AlSi10Mg für Luft- und Raumfahrthalterungen im Metall-3D-Druck
Inhaltsübersicht
Einleitung: Die kritische Rolle von Luft- und Raumfahrtkonsolen und additiver Fertigung
Die Luft- und Raumfahrtindustrie arbeitet auf dem Höhepunkt ihrer technischen Ambitionen und verlangt ein beispielloses Maß an Sicherheit, Leistung und Effizienz. Jede Komponente, unabhängig von ihrer vermeintlichen Einfachheit, spielt eine wichtige Rolle in der komplexen Symphonie des Fliegens. Halterungen für die Luft- und Raumfahrt, die oft unscheinbar aussehen, sind ein Paradebeispiel für solche kritischen Komponenten. Diese Teile erfüllen wesentliche Funktionen, von der Befestigung wichtiger Systeme und der Unterstützung struktureller Lasten bis hin zur Verlegung wichtiger Leitungen für Treibstoff, Hydraulik und Elektronik. Für ihre Konstruktion und Herstellung gelten strengste Normen, bei denen Versagen keine Option und Optimierung ein ständiges Bestreben ist.
Jahrzehntelang verließ man sich bei der Herstellung von Halterungen für die Luft- und Raumfahrt auf traditionelle Fertigungsmethoden wie CNC-Bearbeitung von Knüppeln oder Feinguss. Diese Methoden sind zwar zuverlässig, haben aber oft erhebliche Einschränkungen, insbesondere was die Komplexität der Konstruktion, den Materialabfall und die Vorlaufzeiten betrifft. Die maschinelle Bearbeitung komplizierter Formen kann zeitaufwändig sein und erheblichen Materialausschuss verursachen, während das Gießen teure Werkzeuge erfordert und die Designmöglichkeiten einschränken kann. Darüber hinaus hängt das unablässige Streben nach verbesserter Leistung von Flugzeugen wesentlich von der Gewichtsreduzierung ab. Leichtere Flugzeuge verbrauchen weniger Treibstoff, bieten eine größere Nutzlastkapazität oder haben eine größere Reichweite - entscheidende Faktoren, die sich auf die Betriebskosten und die Einsatzfähigkeit auswirken. Dieser Zwang zur Gewichtsreduzierung setzt die Konstrukteure unter immensen Druck, jede Komponente, einschließlich der Halterungen, zu optimieren, ohne die strukturelle Integrität oder Sicherheit zu beeinträchtigen.
Der Einstieg in die additive Fertigung von Metall (AM), allgemein bekannt als Metall 3D-Druck. Diese bahnbrechende Technologie verändert die Landschaft der Fertigung von Luft- und Raumfahrtkomponenten in rasantem Tempo. Durch den schichtweisen Aufbau von Bauteilen direkt aus digitalen Modellen unter Verwendung von feinen Metallpulvern eröffnet AM eine noch nie dagewesene Designfreiheit und ermöglicht die Herstellung hoch optimierter, leichter Strukturen, deren Herstellung bisher unmöglich oder unerschwinglich war. Die Palette der Materialien, die sich für AM in der Luft- und Raumfahrt eignen, wächst ständig, AlSi10Mgeine Aluminiumlegierung, hat sich zu einer wichtigen Wahl für die Herstellung von Halterungen für die Luft- und Raumfahrt entwickelt. Ihre überzeugende Kombination aus geringer Dichte, guten mechanischen Eigenschaften, hervorragender Verarbeitbarkeit durch Verfahren wie Laser Powder Bed Fusion (LPBF) und relativer Kosteneffizienz macht sie ideal für eine breite Palette von unkritischen und semikritischen Halterungsanwendungen.
Dieser technologische Wandel ermöglicht es Luftfahrtingenieuren und Beschaffungsmanagern, die Konstruktion von Halterungen und die Beschaffung neu zu überdenken. Er ermöglicht die Produktion von Teilen, die nicht nur leichter und potenziell stärker sind, sondern auch schneller, mit weniger Materialabfall und mit größerer Flexibilität in der Lieferkette hergestellt werden können. Als führender Anbieter von Lösungen für die additive Fertigung von Metallteilen, einschließlich fortschrittlicher Drucksysteme und hochwertige Metallpulver für den 3D-DruckMet3dp steht an der Spitze dieser Revolution und ermöglicht es Luft- und Raumfahrtunternehmen, das volle Potenzial von AM für Komponenten wie Halterungen zu nutzen. Dieser Artikel befasst sich mit den Besonderheiten der Verwendung von AlSi10Mg für Halterungen in der Luft- und Raumfahrt mittels 3D-Metalldruck. Dabei werden Anwendungen, Vorteile, Materialüberlegungen, Konstruktionsprinzipien und entscheidende Faktoren für eine erfolgreiche Umsetzung untersucht, um Ingenieure und B2B-Beschaffungsspezialisten bei der Navigation durch diese aufregende technologische Grenze zu unterstützen. Der Schwerpunkt liegt auf der Bereitstellung umsetzbarer Erkenntnisse für Herstellung von Luft- und Raumfahrtkonsolendas Verständnis der Rolle der Additive Fertigung von Luft- und Raumfahrtkomponenten, erreichen leichte Luft- und Raumfahrtteileund Mastering AlSi10Mg 3D-Druck.
Anwendungen: Wo werden 3D-gedruckte AlSi10Mg-Brackets eingesetzt?
Die Vielseitigkeit des 3D-Drucks von Metallen in Verbindung mit den günstigen Eigenschaften von AlSi10Mg eröffnet eine breite Palette von Anwendungen für additiv gefertigte Halterungen in der Luft- und Raumfahrt und darüber hinaus. Während traditionell gefertigte Halterungen nach wie vor weit verbreitet sind, gewinnt die additive Fertigung in bestimmten Anwendungsfällen, in denen ihre einzigartigen Vorteile einen erheblichen Mehrwert bieten, rasch an Bedeutung. Beschaffungsmanager auf der Suche nach innovativen Zulieferer der Luft- und Raumfahrtindustrie wenden sich zunehmend an AM-Spezialisten, die diese optimierten Teile liefern können.
Beispiele für spezifische Luft- und Raumfahrtklammern:
- Strukturelle Halterungen: Diese Halterungen sind fester Bestandteil der Flugzeugzelle und tragen zur Lastverteilung und strukturellen Integrität in Bereichen wie Rumpfspanten, Flügelrippen und Leitwerkstrukturen bei. Während für flugkritische Primärstrukturen oft umfangreiche Zertifizierungen mit Werkstoffen wie Titan erforderlich sind, findet AlSi10Mg in sekundären Strukturanwendungen Verwendung, wo sein Verhältnis von Festigkeit zu Gewicht erhebliche Vorteile gegenüber schwereren herkömmlichen Konstruktionen bietet. Durch die Optimierung der Topologie können diese Halterungen komplexe Lastpfade mit minimalem Materialeinsatz effizient bewältigen.
- System-Montagehalterungen: Flugzeuge sind vollgepackt mit komplexen Systemen, die alle eine sichere Befestigung erfordern. AlSi10Mg AM Halterungen zeichnen sich hier aus:
- Avionik-Tabletts und -Halterungen: Sichere Aufbewahrung empfindlicher elektronischer Geräte, die oft vibrationsdämpfende Eigenschaften erfordern, die in das AM-Design integriert werden können.
- Hydraulische Leitungshalterungen: Verlegung und Befestigung von Hydraulikleitungen, die oft komplexe Geometrien aufweisen, um enge Stellen in der Flugzeugzelle oder in Fahrwerksschächten zu überwinden. AM ermöglicht kundenspezifische Verlegungspfade.
- Kraftstoffleitungshalterungen: Ähnlich wie Hydraulikleitungen erfordern sie eine sichere Befestigung und möglicherweise spezielle Formen für die Verbindung mit anderen Komponenten.
- Halterungen/Klemmen für den elektrischen Kabelbaum: Organisieren und Sichern komplexer Kabelbäume im gesamten Flugzeug. AM ermöglicht die Erstellung komplizierter Klemmengeometrien, die auf spezifische Kabelbaumdurchmesser und -verläufe zugeschnitten sind.
- Kanalisationsstützen: Haltekanäle für das Umweltkontrollsystem (ECS) oder für das Enteisungssystem.
- Innere Halterungen: Wird im Kabineninneren zur Befestigung von Sitzen, Gepäckfächern, Bordküchengeräten oder Trennwänden verwendet. Gewichtseinsparungen tragen hier direkt zur Treibstoffeffizienz über die gesamte Lebensdauer des Flugzeugs bei. AM ermöglicht ästhetisch ansprechende, leichte Designs.
- Halterungen für Motorkomponenten (nicht heißer Bereich): Während Hochtemperatur-Motorenteile Superlegierungen oder Titan erfordern, können in Kühlern AlSi10Mg-Halterungen für die Montage von Zubehör, Sensoren oder externen Rohren verwendet werden.
Funktionale Anforderungen, die von AlSi10Mg erfüllt werden:
Die Eignung von AlSi10Mg für diese Anwendungen ergibt sich aus seiner Fähigkeit, wichtige funktionale Anforderungen zu erfüllen:
- Tragfähigkeit: Nach einer geeigneten Wärmebehandlung (in der Regel T6) bietet AlSi10Mg eine gute Festigkeit und Steifigkeit, die für viele sekundäre Struktur- und Systembefestigungsaufgaben ausreicht.
- Vibrationsbeständigkeit: AM ermöglicht die Konstruktion von Halterungen mit integrierten Dämpfungsmerkmalen oder optimierten Geometrien, die Spannungskonzentrationen bei Vibrationen minimieren, was für Avionik- und Systemhalterungen entscheidend ist.
- Wärmemanagement: AlSi10Mg besitzt im Vergleich zu Titan- oder Stahllegierungen eine gute Wärmeleitfähigkeit. Dies kann bei Halterungen für wärmeerzeugende Geräte von Vorteil sein, da so die Wärme besser abgeleitet werden kann.
- Komplexe Geometrie: Mit AM lassen sich organische, komplizierte Formen herstellen, die häufig erforderlich sind, um Halterungen in begrenzte Räume innerhalb einer Flugzeugstruktur einzupassen oder mehrere Funktionen in einem einzigen Teil zu vereinen.
Jenseits der Luft- und Raumfahrt:
Die Vorteile, die den Einsatz von 3D-gedruckten AlSi10Mg-Brackets in der Luft- und Raumfahrt vorantreiben, sind auch in anderen anspruchsvollen Branchen von Bedeutung:
- Hochleistungs-Automobil/Motorsport: Gewichtsreduzierung ist oberstes Gebot. Halterungen für die Montage von Motorzubehör, Aufhängungskomponenten oder elektronischen Einheiten profitieren erheblich von AlSi10Mg AM.
- Drohnen/Unbemannte Luftfahrzeuge (UAVs): Jedes eingesparte Gramm verlängert die Flugzeit oder erhöht die Nutzlastkapazität. Strukturelle Rahmenkomponenten, Sensorhalterungen und Fahrwerkshalterungen sind die besten Kandidaten. Hersteller von UAV-Halterungen setzen zunehmend auf AM.
- Satelliten: Die Startkosten sind direkt mit der Masse verbunden. Leichtgewichtige Halterungen für die Montage von Antennen, Solarpanels oder internen Instrumenten unter Verwendung von AlSi10Mg sind von großem Vorteil.
- Industrielle Ausrüstung: Kundenspezifische Halterungen für die Montage von Sensoren, Aktoren oder Vorrichtungen in Spezialmaschinen können schnell und kostengünstig ohne Werkzeuge hergestellt werden.
Das Verständnis dieser verschiedenen AlSi10Mg-Anwendungen und Metall-AM-Anwendungsfälle ist entscheidend für Designer und B2B-Lieferanten die sich diese Technologie zunutze machen wollen. Die Fähigkeit, hochgradig maßgeschneiderte Produkte zu produzieren, 3D-gedruckte Strukturkomponenten on-demand verändert die Beschaffungsstrategien und ermöglicht Leistungsverbesserungen in verschiedenen High-Tech-Sektoren.
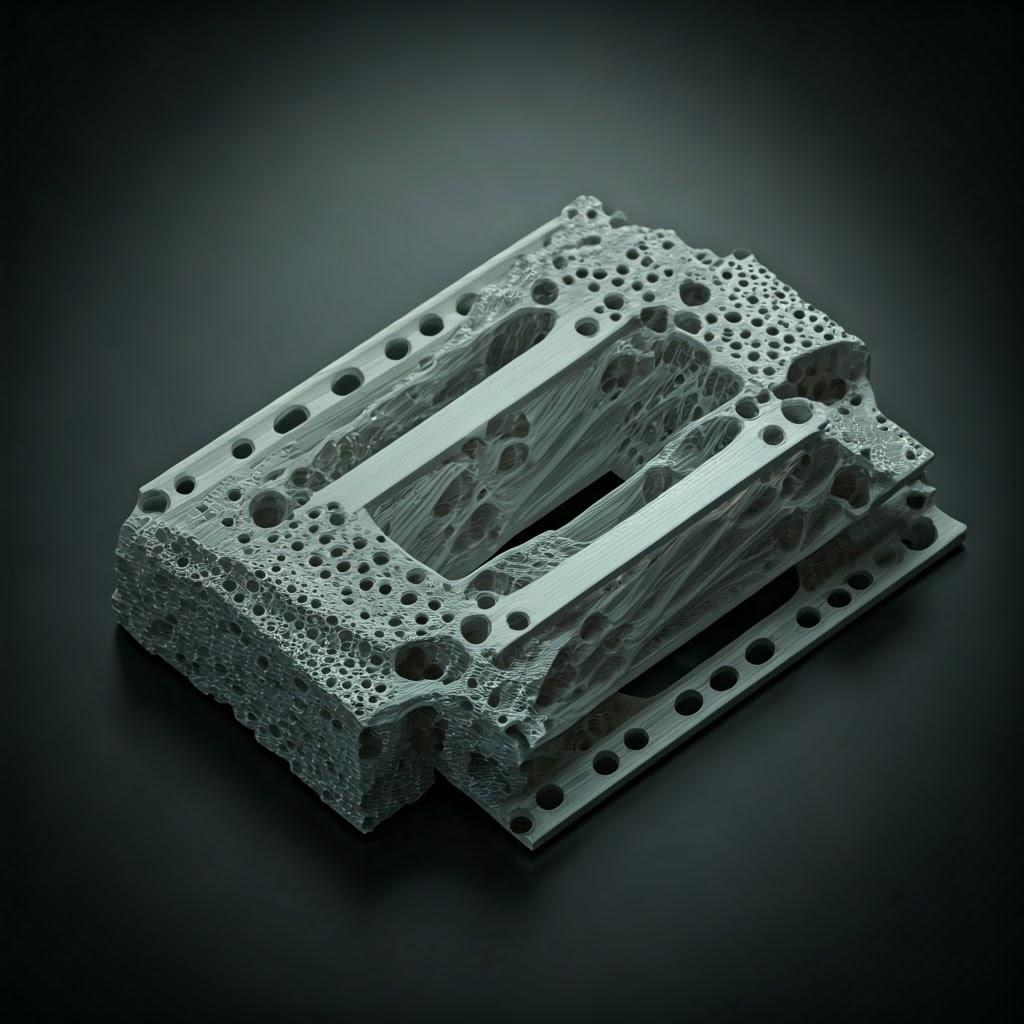
Warum 3D-Metalldruck für Halterungen in der Luft- und Raumfahrt? Vorteile gegenüber traditionellen Methoden
Bei der Entscheidung für die additive Fertigung von Metallteilen für Halterungen in der Luft- und Raumfahrt geht es nicht nur darum, Neues zu entdecken, sondern auch um greifbare, quantifizierbare Vorteile gegenüber etablierten Verfahren wie CNC-Bearbeitung und Feinguss. Für Ingenieure, die sich auf die Leistung konzentrieren, und für Beschaffungsmanager, die die Gesamtbetriebskosten und die Belastbarkeit der Lieferkette bewerten, sind die Vorteile von AM überzeugend. Lassen Sie uns diese Vorteile im Detail untersuchen und aufzeigen, warum versierte Hersteller und Partner für die Herstellung von Luft- und Raumfahrtkomponenten integrieren zunehmend AM.
1. Unerreichte Gestaltungsfreiheit:
- Topologie-Optimierung: Dies ist wohl der größte Vorteil. Mithilfe spezieller Software können Ingenieure Lastfälle, Einschränkungen und Konstruktionsräume definieren, so dass Algorithmen iterativ Material aus nicht tragenden Bereichen entfernen können. Das Ergebnis sind hochgradig organische, skelettartige Strukturen, die auf maximale Steifigkeit und Festigkeit bei minimalem Gewicht optimiert sind. Diese komplizierten Geometrien lassen sich oft nicht durch subtraktive Bearbeitung (bei der Material weggeschnitten wird) oder durch Gießen (bei dem Gussformen verwendet werden) herstellen. Die Topologieoptimierung führt regelmäßig zu Gewichtseinsparungen von 20-60% oder mehr bei Halterungen im Vergleich zu herkömmlich konstruierten Gegenstücken, was sich direkt auf die Kraftstoffeffizienz und die Nutzlastkapazität auswirkt.
- Teil Konsolidierung: Bei herkömmlichen Konstruktionen müssen oft mehrere einfache Teile (Halterungen, Unterlegscheiben, Befestigungselemente) zusammengesetzt werden, um eine komplexe Montage- oder Stützfunktion zu erfüllen. Metall-AM ermöglicht es den Konstrukteuren, diese mehreren Komponenten in einem einzigen, komplexen, monolithischen Teil zu konsolidieren. Dies reduziert den Aufwand drastisch:
- Anzahl der Teile: Vereinfacht Inventarisierung, Logistik und Stücklisten (BOM).
- Montagezeit und Arbeitsaufwand: Reduziert den Bedarf an manueller Montage und die damit verbundenen Kosten.
- Gewicht: Es werden keine schweren Befestigungsmittel (Schrauben, Nieten) mehr benötigt.
- Potenzielle Fehlerpunkte: Weniger Verbindungen und Schnittstellen bedeuten mehr Zuverlässigkeit.
- Komplexe Geometrien und interne Merkmale: AM baut Teile Schicht für Schicht auf und ermöglicht die Schaffung interner Kanäle (z. B. für die Kühlung oder die konforme Verdrahtung), komplexer gekrümmter Oberflächen und dünnwandiger Strukturen ohne die Einschränkungen, die durch Schneidwerkzeuge oder die Entformung entstehen. Dies ermöglicht Halterungen mit integrierten Funktionen, die über eine einfache Montage hinausgehen.
2. Signifikante Gewichtsreduzierung:
Wie bereits erwähnt, ist die Optimierung der Topologie ein wichtiger Faktor, aber AM ermöglicht auch auf andere Weise eine Gewichtsreduzierung:
- Verwendung von Leichtbauwerkstoffen: AM-Verfahren wie LPBF eignen sich besonders gut für leichte Luftfahrtlegierungen wie AlSi10Mg und Ti-6Al-4V.
- Gitterförmige Strukturen: AM ermöglicht den Einbau von internen Gitter- oder Zellstrukturen in massive Teile. Durch diese Strukturen wird die Masse erheblich reduziert, während gleichzeitig ein hohes Maß an Steifigkeit und Festigkeit beibehalten wird - ideal für die Optimierung der Leistung von Halterungen, die über das hinausgeht, was eine einfache Topologieoptimierung erreichen kann. Vergleich von 3D-Metalldruck vs. CNC-BearbeitungDie subtraktiven Verfahren beginnen mit einem massiven Block und tragen Material ab, wobei oft Material zurückbleibt, das strukturell nicht notwendig ist, aber nur schwer entfernt werden kann. AM baut nur das notwendige Material auf, was zu inhärent effizienteren Designs führt.
3. Verkürzte Vorlaufzeiten und Rapid Prototyping:
- Beseitigung von Werkzeugen: Das herkömmliche Gießen erfordert eine beträchtliche Vorlaufzeit (Wochen oder Monate) und hohe Kosten für den Entwurf und die Herstellung von Gussformen. Die CNC-Bearbeitung erfordert Programmierung und möglicherweise komplexe Vorrichtungskonstruktion. AM erfordert nur eine digitale CAD-Datei, was die Einrichtungszeit drastisch reduziert.
- Rapid Prototyping: Die Herstellung von Funktionsprototypen von Halterungsdesigns dauert mit AM nur Tage, im Vergleich zu Wochen oder Monaten bei herkömmlichen Verfahren. Dadurch können die Ingenieure ihre Entwürfe viel schneller wiederholen, die Funktionalität rasch testen und den Produktentwicklungszyklus beschleunigen. Diese Flexibilität ist in der schnelllebigen Luft- und Raumfahrtbranche von entscheidender Bedeutung. Rapid Prototyping von Teilen für die Luft- und Raumfahrt ermöglicht eine schnellere Designvalidierung und eine schnellere Überführung in die Endproduktion.
- Produktion auf Abruf: AM ermöglicht die Produktion von Ersatzteilen oder Kleinserien auf Abruf, was den Bedarf an großen Lagerbeständen und Lagerkosten verringert. Dies ist besonders wertvoll für ältere Flugzeuge oder Situationen, in denen dringender Ersatz benötigt wird.
4. Verbesserte Materialeffizienz und Nachhaltigkeit:
- Near-Net-Shape-Herstellung: Bei AM-Verfahren wird in der Regel nur das Material verwendet, das für die Herstellung des Teils und seiner Stützstrukturen benötigt wird. Zwar wird ein Teil des Pulvers für die Stützstrukturen verwendet, und ungesintertes Pulver muss sorgfältig gehandhabt und recycelt werden, doch ist die Materialausnutzung insgesamt oft deutlich höher als bei der traditionellen subtraktiven Fertigung, insbesondere bei komplexen Teilen, die aus großen Knüppeln hergestellt werden. Die Verringerung des Materialabfalls senkt die Kosten und trägt zu den Zielen der Nachhaltigkeit bei.
- Pulver Wiederverwertbarkeit: Ungeschmolzenes Pulver, das sich während der LPBF in der Baukammer befindet, kann in der Regel gesiebt und mehrfach wiederverwendet werden (mit entsprechenden Qualitätsprüfungen), was die Materialeffizienz weiter verbessert. Führende Anbieter wie Met3dp legen großen Wert auf die Qualität und Rückverfolgbarkeit des Pulvers, die für die Erhaltung der Eigenschaften während des Recyclings entscheidend sind.
5. Verbesserte Flexibilität und Widerstandsfähigkeit der Lieferkette:
- Digitales Inventar: Die Entwürfe liegen als digitale Dateien vor, die elektronisch an jede fähige AM-Anlage auf der ganzen Welt zur Produktion gesendet werden können. Dies ermöglicht eine dezentralisierte Fertigung, die Teile näher am Bedarfsort produziert und die Versandkosten und Vorlaufzeiten reduziert.
- Geringere Abhängigkeit vom Werkzeugbau: Die Abschaffung von harten Werkzeugen vereinfacht die Lieferkette, senkt die Lagerkosten und beseitigt das Risiko der Beschädigung oder des Verlusts von Werkzeugen.
- Abmilderung der Obsoleszenz: Bei älteren Flugzeugen, für die es möglicherweise keine Originalwerkzeuge mehr gibt, ermöglicht AM das Reverse Engineering und die direkte digitale Fertigung veralteter Halterungen, so dass die Lufttüchtigkeit weiterhin gewährleistet ist.
- Agile Beschaffung: Unternehmen können mit einem Netzwerk qualifizierter Anbieter von 3D-Metalldruckdiensten oder 3D-Druckdienste für den Großhandeldie Diversifizierung ihrer Lieferantenbasis und die Verbesserung der Widerstandsfähigkeit gegen Störungen. Optimierung von Lieferkettenlösungen für die Luft- und Raumfahrt ist ein wichtiger Faktor für die Einführung von AM.
Zusammenfassend lässt sich sagen, dass die Vorteile der additiven Fertigung für Halterungen in der Luft- und Raumfahrt gehen weit über die bloße Herstellung komplexer Formen hinaus. Sie umfassen erhebliche Verbesserungen in Bezug auf Leistung (Gewicht), Geschwindigkeit (Durchlaufzeit), Kosten (Materialeffizienz, Reduzierung der Montagekosten) und Lieferkettenstrategie, was sie zu einer überzeugenden Alternative oder Ergänzung zu herkömmlichen Methoden für zukunftsorientierte Luft- und Raumfahrtunternehmen macht.
AlSi10Mg und Ti-6Al-4V: Empfohlene Materialien Deep Dive
Die Wahl des richtigen Materials ist für den Erfolg jeder technischen Anwendung von grundlegender Bedeutung. Dies gilt insbesondere für Komponenten für die Luft- und Raumfahrt, bei denen Leistung und Zuverlässigkeit an erster Stelle stehen. Bei 3D-gedruckten Halterungen für die Luft- und Raumfahrt zeichnen sich zwei Metalllegierungen aus: AlSi10Mg (eine Aluminiumlegierung) und Ti-6Al-4V (eine Titanlegierung). Es gibt zwar noch andere Legierungen, aber diese beiden decken ein breites Spektrum an Bracket-Anforderungen ab und bieten je nach den Anforderungen der jeweiligen Anwendung unterschiedliche Vorteile. Die Kenntnis ihrer Eigenschaften und Verarbeitungsaspekte ist für Ingenieure, die Teile entwerfen, und für Beschaffungsspezialisten, die von Metallpulververteiler oder Full-Service-AM-Anbieter.
AlSi10Mg: Das vielseitige Arbeitspferd
AlSi10Mg ist eine der am häufigsten verwendeten Aluminiumlegierungen in der additiven Fertigung von Metallen, insbesondere mittels Laser Powder Bed Fusion (LPBF). Es handelt sich im Wesentlichen um eine Gusslegierungszusammensetzung, die für AM-Prozesse angepasst wurde.
- Zusammensetzung: Hauptsächlich Aluminium (Al), mit ~9-11% Silizium (Si) und 0,2-0,45% Magnesium (Mg).
- Silizium (Si): Verbessert die Fließfähigkeit der Legierung im geschmolzenen Zustand erheblich und verringert die Erstarrungsschrumpfung. Dies verbessert die "Druckfähigkeit" in LPBF und ermöglicht die erfolgreiche Herstellung von feinen Merkmalen und komplexen Geometrien mit geringerem Risiko von Rissen.
- Magnesium (Mg): Ermöglicht die Ausscheidungshärtung der Legierung durch Wärmebehandlung (in der Regel ein T6-Zyklus mit Lösungsglühen und künstlicher Alterung). Dieser Prozess erhöht die Festigkeit und Härte des Materials im Vergleich zu seinem Ausgangszustand erheblich.
- Wichtigste Eigenschaften und Vorteile für Klammern:
- Ausgezeichnetes Verhältnis von Stärke zu Gewicht: AlSi10Mg ist zwar nicht so hoch wie Titanlegierungen, bietet aber im Vergleich zu herkömmlichem Stahl oder sogar vielen Aluminiumknetlegierungen ein sehr wettbewerbsfähiges Verhältnis zwischen Festigkeit und Gewicht und eignet sich daher ideal für die Herstellung von Leichtbaukonsolen.
- Gute Verarbeitbarkeit (LPBF): Es schmilzt und verfestigt sich vorhersehbar unter Laserbestrahlung, was relativ hohe Baugeschwindigkeiten und eine gute Auflösung der Merkmale ermöglicht. Es ist eines der bewährten und gut charakterisierten Materialien für LPBF.
- Gute Wärmeleitfähigkeit: Aluminiumlegierungen weisen im Allgemeinen eine gute Wärmeleitfähigkeit auf (etwa 130-150 W/m-K für AM AlSi10Mg). Dies ist vorteilhaft für Halterungen, an denen wärmeerzeugende Komponenten angebracht sind, und trägt dazu bei, die Wärme von empfindlichen Systemen abzuleiten.
- Gute Korrosionsbeständigkeit: Bietet ausreichende Beständigkeit gegen atmosphärische Korrosion für viele Umgebungen in der Luft- und Raumfahrt. Die Leistung kann bei Bedarf durch Oberflächenbehandlungen wie Eloxieren oder Lackieren weiter verbessert werden.
- Schweißeignung: Kann geschweißt werden, wobei je nach Nachbearbeitungszustand besondere Verfahren erforderlich sein können.
- Kosten-Nutzen-Verhältnis: Im Vergleich zu Titanlegierungen ist AlSi10Mg-Pulver deutlich preiswerter und damit eine wirtschaftlichere Wahl für Brackets, bei denen die ultimative Leistung von Titan nicht unbedingt erforderlich ist.
- Erwägungen:
- Eignung für niedrigere Temperaturen: Nicht geeignet für Anwendungen, bei denen die Temperaturen deutlich über 150-170°C liegen, da sich die mechanischen Eigenschaften dann merklich verschlechtern.
- Geringere absolute Festigkeit als Titan: Es ist zwar für sein Gewicht stark, erreicht aber nicht die absolute Festigkeit oder Ermüdungsbeständigkeit von Ti-6Al-4V.
- Erforderliche Wärmebehandlung: Zur Erzielung optimaler mechanischer Eigenschaften ist in der Regel eine Wärmebehandlung nach der Herstellung (T6-Zyklus) erforderlich, was einen zusätzlichen Arbeitsschritt und zusätzliche Kosten verursacht.
Met3dp's Verpflichtung zur Pulverqualität: Die Konsistenz und Qualität des Metallpulvers sind entscheidend, um zuverlässige und wiederholbare Ergebnisse in der Luft- und Raumfahrt-AM zu erzielen. Met3dp verwendet branchenführende Gaszerstäubung und Plasma-Rotations-Elektroden-Verfahren (PREP) zur Herstellung von hochwertige Metallpulver, einschließlich AlSi10Mg. Unsere fortschrittlichen Zerstäubungstechniken gewährleisten: * Hohe Sphärizität: Sphärische Pulverpartikel fließen leicht und verdichten sich im Pulverbett, was zu gleichmäßigeren Schichten und Teilen mit geringerer Porosität führt. * Kontrollierte Partikelgrößenverteilung (PSD): Die optimierte PSD gewährleistet eine gute Fließfähigkeit und ein effizientes Schmelzen während des LPBF-Prozesses. * Niedrige Verunreinigungswerte: Strenge Qualitätskontrollen minimieren Sauerstoff und andere Verunreinigungen, die die Materialeigenschaften beeinträchtigen können. * Konsistenz von Charge zu Charge: Unverzichtbar für wiederholbare Fertigungsergebnisse, die von den Normen der Luft- und Raumfahrt gefordert werden. Als zuverlässiger AlSi10Mg-Pulver-Verteiler und Anbieter von AM-Lösungen stellt Met3dp sicher, dass das Ausgangsmaterial die strengen Anforderungen für die Herstellung von Luft- und Raumfahrtkonsolen erfüllt.
Ti-6Al-4V (Grad 5 / Grad 23): Die leistungsstarke Option
Ti-6Al-4V (oft als Ti64 bezeichnet) ist das Arbeitspferd der Titanindustrie und wird aufgrund seiner außergewöhnlichen Eigenschaften häufig in der Luft- und Raumfahrt verwendet. Grade 5 ist der Standard, während Grade 23 (ELI - Extra Low Interstitials) eine verbesserte Duktilität und Bruchzähigkeit bietet, die oft für kritische Anwendungen bevorzugt wird.
- Zusammensetzung: Hauptsächlich Titan (Ti), mit ~6% Aluminium (Al) und ~4% Vanadium (V).
- Wichtigste Eigenschaften und Vorteile für Klammern:
- Hervorragendes Verhältnis von Stärke zu Gewicht: Bietet eines der besten Verhältnisse zwischen Festigkeit und Gewicht unter den technischen Metallen und übertrifft das von AlSi10Mg und hochfesten Stählen. Dies ermöglicht extrem leichte und starke Halterungskonstruktionen.
- Ausgezeichnete Korrosionsbeständigkeit: Hochgradig korrosionsbeständig in einer Vielzahl von aggressiven Umgebungen, einschließlich Salzwasser und verschiedenen Industriechemikalien. Ideal für Halterungen, die rauen Bedingungen ausgesetzt sind.
- Eignung für hohe Temperaturen: Behält gute mechanische Eigenschaften bei hohen Temperaturen (bis zu ~400°C), wodurch es sich für Halterungen in der Nähe von Motoren oder in Hochgeschwindigkeitsflugzeugstrukturen eignet.
- Ausgezeichnete Ermüdungsfestigkeit: Kritisch für Bauteile, die zyklischen Belastungen ausgesetzt sind, wie sie in Flugzeugstrukturen üblich sind.
- Biokompatibilität (weniger relevant für Klammern): Aufgrund seiner Biokompatibilität wird es häufig für medizinische Implantate verwendet.
- Erwägungen:
- Höhere Materialkosten: Titanpulver ist wesentlich teurer als Aluminiumpulver.
- Höhere Dichte: Das Verhältnis von Festigkeit zu Gewicht ist zwar hervorragend, aber die Dichte (~4,43 g/cm³) ist höher als bei AlSi10Mg (~2,67 g/cm³). Eine Ti64-Halterung ist zwar stärker, aber nicht unbedingt leichter als ein gut optimiertes AlSi10Mg-Äquivalent, es sei denn, die Konstruktion nutzt die höhere Festigkeit voll aus.
- Anspruchsvollere Verarbeitung: Titanlegierungen erfordern im Allgemeinen sorgfältiger kontrollierte LPBF-Parameter (z. B. Reinheit der Schutzgasatmosphäre) und können im Vergleich zu AlSi10Mg langsamere Aufbauraten haben. Sie sind auch reaktiver und erfordern strenge Pulverhandhabungsprotokolle.
- Geringere Wärmeleitfähigkeit: Deutlich geringere Wärmeleitfähigkeit (~6,7 W/m-K) im Vergleich zu Aluminium, was ein Nachteil sein kann, wenn die Halterung zur Wärmeableitung beitragen muss.
Tabelle zum Materialvergleich:
Merkmal | AlSi10Mg (LPBF, T6 wärmebehandelt) | Ti-6Al-4V (LPBF, spannungsarmgeglüht) | Einheit | Anmerkungen |
---|---|---|---|---|
Dichte | ~2.67 | ~4.43 | g/cm³ | Signifikanter Unterschied wirkt sich auf das endgültige Teilegewicht aus |
Streckgrenze (0.2%) | ~230 – 290 | ~900 – 1100 | MPa | Ti64 ist deutlich stärker |
Endgültige Zugfestigkeit | ~330 – 430 | ~1000 – 1200 | MPa | Ti64 hat eine höhere Bruchfestigkeit |
Dehnung beim Bruch | ~3 – 10 | ~6 – 15 | % | Variiert je nach Gebäudeausrichtung/Parametern |
Elastizitätsmodul | ~70 | ~110 – 115 | GPa | Misst die Steifigkeit |
Max. Betriebstemp. | ~150 | ~400 | °C | Ungefährer praktischer Grenzwert |
Wärmeleitfähigkeit | ~130 – 150 | ~6.7 | W/(m-K) | AlSi10Mg besser für die Wärmeableitung |
Relative Materialkosten | Unter | Höher | – | Erheblicher Kostenunterschied |
Typische Anwendungen | Sekundärstrukturen, Systemträger, Prototypen, kostensensible Teile | Primär-/Sekundärstrukturen, stark beanspruchte Teile, Hochtemperaturbereiche, kritische Komponenten | – | Die Anwendung bestimmt die Materialwahl |
In Blätter exportieren
(Hinweis: Die Eigenschaftswerte sind Näherungswerte und können je nach spezifischen Prozessparametern, Bauausrichtung, Wärmebehandlung und Prüfstandards variieren. Spezifische Werte finden Sie immer in den Datenblättern der Lieferanten).
Die Wahl zwischen AlSi10Mg und Ti-6Al-4V:
Bei der Auswahl müssen Leistungsanforderungen, Betriebsumgebung und Kosten gegeneinander abgewogen werden:
- Wählen Sie AlSi10Mg wenn:
- Gewichtsreduzierung ist wichtig, aber absolute Höchstfestigkeit ist nicht der wichtigste Faktor.
- Die Betriebstemperaturen sind moderat (<150°C).
- Die Kosten sind ein wichtiger Faktor.
- Eine gute Wärmeleitfähigkeit ist von Vorteil.
- Die Halterung ist für sekundäre Struktur- oder Systemmontageanwendungen vorgesehen.
- Wählen Sie Ti-6Al-4V wenn:
- Ein maximales Verhältnis zwischen Stärke und Gewicht ist entscheidend.
- Eine hohe Dauerfestigkeit ist erforderlich.
- Die Betriebstemperaturen sind hoch (>150°C).
- Eine ausgezeichnete Korrosionsbeständigkeit ist erforderlich.
- Die Anwendung betrifft Primärstrukturen oder flugkritische Komponenten (vorbehaltlich einer strengen Zertifizierung).
- Das Budget erlaubt es, die höheren Material- und Verarbeitungskosten zu berücksichtigen.
Beide AlSi10Mg Eigenschaften und Ti-6Al-4V Luft- und Raumfahrtqualität Fähigkeiten machen sie zu unschätzbaren Werkzeugen für die Vergleich von Materialien für die Luft- und Raumfahrt für die additive Fertigung. Die Zusammenarbeit mit einem erfahrenen AM-Anbieter wie Met3dp, der die Feinheiten dieser Materialien versteht und über fortschrittliche Laser-Pulver-Bett-Fusion (LPBF) und überlegene Pulverqualitätskontrolle durch Techniken wie GaszerstäubungSo wird sichergestellt, dass das gewählte Material die erwartete Leistung für anspruchsvolle Halterungsanwendungen in der Luft- und Raumfahrt erbringt. Sicherstellung der vollen Materialzertifizierung Luft- und Raumfahrt Die Rückverfolgbarkeit ist ein Standardverfahren für seriöse Lieferanten.
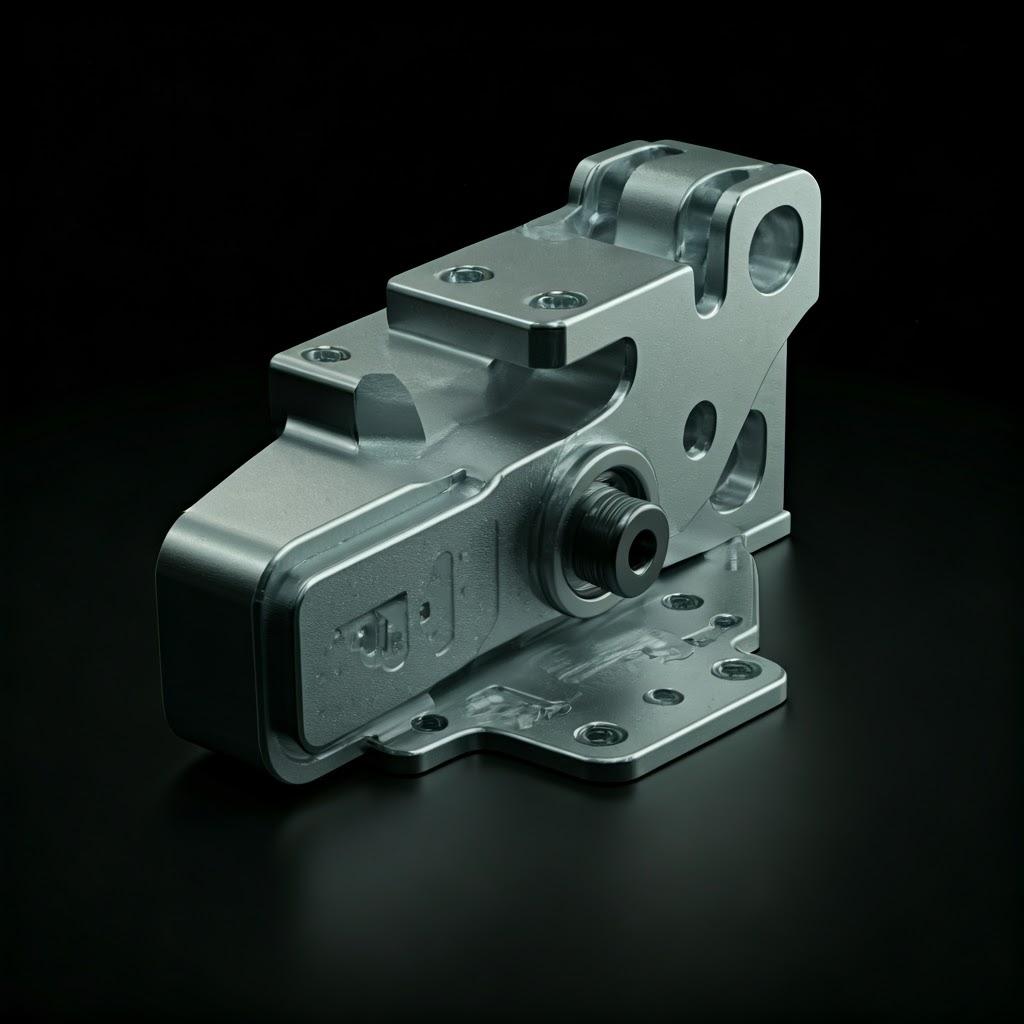
Design for Additive Manufacturing (DfAM) für Luft- und Raumfahrtkonsolen
Wenn man eine ursprünglich für die CNC-Bearbeitung oder den Guss vorgesehene Halterung einfach in einen 3D-Metalldrucker schickt, schöpft man selten das gesamte Potenzial der additiven Fertigung aus. Um die oben genannten Vorteile - erhebliche Gewichtsreduzierung, Teilekonsolidierung und verbesserte Leistung - wirklich nutzen zu können, müssen Ingenieure die folgenden Aspekte berücksichtigen Design für additive Fertigung (DfAM). Bei DfAM geht es nicht nur um die Sicherstellung eines Teils dürfen Es handelt sich um einen grundlegenden Wandel im Designdenken, der die einzigartigen Fähigkeiten des AM-Prozesses nutzt und die spezifischen Einschränkungen berücksichtigt, insbesondere die Laser Powder Bed Fusion (LPBF), die für AlSi10Mg- und Ti-6Al-4V-Halterungen verwendet wird. Luft- und Raumfahrtunternehmen, die mit einem erfahrenen Lieferant für additive Fertigung werden von den gemeinsamen Bemühungen des DfAM stark profitieren.
Verschiebung des Designparadigmas:
Das traditionelle Design for Manufacturing (DfM) konzentriert sich auf die Vereinfachung der Geometrie, um die Bearbeitung zu erleichtern (z. B. Vermeidung tiefer Taschen, Bevorzugung prismatischer Formen) oder das Gießen zu erleichtern (z. B. Entformungswinkel, einheitliche Wandstärke für den Fluss). DfAM hingegen fördert die Komplexität dort, wo sie die Funktion erhöht oder das Gewicht reduziert, während die für den schichtweisen Aufbau kritischen Aspekte sorgfältig verwaltet werden. Schlüssel DfAM-Grundsätze für Luft- und Raumfahrtklammern umfassen:
- Nutzung der Topologie-Optimierung: Wie bereits erwähnt, ist dies ein Eckpfeiler von DfAM für Strukturteile wie Halterungen.
- Prozess: Ingenieure definieren den Konstruktionsraum (das maximal zulässige Volumen für die Halterung), legen die Verbindungspunkte fest (wo die Halterung mit der Flugzeugzelle verschraubt oder an der Ausrüstung befestigt wird), definieren die Belastungsszenarien (Kräfte, Vibrationen, Beschleunigungen, denen die Halterung standhalten muss) und setzen Ziele (z. B. Minimierung der Masse, Maximierung der Steifigkeit).
- Software: Spezialisiert Software zur Topologieoptimierung (oft integriert in CAD-Plattformen wie Siemens NX, CATIA, Creo oder als eigenständige Tools wie Altair Inspire, nTopology, Ansys Discovery) verwendet Algorithmen wie Solid Isotropic Material with Penalization (SIMP) oder Level Set Methods, um die effizientesten Lastpfade zu ermitteln.
- Ausgabe: Das Rohergebnis ist oft eine organische, netzartige Struktur, die verfeinert werden muss. Die Konstrukteure müssen diese Ergebnisse interpretieren, gezackte Kanten glätten und die Geometrie möglicherweise mit CAD-Werkzeugen (Unterteilungsmodellierung oder Standard-B-Rep) rekonstruieren, um die Herstellbarkeit zu gewährleisten und andere Konstruktionsvorgaben zu erfüllen (z. B. Freiraum für die Verkabelung, Zugang für Befestigungselemente).
- Nutzen: Erzeugt die leichtestmögliche Halterung, die dennoch alle Leistungsanforderungen erfüllt, was oft zu biologisch inspirierten, effizienten Formen führt, die auf herkömmliche Weise nicht zu erreichen sind.
- Minimierung der Stützstrukturen: LPBF benötigt aus mehreren Gründen Stützstrukturen:
- Überhänge: Features, die unter einem bestimmten Schwellenwert (in der Regel ~45 Grad relativ zur Bauplatte) abgewinkelt sind, benötigen eine darunter liegende Stütze, um einen Zusammenbruch oder eine Verformung während des Drucks zu verhindern.
- Wärmeleitung: Stützen leiten die Wärme vom Bauteil weg in die Bauplatte und reduzieren so thermische Spannungen und Verformungen.
- Verankerung: Sie verankern das Teil fest auf der Bauplatte und verhindern so Bewegungen oder Verformungen während des Bauprozesses.
- Die Herausforderung: Träger verbrauchen zusätzliches Material (was die Kosten erhöht), verlängern die Druckzeit erheblich, erfordern eine mühsame Nachbearbeitung (was zusätzliche Kosten verursacht und die Oberfläche beschädigen kann) und können Spuren auf der Oberfläche des fertigen Teils hinterlassen. Deshalb, Minimierung der Stützstrukturen ist ein vorrangiges Ziel des DfAM.
- Strategien:
- Design für Selbsthilfe: Wo immer möglich, sollten Konstruktionsmerkmale mit Winkeln, die größer sind als der kritische freistehender Winkel (z. B. >45°). Das Anfasen von nach unten gerichteten Löchern oder die Verwendung von tropfenförmigen Löchern anstelle von einfachen kreisförmigen horizontalen Löchern kann den Bedarf an internen Stützen beseitigen.
- Strategische Teilausrichtung: Die Ausrichtung der Halterung auf der Bauplatte hat einen großen Einfluss auf die Anforderungen an die Abstützung. Teilorientierungsstrategie ist mit komplexen Abwägungen verbunden: Minimierung des Stützvolumens vs. Minimierung der Bauhöhe (Druckzeit) vs. Optimierung der Oberflächengüte auf kritischen Flächen vs. potenzielle Beeinflussung anisotroper mechanischer Eigenschaften. Erfahrene AM-Ingenieure verwenden spezielle Software, um verschiedene Ausrichtungen zu simulieren und das optimale Gleichgewicht zu finden. Wenn beispielsweise eine große flache Halterung vertikal ausgerichtet wird, können die Stützen im Vergleich zum Flachdruck drastisch reduziert werden.
- Cleveres Feature-Design: Einbau von Opferrippen oder leichte Änderung der Geometrie, um flache Überhänge zu vermeiden.
- Optimierung der Wandstärke und der Größe der Elemente:
- Mindestwanddicke: Bei LPBF-Verfahren gibt es Grenzen für die dünnsten Wände, die zuverlässig hergestellt werden können (oft 0,4-0,5 mm), die von den Pulvereigenschaften und den Maschinenparametern beeinflusst werden. Bei einer Konstruktion unterhalb dieser Grenze besteht die Gefahr, dass die Merkmale unvollständig sind oder versagen.
- Maximale Wanddicke: Sehr dicke Profile (> ca. 10-20 mm, je nach Material und Geometrie) können übermäßige thermische Spannungen akkumulieren, die zu Rissen oder Verformungen führen können. Das DfAM empfiehlt die Aushöhlung dicker Profile oder den Einbau von inneren Gitterstrukturen 3D-Druck um die Masse zu reduzieren und thermische Probleme zu mindern, während die Steifigkeit erhalten bleibt.
- Einheitlichkeit: Obwohl AM unterschiedliche Dicken zulässt, kann das Streben nach einer relativ gleichmäßigen Wanddicke helfen, thermische Gradienten zu bewältigen und Spannungen zu reduzieren.
- Kleine Merkmale: Die minimalen druckbaren Lochdurchmesser, Stiftgrößen und Spaltbreiten werden auch durch die Prozessauflösung (Größe des Laserspots, Größe der Pulverpartikel) begrenzt. Diese Einschränkungen müssen bei der Entwicklung berücksichtigt werden (z. B. indem die Löcher etwas größer gestaltet werden, um eine Nachbearbeitung zu ermöglichen, oder indem kleine Löcher nach dem Druck gebohrt werden).
- Einbindung von Gitterstrukturen:
- Funktion: Diese internen, sich wiederholenden zellulären Strukturen (z. B. auf Streben basierende Gitter wie kubische oder Oktett-Fachwerke oder auf Oberflächen basierende TPMS - Triply Periodic Minimal Surfaces) können das Gewicht erheblich reduzieren und gleichzeitig maßgeschneiderte Steifigkeit, Energieabsorption oder sogar Wärmemanagementeigenschaften bieten.
- Anwendung in Klammern: Kann als Füllung für dickere Abschnitte verwendet werden, die durch Topologieoptimierung identifiziert wurden, oder um Halterungen mit spezifischen Schwingungsdämpfungseigenschaften zu schaffen.
- Erwägungen: Erfordert spezielle Software für die Erstellung. Es muss sichergestellt werden, dass die Gitterzellen groß genug sind, um das Pulver nach dem Druck effektiv zu entfernen. Die Prüfung der Integrität des inneren Gitters kann eine Herausforderung sein (oft sind CT-Scans erforderlich).
- Stressbewältigung Konzentrationen:
- Wichtigkeit: Auch wenn AM komplexe Formen ermöglicht, gelten nach wie vor grundlegende mechanische Konstruktionsprinzipien. Scharfe Innenecken erhöhen die Spannungen und können zu Rissen führen, insbesondere bei der in der Luft- und Raumfahrt üblichen Ermüdungsbelastung.
- DfAM-Ansatz: Berücksichtigen Sie großzügige Verrundungen und weiche Übergänge zwischen Features, insbesondere dort, wo die Topologieoptimierung scharfe Übergänge erzeugen könnte. Verwenden Sie die Finite-Elemente-Analyse (FEA), um die Spannungsverteilung in der Geometrie des AM-Teils zu simulieren und das Design zu verfeinern, um Bereiche mit hoher Belastung zu eliminieren.
- Entwerfen für die Nachbearbeitung: Überlegen Sie, wie das Teil nach dem Druck gehandhabt werden soll. Sorgen Sie für den Zugang zu Werkzeugen zum Entfernen von Halterungen, fügen Sie Bearbeitungszugaben für Oberflächen hinzu, die hohe Präzision erfordern, und entwerfen Sie Merkmale, die mit den gewünschten Endbearbeitungsverfahren kompatibel sind (z. B. Oberflächen, die sich zum Eloxieren eignen).
Die Beherrschung dieser Leitlinien für die additive Fertigung ist der Schlüssel zur Herstellung hervorragender Halterungen für die Luft- und Raumfahrt. Dies erfordert oft eine enge Zusammenarbeit zwischen Konstruktionsingenieuren und AM-Prozessexperten, wie denen von Met3dp, die die komplizierte Beziehung zwischen Konstruktionsentscheidungen und Fertigungsergebnissen in Entwerfen für LPBF.
Erreichbare Toleranzen, Oberflächengüte und Maßgenauigkeit
Obwohl Metall-AM eine unglaubliche Designfreiheit bietet, ist es für Ingenieure und Beschaffungsmanager entscheidend, realistische Erwartungen hinsichtlich der erreichbaren Präzision direkt aus dem Drucker zu haben. Die Kenntnis der typischen Toleranzen, der Oberflächenbeschaffenheit und der allgemeinen Maßgenauigkeit von in LPBF hergestellten AlSi10Mg- und Ti-6Al-4V-Brackets ist wichtig, um festzustellen, ob eine Nachbearbeitung erforderlich ist, und um Prüfstrategien zu planen. Diese Faktoren haben direkten Einfluss auf Passform, Montage und Leistung.
Typische Toleranzen:
- Allgemeine Maßgenauigkeit: Als Faustregel gilt, dass bei gut kontrollierten LPBF-Prozessen mit Qualitätsmaschinen und Materialien wie AlSi10Mg und Ti-6Al-4V typische, erreichbare Toleranzen im Bereich von:
- +/- 0,1 mm bis +/- 0,2 mm für kleinere Merkmale (z. B. bis zu 100 mm).
- +/- 0,1% bis +/- 0,2% des Nennmaßes für größere Merkmale.
- Es ist wichtig zu beachten, dass es sich hierbei um allgemeine Leitlinien für die Ist-Zustand Zustand (nach dem Spannungsabbau, aber vor der Bearbeitung). Die spezifischen Toleranzen hängen stark von der Teilegeometrie, der Größe, der Ausrichtung, dem Material und den spezifischen Maschinen- und Prozessparametern ab.
- Vergleich: Diese Toleranzen sind in der Regel geringer als bei der Präzisions-CNC-Bearbeitung (die leicht +/- 0,01 bis 0,05 mm oder weniger erreichen kann). Daher müssen kritische Schnittstellen, Lagerbohrungen oder Oberflächen, die bei AM-Halterungen sehr genau passen müssen, fast immer nachbearbeitet werden.
- GD&T: Die Anwendung der geometrischen Bemaßung und Tolerierung (GD&T) auf AM-Teile ist entscheidend für die eindeutige Definition funktionaler Anforderungen. Aufgrund der besonderen Eigenschaften von AM (schichtweiser Aufbau, Potenzial für geringfügige Anisotropie, Oberflächentextur im eingebauten Zustand) ist bei der Definition von Bezugspunkten und der Angabe von Form-, Orientierungs-, Lage- und Rundlauftoleranzen jedoch eine sorgfältige Prüfung erforderlich. Beratung durch einen AM-Anbieter mit Erfahrung in GD&T Additive Fertigung wird empfohlen.
Faktoren, die die Genauigkeit und Toleranzen beeinflussen:
Erzielung der bestmöglichen Maßhaltigkeit LPBF erfordert eine sorgfältige Kontrolle zahlreicher Faktoren:
- Kalibrierung der Maschine: Die regelmäßige Kalibrierung der Scanner des Druckers, der Laserfokussierung und der Nivellierung der Bauplatte ist entscheidend.
- Prozessparameter: Laserleistung, Scangeschwindigkeit, Schichtdicke, Schraffurabstand und Scanstrategie beeinflussen die Größe und Stabilität des Schmelzbades und wirken sich auf die Maßgenauigkeit und Oberflächengüte aus. Optimierte Parametersätze (oft von Maschinenherstellern oder Experten wie Met3dp entwickelt) sind entscheidend.
- Thermische Effekte: Die schnelle Erwärmung und Abkühlung, die LPBF mit sich bringt, erzeugt thermische Gradienten und Eigenspannungen. Diese können insbesondere bei großen oder komplexen Teilen zu Verformungen und Verwerfungen führen, die sich auf die endgültigen Abmessungen auswirken. Wirksame Stützstrukturen und spannungsreduzierende Wärmebehandlungen sind wichtige Strategien zur Abhilfe.
- Teilegeometrie und -ausrichtung: Große ebene Flächen, die parallel zur Bauplatte verlaufen, sind anfälliger für Verformungen. Hohe, dünne Merkmale können eine Herausforderung für die genaue Herstellung darstellen. Die Ausrichtung wirkt sich auf die Wärmeentwicklung und den Unterstützungsbedarf aus, beides beeinflusst die Genauigkeit.
- Qualität des Pulvers: Eine gleichmäßige Partikelgrößenverteilung, Morphologie (Sphärizität) und Fließfähigkeit des Metallpulvers tragen zu einer gleichmäßigen Pulverbettdichte und einem vorhersehbaren Schmelzen bei, was sich auf die Genauigkeit und die Fehlerquote auswirkt.
- Strategie unterstützen: Unzureichende oder schlecht konstruierte Stützen können dazu führen, dass sich das Teil während der Fertigung verschiebt oder verzieht.
Oberflächengüte (Oberflächenrauhigkeit):
Die Oberflächenbeschaffenheit von AM-Metallteilen ist aufgrund des schichtweisen Prozesses und der teilweise geschmolzenen Pulverpartikel, die an der Oberfläche haften, typischerweise rauer als bei bearbeiteten Oberflächen.
- Messung: Die Oberflächenrauhigkeit wird in der Regel mit dem Parameter Ra (arithmetische mittlere Abweichung des Rauheitsprofils), gemessen in Mikrometern (µm).
- Typische As-Built Ra-Werte (LPBF AlSi10Mg/Ti64):
- Vertikale Mauern: Im Allgemeinen bieten sie die beste Oberfläche, etwa Ra 6 - 15 µm.
- Nach oben gerichtete Oberflächen (Oberhäute): Oft etwas rauer als vertikale Wände, Ra 8 - 20 µm.
- Nach unten gerichtete Oberflächen (unterstützt): Typischerweise die rauesten aufgrund des Kontakts mit Trägerstrukturen, Ra 15 - 30 µm oder höher, je nach Art des Trägers und des Abtragsverfahrens.
- Gestufte Oberflächen (Treppeneffekt): Gekrümmte oder abgewinkelte Oberflächen, die durch Schichten angenähert werden, können sichtbare Abstufungen aufweisen, die die wahrgenommene Glätte beeinträchtigen.
- Vergleich: Bearbeitete Oberflächen erreichen in der Regel Ra 0,8 - 3,2 µm oder sind durch Schleifen/Polieren wesentlich glatter (Ra < 0,1 µm). Gegossene Oberflächen variieren stark, sind aber oft rauer als AM, wenn sie nicht poliert werden.
- Auswirkungen: Der Ist-Zustand Oberflächengüte additive Fertigung kann für einige unkritische Halterungsoberflächen akzeptabel sein. Für Passflächen, Dichtungsflächen oder Bereiche, die für Ermüdungserscheinungen anfällig sind, ist die Rauheit jedoch oft zu hoch und muss durch Nachbearbeitung (z. B. Perlstrahlen, Trommeln, Bearbeiten, Polieren) verbessert werden. Die Website Ra Oberflächenrauhigkeitskarte sollten neben den funktionalen Anforderungen konsultiert werden.
Inspektion und Validierung:
Angesichts der inhärenten Variabilität und der Kritikalität von Luft- und Raumfahrtkomponenten sind robuste Prüfmethoden unverzichtbar:
- Koordinatenmessmaschinen (KMG): Wird für die präzise Messung kritischer Abmessungen, Lochpositionen und geometrischer Toleranzen verwendet, die durch GD&T definiert sind. Erfordert ein sorgfältiges Vorrichtungsdesign für AM-Teile. CMM-Prüfung Luft- und Raumfahrt Die Protokolle sind gut etabliert.
- 3D-Laserscanning / Structured Light Scanning: Erfasst Millionen von Datenpunkten über die gesamte Oberfläche des Teils und erstellt ein 3D-Modell, das direkt mit der ursprünglichen CAD-Datei verglichen werden kann. Hervorragend geeignet für die Überprüfung der Gesamtform, die Erkennung von Verformungen und die Analyse von Oberflächenabweichungen. Wird zunehmend für die Qualifizierung von AM-Teilen verwendet.
- Zerstörungsfreie Prüfung (NDT): Wie in der Nachbearbeitung weiter ausgeführt, können Methoden wie das CT-Scannen die innere Geometrie untersuchen und Fehler (Porosität, Einschlüsse) aufdecken, die die strukturelle Integrität beeinträchtigen, was auch mit dem Erreichen des beabsichtigten Ziels zusammenhängt. intern Abmessungen.
Verständnis für das Erreichbare Toleranzen beim 3D-Druck von Metall und Oberflächenbeschaffenheit ermöglicht es den Ingenieuren, entsprechend zu konstruieren (z. B. durch Hinzufügen von Bearbeitungsmaterial), und ermöglicht es den Beschaffungsmanagern, realistische Anforderungen und angemessene Prüfniveaus bei der Zusammenarbeit mit AM-Dienstleistern festzulegen. Die Zusammenarbeit mit einem Anbieter wie Met3dp, der sowohl über fortschrittliche Drucktechnologie als auch über umfassende messtechnische Fähigkeiten verfügt, stellt sicher, dass die Teile die erforderlichen Spezifikationen erfüllen.
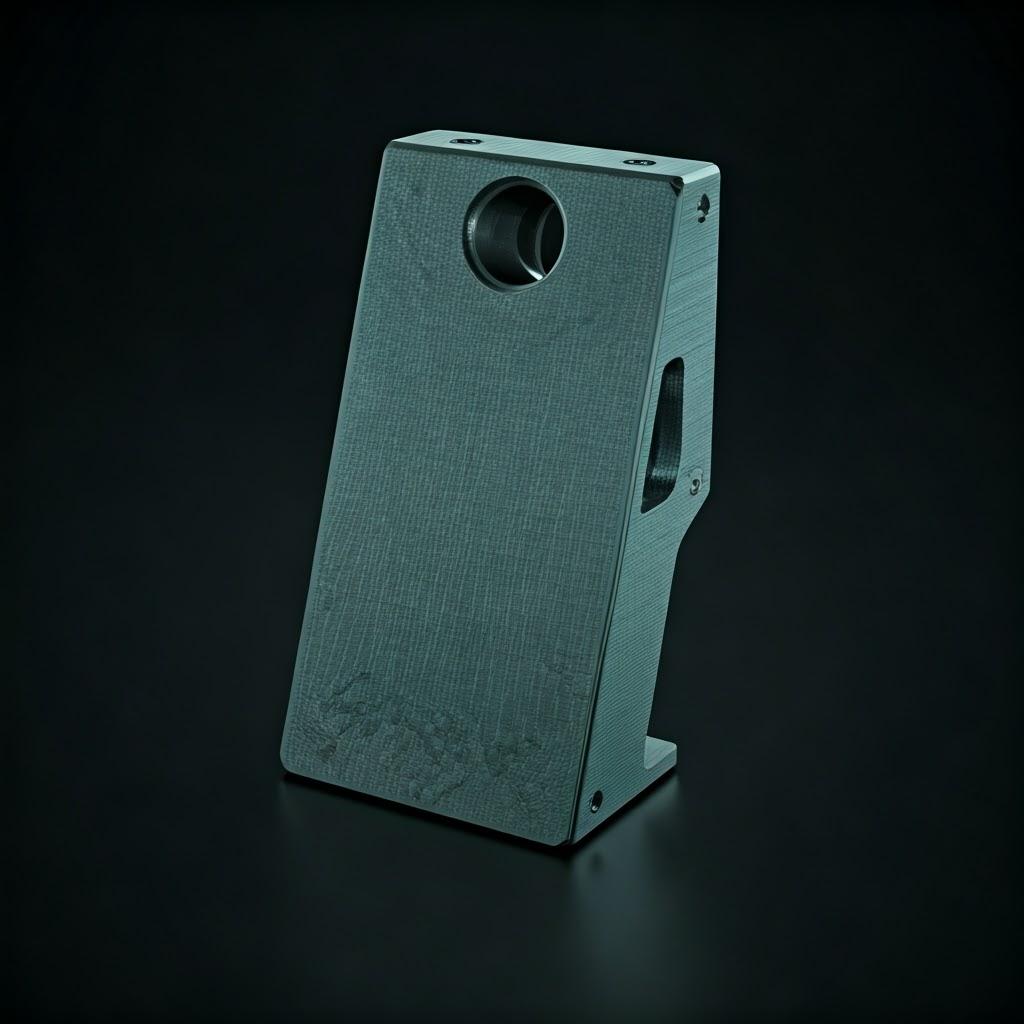
Wichtige Nachbearbeitungsschritte für 3D-gedruckte Brackets
Das Drucken der Halterung für die Luft- und Raumfahrt ist nur der erste große Schritt im Arbeitsablauf der additiven Fertigung. Fast immer ist eine Reihe wichtiger Nachbearbeitungsschritte erforderlich, um das rohe Bauteil in ein funktionsfähiges, flugtaugliches Bauteil zu verwandeln. Diese Schritte sind entscheidend, um die gewünschten mechanischen Eigenschaften, die Maßgenauigkeit, die Oberflächenbeschaffenheit und die von der Luft- und Raumfahrtindustrie geforderte Gesamtqualität zu erreichen. Beschaffungsmanager sollten sicherstellen, dass potenzielle AM-Lieferanten über robuste Fähigkeiten und Qualitätskontrollen für diese entscheidenden Phasen verfügen.
1. Abnehmen von der Bauplatte:
- Die gedruckte(n) Klammer(n) werden zunächst über die ersten Schichten und Stützstrukturen mit der Metallbauplatte verschmolzen.
- Zu den üblichen Entfernungsmethoden gehören:
- Draht-Elektroerosion (Wire EDM): Präzises Verfahren, das häufig für empfindliche Teile verwendet wird oder wenn ein sauberer Schnitt in der Nähe der Teilebasis erforderlich ist.
- Bandsägen: Schnelleres Verfahren, das sich für weniger empfindliche Teile eignet oder bei dem etwas überschüssiges Material in der Nähe der Basis zum späteren Entfernen akzeptiert wird.
- Bei diesem Schritt ist Vorsicht geboten, damit die Teile nicht beschädigt werden.
2. Stressabbau / Wärmebehandlung:
- Dies ist wohl der kritischste Nachbearbeitungsschritt, um die gewünschten Materialeigenschaften zu erreichen und die Maßhaltigkeit zu gewährleisten. Während der schnellen Erwärmungs- und Abkühlungszyklen von LPBF bauen sich Eigenspannungen auf, die zu Verzug und unvorhersehbarem mechanischen Verhalten führen können, wenn sie nicht behoben werden.
- AlSi10Mg: Typischerweise durchläuft ein T6-Wärmebehandlung:
- Lösungsfindung: Erhitzen des Teils auf eine bestimmte hohe Temperatur (z. B. ~530 °C), um die Elemente Mg und Si in der Aluminiummatrix aufzulösen.
- Abschrecken: Schnelles Abkühlen (oft in Wasser oder Polymer), um diese Elemente in einer übersättigten festen Lösung einzuschließen.
- Künstliche Alterung: Wiedererwärmung auf eine niedrigere Temperatur (z. B. ~160-180 °C) für eine bestimmte Dauer, um eine kontrollierte Ausscheidung von Mg2Si-Phasen zu ermöglichen, die die Legierung erheblich verstärken und härten. Die genaue Wärmebehandlung AlSi10Mg T6 Die Zyklusparameter (Zeiten, Temperaturen) beeinflussen das endgültige Gleichgewicht von Festigkeit und Duktilität.
- Ti-6Al-4V:
- Stress Relief Anneal: In der Regel auf 650-800 °C erhitzt und anschließend langsam abgekühlt. Dadurch werden die während des Drucks entstehenden inneren Spannungen reduziert und die Verformung bei nachfolgenden Schritten wie der Entfernung von Trägern oder der Bearbeitung minimiert. Das Mikrogefüge und die Festigkeit, die durch die schnelle Erstarrung beim AM entstehen, werden dabei nicht wesentlich verändert.
- Heiß-Isostatisches Pressen (HIP): Häufig empfohlen, insbesondere für kritische Bauteile in der Luft- und Raumfahrt. Bei diesem Verfahren wird das Teil einer hohen Temperatur (knapp unter dem Schmelzpunkt) ausgesetzt und hoher Inertgasdruck (z. B. Argon) gleichzeitig. HIP-Behandlung Luft- und Raumfahrt schließt effektiv die innere Porosität (Gasporen, fehlende Schmelzhohlräume), die sich während des Drucks gebildet haben könnte, und verbessert so die Ermüdungslebensdauer, die Duktilität und die Bruchzähigkeit erheblich. HIP kann manchmal mit Wärmebehandlungszyklen kombiniert werden.
- Ausrüstung: Diese Behandlungen erfordern genau kontrollierte Öfen, oft mit inerter Atmosphäre (wie Argon oder Stickstoff) oder Vakuum, um Oxidation zu verhindern, was besonders für Titan wichtig ist.
3. Entfernung der Stützstruktur:
- Das Entfernen der während der Erstellung erzeugten Stützstrukturen ist oft ein manueller und arbeitsintensiver Prozess, der die Nachbearbeitungszeit und -kosten erheblich erhöht.
- Die Methoden hängen von der Gestaltung der Unterstützung und der Zugänglichkeit ab:
- Manuelle Entfernung: Verwendung von Zangen, Cuttern, Schleifern oder Spezialwerkzeugen, um Stützen zu brechen oder abzuschneiden. Gut gestaltete Stützen weisen Merkmale auf (z. B. Perforationen, kleinere Kontaktpunkte), die das Abbrechen erleichtern.
- Bearbeitungen: Abfräsen oder Abschleifen von Stützen, besonders nützlich für Stützen in schwer zugänglichen Bereichen oder wenn eine glattere Oberfläche an der Kontaktstelle erforderlich ist.
- Elektrochemische Bearbeitung (ECM): Weniger verbreitet, kann aber für bestimmte Materialien/Geometrien verwendet werden.
- Effektive DfAM-Praktiken, die den Umfang des Supports minimieren und die Zugänglichkeit sicherstellen, sind der Schlüssel zur Verringerung des Aufwands und der Kosten, die mit der Abstützung Metall AM.
4. Bearbeitung für kritische Merkmale:
- Wie unter "Toleranzen" erläutert, erfordern AM-Teile häufig eine Nachbearbeitung, um enge Toleranzen, bestimmte Oberflächengüten oder Merkmale zu erreichen, die im Ist-Zustand nicht möglich sind.
- Zu den üblichen Bearbeitungsvorgängen für Halterungen gehören:
- Fräsen von Gegenflächen, um die Ebenheit zu gewährleisten und GD&T-Anforderungen zu erfüllen.
- Bohren, Reiben oder Aufbohren von Löchern mit präzisen Durchmessern und Positionstoleranzen für Befestigungselemente oder Lager.
- Gewindebohrungen.
- Schaffung spezifischer Dichtungsflächen.
- CNC-Bearbeitung von 3D-Drucken erfordert ein sorgfältiges Vorrichtungsdesign, um die oft komplexe AM-Teilegeometrie sicher und ohne Verzug zu halten. Durch die Kombination von AM und spanender Fertigung (Hybridfertigung) werden die Vorteile beider Verfahren genutzt.
5. Oberflächenveredelung:
- Verschiedene Oberflächenbearbeitung von Luft- und Raumfahrtteilen Techniken werden eingesetzt, um die Rauheit zu verbessern, die Oberfläche zu reinigen, die Ermüdungsfestigkeit zu erhöhen oder Beschichtungen vorzubereiten.
- Gemeinsame Methoden:
- Perlenstrahlen / Sandstrahlen: Schleudern feiner Medien (Glasperlen, Keramik, Aluminiumoxid) auf die Oberfläche. Reinigt das Teil, entfernt teilweise gesinterte Partikel, erzeugt eine gleichmäßige matte Oberfläche und kann die Ermüdungsfestigkeit durch Druckspannung leicht verbessern. Medientyp und Druck müssen kontrolliert werden.
- Shot Peening: Ähnlich wie beim Strahlen, aber unter Verwendung von kugelförmigem Metallkorn mit kontrollierter Intensität, um eine tiefere Druckspannungsschicht zu erzeugen, die die Ermüdungslebensdauer deutlich erhöht - oft eine Anforderung für kritische Komponenten in der Luft- und Raumfahrt.
- Taumeln / Vibrationsgleitschleifen: Einlegen der Teile in einen Tumbler mit Schleifmittel. Gut geeignet zum gleichzeitigen Glätten von Kanten und Oberflächen mehrerer kleiner Teile, allerdings weniger präzise als beim Strahlen oder Bearbeiten.
- Polieren: Verwendung immer feinerer Schleifmittel zur Erzielung einer glatten, reflektierenden Oberfläche (niedriger Ra). In der Regel für spezifische funktionale Anforderungen oder ästhetische Zwecke reserviert.
- Eloxieren (AlSi10Mg): Ein elektrochemisches Verfahren, das eine harte, verschleißfeste und korrosionsbeständige Oxidschicht auf der Oberfläche von Aluminiumteilen erzeugt. Kann auch in verschiedenen Farben eingefärbt werden. Eloxieren von Aluminium ist eine übliche Oberfläche für AlSi10Mg-Klammern.
- Anstrich / Beschichtung: Auftragen spezieller Grundierungen und Decklacke für die Luft- und Raumfahrt zur Verbesserung des Korrosionsschutzes oder spezifischer Eigenschaften (z. B. Wärmedämmschichten, Trockenfilmschmiermittel). Die Oberflächenvorbereitung (Reinigung, ggf. Eloxierung oder Konversionsbeschichtung) ist für die Haftung entscheidend.
6. Qualitätskontrolle und Inspektion (Nachbearbeitungsphase):
- Die Inspektion erfolgt während des gesamten Nachbearbeitungsprozesses.
- Bei der Endkontrolle wird überprüft, ob alle vorangegangenen Schritte korrekt ausgeführt wurden und das Teil alle Spezifikationen erfüllt.
- Dazu gehören:
- Überprüfung der Dimensionen: CMM oder 3D-Scannen nach der Bearbeitung und Wärmebehandlung.
- Messung der Oberflächengüte: Verwendung von Profilometern zur Überprüfung der Ra-Werte.
- Zerstörungsfreie Prüfung (NDT):
- Visuelle Inspektion (VT): Prüfung auf offensichtliche Fehler, Oberflächenmängel.
- Farbeindringprüfung (Dye Penetrant Inspection, PT): Zeigt oberflächliche Risse auf.
- Computertomographie (CT) Scannen: Röntgenbasierte Methode zur Visualisierung interner Strukturen und zur Erkennung interner Defekte wie Porosität oder Einschlüsse, die für die Qualifizierung kritischer AM-Teile für die Luft- und Raumfahrt immer wichtiger werden.
- Überprüfung der Materialeigenschaften: Häufig sind zerstörende Prüfungen an Mustern erforderlich, die neben den Hauptteilen gedruckt werden (z. B. Zugprüfungen zur Bestätigung der Wirksamkeit der Wärmebehandlung).
Die erfolgreiche Durchführung dieser Nachbearbeitungsschritte erfordert ein hohes Maß an Fachwissen, Spezialausrüstung und strenge Qualitätskontrollsysteme. Bei der Auswahl eines AM FertigungspartnerUm die Lieferung flugtauglicher Halterungen für die Luft- und Raumfahrt zu gewährleisten, ist es von entscheidender Bedeutung, dass sie ihre internen oder verwalteten Fähigkeiten für diese kritischen Vorgänge überprüfen. Met3dp bietet umfassende Lösungen für die additive Fertigung die nicht nur den Druck, sondern auch Anleitungen für die notwendige Nachbearbeitung zur Erfüllung der Anwendungsanforderungen umfassen.
Allgemeine Herausforderungen beim Drucken von Halterungen für die Luft- und Raumfahrt und Strategien zur Abhilfe
Der 3D-Metalldruck bietet zwar zahlreiche Vorteile für Halterungen in der Luft- und Raumfahrt, doch der LPBF-Prozess ist komplex und nicht ohne Herausforderungen. Das Verständnis potenzieller Probleme und der von erfahrenen Dienstleistern angewandten Strategien zu deren Entschärfung ist entscheidend, um erfolgreiche Ergebnisse, gleichbleibende Qualität und zuverlässige Teile zu gewährleisten. Ingenieure und Beschaffungsmanager sollten sich dieser Faktoren bewusst sein, wenn sie Lieferanten und die Durchführbarkeit von Projekten bewerten.
1. Verformung und Verzerrung:
- Herausforderung: Aufgrund der intensiven lokalen Erwärmung durch den Laser und der anschließenden schnellen Abkühlung entstehen während des LPBF-Prozesses erhebliche Wärmegradienten innerhalb des Teils und zwischen dem Teil und der Bauplatte. Dies führt zum Aufbau von inneren Eigenspannungen. Wenn diese Spannungen die Streckgrenze des Materials bei hohen Temperaturen überschreiten, kann sich das Teil verziehen, von der Bauplatte abrollen oder von der vorgesehenen Geometrie abweichen. Dies ist eine der häufigsten Fehler beim 3D-Druck von Metall.
- Strategien zur Schadensbegrenzung:
- Optimierte Teileausrichtung: Die Ausrichtung des Teils zur Minimierung großer, flacher Querschnitte parallel zur Bauplatte kann die Spannungsakkumulation verringern. Auch die Minimierung der Bauhöhe kann manchmal helfen.
- Wirksame Unterstützungsstrukturen: Robuste Stützen sind nicht nur für Überhänge entscheidend, sondern auch für die feste Verankerung des Teils auf der Bauplatte, den Widerstand gegen Verformungskräfte und eine gleichmäßigere Wärmeableitung. Das Design der Stützen (Art, Dichte, Kontaktpunkte) ist entscheidend.
- Optimierung der Prozessparameter: Die Feinabstimmung von Laserleistung, Scan-Geschwindigkeit und Scan-Strategie (z. B. Verwendung von Schachbrettmustern oder Insel-Scanning) kann dazu beitragen, die Temperaturverteilung zu steuern und Spannungsspitzen zu reduzieren. Erfahrene Anbieter wie Met3dp investieren viel in die Entwicklung von Prozessparametern.
- Build Plate Heating: Durch das Vorheizen der Bauplatte (üblich bei Ti-6Al-4V, seltener, aber manchmal bei AlSi10Mg) wird das Wärmegefälle zwischen dem geschmolzenen Material und dem darunter liegenden Substrat verringert, was den Spannungsaufbau reduziert.
- Stressabbau Wärmebehandlung: Die Durchführung eines Entspannungszyklus unmittelbar nach dem Druck (in manchen Fällen vor der Entnahme aus der Bauplatte) ist von entscheidender Bedeutung für die Entspannung der inneren Spannungen und die Vermeidung von Verformungen bei der anschließenden Handhabung und Bearbeitung.
2. Eigenspannung:
- Herausforderung: Selbst wenn makroskopische Verformungen vermieden werden, bleiben erhebliche Eigenspannungen im Bauteil eingeschlossen. Diese Spannungen können sich negativ auf die Ermüdungslebensdauer, die Bruchzähigkeit und die Dimensionsstabilität auswirken (und möglicherweise Verformungen verursachen, wenn das Material bei der Bearbeitung entfernt wird). Verringerung der Eigenspannung ist ein Hauptanliegen.
- Strategien zur Schadensbegrenzung:
- Prozesskontrolle: Wie beim Verziehen helfen auch hier optimierte Prozessparameter und Scan-Strategien, die Spannungsinduktion zu minimieren.
- Wärmemanagement: Eine wirksame Konstruktion der Stütze und möglicherweise eine Plattenheizung spielen eine Rolle.
- Obligatorische Wärmebehandlung: Eine geeignete Wärmebehandlung nach der Herstellung (Spannungsarmglühen für Ti-6Al-4V, Lösungsglühen/Aushärten T6 für AlSi10Mg) ist die wichtigste Methode, um die Eigenspannungen auf ein akzeptables Niveau zu reduzieren.
3. Porosität:
- Herausforderung: Kleine Hohlräume oder Poren im gedruckten Material können als Spannungskonzentratoren wirken und die mechanischen Eigenschaften, insbesondere die Ermüdungsfestigkeit und Bruchzähigkeit, erheblich verschlechtern. Porosität ist für kritische Bauteile in der Luft- und Raumfahrt inakzeptabel. Porositätskontrolle LPBF ist unerlässlich.
- Arten und Ursachen:
- Gas Porosität: Typischerweise kugelförmig, verursacht durch gelöstes Schutzgas (Argon), das während der schnellen Erstarrung eingeschlossen wird, oder durch Gas, das aus dem Pulver selbst freigesetzt wird.
- Fehlende Fusionsporosität: Unregelmäßig geformte Hohlräume, die durch unzureichendes Schmelzen und Verschmelzen zwischen benachbarten Schmelzspuren oder Schichten entstehen. Häufig die Folge von falschen Parametern (zu geringe Leistung, zu hohe Geschwindigkeit) oder uneinheitlicher Pulververteilung.
- Strategien zur Schadensbegrenzung:
- Hochwertiges Pulver: Die Verwendung von Pulver mit einem geringen Gehalt an eingeschlossenen Gasen, kontrollierter Sphärizität und optimierter Partikelgrößenverteilung ist entscheidend. Die fortschrittlichen Zerstäubungsprozesse von Met3dp konzentrieren sich auf die Herstellung von Pulver mit diesen Eigenschaften. Eine ordnungsgemäße Handhabung und Lagerung des Pulvers zur Vermeidung von Feuchtigkeitsaufnahme ist ebenfalls entscheidend.
- Optimierte Prozessparameter: Sicherstellung einer ausreichenden Energiedichte (Kombination aus Laserleistung, Geschwindigkeit, Lukenabstand), um das Pulver vollständig zu schmelzen und eine gute Überlappung der Schmelzspuren zu erreichen.
- Abschirmgas-Kontrolle: Die Aufrechterhaltung einer hochreinen Inertgasatmosphäre (Argon) in der Baukammer mit niedrigem Sauerstoffgehalt verhindert Oxidation und verringert Probleme mit der Gasporosität. Eine korrekte Gasflussdynamik ist wichtig.
- Wartung der Maschine: Regelmäßige Kalibrierung und Wartung des Lasers, der Optik und des Pulverzufuhrsystems des Druckers.
- Heiß-Isostatisches Pressen (HIP): Vor allem bei Ti-6Al-4V und kritischen Anwendungen ist HIP sehr effektiv beim Schließen der inneren Porosität durch hohen Druck und hohe Temperatur, was zu nahezu vollständig dichten Teilen führt.
4. Stütze entfernen Schwierigkeitsgrad:
- Herausforderung: Schlecht konstruierte oder zu dichte Halterungen sind zwar notwendig, lassen sich aber nur sehr schwer und zeitaufwändig entfernen, ohne die Oberfläche des Teils zu beschädigen. Halterungen in internen Kanälen oder schwer zugänglichen Bereichen stellen eine große Herausforderung dar.
- Strategien zur Schadensbegrenzung:
- DfAM Fokus: Die beste Strategie ist es, die Teile so weit wie möglich selbsttragend zu gestalten. Siehe Abschnitt DfAM.
- Optimierte Unterstützungsstrukturen: Verwendung spezieller Software zur Erzeugung von Stützen, um Strukturen zu schaffen, die während der Herstellung stabil genug, aber leichter zu entfernen sind (z. B. Verwendung konischer Spitzen, perforierter Wände, Baumstützen). Anpassung des Stützentyps an das Material (AlSi10Mg-Stützen sind im Allgemeinen leichter zu entfernen als Ti-6Al-4V).
- Planung der Zugänglichkeit: Sicherstellen, dass die Konstruktion einen physischen Zugang für die zur Entfernung der Stütze erforderlichen Werkzeuge ermöglicht.
- Geeignete Entfernungstechniken: Auswahl der richtigen Werkzeuge und Methoden je nach Art und Ort der Unterstützung.
5. Handhabung und Sicherheit von Pulver:
- Herausforderung: Feine Metallpulver, insbesondere Aluminium und Titan, sind reaktionsfreudig und stellen bei unsachgemäßer Handhabung eine potenzielle Brand-, Explosions- und Gesundheitsgefahr dar. Sicherheit durch Metallpulver ist von entscheidender Bedeutung.
- Strategien zur Schadensbegrenzung:
- Inerte Umgebungen: Handhabung reaktiver Pulver (insbesondere Ti) unter inerter Argon-Atmosphäre, wann immer dies möglich ist (z. B. beim Laden, Entladen, Sieben).
- Erdung: Sicherstellen, dass alle Geräte (Drucker, Siebe, Staubsauger) ordnungsgemäß geerdet sind, um statische Entladungen zu verhindern, die Pulverwolken entzünden könnten.
- Explosionsgeschützte Geräte: Verwendung von ATEX-zertifizierten oder entsprechend ausgelegten Staubsaugern und anderen Geräten für die Handhabung von Pulver.
- Persönliche Schutzausrüstung (PSA): Obligatorisches Tragen von Atemschutzmasken (zum Schutz vor Einatmen), leitfähigem Schuhwerk, flammhemmender Kleidung und Schutzbrillen.
- Verfahren zur Verwaltung des Pulvers: Strenge Protokolle für Lagerung, Transport, Verladung, Recycling (Sieben) und Entsorgung von Pulver. Begrenzung der Mengen von losem Pulver.
- Entwurf der Einrichtung: Angemessene Belüftung, atmosphärische Überwachung und Maßnahmen zur Eindämmung von Verschüttungen.
- Ausbildung: Sicherstellen, dass alle Mitarbeiter, die mit Pulver umgehen, gründlich in den Risiken und Sicherheitsverfahren geschult werden. Erfahrene Anbieter wie Met3dp halten strenge Sicherheitsprotokolle ein.
6. Unregelmäßigkeiten in der Oberfläche:
- Herausforderung: Es ist schwierig, eine perfekt gleichmäßige Oberflächenbeschaffenheit direkt aus dem Drucker zu erzielen. Zu den Problemen gehören Rauheit auf nach unten gerichteten Oberflächen, sichtbare Schichtlinien ("Treppenstufen") und Abdrücke von Stützstrukturen.
- Strategien zur Schadensbegrenzung:
- Optimierung der Orientierung: Kritische Flächen sollten möglichst vertikal oder nach oben gerichtet sein.
- Einstellung der Parameter: Konturscans und spezifische Hautstrategien können die Oberflächengüte bestimmter Merkmale verbessern.
- Effektive Nachbearbeitung: Auswahl der geeigneten Oberflächenbearbeitungsmethoden (Strahlen, Trowalisieren, Bearbeiten, Polieren) auf der Grundlage der gewünschten Endbearbeitung. Siehe Abschnitt Nachbearbeitung.
Die Bewältigung dieser Herausforderungen erfordert eine Kombination aus robusten DfAM-Praktiken, optimierten und validierten Prozessparametern, hochwertigen Materialien, geeigneten Nachbearbeitungstechniken, strenger Qualitätskontrolle und der Einhaltung strenger Sicherheitsprotokolle. Die Zusammenarbeit mit einem sachkundigen und erfahrenen Metall-AM-Dienstleister wie Met3dp, der sich proaktiv um diese potenziellen Probleme kümmert, ist der Schlüssel zur erfolgreichen Implementierung des Metall-3D-Drucks für anspruchsvolle Halterungsanwendungen in der Luftfahrt.
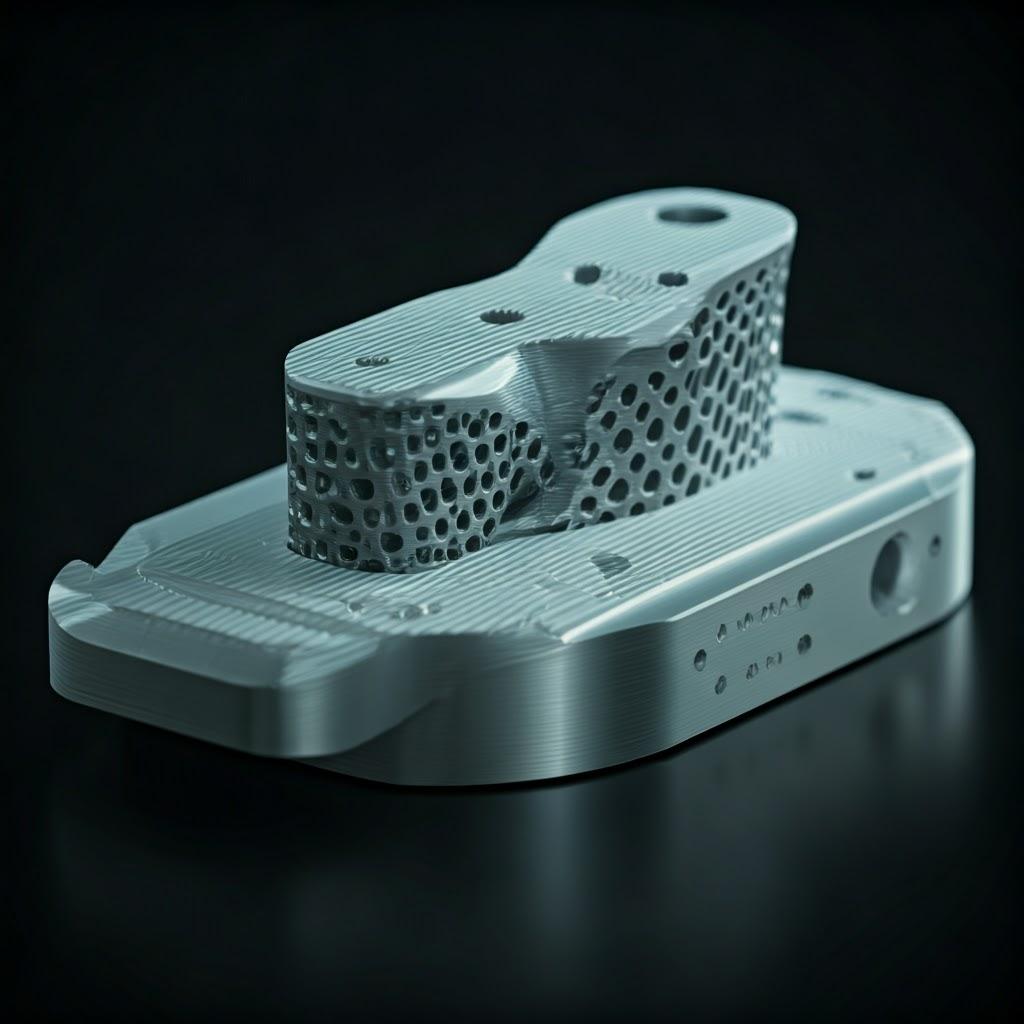
Die Wahl Ihres 3D-Druck-Dienstleisters für Luft- und Raumfahrtkomponenten aus Metall
Die Auswahl des richtigen Fertigungspartners ist wohl eine der wichtigsten Entscheidungen bei der Einführung der additiven Fertigung von Luft- und Raumfahrtkomponenten wie Halterungen. Anders als bei der Beschaffung von Standard-Hardware von der Stange handelt es sich bei der additiven Fertigung um komplizierte Prozesse, bei denen sich das Fachwissen, die Ausrüstung, die Prozesskontrolle und die Qualitätssysteme des Lieferanten direkt auf die Integrität und Leistung des fertigen Teils auswirken. Einfach das billigste Angebot zu wählen, kann bei anspruchsvollen Luft- und Raumfahrtanwendungen zu minderwertigen Teilen, Projektverzögerungen und potenziell katastrophalen Ausfällen führen. Es geht nicht nur darum, einen 3D-Druck-Dienstleister für MetallEs geht um den Aufbau einer Zusammenarbeit mit einem sachkundigen Lieferant für additive Fertigung in der Luft- und Raumfahrt der die einzigartigen Herausforderungen und strengen Anforderungen der Branche kennt.
Ingenieure und Beschaffungsmanager müssen eine gründliche Due-Diligence-Prüfung durchführen, wenn Bewertung von Metall-AM-Büros oder potenziell AM-Partner. Hier sind die wichtigsten Kriterien, die Sie beachten sollten:
Wichtige Bewertungskriterien für AM-Lieferanten in der Luft- und Raumfahrt:
- Zertifizierungen für die Luft- und Raumfahrt und Qualitätsmanagementsysteme (QMS):
- AS9100-Zertifizierung: Dies ist die international anerkannte Norm für Qualitätsmanagementsysteme speziell für die Luft-, Raumfahrt- und Verteidigungsindustrie. 1 AS9100 baut auf ISO 9001 auf, enthält jedoch zusätzliche Anforderungen, die für die Luft- und Raumfahrt von entscheidender Bedeutung sind, und konzentriert sich auf Sicherheit, Lufttüchtigkeit, Produktkonformität, Konfigurationsmanagement, Risikomanagement und Rückverfolgbarkeit in der gesamten Lieferkette. Eine Partnerschaft mit einem AS9100-zertifizierten Lieferanten bietet die Gewissheit, dass robuste Prozesse vorhanden sind. Fragen Sie potenzielle Lieferanten nach ihrem Zertifizierungsstatus oder ihrem dokumentierten Weg dorthin. 1. www.citizensjournal.us www.citizensjournal.us
- NADCAP-Akkreditierung: Während AS9100 das gesamte QMS abdeckt, bietet NADCAP (National Aerospace and Defense Contractors Accreditation Program) eine spezifische Akkreditierung für "Spezialprozesse". Für AM-Zulieferer könnten relevante NADCAP-Akkreditierungen die Wärmebehandlung, die zerstörungsfreie Prüfung (ZfP) und möglicherweise Materialprüflabore umfassen, wenn sie diese Tätigkeiten intern durchführen. Wenn ein Zulieferer diese kritischen Prozesse auslagert, stellen Sie sicher, dass seine Unterauftragnehmer die erforderlichen NADCAP-Zulassungen besitzen.
- Robustes internes QMS: Über die Zertifizierungen hinaus sollten Sie die interne QMS-Dokumentation des Lieferanten bewerten. Wie werden Prozesskontrolle, Dokumentenkontrolle, Korrektur- und Vorbeugungsmaßnahmen (CAPA), Mitarbeiterschulung, Gerätekalibrierung und Lieferantenmanagement gehandhabt? Ein ausgereiftes QMS ist die Voraussetzung für konsistente Ergebnisse. Met3dp weiß, wie wichtig diese Systeme sind, und setzt sich für die Einführung branchenführender Qualitätspraktiken ein. Erfahren Sie mehr über unser Engagement auf unserer Über uns Seite.
- Maschinenkapazität, Kapazität und Technologie:
- Angemessene Technologie: Vergewissern Sie sich, dass der Lieferant Laser Powder Bed Fusion (LPBF) Systeme einsetzt, die für die zuverlässige Verarbeitung von AlSi10Mg und/oder Ti-6Al-4V geeignet sind.
- Maschinenflotte: Mit welchen spezifischen Maschinenmodellen arbeiten sie? Verschiedene Hersteller (z. B. EOS, SLM Solutions, Renishaw, Trumpf, Velo3D, Farsoon - und die eigenen fortschrittlichen Systeme von Met3dp) haben unterschiedliche Fähigkeiten in Bezug auf Bauvolumen, Laserleistung/-anzahl, Mindestgröße der Merkmale und Prozessüberwachung.
- Kapazität und Redundanz: Verfügen sie über ausreichende Maschinenkapazitäten, um die von Ihnen geplanten Mengen zu verarbeiten und die Vorlaufzeiten einzuhalten? Mehrere Maschinen bieten Redundanz im Falle von Wartungsarbeiten oder Ausfallzeiten.
- Prozessüberwachung: Erkundigen Sie sich nach dem Einsatz von In-situ-Prozessüberwachungsinstrumenten (z. B. Schmelzepool-Überwachung, Wärmebildtechnik), die wertvolle Daten für die Qualitätssicherung liefern können, auch wenn sich die effektive Auswertung dieser Daten noch in der Entwicklung befindet.
- Materialkenntnis und Qualitätskontrolle:
- Materieller Schwerpunkt: Sind sie auf die von Ihnen gewünschten Legierungen spezialisiert (AlSi10Mg, Ti-6Al-4V)? Tiefes Fachwissen in der Verarbeitung dieser Materialien ist entscheidend.
- Pulverbeschaffung und -handhabung: Woher beziehen sie ihr Pulver? Verwenden sie Pulver, das nach Luft- und Raumfahrtspezifikationen zertifiziert ist? Welche Verfahren gibt es für die Eingangskontrolle des Pulvers, die Lagerung (Vermeidung von Verunreinigungen/Feuchtigkeit), die Handhabung (insbesondere von reaktivem Ti) und die Rückverfolgbarkeit (Verknüpfung von Pulverchargen mit bestimmten Bauteilen)?
- Pulver-Recycling (Wiederverwendung): Die Verwendung von recyceltem Pulver ist gängige Praxis, um die Kosteneffizienz zu verbessern, aber sie muss sorgfältig gehandhabt werden. Welche Strategie verfolgt das Unternehmen bei der Wiederverwendung von Pulver? Wie oft wird das Pulver wiederverwendet? Wie wird das recycelte Pulver geprüft, um sicherzustellen, dass sich seine Eigenschaften nicht verschlechtert haben (z. B. Chemie, Partikelgrößenverteilung, Fließfähigkeit)? Met3dp konzentriert sich auf die Herstellung von qualitativ hochwertigen Pulvern mit hervorragender Konsistenz und ist sich bewusst, dass die Qualität des Ausgangsmaterials von grundlegender Bedeutung ist.
- Materialzertifizierung: Können sie eine vollständige Materialrückverfolgbarkeit und Konformitätszertifikate (CoCs) sowohl für das verwendete Pulver als auch für die fertigen Teile vorweisen?
- Technische und DfAM-Unterstützung:
- Technisches Fachwissen: Hat der Lieferant erfahrene AM-Ingenieure und Metallurgen im Team? Können sie sinnvolle DfAM-Unterstützung bieten und Ihnen helfen, Ihr Halterungsdesign im Hinblick auf Druckbarkeit, Gewichtsreduzierung und Leistung zu optimieren?
- Kollaborativer Ansatz: Sind sie bereit, mit Ihrem Entwicklungsteam zusammenzuarbeiten und Vorschläge für die Ausrichtung, die Unterstützungsstrategie und das Funktionsdesign zu machen? Dieser partnerschaftliche Ansatz führt oft zu den besten Ergebnissen. Met3dp ist stolz auf seine jahrzehntelange Erfahrung in der Metall-AM und bietet umfassende Lösungen.
- Nachbearbeitungsmöglichkeiten:
- In-House vs. Outsourced: Werden kritische Nachbearbeitungsschritte wie Wärmebehandlung (mit kalibrierten Öfen für die Luft- und Raumfahrt und Atmosphärenkontrolle), Abtragungen, CNC-Präzisionsbearbeitung, Oberflächenbehandlung (Strahlen, Hämmern, Polieren) und zerstörungsfreie Prüfung im Haus durchgeführt? Inhouse-Kapazitäten ermöglichen im Allgemeinen eine bessere Prozesskontrolle, Integration und potenziell kürzere Vorlaufzeiten.
- Verwaltete Lieferkette: Wenn sie bestimmte Schritte auslagern, wie qualifizieren und verwalten sie diese Unterauftragnehmer? Verfügen die Unterauftragnehmer über die erforderlichen Zertifizierungen (z. B. NADCAP für Wärmebehandlung/NDT)?
- Erfolgsbilanz und Erfahrung:
- Erfahrung in der Luft- und Raumfahrt: Haben sie erfolgreich Teile (insbesondere Halterungen oder ähnliche Struktur-/Systemkomponenten) für andere Kunden aus der Luft- und Raumfahrt hergestellt? Nachgewiesene Erfahrung in diesem Sektor ist von unschätzbarem Wert.
- Fallstudien/Referenzen: Können sie nicht vertrauliche Beispiele für relevante Projekte liefern oder Ihnen erlauben, mit bestehenden Kunden zu sprechen?
- Stabilität und Reputation: Achten Sie auf die Stabilität des Unternehmens und den Ruf des Anbieters in der Branche.
- Inspektion und Metrologie:
- Ausrüstung: Verfügen sie über die erforderlichen Messgeräte (CMMs, 3D-Scanner, Oberflächenprofilometer), die nach rückführbaren Standards kalibriert sind?
- NDT-Fähigkeiten: Welche ZfP-Methoden (VT, PT, ggf. UT, RT, CT) bieten sie intern oder über zertifizierte Partner an? Die Möglichkeit des CT-Scannens wird für die interne Prüfung kritischer AM-Teile immer wichtiger.
Potenzielle Lieferanten finden:
Ressourcen zur Identifizierung potenzieller Metall-AM-Serviceverteiler und Anbieter umfassen:
- Online-Marktplätze und -Verzeichnisse für die Fertigung (z. B. Hubs, Xometry, Thomasnet, spezielle AM-Verzeichnisse).
- Messen und Konferenzen der Luft- und Raumfahrt- sowie der AM-Industrie.
- Empfehlungen von Kontakten aus der Industrie.
- Direkte Zusammenarbeit mit etablierten AM-Lösungsanbietern, die für ihre Qualität bekannt sind, wie z. B. Met3dp.
Sorgfältig Auswahl eines AM-Partners auf der Grundlage dieser Kriterien und nicht nur auf der Grundlage des Preises zu wählen, ist eine strategische Investition, die die Wahrscheinlichkeit der erfolgreichen Implementierung zuverlässiger, leistungsstarker 3D-gedruckter AlSi10Mg- oder Ti-6Al-4V-Halterungen für Ihre Luft- und Raumfahrtanwendungen erheblich erhöht.
Kostenanalyse und Vorlaufzeiten für AM Aerospace Brackets
Eine der häufigsten Fragen von Beschaffungsmanagern und Ingenieuren, die eine additive Fertigung von Metallen in Erwägung ziehen, lautet: "Wie viel kostet es und wie lange dauert es?" AM bietet zwar überzeugende Vorteile, aber das Verständnis der Kostenstruktur und der realistischen Vorlaufzeiten ist entscheidend für die Projektplanung, die Budgetierung und den Vergleich von AM mit traditionellen Fertigungsmethoden. Die Preisgestaltung bei der additiven Fertigung Modell unterscheidet sich deutlich von subtraktiven oder formativen Verfahren.
Komplexität der AM-Kostenrechnung:
Anders als bei der CNC-Bearbeitung, wo die Kosten stark von der Maschinenzeit und der Größe des Materialblocks abhängen, oder beim Gießen, wo die Werkzeugkosten einen großen Teil der Vorlaufkosten ausmachen, Kosten für den 3D-Druck von Metall wird durch ein komplexes Zusammenspiel von Faktoren beeinflusst, die mit dem Druckverfahren selbst und der erforderlichen umfangreichen Nachbearbeitung zusammenhängen. Es ist selten so einfach wie die Kosten pro Kilogramm Material.
Schlüsselfaktoren, die die Kosten beeinflussen:
- Materialtyp und Volumen:
- Pulverkosten: Es gibt einen erheblichen Unterschied bei den Rohmaterialkosten. Ti-6Al-4V-Pulver in Luft- und Raumfahrtqualität kann 5-10 Mal teurer sein als AlSi10Mg-Pulver.
- Teilband: Das tatsächliche Volumen des Materials, aus dem die endgültige Klammer besteht, wirkt sich direkt auf die Kosten aus.
- Volumen unterstützen: Auch das für Stützstrukturen verwendete Material trägt zu den Kosten bei. Gut optimierte Entwürfe mit DfAM minimieren die Verschwendung von Stützmaterial.
- Beschaffungsmodell: Die Kosten können unterschiedlich sein, wenn die fertigen Teile von einem Dienstleister bezogen werden, während das Pulver direkt von einem Unternehmen bezogen wird. Metallpulververteiler für den Hausdruck. Großhandel mit 3D-Druckdienstleistungen können Mengenrabatte anbieten.
- Druckzeit (Maschinenauslastung):
- Bauhöhe: LPBF baut Schicht für Schicht auf, d. h. je größer das Teil (in der Bauausrichtung) ist, desto länger dauert der Druckvorgang, unabhängig vom Volumen. Dies ist ein wichtiger Kostentreiber. Die Verschachtelung mehrerer kürzerer Teile in einem einzigen Bauvorgang ist kostengünstiger als der Druck eines sehr hohen Teils.
- Teilvolumen und Dichte: Das Scannen und Schmelzen von Teilen mit größerem Volumen dauert natürlich länger. Dichte, massive Teile brauchen länger als solche mit leichten Gitterstrukturen.
- Anzahl der Teile pro Build: Die Einrichtungszeit (Laden des Pulvers, Vorbereitung der Maschine) amortisiert sich über alle Teile in einem Bau. Das gleichzeitige Drucken mehrerer Halterungen (Nesting) senkt die Kosten pro Teil im Vergleich zum Drucken einer einzelnen Halterung erheblich.
- Suchstrategie und Parameter: Die für Geschwindigkeit und Qualität/Genauigkeit optimierten Bauparameter wirken sich auf die Druckzeit aus.
- Maschine Stundensatz:
- Dieser Satz spiegelt die Kapitalkosten der hochentwickelten LPBF-Maschine, die Wartung, die Gemeinkosten der Einrichtung, den Energieverbrauch und die für den Betrieb der Maschine erforderlichen Fachkräfte wider. Die Preise variieren je nach Anbieter und Maschinentyp.
- Anforderungen an die Nachbearbeitung (oft signifikant):
- Wärmebehandlung: Ofenzeit, Energie und möglicherweise der Verbrauch von Inertgas verursachen zusätzliche Kosten. Komplexe Zyklen wie T6 oder HIP sind teurer als einfacher Spannungsabbau.
- Unterstützung bei der Entfernung: In erster Linie durch den manuellen Arbeitsaufwand bedingt. Komplexe, unzugängliche Träger erhöhen diese Kosten erheblich.
- Bearbeitungen: Die Kosten hängen von der Komplexität der Bearbeitungsvorgänge, der Anzahl der erforderlichen Aufspannungen und der CNC-Maschinenzeit ab.
- Oberflächenveredelung: Arbeitskräfte und Materialien/Verbrauchsmaterialien für Strahlen, Trowalisieren, Polieren, Eloxieren usw. Shotpeening erfordert spezielle Ausrüstung und Kontrolle.
- Inspektion: Arbeitsaufwand für visuelle/maßliche Prüfungen. Die Ausrüstungszeit und spezielle Analysen für CMM, 3D-Scanning und insbesondere NDT-Methoden wie CT-Scanning können erhebliche Kosten verursachen, insbesondere wenn sie für 100%-Teile in kritischen Anwendungen erforderlich sind.
- Auftragsvolumen:
- Skalenvorteile: Während AM für seine Kosteneffizienz bei geringen Stückzahlen (Prototypen, Kleinserien) bekannt ist, sinken die Stückkosten bei größeren Aufträgen aufgrund der Amortisierung der Einrichtungs-/Programmierzeit und der optimierten Verschachtelung der Bauteile. Erkundigen Sie sich bei den Anbietern nach Preisstaffeln für unterschiedliche Mengen.
- Entwurfskomplexität (DfAM Impact):
- Ein nach DfAM-Prinzipien optimiertes Bracket-Design (z. B. minimiertes Volumen/Gewicht, selbsttragende Funktionen, integrierte Funktionalität) ist aufgrund des geringeren Materialverbrauchs, der kürzeren Druckzeiten und des geringeren Nachbearbeitungsaufwands in der Regel kostengünstiger zu produzieren als ein nicht optimiertes oder direkt übersetztes traditionelles Design. Die Investition in DfAM im Vorfeld zahlt sich bei den Produktionskosten aus.
Typische Erwartungen an die Vorlaufzeit:
Vorlaufzeit additive Fertigung ist in der Regel viel schneller als herkömmliche Verfahren, bei denen Werkzeuge hergestellt werden (Gießen), kann aber aufgrund der oben genannten Faktoren stark variieren.
- Prototypen: Für Einzelteile oder sehr kleine Chargen (1-5) mit Standard-Nachbearbeitung (z. B. Spannungsabbau, Entfernen von Grundträgern, Perlstrahlen) gelten Durchlaufzeiten von 5-15 Arbeitstage sind üblich. Eildienste können gegen einen Aufpreis angeboten werden.
- Produktionsserie (kleine bis mittlere Stückzahlen): Bei Chargen von zehn bis hunderten von Klammern können die Vorlaufzeiten zwischen 3 bis 8 Wochenund hängt stark davon ab:
- Komplexität der Teile und Druckzeit pro Bau.
- Gesamtzahl der benötigten Teile.
- Komplexität der Nachbearbeitung (mehrstufige Wärmebehandlungen, umfangreiche Bearbeitungen, komplexe Endbearbeitung, strenge zerstörungsfreie Prüfung).
- Aktuelle Kapazität und Auftragsbestand des Lieferanten.
- Erforderliche Unterlagen und Zertifizierungspaket.
Kostenvergleich: AM vs. traditionelle Methoden:
Oft gibt es eine Break-even-Analyse AM zu berücksichtigen:
- Sehr geringe Lautstärke (1-10s): AM ist oft sehr wettbewerbsfähig, insbesondere bei komplexen Halterungen, da hohe Werkzeugkosten, die beim Gießen anfallen, oder komplexe Vorrichtungen für die Bearbeitung vermieden werden können.
- Geringe bis mittlere Lautstärke (10s-100s): AM ist nach wie vor wettbewerbsfähig, insbesondere wenn Gewichtsreduzierung und Designkomplexität einen bedeutenden Wert darstellen. Der Kostenvergleich mit der mehrachsigen CNC-Bearbeitung hängt stark von der Komplexität der Teile ab.
- Großes Volumen (1000+): Traditionelle Verfahren wie Feinguss oder Hochgeschwindigkeitsbearbeitung werden aufgrund von Skaleneffekten in der Regel pro Teil kostengünstiger, es sei denn, die einzigartigen Vorteile von AM (extreme Gewichtsreduzierung, Konsolidierung von Teilen, die sonst nicht möglich ist) rechtfertigen einen potenziellen Kostenaufschlag pro Teil.
Genaue Angebote einholen:
Um zuverlässige Kostenschätzungen und Kostenanalyse für Luft- und Raumfahrtkomponentenbieten Sie potenziellen Lieferanten an:
- 3D-CAD-Modelle (vorzugsweise im STEP-Format).
- 2D-Zeichnungen mit Angaben zu kritischen Abmessungen, GD&T, erforderlichen Oberflächenbehandlungen und Prüfanforderungen.
- Werkstoffspezifikation (AlSi10Mg oder Ti-6Al-4V, einschließlich spezifischer Güte oder Wärmebehandlung).
- Benötigte Menge und gewünschter Liefertermin.
- Besondere Zertifizierungs- oder Dokumentationsanforderungen.
Das Verständnis dieser Kostentreiber und Vorlaufzeitfaktoren ermöglicht eine bessere Budgetierung, eine realistische Zeitplanung und fundierte Entscheidungen, wenn 3D-gedruckte AlSi10Mg- oder Ti-6Al-4V-Bügel in Luft- und Raumfahrtprojekte integriert werden.
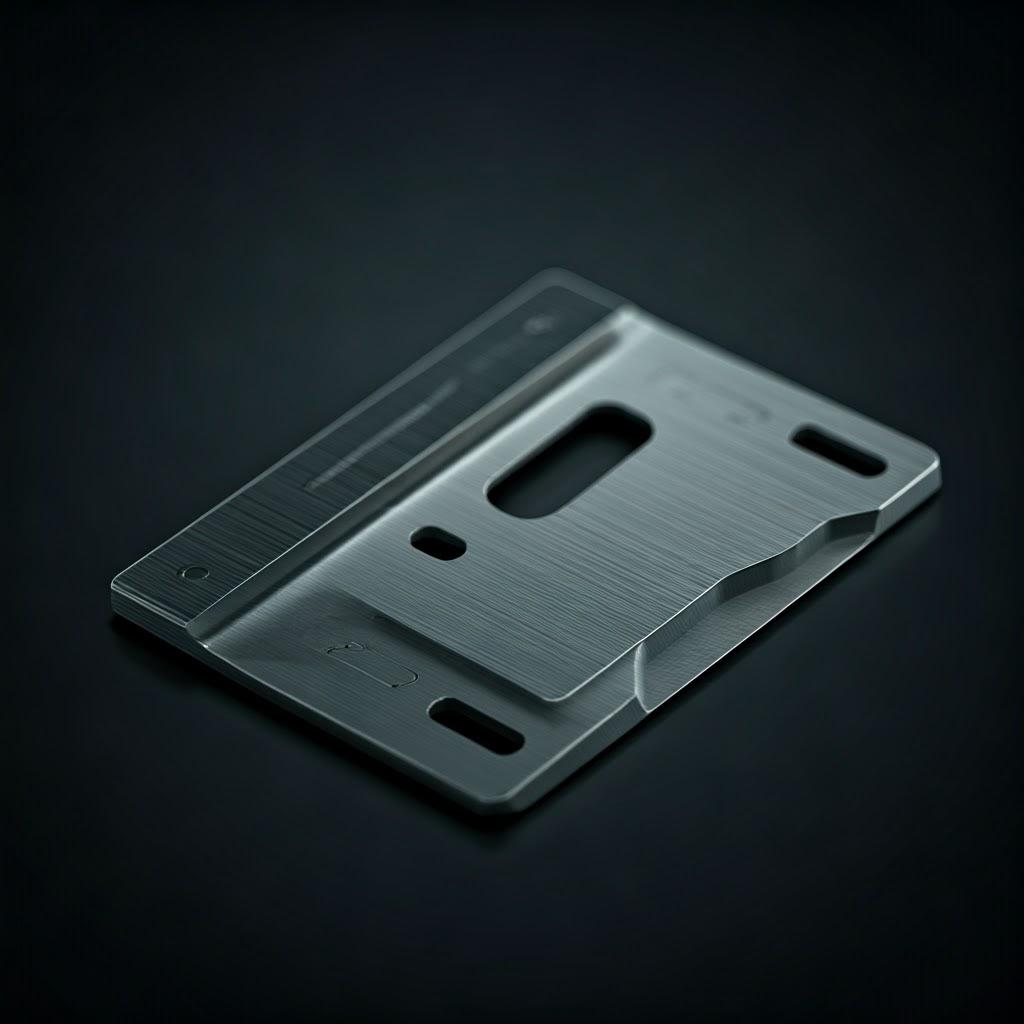
Häufig gestellte Fragen (FAQ) zu AlSi10Mg Aerospace Brackets
Hier finden Sie Antworten auf einige häufig gestellte Fragen von Ingenieuren und Beschaffungsmanagern zur Verwendung von 3D-gedrucktem AlSi10Mg für Halterungen in der Luftfahrt:
1. Ist 3D-gedrucktes AlSi10Mg für flugkritische Anwendungen geeignet?
Im Allgemeinen wird das mittels LPBF hergestellte AlSi10Mg häufiger für sekundäre Strukturelemente und System-Montagebügel und nicht für primäre, flugkritische Strukturen (z. B. Haupttragflächenholme, Fahrwerkskomponenten). Trotz seiner hohen Festigkeit im Verhältnis zum Gewicht sind die Ermüdungseigenschaften und die Bruchzähigkeit in der Regel geringer als bei optimierten Aluminium-Knetlegierungen (wie 7075-T6) oder Titanlegierungen in Luft- und Raumfahrtqualität (wie Ti-6Al-4V). Flugkritische Anwendungen erfordern ein extrem hohes Maß an nachgewiesener Zuverlässigkeit, Schadenstoleranz und vorhersehbarem Verhalten unter extremen Bedingungen, was oft umfangreiche und kostspielige Qualifizierungsprogramme mit statistischen Materialeigenschaften und Komponententests erfordert. Während spezifische, streng kontrollierte AlSi10Mg-Anwendungen für weniger anspruchsvolle kritische Teile mit umfangreichen Analysen und Tests zertifiziert werden können, wird Ti-6Al-4V (oft mit HIP-Behandlung) aufgrund seiner überlegenen intrinsischen Eigenschaften häufiger für additiv gefertigte kritische Komponenten in Betracht gezogen. Die Eignung hängt immer von einer strengen technischen Analyse des Lastfalls des spezifischen Teils, der Betriebsumgebung, der Sicherheitsfaktoren und der von den Aufsichtsbehörden (z. B. FAA, EASA) festgelegten Zertifizierungsanforderungen ab.
2. Wie sind die Ermüdungseigenschaften von AM AlSi10Mg-Klammern im Vergleich zu Knetaluminium?
Dies ist ein entscheidender Faktor für Bauteile in der Luft- und Raumfahrt, die zyklischen Belastungen ausgesetzt sind. Mit LPBF hergestelltes oder spannungsarmgeglühtes/T6-wärmebehandeltes AlSi10Mg weist in der Regel folgende Eigenschaften auf geringere Ermüdungsfestigkeit bei hoher Lastspielzahl (HCF) im Vergleich zu herkömmlichen Aluminium-Knetlegierungen wie 6061-T6 oder 7075-T6. Mehrere Faktoren tragen dazu bei:
- Mikrostruktur: Die schnell erstarrte Mikrostruktur von AM-Teilen unterscheidet sich von der Knetstruktur.
- Potenzielle Defekte: Mikroporosität (selbst bei geringen Werten <0,1%) kann als Initiationsstelle für Ermüdungsrisse dienen.
- Oberfläche: Die inhärente Rauheit von AM-Oberflächen kann die Ermüdungslebensdauer im Vergleich zu glatten, maschinell bearbeiteten Oberflächen erheblich verringern. Nach unten weisende Oberflächen und Bereiche mit Stützkontaktpunkten sind oft besonders kritisch.
- Anisotropie: Die Ermüdungseigenschaften können manchmal abhängig von der Ausrichtung des Bauteils im Verhältnis zur Belastungsrichtung variieren. Milderung/Verbesserung: Nachbearbeitungsschritte wie Heiß-Isostatisches Pressen (HIP) (obwohl weniger verbreitet und bei Al-Legierungen potenziell weniger wirksam als bei Ti) können dazu beitragen, innere Poren zu schließen, und Oberflächenbehandlungen wie Shotpeening kann vorteilhafte Druckeigenspannungen einbringen, die die Ermüdungslebensdauer erheblich verbessern. Die Glättung kritischer Oberflächen ist ebenfalls hilfreich. Die Konstrukteure müssen jedoch geeignete Ermüdungsdaten verwenden, die für das AM-Material und den Prozess (einschließlich Nachbearbeitung) spezifisch sind, und geeignete Sicherheitsfaktoren anwenden, was häufig spezielle Ermüdungstests zur Validierung erfordert, insbesondere bei Teilen, die erheblichen zyklischen Belastungen ausgesetzt sind.
3. Können bestehende Halterungsdesigns (für die Bearbeitung oder den Guss) direkt in 3D gedruckt werden?
Technisch gesehen kann ein für die Bearbeitung konzipiertes CAD-Modell in der Regel in eine STL-Datei umgewandelt und gedruckt werden. Allerdings ist dies höchst suboptimal und im Allgemeinen nicht zu empfehlen. Dabei werden die wichtigsten Vorteile der additiven Fertigung völlig außer Acht gelassen. Das direkte Drucken eines für subtraktive Verfahren optimierten Designs führt in der Regel zu:
- Übermäßiges Gewicht: Der Entwurf enthält wahrscheinlich Schüttgut, das leicht zu entfernen ist, aber aus Sicht des strukturellen Lastpfads ineffizient ist.
- Umfassender Unterstützungsbedarf: Merkmale, die für den Zugang zu Werkzeugen konzipiert sind (z. B. flache Böden, rechtwinklige Überhänge), erfordern in der AM oft erhebliche Stützstrukturen, was die Druckzeit, den Materialabfall und den Nachbearbeitungsaufwand erhöht.
- Längere Druckzeiten: Die nicht optimierten Volumen- und Stützstrukturen erhöhen die Bauzeit.
- Höhere Kosten: Erhöhter Materialverbrauch, Druckzeit und Nachbearbeitungsaufwand machen es teurer als nötig. Um wirklich von AM zu profitieren, sollten Klammern sein nach DfAM-Prinzipien umgestaltet oder neu konzipiert. Dazu gehören die Optimierung der Topologie, die Entwicklung selbsttragender Merkmale, die Konsolidierung von Teilen und die Optimierung des schichtweisen Bauprozesses. Dies erfordert eine Investition in den Designaufwand, führt aber zu deutlich leichteren, oft leistungsfähigeren und letztlich kostengünstigeren AM-Komponenten.
4. Welche Qualitätszertifizierungen sind für AM-Lieferanten in der Luft- und Raumfahrt wichtig?
Wie bereits erwähnt, ist die grundlegende QMS-Zertifizierung AS9100. Dies zeigt, dass der Lieferant luftfahrtspezifische Kontrollen für Qualität, Rückverfolgbarkeit, Risikomanagement und Konfigurationsmanagement eingeführt hat. Für Lieferanten, die "spezielle Prozesse" intern durchführen, NADCAP-Akkreditierung für diese Prozesse (z. B. Wärmebehandlung, zerstörungsfreie Prüfung, Schweißen, Werkstoffprüfung) bietet eine weitere Gewähr für die technische Kompetenz und die Prozesskontrolle speziell für diese Vorgänge. Außerdem sind robuste Materialzertifizierung Prozesse, die sicherstellen, dass das eingehende Pulver die erforderlichen Spezifikationen erfüllt (z. B. AMS-Normen für Chemie und PSD) und eine vollständige Rückverfolgbarkeit von der Pulvercharge bis zum fertigen Teil gewährleisten, sind von entscheidender Bedeutung. Die Kunden sollten den aktuellen Zertifizierungsstatus eines potenziellen Lieferanten und den Umfang seiner Akkreditierungen überprüfen.
5. Wie gewährleistet Met3dp die Qualität seines AlSi10Mg-Pulvers?
Met3dp ist sich bewusst, dass qualitativ hochwertiges Metallpulver die Grundlage für eine leistungsstarke additive Fertigung ist, insbesondere in anspruchsvollen Bereichen wie der Luft- und Raumfahrt. Wir gewährleisten die Qualität unseres AlSi10Mg-Pulvers durch einen vielschichtigen Ansatz, der auf fortschrittlicher Produktionstechnologie und strenger Qualitätskontrolle beruht:
- Fortgeschrittene Produktion: Wir verwenden branchenführende Gaszerstäubung und PREP (Plasma-Rotationselektrodenverfahren) Technologien. Diese Verfahren sind optimiert für die Herstellung von Metallpulvern mit hohe Sphärizität (Verbesserung der Fließfähigkeit und der Packungsdichte) und geringer Satellitenanteildie für ein gleichmäßiges Schmelzen und das Erreichen dichter Teile in LPBF entscheidend sind. Erfahren Sie mehr über unser Unternehmen und unsere Technologie unter Met3dp.com.
- Strenge Kontrolle der Rohmaterialien: Wir wählen die Rohstoffe sorgfältig aus und prüfen sie, um sicherzustellen, dass sie vor der Zerstäubung strenge Reinheitsanforderungen erfüllen.
- Prozesskontrolle: Die Zerstäubungsparameter werden streng kontrolliert, um die gewünschte Partikelgrößenverteilung (PSD) zu erreichen, die für LPBF-Prozesse und spezifische Kundenanforderungen optimiert ist.
- Umfassende Qualitätsprüfung: Jede Pulvercharge wird in unserem gut ausgestatteten Labor umfangreichen Tests unterzogen:
- Analyse der chemischen Zusammensetzung (z. B. mittels ICP-OES), um zu überprüfen, ob es die AlSi10Mg-Spezifikationen erfüllt.
- Messung der Partikelgrößenverteilung (z. B. mittels Laserbeugung).
- Bewertung der Morphologie (z. B. mittels SEM) zur Bestätigung einer hohen Sphärizität und minimaler Satelliten.
- Fließfähigkeitsprüfungen (z. B. Hall-Durchflussmesser) und Messungen der scheinbaren Dichte bzw. Klopfdichte.
- Analyse des Gasgehalts (Sauerstoff, Stickstoff), sofern kritisch.
- Rückverfolgbarkeit der Chargen: Strenge Chargenkontrolle und Dokumentation gewährleisten eine vollständige Rückverfolgbarkeit von den Rohstoffen über die Zerstäubung bis hin zum fertig verpackten Pulver.
- Analysezertifikate (CoA): Wir stellen unseren Kunden detaillierte CoAs für jede Pulvercharge zur Verfügung, die bestätigen, dass sie den vereinbarten Spezifikationen entspricht. Diese Verpflichtung zur Qualität stellt sicher, dass Kunden, die das AlSi10Mg-Pulver von Met3dp verwenden, auf die Konsistenz und Leistung ihrer additiv gefertigten Luft- und Raumfahrtkomponenten vertrauen können.
Schlussfolgerung: Verbesserte Luft- und Raumfahrtentwicklung mit AlSi10Mg Additive Manufacturing
Die Reise durch die Feinheiten der Verwendung von AlSi10Mg für Halterungen in der Luft- und Raumfahrt mittels 3D-Metalldruck offenbart eine Technologie, die vor transformativem Potenzial nur so strotzt. Die additive Fertigung, insbesondere das Laser Powder Bed Fusion, ist nicht nur eine alternative Produktionsmethode, sondern ein Wegbereiter für Innovationen, der es Ingenieuren in der Luft- und Raumfahrt ermöglicht, sich von den Beschränkungen der traditionellen Fertigung zu lösen und ein noch nie dagewesenes Maß an Designoptimierung, Gewichtsreduzierung und Bauteilkonsolidierung zu erreichen.
AlSi10Mg hat sich als vielseitiges und wertvolles Material in der AM-Werkzeugpalette für die Luft- und Raumfahrt etabliert. Seine vorteilhafte Kombination aus geringer Dichte, guten mechanischen Eigenschaften (bei entsprechender Wärmebehandlung), hervorragender Verarbeitbarkeit und relativer Kosteneffizienz macht es zu einem idealen Kandidaten für eine Vielzahl von sekundären strukturellen Halterungen und Systemmontagekomponenten. Die Fähigkeit, Topologieoptimierung und DfAM-Prinzipien mit AlSi10Mg zu nutzen, ermöglicht die Herstellung hocheffizienter, leichter Halterungen, die direkt zu einer verbesserten Treibstoffersparnis, einer erhöhten Nutzlastkapazität und der Gesamtleistung von Flugzeugen beitragen - wichtige Faktoren auf dem wettbewerbsintensiven Luft- und Raumfahrtmarkt. Während Ti-6Al-4V die erste Wahl für Anwendungen mit höherer Belastung und höheren Temperaturen bleibt, bietet AlSi10Mg ein überzeugendes Gleichgewicht zwischen Leistung und Wert für viele Halterungsanforderungen.
Die erfolgreiche Umsetzung von AM für Luft- und Raumfahrtkomponenten erfordert jedoch mehr als nur den Zugang zu einem Drucker und Pulver. Sie erfordert einen ganzheitlichen Ansatz, der Folgendes umfasst:
- Intelligentes Design: Anwendung der DfAM-Prinzipien zur Maximierung des Nutzens.
- Materialwissenschaft: Verständnis der Materialeigenschaften und der entscheidenden Rolle der Pulverqualität.
- Prozesskontrolle: Beherrschung der Komplexität des LPBF-Prozesses.
- Strenge Nachbearbeitung: Durchführung wichtiger Schritte wie Wärmebehandlung, Endbearbeitung und Kontrolle.
- Qualitätssicherung: Einhaltung von strengen Luft- und Raumfahrtnormen wie AS9100.
Am wichtigsten ist vielleicht, dass der Erfolg von folgenden Faktoren abhängt Auswahl des richtigen Produktionspartners. Ein idealer Partner wie Met3dp verfügt nicht nur über hochmoderne Anlagen für den Druck und die Pulverherstellung, sondern auch über fundiertes Fachwissen für den gesamten AM-Workflow. Sie bieten DfAM-Unterstützung, stellen die Prozessstabilität sicher, verwalten komplexe Nachbearbeitungsketten und bieten die von der Luft- und Raumfahrtbranche geforderte strenge Qualitätskontrolle und Rückverfolgbarkeit.
Die Zukunft der Luft- und Raumfahrtindustrie wird die additive Fertigung zweifelsohne eine immer wichtigere Rolle spielen. In dem Maße, in dem die Technologie reift, die Werkstoffe besser werden und die Konstruktionswerkzeuge ausgereifter werden, wird die additive Fertigung weiterhin neue Möglichkeiten für die Herstellung leichterer, stärkerer und effizienterer Flugzeuge eröffnen. 3D-gedruckte Halterungen aus AlSi10Mg sind ein Paradebeispiel für diese laufende Revolution und zeigen bereits heute greifbare Vorteile.
Für Ingenieure und Beschaffungsmanager, die das Potenzial von AlSi10Mg-Klammerlösungen oder andere Metall-AM-Anwendungen, ist es jetzt an der Zeit, sich zu engagieren. Wir laden Sie ein, die Vorteile Met3dp Fähigkeiten in der Luft- und Raumfahrt. Wenden Sie sich noch heute an Met3dp, um Ihre spezifischen Herausforderungen im Bereich der Komponenten zu besprechen und zu erfahren, wie unsere umfassenden Innovation in der additiven Fertigungmit seinen branchenführenden Druckern, fortschrittlichen Metallpulvern und umfangreichem Anwendungs-Know-how kann Ihnen dabei helfen, Ihre Fertigungsziele in der Luft- und Raumfahrt zu erreichen und Ihre Entwürfe auf ein neues Niveau zu heben.
Teilen auf
MET3DP Technology Co., LTD ist ein führender Anbieter von additiven Fertigungslösungen mit Hauptsitz in Qingdao, China. Unser Unternehmen ist spezialisiert auf 3D-Druckgeräte und Hochleistungsmetallpulver für industrielle Anwendungen.
Fragen Sie an, um den besten Preis und eine maßgeschneiderte Lösung für Ihr Unternehmen zu erhalten!
Verwandte Artikel
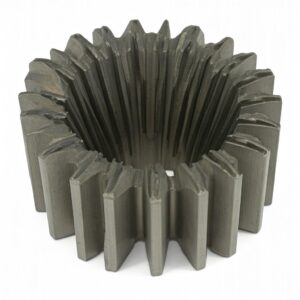
Hochleistungs-Düsenschaufelsegmente: Revolutionierung der Turbineneffizienz mit 3D-Metalldruck
Mehr lesen "Über Met3DP
Aktuelles Update
Unser Produkt
KONTAKT US
Haben Sie Fragen? Senden Sie uns jetzt eine Nachricht! Wir werden Ihre Anfrage mit einem ganzen Team nach Erhalt Ihrer Nachricht bearbeiten.
Holen Sie sich Metal3DP's
Produkt-Broschüre
Erhalten Sie die neuesten Produkte und Preislisten
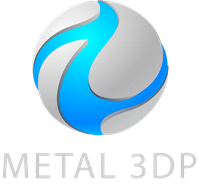
Metallpulver für 3D-Druck und additive Fertigung