und die Höhe des Teils (Anzahl der Schichten). Zu den Faktoren, die ihn beeinflussen, gehören:
- Arbeit und Technik:
- Vorverarbeitung: CAD-Dateivorbereitung, DfAM-Optimierung, Orientierungsplanung, Support-Generierung. Erfordert Zeit für qualifizierte Ingenieure.
- Einrichtung und Überwachung von Gebäuden: Vorbereiten der Maschine, Laden des Pulvers, Überwachung des Baus.
- Nachbearbeitungsarbeiten: Dies kann erheblich sein, insbesondere für:
- Unterstützung bei der Entfernung: Bei komplexen Teilen oft manuell und zeitaufwendig.
- Oberflächenveredelung: Manuelle Nachbearbeitung oder Einrichtung automatisierter Prozesse.
- Inspektion: Manuelle Prüfungen, CMM-Programmierung/Betrieb.
- Nachbearbeitungsvorgänge:
- Wärmebehandlung: Kosten, die mit der Zeit, der Energie und dem Fachwissen der Öfen verbunden sind (insbesondere bei Behandlungen unter Vakuum oder kontrollierter Atmosphäre).
- CNC-Bearbeitung: Kosten für CAM-Programmierung, Maschineneinrichtung, Bearbeitungszeit, Werkzeuge und qualifizierte Arbeitskräfte, wenn enge Toleranzen oder spezielle Oberflächen erforderlich sind.
- Oberflächenbehandlungen: Kosten für Perlstrahlen, Trommeln, Polieren oder Beschichten.
- Qualitätssicherung und Inspektion:
- Der Umfang der erforderlichen Inspektion (Sichtprüfung, Maßprüfung, zerstörungsfreie Prüfung) und Dokumentation wirkt sich auf die Kosten aus. Komponenten für die Luft- und Raumfahrt erfordern in der Regel eine strengere Qualitätssicherung, was den Gesamtpreis in die Höhe treibt.
Tabelle: Kostentreiber und ihre Auswirkungen
Kostentreiber | Typische Auswirkungsebene | Anmerkungen |
---|---|---|
Pulvertyp (Legierung) | Hoch | Scalmalloy®/A7075 ist deutlich teurer als AlSi10Mg. |
Teil Volumen/Größe | Hoch | Wirkt sich direkt auf den Materialverbrauch und die Druckzeit aus. |
Teil Höhe | Hoch | Der wichtigste Faktor für die Druckzeit (Anzahl der Ebenen). |
Komplexität/Unterstützung | Mittel bis Hoch | Erhöht die Druckzeit, den Materialverbrauch und den Nachbearbeitungsaufwand. |
Post-Processing-Anforderungen | Mittel bis Hoch | Maschinelle Bearbeitung, aufwendige Endbearbeitung und komplexe Wärmebehandlungen verursachen zusätzliche Kosten. |
Arbeit (Einrichtung & Post-Pro) | Mittel | Vor allem bei der Entfernung und Veredelung von Stützen. |
Qualitätsanforderungen | Niedrig bis Hoch | Abhängig von der Branche; NDT und umfangreiche Dokumentation verursachen zusätzliche Kosten. |
Produktionsvolumen | Niedrig bis mittel | Die Kosten pro Teil nehmen mit der Menge moderat ab (Amortisation der Einrichtung). |
In Blätter exportieren
Typische Vorlaufzeiten:
Die Vorlaufzeiten für AM-Drohnenrahmen aus Metall werden von vielen der gleichen Faktoren wie die Kosten beeinflusst, insbesondere von der Verfügbarkeit der Maschine, der Druckzeit und dem Umfang der Nachbearbeitung.
- Prototyping: Für einfachere Prototypen mit minimaler Nachbearbeitung können die Vorlaufzeiten zwischen 5 bis 15 Arbeitstage.
- Produktionsteile: Für Rahmen, die eine komplexe Nachbearbeitung erfordern (z. B. Wärmebehandlung, umfangreiche Bearbeitung, strenge Inspektion), können sich die Vorlaufzeiten auf 3 bis 6 Wochen oder längerje nach Komplexität und Menge.
Faktoren, die die Vorlaufzeit beeinflussen:
- Designkomplexität und Druckzeit.
- Maschinenverfügbarkeit und Planungswarteschlange.
- Erforderliche Nachbearbeitungsschritte (jeder einzelne kostet Zeit).
- Anforderungen an die Inspektion.
- Bestellte Menge.
- Die derzeitige Arbeitsbelastung des Lieferanten.
Erlangung einer genauen Angebot für 3D-Druck im Großhandel erfordert die Bereitstellung detaillierter Informationen für den Dienstleister. Eine klare Kommunikation über die Anforderungen, einschließlich CAD-Dateien, Materialspezifikationen, Toleranzen, Endbearbeitungsanforderungen und erforderliche Zertifizierungen, ermöglicht es potenziellen Partnern, realistische Kostenschätzungen und Vorlaufzeiten zu erstellen.
Häufig gestellte Fragen (FAQ) zu 3D-gedruckten Aluminium-UAV-Rahmen
Hier finden Sie Antworten auf einige häufig gestellte Fragen von Ingenieuren und Beschaffungsmanagern zur Verwendung von Metall-AM für UAV-Rahmen:
- F1: Wie stabil sind 3D-gedruckte Aluminium-Drohnenrahmen im Vergleich zu maschinell gefertigten?
- A: Die Festigkeit hängt stark von der verwendeten Aluminiumlegierung und der Nachbearbeitung (insbesondere der Wärmebehandlung) ab. So bietet beispielsweise gedrucktes und auf T6 wärmebehandeltes AlSi10Mg eine gute Festigkeit, die oft mit der von Standard-Aluminiumgussbauteilen vergleichbar ist oder diese übertrifft und an Knetlegierungen wie 6061-T6 heranreicht. Hochleistungs-AM-Legierungen wie Scalmalloy® können eine spezifische Festigkeit (Verhältnis von Festigkeit zu Gewicht) aufweisen, die vielen herkömmlichen hochfesten Aluminiumlegierungen und sogar einigen Titansorten überlegen ist. AM-verarbeitetes A7075 zielt bei entsprechender Wärmebehandlung darauf ab, die sehr hohe Festigkeit von herkömmlichem 7075-T6-Knetwerkstoff zu erreichen. Darüber hinaus ermöglicht die Designfreiheit von AM eine Topologieoptimierung, bei der das Material nur dort platziert wird, wo es benötigt wird. Das Ergebnis sind Rahmen, die bei gleicher Steifigkeit oder Festigkeit im Vergleich zu traditionell konstruierten und hergestellten Teilen deutlich leichter sind.
- F2: Ist der 3D-Druck von Metall für UAV-Rahmen kosteneffizient?
- A: Das hängt von verschiedenen Faktoren ab, aber oft ist es so, vor allem bei bestimmten Szenarien. Metall-AM ist äußerst kosteneffizient für:
- Komplexe Geometrien: Teile mit komplizierten inneren Strukturen, organischen Formen aus der Topologieoptimierung oder integrierten Merkmalen, die auf herkömmliche Weise nur schwer oder gar nicht zu bearbeiten sind.
- Teil Konsolidierung: Das Drucken eines einzigen komplexen Teils anstelle des Zusammenbaus mehrerer einfacher Teile kann Montageaufwand, Befestigungsmittel und potenzielle Fehlerquellen einsparen.
- Rapid Prototyping und Kleinserienfertigung: AM vermeidet die hohen Vorlaufkosten und -zeiten, die mit der Herstellung von Werkzeugen (z. B. Gussformen, Gesenke, komplexe Vorrichtungen) verbunden sind.
- Anpassungen: Die Herstellung einzigartiger oder kundenspezifischer Rahmen ist möglich, ohne dass Kosten für das Umrüsten anfallen.
- Leistungsabhängige Anwendungen: Wenn die Gewichtseinsparungen und Leistungssteigerungen, die durch AM-Designs ermöglicht werden, einen signifikanten betrieblichen Nutzen bieten (z. B. längere Flugzeit, höhere Nutzlast), der die potenziell höheren Kosten pro Teil im Vergleich zu einer einfachen, traditionell hergestellten Alternative aufwiegt. Bei sehr einfachen Rahmendesigns, die in sehr hohen Stückzahlen produziert werden, können herkömmliche Methoden wie Stanzen oder Hochgeschwindigkeits-CNC-Bearbeitung mit der Zeit pro Teil kosteneffizienter werden, aber AM gewinnt oft, wenn Komplexität, kundenspezifische Anpassung oder Vorlaufzeit für die ersten Chargen die entscheidenden Faktoren sind.
- A: Das hängt von verschiedenen Faktoren ab, aber oft ist es so, vor allem bei bestimmten Szenarien. Metall-AM ist äußerst kosteneffizient für:
- Q3: Welche Informationen muss ich angeben, um ein genaues Angebot für einen 3D-gedruckten UAV-Rahmen zu erhalten?
- A: Um einen zuverlässigen Kostenvoranschlag von einem Metall-AM-Dienstleister zu erhalten, sollten Sie so viele Einzelheiten wie möglich angeben, in der Regel einschließlich:
- 3D-CAD-Datei: Ein qualitativ hochwertiges Modell in einem Standardformat (z. B. STEP, IGES). Stellen Sie sicher, dass das Modell wasserdicht und fehlerfrei ist.
- Spezifikation des Materials: Geben Sie eindeutig die gewünschte Aluminiumlegierung an (z. B. AlSi10Mg, Scalmalloy®, A7075 AM Variante).
- Technisches Zeichnen (fakultativ, aber empfohlen): Eine 2D-Zeichnung mit Angabe der kritischen Abmessungen, der erforderlichen Toleranzen (unter Verwendung von GD&T), der spezifischen Anforderungen an die Oberflächengüte (Ra-Werte) der wichtigsten Merkmale und der Stellen für die Nachbearbeitung.
- Menge: Die Anzahl der benötigten Rahmen (für Prototypen oder Serienproduktion).
- Nachbearbeitungsanforderungen: Geben Sie die erforderlichen Schritte wie Wärmebehandlung (z. B. T6-Zustand), gewünschte Oberflächenbeschaffenheit (z. B. mattes Perlstrahlen, spezielle Bearbeitung an den Schnittstellen) und alle erforderlichen Beschichtungen an.
- Prüfung und Zertifizierung: Erwähnen Sie alle erforderlichen Tests (z. B. zerstörungsfreie Prüfung, Überprüfung der Materialeigenschaften) oder Zertifizierungen (z. B. Materialzertifikate, Konformitätszertifikate, Einhaltung von AS9100). Die Bereitstellung umfassender Informationen ermöglicht es dem AM-Anbieter, die Herstellbarkeit genau zu beurteilen, die Kosten abzuschätzen (Druckzeit, Material, Nachbearbeitung) und eine realistische Vorlaufzeit zu bestimmen.
- A: Um einen zuverlässigen Kostenvoranschlag von einem Metall-AM-Dienstleister zu erhalten, sollten Sie so viele Einzelheiten wie möglich angeben, in der Regel einschließlich:
Schlussfolgerung: Höhere Leistung von UAVs mit 3D-gedruckten Aluminiumrahmen aus Metall
Die Landschaft der Konstruktion und Fertigung unbemannter Luftfahrzeuge unterliegt einem bedeutenden Wandel, der durch das Streben nach höherer Leistung, größerer Effizienz und verbesserten Fähigkeiten vorangetrieben wird. Die additive Fertigung von Metallen, insbesondere unter Verwendung von leichten, hochfesten Aluminiumlegierungen wie AlSi10Mg, Scalmalloy® und AM-optimiertem A7075, steht an der Spitze dieser Entwicklung. Wie wir herausgefunden haben, machen die Vorteile der Metall-AM - beispiellose Designfreiheit, die eine Topologieoptimierung und Bauteilkonsolidierung ermöglicht, erhebliche Gewichtsreduzierung, die zu einer verbesserten Flugdauer und Nutzlastkapazität führt, schnelles Prototyping, das Innovationen beschleunigt, und die Fähigkeit, komplexe Geometrien herzustellen, die mit herkömmlichen Mitteln nicht zu erreichen sind - sie zu einem unverzichtbaren Werkzeug für die Entwicklung von UAV-Rahmen der nächsten Generation.
Um diese Vorteile erfolgreich zu nutzen, ist ein ganzheitlicher Ansatz erforderlich. Er beginnt damit, dass man sich die Grundsätze des Design for Additive Manufacturing (DfAM) zu eigen macht und das Bauteildesign neu überdenkt, um das schichtweise Verfahren voll auszuschöpfen. Dazu gehört eine sorgfältige Auswahl der geeigneten Aluminiumlegierung, die die Leistungsanforderungen mit der Druckbarkeit und den Kosten in Einklang bringt. Und ganz entscheidend ist die Wahl des richtigen Fertigungspartners - eines Partners mit fundiertem technischem Know-how, robusten Qualitätssystemen, fortschrittlichen Anlagen und umfassenden Fähigkeiten, die vom Pulver bis zum fertigen Teil reichen. Das Verständnis für die Feinheiten von Toleranzen, Oberflächengüten, wichtigen Nachbearbeitungsschritten und potenziellen Herausforderungen ermöglicht eine realistische Planung und eine effektive Zusammenarbeit. Während Kosten- und Vorlaufzeitfaktoren sorgfältig berücksichtigt werden müssen, geht das Wertversprechen von AM oft über den reinen Teilepreis hinaus und umfasst eine verbesserte Leistung, eine schnellere Markteinführung für innovative Designs und eine vereinfachte Logistik durch Teilekonsolidierung.
Met3dp hat es sich zur Aufgabe gemacht, Unternehmen in die Lage zu versetzen, das volle Potenzial der additiven Fertigung von Metallen auszuschöpfen. Mit unseren branchenführenden Drucksystemen, unserer Erfahrung in der Herstellung Hochleistungsmetallpulver Durch fortschrittliche Zerstäubungstechniken und umfassende Anwendungsunterstützung bieten wir End-to-End-Lösungen, die auf die anspruchsvollen Anforderungen von Branchen wie Luft- und Raumfahrt und UAV-Fertigung zugeschnitten sind. Wir arbeiten mit unseren Kunden zusammen, um die Komplexität der AM-Einführung zu bewältigen, von der ersten Designberatung bis zur Lieferung vollständig qualifizierter, einsatzbereiter Komponenten. Da UAVs in verschiedenen Sektoren eine immer wichtigere Rolle spielen, wird der 3D-Metalldruck maßgeblich dazu beitragen, die Grenzen des Möglichen zu erweitern und leichtere, stärkere, intelligentere und leistungsfähigere Luftplattformen für die Zukunft zu ermöglichen. Setzen Sie sich noch heute mit Met3dp in Verbindung, um zu erfahren, wie unsere Fähigkeiten die Ziele Ihres Unternehmens im Bereich der additiven Fertigung unterstützen und die Leistung Ihres UAVs steigern können.
Teilen auf
MET3DP Technology Co., LTD ist ein führender Anbieter von additiven Fertigungslösungen mit Hauptsitz in Qingdao, China. Unser Unternehmen ist spezialisiert auf 3D-Druckgeräte und Hochleistungsmetallpulver für industrielle Anwendungen.
Fragen Sie an, um den besten Preis und eine maßgeschneiderte Lösung für Ihr Unternehmen zu erhalten!
Verwandte Artikel
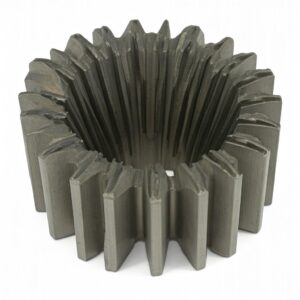
Hochleistungs-Düsenschaufelsegmente: Revolutionierung der Turbineneffizienz mit 3D-Metalldruck
Mehr lesen "Über Met3DP
Aktuelles Update
Unser Produkt
KONTAKT US
Haben Sie Fragen? Senden Sie uns jetzt eine Nachricht! Wir werden Ihre Anfrage mit einem ganzen Team nach Erhalt Ihrer Nachricht bearbeiten.
Holen Sie sich Metal3DP's
Produkt-Broschüre
Erhalten Sie die neuesten Produkte und Preislisten
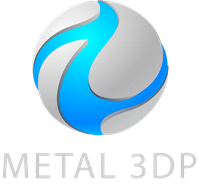
Metallpulver für 3D-Druck und additive Fertigung