3D-gedruckte Raketendüsen aus Hochtemperaturlegierungen
Inhaltsübersicht
Einleitung: Die kritische Rolle von Raketendüsen und der Aufstieg der additiven Fertigung
Raketendüsen gehören zu den anspruchsvollsten und kritischsten Komponenten von Antriebssystemen in der Luft- und Raumfahrt. Diese Komponenten, deren Aufgabe es ist, glühend heiße Hochdruck-Verbrennungsgase auf Überschall- (oft Hyperschall-) Geschwindigkeiten zu beschleunigen, sind extremen thermischen, mechanischen und chemischen Beanspruchungen ausgesetzt. Die Effizienz, Zuverlässigkeit und Leistung eines gesamten Trägerraketen- oder Satellitenantriebssystems hängt wesentlich von der Konstruktion und der Materialintegrität der Düse ab. Ihre Hauptfunktion besteht darin, die in der Brennkammer erzeugte Wärmeenergie in kinetische Energie umzuwandeln und so den für die Überwindung der Schwerkraft und den Antrieb von Raumfahrzeugen erforderlichen Schub zu erzeugen. Jegliches Versagen oder unzureichende Leistung in der Düse kann katastrophale Folgen haben, weshalb ihre Konstruktion, die Materialauswahl und der Herstellungsprozess für Ingenieure und Hersteller in der Luft- und Raumfahrt von größter Bedeutung sind.
Für die Herstellung dieser komplizierten Bauteile waren bisher komplexe, mehrstufige Verfahren wie Gießen, Schmieden und umfangreiche subtraktive Bearbeitungen erforderlich, häufig aus schwer zu bearbeitenden Hochtemperaturwerkstoffen. Diese Methoden haben sich zwar bewährt, weisen aber erhebliche Einschränkungen auf:
- Design-Zwänge: Komplexe interne Merkmale, wie z. B. komplizierte Kühlkanäle, die für die Beherrschung extremer Temperaturen unerlässlich sind, lassen sich mit herkömmlichen Methoden nur schwer oder gar nicht realisieren. Dies zwingt oft zu Kompromissen bei der optimalen Gestaltung.
- Lange Vorlaufzeiten: Der mehrstufige Charakter der konventionellen Fertigung in Verbindung mit den Anforderungen an die Werkzeuge führt zu langen Produktionszyklen und behindert schnelle Iterations- und Entwicklungsprogramme.
- Materialabfälle: Bei der subtraktiven Bearbeitung fällt naturgemäß ein erheblicher Materialabfall an, der besonders kostspielig ist, wenn man mit teuren Superlegierungen arbeitet.
- Gewichtsstrafen: Mit herkömmlichen Methoden lassen sich nur schwer leichte Strukturen ohne Einbußen bei der Festigkeit herstellen - ein entscheidender Faktor in der Luft- und Raumfahrt, wo jedes eingesparte Gramm die Nutzlastkapazität oder die Treibstoffeffizienz erhöht.
- Komplexität der Montage: Düsen erfordern oft den Zusammenbau mehrerer maschinell bearbeiteter oder gegossener Teile, was zu potenziellen Fehlerstellen an den Verbindungsstellen führt und die Montagezeit und -kosten erhöht.
Hier kommt die additive Fertigung von Metallen (AM) ins Spiel, besser bekannt als 3D-Metalldruck. Diese transformative Technologie entwickelt sich rasch zu einer leistungsstarken Lösung für die Herstellung kritischer Luft- und Raumfahrtkomponenten wie Raketendüsen. Durch den schichtweisen Aufbau von Teilen direkt aus digitalen Modellen unter Verwendung von Hochenergiequellen (Laser oder Elektronenstrahlen) zum Verschmelzen von feinen Metallpulvern überwindet AM viele der mit der herkömmlichen Fertigung verbundenen Einschränkungen.
Die wichtigsten Vorteile von AM für Raketendüsen:
- Beispiellose Designfreiheit: AM ermöglicht die Herstellung hochkomplexer Geometrien, einschließlich integrierter konformer Kühlkanäle, die den Konturen der Düse für eine maximale Wärmeübertragungseffizienz genau folgen. Dies ermöglicht Designs, die bisher als nicht herstellbar galten.
- Beschleunigte Entwicklungszyklen: Prototypen und Design-Iterationen können wesentlich schneller hergestellt werden, so dass die Ingenieure die Düsenkonzepte viel schneller testen und verfeinern können, was die Entwicklungsprogramme für Motoren beschleunigt.
- Optimierung des Gewichts: Techniken wie die Topologieoptimierung und die Einbindung von Gitterstrukturen ermöglichen es, Material nur dort zu platzieren, wo es strukturell notwendig ist, was zu erheblichen Gewichtseinsparungen führt, ohne die Leistung zu beeinträchtigen.
- Teil Konsolidierung: Mehrere Komponenten, die zuvor zusammengebaut werden mussten, können oft zu einem einzigen, monolithischen 3D-gedruckten Teil zusammengefasst werden, wodurch sich die Anzahl der Teile verringert, Verbindungsstellen (potenzielle Fehlerstellen) entfallen und die Logistik vereinfacht wird.
- Materialeffizienz: Da es sich um ein additives Verfahren handelt, wird das Material hauptsächlich dort eingesetzt, wo es benötigt wird, wodurch der mit subtraktiven Verfahren verbundene Abfall drastisch reduziert wird - ein entscheidender Vorteil, wenn es um teure Hochtemperatursuperlegierungen geht.
- Widerstandsfähigkeit der Lieferkette: AM bietet das Potenzial für dezentrale Fertigung und Produktion auf Abruf, wodurch die Abhängigkeit von komplexen globalen Lieferketten und Schmiede- oder Gussteilen mit langen Vorlaufzeiten verringert wird.
Die Luft- und Raumfahrtindustrie, die ständig die Grenzen von Leistung und Effizienz verschiebt, hat das immense Potenzial des 3D-Metalldrucks erkannt. Für Raketendüsen, die in extremen Umgebungen eingesetzt werden, bietet AM einen Weg zu verbessertem Wärmemanagement, geringerem Gewicht, schnellerer Innovation und letztendlich zu leistungsfähigeren und kostengünstigeren Antriebssystemen. Da Unternehmen wie Met3dp Durch die weitere Verfeinerung der AM-Prozesse und der speziellen Hochleistungsmetallpulver wird sich der Aufstieg der additiven Fertigung bei der Herstellung von flugkritischer Hardware wie Raketendüsen beschleunigen und die Zukunft der Weltraumforschung und des Zugangs zum Weltraum neu gestalten.
Anwendungen von 3D-gedruckten Raketendüsen: Die Grenzen der Luft- und Raumfahrt verschieben
Die einzigartigen Möglichkeiten, die die additive Fertigung von Metallen bietet, haben ein vielfältiges und wachsendes Spektrum von Anwendungen erschlossen für 3D-gedruckt Raketendüsen in der Luft- und Raumfahrt und im Verteidigungssektor. Die Fähigkeit, komplexe Designs schnell zu iterieren, das Gewicht zu optimieren und fortschrittliche Funktionen wie ausgeklügelte Kühlkanäle zu integrieren, macht AM besonders geeignet für anspruchsvolle Antriebsanwendungen, bei denen die Leistung an erster Stelle steht.
1. Haupt- und Oberstufentriebwerke der Trägerrakete:
- Primäre Anwendung: Am häufigsten werden sie wohl in den Hauptantriebssystemen von Trägerraketen eingesetzt, die Nutzlasten von der Erde in die Umlaufbahn befördern. Dazu gehören sowohl die Booster-Triebwerke der ersten Stufe als auch die Triebwerke der oberen Stufe, die den Eintritt in die Umlaufbahn oder interplanetare Flüge durchführen.
- Warum AM?
- Leistung: Komplexe Kühlkanaldesigns, die durch AM ermöglicht werden (z. B. regenerative Kühlkreisläufe, bei denen der Kraftstoff vor der Verbrennung durch Kanäle in der Düsenwand fließt), ermöglichen es den Motoren, mit höheren Kammerdrücken und -temperaturen zu arbeiten, wodurch der spezifische Impuls (Isp) - ein Schlüsselmaß für die Motoreffizienz - erhöht wird.
- Gewichtsreduzierung: Jedes Kilogramm, das bei der Raketenstruktur eingespart wird, schlägt sich direkt in einer erhöhten Nutzlastkapazität oder Missionsfähigkeit nieder. AM ermöglicht erhebliche Gewichtseinsparungen in der Düsenbaugruppe durch Topologieoptimierung und Teilekonsolidierung.
- Schnellere Entwicklung: Die Entwicklungszyklen für Trägerraketen sind bekanntermaßen lang und teuer. AM beschleunigt den Iterationsprozess für Düsenkonstruktionen erheblich und ermöglicht schnellere Tests und Verfeinerungen, was sowohl für etablierte Unternehmen als auch für neue Raumfahrtunternehmen, die nach kosteneffizienten Lösungen suchen, entscheidend ist.
- Kostenreduzierung: Während die anfänglichen Kosten für AM-Teile in einigen Fällen vergleichbar oder höher sein können, lassen sich die Gesamtsystemkosten durch die Konsolidierung von Teilen (weniger Komponenten, die hergestellt, verfolgt und montiert werden müssen), geringere Werkzeugkosten und kürzere Entwicklungszeiten senken. Großeinkäufer und Beschaffungsmanager profitieren von einer rationalisierten Logistik und potenziell niedrigeren Gesamtprogrammkosten.
2. Satelliten-Antriebssysteme:
- Anwendung: Satelliten benötigen kleinere Triebwerke für die Stationierung (Aufrechterhaltung der korrekten Umlaufbahn), die Lageregelung (Orientierung) und manchmal auch für das Manövrieren in der Umlaufbahn oder den Rückzug aus der Umlaufbahn. Dabei handelt es sich häufig um Mono- oder Bipropellant-Systeme, die in einem kleineren Maßstab als die Triebwerke von Trägerraketen arbeiten.
- Warum AM?
- Miniaturisierung und Integration: AM eignet sich hervorragend für die Herstellung kleiner, komplizierter Komponenten. Schubdüsen, die oft Teil eines größeren integrierten Antriebsmoduls sind, können mit Funktionen wie Einspritzköpfen oder Ventilschnittstellen in einer einzigen Einheit gedruckt werden, was die Masse und potenzielle Leckstellen reduziert.
- Anpassungen: Satellitenkonstellationen können leicht unterschiedliche Triebwerkskonfigurationen erfordern. AM ermöglicht eine effiziente Produktion kundenspezifischer Düsenkonstruktionen, ohne dass für jede Variante ein eigenes Werkzeug benötigt wird.
- Neuartige Materialien: AM erleichtert die Verwendung fortschrittlicher oder spezieller Legierungen, die auf bestimmte Treibstoffchemien oder eine lange Exposition im Weltraum zugeschnitten sind und die Lebensdauer und Leistung von Triebwerken verbessern können.
3. Reaktionskontrollsysteme (RCS):
- Anwendung: RCS-Triebwerke sind kleine Raketentriebwerke, die in den Oberstufen von Raumfahrzeugen und Trägerraketen in erster Linie zur Lageregelung und zum präzisen Manövrieren im Weltraum eingesetzt werden, anstatt große Mengen an Schub zu erzeugen.
- Warum AM?
- Komplexe Geometrien: RCS-Systeme bestehen oft aus mehreren Düsen, die in bestimmten Winkeln angeordnet sind. Mit AM können diese Cluster zusammen mit den zugehörigen Verteilern und Befestigungselementen als eine einzige integrierte Komponente gedruckt werden.
- Gewichtseinsparung: Wie bei größeren Düsen ist die Minimierung der Masse der RCS-Komponenten von entscheidender Bedeutung, insbesondere bei Deep-Space-Missionen oder gewichtssensiblen Satelliten.
- Rapid Prototyping: Die Feinabstimmung der Leistungs- und Abgaseigenschaften von RCS-Triebwerken erfordert häufig iterative Tests. AM ermöglicht eine schnelle Produktion von Designvarianten.
4. Antrieb von Hyperschallfahrzeugen:
- Anwendung: Neu entstehende Hyperschallfahrzeuge (Flugzeuge oder Raketen, die über Mach 5 fliegen) erfordern fortschrittliche luftatmende Triebwerke (wie Scramjets) oder Raketenbooster, die unter extremer aerodynamischer Erwärmung und mechanischer Belastung arbeiten. Das Design der Düsen ist entscheidend für die Leistung und das Wärmemanagement.
- Warum AM?
- Management extremer Temperaturen: AM ermöglicht die Integration hochkomplexer Transpirations- oder Regenerationskühlsysteme direkt in die Düsenwände, die für das Überleben der bei Hyperschallflügen herrschenden Temperaturen von mehreren Tausend Grad unerlässlich sind.
- Fortgeschrittene Materialien: Hyperschallanwendungen erfordern Materialien, die extremen Bedingungen standhalten können. AM-Prozesse werden an die Arbeit mit hochmodernen Refraktärmetallen und Keramikmatrix-Verbundwerkstoffen (CMC) angepasst, die für diese anspruchsvollen Düsenanwendungen geeignet sein könnten.
- Optimierung der Form: Die komplexen Strömungswege und Düsengeometrien, die für einen effizienten Hyperschallantrieb erforderlich sind, eignen sich oft ideal für die Designfreiheit, die AM bietet.
5. Forschung und Entwicklung / Testartikel:
- Anwendung: Bevor die Hardware für den Flug freigegeben wird, sind umfangreiche Bodentests erforderlich. AM wird intensiv genutzt, um Prototyp-Düsen und Brennkammerkomponenten für Testkampagnen herzustellen.
- Warum AM?
- Geschwindigkeit: Durch die schnelle Herstellung von Testartikeln können Forschungsprogramme schneller vorangetrieben werden.
- Kosten-Nutzen-Verhältnis: Die Herstellung von Einzelstücken oder Kleinserien von Testhardware mittels AM ist oft wirtschaftlicher als die Einrichtung herkömmlicher Fertigungsstraßen.
- Instrumentierung: AM ermöglicht die Integration von Anschlüssen und Kanälen für Sensoren und Diagnosegeräte direkt in die Prüfdüse.
Auswirkungen auf die Industrie:
Die Einführung von 3D-gedruckten Raketendüsen hat Auswirkungen auf verschiedene Akteure in der Lieferkette der Luft- und Raumfahrt:
- Motorhersteller: Profitieren Sie direkt von verbesserter Leistung, geringerem Gewicht und schnellerer Entwicklung.
- Anbieter von Startdiensten: Erzielung von Wettbewerbsvorteilen durch effizientere und potenziell kostengünstigere Trägerraketen.
- Satelliten-Betreiber: Profitieren Sie von leichteren, besser integrierten und potenziell langlebigeren Antriebssystemen.
- Auftragnehmer im Verteidigungsbereich: Nutzung von AM für die schnelle Entwicklung und Produktion von fortschrittlichen Raketen- und Hyperschallsystemen.
- Lieferanten und Vertreiber von Luft- und Raumfahrtkomponenten: Sie müssen ihr Angebot und ihre Fähigkeiten anpassen, um AM-Teile und -Materialien einzubeziehen und so zu wichtigen Partnern in der sich entwickelnden Fertigungslandschaft zu werden. Unternehmen, die sich auf hochwertige Metallpulver und fortschrittliche Druckverfahren wie Met3dp sind für dieses Ökosystem von entscheidender Bedeutung.
3D-gedruckte Raketendüsen sind nicht nur eine Neuheit in der Herstellung, sondern ein entscheidender Wegbereiter für die nächste Generation von Luft- und Raumfahrtsystemen, die die Grenzen von Leistung, Effizienz und Einsatzfähigkeit in einem breiten Spektrum von Anwendungen erweitern.
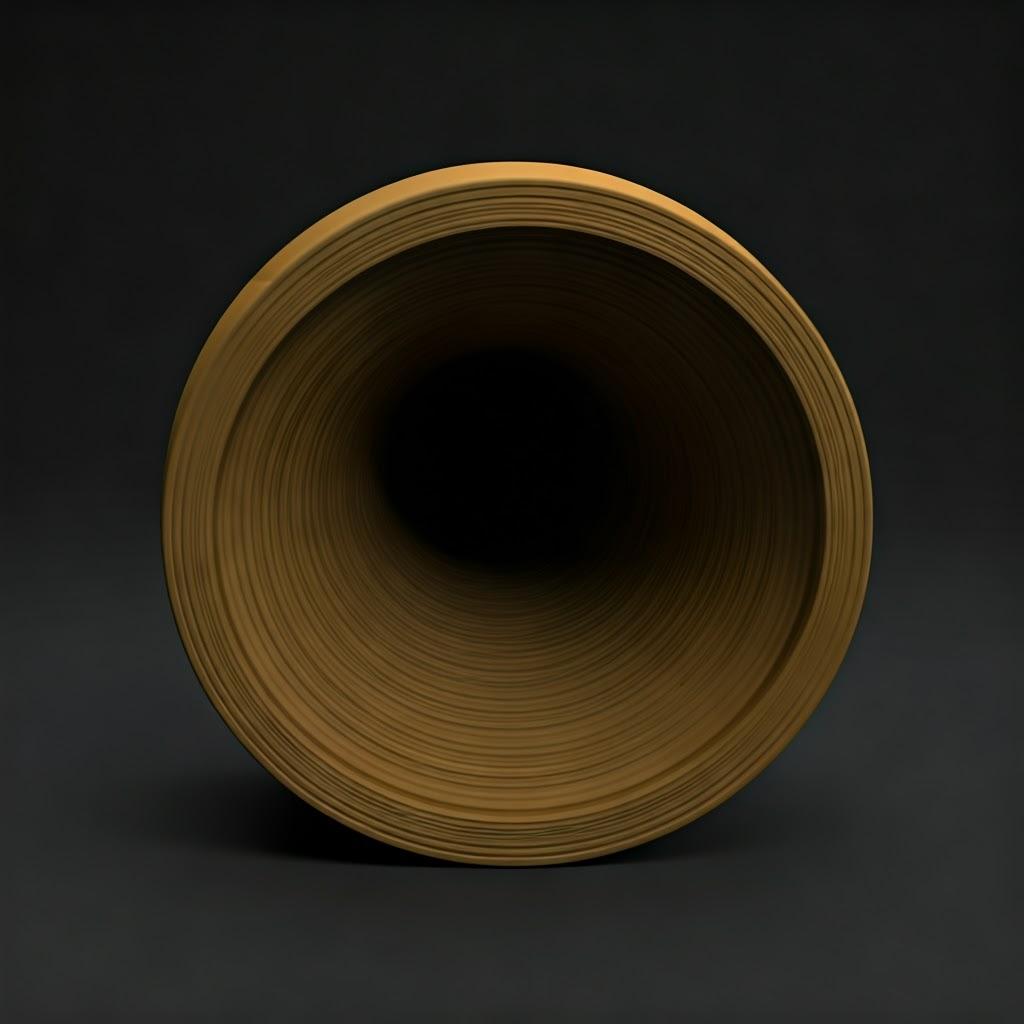
Warum der 3D-Druck von Metall für die Herstellung von Raketendüsen hervorragend geeignet ist
Die Entscheidung, bei einem so kritischen Bauteil wie einer Raketendüse von etablierten, traditionellen Fertigungsverfahren (wie Gießen, Schmieden, Schleudern und Zerspanen) auf die additive Fertigung von Metallen umzusteigen, wird durch eine Reihe von überzeugenden Vorteilen begründet. Der 3D-Metalldruck bietet Lösungen für inhärente Herausforderungen bei herkömmlichen Verfahren, insbesondere bei komplexen Konstruktionen und anspruchsvollen Materialien, die für eine optimale Düsenleistung erforderlich sind. Beschaffungsmanager, Ingenieure und Zulieferer von Luft- und Raumfahrtkomponenten erkennen diese Vorteile als Hauptgründe für die Einführung.
1. Unerreichte geometrische Komplexität:
- Herausforderung (traditionell): Die Herstellung komplizierter interner Merkmale, wie z. B. optimierte konforme Kühlkanäle, die der Innenwandkontur der Düse genau folgen, ist mit Guss oder maschineller Bearbeitung extrem schwierig oder unmöglich. Die Kanäle mussten oft in einfachere Formen gefräst und dann abgedeckt oder durch Zusammenlöten mehrerer Abschnitte geformt werden.
- AM-Lösung: Der schichtweise Aufbau ermöglicht die Erstellung nahezu beliebiger Innengeometrien. Dies ermöglicht:
- Konforme Kühlkanäle: Hocheffiziente Kühlkanäle, die den Wärmeübergang erheblich verbessern und höhere Betriebstemperaturen/-drücke und damit eine bessere Motorleistung (höherer Isp) ermöglichen.
- Integrierte Funktionen: Merkmale wie Einspritzdüsenfrontplatten, Montageflansche oder interne Versteifungsstrukturen können direkt in die Düse als ein einziges Stück eingebaut werden.
- Optimierte Flusspfade: Die Innenkonturen der Düse selbst können für die Strömungsdynamik optimiert werden, ohne dass sie durch herkömmliche Fertigungsbeschränkungen beeinträchtigt werden.
2. Beschleunigte Design-Iteration und Rapid Prototyping:
- Herausforderung (traditionell): Die Herstellung neuer Werkzeuge (Formen, Gesenke, Vorrichtungen) für jede Konstruktionsiteration ist zeitaufwändig und teuer. Die Erprobung neuer Konzepte ist mit langen Vorlaufzeiten verbunden, was die Entwicklungsprogramme für Motoren erheblich verlangsamt.
- AM-Lösung: AM ist ein werkzeugloser Prozess. Die Entwürfe werden direkt vom CAD-Modell zum physischen Teil.
- Geschwindigkeit: Prototyp-Düsen können oft innerhalb von Tagen oder Wochen gedruckt werden, im Vergleich zu Monaten bei herkömmlichen Verfahren.
- Flexibilität: Mehrere Designvariationen können gleichzeitig in einem einzigen Druckvorgang für vergleichende Tests gedruckt werden.
- Geringere Entwicklungskosten: Schnellere Iterationszyklen führen zu kürzeren Entwicklungszeiten und niedrigeren Gesamtprogrammkosten, auch wenn die Kosten pro Teil bei frühen Prototypen höher sind.
3. Erhebliches Potenzial zur Gewichtsreduzierung:
- Herausforderung (traditionell): Um ein geringes Gewicht zu erreichen und gleichzeitig die strukturelle Integrität zu erhalten, sind oft umfangreiche und kostspielige Bearbeitungsvorgänge erforderlich, die zu suboptimalen Konstruktionen führen können.
- AM-Lösung:
- Topologie-Optimierung: Software-Algorithmen können die effizientesten Belastungspfade ermitteln, so dass das Material nur dort platziert wird, wo es strukturell erforderlich ist, was zu organisch anmutenden, hoch optimierten und leichten Konstruktionen führt.
- Gitterförmige Strukturen: Interne Gitter- oder Wabenstrukturen können eine hohe Steifigkeit und Festigkeit bei sehr geringer Dichte bieten, was das Gewicht der Bauteile weiter reduziert.
- Wahl des Materials: Während herkömmliche Methoden die Verwendung einer dichteren Legierung aufgrund von Einschränkungen bei der Herstellbarkeit erzwingen können, kann AM oft optimierte Designs in etwas weniger dichten, aber gleich starken Hochtemperaturlegierungen verarbeiten.
4. Teil Konsolidierung:
- Herausforderung (traditionell): Komplexe Baugruppen wie Düsen bestehen oft aus mehreren Einzelteilen (z. B. Brennkammerschnittstelle, Halsabschnitt, Expansionskegel, Kühlmäntel), die separat hergestellt und dann zusammengefügt werden müssen, in der Regel durch Löten oder Schweißen.
- AM-Lösung: AM ermöglicht die Konsolidierung dieser mehreren Teile zu einer einzigen, monolithischen Komponente.
- Reduzierte Montagezeit und -kosten: Komplexe Fügeverfahren und die damit verbundene Arbeit/Inspektion sind nicht mehr erforderlich.
- Verbesserte Verlässlichkeit: Entfernt Verbindungen, die potenzielle Schwachstellen, Leckagepfade oder Quellen von Eigenspannungen sind.
- Vereinfachte Logistik: Reduziert die Anzahl der Einzelteile, die von Beschaffungsteams und Lieferanten beschafft, verfolgt und verwaltet werden müssen.
5. Verbesserte Materialverwendung und reduzierter Abfall:
- Herausforderung (traditionell): Bei der subtraktiven Bearbeitung, insbesondere von großen Knüppeln oder Schmiedestücken aus teuren Superlegierungen wie Inconel oder Haynes, entsteht ein erheblicher Materialabfall (oft >50-80% des Ausgangsmaterials).
- AM-Lösung: Da es sich um ein additives Verfahren handelt, wird das Material nur dort geschmolzen, wo es benötigt wird.
- Geringeres "Buy-to-Fly"-Verhältnis: Für die Herstellung des Endprodukts wird deutlich weniger Rohmaterial benötigt, was den Abfall drastisch reduziert. Ungenutztes Pulver muss zwar recycelt werden, aber die Materialeffizienz ist insgesamt viel höher.
- Einsparmaßnahmen: Dies gilt insbesondere für teure Superlegierungen, die häufig in Düsen verwendet werden, und führt zu direkten Kosteneinsparungen, die von Großeinkäufern und Herstellern geschätzt werden.
6. Optimierung der Lieferkette und Agilität:
- Herausforderung (traditionell): Die Abhängigkeit von spezialisierten Gießereien oder Schmieden ist oft mit langen Vorlaufzeiten (Monate oder sogar Jahre für bestimmte Legierungen/Formen) und komplexen globalen Lieferketten verbunden.
- AM-Lösung:
- Fertigung auf Abruf: Ermöglicht eine Produktion näher am Ort des Bedarfs oder der Montage, was den Lagerbedarf verringern kann.
- Reduzierte Vorlaufzeiten: Bei etablierten Designs kann AM kürzere Produktionsvorlaufzeiten bieten als das Warten auf Schmiede- oder Gussteile.
- Digitales Inventar: Die Entwürfe können digital gespeichert und bei Bedarf gedruckt werden, was eine größere Flexibilität bietet als die Vorhaltung physischer Bestände. Diese Flexibilität kommt Zulieferern und Händlern von Luft- und Raumfahrtkomponenten zugute, die unterschiedliche Bestände verwalten.
Vergleichende Übersicht: AM vs. Traditionell für Raketendüsen
Merkmal | Traditionelle Fertigung (Guss/Bearbeitung) | Additive Fertigung von Metallen (z. B. LPBF/SEBM) | Vorteil von AM |
---|---|---|---|
Geometrische Komplexität | Begrenzte, insbesondere interne Funktionen | Sehr hoch, ermöglicht konforme Kühlung | Verbesserte Leistung, optimierte Designs |
Entwurf Iteration | Langsam, erfordert Werkzeuge | Schnell, werkzeuglos | Schnelles Prototyping, schnellere Entwicklungszyklen |
Gewicht | Oft schwerer, Optimierung eingeschränkt | Potenzial für eine erhebliche Gewichtsreduzierung | Höhere Nutzlastkapazität, bessere Effizienz |
Anzahl der Teile | Erfordert oft den Zusammenbau mehrerer Teile | Ermöglicht die Konsolidierung in einzelne Teile | Weniger Montageaufwand, höhere Zuverlässigkeit, einfachere Logistik |
Materialabfälle | Hoch (subtraktives Verfahren) | Niedrig (additives Verfahren) | Kosteneinsparungen (insbesondere bei Superlegierungen) |
Vorlaufzeiten | Lang (Werkzeugbau, mehrstufige Prozesse) | Möglicherweise kürzer, insbesondere bei Prototypen | Erhöhte Agilität der Lieferkette |
Werkzeugkosten | Hoch | Keiner | Niedrigere Hürde für neue Designs/geringe Stückzahlen |
In Blätter exportieren
Der 3D-Metalldruck bringt zwar einige besondere Herausforderungen mit sich (auf die später eingegangen wird), doch seine Vorteile in Bezug auf Designfreiheit, Geschwindigkeit, Gewichtsreduzierung und Teilekonsolidierung machen ihn zu einer außerordentlich überzeugenden Technologie für die Herstellung von Hochleistungs-Raketendüsen, die Innovationen in der gesamten Fertigungslandschaft der Luft- und Raumfahrt vorantreibt.
Hochtemperatur-Helden: Empfohlene Metallpulver für Raketendüsen (IN718, IN625, Haynes 282)
Die Fähigkeit einer Raketendüse, dem Inferno der Verbrennung standzuhalten, hängt entscheidend von dem Material ab, aus dem sie hergestellt ist. Bei 3D-gedruckten Düsen bedeutet dies direkt die Wahl des Metallpulvers. Die extremen Temperaturen (oft über 1000 °C, manchmal auch viel höher), der hohe Druck, die korrosiven Verbrennungsprodukte und die starken Temperaturschwankungen erfordern Materialien mit außergewöhnlichen Eigenschaften. Superlegierungen auf Nickelbasis sind die Arbeitspferde in diesem Bereich, da sie ihre Festigkeit auch bei hohen Temperaturen beibehalten, oxidations- und korrosionsbeständig sind und eine gute Ermüdungsfestigkeit aufweisen. Zu den bekanntesten und für die additive Fertigung von Raketendüsen am besten geeigneten Werkstoffen gehören Inconel 718 (IN718), Inconel 625 (IN625) und Haynes 282.
Die Auswahl des richtigen Pulvers ist entscheidend, und die Beschaffung von qualitativ hochwertigem, konsistentem Pulver ist ebenso wichtig. Beschaffungsmanager und Ingenieure sollten mit renommierten Metallpulverlieferanten zusammenarbeiten, die die strengen Anforderungen von Luft- und Raumfahrtanwendungen verstehen. Unternehmen wie Met3dp, die fortschrittliche Pulverherstellungstechniken wie die Gasverdüsung und das Plasma-Rotations-Elektroden-Verfahren (PREP) nutzen, sind auf die Herstellung von Hochleistungs-Sphärische Metallpulver optimiert für AM-Prozesse wie Selective Electron Beam Melting (SEBM) und Laser Powder Bed Fusion (LPBF). Das Portfolio umfasst nicht nur Standardsuperlegierungen, sondern auch innovative Legierungen, die für bestimmte anspruchsvolle Umgebungen maßgeschneidert sind.
Schauen wir uns die Eigenschaften und die Eignung der empfohlenen Pulver genauer an:
1. Inconel 718 (IN718 / Legierung 718)
- Zusammensetzung: Nickel-Chrom-Legierung, ausscheidungshärtbar mit Niob und Molybdän.
- Wichtige Eigenschaften:
- Hohe Festigkeit: Hervorragende Zug-, Ermüdungs- und Kriechbruchfestigkeit bis zu ~700°C (1300°F). Es behält seine gute Festigkeit auch bei höheren Temperaturen für kurze Zeit bei.
- Gut schweißbar/bedruckbar: Eine der am leichtesten mittels AM zu verarbeitenden Superlegierungen, die im Vergleich zu einigen anderen Nickellegierungen gute Schmelzeigenschaften und eine relative Beständigkeit gegen Rissbildung während des Drucks aufweist.
- Korrosionsbeständigkeit: Gute Beständigkeit gegen Oxidation und Korrosion in typischen Verbrennungsumgebungen.
- Verfügbarkeit und Kosten: Relativ weit verbreitet und in der Regel preiswerter als IN625 oder Haynes 282.
- Wärmebehandlung: Erfordert spezielle Ausscheidungshärtungswärmebehandlungen nach dem Druck, um optimale mechanische Eigenschaften zu erzielen.
- Eignung für Raketendüsen:
- Hervorragende Wahl für Anwendungen, bei denen die Betriebstemperaturen anspruchsvoll sind, aber nicht die absoluten Extreme erreichen, die Haynes 282 bewältigt.
- Weit verbreitet für Strukturbauteile im Triebwerk, Düsenflansche und weniger stark beheizte Abschnitte der Düse.
- Seine gute Bedruckbarkeit macht es zu einer häufigen Wahl für komplexe Geometrien und erste Entwicklungsprogramme.
- Erwägungen: Die Festigkeit nimmt oberhalb von ~700°C stärker ab als bei Haynes 282.
2. Inconel 625 (IN625 / Legierung 625)
- Zusammensetzung: Nickel-Chrom-Molybdän-Niob-Legierung, mischkristallverfestigt.
- Wichtige Eigenschaften:
- Ausgezeichnete Korrosionsbeständigkeit: Hervorragende Beständigkeit gegen eine Vielzahl von korrosiven Umgebungen, einschließlich Oxidation und saure Verbrennungsnebenprodukte, selbst bei hohen Temperaturen. Gilt oft als korrosionsbeständiger als IN718.
- Hohe Festigkeit und Zähigkeit: Behält eine gute Festigkeit und Zähigkeit über einen breiten Temperaturbereich bei, von kryogenen Temperaturen bis zu ~815°C (1500°F). Er ist nicht auf Ausscheidungshärtung angewiesen wie IN718.
- Gute Verarbeitbarkeit/Bedruckbarkeit: Gilt allgemein als gut bedruckbar in AM-Verfahren, ähnlich wie IN718.
- Ermüdungsfestigkeit: Weist eine ausgezeichnete Dauerfestigkeit auf.
- Eignung für Raketendüsen:
- Ideal für Bauteile, die stark korrosiven Treibstoffkombinationen oder Umgebungen ausgesetzt sind.
- Wird für Düsenauskleidungen, Brennkammern und Profile verwendet, die eine außergewöhnliche Zähigkeit und Ermüdungsbeständigkeit über ein breites Temperaturspektrum erfordern.
- Sein Festigkeitsprofil ergänzt IN718 und bietet bessere Leistungen in bestimmten Temperatur-/Korrosionsbereichen.
- Erwägungen: Typischerweise geringere Festigkeit als optimal wärmebehandeltes IN718 bei mäßigen Temperaturen (unter ~650°C), behält aber seine Festigkeit bei etwas höheren Temperaturen besser bei. Im Allgemeinen teurer als IN718.
3. Haynes 282
- Zusammensetzung: Nickel-Kobalt-Chrom-Molybdän-Titan-Aluminium-Legierung, ausscheidungshärtbar. Speziell für strukturelle Anwendungen bei hohen Temperaturen entwickelt.
- Wichtige Eigenschaften:
- Außergewöhnliche Festigkeit bei hohen Temperaturen: Bietet im Vergleich zu IN718 und IN625 bei Temperaturen über ~700°C eine höhere Kriechfestigkeit, Zeitstandseigenschaften und Zugfestigkeit und erweitert die Einsatzfähigkeit auf 900°C (1650°F) und höher für bestimmte Belastungsbedingungen.
- Gute Verarbeitbarkeit/Bedruckbarkeit: Sie wurde mit Blick auf die Verarbeitbarkeit entwickelt und weist für eine solche Hochleistungslegierung eine relativ gute Druckbarkeit auf, obwohl sie möglicherweise eine sorgfältigere Parameteroptimierung als IN718/IN625 erfordert.
- Gute Oxidationsbeständigkeit: Ausgezeichnete Beständigkeit gegen Hochtemperaturoxidation.
- Thermische Stabilität: Behält seine mikrostrukturelle Stabilität auch nach langer Exposition bei hohen Temperaturen bei.
- Wärmebehandlung: Erfordert eine Wärmebehandlung durch Ausscheidungshärtung.
- Eignung für Raketendüsen:
- Die erste Wahl für die anspruchsvollsten Anwendungen, wie z. B. die heißesten Abschnitte des Düsenhalses und des Expansionskegels in Hochleistungs-Flüssigkeitsraketentriebwerken oder Hyperschall-Luftatmungsmotoren.
- Wird gewählt, wenn IN718 oder IN625 die erforderlichen Festigkeits- oder Kriechwiderstandskriterien bei Spitzenbetriebstemperaturen nicht erfüllen können.
- Erwägungen: Die teuerste der drei Legierungen. Die Verarbeitungsparameter beim AM müssen sorgfältig kontrolliert werden, um Eigenspannungen zu bewältigen und eine optimale Mikrostruktur zu gewährleisten.
Die Qualität des Pulvers - ein entscheidender Faktor
Unabhängig von der gewählten Legierung ist die Qualität des Metallpulver-Rohmaterials für die Herstellung zuverlässiger, flugtauglicher Raketendüsen unverzichtbar. Zu den wichtigsten Pulvereigenschaften gehören:
- Sphärizität: Hochkugelförmige Partikel gewährleisten eine gute Fließfähigkeit des Pulvers und eine hohe Packungsdichte im Pulverbett, was zu dichteren, gleichmäßigeren Teilen führt. Technologien wie PREP, die von Anbietern wie Met3dp eingesetzt werden, zeichnen sich durch die Herstellung hochsphärischer Pulver aus.
- Partikelgrößenverteilung (PSD): Ein kontrollierter PSD ist entscheidend für ein gleichmäßiges Schmelzverhalten und die Auflösung des fertigen Teils. Das optimale PSD hängt von der jeweiligen AM-Maschine und dem Verfahren ab (LPBF verwendet in der Regel feinere Pulver als SEBM).
- Reinheit und Chemie: Ein geringer Gehalt an Verunreinigungen (insbesondere Sauerstoff und Stickstoff) und die genaue Einhaltung der chemischen Spezifikation der Legierung sind für die Erzielung der gewünschten mechanischen Eigenschaften und die Vermeidung von Defekten unerlässlich.
- Fließfähigkeit: Die gute Fließfähigkeit sorgt für eine gleichmäßige Verteilung der Pulverschichten während des Druckvorgangs und verhindert Hohlräume und Unregelmäßigkeiten.
- Abwesenheit von Satelliten: Die Minimierung kleinerer Partikel, die an größeren Partikeln (Satelliten) haften, verbessert die Fließfähigkeit und die Packungsdichte.
Vergleich der Materialeigenschaften (typische Werte bei Raumtemperatur nach geeigneter Wärmebehandlung)
Eigentum | IN718 (AMS 5663) | IN625 (AMS 5666) | Haynes 282 (AMS 5951) | Einheit | Anmerkungen |
---|---|---|---|---|---|
Endgültige Zugfestigkeit | ~1380 (200) | ~930 (135) | ~1180 (171) | MPa (ksi) | Die Stärke variiert stark mit der Temperatur. |
Streckgrenze (0.2%) | ~1170 (170) | ~520 (75) | ~780 (113) | MPa (ksi) | Die Stärke variiert stark mit der Temperatur. |
Dehnung | ~20% | ~45% | ~30% | % | Indikator für Duktilität |
Maximale Einsatztemperatur (Stärke begrenzt) | ~700 (1300) | ~815 (1500) | ~900+ (1650+) | °C (°F) | Ungefähr, abhängig von Belastung und Zeit |
Dichte | 8.19 | 8.44 | 8.33 | g/cm³ | |
Relative Kosten | Basis | Höher | Höchste | – | Allgemeiner Vergleich |
Mechanismus der primären Stärke | Ausscheidungshärtung | Solide Lösung | Ausscheidungshärtung | – | Beeinflusst den Wärmebehandlungsbedarf |
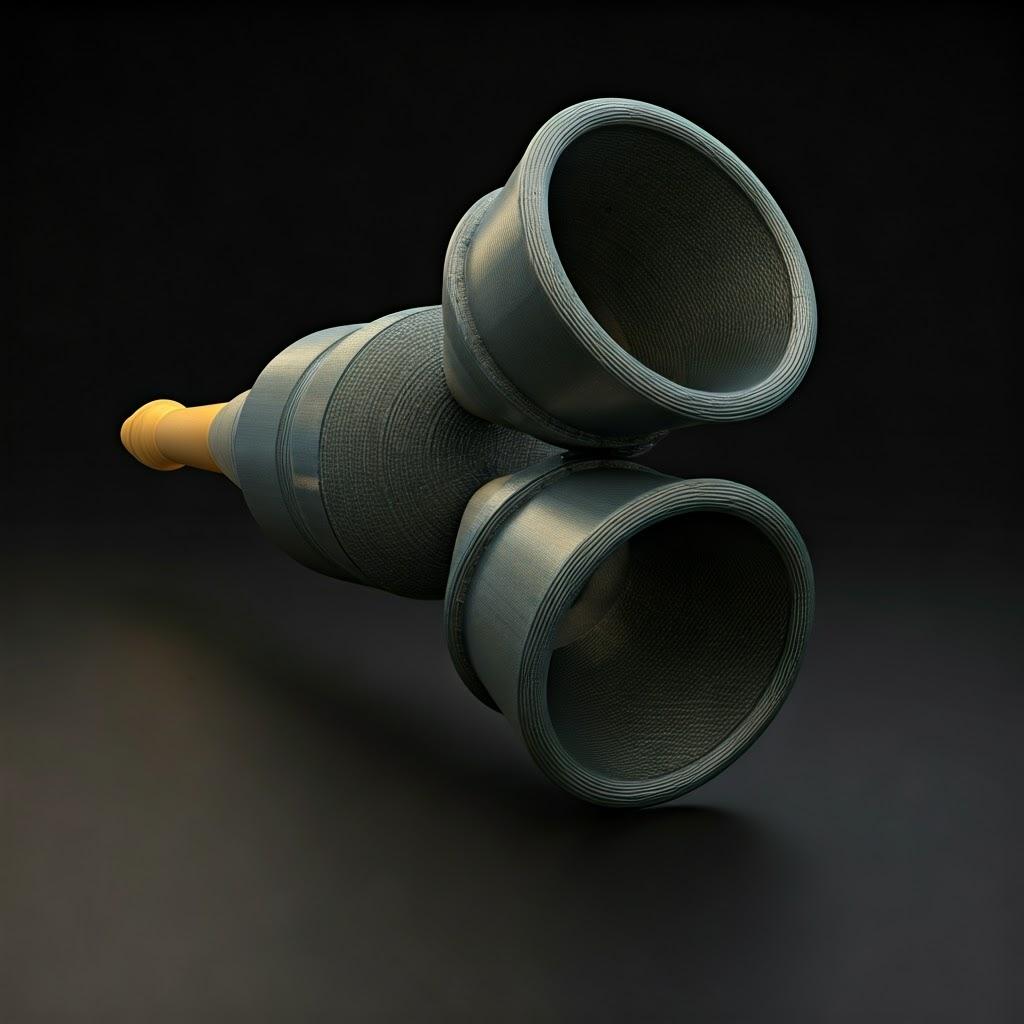
In Blätter exportieren
Hinweis: Dies sind typische Werte; die tatsächlichen Eigenschaften von AM-Teilen hängen stark von den Druckparametern, der Bauausrichtung und den Wärmebehandlungen nach dem Prozess ab.
Die Wahl des richtigen Hochtemperatur-Superlegierungspulvers ist eine Balance zwischen Leistungsanforderungen (Temperatur, Spannung, Korrosion), Herstellbarkeit durch AM und Kosten. IN718 bietet eine solide Grundlage, IN625 bietet eine hervorragende Korrosionsbeständigkeit und Zähigkeit, während Haynes 282 eine unvergleichliche Festigkeit bei höchsten Temperaturen bietet, was die Herstellung von robusten und effizienten 3D-gedruckten Raketendüsen für die anspruchsvollsten Luft- und Raumfahrtanwendungen ermöglicht. Die Zusammenarbeit mit sachkundigen Materiallieferanten und AM-Dienstleistern ist der Schlüssel zum Erfolg bei diesen Entscheidungen. Quellen und verwandte Inhalte
Entwerfen für additiven Erfolg: Optimierung von Raketendüsen für den 3D-Druck
Die additive Fertigung eröffnet eine unglaubliche Designfreiheit, aber wenn man einfach eine konventionell konstruierte Raketendüse nimmt und sie druckt, werden selten optimale Ergebnisse erzielt. Um die Vorteile der additiven Fertigung voll ausschöpfen zu können - insbesondere bei komplexen Komponenten wie Düsen, die unter extremen Bedingungen arbeiten - müssen Ingenieure die Grundsätze des Design for Additive Manufacturing (DfAM) anwenden. DfAM bedeutet, den Konstruktionsprozess von Grund auf zu überdenken und dabei die einzigartigen Fähigkeiten und Einschränkungen des gewählten AM-Prozesses (wie LPBF oder SEBM) und des Materials (wie IN718, IN625 oder Haynes 282) zu berücksichtigen. Die Optimierung eines Raketendüsendesigns für AM ist entscheidend für das Erreichen der gewünschten Leistung, die Gewährleistung der Herstellbarkeit, die Minimierung der Nachbearbeitung und die Kostenkontrolle.
Wichtige DfAM-Überlegungen für Raketendüsen:
- Geometrische Komplexität für mehr Leistung nutzen:
- Konforme Kühlkanäle: Dies ist vielleicht der wichtigste Vorteil, den AM für Düsen bietet. Anstelle von einfachen gebohrten oder gefrästen Kanälen ermöglicht AM den Konstrukteuren, komplizierte Netzwerke zu schaffen, die der exakten Kontur der Düsenwand folgen und einen genauen Abstand zum Heißgasstrom einhalten.
- Vorteile: Maximierte Wärmeabfuhr, gleichmäßigere Wandtemperaturen, geringere thermische Belastung, Potenzial für höhere Kammerdrücke/-temperaturen, was zu einem verbesserten spezifischen Impuls (Isp) führt.
- DfAM-Taktik: Entwerfen Sie Kanäle mit sanften Kurven, vermeiden Sie scharfe Ecken, in denen sich Spannungen konzentrieren können, ziehen Sie unterschiedliche Kanalquerschnitte in Betracht (z. B. elliptisch oder rechteckig), um den Durchfluss und die Wärmeübertragung zu optimieren, und stellen Sie sicher, dass die Kanäle nach Möglichkeit selbsttragend sind oder so konstruiert sind, dass das Pulver leicht entfernt werden kann.
- Integrierte Funktionen: Kombinieren Sie Elemente wie Einspritzflächen, kardanische Schnittstellen, Montageflansche, Sensoranschlüsse oder sogar strukturelle Halterungen direkt in den Düsendruck.
- Vorteile: Geringere Anzahl von Teilen, keine Verbindungen (Schweißnähte/Lötstellen), geringere Komplexität der Montage, Gewichtseinsparungen.
- DfAM-Taktik: Sorgen Sie für weiche Übergänge zwischen den Merkmalen, berücksichtigen Sie Spannungskonzentrationen an Verbindungsstellen und konstruieren Sie Schnittstellen mit angemessenen Toleranzen für eine mögliche Nachbearbeitung.
- Konforme Kühlkanäle: Dies ist vielleicht der wichtigste Vorteil, den AM für Düsen bietet. Anstelle von einfachen gebohrten oder gefrästen Kanälen ermöglicht AM den Konstrukteuren, komplizierte Netzwerke zu schaffen, die der exakten Kontur der Düsenwand folgen und einen genauen Abstand zum Heißgasstrom einhalten.
- Verwaltung von Stützen und Überhängen:
- Selbsttragende Winkel: Die meisten Pulverbettschmelzverfahren können Überhänge bis zu einem bestimmten Winkel (in der Regel etwa 45 Grad zur Horizontalen) drucken, ohne dass Stützstrukturen erforderlich sind. Wenn Sie die Merkmale so gestalten, dass sie innerhalb dieser Grenze bleiben, wird die Verwendung von Stützen minimiert.
- Strategie unterstützen: Wo Stützen erforderlich sind (z. B. bei horizontalen Flächen, steilen Überhängen oder großen inneren Hohlräumen), müssen sie sorgfältig geplant werden.
- Zweck: Verankerung des Teils auf der Bauplatte, Verhinderung von Verformungen durch thermische Spannungen, Unterstützung überhängender Merkmale während des Bauprozesses.
- DfAM-Taktik: Entwerfen Sie Stützen, die stark genug, aber leicht zu entfernen sind, ohne die Oberfläche des Teils zu beschädigen, minimieren Sie die Kontaktfläche zwischen der Stütze und dem Teil ("Stütznarben"), verwenden Sie baumartige oder gitterartige Stützen, um Material zu sparen und die Entfernungszeit zu verringern, und richten Sie das Teil auf der Bauplatte aus, um den Bedarf an Stützen für kritische Oberflächen zu minimieren. Bei internen Kanälen ist es wichtig, dass sie selbsttragend sind oder klare Wege für die Entnahme des Pulvers gewährleistet sind.
- Entfernung von Puder: Interne Kanäle und komplexe Hohlräume müssen so konstruiert sein, dass sie nach dem Bau des Bauteils zugänglich sind, um ungeschmolzenes Pulver zu entfernen. Eingeschlossenes Pulver kann das Gewicht erhöhen und bei der Wärmebehandlung versintern, was zu Problemen führen kann.
- Wanddicke und Größe der Merkmale:
- Mindestwanddicke: AM-Prozesse haben Grenzen für die minimale Wandstärke, die sie zuverlässig herstellen können (abhängig von Maschine, Material und Parametern). Die Konstrukteure müssen sicherstellen, dass die Wände, insbesondere in dünnen Abschnitten der Düsenverlängerung oder der Kühlkanäle, diesen Mindestwerten entsprechen (oft ~0,4-1,0 mm).
- Merkmal Auflösung: Kleine Merkmale wie Kühlkanaleingänge/-ausgänge oder feine Details müssen unter Berücksichtigung der Auflösungsgrenzen des AM-Prozesses (Strahlfleckgröße, Schichtdicke) entworfen werden.
- Einheitlichkeit: Es ist zwar möglich, die Dicke zu variieren, aber die Beibehaltung einer relativ gleichmäßigen Wanddicke kann helfen, thermische Gradienten zu bewältigen und Eigenspannungen während des Drucks zu reduzieren. Abrupte Änderungen sollten fließend ineinander übergehen.
- Wärmemanagement und Eigenspannung:
- Mechanismus: Die schnelle Erwärmung und Abkühlung, die mit AM einhergeht, führt zu erheblichen thermischen Gradienten und damit zu inneren Eigenspannungen innerhalb des Teils. Übermäßige Spannungen können zu Verzug, Verformung beim Entfernen von der Bauplatte oder sogar zu Rissen führen, insbesondere bei spröden Hochtemperaturlegierungen.
- DfAM-Taktik:
- Orientierung: Wählen Sie die Bauausrichtung sorgfältig aus, um die Stressakkumulation zu bewältigen und den Bedarf an Stützen in kritischen Bereichen zu minimieren.
- Geometrie: Verwenden Sie Verrundungen und Radien anstelle von scharfen Ecken, streben Sie nach Möglichkeit eine gleichmäßige Materialverteilung an, und verwenden Sie die Topologieoptimierung, um unnötiges Material zu entfernen, das zu Spannungen beitragen könnte.
- Simulation: Verwenden Sie Prozesssimulationssoftware, um thermische Gradienten und Eigenspannungsverteilung auf der Grundlage des Designs und der geplanten Druckparameter vorherzusagen. Dies ermöglicht Designänderungen vor Drucken, um mögliche Probleme zu entschärfen.
- Unterstützende Strukturen: Gut konzipierte Stützen können dazu beitragen, das Teil zu verankern und Verformungskräften zu widerstehen.
- Topologie-Optimierung und Gewichtsreduzierung:
- Konzept: Verwendung von Software-Tools zur Optimierung der Materialauslegung innerhalb eines definierten Konstruktionsraums auf der Grundlage der angewandten Lasten, Einschränkungen und Leistungsziele (z. B. Maximierung der Steifigkeit bei gleichzeitiger Minimierung des Gewichts).
- Anwendung auf Düsen: Während die primäre Düsenkontur durch die Strömungsdynamik vorgegeben ist, können Strukturelemente wie Flansche, Rippen oder Montagehalterungen häufig topologisch optimiert werden.
- Gitterförmige Strukturen: Durch das Ersetzen von Vollprofilen durch interne Gitterstrukturen kann das Gewicht drastisch reduziert werden, während die erforderliche Steifigkeit und Festigkeit erhalten bleibt. Dies ist besonders nützlich für strukturelle Ummantelungen oder Stützelemente rund um die Düse.
- Erwägungen: Sicherstellen, dass die optimierten Strukturen mittels AM herstellbar sind (z. B. Dicke der Gitterstreben, Knotenverbindungen), Berücksichtigung der Ermüdungsleistung und Validierung der Entwürfe durch Simulation und Tests.
- Entwerfen für die Nachbearbeitung:
- Zulagen für die Bearbeitung: Wenn kritische Schnittstellen (z. B. Montageflansche, Dichtungsflächen) enge Toleranzen erfordern, die nur durch CNC-Bearbeitung erreicht werden können, müssen die Konstrukteure für diese Bereiche im AM-Design zusätzliches Material (Bearbeitungsmaterial) bereitstellen.
- Oberfläche: Informieren Sie sich über die Möglichkeiten der Oberflächenbeschaffenheit des gewählten AM-Prozesses (SEBM erzeugt im Allgemeinen rauere Oberflächen als LPBF). Wenn eine glattere Oberfläche für die Strömungsdynamik oder die Abdichtung erforderlich ist, muss das Teil so konstruiert werden, dass es für das Polieren oder die Bearbeitung zugänglich ist.
- Zugang zur Inspektion: Bei der Konstruktion des Teils ist zu berücksichtigen, wie die zerstörungsfreie Prüfung (ZfP), z. B. durch CT-Scannen oder Ultraschallprüfung, durchgeführt werden soll, um sicherzustellen, dass die innere Integrität überprüft werden kann.
DfAM umarmen:
Die erfolgreiche Umsetzung von DfAM erfordert eine enge Zusammenarbeit zwischen Konstrukteuren, Werkstoffwissenschaftlern und Experten für AM-Verfahren. Oft handelt es sich um einen iterativen Prozess von Design, Simulation, Druck von Testkupons oder Prototypen und Verfeinerung. Dies erfordert zwar eine andere Denkweise als bei der traditionellen spanenden Fertigung, doch der Nutzen in Form von Leistungssteigerungen, Gewichtsreduzierung und Fertigungseffizienz für Komponenten wie Raketendüsen ist beträchtlich. Die Zusammenarbeit mit einem erfahrenen 3D-Druck-Dienstleister für Metall der die DfAM-Prinzipien versteht, ist entscheidend für die Umsetzung fortschrittlicher Designs in flugtaugliche Hardware.
Erreichen von Präzision: Toleranz, Oberflächengüte und Maßgenauigkeit bei 3D-gedruckten Düsen
Während die additive Fertigung eine beispiellose geometrische Freiheit bietet, ist das Verständnis und die Kontrolle der erreichbaren Präzision - Toleranzen, Oberflächengüte und allgemeine Maßgenauigkeit - für funktionale Komponenten wie Raketendüsen von entscheidender Bedeutung. Schnittstellen müssen korrekt zusammenpassen, fluiddynamische Oberflächen benötigen vorhersehbare Eigenschaften, und das endgültige Teil muss den technischen Spezifikationen innerhalb akzeptabler Grenzen entsprechen. Luft- und Raumfahrtingenieure und Beschaffungsmanager müssen realistische Erwartungen haben, die auf dem gewählten AM-Prozess, dem Material und den Nachbearbeitungsschritten basieren.
1. Maßgenauigkeit:
- Definition: Wie genau die Abmessungen des endgültigen gedruckten Teils mit den im CAD-Modell angegebenen Nennmaßen übereinstimmen.
- Beeinflussende Faktoren:
- AM-Prozess: Verschiedene AM-Technologien haben unterschiedliche Genauigkeitsstufen. Das Laser Powder Bed Fusion (LPBF) bietet im Allgemeinen eine höhere Genauigkeit und eine feinere Auflösung der Merkmale als das Elektronenstrahlschmelzen (SEBM), da der Strahlfleck kleiner und die Pulver-/Schichtdicke feiner ist. Allerdings treten beim SEBM häufig geringere Eigenspannungen auf, was bei größeren Teilen zu weniger Verzug führen kann.
- Kalibrierung der Maschine: Die regelmäßige Kalibrierung der Scanner, der Energiequelle und der Bewegungssysteme des AM-Systems ist entscheidend.
- Materialeigenschaften: Die Wärmeausdehnungs- und Schrumpfungseigenschaften der jeweiligen Legierung (IN718, IN625, Haynes 282) beeinflussen die endgültigen Abmessungen.
- Größe und Geometrie der Teile: Größere Teile und komplexe Geometrien sind anfälliger für thermische Verformung und Abweichung.
- Orientierung aufbauen: Die Ausrichtung des Teils auf der Bauplatte hat Auswirkungen auf die Wärmeverteilung, die Anforderungen an die Unterstützung und die möglichen Schrumpfungs-/Verzugsrichtungen.
- Thermische Belastung: Während des Drucks aufgebaute Eigenspannungen können zu Verformungen führen, insbesondere nach der Entnahme des Teils von der Bauplatte oder während spannungsabbauender Wärmebehandlungen.
- Nachbearbeiten: Wärmebehandlungen (z. B. HIP oder Spannungsabbau) können zu leichten Maßänderungen führen. Die maschinelle Bearbeitung wird häufig eingesetzt, um die endgültige Genauigkeit bei kritischen Merkmalen zu erreichen.
- Typische erreichbare Genauigkeit (As-Built):
- LPBF: Im Allgemeinen im Bereich von ±0,1 mm bis ±0,2 mm (±0,004″ bis ±0,008″) oder ±0,1-0,2% der Abmessung für gut kontrollierte Prozesse.
- SEBM: Normalerweise im Bereich von ±0,2 mm bis ±0,4 mm (±0,008″ bis ±0,016″) oder ±0,2-0,4% der Abmessung.
- Erzielung engerer Toleranzen: Für kritische Abmessungen (z. B. Halsdurchmesser, Flanschschnittstellen, Dichtungsnuten) sind oft engere Toleranzen als die des Ist-Zustandes erforderlich. Diese werden in der Regel durch CNC-Bearbeitung nach dem Druck erreicht, wobei Toleranzen von ±0,01 mm bis ±0,05 mm (±0,0004″ bis ±0,002″) machbar sind. Die DfAM-Grundsätze schreiben vor, dass in diesen Bereichen zusätzliches Rohmaterial zu bearbeiten ist.
2. Oberflächengüte (Rauhigkeit):
- Definition: Das Maß für die feinen Unregelmäßigkeiten auf der Oberfläche eines Teils, typischerweise quantifiziert durch Ra (durchschnittliche Rauheit).
- Beeinflussende Faktoren:
- AM-Prozess: SEBM erzeugt naturgemäß rauere Oberflächen (Ra typischerweise 20-40 µm) aufgrund größerer Pulverpartikel und eines höheren Energieeintrags, der ein teilweises Sintern des umgebenden Pulvers bewirkt. LPBF erzeugt glattere Oberflächen (Ra typischerweise 5-15 µm) aufgrund des feineren Pulvers und kleinerer Schmelzbäder.
- Schichtdicke: Dünnere Schichten führen in der Regel zu glatteren Oberflächen, insbesondere bei schrägen oder gekrümmten Flächen (Verringerung des Treppeneffekts).
- Orientierung aufbauen: Oberflächen, die parallel zur Bauplatte verlaufen (nach oben/unten weisend), haben in der Regel andere Rauheitseigenschaften als vertikale Wände. Nach unten weisende Oberflächen, für die Stützen erforderlich sind, weisen nach dem Entfernen der Stützen oft die schlechteste Oberfläche auf.
- Eigenschaften des Pulvers: Partikelgrößenverteilung und Sphärizität beeinflussen das Finish.
- Laser-/Elektronenstrahl-Parameter: Energiedichte, Scangeschwindigkeit und Schraffurstrategie wirken sich auf die Dynamik des Schmelzbades und die Oberflächenbeschaffenheit aus.
- Unterstützung bei der Entfernung: Die mechanische Entfernung von Trägern kann Spuren oder Narben hinterlassen und die lokale Rauheit erhöhen.
- Bedeutung für Düsen:
- Interne Oberflächen: Die Oberflächenrauheit im Inneren der Düse wirkt sich auf die Fluiddynamik (Grenzschichtentwicklung, Reibungsverluste) und die Wärmeübertragung aus. Eine extrem glatte Oberfläche ist zwar nicht immer notwendig oder vorteilhaft (eine leichte Rauheit kann manchmal die turbulente Wärmeübertragung verbessern), aber eine kontrollierte und vorhersehbare Oberfläche ist wichtig.
- Externe Oberflächen: Weniger wichtig für die Leistung, kann aber für die Inspektion oder Ästhetik wichtig sein.
- Versiegeln von Oberflächen: Schnittstellen, die abgedichtet werden müssen, benötigen eine viel glattere Oberfläche, als sie im Ist-Zustand erreicht werden kann, was eine Nachbearbeitung wie z. B. maschinelles Bearbeiten oder Polieren erfordert.
- Verbesserung der Oberflächengüte:
- Optimierung der Parameter: Die Feinabstimmung der Parameter des AM-Prozesses kann die Qualität des Endprodukts geringfügig verbessern.
- Abrasives Strahlen/Trommeln: Kann für ein gleichmäßigeres mattes Finish sorgen und einige lose anhaftende Partikel entfernen, reduziert aber Ra nur geringfügig.
- Chemisches Polieren/Ätzen: Kann Oberflächen deutlich glätten, erfordert aber eine sorgfältige Kontrolle, damit die Abmessungen nicht verändert werden.
- Abrasive Fließbearbeitung (AFM): Lässt abrasive Medien durch interne Kanäle fließen, um sie zu glätten.
- CNC-Bearbeitung/Schleifen/Polieren: Die gängigsten Methoden zur Erzielung glatter (Ra < 1 µm) und präziser Oberflächen an zugänglichen Merkmalen.
3. Tolerierungsnormen:
- GD&T (Geometrische Dimensionierung und Tolerierung): Unverzichtbar für eine klare Kommunikation der Konstruktionsabsicht. Zeichnungen für AM-Teile sollten wie bei traditionell gefertigten Teilen GD&T-Kennzeichnungen verwenden, die Toleranzen für Größe, Form, Ausrichtung, Position und Rundlauf angeben.
- ISO/ASTM-Normen: Normen, die speziell für die additive Fertigung gelten (z. B. die ISO/ASTM 52900-Reihe), bieten eine Terminologie und einen Rahmen, aber spezifische Toleranzklassen verweisen oft immer noch auf allgemeine technische Normen (wie ISO 2768 für allgemeine Toleranzen, obwohl ihre direkte Anwendbarkeit auf AM umstritten ist). Konstrukteure müssen die geforderten Toleranzen auf Zeichnungen ausdrücklich angeben.
Präzision in der Praxis erreichen:
Um die erforderliche Präzision für eine 3D-gedruckte Raketendüse zu erreichen, ist ein ganzheitlicher Ansatz erforderlich:
- DfAM: Entwurf unter Berücksichtigung von Prozessbeschränkungen und Nachbearbeitungsanforderungen.
- Prozesskontrolle: Einsatz von hochwertigen AM-Systemen mit robuster Prozessüberwachung und -steuerung. Met3dp legt bei seinen Druckern Wert auf ein branchenführendes Druckvolumen, Genauigkeit und Zuverlässigkeit.
- Materialqualität: Verwendung von konsistenten, hochwertigen Metallpulvern.
- Simulation: Vorhersage und Kompensation von Verzerrungen.
- Strategische Nachbearbeitung: Planung und Durchführung der erforderlichen Schritte wie Wärmebehandlung und Präzisionsbearbeitung.
- Metrologie und Inspektion: Einsatz genauer Messtechniken (CMM, 3D-Scanning) zur Überprüfung der Konformität.
Durch das Verständnis der Möglichkeiten und Grenzen von AM-Prozessen und die Integration von DfAM- und Nachbearbeitungsstrategien können Ingenieure mit Zuversicht 3D-gedruckte Raketendüsen entwerfen und herstellen, die die anspruchsvollen Präzisionsanforderungen von Luft- und Raumfahrtanwendungen erfüllen.
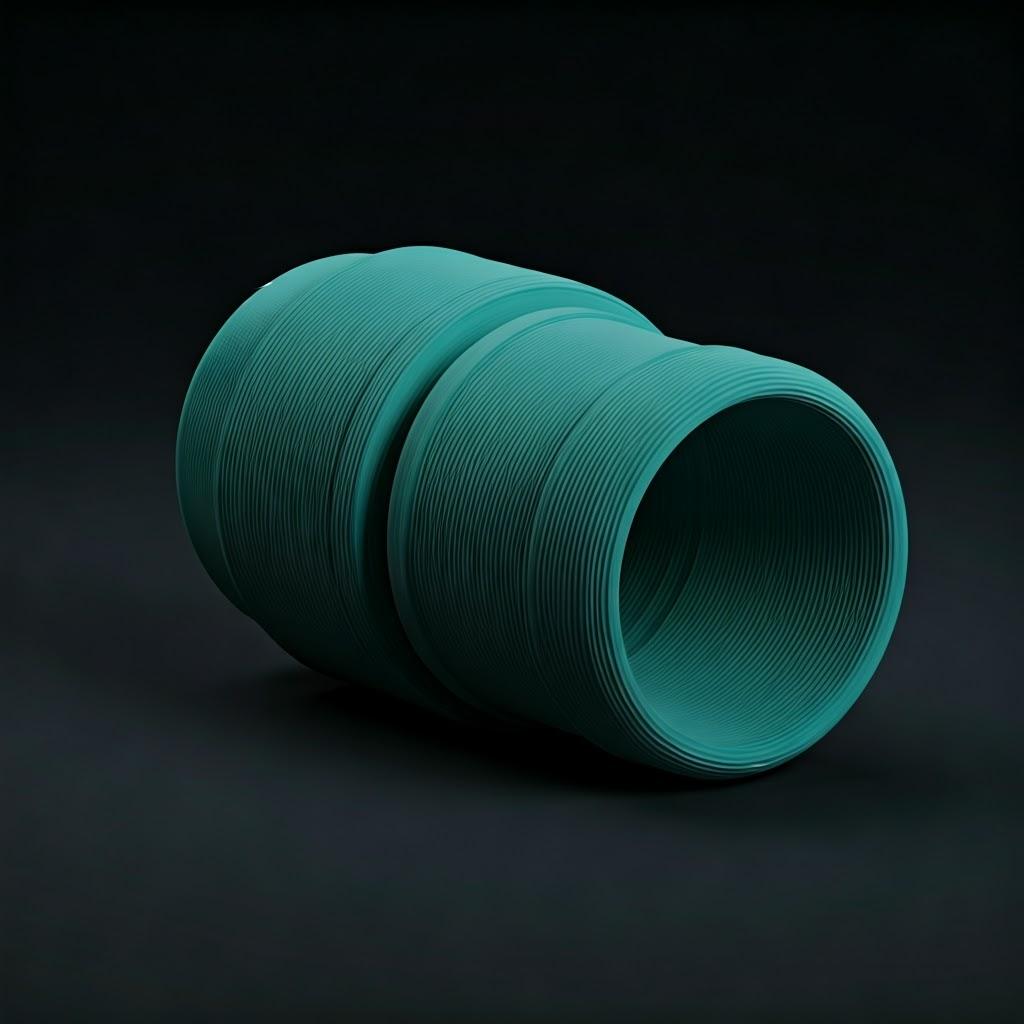
Über den Bau hinaus: Wichtige Nachbearbeitung für 3D-gedruckte Raketendüsen
Der Abschluss des Druckzyklus auf einer additiven Fertigungsmaschine ist ein wichtiger Meilenstein, aber nur selten der letzte Schritt zur Herstellung einer funktionalen, flugfähigen Raketendüse. In der Regel ist eine Reihe entscheidender Nachbearbeitungsschritte erforderlich, um das fertige Bauteil in ein fertiges Teil umzuwandeln, das den strengen Anforderungen der Luft- und Raumfahrtindustrie in Bezug auf mechanische Eigenschaften, Maßhaltigkeit, Oberflächengüte und Gesamtintegrität entspricht. Die Planung dieser Schritte ist ein wesentlicher Bestandteil des Fertigungsablaufs und wirkt sich auf die Gesamtkosten und die Vorlaufzeit aus.
Gemeinsame Nachbearbeitungsschritte für AM-Raketendüsen:
- Entstaubung / Entpuderung:
- Zweck: Zur Entfernung des gesamten ungeschmolzenen Metallpulvers aus dem fertigen Bauteil, insbesondere aus internen Kanälen, Hohlräumen und komplexen Geometrien.
- Methoden: Manuelles Bürsten, Staubsaugen, Ausblasen mit Druckluft, leichtes Vibrieren oder Taumeln. Automatisierte Entpuderungssysteme werden immer häufiger eingesetzt. Die in der DfAM-Phase konzipierten Zugangsöffnungen sind für eine wirksame Reinigung der internen Kühlkanäle von entscheidender Bedeutung.
- Wichtigkeit: Eingeschlossenes Pulver erhöht das Gewicht unnötig, kann nachfolgende Prozesse (wie HIP) stören und sich möglicherweise während des Betriebs lösen. Eine unvollständige Pulverentfernung ist ein erhebliches Qualitätsproblem.
- Stressabbau Wärmebehandlung:
- Zweck: Um die hohen inneren Eigenspannungen zu reduzieren, die während der schnellen Heiz- und Kühlzyklen des AM-Prozesses entstehen. Diese Spannungen können Verformungen verursachen, wenn das Teil von der Bauplatte entfernt wird, oder zu einem vorzeitigen Versagen führen.
- Methode: Erhitzen des Teils (oft noch auf der Bauplatte) auf eine bestimmte Temperatur unterhalb der Alterungs- oder Lösungstemperatur der Legierung, Halten des Teils für einen bestimmten Zeitraum und anschließendes langsames Abkühlen. Die Parameter hängen stark von der Legierung (IN718, IN625, Haynes 282) und der Teilegeometrie ab.
- Wichtigkeit: Unverzichtbar für die Dimensionsstabilität und zur Vermeidung von Rissen, insbesondere vor dem Entfernen von Stützen oder des Teils von der Bauplatte.
- Entfernen von der Bauplatte und Entfernen der Stützstruktur:
- Zweck: Trennen der gedruckten Düse(n) von der Metallgrundplatte, auf der sie gebaut wurden, und Entfernen aller temporären Stützstrukturen, die während des Baus verwendet wurden.
- Methoden: In der Regel wird das Teil durch Drahterodieren (Electrical Discharge Machining) oder Bandsägen von der Platte getrennt. Stützen werden manuell (Brechen, Schneiden, Schleifen) oder manchmal durch maschinelle Bearbeitung entfernt.
- Wichtigkeit: Erfordert eine vorsichtige Handhabung, um eine Beschädigung des Teils zu vermeiden. Das Entfernen von Halterungen kann die Oberflächenbeschaffenheit in den Kontaktbereichen beeinträchtigen ("Zeugenspuren"). DfAM zielt darauf ab, Stützen zu minimieren und sie leicht zugänglich zu machen.
- Heiß-Isostatisches Pressen (HIP):
- Zweck: Eliminierung der internen Porosität (kleine Hohlräume), die in AM-Bauteilen vorhanden sein kann, wodurch mechanische Eigenschaften wie Ermüdungsfestigkeit, Duktilität und Bruchzähigkeit verbessert werden.
- Methode: Das Teil wird in einem speziellen HIP-Gefäß gleichzeitig einer hohen Temperatur (unter dem Schmelzpunkt) und einem hohen Inertgasdruck (normalerweise Argon) ausgesetzt. Der Druck verschließt die inneren Hohlräume, und die hohe Temperatur ermöglicht die Bildung metallurgischer Verbindungen an den geschlossenen Porengrenzflächen.
- Wichtigkeit: Wird häufig für kritische Bauteile in der Luft- und Raumfahrt, einschließlich Düsen, als obligatorisch angesehen, um Eigenschaften zu erzielen, die denen von Knet- oder Gusswerkstoffen gleichwertig oder sogar überlegen sind, und um eine maximale Dichte (in der Regel >99,9%) zu gewährleisten. Außerdem trägt es zur weiteren Reduzierung der Eigenspannung bei.
- Lösungsglühen und Alterungswärmebehandlungen (Ausscheidungshärtung):
- Zweck: Zur Erzielung des gewünschten endgültigen Gefüges und optimaler mechanischer Eigenschaften (Festigkeit, Härte, Kriechfestigkeit) bei ausscheidungshärtbaren Legierungen wie IN718 und Haynes 282. (IN625 ist mischkristallverfestigt und muss möglicherweise nur geglüht werden).
- Methode: Beinhaltet spezifische Heizzyklen:
- Lösungsglühen: Erhitzen auf eine hohe Temperatur, um Ausfällungen aufzulösen und eine homogene feste Lösung zu schaffen, gefolgt von einer schnellen Abkühlung.
- Alterung (Ausscheidungshärtung): Wiedererwärmung auf eine oder mehrere Zwischentemperaturen für bestimmte Zeiten, um eine kontrollierte Bildung feiner verfestigender Ausscheidungen innerhalb der Metallmatrix zu ermöglichen.
- Wichtigkeit: Absolut entscheidend für die Entwicklung der für den Düsenbetrieb erforderlichen Hochtemperaturfestigkeit. Die Rezepte für die Wärmebehandlung sind spezifisch für die jeweilige Legierung und müssen sorgfältig kontrolliert werden.
- CNC-Bearbeitung:
- Zweck: Zur Erzielung enger Toleranzen bei kritischen Abmessungen und Schnittstellen, zur Herstellung spezifischer Merkmale (wie O-Ring-Nuten oder Gewindebohrungen), die sich nur schwer präzise drucken lassen, und zur Erzielung sehr glatter Oberflächen auf Dichtungs- oder Gegenflächen.
- Methode: Einsatz von mehrachsigen CNC-Fräs- oder Drehzentren zum präzisen Abtragen von Material aus bestimmten Bereichen des AM-Teils. Erfordert ein sorgfältiges Vorrichtungsdesign, um die komplexe Geometrie der Düse sicher und ohne Verformung zu halten.
- Wichtigkeit: Schließt die Lücke zwischen der inhärenten Genauigkeit/Finish von AM und den strengen Anforderungen an Endmontage und Funktion. Die DfAM-Planung (Hinzufügen von Bearbeitungsmaterial) ist unerlässlich.
- Oberflächenveredelung:
- Zweck: Verbesserung der Oberflächenbeschaffenheit über den Ist- oder HIP-Zustand hinaus aus Gründen der Fluiddynamik, der Wärmeübertragung, der Abdichtung oder der Inspektion.
- Methoden:
- Strahlen (Körnung/Perlen): Erzeugt ein gleichmäßiges, mattes Finish.
- Taumeln/Gleitschleifen: Verwendet Medien zum Glätten von Oberflächen und Entgraten von Kanten, geeignet für Chargen von kleineren Teilen.
- Polieren/Läppen: Manuelle oder automatisierte Verfahren zur Erzielung sehr glatter, spiegelähnlicher Oberflächen (niedrige Ra) auf bestimmten Oberflächen.
- Abrasive Fließbearbeitung (AFM): Nützlich zum Glätten von inneren Kanälen, indem man Schleifspachtel durch sie hindurchfließen lässt.
- Elektropolieren: Elektrochemisches Verfahren zum Abtragen von Material und Glätten von Oberflächen, wirksam bei komplexen Formen.
- Wichtigkeit: Die Anforderungen hängen vom spezifischen Anwendungsbereich der Düsenoberfläche ab (interner Fließweg vs. externe Struktur vs. Dichtfläche).
- Zerstörungsfreie Prüfung (NDT) und Inspektion:
- Zweck: Überprüfung der Integrität der fertigen Düse, um sicherzustellen, dass sie frei von kritischen Fehlern (Risse, Porositätscluster, Einschlüsse) ist und alle Abmessungsspezifikationen erfüllt.
- Methoden:
- Visuelle Inspektion: Grundlegende Prüfung auf Oberflächenfehler.
- Dimensionelle Metrologie: Koordinatenmessmaschinen (CMM), 3D-Laserscanning zur Überprüfung von Abmessungen und GD&T.
- Computertomographie (CT-Scan): Röntgenbasierte Methode zur Inspektion interner Strukturen und zur Erkennung von volumetrischen Fehlern (Porosität) ohne Zerstörung des Teils. Zunehmend wichtig für AM-Teile.
- Ultraschallprüfung (UT): Nutzt Schallwellen zum Aufspüren von inneren Fehlern.
- Fluoreszierende Eindringprüfung (FPI): Erkennt Risse, die die Oberfläche durchbrechen.
- Durchleuchtungsprüfung (RT): Traditionelle Röntgeninspektion.
- Wichtigkeit: Obligatorischer Qualitätssicherungsschritt für flugkritische Luft- und Raumfahrtteile. Schafft Vertrauen in die strukturelle Integrität des Teils.
Workflow-Integration:
Diese Nachbearbeitungsschritte werden nicht immer in der angegebenen Reihenfolge durchgeführt; der genaue Arbeitsablauf hängt vom Material, der Komplexität der Konstruktion und den spezifischen Anforderungen ab. So kann beispielsweise die Bearbeitung vor der abschließenden Wärmebehandlung erfolgen oder die HIP-Bearbeitung kann mit einem Teil des Wärmebehandlungszyklus kombiniert werden. Sorgfältige Planung und Prozesskontrolle sind in jedem Fall unerlässlich. Die Kosten und der Zeitaufwand für die Nachbearbeitung können beträchtlich sein, oft vergleichbar mit den anfänglichen Druckkosten oder sogar höher als diese, und müssen von den Beschaffungsmanagern und Ingenieuren in den Projektbudgets und Zeitplänen berücksichtigt werden.
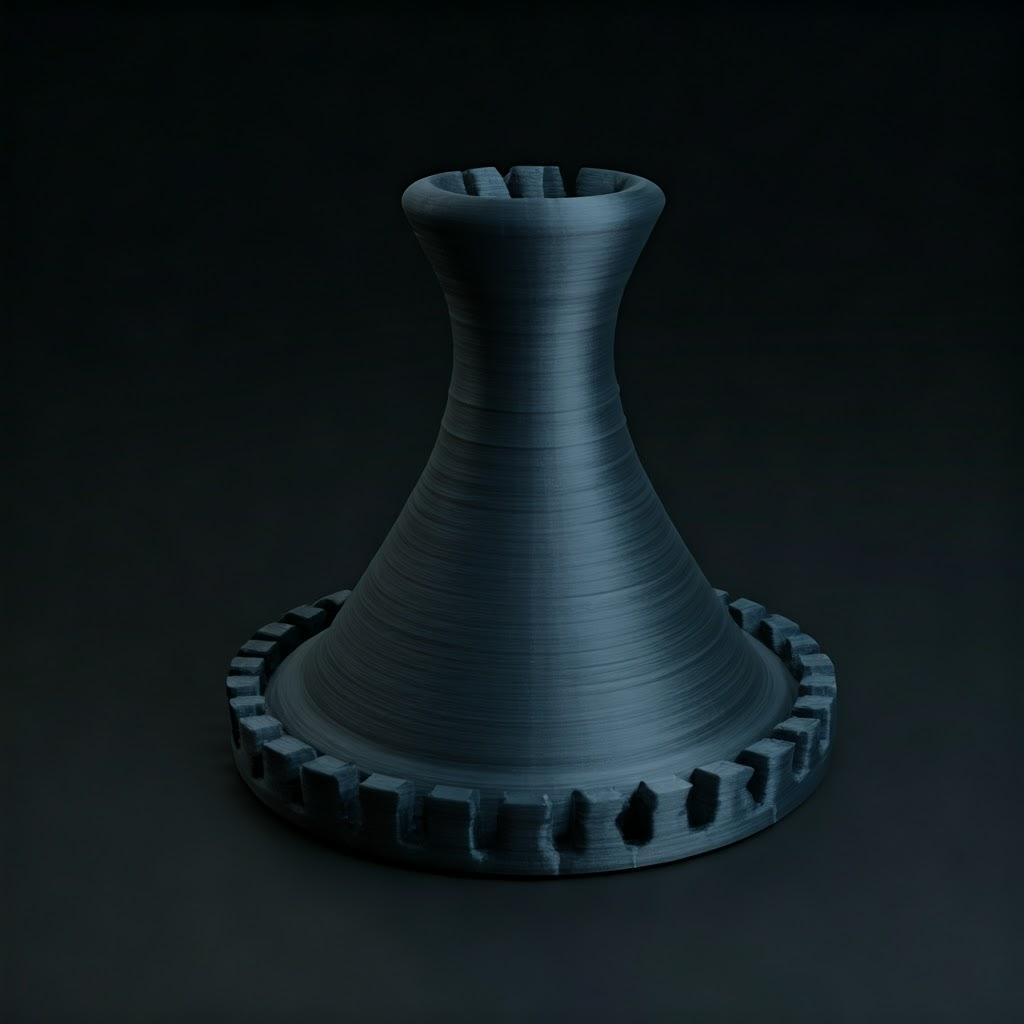
Herausforderungen meistern: Häufige Probleme beim 3D-Druck von Raketendüsen und Lösungen
Die additive Fertigung von Metallen bietet zwar ein revolutionäres Potenzial für die Herstellung von Raketendüsen, ist aber nicht ohne Herausforderungen. Die Kombination aus komplexen Geometrien, anspruchsvollen Hochtemperatur-Superlegierungen und der inhärenten Physik der schichtweisen Verschmelzung kann zu verschiedenen Defekten oder Problemen führen, wenn sie nicht richtig gehandhabt wird. Das Verständnis dieser potenziellen Probleme und die Implementierung robuster Prozesskontrollen und Abhilfestrategien sind entscheidend für die Herstellung zuverlässiger, hochwertiger Düsen.
Gemeinsame Herausforderungen und Abhilfestrategien:
- Eigenspannung, Verformung und Verzerrung:
- Ausgabe: Große thermische Gradienten während des Druckens verursachen innere Spannungen. Wenn diese Spannungen nachlassen, können sie dazu führen, dass sich das Teil verzieht, von der vorgesehenen Geometrie abweicht oder sogar reißt, insbesondere beim Entfernen von der Bauplatte oder bei der Nachbearbeitung. Nickelsuperlegierungen sind aufgrund ihrer hohen Wärmeausdehnung und Festigkeit besonders anfällig.
- Die Ursachen: Schnelle Heiz-/Abkühlzyklen, große Temperaturunterschiede zwischen Schmelzbad und umgebendem Material, Teilegeometrie (dicke Abschnitte neben dünnen), Materialeigenschaften.
- Milderung:
- Prozess-Simulation: Vorhersage von Spannungsakkumulation und Verformung zur Optimierung von Bauausrichtung und Stützstrategie vor Drucken.
- Optimierte Scan-Strategien: Verwenden Sie spezielle Laser-/Elektronenstrahl-Abtastmuster (z. B. Inselabtastung, Schachbrettmuster), um die Wärme gleichmäßiger zu verteilen und den Aufbau lokaler Spannungen zu verringern.
- Plattformheizung (LPBF & SEBM): Durch die Aufrechterhaltung einer hohen Temperatur in der Baukammer werden thermische Gradienten reduziert. SEBM verwendet von Natur aus höhere Kammertemperaturen, was erheblich dazu beiträgt.
- Robuste Stützstrukturen: Konstruieren Sie Stützen, um das Teil wirksam zu verankern und Verformungskräften entgegenzuwirken.
- Stressabbau nach der Bauphase: Durchführung eines geeigneten Wärmebehandlungszyklus vor Entfernen des Teils von der Bauplatte.
- DfAM: Entwerfen Sie Merkmale mit allmählichen Übergängen, vermeiden Sie nach Möglichkeit große, sperrige Abschnitte und ziehen Sie eine Optimierung der Topologie in Betracht.
- Porosität:
- Ausgabe: Kleine innere Hohlräume oder Poren innerhalb des gedruckten Materials. Porosität kann die Dichte verringern, die mechanischen Eigenschaften (insbesondere Ermüdungsfestigkeit und Duktilität) verschlechtern und als Rissauslöser dienen.
- Die Ursachen:
- Gas Porosität: Eingeschlossenes Gas (z. B. Argon-Schutzgas in LPBF, gelöste Gase in Pulver) im Schmelzbad, das vor der Erstarrung nicht entweicht.
- Lack-of-Fusion-Porosität: Ein unzureichender Energieeintrag oder eine unzureichende Überlappung zwischen den Schmelzepools führt zu ungeschmolzenen Pulverpartikeln oder Hohlräumen zwischen den Schichten/Spuren. Schlüssellochinstabilität/Porosität kann bei zu hoher Energiedichte auftreten.
- Fragen zur Pulverqualität: Unregelmäßige Pulverformen, innere Gasporen in den Pulverpartikeln oder Verunreinigungen.
- Milderung:
- Optimierte Prozessparameter: Sorgfältige Steuerung von Laser-/Strahlleistung, Scangeschwindigkeit, Schichtdicke, Schraffurabstand und Fokus zur Gewährleistung eines vollständigen Schmelzvorgangs und einer stabilen Schmelzbaddynamik. Umfassende Parameterentwicklung ist der Schlüssel.
- Hochwertiges Pulver: Verwenden Sie Pulver mit hoher Sphärizität, kontrollierter Partikelgrößenverteilung, geringem internen Gasgehalt und hoher Reinheit. Die Beschaffung bei renommierten Lieferanten wie Met3dp, die für ihre fortschrittlichen Pulverherstellungssysteme bekannt sind, ist entscheidend.
- Kontrollierte Atmosphäre: Sorgen Sie für eine hochreine Inertgasumgebung (LPBF) oder Hochvakuum (SEBM), um die Gasaufnahme zu minimieren.
- Heiß-Isostatisches Pressen (HIP): Hochwirksamer Nachbearbeitungsschritt zum Schließen der inneren Poren und Erreichen der vollen Dichte (>99,9%). Für kritische Düsenkomponenten oft zwingend erforderlich.
- Rissbildung (Verfestigungs- oder Verflüssigungsrissbildung):
- Ausgabe: Rissbildung während der Erstarrung oder in der Wärmeeinflusszone bei nachfolgenden Durchgängen, besonders häufig bei bestimmten komplexen, hochfesten Nickelsuperlegierungen (obwohl IN718, IN625 und Haynes 282 im Allgemeinen eine bessere Schweißbarkeit/Druckbarkeit aufweisen als einige andere).
- Die Ursachen: Hohe Eigenspannungen, die die Festigkeit des Materials bei erhöhten Temperaturen übersteigen, Vorhandensein von niedrigschmelzenden Phasen oder Verunreinigungen, die sich an den Korngrenzen ausscheiden, ungünstige Kornstrukturen.
- Milderung:
- Auswahl der Legierung: Wählen Sie nach Möglichkeit Legierungen, die für bessere Druck-/Schweißbarkeit bekannt sind (IN718/IN625 sind im Allgemeinen gut).
- Optimierung der Parameter: Steuerung des Wärmeeintrags und der Abkühlungsraten durch Scan-Strategie und -Parameter zur Minimierung von Spannungen und zur Förderung günstiger Mikrostrukturen.
- Plattform Heizung: Reduziert Wärmeschock und Stress.
- Stressabbau Wärmebehandlung: Reduziert das allgemeine Stressniveau.
- Reinheit des Pulvers: Minimieren Sie Verunreinigungen, die zur Rissbildung bei der Verflüssigung beitragen können.
- DfAM: Vermeiden Sie scharfe Ecken und abrupte geometrische Veränderungen, in denen sich Spannungen konzentrieren.
- Probleme mit der Oberflächenrauhigkeit und der Merkmalsauflösung:
- Ausgabe: Bestehende Oberflächen können für die Anforderungen der Fluiddynamik zu rau sein, oder feine Merkmale (kleine Kanäle, dünne Wände) können nicht genau aufgelöst werden. Treppeneffekt auf abgewinkelten Oberflächen.
- Die Ursachen: Schicht-für-Schicht-Verfahren, Pulverpartikelgröße, Schmelzbaddynamik, Anhaftung von teilgesintertem Pulver (insbesondere SEBM), Stützkontaktpunkte.
- Milderung:
- Prozessauswahl: LPBF bietet im Allgemeinen eine bessere Oberfläche und Auflösung als SEBM.
- Einstellung der Parameter: Optimieren Sie Schichtdicke, Strahl-/Laserspotgröße und Energieeintrag.
- Orientierung aufbauen: Richten Sie das Teil so aus, dass die Stufenbildung auf kritischen Oberflächen minimiert wird, oder platzieren Sie es so, dass eine Nachbearbeitung möglich ist.
- DfAM: Konstruieren Sie Merkmale innerhalb der Auflösungsgrenzen des gewählten Prozesses. Stellen Sie sicher, dass die Mindestwandstärken eingehalten werden.
- Nachbearbeiten: Planen Sie Bearbeitung, Polieren oder AFM für kritische Oberflächen, die eine hohe Glätte oder Genauigkeit erfordern.
- Unvollständige Entfernung des Pulvers:
- Ausgabe: Schwierigkeiten bei der Entfernung des gesamten ungeschmolzenen Pulvers aus komplexen internen Kanälen oder Hohlräumen.
- Die Ursachen: Äußerst komplizierte oder gewundene Rinnengestaltung, unzureichende Zugänge, Pulvereigenschaften (schlechte Fließfähigkeit).
- Milderung:
- DfAM: Entwerfen Sie Rinnen mit sanften Biegungen, ausreichendem Durchmesser und strategisch platzierten Zugangs-/Abflusslöchern. Ziehen Sie in Erwägung, die Rinnen so zu gestalten, dass sie je nach Bauausrichtung selbstentleerend sind.
- Optimierte Depowdering-Verfahren: Verwenden Sie geeignete Kombinationen aus Vibration, Rotation und gezielter Druckluft/Vakuum.
- Inspektion: Verwenden Sie Methoden wie CT-Scans oder Endoskopie, um die vollständige Entfernung des Pulvers aus kritischen inneren Passagen zu überprüfen.
Herausforderungen meistern - Die Bedeutung von Fachwissen:
Um diese Herausforderungen erfolgreich zu meistern, sind fundierte Kenntnisse in den Bereichen Materialwissenschaft, Physik des AM-Prozesses, Simulation und strenge Qualitätskontrolle erforderlich. Dies beinhaltet:
- Gründliche Parameterentwicklung: Umfassende Tests zur Ermittlung robuster Prozessfenster für bestimmte Legierungs-/Maschinenkombinationen.
- Prozessbegleitende Überwachung: Einsatz von Sensoren (Wärmebildkameras, Fotodioden) zur Überwachung des Schmelzbads und zur Erkennung von Anomalien während des Baus in Echtzeit.
- Strenge Qualitätskontrolle: Implementierung umfassender ZfP und Messtechnik im gesamten Arbeitsablauf.
- Partnerschaft: enge Zusammenarbeit mit erfahrenen AM-Dienstleistern und Materiallieferanten, die nachweislich hochwertige Komponenten für die Luft- und Raumfahrt herstellen. Unternehmen wie Met3dp verkörpern mit ihrem Schwerpunkt auf fortschrittlichen SEBM-Druckern und hochwertigen Metallpulvern in Kombination mit Anwendungsentwicklungsdiensten das integrierte Fachwissen, das erforderlich ist, um diese Herausforderungen effektiv zu bewältigen.
Indem sie diese potenziellen Probleme durch sorgfältiges Design, Prozesskontrolle und Nachbearbeitung proaktiv angehen, können die Hersteller die Leistungsfähigkeit von AM nutzen, um komplexe, leistungsstarke Raketendüsen zuverlässig und wiederholbar herzustellen.
Die Auswahl Ihres Partners: Die Wahl des richtigen 3D-Druckdienstleisters für Luft- und Raumfahrtkomponenten
Die Herstellung von flugkritischer Hardware wie Raketendüsen mittels additiver Fertigung ist keine Aufgabe, die man irgendeinem Dienstleistungsunternehmen anvertrauen kann. Es steht unglaublich viel auf dem Spiel, und die damit verbundene technische Komplexität erfordert einen Partner mit speziellem Fachwissen, robusten Qualitätssystemen und einem tiefen Verständnis der strengen Anforderungen der Luft- und Raumfahrtindustrie. Die Auswahl des richtigen 3D-Druckdienstleisters für Metall ist eine wichtige Entscheidung für Ingenieure, Programmmanager und Beschaffungsspezialisten, die AM erfolgreich nutzen wollen. Im Folgenden finden Sie eine Aufschlüsselung der wichtigsten Kriterien zur Bewertung potenzieller Anbieter:
- Zertifizierungen für die Luft- und Raumfahrt und Qualitätsmanagementsystem (QMS):
- Erfordernis: Der Anbieter muss verfügen über ein zertifiziertes und streng eingehaltenes QMS, das speziell auf die Luft- und Raumfahrtindustrie zugeschnitten ist. Die wichtigste Norm ist AS9100. Diese Zertifizierung belegt, dass der Zulieferer strenge Prozesse für die Rückverfolgbarkeit, das Konfigurationsmanagement, die Prozesskontrolle, die Inspektion und die kontinuierliche Verbesserung einhält, die für Luft- und Raumfahrtkomponenten erforderlich sind.
- Bewertung: Überprüfen Sie den Status und den Umfang der AS9100-Zertifizierung des Lieferanten. Erkundigen Sie sich nach dem Qualitätshandbuch, den internen Auditverfahren und dem Umgang mit Nichtkonformitäten. Ein solides QMS ist nicht verhandelbar.
- Erfahrung mit Hochtemperatursuperlegierungen:
- Erfordernis: Das Drucken von Materialien wie IN718, IN625 und insbesondere Haynes 282 erfordert spezielle Kenntnisse und validierte Prozessparameter. Diese Legierungen verhalten sich in AM-Prozessen anders als gängige Materialien wie Aluminium- oder Titanlegierungen.
- Bewertung: Erkundigen Sie sich nach der Erfahrung des Anbieters mit den spezifischen Legierungen, die für Ihre Düse benötigt werden. Fordern Sie Fallstudien, Daten zu den Materialeigenschaften der Maschinen (Zug-, Ermüdungs- und Kriechdaten, falls verfügbar) sowie Nachweise für erfolgreiche Drucke mit ähnlichen Materialien und ähnlicher Komplexität an. Kennen sie die erforderlichen Wärmebehandlungen? Verfügen sie über festgelegte und validierte Druckparameter für diese Legierungen?
- Einschlägige Technologie und Ausrüstung:
- Erfordernis: Der Lieferant sollte über die entsprechende AM-Technologie (z. B. LPBF, SEBM) verfügen, die für die Anforderungen Ihrer Düse geeignet ist (Genauigkeit, Oberflächengüte, Material). Die Maschinen sollten industrietauglich sein, gut gewartet werden und Teile herstellen können, die den Standards der Luft- und Raumfahrt entsprechen.
- Bewertung: Informieren Sie sich über die Marke und das Modell der verwendeten Drucker. Wie hoch ist die Produktionskapazität? Wie werden Kalibrierung und Konsistenz der Maschine sichergestellt? Stimmt die Technologie mit Ihren Designanforderungen überein (z. B. SEBM für geringere Eigenspannungen bei großen Teilen gegenüber LPBF für feinere Merkmale)? Unternehmen wie Met3dp, die nicht nur Dienstleistungen anbieten, sondern auch ihre eigenen Maschinen herstellen branchenführende SEBM-Drucker und Pulver, verfügen oft über ein tiefes technisches Know-how in ihren spezifischen Systemen.
- Eigene Fähigkeiten vs. ausgelagerte Prozesse:
- Erfordernis: Ein Anbieter mit umfassenden internen Kapazitäten für wichtige Nachbearbeitungsschritte (Spannungsabbau, HIP, Wärmebehandlung, Grundbearbeitung, zerstörungsfreie Prüfung) kann eine bessere Kontrolle, potenziell kürzere Lieferzeiten und eine klarere Verantwortlichkeit bieten.
- Bewertung: Stellen Sie fest, welche Prozesse intern durchgeführt werden und welche ausgelagert sind. Wenn wichtige Schritte wie HIP oder die abschließende Wärmebehandlung ausgelagert werden, sollten Sie die Beziehungen des Lieferanten zu seinen Zulieferern kennen und wissen, wie die Qualitätskontrolle in der gesamten erweiterten Lieferkette gewährleistet wird. Wie wird die Rückverfolgbarkeit über verschiedene Einrichtungen hinweg gehandhabt?
- Technische und DfAM-Unterstützung:
- Erfordernis: Im Idealfall sollte der Anbieter mehr als nur "Print-to-Print"-Dienste anbieten. Suchen Sie nach Partnern, die Sie beim Design for Additive Manufacturing (DfAM) unterstützen und Ihnen helfen, Ihr Düsendesign im Hinblick auf Druckbarkeit, Leistung und Kosteneffizienz zu optimieren.
- Bewertung: Verfügen sie über Anwendungsingenieure oder Metallurgen, die Ihre Konstruktion prüfen und DfAM-Empfehlungen geben können? Können sie bei der Optimierung der Bauausrichtung und der Stützstrategien helfen oder Konstruktionsänderungen vorschlagen, um Risiken wie Eigenspannungen zu mindern?
- Prozesssteuerung und -überwachung:
- Erfordernis: Eine robuste Prozesssteuerung ist für die Wiederholbarkeit und Qualität unerlässlich. Dazu gehört die Überwachung von Schlüsselparametern während der Herstellung (z. B. Sauerstoffgehalt, Kammertemperatur, Eigenschaften des Schmelzbads, falls vorhanden) und die Führung detaillierter Herstellungsprotokolle.
- Bewertung: Fragen Sie nach den Methoden zur Prozessüberwachung. Verwenden sie Schmelzbadüberwachung oder Wärmebildtechnik? Wie werden die Herstellungsprotokolle geführt und überprüft? Wie wird die Konsistenz von Herstellung zu Herstellung sichergestellt?
- Materialhandhabung und Rückverfolgbarkeit:
- Erfordernis: Strenge Verfahren für die Handhabung, Lagerung, Prüfung und das Recycling von Metallpulvern sind unerlässlich, um Verunreinigungen zu vermeiden und die Materialqualität zu gewährleisten. Eine vollständige Rückverfolgbarkeit von der Rohpulvercharge bis zum fertigen Teil ist erforderlich.
- Bewertung: Überprüfen Sie die Verfahren zur Handhabung des Pulvers. Wie werden die eingehenden Pulverchargen qualifiziert? Wie wird das Pulver gelagert und wiederverwendet? Welche Maßnahmen werden ergriffen, um eine Kreuzkontamination zwischen verschiedenen Legierungen zu verhindern? Wie wird die Rückverfolgbarkeit der Chargen dokumentiert?
- Inspektion und zerstörungsfreie Prüfung (NDT):
- Erfordernis: Der Anbieter muss über die notwendige Ausrüstung und zertifiziertes Personal verfügen, um die erforderlichen Prüfungen (dimensionelle Messtechnik mit CMM/3D-Scanning) und zerstörungsfreie Prüfungen (CT-Scanning, FPI, UT, RT) durchzuführen, um die Integrität der Teile gemäß den Spezifikationen der Luft- und Raumfahrt zu überprüfen.
- Bewertung: Bestätigen Sie die internen ZfP-Fähigkeiten und Personalzertifizierungen (z. B. NAS 410). Wenn die zerstörungsfreie Prüfung ausgelagert wird, überprüfen Sie die Qualifikationen des Drittanbieters. Können sie detaillierte Inspektionsberichte, einschließlich CT-Scan-Analysen, vorlegen?
- Nachgewiesene Erfolgsbilanz und Erfahrung:
- Erfordernis: Suchen Sie nach Anbietern mit nachgewiesener Erfahrung in der Herstellung komplexer, hochwertiger Komponenten für die Luft- und Raumfahrt oder ähnlich anspruchsvolle Branchen (z. B. Medizin, Verteidigung).
- Bewertung: Fordern Sie Referenzen und Fallstudien ähnlicher Projekte an (unter Wahrung von Geheimhaltungsvereinbarungen) und erkundigen Sie sich nach der Zusammenarbeit mit führenden Unternehmen der Luft- und Raumfahrtindustrie oder Tier-One-Zulieferern. Wie lange bieten sie schon Metall-AM-Dienstleistungen für kritische Anwendungen an?
- Kapazität, Vorlaufzeit und Kommunikation:
- Erfordernis: Vergewissern Sie sich, dass der Anbieter in der Lage ist, Ihre Projektfristen und Ihr Produktionsvolumen einzuhalten. Klare Kommunikation und Projektmanagement sind ebenfalls von entscheidender Bedeutung.
- Bewertung: Erläutern Sie die aktuelle Maschinenverfügbarkeit und die typischen Vorlaufzeiten für Teile ähnlicher Komplexität und Materialien. Wie sieht das Verfahren für die Erstellung von Angeboten und Status-Updates aus? Wer wird Ihr Hauptansprechpartner sein? Dies ist von entscheidender Bedeutung für Beschaffungsmanager, die Projektpläne verwalten, und für Großeinkäufer, die zuverlässige Kostenvoranschläge benötigen.
Checkliste zur Lieferantenbewertung:
Kriterien | Zentrale Fragen | Bedeutung |
---|---|---|
AS9100-Zertifizierung | Ist die Zertifizierung aktuell? Was ist der Geltungsbereich? Kann das Qualitätshandbuch überprüft werden? | Kritisch |
Kompetenz bei Hochtemperaturlegierungen | Erfahrung mit IN718/IN625/Haynes 282? Validierung der Parameter? Sind Materialdaten verfügbar? | Kritisch |
Technologie & Ausstattung | Geeigneter AM-Prozess (LPBF/SEBM)? Industrielle Qualität? Bauvolumen? Aufzeichnungen über Wartung/Kalibrierung? | Hoch |
In-House vs. Ausgelagert | Welche Nachbearbeitungsschritte werden intern durchgeführt (HIP, Wärmebehandlung, Bearbeitung, NDT)? Wie werden die Zulieferer verwaltet? | Hoch |
DfAM-Unterstützung | Entwurfsprüfung/Optimierung anbieten? Fachwissen der Mitarbeiter (Ingenieure, Metallurgen)? | Hoch |
Prozesssteuerung/Überwachung | Techniken zur prozessbegleitenden Überwachung? Protokolle erstellen? Konsistenzmaßnahmen? | Hoch |
Materialhandhabung/Rückverfolgbarkeit | Qualifikation des Pulvers? Verfahren zur Lagerung/Wiederverwendung? Vermeidung von Kontaminationen? Vollständige Rückverfolgbarkeit der Charge? | Kritisch |
Inspektion & NDT | Eigene ZfP (CT, FPI usw.)? Zertifiziertes Personal (NAS 410)? Fähigkeiten zur Dimensionsprüfung (CMM/Scan)? | Kritisch |
Erfolgsbilanz und Erfahrung | Beispiele für Luft- und Raumfahrtprojekte? Referenzen? Jahre im Geschäft? | Hoch |
Kapazität und Vorlaufzeit | Verfügbarkeit von Maschinen? Realistische Durchlaufzeiten? Projektmanagement-Prozess? Klare Kommunikation? | Hoch |
In Blätter exportieren
Bei der Wahl des richtigen AM-Dienstleisters geht es darum, einen echten Partner zu finden, der die technischen Feinheiten und Qualitätsanforderungen der Luft- und Raumfahrtindustrie versteht. Eine gründliche Due-Diligence-Prüfung anhand dieser Kriterien wird die Erfolgswahrscheinlichkeit Ihres 3D-gedruckten Raketendüsenprojekts deutlich erhöhen.
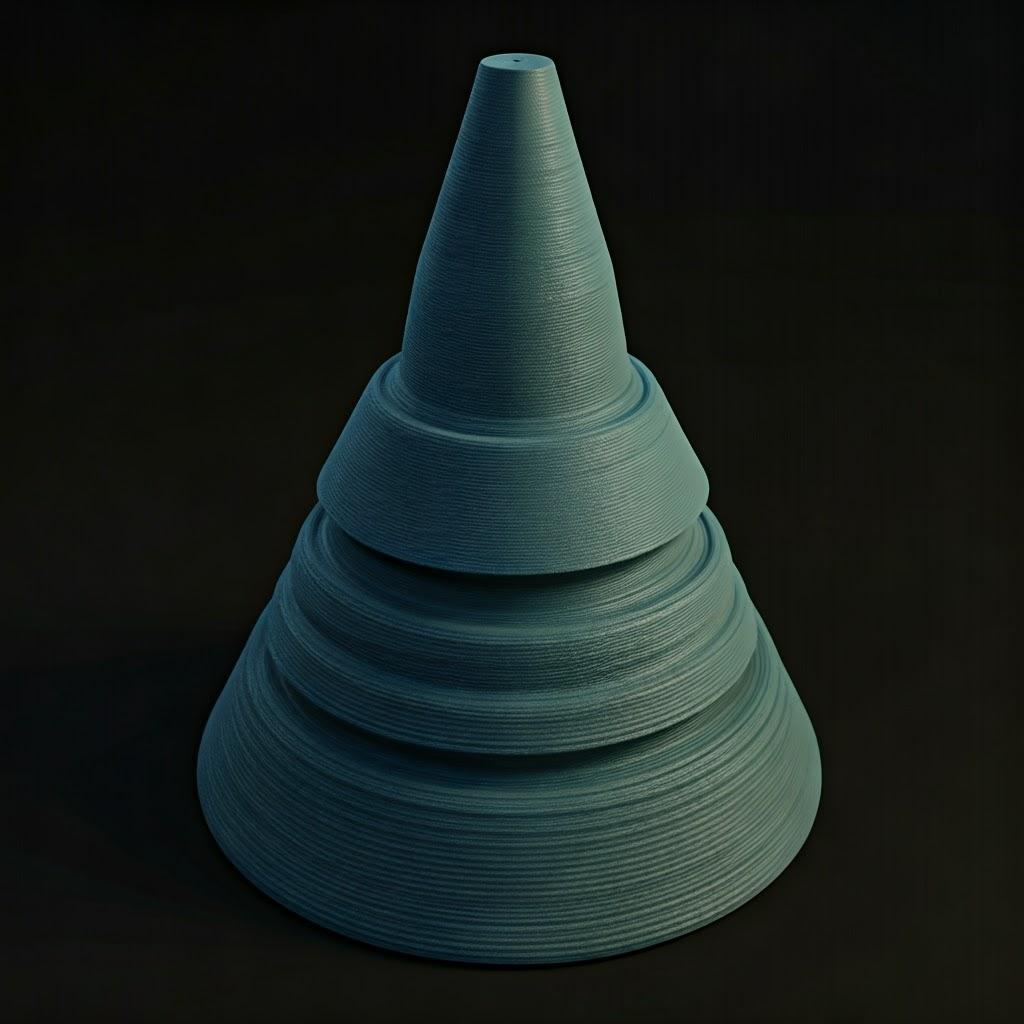
Die Investition verstehen: Kostenfaktoren und Vorlaufzeiten für 3D-gedruckte Raketendüsen
Die additive Fertigung bietet überzeugende technische Vorteile für Raketendüsen, aber das Verständnis der damit verbundenen Kosten und typischen Vorlaufzeiten ist entscheidend für die Projektplanung, die Budgetierung und den Vergleich von AM mit traditionellen Methoden. Beschaffungsmanager, Projektingenieure und Großeinkäufer brauchen ein klares Bild davon, was den Endpreis und den Lieferplan für diese komplexen, hochwertigen Komponenten bestimmt.
Die wichtigsten Kostentreiber für 3D-gedruckte Raketendüsen:
- Materialart und Verbrauch:
- Legierung Kosten: Hochtemperatur-Nickel-Superlegierungen (IN718, IN625, Haynes 282) sind wesentlich teurer als gewöhnliche technische Metalle wie Edelstahl oder Aluminium. Haynes 282 ist im Allgemeinen am teuersten, gefolgt von IN625 und IN718. Die Pulverkosten sind ein wesentlicher Bestandteil des Gesamtpreises.
- Teilvolumen und Dichte: Die schiere Menge des benötigten Materials wirkt sich direkt auf die Kosten aus. Größere oder dichtere Düsen verbrauchen mehr teures Pulver. DfAM-Techniken wie Topologieoptimierung und Gitterstrukturen können den Materialverbrauch und damit die Kosten senken.
- Unterstützungsstruktur Volumen: Das für die Stützstrukturen verwendete Material trägt ebenfalls zu den Kosten bei, obwohl nicht verwendetes Pulver oft wiederverwertet werden kann (bei strenger Qualitätskontrolle). Die Minimierung der Träger durch DfAM hilft, diesen Faktor zu reduzieren.
- Maschinenzeit (Bauzeit):
- Größe und Komplexität der Teile: Größere Teile oder solche mit sehr komplizierten Merkmalen benötigen mehr Zeit zum Drucken, was wertvolle Maschinenzeit verbraucht. Die Bauhöhe ist oft ein Hauptfaktor für die Druckzeit.
- Anzahl der Teile pro Build: Druckdienstleister versuchen, die Anzahl der gleichzeitig auf einer einzigen Bauplatte gedruckten Teile zu maximieren ("Verschachtelung"), um die Rüstzeit zu amortisieren und die Maschinenauslastung zu maximieren. Bei großen Düsen passt möglicherweise nur ein Teil pro Bauplatte.
- Schichtdicke & Parameter: Dünnere Schichten bieten eine bessere Auflösung, verlängern aber die Druckzeit erheblich. Optimierte Druckparameter sorgen für ein Gleichgewicht zwischen Geschwindigkeit und Qualität.
- Maschine Stundensatz: Die Dienstleister kalkulieren in ihre Stundensätze die Kapitalkosten für teure industrielle AM-Maschinen, Wartung, Anlagen, Energie und Fachkräfte ein.
- Design und technischer Input (NRE - Non-Recurring Engineering):
- DfAM und Optimierung: Wenn der Dienstleister bei der Optimierung des Designs, der Simulation oder der Entwicklung spezifischer Konstruktionsstrategien behilflich ist, trägt dieser anfängliche technische Aufwand zu den NRE-Kosten bei, insbesondere bei Erstdrucken oder komplexen neuen Designs.
- Entwicklung der Parameter: Wenn eine neuartige Geometrie gedruckt werden soll oder besondere Eigenschaften erforderlich sind, müssen möglicherweise umfangreiche Parameter entwickelt und getestet werden, was die Vorabkosten erhöht.
- Nachbearbeitungsanforderungen:
- Komplexität und Ausmaß: Die Nachbearbeitungsschritte können 50% oder mehr der Gesamtkosten ausmachen. Die spezifischen erforderlichen Schritte (Spannungsarmglühen, HIP, Wärmebehandlung, Entfernen von Halterungen, maschinelle Bearbeitung, Endbearbeitung, zerstörungsfreie Prüfung) und ihre Komplexität beeinflussen den Preis erheblich.
- HIP: Isostatisches Heißpressen ist ein teures Batch-Verfahren, das spezielle Anlagen erfordert.
- CNC-Bearbeitung: Der Bearbeitungsaufwand (Einrichtzeit, Programmierung, Bearbeitungszeit) ist ein wichtiger Faktor, insbesondere wenn es darum geht, enge Toleranzen bei mehreren Merkmalen zu erreichen.
- ZfP und Inspektion: Umfassende Inspektionen, insbesondere CT-Scans für die interne Validierung, verursachen erhebliche Kosten, sind aber für die Qualitätssicherung unerlässlich.
- Qualitätssicherung und Zertifizierung:
- Normen für die Luft- und Raumfahrt (AS9100): Die Aufrechterhaltung der strengen Qualitätssysteme, der Dokumentation und der Rückverfolgbarkeit, die AS9100 vorschreibt, ist mit Gemeinkosten verbunden, die in den Teilepreis eingerechnet werden.
- Testanforderungen: Wenn spezielle zerstörende Prüfungen (z. B. Zugversuche an Prüfmustern) oder umfangreiche Dokumentationspakete erforderlich sind, erhöht dies die Kosten.
- Auftragsvolumen und Dringlichkeit:
- Menge: Die Stückkosten sinken in der Regel bei größeren Chargengrößen aufgrund der Amortisierung der Einrichtungskosten und der möglichen Optimierung der Fertigungslayouts (obwohl der Effekt bei sehr großen Teilen, die auf ein Stück pro Fertigung beschränkt sind, weniger ausgeprägt sein kann). Großhandelsanfragen für größere Mengen können zu Vorzugspreisen bearbeitet werden.
- Vorlaufzeit: Für Eilanträge, die eine vorrangige Terminierung oder Überstunden erfordern, werden in der Regel Aufschläge erhoben.
Typische Vorlaufzeiten:
Die Vorlaufzeiten für 3D-gedruckte Raketendüsen für die Luft- und Raumfahrt sind sehr unterschiedlich, liegen aber im Allgemeinen zwischen mehrere Wochen bis mehrere Monateje nach Komplexität, Größe, Materialverfügbarkeit, erforderlicher Nachbearbeitung und Auftragsbestand des Anbieters.
- Drucken: Bei großen/komplexen Düsen dauert dies in der Regel mehrere Tage bis über eine Woche.
- Zeit in der Warteschlange: Das Warten auf die Verfügbarkeit einer Maschine kann Tage oder Wochen dauern.
- Nachbearbeiten:
- Stressabbau/Bauplattenentfernung: 1-3 Tage
- HIP: Häufig in Chargen, kann 1-2 Wochen länger dauern (einschließlich Planung und Zykluszeit).
- Wärmebehandlung (Lösung/Alterung): Mehrere Tage, je nach den erforderlichen spezifischen Zyklen.
- CNC-Bearbeitung: Sehr variabel, von Tagen bis Wochen, je nach Komplexität und Auslastung der Werkstatt.
- ZfP und Inspektion: Tage bis über eine Woche, abhängig von den Methoden und der erforderlichen Berichterstattung.
- Versand: Je nach Standort unterschiedlich.
Faktoren, die die Vorlaufzeit beeinflussen:
- Komplexität und Größe der Teile (längere Druck- und Bearbeitungszeiten).
- Verfügbarkeit von qualifiziertem Pulver.
- Maschinenverfügbarkeit und Planungswarteschlange.
- Komplexität und Zeitplanung der Nachbearbeitungsschritte (insbesondere HIP und komplexe Bearbeitung).
- Notwendigkeit einer iterativen zerstörungsfreien Prüfung oder Nacharbeit.
- Aktuelle Arbeitsbelastung und Kapazität des Dienstleisters und aller externen Anbieter.
Kosten im Vergleich zu traditionellen Methoden:
Ein direkter Kostenvergleich von Teil zu Teil kann irreführend sein. Während die Kosten für ein AM-Teil manchmal höher sein können als die eines traditionell hergestellten Äquivalents (insbesondere bei einfacheren Designs), sind die Gesamtnutzenversprechen begünstigt oft AM aufgrund von:
- Geringere Entwicklungszeit: Schnellere Iterationen sparen erhebliche Programmkosten.
- Verbesserte Leistung: Ein höherer Wirkungsgrad durch bessere Kühlung kann zu Vorteilen für den Einsatz führen.
- Gewichtseinsparung: Geringere Startkosten oder höhere Nutzlastkapazität.
- Teil Konsolidierung: Niedrigere Montagekosten und höhere Zuverlässigkeit.
- Geringere Werkzeugkosten: Eliminiert teure Formen, Gesenke oder Vorrichtungen.
Ingenieure und Beschaffungsmanager sollten eine Analyse der Gesamtbetriebskosten durchführen und dabei diese umfassenderen Vorteile auf Systemebene berücksichtigen, wenn sie die Investition in 3D-gedruckte Raketendüsen bewerten. Die Zusammenarbeit mit einem transparenten Dienstleister, der detaillierte Angebote mit diesen Kostenfaktoren vorlegen kann, ist für eine effektive Budgetierung und Entscheidungsfindung unerlässlich.
Häufig gestellte Fragen (FAQ) zu 3D-gedruckten Raketendüsen
Hier finden Sie Antworten auf einige häufig gestellte Fragen zum Einsatz der additiven Fertigung bei der Herstellung von Raketendüsen:
1. Wie ist die Leistung (z. B. Effizienz, Lebensdauer) einer 3D-gedruckten Raketendüse im Vergleich zu einer traditionell hergestellten?
- Bei korrektem Entwurf, Herstellung und Nachbearbeitung mit geeigneten Materialien wie IN718, IN625 oder Haynes 282 können 3D-gedruckte Raketendüsen die Leistung ihrer herkömmlichen Gegenstücke erreichen oder sogar übertreffen. Der Hauptvorteil liegt oft in der Möglichkeit, mittels AM hoch optimierte konforme Kühlkanäle einzubauen. Dank dieser verbesserten Kühlung können Triebwerke bei höheren Temperaturen und Drücken betrieben werden, was zu einem höheren spezifischen Impuls (Isp) oder Wirkungsgrad führt. Darüber hinaus stellen Nachbearbeitungsschritte wie HIP sicher, dass die Materialdichte und die mechanischen Eigenschaften (Festigkeit, Ermüdungsfestigkeit) mit denen von Guss- oder Knetwerkstoffen vergleichbar oder sogar besser sind, was zu einer potenziell längeren Betriebslebensdauer beiträgt, insbesondere unter anspruchsvollen thermischen Zyklusbedingungen. Die Gleichwertigkeit oder Überlegenheit der Leistung hängt jedoch in hohem Maße von einer strengen Prozesskontrolle, DfAM, einer geeigneten Materialauswahl und gründlichen Validierungstests ab.
2. Ist der 3D-Druck von Raketendüsen teurer als herkömmliche Verfahren wie Gießen und Bearbeiten?
- Der Kostenvergleich ist nuanciert. Bei hochkomplexen Konstruktionen mit komplizierter Innenkühlung, erheblicher Teilekonsolidierung oder geringen Produktionsmengen (Prototypen, Kleinserien) kann der 3D-Druck insgesamt kostengünstiger sein. Dies liegt an den wegfallenden Werkzeugkosten, dem geringeren Arbeitsaufwand bei der Montage, dem Potenzial für Gewichtseinsparungen (was die Startkosten senkt) und den deutlich schnelleren Entwicklungszyklen. Bei einfacheren Düsenkonstruktionen, die in sehr hohen Stückzahlen hergestellt werden, können herkömmliche Methoden immer noch einen Kostenvorteil pro Teil bieten. Betrachtet man jedoch die Gesamtbetriebskosten, einschließlich der Entwicklungsgeschwindigkeit, der Leistungssteigerung und der Faktoren in der Lieferkette, so ist AM für fortschrittliche Düsenanwendungen oft vorzuziehen. Die hohen Kosten von Superlegierungspulvern und die umfangreichen erforderlichen Nachbearbeitungen (HIP, Bearbeitung, NDT) sind wichtige Kostentreiber für AM-Düsen.
3. Wie wird die Materialqualität und -zertifizierung für flugkritische 3D-gedruckte Düsen gehandhabt? Wie können wir sicher sein, dass die Materialeigenschaften konsistent und zuverlässig sind?
- Die Sicherstellung von Materialqualität und -konsistenz ist von größter Bedeutung und erfordert einen vielschichtigen Ansatz, der durch Luft- und Raumfahrtstandards wie AS9100 vorgeschrieben ist:
- Pulver Zertifizierung: Seriöse Anbieter (wie Met3dp) stellen chargenspezifische Analysezertifikate für ihre Pulver zur Verfügung, in denen die chemische Zusammensetzung und die physikalischen Eigenschaften (PSD, Morphologie, Fließfähigkeit) überprüft werden. Eingehende Pulverchargen werden häufig von dem AM-Dienstleister unabhängig geprüft.
- Prozess-Validierung: Die AM-Parameter (Laser-/Strahlleistung, Geschwindigkeit, Schichtdicke usw.) werden für jede spezifische Legierung und Maschine sorgfältig entwickelt und validiert, um eine gleichmäßige Schmelz- und Mikrostrukturbildung zu gewährleisten.
- Gutscheine bezeugen: Prüfmuster (Coupons) werden oft zusammen mit den eigentlichen Teilen auf derselben Bauplatte gedruckt. Diese Proben werden einer zerstörenden Prüfung unterzogen (Zugprüfung, Ermüdungsprüfung, Mikrostrukturanalyse), um zu überprüfen, ob der Druck die für den jeweiligen Druckauftrag erforderlichen mechanischen Eigenschaften aufweist.
- Zerstörungsfreie Prüfung (NDT): Die fertigen Teile werden einer umfassenden zerstörungsfreien Prüfung (z. B. CT-Scannen) unterzogen, um die innere Unversehrtheit sicherzustellen und sie auf Defekte wie Porosität oder Risse zu überprüfen.
- Rückverfolgbarkeit: Eine strenge Dokumentation verfolgt die Pulvercharge, die Maschinenparameter, den Bediener, die Nachbearbeitungsschritte und die Prüfergebnisse für jedes einzelne Teil und gewährleistet so die vollständige Rückverfolgbarkeit vom Rohmaterial bis zum zertifizierten Endprodukt.
Diese Kombination aus kontrollierten Ausgangsmaterialien, validierten Prozessen, In-situ-Überwachung (sofern verfügbar), Tests nach der Herstellung und umfassender zerstörungsfreier Prüfung bietet das notwendige Vertrauen in die Zuverlässigkeit und Konsistenz von 3D-gedruckten Düsen für flugkritische Anwendungen.
Schlussfolgerung: Mit additiv gefertigten Raketendüsen in die Zukunft starten
Der Weg einer Raketendüse vom digitalen Entwurf bis zum Start stellt einen Höhepunkt der technischen Leistung dar. Die additive Fertigung hat die Möglichkeiten für diese kritischen Komponenten grundlegend verändert und die Beschränkungen traditioneller Methoden überwunden, um ein bisher nicht gekanntes Maß an Leistung, Effizienz und Designinnovation zu ermöglichen. Durch die Schaffung komplexer konformer Kühlkanäle, die Konsolidierung mehrerer Teile zu monolithischen Strukturen, die erhebliche Gewichtsreduzierung und die Beschleunigung der Entwicklungszyklen ist der 3D-Metalldruck nicht nur ein alternatives Fertigungsverfahren, sondern auch ein wichtiger Wegbereiter für die nächste Generation der Weltraumforschung und des Hyperschallflugs.
Die erfolgreiche Implementierung von AM für Raketendüsen hängt von der Synergie zwischen fortschrittlichen Designtechniken (DfAM), Hochleistungswerkstoffen wie den Nickelsuperlegierungen IN718, IN625 und Haynes 282 und sorgfältig kontrollierten Fertigungsprozessen ab. Durch die Möglichkeit, die Wärmemanagementsysteme innerhalb der Düsenstruktur genau zuzuschneiden, können die Triebwerke ihre Leistungsgrenzen erweitern, während Gewichtseinsparungen direkt zur Einsatzfähigkeit beitragen. Die Herausforderungen bleiben bestehen, insbesondere im Hinblick auf das Management von Eigenspannungen, die Sicherstellung der Materialintegrität und die Verfeinerung der Nachbearbeitungsabläufe, aber die Branche reift schnell, angetrieben durch strenge Qualitätsstandards und kontinuierliche Innovation.
Die Wahl der richtigen Partner ist in diesem anspruchsvollen Bereich von entscheidender Bedeutung. Die Zusammenarbeit mit fachkundigen AM-Dienstleistern und Werkstoffspezialisten wie Met3dp, die über zertifizierte Qualitätssysteme (AS9100), tiefgreifende Kenntnisse über Hochtemperaturlegierungen, fortschrittliche Drucktechnologien wie SEBM und umfassende Lösungen für die additive Fertigungist entscheidend, um die Komplexität zu beherrschen und die Produktion zuverlässiger, flugtauglicher Hardware zu gewährleisten.
Da die Luft- und Raumfahrt weiterhin nach einem schnelleren, günstigeren und leistungsfähigeren Zugang zum Weltraum und darüber hinaus strebt, sind 3D-gedruckte Raketendüsen ein Beweis für die Leistungsfähigkeit der additiven Fertigung. Sie stellen einen bedeutenden Sprung nach vorn dar und versprechen effizientere Antriebssysteme, schnellere Innovationen und letztlich einen weiteren Start der Menschheit in die Zukunft.
Teilen auf
MET3DP Technology Co., LTD ist ein führender Anbieter von additiven Fertigungslösungen mit Hauptsitz in Qingdao, China. Unser Unternehmen ist spezialisiert auf 3D-Druckgeräte und Hochleistungsmetallpulver für industrielle Anwendungen.
Fragen Sie an, um den besten Preis und eine maßgeschneiderte Lösung für Ihr Unternehmen zu erhalten!
Verwandte Artikel
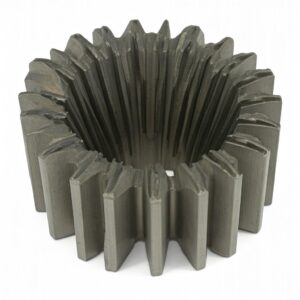
Hochleistungs-Düsenschaufelsegmente: Revolutionierung der Turbineneffizienz mit 3D-Metalldruck
Mehr lesen "Über Met3DP
Aktuelles Update
Unser Produkt
KONTAKT US
Haben Sie Fragen? Senden Sie uns jetzt eine Nachricht! Wir werden Ihre Anfrage mit einem ganzen Team nach Erhalt Ihrer Nachricht bearbeiten.
Holen Sie sich Metal3DP's
Produkt-Broschüre
Erhalten Sie die neuesten Produkte und Preislisten
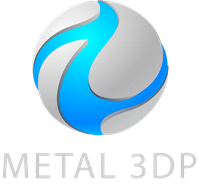
Metallpulver für 3D-Druck und additive Fertigung